Абразивный проволочно-вырезной станок с ЧПУ SX7720 – АлеКо
Описание станка:
Проволочно-вырезные станки абразивные с ЧПУ серии SX77 широко используются для резки графитовых электродов, пластин из эпоксидных смол, карбидных материалов, мрамора, нефрита, оптического стекла, керамики, ферритов, полупроводниковых материалов, огнеупорного кирпича и прочих материалов.
Модели отличаются величиной перемещения по осям, габаритами рабочего стола и соответственно размерами обрабатываемой заготовки.
Обрабатываемая деталь фиксируется на рабочем столе, который перемещает деталь по траектории, заданной программой. Рез происходит в результате трения между заготовкой и абразивной нитью.
- Комплектация
- Технические характеристики
- Дополнительная информация
Стандартная комплектация
- Система подачи рабочей жидкости
- Система смазки
- Проволока абразивная с алмазным напылением Ø 0,33 мм – 1000 м
- Шкаф управления ЧПУ
- Концентрат СОЖ (эмульсия JR-3A) 1:40, 2 кг – 1 шт.
- Комплект направляющих роликов Ø 100, мм (4 шт.) – 1 к-т
- Комплект инструкций по эксплуатации на русском языке – 1 к-т
Дополнительная комплектация:
- Комплект оптических линеек с УЦИ для SX7720 с установкой
- Система подачи воздуха.
Параметры | Значение |
Рабочий ход стола, мм | 200 х 250 |
Размер рабочего стола, мм | 270 х 420 |
Максимальная толщина разрезаемой заготовки, мм | 200 |
Диаметр абразивной проволоки, мм | Ф0.19-Ф0.45 |
Шаговый двигатель | 90BF006 |
Шаг импульса, мм | 0.001 |
Потребляемая мощность | 2 кВт, переменный ток 380В/220ВБ 50 Гц |
Программируемая система (опционально) | HF/HL/Autocut/ X8 |
Расстояние перемещения рабочего стола за один оборот штурвала, мм | 4 |
Габаритные размеры, мм | 1050*720* 1700 |
Вес, кг | 800 |
- Проволока абразивная с алмазным напылением.
На абразивных проволочно – вырезных станках серии SX77 применяется
проволока абразивная с алмазным напылением Ø 0,33 – 0,45 мм.
Одна намотка проволоки составляет 300 м, использование которой, в зависимости от обрабатываемого материала, может достигать 72 и более часа. - Комплект направляющих роликов. На станке установлено четыре направляющих ролика, изготовленных из высокопрочного материала. Ресурс работы роликов зависит от обрабатываемого материала и составляет 15-20 дней эксплуатации оборудования.
Напольные отрезные станки для влажной абразивной резки
Напольные станки QATM для влажной абразивной резки – это надежный и мощный инструмент для резки сложных и крупных металлических деталей. Эти режущие станки подходят для промышленного применения и обладают различными степенями автоматизации с возможностью резки по пяти осям.
- Макс.
отрезная способность: Ø 190 мм
- Движение по оси X: 420 мм, автоматически
- Движение по оси Y: 280мм, автоматически
- Движение по оси Z (опция): 200мм, автоматически
- D-ось: +/- 90 °
- E-ось: +/- 100 °
- Подробное описание
- Макс. отрезная способность: Ø 150 мм
- Движение по оси X: 365 мм, вручную
- Движение по оси Y: 170 мм, вручную
- Движение по оси Z (опция): 150 мм, вручную
- Подробное описание
- Макс.
отрезная способность: Ø 150 мм
- Движение по оси X: 345мм, автоматически
- Движение по оси Y: 200мм, автоматически
- Движение по оси Z (опция): 150 мм, вручную / автоматически
- Подробное описание
- Макс. отрезная способность: Ø 190 мм
- Движение по оси X: 420 мм, автоматически
- Движение по оси Y: 280 мм, автоматически
- Движение по оси Z (опция): 200 мм, автоматически
- Подробное описание
- Макс.
отрезная способность: Ø 244 мм
- Движение по оси X: 550 мм, автоматически
- Движение по оси Y: 360 мм, автоматически
- Движение по оси Z 550 мм, автоматически
- Подробное описание
- Макс. отрезная способность: Ø 295 мм
- Движение по оси X: 700 мм, автоматически
- Движение по оси Y: 450 мм, автоматически
- Движение по оси Z 700 мм, автоматически
- Подробное описание
Что такое абразивная обработка?
