Обороты шпинделя: задаём оптимальную частоту вращения
Чтобы не ошибиться с “оборотами”, надо знать всего две вещи: диаметр фрезы D (это просто) и скорость резания данного материала Vr (это тоже). Скорость резания можно подсмотреть здесь:
- алюминий и алюминиевые сплавы — 200-400 м/мин,
- латунь — 150-300 м/мин,
- бронза — 100-150 м/мин,
- бакелит — 50-100 м/мин,
- ПВХ — 100-200 м/мин,
- термопласты стандартные (акрил, нейлон и проч.) — 300-500 м/мин,
- древесина — 300-400 м/мин,
- нержавеющая сталь — 50-90 м/мин.
Теперь, когда мы всё это знаем, подставляем значения в формулу:
n = (1000 * Vr) / (3,14 * D),
где n — частота вращения шпинделя (об./мин), а всё остальное Вы уже знаете, потому что внимательно читали первое предложение 🙂
Например: режем древесину 6-миллиметровой фрезой.
Внимание: расчёты верны только для фрез со стандартным соотношением диаметра и рабочей длины — 1/3-1/5. При меньшем соотношении (при большей длине фрезы) обороты необходимо уменьшать!
Вернёмся к примеру. Еесли у нас не обычная фреза на 6 мм с рабочей длиной 22 мм, а удлинённая — допустим, с длиной 52 мм, обороты могут быть подобраны только экспериментально, начиная со стандартного значения, делённого на 4 или даже 5. То есть, ставить надо не 16 тыс., а 3200 об/мин (16000 / 5) и, если не возникает посторонних шумов, понемногу увеличивать до устраивающих значений, при которых всё ещё не возникает вибраций.
Важно помнить, что частота вращения — это полдела, потому что ещё надо правильно выбрать подачу. Она может быть тем быстрее, чем выше “обороты” шпинделя, но с их увеличением неизбежно ускоряется и износ режущих кромок фрезы.
как её выбрать? — MULTICUT
При составлении технологической карты токарной или фрезерной обработки специалисту нужно найти оптимальный баланс между производительностью станка и требованиями к чистоте поверхности готовой детали. Основные параметры, на которые он может повлиять — это частота вращения шпинделя и скорость подачи. Выбор режимов обработки проводится расчетным или опытным путем.
Сложность работы на портальных фрезерно-гравировальных станках состоит в их многозадачности. В одной управляющей программе может быть несколько видов обработки: контурная резка, фрезерование пазов и сквозных отверстий, гравирование. При этом материалы — дерево, пластик и композиты, различаются сопротивлением резанию и структурой. Многие начинающие операторы сталкиваются с такими неприятными моментами как прижог, недостаточная чистота обработки, преждевременный износ режущей кромки.
Что такое скорость вращения шпинделя и подача?
Скорость вращения — один из основных параметров шпинделя. Он выражается в оборотах в минуту (об/мин) или герцах (Гц). В портальных станках с ЧПУ не используется сложных по конструкции механических коробок передач и скорость регулируется электронными компонентами. С увеличением скорости вращения растет производительность станка и снижается ресурс режущего инструмента. Последнее связано с выделением избыточного количества тепла, которое не успевает рассеиваться. В результате перегрева падает твердость режущих кромок, и они теряют свою остроту.
Скорость подачи, или линейного перемещения, измеряется в миллиметрах в минуту (мм/мин) и влияет на объем снимаемого материала в единицу времени. На портальных станках без механизма вращения заготовки регулируются скорости перемещения портала, каретки и вертикального движения шпинделя. При составлении управляющих программ стараются задать максимально возможные подачи, при этом должно выполняться условие сохранения целостности фрезы. Избыточная скорость приводит к появлению сколов на режущих кромках поломка или деформация хвостовика.
Распространенные ошибки при выборе режимов резания
Одно из важных условий правильной работы станка — согласование скоростей вращения и подачи фрезы между собой. Некоторые начинающие станочники при выборе режимов резания допускают ошибки в попытках сохранить инструмент.
Работа на минимальных скоростях приводит к снижению качества обработки. Если величина подачи сопоставима с толщиной режущей кромки, то вместо снятия стружки фреза надавит на заготовку и будет только шлифовать ее своей поверхностью. Чтобы понять, что в этот момент происходит с обрабатываемой поверхностью, представьте, что вы включили реверс на шпинделе, в котором зажато спиральное сверло, и пытаетесь «продавить» отверстие. На высоких оборотах будет наблюдаться прижог обрабатываемой поверхности и режущей кромки, отгибание фрезы.
Обратная ситуация, когда при высокой подаче шпиндель работает на малых оборотах, заставит фрезу снимать слишком толстую стружку. Из-за высокой нагрузки откалываются режущие кромки, а на обрабатываемой поверхности будут оставаться заметные «следы».
Для каждой фрезерной операции существует оптимальное соотношение скоростей подачи и вращения инструмента, на которых обработка будет проходить с достаточной скоростью и точностью. Это не фиксированные величины, а диапазоны. Поломка или преждевременный износ будут наблюдаться при критической ошибке.
Обработка чаще всего состоит из двух этапов: чернового, направленного на максимальный съем материала и чистового, при котором достигается требуемая шероховатость поверхности. Для чистового прохода снижают скорость подачи при сохранении оборотов шпинделя, а в станках со сменой режущего инструмента его выполняют другой, чистовой, фрезой.
Рекомендации по выбору режимов резания
Существует несколько типичных ситуаций, при которых можно воспользоваться общими рекомендациями.
Слишком большие обороты шпинделя
- Заменить фрезу из быстрорежущей стали на твердосплавную, по возможности — с покрытием, которое работает при повышенных температурах.
- Уменьшить диаметр фрезы. При этом снизится окружная скорость, с которой движется режущая кромка.
- Использовать технологию HSM. Высокоскоростная обработка позволяет повысить частоту вращения шпинделя и скорость подачи без увеличения износа режущего инструмента. Первый проход выполняется на полную ширину фрезы, а все последующие — на ¼ диаметра.
Слишком малая скорость подачи
В ситуациях, когда привода перемещения не могут обеспечить требуемую скорость подачи, можно поступить следующим образом:
- Уменьшать скорость вращения шпинделя вплоть до минимально допустимой мощности.
- Использовать фрезу с меньшим количеством зубьев. Такое решение дает хорошие результаты при работе с вязкими материалами, поскольку улучшаются условия отвода стружки с обрабатываемой поверхности. Замена фрезы с 3 зубьями (заходами) на однозаходную фактически означает увеличение скорости подачи в 3 раза (на каждый зуб).
- Использовать фрезу большего диаметра.
Налипание стружки при фрезеровании алюминия
Из-за относительно низкой температуры плавления алюминий имеет свойство налипать на поверхность фрезы. Многие начинающие фрезеровщики пытаются решить эту проблему регулированием оборотов шпинделя или скоростей перемещения. В результате оптимальный для фрезы режим резания становится неоптимальным для владельца предприятия: скорость обработки оказывается слишком низкой.
Главная причина налипания стружки — недостаточная подача или неправильный состав СОЖ. Если у станка нет возможности подавать смазочно-охлаждающую жидкость, необходимо организовать вакуумное удаление стружки или продувку сжатым воздухом.
Работа с глубокими отверстиями
Если глубина отверстия в 6 и более раз превышает его диаметр, оно считается глубоким. Неопытные станочники часто сталкиваются с такими проблемами как уход инструмента с оси и его поломка. Существует несколько приемов, которые позволят выполнить обработку точно и без потерь:
- Пользоваться сверлами, а не фрезами. По возможности они должны иметь параболические канавки, которые обеспечивают лучший отвод стружки.
- Подавать СОЖ под давлением. Жидкость будет вымывать стружку из отверстия.
- По возможности производить последовательную обработку двумя сверлами с разными диаметрами: проходить половину глубины отверстия меньшим диаметром и рассверливать до чертежного. Затем пройти отверстие до конца.
- При работе одним сверлом как можно чаще вынимать его из отверстия для удаления стружки.
- Увеличить скорость подачи, чтобы стружка представляла собой непрерывную спираль.
Как фрезеровать пазы?
При фрезеровании торцов деталей и внутренних поверхностей пазов цилиндрическими фрезами важно выбрать правильное соотношение ширины и глубины снимаемого материала в соответствии с максимальными скоростными возможностями станка. При увеличении глубины фрезерования нагрузка на канавки распределяется более равномерно, но вместе с этим наблюдается более сильный отгиб режущего инструмента. Кроме того, ухудшаются условия удаления стружки. При увеличении ширины снимаемого материала существует возможность увеличения скорости вращения шпинделя. Однако есть некоторые граничные значения частот, при которых скорость съема материала начинает падать.
Единственный способ получения оптимального сочетания этих двух параметров — тестирование станка в разных режимах. При этом материал «пробной» и «рабочей» заготовок должен быть одинаковым.
Сотрудники компании MULTICUT посвятили много времени изучению режимов обработки разных материалов. Выбор базовой комплектации станков собственного производства выполнялся с учетом полученного опыта. Сотрудники компании готовы оказать консультационную и практическую помощь в освоении оборудования и выборе оптимальных режимов резания. Любой желающий может поработать на действующем станке MULTICUT в демонстрационном центре и получить советы опытных мастеров. Получить консультации и справки можно, позвонив по контактному телефону.
Какая может быть частота вращения шпинделя?
Шпинделем принято называть вращающуюся часть станка, фрезерного или токарного. Если рассматривать токарный станок, то на шпинделе, в патроне закрепляется заготовка, а если рассматривать фрезерный – то вращается фреза. Так как размеры заготовок и фрез могут очень отличаться друг от друга, то и обороты шпинделя могут варьироваться в очень больших пределах.
Напомним, что определяющим параметром для расчета скорости вращения шпинделя, является скорость резания, из чего следует что чем больше размер заготовки для токарной обработки и чем больше диаметр фрезы, тем меньшие требуются обороты. Для токарных станков характерны обороты от 100 и менее до 3000 об/мин, которые сравнительно легко получить, используя самые обычные асинхронные двигатели вместе с коробкой передач или преобразователем частоты.
То же касается и обычных вертикальных фрезерных станков, у которых обороты редко превышают 3000…5000 об/мин, так как они в основной своей массе предназначены для силового фрезерования фрезами крупного диаметра.
По-иному обстоит дело для шпинделей современных обрабатывающих центров и более простых портальных фрезерных станков, а также гравировальных машин. Недавно появившаяся технология высокоскоростной обработки материалов получила массовое распространение ввиду появления приемлемых по цене высокоскоростных шпинделей.
Основной целью, к которой стремятся производители высокоскоростных шпинделей и станков является повышение производительности операций фрезерования, и в особенности фрезерования мелким инструментом с диаметром меньше 3мм.
Рассмотрим основные категории высокоскоростных шпинделей, которые встречаются на фрезерных станках:
- шпиндели высокой мощности от 5 кВт и более: применяются в основном на обрабатывающих центрах или крупных станках, имеют диапазон оборотов до 12000…18000 об/мин и предназначены для высокопроизводительной обработки, в том числе труднообрабатываемых материалов.
- шпиндели средней мощности 1.5…5 кВт: применяются на среднеразмерных портальных фрезерных станках. Такие станки чаще всего применяют для резки различного рода пластиков, дерева и мягких металлов. Верхний диапазон оборотов этих шпинделей лежит в диапазоне 18000…24000 об/мин.
- шпиндели малой мощности 0.8 кВт и менее: применяются на малоразмерных фрезерных и гравировальных станках, а также на сверлильных станках для производства печатных плат. Верхний предел оборотов таких шпинделей доходит до 40000 об/мин, а для некоторых моделей – до 60000…70000 об/мин.
Выше мы рассмотрели шпиндели, построенные на основе асинхронной трехфазной машины и классических подшипниках. Дальнейший рост скорости вращения в такой схеме затруднен ввиду наличия механического трения и конечной точности изготовления подшипников. Поэтому на самых высококлассных шпинделях используют газодинамические подшипники, питаемые сжатым воздухом. Также существуют модели шпинделей построенных на основе воздушной турбины. Шпиндели такой конструкции при правильной эксплуатации исключительно надежны и имеют долгий срок службы.
Однако вернемся к шпинделям, построенным на основе асинхронной машины. Асинхронный двигатель имеет один существенный недостаток – невозможность работы на частотах значительно ниже номинальной. С понижением частоты вращения падает и выходной момент шпинделя. Хотя современные преобразователи и могут улучшить ситуацию, принципиально изменить ее нельзя. Ситуацию осложняет специфическое применение асинхронного двигателя в качестве шпинделя, так как обычно пониженные обороты нужны для вращения крупного инструмента, которому требуется как раз более высокий момент.
Практические значения нижней границы оборотов лежат в диапазоне 20…30% от максимальных заявленных оборотов шпинделя, они сильно зависят от выполняемой задачи и нагрузки на двигатель. Также заметим, что заявленные максимальные обороты не являются физическим пределом. Все высокоскоростные шпиндели можно легко разгонять до 120% от номинальных оборотов и даже выше, но при этом следует помнить, что ресурс подшипников может резко снизиться.
Резюмируя все вышеизложенное можно сказать, что не существует универсального шпинделя с большим диапазоном оборотов. Правильно подобрать размер, мощность и максимальные обороты шпинделя можно лишь четко обозначив задачу, для решения которой он будет использоваться.
Шпиндель частота вращения – Энциклопедия по машиностроению XXL
При внутреннем шлифовании поверхностей отверстий малых диаметров (в несколько миллиметров) станки снабжают специальными быстроходными шпинделями. Частота вращения круга доходит до 300 ООО 1/мин. [c.416]Число скоростей сверлильного шпинделя Частота вращения сверлильного шпинделя, мин [c.45]
Число скоростей шпинделя Частота вращения шпинделей, об/мин 21 39 27 40 21 25 39
[c. 14]
Число скоростей шпинделя Частота вращения шпинделей, об/мин 29 40 25 9 8 40 [c.15]
Число скоростей шпинделя Частота вращения шпинделя, об/мин 50 50 22 21 21 [c.17]
Число скоростей шпинделя Частота вращения шпинделя, об/мин 21 20-2000 18-2000 21 10-1000 21 20-2000 22 12,5-1600 22 10-1250 [c.30]
Частота вращения шпинделя, мин Ступень коробки скоростей Код частоты вращения шпинделя Частота вращения щпинделя, мин Ступень коробки скоростей Код частоты вращения шпинделя [c.499]
Важным является тот факт, что центробежная сила дисбаланса находится в квадратичной зависимости от угловой скорости шпинделя. Частота вращения определяется заданной скоростью резания V при заданном диаметре инструмента d [c.245]
После вычисления скорости резания определяют частоту вращения шпинделя станка, соответствующую этой скорости резания, об/мин
[c. 276]
Так как на станке точно такой частоты вращения шпинделя может не быть вследствие ступенчатого регулирования, то назначают ближайшую меньшую частоту вращения. [c.276]
Приводы станков бывают со ступенчатым и бесступенчатым регулированием частоты вращения шпинделя и величины подач. Приводы со ступенчатым регулированием выполняют в виде зубчатых коробок передач, обеспечивающих получение определенного ряда значений частоты вращения или подач. Системы бесступенчатого регулирования позволяют получать частоту вращения шпинделя и величины подач в определенных пределах, что обеспечивает возможность работы на расчетном режиме резания. [c.284]
С вала IV движение клиноременной передачей с диаметрами шкивов 174—174 мм передается полому валу V, а далее через зубчатые передачи 34—68 и 20—80 — на шпиндель VII. Переключением муфты All влево вращение вала V передается шпинделю VII. Шпиндель станка имеет 24 частоты вращения (И—2240 об/мии).
