Электроэрозионная обработка. Описание процесса, принципы, установки электроэрозионной обрботки.
1. Сущность и назначение электроэрозионной обработки
Электроэрозия – это разрушение поверхности изделия под действием электрического разряда. Основателями технологии являются советские ученые-технологи Б.Р. Лазаренко и Н.И. Лазаренко.
Электроэрозионная обработка (ЭЭО) широко применяется для изменения размеров металлических изделий – для получения отверстий различной формы, фасонных полостей, профильных канавок и пазов в деталях из твердых сплавов, для упрочнения инструмента, для электропечатания, шлифования, резки и др.
Рис. 1.9. Схема электроэрозионной обработки материалов: 1 – электрод-инструмент, 2 – обрабатываемая деталь, 3 – среда, в которой производится разряд, 4 – конденсатор, 5 – реостат, 6 – источник питания, 1р – режим электроискровой обработки, 2р – режим электроимпульсной обработки
Схема электроэрозионной обработки материалов приведена на рис. 1.9. Схема запитывается импульсным напряжением разной полярности, что соответствует электроискровому режиму (1р) и электроимпульсному режиму (2р). Напряжение питания заряжает конденсатор (4), параллельно которому включен разрядный промежуток между электродом-инструментом (1) и обрабатываемой деталью (2), которые помещены в жидкость с низкой диэлектрической проницаемостью. Когда напряжение на конденсаторе превысит потенциал зажигания разряда, происходит пробой жидкости. Жидкость нагревается до температуры кипения и образуется газовый пузырь из паров жидкости. Далее электрический разряд развивается в газовой среде, что приводит к интенсивному локальному разогреванию детали, приповерхностные слои материала плавятся и продукты расплава в виде шариков застывают в проточной жидкости и выносятся из зоны обработки.
2. Стадии электроэрозионной обработки Режим электроискровой обработки
Обрабатываемая деталь является анодом (+), то есть в данном случае деталь обрабатывается электронным потоком, то есть работает электронный стример, расплавляя объем анода-детали в виде лунки. Для того чтобы ионный поток не разрушал электрод-инструмент, используются импульсы напряжения длительностью не более 10-3 с. Электроискровой режим используется для чистовой, точной обработки, поскольку съем металла в данном случае небольшой.
Режим электроимпульсной обработки
Обрабатываемая деталь является катодом, то есть на нее подается отрицательный импульс длительностью больше 10-3 с. При электроимпульсной обработке между электродами зажигается дуговой разряд и обработка деталей ведется ионным потоком. Данный режим характеризуется большой скоростью съема металла, превышающей производительность электроискрового режима в 8-10 раз, но при этом чистота обработки существенно хуже. При обоих режимах в качестве рабочей жидкости, как правило, используется керосин или изоляционные масла.
3. Физика электроэрозионной обработки
Явления, происходящие в межэлектродном промежутке, весьма сложны и являются предметом специальных исследований. Здесь же будет рассмотрена простейшая схема удаления металла из области обработки посредством электрической эрозии.
Как показано на рис. 1.10, к электродам 1 подведено напряжение, которое создает электрическое поле в межэлектродном промежутке. При сближении электродов на критическое расстояние, возникает электрический разряд в виде проводящего канала. Для повышения интенсивности разряда электроды погружают в диэлектрическую жидкость 2 (керосин, минеральное масло и др.) На поверхности электродов имеются микронеровности различной величины. Напряженность электрического поля будет наибольшей между двумя наиболее близкими друг к другу выступами на поверхности электродов, поэтому именно здесь возникают проводящие мостики из примесных частиц жидкости. Ток по мостикам нагревает жидкость до испарения и образуется газовый пузырь (4), внутри которого и развивается мощный искровой или дуговой разряд, сопровождающийся ударной волной. Возникают потоки электронов и ионов (положительные и отрицательные стримеры), которые бомбардируют электроды. Образуется плазменный канал разряда. Благодаря высокой концентрации энергии в зоне разряда температура достигает тысячи и десятков тысяч градусов. Металл на поверхности электродов плавится и испаряется. Капли расплавленного металла в результате движения потока жидкости в рабочей зоне выбрасываются за пределы электродов и застывают в окружающей электроды жидкости в виде мелких частиц сферической формы (5).
От взаимодействия жидкости с участками электродов, нагретых до температуры 100-400 0С, на границах плазменного канала разряда происходит пиролиз диэлектрической жидкости. В результате в жидкости образуются газы, а также асфальтосмолистые вещества. Из газовой среды выделяется углерод, отлагающийся на нагретых поверхностях электродов в виде тонкой пленки кристаллического графита. В месте действия импульса тока на поверхностях электродов остаются небольшие углубления – лунки, образовавшиеся вследствие удаления разрядом некоторого количества металла.
В табл. 1.2 приведена зависимость величины эрозии стального электрода от энергии и длительности одиночного импульса.
Таблица 1.2
Зависимость величины эрозии стального электрода (анода) от энергии и длительности одиночного импульса
Характеристика импульса | Размеры лунки | |||
Энергия, Дж | Длительность, мкс | Глубина, мм | Диаметр, мм | Объем, м3 |
0,001 0,1 1,0 2,0 | 9 40 60 1500 | 0,015 0,025 0,042 0,050 | 0,1 0,75 1,65 2,00 | 0,000078 0,0074 0,06 0,10 |
Рис. 1.10. Режим электроэрозионной обработки: 1 – электроды, 2 – жидкость, 3 – лунки, 4 – газовый пузырь, 5 – продукты эрозии
После разряда в течение некоторого времени происходит остывание столба канала и деионизация вещества плазмы в межэлектродном промежутке. Электрическая прочность межэлектродного промежутка восстанавливается. Время деионизации жидкого диэлектрика составляет 106-10-2 с. Следующий разряд обычно возникает уже в новом месте, между двумя другими ближайшими точками электродов.
Длительность интервалов между импульсами должна быть достаточной для удаления из зоны разряда продуктов эрозии, а также газового пузыря, являющегося главным препятствием для возникновения следующего разряда. В связи с этим частота разрядов с возрастанием их энергии снижается.
Так происходит до тех пор, пока разряды не удалят с поверхности электродов все участки металла, которые находятся на расстоянии пробоя при величине приложенного напряжения. Когда расстояние между электродами превысит пробивное, для возобновления разрядов электроды должны быть сближены. Обычно электроды сближают в течение всего времени обработки так, чтобы электрические разряды не прекращались.
Параметры рабочих импульсов. Основными параметрами электрических импульсов, подаваемых на межэлектродный промежуток, являются их частота повторения, длительность, амплитуда и скважность, а также форма, определяющие максимальную мощность и энергию. Форма и параметры импульсов оказывают существенное влияние на износ электрода-инструмента, производительность и шероховатость обработанной поверхности.
Обозначим частоту повторения импульсов, т. е. их число в секунду, через f. Тогда Т = 1/f будет являться периодом. Он определяет промежуток времени, через который следует очередной импульс.
Импульс характеризуется амплитудным значением (или амплитудой) напряжения и тока Um и Im. Это максимальные значения, которые приобретают напряжение и ток за время импульса. При электроэрозионной обработке амплитуда напряжения изменяется от нескольких вольт до нескольких сотен вольт, а амплитуда тока от доли ампера до десятков тысяч ампер. Диапазон скважностей импульса при электроэрозионной обработке заключен в пределах от 1 до 30.
Полярный эффект и полярность импульса. Высокая температура в канале разряда и происходящие динамические процессы вызывают эрозию обоих электродов. Повышение эрозии одного электрода по сравнению с другим электродом называется полярным эффектом. Полярный эффект определяется материалом электродов, энергией и длительностью импульсов, знаком подведенного к электроду потенциала.
Процессы изменения напряжения и тока имеют колебательный характер относительно их нулевого значения. При электроэрозионной обработке принято считать рабочей или прямой полярностью импульса ту его часть, которая вызывает наибольший эффект эрозии обрабатываемой заготовки, а обратной – часть импульса, вызывающую усиленную эрозию электрода-инструмента. Обрабатываемую заготовку присоединяют к тому полюсу, эффект эрозии которого в данных условиях больше. К противоположному полюсу присоединяют электрод- инструмент. Например, при коротких импульсах электроискровой обработки энергия преимущественно поступает на анод, в качестве которого здесь следует использовать заготовку (прямая полярность). При увеличении длительности импульсов наступает перераспределение теплового потока на электродах. Это приводит к тому, что при определенных режимах электроимпульсной обработки эрозия анода становится меньше, чем эрозия катода. В этом случае следует применять обратную полярность, используя заготовку в качестве катода.
Электроэрозионная обрабатываемость. Эффект эрозии различных металлов и сплавов, производимый одинаковыми по своим параметрам электрическими импульсами, различен. Зависимость интенсивности эрозии от свойств металлов называют электроэрозионной обрабатываемостью.
Различное влияние импульсных разрядов на металлы и сплавы зависит от их теплофизических констант: – температур плавления и кипения, теплопроводности, теплоемкости. Если принять электроэрозионную обрабатываемость стали за единицу, то электроэрозионная обрабатываемость других металлов (при тех же условиях) может быть представлена в следующих относительных единицах: вольфрам – 0,3; твердый сплав – 0,5; титан – 0,6; никель – 0,8; медь – 1,1; латунь – 1,6; алюминий – 4; магний – 6 (указанные данные справедливы только при конкретных условиях: энергия импульса 0,125 Дж, длительность 1.4-10-5 с, частота 1200 1/с, амплитуда тока 250 А).
Рабочая среда. Большинство операций при электроэрозионной обработке производят в жидкости. Она обеспечивает условия, необходимые для удаления продуктов эрозии из межэлектродного промежутка, стабилизирует процесс, влияет на электрическую прочность межэлектродного промежутка. Жидкости, пригодные для электроискровой обработки, должны обладать соответствующей вязкостью, электроизоляционными свойствами, химической устойчивостью к действию разрядов.
С повышением частоты импульсов и снижением рабочего тока стабильность рабочего процесса ухудшается. Это вызывает необходимость увеличить скважность импульсов. Применение прямоугольных импульсов существенно повышает производительность.
Производительность обработки можно повысить, если применять принудительное удаление продуктов эрозии из межэлектродного промежутка. Для этого в межэлектродный промежуток под давлением нагнетают жидкость (рис. 1.11).
Рис. 1.11. Схема подвода жидкости в межэлектродный промежуток через полый электрод при прошивании отверстия
Хорошие результаты дает наложение вибраций на электрод-инструмент, а также вращение одного или обоих электродов. Давление жидкости зависит от глубины отверстия и величины межэлектродного промежутка. Вибрации особенно необходимы при электроискровой обработке глубоких отверстий малого диаметра и узких щелей. Большинство электроэрозионных станков снабжено специальной вибрационной головкой.
Качество поверхности и точность обработки. Металл электродов подвергается хотя и локальному, кратковременному, но весьма интенсивному электротермическому воздействию. Наивысшая температура существует на обрабатываемой поверхности и быстро уменьшается на некотором расстоянии от поверхности. Большая часть расплавленного металла и его паров удаляется из зоны разряда, но некоторая часть остается в лунке (рис. 1.12). При застывании металла на поверхности лунки образуется пленка, по своим свойствам отличающаяся от основного металла.
Рис. 1.12. Лунка, полученная в результате воздействия единичного импульса: 1 – пространство, оставшееся после выплавления металла; 2 – белый слой; 3 – валик вокруг лунки; 4 – обрабатываемая заготовка; БЛ, НЛ – диаметр и глубина лунки
Поверхностный слой в расплавленном состоянии активно вступает в химическое взаимодействие с парами и продуктами разложения рабочей жидкости, образующимися в зоне высоких температур. Результатом этого взаимодействия является интенсивное насыщение металла компонентами, содержащимися в жидкой среде, а также веществами, входящими в состав электрода-инструмента. Таким образом, в поверхностный слой могут быть внесены титан, хром, вольфрам и т. д. При электроэрозионной обработке стальных заготовок в среде, состоящей из жидких углеводородов (керосин, масло), поверхностный слой насыщается углеродом, т. е. образуются карбиды железа. Следовательно, при электроэрозионной обработке происходит упрочнение поверхности детали.
Интенсивный теплоотвод из зоны разряда через прилегающие к ней массы холодного металла и рабочую жидкость создает условия для сверхскоростной закалки, что одновременно с науглероживанием приводит к образованию очень твердого слоя. Закаленный поверхностный слой стали обладает повышенной стойкостью на истирание и меньшим, чем у нетермообработанной стали коэффициентом трения. Структура поверхностного слоя существенно отличается от структуры основного металла и схожа со структурой отбеленного слоя, возникающего на поверхности некоторых чугунов. Поэтому этот слой получил название «белый слой». Глубина белого слоя зависит от энергии импульсов, их длительности и теплофизических свойств обрабатываемого материала. При длительных импульсах тока большой энергии глубина белого слоя равна десятым долям миллиметра, а при коротких импульсах – сотым долям миллиметра и микронам.
Упрочнение поверхностного слоя металлов (электроэрозионное легирование). Одним из преимуществ электроискрового метода обработки материалов является то, что при определенных условиях резко повышаются прочностные свойства поверхности заготовки: твердость, износостойкость, жаростойкость и эрозионная стойкость. Эту особенность используют для повышения износостойкости режущего инструмента, штампов, пресс-форм и деталей машин, упрочняя металлические поверхности электроискровым способом.
При электроискровом легировании применяют обратную полярность (заготовка является катодом, инструмент – анодом) обработку производят обычно в воздушной среде и, как правило, с вибрацией электрода. Аппаратура, с помощью которой осуществляется процесс упрочнения, малогабаритна и очень проста в эксплуатации. Основные преимущества электроискрового способа нанесения покрытий заключаются в следующем: покрытия имеют большую прочность сцепления с материалом основы; покрываемые поверхности не требуют предварительной подготовки; возможно нанесение не только металлов и их сплавов, но и их композиций. Процессы, происходящие при электроискровом упрочнении, сложны и являются предметом тщательных исследований. Сущность упрочнения состоит в том, что при электроискровом разряде в воздушной среде происходит полярный перенос материала электрода на заготовку. Перенесенный материал электрода легирует металл заготовки и, химически соединяясь с диссоциированным атомарным азотом воздуха, углеродом и материалом заготовки, образует диффузионный износоустойчивый упрочненный слой. При этом в слое возникают сложные химические соединения, высокостойкие нитриды и карбонитриды, а также закалочные структуры. По мнению специалистов, при электроискровом упрочнении в поверхностном слое, например, стали происходят процессы, приведенные в табл. 1.3.
Таблица 1.3
Упрочняемый материал | Процесс | |
Вид | Особенности | |
Углеродистая сталь, содержащая углерод в количестве свыше 0,6 %, а также легирующие элементы в большом количестве | Сверхскоростная закалка | Кратковременный нагрев до высокой температуры и мгновенное охлаждение нагретых и расплавленных участков массой холодного металла |
Инструментальная сталь | Азотирование | Диссоциация атмосферного азота в разряде с образованием атомарного азота. |
При электроискровом упрочнении микротвердость белого слоя в углеродистых сталях может быть доведена до 230 МПа, высота микронеровностей обработанной поверхности до 2,5 мкм. Толщина слоя покрытия, получаемого на некоторых установках, составляет 0,003-0,2 мм.
4. Основные технологии электроэрозионной обработки металлов
Технологии размерной обработки металлических деталей.
Формообразование деталей электроэрозионным методом можно осуществить по следующим схемам.
1. Копирование формы электрода или его сечения. При этом обрабатываемый элемент заготовки по форме является обратным отображением рабочей поверхности инструмента. Данную операцию называют прошиванием. Существуют методы прямого и обратного копирования. При прямом копировании инструмент находится над заготовкой, а при обратном – под ней. Метод прошивания прост в исполнении, и он широко применяется в промышленности. На рис. 1.13 представлена схема электроэрозионной обработки методом копирования формы электрода- инструмента. По мере электроэрозионной обработки электрод (1) внедряется в деталь, обеспечивая копирование электрода.
2. Взаимное перемещение обрабатываемой заготовки и электрода- инструмента. При этой схеме возможны операции вырезания сложно- профильных деталей и разрезание заготовок электродами, электроэрозионного шлифования и растачивания деталей.
Рис. 1.13. Схема копирования формы электрода: 1 – электрод-инструмент, 2 – обрабатываемая деталь, 3 – жидкость, 4 – сосуд
Прошивание окон, щелей и отверстий. Эта операция осуществляется на универсальных станках. Электроэрозионным способом прошивают щели шириной (2,5-10) мм, глубиной до 100 мм. Для обеспечения удаления продуктов эрозии из межэлектродного промежутка, электрод-инструмент делают Т-образной формы или уменьшают толщину хвостовой части по сравнению с рабочей частью на несколько десятых долей миллиметра. Скорость прошивания щелей составляет (0,5-0,8) мм/мин, шероховатость обработанной поверхности – до 2,5 мкм.
Обработка деталей типа сеток и сит. Созданы электроэрозионные станки, позволяющие обрабатывать сеточные детали с числом отверстий до нескольких тысяч. Станки могут обрабатывать одновременно более 800 отверстий диаметром (0,2-2) мм в листах из коррозионно- стойких сталей, латуни и других материалов толщиной до 2 мм. Производительность обработки до 10000 отверстий в час.
Электроэрозионное шлифование. Это одна из разновидностей электроэрозионной обработки, которая используется для обработки высокопрочных заготовок из сталей и твердых сплавов. Удаление металла при этом происходит под воздействием импульсных разрядов между вращающимся электродом-инструментом и обрабатываемой заготовкой, а не в результате механического воздействия, как при абразивном шлифовании.
Сложноконтурная проволочная вырезка. Методы прямого и обратного копирования имеют существенный недостаток, заключающийся в необходимости использования сложных фасонных электродов- инструментов. Износ электродов отражается на точности изготовления деталей, поэтому одним электродом-инструментом удается изготовить не более 5-10 деталей.
Электроискровой метод сложноконтурной проволочной вырезки выгодно отличается от методов копирования тем, что здесь инструментом является тонкая проволока из меди, латуни или вольфрама диаметром от нескольких микрон до 0,5 мм, включаемая в электрическую схему как катод (см. рис. 1.14).
Рис. 1.14. Сложноконтурная проволочная вырезка: 1 – проволока, 2 – обрабатываемая деталь, 3 – направляющие ролики, 4 – устройство для регулирования скорости протяжки проволоки
Для устранения влияния износа проволоки на точность обработки, проволока перематывается с одной катушки на другую, что позволяет все новым элементам участвовать в работе. При перемотке осуществляется небольшой натяг. Возле обрабатываемой заготовки установлены ролики, ориентирующие проволоку относительно обрабатываемой детали. Сложноконтурная проволочная вырезка применяется при прецизионном резании заготовок, прорезании точных щелей, резании полупроводниковых материалов, обработке цилиндрических, конических наружных и внутренних поверхностей.
К основным достоинствам электроэрозионной обработки проволочным электродом-инструментом относится высокая точность и возможность широкой автоматизации процесса.
Электроконтактный способ обработки. Электроконтактная обработка материалов является разновидностью электроэрозионной обработки. Отличие ее состоит в том, что импульсы электрической энергии генерируются в результате взаимного перемещения электродов или прерывания электрического разряда при прокачке жидкости под давлением. Электроконтактную обработку можно проводить при постоянном и переменном токе, в воздухе или жидкости (вода с антикоррозионными добавками). При обработке электрод-инструмент и заготовку полностью погружают в жидкость либо подают жидкость в межэлектродный промежуток распылением. Обработку производят при значительных токах (до 5000 А) и напряжениях холостого хода источника питания 18-40 В. Электроконтактным методом производят получистовое точение тел вращения, чистовую резку, прошивание цилиндрических, фасонных отверстий и объемных полостей, фрезерование, шлифование. Электроконтактный метод особенно эффективен при обработке заготовок из труднообрабатываемых сталей и сплавов, а также чугунов высокой твердости, монокристаллов, материалов с высокими теплофизическими свойствами.
