область применения и принцип работы
Если раньше электроэрозионный станок был редкостью, то сегодня таким оборудованием уже никого не удивить. Под электроэрозией понимают разрушение межатомных сил взаимодействия в металлах под воздействием электрического заряда. Своим появлением электроэрозионный станок обязан разработкам советских ученых Б. Р. Лазаренко и Н. И. Лазаренко. Такое оборудование является универсальным. Оно позволяет обрабатывать и придавать форму любым маркам металлов и сплавов. Причем твердость обрабатываемого материала не имеет никакого значения. Возможность обрабатывать любые материалы является одним из основных преимуществ электроэрозионной обработки перед традиционной обработкой резанием.
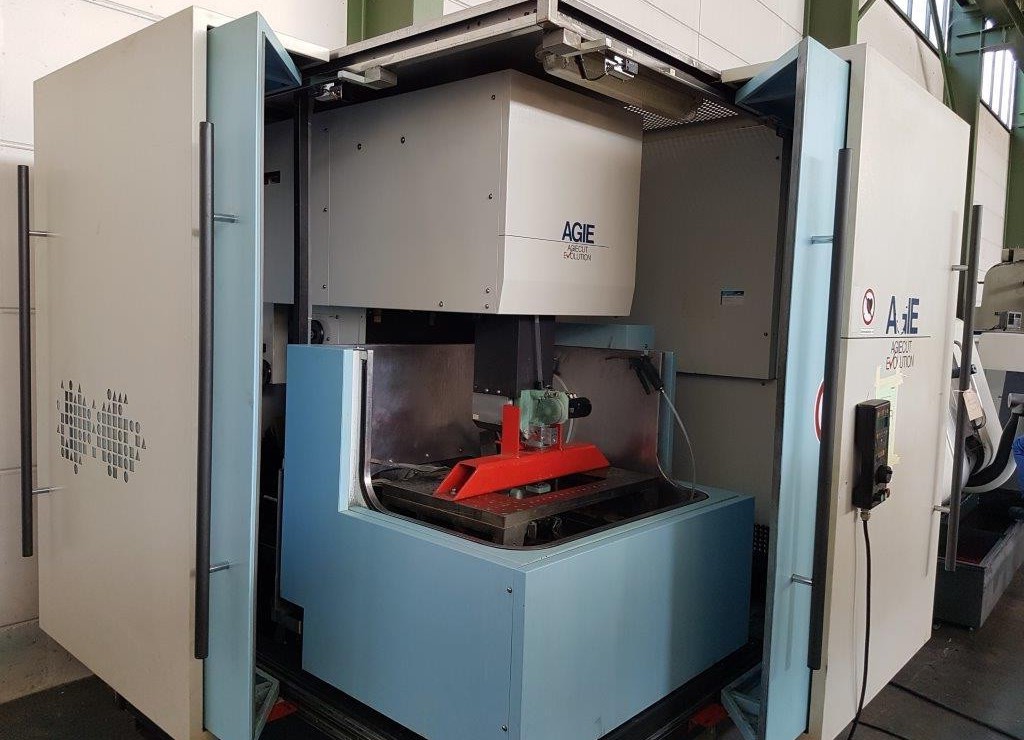
Принцип работы электроэрозионного станка
При ознакомлении с принципом работы подобного оборудования у многих возникает ассоциация с электродуговой сваркой. И это вполне логично. Ведь для протекания эрозионных процессов необходимо получить электрический разряд. С этой целью между электродами создается разница потенциалов. Одним из электродов при этом служит обрабатываемое изделие, а вторым – электрод станка.
Когда электрод приближается к заготовке на критическое расстояние, то происходит так называемый пробой. Иными словами, электроны совершают работу выхода и устремляются по воздуху к катоду (обрабатываемой заготовке).
Электроны, соударяясь с поверхностью обрабатываемого изделия, в считаные доли секунды разогревают его до невероятно больших температур (10 000 и более градусов по Цельсию). Температура плавления даже самых тугоплавких материалов в разы меньше. Таким образом, слой металла моментально испаряется, образуются углубления по форме рабочего инструмента электроэрозионного станка.
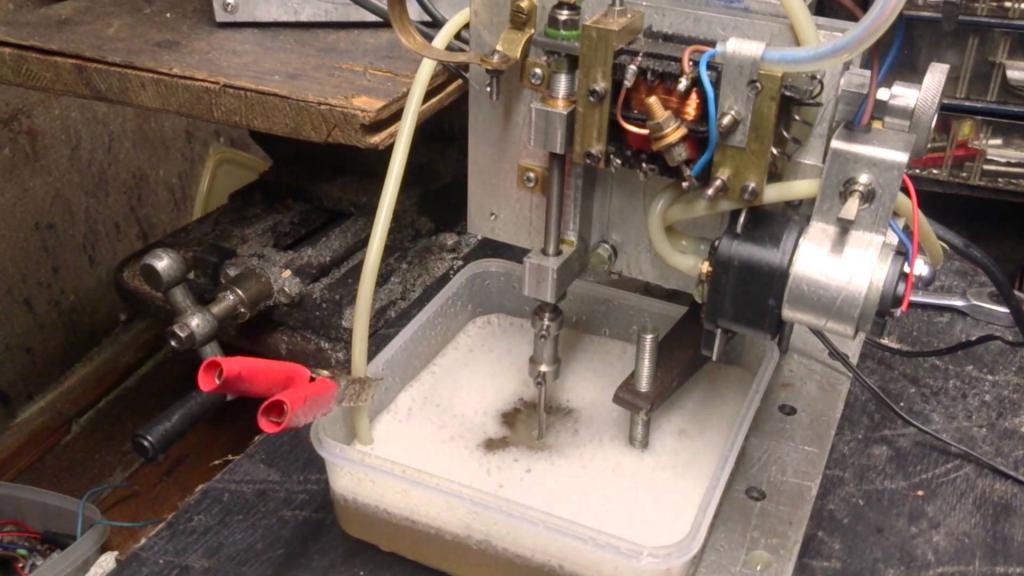
Зачем нужен электролит?
Для усиления эффекта анод и катод помещаются в диэлектрический раствор. В качестве такового может быть использован керосин. Однако он может в любой момент воспламениться. Поэтому предпочтение следует отдавать специальным минеральным маслам. Масло тоже может гореть, однако температуры вспышки значительно выше, чем у керосина. Кроме того, керосин источает вредные для производственного персонала пары.
Диэлектрическая жидкость сильно нагревается и образует так называемую паровую рубашку (мелкие воздушные пузырьки). Именно по воздуху, заключенному в диэлектрическую жидкость, и протекает ток (направленное движение электронов). Это позволяет концентрировать поток электронов и усиливать полезный эффект.
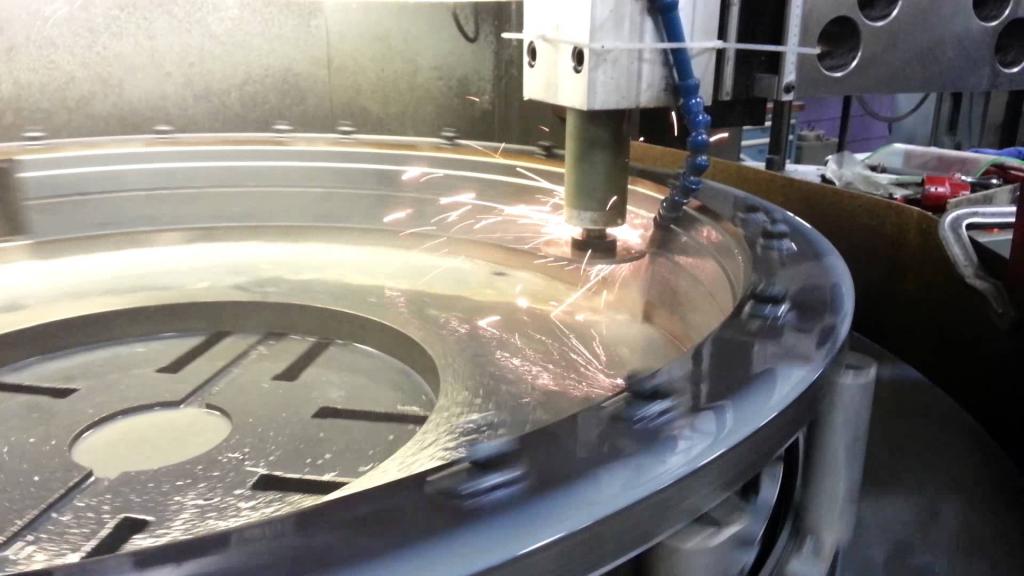
Влияние обработки на прочностные характеристики обработанной поверхности
После обработки химический состав и концентрация различных элементов в приповерхностном слое заготовки несколько изменяются. Например, может повыситься концентрация углерода. Кроме того, поверхностный слой может легироваться элементами, которые содержались в расплавленном электроде. Подбором электродов можно осуществлять легирование поверхности такими элементами, как алюминий, цинк, хром, никель, вольфрам и другие. В зависимости от условий последующей эксплуатации детали, это может играть как положительную, так и отрицательную роль.
Достоинства электроэрозионной технологии и оборудования
Одним из основных достоинств данной технологии является очень высокая точность обработки изделий. Это обусловило широкое применение электроэрозионной технологии в таких отраслях, как военная промышленность, точное машиностроение, а также в производстве медицинских изделий ответственного назначения.
Дефицит производственных площадей – одна из главных проблем современных машиностроительных компаний. Электроэрозионные станки, как правило, довольно компактны и позволяют частично разрешить эту проблему. Таким образом, компактность оборудования также является неоспоримым преимуществом станков данного типа.
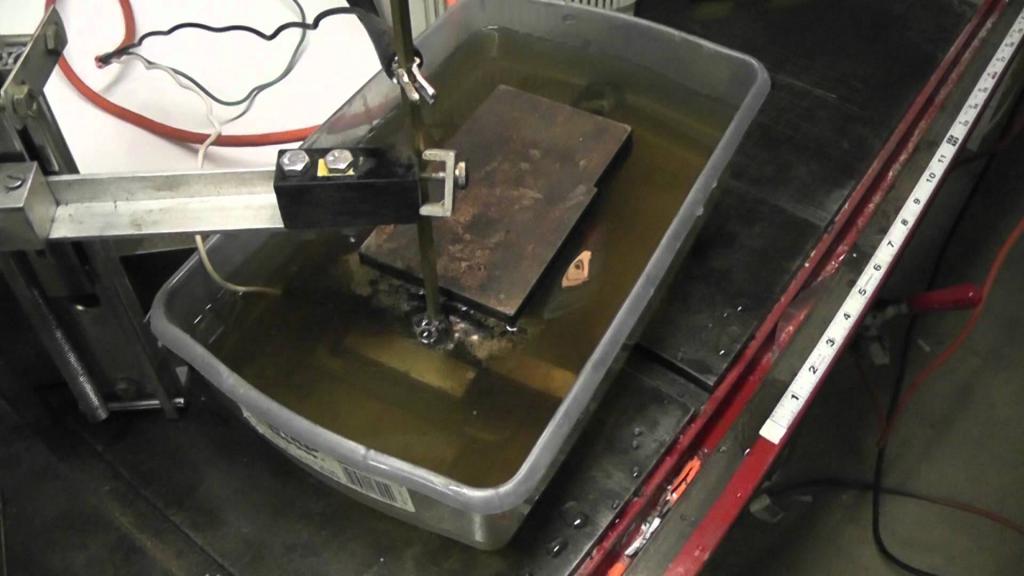
Устройство электроэрозионного станка
Существует множество типов станков. Однако вышеописанные принципы работы справедливы абсолютно для каждого из них, будь то электроэрозионный прошивной станок или станок для электроискровой обработки.
Может показаться, что данное технологическое оборудование является невероятно сложным и дорогостоящим. Дорогостоящим, возможно. Особенно если станок произведет именитым брендом. Однако сам принцип работы оборудования довольно прост. В Сети появилось множество видеороликов, в которых умельцы воспроизводят эти процессы. Причем они собирают электроэрозионные станки своими руками в условиях домашних любительских мастерских.
Сам станок, как и любой другой станок для обработки металлов и других материалов, включает станину (основание), ванну для электролита, шпиндельную головку, пульт управления для оператора (это может быть и полноценная система числового программного управления), различную автоматику. Это основные компоненты. Отдельные станки могут дополнительно оснащаться системой фильтрации электролита и другими устройствами.
Процесс электроэрозионной обработки (ЭЭО) токопроводящих материалов основан на принципе направленного разрушения анода (заготовки), который находится в жидкой диэлектрической среде, в результате прохождения между ним и катодом (рабочим инструментом) электрического разряда большой мощности. Ввиду значительных технологических возможностей метода, он реализуется на электроэрозионных станках различного исполнения.


Структура и разновидности оборудования для ЭЭО
Типовой электроэрозионный станок включает в себя:
- несколько автономно действующих друг от друга электродвигателей;
- узел подачи электрода-инструмента;
- ванну с рабочей средой;
- стол для размещения обрабатываемой заготовки;
- схему управления.
Классификация рассматриваемого оборудования производится по следующим признакам:
- По технологическому предназначению. Можно выделить универсальные, специализированные и специальные станки для ЭЭО;
- По принципу компоновки основных узлов. Её можно сделать горизонтальной и наклонной, но чаще используется вертикальная компоновка;
- По типу стола: неподвижный или координатный;
- По типу ванны – съёмная или поднимающаяся;
- По степени точности – оборудование для работ обычной точности и прецизионное;
- По принципу возбуждения и последующего регулирования параметров электрического разряда.
Размерный ряд видов электроэрозионного оборудования отечественного производства определяется требованиями ГОСТ 15954.
Способы получения электрического разряда в рабочих цепях станков
Размерную обработку можно производить искровым, импульсным и дуговым разрядами. В первом случае между катодом и анодом образуется искровой разряд малой скважности, но с точно заданными характеристиками межэлектродного промежутка. Такие станки компактны, отличаются высокой точностью работы и качеством поверхности после электроэрозии, удобством регулирования технологическими показателями, но одновременно имеют малую мощность, и, следовательно – производительность. Области целесообразного использования таких станков – точная разрезка труднообрабатываемых материалов (в частности, твёрдых сплавов), получение деталей со сложными контурами. Их можно также использовать для извлечения сломанного инструмента и т.п.


Схема проволочно-вырезного электроэрозионного станка
Повышение энергии электрического разряда достигается введением в схему генератора импульсов, который увеличивает интервал между смежными разрядами и одновременно увеличивает тепловую мощность при единичном электроэрозионном акте. Как следствие, производительность работы увеличивается, но зато снижаются точность, а поверхность обработанной детали может иметь довольно протяжённую зону термического влияния, что не всегда допустимо. Электроимпульсные станки применяются там, где требуется более значительный съём металла в единицу времени.
При необходимости обеспечить ещё более высокий съём металла (причём не только для формоизменения исходной заготовки, но и для её упрочнения) применяются электродуговые станки. Производительность такого оборудования увеличивается в несколько десятков раз, поскольку дуга, в отличие от остальных видов электрического разряда, горит непрерывно. Для управления технологическими параметрами дугового разряда он сжимается поперечным потоком среды-диэлектрика, которая постоянно, и под большим давлением прокачивается через зону горения дуги насосной установкой, предусмотренной в схеме станка. Электродуговыми станками можно изготовить крупные заготовки под валки, молотовые штампы горячей штамповки и т.д.
Применение электроэрозионных станков разных типов
Из оборудования электроискрового типа одним из наиболее точных считается копировально-прошивочный станок МА4720. Он предназначен для работы с труднообрабатываемыми заготовками сложной конфигурации, например, для твёрдосплавной штамповой оснастки, пресс-форм, кокилей. Производительность станка не превышает 70 мм3/мин, зато можно достичь точности в 0,03…0,04 мм, при достаточно невысокой шероховатости конечной поверхности (не выше Rz 0,32…0,4 мкм на чистовых режимах обработки). Перемещение рабочего стола производится системой ЧПУ. Размеры рабочего стола и допустимый диапазон значений межэлектродного зазора между анодом и катодом не позволяет получать на данном станке изделия с габаритными размерами более 120?180?75 мм.
