Вспомогательный инструмент для станков с ЧПУ
ТокарныйВспомогательный инструмент для станков с ЧПУ – оборудование, обеспечивающее высокую производительность и качество исполнения работы аппаратурой.
Вспомогательный инструмент для станков с ЧПУ – оборудование, позволяющее осуществить точную и качественную обработку материала. Наличие подобных аппаратов позволяет повысить производительность и скорость производства. ЧПУ делится на два типа: полуавтоматический и автоматический. При работе с различными станками задействуются элементы с определенной комплектацией. Но без вспомогательных инструментов спектр выполняемых функций ограничен.
Комплекс деталей, составляющих собой наиболее важную часть комплектации станка с ЧПУ, представлен:
- станочными приспособлениями;
- режущим прибором;
- вспомогательным инструментом.
Функции
Вспомогательный инструмент представляет собой группу систем, главной функцией которых является компоновка блоков с запчастями, отвечающими за работоспособность агрегата. Блок представляет собой сочетание оборудования для режущих и дополнительных задач.
Наиболее распространенным прибором такого типа является вспомогательный инструмент для токарных станков с ЧПУ. Благодаря им крепятся:
- резцы;
- зенкеры;
- сверла;
- метчики;
- развертки.
Качественному вспомогательному инструменту характерен высокий показатель жесткости. Он должен уметь обеспечить точность и стабильность применения орудия для резки. Аппарат предназначен для поддержки всех типов работ, которые способен выполнять станок. Достоинством устройства является легкая и быстрая установка. Универсальный станок должен обладать аналогичной комплектацией для разных модификаций. Настройку прибора можно произвести, не устанавливая его на станок.
Конструкция
Закрепление оборудования на станке производится благодаря унифицированной хвостовой части. Крепление усиливают элементы для соединения с режущим механизмом. Крепление осуществляется ручным методом. Хвостовик устройства имеет цилиндрическую форму и лыску рифленого типа. Такая конструкция обеспечивает более высокий показатель надежности крепления.
Системы инструментов изменяются в зависимости от того, для каких задач используется станок. Быстрая смена системы требуется, если производятся работы по сверлению и фрезеровке. Станок переналаживается путем замены носителя программы. Чем выше жесткость дополнительного механизма, тем более интенсивной будет его работа. От интенсивности работы зависит, насколько быстро она будет выполнена.
Жесткость обеспечивается за счет прочного крепления. Для достижения высокой прочности крепления используются детали, изготовленные из твердых сплавов. Добавочный механизм рекомендуется настраивать до установки на станок. Это поможет сократить время работы. Многошпиндельные головки упрощают установку технологии на прибор с ЧПУ. Такое оборудование особо эффективно при мелкосерийных задачах.
Достоинства
Вспомогательный инструмент обеспечивает станок с ЧПУ целым рядом преимуществ:
- время, затраченное на осуществление задачи, сокращается вполовину;
- повышается показатель точности, благодаря чему обеспечивается экономия материала;
- обеспечивается стабильная эксплуатация;
- появляется возможность обслуживать сразу несколько станков;
- отсутствует необходимость в использовании приспособлений, имеющих сложную конструкцию;
- идентичная конструкция устройств позволяет устанавливать их на различные станки;
- настройка аппаратуры может проводиться до установки на станок;
- упрощено использование аппарата;
- увеличилось разнообразие позиций для обработки материала;
- участие человека в управлении агрегатом уменьшилось;
- увеличилась производительность станка;
- появилась возможность изготовления деталей сложной формы;
- изделия стали более качественными;
- повысилась производительность оборудования;
- использование устройства стало более простым и безопасным.
Наладка
Приведение устройства в рабочее состояние делится на две части: наладки и подналадка. Процесс наладки представляет собой подготовку оборудования к выполнению рабочей цели. Подналадка – дополнительная подготовка механизмов агрегата. Первая часть связана с основной частью станка, выполняющей поставленную задачу. Вторая часть представляет собой взаимодействие с технологической оснасткой. Именно во второй части производится наладка вспомогательного инструмента.
На первом этапе наладки производится сборка и установка режущего приспособления и его элементов. На втором этапе устанавливается заранее настроенный добавочный механизм. На третьем этапе выбирается режим работы аппарата.
Установка на станках производится тремя вариантами:
- на стол;
- в приспособление на столе;
- на координатную плиту.
Приспособление может быть установлено на координатной плите.
Особенности настройки
Настройку оборудования рекомендуется проводить перед установкой на станок. Это не только упрощает процесс настройки, но и позволяет сэкономить время. Режущая часть прибора имеет два направления: радиальное и осевое. Установка производится в выбранном направлении на определенном расстоянии от основной части прибора. Оптимальное расстояние зависит от используемого агрегата.
Для элементов имеются посадочные места. Каждый элемент имеет свой размер, который соответствует указанному месту. Правильное распределение элементов обеспечит точность работы агрегата. Для сверл, расточных оправок, зенкеров, и еще ряда элементов имеется только одна координата настройки. Для настройки используется вставка в виде ножа или индикатор. Точную настройку практически невозможно произвести без окулярного микроскопа.
