Электроэрозионные(электроискровые) станки с ЧПУ фирмы AgieCharmilles.
GF Machining Solutions входящая в корпорацию Georg Fischer — крупный мировой производитель металлообрабатывающего оборудования, средств автоматизации, крепежной оснастки и программного обеспечения. Штат — около 3000 сотрудников, а ежегодный оборот превышает 900 млн. швейцарских франков. Компания выпускает станки известных всему миру старейших брендов.
Электроэрозионные станки AgieCharmilles включая: проволочно-вырезные, прошивочные и супердрели под любую задачу и типоразмер.
Высокоскоростные и производительные фрезерные обрабатывающие центры Mikron в 3-5 осевом исполнении.
Специализированные фрезерные станки Liechti для обработки турбинных лопаток.
Крепёжная оснастка и палетные системы System 3R для электроэрозионных станков и фрезерных обрабатывающих центров.
Скоростные шпиндели Steptec покрывают внутренние потребности и поставляются европейским
производителям фрезерных станков.
GFMS предлагает 3D принтеры для изготовления пресс-форм и 5-осевые лазерные станки для нанесения тонких текстур, включая голографические, на их поверхность.
Группа GFMS владеет научно-производственными центрами в Европе и Азии. Компания поддерживает региональные представительства в более чем 50 стран мира, предлагающих обучение и демонстрацию продуктов отвечающих новейшим технологическим тенденциям.
Технические центры предлагают специализированные решения для конкретных промышленных сегментов. Сервисные центры осуществляют техническое поддержку но протяжении всего срока службы оборудования, поставку запасных частей и расходных материалов.
В странах СНГ компанию GFMS представляет швейцарская фирма GALIKA AG, которая начала свою деятельность еще в 1986, как эксклюзивный дистрибьютор на территории СССР швейцарского производителя электроэрозионного оборудования AGIE.
GALIKA AG поставляет весь спектр металлообрабатывающего оборудования GFMS, имеет развитую
дилерскую сеть, региональные представительства по всей России и странах СНГ.
Головной офис фирмы GALIKA в Москве на Пушкинской набережной. Фирма владеет собственным зданием — выставочным технологическим центром, демонстрационными залами с металлообрабатывающим оборудованием, сервисным центром, складом запасных частей и расходных материалов.
Электроискровые станки Основу электроискрового метода обработки металлов составляет процесс электроэрозии металлов. Сущность его заключается в том, что под воздействием коротких искровых разрядов, посылаемых источником электрического тока, металл разрушается. При обработке на электроискровом станке для прошивки отверстий заготовку погружают в бак с жидкостью и соединяют с положительным полюсом, выполняющим функции анода. Электрод (инструмент), являющийся катодом, соединяют с отрицательным полюсом и укрепляют на ползуне, имеющем вертикальное перемещение по направляющим. Заготовка, стол, на котором ее закрепляют, корпус бака и станина станка электрически соединены между собой и заземлены, так что их электрический потенциал всегда равен нулю. Если, опустив ползун, прикоснуться электродом к заготовке, то в электрической цепи пойдет электрический ток от отрицательной клеммы генератора к положительной клемме. В электрическую цепь включен резистор. Это катушка из длинной тонкой проволоки. Изменяя сопротивление, можно регулировать силу тока, контролируя ее по амперметру. Для того чтобы получить импульсные разряды, непрерывно следующие друг за другом, между электродом и заготовкой в электрическую схему станка включается конденсаторная батарея. Ее включают параллельно заготовке и электроду. Если замкнуть выключатель электрической цепи при разведенных электродах станка, то в первый момент стрелка амперметра резко отклонится и постепенно возвратится на 0. Стрелка вольтметра, наоборот, плавно отклонится от того значения напряжения, которое создается генератором. Это означает, что произошла зарядка конденсаторов Технический вуз . Теперь можно приблизить электрод к заготовке. ![]() После разряда электрический ток между электродом и деталью исчезнет, так как вся энергия, накопленная в конденсаторах, израсходована, и снова начинается зарядка конденсаторной батареи. Следующий разряд произойдет как только конденсаторы зарядятся. Этот процесс происходит непрерывно, импульсные разряды следуют один за другим до тех пор, пока не закончится обработка. ![]() Когда электрод прикоснется к заготовке, электрическая цепь станка замкнется и в ней потечет электрический ток. Тогда на концах катушки создается разность потенциалов, и в ней также потечет электрический ток. Сердечник намагнитится и втянется в катушку, т. е. поднимется, поднимая вместе с собой ползун и электрод. Искровой промежуток между электродом и заготовкой восстановится, и основная электрическая цепь окажется разорванной – ток в ней исчезнет. Одновременно исчезнет ток и в катушке соленоида. Сердечник размагнитится, перестанет втягиваться в катушку и под действием собственной массы опустится. Вместе с ним опустятся ползун и электрод. Между электродом и заготовкой снова произойдет электрический разряд. По мере углубления отверстия электрод будет опускаться под действием силы тяжести. Так будет продолжаться, пока идет процесс прошивки отверстия. Соленоидный регулятор автоматически постепенно опускает) электрод по мере увеличения глубины отверстия. ![]() Электроискровой прошивкой удается изготовлять отверстия с криволинейной осью. Электрод из латунной проволоки изогнут по дуге окружности, радиус которой равен радиусу закрепления оси отверстия. Электрод укреплен в держателе, который может поворачиваться вокруг оси. Держатель вокруг оси поворачивается с помощью шнура, верхний конец которого прикреплен к соленоидному регулятору. В остальном процесс совершается так же, как и при прошивке отверстий с прямолинейной осью. Универсальные электроискровые станки обычно имеют вертикальную компоновку. Автоматический регулятор подач сообщает вертикальные перемещения электроду-инструменту. Ванну с заготовкой, установленной на столе, можно перемещать в вертикальном направлении с помощью электродвигателя. ![]() 2005-2007 @ www.swedishbranch.ru |
Электроискровые станки – Большая Энциклопедия Нефти и Газа, статья, страница 1
Электроискровые станки
Cтраница 1
Электроискровые станки используют при обработке отверстий малого диаметра, узких щелей и других поверхностей деталей из труднообрабатываемых материалов. Производительность станков невелика – порядка 20 м3 / мин. [1]
Специальные электроискровые станки моделей 159 – 162 предназначены для получения отверстии в распылителях дизельной топливной аппаратуры и в других аналогичных деталях.
[4]
Специальные электроискровые станки моделей 159 – 162 предназначены для получения отверстий в распылителях дизельной топливной аппаратуры и в других аналогичных деталях. [5]
Промышленностью выпускаются электроискровые станки модели 18В для извлечения обломков сверл и других инструментов из глубоких отверстий, станки модели 37М для плоского шлифования и автоматические станки модели 62 для получения отверстий диаметром до 0 15 мм с точностью обработки до 0 01 мм. [6]
Промышленность выпускает электроискровые станки модели 18В для извлечения обломков сверл и других инструментов из глубоких отверстий, станки модели 37М для плоского шлифования и автоматические станки модели 62 для получения отверстий диаметром до 0 15 мм с точностью обработки до 0 01 мм. [7]
Значительно более производительны многоканальные электроискровые станки, позволяющие работать с многоинструментальной настройкой. Ниже рассмотрено несколько целесообразных вариантов конструкции таких станков.
