Что такое фрезер и его принципы работы — Обзоры
Как устроен фрезер?
Фрезер похож на гигантскую канцелярскую печать. В основании по центру находится отверстие, где располагается поверхность детали. Сама «печать» опускается при помощи двух ручек, расположенных по бокам. В центре шпиндель с фрезой. Конструкция вручную вдоль плоскости двигается по нужной траектории, на заданную глубину снимая слой материала. Для упрощения процесса разработаны шаблоны, копировальные диски с втулками (см. ниже), прочие направляющие устройства. Состав в совокупности позволяет на поверхности получать разнообразные углубления нужной формации.
Виды фрезеров описанием не ограничиваются. Известны кромочные, предназначенные для формирования торцов деталей. С этой целью в продажу поступают столь изощрённые по профилю резцы, что диву даёшься. Рассмотрим некоторые технические характеристики фрезеровальных машин.
Опции и функции фрезера
Внутри фрезера стоит коллекторный двигатель с регуляцией оборотов или без.
- Когда работает фреза, возникают нагрузки.
- В результате крепление расшатывается, зажим на хвостовике ослаблен.
- При работе фреза способна уходить вверх или вниз. Последнее всегда заметно. В первом случае, если глубина патрона мала, хвостовик упрётся в дно, и не удастся определить, что фреза расшатана.
- Высокая скорость вращения шпинделя фрезера спровоцирует ситуацию: как патрон, режущий инструмент вылетит в неизвестном направлении. Это станет причиной серьёзной травмы.
- Если запасная глубина достаточная, удастся вовремя заметить дефект и вращение остановить.
Если изменение скорости вращения в фрезере не слишком востребовано, поддержание оборотов на постоянном уровне придаст стабильности работе. Согласитесь, плохо, когда вращение нестабильное. За постоянством работы фрезера следит специальная схема, реагирующая на уровень искрения. Наличие описывается в технических характеристиках, как поддержание уровня оборотов. Смысл — от скорости вращения вала зависит сила искрения. Схема отслеживает ситуацию и меняет угол отсечки напряжения питания, обороты фрезера восстанавливаются до исходных. Подобные опции отсутствуют в дешёвых моделях.
Домашний ЧПУ-фрезер как альтернатива 3D принтеру, часть четвертая. Общие понятия обработки
Начав писать про стратегии обработки, я понял что творю «обезьяний набор» — пошаговое руководство даже не для чайников, а для идиотов, мои шаги повторить можно, сделать свои по образцу тоже, но понимания не добавляется. В свое время, когда я внезапно решил стать фрезеровщиком, имея в бэкграунде высшее медицинское, МБА и 10 лет компьютерного ритейла, мне было очень сложно продираться через терминологию и абсолютно новый понятийный аппарат.
Конечно, большинство CAM программ оснащено хорошей справкой, но она все-таки написана технологами для операторов, и человек с улицы не всегда может понять что такое «оба в приращениях», зачем нужна «область безопасности цилиндр», какой тип подвода выбирать и что это вообще такое.
Ниже — моя скромная попытка пробежаться по базовым понятиям фрезерной обработки с краткой расшифровкой. Терминологию я использовал русскую из делкамовских учебников, она может не совпадать с другими CAM программами, но я думаю тут уже интуиция и гугл спасут. Ну и как всегда, капелька личного опыта по обработке пластиков на хоббийных станках.
Скорость шпинделя
В действительности, скорость вращения шпинделя — несамостоятельный параметр, он зависит от инструмента и материала. В документации к нормальным взрослым фрезам есть параметр «скорость резания» в м/мин для разных материалов, это скорость кромки относительно материала.
Чтобы вычислить скорость вращения шпинделя, необходимо поделить рекомендованную скорость на длину окружности. Но тут есть 2 проблемы: во-первых, мы режем «домашние» материалы типа пластиков и дерева, для которых производители параметры реза не указывают, а во вторых, используем хоббийные фрезы, на которых вообще никаких режимов не написано. Так что скорость вычисляем эмпирически: рисуем простую траекторию типа паза, запускаем фрезу в материал на небольшой (700-1000 мм/мин) подаче и начинаем от 6000 потихоньку поднимать. Начало плавиться/подгорать — снижаем на пару шагов. По опыту для фрезы диаметром 6 мм скорость в вязких пластиках (капролон, ПП, ПЭ) — 6-8К, в жестких (АБС, ПС, ПК) — 8-12к, в дереве — 15-18К, в цветнине — 10-20К. При уменьшении диаметра скорость увеличиваем, на чистовых — тоже увеличиваем.
Скорость подачи
Скорость подачи — тоже производная величина, но тут все еще хуже — если с одной стороны она зависит от вполне себе считаемых/документированных цифр типа «подача на зуб», то с другой — от жесткости системы станок-приспособление-инструмент-деталь (ака СПИД). Подачу на зуб Sz или Fz можно посмотреть в документации на фрезу, там она описана в мм/зуб (mm/t). При перемножении на количество зубов фрезы и частоту вращения она даст максимальную теоретическую скорость подачи.