Этот процесс может заменить традиционные операции обработки с крупной стружкой, такие как фрезерование, строгание, протяжка и токарная обработка.
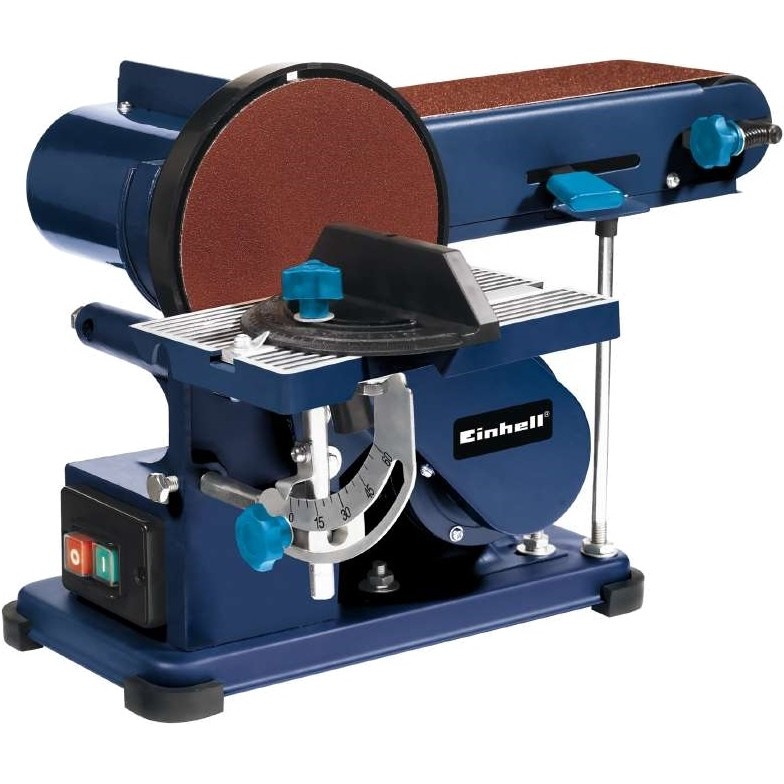
Существует прецизионное шлифование и абразивная обработка. Итак, в чем разница?
Что касается процессов шлифования, не может быть двух процессов, которые выглядят так похоже, но при этом так тесно связаны друг с другом. Простое упоминание слова «шлифовка» для некоторых специалистов-производителей вызывает в воображении кошмарные сценарии процессов, которые требуют вечности для удаления практически любого материала, на этапе, когда деталь представляет большую ценность, а любая неудача будет дорого стоить. Известно, что некоторые из них покрываются крапивницей.
Абразивная обработка – это , а не прецизионное шлифование. Целью является не сверхточность и не блестящая поверхность. Абразивная обработка в первую очередь обеспечивает высокий съем материала. Абразивная обработка не считается процессом точной шлифовки, но это не значит, что она не является точной.
Абразивная обработка может заменить процессы обработки с «крупной стружкой», такие как фрезерование, строгание, протяжка и токарная обработка. Сравните шероховатость поверхности и точность, достигаемые при обработке с крупной стружкой, с шероховатостью поверхности и точностью, достигаемой при абразивной обработке, и не будет никакого сравнения — абразивная обработка намного лучше. Абразивная обработка не только более точна, чем обработка крупной стружки (допуски по размеру в пределах 0,001 дюйма или 0,025 мм и допуски формы в пределах 0,0005 дюйма или 0,0127 мм), она также обеспечивает значительно лучшее качество поверхности. Дополнительным бонусом является то, что практически не образуется заусенцев. У абразивной обработки есть еще одна важная особенность — это средство, с помощью которого труднообрабатываемые материалы становятся пригодными для обработки, будь то металлы или неметаллы.
Абразивная обработка укоренилась в аэрокосмической промышленности в конце 1950-х годов, когда фрезерование и протяжка ласточкина хвоста и елочки на концах лопаток компрессора и турбины считались трудными, если не невозможными. В конце 50-х Эдмунд Ланг (основатель ELB в Бабенхаузене, Германия) и его сын Герхард экспериментировали с электрохимическим измельчением. Один из их экспериментов оказался неудачным, когда шлифовальный круг медленно проходил через заготовку с большой глубиной резания, но без подачи электрического тока. К их удивлению и изумлению, круг прошел прямо через заготовку, как если бы это была фреза — так родилась технология глубинного шлифования (CFG).