Перед использованием микроскопа, для его оптических элементов требуется задать координаты, которые обеспечат точность настройки.
Самые популярные станки с вспомогательным инструментом
Вспомогательный инструмент может использоваться с любыми моделями станков современного типа, оснащенных ЧПУ. Их популярность зависит от востребованности. Наиболее часто используемыми типами аппаратов являются:
- токарным-револьверным;
- вертикально-сверлильным;
- вертикально-фрезерным.
Сборка устройства производится по ГОСТу 23597-79. Он предполагает оптимальные настройки для оборудования, обеспечивающие точность производства. Показатель точности является частично регулируемым. Уровень искажения может меняться в зависимости от того, насколько профессионально была установлена программа.
Программа должна учитывать функции, которые дает дополнительная аппаратура. Вместе они могут:- предупредить показатель искажения траектории движения прибора;
- уменьшить подачу при использовании аппарата;
- регулировать размер рабочего приспособления.
Конструкция вспомогательного инструмента может изменяться в зависимости от того, для какого типа станков он используется. Но основная задача остается неизменной – закрепление рабочих элементов прибора. Без подобного оборудования производительность и период бесперебойной эксплуатации аппарата будет значительно ниже. Режущее устройств будет хуже закреплено, по причине чего снизится качество изготовляемых изделий, и многообразие возможных форм.
Вспомогательный инструмент
Основная задача вспомогательного инструмента – надежная фиксация режущего инструмента в шпинделе и передача ему крутящего момента от станка. В качестве вспомогательного инструмента на операциях фрезерования используютпатроны и оправки.
Оправки главным образом предназначены для операций с большими усилиями резания, таких как торцовое фрезерование, фрезерование пазов дисковыми фрезами, растачивание отверстий большого диаметра.
Элементом, передающим крутящий момент у оправок, является шпонка, которая предотвращает проворот режущего инструмента относительно оправки. Этим обеспечиваются надежное закрепление и передача крутящего момента. Однако оправки не способны обеспечить хорошее центрирование инструмента, поэтому основное их применение – черновые операции с удалением основного объема материала.
Патроны обеспечивают лучшее центрирование и обычно используются для зажатия режущих инструментов небольшого размера. Следует различать патроны с механическим креплением режущего инструмента (для сверл, инструментов с коническими хвостовиками типа конусов Морзе, Whistle Notch, Weldon и др.) и патроны с упруго-деформируемой зажимной частью (цанговые, гидромеханические, гидропластовые и др.).
Особое внимание следует уделить цанговым патронам (рис. 2.10), которые наиболее час то используются при работе на станках с ЧПУ. Принцип действия такого пат рона очень прост. В коническое отверстие патрона вставляются сменные цанги. Цанга имеет цилиндрическое отверстие, в которое устанавливается цилиндрический хвостовик режущего инструмента (диаметр хвостовика режущего инструмента должен соответствовать номеру цанги). При затягивании гайки давление передается на торец цанги, что приводит к вдавливанию последней в коническое отверстие патрона и сжатию в радиальном направлении. Сжимаясь, цанга передает давление на цилиндрический хвостовик режущего инструмента и надежно его закрепляет. После снятия давления (откручивания гайки) с цанги она разжимается и позволяет извлечь режущий инструмент из патрона.
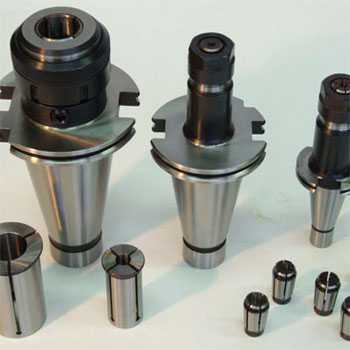
Рис. 2.10. Цанговые патроны и сменные цанги
Основное преимущество цангового патрона – способность осуществлять закрепление широкого диапазона режущих инструментов при помощи комплекта сменных цанг. В комплекте цанг к одному и тому же патрону вы, как правило, найдете цанги для закрепления инструментов с хвостовиками от 6 до 30 мм и более. Цанга производит хорошее центрирование инструмента и надежное закрепление, однако плохо сбалансирована для скоростных методов обработки.
Следует уделять должное внимание вспомогательному инструменту, так как от него зависят: стойкость режущего инструмента, стабильность технологического процесса, точность и качество обработки.
planetacam.ru
Система вспомогательного инструмента сверлильно-фрезерно-расточных станков с чпу
Для этих станков инструментальные системы строятся аналогичным образом. Только в качестве элемента крепления на станке используются патроны с хвостовиками 7:24 или с конусом Морзе.