[c.288]
Частота вращения шпинделя, об/мин, [c.288]
Например, наименьшая частота вращения шпинделя [c.290]
С помощью гитары скоростей 9 устанавливают частоту вращения шпинделя в минуту. Гитара деления (обкатки) II служит для сообщения заготовке окружной скорости, необходимой для автоматического деления заготовки на заданное число зубьев. С помощью гитары подач 10 устанавливают вертикальную подачу фрезы или горизонтальную подачу заготовки. Гитара дифференциала (находится в одной коробке с гитарой подач) сообщает заготовке дополнительное вращательное движение при нарезании колес с косым зубом. Она позволяет увеличить или уменьшить скорость вращения заготовки, которая определяется настройкой делительной гитары, и получить левый или правый наклон зубьев колеса. На зуборезных станках G программным управлением [c.352]
Для согласования значений подачи 5 и частоты вращения шпинделя п с паспортными данными оборудования используют коэффициенты геометрических рядов подач (фа) и частот вращения шпинделя (фп) [c.

Режимы обработки частота вращения шпинделя и подача Sj находятся в пределах паспортных данных станка. В качестве целевой функции принимается себестоимость С выполнения р-пе- [c.121]
Подп]ипники более высоких классов точности применяют для валов, требующих точного вращения в связи с назначением машины, например шпинделей металлорежущих станков, валов и осей приборов, или в связи с особо высокими частотами вращения. [c.346]
Более точным и перспективным в отношении автоматизации процесса балансировки является способ определения статической неуравновешенности в процессе вращения ротора, т. е. в динамическом режиме. Одним из примеров оборудования, работающего по этому принципу, служит балансировочный станок, изображенный на рис. 6.15. Неуравновешенный ротор /, закрепленный на шпинделе 4, вращается с постоянной скоростью ojr, в подшипниках, смонтированных в плите 2. Эта плита опирается на станину посредством упругих элементов 3. С плитой 2 с помощью мягкой пружины 5 связана масса 6 сейсмического датчика. Собственная частота колебаний массы датчика должна быть значительно ниже частоты вращения ротора. Массе 6 дана свобода прямолинейного перемещения вдоль оси х, проходящей через центр масс S(i плиты.
[c.218]
Частоту вращения шпинделя (гидромотора) и мощность, потребляемую насосом, при площади проходного сечения дросселя 5др = 0,03 см1 [c.130]
Максимально возможную частоту вращения шпинделя. [c.130]
Пример функциональных связей, определяющих параме> трическую надежность изделия В качестве примера оценки изменения выходного параметра рассмотрим погрешность обработки на револьверном станке-автомате (рис. 63), Обрабатываемая за готовка (пруток) вращается с частотой вращения /г в, шпинделе станка 7, а инструмент закреплен в шестипозиционной револьверной головке и последовательно подводится к изделию. На рисунке изображена обточка прутка при подаче головки со скоростью s, причем диаметр детали d должен быть обработан с заданной точностью. Выходным параметром является погрешность
[c.196]
Диаметр рабочей поверхности стола, мм Наибольший расчетный диаметр фрезы, мм Наибол1>шее перемещение гильзы, мм Наибольшее перемещение фрезерной бабки, мм Размер конца шпинделя по ГОСТ 836-72 Число скоростей шпинделя Частота вращения шпинделя, мин
[c. 41]
Черновое нарезание зубьев выполняют 10 блоков (50 резцов). Линии резов при черновом нарезании в осевом сечении зуба показаны на рис. 11.11, б, а в поперечном сечении—на рис. 11.11, в. После чернового нарезания зуб не имеет правильной конусной формы. Поверхность зуба, расположенная слева от линии аЬ (рис. 11.11, б), подготовлена для чистового нарезания, а поверхность зуба, находящаяся справа от линии аЬ, по высоте профиля и впадине зуба имеет значительно больший припуск, который снимается пятью получистовымн резцами одиннадцатого блока 4 (см. рис. 11.11, а) при перемещении заготовки вверх из точки В в точку С. Во время прохождения безрезцового участка 6 протяжки мимо заготовки происходит снятие фаски резцом 12 (рис. 11.11, г) сначала со дна впадины, а затем с боковых сторон зуба на внешнем торце.Фасочный резец получает вращение от зубчатого колеса, закрепленного на инструментальном шпинделе.

При включении муфты 10 вращение через зубчатые колеса г = 57 и г 76 передается на широкое зубчатое колесо г = 38 револьверного суппорта. Далее вращение через конические зубчатые колеса г = 23 и 2 = 46 передается диску 13, его палец заходит в один из шести пазов мальтийского креста 12, сидящего на оси револьверной головкн 21, и поворачивает ее. За один оборот диска с пальцем револьверная головка поворачивается на одну позицию (угол 60°). Если инструменты на ней установлены только в трех позициях (через одну), то на диске 13 устанавливаются два пальца. Тогда за один оборот диска головка повернется сразу же на две позиции (угол 120°). Торцовый цилиндрический кулачок 20, установленный на кривошипном валу XI, выводит фиксатор из револьверной головки. Ввод фиксатора осуществляется пружиной. На валу /X установлен поводок 14, переключающий через мальтийский крест переключатель 15 частоты вращения шпинделя. Частота вращения кривошипного вала X/ с диском /3 всегда постоянна и равна = 90 об/мин, а время поворота револьверной головки на одну позицию = 0,667 с. На распределительные валы Х/1 и X//I вращение передается от вспомогательного вала V/I через зубчатые колеса г = 29, г = 79 и сменные зубчатые колеса а, Ь, с, d. Далее через червячную передачу 2=1 и г = 40 вращение передается на поперечный распределительный вал X//, а через коннческне зубчатые колеса z = 44 н г -= 44 на продольный распределительный вал X//I. На поперечном распределительном валу X// кроме дискового кулачка 17 подачи револьверного суппорта установлены кулачки 19, переключающие конечный выключатель 18 реверса вращения шпинделя автомата. На продольном распределительном валу X/// кроме командных кулачков 24 и 26 установлены дисковые кулачки 27, 28, 29 подачи поперечных суппортов и кулачок 25 подвода лотка для сбора готовых деталей.
[c.281]
Установить требуемую частоту вращения шпинделя. Частоту вращения шпинделя определить по выбранной скорости резания и диаметру обрабатьшаемой заготовки.
[c.43]
На рис. 6.19 показана кинематическая схема вертикально-фрезерного станка с ЧПУ модели 6Р13ФЗ. Механизм главного движения станка представляет собой обычную коробку скоростей, в которой 18 частот вращений шпинделя получают переключением двух тронных и одного двойного блока 19—22—16 37—46—26 и 82—19). Источником движения служит электродвигатель /VIj (N = 7,5 кВт, п = 1450 об/мин). Диапазон частот вращення шпинделя 40— 2000 об/мин. [c.292]
В передней бабке 6 смонтированы коробка скоростей станка и шпиндель. Механизмы и передачи коробки скоростей позволяют получать разные частоты вращения шпинделя. На шпинделе закрепляют зажимные приспособления для передачи крутящего момеига обрабатываемой заготовке. На лицевой стороне передней бабки установлена панель управления 5 механизмами коробки скоростей. [c.296]
Критерий оценки выбранного маршрута обработки поверхности — минимальное число оборотов шпинделя, необходимое для обработки поверхности при нормативной подаче [19]. При обработке проходным резцом необходимая частота вращения шпинделя rtnp = L/snp, а при обработке фасонным резцом Пф = го/5ф, где L — длина обработки Snp и 5ф — соответственно значения подачи при обработке проходным и фасонным резцами Zo — общий припуск на обработку.
[c.124]
Возможные варианты маршрутов сравниваются по частоте вращения шпинделя, необходимой для обработки конкретной поверхности детали (в случае однопереходных маршрутов), т. е. сравниваются отношения -Е/ пр.ср и 2о/5ф,ср И средние значения подач Snp. p и ф.ср, рекомендуемых по нормативам. Из просмотренных вариантов маршрутов выбирается более производительный. [c.124]
Для каждой Е1елимитирующей позиции можно указать множество пар niSj (частот вращения шпинделя и подач), удовлетворяющих требованиям по точности обработки диаметрального размера, шероховатости обработанной поверхности, мощности, потребной на резание. Кроме того, необходимо, чтобы время обработки на иелимнтирующих позициях было не больше времени обработки на лимитирующей позиции [c. 140]
Таким образом, при обработке на станке число работ я заменяется на число рабочих позиций и многошпинделыюго автомата II я кандидатов на выполнение каждой работы — на число возможных сочетаний о пар режимов резания (n Sj)—частот вращения шпинделя я, и подач Зу [c.140]
Номер отиер-стии под шпиндель, мм Диаметр отверстия п шпинделе, мм Наружный диаметр шпинделя, мм Длина шпинделя, мм Частота вращения, об/мин [c.179]
Технологические возможности станков с ЧПУ обусловлены их универсальностью, повышенными жесткостью, мощностью привода и точностью, многоинструментальностью, автоматизацией цикла технологических операций, широким диапазоном частот вращения шпинделя и подач, наличием корректоров положения инструментов, возможностью ручной коррекции подач, режимов интерполяции, сокращением вспомогательного времени благодаря высоким скоростям вспомогательных ходов и малым затратам времени на смену инструментов.
[c. 218]
При необходимости вращения детали относительно вертикальной осп (круговые, кольцевые угловые швы) используют поворотный стол для установки и съема деталей и их вращения относительно неподвижной сварочной головки. Примером такого станка для сварки круговых швов детали малого размера (рис. 10.31) является полуавтомат, обеспечивающий одновременную сварку двух разных швов на позициях IV и VI поворотного стола (рис. 10.32, а). Периодический поворот планшайбы стола на 1/8 оборота осуществляется мальтийским механизмом. Привод вращения деталей на сварочных позициях /V п VI достигается прижатием к каждой из них подпружиненных поверхностей постоянно вращающихся шпинделе (рис. 10.32, б). Частота вращения подбирается с помощью сменных шестерен, длительность цикла сварки составляет 14… 17 с. Привод движения всех механизмов станка (рис, 10,33) осуществляется от одного непрерывно работаюп его электродвигателя /.
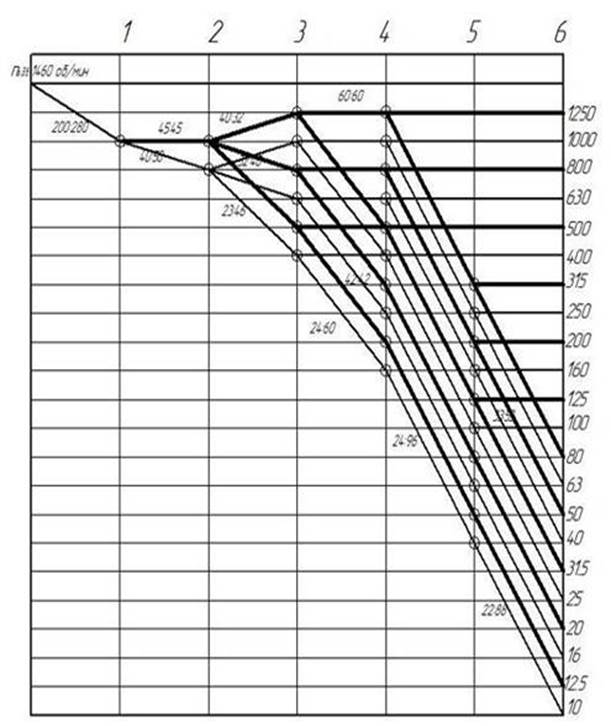
Пример I. Рассчитать передачу роликой цепью для привода шпинделя токарного автомата по следующим данным мощность на ведущей звездочке Ni = 2,6 кВт, частота- вращения ведомой звездочки 2 = 400 об/мин, передаточное число передачи и = 2, межосевое расстояние не более а = 750 мм, регулировка передачи производится смещением оси ведущей звездочки, нагрузка — с умеренными толчками, смазка — периодическая, работа — двухсменная, линпя центров звездочек наклонена к горизонту под углом 80°. [c.264]
Расчетную частоту вращения вала, об/мии, выбирают соответственно по частоте вращения шиинделя п пп или выходного вала коробки, при которой они передают наибольшие моменты (обычно берут минимальную частоту вращения шпинделя, при которой передается полная мощность).
[c.18]
В совремешшх станках окружные скорости на шейке вала доходят до 12 м/с. Удельные давления р в подшипниках валов и шпинделей станков, имеющих среднюю частоту вращения, обычно не превыпиют 30 кгс/см2, в подшипниках тихоходных валов при малых окружных скоростях (измеряемых долями м/с) удельные давления иногда доходят до 100 кгс/см . [c.28]
Частота вращения шпинделя определение, ряды и график частот определение, формула, расчет
Для обработки самых разных заготовок и получения определенных изделия практически всегда используется фрезеровальное или токарное оборудование. Оно отличается просто очень большим кол-во самых разных свойств, посреди которых отметим наличие шпинделя. Назначение аналогичного узла состоит в креплении заготовки или инструмента на момент работы. Выделяют довольно очень много самых разных показателей, которые должны предусматриваться.
Примером можно назвать то, что скорость вращения шпинделя варьируется в довольно обширном диапазоне, подбирается в зависимости от сфере использования оборудования и множества прочих факторов. Собственными силами определить частоту вращения шпинделя можно только при проведении теоретических расчетов, практический критерий указывается изготовителем оборудования в инструкции по эксплуатированию. Рассмотрим детальнее то, как высчитать частота вращения шпинделя и какими характерностями обладает устанавливаемый узел на станках.
Обозначение скорости вращения
Часто обозначение скорости вращения шпинделя проходит при разработке технологичной карты получения того либо другого изделия. Собственно поэтому для определения точного значение необходимо уделять большое внимание исходным данным. Во многих случаях они смотрятся так:
- Вид используемого материала при разработке заготовки. Во многих случаях эта сталь, которая обладает конкретным критерием твердости, а еще пределом прочности. Во многих случаях заготовка представлена углеродистой сталью, отличающаяся практически небольшой степенью обрабатываемости. Также могут применяться разные разноцветные сплавы, а еще чугун.