[8]
Наиболее удобными для переоборудования под электроискровые станки
В настоящее время отечественная промышленность выпускает электроискровые станки конденсаторного действия, различающиеся по назначению, конструкции, производительности и другим параметрам. Что же касается электроискровых станков бесконденсаторного действия, то таковые пока не изготовляются промышленностью. [10]
Для отверстий диаметром менее 1 мм обычно применяют электроискровые станки с релаксационными генераторами. Однако при изготовлении щелей ( вследствие увеличения площади за счет длины щели) электроимпульсные источники могут применяться при ширине щели и менее 1 мм. Так, специальный двухшпиндель-ный электроимпульсный станок модели 4Ц24М позволяет изготовлять щели шириной от 0 5 мм, длиной до 75 – 80 мм и глубиной до 5 мм.
[11]
Кроме того, все колебания напряжения сети, питающей электроискровые станки, скажутся на работе регулятора подачи и, в CBOIO очередь, также приведут к колебаниям величины зазора. [12]
Рабочий инструмент и изделие, к которым по условиям работы подводится электрический ток, например электроискровые станки, установки для электрогидравлического удара, следует изолировать от корпуса оборудования. Корпуса указанного и аналогичного оборудования не следует заземлять, чтобы исключить возможную опасность поражения током рабочих, обслуживающих такое оборудование. [13]
На небольших предприятиях с малой потребностью в резцах для изготовления стружкозавивательных канавок могут быть использованы электроискровые станки типа настольного станка ОКБ ММ. На этом станке можно обработать до 150 резцов в смену. На крупных предприятиях, использующих твердосплавные резцы со стружкозавивательными канавками в большом количестве, обычно применяют специализированный электроискровый станок с большой производительностью, например, станок модели 4382, выпускаемый ОКБММ, описание которого приведено ниже.
[14]
Страницы: 1 2
станок для электроискровой обработки – Перевод на английский – примеры русский
На основании Вашего запроса эти примеры могут содержать грубую лексику.
На основании Вашего запроса эти примеры могут содержать разговорную лексику.
Предложить пример
В контрольные списки включены только такие станки для электроискровой обработки, которые имеют две или более поворотных оси, – а количество этих осей зависит от используемого программного обеспечения.
У моей тети есть станок для этого.
Он обнаружил остатки гончарной печи овальной формы, станок для обработки глины и глубокий резервуар для воды.
Йохман, принеси станок для арматуры.
Это станок для печати открыток, приглашений на свадьбу, поздравлений.
It’s how I put out my line of letterpress cards, wedding invitations, invites. Отсюда это похоже на станок для пирсинга.
СТАНОК ДЛЯ НАНЕСЕНИЯ И УДАЛЕНИЯ СУБСТАНЦИИ НА ПОВЕРХНОСТЬ ДЛИННОМЕРНОГО ИЗДЕЛИЯ
MACHINE FOR APPLYING AND REMOVING SUBSTANCES TO AND FROM A LONG ARTICLEОсновными потребителями станка являются мастерские и предприятия по ремонту и обслуживанию бензопил и частные лица, приобретающие станок для индивидуального пользования.
The basic users of the grinder are the workshops and facilities for maintenance and overhaul of petrol power saws as well as the individuals procuring the grinder for personal use.RM.CBBK ДВОЙНЫ ТОРЦОВАЧНИЙ СТАНОК ДЛЯ ПОПЕРЕЧНЕГО СРЕЗА, ДЛИНА СРЕЗА 6мт.
Мы оставим станок для изготовления ключей!
Присланный в Шри-Ланку станок для изготовления пластиковых пакетов – это чисто коммерческая сделка, в которой участвовал г-н Джаясундарам.
Компактный станок для экономичного серийного производства деталей из латуни ХЗ, алюминия и стали. Новый модельный ряд MSL с несколькими салазками идеально отвечает запросам пользователей.
The MSL series is the optimal complement to cam-controlled turning machines, and is best suited for smaller lot sizes and for efficient serial production, ranging from simple to complex work pieces.Станок для изгибания профилей, предназначеный для изгибания профилей с определенным радиусом.
The machine is intended for bending of profiles with a particular radius. Еммё Elle Станок для полирования поверхностей – бывший в употреблении L. B.A.
Glimåkra Идеал – это удобный компактный ткацкий станок для человека, который увлеченно занимается ткачеством, но не имеет достаточно места для установки станка большего размера.
Glimåkra Ideal is a well proportioned small loom for the weaver, who has a great interest in weaving, but who doesn’t have enough room for a bigger loom.В 1926 году Гуннар Андерссон приобрел свой первый станок для производства бёрд и основал компанию Gunnar Anderssons Vävskedsfabrik AB, GAV.
In 1926 Gunnar Andersson bought his first reed-making machine and started the limited company Gunnar Anderssons Vävskedsfabrik AB, GAV. Что касается финансов, то реформа позволит обуздать инфляцию, предотвратить растрату государственных средств и избегнуть необходимости пускать в ход станок для печатания денег, а также бороться с неэффективностью государственного управления, с безнаказанностью и коррупцией.
За выпуск вибропрессов – линий Рефей, “Стройтехника” награждена десятками дипломов и золотыми медалями ВВЦ (ВДНХ), которые подтвердили что линия “Рифей” – это самый надёжный, качественный и экономичный станок для вибропрессования.
For the vibropress “RIFEY” line production, the plant was awarded numerous certificates and VVC(VDNH) gold medals.
Станок для плетения тесьмы относится к традиционным скандинавским станкам и используется для изготовления лент, декоративной тесьмы и поясов.