Примером электроимпульсного станка является распространённая модель 4Е723, также оснащаемая ЧПУ. Более высокие показатели удельной мощности позволяют достигать производительности ЭЭО до 1200м3/мин, при погрешности обработки на чистовых режимах в пределах 0,25…0,1 мм. Более высокая точность достигается при ЭЭО фасонных поверхностей. Станок также используется преимущественно в инструментальном производстве, однако шероховатость поверхности заметно увеличивается – до Ra 2,5 мкм, поэтому после обработки в большинстве случаев потребуется шлифование. На станке можно выполнять ЭЭО деталей с габаритными размерами 620?380?380 мм, а также прорезание фасонных пазов.
Данные виды относятся к универсальным электроэрозионным станкам. Примером специализированного оборудования является электроэрозионный станок модели 4531, производящий профильную вырезку сложных контуров при помощи непрофилированного электрода. На станке 4531 применяется латунная проволока, которая непрерывно перематывается через межэлектродный промежуток, возбуждая разряд между катодом и анодом. При относительно невысокой производительности (не более 16…18 мм3/мин по стали; для твёрдого сплава производительность ещё ниже), станок 4531 в принципе позволяет обеспечить погрешность ±0,01 мм, поэтому рассматриваемое оборудование эффективно при производстве матриц вырубных штампов особо сложной конфигурации и шаблонов. Максимальные размеры вырезаемого контура составляют 100?60 мм.
Принципы оптимального выбора технологии и типоразмера станка для ЭЭО
Исходными данными являются точность контура, размеры (глубина) термически изменённой зоны, а также желаемое значение съёма в единицу времени. Для станков, работающих с непрофилированными электродами, важно наличие устройств для автоматической заправки проволоки, а для импульсных станков – генераторов, позволяющих использовать биметаллическую проволоку, которая повышает производительность ЭЭО.
Для повышения качества процесса и снижения эрозионного износа электрода-инструмента в качестве рабочих сред лучше использовать масло (наиболее употребительна смесь масла «индустриальное-20» с керосином). В принципе, для изделий с увеличенными допусками, возможно использование и воды.
Технологические возможности электроэрозионных станков значительно расширяются наличием дополнительных приспособлений (например, для получения конических поверхностей).
Для съёма металла от 20000 мм3/мин и выше нужно применять только электродуговые станки. Наименьшая погрешность работы такого оборудования достигается на обратной полярности при использовании графитовых электродов. Вместе с тем, сравнительно высокая шероховатость поверхности – не ниже Rz 0,8…1,6 мкм – вынуждает после ЭЭО дуговым разрядом предусматривать чистовое шлифование полученного контура. Давление прокачки рабочей среды должно быть не менее 50…60 кПа.
Одним из вариантом зачистки металлов является электроэрозионная обработка. Принцип работы технологии прост. К заготовке и электроду подключается источник постоянного тока, который генерирует кратковременные импульсы, проходящие через электроды. Электричество в активной зоне создает электронную дугу, которая легко прожигает металлическую поверхность. Дуга живет небольшой период во времени, поэтому она не деформирует металл, не оставляет следов, сохраняет целостность электрода.
Электроэрозионная обработка металлов обычно выполняется с помощью специальных станков, которые обладают множеством преимуществ — высокая мощность, универсальность, простота использования. Но как происходит такая обработка металлов? В каких режимах работы могут функционировать эрозионные станки? И о чем нужно знать при их выборе? В статье эти вопросы будут рассмотрены.
Физические и химические основы электроэрозии
Электроэрозионная обработка (ЭЭО) — это технология, которая позволяет разрушать поверхность металлических изделий с помощью электрических разрядов. Явление электрической эрозии основано на разрушении электродов под действием электрического тока, пропускаемого через электроды. Технология была изобретена советскими инженерами и учеными Б. Лазаренко и Н. Лазаренко в 1943 году.
Технология электроэрозии позволяет изменить размеры, форму металлических деталей — ее можно использовать для создания отверстий, для шлифовки, для обработки фасонных полостей, для создания углублений и так далее. Технология является очень точной и надежной, что позволяет использовать для высокоточной обработки металлов.
На физическом уровне ЭЭО выглядит так:
- Для электрической эрозии применяются станки, которые имеет приблизительно одинаковую конструкцию. Главным их элементом является обрабатывающий инструмент-электрод, который выступает в роли резака. Вторым важным элементом является сама обрабатываемая деталь. Третий элемент — источник постоянного тока, к которому подключаются электрод и обрабатываемая деталь.
- Чтобы избежать перегрева деталей, обработка выполняется в жидкой среде. В качестве жидкости выступают диэлектрики, которые плохо проводят ток (керосин, минеральное масло). Для удобства работы станок может оборудоваться дополнительными деталями (реостаты, конденсаторы и другие). Большинство современных станков также оборудованы электронной панелью управления.
- Установка может работать в двух режимах — электроискровой и электроимпульсный. В случае электроискрового режима ток подается таким образом, что электрод выступает в роли минус-катода, а сама деталь — плюс-анода. Во время работы электрод генерирует электрическую дугу, которая ионизирует поверхность металлической заготовки. Ионы имеют очень высокую температуру, что приводит к расплавлению металла с образованием небольшой лунки. Чтобы не расплавить электрод-катод, электричество подается короткими импульсами. Длительность подачи электричества для генерации 1 импульса — 0,001 секунд. Во время электроискровой обработки срезается небольшое количество металла, поэтому эту технологию используют для финальной обработки заготовки.
- В случае электроимпульсного режима работы меняется электрическая полярность. На электрод подается положительный ток, а на деталь — отрицательный. Это также приводит к образованию ионизированной плазмы, которая прожигает металл с образованием лунки-углубления. Однако из-за особенностей кристаллической решетки металлов генерируется более мощный поток ионов, поэтому электроимпульсный режим мощнее электроискрового в 10-11 раз. Чтобы защитить электрод от расплавления, ток подается небольшими порциями, где длительность подачи 1 импульса составляет 0,001 секунд. Электроимпульсный режим из-за повышенной мощности используется для черновой обработки, а также для резки сверхпрочных металлических сплавов.
Частички металла, которые срезаются ионным потоком, попадают в жидкость-диэлектрик. Они не растворяются, а находятся в диэлектрике в виде мелкой взвеси. Сперва частички обладают очень высокой температурой, однако при контакте с жидкостью они быстро остывают, достигая температуры окружающей среды. После проведения работ не рекомендуется использовать «раствор» по прямому назначению, поскольку металлическая взвесь может ухудшать технические свойства эксплуатируемого прибора.
Электроэрозионная обработка металлов
Электроэрозионная обработка подходит для обработки любых металлов и их сплавов (чугун, сталь, латунь, алюминий и так далее). Температура ионизированной плазмы является очень высокой (более 10 тысяч градусов), что делает возможной работу со всеми видами металлов. Плазма обладает коротким периодом жизни, поэтому она не повреждает металлическую деталь, а контролировать мощность ионного потока не слишком сложно. Технология востребована в высокоточных отраслях промышленности; в мелкосерийном и домашнем производстве станки для ЭЭО используются редко в связи с их высокой стоимостью.
На практике технология ЭЭО обычно применяется для обработки сложных фасадных конструкций, а также при работе со сверхпрочными деталями для самолетов, автомобилей, кораблей, электронных устройств. В случае правильного использования оборудования не возникают микротрещины и микроповреждении металлической заготовки, что положительно сказывается на качестве обработки. Для создания электрода используются графит, вольфрам, алюминий или латунь. Эти материалы не разрушаются при контакте с нагретой плазмой, сохраняют свою форму. ЭЭО позволяет изменить форму, размеры, шероховатость исходной детали.
Преимущества
У технологии ЭЭО есть как преимущества, так и недостатки. Рассмотрим сперва преимущества технологии ЭЭО:
- Универсальность (для металлов). Поток разогретой плазмы обладает очень высокой температурой, а с его помощью можно прожечь любой металлический сплав. С помощью разогретой плазмы можно создать отверстие, разрезать деталь, выполнить высокоточную шлифовку, создать углубление. Это делает ЭЭО-станки универсальными, удобными в использовании.
- Высокое качество резки. Толщина ионизированной плазмы составляет менее 1 миллиметра, поэтому с ее помощью можно делать точную обработку металлических деталей. Разогретая плазма быстро остывает, поэтому края заготовки остаются ровными, прочными, без расплавленных частей. Электрическая дуга не испаряет раствор-диэлектрик, поэтому защитную жидкость можно использовать долгое время (потери жидкости от испарения составляют менее 0,1%).
- Простота применения. ЭЭО-станки просты в использовании, не нуждаются в особом уходе. Почти все модели оборудованы электронной панелью, которая позволяет контролировать режим работы (мощность разряда, длительность импульса, глубина подачи плазмы и другие). Во время работы не образуются вредоносные испарения и газы, поэтому рабочему не нужно носить защитную одежду.
- Несколько режимов работы. Основные режимы — электроискровой и электроимпульсный. Первая методика применяется для разрезания детали, вторая используется для полировки, выравнивания поверхности. Также существуют вспомогательные методы обработки материалов — эрозионно-химическая технология, проволочная, анодно-механическая, электроконтактная и другие.
Недостатки
- Нельзя обрабатывать диэлектрические материалы. Электрическая дуга, которая создает высокотемпературную плазму, возникает за счет контакта электрода с металлической поверхности обрабатываемой деталью. Если деталь будет выполнена из диэлектрического материала (дерево, бетон, пластик), то в таком случае режущая дуга не возникнет, а станок будет бесполезен.
- Высокое электропотребление. Для работы ЭЭО-станка требуется большое количество электроэнергии, что увеличивает себестоимость обработки. Во время работы станка должны поддерживаться постоянные параметры электрического тока (напряжение, мощность, сила). Поэтому многие установки оборудуются защитным оборудованием, позволяющего изменить параметры станка в случае скачка напряжения.
- Низкая производительность. Большинство моделей станков проводят резку с небольшой скоростью (от 0,1 до 7-8 миллиметров в секунду в зависимости от способа обработки металла). Поэтому ЭЭО-станки не подходят для фабрик с большой производственной загруженностью.
- Высокая стоимость. ЭЭО-оборудование стоит достаточно дорого, что снижает его универсальность и доступность. Большинство станков производятся иностранными компаниями (Япония, Германия, Польша), что также негативно влияет на ценообразование. Помимо этого придется оплачивать вспомогательные расходы — на покупку защитной жидкости, на замену отработанных электродов, на потребление электричества и другие.
Способы обработки
Перечислим основные способы электроэрозионной обработки:
- Создание отверстий. Пучок плазмы позволяет создать очень глубокие отверстия в металлической поверхности (от 20 до 40 диаметров в зависимости от типа электрода). Увеличить глубину отверстия можно за счет кручения детали, перемещения электрода, использования нестандартного вспомогательного оборудования. Средняя скорость сверления составляет 0,1-1 миллиметр в секунду.
- Резка металлические объектов. С помощью плазменного пучка можно разрезать заготовку на любое количество частей. Глубина резки практически не имеет ограничений по глубине — стандартная глубина составляет 20-40 диаметров, однако ее можно увеличить за счет применения нестандартных электродов и вращения заготовки. Средняя скорость резки — 0,1-0,5 миллиметров в секунду.
- Вырезание деталей. С помощью технологии ЭЭО можно вырезать объекты любой формы. Эта технология широко применяется для резки драгоценных камней для создания необычных украшений. Также ее применяют для производства фасонных резцов, матриц, пуансонов и других объектов.
- Шлифование, легирование. Технологию ЭЭО можно выполнять для выравнивания шероховатых поверхностей, а также для устранения внешних дефектов. Шлифовка выполняется точечным методом с помощью электрода, поэтому ЭЭО-легирование не рекомендуется использовать для работы с большими поверхностями. Однако эта технология может применяться для работы с деталями сложной формы, для устранения дефектов на поверхности магнитных сплавов. Средняя скорость шлифовки — 4-5 квадратных миллиметров в секунду.
ЭЭО-технику можно также применять для маркирования металлов и создание надписей на их поверхности. Для маркировки могут использоваться любые символы — буквы, цифры, специальные обозначения. Де-факто маркировка представляет собой создание несквозных отверстий, а нанести код можно на любой участок металлической детали. Средняя производительность ЭЭО-оборудования составляет 4-10 миллиметров в секунду, что является хорошим показателем для техники такого класса.
Станки для электроэрозии металлов
Перечислим основные модели станков, которые представлены в России:
- INTEGRAL 2 (AGIE). Производится одноименной швейцарской компанией. Позволяет работать с деталями размером не более 80 х 60 х 25 сантиметров. Основной режим работы — электроискровая эрозия в защитной среде диэлектрической жидкости. Имеет встроенную панель ЧПУ, которая позволяет контролировать технологические особенности операции (мощность ионного потока, точность обработки, итоговый уровень шероховатости).
- AQ535 (SODICK). Производится японской компанией. Позволяет обрабатывать заготовки, размеры которых составляют не более 105 x 65 x 30 сантиметров. Электроэрозионная обработка выполняется с помощью режущей проволоки, которая может делать все основные операции (создание отверстий, маркировка, шлифовка, вырезание). Модель оснащена продвинутой ЧПУ-панелью и имеет встроенную систему, экономящую электричество, что снижает себестоимость обработки.
- Модель 4531. Производилась в СССР; новые станки 4531 больше не выпускаются. Однако в продаже можно встретить множество неиспользованных моделей, а также станков Б/У. Для работы применяется электроискровая обработка металлических заготовок. Максимальные габариты обрабатываемых деталей — 16 x 12 x 3 сантиметра. Управление осуществляется в основном механическим способом + есть несколько информационных панелей, позволяющих узнать технологические особенности процедуры.
Заключение
Технология позволяет резать металлы любой прочности. Обработка выполняется за счет создания ионизированного потока частиц, которые прожигают металл. Разогретые ионы создаются с помощью электрической дуги, которая возникает между проводящим электродом и металлической поверхностью обрабатываемой детали при прохождении между ними электрического тока. Чтобы не повредить деталь и не испарить электрод, используется защитная жидкость-диэлектрик, а электрический ток подается небольшими порциями-импульсами (частота — 0,001 с).
ЭЭО-станки выполняют все основные операции — создание отверстий, резка, нанесение маркировки. Электроэрозионная обработка металла обладает множеством преимуществ — высокая точность, универсальность (для металлов), простота применения станков. Однако есть и недостатки — нельзя резать пластик, бетон или дерево, большое потребление электричества, высокая стоимость станка. Использовать ЭЭО-станки рекомендуется для производства высокоточных деталей. Основные модели станков — AGIE INTEGRAL 2, модель 4531, SODICK AQ535.
Используемая литература и источники:
- Электрофизические и электрохимические методы обработки / Юдин Д.Л. // Экслибрис — Яя. — М. : Советская энциклопедия, 1978.
- Немилов Е.Ф. Электроэрозионная обработка материалов. — Л.: Машиностроение, 1983.
- Ставицкий Б.И. Из истории электроискровой обработки материалов // Оборудование и инструмент для профессионалов. Металлообработка. — 2006.
- Статья на Википедии
Поделиться в социальных сетях
Электроэрозионная обработка металлов и других токопроводящих материалов (ЭЭО) – самостоятельный вид металлообработки, который используется для получения отверстий и полостей сложной формы. ЭЭО эффективна при размерном формообразовании труднообрабатываемых материалов, применяется для целей поверхностного упрочнения инструмента, а также в ремонтном производстве, для извлечения из стальных изделий сломанных свёрл, метчиков и т.п. По вышеперечисленным направлениям выпускается и соответствующее оборудование.
Принцип работы станков электроэрозионной обработки
Независимо от технологического назначения, в ЭЭО-станках используется явление размерного плавления металла или сплава в результате термического воздействия электрического разряда весьма большой мощности. Им может быть электрическая искра или электрическая дуга. С этой целью обрабатываемую заготовку включают в электрическую цепь станка. В результате последовательно реализуются следующие переходы:
- Заготовка и инструмент
- При включении энергетической части привода станка происходит накапливание электрического потенциала на границах смежных электродов заготовки и инструмента. Его конфигурация должна соответствовать размерам полости или контура на будущем изделии.
