ΠΠ΅Π½ΠΊΠ΅ΡΠΎΠ²Π°Π½ΠΈΠ΅ ΠΈ ΡΠ°Π·Π²Π΅ΡΡΡΠ²Π°Π½ΠΈΠ΅ ΠΎΡΠ²Π΅ΡΡΡΠΈΠΉ
ΠΠΏΠ΅ΡΠ°ΡΠΈΠΈ ΠΌΠ΅Ρ Π°Π½ΠΈΡΠ΅ΡΠΊΠΎΠΉ ΠΎΠ±ΡΠ°Π±ΠΎΡΠΊΠΈ Π·Π°Π³ΠΎΡΠΎΠ²ΠΎΠΊ Π½Π° ΡΠΎΠΊΠ°ΡΠ½ΡΡ ΡΡΠ°Π½ΠΊΠ°Ρ ΡΠ΅Π΄ΠΊΠΎ ΡΡΠ°Π½ΠΎΠ²ΡΡΡΡ ΡΠΈΠ½Π°Π»ΡΠ½ΡΠΌΠΈ Π² ΡΠ΅Ρ Π½ΠΎΠ»ΠΎΠ³ΠΈΡΠ΅ΡΠΊΠΎΠΌ ΠΏΡΠΎΡΠ΅ΡΡΠ΅. Π‘ΠΎΠ·Π΄Π°Π½ΠΈΠ΅ ΠΎΡΠ²Π΅ΡΡΡΠΈΠΉ β ΡΡΠΎ ΠΎΡΠ½ΠΎΠ²Π½ΠΎΠΉ ΡΡΠ°ΠΏ Π² ΠΏΠΎΠ»ΡΡΠ΅Π½ΠΈΠΈ Π½Π΅ΠΎΠ±Ρ ΠΎΠ΄ΠΈΠΌΠΎΠΉ ΡΠΎΡΠΌΡ Π΄Π΅ΡΠ°Π»ΠΈ. ΠΠΎ Π·Π° Π½ΠΈΠΌ, ΠΊΠ°ΠΊ ΠΏΡΠ°Π²ΠΈΠ»ΠΎ, ΡΠ»Π΅Π΄ΡΠ΅Ρ ΡΡΠ°ΠΏ Π΄ΠΎΡΠ°Π±ΠΎΡΠΊΠΈ. ΠΡΡΠ°ΡΡΠΈ ΡΡΠΎ ΠΌΠ΅ΡΠΎΠΏΡΠΈΡΡΠΈΡ ΡΠΈΡΡΠΎΠ²ΠΎΠΉ ΠΊΠΎΡΡΠ΅ΠΊΡΠΈΠΈ, Π½ΠΎ ΠΈΠ½ΠΎΠ³Π΄Π° ΠΏΡΠΈΠΌΠ΅Π½ΡΡΡΡΡ ΠΈ ΠΌΠ΅ΡΠΎΠ΄Ρ Π±Π°Π·ΠΎΠ²ΠΎΠ³ΠΎ ΠΈΠ·ΠΌΠ΅Π½Π΅Π½ΠΈΡ ΠΏΠ°ΡΠ°ΠΌΠ΅ΡΡΠΎΠ² Π²ΡΠΏΠΎΠ»Π½Π΅Π½Π½ΠΎΠ³ΠΎ ΡΠ΅Π·Π°. Π ΡΠ°ΠΊΠΈΠΌ ΠΎΠΏΠ΅ΡΠ°ΡΠΈΡΠΌ ΠΎΡΠ½ΠΎΡΡΡ Π·Π΅Π½ΠΊΠΎΠ²Π°Π½ΠΈΠ΅ ΠΈ ΡΠ°Π·Π²Π΅ΡΡΡΠ²Π°Π½ΠΈΠ΅ ΠΎΡΠ²Π΅ΡΡΡΠΈΠΉ, Π² ΡΠ΅Π·ΡΠ»ΡΡΠ°ΡΠ΅ ΡΠ΅Π³ΠΎ ΠΎΠΏΠ΅ΡΠ°ΡΠΎΡ ΠΏΠΎΠ»ΡΡΠ°Π΅Ρ ΠΎΠΏΡΠΈΠΌΠ°Π»ΡΠ½ΡΡ ΠΏΠΎ Ρ Π°ΡΠ°ΠΊΡΠ΅ΡΠΈΡΡΠΈΠΊΠ°ΠΌ Π·Π°Π³ΠΎΡΠΎΠ²ΠΊΡ. ΠΠΎ-ΠΏΠ΅ΡΠ²ΡΡ , ΠΏΠΎΠ΄Π³ΠΎΡΠΎΠ²Π»Π΅Π½Π½ΠΎΠ΅ ΡΠ³Π»ΡΠ±Π»Π΅Π½ΠΈΠ΅ ΠΎΠ±ΡΠ΅ΡΠ°Π΅Ρ Π½Π΅ΠΎΠ±Ρ ΠΎΠ΄ΠΈΠΌΡΠ΅ ΡΠ°Π·ΠΌΠ΅ΡΡ, Π° Π²ΠΎ-Π²ΡΠΎΡΡΡ , Π΅Π³ΠΎ ΠΊΡΠΎΠΌΠΊΠΈ ΠΈ ΠΏΠΎΠ²Π΅ΡΡ Π½ΠΎΡΡΠΈ ΠΎΡΠΈΡΠ°ΡΡΡΡ ΠΎΡ Π»ΠΈΡΠ½ΠΈΡ Π·Π°ΡΡΠ΅Π½ΡΠ΅Π² ΠΈ ΡΡΡΡΠΆΠΊΠΈ.
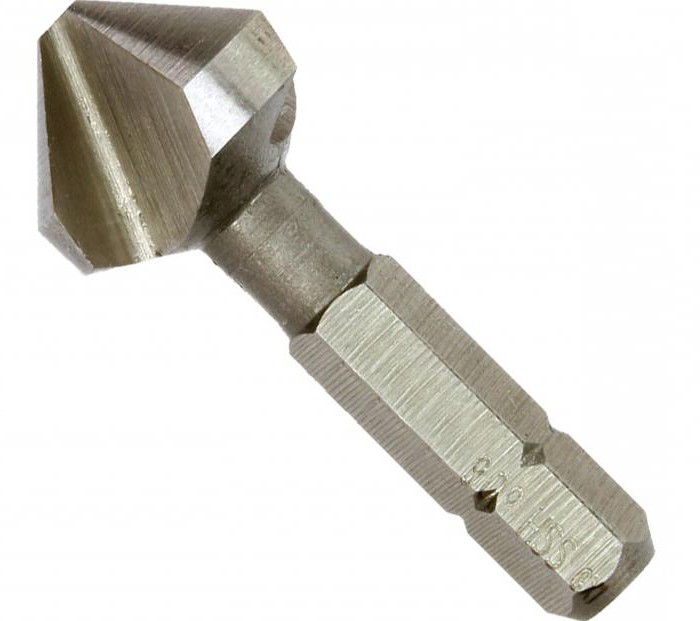
ΠΠ°ΠΊΠΈΠ΅ Π·Π°Π΄Π°ΡΠΈ ΡΠ΅ΡΠ°Π΅Ρ Π·Π΅Π½ΠΊΠ΅ΡΠΎΠ²Π°Π½ΠΈΠ΅?
Π ΠΏΡΠΎΡΠ΅Π΄ΡΡΠ΅ Π·Π΅Π½ΠΊΠ΅ΡΠΎΠ²Π°Π½ΠΈΡ Π΄ΠΎΠΏΡΡΠΊΠ°ΡΡΡΡ ΠΎΡΠ²Π΅ΡΡΡΠΈΡ ΡΠ°Π·Π½ΠΎΠ³ΠΎ ΠΏΡΠΎΠΈΡΡ ΠΎΠΆΠ΄Π΅Π½ΠΈΡ. ΠΡΠΎ ΠΌΠΎΠ³ΡΡ Π±ΡΡΡ Π»ΠΈΡΡΠ΅, ΡΡΠ°ΠΌΠΏΠΎΠ²Π°Π½Π½ΡΠ΅ ΠΈΠ»ΠΈ ΠΏΡΠΎΡΠ²Π΅ΡΠ»Π΅Π½Π½ΡΠ΅ Π½ΠΈΡΠΈ, Π½Π°Π΄ ΠΊΠΎΡΠΎΡΡΠΌΠΈ Π² Π΄Π°Π»ΡΠ½Π΅ΠΉΡΠ΅ΠΌ Π±ΡΠ΄Π΅Ρ ΡΠ°Π±ΠΎΡΠ°ΡΡ ΠΌΠ°ΡΡΠ΅Ρ ΠΏΠΎ Π·Π΅Π½ΠΊΠ΅ΡΠΎΠ²Π°Π½ΠΈΡ. Π ΡΠ΅ΠΌ ΠΆΠ΅ Π·Π°ΠΊΠ»ΡΡΠ°Π΅ΡΡΡ ΡΡΡΡ Π΄Π°Π½Π½ΠΎΠΉ ΠΎΠΏΠ΅ΡΠ°ΡΠΈΠΈ? Π£ Π½Π΅Π΅ ΠΌΠΎΠ³ΡΡ Π±ΡΡΡ Π΄Π²Π΅ ΡΠ΅Π»ΠΈ. ΠΠ°ΠΊ ΠΌΠΈΠ½ΠΈΠΌΡΠΌ Π±ΡΠ΄Π΅Ρ ΠΎΠ±Π΅ΡΠΏΠ΅ΡΠ΅Π½Π° Π·Π°ΡΠΈΡΡΠΊΠ° ΠΏΠΎΠ²Π΅ΡΡ Π½ΠΎΡΡΠ΅ΠΉ ΠΎΡΠ²Π΅ΡΡΡΠΈΡ. ΠΡΠΎ ΠΎΡΠΎΠ±Π΅Π½Π½ΠΎ Π²Π°ΠΆΠ½ΠΎ Π² ΡΠ΅Ρ ΡΠ»ΡΡΠ°ΡΡ , Π΅ΡΠ»ΠΈ ΠΏΡΠ΅Π΄Π²Π°ΡΠΈΡΠ΅Π»ΡΠ½ΠΎ Π²ΡΠΏΠΎΠ»Π½ΡΠ΅ΡΡΡ Π³ΡΡΠ±ΠΎΠ΅ ΡΠ²Π΅ΡΠ»Π΅Π½ΠΈΠ΅ ΠΈ ΡΠ°Π·Π²Π΅ΡΡΡΠ²Π°Π½ΠΈΠ΅ ΠΎΡΠ²Π΅ΡΡΡΠΈΠΉ, ΠΊΡΠΎΠΌΠΊΠΈ ΠΊΠΎΡΠΎΡΡΡ Π½ΡΠΆΠ΄Π°ΡΡΡΡ Π² Π΄ΠΎΡΠ°Π±ΠΎΡΠΊΠ΅. Π Π·Π°Π²ΠΈΡΠΈΠΌΠΎΡΡΠΈ ΠΎΡ ΠΊΠ°ΡΠ΅ΡΡΠ²Π° ΡΠΎΡΠΌΠΈΡΠΎΠ²Π°Π½ΠΈΡ ΠΎΡΠ²Π΅ΡΡΡΠΈΡ ΠΌΠΎΠΆΠ΅Ρ ΠΏΡΠΈΠΌΠ΅Π½ΡΡΡΡΡ ΠΏΠΎΠ»ΡΡΠΈΡΡΠΎΠ²ΠΎΠ΅ ΠΈΠ»ΠΈ ΡΠΈΡΡΠΎΠ²ΠΎΠ΅ Π·Π΅Π½ΠΊΠ΅ΡΠΎΠ²Π°Π½ΠΈΠ΅. Π ΡΠ΅Π·ΡΠ»ΡΡΠ°ΡΠ΅ ΠΌΠ΅Π½ΡΠ΅ΡΡΡ ΠΈ ΡΡΠ΅ΠΏΠ΅Π½Ρ ΡΠ³Π»Π°ΠΆΠΈΠ²Π°Π½ΠΈΡ ΡΠ°Π±ΠΎΡΠΈΡ ΠΏΠΎΠ²Π΅ΡΡ Π½ΠΎΡΡΠ΅ΠΉ. ΠΡΠ΅ Π±ΠΎΠ»Π΅Π΅ ΠΎΡΠ²Π΅ΡΡΡΠ²Π΅Π½Π½Π° Π·Π°Π΄Π°ΡΠ° ΠΊΠ°Π»ΠΈΠ±ΡΠΎΠ²ΠΊΠΈ. Π ΡΡΠΎΠΌ ΡΠ»ΡΡΠ°Π΅ ΠΌΠ°ΡΡΠ΅Ρ Π½Π΅ ΠΎΠ³ΡΠ°Π½ΠΈΡΠΈΠ²Π°Π΅ΡΡΡ Π·Π°ΡΠΈΡΡΠΊΠΎΠΉ ΠΈ ΠΊΠΎΡΡΠ΅ΠΊΡΠΈΡΡΠ΅Ρ ΠΏΠ°ΡΠ°ΠΌΠ΅ΡΡΡ ΠΎΡΠ²Π΅ΡΡΡΠΈΡ, Π½Π°ΠΏΡΠΈΠΌΠ΅Ρ Π³Π»ΡΠ±ΠΈΠ½Ρ ΠΈ ΡΠΎΠ»ΡΠΈΠ½Ρ. ΠΠΎΡΡΠ΅Π±Π½ΠΎΡΡΡ Π² ΡΠ°ΠΊΠΈΡ Π΄Π΅ΠΉΡΡΠ²ΠΈΡΡ Π²ΠΎΠ·Π½ΠΈΠΊΠ°Π΅Ρ, Π΅ΡΠ»ΠΈ ΠΈΠ·Π½Π°ΡΠ°Π»ΡΠ½ΠΎ ΠΏΠΎΠ»ΡΡΠ΅Π½Π½ΠΎΠ΅ ΠΎΡΠ²Π΅ΡΡΡΠΈΠ΅ Π½Π΅ ΠΏΠΎΠ΄Ρ ΠΎΠ΄ΠΈΡ ΠΏΠΎ ΡΠ°Π·ΠΌΠ΅ΡΠ°ΠΌ ΠΊ ΡΠ΅Π»Π΅Π²ΠΎΠΉ ΡΠΏΠΈΠ»ΡΠΊΠ΅, Π²ΠΈΠ½ΡΡ ΠΈΠ»ΠΈ Π΄ΡΡΠ³ΠΎΠΉ ΠΊΡΠ΅ΠΏΠ΅ΠΆΠ½ΠΎΠΉ Π΄Π΅ΡΠ°Π»ΠΈ. ΠΠΎΡΠ»Π΅ Π·Π΅Π½ΠΊΠ΅ΡΠΎΠ²Π°Π½ΠΈΡ ΠΊΠ°ΠΊ ΡΠ°Π· Π²ΡΠΏΠΎΠ»Π½ΡΠ΅ΡΡΡ Π½Π°ΡΠ΅Π·ΠΊΠ° ΡΠ΅Π·ΡΠ±Ρ Π² ΡΠΎΠΎΡΠ²Π΅ΡΡΡΠ²ΠΈΠΈ Ρ ΡΠ°Π·ΠΌΠ΅ΡΠ°ΠΌΠΈ ΠΌΠ΅ΡΠΈΠ·Π°.
Π§ΡΠΎ ΠΏΡΠ΅Π΄ΡΡΠ°Π²Π»ΡΠ΅Ρ ΡΠΎΠ±ΠΎΠΉ Π·Π΅Π½ΠΊΠ΅Ρ?
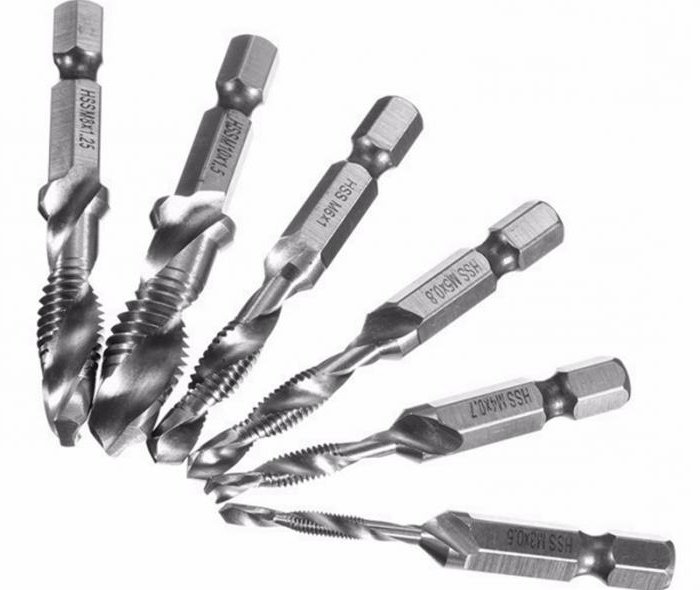
ΠΡΠΎ ΡΠ΅ΠΆΡΡΠΈΠΉ ΠΈΠ½ΡΡΡΡΠΌΠ΅Π½Ρ, ΠΊΠΎΠ½ΡΡΡΡΠΊΡΠΈΡ ΠΊΠΎΡΠΎΡΠΎΠ³ΠΎ ΡΠΎΡΠΌΠΈΡΡΠ΅ΡΡΡ ΡΡΠ½ΠΊΡΠΈΠΎΠ½Π°Π»ΡΠ½ΠΎΠΉ ΠΎΠ±ΡΠ°Π±Π°ΡΡΠ²Π°ΡΡΠ΅ΠΉ ΡΠ°ΡΡΡΡ ΠΈ Ρ Π²ΠΎΡΡΠΎΠ²ΠΈΠΊΠΎΠΌ-Π΄Π΅ΡΠΆΠ°Π²ΠΊΠΎΠΉ. ΠΠ½Π΅ΡΠ½Π΅ Π½Π΅ΠΊΠΎΡΠΎΡΡΠ΅ Π²ΠΈΠ΄Ρ Π·Π΅Π½ΠΊΠ΅ΡΠ° Π½Π°ΠΏΠΎΠΌΠΈΠ½Π°ΡΡ ΡΠ²Π΅ΡΠ»Π°, Π½ΠΎ ΠΎΠ½ΠΈ Π³ΠΎΡΠ°Π·Π΄ΠΎ ΠΏΡΠΎΡΠ½Π΅Π΅. Π Π΅ΡΠ΅ Π±ΠΎΠ»Π΅Π΅ Π²Π°ΠΆΠ½Π°Ρ ΡΠ°Π·Π½ΠΈΡΠ° Π·Π°ΠΊΠ»ΡΡΠ°Π΅ΡΡΡ Π² Π½Π°Π»ΠΈΡΠΈΠΈ ΠΊΠ°ΠΊ ΠΌΠΈΠ½ΠΈΠΌΡΠΌ ΡΡΠ΅Ρ ΡΠ΅ΠΆΡΡΠΈΡ ΠΊΡΠΎΠΌΠΎΠΊ, ΠΎΠ±Π΅ΡΠΏΠ΅ΡΠΈΠ²Π°ΡΡΠΈΡ Π±ΠΎΠ»Π΅Π΅ ΡΡΡΠ΅ΠΊΡΠΈΠ²Π½ΡΠΉ ΡΡΠ΅ΠΌ Π»ΠΈΡΠ½Π΅ΠΉ ΠΌΠ°ΡΡΡ ΠΌΠ΅ΡΠ°Π»Π»Π°. ΠΡΡΠ°ΡΠΈ, ΡΡΠΈΠΌ ΠΎΡΠ»ΠΈΡΠ°Π΅ΡΡΡ ΠΈ ΡΠ°Π·Π²Π΅ΡΡΡΠ²Π°Π½ΠΈΠ΅ ΠΎΡΠ²Π΅ΡΡΡΠΈΠΉ, Π΄Π»Ρ ΠΊΠΎΡΠΎΡΠΎΠ³ΠΎ ΠΈΠ½ΠΎΠ³Π΄Π° ΡΡΠ΅Π±ΡΠ΅ΡΡΡ ΠΈΠ½ΡΠ΅Π½ΡΠΈΠ²Π½Π°Ρ Π»ΠΈΠΊΠ²ΠΈΠ΄Π°ΡΠΈΡ ΡΡΡΡΠΆΠΊΠΈ Ρ ΡΠ΅Π»ΡΡ Π΄ΠΎΡΡΠΈΠΆΠ΅Π½ΠΈΡ Π±ΠΎΠ»Π΅Π΅ ΡΠΎΡΠ½ΠΎΠΉ ΡΠΎΡΠΌΡ Π·Π°Π³ΠΎΡΠΎΠ²ΠΊΠΈ. ΠΠΎ Ρ Π·Π΅Π½ΠΊΠ΅ΡΠ° Π½Π΅ΡΠΊΠΎΠ»ΡΠΊΠΎ ΡΠ΅ΠΆΡΡΠΈΡ ΠΊΡΠΎΠΌΠΎΠΊ ΡΠ°ΠΊΠΆΠ΅ Π²ΡΡΡΡΠΏΠ°ΡΡ Π² Π½Π΅ΠΊΠΎΡΠΎΡΠΎΠΌ ΡΠΎΠ΄Π΅ ΡΡΠ°Π±ΠΈΠ»ΠΈΠ·Π°ΡΠΎΡΠΎΠΌ ΠΈΠ½ΡΡΡΡΠΌΠ΅Π½ΡΠ°. ΠΡΠΎΡ Π°ΡΠΏΠ΅ΠΊΡ Π³Π°ΡΠ°Π½ΡΠΈΡΡΠ΅Ρ ΠΎΠ±Π΅ΡΠΏΠ΅ΡΠ΅Π½ΠΈΠ΅ ΡΠ°Π²Π½ΠΎΠΌΠ΅ΡΠ½ΠΎΡΡΠΈ ΠΎΠ±ΡΠ°Π±ΠΎΡΠΊΠΈ ΠΊΡΠΎΠΌΠΎΠΊ, ΡΡΠΎ ΡΠΊΠ°Π·ΡΠ²Π°Π΅ΡΡΡ Π½Π° ΡΠΎΡΠ½ΠΎΡΡΠΈ Π²ΡΠΏΠΎΠ»Π½Π΅Π½ΠΈΡ ΠΎΠΏΠ΅ΡΠ°ΡΠΈΠΈ. ΠΠΏΡΠΎΡΠ΅ΠΌ, ΠΊΠ°ΡΠ΅ΡΡΠ²ΠΎ ΡΠ΅Π·ΡΠ»ΡΡΠ°ΡΠ° Π±ΡΠ΄Π΅Ρ Π·Π°Π²ΠΈΡΠ΅ΡΡ ΠΈ ΠΎΡ ΡΠΎΠ³ΠΎ, Π½Π°ΡΠΊΠΎΠ»ΡΠΊΠΎ ΠΏΡΠ°Π²ΠΈΠ»ΡΠ½ΠΎ Π±ΡΠ» Π²ΡΠ±ΡΠ°Π½ ΡΠΈΠΏ ΠΈΠ½ΡΡΡΡΠΌΠ΅Π½ΡΠ°.
Π Π°Π·Π½ΠΎΠ²ΠΈΠ΄Π½ΠΎΡΡΠΈ Π·Π΅Π½ΠΊΠ΅ΡΠΎΠ²
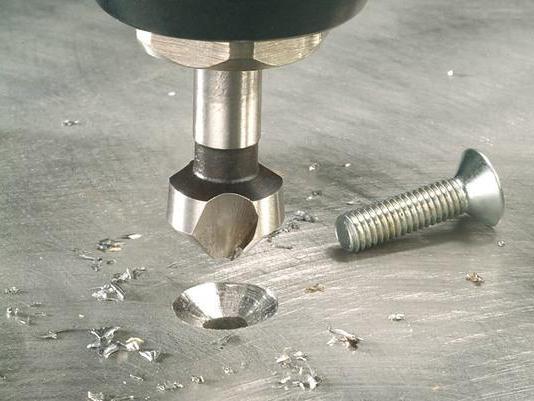
ΠΡΠΎΡΡΠ΅ΠΉΡΠΈΠ΅ ΠΊΠΎΠ½ΠΈΡΠ΅ΡΠΊΠΈΠ΅ ΠΌΠΎΠ΄Π΅Π»ΠΈ Π·Π΅Π½ΠΊΠΎΠ²ΠΎΠΊ ΡΠΎΡΡΠΎΡΡ ΠΈΠ· ΡΠ΅Π·ΡΠΈΠΊΠ° ΠΈ Ρ Π²ΠΎΡΡΠΎΠ²ΠΈΠΊΠ°. Π£Π³ΠΎΠ» ΠΊΠΎΠ½ΡΡΠ° Π² ΡΠ°Π±ΠΎΡΠ΅ΠΉ ΡΠ°ΡΡΠΈ ΠΌΠΎΠΆΠ΅Ρ Π²Π°ΡΡΠΈΡΠΎΠ²Π°ΡΡΡΡ ΠΎΡ 30 Π΄ΠΎ 120 Β°. ΠΠΎΠ»Π΅Π΅ ΡΠ»ΠΎΠΆΠ½ΠΎΠΉ Π²Π°ΡΠΈΠ°ΡΠΈΠ΅ΠΉ ΠΈΠ½ΡΡΡΡΠΌΠ΅Π½ΡΠ° ΡΠ²Π»ΡΠ΅ΡΡΡ ΡΠ΅Π·ΡΠΈΠΊ Ρ ΡΠΎΡΡΠ΅Π²ΡΠΌΠΈ Π·ΡΠ±ΡΠ°ΠΌΠΈ. ΠΠΎΠ»ΠΈΡΠ΅ΡΡΠ²ΠΎ Π·ΡΠ±ΡΠ΅Π² Π² ΡΡΠ΅Π΄Π½Π΅ΠΌ ΡΠΎΡΡΠ°Π²Π»ΡΠ΅Ρ ΠΎΡ 4 Π΄ΠΎ 8. Π‘ΠΎΠΎΡΠ²Π΅ΡΡΡΠ²Π΅Π½Π½ΠΎ, ΡΠ΅ΠΌ ΡΠΎΡΠ½Π΅Π΅ ΡΡΠ΅Π±ΡΠ΅ΡΡΡ Π·Π΅Π½ΠΊΠ΅ΡΠΎΠ²Π°Π½ΠΈΠ΅, ΡΠ΅ΠΌ ΠΌΠ΅Π½ΡΡΠ΅ Π΄ΠΎΠ»ΠΆΠ½Π° Π±ΡΡΡ ΠΏΠΎΠ²Π΅ΡΡ Π½ΠΎΡΡΡ ΡΠ΅Π·ΡΠΈΠΊΠ°. Π’Π°ΠΊΠΆΠ΅ ΡΡΡΠ΅ΡΡΠ²ΡΡΡ ΡΠΈΠ»ΠΈΠ½Π΄ΡΠΈΡΠ΅ΡΠΊΠΈΠ΅ ΡΡΡΡΠΎΠΉΡΡΠ²Π°, Π² ΠΊΠΎΡΠΎΡΡΡ ΠΏΡΠ΅Π΄ΡΡΠΌΠΎΡΡΠ΅Π½Π° Π½Π°ΠΏΡΠ°Π²Π»ΡΡΡΠ°Ρ ΡΠ°ΠΏΡΠ°. ΠΠ½Π° Π²Ρ ΠΎΠ΄ΠΈΡ Π² ΡΠΎΡΠΌΠΈΡΡΠ΅ΠΌΡΠ΅ ΠΎΡΠ²Π΅ΡΡΡΠΈΡ, ΠΎΠ±Π΅ΡΠΏΠ΅ΡΠΈΠ²Π°Ρ, ΡΠ°ΠΊΠΈΠΌ ΠΎΠ±ΡΠ°Π·ΠΎΠΌ, ΡΠΎΠ²ΠΏΠ°Π΄Π΅Π½ΠΈΠ΅ ΠΎΠ±ΡΠ°Π·ΠΎΠ²Π°Π½Π½ΠΎΠ³ΠΎ ΡΠΈΠ»ΠΈΠ½Π΄ΡΠΈΡΠ΅ΡΠΊΠΎΠ³ΠΎ ΡΠ³Π»ΡΠ±Π»Π΅Π½ΠΈΡ ΠΈ ΠΎΡΠΈ ΠΎΡΠ²Π΅ΡΡΡΠΈΡ. ΠΡΠΎ ΡΠ½ΠΈΠ²Π΅ΡΡΠ°Π»ΡΠ½Π°Ρ ΡΠ΅Ρ Π½ΠΈΠΊΠ°, ΠΏΡΠΈ ΠΊΠΎΡΠΎΡΠΎΠΉ ΡΠ²Π΅ΡΠ»Π΅Π½ΠΈΠ΅, Π·Π΅Π½ΠΊΠ΅ΡΠΎΠ²Π°Π½ΠΈΠ΅ ΠΈ ΡΠ°Π·Π²Π΅ΡΡΡΠ²Π°Π½ΠΈΠ΅ ΠΎΡΠ²Π΅ΡΡΡΠΈΠΉ ΠΏΡΠΎΠΈΠ·Π²ΠΎΠ΄ΡΡΡΡ ΠΈΠ½ΡΡΡΡΠΌΠ΅Π½ΡΠΎΠΌ Π΅Π΄ΠΈΠ½ΠΎΠΉ ΡΠΎΡΠΌΠ°ΡΠΈΠΈ. Π ΠΈΡΠΎΠ³Π΅ ΡΠΏΡΠΎΡΠ°Π΅ΡΡΡ ΡΠΈΠΊΠ» ΡΠΎΡΠΌΠΈΡΠΎΠ²Π°Π½ΠΈΡ ΠΎΡΠ²Π΅ΡΡΡΠΈΡ ΠΈ ΠΏΠΎΠ²ΡΡΠ°Π΅ΡΡΡ ΠΊΠ°ΡΠ΅ΡΡΠ²ΠΎ ΠΎΡΠΈΡΡΠΊΠΈ ΠΏΡΠΈΠ»Π΅Π³Π°ΡΡΠΈΡ ΠΏΠΎΠ²Π΅ΡΡ Π½ΠΎΡΡΠ΅ΠΉ. ΠΠΎΡΡΠΈ Π²ΡΠ΅ ΠΌΠΎΠ΄Π΅Π»ΠΈ Π·Π΅Π½ΠΊΠ΅ΡΠΎΠ² ΠΈΠ·Π³ΠΎΡΠ°Π²Π»ΠΈΠ²Π°ΡΡΡΡ ΠΈΠ· ΠΈΠ½ΡΡΡΡΠΌΠ΅Π½ΡΠ°Π»ΡΠ½ΡΡ Π»Π΅Π³ΠΈΡΠΎΠ²Π°Π½Π½ΡΡ ΠΈ ΡΠ³Π»Π΅ΡΠΎΠ΄ΠΈΡΡΡΡ ΡΡΠ°Π»Π΅ΠΉ.
Π’Π΅Ρ Π½ΠΈΠΊΠ° Π²ΡΠΏΠΎΠ»Π½Π΅Π½ΠΈΡ Π·Π΅Π½ΠΊΠ΅ΡΠΎΠ²Π°Π½ΠΈΡ
ΠΠ±ΡΡΠ½ΠΎ Π·Π΅Π½ΠΊΠ΅ΡΠΎΠ²Π°Π½ΠΈΠ΅ Π²ΡΠΏΠΎΠ»Π½ΡΠ΅ΡΡΡ Π½Π° ΡΠ²Π΅ΡΠ»ΠΈΠ»ΡΠ½ΡΡ ΡΡΠ°Π½ΠΊΠ°Ρ . Π’Π°ΠΊ ΠΆΠ΅ ΠΊΠ°ΠΊ ΠΈ ΡΠ²Π΅ΡΠ»Π°, Π·Π΅Π½ΠΊΠ΅ΡΡ ΡΡΡΠ°Π½Π°Π²Π»ΠΈΠ²Π°ΡΡΡΡ Π² ΡΠΎΠΎΡΠ²Π΅ΡΡΡΠ²ΡΡΡΠΈΡ ΠΏΠ°ΡΡΠΎΠ½Π°Ρ ΠΈΠ»ΠΈ Π·Π°ΠΆΠΈΠΌΠ½ΡΡ ΠΌΠ΅Ρ Π°Π½ΠΈΠ·ΠΌΠ°Ρ . ΠΠ°Π»Π΅Π΅ Π²ΡΡ ΠΎΠ΄Π½ΡΠ΅ ΡΠ°ΡΡΠΈ ΠΎΡΠ²Π΅ΡΡΡΠΈΠΉ ΠΎΠ±ΡΠ°Π±Π°ΡΡΠ²Π°ΡΡΡΡ ΠΊΠΎΠ½ΠΈΡΠ΅ΡΠΊΠΈΠΌΠΈ Π·Π΅Π½ΠΊΠΎΠ²ΠΊΠ°ΠΌΠΈ. ΠΠΎ ΡΡΠΎΠΉ ΡΠ΅Ρ Π½ΠΈΠΊΠ΅ ΡΠΎΡΠΌΠΈΡΡΡΡΡΡ ΠΊΠΎΠ½ΡΡΠ½ΡΠ΅ ΡΠ³Π»ΡΠ±Π»Π΅Π½ΠΈΡ, ΠΏΠΎΠ΄Ρ ΠΎΠ΄ΡΡΠΈΠ΅ Π΄Π»Ρ Π³ΠΎΠ»ΠΎΠ²ΠΎΠΊ Π·Π°ΠΊΠ»Π΅ΠΏΠΎΠΊ ΠΈ ΠΏΠΎΡΠ°ΠΉΠ½ΡΡ Π²ΠΈΠ½ΡΠΎΠ². Π£Π³Π»ΡΠ±Π»Π΅Π½ΠΈΡ Π΄Π»Ρ Π±ΠΎΠ»ΡΠΎΠ² ΠΏΡΠΎΠΈΠ·Π²ΠΎΠ΄ΡΡΡΡ ΡΠ°ΠΊΠΈΠΌ ΠΆΠ΅ ΠΎΠ±ΡΠ°Π·ΠΎΠΌ, Π½ΠΎ ΡΠΆΠ΅ ΡΠΈΠ»ΠΈΠ½Π΄ΡΠΈΡΠ΅ΡΠΊΠΈΠΌΠΈ Π·Π΅Π½ΠΊΠΎΠ²ΠΊΠ°ΠΌΠΈ. ΠΠ°Π½Π½ΡΠΌ ΠΈΠ½ΡΡΡΡΠΌΠ΅Π½ΡΠΎΠΌ ΡΠ°ΠΊΠΆΠ΅ Π²ΡΠΏΠΎΠ»Π½ΡΡΡ ΠΏΠΎΠ΄ΡΠ΅Π·ΠΊΡ ΡΠΎΡΡΠΎΠ², Π²ΡΠ±ΠΎΡΠΊΡ ΡΠ³Π»ΠΎΠ² ΠΈ Π²ΡΡΡΡΠΏΠΎΠ². Π Π·Π΅Π½ΠΊΠ΅ΡΠΎΠ²Π°Π½ΠΈΠ΅, ΠΈ ΡΠ°Π·Π²Π΅ΡΡΡΠ²Π°Π½ΠΈΠ΅ ΠΎΡΠ²Π΅ΡΡΡΠΈΠΉ Π½Π° ΡΡΠ°Π½ΠΊΠ΅ ΠΊΠΎΠ½ΡΡΠΎΠ»ΠΈΡΡΡΡΡΡ ΠΎΠΏΠ΅ΡΠ°ΡΠΎΡΠΎΠΌ. Π ΡΠΎΠ²ΡΠ΅ΠΌΠ΅Π½Π½ΡΡ ΠΌΠΎΠ΄Π΅Π»ΡΡ ΠΏΠ½Π΅Π²ΠΌΠ°ΡΠΈΡΠ΅ΡΠΊΠΈΡ ΠΈ ΡΠ»Π΅ΠΊΡΡΠΈΡΠ΅ΡΠΊΠΈΡ ΡΡΠ°Π½ΠΊΠΎΠ² Π΄ΠΎΠΏΡΡΠΊΠ°Π΅ΡΡΡ Π²ΠΎΠ·ΠΌΠΎΠΆΠ½ΠΎΡΡΡ ΠΎΠ±ΡΠ°Π±ΠΎΡΠΊΠΈ Π² ΠΏΠΎΠ»ΡΠ°Π²ΡΠΎΠΌΠ°ΡΠΈΡΠ΅ΡΠΊΠΎΠΌ ΠΈ Π°Π²ΡΠΎΠΌΠ°ΡΠΈΡΠ΅ΡΠΊΠΎΠΌ ΡΠ΅ΠΆΠΈΠΌΠ°Ρ . Π‘ΡΠ°Π½ΠΊΠΈ Ρ ΠΏΡΠΎΠ³ΡΠ°ΠΌΠΌΠ½ΡΠΌ ΡΠΏΡΠ°Π²Π»Π΅Π½ΠΈΠ΅ΠΌ ΠΌΠΎΠ³ΡΡ ΠΈΡΠΏΠΎΠ»ΡΠ·ΠΎΠ²Π°ΡΡ Π°Π½Π°Π»ΠΎΠ³ΠΈΡΠ½ΡΠ΅ Π½Π°ΡΡΡΠΎΠΉΠΊΠΈ ΠΎΠ±ΡΠ°Π±ΠΎΡΠΊΠΈ Π·Π΅Π½ΠΊΠ΅ΡΠ°ΠΌΠΈ Π΄Π»Ρ ΡΠ΅ΡΠΈΠΉΠ½ΠΎΠ³ΠΎ ΠΎΠ±ΡΠ»ΡΠΆΠΈΠ²Π°Π½ΠΈΡ Π΄Π΅ΡΠ°Π»Π΅ΠΉ.
ΠΠ°Π·Π½Π°ΡΠ΅Π½ΠΈΠ΅ ΠΎΠΏΠ΅ΡΠ°ΡΠΈΠΈ ΡΠ°Π·Π²Π΅ΡΡΡΠ²Π°Π½ΠΈΡ
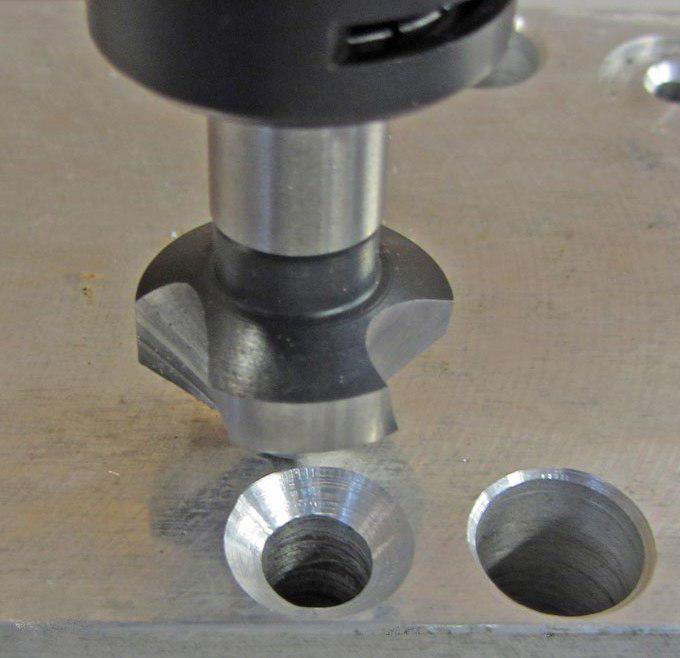
ΠΠΏΠ΅ΡΠ°ΡΠΈΡ ΡΠ°Π·Π²Π΅ΡΡΡΠ²Π°Π½ΠΈΡ Π²ΠΎ ΠΌΠ½ΠΎΠ³ΠΎΠΌ ΡΡ ΠΎΠΆΠ° Ρ Π·Π΅Π½ΠΊΠ΅ΡΠΎΠ²Π°Π½ΠΈΠ΅ΠΌ. ΠΠ½Π° ΡΠ°ΠΊΠΆΠ΅ ΡΠ°ΡΡΡΠΈΡΠ°Π½Π° Π½Π° ΡΠΎΡΠΌΠΈΡΠΎΠ²Π°Π½ΠΈΠ΅ ΠΎΠΏΡΠΈΠΌΠ°Π»ΡΠ½ΡΡ ΠΏΠΎ ΡΠ°Π·ΠΌΠ΅ΡΠ°ΠΌ ΠΎΡΠ²Π΅ΡΡΡΠΈΠΉ Ρ Π²ΠΎΠ·ΠΌΠΎΠΆΠ½ΠΎΡΡΡΡ ΠΊΠΎΡΡΠ΅ΠΊΡΠΈΠΈ ΡΠΎΡΠΌΡ. ΠΠΎ Π΅ΡΠ»ΠΈ Π·Π΅Π½ΠΊΠ΅ΡΡ ΠΏΠΎΠ΄Π³ΠΎΡΠ°Π²Π»ΠΈΠ²Π°ΡΡ ΠΎΡΠ²Π΅ΡΡΡΠΈΡ Π΄Π»Ρ ΠΏΠΎΡΠ»Π΅Π΄ΡΡΡΠ΅Π³ΠΎ ΠΈΡΠΏΠΎΠ»ΡΠ·ΠΎΠ²Π°Π½ΠΈΡ Π·Π°ΠΊΠ»Π΅ΠΏΠΎΠΊ ΠΈ Π±ΠΎΠ»ΡΠΎΠ², ΡΠΎ ΡΠ°Π·Π²Π΅ΡΡΡΠ²Π°Π½ΠΈΠ΅ ΠΏΠΎΠ·Π²ΠΎΠ»ΡΠ΅Ρ ΠΏΠΎΠ»ΡΡΠ°ΡΡ ΡΠΎΡΠ½ΡΠ΅ ΠΊΠ°Π»ΠΈΠ±ΡΠΎΠ²Π°Π½Π½ΡΠ΅ Π½ΠΈΡΠΈ Π΄Π»Ρ Π²Π°Π»ΠΎΠ², ΠΏΠ»ΡΠ½ΠΆΠ΅ΡΠ½ΡΡ Π΄Π΅ΡΠ°Π»Π΅ΠΉ ΠΈ ΠΏΠΎΠ΄ΡΠΈΠΏΠ½ΠΈΠΊΠΎΠ². Π’Π°ΠΊΠΆΠ΅ ΡΠ°Π·Π²Π΅ΡΡΡΠ²Π°Π½ΠΈΠ΅ ΠΎΡΠ²Π΅ΡΡΡΠΈΠΉ ΠΏΠΎΠ·Π²ΠΎΠ»ΡΠ΅Ρ ΠΌΠΈΠ½ΠΈΠΌΠΈΠ·ΠΈΡΠΎΠ²Π°ΡΡ ΡΡΠ΅Π½ΠΈΠ΅ Π² ΠΎΠ±ΡΠ°Π±Π°ΡΡΠ²Π°Π΅ΠΌΠΎΠΉ Π·ΠΎΠ½Π΅ ΠΈ ΠΎΠ±Π΅ΡΠΏΠ΅ΡΠΈΠ²Π°ΡΡ Π²ΡΡΠΎΠΊΡΡ ΠΏΠ»ΠΎΡΠ½ΠΎΡΡΡ ΠΊΠΎΠ½ΡΠ°ΠΊΡΠ° ΠΌΠ΅ΠΆΠ΄Ρ ΡΠ»Π΅ΠΌΠ΅Π½ΡΠ°ΠΌΠΈ. ΠΡΠΈ Π·Π°Π΄Π°ΡΠΈ Π΄ΠΎΡΡΠΈΠ³Π°ΡΡΡΡ Π·Π° ΡΡΠ΅Ρ ΡΠΎΠΊΡΠ°ΡΠ΅Π½ΠΈΡ ΡΠ΅ΡΠΎΡ ΠΎΠ²Π°ΡΠΎΡΡΠΈ ΠΏΠΎΠ²Π΅ΡΡ Π½ΠΎΡΡΠ΅ΠΉ ΠΎΡΠ²Π΅ΡΡΡΠΈΡ.
ΠΠ½ΡΡΡΡΠΌΠ΅Π½Ρ Π΄Π»Ρ ΡΠ°Π·Π²Π΅ΡΡΡΠ²Π°Π½ΠΈΡ
Π Π°Π·Π²Π΅ΡΡΠΊΠΈ ΡΠ°ΠΊΠΆΠ΅ ΠΏΡΠ΅Π΄ΡΡΠ°Π²Π»ΡΡΡ ΡΠΎΠ±ΠΎΠΉ ΠΈΠ½ΡΡΡΡΠΌΠ΅Π½Ρ, Π½Π°ΠΏΠΎΠΌΠΈΠ½Π°ΡΡΠΈΠΉ ΡΠ²Π΅ΡΠ»Π°. Π Π°Π±ΠΎΡΠ°Ρ ΡΠ°ΡΡΡ Π² Π΄Π°Π½Π½ΠΎΠΌ ΡΠ»ΡΡΠ°Π΅ ΠΎΠ±Π΅ΡΠΏΠ΅ΡΠΈΠ²Π°Π΅ΡΡΡ ΡΠ°ΡΠΏΠΎΠ»ΠΎΠΆΠ΅Π½Π½ΡΠΌΠΈ ΠΏΠΎ ΠΎΠΊΡΡΠΆΠ½ΠΎΡΡΠΈ ΡΡΠ΅ΡΠΆΠ½Ρ Π·ΡΠ±ΡΡΠΌΠΈ. ΠΠΎΠΌΠΈΠΌΠΎ ΡΡΠΎΠ³ΠΎ, ΡΡΡΠ΅ΡΡΠ²ΡΡΡ Π²ΡΠΏΠΎΠΌΠΎΠ³Π°ΡΠ΅Π»ΡΠ½ΡΠ΅ ΡΡΠ½ΠΊΡΠΈΠΎΠ½Π°Π»ΡΠ½ΡΠ΅ ΡΠ°ΡΡΠΈ ΡΠ΅Π·ΡΠΈΠΊΠ°. ΠΡΠΎ Π·Π°Π±ΠΎΡΠ½Π°Ρ, ΠΊΠ°Π»ΠΈΠ±ΡΡΡΡΠ°Ρ ΠΈ ΡΠΈΠ»ΠΈΠ½Π΄ΡΠΈΡΠ΅ΡΠΊΠ°Ρ ΡΠ°ΡΡΠΈ. ΠΠ΅ΠΏΠΎΡΡΠ΅Π΄ΡΡΠ²Π΅Π½Π½ΡΡ ΡΠ΅Π·ΠΊΡ ΠΏΡΠΎΠΈΠ·Π²ΠΎΠ΄ΠΈΡ Π½Π°ΠΏΡΠ°Π²Π»ΡΡΡΠΈΠΉ ΠΊΠΎΠ½ΡΡ, ΠΊΡΠ°Ρ ΠΊΠΎΡΠΎΡΠΎΠ³ΠΎ ΡΠ½ΠΈΠΌΠ°ΡΡ ΠΏΡΠΈΠΏΡΡΠΊ ΠΌΠ΅ΡΠ°Π»Π»Π°, Π½ΠΎ Π² ΡΠΎ ΠΆΠ΅ Π²ΡΠ΅ΠΌΡ ΠΏΡΠ΅Π΄ΠΎΡ ΡΠ°Π½ΡΡΡ Π²Π΅ΡΡΠΈΠ½Ρ ΡΠ΅ΠΆΡΡΠ΅ΠΉ ΠΊΡΠΎΠΌΠΊΠΈ ΠΎΡ Π·Π°Π±ΠΎΠΈΠ½. Π Π·Π΄Π΅ΡΡ ΠΌΠΎΠΆΠ½ΠΎ Π²ΡΠ΄Π΅Π»ΠΈΡΡ ΠΎΡΠ΄Π΅Π»ΡΠ½ΡΠ΅ ΠΊΠΎΠ½ΡΡΡΡΠΊΡΠΈΠ²Π½ΡΠ΅ ΡΠ°ΡΡΠΈ, ΡΠ°Π·Π»ΠΈΡΠ°ΡΡΠΈΠ΅ Π΄Π°Π½Π½ΡΡ ΠΌΠ΅ΡΠΎΠ΄ΠΈΠΊΡ ΠΈ Π·Π΅Π½ΠΊΠΎΠ²Π°Π½ΠΈΠ΅. ΠΠ΅Π½ΠΊΠ΅ΡΠΎΠ²Π°Π½ΠΈΠ΅ ΠΈ ΡΠ°Π·Π²Π΅ΡΡΡΠ²Π°Π½ΠΈΠ΅ ΠΎΡΠ²Π΅ΡΡΡΠΈΠΉ ΡΡ ΠΎΠ΄ΡΡΡΡ Π² ΠΎΠΏΠ΅ΡΠ°ΡΠΈΡΡ ΡΠ΅Π·ΠΊΠΈ, ΠΎΠ΄Π½Π°ΠΊΠΎ ΠΊΠ°Π»ΠΈΠ±ΡΡΡΡΠ°Ρ ΡΠ°ΡΡΡ ΡΠ°Π·Π²Π΅ΡΡΠΊΠΈ ΡΠ°ΠΊΠΆΠ΅ Π²ΡΠΏΠΎΠ»Π½ΡΠ΅Ρ ΡΡΠ½ΠΊΡΠΈΠΈ Π½Π°ΠΏΡΠ°Π²Π»Π΅Π½ΠΈΡ ΠΈ ΠΎΡΠ²ΠΎΠ΄Π° ΡΡΡΡΠΆΠΊΠΈ. ΠΠ»Ρ ΡΡΠΎΠ³ΠΎ ΠΏΡΠ΅Π΄Π½Π°Π·Π½Π°ΡΠ΅Π½Ρ ΡΠΏΠ΅ΡΠΈΠ°Π»ΡΠ½ΡΠ΅ ΠΊΠ°Π½Π°Π²ΠΊΠΈ, Π΄Π΅Π»Π°ΡΡΠΈΠ΅ ΠΈΠ½ΡΡΡΡΠΌΠ΅Π½Ρ Π±ΠΎΠ»Π΅Π΅ ΡΠ°ΠΌΠΎΡΡΠΎΡΡΠ΅Π»ΡΠ½ΡΠΌ.
ΠΠ°ΡΠΈΠ½Π½ΡΠ΅ ΠΈ ΡΡΡΠ½ΡΠ΅ ΡΠ°Π·Π²Π΅ΡΡΠΊΠΈ
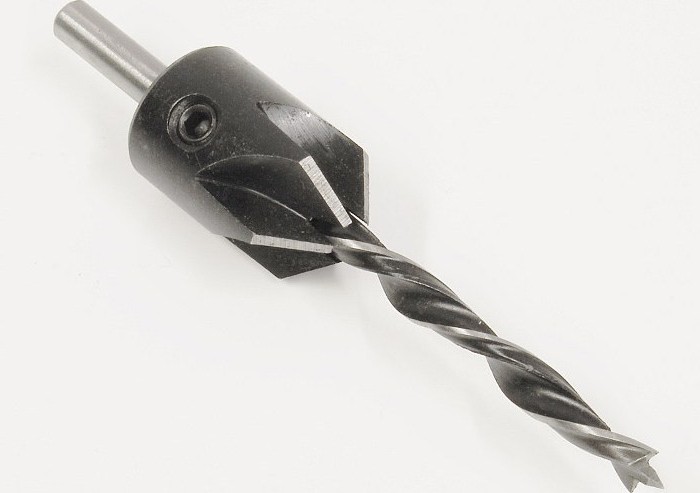
Π Π°Π·Π²Π΅ΡΡΡΠ²Π°Π½ΠΈΠ΅ ΠΌΠΎΠΆΠ΅Ρ Π²ΡΠΏΠΎΠ»Π½ΡΡΡΡΡ ΡΡΡΠ½ΡΠΌ ΠΈ ΠΌΠ°ΡΠΈΠ½Π½ΡΠΌ ΡΠΏΠΎΡΠΎΠ±ΠΎΠΌ, ΡΠΎ Π΅ΡΡΡ Π½Π° ΡΠ΅Ρ ΠΆΠ΅ ΡΡΠ°Π½ΠΊΠ°Ρ . ΠΠ½ΡΡΡΡΠΌΠ΅Π½Ρ, ΠΏΡΠΈΠΌΠ΅Π½ΡΠ΅ΠΌΡΠΉ Π΄Π»Ρ ΡΡΡΠ½ΡΡ ΠΎΠΏΠ΅ΡΠ°ΡΠΈΠΉ, ΠΎΡΠ»ΠΈΡΠ°Π΅ΡΡΡ ΡΠ΄Π»ΠΈΠ½Π΅Π½Π½ΠΎΠΉ ΡΠ°Π±ΠΎΡΠ΅ΠΉ ΡΠ°ΡΡΡΡ. ΠΠΈΠ°ΠΌΠ΅ΡΡ ΠΎΠ±ΡΠ°ΡΠ½ΠΎΠ³ΠΎ ΠΊΠΎΠ½ΡΡΠ° Π² Π΄Π°Π½Π½ΠΎΠΌ ΡΠ»ΡΡΠ°Π΅ Π²Π°ΡΡΠΈΡΡΠ΅ΡΡΡ ΠΎΡ 0,06 Π΄ΠΎ 0,1 ΠΌΠΌ Π² ΡΡΠ΅Π΄Π½Π΅ΠΌ. ΠΠ»Ρ ΡΡΠ°Π²Π½Π΅Π½ΠΈΡ, ΡΡΠ°Π½ΠΎΡΠ½ΡΠ΅ ΡΠ°Π·Π²Π΅ΡΡΠΊΠΈ ΠΈΠΌΠ΅ΡΡ ΡΠΎΠ»ΡΠΈΠ½Ρ ΠΊΠΎΠ½ΡΡΠ° ΠΎΡ 0,05 Π΄ΠΎ 0,3 ΠΌΠΌ. Π‘ ΠΏΠΎΠΌΠΎΡΡΡ ΡΡΡΠ½ΠΎΠ³ΠΎ ΡΠ°Π·Π²Π΅ΡΡΡΠ²Π°Π½ΠΈΡ ΠΌΠΎΠΆΠ½ΠΎ ΠΏΠΎΠ»ΡΡΠ°ΡΡ ΠΎΡΠ²Π΅ΡΡΡΠΈΡ Π΄ΠΈΠ°ΠΌΠ΅ΡΡΠΎΠΌ ΠΎΡ 3 Π΄ΠΎ 60 ΠΌΠΌ. ΠΡΠΈ ΡΡΠΎΠΌ ΡΡΠ΅ΠΏΠ΅Π½Ρ ΡΠΎΡΠ½ΠΎΡΡΠΈ Π±ΡΠ΄Π΅Ρ Π½Π΅Π²Π΅Π»ΠΈΠΊΠ°. ΠΠ°ΡΠΈΠ½Π½ΡΠΉ ΠΈΠ½ΡΡΡΡΠΌΠ΅Π½Ρ ΠΎΡΠΈΠ΅Π½ΡΠΈΡΡΠ΅ΡΡΡ ΠΏΠΎΠ΄ ΠΎΠΏΡΠ΅Π΄Π΅Π»Π΅Π½Π½ΡΠ΅ ΡΠΈΠΏΠΎΡΠ°Π·ΠΌΠ΅ΡΡ, Π·Π°ΡΠ°ΡΡΡΡ ΠΏΠΎ ΡΠΏΠ΅ΡΠ·Π°ΠΊΠ°Π·Π°ΠΌ. ΠΠ°ΠΏΡΠΈΠΌΠ΅Ρ, ΡΠ°Π·Π²Π΅ΡΡΡΠ²Π°Π½ΠΈΠ΅ ΠΎΡΠ²Π΅ΡΡΡΠΈΠΉ Π² Π΄Π΅ΡΠ°Π»ΡΡ Π΄Π»Ρ ΡΡΡΠΎΠΈΡΠ΅Π»ΡΠ½ΡΡ ΠΊΠΎΠ½ΡΡΡΡΠΊΡΠΈΠΉ ΠΌΠΎΠΆΠ΅Ρ Π²ΡΠΏΠΎΠ»Π½ΡΡΡΡΡ Π² ΡΠΎΠΎΡΠ²Π΅ΡΡΡΠ²ΠΈΠΈ Ρ ΡΠ΅Ρ Π½ΠΈΡΠ΅ΡΠΊΠΈΠΌΠΈ Π΄Π°Π½Π½ΡΠΌΠΈ ΠΏΠΎ ΠΊΠΎΠ½ΠΊΡΠ΅ΡΠ½ΠΎΠΌΡ ΠΏΡΠΎΠ΅ΠΊΡΡ. Π ΠΏΡΠ΅ΠΈΠΌΡΡΠ΅ΡΡΠ²Π°ΠΌ ΡΠ°ΠΊΠΎΠ³ΠΎ ΡΠΏΠΎΡΠΎΠ±Π° ΠΎΡΠ½ΠΎΡΡΡ Π²ΡΡΠΎΠΊΡΡ ΡΠΎΡΠ½ΠΎΡΡΡ ΡΠ΅Π·ΠΊΠΈ, ΠΊΠ°ΡΠ΅ΡΡΠ²Π΅Π½Π½ΡΡ Π·Π°ΡΠΈΡΡΠΊΡ ΠΈ ΠΎΡΡΡΡΡΡΠ²ΠΈΠ΅ Π΄Π΅ΡΠΎΡΠΌΠ°ΡΠΈΠΎΠ½Π½ΠΎΠ³ΠΎ ΡΡΡΠ΅ΠΊΡΠ°.
ΠΡΠΏΠΎΠ»Π½Π΅Π½ΠΈΠ΅ ΡΠ°Π·Π²Π΅ΡΡΡΠ²Π°Π½ΠΈΡ
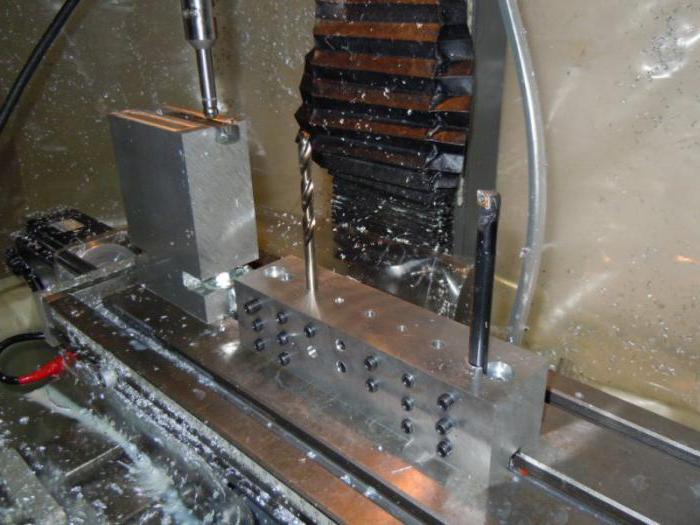
ΠΠ°ΡΠΈΠ½Π½ΠΎΠ΅ ΡΠ°Π·Π²Π΅ΡΡΡΠ²Π°Π½ΠΈΠ΅ Π²ΡΠΏΠΎΠ»Π½ΡΠ΅ΡΡΡ ΠΏΠΎ ΡΠ΅ΠΌ ΠΆΠ΅ ΠΏΡΠΈΠ½ΡΠΈΠΏΠ°ΠΌ, ΡΡΠΎ ΠΈ Π·Π΅Π½ΠΊΠΎΠ²Π°Π½ΠΈΠ΅. ΠΠ½ΡΡΡΡΠΌΠ΅Π½Ρ ΡΠΈΠΊΡΠΈΡΡΠ΅ΡΡΡ Π² ΠΏΠ°ΡΡΠΎΠ½Π΅, Π° Π·Π°ΡΠ΅ΠΌ Π½Π°ΠΏΡΠ°Π²Π»ΡΠ΅ΡΡΡ Π² ΠΎΠ±ΡΠ°Π±Π°ΡΡΠ²Π°Π΅ΠΌΡΡ Π·ΠΎΠ½Ρ ΡΡΠ°Π½ΠΊΠΎΠΌ. ΠΠ΄ΠΈΠ½ΡΡΠ²Π΅Π½Π½ΡΠΌ ΠΎΡΠ»ΠΈΡΠΈΠ΅ΠΌ ΡΠ²Π»ΡΡΡΡΡ Π±ΠΎΠ»Π΅Π΅ Π²ΡΡΠΎΠΊΠΈΠ΅ ΡΡΠ΅Π±ΠΎΠ²Π°Π½ΠΈΡ ΠΊ ΠΎΡ Π»Π°ΠΆΠ΄Π΅Π½ΠΈΡ ΡΠ°Π±ΠΎΡΠ΅ΠΉ ΠΎΡΠ½Π°ΡΡΠΊΠΈ Π² ΠΏΡΠΎΡΠ΅ΡΡΠ΅ ΡΠ°Π±ΠΎΡΡ ΠΈ ΡΠΌΠ°Π·ΠΊΠ΅ ΠΎΡΠ²Π΅ΡΡΡΠΈΠΉ. Π ΠΊΠ°ΡΠ΅ΡΡΠ²Π΅ ΡΠΌΠ°Π·ΡΠ²Π°ΡΡΠ΅Π³ΠΎ ΡΠΎΡΡΠ°Π²Π° ΠΈΡΠΏΠΎΠ»ΡΠ·ΡΡΡ ΠΌΠΈΠ½Π΅ΡΠ°Π»ΡΠ½ΠΎΠ΅ ΠΌΠ°ΡΠ»ΠΎ, ΡΠΊΠΈΠΏΠΈΠ΄Π°Ρ ΠΈ ΡΠΈΠ½ΡΠ΅ΡΠΈΡΠ΅ΡΠΊΠΈΠ΅ ΡΠΌΡΠ»ΡΡΠΈΠΈ. ΠΠ½Π°ΡΠ΅ Π²ΡΠΏΠΎΠ»Π½ΡΠ΅ΡΡΡ ΡΡΡΠ½Π°Ρ ΠΎΠ±ΡΠ°Π±ΠΎΡΠΊΠ° ΠΎΡΠ²Π΅ΡΡΡΠΈΠΉ. Π Π°Π·Π²Π΅ΡΡΡΠ²Π°Π½ΠΈΠ΅ ΡΠ°ΠΊΠΎΠ³ΠΎ ΡΠΈΠΏΠ° ΠΏΡΠ΅Π΄ΠΏΠΎΠ»Π°Π³Π°Π΅Ρ ΠΈΠ·Π½Π°ΡΠ°Π»ΡΠ½ΡΡ ΡΠΈΠΊΡΠ°ΡΠΈΡ Π·Π°Π³ΠΎΡΠΎΠ²ΠΊΠΈ Π² ΡΠΈΡΠΊΠ°Ρ . ΠΠ°Π»Π΅Π΅ Π² ΠΎΡΠ²Π΅ΡΡΡΠΈΠ΅ Π²ΡΡΠ°Π²Π»ΡΠ΅ΡΡΡ Π½Π°ΠΊΠΎΠ½Π΅ΡΠ½ΠΈΠΊ ΡΠ°Π·Π²Π΅ΡΡΠΊΠΈ ΠΈ ΠΏΡΡΠ΅ΠΌ ΠΊΡΡΡΠ΅Π½ΠΈΡ Π²ΠΎΡΠΎΡΠΊΠ° Π΄ΠΎΡΡΠΈΠ³Π°Π΅ΡΡΡ ΡΠ΅Π·ΡΠ»ΡΡΠ°Ρ. ΠΡΠΈΡΠ΅ΠΌ Π²ΡΠ°ΡΠ°ΡΡ ΠΈΠ½ΡΡΡΡΠΌΠ΅Π½Ρ ΠΌΠΎΠΆΠ½ΠΎ ΡΠΎΠ»ΡΠΊΠΎ Π² ΠΎΠ΄Π½ΠΎΠΌ Π½Π°ΠΏΡΠ°Π²Π»Π΅Π½ΠΈΠΈ β Π΄ΠΎ ΡΠΎΡΠΌΠΈΡΠΎΠ²Π°Π½ΠΈΡ Π½Π΅ΠΎΠ±Ρ ΠΎΠ΄ΠΈΠΌΡΡ ΠΏΠ°ΡΠ°ΠΌΠ΅ΡΡΠΎΠ² ΠΈΠ·Π΄Π΅Π»ΠΈΡ.
