Разновидность волок (фильеров) для волочения проволоки
По существу волока – это рабочий инструмент для механической обработки металла. Он имеет специфическую конструкцию, представленную внутренним каналом воронкообразного типа. Именно через него и выполняется процесс протягивания металлической трубы, проволоки или же прутка.
Выбор фильер в зависимости от целей
Учитывая, что волоки (фильеры) для волочения проволоки (или другие их виды) испытывает огромное динамическое и температурное воздействие особое внимание уделяется технологии их производства. Для этих целей преимущественно используют синтетическую, алмазную структуру или твёрдые сплавы особой прочности. Также достаточно часто используют и так называемую инструментальную сталь. Сам же выбор изделия напрямую зависит от особенностей производственного процесса и его планируемых экономических показателей.
Так, например, волоки (фильеры) напорная способна эффективно обеспечивать поступление смазочного, обслуживающего агента непосредственно в зону деформации.
На что обратить в первую очередь внимание?
Вообще не стоит забывать, что перед покупкой волок (фильер) для волочения проволоки или других их модификаций стоит убедиться в её эксплуатационных характеристиках. Важнее всего получить информацию о её реальной стойкости. Это параметр говорит о фактическом количестве проволоки, которая протягивается до механической поломки самого инструмента. Отдельно оценивается стойкость износа, что подразумевает число полученной продукции на 1 единицу внутреннего канала (измеряется в микронах).
Решения для разных технологических задач
А вот фильеры (волоки) скальпирующие позволяют получать более качественную и конкурентоспособную проволоку благодаря специальному, механическому воздействию. В результате на выходе проволока получает свойства улучшенной сопротивляемости коррозийным процессам, а также борьбе с агрессивными примесями, воздействующими на поверхность металла. Больше того – фильеры (волоки) скальпирующие могут использоваться для материала с диаметром 16 мм (в том числе и латунь, медь и алюминий).
Если целью вашего технологического процесса является необходимость протягивания хромоникелевых сталей, то целесообразно будет купить волоки (фильера) твёрдосплавные. Дело в том, что именно этот тип изделий выделяется идеальным балансом рабочей производительности и общего КПД. Не будет лишним сказать и об их высокой устойчивости к трению в условиях ежедневной, безостановочной эксплуатации. Да и хорошая пригодность к шлифованию волок (фильер) твёрдосплавных не подлежит сомнению.
Один из самых надёжных вариантов
Ну и, пожалуй, в конце стоит сказать о самых востребованных и популярных волоках (фильерах) алмазных на современном рынке. Например, наше предприятие занимается изготовлением сразу двух видов – из монокристаллических и природных алмазов. Они обладают очень высокой прочностью, а стало быть и огромным, эксплуатационным ресурсом. При этом способны и выдерживать большой, температурный нагрев (для волоков (фильер) алмазных природных это не менее 2300 W/Mk).
Изготовление фильер для волочения проволоки
Оборудование
Комплектующие
Материалы
Эмульсии
Санкт-Петербург
Канал ООО «СЗКСК»
ТАКЖЕ МЫ ПОСТАВЛЯЕМ СОЖ ОТ КОМПАНИИ RICHARDSAPEX |
Эмульсии для волочения медной проволоки… Масло и эмульсии для волочения алюминиевой проволоки… Эмульсии для волочения проволоки из стали и других металлов… |
Для производства металлической проволоки применяются специализированные линии, станки и комплектующие для этих станков – фильеры (волоки), бандажные кольца и конусы, глазки, вкладыши, вставки. В процессе волочения материал проволоки и детали, с ним контактирующие, испытывают значительные механические нагрузки. Поэтому фильера для проволоки должна обладать высоким качеством и иметь выше среднего показатели прочности, твёрдости, износостойкости. Только в этом случае в конечном итоге вы получите качественную продукцию, а ваша технологическая линия волочения будет работать ритмично и бесперебойно, без непродуктивных простоев и излишних затрат на ремонт.
Изготовление фильер в настоящее время ведется в основном с применением твердосплавных и алмазных заготовок. Именно эти материалы обеспечивают выполнение требований к фильерам, которые упомянуты выше.
