Рекомендации по фрезерованию
Выбор диаметра фрезы зависит, как правило, от ширины обрабатываемой заготовки, а также от мощностных характеристик станка. При этом важным фактором, определяющим успешное выполнение операции фрезерования, является взаимное расположение обрабатываемой поверхности и фрезы.
Ширина фрезерования особенно сильно влияет на выбор диаметра фрезы при обработке торцовыми фрезами. В этом случае рекомендуется выбирать диаметр фрезы, превышающий ширину фрезерования на 20–50%.
Если обработка может быть произведена за несколько проходов, то ширина резания за каждый проход должна быть равной 3/4 диаметра фрезы. При этом формирование стружки и нагрузка на режущую кромку будут оптимальными.

Когда диаметр фрезы значительно превышает ширину заготовки, то ось фрезы следует сместить с оси симметрии заготовки. Конечно, близкое расположение оси фрезы к оси заготовки позволяет обеспечить наикратчайший путь зубьев фрезы в металле, надежное формирование стружки на входе и благоприятную ситуацию относительно ударных нагрузок на пластину. Но когда ось фрезы расположена точно по оси симметрии заготовки, циклическое изменение силы резания при врезании и выходе может привести к возникновению вибраций, которые приведут к повреждению пластины и плохой шероховатости поверхности.
При торцевом фрезеровании по возможности избегайте фрезерования плоскостей с пересечением пазов и отверстий, так как при этом режущие кромки будут работать в неудовлетворительных условиях прерывистого резания. Выполняйте операцию изготовления отверстий после фрезерования. Если такой вариант невозможен, то при пересечении фрезой отверстия снижайте величину подачи на 50% от рекомендованной.
При обработке больших плоскостей старайтесь не прерывать контакт фрезы с заготовкой, обходя поверхность по периметру, а не за несколько параллельных проходов. Обработку углов необходимо осуществлять по радиусу, превышающему радиус фрезы, чтобы исключить возможность возникновения вибраций, связанных с резким увеличением угла охвата фрезы.
При обработке закрытого паза (замкнутой области) основная проблема заключается в трудности первоначального входа инструмента в материал заготовки, так как большинство концевых фрез плохо работают на засверливание. Существует несколько способов решения этой проблемы. Самый простой выход из ситуации – предварительно просверлить технологическое отверстие и затем спокойно опустить в него фрезу. Более интересные способы – маятниковое и спиральное врезания. В этом случае отпадает необходимость предварительного сверления, режущий инструмент входит в материал заготовки плавно.
Рис. ![]() |
Рис. 2.13. Маятниковое врезание (фрезерование) |
Рис. 2.14. Траектория спирального врезания с выходом в плоскость обработки |
Особую осторожность нужно соблюдать при обработке тонкостенных карманов. Желательно, чтобы материал выбирался постепенно и обязательно при попутном способе фрезерования. В противном случае появляется вероятность «подрыва» тонкой стенки.
Обрабатывая внутренние радиусы, старайтесь, чтобы радиус фрезы был немного меньше, чем радиус в углу кармана (контура). Дело в том, что в момент, когда фреза входит в угол, ширина фрезерования возрастает скачкообразно, что может привести к «подхвату» инструмента и, как следствие, подрезать обрабатываемый контур или сломать фрезу. При назначении диаметра фрезы для черновой обработки внутренних радиусов желательно, чтобы оставляемый в углах припуск не превышал 0,20×D, где D – диаметр последующей чистовой фрезы.
При обработке глубоких контуров и уступов необходимо обеспечить достаточную жесткость инструмента во избежание его отжима и исключения «конусности» обработанной поверхности. Желательно, чтобы диаметр инструмента D удовлетворял условию H
Часто фрезерование производится в два этапа: черновой – контур обрабатывается послойно с небольшим припуском, чистовой – оставшийся припуск удаляется за один проход фрезы на финальной глубине.
Рис. 2.15. Простейшие способы подвода инструмента
При выполнении чернового и особенно чистового фрезерования инструмент следует подводить к обрабатываемой поверхности по касательной или по прямой линии под острым углом. Следуя этому правилу, необходимо и отводить инструмент. Дело в том, что при первоначальном врезании в материал заготовки фреза подвергается резкой нагрузке, что может привести к ее поломке или к тому, что на поверхности детали в месте входа фрезы в материал останется след или неровность. Если врезание будет плавным, то нагрузка на инструмент будет возрастать постепенно и поверхность останется «чистой».
Фрезы — Диаметр и ширина
Корпус I конструктивно выполнен с расчетом возможности размещения в нем фрез различного диаметра и ширины (по труп, нам, см. МН 3611—62) и возможности, кроме обработки пло. скостей, производить выборку пазов и отрезку. Для этого пред. [c.122]Корпус 2 конструктивно выполнен с расчетом на возможность размеш ения в нем фрез различного диаметра и ширины (по группам, см. МН 3611-62) II па возможность, кроме обработки плоскостей, производить выборку пазов и отрезку. Для этого предусмотрена регулировка положения корпуса (с приемным па-
[c. 120]
Для обработки прямых ящичных шипов используют комплект из 25 фрез. В комплекте должны быть фрезы одинакового диаметра и шириной, равной ширине вырабатываемой проушины. Отклонение ширины фрез допускается не более 0,03 мм.
Диаметр и ширина фрез. Диаметр и ширина фрез нормализованы в геометрический ряд со знаменателем прогрессии ф= 1,26. Диаметр фрезы выбирают в основном в зависимости от ширины фрезерования В и глубины резания t (табл. 5—7). Допускаемые отклонения на диаметр [c.466]
Ниже приводится графический метод расчёта контура наибольшего диаметра и ширины двухугловой фрезы. Профиль канавки обрабатываемой фрезы задаётся в плоскости, перпендикулярной оси фрезы. [c.304]
Конструктивные элементы фрез. Червячные фрезы для шлицевых валиков изготовляются 1) без усиков — для шлицевых соединений всех трёх серий при центрировании по наружному диаметру и ширине шлицев
[c.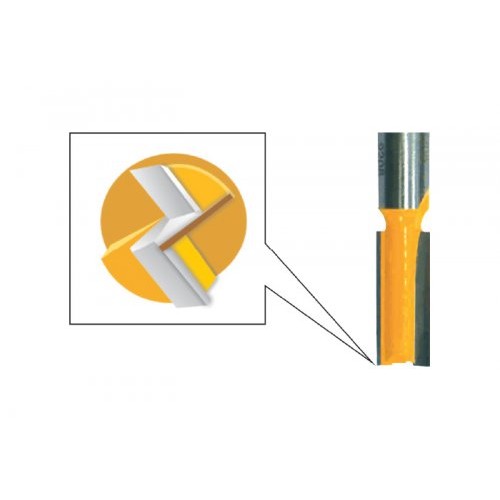
Диаметр и ширина фрез. Диаметр и ширина фрез нормализованы их величины образуют геометрический ряд со знаменателем прогрессии ср = 1,26. [c.252]
Шпоночные пазы, представленные на фиг. 91, б, фрезеруются при помощи дисковой фрезы диаметром 50 мм и толщиной, равной ширине паза. Шпоночные пазы, представленные на фиг. 91, б, фрезеруются при помощи пальцевой фрезы с диаметром, равным ширине паза. [c.158]
Диаметр и ширина фрез. Диаметр и ширина фрез нормализованы, их величины образуют геометрический ряд со знаменателем прогрессии Диаметр фрезы выбирают в зависимости от ширины фрезерования В и глубины резания 1 (табл. 3—5). Допускаемые отклонения на диаметр по Bg, конусность не должна превышать 0,02 мм для фрез шириной до 50 мм и 0,03 мм для фрез шириной более 50 мм. Диаметры шпоночных фрез нормализованы в соответствии с размерами шпоночных соединений в ряд 3 4 (5) 6 8 10 12 14 16 18 20 22 и т. д.
Фрезы — Диаметр и ширина 376 377
[c. 747]
Технологические углубления фрезеруют стандартными фрезами, например дисковыми трехсторонними по ГОСТ 28527-90. Выбор фрезы осуществляют по диаметру и ширине с учетом номинальной ширины паза вала оправки и глубины врезания в вал оправки. [c.169]
Задний угол а получается путем затачивания зуба. Ширина вершины зуба р (фиг. 122, а) не должна быть большой, так как иначе могут ухудшиться условия резания. Она выбирается в пределах 0,5— 2,0 мм в зависимости от диаметра фрезы. Зуб затачивается до остроты или с оставлением небольшой ленточки порядка 0,02—0,03 мм. Наличие ленточки облегчает измерение фрезы по диаметру и биение вершин ее зубьев.
[c.285]Наружный диаметр и ширина В фрезы по ГОСТ 7614—55 определяются по табл. 182. [c.474]
Диаметр и ширина фрез [c.97]
В настоящее время диаметры и ширина фрез во всем мире нормализованы в геометрический ряд со знаменателем прогрессии ф = 1,26. Доказано, что применяя нормальные (т. е. не специальные) фрезы означенного ряда, можно сократить на 40% общее число типоразмеров фрез, работая при этом с наивыгоднейшими режимами резания.