The Bandloom is a traditional style of Scandinavian loom for making ribbons, decorative bands and belts.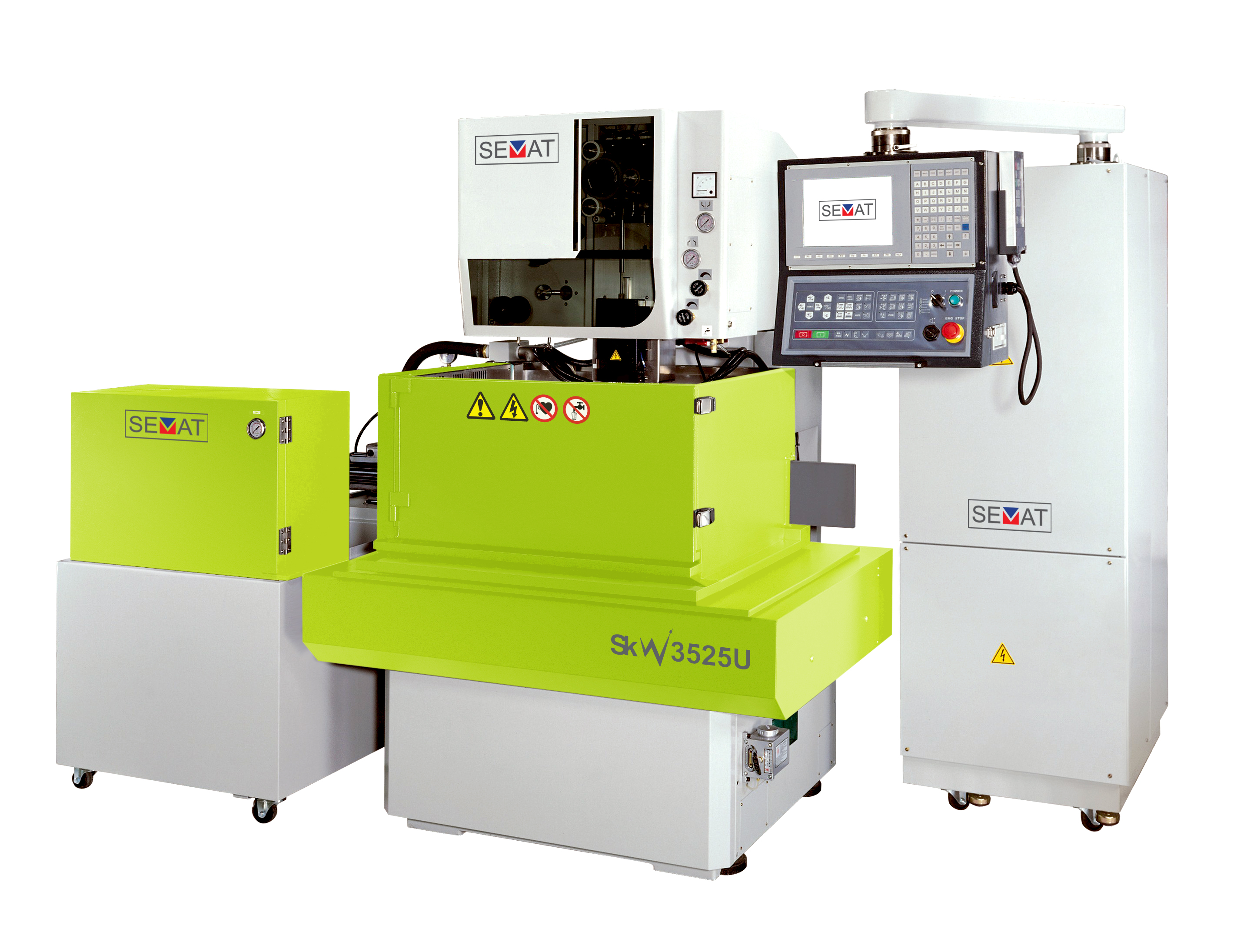
Начиная с 1981 года, наша фирма вновь выступила в секторе упаковочного оборудования и стала производить МАШИНУ ДЛЯ ФЛЕКСОГРАФИЧЕСКОЙ ПЕЧАТИ и СТАНОК ДЛЯ РЕЗКИ РУЛОННОЙ БУМАГИ ПО ЗАДАННЫМ РАЗМЕРАМ, и стала предлагать их на рынок.
Since 1981, we are producing and representing to market Flesko Printing and Bobin Size Cutting Machine for packaging sector.SODICK (СОДИКОМ)
Sodick Сo., Ltd . основана в августе 1976 года. Уже в конце 80-х годов компания прочно заняла ведущее место в мире по объемам производства и продаж электроискрового (электроэрозионного) оборудования. Sodick буквально взорвала рынок электроэрозии, обойдя за кратчайший срок целый ряд именитых фирм-производителей. К середине 90-х годов Sodick производила в год более 2000 ЭИ станков с компьютерными ЧПУ – на тот период четверть продаж мирового рынка ЭИ станков с КЧПУ (в 1996 г. продано 2284 электроискровые (электроэрозионные) системы с Sodick с КЧПУ). В 2007 – 2008 финансовом году производственники во всем мире купили уже свыше 4000 станков Sodick – больше, чем произвели все европейские фирмы, вместе взятые (включая европейское производство в Китае и т.д.). Такой рост объясняется не только надежностью и качеством оборудования, но, прежде всего, рядом новых эксклюзивных технических инноваций и новых технологических направлений в ЭИ обработке, открывающих потребителям совершенно новые возможности. Самое значительное нововведение – линейные двигатели в электроискровых станках. Первые линейные ЭИ станки – фактически революция в ЭИ обработке – появились на рынке в конце 1998 года. На октябрь 2008 г. у пользователей работало уже более 20 тысяч линейных электроискровых (электроэрозионных) станков. Доля Sodick на рынке Японии – около 50%. Более 70% продукции Sodick поставляется на экспорт. Всего в мире эксплуатируется 50 с лишним тысяч ЭИ станков фирмы Sodick С o ., Ltd .
Электроискровое (электроэрозионное) оборудование Sodick – это синтез самых передовых, часто уникальных технологий с изящными и лаконичными конструкторскими решениями, это высокотехнологичные функции, аналогов которым нет в ЭИ машинах других изготовителей. Добавьте к этому непревзойденное японское качество, надежность и долголетнюю безотказность, и станут понятны причины, по которым “электроэрозию Sodick R21; выбрали и выбирают для своих предприятий известнейшие производственные фирмы.
В перечне только именитых фирм, на заводах которых работает ЭИ оборудование Sodick , свыше 1000 имен. В аэрокосмическом производстве – это Boeing и Pratt&Whitney , G е n е r а l Е l е ctric и SNECMA , американское Национальное управление по аэронавтике и космосу ( NASA ), ряд ведущих предприятий России и СНГ, включая «Мотор Сич» . В электронной промышленности – IBM, Bell Labs, AT&T, Hеwlеtt Pаckаrd, NEC, Toshiba. На ЭИ станках Sodick делают инструмент на заводах Маtsushitа для знаменитых телевизоров и электронных приборов Pаnаsonic, Nаtionаl, Tеchnics. ЭИ системы Sodick работают на автомобильных заводах Chryslеr, Fiat, Ford, GM, Hondа, Hyundаi, MAN, Nissan, Opel, SAAB, Toyota, Volvo и всех японских автопроизводителей (за исключением одного, самого убыточного). В списках пользователей: Саnon, Кyosеrа, JVС, Samsung, LG (Gold Star), Bosch, Siemens, Сitizеn, Polaroid, Phillips, Gillette, Proctor&Gаmblе, Blаck&Deckel, De Beers, Мikron, Daewoo, Kawasaki, Pilot Pen, Omron, Huskey, 3M. В начале 2000-х годов ультрапрецизионный ЭИ станок Sodick AP200L стал самым продаваемым ЭИ вырезным станком в часовой промышленности Швейцарии (не можем назвать названия фирм из-за соглашений о неразглашении, но это самые именитые и дорогие бренды!)
Поразительный успех за невероятно короткий срок в значительной степени объясняется тем, что фирму Sodick создали талантливые конструкторы-эрозионщики, которые после многих лет работы ушли с “фирмы-пионера” в электроэрозии Japax (“Джапакс”), чтобы воплощать свои оригинальные идеи в электроэрозии самостоятельно, на новом качественном уровне. J apax Inc . выпускала ЭИ станки с 1953 г. и была основана “отцом японской электроэрозии” Киёси.Иноуэ, который вслед за первооткрывателями электроэрозии супругами Б.Р. и Н.И. Лазаренко и другими российскими учеными, начал работы над проблемами ЭИ в Японии и внес наибольший вклад в создание производства ЭИ станков в Японии. Опыт, приобретенный и наработанный основателями Sodick за годы работы на Japax , послужил пусковой площадкой и стартовым научно-техническим капиталом для успешного и быстрого взлета новой фирмы. “Кадровая подпитка” ведущими специалистами с J apax шла на фирму Sodick вплоть до апреля 1992 г., когда J apax Inc . формально вошла в SОDIСК.
