Ремонт шаровых опор полимером по технологии sjr, как сделать экструдер своими руками
Ремонт / От Владимир
Содержание
Почему нужен ремонт шаровых опор
Восстановление полимером по технологии SJR
Что необходимо для проведения работ
Изготовление экструдера своими руками: подробно о сложном
Схема работы оборудования на видео
Восстановление шаровых с помощью самодельного экструдера
Заливка шаровых на Тойоте Королле: видео
Каждый владелец собственного авто мечтает сэкономить на его обслуживании. Замена шаровых опор — одна из статей расхода, особенно с учётом наших дорог. А если конструкция подвески предполагает одновременную замену шаровой и рычага — вопрос встаёт в копеечку. В помощь водителям изобретена технология SJR — восстановление (ремонт) шаровых опор полимером.
Почему нужен ремонт шаровых опор
Рычаги подвески с помощью шаровых опор удерживают поворотный кулак со ступицей. Фактически это ось поворота колеса. Узел испытывает нагрузки со всех сторон и достаточно быстро изнашивается на неровной дороге. Люфт в шаровой опоре приводит к разболтанности подвески, и что более опасно — к неточностям в рулевом управлении. Критический износ может привести к разрушению опоры — и тогда у автомобиля банально отвалится колесо. Наверное, многие наблюдали подобную картину.
Хорошо, если подобное случится на незагруженной дороге и малой скорости. А если на трассе и с высокой? Последствия могут быть печальными. Поэтому при появлении минимального люфта следует попытаться определить возможные неисправности шаровых опор.
Восстановление полимером по технологии SJR
Диагностика выявила опасный зазор между шаром и вкладышем опоры? Возникает дилемма: менять или восстанавливать. Опишем вкратце устройство шаровой опоры.
В зонах, отмеченных красным, износ максималенУзел состоит из двух частей, обоймы и поворотного шара. Между ними находится полимер, который демпфирует жёсткие удары и снижает трение между металлическими частями. Система работает по принципу суставной сумки в ногах человека. Именно этот полимер со временем изнашивается, и появляется опасный люфт.
Поскольку разобрать шаровую опору для замены вкладыша невозможно, остаётся одно — расплавить полимер и залить его внутрь. Это и есть суть метода sjr.
Полимеры для заливки могут быть разных видов- Во внешнем корпусе (обойме) шаровой опоры проделывается отверстие. Можно использовать готовый штуцер для пресс-маслёнки, если таковой имеется.
- С помощью газовой горелки шаровая опора прогревается до температуры плавления полиамида.
- Одновременно в специальном экструдере разогреваются заготовки (картриджи) из полиамида, аналогичного штатному.
- С помощью экструдера под высоким давлением расплав впрыскивается в полость между обоймой и подвижным шаром. Причём заполняются все трещины, щели и выработки штатного вкладыша.
- Полимер застывает, принимая форму зазора.
Люфт устранён, шаровая опора восстановлена.
Преимущества данного способа:
- Универсальность и ценовая доступность.
- Компактность и мобильность оборудования.
- Возможность применения как на небольшой СТО, так и в условиях собственного гаража.
- Доступные расходные материалы.
Существуют ещё способы с применением стационарного оборудования. Технология ремонта близка к заводской, используемой при изготовлении новых шаровых опор. Стоимость ремонта приближается к цене нового узла, что делает процесс нерентабельным.
Что необходимо для проведения работ
Комплект эконом-класса изображён на фото:
Стоимость комплекта отобьётся лишь спустя время. На один раз его редко кто покупает — невыгодно- Самая важная часть комплекта — это экструдер. В нём происходит нагрев и формирование консистенции полиамида.
- Переходные штуцеры, с помощью которых расплав под давлением заливается в шаровую опору.
- Газовая горелка или строительный фен для разогрева шаровой опоры (если этого не сделать, полимер будет застывать при заливке, и 100% заполнения не будет).
- Дистанционный термометр для контроля за нагревом.
- Воздушный компрессор, создающий давление подпора воздуха для экструдера.
Более продвинутый вариант имеет поршень, создающий давление для экструдера без применения сжатого воздуха.