Глубинное шлифование показало, как оно может легко и экономично удалять труднообрабатываемые материалы с минимальным образованием заусенцев и точным сохранением формы. CFG был первым из процессов абразивной обработки, хотя, как мы увидим позже, абразивная резка также может считаться абразивной обработкой. Затем, вдали от аэрокосмической промышленности, CFG начал распространяться на другие приложения. Заготовка может быть предварительно обработана черновой фрезеровкой в мягком состоянии, подвергнута термообработке и закалке перед чистовой шлифовкой. CFG позволяет проводить сквозную закалку таких деталей и шлифовать их методом ползучести из массива. В те первые дни CFG цикл обработки считался быстрым для обработки того, что невозможно обработать. Общая стоимость была разумной, а целостность поверхности была намного выше, чем при фрезеровании или протяжке. Сегодня часто общая стоимость фрезерования по сравнению со глубинным шлифованием может быть незначительной, но качество обработки поверхности и практически отсутствие заусенцев в процессе обеспечивают значительную экономию на операциях после механической обработки.
Хотя CFG очень похож на фрезерование, использует шлифовальный круг вместо фрезы. В отличие от обычного плоского шлифования, для CFG требуется станок с высокой жесткостью и мощностью. Первые глубинные шлифовальные машины использовали обычные абразивы на керамической связке с зерном из оксида алюминия или карбида кремния, с очень открытой структурой и довольно хрупкими связками. В то время производство такого инструмента было проблемой для производителей шлифовальных кругов. В этом процессе также использовались дробильные правящие машины или алмазные валки для прерывистой правки полноразмерных форм на шлифовальные круги за очень короткое время правки. Шлифовальный круг делал один черновой проход по материалу. Затем его нужно было обработать, чтобы заточить поверхность колеса, а также восстановить форму, и был сделан окончательный, более легкий разрез для окончательного размера. Затем цикл повторялся.
Необходимо улучшить пропускную способность и производительность CFG, а также возможность избежать поверхностных трещин и пригорания заготовки. В конце 1970-х годов на сцену вышло непрерывное полирующее шлифование (CDCF). Вместо правки между деталями или проходами шлифовальный круг постоянно правится во время обработки. Точильный круг не только постоянно удерживается в постоянном состоянии максимальной остроты, но и точно поддерживается форма. Уровень остроты шлифовального круга таков, что скорость снятия припуска может увеличиться в 20 и более раз по сравнению с обычным шлифованием даже при обработке самых труднообрабатываемых жаропрочных сплавов на основе никеля и кобальта. То, на что у старого процесса CFG уходили минуты, с CDCF укладывается в секунды. Этот новый процесс произвел революцию в производстве турбинных лопаток и стимулировал разработку автоматизированных шлифовальных ячеек, которые превращали черновую отлитую лопатку турбины в полностью проверенную готовую деталь — без прикосновения к заготовке рукой человека.
Исследования по абразивам тоже шли полным ходом. Суперабразивные материалы (алмазные и эльборовые) зарекомендовали себя, в основном, в полимерных связках и в других областях, используемых для прецизионного шлифования. Затем появились застеклованные суперабразивные круги. Очевидно, что они не подходили для какой-либо непрерывной правки из-за высокой стоимости абразива, но срок службы круга из CBN был значительно выше, чем у круга из оксида алюминия или карбида кремния. В высокопроизводительных системах стали использовать круги с прерывистой правкой на керамической суперабразивной основе в режиме глубинной подачи. Однако было необходимо, чтобы приложение было высокопроизводительным или, по крайней мере, имело общую форму, потому что стоимость частого исправления другой формы на круге из стекловолокна CBN по сравнению с кругом из оксида алюминия непомерно высока.
«Промежуточный» абразив, появившийся в конце 1970-х годов, представляет собой керамический оксид алюминия. Компания 3M Co. назвала свой продукт Cubitron, а Norton выбрала название SG (от Sol-Gel или Seeded Gel). Абразив агрессивной формы, керамический оксид алюминия имеет более длительный срок службы, чем плавленый оксид алюминия. Керамический абразив, однако, требует большой силы на отдельные зерна, чтобы инициировать разрушение зерен и самозатачивание. CFG, с другой стороны, создает очень небольшие усилия на отдельные зерна. Первоначально керамический абразив плохо подходил для CFG, поэтому стали популярными гибридные круги, сочетающие плавленый и керамический оксид алюминия. Позже керамическая технология позволила производить зерна с высоким соотношением сторон, которые лучше подходили для CFG, особенно при обработке более мягких и вязких материалов, таких как нержавеющая сталь и суперсплавы. Высокое соотношение сторон может варьироваться от 4:1 до 8:1, придавая зерну направленную рыхлость. В зависимости от сложности формы круг из керамического оксида алюминия может составить конкуренцию CDCF.