[c.97]
При заказе фрез следует указать название, диаметр и ширину фрезы и допускаемое отклонение по ширине фрезы. [c.330]
Выбор периода стойкости фрез. Стойкость фрезы зависит от ее габаритов, т. е. от диаметра и ширины фрезы. Ориентировочно стойкость фрезы можно подсчитать следующим образом
Значения диаметров и ширины фрез нормализованы. Они образуют геометрический ряд со знаменателем прогрессии ф = 1,26. Наружные диаметры стандартных фрез принимаются равными 16, 20, 25, 32, 40, 50, 63, 100, 125, 160, 200, 250 й т. д. до 630 мм. Нормальная ширина цилиндрических фрез составляет ряд с размерами 40, 50, 63, 100, 125 и 160 мм. В отверстиях фрез предусмотрены продольный шпоночный паз для передачи крутящего момента от шпинделя с помощью шпонки и внутренняя выточка (во фрезах шириной больше 24 мм).
[c.30]
При обработке паза закрепим заготовку кулачка на оправке в шпинделе делительной головки, а в шпинделе накладной фрезерной головки закрепляется концевая фреза Ф диаметром, равным ширине паза. Шпиндель головки и концевая фреза располагаются вертикально (рис. 98, а). [c.346]
Диаметр и ширина (полная высота) в зависимости от номера фрезы в комплекте. Максимальный диаметр резания р —по следующему графику. [c.126]
Размеры диаметров и ширины фрез нормализованы. Они образуют геометрический ряд со знаменателем прогрессии ф=1,26. Наружные диаметры стандартных фрез изготовляются равными 16. 20, 25, 32, 40, 50, 63, 100, 125, 160, 200, 250 и т. д. до 630 мм. [c.119]
Диаметр и ширина фрез. Диаметр и ширина фрез нормализованы [c.707]
После выбора указанных параметров выбирают фрезу по диаметру и числу зубьев. Чем больше диаметр фрезы, тем большего сечения можно снимать стружку. Ориентировочно можно определять диаметр фрезы по соотношению О = 1,65, где В — ширина фрезерования. Для грубых работ следует выбирать фрезы с крупными зубьями.
[c.358]
Подобрать цилиндрическую фрезу как можно меньшего диаметра и шириной, позволяющей обработать сразу всю ширину обрабатываемой поверхности [c.173]
Глубина вспашки мотоблоком МБ-1 с оборотным плугом ПСН-1-18 составляет около 20 см. Скорость движения с плугом 4 км/ч. Для работы с плугом на тяжелых почвах предназначаются сварные металлические колеса, имеющие увеличенные диаметр и ширину. Грунтозацепы, выполненные на ободе колес, имеют вид угольников, что исключает их пробуксовку, поэтому тяговое усилие агрегата с этими колесами, возрастает до 2 кН. Глубина обработки вспаханной почвы фрезой достигает 10—15 см за один проход. Ширина захвата фронтальной навесной косилки 110 см при скорости от 2,5 до 5 км/ч. Производительность косилки при средней скорости составляет 0,35 га/ч 118, 211.
[c.250]
При заказе фрез необходимо указать название, диаметр и ширину фрезы. [c.51]
При заказе фрез необходимо указать диаметр и ширину фрезы и номер ГОСТ на основные размеры. [c.53]
При заказе фрез необходимо указывать диаметр и ширину фрезы, диаметр посадочного отверстия, марку твердого сплава и номер ГОСТ на основные размеры. [c.57]
При заказе следует указывать наименование, диаметр и ширину фрезы и марку твердого сплава. [c.62]
Торцовые фрезы имеют ряд преимуществ по сравнению с цилиндрическими. Они обеспечивают равномерное фрезерование даже при небольших припусках на обработку, так как угол контакта фрезы с заготовкой зависит только от диаметра фрезы и ширины заготовки. Длина дуги контакта в этом случае больше, чем при фрезеровании цилиндрическими фрезами. Установка торцовой фрезы непосредственно в шпиндель станка исключает необходимость в применении длинных и недостаточно жестких оправок, неизбежных при работе цилиндрическими насадными фрезами, и позволяет использовать фрезы диаметром до 800. .. 1000 мм и более.
[c.151]
Для обработки канавок и прорезей применяют фрезы с заданной шириной режущей кромки при произвольном диаметре для обработки открытых плоскостей и фигурных поверхностен — с заданным диаметром и произвольной шириной. [c.363]
Шпоночные пазы закрытого типа обрабатывают на валах двухзубой концевой фрезой по челночной схеме с ручной или автоматической осевой подачей в конце каждого продольного хода. Шпоночные пазы, расположенные на валах с угловым шагом, фрезеруют последовательно с поворотом вокруг оси, а диаметрально расположенные пазы — одновременно на двусторонних фрезерных станках. Для компенсации износа фрезы по диаметру и получения точных по ширине пазов применяют патроны, регулирующие эксцентриситет фрезы (рис. 182). При фрезеровании сег- [c.328]
Торц вые фрезы широко. применяются при обработке плоскостей. Ось их устанавливается перпендикулярно к обработанной поверхности детали. В связи с этим торцовые фрезы имеют зубья на цилиндрической поверхности и торце. Главными режущими кромками, которые выполняют основную работу, являются кромки, расположенные на цилиндре, а торцовые — вспомогательными. Торцовые фрезы обеспечивают плавную работу даже при небольшой величине припуска. У торцовых фрез угол контакта с заготовкой не зависит от величины припуска и определяется шириной фрезерования и диаметром фрезы. Торцовые фрезы зачастую оснащаются твердым сплавом. Пластинки из твердого сплава у фрез малого диаметра припаиваются непосредственно к корпусу. Подобная наиболее простая конструкция фрез, оснащенных твердым сплавом, обеспечивая достаточную надежность крепления, имеет и существенные недостатки. У таких фрез нельзя- регулировать размеры диаметра и ширины, трудно заменить отдельные зубья в случае их поломки. При заточке со всех зубьев приходится снимать слои металла, соответствующие наиболее изношенному зубу. С этой точки зрения более целесообразны фрезы (фиг. 43) с механическим креплением ножей.
Они состоят из корпуса, в пазах которого устанавливаются и закрепляются ножи. По своей конструкции ножи напоминают резцы с припаянными пластинками из твердого сплава. Обычно предварительная заточка ножей производится отдельно от корпуса, а окончательная — в собранном виде.
[c.68]
Важными ковструктивными параметрами фрезы являются высота винтовой лопасти, угол подъема винтовой линии наружной кромки, соотношение диаметра и ширины захвата. Эти параметры [c.55]
Выбор режимов резания. Настройка станка. После установки центровой оправки с фрезой и закрепления заготовки переходят к выбору и назначению режимов резания, которые должны обеспечить экономически наиболее выгодные условия изготовления конкретной детали при соблюдении заданных технических условий. Выбор режимов резания заключается в определении величин глубины резания, подачи, скорости резания и мощности резания. Необходимо также определить ширину фрезерования, диаметр и ширину фрезы, тип станка и другие данные. Выбор режимов резания зависит от многих факторов, взаимно влияющих друг на друга. При назначении режимов резания необходимо придерживаться определенной последовательности в выборе составляющих элементов при обязательном учете условий обработки. Выбор режимов резания производят по таблицам режимов резания, составленных на основе исследовательских работ и опыта передовых заводов. Таблицы режимов резания составлены для обработки черных и цветных металлов инструментами из быстрорежущей стали, твердых сплавов и минера-локерамики.
[c.60]
Выбор диаметра фрезы зависит от глубины и ширины фрезерования. При обработке плоскостей цилиндрическими фрезами можно брать следующие значения диаметров фрез D =60- 75 мм при глубине фрезерования до i =5 мм и ширине фрезерования до В =70 мм D =90 -4- 110 мм при / = до 8 мм и В = до 90 лш D = 110ч-130 мм при / = 10 мм и В = 100 мм. Конкретные величины диаметра и ширины фрезы подбирают из стандартного набора цилиндрических фрез.
[c. 61]
Геометрия цилиндрическои фрезы с прямыми зубьями (фиг. 275). Обратимся к общим определениям первой координатной (основной) плоскости и второй координатной плоскости, к ней перпендикулярной. Основная плоскость при точении определяется направлениями радиальной и продольной подач. При фрезовании направления этих величин определяется направлениями радиуса R фрезы и ее оси. Эти величины меняются с диаметром и шириной фрезы. Таким образом, основная плоскость фрезы будет для каждого зуба диаметральной плоскостью, проходящей через вершину каждого зуба. Вторая координатная плоскость определяется вектором враще- Оснобная ния фрезы Vep и ее лезвием. плосность [c.395]
Л)-+-Л1, где / 1 —высота заготовки ножа Д—зазор между торцом ножа и дном паза А1=0,2…0,3 мм—припуск на шлифование фрезы по диаметру и затачивание после сборки. Ширина паза под нож зависит от его торщины и способа крепления. [c.90]
В одном из опытов прорезной фрезой диаметром D = 80 мм и шириной 6=4 мм, выполненной из быстрорежущей стали Р6М5, фрезеровалась заготовка из стали 12Х18Н10Т при скорости резания и = 63 м/мин, глубине резания t = 3 мм, подаче S = 64 мм/мин. Прорези фрезеровались по всей длине заготовки
[c.198]
На фиг. 627, а изображена вилка механизма блокировки автоматического включения фрикциона шестишпиндельного токарного автомата, тре-бующ,ая обработки наружных и внутренних поверхностей с обеспечением , при этом точных размеров. Наиболее затруднительна здесь обработка внутреннего паза шириной 40 ° мм, которая требует применения фрезы большого диаметра либо подрезки внутренних торцов при сверлении или расточке отверстий в ушках вилки. [c.606]
Фрезы по дереву для ручного фрезера
Универсальность вертикального фрезера во многом обусловлена разнообразием оснастки для него. Какими бывают фрезы и на что следует обратить внимание перед покупкой?