Как видно, разновидностей оборудования тоже множествоНет необходимости покупать компрессор, но и сам комплект стоит дороже. Зато можно контролировать температуру нагрева с помощью собственного термометра (опять же, отпадает необходимость его приобретения). Газовая горелка или фен по-прежнему нужны для прогрева шаровой опоры перед заполнением.
Верстак обеспечит удобство и безопасностьВажно! Мобильный комплект позволяет выполнять работы прямо под днищем автомобиля, не снимая шаровой опоры. Однако делать это не рекомендуется, поскольку локальный нагрев с помощью горелки невозможен, есть опасность повредить тормозные шланги или резиновые пыльники. Поэтому не поленитесь демонтировать шаровую опору и проводите работы на верстаке.
Изготовление экструдера своими руками: подробно о сложном
При наличии домашней слесарной мастерской можно изготовить прибор самостоятельно, в крайнем случае стоит воспользоваться услугами токаря.
- Необходимо сделать плотно подогнанные поршень и цилиндр. Диаметр 10–15 см, длины 20–30 см.
Деталь не должна быть слишком громоздкой
- Уплотнительные кольца можно использовать из резины, но в большинстве случаев достаточно густой консистентной смазки.
Изготовьте уплотнительные кольца из качественной резины
- С глухой стороны к цилиндру подсоединяется штуцер для подачи сжатого воздуха. Он снабжается шаровым краном.
Подцепите штуцер для нагнетения воздуха
- В открытую часть воздушного цилиндра вкручивается переходник. Он оборудуется замком для фиксации цилиндра, в котором разогревается полимер.
Оборудуйте приспособление переходником
- Цилиндр для полимера имеет меньшие размеры. За счёт разности в диаметрах давление при запрессовке полимера выше, чем подаваемое от компрессора.
Обратите внимание на пропорции цилиндра для полимера и самого корпуса экструдера
Иногда экструдер называют станком или стендом для восстановления.
Схема работы оборудования на видео
https://youtube.com/watch?v=hVkDLYx7zoc
Восстановление шаровых с помощью самодельного экструдера
После сборки экструдера вам достаточно просто загрузить полимерный картридж в цилиндр и соединить его с подготовленным отверстием в шаровой опоре. Одновременно прогревая корпус шаровой и цилиндр с полиамидом, вы покачиваете палец шаровой опоры для равномерного проникновения расплава. После того как воздушный цилиндр в экструдере остановится, процесс считается оконченным. Дайте возможность застыть полимеру внутри детали, и можно устанавливать шаровую на автомобиль.
Заливка шаровых на Тойоте Королле: видео
Извлекать полиамид из цилиндра после проведения работ не требуется. Он снова расплавится при восстановлении следующей детали.
Изготовив такое приспособление, вы не только сможете экономить на обслуживании подвески, но и зарабатывать, предоставляя подобные услуги знакомым. Затраты на приобретение компонентов для экструдера окупаются после восстановления пары шаровых опор.
Шаровая опора своими руками: замена, диагностика, восстановление
Случается, что отреставрированная шаровая опора своими руками, может прослужить дольше, чем дешевые дубликаты. Замену этого узла сможет осуществить даже начинающий автолюбитель.
Устройство и назначение узла
Шаровая опора предназначена для надежного подвижного крепления ступицы колеса к рычагу подвески. Состоит шаровая опора из шарового пальца, корпуса и пластмассового вкладыша. Корпус шаровой опоры либо сваривается точечной сваркой из двух половинок со штампованными, сферическими углублениями с отверстием под палец в одной из них или является толстостенным металлическим стаканом в который вставляется вкладыш с пальцем, после чего ставится дно, а край завальцовывается чтобы конструкция не разбиралась. Иногда вкладыш не изготавливают, а наполняют промежуток между корпусом и шаром размягченной полиамидной пластмассой. Используют для этого обычно экструдер. Он же используется как основное оборудование в фирмах для реставрации шаровых опор. Для защиты сопрягаемых поверхностей шарнира от воды с грязью сверху надевают резиновый пыльник.