Мы предлагаем своим клиентам исключительно высококачественные фильеры для волочения, как стандартных размеров, типов и форм, так и выполненные под заказ по вашим индивидуальным конкретным запросам и чертежам.
Твердосплавные волоки (фильеры) Для волочения проволоки преимущественно из черных металлов, а также для изготовления деталей, имеющих большой диаметр, применяются твердосплавные волоки (фильеры).
Read more…
Алмазные волоки для волочения (фильеры) В процессе изготовления проволоки методом волочения решающую роль для получения качественного продукта играют волоки алмазные. При протягивании сквозь волоку металл значительно деформируется. Процессы, происходящие при этом с металлом, сходны…
Read more…
Волочильные бандажные кольца и конусы Любые по конструкции конусы, кольца волочильные бандажные, втулки, вставки, направляющие, барабаны волочильные, разнообразные ролики и другие детали и запасные части для волочения с повышенной износостойкостью производства итальянской фирмы «Paganoni…
Read more…
Твердосплавные заготовки (вставки, вкладыши) глазки Твердосплавные заготовки (вкладыши, вставки, глазки), которые используются при изготовлении дорнов, штампов и фильер, а также других приспособлений, производят по стандартам качества ISO 9001:2000.
Read more…
Алмазные заготовки фильер Поликристаллические заготовки изготавливаются из сверхтвердых синтетических материалов и применяются для изготовления инструментов, требующих высоких характеристик. PCD вставки для фильер Типоразмеры заготовок Изготавливаются из поликристаллического алмаза, синтезируемого при высокой температуре…
Read more…
Эмульсии и воски для проката к…
Подробнее…
Шнеки и шнековые пары для лить…
Подробнее…
Слюдяные ленты с покрытием – с…
Подробнее. ..
Оборудование для производства кабеля
8 (812) 244-07-34, 8-800-301-05-59,
This email address is being protected from spambots. You need JavaScript enabled to view it.
Комплектующие для кабельных производств
8 (812) 244-07-39, 8-800-301-05-59 ,
Материалы обмоточные ленты и нити
8(812)244-07-38, 8800-301-05-59,
This email address is being protected from spambots. You need JavaScript enabled to view it.
Эмульсии и др. продукты RichardsApex
8(812)244-48-14, 8800-301-05-59,
This email address is being protected from spambots. You need JavaScript enabled to view it.
Политика конфиденциальности
Наш адрес: 196603, Россия, Санкт-Петербург, Пушкин, ул. Гусарская д.4, лит.Ц.
Сайт: www.czksk.ru
Комплексные решения для кабельных производств. Будем рады видеть Вас в числе наших клиентов!
Статьи, новости отрасли
Карта сайта
Наш офис в Москве: 117545, Россия, Москва, ул.Дорожная, д.8, корп. 1, офис 110. Перед приездом обязательно позвоните нам!
› ‹
Матрицы для волочения проволоки для производства сварочных материалов – WESPEC
Свойства и характеристики типов волочильных головок:
В следующих разделах описаны свойства и характеристики различных типов волочильных головок карбидный композит, изготовленный из порошка карбида вольфрама и подходящего связующего материала. Например, кобальт. Наиболее распространенные наконечники из карбида вольфрама изготавливаются из порошка карбида вольфрама средней зернистости с 6-13% связующего кобальта.
Основными преимуществами наконечников из карбида вольфрама являются ударная вязкость и сопротивление разрушению, которые зависят от размера зерна вольфрамового порошка и количества используемого кобальта. Более высокое содержание связующего кобальта приводит к получению более пластичного материала штампа с более низкой твердостью и износостойкостью. эти матрицы используются для волочения проволоки большего диаметра с большим обжатием на более низкой скорости без больших потерь в сроке службы матрицы.
танталовые добавки Улучшают стойкость к образованию лунок и уменьшают повреждения, вызываемые истиранием и царапаньем штампа. Матрицы с добавлением тантала используются для волочения нержавеющей стали, алюминиевых сплавов, оцинкованной проволоки. Добавки титана повышают твердость, улучшают стойкость к истиранию и снижают плотность, но повышают хрупкость.