Но мерить жесткость системы СПИД — сложно, да и неоправданно, поэтому как всегда у самодельщиков, подача параметр подбирается по опыту: пробуем разные подачи, начиная с 500 мм/мин (мы говорим о пластиках, да) когда нам перестает нравится звук (или ломается фреза, или вылетает заготовка) — снижаем скорость. Не забываем что подача для разных фрез и разных обработок будет разной. Общее правило такое: при уменьшении съема на зуб скорость повышаем, при увеличении — снижаем. Хотя в пластиках иногда случаются парадоксальные эффекты, например, качество вертикальных поверхностей ПОМ выше на более высоких скоростях. На моих станках при обработке пластиков чаще всего использую скорости от 1500 до 3000 мм/мин, поверхности получаются вполне.
Область безопасности
Область безопасности, она же ОБ — совокупность областей станка, где CAM считает что он гарантированно не встретит ни заготовки, ни крепежа. Через эту область осуществляются переходы, в ней разрешено по умолчанию ходить на ускоренной подаче. При обычных 2,5D обработках это плоскость — мы закрепляем деталь так, чтобы над всей зоной обработки было чисто и безоблачно. Тем не менее, иногда имеет смысл задать ОБ иначе, например, если мы фрезеруем только стороны заготовки, а крепимся через отверстия в заготовке в центре. Кроме того, некоторые фрезы не предполагают возможности вертикального или даже наклонного врезания в материал и надо объяснить CAMу что переходы и подводы должны быть только сбоку. В большинстве нормальных CAM для этого предусмотрены типы ОБ «блок», «цилиндр» или даже «модель», задающие ОБ соответственно.
Подводы и отводы
Многие материалы и типы обработок позволяют не заморачиваться с понятием подводов вообще — ПВХ, ПС, мягкие сорта дерева режутся в любом направлении любой фрезой на штатном режиме обработки. Подачу врезания выставили и поехали. Тем не менее, момент входа в материал и выхода из него отличаются как для фрезы (неравномерная нагрузка на плоскость, работа центром фрезы при вертикальном врезании многоперых фрез), так и для материала (зависание заусенки, выбивание щепки).
- Подвод «по вертикальной дуге»
- Отвод «прямо»
- Переход «обе в приращениях»
- Подвод — перемещение на ускоренной
- Подъем — перемещение на ускоренной
С одной стороны в лагере самодельщиков тут все просто: материалы мягкие, режимы и так щадящие, поэтому многие вообще брезгуют этим параметром и ставят вертикальные подводы и отводы. С другой стороны, выбитая щепка на деревянном барельефе в самом конце многочасовой обработки или побитая вибрацией фрезы при самом нижнем из 50 проходов вертикальная стенка — это очень неприятно. Поэтому пользуемся разумно: при черновых обработках с нормальными (заведомо бОльшими потенциального дефекта) припусками работаем жестко, ставим минимальные вертикальные подводы, при чистовых или тонких работах — подводим в зависимости от операции по дуге или наклонно. Но опять же не стоит юродствовать, длинные подводы и отводы сильно увеличивают общее время обработки.
Высоты
Собственно, с высотами все относительно просто. Существует абсолютная безопасная Z, определяемая ОБ. Но представьте себе, что Вы прорабатываете надпись на дне коробочки смещением с очень маленьким шагом. Масса мелких переходов, на каждом CAM уводит фрезу в ОБ, переводит на пару миллиметров и потом мучительно едет вниз. Чтобы такого избежать, придумали относительную безопасную Z — высоту, на которой можно ходить при чистовых обработках после прошедшей выборки. Только надо помнить при этом, что если выборка в реале не сделана, например, оператор перепутал порядок траекторий, инструмент попробует перейти между сегментами в материале, попутно разворотив заготовку и сломавшись.
Мои личные параметры для мелких деталек абсолютная безопасная — 5-10 мм, относительная — 2-5 мм.
Переходы и зазоры
Переход — участок траектории между рабочими ходами фрезы. Как уже было сказано, может осуществляться на абсолютной или относительной безопасной высоте, в powermill’e соответствующие настройки называются «безопасный» и «оба в приращениях». Но иногда, особенно на чистовых или доборочных траекториях, имеет смысл организовать переход иначе, поэтому в CAM программах предусмотрены варианты:
- По поверхности. Несмотря на то что правильно настроенные подводы и отводы практически не оставляют следов отрыва инструмента на заготовке, иногда, например если расстояние перехода невелико, имеет смысл сделать переход не отрывая фрезы вообще.
- Шаг по Z. Правильный выбор для траекторий с постоянной замкнутой обработкой вертикальных стенок, например, постоянной Z
- Прямо. Настоящий хардкорный вариант, CAM игнорирует все и тупо прокладывает прямую между отводом и подводом. И горе встретившемуся на пути материалу, минус в зарплату оператору, запоровшему и фрезу и заготовку.
Зато респект и уважуха герою, грамотно воспользовавшемуся инструментом и сократившим время переходов на часы (не шутка, такое было).
Тут даже рекомендовать что-то сложно. Наверное для начинающего общее правило такое: выборки — «безопасный» или «оба в приращениях», вертикальные стенки — «шаг по Z», 3D смещение или поверхности — «по поверхности».
Припуски и допуски
Совсем простой, интуитивно понятный пункт.
Допуск — размер, который Вам безразличен и в пределах которого CAM может изголяться как хочет. С одной стороны, больше допуск — больше свободы для CAM, плавнее траектория, меньше изменений направления и так далее. С другой — в редких случаях CAM может, например, разгрузочный заход выборки разместить посреди вертикальной поверхности, и вне зависимости от того что в общем Вам на размер этой области по барабану, поверхность станет некрасивой. В наш век больших объемов памяти и мощных компов, считающих траекторию, пусть лучше CAM подумает немножко дольше и напишет лишних пару мегабайт в программе, чем потом чесать репу на тему что делать с огрехами. Я ставлю допуск в сотку на пластиках, вроде всем доволен.