Чем выше скорость круга, тем быстрее сокращается время резки и увеличивается срок службы круга. Давно известно, что оксид алюминия плохо работает на очень высоких скоростях. Фактически, скорости свыше 6000 футов в минуту (30 м/с) вызывают ускоренный истирание абразивного зерна. Однако в пластиковой связке (не смоляной, в которой используется термореактивный пластик, а термопластичный пластик) оксид алюминия хорошо показал себя при более высоких скоростях вращения колеса.
При высокой скорости CFG обычно выполняется с использованием покрытых суперабразивных шлифовальных кругов (12 000–24 000 футов в минуту или 60–120 м/с). Это называется HEDG — высокоэффективное глубокое измельчение. Сегодня колеса также могут изготавливаться с застеклованными суперабразивными сегментами, прикрепленными к периферии металлического сердечника. Для перевода скорости шлифовального круга в режим сверхвысокой скорости шлифования (UHSG) (выше 40 000 футов в минуту или 200 м/с) сердцевина круга должна быть металлической, а абразив, скорее всего, покрыт металлом. Такие колеса могут двигаться с околозвуковой скоростью (66 000 футов в минуту или 335 м/с), не опасаясь разрыва. Проблема безопасности здесь больше похожа на ситуацию «с выключенным колесом». Вероятность разрыва колеса с металлическим сердечником невелика. Но установка колеса на шпиндель на конусе приводит к возникновению слабых участков конструкции вблизи отверстия колеса, где напряжение является самым высоким. Сверхскоростные машины должны проектироваться с учетом состояния «снятого колеса». На сегодняшний день UHSG проводится только в лаборатории. Сегодня лишь немногие производственные системы работают со скоростью, превышающей 30 000 футов в минуту (150 м/с).
Что касается безопасности, то человеческая жизнь вряд ли будет в опасности во время операции UHSG, потому что скорость съема материала настолько высока, что загрузка и выгрузка деталей, а также замена круга будут выполняться автоматически. В отличие от ручных машин прошлых лет, рядом не будет травмированных людей.
Балансировка колес будет важна при более высоких периферийных скоростях колес. На таких скоростях балансировку необходимо проводить правильно, последовательно и быстро. Конструкции шпинделя станка будут сильно отличаться от используемых на обычном шлифовальном станке. Абразивно-шлифовальные станки будут включать в себя гидростатическую, воздушную и комбинированную технологию пресс-пленки. Такие шпиндели будут передавать гораздо более высокую мощность (от 40 до более 100 л.с. или 30–75 кВт), чем та, которая используется в обычной системе плоского шлифования с аналогичным размером стола. Это главное отличие прецизионного шлифования от абразивной обработки.
Прецизионное шлифование требует очень малой глубины резания при высокой скорости подачи. Действие больше похоже на полировку/трение, чем на снятие припуска. Удельная энергия (энергия, необходимая для удаления единицы объема материала) высока, и большая часть этой энергии передается поверхности заготовки. Удаление 1 дюйма3 (16,4 см3) материала занимает более 200 с. Требуемая мощность шпинделя составляет всего 12 л. с. (9 кВт).
CFG имеет более высокую удельную энергию из-за длины дуги реза, большой тонкая стружка и круг, который постоянно изнашивается, что ограничивает длину детали (3″ или 76,2 мм), которую можно шлифовать до начала термического повреждения. Большая часть энергии при шлифовании передается стружечной стружке. для удаления материала толщиной 1 дюйм 3 требуется всего 117 с. Требуемая мощность шпинделя значительна — 51 л.с. (38 кВт) при обычной скорости вращения шпинделя 9.0005
CDCF имеет самую низкую удельную энергию из-за максимального состояния остроты зерна и отсутствия энергии трения. Колесо «никогда не тупится», поэтому длина детали не ограничена. Большая часть энергии при помоле передается стружечной стружке. Чтобы удалить 1 дюйм3 материала, требуется всего 17 секунд. Требуемая мощность шпинделя составляет 38 л.с. (28 кВт), а скорость шпинделя должна быть от низкой до обычной.