От типа используемого материала в большинстве случаев зависит то, какая нагрузка должна оказываться на поверхность для снимания конкретного слоя материала. В большинстве случаев собственно вид материала определяет частота вращения шпинделя, который подбирается в любых ситуациях обработки.
- Диаметр заготовки может изменяться в очень широком диапазоне. При этом для расчета ключевых показателей принимается во внимание величина припуска. Она делится на несколько проходов в зависимости от того, какой точности размеров и качества поверхности необходимо добиться после обработки механическим способом. Очень часто точение разбивается на несколько ключевых операций: черновое, чистовое и финишное. При черновом, в основном, подбирается больший критерий снимаемого материала, благодаря чему проходит Понижение частоты вращения шпинделя. При чистовой отделке критерий может быть значительно повышен, так как нагрузка на важные элементы значительно уменьшается. Финишное резание дает возможность получить невысокую уровень шершавости, которая свойственна деталям, которые используются при разработке ответственных механизмов.
- Длина отделываемой детали имеет большое значение при подборе ключевых показателей резания. Связывают это с тем, что обработка может проходит поэтапно. Очень велика длина изделия определяет значительное увеличение нагрузки на шпиндель и крепление инструмента для резки.
- Квалитет точности и требуемая шероховатость считаются основными параметрами, которые влияют на число оборотов шпинделя. Большую точность можно достичь только при выборе высокой частоты вращения шпинделя и использовании более нового оборудования. Наиболее больший коэффициент квалитета точности можно достичь при использовании станков с числовым программным управлением, так как их конструкция отличается высокой жесткостью и точностью позиционирования некоторых узлов по отношению друг к другу.
Для определения рассматриваемого критерия применяется формула, которая выглядит так: n=1000V/nd. Вышеприведенная информация указывает на то, что скорость вращения в большинстве случаев зависит от диаметра и скорости резания, устанавливается в разных случаях.
Меряется рассматриваемый критерий в единице, которая определяет число выполненных оборотов за минуту. Эта единица считается мировой, применяется во многих случаях и может переводится в прочие. При расчетах нечасто выходит точный результат, по этому берется приближенный параметр из таблицы.
Расчет режима резания вызывает очень много сложностей при отсутствии требующейся информации. Важными параметрами можно назвать следующее:
- Для начала уделяют внимание типу подходящего инструмента для резки, его материалу и геометрическим показателям. В продаже встречается просто очень большое число самых разнообразных вариантов выполнения инструментов, по этому выбору необходимо выделять довольно достаточно внимания. Режущая часть часто делается из быстрорежущей стали, но еще бывают варианты выполнения, кромка которых представлена твёрдым устойчивым к износу сплавом. На токарном станке ставятся резцы, кромка резки которых может повторить разную форму.
Примером можно назвать проходные, отрезные резцы, а еще варианты выполнения, предназначающиеся для получения канавок. Куда более непростая специфична для фрез, которые могут использоваться для получения ровной поверхности. При непосредственном выборе инструмента лучше всего проводить его зрительный осмотр, так как изъяны могут оказаться причиной повреждения инструмента и его быстрого износа, появления множества прочих проблем.
- Второй шаг состоит в непосредственном выборе подходящего станка для получения детали. В данном случае необходимо помнить про то, что все оборудование способна работать при определенном диапазоне вращения шпинделя. По мимо этого, выбор проходит в зависимости от типа проводимой работы. Примером можно назвать то, что токарное оборудование может проводить лишь внешнее точение, а еще отрезание и расстачивание и некоторые прочие работы. Очень непосильной задачей можно назвать нарезание резьбы, для чего также проходит выбор скорости вращения. Для получения корпусных деталей, высверливания и прочих аналогичных операций часто подбирается фрезеровальное оборудование, работа которого возможна от блока числового программного управления.
На данное время проходит выпуск достаточно немалого количества самых разных моделей станков, отдельные из них как правило ставятся в мастерской дома и при этом имеют очень широкий диапазон скорости вращения.
- Нужно провести расчет режимов резания. Наиболее основными параметрами можно назвать скорость резания, величина подачи и остальные моменты. Технологическая карта, в основном, предоставлена чертежом с режимами резания, которые выведены в индивидуальной таблице. В таком случае также проходит указание критерия скорости вращения шпинделя, который подбирается с рекомендуемого диапазона. Скорость вращения шпинделя – параметр, определяющий многое на момент обработки: нагревательная степень кромки, ее износа, эффективность оборудования и многое иное. Все оборудование способна работать при конкретной скорости вращения, которая подбирается путем выбора соответствующего режима резания. Важные параметры рассчитываются при использовании конкретных формул, которые можно повстречать в самой разной техдокументации.
- Рекомендуется также проверять подобранных режимов резания. При этом делаются расчёты мощности привода, крепость механизма подач, уделяют внимание прочности державки и пластинки твёрдого сплава. Необходимо помнить про то, что неверный выбор ключевых показателей оказывается основой не только получения низкокачественного изделия, но и изнашиванию ключевых узлов. Аналогичные расчеты проводятся только с учетом технических свойств оборудования, а еще подобранной оснастки.
- Наиболее основным параметром в большинстве случаев считают также кол-во времени, которое необходимо для выполнения определенной операции. Данный показатель используется для определения продуктивности и себестоимости изделия. Минимальный параметр свойственен для станков с числовым программным управлением, так как они как правило будут работать при больших показателях скорости вращения шпинделя, а на перемещение ключевых узлов уходит короткое время. Собственно поэтому аналогичное оборудование монтируется в случае, когда необходимо достичь большой параметр продуктивности.
Последний этап связан с проверкой эффективности подобранного режима резания, а еще правильности выбранного обрабатывающего оборудования.
При отсутствии ключевой информации высчитать частоту вращения шпинделя оборотов в минуту как правило невозможно. Впрочем, прибора, который позволит найти значение очень точно, фактически нет. Мерная единица конкретного шпинделя может переводится в прочие значения, например, численность оборотов в течение минуты или часа.
Главное не забыть учесть тот фактор, что количеству оборотов будут подходить конкретные условия обработки заготовки. Например, чрезмерно высокое значение оказывается основой повреждения инструмента, при чрезмерно малом достичь требуемых показателей будет почти что нереально.
Частота вращения шпинделя
При рассмотрении формулы, которая используется для расчетов скорости вращения шпинделя, уделяют внимание скорости. Она также должна выбираться в зависимости от определенных эксплуатационных условий оборудования. Для расчета частоты вращения -шпинделя станка может использоваться формула: v=пdn/1000.
Частота вращения токарного станка по металлу применяется в качестве критерия скорости резания. От него зависит следующее:
- Продуктивность труда. Цена изделия в большинстве случаев зависит от того, какое количество времени было затрачено на его получение. Для повышений продуктивности труда следует значительно увеличить значение скорости резания. Но это не всегда есть возможность провести, так как слишком больший коэффициент может привести к большим проблемам, например, нагреву инструмента или изнашиванию весомой части.
- Шероховатость получившейся поверхности также варьирует в огромном диапазоне. С увеличением скорости резания можно значительно увеличить качество готового изделия. По этому высокие значения применяются во многих случаях при чистовом точении.
Выбор конкретного критерия частоты вращения шпинделя проходит в зависимости от возможностей используемого оборудования. Слишком больший коэффициент нельзя ставить из-за причины того, что аналогичная работа оборудования приводит к большому износу.
Напоследок напомним, что неверный расчет скорости вращения может привести к очень тяжёлым последствиям. Это связано с возможностью износа привода, а еще иных элементов. Не лучше подбирать самые большие показателе скорости вращения и скорости резания, так как это приведет к максимальному изнашиванию и возможности износа используемого инструмента.
Если вы нашли погрешность, пожалуйста, выдилите фрагмент текста и нажмите Ctrl+Enter.
Похожие статьи
Скорость резания от диаметра Таблица / Surface speed to RPM conversion
Перевод оборотов в минуту в линейную скорость Справочная таблица Скорости резания в зависимости от диаметра режущего инструмента
Перевод оборотов в минуту в линейную скорость Справочная таблица Скорости резания в зависимости от диаметра режущего инструмента _ Расчет частоты вращения vc Скорость резания (Vc, м/ ин) Диаметр 20 30 40 50 60 70 80 90 100 120 140 150 180 200 250 300 0. 2 31,831 47,746 63,662 79,577 95,493 111,408 127,324 143,239 159,155 190,986 222,817 23,872 286,479 318,310 397,887 477,465 0.3 21,221 31,831 42,441 53,052 63,662 74,272 84,883 95,493 106,103 127,324 148,545 159,155 190,986 212,207 265,258 318,310 0.4 15,915 23,873 31,831 39,789 47,746 55,704 63,662 71,620 79,577 95,493 111,408 119,366 143,239 159,155 198,944 238,732 0.5 12,732 19,099 25,465 31,831 38,197 44,563 50,930 57,296 63,662 76,394 89,127 95,493 114,592 127,324 159,155 190,986 0.6 10,610 15,915 21,221 26,526 31,831 37,136 42,441 47,746 53,052 63,662 74,272 79,577 95,493 106,103 132,629 159,155 0.7 9,095 13,642 18,189 22,736 27,284 31,831 36,378 40,926 45,473 54,567 63,662 68,209 81,851 90,946 113,682 136,419 0.8 7,958 11,937 15,915 19,894 23,873 27,852 31,831 35,810 39,789 47,746 55,704 59,683 71,620 79,577 99,472 119,366 0.9 7,074 10,610 14,147 17,684 21,221 24,757 28,294 31,831 35,368 42,441 49,515 53,052 63,662 70,736 88,419 106,103 6,366 9,549 12,732 15,915 19,009 22,282 25,465 28,648 31,831 38,197 44,563 47,746 57,296 63,662 79,577 95,793 1.
5 4,244 6,366 8,488 10,610 12,732 14,854 16,977 19,099 21,221 25,465 29,709 31,831 38,197 42,441 53,052 63,662 2 3,183 4,775 6,366 7,958 9,549 11,141 12,732 14,324 15,915 19,099 22,282 23,873 28,648 31,831 39,789 47,746 2.5 2,546 3,820 5,093 6,366 7,639 8,913 10,186 11,459 12,732 15,279 17,825 19,099 22,918 25,465 31,831 38,197 3 2,122 3,183 4,244 5,305 6,366 7,427 8,488 9,549 10,610 12,732 14,854 15,915 19,099 21,221 26,526 31,831 3.5 1,819 2,728 3,638 4,547 5,457 6,366 7,276 8,185 9,095 10,913 12,732 13,642 16,370 18,189 22,736 27,284 4 1,592 2,387 3,183 3,979 4,775 5,570 6,366 7,162 7,958 9,549 11,141 11,937 14,324 15,915 19,894 23,873 4.5 1,415 2,122 2,829 3,537 4,244 4,951 5,659 6,366 7,074 8,488 9,903 10,610 12,732 14,147 17,684 21,221 5 1,273 1,910 2,546 3,183 3,820 4,456 5,093 5,730 6,366 7,639 8,913 9,549 11,459 12,732 15,915 19,099 5.5 1,157 1,736 2,315 2,894 3,472 4,051 4,630 5,209 5,787 6,945 8,102 8,681 10,417 11,575 14,469 17,362 6 1,061 1,592 2,122 2,653 3,183 3,714 4,244 4,775 5,305 6,366 7,427 7,958 9,549 10,610 13,263 15,915 6.
5 979 1,469 1,959 2,449 2,938 3,428 3,918 4,407 4,897 5,876 6,856 7,346 8,815 9,794 12,243 14,691 7 909 1,364 1,819 2,274 2,728 3,183 3,638 4,093 4,547 5,457 6,366 6,821 8,185 9,095 11,368 13,642 7.5 849 1,273 1,698 2,122 2,546 2,971 3,395 3,820 4,244 5,093 5,942 6,366 7,639 8,488 10,610 12,732 8 796 1,194 1,592 1,989 2,387 2,785 3,183 3,581 3,979 4,775 5,570 5,968 7,162 7,958 9,947 11,937 8.5 749 1,123 1,498 1,872 2,247 2,621 2,996 3,370 3,745 4,494 5,243 5,617 6,741 7,490 9,362 11,234 9 707 1,061 1,415 1,768 2,122 2,476 2,829 3,183 3,537 4,244 4,951 5,305 6,366 7,074 8,842 10,610 9.5 670 1,005 1,340 1,675 2,010 2,345 2,681 3,016 3,351 4,021 4,691 5,026 6,031 6,701 9,377 10,052 10 637 955 1,273 1,592 1,910 2,228 2,546 2,865 3,183 3,820 4,456 4,775 5,730 6,366 7,958 9,549 11 579 868 1,157 1,447 1,736 2,026 2,315 2,604 2,894 3,472 4,051 4,341 5,209 5,787 7,234 8,681 12 531 796 1,061 1,326 1,592 1,857 2,122 2,387 2,653 3,183 3,714 3,979 4,775 5,305 6,631 7,958 13 490 735 979 1,224 1,469 1,714 1,959 2,204 2,449 2,938 3,428 3,673 4,407 4,897 6,121 7,346 14 455 682 909 1,137 1,364 1,592 1,819 2,046 2,274 2,728 3,183 3,410 4,093 4,547 5,684 6,821 15 424 637 849 1,061 1,273 1,485 1,698 1,910 2,122 2,546 2,971 3,183 3,820 4,244 5,305 6,366 16 398 597 796 995 1,194 1,393 1,592 1,790 1,989 2,387 2,785 2,984 3,581 3,979 4,974 5,968 17 374 562 749 969 1,123 1,311 1,498 1,685 1,872 2,247 2,621 2,809 3,370 3,745 4,681 5,617 18 354 531 707 884 1,061 1,238 1,415 1,592 1,768 2,122 2,476 2,653 3,183 3,537 4,421 5,305 19 335 503 670 838 1,005 1,173 1,340 1,508 1,675 2,010 2,345 2,513 3,016 3,351 4,188 5,026 20 318 477 637 796 955 1,114 1,273 1,432 1,592 1,910 2,228 2,387 2,865 3,183 3,979 4,775 21 303 455 606 758 909 1,061 1,213 1,364 1,516 1,819 2,122 2,274 2,728 3,032 9,789 4,547 22 289 434 579 723 868 1,013 1,157 1,302 1,447 1,736 2,026 2,170 2,604 2,894 3,617 4,341 23 277 415 554 692 830 969 1,107 1,246 1,384 1,661 1,938 2,076 2,491 2,768 3,460 4,152 24 265 398 531 663 796 928 1,061 1,194 1,326 1,592 1,857 1,989 2,387 2,653 3,316 3,979 25 255 382 509 637 764 891 1,019 1,146 1,273 1,528 1,783 1,910 2,292 2,546 3,183 3,820 гНННЬ 28 Влияние длины рабочей части (вылета фрезы) Концевые фрезы Влияние рабочей части на деформацию изгиба Относительная длина рабочей части фрезы Длину рабочей части фрезы принято измерять в количестве её диаметров I Id При мер) 3D, 15D, 22D Деформация изгиба определяется силой упругости.