шпиндель станка
оправка для насадных фрез с поперечной штангой
патрон цанговый
втулка переходная для концевых фрез с конусом Морзе и резьбовым отверстием
державка для регулируемых втулок, патронов и оправок
оправка расточная для чернового растачивания
оправка расточная для чистового растачивания
патрон регулируемый цанговый
втулка регулируемая с внутренним конусом Морзе
втулка регулируемая длинная с внутренним конусом Морзе
оправка регулируемая для насадных зенкеров и разверток
патрон регулируемый резьбонарезной
оправка регулируемая для чернового растачивания
оправка регулируемая для крепления перовых сверл
оправка регулируемая для дисковых фрез
расточной регулируемый патрон
Принцип построения системы инструментальной оснастки для станков с ЧПУ сверлильно-фрезерно-расточной группы
В качестве примера на рисунке показаны небольшая часть этой системы и некоторые способы крепления разных по назначению режущих инструментов: торцовая фреза, осевой инструмент, расточная оправка. Для передачи крутящего момента фланец патрона с конусом 7:24 имеет пазы, в которые входят торцовые шпонки шпинделя станка. Смена инструментов производится автоматически по программе с помощью манипуляторов (автооператоров), которые передают инструментальные блоки из магазина в шпиндель и обратно.
Сборный переходной патрон для крепления инструмента с коническим хвостовиком
Для крепления инструмента с конусом Морзе с возможностью регулировки вылета сверла от торца шпинделя (поз. 9 и 10 на рис. система вспомогательного инструмента для сверлильно-фрезерно-расточных станков с ЧПУ с коническим хвостовиком) может быть использован сборный переходной патрон. 1-корпус патрона с конусом 7:24 имеет внутреннее цилиндрическое отверстие диаметром 36 или 48мм. В этом отверстие предусмотрен шпоночный паз 2. В этом цилиндрическом отверстии находится внутренняя регулируемая втулка 3. Во втулке 3 устанавливается инструмент 8. Регулирование вылета инструмента осуществляется за счет вращения регулировочной гайки 5. Эта гайка вращается по наружной трапециевидной резьбе втулки 3. После достижения нужной длины вылета, гайка фиксируется гайкой 7 и прокладкой 6. Втулка 3 фиксируется в корпусе патрона с помощью винтов 4. Для предотвращения вытягивания втулки из корпуса патрона, на ее поверхности делается косой срез.
Распространенными являются хвостовики с конусами конусностью 7:24. Стандартная конструкция по DIN 2080 применяется на фрезерных и расточных станках с ручной сменой инструмента. Для станков с автоматической сменой инструмента используют хвостовики по ГОСТ 25827-93, исполнение 3, имеющие тот же размерный ряд, что и по DIN 2080, но отличающиеся трапецеидальной проточкой во фланце под захват устройства с автоматической сменой инструмента.
Недостатки соединения с конусом SK 7:24
studfiles.net
Режущий и вспомогательный инструмент к фрезерным станкам
Наиболее распространенный режущий инструмент для работы на фрезерных станках с ЧПУ – фрезы. Они бывают стандартными и специальными, приспособленными для работы в особых, трудных условиях.
Специальная конструкция
Например, для концевых фрез можно отметить следующие особые случаи, требующие специальных конструктивных решений:
- облегчение выхода стружки при обработке глубоких глухих колодцев в результате уменьшения числа зубьев и увеличения угла наклона спирали
- изменение направления осевой составляющей силы резания таким образом, чтобы за счет этой составляющей деталь прижималась к столу станка; достигается это применением праворежущих фрез с левой спиралью и леворежущих с правой спиралью
- уменьшение вибраций при резании, что обеспечивается несимметричным расположением зубьев фрезы
- особое затачивание торца двузубых и четырехзубых фрез, позволяющее осуществлять вертикальное врезание в металл
- повышение жесткости режущей части инструмента в результате того, что канавки имеют переменную глубину (конический сердечник)
- увеличение вылета инструмента с сохранением его жесткости за счет усиленного тела фрезы (рис. 105, а)
- конические концевые (рис. 105, б) и фасонные фрезы для образования сложных криволинейных поверхностей.
Рис. 105. Специальные концевые фрезы
Торцовые фрезы в основном имеют стандартную конструкцию. Все более широкое использование находят фрезы с механическим креплением пластин из твердого сплава или сверхтвердых режущих материалов.
Рис. 106. Крепление режущих инструментов: а – торцовой фрезы; б – концевой фрезы; в концевой фрезы через переходную втулку; г – сверла
Закрепление инструмента
Режущие инструменты закрепляют в переходных втулках, патронах, оправках. На рис. 106 изображено крепление концевых и торцовых фрез, а также сверл. Концевые фрезы необходимо затягивать непосредственно или через переходные втулки в коническое отверстие вспомогательного инструмента с помощью специальных винтов.
Рис. 107. Цанговый патрон для крепления инструментов с цилиндрическим хвостовиком
Для крепления концевых фрез большого диаметра (40, 50, 63 мм) с цилиндрическим хвостовиком разработана конструкция цангового патрона (рис. 107). Такой патрон обеспечивает передачу крутящего момента и восприятие осевой и радиальной сил, действующих при фрезеровании. В передней части корпуса / размещена цанга 2, которая гайкой 5 крепит хвостовик фрезы.