Припуск — изначально понятие о черновой обработке. На уровне CAM припуск выглядит как построение эквидистантной (равномерно офсетнутой) от оригинальной модели. Общее правило выше я уже давал — размер припуска должен быть заведомо больше размера потенциального дефекта обработки, тогда даже при неприятности Вы сможете исправить огрех дальнейшей обработкой. Кроме этого, припуском можно пользоваться и в других целях, например, для масштабирования модели при подгонке совмещающихся пазов/бобышек. На пластиках в черновых обработках я ставлю припуск в 0,3-0,7 мм, этого хватает.
В общем где-то так. Теперь можно начинать статью о построении обработки в CAM, не отвлекаясь поминутно на размышления достаточно ли понятно я пишу и не закидывая статью сносками. Если что забыл или непонятно выразился — пишите комментарии, задавайте вопросы, постараюсь ответить.
Если кто пропустил, но интересно, предыдущие статьи цикла:
Домашний ЧПУ-фрезер как альтернатива 3D принтеру, часть первая — выбор станка
Домашний ЧПУ-фрезер как альтернатива 3D принтеру, часть вторая
Домашний ЧПУ-фрезер как альтернатива 3D принтеру, часть третья, ПО и G-code
Чем отличается кромочный фрезер от обычного, выбираем кромочный ручной фрезер
11. 07.2020
Профессиональный столяр хорошо понимает, насколько важно при выполнении тонкой и ответственной работы, использовать качественный современный инструмент. Использование такого инструмента позволяет выполнить сложную работу не только аккуратно, но и максимально быстро. Именно таким электроинструментом является кромочный фрезер, используемый столярами не только в домашних мастерских, но и в производственных условиях.
Какими особенностями выделяется этот агрегат, на фоне остальных разновидностей столярного электроинструмента? Для чего нужен фрезер кромочный? Почему купить кромочный фрезер в нашей компании, это удобно и выгодно?
Выбираем кромочный ручной фрезер, ориентируясь на преимущества инструмента
Основными видами работ, которые можно эффективно и быстро выполнить с помощью кромочного фрезера, являются:
- Снятие фасок с изделий и заготовок;
- Скругление краев изделия или придание ему сложного профиля;
- Формирование аккуратных и красивых желобков вдоль кромки;
- Подгонка шпоночного слоя по размерам;
- Вырезание пазов под петли.
Хотя многие работы столяра выполняют также при помощи стандартного вертикального фрезера, кромочная модель отличается целым рядом привлекательных особенностей и преимуществ. Главные выдающиеся преимущества кромочного фрезера, побуждающими клиентов покупать инструмент в нашей компании, это:
- Ø Маневренность. Рабочая часть инструмента сделана таким образом, чтобы мастер мог легко обрабатывать изделия даже в труднодоступных местах, четко контролируя соблюдение глубины и ширины паза или других, кромки или желобка.
- Ø Мощность. Относительно небольшая мощность, которая в зависимости от модели может составлять 450-720 Вт, позволяет справляться с работой любой сложности, а также экономить электроэнергию, даже если работать с агрегатом приходится на протяжении полного рабочего дня.
- Ø Удобство. Кромочный фрезер можно вести при выполнении работы по заготовке, одной рукой, что позволяет удерживать изделие, не фиксируя его предварительно на верстаке.
- Ø Регулировка. Глубину погружения фрезы позволяет отрегулировать специальная шкала, а чтобы вдоль края был выполнен точный, равномерный и аккуратный узор, мастер может использовать параллельный упор.
- Ø Дополнительные аксессуары. В некоторых моделях кромочных фрезеров, производителем предусмотрено использование пылесоса, за счет чего во время работы в помещении наблюдается минимальное количество древесной пыли.
- Ø Регулировка скорости. Этой функцией оснащены только некоторые дорогостоящие модели, а в большинстве фрезеров частота вращения фрезы составляет от 30 до 33 тысяч об/мин.
Покупаем профессиональный инструмент с гарантией качества
Наша компания – это известный в своем регионе поставщик и реализатор профессионального оборудования и инструментов, представленных мировыми производителями. Покупка кромочного фрезера в нашем интернет-магазине будет не только выгодной, но и удобной, потому что для наших клиентов мы создали максимально комфортные условия, представленные следующими возможностями:
- 1) Широкий выбор инструмента.
Ассортимент нашего магазина представлен как дорогостоящими фрезерами для профессиональной работы в мастерской, так бюджетными вариантами, предназначенными для домашних мастеров.
- 2) Гарантия качества. Идеальное качество всех представленных агрегатов гарантировано известными производителями, а на любую модель мы предоставляем документально подтверждение гарантии, в течение срока действия которой, покупатель сможет абсолютно бесплатно проводить ремонт, обслуживание и профилактику в нашем сервисном центре.
- 3) Квалифицированные консультации. Специалисты нашей компании всегда готовы помочь клиенту с выбором кромочного фрезера, ориентируясь на его потребности, особенности выполняемой работы и финансовые возможности.
- 4) Обоснованная стоимость. Цена кромочного фрезера любой модели, является разумной и доступной для большинства наших покупателей, а для постоянных клиентов мы готовы сделать приятные скидки.