HEDG имеет низкую удельную энергию из-за агрессивной природы суперабразивного зерна и может работать с большей длиной деталей, чем CFG. Большая часть энергии при измельчении передается стружечной стружке и шлифовальному кругу. Чтобы удалить 1 дюйм3 материала, требуется 83 секунды. Требуемая мощность шпинделя высока — 44 л.с. (33 кВт) при высоких скоростях шпинделя.
Что касается абразивного отрезания, отрезание куска квадратного прутка диаметром 1 дюйм (25,4 мм) имеет умеренно высокую удельную энергию из-за энергии шлифования, используемой для «самозачистки» круга во время его работы. Энергия при шлифовании передается стружечной стружке и шлифовальному кругу, а также в массу материала заготовки, которая действует как теплоотвод. Удаление 1 дюйма 3 материала (восемь разрезов) занимает всего 16 секунд. Требуемая мощность шпинделя высока, 41 л.с. (31 кВт) при обычных скоростях круга.
UHSG имеет относительно низкую удельную энергию из-за механизма хрупкого разрушения съема припуска. Большая часть энергии при шлифовании представляет собой энергию трения и распределяется между заготовкой и кругом. Удаление 1 дюйма 3 материала занимает 41 секунду. Требуемая мощность шпинделя высока, 52 л.с. (39 кВт) при значительно высоких скоростях вращения шпинделя.
Это противопоставление процессов обобщено для некоторого общего понимания; результаты могут значительно отличаться в зависимости от обрабатываемых материалов, используемых шлифовальных кругов и методов правки, применяемых для правящихся кругов.
Основное преимущество использования покрытых суперабразивных кругов в HEGD или UHSG заключается в том, что круги не нужно затачивать. Для цикла правки не нужно выделять время, и для правки круга не требуется капитального оборудования или системы управления. Однако может быть довольно большой разброс в сроке службы круга с покрытием из-за неравномерности покрытия и обработки. Мониторинг рабочих характеристик колеса в виде датчиков силы должен быть встроен в станок либо на корпусе шпинделя, либо в приспособлении для детали, чтобы персонал, контролирующий колесо, мог решить, когда необходимо произвести замену колеса.
Шлифовальные круги с покрытием не только быстро изнашиваются, но также засоряются и загружаются материалом. Покрытия с твердой смазкой использовались для обеспечения «скользкой» поверхности между зернами и, таким образом, увеличения срока службы круга благодаря дополнительному выступу зерна, достигаемому за счет устранения любой нагрузки на круг.
По мере увеличения скорости шлифовального круга силы шлифования уменьшаются, что увеличивает срок службы круга, но при этом генерирует больше энергии трения по мере износа круга. Следовательно, при высоких окружных скоростях охлаждение становится более важным, чем смазка. Криогеника успешно использовалась в очень специальных приложениях, где важно было не только охлаждение деталей, но и их жесткость.
CFG, CDCF, HEDG и UHSG считаются процессами абразивной обработки, как и «шлифование отслаиванием». Измельчение кожуры было изобретено и запатентовано компанией Erwin Junker Maschinenfabrik GmbH (Нордрах, Германия) в 1985 году под названием Quickpoint. Это процесс абразивной обработки, при котором тонкий суперабразивный шлифовальный круг работает на высокой скорости и используется в качестве передней части «токарного инструмента» для обработки цилиндрических компонентов; даже детали с большим соотношением длины к диаметру, такие как штоки автомобильных клапанов, могут быть обработаны шлифованием кожухом. Это универсальный процесс из-за общей формы формы на колесе, хотя ее можно модифицировать или изменить при необходимости.
Процесс абразивной обработки, при котором материал удаляется быстрее, чем любой другой, называется VIPER (Very Impressive Performance Extreme Removal). Первая машина была запущена в производство в 1999 году для аэрокосмической промышленности, снова производящей турбинные лопатки. VIPER сочетает в себе открытую структуру, шлифовальные круги из оксида алюминия с высокой скоростью круга, в режиме непрерывной правки и с соплами высокого давления с высокой скоростью потока, управляемыми ЧПУ, которые направляют охлажденную шлифовальную жидкость точно в то место, где это требуется, непосредственно перед до дуги реза и по всему пропилу и всем диаметрам круга. Этот процесс лучше всего выполнять на обрабатывающем центре, где замена круга и правящего инструмента может происходить автоматически и под полным контролем ЧПУ. В запатентованном Rolls-Royce процессе используются специальные колеса производства Tyrolit.