Для затягивания цанги в конус и вытягивания из конуса гайка снабжена сборным буртом (кольцом) 4, связанным с гайкой шариками 3. При вращении гайки шарики передают на кольцо и далее на цангу осевую силу, разгружая цангу от действия тангенциальных сил, что приводит к повышению точности крепления инструментов. Крутящий момент на хвостовик фрезы передается сухарем 8, который зафиксирован штифтом 7 в корпусе 1. Для предотвращения вытягивания концевых фрез из патрона предусмотрен боковой фиксирующий винт 6, передняя часть которого упирается в соответствующую лыску фрезы.
Похожие материалы
www.metalcutting.ru
Инструмент, применяемый при работе на фрезерных станках
Режущий инструмент, применяемый при работе на фрезерных станках, весьма разнообразен.
1Цилиндрические фрезы используются для обработки открытых поверхностей. Зубцы располагаются на цилиндрической основе и наклонены к оси под углом 30-40%. Эти фрезы используются для комплексной обработки многоступенчатой поверхности и различных пластиков.
2Торцевые фрезы предназначены для обработки открытых поверхностей. Ось фрезы размещена под прямым углом к обрабатываемой поверхности. Зубцы расположены на цилиндрической и торцевой поверхностях фрезы. Преимуществом торцевых фрез перед цилиндрическими является большое число зубцов, что снижает вибрации и улучшает качество обработки.
3Концевые фрезы имеют очень широкое техническое применение. Применяются для обработки глубоких пазов, уступов, взаимно перпендикулярных плоскостей, для осуществления контурной обработки наружных и внутренних поверхностей сложного профиля.
4Дисковые фрезы используются для резки пазов, канавок, раскроя металла. Исходя из конструктивных особенностей, их можно разделить на две категории цельные и сборные.
5Угловые фрезы, по сути, это одна из разновидностей дисковых фрез. Они применяются для прорезки канавок с угловым профилем. Однако наиболее часто, угловые фрезы используют для прорезки стружечных канавок у фрез, разверток и зенкеров. Сейчас на рынке представлены четыре вида угловых фрез :правые и левые фрезы двухсторонние, симметричные и несимметричные двух угловые фрезы. Производятся они цельнометаллическими из быстрорежущей стали.
6.Фасонные фрезы используются для работы с канавками сложного профиля. Фасонные фрезы отличаются от всех остальных видов фрез, так как проектируются в зависимости от габаритных размеров и профиля обрабатываемой поверхности.
Его можно классифицировать следующим образом:
1. Фрезы насадные цельные.
2. Фрезы насадные составные.
3. Фрезы насадные сборные со вставными ножами.
4. Фрезы концевые (цельные).
Рис. 8. Обозначение угловой фрезы
Плоские ножи, применяемые для насадных сборных фрез, бывают односторонние или двухсторонние и имеют прямолинейные режущие кромки для плоского фрезерования или криволинейные режущие кромки для выборки профилей.
Преимущества сборных фрез заключаются в простоте, дешевизне и быстроте изготовления резцов, а также возможности сохранения постоянного диаметра окружности резания. Отрицательными качествами являются трудность заточки профильных ножей с подгонкой по шаблону, необходимость балансировки головок и менее выгодные углы резания.
Цельные фрезы по сравнению со сборными имеют ряд преимуществ. Они, как правило, обладают большим числом резцов (четыре, шесть и более), исключают необходимость балансировки, более безопасны, так как не имеют частей, которые могут вылететь из крепления во время работы, обеспечивают большую производительность и легко сменяются.
Основным недостатком цельных фрез является изменение диаметра по мере стачивания. Для заточки насадочных и концевых фрез имеются специальные заточные станки.
Улучшенные конструкции фрез
Безопасная фланцевая ножевая головка с плоскими ножами (рис. 9). Основной особенностью конструкции новой фланцевой ножевой головки в отличие от ранее применявшихся является безопасность ее эксплуатации, так как вылет ножей во время работы исключается. Одновременно обеспечивается возможность регулирования положения режущих кромок ножей во время их установки с высокой степенью точности при минимальной затрате времени.
На шпинделе фланцевая ножевая головка, состоящая из верхнего и нижнего фланцев и двух плоских ножей, крепится гайкой. Между гайкой и верхним фланцем рекомендуется устанавливать прокладочное кольцо. При затягивании гайки не следует применять большое усилие, так как в этом нет необходимости и, кроме того, усилие может привести к искривлению шпинделя станка и ненормальной его работе.
Рис. 9. Безопасная фланцевая ножевая головка с плоскими ножами: 1 — нож, 2 — верхний фланец, 3 — прокладочное кольцо, 4, — гайка, 5 — шпиндель, 6 — стопорный винт, 7 — вилки, 8 — предохранительный винт, 9 — нижний фланец
Верхняя боковая кромка ножей выполнена в виде рейки, зубцы которой входят во впадины между витками предохранительного винта 8, препятствуют вылету их во время работы.
Между зубцами рейки и впадинами винтовой нарезки предохранительного винта необходим небольшой зазор, обеспечивающий зажим ножа в пазу верхнего фланца.