ΠΠ°ΠΊΠ»ΡΡΠ΅Π½ΠΈΠ΅
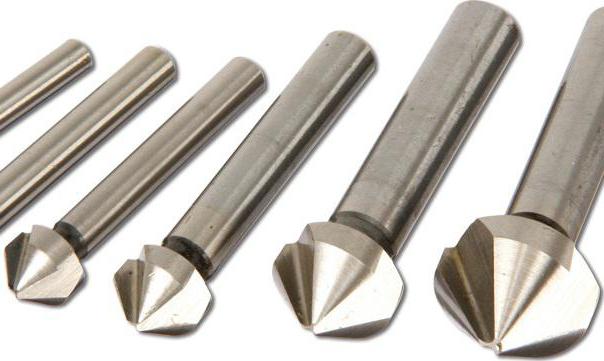
ΠΠ΅Ρ Π°Π½ΠΈΡΠ΅ΡΠΊΠ°Ρ ΠΎΠ±ΡΠ°Π±ΠΎΡΠΊΠ° ΠΌΠ΅ΡΠ°Π»Π»ΠΎΠ² ΠΏΠΎΡΡΠ΅ΠΏΠ΅Π½Π½ΠΎ ΡΡΡΡΠΏΠ°Π΅Ρ ΠΌΠ΅ΡΡΠΎ ΡΠ΅Ρ Π½ΠΎΠ»ΠΎΠ³ΠΈΡΠ½ΡΠΌ Π»Π°Π·Π΅ΡΠ½ΡΠΌ ΠΈ ΡΠ΅ΡΠΌΠΈΡΠ΅ΡΠΊΠΈΠΌ ΠΌΠ΅ΡΠΎΠ΄Π°ΠΌ. Π’Π°ΠΊΠΆΠ΅ ΠΊΠΎΠ½ΠΊΡΡΠ΅Π½ΡΠΈΡ ΡΡΠ°Π΄ΠΈΡΠΈΠΎΠ½Π½ΡΠΌ ΡΠΏΠΎΡΠΎΠ±Π°ΠΌ ΡΠ΅Π·ΠΊΠΈ ΡΠΎΡΡΠ°Π²Π»ΡΠ΅Ρ Π³ΠΈΠ΄ΡΠΎΠ°Π±ΡΠ°Π·ΠΈΠ²Π½Π°Ρ ΡΠ΅Ρ Π½ΠΈΠΊΠ°, ΠΎΡΠ»ΠΈΡΠ°ΡΡΠ°ΡΡΡ Π²ΡΡΠΎΠΊΠΎΠΉ ΡΠΊΠΎΡΠΎΡΡΡΡ ΡΠ°ΡΠΊΡΠΎΡ ΠΈ ΡΠΎΡΠ½ΠΎΡΡΡΡ. Π§ΡΠΎ Π½Π° ΡΡΠΎΠΌ ΡΠΎΠ½Π΅ ΠΌΠΎΠ³ΡΡ ΠΏΡΠ΅Π΄Π»ΠΎΠΆΠΈΡΡ Π² ΠΊΠ°ΡΠ΅ΡΡΠ²Π΅ ΠΏΡΠ΅ΠΈΠΌΡΡΠ΅ΡΡΠ² Π·Π΅Π½ΠΊΠΎΠ²ΠΊΠ°, Π° ΡΠ°ΠΊΠΆΠ΅ ΡΠ°Π·Π²Π΅ΡΡΡΠ²Π°Π½ΠΈΠ΅ ΠΎΡΠ²Π΅ΡΡΡΠΈΠΉ? Π ΠΏΠ΅ΡΠ²ΡΡ ΠΎΡΠ΅ΡΠ΅Π΄Ρ ΡΡΠΎ Π²ΠΎΠ·ΠΌΠΎΠΆΠ½ΠΎΡΡΡ ΡΡΡΠ½ΠΎΠΉ ΠΎΠ±ΡΠ°Π±ΠΎΡΠΊΠΈ Π±Π΅Π· ΠΏΡΠΈΠΌΠ΅Π½Π΅Π½ΠΈΡ ΡΠ»ΠΎΠΆΠ½ΠΎΠ³ΠΎ ΠΎΠ±ΠΎΡΡΠ΄ΠΎΠ²Π°Π½ΠΈΡ Π² Π²ΠΈΠ΄Π΅ ΡΡΠ°Π½ΠΊΠΎΠ². ΠΡΠΎΠΌΠ΅ ΡΠΎΠ³ΠΎ, Π² ΠΎΡΠ»ΠΈΡΠΈΠ΅ ΠΎΡ Π³ΠΈΠ΄ΡΠΎΠ°Π±ΡΠ°Π·ΠΈΠ²ΠΎΠ² ΠΈ ΡΠ΅ΡΠΌΠΈΡΠ΅ΡΠΊΠΈΡ Π°ΠΏΠΏΠ°ΡΠ°ΡΠΎΠ², Π΄Π°Π½Π½ΡΠ΅ ΡΠ΅Ρ Π½ΠΎΠ»ΠΎΠ³ΠΈΠΈ Π½Π΅ ΡΡΠ΅Π±ΡΡΡ ΠΏΠΎΠ΄ΠΊΠ»ΡΡΠ΅Π½ΠΈΡ Π΄ΠΎΠΏΠΎΠ»Π½ΠΈΡΠ΅Π»ΡΠ½ΡΡ ΡΠ°ΡΡ ΠΎΠ΄Π½ΡΡ ΠΌΠ°ΡΠ΅ΡΠΈΠ°Π»ΠΎΠ². ΠΠΎΡΡΠΎΠΌΡ ΠΌΠΎΠΆΠ½ΠΎ Π³ΠΎΠ²ΠΎΡΠΈΡΡ ΠΎ ΠΏΡΠ΅ΠΈΠΌΡΡΠ΅ΡΡΠ²Π°Ρ ΡΠΊΠΎΠ½ΠΎΠΌΠΈΡΠ΅ΡΠΊΠΎΠ³ΠΎ, ΠΎΡΠ³Π°Π½ΠΈΠ·Π°ΡΠΈΠΎΠ½Π½ΠΎΠ³ΠΎ ΠΈ ΡΡΠ³ΠΎΠ½ΠΎΠΌΠΈΡΠ΅ΡΠΊΠΎΠ³ΠΎ Ρ Π°ΡΠ°ΠΊΡΠ΅ΡΠ°. ΠΠΎ ΠΊΠ°ΡΠ΅ΡΡΠ²ΠΎΠΌ ΠΎΠ±ΡΠ°Π±ΠΎΡΠΊΠΈ ΠΈ ΡΠ΅ΠΌΠΏΠ°ΠΌΠΈ ΠΏΡΠΎΠΈΠ·Π²ΠΎΠ΄ΡΡΠ²Π΅Π½Π½ΠΎΠ³ΠΎ ΠΏΡΠΎΡΠ΅ΡΡΠ°, ΠΊΠΎΠ½Π΅ΡΠ½ΠΎ, ΠΏΡΠΈΠ΄Π΅ΡΡΡ ΠΏΠΎΠΆΠ΅ΡΡΠ²ΠΎΠ²Π°ΡΡ.
Π‘Π²Π΅ΡΠ»Π°, Π·Π΅Π½ΠΊΠ΅ΡΡ, ΡΠ°Π·Π²Π΅ΡΡΠΊΠΈ β Π‘ΡΡΠ΄ΠΎΠΏΠ΅Π΄ΠΈΡ
ΠΠ»Ρ ΠΎΠ±ΡΠ°Π±ΠΎΡΠΊΠΈ ΠΎΡΠ²Π΅ΡΡΡΠΈΠΉ Π½Π° ΡΠΎΠΊΠ°ΡΠ½ΡΡ ΡΡΠ°Π½ΠΊΠ°Ρ ΠΏΡΠΈΠΌΠ΅Π½ΡΡΡ ΡΠ²Π΅ΡΠ»Π°, Π·Π΅Π½ΠΊΠ΅ΡΡ ΠΈ ΡΠ°Π·Π²Π΅ΡΡΠΊΠΈ, ΠΊΠΎΡΠΎΡΡΠ΅ Π²ΡΠ±ΠΈΡΠ°ΡΡ Π² Π·Π°Π²ΠΈΡΠΈΠΌΠΎΡΡΠΈ ΠΎΡ Π²ΠΈΠ΄Π° Π·Π°Π³ΠΎΡΠΎΠ²ΠΊΠΈ, ΡΡΠ΅Π±ΡΠ΅ΠΌΠΎΠΉ ΡΠΎΡΠ½ΠΎΡΡΠΈ ΡΠ°Π·ΠΌΠ΅ΡΠΎΠ² ΠΈ ΡΠ΅ΡΠΎΡ ΠΎΠ²Π°ΡΠΎΡΡΠΈ ΠΎΠ±ΡΠ°Π±ΠΎΡΠ°Π½Π½ΠΎΠΉ ΠΏΠΎΠ²Π΅ΡΡ Π½ΠΎΡΡΠΈ.
Π‘Π²Π΅ΡΠ»Π° ΠΏΡΠ΅Π΄Π½Π°Π·Π½Π°ΡΠ΅Π½Ρ Π΄Π»Ρ ΡΠ²Π΅ΡΠ»Π΅Π½ΠΈΡ ΡΠΊΠ²ΠΎΠ·Π½ΡΡ ΠΈΠ»ΠΈ Π³Π»ΡΡ ΠΈΡ ΠΎΡΠ²Π΅ΡΡΡΠΈΠΉ Π² ΡΠΏΠ»ΠΎΡΠ½ΠΎΠΌ ΠΌΠ°ΡΠ΅ΡΠΈΠ°Π»Π΅, Π° ΡΠ°ΠΊ ΠΆΠ΅ Π΄Π»Ρ ΡΠ²Π΅Π»ΠΈΡΠ΅Π½ΠΈΡ Π΄ΠΈΠ°ΠΌΠ΅ΡΡΠ° ΡΠ°Π½Π΅Π΅ ΠΏΡΠΎΡΠ²Π΅ΡΠ»Π΅Π½Π½ΡΡ ΠΎΡΠ²Π΅ΡΡΡΠΈΠΉ (ΡΠ°ΡΡΠ²Π΅ΡΠ»ΠΈΠ²Π°Π½ΠΈΠ΅), Π° ΡΠ°ΠΊ ΠΆΠ΅ Π΄Π»Ρ Π½Π°Π΄ΡΠ²Π΅ΡΠ»ΠΈΠ²Π°Π½ΠΈΡ.
ΠΠΎ ΠΊΠΎΠ½ΡΡΡΡΠΊΡΠΈΠΈ ΡΠ΅ΠΆΡΡΠ΅ΠΉ ΡΠ°ΡΡΠΈ ΡΠ²Π΅ΡΠ»Π° ΡΠ°Π·Π΄Π΅Π»ΡΡΡΡΡ Π½Π° ΡΠΏΠΈΡΠ°Π»ΡΠ½ΡΠ΅, ΠΈΠ»ΠΈ ΡΠΎΡΠ½Π΅Π΅, ΡΠ²Π΅ΡΠ»Π° Ρ Π²ΠΈΠ½ΡΠΎΠ²ΡΠΌΠΈ ΠΊΠ°Π½Π°Π²ΠΊΠ°ΠΌΠΈ, ΡΠ²Π΅ΡΠ»Π° Ρ ΠΏΡΡΠΌΡΠΌΠΈ ΠΊΠ°Π½Π°Π²ΠΊΠ°ΠΌΠΈ, ΡΠ²Π΅ΡΠ»Π° Π΄Π»Ρ Π³Π»ΡΠ±ΠΎΠΊΠΈΡ ΠΎΡΠ²Π΅ΡΡΡΠΈΠΉ (ΡΡΠΆΠ΅ΠΉΠ½ΡΠ΅ ΠΈ ΠΏΡΡΠ΅ΡΠ½ΡΠ΅), ΡΠ½ΠΈΠ²Π΅ΡΡΠ°Π»ΡΠ½ΡΠ΅ ΠΈ Π΄Ρ.
Π‘ΠΏΠΈΡΠ°Π»ΡΠ½ΡΠ΅ ΡΠ²Π΅ΡΠ»Π° ΠΏΡΠΈΠΌΠ΅Π½ΡΡΡ Π΄Π»Ρ ΡΠ²Π΅ΡΠ»Π΅Π½ΠΈΡ ΡΡΠ°Π²Π½ΠΈΡΠ΅Π»ΡΠ½ΠΎ Π½Π΅Π³Π»ΡΠ±ΠΎΠΊΠΈΡ ΠΎΡΠ²Π΅ΡΡΡΠΈΠΉ, Π³Π»ΡΠ±ΠΈΠ½Π° ΠΊΠΎΡΠΎΡΡΡ Π½Π΅ ΠΏΡΠ΅Π²ΡΡΠ°Π΅Ρ ΡΠ΅ΡΡΠΈ Π΄ΠΈΠ°ΠΌΠ΅ΡΡΠΎΠ² ΡΠ²Π΅ΡΠ»Π°. ΠΠ½ΠΈ ΠΈΠ·Π³ΠΎΡΠ°Π²Π»ΠΈΠ²Π°ΡΡΡΡ ΠΈΠ· ΡΠ³Π»Π΅ΡΠΎΠ΄ΠΈΡΡΠΎΠΉ ΡΡΠ°Π»ΠΈ Π£10Π ΠΈ Π£12Π, Π»Π΅Π³ΠΈΡΠΎΠ²Π°Π½Π½ΠΎΠΉ ΡΡΠ°Π»ΠΈ 9Π₯Π‘, Π±ΡΡΡΡΠΎΡΠ΅ΠΆΡΡΠ΅ΠΉ ΡΡΠ°Π»ΠΈ Π 9 ΠΈ Π 18, Π° ΡΠ°ΠΊ ΠΆΠ΅ ΠΎΡΠ½Π°ΡΠ°ΡΡΡΡ ΠΏΠ»Π°ΡΡΠΈΠ½ΠΊΠ°ΠΌΠΈ ΠΈΠ· ΡΠ²Π΅ΡΠ΄ΠΎΠ³ΠΎ ΡΠΏΠ»Π°Π²Π°.
ΠΠ»Ρ ΡΠ²Π΅Π»ΠΈΡΠ΅Π½ΠΈΡ Π΄ΠΈΠ°ΠΌΠ΅ΡΡΠ° ΠΏΡΠ΅Π΄Π²Π°ΡΠΈΡΠ΅Π»ΡΠ½ΠΎ ΠΏΡΠΎΡΠ²Π΅ΡΠ»Π΅Π½Π½ΡΡ ΠΎΡΠ²Π΅ΡΡΡΠΈΠΉ, Π° ΡΠ°ΠΊ ΠΆΠ΅ Π΄Π»Ρ Π΄Π°Π»ΡΠ½Π΅ΠΉΡΠ΅ΠΉ ΠΎΠ±ΡΠ°Π±ΠΎΡΠΊΠΈ ΠΎΡΠ²Π΅ΡΡΡΠΈΠΉ Π² ΠΎΡΠ»ΠΈΠ²ΠΊΠ°Ρ , ΠΏΠΎΠΊΠΎΠ²ΠΊΠ°Ρ ΠΈ ΡΡΠ°ΠΌΠΏΠΎΠ²ΠΊΠ°Ρ ΡΠΈΡΠΎΠΊΠΎ ΠΏΡΠΈΠΌΠ΅Π½ΡΡΡ ΠΈΠ½ΡΡΡΡΠΌΠ΅Π½Ρ, Π½Π°Π·ΡΠ²Π°Π΅ΠΌΡΠΉ Π·Π΅Π½ΠΊΠ΅ΡΠΎΠΌ. ΠΠ΅Π½ΠΊΠ΅ΡΡ ΠΎΡΠ»ΠΈΡΠ°ΡΡΡΡ ΠΎΡ ΡΠΏΠΈΡΠ°Π»ΡΠ½ΡΡ ΡΠ²Π΅ΡΠΈΠ» ΡΠ΅ΠΌ, ΡΡΠΎ ΠΈΠΌΠ΅ΡΡ ΡΡΠΈ ΠΈΠ»ΠΈ ΡΠ΅ΡΡΡΠ΅ Π³Π»Π°Π²Π½ΡΠ΅ ΡΠ΅ΠΆΡΡΠΈΠ΅ ΠΊΡΠΎΠΌΠΊΠΈ (ΡΡΠ΅Ρ - ΠΈΠ»ΠΈ ΡΠ΅ΡΡΡΠ΅Ρ Π·ΡΠ±ΡΠ΅ Π·Π΅Π½ΠΊΠ΅ΡΡ), ΡΠ°ΡΠΏΠΎΠ»ΠΎΠΆΠ΅Π½Π½ΡΡ Π½Π° ΠΏΠΎΠ²Π΅ΡΡ Π½ΠΎΡΡΠΈ ΡΡΠ΅ΡΠ΅Π½Π½ΠΎΠ³ΠΎ ΠΊΠΎΠ½ΡΡΠ°, ΠΈ Π½Π΅ ΠΈΠΌΠ΅ΡΡ ΠΏΠ΅ΡΠ΅ΠΌΡΡΠΊΠΈ. Π‘Π»Π΅Π΄ΠΎΠ²Π°ΡΠ΅Π»ΡΠ½ΠΎ, Π·Π΅Π½ΠΊΠ΅ΡΡ Π½Π΅ ΠΏΡΠΈΡΠΏΠΎΡΠΎΠ±Π»Π΅Π½Ρ Π΄Π»Ρ ΠΏΠΎΠ»ΡΡΠ΅Π½ΠΈΡ ΠΎΡΠ²Π΅ΡΡΡΠΈΠΉ Π² ΡΠΏΠ»ΠΎΡΠ½ΠΎΠΌ ΠΌΠ°ΡΠ΅ΡΠΈΠ°Π»Π΅, Π° ΡΠ»ΡΠΆΠΈΡ Π»ΠΈΡΡ Π΄Π»Ρ ΡΠ²Π΅Π»ΠΈΡΠ΅Π½ΠΈΡ ΠΈΠΌΠ΅ΡΡΠΈΡ ΡΡ ΠΎΡΠ²Π΅ΡΡΡΠΈΠΉ. ΠΠ°ΠΏΡΠ°Π²Π»Π΅Π½ΠΈΠ΅ Π·Π΅Π½ΠΊΠ΅ΡΠ° Π² ΠΎΡΠ²Π΅ΡΡΡΠΈΠ΅ Π»ΡΡΡΠ΅, ΡΠ΅ΠΌ Ρ ΡΠ²Π΅ΡΠ»Π°, Ρ. ΠΊ. Ρ Π·Π΅Π½ΠΊΠ΅ΡΠ° ΠΈΠΌΠ΅ΡΡΡΡ Π΄Π»Ρ ΡΡΠΎΠ³ΠΎ ΡΡΠΈ ΠΈΠ»ΠΈ ΡΠ΅ΡΡΡΠ΅ Π½Π°ΠΏΡΠ°Π²Π»ΡΡΡΠΈΠ΅ Π»Π΅Π½ΡΠΎΡΠΊΠΈ (ΡΠ°ΡΠΊΠΈ). ΠΠΎ ΡΠ΅ΠΌ ΠΆΠ΅ ΠΏΡΠΈΡΠΈΠ½Π°ΠΌ Π·Π΅Π½ΠΊΠ΅Ρ Π΄Π°Π΅Ρ Π±ΠΎΠ»Π΅Π΅ ΡΠΎΡΠ½ΠΎΠ΅ ΠΎΡΠ²Π΅ΡΡΡΠΈΠ΅, ΡΠ΅ΠΌ ΡΠ²Π΅ΡΠ»ΠΎ.
ΠΠ΅Π½ΠΊΠ΅Ρ ΠΏΠΎΠ΄ΠΎΠ±Π½ΠΎ ΡΠ²Π΅ΡΠ»Ρ Π·Π°ΠΊΡΠ΅ΠΏΠ»ΡΡΡ Π² ΠΊΠΎΠ½ΠΈΡΠ΅ΡΠΊΠΎΠΌ ΠΎΡΠ²Π΅ΡΡΡΠΈΠΈ ΠΏΠΈΠ½ΠΎΠ»ΠΈ Π·Π°Π΄Π½Π΅ΠΉ Π±Π°Π±ΠΊΠΈ, ΠΏΠΎΠ΄Π°ΡΡ Π΅Π³ΠΎ Π²ΡΡΡΠ½ΡΡ, Π²ΡΠ°ΡΠ°Ρ ΠΌΠ°Ρ ΠΎΠ²ΠΈΡΠΎΠΊ Π·Π°Π΄Π½Π΅ΠΉ Π±Π°Π±ΠΊΠΈ. ΠΠ΄Π½Π°ΠΊΠΎ ΠΌΠΎΠΆΠ½ΠΎ ΠΌΠ΅Ρ Π°Π½ΠΈΠ·ΠΈΡΠΎΠ²Π°ΡΡ ΠΏΠΎΠ΄Π°ΡΡ, Π΅ΡΠ»ΠΈ Π·Π°ΠΊΡΠ΅ΠΏΠΈΡΡ Π·Π΅Π½ΠΊΠ΅Ρ Π² ΡΠΏΠ΅ΡΠΈΠ°Π»ΡΠ½ΠΎΠΌ ΠΏΡΠΈΡΠΏΠΎΡΠΎΠ±Π»Π΅Π½ΠΈΠΈ.
Π Π·Π°Π²ΠΈΡΠΈΠΌΠΎΡΡΠΈ ΠΎΡ Π΄ΠΈΠ°ΠΌΠ΅ΡΡΠ° ΠΎΠ±ΡΠ°Π±Π°ΡΡΠ²Π°Π΅ΠΌΡΡ ΠΎΡΠ²Π΅ΡΡΡΠΈΠΉ ΠΏΡΠΈΠΌΠ΅Π½ΡΡΡ ΡΠ°Π·Π»ΠΈΡΠ½ΡΠ΅ ΠΊΠΎΠ½ΡΡΡΡΠΊΡΠΈΠΈ Π·Π΅Π½ΠΊΠ΅ΡΠΎΠ². ΠΠ»Ρ ΠΌΠ°Π»ΡΡ ΠΎΡΠ²Π΅ΡΡΡΠΈΠΉ (12 β35 ΠΌΠΌ) ΠΏΡΠΈΠΌΠ΅Π½ΡΡΡ ΡΡΠ΅Π·ΡΠ±ΡΠ΅ Π·Π΅Π½ΠΊΠ΅ΡΡ Ρ ΠΊΠΎΠ½ΠΈΡΠ΅ΡΠΊΠΈΠΌ Ρ Π²ΠΎΡΡΠΎΠ²ΠΈΠΊΠΎΠΌ. ΠΠ»Ρ Π±ΠΎΠ»ΡΡΠΈΡ ΠΎΡΠ²Π΅ΡΡΡΠΈΠΉ Π·Π΅Π½ΠΊΠ΅ΡΠ° ΠΈΠ·Π³ΠΎΡΠΎΠ²Π»ΡΡΡ Π½Π°ΡΠ°Π΄Π½ΡΠΌΠΈ Ρ ΡΠ΅ΡΡΡΡΠΌΡ Π·ΡΠ±ΡΡΠΌΠΈ. ΠΡ Π½Π°ΡΠ°ΠΆΠΈΠ²Π°ΡΡ Π½Π° ΠΎΠΏΡΠ°Π²ΠΊΠΈ ΠΈΠ· ΡΠ³Π»Π΅ΡΠΎΠ΄ΠΈΡΡΠΎΠΉ ΡΡΠ°Π»ΠΈ.
Π‘Π²Π΅ΡΠ»Π° ΠΈΠ· Π±ΡΡΡΡΠΎΡΠ΅ΠΆΡΡΠ΅ΠΉ ΡΡΠ°Π»ΠΈ ΠΎΠ±Π΅ΡΠΏΠ΅ΡΠΈΠ²Π°ΡΡ ΠΎΠ±ΡΠ°Π±ΠΎΡΠΊΡ ΠΎΡΠ²Π΅ΡΡΡΠΈΠΉ ΠΏΠΎ 4β5-ΠΌΡ ΠΊΠ»Π°ΡΡΡ, ΡΠΎΡΠ½ΠΎΡΡΠΈ ΠΈ ΠΏΠΎ 3β4-ΠΌΡ ΠΊΠ»Π°ΡΡΡ ΡΠ΅ΡΠΎΡ ΠΎΒΠ²Π°ΡΠΎΡΡΠΈ. Π‘Π²Π΅ΡΠ»Π° Ρ ΠΏΠ»Π°ΡΡΠΈΠ½ΠΊΠ°ΠΌΠΈ ΠΈΠ· ΡΠ²Π΅ΡΠ΄ΡΡ ΡΠΏΠ»Π°Π²ΠΎΠ², ΡΠ°Π±ΠΎΡΠ°ΡΡΠΈΠ΅ Π½Π° Π±ΠΎΠ»Π΅Π΅ Π²ΡΡΠΎΠΊΠΈΡ ΡΠΊΠΎΡΠΎΡΡΡΡ , ΡΠ΅Π·Π°Π½ΠΈΡ ΠΎΠ±Π΅ΡΠΏΠ΅ΡΠΈΠ²Π°ΡΡ ΠΎΠ±ΡΠ°Π±ΠΎΡΠΊΡ ΠΎΡΠ²Π΅ΡΡΡΠΈΠΉ ΠΏΠΎ 3β4-ΠΌΡ ΠΊΠ»Π°ΡΡΡ ΡΠΎΡΠ½ΠΎΡΡΠΈ ΠΈ 4β5-ΠΌΡ ΠΊΠ»Π°ΡΡΡ ΡΠ΅ΡΠΎΡ ΠΎΠ²Π°ΡΠΎΒΡΡΠΈ. ΠΠ»Ρ ΠΏΠΎΠ»ΡΡΠ΅Π½ΠΈΡ Π±ΠΎΠ»Π΅Π΅ ΡΠΎΡΠ½ΡΡ ΠΎΡΠ²Π΅ΡΡΡΠΈΠΉ (3β-4-ΠΉ ΠΊΠ»Π°ΡΡ ΡΠΎΡΠ½ΠΎΡΡΠΈ, 6-ΠΉ ΠΊΠ»Π°ΡΡ ΡΠ΅ΡΠΎΡ ΠΎΠ²Π°ΡΠΎΡΡΠΈ) ΠΏΡΠΈΠΌΠ΅Π½ΡΡΡ Π·Π΅Π½ΠΊΠ΅ΡΠΎΠ²Π°Π½ΠΈΠ΅.
ΠΡΠΎΡΠ΅ΡΡ Π·Π΅Π½ΠΊΠ΅ΡΠΎΠ²Π°Π½ΠΈΡ ΠΎΡΡΡΠ΅ΡΡΠ²Π»ΡΠ΅ΡΡΡ Π·Π΅Π½ΠΊΠ΅ΡΠΎΠΌ (ΡΠΈΡ. 10), ΠΊΠΎΡΠΎΡΡΠΉ ΡΠ»ΡΠΆΠΈΡ Π΄Π»Ρ Π΄Π°Π»ΡΠ½Π΅ΠΉΡΠ΅ΠΉ ΠΎΠ±ΡΠ°Π±ΠΎΡΠΊΠΈ ΠΎΡΠ²Π΅ΡΡΡΠΈΠΉ, ΠΏΠΎΠ»ΡΡΠ΅Π½Π½ΡΡ ΠΏΠΎΡΠ»Π΅ Π»ΠΈΡΡΡ, ΡΡΠ°ΠΌΠΏΠΎΠ²ΠΊΠΈ ΠΈΠ»ΠΈ ΡΠ²Π΅ΡΠ»Π΅Π½ΠΈΡ. ΠΡΠ° ΠΎΠ±ΡΠ°Π±ΠΎΡΠΊΠ° ΠΎΡΠ²Π΅ΡΡΡΠΈΡ ΠΌΠΎΠΆΠ΅Ρ Π±ΡΡΡ Π»ΠΈΠ±ΠΎ ΠΎΠΊΠΎΠ½ΡΠ°ΡΠ΅Π»ΡΠ½ΠΎΠΉ, Π»ΠΈΠ±ΠΎ ΠΏΡΠΎΠΌΠ΅ΠΆΡΡΠΎΡΠ½ΠΎΠΉ ( ΠΏΠΎΠ»ΡΡΠΈΡΡΠΎΠ²ΠΎΠΉ ) ΠΏΠ΅ΡΠ΅Π΄ ΡΠ°Π·Π²Π΅ΡΡΡΠ²Π°Π½ΠΈΠ΅ΠΌ, Π΄Π°ΡΡΠΈΠ΅ Π΅ΡΠ΅ Π±ΠΎΠ»Π΅Π΅ ΡΠΎΡΠ½ΡΠ΅ ΠΎΡΠ²Π΅ΡΡΡΠΈΡ(Ρ 3 ΠΏΠΎ 1 ΠΊΠ»Π°ΡΡ ΡΠΎΡΠ½ΠΎΡΡΠΈ, 7-9 ΠΊΠ»Π°ΡΡ ΡΠ΅ΡΠΎΡ ΠΎΠ²Π°ΡΠΎΡΡΠΈ).
Π€ΡΠ΅Π·Ρ.
Π’Π΅ΠΎΡΠ΅ΡΠΈΡΠ΅ΡΠΊΠΈΠ΅ ΡΠ²Π΅Π΄Π΅Π½ΠΈΡ. Π€ΡΠ΅Π·Ρ ΠΊΠ»Π°ΡΡΠΈΡΠΈΡΠΈΡΡΡΡ ΠΏΠΎ Ρ Π°ΡΠ°ΠΊΡΠ΅ΡΡ Π²ΡΠΏΠΎΠ»Π½ΡΠ΅ΠΌΠΎΠΉ ΡΠ°Π±ΠΎΡΡ, ΠΏΠΎ ΠΊΠΎΠ½ΡΡΡΡΠΊΡΠΈΠΈ, ΠΈ ΠΊΡΠ΅ΠΏΠ»Π΅Π½ΠΈΡ Π·ΡΠ±ΡΠ΅Π² ΠΎΡΠ½ΠΎΡΠΈΡΠ΅Π»ΡΠ½ΠΎ ΠΎΡΠΈ ΡΡΠ΅Π·Ρ ΠΈ Π΄ΡΡΠ³ΠΈΠΌΠΈ ΠΏΡΠΈΠ·Π½Π°ΠΊΠ°ΠΌΠΈ. ΠΡΠ½ΠΎΠ²Π½ΡΠ΅ ΡΠΈΠΏΡ ΡΡΠ΅Π· ΠΏΠΎΠΊΠ°Π·Π°Π½Ρ Π½Π° ΡΠΈΡ. 12, 13. Π¦ΠΈΠ»ΠΈΠ½Π΄ΡΠΈΡΠ΅ΡΠΊΠΈΠ΅ ΡΡΠ΅Π·Ρ ΠΏΡΠΈΠΌΠ΅Π½ΡΡΡ Π΄Π»Ρ ΠΎΠ±ΡΠ°Π±ΠΎΡΠΊΠΈ ΠΎΡΠΊΡΡΡΡΡ ΠΏΠ»ΠΎΡΠΊΠΎΡΡΠ΅ΠΉ. Π’ΠΎΡΡΠ΅Π²ΡΠ΅ ΡΡΠ΅Π·Ρ ΠΈΠΌΠ΅ΡΡ Π·ΡΠ±ΡΡ Π½Π° ΡΠΈΠ»ΠΈΠ½Π΄ΡΠΈΡΠ΅ΡΠΊΠΎΠΉ ΠΈ ΡΠΎΡΡΠ΅Π²ΠΎΠΉ ΠΏΠΎΠ²Π΅ΡΡ Π½ΠΎΡΡΡΡ . ΠΡΠΈ ΡΡΠ΅Π·Ρ ΠΏΡΠΈΠΌΠ΅Π½ΡΡΡ Π΄Π»Ρ ΠΎΠ±ΡΠ°Π±ΠΎΡΠΊΠΈ ΡΡΡΡΠΏΠΎΠ², ΠΏΠ°Π·ΠΎΠ², Π»ΡΡΠΎΠΊ, ΠΌΠ½ΠΎΠ³ΠΎΠ³ΡΠ°Π½Π½ΡΡ ΠΈ Π΄ΡΡΠ³ΠΈΡ Π±ΠΎΠΊΠΎΠ²ΡΡ ΠΏΠΎΠ²Π΅ΡΡ Π½ΠΎΡΡΡΡ Π½Π° ΠΏΡΡΠΌΠΎΡΠ³ΠΎΠ»ΡΠ½ΡΡ ΠΈ ΠΊΡΠΈΠ²ΡΡ Π·Π°Π³ΠΎΡΠΎΠ²ΠΊΠ°Ρ . ΠΠΈΡΠΊΠΎΠ²ΡΠ΅ ΡΡΠ΅Π·Ρ ΠΌΠΎΠ³ΡΡ Π±ΡΡΡ ΠΎΠ΄Π½ΠΎ,- Π΄Π²ΡΡ - ΡΡΠ΅Ρ ΡΡΠΎΡΠΎΠ½Π½ΠΈΠΌΠΈ. Π Π΅ΠΆΡΡΠΈΠ΅ ΠΊΡΠΎΠΌΠΊΠΈ ΡΡΠ΅Ρ ΡΡΠΎΡΠΎΠ½Π½Π΅ΠΉ Π΄ΠΈΡΠΊΠΎΠ²ΠΎΠΉ ΡΡΠ΅Π·Ρ ΡΠ°ΡΠΏΠΎΠ»ΠΎΠΆΠ΅Π½Ρ Π½Π° ΠΎΠ±ΠΎΠΈΡ ΡΠΎΡΡΠ°Ρ ΠΈ Π½Π° ΡΠΈΠ»ΠΈΠ½Π΄ΡΠΈΡΠ΅ΡΠΊΠΎΠΉ ΡΠ°ΡΡΠΈ, ΠΌΠΎΠ³ΡΡ ΡΠ°ΡΠΏΠΎΠ»Π°Π³Π°ΡΡΡΡ ΠΏΠ°ΡΠ°Π»Π»Π΅Π»ΡΠ½ΠΎ ΠΎΡΠΈ ΡΡΠ΅Π·Ρ ΠΈΠ»ΠΈ ΠΏΠΎΠ΄ Π½Π΅ΠΊΠΎΡΠΎΡΡΠΌ ΡΠ³Π»ΠΎΠΌ ΠΊ Π½Π΅ΠΉ.
ΠΠ²ΡΡ ΡΡΠΎΡΠΎΠ½Π½ΡΡ Π΄ΠΈΡΠΊΠΎΠ²Π°Ρ ΡΡΠ΅Π·Π° ΠΈΠΌΠ΅Π΅Ρ ΡΠ΅ΠΆΡΡΠΈΠ΅ ΠΊΡΠΎΠΌΠΊΠΈ Π½Π° ΠΎΠ΄Π½ΠΎΠΌ ΡΠΎΡΡΠ΅ ΠΈ Π½Π° ΡΠΈΠ»ΠΈΠ½Π΄ΡΠΈΡΠ΅ΡΠΊΠΎΠΉ ΡΠ°ΡΡΠΈ, ΠΎΠ΄Π½ΠΎΡΡΠΎΡΠΎΠ½Π½ΡΡ Π΄ΠΈΡΠΊΠΎΠ²Π°Ρ ΡΡΠ΅Π·Π° ΠΈΠΌΠ΅Π΅Ρ ΡΠ΅ΠΆΡΡΠΈΠ΅ ΠΊΡΠΎΠΌΠΊΠΈ ΡΠΎΠ»ΡΠΊΠΎ Π½Π° ΡΠΈΠ»ΠΈΠ½Π΄ΡΠΈΡΠ΅ΡΠΊΠΎΠΉ ΡΠ°ΡΡΠΈ. ΠΡΠΎΡΠ΅Π·Π½ΡΠ΅ ΠΈ ΠΎΡΡΠ΅Π·Π½ΡΠ΅ ΡΡΠ΅Π·Ρ ΠΏΡΠΈΠΌΠ΅Π½ΡΡΡ Π΄Π»Ρ ΡΡΠ΅Π·Π΅ΡΠΎΠ²Π°Π½ΠΈΡ ΡΠ·ΠΊΠΈΡ ΠΏΠ°Π·ΠΎΠ² (ΡΠ»ΠΈΡΡ Π²ΠΈΠ½ΡΠΎΠ² ΠΈ Π΄Ρ.) ΠΈ ΠΎΡΡΠ΅Π·ΠΊΠΈ (ΡΠ°Π·ΡΠ΅Π·Π°Π½ΠΈΡ) Π·Π°Π³ΠΎΡΠΎΠ²ΠΎΠΊ.
ΠΠΎΠ½ΡΠ΅Π²ΡΠ΅ ΡΡΠ΅Π·Ρ ΠΏΡΠΈΠΌΠ΅Π½ΡΡΡ Π΄Π»Ρ ΠΎΠ±ΡΠ°Π±ΠΎΡΠΊΠΈ ΠΏΠ»ΠΎΡΠΊΠΎΡΡΠ΅ΠΉ, ΡΡΡΡΠΏΠΎΠ², ΠΏΠ°Π·ΠΎΠ². ΠΠ½ΠΈ ΠΈΠΌΠ΅ΡΡ ΡΠ΅ΠΆΡΡΠΈΠ΅ ΠΊΡΠΎΠΌΠΊΠΈ Π½Π° ΡΠΈΠ»ΠΈΠ½Π΄ΡΠΈΡΠ΅ΡΠΊΠΎΠΉ ΡΠ°ΡΡΠΈ ΠΈ Π½Π° ΡΠΎΡΡΠ΅. ΠΡΠ½ΠΎΠ²Π½ΠΎΠ΅ ΠΎΡΠ»ΠΈΡΠΈΠ΅ ΠΎΡ ΡΠΎΡΡΠ΅Π²ΡΡ ΡΡΠ΅Π· Π² ΡΠΎΠΌ ΡΡΠΎ ΠΊΠΎΠ½ΡΠ΅Π²ΡΠ΅ Π±ΠΎΠ»Π΅Π΅ Π²ΡΡΡΠ½ΡΡΡΠ΅, Π° Ρ ΡΠΎΡΡΠ΅Π²ΡΠ΅ Π½Π°ΠΎΠ±ΠΎΡΠΎΡ D > H (ΡΠΏΠ»ΡΡΠ½ΡΡΡΠ΅).
Π£Π³Π»ΠΎΠ²ΡΠ΅ ΡΡΠ΅Π·Ρ ΠΏΡΠΈΠΌΠ΅Π½ΡΡΡ Π΄Π»Ρ ΠΎΠ±ΡΠ°Π±ΠΎΡΠΊΠΈ ΠΏΠΎΠ²Π΅ΡΡ Π½ΠΎΡΡΠ΅ΠΉ, ΡΠ°ΡΠΏΠΎΠ»ΠΎΠΆΠ΅Π½Π½ΡΡ ΠΏΠΎΠ΄ Π½Π΅ΠΊΠΎΡΠΎΡΡΠΌ ΡΠ³Π»ΠΎΠΌ Π΄ΡΡΠ³ Π΄ΡΡΠ³Ρ.
Π ΠΈΡ. 9. Π§Π°ΡΡΠΈ ΠΈ ΡΠ»Π΅ΠΌΠ΅Π½ΡΡ ΡΠΏΠΈΡΠ°Π»ΡΠ½ΠΎΠ³ΠΎ ΡΠ²Π΅ΡΠ»Π°.
Π ΠΈΡ. 10. ΠΡΠ½ΠΎΠ²Π½ΡΠ΅ ΡΠ°ΡΡΠΈ Π·Π΅Π½ΠΊΠ΅ΡΠΎΠ²
Π° β ΡΠ΅Π»ΡΠ½ΡΠΉ Ρ ΠΊΠΎΠ½ΡΡΠ½ΡΠΌ Ρ Π²ΠΎΡΡΠΎΠ²ΠΈΠΊΠΎΠΌ, Π± β Π½Π°ΡΠ°Π΄Π½ΠΎΠΉ ΡΠ΅Π»ΡΠ½ΡΠΉ
Π ΠΈΡ. 11. ΠΡΠ½ΠΎΠ²Π½ΡΠ΅ ΡΠ°ΡΡΠΈ ΡΠ°Π·Π²Π΅ΡΡΠΊΠΈ.
Π ΠΈΡ. 12. Π€Π°ΡΠΎΠ½Π½ΡΠ΅ ΡΡΠ΅Π·Ρ: Π° β Ρ Π²ΡΠΏΡΠΊΠ»ΡΠΌ ΠΏΡΠΎΡΠΈΠ»Π΅ΠΌ;
Π± β Ρ Π²ΠΎΠ³Π½ΡΡΡΠΌ ΠΏΡΠΎΡΠΈΠ»Π΅ΠΌ; Π² β ΡΠ³Π»ΠΎΠ²ΡΠ΅
![]() |
![]() |
Π ΠΈΡ. 13. ΠΠΈΠ΄Ρ ΡΡΠ΅Π·Π΅ΡΠΎΠ²Π°Π½ΠΈΡ ΠΈ ΠΎΡΠ½ΠΎΠ²Π½ΡΠ΅ ΡΠΈΠΏΡ ΡΡΠ΅Π·:
Π° β ΡΠΈΠ»ΠΈΠ½Π΄ΡΠΈΡΠ΅ΡΠΊΠΈΠ΅; Π± β ΡΠΎΡΡΠΎΠ²ΡΠ΅; Π² ΠΈ Π³ β Π΄ΠΈΡΠΊΠΎΠ²ΡΠ΅;
Π΄ β ΠΏΡΠΎΡΠ΅Π·Π½ΡΠ΅ ΠΈ ΠΎΡΡΠ΅Π·Π½ΡΠ΅; Π΅ ΠΈ ΠΆ β ΠΊΠΎΠ½ΡΠ΅Π²ΡΠ΅
Π€Π°ΡΠΎΠ½Π½ΡΠ΅ ΡΡΠ΅Π·Ρ ΠΏΡΠΈΠΌΠ΅Π½ΡΡΡ Π΄Π»Ρ ΠΎΠ±ΡΠ°Π±ΠΎΡΠΊΠΈ ΡΠ»ΠΎΠΆΠ½ΠΎ- ΡΠ°ΡΠΎΠ½Π½ΡΡ ΠΏΠΎΠ²Π΅ΡΡ Π½ΠΎΡΡΠ΅ΠΉ: ΠΏΡΠΎΡΠΈΠ»Ρ ΡΠ°ΡΠΎΠ½Π½ΠΎΠΉ ΡΡΠ΅Π·Ρ Π΄ΠΎΠ»ΠΆΠ΅Π½ ΡΠΎΠΎΡΠ²Π΅ΡΡΡΠ²ΠΎΠ²Π°ΡΡ ΠΏΡΠΎΡΠΈΠ»Ρ ΠΎΠ±ΡΠ°Π±Π°ΡΡΠ²Π°Π΅ΠΌΠΎΠΉ Π΄Π΅ΡΠ°Π»ΠΈ.
Π°)
Π±)
Π²)
Π ΠΈΡ.14 ΠΡΠ±ΠΎΡΠ΅Π·Π½ΡΠΉ ΠΈΠ½ΡΡΡΡΠΌΠ΅Π½Ρ: Π°- Π΄ΠΈΡΠΊΠΎΠ²Π°Ρ ΠΌΠΎΠ΄ΡΠ»ΡΠ½Π°Ρ ΡΡΠ΅Π·Π°;
Π±- ΠΏΠ°Π»ΡΡΠ΅Π²Π°Ρ ΠΌΠΎΠ΄ΡΠ»ΡΠ½Π°Ρ ΡΡΠ΅Π·Π°; Π²- ΡΠ΅ΡΠ²ΡΡΠ½Π°Ρ ΠΌΠΎΠ΄ΡΠ»ΡΠ½Π°Ρ ΡΡΠ΅Π·Π°
ΠΠΎ ΡΠΏΠΎΡΠΎΠ±Ρ ΡΡΡΠ°Π½ΠΎΠ²ΠΊΠΈ Π½Π° ΡΡΠ°Π½ΠΊΠ΅ Π·Π΅Π½ΠΊΠ΅ΡΡ Π΄Π΅Π»ΡΡΡΡ Π½Π° Ρ Π²ΠΎΡΡΠΎΠ²ΡΠ΅ ΠΈ Π½Π°ΡΠ°Π΄Π½ΡΠ΅, Π° ΠΏΠΎ ΠΊΠΎΠ½ΡΡΡΡΠΊΡΠΈΠΈ ΡΠ°Π±ΠΎΡΠ΅ΠΉ ΡΠ°ΡΡΠΈ β Π½Π° ΡΠ΅Π»ΡΠ½ΡΠ΅ ΠΈ ΡΠ±ΠΎΡΠ½ΡΠ΅.
Π₯Π²ΠΎΡΡΠΎΠ²ΠΎΠΉ Π·Π΅Π½ΠΊΠ΅Ρ (ΡΠΈΡ. 86, Π°) ΠΏΠΎ Π²Π½Π΅ΡΠ½Π΅ΠΌΡ Π²ΠΈΠ΄Ρ Π½Π°ΠΏΠΎΠΌΠΈΠ½Π°Π΅Ρ ΡΠ²Π΅ΡΠ»ΠΎ ΠΈ ΡΠΎΡΡΠΎΠΈΡ ΠΈΠ· ΡΠ΅Ρ ΠΆΠ΅ ΠΊΠΎΠ½ΡΡΡΡΠΊΡΠΈΠ²Π½ΡΡ ΡΠ°ΡΡΠ΅ΠΉ ΠΈ ΡΠ»Π΅ΠΌΠ΅Π½ΡΠΎΠ². ΠΠ΄Π½Π°ΠΊΠΎ Π² ΠΎΡΠ»ΠΈΡΠΈΠ΅ ΠΎΡ ΠΏΠΎΡΠ»Π΅Π΄Π½Π΅Π³ΠΎ Π·Π΅Π½ΠΊΠ΅Ρ ΠΈΠΌΠ΅Π΅Ρ 3β4 Π·ΡΠ±Π° ΠΈ ΡΠ΅ΠΆΡΡΡΡ ΡΠ°ΡΡΡ ΠΏΠΎ ΡΠΎΡΠΌΠ΅ ΡΡΠ΅ΡΠ΅Π½Π½ΠΎΠ³ΠΎ ΠΊΠΎΠ½ΡΡΠ°. ΠΠ΅Π³Π»ΡΠ±ΠΎΠΊΠΈΠ΅ ΡΡΡΡΠΆΠ΅ΡΠ½ΡΠ΅ ΠΊΠ°Π½Π°Π²ΠΊΠΈ ΠΎΠ±Π΅ΡΠΏΠ΅ΡΠΈΠ²Π°ΡΡ ΠΏΠΎΠ²ΡΡΠ΅Π½Π½ΡΡ ΠΏΡΠΎΡΠ½ΠΎΡΡΡ ΠΈ ΠΆΠ΅ΡΡΠΊΠΎΡΡΡ Π·Π΅Π½ΠΊΠ΅ΡΠ°, Π° ΡΠ²Π΅Π»ΠΈΡΠ΅Π½Π½ΠΎΠ΅ ΠΊΠΎΠ»ΠΈΡΠ΅ΡΡΠ²ΠΎ Π»Π΅Π½ΡΠΎΡΠ΅ΠΊ Π½Π° ΠΊΠ°Π»ΠΈΠ±ΡΡΡΡΠ΅ΠΉ ΡΠ°ΡΡΠΈ ΡΠΎΠ·Π΄Π°Π΅Ρ Π΅ΠΌΡ Π»ΡΡΡΠ΅Π΅ Π½Π°ΠΏΡΠ°Π²Π»Π΅Π½ΠΈΠ΅ Π² ΠΎΡΠ²Π΅ΡΡΡΠΈΠΈ. ΠΠ»Π°Π³ΠΎΠ΄Π°ΡΡ ΡΡΠΎΠΌΡ ΠΎΠ±Π΅ΡΠΏΠ΅ΡΠΈΠ²Π°Π΅ΡΡΡ Π½Π΅ ΡΠΎΠ»ΡΠΊΠΎ Π±ΠΎΠ»Π΅Π΅ Π²ΡΡΠΎΠΊΠ°Ρ ΡΠΎΡΠ½ΠΎΡΡΡ ΠΈ ΡΠΈΡΡΠΎΡΠ° ΠΎΠ±ΡΠ°Π±ΠΎΡΠΊΠΈ, Π½ΠΎ ΡΠ°ΠΊΠΆΠ΅ Π±ΠΎΠ»Π΅Π΅ ΡΡΡΠΎΠ³Π°Ρ ΠΏΡΡΠΌΠΎΠ»ΠΈΠ½Π΅ΠΉΠ½ΠΎΡΡΡ ΠΎΡΠΈ ΠΎΠ±ΡΠ°Π±Π°ΡΡΠ²Π°Π΅ΠΌΠΎΠ³ΠΎ ΠΎΡΠ²Π΅ΡΡΡΠΈΡ.
Π£Π³ΠΎΠ» ΠΊΠΎΠ½ΡΡΠ° ΡΠ΅ΠΆΡΡΠ΅ΠΉ ΡΠ°ΡΡΠΈ.2Ρ Π΄Π»Ρ Π·Π΅Π½ΠΊΠ΅ΡΠΎΠ² ΠΎΠ±ΡΠ΅Π³ΠΎ Π½Π°Π·Π½Π°ΡΠ΅Π½ΠΈΡ Π²ΡΠΏΠΎΠ»Π½ΡΠ΅ΡΡΡ 120Β°.
ΠΠ°ΡΠ°Π΄Π½ΡΠ΅ Π·Π΅Π½ΠΊΠ΅ΡΡ (ΡΠΈΡ. 86, Π± ΠΈ Π²) ΠΈΠΌΠ΅ΡΡ ΠΊΠΎΠ½ΠΈΡΠ΅ΡΠΊΠΎΠ΅ ΠΎΡΠ²Π΅ΡΡΡΠΈΠ΅ Ρ ΠΊΠΎΠ½ΡΡΠ½ΠΎΡΡΡΡ 1: 30 ΠΈ ΠΏΠ°Π· ΠΏΠΎΠ΄ ΡΠΎΡΡΠΎΠ²ΡΡ ΡΠΏΠΎΠ½ΠΊΡ Π΄Π»Ρ ΠΊΡΠ΅ΠΏΠ»Π΅Π½ΠΈΡ Π½Π° ΠΎΠΏΡΠ°Π²ΠΊΠ΅ (ΡΠΈΡ. 87).
Π‘Π±ΠΎΡΠ½Π°Ρ ΠΊΠΎΠ½ΡΡΡΡΠΊΡΠΈΡ Π·Π΅Π½ΠΊΠ΅ΡΠΎΠ² (ΡΠΈΡ. 86, Π²) ΠΏΠΎΠ·Π²ΠΎΠ»ΡΠ΅Ρ ΠΌΠ½ΠΎΠ³ΠΎΠΊΡΠ°ΡΠ½ΠΎ
Π²ΠΎΡΡΡΠ°Π½Π°Π²Π»ΠΈΠ²Π°ΡΡ ΠΈΡ ΠΏΠΎ ΠΌΠ΅ΡΠ΅ ΠΏΠΎΡΠ΅ΡΠΈ ΡΠ°Π·ΠΌΠ΅ΡΠ°. Π’Π°ΠΊΠΈΠ΅ Π·Π΅Π½ΠΊΠ΅ΡΡ ΡΠΎΡΡΠΎΡΡ ΠΈΠ· ΠΊΠΎΡΠΏΡΡΠ°
3, ΠΈΠ·Π³ΠΎΡΠΎΠ²Π»Π΅Π½Π½ΠΎΠ³ΠΎ ΠΈΠ· ΠΊΠΎΠ½ΡΡΡΡΠΊΡΠΈΠΎΠ½Π½ΠΎΠΉ ΡΡΠ°Π»ΠΈ, ΠΈ Π½ΠΎΠΆΠ΅ΠΉ 2, Π·Π°ΠΊΡΠ΅ΠΏΠ»ΡΠ΅ΠΌΡΡ Π² ΠΏΠ°Π·Π°Ρ ΠΊΠΎΡΠΏΡΡΠ° ΠΊΠ»ΠΈΠ½ΡΡΠΌΠΈ 1.
Π‘ΡΠ°Π½Π΄Π°ΡΡΠ°ΠΌΠΈ ΠΏΡΠ΅Π΄ΡΡΠΌΠΎΡΡΠ΅Π½ Π²ΡΠΏΡΡΠΊ Π·Π΅Π½ΠΊΠ΅ΡΠΎΠ² Π΄Π»Ρ ΠΎΡΠ²Π΅ΡΡΡΠΈΠΉ Π΄ΠΈΠ°ΠΌΠ΅ΡΡΠΎΠΌ 10β100 ΠΌΠΌ Π΄Π²ΡΡ Π½ΠΎΠΌΠ΅ΡΠΎΠ². ΠΠ΅Π½ΠΊΠ΅ΡΡ β 1 ΠΏΡΠ΅Π΄Π½Π°Π·Π½Π°ΡΠ°ΡΡΡΡ
Π΄Π»Ρ ΠΏΡΠ΅Π΄Π²Π°ΡΠΈΡΠ΅Π»ΡΠ½ΠΎΠΉ ΠΎΠ±ΡΠ°Π±ΠΎΡΠΊΠΈ ΠΎΡΠ²Π΅ΡΡΡΠΈΠΉ Ρ ΠΏΡΠΈΠΏΡΡΠΊΠΎΠΌ ΠΏΠΎΠ΄ ΡΠ°Π·Π²Π΅ΡΡΡΠ²Π°Π½ΠΈΠ΅, β 2 β Π΄Π»Ρ ΠΎΠΊΠΎΠ½ΡΠ°ΡΠ΅Π»ΡΠ½ΠΎΠΉ ΠΎΠ±ΡΠ°Π±ΠΎΡΠΊΠΈ Ρ ΡΠΎΡΠ½ΠΎΡΡΡΡ 4-Π³ΠΎ ΠΊΠ»Π°ΡΡΠ°.
Π Π°Π±ΠΎΡΠ°Ρ ΡΠ°ΡΡΡ Π·Π΅Π½ΠΊΠ΅ΡΠΎΠ² Π²ΡΠΏΠΎΠ»Π½ΡΠ΅ΡΡΡ ΠΈΠ· Π±ΡΡΡΡΠΎΡΠ΅ΠΆΡΡΠΈΡ ΡΡΠ°Π»Π΅ΠΉ Π»ΠΈΠ±ΠΎ ΠΎΡΠ½Π°ΡΠ°Π΅ΡΡΡ ΠΏΠ»Π°ΡΡΠΈΠ½ΠΊΠ°ΠΌΠΈ ΡΠ²Π΅ΡΠ΄ΠΎΠ³ΠΎ ΡΠΏΠ»Π°Π²Π° ΠΠ8 ΠΈΠ»ΠΈ Π’15Π6. ΠΠ° ΡΠ΅ΠΉΠΊΠ΅ Π·Π΅Π½ΠΊΠ΅ΡΠ° ΠΌΠ°ΡΠΊΠΈΡΡΡΡΡΡ Π½ΠΎΠΌΠΈΠ½Π°Π»ΡΠ½ΡΠΉ Π΄ΠΈΠ°ΠΌΠ΅ΡΡ, Π½ΠΎΠΌΠ΅Ρ ΠΈ ΠΌΠ°ΡΠΊΠ° ΠΌΠ°ΡΠ΅ΡΠΈΠ°Π»Π°.
2. ΠΡΠΈΠ΅ΠΌΡ Π·Π΅Π½ΠΊΠ΅ΡΠΎΠ²Π°Π½ΠΈΡ. ΠΠ΅Π½ΠΊΠ΅ΡΠΎΠ²Π°Π½ΠΈΠ΅ Π½Π° ΡΠΎΠΊΠ°ΡΠ½ΠΎΠΌ ΡΡΠ°Π½ΠΊΠ΅ Π²ΡΠΏΠΎΠ»Π½ΡΠ΅ΡΡΡ Π°Π½Π°Π»ΠΎΠ³ΠΈΡΠ½ΠΎ ΡΠ²Π΅ΡΠ»Π΅Π½ΠΈΡ (ΡΠΈΡ. 88). ΠΠ°Π³ΠΎΡΠΎΠ²ΠΊΡ Π·Π°ΠΊΡΠ΅ΠΏΠ»ΡΡΡ Π² ΠΏΠ°ΡΡΠΎΠ½Π΅ ΠΈ ΠΏΡΠΈ Π½Π΅ΠΎΠ±Ρ ΠΎΠ΄ΠΈΠΌΠΎΡΡΠΈ Π²ΡΠ²Π΅ΡΡΡΡ ΠΏΠΎ ΠΎΡΠ²Π΅ΡΡΡΠΈΡ. ΠΠ΅Π½ΠΊΠ΅Ρ ΡΡΡΠ°Π½Π°Π²Π»ΠΈΠ²Π°ΡΡ Π² ΠΏΠΈΠ½ΠΎΠ»Ρ Π·Π°Π΄Π½Π΅ΠΉ Π±Π°Π±ΠΊΠΈ, ΠΎΡΡ ΠΊΠΎΡΠΎΡΠΎΠΉ Π΄ΠΎΠ»ΠΆΠ½Π° ΡΡΡΠΎΠ³ΠΎ ΡΠΎΠ²ΠΏΠ°Π΄Π°ΡΡ Ρ ΠΎΡΡΡ ΡΠΏΠΈΠ½Π΄Π΅Π»Ρ. ΠΠ°Π΄Π½ΡΡ Π±Π°Π±ΠΊΡ Π·Π°ΠΊΡΠ΅ΠΏΠ»ΡΡΡ Π½Π° ΡΡΠ°Π½ΠΈΠ½Π΅ Π² ΡΠ°ΠΊΠΎΠΌ ΠΌΠ΅ΡΡΠ΅, ΡΡΠΎΠ±Ρ Π²ΡΠ»Π΅Ρ ΠΏΠΈΠ½ΠΎΠ»ΠΈ Π²ΠΎ Π²ΡΠ΅ΠΌΡ ΡΠ°Π±ΠΎΡΡ Π±ΡΠ» Π½Π°ΠΈΠΌΠ΅Π½ΡΡΠΈΠΌ. Π ΡΡΠ½ΠΎΠΉ ΠΏΠΎΠ΄Π°ΡΠ΅ΠΉ Π·Π΅Π½ΠΊΠ΅Ρ ΠΏΠΎΠ΄Π°ΡΡ Π² ΠΎΡΠ²Π΅ΡΡΡΠΈΠ΅ Π·Π°Π³ΠΎΡΠΎΠ²ΠΊΠΈ ΠΈ ΠΏΠΎ
ΠΎΠΊΠΎΠ½ΡΠ°Π½ΠΈΠΈ ΠΎΠ±ΡΠ°Π±ΠΎΡΠΊΠΈ Π²ΡΠ²ΠΎΠ΄ΡΡ ΠΈΠ· Π½Π΅Π³ΠΎ Π΄ΠΎ Π²ΡΠΊΠ»ΡΡΠ΅Π½ΠΈΡ ΡΡΠ°Π½ΠΊΠ°.
ΠΡΠΈΠΏΡΡΠΊ ΠΏΠΎΠ΄ Π·Π΅Π½ΠΊΠ΅Ρ Ρ ΠΏΡΠ΅Π΄Π²Π°ΡΠΈΡΠ΅Π»ΡΠ½ΠΎ ΠΏΡΠΎΡΠ²Π΅ΡΠ»Π΅Π½Π½ΡΡ ΠΎΡΠ²Π΅ΡΡΡΠΈΠΉ Π΄ΠΎΠ»ΠΆΠ΅Π½ ΡΠΎΡΡΠ°Π²Π»ΡΡΡ 1β3 ΠΌΠΌ Π½Π° Π΄ΠΈΠ°ΠΌΠ΅ΡΡ Π² Π·Π°Π²ΠΈΡΠΈΠΌΠΎΡΡΠΈ ΠΎΡ ΡΠ°Π·ΠΌΠ΅ΡΠ° ΠΎΡΠ²Π΅ΡΡΡΠΈΡ.
ΠΡΠΈ Π·Π΅Π½ΠΊΠ΅ΡΠΎΠ²Π°Π½ΠΈΠΈ Π»ΠΈΡΡΡ ΠΈ ΠΊΠΎΠ²Π°Π½ΡΡ ΠΎΡΠ²Π΅ΡΡΡΠΈΠΉ Ρ Π½Π΅ΡΠ°Π²Π½ΠΎΠΌΠ΅ΡΠ½ΡΠΌ ΠΏΡΠΈΠΏΡΡΠΊΠΎΠΌ ΠΈΡ ΡΠ΅ΠΊΠΎΠΌΠ΅Π½Π΄ΡΠ΅ΡΡΡ Π²Π½Π°ΡΠ°Π»Π΅ ΡΠ°ΡΡΠΎΡΠΈΡΡ Π½Π° Π³Π»ΡΠ±ΠΈΠ½Ρ 5β10 ΠΌΠΌ Π΄Π»Ρ ΡΠΎΠ·Π΄Π°Π½ΠΈΡ Π½Π°ΠΏΡΠ°Π²Π»Π΅Π½ΠΈΡ Π·Π΅Π½ΠΊΠ΅ΡΡ.