- По достижении требуемой разности потенциалов происходит бой межэлектродного промежутка с созданием направленного разряда, вызывающего электрическую эрозию материала. Если преимущественному разрушению подвергается катод, то говорят об ЭЭО на прямой полярности электрического тока, а если анод – то об обратной полярности.
- Продукты эрозии либо принудительно удаляются из зоны обработки специальной насосной установкой, либо скапливаются на дне емкости, и извлекаются оттуда после окончания цикла ЭЭО.
- После отключения напряжения ионизированные высоковольтным разрядом частицы в рабочей жидкости исчезают, и её диэлектрическая прочность восстанавливается.
Если электрическая эрозия вызывается нестационарным электрическим разрядом, то такое оборудование называют электроискровыми или электроимпульсными ЭЭО-станками.
Разница между ними заключается в следующем. Электроимпульсные станки, в отличие от электроискровых, имеют в своём составе специальный узел – шаговый генератор импульсов – который обеспечивает периодическое формирование высоковольтного разряда. Его параметры должны быть достаточными для размерного плавления и испарения обрабатываемого материала. В результате возрастает мощность и производительность ЭЭО.
Кроме того, управляя параметрами импульса – его продолжительностью, интенсивностью и скважностью (соотношением времени действия импульса ко времени его накопления) –
При электродуговой обработке источником тепла, производящего разрушение металла заготовки, является стационарный разряд. Дуга горит непрерывно, поэтому станки такого типа отличаются повышенной производительностью, но меньшей точностью обработки. При дуговой обработке главным параметром считается сила тока, а не напряжение на электродах. Поэтому для привода таких станков применяются сварочные генераторы или преобразователи – оборудование, гораздо более дешёвое и простое в управлении, чем генераторы импульсов. Область рационального использования электродугового оборудования – получение отверстий и полостей
значительных размеров при повышенных требованиях к производительности обработки.Классификация ЭЭО-станков
Электроэрозионные станки различают в зависимости от их технологического назначения. Выпускаются как универсальное, так и специализированное оборудование, которое может оснащаться ЧПУ, либо действовать в ручном режиме.
Основными операциями, на которых целесообразно использовать ЭЭО-станки, являются:
- Вырезка по сложному контуру. Она может выполняться профилированным электродом-инструментом, либо проволочкой из токопроводящего материала.
- Прошивка-копирование, при которой форма электрода-инструмента должна соответствовать размерам и конфигурации полости или сквозного отверстия. При извлечении сломанных инструментов используется обычная прошивка сплошным или трубчатым электродом.
- Электроэрозионное шлифование, при котором выполняется доводка полученной заготовки по параметрам точности и шероховатости поверхности. Электродуговые станки могут выполнять как грубую так и точную ЭЭО: для этого им достаточно только скорректировать некоторые технические характеристики процесса.
- Поверхностное электроупрочнение, при котором съёма металла практически не происходит, а обрабатываемая поверхность заготовки насыщается атомами химических элементов, содержащихся в электроде-инструменте. Направленный перенос возможен не только из электрода, но и из состава рабочей жидкости, которая пиролизуется под действием высокотемпературного разряда.
- Электроэрозионная маркировка, в результате которой на поверхности могут наноситься клейма или иные условные обозначения.
- Электроэрозионная приработка сопрягаемых деталей (шестерён, пуансонов, матриц). Она ведётся при малых значениях тока и напряжения.
Классификация станков для ЭЭО может быть выполнена и по их компоновке. В основном такое оборудование – вертикального исполнения, однако для электродуговой обработки длинномерных заготовок, например, твердосплавных валков прокатных станов, изготавливаются и станки горизонтального типа.
Из основных конструктивных различий ЭЭО-станков необходимо отметить исполнение и размеры стола (координатный или обычный), а также ванны с рабочей жидкостью, которая может быть съёмной или перемещающейся вверх-вниз.
Важным классификационным признаком рассматриваемого оборудования считается его возможность программного управления, что немаловажно из-за высокой продолжительности обработки заготовок. Поэтому станки электроимпульсного и электроискрового типа часто изготавливаются с системами ЧПУ (для электродуговых станков, имеющих на порядок более высокую производительность, это не существенно).
Отечественные ЭЭО-станки выпускаются в соответствии с требованиями ГОСТ 15894. Из зарубежного аналогичного оборудования наилучшим качеством отличаются станки швейцарской фирмы Agie, японской торговой марки Mitsubishi и итальянской компании Сarbomatic.
Основные узлы ЭЭО-станков и их действие
Копировально-прошивочный станок
Типовой копировально-прошивочный станок вертикальной компоновки, снабжённый электрогидравлической системой привода рабочих органов, состоит из следующих узлов:
- Г-образной станины, регулируемой по высоте.
- Рабочей головки, в которой смонтирован узел электрода-инструмента.
- Привода двухкоординатного перемещения рабочей головки (на некоторых типоразмерах станков имеется ещё и орбитальная головка, благодаря которой электрод-инструмент может вращаться).
- Рабочего стола, на котором закрепляется обрабатываемая заготовка.
- Ванна с рабочей жидкостью, которая снабжена винтовой передачей для своего подъёма-опускания.
- Электродвигателей: главного привода, привода рабочей ёмкости и орбитальной головки.
- Системы управления.
В самостоятельном корпусе размещается шаговый генератор импульсов, который включается в общую электрическую схему станка. Эти устройства должны отвечать следующим требованиям:
- Отличаться возможно более высоким КПД;
- Стабилизировать во времени все параметры электрического разряда;
- Иметь возможность максимального регулирования рабочей частоты импульса;
- Обеспечивать такие параметры электрического разряда, при которых износ электрода-инструмента, производительность процесса и качество обработки заготовки будут оптимальными.
Отечественные генераторы импульсов системы ШГИ оснащаются встроенными регуляторами подачи электрода-инструмента и блоками предотвращения короткого замыкания.
Узлы подачи рабочей головки в станках, использующих для ЭЭО нестационарный электрический разряд, могут быть трёх основных типов –
Электродуговые станки
Электродуговые станки состоят из:
- Станины рамного типа.
- Рабочей головки с электродом-инструментом и контрольно-следящей системой его перемещения во время ЭЭО.
- Насосной станции для прокачки рабочей жидкости под повышенным давлением (это необходимо для повышения качества ЭЭО стационарным дуговым разрядом).
- Герметизирующей камеры , внутрь которой устанавливается заготовка.
- Рабочего стола.
- Источника питания постоянного тока.
Рабочий цикл такого оборудования включает в себя установку на стол заготовки, подлежащей ЭЭО, последующего размещения герметизирующей камеры, подвода инструментальной головки с электродом-инструментом и включения насосного привода подачи рабочей среды. После этого включается источник питания, возбуждается дуговой разряд и производится обработка. Подача электрода-инструмента выполняется автоматически. По достижении требуемого значения напряжения на дуге происходит пробой межэлектродного промежутка, и возникающий столб дуги, сжатый потоком рабочей среды производит размерное формообразование. Продукты эрозии удаляются насосной установкой через рабочие отверстия в электроде-инструменте.
Электроэрозионные станки работают по принципу воздействия электрическими зарядами на обрабатываемую поверхность детали находящейся в электропроводной среде.
Электроэрозионный прошивной станок
За счет этого возникает электрическая эрозия в заданном направлении, что позволяет получить конкретную форму или размеры детали.
1 Принцип РАБОТЫ
Электроэрозионная резка происходит во время возникновения импульса газового электрического разряда, который имеет направленное действие. Схема такова, что при этом происходит разрушение и удаление части материала в зоне воздействия.
Под влиянием высокой температуры в области возникновения разрядов происходит плавление металла (латунная или медная проволока) с частичным его испарением. Для того чтобы получить необходимую температуру, схема использует генератор импульсов, позволяющий сконцентрировать большое количество энергии.
Электродами, между которыми возникает разряд, являются сама деталь, с одной стороны, и инструмент — с другой. Пространство между ними заполняется рабочей жидкостью, которая постоянно подается при работе станка через подводящую трубку (латунная или медная), если обработка не происходит в специальной ванной.
Электроэрозионный станок процессе работы
Электроэрозионные станки, в которых используются электрические разряды различных видов и способов их получения, могут производить несколько разновидностей электроэрозионной обработки металла:
- электроискровая схема;
- электроконтактная схема;
- электроимпульсная схема;
- анодно-механическая (комбинированная схема).
В работе с различными материалами прошивочный электроэрозионный станок с ЧПУ имеет одно ограничение — у них должна быть хорошая электрическая проводимость. Если материал не обладает этим свойством, то прошивной станок работать не сможет.
1.1 Процесс работы электроэрозионного станка (видео)
к меню ↑
2 Основные виды электроэрозионной обработки
Электроэрозионный проволочно вырезной станок применяется при следующих видах электроэрозионной обработки деталей из металла:
- прошивании;
- объемном копировании;
- вырезании/отрезании;
- шлифовании;
- доводке;
- маркировании;
- упрочнении.
Возможна электроконтактная обработка при выполнении:
- резки;
- работы с телами вращения;
- обработки внутренних полостей;
- зубчатых поверхностей;
- обработки плоских и конических поверхностей;
- упрочнения.
2.1 Станки фирмы Sodick
Японская производственная компания Sodick Co LTD, которая начала свою деятельность в 1976 году, на сегодняшний день является мировым лидером по производству и продажам электроэрозионных станков.
Электроэрозионный станок Sodick AD35L
Представительства компании Sodick имеются в Азии, США, Европе и ее продукция пользуется заслуженной популярностью у промышленных предприятий, которые имеют дело с обработкой таких материалов как титан и инструментальная сталь.
Sodick — единственный в мире производитель, который выпускает электроэрозионный прошивной станок с ЧПУ, имеющий линейные двигатели и рабочую зону сделанную из керамики. Специалисты компании Sodick разработали революционную электроискровую технологию зеркальной полировки обрабатываемого материала.
Схема оборудования Sodick работает по принципу прямого воздействия тепловой энергии на обрабатываемую поверхность металла. При этом отсутствует какое-либо силовое воздействие на материал, что значительно повышает качество производимых работ.
Изготовленные на электроэрозионных станках Sodick детали получают дополнительную прочность и устойчивость к обычной коррозии, так как в процессе работы над ними происходит изменение физических характеристик металла.
2.2 Копировально-прошивочный станок 4л721ф1
Прошивочный станок 4л721ф1 имеет адаптивное ЧПУ и используется при обработке отверстий и полостей в заготовках из металла трудно поддающегося обработке. С его помощью, также можно изготовить штампы, пресс-формы, фильеры и т.д.
Электроэрозионный копировально-прошивочный станок 4Л721Ф1
Установленные в прошивочный станок 4л721ф1 генератор импульсов ШГИ-80-440М2, высокоскоростной привод, устройство индикации в цифровом виде, быстросъемные приспособления, дают возможность значительно увеличить его производительность и качество обработки.
Станок 4л721ф1 не требует наличия особо прочного фундамента в производственном помещении, так как устанавливается на виброустойчивые опоры.
На станке 4л721ф1 возможна обработка деталей, которые имеют максимальные размеры по длине, ширине и высоте — 280×250х120 мм.
к меню ↑
2.3 Станки компании P&G (dk7732, dk7740, dk7725)
Станки dk7732, dk7740, dk7725 предназначены для изготовления измерительных инструментов, инструментальной оснастки, деталей для машин и механизмов (шестерни, зубчатые колеса и т.д.).
У проволочно-вырезных станков dk7732, dk7740, dk7725 имеется несколько особенностей:
- при работе используется молибденовая проволока, что позволяет использовать ее многократно. Для работы станка в течение недели достаточно 200 метров;
- станки оснащены удобным ЧПУ. Достаточно выполнить чертеж детали в программе CAD и загрузить его в ЧПУ станка при помощи съемного носителя;
- у них высокая производительность — обработка до 160 кв. мм поверхности за минуту.
2.4 Станок своими руками
Самодельный электроэрозионный станок можно собрать при наличии искрового генератора. Это самый сложный элемент в конструкции инструмента, который создается своими руками. За короткий отрезок времени должна быть собрана электрическая энергия в достаточном количестве для ее мгновенного выброса.
Простейшая схема для создания станка должна содержать в себе электрод соответствующего состава
Многие комплектующие для электроэрозионного станка который планируется сделать своими руками можно найти в старом телевизоре. К примеру — конденсатор емкостью 1000 мкФ. Все необходимые детали размещаются в коробе сделанном из фторопласта, который должен быть полностью изолирован. Направляющую втулку электрода можно сделать из заземляющего штыря розетки европейского типа.
Электродом является молибденовая проволока, которая по мере испарения продвигается с использованием винтового зажима. Втулка должна иметь отверстие для прохождения охлаждающей жидкости и одновременно рабочей среды по оси совпадающей с расположением электрода.
1. Сущность и назначение электроэрозионной обработки
Электроэрозия – это разрушение поверхности изделия под действием электрического разряда. Основателями технологии являются советские ученые-технологи Б.Р. Лазаренко и Н.И. Лазаренко.
Электроэрозионная обработка (ЭЭО) широко применяется для изменения размеров металлических изделий – для получения отверстий различной формы, фасонных полостей, профильных канавок и пазов в деталях из твердых сплавов, для упрочнения инструмента, для электропечатания, шлифования, резки и др.
Рис. 1.9. Схема электроэрозионной обработки материалов: 1 – электрод-инструмент, 2 – обрабатываемая деталь, 3 – среда, в которой производится разряд, 4 – конденсатор, 5 – реостат, 6 – источник питания, 1р – режим электроискровой обработки, 2р – режим электроимпульсной обработки
Схема электроэрозионной обработки материалов приведена на рис. 1.9. Схема запитывается импульсным напряжением разной полярности, что соответствует электроискровому режиму (1р) и электроимпульсному режиму (2р). Напряжение питания заряжает конденсатор (4), параллельно которому включен разрядный промежуток между электродом-инструментом (1) и обрабатываемой деталью (2), которые помещены в жидкость с низкой диэлектрической проницаемостью. Когда напряжение на конденсаторе превысит потенциал зажигания разряда, происходит пробой жидкости. Жидкость нагревается до температуры кипения и образуется газовый пузырь из паров жидкости. Далее электрический разряд развивается в газовой среде, что приводит к интенсивному локальному разогреванию детали, приповерхностные слои материала плавятся и продукты расплава в виде шариков застывают в проточной жидкости и выносятся из зоны обработки.
2. Стадии электроэрозионной обработки Режим электроискровой обработки
Обрабатываемая деталь является анодом (+), то есть в данном случае деталь обрабатывается электронным потоком, то есть работает электронный стример, расплавляя объем анода-детали в виде лунки. Для того чтобы ионный поток не разрушал электрод-инструмент, используются импульсы напряжения длительностью не более 10-3 с. Электроискровой режим используется для чистовой, точной обработки, поскольку съем металла в данном случае небольшой.
Режим электроимпульсной обработки
Обрабатываемая деталь является катодом, то есть на нее подается отрицательный импульс длительностью больше 10-3 с. При электроимпульсной обработке между электродами зажигается дуговой разряд и обработка деталей ведется ионным потоком. Данный режим характеризуется большой скоростью съема металла, превышающей производительность электроискрового режима в 8-10 раз, но при этом чистота обработки существенно хуже. При обоих режимах в качестве рабочей жидкости, как правило, используется керосин или изоляционные масла.
3. Физика электроэрозионной обработки
Явления, происходящие в межэлектродном промежутке, весьма сложны и являются предметом специальных исследований. Здесь же будет рассмотрена простейшая схема удаления металла из области обработки посредством электрической эрозии.
Как показано на рис. 1.10, к электродам 1 подведено напряжение, которое создает электрическое поле в межэлектродном промежутке. При сближении электродов на критическое расстояние, возникает электрический разряд в виде проводящего канала. Для повышения интенсивности разряда электроды погружают в диэлектрическую жидкость 2 (керосин, минеральное масло и др.) На поверхности электродов имеются микронеровности различной величины. Напряженность электрического поля будет наибольшей между двумя наиболее близкими друг к другу выступами на поверхности электродов, поэтому именно здесь возникают проводящие мостики из примесных частиц жидкости. Ток по мостикам нагревает жидкость до испарения и образуется газовый пузырь (4), внутри которого и развивается мощный искровой или дуговой разряд, сопровождающийся ударной волной. Возникают потоки электронов и ионов (положительные и отрицательные стримеры), которые бомбардируют электроды. Образуется плазменный канал разряда. Благодаря высокой концентрации энергии в зоне разряда температура достигает тысячи и десятков тысяч градусов. Металл на поверхности электродов плавится и испаряется. Капли расплавленного металла в результате движения потока жидкости в рабочей зоне выбрасываются за пределы электродов и застывают в окружающей электроды жидкости в виде мелких частиц сферической формы (5).
