Самодельный очень точный отрезной станок из болгарки
Здравствуйте. Сегодня я хочу рассказать о том, как я сделал из не нужной мне болгарки отрезной станок. Мне часто приходится резать трубы. Особенно, профильные. Кто это делал, знает, что отрезать ровно профильную трубу болгаркой достаточно сложно. Это занимает много времени — приходится при помощи угольника отчерчивать под прямой угол каждую сторону, потом аккуратно прорезать по одной грани. И всё равно, бывает, что одна сторона получается на полмиллиметра короче, и потом, при сваривании тонкий металл стенки в этом месте начинает гореть из за неплотного прилегания. В идеале ровно можно отрезать только за один рез. А для этого нужен отрезной станок.
У меня была не нужная мне УШМ «DWT ws-180s». Её мне отдали бесплатно по причине неисправности — оторвалась крыльчатка ротора и болгарка заклинила. Хозяин хотел её выбрасывать и предложил отдать мне её на запчасти бесплатно.
..Но оказалось, что такая болгарка мне не нужна. Она очень тяжёлая и массивная для 180-го круга. Мощности там хватает и для 230-го (2200 Вт), но, почему-то, производитель оборудовал её защитой именно под 180-й круг. Поэтому она у меня несколько лет висела в мастерской невостребованная — у меня есть более лёгкая «180-ка». Я собирался переделать защиту под 230-й круг (тогда она пригодится для работ по бетону, например), но так и не собрался! )))). Ведь 230-я у меня тоже есть…
И вот мне пришла в голову мысль купить для неё станину и сделать отрезной стационарный станок. Но рассмотрев покупные варианты, я обнаружил, что они, в большинстве своём, не обладают достаточной жёсткостью, а значит, и точностью! Поэтому, я пришёл к выводу,что нужно сделать самому.
Что мне понадобилось:
1. Собственно УШМ.
2. Уголок стальной 50 на 50 и 40 на 40.
3. Обрезок водопроводной трубы ДУ32-3,5
5.
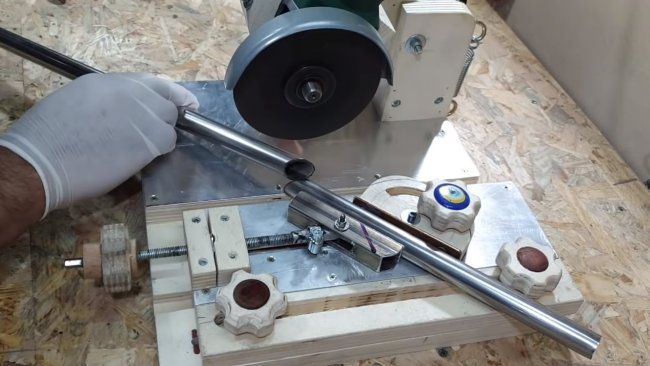
6. Подшипник опорный.
7. Шпилька М14.
8. Профильные трубы 15 на 15, 20 на 20, 25 на 25
9. Болты и гайки М6, М8, М14.
10. Обрезки жести.
Итак, для начала я решил собрать крепление болгарки. В покупных вариантах, рассчитанных на различные болгарки, крепление осуществляется тремя длинными болтами с контргайками, что сказывается на жёсткости. К тому же, закрепив УШМ в трёх точках, её приходится располагать вертикально, что немного «ворует» глубину реза — как правило, впереди корпус редуктора чуть вытянут. А посему я решил закрепить её горизонтально, в двух точках, с плотным прилеганием рамы к редуктору.. Минус такого крепления — оно подходит только к одной модели УШМ. Но я решил этим пренебречь, посчитав, что если мне и придётся заменить болгарку, то я просто сварю новое крепление.))))
Просверлил в них отверстия диаметром 14 мм:
И прикрутил к редуктору, используя места крепления ручки:
При этом у меня не нашлось болтов М14, и я временно заменил их обрезками шпильки с гайками.

После этого я прямо на болгарке прихватил уголки друг к другу сваркой, потом снял и накрепко проварил:
Далее я приступил к изготовлению каретки. Для этого мне понадобился отрезок толстостенной трубы 32-ки. Так как отрезать нужно было ровно, а под рукой пока не было отрезного станка, я использовал в качестве разметки широкую малярную ленту:
После этого я вырезал кусок трубы ДУ-25, на 20 мм короче 32-ки:
Вложил одну в другую:
Забил с двух сторон по 202-му подшипнику:
И стянул шпилькой М14, используя шайбы и гайки:
Потом вырезал кусок уголка и прихватил его к трубе. При этом прожёг электродом наружную трубу так, чтобы сварить её с внутренней:
Сейчас надо сделать стойки для крепления каретки. Их я делал из того-же уголка 50. Чтобы они получились одинаковыми, я стянул их струбциной, и в таком положении обрезал и просверлил отверстия:
Далее я собрал и сварил всю крепёжную конструкцию каретки:
Тяги на которых будет крепиться к каретке УШМ, я изготовил из толстостенной профильной трубы 20 на 20.