Принципиальная схема установки для электроконтактной обработки выглядит следующим образом. Заготовка и электрод-инструмент, имеющие ось вращательной симметрии и включенные в цепь с источником питания, после соприкосновения совершают вращательное движение друг относительно друга.
При соблюдении условий, необходимых для реализации электроэрозионных процессов, происходит съем металла с заготовки.
Упрочнение поверхностного слоя металла (электроэрозионное легирование)
Одним из преимуществ электроэрозионной обработки металлов является то, что при определенных условиях резко повышаются прочностные свойства поверхности заготовки. Эту особенность используют для улучшения износостойкости режущего инструмента, штампов, пресс-форм и т.д. При электроэрозионном легировании применяют обратную полярность (заготовка является катодом, инструмент – анодом) обработку производят обычно атомами инструмента-электрода в электроимпульсном режиме (см. рис. 1.15) в воздушной среде и, как правило, с вибрацией электрода.
Рис. 1.15 Схема электроэрозионного легирования: 1 – легирующий электрод-инструмент, 2 – легируемая деталь
Основные преимущества электроэрозионного легирования заключаются в следующем: покрытия имеют большую степень сцепления с материалом основы; покрываемые поверхности не требуют предварительной подготовки; возможно нанесение не только металлов и сплавов, но и их композиций.
Процессы, происходящие при электроэрозионном упрочнении, сложны и являются предметом тщательных исследований. Однако, сущность упрочнения состоит в том, что при электроискровом разряде в воздушной среде происходит перенос материала электрода на заготовку (см. рис. 1.15). Перенесенный материал электрода легирует металл заготовки и, химически соединяясь с ионами азота воздуха, углеродом и материалом заготовки, образует износоустойчивый упрочненный слой, состоящий из нитридов, карбонитридов и других закалочных структур.
При электроискровом легировании микротвердость белого слоя в углеродистых сталях может быть доведена до 230 МПа. Толщина слоя покрытия, получаемого на некоторых установках, составляет 0,003-0,2 мм. При упрочнении поверхности деталей машин (например, на установке ИЕ-2М) можно получить глубину слоя до 0,5-1,6 мм с микротвердостью 50-60 МПа (при упрочнении феррохромом).
Различают чистую обработку, которая соответствует высоким напряжениям и небольшим значениям токов короткого замыкания (до 20 А), и грубую (грубое легирование) при низких напряжениях 50-60 В и токах короткого замыкания свыше 20 А.
Работа на электроэрозионных станках. Подготовка электроэрозионных станков к работе заключается в установке заготовки и электрода-инструмента и выверке их взаимного расположения, подготовке ванны к работе и системы прокачки рабочей жидкости, выбору и настройке режимов генератора. Заготовку устанавливают и закрепляют непосредственно на столе станка или в приспособлении. Электрод-инструмент устанавливают хвостиком в шпиндель головки. При выверке используют индикаторы, оптические приборы, приспособления, позволяющие изменять положение инструмента по отношению к заготовке и угол наклона.
Осуществив выверку положения электрод-инструмента, заполняют ванну рабочей жидкостью, проверяют работу системы прокачки, устанавливают необходимое давление прокачки. Задают режим генератора импульсов (полярность, форма импульсов, скважность, частоту следования импульсов, средний ток), пользуясь соответствующими таблицами и номограммами. Изменение полярности напряжения генератора импульсов производится путем переключения на штепсельном разъеме токоподводов к станку. При работе с прямой полярностью (электроискровой режим) на электрод подается отрицательный потенциал, а на заготовку – положительный. Для работы с обратной полярностью (электроимпульсный режим) производят обратное переключение. Установку электрических параметров и режимов работы осуществляют с помощью переключателей, расположенных на панели пульта управления. Настраивают регулятор подачи, устанавливая рекомендуемое напряжение регулятора.
Электроэрозионная обработка. Описание процесса, принципы, установки электроэрозионной обрботки. Границы применения электроэрозионной обработки
Чтобы изменять размеры металлических деталей без каких-либо изменений их физических свойств, используется электроэрозионная обработка, выполнение которой требует наличия специального оборудования и хорошего знания соответствующих технологий.
Электроэрозионная обработка металлов, помимо изменения размеров различных деталей, дает возможность также получить отверстия требуемой формы и конфигурации, сделать при необходимости фасонные полости, а также изготовить профильные канавки и пазы на тех заготовках, которые созданы на основе твердых сплавов.
На видео в статье наглядно показано, как проводится данный вид обработки и какие проблемы могут возникнуть в процессе.
Кроме этого, данный метод дает возможность сделать различный инструмент более прочным, позволяет про
>изводить качественное электропечатание, высокоточное шлифование, выполнять резку деталей, а также многое другое.
Простейшая схема, при которой возможна обработка, в обязательном порядке содержит определенный электрод, состав, который подходит для выполнения электрического разряда, а также такие элементы, как конденсатор, реостат и непосредственно сам источник питания.
Выполнять данный вид обработки металлических деталей следует при полном соблюдении соответствующих правил по технике безопасности.
Для того чтобы на практике выполнить данный вид обработки, необходимо, для начала, правильно собрать в единую цепь все необходимые элементы, а также выполнить предварительную подготовку деталей, с которыми предстоит работать.
В настоящее время на промышленных предприятиях используют несколько видов электроэрозионной обработки металлических деталей.
Следует отметить, что одним из главнейших элементов в схеме, по которой выполняется электроэрозионная обработка, является электрод, который должен обладать достаточной эрозионной стойкостью.
В этом случае целесообразно использовать в качестве электрода такие металлы, как медь, графит, вольфрам, а также латунь и алюминий.
Если посмотреть со стороны химии, то данный метод термического воздействия непосредственно на металл определенным образом разрушает его кристаллическую решетку, за счет чего происходит высвобождение некоторых категорий ионов.
Достаточно часто для обработки металла используют электроимпульсный и электроискровой методы. Кроме этого, можно встретить так же электроконтактный и анодно-механический способы. Более детально об этом смотрите в видео в статье.
В том случае, когда для металлических деталей требуется черновая обработка, как правило, используется электроимпульсная схема обработки.
В этом случае при проведении необходимых работ температура вырабатываемых импульсов может подниматься до пяти тысяч градусов по Цельсию.
При необходимости выполнить данный тип обработки заготовок с небольшими габаритами и размерами, целесообразно использовать электроискровой способ.
В свою очередь, при работе со сплавами в жидкой среде, в большинстве случаев применяют электроконтактную обработку.
Следует отметить, что те свойства, которые приобретает металл после того, как будет произведена такая обработка, могут совершенно по-разному сказаться на эксплуатационных характеристиках деталей.
В большинстве случаев, под воздействием высоких температуры и токов у обрабатываемых деталей значительно повышается прочность, притом, что в самой структуре сохраняется мягкость.
Типы используемого оборудования
Как известно, существуют самые разные методы и способы обработки поверхностей металлов, при этом данный вид является более эффективным, чем механические.
Связано это главным образом с тем, что тот инструмент, который используется для проведения механических типов обработки, стоит гораздо дороже, чем проволока, которая применяется при электроэрозионной обработке.
На промышленных предприятиях для электроэрозионной обработки самых разных деталей используется специальное оборудование.
В том случае, когда необходимо изготовить пресс-формы и детали со сложной формой, а также при производстве некоторых материалов, к которым применяются высокие требования к точности обработки, используют проволочно-вырезные электроэрозионные агрегаты.
Как правило, на таком типе оборудования изготавливают самые разные детали для самолетов, электроники и даже космической сферы.
На видео, которое размещено ниже, можно увидеть, как проводится такая обработка с использованием электроэрозионного оборудования.
Для массового и серийного производства деталей по данному методу в большинстве случаев используют копировально-прошивочные агрегаты.
Такие станки позволяют получить достаточно точные сквозные контуры, а также мелкие отверстия, что успешно используется при производстве сеток, а также штампов в инструментальной сфере промышленности.
Как правило, оборудование данного типа подбирается, исходя из поставленных задач, а также финансовой окупаемости. Следует отметить и то, что электроэрозионную обработку относят к сложным и достаточно трудоемким рабочим процессам.
Ее невозможно провести в домашних условиях своими руками. К работе на станках для данного вида обработки деталей допускаются только квалифицированные и аттестованные люди, которые имеют соответствующий опыт работы в данной сфере.
При выполнении электроэрозионной обработки необходимо не только соблюдать технику безопасности, но и обязательно надеть спецодежду.
Преимущества обработки
Электроэрозионное воздействие на металл должно выполняться только на специальном оборудовании и под присмотром квалифицированного человека, который имеет соответствующий допуск.
Несмотря на то, что данный способ делает заготовку более качественной и точной, все же на промышленных предприятиях больше всего распространена механическая обработка металлических поверхностей.
В этом случае следует отметить все основные преимущества электроэрозионного воздействия на различные типы заготовок.
В первую очередь, при использовании данного метода удается добиться высочайшего качества поверхности металла, она становится однородной и максимально точной.
Следует отметить и то, что в этом случае необходимость в проведении финишной обработки полностью исключается. Кроме этого, данный метод дает возможность получать на выходе поверхность с самой разной структурой.
К достоинствам электроэрозионного воздействия следует отнести и возможность работать с поверхностью практически любой твердости.
Также при данном методе полностью исключается деформация поверхности у деталей с небольшой толщиной.
Это происходит по причине того, что метод не предполагает какой-либо механической нагрузки. При данном способе воздействия на металлическую поверхность рабочий анод имеет минимальный износ.
Следует отметить и то, что электроэрозионное воздействие позволяет получить при минимальных усилиях поверхности самых разных конфигураций и геометрических форм.
Еще одним достоинством данного процесса является полное отсутствие шума во время работы на специальном оборудовании.
Конечно, есть и свои проблемы такого воздействия на металлическую деталь, однако они не сильно сказываются на ее эксплуатационных свойствах.
Электроэрозионный станок, используемый для обработки различных металлов, можно увидеть на видео, которое размещено ниже.
Технология обработки
Для того чтобы досконально разобраться во всех преимуществах электроэрозионного воздействия на металлические заготовки и понять сам принцип, необходимо подробно рассмотреть один из способов.
Так, простейшая электроэрозионная схема должна в обязательном порядке состоять из таких элементов, как электрод, емкость для рабочей среды, а также конденсатора, реостата и непосредственно источника, обеспечивающего необходимое электропитание.
В данную схему должны быть включены все необходимые элементы в определенной последовательности. Питание данной схемы осуществляется от напряжения импульсного типа, при этом оно должно иметь разную полярность.
Это даст возможность получить необходимые для работы электроимпульсный и электроискровый режимы.
При подаче напряжения идет зарядка конденсатора, от которого разрядный ток поступает на электрод, который должен быть предварительно опущен в емкость с рабочим составом и заготовкой.
После того, как на конденсаторе напряжение достигнет необходимого потенциала, произойдет пробой жидкости, которая быстро нагреется до температуры кипения, а кроме этого, в ней возникнет пузырь из газов.
Этот пузырь будет способствовать локальному нагреву заготовки, у которой произойдет плавление самых верхних слоев, что позволит обеспечить заданную форму.
В данном способе есть определенные проблемы, которые требуют постоянного контроля самого процесса, а поэтому лучше воспользоваться более совершенными методами.
На видео выше показана обработка, проводимая на профессиональном оборудовании.
Электроэрозионная обработка
(CNC Wire Cut EDM Machine) металлов, сплавов, деталей, узлов, инструментов.
Наше оборудование позволяет выполнять электроэрозионную обработку токопроводящих материалов и изготавливать детали различной формы и сложности.
- обработка стали любой твердости;
- обработка титана;
- твердых сплавов;
- жаропрочных сплавов;
- обработка магнитов;
- прошивка отверстий, полостей, углублений;
- получение методом копирования профилированных поверхностей, отверстий любого сечения;
- нанесение надписей и маркировки на металлах;
- изготовление прототипов статоров электродвигателей из магнитной стали;
- изготовление планетарных редукторов.
ПРИМЕРЫ НАШИХ РАБОТ
Электроэрозионная обработка
Сущностью процесса электроэрозионной резки является воздействие на деталь искровых разрядов,
образующихся вследствие протекания импульсного тока с частотой в районе 240 кГц между электродом-проволокой и
деталью, находящихся в непосредственной близости друг от друга в среде жидкого диэлектрика. В результате этих
разрядов из материала детали выбиваются микрочастицы, которые выносятся из межэлектродного зазора (GAP) струей
диэлектрика. Кроме этого, диэлектрик играет роль катализатора процесса распада, так как при высочайшей
температуре разряда диэлектрик в зоне эрозии превращается в пар. Происходит дополнительный микровзрыв пара,
который не может сразу выйти из межэлектродного зазора.
За последние годы электроэрозионная обработка не только окончательно закрепила свои позиции в современном
инструментальном производстве, но и продолжает развиваться быстрыми темпами в направлении улучшения
качественных показателей и предложения новых конструктивных решений.
Открытие формообразующего воздействия электрической эрозии на токопроводящие материалы состоялось в 1943
году и принадлежит нашим соотечественникам – супругам Б. и Н. Лазаренко. Когда повсюду в мире в 50-х годах
лучшие умы всерьез взялись за эту технологию, чья-то советская руководящая воля свернула перспективные
разработки и ввергла нас в отставание на многие десятки лет в области электроэрозионной обработки. Ну что
же, как это не горько, поговорим об успехах других.
Диэлектрик в электроэрозионной обработке
Советские исследователи, супруги Лазаренко, которые впервые и открыли возможность использования
явления электрической эрозии для обработки токопроводящих материалов, в качестве диэлектрика вначале
использовали окружающий воздух. Однако скоро выяснилось, что производные минеральных масел имеют в этом плане
несравнимые преимущества: сила разряда – больше, можно
работать с меньшими искровыми промежутками, что улучшает точность операции. Новый материал диэлектрика также
позволил увеличить частоту разрядов и лучше вымывать частички эродированного металла.
С 1960 года на рынок стали выходить химические компании, предлагающие специальные составы для использования
в электроэрозионных установках.
О сути процесса:
Электроды – инструмент и заготовка – закреплены оснасткой станка и не соприкасаются друг с другом. Генератор электрических импульсов задает периодичность и напряженность электрического поля вокруг электродов.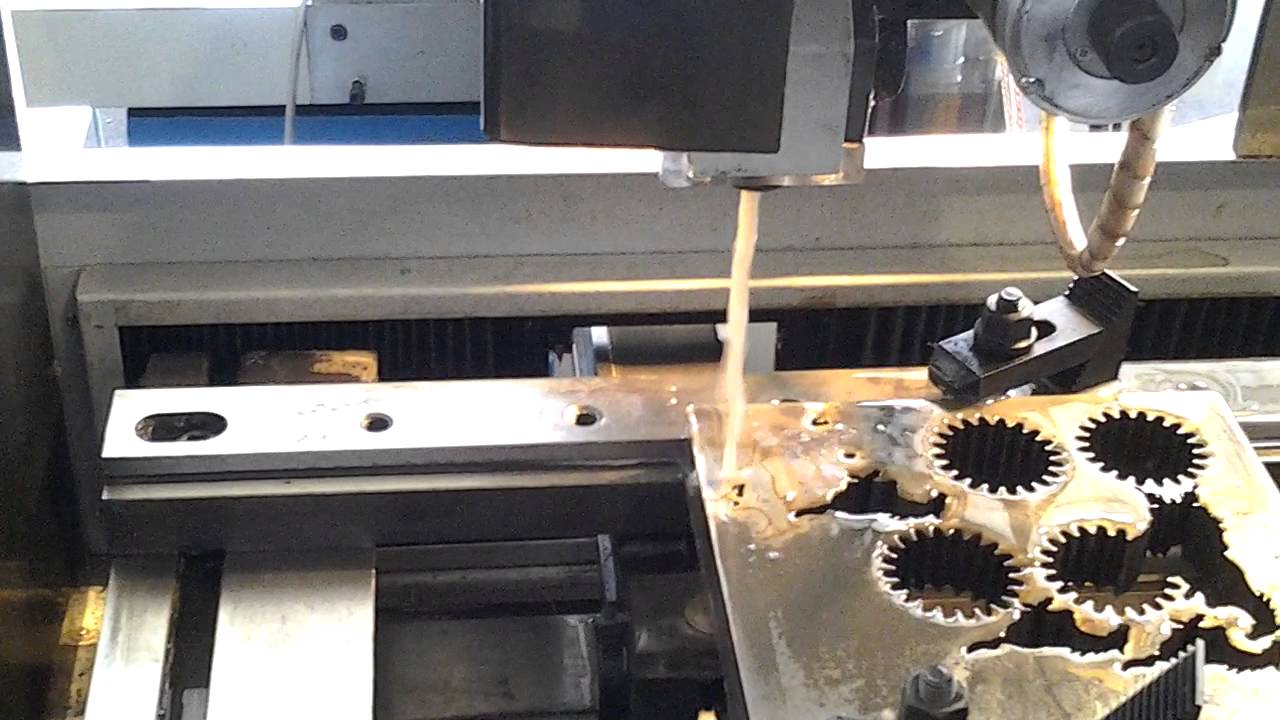
В точке, где напряженность электрического поля достигает максимума, происходит электрический разряд – молния в “микроатюре”. Под действием электрического поля электроны и свободные положительные ионы разгоняются до высоких скоростей и моментально образуют ионизационный туннель, обладающий электрической проводимостью. Возникает электроток, и между электродом и заготовкой образуется искровой разряд, приводящий к столкновениям элементарных частиц. Во время этого процесса образуется газовый пузырек, давление которого непрерывно нарастает до образования плазменной зоны. Плазменная зона быстро достигает сверхвысоких температур – от 8000 до 12000°С – благодаря нарастающему числу столкновений элементарных частиц. Этот процесс приводит к моментальному плавлению микрослоев вещества у электрода. При исчезновении электрического поля внезапное снижение температуры приводит к взрыву плазменного пузырька, что сопровождается отрывом части материала с заготовки, и к образованию на этом месте микроскопического кратера.
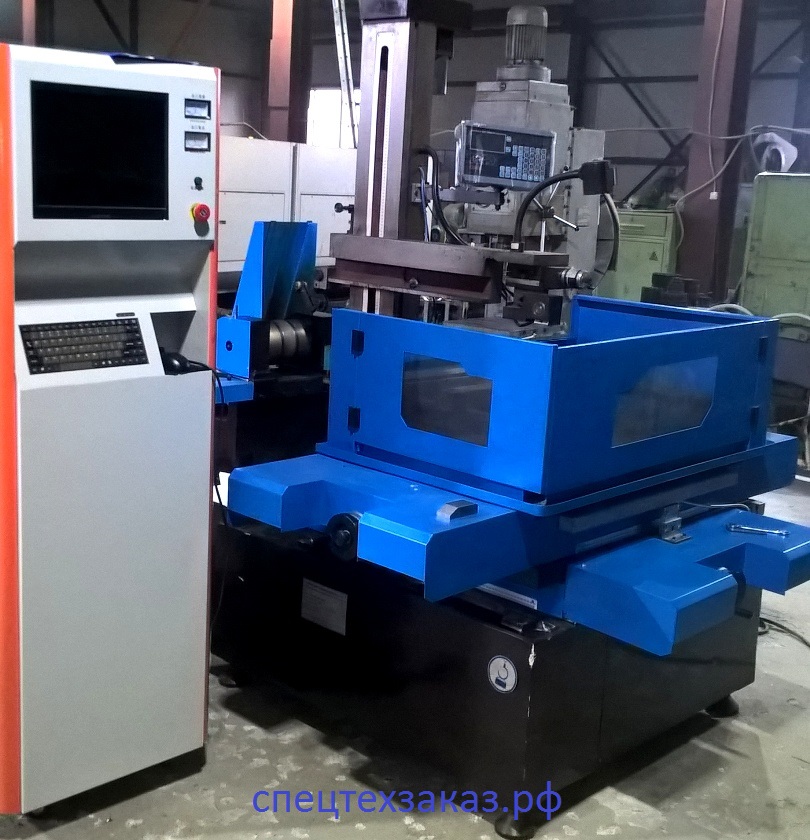

Неблизнецы-братья
Технология электроэрозионной обработки продолжает развиваться по двум основным направлениям: проволочная электроэрозионная резка (wire electric discharge machining) и копировально-прошивная электроэрозионная обработка (ram (die sinking) electric discharge machining).