UMI.CMS – Проволочно-вырезные станки
Электроэрозионные проволочно вырезные станки общего назначения от компании GF Agie Charmilles
Серия электроэрозионных станков GF Agie Charmilles CUT 20/30 специально создана для производства штампов и пресс-форм, поэтому эти станки оптимальны для использования в инструментальном производстве. По итогам 2012 года эта серия является самой продаваемой в СНГ среди проволочно-вырезных станков иностранного производства*.
Станок | Габариты заготовки (ДхГхВ) | Хода X, Y, Z |
Электроэрозионный CUT 20 P | 900 x 680 x 250 мм | 350 x 250 x 250 мм |
Электроэрозионный CUT 30 P | 1050 x 800 x 350 мм | 600 x 400 x 350 мм |
Электроискровые проволочно вырезные станки повышенной точности от компании GF Agie Charmilles
Специальная серия электроэрозионных станков, позволяющая вести обработку с ультрапрецизионной точностью, имеющая целый ряд особенностей: микрообработка, работа в масле, проволока Ø20 мкм, получение шероховатости менее Ra 0,03 мкм, функция двухпроволочной обработки, системы оптического контроля. Комплекс этих возможностей делает данные станки уникальными, не имеющими аналогов на рынке электроэрозионного оборудования.
Станок | Габариты заготовки (ДхГхВ) | Хода X, Y, Z |
Электроискровой CUT 1000 |
300 х 200 х 80 мм | 220 х 160 х 100 мм |
Электроискровой CUT 1000 OilTech |
300 x 200 x 80 мм | 220 х 160 х 100 мм |
Электроискровой CUT 2000 |
750 x 550 x 250 мм | 350 x 250 x 256 мм |
Электроискровой CUT 2000 OilTech |
750 x 550 x 250 мм | 350 x 250 x 256 мм |
Электроискровой CUT 3000 |
1050 x 650 x 250 мм | 500 x 350 x 256 мм |
Электроэрозионные высокопроизводительные проволочно вырезные станки от GF Agie Charmilles
В дополнение к возможностям электроэрозионных станков CUT 20/30 данные станки позволяют решать ряд специальных задач: высокоскоростная обработка деталей основного производства, обработка крупногабаритных заготовок, получение сверхбольших углов на высоких деталях, изготовление деталей для медицины и аэрокосмической промышленности с минимальным измененным слоем и отсутствием электролитически х эффектов, обработка специальных материалов.
Станок | Габариты заготовки (ДхГхВ) | Хода X, Y, Z |
Электроэрозионный AC Progress VP2 |
750 x 550 x 250 мм | 350 x 250 x 256 мм |
Электроэрозионный AC Progress VP3 |
1050 x 650 x 420 мм | 500 x 350 x 426 мм |
Электроэрозионный AC Progress VP4 |
1300 x 1000 x 510 мм | 800 x 550 x 525 мм |
Электроэрозионный CUT 200 mS/Sp |
1000 x 550 x 220 мм | 350 x 220 x 220 мм |
Электроэрозионный CUT 300 mS/Sp |
1200 x 700 x 400 мм | 550 x 350 x 400 мм |
Электроэрозионный CUT 400 Sp |
1300 x 1000 x 510 мм | 800 x 550 x 510 мм |
Электроэрозионный CUT 200 Dedicated |
Ø150…Ø500 мм | 350 x 220 x 220 мм |
Эрозионные проволочно вырезные станки серии Фастваэр от компании GF Agie Charmilles
Эта серия проволочно вырезных электроэрозионных станков GF AgieCharmilles специально разработана для решения задач, требующих применения электроэрозионного оборудования при условии, что использование традиционных станков является экономически невыгодным. Демократичная цена, низкие эксплуатационные расходы делают станок очень привлекательным в современных экономических условиях.
Станок | Габариты заготовки (ДхГхВ) | Хода X, Y, Z |
Эрозионный FW1U |
900 x 680 x 250 мм | 350 x 250 x 250 мм |
Эрозионный FW2U |
1050 x 800 x 350 мм | 600 x 400 x 350 мм |
Эрозионный FW3U |
1050 x 800 x 350 мм | 600 x 400 x 350 мм |
Электроимпульсные станки | Электроискровая обработка металла
Электроимпульсные станки отличаются от электроискровых тем, что работают на основе использования импульсных луговых разрядов малой скважности, по разной энергии и частоты. Черновая обработка происходит при большой энергии и низкой частоте, а чистовая обработка – при малой энергии и высокой частоте. Возбуждение разрядов осуществляется электрическим независимым генератором. В отличие от электроискровых, в электроимпульсных станках обрабатываемая деталь соединяется с катодом ( – ), а инструмент – с анодом (+). Съем металла осуществляется в основном в его капельно-жидком состоянии, что положительно отражается на энергоемкости процесса.
Электроды
Электрод-инструмент изготовляют из материалов с высокой теплопроводностью, таких как медь, алюминий и его сплавы, специальные графитизированные материалы, вольфрам.
В зоне обработки выделяется большое количество тепла, которое для обеспечения непрерывности обработки необходимо интенсивно отводить. Кроме того, в процессе обработки появляются частицы снятого материала и продукты износа электрода. При малых энергиях разрядов значительно ухудшается очистка межэлектродного промежутка, чем снижается эффективность процесса. Указанные обстоятельства заставляют электроимпульсную обработку осуществлять в два приема. Сначала используют разряды большой энергии с низкой частотой (черновая обработка). На этом режиме удаляют основную часть металла, оставляя припуск порядка 0,5 – 1 мм. После этого снижают энергию разрядов, повышают частоту и удаляют образовавшуюся неровность (чистовая обработка).
Интенсивность съема металла
Интенсивность съема металла с 1 см2 обрабатываемой поверхности при оптимальной подводимой мощности составляет для сталей 35-60 мм3/мин. Это позволяет вести обработку со скоростью углубления инструмента в деталь 0,35-0,6 мм/мин независимо от размеров обрабатываемой поверхности. Шероховатость поверхности при обработке деталей из стали соответствует 2,5 < Ra < 5 мкм, а при обработке деталей из твердого сплава 1.25 < Ra < 2,5 мкм. Исследования и практика указывают на возможность получения размеров с точностью до 0,08-0,2 мм при обработке поверхностей и 0,01-0,03 мм при обработке отверстии.
Электроимпульсный метод используется при обработке средних и крупных штампов, пресс-форм и их деталей из закаленных и труднообрабатываемых материалов.
Похожие материалы
Что такое электроискровое осаждение (ESD)?
Электроискровое осаждение (ESD) – это процесс импульсной микросварки, который используется для мелкомасштабного и точного ремонта дорогостоящих изношенных или неправильно изготовленных компонентов. Электроискровое осаждение также известно как искровое упрочнение, электроискровое упрочнение, электроискровое легирование, наплавка импульсным плавлением и наплавка импульсным электродом. Основные промышленные применения включают ремонт дефектов литейных форм и оснастки для литья под давлением.
Системы электроискрового осаждения содержат конденсаторный источник питания, который генерирует короткие импульсы сильного тока через вращающийся проволочный расходуемый электрод.Материал расходуемого электрода осаждается на заготовку с помощью электрических искр способом, обратным искровой эрозии. В процессе электроискрового осаждения электрод является анодом, а заготовка – катодом.
Когда энергия конденсатора высвобождается, постоянный ток генерирует плазменную дугу с высокой температурой (от 8000 до 25000 ° C) между концом электрода и заготовкой. Плазменная дуга ионизирует расходные детали, и небольшое количество расплавленного электродного материала переносится на заготовку.Перенос материала происходит быстро, а самозатухание происходит очень быстро.