Осталось вырезать и сварить всё воедино:
На этом этапе я «примерил» болгарку:
Теперь подошла очередь стола. Его я изготовил из листа стали, толщиной 4мм, размером 60 на 60 см:
Закрепил на этом листе всю конструкцию:
Из профильной трубы 15 на 15 сделал две квадратных рамки, размером 50 на 50 см. При этом в трубе, в местах сгиба прорезал только по три стенки, четвёртую оставил.
После этого вварил в углах вертикальные стойки из той-же трубы, и на получившийся параллелепипед закрепил мою конструкцию.
На данном этапе возникла необходимость выставить прямой угол между отрезным кругом и столом. Как я уже говорил, я исключил все регулировки в угоду жёсткости (читай: точности) конструкции. В моих планах было просто подогнуть тяги, а потом укрепить их в нужном положении, приварив к ним в качестве усиления уголки. Но, когда я попробовал их подогнуть сперва двумя монтажками… (У-у-у! Какой я оптимист! )))). Потом ломом! (Результат тот же)….. Я понял, что усиливать конструкцию не придётся!! Две толстостенные профильные трубы небольшой длины, к тому-же, проваренные на концах к уголкам швами по 5 см длиной с каждой стороны, дают неимоверную жёсткость! …
…Подогнуть я смог, лишь вставив между ними двухметровую (!) трубу, сечением 60 на 20. (Благо, между тягами как раз 60 мм.
Итак, вертикаль выставлена! Теперь прорезал стол:
После этого расширил и удлинил прорезь малой болгаркой. (На случай установки, к примеру, круга по дереву.)
..Кстати…Изначально у меня возникла мысль сделать «2 в 1». Т.е., предусмотреть возможность переворачивания стола болгаркой вниз, с целью получения циркулярки! И я даже начал это воплощать. К примеру, шляпки всех крепёжных болтов с обратной стороны я проварил, расплавил и зачистил, чтобы получить ровный циркулярочный стол:
По той же причине сделал симметрично отверстия для крепёжных болтов, которыми стол крепится к «параллелепипеду»… Но эйфория от того, что «классно я придумал» прошла, и я понял, что я просто «повёлся», и погнался не за практичностью, а за «классно получилось».
…А на деле я НЕ БУДУ ЭТИМ ПОЛЬЗОВАТЬСЯ!!! Ведь у меня циркулярка есть. И она, в любом случае, лучше, чем сделанная из болгарки! К тому-же, работая циркуляркой с деревом, хорошо поставить рядом этот станок с кругом по дереву, чтобы торцевать. А не переворачивать стол ради каждой доски…
В общем, отбросил я эту глупую затею….
..
Дальше я приступил к сооружению упора для заготовки. Я приложил угольник к кругу, отчертил линию под прямым углом, и закрепил по ней упорный уголок 40 на 40.
После этого я открутил уголок и по его отверстиям, приложив на этот раз угольник 45 градусов, просверлил отверстие в столе.
Забыл сфотографировать, но тут, думаю, понятно….Теперь, чтобы отрезать под 45, нужно извлечь один болт, повернуть уголок и закрепить в другое отверстие.
Следующий этап. Я приступил к сборке инструментальных тисков. Ведь точно отрезать можно только хорошо закреплённую заготовку.Вырезал кусок трубы 20 на 20.

Приварил её.
И обработал болгаркой, придав ей наружные размеры трубы: Далее я ещё понаваривал, там где не хватило и ещё обработал. (не фотографировал).
Потом вырезал кусок 25-й трубы (в неё легко и достаточно плотно входит 20-ка) и приварил к ней поперёк обрезок полосы, чтобы можно было, просверлив отверстия, закрепить её к столу. Это будет направляющая: На краю шпильки я сделал выборку и изготовил туда маховичок.
Далее, на краю стола закрепил уголок с отверстием, и собрал тиски. шпильку вкрутил в трубу с приваренной гайкой, одел на неё направляющую, и всё это пропустил через упорный уголок, подложив опорный подшипник, который зафиксирован зашплинтованной гайкой: Короче, поймёте по фото:
Рукоятку маховичка сделал из мебельного болта, одев на него металлическую трубку.
На конце сделал широкий упор. И получились вот такие инструментальные тиски:
При вращении маховичка, труба с приваренной гайкой вылезает из направляющей и плотно прижимает заготовку к упору.