Проволочная электроэрозионная резка
Проволочная резка начала свое развитие с чистого листа в начале 70-х годов. Глобальное совершенствование
процесса пришлось на период с середины 80-х до середины 90-х годов. Прогресс обозначился по шести ключевым
направлениям известного соотношения цена-качество:

Функции диэлектрика:
Электроизолирующая . Диэлектрик должен разделять заготовку и электрод. Искровой разряд
должен происходить в максимально узком промежутке между заготовкой и электродом, что позволяет сделать
процесс производительным и точным.
Ионизационная . За очень короткое время необходимо создать все условия для формирования электрического
поля. После импульса зона разряда должна быть очень быстро деионизирована для возможности повторного
разряда. Диэлектрик должен способствовать максимальному сужению искровой зоны, чтобы добиться высокой
плотности энергии в этой зоне.
Охлаждающая . Искровой разряд имеет сверхвысокую температуру, поэтому диэлектрик должен остудить и
электрод, и заготовку. Также важно увести металлические газы, образующиеся в процессе электроэрозии.
Промывочная . Чтобы избежать электрического пробоя диэлектрик должен эффективно удалять эродированные крупицы металла.
Скорость . Номинальная максимальная скорость резки на сегодняшний день превышает 300 кв. мм/мин, (в лабораторных
условиях реализована скорость вырезки 600 кв. мм/мин.). Конечно, средняя скорость резки в реальных
производственных условиях ниже номинальных величин, однако и это впечатляет по сравнению с показателями
четвертьвековой давности (25-30 кв. мм/мин.). Появление новых сплавов для проволоки может отодвинуть и эти рубежи.
Размер заготовки . Максимальные размеры заготовок, пригодных для обработки на вырезных станках, по осям Х и V
достигают метра и даже больше (1300-1380 мм – по оси X). Однако особенно сильно за последние десятилетия
вырос габаритный размер заготовки по оси 2, который сейчас доходит до 400 мм. До этой же отметки поднялись
и координатные перемещения по оси 2. Всего этого удалось добиться благодаря новым конструктивным решениям,
объединившим принципы неподвижности заготовки и более точной и жесткой реализации осевых движений.
Угол конусной резки . В современных установках достигаются углы вырезки конических отверстий до 30 градусов
для заготовок толщиной до 400 мм. Более того, некоторые фирмы в качестве опциона предлагают установки с
возможностью достижения конусности до 45 градусов. Такие возможности позволили с начала 90-х годов значительно
расширить область применения электроэрозионной резки. Так, если раньше головки для экструзионных установок
собирались из набора отдельно обработанных тонких пластин, то новые возможности электроэрозионных станков
позволили изготавливать экструзионные головки из одной заготовки и за одну операцию. За счет этого
удалось значительно снизить объем скрапа и увеличить производительность экструзионного процесса.
Цена . За более чем четверть века непрерывных работ на порядок улучшились характеристики вырезных станков, в
то время как за этот же период оборудование подешевело приблизительно на 75% (с учетом фактора инфляции). Целый
ряд обстоятельств способствовал снижению цены. Электронная начинка оборудования вобрала много решений, пришедших
из компьютерной индустрии, которые уже тогда отличались прекрасным соотношением цена-качество – возросшая
вычислительная мощь за меньшие деньги. Сильно увеличился объем производства электроэрозионного оборудования, что
повысило эффективность таких производств. Кроме того, все новые и новые технические решения также способствовали
планомерному снижению цен на установки.
Точность . Еще в 70-х и начале 80-х годов оператору станка приходилось вначале делать пробный рез образца и затем
корректировать первоначальные настройки, прежде чем выйти на точные геометрические размеры изделия.
Искровые промежутки
Искровой промежуток разделяет заготовку и электрод. Даже при малой глубине обработки
различают два типа промежутка: фронтальный и боковой. Фронтальный задается системой управления, в то время
как боковой искровой промежуток зависит от продолжительности и высоты разрядного импульса, сочетания
материалов, напряжения холостого хода и других заданных параметров.
Блок питания является важнейшим элементом электроэрозионной установки. Он преобразует переменный ток из
силовой сети в прямоугольные импульсы определенной полярности. Размер импульсов и интервал между ними
задается системой управления в соответствии с выполняемым режимом обработки. Сила тока разряда пропорциональна
высоте импульса. Интервал между импульсами соответствует моменту отсутствия искрового разряда, а протяженность
импульса соответствует длительности искрового разряда. Обе эти величины составляют тысячные или даже
миллионные доли секунды.
Интервал между отдельными импульсами (длительность отсутствия электрического тока) также задается системой
управления. Интервал измеряется в процентном отношении собственной длительности к длительности импульса.
Теперь все эти мытарства остались в прошлом и сегодняшняя точность станков достигает 0,001 мм.
Вовлечение современных информационных технологий (САD/САМ – системы) в технологический процесс также
позволило увеличить точность обработки – новые установки со всем комплексом современного оснащения гарантировали
повторение заложенной в программе геометрии с большой степенью точности.
Как уже отмечалось, современные модели станков на 75% дешевле своих ранних предшественников, в то же самое
время они в 3-5 раз точнее.
Длительная работа без вмешательства человека. В 70-х годах электроэрозионные установки могли работать целыми
часами без вмешательства оператора – тогда скорости резки были слишком малыми. В современных
условиях, когда значительно возросли скорости обработки, практически полностью безлюдное производство
обеспечивается за счет использования продвинутых систем автоматизации: устройства автоматической заправки
проволоки, поиска отверстия, предотвращения обрыва проволоки, системы автоматизированной загрузки
заготовок, удаления перемычек и т. д.
Износ электрода
Эрозия при малом токе снимает мало материала заготовки, тогда как большой ток позволяет
добиться больших скоростей снятия материала.
Однако и износ инструмента возрастает, особенно при обработке стали медными электродами. Графитовые электроды
ведут себя иначе – износ до определенного момента растет, затем более или менее стабилизируется.
Короткие импульсы также приводят к ускоренному износу электрода. И наоборот, износ идет значительно медленней
при длинных импульсах. На практике, при черновой обработке стали медным и графитовым инструментом оптимальная
величина длительности импульса лежит на отрезке, на одном конце которого длительность импульса с максимальным
съемом, а на другом – длительность импульса с минимальной интенсивностью износа инструмента.
Копировально-прошивочная обработка
Впервые об электроэрозионных станках стало известно с появлением в 1955 году первой
копировально-прошивочной установки с ручным управлением. Возможности станков были значительно улучшены к
концу 70-х годов, когда применение спутников позволило значительно уменьшить время цикла и число используемых
электродов. Примерно в 1980 году была представлена первая модель станка с СNС-управлением. К этому времени
процесс копировальной прошивки уже успел претерпеть все возможные усовершенствования, и характеристики
прошивочных СNС-станков улучшались более медленными темпами по сравнению с более “молодыми” проволочно-вырезными
станками. Наиважнейшим усовершенствованием по сравнению с ранними станками с ручным управлением было не
столько само время цикла, сколько число рабочих часов, необходимых для образования заданной полости в материале.
Ранее было замечено, что в случае проволочной резки увеличение производительности и снижение производственных
затрат в большей степени достигалось благодаря скорости резания. Что касается электроэрозионной прошивки, то
соответствующие улучшения были достигнуты благодаря существенному увеличению количества часов, которые способен
работать СNС-станок в течение дня. Обе технологии много выиграли от снижения нормочасов на каждой
детали. Переход с ручного управления на числовое программное позволил станкам работать практически всю первую
смену, интенсивно во вторую и третью в безлюдном режиме. Если для станка с ручным управлением наиболее типичной
является работа в течение 6 часов, то в случае станка с СNС-управлением реально выполнимой задачей может
быть 16 часов. Хотя на многих производствах достигаются и более высокие показатели.
Цена. Ведущие производители прошивочных станков предлагают сегодня СNС-станки (без системы автоматической смены
инструмента и оси С) примерно по той же цене, по которой в середине 70-х продавались станки с ручным
управлением (инфляция учитывается). Даже если добавить стоимость необходимых опций, то скорректированная цена
такого нового станка примерно будет равна цене станка 70-х с ручным управлением, который оснащен спутником.
Любое повышение цены будет существенно перевешиваться снижением времени цикла, нормочасов и увеличением времени,
которое оборудование реально работает в течение суток.
Точность обработки. Учитывая характер процесса формообразования при электроэрозионной прошивке, точность
обработки в большей степени будет зависеть от качества и точности изготовления электрода. Графит – более дешевый
и удобнообрабатываемый материал – в сочетании с современными технологиями высокоскоростной
фрезерной обработки
позволяет получать электроды большой сложности и высокой точности.
Определенные успехи были достигнуты и в отношении плоскостности обработанных поверхностей. Например, суммарное
отклонение для прямоугольной полости 150х200 мм, полученной на современном станке, составляет всего 0,008 мм.
Наш завод производит работы по электроэрозионной обработке металлических деталей, узлов, инструмента клиента на заказ. Мы берем заказы на электроэрозионные работы в Москве. Мы принимаем разовые заказы на электроэрозионную обработку отдельных металлических деталей и стальных узлов.
Заказать электроэрозионные работы можно обратившись в отдел продаж нашего завода по телефону +7 495 952-3966 или по электронной почте
Этот e-mail адрес защищен от спам-ботов, для его просмотра у Вас должен быть включен Javascript
. Для ускорения ответа по стоимости и срокам выполнения работ просим направить эскизы или чертежи по электронной почте Этот e-mail адрес защищен от спам-ботов, для его просмотра у Вас должен быть включен Javascript или по факсу.
Завод СТАНКОКОНСТРУКЦИЯ оказывает следующие услуги по электроэрозионной обработке:
Электроэрозионная обработка деталей сложного профиля с прямолинейной вертикальной или наклонной образующей из то копроводящих материалов независимо от их твердости. Фигурная резка металла, вырезка стали по контуру, высокоточный раскрой металла.
Услуги по электроэрозионной обработке любых токопроводящих материалов (любой твёрдости и хрупкости) на проволочных (вырезных) и копировально-прошивных электроэрозионных станках. Создание сложнопрофильного контура с точностью 0.01 мм.
Изготовление штампов, пресс-форм, лекальных шаблонов, нестандартного инструмента на электроэрозионных станках.
Резка на электроэрозионных станках твёрдых сплавов, магнитов, поликристаллического алмаза, кубического нитрита бора, титана, вольфрама, молибдена, полупроводников и т.п. и их электроэрозионная обработка.
Изготовление электроэрозионных станков, ремонт электроэрозионных станков, оснастка электроэрозионных станков, наладка электроэрозионных станков, модернизация электроэрозионных станков с заменой устаревших генераторов тока и ЧПУ.
Электроэрозионная обработка основана на вырывании частиц материала с поверхности импульсом электрического разряда. Если задано напряжение (расстояние) между электродами, погруженными в жидкий диэлектрик, то при их сближении (увеличении напряжения) происходит пробой диэлектрика возникает электрический разряд, в канале которого образуется плазма с высокой температурой.
Электроэрозионные методы обработки особенно эффективны при обработке твёрдых материалов и сложных фасонных изделий. При обработке твёрдых материалов механическими способами большое значение приобретает износ инструмента. Преимущество электроэрозионных методов состоит в том, что для изготовления инструмента используются более дешёвые, легко обрабатываемые материалы. Часто при этом износ инструментов незначителен. Например, при изготовлении некоторых типов штампов механическими способами более 50% технологической стоимости обработки составляет стоимость используемого инструмента. При обработке этих же штампов электроэрозионными методами стоимость инструмента не превышает 3,5%. Условно технологические приёмы электроэрозионной обработки можно разделить на прошивание и копирование. Прошиванием удаётся получать отверстия диаметром менее 0,3 мм, что невозможно сделать механическими методами. В этом случае инструментом служит тонкая проволочка. Этот приём на 20 70% сократил затраты на изготовление отверстий в фильерах, в том числе алмазных. Более того, электроэрозионные методы позволяют изготовлять спиральные отверстия.
Более распространена обработка проволочным электродом. Этим способом, например, можно получать из единого куска материала одновременно пуансон и матрицу штампа, причём их соответствие практически идеально.
Какой термин правильный: электроискровой или электроэрозионный метод обработки?
Электроискровым, а не электроэрозионным новый электрофизический метод обработки именовался еще своими первооткрывателями супругами Лазаренко, Борисом Романовичем Лазаренко и Натальей Иоасафовной Лазаренко, в конце 30-хх годов ХХ века. И в первых публикациях об открытии Лазаренко (1943 г.), и в докторской диссертации Бориса Романовича Лазаренко (1947 г.) использовался термин “электроискровой метод”. Термин “электроэрозия” применительно к этой технологии появился в 50-х годах скорее как результат “идейного противостояния” различных коллективов, занимавшихся к тому времени проблемами новой технологии. Создатель первого в мире проволочно-вырезного станка (1954 г.) Борис Иванович Ставицкий, ученик Лазаренко, во всех своих работах использует термины “электроискровая” и “электроискровой” применительно как к технологии, так и процессу и методу обработки.
Некоторым представляется, что термин “электроискровая” обработка подходит к названию процесса лучше, чем “электроэрозионная”. Электрическая искра – это инструмент, который работает в процессе обработки, электроэрозия – это результат, разрушение металла под действием электроискровых разрядов. Если по той же логике, по которой обработку называют “электроэрозионной”, называть другие процессы, то сверление, к примеру, будет именоваться “дырением”. Как бы то ни было, термин “электроэрозия” является более устоявшимя и официальным. На производствах электроискровую (электроэрозионную) обработку именуют иногда “эрозийной”, “электроимпульсной”, координатно-прошивочную электроискровую (электроэрозионную) обработку зачастую называют “прожигом”. Некоторые считают правильными терминами “электроискровая обработка”, “электроискровой станок”, электроэрозийная обработка”, электроэрозийный станок” и т.д., однако общепринято использование термина – “электроэрозионная обработка”, “электроэрозионный станок”.
Вот как одни и теже названия будут именоваться в разных терминологиях:
электроэрозионная обработка (ЭИ обработка)
электроэрозийная обработка
электроискровая обработка (ЭИ обработка)
электроэрозия
электроэрозионный станок (ЭЭС)
электроэрозийный станок
электроискровой станок (ЭИС)
электроэрозионные технологии (ЭЭ технологии)
электроэрозийные технологии
элекроискровые технологии (ЭИ технологии)
электроэрозионный координатно-прошивочный станок
электроэрозийный координатно-прошивочный станок
электроэрозийный прожигной станок
электроискровой координатно-прошивочный станок
электроэрозионный проволочно-вырезной станок
электроэрозийный проволочно-вырезной станок
электроискровой проволочно-вырезной станок
электроэрозионная “супердрель”
электроэрозийная “супердрель”
электроискровая “супердрель”
услуги по электроэрозионной обработке деталей, ремонту и наладке электроэрозионных станков
услуги по электроэрозийной обработке деталей, ремонту и наладке электроэрозийных станков
услуги по электроискровой обработке деталей, ремонту и наладке электроискровых станков
Электроэрозионная обработка металлов и сплавов в Москве – это услуга, которую предоставляет своим заказчикам наш завод. У нас есть все необходимое оборудование, за которым работают квалифицированные специалисты. Все заказы мы выполняем качественно и в установленные сроки.
Лазерная резка
Материал из Википедии – свободной энциклопедии
Текущая версия.
Лазерная резка листа стали.
Технология резки и раскроя материалов, использующая лазер высокой мощности и обычно применяемая на промышленных производственных линиях. Сфокусированный лазерный луч, обычно управляемый компьютером, обеспечивает высокую концентрацию энергии и позволяет разрезать практически любые материалы независимо от их теплофизических свойств. В процессе резки, под воздействием лазерного луча материал разрезаемого участка плавится, возгорается, испаряется или выдувается струей газа. При этом можно получить узкие резы с минимальной зоной термического влияния. Лазерная резка отличается отсутствием механического воздействия на обрабатываемый материал, возникают минимальные деформации, как временные в процессе резки, так и остаточные после полного остывания. Вследствие этого лазерную резку, даже легкодеформируемых и нежестких заготовок и деталей, можно осуществлять с высокой степенью точности. Благодаря большой мощности лазерного излучения обеспечивается высокая производительность процесса в сочетании с высоким качеством поверхностей реза. Легкое и сравнительно простое управление лазерным излучением позволяет осуществлять лазерную резку по сложному контуру плоских и объемных деталей и заготовок с высокой степенью автоматизации процесса.
Процесс
Для лазерной резки металлов применяют технологические установки на основе твердотельных и газовых CO2-лазеров, работающих как в непрерывном, так и в импульсно-периодическом режимах излучения. Промышленное применение газолазерной резки с каждым годом увеличивается, но этот процесс не может полностью заменить традиционные способы разделения металлов. В сопоставлении со многими из применяемых на производстве установок стоимость лазерного оборудования для резки ещё достаточно высока, хотя в последнее время наметилась тенденция к её снижению. В связи с этим процесс лазерной резки становится эффективным только при условии обоснованного и разумного выбора области применения, когда использование традиционных способов трудоемко или вообще невозможно.
Лазерная резка осуществляется путём сквозного прожига листовых металлов лучом лазера. Такая технология имеет ряд очевидных преимуществ перед другими способами раскроя:
Отсутствие механического контакта позволяет обрабатывать хрупкие и деформирующиеся материалы;
Обработке поддаются материалы из твердых сплавов;
При выпуске небольших партий продукции целесообразней провести лазерный раскрой материала, чем изготавливать для этого дорогостоящие пресс-формы или формы для литья;
Для автоматического раскроя материала достаточно подготовить файл рисунка в любой чертежной программе и перенести файл на компьютер установки, которая выдержит погрешности в очень малых величинах;
Литература
С. А. Астапчик, В. С. Голубев, А. Г. Маклаков Лазерные технологии в машиностроении и металлообработке. – Белорусская наука. – ISBN 978-985-08-0920-9
Черпаков Б.И., Альперович Т.А. Металлорежущие станки. – ISBN 5-7695-1141-9
Colin E. Webb, Julian D.C. Jones Handbook Of Laser Technology And Applications (Справочник по лазерным технологиям и их применению) book 1. – IOP. – ISBN 0-7503-0960-1
Colin E. Webb, Julian D.C. Jones Handbook Of Laser Technology And Applications (Справочник по лазерным технологиям и их применению) book 2. – IOP. – ISBN 0-7503-0963-6
Wlliam M. Steen Laser Material Processing. – 2nd edition. – Great Britain: Springer-Verlag. – ISBN 3-540-76174-8
ЭЭО профилированной полости. Включение на обратную полярность. 1 – обрабатываемая заготовка, 2 – разряды в зазоре, 3 – электрод-инструмент, 4 – генератор импульсов технологического тока.
Обработка заготовки на электроэрозионном копировально-прошивочном станке. Заготовка находится в рабочей ванне, наполненной рабочей жидкостью.
Электроэрозионная обработка (аббр. ЭЭО) – Обработка, заключающаяся в изменении формы, размеров, шероховатости и свойств поверхности электропроводной заготовки под действием электрических разрядов возникающих между заготовкой и электродом-инструментом.