Основываясь на коротких длительностях сильноточных импульсов, процесс обеспечивает низкое тепловложение материала подложки, что приводит к незначительным изменениям микроструктуры подложки или совсем без них. Следовательно, этот процесс имеет преимущество перед процессами сварки плавлением (включая дуговую, лазерную и контактную сварку) при ремонте материалов, которые трудно сваривать из-за плохих свойств зоны термического влияния (например, ликвационного растрескивания, высокой твердости, низкой ударной вязкости).Компоненты могут быть восстановлены до их первоначальных размеров, поскольку при таком низком тепловложении объемный материал основы остается близкой к температуре окружающей среды, что позволяет избежать термической деформации, усадки и высоких остаточных напряжений. Кроме того, этот процесс обеспечивает хорошую металлургическую связь между покрытием и подложкой.
Электроискровое напыление особенно подходит для ремонта мелких и неглубоких дефектов, но не подходит для крупных дефектов, так как процесс идет медленно, а максимальная толщина покрытия составляет около 2 мм.Электроискровое осаждение также можно рассматривать как процесс повышения износостойкости и эрозионной стойкости небольших участков поверхности.
См. Дополнительную информацию о материалах и управлении коррозией или свяжитесь с нами.
Схематическое изображение электроискрового осаждения
Электроискровой дефектоскоп “Корона 2.2” | AmasEnergy
(Оборудование / Материал)
Номер модели: Корона 2. 2
Состояние: Новое
Расположение или страна хранения: Россия
Техническая поддержка: Да
Гарантия: Нет
Цена: 85 620 руб.
Описание:
Корона 2.2 – электроискровой дефектоскоп, предназначенный для ручного контроля качества диэлектрических покрытий на токопроводящих подложках.Обнаруживает локальные сквозные и структурные дефекты в сухих изоляционных покрытиях толщиной до 16 мм. Диапазон импульсного испытательного напряжения от 5 до 40 кВ. Комплектуется вентилятором и Т-образными электродами.
Обзор:
Дефектоскоп Corona 2.2 можно использовать для проверки структурной целостности лакокрасочного покрытия, порошка, пленки, битума и других защитных покрытий. Подходит для исследования покрытий на изделиях из железа, бетона и других токопроводящих материалов на любом этапе эксплуатации объекта. Электроискровый дефектоскоп способен обнаруживать в покрытиях места пустот, непокрашенных красок, трещин, отслоений, микролунок, пористости, недопустимого истончения и различных посторонних включений.
Характеристики
- Диапазон испытательного напряжения 5-40 кВ;
- Наименьшее расстояние между двумя дефектами, закрепленными по отдельности, составляет 25 мм;
- цифровая индикация испытательного напряжения на дисплее с разрешением 0,1 кВ;
- позволяет контролировать как внутренние, так и внешние поверхности трубопроводов;
- время непрерывной работы от заряженного аккумулятора от 5 до 8 часов;
- световая и звуковая индикация искрового пробоя;
- толщина контролируемых покрытий: до 16 мм;
- большое количество сменных электродов для контроля изделий различного назначения; №
- с помощью пружинного электрода можно обследовать трубы диаметром до 1520 мм;
- небольшое усилие нажатия кнопки «КОНТРОЛЬ» облегчает длительную работу с устройством;
- Контроль разряда аккумулятора и автоматическое отключение питания при падении напряжения до 11 В;
- возможность быстрой замены АКБ.
Оборудование
- держатель трансформатора высокого напряжения;
- электронный блок управления;
- щеточный вентиляторный электрод;
- Электрод Т-образный;
- удлинитель для электрода;
- зажим;
- заземляющий провод с магнитом и зажимом;
- штырь заземления;
- переходные кабели для зарядки аккумулятора;
- Зарядное устройство;
- аккумулятор 2 шт .;
- термопакет для блока управления;
- чемодан для хранения и транспортировки;
- инструкция.
Принадлежности
пружинный электрод диаметром до 1520 мм;
- вспомогательный резиновый электрод с электробезопасной ручкой;
- малый Т-образный электрод;
- кольцевой резиновый электрод;
- щеточный волосяной электрод;
- плоский резиновый электрод;
- серповидный электрод;
- внутритрубный дисковый электрод;
- удлинители электродов длиной 0,3 – 2 м;
- заземляющий провод длиной до 20 м;
- дополнительные батареи;
- ручка электробезопасности;
- ручка съемная.
Чтобы увидеть информацию о компании, вам необходимо войти в систему.
Принципы и применение электроискрового осаждения (Конференция)
Джонсон, Р. Н. Принципы и применения электроискрового осаждения . США: Н. П., 1987.
Интернет.
Джонсон, Р. Н. Принципы и применения электроискрового осаждения . Соединенные Штаты.
Джонсон, Р. Н. Вт.
«Принципы и применение электроискрового осаждения». Соединенные Штаты.
@article {osti_7006599,
title = {Принципы и применение электроискрового осаждения},
author = {Johnson, R N},
abstractNote = {Электроискровое осаждение (ESD) - это процесс микросварки с импульсной дугой, использующий короткие сильноточные электрические импульсы для нанесения электродного материала на металлическую подложку. Это один из немногих доступных методов, с помощью которых сплавленное металлургически связанное покрытие может быть нанесено с таким низким общим тепловложением, что объемный материал основы остается при температуре окружающей среды или близкой к ней. Короткая длительность электрического импульса обеспечивает чрезвычайно быстрое затвердевание нанесенного материала и приводит к исключительно мелкозернистому однородному покрытию, которое приближается к аморфной структуре. Считается, что эта структура способствует хорошим трибологическим и коррозионным характеристикам, наблюдаемым для материалов для упрочнения, используемых в сложных условиях.Дан краткий исторический обзор процесса, за которым следует описание современного состояния, характеристик и применения покрытий электроискрового осаждения в ядерной и ископаемой энергетике, а также потенциальных приложений в разработке. 23 исх., 23 рис., 3 таб.},
doi = {},
url = {https://www.osti.gov/biblio/7006599},
journal = {},
number =,
объем =,
place = {United States},
год = {1987},
месяц = {12}
}
Ремонт алюминиевого сплава 2024 года методом электроискрового осаждения: технико-экономическое обоснование
Метод электроискрового осаждения (ESD) был изучен в качестве потенциального метода ремонта локально поврежденных катаных листов 2024 года, поставляемых с естественным старением (T4) и искусственным старением (T6 ) условия. На образцах для растяжения 2024-T4 и 2024-T6 сначала были сделаны надрезы, а затем надрезы были заполнены (отремонтированы) с помощью электростатического разряда тем же алюминиевым сплавом. Влияние параметров процесса на микроструктуру материала наполнителя и свойства подложки исследовали методами оптической и растровой электронной микроскопии. Были проведены испытания на растяжение и твердость. Испытание на растяжение показало, что образцы Т4 и Т6 в отремонтированном состоянии имели низкие свойства на растяжение, что было связано с дефектами и остаточными напряжениями, вызванными высокой скоростью охлаждения во время ремонта.Однако образцы после ремонта подвергались термообработке при температуре 135 ° C или 190 ° C для улучшения механических свойств. Более высокий предел текучести наблюдался у термообработанного сплава Т4. Пластичность и предел прочности при растяжении не изменились, на них в основном влияют пустоты и микротрещины.