Предохранительные винты удерживаются в отверстиях верхнего фланца с помощью вилок, которые в свою очередь фиксируются в своих гнездах стопорными винтами. Нижней боковой кромкой оба ножа входят в соответствующие пазы нижнего фланца, который предохранительных винтов не имеет. Регулирование положения режущих кромок ножей при их установке достигается вращением предохранительных винтов, имеющих внутренние шестигранные отверстия под торцовый ключ. При регулировании ножи лишь слабо зажимаются между фланцами.
Рис. 10. Безопасная сборная фреза
Режущая кромка ножей всегда должна выступать со стороны глухого конца отверстия для предохранительных винтов в верхнем фланце.
В зависимости от сложности профиля обрабатываемой детали применяется одно или несколько предохранительных колец с распорными втулками соответствующих размеров и формы.
Насадная цельная пазовая фреза (рис. 11) имеет шесть зубьев, из них три зуба подрезающих и три зуба зачищающих. Подрезающие зубья выступают над окружностью резания зачищающих зубьев на 0,2 мм.
Подрезатели делаются с положительным или отрицательным передним углом. Подрезающие зубья такой фрезы формируют боковые поверхности паза с двух сторон.
Работа на фрезерных станках
При фрезеровании прямолинейных кромок деталей различают три случая:
1) фрезерование прямолинейных гладких кромок под линейку;
2) отборка профиля на всю длину детали (сквозное фрезерование) ;
3) отборка профиля на определенной части длины детали (несквозное фрезерование).
Во всех трех случаях фрезерование производится по направляющей линейке. При фрезеровании гладких кромок выходную половину линейки (вторую от станочника) устанавливают в одной плоскости с режущими кромками резцов, а переднюю заглубляют от линии резания на толщину стружки.
Рис. 11. Насадная цельная пазовая фреза
При сквозном фрезеровании, когда часть ширины обрабатываемой кромки не фрезеруют, обе половинки линейки устанавливают в одной плоскости. В этом случае режущие кромки резцов выступают за линейку на глубину фрезерования. В таких случаях к направляющей линейке прикрепляют сплошную планку с прорезью для режущей части инструмента.
При несквозном фрезеровании пользуются двумя упорами. Сначала деталь, уложенную на столе под некоторым углом к направляющей линейке, упирают торцом в передний упор (перед резцами) и прижимают к ней. Затем в таком положении деталь продвигают под резцами до противоположного упора (рис. 8).
Для обеспечения безопасности работы при прямолинейном фрезеровании, особенно при фрезеровании узких деталей, обязательно следует пользоваться верхними и боковыми прижимами.
При массовой работе удобно применять подающие устройства, пристраиваемые к любому фрезерному станку. Подача в этом случае осуществляется валиками или цепью. Аппараты эти применимы только для сквозного фрезерования.
Фрезерование внешних криволинейных кромок деталей производится с (помощью шаблонов (цулаг). Шаблон-цулага служит для прочного закрепления обрабатываемой детали во время фрезерования и обеспечивает точность обработки и соответствие контуру шаблона. Для направления шаблона применяется упорное кольцо (рис. 9), надеваемое на шпиндель станка и вращающееся на нем.
При обработке шаблон с закрепленной деталью продвигается под резцами так, что кромка его все время плотно прижимается к упорному кольцу, что обеспечивает обработку детали точно по шаблону.
infopedia.su
Вспомогательный инструмент для станков с чпу
Вспомогательный инструмент для станков с ЧПУ
Вспомогательный инструмент для станков с ЧПУ – оборудование, позволяющее осуществить точную и качественную обработку материала. Наличие подобных аппаратов позволяет повысить производительность и скорость производства. ЧПУ делится на два типа: полуавтоматический и автоматический. При работе с различными станками задействуются элементы с определенной комплектацией. Но без вспомогательных инструментов спектр выполняемых функций ограничен.
Комплекс деталей, составляющих собой наиболее важную часть комплектации станка с ЧПУ, представлен:
- станочными приспособлениями;
- режущим прибором;
- вспомогательным инструментом.
Функции
Вспомогательный инструмент представляет собой группу систем, главной функцией которых является компоновка блоков с запчастями, отвечающими за работоспособность агрегата. Блок представляет собой сочетание оборудования для режущих и дополнительных задач.
Наиболее распространенным прибором такого типа является вспомогательный инструмент для токарных станков с ЧПУ. Благодаря им крепятся:
- резцы;
- зенкеры;
- сверла;
- метчики;
- развертки.
Качественному вспомогательному инструменту характерен высокий показатель жесткости. Он должен уметь обеспечить точность и стабильность применения орудия для резки. Аппарат предназначен для поддержки всех типов работ, которые способен выполнять станок. Достоинством устройства является легкая и быстрая установка. Универсальный станок должен обладать аналогичной комплектацией для разных модификаций. Настройку прибора можно произвести, не устанавливая его на станок.