Пока цел пыльник ― шаровая практически не изнашивается. Интенсивный износ шаровой начинается после прихода пыльника в негодность, с попаданием внутрь грязи. Поэтому следите за пыльниками, так как своевременная замена негодного пыльника ― это продление срока работы узла.
Правда, стык сварного корпуса не герметичен поэтому через него внутрь корпуса набирается вода даже с целым пыльником. Потому если корпус узла состоит из двух частей, желательно наполнять его через тавотницу литолом.
Диагностика
Если во время движения автомобиля по неровной дороге слышен стук или скрип подвески, возможно эти звуки идут от изношенных шаровых опор. Определять источник неприятных звуков лучше вдвоем: одному спуститься в смотровую яму и положить руку на шаровую, а другому раскачивать машину. Когда вы почувствуете звук своими руками снимете опору, зажмете ее в тисах, и проверьте люфт шарнира. Палец не должен двигаться от небольших усилий, но закусывать его тоже не должно иначе узлу требуется ремонт или замена.
Обязательно следует провести эту проверку также в следующих случаях:
- Скрип при повороте руля.
- Самопроизвольное виляние при езде по прямой.
- Тугой руль.
Снятие & установка
Съемник
Необходимое оборудование:
- Съемник шаровых опор.
- Домкрат.
- Подставка под машину.
- Набор ключей.
- Пассатижи.
- Монтировка.
Съемник шаровых, как правило, не универсален. Если вы не нашли, подходящий съемник его можно с успехом заменить молотком. Только нужно знать куда бить. Не нужно выбивать палец из посадочного места. Удар должен быть перпендикулярен пальцу, а бить нужно по проушине (так как палец конусный небольшое давление посадочного выдавит его из проушины). Молоток ― универсальный съемник. Он не должен быть ни слишком тяжелым ни слишком легким 600 грамм будет в самый раз.
Снятие: Ослабить крепление колеса. Поднимите машину на домкрате. Снимите колесо. Поверните руль так чтобы было удобно работать. Если гайка пальца шплинтуется снимите шплинт пассатижами. Отверните гайку. Возьмите съемник, выдавите им палец. Отвернете крепление корпуса шаровой. Монтировкой отожмете нижний рычаг и снимите шаровую. Снятие и ремонт наконечников рулевых тяг и шаровых опор ничем не отличается нужно только взять другой съемник. Методы же восстановления идентичны.
Установка: Прикрепить корпус шарнира к нижнему рычагу, затянуть крепеж, монтировкой отжать нижний рычаг, вставить палец в посадочное место. Накрутить гайку на палец, затянуть ее. Если палец будет проворачиваться потянуть рычаг монтировкой вверх (палец с посадочным конусные поэтому при вдавливании пальца он перестает проворачиваться в посадочном). Не забудьте зашплинтовать гайку. Съемник для установки не нужен. Следующая замена опор не заставит вас возиться со шплинтами если вы поменяете гайки на самоконтрящиеся.
Восстановление
Необходимое оборудование:
- Наждак или болгарка.
- Экструдер.
- Электродрель с большим патроном (чтобы можно было зажать в него палец для шлифовки шара наждачной бумагой).
- Слесарные тисы.
- Сварочный аппарат (лучше полуавтомат).
- Компрессор.
Реставрация опор может происходить двумя способами:
- Переделывание неразборного шарнира в разборный, шлифовка шара пальца и замена вкладышей.
- Ремонт за счет нагнетания размягченной пластмассы в зазор между шаром и корпусом применяя экструдер.
Конечно, не стоит закупать оборудование для разового ремонта, но простейший экструдер можно быстро сделать своими руками из старого главного тормозного цилиндра, приладив к нему рычаг для надавливания на поршень. Подогревать его для размягчения пластмассы можно горелкой или паяльной лампой.