Субмикронный вольфрам, содержащий титан, увеличивает срок службы штампа при волочении тонкой проволоки из высокоуглеродистой стали, такой как шинный корд. Эти легирующие добавки задерживают точку, в которой кратеры на поверхности штампа делают его непригодным для дальнейшего использования. При выборе марки карбида вольфрама всегда желательно использовать самую твердую марку с наименьшим содержанием связующего и максимально возможным размером зерна, не сталкиваясь с комплектом штампов. это даст максимальный срок службы.
Для любого конкретного применения обычно существует одна оптимальная комбинация размера зерна и содержания связующего. Однако, чтобы поставлять штампы для каждого отдельного применения, производители карбида должны иметь в наличии сотни марок. Поскольку это невозможно, производители выбрали в качестве эталонов самые популярные композиции. В приведенной ниже таблице показано содержание кобальта и размер зерна карбида вольфрама для наиболее распространенных марок, используемых для волочения проволоки через прутки (РИС. 9).0019 h5 ) .
Матрицы из карбида вольфрама – лучший выбор для волочильного оборудования в проволочной промышленности, когда требуется экономичный вариант, а не лучшая износостойкость и чистота поверхности проволоки. Матрицы из карбида вольфрама представляют собой небольшой сверхтвердый прецизионный инструмент с небольшим отверстием в центре.
Матрица из карбида вольфрама обычно приобретается как матрица с грубым сердечником, что требует шлифовки и полировки матрицы для подготовки ее к волочению. Если готовые штампы приобретаются у поставщика штампов, они обычно возвращаются поставщику по мере износа. Затем использованные штампы должны быть очищены, осмотрены и, если они сильно изношены, перерезаны до большего диаметра перед повторным использованием в волочильной машине.
Карбид вольфрама почти в три раза тверже стали и имеет большую плотность, чем титан. Для компаний, использующих штампы, это означает, что штампы из карбида вольфрама обладают превосходной износостойкостью по сравнению с штампами, изготовленными из других материалов. Когда штампы служат дольше, это равнозначно снижению стоимости денег за счет отсутствия затрат на их замену и сокращению времени простоя оборудования, ожидающего установки новых штампов.
Карбид вольфрама имеет твердость от 85HRA до 92ХРА. Алмаз имеет рейтинг твердости 10, однако алмазы не так универсальны и, очевидно, являются очень дорогим материалом для штампов. В частности, он обладает самой высокой твердостью и теплопроводностью среди всех сыпучих материалов. Эти свойства определяют основные промышленные применения алмаза в режущих и полировальных инструментах.
Алмазные матрицы:
— это углерод со специальной кубической кристаллической структурой. Это самый твердый из всех материалов для штампов. Природный алмаз также обладает лучшей теплопроводностью. три типа алмазов используются для волочильных волок:
– SCN : монокристаллический натуральный
– SCS : монокристаллический синтетический
– PCD : поликристаллинный бриллиант
SCN Dies:
С 1
.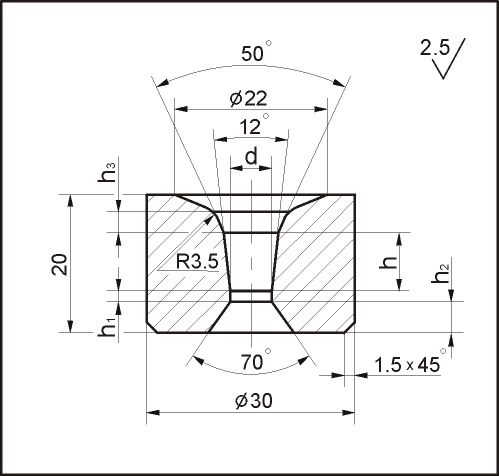
SCS Dies:
производится синтетически, но расположение атомов углерода в монокристалле такое же, как в природных алмазах. Синтетический алмаз обеспечивает более равномерный износ матрицы, чем матрицы из монокристаллического природного алмаза. Матрицы SCS имеют немного меньшую стойкость к истиранию и немного меньшую вязкость разрушения, чем натуральные алмазы. Теплопроводность в 2-3 раза лучше, чем у матрицы с природными алмазами, что было бы выгодно при высокоскоростном волочении, когда выделяемое тепло выше и вызывает быстрый износ матрицы, плохое качество проволоки и разрушение смазки. Матрицы из природного алмаза и синтетического монокристалла обычно используются для волочения проволоки малого диаметра на машинах для волочения проволоки во влажном состоянии.