1. Введение
Необходимость снижения эксплуатационных расходов, затрат на техническое обслуживание и связанных с отходами воздушных судов побудила авиационную промышленность разработать новые процедуры ремонта авиационных компонентов. Кроме того, из-за высокой стоимости материалов и рабочей силы для изготовления дорогостоящих компонентов, также необходимо отремонтировать все те компоненты, которые подвержены вдавливанию фрезерного шара и вырыванию резца, которые возникают в процессе изготовления [1, 2]. Новые ремонтные технологии должны преодолевать ограничения существующих и быть в состоянии работать в ремонтной мастерской, что позволит избежать транспортировки в ремонтную мастерскую или отправки изношенной детали оригинальному производителю [3].
Алюминиевый сплав 2024 был предшественником различных сплавов серии 2xxx, которые широко применяются в аэрокосмической промышленности благодаря своим превосходным свойствам, таким как высокое отношение прочности к массе, очень хорошее сопротивление росту усталостных трещин и хорошая вязкость разрушения [ 4, 5]. Обычно он поставляется в состоянии T4 или T6, поскольку такая обработка дает хорошие механические свойства. Как правило, детали 2024, используемые в авиации для обеспечения устойчивости к повреждениям, такие как нижняя обшивка крыла и конструкция фюзеляжа коммерческих самолетов, обычно легко подвергаются локальной коррозии (т. например, точечная коррозия и расслоение), особенно в хлоридсодержащей среде [6, 7].
К сожалению, обычные методы сварки плавлением (например, сварка вольфрамовым электродом в инертном газе (TIG), дуговая и электронно-лучевая сварка с переносом плазмы и лазерная наплавка) не подходят для ремонта этого сплава [1, 5]. Было доказано, что некоторые проблемы, такие как растрескивание при затвердевании, плавление границ зерен в основном металле (ликвационное растрескивание) и изменения в металлургической структуре, могут возникать в основном из-за высоких затрат термического процесса [8–14].
Технология электроискрового осаждения (ESD) – эффективный метод нанесения антикоррозионных и износостойких покрытий. Это импульсный процесс микробондинга с малым тепловложением, в котором используются высокая плотность энергии и короткие электрические импульсы, обычно от нескольких микросекунд до миллисекунд, для нанесения материала электрода на поверхность компонента. Это представляется очень интересным и экономичным решением для восстановления изношенных или поврежденных дорогостоящих деталей, особенно тех материалов, которые обычно считаются плохо свариваемыми с помощью традиционных процессов ремонта [2, 15–21].
В этом методе электрическая дуга генерируется в импульсном режиме между вращающимся расходуемым электродом (анодом) и заготовкой / подложкой (катодом) для образования осадка путем отделения небольших капель материала от электрода и выброса в сторону подложки. Во время процесса электрическая дуга генерируется импульсами с частотой от 0,1 до 4 кГц с использованием высокочастотного источника питания [22, 23].
Короткая длительность импульса и высокая частота импульсов вызывают как очень высокую скорость охлаждения, так и быстрый процесс затвердевания в сочетании с небольшим количеством материала, переносимого во время каждого импульса технологии ESD.Эта высокая скорость затвердевания, которая, как считается, приближается к 10 5 -10 6 ° C / с, приводит к уточнению микроструктуры до наноструктурированного или аморфного уровня [23]. Режим затвердевания наплавленного сплава, а также морфология получаемых зерен в основном контролируются тепловыми условиями, которые существуют в начале затвердевания. В противном случае микроструктура мелкого масштаба контролируется в первую очередь скоростью охлаждения после затвердевания [17].
Эта инновационная технология вызвала большой интерес в области ремонта, поскольку она может предложить ряд преимуществ, включая низкий уровень загрязнения, техническую возможность осаждения металла при атмосферном давлении, а также транспортировку и транспортировку сварочного оборудования.Более того, снижение остаточного напряжения и деформации по сравнению с другими процессами плавления делает этот метод очень применимым к тем материалам, которые обладают высокой склонностью к растрескиванию во время сварки, таким как суперсплавы, MCrAlY и термочувствительные материалы (алюминиевый сплав серии 2000) [22 –24].
Во многих работах изучается массоперенос, который происходит во время процесса ESD [25–27], что имеет первостепенное значение для получения покрытия с высокой износостойкостью [28–32]. Также исследовалась взаимосвязь между параметрами процесса и структурой осадка [33–36]. Лишь несколько исследований связаны с использованием электростатического разряда в качестве технологии ремонта. Фархат [24] определил, что ремонт локально поврежденного покрытия NiCoCrAlY или CoNiCrAlY может выполняться с помощью электростатического разряда для дальнейшего продления срока службы покрытий. В то время как Джонсон показал возможность ремонта монокристаллической лопатки турбины с низким полезным тепловложением без деформации [37].
Кроме того, на сегодняшний день исследования сосредоточены на оценке ESD как технологии ремонта, а не на термочувствительных материалах, таких как сплав 2024.
В этой статье было представлено сравнительное исследование отложений, приготовленных методом ESD на стандартных субстратах из кости собаки AA2024 как в состояниях естественного (T4), так и искусственно состаренного (T6) состояния. Был проведен детальный анализ модификации микроструктуры наполняющего сплава и влияния параметров процесса на свойства и микроструктуру подложки.
Кроме того, образцы после ремонта были подвергнуты термообработке при 135 ° C и 190 ° C для уменьшения отрицательного влияния остаточных напряжений на механические свойства. Таким образом, также было исследовано влияние послеремонтной термообработки (PRHT) на микроструктуру и механические свойства отремонтированных образцов.
2. Экспериментальные методы
Алюминиевый сплав AA2024 использовался для материалов электрода и подложки. Подложка ESD поставлялась в виде катаных пластин Т4 и Т6. Химические компоненты (мас.%) Сплава AA2024 приведены в таблице 1.
|
Образцы собачьей кости были изготовлены из пластин толщиной 4 мм (Рисунок 1 (а)). На образцах собачьей кости среднего размера был вырезан надрез, который позже был заполнен электродным материалом, как показано на рисунке 1 (b). Осаждение проводилось с помощью ручного пистолета при комнатной температуре с защитой аргоном (Ar), что позволяет избежать загрязнения зоны осаждения промежуточными элементами, такими как кислород или азот.Во время напыления электрод вращался со скоростью 1200 об / мин. Параметры процесса электроискрового осаждения приведены в таблице 2, где E – значение энергии импульса электрической дуги в Джоулях. Эти параметры основаны на предыдущем исследовании Leo et al. [36].
|
Подложка удерживалась в фиксированном положении, в то время как ручной пистолет перемещался по трем ортогональным осям XYZ . Вначале надрез полукруглой формы покрывали смежными напылениями. Наплавки имели круглую форму, чтобы соответствовать полукруглой форме надреза. Плотные полукруглые наплавки были реализованы для покрытия всей поверхности надреза по оси y .Заполнение было получено путем наложения нескольких отложений по направлению Z (рис. 1 (б)). Затем образцы подвергались послеремонтной термообработке (ППВТ) в течение 2 ч при 135 ° С и 6 ч при 190 ° С. Все образцы охлаждались воздухом. Время выдержки и температуры показаны в таблице 3. Образцы были разрезаны по центру отложения, залиты эпоксидной смолой и затем отполированы до зеркального блеска. Анализы были выполнены на секции XZ в состоянии после полировки, чтобы оценить металлургическое состояние месторождения и зоны соединения.Микроструктура была выявлена травлением реактивом Келлера. Для изучения микроструктуры использовались три дополнительных метода: стереомикроскопия (SM), оптическая микроскопия (OM) и сканирующая электронная микроскопия (SEM) с EDS.