Далее, я приступил к изготовлению защитного кожуха. Как я уже говорил, кожух на болгарке был под 180-й круг, а я решил использовать 230-й. (Мощности хватает. Обороты тоже подходящие.). К тому-же, так как мне нужна точность, то резать я буду толстыми кругами (2,6, или 3 мм). Потому как более тонкие немного болтаются при нажиме. А посему количество искр будет неимоверным!!! Поэтому я решил сделать наиболее закрытый кожух, и закрепить его непосредственно к станине.
Сперва я сделал шаблон из картона:
Потом по нему вырезал из жести две зеркальных развёртки. (При этом использовал обрезки — один из оцинковки, другой — из корпуса микроволновки! Не пропадать же добру! )))))):
На этом этапе я закрепил крепёжный уголок, т.к., приклёпывать его нужно изнутри — иначе, торчащие заклёпки будут мешать кругу. Сделал я его из обрезка алюминиевого уголка:
После чего сложил половинки, склепал и закрепил на тяге, просверлив отверстия и нарезав резьбу М6:
Ещё расскажу, как я реализовал подпружинивание. Пружина у меня была (не знаю, от чего), я отрезал от неё кусок, и, как временное решение сделал вот так:
Трубка просто вставлена! Так я хотел найти идеальный вылет рычага и жёсткость пружины. Да так и оставил!!! Это очень удобно! Во первых, я могу регулировать жёсткость и угол подъёма, просто заглубляя, или вытягивая трубку. Во вторых, можно легко, чуть приподняв болгарку одной рукой, второй вытащить трубку полностью. И тогда станок переводится в «транспортное положение» — болгарка ложится кожухом на стол, ничего не вихляется, не растягивается пружина.
Вот, собственно, и всё… Вот такой агрегат получился:
Планирую ещё продлить на правую сторону упор. Так будет удобно что-то к примеру, подторцевать. И закрепить на нём металлическую слесарную линейку — так удобно будет отрезать небольшие куски, не отмеряя каждый раз.
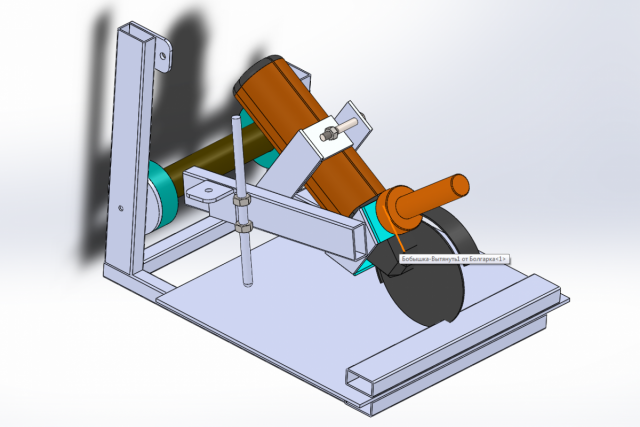
…А пока я экстренно «ввёл его в эксплуатацию», потому что делаю сейчас трубогиб, и там очень много чего резать нужно.
Угол держит идеально!!!! Разрезал им даже валы к трубогибу (круг 40 мм), и потом на станке биение было настолько мизерным, что от торцовки отказался. Трубы профильные вообще идеально режутся — потом угольник на свет никакой, даже мизерной щёлочки не даёт.
Diy Grinder – Etsy.de
Etsy больше не поддерживает старые версии вашего веб-браузера, чтобы обеспечить безопасность пользовательских данных. Пожалуйста, обновите до последней версии.
Воспользуйтесь всеми преимуществами нашего сайта, включив JavaScript.
Найдите что-нибудь памятное, присоединяйтесь к сообществу, делающему добро.
( 212 релевантных результатов, с рекламой Продавцы, желающие расширить свой бизнес и привлечь больше заинтересованных покупателей, могут использовать рекламную платформу Etsy для продвижения своих товаров. Вы увидите результаты объявлений, основанные на таких факторах, как релевантность и сумма, которую продавцы платят за клик. Учить больше. )
Самодельная мясорубка с двигателем от стиральной машины
Слово мясорубка вводит некоторых обывателей в ступор, но между тем ничего необычного в этом слове нет. Болгаркой называют разновидность шлифовального станка, который предназначен для более тонкой финишной шлифовки какой-либо детали. В этой статье мы расскажем о том, как сделать самодельную мясорубку с двигателем из стиральной машины автомат, надеемся, эта информация будет вам полезна.