Проведение работ
Ремонт и восстановление первым способом начинается с разборки опор. Для разборки корпуса сваренного из двух чашек, нужно высверлить на одной из чашек точки сварки и разделить чашки при помощи зубила и молотка. На корпусе со вставленным донцем, при помощи наждака или болгарки стачивают развальцованные края, и ударом молотка в торец пальца выбивают дно. В корпус из двух чашек вставляется вкладыш с пальцем, половинки прижимаются друг к другу и делается несколько прихваток сваркой, стараясь не перегреть вкладыш. У корпуса с вынутым дном измерьте наружный и внутренний диаметр и изготовьте стальное кольцо в соответствии с этими размерами высотой около 10 мм с резьбой внутри и пробкой, ввинчивающейся в него. Приварите кольцо к корпусу, остудите, вставите вкладыш с пальцем в корпус ввинтите пробку, подожмите ей вкладыш, просверлите в кольце отверстие Ø 2 мм вплотную к пробке и зашплинтуйте.
Ремонт и восстановление своими руками вторым способом обычно проходит без разборки узла.
В дне корпуса сверлят отверстие диаметром около 6 мм, его размер зависит от того какой экструдер вам доступен. Зазор между шаром и вкладышам очищается от грязи и продувается сжатым воздухом от песка и стружки. Через просверленное в днище отверстие используя экструдер в зазор между шаром пальца и корпусом, нагнетается размягченная пластмасса. Дайте ей остыть и ремонт готов. Недостатком этого способа является то что вы не видите сохранилась ли геометрия шара и не можете отшлифовать его, убрав следы коррозии, поэтому результаты восстановления будут недолговечны.
Полезные советы
- Не беритесь за восстановление шарнира, если палец вынимается из него без разборки, такому узлу не поможет ремонт, а только замена. Отверстие под палец в корпусе должно быть меньше диаметра шара чтобы. В случае износа вкладыша, палец не мог вылететь из корпуса, став причиной аварии.
- Восстанавливая шарнир своими руками, разбирайте его полностью и шлифуйте шар пальца, каким бы способом вы ни собирались реставрировать узел.
Тогда плоду вашей работы не так скоро понадобится замена. Даже собираясь, использовать для восстановления экструдер не поленитесь разобрать шарнир чтобы посмотреть не нужна ли замена пальцу. Если не нужна, тогда только отшлифуете его шар.
Клон Prusa MK3S — Часть 3: Экструдер
Экструдер — сердце 3D-принтера. Он извергает нить при правильной температуре через нагретое сопло.
Я начал с 3D-печати всех необходимых деталей экструдера с использованием черной нити PETG, за исключением части кожуха вентилятора, для которой используется нить ASA. Их можно найти в разделе оси E на этой странице деталей для печати i3 MK3S+.
Компания PCBWay любезно предложила спонсировать эту сборку 3D-принтера. Помимо услуг по производству и сборке печатных плат, они также предлагают услуги 3D-печати с использованием различных технологий печати, таких как FDM, SLA, SLS, MJF, DMLS и Polyjet.
Первоначально я думал, что мне удастся использовать все клонированные детали экструдера E3D V6, и я проделал долгий путь,
, но после полной сборки мне не понравился термистор. на пути кожуха вентилятора
, поэтому я решил получить оригинальный цельнометаллический экструдер E3D V6 Prusa 24 В, который поставляется с термистором Semitec 104NT. Это также избавит меня от хлопот при последующей установке оригинальной прошивки Prusa.
Экструдер в разобранном виде состоит из следующих частей:
Чтобы сначала собрать экструдер, полностью ввинтите сопло в нагревательный блок.
Затем открутите его на один полный оборот.
Затем полностью вкрутите терморазрыв в блок нагревателя.
Нанесите термопасту на обмотки терморазрыва.
Прикрутите радиатор к терморазрыву.
Вставьте маленькую черную цангу.
Затем вставьте маленькую тефлоновую трубку.
Эту трубку можно найти в запасной сумке с креплениями MK3S, которую можно купить в интернет-магазине Prusa. Если у вас есть трубка из ПТФЭ с размерами OD: 4 мм, ID: 2 мм, вы также можете вырезать ее самостоятельно.
Подготовьте картридж нагревателя и термистор вместе с прилагающимися винтами и шестигранными ключами.
Слегка затяните винты на блоке нагревателя.
Затем вставьте картридж нагревателя, убедитесь, что он выровнен посередине, и затяните винт.
Проделайте то же самое с термистором.