которая пропорциональна прогибу стержня. Вел ичин а деформация изгиба определяется по закону Гука С ув еличением вылета фрезы увеличивается деформация изгиба. С увел ичением количества зубьев жесткость возрастает. Малый размер стружечной канавки обеспечивает более высокую жесткость. 5 = Относительная деформация I = Длина рабочей части P = Сила резания Е = Модуль Юнга I = Момент инерции ( 1 5 = ltd4 14 >218 >51 -> 51 =851 =52 3
Основная характеристики жестких дисков – скорость вращения шпинделя
С каждым годом IT-индустрия практически в каждом из компонентов системного блока, стремится повысить скорость. Скорость вычислений, скорость доступа, скорость передачи – все это увеличивается ежеквартально.
Не обошли стороной эти скоростные изменения и сферу накопителей информации – жестких дисков. Здесь постоянно увеличивалась и увеличивается скорость вращения шпинделя жесткого диска, которая, в свою очередь влияет на скорость доступа к данным, скорость записи и скорость чтения информации.
Скорость вращения шпинделя жесткого диска
Скорость вращения шпинделя жесткого диска – это основная характеристика жесткого диска, которая напрямую влияет на результирующую производительность устройства.
На данный момент для десктопных вариантов систем, популярностью пользуются три вида жестких дисков по скорости вращения шпинделя – это 5400 об/мин., 7200 об./мин и 10 000 об./мин.
Естественно, у более скоростных жестких дисков помимо достоинств перед собратьями меньшими, существуют и недостатки для потребителя – это повышенная цена, более высокий уровень шума и большее энергопотребление. По поводу уровня шума – это довольно спорный и незначительный момент. На фоне подавляющего большинства шумных кулеров для обычных систем – может быть вообще не заметен.
Что же дает более высокая скорость вращения шпинделя для повышения скорости работы системы? Во-первых, это скорость случайного доступа к какой-либо информации на жестком диске. Естественно, время за которое головка чтения доходит до определенного места на пластине жесткого диска, в случае с 5400 об./мин. – существенно падает, по сравнению с 7200 об./мин или же 10 000 об./мин. Такая же ситуация и со скоростью записи.
Тестирование жестких дисков
Теперь давайте все это рассмотрим на показательных примерах. На ixbt.com провели тестирование четырех жестких дисков, которые существенно разнятся по параметрам. В результате были получены очень показательные графики, на которых четко видно превосходство более высокой скорости вращения шпинделя.
Итак, модели для тестирования:
- Western Digital Green – WD10EZRX (5400 об./мин. )
- Western Digital Blue – WD10EALX (7200 об./мин.)
- Western Digital Black WD1002FAEX (7200 об./мин.)
- Western Digital VelociRaptor WD1000DHTZ (10 000 об./мин.)
В большей мере нас интересуют три модели с разной скоростью вращения.
Теперь давайте рассмотрим графики тестирования:
1. Скорость чтения и скорость записи
Как видно из графиков тестирования, Green-серия с 5400 об./мин, провально отстает от всех. Особенно четко можно увидеть градацию по скорости вращения шпинделя, именно на графике времени доступа при чтении.
2. Произвольный доступ
Опять же, четко прослеживается заметное преимущество жестких дисков с 7200 об./мин. над «низкооборотистой» Green-серией, при чем на одном из графиков они вплотную подбираются к Veloci Raptor с 10 000 об./мин.
При тестировании жестких дисков в большинстве приложений, а также в игровых нагрузках, соблюдается все то же отставание Green-серии.
Итоги
После всего этого остается только подвести небольшие итоги. Безусловно, не все тесты были провальны со стороны Green с 5400 об./мин, так как скорость вращения шпинделя решает не все, но подавляющее большинство тестов, оказались печальными для Green-диска. В любом случае не стоит заострять внимание на одной характеристике. Для того же копирования файлов необходимо увеличении плотности записи, а не повышение скоростей вращающихся элементов накопителя. Так что комплексность анализа характеристик остается единственным правильным решением при выборе жесткого диска. Также важно помнить про основную характеристику жесткого диска – это объем памяти HDD, ведь «как ни крути», основная задача накопителя – хранить информацию.
, когда скорость шпинделя является ограничением
Фраза «высокоскоростная обработка» подчеркивает слово «скорость», но работа с высокой скоростью шпинделя никогда не была основной целью. Наоборот, высокоскоростная обработка направлена только на усиление скорости шпинделя – достижение высокой скорости съема металла в пределах одного цикла фрезерования, что приближает необработанную заготовку к готовой, насколько это возможно. Готовая деталь и высокая производительность съема металла – две цели. Скорость – это только средство, а скорость – даже не единственное средство для объединения этих двух целей.
За последние несколько лет усовершенствования в технологии режущего инструмента позволили цехам достичь высокой скорости съема металла при более низких скоростях шпинделя. В результате команда Boeing в Сент-Луисе, штат Миссури, которая обучает поставщиков Boeing методам высокоскоростной обработки, теперь также обучает методам работы на более низких оборотах – часто для цехов, которым не хватает высокоскоростных мощностей. Для Boeing этот новый набор методов получил обманчиво скромный ярлык «низкоскоростная обработка» – термин, который на самом деле влечет за собой высокий уровень производительности.
Одна часть, в частности, иллюстрирует это. Алюминиевая деталь на фотографии справа была изготовлена путем высокоскоростной обработки на большом обрабатывающем центре Boeing – машине, способной развивать скорость 24 000 об / мин. Но эта машина была перегружена, что вызывало давление, заставляющее делать часть по-другому. В наличии оказался обрабатывающий центр с частотой вращения 4000 об / мин.
Команда Boeing разработала процесс максимального использования возможностей этой низкоскоростной машины, чтобы одна только эта машина могла эффективно производить детали.При этом команда также усовершенствовала подход к низкоскоростной обработке, который с тех пор помог внедрить различным поставщикам. Этот процесс включает черновую обработку с использованием фрез с большой подачей, а также твердосплавных концевых фрез, способных выдерживать большие глубины резания и стружку. Этот процесс также включает в себя функции быстрой чистовой обработки с использованием концевых фрез с большим числом канавок.
Время работы детали составило 61 минуту. Это было реальное время для высокоскоростного цикла обработки, включая смену инструмента и ускорение / замедление.
Для той же части нового низкоскоростного процесса время выполнения было почти таким же – 67 минут.
Инженер Boeing Эрик Стерн – член группы механической обработки в Сент-Луисе, которая входит в исследовательскую и технологическую группу компании. Он подчеркивает, что все же предпочтительнее высокоскоростная обработка. Обычно HSM будет более продуктивным, а зачастую и заметно. Даже вышеупомянутый высокоскоростной цикл, вероятно, длился бы лучше, чем 61 минута, если бы его программирование и другие аспекты процесса подверглись такому же анализу, как и низкоскоростной процесс в конечном итоге.Однако на этот раз это стало общепринятым эталоном, и производительность низкоскоростной обработки оказалась довольно близкой.
Для многих поставщиков это важно. У многих нет обрабатывающих центров с высокой частотой вращения, не говоря уже о достаточном количестве работ, которые могли бы его оправдать. Многие другие сталкиваются с перегрузкой высокоскоростных машин, в то время как низкоскоростные машины в магазине остаются доступными. Помогая магазинам повысить производительность на всех уровнях скорости, команда Boeing надеется расширить возможности всей цепочки поставок компании.
Вот несколько советов, которые предлагает команда для реализации более производительной низкоскоростной обработки:
Вернуться к черновой обработке
Черновая и чистовая обработка – это различия, которые могут стать ненужными при высокоскоростной обработке деталей самолетов, поскольку обработка выполняется посредством точных тяжелых пропилов, которые одновременно вытаскивают материал и достигают конечных размеров. Однако, по словам Боинга, низкоскоростная обработка требует возврата к черновой и чистовой обработке. Это связано с тем, что черновая обработка может повлечь за собой резку с высокой мощностью, которая не подходит для достижения окончательных допусков на размеры элементов детали.
При черновой обработке главное – максимально использовать доступную мощность станка. На станке, где нет высокой скорости вращения шпинделя, эта мощность является альтернативой высокой производительности.
Чтобы максимально использовать мощность, можно поэкспериментировать с различными инструментами. В части, упомянутой ранее, команда Boeing первоначально применила стандартную концевую фрезу для черновой обработки алюминия. Инструмент допускал максимальную скорость съема металла 6.3 кубических дюйма в минуту при мощности всего 2 л.с. Напротив, другой инструмент, более грубый SwiftCarb, показанный на этой странице, позволил машине развить 14,5 л.с. при этом резании – частично из-за зазора между стружкой, обеспечиваемого режущим эффектом конструкции канавки. Соответствующая скорость съема металла с помощью этого инструмента составляла 45 кубических дюймов в минуту.
Используйте канавки для чистовой обработки
Для чистовой обработки лучший выбор инструмента другой. Концевая фреза с большим количеством канавок может обеспечить производительную скорость подачи дюйм / мин при низких скоростях шпинделя.Фрезерный инструмент с 10 зубьями, показанный на лицевой странице, является стандартным инструментом, который компания Boeing рекомендует для чистовой обработки титана. Инструмент также эффективно работает при чистовой обработке алюминия. Фактически, в алюминии инструмент диаметром 1 дюйм может работать при радиальном погружении на 0,3 дюйма с осевой глубиной резания 1 дюйм – параметры, которые не учитывались бы для титана
.
Недостаток этого инструмента (и при низкоскоростной обработке компонентов самолета в целом) заключается в том, что сначала необходимо обработать внутренние углы детали.Многочисленные внутренние углы типичны для элементов конструкции самолета, которые часто состоят из множества карманов. Для чистового фрезерования инструмента с небольшой радиальной глубиной резания радиальное зацепление резко увеличивается, когда инструмент входит в угол. Следовательно, для защиты как инструмента, так и заготовки, перед выполнением этих быстрых чистовых проходов необходимо обработать материал по углам (используя какой-либо другой тип инструмента).
Прочие инструменты для черновой обработки
Другие типы инструментов также могут оказаться ценными.По словам Боинга, главными из них являются комбикормовые заводы. На последней фотографии выше – кадре из видеозаписи Boeing в разделе «Выбор редактора» справа – показан фрезерный инструмент с высокой подачей от Iscar. В инструментах с «высокой подачей» используется геометрия режущей кромки, которая использует преимущества осевого утонения стружки для достижения более высокой скорости подачи, чем мог бы реализовать сопоставимый инструмент с более стандартной геометрией. По словам г-на Стерна, когда объемы черновой обработки достаточно велики для использования этого типа инструмента, фрезерный станок с высокой подачей может быть надежным способом достичь производительности от 50 до 60 кубических дюймов в минуту, даже при низкой скорости вращения шпинделя.
Последний инструмент, который также заслуживает внимания, – это врезной стан для черновой обработки. Немногие магазины рассматривали бы такой инструмент для алюминия. Вместо этого большинство считает врезку методом обработки твердых металлов. Однако, когда низкая скорость шпинделя является ограничением процесса, врезная черновая обработка может быть наиболее продуктивным методом даже при работе с мягким материалом. Выбор сводится к форме кармана, а именно к тому, сколько материала останется после погружения, что потребует дополнительной обработки. По словам Боинга, черновая обработка врезанием не имела бы смысла, если бы была доступна высокая скорость шпинделя.Однако для низкоскоростной машины этот метод может быть элементом процесса, обеспечивающим наивысшую производительность.
Краткие сведения о низкоскоростной обработке
Обрабатывающий центр с частотой вращения 4000 об / мин может быть высокопроизводительным станком для фрезерования алюминия. Группа исследований и технологий в области механической обработки в Сент-Луисе говорит, что это ключи к достижению максимальной производительности, когда частота вращения шпинделя является ограничением:
• Увеличьте мощность! При черновой обработке стремитесь максимально использовать мощность шпинделя.
• Увеличьте скорость шпинделя, осевую глубину резания и радиальную глубину резания. Постарайтесь установить все эти параметры настолько высоко, насколько позволяет качество резки.
• Используйте высокую стружку при черновой обработке. Для цельнотвердосплавных концевых фрез из алюминия реалистична стружкодетальная нагрузка не менее 0,010 дюйма на зуб. Фрезы с высокой подачей могут допускать стружку до 0,050 дюйма на зуб.
• При чистовой обработке инструменты с большим количеством канавок могут достигать высокой скорости подачи, несмотря на низкую скорость.
• Обработайте внутренние углы перед чистовой обработкой ребер.
Feeds & Speeds Sweet Spots [Урок 1: электронная почта от F&S]
Есть какой-то жаргон, связанный с фидами и скоростями, но выучить его несложно.
Часть «Скорости» в комбинации «Подача и скорость» относится к оборотам вашего шпинделя. Определение правильной скорости для работы в значительной степени связано с определением скорости вращения инструмента без его перегрева в обрабатываемом материале. Или, в мягких материалах, таких как пластик и дерево, перегрев может сжечь или расплавить материал.
В серии экспериментов, проведенных на ранних этапах обработки, было установлено, что скорость вращения шпинделя является самым важным фактором, определяющим срок службы вашего инструмента. Слишком высокая скорость приводит к возникновению избыточного тепла (есть и другие способы нагрева), что смягчает инструмент и в конечном итоге приводит к потускнению кромки. В нашей серии статей мы поговорим о том, как увеличить срок службы инструмента, но пока считайте, что скорость вращения шпинделя в значительной степени зависит от увеличения срока службы инструмента. Будьте очень осторожны при превышении рекомендованной скорости вращения шпинделя!
«Подача» означает скорость подачи в некоторых линейных единицах измерения в минуту (дюймы в минуту или миллиметры в минуту в зависимости от того, используете ли вы метрическую или британскую систему мер).Скорость подачи – это компромисс между увеличением скорости съема материала и возможностью удаления стружки из реза. Скорость съема материала – это то, насколько быстро ваш станок с ЧПУ производит стружку в кубических единицах. Чем быстрее, тем лучше для большинства машинистов, вплоть до возникновения проблем. Наиболее частая проблема – поломка инструмента или сколы при слишком быстрой подаче.
Инструмент ломается, потому что стружка застревает в канавках, резец застревает, и довольно скоро он ломается.
Я новичок. Как насчет того, чтобы запустить тренажер на сверхмедленной скорости? (Большая ошибка!)
Подождите, слишком медленная работа – это плохо?
Распространенное заблуждение, что можно «детить» стрижку, чтобы быть ультраконсервативным.Просто увеличьте скорость вращения шпинделя и скорость подачи, и вы ничего не сломаете, верно? Не совсем так. Вот несколько примеров того, что может случиться, если вы бежите слишком медленно:
– Если вы уменьшите скорость шпинделя слишком сильно по сравнению со скоростью подачи, вы заставите канавки фрезы снимать слишком много материала. Концевая фреза слишком быстро вдавливается в пропил, и стружка становится слишком большой. Таким образом можно легко сломать резак.