Один из электродов является обрабатываемой заготовкой, другой – электрод-инструментом. Разряды производятся периодически, импульсно, так чтобы среда между электродами восстановила свою электрическую прочность. Для уменьшения износа электрода-инструмента подаются униполярные импульсы технологического тока. Полярность зависит от длительности импульса, поскольку при малой продолжительности импульса преобладает эрозия (износ) анода , а при большой длительности импульса преобладает эрозия (износ) катода . На практике используются оба способа подачи униполярных импульсов: с подключением заготовки к положительному полюсу генератора импульсов (т. н. включение на прямую полярность), и с подключением заготовки к отрицательному полюсу (т. н. включение на обратную полярность).
Виды ЭЭО
- Комбинированная электроэрозионная обработка — выполняется одновременно с другими видами обработки
- Электроэрозионно-химическая обработка (ЭЭХО) — комбинированная электроэрозионная обработка, осуществляемая одновременно с электрохимическим растворением материала заготовки в электролите
- Электроэрозионная абразивная обработка — абразивная обработка с использованием электроэрозионного разрушения металла
- Анодно-механическая обработка — электрохимическая обработка в жидкой среде, при которой осуществляется растворение материала электрода-заготовки под действием электрического тока с образованием на обрабатываемой поверхности окисных плёнок и их удаление механическим действием.
Может сопровождаться электроэрозионной обработкой
- Электроэрозионное упрочнение — электроэрозионная обработка, при которой увеличивается прочность поверхностного слоя заготовки
- Электроэрозионное объёмное копирование — электроэрозионная обработка, при которой на электроде-заготовке отображается форма поверхности электрода-инструмента
- Электроэрозионное прошивание — электроэрозионная обработка, при которой электрод-инструмент, углубляясь в электрод-заготовку, образует отверстие постоянного сечения
- Электроэрозионное маркирование
- Электроэрозионное вырезание — электроэрозионная обработка, при которой электрод-инструмент в виде непрерывно перематывающейся проволоки при движении подачи осуществляет обход заготовки по заданной траектории, образуя поверхность заданного контура
- Электроэрозионная отрезка — электроэрозиониая обработка, при которой заготовка разделяется на части
- Электроэрозионное шлифование — шлифование с использованием электроэрозионного разрушения металла
- Электроэрозионная доводка
- Электроэрозионная обработка с прямой полярностью
- Электроэрозионная обработка с обратной полярностью
- Многоэлектродная эрозионная обработка
- Многоконтурная обработка
Характеристики электрического разряда при ЭЭО
Электрический разряд между электродами идёт в несколько этапов: сначала происходит электрический пробой , который может сопровождаться искровыми разрядами ; затем устанавливается дуговой разряд . Поэтому многие генераторы способны выдавать многоступенчатую форму импульса.
Частота импульсов и их длительность выбирается исходя из технологических требований к обрабатываемой поверхности. Длительность импульса обычно лежит в диапазоне 0,1 .. 10 −7 секунды, частота от 5 кГц до 0,5 МГц. Чем меньше длительность импульса, тем меньше шероховатость получаемой поверхности. Средний ток во время ЭЭО зависит от площади обрабатываемой поверхности. При площади 3600 мм² оптимальный ток приблизительно равен 100 .
Особенности ЭЭО
Электрод-инструмент может иметь достаточно произвольную форму, что позволяет обрабатывать закрытые каналы, недоступные обычной механической обработке.
ЭЭО могут подвергаться любые токопроводящие материалы. Основные недостатки ЭЭО это невысокая производительность (скорость подачи обычно ~10 мм/мин) и высокое энергопотребление.
История
Роберт Бойль (1694), Бенджамин Франклин (1751), Джозеф Пристли (1766) Лихтенберг Георг Кристиан (1777): делали первые сообщения об электрических разрядах и эффектах, их сопровождающих.
В 1941 году докторам Борису Романовичу Лазаренко и Наталье Иосифовне Лазаренко (Московский Государственный Университет) было поручено найти методы увеличения срока службы прерывателей-распределителей зажигания автомобильных двигателей.
В результате исследований и экспериментов с вольфрамом было обращено внимание на направленное разрушение электрическими разрядами, создаваемыми импульсами определённой формы тока, что послужило толчком к созданию в 1943 году нового технологического процесса обработки заготовок с помощью электроэрозии.
В 1943 году советские учёные – супруги Борис Романович Лазаренко и Наталия Иоасафовна Лазаренко, предложили использовать электроэрозионные свойства разрядов в воздушном промежутке для формообразования (электроискровой метод электроэрозионной обработки) . На изобретение было получено авторское свидетельство № 70010 от 3.04.1943 года, патент Франции № 525414 от 18.06.1946 года, патент Великобритании № 285822 от 24.09.1946 года, патент США № 6992718 от 23.08.1946 года (указанный патент имеет совсем иную дату и тему ), патент Швейцарии № 8177 от 14.07.1946 года, патент Швеции № 9992/46 от 1.11.1946 года См. также
Примечания
Ссылки
- ГОСТ 25331-82 Обработка электроэрозионная. Термины и определения
- Немилов Е.Ф. Электроэрозионная обработка материалов. – Л. : Машиностроение, 1983. *
Похожие статьи
Электроэрозионная обработка: состояние и перспективы развития, часть 1
Сложноконтурная электроэрозионная обработкаТехнологии электроэрозионной обработки материалов обладают всеми признаками ключевых технологий. За относительно короткий срок (около 60 лет) производство электроэрозионных станков по объему продаж заняло четвертое место на рынке металлообрабатывающего оборудования. Развиваясь синхронно с производством оборудования других типов, оно в то же время стало площадкой для внедрения ряда нововведений — обработки нанообъектов, применения линейных приводов и специальных конструкционных керамик.
Наибольшее распространение на предприятиях машинои приборостроения получили следующие технологии электроэрозионной обработки:
- Обработка сложноконтурных поверхностей и отверстий (операция электроэрозионная копировально-прошивочная)
- О обработка сложноконтурных линейчатых поверхностей (операция электроэрозионная профильно-вырезная)
- О прошивка глубоких отверстий малого диаметра (операция электроэрозионная прошивочная)
Электроэрозионная обработка сложноконтурных полостей и отверстий осуществляется на копировально-прошивочных станках.
Станки японских компаний Makino и Mitsubishi обладают широкими технологическими возможностями. Они снабжены целым рядом проектно-технологических функций. Так, на станках S-серии компании Makino используется система HQSF для ЭЭО с параметром шероховатости поверхности Ra = 0,2 мкм (зеркальная обработка). Имеется функция Super Edge для получения радиусов 0,01 мм при обработке точных углов. Станки фирмы Mitsubishi компонуются по схеме «неподвижный стол — подвижная головка», использованы линейные направляющие качения. Станки оснащены системой адаптивного управления процессом, системой быстрой прошивки узких глубоких полостей.
Копировально-прошивочные станки фирмы Sodick оснащены КЧПУ генераторами серии LN/LQ с максимальным током 40, 80, 160, 240 А. Базовый генератор обеспечивает максимальную производительность до 600 мм3/мин при обработке стали графитовым ЭИ. Имеется функция чистовой обработки (зеркальное выхаживание, Ra = 0,06 мкм) без замены диэлектрика или в специальном диэлектрике. Функция Pikagen pulse обеспечивает пониженный износ электродовинструментов (ЭИ), функция MAP11 — оптимизацию параметров режима по мере изменения геометрии межэлектродного промежутка. Используется объектно-ориентированная 3D CAD-CAM система сквозного проектирования. Линейные двигатели привода осей и высокоточные датчики линейного положения обеспечивают по данным компании точность позиционирования ± 0,01 мкм. Достижимая точность обработки по стандартной технологии фирмы составляет от ± 1,5 до ± 5 мкм на 300 мм длины в зависимости от модели станка. В качестве опции поставляется ось С углового позиционирования со шпинделем вращения. Предусмотрена обработка с орбитальными осцилляциями ЭИ (5 базовых траекторий и 72 производных). В зависимости от модели станка линейные перемещения по осям осуществляются за счет перемещения стола или головки.
Европейские производители электроэрозионных копировально-прошивочных станков представлены фирмами AGIE, Charmille (Швейцария), ONA (Испания), Winbro Group (Великобритания), Zimmer + Krein GmbH & Co (Германия).
Фирма ONA предлагает широкую гамму станков, которые отличаются современным дизайном и высокими технологическими характеристиками. Станки оснащены системой КЧПУ ONA, осью С с углом поворота 360о. Максимальный ток генератора импульсов 60 А (опция 120 А). Используются современные системы очистки рабочей жидкости без применения сменных картриджей, обеспечивающие отделение твердых частиц размерами до 3 мкм.
Гамма станков серии Genius фирмы Zimmer + Krein GmbH & Co. KG выгодно отличается компактностью конструкции и относительно малой потребной производственной площадью при достаточно высокой производительности и точности обработки. Разрешение по линейным осям ± 1 мкм, по оси С ± 0,001о. Все станки этой серии конструктивно выполнены с неподвижным столом, регулируемой по высоте ванной и встроенной осью С. Модульный принцип, заложенный в конструкцию станков, позволяет выбрать оптимальную конфигурацию. Жесткая литая конструкция станины в комбинации с направляющими качения с предварительным натягом обеспечивают высокие точностные параметры обработки.
Станки комплектуются устройством смены инструментов роторного типа на 16 или 24 позиции или линейным устройством Eagle магазинного типа на 50 позиций. Станки могут комплектоваться загрузочно-разгрузочным устройством «Chameleon», обеспечивающим любую комбинацию паллет с заготовками и электродами, поворотным устройством (пятая ось).
Станки серии Genius могут комплектоваться встраиваемым модулем, обеспечивающим финишную обработку с параметром Ra менее 0,8 мм, специальным модулем для повышения производительности при обработке твердых сплавов. Предусмотрена опция в виде вращающейся головки и насосной установки высокого давления для прошивки глубоких отверстий диаметром 0,1…6 мм и полостей с помощью полых электродов (функция Superdrill).
Станки швейцарских компаний Agie и Charmille получили широкое распространение на российских предприятиях. Многие новые идеи и технические решения получили материальное воплощение в этих компаниях. Так, модель 2400QCR интегрирована с роботом, управляемым от ЧПУ и способным заменять 8 паллет и 76 инструментов. В большинстве станков используются генераторы импульсов типа ISOPULS, вырабатывающих «изоэнергетические» импульсы с блоком защиты от КЗ типа SPAC.
Разнообразное по назначению и технологическим возможностям электроэрозионное оборудование поставляют производители Тайваня. Так, станок ЕВ600L (фирмы JSEDM) имеет С— ось, смонтированную внутри головки станка. Используя эту ось, можно изготовлять поверхности вращения, поверхности сложного профиля, выполнять различные операции с использованием вращающегося дискового или цилиндрического электродов. Генератор импульсов станков данного типа обеспечивает максимальный ток 60 или 90 А. Максимальная производительность 400/600 мм3/мин, наименьшая шероховатость Ra = 0,3 мкм.
В последние годы на рынке электроэрозионного оборудования появились китайские производители, станки которых, как правило, дешевле функциональных аналогов других компаний.
Конкурентоспособность современного станочного оборудования обеспечивается высоким уровнем автоматизации. Поэтому ведущие фирмы-производители оснащают станки автоматическими устройствами для смены заготовок и инструмента. Так, например, компактный агрегат, созданный компанией Sodick, обеспечивает смену 40 электродов и 8 паллет с заготовками и позволяет решить проблему непрерывной и долговременной работы станка в автоматическом режиме. Агрегат представляет собой автономную, компактную и интегрируемую конструкцию. Для расширения технологических возможностей оборудования многие компании—производители предлагают в качестве опций дополнительные оси А и С. Ось А реализуется за счет применения поворотного устройства, устанавливаемого на штатном столе станка. Это позволяет решать технологические задачи, связанные с непрерывным или дискретным поворотом заготовки вокруг оси, перпендикулярной оси шпинделя. Ось С обеспечивает поворот инструмента относительно оси Z и реализуется с помощью специальной головки, закрепляемой на шпинделе станка.
Обработка сложноконтурных линейчатых поверхностей осуществляется на проволочно-вырезных электроэрозионных станках. К настоящему времени технологии и оборудование для электроэрозионной вырезки электродомпроволокой (ЭП) получили широкое распространение, создан обширный рынок соответствующих станков. Для точного относительного перемещения стола и рабочего участка проволоки по заданному контуру используются современные приводы с ЧПУ или КЧПУ.
На этой операции удается получать поверхности, образованные не только поступательным перемещением рабочего участка проволоки, но и более сложные поверхности с использованием дополнительного пространственного вращения рабочего участка. Это достигается применением таких схем обработки, в которых верхняя и нижняя направляющие проволоки перемещаются независимо друг от друга по заданной программе. Отметим, что использование многокоординатных проволочно-вырезных станков позволяет существенно расширить возможности конструктора при проектировании новых технических объектов.
Разработаны различные технические решения, направленные на повышение жесткости рабочего участка проволоки. Так, предложен способ обработки, по которому одна из находящихся в плотном контакте проволока является рабочей, а вторая — поддерживающей, препятствующей изгибу рабочего участка ЭИ и его вибрации. Такая система позволила вдвое снизить прогиб рабочей проволоки.
Рабочими средами в технологиях электроэрозионной проволочной вырезки являются маловязкие диэлектрические жидкости: масло, керосин или вода (промышленная, дистиллированная или деионизированная). Заметим, что как водные, так и углеводородные среды в качестве рабочих жидкостей для ЭЭО имеют свои преимущества и недостатки, что необходимо учитывать при выборе рабочей жидкости.
Практически все ведущие производители оборудования оснащают станки антиэлектролизными генераторами импульсов или соответствующими приставками. Это позволяет исключить окисление поверхности при обработке в воде за счет применения биполярных импульсов тока.
В качестве электрода-инструмента используется проволока, изготовленная по первому и второму классам точности, с максимальным отклонением диаметра от номинального не более 0,005 мм. Латунная проволока — наиболее подходящий инструмент для проволочной вырезки, так как ее прочность в зависимости от состава лежит в пределах 400…900 МПа, а относительное удлинение составляет от 3 до 30%. Ряд фирм специализируется на выпуске высококачественной проволоки для проволочно-вырезных станков (SEI, Primatec GmbH). Установлено, что применение покрытия с высоким содержанием цинка обеспечивает повышение производительности на 40…50% для заданной толщины реза или существенно повышает толщину реза при заданной производительности. Легирование латуни специальными компонентами приводит к заметному увеличению максимальных растягивающих напряжений.
Выбор параметров режима работы генератора импульсов зависит от требований к качеству поверхности детали, ее материала и толщины (высоты реза). На выбранном режиме не должно быть разрывов электрода-проволоки. Современные генераторы импульсов обеспечивают создание униполярных и биполярных импульсов различной энергии с частотой до сотен кГц. Созданы генераторы или приставки к ним для «зеркальной» обработки, обеспечивающие шероховатость поверхности до Ra = 0,04 мкм и генераторы для высокопроизводительной резки (до 600 мм2/мин). Последние модели станков оснащаются КЧПУ-генераторами и обеспечивают работу в режиме «интеллектуального» управления процессом резания.
Современные проволочно-вырезные станки отличаются высоким уровнем автоматизации, надежностью, гибкостью и позволяют эффективно решать многие технологические задачи основного и инструментального производства. Выпускаются двух-, четырехи пятикоординатные проволочно-вырезные станки. Их программное обеспечение содержит базу технологических данных и предполагает использование ряда специальных функций, созданных для достижения высокой точности обработки отдельных геометрических элементов детали (прямолинейность пазов, точность углов).
Проволочно-вырезные станки фирмы Sodick поставляются со встроенной объектно-ориентированной трехмерной системой CALS (3D CAD-CAM) и системой автоматизированного програм-мирования с рядом функциональных полусистем. Процессорные системы обеспечивают управление по 4-5 координатам (X, Y, U, V, +Z) c максимальной скоростью сервоподач до 5 м/мин.
Станок EXL100L и его модификации названы компанией ультрапрецизионными и рекламируются как самые точные электроэрозионные проволочно-вырезные станки. В его конструкции использованы сдвоенные линейные двигатели без сердечников, закрытые керамические направляющие аэростатического типа, керамическая станочная конструкция на гранитной станине, высокоточный холодильник-термостат диэлектрика, нанометровые линейные датчики положения Heidenhein и специально разработанная система управления Sodick Motion Controller (SMC). Конструкция привода обеспечивает дискретность подач 10 нм по осям X, Y, U, V. Станок укомплектован системой автоматической заправки проволоки диаметром от 0,03 мм. Диэлектрическая среда — масло.
Станки AP200L и AP450L являются станками повышенной точности (прецизионными). Первый из них предназначен для обработки в масле или воде и оснащен одним баком (объем 420 л), а второй оснащен двумя баками — для масла и деионизированной воды объемом 550 л каждый. Дискретность подач приводов осей составляет 100 нм. Плита стола, опоры заготовки, кронштейны и детали механизма протяжки проволоки выполнены из новых видов керамики.
Станки серии AQ предназначены для резания в воде. Модели AQ325L, AQ535L, AQ550L обеспечивают как обработку в ванне, так и струйную обработку, станок модели AQ750L — погружного типа, AQ800LF — струйного типа. Последняя модель создана для обработки габаритных заготовок.
Станки, работающие на воде, имеют в своем составе антиэлектролизный генератор биполярных импульсов. Такой источник питания компании Sodick генерирует импульсы малой длительности на первых двух проходах и биполярные импульсы на 3 проходе.
Для расширения технологических возможностей оборудования в некоторых моделях станков предусмотрены добавочные координаты. Так, наряду с 5 координатами, рассмотренными выше, предусмотрен поворот стола (ось W). Кроме углового позиционирования ось W используется для вращения детали, что расширяет технологические возможности станка.
Станок RA-90AT компании Mitsubishi с габаритными размерами 1440×2075×2030 мм обеспечивает производительность до 330 мм2/мин и достижимую шероховатость Ra = 0,6 мкм. Станок оснащен антиэлектролизным генератором, устройством высокоскоростной автозаправки проволоки, системой адаптивного управления (функция Rower Master-3) c функцией экономичного расхода проволоки. Используется функция адаптивного управления Rower Master-4. Проектирование технологий обработки на данных станках осуществляется на основе развитого программного обеспечения.
Высококачественные станки для проволочной вырезки выпускают японские компании Makino, Fanuc Ltd и Seibu Electric and Machinery Co., Ltd.
Станки серии «Robocut a-ic» отличаются качественной системой слежения за состоянием межэлектродного промежутка. Эта система определяет принцип оптимального управления процессом резания, который разработчики называют импульсным управлением на базе искусственного интеллекта. В результате использования высококачественной системы ЧПУ Fanuc и системы обратной связи по состоянию межэлектродного промежутка обеспечивается устойчивый высокоскоростной режим резания с поддержкой постоянной мощности резания и предотвращением разрыва проволоки.
В результате при резке латунной проволокой диаметром 0,25 мм достигается производительность около 250 мм2/мин, а проволокой диаметром 0,3 мм — 330 мм2/мин. Применение проволоки с покрытием позволяет повысить производительность до 360 мм2/мин. Высокопроизводительная резка на данных станках осуществляется переменным током высокой частоты, что позволяет практически предотвратить анодное окисление (антиэлектролизный эффект). В качестве опции поставляется специальный источник питания для «зеркальной» отделки, обеспечивающий достижение шероховатости поверхности Ra = 0,04…0,08 мкм.
Компания Fanuc Ltd рекламирует самую быстродействующую систему автоматической заправки проволоки с величиной рабочего цикла 12 с. В станках серии М компании Seibu (ELO Erosion GmbH) также используются современные средства автоматизации процесса резания, в частности система автоматической заправки проволоки и эффективная система управления процессом резания.