И мы закончили сборку экструдера. Соедините кабели вместе, чтобы они не мешали в процессе сборки.
Подготовьте детали для 3D-печати: корпус экструдера, адаптер-принтер и fs-рычаг.
Вам также понадобится датчик накаливания с кабелем, неодимовые магниты, небольшой стальной шарик, 2 шестигранные гайки M3, 2 квадратные гайки M3, винты M3x18 и M3x10. Все эти детали входят в комплект, который можно купить на сайте Aliexpress. Магниты и стальной шарик также являются частью сумки с запасными частями, о которой я упоминал ранее.
Начните с вставки шестигранных гаек M3 в корпус экструдера. Вы можете использовать винт M3, чтобы втянуть гайки в отверстия.
Затем вставьте обе гайки M3.
Вторая квадратная гайка будет удерживать датчик приближения на месте
с помощью этого винта M3x10.
Затем вставьте меньший неодимовый магнит в 3D-печатную деталь fs-рычага
и поместите деталь внутрь корпуса экструдера и закрепите ее с помощью винта M3x18.
Деталь должна иметь возможность свободно двигаться.
Вставьте второй магнит так, чтобы два магнита отталкивались друг от друга.
Теперь вставьте небольшой стальной шарик внутрь части адаптера-принтера и вставьте его в корпус экструдера, как показано на рисунке.
Подготовьте следующие детали: напечатанную на 3D-принтере плиту двигателя экструдера, шестерню Btech и шаговый двигатель оси E. Обратите внимание, что сначала я попытался использовать шаговый двигатель с пластиковым разъемом, но он не подходил к сборке, и мне пришлось заменить его на один из этого набора шаговых двигателей-клонов Prusa.
Прикрепите пластину двигателя экструдера к двигателю экструдера с помощью 2 винтов M3x10.
Закрепите одну из шестерен BTech на валу шагового двигателя таким образом, чтобы нить могла захватить ее зубьями.
Подготовьте крышку экструдера и вставьте в нее квадратную гайку M3.
Вставьте 2 винта M3x10 в отверстия в корпусе экструдера.
Затем возьмите собранный экструдер и поместите его внутрь корпуса экструдера.
И поместите на него двигатель экструдера в сборе.
.
Используя 2x M3x40, соедините две детали вместе. Обратите внимание, что винты будут торчать из собранного корпуса, это нормально.
Подготовьте напечатанную на 3D-принтере часть x-каретки с 4 квадратными гайками M3, 2 шестигранными гайками M3 и кабелем датчика накаливания.
Вставьте две шестигранные гайки M3 в предусмотренные отверстия. При необходимости используйте технику вытягивания винта.
Вставьте три квадратных гайки M3, как показано на рисунке.
И последний здесь.
Поместите кабель датчика накаливания в канавку х-образной каретки. Убедитесь, что разъем выступает примерно на 15 мм.
Направьте кабель экструдера, как показано на рисунке ниже, и совместите часть x-каретки с винтами другой части.
Закройте его с помощью уже вставленных винтов M3x10.
Прикрепите датчик накаливания. Обратите внимание на ориентацию! Провод заземления черный.
Установите его сверху и закрепите винтом M2x8.
Закрепите узел с помощью M3x40.
Для охлаждения экструдера я использовал вентилятор Noctura NF-A4x10 5V. Он имеет 3-контактное соединение, такое же, как у Prusa. Также подготовьте 3 винта M3x16 и винт M3x20.
Затяните 3 винта M3x16, но оставьте последний.
Вставьте квадратную гайку M3 в кожух вентилятора.
Так же не забудьте снять с него опору.
Затем наденьте его на нижнюю часть сборки.
И, наконец, закрепите его винтом M3x20.
Соберите остальную часть комплекта шестерен BTech вместе с распечатанной на 3D-принтере деталью экструдера-натяжителя.
Вставьте шестигранную гайку M3 в натяжную часть экструдера.
Соберите шестерню, поместив оба подшипника внутрь шкива.
Вставьте вал в промежуточную часть
и убедитесь, что он свободно вращается.