– Если вы слишком сильно уменьшите скорость подачи по сравнению со скоростью шпинделя, вы скоро заставите канавки фрезы начать «натирать» или «полировать» заготовку вместо срезания или обрезки стружки.Многие механики скажут вам, что самый быстрый способ затупить фрезу – просто запустить ее с перевернутым шпинделем и сделать проход, но слишком низкая скорость подачи создает аналогичный эффект. Мы поговорим подробнее о том, как это происходит, позже в этом мастер-классе, но достаточно сказать, что слишком медленный бег – это так же тяжело для ваших резаков, как и слишком быстрый, если не более тяжелый.
Это настоящий сюрприз, правда?
Лучшее место для подачи и скорости
Да! Совершенно верно, для каждой операции резки есть своя зона наилучшего восприятия.
Если мы можем навредить закройщикам, двигаясь слишком быстро или слишком медленно, то есть золотая середина – золотая середина.
Это не та точка, в которую нужно попасть точно, но в то же время она тоже не очень большая, и если вы ее полностью пропустите, есть штрафы. Чем сложнее материал, который вы режете, тем меньше зона наилучшего восприятия и тем больше штрафов. Как только вы узнаете, где находится зона наилучшего восприятия, вы можете настроить параметры резки в этом диапазоне, чтобы максимизировать скорость съема материала, чистоту поверхности или срок службы инструмента.Фактически, вы часто можете максимизировать любые два из трех, но не все три сразу.
Давайте посмотрим на «золотые точки» для различных целей, а также на «опасные зоны»: эта диаграмма относительна, то есть вы не можете делать никаких предположений относительно пропорций или масштаба. Просто посмотрите на положение областей относительно друг друга и относительно идеи более высоких и низких скоростей шпинделя и скорости подачи.
Давайте рассмотрим различные помеченные зоны, слева направо, сверху вниз:
Слишком большая подача Загрузка чипа: Как мы уже обсуждали, когда вы подаете слишком быстро для данной скорости вращения шпинделя, вы, скорее всего, сломаете инструмент.Чем больше вы превысите соответствующую скорость, тем больше вероятность. В какой-то момент вы всегда сломаете инструмент. Рассмотрим абсурдный случай, когда частота вращения шпинделя равна нулю, и вы ускоряете инструмент в работу. Поп! Просто сломал другой инструмент. Между прочим, я подкрался немного жаргона: «Chipload». Нагрузка на стружку измеряется в единицах на зуб. Например, дюймы или мм на зуб фрезы. Скорость подачи зависит от частоты вращения шпинделя. Если мы изменим частоту вращения, мы должны изменить скорость подачи, чтобы сохранить ту же стружколомную нагрузку. И в этом преимущество загрузки микросхем – это единое число, которое работает для всех оборотов в минуту.Поздравляем, вы выучили новый термин.
MRR : MRR означает «скорость удаления материала», еще один термин из жаргона обработки. Он измеряет кубические единицы чипов, произведенных за временной интервал. Например, кубические дюймы в минуту. Максимально возможная скорость вращения шпинделя без сжигания инструмента и максимальная скорость подачи без поломки инструмента – это идеальное место для максимальной скорости съема материала. Если вы занимаетесь производством, именно здесь вы зарабатываете деньги, поднимаясь выше и правее, чем конкуренты.Мы увеличиваем скорость съема материала, чтобы сократить время, необходимое для обработки детали.
Too Fast : Слишком высокая скорость шпинделя приведет к выделению избыточного тепла, которое размягчит инструмент и быстрее затупит его. Есть исключения и смягчающие обстоятельства, о которых мы поговорим в более сложных частях.
Лучший срок службы инструмента : Немного замедляя шпиндель и подавая немного меньше, чем необходимо для максимального MRR, можно добиться максимальной стойкости инструмента. Позже мы подробнее поговорим об уравнениях Тейлора для стойкости инструмента, но достаточно сказать, что снижение частоты вращения шпинделя более важно, чем снижение скорости подачи, но оба помогут.
Чистота поверхности : Снижение скорости подачи при сохранении высокой скорости шпинделя снижает нагрузку на стружку и приводит к более качественной обработке поверхности. Существуют ограничения, самый большой из которых заключается в том, что вы в конечном итоге слишком сильно уменьшите скорость подачи, ваши инструменты начнут тереться, а срок службы инструмента значительно снизится из-за избыточного тепла, выделяемого при трении.
Старые станки : Значит, скорость вашего шпинделя сильно упала, и, кроме того, снизилась и скорость подачи. Вероятно, вы работаете на более старом станке, на котором вы не можете работать со скоростью, необходимой для использования твердосплавных инструментов.Возможно, вам придется перейти на HSS (быстрорежущая сталь, материал, используемый в более дешевых фрезах с низкой производительностью). Для многих является неожиданностью, что есть области диапазона подачи и скорости, в которых HSS может превзойти твердосплавные сплавы, но это правда, в зависимости от возможностей вашего станка и материала, который вы режете. Прочтите статью «Всегда ли карбид быстрее, чем HSS» для получения дополнительной информации.
Слишком медленная подача : Как уже говорилось, слишком медленная подача приводит к трению вместо резания, что может радикально сократить срок службы инструмента, и этого следует избегать.Теперь, когда вы знаете, как распадаются зоны наилучшего восприятия, вы лучше понимаете, как направлять поток и скорость для достижения желаемых результатов.
Мне всегда легче запоминать концепции с помощью наглядного пособия, поэтому, надеюсь, диаграмма зоны наилучшего восприятия облегчит вам задачу. Распечатайте его и приклейте на видном месте в магазине, если это поможет.
Нагрузка на стружку: толщина стружки на зуб
Загрузка стружки – это толщина стружки, отрезанной фрезой. Изображение любезно предоставлено Onsrud.
Я кратко описал загрузку микросхем выше, но давайте углубимся немного глубже (не волнуйтесь, не слишком глубоко).
Хотя скорость подачи с ЧПУ указывается в единицах длины в минуту, более важным измерением является то, что называется «загрузка стружки». Думайте о микросхеме, как о чем-то вроде запятой в поперечном сечении или, возможно, апострофа. Один начинается с большого, а в конце становится меньше. Другой начинается с малого, а в конце становится больше. На мгновение мы проигнорируем эту разницу, хотя она важна, как мы увидим позже.Если мы измеряем толщину стружки в самом толстом месте, то это и есть стружка. Все просто, правда?
Загрузка стружки – это измерение, которое не зависит от частоты вращения шпинделя, скорости подачи или количества канавок. Он говорит о том, насколько тяжело работает инструмент. Как вы могли догадаться, это очень полезная вещь. Следовательно, производители и механики обычно любят говорить о загрузке стружки для конкретного инструмента.
Вы можете видеть, что инструмент с большим количеством канавок (режущих кромок) должен подаваться быстрее, чтобы поддерживать определенную нагрузку стружки для всех канавок.Поскольку каждый зуб будет резаться при каждом обороте, у зуба есть только часть оборота, чтобы вырезать стружку, которая достигает толщины нагрузки стружки. За время, необходимое для вращения следующего зуба, чтобы начать резку, инструмент должен продвинуться достаточно далеко, чтобы срезать стружку достаточно большой толщины. Следовательно, инструменты с большим количеством канавок можно подавать быстрее. Концевую фрезу с 4 зубьями можно подавать в два раза быстрее, чем с концевой фрезой с 2 зубьями, при прочих равных условиях.
Сейчас вы думаете: «А что, если бы я с помощью фрезы с 32 зубьями действительно смог летать с этой штукой, не так ли?» Не так быстро.Количество канавок, которые вы можете использовать в материале, во многих случаях ограничено. Например, в алюминии резак делает большие толстые стружки, которые скручиваются и становятся еще толще. Вы можете использовать только 2 или 3 канавки, иначе ваш резак захлебнется крупной стружкой и сломается. Как правило, для большинства вещей, кроме алюминия, можно использовать 4 канавки, а для алюминия – 2 или 3. Есть много исключений, но если вы новичок, придерживайтесь этого практического правила.
Почему инструменты ломаются из-за слишком большой стружкодробной нагрузки?
Вы можете себе представить, что силы просто становятся слишком большими, если инструмент пытается «укусить» слишком много из-за слишком большой рабочей нагрузки.Это может сломать или сломать резак. Но есть вторая проблема, которая возникает из-за слишком большой загрузки стружки – стружка становится больше и в конечном итоге не может ускользнуть от фрезы.
Начинающие станочники, вероятно, сломают больше инструментов, потому что они не убирают стружку с пути достаточно быстро, чем потому, что сила подачи ломает инструмент. Если резак находится в глубоком пазу, стружки особенно трудно убрать с пути. Мы используем воздушные струи, туман и охлаждающую жидкость, чтобы попытаться убрать стружку с пути, но если они попадают в отверстие или прорезь, это значительно усложняет задачу, и нам приходится снижать скорость.Что еще хуже, щепки всегда занимают больше места, когда они являются щепками, чем эквивалентный вес материала занимает твердое тело. Единственное, куда они должны пойти, – это зазоры между канавками фрезы. Конечно, чем больше у нас флейт, тем меньше остается места в зазорах.
Вы видите, что приближается точка уменьшения отдачи?
Это огромная роль калькуляторов каналов и скоростей, таких как G-Wizard. Данные производителя инструмента дают вам один или два образца загрузки микросхем или диапазон загрузок микросхем.Но такой калькулятор, как G-Wizard, точно определит, какую нагрузку на стружку вы можете использовать, основываясь на рекомендуемой стружкодробной нагрузке фрезы и условиях того, насколько глубоко в отверстии проходит рез (глубина резания) и какая часть резца работает в разрез (ширина реза или шаг в сторону). Эти расчеты трудно сделать без изрядной математики, поэтому калькуляторы каналов и скоростей могут сэкономить время (и инструменты) в реальном времени.
Скорость резания: насколько быстро инструмент скользит по заготовке при резке
Вы довольно быстро встретите термин «поверхностная скорость» с помощью Feeds & Speeds, потому что мы используем его для определения правильной скорости вращения шпинделя.Вы также можете услышать, как скорость резания называется «скорость резания».
При указании работы инструмента скорость резания идет рука об руку с нагрузкой на стружку. Так же, как загрузка стружки – лучший способ говорить о скорости подачи с ЧПУ, потому что она не зависит от многих факторов, скорость резания – лучший способ говорить об оборотах шпинделя. Представьте себе, что вместо вращающегося цилиндра с режущими кромками ваш инструмент представляет собой плоский кусок металла, скользящий по заготовке. Рекомендуемая скорость скольжения при резке – это поверхностная скорость.
Вот изображение:
Визуализация поверхностной скорости…
Скорость движения поверхности измеряется в линейных единицах измерения в минуту: футы в минуту (SFM) для британской системы мер и метры в минуту для метрической системы.
Вы не можете обмануть Surface Speed. Это то, что есть, и превышение рекомендаций производителя обязательно приведет к значительному сокращению срока службы инструмента, за исключением некоторых очень специальных случаев HSM (высокоскоростная обработка) и усовершенствованной СОЖ (под высоким давлением через СОЖ шпинделя), о которых следует беспокоиться только тогда, когда вы освоите основы.
Чтобы дать вам представление, вот диаграмма скорости резания (диаграмма поверхностных футов в минуту), которая показывает вам поверхностную скорость в футах в минуту для типичных материалов при резке концевой фрезой из быстрорежущей стали (HSS):
Таблица скоростей резания для концевых фрез из быстрорежущей стали в SFM | |
Материал | Поверхностная скорость (SFM) |
Алюминий – Кованый (6061) | 250 |
Латунь | 200 |
Чугун – ковкий | 90 |
Чугун – серый | 100 |
Медный сплав – деформируемый | 120 |
Магниевый сплав | 250 |
Нержавеющая сталь | 30 |
Сталь – мягкая | 110 |
Сталь – твердый сплав | 60 |
Сталь – Инструмент | 60 |
В целом поверхностные скорости выше для более мягких материалов и медленнее для более твердых / твердых материалов.Твердосплавные концевые фрезы могут работать на гораздо более высоких скоростях, чем HSS (быстрорежущая сталь), поэтому карбид так популярен при обработке. Фактически, переход от HSS к твердому сплаву был первым большим увеличением производительности в истории обработки, а переход от ручного управления к ЧПУ стал вторым большим увеличением производительности.
Кстати, это еще одна вещь, с которой G-Wizard Feeds and Speeds Calculator может помочь. Он имеет огромную базу данных материалов наряду с поверхностными скоростями. Речь идет не только об алюминии и стали, но и о сплавах и даже об условиях (закалке, отжиге и т. Д.).) сплавов. Например, существуют только сотни пород дерева.
Взаимодействие скорости резания и частоты вращения шпинделя
Рассмотрим эту таблицу, в которой показан диаметр инструмента в зависимости от скорости резания при 10000 об / мин:
Зависимость скорости движения от диаметра при 10 000 об / мин…
Если мы будем поддерживать постоянную скорость вращения, поверхностная скорость будет прямо пропорциональна диаметру. Концевая фреза 1/16 дюйма внизу движется на 1/8 скорости с точки зрения поверхностной скорости, чем концевая фреза 1/2 дюйма вверху.Следовательно, для достижения заданной поверхностной скорости маленькие инструменты должны будут вращаться быстрее, а инструменты большого диаметра – медленнее.
Вот классическая формула наземной скорости или SFM, которой учат в мастерских:
Формула об / мин шпинделя = (12 * SurfacceSpeed) / (PI * CutterDiameter)
Существует ряд причин, по которым эта формула идеализирована и не подходит для использования в реальном мире, но вы поняли.
Где я могу найти информацию о поверхностной скорости и загрузке чипов?
Обычно эта информация берется из каталога инструментов производителя вашей концевой фрезы.Более общий источник мог бы быть чем-то вроде Справочника по машинному оборудованию.
Намного проще получить и использовать информацию в калькуляторе каналов и скорости, таком как наш калькулятор G-Wizard. Посмотрите на экран G-Wizard:
Двигаясь сверху вниз, следующие строки содержат информацию о поверхностной скорости или загрузке чипа (строки обозначены синим цветом на черных этикетках в левых столбцах):
Mfg : Этот столбец предназначен для начальной поверхностной скорости и нагрузки чипа, обычно берется у производителя, отсюда и название строки «Mfg».G-Wizard имеет отличные настройки по умолчанию, если вы не укажете значения в этой строке. Фактически, единственная веская причина для их заполнения – если вы используете резаки премиум-класса и нуждаетесь в них до последней капли. В противном случае расслабьтесь и просто используйте настройки G-Wizard по умолчанию. Честно говоря, вы не нарушите свои инструменты с настройками по умолчанию.