Современный кромочный фрезер – это качественный, практичный и надежный помощник при выполнении сложных столярных работ.
Тег: фрезы | M&M Sales & Equipment
В наши дни кажется, что все движется с молниеносной скоростью, и многие люди думают, что чем быстрее, тем лучше. От закупки до доставки мы хотим, чтобы это было сделано, и мы хотим, чтобы это было сделано вчера. Однако, когда дело доходит до обработки, эти скорость и скорость подачи могут повлиять на надежность ваших фрез и привести к повреждению дорогостоящих станков. Некоторые из главных факторов, которые следует учитывать при сложных и сложных операциях фрезерования, – это нагрев, вибрация, стабильность, функциональность и адекватная скорость удаления металла и стружки, а также высокая надежность процесса.
Вот почему так важно, чтобы вы понимали основы режущих инструментов и оборудования, которые вы используете ежедневно. Без правильных фрез, корпусов фрез и режущего инструмента эти высокие скорости могут не только замедлить или остановить производительность вашего цеха, но и подорвать вашу прибыль.
К счастью, наше партнерство с Sandvik Coromant, самым передовым в отрасли производителем технологического инструмента, дало нам полезные советы и подсказки, которые помогут вам получить максимальную отдачу от обработки. Нужны ответы прямо сейчас ? Позвоните нам напрямую по телефону 800-592-4516.
Хвостовик – это часть инструмента цилиндрической формы, которая используется для удержания и размещения его в держателе инструмента. Он может быть круглым и удерживаться трением или удерживаться на месте установочным винтом.
Флейта фрезы – это глубокие винтовые канавки, идущие вверх по фрезу.
Зуб – это острое лезвие по краю канавки, которое разрезает материал.Канавка с помощью вращения самого фрезы помогает выталкивать материал вверх и от режущей поверхности.
Угол наклона спирали описывает канавки фрезы. Обычно канавки имеют спиральную форму, что позволяет постепенно входить в заготовку. Если бы канавки были прямыми, они одновременно входили бы в заготовку, вызывая вибрацию и потенциальное повреждение. Более узкие углы винтовой линии и более высокие передние углы часто обеспечивают лучшее качество обработки.
Фрезы Материалы часто представляют собой быстрорежущую сталь (HSS) или твердый сплав.Как показывает практика, более мягкие материалы можно обрабатывать с помощью HSS, а для более твердых материалов требуется твердый сплав. Но учтите, что, хотя HSS дешевле, чем карбид, она изнашивается быстрее, что требует более частой замены.
Покрытия помогают повысить твердость режущей кромки и уменьшить трение о материалы, которые имеют низкую теплопроводность или не могут контролировать нагрев как фрезы, так и заготовки.
Срок службы инструмента вашей фрезы имеет решающее значение.Если у вас высокая производительность и большие рабочие нагрузки, очень важно инвестировать в правильный инструментарий, который сможет справиться с объемом работы. Выбор недорогого или неадекватного инструмента требует времени и денег на потраченный впустую материал, лом, потраченный впустую инструмент и дополнительный износ вашего оборудования.
Недостаточно просто выбрать фрезу, подходящую для работы. Вам также необходимо понимать, как фреза, заготовка и станок работают вместе, чтобы получить наилучшие результаты обработки.
Основы фрезерования и фрезерных операцийСледующее взято из Sandvik Coromant:
A. Фреза
Фрезерование – это не универсальная операция. Фрезы охватывают широкий спектр традиционных операций по удалению металла с заготовок, но фрезы также могут использоваться альтернативными способами для создания отверстий, резьбы, полостей или карманов. Детали, подлежащие фрезерованию, требуют тщательного рассмотрения, поскольку фрезы бывают разных форм, размеров, покрытий и поверхностей резания.Требуется ли глубина фрезерования расширенного инструмента или фрезеруемый элемент содержит прерывания или включения? Это общие вопросы, которые вы должны задать себе.
B. Заготовка
Рассмотрите заготовку и ее обрабатываемость. Размер обрабатываемой детали ограничен возможностями станка и необходимой глубиной резания. Кроме того, характеристики материала будут определять общую функциональность. Такие характеристики, как твердость, толщина, жесткость, химическая стойкость, способность к термообработке и термическая стабильность, играют решающую роль, поэтому особое внимание следует уделять выбору специального инструмента и стратегий фрезерования.
C. Станок
Выбранный вами метод фрезерования повлияет на тип нужного вам станка. Обычно бывает двух конфигураций: вертикальные фрезерные станки и горизонтально-фрезерные станки. Существуют многозадачные станки (MTM), которые могут выполнять множество операций, включая фрезерование и токарную обработку, но есть ограничения. Выбор подходящей машины для работы сэкономит вам деньги на ремонте и замене оборудования, а также на расходах на металлолом.
Связано: Увеличьте нагрузку на ваш механический цех
Мы уже много лет сотрудничаем с Sandvik Coromant в Одессе, Лаббоке, Амарилло и Форт-Уэрте, штат Техас. M&M Sales & Equipment с гордостью предлагает всю линейку фрезерных инструментов Sandvik Coromant, в том числе:
- Инструменты для фрезерования уступов
- Инструменты для торцевого фрезерования
- Инструменты для торцевого фрезерования
- Инструменты для профильного фрезерования
- Диск Фрезерные инструменты
- Инструменты для фрезерования канавок
- Инструменты для резьбонарезания
- Инструменты для фрезерования фасок
M&M Sales & Equipment – ваш специалист по режущим инструментам, и мы гордимся тем, что являемся дистрибьютором Sandvik Coromant со статусом Gold Tier.Для получения дополнительной информации об этих и других фрезах, инструментах и принадлежностях, доступных через M&M Sales & Equipment, зайдите в один из четырех наших удобных офисов в Техасе или позвоните нам по телефону 800-592-4516 .