Штампы из поликристаллического алмаза:
Заготовки из поликристаллического алмаза в настоящее время производятся в виде самонесущих заготовок или заготовок с опорой из карбида вольфрама, которые чаще используются для волочения проволоки из черных металлов.
Самонесущие заготовки, как правило, предлагаются с двумя размерами зерна (≤1-5 микрон) и двумя сортами (термически стабильный катализатор с удаленным металлом-TS и наполненный металлом, содержащий катализатор-металл-MF). Заготовки с опорой из карбида вольфрама имеют сердцевину, неразрывно связанную с кольцом на основе карбида вольфрама. эти заготовки обычно предлагаются в четырнадцати размерах и четырех размерах зерна (3-5-25-50 мкм).
Поликристаллические алмазы характеризуются в зависимости от размера зерна, обычно в четырех категориях: крупный, средний, мелкий, сверхмелкий. Размер зерна трудно классифицировать, потому что каждый производитель оценивает размер зерна по-разному. Существуют определенные тенденции производительности, связанные с размером зерна, как показано на (РИС. J4).
Выбор сплава следует обсудить с поставщиком матрицы, чтобы обеспечить наилучший технический подход для конкретных применений волочения проволоки. Имейте в виду, что алмазные заготовки имеют ограниченную высоту, поэтому угол подхода и длина подшипника должны быть скомпрометированы, чтобы обеспечить контакт проволоки с правильным местом внутри заготовки для данного уменьшения. Как правило, в штампах PCD используются более широкие углы и короткие подшипники. Рисунок K4 показывает применение различных типов штампов PCD.
Поставщики штампов используют ряд методов для установки заготовок штампов из ПКА в подходящий корпус. На рис. L4 показан типичный способ крепления поддерживаемой заготовки.
Спецификация алмазных фильер
Алмазные фильеры используются на машинах для влажного волочения, когда требуется очень жесткий допуск на диаметр или высокое качество поверхности, а также для стальной проволоки (0,18 мм) и меньше. давление матрицы при волочении тонкой проволоки относительно низкое, и поломка алмазной матрицы маловероятна.
Алмазные матрицы используются для проволоки диаметром от (0,18 до 0,76 мм) при более высоких скоростях волочения, где важна теплопроводность. поликристаллический алмаз заменяет карбид вольфрама и природный алмаз во многих областях применения, в которых желательны следующие параметры:
– повышенная скорость волочильного станка
– лучший допуск на размер
– более стабильное качество проволоки
– лучшая экономическая эффективность
Технические характеристики для монокристаллических и поликристаллических алмазных штампов для волочения различных металлов перечислены на (РИС М4) .
Как правило, сухой процесс волочения проволоки используется для волочения стали и проволоки больших размеров. В случае меди, алюминия и их сплавов обычно используется мокрое волочение проволоки.
В центре внимания машины и матрицы для волочения проволоки
Майк Макналти, редактор
Wire & Cable Technology International (WCTI)
Несмотря на то, что процесс использования машины для протягивания проволоки через матрицу для уменьшения ее диаметра и увеличения ее длины очень старый, и основы не сильно изменились с 19-й -й век, машины, процессы и инструменты, используемые для волочения проволоки, менялись и будут меняться. Имейте в виду, что это не быстрые инновации, а те, которые развиваются и совершенствуются.
В области машин для волочения проволоки у нас есть долгосрочные тенденции к технологии многопроволочного волочения, более высоким скоростям, гибкости, автоматизации, системам быстрой смены матрицы, увеличенным уровням производительности и диапазонам, переменной вытяжке, снижению затрат и улучшенной смазке. . Что касается матрицы для волочения проволоки, значительная часть новостей сосредоточена на улучшении обслуживания, и мы стали свидетелями введения бесплатных инженерных услуг, бесплатных пробных версий, программ управления запасами, лизинга и подбора матрицы. Что касается технологии изготовления волочильных штампов, разработки происходят в области материалов и источников инструментов, технологий изготовления инструментов и отделки поверхности. Одним из примеров являются матрицы из карбида вольфрама, покрытые тонким слоем нанокристаллических алмазных частиц для улучшения характеристик и срока службы матрицы.