На фото:
Диаметр хвостовика
В миллиметрах или дюймах. Диаметр хвостовика — это одна из ключевых характеристик фрезы. Данный параметр показывает совместимость оснастки с той или иной моделью фрезера, ведь далеко не у каждой машины в комплекте имеются цанги (специальные втулки, обжимающие хвостовик) всех наиболее распространенных размеров, а именно 6, 8 и 12 мм.
Еще нужно отметить, что на рынке встречаются фрезы с хвостовиком 1/4 или ½ дюйма (при переводе в миллиметры получится 6,35 и 12,7 мм). Так вот, они не совместимы с 6- и 12-миллиметровыми цангами, им требуются «свои» втулки. Диаметр хвостовика должен строго соответствовать диаметру цанги.
Конструкция фрезы
Монолитные, сборные, со сменными лезвиями. Чаще всего фреза по дереву для ручного фрезера представляют собой стальную «болванку» с хвостовиком, к которой припаяны лезвия. Иногда лезвия выполнены в виде съемных пластин с двусторонней заточкой: если острие затупилось, нож переворачивают. Также встречаются цельные фрезы, то есть выполненные в качестве монолитной металлической детали с выточенными лезвиями.
Типы лезвий
На фото: вертикальный фрезер Of E 1229 Signal компании Metabo.
Что означает «HM» и «HSS»?. Лезвия у фрезы для ручного фрезера бывают твердосплавными (HM) и быстрорежущими (HSS). Вторые оптимальны для обработки мягкой древесин или алюминия, первые успешно справятся с разными древесными материалами, включая твердые породы.
В большинстве случаев лезвия расположены строго вертикально, а значит, они рубят, а не срезают материал. Но иногда ножи делают наклонными либо спиральными. В этом случае оснастка именно срезает материал, поэтому он меньше скалывается по краям, а качество обработки становится лучше.
Фрезы с опорным подшипником
Удобно, быстро и точно! Многие фрезы оснащены небольшим подшипником, установленным заподлицо с лезвиями сверху или снизу. Такое дополнение позволяет с минимальными затратами времени выполнить точное фрезерование края, ведь теперь не нужно возиться с упорами для ровного ведения машины: подшипник упирается в «ребро» заготовки и тем самым точно направляет фрезер. Риск ошибки исключен.
Разновидности фрез
Пазовые, галтельные, профильные и т.д. Фрезы для ручного фрезера классифицируют в зависимости от решаемых задач. Разновидностей очень много (советуем посмотреть каталоги производителей), поэтому выделим лишь наиболее распространенные виды.
Пазовые фрезы предназначены для выборки паза. Такие фрезы встречаются в самых разных вариантах: как маленького диаметра, так и «крупнокалиберные», короткие и длинные, с одним или двумя лезвиями. Чаще подобная оснастка предназначена для фрезерования прямоугольных пазов, но бывают, к примеру, и фрезы для выборки V-образных канавок или декоративных пазов со скругленными краями.
Фрезы «ласточкин хвост» служат для выборки трапециевидных пазов и шипов, которые впоследствии образуют стык. Кстати, соединение типа «ласточкин хвост» — это показатель добротной работы столяра.
На фото: вертикальный фрезер RP2300FC компании Makita.
Широкое распространение получили профильные фрезы с опорным подшипником и лезвиями различной формы. Такой оснасткой можно скруглять край, придавать ему благородный профиль с декоративными выступами или скруглениями.
Галтельные фрезы служат для выемки U-образного паза или выкружки, если речь идет фрезе с подшипником.
Пригоночные фрезы с верхним или нижним подшипником, который расположен заподлицо с прямыми лезвиями, помогут скопировать деталь, то есть подогнать еще по форме и размерам. Или просто снять припуск в нужных местах.
Фальцевые фрезы с подшипником помогут выбрать четверть или вырезать продольный паз в кромке заготовки.
В статье использованы изображения: bosch-professional.com, metabo.ru, makita.com.ru
Комплекты фрез для чашкорезных станков недорого в Москве
Инструмент для чашкорезных станков – это пазовые фрезы различной геометрии большого диаметра.
Эти инструменты могут быть как стандартными, так и под конкретную технологическую задачу.
Это пример фрезы для чашкорезного станка, не имеющей регулировок.
Такими фрезами можно обрабатывать пазы фиксированного размера по ширине – 100 мм. Диаметр подбирается под конкретный станок. В данном случае диаметр фрезы 280 мм, посадочный диаметр 45 мм.
При заказе данного инструмента необходимо указывать наличие шпонки (шпонок) на валу станка. Фреза предусматривает наличие на станке двух шпонок шириной 12мм.
Помимо насадных пазовых фрез в комплект включаются концевые пазовы фрезы, которые также отличает большой размер.
Фреза концевая пазовая спиральная из массивного твёрдого сплава. Диаметр фрезы 40 мм, длина рабочей части 250 мм. Также фреза имеет мощный хвостовик диаметром 30 мм и длиной 50 мм.
Комплект чашкорезных фрез с регулировками для обработки пазов с фасками:
Комплект состоит из двух и более фрезерных гарнитур для обработки прямых пазов и двух гарнитур для обработки пазов с фасками:
Комплекты состоят из отдельных элементов и могут собираться как конструктор.
Если изначально комплект рассчитан на чашку шириной от 40 до 80 мм, то впоследствии всегда можно дозаказать дополнительные вставки и увеличить диапазон регулировки и размеры обрабатываемых пазов.
Так этот инструмент выглядит на станке:
Вариант инструмента под прямоугольный паз может выглядеть так:
Сами фрезы представляют собой наборы фрезерных гарнитур, выполненных, как правило, из облегчённого дюралевого сплава со сменными твёрдосплавными ножами:
Инструмент на станке:
Фрезы прямые, пазовые и спиральные
Серия 04, 12 Фрезы прямые пазовые диаметром от 2 до 25 мм. с твердосплавной напайкой или цельнотвердосплавные (фрезы с диаметром от 2 до 6 мм.) Хвостовик 6, 8 и 12 мм. |
|
Серия 14 Фрезы прямые пазовые с разнесенными ножами. Диаметр 9,5 и 12,7 мм. Хвостовик 12 мм. |
|
Серия 16 Фрезы прямые пазовые для выборки пазов под петли. Диаметр 12,7; 19 и 31,8 мм. Хвостовик 6, 8 и 12 мм. |
|
Серия 17 Фрезы прямые пазовые врезные с торцевым зубом. ![]() |
|
Серия 26, 28 Фрезы прямые вырезные. Диаметр 6, 8 и 12,7 мм. Высота рабочей части 19 и 31,8 мм. Хвостовик 6, 8 и 12 мм. |
|
Серия 32 Фрезы прямая кромочная с набором подшипников для выборки четверти. Глубина выборки от 0 до 12,7 мм. высота обработки 12,7 мм. Хвостовик 6, 8 и 12 мм. |
|
Серия 32 Фрезы прямая кромочныая с подшипником для выборки четверти. Глубина выборки 9,5 и 11,1 мм. Выстота обработки 12,7 мм. Хвостовик 6, 8 и 12 мм. |
|
Серия 42 Фрезы прямые кромочные с подшипником для обработки торца заготовки. Высота обработки от 12,7 до 50,8 мм. Хвостовик 6, 8 и 12 мм. |
|
Серия 48 Фрезы прямые кромочные с одновременной выборкой v-образного паза с подшипником. Высота обработки 25,4 мм. Хвостовик диаметром 6, 8 и 12 мм. |
|
Серия 50 Фрезы прямые кромочные с верхним подшипником. ![]() |
|
Серия 56 Фрезы пазовые дисковые. Диаметр 50,8 мм. ширина паза от 1,5 до 6,35 мм. Внутренний диаметр 8 мм. Используется совместно с оправками серии 60. |
|
Серия 60 Оправка для пазовых дисковых фрез серии 56. Хвостовик 6, 8 и 12 мм. |
|
Серия 75 Фрезы прямые спиральные цельнотвердосплавные с верхним отводом стружки. Диаметр от 3 до 12 мм. Высота обработки от 13 до 42 мм. Хвостовик 6, 8 и 12 мм. |
|
Серия 76 Фрезы прямые спиральные цельнотвердосплавные с нижнним отводом стружки. Диаметр от 3 до 12 мм. Высота обработки от 13 до 32 мм. Хвостовик 6, 8 и 12 мм. |
|
Серия 77 Фрезы прямые спиральные с двунаправленным (вверх и вниз) отводом стружки. Диаметр 8 и 12 мм. Высота обработки 32 и 42 мм. Хвостовик 8 и 12 мм. |
VMA – Диспергирование – фрезами
Содержание
1.

Речь идет о следующих процессах:
- Процесс диспергирования:
Смачивание, разделение, стабилизация.
- Смачивание поверхности частиц твердого вещества жидкой средой
- Механическое разделение и измельчение ассоциированных частиц (агрегатов и агломератов)
- Стабилизация возникших в результате диспергирования новых, более мелких частиц и предотвращение их повторного слипания (флокуляции)
Процесс смачивания частиц твердого вещества и их стабилизации для защиты от дополнительной флокуляции зависит от взаимодействия между твердой и жидкой фазами.
↑ назад к содержанию
Эффект Doughnut
Наилучшие результаты диспергирования смеси на диссольвере DISPERMAT достигаются в том случае, когда основные параметры процесса согласованы между собой: Геометрия и диаметр рабочей емкости, окружная скорость вращения фрезы и глубина ее погружения в смесь, а также реологические свойства смеси.
- Все зависит от эффекта Doughnut!