Подпишитесь на нашу рассылку новостей
Будьте в курсе последних новостей, получайте полезные ресурсы и ознакомьтесь с рекламными акциями в информационном бюллетене M&M Sales & Equipment.Теги фрезы, Sandvik Coromant, Sandvik Coromant Фрезерные инструменты
Walter Tools »Engineering Kompetenz
Используемый вами браузер устарел и больше не поддерживается.Пожалуйста, обновитесь до более новой версии.
Что такое торцевое фрезерование и зачем вам это нужно?
Когда дело доходит до обработки, всегда есть несколько способов выполнить один и тот же рез.
Спросите пять машинистов, как выполнить ту или иную операцию, и вы обязательно получите восемь разных ответов. Торцевое фрезерование ничем не отличается. Когда вы хотите получить точно ровную поверхность или хотите отделку, которая действительно заставит вашу деталь сиять (в прямом и / или переносном смысле), процесс торцевого фрезерования может помочь вам в этом. Самый распространенный инструмент, используемый при механической обработке, – это концевая фреза. Обычно в процессе резки концевой фрезой используется как конец фрезы, так и боковые стороны, что позволяет выполнять операции резания с выемками и наклонной резкой.Торцевое фрезерование, в общем, определяется как процесс резки поверхностей, перпендикулярных оси фрезы или граням детали. Для торцевого фрезерования чаще всего используются ракушечные фрезы и фрезы, но в зависимости от того, какую обработку поверхности вы ищете, вы также можете использовать концевую фрезу.
Концевые фрезы
Использование концевой фрезы для торцевого фрезерования часто неэффективно, но может создать привлекательные узоры на вашей отделке, если это то, что вам нужно.
Концевая фреза часто достигает острого края в одном углу, а нижняя кромка обычно находится под углом 1 °, когда идет к центру, поэтому она не перекрывается с предыдущим проходом. Это может создать некоторые замысловатые узоры и отделку поверхности, которые было бы трудно найти где-либо еще.
Shell Mills
Если вы ищете однородную отделку, то ракушечная мельница – хороший выбор. Shell-фрезы также известны как торцевые фрезы, поэтому они известны своим качественным торцевым фрезерованием.Фрезы Shell имеют несколько вставок на внешнем крае фрезы, поэтому, когда фреза впервые попадает в материал, она удаляет небольшое количество припуска – в зависимости от глубины резания. Когда фреза проходит над заготовкой, другие зубья фактически работают, чтобы удалить припуск, который остался в виде бора или в результате подпружинивания заготовки или фрезы. Если все вставки на вашей ракушной фрезы выровнены и изношены равномерно, это обеспечивает высококачественную отделку поверхности.
Мельницы Shell также подходят для обработки почти всех материалов.Иногда может возникнуть необходимость в замене вставок для разных материалов, но сам инструмент достаточно прочен, чтобы работать с большинством материалов. Хотя наличие нескольких режущих зубьев на ракушечнике можно считать преимуществом, наличие всех этих пластин может вызвать больше головных болей. Различная высота и небольшие различия в геометрии могут вызвать различную стружкодробную нагрузку на пластины. Это плохо скажется на отделке поверхности
Мухорезы
Фрезы Shell обеспечивают качественную обработку поверхности на более высоких скоростях, в то время как мухорезка может создавать гораздо более тонкую поверхность с меньшей мощностью.Для этого в летучей фрезе используется только одна пластина, которая, хотя и работает медленнее, может обеспечить более однородную обработку поверхности. Прочтите: Наука торцевого фрезерования с помощью Flycutter Если вы хотите получить фантастическую чистоту поверхности, и скорость выполнения операции не так важна, вы можете выбрать фрезу TTS Superfly, укомплектованную пластинами для обоих более мягких материалов ( например, алюминий) и более твердые материалы (например, сталь) менее чем за 150 долларов.
Наконечники для торцевого фрезерования
Во-первых, примите во внимание устойчивость вашего инструмента и мощность вашего шпинделя.Со всеми этими зубьями и меньшим шпинделем ракушечная фреза с миллионом зубьев очень быстро увязнет. Что касается станков Tormach, мы рекомендуем придерживаться нашей ракушечной мельницы, если вы собираетесь резать такие вещи, как сталь. Корпусная фреза 38 мм может выполнять операцию с более твердыми металлами немного быстрее, но фреза с соответствующими пластинами также может справиться с такими операциями, она будет немного медленнее, но она справится с резками и при этом даст вам хороший результат. Конец. В более мягких материалах, таких как алюминий, мухорезка по-прежнему дает фантастические результаты, или известно, что Shear Hog отлетает немного стружки, оставляя красивый отражающий блеск.Независимо от того, какой материал вы режете, при торцевом фрезеровании обычно рекомендуется располагать фрезу вне центра заготовки.