Краткий обзор разработок, которые мы наблюдали за последние несколько лет, включает следующее:
- Современные многопроволочные линии волочения для производства проволоки из меди, алюминия и других цветных металлов.
- Гибкая машина
- Компактный волочильный станок для различных применений, включая исследования и разработку материалов.
- Волочение проволоки из сверхтонкой высокопрочной стали
- Кабестаны для волочения проволоки с индивидуальным приводом и электронным управлением с минимальным проскальзыванием.
- Улучшенная конечная поверхность проволоки
- Программируемая пользователем настройка обратного натяжения с автоматическим измерением и регулировкой.
- Волочение проволоки из нанокристаллического алмаза
- Заготовки штампов из нового высокоэффективного сплава
- Улучшенная подача смазки на трос
- Экономия материала за счет более жестких допусков по диаметру или проводимости.
- Модульные конструкции машин всех размеров: мелкозернистые, промежуточные, аварийные.
- Волочение специальных материалов, включая алюминий, сплавы, сверхпроводники и биметаллы.
- Пониженная энергия
- Миниатюризация: сверхтонкое волочение проволоки многих типов материалов на высоких уровнях производства.
Достижения в процессе волочения проволоки, а также разработка новых материалов для проволоки привели к стремлению к более последовательной и точной геометрии штампов, материалам с более длительным сроком службы и специальным комплектам штампов, таким как штампы, соответствующие удлинению для использования в многопроволочном волочении. .
Некоторые нововведения в области оборудования для обработки штампов включают:
- Автоматизированное полирование углов и размер
- Многопозиционная ультразвуковая штамповка
- Мощный осмотр
В дополнение к тому, чтобы быть в курсе последних событий, для успешного выбора, использования и технического обслуживания машин для волочения проволоки и штампов необходимо хорошее знание основ волочения проволоки.
Основы волочения проволоки
Волочение проволоки — это стационарный процесс холодной штамповки, при котором стержень или проволока протягивается или протягивается через одну матрицу или серию последовательных матриц. Каждая матрица и последующие матрицы имеют диаметры, меньшие диаметра исходного материала, а площадь поперечного сечения проволоки уменьшается по мере ее прохождения через каждую матрицу. Теоретически волочение проволоки представляет собой «процесс без стружки», при котором не предполагается удаление материала. Из-за этого объем проволоки практически остается таким же, как и при вытягивании, но длина проволоки увеличивается или удлиняется в соответствии с ее новым диаметром. На практике, в зависимости от вытягиваемого материала и условий смазывания, происходит некоторое образование мелких частиц металла.
Процесс волочения проволоки считается холодным, потому что тепло не применяется для облегчения формирования металла. Во время волочения свойства входного материала изменяются из-за холодной обработки, и температура действительно повышается, часто резко, по мере того, как проволока вытягивается до меньших диаметров.
Для волочения проволоки вам понадобится волочильная машина, проволока, смазка и матрицы. Процесс может быть мокрым или сухим, что определяется типом используемой смазки: продукты на водной или масляной основе для мокрого волочения и сухие смазки для сухого волочения.
В процессе волочения проволоки используются машины с одним, но чаще многоштыревым (многовытяжным или тандемным) устройством, предназначенным для волочения одной или нескольких проволок одновременно. Когда стержень или проволока протягивается через каждую матрицу, диаметр уменьшается (уменьшение площади) и увеличивается длина (удлинение).