В последние десять пятнадцать лет значительную активность на рынке электроэрозионного оборудования проявляют предприятия Тайваня (MAX SEE, ECOWIN, Fair Friend Group, CHMER и др.).
Так, компания MAX SEE производит и поставляет следующие станки:
- Электроэрозионные копировально-прошивные с подвижным столом (модели Р 26, 36, 46, 56), с подвижным хоботом (модели Р40, 50, 58, 66, 207, 307), ZNC (одна ось Z управляемая от ЧПУ) и CNC (4 оси управляемые от ЧПУ)
- Электроэрозионные проволочно-вырезные струйного (модели FW 325, 530, 540, 645, 840, 1270) и погружного (модели SW 325, 530, 540, 645, 840, 1270) типа, с автоматической заправкой проволоки (серии BFW и BSW)
- Показательным является опыт эксплуатации 30 единиц станков фирмы MAX SEE на крупнейшем авиадвигателестроительном предприятии ФГУП «НТП ГТС «Салют», использующем в основном производстве
Среди европейских производителей оборудования наиболее известны компании CHARMILLES, AGIE (Швейцария), ONA (Испания). Станок «Robofil 690» компании Charmilles обеспечивает максимальную производительность 300 мм2/мин при достижимой шероховатости Ra = 0,28 мкм. Рекомендуемый диаметр проволоки 0,25 мм, дополнительные диаметры 0,1, 0,2 и 0,3 мм. В конструкции станка использована станина из полимербетона и система термостабилизации диэлектрика, что существенно сказывается на точности обработки. Использованы беззазорные алмазные направляющие проволоки и надежная система ее заправки. Предусмотрена возможность обработки как при погружении в ванну, так и при прокачке диэлектрика вдоль ЭП. Благодаря оптическим линейкам обеспечивается точность позиционирования ± 0,5 мкм.
Модификации станков 2030SI-TW, 4030SI-TW, 6030SI-TW обеспечивают последовательный обход контура в два перехода с использованием проволоки диаметром 0,25 мм (черновой проход) и 0,1 мм (чистовой проход). На автоматическую замену проволоки затрачивается около 45 с. По данным фирмы-изготовителя, двухпроволочная вырезка (twin-wire cutting) позволяет повысить производительность обработки на 30…60%.
Отечественные производители представлены на рынке проволочно-вырезным оборудованием среднего технического уровня. Станок модели СК96Ф3/Ф5 позволяет осуществлять пятикоординатную обработку заготовок с максимальными размерами 460×410×150 мм и массой до 150 кг. Ход по координатам X и Y — 250 мм, по координатам U и V — 20 мм, по координате Z (пиноль головки) — 150 мм. Угол наклона проволоки зависит от высоты заготовки и для заготовок высотой 20, 70 и 150 мм составляет соответственно ±30о, ±15о, ±7о. Станок оснащен системой КЧПУ «Арта-тест», обеспечивающей графический контроль контуров детали с визуализацией процесса обработки, просмотр и редактирование УП в процессе обработки.
Станок ЭИ250Ф4 производится ОАО «Санкт-Петербургский завод прецизионного станкостроения». Станок предназначен для изготовления деталей сложной конфигурации в том числе профилей с переменным углом наклона и линейчатых поверхностей с различными контурами в верхней и нижней плоскостях обрабатываемого изделия. Предусмотрено выполнение операций копирования формы электрода-инструмента небольшой площади (клейма различной сложности) и гравировки с нанесением знаковой информации.
Станок имеет 5 управляемых координат с величинами перемещений в миллиметрах по осям X, Y, Z, U, V соответственно 300/250/150/±30/±30 мм. Наибольшая скорость перемещений по осям X и Y составляет 100 мм/мин.
В конструкции использованы круглые алмазные направляющие для проволоки диаметром 0,1/0,2/0,25 мм и керамические направляющие для проволоки диаметром 0,05…0,07 мм. Скорость протяжки проволоки регулируется в пределах 0…6 м/мин. Наибольший угол наклона проволоки при соответствующей толщине реза, град/мм: ± 44/30, ± 23/70 и ±12/150. Генератор импульсов, собранный на базе современных MOSтранзисторов, обеспечивает регулировку частоты в пределах 10…200 кГц с шагом 1 кГц и длительности импульсов в пределах 0,2…3,2 мкс с шагом 0,1 мкс. Амплитуда напряжения рабочих импульсов 150 В, максимально потребляемый средний ток 20 А. Станок оснащен эффективной системой КЧПУ и адаптирован к САПР UNICAM. Габаритные размеры станка 3×2,76×1,7 м, масса 1410 кг.
НПК «Дельта-Тест» выпускает и модернизирует электроэрозионные проволочно-вырезные станки нескольких моделей. Технические характеристики выпускаемых станков приведены в таблице ниже.
Используется погружная схема обработки с подъемом ванны. Габариты системы ЧПУ/генератор импульсов 470×550×1600 мм. Рабочие среды: водопроводная и деионизированная вода. Применяется латунная, медная, молибденовая проволоки диаметром 0,05…0,3 мм (опция — 0,012 мм). Максимальная скорость резания по стали, мм2/мин — 110. Точность координатных перемещений — ± 5 мкм.
В станках применяется система ЧПУ АРТА-Х7 на основе промышленных компьютеров фирмы Advantech. Генератор импульсов АРТА-3М-5 на базе мощных MOS-транзисторов с микропроцессорным управлением гарантирует высокую производительность при использовании в качестве рабочей среды даже технической воды. СЧПУ обеспечивает широкий диапазон регулировки параметров тока, защиту от обрыва проволоки, выбор оптимальных параметров режима обработки, работу с проволокой малого диаметра (0,012…0,05 мм). Достигаемая шероховатость поверхности Ra = 0,5 мкм. СЧПУ обеспечивает набор автоматических циклов и дополнительных функций, автоматическое сохранение параметров, включает в себя встроенную подсистему справочной информации и диагностики.
Одна из последних разработок компании — станок Арта-450 — представлена на рисунке.
Б. П. Саушкин
Описание технологии электроэрозионной обработки — Центр эрозионных технологий им. Лазаренко
В настоящее время широкое развитие получили 3 типа электроэрозионной обработки:
- Вырезание проволокой
- Прошивка электродом
- Прошивка (прожиг, сверление) тонких глубоких отверстий
Все эти операции показаны ниже.
Смотрите все наши работы, полученных электроэрозионной обработкой.
Вырезание проволокой
Вырезание фасонных отверстий в толщине 650 мм. Видео 1а. Вырезание лопатки для испытания на прочность. Фото 1. Лопатка, вырезанная на проволочном станке, для проведения испытаний на прочность. Вырезка образцов для испытаний механических свойств соединения титана диффузионной и электронно-лучевой сваркой Видео 1б. Вырезание восьмигранника для измерения точности проволочно — вырезного станкаDK 7732 в г.Тольятти. Точность станка оказалась 7 мкм, при паспортной 12. Отчет, согласованный с Заказчиком здесь.
Надпись на части кольца подшипника. Вырезано проволокой 0,18 мм. Фото повернуто.Смотрите еще примеры изделий, полученных электроэрозионной обработкой.
Прошивка (прожиг, сверление) тонких глубоких отверстий
Прожиг охлаждающих отверстий в лопатках газовой турбины В настоящее время на электростанциях и газоперекачивающих станциях парк газовых турбин импортного производства, в первую очередь производства «Simens» и «General Electric», исчисляется сотнями и вопрос уменьшения затрат при ремонтах для собственников оборудования приобретает особое значение.
Исчерпавшие моторесурс рабочие лопатки, снимаются с ротора турбины, закупается новый комплект рабочих лопаток и устанавливается на место старых.
Между тем, в 80 % случаев технологии ремонта позволяют проводить ремонт и восстановление направляющих (сопловых) рабочих лопаток и назначать им новый гарантированный ресурс равный первоначальному. Такое восстановление лопаток можно проводить 3-4 раза. То есть, вместо назначенного изготовителем рабочих лопаток рабочего ресурса до их замены в 35-40 тысяч часов, жизнь лопаток может быть продлена до 90-120 тысяч. Стоимость восстановленных лопаток с гарантированным ресурсом, таким же, какой имеют вновь изготовленные лопатки, на 35-50 % ниже. Таким образом, потребитель получает комплект лопаток, соответствующий по своим свойствам новым лопаткам, за цену вдвое меньшую.
Смотрите еще примеры изделий, полученных электроэрозионной обработкой.
Прошивка электродом.
Видео 2. Прошивка матрицы медным электродом. Видео 3. Прошивка электродом диаметром 1 мм.Смотрите еще примеры изделий, полученных электроэрозионной обработкой.
Электроэрозионная обработка основана на вырывании частиц материала с поверхности импульсом электрического разряда. Если задано напряжение (расстояние) между электродами, погруженными в жидкий диэлектрик, то при их сближении (увеличении напряжения) происходит пробой диэлектрика — возникает электрический разряд, в канале которого образуется плазма с высокой температурой.
Так как длительность используемых в данном методе обработки электрических импульсов не превышает 10—2сек, выделяющееся тепло не успевает распространиться в глубь материала и даже незначительной энергии оказывается достаточно, чтобы разогреть, расплавить и испарить небольшое количество вещества. Кроме того, давление, развиваемое частицами плазмы при ударе об электрод, способствует выбросу (эрозии) не только расплавленного, но и просто разогретого вещества. Поскольку электрический пробой, как правило, происходит по кратчайшему пути, то прежде всего разрушаются наиболее близко расположенные участки электродов. Таким образом, при приближении одного электрода заданной формы (инструмента) к другому (заготовке) поверхность последнего примет форму поверхности первого (рис. 1). Производительность процесса, качество получаемой поверхности в основном определяются параметрами электрических импульсов — их длительностью, частотой следования, энергией в импульсе. Электроэрозионный метод обработки объединил электроискровой и электроимпульсный методы.
Электроэрозионные методы особенно эффективны при обработке твёрдых материалов и сложных фасонных изделий. При обработке твёрдых материалов механическими способами большое значение приобретает износ инструмента. Преимущество электроэрозионных методов, как и вообще всех электрофизических и электрохимических методы обработки, состоит в том, что для изготовления инструмента используются более дешёвые, легко обрабатываемые материалы. Часто при этом износ инструментов незначителен.
Например, при изготовлении некоторых типов штампов механическими способами более 50% технологической стоимости обработки составляет стоимость используемого инструмента. При обработке этих же штампов электроэрозионными методами стоимость инструмента не превышает 3,5%. Условно технологические приёмы электроэрозионной обработки можно разделить на прошивание и копирование. Прошиванием удаётся получать отверстия диаметром менее 0,3 мм,что невозможно сделать механическими методами. В этом случае инструментом служит тонкая проволочка. Этот приём на 20—70% сократил затраты на изготовление отверстий в фильерах, в том числе алмазных. Более того, электроэрозионные методы позволяют изготовлять спиральные отверстия. При копировании получила распространение обработка ленточным электродом. Лента, перематываясь с катушки на катушку, огибает копир, повторяющий форму зуба. На грубых режимах лента «прорезает» заготовку на требуемую глубину, после чего вращением заготовки щель расширяется на нужную ширину. Более распространена обработка проволочным электродом, то есть лента заменяется проволокой. Этим способом, например, можно получать из единого куска материала одновременно пуансон и матрицу штампа, причём их соответствие практически идеально.
Разрушение поверхностных слоев материала под влиянием внешнего воздействия электрических разрядов называется электрической эрозией. На этом явлении основан принцип электроэрозионной обработки.
Электроэрозионная обработка заключается в изменении формы, размеров, шероховатости и свойств поверхности заготовки под воздействием электрических разрядов в результате электрической эрозии.
Под воздействием высоких температур в зоне разряда происходят нагрев, расплавление, и частичное испарение металла. Для получения высоких температур в зоне разряда необходима большая концентрация энергии. Для достижения этой цели используется генератор импульсов. Процесс электроэрозионной обработки происходит в рабочей жидкости, которая заполняет пространство между электродами; при этом один из электродов — заготовка, а другой — электрод-инструмент.
Под действием сил, возникающих в канале разряда, жидкий и парообразный материал выбрасывается из зоны разряда в рабочую жидкость, окружающую его, и застывает в ней с образованием отдельных частиц. В месте действия импульса тока на поверхности электродов появляются лунки. Таким образом осуществляется электрическая эрозия токопроводящего материала, показанная на примере действия одного импульса тока, и образование одной эрозионной лунки.
Материалы, из которых изготавливается электрод-инструмент, должны иметь высокую эрозионную стойкость. Наилучшие показатели в отношении эрозионной стойкости электродов-инструментов и обеспечения стабильности протекания электроэрозионного процесса имеют медь, латунь, вольфрам, алюминий, графит и графитовые материалы.
Общая характеристика процесса электроэрозионной обработки
Типовой технологический процесс электроэрозионной обработки на копировально-прошивочных станках заключается в следующем:
- Заготовку фиксируют и жестко крепят на столе станка или в приспособлении. Тяжелые установки (весом выше 100 кг) устанавливают без крепления. Устанавливают и крепят в электродержателе электрод-инструмент. Положение электрода-инструмента относительно обрабатываемой заготовки выверяют по установочным рискам с помощью микроскопа или по базовым штифтам. Затем ванну стакана поднимают и заполняют рабочей жидкостью выше поверхности обрабатываемой заготовки.
- Устанавливают требуемый электрический режим обработки на генераторе импульсов, настраивают глубинометр и регулятор подачи. В случае необходимости включают вибратор и подкачку рабочей жидкости.
- В целях повышения производительности и обеспечения заданной шероховатости поверхности обработку производят в три перехода: предварительный режим — черновым электродом-инструментом и окончательный — чистовым и доводочным.
4.1 Типовые операции электроэрозионной обработки
Прошивание отверстий
При электроэрозионной обработке прошивают отверстия на глубину до 20 диаметров с использованием стержневого электрода-инструмента и до 40 диаметров — трубчатого электрода-инструмента. Глубина прошиваемого отверстия может быть значительно увеличена, если вращать электрод-инструмент, или обрабатываемую поверхность, или и то и другое с одновременной прокачкой рабочей жидкости через электрод-инструмент или с отсосом ее из зоны обработки. Скорость электроэрозионного прошивания достигает 2-4 мм/мин.
Маркирование
Маркирование выполняется нанесением на изделие цифр, букв, фирменных знаков и др. Электроэрозионное маркирование обеспечивает высокое качество, не вызывает деформации металла и не создает зоны концентрации внутреннего напряжения, которое возникает при маркировании ударными клеймами. Глубина нанесения знаков может колебаться в пределах от 0,1 до 1 мм.
Операция может выполняться одним электродом-инструментом и по многоэлектродной схеме. Изготавливаются электроды-инструменты из графита, меди, латуни, алюминия.
Производительность составляет около 3-8 мм/с. Глубина знаков зависит от скорости движения электрода. При скорости движения электрода более 6 мм/с четкость знаков ухудшается. В среднем на знак высотой 5 мм затрачивается около 4.
Вырезание
В основном производстве электроэрозионное вырезание применяют при изготовлении деталей электро-вакуумной и электронной техники, ювелирных изделий и т.д. в инструментальном производстве, при изготовлении матриц, пуансонов, пуансонодержателей и других деталей, а также вырубных штампов, копиров, шаблонов, цанг, лекал, фасонных резцов и др.
Шлифование
Процесс электроэрозионного шлифования применяют для чистовой обработки труднообрабатываемых материалов, магнитных и твердых сплавов.
Отклонение размеров профиля после электроэрозионного шлифования находится в пределах от 0,005 до 0,05 мм, шероховатость Ra = 2,50,25, производительность — 260 мм2/мин.
С появлением электрических способов обработки оказалось в принципе возможным осуществление методами электротехнологии всего комплекса операций, необходимых для превращения заготовки в готовую деталь, включая и ее термическую обработку.
6.10.13. Электроэрозионные станки “МЕЖОТРАСЛЕВЫЕ ПРАВИЛА ПО ОХРАНЕ ТРУДА ПРИ ХОЛОДНОЙ ОБРАБОТКЕ МЕТАЛЛОВ. ПОТ Р М 006-97” (утв. Постановлением Минтруда РФ от 27.10.97 N 55)
не действует Редакция от 27.10.1997 Подробная информацияНаименование документ | “МЕЖОТРАСЛЕВЫЕ ПРАВИЛА ПО ОХРАНЕ ТРУДА ПРИ ХОЛОДНОЙ ОБРАБОТКЕ МЕТАЛЛОВ. ПОТ Р М 006-97” (утв. Постановлением Минтруда РФ от 27.10.97 N 55) |
Вид документа | правила, перечень, нормы |
Принявший орган | минтруд рф |
Номер документа | 55 |
Дата принятия | 01.01.1970 |
Дата редакции | 27.10.1997 |
Дата регистрации в Минюсте | 01.01.1970 |
Статус | не действует |
Публикация |
|
Навигатор | Примечания |
6.10.13. Электроэрозионные станки
6.10.13.1. При устройстве электроустановок, оборудовании силовых и осветительных сетей электроэрозионных цехов и участков необходимо следовать требованиям Правил устройства электроустановок.
Эксплуатация электроэрозионных станков должна осуществляться в соответствии с Правилами эксплуатации электроустановок потребителей и Правилами техники безопасности при эксплуатации электроустановок потребителей.
6.10.13.2. К работе на электроэрозионных станках должны допускаться только лица, прошедшие специальное обучение по эксплуатации станка, технике безопасности и противопожарной технике при выполнении технологических операций, имеющие соответствующие удостоверения о допуске к работе на этих станках и необходимую группу электробезопасности.
6.10.13.3. Для исключения разрядов статического электричества, возникающего при протекании токонепроводящих жидкостей в трубопроводах, трубопроводы должны быть заземлены.
6.10.13.4. Станки, на которых применяются открытые электроды и осуществляется полив зоны обработки, должны иметь ограждение рабочей зоны, изготовленное из негорючего материала, для защиты обслуживающего персонала от брызг рабочей жидкости.
6.10.13.5. Станки должны оснащаться местным отсосом, обеспечивающим отвод образующихся при работе газов в соответствии с разделом 6.7.
Пуск станка должен быть сблокирован с включением системы отсоса воздуха из рабочей зоны. В случае выключения отсасывающей системы станок должен автоматически отключаться.
6.10.13.6. Воздуховоды местных отсосов станка должны иметь люки для периодической очистки от масла, сажи и других загрязнений.
6.10.13.7. Пульт управления должен быть оборудован световой сигнализацией, указывающей наличие напряжения на электродах.
6.10.13.8. В станках, где в качестве рабочей жидкости применяются горючие материалы (керосин, масло и др.), токопроводы к электроду-инструменту, электроду-детали, приспособлениям и сборочным единицам, расположенным в рабочей зоне, должны иметь исполнение, исключающее искрообразование в легковоспламеняющихся парах и газах, выделяющихся при электроэрозионном процессе.
6.10.13.9. Станки с ванной емкостью более 20 л, заполняемой горючей жидкостью (керосин, масло и др.), должны иметь автоматическое устройство, отключающее подачу напряжения на электроды при понижении уровня жидкости в ванне ниже допустимой.
6.10.13.10. Ванны должны быть оборудованы переливными устройствами.
6.10.13.11. На станке должна быть табличка с указанием установленного для станка уровня рабочей жидкости над обрабатываемой деталью.
6.10.13.12. Если при работе станка используемая для работы жидкость нагревается до температуры на 10 град. C ниже температуры вспышки (керосин – не более 30 град. C, смесь керосина с маслом – не более 50 град. C), станок должен оснащаться охлаждающим устройством, устраняющим возможность нагрева жидкости выше указанного предела.
6.10.13.13. Электроконтактные станки должны быть оборудованы защитой обслуживающего персонала от светового излучения.