3. Π Π΅ΠΆΠΈΠΌ ΡΠ΅Π·Π°Π½ΠΈΡ ΠΏΡΠΈ Π·Π΅Π½ΠΊΠ΅ΡΠΎΠ²Π°Π½ΠΈΠΈ. ΠΡΠΈ Π²ΡΠ±ΠΎΡΠ΅ ΡΠ΅ΠΆΠΈΠΌΠ° ΡΠ΅Π·Π°Π½ΠΈΡ Π΄Π»Ρ ΡΠ°Π±ΠΎΡΡ Π·Π΅Π½ΠΊΠ΅ΡΠΎΠΌ ΡΠ»Π΅Π΄ΡΠ΅Ρ ΡΡΠΈΡΡΠ²Π°ΡΡ, ΡΡΠΎ Π³Π»ΡΠ±ΠΈΠ½Π° ΡΠ΅Π·Π°Π½ΠΈΡ Π΄Π»Ρ Π½Π΅Π³ΠΎ Π‘ΠΎΡΡΠ°Π²Π»ΡΠ΅Ρ 1/2 ΠΏΡΠΈΠΏΡΡΠΊΠ° Π½Π° Π΄ΠΈΠ°ΠΌΠ΅ΡΡ ΠΎΡΠ²Π΅ΡΡΡΠΈΡ’. ΠΠΎΠ΄Π°ΡΡ Π΄Π»Ρ Π·Π΅Π½ΠΊΠ΅ΡΠΎΠ²Π°Π½ΠΈΡ ΠΌΠΎΠΆΠ½ΠΎ ΡΠ²Π΅Π»ΠΈΡΠΈΡΡ Π² 1,5β2 ΡΠ°Π·Π° ΠΏΠΎ ΡΡΠ°Π²Π½Π΅Π½ΠΈΡ Ρ Π΅Π΅ Π·Π½Π°ΡΠ΅Π½ΠΈΡΠΌΠΈ Π΄Π»Ρ ΡΠ²Π΅ΡΠ»Π΅Π½ΠΈΡ, Π° ΡΠΊΠΎΡΠΎΡΡΡ ΡΠ΅Π·Π°Π½ΠΈΡ ΠΏΡΠΈΠ½ΠΈΠΌΠ°ΡΡ Π² ΡΠ΅Ρ ΠΆΠ΅ ΠΏΡΠ΅Π΄Π΅Π»Π°Ρ (ΡΠΌ. Β§ 2, ΠΏ.-7 Π΄Π°Π½Π½ΠΎΠΉ Π³Π»Π°Π²Ρ).
ΠΡΠΈ ΡΠ°ΡΡΠ΅ΡΠ°Ρ ΡΠ»Π΅ΠΌΠ΅Π½ΡΠΎΠ² ΡΠ΅ΠΆΠΈΠΌΠ° ΡΠ΅Π·Π°Π½ΠΈΡ ΠΌΠΎΠΆΠ½ΠΎ ΠΏΠΎΠ»ΡΠ·ΠΎΠ²Π°ΡΡΡΡ ΡΠΎΡΠΌΡΠ»Π°ΠΌΠΈ 2β5 (ΡΠΌ. Π³Π». I, Β§ 10).
ΠΠ±ΡΠ°Π±ΠΎΡΠΊΡ ΠΎΡΠ²Π΅ΡΡΡΠΈΠΉ Π² ΡΡΠ°Π»ΡΠ½ΡΡ Π·Π°Π³ΠΎΡΠΎΠ²ΠΊΠ°Ρ Π±ΡΡΡΡΠΎΡΠ΅ΠΆΡΡΠΈΠΌΠΈ Π·Π΅Π½ΠΊΠ΅ΡΠ°ΠΌΠΈ Π½Π΅ΠΎΠ±Ρ ΠΎΠ΄ΠΈΠΌΠΎ ΠΏΡΠΎΠΈΠ·Π²ΠΎΠ΄ΠΈΡΡ Ρ ΠΎΡ Π»Π°ΠΆΠ΄Π΅Π½ΠΈΠ΅ΠΌ ΡΠΌΡΠ»ΡΡΠΈΠΉ. ΠΡΠΈ ΠΎΠ±ΡΠ°Π±ΠΎΡΠΊΠ΅ ΡΡΠ³ΡΠ½Π° ΠΈ ΡΠ²Π΅ΡΠ½ΡΡ ΠΌΠ΅ΡΠ°Π»Π»ΠΎΠ², Π°/ΡΠ°ΠΊΠΆΠ΅ ΠΏΡΠΈ ΠΈΡΠΏΠΎΠ»ΡΠ·ΠΎΠ²Π°Π½ΠΈΠΈ ΡΠ²Π΅ΡΠ΄ΠΎΡΠΏΠ»Π°Π²Π½ΡΡ Π·Π΅Π½ΠΊΠ΅ΡΠΎΠ² ΠΎΡ Π»Π°ΠΆΠ΄Π΅Π½ΠΈΠ΅ ΠΎΠ±ΡΡΠ½ΠΎ Π½Π΅ ΠΏΡΠΈΠΌΠ΅Π½ΡΡΡ.
4. ΠΡΠ°ΠΊ ΠΎΡΠΈ Π·Π΅Π½ΠΊΠ΅ΡΠΎΠ²Π°Π½ΠΈΠΈ. ΠΠΎΠ·ΠΌΠΎΠΆΠ½ΡΠ΅ Π²ΠΈΠ΄Ρ Π±ΡΠ°ΠΊΠ° ΠΎΡΠ²Π΅ΡΡΡΠΈΠΉ ΠΏΡΠΈ Π·Π΅Π½ΠΊΠ΅ΡΠΎΠ²Π°Π½ΠΈΠΈ ΠΏΡΠΈΠ²Π΅Π΄Π΅Π½Ρ Π² ΡΠ°Π±Π». 7.
1. ΠΠ°Π·Π½Π°ΡΠ΅Π½ΠΈΠ΅ ΠΈ ΠΈΠ½ΡΡΡΡΠΌΠ΅Π½ΡΡ. Π Π°Π·Π²Π΅ΡΡΡΠ²Π°Π½ΠΈΠ΅ ΠΏΡΠΈΠΌΠ΅Π½ΡΡΡ Π΄Π»Ρ ΡΠΈΡΡΠΎΠ²ΠΎΠΉ ΠΎΠ±ΡΠ°Π±ΠΎΡΠΊΠΈ ΠΎΡΠ²Π΅ΡΡΡΠΈΠΉ 2β3-Π³ΠΎ ΠΊΠ»Π°ΡΡΠΎΠ² ΡΠΎΡΠ½ΠΎΡΡΠΈ ΠΈ 6β8-Π³ΠΎ ΠΊΠ»Π°ΡΡΠΎΠ² ΡΠΈΡΡΠΎΡΡ ΠΏΠΎΡΠ»Π΅ ΡΠ²Π΅ΡΠ»Π΅Π½ΠΈΡ (ΡΠΎΠ»ΡΠΊΠΎ ΠΏΡΠΈ Π΄ΠΈΠ°ΠΌΠ΅ΡΡΠ΅ Π΄ΠΎ 10 ΠΌΠΌ), Π·Π΅Π½ΠΊΠ΅ΡΠΎΠ²Π°Π½ΠΈΡ ΠΈΠ»ΠΈ ΡΠ°ΡΡΠ°ΡΠΈΠ²Π°Π½ΠΈΡ. Π Π΅ΠΆΡΡΠΈΠΌΠΈ ΠΈΠ½ΡΡΡΡΠΌΠ΅Π½ΡΠ°ΠΌΠΈ Π΄Π»Ρ ΡΠ°ΡΡΠΌΠ°ΡΡΠΈΠ²Π°Π΅ΠΌΠΎΠ³ΠΎ ΡΠΏΠΎΡΠΎΠ±Π° ΠΎΠ±ΡΠ°Π±ΠΎΡΠΊΠΈ Π½Π° ΡΠΎΠΊΠ°ΡΠ½ΡΡ
ΡΡΠ°Π½ΠΊΠ°Ρ
ΡΠ»ΡΠΆΠ°Ρ ΠΌΠ°ΡΠΈΠ½Π½ΡΠ΅ ΡΠ°Π·Π²Π΅ΡΡΠΊΠΈ (ΡΠΈΡ. 89). ΠΠ½ΠΈ ΠΎΡΠ»ΠΈΡΠ°ΡΡΡΡ ΠΎΡ Π·Π΅Π½ΠΊΠ΅ΡΠΎΠ² Π±ΠΎΠ»ΡΡΠΈΠΌ ΠΊΠΎΠ»ΠΈΡΠ΅ΡΡΠ²ΠΎΠΌ Π·ΡΠ±ΡΠ΅Π² (ΠΎΠ±ΡΡΠ½ΠΎ ΠΎΡ 6 Π΄ΠΎ 14), ΠΊΠΎΡΠΎΡΡΠ΅, ΡΡΠ΅Π·Π°Ρ ΠΌΠ΅Π»ΠΊΠΈΠ΅ ΡΡΡΡΠΆΠΊΠΈ, ΠΎΠ±Π΅ΡΠΏΠ΅ΡΠΈΠ²Π°ΡΡ Π±ΠΎΠ»Π΅Π΅ Π²ΡΡΠΎΠΊΡΡ ΡΠΎΡΠ½ΠΎΡΡΡ ΠΈ ΡΠΈΡΡΠΎΡΡ ΠΎΠ±ΡΠ°Π±ΠΎΡΠΊΠΈ.
ΠΠΎ ΡΠΏΠΎΡΠΎΠ±Ρ ΡΡΡΠ°Π½ΠΎΠ²ΠΊΠΈ Π½Π° ΡΡΠ°Π½ΠΊΠ΅ ΡΠ°Π·Π²Π΅ΡΡΠΊΠΈ Π΄Π΅Π»ΡΡΡΡ Π½Π° Ρ
Π²ΠΎΡΡΠΎΠ²ΡΠ΅ ΠΈ Π½Π°ΡΠ°Π΄Π½ΡΠ΅, ΠΏΠΎ ΠΊΠΎΠ½ΡΡΡΡΠΊΡΠΈΠΈ ΡΠ°Π±ΠΎΡΠ΅ΠΉ ΡΠ°ΡΡΠΈ β Π½Π° ΡΠ΅Π»ΡΠ½ΡΠ΅ ΠΈ ΡΠ±ΠΎΡΠ½ΡΠ΅. ΠΠΎΡΠ»Π΅Π΄Π½ΠΈΠ΅ ΡΠΎΡΡΠΎΡΡ ΠΈΠ· ΠΊΠΎΡΠΏΡΡΠ° ΠΈ Π·Π°ΠΊΡΠ΅ΠΏΠ»Π΅Π½Π½ΡΡ
Π² Π΅Π³ΠΎ ΠΏΠ°Π·Π°Ρ
Π½ΠΎΠΆΠ΅ΠΉ.
ΠΠ° ΡΠ΅ΠΆΡΡΠ΅ΠΉ ΡΠ°ΡΡΠΈ ΡΠ°ΡΠΏΠΎΠ»Π°Π³Π°ΡΡΡΡ Π³Π»Π°Π²Π½ΡΠ΅ ΡΠ΅ΠΆΡΡΠΈΠ΅ ΠΊΡΠΎΠΌΠΊΠΈ. ΠΠ°ΠΊΠ»ΠΎΠ½ ΠΈΡ ΠΊ ΠΎΡΠΈ ΠΎΠΏΡΠ΅Π΄Π΅Π»ΡΠ΅ΡΡΡ ΡΠ³Π»ΠΎΠΌ Π² ΠΏΠ»Π°Π½Π΅ Ρ, Π²Π΅Π»ΠΈΡΠΈΠ½Π° ΠΊΠΎΡΠΎΡΠΎΠ³ΠΎ Π·Π°Π²ΠΈΡΠΈΡ ΠΎΡ Π½Π°Π·Π½Π°ΡΠ΅Π½ΠΈΡ ΡΠ°Π·Π²Π΅ΡΡΠΊΠΈ. ΠΠ»Ρ ΡΠΊΠ²ΠΎΠ·Π½ΡΡ ΠΎΡΠ²Π΅ΡΡΡΠΈΠΉ ΠΏΡΠΈ ΠΎΠ±ΡΠ°Π±ΠΎΡΠΊΠ΅ ΡΡΠ°Π»Π΅ΠΉ ΠΈ Π΄ΡΡΠ³ΠΈΡ ΠΏΠ»Π°ΡΡΠΈΡΠ½ΡΡ ΠΌΠ΅ΡΠ°Π»Π»ΠΎΠ² Ρ=15Β°, Π΄Π»Ρ Ρ ΡΡΠΏΠΊΠΈΡ ΠΌΠ΅ΡΠ°Π»Π»ΠΎΠ² Ρ = 5Β°. Π£ ΡΠ°Π·Π²Π΅ΡΡΠΎΠΊ Π΄Π»Ρ Π³Π»ΡΡ ΠΈΡ ΠΎΡΠ²Π΅ΡΡΡΠΈΠΉ Ρ = 60Β°.
ΠΠ°Π»ΠΈΠ±ΡΡΡΡΠ°Ρ ΡΠ°ΡΡΡ ΠΈΠΌΠ΅Π΅Ρ ΡΠΈΠ»ΠΈΠ½Π΄ΡΠΈΡΠ΅ΡΠΊΡΡ ΡΠΎΡΠΌΡ. ΠΠ° Π½Π΅ΠΉ ΡΠ°ΡΠΏΠΎΠ»Π°Π³Π°ΡΡΡΡ Π²ΡΠΏΠΎΠΌΠΎΠ³Π°ΡΠ΅Π»ΡΠ½ΡΠ΅ ΡΠ΅ΠΆΡΡΠΈΠ΅ ΠΊΡΠΎΠΌΠΊΠΈ, ΠΏΡΠ΅Π΄Π½Π°Π·Π½Π°ΡΠ΅Π½Π½ΡΠ΅ -Π΄Π»Ρ Π·Π°ΡΠΈΡΡΠΊΠΈ ΠΈ ΠΊΠ°Π»ΠΈΠ±ΡΠΎΠ²Π°Π½ΠΈΡ ΠΎΡΠ²Π΅ΡΡΡΠΈΡ. Π§ΡΠΎΠ±Ρ ΠΏΡΠ΅Π΄ΡΠΏΡΠ΅Π΄ΠΈΡΡ ΠΏΠΎΠ²ΡΠ΅ΠΆΠ΄Π΅Π½ΠΈΡ ΠΎΡΠ²Π΅ΡΡΡΠΈΡ ΠΊΠΎΠ½ΡΠ°ΠΌΠΈ Π·ΡΠ±ΡΠ΅Π² ΠΊΠ°Π»ΠΈΠ±ΡΡΡΡΠ΅ΠΉ ΡΠ°ΡΡΠΈ, Π² ΠΊΠΎΠ½ΡΠ΅ Π΅Π΅ Π½Π° Π½Π΅Π±ΠΎΠ»ΡΡΠΎΠΉ Π΄Π»ΠΈΠ½Π΅ Π²ΡΠΏΠΎΠ»Π½ΡΠ΅ΡΡΡ Π½Π΅Π·Π½Π°ΡΠΈΡΠ΅Π»ΡΠ½ΡΠΉ ΠΎΠ±ΡΠ°ΡΠ½ΡΠΉ ΠΊΠΎΠ½ΡΡ Ρ Π²Π΅Π»ΠΈΡΠΈΠ½ΠΎΠΉ Π·Π°Π½ΠΈΠΆΠ΅Π½ΠΈΡ Π΄ΠΈΠ°ΠΌΠ΅ΡΡΠ° Π½Π° 0,04β0,07 ΠΌΠΌ.
Π ΡΠ²ΡΠ·ΠΈ Ρ ΡΠ°Π·Π»ΠΈΡΠ½ΡΠΌ Π½Π°Π·Π½Π°ΡΠ΅Π½ΠΈΠ΅ΠΌ Π³Π»Π°Π²Π½ΡΡ
ΠΈ Π²ΡΠΏΠΎΠΌΠΎΠ³Π°ΡΠ΅Π»ΡΠ½ΡΡ
ΡΠ΅ΠΆΡΡΠΈΡ
ΠΊΡΠΎΠΌΠΎΠΊ ΡΠΎΡΠΌΠ°- Π·Π°ΡΠΎΡΠΊΠΈ Π·ΡΠ±ΡΠ΅Π² ΠΏΠΎ Π΄Π»ΠΈΠ½Π΅ ΡΠ°Π·Π»ΠΈΡΠ½Π°. ΠΠ° ΡΠ΅ΠΆΡΡΠ΅ΠΉ ΡΠ°ΡΡΠΈ (ΡΠΈΡ. 89, Π°, ΡΠ΅Ρ. ΠβΠ) Π·ΡΠ±ΡΡ Π·Π°ΡΠ°ΡΠΈΠ²Π°ΡΡΡΡ Π΄ΠΎ ΠΎΡΡΡΠΎΡΡ Ρ ΡΠ³Π»ΠΎΠΌ Π°=6β8Β°.. ΠΠ° ΠΊΠ°Π»ΠΈΠ±ΡΡΡΡΠ΅ΠΉ ΡΠ°ΡΡΠΈ (ΡΠΈΡ. 89, Π°, ΡΠ΅Ρ. Π β Π) Π½ΠΎ Π·Π°Π΄Π½ΠΈΠΌ ΠΏΠΎΠ²Π΅ΡΡ
Π½ΠΎΡΡΡΠΌ Π·ΡΠ±ΡΠ΅Π² ΠΎΡΡΠ°Π²Π»ΡΡΡΡΡ ΡΠΈΠ»ΠΈΠ½Π΄ΡΠΈΡΠ΅ΡΠΊΠΈΠ΅ Π»Π΅Π½ΡΠΎΡΠΊΠΈ ΡΠΈΡΠΈΠ½ΠΎΠΉ 0,08β0,5 ΠΌΠΌ, ΠΊΠΎΡΠΎΡΡΠ΅ ΡΠ³Π»Π°ΠΆΠΈΠ²Π°ΡΡ ΠΏΠΎΠ²Π΅ΡΡ
Π½ΠΎΡΡΡ ΠΎΡΠ²Π΅ΡΡΡΠΈΡ, ΡΠ»ΡΡΡΠ°ΡΡ Π½Π°ΠΏΡΠ°Π²Π»Π΅Π½ΠΈΠ΅ ΡΠ°Π·Π²Π΅ΡΡΠΊΠΈ ΠΈ ΡΠ²Π΅Π»ΠΈΡΠΈΠ²Π°ΡΡ Π΅Π΅ ΡΠΈΡΠ»ΠΎ ΠΏΠ΅ΡΠ΅ΡΠΎΡΠ΅ΠΊ.
ΠΠ΅ΡΠ΅Π΄Π½ΠΈΠΉ ΡΠ³ΠΎΠ» Ρ Ρ ΡΠ°Π·Π²Π΅ΡΡΠΎΠΊ ΠΎΠ±ΡΡΠ½ΠΎ Π²ΡΠΏΠΎΠ»Π½ΡΡΡ 0Β°. ΠΡΠΈ ΠΏΠΎΠ²ΡΡΠ΅Π½Π½ΡΡ
ΡΡΠ΅Π±ΠΎΠ²Π°Π½ΠΈΡΡ
ΠΊ ΠΊΠ°ΡΠ΅ΡΡΠ²Ρ ΠΎΠ±ΡΠ°Π±ΠΎΡΠΊΠΈ Π΅Π³ΠΎ ΡΠ΅ΠΊΠΎΠΌΠ΅Π½Π΄ΡΠ΅ΡΡΡ Π΄Π΅Π»Π°ΡΡ ΠΎΡΡΠΈΡΠ°ΡΠ΅Π»ΡΠ½ΡΠΌ ΠΎΡ β3 Π΄ΠΎ β6Β°. ΠΡΠ»Π΅Π΄ΡΡΠ²ΠΈΠ΅ ΡΡΠΎΠ³ΠΎ ΡΠ΅Π·Π°Π½ΠΈΠ΅ ΠΏΡΠΈ ΡΠ°Π·Π²Π΅ΡΡΡΠ²Π°Π½ΠΈΠΈ Π½Π°ΠΏΠΎΠΌΠΈΠ½Π°Π΅Ρ ΡΠΊΠΎΠ±Π»Π΅Π½ΠΈΠ΅.
Π£ ΡΠ°Π·Π²Π΅ΡΡΠΎΠΊ Π΄Π»Ρ ΡΠΊΠ²ΠΎΠ·Π½ΡΡ
ΠΎΡΠ²Π΅ΡΡΡΠΈΠΉ Π½Π° ΠΏΠ΅ΡΠ΅Π΄Π½Π΅ΠΌ ΡΠΎΡΡΠ΅ Π²ΡΠΏΠΎΠ»Π½ΡΠ΅ΡΡΡ ΡΠ°ΡΠΊΠ° ΡΠΈΡΠΈΠ½ΠΎΠΉ 1,5β2,5 ΠΌΠΌ ΠΏΠΎΠ΄ ΡΠ³Π»ΠΎΠΌ 45Β°, ΠΊΠΎΡΠΎΡΠ°Ρ ΠΏΡΠ΅Π΄ΠΎΡ
ΡΠ°Π½ΡΠ΅Ρ ΡΠ³ΠΎΠ»ΠΊΠΈ Π·ΡΠ±ΡΠ΅Π² ΠΎΡ Π²ΡΠΊΡΠ°ΡΠΈΠ²Π°Π½ΠΈΡ ΠΏΡΠΈ Π²Ρ
ΠΎΠ΄Π΅ Π² ΠΎΡΠ²Π΅ΡΡΡΠΈΠ΅.
ΠΠ»Ρ ΠΏΠΎΠ²ΡΡΠ΅Π½ΠΈΡ ΡΠΈΡΡΠΎΡΡ ΠΎΠ±ΡΠ°Π±ΠΎΡΠΊΠΈ Π·ΡΠ±ΡΡ ΡΠ°Π·Π²Π΅ΡΡΠΎΠΊ ΡΠ°ΡΠΏΠΎΠ»Π°Π³Π°ΡΡ ΠΏΠΎ ΠΎΠΊΡΡΠΆΠ½ΠΎΡΡΠΈ Π½Π΅ΡΠ°Π²Π½ΠΎΠΌΠ΅ΡΠ½ΠΎ. ΠΡΠΎ ΠΎΠ±ΡΡΡΠ½ΡΠ΅ΡΡΡ ΡΠ΅ΠΌ, ΡΡΠΎ Π² ΠΏΡΠΎΡΠ΅ΡΡΠ΅ ΡΠ΅Π·Π°Π½ΠΈΡ Π²ΡΠ΅Π³Π΄Π° ΠΈΠΌΠ΅Π΅Ρ ΠΌΠ΅ΡΡΠΎ ΠΊΠΎΠ»Π΅Π±Π°Π½ΠΈΠ΅ Π½Π°Π³ΡΡΠ·ΠΊΠΈ Π½Π° Π·ΡΠ±, Π²ΡΠ·Π²Π°Π½Π½ΠΎΠ΅ Π½Π΅ΡΠ°Π²Π½ΠΎΠΌΠ΅ΡΠ½ΠΎΠΉ ΠΏΠ»ΠΎΡΠ½ΠΎΡΡΡΡ ΠΎΠ±ΡΠ°Π±Π°ΡΡΠ²Π°Π΅ΠΌΠΎΠ³ΠΎ ΠΌΠ°ΡΠ΅ΡΠΈΠ°Π»Π° ΠΈ ΡΠ°Π·Π»ΠΈΡΠ½ΡΠΌΠΈ Π²ΠΊΠ»ΡΡΠ΅Π½ΠΈΡΠΌΠΈ Π² Π½Π΅ΠΌ. ΠΠ΅ΡΠΈΠΎΠ΄ΠΈΡΠ΅ΡΠΊΠΈ ΠΏΠΎΠ²ΡΠΎΡΡΡΡΠΈΠ΅ΡΡ ΠΊΠΎ-
Π»Π΅Π±Π°Π½ΠΈΡ ΠΏΡΠΈ ΡΠ°Π²Π½ΠΎΠΌΠ΅ΡΠ½ΠΎΠΌ ΡΠ°ΡΠΏΠΎΠ»ΠΎΠΆΠ΅Π½ΠΈΠΈ Π·ΡΠ±ΡΠ΅Π² ΡΠΎΠ·Π΄Π°ΡΡ ΠΌΠ΅ΡΡΠ½ΡΠ΅ ΡΠ³Π»ΡΠ±Π»Π΅Π½ΠΈΡ Π½Π° ΠΏΠΎΠ²Π΅ΡΡ
Π½ΠΎΡΡΠΈ ΡΠ°Π·Π²Π΅ΡΠ½ΡΡΠΎΠ³ΠΎ ΠΎΡΠ²Π΅ΡΡΡΠΈΡ. ΠΠ΅ΡΠ°Π²Π½ΠΎΠΌΠ΅ΡΠ½ΠΎΠ΅ ΡΠ°ΡΠΏΠΎΠ»ΠΎΠΆΠ΅Π½ΠΈΠ΅ Π·ΡΠ±ΡΠ΅Π² ΠΈΡΠΊΠ»ΡΡΠ°Π΅Ρ ΡΠΊΠ°Π·Π°Π½Π½ΠΎΠ΅ ΡΠ²Π»Π΅Π½ΠΈΠ΅.
Π Π°Π·Π²Π΅ΡΡΠΊΠΈ ΠΎΠ±ΡΡΠ½ΠΎ ΠΈΠΌΠ΅ΡΡ ΠΏΡΡΠΌΡΠ΅ Π·ΡΠ±ΡΡ. Π Π½Π΅ΠΊΠΎΡΠΎΡΡΡ
ΡΠ»ΡΡΠ°ΡΡ
Π΄Π»Ρ ΠΎΠ±ΡΠ°Π±ΠΎΡΠΊΠΈ ΠΎΡΠ²Π΅ΡΡΡΠΈΠΉ Ρ ΠΏΠ°Π·Π°ΠΌΠΈ ΠΈΠ»ΠΈ ΠΊΠ°Π½Π°Π²ΠΊΠ°ΠΌΠΈ ΠΏΡΠΈΠΌΠ΅Π½ΡΡΡ ΡΠ°Π·Π²Π΅ΡΡΠΊΠΈ Ρ Π²ΠΈΠ½ΡΠΎΠ²ΡΠΌΠΈ Π·ΡΠ±ΡΡΠΌΠΈ, Π½Π°ΠΏΡΠ°Π²Π»Π΅Π½ΠΈΠ΅ ΠΊΠΎΡΠΎΡΡΡ
Π΄Π΅Π»Π°ΡΡ ΠΏΡΠΎΡΠΈΠ²ΠΎΠΏΠΎΠ»ΠΎΠΆΠ½ΡΠΌ Π½Π°ΠΏΡΠ°Π²Π»Π΅Π½ΠΈΡ ΡΠ΅Π·Π°Π½ΠΈΡ Ρ ΡΠ΅ΠΌ, ΡΡΠΎΠ±Ρ ΡΠ°Π·Π²Π΅ΡΡΠΊΠ° Π½Π΅ Π·Π°ΡΡΠ³ΠΈΠ²Π°Π»Π°ΡΡ Π² ΠΎΡΠ²Π΅ΡΡΡΠΈΠ΅.
Π ΡΠΎΠΎΡΠ²Π΅ΡΡΡΠ²ΠΈΠΈ Ρ Π΄Π΅ΠΉΡΡΠ²ΡΡΡΠΈΠΌΠΈ ΡΡΠ°Π½Π΄Π°ΡΡΠ°ΠΌΠΈ ΡΠ°Π·Π²Π΅ΡΡΠΊΠΈ ΠΎΠ±ΡΠ΅Π³ΠΎ Π½Π°Π·Π½Π°ΡΠ΅Π½ΠΈΡ Π²ΡΠΏΡΡΠΊΠ°ΡΡΡΡ Π΄ΠΈΠ°ΠΌΠ΅ΡΡΠΎΠΌ ΠΎΡ 0,1 Π΄ΠΎ 300 ΠΌΠΌ Π² Π΄ΠΎΠ²Π΅Π΄Π΅Π½Π½ΠΎΠΌ Π²ΠΈΠ΄Π΅ Π΄Π»Ρ ΠΎΡΠ²Π΅ΡΡΡΠΈΠΉ 2β3-Π³ΠΎ ΠΊΠ»Π°ΡΡΠΎΠ² ΡΠΎΡΠ½ΠΎΡΡΠΈ (Π, Π2Π°, Π3, Π) Π»ΠΈΠ±ΠΎ Ρ ΠΏΡΠΈΠΏΡΡΠΊΠΎΠΌ ΠΏΠΎΠ΄ Π΄ΠΎΠ²ΠΎΠ΄ΠΊΡ. ΠΠΎΡΠ»Π΅Π΄Π½ΠΈΠ΅ ΠΈΠ·Π³ΠΎΡΠ°Π²Π»ΠΈΠ²Π°ΡΡΡΡ ΡΠ΅ΡΡΠΈ Π½ΠΎΠΌΠ΅ΡΠΎΠ², ΠΊΠΎΡΠΎΡΡΠ΅ ΡΠΎΠ»ΡΠΊΠΎ ΠΏΠΎΡΠ»Π΅ Π΄ΠΎΠ²ΠΎΠ΄ΠΊΠΈ ΠΏΠΎ ΠΊΠ°Π»ΠΈΠ±ΡΡΡΡΠ΅ΠΉ ΡΠ°ΡΡΠΈ ΠΌΠΎΠΆΠ½ΠΎ ΠΏΡΠΈΠΌΠ΅Π½ΡΡΡ Π΄Π»Ρ ΠΎΠ±ΡΠ°Π±ΠΎΡΠΊΠΈ ΠΎΡΠ²Π΅ΡΡΡΠΈΠΉ ΠΏΡΠ΅Π΄ΡΡΠΌΠΎΡΡΠ΅Π½Π½ΠΎΠΉ ΡΠΎΡΠ½ΠΎΡΡΠΈ.’
Π Π°Π±ΠΎΡΠ°Ρ ΡΠ°ΡΡΡ ΡΠ°Π·Π²Π΅ΡΡΠΎΠΊ Π²ΡΠΏΠΎΠ»Π½ΡΠ΅ΡΡΡ ΠΈΠ· Π±ΡΡΡΡΠΎΡΠ΅ΠΆΡΡΠ΅ΠΉ ΡΡΠ°Π»ΠΈ Π 18 ΠΈΠ»ΠΈ ΠΎΡΠ½Π°ΡΠ°Π΅ΡΡΡ ΡΠ²Π΅ΡΠ΄ΡΠΌ ΡΠΏΠ»Π°Π²ΠΎΠΌ Π΄Π»Ρ ΠΏΠΎΠ²ΡΡΠ΅Π½ΠΈΡ ΡΡΠΎΠΉΠΊΠΎΡΡΠΈ.
ΠΠ° ΡΠ°Π·Π²Π΅ΡΡΠΊΠ°Ρ
ΠΌΠ°ΡΠΊΠΈΡΡΠ΅ΡΡΡ Π½ΠΎΠΌΠΈΠ½Π°Π»ΡΠ½ΡΠΉ Π΄ΠΈΠ°ΠΌΠ΅ΡΡ, ΠΊΠ»Π°ΡΡ ΡΠΎΡΠ½ΠΎΡΡΠΈ ΠΈ ΠΌΠ°ΡΠΊΠ° ΠΌΠ°ΡΠ΅ΡΠΈΠ°Π»Π°.
2. ΠΡΠΈΠ΅ΠΌΡ ΡΠ°Π·Π²Π΅ΡΡΡΠ²Π°Π½ΠΈΡ. ΠΠΎΠ΄Π³ΠΎΡΠΎΠ²ΠΊΠ° ΠΊ ΡΠ°Π·Π²Π΅ΡΡΡΠ²Π°Π½ΠΈΡ ΠΈ Π΅Π³ΠΎ Π²ΡΠΏΠΎΠ»Π½Π΅Π½ΠΈΠ΅ (ΡΠΈΡ. 90) ΠΎΡΡΡΠ΅ΡΡΠ²Π»ΡΡΡΡΡ Π°Π½Π°Π»ΠΎΠ³ΠΈΡΠ½ΠΎ Π·Π΅Π½ΠΊΠ΅ΡΠΎΠ²Π°Π½ΠΈΡ. ΠΠ΄Π½Π°ΠΊΠΎ Π² ΡΠ²ΡΠ·ΠΈ Ρ Π±ΠΎΠ»Π΅Π΅ Π²ΡΡΠΎΠΊΠΎΠΉ ΡΠΎΡΠ½ΠΎΡΡΡΡ ΠΎΠ±ΡΠ°Π±ΠΎΡΠΊΠΈ ΠΎΠ½ΠΈ ΠΈΠΌΠ΅ΡΡ Π½Π΅ΠΊΠΎΡΠΎΡΡΠ΅ ΠΎΡΠΎΠ±Π΅Π½Π½ΠΎΡΡΠΈ.
1. Π Π°Π·Π²Π΅ΡΡΠΊΠ° ΡΡΠ΅Π·Π°Π΅Ρ ΡΠΎΠ½ΠΊΠΈΠ΅ ΡΠ»ΠΎΠΈ ΠΌΠ΅ΡΠ°Π»Π»Π° ΠΈ Π½Π΅ ΠΌΠΎΠΆΠ΅Ρ ΠΈΡΠΏΡΠ°Π²ΠΈΡΡ Π½Π°ΠΏΡΠ°Π²Π»Π΅Π½ΠΈΠ΅ ΠΎΡΠ²Π΅ΡΡΡΠΈΡ, ΠΎΡΡ ΠΊΠΎΡΠΎΡΠΎΠ³ΠΎ Π±ΡΠ»Π° ΡΠΌΠ΅ΡΠ΅Π½Π° ΠΏΡΠ΅Π΄Π²Π°ΡΠΈΡΠ΅Π»ΡΠ½ΠΎΠΉ ΠΎΠ±ΡΠ°Π±ΠΎΡΠΊΠΎΠΉ. ΠΠΎΡΡΠΎΠΌΡ ΠΎΡΠ²Π΅ΡΡΡΠΈΡ ΠΏΠΎΠ΄ ΡΠ°Π·Π²Π΅ΡΡΡΠ²Π°Π½ΠΈΠ΅ ΠΏΠΎΠ΄Π³ΠΎΡΠ°Π²Π»ΠΈΠ²Π°ΡΡ Π·Π΅Π½ΠΊΠ΅ΡΠΎΠ²Π°Π½ΠΈΠ΅ΠΌ ΠΈΠ»ΠΈ ΡΠ°ΡΡΠ°ΡΠΈΠ²Π°Π½ΠΈΠ΅ΠΌ. ΠΡΠ²Π΅ΡΡΡΠΈΡ Π½Π΅Π±ΠΎΠ»ΡΡΠΎΠ³ΠΎ Π΄ΠΈΠ°ΠΌΠ΅ΡΡΠ° (Π΄ΠΎ 10 ΠΌΠΌ) Π² ΡΠ²ΡΠ·ΠΈ ΡΠΎ ΡΠ»ΠΎΠΆΠ½ΠΎΡΡΡΡ ΡΠ°ΡΡΠΎΡΠΊΠΈ ΠΈ ΠΎΡΡΡΡΡΡΠ²ΠΈΠ΅ΠΌ Π΄Π»Ρ Π½ΠΈΡ
Π·Π΅Π½ΠΊΠ΅ΡΠΎΠ² ΠΎΠ±ΡΠ΅Π³ΠΎ Π½Π°Π·Π½Π°ΡΠ΅Π½ΠΈΡ ΡΠ°Π·Π²Π΅ΡΡΡΠ²Π°ΡΡ ΠΏΠΎΡΠ»Π΅ ΡΠ²Π΅ΡΠ»Π΅Π½ΠΈΡ, ΠΊΠΎΡΠΎΡΠΎΠ΅ ΡΠ»Π΅Π΄ΡΠ΅Ρ Π²ΡΠΏΠΎΠ»Π½ΠΈΡΡ Ρ ΠΎΡΠΎΠ±ΠΎΠΉ ΡΡΠ°ΡΠ΅Π»ΡΠ½ΠΎΡΡΡΡ.
2. ΠΡΠΈΠΏΡΡΠΊ ΠΏΠΎΠ΄ ΡΠ°Π·Π²Π΅ΡΡΡΠ²Π°Π½ΠΈΠ΅ ΠΎΡΡΠ°Π²Π»ΡΡΡ Π½Π΅Π±ΠΎΠ»ΡΡΠΎΠΉ, ΠΏΡΠΈΡΠ΅ΠΌ, ΡΠ΅ΠΌ ΠΎΠ½ ΠΌΠ΅Π½ΡΡΠ΅, ΡΠ΅ΠΌ ΡΠΎΡΠ½ΠΎΡΡΡ ΠΎΠ±ΡΠ°Π±ΠΎΡΠΊΠΈ Π²ΡΡΠ΅. ΠΠ»Ρ Π΅Π³ΠΎ Π²ΡΠ±ΠΎΡΠ° ΠΌΠΎΠΆΠ½ΠΎ ΡΡΠΊΠΎΠ²ΠΎΠ΄ΡΡΠ²ΠΎΠ²Π°ΡΡΡΡ ΡΠ»Π΅Π΄ΡΡΡΠΈΠΌΠΈ Π΄Π°Π½Π½ΡΠΌΠΈ, ΠΌΠΌ:
ΠΠΈΠ°ΠΌΠ΅ΡΡ ΠΎΡΠ²Π΅ΡΡΡΠΈΡ ΠΠΎ 5 5β20 20β30 30β50 50β80 80β100
ΠΡΠΈΠΏΡΡΠΊ Π½Π° Π΄ΠΈΠ°ΠΌΠ΅ΡΡ 0,1 0,2 0,25 0,3 0,35 0,4
3. ΠΠ΅ΡΠ΅Π΄ ΠΎΠ±ΡΠ°Π±ΠΎΡΠΊΠΎΠΉ ΡΠ°Π·Π²Π΅ΡΡΠΊΡ Π½Π°Π΄ΠΎ Π²Π½ΠΈΠΌΠ°ΡΠ΅Π»ΡΠ½ΠΎ ΠΎΡΠΌΠΎΡΡΠ΅ΡΡ. Π’ΠΎΡΠ½ΠΎΡΡΡ Π΅Π΅ Π΄ΠΎΠ»ΠΆΠ½Π° ΡΠΎΠΎΡΠ²Π΅ΡΡΡΠ²ΠΎΠ²Π°ΡΡ ΠΊΠ»Π°ΡΡΡ ΡΠΎΡΠ½ΠΎΡΡΠΈ ΠΎΠ±ΡΠ°Π±Π°ΡΡΠ²Π°-
Π΅ΠΌΠΎΠ³ΠΎ ΠΎΡΠ²Π΅ΡΡΡΠΈΡ. Π Π΅ΠΆΡΡΠΈΠ΅ ΠΊΡΠΎΠΌΠΊΠΈ Π΄ΠΎΠ»ΠΆΠ½Ρ Π±ΡΡΡ ΠΎΡΡΡΡΠΌΠΈ, Π±Π΅Π· Π·Π°Π²Π°Π»ΠΎΠ² ΠΈ Π·Π°Π±ΠΎΠΈΠ½. Π Π°Π΄ΠΈΠ°Π»ΡΠ½ΠΎΠ΅ Π±ΠΈΠ΅Π½ΠΈΠ΅ ΠΊΡΠΎΠΌΠΎΠΊ Π½Π° ΡΠ΅ΠΆΡΡΠ΅ΠΉ ΡΠ°ΡΡΠΈ Π½Π΅ Π΄ΠΎΠ»ΠΆΠ½ΠΎ ΠΏΡΠ΅Π²ΡΡΠ°ΡΡ 0,02 ΠΌΠΌ.
4. ΠΠ»Ρ ΠΊΠ°ΡΠ΅ΡΡΠ²Π΅Π½Π½ΠΎΠ³ΠΎ ΡΠ°Π·Π²Π΅ΡΡΡΠ²Π°Π½ΠΈΡ Π½Π΅ΠΎΠ±Ρ
ΠΎΠ΄ΠΈΠΌΠΎ ΠΎΠ±Π΅ΡΠΏΠ΅ΡΠΈΡΡ ΡΡΡΠΎΠ³ΡΡ ΡΠΎΠΎΡΠ½ΠΎΡΡΡ ΡΠ°Π·Π²Π΅ΡΡΠΊΠΈ ΠΈ ΠΎΠ±ΡΠ°Π±Π°ΡΡΠ²Π°Π΅ΠΌΠΎΠ³ΠΎ ΠΎΡΠ²Π΅ΡΡΡΠΈΡ. ΠΠ»Ρ ΡΡΠΎΠ³ΠΎ ΠΏΡΠ΅ΠΆΠ΄Π΅ Π²ΡΠ΅Π³ΠΎ ΡΠ»Π΅Π΄ΡΠ΅Ρ ΡΡΠ°ΡΠ΅Π»ΡΠ½ΠΎ Π²ΡΠ²Π΅ΡΠΈΡΡ ΡΠΎΠ²ΠΏΠ°Π΄Π΅Π½ΠΈΠ΅ ΠΎΡΠ΅ΠΉ ΠΏΠΈΠ½ΠΎΠ»ΠΈ Π·Π°Π΄Π½Π΅ΠΉ Π±Π°Π±ΠΊΠΈ ΠΈ ΡΠΏΠΈΠ½Π΄Π΅Π»Ρ. ΠΡΠΎΠΌΠ΅ ΡΠΎΠ³ΠΎ, ΡΡΠΎΠ±Ρ ΠΈΡΠΊΠ»ΡΡΠΈΡΡ Π²Π»ΠΈΡΠ½ΠΈΠ΅ ΠΏΠΎΠ³ΡΠ΅ΡΠ½ΠΎΡΡΠΈ ΡΡΡΠ°Π½ΠΎΠ²ΠΊΠΈ Π·Π°Π³ΠΎΡΠΎΠ²ΠΊΠΈ Π² ΠΏΠ°ΡΡΠΎΠ½Π΅ Π½Π° ΠΊΠ°ΡΠ΅ΡΡΠ²ΠΎ ΠΎΡΠ²Π΅ΡΡΡΠΈΡ, ΡΠ°Π·Π²Π΅ΡΡΡΠ²Π°Π½ΠΈΠ΅ ΠΎΠ±ΡΡΠ½ΠΎ Π²ΡΠΏΠΎΠ»Π½ΡΡΡ Π·Π° ΠΎΠ΄Π½Ρ ΡΡΡΠ°Π½ΠΎΠ²ΠΊΡ Π½Π΅ΠΏΠΎΡΡΠ΅Π΄ΡΡΠ²Π΅Π½Π½ΠΎ ΠΏΠΎΡΠ»Π΅ ΠΏΠΎΠ΄Π³ΠΎΡΠΎΠ²ΠΈΡΠ΅Π»ΡΠ½ΡΡ
ΡΠΏΠΎΡΠΎΠ±ΠΎΠ² ΠΎΠ±ΡΠ°Π±ΠΎΡΠΊΠΈ ΠΎΡΠ²Π΅ΡΡΡΠΈΡ.
ΠΠ½ΠΎΠ³Π΄Π° ΠΌΠΎΠΆΠ΅Ρ Π²ΠΎΠ·Π½ΠΈΠΊΠ½ΡΡΡ ΡΠ΅Ρ
Π½ΠΎΠ»ΠΎΠ³ΠΈΡΠ΅ΡΠΊΠ°Ρ Π½Π΅ΠΎΠ±Ρ
ΠΎΠ΄ΠΈΠΌΠΎΡΡΡ ΡΠ°Π·Π²Π΅ΡΡΡΠ²Π°Π½ΠΈΡ ΠΎΡΠ²Π΅ΡΡΡΠΈΡ Π·Π° ΠΎΡΠ΄Π΅Π»ΡΠ½ΡΡ ΡΡΡΠ°Π½ΠΎΠ²ΠΊΡ Π·Π°Π³ΠΎΡΠΎΠ²ΠΊΠΈ Π² ΠΏΠ°ΡΡΠΎΠ½Π΅. Π ΡΠ°ΠΊΠΈΡ
ΡΠ»ΡΡΠ°ΡΡ
ΡΠ°Π·Π²Π΅ΡΡΠΊΡ Π½Π΅ΠΎΠ±Ρ
ΠΎΠ΄ΠΈΠΌΠΎ ΡΡΡΠ°Π½Π°Π²Π»ΠΈΠ²Π°ΡΡ Π½Π° ΡΡΠ°Π½ΠΊΠ΅ Π² ΠΊΠ°ΡΠ°ΡΡΠΈΡ
ΡΡ (ΡΠΈΡ. 91) ΠΈΠ»ΠΈ ΡΠΏΠ΅ΡΠΈΠ°Π»ΡΠ½ΡΡ
ΠΏΠ»Π°Π²Π°ΡΡΠΈΡ
ΠΏΠ°ΡΡΠΎΠ½Π°Ρ
, ΠΏΠΎΠ·Π²ΠΎΠ»ΡΡΡΠΈΡ
Π΅ΠΉ ΡΠ°ΠΌΠΎΡΡΡΠ°Π½Π°Π²Π»ΠΈΠ²Π°ΡΡΡΡ ΠΏΠΎ ΠΎΡΠΈ ΠΎΠ±ΡΠ°Π±Π°ΡΡΠ²Π°Π΅ΠΌΠΎΠ³ΠΎ ΠΎΡΠ²Π΅ΡΡΡΠΈΡ.
5. ΠΡΠ²Π΅ΡΡΡΠΈΡ 2-Π³ΠΎ ΠΊΠ»Π°ΡΡΠ° ΡΠΎΡΠ½ΠΎΡΡΠΈ ΡΠ΅ΠΊΠΎΠΌΠ΅Π½Π΄ΡΠ΅ΡΡΡ ΠΎΠ±ΡΠ°Π±Π°ΡΡΠ²Π°ΡΡ Π΄Π²ΡΠΌΡ ΡΠ°Π·Π²Π΅ΡΡΠΊΠ°ΠΌΠΈ β ΡΠ΅ΡΠ½ΠΎΠ²ΠΎΠΉ ΠΈ ΡΠΈΡΡΠΎΠ²ΠΎΠΉ: ΠΏΠ΅ΡΠ²Π°Ρ ΡΡΠ΅Π·Π°Π΅Ρ 2/3, Π²ΡΠΎΡΠ°Ρ β 1/3 ΠΏΡΠΈΠΏΡΡΠΊΠ°.
Π§Π΅ΡΠ½ΠΎΠ²ΡΡ ΡΠ°Π·Π²Π΅ΡΡΠΊΡ ΠΎΠ±ΡΡΠ½ΠΎ ΠΈΠ·Π³ΠΎΡΠ°Π²Π»ΠΈΠ²Π°ΡΡ ΠΈΠ· ΠΏΠΎΡΠ΅ΡΡΠ²ΡΠ΅ΠΉ ΡΠ°Π·ΠΌΠ΅Ρ ΡΠΈΡΡΠΎΠ²ΠΎΠΉ ΡΠ°Π·Π²Π΅ΡΡΠΊΠΈ ΠΏΡΡΠ΅ΠΌ ΡΠ»ΠΈΡΠΎΠ²Π°Π½ΠΈΡ ΠΈ Π΄ΠΎΠ²ΠΎΠ΄ΠΊΠΈ ΠΊΠ°Π»ΠΈΠ±ΡΡΡΡΠ΅ΠΉ ΡΠ°ΡΡΠΈ.
ΠΠ²ΡΠΎΡ – nastia19071991
ΠΠ΅Π½ΠΊΠΎΠ²Π°Π½ΠΈΠ΅ ΠΈ Π·Π΅Π½ΠΊΠ΅ΡΠΎΠ²Π°Π½ΠΈΠ΅, Π½Π΅ΡΠΌΠΎΡΡΡ Π½Π° ΡΡ ΠΎΠΆΠ΅ΡΡΡ Π½Π°Π·Π²Π°Π½ΠΈΠΉ, ΡΠ²Π»ΡΡΡΡΡ ΡΠ°Π·Π½ΡΠΌΠΈ ΠΎΠΏΠ΅ΡΠ°ΡΠΈΡΠΌΠΈ ΠΌΠ΅ΡΠ°Π»Π»ΠΎΠΎΠ±ΡΠ°Π±ΠΎΡΠΊΠΈ Ρ ΡΠΎΠΎΡΠ²Π΅ΡΡΡΠ²ΡΡΡΠΈΠΌ ΠΈΠ½ΡΡΡΡΠΌΠ΅Π½ΡΠΎΠΌ. Π‘Ρ ΠΎΠΆΠ΅ΡΡΡ ΠΎΠΏΠ΅ΡΠ°ΡΠΈΠΉ Π² ΡΠΈΠΏΠ΅ ΠΎΠ±ΡΠ°Π±ΠΎΡΠΊΠΈ ΠΈ ΠΎΠ±ΡΠ°Π±Π°ΡΡΠ²Π°Π΅ΠΌΠΎΠΉ ΠΏΠΎΠ²Π΅ΡΡ Π½ΠΎΡΡΠΈ. Π Π·Π΅Π½ΠΊΠΎΠ²Π°Π½ΠΈΠ΅, ΠΈ Π·Π΅Π½ΠΊΠ΅ΡΠΎΠ²Π°Π½ΠΈΠ΅ ΠΏΠΎΠ΄ΡΠ°Π·ΡΠΌΠ΅Π²Π°Π΅Ρ ΠΌΠ΅Ρ Π°Π½ΠΈΡΠ΅ΡΠΊΡΡ ΠΎΠ±ΡΠ°Π±ΠΎΡΠΊΡ ΡΠ΅Π·Π°Π½ΠΈΠ΅ΠΌ Π²Π½ΡΡΡΠ΅Π½Π½Π΅ΠΉ ΠΏΠΎΠ²Π΅ΡΡ Π½ΠΎΡΡΠΈ ΠΎΡΠ²Π΅ΡΡΡΠΈΠΉ. Π Π°Π·Π»ΠΈΡΠΈΡ Π² Ρ Π°ΡΠ°ΠΊΡΠ΅ΡΠ΅ ΠΎΠ±ΡΠ°Π±ΠΎΡΠΊΠΈ ΠΈ, ΡΠΎΠΎΡΠ²Π΅ΡΡΡΠ²Π΅Π½Π½ΠΎ, ΠΏΠΎΠ»ΡΡΠ°Π΅ΠΌΠΎΠΌ ΡΠ΅Π·ΡΠ»ΡΡΠ°ΡΠ΅.
ΠΠ΅Π½ΠΊΠ΅ΡΠΎΠ²Π°Π½ΠΈΠ΅: ΠΈΠ½ΡΡΡΡΠΌΠ΅Π½Ρ ΠΈ ΠΎΡΠΎΠ±Π΅Π½Π½ΠΎΡΡΠΈ
ΠΠ΅Π½ΠΊΠ΅ΡΠΎΠ²Π°Π½ΠΈΠ΅ β ΡΡΠΎ ΠΏΡΠΎΠΌΠ΅ΠΆΡΡΠΎΡΠ½ΡΠΉ ΠΏΡΠΎΡΠ΅ΡΡ ΠΎΠ±ΡΠ°Π±ΠΎΡΠΊΠΈ ΠΎΡΠ²Π΅ΡΡΡΠΈΠΉ ΡΠ°ΡΠΏΠΎΠ»Π°Π³Π°Π΅ΠΌΡΠΉ, ΠΊΠ°ΠΊ ΠΏΡΠ°Π²ΠΈΠ»ΠΎ, ΠΌΠ΅ΠΆΠ΄Ρ ΡΠ²Π΅ΡΠ»Π΅Π½ΠΈΠ΅ΠΌ ΠΈ ΡΠ°Π·Π²Π΅ΡΡΠΊΠΎΠΉ. ΠΡΠΎ ΠΏΠΎΠ»ΡΡΠΈΡΡΠΎΠ²Π°Ρ ΠΎΠ±ΡΠ°Π±ΠΎΡΠΊΠ° ΠΎΡΠ²Π΅ΡΡΡΠΈΡ Ρ ΡΠ΅Π»ΡΡ:
- ΠΏΠΎΠ²ΡΡΠ΅Π½ΠΈΡ ΡΠΎΡΠ½ΠΎΡΡΠΈ ΠΎΡΠ²Π΅ΡΡΡΠΈΡ Π΄ΠΎ 4-Π³ΠΎ ΠΈ Π΄Π°ΠΆΠ΅ 5-Π³ΠΎ ΠΊΠ»Π°ΡΡΠ°;
- ΡΠ»ΡΡΡΠ΅Π½ΠΈΡ ΡΠ΅ΡΠΎΡ ΠΎΠ²Π°ΡΠΎΡΡΠΈ;
- ΠΏΡΠΈΠ΄Π°Π½ΠΈΡ ΡΡΡΠΎΠ³ΠΎΠΉ Π³Π΅ΠΎΠΌΠ΅ΡΡΠΈΡΠ΅ΡΠΊΠΎΠΉ ΡΠΎΡΠΌΡ.
Π’Π°ΠΊΠΆΠ΅ Π·Π΅Π½ΠΊΠ΅ΡΠΎΠ²Π°Π½ΠΈΠ΅ ΠΏΡΠΈΠΌΠ΅Π½ΡΠ΅ΡΡΡ ΠΏΡΠΈ ΠΎΠ±ΡΠ°Π±ΠΎΡΠΊΠ΅ ΠΎΡΠ²Π΅ΡΡΡΠΈΠΉ ΠΏΠΎΠ»ΡΡΠ΅Π½Π½ΡΡ Π»ΠΈΡΡΡΠΌ ΠΈΠ»ΠΈ ΠΎΠ±ΡΠ°Π±ΠΎΡΠΊΠΎΠΉ Π΄Π°Π²Π»Π΅Π½ΠΈΠ΅ΠΌ.Β
ΠΠ±ΡΠ°Π±ΠΎΡΠΊΠ° ΠΏΡΠΎΠΈΠ·Π²ΠΎΠ΄ΠΈΡΡΡ Ρ ΠΏΠΎΠΌΠΎΡΡΡ Π·Π΅Π½ΠΊΠ΅ΡΠ°, ΠΈΠ½ΡΡΡΡΠΌΠ΅Π½ΡΠ° Π²Π½Π΅ΡΠ½Π΅ ΠΏΠΎΡ ΠΎΠΆΠ΅Π³ΠΎ Π½Π° ΡΠ²Π΅ΡΠ»ΠΎ, Π½ΠΎ ΠΈΠΌΠ΅ΡΡΠ΅Π³ΠΎ ΡΡΠ΄ ΠΊΠΎΠ½ΡΡΡΡΠΊΡΠΈΠ²Π½ΡΡ ΠΎΡΠ»ΠΈΡΠΈΠΉ. ΠΡΠ½ΠΎΠ²Π½ΡΠ΅ ΠΎΡΠ»ΠΈΡΠΈΡ β ΡΡΠΎ ΡΠ²Π΅Π»ΠΈΡΠ΅Π½Π½Π°Ρ ΠΏΠ΅ΡΠ΅ΠΌΡΡΠΊΠ° ΠΌΠ΅ΠΆΠ΄Ρ ΡΠ΅ΠΆΡΡΠΈΠΌΠΈ ΠΊΡΠΎΠΌΠΊΠ°ΠΌΠΈ, ΡΠ²Π΅Π»ΠΈΡΠ΅Π½Π½ΠΎΠ΅ ΠΊΠΎΠ»ΠΈΡΠ΅ΡΡΠ²ΠΎ ΡΠ°Π±ΠΎΡΠΈΡ ΠΊΡΠΎΠΌΠΎΠΊ ΠΈ ΡΡΠ΅Π·Π°Π½Π½ΡΠΉ ΡΠ³ΠΎΠ». ΠΡΡ ΡΡΠΎ ΠΎΠ±Π΅ΡΠΏΠ΅ΡΠΈΠ²Π°Π΅Ρ Π²ΡΡΠΎΠΊΡΡ ΡΡΡΠΎΠΉΡΠΈΠ²ΠΎΡΡΡ Π·Π΅Π½ΠΊΠ΅ΡΠ° ΠΈ Π΅Π³ΠΎ ΡΠΎΠΎΡΠ½ΠΎΡΡΡ Ρ ΠΎΠ±ΡΠ°Π±Π°ΡΡΠ²Π°Π΅ΠΌΡΠΌ ΠΎΡΠ²Π΅ΡΡΡΠΈΠ΅ΠΌ. Π’Π°ΠΊ, Π½Π°Π»ΠΈΡΠΈΠ΅ 3-4 ΡΠ΅ΠΆΡΡΠΈΡ ΠΊΡΠΎΠΌΠΎΠΊ ΠΎΠ±Π΅ΡΠΏΠ΅ΡΠΈΠ²Π°Π΅Ρ ΠΏΠ»Π°Π²Π½ΠΎΠ΅ ΡΠ°ΡΠΏΡΠ΅Π΄Π΅Π»Π΅Π½ΠΈΠ΅ ΡΠΈΠ» Π² Π·ΠΎΠ½Π΅ ΠΊΠΎΠ½ΡΠ°ΠΊΡΠ° Π·Π΅Π½ΠΊΠ΅ΡΠ° Ρ ΠΎΠ±ΡΠ°Π±Π°ΡΡΠ²Π°Π΅ΠΌΠΎΠΉ Π΄Π΅ΡΠ°Π»ΡΡ. ΠΠ΅ΠΎΠΌΠ΅ΡΡΠΈΡ ΡΠ΅ΠΆΡΡΠ΅ΠΉ ΡΠ°ΡΡΠΈ ΠΎΠ±Π΅ΡΠΏΠ΅ΡΠΈΠ²Π°Π΅Ρ ΠΎΠ±ΡΠ°Π±ΠΎΡΠΊΡ ΠΎΡΠ²Π΅ΡΡΡΠΈΡ Π±Π΅Π· ΡΡΠ΅ΠΌΠ° ΠΌΠ΅ΡΠ°Π»Π»Π° Π² ΠΏΡΠΎΠ΄ΠΎΠ»ΡΠ½ΠΎΠΌ Π½Π°ΠΏΡΠ°Π²Π»Π΅Π½ΠΈΠΈ.
ΠΠ΅Π½ΠΊΠ΅ΡΡ ΡΠ°Π·Π»ΠΈΡΠ°ΡΡΡΡ ΠΏΠΎ ΠΊΠΎΠ»ΠΈΡΠ΅ΡΡΠ²Ρ Π·ΡΠ±ΡΠ΅Π² (3 ΠΈΠ»ΠΈ 4) ΠΈ ΠΊΠΎΠ½ΡΡΡΡΠΊΡΠΈΠΈ β Π½Π°ΡΠ°Π΄Π½ΡΠ΅, ΡΠ΅Π»ΡΠ½ΡΠ΅ ΠΈ Π²ΡΡΠ°Π²Π½ΡΠ΅. ΠΡΠ±ΠΎΡ ΠΈΠ½ΡΡΡΡΠΌΠ΅Π½ΡΠ° Π·Π°Π²ΠΈΡΠΈΡ ΠΎΡ Π΄ΠΈΠ°ΠΌΠ΅ΡΡΠ° ΠΎΡΠ²Π΅ΡΡΡΠΈΡ. Π’Π°ΠΊ, ΠΏΡΠΈΠΌΠ΅Π½Π΅Π½ΠΈΠ΅ Π²ΡΡΠ°Π²Π½ΡΡ Π·Π΅Π½ΠΊΠ΅ΡΠΎΠ² (Ρ Π²ΡΡΠ°Π²Π½ΡΠΌΠΈ Π½ΠΎΠΆΠ°ΠΌΠΈ) ΡΠ΅ΠΊΠΎΠΌΠ΅Π½Π΄ΡΠ΅ΡΡΡ Π΄Π»Ρ ΠΎΡΠ²Π΅ΡΡΡΠΈΠΉ Π΄ΠΈΠ°ΠΌΠ΅ΡΡΠΎΠΌ ΠΎΡ 20 ΠΌΠΌ., ΡΠ΅Π»ΡΠ½ΡΠ΅ ΠΏΡΠΈΠΌΠ΅Π½ΡΡΡΡΡ Π΄Π»Ρ ΠΌΠ°Π»ΡΡ Π΄ΠΈΠ°ΠΌΠ΅ΡΡΠΎΠ² (ΠΎΡ 12 ΠΌΠΌ.).Β
ΠΠ»Ρ ΠΏΠΎΠ»ΡΡΠ΅Π½ΠΈΡ Π±ΠΎΠ»Π΅Π΅ ΡΠΎΡΠ½ΡΡ ΠΈ ΡΠ»ΠΎΠΆΠ½ΡΡ ΠΏΠΎΠ²Π΅ΡΡ Π½ΠΎΡΡΠ΅ΠΉ ΠΈΡΠΏΠΎΠ»ΡΠ·ΡΡΡΡΡ ΠΊΠΎΠΌΠ±ΠΈΠ½ΠΈΡΠΎΠ²Π°Π½Π½ΡΠ΅ ΡΠΈΠΏΡ ΠΈΠ½ΡΡΡΡΠΌΠ΅Π½ΡΠ° Ρ Π±ΠΎΠ»ΡΡΠΈΠΌ ΠΊΠΎΠ»ΠΈΡΠ΅ΡΡΠ²ΠΎΠΌ ΡΠ΅ΠΆΡΡΠΈΡ ΠΊΡΠΎΠΌΠΎΠΊ (Π΄ΠΎ 8). ΠΡΠΈ ΡΡΠΎΠΌ ΡΠ±ΠΎΡΠ½ΡΠ΅ Π·Π΅Π½ΠΊΠ΅ΡΡ ΠΏΡΠΈΠΌΠ΅Π½ΡΡΡΡΡ ΡΠΎΠ²ΠΌΠ΅ΡΡΠ½ΠΎ Ρ Π΄ΡΡΠ³ΠΈΠΌ ΠΌΠ΅ΡΠ°Π»Π»ΠΎΡΠ΅ΠΆΡΡΠΈΠΌ ΠΈΠ½ΡΡΡΡΠΌΠ΅Π½ΡΠΎΠΌ β ΡΠ²Π΅ΡΠ»Π°ΠΌΠΈ, ΡΠ°Π·Π²Π΅ΡΡΠΊΠ°ΠΌΠΈ ΠΈ Ρ. Π΄.