Поместите собранный ролик экструдера в сборку и закрепите его с помощью винта M3x40.
Найдите часть fs-крышки вместе с винтом M3x10
и поместите ее поверх ИК-датчика накаливания.
Используйте M3x40 с пружиной, чтобы усилить натяжение натяжного ролика. Винт с частичной резьбой и пружина входят в комплект запасного мешка с креплениями MK3S. Вы также можете приобрести пружину экструдера со следующими характеристиками:
Длина: 15 мм
Диаметр проволоки 0,8 мм
Внешний диаметр: 0,5 мм
Для подключения вентилятора печати соберите опорную часть вентилятора печати, шестигранную гайку M3 и винт M3x10.
Вставьте шестигранную гайку M3 внутрь пластиковой детали.
И прикрепите к сборке.
Я заказал оригинальный вентилятор для печати 5015 5V в магазине Prusa, так как думал, что он будет лучшего качества, чем те, что можно найти на Aliexpress. Но я не знаю, может быть, они такого же качества.
Для крепления вам также понадобятся 2 винта M3x20 и квадратная гайка M3.
Теперь можно приступить к сборке датчика приближения. Этот датчик называется Super PINDA от Prusa. Я тоже купил оригинал, просто чтобы избежать проблем с клонами. Я заказал один на Aliexpress, но не пробовал, чтобы увидеть разницу.
Вставьте датчик в держатель и проведите провода, как показано на рисунке. На данный момент точное размещение не имеет значения. Датчик будет откалиброван в конце сборки.
Затем вставьте две стяжки в отверстия в задней части собранного экструдера.
К этому моменту у вас должен быть полностью собранный экструдер с множеством торчащих из него проводов.
Закрепите стяжки на линейных подшипниках оси X. Убедитесь, что кабели выведены наружу, как показано на рисунке. Управление кабелями — важная часть сборки принтера Prusa.
Они должны выглядеть так. Теперь вы можете отрезать торчащие части стяжек.
Пришло время подключить зубчатый ремень GT2 6 мм к собранному экструдеру. Длина ремня оси X составляет 850 мм. Сначала вставьте конец кабеля в канавку.
Затем проведите его в сторону через натяжной ролик.
Назад к другой стороне, где расположен 16-зубый шкив ремня ГРМ GT2 .
И, наконец, вернемся к пазу на задней части крестовины. Натяните ремень как можно туже, но не перетягивайте его.
Если ремень слишком ослаблен, вы можете отрегулировать его с помощью винтов на х-образном направляющем ролике.
Когда вас устраивает натяжение, вы можете отрезать оставшуюся часть ремня. Натяжение ремня также является частью процесса калибровки, так что не беспокойтесь об этом на этом этапе сборки.
Чтобы завершить укладку кабелей экструдера, мы начнем с того, что отложим в сторону заднюю часть каретки и держатель кабеля, напечатанные на 3D-принтере. Вам также понадобится винт M3x40 и шестигранная гайка M3.
Вставьте шестигранную гайку M3 в предназначенное для этого отверстие в задней части крестообразной каретки.
Затем вставьте винт M3x40 в держатель кабеля.
Соберите две части вместе.
Оригинальная Prusa использует нейлоновую нить 2,75 мм в качестве опоры для проводов, но у меня ее не было, и вместо нее я использовал нить 1,75 PETG и обернул ее вокруг термоусадочной трубки 3 мм. Возможно, позже заменю, но пока придется.
Затем его можно вставить в отверстие, которое выступает из х-образной части каретки.
Проведите все кабели, за исключением кабеля горячего конца и термистора, через отверстие в задней части каретки.
И закрепите его с помощью 4 винтов M3x10.
Я также отрезал конец разъема вентилятора Noctura и подключил к нему удлинительные провода.
На конце я добавил 3-контактный разъем Dupont. Обратите внимание, что цвета должны быть расположены, как на картинке ниже.
Затем вставьте все провода в текстильный рукав длиной 50 см и диаметром 13 мм.
И закрепил их стяжками.
Проделайте то же самое с горячим концом и кабелем термистора в нижней части держателя кабеля.