Конструкция
Закрепление оборудования на станке производится благодаря унифицированной хвостовой части. Крепление усиливают элементы для соединения с режущим механизмом. Крепление осуществляется ручным методом. Хвостовик устройства имеет цилиндрическую форму и лыску рифленого типа. Такая конструкция обеспечивает более высокий показатель надежности крепления.
Системы вспомогательных инструментов изменяются в зависимости от того, для каких задач используется станок. Быстрая смена системы требуется, если производятся работы по сверлению и фрезеровке. Станок переналаживается путем замены носителя программы. Чем выше жесткость дополнительного механизма, тем более интенсивной будет его работа. От интенсивности работы зависит, насколько быстро она будет выполнена.
Жесткость обеспечивается за счет прочного крепления. Для достижения высокой прочности крепления используются детали, изготовленные из твердых сплавов. Добавочный механизм рекомендуется настраивать до установки на станок. Это поможет сократить время работы. Многошпиндельные головки упрощают установку технологии на прибор с ЧПУ. Такое оборудование особо эффективно при мелкосерийных задачах.
Достоинства
Вспомогательный инструмент обеспечивает станок с ЧПУ целым рядом преимуществ:
- время, затраченное на осуществление задачи, сокращается вполовину;
- повышается показатель точности, благодаря чему обеспечивается экономия материала;
- обеспечивается стабильная эксплуатация;
- появляется возможность обслуживать сразу несколько станков;
- отсутствует необходимость в использовании приспособлений, имеющих сложную конструкцию;
- идентичная конструкция устройств позволяет устанавливать их на различные станки;
- настройка аппаратуры может проводиться до установки на станок;
- упрощено использование аппарата;
- увеличилось разнообразие позиций для обработки материала;
- участие человека в управлении агрегатом уменьшилось;
- увеличилась производительность станка;
- появилась возможность изготовления деталей сложной формы;
- изделия стали более качественными;
- повысилась производительность оборудования;
- использование устройства стало более простым и безопасным.
Наладка
Приведение устройства в рабочее состояние делится на две части: наладки и подналадка. Процесс наладки представляет собой подготовку оборудования к выполнению рабочей цели. Подналадка – дополнительная подготовка механизмов агрегата. Первая часть связана с основной частью станка, выполняющей поставленную задачу. Вторая часть представляет собой взаимодействие с технологической оснасткой. Именно во второй части производится наладка вспомогательного инструмента.
На первом этапе наладки производится сборка и установка режущего приспособления и его элементов. На втором этапе устанавливается заранее настроенный добавочный механизм. На третьем этапе выбирается режим работы аппарата.
Установка на станках производится тремя вариантами:
- на стол;
- в приспособление на столе;
- на координатную плиту.
Приспособление может быть установлено на координатной плите.
Особенности настройки
Настройку оборудования рекомендуется проводить перед установкой на станок. Это не только упрощает процесс настройки, но и позволяет сэкономить время. Режущая часть прибора имеет два направления: радиальное и осевое. Установка производится в выбранном направлении на определенном расстоянии от основной части прибора. Оптимальное расстояние зависит от используемого агрегата.
Для элементов имеются посадочные места. Каждый элемент имеет свой размер, который соответствует указанному месту. Правильное распределение элементов обеспечит точность работы агрегата. Для сверл, расточных оправок, зенкеров, и еще ряда элементов имеется только одна координата настройки. Для настройки используется вставка в виде ножа или индикатор. Точную настройку практически невозможно произвести без окулярного микроскопа.
Перед использованием микроскопа, для его оптических элементов требуется задать координаты, которые обеспечат точность настройки.
Самые популярные станки с вспомогательным инструментом
Вспомогательный инструмент может использоваться с любыми моделями станков современного типа, оснащенных ЧПУ. Их популярность зависит от востребованности. Наиболее часто используемыми типами аппаратов являются:
- токарным-револьверным;
- вертикально-сверлильным;
- вертикально-фрезерным.
Сборка устройства производится по ГОСТу 23597-79. Он предполагает оптимальные настройки для оборудования, обеспечивающие точность производства. Показатель точности является частично регулируемым. Уровень искажения может меняться в зависимости от того, насколько профессионально была установлена программа. Программа должна учитывать функции, которые дает дополнительная аппаратура. Вместе они могут:
- предупредить показатель искажения траектории движения прибора;
- уменьшить подачу при использовании аппарата;
- регулировать размер рабочего приспособления.
Конструкция вспомогательного инструмента может изменяться в зависимости от того, для какого типа станков он используется. Но основная задача остается неизменной – закрепление рабочих элементов прибора. Без подобного оборудования производительность и период бесперебойной эксплуатации аппарата будет значительно ниже. Режущее устройств будет хуже закреплено, по причине чего снизится качество изготовляемых изделий, и многообразие возможных форм.
i-perf.ru
Вспомогательный инструмент для станков сверлильно-расточной и фрезерной групп
Служебное назначение вспомогательного инструмента для мно- гоцелевых станков полностью соответствует инструменту токарных станков с ЧПУ. Отличительные особенности такого инструмента [3]:
— в связи с тем, что инструмент устанавливается в шпиндель станка, хвостовики обычно имеют форму конуса Морзе;
— так как смена и закрепление инструмента выполняется авто- матически, на хвостовике предусмотрены специальные поверхности, предназначенные для захвата инструмента автооператором, а также для удержания инструмента в магазине.