ΠΡΠΎΠ±Π΅Π½Π½ΠΎΡΡΠΈ Π·Π΅Π½ΠΊΠΎΠ²Π°Π½ΠΈΡ
ΠΠ΅Π½ΠΊΠΎΠ²Π°Π½ΠΈΠ΅ β ΡΡΠΎ ΠΌΠ΅Ρ Π°Π½ΠΈΡΠ΅ΡΠΊΠ°Ρ ΠΎΠ±ΡΠ°Π±ΠΎΡΠΊΠ° ΠΎΡΠ²Π΅ΡΡΡΠΈΠΉ Ρ ΡΠ΅Π»ΡΡ ΡΠΎΠ·Π΄Π°Π½ΠΈΡ ΡΠ°Π·Π»ΠΈΡΠ½ΡΡ Π³Π΅ΠΎΠΌΠ΅ΡΡΠΈΡΠ΅ΡΠΊΠΈΡ ΡΠ³Π»ΡΠ±Π»Π΅Π½ΠΈΠΉ Π΄Π»Ρ ΠΏΠΎΡΠ°ΠΉΠ½ΠΎΠ³ΠΎ ΡΠ°Π·ΠΌΠ΅ΡΠ΅Π½ΠΈΡ ΠΊΡΠ΅ΠΏΠ΅ΠΆΠ½ΡΡ ΠΈΠ·Π΄Π΅Π»ΠΈΠΉ. Π’Π°ΠΊΠΆΠ΅ ΠΎΠ½Π° ΠΏΡΠΈΠΌΠ΅Π½ΡΠ΅ΡΡΡ Π΄Π»Ρ Π½Π°ΡΠ΅Π·ΠΊΠΈ Π²Π½ΡΡΡΠ΅Π½Π½ΠΈΡ ΡΠ°ΡΠΎΠΊ. ΠΠ»Ρ ΡΡΠΈΡ ΡΠ΅Π»Π΅ΠΉ Π΅ΡΡΡ ΡΠΏΠ΅ΡΠΈΠ°Π»ΡΠ½ΡΠΉ ΠΈΠ½ΡΡΡΡΠΌΠ΅Π½Ρ β Π·Π΅Π½ΠΊΠΎΠ²ΠΊΠ°, ΠΈΠΌΠ΅ΡΡΠΈΠ΅ ΡΠ°Π·Π»ΠΈΡΠ½ΡΡ ΡΠΎΡΠΌΡ. ΠΡΠ±ΠΎΡ Π·Π΅Π½ΠΊΠΎΠ²ΠΊΠΈ Π·Π°Π²ΠΈΡΠΈΡ ΠΎΡ Π½Π΅ΠΎΠ±Ρ ΠΎΠ΄ΠΈΠΌΠΎΠ³ΠΎ ΠΊΠΎΠ½Π΅ΡΠ½ΠΎΠ³ΠΎ ΡΠ΅Π·ΡΠ»ΡΡΠ°ΡΠ°.Β
ΠΡΠ½ΠΎΠ²Π½ΡΠ΅ Π²ΠΈΠ΄Ρ Π·Π΅Π½ΠΊΠΎΠ²ΠΎΠΊ
- Π¦ΠΈΠ»ΠΈΠ½Π΄ΡΠΈΡΠ΅ΡΠΊΠΈΠ΅ Π·Π΅Π½ΠΊΠΎΠ²ΠΊΠΈ. ΠΡΠΈΠΌΠ΅Π½ΡΡΡΡΡ Π΄Π»Ρ ΠΏΠΎΠ»ΡΡΠ΅Π½ΠΈΡ ΡΠΈΠ»ΠΈΠ½Π΄ΡΠΈΡΠ΅ΡΠΊΠΈΡ
Π²ΡΠ΅ΠΌΠΎΠΊ Π² ΠΏΡΠΎΡΠ²Π΅ΡΠ»Π΅Π½Π½ΡΡ
ΠΎΡΠ²Π΅ΡΡΡΠΈΡΡ
ΠΏΠΎΠ΄ ΡΡΡΠ°Π½ΠΎΠ²ΠΊΡ Π±ΠΎΠ»ΡΠΎΠ² ΠΈ Π²ΠΈΠ½ΡΠΎΠ².
Β
- ΠΠΎΠ½ΠΈΡΠ΅ΡΠΊΠΈΠ΅ Π·Π΅Π½ΠΊΠΎΠ²ΠΊΠΈ. ΠΡΠΏΠΎΠ»ΡΠ·ΡΡΡΡΡ Π΄Π»Ρ Π²ΡΡΠ΅Π·Π°Π½ΠΈΡ ΠΎΡΠ²Π΅ΡΡΡΠΈΠΉ ΠΊΠΎΠ½ΡΡΠ½ΠΎΠΉ ΡΠΎΡΠΌΡ Π²Π½ΡΡΡΠΈ Π΄Π΅ΡΠ°Π»ΠΈ, Π° ΡΠ°ΠΊΠΆΠ΅ Π΄Π»Ρ Π·Π°ΡΠΈΡΡΠΊΠΈ ΠΎΡΡΡΡΡ ΠΊΡΠΎΠΌΠΎΠΊ, ΡΠ½ΡΡΠΈΡ ΡΠ°ΡΠΎΠΊ ΠΈ ΠΏΠΎΠ΄Π³ΠΎΡΠΎΠ²ΠΊΠΈ ΡΠ³Π»ΡΠ±Π»Π΅Π½ΠΈΠΉ ΠΏΠΎΠ΄ ΠΊΡΠ΅ΠΏΠ΅ΠΆΠ½ΡΠ΅ ΡΠ»Π΅ΠΌΠ΅Π½ΡΡ. Π§Π°ΡΠ΅ Π²ΡΠ΅Π³ΠΎ ΠΏΡΠΈΠΌΠ΅Π½ΡΠ΅ΡΡΡ ΠΈΠ½ΡΡΡΡΠΌΠ΅Π½Ρ Ρ ΠΊΠΎΠ½ΡΡΠ½ΡΠΌ ΡΠ³Π»ΠΎΠΌ 90Β° ΠΈ 120Β°.
- ΠΠ»ΠΎΡΠΊΠΈΠ΅ ΠΈΠ»ΠΈ ΡΠΎΡΡΠ΅Π²ΡΠ΅ Π·Π΅Π½ΠΊΠΎΠ²ΠΊΠΈ, ΡΠ°ΠΊΠΆΠ΅ ΠΌΠΎΠΆΠ½ΠΎ Π²ΡΡΡΠ΅ΡΠΈΡΡ Π½Π°Π·Π²Π°Π½ΠΈΠ΅ ΡΠ΅ΠΊΠΎΠ²ΠΊΠΈ. ΠΡΠ΅ΠΈΠΌΡΡΠ΅ΡΡΠ²Π΅Π½Π½ΠΎ ΠΏΡΠΈΠΌΠ΅Π½ΡΡΡΡΡ Π΄Π»Ρ Π·Π°ΡΠΈΡΡΠΊΠΈ ΠΈ ΠΎΠ±ΡΠ°Π±ΠΎΡΠΊΠΈ ΡΠ³Π»ΡΠ±Π»Π΅Π½ΠΈΠΉ ΠΏΠ΅ΡΠ΅Π΄ ΡΡΡΠ°Π½ΠΎΠ²ΠΊΠΎΠΉ ΠΊΡΠ΅ΠΏΠ΅ΠΆΠ½ΡΡ ΠΈΠ·Π΄Π΅Π»ΠΈΠΉ.
ΠΠ΅Π½ΠΊΠΎΠ²ΠΊΠ° ΡΠΎΡΡΠΎΠΈΡ ΠΈΠ· ΡΠ°Π±ΠΎΡΠ΅ΠΉ ΡΠ°ΡΡΠΈ ΠΈ Ρ Π²ΠΎΡΡΠΎΠ²ΠΈΠΊΠ° ΡΠΎ ΡΠΏΠ΅ΡΠΈΠ°Π»ΡΠ½ΠΎΠΉ ΡΠ°ΠΏΡΠΎΠΉ Π²ΡΠΏΠΎΠ»Π½ΡΡΡΠ΅ΠΉ ΡΡΠ½ΠΊΡΠΈΡ Π½Π°ΠΏΡΠ°Π²Π»ΡΡΡΠ΅Π³ΠΎ ΠΏΠΎΡΡΠ°. Π¦Π°ΠΏΡΠ° Π½Π΅ΠΎΠ±Ρ ΠΎΠ΄ΠΈΠΌΠ° Π΄Π»Ρ ΠΊΠΎΠ½ΡΡΠΎΠ»Ρ ΡΠΎΠΎΡΠ½ΠΎΡΡΠΈ Π² ΠΏΡΠΎΡΠ΅ΡΡΠ΅ Π½Π°ΡΠ΅Π·ΠΊΠΈ ΡΠ³Π»ΡΠ±Π»Π΅Π½ΠΈΠΉ.
ΠΠ±ΠΎΡΡΠ΄ΠΎΠ²Π°Π½ΠΈΠ΅
ΠΠ»Ρ Π·Π΅Π½ΠΊΠΎΠ²Π°Π½ΠΈΡ ΠΈ Π·Π΅Π½ΠΊΠ΅ΡΠΎΠ²Π°Π½ΠΈΡ ΠΈΡΠΏΠΎΠ»ΡΠ·ΡΠ΅ΡΡΡ, ΡΠ°ΡΠ΅ Π²ΡΠ΅Π³ΠΎ, ΡΠ²Π΅ΡΠ»ΠΈΠ»ΡΠ½ΡΠ΅ ΡΡΠ°Π½ΠΊΠΈ ΡΠ°Π·Π»ΠΈΡΠ½ΠΎΠ³ΠΎ ΡΠΈΠΏΠ°. Π’Π°ΠΊΠΆΠ΅ ΠΌΠΎΠΆΠ΅Ρ Π±ΡΡΡ ΠΈΡΠΏΠΎΠ»ΡΠ·ΠΎΠ²Π°Π½ ΠΎΠ±ΡΠ°Π±Π°ΡΡΠ²Π°ΡΡΠΈΠΉ ΡΠ΅Π½ΡΡ ΠΈΠ»ΠΈ ΡΠΎΠΊΠ°ΡΠ½ΡΠΉ ΡΡΠ°Π½ΠΎΠΊ β ΠΏΡΠ°ΠΊΡΠΈΡΠ΅ΡΠΊΠΈ ΡΠΎΠΆΠ΅ ΡΠ°ΠΌΠΎΠ΅ ΠΎΠ±ΠΎΡΡΠ΄ΠΎΠ²Π°Π½ΠΈΠ΅, Π½Π° ΠΊΠΎΡΠΎΡΠΎΠΌ Π²ΡΠΏΠΎΠ»Π½ΡΡΡΡΡ ΠΈ ΠΎΠΏΠ΅ΡΠ°ΡΠΈΠΈ ΡΠ²Π΅ΡΠ»Π΅Π½ΠΈΡ. ΠΠ»Ρ ΠΎΠ±Π΅ΠΈΡ ΠΎΠΏΠ΅ΡΠ°ΡΠΈΠΉ Π½Π΅ ΡΠ΅ΠΊΠΎΠΌΠ΅Π½Π΄ΡΠ΅ΡΡΡ ΠΈΡΠΏΠΎΠ»ΡΠ·ΠΎΠ²Π°ΡΡ ΡΡΡΠ½ΠΎΠΉ ΠΈΠ½ΡΡΡΡΠΌΠ΅Π½Ρ ΠΈΠ·-Π·Π° Π½Π΅Π΄ΠΎΡΡΠ°ΡΠΎΡΠ½ΠΎΠΉ ΡΠΎΡΠ½ΠΎΡΡΠΈ ΠΏΠΎΠ·ΠΈΡΠΈΠΎΠ½ΠΈΡΠΎΠ²Π°Π½ΠΈΡ.
Π½Π°Π·Π½Π°ΡΠ΅Π½ΠΈΠ΅, Π²ΠΈΠ΄Ρ, ΠΏΡΠΎΡΠ΅ΡΡ, ΠΎΡΠ»ΠΈΡΠΈΠ΅ ΠΎΡ Π·Π΅Π½ΠΊΠΎΠ²Π°Π½ΠΈΡ
ΠΠ΄Π½ΠΈΠΌ ΠΈΠ· ΠΎΡΠ½ΠΎΠ²Π½ΡΡ ΠΈΠ½ΡΡΡΡΠΌΠ΅Π½ΡΠΎΠ², ΠΏΡΠΈΠΌΠ΅Π½ΡΠ΅ΠΌΡΡ ΠΏΡΠΈ ΠΎΠ±ΡΠ°Π±ΠΎΡΠΊΠ΅ ΠΎΡΠ²Π΅ΡΡΡΠΈΠΉ Π² ΠΌΠ΅ΡΠ°Π»Π»ΠΈΡΠ΅ΡΠΊΠΈΡ Π΄Π΅ΡΠ°Π»ΡΡ , ΡΠ²Π»ΡΠ΅ΡΡΡ Π·Π΅Π½ΠΊΠ΅Ρ. Π‘ Π΅Π³ΠΎ ΠΏΠΎΠΌΠΎΡΡΡ ΡΠ²Π΅Π»ΠΈΡΠΈΠ²Π°ΡΡ Π΄ΠΈΠ°ΠΌΠ΅ΡΡ, ΡΠ»ΡΡΡΠ°ΡΡ ΠΊΠ°ΡΠ΅ΡΡΠ²ΠΎ Π±ΠΎΠΊΠΎΠ²ΡΡ ΠΏΠΎΠ²Π΅ΡΡ Π½ΠΎΡΡΠ΅ΠΉ ΠΎΡΠ²Π΅ΡΡΡΠΈΡ, ΡΠ°ΠΊΠΆΠ΅ ΡΠ΄Π°ΡΡΡΡ ΠΏΠΎΠ»ΡΡΠΈΡΡ Π±ΠΎΠ»Π΅Π΅ Π²ΡΡΠΎΠΊΠΈΠΉ ΠΊΠ»Π°ΡΡ ΡΠΎΡΠ½ΠΎΡΡΠΈ. ΠΠ΅Π½ΠΊΠ΅ΡΠΎΠ²Π°Π½ΠΈΠ΅, Π° ΠΈΠΌΠ΅Π½Π½ΠΎ ΡΠ°ΠΊ Π½Π°Π·ΡΠ²Π°Π΅ΡΡΡ ΡΡΠ° ΠΎΠΏΠ΅ΡΠ°ΡΠΈΡ, ΡΠΎΠ·Π²ΡΡΠ½ΠΎ Π·Π΅Π½ΠΊΠΎΠ²Π°Π½ΠΈΡ, ΡΡΠΎ ΠΌΠΎΠΆΠ΅Ρ Π²Π²Π΅ΡΡΠΈ Π½Π΅ΡΠΏΠ΅ΡΠΈΠ°Π»ΠΈΡΡΠ° Π² Π·Π°Π±Π»ΡΠΆΠ΄Π΅Π½ΠΈΠ΅. Π Π°Π·Π½ΠΈΡΠ° ΠΌΠ΅ΠΆΠ΄Ρ ΡΡΠΈΠΌΠΈ Π΄Π²ΡΠΌΡ ΠΊΠ°ΡΠ΅Π³ΠΎΡΠΈΡΠΌΠΈ ΡΠΎΠΆΠ΅ Π±ΡΠ΄Π΅Ρ ΠΎΠ±ΡΡΡΠ½Π΅Π½Π° Π² Π΄Π°Π½Π½ΠΎΠΉ ΡΡΠ°ΡΡΠ΅.
ΠΠ΅Π½ΠΊΠ΅Ρ. ΠΠ°Π·Π½Π°ΡΠ΅Π½ΠΈΠ΅ ΠΈ Π²ΠΈΠ΄Ρ ΠΈΠ½ΡΡΡΡΠΌΠ΅Π½ΡΠ°
ΠΠ΅Π½ΠΊΠ΅Ρ β ΠΈΠ½ΡΡΡΡΠΌΠ΅Π½Ρ, ΠΏΡΠ΅Π΄Π½Π°Π·Π½Π°ΡΠ΅Π½Π½ΡΠΉ Π΄Π»Ρ ΠΏΠΎΠ»ΡΡΠΈΡΡΠΎΠ²ΠΎΠΉ ΠΎΠ±ΡΠ°Π±ΠΎΡΠΊΠΈ ΠΌΠ΅ΡΠ°Π»Π»Π°. ΠΠ½Π΅ΡΠ½Π΅ ΠΏΡΠ΅Π΄ΡΡΠ°Π²Π»ΡΠ΅Ρ ΡΠΎΠ±ΠΎΠΉ ΠΌΠ΅ΡΠ°Π»Π»ΠΈΡΠ΅ΡΠΊΠΈΠΉ Π²Π°Π» Ρ ΡΠ΅ΠΆΡΡΠΈΠΌΠΈ ΠΏΠΎΠ²Π΅ΡΡ Π½ΠΎΡΡΡΠΌΠΈ, Π½Π°ΠΏΠΎΠΌΠΈΠ½Π°ΡΡΠΈΠΉ ΡΠ²Π΅ΡΠ»ΠΎ. ΠΠ½ ΡΠΎΠ·Π΄Π°Π½ ΡΠΏΠ΅ΡΠΈΠ°Π»ΡΠ½ΠΎ Π΄Π»Ρ ΠΌΠ΅ΡΠ°Π»Π»ΠΎΠΎΠ±ΡΠ°Π±Π°ΡΡΠ²Π°ΡΡΠ΅ΠΉ ΠΏΡΠΎΠΌΡΡΠ»Π΅Π½Π½ΠΎΡΡΠΈ. ΠΡΠΏΡΡΠΊΠ°Π΅ΡΡΡ ΠΏΠΎ ΠΠΠ‘Π’ 12489-71, ΠΠΠ‘Π’ 3231-71 ΠΈΠ»ΠΈ Π’Π£ 2-035-923-83 Π² ΡΠΎΠΎΡΠ²Π΅ΡΡΡΠ²ΠΈΠΈ ΡΒ ΡΠ°Π·Π½ΠΎΠ²ΠΈΠ΄Π½ΠΎΡΡΡΡ ΡΡΡΡΠΎΠΉΡΡΠ²Π°.
Π‘ΠΊΠ°ΡΠ°ΡΡ ΠΠΠ‘Π’ 12489-71
Π‘ΠΊΠ°ΡΠ°ΡΡ ΠΠΠ‘Π’ 3231-71
ΠΠ΅Π½ΠΊΠ΅ΡΡ ΠΏΠΎΠ΄ΡΠ°Π·Π΄Π΅Π»ΡΡΡΡΡ:
ΠΠΎ ΡΠΈΠΏΡ Π·Π°ΠΊΡΠ΅ΠΏΠ»Π΅Π½ΠΈΡ Π² ΠΏΠ°ΡΡΠΎΠ½Π΅ ΡΡΠ°Π½ΠΊΠ°:
- Ρ Π²ΠΎΡΡΠΎΠ²ΡΠ΅;
- Π½Π°ΡΠ°Π΄Π½ΡΠ΅.
ΠΠΎ ΠΎΡΠΎΠ±Π΅Π½Π½ΠΎΡΡΡΠΌ ΠΊΠΎΠ½ΡΡΡΡΠΊΡΠΈΠΈ:
- ΡΠ΅Π»ΡΠ½ΡΠ΅;
- ΡΠ±ΠΎΡΠ½ΡΠ΅;
- ΡΠ²Π°ΡΠ½ΡΠ΅;
- Ρ ΡΠ²Π΅ΡΠ΄ΠΎΡΠΏΠ»Π°Π²Π½ΡΠΌΠΈ ΠΏΠ»Π°ΡΡΠΈΠ½Π°ΠΌΠΈ ΠΈ Π±Π΅Π· Π½ΠΈΡ .
ΠΠΎ Π³Π΅ΠΎΠΌΠ΅ΡΡΠΈΡΠ΅ΡΠΊΠΎΠΉ ΡΠΎΡΠΌΠ΅:
- ΡΠΈΠ»ΠΈΠ½Π΄ΡΠΈΡΠ΅ΡΠΊΠΈΠ΅;
- ΠΊΠΎΠ½ΠΈΡΠ΅ΡΠΊΠΈΠ΅;
- ΠΎΠ±ΡΠ°ΡΠ½ΡΠ΅.
ΠΠΎ Π½Π°ΠΏΡΠ°Π²Π»Π΅Π½ΠΈΡ Π»Π΅Π½ΡΠΎΡΠ΅ΠΊ ΠΈ ΠΊΠ°Π½Π°Π²ΠΎΠΊ:
- ΠΏΡΠ°Π²ΠΎΠ³ΠΎ Π²ΡΠ°ΡΠ΅Π½ΠΈΡ;
- Π»Π΅Π²ΠΎΠ³ΠΎ Π²ΡΠ°ΡΠ΅Π½ΠΈΡ.
Π¦Π΅Π»ΡΠ½ΡΠ΅ Ρ Π²ΠΎΡΡΠΎΠ²ΡΠ΅ Π·Π΅Π½ΠΊΠ΅ΡΡ Π½Π°ΠΈΠ±ΠΎΠ»Π΅Π΅ ΠΏΠΎΡ ΠΎΠΆΠΈ Π½Π° ΡΠ²ΡΡΠ»Π°, Π½ΠΎ ΠΎΡΠ»ΠΈΡΠ°ΡΡΡΡ Π½Π°Π»ΠΈΡΠΈΠ΅ΠΌ Π±ΠΎΠ»ΡΡΠ΅Π³ΠΎ ΠΊΠΎΠ»ΠΈΡΠ΅ΡΡΠ²Π° ΡΠ΅ΠΆΡΡΠΈΡ ΠΊΡΠΎΠΌΠΎΠΊ. Π ΠΈΡ ΠΏΠΎΠΏΠ΅ΡΠ΅ΡΠ½ΠΎΠΌ ΡΠ΅ΡΠ΅Π½ΠΈΠΈ Π½Π°ΡΡΠΈΡΡΠ²Π°Π΅Ρ ΠΎΡ 3 Π΄ΠΎ 6 ΡΠ°ΠΊΠΈΡ ΠΎΡΡΡΡΡ Π·ΡΠ±ΡΠΈΠΊΠΎΠ². ΠΠ»Ρ ΠΈΠ·Π³ΠΎΡΠΎΠ²Π»Π΅Π½ΠΈΡ ΠΏΡΠΈΠΌΠ΅Π½ΡΠ΅ΡΡΡ Π±ΡΡΡΡΠΎΡΠ΅ΠΆΡΡΠΈΠ΅ ΠΈΠ½ΡΡΡΡΠΌΠ΅Π½ΡΠ°Π»ΡΠ½ΡΠ΅ ΡΡΠ°Π»ΠΈ Π 9, Π 18, Π° ΡΠ°ΠΊΠΆΠ΅ Π»Π΅Π³ΠΈΡΠΎΠ²Π°Π½Π½ΡΠ΅ ΠΏΠ»Π°ΡΡΠΈΠ½Ρ Ρ ΠΏΠΎΠ²ΡΡΠ΅Π½Π½ΠΎΠΉ ΡΠ²ΡΡΠ΄ΠΎΡΡΡΡ ΠΈ ΠΈΠ·Π½ΠΎΡΠΎΡΡΡΠΎΠΉΡΠΈΠ²ΠΎΡΡΡΡ ΠΠ4, ΠΠ6, ΠΠ8, Π’15Π6. ΠΠΎΠΏΡΡΡΠΈΠΌΠ°Ρ ΡΠΊΠΎΡΠΎΡΡΡ ΡΠ΅Π·Π°Π½ΠΈΡ Ρ ΠΌΠΎΠ΄Π΅Π»Π΅ΠΉ Ρ ΡΠ²Π΅ΡΠ΄ΠΎΡΠΏΠ»Π°Π²Π½ΡΠΌΠΈ Π²ΡΡΠ°Π²ΠΊΠ°ΠΌΠΈ Π²ΡΡΠ΅, ΡΡΠΎ ΡΠ²Π΅Π»ΠΈΡΠΈΠ²Π°Π΅Ρ ΠΈΡ ΠΠΠ.
ΠΠ°ΡΠ°Π΄Π½ΡΠ΅ Π·Π΅Π½ΠΊΠ΅ΡΡ Π½Π΅ ΠΈΠΌΠ΅ΡΡ Ρ Π²ΠΎΡΡΠΈΠΊΠ° ΠΈ ΠΊΡΠ΅ΠΏΡΡΡΡ Ρ ΠΏΠΎΠΌΠΎΡΡΡ ΠΎΠΏΡΠ°Π²ΠΊΠΈ, Π΄Π»Ρ ΡΠ΅Π³ΠΎ Π² ΡΠ΅Π»Π΅ ΠΈΠ½ΡΡΡΡΠΌΠ΅Π½ΡΠ° ΠΏΡΠ΅Π΄ΡΡΠΌΠΎΡΡΠ΅Π½ ΠΏΠ°Π·.
Π ΠΈΡ ΠΏΠΎΠΏΠ΅ΡΠ΅ΡΠ½ΠΈΠΊΠ΅ ΡΡΡΠΎΠ³ΠΎ 4 Π·ΡΠ±ΡΠ°. Π‘Π°ΠΌΠ° Π½Π°ΡΠ°Π΄ΠΊΠ° ΠΈΠ½ΠΎΠ³Π΄Π° ΠΊΠΎΠΌΠΏΠ»Π΅ΠΊΡΡΠ΅ΡΡΡ ΡΡΡΠΌΠ½ΡΠΌΠΈ ΡΠ°Π±ΠΎΡΠΈΠΌΠΈ Π»Π΅Π·Π²ΠΈΡΠΌΠΈ ΠΈΠ· ΡΠ²ΡΡΠ΄ΡΡ ΡΠΏΠ»Π°Π²ΠΎΠ². Π€ΠΈΠΊΡΠΈΡΡΡΡΡΡ ΡΠ΅Π·Π°ΠΊΠΈ ΠΊΠ»ΠΈΠ½ΡΡΠΌΠΈ, ΠΈ ΠΌΠΎΠ³ΡΡ Π·Π°ΠΌΠ΅Π½ΡΡΡΡΡ ΠΏΠΎ ΠΌΠ΅ΡΠ΅ Π½Π°Π΄ΠΎΠ±Π½ΠΎΡΡΠΈ.
ΠΠΎΠ½ΠΈΡΠ΅ΡΠΊΠΈΠΉ Π·Π΅Π½ΠΊΠ΅Ρ ΠΏΠΎΡ ΠΎΠΆ Π½Π° Π±ΡΡ, ΡΠ°Π±ΠΎΡΠ°Ρ ΡΠ°ΡΡΡ ΠΈΠ½ΡΡΡΡΠΌΠ΅Π½ΡΠ° ΡΡΠΆΠ°Π΅ΡΡΡ ΠΊ Π΅Π³ΠΎ ΠΊΠΎΠ½ΡΡ. ΠΡΠΈΠΌΠ΅Π½ΡΠ΅ΡΡΡ Π΄Π»Ρ ΠΎΠ±ΡΠ°Π±ΠΎΡΠΊΠΈ Π½Π°ΠΊΠ»ΠΎΠ½Π½ΡΡ ΠΊΡΡΠ³ΠΎΠ²ΡΡ ΠΏΠΎΠ²Π΅ΡΡ Π½ΠΎΡΡΠ΅ΠΉ. ΠΠ·Π³ΠΎΡΠΎΠ²Π»ΡΡΡΡΡ ΠΈΠ· Π»Π΅Π³ΠΈΡΠΎΠ²Π°Π½Π½ΠΎΠΉ ΡΡΠ°Π»ΠΈ ΠΈ ΠΌΠ΅ΡΠ°Π»Π»ΠΎΠΊΠ΅ΡΠ°ΠΌΠΈΠΊΠΈ.
ΠΠ΅Π½ΡΠΎΡΠΊΠΈ ΡΠ²Π΅ΡΠ»Π°-Π·Π΅Π½ΠΊΠ΅ΡΠ° ΠΌΠΎΠ³ΡΡ Π±ΡΡΡ Π·Π°ΠΊΡΡΡΠ΅Π½Ρ Π² ΡΠ°Π·Π½ΡΡ Π½Π°ΠΏΡΠ°Π²Π»Π΅Π½ΠΈΡΡ , ΡΠΎΠΎΡΠ²Π΅ΡΡΡΠ²Π΅Π½Π½ΠΎ Π²ΡΠ΄Π΅Π»ΡΡΡ ΠΏΡΠΎΡΠΈΠ»ΠΈ ΠΏΡΠ°Π²ΠΎΠ³ΠΎ ΠΈ Π»Π΅Π²ΠΎΠ³ΠΎ Π²ΡΠ°ΡΠ΅Π½ΠΈΡ. ΠΠ΅Π½ΠΊΠ΅ΡΡ Π»Π΅Π²ΠΎΠ³ΠΎ Π²ΡΠ°ΡΠ΅Π½ΠΈΡ ΠΏΡΠΈΠΌΠ΅Π½ΡΡΡΡΡ Π² ΡΠΎΠΊΠ°ΡΠ½ΡΡ ΠΏΠΎΠ»ΡΠ°Π²ΡΠΎΠΌΠ°ΡΠ°Ρ , ΠΎΡΡΡΠ΅ΡΡΠ²Π»ΡΡΡΠΈΡ ΠΏΠΎΠ΄Π°ΡΡ ΠΌΠ°ΡΠ΅ΡΠΈΠ°Π»Π° Ρ ΠΏΡΠ°Π²ΠΎΠΉ ΡΡΠΎΡΠΎΠ½Ρ.
ΠΡΠ±ΠΎΡ ΡΠ°Π·Π½ΠΎΠ²ΠΈΠ΄Π½ΠΎΡΡΠΈ Π·Π΅Π½ΠΊΠ΅ΡΠ° Π½Π°ΠΏΡΡΠΌΡΡ ΠΎΠ±ΡΡΠ»ΠΎΠ²Π»Π΅Π½ ΡΠ°Π·ΠΌΠ΅ΡΠΎΠΌ ΠΎΡΠ²Π΅ΡΡΡΠΈΡ Π² Π·Π°Π³ΠΎΡΠΎΠ²ΠΊΠ΅ ΠΈ Π΅Ρ ΠΌΠ°ΡΠ΅ΡΠΈΠ°Π»ΠΎΠΌ. ΠΡΠΈ Π΄ΠΈΠ°ΠΌΠ΅ΡΡΠ΅ Π΄ΠΎ 12 ΠΌΠΌ ΡΠ°Π±ΠΎΡΠ°ΡΡ ΡΠ΅Π»ΡΠ½ΡΠΌΠΈ Π·Π΅Π½ΠΊΠ΅ΡΠ°ΠΌΠΈ, Π½Π°ΡΠΈΠ½Π°Ρ ΠΎΡ 20 ΠΌΠΌ β Π·Π΅Π½ΠΊΠ΅ΡΠ°ΠΌΠΈ-Π½Π°ΡΠ°Π΄ΠΊΠ°ΠΌΠΈ ΠΈ ΠΈΠ½ΡΡΡΡΠΌΠ΅Π½ΡΠΎΠΌ ΡΠΎ Π²ΡΡΠ°Π²Π½ΡΠΌΠΈ Π»Π΅Π³ΠΈΡΠΎΠ²Π°Π½Π½ΡΠΌΠΈ Π»Π΅Π·Π²ΠΈΡΠΌΠΈ. ΠΠΎΠ³Π΄Π° ΡΡΠ΅Π±ΡΠ΅ΡΡΡ ΡΠ΄Π΅Π»Π°ΡΡ Π±ΠΎΠ»Π΅Π΅ Π³Π»Π°Π΄ΠΊΠΈΠ΅ ΠΈ ΠΊΡΡΠΏΠ½ΡΠ΅ ΠΎΡΠ²Π΅ΡΡΡΠΈΡ Π² ΡΡΠ°Π½ΠΎΠΊ ΡΡΡΠ°Π½Π°Π²Π»ΠΈΠ²Π°ΡΡΡΡ ΠΊΠΎΠΌΠ±ΠΈΠ½ΠΈΡΠΎΠ²Π°Π½Π½ΡΠ΅ ΠΌΠΎΠ΄Π΅Π»ΠΈ, Π³Π΄Π΅ ΠΌΠΎΠΆΠ΅Ρ Π±ΡΡΡ Π΄ΠΎ Π²ΠΎΡΡΠΌΠΈ ΠΎΡΡΡΡΡ Π·ΡΠ±ΡΠΈΠΊΠΎΠ², ΠΏΡΠΈ ΡΡΠΎΠΌ Π΄Π°Π½Π½ΡΠ΅ Π·Π΅Π½ΠΊΠ΅ΡΡ ΠΎΠΏΡΠΈΠΎΠ½Π°Π»ΡΠ½ΠΎ ΠΊΠΎΠΌΠ±ΠΈΠ½ΠΈΡΡΡΡΡΡ ΡΠΎ ΡΠ²Π΅ΡΠ»Π°ΠΌΠΈ, ΡΠ°Π·Π²Π΅ΡΡΠΊΠ°ΠΌΠΈ ΠΈ Π΄ΡΡΠ³ΠΈΠΌΠΈ ΡΠ²Π΅ΡΠ»ΠΈΠ»ΡΠ½ΠΎ-ΡΠ΅ΠΆΡΡΠΈΠΌΠΈ ΠΈΠ½ΡΡΡΡΠΌΠ΅Π½ΡΠ°ΠΌΠΈ.
ΠΡΠ»ΠΈΡΠΈΠ΅ Π·Π΅Π½ΠΊΠ΅ΡΠΎΠ²Π°Π½ΠΈΡ ΠΎΡ ΡΠΌΠ΅ΠΆΠ½ΡΡ ΠΎΠΏΠ΅ΡΠ°ΡΠΈΠΉ
ΠΠ΅Π½ΠΊΠ΅ΡΠΎΠ²Π°Π½ΠΈΠ΅ ΡΡ ΠΎΠ΄Π½ΠΎ Ρ ΡΠ°Π·Π²ΡΡΡΡΠ²Π°Π½ΠΈΠ΅ΠΌ ΠΎΡΠ²Π΅ΡΡΡΠΈΠΉ, ΡΠ΅ΠΆΡΡΠΈΠ΅ ΠΊΡΠΎΠΌΠΊΠΈ ΠΈΠ½ΡΡΡΡΠΌΠ΅Π½ΡΠ° ΡΠ½ΠΈΠΌΠ°ΡΡ Π»ΠΈΡΠ½ΠΈΠΉ ΠΌΠ°ΡΠ΅ΡΠΈΠ°Π» ΡΠΎ ΡΡΠ΅Π½ΠΎΠΊΡΠΈΡ, ΡΠΌΠ΅Π½ΡΡΠ°ΡΡ ΡΠ΅ΡΠΎΡ ΠΎΠ²Π°ΡΠΎΡΡΡ ΠΈ ΡΠ²Π΅Π»ΠΈΡΠΈΠ²Π°ΡΡ Π΄ΠΈΠ°ΠΌΠ΅ΡΡ. ΠΡΠΎ ΠΏΠΎΠ»ΡΡΠΈΡΡΠΎΠ²Π°Ρ ΠΎΠΏΠ΅ΡΠ°ΡΠΈΡ, ΡΡΠΎ Π·Π½Π°ΡΠΈΡ, Π·Π° Π½Π΅ΠΉ ΡΠ»Π΅Π΄ΡΠ΅Ρ Π΅ΡΡ ΠΎΠ΄ΠΈΠ½ ΡΡΠ°ΠΏ ΠΎΠ±ΡΠ°Π±ΠΎΡΠΊΠΈ. Π Π°Π·Π²ΡΡΡΡΠ²Π°Π½ΠΈΠ΅ β ΡΠΈΠ½ΠΈΡΠ½Π°Ρ ΠΏΡΠΎΡΠ΅Π΄ΡΡΠ°. ΠΠΎ Π²ΡΠ΅ΠΌΡ Π·Π΅Π½ΠΊΠ΅ΡΠΎΠ²Π°Π½ΠΈΡ ΡΡΡΡΠ°Π½ΡΡΡΡΡ Π΄Π΅ΡΠ΅ΠΊΡΡ ΡΠ²Π΅ΡΠ»Π΅Π½ΠΈΡ, ΡΡΠ°ΠΌΠΏΠΎΠ²ΠΊΠΈ ΠΈ Π»ΠΈΡΡΡ. Π ΠΏΡΠΎΡΠ΅ΡΡΠ΅ ΠΌΠΎΠΆΠ½ΠΎ Π½Π΅ΠΌΠ½ΠΎΠ³ΠΎ ΠΎΡΠΊΠΎΡΡΠ΅ΠΊΡΠΈΡΠΎΠ²Π°ΡΡ ΠΏΡΠΈΠ²ΡΠ·ΠΊΡ, Π΄ΠΎΠ±ΠΈΡΡΡΡ Π»ΡΡΡΠ΅ΠΉ ΡΠΎΠΎΡΠ½ΠΎΡΡΠΈ Π΄Π»Ρ Π±ΡΠ΄ΡΡΠ΅Π³ΠΎ ΡΠΎΠ΅Π΄ΠΈΠ½Π΅Π½ΠΈΡ. Π’ΠΎΡΠ½ΠΎΡΡΡ ΡΠ΄Π°ΡΡΡΡ ΠΏΠΎΠ²ΡΡΠΈΡΡ Π΄ΠΎ 5, Π° ΠΈΠ½ΠΎΠ³Π΄Π° Π΄Π°ΠΆΠ΅ Π΄ΠΎ 4-Π³ΠΎ ΠΊΠ»Π°ΡΡΠ°.
ΠΡΠΈ ΡΡΡΠ°Π½ΠΎΠ²ΠΊΠ΅ ΡΠ΅ΠΆΠΈΠΌΠ° ΡΠ΅Π·Π°Π½ΠΈΡ Π½ΡΠΆΠ½ΠΎ ΠΏΠΎΠΌΠ½ΠΈΡΡ, ΡΡΠΎ ΡΠΎΠ»ΡΠΈΠ½Π° ΡΠ΄Π°Π»ΡΠ΅ΠΌΠΎΠ³ΠΎ ΠΌΠ΅ΡΠ°Π»Π»Π° ΠΏΡΠΈ Π·Π΅Π½ΠΊΠ΅ΡΠΎΠ²Π°Π½ΠΈΠΈ ΡΠ°Π²Π½Π° ΠΏΠΎΠ»ΠΎΠ²ΠΈΠ½Π΅ ΠΏΡΠΈΠΏΡΡΠΊΠ° Π΄Π»Ρ Π·Π°Π΄Π°Π½Π½ΠΎΠ³ΠΎ Π΄ΠΈΠ°ΠΌΠ΅ΡΡΠ° ΠΎΡΠ²Π΅ΡΡΡΠΈΡ. ΠΡΠ»ΠΈ ΡΡΠ°Π²Π½ΠΈΠ²Π°ΡΡ ΡΠΎ ΡΠ²Π΅ΡΠ»Π΅Π½ΠΈΠ΅ΠΌ, ΡΠΎ ΠΏΠΎΠ΄Π°ΡΡ ΠΌΠΎΠΆΠ½ΠΎ ΡΠ΄Π΅Π»Π°ΡΡ Π±ΠΎΠ»ΡΡΠ΅ Π² 1,5-2 ΡΠ°Π·Π°, Π° ΡΠΊΠΎΡΠΎΡΡΡ ΠΎΡΡΠ°Π²ΠΈΡΡ ΡΠ°ΠΊΠΎΠΉ ΠΆΠ΅. ΠΠΎΠ½ΠΊΡΠ΅ΡΠ½ΡΠ΅ ΠΏΠ°ΡΠ°ΠΌΠ΅ΡΡΡ ΡΠ΅Π·Π°Π½ΠΈΡ ΡΠ°ΡΡΡΠΈΡΡΠ²Π°ΡΡΡΡ ΠΏΠΎ ΡΠΎΡΠΌΡΠ»Π°ΠΌ, ΠΏΡΠΈΠ²ΠΎΠ΄ΠΈΠΌΡΠΌ Π² Π½ΠΎΡΠΌΠ°ΡΠΈΠ²Π½ΠΎΠΉ Π»ΠΈΡΠ΅ΡΠ°ΡΡΡΠ΅.
Π’Π°ΠΊ ΠΊΠ°ΠΊ Π·Π΅Π½ΠΊΠ΅Ρ ΠΎΠ±Π»Π°Π΄Π°Π΅Ρ Π±ΠΎΠ»ΡΡΠ΅ΠΉ Π² ΡΡΠ°Π²Π½Π΅Π½ΠΈΠΈ ΡΠΎ ΡΠ²Π΅ΡΠ»ΠΎΠΌ ΠΆΡΡΡΠΊΠΎΡΡΡΡ, ΠΈΠ·-Π·Π° ΠΏΠΎΠ²ΡΡΠ΅Π½Π½ΠΎΠ³ΠΎ ΡΠΈΡΠ»Π° ΠΎΡΡΡΡΡ Π²ΡΡΡΡΠΏΠΎΠ², Π²ΠΎΠ·ΡΠ°ΡΡΠ°Π΅Ρ ΡΠΎΡΠ½ΠΎΡΡΡ Π½Π°ΠΏΡΠ°Π²Π»Π΅Π½ΠΈΡ Π΄Π²ΠΈΠΆΠ΅Π½ΠΈΡ, Π° ΡΠ°ΠΊΠΆΠ΅ ΠΊΠ°ΡΠ΅ΡΡΠ²ΠΎ ΠΎΠ±ΡΠ°Π±ΠΎΡΠΊΠΈ, Π³Π»Π°Π΄ΠΊΠΎΡΡΡ ΠΈ ΡΠΈΡΡΠΎΡΠ° ΠΏΠΎΠ²Π΅ΡΡ Π½ΠΎΡΡΠΈ. ΠΠ»Ρ ΡΡΠ°Π²Π½Π΅Π½ΠΈΡ ΡΠ²Π΅ΡΠ»Π΅Π½ΠΈΠ΅ Π΄Π°ΡΡ ΡΠ΅ΡΠΎΡ ΠΎΠ²Π°ΡΠΎΡΡΡ 20 ΠΌΠΊΠΌ ΠΈ ΠΊΠ²Π°Π»ΠΈΡΠ΅ΡΡ 11β12, Π·Π΅Π½ΠΊΠ΅ΡΠΎΠ²Π°Π½ΠΈΠ΅ β ΡΠ΅ΡΠΎΡ ΠΎΠ²Π°ΡΠΎΡΡΡ 2,5 ΠΌΠΊΠΌ, ΠΊΠ²Π°Π»ΠΈΡΠ΅ΡΡ 9β11, Π° ΡΠ°Π·Π²ΡΡΡΡΠ²Π°Π½ΠΈΠ΅ β ΡΠ΅ΡΠΎΡ ΠΎΠ²Π°ΡΠΎΡΡΡ 0,25-1,25 ΠΌΠΊΠΌ ΠΈ ΠΊΠ²Π°Π»ΠΈΡΠ΅ΡΡ 6β9. ΠΠ²Π°Π»ΠΈΡΠ΅ΡΠΎΠΌ Π½Π°Π·ΡΠ²Π°ΡΡ ΡΠΎΡΠ½ΠΎΡΡΡ ΠΈΠ·Π³ΠΎΡΠΎΠ²Π»Π΅Π½ΠΈΡ Π΄Π΅ΡΠ°Π»ΠΈ, Ρ ΡΠ²Π΅Π»ΠΈΡΠ΅Π½ΠΈΠ΅ΠΌ Π΅Π³ΠΎ Π·Π½Π°ΡΠ΅Π½ΠΈΡ Π΄ΠΎΠΏΡΡΠΊΠΈ ΡΠ°ΡΡΡΡ, Π° ΡΠΎΡΠ½ΠΎΡΡΡ ΠΏΠ°Π΄Π°Π΅Ρ. ΠΡΠ»ΠΈ ΡΠ΅Ρ Π½ΠΎΠ»ΠΎΠ³ΠΈΡΠ΅ΡΠΊΠΈΠΌ ΠΏΡΠΎΡΠ΅ΡΡΠΎΠΌ Π΄Π»Ρ ΠΎΠ±ΡΠ°Π±ΠΎΡΠΊΠΈ ΠΈΠ·Π΄Π΅Π»ΠΈΡ ΡΡΠ΅Π±ΡΠ΅ΡΡΡ ΠΈ Π·Π΅Π½ΠΊΠ΅ΡΠΎΠ²Π°Π½ΠΈΠ΅ ΠΈ ΡΠ°Π·Π²ΡΡΡΠΊΠ°, ΡΠΎ ΠΎΠ½ΠΈ ΠΏΡΠΎΠΈΠ·Π²ΠΎΠ΄ΡΡΡΡ Π·Π° ΠΎΠ΄Π½Ρ ΡΡΡΠ°Π½ΠΎΠ²ΠΊΡ ΠΈ Π²ΡΠ²Π΅ΡΠΊΡ Π·Π°Π³ΠΎΡΠΎΠ²ΠΊΠΈ Π½Π° ΡΡΠ°Π½ΠΊΠ΅.
ΠΠ΅Π½ΠΊΠΎΠ²Π°Π½ΠΈΠ΅ ΠΈ Π·Π΅Π½ΠΊΠ΅ΡΠΎΠ²Π°Π½ΠΈΠ΅ Π½Π΅ΡΠ΅Π΄ΠΊΠΎ ΠΏΡΡΠ°ΡΡ ΠΈΠ·-Π·Π° ΠΏΠΎΡ ΠΎΠΆΠ΅ΡΡΠΈ Π½Π°Π·Π²Π°Π½ΠΈΠΉ. ΠΠ° ΡΠ°ΠΌΠΎΠΌ Π΄Π΅Π»Π΅, Π·Π΅Π½ΠΊΠΎΠ²Π°Π½ΠΈΠ΅ ΠΈΠΌΠ΅Π΅Ρ ΡΠΎΠ²Π΅ΡΡΠ΅Π½Π½ΠΎ ΠΈΠ½ΡΡ ΡΠ΅Π»Ρ, ΠΈ Π΄Π»Ρ Π½Π΅Π³ΠΎ ΠΈΡΠΏΠΎΠ»ΡΠ·ΡΠ΅ΡΡΡ ΠΎΡΠ»ΠΈΡΠ½ΡΠΉ ΠΈΠ½ΡΡΡΡΠΌΠ΅Π½Ρ, Π½Π°Π·Π²Π°Π½ΠΈΠ΅ ΠΊΠΎΡΠΎΡΠΎΠΌΡ Π·Π΅Π½ΠΊΠΎΠ²ΠΊΠ°.
ΠΡΠΈ ΡΡΠΎΠΌ Π²ΠΈΠ΄Π΅ ΠΎΠ±ΡΠ°Π±ΠΎΡΠΊΠΈ ΡΠΎΠ·Π΄Π°ΡΡΡΡ ΡΠ³Π»ΡΠ±Π»Π΅Π½ΠΈΡ Π΄Π»Ρ ΡΠ°Π·ΠΌΠ΅ΡΠ΅Π½ΠΈΡ ΠΊΡΠ΅ΠΏΠ΅ΠΆΠ° Π·Π°ΠΏΠΎΠ΄Π»ΠΈΡΠΎ Ρ ΠΏΠΎΠ²Π΅ΡΡ Π½ΠΎΡΡΡΡ Π΄Π΅ΡΠ°Π»ΠΈ. ΠΠΎΠΌΠΈΠΌΠΎ ΡΠ½ΡΡΠΈΡ ΡΠ°ΡΠΎΠΊ, Π·Π΅Π½ΠΊΠΎΠ²ΠΊΡ ΠΏΡΠΈΠΌΠ΅Π½ΡΡΡ Π΄Π»Ρ Π²ΡΡΠ΅Π·Π°Π½ΠΈΡ ΡΠ³Π»ΡΠ±Π»Π΅Π½ΠΈΠΉ ΠΊΠΎΠ½ΠΈΡΠ΅ΡΠΊΠΎΠΉ ΡΠΎΡΠΌΡ. ΠΡΡ ΠΎΠ΄Π½ΠΈΠΌ Π½Π°Π·Π½Π°ΡΠ΅Π½ΠΈΠ΅ΠΌ Π±ΡΠ΄Π΅Ρ Π·Π°ΡΠΈΡΡΠΊΠ° ΠΈ ΠΎΠ±ΡΠ°Π±ΠΎΡΠΊΠ° Π²ΡΠ΅ΠΌΠΎΠΊ ΠΏΠ΅ΡΠ΅Π΄ ΠΌΠΎΠ½ΡΠ°ΠΆΠΎΠΌ ΠΊΡΠ΅ΠΏΠ΅ΠΆΠ°, ΡΡΠΎ Π΄Π΅Π»Π°Π΅ΡΡΡ ΠΏΡΠΈ ΠΏΠΎΠΌΠΎΡΠΈ ΠΏΠ»ΠΎΡΠΊΠΈΡ ΠΈΠ»ΠΈ ΠΆΠ΅ ΡΠΎΡΡΠ΅Π²ΡΡ Π·Π΅Π½ΠΊΠΎΠ²ΠΎΠΊ, ΠΈΠΌΠ΅Π½ΡΠ΅ΠΌΡΡ Π΅ΡΡ ΡΠ΅ΠΊΠΎΠ²ΠΊΠ°ΠΌΠΈ, ΡΡΠΎ Π±ΠΎΠ»Π΅Π΅ Π³ΡΠ°ΠΌΠΎΡΠ½ΠΎ.
ΠΠ°ΠΈΠ±ΠΎΠ»ΡΡΠ΅Π΅ ΡΠ°ΡΠΏΡΠΎΡΡΡΠ°Π½Π΅Π½ΠΈΠ΅ Π½Π° ΡΡΠ½ΠΊΠ΅ ΠΏΠΎΠ»ΡΡΠΈΠ»ΠΈ ΠΊΠΎΠ½ΠΈΡΠ΅ΡΠΊΠΈΠ΅ Π·Π΅Π½ΠΊΠΎΠ²ΠΊΠΈ Ρ ΡΠ°Π±ΠΎΡΠΈΠΌΠΈ ΡΠ³Π»Π°ΠΌΠΈ Π² 90 ΠΈ 120ΒΊ, ΠΊΠΎΡΠΎΡΡΠΌΠΈ ΡΠΎΠ·Π΄Π°ΡΡΡΡ ΡΠ³Π»ΡΠ±Π»Π΅Π½ΠΈΡ, ΡΡΠΎΠ±Ρ ΠΏΡΡΡΠ°ΡΡ ΡΠ»ΡΠΏΠΊΠΈ Π±ΠΎΠ»ΡΠΎΠ² ΠΈ Π²ΠΈΠ½ΡΠΎΠ². Π ΠΌΠ΅ΡΠ°Π»Π»ΠΎΠΎΠ±ΡΠ°Π±Π°ΡΡΠ²Π°ΡΡΠ΅ΠΉ ΠΏΡΠΎΠΌΡΡΠ»Π΅Π½Π½ΠΎΡΡΠΈ Π½Π°Ρ ΠΎΠ΄ΡΡ ΡΠ²ΠΎΡ ΠΏΡΠΈΠΌΠ΅Π½Π΅Π½ΠΈΠ΅ ΠΈ Π·Π΅Π½ΠΊΠΎΠ²ΠΊΠΈ Ρ ΠΏΠ»ΠΎΡΠΊΠΈΠΌ ΠΊΠΎΠ½ΡΠΈΠΊΠΎΠΌ, ΡΠ»ΡΠΆΠ°ΡΠΈΠ΅ Π΄Π»Ρ Π·Π°ΡΠΈΡΡΠΊΠΈ Π²ΡΠ΅ΠΌΠΎΠΊ ΠΏΠΎΠ΄ ΠΊΡΠ΅ΠΏΠ΅ΠΆΠ½ΡΠ΅ ΡΠ»Π΅ΠΌΠ΅Π½ΡΡ. Π£ΡΡΠ°Π½Π°Π²Π»ΠΈΠ²Π°ΡΡ Π·Π΅Π½ΠΊΠΎΠ²ΠΊΠΈ Π² ΡΠ΅ ΠΆΠ΅ ΡΡΠ°Π½ΠΊΠΈ, ΡΡΠΎ ΠΈ Π΄ΡΡΠ³ΠΎΠΉ ΠΈΠ½ΡΡΡΡΠΌΠ΅Π½Ρ Π΄Π»Ρ ΠΎΠ±ΡΠ°Π±ΠΎΡΠΊΠΈ ΠΎΡΠ²Π΅ΡΡΡΠΈΠΉ Π΄Π»Ρ ΠΊΡΠ΅ΠΏΠ΅ΠΆΠ°.
ΠΠ°ΠΊ Π·Π΅Π½ΠΊΠ΅ΡΠΎΠ²Π°ΡΡ ΠΌΠ΅ΡΠ°Π»Π» ΠΏΡΠ°Π²ΠΈΠ»ΡΠ½ΠΎ
ΠΡΠ»ΠΈ ΠΌΠ°ΡΡΠ΅Ρ-Π»ΡΠ±ΠΈΡΠ΅Π»Ρ ΠΌΠΎΠΆΠ΅Ρ Π²Π·ΡΡΡ Π΄Π»Ρ Π·Π΅Π½ΠΊΠ΅ΡΠΎΠ²Π°Π½ΠΈΡ ΡΠ²Π΅ΡΠ»ΠΎ ΠΈ Π΄ΡΠ΅Π»Ρ, ΡΠΎ Π² ΡΡΠ»ΠΎΠ²ΠΈΡΡ ΠΏΡΠΎΠΌΡΡΠ»Π΅Π½Π½ΠΎΡΡΠΈ Π΄Π»Ρ ΡΡΠΎΠ³ΠΎ ΠΌΠΎΠ³ΡΡ ΠΈΡΠΏΠΎΠ»ΡΠ·ΠΎΠ²Π°ΡΡ ΡΠ»Π΅Π΄ΡΡΡΠ΅Π΅ ΡΡΠ°Π½ΠΊΠΈ:
- ΡΠ²Π΅ΡΠ»ΠΈΠ»ΡΠ½ΡΠ΅;
- ΡΠΎΠΊΠ°ΡΠ½ΡΠ΅;
- ΡΠ°ΡΡΠΎΡΠ½ΡΠ΅;
- ΡΡΠ΅Π·Π΅ΡΠ½ΡΠ΅;
- Π°Π³ΡΠ΅Π³Π°ΡΠ½ΡΠ΅.
ΠΡΠΎΡΠ΅ΡΡ Π·Π΅Π½ΠΊΠ΅ΡΠΎΠ²Π°Π½ΠΈΡ ΠΏΡΠΎΡ ΠΎΠ΄ΠΈΡ Π² ΡΡΡΠΎΠ³ΠΎΠΌ ΡΠΎΠΎΡΠ²Π΅ΡΡΡΠ²ΠΈΠΈ Ρ ΡΠ΅Ρ Π½ΠΎΠ»ΠΎΠ³ΠΈΠ΅ΠΉ, ΠΎΠ±ΡΠΈΠ΅ ΠΌΠΎΠΌΠ΅Π½ΡΡ Π² ΠΊΠΎΡΠΎΡΠΎΠΉ ΠΌΠΎΠΆΠ½ΠΎ ΠΎΠΏΠΈΡΠ°ΡΡ Π² Π²ΠΈΠ΄Π΅ ΡΠ»Π΅Π΄ΡΡΡΠΈΡ ΡΠ΅ΠΊΠΎΠΌΠ΅Π½Π΄Π°ΡΠΈΠΉ:
- Π Π»ΠΈΡΡΡ Π΄Π΅ΡΠ°Π»ΡΡ Ρ Π½Π΅ΡΠ°Π²Π½ΠΎΠΌΠ΅ΡΠ½ΡΠΌ Π·Π°ΠΏΠ°ΡΠΎΠΌ Π½Π° ΠΏΠΎΡΠ»Π΅Π΄ΡΡΡΡΡ ΠΌΠ΅ΡΠ°Π»Π»ΠΎΠΎΠ±ΡΠ°Π±ΠΎΡΠΊΡ Π½Π΅ΠΎΠ±Ρ ΠΎΠ΄ΠΈΠΌΠΎ ΡΠ°ΡΡΠΎΡΠΈΡΡ ΠΎΡΠ²Π΅ΡΡΡΠΈΠ΅ Π½Π° Π³Π»ΡΠ±ΠΈΠ½Ρ 5β10 ΠΌΠΌ Π΄Π»Ρ ΠΏΡΠ°Π²ΠΈΠ»ΡΠ½ΠΎΠ³ΠΎ Π½Π°ΠΏΡΠ°Π²Π»Π΅Π½ΠΈΡ Π΄Π²ΠΈΠΆΠ΅Π½ΠΈΡ ΡΠ΅ΠΆΡΡΠ΅Π³ΠΎ ΠΈΠ½ΡΡΡΡΠΌΠ΅Π½ΡΠ°.
- ΠΠ»Ρ ΠΎΠΏΠ΅ΡΠ°ΡΠΈΠΈ Π·Π΅Π½ΠΊΠ΅ΡΠΎΠ²Π°Π½ΠΈΡ ΠΎΡΠ²Π΅ΡΡΡΠΈΠΉ ΠΎΡΡΠ°Π²Π»ΡΠ΅ΡΡΡ ΠΏΡΠΈΠΏΡΡΠΊ 1β3 ΠΌΠΌ Π² Π·Π°Π²ΠΈΡΠΈΠΌΠΎΡΡΠΈ ΠΎΡ ΠΈΡΠΎΠ³ΠΎΠ²ΠΎΠ³ΠΎ Π΄ΠΈΠ°ΠΌΠ΅ΡΡΠ°.
- ΠΠ΅Π½ΠΊΠ΅ΡΠΎΠ²Π°Π½ΠΈΠ΅ ΡΡΠ°Π»ΡΠ½ΡΡ ΠΈΠ·Π΄Π΅Π»ΠΈΠΉ Π½Π΅ ΠΎΠ±Ρ ΠΎΠ΄ΠΈΡΡΡ Π±Π΅Π· ΠΎΡ Π»Π°ΠΆΠ΄Π΅Π½ΠΈΡ ΡΠΏΠ΅ΡΠΈΠ°Π»ΡΠ½ΡΠΌΠΈ ΠΌΠ°ΡΠ»ΡΠ½ΡΠΌΠΈ ΡΠ°ΡΡΠ²ΠΎΡΠ°ΠΌΠΈ. ΠΡΠΈ ΡΠ°Π±ΠΎΡΠ΅ Ρ ΡΡΠ³ΡΠ½ΠΎΠΌ, Π° ΡΠ°ΠΊΠΆΠ΅ ΡΠ²Π΅ΡΠΌΠ΅ΡΠΎΠΌ ΠΎΠ½ΠΎ Π½Π΅ ΡΠ²Π»ΡΠ΅ΡΡΡ ΠΎΠ±ΡΠ·Π°ΡΠ΅Π»ΡΠ½ΡΠΌ.
- ΠΠΏΡΠΈΠΌΠ°Π»ΡΠ½ΡΠΉ Π²Π°ΡΠΈΠ°Π½Ρ Π·Π΅Π½ΠΊΠ΅ΡΠ° ΠΈ ΡΠ΅ΠΆΠΈΠΌ ΡΠ°Π±ΠΎΡΡ ΠΏΠΎΠ΄Π±ΠΈΡΠ°ΡΡ Ρ ΡΡΡΡΠΎΠΌ Π½Π΅ΠΎΠ±Ρ ΠΎΠ΄ΠΈΠΌΠΎΠ³ΠΎ Π΄ΠΈΠ°ΠΌΠ΅ΡΡΠ° ΠΎΡΠ²Π΅ΡΡΡΠΈΡ, ΡΠΎΡΠ½ΠΎΡΡΠΈ ΠΎΠ±ΡΠ°Π±ΠΎΡΠΊΠΈ, Π΅Ρ Π³Π»ΡΠ±ΠΈΠ½Ρ, ΠΌΠ΅ΡΠ°Π»Π»Π° Π΄Π΅ΡΠ°Π»ΠΈ ΠΈ ΠΎΠΏΡΠΈΠΉ ΠΏΡΠΎΠΈΠ·Π²ΠΎΠ΄ΡΡΠ²Π΅Π½Π½ΠΎΠ³ΠΎ ΡΡΠ°Π½ΠΊΠ°.
- ΠΡΠ΅ΠΏΠ»Π΅Π½ΠΈΠ΅ ΡΠ΅ΠΆΡΡΠ΅Π³ΠΎ ΠΈΠ½ΡΡΡΡΠΌΠ΅Π½ΡΠ° Π΄ΠΎΠ»ΠΆΠ½ΠΎ ΡΡΡΠΊΠΎΠ²Π°ΡΡΡΡ Ρ ΡΠ΅ΠΌ ΡΠ»ΠΎΡΠΎΠΌ, ΡΡΠΎ Π΅ΡΡΡ Π½Π° ΡΠ°Π±ΠΎΡΠ΅ΠΉ ΡΡΠ°Π½ΡΠΈΠΈ.
- Π ΡΠ»ΡΡΠ°Π΅, ΠΊΠΎΠ³Π΄Π° ΠΏΡΠ΅Π΄ΠΏΠΎΠ»Π°Π³Π°Π΅ΡΡΡ ΡΠΈΡΡΠΎΠ²Π°Ρ ΠΎΠ±ΡΠ°Π±ΠΎΡΠΊΠ° ΡΠ°Π·Π²ΡΡΡΠΊΠΎΠΉ, ΡΠΎ ΠΏΡΠΈ Π·Π΅Π½ΠΊΠ΅ΡΠΎΠ²Π°Π½ΠΈΠΈ ΡΠ°ΡΡΡ ΠΏΡΠΈΠΏΡΡΠΊΠ°, ΠΎΡ 0,15 Π΄ΠΎ 0,3 ΠΌΠΌ ΠΎΡΡΠ°Π²Π»ΡΡΡ Π΄Π»Ρ Π΄Π°Π»ΡΠ½Π΅ΠΉΡΠ΅ΠΉ ΡΠ°Π±ΠΎΡΡ.
- ΠΠ»Ρ ΠΎΠ±ΡΠ°Π±ΠΎΡΠΊΠΈ ΠΈΠ·Π΄Π΅Π»ΠΈΠΉ ΠΈΠ· Π·Π°ΠΊΠ°Π»ΡΠ½Π½ΡΡ ΠΈ Π»Π΅Π³ΠΈΡΠΎΠ²Π°Π½Π½ΡΡ ΡΡΠ°Π»Π΅ΠΉ ΠΈΡΠΏΠΎΠ»ΡΠ·ΡΡΡ Π·Π΅Π½ΠΊΠ΅ΡΡ Ρ ΡΠ²Π΅ΡΠ΄ΠΎΡΠΏΠ»Π°Π²Π½ΡΠΌΠΈ Π²ΡΡΠ°Π²ΠΊΠ°ΠΌΠΈ Π΄ΠΈΠ°ΠΌΠ΅ΡΡΠΎΠΌ 14-50 ΠΌΠΌ ΠΈ 3-4 Π·ΡΠ±ΡΠΈΠΊΠ°ΠΌΠΈ.
- ΠΡΠΈ ΠΎΠ±ΡΠ°Π±ΠΎΡΠΊΠ΅ ΡΠ²Π΅ΡΠ½ΡΡ ΠΌΠ΅ΡΠ°Π»Π»ΠΎΠ² ΠΈ ΡΠΏΠ»Π°Π²ΠΎΠ² ΠΆΠ΅Π»Π΅Π·Π° Ρ Π²ΡΡΠΎΠΊΠΈΠΌ ΡΠΎΠ΄Π΅ΡΠΆΠ°Π½ΠΈΠ΅ΠΌ ΡΠ³Π»Π΅ΡΠΎΠ΄Π° Π² Π΄Π΅Π»ΠΎ ΠΈΠ΄ΡΡ ΠΏΠ΅ΡΠΎΠ²ΡΠ΅ Π·Π΅Π½ΠΊΠ΅ΡΡ.