Зернистую структуру подложки выявляли электрополировкой (20% хлорная кислота и 80% этанол при 0 ° C; параметр электрополировки: 15 В и 60 с), анодным окислением (травление Баркера; параметры анодирования: 20 В и 80 с) и последующее исследование в поляризованном свете в ОМ.
|
Дефектные области отложения внутри отложения и длина трещин на границе раздела плоскость XZ (рис. 1 (b)) были получены с использованием программного обеспечения NIS для анализа изображений.NIS-Elements – это программное обеспечение NIKON, поставляемое с Epiphot 200 OM. Процент площади дефектов измерялся как сумма площадей дефектов, деленная на площадь восстановленной зоны. Кроме того, с помощью программного обеспечения ImageJ были оценены как диаметр Ферета, так и коэффициент формы ( f круг ) дефектов заполнения. Фактор формы получается из следующего уравнения: где – периметр, а – площадь дефекта. Для идеального сферического дефекта коэффициент формы равен единице, а для сильно вытянутого дефекта он очень близок к нулю.В частности, в данном исследовании были рассмотрены два основных морфологических класса дефектов: (i) дефекты с 0 <≤ 0,5 (ii) дефекты с 0,5 <≤ 1
Испытания на микротвердость были выполнены с нагрузкой 100 г в течение 15 с. Измерения микротвердости проводили на плоскости XZ по сетке, параллельной верхней поверхности покрытия, в соответствии с ISO 6507-1: 2005. Расстояние между углублениями как по горизонтали, так и по вертикали составляло 100 мкм м.Затем рассчитывали средние значения микротвердости с учетом всех отпечатков, сделанных в зоне наплавки и в ОМ соответственно. Эти меры проводились как на отремонтированных образцах, так и на образцах после ППВТ. Испытания на растяжение проводились при комнатной температуре на универсальной испытательной машине в соответствии с ISO 6892-1: 2009 перпендикулярно направлению прокатки (RD). Использовался контроль смещения при начальной скорости деформации 0,25 мм / мин. Деформации измеряли с помощью осевого экстензометра с измерительной длиной 12.5 мм.
3. Результаты и обсуждение
3.1. Характеристика основного материала
В сплаве AA2024-T4 механизм упрочнения обусловлен зоной Гинье – Престона (зона G – P) в зернах, которые препятствуют перемещению дислокаций. Хотя AA2024-T6 достигает максимальной твердости из-за более тонкого переходного распределения выделений, которые остаются когерентными с матрицей твердого раствора, он способствует дисперсионному упрочнению. И зона G – P (∼10 нм толщиной и 100 нм в диаметре), и частицы осадка (больше, чем зона G – P) слишком малы, чтобы их можно было четко разделить с помощью микроскопии OM или SEM [4, 5, 38]. На рис. 2 (а) представлена микроструктура основного материала из сплава AA2024 (BM) в направлении, перпендикулярном производству прокатки. Микрофотографии ОМ и СЭМ 2024 года в состояниях Т4 (рис. 2 (а)) и Т6 (рис. 2 (б)), соответственно, показывают алюминиевую матрицу вместе с рядом интерметаллических частиц различной морфологии и размеров. Согласно литературным данным и анализу SEM / EDS, основными сферическими интерметаллическими частицами являются Al 2 CuMg (S-фаза) (1, рисунки 2 (a) и 2 (b)), а светло-серые частицы – Al . 2 Cu ( θ фаза) (2, на рисунках 2 (а) и 2 (б)).Кроме того, (Mn, Fe) 3 SiAl 12 (светло-коричневый, 3, рисунки 2 (а) и 2 (б)) и фазы Al (Cu, Fe, Mn) (темно-коричневый, 4, рисунки 2 ( а) и 2 (б)). Они были размером до 10 м и имели неправильную форму. Кроме того, согласно литературным данным, мелкодисперсные дисперсоиды в матрице Al могут быть либо Cu 2 Mn 3 Al 20 , либо Al 2 Cu [5, 39].
Картирование элементов (рис. 3) BM подтвердило наличие этих фаз.
Механические свойства основного материала в условиях Т4 и Т6 при комнатной температуре представлены в таблице 4 [5].
| ||||||||||
AA2024-T4 | 339 | 485 | 29 | 141 ± 1,1 | ||||||
AA2024-T6 | 482 | 516 | . 166 | |||||||
3.2. Дефектность и микроструктура в пломбах
На рисунках 4 (a) и 4 (b) показаны SM-изображения надреза после заполнения с помощью процесса ESD. Рисунок 4 (c) представляет собой микрофотографию ОМ плоскости XZ электроискрового заполнения. Хорошо видно, что верхняя поверхность была сплошной и без видимых трещин или других дефектов (Рисунки 4 (а) и 4 (б)). Однако некоторые дефекты показаны на рисунке 4 (c).Основными дефектами, обнаруженными в анализируемых пломбах, были пустоты различной морфологии и микротрещины, простирающиеся как перпендикулярно, так и параллельно границе раздела подложка / пломба. В частности, типичные пустоты, идентифицированные внутри заполнения, имели три геометрии, а именно: небольшие сферические пустоты (газовая пористость), большие пустоты произвольной формы (мостиковая пористость) и тонкий слой пустот (ламинарная пористость) [36]. Формирование этих несплошностей сильно зависело от количества и локализации оплавленного материала.Во время ручного напыления выбранные электрические параметры, расстояние от электрода до поверхности детали и сила, действующая на электрод, не оставались постоянными во время процесса напыления [19, 36]. Все предыдущие аспекты изменили количество металла, который расплавился и / или испарился. Поэтому на поверхности образовывались пики и впадины, которые выглядели гофрированными с пустотами [19, 30, 31].
Считается, что растрескивание внутри наполнителя является результатом теплового напряжения, которое накапливается во время охлаждения и затвердевания осажденного материала.Остаточное термическое напряжение в заполнении всегда было растягивающим [40, 41]. Кроме того, из анализа границы раздела подложка / заполнение было также замечено, что обе подложки в состояниях T4 и T6 характеризовались трещинами, которые преимущественно простирались вдоль границ зерен (рис. 5 (а)). СЭМ-изображение с большим увеличением очерчивает путь трещины по повторно затвердевшим продуктам, которые типичны для явления ликвационного растрескивания (рис. 5 (b)). Одновременно быстрое охлаждение в результате процесса электростатического разряда вызвало большую тепловую деформацию, которая открыла ликвидированные зоны.Фактически, алюминиевый сплав 2024 подвержен затвердеванию и ликвационному растрескиванию, имеет большой диапазон затвердевания, высокое тепловое расширение, большую усадку и множество легирующих элементов [10, 41].