Более высокая скорость вращения колеса кажется целесообразной, но «Почему сверхвысокая скорость? Это просто трюк?» Существует дополнительное преимущество перехода в область сверхвысоких скоростей (выше 35 000 футов в минуту или 178 м/с). По мере увеличения скорости круга изменяется морфология стружки. Большинство металлов обрабатывается в пластичном режиме, тогда как керамика обрабатывается в хрупком режиме. Металлическая стружка длинная и тонкая и может закупоривать поры шлифовального круга, уменьшая зазор между абразивными зернами. Керамическая (ломкая) стружка больше похожа на пылинки. Было показано, что когда окружная скорость круга и, следовательно, скорость зерна превышает скорость распространения напряжений в материале, стружкообразование меняется с пластичного на хрупкое. Аналогия может заключаться в том, чтобы сначала визуализировать обработку с нормальной скоростью, когда стружка формируется в пластичном режиме, а затем, по мере увеличения скорости резания, наступает момент времени, когда материал сжимается перед зерном и не может двигаться наружу. пути и действует как хрупкий материал. При сверхвысоких скоростях круга твердые и мягкие материалы будут обрабатываться одинаково.
Эти очень быстрые операции резки потребуют автоматизации для загрузки деталей и замены круга. Оглядываясь назад, когда компания CDCF произвела революцию в производстве турбинных лопаток и появились шлифовальные станки, можно сказать, что именно автоматизация вывела производительность на новый уровень, но она была сосредоточена вокруг конструкций станков ушедшей эпохи. Для высокоскоростных шлифовальных систем необходимо перепроектировать станок в сочетании с необходимой автоматизацией и безопасностью. Это будет не новая эра, это будет совсем другой мир.
Абразивная обработка — это более быстрый и экономичный способ обработки труднообрабатываемых материалов, конкурирующий с фрезерованием, протяжкой, строганием и токарной обработкой. За последние пять или около того лет сложилась тенденция, когда производители станков объединяют абразивную обработку с обработкой крупной стружки на одном устройстве, которое должно обрабатывать большие объемы шлифовальной стружки «Brillo» или «SOS» и, возможно, некоторое количество рыхлого абразивного зерна. , а также крупную стружку от операций сверления и фрезерования. Однако крайне важно иметь систему фильтрации жидкости, которая может надлежащим образом справиться со всем спектром стружки и стружки.
Лосьон «Каламин» может облегчить боль от крапивницы, но для того, чтобы по-настоящему увидеть высокий съем практически любого материала практически без заусенцев, необходима абразивная обработка.
Что такое абразивная обработка? (с изображением)
`;
Промышленность
Факт проверен
М.

Абразивная обработка — это процесс использования абразивов для очистки поверхности твердых предметов. Мелкие зерна, называемые зернистостью, используются для удаления материала небольшими порциями. Этот процесс используется для полировки поверхностей, резки твердых материалов или изменения формы стали.
Зернистость – это то, что делает абразивную обработку эффективной. Используя песок в качестве абразива, оператор может проникать в материалы, слишком твердые для обычных режущих инструментов. Он работает, когда песок вступает в контакт с поверхностью с большим усилием. Отдельные частицы песка постепенно изнашивают поверхность. В конечном итоге процесс удаляет достаточно материала, чтобы создать надрез или выровнять поверхность, которая полирует объект.
Одним из распространенных примеров является наждачная бумага.
Сыпучие абразивы идеально подходят для больших или труднодоступных поверхностей. Абразивоструйная очистка – это один из методов, в котором используются свободные абразивы. Он использует высокое давление для перемещения абразивов по поверхности для сглаживания, придания шероховатости или удаления поверхностного слоя.

Гидроабразивная обработка отличается от обычных абразивных станков тем, что в ней не используется твердое зерно. Вода находится под давлением и выбрасывается концентрированной струей, чтобы направить поток на поверхность цели. Используя воду в качестве абразива, операторы обходят два обычных недостатка обычных абразивных машин.
Во-первых, некоторые твердые абразивы дороги. Карбид кремния и алмаз, используемые в качестве промышленных абразивов, требуют больших затрат как в производстве, так и в приобретении. Во-вторых, трение, создаваемое абразивом, вызывает сильное нагревание, что увеличивает затраты на охлаждение процесса. Вода действует как охлаждающая жидкость и как абразив, что экономит оператору дополнительные расходы.
Использование различных сортов абразива особенно полезно для абразивной обработки. Различные сорта позволяют оператору подобрать абразив в соответствии с его назначением. Абразивная обработка используется в тех работах, где допустима небольшая погрешность. Правильная марка абразива иногда может быть фактором хорошо выполненной работы.