Пример комплекта вспомогательного инструмента показан на рис. 3.32.
В систему включены оправки насадных фрез 1, 2 (рис. 3.32), предназначенные для крепления торцовых, трехсторонних, цилинд- рических и других фрез. Цанговые патроны 3, 4, 16 (рис. 52) предна- значены для крепления инструмента с цилиндрическим хвостовиком, стандартных сверл, зенкеров, разверток, фрез диаметром 3—20 мм и специальных фрез диаметром 20—50 мм. Нерегулируемые переход- ные втулки 5, 6 (рис. 3.32) предназначены для инструмента с конусом Морзе от 2—5.
1 2 3 4 5 6 7 8 9
16 10 11 12
13 14 15
Рис. 3.32. Состав комплекта вспомогательного инструмента для многоцелевых станков с ЧПУ
Системой предусмотрена номенклатура расточных оправок для чистовой и черновой обработок. Включены оправки 9 для чистовой обработки отверстий диаметром 50—180 мм, изготовляемые с наклонными гнездами под резцовые расточные вставки с микрометрическим регули- рованием. В однолезвийных оправках 8 для чернового растачивания отверстий диаметром 50—180 мм преду- смотрено использование стандартных расточных резцов, устанавливаемых в державку.
В качестве адаптера в системе используются переход- ные державки, состоящие из корпуса с внутренним цилин- дрическим отверстием и винта для фиксации положения закрепляемого хвостовика 7. В державках закрепляются переходные цилиндрические втулки 10, оправки для на- садных зенкеров и разверток 12, патроны для метчиков 13, расточные оправки 14 и расточные патроны 15 ( рис. 3.32). Комплект вспомогательного инструмента фирмы
Sandvik Coromant показан на рис. 3.33. В состав комплек- та входят набор хвостовиков, отвечающих требованиям различных стандартов; переходники, предназначенные для увеличения вылета инструмента; набор патронов для кре- пления насадных фрез и концевого инструмента; набор черновых и чистовых расточных оправок, а также конце- вых фрез и сверл, имеющих унифицированные присоеди- нительные поверхности Coromant Capto.
При работе с высокими частотами вращения шпинде- ля ( более 10000 об/ мин) одним из основных требований к вспомогательному инструменту являются высокие и ста- бильные усилия закрепления и минимальное биение инст- румента [12]. Им соответствуют оправки с гидропластом, гидромеханическим и термическим зажимами ( рис. 3.34).
В оправках первого типа давление зажима создает ма- лосжимаемое вещество гидропласт при завинчивании вин- та в корпус.
Рис. 3.33. Состав комплекта вспомогательного инструмента для многоцелевых станков фирмы Sandvik Coromant.
При работе с высокими частотами вращения шпинделя (более 10000об/мин) одним из основных требований к вспомогатель- ному инструменту являются высокие и стабильные усилия закрепле- ния и минимальное биение инструмента [12]. Им соответствуют оп- равки с гидропластом, гидромеханическим и термическим зажимами (рис. 3.34).
В оправках первого типа давление зажима создает малосжимае- мое вещество гидропласт при завинчивании винта в корпус.
Принцип работы гидромеханических оправок схож с предыду- щим, только давление создается не винтом, а специальным насосом. При этом жидкость, находящаяся в корпусе, действует на клиновой механизм, зажимающий инструмент.
Последний тип основан на свойстве металлов расширяться при нагревании. Корпус помещается в специальное устройство индукци- онного нагрева, нагревается и в него устанавливается инструмент. После охлаждения посадочный диаметр уменьшается и инструмент закрепляется силами упругости. Данный тип оправок используется только для твердосплавного инструмента, т. к. его коэффициент теп- лового расширения ниже, чем у стали.
![]() | ![]() | ||
Рис. 3.34. Оправки с зажимом инструмента гидропластом и гидравлическим способом
Существует отдельная группа вспомогательного инструмента, предназначенного для расширения технологических возможностей станка и носящего название «специальный вспомогательный инст- румент».
К такому инструменту относятся многошпиндельные, угловые и ускорительные головки, устройства удаления стружки, дозаторы.
Автоматически сменяемые многошпиндельные головки имеют, как правило, два, три или четыре шпинделя. Вращение этих шпинде- лей осуществляется с той же частотой, что и вращение шпинделя с сохранением направления вращения. В двухшпиндельной головке (рис. 3.35) центральная шестерня 1, размещенная на хвостовике 15, вращающаяся в подшипниках 14, через блоки колес 13 и 12 передает крутящий момент от шпинделя станка на шестерни 9, размещенные на шпинделях 6 головки. Шпиндели 6 размещены в корпусах 5 с экс- центриситетом относительно осей 2 и 10, расположенных в корпусе 4 головки с межосевым расстоянием, равным 68 мм. При вращении корпусов 5 вокруг осей 10 расстояние между шпинделями 6 головки изменяется от минимального до максимального. Режущий инстру- мент цилиндрическим хвостовиком диаметром до 13 мм закрепля- ется в цангах 8 с помощью гаек 7.