Микрофотографии в оптическом и сканирующем электронном микроскопах на плоскости заполнения XZ показаны на рис. 6. Четко просматриваются многочисленные наложенные линейные дорожки (рис. 6 (b) и 6 (c)) из-за переплава что было вызвано наложенным слоем (интерфейс слой-слой).Причем эти слои различались по размеру и накладывались друг на друга. Слои случайного размера просто показали нестабильность в процессе ручного нанесения. Средняя толщина нескольких наплавленных слоев рассчитывалась методом пересечения. Затем было определено, что она составляет ∼12,4 ± 6,1 µ м. Кроме того, столбчатая зернистая структура росла перпендикулярно подложке (рисунки 6 (а) и 6 (б)). Эти столбчатые зерна росли эпитаксиально вдоль кристаллографического направления ранее затвердевшего зерна через несколько слоев, создавая микроструктуру, нормальную к слоям осаждения [10, 36, 38, 42].Микроструктура покрытия была прекрасной из-за высокой скорости охлаждения [15, 16]. Более того, некоторые слои характеризовались ячеистой дендритной микроструктурой (выделена кружком B на рисунке 6 (d)), а некоторые другие слои демонстрировали равномерное распределение мелких мелких частиц второй фазы (появляющиеся в виде светлой точки в кружке A на рисунке. 6 (г)). Более того, межслойная тонкая зона демонстрирует грубую микроструктуру, как правило, равноосную (выделена прямоугольником C на рисунке 6 (d)). Эти разные морфологии микроструктуры в тонких слоях осадка можно объяснить различными условиями затвердевания в объеме расплавленного пятна (жидкой фазы) [16, 43].Граница раздела между наполнителем и подложкой показана на рисунке 7. Заполнение образовало металлургическую связь с подложкой (рисунок 7).
3.3. Анализ дефектов
Дефекты в материале пломбы и на границе раздела пломба / подложка были исследованы подробно. В заливке для всех полученных образцов в объеме осадка наблюдались случайно распределенные дефекты сферической и ламинарной формы. Средняя доля площади этих дефектов составила 2.5%, что можно считать приемлемым. На рисунках 8 (a) и 8 (b) показаны графики зависимости диаметра Ферета от коэффициента формы и процентного распределения дефектов, имеющих коэффициент формы от 0 до 0,5 и от 0,5 до 1, соответственно. Как показано на Фигуре 8 (а), дефекты большего размера были наиболее неправильными, а пломбы в основном характеризовались ламинарными дефектами (коэффициент формы составлял от 0 до 0,5). Фактически, распределение дефектов по диаметру Ферета, показанное на Рисунке 8 (b), показывает, как почти все дефекты имеют значение от 0 до 0.5 имели длину меньше 20 м. Кроме того, 50% из них имели диаметр от 10 м до 20 м, но с дефектами значительной протяженности. Растягивающее термическое напряжение увеличивалось во время роста заполнения, вызывая большие трещины в заполнении и отслаивание в местах слабого межфазного соединения. Пустоты небольшого размера создавались за счет образования неровностей или захваченного газа. Рисунок 8 (b) показывает, что сферические дефекты (0,5–1) в основном были распределены (90%) в нижнем классе диаметров Ферета (до 10 м), в то время как остальные имели диаметр Ферета от 10 до 30 мкм.
Что касается дефектов на границе раздела подложка / заполнение, для двух различных условий обработки BM (состояния T4 и T6) получены значения средней длины трещины и отношения между числом трещин и длиной границы раздела (мм), исследованных и представлены в таблице 5. Кроме того, на рисунке 9 показано распределение длины трещин, которые распространяются в подложке от границы раздела подложка / заполнение в состояниях BM T4 и T6. Примечательно, что процесс ESD генерировал одно и то же значение / мм независимо от состояния BM (T4 или T6) и значительного увеличения средней длины трещины в BM T6.Увеличение средней длины трещины, наблюдаемое в образце 2024-Т6, было связано с высокой твердостью подложки. После срабатывания трещины легче распространяются благодаря хрупкости области. Фактически, наблюдая графики распределения длин трещин, осаждение на образце 2024-T6 привело к более низкому процентному содержанию трещин для полей длины менее 15 µ м и увеличению процента более длинных трещин с последующим увеличением изменения поля длины трещины.
Следовательно, напыления, сделанные на 2024-T6, вызвали больше дефектов на границе раздела, чем напыления, сделанные на 2024-T4.
|
3.4. Механическая характеристика
3.4.1. Микротвердость
На рис. 10 показаны профили микротвердости пломб и подложки AA2024 для условий T4 и T6.На графике показаны средние значения микротвердости, обнаруженные на увеличивающихся расстояниях от границы раздела подложка / осаждение. В таблице 6 приведены средние значения микротвердости. Кроме того, указаны средние значения микротвердости подложки, измеренные на расстоянии 100 мкм м от поверхности раздела покрытия. Во всех исследованных образцах твердость наполнителя была обычно ниже, чем у подложки (Рисунок 10 и Таблица 6). Уменьшение твердости было связано со старением основного материала и некоторыми дефектами, которые образовались внутри покрытия.Более того (рисунок 10) в зоне ремонта средние значения микротвердости оставались практически постоянными, что подтверждает отсутствие значительных микроструктурных изменений по толщине зоны ремонта. Результаты в таблице 6 показывают, что микротвердость подложки вблизи границы раздела не изменилась по сравнению с микротвердостью зоны BM. Следовательно, механические свойства подложки не изменились. Кроме того, результаты показали, что послеремонтная термообработка (PRHT), проведенная на образцах, не повлияла на твердость пломбы.Фактически, она оставалась почти постоянной независимо от применяемой температуры термообработки. Твердость подложки 2024-T4, которая не выдерживалась, увеличилась после Т 190_6 PRHT из-за осаждения более твердой частицы [38].
Из-за усреднения значение твердости подложки 2024-T6, которая подверглась пиковому старению, уменьшалось с увеличением времени и температуры термообработки. Фактически, известно, что если частицы преципитата велики и широко разнесены, их можно легко обойти, перемещая дислокации, которые изгибаются между ними и снова соединяются с помощью механизма, впервые предложенного Орованом [4].
4.![]() Исследование процесса электроискрового осаждения алюминиевого сплава 2024 года на аналогичной подложке дало следующие доказательства: (1) Микроструктура заполнения была слоистой. послойно, очень мелко и смешано как с клеточными, так и с равноосными дендритами. В заполняющих слоях зерна образовывали длинные столбчатые зерна с преимущественным ростом в направлении нарастания. Микроструктура была сильно неоднородной из-за разной скорости охлаждения в процессе осаждения.Твердость наплавленного металла была ниже, чем у подложки. На подложке не было зоны термического влияния. (2) Ремонт показал наличие некоторых дефектов. Эти дефекты, случайно распределенные в микроструктуре, имели сферическую, случайную и ламинарную формы. Средняя доля площади этих дефектов составила 2,5%, что считается приемлемым. Было подсчитано, что пломбы имели 63% ламинарных и 37% дефектов сферической формы. Образование дефектов ламинарной морфологии в основном связано с растягивающими остаточными напряжениями. Конфликты интересовАвторы заявляют об отсутствии конфликта интересов. Система создания оснастки для электроискрового упрочнения поверхностей Ясев А. https://doi.org Резюме: Приведены результаты использования системы математического моделирования (включающей математическое моделирование, разработку конструктивно-технологических предложений, оптимизацию параметров оснастки) для повышения производительности электроискрового деформационного упрочнения сложных поверхностей. Ключевые слова:система, создающая, оснастка, электроискровая, наклеп, поверхность ССЫЛКА:
Заявления об условиях получения полного текста статьи: По предоплаченной подписке журнала на 1 месяц.
|