Готово! Должен сказать, что это была самая трудоемкая и сложная часть сборки 3D-принтера, но было очень приятно увидеть готовый экструдер, готовый печатать красивые 3D-объекты.
Матричный экструдер
ПримечаниеВсе товары, приобретенные на этом веб-сайте, не включают налог, включая, но не ограничиваясь: налог на потребление, налог на добавленную стоимость, таможенные пошлины и т. д.,
Перед размещением заказа ознакомьтесь с политикой и правилами вашей страны в отношении налогов на онлайн-покупки.
Сумма, которую вы платите, не включает налог, и вам нужно будет заплатить ее самостоятельно.
Чтобы приобрести товары с включенным налогом, нажмите на ссылку ниже:
https://trianglelab.aliexpress.com/store/1654223
▉О описании логистики:
Поскольку упаковка содержит сильные магниты, обычная логистика не может быть транспортирована. Поэтому независимо от того, какой вид логистики вы выберете.
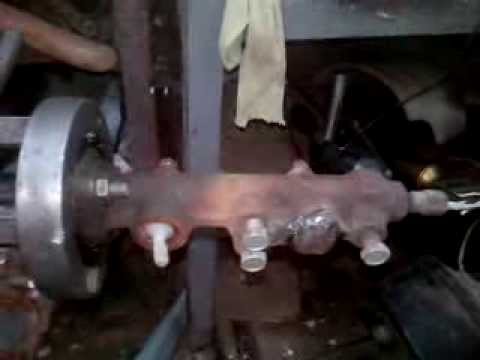
▉ Имя:
Triangle Lab – Matrix Extruder
▉ Installation guide:
https://drive.google.com/drive/folders/1K_Jj4JfczDlKiNnwk-SYakOIQqm4zllD?usp=sharing
▉ Highlight:
·двойной привод с регулируемым натяжным роликом
· очень короткий путь нити
· тонкостенный биметаллический термовыключатель
·компактная экструзионная система
▉ Совместимость:
Совместим с Prusa
Совместим с Ender 3/3 PRO/ 5
Совместим с CR-10/CR-10S
Другие модели могут найти кронштейны здесь.
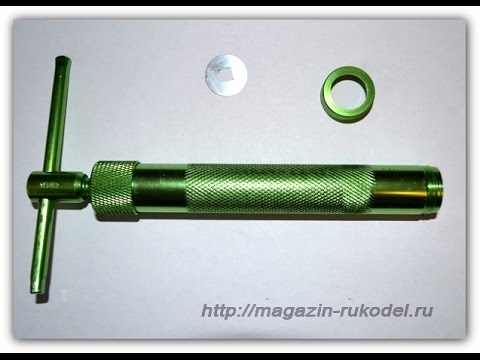
https://www.thingiverse.com/
Пользователи сети представили:
1: для принтера Lulzbot Taz
https://www.thingiverse.com/thing:4686413
♥Матричный экструдер-3D печать с интервальной съемкой:
https://youtu.be/GREhHw2ynsc
◆ Резюме
Тип привода: Двойной привод с регулируемым натяжным роликом
Максимальная температура печати: 285°C (с возможностью повышения до 450°C)
Масса: 357 г (включая горячую сторону)
Номинальное количество шагов на мм (16x): 335,4 шага на мм (требуется дополнительная калибровка)
Ток двигателя: 1,2 А
Диаметр нити и допуски: 1,75±0,05 мм
Максимальное толкающее усилие: 8,6 кг. Стандартный PLA 10 мм/мин при 24 В. Драйвер
66,7x44x78,7 мм
◆
Совместимость с HotsideV6 Volcano Super Volcano
Электрика
Мощность нагревателя 40 Вт 12/24 В дополнительно
Вентилятор 40x40x10 мм, постоянный ток, шарикоподшипник , 12/24 В, опционально
Термистор Semitec 104NT-4-R025х52G
Двигатель
Номер фазы 2 фазы
Сопротивление 2oum
Удерживающий момент 29Н см
Ток 1,2 А
Длина кабеля двигателя 90 см
▉ Комплектация:
Trianglelab-Matrix ExtruderX 1
*Дружеское напоминание.