От взаимодействия жидкости с участками электродов, нагретых до температуры 100-400 0С, на границах плазменного канала разряда происходит пиролиз диэлектрической жидкости. В результате в жидкости образуются газы, а также асфальтосмолистые вещества. Из газовой среды выделяется углерод, отлагающийся на нагретых поверхностях электродов в виде тонкой пленки кристаллического графита. В месте действия импульса тока на поверхностях электродов остаются небольшие углубления – лунки, образовавшиеся вследствие удаления разрядом некоторого количества металла.
В табл. 1.2 приведена зависимость величины эрозии стального электрода от энергии и длительности одиночного импульса.
Таблица 1.2
Зависимость величины эрозии стального электрода (анода) от энергии и длительности одиночного импульса
Характеристика импульса | Размеры лунки | |||
Энергия, Дж | Длительность, мкс | Глубина, мм | Диаметр, мм | Объем, м3 |
0,001 0,1 1,0 2,0 | 9 40 60 1500 | 0,015 0,025 0,042 0,050 | 0,1 0,75 1,65 2,00 | 0,000078 0,0074 0,06 0,10 |
Рис. 1.10. Режим электроэрозионной обработки: 1 – электроды, 2 – жидкость, 3 – лунки, 4 – газовый пузырь, 5 – продукты эрозии
После разряда в течение некоторого времени происходит остывание столба канала и деионизация вещества плазмы в межэлектродном промежутке. Электрическая прочность межэлектродного промежутка восстанавливается. Время деионизации жидкого диэлектрика составляет 106-10-2 с. Следующий разряд обычно возникает уже в новом месте, между двумя другими ближайшими точками электродов.
Длительность интервалов между импульсами должна быть достаточной для удаления из зоны разряда продуктов эрозии, а также газового пузыря, являющегося главным препятствием для возникновения следующего разряда. В связи с этим частота разрядов с возрастанием их энергии снижается.
Так происходит до тех пор, пока разряды не удалят с поверхности электродов все участки металла, которые находятся на расстоянии пробоя при величине приложенного напряжения. Когда расстояние между электродами превысит пробивное, для возобновления разрядов электроды должны быть сближены. Обычно электроды сближают в течение всего времени обработки так, чтобы электрические разряды не прекращались.
Параметры рабочих импульсов. Основными параметрами электрических импульсов, подаваемых на межэлектродный промежуток, являются их частота повторения, длительность, амплитуда и скважность, а также форма, определяющие максимальную мощность и энергию. Форма и параметры импульсов оказывают существенное влияние на износ электрода-инструмента, производительность и шероховатость обработанной поверхности.
Обозначим частоту повторения импульсов, т. е. их число в секунду, через f. Тогда Т = 1/f будет являться периодом. Он определяет промежуток времени, через который следует очередной импульс.
Импульс характеризуется амплитудным значением (или амплитудой) напряжения и тока Um и Im. Это максимальные значения, которые приобретают напряжение и ток за время импульса. При электроэрозионной обработке амплитуда напряжения изменяется от нескольких вольт до нескольких сотен вольт, а амплитуда тока от доли ампера до десятков тысяч ампер. Диапазон скважностей импульса при электроэрозионной обработке заключен в пределах от 1 до 30.
Полярный эффект и полярность импульса. Высокая температура в канале разряда и происходящие динамические процессы вызывают эрозию обоих электродов. Повышение эрозии одного электрода по сравнению с другим электродом называется полярным эффектом. Полярный эффект определяется материалом электродов, энергией и длительностью импульсов, знаком подведенного к электроду потенциала.
Процессы изменения напряжения и тока имеют колебательный характер относительно их нулевого значения. При электроэрозионной обработке принято считать рабочей или прямой полярностью импульса ту его часть, которая вызывает наибольший эффект эрозии обрабатываемой заготовки, а обратной – часть импульса, вызывающую усиленную эрозию электрода-инструмента. Обрабатываемую заготовку присоединяют к тому полюсу, эффект эрозии которого в данных условиях больше. К противоположному полюсу присоединяют электрод- инструмент. Например, при коротких импульсах электроискровой обработки энергия преимущественно поступает на анод, в качестве которого здесь следует использовать заготовку (прямая полярность). При увеличении длительности импульсов наступает перераспределение теплового потока на электродах. Это приводит к тому, что при определенных режимах электроимпульсной обработки эрозия анода становится меньше, чем эрозия катода. В этом случае следует применять обратную полярность, используя заготовку в качестве катода.
Электроэрозионная обрабатываемость. Эффект эрозии различных металлов и сплавов, производимый одинаковыми по своим параметрам электрическими импульсами, различен. Зависимость интенсивности эрозии от свойств металлов называют электроэрозионной обрабатываемостью.
Различное влияние импульсных разрядов на металлы и сплавы зависит от их теплофизических констант: – температур плавления и кипения, теплопроводности, теплоемкости. Если принять электроэрозионную обрабатываемость стали за единицу, то электроэрозионная обрабатываемость других металлов (при тех же условиях) может быть представлена в следующих относительных единицах: вольфрам – 0,3; твердый сплав – 0,5; титан – 0,6; никель – 0,8; медь – 1,1; латунь – 1,6; алюминий – 4; магний – 6 (указанные данные справедливы только при конкретных условиях: энергия импульса 0,125 Дж, длительность 1.4-10-5 с, частота 1200 1/с, амплитуда тока 250 А).
Рабочая среда. Большинство операций при электроэрозионной обработке производят в жидкости. Она обеспечивает условия, необходимые для удаления продуктов эрозии из межэлектродного промежутка, стабилизирует процесс, влияет на электрическую прочность межэлектродного промежутка. Жидкости, пригодные для электроискровой обработки, должны обладать соответствующей вязкостью, электроизоляционными свойствами, химической устойчивостью к действию разрядов.
С повышением частоты импульсов и снижением рабочего тока стабильность рабочего процесса ухудшается. Это вызывает необходимость увеличить скважность импульсов. Применение прямоугольных импульсов существенно повышает производительность.
Производительность обработки можно повысить, если применять принудительное удаление продуктов эрозии из межэлектродного промежутка. Для этого в межэлектродный промежуток под давлением нагнетают жидкость (рис. 1.11).
Рис. 1.11. Схема подвода жидкости в межэлектродный промежуток через полый электрод при прошивании отверстия
Хорошие результаты дает наложение вибраций на электрод-инструмент, а также вращение одного или обоих электродов. Давление жидкости зависит от глубины отверстия и величины межэлектродного промежутка. Вибрации особенно необходимы при электроискровой обработке глубоких отверстий малого диаметра и узких щелей. Большинство электроэрозионных станков снабжено специальной вибрационной головкой.
Качество поверхности и точность обработки. Металл электродов подвергается хотя и локальному, кратковременному, но весьма интенсивному электротермическому воздействию. Наивысшая температура существует на обрабатываемой поверхности и быстро уменьшается на некотором расстоянии от поверхности. Большая часть расплавленного металла и его паров удаляется из зоны разряда, но некоторая часть остается в лунке (рис. 1.12). При застывании металла на поверхности лунки образуется пленка, по своим свойствам отличающаяся от основного металла.
Рис. 1.12. Лунка, полученная в результате воздействия единичного импульса: 1 – пространство, оставшееся после выплавления металла; 2 – белый слой; 3 – валик вокруг лунки; 4 – обрабатываемая заготовка; БЛ, НЛ – диаметр и глубина лунки
Поверхностный слой в расплавленном состоянии активно вступает в химическое взаимодействие с парами и продуктами разложения рабочей жидкости, образующимися в зоне высоких температур. Результатом этого взаимодействия является интенсивное насыщение металла компонентами, содержащимися в жидкой среде, а также веществами, входящими в состав электрода-инструмента. Таким образом, в поверхностный слой могут быть внесены титан, хром, вольфрам и т. д. При электроэрозионной обработке стальных заготовок в среде, состоящей из жидких углеводородов (керосин, масло), поверхностный слой насыщается углеродом, т. е. образуются карбиды железа. Следовательно, при электроэрозионной обработке происходит упрочнение поверхности детали.
Интенсивный теплоотвод из зоны разряда через прилегающие к ней массы холодного металла и рабочую жидкость создает условия для сверхскоростной закалки, что одновременно с науглероживанием приводит к образованию очень твердого слоя. Закаленный поверхностный слой стали обладает повышенной стойкостью на истирание и меньшим, чем у нетермообработанной стали коэффициентом трения. Структура поверхностного слоя существенно отличается от структуры основного металла и схожа со структурой отбеленного слоя, возникающего на поверхности некоторых чугунов. Поэтому этот слой получил название «белый слой». Глубина белого слоя зависит от энергии импульсов, их длительности и теплофизических свойств обрабатываемого материала. При длительных импульсах тока большой энергии глубина белого слоя равна десятым долям миллиметра, а при коротких импульсах – сотым долям миллиметра и микронам.
Упрочнение поверхностного слоя металлов (электроэрозионное легирование). Одним из преимуществ электроискрового метода обработки материалов является то, что при определенных условиях резко повышаются прочностные свойства поверхности заготовки: твердость, износостойкость, жаростойкость и эрозионная стойкость. Эту особенность используют для повышения износостойкости режущего инструмента, штампов, пресс-форм и деталей машин, упрочняя металлические поверхности электроискровым способом.
При электроискровом легировании применяют обратную полярность (заготовка является катодом, инструмент – анодом) обработку производят обычно в воздушной среде и, как правило, с вибрацией электрода. Аппаратура, с помощью которой осуществляется процесс упрочнения, малогабаритна и очень проста в эксплуатации. Основные преимущества электроискрового способа нанесения покрытий заключаются в следующем: покрытия имеют большую прочность сцепления с материалом основы; покрываемые поверхности не требуют предварительной подготовки; возможно нанесение не только металлов и их сплавов, но и их композиций. Процессы, происходящие при электроискровом упрочнении, сложны и являются предметом тщательных исследований. Сущность упрочнения состоит в том, что при электроискровом разряде в воздушной среде происходит полярный перенос материала электрода на заготовку. Перенесенный материал электрода легирует металл заготовки и, химически соединяясь с диссоциированным атомарным азотом воздуха, углеродом и материалом заготовки, образует диффузионный износоустойчивый упрочненный слой. При этом в слое возникают сложные химические соединения, высокостойкие нитриды и карбонитриды, а также закалочные структуры. По мнению специалистов, при электроискровом упрочнении в поверхностном слое, например, стали происходят процессы, приведенные в табл. 1.3.
Таблица 1.3
Упрочняемый материал | Процесс | |
Вид | Особенности | |
Углеродистая сталь, содержащая углерод в количестве свыше 0,6 %, а также легирующие элементы в большом количестве | Сверхскоростная закалка | Кратковременный нагрев до высокой температуры и мгновенное охлаждение нагретых и расплавленных участков массой холодного металла |
Инструментальная сталь | Азотирование | Диссоциация атмосферного азота в разряде с образованием атомарного азота. Соединение азота с элементами поверхностного слоя и образование нитридов металлов (титана, хрома, железа и др.) |
При электроискровом упрочнении микротвердость белого слоя в углеродистых сталях может быть доведена до 230 МПа, высота микронеровностей обработанной поверхности до 2,5 мкм. Толщина слоя покрытия, получаемого на некоторых установках, составляет 0,003-0,2 мм.
4. Основные технологии электроэрозионной обработки металлов
Технологии размерной обработки металлических деталей.
Формообразование деталей электроэрозионным методом можно осуществить по следующим схемам.
1. Копирование формы электрода или его сечения. При этом обрабатываемый элемент заготовки по форме является обратным отображением рабочей поверхности инструмента. Данную операцию называют прошиванием. Существуют методы прямого и обратного копирования. При прямом копировании инструмент находится над заготовкой, а при обратном – под ней. Метод прошивания прост в исполнении, и он широко применяется в промышленности. На рис. 1.13 представлена схема электроэрозионной обработки методом копирования формы электрода- инструмента. По мере электроэрозионной обработки электрод (1) внедряется в деталь, обеспечивая копирование электрода.
2. Взаимное перемещение обрабатываемой заготовки и электрода- инструмента. При этой схеме возможны операции вырезания сложно- профильных деталей и разрезание заготовок электродами, электроэрозионного шлифования и растачивания деталей.
Рис. 1.13. Схема копирования формы электрода: 1 – электрод-инструмент, 2 – обрабатываемая деталь, 3 – жидкость, 4 – сосуд
Прошивание окон, щелей и отверстий. Эта операция осуществляется на универсальных станках. Электроэрозионным способом прошивают щели шириной (2,5-10) мм, глубиной до 100 мм. Для обеспечения удаления продуктов эрозии из межэлектродного промежутка, электрод-инструмент делают Т-образной формы или уменьшают толщину хвостовой части по сравнению с рабочей частью на несколько десятых долей миллиметра. Скорость прошивания щелей составляет (0,5-0,8) мм/мин, шероховатость обработанной поверхности – до 2,5 мкм.
Обработка деталей типа сеток и сит. Созданы электроэрозионные станки, позволяющие обрабатывать сеточные детали с числом отверстий до нескольких тысяч. Станки могут обрабатывать одновременно более 800 отверстий диаметром (0,2-2) мм в листах из коррозионно- стойких сталей, латуни и других материалов толщиной до 2 мм. Производительность обработки до 10000 отверстий в час.
Электроэрозионное шлифование. Это одна из разновидностей электроэрозионной обработки, которая используется для обработки высокопрочных заготовок из сталей и твердых сплавов. Удаление металла при этом происходит под воздействием импульсных разрядов между вращающимся электродом-инструментом и обрабатываемой заготовкой, а не в результате механического воздействия, как при абразивном шлифовании.
Сложноконтурная проволочная вырезка. Методы прямого и обратного копирования имеют существенный недостаток, заключающийся в необходимости использования сложных фасонных электродов- инструментов. Износ электродов отражается на точности изготовления деталей, поэтому одним электродом-инструментом удается изготовить не более 5-10 деталей.
Электроискровой метод сложноконтурной проволочной вырезки выгодно отличается от методов копирования тем, что здесь инструментом является тонкая проволока из меди, латуни или вольфрама диаметром от нескольких микрон до 0,5 мм, включаемая в электрическую схему как катод (см. рис. 1.14).
Рис. 1.14. Сложноконтурная проволочная вырезка: 1 – проволока, 2 – обрабатываемая деталь, 3 – направляющие ролики, 4 – устройство для регулирования скорости протяжки проволоки
Для устранения влияния износа проволоки на точность обработки, проволока перематывается с одной катушки на другую, что позволяет все новым элементам участвовать в работе. При перемотке осуществляется небольшой натяг. Возле обрабатываемой заготовки установлены ролики, ориентирующие проволоку относительно обрабатываемой детали. Сложноконтурная проволочная вырезка применяется при прецизионном резании заготовок, прорезании точных щелей, резании полупроводниковых материалов, обработке цилиндрических, конических наружных и внутренних поверхностей.
К основным достоинствам электроэрозионной обработки проволочным электродом-инструментом относится высокая точность и возможность широкой автоматизации процесса.
Электроконтактный способ обработки. Электроконтактная обработка материалов является разновидностью электроэрозионной обработки. Отличие ее состоит в том, что импульсы электрической энергии генерируются в результате взаимного перемещения электродов или прерывания электрического разряда при прокачке жидкости под давлением. Электроконтактную обработку можно проводить при постоянном и переменном токе, в воздухе или жидкости (вода с антикоррозионными добавками). При обработке электрод-инструмент и заготовку полностью погружают в жидкость либо подают жидкость в межэлектродный промежуток распылением. Обработку производят при значительных токах (до 5000 А) и напряжениях холостого хода источника питания 18-40 В. Электроконтактным методом производят получистовое точение тел вращения, чистовую резку, прошивание цилиндрических, фасонных отверстий и объемных полостей, фрезерование, шлифование. Электроконтактный метод особенно эффективен при обработке заготовок из труднообрабатываемых сталей и сплавов, а также чугунов высокой твердости, монокристаллов, материалов с высокими теплофизическими свойствами.