Машинное применение
Прежде чем приступить к сборке машины с использованием двигателя от стиральной машины, помните о технике безопасности. Процесс сборки и дальнейшего использования самодельного станка может быть опасен для вашего здоровья. Будьте предусмотрительны и осторожны, если вы не уверены в своих силах, лучше не браться за изготовление самодельного станка.
Итак, где применяется болгарка, зачем она вообще нужна в хозяйстве? По большей части наждак требуется для хозяйственных нужд. Кстати наждак из стиральной машины своими руками сделать даже проще, чем болгарку, если интересно, читайте одноименную публикацию, размещенную на нашем сайте. Болгарка, в отличие от наждака, требуется в тех случаях, когда нужно быстро и качественно отшлифовать любую поверхность.
Внимание! Ленты (75х457 мм) с любой рабочей поверхностью продаются на шлифовальных машинах, так что никаких проблем в дальнейшем возникнуть не должно.
Например, если вы делаете ручку для сельхозинвентаря или планки для пчелиных рамок, то эти детали нужно в финале отшлифовать, чтобы потом не было проблем. Можно выполнить эту работу вручную, но тогда будет потрачено много сил и энергии. Гриндер сделает процесс снятия шкур простым и незатейливым.
Изготавливаем механизм
Важнейшим элементом, помимо двигателя от стиральной машины, является самодельный подвижный узел, с помощью которого происходит натяжение ленты и регулировка ее положения. Можно купить готовый подвижный механизм для такой машины или заказать его изготовление у мастеров, но тогда стоимость готового изделия будет приближаться к цене заводской болгарки, что, конечно же, недопустимо. Вот и попробуем сделать эту самую главную деталь своими руками. Какие материалы потребуются:
- несколько штук уголка 30 мм, один длинный – 40 см и два коротких 15 и 25 см;
- два длинных болта и дюжина гаек;
- шпилька;
- пружина на болт;
- полоса металлическая 30х100 мм;
- короткие болты, шайбы, гайки.
Детали ролика пришлось обтачивать на токарном станке. Вы можете увидеть их на рисунке ниже. Два подшипника, гайка, сам ролик и своеобразный вал.
Соответственно из инструментов нам потребуются: токарный станок, болгарка, дрель, электросварка, гаечные ключи, пассатижи и “ангельское терпение”. Делаем следующее. Привариваем друг к другу уголки и пластины так, как показано на рисунке ниже. В конце конструкции вставляем болт с пружинкой. Этот болт нам понадобится для регулировки натяжения ленты.
! Основной болт будут удерживать две небольшие пластины с отверстиями и резьбой, которые приварены к низу уголка перпендикулярно ему.
Далее в верхней части основного уголка просверлите отверстие, вставьте в него короткий болт и закрепите короткий кусок уголка. Эта деталь должна немного двигаться из стороны в сторону и в свою очередь к ней будет крепиться ролик с подшипниковым механизмом. Движение этого кусочка уголка впоследствии позволяет регулировать положение ленты.
Собираем механизм ролика и крепим его к уголку. Сильно затягивать не нужно, чтобы ролик свободно вращался, но и он не должен соскочить с подшипников, поэтому подшипники прихватываем к ролику сваркой, и затягиваем контргайки на концах вала. ролика в уголке, потребуется просверлить еще одно отверстие и закрепить в нем шпильку, на одном конце которой нужно закрутить две гайки, а другой конец будет упираться в основной уголок. Очень важно, чтобы шпилька была закручена и закручена ниткой.
Короткий уголок, приваренный перпендикулярно основному уголку с прикрученным к нему куском ДСП, служит направляющей, а главное защищает руки мастера при регулировке движения ленты. Для безопасности это важно, так как самодельная болгарка регулируется шпилькой, которая находится в опасной близости от активно движущегося ремня. Ну вот и все, механизм готов, теперь можно подключить двигатель, надеть на его вал втулку, соединить все это с подвижным механизмом и приступить к испытаниям.
Двигатель и вал
О том, как подключить двигатель от стиральной машины Мы уже достаточно много говорили и не будем повторяться. Переходим сразу к следующему и завершающему этапу сборки болгарки. Мы будем подключать двигатель от старой стиральной машины-полуавтомата. Кожух двигателя защищаем листом тонкой жести и закрепляем на подходящей станине . В нашем случае станину мы сварили из уголков, но можно закрепить двигатель прямо на верстаке.
! Конденсатор, управляющий запуском двигателя, можно взять из того же полуавтомата стиральной машины.
Как видите двигатель мы взяли сразу с длинным валом, но если у вас обычный двигатель от стиральной машины с коротким валом, то придется что-то изобретать и увеличивать его длину. На рисунке выше вы видите, что на вал двигателя надевается специальная деревянная втулка, которую мы выточили на станке.