Этим самым Вы достигаете самое эффективное разрушение агломератов, которое происходит в районе движения фрезы. Эффект Doughnut образуется при ламинарном течении в тех случаях, когда смесь отбрасывается вращающейся зубчатой фрезой наружу к стенкам емкости, где поток разделяется на две части.
Нижний поток смеси устремляется к центру дна емкости под вращающийся вал, а затем снова поднимается наверх к зубчатой фрезе. Второй поток образует воронку, которая хорошо видна сверху.
Характер текучести воронки при эффекте Doughnut зависит от количества твердых компонентов в смеси. При пониженном содержании твердых компонентов вязкость смеси оказывается слишком низкой, что приводит к разбрызгиванию и вспениванию смеси.
↑ назад к содержанию
3. принцип работы фрезы по разрушению агломе- рированных твердых компонентов смеси
При вращении фрезы с повышенной скоростью перед ее зубцами образуется зона повышенного давления, а за ними – зона разрежения. Попеременное воздействие повышенного давления и разрежения на агломераты твердых частиц приводит к их разрушению.Кроме того, зубцы фрезы оказывают также ударное действие на частицы смеси. Значительная часть работы по диспергированию частиц происходит также на верхней и нижней поверхностях фрезы. При скоростном вращении фрезы на ее поверхностях образуются вихревые потоки массы, в которых разрушаются агломераты твердых частиц. Вихревой поток, образующийся, прежде всего, на нижней поверхности фрезы, в значительной степени зависит также от расстояния между фрезой и дном емкости. При уменьшении этого расстояния интенсивность этого вихревого потока увеличивается. Благодаря этому увеличивается скорость потока между нижней поверхностью фрезы и дном емкости и геометрия в рабочей емкости появляется возможность увеличения скорости вращения диссольверного вала, так как в этом случае переход от ламинарного к турбулентному течению массы происходит значительно позднее.
Кроме того, благодаря увеличению частоты вращения вала становится возможным дальнейшее увеличение механической энергии смешивания, обеспечивающей эффективность диспергирования. Как правило, наилучшие результаты диспергирования достигаются в том случае, когда работа проводится с максимальной механической энергией смешивания без разрушения образующейся в емкости воронки (эффекта Doughnut).
Механическая энергия смешивания P (W) определяется по частоте вращения n (1/с) и вращающему моменту M (Nm) вала (π = 3,141…..).
геометрия в рабочей емкости
окружная скорость вращения в зависимости от числа оборотов и диаметра фрезы
рекомендуемый диаметр фрезы в зависимости от вязкости и размера рабочей емкости.
↑ назад к содержанию
4. метод работы и оптимизация состава смеси
Чаще всего на практике применяется следующая технологическая последовательность: Сначала в рабочую емкость вводят жидкие компоненты. Затем при медленном вращении вала порциями вводят такое количество порошкообразных компонентов, при котором с увеличением скорости вращения вала до 18 – 25 м/с происходит образование воронки (эффект Dougnut).- Не надо бояться больших оборотов!
Только после этого проводится собственно диспергирование предварительно перемешанной смеси, при этом в диспергируемой массе должна образоваться воронка. При проведении этой работы следует использовать преимущества диссольверов DISPERMAT®. Не надо бояться высоких скоростей вращения вала! При использовании фрезы диаметром 25 мм вал диссольвера должен вращаться со скоростью 15000 мин-1, чтобы фреза могла достичь окружной скорости 20 м/с. Окончательный эффект диспергирования на диссольверах DISPERMAT® достигается через 10 – 15 минут работы. Дальнейшая работа диссольвера, как правило, не приводит к улучшению результатов диспергирования агломератов; как показывают анализы проб, устанавливается окончательный размер частиц. Если предъявляются повышенные требования к размеру частиц или к обработке агломератов, плохо поддающихся диспергированию, требуется применение мельницы.
↑ назад к содержанию
5. перенос лабораторных результатов в производственные условия
Одним из важнейших условий успешной работы является возможность переноса результатов диспергирования, полученных на диссольверах, в основное производство.Рис.: Диссольвер DISPERMAT® CV3-PLUS и диссольвер DISPERMAT® SC122
Ранее уже отмечалось, что результат диспергирования зависит как от движения агломератов вокруг зубчатой фрезы, так и от количества механической энергии, вводимой в смесь в емкости для диспергирования. Количество механической энергии является тем параметром, который определяет максимальный конечный результат разрушения агломератов, а движение агломератов определяет длительность процесса, которая необходима для достижения конечного результата диспергирования. Диспергирование агломератов происходит, как правило, в зоне действия усилий сдвига, которая образуется на рабочих поверхностях зубчатой фрезы. Величина образующихся усилий сдвига (оптимальные результаты диспергирования) определяется краевой конструкцией зубчатой фрезы, поскольку именно эта часть фрезы вращается в массе с максимальной скоростью.
По этой причине скорость (окружная скорость вращения 12 фрезы) может быть использована в качестве критерия при переносе результатов лабораторных исследований в производственные условия. Однако данное утверждение относится только к оценке конечного результата процесса диспергирования, но не к его длительности.
В диссольверах DISPERMAT® конечный результат обычно достигается быстрее, так как в лабораторном диссольвере траектория движения агломератов до зубчатой фрезы короче, чем в промышленных диссольверах. Точное воспроизведение окончательных результатов диспергирования достигается в тех случаях, когда температура массы в лабораторном диссольвере соответствует температуре массы в промышленном оборудовании. По этой причине при работе с диссольверами DISPERMAT® рекомендуется использовать двухстенные темперированные емкости. Для достижения в лабораторном диссольвере такой же окружной скорости вращения фрезы, как и в промышленном оборудовании, вал лабораторного диссольвера должен вращаться постоянно и стабильно с повышенной скоростью. При использовании различных зубчатых фрез окружная скорость легко рассчитывается по вышеуказанной формуле.
↑ назад к содержанию
6. окружная скорость вращения в зависимости от числа оборотов и диаметра фрезы
Ниже приведены три примера, на которых приведена зависимость окружной скорости от числа оборотов и диаметра фрезы. Зеленым цветом отмечен наиболее благоприятный интервал величин окружной скорости (18 – 25 м/с).пример для смеси объемом 100 мл, обрабатываемой на лабораторном диссольвере DISPERMAT®
пример для смеси объемом 2500 мл, обрабатываемой на лабораторно- исследовательском диссольвере DISPERMAT®
пример для смеси объемом 30 л, обрабатываемой на лабораторно- исследовательском диссольвере DISPERMAT®
↑ назад к содержанию
7. что следует предпринять, если не достигнут желаемый Эффект диспергирования ?
В случае, если результат диспергирования не соответствует предъявляемым требованиям, необходимо проверить следующие параметры процесса:↑ назад к содержанию
8. реологические свойства смеси
Для достижения оптимальных результатов диспергирования необходимо контролировать реологические свойства смеси. К сожалению, реологические свойства нельзя охарактеризовать одним параметром, например, только вязкостью. Вязкость представляет собой способность вещества растекаться под действием внешних усилий сдвига и подвергаться необратимым деформациям.Коэффициент вязкости, часто называемый просто вязкость, зависит от свойств вещества и определяется как соотношение касательного напряжения сдвига и скорости сдвига. Только в ньютоновских жидкостях вязкость является постоянной (например, в воде, минеральных маслах). Все другие жидкости, не имеющие такого свойства, называются неньютоновскими, они встречаются гораздо чаще. В рецептурах смесей используются сложные по реологическим свойствам вещества. Для их характеристики используются такие термины, как кажущаяся вязкость, пластическое поведение, граница текучести, тиксотропия, реопексия и дилатансия.
общевзятый диапазон вязкости:
низкая вязкость μ < 500 мПа.с
высокая вязкость > 5000 мПа.с
средняя вязкость μ = 500 – 5000 мПа.с
↑ назад к содержанию
9. Диспергирование в вакууме
При диспергировании с помощью диссольвера воздух часто попадает в диспергируемую смесь. При использовании веществ низкой и средней вязкости воздух удаляется сам уже во время или, в крайнем случае, после процесса диспергирования; часто этому способствует введение в смесь добавки. Однако при использовании продуктов с более высокой степенью вязкости и пределом текучести (см. также «Реологические свойства смеси») воздух, попавший в смесь, не всегда выходит наружу.
В данном случае процесс диспергирования должен обязательно осуществляться с применением вакуума во избежание попадание воздуха и микропузырьков, которые могут проникнуть в используемую массу через мельчайшие поры и отверстия в поверхности. Кроме того, часто необходимо применять скребковую систему для счищения диспергируемой смеси с внутренней стенки емкости и доставки ее в центральную часть емкости. Благодаря такому подходу в процессе диспергирования будет задействован весь загруженный материал.
Рис.: Диссольвер DISPERMAT® CA диспергирующая Вакуумная система CDS
Основные преимущества вакуумного диспергирования:
- Возможность получать высоковязкие смеси без пузырьков воздуха
- Образование пены сводится к минимуму, особенно в водянистой среде
- С применением вакуума можно легко получать продукты, которые вступают в реакции с образованием кислорода или влажности.
- При вакуумном диспергировании качество продукта (тонкодисперсность) заметно выше
отите узнать больше о преимуществах диспергирования в вакууме? Мы охотно проконсультируем вас. Посетите нашу лабораторию и экспериментальный цех, полностью оснащенные оборудованием. Здесь вы сможете провести пробное диспергирование с использованием своих продуктов, при этом не связывая себя никакими обязательствами. Наши опытные инженеры окажут вам радушный прием.