Принципиальная схема установки для электроконтактной обработки выглядит следующим образом. Заготовка и электрод-инструмент, имеющие ось вращательной симметрии и включенные в цепь с источником питания, после соприкосновения совершают вращательное движение друг относительно друга.
При соблюдении условий, необходимых для реализации электроэрозионных процессов, происходит съем металла с заготовки.
Упрочнение поверхностного слоя металла (электроэрозионное легирование)
Одним из преимуществ электроэрозионной обработки металлов является то, что при определенных условиях резко повышаются прочностные свойства поверхности заготовки. Эту особенность используют для улучшения износостойкости режущего инструмента, штампов, пресс-форм и т.д. При электроэрозионном легировании применяют обратную полярность (заготовка является катодом, инструмент – анодом) обработку производят обычно атомами инструмента-электрода в электроимпульсном режиме (см. рис. 1.15) в воздушной среде и, как правило, с вибрацией электрода.
Рис. 1.15 Схема электроэрозионного легирования: 1 – легирующий электрод-инструмент, 2 – легируемая деталь
Основные преимущества электроэрозионного легирования заключаются в следующем: покрытия имеют большую степень сцепления с материалом основы; покрываемые поверхности не требуют предварительной подготовки; возможно нанесение не только металлов и сплавов, но и их композиций.
Процессы, происходящие при электроэрозионном упрочнении, сложны и являются предметом тщательных исследований. Однако, сущность упрочнения состоит в том, что при электроискровом разряде в воздушной среде происходит перенос материала электрода на заготовку (см. рис. 1.15). Перенесенный материал электрода легирует металл заготовки и, химически соединяясь с ионами азота воздуха, углеродом и материалом заготовки, образует износоустойчивый упрочненный слой, состоящий из нитридов, карбонитридов и других закалочных структур.
При электроискровом легировании микротвердость белого слоя в углеродистых сталях может быть доведена до 230 МПа. Толщина слоя покрытия, получаемого на некоторых установках, составляет 0,003-0,2 мм. При упрочнении поверхности деталей машин (например, на установке ИЕ-2М) можно получить глубину слоя до 0,5-1,6 мм с микротвердостью 50-60 МПа (при упрочнении феррохромом).
Различают чистую обработку, которая соответствует высоким напряжениям и небольшим значениям токов короткого замыкания (до 20 А), и грубую (грубое легирование) при низких напряжениях 50-60 В и токах короткого замыкания свыше 20 А.
Работа на электроэрозионных станках. Подготовка электроэрозионных станков к работе заключается в установке заготовки и электрода-инструмента и выверке их взаимного расположения, подготовке ванны к работе и системы прокачки рабочей жидкости, выбору и настройке режимов генератора. Заготовку устанавливают и закрепляют непосредственно на столе станка или в приспособлении. Электрод-инструмент устанавливают хвостиком в шпиндель головки. При выверке используют индикаторы, оптические приборы, приспособления, позволяющие изменять положение инструмента по отношению к заготовке и угол наклона.
Осуществив выверку положения электрод-инструмента, заполняют ванну рабочей жидкостью, проверяют работу системы прокачки, устанавливают необходимое давление прокачки. Задают режим генератора импульсов (полярность, форма импульсов, скважность, частоту следования импульсов, средний ток), пользуясь соответствующими таблицами и номограммами. Изменение полярности напряжения генератора импульсов производится путем переключения на штепсельном разъеме токоподводов к станку. При работе с прямой полярностью (электроискровой режим) на электрод подается отрицательный потенциал, а на заготовку – положительный. Для работы с обратной полярностью (электроимпульсный режим) производят обратное переключение. Установку электрических параметров и режимов работы осуществляют с помощью переключателей, расположенных на панели пульта управления. Настраивают регулятор подачи, устанавливая рекомендуемое напряжение регулятора.
Эрозионные станки
Всемирная локализация производственных процессов привела к расширению номенклатурных позиций для всех ведущих производителей технических средств, осуществляющих механическую обработку металлов. Наш концерн Knuth, находящийся в г. Вазбек, Германия, предлагает российским промышленным предприятиям станки, оборудование высокого качества с длительным сроком эксплуатации.
Технологическая схема электроэрозионной проволочно-вырезной обработки, которую предлагает наша компания, гарантирует повышенные качественные характеристики конечного продукта. Одновременно работа наших станков и оборудования сопровождается чрезвычайно низкими затратами на их эксплуатацию, высокой надежностью, полнейшей автоматизацией, экономящей время пользователей.
Расширенный ассортиментный ряд массогабаритных показателей, технического оснащения, классов точности, и, как следствие, диапазонов стоимости привлекает все больше предприятий, заинтересованных в нашей продукции. Клиентская база концерна Knuth неуклонно расширяется, номенклатура растет соответственно спросу. Нашими постоянными заказчиками есть как небольшие частные предприятия, так и промышленные гиганты мирового значения.
Раздел «Эрозионные станки» в настоящее время представляют три наиболее популярные позиции:
1. Электроэрозионные проволочно-вырезные станки.
2. Электроэрозионные сверлильные станки (Супердрель).
3. Электроэрозионные копировально-прошивные станки.
Ниже предлагается подробное описание каждой позиции.
Сферы использования
Данная группа станков предназначена для пространственной обработки металла с соблюдением высокой точности. Машина осуществляет контурную обработку узлов, деталей, механизмов, изготовленных из электропроводящих материалов. Это могут быть: алюминиевые, медные, стальные заготовки любой твердости, твердые сплавы, цветные металлы.
Электроэрозионные проволочно-вырезные станки применяются для производства деталей, инструментов, оборудования со сложной геометрической формой: токарные кулачки, фасонные резцы, копиры, пуансоны, матрицы, постоянно задействованные в условиях серийного и мелкосерийного производства. Главной конструктивной особенностью данного оборудования является использование координат на линейных двигателях с прецизионными направляющими.
Станки оборудованы точными датчиками линейного перемещения. Это позволяет получать самую высокую степень точности при изготовлении ответственных деталей. Постоянный контроль с помощью высокоточных датчиков полностью исключает износ механики станка. Протяжка проволоки осуществляется через алмазные направляющие, имеющие чрезвычайно высокие прочностные характеристики.
Принцип работы
Электроэрозионные проволочно-вырезные станки производятся компанией Knuth с наличием числового программного управления. Система включает в себя:
- режим детального позиционирования от пункта к пункту;
- винтовую, круговую, линейную, сферическую интерполяции;
- профилирование скоростей;
- электронную синхронизацию;
- перемены траекторий;
- высокоскоростные входы и выходы.
Связь между приводами и контроллером осуществляется по интерфейсу с коммерческой доступностью. Цифровой токопроводящий контур обеспечивает высокую управляемость и устойчивость для всей системы. Программное обеспечение данной группы станков позволяет осуществлять обработку деталей, выполняя файлы-задания.
Информеры состоят из чертежей, характеристик для технологических процессов обработки, необходимых генератору с движущей системой. ПО способно выполнять функции самодиагностики для всей системы в процессе работы. Станки с успехом могут получать задание для обработки деталей, введенное в виде управляющих чертежей формата .dxf из любых САПР.
Группы, виды станков
Компания Knuth изготавливает и реализует электроэрозионные проволочно-вырезные станки близко 20 конструктивных исполнений. Это агрегаты общим весом от 800 кг до 14000 кг. Станки выполнены в различных функциональных категориях:
- однопроходные;
- многопроходные;
- станки с ЧПУ.
Размеры столов для каждой машины различные. Основные типоразмеры рабочих станин варьируются от 380х490 мм до 2600х1680 мм. Мощность генераторной установки находится в пределах от <1 кВт до 4,5 кВА. Минимальные габаритные размеры станка 1200х900х1300 мм, максимальные 5300х4800х3000 мм.
Особенности выбора
Для правильного выбора электроэрозионного станка со всей массы предложений, необходимо четко представлять себе особенности собственного производства, характеристики обрабатываемых деталей, ежедневную, месячную, годичную загруженность станков.
Остановив свой выбор на оборудовании концерна Knuth, каждый потребитель имеет возможность гарантированно выбрать станок необходимого типа и результативности. Поставка с центрального склада в Германии занимает всего от 2 до 8 недель, начиная от даты заявки.
Применяемость
Основная производственная задача оборудования, принадлежащего к большой группе, называемой электроэрозионные сверлильные станки (Супердрель), заключается в получении глубоких отверстий сечением 0,2 – 3,0 мм. Отверстия такого диаметра необходимы в материалах, проводящих электрический ток. Вещества могут быть любой твердости, толщины. Также различная геометрическая форма их поверхности.
Благодаря высокой степени универсальности, станки супердрель получили широкое распространение во многих сферах промышленности. Их используют в машиностроении при нарезании шлицевых, шпоночных пазов, выполнении отверстий в труднодоступных местах. Штампы, элементы прессформ также изготовлены на данном оборудовании. Оно применяется при обработке медицинских изделий, высокоточных деталей аэрокосмических механизмов, лазерной техники.
Устройство
Повышенная степень надежности, долговечность агрегатов позволяет их успешно использовать в процессах выпуска крупносерийной и мелкосерийной продукции. Супердрели работают на повышенных рабочих скоростях. По сравнению с обычными, привычными для нас дрелями, электроэрозионные сверлильные станки (Супердрель) имеют существенные принципиальные различия по ряду характеристик:
- конструкция;
- принцип работы;
- сечение обрабатываемых поверхностей.
Простые, но вместе с тем надежные механизмы позволяют быстро добиваться успеха в местах, труднодоступных и сложновыполнимых при использовании традиционных механических способов обработки. Единственное обязательное условие гарантированного успешного сверления нашим станком – хорошая проводимость электрического тока используемым материалом.
Супердрель электроэрозионного принципа действия состоит из двух электродов. Один из них представляет режущий инструмент. Это углеродный контакт, выдерживающий большую силу тока. Он помещается в одну из оправок, набор которых входит в базовую комплектацию станка. Другим электродом является зажимное устройство для обрабатываемой заготовки. Ток от механизма переходит к токопроводящей детали.
Принцип действия
Настроив углеродный контакт на сверление отверстий необходимого сечения, зажав заготовку в специальном кондукторе, оператор включает подачу электрического напряжения к исполнительным механизмам. За счет разницы потенциалов, на электроде возникает режущая сила. Параметры сверления заданы заранее электронной программой.
Электроэрозионные сверлильные станки (Супердрель) быстро, аккуратно, надежно справляются со всеми поставленными задачами. Исходя из высоких скоростей резания, агрегаты могут выполнять повышенные объемы обработки на любых участках обработки металлов.
Виды станков
Компания Knuth производит и реализует следующие виды станков типа супердрель:
Выбор
При необходимости покупки и эксплуатации высокотехнологичных станков моделей супердрель, изготовленных концерном Knuth, каждый потребитель должен сначала определиться с уровнем собственного производства, программой выпуска тех или иных деталей.
Наше оборудование, работая в условиях крупносерийного и мелкосерийного изготовления продукции, приносит значительную экономию времени, трудовых ресурсов, денежных средств. Работать с электроэрозионными сверлильными станками выгодно, экономично, целесообразно.
Принцип действия
Процесс электрической эрозии заключается в разрушении поверхностного слоя металлического изделия в результате воздействия на него электрического разряда. На данном принципе построена большая группа металлообрабатывающих станков немецкого концерна Knuth. Технологию работы с электрической эрозией разработали советские ученые-технологи Лазаренко Б. Р. и Лазаренко Н. И.
В настоящее время электроэрозионная обработка – ЭЭО, массово используется при изменении параметров металлических заготовок, проводящих электрический ток. Благодаря данной методике, получают отверстия различных сечений и конфигураций, фасонные полости, профильные канавки, пазы в деталях из твердосплавных материалов.
Наиболее популярной продукцией компании Knuth являются малогабаритные электроэрозионные копировально-прошивные станки модели D7120. Для различных производственных нужд предприятие производит станки различной мощности, исполнения, габаритных размеров. Оборудование имеет разные размеры станин, они различные по массе и выполняемым операциям.
Группы станков
Немецкая фирма Knuth производит и реализует по всей территории Российской Федерации уникальные высокоэффективные станки для электроэрозионной обработки металлов и сплавов. Самые компактные станки имеют массу от 1000 кг, наиболее металлоемкие выпускаются весом до 5500. Габаритные размеры выпускаемого оборудования: от 1200х1000х1800 мм до 2200х3600х2920 мм.
Электроэрозионные копировально-прошивные станки производятся с различной мощностью генераторной установки: от 2 кВт до 10 кВт. Предприятие изготавливает 14 моделей копировально-прошивных станков, предназначенных для выполнения самых разнообразных операций по обработке металлических заготовок по всему технологическому циклу. При этом используются различные размеры станин: от 200х160 мм до 1250х800 мм.
Устройство
Основные технологические функции предлагаемого оборудования будут рассмотрены на примере однокоординатного прошивного станка. Данный тип станков имеет только одну управляемую ось Z. Это вертикальная функция, которая определяет глубину электроэрозионного прожига. Перемещение по осям X, Y производится либо вручную, путем вращения рукояток, либо с помощью автоматики.
Когда на данном типе станка обрабатывается заготовка, оси X и Y должны оставаться неподвижными. С этой целью в районе рукояток установлены зажимы для фиксации. Они не позволяют ШВП проворачиваться. На все три оси станков: X, Y, Z, помещены оптические линейки с дискретностью 0,005 мм.
Выполняемые операции
Станки подобного типа с ЧПУ оснащены двумя системами координат. Осуществляя операции по обработке заготовок, одну из них удобно будет принять за абсолютную, вторую – за относительную. Данное обстоятельство, а также то, что полученное значение координат можно разделить на 2, позволяет легко базироваться, прожигать многоместные формы, измерять геометрические характеристики деталей, точно находить центры отверстий, более совершенно работать над производством и совершенствованием каждой отдельной детали.
Эксплуатируя электроэрозионные копировально-прошивные станки, операции эффективного прожига металла можно разбить на несколько этапов. Это усовершенствование позволит в процессе изготовления деталей обходиться одним электродом. Доглаживание обрабатываемой поверхности осуществляется на последнем этапе пониженными токами.
Данная хитрость позволяет значительно уменьшить износ электрода. На начальном этапе обработки ток прожига будет соблюдаться меньший. Постепенно увеличивая ток и глубину прожига, площадь обрабатываемой поверхности, добиваемся поставленной цели и экономим на расходе используемых электродов.