- ΠΠ½ΡΡΡΡΠΌΠ΅Π½ΡΠΎΠΌ ΠΈΠ· Π±ΡΡΡΡΠΎΡΠ΅ΠΆΡΡΠ΅ΠΉ ΡΡΠ°Π»ΠΈ ΠΎΠ±ΡΠ°Π±Π°ΡΡΠ²Π°ΡΡ ΠΈΠ·Π΄Π΅Π»ΠΈΡ ΠΈΠ· ΠΎΠ±ΡΡΠ½ΠΎΠΉ ΠΊΠΎΠ½ΡΡΡΡΠΊΡΠΈΠΎΠ½Π½ΠΎΠΉ ΡΡΠ°Π»ΠΈ. ΠΡΠΈ ΠΎΡΠ²Π΅ΡΡΡΠΈΡΡ Π±ΠΎΠ»Π΅Π΅ 40 ΠΌΠΌ ΠΎΡΠ½Π°ΡΡΠΊΡ Π΄ΠΎΠΏΠΎΠ»Π½ΡΡΡ Π½Π°ΡΠ°Π΄ΠΊΠ°ΠΌΠΈ Ρ Π΄ΠΈΠ°ΠΌΠ΅ΡΡΠΎΠΌ 32β80 ΠΌΠΌ.
ΠΠ΅ΡΠΎΠΎΡΠ²Π΅ΡΡΡΠ²ΠΈΠ΅ ΠΏΡΠΎΡΠ΅ΡΡΠ° ΡΡΡΠ°Π½ΠΎΠ²Π»Π΅Π½Π½ΠΎΠΉ ΡΠ΅Ρ Π½ΠΎΠ»ΠΎΠ³ΠΈΠΈ ΡΠ°ΡΡΠΎ Π²ΡΡΡΡΠΏΠ°Π΅Ρ ΠΏΡΠΈΡΠΈΠ½ΠΎΠΉ Π±ΡΠ°ΠΊΠ°. ΠΡΠΈ Π±ΠΎΠ»ΡΡΠΎΠΌ ΠΈΠ·Π½ΠΎΡΠ΅ ΠΈΠ½ΡΡΡΡΠΌΠ΅Π½ΡΠ° ΠΏΠΎΠ»ΡΡΠΈΠ²ΡΠ΅Π΅ΡΡ ΠΎΡΠ²Π΅ΡΡΡΠΈΠ΅ Π±ΡΠ΄Π΅Ρ ΠΌΠ΅Π½ΡΡΠ΅, ΡΠ΅ΠΌ ΠΏΠΎ ΠΏΡΠΎΠ΅ΠΊΡΡ. ΠΠΎΠ³Π΄Π° ΠΌΠ°ΡΡΠ΅Ρ Π·Π°Π²ΡΡΠΈΠ» ΠΏΠΎΠ΄Π°ΡΡ, ΠΈΠ»ΠΈ Π½Π° Π·ΡΠ±ΡΡ Π·Π΅Π½ΠΊΠ΅ΡΠ° Π½Π°Π»ΠΈΠΏΠ»ΠΈ ΠΎΡΡ ΠΎΠ΄Ρ, ΡΠΈΡΡΠΎΡΠ° ΠΎΠ±ΡΠ°Π±ΠΎΡΠΊΠΈ ΠΌΠΎΠΆΠ΅Ρ Π½Π΅ ΡΠ΄ΠΎΠ²Π»Π΅ΡΠ²ΠΎΡΡΡΡ ΠΊΠ°ΡΠ΅ΡΡΠ²Ρ. ΠΡΡΠ³ΠΈΠ΅ Π΄Π΅ΡΠ΅ΠΊΡΡ: ΡΠ°ΡΡΡ ΠΏΠΎΠ²Π΅ΡΡ Π½ΠΎΡΡΠΈ Π½Π΅ ΠΎΠ±ΡΠ°Π±ΠΎΡΠ°Π½Π°, ΠΏΠΎΠ»ΡΡΠ΅Π½Π½ΡΠΉ Π΄ΠΈΠ°ΠΌΠ΅ΡΡ Π±ΠΎΠ»ΡΡΠ΅ ΡΡΠ΅Π±ΡΠ΅ΠΌΠΎΠ³ΠΎ, ΡΠ²Π»ΡΡΡΡΡ ΡΠ»Π΅Π΄ΡΡΠ²ΠΈΠ΅ΠΌ Π½Π΅ΠΏΡΠ°Π²ΠΈΠ»ΡΠ½ΠΎΠ³ΠΎ Π²ΡΠ±ΠΎΡΠ° Π·Π΅Π½ΠΊΠ΅ΡΠ° ΠΈΠ»ΠΈ Π΅Π³ΠΎ Π½Π΅ΠΏΡΠ°Π²ΠΈΠ»ΡΠ½ΠΎΠΉ ΡΡΡΠ°Π½ΠΎΠ²ΠΊΠΈ.
Π Π°Π·Π²ΡΡΡΡΠ²Π°Π½ΠΈΠ΅ Π΄Π»Ρ ΠΎΠ±Π΅ΡΠΏΠ΅ΡΠ΅Π½ΠΈΡ ΠΌΠ°ΠΊΡΠΈΠΌΠ°Π»ΡΠ½ΠΎΠΉ ΡΠΎΡΠ½ΠΎΡΡΠΈ ΠΏΠΎΠ²Π΅ΡΡ Π½ΠΎΡΡΠΈ
Π’ΠΎΡΠ½ΠΎΡΡΡ Π΄Π΅ΡΠ°Π»Π΅ΠΉ ΠΎΠΏΡΠ΅Π΄Π΅Π»ΡΠ΅ΡΡΡ ΡΠ΅ΡΠ΅Π· ΡΠ°ΠΊΠΈΠ΅ ΠΏΠΎΠ½ΡΡΠΈΡ ΠΊΠ°ΠΊ ΠΊΠ»Π°ΡΡ ΠΈ ΠΊΠ²Π°Π»ΠΈΡΠ΅Ρ. ΠΡΠΎΡΠΎΠ΅ ΡΠ΅ΠΉΡΠ°Ρ Π±ΠΎΠ»Π΅Π΅ ΡΠΏΠΎΡΡΠ΅Π±ΠΈΠΌΠΎ, Ρ. ΠΊ. Π΄Π°ΡΡ Π±ΠΎΠ»Π΅Π΅ ΡΠΎΡΠ½ΡΡ ΠΈΠ½ΡΠΎΡΠΌΠ°ΡΠΈΡ ΠΎ Π΄ΠΎΠΏΡΡΡΠΈΠΌΡΡ Π΄ΠΎΠΏΡΡΠΊΠ°Ρ Π½Π΅ΡΠΎΠΎΡΠ²Π΅ΡΡΡΠ²ΠΈΡ ΡΠ°Π·ΠΌΠ΅ΡΠΎΠ². ΠΠ΅ΠΆΠ΄Ρ ΡΠ΅ΠΌ ΡΠΈΡΡΠ΅ΠΌΠ° ΠΊΠ»Π°ΡΡΠΎΠ² Π²ΡΡ Π΅ΡΡ ΠΏΡΠΎΠ΄ΠΎΠ»ΠΆΠ°Π΅Ρ ΠΆΠΈΡΡ Π² ΠΏΡΠΎΡΠ΅ΡΡΠΈΠΎΠ½Π°Π»ΡΠ½ΠΎΠΉ ΡΡΠ΅Π΄Π΅, ΠΈΡΠΏΠΎΠ»ΡΠ·ΡΠ΅ΡΡΡ ΠΊΠ²Π°Π»ΠΈΡΠΈΡΠΈΡΠΎΠ²Π°Π½Π½ΡΠΌΠΈ ΠΊΠ°Π΄ΡΠ°ΠΌΠΈ Π½Π° ΠΏΡΠΎΠΈΠ·Π²ΠΎΠ΄ΡΡΠ²Π°Ρ .Β Π ΠΎΡΠ΅ΡΠ΅ΡΡΠ²Π΅Π½Π½ΠΎΠΌ ΠΌΠ°ΡΠΈΠ½ΠΎΡΡΡΠΎΠ΅Π½ΠΈΠΈ ΠΏΡΠΈΠΌΠ΅Π½ΡΡΡΡΡ ΡΠΎΠ»ΡΠΊΠΎ ΠΏΠ΅ΡΠ²ΡΠ΅ 9 ΠΊΠ»Π°ΡΡΠΎΠ² ΠΏΠΎ ΡΠΎΡΠ½ΠΎΡΡΠΈ, ΠΈ ΠΏΠΎΠ»Π΅Π·Π½ΠΎ Π·Π½Π°ΡΡ ΠΊΠ°ΠΊΠΈΠΌ ΠΊΠ²Π°Π»ΠΈΡΠ΅ΡΠ°ΠΌ ΠΎΠ½ΠΈ ΡΠΎΠΎΡΠ²Π΅ΡΡΡΠ²ΡΡΡ.
ΠΠ»Π°ΡΡ ΡΠΎΡΠ½ΠΎΡΡΠΈ | ΠΠ²Π°Π»ΠΈΡΠ΅Ρ (ΠΎΡΠ²./Π²Π°Π») | ΠΠΎΠΏΡΡΠΊ Π΄Π»Ρ Γ18-30 ΠΌΠΌ (ΠΎΡΠ²./Π²Π°Π»), ΠΌΠΊΠΌ |
1 | 6/5 | 13/9 |
2 | 7/6; 7/7 | 21/13 |
2Π° | 8/7; 8/8 | 33/21 |
3 | 9/8; 9/9 | 52/33 |
3Π° | 10/10 | 84/84 |
4 | 11/11 | 130/130 |
5 | 12/12 | 210/210 |
7 | 14/14 | 520/520 |
8 | 15/15 | 840/840 |
9 | 16/16 | 1300/1300 |
Β
ΠΡΠΎΠΏΡΡΠ΅Π½ 6-ΠΉ ΠΊΠ»Π°ΡΡ ΡΠΎΡΠ½ΠΎΡΡΠΈ, Ρ. ΠΊ. ΠΎΠ½ ΠΈΡΠΏΠΎΠ»ΡΠ·ΡΠ΅ΡΡΡ ΠΊΡΠ°ΠΉΠ½Π΅ ΡΠ΅Π΄ΠΊΠΎ. Π£ΡΡΠ°Π½ΠΎΠ²Π»Π΅Π½ ΠΎΠ½ Π΄Π»Ρ Π½Π΅ΠΎΡΠ²Π΅ΡΡΡΠ²Π΅Π½Π½ΡΡ Π½Π΅ΡΠΎΠΏΡΡΠ³Π°Π΅ΠΌΡΡ ΠΏΠΎΠ²Π΅ΡΡ Π½ΠΎΡΡΠ΅ΠΉ. Π‘ΠΈΡΡΠ΅ΠΌΠ° Π΄ΠΎΠΏΡΡΠΊΠΎΠ² Π·Π°ΡΠΈΠΊΡΠΈΡΠΎΠ²Π°Π½Π° Π² ΠΠΠ‘Π’ 11472-69, ΠΠΠ‘Π’ 7713-62 ΠΈ Π΄ΡΡΠ³ΠΈΡ .
Π‘ΠΊΠ°ΡΠ°ΡΡ ΠΠΠ‘Π’ 7713-62
Π‘ΠΊΠ°ΡΠ°ΡΡ ΠΠΠ‘Π’ 11472-69
ΠΠ°ΠΊΡΠΈΠΌΠ°Π»ΡΠ½Π°Ρ ΡΠΎΡΠ½ΠΎΡΡΡ ΠΏΠΎΠ»ΡΡΠ°Π΅ΠΌΡΡ ΠΎΡΠ²Π΅ΡΡΡΠΈΠΉ Π·Π°Π²ΠΈΡΠΈΡ ΠΎΡ ΡΠΏΠΎΡΠΎΠ±Π° ΠΈΡ ΠΎΠ±ΡΠ°Π±ΠΎΡΠΊΠΈ ΠΈ ΠΏΡΠΈΠΌΠ΅Π½ΡΠ΅ΠΌΠΎΠ³ΠΎ ΠΈΠ½ΡΡΡΡΠΌΠ΅Π½ΡΠ°. ΠΠ΅Π½ΠΊΠ΅ΡΠΎΠ²Π°Π½ΠΈΠ΅ ΠΈ ΡΠ°Π·Π²ΡΡΡΡΠ²Π°Π½ΠΈΠ΅ ΠΈΠΌΠ΅ΡΡ ΡΠ°Π·Π½ΡΠΉ ΠΏΠΎΠΊΠ°Π·Π°ΡΠ΅Π»Ρ ΠΌΠ°ΠΊΡΠΈΠΌΠ°Π»ΡΠ½ΠΎ Π²ΠΎΠ·ΠΌΠΎΠΆΠ½ΠΎΠ³ΠΎ ΠΊΠ²Π°Π»ΠΈΡΠ΅ΡΠ° ΠΈ ΠΊΠ»Π°ΡΡΠ°. ΠΠ±ΡΡΠ½ΠΎ ΡΡΠΈ ΠΎΠΏΠ΅ΡΠ°ΡΠΈΠΈ Π²ΡΠΏΠΎΠ»Π½ΡΡΡΡΡ ΠΏΠΎΡΠ»Π΅Π΄ΠΎΠ²Π°ΡΠ΅Π»ΡΠ½ΠΎ ΠΎΠ΄Π½Π° Π·Π° Π΄ΡΡΠ³ΠΎΠΉ.
Π‘Π½Π°ΡΠ°Π»Π° Π΄Π΅ΡΠ°Π»Ρ Π·Π΅Π½ΠΊΠ΅ΡΡΡΡ, Ρ Π±ΠΎΠΊΠΎΠ²ΡΡ ΠΏΠΎΠ²Π΅ΡΡ Π½ΠΎΡΡΠ΅ΠΉ ΠΎΡΠ²Π΅ΡΡΡΠΈΡ ΡΠ΄Π°Π»ΡΠ΅ΡΡΡ Π»ΠΈΡΠ½ΠΈΠΉ ΠΌΠ°ΡΠ΅ΡΠΈΠ°Π», ΠΏΡΠ°Π²ΡΡΡΡ Π²ΠΎΠ·ΠΌΠΎΠΆΠ½ΡΠ΅ Π½Π΅Π·Π½Π°ΡΠΈΡΠ΅Π»ΡΠ½ΡΠ΅ ΠΎΡΠΊΠ»ΠΎΠ½Π΅Π½ΠΈΡ Π΅Π³ΠΎ ΡΠ°ΡΠΏΠΎΠ»ΠΎΠΆΠ΅Π½ΠΈΡ. ΠΠ»Π°Π²Π½ΠΎΠ΅ ΡΠ΅Π³ΠΎ ΡΠ΄Π°ΡΡΡΡ Π΄ΠΎΠ±ΠΈΡΡΡΡ Π½Π° ΡΡΠΎΠΌ ΡΡΠ°ΠΏΠ΅ β ΡΠΌΠ΅Π½ΡΡΠΈΡΡ Π½Π΅ΡΠΎΠ²Π½ΠΎΡΡΡ ΡΡΠ΅Π½ΠΎΠΊ. ΠΠΎΡΡΠΈΠΆΠΈΠΌΡΠΉ ΡΠ΅Π·ΡΠ»ΡΡΠ°Ρ β 4-ΠΉ ΠΊΠ»Π°ΡΡ ΡΠΎΡΠ½ΠΎΡΡΠΈ ΠΈ 11 ΠΊΠ²Π°Π»ΠΈΡΠ΅Ρ.
ΠΠ°Π»Π΅Π΅ Π΄Π΅ΡΠ°Π»Ρ ΠΎΠ±ΡΠ°Π±Π°ΡΡΠ²Π°ΡΡ Ρ ΠΏΠΎΠΌΠΎΡΡΡ ΡΠ°Π·Π²ΡΡΡΠΊΠΈ, ΡΠ°Π±ΠΎΡΠ° ΠΌΠΎΠΆΠ΅Ρ ΠΏΡΠΎΠ²ΠΎΠ΄ΠΈΡΡΡΡ Π½Π° ΡΠ΅Ρ ΠΆΠ΅ ΡΠ°ΠΌΡΡ ΡΡΠ°Π½ΠΊΠ°Ρ . ΠΠ½ΡΡΡΡΠΌΠ΅Π½Ρ, ΡΠ°ΠΊ ΠΆΠ΅ ΠΊΠ°ΠΊ ΠΈ Π·Π΅Π½ΠΊΠ΅Ρ, ΡΠ΄Π΅Π»Π°Π½ ΠΈΠ· Π»Π΅Π³ΠΈΡΠΎΠ²Π°Π½Π½ΠΎΠΉ ΡΡΠ°Π»ΠΈ ΠΈ ΠΎΡΠ½Π°ΡΡΠ½ ΡΠ²ΡΡΠ΄ΡΠΌΠΈ ΡΠΏΠ»Π°Π²Π°ΠΌΠΈ, ΠΊΠΎΠ»ΠΈΡΠ΅ΡΡΠ²ΠΎ Π·ΡΠ±ΡΠ΅Π² Ρ Π½Π΅Π³ΠΎ ΡΠ²Π΅Π»ΠΈΡΠ΅Π½ΠΎ. Π Π°Π·Π²ΡΡΡΠΊΠ° ΡΡΠ΅Π·Π°Π΅Ρ Π±ΠΎΠ»Π΅Π΅ ΠΌΠ΅Π»ΠΊΡΡ ΡΡΡΡΠΆΠΊΡ, ΡΠ°ΠΊ Π΄ΠΎΡΡΠΈΠ³Π°Π΅ΡΡΡ ΡΠΎΡΠ½ΠΎΡΡΡ ΠΎΡΠ²Π΅ΡΡΡΠΈΠΉ ΡΠΎΠΎΡΠ²Π΅ΡΡΡΠ²ΡΡΡΠ°Ρ 2β3 ΠΊΠ»Π°ΡΡΡ. ΠΠ»Ρ Π²ΡΡΠΎΠΊΠΎΡΠΎΡΠ½ΡΡ Π΄Π΅ΡΠ°Π»Π΅ΠΉ 1-Π³ΠΎ ΠΊΠ»Π°ΡΡΠ° ΡΠ°Π·Π²ΡΡΡΠΊΡ ΠΏΡΠΈΠΌΠ΅Π½ΡΡΡ ΠΌΠ½ΠΎΠ³ΠΎΠΊΡΠ°ΡΠ½ΠΎ, ΡΡΡΠ΅ΡΡΠ²ΡΡΡ ΠΈ Π΄ΡΡΠ³ΠΈΠ΅ Π΄ΠΎΠ²ΠΎΠ΄ΠΎΡΠ½ΡΠ΅ ΠΎΠΏΠ΅ΡΠ°ΡΠΈΠΈ.
ΠΡΠ±ΡΡ Ρ ΡΠ°Π·Π²ΡΡΡΠΎΠΊ ΡΠ°ΡΠ΅ ΠΏΡΡΠΌΡΠ΅. ΠΠΈΠ½ΡΠΎΠ²ΡΠ΅ ΠΈΡΠΏΠΎΠ»ΡΠ·ΡΡΡΡΡ Π΄Π»Ρ ΠΎΠ±ΡΠ°Π±ΠΎΡΠΊΠΈ ΠΎΡΠ²Π΅ΡΡΡΠΈΠΉ Ρ ΠΏΠ°Π·Π°ΠΌΠΈ, Π·Π°ΠΊΡΡΡΠΈΠ²Π°Π½ΠΈΠ΅ ΠΏΡΠΎΡΠΈΠ»Ρ ΠΈΠ½ΡΡΡΡΠΌΠ΅Π½ΡΠ° Π±Π΅ΡΡΡ ΠΏΡΠΎΡΠΈΠ²ΠΎΠΏΠΎΠ»ΠΎΠΆΠ½ΡΠΌ Π½Π°ΠΏΡΠ°Π²Π»Π΅Π½ΠΈΡ ΡΠ΅Π·Π°Π½ΠΈΡ, Π΄Π»Ρ ΡΠΎΠ³ΠΎ ΡΡΠΎΠ±Ρ Π΅Π³ΠΎ Π½Π΅ Π·Π°ΡΡΠ³ΠΈΠ²Π°Π»ΠΎ Π² ΠΎΡΠ²Π΅ΡΡΡΠΈΠ΅. Π Π΅ΠΆΡΡΠΈΠ΅ Π²ΡΠΏΡΠΊΠ»ΠΎΡΡΠΈ ΡΠ°ΡΠΏΠΎΠ»ΠΎΠΆΠ΅Π½Ρ Π½Π° ΡΡΠ΅ΡΠΆΠ½Π΅ ΡΠ°Π·Π²ΡΡΡΠΊΠΈ Π½Π΅ΡΠ°Π²Π½ΠΎΠΌΠ΅ΡΠ½ΠΎ Ρ ΡΠ΅ΠΌ, ΡΡΠΎΠ±Ρ ΠΈΡΠΊΠ»ΡΡΠΈΡΡ Π²Π»ΠΈΡΠ½ΠΈΠ΅ Π½Π΅ΠΎΠ΄Π½ΠΎΡΠΎΠ΄Π½ΠΎΡΡΠΈ ΠΌΠ΅ΡΠ°Π»Π»Π° Π·Π°Π³ΠΎΡΠΎΠ²ΠΊΠΈ. ΠΠ°Π»ΠΈΡΠΈΠ΅ Π²ΠΊΡΠ°ΠΏΠ»Π΅Π½ΠΈΠΉ Ρ ΠΎΡΠ»ΠΈΡΠ½ΠΎΠΉ ΠΏΠ»ΠΎΡΠ½ΠΎΡΡΡΡ ΠΈΠ·ΠΌΠ΅Π½ΡΠ΅Ρ Π½Π°Π³ΡΡΠ·ΠΊΡ Π½Π° ΠΊΠΎΠ½ΡΠ°ΠΊΡΠΈΡΡΡΡΠΈΠΉ Π·ΡΠ±, ΠΈ ΠΏΡΠΈ ΠΎΡΡΡΡΡΡΠ²ΠΈΠΈ Ρ Π½ΠΈΡ ΡΠ°Π·Π±Π΅ΠΆΠΊΠΈ, Π½Π° ΡΡΠΎΠΌ ΠΌΠ΅ΡΡΠ΅ ΠΏΠΎΡΠ²ΠΈΡΡΡΡ ΠΌΠ΅ΡΡΠ½ΠΎΠ΅ ΡΠ³Π»ΡΠ±Π»Π΅Π½ΠΈΠ΅ ΠΈΠ»ΠΈ Π²ΡΠΏΡΠΊΠ»ΠΎΡΡΡ.
ΠΠΎ ΡΠΎΠΉ ΠΏΡΠΈΡΠΈΠ½Π΅, ΡΡΠΎ ΡΠ°Π·Π²ΡΡΡΠΊΠ° ΡΡΠ΅Π·Π°Π΅Ρ ΠΏΡΠΈ ΠΎΠ±ΡΠ°Π±ΠΎΡΠΊΠ΅ ΠΌΠ΅Π½ΡΡΠ΅ ΠΌΠ΅ΡΠ°Π»Π»Π°, ΠΎΠ½Π° Π½Π΅ ΠΈΡΠΏΠΎΠ»ΡΠ·ΡΠ΅ΡΡΡ Π΄Π»Ρ ΠΈΡΠΏΡΠ°Π²Π»Π΅Π½ΠΈΡ Π½Π°ΠΏΡΠ°Π²Π»Π΅Π½ΠΈΡ ΠΎΡΠ²Π΅ΡΡΡΠΈΡ, ΠΏΠΎΠ΄ΠΎΠ±Π½ΠΎΠ΅ ΠΏΡΠΎΡΡΠΎ Π½Π΅ ΡΠ°ΡΠΈΠΎΠ½Π°Π»ΡΠ½ΠΎ. Π‘Π»Π΅Π΄ΠΎΠ²Π°ΡΠ΅Π»ΡΠ½ΠΎ, ΠΏΠ΅ΡΠ΅Π΄ ΡΠΈΡΡΠΎΠ²ΠΎΠΉ ΠΎΠΏΠ΅ΡΠ°ΡΠΈΠ΅ΠΉ ΡΠ°Π·Π²ΡΡΡΡΠ²Π°Π½ΠΈΡ Π΄ΠΎΠ»ΠΆΠ½Π° ΠΈΠ΄ΡΠΈ Π±ΠΎΠ»Π΅Π΅ Π³ΡΡΠ±Π°Ρ ΠΎΠ±ΡΠ°Π±ΠΎΡΠΊΠ°, Π·Π΅Π½ΠΊΠ΅ΡΠΎΠ²Π°Π½ΠΈΠ΅ ΠΈΠ»ΠΈ ΡΠ°ΡΡΠ°ΡΠΈΠ²Π°Π½ΠΈΠ΅. ΠΡΠΊΠ»ΡΡΠ΅Π½ΠΈΠ΅ ΡΠΎΡΡΠ°Π²Π»ΡΡΡ ΠΎΡΠ²Π΅ΡΡΡΠΈΡ Π΄ΠΎ 10 ΠΌΠΌ Π΄ΠΈΠ°ΠΌΠ΅ΡΡΠΎΠΌ, ΡΠ°ΡΡΠΎΡΠΊΠ° ΠΊΠΎΡΠΎΡΡΡ ΡΠ»ΠΎΠΆΠ½Π°, Π° Π·Π΅Π½ΠΊΠ΅ΡΠΎΠ² ΠΏΠΎΠ΄Ρ ΠΎΠ΄ΡΡΠΈΡ Π³Π°Π±Π°ΡΠΈΡΠΎΠ² ΠΏΠΎΠΏΡΠΎΡΡΡ Π½Π΅Ρ, ΡΠΎΠ³Π΄Π° ΡΠ°Π·Π²ΡΡΡΠΊΠ° ΠΈΠ΄ΡΡ ΡΡΠ°Π·Ρ ΠΏΠΎΡΠ»Π΅ ΡΠ²Π΅ΡΠ»Π΅Π½ΠΈΡ ΠΈ Π²ΡΠΏΠΎΠ»Π½ΡΠ΅ΡΡΡ ΠΎΡΠΎΠ±ΠΎ Π°ΠΊΠΊΡΡΠ°ΡΠ½ΠΎ.
Π§ΡΠΎΠ±Ρ Π΄ΠΎΡΡΠΈΡΡ Π²ΡΡΠΎΠΊΠΈΡ ΠΏΠΎΠΊΠ°Π·Π°ΡΠ΅Π»Π΅ΠΉ ΠΊΠ°ΡΠ΅ΡΡΠ²Π° Π½ΡΠΆΠ½ΠΎ ΠΎΠ±Π΅ΡΠΏΠ΅ΡΠΈΡΡ ΡΡΡΠΊΡΡ ΡΠΎΠΎΡΠ½ΠΎΡΡΡ ΠΎΠ±ΡΠ°Π±Π°ΡΡΠ²Π°Π΅ΠΌΠΎΠ³ΠΎ ΠΎΡΠ²Π΅ΡΡΡΠΈΡ ΠΈ ΠΈΠ½ΡΡΡΡΠΌΠ΅Π½ΡΠ°. ΠΡΠΏΠΎΠ»Π½Π΅Π½ΠΈΠ΅ ΡΡΠ°Π·Ρ ΠΏΠΎΡΠ»Π΅ Π·Π΅Π½ΠΊΠ΅ΡΠΎΠ²Π°Π½ΠΈΡ Π½Π° ΡΠΎΠΌ ΠΆΠ΅ ΡΡΠ°Π½ΠΊΠ΅ ΠΏΠΎΠΌΠΎΠ³Π°Π΅Ρ ΠΈΠ·Π±Π΅ΠΆΠ°ΡΡ ΠΏΠΎΠ³ΡΠ΅ΡΠ½ΠΎΡΡΠ΅ΠΉ ΠΏΡΠΈ ΠΏΠ΅ΡΠ΅ΡΡΡΠ°Π½ΠΎΠ²ΠΊΠ΅ Π·Π°Π³ΠΎΡΠΎΠ²ΠΊΠΈ Π² ΠΏΠ°ΡΡΠΎΠ½Π΅. ΠΠ΅ΡΠ°Π»ΠΈ Ρ ΠΎΡΠ²Π΅ΡΡΡΠΈΡΠΌΠΈ 2-Π³ΠΎ ΠΊΠ»Π°ΡΡΠ° ΡΠΎΡΠ½ΠΎΡΡΠΈ ΠΏΡΠ°Π²ΠΈΠ»ΡΠ½ΠΎ ΠΎΠ±ΡΠ°Π±Π°ΡΡΠ²Π°ΡΡ Π·Π° 2 ΠΏΡΠΎΡ ΠΎΠ΄Π°, ΠΏΠ΅ΡΠ²ΡΠΉ β ΡΠ΅ΡΠ½ΠΎΠ²ΠΎΠΉ ΡΠ°Π·Π²ΡΡΡΠΊΠΎΠΉ, Π²ΡΠΎΡΠΎΠΉ β ΡΠΈΡΡΠΎΠ²ΠΎΠΉ. ΠΠ΅Π»ΠΈΡΠΈΠ½Π° ΠΏΡΠΈΠΏΡΡΠΊΠ° Π΄Π»Ρ ΠΏΠ΅ΡΠ²ΠΎΠ³ΠΎ ΡΠ°Π·Π° β 2/3 ΠΎΠ±ΡΠ΅Π³ΠΎ Π·Π½Π°ΡΠ΅Π½ΠΈΡ. Π Π΅Π·Π°ΠΊ Π΄Π»Ρ ΡΠ°ΠΊΠΎΠΉ ΠΌΠ΅Π½Π΅Π΅ ΡΡΠ΅Π±ΠΎΠ²Π°ΡΠ΅Π»ΡΠ½ΠΎΠΉ ΠΏΡΠΎΡΠ΅Π΄ΡΡΡ β ΡΡΠΎ ΠΎΡΡΠ»ΠΈΡΠΎΠ²Π°Π½Π½Π°Ρ ΠΈ ΠΎΡΠΊΠ°Π»ΠΈΠ±ΡΠΎΠ²Π°Π½Π½Π°Ρ ΠΏΠΎΡΠ΅ΡΡΠ²ΡΠ°Ρ ΡΠ°Π·ΠΌΠ΅Ρ ΡΠ°Π·Π²ΡΡΡΠΊΠ°.
Π Π΅Π·ΡΠΌΠΈΡΡΡ, ΡΡΠΎΠΈΡ ΠΎΡΠΌΠ΅ΡΠΈΡΡ, ΡΡΠΎ Π·Π΅Π½ΠΊΠ΅ΡΠΎΠ²Π°Π½ΠΈΠ΅ β ΠΎΠ±ΠΎΡΠΎΠ±Π»Π΅Π½Π½Π°Ρ ΠΎΠΏΠ΅ΡΠ°ΡΠΈΡ ΠΏΠΎ ΠΎΠ±ΡΠ°Π±ΠΎΡΠΊΠ΅ ΠΎΡΠ²Π΅ΡΡΡΠΈΠΉ Π² ΠΌΠ΅ΡΠ°Π»Π»ΠΈΡΠ΅ΡΠΊΠΈΡ ΠΈΠ·Π΄Π΅Π»ΠΈΡΡ , ΠΎΡΠ»ΠΈΡΠ½Π°Ρ ΠΎΡ ΡΠ°Π·Π²ΡΡΡΠΊΠΈ, ΠΈ Π½Π΅ ΠΈΠΌΠ΅ΡΡΠ°Ρ ΠΏΡΠ°ΠΊΡΠΈΡΠ΅ΡΠΊΠΈ Π½ΠΈΡΠ΅Π³ΠΎ ΠΎΠ±ΡΠ΅Π³ΠΎ Ρ Π·Π΅Π½ΠΊΠΎΠ²Π°Π½ΠΈΠ΅ΠΌ. ΠΠ»Π°Π²Π½ΠΎΠ΅ Π½Π°Π·Π½Π°ΡΠ΅Π½ΠΈΠ΅ Π·Π΅Π½ΠΊΠ΅ΡΠ° β ΡΠΌΠ΅Π½ΡΡΠΈΡΡ ΡΠ΅ΡΠΎΡ ΠΎΠ²Π°ΡΠΎΡΡΠΈ ΡΡΠ΅Π½ΠΎΠΊ ΠΎΡΠ²Π΅ΡΡΡΠΈΡ ΠΈ ΡΠ²Π΅Π»ΠΈΡΠΈΡΡ ΡΠΎΡΠ½ΠΎΡΡΡ Π²ΡΠΏΠΎΠ»Π½Π΅Π½ΠΈΡ ΠΎΡΠ²Π΅ΡΡΡΠΈΡ. ΠΠΏΠ΅ΡΠ°ΡΠΈΡ Π²ΡΠΏΠΎΠ»Π½ΡΠ΅ΡΡΡ ΠΏΠΎΡΠ»Π΅ ΡΠ²Π΅ΡΠ»Π΅Π½ΠΈΡ, Π»ΠΈΡΡΡ ΠΈΠ»ΠΈ ΡΡΠ°ΠΌΠΏΠΎΠ²ΠΊΠΈ ΠΈ ΠΏΡΠ΅Π΄ΡΠ΅ΡΡΠ²ΡΠ΅Ρ ΡΠΈΡΡΠΎΠ²ΠΎΠΉ ΠΎΠ±ΡΠ°Π±ΠΎΡΠΊΠ΅. Π‘Π±ΠΎΡΠ½ΡΠΉ Π·Π΅Π½ΠΊΠ΅Ρ ΠΌΠΎΠΆΠ΅Ρ ΡΠΎΠ²ΠΌΠ΅ΡΠ°ΡΡΡΡ ΡΠΎ ΡΠ²Π΅ΡΠ»ΠΎΠΌ, ΡΠ°Π·Π²ΡΡΡΠΊΠΎΠΉ ΠΈ Π΄ΡΡΠ³ΠΈΠΌΠΈ ΠΈΠ½ΡΡΡΡΠΌΠ΅Π½ΡΠ°ΠΌΠΈ.Β ΠΠ°Π» ΠΏΡΠΈΠ±ΠΎΡΠ° ΡΠΎΡΡΠΎΠΈΡ ΠΈΠ· Π±ΡΡΡΡΠΎΡΠ΅ΠΆΡΡΠ΅ΠΉ ΡΡΠ°Π»ΠΈ, Π° ΡΠ°Π±ΠΎΡΠΈΠ΅ Π·ΡΠ±ΡΡ, ΠΈΠ½ΠΎΠ³Π΄Π°, ΠΈΠ· ΡΠ²ΡΡΠ΄ΠΎΡΠΏΠ»Π°Π²Π½ΡΡ Π²ΡΡΠ°Π²ΠΎΠΊ. Π‘ΠΎΠ²ΠΌΠ΅ΡΡΠΈΠΌΡΠ΅ Ρ ΡΡΠΈΠΌ ΠΎΡΠ΄Π΅Π»ΠΎΡΠ½ΡΠΌ ΡΠ²Π΅ΡΠ»ΠΎΠΌ Π°ΠΏΠΏΠ°ΡΠ°ΡΡ β ΡΡΠ΅Π·Π΅ΡΠΎΠ²ΠΎΡΠ½ΡΠΉ, ΡΠΎΠΊΠ°ΡΠ½ΡΠΉ, ΡΠ°ΡΡΠΎΡΠ½ΡΠΉ ΠΈ ΡΠ²Π΅ΡΠ»ΠΈΠ»ΡΠ½ΡΠΉ.
ΠΡΠ±ΠΎΡ ΠΊΠΎΠ½ΠΊΡΠ΅ΡΠ½ΠΎΠ³ΠΎ Π·Π΅Π½ΠΊΠ΅ΡΠ° ΠΎΡΡΡΠ΅ΡΡΠ²Π»ΡΠ΅ΡΡΡ Π² Π·Π°Π²ΠΈΡΠΈΠΌΠΎΡΡΠΈ ΠΎΡ Π΄ΠΈΠ°ΠΌΠ΅ΡΡΠ° ΠΎΡΠ²Π΅ΡΡΡΠΈΡ, ΡΡΠ΅ΠΏΠ΅Π½ΠΈ ΠΎΠ±ΡΠ°Π±ΠΎΡΠΊΠΈ ΠΈ ΠΌΠ°ΡΠ΅ΡΠΈΠ°Π»Π° Π·Π°Π³ΠΎΡΠΎΠ²ΠΊΠΈ.
Π Π΅ΠΆΠΈΠΌ ΡΠ°Π±ΠΎΡΡ ΡΡΠ°Π½ΠΊΠ° ΠΈ Π΄ΡΡΠ³ΠΈΠ΅ Π½Π΅ΠΎΠ±Ρ ΠΎΠ΄ΠΈΠΌΡΠ΅ Π΄Π°Π½Π½ΡΠ΅ β ΡΠ°ΡΡΡΡΠ½ΡΠ΅ Π²Π΅Π»ΠΈΡΠΈΠ½Ρ, ΠΊΠΎΡΠΎΡΡΠ΅ ΠΎΡΠΎΠ±ΡΠ°ΠΆΠ°ΡΡΡΡ Π² ΡΠ°Π±ΠΎΡΠΈΡ ΡΠ΅ΡΡΠ΅ΠΆΠ°Ρ ΠΈΠ·Π³ΠΎΡΠΎΠ²Π»ΡΠ΅ΠΌΡΡ Π΄Π΅ΡΠ°Π»Π΅ΠΉ. ΠΡΡΡΡΠΏΠ»Π΅Π½ΠΈΠ΅ ΠΎΡ ΡΡΠΈΡ Π²Π΅Π»ΠΈΡΠΈΠ½ ΠΈ ΠΎΠ±ΡΠ΅ΠΉ ΡΠ΅Ρ Π½ΠΎΠ»ΠΎΠ³ΠΈΠΈ Π·Π΅Π½ΠΊΠ΅ΡΠΎΠ²Π°Π½ΠΈΡ ΡΠ²Π»ΡΠ΅ΡΡΡ ΠΎΠ΄Π½ΠΎΠΉ ΠΈΠ· ΠΎΡΠ½ΠΎΠ²Π½ΡΡ ΠΏΡΠΈΡΠΈΠ½ Π²ΠΎΠ·Π½ΠΈΠΊΠ½ΠΎΠ²Π΅Π½ΠΈΡ ΠΏΡΠΎΠΈΠ·Π²ΠΎΠ΄ΡΡΠ²Π΅Π½Π½ΠΎΠ³ΠΎ Π±ΡΠ°ΠΊΠ°. Π ΠΊΠ°ΡΠ΅ΡΡΠ²Π΅ ΡΠΈΠ½ΠΈΡΠ½ΠΎΠΉ ΠΎΠΏΠ΅ΡΠ°ΡΠΈΠΈ Π·Π΅Π½ΠΊΠ΅ΡΠΎΠ²Π°Π½ΠΈΠ΅ ΠΈΡΠΏΠΎΠ»ΡΠ·ΡΠ΅ΡΡΡ Π΄ΠΎΠ²ΠΎΠ»ΡΠ½ΠΎ ΡΠ΅Π΄ΠΊΠΎ, ΡΠΎΠ»ΡΠΊΠΎ ΠΏΡΠΈ ΠΏΠΎΠ½ΠΈΠΆΠ΅Π½Π½ΡΡ ΡΡΠ΅Π±ΠΎΠ²Π°Π½ΠΈΡΡ ΠΊ ΡΠΎΡΠ½ΠΎΡΡΠΈ, ΠΏΡΠΈ ΠΊΠ»Π°ΡΡΠ΅ Π½ΠΈΠΆΠ΅ 4-Π³ΠΎ. ΠΠ° ΡΡΠ½ΠΊΠ΅ ΠΏΡΠΎΠ΄Π°ΡΡΡΡ ΠΌΠ½ΠΎΠΆΠ΅ΡΡΠ²ΠΎ Π·Π΅Π½ΠΊΠ΅ΡΠΎΠ² Ρ ΡΠ°Π·Π½ΡΠΌΠΈ Ρ Π°ΡΠ°ΠΊΡΠ΅ΡΠΈΡΡΠΈΠΊΠ°ΠΌΠΈ, ΠΎΠΏΡΠΈΠΌΠΈΠ·ΠΈΡΠΎΠ²Π°Π½Π½ΡΠΌΠΈ Π΄Π»Ρ ΡΠ°Π±ΠΎΡΡ Π² ΡΠ°Π·Π½ΡΡ ΡΡΠ»ΠΎΠ²ΠΈΡΡ , ΠΏΠΎΠ΄ ΡΠ°Π·Π½ΡΠΉ ΠΌΠ΅ΡΠ°Π»Π» ΠΈ Π΄ΠΈΠ°ΠΌΠ΅ΡΡΡ ΠΎΡΠ²Π΅ΡΡΡΠΈΠΉ.
ΠΠ΅Π½ΠΊΠ΅ΡΡ
Β
ΠΠ΅Π½ΠΊΠ΅ΡΡ (ΡΠΈΡ. 3.34, Π°) ΠΏΡΠ΅Π΄Π½Π°Π·Π½Π°ΡΠ΅Π½Ρ Π΄Π»Ρ ΠΎΠ±ΡΠ°Π±ΠΎΡΠΊΠΈ ΠΎΡΠ²Π΅ΡΡΡΠΈΠΉ Π² Π·Π°Π³ΠΎΡΠΎΠ²ΠΊΠ°Ρ , ΠΏΠΎΠ»ΡΡΠ΅Π½Π½ΡΡ ΠΎΡΠ»ΠΈΠ²ΠΊΠΎΠΉ, ΡΡΠ°ΠΌΠΏΠΎΠ²ΠΊΠΎΠΉ ΠΈΠ»ΠΈ ΠΏΡΠ΅Π΄Π²Π°ΡΠΈΡΠ΅Π»ΡΠ½ΡΠΌ ΡΠ²Π΅ΡΠ»Π΅Π½ΠΈΠ΅ΠΌ. Π ΠΎΡΠ»ΠΈΡΠΈΠ΅ ΠΎΡ ΡΠ²Π΅ΡΠ»Π° Π·Π΅Π½ΠΊΠ΅Ρ ΠΈΠΌΠ΅Π΅Ρ Π±ΠΎΠ»ΡΡΠ΅Π΅ ΡΠΈΡΠ»ΠΎ ΡΠ΅ΠΆΡΡΠΈΡ ΠΊΡΠΎΠΌΠΎΠΊ (ΡΡΠΈ ΠΈΠ»ΠΈ ΡΠ΅ΡΡΡΠ΅), ΡΡΠΎ ΠΎΠ±Π΅ΡΠΏΠ΅ΡΠΈΠ²Π°Π΅Ρ ΠΏΠΎΠ»ΡΡΠ΅Π½ΠΈΠ΅ ΠΏΠΎΠ²Π΅ΡΡ Π½ΠΎΡΡΠ΅ΠΉ Ρ Π±ΠΎΠ»Π΅Π΅ Π²ΡΡΠΎΠΊΠΈΠΌΠΈ ΠΏΠΎΠΊΠ°Π·Π°ΡΠ΅Π»ΡΠΌΠΈ ΡΠΎΡΠ½ΠΎΡΡΠΈ ΠΈ ΡΠ΅ΡΠΎΡ ΠΎΠ²Π°ΡΠΎΡΡΠΈ.
ΠΠΎ ΠΊΠΎΠ½ΡΡΡΡΠΊΡΠΈΠΈ Π·Π΅Π½ΠΊΠ΅ΡΡ Π±ΡΠ²Π°ΡΡ Π½Π°ΡΠ°Π΄Π½ΡΠ΅ ΠΈ ΡΠ΅Π»ΡΠ½ΡΠ΅ ΠΈ ΠΌΠΎΠ³ΡΡ ΠΈΠΌΠ΅ΡΡ ΡΠ°Π·Π»ΠΈΡΠ½ΠΎΠ΅ Π½Π°ΠΏΡΠ°Π²Π»Π΅Π½ΠΈΠ΅ ΡΠ³Π»Π° ΡΠΏΠΈΡΠ°Π»ΠΈ (ΠΏΡΠ°Π²ΠΎΠ΅, Π»Π΅Π²ΠΎΠ΅, ΠΏΡΡΠΌΠΎΠ΅). ΠΠ΅Π½ΠΊΠ΅ΡΡ ΠΈΠ·Π³ΠΎΡΠ°Π²Π»ΠΈΠ²Π°ΡΡ ΠΈΠ· Π±ΡΡΡΡΠΎΡΠ΅ΠΆΡΡΠ΅ΠΉ ΡΡΠ°Π»ΠΈ ΠΈΠ»ΠΈ ΠΎΡΠ½Π°ΡΠ°ΡΡ ΠΏΠ»Π°ΡΡΠΈΠ½Π°ΠΌΠΈ ΠΈΠ· ΡΠ²Π΅ΡΠ΄ΠΎΠ³ΠΎ ΡΠΏΠ»Π°Π²Π° ΠΌΠ°ΡΠΎΠΊ ΠΠ6, ΠΠ8, BKbM, ΠΠ8Π, Π’5Π10, Π’15Π6. ΠΠ»Π°ΡΡΠΈΠ½Ρ ΠΈΠ· ΡΠ²Π΅ΡΠ΄ΠΎΠ³ΠΎ ΡΠΏΠ»Π°Π²Π° Π·Π°ΠΊΡΠ΅ΠΏΠ»ΡΡΡΡΡ Π² Π·Π΅Π½ΠΊΠ΅ΡΠ΅ ΠΏΡΠΈ ΠΏΠΎΠΌΠΎΡΠΈ ΠΏΠ°ΠΉΠΊΠΈ ΠΈΠ»ΠΈ ΠΊΠ»ΠΈΠ½ΠΎΠ²ΠΎΠ³ΠΎ ΠΊΡΠ΅ΠΏΠ»Π΅Π½ΠΈΠ΅, ΡΡΠΎ ΠΏΠΎΠ·Π²ΠΎΠ»ΡΠ΅Ρ ΠΌΠ½ΠΎΠ³ΠΎΠΊΡΠ°ΡΠ½ΠΎ ΠΈΡΠΏΠΎΠ»ΡΠ·ΠΎΠ²Π°ΡΡ ΠΊΠΎΡΠΏΡΡ Π·Π΅Π½ΠΊΠ΅ΡΠ°. Π Π°Π±ΠΎΡΠ°Ρ ΡΠ°ΡΡΡ Π·Π΅Π½ΠΊΠ΅ΡΠΎΠ², ΠΈΠ·Π³ΠΎΡΠΎΠ²Π»Π΅Π½Π½ΡΡ ΠΈΠ· Π±ΡΡΡΡΠΎΡΠ΅ΠΆΡΡΠ΅ΠΉ ΡΡΠ°Π»ΠΈ, ΠΈΠΌΠ΅Π΅Ρ ΠΎΠ±ΡΠ°ΡΠ½ΡΡ ΠΊΠΎΠ½ΡΡΠ½ΠΎΡΡΡ (ΠΏΠΎ Π½Π°ΠΏΡΠ°Π²Π»Π΅Π½ΠΈΡ ΠΊ Ρ Π²ΠΎΡΡΠΎΠ²ΠΈΠΊΡ) ΠΏΠΎΡΡΠ΄ΠΊΠ° 0,05β¦ 0,1 Π½Π° 100 ΠΌΠΌ Π΄Π»ΠΈΠ½Ρ ΡΠ°Π±ΠΎΡΠ΅ΠΉ ΡΠ°ΡΡΠΈ ΠΈ ΡΠΎΠ΅Π΄ΠΈΠ½ΡΠ΅ΡΡΡ Ρ Ρ Π²ΠΎΡΡΠΎΠ²ΠΈΠΊΠΎΠΌ ΡΠ°ΠΊ ΠΆΠ΅, ΠΊΠ°ΠΊ ΠΈ Ρ ΡΠ²Π΅ΡΠ», ΡΠ΅ΠΉΠΊΠΎΠΉ. Π¦Π΅Π»ΡΠ½ΡΠ΅ Π·Π΅Π½ΠΊΠ΅ΡΡ Π·Π°ΠΊΡΠ΅ΠΏΠ»ΡΡΡΡΡ Π½Π΅ΠΏΠΎΡΡΠ΅Π΄ΡΡΠ²Π΅Π½Π½ΠΎ Π² ΠΊΠΎΠ½ΠΈΡΠ΅ΡΠΊΠΎΠΌ ΠΎΡΠ²Π΅ΡΡΡΠΈΠΈ ΡΠΏΠΈΠ½Π΄Π΅Π»Ρ ΡΡΠ°Π½ΠΊΠ°, Π° Π½Π°ΡΠ°Π΄Π½ΡΠ΅ ΡΡΡΠ°Π½Π°Π²Π»ΠΈΠ²Π°ΡΡΡΡ Π½Π° ΡΠΏΠ΅ΡΠΈΠ°Π»ΡΠ½ΡΡ ΠΎΠΏΡΠ°Π²ΠΊΡ, ΡΠ°ΠΊΠΆΠ΅ ΠΈΠΌΠ΅ΡΡΡΡ ΠΊΠΎΠ½ΠΈΡΠ΅ΡΠΊΠΈΠΉ Ρ Π²ΠΎΡΡΠΎΠ²ΠΈΠΊ Π΄Π»Ρ ΡΡΡΠ°Π½ΠΎΠ²ΠΊΠΈ Π² ΡΠΏΠΈΠ½Π΄Π΅Π»Π΅ ΡΡΠ°Π½ΠΊΠ°.
Β
Π ΠΊΠ°ΡΠ΅ΡΡΠ²Π΅ ΡΠ΅ΠΆΡΡΠ΅ΠΉ ΡΠ°ΡΡΠΈ Π½Π°ΡΠ°Π΄Π½ΡΡ Π·Π΅Π½ΠΊΠ΅ΡΠΎΠ² ΠΈΡΠΏΠΎΠ»ΡΠ·ΡΡΡΡΡ ΠΌΠ½ΠΎΠ³ΠΎΠ³ΡΠ°Π½Π½ΡΠ΅ ΡΠ²Π΅ΡΠ΄ΠΎΡΠΏΠ»Π°Π²Π½ΡΠ΅ ΠΏΠ»Π°ΡΡΠΈΠ½Ρ. ΠΡΠ΅ΠΏΠ»Π΅Π½ΠΈΠ΅ ΡΠ°ΠΊΠΈΡ ΠΏΠ»Π°ΡΡΠΈΠ½ Π² ΠΊΠΎΡΠΏΡΡΠ΅ Π½Π°ΡΠ°Π΄Π½ΠΎΠ³ΠΎ Π·Π΅Π½ΠΊΠ΅ΡΠ° ΠΎΡΡΡΠ΅ΡΡΠ²Π»ΡΡΡ ΠΌΠ΅Ρ Π°Π½ΠΈΡΠ΅ΡΠΊΠΈΠΌ ΠΏΡΡΠ΅ΠΌ (ΡΠΈΡ. 3.35). Π Π΅ΠΆΡΡΠΈΠ΅ ΠΏΠ»Π°ΡΡΠΈΠ½Ρ 1 Π·Π°ΠΊΡΠ΅ΠΏΠ»ΡΡΡΡΡ Π² ΠΊΠΎΡΠΏΡΡΠ΅ 2 ΠΏΡΠΈ ΠΏΠΎΠΌΠΎΡΠΈ ΡΡΠ³ΠΈ 3, ΡΡΠΎ ΠΏΠΎΠ·Π²ΠΎΠ»ΡΠ΅Ρ ΠΏΡΠΎΠΈΠ·Π²ΠΎΠ΄ΠΈΡΡ Π·Π°ΠΌΠ΅Π½Ρ ΠΏΠ»Π°ΡΡΠΈΠ½ Π½Π΅ΠΏΠΎΡΡΠ΅Π΄ΡΡΠ²Π΅Π½Π½ΠΎ Π½Π° ΡΡΠ°Π½ΠΊΠ΅. ΠΠ»Ρ ΡΡΠΎΠ³ΠΎ Π΄ΠΎΡΡΠ°ΡΠΎΡΠ½ΠΎ ΡΠΌΠ΅ΡΡΠΈΡΡ ΡΡΠ³Ρ 3, ΠΏΠΎΠ²Π΅ΡΠ½ΡΡΡ ΠΏΠ»Π°ΡΡΠΈΠ½Ρ ΡΠ»Π΅Π΄ΡΡΡΠ΅ΠΉ Π³ΡΠ°Π½ΡΡ ΠΈΠ»ΠΈ Π·Π°ΠΌΠ΅Π½ΠΈΡΡ Π΅Π΅ Π½Π° Π½ΠΎΠ²ΡΡ, ΡΠ½ΠΎΠ²Π° Π·Π°ΠΊΡΠ΅ΠΏΠΈΡΡ ΡΡΠ³Ρ ΠΈ ΠΏΡΠΎΠ΄ΠΎΠ»ΠΆΠ°ΡΡ ΡΠ°Π±ΠΎΡΡ. ΠΠΎΠ·ΠΌΠΎΠΆΠ½ΠΎΡΡΡ ΠΎΡΠ½Π°ΡΠ΅Π½ΠΈΡ ΡΠ°ΠΊΠΈΡ Π·Π΅Π½ΠΊΠ΅ΡΠΎΠ² ΠΏΠ»Π°ΡΡΠΈΠ½Π°ΠΌΠΈ ΠΈΠ· ΡΠ°Π·Π»ΠΈΡΠ½ΡΡ ΠΈΠ½ΡΡΡΡΠΌΠ΅Π½ΡΠ°Π»ΡΠ½ΡΡ ΠΌΠ°ΡΠ΅ΡΠΈΠ°Π»ΠΎΠ² ΠΏΠΎΠ·Π²ΠΎΠ»ΡΠ΅Ρ ΡΡΡΠ΅ΡΡΠ²Π΅Π½Π½ΠΎ ΡΠ°ΡΡΠΈΡΠΈΡΡ ΡΠ΅Ρ Π½ΠΎΠ»ΠΎΠ³ΠΈΡΠ΅ΡΠΊΠΈΠ΅ Π²ΠΎΠ·ΠΌΠΎΠΆΠ½ΠΎΡΡΠΈ ΠΈ ΠΏΡΠΎΠΈΠ·Π²ΠΎΠ΄ΠΈΡΠ΅Π»ΡΠ½ΠΎΡΡΡ ΠΏΡΠΈ Π·Π΅Π½ΠΊΠ΅ΡΠΎΠ²Π°Π½ΠΈΠΈ.
ΠΠ΅ΠΎΠΌΠ΅ΡΡΠΈΡΠ΅ΡΠΊΠΈΠ΅ ΠΏΠ°ΡΠ°ΠΌΠ΅ΡΡΡ ΡΠ΅ΠΆΡΡΠ΅ΠΉ ΡΠ°ΡΡΠΈ Π·Π΅Π½ΠΊΠ΅ΡΠΎΠ² (ΡΠΌ. ΡΠΈΡ. 3.34, Π±) Π²ΡΠ±ΠΈΡΠ°ΡΡΡΡ Π² Π·Π°Π²ΠΈΡΠΈΠΌΠΎΡΡΠΈ ΠΎΡ ΡΡΠ»ΠΎΠ²ΠΈΠΉ ΠΎΠ±ΡΠ°Π±ΠΎΡΠΊΠΈ: Π³Π»Π°Π²Π½ΡΠΉ ΡΠ³ΠΎΠ» Π² ΠΏΠ»Π°Π½Π΅ Ρ = 30β¦ 60 ΠΏΠ΅ΡΠ΅Π΄Π½ΠΈΠΉ ΡΠ³ΠΎΠ» Ρ = 3β¦ 30 Β° Π΄Π»Ρ Π·Π΅Π½ΠΊΠ΅ΡΠΎΠ² ΠΈΠ· Π±ΡΡΡΡΠΎΡΠ΅ΠΆΡΡΠ΅ΠΉ ΡΡΠ°Π»ΠΈ,Π΄Π»Ρ Π·Π΅Π½ΠΊΠ΅ΡΠΎΠ², ΠΎΡΠ½Π°ΡΠ΅Π½Π½ΡΡ ΠΏΠ»Π°ΡΡΠΈΠ½Π°ΠΌΠΈ ΡΠ²Π΅ΡΠ΄ΠΎΠ³ΠΎ ΡΠΏΠ»Π°Π²Π°, ΡΡΠΎΡ ΡΠ³ΠΎΠ» ΡΠΎΡΡΠ°Π²Π»ΡΠ΅Ρ ΠΎΡ 5 Π΄ΠΎ -5Β°; Π·Π°Π΄Π½ΠΈΠΉ ΡΠ³ΠΎΠ» Π° Π½Π° Π³Π»Π°Π²Π½ΡΡ ΡΠ΅ΠΆΡΡΠΈΡ ΠΊΡΠΎΠΌΠΊΠ°Ρ ΡΠΎΡΡΠ°Π²Π»ΡΠ΅Ρ 8β¦ 15 ΠΡΠ±ΠΎΡ ΠΊΠΎΠ½ΡΡΡΡΠΊΡΠΈΠΈ Π·Π΅Π½ΠΊΠ΅ΡΠ° ΠΈ ΠΌΠ°ΡΠ΅ΡΠΈΠ°Π»Π° ΡΠ°Π±ΠΎΡΠ΅ΠΉ ΡΠ°ΡΡΠΈ Π² Π·Π½Π°ΡΠΈΡΠ΅Π»ΡΠ½ΠΎΠΉ ΡΡΠ΅ΠΏΠ΅Π½ΠΈ Π·Π°Π²ΠΈΡΠΈΡ ΠΎΡ ΠΎΠ±ΡΠ°Π±Π°ΡΡΠ²Π°Π΅ΠΌΠΎΠ³ΠΎ ΠΌΠ°ΡΠ΅ΡΠΈΠ°Π»Π° ΠΈ ΠΏΠ°ΡΠ°ΠΌΠ΅ΡΡΠΎΠ² ΠΎΠ±ΡΠ°Π±Π°ΡΡΠ²Π°Π΅ΠΌΠΎΠ³ΠΎ ΠΎΡΠ²Π΅ΡΡΡΠΈΡ:
β’ Π·Π΅Π½ΠΊΠ΅ΡΡ ΠΈΠ· Π±ΡΡΡΡΠΎΡΠ΅ΠΆΡΡΠ΅ΠΉ ΡΡΠ°Π»ΠΈ, ΠΈΠΌΠ΅ΡΡΠΈΠ΅ ΡΡΠΈ-ΡΠ΅ΡΡΡΠ΅ Π·ΡΠ±Π° ΠΈ Π΄ΠΈΠ°ΠΌΠ΅ΡΡ ΠΎΡ 10 Π΄ΠΎ 40 ΠΌΠΌ, ΠΏΡΠΈΠΌΠ΅Π½ΡΡΡΡΡ Π΄Π»Ρ ΠΎΠ±ΡΠ°Π±ΠΎΡΠΊΠΈ ΠΎΡΠ²Π΅ΡΡΡΠΈΠΉ Π² Π·Π°Π³ΠΎΡΠΎΠ²ΠΊΠ°Ρ ΠΈΠ· ΠΊΠΎΠ½ΡΡΡΡΠΊΡΠΈΠΎΠ½Π½ΠΎΠΉ ΡΡΠ°Π»ΠΈ;
β’Β Β Π·Π΅Π½ΠΊΠ΅ΡΡ, ΠΎΡΠ½Π°ΡΠ΅Π½Π½ΡΠ΅ ΠΏΠ»Π°ΡΡΠΈΠ½Π°ΠΌΠΈ ΠΈΠ· ΡΠ²Π΅ΡΠ΄ΠΎΠ³ΠΎ ΡΠΏΠ»Π°Π²Π°, ΠΈΠΌΠ΅ΡΡΠΈΠ΅ ΡΡΠΈ-ΡΠ΅ΡΡΡΠ΅ Π·ΡΠ±Π° ΠΈ Π½ΠΎΠΌΠΈΠ½Π°Π»ΡΠ½ΡΠΉ Π΄ΠΈΠ°ΠΌΠ΅ΡΡ ΠΎΡ 14 Π΄ΠΎ 50 ΠΌΠΌ, ΠΈΡΠΏΠΎΠ»ΡΠ·ΡΡΡΡΡ ΠΏΡΠΈ ΠΎΠ±ΡΠ°Π±ΠΎΡΠΊΠ΅ ΠΎΡΠ²Π΅ΡΡΡΠΈΠΉ Π² Π·Π°Π³ΠΎΡΠΎΠ²ΠΊΠ°Ρ ΠΈΠ· ΡΡΡΠ΄Π½ΠΎΠΎΠ±ΡΠ°Π±Π°ΡΡΠ²Π°Π΅ΠΌΡΡ ΠΈ Π·Π°ΠΊΠ°Π»Π΅Π½Π½ΡΡ ΡΡΠ°Π»Π΅ΠΉ;
β’Β Π·Π΅Π½ΠΊΠ΅ΡΡ Ρ Π½Π°ΡΠ°Π΄Π½ΡΠΌΠΈ Π³ΠΎΠ»ΠΎΠ²ΠΊΠ°ΠΌΠΈ ΠΈΠ· Π±ΡΡΡΡΠΎΡΠ΅ΠΆΡΡΠ΅ΠΉ ΡΡΠ°Π»ΠΈ Π½ΠΎΠΌΠΈΠ½Π°Π»ΡΠ½ΡΠΌ Π΄ΠΈΠ°ΠΌΠ΅ΡΡΠΎΠΌ ΠΎΡ 32 Π΄ΠΎ 80 ΠΌΠΌ ΠΏΡΠ΅Π΄Π½Π°Π·Π½Π°ΡΠ΅Π½Ρ Π΄Π»Ρ ΠΎΠ±ΡΠ°Π±ΠΎΡΠΊΠΈ ΠΎΡΠ²Π΅ΡΡΡΠΈΠΉ Π² Π·Π°Π³ΠΎΡΠΎΠ²ΠΊΠ°Ρ ΠΈΠ· ΠΊΠΎΠ½ΡΡΡΡΠΊΡΠΈΠΎΠ½Π½ΠΎΠΉ ΡΡΠ°Π»ΠΈ;
β’Β ΠΏΠ΅ΡΠΎΠ²ΡΠ΅ Π·Π΅Π½ΠΊΠ΅ΡΡ ΡΠ»ΡΠΆΠ°Ρ Π΄Π»Ρ ΠΎΠ±ΡΠ°Π±ΠΎΡΠΊΠΈ Π³Π»ΡΡ ΠΈΡ ΠΎΡΠ²Π΅ΡΡΡΠΈΠΉ Π² Π·Π°Π³ΠΎΡΠΎΠ²ΠΊΠ°Ρ ΠΈΠ· ΡΡΠ³ΡΠ½Π° ΠΈ ΡΠ²Π΅ΡΠ½ΡΡ ΠΌΠ΅ΡΠ°Π»Π»ΠΎΠ²;
β’Β Π΄Π»Ρ ΠΎΠ±ΡΠ°Π±ΠΎΡΠΊΠΈ Π³Π»ΡΡ ΠΈΡ ΠΎΡΠ²Π΅ΡΡΡΠΈΠΉ Π΄ΠΈΠ°ΠΌΠ΅ΡΡΠΎΠΌ ΠΎΡ 15 Π΄ΠΎ 25 ΠΌΠΌ ΠΏΡΠΈΠΌΠ΅Π½ΡΠ΅ΡΡΡ ΡΠΏΠ΅ΡΠΈΠ°Π»ΡΠ½ΡΠΉ Π·Π΅Π½ΠΊΠ΅Ρ, Ρ ΠΊΠΎΡΠΎΡΠΎΠ³ΠΎ Π² ΠΊΠΎΡΠΏΡΡΠ΅ Π²ΡΠΏΠΎΠ»Π½Π΅Π½ΠΎ ΡΠΏΠ΅ΡΠΈΠ°Π»ΡΠ½ΠΎΠ΅ ΠΎΡΠ²Π΅ΡΡΡΠΈΠ΅ Π΄Π»Ρ ΠΏΠΎΠ΄Π°ΡΠΈ Π‘ΠΠ Π² Π·ΠΎΠ½Ρ ΡΠ΅Π·Π°Π½ΠΈΡ (ΡΠΈΡ. 3.36).