Подать заявку на пробное диспергирование
↑ назад к содержанию
Термины и единицы измерения Фрезерование Dc c Рабочий диаметр фрезы mm zc Эффективное число зубьев шт m Длина обработки mm kc1 c1 Удельная сила р
Режущий инструмент, инструментальная оснастка и приспособления / Cutting tools, tooling system and workholding SANDVIK COROMANT | Руководство SANDVIK COROMANT 2005 по обработке металлов резанием (Всего 564 стр.) | ||||||||
185 Руководство SANDVIK COROMANT 2005 по обработке металлов резанием на станках Стр.D23 | ||||||||
Термины и единицы измерения Фрезерование Dc c Рабочий диаметр фрезы mm zc Эффективное число зубьев шт. m Длина обработки mm kc1 c1 Удельная сила резания De Эффективный рабочий диаметр mm (для hex 1 мм) Н мм2 a P Глубина резания mm n Скорость вращения шпинделя об/мин Pc c Мощность необходимая на резание кВт a e Ширина обработки mm n КПД v c Скорость резания м/мин Qc Производительность снятия см3 мин к r Главный угол в плане град. Tc материала мин vc0 Постоянная скорости резания z n Время резания шт. cvc Коэффициент изменения скорости Количество режущих кромок резания (зубьев фрезы) mm m c Увеличение удельной силы резания mm (kc) fz z Подача на зуб фрезы мм/мин как функция толщины стружки fn n Подача на оборот mm iC Диаметр вписанной окружности vf Подача стола (скорость подачи) mm пластины h ex Max толщина стружки hm m Средняя толщина стружки Основные формулы Скорость резания (м/мин) Скорость вращения шпинделя (об/мин) Подача стола (скорость подачи) (мм/мин) Подача на зуб фрезы (мм) Подача на оборот (мм/об) Скорость удаления материала (см3) Удельная сила резания (Н мм2) Средняя толщина стружки (мм) (торцово-цилиндрическое фрезерование) когда ae Dc 0.1 Средняя толщина стружки (мм) когда ae Dc 0.1 Время резания (мин) Потребная мощность (кВт) 1000 n v х 1000 xD v f x n xz f z n fz Vf n xz a xa xv Q p -e f- 1000 k k x h c c1 m sin к x180 x a xf h -r – e -z m x Dc x arcsin a ) T m c Vf a xa xv xk P P e f c c 60 x106 x n SANDVIK Coromant D 23 | ||||||||
См.также / See also : | ||||||||
Соотношение твердостей Таблица / Hardness equivalent table | Аналоги марок стали / Workpiece material conversion table | |||||||
Отклонение размера детали / Fit tolerance table | Перевод оборотов в скорость / Surface speed to RPM conversion | |||||||
Диаметр под резьбу / Tap drill sizes | Виды резьбы в машиностроении / Thread types and applications | |||||||
Дюймы в мм Таблица / Inches to mm Conversion table | Современные инструментальные материалы / Cutting tool materials | |||||||
SANDVIK COROMANT | ||||||||
| ||||||||
Каталог SANDVIK COROMANT 2017 Инструмент токарный и оснастка (656 страниц) | Каталог SANDVIK COROMANT 2017 Инструмент вращающийся и оснастка (515 страниц) | Каталог SANDVIK COROMANT 2016 Металлорежущий цельный инструмент (866 страниц) | Каталог SANDVIK COROMANT 2016 Обработка глубоких отверстий (226 страниц) | Каталог SANDVIK COROMANT 2015 Токарные инструменты (1253 страницы) | Каталог SANDVIK COROMANT 2015 Вращающиеся инструменты (1500 страниц) | |||
Каталог SANDVIK COROMANT 2015 Комплектующие для инструмента (670 страниц) | Каталог SANDVIK COROMANT 2015 Специальный инструмент (163 страницы) | Каталог SANDVIK COROMANT 2001 Вращающиеся инструменты (751 страницы) | Каталог SANDVIK COROMANT 2000 Токарный инструмент (573 страницы) | Каталог SANDVIK COROMANT 2017 Инструмент Сандвик-МКТС (104 страницы) | Каталог SANDVIK COROMANT 2000 Инструмент и сменные пластины Сандвик МКТС (172 страницы) | |||
Руководство SANDVIK COROMANT 2010 по металлообработке (800 страниц) | Каталог SANDVIK COROMANT 2010 CoroKey Режущий инструмент (216 страниц) | Пособие SANDVIK COROMANT 2009 Обработка металлов резанием (359 страниц) | Каталог SANDVIK COROMANT 2006 CoroKey Металлорежущий инструмент (195 страниц) | Руководство SANDVIK COROMANT 2005 по обработке металлов резанием (564 страницы) | Учебник SANDVIK COROMANT 2003 Обработка резанием (301 страница) | |||
Каталоги инструмента и оснастки для металлообработки на станках / | ||||||||
Руководство SANDVIK COROMANT 2005 по обработке металлов резанием (Всего 564 стр.) | ||||||||
| ||||||||
182 Проблемой трехстороннего фрезерования на станках являются вибрации для борьбы с которыми существует простой и эффективный способ Помимо использов | 183 | 184 | 186 | 187 | 188 | |||
— — |
Расчет диаметра фрезы (с учетом глубины резания) «Super Tool – Производитель прецизионных режущих инструментов
Недавно я обучал сотрудника тому, как определить подходящий диаметр продольно-продольной пилы после того, как наш клиент дал ей желаемую глубину пропила. Хотя это простой расчет, он не так прост, как вы думаете. Для того, чтобы рассчитать диаметр, нужно знать, каким будет отверстие продольной пилы / фрезы. После того как вы размер оправки отверстия, вы должны смотреть на то, что диаметр беседки спейсера для этой оправки отверстия.Ниже приведена таблица, которая показывает стандартное отверстие диаметр оправки вместе со стандартным диаметром оправки распорного для этой оправки отверстия.
Диаметр отверстия стандартной оправки | Диаметр проставки стандартной оправки |
3/4 | 1–1 / 8 |
7/8 | 1-3 / 8 |
1 | 1–1 / 2 |
1-1 / 4 | 1-3 / 4 |
1–1 / 2 | 2-1 / 8 |
Когда у вас есть диаметр проставки для посадочного отверстия, вы можете рассчитать диаметр фрезы, если вы знаете желаемую глубину резания.Формула:
[(глубина резания) x 2] + (диаметр проставки вала) = минимальный диаметр фрезы
Допустим, у вас глубина пропила 1,6 дюйма и вам нужна пила для продольной резки с отверстием диаметром 1 дюйм. Из приведенной выше таблицы мы знаем, что распорная втулка для посадочного отверстия диаметром 1 дюйм имеет диаметр 1-1 / 2 дюйма.
(1,6 × 2) + 1,5 = 4,7
Итак, для этого примера минимальный диаметр фрезы для достижения глубины резания 1,6 дюйма составляет 4,7 дюйма.
Хотя 4,7 дюйма – это минимальный диаметр, я бы рекомендовал использовать фрезу немного большего размера, если это позволяет ваше приложение, потому что прокладка, скорее всего, будет тереться о деталь, которую вы обрабатываете.В этом случае будет лучше 4,75 или 5 дюймов.
Допущения
В приведенном выше примере предполагается несколько вещей:
Во-первых, используемая вами распорка оправки является стандартной распоркой. Если вы используете проставку, изготовленную на заказ, или стандартная проставка была изменена, введите диаметр проставки в (Диаметр проставки оправки) в приведенной выше формуле.
Второе допущение заключается в том, что ширина ступицы фрезы меньше ширины реза. Если ширина ступицы больше ширины реза И диаметр ступицы больше диаметра проставки, то диаметр ступицы является важным числом.В этом сценарии глубина резания будет:
(Диаметр фрезы) – (Диаметр ступицы) = Глубина резания
2
Если у вас есть какие-либо вопросы по расчету соответствующего диаметра фрезы (или любые другие вопросы по режущему инструменту), не стесняйтесь оставлять нам комментарий здесь в нашем блоге или заполнить форму на странице контактов Super Tool.
Брайан Энандер
Президент
Super Tool, Inc
Выбор оптимальной глубины и ширины резания при фрезеровании
Недавно я получил заметку от пользователя G-Wizard, который хотел узнать, как выбрать наилучшую глубину и ширину резания при фрезеровании.Отличный вопрос. Я подозреваю, что большинство машинистов используют практические правила и привычки больше, чем что-либо еще, если только ситуация не диктует что-то, в частности, исходя из размеров обрабатываемого элемента. Они привыкли использовать какую-то часть диаметра фрезы или какую-то цифру, которую они получили другим способом по привычке (40 тысячных или около того – это то, что они всегда использовали). Возможно, их программа CAM имеет жесткую настройку по умолчанию, которая составляет процент от диаметра фрезы.
Но эти значения, хотя они и работали с течением времени, не обязательно являются оптимальными цифрами в отношении скорости съема материала, допусков на отклонение инструмента или множества других переменных, которые мы могли бы принять во внимание.Как можно более систематически подойти к проблеме?
Во-первых, у нас есть две переменные (ширина и глубина резания), поэтому будет трудно добиться прогресса, если мы не сможем определить одну из двух переменных и сосредоточиться на взаимосвязи другой. Обычно довольно легко определить одну из переменных в зависимости от ситуации. Разделим нашу работу на две категории:
– Прорезание пазов: я буду обобщать это как любую ситуацию, когда удаляемый материал очень близок к диаметру фрезы.Это может быть паз или интерполяция отверстия или кармана, которые лишь немного больше диаметра концевой фрезы.