В машинах для волочения проволоки протягивание материала, подлежащего волочению, осуществляется с помощью приводных шпилей. На одной тяговой машине существует только одна тяга, а несколько тяговых машин обычно имеют количество тяг, равное количеству тяг. Шпили могут быть расположены в линию (тандем), когда каждый шпилек приводится в движение одним валом, или в виде конуса, когда на одном валу находится более одного шпиля. Ключевыми параметрами волочения проволоки являются уменьшение площади, удлинение проволоки и проскальзывание:
Уменьшение площади, AR, % AR = (A1 – A2)/A1 x 100 AR = (1 – A2/A1) x 100 AR = (1 – (D2/D1)2) x 100
где, A1 = входная площадь поперечного сечения; A2 = выходное поперечное сечение;
D1 = входной диаметр; D2 = выходной диаметр
Удлинение проволоки, E, % E = (L2 – L1)/L1 x 100 E = (L2/L1 – 1) x 100
E = ((D1/D2)2 – 1) x 100
где L1 = входная длина; L2 = выходная длина; D1 = входной диаметр; D2 = выходной диаметр Соотношение между удлинением и уменьшением площади: E = 100/(100 – AR) – 100
Проскальзывание в % представляет собой разницу в скорости между канатом
и волочильным шпилем следующим образом:
Проскальзывание в %, S
S = (Vc – V)/Vc x 100
, где V = скорость провода; Vc = скорость вращения шпиля
В волочильном станке с многоступенчатой тягой проскальзывание будет накапливаться по всему станку, пока не достигнет конечного тянущего шпиля, где % скольжения теоретически равен нулю. В машине с нулевым скольжением стержень или проволока вытягиваются с одинаковой скоростью каждого волочильного шпиля. Другие полезные и интересные расчеты могут быть сделаны относительно скорости и производительности машин для волочения проволоки. Это полезно при составлении планов емкости. При выборе параметров волочильного станка необходимо учитывать множество факторов, включая материал входной проволоки, количество проволок, окончательный диаметр проволоки, конечную скорость проволоки, стиль работы, условия смазки и требования к качеству поверхности.
В основе процесса волочения проволоки лежит волочильная матрица, которая представляет собой инструмент, который находится в непосредственном контакте с проволокой во время ее обработки. Существуют десятки поставщиков фильер для волочения проволоки. По моему мнению, при выборе поставщика и приобретении волок для волочения проволоки важны следующие аспекты: согласованность и качество деталей, сервис, опыт и ноу-хау, помощь в проектировании, цена и сроки поставки.
Матрицы для волочения проволоки должны иметь правильную геометрию для соответствующего применения, если можно ожидать хороших результатов. Матрица может быть разбита на несколько зон: входная зона, где проволока и смазка входят в матрицу, зона редуцирования, где проволока соприкасается с матрицей и начинает деформироваться, зона калибровки, где задается диаметр проволоки, и выходная зона, где проволока покидает матрицу. Для описания частей штампа используются различные термины, но наиболее важными атрибутами являются угол наклона штампа, длина опоры и диаметр. Кроме того, хорошо работающие матрицы должны обеспечивать некоторый тип смешивания от одной зоны к другой, чтобы поверхность проволоки не повреждалась и не напрягалась.
Оптимальный угол матрицы и длина подшипника зависят от вытягиваемого материала и площади обжатия. Есть много хороших технических работ по геометрии штампов. Эти знания в сочетании с практическим опытом, тестированием и, возможно, программным обеспечением для моделирования приведут вас в правильном направлении для получения оптимальной геометрии матрицы.
Материалы, используемые для волок для волочения проволоки, включают карбид вольфрама (TC или WC), монокристаллический природный алмаз (SCND), монокристаллический синтетический алмаз (SCSD) и поликристаллический синтетический алмаз (PCD). Для каждого материала доступны различные «классы» в зависимости от таких факторов, как размер зерна, уровень полировки, плотность, процентное содержание алмазов и т. д. Каждый материал и класс имеют свои преимущества и ограничения, и по этому вопросу есть опубликованные мнения.
Многие факторы влияют на решение, включая обрабатываемый материал, требования к качеству поверхности, диаметр и форму изделия, температуру, скорость, % проскальзывания при вытяжке, стоимость и т. д. Наиболее важные данные об этих факторах, вероятно, будут получены из практического опыта, сбора и анализа. данных о производительности отдельных заводов. Материалы были усовершенствованы в направлении повышения прочности PCD, увеличения диаметра в материалах PCD и SCSD, обработки поверхности для снижения коэффициента трения, использования запатентованных технологических инструментальных сталей и использования одноразовых вставок.