ΠΠ·Π½Π°ΡΠΈΠ²Π°Π½ΠΈΠ΅ Π·Π΅Π½ΠΊΠ΅ΡΠΎΠ² (ΡΠΈΡ. 3.37) ΠΏΡΠΎΠΈΡΡ ΠΎΠ΄ΠΈΡ ΠΏΠΎ Π·Π°Π΄Π½ΠΈΠΌ ΠΏΠΎΠ²Π΅ΡΡ Π½ΠΎΡΡΡΠΌ, Π³Π΄Π΅ ΠΎΠ±ΡΠ°Π·ΡΡΡΡΡ ΠΏΠ»ΠΎΡΠ°Π΄ΠΊΠΈ Ρ Π·Π°Π΄Π½ΠΈΠΌ ΡΠ³Π»ΠΎΠΌ, ΡΠ°Π²Π½ΡΠΌ Π½ΡΠ»Ρ, ΠΈ ΡΠΈΡΠΈΠ½ΠΎΠΉ h4; ΠΏΠΎ ΠΏΠ΅ΡΠ΅Π΄Π½ΠΈΠΌ ΠΏΠΎΠ²Π΅ΡΡ Π½ΠΎΡΡΡΠΌ Ρ ΠΎΠ±ΡΠ°Π·ΠΎΠ²Π°Π½ΠΈΠ΅ΠΌ Π»ΡΠ½ΠΊΠΈ; ΠΏΠΎ Π»Π΅Π½ΡΠΎΡΠΊΠ΅ Ρ ΠΎΠ±ΡΠ°Π·ΠΎΠ²Π°Π½ΠΈΠ΅ΠΌ ΠΏΠΎΠΏΠ΅ΡΠ΅ΡΠ½ΡΡ ΠΏΡΠΎΡΠΎΡΠΈΠ½ Π½Π° Π΄Π»ΠΈΠ½Π΅ ΠΠ»; ΠΏΠΎ ΡΠ³ΠΎΠ»ΠΊΠ°ΠΌ Ρ ΠΎΠ±ΡΠ°Π·ΠΎΠ²Π°Π½ΠΈΠ΅ΠΌ ΠΊΠΎΠ½ΠΈΡΠ΅ΡΠΊΠΈΡ ΠΈΠ»ΠΈ ΡΠΈΠ»ΠΈΠ½Π΄ΡΠΈΡΠ΅ΡΠΊΠΈΡ ΡΡΠ°ΡΡΠΊΠΎΠ² hy. Π ΠΊΠ°ΡΠ΅ΡΡΠ²Π΅ ΠΊΡΠΈΡΠ΅ΡΠΈΡ ΠΈΠ·Π½ΠΎΡΠ° Π·Π΅Π½ΠΊΠ΅ΡΠΎΠ² ΠΏΡΠΈ ΠΎΠ±ΡΠ°Π±ΠΎΡΠΊΠ΅ Π·Π°Π³ΠΎΡΠΎΠ²ΠΎΠΊ ΠΈΠ· ΡΡΠ°Π»ΠΈ ΠΏΡΠΈΠ½ΡΡ ΠΈΠ·Π½ΠΎΡ Π·Π΅Π½ΠΊΠ΅ΡΠ° ΠΏΠΎ ΡΠ³ΠΎΠ»ΠΊΠ°ΠΌ, ΡΠ°Π²Π½ΡΠΉ 1,2β¦ 1,5 ΠΌΠΌ, Π° ΠΏΡΠΈ ΠΎΠ±ΡΠ°Π±ΠΎΡΠΊΠ΅ Π·Π°Π³ΠΎΡΠΎΠ²ΠΎΠΊ ΠΈΠ· ΡΡΠ³ΡΠ½Π° β 0,8β¦ 1,5 ΠΌΠΌ. ΠΠ°ΡΠ°ΡΠΈΠ²Π°Π½ΠΈΠ΅ ΠΈ ΠΏΠ΅ΡΠ΅ΡΠ°ΡΠΈΠ²Π°Π½ΠΈΠ΅ ΠΈΠ·Π½ΠΎΡΠ΅Π½Π½ΡΡ Π·Π΅Π½ΠΊΠ΅ΡΠΎΠ² ΠΎΡΡΡΠ΅ΡΡΠ²Π»ΡΠ΅ΡΡΡ, ΠΊΠ°ΠΊ ΠΏΡΠ°Π²ΠΈΠ»ΠΎ, Π½Π° ΡΠΏΠ΅ΡΠΈΠ°Π»ΡΠ½ΠΎΠΌ ΠΎΠ±ΠΎΡΡΠ΄ΠΎΠ²Π°Π½ΠΈΠΈ Π² Π·Π°ΡΠΎΡΠ½ΡΡ ΡΠ΅Ρ Π°Ρ .
Β
ΠΠ΅Π½ΠΊΠΎΠ²ΠΊΠΈ ΠΈ ΡΠ΅ΠΊΠΎΠ²ΠΊΠΈ
Β
ΠΠ΅Π½ΠΊΠΎΠ²ΠΊΠΈ ΠΈ ΡΠ΅ΠΊΠΎΠ²ΠΊΠΈ (ΡΠΈΡ. 3.38) Π΄Π»Ρ ΠΎΠ±ΡΠ°Π±ΠΎΡΠΊΠΈ ΠΎΠΏΠΎΡΠ½ΡΡ ΠΏΠΎΠ²Π΅ΡΡ Π½ΠΎΡΡΠ΅ΠΉ ΠΏΠΎΠ΄ ΠΊΡΠ΅ΠΏΠ΅ΠΆΠ½ΡΠ΅ Π²ΠΈΠ½ΡΡ Π² ΠΎΡΠ»ΠΈΡΠΈΠ΅ ΠΎΡ Π·Π΅Π½ΠΊΠ΅ΡΠΎΠ² ΠΈΠΌΠ΅ΡΡ ΡΠ΅ΠΆΡΡΠΈΠ΅ Π·ΡΠ±ΡΡ Π½Π° ΡΠΎΡΡΠ΅ ΠΈ Π½Π°ΠΏΡΠ°Π²Π»ΡΡΡΠΈΠ΅ ΡΠ°ΠΏΡΡ, ΠΊΠΎΡΠΎΡΡΠ΅ ΠΎΠ±Π΅ΡΠΏΠ΅ΡΠΈΠ²Π°ΡΡ Π½ΡΠΆΠ½ΠΎΠ΅ Π½Π°ΠΏΡΠ°Π²Π»Π΅Π½ΠΈΠ΅ Π·Π΅Π½ΠΊΠΎΠ²ΠΎΠΊ ΠΈ ΡΠ΅ΠΊΠΎΠ²ΠΎΠΊ Π² ΠΏΡΠΎΡΠ΅ΡΡΠ΅ ΠΎΠ±ΡΠ°Π±ΠΎΡΠΊΠΈ. Π¦Π°ΠΏΡΠ° Π²Π²ΠΎΠ΄ΠΈΡΡΡ Π² ΠΏΡΠ΅Π΄Π²Π°ΡΠΈΡΠ΅Π»ΡΠ½ΠΎ ΠΏΡΠΎΡΠ²Π΅ΡΠ»Π΅Π½Π½ΠΎΠ΅ ΠΎΡΠ²Π΅ΡΡΡΠΈΠ΅, ΠΏΡΠΈ ΡΡΠΎΠΌ ΠΎΡΠΈ ΠΎΡΠ²Π΅ΡΡΡΠΈΡ ΠΈ ΠΎΠ±ΡΠ°Π·ΠΎΠ²Π°Π½Π½ΠΎΠ³ΠΎ Π·Π΅Π½ΠΊΠΎΠ²ΠΊΠΎΠΉ ΡΠ³Π»ΡΠ±Π»Π΅Π½ΠΈΡ ΡΠΎΠ²ΠΏΠ°Π΄Π°ΡΡ. ΠΠ΅Π½ΠΊΠΎΠ²ΠΊΠΈ Π΄Π»Ρ ΠΎΠ±ΡΠ°Π±ΠΎΡΠΊΠΈ ΠΎΡΠ²Π΅ΡΡΡΠΈΠΉ ΠΏΠΎΠ΄ ΡΠΈΠ»ΠΈΠ½Π΄ΡΠΈΡΠ΅ΡΠΊΠΈΠ΅ Π³ΠΎΠ»ΠΎΠ²ΠΊΠΈ Π²ΠΈΠ½ΡΠΎΠ² ΠΈΠ·Π³ΠΎΡΠ°Π²Π»ΠΈΠ²Π°ΡΡΡΡ Ρ ΡΠΈΠ»ΠΈΠ½Π΄ΡΠΈΡΠ΅ΡΠΊΠΈΠΌ ΠΈ ΠΊΠΎΠ½ΠΈΡΠ΅ΡΠΊΠΈΠΌ Ρ Π²ΠΎΡΡΠΎΠ²ΠΈΠΊΠΎΠΌ. ΠΠ΅Π½ΠΊΠΎΠ²ΠΊΠΈ Ρ ΡΠΈΠΏΠΈΠ½Π΄ΡΠΈΡΠ΅ΡΠΊΠΈΠΌ Ρ Π²ΠΎΡΡΠΎΠ²ΠΈΠΊΠΎΠΌ (ΡΠΈΡ. 3.38, ΠΈ) Π²ΡΠΏΡΡΠΊΠ°ΡΡΡΡ Π΄ΠΈΠ°ΠΌΠ΅ΡΡΠΎΠΌ 15; 18; 20; 22 ΠΈ 24 ΠΌΠΌ: Π° Π·Π΅Π½ΠΊΠΎΠ²ΠΊΠΈ Ρ ΠΊΠΎΠ½ΠΈΡΠ΅ΡΠΊΠΈΠΌ Ρ Π²ΠΎΡΡΠΎΠ²ΠΈΠΊΠΎΠΌ (ΡΠΈΡ. 3.38, Π±) β Π΄ΠΈΠ°ΠΌΠ΅ΡΡΠΎΠΌ 15; 18; 20; 22; 24; 26; 30; 32; 33; 34; 36 ΠΈ 40 ΠΌΠΌ.
Β
ΠΠ΅Π½ΠΊΠΎΠ²ΠΊΠΈ Π΄Π»Ρ ΠΎΠ±ΡΠ°Π±ΠΎΡΠΊΠΈ ΠΊΠΎΠ½ΠΈΡΠ΅ΡΠΊΠΈΡ ΡΠ³Π»ΡΠ±Π»Π΅Π½ΠΈΠΉ Ρ ΡΠ³Π»Π°ΠΌΠΈ 60, 90 ΠΈ 120Β° (ΡΠΈΡ. 3.38, Π², Π³) ΡΠ°ΠΊΠΈΠ΅Β», ΠΈΠ·Π³ΠΎΡΠ°Π²Π»ΠΈΠ²Π°ΡΡ ΠΈ Ρ ΡΠΈΠ»ΠΈΠ½Π΄ΡΠΈΡΠ΅ΡΠΊΠΈΠΌ, ΠΈ Ρ ΠΊΠΎΠ½ΠΈΡΠ΅ΡΠΊΠΈΠΌ Ρ Π²ΠΎΡΡΠΎΠ²ΠΈΠΊΠΎΠΌ. ΠΠ΅Π½ΠΊΠΎΠ²ΠΊΠΈ Ρ ΡΠΈΠ»ΠΈΠ½Π΄ΡΠΈΡΠ΅ΡΠΊΠΈΠΌ Ρ Π²ΠΎΡΡΠΎΠ²ΠΈΠΊΠΎΠΌ ΠΈΠ·Π³ΠΎΡΠ°Π²Π»ΠΈΠ²Π°ΡΡ Π΄ΠΈΠ°ΠΌΠ΅ΡΡΠΎΠΌ 8; 10; 12; 16; 20; 25 ΠΌΠΌ, Π° Ρ ΠΊΠΎΠ½ΠΈΡΠ΅ΡΠΊΠΈΠΌ Ρ Π²ΠΎΡΡΠΎΠ²ΠΈΠΊΠΎΠΌ β Π΄ΠΈΠ°ΠΌΠ΅ΡΡΠΎΠΌ 16; 20; 25; 31,5; 40; 50; 63 ΠΈ 80 ΠΌΠΌ.
ΠΠ»Ρ ΠΏΠΎΠ΄ΡΠ΅Π·Π°Π½ΠΈΡ ΡΠΎΡΡΠ΅Π² ΠΏΡΠΈΠ»ΠΈΠ²ΠΎΠ² ΠΈ Π±ΠΎΠ±ΡΡΠ΅ΠΊ Π² Π»ΠΈΡΡΡ ΠΊΠΎΡΠΏΡΡΠ½ΡΡ Π΄Π΅ΡΠ°Π»ΡΡ ΠΏΡΠΈΠΌΠ΅Π½ΡΡΡΡΡ ΠΎΠ΄Π½ΠΎ- ΠΈ Π΄Π²ΡΡ ΡΡΠΎΡΠΎΠ½Π½ΠΈΠ΅ ΠΏΠ΅ΠΊΠΎΠ²ΠΊΠΈ (ΡΠΈΡ. 3.38, Π΄, Π΅) ΠΈΠ· Π±ΡΡΡΡΠΎΡΠ΅ΠΆΡΡΠ΅ΠΉ ΡΡΠ°Π»ΠΈ ΠΈΠ»ΠΈ ΠΎΡΠ½Π°ΡΠ΅Π½Π½ΡΠ΅ ΠΏΠ»Π°ΡΡΠΈΠ½Π°ΠΌΠΈ ΡΠ²Π΅ΡΠ΄ΠΎΠ³ΠΎ ΡΠΏΠ»Π°Π²Π°. ΠΠ½ΠΈ ΠΊΡΠ΅ΠΏΡΡΡΡ Π½Π° ΡΠΏΠ΅ΡΠΈΠ°Π»ΡΠ½ΡΡ ΠΎΠΏΡΠ°Π²ΠΊΠ°Ρ Ρ ΠΏΠΎΠΌΠΎΡΡΡ Π±Π°ΠΉΠΎΠ½Π΅ΡΠ½ΠΎΠ³ΠΎ Π·Π°ΠΌΠΊΠ°. ΠΡΠΏΡΡΠΊΠ°ΡΡΡΡ ΡΠ΅ΠΊΠΎΠ²ΠΊΠΈ Π΄ΠΈΠ°ΠΌΠ΅ΡΡΠΎΠΌ 25; 32; 40; 50; Π¬Π; 80 ΠΈ 10Π‘ ΠΌΠΌ.
Β
Π Π°Π·Π²Π΅ΡΡΠΊΠΈ
Β
Π Π°Π·Π²Π΅ΡΡΠΊΠΈ (ΡΠΈΡ. 3.39) ΠΈΠ·Π³ΠΎΡΠΎΠ²Π»ΡΡΡΡΡ ΡΠ΅Π»ΡΠ½ΡΠΌΠΈ ΠΈ Π½Π°ΡΠ°Π΄Π½ΡΠΌΠΈ Ρ ΠΊΠΎΠ½ΠΈΡΠ΅ΡΠΊΠΈΠΌ ΠΈ ΡΠΈΠ»ΠΈΠ½Π΄ΡΠΈΡΠ΅ΡΠΊΠΈΠΌ Ρ Π²ΠΎΡΡΠΎΠ²ΠΈΠΊΠΎΠΌ, ΠΎΡΠ½Π°ΡΠ°ΡΡΡΡ Π²ΡΡΠ°Π²Π½ΡΠΌΠΈ Π½ΠΎΠΆΠ°ΠΌΠΈ, Π²ΠΏΠ°ΡΠ½Π½ΡΠΌΠΈ ΠΏΠ»Π°ΡΡΠΈΠ½Π°ΠΌΠΈ ΠΈΠ· ΡΠ²Π΅ΡΠ΄ΠΎΠ³ΠΎ ΡΠΏΠ»Π°Π²Π° Π»ΠΈΠ±ΠΎ ΠΈΠ·Π³ΠΎΡΠΎΠ²Π»ΡΡΡΡΡ ΠΈΠ· Π±ΡΡΡΡΠΎΡΠ΅ΠΆΡΡΠ΅ΠΉ ΡΡΠ°Π»ΠΈ. Π Π°Π·Π²Π΅ΡΡΠΊΠΈ Π² ΠΎΡΠ»ΠΈΡΠΈΠ΅ ΠΎΡ ΡΠ²Π΅ΡΠ»Π° ΠΈ Π·Π΅Π½ΠΊΠ΅ΡΠ° ΠΈΠΌΠ΅ΡΡ Π±ΠΎΠ»ΡΡΠ΅Π΅ ΠΊΠΎΠ»ΠΈΡΠ΅ΡΡΠ²ΠΎ ΡΠ΅ΠΆΡΡΠΈΡ ΠΊΡΠΎΠΌΠΎΠΊ, ΡΡΠΎ ΠΏΠΎΠ·Π²ΠΎΠ»ΡΠ΅Ρ ΠΏΡΠΈ ΠΎΠ±ΡΠ°Π±ΠΎΡΠΊΠ΅ ΡΠ½ΠΈΠΌΠ°ΡΡ ΡΠ»ΠΎΠΉ ΠΌΠ°ΡΠ΅ΡΠΈΠ°Π»Π° Π½Π΅Π±ΠΎΠ»ΡΡΠΎΠΉ ΡΠΎΠ»ΡΠΈΠ½Ρ, ΡΠΎΡΡΠ°Π²Π»ΡΡΡΠΈΠΉ Π΄Π΅ΡΡΡΡΠ΅ ΠΈ Π΄Π°ΠΆΠ΅ ΡΠΎΡΡΠ΅ Π΄ΠΎΠ»ΠΈ ΠΌΠΈΠ»Π»ΠΈΠΌΠ΅ΡΡΠ°. ΠΡΠΈΠΏΡΡΠΊΠΈ Π½Π° ΡΠ°Π·Π²Π΅ΡΡΡΠ²Π°Π½ΠΈΠ΅ Π²ΡΠ±ΠΈΡΠ°ΡΡΡΡ ΠΏΠΎ ΡΠ°Π±Π»ΠΈΡΠ°ΠΌ Π² Π·Π°Π²ΠΈΡΠΈΠΌΠΎΡΡΠΈ ΠΎΡ Π΄ΠΈΠ°ΠΌΠ΅ΡΡΠ° ΠΎΠ±ΡΠ°Π±Π°ΡΡΠ²Π°Π΅ΠΌΠΎΠ³ΠΎ ΠΎΡΠ²Π΅ΡΡΡΠΈΡ Π Π°Π·Π»ΠΈΡΠ°ΡΡ ΡΠ°Π·Π²Π΅ΡΡΠΊΠΈ Π΄Π»Ρ ΡΡΡΠ½ΠΎΠ³ΠΎ ΠΈ ΠΌΠ°ΡΠΈΠ½Π½ΠΎΠ³ΠΎ ΡΠ°Π·Π²Π΅ΡΡΡΠ²Π°Π½ΠΈΡ, ΡΠΈΠ»ΠΈΠ½Π΄ΡΠΈΡΠ΅ΡΠΊΠΈΠ΅ ΠΈ ΠΊΠΎΠ½ΠΈΡΠ΅ΡΠΊΠΈΠ΅. Π Π°Π·Π²Π΅ΡΡΠΊΠΈ Π΄Π»Ρ ΡΡΡΠ½ΠΎΠ³ΠΎ ΡΠ°Π·Π²Π΅ΡΡΡΠ²Π°Π½ΠΈΡ Π½Π° ΠΊΠΎΠ½ΡΠ΅ ΡΠΈΠ»ΠΈΠ½Π΄ΡΠΈΡΠ΅ΡΠΊΠΎΠ³ΠΎ Ρ Π²ΠΎΡΡΠΎΠ²ΠΈΠΊΠ° ΠΈΠΌΠ΅ΡΡ ΠΊΠ²Π°Π΄ΡΠ°ΡΠ½ΡΡ ΡΠ°ΡΡΡ, Π½Π° ΠΊΠΎΡΠΎΡΡΡ ΡΡΡΠ°Π½Π°Π²Π»ΠΈΠ²Π°ΡΡ Π²ΠΎΡΠΎΡΠΎΠΊ Π΄Π»Ρ Π²ΡΠ°ΡΠ΅Π½ΠΈΡ ΡΠ°Π·Π²Π΅ΡΡΠΊΠΈ Π² ΠΎΠ±ΡΠ°Π±Π°ΡΡΠ²Π°Π΅ΠΌΠΎΠΌ ΠΎΡΠ²Π΅ΡΡΡΠΈΠΈ.
Β
ΠΠΎΠ½ΡΡΡΡΠΊΡΠΈΠ²Π½ΠΎ ΡΠ°Π·Π²Π΅ΡΡΠΊΠ° Π΄Π»Ρ ΡΡΡΠ½ΠΎΠ³ΠΎ ΡΠ°Π·Π²Π΅ΡΡΡΠ²Π°Π½ΠΈΡ ΡΠΎΡΡΠΎΠΈΡ ΠΈΠ· ΡΠ°Π±ΠΎΡΠ΅ΠΉ ΡΠ°ΡΡΠΈ, Ρ Π²ΠΎΡΡΠΎΠ²ΠΈΠΊΠ° ΠΈ ΡΠ΅ΠΉΠΊΠΈ. Π Π°Π±ΠΎΡΠ°Ρ ΡΠ°ΡΡΡ ΠΊΠΎΠ½ΡΡΠ° Π²ΠΊΠ»ΡΡΠ°Π΅Ρ Π² ΡΠ΅Π±Ρ ΡΠ΅ΠΆΡΡΡΡ ΡΠ°ΡΡΡ (Π·Π°Π±ΠΎΡΠ½ΡΠΉ ΠΊΠΎΠ½ΡΡ ΠΈ Π½Π°ΠΏΡΠ°Π²Π»ΡΡΡΠΈΠΉ ΠΊΠΎΠ½ΡΡ, ΠΊΠΎΡΠΎΡΡΠΉ ΠΎΠ±Π΅ΡΠΏΠ΅ΡΠΈΠ²Π°Π΅Ρ ΡΠ΅Π½ΡΡΠΈΡΠΎΠ²Π°Π½ΠΈΠ΅ ΡΠ°Π·Π²Π΅ΡΡΠΊΠΈ Π² ΠΎΡΠ²Π΅ΡΡΡΠΈΠΈ) ΠΈ ΠΊΠ°Π»ΠΈΠ±ΡΡΡΡΡΡ ΡΠ°ΡΡΡ, ΠΎΠ±Π΅ΡΠΏΠ΅ΡΠΈΠ²Π°ΡΡΡΡ ΠΏΠΎΠ»ΡΡΠ΅Π½ΠΈΠ΅ ΠΎΡΠ²Π΅ΡΡΡΠΈΡ Ρ Π·Π°Π΄Π°Π½Π½ΠΎΠΉ ΡΠΎΡΠ½ΠΎΡΡΡΡ ΠΈ ΡΠ΅ΡΠΎΡ ΠΎΠ²Π°ΡΠΎΡΡΡΡ ΠΎΠ±ΡΠ°Π±ΠΎΡΠ°Π½Π½ΠΎΠΉ ΠΏΠΎΠ²Π΅ΡΡ Π½ΠΎΡΡΠΈ.
Π Π΅ΠΆΡΡΠ°Ρ ΡΠ°ΡΡΡ Π·Π°Π±ΠΎΡΠ½ΠΎΠ³ΠΎ ΠΊΠΎΠ½ΡΡΠ° ΡΠ°Π·Π²Π΅ΡΡΠΊΠΈ ΠΈΠΌΠ΅Π΅Ρ ΡΠ³ΠΎΠ» ΠΏΡΠΈ Π²Π΅ΡΡΠΈΠ½Π΅ 2Ρ. ΠΠ»Ρ ΠΎΠ±ΡΠ°Π±ΠΎΡΠΊΠΈ Π²ΡΠ·ΠΊΠΈΡ ΠΌΠ΅ΡΠ°Π»Π»ΠΎΠ² ΡΡΠΎΡ ΡΠ³ΠΎΠ» ΡΠΎΡΡΠ°Π²Π»ΡΠ΅Ρ 12β¦ 15Β°, Π° Π΄Π»Ρ ΠΎΠ±ΡΠ°Π±ΠΎΡΠΊΠΈ Ρ ΡΡΠΏΠΊΠΈΡ ΠΈ ΡΠ²Π΅ΡΠ΄ΡΡ ΠΌΠ°ΡΠ΅ΡΠΈΠ°Π»ΠΎΠ² β ΠΎΡ 3 Π΄ΠΎ 5Β°.
Β
Β
Π’Π²Π΅ΡΠ΄ΠΎΡΠΏΠ»Π°Π²Π½ΡΠ΅ ΡΠ°Π·Π²Π΅ΡΡΠΊΠΈ ΠΈΠΌΠ΅ΡΡ ΡΠ³ΠΎΠ» ΠΏΡΠΈ Π²Π΅ΡΡΠΈΠ½Π΅ 30β¦ 45 ΠΠ°ΠΏΡΠ°Π²Π»ΡΡΡΠΈΠΉ ΠΊΠΎΠ½ΡΡ ΡΠ°Π±ΠΎΡΠ΅ΠΉ ΡΠ°ΡΡΠΈ ΡΠ°Π·Π²Π΅ΡΡΠΊΠΈ ΡΠ°ΡΠΏΠΎΠ»ΠΎΠΆΠ΅Π½ ΠΏΠΎΠ΄ ΡΠ³Π»ΠΎΠΌ 45 Ρ ΠΊ Π΅Π΅ ΠΎΡΠΈ. ΠΠ°Π΄Π½ΠΈΠΉ ΡΠ³ΠΎΠ» Π° Π½Π° ΡΠ΅ΠΆΡΡΠ΅ΠΉ ΡΠ°ΡΡΠΈ ΡΠΎΡΡΠ°Π²Π»ΡΠ΅Ρ ΠΎΡ 6 Π΄ΠΎ 15Β°, Π½Π° ΠΊΠ°Π»ΠΈΠ±ΡΡΡΡΠ΅ΠΉ ΡΠ°ΡΡΠΈ ΡΡΠΎΡ ΡΠ³ΠΎΠ» ΠΎΠ±ΡΡΠ½ΠΎ ΡΠ°Π²Π΅Π½ Π½ΡΠ»Ρ, Π° ΠΏΠ΅ΡΠ΅Π΄Π½ΠΈΠΉ ΡΠ³ΠΎΠ» Ρ β 0β¦ 15 . ΠΠ»Ρ Ρ ΡΡΠΏΠΊΠΈΡ ΠΌΠ°ΡΠ΅ΡΠΈΠ°Π»ΠΎΠ² ΠΏΠ΅ΡΠ΅Π΄Π½ΠΈΠΉ ΡΠ³ΠΎΠ» ΡΠ°Π²Π΅Π½ Π½ΡΠ»Ρ, Π° Π΄Π»Ρ ΡΠ²Π΅ΡΠ΄ΠΎΡΠΏΠ»Π°Π²Π½ΡΡ ΡΠ°Π·Π²Π΅ΡΡΠΎΠΊ ΠΎΠ½ ΡΠΎΡΡΠ°Π²Π»ΡΠ΅Ρ ΠΎΡ 0 Π΄ΠΎ -5Β°. Π ΡΡΠ½ΡΠ΅ ΡΠ°Π·Π²Π΅ΡΡΠΊΠΈ ΠΈΡΠΏΠΎΠ»ΡΠ·ΡΡΡ, ΠΊΠ°ΠΊ ΠΏΡΠ°Π²ΠΈΠ»ΠΎ, ΠΏΡΠΈ ΠΎΠ±ΡΠ°Π±ΠΎΡΠΊΠ΅ ΠΎΡΠ²Π΅ΡΡΡΠΈΠΉ Π΄ΠΈΠ°ΠΌΠ΅ΡΡΠΎΠΌ ΠΎΡ 3 Π΄ΠΎ 50 ΠΌΠΌ Π² ΠΌΠ°ΡΠ΅ΡΠΈΠ°Π»Π°;, Π½Π΅Π²ΡΡΠΎΠΊΠΎΠΉ ΡΠ²Π΅ΡΠ΄ΠΎΡΡΠΈ (ΠΊΠΎΠ½ΡΡΡΡΠΊΡΠΈΠΎΠ½Π½ΡΠ΅ ΡΡΠ°Π»ΠΈ, ΡΠ²Π΅ΡΠ½ΡΠ΅ ΠΌΠ΅ΡΠ°Π»Π»Ρ). ΠΠΎΠ½ΠΈΡΠ΅ΡΠΊΠΈΠ΅ ΡΠ°Π·Π²Π΅ΡΡΠΊΠΈ (ΡΠΈΡ. 3.40) ΠΏΡΠΈΠΌΠ΅Π½ΡΡΡΡΡ Π΄Π»Ρ ΡΠ°Π·Π²Π΅ΡΡΡΠ²Π°Π½ΠΈΡ ΠΊΠΎΠ½ΠΈΡΠ΅ΡΠΊΠΈΡ ΠΎΡΠ²Π΅ΡΡΡΠΈΠΉ ΠΈ, ΠΊΠ°ΠΊ ΠΏΡΠ°Π²ΠΈΠ»ΠΎ, ΡΠ°Π±ΠΎΡΠ°ΡΡ Π² ΠΊΠΎΠΌΠΏΠ»Π΅ΠΊΡΠ΅ ΠΈΠ· Π΄Π²ΡΡ ΡΡΠ΅Ρ ΡΡΡΠΊ.
ΠΠ°ΡΠΈΠ½Π½ΡΠ΅ ΡΠ°Π·Π²Π΅ΡΡΠΊΠΈ Π±ΡΠ²Π°ΡΡ ΡΠΈΠ»ΠΈΠ½Π΄ΡΠΈΡΠ΅ΡΠΊΠΈΠΌΠΈ ΠΈ ΠΊΠΎΠ½ΠΈΡΠ΅ΡΠΊΠΈΠΌΠΈ, Π½Π°ΡΠ°Π΄Π½ΡΠΌΠΈ ΠΈ ΡΠ΅Π»ΡΠ½ΡΠΌΠΈ. Π¦Π΅Π»ΡΠ½ΡΠ΅ ΠΌΠ°ΡΠΈΠ½Π½ΡΠ΅ ΡΠ°Π·Π²Π΅ΡΡΠΊΠΈ ΠΏΡΠ΅Π΄Π½Π°Π·Π½Π°ΡΠ΅Π½Ρ Π΄Π»Ρ ΠΎΠ±ΡΠ°Π±ΠΎΡΠΊΠΈ ΠΎΡΠ²Π΅ΡΡΡΠΈΠΉ Π΄ΠΈΠ°ΠΌΠ΅ΡΡΠΎΠΌ ΠΎΡ 3 Π΄ΠΎ 100 ΠΌΠΌ, Π° Π΄Π»Ρ ΡΠ°Π·Π²Π΅ΡΡΡΠ²Π°Π½ΠΈΡ ΠΎΡΠ²Π΅ΡΡΡΠΈΠΉ Π΄ΠΈΠ°ΠΌΠ΅ΡΡΠΎΠΌ ΠΎΡ 25 Π΄ΠΎ 300 ΠΌΠΌ ΠΈΡΠΏΠΎΠ»ΡΠ·ΡΡΡΡΡ Π½Π°ΡΠ°Π΄Π½ΡΠ΅ ΡΠ°Π·Π²Π΅ΡΡΠΊΠΈ. Π ΡΠ΅Π»ΡΠ½ΡΠ΅ (ΡΠΈΡ. 3.41, Π°, Π±), ΠΈ Π½Π°ΡΠ°Π΄Π½ΡΠ΅ (ΡΠΈΡ. 3.41, Π², Π³) ΡΠ°Π·Π²Π΅ΡΡΠΊΠΈ ΠΈΠ·Π³ΠΎΡΠ°Π²Π»ΠΈΠ²Π°ΡΡ ΠΈΠ· Π±ΡΡΡΡΠΎΡΠ΅ΠΆΡΡΠ΅ΠΉ ΡΡΠ°Π»ΠΈ ΠΈΠ»ΠΈ ΠΎΡΠ½Π°ΡΠ°ΡΡ ΠΏΠ»Π°ΡΡΠΈΠ½Π°ΠΌΠΈ ΠΈΠ· ΡΠ²Π΅ΡΠ΄ΠΎΠ³ΠΎ ΡΠΏΠ»Π°Π²Π°. ΠΠΎΠ½ΡΡΡΡΠΊΡΠΈΡ ΠΈ ΠΌΠ°ΡΠ΅ΡΠΈΠ°Π» ΠΌΠ°ΡΠΈΠ½Π½ΠΎΠΉ ΡΠ°Π·Π²Π΅ΡΡΠΊΠΈ Π²ΡΠ±ΠΈΡΠ°Π΅ΡΡΡ Π² Π·Π°Π²ΠΈΡΠΈΠΌΠΎΡΡΠΈ ΠΎΡ Ρ Π°ΡΠ°ΠΊΡΠ΅ΡΠ° Π²ΡΠΏΠΎΠ»Π½ΡΠ΅ΠΌΡΡ ΡΠ°Π±ΠΎΡ, ΠΌΠ°ΡΠ΅ΡΠΈΠ°Π»Π° ΠΎΠ±ΡΠ°Π±Π°ΡΡΠ²Π°Π΅ΠΌΠΎΠΉ Π·Π°Π³ΠΎΡΠΎΠ²ΠΊΠΈ ΠΈ ΡΡΠ΅Π±ΠΎΠ²Π°Π½ΠΈΠΉ, ΠΏΡΠ΅Π΄ΡΡΠ²Π»ΡΠ΅ΠΌΡΡ ΠΊ ΠΊΠ°ΡΠ΅ΡΡΠ²Ρ ΠΎΠ±ΡΠ°Π±ΠΎΡΠ°Π½Π½ΠΎΠΉ ΠΏΠΎΠ²Π΅ΡΡ Π½ΠΎΡΡΠΈ.
14.7. ΠΠ΅Π½ΠΊΠ΅ΡΠΎΠ²Π°Π½ΠΈΠ΅ ΠΈ ΡΠ°Π·Π²Π΅ΡΡΡΠ²Π°Π½ΠΈΠ΅
14.7.1. ΠΠ»Π΅ΠΌΠ΅Π½ΡΡ ΠΈ Π³Π΅ΠΎΠΌΠ΅ΡΡΠΈΡΠ΅ΡΠΊΠΈΠ΅ ΠΏΠ°ΡΠ°ΠΌΠ΅ΡΡΡ Π·Π΅Π½ΠΊΠ΅ΡΠ° ΠΈ ΡΠ°Π·Π²Π΅ΡΡΠΊΠΈ
ΠΠ»Π΅ΠΌΠ΅Π½ΡΡ Π·Π΅Π½ΠΊΠ΅ΡΠ°. ΠΠ° ΡΠΈΡ. 14.22 ΠΏΠΎΠΊΠ°Π·Π°Π½Ρ ΡΠ»Π΅ΠΌΠ΅Π½ΡΡ ΠΈ ΡΠ°ΡΡΠΈ ΡΠΈΠ»ΠΈΠ½Π΄ΡΠΈΡΠ΅ΡΠΊΠΎΠ³ΠΎ Π·Π΅Π½ΠΊΠ΅ΡΠ°. ΠΠΎ ΡΠΎΡΠΌΠ΅ ΡΠ΅ΠΆΡΡΠ΅ΠΉ ΡΠ°ΡΡΠΈ Π·Π΅Π½ΠΊΠ΅Ρ Π½Π°ΠΏΠΎΠΌΠΈΠ½Π°Π΅Ρ ΡΠΏΠΈΡΠ°Π»ΡΠ½ΠΎΠ΅ ΡΠ²Π΅ΡΠ»ΠΎ, Π½ΠΎ Π² ΠΎΡΠ»ΠΈΡΠΈΠ΅ ΠΎΡ ΡΠ²Π΅ΡΠ»Π° ΠΎΠ½ ΠΈΠΌΠ΅Π΅Ρ Π½Π΅ Π΄Π²Π΅, Π° ΡΡΠΈ ΠΈΠ»ΠΈ ΡΠ΅ΡΡΡΠ΅ Π³Π»Π°Π²Π½ΡΠ΅ ΡΠ΅ΠΆΡΡΠΈΠ΅ ΠΊΡΠΎΠΌΠΊΠΈ, ΡΠ°ΡΠΏΠΎΠ»ΠΎΠΆΠ΅Π½Π½ΡΠ΅ Π½Π° ΡΠ΅ΠΆΡΡΠ΅ΠΉ ΡΠ°ΡΡΠΈ; ΠΊΡΠΎΠΌΠ΅ ΡΠΎΠ³ΠΎ, Π·Π΅Π½ΠΊΠ΅Ρ Π½Π΅ ΠΈΠΌΠ΅Π΅Ρ ΠΏΠΎΠΏΠ΅ΡΠ΅ΡΠ½ΠΎΠΉ ΠΊΡΠΎΠΌΠΊΠΈ.
Π¦ΠΈΠ»ΠΈΠ½Π΄ΡΠΈΡΠ΅ΡΠΊΠΈΠΉ Π·Π΅Π½ΠΊΠ΅Ρ ΠΈΠΌΠ΅Π΅Ρ ΡΠ»Π΅Π΄ΡΡΡΠΈΠ΅ ΡΠ°ΡΡΠΈ: 1) ΡΠ΅ΠΆΡΡΠ°Ρ (Π·Π°Π±ΠΎΡΠ½Π°Ρ) ΡΠ°ΡΡΡ, Π½Π΅ΡΡΡΠ°Ρ ΡΠ΅ΠΆΡΡΠΈΠ΅ ΠΊΡΠΎΠΌΠΊΠΈ, ΡΠ°ΡΠΏΠΎΠ»ΠΎΠΆΠ΅Π½Π½ΡΠ΅ ΠΏΠΎΠ΄ ΡΠ³Π»ΠΎΠΌ Π² ΠΏΠ»Π°Π½Π΅ Ο = 45β¦60Β°; ΠΎΠ½Π° Π²ΡΠΏΠΎΠ»Π½ΡΠ΅Ρ ΠΎΡΠ½ΠΎΠ²Π½ΡΡ ΡΠ°Π±ΠΎΡΡ ΡΠ΅Π·Π°Π½ΠΈΡ; 2) ΠΊΠ°Π»ΠΈΠ±ΡΡΡΡΠ°Ρ (Π½Π°ΠΏΡΠ°Π²Π»ΡΡΡΠ°Ρ) ΡΠ°ΡΡΡ, ΠΈΠΌΠ΅ΡΡΠ°Ρ ΡΠ·ΠΊΠΈΠ΅ ΡΠ°ΡΠΊΠΈ ΠΈ ΡΠ»ΡΠΆΠ°ΡΠ°Ρ Π΄Π»Ρ Π½Π°ΠΏΡΠ°Π²Π»Π΅Π½ΠΈΡ Π·Π΅Π½ΠΊΠ΅ΡΠ° Π² ΠΎΡΠ²Π΅ΡΡΡΠΈΠΈ Π² ΠΏΡΠΎΡΠ΅ΡΡΠ΅ ΡΠ΅Π·Π°Π½ΠΈΡ; 3) Ρ Π²ΠΎΡΡΠΎΠ²ΠΈΠΊ, ΡΠ»ΡΠΆΠ°ΡΠΈΠΉ Π΄Π»Ρ Π·Π°ΠΊΡΠ΅ΠΏΠ»Π΅Π½ΠΈΡ Π·Π΅Π½ΠΊΠ΅ΡΠ°.
Π ΠΈΡ. 14.22. ΠΠ»Π΅ΠΌΠ΅Π½ΡΡ ΠΈ ΡΠ°ΡΡΠΈ ΡΠΈΠ»ΠΈΠ½Π΄ΡΠΈΡΠ΅ΡΠΊΠΎΠ³ΠΎ Π·Π΅Π½ΠΊΠ΅ΡΠ°
ΠΠ΅ΠΎΠΌΠ΅ΡΡΠΈΡΠ΅ΡΠΊΠΈΠ΅ ΠΏΠ°ΡΠ°ΠΌΠ΅ΡΡΡ Π·Π΅Π½ΠΊΠ΅ΡΠ° ΠΏΠΎΠΊΠ°Π·Π°Π½Ρ Π½Π° ΡΠΈΡ. 14.23. ΠΠ΅ΡΠ΅Π΄Π½ΠΈΠΉ ΡΠ³ΠΎΠ»Ξ³ ΠΈΠ·ΠΌΠ΅ΡΡΠ΅ΡΡΡ Π² Π³Π»Π°Π²Π½ΠΎΠΉ ΡΠ΅ΠΊΡΡΠ΅ΠΉ ΠΏΠ»ΠΎΡΠΊΠΎΡΡΠΈ PΟ β PΟ, ΠΏΠ΅ΡΠΏΠ΅Π½Π΄ΠΈΠΊΡΠ»ΡΡΠ½ΠΎΠΉ ΠΊ ΠΏΡΠΎΠ΅ΠΊΡΠΈΠΈ ΡΠ΅ΠΆΡΡΠ΅ΠΉ ΠΊΡΠΎΠΌΠΊΠΈ Π½Π° ΠΎΡΠ½ΠΎΠ²Π½ΡΡ ΠΏΠ»ΠΎΡΠΊΠΎΡΡΡ; Π² Π·Π°Π²ΠΈΡΠΈΠΌΠΎΡΡΠΈ ΠΎΡ ΠΌΠ΅Ρ Π°Π½ΠΈΡΠ΅ΡΠΊΠΈΡ ΡΠ²ΠΎΠΉΡΡΠ² ΠΎΠ±ΡΠ°Π±Π°ΡΡΠ²Π°Π΅ΠΌΠΎΠ³ΠΎ ΠΌΠ°ΡΠ΅ΡΠΈΠ°Π»Π° ΠΈ ΠΌΠ°ΡΠ΅ΡΠΈΠ°Π»Π° Π·Π΅Π½ΠΊΠ΅ΡΠ° Ξ³ Π½Π°Π·Π½Π°ΡΠ°Π΅ΡΡΡ ΠΎΡ 0 Π΄ΠΎ 15Β°. ΠΠ°Π΄Π½ΠΈΠΉ ΡΠ³ΠΎΠ» Ξ± ΠΈΠ·ΠΌΠ΅ΡΡΠ΅ΡΡΡ ΡΠ°ΠΊΠΆΠ΅ Π² ΠΏΠ»ΠΎΡΠΊΠΎΡΡΠΈ PΟ β PΟ ΠΈ Π΄Π΅Π»Π°Π΅ΡΡΡ Π² ΠΏΡΠ΅Π΄Π΅Π»Π°Ρ 8β¦10Β°. Π£Π³ΠΎΠ» Π½Π°ΠΊΠ»ΠΎΠ½Π° Π²ΠΈΠ½ΡΠΎΠ²ΠΎΠΉ ΠΊΠ°Π½Π°Π²ΠΊΠΈ Ο ΠΏΡΠΈΠ½ΠΈΠΌΠ°ΡΡ Π² ΠΏΡΠ΅Π΄Π΅Π»Π°Ρ Β 10β¦30Β°. ΠΠ΅Π½ΠΊΠ΅Ρ ΠΈΠΌΠ΅Π΅Ρ ΠΎΠ±ΡΠ°ΡΠ½ΡΠΉ ΠΊΠΎΠ½ΡΡ ΠΏΠΎΠ΄ ΡΠ³Π»ΠΎΠΌ Ο1 = 1β¦2,0Β°.
Π ΠΈΡ. 14.23. ΠΠ΅ΠΎΠΌΠ΅ΡΡΠΈΡΠ΅ΡΠΊΠΈΠ΅ ΠΏΠ°ΡΠ°ΠΌΠ΅ΡΡΡ Π·Π΅Π½ΠΊΠ΅ΡΠ°
ΠΠ»Π΅ΠΌΠ΅Π½ΡΡ ΡΠ°Π·Π²Π΅ΡΡΠΊΠΈ. Π Π°Π·Π²Π΅ΡΡΠΊΠ° (ΡΠΈΡ. 14.24) Π²Π½Π΅ΡΠ½Π΅ ΠΏΠΎΡ ΠΎΠΆΠ° Π½Π° Π·Π΅Π½ΠΊΠ΅Ρ, Π½ΠΎ ΠΎΡΠ»ΠΈΡΠ°Π΅ΡΡΡ ΠΎΡ Π½Π΅Π³ΠΎ Π±ΠΎΠ»ΡΡΠΈΠΌ ΡΠΈΡΠ»ΠΎΠΌ ΡΠ΅ΠΆΡΡΠΈΡ ΠΊΡΠΎΠΌΠΎΠΊ (ΠΎΡ 6 Π΄ΠΎ 12) ΠΈ Π±ΠΎΠ»Π΅Π΅ ΠΏΠΎΠ»ΠΎΠ³ΠΎΠΉ ΡΠ΅ΠΆΡΡΠ΅ΠΉ (Π·Π°Π±ΠΎΡΠ½ΠΎΠΉ) ΡΠ°ΡΡΡΡ; Π½Π°Π³ΡΡΠ·ΠΊΠ°, ΠΏΡΠΈΡ ΠΎΠ΄ΡΡΠ°ΡΡΡ Π½Π° ΡΠ΅ΠΆΡΡΠΈΠ΅ ΠΊΡΠΎΠΌΠΊΠΈ ΡΠ°Π·Π²Π΅ΡΡΠΊΠΈ, Π·Π½Π°ΡΠΈΡΠ΅Π»ΡΠ½ΠΎ ΠΌΠ΅Π½ΡΡΠ΅, ΡΠ΅ΠΌ Ρ Π·Π΅Π½ΠΊΠ΅ΡΠ°. ΠΡΠ΅ ΡΡΠΎ Π²Π»ΠΈΡΠ΅Ρ Π½Π° ΠΏΠΎΠ²ΡΡΠ΅Π½ΠΈΠ΅ ΡΠΎΡΠ½ΠΎΡΡΠΈ ΠΈ ΡΠΌΠ΅Π½ΡΡΠ΅Π½ΠΈΠ΅ ΡΠ΅ΡΠΎΡ ΠΎΠ²Π°ΡΠΎΡΡΠΈ ΡΡΠ΅Π½ΠΎΠΊ ΠΎΡΠ²Π΅ΡΡΡΠΈΡ ΠΏΠΎΡΠ»Π΅ ΡΠ°Π·Π²Π΅ΡΡΡΠ²Π°Π½ΠΈΡ.
Π Π°Π·Π²Π΅ΡΡΠΊΠ°, ΠΊΠ°ΠΊ ΠΈ Π·Π΅Π½ΠΊΠ΅Ρ, ΡΠΎΡΡΠΎΠΈΡ ΠΈΠ· ΡΠ°Π±ΠΎΡΠ΅ΠΉ ΡΠ°ΡΡΠΈ, ΡΠ΅ΠΉΠΊΠΈ ΠΈ Ρ Π²ΠΎΡΡΠΎΠ²ΠΈΠΊΠ°.
Π ΠΈΡ. 14.24. ΠΠ»Π΅ΠΌΠ΅Π½ΡΡ ΡΠΈΠ»ΠΈΠ½Π΄ΡΠΈΡΠ΅ΡΠΊΠΎΠΉ ΡΠ°Π·Π²Π΅ΡΡΠΊΠΈ
Π Π°Π±ΠΎΡΠ°Ρ ΡΠ°ΡΡΡ ΡΠ°Π·Π²Π΅ΡΡΠΊΠΈ ΡΠΎΡΡΠΎΠΈΡ ΠΈΠ· ΡΡΠ΅Ρ ΡΠ»Π΅ΠΌΠ΅Π½ΡΠΎΠ²: ΡΠ΅ΠΆΡΡΠ΅ΠΉ ΡΠ°ΡΡΠΈ, ΡΠΈΠ»ΠΈΠ½Π΄ΡΠΈΡΠ΅ΡΠΊΠΎΠΉ (ΠΊΠ°Π»ΠΈΠ±ΡΡΡΡΠ΅ΠΉ) ΡΠ°ΡΡΠΈ ΠΈ ΠΎΠ±ΡΠ°ΡΠ½ΠΎΠ³ΠΎ ΠΊΠΎΠ½ΡΡΠ°; Π² Π΄Π»ΠΈΠ½Ρ ΡΠ°Π±ΠΎΡΠ΅ΠΉ ΡΠ°ΡΡΠΈ Π²Ρ ΠΎΠ΄ΠΈΡ ΠΈ Π½Π°ΠΏΡΠ°Π²Π»ΡΡΡΠΈΠΉ ΠΊΠΎΠ½ΡΡ, ΠΈΠΌΠ΅ΡΡΠΈΠΉ ΡΠ³ΠΎΠ» ΠΏΡΠΈ Π²Π΅ΡΡΠΈΠ½Π΅ 90Β°. Π Π΅ΠΆΡΡΠ°Ρ ΡΠ°ΡΡΡ ΡΠ²Π»ΡΠ΅ΡΡΡ Π³Π»Π°Π²Π½ΡΠΌ ΡΠ»Π΅ΠΌΠ΅Π½ΡΠΎΠΌ ΡΠ°Π±ΠΎΡΠ΅ΠΉ ΡΠ°ΡΡΠΈ Π·ΡΠ±Π°; ΠΎΠ½Π° ΠΏΡΠΎΠΈΠ·Π²ΠΎΠ΄ΠΈΡ ΠΎΡΠ½ΠΎΠ²Π½ΡΡ ΡΠ°Π±ΠΎΡΡ ΡΠ°Π·Π²Π΅ΡΡΡΠ²Π°Π½ΠΈΡ Ρ ΠΏΠΎΠΌΠΎΡΡΡ Π³Π»Π°Π²Π½ΡΡ ΡΠ΅ΠΆΡΡΠΈΡ ΠΊΡΠΎΠΌΠΎΠΊ, Π½Π°ΠΊΠ»ΠΎΠ½Π΅Π½Π½ΡΡ ΠΊ ΠΎΡΠΈ ΠΏΠΎΠ΄ ΡΠ³Π»ΠΎΠΌ Π² ΠΏΠ»Π°Π½Π΅ Ο ΠΈ ΠΎΠ±ΡΠ°Π·ΡΡΡΠΈΡ ΡΠ³ΠΎΠ» Π·Π°Π±ΠΎΡΠ½ΠΎΠ³ΠΎ ΠΊΠΎΠ½ΡΡΠ° 2Ο. Π£ ΡΡΡΠ½ΡΡ ΡΠ°Π·Π²Π΅ΡΡΠΎΠΊ Ο = 0,5β¦1,5Β°, Π° Ρ ΠΌΠ°ΡΠΈΠ½Π½ΡΡ ΠΏΡΠΈ ΠΎΠ±ΡΠ°Π±ΠΎΡΠΊΠ΅ ΡΠΊΠ²ΠΎΠ·Π½ΡΡ ΠΎΡΠ²Π΅ΡΡΡΠΈΠΉ Π² ΡΡΠ°Π»ΡΠ½ΡΡ Π·Π°Π³ΠΎΡΠΎΠ²ΠΊΠ°Ρ Ο = 15Β° ΠΈ Π² ΡΡΠ³ΡΠ½Π½ΡΡ Π·Π°Π³ΠΎΡΠΎΠ²ΠΊΠ°Ρ Ο = 5Β°. ΠΠ»Ρ ΡΠ²Π΅ΡΠ΄ΠΎΡΠΏΠ»Π°Π²Π½ΡΡ ΡΠ°Π·Π²Π΅ΡΡΠΎΠΊ Ο = 30β¦45Β°.
Π¦ΠΈΠ»ΠΈΠ½Π΄ΡΠΈΡΠ΅ΡΠΊΠ°Ρ ΡΠ°ΡΡΡ ΡΠ»ΡΠΆΠΈΡ Π΄Π»Ρ ΠΊΠ°Π»ΠΈΠ±ΡΠΎΠ²Π°Π½ΠΈΡ ΠΎΡΠ²Π΅ΡΡΡΠΈΡ ΠΈ Π½Π°ΠΏΡΠ°Π²Π»Π΅Π½ΠΈΡ ΡΠ°Π·Π²Π΅ΡΡΠΊΠΈ Π² ΠΎΡΠ²Π΅ΡΡΡΠΈΠΈ. ΠΠ±ΡΠ°ΡΠ½ΡΠΉ ΠΊΠΎΠ½ΡΡ Π΄Π΅Π»Π°ΡΡ Π΄Π»Ρ ΡΠΌΠ΅Π½ΡΡΠ΅Π½ΠΈΡ ΡΡΠ΅Π½ΠΈΡ ΡΠ°Π±ΠΎΡΠ΅ΠΉ ΡΠ°ΡΡΠΈ ΡΠ°Π·Π²Π΅ΡΡΠΊΠΈ ΠΎ ΡΡΠ΅Π½ΠΊΠΈ ΠΎΡΠ²Π΅ΡΡΡΠΈΡ.
Π Π΅ΠΆΡΡΠΈΠ΅ Π·ΡΠ±ΡΡ ΡΠ°Π·Π²Π΅ΡΡΠΊΠΈ Π΄ΠΎΠ»ΠΆΠ½Ρ ΠΈΠΌΠ΅ΡΡ ΠΏΡΠ°Π²ΠΈΠ»ΡΠ½ΠΎ ΠΏΠΎΠ΄ΠΎΠ±ΡΠ°Π½Π½ΡΠ΅ ΡΠ³Π»Ρ β ΠΏΠ΅ΡΠ΅Π΄Π½ΠΈΠΉ Ξ³ ΠΈ Π·Π°Π΄Π½ΠΈΠΉ ο‘. ΠΡΠΈ ΡΠ³Π»Ρ ΠΈΠ·ΠΌΠ΅ΡΡΡΡ Π² ΠΏΠ»ΠΎΡΠΊΠΎΡΡΠΈ PΟ β PΟ, ΠΏΠ΅ΡΠΏΠ΅Π½Π΄ΠΈΠΊΡΠ»ΡΡΠ½ΠΎΠΉ ΠΊ ΡΠ΅ΠΆΡΡΠ΅ΠΉ ΠΊΡΠΎΠΌΠΊΠ΅; Π²ΡΠ±ΠΈΡΠ°ΡΡ ΠΈΡ Π² Π·Π°Π²ΠΈΡΠΈΠΌΠΎΡΡΠΈ ΠΎΡ ΠΎΠ±ΡΠ°Π±Π°ΡΡΠ²Π°Π΅ΠΌΠΎΠ³ΠΎ ΠΌΠ°ΡΠ΅ΡΠΈΠ°Π»Π° ΠΈ Π½Π°Π·Π½Π°ΡΠ΅Π½ΠΈΡ ΡΠ°Π·Π²Π΅ΡΡΠΊΠΈ.
ΠΠ»Ρ ΡΠ°Π·Π²Π΅ΡΡΠΎΠΊ ΠΈΠ· ΠΈΠ½ΡΡΡΡΠΌΠ΅Π½ΡΠ°Π»ΡΠ½ΡΡ ΡΡΠ°Π»Π΅ΠΉ ΠΏΡΠΈ ΡΠ΅ΡΠ½ΠΎΠ²ΠΎΠΉ ΠΎΠ±ΡΠ°Π±ΠΎΡΠΊΠ΅ Π²ΡΠ·ΠΊΠΈΡ ΠΌΠ΅ΡΠ°Π»Π»ΠΎΠ² ΠΏΠ΅ΡΠ΅Π΄Π½ΠΈΠΉ ΡΠ³ΠΎΠ» Ξ³ Π²ΡΠ±ΠΈΡΠ°ΡΡ Π² ΠΏΡΠ΅Π΄Π΅Π»Π°Ρ 5β¦10Β°, Π° ΠΏΡΠΈ ΡΠΈΡΡΠΎΠ²ΠΎΠΉ ΠΎΠ±ΡΠ°Π±ΠΎΡΠΊΠ΅ Ξ³ = 0Β°. ΠΠ»Ρ ΡΠ°Π·Π²Π΅ΡΡΠΎΠΊ, ΠΎΡΠ½Π°ΡΠ΅Π½Π½ΡΡ ΠΏΠ»Π°ΡΡΠΈΠ½ΠΊΠ°ΠΌΠΈ ΠΈΠ· ΡΠ²Π΅ΡΠ΄ΠΎΠ³ΠΎ ΡΠΏΠ»Π°Π²Π°, ΠΎΠΏΡΠΈΠΌΠ°Π»ΡΠ½ΡΠΌ ΠΏΠ΅ΡΠ΅Π΄Π½ΠΈΠΌ ΡΠ³Π»ΠΎΠΌ, ΡΠ²Π»ΡΠ΅ΡΡΡ Ξ³ = 0β¦15Β°. ΠΠ°Π΄Π½ΠΈΠΉ ΡΠ³ΠΎΠ» Π½Π° ΡΠ΅ΠΆΡΡΠ΅ΠΉ ΡΠ°ΡΡΠΈ ΠΈΠ·ΠΌΠ΅ΡΡΡΡ ΡΠ°ΠΊΠΆΠ΅ Π² ΠΏΠ»ΠΎΡΠΊΠΎΡΡΠΈ PΟ β PΟ; Π²ΡΠ±ΠΈΡΠ°ΡΡ ΡΡΠΎΡ ΡΠ³ΠΎΠ» Π² Π·Π°Π²ΠΈΡΠΈΠΌΠΎΡΡΠΈ ΠΎΡ ΠΎΠ±ΡΠ°Π±Π°ΡΡΠ²Π°Π΅ΠΌΠΎΠ³ΠΎ ΠΌΠ°ΡΠ΅ΡΠΈΠ°Π»Π°: ΠΎΡ 10 Π΄ΠΎ 12Β° Π΄Π»Ρ Π°Π»ΡΠΌΠΈΠ½ΠΈΡ ΠΈ Π΅Π³ΠΎ ΡΠΏΠ»Π°Π²ΠΎΠ² ΠΈ ΠΎΡ 6 Π΄ΠΎ 10Β° Π΄Π»Ρ ΡΠ³Π»Π΅ΡΠΎΠ΄ΠΈΡΡΠΎΠΉ ΠΈ Π»Π΅Π³ΠΈΡΠΎΠ²Π°Π½Π½ΠΎΠΉ ΡΡΠ°Π»Π΅ΠΉ Ρ ΟΠ² > 500 ΠΠΠ°.
Π£Π³Π»Ρ Π½Π° ΠΊΠ°Π»ΠΈΠ±ΡΡΡΡΠ΅ΠΉ ΡΠ°ΡΡΠΈ ΡΠ°Π·Π²Π΅ΡΡΠΊΠΈ ΠΈΠ·ΠΌΠ΅ΡΡΡΡ Π² ΠΏΠ»ΠΎΡΠΊΠΎΡΡΠΈΒ NβN.
14.7.2. ΠΠ»Π΅ΠΌΠ΅Π½ΡΡ ΡΠ΅ΠΆΠΈΠΌΠ° ΡΠ΅Π·Π°Π½ΠΈΡ, ΡΠΈΠ»Ρ, ΠΈΠ·Π½ΠΎΡ ΠΈ ΡΡΠΎΠΉΠΊΠΎΡΡΡ ΠΏΡΠΈ Π·Π΅Π½ΠΊΠ΅ΡΠΎΠ²Π°Π½ΠΈΠΈ ΠΈ ΡΠ°Π·Π²Π΅ΡΡΡΠ²Π°Π½ΠΈΠΈ
ΠΠ»ΡΠ±ΠΈΠ½Π° ΡΠ΅Π·Π°Π½ΠΈΡ, ΠΌΠΌ, ΡΠ°Π²Π½Π° ΠΏΠΎΠ»ΡΡΠ°Π·Π½ΠΎΡΡΠΈ Π΄ΠΈΠ°ΠΌΠ΅ΡΡΠΎΠ² ΠΎΡΠ²Π΅ΡΡΡΠΈΡ Π΄ΠΎ ΠΈ ΠΏΠΎΡΠ»Π΅ ΠΎΠ±ΡΠ°Π±ΠΎΡΠΊΠΈ (ΡΠΈΡ. 14.25), Ρ.Π΅.
.
ΠΠΎΠ΄Π°ΡΠ° ΠΏΡΠΈ Π·Π΅Π½ΠΊΠ΅ΡΠΎΠ²Π°Π½ΠΈΠΈ ΠΈΠ»ΠΈ ΡΠ°Π·Π²Π΅ΡΡΡΠ²Π°Π½ΠΈΠΈ Π²ΡΡΠ°ΠΆΠ°Π΅ΡΡΡ Π² ΠΌΠΈΠ»Π»ΠΈΠΌΠ΅ΡΡΠ°Ρ Π·Π° ΠΎΠ΄ΠΈΠ½ ΠΎΠ±ΠΎΡΠΎΡ ΠΈΠ½ΡΡΡΡΠΌΠ΅Π½ΡΠ° (ΠΌΠΌ/ΠΎΠ±). ΠΡΠ»ΠΈ ΠΎΠ±ΠΎΠ·Π½Π°ΡΠΈΡΡ ΠΏΠΎΠ΄Π°ΡΡ Π·Π΅Π½ΠΊΠ΅ΡΠ° ΠΈΠ»ΠΈ ΡΠ°Π·Π²Π΅ΡΡΠΊΠΈ ΡΠ΅ΡΠ΅Π· s, Π° ΡΠΈΡΠ»ΠΎ Π·ΡΠ±ΡΠ΅Π² ΡΠ΅ΡΠ΅Π· z, ΡΠΎ ΠΏΠΎΠ΄Π°ΡΠ° Π½Π° ΠΎΠ΄ΠΈΠ½ Π·ΡΠ±, ΠΌΠΌ/Π·ΡΠ± (ΡΠ΅ΠΆΡΡΡΡ ΠΊΡΠΎΠΌΠΊΡ)
.