– Карманы: здесь я снова буду обобщать это как любую ситуацию, когда диаметр фрезы немного меньше, чем размеры удаляемого материала. Это не означает, что нет какого-либо внутреннего радиуса или другой функции, которая больше не похожа на пример прорезания, но по большей части у нас есть место для работы. Обратите внимание, что профилирование будет считаться таким же, как и карманы для этого обсуждения.
Хорошо, теперь мы должны взять перед собой задачу и решить, что ближе к прорезанию или врезке в карман. Причина, по которой я определил эти два способа, заключается в том, что он сообщает нам, с какой переменной работать в первую очередь. Если мы выполняем паз, ширина резки является первой переменной. Если мы обрабатываем карманы, глубина резания является первой переменной. Почему?
При прорезании пазов размер элемента очень близок к диаметру фрезы. Мы не можем взять концевую фрезу 1/2 дюйма и использовать ее для изготовления паза 1/4 дюйма.В общем, мы хотим использовать концевую фрезу наибольшего диаметра, которая подходит для данной детали, и тогда нам в значительной степени нужно сделать хотя бы один пропил на всю ширину. Как только мы уберем этот разрез, все оставшееся будет обработано так же, как и в кармане. Итак, при прорезании пазов мы в первую очередь ориентируемся на ширину реза и устанавливаем ширину фрезы, чтобы начать работу.
При формировании кармана нашим ограничением будет наименьший внутренний радиус, с которым нам придется иметь дело, а также глубина кармана. Помните, что может быть выгодно сделать два прохода.Первый с фрезой, диаметр которой слишком велик для наименьших внутренних радиусов, с которыми нам приходится иметь дело. Это черновой проход, при котором используется фреза большего размера, чтобы сделать его быстрее. Второй проход является чистовым, и для него необходимо использовать фрезу, диаметр которой меньше или равен диаметру, необходимому для достижения наименьшего внутреннего радиуса, удерживаемого карманом. Обратите внимание, что мы можем обойти внешний радиус (выступ) с помощью фрезы любого диаметра, это внутренний радиус, который нас ограничивает.
Итак, мы выбираем фрезу, размер которой равен наименьшему радиусу, или выбираем два прохода и выбираем фрезу большего размера.Давайте пока оставим проблему двух проходов в стороне, потому что определение того, когда это оптимально, может занять некоторое время методом проб и ошибок. Это похоже на мысль об одном проходе. Учитывая, что резак выбран, мы можем выбрать практически любую ширину реза, какую захотим. Так как же нам зафиксировать переменную, когда кладем в карман? В случае прорези я люблю прибивать ширину реза. Что касается кармана, я предпочитаю прибивать глубину пропила.
В целом, мы получим более красивую отделку, если разрежем карман на как можно меньше слоев.Программы CAM хорошо складываются в карман, поэтому мы можем выбирать произвольную глубину резания. Если есть возможность, я предпочитаю делать это одним слоем для кармана, глубина которого меньше двух. В противном случае я предпочитаю, чтобы глубина слоев была одинаковой. Другими словами, я не стал бы опускаться на 1/4 дюйма, 1/4 дюйма, а затем на 0,19 дюйма на третьем слое. Поэтому выберите глубину слоя, которая удовлетворяет этому критерию.
Теперь в обоих случаях мы заблокировали одну из двух переменных – ширину замков прорезания, глубину замков прорези. Нам нужно определить наилучшее значение для переменной, которую мы оставили плавающей, на основе значения той, которую мы заблокировали.Именно здесь G-Wizard Cut Optimizer упрощает задачу. Введите известные вам значения для разреза и позвольте оптимизатору вычислить значение для плавающей переменной.
Например, предположим, что нам нужно вырезать карман глубиной 3/4 дюйма в алюминии 6061. Наименьший внутренний радиус составляет 1/4 дюйма, поэтому мы решили использовать твердосплавную концевую фрезу 1/4 дюйма с 3 канавками. Вот проблема, созданная в G-Wizard:
Материал, инструмент, диаметр инструмента, канавки и глубина резания 3/4 дюйма…
Теперь мы можем вызвать оптимизатор резки, просто нажав кнопку «Rough»:
Как вы можете видеть из красных стрелок, которые я добавил, для глубины резания 3/4 дюйма эта концевая фреза может обрабатывать не более 0.1799 ″ ширина пропила при черновой обработке. Давайте округлим это вниз и возьмем 0,170 ″
Нажмите кнопку финиша, чтобы увидеть, какой припуск на финиш мы должны оставить САМ для нашего финишного пути, и мы получим 0,0052 ″. Это довольно легкий проход, но 3/4 дюйма для этой концевой фрезы 1/4 дюйма. Вот интересная мысль: если мы уменьшим длину державки инструмента до 0,9 дюйма вместо 1 дюйма, мы сможем увеличить длину резания до 0,0095 дюйма. Это дает вам представление о том, насколько важно, чтобы инструмент как можно меньше выступал.Я бы предпочел забить инструмент и получить чистовую ширину пропила 0,009 дюйма, если бы это была моя работа. Еще нужно учитывать два уровня финишного прохода. Если мы не против взять два уровня и по-прежнему захлебнуться инструментом, мы можем получить ширину пропила 0,015 дюйма для чистовой обработки. Это примерно столько же, сколько мне нравится делать финишную передачу.
Проблема с этим фрезом в том, что он немного глубок для нашей концевой фрезы 1/4 дюйма. Это соотношение диаметра к глубине 3: 1. Мы можем сказать, что это натяжение, потому что максимальная рекомендуемая ширина реза очень мала.Если бы у меня была программа CAM, которая упростила бы выполнение чернового прохода с помощью большей фрезы, у меня возникло бы соблазн прыгнуть с концевой фрезой 1/2 дюйма (или, может быть, даже больше) для чернового прохода, а затем перейти к 1 / 4 ″ под чистовую отделку, но вы поняли.
Случай прорезания почти аналогичен, за исключением этого случая, вместо того, чтобы пытаться вычислить ширину пропила, мы хотим использовать оптимизатор для определения глубины. Например, если мы продолжим работу с флейтой 1/4 дюйма 3, предположим, что нам нужно вырезать прорезь 0.Ширина от 300 ″ до глубины 3/4 ″. Наш план состоит в том, чтобы вырезать полную прорезь шириной 0,250 дюйма посередине, а затем закончить ее, разрезав оставшуюся часть с каждой стороны. Насколько глубоко мы можем сделать наши проходы на все слоты? Еще раз наберите начальные параметры и на этот раз нажмите кнопку «Слот». Для черновой обработки оптимизатор резки сообщает нам, что мы можем резать на глубину 0,3466 дюйма, прежде чем мы получим слишком большой прогиб. Два прохода на этой глубине приведут нас к глубине 0,6932 дюйма. Остается 0,0568 ″ снизу для финиша и 0,0259 ″ с каждой стороны для финишного прохода.Помните, что мы не прорезаем полный паз для чистового прохода, поэтому мы относимся к нему так же, как и к карману, чтобы определить ширину и глубину пропила.
Вот и все. Подводя итог:
1. Решите, будете ли вы прорезать пазы или карманы.
2. При прорезании пазов выберите значение ширины и используйте оптимизатор обрезки для определения глубины.
3. При прорезании карманов выберите значение глубины и используйте Cut Optimizer для определения ширины.
Если вы подойдете к проблеме таким образом, вы максимизируете MRR, сведя к минимуму отклонение инструмента как для черновой, так и для чистовой обработки.Это гораздо более оптимальный подход, чем старый мокрый палец на ветру!
Дополнительные сведения о параметрах резания при фрезеровании см. На странице «Чистота поверхности фрезерования».
Присоединяйтесь к более чем 100 000 ЧПУ! Получайте наши последние сообщения в блоге бесплатно раз в неделю прямо на ваш почтовый ящик. Кроме того, мы предоставим вам доступ к некоторым отличным справочным материалам для ЧПУ, включая:
фрез – Shaper
Размеры фрезы для ключей
Обратите внимание:
- Origin поставляется с цанговым патроном 1/4 дюйма, что означает, что он принимает фрезы с хвостовиком 1/4 дюйма.
- Максимальный диаметр фрезы составляет 1 дюйм. Никогда не пытайтесь воздействовать на фрезы с большим диаметром хвостовика. При использовании фрез с диаметром более 1/4 дюйма начинайте с неглубоких проходов по мере того, как вы привыкните к материалу и фрезу.
- Origin не принимает фрезы с направляющими подшипниками.
- Поскольку Origin втягивается всякий раз, когда обнаруживает ошибку отслеживания, фрезы для замочной скважины и фрезы “ласточкин хвост” необходимо использовать очень осторожно. Отклонение от корректирующего круга приведет к втягиванию фрезы вертикально через обрабатываемый вами материал.
- Никогда не пытайтесь резать глубже, чем длина режущей канавки.
Фрезы в комплекте:
Origin поставляется с 3 высококачественными резаками. Они изготовлены из карбида – материала, который долгое время сохраняет остроту режущей кромки. Фрезы в первую очередь предназначены для резки дерева с помощью Origin.
Бирка сбоку содержит важные данные:
UC. 1/4. 3/4
UC = подрезка, 1/4 “ диаметр резания, 3/4″ Концевая фреза с длиной канавки
Это наша наиболее часто используемая фреза для обработки любых пород дерева.Эта фреза может резать на глубину 1/4 дюйма за проход до максимальной глубины 3/4 дюйма. Две режущие канавки позволяют резчику быстро перемещаться через большие панели. При резке древесины этой фрезой начните со скорости шпинделя 5-6 и при необходимости отрегулируйте.