6.10.13.14. Станки должны иметь устройства для автоматического отключения напряжения, подаваемого на электроды и разрядники для разрядки конденсаторов при выполнении операций, во время которых возможно прикосновение оператора к токоведущим частям (при смене электрода-инструмента, при снятии и установке обрабатываемой детали на станке и т.д.).
6.10.13.15. Установки для поверхностного упрочнения металла должны иметь электрическую изоляцию приспособления, используемого для закрепления обрабатываемой заготовки.
Стержень вибровозбудителя должен быть надежно изолирован по всей длине до места крепления электрода, которым производится упрочнение поверхности детали.
6.10.13.16. Операции упрочнения ручными вибраторами должны выполняться в диэлектрических резиновых перчатках.
6.10.13.17. Электрические части установки (конденсаторы, сопротивления, выпрямители и т.п.) должны быть обеспечены достаточным охлаждением сопротивлений, термоизоляцией конденсаторов, а также надежно изолированы от корпуса станка (установки) и пульта управления.
Электропровода и кабели должны быть защищены от воздействия жидкой рабочей среды.
6.10.13.18. Конструкция и расположение пусковых механизмов должны исключать возможность их случайного включения.
Для этого они должны быть различными по форме и окраске, а также снабжены блокировками, фиксаторами и четкими надписями об их назначении.
6.10.13.19. Система управления электроэрозионными станками, сигнальные устройства должны быть защищены от случайных механических повреждений, запыления, влияния температуры и других факторов.
6.10.13.20. В электроэрозионных станках, оснащенных генераторами импульсов с высоким напряжением питания (3 – 15 кВ), дополнительно следует предусматривать замыкатели, автоматические разъединители, разряжающие батареи рабочих конденсаторов при открывании электроблока генераторов.
На время ремонта генераторов должна быть предусмотрена блокировка, обеспечивающая выключение всех цепей при открытых дверцах.
6.10.13.21. Все токоведущие части станков должны быть ограждены. Конструкция блокировок должна исключать снятие ограждений до отключения напряжения.
6.10.13.22. Все нетоковедущие металлические конструкции станка должны быть заземлены.
6.10.13.23. Для предотвращения поражения работающих электрическим током в помещении, где установлены электроэрозионные станки, должны устраиваться полы из электроизолирующих материалов или на рабочих местах операторов пол должен быть покрыт диэлектрическим настилом, ковриками из маслобензостойких материалов или применяться электроизолирующие подставки.
6.10.13.24. Запрещается работать в одиночку на электроэрозионном оборудовании. Во время работы электроэрозионного станка в помещении должно находиться не менее двух человек.
Настройка аппаратуры и регулировка технологических режимов должны осуществляться не менее чем двумя лицами.
6.10.13.25. Вода для охлаждения деталей высокочастотных ламповых генераторов должна подаваться через шланги из электроизоляционного материала.
6.10.13.26. На неработающем станке ванны должны быть опущены и закрыты металлической крышкой.
6.10.13.27. Шлам, удаляемый при очистке расходных баков и рабочих ванн, должен вывозиться в специально отведенное место или сдаваться на переплавку. Спуск шлама в поглощающие колодцы и буровые скважины не допускается.
Удаление шлама из расходных баков емкостью более 300 л должно быть механизировано.
6.10.13.28. Огнеопасная рабочая жидкость (керосин, масло и др.) в помещениях, где находятся электроэрозионные станки, может храниться в количестве, не превышающем сменной потребности, в закрытой таре и с разрешения пожарной охраны.
6.10.13.29. Вблизи каждой электроэрозионной установки должны быть средства пожаротушения. Их количество и состав согласовываются с пожарной охраной.
6.10.13.30. Принимать пищу и курить на участках, где установлены электроэрозионные станки, запрещается. Для этих целей должны быть отведены специальные помещения.
Электроды для электроэрозионной обработки | Plansee
Высокая износостойкость — благодаря высокой температуре плавления вольфрама (3420 °C) электроды из WCu обладают намного более долгим сроком службы по сравнению с медными или графитовыми электродами, в частности в случае электродов малых размеров, подвергающихся сложной машинной обработке. Поскольку стоимость производства сложных электродов обычно намного превышает стоимость чистых материалов, применение Sparkal® обеспечивает заметную экономию расходов за счет увеличенного срока службы электродов.
Высокая четкость контуров — высокая износостойкость электродов для электроэрозионной обработки Sparkal® позволяет точно сфокусировать дугу и достичь большей геометрической точности заготовки, чем это возможно при использовании медных или графитовых электродов. Вы можете обрабатывать изделия с высокой точностью и выдерживать малые допуски машинной обработки.
Высокое качество поверхности – использование Sparkal® в процессе электроэрозионной обработки обеспечивает отличное качество поверхности, в частности, снимает необходимость во круговых движениях электродов. Это становится возможным благодаря мелкой однородной микроструктуре и отсутствию пор в электродах Sparkal®.
Очень хорошая обрабатываемость – заметно больший модуль упругости и повышенная твердость электродов Sparkal® обеспечивают исключительно хорошую обрабатываемость. По сравнению с медью здесь практически не наблюдается деформаций материала, а уровень образования заусенцев пренебрежительно мал. В отличие от графита не наблюдается скалывания материала и обеспечивается лучшая геометрическая точность электродов. Благодаря этим свойствам материала из Sparkal® можно изготовлять прутки и трубки необычайно малого диаметра и особо большой длины.
Улучшенные экологические и рабочие условия — механическая обработка графита требует применения специальных вытяжных систем для удаления пыли, предотвращения образования слоев графита на полу и обеспечения чистоты воздуха. Механическая обработка Sparkal®, напротив, не требует никакого дополнительного оборудования.
Статья – Электроэрозионная обработка
Электроэрозионная обработка
автор: Евгений Дряхлов
Сущностью процесса электроэрозионной резки является воздействие на деталь искровых разрядов, образующихся вследствие протекания импульсного тока с частотой в районе 240 кГц между электродом-проволокой и деталью, находящихся в непосредственной близости друг от друга в среде жидкого диэлектрика. В результате этих разрядов из материала детали выбиваются микрочастицы, которые выносятся из межэлектродного зазора (GAP) струей диэлектрика. Кроме этого, диэлектрик играет роль катализатора процесса распада, так как при высочайшей температуре разряда диэлектрик в зоне эрозии превращается в пар. Происходит дополнительный микровзрыв пара, который не может сразу выйти из межэлектродного зазора.
За последние годы электроэрозионная обработка не только окончательно закрепила свои позиции в современном инструментальном производстве, но и продолжает развиваться быстрыми темпами в направлении улучшения качественных показателей и предложения новых конструктивных решений.
Открытие формообразующего воздействия электрической эрозии на токопроводящие материалы состоялось в 1943 году и принадлежит нашим соотечественникам – супругам Б. и Н. Лазаренко. Когда повсюду в мире в 50-х годах лучшие умы всерьез взялись за эту технологию, чья-то советская руководящая воля свернула перспективные разработки и ввергла нас в отставание на многие десятки лет в области электроэрозионной обработки. Ну что же, как это не горько, поговорим об успехах других.
Диэлектрик в электроэрозионной обработке
Советские исследователи, супруги Лазаренко, которые впервые и открыли возможность использования явления электрической эрозии для обработки то-копроводящих материалов, в качестве диэлектрика вначале использовали окружающий воздух. Однако скоро выяснилось, что производные минеральных масел имеют в этом плане несравнимые преимущества: сила разряда – больше, можно работать с меньшими искровыми промежутками, что улучшает точность операции. Новый материал диэлектрика также позволил увеличить частоту разрядов и лучше вымывать частички эродированного металла.
С 1960 года на рынок стали выходить химические компании, предлагающие специальные составы для использования в электроэрозионных установках.
О сути процесса:
Электроды – инструмент и заготовка – закреплены оснасткой станка и не соприкасаются друг с другом. Генератор электрических импульсов задает периодичность и напряженность электрического поля вокруг электродов. Во время процесса электроискрового воздействия серия периодических блуждающих электрических разрядов снимает тончайший слой материала с заготовки.
В точке, где напряженность электрического поля достигает максимума, происходит электрический разряд – молния в “микроатюре”. Под действием электрического поля электроны и свободные положительные ионы разгоняются до высоких скоростей и моментально образуют ионизационный туннель, обладающий электрической проводимостью. Возникает электроток, и между электродом и заготовкой образуется искровой разряд, приводящий к столкновениям элементарных частиц.
Во время этого процесса образуется газовый пузырек, давление которого непрерывно нарастает до образования плазменной зоны. Плазменная зона быстро достигает сверхвысоких температур – от 8000 до 12000°С – благодаря нарастающему числу столкновений элементарных частиц. Этот процесс приводит к моментальному плавлению микрослоев вещества у электрода. При исчезновении электрического поля внезапное снижение температуры приводит к взрыву плазменного пузырька, что сопровождается отрывом части материала с заготовки, и к образованию на этом месте микроскопического кратера. Эродированный материал затем формируется заново в виде маленьких сфер, которые вымываются жидкостью-диэлектриком.
При очень коротком разрядном импульсе в движение приводится больше отрицательно заряженных частиц, нежели положительно заряженных. Чем больше частиц определенного заряда движутся к электроду, тем больше тепла вырабатывается на его поверхности. Из-за большего размера положительные частицы способствуют выработке большего тепла при тех же скоростях бомбардировки электрода-цели. Чтобы минимизировать снятие материала заготовки или износ инструмента, полярность выбирается таким образом, чтобы как можно больше тепла высвобождалось со стороны заготовки до завершения разряда. Для чего при коротких разрядах электрод-инструмент соединяется с отрицательной клеммой и, таким образом, имеет отрицательную полярность.
При длительных разрядах, наоборот, электрод-инструмент подключается к положительному полюсу. На протяженность импульса, при которой должна поменяться полярность на заготовке и электроде-инструменте влияет целый ряд факторов, в большей степени зависящих от физических параметров инструмента и свойств материала электрода. Когда идет обработка стали медным электродом, продолжительность периодичного генерируемого импульса составляет порядка 8 микросекунд.
Неблизнецы-братья
Технология электроэрозионной обработки продолжает развиваться по двум основным направлениям: проволочная электроэрозионная резка (wire electric discharge machining) и копировально-прошивная электроэрозионная обработка (ram (die sinking) electric discharge machining).
Проволочная электроэрозионная резка
Проволочная резка начала свое развитие с чистого листа в начале 70-х годов. Глобальное совершенствование процесса пришлось на период с середины 80-х до середины 90-х годов. Прогресс обозначился по шести ключевым направлениям известного соотношения цена-качество:
– скорость обработки;
– размер заготовки;
– угол конусной резки;
– цена;
– точность;
– длительная работа без вмешательства человека.
Функции диэлектрика:
Электроизолирующая. Диэлектрик должен разделять заготовку и электрод. Искровой разряд должен происходить в максимально узком промежутке между заготовкой и электродом, что позволяет сделать процесс производительным и точным.
Ионизационная. За очень короткое время необходимо создать все условия для формирования электрического поля. После импульса зона разряда должна быть очень быстро деионизирована для возможности повторного разряда. Диэлектрик должен способствовать максимальному сужению искровой зоны, чтобы добиться высокой плотности энергии в этой зоне.
Охлаждающая. Искровой разряд имеет сверхвысокую температуру, поэтому диэлектрик должен остудить и электрод, и заготовку. Также важно увести металлические газы, образующиеся в процессе электроэрозии.
Промывочная. Чтобы избежать электрического пробоя диэлектрик должен эффективно удалять эродированные крупицы металла.
Скорость. Номинальная максимальная скорость резки на сегодняшний день превышает 300 кв. мм/мин, (в лабораторных условиях реализована скорость вырезки 600 кв. мм/мин.). Конечно, средняя скорость резки в реальных производственных условиях ниже номинальных величин, однако и это впечатляет по сравнению с показателями четвертьвековой давности (25-30 кв. мм/мин.). Появление новых сплавов для проволоки может отодвинуть и эти рубежи.
Размер заготовки. Максимальные размеры заготовок, пригодных для обработки на вырезных станках, по осям Х и Y достигают метра и даже больше (1300-1380 мм – по оси X). Однако особенно сильно за последние десятилетия вырос габаритный размер заготовки по оси Z, который сейчас доходит до 400 мм. До этой же отметки поднялись и координатные перемещения по оси Z. Всего этого удалось добиться благодаря новым конструктивным решениям, объединившим принципы неподвижности заготовки и более точной и жесткой реализации осевых движений.
Угол конусной резки. В современных установках достигаются углы вырезки конических отверстий до 30 градусов для заготовок толщиной до 400 мм. Более того, некоторые фирмы в качестве опциона предлагают установки с возможностью достижения конусности до 45 градусов. Такие возможности позволили с начала 90-х годов значительно расширить область применения электроэрозионной резки. Так, если раньше головки для экструзионных установок собирались из набора отдельно обработанных тонких пластин, то новые возможности электроэрозионных станков позволили изготавливать экструзионные головки из одной заготовки и за одну операцию. За счет этого удалось значительно снизить объем скрапа и увеличить производительность экструзионного процесса.
Цена. За более чем четверть века непрерывных работ на порядок улучшились характеристики вырезных станков, в то время как за этот же период оборудование подешевело приблизительно на 75% (с учетом фактора инфляции). Целый ряд обстоятельств способствовал снижению цены. Электронная начинка оборудования вобрала много решений, пришедших из компьютерной индустрии, которые уже тогда отличались прекрасным соотношением цена-качество – возросшая вычислительная мощь за меньшие деньги. Сильно увеличился объем производства электроэрозионного оборудования, что повысило эффективность таких производств. Кроме того, все новые и новые технические решения также способствовали планомерному снижению цен на установки.
Точность. Еще в 70-х и начале 80-х годов оператору станка приходилось вначале делать пробный рез образца и затем корректировать первоначальные настройки, прежде чем выйти на точные геометрические размеры изделия.
Искровые промежутки
Искровой промежуток разделяет заготовку и электрод. Даже при малой глубине обработки различают два типа промежутка: фронтальный и боковой. Фронтальный задается системой управления, в то время как боковой искровой промежуток зависит от продолжительности и высоты разрядного импульса, сочетания материалов, напряжения холостого хода и других заданных параметров.
Блок питания является важнейшим элементом электроэрозионной установки. Он преобразует переменный ток из силовой сети в прямоугольные импульсы определенной полярности. Размер импульсов и интервал между ними задается системой управления в соответствии с выполняемым режимом обработки. Сила тока разряда пропорциональна высоте импульса. Интервал между импульсами соответствует моменту отсутствия искрового разряда, а протяженность импульса соответствует длительности искрового разряда. Обе эти величины составляют тысячные или даже миллионные доли секунды.
Интервал между отдельными импульсами (длительность отсутствия электрического тока) также задается системой управления. Интервал измеряется в процентном отношении собственной длительности к длительности импульса.
Теперь все эти мытарства остались в прошлом и сегодняшняя точность станков достигает 0,001 мм.
Вовлечение современных информационных технологий (САD/САМ -системы) в технологический процесс также позволило увеличить точность обработки – новые установки со всем комплексом современного оснащения гарантировали повторение заложенной в программе геометрии с большой степенью точности.
Как уже отмечалось, современные модели станков на 75% дешевле своих ранних предшественников, в то же самое время они в 3-5 раз точнее.
Длительная работа без вмешательства человека. В 70-х годах электроэрозионные установки могли работать целыми часами без вмешательства оператора – тогда скорости резки были слишком малыми. В современных условиях, когда значительно возросли скорости обработки, практически полностью безлюдное производство обеспечивается за счет использования продвинутых систем автоматизации: устройства автоматической заправки проволоки, поиска отверстия, предотвращения обрыва проволоки, системы автоматизированной загрузки заготовок, удаления перемычек и т. д.
Износ электрода
Эрозия при малом токе снимает мало материала заготовки, тогда как большой ток позволяет добиться больших скоростей снятия материала.
Однако и износ инструмента возрастает, особенно при обработке стали медными электродами. Графитовые электроды ведут себя иначе – износ до определенного момента растет, затем более или менее стабилизируется.
Короткие импульсы также приводят к ускоренному износу электрода. И наоборот, износ идет значительно медленней при длинных импульсах. На практике, при черновой обработке стали медным и графитовым инструментом оптимальная величина длительности импульса лежит на отрезке, на одном конце которого длительность импульса с максимальным съемом, а на другом – длительность импульса с минимальной интенсивностью износа инструмента.
Копировально-прошивочная обработка
Впервые об электроэрозионных станках стало известно с появлением в 1955 году первой копировально-прошивочной установки с ручным управлением. Возможности станков были значительно улучшены к концу 70-х годов, когда применение спутников позволило значительно уменьшить время цикла и число используемых электродов. Примерно в 1980 году была представлена первая модель станка с СNС-управлением. К этому времени процесс копировальной прошивки уже успел претерпеть все возможные усовершенствования, и характеристики прошивочных СNС-станков улучшались более медленными темпами по сравнению с более “молодыми” проволочно-вырезными станками. Наиважнейшим усовершенствованием по сравнению с ранними станками с ручным управлением было не столько само время цикла, сколько число рабочих часов, необходимых для образования заданной полости в материале.
Ранее было замечено, что в случае проволочной резки увеличение производительности и снижение производственных затрат в большей степени достигалось благодаря скорости резания. Что касается электроэрозионной прошивки, то соответствующие улучшения были достигнуты благодаря существенному увеличению количества часов, которые способен работать СNС-станок в течение дня. Обе технологии много выиграли от снижения нормочасов на каждой детали. Переход с ручного управления на числовое программное позволил станкам работать практически всю первую смену, интенсивно во вторую и третью в безлюдном режиме. Если для станка с ручным управлением наиболее типичной является работа в течение 6 часов, то в случае станка с СNС-управлением реально выполнимой задачей может быть 16 часов. Хотя на многих производствах достигаются и более высокие показатели.
Цена. Ведущие производители прошивочных станков предлагают сегодня СNС-станки (без системы автоматической смены инструмента и оси С) примерно по той же цене, по которой в середине 70-х продавались станки с ручным управлением (инфляция учитывается). Даже если добавить стоимость необходимых опций, то скорректированная цена такого нового станка примерно будет равна цене станка 70-х с ручным управлением, который оснащен спутником. Любое повышение цены будет существенно перевешиваться снижением времени цикла, нормочасов и увеличением времени, которое оборудование реально работает в течение суток.
Точность обработки. Учитывая характер процесса формообразования при электроэрозионной прошивке, точность обработки в большей степени будет зависеть от качества и точности изготовления электрода. Графит – более дешевый и удобнообрабатываемый материал – в сочетании с современными технологиями высокоскоростной фрезерной обработки позволяет получать электроды большой сложности и высокой точности.
Определенные успехи были достигнуты и в отношении плоскостности обработанных поверхностей. Например, суммарное отклонение для прямоугольной полости 150х200 мм, полученной на современном станке, составляет всего 0,008 мм
Электроэрозионный электроэрозионный станок | Makino
Большинство электроэрозионных станков перерабатывают более одного фунта проволоки в час, что делает потребление проволоки самым большим расходом при эксплуатации электроэрозионных станков. Электроэрозионный станок Makino использует половину этого количества, обеспечивая значительную долгосрочную экономию в размере 1000 долларов в год на эксплуатационных расходах.Скорость разматывания проволоки на электроэрозионных станках Makino установлена на постоянный низкий уровень, при котором оптимальная скорость обработки может поддерживаться без обрыва проволоки. Компания Makino также разработала уникальную технологию адаптивного управления под названием BellyWIZARD, которая автоматически компенсирует и регулирует проволоку механически в зависимости от толщины заготовки, чтобы обеспечить лучшую прямолинейность и точность, а также включает передовую систему транспортировки и натяжения проволоки HyperDrive.