Π’ΠΎΠ»ΡΠΈΠ½Π° ΡΡΠ΅Π·Π°, ΠΌΠΌ, ΡΠ½ΠΈΠΌΠ°Π΅ΠΌΠ°Ρ ΠΊΠ°ΠΆΠ΄ΡΠΌ Π·ΡΠ±ΠΎΠΌ Π·Π΅Π½ΠΊΠ΅ΡΠ° (ΡΠ°Π·Π²Π΅ΡΡΠΊΠΈ),
.
Π¨ΠΈΡΠΈΠ½Π° ΡΡΠ΅Π·Π°, ΠΌΠΌ,
.
Π°) Π±)
Π ΠΈΡ. 14.25. Π‘Ρ Π΅ΠΌΠ° ΡΠ°Π±ΠΎΡΡ Π·Π΅Π½ΠΊΠ΅ΡΠ° (Π°) ΠΈ ΡΠ°Π·Π²Π΅ΡΡΠΊΠΈ (Π±)
ΠΠ»ΠΎΡΠ°Π΄Ρ ΠΏΠΎΠΏΠ΅ΡΠ΅ΡΠ½ΠΎΠ³ΠΎ ΡΠ΅ΡΠ΅Π½ΠΈΡ ΡΡΠ΅Π·Π°, ΠΌΠΌ2, ΠΏΡΠΈΡ ΠΎΠ΄ΡΡΠ°ΡΡΡ Π½Π° ΠΎΠ΄Π½Ρ ΡΠ΅ΠΆΡΡΡΡ ΠΊΡΠΎΠΌΠΊΡ Π·Π΅Π½ΠΊΠ΅ΡΠ° (ΡΠ°Π·Π²Π΅ΡΡΠΊΠΈ),
.
ΠΠ±ΡΠ°Ρ ΠΏΠ»ΠΎΡΠ°Π΄Ρ ΠΏΠΎΠΏΠ΅ΡΠ΅ΡΠ½ΠΎΠ³ΠΎ ΡΠ΅ΡΠ΅Π½ΠΈΡ ΡΡΠ΅Π·Π°, ΠΌΠΌ2,
.
Π‘ΠΊΠΎΡΠΎΡΡΡ ΡΠ΅Π·Π°Π½ΠΈΡ, ΠΌ/ΠΌΠΈΠ½, ΠΏΡΠΈ Π·Π΅Π½ΠΊΠ΅ΡΠΎΠ²Π°Π½ΠΈΠΈ (ΡΠ°Π·Π²Π΅ΡΡΡΠ²Π°Π½ΠΈΠΈ) ΠΎΠΏΡΠ΅Π΄Π΅Π»ΡΠ΅ΡΡΡ ΠΏΠΎ ΡΠΎΠΉ ΠΆΠ΅ ΡΠΎΡΠΌΡΠ»Π΅, ΡΡΠΎ ΠΈ ΠΏΡΠΈ ΡΠ²Π΅ΡΠ»Π΅Π½ΠΈΠΈ, Ρ.Π΅.
,
Π³Π΄Π΅ D β Π΄ΠΈΠ°ΠΌΠ΅ΡΡ Π·Π΅Π½ΠΊΠ΅ΡΠ° (ΡΠ°Π·Π²Π΅ΡΡΠΊΠΈ), ΠΌΠΌ; ΠΏ β ΡΠΈΡΠ»ΠΎ ΠΎΠ±ΠΎΡΠΎΡΠΎΠ² Π² ΠΌΠΈΠ½.
ΠΡΠ½ΠΎΠ²Π½ΠΎΠ΅ ΠΌΠ°ΡΠΈΠ½Π½ΠΎΠ΅ Π²ΡΠ΅ΠΌΡ, ΠΌΠΈΠ½, ΠΏΡΠΈ Π·Π΅Π½ΠΊΠ΅ΡΠΎΠ²Π°Π½ΠΈΠΈ (ΡΠ°Π·Π²Π΅ΡΡΡΠ²Π°Π½ΠΈΠΈ) ΠΎΠΏΡΠ΅Π΄Π΅Π»ΡΠ΅ΡΡΡ ΠΏΠΎ ΡΠΎΡΠΌΡΠ»Π΅
,
Π³Π΄Π΅ L β ΠΏΠΎΠ»Π½Π°Ρ Π΄Π»ΠΈΠ½Π° ΠΏΡΡΠΈ, ΠΏΡΠΎΡ ΠΎΠ΄ΠΈΠΌΠ°Ρ Π·Π΅Π½ΠΊΠ΅ΡΠΎΠΌ (ΡΠ°Π·Π²Π΅ΡΡΠΊΠΎΠΉ) Π² Π½Π°ΠΏΡΠ°Π²Π»Π΅Π½ΠΈΠΈ Π΄Π²ΠΈΠΆΠ΅Π½ΠΈΡ ΠΏΠΎΠ΄Π°ΡΠΈ, ΠΌΠΌ; l β Π³Π»ΡΠ±ΠΈΠ½Π° Π·Π΅Π½ΠΊΠ΅ΡΠΎΠ²Π°Π½ΠΈΡ (ΡΠ°Π·Π²Π΅ΡΡΡΠ²Π°Π½ΠΈΡ), ΠΌΠΌ; Ρ β ΠΏΡΡΡ Π²ΡΠ΅Π·Π°Π½ΠΈΡ, ΠΌΠΌ, ΠΎΠΏΡΠ΅Π΄Π΅Π»ΡΠ΅ΠΌΡΠΉ ΠΏΠΎ ΡΠΎΡΠΌΡΠ»Π΅
,
Π·Π΄Π΅ΡΡ Ο β Π³Π»Π°Π²Π½ΡΠΉ ΡΠ³ΠΎΠ» Π² ΠΏΠ»Π°Π½Π΅; l1 β ΠΏΠ΅ΡΠ΅Π±Π΅Π³ ΠΈΠ½ΡΡΡΡΠΌΠ΅Π½ΡΠ°, ΡΠ°Π²Π½ΡΠΉ 1β¦3 ΠΌΠΌ.
Π‘ΠΈΠ»Ρ ΡΠ΅Π·Π°Π½ΠΈΡ. Π Π°Π²Π½ΠΎΠ΄Π΅ΠΉΡΡΠ²ΡΡΡΡΡ ΡΠΈΠ» ΡΠΎΠΏΡΠΎΡΠΈΠ²Π»Π΅Π½ΠΈΡ ΡΠ΅Π·Π°Π½ΠΈΡ ΠΏΡΠΈ Π·Π΅Π½ΠΊΠ΅ΡΠΎΠ²Π°Π½ΠΈΠΈ (ΡΠ°Π·Π²Π΅ΡΡΡΠ²Π°Π½ΠΈΠΈ) ΠΌΠΎΠΆΠ½ΠΎ ΡΠ°Π·Π»ΠΎΠΆΠΈΡΡ ΡΠ°ΠΊ ΠΆΠ΅, ΠΊΠ°ΠΊ ΠΈ ΠΏΡΠΈ ΡΠ²Π΅ΡΠ»Π΅Π½ΠΈΠΈ, Π½Π° ΡΠΎΡΡΠ°Π²Π»ΡΡΡΠΈΠ΅ ΡΠΈΠ»Ρ Pz, Py ΠΈ Π Ρ , Π΄Π΅ΠΉΡΡΠ²ΡΡΡΠΈΠ΅ Π² ΡΡΠ΅Ρ Π½Π°ΠΏΡΠ°Π²Π»Π΅Π½ΠΈΡΡ .
ΠΠ°ΡΠ°ΡΠ΅Π»ΡΠ½ΡΠ΅ ΡΠΈΠ»Ρ, Π΄Π΅ΠΉΡΡΠ²ΡΡΡΠΈΠ΅ Π² ΠΏΠ»ΠΎΡΠΊΠΎΡΡΠΈ Π²ΡΠ°ΡΠ΅Π½ΠΈΡ Π·Π΅Π½ΠΊΠ΅ΡΠ° (ΡΠ°Π·Π²Π΅ΡΡΠΊΠΈ), ΡΠΎΠ·Π΄Π°ΡΡ ΠΌΠΎΠΌΠ΅Π½Ρ ΡΠΎΠΏΡΠΎΡΠΈΠ²Π»Π΅Π½ΠΈΡ ΡΠ΅Π·Π°Π½ΠΈΡ Π, ΠΏΡΠ΅ΠΎΠ΄ΠΎΠ»Π΅Π²Π°Π΅ΠΌΡΠΉ ΠΌΠ΅Ρ Π°Π½ΠΈΠ·ΠΌΠΎΠΌ Π³Π»Π°Π²Π½ΠΎΠ³ΠΎ Π΄Π²ΠΈΠΆΠ΅Π½ΠΈΡ ΡΡΠ°Π½ΠΊΠ°. Π‘ΠΈΠ»Ρ, Π΄Π΅ΠΉΡΡΠ²ΡΡΡΠΈΠ΅ Π²Π΄ΠΎΠ»Ρ ΠΎΡΠΈ, ΠΏΡΠ΅ΠΎΠ΄ΠΎΠ»Π΅Π²Π°ΡΡΡΡ ΠΏΡΠΈΠ»ΠΎΠΆΠ΅Π½ΠΈΠ΅ΠΌ Π² ΠΌΠ΅Ρ Π°Π½ΠΈΠ·ΠΌΠ΅ ΠΏΠΎΠ΄Π°ΡΠΈ ΡΠΎΠΎΡΠ²Π΅ΡΡΡΠ²ΡΡΡΠ΅ΠΉ ΠΎΡΠ΅Π²ΠΎΠΉ ΡΠΈΠ»Ρ Π 0. Π‘ΠΈΠ»Ρ Py, ΠΏΡΠΎΡΠΈΠ²ΠΎΠΏΠΎΠ»ΠΎΠΆΠ½ΡΠ΅ ΠΏΠΎ Π½Π°ΠΏΡΠ°Π²Π»Π΅Π½ΠΈΡ, Π²Π·Π°ΠΈΠΌΠ½ΠΎ ΡΡΠ°Π²Π½ΠΎΠ²Π΅ΡΠΈΠ²Π°ΡΡΡΡ.
ΠΠΎΠΌΠ΅Π½Ρ, ΠοΠΌ, ΠΈ ΡΠΈΠ»Ρ ΠΏΠΎΠ΄Π°ΡΠΈ, Π, ΠΏΡΠΈ Π·Π΅Π½ΠΊΠ΅ΡΠΎΠ²Π°Π½ΠΈΠΈ (ΡΠ°Π·Π²Π΅ΡΡΡΠ²Π°Π½ΠΈΠΈ) ΠΌΠΎΠΆΠ½ΠΎ ΠΎΠΏΡΠ΅Π΄Π΅Π»ΠΈΡΡ ΠΏΠΎ ΡΠΎΡΠΌΡΠ»Π°ΠΌ
;
,
Π³Π΄Π΅ Π‘ΠΌ ΠΈ Π‘Ρ β ΠΊΠΎΡΡΡΠΈΡΠΈΠ΅Π½ΡΡ, Ρ Π°ΡΠ°ΠΊΡΠ΅ΡΠΈΠ·ΡΡΡΠΈΠ΅ ΠΎΠ±ΡΠ°Π±Π°ΡΡΠ²Π°Π΅ΠΌΡΠΉ ΠΌΠ°ΡΠ΅ΡΠΈΠ°Π» ΠΈ ΡΡΠ»ΠΎΠ²ΠΈΡ ΡΠ΅Π·Π°Π½ΠΈΡ; D β Π΄ΠΈΠ°ΠΌΠ΅ΡΡ Π·Π΅Π½ΠΊΠ΅ΡΠ° (ΡΠ°Π·Π²Π΅ΡΡΠΊΠΈ), ΠΌΠΌ; s β ΠΏΠΎΠ΄Π°ΡΠ°, ΠΌΠΌ/ΠΎΠ±; t β Π³Π»ΡΠ±ΠΈΠ½Π° ΡΠ΅Π·Π°Π½ΠΈΡ (ΠΏΡΠΈΠΏΡΡΠΊ Π½Π° ΠΎΠ±ΡΠ°Π±ΠΎΡΠΊΡ), ΠΌΠΌ; xΠΌ, yΠΌ, uΠΌ, xp, yp ΠΈ up β ΠΏΠΎΠΊΠ°Π·Π°ΡΠ΅Π»ΠΈ ΡΡΠ΅ΠΏΠ΅Π½Π΅ΠΉ.
ΠΠ½Π°ΡΠ΅Π½ΠΈΡ ΠΊΠΎΡΡΡΠΈΡΠΈΠ΅Π½ΡΠΎΠ² ΠΈ ΠΏΠΎΠΊΠ°Π·Π°ΡΠ΅Π»Π΅ΠΉ ΡΡΠ΅ΠΏΠ΅Π½Π΅ΠΉ ΠΏΡΠΈΠ²Π΅Π΄Π΅Π½Ρ Π² ΡΠΎΠΎΡΠ²Π΅ΡΡΡΠ²ΡΡΡΠΈΡ ΡΠΏΡΠ°Π²ΠΎΡΠ½ΠΈΠΊΠ°Ρ .
ΠΡΠΈ Π·Π΅Π½ΠΊΠ΅ΡΠΎΠ²Π°Π½ΠΈΠΈ ΡΡΠ°Π»ΡΠ½ΡΡ Π·Π°Π³ΠΎΡΠΎΠ²ΠΎΠΊ, ΠΈΠΌΠ΅ΡΡΠΈΡ ΟΠ² = 750 Π/ΠΌΠΌ2, Π·Π΅Π½ΠΊΠ΅ΡΠΎΠΌ, ΠΎΡΠ½Π°ΡΠ΅Π½Π½ΡΠΌ ΠΏΠ»Π°ΡΡΠΈΠ½ΠΊΠ°ΠΌΠΈ ΠΈΠ· ΡΠΏΠ»Π°Π²Π° Π’15Π6, Π‘ΠΌ = 943; Ρ ΠΌ = 0,75; yΠΌ = 0,95; uΠΌ = 0,8.
ΠΡΡΠ΅ΠΊΡΠΈΠ²Π½ΡΡ ΠΌΠΎΡΠ½ΠΎΡΡΡ, ΠΊΠΡ, Π·Π°ΡΡΠ°ΡΠΈΠ²Π°Π΅ΠΌΡΡ Π½Π° Π·Π΅Π½ΠΊΠ΅ΡΠΎΠ²Π°-Π½ΠΈΠ΅ (ΡΠ°Π·Π²Π΅ΡΡΡΠ²Π°Π½ΠΈΠ΅), ΠΎΠΏΡΠ΅Π΄Π΅Π»ΡΡΡ ΠΏΠΎ ΡΠΎΡΠΌΡΠ»Π΅
.
ΠΠ·Π½ΠΎΡ Π·Π΅Π½ΠΊΠ΅ΡΠΎΠ². ΠΠ΅Π½ΠΊΠ΅ΡΡ ΠΎΠ±ΡΡΠ½ΠΎ ΠΈΠ·Π½Π°ΡΠΈΠ²Π°ΡΡΡΡ ΠΏΠΎ Π·Π°Π΄Π½Π΅ΠΉ ΠΏΠΎΠ²Π΅ΡΡ Π½ΠΎΡΡΠΈ, ΠΏΠΎ ΠΏΠ΅ΡΠ΅Π΄Π½Π΅ΠΉ ΠΏΠΎΠ²Π΅ΡΡ Π½ΠΎΡΡΠΈ (Ρ ΠΎΠ±ΡΠ°Π·ΠΎΠ²Π°Π½ΠΈΠ΅ΠΌ Π½Π΅Π±ΠΎΠ»ΡΡΠΎΠΉ Π»ΡΠ½ΠΊΠΈ), ΠΏΠΎ ΡΠ³ΠΎΠ»ΠΊΠ°ΠΌ ΠΈ ΠΏΠΎ Π»Π΅Π½ΡΠΎΡΠΊΠ΅ (ΡΠΈΡ. 14.26). ΠΠ° ΠΊΡΠΈΡΠ΅ΡΠΈΠΉ Π·Π°ΡΡΠΏΠ»Π΅Π½ΠΈΡ Π·Π΅Π½ΠΊΠ΅ΡΠΎΠ² ΠΈΠ· Π±ΡΡΡΡΠΎΡΠ΅ΠΆΡΡΠ΅ΠΉ ΡΡΠ°Π»ΠΈ ΠΏΡΠΈΠ½ΠΈΠΌΠ°ΡΡ:
Π°) ΠΏΡΠΈ ΠΎΠ±ΡΠ°Π±ΠΎΡΠΊΠ΅ ΠΊΠΎΠ½ΡΡΡΡΠΊΡΠΈΠΎΠ½Π½ΡΡ ΡΠ³Π»Π΅ΡΠΎΠ΄ΠΈΡΡΡΡ ΠΈ Π»Π΅Π³ΠΈΡΠΎΠ²Π°Π½Π½ΡΡ ΡΡΠ°Π»Π΅ΠΉ Ρ ΠΎΡ Π»Π°ΠΆΠ΄Π΅Π½ΠΈΠ΅ΠΌ β ΠΈΠ·Π½ΠΎΡ ΠΏΠΎ Π·Π°Π΄Π½Π΅ΠΉ ΠΏΠΎΠ²Π΅ΡΡ Π½ΠΎΡΡΠΈ hΠ· = =Β 1,2β¦1,5 ΠΌΠΌ;
Π±) ΠΏΡΠΈ ΠΎΠ±ΡΠ°Π±ΠΎΡΠΊΠ΅ ΠΆΠ°ΡΠΎΠΏΡΠΎΡΠ½ΠΎΠΉ ΡΡΠ°Π»ΠΈ Π₯18Π9Π’ Ρ ΠΎΡ Π»Π°ΠΆΠ΄Π΅Π½ΠΈΠ΅ΠΌ β ΠΈΠ·Π½ΠΎΡ ΠΏΠΎ Π·Π°Π΄Π½Π΅ΠΉ ΠΏΠΎΠ²Π΅ΡΡ Π½ΠΎΡΡΠΈ hΠ· = 0,4 ΠΌΠΌ;
Π²) Π΄Π»Ρ Π·Π΅Π½ΠΊΠ΅ΡΠΎΠ², ΠΎΡΠ½Π°ΡΠ΅Π½Π½ΡΡ ΠΏΠ»Π°ΡΡΠΈΠ½ΠΊΠ°ΠΌΠΈ ΠΈΠ· ΡΠ²Π΅ΡΠ΄ΠΎΠ³ΠΎ ΡΠΏΠ»Π°Π²Π°, Π·Π° ΠΊΡΠΈΡΠ΅ΡΠΈΠΉ Π·Π°ΡΡΠΏΠ»Π΅Π½ΠΈΡ ΠΏΡΠΈΠ½ΠΈΠΌΠ°ΡΡ ΠΈΠ·Π½ΠΎΡ ΠΏΠΎ Π·Π°Π΄Π½Π΅ΠΉ ΠΏΠΎΠ²Π΅ΡΡ Π½ΠΎΡΡΠΈ Ρ Π»Π΅Π½ΡΠΎΡΠΊΠΈ; Π²Π΅Π»ΠΈΡΠΈΠ½Π° Π΄ΠΎΠΏΡΡΡΠΈΠΌΠΎΠ³ΠΎ ΠΈΠ·Π½ΠΎΡΠ° ΠΏΡΠΈΠ²Π΅Π΄Π΅Π½Π° Π² ΠΏΡΠΎΠΌΡΡΠ»Π΅Π½Π½ΡΡ Π½ΠΎΡΠΌΠ°ΡΠΈΠ²Π°Ρ .
ΠΠ°ΠΏΡΠΈΠΌΠ΅Ρ, ΠΏΡΠΈ ΠΎΠ±ΡΠ°Π±ΠΎΡΠΊΠ΅ Ρ ΡΠΎΠΌΠΎΠΊΡΠ΅ΠΌΠ½ΠΈΠ΅ΠΌΠ°ΡΠ³Π°Π½ΡΠΎΠ²ΠΈΡΡΠΎΠΉ ΡΡΠ°Π»ΠΈ, ΠΈΠΌΠ΅ΡΡΠ΅ΠΉ ΟΠ² =1150β¦1700 ΠΠΠ° Ρ ΠΎΡ Π»Π°ΠΆΠ΄Π΅Π½ΠΈΠ΅ΠΌ, Π΄ΠΎΠΏΡΡΡΠΈΠΌΡΠΉ ΠΈΠ·Π½ΠΎΡ hΠ· = 0,6 ΠΌΠΌ.
Π°) Π±)
Π ΠΈΡ. 14.26. ΠΠ·Π½ΠΎΡ Π·Π΅Π½ΠΊΠ΅ΡΠΎΠ²: Π°) Π±ΡΡΡΡΠΎΡΠ΅ΠΆΡΡΠ΅Π³ΠΎ;
Π±) ΠΎΡΠ½Π°ΡΠ΅Π½Π½ΠΎΠ³ΠΎ ΠΏΠ»Π°ΡΡΠΈΠ½ΠΊΠ°ΠΌΠΈ ΠΈΠ· ΡΠ²Π΅ΡΠ΄ΡΡ ΡΠΏΠ»Π°Π²ΠΎΠ²
Π ΠΈΡ. 14.27. ΠΠ·Π½ΠΎΡ Π·ΡΠ±ΡΠ΅Π² ΡΠ°Π·Π²Π΅ΡΡΠΊΠΈ
ΠΠ·Π½ΠΎΡ ΡΠ°Π·Π²Π΅ΡΡΠΎΠΊ. Π Π°Π·Π²Π΅ΡΡΠΊΠΈ, ΡΡΠ΅Π·Π°ΡΡΠΈΠ΅ ΠΎΡΠ΅Π½Ρ ΡΠΎΠ½ΠΊΠΈΠ΅ ΡΠ»ΠΎΠΈ ΠΌΠ΅ΡΠ°Π»Π»Π°, ΠΈΠ·Π½Π°ΡΠΈΠ²Π°ΡΡΡΡ Π² ΠΎΡΠ½ΠΎΠ²Π½ΠΎΠΌ ΠΏΠΎ Π·Π°Π΄Π½Π΅ΠΉ ΠΏΠΎΠ²Π΅ΡΡ Π½ΠΎΡΡΠΈ ΠΈ ΡΠ³ΠΎΠ»ΠΊΡ Π² ΠΌΠ΅ΡΡΠ΅ ΠΏΠ΅ΡΠ΅Ρ ΠΎΠ΄Π° ΡΠ΅ΠΆΡΡΠ΅ΠΉ ΡΠ°ΡΡΠΈ Π² ΡΠΈΠ»ΠΈΠ½Π΄ΡΠΈΡΠ΅ΡΠΊΡΡ (ΠΊΠ°Π»ΠΈΠ±ΡΡΡΡΡΡ) ΡΠ°ΡΡΡ (ΡΠΈΡ. 14.27). ΠΡΠΈ ΡΡΠΎΠΌ Π²ΡΠ»Π΅Π΄ΡΡΠ²ΠΈΠ΅ ΠΈΠ·ΠΌΠ΅Π½Π΅Π½ΠΈΡ ΡΠ°Π·ΠΌΠ΅ΡΠΎΠ² ΡΠ°Π·Π²Π΅ΡΡΠΊΠΈ ΡΠ²Π΅Π»ΠΈΡΠΈΠ²Π°Π΅ΡΡΡ ΡΠ΅ΡΠΎΡ ΠΎΠ²Π°ΡΠΎΡΡΡ ΠΎΠ±ΡΠ°Π±ΠΎΡΠ°Π½Π½ΠΎΠΉ ΠΏΠΎΠ²Π΅ΡΡ Π½ΠΎΡΡΠΈ ΠΈ ΡΠΌΠ΅Π½ΡΡΠ°Π΅ΡΡΡ ΡΠΎΡΠ½ΠΎΡΡΡ ΡΠ°Π·ΠΌΠ΅ΡΠΎΠ² ΠΎΡΠ²Π΅ΡΡΡΠΈΡ. ΠΠΎΡΡΠΎΠΌΡ Π·Π° ΠΊΡΠΈΡΠ΅ΡΠΈΠΉ Π·Π°ΡΡΠΏΠ»Π΅Π½ΠΈΡ ΡΠ°Π·Π²Π΅ΡΡΠΊΠΈ ΠΏΡΠΈΠ½ΠΈΠΌΠ°ΡΡ ΡΠ°ΠΊΡΡ Π²Π΅Π»ΠΈΡΠΈΠ½Ρ ΠΈΠ·Π½ΠΎΡΠ°, ΠΏΡΠΈ ΠΊΠΎΡΠΎΡΠΎΠΉ ΠΎΠ±ΡΠ°Π±ΠΎΡΠ°Π½Π½ΠΎΠ΅ ΡΠ°Π·Π²Π΅ΡΡΠΊΠΎΠΉ ΠΎΡΠ²Π΅ΡΡΡΠΈΠ΅ ΠΏΠ΅ΡΠ΅ΡΡΠ°Π΅Ρ ΡΠ΄ΠΎΠ²Π»Π΅ΡΠ²ΠΎΡΡΡΡ ΡΠ΅Ρ Π½ΠΈΡΠ΅ΡΠΊΠΈΠΌ ΡΡΠ»ΠΎΠ²ΠΈΡΠΌ, Ρ.Π΅. Π²ΡΡ ΠΎΠ΄ΠΈΡ Π·Π° ΠΏΡΠ΅Π΄Π΅Π»Ρ Π΄ΠΎΠΏΡΡΠΊΠ° ΠΈ ΠΏΠ΅ΡΠ΅ΡΡΠ°Π΅Ρ ΡΠ΄ΠΎΠ²Π»Π΅ΡΠ²ΠΎΡΡΡΡ ΡΡΠ΅Π±ΠΎΠ²Π°Π½ΠΈΡΠΌ ΡΠ΅ΡΠΎΡ ΠΎΠ²Π°ΡΠΎΡΡΠΈ. ΠΡΠΎ ΡΠ°ΠΊ Π½Π°Π·ΡΠ²Π°Π΅ΠΌΡΠΉ ΡΠ΅Ρ Π½ΠΎΠ»ΠΎΠ³ΠΈΡΠ΅ΡΠΊΠΈΠΉ ΠΊΡΠΈΡΠ΅ΡΠΈΠΉ ΠΈΠ·Π½ΠΎΡΠ° ΠΈΠ½ΡΡΡΡΠΌΠ΅Π½ΡΠ°.ΠΠ°ΠΊΡΠΈΠΌΠ°Π»ΡΠ½ΠΎ Π΄ΠΎΠΏΡΡΡΠΈΠΌΡΠΌΠΈ Π²Π΅Π»ΠΈΡΠΈΠ½Π°ΠΌΠΈ ΠΈΠ·Π½ΠΎΡΠ° ΡΠ°Π·Π²Π΅ΡΡΠΎΠΊ ΠΈΠ· Π±ΡΡΡΡΠΎΡΠ΅ΠΆΡΡΠ΅ΠΉ ΡΡΠ°Π»ΠΈ ΡΠ²Π»ΡΡΡΡΡ hΠ· = 0,6β¦0,8 ΠΌΠΌ ΠΏΡΠΈ ΠΎΠ±ΡΠ°Π±ΠΎΡΠΊΠ΅ ΡΠ³Π»Π΅ΡΠΎΠ΄ΠΈΡΡΡΡ ΠΈ Π»Π΅Π³ΠΈΡΠΎΠ²Π°Π½Π½ΡΡ ΠΌΠ°ΡΠΈΠ½ΠΎΠΏΠΎΠ΄Π΅Π»ΠΎΡΠ½ΡΡ ΡΡΠ°Π»Π΅ΠΉ Ρ ΠΎΡ -Π»Π°ΠΆΠ΄Π΅Π½ΠΈΠ΅ΠΌ ΠΈ hΠ· = 0,25β¦0,3 ΠΌΠΌ ΠΏΡΠΈ ΠΎΠ±ΡΠ°Π±ΠΎΡΠΊΠ΅ ΠΆΠ°ΡΠΎΠΏΡΠΎΡΠ½ΠΎΠΉ ΡΡΠ°Π»ΠΈ Π₯18Π10Π’ Ρ ΠΎΡ Π»Π°ΠΆΠ΄Π΅Π½ΠΈΠ΅ΠΌ.
ΠΠ° ΠΊΡΠΈΡΠ΅ΡΠΈΠΉ Π·Π°ΡΡΠΏΠ»Π΅Π½ΠΈΡ ΡΠ²Π΅ΡΠ΄ΠΎΡΠΏΠ»Π°Π²Π½ΡΡ ΡΠ°Π·Π²Π΅ΡΡΠΎΠΊ ΠΏΡΠΈΠ½ΠΈΠΌΠ°ΡΡ:
Π°) ΠΏΡΠΈ ΠΎΠ±ΡΠ°Π±ΠΎΡΠΊΠ΅ Π½Π΅Π·Π°ΠΊΠ°Π»Π΅Π½Π½ΡΡ ΠΌΠ°ΡΠΈΠ½ΠΎΠΏΠΎΠ΄Π΅Π»ΠΎΡΠ½ΡΡ ΡΡΠ°Π»Π΅ΠΉ ΠΈΠ·Π½ΠΎΡ ΠΏΠΎ Π·Π°Π΄Π½Π΅ΠΉ ΠΏΠΎΠ²Π΅ΡΡ Π½ΠΎΡΡΠΈ hΠ· = 0,4β¦0,7 ΠΌΠΌ;
Π±) ΠΏΡΠΈ ΠΎΠ±ΡΠ°Π±ΠΎΡΠΊΠ΅ Π·Π°ΠΊΠ°Π»Π΅Π½Π½ΠΎΠΉ ΡΡΠ°Π»ΠΈ Ρ ΟΠ² = 1800Β Π/ΠΌΠΌ2 hΠ· = =Β 0,4β¦0,35 ΠΌΠΌ.
Π‘ΠΊΠΎΡΠΎΡΡΡ ΡΠ΅Π·Π°Π½ΠΈΡ ΠΏΡΠΈ Π·Π΅Π½ΠΊΠ΅ΡΠΎΠ²Π°Π½ΠΈΠΈ ΠΈ ΡΠ°Π·Π²Π΅ΡΡΡΠ²Π°Π½ΠΈΠΈ Π·Π°Π²ΠΈΡΠΈΡ ΠΎΡ ΠΎΠ±ΡΠ°Π±Π°ΡΡΠ²Π°Π΅ΠΌΠΎΠ³ΠΎ ΠΌΠ°ΡΠ΅ΡΠΈΠ°Π»Π° ΠΈ ΠΌΠ°ΡΠ΅ΡΠΈΠ°Π»Π° ΠΈΠ½ΡΡΡΡΠΌΠ΅Π½ΡΠ°, Π΄ΠΈΠ°ΠΌΠ΅ΡΡΠ° ΠΈΠ½ΡΡΡΡΠΌΠ΅Π½ΡΠ° D, ΠΏΠ΅ΡΠΈΠΎΠ΄Π° ΡΡΠΎΠΉΠΊΠΎΡΡΠΈ Π’, Π³Π»ΡΠ±ΠΈΠ½Ρ ΡΠ΅Π·Π°Π½ΠΈΡ t, ΠΏΠΎΠ΄Π°ΡΠΈ s ΠΈ Π΄ΡΡΠ³ΠΈΡ ΡΠ°ΠΊΡΠΎΡΠΎΠ².
Π‘ΠΊΠΎΡΠΎΡΡΡ ΡΠ΅Π·Π°Π½ΠΈΡ, ΠΌ/ΠΌΠΈΠ½, Π΄ΠΎΠΏΡΡΠΊΠ°Π΅ΠΌΠ°Ρ ΡΠ΅ΠΆΡΡΠΈΠΌΠΈ ΡΠ²ΠΎΠΉΡΡΠ²Π°ΠΌΠΈ Π·Π΅Π½ΠΊΠ΅ΡΠΎΠ² ΠΈ ΡΠ°Π·Π²Π΅ΡΡΠΎΠΊ, ΠΎΠΏΡΠ΅Π΄Π΅Π»ΡΠ΅ΡΡΡ ΠΏΠΎ ΡΠΎΡΠΌΡΠ»Π΅
.
ΠΠ½Π°ΡΠ΅Π½ΠΈΡ ΠΊΠΎΡΡΡΠΈΡΠΈΠ΅Π½ΡΠΎΠ², ΠΏΠΎΠΊΠ°Π·Π°ΡΠ΅Π»Π΅ΠΉ ΡΡΠ΅ΠΏΠ΅Π½Π΅ΠΉ ΠΈ ΡΠ΅ΠΊΠΎΠΌΠ΅Π½Π΄ΡΠ΅ΠΌΠΎΠΉ ΡΡΠΎΠΉΠΊΠΎΡΡΠΈ ΠΏΡΠΈΠ²ΠΎΠ΄ΡΡΡΡ Π² ΡΠΏΡΠ°Π²ΠΎΡΠ½ΠΈΠΊΠ°Ρ ΠΏΠΎ ΡΠ΅ΠΆΠΈΠΌΠ°ΠΌ ΡΠ΅Π·Π°Π½ΠΈΡ.
Π Π°Π·Π½ΠΈΡΠ° ΠΌΠ΅ΠΆΠ΄Ρ Π·Π΅Π½ΠΊΠΎΠ²ΠΊΠΎΠΉ ΠΈ Π·Π΅Π½ΠΊΠΎΠ²ΠΊΠΎΠΉ
ΠΠ»Ρ Π±ΠΎΠ»ΡΡΠΈΠ½ΡΡΠ²Π° ΠΏΠ΅ΡΠ°ΡΠ½ΡΡ ΠΏΠ»Π°Ρ ΡΡΠ΅Π±ΡΠ΅ΡΡΡ ΠΎΠΏΡΠ΅Π΄Π΅Π»Π΅Π½Π½ΡΠΉ ΡΠΈΠΏ ΠΌΠΎΠ½ΡΠ°ΠΆΠ½ΠΎΠ³ΠΎ ΠΎΠ±ΠΎΡΡΠ΄ΠΎΠ²Π°Π½ΠΈΡ. ΠΠ»Ρ ΡΡΠΎΠΉ ΡΠ΅Π»ΠΈ Π±ΠΎΠ»ΡΡΠΈΠ½ΡΡΠ²ΠΎ ΠΈΠ·Π³ΠΎΡΠΎΠ²Π»Π΅Π½ΠΈΠΉ ΠΏΠ΅ΡΠ°ΡΠ½ΡΡ ΠΏΠ»Π°Ρ Π²ΠΊΠ»ΡΡΠ°ΡΡ Π² ΡΠ΅Π±Ρ Π½Π΅ΠΏΠΎΠΊΡΡΡΡΠ΅ ΠΌΠΎΠ½ΡΠ°ΠΆΠ½ΡΠ΅ ΠΎΡΠ²Π΅ΡΡΡΠΈΡ. ΠΠ²ΡΠΌΡ Π½Π°ΠΈΠ±ΠΎΠ»Π΅Π΅ ΡΠ°ΡΠΏΡΠΎΡΡΡΠ°Π½Π΅Π½Π½ΡΠΌΠΈ ΠΈΠ· ΡΠ°ΠΊΠΈΡ ΠΎΡΠ²Π΅ΡΡΡΠΈΠΉ ΡΠ²Π»ΡΡΡΡΡ ΠΎΡΠ²Π΅ΡΡΡΠΈΡ Ρ Π·Π΅Π½ΠΊΠΎΠ²ΠΊΠΎΠΉ ΠΈ Π·Π΅Π½ΠΊΠΎΠ²ΠΊΠΎΠΉ, ΠΊΠΎΡΠΎΡΡΠ΅ ΡΠ²Π»ΡΡΡΡΡ ΠΎΡΠΎΠ±ΡΠΌΠΈ ΡΡΠ΅Π±ΠΎΠ²Π°Π½ΠΈΡΠΌΠΈ Π΄Π»Ρ ΡΠ²Π΅ΡΠ»Π΅Π½ΠΈΡ ΠΏΠ΅ΡΠ°ΡΠ½ΡΡ ΠΏΠ»Π°Ρ, Π½ΠΎ ΠΎΠ±ΡΡΠ½ΠΎ Π²Π·Π°ΠΈΠΌΠΎΠ·Π°ΠΌΠ΅Π½ΡΠ΅ΠΌΡ.
ΠΠ²Π° ΡΠΈΠΏΠ° ΠΎΡΠ²Π΅ΡΡΡΠΈΠΉ ΠΎΡΠ½ΠΎΡΡΡΡΡ ΠΊ ΠΌΠ΅ΡΠΎΠ΄Π°ΠΌ ΡΠ²Π΅ΡΠ»Π΅Π½ΠΈΡ, ΠΊΠΎΡΠΎΡΡΠ΅ ΠΏΠΎΠ·Π²ΠΎΠ»ΡΡΡ ΡΠΈΠΊΡΠΈΡΠΎΠ²Π°ΡΡ ΠΊΡΠ΅ΠΏΠ΅ΠΆΠΈ Π½Π° ΠΎΠ΄Π½ΠΎΠΌ ΡΡΠΎΠ²Π½Π΅ Ρ ΠΏΠΎΠ²Π΅ΡΡ Π½ΠΎΡΡΡΡ ΡΠ»ΠΎΠΈΡΡΠΎΠ³ΠΎ ΠΌΠ°ΡΠ΅ΡΠΈΠ°Π»Π° ΠΏΠ΅ΡΠ°ΡΠ½ΠΎΠΉ ΠΏΠ»Π°ΡΡ.ΠΡΠΎΡΠ΅ΡΡ ΠΎΠ±ΡΡΠ½ΠΎ Π·Π°ΠΊΠ»ΡΡΠ°Π΅ΡΡΡ Π² Π²ΡΡΠ²Π΅ΡΠ»ΠΈΠ²Π°Π½ΠΈΠΈ ΠΎΡΠ²Π΅ΡΡΡΠΈΠΉ Π±ΠΎΠ»ΡΡΠ΅Π³ΠΎ Π΄ΠΈΠ°ΠΌΠ΅ΡΡΠ° Π΄Π»Ρ Π²Π΅ΡΡ Π½ΠΈΡ Π½Π΅ΡΠΊΠΎΠ»ΡΠΊΠΈΡ ΠΌΠΈΠ»Π»ΠΈΠΌΠ΅ΡΡΠΎΠ² ΠΎΡΠ²Π΅ΡΡΡΠΈΡ, ΡΡΠΎΠ±Ρ Π³ΠΎΠ»ΠΎΠ²ΠΊΠ° Π²ΠΈΠ½ΡΠ° ΠΌΠΎΠ³Π»Π° Π±ΡΡΡ ΠΏΠ»ΠΎΡΠ½ΠΎ ΡΠ°Π·ΠΌΠ΅ΡΠ΅Π½Π°.
Π‘ ΡΡΠΈΠΌΠΈ Π΄Π²ΡΠΌΡ ΠΏΡΡΠ°Π½ΠΈΡΠ° Π²ΡΠ΅Π³Π΄Π° ΡΠ°ΡΠΏΡΠΎΡΡΡΠ°Π½Π΅Π½Π° ΠΎΡΠ½ΠΎΡΠΈΡΠ΅Π»ΡΠ½ΠΎ ΡΠΎΠ³ΠΎ, ΡΡΠΎ ΠΊΠ°ΠΆΠ΄ΡΠΉ ΠΎΠ±ΠΎΠ·Π½Π°ΡΠ°Π΅Ρ. Π’Π°ΠΊΠΈΠΌ ΠΎΠ±ΡΠ°Π·ΠΎΠΌ, ΡΡΡΠ΅ΠΌΠ»Π΅Π½ΠΈΠ΅ ΠΏΡΠΎΠ²Π΅ΡΡΠΈ ΡΠ΅ΡΠΊΡΡ Π³ΡΠ°Π½Ρ ΠΌΠ΅ΠΆΠ΄Ρ Π½ΠΈΠΌΠΈ ΠΎΡΠ΅Π½Ρ ΠΏΠΎΠΌΠΎΠΆΠ΅Ρ.
Π§ΡΠΎ ΡΠ°ΠΊΠΎΠ΅ Counterbore?
ΠΡΠ²Π΅ΡΡΡΠΈΠ΅ Π² ΠΎΡΠ²Π΅ΡΡΡΠΈΠΈ ΠΎΠΏΡΠ΅Π΄Π΅Π»ΡΠ΅ΡΡΡ ΠΊΠ°ΠΊ ΡΠΈΠ»ΠΈΠ½Π΄ΡΠΈΡΠ΅ΡΠΊΠΎΠ΅ ΠΎΡΠ²Π΅ΡΡΡΠΈΠ΅ Ρ ΠΏΠ»ΠΎΡΠΊΠΈΠΌ Π΄Π½ΠΎΠΌ, ΠΊΠΎΡΠΎΡΠΎΠ΅ ΠΎΠ±ΡΡΠ½ΠΎ ΡΠ°ΡΡΠΈΡΡΠ΅ΡΡΡ Π² Π΄ΡΡΠ³ΠΎΠ΅ ΡΠΎΠΎΡΠ½ΠΎΠ΅ ΠΎΡΠ²Π΅ΡΡΡΠΈΠ΅.ΠΡΠ²Π΅ΡΡΡΠΈΠ΅ ΠΎΠ±ΡΡΠ½ΠΎ ΠΈΡΠΏΠΎΠ»ΡΠ·ΡΠ΅ΡΡΡ Π²ΡΡΠΊΠΈΠΉ ΡΠ°Π·, ΠΊΠΎΠ³Π΄Π° ΡΡΠ΅Π±ΡΠ΅ΡΡΡ ΠΊΡΠ΅ΠΏΠ΅ΠΆΠ½ΡΠΉ ΡΠ»Π΅ΠΌΠ΅Π½Ρ, Π½Π°ΠΏΡΠΈΠΌΠ΅Ρ, Π²ΠΈΠ½Ρ Ρ Π³ΠΎΠ»ΠΎΠ²ΠΊΠΎΠΉ ΠΏΠΎΠ΄ ΡΠΎΡΡΠ΅Π²ΠΎΠΉ ΠΊΠ»ΡΡ, ΡΡΠΎΠ±Ρ ΠΎΠ½ Π½Π°Ρ ΠΎΠ΄ΠΈΠ»ΡΡ Π·Π°ΠΏΠΎΠ΄Π»ΠΈΡΠΎ Π½ΠΈΠΆΠ΅ ΠΈΠ»ΠΈ Π²Π½ΡΡΡΠΈ ΡΡΠΎΠ²Π½Ρ ΠΏΠΎΠ²Π΅ΡΡ Π½ΠΎΡΡΠΈ Π·Π°Π³ΠΎΡΠΎΠ²ΠΊΠΈ.
Π’Π΅ΡΠΌΠΈΠ½ ΡΠ°ΠΊΠΆΠ΅ ΠΈΡΠΏΠΎΠ»ΡΠ·ΡΠ΅ΡΡΡ Π΄Π»Ρ ΠΎΠ±ΠΎΠ·Π½Π°ΡΠ΅Π½ΠΈΡ ΡΡΠ΅Π·Ρ, ΠΊΠΎΡΠΎΡΠ°Ρ ΠΏΡΠΎΠΈΠ·Π²ΠΎΠ΄ΠΈΡ ΠΎΡΠ²Π΅ΡΡΡΠΈΡ Π΄Π»Ρ ΡΠ°ΡΡΠΎΡΠΊΠΈ ΠΎΡΠ²Π΅ΡΡΡΠΈΠΉ. ΠΠ΄Π½Π°ΠΊΠΎ ΡΠ΅ΡΠΌΠΈΠ½ Β«Π·Π΅Π½ΠΊΠΎΠ²Π°Π½Π½ΡΠΉ ΡΠ΅Π·Π΅ΡΒ» ΠΎΠ±ΡΡΠ½ΠΎ ΠΈΡΠΏΠΎΠ»ΡΠ·ΡΠ΅ΡΡΡ Π΄Π»Ρ ΡΡΠ΅Π·Π΅ΡΠΎΠ²Π°Π½ΠΈΡ, ΡΡΠΎΠ±Ρ ΡΠΌΠ΅Π½ΡΡΠΈΡΡ Π½Π΅ΠΎΠ΄Π½ΠΎΠ·Π½Π°ΡΠ½ΠΎΡΡΡ.
Π§ΡΠΎ ΡΠ°ΠΊΠΎΠ΅ Π·Π΅Π½ΠΊΠΎΠ²ΠΊΠ°?
ΠΠ΅Π½ΠΊΠΎΠ²ΠΊΠ° – ΡΡΠΎ ΡΠ΅ΡΠΌΠΈΠ½, ΠΈΡΠΏΠΎΠ»ΡΠ·ΡΠ΅ΠΌΡΠΉ Π΄Π»Ρ ΠΎΠ±ΠΎΠ·Π½Π°ΡΠ΅Π½ΠΈΡ ΠΊΠΎΠ½ΠΈΡΠ΅ΡΠΊΠΎΠ³ΠΎ ΠΎΡΠ²Π΅ΡΡΡΠΈΡ, ΠΊΠΎΡΠΎΡΠΎΠ΅ Π²ΡΡΠ΅Π·Π°Π½ΠΎ Π² ΠΎΠ±ΡΠ΅ΠΊΡΠ΅.ΠΡΠΎ ΠΌΠΎΠΆΠ΅Ρ ΡΠ°ΠΊΠΆΠ΅ ΠΈΡΠΏΠΎΠ»ΡΠ·ΠΎΠ²Π°ΡΡΡΡ, ΡΡΠΎΠ±Ρ ΠΎΠ±ΡΠ°ΡΠΈΡΡΡΡ ΠΊ ΡΠ΅Π·ΡΡ, ΠΊΠΎΡΠΎΡΡΠΉ Π΄Π΅Π»Π°Π΅Ρ ΠΎΡΠ²Π΅ΡΡΡΠΈΠ΅. ΠΠ±ΡΡΠ½ΠΎ ΡΡΠΎ Π΄Π΅Π»Π°Π΅ΡΡΡ Π΄Π»Ρ ΡΠΎΠ³ΠΎ, ΡΡΠΎΠ±Ρ Π³ΠΎΠ»ΠΎΠ²ΠΊΠ° ΠΏΠΎΡΠ°ΠΉΠ½ΠΎΠΉ Π·Π°ΠΊΠ»Π΅ΠΏΠΊΠΈ, Π²ΠΈΠ½ΡΠ° ΠΈΠ»ΠΈ Π±ΠΎΠ»ΡΠ° Π½Π°Ρ ΠΎΠ΄ΠΈΠ»Π°ΡΡ Π·Π°ΠΏΠΎΠ΄Π»ΠΈΡΠΎ Ρ ΠΏΠΎΠ²Π΅ΡΡ Π½ΠΎΡΡΡΡ ΠΎΠΊΡΡΠΆΠ°ΡΡΠΈΡ ΠΌΠ°ΡΠ΅ΡΠΈΠ°Π»ΠΎΠ² ΠΈΠ»ΠΈ ΠΏΠΎΠ΄ Π½ΠΈΠΌΠΈ, ΠΊΠΎΠ³Π΄Π° ΠΎΠ½ΠΈ ΠΏΠΎΠΌΠ΅ΡΠ΅Π½Ρ Π² ΠΎΡΠ²Π΅ΡΡΡΠΈΠ΅.
ΠΠ½ ΡΠ°ΠΊΠΆΠ΅ ΠΌΠΎΠΆΠ΅Ρ Π±ΡΡΡ ΠΈΡΠΏΠΎΠ»ΡΠ·ΠΎΠ²Π°Π½ Π΄Π»Ρ ΡΠ΄Π°Π»Π΅Π½ΠΈΡ Π·Π°ΡΡΠ΅Π½ΡΠ΅Π², ΠΎΡΡΠ°Π²ΡΠΈΡ ΡΡ ΠΏΠΎΡΠ»Π΅ ΠΎΠΏΠ΅ΡΠ°ΡΠΈΠΈ Π½Π°ΡΠ΅Π·Π°Π½ΠΈΡ ΡΠ΅Π·ΡΠ±Ρ ΠΈΠ»ΠΈ ΡΠ²Π΅ΡΠ»Π΅Π½ΠΈΡ, ΡΡΠΎ ΠΏΠΎΠΌΠΎΠ³Π°Π΅Ρ ΡΠ»ΡΡΡΠΈΡΡ ΠΊΠ°ΡΠ΅ΡΡΠ²ΠΎ ΠΎΡΠ΄Π΅Π»ΠΊΠΈ ΠΈΠ·Π΄Π΅Π»ΠΈΡ. ΠΡΠΎ ΡΠ°ΠΊΠΆΠ΅ ΠΏΠΎΠΌΠΎΠ³Π°Π΅Ρ ΡΠ΄Π°Π»ΠΈΡΡ Π»ΡΠ±ΡΠ΅ ΠΎΠΏΠ°ΡΠ½ΡΠ΅ ΠΎΡΡΡΡΠ΅ ΠΊΡΠ°Ρ Π² ΠΏΡΠΎΡΠ΅ΡΡΠ΅.
Π Π°Π·Π½ΠΈΡΠ° ΠΌΠ΅ΠΆΠ΄Ρ Π·Π΅Π½ΠΊΠΎΠ²ΠΊΠΎΠΉ ΠΈ Π·Π΅Π½ΠΊΠΎΠ²ΠΊΠΎΠΉ
ΠΡΠ½ΠΎΠ²Π½ΡΠ΅ ΡΠ°Π·Π»ΠΈΡΠΈΡ ΠΌΠ΅ΠΆΠ΄Ρ Π΄Π²ΡΠΌΡ ΠΎΡΠ²Π΅ΡΡΡΠΈΡΠΌΠΈ Π²ΠΊΠ»ΡΡΠ°ΡΡ Π² ΡΠ΅Π±Ρ:
ΠΠΏΡΠ΅Π΄Π΅Π»Π΅Π½ΠΈΠ΅ Counterbore Vs.ΠΠ΅Π½ΠΊΠΎΠ²ΠΊΠ°
ΠΠ΅Π½ΠΊΠΎΠ²ΠΊΠ° – ΡΡΠΎ ΠΊΡΡΠ³Π»ΠΎΠ΅ ΠΎΡΠ²Π΅ΡΡΡΠΈΠ΅, ΠΎΠ±ΡΡΠ½ΠΎ Ρ ΠΏΡΠΎΡΠΈΠ»ΡΠΌΠΈ ΡΠ°Π·Π½ΠΎΠ³ΠΎ Π΄ΠΈΠ°ΠΌΠ΅ΡΡΠ°. ΠΠ½ ΠΏΡΠΎΡΠ²Π΅ΡΠ»Π΅Π½, ΡΡΠΎΠ±Ρ ΠΏΠΎΠ·Π²ΠΎΠ»ΠΈΡΡ Π½Π΅Π²ΡΠΏΠ°Π΄Π°ΡΡΠ΅ΠΉ Π³ΠΎΠ»ΠΎΠ²ΠΊΠ΅ ΠΈΠ»ΠΈ Π»ΡΠ±ΡΠΌ Π΄ΡΡΠ³ΠΈΠΌ ΠΊΡΠ΅ΠΏΠ΅ΠΆΠ°ΠΌ Ρ ΠΊΠ²Π°Π΄ΡΠ°ΡΠ½ΡΠΌΠΈ ΠΏΠ»Π΅ΡΠ°ΠΌΠΈ ΠΏΠ»Π°Π²Π½ΠΎ ΠΏΠΎΠ³ΡΡΠΆΠ°ΡΡΡΡ Π² ΠΏΡΠΎΡΠ²Π΅ΡΠ»Π΅Π½Π½ΡΠΉ ΠΌΠ°ΡΠ΅ΡΠΈΠ°Π». Π‘ Π΄ΡΡΠ³ΠΎΠΉ ΡΡΠΎΡΠΎΠ½Ρ, Π·Π΅Π½ΠΊΠΎΠ²Π°Π½Π½ΠΎΠ΅ ΠΎΡΠ²Π΅ΡΡΡΠΈΠ΅ – ΡΡΠΎ Π±ΠΎΠ»ΡΡΠΎΠΉ ΡΠ΅Π»ΡΠ΅Ρ Ρ ΡΡΠΏΡΠΌ ΡΠ³Π»ΠΎΠΌ ΠΈΠ»ΠΈ ΡΠΊΠΎΡ, ΠΏΡΠΎΡΠ²Π΅ΡΠ»Π΅Π½Π½ΡΠΉ Π½Π° ΠΊΡΠ°Ρ ΠΊΡΡΠ³Π»ΠΎΠ³ΠΎ ΠΎΡΠ²Π΅ΡΡΡΠΈΡ ΠΈ ΠΏΡΠ΅Π΄Π½Π°Π·Π½Π°ΡΠ΅Π½Π½ΡΠΉ Π΄Π»Ρ ΠΊΡΠ΅ΠΏΠ»Π΅Π½ΠΈΡ Ρ ΡΡΠΎΠΏΠ»Π΅Π½Π½ΡΠΌΠΈ Π³ΠΎΠ»ΠΎΠ²ΠΊΠ°ΠΌΠΈ, ΡΠ°ΠΊΠΈΠΌΠΈ ΠΊΠ°ΠΊ Π·Π°ΠΊΠ»Π΅ΠΏΠΊΠΈ ΠΈ Π²ΠΈΠ½ΡΡ. ΠΡΠ²Π΅ΡΡΡΠΈΠ΅ ΠΏΠΎΠ·Π²ΠΎΠ»ΡΠ΅Ρ Π²Π΅ΡΡ Π½Π΅ΠΉ ΡΠ°ΡΡΠΈ ΠΊΡΠ΅ΠΏΠ΅ΠΆΠ° ΡΠΎΠΎΡΠ²Π΅ΡΡΡΠ²ΠΎΠ²Π°ΡΡ Π·Π°ΠΏΠΎΠ΄Π»ΠΈΡΠΎ Ρ ΠΌΠ°ΡΠ΅ΡΠΈΠ°Π»ΠΎΠΌ.
Π€ΠΎΡΠΌΠ° ΠΈ ΡΠ°Π·ΠΌΠ΅Ρ ΠΎΡΠ²Π΅ΡΡΡΠΈΡ Π² Counterbore Vs.Π² Π·Π΅Π½ΠΊΠΎΠ²ΠΊΠ΅
ΠΡΠ²Π΅ΡΡΡΠΈΡ Ρ ΠΎΡΠ²Π΅ΡΡΡΠΈΡΠΌΠΈ Π±ΠΎΠ»Π΅Π΅ ΠΊΠ²Π°Π΄ΡΠ°ΡΠ½ΡΠ΅ ΠΈ Π±ΠΎΠ»Π΅Π΅ ΡΠΈΡΠΎΠΊΠΈΠ΅, ΡΡΠΎ ΠΏΠΎΠ·Π²ΠΎΠ»ΡΠ΅Ρ Π΄ΠΎΠ±Π°Π²Π»ΡΡΡ ΡΠ°ΠΉΠ±Ρ ΠΏΠ΅ΡΠ΅Π΄ Π·Π°ΠΊΡΠ΅ΠΏΠ»Π΅Π½ΠΈΠ΅ΠΌ ΠΊΡΠ΅ΠΏΠ΅ΠΆΠ°, Π² ΡΠΎ Π²ΡΠ΅ΠΌΡ ΠΊΠ°ΠΊ ΠΎΡΠ²Π΅ΡΡΡΠΈΡ Ρ Π·Π΅Π½ΠΊΠΎΠ²ΠΊΠΎΠΉ ΠΈΠΌΠ΅ΡΡ ΠΊΠΎΠ½ΠΈΡΠ΅ΡΠΊΡΡ ΡΠΎΡΠΌΡ, ΠΊΠΎΡΠΎΡΠ°Ρ ΡΠΎΠΎΡΠ²Π΅ΡΡΡΠ²ΡΠ΅Ρ ΡΠ³Π»ΠΎΠ²ΠΎΠΉ ΡΠΎΡΠΌΠ΅ Π½Π° Π½ΠΈΠΆΠ½Π΅ΠΉ ΡΡΠΎΡΠΎΠ½Π΅ Π²ΠΈΠ½ΡΠΎΠ² Ρ ΠΏΠ»ΠΎΡΠΊΠΎΠΉ Π³ΠΎΠ»ΠΎΠ²ΠΊΠΎΠΉ.
Π§ΡΠΎ ΠΊΠ°ΡΠ°Π΅ΡΡΡ ΡΠ°Π·ΠΌΠ΅ΡΠ° ΠΎΡΠ²Π΅ΡΡΡΠΈΡ, ΠΎΡΠ²Π΅ΡΡΡΠΈΠ΅ Π·Π΅Π½ΠΊΠΎΠ²ΠΊΠΈ Π±ΠΎΠ»ΡΡΠ΅, ΡΠ΅ΠΌ Π² Π·Π΅Π½ΠΊΠΎΠ²ΠΊΠ΅.
Counterbore Vs. ΠΠ΅Π½ΠΊΠΎΠ²ΠΊΠ°: Π‘ΡΠ°Π²Π½ΠΈΡΠ΅Π»ΡΠ½Π°Ρ ΡΠ°Π±Π»ΠΈΡΠ°
Π Π΅Π·ΡΠΌΠ΅ Counterbore Vs. ΠΠ΅Π½ΠΊΠΎΠ²ΠΊΠ°
Π ΠΌΠΈΡΠ΅ ΠΏΠ΅ΡΠ°ΡΠ½ΡΡ ΠΏΠ»Π°Ρ ΠΈΡΠΏΠΎΠ»ΡΠ·ΡΡΡΡΡ Π΄Π²Π° ΡΠ΅ΡΠΌΠΈΠ½Π°: Π·Π΅Π½ΠΊΠΎΠ²Π°Π½ΠΈΠ΅ ΠΈ Π·Π΅Π½ΠΊΠΎΠ²ΠΊΠ°.ΠΠ΅ΡΠΌΠΎΡΡΡ Π½Π° ΡΠΎ, ΡΡΠΎ ΠΎΠ½ΠΈ Π±ΠΎΠ»Π΅Π΅ ΡΠ΅ΠΌ ΡΠ°ΡΡΠΎ Π²Π·Π°ΠΈΠΌΠΎΠ·Π°ΠΌΠ΅Π½ΡΠ΅ΠΌΡ, ΠΎΠ½ΠΈ ΠΎΡΠ½ΠΎΡΡΡΡΡ ΠΊ ΡΠ°Π·Π½ΡΠΌ ΡΠΈΠΏΠ°ΠΌ ΠΎΡΠ²Π΅ΡΡΡΠΈΠΉ, ΡΠΎΡΠΌΠ°ΠΌ ΠΈ ΡΠ°Π·ΠΌΠ΅ΡΠ°ΠΌ. ΠΠ½ΠΈ ΡΠ°ΠΊΠΆΠ΅ ΠΎΡΠ½ΠΎΡΡΡΡΡ ΠΊ ΡΠ΅Π·ΡΠ°ΠΌ, ΠΈΡΠΏΠΎΠ»ΡΠ·ΡΠ΅ΠΌΡΠΌ Π΄Π»Ρ ΠΈΠ·Π³ΠΎΡΠΎΠ²Π»Π΅Π½ΠΈΡ ΠΎΡΠ²Π΅ΡΡΡΠΈΠΉ Π΄Π»Ρ ΠΊΠ°ΠΆΠ΄ΠΎΠ³ΠΎ ΡΠΎΠΎΡΠ²Π΅ΡΡΡΠ²ΡΡΡΠ΅Π³ΠΎ ΡΠΈΠΏΠ° ΠΎΡΠ²Π΅ΡΡΡΠΈΡ. Π‘ΡΡΡ, ΠΎΠ΄Π½Π°ΠΊΠΎ, Π² ΡΠΎΠΌ, ΡΡΠΎ ΠΊΠ°ΠΆΠ΄ΡΠΉ ΠΈΠ· Π½ΠΈΡ ΠΎΡΠ»ΠΈΡΠ°Π΅ΡΡΡ ΠΎΡ Π΄ΡΡΠ³ΠΎΠ³ΠΎ Π² ΡΠ°Π·Π»ΠΈΡΠ½ΡΡ Π°ΡΠΏΠ΅ΠΊΡΠ°Ρ , Π²ΠΊΠ»ΡΡΠ°Ρ ΠΎΠΏΡΠ΅Π΄Π΅Π»Π΅Π½ΠΈΡ.
Π‘Π°ΡΠ° Π€ΠΈΠ»ΠΈΡ ΠΡΠ°ΡΠ½
ΠΡΠΎΠΈΡΡ
ΠΎΠΆΠ΄Π΅Π½ΠΈΠ΅: Π₯ΡΡΡΡΠΎΠ½, Π’Π΅Ρ
Π°Ρ
ΠΠ±ΡΠ°Π·ΠΎΠ²Π°Π½ΠΈΠ΅: ΠΌΠ°Π³ΠΈΡΡΡ ΠΈΠ·ΡΡΠ½ΡΡ
ΠΈΡΠΊΡΡΡΡΠ² (ΠΌΠ°Π³ΠΈΡΡΡ ΠΈΡΠΊΡΡΡΡΠ²) | Π£Π½ΠΈΠ²Π΅ΡΡΠΈΡΠ΅Ρ ΠΠ°ΡΡΠ°ΡΡΡΠ΅ΡΡΠ° ΠΠΌΡ
Π΅ΡΡΡ. ΠΠ½Π° ΡΠ°ΠΊΠΆΠ΅ ΠΈΠΌΠ΅Π΅Ρ ΡΠ΅ΡΡΠΈΡΠΈΠΊΠ°Ρ Π² ΡΡΠ°ΡΠΈΡΡΠΈΡΠ΅ΡΠΊΠΈΡ
ΠΏΡΠΈΠ»ΠΎΠΆΠ΅Π½ΠΈΡΡ
.ΠΠ½Π° Π½Π°ΠΏΠΈΡΠ°Π»Π° ΠΌΠ½ΠΎΠΆΠ΅ΡΡΠ²ΠΎ ΡΡΠ°ΡΠ΅ΠΉ, ΠΏΠΎΡΡΠΎΠ² Π² Π±Π»ΠΎΠ³Π°Ρ
, ΡΡΠ°ΡΠ΅ΠΉ, ΠΎΠΏΠΈΡΠ°Π½ΠΈΠΉ ΠΏΡΠΎΠ΄ΡΠΊΡΠΎΠ², ΠΎΠ±Π·ΠΎΡΠΎΠ² ΠΏΡΠΎΠ΄ΡΠΊΡΠΎΠ², Ghost, Fiction ΠΈ ΡΡΠ΅Π½Π°ΡΠΈΠ΅Π².