UC. 1/8. 1/2
UC = подрезка, 1/8 “ диаметр резания, 1/2″ длина режущей канавки Концевая фреза
При резке более мелких деталей идеально подходит фрезер 1/8 дюйма.Длина канавки ограничивает общую глубину пропила до 1/2 дюйма. При резке древесины этой фрезой начните со скорости шпинделя 5-6 и при необходимости отрегулируйте.
V60. 1/4. 1/4
V60 = 60 градусов V бит, 1/4 “ диаметр резания, приблизительно 1/4″ длина канавки.
Для гравировки сверло V отлично работает на различных материалах. Очень тонкие линии можно получить с небольшой глубиной резания. При резке древесины этой фрезой начните со скорости шпинделя 3 и при необходимости отрегулируйте.
Уход за резаком
Тепло – основная причина ухудшения качества режущей кромки. Все, что можно сделать, чтобы уменьшить накопление тепла на резаке, поможет им сохранить остроту кромки в течение более длительного времени.
- Не задерживайтесь: Легко получить боковые корректировки смещений в пользовательском интерфейсе, если резак опущен, а агрегат неподвижен. Всегда убирайте резак, когда он не работает активно, даже если вы планируете остановиться всего на несколько секунд.Это предотвращает перегрев и износ режущей кромки.
- Не устанавливайте число оборотов шпинделя выше, чем необходимо: Звук правильно загруженного резака станет музыкой для ваших ушей после того, как вы некоторое время воспользуетесь Origin. Хорошее практическое правило – установить шпиндель на самую низкую скорость, чтобы обеспечить хорошее качество резки. Чрезмерная частота вращения шпинделя приведет к трению, выделению тепла, подгоранию или плавлению рабочей поверхности и ухудшению качества режущей кромки.
- Очистите резаки. : Смола, сок и клеи создают большее трение, если они могут накапливаться на резце.В свою очередь, это трение может ускорить деградацию кромок. Найдите минутку, чтобы очистить резаки с помощью небольшой латунной щетки, средства для чистки цитрусовых и тряпки.
- Очистите цангу: Накопление материала внутри цанги снижает эффективность зажима цанги. Это может привести к смещению фрезы, вызывая “биение”, что в конечном итоге снижает качество резки. Обязательно регулярно проверяйте и очищайте цангу.
Геометрия канавки фрезы:
- Up Spiral: Это стандартная геометрия фрезы, используемая в Origin.Он вытягивает стружку из вырезанной панели и прижимает Origin к поверхности. Это создает плавный и предсказуемый пользовательский интерфейс. Такая геометрия может оставлять небольшой ворс на верхнем крае вырезов в хорошем слое, но этот ворс легко удаляется быстрой шероховатой обработкой мелкозернистой наждачной бумагой.)
- Down Spiral : Эта геометрия выталкивает стружку в рез, что приводит к ухудшению ее удаления и удаления пыли. Фрезы со спиральной спиралью вниз также отталкивают Origin от режущей поверхности, что приводит к более резкому резанию с рывками.
- Компрессионная спираль : Эта геометрия сочетает в себе режущие спирали вверх и вниз для достижения чистых срезов сверху и снизу рабочей поверхности. Эти фрезы идеально подходят для резки материалов с деликатными верхней и нижней поверхностями (например, ламинатной фанеры, меламина и т. Д.).
- Прямая канавка: Такая геометрия не способствует хорошему удалению стружки. Эти фрезы обычно используются на фрезерных станках, где врезание в материал встречается реже. Многие долота с прямой канавкой не способны врезаться врезанием; мы не рекомендуем использовать эти резаки с Origin.Прямые фрезы часто включают твердосплавные пластины, что делает их пригодными для шлифования в специальные профили (круглые фрезы, фрезы для замочной скважины, фрезы “ласточкин хвост” и т. Д.).
- Заусенец: Заусенцы, часто используемые для резки композитных материалов, шлифуются с помощью множества мелких канавок, напоминающих напильник.
Длина канавки:
- Длина режущей канавки представляет собой максимальную глубину, которую может резать конкретная фреза. Самый длинный резак, который мы поставляем, – это резак 1/4 дюйма с длиной канавки 3/4 дюйма.
- Вы заметите, что длина канавки и диаметр фрезы взаимосвязаны. Чем больше длина канавки относительно диаметра фрезы, тем более гибкая фреза. Обычное практическое правило, которое используют многие производители, – стремиться к тому, чтобы длина канавки была в три раза больше диаметра фрезы. Длина канавки, превышающая это соотношение, обычно не так стабильна.
Кол-во канавок:
- 1 Канавка: Отлично подходит для удаления стружки и более медленных скоростей подачи, подходит для акрила / пластика и мягких металлов.
- 2 канавки: Хороший компромисс для дерева. Две канавки позволяют сочетать хорошую скорость подачи и разумный отвод стружки.
- 3+ канавки: Эти фрезы обычно используются в быстродвижущихся портальных станках с ЧПУ для резки металлов, которые не подходят для резки с использованием Origin.
Материалы
- Быстрорежущая сталь: (сокращенно HSS) Твердые, жаропрочные и прочные стальные сплавы, обычно используемые в недорогих резцах.
- Твердый сплав: Более прочный, твердый, более устойчивый к нагреванию и истиранию, чем HSS, твердый сплав – идеальный материал для фрез. Имейте в виду, что они также более хрупкие, чем HSS, поэтому относитесь к ним как к керамике. Избегайте резких ударных нагрузок, например, в результате падения на пол.
- Твердосплавная пластина: Твердосплав, припаянный к более мягкой стальной опоре и хвостовику.
Покрытия:
- Покрытия используются для уменьшения трения и защиты от нагрева, повышая долговечность резца.Типичными примерами являются TiN (нитрид титана) и ZrN (нитрид циркония).
Следующие подшипники:
- Origin не поддерживает резку НЕ следующими фрезами. Используйте их обычным ручным или настольным маршрутизатором.
Параллельные фрезы 11/64 – это инструменты с прямыми параллельными режущими кромками, которые обеспечивают резание с параллельными кромками и плоским днищем
Параллельный резак – это инструмент с прямой кромкой, который производит рез с параллельной кромкой и плоским дном
Фреза параллельная
11/64 “(.1719 дюймов) Диаметр хвостовика инструмента
Цельнотвердосплавная фреза с параллельными кромками
Выполняйте гравировку и резку на самых разных материалах, когда требуется резка по прямой кромке.
- Parallel Cutter – твердосплавный режущий инструмент с прямыми кромками и диаметром фрезы от 0,050 ‘до 0,250 дюйма
- Стандартная глубина фрезы в 3 раза больше диаметра до максимальной глубины 1/2 дюйма.
- Этот инструмент предназначен для вращающихся приложений.
- Он используется для множества гравировальных и режущих задач, где требуются прямые режущие кромки, в отличие от типичного V-образного среза.
- Эти инструментальные насадки размером 11/64 дюйма обычно используются в настольных и гравировальных станках с верхней загрузкой.
- Премиум, ультратонкий твердый сплав нано-класса для максимальной прочности и долговечности инструмента.
- Произведено на собственном производстве.
Закажите ниже или позвоните нам: (978) 567-8867.
У нас есть запас инструментов разных размеров!
Фреза параллельная
11/64 “(.1719 дюймов) Диаметр хвостовика инструмента
Диаметр хвостовика инструмента | Общая длина | Диаметр фрезы | Глубина резания | С разрезом | Деталь № | Цена (за каждый) | Порядок ниже |
---|---|---|---|---|---|---|---|
11/64 “ (.1719″) | 6,5 дюйма | 0,050 “ | 0,150 “ | .65 “ | PC-1719×6.5-.050 | 19 долларов.50 | |
11/64 “ (.1719″) | 6,5 дюйма | .060 “ | 0,180 дюйма | .65 “ | PC-1719×6.5-.060 | $ 19,50 | |
11/64 “ (.1719″) | 6,5 дюйма | .075 “ | 0,225 дюйма | .65 “ | PC-1719×6.5-.075 | 19 долларов.50 | |
11/64 “ (.1719″) | 6,5 дюйма | .090 “ | 0,270 дюйма | .65 “ | PC-1719×6.5-.090 | $ 19,50 | |
11/64 “ (.1719″) | 6,5 дюйма | .125 “ | 0,375 “ | .65 “ | PC-1719×6,5-.125 | 19 долларов.50 | |
11/64 “ (.1719″) | 6,5 дюйма | . 1719 “ | 0,500 “ | .65 “ | PC-1719×6,5-.1719 | $ 19,50 | |
Ручки резака 11/64 дюйма для гравировальных машин с верхней загрузкой / настольных | 10317 | 20 долларов.00 (Упаковка из 10) |
Если вы не видите нужный размер:
Свяжитесь с нами или отправьте специальный чертеж инструмента (загрузите pdf).
Пользовательские инструменты быстро меняются.
Посмотреть все Параллельные фрезы
Посмотреть все Гравировальные инструменты
Tungaloy добавляет новые диаметры фрезы к своей линии мельниц с высокой подачей TungForceFeed
Иваки, июнь 2020 г. – Компания Tungaloy расширила линейку фрез TungForceFeed для фрез малого диаметра с большой подачей, добавив фрезы нового диаметра.
TungForceFeed отличается большим передним углом и положительным углом наклона режущей кромки, что обеспечивает отличный стружкодробление при одновременном снижении нагрузки на шпиндель и энергопотребления. Это позволяет применять более высокую скорость подачи или большую глубину резания для повышения эффективности и, работая в синергии с конструкцией режущих пластин с высокой плотностью резания, обеспечивает прирост скорости съема металла на 130% -150%.