В наших электроэрозионных станках также используется уникальная полностью цифровая конфигурация насоса двойной промывки, которая обеспечивает автоматическое динамическое адаптивное управление промывкой верхней и нижней головок машины в режиме реального времени во время работы. Эта интеллектуальная и высокоэффективная конфигурация обеспечивает вдвое большую мощность промывки и гарантирует, что необходимая промывка применяется оптимально там и тогда, когда и где она необходима для достижения наилучшей производительности и производительности.
Другие преимущества Makino EDM:
- Снижение затрат на техническое обслуживание до 50%, что является важным преимуществом по сравнению с обычными требованиями к высокому техническому обслуживанию, связанными с производством электроэрозионной обработки.В электроэрозионных станках Makino также меньше расходуемых изнашиваемых деталей.
- Большой сенсорный экран высокой четкости, работающий как смартфон. Операторы любого уровня подготовки могут использовать этот оптимизированный интерфейс, который снижает требования к машинному обучению. Только Makino может предоставить расширенное управление Hyper-i, которое обеспечивает идентичный производительный интерфейс для всех станков Makino Wire EDM, Sinker EDM и EDM Drilling, что еще больше снижает потребность в поддержке обучения.
- Простая автоматизация. Получите заранее определенные оптимизированные настройки для любого приложения и круглосуточное производство без необходимости участия оператора.
Сенсорное управление
EDMMakino отличаются интуитивно понятной системой управления Hyper-i, оптимизированным и эффективным интерфейсом, который помогает выполнять работу быстрее. Большой 24-дюймовый сенсорный экран высокой четкости работает как интеллектуальное устройство (телефон / планшет), позволяя операторам любого уровня подготовки извлекать выгоду из его привлекательного и привычного управления, которое существенно снижает требования к обучению. Управление Hyper-i еще больше повышает возможности оператора с помощью нескольких интегрированных расширенных функций, таких как цифровые руководства и видеоуроки с гиперссылками, E-Tech Doctor и EZ-Cut, которые обеспечивают более высокий уровень производительности для оператора.
Какой электроэрозионный станок Makino вам подходит?
Makino предлагает широкий спектр решений для электроэрозионных станков.
Серия UPN
Разработан для автономной работы с мелкими проводами и мелкими деталями. Эти горизонтальные проволочные электроэрозионные станки на масляной основе с диэлектриком с субмикронной точностью и превосходной обработкой поверхности идеально подходят для небольших электронных устройств, медицины и микрообработки.
Серия UP
Сверхвысокая точность и наилучшее качество поверхности – отличительные черты этих электроэрозионных станков.Стационарный рабочий стол и программируемый 3-сторонний рабочий бак для подъема и опускания обеспечивают легкий доступ к рабочей зоне и упрощают автоматизацию, а также доступна конфигурация диэлектрика на масляной основе, которая дополнительно улучшает чистоту поверхности обрабатываемой детали и металлургическое качество.
Серия U
Серия U включает в себя самые быстрые в отрасли электроэрозионные станки. Уникальные для отрасли, они могут быть сконфигурированы с выбором систем направляющих для проволоки, которые наилучшим образом соответствуют вашим требованиям к деталям и процессу.Все машины оснащены двойными независимыми промывочными насосами, превращающими промывку в программируемый элемент ЧПУ, а система H.E.A.T. конфигурация обеспечивает более высокую производительность промывки для более быстрой обработки.
Узнайте, как инновации Makino стимулируют производство
Makino – мировой лидер в области электроэрозионной обработки. Имея более 140 патентов, электроэрозионный станок Makino означает сокращение времени обработки и превосходное качество поверхности даже для деталей самой сложной формы. Посмотрите, как Makino превращает инновации и технологии в увеличение производства и снижение стоимости детали для наших клиентов.
Целевой рынок | РАЗМЕР МАШИНЫ | ||||
Малый | <---- | Средний | —-> | Большой | |
Micromachining | УПН-01 | УП6 ВЫСОКАЯ ТЕМПЕРАТУРА. | |||
Высокая точность / чистовая обработка | УПВ-3U3i | УПВ-5 | U6i | ||
| U3ВЫСОКАЯ ТЕМПЕРАТУРА. | U6ВЫСОКАЯ ТЕМПЕРАТУРА. U6ВЫСОКАЯ ТЕМПЕРАТУРА. Экстрим | U86 | U1310 | |
Прецизионная обработка | U3 | U6 | U86 | U1310 |
Обычный EDM по сравнению с Wire EDM
СодержаниеВ сфере механической обработки часто можно использовать традиционные режущие инструменты, такие как шлифовальные станки и концевые фрезы, для создания деталей и других изделий определенной формы.Но что делать, если обычные режущие инструменты не справляются с этой задачей?
В этом случае используется электроэрозионная обработка, известная в отрасли как электроэрозионная обработка. Электроэрозионная обработка выполняется в двух основных формах, которые охватывают множество приложений для точной обработки в разных отраслях промышленности.
В этом руководстве мы обсудим, что такое EDM, каковы два основных типа электроэрозионных станков и какие преимущества у каждого из них.
EDM – это нетрадиционный метод обработки, при котором создаются элементы с использованием тепловой энергии для удаления материала – например, аналогично лазерной резке.EDM использует инструменты из графита или мягкого металла в качестве электродов и пропускает через них напряжение для генерации высокочастотных искровых разрядов. Во время обработки и электрод, и обрабатываемый материал обычно погружаются в ванну с диэлектрической жидкостью, которая охлаждает электрод и заготовку, действует как проводник тока и вымывает мусор.
Электрические разряды могут легко прорезать проводящие материалы, такие как металлы. Электроэрозионная сварка ценна, потому что она полезна для обработки любого проводящего металла, независимо от его физических свойств.
Использование тепловой энергии EDM для обработки дает несколько преимуществ. Это выгодно с известными твердыми материалами, такими как титан, вольфрам, закаленная сталь или карбиды, где традиционные инструменты часто не подходят. EDM также полезен для создания предметов сложной замысловатой формы.
Ниже представлены два основных типа электроэрозионных станков:
1. Обычные электроэрозионные станкиТрадиционный электроэрозионный электроэрозионный станок также известен под несколькими другими названиями, например, электроэрозионный электроэрозионный станок с грузилом, электроэрозионный электроэрозионный станок, электроэрозионный электроэрозионный станок с полостью, объемный электроэрозионный электроэрозионный станок и электроэрозионный электроэрозионный станок с плунжером.Этот тип EDM популярен из-за его пригодности для создания сложных форм.
Обычный электроэрозионный станок использует механическую обработку для создания электрода отличительной формы. Затем он погружает электрод глубоко в материал, который требует формовки. Электрод создает негативное впечатление о своей форме, образуя форму.
2. Электроэрозионные станкиЭлектроэрозионный электроэрозионный электродвигатель, также известный как электроэрозионный электроэрозионный электродвигатель, обжиг проволоки и эрозия проволоки, использует в качестве электрода тонкую нагретую проволоку.Твердые алмазные направляющие надежно удерживают канат. Проволочный электрод движется через металл, чтобы создать определенную форму – хотя сама проволока на самом деле не касается металла, но ее электрические разряды касаются. Во время электроэрозионной обработки проволока постоянно разматывается из автоматического подающего устройства, поэтому проволока всегда доступна для резки в гладкой, непрерывной форме.
Иногда форма требует разреза посередине, а не снаружи. В этом случае машинисты соединяют электроэрозионный электроэрозионный станок с так называемым электроэрозионным электродвигателем с просверливанием отверстий.Как следует из названия этой техники, электроэрозионный электроэрозионный станок предполагает просверливание небольшого отверстия в середине заготовки. Затем проволока может продеться через отверстие, чтобы продолжить ее точное формирование. В этом случае электроды имеют форму трубки, и через них к отверстию течет диэлектрическая жидкость.
В общем, электроэрозионная обработка имеет смысл в качестве метода обработки, когда рассматриваемый материал является проводящим – в основном, любой металл, даже очень твердый. А электроэрозионная обработка позволяет создавать сложные формы, такие как острые углы и тонкие прорези, а также глубины, недоступные обычным режущим инструментам.
EDM также идеально подходит для многих применений, поскольку требует минимального усилия. Таким образом, он подходит даже для деликатных форм и хрупких материалов, поскольку не повредит их чрезмерной механической энергией в процессе обработки.
Выбор обычного или проволочного электроэрозионных станков иногда более сложен. Ниже приведены некоторые возможности и применения двух основных типов электроэрозионных станков:
Возможности и области применения обычных электроэрозионных станковТрадиционный электроэрозионный электроэрозионный электродвигатель из-за использования профилированных электродов особенно полезен для изготовления штампов и пресс-форм.Это также выгодно для мелкосерийного производства, особенно для изготовления прототипов. Он находит широкое применение в таких отраслях, как автомобилестроение и авиакосмическая промышленность, поскольку может точно производить сложные детали двигателя. Он также широко используется в различных отраслях промышленности для процессов литья под давлением.
Возможности и применение электроэрозионных станков ВозможностиWire EDM предлагают несколько явных преимуществ. Они обеспечивают прочную, надежную, ультрасовременную производительность, оставаясь при этом удобными для пользователя.Вот некоторые из преимуществ электроэрозионных станков по сравнению с обычными:
- Удобство производства
- Скорость
- Низкие эксплуатационные расходы
При использовании традиционных электроэрозионных электродов электроды подвержены эрозии и должны регулярно заменяться, если они слишком изношены для работы. Традиционный электроэрозионный станок также требует обработки электродов определенной формы, и эта дополнительная предварительная обработка требует много времени.
С другой стороны, электроэрозионный электроэрозионный станок готов к работе сразу после установки проволоки и не требует временных и материальных затрат, связанных с подготовительной обработкой.Он подходит для чувствительных ко времени приложений и форм, где обработка согласующих электродов представляет собой проблему. Он также обычно используется в фильерах для экструзии.
Ниже приведены некоторые компоненты, используемые в двух основных типах электроэрозионных станков:
Компоненты и конструкция обычных электроэрозионных станков
В обычных электроэрозионных станках для приведения в движение используется профилированный электрод, источник энергии и плунжер. Эти машины часто включают в себя числовые компьютерные системы управления (ЧПУ), которые помогают в процессе автоматизации.
Электроды, используемые в обычных электроэрозионных станках с штамповкой, обычно изготавливаются из меди или графита. Выбор между ними часто зависит от идеальной проводимости и эрозионной стойкости электродов. Графит более податлив, поэтому он позволяет упростить изготовление электродов электроэрозионных станков. С другой стороны, медь более прочная и более проводящая, поэтому ее можно использовать для обработки более прочных металлов.
Компоненты и конструкция электроэрозионных станков
Электроэрозионные станкиоснащены катушкой с проволокой, алмазными направляющими и автоматическим механизмом подачи проволоки.
Проволочные электроды, используемые в электроэрозионных станках, часто изготавливаются из меди, а иногда из латуни, сплава меди и цинка. Латунь также используется для изготовления трубчатых электродов, необходимых для электроэрозионных станков.
Однако, в отличие от компонентов обычных электроэрозионных станков, проволока, используемая в электроэрозионных станках, не обязательно должна обладать высокими сопротивляемыми свойствами. Причина в том, что автоподатчик постоянно разматывает новую проволоку для использования при обработке, поэтому, когда старая проволока тускнеет, ее место занимает новая.
Чтобы увидеть преимущества электроэрозионной обработки в своих операциях, сделайте Astro Machine Works своим надежным партнером по оказанию услуг электроэрозионной обработки на проволоке.
Мы предоставляем комплексные решения по механической обработке в различных отраслях промышленности, от оборонных и государственных предприятий до производства фармацевтических препаратов и пищевой промышленности. Наш 35-летний опыт работы в сфере машиностроения, обработки и изготовления на заказ означает, что мы можем помочь вам получить услуги по механической обработке и детали, необходимые для обеспечения качества, своевременности и производительности продукции.
Свяжитесь с нами сегодня, чтобы узнать больше.
Не знаете, какой тип электроэрозионного станка вам нужен?
Многие из долговечных предметов, которые нас окружают, имеют замысловатый дизайн и конфигурации, созданные с помощью металлообработки, и, как мы все знаем, металлообработка состоит из трех неотъемлемых частей; формирование, соединение и резка. В производстве металлов, как и при прецизионной обработке, используются несколько методов формования, резки и соединения металлов. В то время как большинство традиционных методов дали отличные результаты, открытие электроэрозионной обработки (EDM) стало для них передышкой.Это связано с тем, что электроэрозионные станки эффективны и надежны и позволяют достичь высочайшей точности, а также деталей. Кроме того, они могут использоваться в самых современных областях обработки и сложных областях металлообработки, где традиционные методы затруднены. В этой статье мы расскажем, что такое электроэрозионные станки, для чего они могут использоваться, о различных типах электроэрозионных станков и о том, как выбрать то, что подходит для ваших нужд.
Что такое электроэрозионный станок?Электроэрозионная обработка (EDM) – это нетрадиционный процесс с электрическим управлением, при котором металл удаляется с заготовки за счет использования тепловой энергии.Электроэрозионная машина использует термическую эрозию для удаления небольших кусков проводящего металла за счет использования электрического разряда между режущим инструментом, обрабатываемой деталью и диэлектрической жидкостью.
В процессе электроэрозионной обработки в зазоре между режущим инструментом (электродом) и обрабатываемой деталью возникает высокочастотный электрический разряд. Тепло испаряет мелкие кусочки металла в местах фокусировки электрического заряда, которые смываются потоком диэлектрической жидкости.Во время этого процесса температура может подняться до 15000 градусов по Фаренгейту.
Процесс EDM помогает изготовителям и производителям решить проблему твердости. При использовании традиционных методов твердые металлы и металлические сплавы необходимо размягчить для резки или придания им различной формы. Однако электроэрозионные станки могут выполнять уникальные вырезы и отверстия на твердых металлах и металлических сплавах без необходимости их разупрочнения. Кроме того, когда используются обычные методы обработки, они должны сопровождаться еще несколькими процессами для достижения желаемого резания или формы, но электроэрозионные станки могут резать закаленные материалы и экзотические сплавы и обеспечивать отличное качество обработки поверхности в качестве бонуса.Все, что требуется, – это проводимость. Хотя все электроэрозионные станки используют электрический ток для резки материалов, они бывают разных видов.
3 распространенных типа электроэрозионных станковПроволока или резак для сыра
В электроэрозионном станкеиспользуется проволочный электрод и движение ЧПУ для получения желаемой формы или контура. Этот метод удаляет проводящий материал с помощью искровой эрозии, которая является основным принципом процесса электроэрозионной обработки. Проволока проходит от катушки по прецизионным направляющим, управляемым ЧПУ.Промытый диэлектриком (деионизированной водой) для охлаждения тонкой проволоки и удаления эродированных частиц, ленточную пилу для проволоки можно рассматривать как очень точную и точную ленточную пилу.
EDM для сверл или отверстий
Этот электроэрозионный станок используется для выполнения небольших отверстий в металлических деталях. В машине используется токопроводящая трубка в качестве электрода и непрерывный поток диалектной жидкости через этот электрод и вокруг него для вымывания испарившихся металлов. Способность машины сверлить точные и точные отверстия даже в твердых и экзотических материалах остается одной из перспективных отраслей промышленного производства.
RAM или Sinker EDM
Будучи самой старой формой электроэрозионной обработки, RAM EDM состоит из электрода особой формы, который погружается в заготовку для создания сложных разрезов и полостей глухой формы. Как следует из названия, в электроэрозионных станках Sinker и заготовка, и электроды погружаются в диэлектрическую жидкость (легкие и вязкие масла) и через соответствующий генератор для достижения желаемых результатов.
Как определить, какой электроэрозионный станок подходит именно вамОдним из наиболее значительных преимуществ EDM является то, что его можно использовать для всех материалов, если они являются проводящими.Он позволяет создавать формы и глубину, которые трудно достичь другими методами. Однако когда дело доходит до выбора лучшего электроэрозионного станка, все сводится к нескольким факторам.
Для начала, тип конструкции, которую вы хотите создать, должен подсказать вам, какой тип электроэрозионного станка вам нужен. Кроме того, тип станка, который лучше всего подходит для вашего проекта, будет зависеть от материала, который вы режете, требуемой точности и желаемой отделки поверхности. Электроэрозионные станки известны тем, что обеспечивают большую точность, если вы хотите сделать точные надрезы на толстом куске металла или сплава.Разрез и контуры на этой машине невозможно получить другими методами.
Если вам нужен станок, сочетающий надежность и точность, и в вашей работе есть глухие отверстия или полости (формование), лучшим выбором будет Sinker или RAM EDM. Этот тип станка обеспечивает более гладкую поверхность и точную отделку деталей. Наконец, электроэрозионные станки Drill EDM лучше всего подходят для проектов, связанных с выполнением точных и небольших отверстий в заготовке. Суть в том, что; не существует универсальных критериев для выбора типа электроэрозионного станка, который подходит именно вам.Все зависит от материала, который вы хотите разрезать, точности, которую вы хотите достичь, и типа отделки, которую вы хотите.
В компании Southern Fabricating Machinery Sales наша команда имеет многолетний опыт работы с электроэрозионным оборудованием и может помочь вам выбрать подходящий станок для ваших деталей и бюджета. Позвоните нам сегодня по телефону 813-444-4555 или посетите наш веб-сайт www.s Southernfabsales.com, чтобы узнать больше.
EDM компаний | Услуги EDM
Список компаний EDM
В этих отраслях он популярен для использования в приложениях, требующих создания сложных деталей или сложной геометрии, таких как изготовление пресс-форм.
Еще одно популярное применение электроэрозионной обработки – это обработка методом дробления металла. При механической обработке распада металла производители используют электроэрозионные машины для разрушения сломанных деталей инструмента, застрявших внутри заготовок. Примеры таких деталей инструмента включают шпильки, метчики, сверла и болты. Удаляя их из центра заготовки, производители могут переработать или вернуть материал заготовки.
Произведенная продукцияИспользуя электроэрозионную обработку, производители производят формы, инструменты и штампы для формования, литья и ковки таких изделий и деталей, как пластиковые формы, лопатки компрессора, различные детали двигателя, ювелирные изделия, значки, чеканки монет, Производство пластиковых форм, производство лопаток компрессора и производство других деталей двигателя.
С помощью EDM производители также создают прототипы и образцы деталей для клиентов в автомобильной, аэрокосмической и электронной промышленности.
Электроэрозионная обработка – Avon Broach and Production Company История
В 1770 году Джозеф Пристли обнаружил, что с помощью электрического разряда можно создать эрозию. Теперь мы знаем этот эффект как электроразрядную эрозию.
Спустя почти 200 лет после наблюдения Пристли пара советских исследователей сделала первые шаги в направлении разработки современной технологии электроэрозионной обработки.Ученые Н.И. Лазаренко и Б. Бутинцки, соответственно, проводя другие исследования, обнаружил, что они могут контролировать вызванную искрой эрозию вольфрамовых электрических контактов, погружая электроды в диэлектрическую жидкость. (Электроды – это проводящие материалы, через которые может проходить электричество.) Вдохновленные этим открытием, ученые решили создать машину, в которой использовались электроды и диэлектрическая жидкость, чтобы помочь им работать с вольфрамом и другими сложными материалами. Они назвали свою машину машиной типа резисторно-конденсаторной цепи (RC-цепи), или, для краткости, машиной типа R-C.RC-цепи заряжают электроды.
Между тем, примерно в то же время в Соединенных Штатах группа американских ученых создала еще один электроэрозионный станок, работающий с электродами. Они использовали свою технологию, чтобы вытащить сломанные метчики и сломанные сверла из алюминиевых отливок. Они добились успеха, используя машины с электродами, мощными искровыми устройствами, автоматическим повторением искры, устройством электромагнитного прерывателя и заменой жидкости. Их первые успешные машины могли генерировать до 60 искр в секунду.