![]() |
Рис. 3.35. Конструктивное исполнение двухшпиндельной регулируемой головки
Для сокращения времени, затрачиваемого на базирование и за- крепление заготовок, используются сменные головки, в которых шпиндель головки расположен относительно оси шпинделя станка под углом.
На рис. 3.36 представлена конструкция головки с углом α = 45°.
На хвостовике 1 размещена коническая шестерня 2, которая
находится в зацеплении с шестерней 3,
закрепленной с проставкой 4 на шпинделе
5 с конусом Морзе. Достижение произвольного положения оси инструмента относительно оси шпинделя достигается с помощью регулируемых угловых головок, Они выполняются с двумя разъемами, каждый из которых обеспечивает поворот соединяемых частей относительно друг друга на 360°. В результате может быть об- работана любая точка в пределах полусферы.
Ускорительные головки (мультипликаторы) предназначены для обработки на станках с ЧПУ конструкци- онных сталей и чугунов нормальной обра-
2
Рис.3.36. Конструктивная схема головки с шпинделем, расположенным под углом α = 45º
Рис. 3.37. Ускорительная головка
батываемости концевыми твердосплавным и быстрорежущим инструментами диаметром до 12 мм (сверла, центровки, зенкеры, концевые и шпоночные фрезы и т. п.) со скоростями резания, имеющими оптимальные значения. Необходимость в таких головках предопределяется тем, что ряд станков для обработки корпусных деталей имели ограниченную частоту вращения шпинделя, недостаточную для достижения необходимой скорости резания.
Пример конструкции ускорительной головки представлен на рис. 3.37. Корпус 1 выполняет роль водила, в котором на осях 9 закреплены сателлиты 7. Корпус 1 неподвижно соединен с хвостовиком 3, устанавливаемым в шпиндель станка. Сателлиты 7 находятся в зацеплении с корончатым колесом 8, которое может
быть остановлено путем соединения с позиционирующим блоком. Через солнечное колесо 2 вращение передается на выходной вал 5, который движется с частотой, в пять раз большей частоты вращения шпинделя. На открытом конце выходного вала размещен цанговый патрон с цангой 10, которая с помощью
гайки 11 закрепляет цилиндрический хвостовик инструмента 12. На другом конце выходного вала 5 с помощью шайбы 4 закреплен маховик 6, предна- значенный для повышения равномерно- сти вращения инструмента.
После сверления глухого отверстия оставшуюся в нем стружку удаляют с помощью специального устройства-отсоса стружки (рис. 3.38), который подключается к
индустриальному пылесосу через специальный разъем 2. Подвод сменного наконечника 6 к детали
Рис. 3.38. Конструктивное ис- полнение устройства для удале-
Рис. 3.39. Конструктивное исполнение дозатора для по- дачи масла
осуществляется при подаче 4—6 м/мин. После упора в деталь наконечника 6 колено 7 перемещается относительно хвостовика 1 и через трубу 5 перемещает плунжер 4 разъема 2 до срабатывания конечного выключателя 3, который подает команду на прекращение подачи устройства.
Дозатор для подачи масла (рис. 3.38) пригоден как для станков с вертикальным, так и с горизонтальным расположением оси шпинделя. Дозатор позволяет вводить масло в отверстие или в другие зоны, которые требуют сма- зывания, а также в тех случаях, когда СОЖ, находящаяся в системе станка, не пригодна для этих целей. Объем дозатора
составляет 400, 600 и 800 см3, доза масла может регулироваться от 0 до 2 см3.
Дозатор (рис. 3.39) имеет хвостовик 1 для установки в шпинделе станка, который соединяется с емкостью 2. Емкость 2 снабжена перепускным клапаном 8, втулкой 3 с запорной иглой 4, который функционирует как в вертикальном , так и в горизонтальном положениях, однако в последнем случае необходима ориентация дозатора по углу вращения шпинделя.
Из камеры 8 масло поступает в наконечник 5, в котором находится плунжер 6 с шариковым клапаном 7. При наличии масла в камере 8 дозатор со скоростью 4—6 м/мин прижимается к детали до упора форсункой 10. При этом плунжер 6 перемещается в наконечнике 5, создавая давление в камере 8. Под этим давлением срабатывает шариковый клапан 7, и порция масла выбрасывается в зону предстоящей обработки. Сменные форсунки 10 обеспечивают различную форму впрыска для достижения наилучшего эффекта смазки.
После впрыска дозатор отводится от детали и плунжер 6 под действием пружины 9 возвращается в исходное положение, функционируя при этом как поршень насоса. В камере 8 создается разрежение, клапан 4 открывается и камера заполняется маслом. Количество масла определяется величиной хода плунжера 5. При
максимальном ходе 15мм обеспечивается подача 2 см3 масла.
infopedia.su