90000 Electrical Discharge Machining Basics> ENGINEERING.com 90001 90002 90003 (Image courtesy of Makino.) 90004 Electrical discharge machining (EDM) has long been the answer for high accuracy, demanding machining applications where conventional metal removal is difficult or impossible. 90003 Known by many other names, including spark machining, arc machining and (inaccurately) burning, the EDM process is conceptually very simple: an electrical current passes between an electrode and a workpiece which are separated by a dielectric liquid.The dielectric fluid acts as an electrical insulator unless enough voltage is applied to bring it to its ionization point, when it becomes an electrical conductor. The resulting spark discharge erodes the workpiece to form a desired final shape. 90004 90007 90008 90007 3 Types of EDM Machines 90008 90003 While there are many specialized forms of electrical discharge machining, industrial EDM machines are commonly grouped into three categories: 90004 90013 90014 Die Sinker or “Ram” EDM 90015 90014 Wire or “Cheese Cutter” EDM 90015 90014 Hole Drilling or “Hole Popper” EDM 90015 90020 90003 All three types operate on the same principal of erosion by electrical discharge discovered by Joseph Priestley in 1770 but their history, methods and applications are notably different.90004 90023 Die Sinker EDM 90024 90025 90003 (Image courtesy of MC Machinery.) 90004 Like the electric telegraph and the jet engine, die sinker EDM was invented independently and almost simultaneously by more than one person. In 1941 Russian scientists Boris and Natalya Lazarenko were tasked with finding a way to increase the lifespan of tungsten breaker points. In the course of their research, they discovered that they could control the erosion of tungsten electrical contacts by immersing them in a dielectric fluid.By 1943 року, the Lazarenkos had developed a spark machining process based on this discovery that eventually became known as a resistor-capacitor (R-C) circuit for EDM. 90003 At nearly the same time, an American engineering team-consisting of Harold Stark, Victor Harding and Jack Beaver-was working on a way to remove broken drills and taps. Harding, an electrical engineer, proposed using sparks to erode them away. The idea showed promise, but it was not until water was added as a coolant that this approach became practical.Stark, Harding and Beaver continued to refine their process, which eventually became the basis for the vacuum-tube EDM, which made it possible to increase spark frequency from 60 times per second to well over 1,000. 90004 90003 As it exists today, die sinker EDM is used to create complex cavity shapes in tool and die applications, such as metal stamping dies and plastic injection molds. The die sinker process begins with machining a graphite electrode to form a “positive” of the desired cavity.This electrode is then carefully plunged into the workpiece, causing sparking over its surface as features close the sparking gap-the distance required for sparking. 90004 90023 Wire EDM 90024 90034 90003 (Image courtesy of MC Machinery.) 90004 This history of wire EDM is less clear cut than die sinker EDM, but what is known is that it was developed over roughly a decade between the 1960s and 1970s as a new method for making dies from hardened steel. As the name implies, wire EDM uses a thin wire for an electrode.The wire moves in a carefully controlled pattern, roughly analogous to a woodworker’s scroll saw, causing sparking to occur between the wire and the workpiece. Because the electrical discharge erodes by the wire and the workpiece, wire EDM machines use a spool of wire that’s continuously moving to present a fresh discharge path in the cut. 90003 This “cheese cutter” approach to EDM works well, but it has an important limitation: the wire must pass entirely through the workpiece, making an essentially two-dimensional cut in a three-dimensional part.Control of the wire’s movement in an XY plane on modern-day machines is similar to other CNC-driven technologies. 90004 90023 Hole Drilling EDM 90024 90041 Beaumont Fast Hole EDM Drill. (Image courtesy of Global EDM.) The principle benefits of EDM-its excellent surface finish, minimal heat-affected zone (HAZ) and ability to cut hardened materials and exotic alloys-make it ideal for certain hole-making applications. If a small pilot hole is pre-drilled into workpiece, wire can be threaded through it to complete the operation using wire EDM.90003 Cases where this is impossible-blind hole applications, for example-call for a specialized EDM hole making machine. Commonly called a “hole popper” this machine uses a rotating conductive tube for its electrode and a continuous flow of dielectric fluid (usually deionized water) to flush the cut. Hole popper EDM can also be used to create the pilot hole necessary for wire threading. 90004 90003 The ability to create accurate and precise holes, even in hardened or exotic materials has been a key development for several advanced technologies, such as EDM-created cooling holes in high-temperature alloy turbine blade sections.This permits a “film cooling” process, which allows jet engines to operate at higher temperatures for greater durability and efficiency. 90004 90007 90008 90007 Dielectric Fluid 90008 90003 Die-sinker EDM machines typically use hydrocarbon oil for their dielectric fluid, into which both the workpiece and spark are immersed. In contrast, wire EDM machines normally use deionized water, into which only the sparking area is immersed. Whether oil-based or water-based, the dielectric fluid used in EDM machines serves three critical functions: 90004 90052 90014 Controlling the spacing of the sparking gap between the electrode and workpiece 90015 90014 Cooling the heated material to form the EDM chips 90015 90014 Removing EDM chips from the sparking area 90015 90059 90003 Although they’re considerably smaller than those produced in milling or turning processes, EDM does produce chips.These tiny, hollow spheroids are composed of material from both the electrode as well as the workpiece. Just like any chip, they need to be removed from the cutting zone, which is accomplished by flowing the dielectric fluid through the sparking gap. 90004 90003 As the dielectric fluid breaks down-whether as the result of age or contamination-the risk of unstable discharge increases. Control electronics can compensate to a certain extent, but the only real solution is to continually pump clean dielectric fluid through the cutting zone to flush it.The more conductive particles in the fluid, the more difficult it is for the machine to maintain stable electrical thresholds inside the sparking gap. 90004 90064 Because the lifespan of dielectric fluid depends on a host of factors, such as its type and the efficiency and quality of your EDM fluid filters, it has no definitive expiry date. As a rule of thumb, however, if you’re using a oil-based fluid and it’s over five years old, it should probably be replaced. You can also perform sight and smell comparisons between used and virgin fluids, but the best way to determine whether your dielectric fluid needs to be replaced is with a refractometer.90003 Choosing the right dielectric fluid for your EDM application is not always as straightforward as it might seem. Many criteria need to be taken into account. Some are obvious, such as degree of metal removal and electrode wear, while others are much more subtle. 90004 90003 For example, particle suspension is a key property for machining efficiency, since the fluid needs to be able to remove EDM chips and other waste particles from the cutting zone. However, if particle suspension is too high, these impurities will not separate from the fluid during filtration.90004 90003 To ensure that you’re using the best dielectric fluid for your particular machine, consult its manufacturer. 90004 90007 EDM Materials 90008 90003 Obviously, any workpiece that’s going to be machined with EDM has to be electrically conductive, but there’s more to the material limitations of electrical discharge machining than that. For one, certain materials, such as high-nickel alloys-like those found in the aerospace industry-and carbide materials can present a greater challenge for EDM compared to standard tool steels.However, the solutions to the material issues in these cases lie in variations of electrode materials and slower EDM cycle times. 90004 90003 Moreover, while EDM is technically a stress-free machining process-since no direct mechanical force is applied to the workpiece), it’s still a thermal process and so has the potential to alter the metallurgy of the workpiece via heat affected zones (HAZs) , recasts and micro-cracking. 90004 90077 ONA AV wire EDM. (Image courtesy of ONA.) “Most EDMs from the year 2000 on are capable of producing excellent metallurgical quality thanks to the advancement of EDM technology and adaptive power controls,” said Brian Pfluger, EDM Product Line Manager at Makino.90003 Of course, some electrically conductive materials still do not play well with EDM. “I’ve been asked to cut silicon wafer material, which is almost glass-like,” said Greg Langenhorst, Technical Marketing Manager at MC Machinery. “That does not work too well: it’s way too brittle and the spark energy just shatters it like glass. Some of it is conductive enough that you can cut it a little bit, but not very well. ” 90004 90003 Heterogenous materials, especially those with impurities, can also present a problem for EDM, as Langenhorst explained: 90004 90003 “With carbon fiber composites, even though they are electrically conductive, the adhesives in them create some problems because they’re non-conductive.I’ve even run into that when someone buys cheap tool steel. When it has a lot of particulate-I call it ‘melted car bumpers’-that’s non-conductive, if you hit one of those, it’s like hitting a stone: you just can not get through it. ” 90004 90007 Why Use EDM? 90008 90003 In practical terms, electrical discharge machining overcomes a major issue found in contact machining: hardness. In traditional processes, metal workpieces are made from special grades of hardenable tool steels machined in an anneal of soft state to facilitate cutting.90004 90003 One the desired shape has been machined, the parts are then hardened by one or more heat treatments. This adds time, cost and can alter the finished parts ‘dimensions, especially if the heat treatment process is not properly controlled. The advantage of EDM is that it can cut hardened materials and exotic alloys while also providing excellent surface finishes as a bonus. The result is often a reduced need for post-processing or surface treatment. 90004 90090 90003 Basic machine components for a wire EDM.(Image courtesy of Makino.) 90004 Like all machining processes, EDM requires a balancing act between speed and surface finish. In wire EDM, for example, it’s common to use faster, rougher cuts followed by finishing or skimming cuts that use a less aggressing flushing profile to minimize wire deflection. Sinker EDM sees a similar pattern, with most jobs using two electrodes: one for roughing and one for finishing. 90003 “With sinkers, there’s a standing joke that you do not want to use a sinker EDM unless you absolutely have to: if there’s no other way to get the shape you need into the part,” said Langenhorst.”Over the years, sinkers have become less and less utilized because of high-speed hard milling. As that process improved, there’s less sinker cavity work that needs to be done. The areas you can not do with hard milling are sharp inside corners or very deep, thin ribs. That’s where sinker EDM is a must. ” 90004 90003 The principle advantages of EDM are that the process is very predictable, accurate and repeatable. “All EDM machining is performed unattended, so the direct labor rate and manufacturing cost are typically lower for EDM than other methods,” said Pfluger.”In general, the EDM process is reserved for parts with smaller feature sizes and higher accuracy requirements (+/- 0.0005″ or + / – 0.012mm or finer accuracy). ” 90004 90003 “Once you have a wire EDM in your shop, it becomes very obvious that you can do a lot more with it than just what you bought it for,” said Langenhorst. “All of a sudden, they realize that can cut strippers, knockouts, die buttons, inserts, slides, all kinds of parts. If you need to do die tryouts on a form die, you can actually cut the sheet metal blanks to test the form die.”90004 90007 Electrical Discharge Machining vs. Other Machining Processes 90008 90003 “There’s more than one way to skin a cat,” as the old expression goes. Similarly, there’s typically more than one way to cut parts. Compared with conventional machining-from basic CNC turning all the way up to 5-axis-EDM has certain advantages and disadvantages. So, if you’re wondering whether EDM is the best bet for your particular application, the answer is always the same: it depends on your application.90004 90003 Generally speaking, however, the principle characteristics of electrical discharge machining should give you a sense of whether EDM is a good fit for your application. For example, EDM is typically slower than other machining methods, but it also tends to be more predictable, accurate and repeatable. There are other benefits as well, as Pfluger pointed out: “All EDM machining is performed unattended,” he said, “so the direct labor rate and the cost of manufacture with EDM are typically lower than other methods.”90004 90003 The combination of predictability, accuracy and repeatability-combined with its relatively slow machining speed-explains why EDM is most at home in low-volume operations with tight tolerances, such as the aerospace and medical device industries. 90004 90107 “The biggest point in favor of piece part manufacturing with wire EDM is when you get into part detail and you’re trying to do it with a slitting saw or a grinder, or any type of friction machining, which is going to create a burr , “said Langenhorst.”In that case, you have to have a secondary process for burr removal, whether it’s vibratory or having a bunch of workers scratching the burrs off with hand tools. On the other hand, when you take a part off an EDM machine, there is no burr: it’s perfect. ” 90003 Pfluger pointed out another advantage to using electrical discharge machining for parts with small or complex features: “The EDM process becomes more attractive as workpiece materials become harder, and as the part geometry becomes smaller and deeper,” he said.”Unlike conventional milling, EDM does not encounter limitations with L: D as internal radii features become smaller and workpiece thickness increases. In general, the EDM process is reserved for smaller part feature sizes and higher accuracy requirement applications (+/- 0.0005 “or +/- 0.012mm or finer accuracy).” 90004 90003 Moreover, since EDM is a non-contact machining process, the fixturing requirements for cutting small parts are considerably less onerous compared to those of a standard CNC mill.”There’s no cutting pressure, so if you’re working with little tiny pieces, you do not need much of a fixture to hold them,” said Langenhorst. “If you tried to mill them, have you to have it held tight enough that your machining process will not pick it up or bend it. For example, if you’re doing core pins for molds and you try to grind them, they’ll move all over the place. You can wire cut those with just a 90-degree flip fixture and they come out great. ” 90004 90007 EDM & Additive Manufacturing 90008 90003 Anyone who’s been paying attention to manufacturing technology over the last decade or so knows there are some big changes coming.Often presented under the banner of Industry 4.0 or the fourth industrial revolution, the conjunction of various technologies, including robotics, artificial intelligence and the Industrial Internet of Things (IIoT) -will forever change the manufacturing sector, from machine tools to quality assurance. 90004 90116 Cabin brackets for the Airbus A350 XWB with support structure. (Image courtesy of Concept Laser.) Additive manufacturing is one of the most frequently cited examples of an Industry 4.0 technology, one which could potentially replace so-called subtractive processes (like EDM) entirely. Interestingly, both Langenhorst and Pfluger see additive and EDM as more complimentary than competitive, as Langenhorst explained: 90003 “The biggest thing with metal additive manufacturing is that you have to build on a base plate and then separate the part from that,” he said. “Depending on the complexity of the attachment layer, it can be a pain to separate them. People have tried bandsaws, grinding, slitting wheels and all different kinds of things, and we’ve done quite well cutting the parts off the base plates using wire EDM.Obviously, it takes a submerged machine to do that, and in some cases you get this honeycomb structure between the workpiece and the baseplate that acts as a heatsink; if you do not build that just right, it can trap powder, which really raises hell on the controls for an adaptive wire EDM machine. ” 90004 90003 Pfluger agreed, adding that “Sinker EDM is also commonly used to finish certain features on additively manufactured components, such as small features that require high accuracy and finer surface finishes than what can be produced by additive manufacturing.”90004 90003 “We’re even trying to figure out how to create a less-expensive wire EDM machine to be used specifically for separating additively built workpieces from their baseplates, so basically an electric bandsaw,” Langenhorst added. 90004 90007 Electrical Discharge Machining & Automation 90008 90003 The process of automating one or more EDM machines is similar to that of other conventional machine tools. “Generally, workpieces are mounted on a pallet system and the automation changes the pallets in and out of a chuck on the machine,” said Langenhorst.90004 90003 “We have done some things with our Mitsubishi six-axis robots, which do not have a lot of weight capacity,” he added, “but we have had some applications with smaller parts where the robots were able to pick the parts and place them in a fixture on a machine that had its own clamping mechanism. ” 90004 90129 Nevertheless, there are some key differences between automating EDM and automating other machining processes, as Lagenhorst explained: 90003 “A lot of milling applications do not need stainless steel, hardened tooling to hold the workpieces, because you’re running a water-soluble coolant on the machine,” he said.”With wire EDM, you’re working in deionized water, so unless it’s made from 420 stainless steel or something like that, a robot’s not going to last very long.” 90004 90003 This is one reason sinker EDM fits more naturally with industrial robots compared to wire EDM. With sinker EDM, you can automate the machining electrode tool as well as the workpiece. “It’s very common to automate a VMC mill with a sinker EDM so the mill can produce the needed electrode tool with a robot automatically moving it between the different machines,” said Pfluger.90004 90007 90008 90007 Bottlenecks to EDM Efficiency 90008 90003 As with any manufacturing technology, EDM faces certain hurdles that must be overcome to ensure that you’re getting the most from your machines. Some of these are the same bottlenecks the arise for other machining processes, as Pfluger explained. “The biggest bottleneck to overcome with EDM processing is managing part throughput by maximizing the unattended operation and overall machine utilization,” he said. “Workholding and the required machine setup time are often a bottleneck for many shops.This necessary time can be kept to a minimum with proper investment in workholding tooling that provides faster and more precise setups. ” 90004 90140 90003 (Left) Side-clamp vise. (Right) Top-Clamp Vise. (Image courtesy of Makino.) 