Пределы : В этой строке указаны пределы вашей машины в крайнем левом столбце, а также ряд актуальных статистических данных по фактическому резанию. Это включает в себя фактическую скорость резания и нагрузку на стружку, а также скорректированную нагрузку на стружку для данного реза.Почему эти числа отличаются от поверхностной скорости и загрузки чипа в строке Mfg? Это потому, что эти числа скорректированы с учетом условий резания . При сверхглубокой резке сложнее избавиться от стружки, поэтому нам нужно уменьшить поверхностную скорость и нагрузку на стружку с теоретических максимумов, чтобы учесть их более сложный рез. Вы можете переопределить вычисления G-Wizard, но делать это не рекомендуется, если вы не опытный пользователь, который точно знает, что делает. Параметр «Adj. Chipload »- это дополнительная настройка для так называемого« Chip Thinning », о котором мы поговорим в Уроке 3.
Суть в том, что вам не нужно беспокоиться о поверхностной скорости или загрузке микросхем, когда вы используете G-Wizard. Он имеет интеллектуальные настройки по умолчанию и регулирует их в соответствии с условиями резки. Если вам действительно нужна максимальная производительность ваших резаков по производственным причинам, G-Wizard может принять эту информацию и усовершенствовать ее для получения еще лучших результатов. Мы объясним, как это работает, на следующем уроке.
Что это? У вас еще нет G-Wizard?
Хорошие новости: мы предлагаем бесплатную 30-дневную пробную версию.Вам действительно стоит этим воспользоваться!
Получите бесплатную пробную версию G-Wizard. Это поможет вам поэкспериментировать с концепциями этого курса, чтобы вы поняли и могли лучше применять их.
Вы можете перейти к Уроку 2: Как использовать калькулятор каналов и скорости или дождаться его в электронном письме на следующей неделе.
Скорость шпинделя заставит вашу голову кружиться
Как только вы думаете, что все это выяснилось, появляются улучшенные инструменты и более быстрые шпиндели, которые бросают вызов арифметике скорости и создают новые нормы.Например, несколько производителей теперь предлагают шпиндели, которые могут работать почти в два раза выше максимальной скорости, к которой мы привыкли.
В конце прошлого года немецкий производитель Precision Drive Systems представил новый шпиндель, который вращается со скоростью 40 000 об / мин вместо стандартных 24 000 об / мин. Хотя PDS не был первым производителем, который сделал это, производитель платформ с ЧПУ AXYZ International назвал это «следующим шагом в процессах высокоскоростной обработки». По словам компаний, шпиндель, названный XLC70, представляет собой быстросъемное устройство мощностью 3 л.с., которое предназначено для поддержания высокого качества обработки кромок при увеличении числа оборотов (не обязательно производства) на 67 процентов.Но скорость резки может быть здесь не единственным преимуществом: качество многих резов, по-видимому, также становится немного лучше, особенно для вывески и производителей мебели, которые занимаются фрезеровкой пластмасс, акрила и цветных металлов.
Что особенно хорошо в XLC70 и некоторых других моделях, так это то, что они не нуждаются в водяном охлаждении. Обладая рейтингом S1 от IEC, он может работать на полную мощность в течение всего дня, используя для охлаждения сжатый воздух. Заказчики могут установить шпиндель PDS XLC70 на все станки серии Pacer и Trident от AXYZ, с автоматической сменой инструмента или без нее.Кроме того, шпиндель доступен для модернизации существующих станков в зависимости от спецификации.
Скорость растет повсюду. Например, в каталоге Colombo USA (www.colombospindles.com) имеется довольно много шпинделей с частотой вращения 40 000 об / мин, многие из которых имеют воздушное охлаждение (например, модели RC 73 с автоматической заменой на 2 и 3 л.с.). Colombo, подразделение Милана, итальянская компания Elettromeccanica Giordano Colombo, также предлагает меньший шпиндель цангового типа (RC55), максимальная частота вращения которого составляет 40 000 об / мин, а также охлаждение сжатым воздухом.
Вопрос о том, стоит ли вам переходить на более быстрые шпиндели, требует большого внимания и, возможно, долгих разговоров с вашим представителем ЧПУ. Некоторые из вопросов могут включать в себя вопрос о том, что более быстрая революция может означать как для вашего существующего инструмента, так и для качества деталей. Отличным местом для проведения такой встречи будет IWF в Атланте (24-27 августа), где владелец или менеджер столярного цеха сможет встретиться почти со всеми крупными производителями и запросить информированное мнение о тенденции к более высоким скоростям.Суть в том, что более быстрые шпиндели, вероятно, означают более короткое время производства, но могут быть некоторые обратные стороны.
Ограничения скорости
Скорость шпинделя (измеряемая в оборотах в минуту или об / мин, также широко известная как «скорость резания») является наиболее важным фактором при определении того, как долго фреза будет сохранять свою кромку. Если число оборотов слишком велико для металлургии и массы инструмента, то тепло накапливается слишком быстро, и тонкая кромка становится хрупкой и быстро тускнеет.Переход на шпиндель, который почти вдвое увеличивает скорость, почти наверняка будет означать, что нужно что-то изменить. Либо нужно обновить инструмент (например, больше или меньше канавок, другой твердый сплав), либо уменьшить глубину резания, либо, возможно, нужно уменьшить скорость подачи (скорость, с которой шпиндель движется по заготовке). вниз или ускориться. Все эти переменные могут быть частью разговоров с производителями оборудования на торговой выставке. Это также вопросы, которые можно обсудить на онлайн-форумах или с другими владельцами / менеджерами магазинов, которые уже сделали шаг.
Большинство производителей шпинделей могут указать имена клиентов, которые готовы ответить на ваш звонок и ответить на некоторые вопросы. Самая большая проблема заключается в том, что нет простых ответов, потому что индивидуальные мастерские по дереву подвержены очень многим переменным. На некоторых рынках профили, выбранные дизайнерами, являются тонкими и аккуратными, в то время как на других можно использовать фрезу для фрезерования очень сложной декоративной лепки или кромки. Некоторые магазины работают почти исключительно с МДФ, в то время как другие просят свои инструменты и шпиндели обрабатывать дюжину различных пород древесины.Поэтому трудно сказать, являются ли более быстрые веретена разумным решением для какого-либо конкретного цеха.
Подача – важный фактор в сохранении кромки, и необходимо выяснить влияние более быстрого шпинделя на это. Самый большой вопрос в производственной работе – решить, с какой скоростью может двигаться шпиндель, не подвергая сверло так много, что оно либо перегреется, либо застрянет. Слишком большая поспешность обычно приводит либо к поломке инструмента, либо к образованию сколов, а это означает переделку деталей или отключение для повторной настройки.Слишком большая нагрузка на двигатель шпинделя также может быть дорогостоящей, особенно со временем.
И дело не только в скорости: слишком медленная подача с более быстрым шпинделем также является потенциальной проблемой. Недостаток скорости не только заставляет работать в цехе, но и заставляет инструмент сжигать древесину, особенно на поворотах и углах, потому что он слишком долго трется в одном месте и нагревается. И чипы тоже становятся больше. Фактически, слишком медленное движение (будь то скорость шпинделя или скорость подачи) иногда может быть сложнее для инструментов, шпинделей и двигателей, чем слишком быстрое движение.Есть окно, в котором нужная скорость, подача, инструменты и материалы поют одну и ту же песню. Это не очень широкое окно, и это тоже не точная формула, а скорее узкий диапазон.
Здесь играет роль множество факторов. Например, размер профиля является ключевым: для сверл большего диаметра требуются более низкие скорости, поэтому при фрезеровании большого количества декоративных кромок может потребоваться рассмотреть, какое преимущество высокоскоростной шпиндель дает столу. С другой стороны, мастерская, работающая с более мягкими, менее смолистыми материалами и занимающаяся чем-то менее ударным, например гравировкой, может найти значительное улучшение в более быстром шпинделе.
Мощность шпинделя также учитывается. При достаточной мощности скорость подачи становится немного менее критичной. Например, PDS предлагает шпиндель XLerator со скоростью до 40 000 об / мин и мощностью до 56 л.с. Такой тип мышц, конечно, работает в полностью автоматизированном процессе, где допуски очень предсказуемы и легко анализируются. Но в конфигурациях небольшого цеха с очень низким диапазоном от 2 до 5 л.с. скорость подачи может быть весьма резкой, и небольшое отклонение может иметь серьезные последствия.
Пневматические амортизаторы
Помимо скорости, еще одним аспектом шпинделей, который может достичь некоторых технических достижений в ближайшем будущем, является точность. В течение последних нескольких десятилетий несколько компаний работали над созданием пневматических шпинделей, в которых струя сжатого воздуха используется вместо физических подшипников для амортизации движущихся частей и обеспечения более плавного хода.
«Азом» (www.azom.com) – это издательское средство, используемое учеными-материаловедами для обмена информацией. Он базируется в Манчестере, Англия, и возглавляется командой британских, канадских и австралийских университетских профессоров.В недавнем сообщении доктора Ральфа Дюпона, президента немецкого производителя Levicron GmbH, команда Azom обсуждала разработки в этой области. В частности, речь шла о технологии, лежащей в основе бесконтактных (воздушных или «аэростатических») подшипников Levicron. Изначально компания начала обсуждение на своем веб-сайте с заявления: «При отсутствии контакта металл-металл большинству инженеров трудно поверить в то, что бесконтактный подшипник может быть таким же прочным и жестким, как роликовый подшипник. и в то же время еще точнее и быстрее.”
Нетрудно поверить, что большинство высокоскоростных двигателей, включая шпиндели для деревянных мастерских, испытывающие напряжение сдвига (вбок), скоро будут изготавливаться без каких-либо металлических подшипников и без какого-либо физического контакта между валом и корпусом. По сути, именно это уже происходит со многими системами жидкостного охлаждения. Но даже это низкоуровневое жидкостное трение можно устранить с помощью нового поколения шпинделей для аэростатических инструментов, разработанного Levicron. Ключом к этой технологии являются струи сжатого воздуха или газа, проходящие через цилиндр, которые создают восстанавливающую силу, которая перемещает даже самый малый эксцентричный вал обратно в центр.Чем точнее концентричность (чем меньше шатание), тем быстрее шпиндель может вращаться без трения или нагрева.
Levicron уже производит модели, способные развивать скорость до 100 000 об / мин. И хотя его аэростатические шпиндели создают волны в производственных процессах на базе ЧПУ, требующих высочайшего уровня точности (например, линзы камер и оптические компоненты), может пройти некоторое время, прежде чем они попадут в деревообрабатывающие цеха.
Для среднего столярного цеха инвестировать в сверхточные аэростатические шпиндели, вероятно, не будет иметь большого смысла с точки зрения бюджета.Но руководители производственных цехов, которые производят детали для высокотехнологичных компонентов, могут захотеть время от времени проверять их прогресс. Без какого-либо трения эти шпиндели с пневмоподвеской могут прослужить очень долго.
Эта статья впервые появилась в номере за август 2016 года.
Расчет скорости вращения шпинделя и скорости подачи
Предпосылкой для достижения максимальной производительности станка, стойкости инструмента и эффективности стружки является баланс между оптимальным удалением стружки, скоростью резания и скоростью подачи станка.В следующей статье содержится ценная информация о том, как добиться максимальной производительности обработки.
Скорость шпинделя
Неправильная скорость шпинделя – распространенная ошибка при обработке с ЧПУ. Для каждого материала и вида обработки требуется идеальный профиль инструмента и скорость резания. Инструменты большего диаметра требуют меньших скоростей резания. Важно согласовать скорость шпинделя и скорость подачи для любой конкретной задачи обработки, чтобы добиться максимального качества, срока службы инструмента и срока службы шпинделя.При этом скорость шпинделя регулируется преобразователем частоты. Все шпиндели представляют собой трехфазные асинхронные двигатели с плавно регулируемой скоростью от 0 об / мин до максимальной номинальной скорости.
Подача
Скорость подачи режущего инструмента должна быть сбалансирована пропорционально скорости вращения шпинделя. Изменение одного фактора влияет на другие факторы. Слишком медленная установка скорости подачи снижает срок службы режущего инструмента и может вызвать перегрев и, как следствие, привести к ожогам на заготовке.В результате снимается недостаточное количество материала и острие реза недостаточно охлаждается. В приведенной ниже таблице скорости подачи представлена информация о значениях начальной точки. Мы рекомендуем установить указанные средние значения для первого запуска. Обратитесь к поставщику режущего инструмента за индивидуальным советом для вашего конкретного применения.
Чип нагрузка
Нагрузка стружки – это термин, используемый для описания толщины стружки, удаляемой перпендикулярно направлению резания, измеренной вертикально к направлению резания.Нагрузка на стружку иногда также называется «подача на зуб» и рассчитывается следующим образом:
Нагрузка на стружку – важный фактор для определения скорости резания и подачи. Что касается древесины, то слишком низкая нагрузка на стружку приводит к слишком большому нагреву точки резания. «Пылеобразные» стружки, в свою очередь, могут вызвать ожоги на поверхности. Слишком большая нагрузка на стружку толкает фрезу сквозь материал, вызывая слишком большое давление. Возникающие в результате высокие радиальные нагрузки на подшипник шпинделя могут со временем вызвать отказ шпинделя, чрезмерный износ инструмента и поломку инструмента.Что касается фрезерования, обычно существует два вида фрезерования: синхронное фрезерование и обычное фрезерование. При обработке дерева синхронное фрезерование обеспечивает лучшее качество фрезерования, поскольку образующаяся стружка вырывается в меньшей степени. Следует отдавать предпочтение синхронному фрезерованию, так как нагрузки ниже, а срок службы инструмента больше.
Нагрузка на стружку – это один из многих факторов, используемых для определения размера шпинделя и параметров станка, например:
- Диапазон скоростей и потребляемая мощность шпинделя
- Определение нагрузки на инструмент в зависимости от модели режущего инструмента
- Расчет крутящего момента для доступного приложения
Мы рекомендуем связаться с техническим специалистом PDS в случае применения новых шпинделей, чтобы помочь вам в установлении базовых значений резания.Наши сотрудники будут рады ответить на ваши технические вопросы по телефону или электронной почте. В таблице ниже представлена информация о нагрузке на стружку для обычных фрезерных инструментов. Это начальные значения, которые нельзя превышать при первоначальной настройке. Фактические значения, конечно, могут отличаться в результате различных машинных факторов. К этим факторам относятся: жесткость, мощность, зажим инструмента, фиксация шпинделя, зажим заготовки и другие.
Какова формула скорости шпинделя? – MVOrganizing
Какова формула скорости шпинделя?
Следующее уравнение используется для расчета скорости шпинделя: об / мин = sfm ÷ диаметр × 3.82, где диаметр – это диаметр режущего инструмента или диаметр детали на токарном станке в дюймах, а 3,82 – константа, полученная в результате алгебраического упрощения более сложной формулы: об / мин = (sfm × 12) ÷ (диаметр × π ).
Что такое скорость резания при токарной обработке?
Скорость резания определяется как скорость, с которой деталь движется по отношению к инструменту (обычно измеряется в футах в минуту). Подача определяется как расстояние, которое инструмент проходит за один оборот детали. Скорость резания и подача определяют качество поверхности, потребляемую мощность и скорость съема материала.
В чем разница между скоростью резания и скоростью шпинделя?