Прочный угол пластины изготовлен с дополнительной толщиной, которая выдерживает высокие усилия резания и предотвращает растрескивание режущей кромки.Державка оснащена прочными винтами M2, которые упрощают работу и уменьшают срезание шейки винта, которое может быть обычным явлением при работе с большими усилиями резания.
Доказанный успех линейки фрез со сменными пластинами для большой подачи TungForce-Feed способствовал ее расширению за счет включения фрез с метрическими диаметрами 20 мм и 25 мм и дюймовыми диаметрами 0,75 и 1,00 дюйма. Эти новые диаметры фрезы дополняют существующий диапазон от 8 мм до 16 мм. Это дополнение расширяет диапазон применения фрез для экзотических материалов с глубиной резания 0.5 мм или меньше.
TungForce-Feed может похвастаться более высокой плотностью пластины по сравнению с фрезами конкурентов того же размера, что позволяет применять более высокие подачи стола для исключительной экономии производства. Фреза особенно эффективна и полезна для производителей деталей из экзотических материалов, типичных для авиакосмической и тяжелой промышленности, которые борются с неэффективностью обработки с непредсказуемым сроком службы инструмента. Он позволяет увеличить подачу на зуб с высокой плотностью пластины для повышения скорости съема металла и длительного предсказуемого срока службы инструмента
Краткий обзор
- Расширенная линейка инструментов для расширенного охвата
- Высокая плотность пластин для повышения производительности
- Прочная конструкция фрезы обеспечивает надежность процесса обработки небольших пластин
- Всего будет добавлено 16 фрез, включая 10 метрических и 6 дюймовых фрез
Фреза APT Slot Master с регулируемой шириной
|
Основы конструирования концевых фрез – Mastercut Tool Corp
Угловая кромка – Режущая кромка представляет собой прямую линию и образует угол с осью фрезы.Срез, который производит инструмент с угловой кромкой, не будет таким плоским, как винтовая режущая кромка.
Осевое биение – Разница между самым высоким и самым низким показанием индикатора, которое снимается на торце фрезы около внешнего диаметра.
Обратный конус – Небольшой конус, в результате которого хвостовик с диаметром резания меньше режущего конца. Это условие помогает не только при погружении или сверлении, но также имеет тенденцию компенсировать прогиб.
Фаска – Плоская фаска с короткой кромкой, устанавливаемая на стыке периферии и торца фрезы. Он используется для усиления слабого в противном случае угла.
Стружколомы – Специальная геометрия передней поверхности, которая заставляет стружку плотно скручиваться и ломаться.
Стружколомители – Пазы по окружности концевой фрезы типа кукурузных початков, приводящие к узкой стружке. Подходит для черновой обработки.
Зазор – Пространство, создаваемое удалением дополнительного инструментального материала из-за заданного угла.
Свободный угол – Угол, образованный очищенной поверхностью и линией, касательной к режущей кромке.
- Зазор: первичный (первый угол 5–9 градусов) – Рельеф рядом с режущей кромкой.
- Зазор: Вторичный (2-й угол 14-17 градусов) – Рельеф рядом с режущей кромкой.
- Зазор: третичный (3-й) – Дополнительный зазор для разгрузки предусмотрен рядом со второстепенным уголком.
Подбарабанье – На торце концевой фрезы требуется небольшая полость. Эта особенность достигается за счет установки уголка тарелки на резак.
Выпуклый – Радиус выступа наружу на торце шаровой мельницы.
Диаметр сердечника – Диаметр цилиндра (или конуса с коническими концевыми фрезами) по касательной к канавкам в самой глубокой точке.
Зенковка – выемка в режущем инструменте без конца для облегчения шлифования.
Резак (биение) – Инструментальный материал удаляется фрезой (или шлифовальным кругом) на конце канавки.
Режущая кромка – Передняя кромка режущего зуба. Пересечение двух чистовых поверхностей, как правило, под углом менее 90 градусов.
Угол режущей кромки – Угол, образованный режущей кромкой и осью инструмента.
Фрезы с дифференциальным шагом – Специально разработанное изменение радиального расстояния между зубьями фрезы.Это обеспечивает изменение расстояния между зубьями и может быть полезно для уменьшения вибрации. Эта концепция основана на уменьшении гармонического воздействия инструмента, контактирующего с деталью в точный момент вибрации.
Угол тарелки – Угол, образованный торцевой режущей кромкой и плоскостью, перпендикулярной оси резца. Блюдо гарантирует, что резак будет производить ровную поверхность.
Угол входа – Угол, образованный линией, проходящей через центр фрезы под углом 90 к направлению подачи, и радиальной линией, проходящей через начальную точку контакта.Когда этот угол приближается к 90 градусам, ударная нагрузка увеличивается.
Угол входа: наклон в – значение угла или радиуса для входа фрезы в поверхность детали.
Скругление – Радиус в нижней части канавки, по которому определяется диаметр сердечника.
Флейта – Расстояние между режущими зубьями, обеспечивающее пространство для стружки и возможность переточки. Количество режущих кромок. Иногда его называют «зубами» или «глоткой». Число на концевой фрезы определяет скорость подачи.
Длина канавки – Длина канавок или канавок. Часто используется неправильно для обозначения длины резки.
Зазор (выемка) – Вторичные надрезы на инструменте, обеспечивающие пространство для стружки по углам и концам. Пространство, образующее концевую режущую кромку, которая используется при подаче в осевом направлении.
Угол зазора – Угол зазора зазора.
Ширина зазора – Ширина зазора. Расстояние между режущими кромками, обеспечивающее пространство для стружки и возможность переточкиИногда называют флейтой.
Каблук – Задний край рельефной земли. Это поверхность зуба за режущей кромкой.
Helical – Режущая кромка или канавка, равномерно проходящая по цилиндрической поверхности в осевом направлении. Нормальное направление спирали – это спираль прямого направления.
Угол винтовой линии – Угол, образованный линией, касательной к спирали и плоскостью, проходящей через ось фрезы, или углом режущей кромки, который спиральная режущая кромка образует с плоскостью, содержащей ось цилиндрической фрезы.
Крючок – термин, используемый для обозначения вогнутого состояния поверхности зуба. Этот термин означает изогнутую поверхность, а не прямую поверхность. Крючок необходимо измерять по режущей кромке, что затрудняет измерение.
Land – Узкая поверхность профильного зуба фрезы непосредственно за режущей кромкой,
(A) Цилиндрическая – узкая часть периферийной кромки, прилегающая к режущей кромке, без радиального рельефа .
(B) Рельефный – Часть площадки, прилегающая к режущей кромке, которая обеспечивает рельеф.
Свинец – продвижение винтовой режущей кромки в осевом направлении за один оборот.
Шаг = (Диаметр фрезы x Pi) / Угол касательной спирали
Длина реза (длина канавки) – Эффективная осевая длина периферийной режущей кромки, которая была снята для резки.
Радиальный передний угол – Угол между передним торцом и радиус, измеренный в плоскости, перпендикулярной оси.
Грабли – Угловое соотношение между лицевой стороной зуба или касательной к поверхности зуба в данной точке и базовой плоскостью или линией. Угловой элемент, отшлифованный на поверхности концевой фрезы.
- Осевой передний угол – Угол, образованный плоскостью, проходящей через ось, и линией, совпадающей с поверхностью зуба или касательной к ней.
- Эффективный передний угол – Передний угол, который больше всего влияет на стружкообразование. На эффективный передний угол в значительной степени влияют радиальные и осевые передние планки только при наличии угловых углов.
- Винтовая грабля – В большинстве случаев термины винтовой и осевой грабли могут использоваться как синонимы. Это наклон поверхности зуба относительно плоскости, проходящей через ось фрезы.
- Отрицательный передний угол – Имеется, когда начальный контакт между инструментом и заготовкой происходит в точке или линии на зубе, отличной от режущей кромки. Передняя поверхность ведет к режущей кромке.
- Положительный передний угол – Имеется, когда начальный контакт между фрезой и заготовкой происходит на режущей кромке.Режущая кромка ведет к передней поверхности.
Рельефное пространство – Обеспечивается удалением материала непосредственно за режущей кромкой. Сделано так, чтобы исключить возможность пятки или натирания.
- Осевой угол наклона – Угол, образованный линией, касательной к снятой поверхности на торцевой режущей кромке, и плоскостью, перпендикулярной оси.
- Осевой задел – Подъем, измеренный в осевом направлении между плоскостью, перпендикулярной оси на режущей кромке и обработанной поверхностью.Помогает предотвратить трение при изнашивании уголка.
- Вогнутый рельеф – рельефная поверхность за режущей кромкой, имеющая вогнутую форму. Производится шлифовальным кругом, установленным под углом 90 градусов к оси фрезы.
- Эксцентриковый рельеф – рельефная поверхность за режущей кромкой, имеющая выпуклую форму. Производится колесом типа I, расположенным под углом к оси фрезы.
- Торцевой фиксатор – Разгрузка на конце концевой фрезы.Требуется только для погружных фрез и для уменьшения трения в результате износа углов.
- Плоский рельеф – Рельефная поверхность за режущей кромкой, имеющая плоскую поверхность, образованную лицевой стороной чашечного колеса.
- Радиальный рельеф – Рельеф в радиальном направлении, измеренный в плоскости вращения. Его можно измерить по количеству падения индикатора на заданном радиусе при заданном угловом вращении.
Тангенциальный передний угол – Угол, образованный линией, касательной к зацепленному зубу на режущей кромке, и радиусом, проходящим через ту же точку в плоскости, перпендикулярной оси.
Зуб – Режущая кромка концевой фрезы.
Зубчатая поверхность – Также известна как грабельная поверхность.