ΠΠ½Π° Π²ΠΎΠ·Π³Π»Π°Π²Π»ΡΠ»Π° Π³ΡΡΠΏΠΏΡ ΡΠΊΡΠΏΠ΅ΡΡΠΎΠ² ΠΏΠΎ ΡΡΡΠ°Π½ΠΎΠ²Π»Π΅Π½ΠΈΡ Π²ΠΎΠ·Π΄Π΅ΠΉΡΡΠ²ΠΈΡ ΡΡΠ±ΡΠΈΠ΄ΠΈΡΡΠ΅ΠΌΡΡ
ΠΊΠ°Π½Π°Π»ΠΈΠ·Π°ΡΠΈΠΎΠ½Π½ΡΡ
ΡΠ΅ΡΠ΅ΠΉ Π² ΡΠ΅Π»ΡΡΠΊΠΈΡ
ΡΡΡΡΠΎΠ±Π°Ρ
ΠΠ΅Π½ΠΈΠΈ (ΠΏΠΎΠ΄ ΡΠ³ΠΈΠ΄ΠΎΠΉ ΠΡΠ΅ΠΌΠΈΡΠ½ΠΎΠ³ΠΎ Π±Π°Π½ΠΊΠ°).
: ΠΡΠ»ΠΈ Π²Π°ΠΌ ΠΏΠΎΠ½ΡΠ°Π²ΠΈΠ»Π°ΡΡ ΡΡΠ° ΡΡΠ°ΡΡΡ ΠΈΠ»ΠΈ Π½Π°Ρ ΡΠ°ΠΉΡ. ΠΠΎΠΆΠ°Π»ΡΠΉΡΡΠ°, ΡΠ°ΡΠΏΡΠΎΡΡΡΠ°Π½ΠΈΡΠ΅ ΡΠ»ΠΎΠ²ΠΎ. ΠΠΎΠ΄Π΅Π»ΠΈΡΠ΅ΡΡ ΡΡΠΈΠΌ ΡΠΎ ΡΠ²ΠΎΠΈΠΌΠΈ Π΄ΡΡΠ·ΡΡΠΌΠΈ / ΡΠ΅ΠΌΡΠ΅ΠΉ.
Π¦ΠΈΡΠΈΡΠΎΠ²Π°ΡΡ
Π‘Π°ΡΠ° ΠΡΠ°ΡΠ½.Β«Π Π°Π·Π½ΠΈΡΠ° ΠΌΠ΅ΠΆΠ΄Ρ Π·Π΅Π½ΠΊΠΎΠ²ΠΊΠΎΠΉ ΠΈ Π·Π΅Π½ΠΊΠΎΠ²ΠΊΠΎΠΉΒ». DifferenceBetween.net. 10 ΠΈΡΠ½Ρ 2019 Π³.
Sweeped ΠΈΠ»ΠΈ Swept – ΡΡΠΎ ΠΏΡΠ°Π²ΠΈΠ»ΡΠ½ΠΎ?
Π Π°Π½Π³Π»ΠΈΠΉΡΠΊΠΎΠΌ ΡΠ·ΡΠΊΠ΅ Π΅ΡΡΡ ΠΌΠ½ΠΎΠ³ΠΎ Π³Π»Π°Π³ΠΎΠ»ΠΎΠ², ΠΊΠΎΡΠΎΡΡΠ΅ Π½Π΅ ΡΠΎΠΎΡΠ²Π΅ΡΡΡΠ²ΡΡΡ ΡΡΠ°Π½Π΄Π°ΡΡΠ½ΡΠΌ ΠΏΡΠ°Π²ΠΈΠ»Π°ΠΌ ΡΠΏΡΡΠΆΠ΅Π½ΠΈΡ. ΠΡΠΈ Π³Π»Π°Π³ΠΎΠ»Ρ Π½Π΅ΠΏΡΠ°Π²ΠΈΠ»ΡΠ½ΡΡ Π³Π»Π°Π³ΠΎΠ»ΠΎΠ² . ΠΠ½ΠΈ ΡΠ»Π΅Π΄ΡΡΡ ΡΠ²ΠΎΠΈΠΌ ΡΠΎΠ±ΡΡΠ²Π΅Π½Π½ΡΠΌ ΠΏΡΠ°Π²ΠΈΠ»Π°ΠΌ, ΠΈ Π·Π°ΡΠ°ΡΡΡΡ Π½Π΅Ρ ΠΏΡΠΎΡΡΠΎΠ³ΠΎ ΡΠΏΠΎΡΠΎΠ±Π° Π·Π°ΠΏΠΎΠΌΠ½ΠΈΡΡ ΡΡΠΈ ΠΏΡΠ°Π²ΠΈΠ»Π°, ΠΏΠΎΡΠΊΠΎΠ»ΡΠΊΡ ΠΎΠ½ΠΈ ΡΠ°ΠΊ ΡΠΈΠ»ΡΠ½ΠΎ ΡΠ°Π·Π»ΠΈΡΠ°ΡΡΡΡ.
Sweep ΡΠ²Π»ΡΠ΅ΡΡΡ ΠΎΠ΄Π½ΠΈΠΌ ΠΈΠ· ΡΠ°ΠΊΠΈΡ Π³Π»Π°Π³ΠΎΠ»ΠΎΠ². Π ΡΠΎ Π²ΡΠ΅ΠΌΡ ΠΊΠ°ΠΊ ΠΎΠ±ΡΡΠ½ΡΠ΅ Π°Π½Π³Π»ΠΈΠΉΡΠΊΠΈΠ΅ Π³Π»Π°Π³ΠΎΠ»Ρ ΠΏΡΠΈΠ½ΠΈΠΌΠ°ΡΡ ΡΡΡΡΠΈΠΊΡ -ed Π² ΠΏΡΠΎΡΠ΅Π΄ΡΠ΅ΠΌ Π²ΡΠ΅ΠΌΠ΅Π½ΠΈ, ΡΠ°Π·Π²Π΅ΡΡΠΊΠ° ΡΠ»Π΅Π΄ΡΠ΅Ρ Π΄ΡΡΠ³ΠΈΠΌ ΠΏΡΠ°Π²ΠΈΠ»Π°ΠΌ, Π½Π°ΡΡΠ΄Ρ Ρ Π΄ΡΡΠ³ΠΈΠΌΠΈ Π³Π»Π°Π³ΠΎΠ»Π°ΠΌΠΈ, ΡΠ°ΠΊΠΈΠΌΠΈ ΠΊΠ°ΠΊ , ΡΠΎΡ ΡΠ°Π½ΡΡΡ ΠΈ ΡΠΊΠ°ΡΠΊΠΎΠΌ .ΠΡΠΎΠ΄ΠΎΠ»ΠΆΠ°ΠΉΡΠ΅ ΡΠΈΡΠ°ΡΡ, ΡΡΠΎΠ±Ρ ΡΠ·Π½Π°ΡΡ Π±ΠΎΠ»ΡΡΠ΅ ΠΎΠ± ΡΡΠΈΡ Π·Π°ΠΏΡΡΠ°Π½Π½ΡΡ ΡΠ»ΠΎΠ²Π°Ρ .
ΠΠ°ΠΊΠ°Ρ ΡΠ°Π·Π½ΠΈΡΠ° ΠΌΠ΅ΠΆΠ΄Ρ ΡΠ±ΠΎΡΠΊΠΎΠΉ ΠΈ ΡΠ±ΠΎΡΠΊΠΎΠΉ?
Π ΡΡΠΎΠΌ ΠΏΠΎΡΡΠ΅ Ρ Π±ΡΠ΄Ρ ΡΡΠ°Π²Π½ΠΈΠ²Π°ΡΡ ΡΠ°Π·Π²Π΅ΡΠ½ΡΡΡΡ Ρ ΡΠ°Π·Π²Π΅ΡΠ½ΡΡΡΠΌΠΈ . Π― Π½Π°ΡΠΈΡΡΡ ΠΏΡΠ°Π²ΠΈΠ»ΡΠ½ΠΎΠ΅ ΡΠΏΡΡΠΆΠ΅Π½ΠΈΠ΅ ΠΈ Π±ΡΠ΄Ρ ΠΈΡΠΏΠΎΠ»ΡΠ·ΠΎΠ²Π°ΡΡ Π΅Π³ΠΎ Π² Π½Π΅ΡΠΊΠΎΠ»ΡΠΊΠΈΡ ΠΏΡΠΈΠΌΠ΅ΡΠ°Ρ . Π’Π°ΠΊΠΈΠΌ ΠΎΠ±ΡΠ°Π·ΠΎΠΌ, Π²Ρ ΠΌΠΎΠΆΠ΅ΡΠ΅ ΡΠ²ΠΈΠ΄Π΅ΡΡ, ΠΊΠ°ΠΊ ΡΡΠΎ Π²ΡΠ³Π»ΡΠ΄ΠΈΡ Π² ΠΊΠΎΠ½ΡΠ΅ΠΊΡΡΠ΅.
Plus, Ρ ΠΏΠΎΠΊΠ°ΠΆΡ Π²Π°ΠΌ ΠΏΠΎΠ»Π΅Π·Π½ΡΠΉ ΠΈΠ½ΡΡΡΡΠΌΠ΅Π½Ρ ΠΏΠ°ΠΌΡΡΠΈ, ΠΊΠΎΡΠΎΡΡΠΉ ΠΏΠΎΠ·Π²ΠΎΠ»ΠΈΡ Π²Π°ΠΌ ΠΊΠ°ΠΆΠ΄ΡΠΉ ΡΠ°Π· ΠΏΡΠ°Π²ΠΈΠ»ΡΠ½ΠΎ Π²ΡΠ±ΠΈΡΠ°ΡΡ ΡΠ°Π·Π²Π΅ΡΠ½ΡΡΡΠΉ ΠΈΠ»ΠΈ ΡΠ°Π·Π²Π΅ΡΠ½ΡΡΡΠΉ Π² ΡΠ²ΠΎΠ΅ΠΌ ΡΠΎΠ±ΡΡΠ²Π΅Π½Π½ΠΎΠΌ ΠΏΠΈΡΡΠΌΠ΅.
ΠΠΎΠ³Π΄Π° ΠΈΡΠΏΠΎΠ»ΡΠ·ΠΎΠ²Π°ΡΡ Swept
Π§ΡΠΎ Π·Π½Π°ΡΠΈΡ Β«ΠΏΡΠΎΠΊΠ°ΡΠΈΠ»ΡΡΒ»? ΠΠ΅Π» Π³Π»Π°Π³ΠΎΠ». Π ΡΠ°ΡΡΠ½ΠΎΡΡΠΈ, ΡΡΠΎ Π²Π΅ΡΡΠΈΡ ΠΏΡΠΎΡΠ΅Π΄ΡΠ΅Π³ΠΎ Π²ΡΠ΅ΠΌΠ΅Π½ΠΈ Π³Π»Π°Π³ΠΎΠ»Π° ΡΠ°Π·Π²Π΅ΡΡΠΊΠΈ . ΠΠΎΠ΄ΠΌΠ΅ΡΠ°Π½ΠΈΠ΅ ΠΌΠΎΠΆΠ΅Ρ ΠΎΠ·Π½Π°ΡΠ°ΡΡ Π΄Π»Ρ ΠΎΡΠΈΡΡΠΊΠΈ ΠΏΠΎΠ»Π° ΠΈΠ»ΠΈ Π΄Π»Ρ Π±ΡΡΡΡΠΎΠ³ΠΎ ΠΏΠ΅ΡΠ΅ΠΌΠ΅ΡΠ΅Π½ΠΈΡ .
ΠΠΎΡ ΠΏΡΠΈΠΌΠ΅Ρ ΠΊΠ°ΠΆΠ΄ΠΎΠ³ΠΎ,
- ΠΠΎΠ»ΡΡΠΊΠ° Π½Π΅ΡΡΠΎΠΌΠΈΠΌΠΎ ΠΏΠΎΠ΄ΠΌΠ΅ΡΠ°Π»Π° ΠΏΠΎΠ»Ρ ΠΊΠ°ΠΆΠ΄ΡΠΉ Π΄Π΅Π½Ρ ΡΠ²ΠΎΠ΅ΠΉ ΠΆΠΈΠ·Π½ΠΈ, ΠΏΠΎΠΊΠ° Π½Π΅ ΠΏΠΎΠ»ΡΡΠΈΠ»Π° ΠΏΡΠΈΠ³Π»Π°ΡΠ΅Π½ΠΈΠ΅ Π½Π° Π΄Π²ΠΎΡΡΠΎΠ²ΡΠΉ Π±Π°Π».
- ΠΠΠ ΠΏΡΠΎΠ½Π΅ΡΡΡ ΠΏΠΎ Π½Π΅Π±Ρ Π½Π° Π°ΠΌΠ΅ΡΠΈΠΊΠ°Π½ΡΠΊΠΎΠΌ ΡΠ³ΠΎ-Π·Π°ΠΏΠ°Π΄Π΅, Π²ΡΠ·Π²Π°Π² ΡΡΠ΅Π²ΠΎΠ³Ρ ΠΈ ΠΈΠ·ΡΠΌΠ»Π΅Π½ΠΈΠ΅ Π² ΡΡΠ΅Ρ ΡΡΠ°ΡΠ°Ρ .
ΠΠ»Π°Π³ΠΎΠ» Sweep ΡΠ°ΠΊΠΆΠ΅ ΠΌΠΎΠΆΠ΅Ρ ΠΎΠ·Π½Π°ΡΠ°ΡΡ , ΡΡΠΎΠ±Ρ Π²ΡΠΈΠ³ΡΠ°ΡΡ Π²ΡΠ΅ ΠΈΠ³ΡΡ ΡΠ΅ΡΠΈΠΈ . ΠΠΎΠΈΠ½Ρ ΠΠΎΠ»Π΄Π΅Π½ Π‘ΡΡΠΉΡ ΠΊΠ»Π°ΡΡΠ½ΠΎ ΠΎΠ΄ΠΎΠ»Π΅Π»ΠΈ ΠΠ»ΠΈΠ²Π»Π΅Π½Π΄ ΠΠ°Π²Π°Π»ΡΠ΅ΡΡ Π² ΡΠΈΠ½Π°Π»Π΅ ΠΠΠ Π² 2018 Π³ΠΎΠ΄Ρ, ΠΏΠΎΠ±Π΅Π΄ΠΈΠ² ΡΡΡ ΠΊΠΎΠΌΠ°Π½Π΄Ρ Π² ΡΡΠ΅ΡΠΈΠΉ ΡΠ°Π· Π·Π° ΡΠ΅ΡΡΡΠ΅ Π³ΠΎΠ΄Π°.
ΠΠΎΡ Π΅ΡΠ΅ Π΄Π²Π° ΠΏΡΠΈΠΌΠ΅ΡΠ°,
,ΠΠ°ΠΊΠ°Ρ ΡΠ°Π·Π½ΠΈΡΠ° ΠΌΠ΅ΠΆΠ΄Ρ ΠΊΡΠ·Π½Π΅ΡΠΈΠΊΠ°ΠΌΠΈ ΠΈ ΡΠ°ΡΠ°Π½ΡΠΎΠΉ?
ΠΠ΅Π½Π΄ΠΆΠ°ΠΌΠΈΠ½ ΠΠ»ΠΈΡΠ° Π‘Π°Π²Π΅ 1 Π°Π²Π³ΡΡΡΠ° 2017 Π³ΠΎΠ΄Π° Π² ΡΡΠ΅Π΄Π΅
ΠΡΠ·Π½Π΅ΡΠΈΠΊΠΈ ΠΈ ΡΠ°ΡΠ°Π½ΡΠ° – Π±Π»ΠΈΠ·ΠΊΠΎΡΠΎΠ΄ΡΡΠ²Π΅Π½Π½ΡΠ΅ Π½Π°ΡΠ΅ΠΊΠΎΠΌΡΠ΅, ΠΏΡΠΈΠ½Π°Π΄Π»Π΅ΠΆΠ°ΡΠΈΠ΅ ΠΊ ΡΠ΅ΠΌΠ΅ΠΉΡΡΠ²Ρ Acrididae . Π‘Π°ΡΠ°Π½ΡΠ° – ΡΡΠΎ Π½Π° ΡΠ°ΠΌΠΎΠΌ Π΄Π΅Π»Π΅ ΠΊΡΠ·Π½Π΅ΡΠΈΠΊΠΈ, ΠΊΠΎΡΠΎΡΡΠ΅ ΡΠ°Π·Π²ΠΈΠ²Π°ΡΡ ΠΎΠ±ΡΠΈΡΠ΅Π»ΡΠ½ΠΎΠ΅ ΠΏΠΎΠ²Π΅Π΄Π΅Π½ΠΈΠ΅ ΠΏΡΠΈ ΠΎΠΏΡΠΈΠΌΠ°Π»ΡΠ½ΡΡ ΡΡΠ»ΠΎΠ²ΠΈΡΡ ΠΎΠΊΡΡΠΆΠ°ΡΡΠ΅ΠΉ ΡΡΠ΅Π΄Ρ, ΠΊΠΎΡΠΎΡΡΠ΅ Π²ΠΊΠ»ΡΡΠ°ΡΡ ΠΏΡΠΈΡΡΡΡΡΠ²ΠΈΠ΅ Π±ΠΎΠ»ΡΡΠΎΠ³ΠΎ ΠΊΠΎΠ»ΠΈΡΠ΅ΡΡΠ²Π° ΠΊΡΠ·Π½Π΅ΡΠΈΠΊΠΎΠ². Π‘Π°ΡΠ°Π½ΡΠ° Π½Π΅ Π²ΠΈΠ΄. ΠΠ²Π° Π½Π°ΡΠ΅ΠΊΠΎΠΌΡΡ – ΡΡΠΎ ΠΏΡΠ΅ΠΆΠ΄Π΅ Π²ΡΠ΅Π³ΠΎ ΡΡΠ°Π²ΠΎΡΠ΄Π½ΡΠ΅, ΠΊΠΎΡΠΎΡΡΠ΅ ΠΏΠΈΡΠ°ΡΡΡΡ Π»ΡΠ±ΡΠΌ Π·Π΅Π»Π΅Π½ΡΠΌ Π²Π΅ΡΠ΅ΡΡΠ²ΠΎΠΌ, Ρ ΠΊΠΎΡΠΎΡΡΠΌ ΠΎΠ½ΠΈ ΡΡΠ°Π»ΠΊΠΈΠ²Π°ΡΡΡΡ, ΠΈ ΠΈΠ½ΠΎΠ³Π΄Π° ΡΡΠΈΡΠ°ΡΡΡΡ ΡΠ΅Π»ΡΡΠΊΠΎΡ ΠΎΠ·ΡΠΉΡΡΠ²Π΅Π½Π½ΡΠΌΠΈ Π²ΡΠ΅Π΄ΠΈΡΠ΅Π»ΡΠΌΠΈ, ΠΊΠΎΠ³Π΄Π° ΠΎΠ½ΠΈ ΠΏΠΈΡΠ°ΡΡΡΡ ΡΠ΅Π»ΡΡΠΊΠΎΡ ΠΎΠ·ΡΠΉΡΡΠ²Π΅Π½Π½ΡΠΌΠΈ ΠΏΡΠΎΠ΄ΡΠΊΡΠ°ΠΌΠΈ. Π ΠΊΡΠ·Π½Π΅ΡΠΈΠΊΠΈ ΠΈ ΡΠ°ΡΠ°Π½ΡΠ° ΠΏΠΎΡΡΠ΅Π±Π»ΡΡΡΡΡ Π² Π½Π΅ΠΊΠΎΡΠΎΡΡΡ ΡΠ°ΡΡΡΡ ΠΌΠΈΡΠ°, Π³Π΄Π΅ ΠΎΠ½ΠΈ ΡΠ°ΡΡΠΌΠ°ΡΡΠΈΠ²Π°ΡΡΡΡ ΠΊΠ°ΠΊ Π±ΠΎΠ³Π°ΡΡΠΉ ΠΈΡΡΠΎΡΠ½ΠΈΠΊ Π±Π΅Π»ΠΊΠ°.
Π§ΡΠΎ ΡΠ°ΠΊΠΎΠ΅ ΠΊΡΠ·Π½Π΅ΡΠΈΠΊΠΈ?
ΠΡΠ·Π½Π΅ΡΠΈΠΊΠΈ – ΡΡΠΎ Π½Π°Π·Π΅ΠΌΠ½ΡΠ΅ Π½Π°ΡΠ΅ΠΊΠΎΠΌΡΠ΅, ΠΊΠΎΡΠΎΡΡΠ΅ ΠΏΡΠΎΡ ΠΎΠ΄ΡΡ ΡΠ°Π·Ρ Π½Π΅ΠΏΠΎΠ»Π½ΠΎΠ³ΠΎ ΠΌΠ΅ΡΠ°ΠΌΠΎΡΡΠΎΠ·Π°, ΠΏΡΠ΅ΠΆΠ΄Π΅ ΡΠ΅ΠΌ ΠΏΠ΅ΡΠ΅ΡΠ°ΡΡΡΡ Π²ΠΎ Π²Π·ΡΠΎΡΠ»ΡΡ ΡΡΠ°Π΄ΠΈΡ.ΠΠΎΡΠΊΠΎΠ»ΡΠΊΡ ΠΊΡΠ·Π½Π΅ΡΠΈΠΊΠΈ Π² ΠΎΡΠ½ΠΎΠ²Π½ΠΎΠΌ ΠΆΠΈΠ²ΡΡ Π½Π° Π·Π΅ΠΌΠ»Π΅, Ρ Π½ΠΈΡ ΠΎΡΠ΅Π½Ρ ΠΌΠΎΡΠ½ΡΠ΅ Π·Π°Π΄Π½ΠΈΠ΅ Π»Π°ΠΏΡ, ΠΊΠΎΡΠΎΡΡΠ΅ ΠΏΡΠΈΡΠΏΠΎΡΠΎΠ±Π»Π΅Π½Ρ Π΄Π»Ρ ΠΏΠΎΠ±Π΅Π³Π° Π½Π° ΡΠ»ΡΡΠ°ΠΉ, Π΅ΡΠ»ΠΈ ΠΈΠΌ ΡΠ³ΡΠΎΠΆΠ°ΡΡ. ΠΡΠ·Π½Π΅ΡΠΈΠΊΠΈ ΠΎΡΠ΅Π½Ρ ΠΏΠΎΡ ΠΎΠΆΠΈ Π½Π° ΡΠ°ΡΠ°Π½ΡΡ, Ρ ΠΎΡΡ ΠΊΡΠ·Π½Π΅ΡΠΈΠΊΠΈ ΠΌΠΎΠ³ΡΡ Π»Π΅ΡΠ°ΡΡ ΡΠΎΠ»ΡΠΊΠΎ Π½Π° Π±ΠΎΠ»Π΅Π΅ ΠΊΠΎΡΠΎΡΠΊΠΈΠ΅ ΡΠ°ΡΡΡΠΎΡΠ½ΠΈΡ. ΠΡΠ·Π½Π΅ΡΠΈΠΊΠΈ Π² ΠΎΡΠ½ΠΎΠ²Π½ΠΎΠΌ ΡΡΡΠ΅ΡΡΠ²ΡΡΡ Π² ΠΎΠ΄ΠΈΠ½ΠΎΡΠ½ΠΎΠΉ ΡΠ°Π·Π΅ ΠΏΡΠ°ΠΊΡΠΈΡΠ΅ΡΠΊΠΈ Π±Π΅Π· ΡΠ³ΡΠΎΠ·Ρ Π΄Π»Ρ ΡΠ΅Π»ΡΡΠΊΠΎΡ ΠΎΠ·ΡΠΉΡΡΠ²Π΅Π½Π½ΡΡ ΠΊΡΠ»ΡΡΡΡ. Π ΠΎΠ΄ΠΈΠ½ΠΎΡΠ½ΠΎΠΉ ΡΠ°Π·Π΅ ΠΊΡΠ·Π½Π΅ΡΠΈΠΊΠΈ Π΄Π΅Π·ΠΎΡΠ³Π°Π½ΠΈΠ·ΠΎΠ²Π°Π½Ρ, ΠΊΠ°ΠΆΠ΄ΡΠΉ Π²Π΅Π΄Π΅Ρ ΡΠ²ΠΎΠΉ ΠΎΠ±ΡΠ°Π· ΠΆΠΈΠ·Π½ΠΈ. Π’Π΅ΠΌ Π½Π΅ ΠΌΠ΅Π½Π΅Π΅, Π½Π΅ΠΊΠΎΡΠΎΡΡΠ΅ Π²ΠΈΠ΄Ρ ΠΊΡΠ·Π½Π΅ΡΠΈΠΊΠ° ΡΠ°Π·Π²ΠΈΠ²Π°ΡΡ ΠΎΠ±ΡΠΈΡΠ΅Π»ΡΠ½ΠΎΠ΅ ΠΏΠΎΠ²Π΅Π΄Π΅Π½ΠΈΠ΅ Π² ΠΏΠΎΠ΄Ρ ΠΎΠ΄ΡΡΠΈΡ ΡΡΠ»ΠΎΠ²ΠΈΡΡ , ΠΏΡΠ΅Π²ΡΠ°ΡΠ°ΡΡΡ Π² ΡΠ°ΡΠ°Π½ΡΡ.
Π§ΡΠΎ ΡΠ°ΠΊΠΎΠ΅ ΡΠ°ΡΠ°Π½ΡΠ°?
Π‘Π°ΡΠ°Π½ΡΠ° – ΡΡΠΎ ΠΊΡΠ·Π½Π΅ΡΠΈΠΊΠΈ, ΠΊΠΎΡΠΎΡΡΠ΅ ΡΠ°Π·Π²ΠΈΠ²Π°ΡΡ ΠΎΠ±ΡΠΈΡΠ΅Π»ΡΠ½ΡΠ΅ Ρ Π°ΡΠ°ΠΊΡΠ΅ΡΠΈΡΡΠΈΠΊΠΈ Π² ΠΏΠΎΠ΄Ρ ΠΎΠ΄ΡΡΠΈΡ ΡΡΠ»ΠΎΠ²ΠΈΡΡ ΠΎΠΊΡΡΠΆΠ°ΡΡΠ΅ΠΉ ΡΡΠ΅Π΄Ρ, ΠΎΠ±ΡΠ°Π·ΡΡ ΠΎΡΠ³Π°Π½ΠΈΠ·ΠΎΠ²Π°Π½Π½ΡΡ Π³ΡΡΠΏΠΏΡ. Π’Π°ΠΊΠΈΠ΅ ΡΡΠ»ΠΎΠ²ΠΈΡ ΠΎΡΠΎΠ±Π΅Π½Π½ΠΎ ΠΎΠ±ΡΡΠ»ΠΎΠ²Π»Π΅Π½Ρ ΠΏΠ΅ΡΠΈΠΎΠ΄ΠΎΠΌ ΠΏΠ»ΠΎΡΠ½ΠΎΠ³ΠΎ Π²Π΅Π³Π΅ΡΠ°ΡΠΈΠ²Π½ΠΎΠ³ΠΎ ΡΠΎΡΡΠ° ΠΏΠΎΡΠ»Π΅ ΡΡΡ ΠΎΠ³ΠΎ ΠΏΠ΅ΡΠΈΠΎΠ΄Π°.ΠΠ°ΡΡΡ Π° Π·Π°ΡΡΠ°Π²Π»ΡΠ΅Ρ ΡΠ°ΡΠ°Π½ΡΡ ΡΠΎΠ»ΠΏΠΈΡΡΡΡ Π½Π° Π½Π΅Π±ΠΎΠ»ΡΡΠΈΡ ΡΡΠ°ΡΡΠΊΠ°Ρ , Π³Π΄Π΅ Π΅ΡΡΡ ΡΠ°ΡΡΠΈΡΠ΅Π»ΡΠ½ΠΎΡΡΡ. Π‘Π°ΡΠ°Π½ΡΠ° Π·Π°ΡΠ΅ΠΌ ΠΏΠΎΠΊΠΈΠ΄Π°Π΅Ρ ΡΠ²ΠΎΡ ΡΠ΅Π΄ΠΈΠ½Π΅Π½Π½ΡΡ ΡΠ°Π·Ρ ΠΊΠ°ΠΊ ΠΊΡΠ·Π½Π΅ΡΠΈΠΊΠΈ ΠΈ ΡΠ°Π·ΠΌΠ½ΠΎΠΆΠ°Π΅ΡΡΡ Ρ Π½Π΅Π²Π΅ΡΠΎΡΡΠ½ΠΎ Π²ΡΡΠΎΠΊΠΎΠΉ ΡΠΊΠΎΡΠΎΡΡΡΡ, ΠΎΠ±ΡΠ°Π·ΡΡ ΠΏΠΎΠ»ΠΎΡΡ Π½ΠΈΠΌΡ ΠΈ ΡΡΠ°ΠΉ ΠΊΠ°ΠΊ Π²Π·ΡΠΎΡΠ»ΡΠ΅. ΠΠ΅ΡΠ΅Ρ ΠΎΠ΄ ΠΈΠ· ΠΎΠ΄ΠΈΠ½ΠΎΡΠ½ΠΎΠΉ ΡΠ°Π·Ρ Π²ΡΠ·Π²Π°Π½ ΡΠ΅ΠΊΡΠ΅ΡΠΈΠ΅ΠΉ Π³ΠΎΡΠΌΠΎΠ½Π° ΡΠ΅ΡΠΎΡΠΎΠ½ΠΈΠ½Π°, ΠΊΠΎΡΠΎΡΡΠΉ Π±ΡΠ» ΡΠ²ΡΠ·Π°Π½ Ρ ΠΏΠΎΠ²ΡΡΠ΅Π½ΠΈΠ΅ΠΌ Π½Π°ΡΡΡΠΎΠ΅Π½ΠΈΡ Ρ Π»ΡΠ΄Π΅ΠΉ. Π ΠΈΡ ΡΠΎΡΡ ΡΠ°ΡΠ°Π½ΡΠ° Π΄Π²ΠΈΠΆΠ΅ΡΡΡ Π² ΠΎΠ΄Π½ΠΎΠΌ Π½Π°ΠΏΡΠ°Π²Π»Π΅Π½ΠΈΠΈ, Π΄Π΅Π»Π°Ρ ΠΎΡΡΠ°Π½ΠΎΠ²ΠΊΠΈ Π² Π»ΡΠ±ΠΎΠΉ Π·Π΅Π»Π΅Π½ΠΎΠΉ Π·ΠΎΠ½Π΅, ΠΊΠΎΡΠΎΡΡΡ ΠΎΠ½ΠΈ Π·Π°ΠΌΠ΅ΡΠ°ΡΡ. ΠΡΠΎ Π΄Π²ΠΈΠΆΠ΅Π½ΠΈΠ΅ Π½Π°Π½ΠΎΡΠΈΡ Π·Π½Π°ΡΠΈΡΠ΅Π»ΡΠ½ΡΠΉ ΡΡΠ΅ΡΠ± ΠΏΠΎΡΠ΅Π²Π°ΠΌ.ΠΠ·Π²Π΅ΡΡΠ½ΠΎ, ΡΡΠΎ ΡΠ°ΡΠ°Π½ΡΠ° ΠΏΡΠ΅ΠΎΠ΄ΠΎΠ»Π΅Π²Π°Π΅Ρ Π±ΠΎΠ»ΡΡΠΈΠ΅ ΡΠ°ΡΡΡΠΎΡΠ½ΠΈΡ Π·Π° ΠΊΠΎΡΠΎΡΠΊΠΈΠ΅ ΠΏΡΠΎΠΌΠ΅ΠΆΡΡΠΊΠΈ Π²ΡΠ΅ΠΌΠ΅Π½ΠΈ, ΠΎΡΡΠ°Π²Π»ΡΡ Π·Π° ΡΠΎΠ±ΠΎΠΉ ΡΠ»Π΅Π΄ ΠΏΠΎΠ²ΡΠ΅ΠΆΠ΄Π΅Π½ΠΈΡ.
Π‘ΡΡΡΠΊΡΡΡΠ½ΡΠ΅ ΡΠ°Π·Π»ΠΈΡΠΈΡ ΠΌΠ΅ΠΆΠ΄Ρ ΡΠ°ΡΠ°Π½ΡΠΎΠΉ ΠΈ ΠΊΡΠ·Π½Π΅ΡΠΈΠΊΠ°ΠΌΠΈ
Π₯ΠΎΡΡ ΠΊΡΠ·Π½Π΅ΡΠΈΠΊΠΈ ΠΏΠΎΡ ΠΎΠΆΠΈ ΠΏΠΎ Π²Π½Π΅ΡΠ½Π΅ΠΌΡ Π²ΠΈΠ΄Ρ, ΠΎΠ½ΠΈ ΡΡΡΡΠΊΡΡΡΠ½ΠΎ ΠΎΡΠ»ΠΈΡΠ°ΡΡΡΡ ΠΎΡ ΡΠ°ΡΠ°Π½ΡΠΈ. ΠΠ±Π° ΡΠ°ΠΊΠΆΠ΅ ΠΎΡΠ»ΠΈΡΠ°ΡΡΡΡ ΠΏΠΎ ΡΠ²ΠΎΠ΅ΠΌΡ ΠΏΠΎΠ²Π΅Π΄Π΅Π½ΠΈΡ.Π£ ΠΊΡΠ·Π½Π΅ΡΠΈΠΊΠΎΠ² ΠΏΠ΅ΡΠ΅Π΄Π½ΠΈΠ΅ ΠΊΡΡΠ»ΡΡ ΡΠΎΠ½ΠΊΠΈΠ΅ ΠΈ ΠΆΠ΅ΡΡΠΊΠΈΠ΅, Π° Π²Π½Π΅ΡΠ½ΠΈΠ΅ – ΡΠΈΡΠΎΠΊΠΈΠ΅ ΠΈ Π³ΠΈΠ±ΠΊΠΈΠ΅. Π£ ΡΠ°ΡΠ°Π½ΡΠΈ ΠΊΡΡΠ»ΡΡ ΡΡΠ°Π½ΠΎΠ²ΡΡΡΡ Π΄Π»ΠΈΠ½Π½Π΅Π΅ ΠΈ ΡΠΈΠ»ΡΠ½Π΅Π΅, ΡΡΠΎ ΠΏΠΎΠ·Π²ΠΎΠ»ΡΠ΅Ρ ΡΠΎΠ²Π΅ΡΡΠ°ΡΡ ΠΏΠ΅ΡΠ΅Π»Π΅ΡΡ Π½Π° Π±ΠΎΠ»ΡΡΠΈΠ΅ ΡΠ°ΡΡΡΠΎΡΠ½ΠΈΡ. Π’Π΅Π»ΠΎ ΡΠ°ΡΠ°Π½ΡΠΈ ΠΌΠ΅Π½ΡΡΠ΅, ΡΠ΅ΠΌ Ρ ΠΊΡΠ·Π½Π΅ΡΠΈΠΊΠΎΠ². Π ΡΠ²ΠΎΠ΅ΠΌ ΠΎΠ΄ΠΈΠ½ΠΎΡΠ½ΠΎΠΌ ΡΠΎΡΡΠΎΡΠ½ΠΈΠΈ ΡΠ°ΠΌΠΊΠ° ΡΠ°ΡΠ°Π½ΡΠΈ Π±ΠΎΠ»ΡΡΠ΅, ΡΠ΅ΠΌ ΠΈΡ ΠΊΠΎΠ»Π»Π΅Π³ΠΈ-ΠΌΡΠΆΡΠΈΠ½Ρ, Ρ ΠΎΡΡ ΠΈΡ ΡΠ°Π·ΠΌΠ΅ΡΡ Π½Π° ΡΡΠ°Π΄ΠΈΠΈ ΡΠΎΠ΅Π½ΠΈΡ Π΄Π΅ΠΉΡΡΠ²ΠΈΡΠ΅Π»ΡΠ½ΠΎ ΡΠΌΠ΅Π½ΡΡΠ°ΡΡΡΡ.
ΠΏΠΎΠ²Π΅Π΄Π΅Π½ΡΠ΅ΡΠΊΠΈΡ ΡΠ°Π·Π»ΠΈΡΠΈΠΉ ΠΌΠ΅ΠΆΠ΄Ρ ΡΠ°ΡΠ°Π½ΡΠΎΠΉ ΠΈ ΠΊΡΠ·Π½Π΅ΡΠΈΠΊΠ°ΠΌΠΈ
ΠΡΠ·Π½Π΅ΡΠΈΠΊΠΈ – ΡΡΠΎ, ΠΏΡΠ΅ΠΆΠ΄Π΅ Π²ΡΠ΅Π³ΠΎ, ΠΎΠ΄ΠΈΠ½ΠΎΡΠ½ΡΠ΅ ΡΡΡΠ΅ΡΡΠ²Π° Π½Π° ΠΏΡΠΎΡΡΠΆΠ΅Π½ΠΈΠΈ Π²ΡΠ΅ΠΉ ΡΠ²ΠΎΠ΅ΠΉ ΠΆΠΈΠ·Π½ΠΈ, ΠΊΠΎΡΠΎΡΡΠ΅ ΡΠΎΠ±ΠΈΡΠ°ΡΡΡΡ Π²ΠΌΠ΅ΡΡΠ΅ ΡΠΎΠ»ΡΠΊΠΎ Π΄Π»Ρ ΡΠ°Π·ΠΌΠ½ΠΎΠΆΠ΅Π½ΠΈΡ.Π₯ΠΎΡΡ ΡΠ°ΡΠ°Π½ΡΠ° ΠΌΠΎΠΆΠ΅Ρ Π±ΡΡΡ Π½Π°ΠΉΠ΄Π΅Π½Π° Π² ΠΈΠ·ΠΎΠ»ΡΡΠΈΠΈ, Π² ΠΎΡΠ½ΠΎΠ²Π½ΠΎΠΌ ΠΎΠ½ΠΈ Π²ΡΡΡΠ΅ΡΠ°ΡΡΡΡ Π² Π³ΡΡΠΏΠΏΠ°Ρ , Π² ΠΊΠΎΡΠΎΡΡΡ ΠΎΠ½ΠΈ Π΄ΠΎΠ±ΡΠ²Π°ΡΡ ΠΏΠΈΡΡ, Π³ΡΠ΅ΡΡΡΡ ΠΈ Π½Π°ΡΠ΅Π»ΡΡΡ. ΠΡΠ·Π½Π΅ΡΠΈΠΊΠΈ – ΠΎΡΠ½ΠΎΡΠΈΡΠ΅Π»ΡΠ½ΠΎ ΡΠΈΠ΄ΡΡΠΈΠ΅ Π²ΠΈΠ΄Ρ, ΡΠΎΡ ΡΠ°Π½ΡΡΡΠΈΠ΅ ΠΎΠ΄Π½Ρ ΠΈ ΡΡ ΠΆΠ΅ ΡΡΠ΅Π΄Ρ ΠΎΠ±ΠΈΡΠ°Π½ΠΈΡ Π² ΡΠ΅ΡΠ΅Π½ΠΈΠ΅ Π΄Π»ΠΈΡΠ΅Π»ΡΠ½ΡΡ ΠΏΠ΅ΡΠΈΠΎΠ΄ΠΎΠ². ΠΡΠ·Π½Π΅ΡΠΈΠΊΠΈ Π΄Π²ΠΈΠ³Π°ΡΡΡΡ ΡΠΎΠ»ΡΠΊΠΎ ΡΠΎΠ³Π΄Π°, ΠΊΠΎΠ³Π΄Π° ΠΈΠΌ ΡΠ³ΡΠΎΠΆΠ°ΡΡ, ΠΈ Π²ΠΎ Π²ΡΠ΅ΠΌΡ ΠΊΠΎΡΠΌΠ»Π΅Π½ΠΈΡ. Π‘Π°ΡΠ°Π½ΡΠ°, ΠΎΠ΄Π½Π°ΠΊΠΎ, ΡΠ²Π»ΡΠ΅ΡΡΡ ΠΌΠΈΠ³ΡΠΈΡΡΡΡΠΈΠΌ Π²ΠΈΠ΄ΠΎΠΌ, ΡΠ°ΡΡΠΎ ΠΏΠ΅ΡΠ΅ΠΌΠ΅ΡΠ°ΡΡΠΈΠΌΡΡ ΠΈΠ· ΠΎΠ΄Π½ΠΎΠ³ΠΎ ΡΠ°ΠΉΠΎΠ½Π° Π² Π΄ΡΡΠ³ΠΎΠΉ Π² ΠΏΠΎΠΈΡΠΊΠ°Ρ ΠΏΠΈΡΠΈ. ΠΠ·Π²Π΅ΡΡΠ½ΠΎ, ΡΡΠΎ Π΄Π°ΠΆΠ΅ Π² ΡΠ²ΠΎΠ΅ΠΌ ΡΠ΅Π΄ΠΈΠ½Π΅Π½Π½ΠΎΠΌ ΡΠΎΡΡΠΎΡΠ½ΠΈΠΈ ΡΠ°ΡΠ°Π½ΡΠ° Π»Π΅ΡΠΈΡ Π½Π° Π±ΠΎΠ»ΡΡΠΈΠ΅ ΡΠ°ΡΡΡΠΎΡΠ½ΠΈΡ.
ΠΠ·Π°ΠΈΠΌΠΎΠ΄Π΅ΠΉΡΡΠ²ΠΈΠ΅ ΡΠ΅Π»ΠΎΠ²Π΅ΠΊΠ° Ρ ΡΠ°ΡΠ°Π½ΡΠΎΠΉ ΠΈ ΠΊΡΠ·Π½Π΅ΡΠΈΠΊΠ°ΠΌΠΈ
ΠΡΠ·Π½Π΅ΡΠΈΠΊΠΈ ΠΈ ΡΠ°ΡΠ°Π½ΡΠ° ΠΈΡΠΏΠΎΠ»ΡΠ·ΡΡΡΡΡ Π»ΡΠ΄ΡΠΌΠΈ Π² ΠΊΠ°ΡΠ΅ΡΡΠ²Π΅ ΠΏΠΈΡΠ΅Π²ΠΎΠ³ΠΎ ΡΠ΅ΡΡΡΡΠ°.ΠΠ½ΠΈ ΡΠ°ΠΊΠΆΠ΅ ΡΠ°ΡΡΠΌΠ°ΡΡΠΈΠ²Π°ΡΡΡΡ ΠΊΠ°ΠΊ Π²ΡΠ΅Π΄ΠΈΡΠ΅Π»ΠΈ ΠΈΠ·-Π·Π° ΠΈΡ ΡΠΏΠΎΡΠΎΠ±Π½ΠΎΡΡΠΈ ΡΠ½ΠΈΡΡΠΎΠΆΠ°ΡΡ ΠΏΠΎΡΠ΅Π²Ρ, ΠΈ ΡΡΠ° ΠΏΡΠΎΠ±Π»Π΅ΠΌΠ° ΠΏΡΠ΅ΡΠ»Π΅Π΄ΠΎΠ²Π°Π»Π° ΡΠ΅ΡΠΌΠ΅ΡΠΎΠ² Π½Π° ΠΏΡΠΎΡΡΠΆΠ΅Π½ΠΈΠΈ Π²Π΅ΠΊΠΎΠ². Π’Π°ΠΊΠΈΠΌ ΠΎΠ±ΡΠ°Π·ΠΎΠΌ, ΠΏΠ΅ΡΡΠΈΡΠΈΠ΄Ρ ΠΈ Π±ΠΈΠΎΠ»ΠΎΠ³ΠΈΡΠ΅ΡΠΊΠΈΠ΅ ΠΌΠ΅ΡΠΎΠ΄Ρ Π±ΠΎΡΡΠ±Ρ Ρ ΡΡΠΈΠΌΠΈ Π½Π°ΡΠ΅ΠΊΠΎΠΌΡΠΌΠΈ Π±ΡΠ»ΠΈ ΡΠ°Π·ΡΠ°Π±ΠΎΡΠ°Π½Ρ ΠΈΡΡΠ»Π΅Π΄ΠΎΠ²Π°ΡΠ΅Π»ΡΠΌΠΈ. Π‘Π°ΡΠ°Π½ΡΠ° ΠΏΠΎΠΌΠΎΠ³Π°Π΅Ρ ΡΠ΅ΡΠΌΠ΅ΡΠ°ΠΌ ΠΏΠΎΠ΄Π³ΠΎΡΠΎΠ²ΠΈΡΡΡΡ ΠΊ Π·Π°ΡΡΡ Π΅, ΠΏΠΎΡΠΊΠΎΠ»ΡΠΊΡ ΡΡΠ°ΠΈ ΡΠ°ΡΠ°Π½ΡΠΈ Π² ΠΎΠ±Π»Π°ΡΡΠΈ ΡΠΊΠ°Π·ΡΠ²Π°ΡΡ Π½Π° Π½Π°ΡΡΡΠΏΠ»Π΅Π½ΠΈΠ΅ Π·Π°ΡΡΡΠ»ΠΈΠ²ΠΎΠ³ΠΎ ΠΏΠ΅ΡΠΈΠΎΠ΄Π°.
,ΠΠ°ΠΊΠ°Ρ ΡΠ°Π·Π½ΠΈΡΠ° ΠΌΠ΅ΠΆΠ΄Ρ ΠΠΎΠΊΡΡΠΎΠΌ ΠΈ ΠΠ΅ΡΠ²ΠΈΡΠ½ΡΠΌ?
Π Π΅ΠΊΠ»Π°ΠΌΠ°
ΠΠ°ΠΆΠ΄ΡΠ΅ ΡΠ΅ΡΡΡΠ΅ Π³ΠΎΠ΄Π° ΡΠ΅Π»Π΅Π²ΠΈΠ·ΠΈΠΎΠ½Π½ΡΠ΅ Π½ΠΎΠ²ΠΎΡΡΠ½ΡΠ΅ Π³ΡΡΠΏΠΏΡ ΠΈΠ· ΠΡΡ-ΠΠΎΡΠΊΠ° Π² ΠΠΎΡ-ΠΠ½Π΄ΠΆΠ΅Π»Π΅Ρ ΡΠ°Π·Π±ΠΈΠ²Π°ΡΡ Π»Π°Π³Π΅ΡΡ Π½Π° Ρ ΠΎΠ»ΠΎΠ΄Π½ΡΡ ΠΊΡΠΊΡΡΡΠ·Π½ΡΡ ΠΏΠΎΠ»ΡΡ ΡΠ΅Π»ΡΡΠΊΠΎΠΉ ΠΠΉΠΎΠ²Ρ. ΠΠ°Π²Π°Π»Π΅ΡΡ Π² ΠΠΉΠΎΠ²Π΅, ΡΠΎΡΡΠΎΡΠ²ΡΠΈΠ΅ΡΡ Π² Π½Π°ΡΠ°Π»Π΅ ΡΠ΅Π²ΡΠ°Π»Ρ, ΠΏΡΠ΅Π΄ΠΎΡΡΠ°Π²Π»ΡΡΡ ΠΎΠ±ΡΡΠ½ΡΠΌ Π°ΠΌΠ΅ΡΠΈΠΊΠ°Π½ΡΠ°ΠΌ ΠΈΠ· ΠΎΠ±Π΅ΠΈΡ ΠΎΡΠ½ΠΎΠ²Π½ΡΡ ΠΏΠΎΠ»ΠΈΡΠΈΡΠ΅ΡΠΊΠΈΡ ΠΏΠ°ΡΡΠΈΠΉ ΠΏΠ΅ΡΠ²ΡΠΉ ΡΠ°Π½Ρ ΠΏΠΎΠ΄Π΄Π΅ΡΠΆΠ°ΡΡ ΠΊΠ°Π½Π΄ΠΈΠ΄Π°ΡΠ° Π² ΠΏΡΠ΅Π·ΠΈΠ΄Π΅Π½ΡΡ. ΠΠ°ΡΠΈΠΎΠ½Π°Π»ΡΠ½Π°Ρ ΠΏΡΠ΅ΡΡΠ° ΠΎΡΠ²Π΅ΡΠ°Π΅Ρ ΠΊΠ°ΠΆΠ΄ΡΡ ΠΌΠΈΠ½ΡΡΡ Π²ΠΎΠ»Π½Π΅Π½ΠΈΡ ΠΏΠ΅ΡΠ΅Π΄ ΡΠΎΠ±ΡΠ°Π½ΠΈΠ΅ΠΌ, ΡΠ°ΠΊ ΠΊΠ°ΠΊ ΠΊΠ°Π½Π΄ΠΈΠ΄Π°ΡΡ Π² ΠΏΡΠ΅Π·ΠΈΠ΄Π΅Π½ΡΡ ΡΠ°ΡΠΏΡΠΎΡΡΡΠ°Π½ΡΡΡΡΡ ΠΏΠΎ Π²ΡΠ΅ΠΌ 99 ΠΎΠΊΡΡΠ³Π°ΠΌ ΠΠΉΠΎΠ²Ρ, ΡΡΠΎΠ±Ρ ΠΏΠΎΠΆΠ°ΡΡ ΡΡΠΊΡ ΠΌΠ΅ΡΡΠ½ΡΠΌ ΠΏΠΎΡΠ΅ΡΠΈΡΠ΅Π»ΡΠΌ ΠΈ ΠΏΡΠΎΠΈΠ·Π½Π΅ΡΡΠΈ ΠΏΠ΅Π½Ρ Ρ ΡΠ΅ΡΡΡ Π² ΡΠΏΠΎΡΡΠΈΠ²Π½ΡΡ Π·Π°Π»Π°Ρ Π½Π°ΡΠ°Π»ΡΠ½ΠΎΠΉ ΡΠΊΠΎΠ»Ρ.
ΠΠ°ΠΊ ΡΠ°ΠΌΠΎΠ΅ ΡΠ°Π½Π½Π΅Π΅ ΡΠΎΠ±ΡΡΠΈΠ΅ ΡΠ΅Π·ΠΎΠ½Π° ΠΏΠ΅ΡΠ²ΠΈΡΠ½ΡΡ Π²ΡΠ±ΠΎΡΠΎΠ² – Π²Ρ Π·Π½Π°Π΅ΡΠ΅, ΡΠ²ΠΎΠ±ΠΎΠ΄Π½ΡΠΉ Π΄Π»Ρ Π²ΡΠ΅Ρ , ΠΊΠΎΡΠΎΡΡΠΉ ΠΎΠΏΡΠ΅Π΄Π΅Π»ΡΠ΅Ρ ΠΊΠ°Π½Π΄ΠΈΠ΄Π°ΡΠΎΠ² Π² ΠΊΠ°ΠΆΠ΄ΠΎΠΉ ΠΏΠ°ΡΡΠΈΠΈ – ΠΠΉΠΎΠ²Π° Π²ΡΡΡΡΠΏΠ°Π΅Ρ Π² ΡΠΎΠ»ΠΈ Π»ΠΈΠ΄Π΅ΡΠ° Π½Π°ΡΠΈΠΎΠ½Π°Π»ΡΠ½ΡΡ Π½Π°ΡΡΡΠΎΠ΅Π½ΠΈΠΉ, ΠΏΠΎΠΌΠΎΠ³Π°Ρ Π²ΡΠ΄Π²ΠΈΠ³Π°ΡΡ ΠΈΠ»ΠΈ ΠΎΠΏΡΡΠΊΠ°ΡΡ ΠΊΠ°Π½Π΄ΠΈΠ΄Π°ΡΡΡΡ ΠΈ ΠΎΡΠ΄Π΅Π»ΡΡΡ ΠΏΡΠ΅Π½ΠΈΡΡ ΠΎΡ ΠΏΠ»Π΅Π²Π΅Π». – ΠΈΠ»ΠΈ, Π² ΡΠ»ΡΡΠ°Π΅ ΠΠΉΠΎΠ²Ρ, ΠΊΡΠΊΡΡΡΠ·Π° ΠΈΠ· ΡΠ΅Π»ΡΡ ΠΈ. ΠΠΎ ΡΡΠΎ ΡΠ°ΠΊΠΎΠ΅ ΡΠΎΠ±ΡΠ°Π½ΠΈΠ΅? Π ΡΠ΅ΠΌ ΠΎΠ½ ΠΎΡΠ»ΠΈΡΠ°Π΅ΡΡΡ ΠΎΡ ΠΎΡΠ½ΠΎΠ²Π½ΠΎΠ³ΠΎ?
ΠΠΎΠΊΡΡΡ ΠΈ ΠΏΠ΅ΡΠ²ΠΈΡΠ½ΡΠ΅ Π²ΡΠ±ΠΎΡΡ – ΡΡΠΎ Π΄Π²Π° ΡΠΏΠΎΡΠΎΠ±Π°, ΠΊΠΎΡΠΎΡΡΠΌΠΈ Π΄Π΅ΠΌΠΎΠΊΡΠ°ΡΠΈΡΠ΅ΡΠΊΠ°Ρ ΠΈ ΡΠ΅ΡΠΏΡΠ±Π»ΠΈΠΊΠ°Π½ΡΠΊΠ°Ρ ΠΏΠ°ΡΡΠΈΠΈ Π²ΡΠ±ΠΈΡΠ°ΡΡ Π΄Π΅Π»Π΅Π³Π°ΡΠΎΠ², ΠΊΠΎΡΠΎΡΡΠ΅ Π±ΡΠ΄ΡΡ ΠΏΡΠΈΡΡΡΡΡΠ²ΠΎΠ²Π°ΡΡ Π½Π° Π½Π°ΡΠΈΠΎΠ½Π°Π»ΡΠ½ΡΡ ΡΡΠ΅Π·Π΄Π°Ρ ΡΡΠΎΡΠΎΠ½.ΠΠ° Π½Π°ΡΠΈΠΎΠ½Π°Π»ΡΠ½ΠΎΠΌ ΡΡΠ΅Π·Π΄Π΅ Π΄Π΅Π»Π΅Π³Π°ΡΡ ΠΎΡΠΈΡΠΈΠ°Π»ΡΠ½ΠΎ Π²ΡΠ±ΠΈΡΠ°ΡΡ ΠΊΠ°Π½Π΄ΠΈΠ΄Π°ΡΠ° ΠΎΡ ΠΏΠ°ΡΡΠΈΠΈ Π½Π° ΠΏΡΠ΅Π·ΠΈΠ΄Π΅Π½ΡΡΠΊΡΡ Π³ΠΎΠ½ΠΊΡ.
ΠΡΠ°ΠΉΠΌΠ΅ΡΠΈΠ· ΠΏΡΠ΅Π΄Π»Π°Π³Π°ΡΡ ΠΎΡΠ½ΠΎΡΠΈΡΠ΅Π»ΡΠ½ΠΎ ΠΏΡΠΎΡΡΠΎΠΉ ΡΠΏΠΎΡΠΎΠ± Π½Π°Π·Π½Π°ΡΠ΅Π½ΠΈΡ Π΄Π΅Π»Π΅Π³Π°ΡΠΎΠ² Π½Π° Π½Π°ΡΠΈΠΎΠ½Π°Π»ΡΠ½ΡΡ ΠΊΠΎΠ½Π²Π΅Π½ΡΠΈΡ. ΠΠ·Π±ΠΈΡΠ°ΡΠ΅Π»ΠΈ ΠΎΡ ΠΊΠ°ΠΆΠ΄ΠΎΠΉ ΠΏΠ°ΡΡΠΈΠΈ Π³ΠΎΠ»ΠΎΡΡΡΡ Π·Π° ΠΎΠ΄Π½ΠΎΠ³ΠΎ ΠΈΠ· ΠΊΠ°Π½Π΄ΠΈΠ΄Π°ΡΠΎΠ² Π² ΠΏΠ΅ΡΠ²ΠΈΡΠ½ΠΎΠΌ Π³ΠΎΠ»ΠΎΡΠΎΠ²Π°Π½ΠΈΠΈ. ΠΠ°ΠΊ ΠΈ Π²ΡΠ΅ΠΎΠ±ΡΠΈΠ΅ ΠΏΡΠ΅Π·ΠΈΠ΄Π΅Π½ΡΡΠΊΠΈΠ΅ Π²ΡΠ±ΠΎΡΡ, ΠΏΠ΅ΡΠ²ΠΈΡΠ½ΠΎΠ΅ Π³ΠΎΠ»ΠΎΡΠΎΠ²Π°Π½ΠΈΠ΅ ΠΏΡΠΎΠ²ΠΎΠ΄ΠΈΡΡΡ Π² Π½Π°Π·Π½Π°ΡΠ΅Π½Π½ΡΠΉ Π΄Π΅Π½Ρ Π½Π° Π½Π°Π·Π½Π°ΡΠ΅Π½Π½ΠΎΠΌ ΠΈΠ·Π±ΠΈΡΠ°ΡΠ΅Π»ΡΠ½ΠΎΠΌ ΡΡΠ°ΡΡΠΊΠ΅. ΠΠΎΠ»ΠΎΡΠΎΠ²Π°Π½ΠΈΠ΅ ΡΠ²Π»ΡΠ΅ΡΡΡ ΡΠ°ΡΡΠ½ΡΠΌ ΠΈ Π°Π½ΠΎΠ½ΠΈΠΌΠ½ΡΠΌ. Π Π·Π°Π²ΠΈΡΠΈΠΌΠΎΡΡΠΈ ΠΎΡ ΠΏΡΠ°Π²ΠΈΠ» ΡΡΠ°ΡΠ°, Π΄Π΅Π»Π΅Π³Π°ΡΡ ΡΠ°ΡΠΏΡΠ΅Π΄Π΅Π»ΡΡΡΡΡ Π»ΠΈΠ±ΠΎ ΠΏΡΠΎΠΏΠΎΡΡΠΈΠΎΠ½Π°Π»ΡΠ½ΠΎ ΠΊΠΎΠ»ΠΈΡΠ΅ΡΡΠ²Ρ Π³ΠΎΠ»ΠΎΡΠΎΠ², ΠΏΠΎΠ»ΡΡΠ΅Π½Π½ΡΡ ΠΊΠ°ΠΆΠ΄ΡΠΌ ΠΊΠ°Π½Π΄ΠΈΠ΄Π°ΡΠΎΠΌ (ΠΈΠ·Π²Π΅ΡΡΠ½ΡΠΉ ΠΊΠ°ΠΊ ΠΏΡΠΎΠΏΠΎΡΡΠΈΠΎΠ½Π°Π»ΡΠ½ΡΠΉ ΠΏΠ΅ΡΠ²ΠΈΡΠ½ΡΠΉ ), Π»ΠΈΠ±ΠΎ Π²ΡΠ΅ Π΄Π΅Π»Π΅Π³Π°ΡΡ ΠΏΡΠ΅Π΄ΠΎΡΡΠ°Π²Π»ΡΡΡΡΡ ΠΊΠ°Π½Π΄ΠΈΠ΄Π°ΡΡ, ΠΏΠΎΠ»ΡΡΠΈΠ²ΡΠ΅ΠΌΡ Π½Π°ΠΈΠ±ΠΎΠ»ΡΡΠ΅Π΅ ΠΊΠΎΠ»ΠΈΡΠ΅ΡΡΠ²ΠΎ Π³ΠΎΠ»ΠΎΡΠΎΠ² (Π½Π°Π·ΡΠ²Π°Π΅ΠΌΠΎΠΌΡ ΠΏΠΎΠ±Π΅Π΄ΠΈΡΠ΅Π»Π΅ΠΌ ). Π²Π·ΡΡΡ Π²ΡΠ΅ “ΠΏΠ΅ΡΠ²ΠΈΡΠΊΠΈ ).
Π‘ΠΎΠ±ΡΠ°Π½ΠΈΠ΅, Ρ Π΄ΡΡΠ³ΠΎΠΉ ΡΡΠΎΡΠΎΠ½Ρ, Π΄Π°Π»Π΅ΠΊΠΎ Π½Π΅ ΠΎΠ΄Π½ΠΎΠ·Π½Π°ΡΠ½ΠΎ. (ΠΠ½ΡΠ΅ΡΠ΅ΡΠ½ΠΎ, ΡΡΠΎ Π΄ΠΎ 1960-Ρ ΠΈ 1970-Ρ Π³ΠΎΠ΄ΠΎΠ² Π±ΠΎΠ»ΡΡΠΈΠ½ΡΡΠ²ΠΎ ΡΡΠ°ΡΠΎΠ² Π²ΡΠ±ΠΈΡΠ°Π»ΠΈ ΡΠ²ΠΎΠΈΡ Π΄Π΅Π»Π΅Π³Π°ΡΠΎΠ² Π½Π° ΠΊΠΎΠΊΡΡΠ°Ρ , Π° Π½Π΅ Π½Π° ΠΏΡΠ°ΠΉΠΌΠ΅ΡΠΈΠ·.) Π‘ ΠΎΠ΄Π½ΠΎΠΉ ΡΡΠΎΡΠΎΠ½Ρ, ΠΊΠΎΠΊΡΡΡ Π½Π΅ ΠΏΡΠ΅Π΄Π½Π°Π·Π½Π°ΡΠ΅Π½Ρ ΠΈΡΠΊΠ»ΡΡΠΈΡΠ΅Π»ΡΠ½ΠΎ Π΄Π»Ρ ΠΏΡΠ΅Π·ΠΈΠ΄Π΅Π½ΡΡΠΊΠΈΡ Π²ΡΠ±ΠΎΡΠΎΠ². ΠΡΠΎΠΌΠ΅ ΡΠΎΠ³ΠΎ, ΠΊΠΎΠΊΡΡΡ ΡΡΠ°Π΄ΠΈΡΠΈΠΎΠ½Π½ΠΎ ΠΏΡΠΎΠ²ΠΎΠ΄ΠΈΠ»ΠΈΡΡ ΠΊΠ°ΠΆΠ΄ΡΠ΅ Π΄Π²Π° Π³ΠΎΠ΄Π°, ΡΡΠΎΠ±Ρ ΠΌΠ΅ΡΡΠ½ΡΠ΅ ΡΠ»Π΅Π½Ρ ΠΊΠ°ΠΆΠ΄ΠΎΠΉ ΠΏΠΎΠ»ΠΈΡΠΈΡΠ΅ΡΠΊΠΎΠΉ ΠΏΠ°ΡΡΠΈΠΈ ΠΌΠΎΠ³Π»ΠΈ Π²ΡΡΡΠ΅ΡΠ°ΡΡΡΡ, ΠΎΠ±ΡΡΠΆΠ΄Π°ΡΡ Π°ΠΊΡΡΠ°Π»ΡΠ½ΡΠ΅ Π²ΠΎΠΏΡΠΎΡΡ ΠΈ ΠΏΠΎΠΌΠΎΠ³Π°ΡΡ ΡΠΎΡΠΌΠΈΡΠΎΠ²Π°ΡΡ ΠΏΠΎΠ»ΠΈΡΠΈΡΠ΅ΡΠΊΡΡ ΠΏΠ»Π°ΡΡΠΎΡΠΌΡ Π³ΠΎΡΡΠ΄Π°ΡΡΡΠ²Π° ΠΈ Π½Π°ΡΠΈΠΎΠ½Π°Π»ΡΠ½ΠΎΠΉ ΠΏΠ°ΡΡΠΈΠΈ [ΠΈΡΡΠΎΡΠ½ΠΈΠΊ: Redlawski et al].
ΠΠ°ΠΊ ΡΠ΅Π³ΠΎΠ΄Π½Ρ Π΄Π΅ΠΉΡΡΠ²ΡΡΡ ΠΊΠΎΠΊΡΡΡ ΠΈ ΠΏΡΠ°ΠΉΠΌΠ΅ΡΠΈΠ·? Π£Π·Π½Π°ΠΉ Π΄Π°Π»ΡΡΠ΅.
,