Угловая скорость заготовки (об / мин) машинистами называется «скоростью шпинделя». Его тангенциально-линейный эквивалент на поверхности заготовки (м / мин или sfm) машинистами называют «скоростью резания», «поверхностной скоростью» или просто «скоростью». Эту скорость машинисты называют «подачей».
На каком количестве оборотов следует переключаться?
Переключайте передачи между 2000 и 2500 об / мин для оптимальной эффективности двигателя.Повышение числа оборотов до 3000 об / мин или выше увеличивает скорость, но заставляет двигатель работать тяжелее, что снижает экономию топлива.
Насколько быстро 7 000 об / мин?
около 91,7 миль / ч
На каких оборотах должна быть моя машина на скорости 70 миль в час?
около 2500 об / мин
Где мои обороты должны быть на холостом ходу?
Обычно двигатели работают на холостом ходу около 600-800 об / мин. Старые двигатели могут развивать скорость до 1200 об / мин и более во время прогрева. Но если двигатель набирает обороты на холостом ходу, даже после того, как он достаточно прогрет, у вас может быть проблема.
Должны быть 0 об / мин на холостом ходу?
Двигатель будет работать на холостом ходу, а частота вращения будет составлять от 800 до 1000 об / мин. Когда вы выключите двигатель, счетчик оборотов покажет 0 об / мин. Для получения нулевого значения ваш двигатель не должен работать. Большинство двигателей работают на холостом ходу от 600 до 900 об / мин.
1000 об / мин на холостом ходу – это плохо?
В большинстве современных автомобилей скорость холостого хода от 600 до 1000 об / мин является средней. Однако, если ваша машина едет на холостом ходу, она не будет плавной. Неровный холостой ход легко обнаружить при запуске двигателя, и он может зависеть от температуры двигателя при запуске двигателя.
Может ли грубый холостой ход повредить двигатель?
Обратными сторонами грубого холостого хода могут быть снижение расхода топлива, низкая производительность, проблемы с запуском или потенциальные серьезные проблемы с двигателем в ближайшем будущем. Лучше всего попытаться диагностировать и исправить грубый холостой ход до того, как он станет хуже и до того, как он станет дорогостоящим!
Что может вызвать резкую работу двигателя на холостом ходу?
Неровная работа двигателя на холостом ходу может быть вызвана свечами зажигания или проводами свечей зажигания. Поврежденная или неправильно установленная свеча может привести к непостоянному сжиганию топлива.Если повреждение достаточно велико, вы также можете заметить, что ваш двигатель работает неровно во время движения.
Почему двигатель плохо работает на холостом ходу?
Это плохо для вашего двигателя. Поскольку ваш двигатель не работает при максимальной температуре на холостом ходу, топливо не сгорает полностью, оставляя остатки, которые в конечном итоге могут повредить вашу выхлопную систему.
Как сгладить резкий холостой ход?
Как исправить грубый холостой ход
- Отвезите автомобиль в авторитетный сервисный центр, у которого есть сканер кода.
- Установите коробку передач в нейтральное положение или парковку.
- Запустите двигатель и дайте ему прогреться.
- Проверьте состояние каждой свечи.
- Установите свечи на место и запустите двигатель.
- Найдите винты холостого хода и смеси холостого хода на карбюраторе, если они есть.
Может ли слишком много масла вызвать резкий холостой ход?
Двигатель с обратным зажиганием Добавление слишком большого количества масла в двигатель может вызвать резкую работу двигателя и обратный огонь. Поскольку моторное масло будет циркулировать по двигателю в областях, которые ему не нравятся, двигатель не будет работать так хорошо и даже может вызвать обратный огонь.
Можно ли оставлять машину без дела в течение часа?
Перво-наперво, работа на холостом ходу не обязательно вредна для вашего автомобиля, но имеет свои последствия. Вы можете потратить почти галлон бензина, если оставите машину на холостом ходу более часа. Пригорает масло. Чем дольше двигатель работает, тем больше циркулирует и сгорает моторное масло.
Это плохо – оставлять машину включенной на 30 минут?
Обычно нет. Большинство современных транспортных средств могут выдерживать работу кондиционера в течение 30 минут без каких-либо побочных эффектов.Тем не менее, это повышает рабочую температуру двигателя, и если это очень жаркий день и система охлаждения автомобиля каким-либо образом скомпрометирована, это может иметь негативный эффект.
Стабильность процесса фрезерования с переменной скоростью шпинделя с использованием полного метода на основе Рунге – Кутты
Метод переменной скорости шпинделя (VSS) эффективен в предотвращении регенеративной вибрации в процессах фрезерования. Однако параметры модуляции скорости шпинделя следует выбирать намеренно, чтобы увеличить скорость съема материала.Алгоритмы прогнозирования стабильности играют важную роль в этом отношении, поскольку они позволяют прогнозировать стабильность для всех диапазонов заданной скорости шпинделя. Увеличение времени расчета при фрезеровании с регулируемой частотой вращения шпинделя, вызванное частотой модуляции, затрудняет его практическое использование в мастерской. В этой статье представлен основанный на Рунге – Кутте метод полной дискретизации (RKCDM) для прогнозирования стабильности фрезерования с переменной скоростью шпинделя, которая описывается набором дифференциальных уравнений запаздывания (DDE) с периодическими по времени коэффициентами и временными коэффициентами. переменная задержка.Сходимость и эффективность вычислений сравниваются с таковыми метода полудискретизации (SDM) при различных конфигурациях тестирования и условиях измельчения. Результаты показывают, что RKCDM более точен и экономит не менее 50% времени расчета SDM. Влияние параметров модуляции на стабильность фрезерования VSS исследуется с помощью диаграмм лепестков стабильности, полученных с помощью RKCDM.
1. Введение
В процессе фрезерования вибрации, вызванные вибрациями между фрезой и заготовкой, затрудняют производственное производство.Это не только снижает производительность обработки, но и может привести к ухудшению качества обработки поверхности детали, увеличению износа инструмента и сокращению срока службы самого станка.
Chatter обычно делится на две категории. Первичная вибрация обычно возникает из-за трения между фрезой и заготовкой. Вторичная вибрация, вызванная механизмом регенерации, является наиболее частым фактором. Поэтому во многих публикациях обсуждается только регенеративная болтовня.
Было предложено несколько стратегий для подавления или предотвращения болтовни.Их можно примерно разделить на следующие категории: (1) Стратегии, основанные на диаграмме лепестков устойчивости (SLD) и выборе параметров резания (2) Активные методы подавления вибрации для уменьшения вибрации системы станка (3) Полуактивная вибрация- стратегии подавления (4) Стратегии пассивного подавления вибрации, учитывающие соответствие станка или его конфигурацию (5) Другие стратегии, основанные на отслеживании сигналов в процессе фрезерования для настройки параметров фрезерования
SLD является наиболее логичным и широко распространенным методом выбора параметры резки, чтобы избежать дребезга.Исследователи предложили множество методов прогнозирования стабильности обработки. К ним относятся частотный метод нулевого порядка [1], метод численного интегрирования [2], временной анализ конечных элементов (TFEA) [3], метод полудискретизации (SDM) [4, 5], метод полудискретизации на стандартной ортогональной основе Шеннона [ 6, 7], метод на основе W-функций Ламберта [8], метод на основе полиномов Лежандра [9], метод на основе Адамса – Симпсона [10], метод полной дискретизации на основе Рунге – Кутты [11] и метод коллокаций Чебышева. для дифференциальных уравнений с запаздыванием [12].
Поскольку регенерирующая вибрация является результатом неправильной разницы фаз между волнистыми поверхностями, вызванной последовательными резками инструментом, альтернативные методы обычно изменяют временную задержку между зубьями фрезы. Slavicek [13] продемонстрировал, что этого можно достичь с помощью фрез с переменным шагом. Altintas et al. [14], Olgac и Sipahi [15], Jin et al. [16] и Sims et al. [17] продемонстрировали, что фрезы с переменным шагом могут избежать или значительно подавить вибрацию.
Идея изменения скорости шпинделя для подавления или предотвращения дребезга при обработке восходит к 1970-м годам и новаторским исследованиям Stoferle и Grab [18].После этого Takemura et al. [19] изучали стабильность токарной обработки с переменной скоростью вращения шпинделя, и экспериментальные испытания показали лишь небольшое улучшение глубины резания, хотя стабильность VSS была выше, чем у фрезерования с постоянной скоростью шпинделя (CSS). Altintas и Chan [20] исследовали стабильность VSS с синусоидальной модуляцией, используя метод временного моделирования. Tsao et al. [21] описал систему фрезерования VSS в области углов и показал, что вибрация может быть подавлена или устранена в значительной степени путем правильного выбора параметров модуляции.Лонг и Балачандран [22] проанализировали стабильность восходящего и нисходящего фрезерования с синусоидальной модуляцией, используя метод полудискретизации. В частотной области Zatarain et al. [23] предложил общую теорию для анализа устойчивости фрезерования VSS. Seguy et al. [24, 25] использовали метод полудискретизации для изучения стабильности VSS фрезерования в высокоскоростной области и сообщили, что VSS был эффективным методом для уменьшения вибрации удвоения периода. Основываясь на методе полной дискретизации, Се и Чжан [26, 27] представили улучшенный SDM для прогнозирования стабильности VSS фрезерования.Ding et al. [28] исследовали стабильность фрезерной системы VSS с использованием численного метода постоянного шага. Niu et al. [29] унифицировали различные периодические схемы изменяющейся во времени модуляции скорости шпинделя в единую структуру, вывели и вычислили изменяющуюся во времени задержку на основе метода Рунге – Кутта четвертого порядка, а также вычислили и сравнили стабильность VSS фрезерования с различными схемы модуляции с использованием численного интегрирования с переменным шагом. Totis et al. [30] исследовали стабильность фрезерования с VSS в угловой области.Jin et al. [31] изучали стабильность фрезерования с постоянным шагом, переменным шагом и VSS, используя метод полной дискретизации.
Как упоминалось выше, было проведено много исследований для прогнозирования стабильности фрезерования VSS. Однако требуемое время вычислений сильно увеличивается из-за частотной модуляции, что затрудняет применение VSS [29]. Niu et al. [32] и Ли и др. [11] недавно предложили основанный на Рунге – Кутте метод полной дискретизации (RKCDM) с использованием схемы полной дискретизации [33], но их исследования были основаны исключительно на механической обработке CSS.В этой статье мы представляем динамическую модель фрезерования с двумя степенями свободы, выраженную DDE, и основанный на методе Рунге – Кутты метод полной дискретизации для эффективного анализа VSS фрезерования. Сходимость и вычислительная эффективность сравниваются с современным методом полудискретизации. Наконец, мы обсуждаем влияние модуляции VSS на стабильность фрезерования с помощью карт и контурных графиков осевой глубины резания (ADOC), рассчитанных RKCDM.
2. Моделирование процесса VSS
2.1. VSS
В этой статье будет рассмотрено и проанализировано периодическое изменение скорости шпинделя с синусоидальной модуляцией. Как показано на рисунке 1, синусоидальное изменение скорости шпинделя является периодическим в определенный период времени с номинальным значением и амплитудой изменения скорости. Функция формы синусоидальной модуляции моделируется следующим образом: где – отношение амплитуды изменения скорости к номинальной скорости шпинделя, – отношение частоты изменения скорости к номинальной скорости шпинделя и – фазовый угол синусоидальной модуляции при время т = 0.
2.2. Структурная модель
В процессе обработки относительно более гибкие детали будут подвергаться динамическому прогибу и образовывать волнистую поверхность. Таким образом, систему можно упростить до осциллятора, который движется силой фрезерования. Мы показываем пример модели [34] на рисунке 2. Основное уравнение модели: где – относительное демпфирование, – угловая собственная частота, – осевая глубина резания и – модальная масса зубьев. Предполагается, что динамические характеристики идентичны в направлениях и, поэтому масса модели, относительное демпфирование и собственная частота одинаковы в обоих направлениях.Изменяющиеся во времени коэффициенты силы резания,,, и, выражаются как где – количество зубьев фрезы, и -, соответственно, тангенциальный и нормальный линеаризованные коэффициенты силы резания. Угловое положение j -го зуба определяется как
. Оконная функция может быть определена как где и являются, соответственно, начальным и выходным углами j -го фрезерного зуба. Для фрезерования и. Для фрезерования вниз, где – коэффициент радиального погружения, – это радиальная глубина резания и – диаметр фрезы.
2.3. Расчет переменных временных задержек
Подставив (1) в (4), угловое положение j -го зуба может быть выражено как где – угловая скорость.
В этом случае временная задержка не может быть указана в явном виде, так как она определяется уравнением:
Прямое вычисление занимает много времени [28], поэтому мы упрощаем интегральное уравнение. Подставляя (1) в (7), мы получаем неявное соотношение:
Функция не может быть решена в явном виде; следовательно, он должен быть рассчитан численно.Однако, если RVA и RVF достаточно малы; то приблизительно равно [22] где и. Как показано на рисунке 3, точное время задержки, которое рассчитывается с использованием численного решения из (8) и приблизительных значений из (9), является согласованным. Итак, приближение (9) эффективно. Рисунки 3 (a) и 3 (b) показывают, что приближенная ошибка для RVA = 0,1 меньше, чем RVF = 0,2, потому что небольшое значение RVA является условием (9). Ниже мы рассчитаем изменяющуюся во времени задержку с помощью (9).
3. Стабильность фрезерования с VSS
Следует отметить, что хотя здесь обсуждается VSS с синусоидальной модуляцией, предлагаемый RKCDM может справиться с другими типами модуляции VSS без каких-либо дополнительных трудностей.Посредством алгебраического преобразования (2) может быть записано как где
Первым шагом дискретизации является построение дискретизации временного интервала с длиной, так что, где – целое число, которое можно рассматривать как параметр аппроксимации, относящийся к периоду времени. Временной шаг может быть выражен как
Средняя задержка для интервала дискретизации определяется как
Ряд целых чисел вводится следующим образом: поскольку и где int ( * ) – это функция, округляющая положительные числа до нуля (например,г., int (7,875) = 7). Поскольку задержка периодически меняется во времени, целое число m i может изменяться для разных шагов полудискретизации.
Максимальное значение вводится как
Обратите внимание, что M можно рассматривать как параметр аппроксимации относительно длительности временной задержки.
Самая популярная версия алгоритма Рунге – Кутта – [35], где обозначает, обозначает и представляет и 0 ≤ i ≤ m i .Для решения (10) можно последовательно вывести следующие уравнения: где
Подставляя (19) – (21) в (18), мы можем получить следующую итерационную формулу: где коэффициенты могут быть выражены как где I равно единичная матрица и размерность вектора.
Чтобы получить матрицу перехода, мы сначала определяем новый размерный вектор как
Наконец, результирующая дискретная карта выражается как где матрица коэффициентов может быть построена как -мерная матрица:
Следовательно, приближенная матрица перехода Флоке может быть описывается как
Тогда устойчивость системы может быть рассчитана на основе теории Флоке.Если модули всех собственных значений матрицы перехода меньше единицы, то система устойчива; в противном случае он нестабилен.