Это обеспечивает самую тонкую стружку на выходе из фрезы, что приводит к более чистому срезу и более качественной отделке. С этой целью следует избегать частого входа в заготовку и выхода из нее – это может создать некоторые напряжения на режущей кромке, которые могут привести к задержке и вибрации. Таким образом, траектории движения инструмента должны быть максимально точно привязаны к заготовке. По той же причине вы также должны стараться избегать торцевого фрезерования отверстий или пазов, потому что эти кромки вызывают множественные входы и выходы при резке.Если вы сочтете необходимым резать поверхности с такими перерывами, вы можете уменьшить нагрузку на резак, снизив скорость подачи. Операции торцевого фрезерования – отличный способ удалить часть материала и получить красивую ровную поверхность, но настоящая радость приходит, когда вы видите эту поверхность. Будьте уверены, если вы еще не пристрастились к облицовке, вы обязательно почувствуете это, когда увидите это сияние.
В чем разница между левыми и правыми концевыми фрезами?
Фреза – самый важный инструмент станков с ЧПУ.
В повседневной жизни мы используем множество видов фрез, из которых наиболее распространены концевые фрезы. Концевые фрезы можно разделить на фрезы левые и фрезы правые. Вы до сих пор не представляете, как фреза вращается влево и вправо? Как поставщик металлорежущего инструмента UKO специализируется на производстве твердосплавных пластин с ЧПУ, металлокерамических пластин с ЧПУ, концевых фрез и т.д.
Как определить правую и левую концевую фрезу?
Чтобы определить, является ли фреза левосторонней или правосторонней, мы можем использовать следующие методы.Поставьте край фрезы вертикально вверх. Если направление подъема режущей кромки низкое влево и высокое вправо, то есть слева направо, это правая фреза. Мы можем сжать кулаки и вытянуть большие пальцы рук. Направление подъема канавки режущей кромки такое же, как и у большого пальца правой руки, что означает, что если канавка режущей кромки поднимается снизу справа в верхний левый угол, это вращение влево.
Принципиальная схема различения левого и правого вращения концевой фрезы Мы видим, что когда винт вращается, если его заставляют не «вкручивать», гайка входит.
По сравнению с фрезой это резка металлического мусора. Следовательно, когда направление вращения фрезы не изменяется, направление удаления стружки левой и правой фрезой будет различным.
При фрезеровании направление вращения левой фрезы должно совпадать с направлением вращения правой фрезы, чтобы можно было изменить направление удаления стружки. Для изменения направления удаления стружки направление режущей кромки левой фрезы должно быть таким же, как и у правой фрезы, то есть «правое резание», то есть То есть, режим удаления стружки правой фрезой противоположен режиму левой фрезы.
против часовой стрелки Деталь Концевая фреза правая Концевая фреза левая Форма правая спираль Левая спираль Направление вращения Направление подачи инструмента влево вправо Применение общее фрезерование требования к высокоточной обработке удаления стружки
Разница между правой концевой фрезой и левой ручная концевая фреза Применение левой фрезы
Как правило, левая фреза представляет собой инструмент, который может быть выбран только для высокоточных требований обработки удаления стружки, таких как панель переключения пленки, обработка клавиш мобильного телефона, акрилового объектива и ЖК-панели.
Но есть некоторые высокие требования, особенно некоторые кнопки мобильных телефонов или обработка электрической панели, высокие требования к отделке также очень высоки, вам нужно выбрать левую фрезу с удалением стружки.
В чем преимущества удаления стружки под левой фрезой? Таким образом поверхность заготовки не очищается. Сила резания сильно опускается, заготовка не поднимается, заготовку нелегко сдвинуть. Удаление стружки снизу также позволяет избежать побеления режущей кромки и пропуска кромок обработанных деталей.
Применение правой фрезы
Во всей обрабатывающей промышленности для обработки обычно используется правый инструмент. Покупатели UKO, как отечественные, так и иностранные, приобретают большинство правосторонних режущих инструментов. Для фрезы канавка на корпусе инструмента определяет направление выброса режущего мусора. Однако, если детали изготовлены из прецизионных деталей и внизу есть место для удаления стружки, рекомендуется использовать левую фрезу.
Левая фреза имеет определенные преимущества при обработке прецизионных деталей с особыми требованиями.
По поводу левого и правого вращения концевой фрезы, если у вас есть другие мнения, поделитесь, пожалуйста, с UKO. Если у вас есть спрос на концевые фрезы, вы также можете связаться с нами в любое время. Мы производим не только твердосплавные концевые фрезы, но и концевые фрезы из быстрорежущей стали. Кроме того, наши твердосплавные фрезерные пластины имеют хорошие отзывы клиентов, обращайтесь к нам.
Концевые фрезы – Двусторонние – 2 канавки
Описание
• Сверло может резать только в осевом направлении, фрезу можно резать во всех направлениях, хотя некоторые не могут резать в осевом направлении.
• Концевые фрезы режут материал как по периферии, так и по торцу, одновременно создавая напряжение, поскольку инструмент удерживается только на шпинделе.
• Фрезы используются в таких приложениях фрезерования, как профильное фрезерование, трассировочное фрезерование, торцевое фрезерование, врезание.
• С центрированием и без центрирования.
• Также доступны концевые фрезы с резьбой.
• COBALT STEEL подходят для использования с более прочными материалами и для всех тяжелых условий эксплуатации, где требуется увеличенная глубина резания.Добавление кобальта дает оптимальную твердость и ударную вязкость, улучшая, таким образом, режущие характеристики.