90004 Keep in mind that the relatively slowness of the EDM process means that efficient workholding may not be as much of an issue as it is in milling, where cycle times are considerably shorter, and changeover consequently represents a more significant portion of machine time.Regardless, workholding is an issue for both wire and sinker EDM, but not all bottlenecks are shared by both types of electrical discharge machining. 90003 “The bottleneck for sinkers is electrode manufacturing: if you do not have a graphite mill in-house, then you’re going to have to outsource your electrodes and the more complicated the shape, the longer the lead time,” said Langenhorst . “Newer machines are getting better as far as electrode wear goes, but to get high detail on a finished part with a sinker, you generally need at least two electrodes: a rougher and a finisher.That’s why most people pair a graphite mill along with a couple of sinkers; generally one mill can keep up with two or three sinkers. ” 90004 90003 Regarding wire EDM, Pfluger noted that the machines call for considerably more maintenance and upkeep than a milling machine. “The fundamental difference is that wire EDM maintenance MUST be performed as a proactive and preventative measure,” he said. “The goal is to ensure flawless, unattended machine operation over long hours, as this is where the process gains its productivity and lower manufacturing costs.”90004 90147 90003 EDM accessories and consumables (Image courtesy of MC Machinery.) 90004 Fortunately, the maintenance for wire EDM is relatively straightforward, as Langenhorst explained: “Wire a wire EDM machine, all your consumables are very simple: make sure you have clean filters in the tank and that your power feeders are up to snuff, throw a new roll of wire on, and anything you can program in a CAM system, you can pretty much cut. ” 90007 Is Electrical Discharge Machining Right for You? 90008 90003 If you need to rough cut a lot of parts quickly, electrical discharge machining probably is not the right process for you.(It should be noted that Langenhorst did point out that you can use wire EDM to cut shims by stacking the stock, sandwiching it between two pieces of quarter-inch steel, and cutting off a stack.) However, if you’re looking for a machining process that’s accurate, precise and stress-free-at least on the workpiece-EDM could be just what you need. 90004 90003 To learn more about other machining and fabricating processes, check out An Engineer’s Guide to Waterjet Cutting, The What, Why and How of 5-Axis CNC Machining and An Engineer’s Guide to CNC Turning Centers.90004 .90000 machine tool | Description, History, Types, & Facts 90001 90002 90003 Machine tool 90004, any stationary power-driven machine that is used to shape or form parts made of metal or other materials. The shaping is accomplished in four general ways: (1) by cutting excess material in the form of chips from the part; (2) by shearing the material; (3) by squeezing metallic parts to the desired shape; and (4) by applying electricity, ultrasound, or corrosive chemicals to the material. The fourth category covers modern machine tools and processes for machining ultrahard metals not machinable by older methods.90005 90003 drill press 90004 Drill press. 90008 Plbcr 90009 90002 Machine tools that form parts by removing metal chips from a workpiece include lathes, shapers and planers, drilling machines, milling machines, grinders, and power saws. The cold forming of metal parts, such as cooking utensils, automobile bodies, and similar items, is done on punch presses, while the hot forming of white-hot blanks into appropriately shaped dies is done on forging presses. 90005 90002 Modern machine tools cut or form parts to tolerances of plus or minus one ten-thousandth of an inch (0.0025 millimetre). In special applications, precision lapping machines can produce parts that are within plus or minus two millionths of an inch (0.00005 millimetre). Because of the precise dimensional requirements of the parts and the heavy cutting forces exerted on the cutting tool, machine tools combine weight and rigidity with delicate accuracy. 90005 90014 History 90015 90002 Before the Industrial Revolution of the 18th century, hand tools were used to cut and shape materials for the production of goods such as cooking utensils, wagons, ships, furniture, and other products.After the advent of the steam engine, material goods were produced by power-driven machines that could only be manufactured by machine tools. Machine tools (capable of producing dimensionally accurate parts in large quantities) and jigs and fixtures (for holding the work and guiding the tool) were the indispensable innovations that made mass production and interchangeable parts realities in the 19th century. 90005 Get exclusive access to content from our тисяча сімсот шістьдесят вісім First Edition with your subscription.Subscribe today 90002 The earliest steam engines suffered from the imprecision of early machine tools, and the large cast cylinders of the engines often were bored inaccurately by machines powered by waterwheels and originally designed to bore cannon. Within 50 years of the first steam engines, the basic machine tools, with all the fundamental features required for machining heavy metal parts, were designed and developed. Some of them were adaptations of earlier woodworking machines; the metal lathe derived from woodcutting lathes used in France as early as the 16th century.In тисячу сімсот сімдесят п’ять John Wilkinson of England built a precision machine for boring engine cylinders. In 1797 Henry Maudslay, also of England and one of the great inventive geniuses of his day, designed and built a screw-cutting engine lathe. The outstanding feature of Maudslay’s lathe was a lead screw for driving the carriage. Geared to the spindle of the lathe, the lead screw advanced the tool at a constant rate of speed and guaranteed accurate screw threads. By 1800 Maudslay had equipped his lathe with 28 change gears that cut threads of various pitches by controlling the ratio of the lead-screw speed to the spindle speed.90005 90002 The shaper was invented by James Nasmyth, who had worked in Henry Maudslay’s shop in London. In Nasmyth’s machine, a workpiece could be clamped horizontally to a table and worked by a cutter using a reciprocating motion to plane small surfaces, cut keyways, or machine other straight-line surfaces. A few years later, in 1839 Nasmyth invented the steam hammer for forging heavy pieces. Another disciple of Maudslay, Joseph Whitworth, invented or improved a great number of machine tools and came to dominate the field; at the International Exhibition of тисячі вісімсот шістьдесят два, his firm’s exhibits took up a quarter of all the space devoted to machine tools.90005 90002 Britain tried to keep its lead in machine-tool development by prohibiting exports, but the attempt was foredoomed by industrial development elsewhere. British tools were exported to continental Europe and to the United States despite the prohibition, and new tools were developed outside Britain. Notable among these was the milling machine invented by Eli Whitney, produced in the United States in 1818 and used by Simeon North to manufacture firearms. The first fully universal milling machine was built in 1862 by J.R. Brown of the United States and was used to cut helical flutes in twist drills. The turret lathe, also developed in the United States in the middle of the 19th century, was fully automatic in some operations, such as making screws, and it presaged the momentous developments of the 20th century. Various gear-cutting machines reached their full development in 1896 when F.W. Fellows, an American, designed a gear shaper that could rapidly turn out almost any type of gear. 90005 90002 The production of artificial abrasives in the late 19th century opened up a new field of machine tools, that of grinding machines.C.H. Norton of Massachusetts dramatically illustrated the potential of the grinding machine by making one that could grind an automobile crankshaft in 15 minutes, a process that previously had required five hours. 90005 90002 By the end of the 19th century a complete revolution had taken place in the working and shaping of metals that created the basis for mass production and an industrialized society. The 20th century has witnessed the introduction of numerous refinements of machine tools, such as multiple-point cutters for milling machines, the development of automated operations governed by electronic and fluid-control systems, and nonconventional techniques, such as electrochemical and ultrasonic machining.Yet even today the basic machine tools remain largely the legacy of the 19th century. 90005 90014 Machine-tool characteristics 90015 90002 All machine tools must provide work-holding and tool-holding devices and means for accurately controlling the depth of the cut. The relative motion between the cutting edge of the tool and the work is called the cutting speed; the speed in which uncut material is brought into contact with the tool is called the feed motion. Means must be provided for varying both.90005 90002 Because an overheated tool may lose its cutting ability, temperatures must be controlled. The amount of heat that is generated depends on the shearing force and the cutting speed. Because the shearing force varies with the material being cut and the tool material varies in its tolerance for high temperatures, the optimum cutting speed depends both on the material being cut and the cutting-tool material. It is also influenced by the rigidity of the machine, the shape of the workpiece, and the depth of the cut.90005 90002 Metal-cutting tools are classified as single point or multiple point. A single-point cutting tool can be used for increasing the size of holes, or boring. Turning and boring are performed on lathes and boring mills. Multiple-point cutting tools have two or more cutting edges and include milling cutters, drills, and broaches. 90005 90002 There are two types of operation; either the tool is moving on a straight path against the stationary workpiece, as on a shaper, or the workpiece is moving against the stationary tool, as on a planer.Relief or clearance angles must be provided to prevent the tool surface below the cutting edge from rubbing against the workpiece. Rake angles are often provided on cutting tools to cause a wedging action in the formation of chips and to reduce friction and heat. 90005.90000 PPT – Electrical Discharge Machining (EDM) PowerPoint Presentation, free download 90001 90002 90003 90004 Electrical Discharge Machining (EDM) 90005 90006 90007 90008 90003 90004 Introduction 90005 • Sometimes it is referred to as spark machining, spark eroding, burning, die sinking or wire erosion • Its a manufacturing process whereby a desired shape is obtained using electrical discharges (sparks). • Material is removed from the workpiece by a series of rapidly recurring current discharges between two electrodes, separated by a dielectric liquid and subject to an electric voltage.• One of the electrodes – ‘tool-electrode’ or ‘tool’ or ‘electrode’. • Other electrode – workpiece-electrode or ‘workpiece’. • As distance between the two electrodes is reduced, the current intensity becomes greater than the strength of the dielectric (at least in some points) causing it to break. 2 90006 90007 90014 90003 90004 History 90005 • This allows current to flow between the two electrodes. • This phenomenon is the same as the breakdown of a capacitor. • As a result, material is removed from both the electrodes.• Once the current flow stops, new liquid dielectric is usually conveyed into the electrode zone enabling the solid particles (debris) to be carried away. • Adding new liquid dielectric in the electrode volume is commonly referred to as flushing. • Also, after a current flow, a difference of potential between the two electrodes is restored to what it was before the breakdown, so that a new liquid dielectric breakdown can occur. 3 90006 90007 90020 90003 90004 History 90005 • In 1770 English Physicist Joseph Priestley studied the erosive effect of electrical discharges.• Furthering Priestley’s research, the EDM process was invented by two Russian scientists, Dr. B.R. Lazarenko and Dr. N.I. Lazarenko in 1943. • In their efforts to exploit the destructive effects of an electrical discharge, they developed a controlled process for machining of metals. • Their initial process used a spark machining process, named after the succession of sparks (electrical discharges) that took place between two electrical conductors immersed in a dielectric fluid. • The discharge generator effect used by this machine, known as the Lazarenko Circuit, was used for many years in the construction of generators for electrical discharge.4 90006 90007 90026 90003 90004 History 90005 • New researchers entered the field and contributed many fundamental characteristics of the machining method we know today. • In 1952 the manufacturer Charmilles created the first machine using the spark machining process and was presented for the first time at the European Machine Tool Exhibition in 1955. • In 1969 Agie launched the world’s first numerically controlled wire-cut EDM machine. • Seibu developed the first CNC wire EDM machine in тисячі дев’ятсот сімдесят дві and the first system was manufactured in Japan.• Recently, the machining speed has gone up by 20 times. • This has decreased machining costs by at least 30 percent and improved the surface finish by a factor of 1.5 5 90006 90007 90032 90003 90004 General Aspects of EDM 90005 • EDM is a machining method primarily used for hard metals or those that would be very difficult to machine with traditional techniques. • EDM typically works with materials that are electrically conductive, although methods for machining insulating ceramics with EDM have been proposed.• EDM can cut intricate contours or cavities in hardened steel without the need for heat treatment to soften and re-harden them. • This method can be used with any other metal or metal alloy such as titanium, hastelloy, kovar, and inconel. • Also, applications of this process to shape polycrystalline diamond tools have been reported. 6 90006 90007 90038 90003 90004 EDM – System 90005 7 90006 90007 90044 90003 90004 EDM – Components 90005 8 90006 90007 90050 90003 90004 EDM – Components 90005 • The main components in EDM: • Electric power supply • Dielectric medium • Work piece & tool • Servo control unit.• The work piece and tool are electrically connected to a DC power supply. • The current density in the discharge of the channel is of the order of 10000 A / cm2 and power density is nearly 500 MW / cm2. • A gap, known as SPARK GAP in the range, from 0.005 mm to 0.05 mm is maintained between the work piece and the tool. • Dielectric slurry is forced through this gap at a pressure of 2 kgf / cm2 or lesser. 9 90006 90007 90056 90003 90004 EDM – Working Principle 90005 • It is a process of metal removal based on the principle of material removal by an interrupted electric spark discharge between the electrode tool and the work piece.• In EDM, a potential difference is applied between the tool and workpiece. • Essential – Both tool and work material are to be conductors. • The tool and work material are immersed in a dielectric medium. • Generally kerosene or deionised water is used as the dielectric medium. • A gap is maintained between the tool and the workpiece. • Depending upon the applied potential difference (50 to 450 V) and the gap between the tool and workpiece, an electric field would be established. • Generally the tool is connected to the negative terminal (cathode) of the generator and the workpiece is connected to positive terminal (anode).10 90006 90007 90062 90003 90004 EDM – Working Principle 90005 • As the electric field is established between the tool and the job, the free electrons on the tool are subjected to electrostatic forces. • If the bonding energy of the electrons is less, electrons would be emitted from the tool. • Such emission of electrons are called or termed as ‘cold emission’. • The “cold emitted” electrons are then accelerated towards the job through the dielectric medium. • As they gain velocity and energy, and start moving towards the job, there would be collisions between the electrons and dielectric molecules.• Such collision may result in ionization of the dielectric molecule. • Ionization depends on the ionization energy of the dielectric molecule and the energy of the electron. 11 90006 90007 90068 90003 90004 EDM – Working Principle 90005 • As the electrons get accelerated, more positive ions and electrons would get generated due to collisions. • This cyclic process would increase the concentration of electrons and ions in the dielectric medium between the tool and the job at the spark gap. • The concentration would be so high that the matter existing in that channel could be characterised as “plasma”.• The electrical resistance of such plasma channel would be very less. • Thus all of a sudden, a large number of electrons will flow from tool to job and ions from job to tool. • This is called avalanche motion of electrons. • Such movement of electrons and ions can be visually seen as a spark. • Thus the electrical energy is dissipated as the thermal energy of the spark. 12 90006 90007 90074 90003 90004 EDM – Working Principle 90005 • The high speed electrons then impinge on the job and ions on the tool.• The kinetic energy of the electrons and ions on impact with the surface of the job and tool respectively would be converted into thermal energy or heat flux. • Such intense localized heat flux leads to extreme instantaneous confined rise in temperature which would be in excess of 10,000oC. • Such localized extreme rise in temperature leads to material removal. • Material removal occurs due to instant vaporization of the material as well as due to melting. • The molten metal is not removed completely but only partially.13 90006 90007 90080 90003 90004 EDM – Working Principle 90005 • Upon withdrawal of potential difference, plasma channel collapses. • This ultimately creates compression shock waves on both the electrode surface. • Particularly at high spots on work piece surface, which are closest to the tool. • This evacuates molten material and forms a crater around the site of the spark. • The whole sequence of operation occurs within a few microseconds. 14 90006 90007 90086 90003 90004 EDM – Schematic 90005 15 90006 90007 90092 90003 90004 EDM – Working Principle 90005 • Thus to summarise, the material removal in EDM mainly occurs due to formation of shock waves as the plasma channel collapse owing to discontinuation of applied potential difference • Generally the workpiece is made positive and the tool negative.• Hence, the electrons strike the job leading to crater formation due to high temperature and melting and material removal. • Similarly, the positive ions impinge on the tool leading to tool wear. • In EDM, the generator is used to apply voltage pulses between the tool and job. • A constant voltage is not applied. Only sparking is desired rather than arcing. • Arcing leads to localized material removal at a particular point whereas sparks get distributed all over the tool surface leading to uniform material removal.16 90006 90007 90098 90003 90004 EDM – Working Principle 90005 17 90006 90007 90104 90003 90004 EDM – Power & Control Circuits 90005 • Two broad categories of generators (power supplies) are in use on EDM. • Commercially available: RC circuits based and transistor controlled pulses. • In the first category, the main parameters to choose from at setup time are the resistance (s) of the resistor (s) and the capacitance (s) of the capacitor (s). • In an ideal condition, these quantities would affect the maximum current delivered in a discharge.