4. Моделирование и обсуждение
В этом разделе экспериментальный пример [3] используется для проверки точности и эффективности RKCDM. Модальными параметрами фрезерных систем являются диаметр инструмента, количество зубьев, коэффициент тангенциальной силы резания, коэффициент радиальной силы резания, собственная частота, модальный коэффициент демпфирования и модальная масса.Все расчеты выполняются в MATLAB R2014a на настольном компьютере (центральный процессор Intel Core ™ i7-6700K, 4,0 ГГц, 16 ГБ). Сначала мы обсудим конвергенцию RKCDM и SDM.
4.1. Сходимость и эффективность вычислений
Скорости сходимости RKCDM и SDM в различных условиях сравниваются на рисунке 4. Дискретное количество временных задержек τ (для фрезерования VSS) установлено как для фрезерования с постоянной скоростью, и M для VSS фрезерования и определяется согласно (17), а максимальный модуль собственных значений матрицы перехода задается равным.Для сравнения сходимости RKCDM и SDM значение при условии записывается как точное значение для оценки скорости сходимости. При увеличении ошибка аппроксимации RKCDM ниже, чем SDM. То же явление можно получить для фрезерования VSS с увеличением M . Это означает, что RKCDM сходится быстрее, чем SDM, с увеличением дискретного числа временных задержек, потому что для SDM ошибка дискретизации составляет [36]. Однако погрешность дискретизации для RKCDM составляет.Niu et al. [32] использовали двухточечные барицентрические точки Лагранжа для аппроксимации средних точек, так что оставшаяся часть двухточечной интерполяции равна. Чтобы повысить точность RKCDM, дискретные точки берутся в одном интервале прохождения зубьев для расчета коэффициентов силы резания,, и для следующих примеров. Таким образом, для временного интервала,, и, могут быть вычислены с использованием четных точек, а и рассчитываются с использованием левых точек. Преимущество этого состоит в том, что точность RKCDM такая же, как и у классического метода Рунге – Кутты четвертого порядка.Для повышения точности прогнозирования дискретное число M изменяющихся во времени задержек всегда больше 80, и, согласно рисунку 4, RKCDM может иметь минимальную ошибку аппроксимации.
Чтобы сравнить вычислительную эффективность, мы обратимся к рисунку 5, на котором показано потребление времени при использовании RKCDM и SDM. Для фрезерования VSS время, необходимое для достижения стабильности, увеличивается с уменьшением RVA. Для небольших RVA с RKCDM можно сэкономить больше времени, чем с SDM. Отсюда можно сделать вывод, что потребление времени увеличивается с увеличением числа дискретных задержек.Результаты на Рисунке 5 показывают, что 54% времени можно сэкономить, используя RKCDM вместо SDM.
4.2. Анализ влияния параметров модуляции на стабильность фрезерования VSS
На рисунке 6 показан SLD фрезерования VSS и CSS. При использовании VSS граница устойчивости, очевидно, увеличивается, особенно при низких скоростях шпинделя. Хотя глубина реза увеличивается с использованием VSS, модуляция также оказывает важное влияние на стабильность. На Рисунке 6 (а) в качестве примера видно, что глубина резания при номинальной скорости вращения шпинделя 22 000 об / мин резко уменьшается.Чтобы всесторонне изучить влияние параметров модуляции на стабильность фрезерования, отношения между глубиной резания, RVA и RVF показаны на трехмерных графиках на рисунках 7 и 8. Согласно рисунку 6 (а) осевая глубина резания имеет минимальное значение 1 мм для фрезерования CSS.
После использования VSS, ADOC на этих двух номинальных скоростях шпинделя значительно увеличивается, как показано на рисунках 7 и 8. Рисунок 7 показывает, что ADOC изменяется с изменением параметров синусоидальной модуляции RVA и RVF около номинальной скорости шпинделя, равной 4900 об / мин.Очевидно, что при использовании VSS самая низкая точка выше, чем при фрезеровании CSS. Из рисунка 7 мы знаем, что ADOC более чувствителен к RVA, чем к RVF; Итак, для машиниста выбор параметров модуляции более интересен, чем выбор скорости шпинделя. Если взять в качестве примера номинальную скорость шпинделя 4900 об / мин, с параметрами модуляции RVA = 0,10 и RVF = 0,17, ADOC увеличится до 4,16 мм. Контурный график на Рисунке 7 (b) показывает, что не только вблизи точки (0,10, 0,17), но и все стабильные пределы ADOC на этих двух рисунках (Рисунки 7 и 8) также превышают 1 мм.Таким образом, VSS всегда может увеличить ADOC примерно до номинальной скорости шпинделя 4900 об / мин. Когда RVA находится в диапазоне [0,26, 0,33], ADOC все еще может достичь локального максимума. Поскольку выбор RVA ограничен движущей силой скорости шпинделя, низкий RVA более подходит для фрезерования с VSS.
Результаты при номинальной скорости вращения шпинделя 22 000 об / мин отличаются от результатов при 4 900 об / мин. ADOC резко падает около номинальной скорости шпинделя 22 000 об / мин. Чтобы изучить влияние техники VSS на стабильность фрезерования, мы показываем трехмерную диаграмму стабильности при номинальной скорости шпинделя 22000 об / мин на рисунке 8.С VSS ADOC всегда выше, чем CSS на рис. 7. Однако это отличается при номинальной скорости шпинделя 22000 об / мин, где ADOC не всегда увеличивается при фрезеровании VSS по сравнению с фрезерованием CSS. На рисунке 6 показано, что ADOC составляет 7,83 мм без VSS. На рисунке 8 ADOC всегда ниже 7,83 мм с RVA в диапазоне [0,2, 0,3]. Таким образом, важно правильно выбрать параметры модуляции, чтобы улучшить стабильность с помощью техники VSS. На рисунке 8 ADOC увеличивается до локальной вершины с изменением RVA и RVF, например, около RVA = 0.06 и RVF = 0,16, RVA = 0,08 и RVF = 0,13, а также RVA = 0,14 и RVF = 0,15. Взяв, например, RVA = 0,06 и RVF = 0,16, ADOC может достигать 9,99 мм в этой области. Таким образом, ADOC все еще может быть увеличен при соответствующем выборе параметров модуляции.
5. Заключение
Был разработан новый алгоритм для прогнозирования стабильности VSS-фрезерования, и были сделаны следующие выводы: (1) Управляющая DDE периодического во времени процесса фрезерования, включая регенеративный эффект, описывается набором алгебраических уравнения, а устойчивость системы предсказывается теорией Флоке.(2) Были проведены сравнения скорости сходимости и вычислительной эффективности. RKCDM показывает более высокую скорость сходимости, чем SDM, поэтому RKCDM является более точным. (3) Результаты моделирования показывают, что RKCDM можно использовать для выбора параметров при фрезеровании VSS. Карты и контурные графики ADOC, полученные из RKCDM, показывают стабильность фрезерования VSS с изменениями синусоидальной модуляции с RVA и RVF, а стабильность более чувствительна к изменению RVA. Карты и контурные графики ADOC могут использоваться для выбора оптимальных параметров модуляции для фрезерования VSS.
Наконец, хотя оптимальные параметры метода VSS были выбраны с помощью предложенного здесь метода, очевидно, что параметры должны быть дополнительно протестированы, и это будет нашей будущей работой.
Доступность данных
Данные, использованные для подтверждения результатов этого исследования, включены в статью.
Конфликт интересов
Авторы заявляют об отсутствии конфликта интересов.
Благодарности
Эта работа финансировалась Комиссией по науке и технологиям муниципалитета Шанхая (17DZ2283300).
Технологическая эффективность и применимость к реальным промышленным случаям
Электродвигательбыл оценен и сравнен со спецификациями данных двигателя
.
Дальнейшие исследования будут сосредоточены на влиянии
модуляции скорости на явления износа инструмента
и на потребление энергии двигателем шпинделя.
Кроме того, будет разработана более сложная реализация SSV
: идея состоит в разработке приложения
в мягком реальном времени, которое способно как обнаруживать вибрацию
, так и реализовать стратегию смягчения вибрации на основе
на основе SSSV.Оптимальные параметры SSSV (то есть параметры
, которые обеспечивают условие резания без вибрации
, ограничивающее перегрузку двигателя и энергопотребление)
будут выбираться адаптивно.
Благодарности Авторы выражают признательность консорциуму MUSP-
tium и итальянскому национальному проекту «Микеланджело», который предоставил
финансовую и научную основу для настоящего исследования. Паоло
Альбертелли особо благодарит фонд «Fondazione Polizzotto», который поддержал его стипендию для образования
за рубежом.
Ссылки
1. Altintas Y, Weck M (2004) Устойчивость к вибрации при резании металла и шлифовании
. CIRP Ann Manuf Technol 53 (2): 619–642
2. Quintana G, Ciurana J (2011) Дребезжание в процессах обработки: обзор
. Int J Mach Tool Manu 51: 363–376
3. Stoferle T, Grab H (1972) Vermeiden von Ratterschwingungen
durch Periodische Drehzahlanderung. Werkstatt und Betrieb
105: 727–730
4. Radulescu R, Kapoor SG, DeVor RE (1997) Исследование торцевого фрезерования
с регулируемой скоростью шпинделя для инструментальных конструкций со сложной динамикой
, часть 1: моделирование полученные результаты.J Manuf Sci E T
ASME 119: 266–272
5. Радулеску Р., Капур С.Г., Девор Р.Э. (1997) Исследование торцевого фрезерования
с регулируемой скоростью шпинделя для инструментальных конструкций со сложной динамикой
. Часть 2. Физическое объяснение. J Manuf Sci E T
ASME 119: 273–280
6. Altintas Y, Chan PK (1992) Обнаружение и подавление
вибрации при фрезеровании в процессе обработки. Int J Mach Tool Manu 32 (3): 329–347
7. Затарин М., Бедиага И., Муноа Дж., Лизарральде Р. (2008) Стабильность
процессов фрезерования с непрерывным изменением скорости шпинделя: анализ
по частоте и временные области и экспериментальная корреляция.
CIRP Ann 57: 379–384
8. Seguy S, Insperger T, Arnaud L, Dessein G, Peigné G (2010) На
стабильность высокоскоростного фрезерования при изменении скорости шпинделя. Int
J Adv Manuf Technol. DOI: 10.1007 / s00170-009-2336-9
9. Инамура Т., Сата Т. (1974) Анализ устойчивости резания при изменении скорости шпинделя
. CIRP Ann 23 (1): 119–120
10. Такемура Т., Китамура Т., Хоши Т., Окусимо К. (1974) Активное
подавление вибрации путем запрограммированного изменения скорости шпинделя.
CIRP Ann 23 (1): 121–122
11. Секстон Дж. С., Милн Р. Д., Стоун Б. Дж. (1977) Анализ устойчивости согласования по одной точке
с переменной скоростью шпинделя. Appl Math
Модель 1: 310–318
12. Секстон Дж. С., Стоун Б. Дж. (1978) Стабильность обработки с постоянно меняющейся скоростью шпинделя
. CIRP Ann 27 (1): 321–326
13. Секстон Дж. С., Стоун Б. Дж. (1980) Исследование переменных переходных эффектов
во время резки с переменной скоростью.J Mech Eng Sci
22: 107–118
14. Де Каньер Дж., Ван Брюссель Х., Ван Богерт Дж. (1981) Вклад
в математический анализ обработки с регулируемой скоростью шпинделя.
Appl Math Model 5 (3): 158–164
15. Лин С.К., Девор Р.Е., Капур С.Г. (1990) Влияние переменной скорости резания
на контроль вибрации при торцевом фрезеровании. Trans ASME J
Eng Ind 112: 1–11
16. Джемельняк К., Видота А. (1984) Подавление самовозбуждающейся вибрации
методом изменения скорости шпинделя.Int J Mach Tool Des Res
24 (3): 207–214
17. Yilmaz A, AL-Regib E, Ni J (2002) Подавление вибрации станка
за счет многоуровневого случайного изменения скорости шпинделя. Trans ASME J
Manuf Sci Eng 124 (2): 208–216
18. Jayaram S, Kapoor SG, DeVor RE (2000) Аналитическая стабильность
анализ обработки с регулируемой скоростью шпинделя. Trans ASME J
Manuf Sci Eng 122: 391–397
19. Ян Ф, Чжан Б., Ю Дж (2003) Подавление дребезга с несколькими изменяющимися во времени параметрами
при токарной обработке.J Mater Proc Technol 141
(3): 431–438
20. Al Regib E, Ni J, Lee SH (2003) Программирование скорости шпинделя
Вариантдля подавления вибрации станка. Int J Mach Tool
Manu 43 (12): 1229–1240
21. Insperger T, Schmitz T, Burn TJ, Stépán G (2003) Сравнение аналитического и численного моделирования
для переменной скорости шпинделя
токарная обработка. SME 2003 International Mechanical Engineering Con-
gress and Exposition (IMECE2003), Вашингтон, округ Колумбия, США, 15–
21 ноября 2003 г.
22.Insperger T, Stepan G (2004) Анализ устойчивости с периодической модуляцией скорости шпинделя
посредством полудискретизации. J Vib Control
10: 1835–1855
23. Намаччивая Н.С., Беддини Р. (2003) Изменение скорости вращения шпинделя для
подавление регенеративной вибрации. J Nonlienear Sci 13: 265–
288
24. Демир А., Хасанов А., Намаччивая Н.С. (2006) Уравнения задержки
с флуктуирующей задержкой, связанной с регенеративной вибрацией. Int J
Nonlienear Mech 41: 464–474
25.Ву Д., Чен К. (2010) Подавление дребезга в быстром сервоприводе инструмента
с помощью токарной обработки путем изменения скорости шпинделя. Int J Mach Tool Manu
50 (12): 1038–1047
26. Kalmár-Nagy T (2002) Модели динамики режущего инструмента
с дифференциалом задержки с нелинейными эффектами и эффектами взаимодействия мод. Докторская диссертация,
Корнельский университет, Нью-Йорк
27. Инспергер Т., Бартон Д.А. (2008) Критичность бифуркации Хопфа в модели
с зависимой от состояния задержкой токарных процессов.Int J Non Lin
Mech 43 (2): 140–149
28. Moon FC, Kalmár-Nagy T (2001) Нелинейные модели для сложной динамики
в режущих материалах. Phil Trans Math Phys Eng Sci 359
(1781): 695–711
29. Дешпанде Н., Фофана М. (2001) Нелинейная регенеративная вибрация при токарной обработке
. Robot Comput Integrated Manuf 17 (1–2): 107–112
30. Чандирамани Н.К., Потала Т. (2006) Динамика регенеративной вибрации 2-степеней свободы
во время токарной обработки. J Sound Vibrat 290: 448–464
31.Алтинтас Ю. (2000) Автоматизация производства: металлорежущие станки
, вибрации станков и проектирование ЧПУ.