• ВЫСОКОСКОРОСТНАЯ СТАЛЬ демонстрирует исключительные результаты при обработке низкоуглеродистой, легированной и инструментальной стали и является превосходным инструментом для чистовой обработки, используемым в производственных процессах.
• Также доступны нестандартные длины и размеры в мм.
Доступны следующие материалы
(a) ВЫСОКОСКОРОСТНАЯ СТАЛЬ (HSS)
(1) Качество M2 (Single H)
(b) СТАЛЬ КОБАЛЬТА
(1) Качество M-35 (5% кобальта) (двойной H)
(2) Качество M42 (8% кобальта) (Triple H)
Концевая фреза – 2 канавки
2 канавки
Код товара No.
Размер Диаметр хвостовика Длина канавки Общая длина ABM-CT-13790 1/8 ” 3/8” 3/8 ” 3-1 / 16” ABM-CT-13791 5/32 ” 3/8” 7/16 ” 3-1 / 8” ABM-CT-13792 3/16 дюйма 3/8 дюйма 7/16 дюйма 3-1 / 8 дюйма ABM-CT-13793 7/32 ” 3/8” 1/2 ” 3-1 / 8” ABM-CT-13794 1/4 ” 3/8” 1/2 ” 3-1 / 8” ABM-CT-13795 9/32 ” 3/8” 9/16 ” 3-1 / 8” ABM-CT-13796 5/16 ” 3/8” 9/16 ” 3-1 / 8” ABM-CT-13797 11/32 ” 3/8” 9/16 ” 3-1 / 8” ABM-CT-13798 3/8 дюйма 3/8 дюйма 9/16 дюйма 3-1 / 8 дюйма ABM-CT-13799 13/32 ” 1/2” 13/16 ” 3-3 / 4” ABM-CT-13800 7/16 ” 1/2” 13/16 ” 3-3 / 4” ABM-CT-13801 15/32 ” 1/2” 13/16 ” 3-3 / 4” ABM-CT-13802 1/2 ” 1/2” 13/16 ” 3-3 / 4” ABM-CT-13803 9/16 ” 5/8” 1-1 / 8 ” 4-1 / 2” ABM-CT-13804 5/8 ” 5/8” 1-1 / 8 ” 4-1 / 2” ABM-CT-13805 11/16 ” 3/4” 1-5 / 16 ” 5” ABM-CT-13806 3/4 ” 3/4” 1-5 / 16 ” 5” ABM-CT-13807 13/16 ” 7/8” 1-9 / 16 ” 5-1 / 2” ABM-CT-13808 7/8 ” 7/8” 1-9 / 16 ” 5-1 / 2” ABM-CT-13809 15/16 ” 1” 1-5 / 8 ” 5-7 / 8” ABM-CT-13810 1 ” 1” 1-5 / 8 ” 5-7 / 8” При оформлении заказа укажите Материал M2, M35 и M42.
Также укажите, с центральной резкой или без нее
Выбор подходящей конструкции зубофрезерной фрезы для обработки высококачественных параллельных осей, цилиндрических зубчатых колес и шлицев
Инженер-технолог должен принять ряд решений при планировании необходимых процессов для производства параллельных осей, цилиндрических прямозубых или косозубых шестерен и шлицев. Зуборезание, конечно, является наиболее распространенным процессом удаления металла для создания надлежащего зазора между зубьями, необходимого для изготовления этих шестерен.Этот процесс существует уже более 100 лет и доказал свою эффективность. Это процесс формирования формы посредством последовательных и пошаговых разрезов, которые создают правильную форму с помощью ряда режущих зубьев реечного типа с прямым профилем. В процессе фрезерования зубчатое колесо вращается по мере вращения варочной панели и продвигается в осевом направлении по своей поверхности.
Рис. 1: Зубофрезерование – типичная схема создания последовательных зубьев червячной фрезы Но есть и другой способ выполнить эту задачу.
Также эффективны зубофрезерные фрезы, которые фрезеруют все пространство между зубьями при неподвижном зубчатом колесе.Многие инженеры задают следующие вопросы: когда зубофрезерование предпочтительнее зубофрезерования? Какой тип станка нужен для зубофрезерования? Как выбрать подходящий инструмент для зубофрезерования? Как оценивается время цикла? Какие у меня должны быть проблемы с качеством? А как насчет зажима, крепления инструмента, скорости и подачи?
Вооружившись необходимой информацией, продуманным планированием, а также необходимыми инструментами и оборудованием, можно будет найти ответы на эти вопросы. При необходимости могут применяться стабильные и экономичные процессы зубофрезерования или заделки зубьев.Эта статья предназначена для инженеров-технологов, которые, возможно, плохо знакомы с производством зубчатых колес. Это не научный анализ высокого уровня. Он носит практический характер и призван служить ценным руководством для разработки процесса изготовления зубчатых передач.
Основы процесса зубофрезерования
Инженер-технолог должен сначала понять основы фрезерования, чтобы принять рациональное решение о зарезке по сравнению с фрезерованием. Как уже говорилось, зубофрезерование – это порождающий процесс.Зубофрезерование требует сложной кинематики резания. Лучший способ понять это – наблюдать за образующимися рисунками, возникающими при фрезеровании (см. Рисунок 1). Обратите внимание на узор трохоидных петель, как показано.