• Current delivery in a discharge is associated with the charge accumulated on the capacitors at a certain moment. • Little control is expected over the time of discharge, which is likely to depend on the actual spark-gap conditions. • Advantage: RC circuit generator can allow the use of short discharge time more easily than the pulse-controlled generator. 18 90006 90007 90110 90003 90004 EDM – Power & Control Circuits 90005 • Also, the open circuit voltage (i.e. voltage between electrodes when dielectric is not broken) can be identified as steady state voltage of the RC circuit.• In generators based on transistor control, the user is usually able to deliver a train of voltage pulses to the electrodes. • Each pulse can be controlled in shape, for instance, quasi-rectangular. • In particular, the time between two consecutive pulses and the duration of each pulse can be set. • The amplitude of each pulse constitutes the open circuit voltage. • Thus, maximum duration of discharge is equal to duration of a voltage pulse. • Maximum current during a discharge that the generator delivers can also be controlled.19 90006 90007 90116 90003 90004 EDM – Power & Control Circuits 90005 • Details of generators and control systems on EDMs are not always easily available to their user. • This is a barrier to describing the technological parameters of EDM process. • Moreover, the parameters affecting the phenomena occurring between tool and electrode are also related to the motion controller of the electrodes. • A framework to define and measure the electrical parameters during an EDM operation directly on inter-electrode volume with an oscilloscope external to the machine has been recently proposed by Ferri et al.• This would enable the user to estimate directly the electrical parameter that affect their operations without relying upon machine manufacturer’s claims. • When machining different materials in the same setup conditions, the actual electrical parameters are significantly different. 20 90006 90007 90122 90003 90004 EDM – Power & Control Circuits 90005 • When using RC generators, the voltage pulses, shown in Fig. are responsible for material removal. • A series of voltage pulses (Fig.) Of magnitude about 20 to 120 V and frequency on the order of 5 kHz is applied between the two electrodes.21 90006 90007 90128 90003 90004 EDM – Power & Control Circuits 90005 22 90006 90007 90134 90003 90004 EDM – Power & Control Circuits 90005 23 90006 90007 90140 90003 90004 EDM – Power & Control Circuits 90005 24 90006 90007 90146 90003 90004 EDM – Electrode Material 90005 • Electrode material should be such that it would not undergo much tool wear when it is impinged by positive ions. • Thus the localised temperature rise has to be less by properly choosing its properties or even when temperature increases, there would be less melting.• Further, the tool should be easily workable as intricate shaped geometric features are machined in EDM. • Thus the basic characteristics of electrode materials are: • High electrical conductivity – electrons are cold emitted more easily and there is less bulk electrical heating • High thermal conductivity – for the same heat load, the local temperature rise would be less due to faster heat conducted to the bulk of the tool and thus less tool wear. 25 90006 90007 90152 90003 90004 EDM – Electrode Material 90005 • Higher density – for less tool wear and thus less dimensional loss or inaccuracy of tool • High melting point – high melting point leads to less tool wear due to less tool material melting for the same heat load • Easy manufacturability • Cost – cheap • The followings are the different electrode materials which are used commonly in the industry: • Graphite • Electrolytic oxygen free copper • Tellurium copper – 99% Cu + 0.5% tellurium • Brass 26 90006 90007 90158 90003 90004 EDM – Electrode Material 90005 • Graphite (most common) – has fair wear characteristics, easily machinable. • Small flush holes can be drilled into graphite electrodes. • Copper has good EDM wear and better conductivity. • It is generally used for better finishes in the range of Ra = 0.5 μm. • Copper tungsten and silver tungsten are used for making deep slots under poor flushing conditions especially in tungsten carbides. • It offers high machining rates as well as low electrode wear.• Copper graphite is good for cross-sectional electrodes. • It has better electrical conductivity than graphite while the corner wear is higher. • Brass ensures stable sparking conditions and is normally used for specialized applications such as drilling of small holes where the high electrode wear is acceptable. 27 90006 90007 90164 90003 90004 EDM – Electrode Movement 90005 • In addition to the servo-controlled feed, the tool electrode may have an additional rotary or orbiting motion. • Electrode rotation helps to solve the flushing difficulty encountered when machining small holes with EDM.• In addition to the increase in cutting speed, the quality of the hole produced is superior to that obtained using a stationary electrode. • Electrode orbiting produces cavities having the shape of the electrode. • The size of the electrode and the radius of the orbit (2.54 mm maximum) determine the size of the cavities. • Electrode orbiting improves flushing by creating a pumping effect of the dielectric liquid through the gap. 28 90006 90007 90170 90003 90004 EDM – Electrode Wear 90005 29 90006 90007 90176 90003 90004 EDM – Electrode Wear 90005 • The melting point is the most important factor in determining the tool wear.• Electrode wear ratios are expressed as end wear, side wear, corner wear, and volume wear. • “No wear EDM” – when the electrode-to-workpiece wear ratio is 1% or less. • Electrode wear depends on a number of factors associated with the EDM, like voltage, current, electrode material, and polarity. • The change in shape of the tool electrode due to the electrode wear causes defects in the workpiece shape. • Electrode wear has even more pronounced effects when it comes to micromachining applications.• The corner wear ratio depends on the type of electrode. • The low melting point of aluminum is associated with the highest wear ratio. 30 90006 90007 90182 90003 90004 EDM – Electrode Wear 90005 31 90006 90007 90188 90003 90004 EDM – Electrode Wear 90005 • Graphite has shown a low tendency to wear and has the possibility of being molded or machined into complicated electrode shapes. • The wear rate of the electrode tool material (Wt) and the wear ratio (Rw) are given by Kalpakjian (1997).32 90006 90007 90194 90003 90004 EDM – Dielectric 90005 • In EDM, material removal mainly occurs due to thermal evaporation and melting. • As thermal processing is required to be carried out in absence of oxygen so that the process can be controlled and oxidation avoided. • Oxidation often leads to poor surface conductivity (electrical) of the workpiece hindering further machining. • Hence, dielectric fluid should provide an oxygen free machining environment. • Further it should have enough strong dielectric resistance so that it does not breakdown electrically too easily.• But at the same time, it should ionize when electrons collide with its molecule. • Moreover, during sparking it should be thermally resistant as well. • Generally kerosene and deionised water is used as dielectric fluid in EDM. 33 90006 90007 90200 90003 90004 EDM – Dielectric 90005 • Tap water can not be used as it ionises too early and thus breakdown due to presence of salts as impurities occur. • Dielectric medium is generally flushed around the spark zone. • It is also applied through the tool to achieve efficient removal of molten material.• Three important functions of a dielectric medium in EDM: • Insulates the gap between the tool and work, thus preventing a spark to form until the gap voltage are correct. • Cools the electrode, workpiece and solidifies the molten metal particles. • Flushes the metal particles out of the working gap to maintain ideal cutting conditions, increase metal removal rate. • It must be filtered and circulated at constant pressure. 34 90006 90007 90206 90003 90004 EDM – Dielectric 90005 • The main requirements of the EDM dielectric fluids are adequate viscosity, high flash point, good oxidation stability, minimum odor, low cost, and good electrical discharge efficiency.• For most EDM operations kerosene is used with certain additives that prevent gas bubbles and de-odoring. • Silicon fluids and a mixture of these fluids with petroleum oils have given excellent results. • Other dielectric fluids with a varying degree of success include aqueous solutions of ethylene glycol, water in emulsions, and distilled water. 35 90006 90007 90212 90003 90004 EDM – Flushing 90005 • One of the important factors in a successful EDM operation is the removal of debris (chips) from the working gap.• Flushing these particles out of the working gap is very important, to prevent them from forming bridges that cause short circuits. • EDMs have a built-in power adaptive control system that increases the pulse spacing as soon as this happens and reduces or shuts off the power supply. • Flushing – process of introducing clean filtered dielectric fluid into spark gap. • If flushing is applied incorrectly, it can result in erratic cutting and poor machining conditions. • Flushing of dielectric plays a major role in the maintenance of stable machining and the achievement of close tolerance and high surface quality.• Inadequate flushing can result in arcing, decreased electrode life, and increased production time. 36 90006 90007 90218 90003 90004 EDM – Flushing 90005 • Four methods: 1. Normal flow 2. Reverse flow 3. Jet flushing 4. Immersion flushing 37 90006 90007 90224 90003 90004 EDM – Flushing 90005 • Normal flow (Majority) • Dielectric is introduced , under pressure, through one or more passages in the tool and is forced to flow through the gap between tool and work. • Flushing holes are generally placed in areas where the cuts are deepest.• Normal flow is sometimes undesirable because it produces a tapered opening in the workpiece. • Reverse flow • Particularly useful in machining deep cavity dies, where the taper produced using the normal flow mode can be reduced. • The gap is submerged in filtered dielectric, and instead of pressure being applied at the source a vacuum is used. • With clean fluid flowing between the workpiece and the tool, there is no side sparking and, therefore, no taper is produced. 38 90006 90007 90230 90003 90004 EDM – Flushing 90005 • Jet flushing • In many instances, the desired machining can be achieved by using a spray or jet of fluid directed against the machining gap.• Machining time is always longer with jet flushing than with the normal and reverse flow modes. • Immersion flushing • For many shallow cuts or perforations of thin sections, simple immersion of the discharge gap is sufficient. • Cooling and debris removal can be enhanced during immersion cutting by providing relative motion between the tool and workpiece. • Vibration or cycle interruption comprises periodic reciprocation of the tool relative to the workpiece to effect a pumping action of the dielectric.39 90006 90007 90236 90003 90004 EDM – Flushing 90005 • Synchronized, pulsed flushing is also available on some machines. • With this method, flushing occurs only during the non-machining time as the electrode is retracted slightly to enlarge the gap. • Increased electrode life has been reported with this system. • Innovative techniques such as ultrasonic vibrations coupled with mechanical pulse EDM, jet flushing with sweeping nozzles, and electrode pulsing are investigated by Masuzawa (1990).40 90006 90007 90242 90003 90004 EDM – Flushing 90005 • For proper flushing conditions, Metals Handbook (1989) recommends: • Flushing through the tool is more preferred than side flushing. • Many small flushing holes are better than a few large ones. • Steady dielectric flow on the entire workpiece-electrode interface is desirable. • Dead spots created by pressure flushing, from opposite sides of the workpiece, should be avoided. • A vent hole should be provided for any upwardly concave part of the tool-electrode to prevent accumulation of explosive gases.• A flush box is useful if there is a hole in the cavity. 41 90006 90007 90248 90003 90004 EDM – Process Parameters 90005 The waveform is characterized by the: • The open circuit voltage – Vo • The working voltage – Vw • The maximum current – Io • The pulse on time – the duration for which the voltage pulse is applied – ton • The pulse off time – toff • The gap between the workpiece and the tool – spark gap – δ • The polarity – straight polarity – tool (-ve) • The dielectric medium • External flushing through the spark gap.42 90006 90007 90254 90003 90004 EDM – Process Parameters 90005 • The process parameters – mainly related to the waveform characteristics. 43 90006 90007 90260 90003 90004 EDM – Types – Sinker EDM 90005 • Sinker EDM, also called cavity type EDM or volume EDM. • Consists of an electrode and workpiece submerged in an insulating liquid such as oil or other dielectric fluids. • The electrode and workpiece are connected to a suitable power supply. • The power supply generates an electrical potential between the two parts.• As the electrode approaches the workpiece, dielectric breakdown occurs in the fluid, forming a plasma channel, and a small spark jumps. • These sparks happen in huge numbers at seemingly random locations. • As the base metal is eroded, and the spark gap subsequently increased, the electrode is lowered automatically so that the process can continue. • Several hundred thousand sparks occur per second, with the actual duty cycle carefully controlled by the setup parameters. • These controlling cycles are sometimes known as “on time” and “off time”.44 90006 90007 90266 90003 90004 EDM – Types – Sinker EDM 90005 • The on time setting determines the length or duration of the spark. • Hence, a longer on time produces a deeper cavity for that spark and all subsequent sparks for that cycle. • This creates rougher finish on the workpiece. • The reverse is true for a shorter on time. • Off time is the period of time that one spark is replaced by another. • A longer off time, for example, allows the flushing of dielectric fluid through a nozzle to clean out the eroded debris, thereby avoiding a short circuit.• These settings can be maintained in micro seconds. • The typical part geometry is a complex 3D shape, often with small or odd shaped angles. 45 90006 90007 90272 90003 90004 EDM – Types – Wire EDM (WEDM) 90005 • Also known as wire-cut EDM and wire cutting. • A thin single-strand metal wire (usually brass) is fed through the workpiece submerged in a tank of dielectric fluid (typically deionized water). • Used to cut plates as thick as 300 mm and to make punches, tools, and dies from hard metals that are difficult to machine with other methods.• Uses water as its dielectric fluid; its resistivity and other electrical properties are controlled with filters and de-ionizer units. • The water flushes the cut debris away from the cutting zone. • Flushing is an important factor in determining the maximum feed rate for a given material thickness. • Commonly used when low residual stresses are desired, because it does not require high cutting forces for material removal. 46 90006 90007 90278 90003 90004 EDM – Material Removal Rate 90005 47 90006 90007 90284 90003 90004 EDM – Material Removal Rate 90005 • In EDM, the metal is removed from both workpiece and tool electrode.• MRR depends not only on the workpiece material but on the material of the tool electrode and the machining variables such as pulse conditions, electrode polarity, and the machining medium. • In this regard a material of low melting point has a high metal removal rate and hence a rougher surface. • Typical removal rates range from 0.1 to 400 mm3 / min. • MRR or volumetric removal rate (VRR), in mm3 / min, was described by Kalpakjian (1997): where I – EDM current (A) Tw – Melting point of the workpiece (° C).48 90006 90007 90290 90003 90004 EDM – Material Removal Rate 90005 Effect of pulse current (energy) on MRR & surface roughness. 49 90006 90007 90296 90003 90004 EDM – Material Removal Rate 90005 Effect of pulse on-time (energy) on MRR & surface roughness. 50 90006 90007 Load More ….90000 Cnc Portable Electric Sparking Strengthening Edm Machine 90001 90002 Product Description 90003 90002 90003 90002 SD-260A Parameter 90003 90008 90009 90010 90011 Machine model 90012 90011 SD-260A 90012 90015 90010 90011 Input Power 90012 90011 AC220V 50 / 60HZ 90012 90015 90010 90011 Power 90012 90011 260W 90012 90015 90010 90011 Maximum finish 90012 90011 6 90012 90015 90010 90011 Size 90012 90011 270 * 145 * 220mm 90012 90015 90010 90011 Frequency 90012 90011 1-10HZ 90012 90015 90010 90011 Coating thickness 90012 90011 40micron 90012 90015 90010 90011 Weight 90012 90011 7kg 90012 90015 90010 90011 Usage 90012 90011 Mainly with various types of mold, all kinds of steel.Strengthen the processing, sand processing. 90012 90015 90064 90065 90002 90067 90003 90002 Application & Samples 90003 90002 Electric spark strengthening machine help you increase the wear resistance of the surface of the workpiece and extend the service life by 1-3 times. 90003 90002 90003 90002 Company Introduction 90003 90002 ———————— OUR COMPANY —————- – 90003 90002 We are a EDM equipment company and has 15 years of experience in production. 90067 We have our own installation and maintenance team, can provide better service.90003 90002 90003 90002 90003 90002 90003 90002 ————————- CERTIFICATE —————- —– 90003 90002 90003 90002 ————————– EXHIBITION ————– ——– 90003 90002 FAQ 90003 90002 1. What’s your MOQ? 90003 90002 Our MOQ is 1 set for each machine. 90003 90002 2. Could we use our own brand on your machine? 90003 90002 Yes, we could love to accept. 90003 90002 3. Could your engineers go to our factory to install the machine and train our workers? 90003 90002 Yes, our engineers could go to your factory and assist you.90003 90002 4. What’s your fast deliver time? 90003 90002 According to machine, our production time is from 7 days to 30 days, and some machines are in stock. 90003 90002 5. Could i visit your factory? 90003 90002 Yes, sure, welcome. 90003 90002 OEM Service 90003 90002 1.Warranty is one year and if any parts broken within one year (consumbles not included and under correct operation), 90003 90002 we will send you new one by express for your change. 90067 2.Your problems will be replied within 24 hours and solutions provide within 3 working days 90003 90002 3.Free Installation instructions and other helps from our engineers. 90003 90002 4.Cost-free training video for you. 90003 90002 90003 90002 90003 90002 Technical support 90067 1.Provide the necessary professional training in factory. 90067 2.Comprehensive technical support provide pre-sales & after-sales. 90067 3.Presentation & promotion of the new innovative products & technology. 90003 90002 90003 90002 90003 90002 Spare part support 90067 1.Provide certain spare parts in every order shipment.90067 2.Provide free maintenance or replacement spare parts within the given warranty period. 90067 3.Provide free maintenance technology and spare parts chargeable under out of warranty. 90003 90002 90003 90002 90003 90002 After sale service 90067 1.Provide the pre-sales, in-sales and after-sales services. 90067 2.Provide all technical training. 90067 3.1 year warranty for offline UPS, online UPS and battery. 90003 90002 90003 90002 Maintenance service 90067 1.Provide the long time maintenance service.90067 2.Provide the extended warranty as expected. 90067 3.Provide the regular routime maintenance service. 90003 90002 Contact us 90003 90002 If you have any questions, please contact us.We’ll response you quickly. 90003 90002 90166 Address: NO.168, West Fenghuang Road, Taizhou, Jiangsu, China (Mainland) 90167 90003 90002 90166 Mobile: +8613801423565 90167 90003 90002 90166 Tel: 86 (0523) 86330266 90167 90003 90002 90166 QQ: 1065309566 90167 90003 90002 90166 WhatsAPP: +8613801423565 90167 90003.