Спустя годы другие ученые улучшили свою конструкцию, заменив схемы на электронных лампах. С их помощью их электроэрозионные станки могут производить тысячи искр в секунду и производить высечки с головокружительной скоростью.
В 60-е годы инженеры США и Советского Союза первыми разработали электроэрозионное оборудование для резки проволокой. В электроэрозионных станках для резки проволоки в качестве электрода инструмента используется проволока. Инженеры хотели использовать электроэрозионное оборудование для резки проволокой для создания штампов из закаленной стали.
В 1967 году Советы выпустили первый коммерчески жизнеспособный электроэрозионный станок с числовым программным управлением (ЧПУ) для резки проволоки. Числовое управление было предшественником компьютерного числового контроля. В 1974 году американская группа под руководством Дэвида Х. Дулебона разработала первый электроэрозионный станок для резки проволоки, в котором для построения линий использовалась технология ЧПУ. Два года спустя компания Dulebohn усовершенствовала электроэрозионный станок CN, выпустив первый электроэрозионный станок с ЧПУ.
В 70-х годах инженеры и ученые начали пытаться выяснить, как и почему работает электроэрозионная обработка.Одним из первых, кто попытался это сделать, был Франс Ван Дейк, который в 1973 году написал докторскую диссертацию, в которой объяснил это с помощью математики. Однако, по собственному признанию Ван Дейка, большая часть его работ была построена на предположениях, а не на эмпирических данных. В 1989 году обучение продолжили студенты Техасского университета A&M. Они выдвинули претензию с достаточным количеством доказательств в пользу того, что электроэрозионный электроэрозионный станок работает посредством термической обработки.
Никто еще не выступил с заявлением, подкрепленным достаточным количеством доказательств, чтобы мы могли с уверенностью сказать, почему EDM работает.Тем не менее, сегодня электроэрозионная обработка стремительно улучшилась. С его помощью производители теперь могут создавать высокоточные разрезы, замысловатые отметки на поверхности и отделку всех видов материалов. Они также могут делать это со скоростью, о которой первые разработчики EDM могли только мечтать. Производители электроэрозионных станков также активно работают над предотвращением легкой эрозии графитовых электродов. Промышленность была и будет оставаться важной, поскольку сложные конструкции и разрезы на металлах необходимы для успешной электроники.
Подробности процессаЭлектроэрозионная обработка использует электрическую энергию для травления, сверления, обработки и резки металлических деталей. Также часто используются электроэрозионные станки с ЧПУ для тщательного управления процессом, что позволяет получать невероятно точные результаты как на очень хрупких или ломких материалах, так и на твердых металлических материалах, которые плохо реагируют на другие процессы обработки (например, закаленная сталь, титановые сплавы и никелевые сплавы. суперсплавы).
Производители имеют в своем распоряжении различные виды электроэрозионной обработки.Однако все процессы следуют общей схеме, которую мы здесь рассмотрим.
1. Для начала производители погружают электроэрозионный инструмент и заготовку в ванну с диэлектрической жидкостью на водной основе. Ванна помогает, проводя электричество между обрабатываемой деталью и электроэрозионным инструментом (быстрее изнашивая ненужный материал), смывая мусор и предотвращая преждевременное искрение.
2. После погружения с помощью электрических разрядов электроэрозионный инструмент создает токопроводящий путь или дугу между собой и заготовкой, создавая между ними сильное электрическое поле.Это генерируемое электрическое поле затем размывает поверхность заготовки по заранее заданному рисунку или форме. Вот почему электроэрозионную обработку также иногда называют электроэрозионной обработкой, электроискровой обработкой или штамповкой.
ДизайнЭлектроэрозионные станки могут резать практически любой материал, металл или любой другой материал. Примеры материалов, с которыми они работают, включают алюминий, бронзу, кобальт, медь, золото, свинец, никель, кремний, нержавеющую сталь, титан и вольфрам.
При принятии решения о том, какой инструмент или инструменты лучше всего подходят для их применения, производители учитывают такие переменные, как предполагаемая форма и размер конечного продукта, а также материал заготовки (который должен соответствовать материалу электрода или материалу / конструкции инструмента, чтобы чтобы нормально работать).
Используемое оборудованиеИнструменты EDM обычно состоят из электрода, проволоки или фасонного инструмента и источника питания, к которому он подключен. Этот источник питания помогает создавать электрический разряд или искры, которые могут выделять высокую температуру в диапазоне от восьми до двадцати тысяч градусов.
Независимо от процесса или инструмента электроэрозионной обработки, большая часть оборудования для электроэрозионной обработки управляется, контролируется или контролируется станками с ЧПУ или программным обеспечением CAM / CAD.
Варианты и аналогичные процессыНекоторые из многих методов, которые производители могут использовать для завершения электроэрозионной обработки, включают обычный электроэрозионный электроэрозионный станок (электроэрозионный электроэрозионный станок), проволочный электроэрозионный электроэрозионный станок, электроэрозионный электроэрозионный станок с малым отверстием, электроэрозионный электроэрозионный станок с быстрым сверлением и электроэрозионный электроэрозионный микроэлектрод.
Обычный электроэрозионный электроэрозионный станок , также известный как электроэрозионный электроэрозионный станок с грузилом, или погружной электроэрозионный станок, является старейшим и одним из двух наиболее широко используемых видов электроэрозионной обработки. Sinker EDM – лучший процесс для создания сложной геометрии.
В электроэрозионном методе с грузилом используется электрод. Электрод чаще всего изготавливают из обработанного графита, хотя он также может быть медным. Электрод погружается в металл, создавая сложные трехмерные формы, отверстия и узоры.
Электроэрозионная обработка проволокой , иногда называемая эрозией проволоки, является другим основным типом электроэрозионной обработки. Процесс электроэрозионной обработки проволоки, который может быть довольно эффективным, хорошо подходит для резки фигур как на отдельные детали, так и на целые сборки. Электроэрозионный электроэрозионный станок также может создавать переделанные слои. Вместо электрода в электроэрозионных станках используется проволока для передачи искр на заготовку. Эта проволока, которая сделана из проводящего материала, такого как латунь, подается с катушки через заготовку, а затем зажимается с обоих концов алмазными направляющими с ЧПУ.
Для создания фигур и узоров проволока в виде узора разрезает металл. Рисунок, который режет проволока, основан на движении рычагов направляющих с ЧПУ. Для того, чтобы произошла электроэрозионная обработка проволокой, производители должны сначала провести большую часть обрабатываемой детали с помощью следующего процесса – электроэрозионной обработки с маленькими отверстиями.
Малое отверстие EDM – это метод EDM-сверления, при котором создаются отверстия и перфорации. Производители используют его перед электроэрозионным станком для создания отверстия, через которое может проходить проволока.Таким образом, он действует как альтернатива предварительному сверлению. Чаще всего производители используют EDM с маленькими отверстиями для пропуска проволоки через такие детали и изделия, как реактивные двигатели, лопатки турбин, фильеры (инструменты, предназначенные для экструзии полимеров в синтетические волокна) и детали топливной системы.
Быстрое сверление отверстий EDM – это тип электроэрозионной обработки, который технические специалисты используют для быстрого создания небольших глубоких отверстий в заготовке. Обычно они могут вырезать отверстие глубиной в дюйм примерно за одну минуту.Электроэрозионный электроэрозионный станок для быстрого сверления отверстий работает с использованием вращающегося трубчатого электрода, распыляющего струю диэлектрической жидкости под высоким давлением. Он популярен при бурении в авиакосмической и энергетической сферах.
Micro EDM – это процесс обработки сверхточных деталей. Также известный как μ EDM (μ – это символ микрон), микро EDM создает эрозии в наноразмерных размерах и предоставляет способ резки и инструментальных деталей, которые иначе не могли бы получить точную обработку. Процессы микроэлектроэрозионной обработки хорошо подходят для чувствительных медицинских инструментов, оптических инструментов, отверстий и т. Д.
ПреимуществаЭлектроэрозионная обработка дает широкий спектр преимуществ как производителям, так и клиентам. Во-первых, электроэрозионная обработка позволяет создавать изделия и детали с очень точной маркировкой, углами, разрезами и т. Д. Во-вторых, электроэрозионные станки могут обрабатывать даже самые маленькие детали или мельчайшие линии. Сложные формы, которые производители могут создавать с помощью инструментов EDM, были бы трудны или невозможны с помощью традиционных инструментов. Кроме того, все электроэрозионные станки могут точно резать даже самые твердые металлы без предварительного нагрева.Удаление этого шага в процессе обработки экономит время и деньги производителей.
В отличие от многих других методов обработки, EDM не использует удары или истирание для достижения своих целей. Фактически, электроэрозионный инструмент никогда не вступает в физический контакт с обрабатываемой деталью. Это существенное преимущество. Поскольку электроэрозионный инструмент никогда не соприкасается с обрабатываемой деталью, эта деталь не деформируется и не имеет тепловых повреждений или дефектов, таких как заусенцы. Аналогичным образом, с помощью электроэрозионной обработки производители могут с первого раза обработать поверхность с отличным качеством обработки.
На что следует обратить вниманиеПрежде чем вводить в эксплуатацию компанию по электроэрозионной обработке, вам необходимо провести исследование. Поскольку EDM создает такие деликатные и сложные разрезы и линии, вы должны быть уверены, что поставщик услуг, выполняющий эти разрезы и линии, справится с этой задачей. Вы также хотите убедиться, что у них есть правильное оборудование EDM, соответствующая сертификация и солидный послужной список для их поддержки.
Рынок EDM наводнен списками поставщиков услуг в Интернете.Некоторые из них хороши, а некоторые нет. Чтобы сузить круг кандидатов для вас и убедиться, что вы в конечном итоге получите высококачественного поставщика услуг, мы составили список из нескольких компаний EDM и контрактных производителей, которым мы доверяем. Вы найдете этот список со ссылками и профилями в середине этой страницы. Мы считаем, что лучший способ приблизиться к ним – это иметь под рукой ваши спецификации. Запишите свои спецификации перед тем, как начать просмотр, чтобы вы могли быстро принять обоснованное решение относительно того, какие производители будут или не будут работать для вас.В зависимости от предлагаемых ими услуг выберите трех или четырех поставщиков EDM, с которыми вы хотели бы поговорить, и обратитесь к ним. Подробно изучите свое приложение с каждым из них, затем сравните и сопоставьте то, что они предлагают. Решите, какая компания вам подходит, и приступайте к работе.
Производители электроэрозионной обработки Информационное видео
FANUC запускает крупнейший на сегодняшний день электроэрозионный электроэрозионный станок
Серия станков FANUC α-CiB включает компактные, высокопроизводительные станки для резки под флюсом с высокой жесткостью и точностью резки.
В варианте α-C800iB используется проволока диаметром 0,1–0,3 мм для обработки толстых, ступенчатых и конических заготовок толщиной до 300 мм и весом 3000 кг. Он также имеет увеличенный ход по оси XY до 800 мм x 600 мм, а также ход по оси Z на 310 мм, который по запросу может быть увеличен до 510 мм.
Одной из выдающихся особенностей α-C800iB является встроенная функция CORE STITCH, которая позволяет операторам продлить часы обработки без участия человека за счет лучшего планирования работ по резке.Точки стежка устанавливаются непосредственно в ЧПУ станка без необходимости какого-либо предварительного программирования, а при использовании в сочетании с функцией повторной заправки проволоки он предлагает идеальное решение для длительной обработки без участия человека и обработки нескольких деталей. После завершения работы операторы просто выбивают стержни вручную, избегая любого риска повреждения машины.
Симметричная чугунная конструкция α-C800iB была оптимизирована для обеспечения большей жесткости и термической стабильности, чтобы удовлетворить требования высокой точности резки.Его компактный дизайн также сочетает в себе большой стол для резки с компактными размерами и самой низкой высотой в своем классе.
Как и в других машинах этой серии, в α-C800iB используется технология заправки проволоки AWF2 Automatic Wire Feed, обеспечивающая быструю и надежную автоматическую заправку всего за 10 секунд. В отличие от других машин, серии ROBOCUT не нужно возвращаться в исходную точку после обрыва проволоки, что радикально сокращает время цикла. Чтобы гарантировать надежную заправку и повторную заправку, проволока обрезается с помощью электроники, оставляя заостренный конец, который действительно прямой и без заусенцев.
Улучшенное управление резкой также может быть достигнуто за счет встроенной функции резки iPulse 2, которая обеспечивает высокоточный контроль углов независимо от толщины материала или шероховатости поверхности.
Система контроля натяжения проволоки с двумя сервоприводамиFANUC также поддерживает натяжение проволоки с точностью до ± 15 г, что дополнительно повышает надежность и стабильность. Таким образом, катушка с проволокой весом 30 кг может обеспечить 140 часов обработки без участия человека, что более чем вдвое превышает ожидаемый отраслевой стандарт.
Чтобы продлить срок службы, встроенные датчики измеряют давление воды на дне бака машины и саморегулируются с помощью серводвигателей в зависимости от высоты оси Z, чтобы гарантировать поддержание оптимального уровня воды повсюду.
Как и во всех моделях этой линейки, центральным элементом α-C800iB является надежный высокопроизводительный регулятор 31i-WB. В комплекте с 15-дюймовым цветным сенсорным дисплеем с интуитивно понятным начальным экраном iHMI он позволяет быстро и легко вводить и контролировать данные, а интуитивно понятный интерфейс визуального обслуживания включает встроенную систему раннего предупреждения для выявления потенциальных ошибок до их возникновения.
Энди Спенс, менеджер по продукции ROBOCUT в FANUC UK, прокомментировал: «Новая α-C800iB – это не только наша самая большая машина ROBOCUT, выпущенная на сегодняшний день, но и самая универсальная.Благодаря способности обрабатывать детали размером до 1250 x 975 x 500 мм, это идеальное решение для электроэрозионной обработки проволоки будущего для рынка, который становится все более непредсказуемым. Если конструкция заготовки изменится, α-C800iB будет идеально адаптирован ».
www.fanuc.eu/uk/en/robocut
Крупнейшая мастерская EDM в Северной Америке
Специалисты EDM
Электроэрозионный электроэрозионный станок • Электроэрозионный станок с трамбовкой / грузилом • Электроэрозионный станок с малым отверстием Быстрый ремонт – круглосуточная работаУ нас есть более 80 электроэрозионных станков , которые способны выполнять все виды электроэрозионной обработки, от небольших медицинских деталей до высоких деталей для нефтяной промышленности или больших турбин для энергетической промышленности.
Проволока EDM
- Электроэрозионные станки с модифицированной проволокой для резки высотой до 64 дюймов
- EDM детали весом до 10 000 фунтов
- EDM сужается до 45 градусов
- Автоматическая резка с автоматической нарезкой резьбы
- Точность до +/- .0001 “
- Обработка поверхности до 12 RMS
Барабан / грузило EDM
- 16 держателей инструментов
- Точная индексация и наведение по орбите
- Угловые возможности
- Машинная резьба в закаленные материалы
- Точность до +/-.0002 “
- Обработка поверхности до 16 RMS
EDM с малым отверстием
- Модифицированные станки для сверления отверстий EDM в высокие детали
- EDM с малым отверстием – более 30 дюймов (EDM с обеих сторон)
- Отверстия без заусенцев
- Отверстия EDM от 0,012 до 0,187 дюйма
Другие возможности
- Шесть специализированных программных станций для электроэрозионных станков
- Обратное проектирование
- Вице-президент, Стив Соммер, инженер-механик
- Получение файлов AutoCAD, DXF, IGES и STEP по электронной почте
- Контроль: оптическое измерительное устройство
- Координатно-измерительная машина с ЧПУ
- Переносная координатно-измерительная машина и др.
электроэрозионных станков | Продажа электроэрозионных станков
Absolute Machine Tools предлагает комплексные электроэрозионные решения для самых разных отраслей и сфер применения.Оснащен электроэрозионным станком AccuteX Wire & Sinker, высокоскоростными фрезерными станками для обработки графита и твердого сплава, а также системами ESPRIT CAD / CAM. Absolute Machine Tools также сотрудничает со всеми основными производителями инструментов, оснастки и автоматизации, чтобы предоставить лучшие решения для каждого клиента и для каждой области применения.
Электроэрозионные станкиAccuteX с ЧПУ стандартно поставляются с лучшим и самым надежным в отрасли автоматическим устройством для заправки проволоки. Как мы можем подтвердить это требование? Потому что запатентованный AccuteX резьбонарезной станок для проволоки отжига каждый день проверяется лучшими источниками… нашими клиентами.Один производитель пистолетов выполняет более 750 проволочных ниток в день, а другой производитель заявляет о тысячах часов автономных операций из-за надежности запатентованного устройства для заправки проволоки AccuteX. Узнать больше
AccuteX EDM также с гордостью представляет свою собственную линейку штамповочных грузил как с ручным ZNC, так и с полностью программируемым ЧПУ для производства трехмерных деталей.
Absolute Machine Tools продолжает предлагать широкий ассортимент расходных материалов для электроэрозионных станков всех марок, представленных на рынке сегодня.
AccuteX EDM также гордится тем фактом, что наш автоматический нитевдеватель обеспечивает самое низкое обслуживание среди всех наших конкурентов. Опять же, как мы можем это доказать? Что ж, один клиент утверждает, что единственный инструмент, который ему нужен для обслуживания нитевдевателя AccuteX, – это Q-наконечник. Благодаря почти 100% успешной нарезке резьбы, электроэрозионное оборудование AccuteX обеспечивает время цикла от искры до искры в течение 15 секунд, что позволяет производителям экономить материалы, время и деньги.
Интеллектуальное управление углом / дугой активно от черновой до чистовой обработки, управляя критически важными функциями для значительного повышения точности углов и чистовой обработки.Контролируя мощность через проволоку, промывку и работу серводвигателя, электроэрозионный станок AccuteX Wire EDM может создавать высокоточные и качественные результаты при обработке заготовок любой формы.
SD-Master обеспечивает повторяемость обработки за счет стабилизации высокоскоростной обработки и обрыва проволоки, делая продолжительность цикла и поставки надежными и предсказуемыми. С SD-Master от AccuteX нет необходимости настраивать условия резки и программировать смещения проволоки, потому что блок SD (стабильная разгрузка) способен справляться с изменяющимися условиями толщины заготовки и требований к промывке водой при высоких скоростях резания.Стабилизируя условия, SD-Master AccuteX также снижает риск обрыва провода, повышая пропускную способность вашего магазина.
Электроэрозионные станкиAccuteX Wire выпускаются четырех типов. Наша серия AL (двигатели с линейным валом) – это самый быстрый и энергоэффективный электроэрозионный электроэрозионный станок с погружным электродвигателем AccuteX. Серия AU состоит из проволочных электроэрозионных станков погружного типа с большой подвижной колонной (с удлиненной осью Z) и с промывкой с открытым столом. Новинка AccuteX – это машина серии GE. В целом экономичная серия GE имеет многие из тех же стандартных (и дополнительных) функций, что и другие модели AccuteX EDM, по цене от 89 900 долларов.AccuteX EDM также предлагает полную линейку вспомогательных электроэрозионных станков, таких как электроэрозионные сверла и штамповочные прессы для электроэрозионных станков как в экономичных ZNC, так и в многоосных моделях с ЧПУ.
AccuteX Technology была основана в 1991 году после того, как группа ведущих инженеров-исследователей из Тайваньского научно-исследовательского института промышленных технологий (ITRI) запустила первый электроэрозионный станок на базе ПК. Базовая технология, оборудование, программное обеспечение, контроллер и источник питания были предоставлены OEM-производителям, таким как Chmer, Jiann Sheng, Maxsee, Sure First и Joemars, которые, в свою очередь, успешно монополизировали рынки электроэрозионной обработки в Японии и Швейцарии.