Рисунок 2: Изменение расстояния между зубьями в зависимости от количества зубьев Как показано, каждый зуб червячной фрезы режет в разных положениях в пространстве между зубьями и имеет разные характеристики стружкообразования. По мере того, как шестерня становится меньше в диаметре и имеет меньше зубьев для заданного диаметрального шага (DP) или модуля, пространство между зубьями увеличивается.(См. Рисунок 2.)
По мере увеличения зазора между зубьями и уменьшения диаметра шестерни меньшее количество зубьев червячной фрезы участвует в процессе резания, поскольку длина хорды фрезы уменьшается; следовательно, толщина стружки увеличивается при заданной скорости подачи на оборот шестерни.
Кроме того, по мере того, как зазор становится больше, каждый зуб фрезы теперь должен принимать больший кусок. Площадь поперечного сечения чипа больше.
Рис. 3. Поднутрение корня, образованное выступом. Это означает, что шестерни с меньшим количеством зубьев и большими зазорами, чем их сопряженная шестерня, могут быть весьма требовательными.Именно тогда зубчатые фрезы становятся лучшей технологической альтернативой зубофрезерованию.
Другой фактор, который следует учитывать при фрезеровании, – это конфигурация корня и любой необходимый подрез. Поднутрения требуются, когда требуется последующая чистовая операция, например, шлифование. Поднутрения корня достигаются с помощью выступа на кончике зуба фрезы. Эта функция выпуклости создает поднутрение корня с широким трохоидальным рисунком режущего действия.(См. Рисунок 3.)
Величину поднутрения из-за фрезерования небольшого числа зубьев или шага можно контролировать с помощью фрезерных фрез с коротким шагом. Конструкции варочных панелей специальной конструкции считаются нестандартными, возможно, с более длительным сроком изготовления и более высокой стоимостью, чем у обычных варочных панелей.
Это был успешный метод борьбы с чрезмерным подрезом на протяжении многих лет, но подробный анализ этих варочных панелей выходит за рамки данной статьи.
Рисунок 4: Пример зубчато-фрезерного профиля с шлифовальной заготовкой по боковой поверхности, но обработанной корневой частью Основы процесса зубофрезерования или зарезки
При зарезании зубчатое колесо удерживается неподвижно, в то время как фреза продвигается в осевом направлении по ширине торца заготовки зубчатого колеса.Этот процесс можно использовать для черновой или получистовой обработки пространства между зубьями с дополнительным припуском для последовательных операций фрезерования, шлифования, бритья или хонингования. Или он может довести пространство между зубами до окончательной формы. Это можно сделать за один или несколько проходов. Зубофрезерные фрезы могут быть установлены в тандеме для создания двух или более пространств, и они могут быть сконструированы из стальных корпусов со съемными твердосплавными пластинами.
В некоторых редких случаях их заставляют использовать повторно шлифуемые твердосплавные лезвия, но с современными технологиями прецизионного шлифования твердосплавных пластин для таких инструментов нет (если вообще есть) оправдания.Иногда используются твердосплавные инструменты, но из-за высокой стоимости и ограничений по размеру твердосплавных инструментов они также становятся менее популярными. Фрезы из быстрорежущей стали можно изготавливать по относительно низкой цене, но они обладают ограниченными скоростными характеристиками и лучше всего подходят для зубчатых колес очень малого объема и модулей меньшего размера, поскольку высокая стоимость материала из быстрорежущей стали делает резцы большего размера непрактичными. (Примеры различных конструкций зубофрезерных фрез показаны на рисунках 5, 6, 7 и 8.)
Рис. 5: Зубофрезерование твердым инструментом (быстрорежущая сталь или твердый сплав) Зубофрезерные фрезы с тангенциально установленными пластинами довольно распространены.Они отличаются хорошей экономичностью, так как большинство из них имеют твердосплавные пластины с несколькими кромками.
Большинство из них предназначены для модулей размером более 8 (DP 3). Требования к мощности и крутящему моменту выше, поскольку их режущая геометрия традиционно подразумевает отрицательные осевые и радиальные передние углы. Некоторые новые конструкции имеют пластины с положительной геометрией резания, но обычно это ограничивается инструментами для черновой и получистовой обработки, для которых не требуются точные полнопрофильные пластины. Такие пластины отшлифованы в соответствии с требованиями производителя зубчатых колес; поэтому дорогостоящие прессовые инструменты со вставками обычно не производятся, если это не оправдано очень большими объемами.
Внешний шлицевой фрезерный инструмент и пластины показаны на Рис. 9 и Рис. 10. В прошлом, будь то эвольвентные шлицы или шлицы с прямой стороной, зубофрезерование было почти исключительным методом обработки. Благодаря усовершенствованию станков с ЧПУ с точной индексацией 4-й оси, теперь предпочтительным процессом становится зарезка.
Разгрузка шлифования (чистовая фрезеровка) в корневой зоне для предотвращения ступенек в активном профиле (см. Рисунок 4) также может выполняться с помощью зубофрезерных фрез. Поскольку процесс зубофрезеровки приводит к более выраженному подрезу по мере уменьшения количества зубьев шестерни и уменьшения диаметра делительной окружности, площадь поперечного сечения корня становится тоньше (см. Рисунок 3).Более толстая корня по сравнению с зубофрезерованием дает преимущество в прочности конструкции при зарезании по сравнению с зубофрезерованием.
На Рисунке 4 компоненты с 1 по 6 представляют собой сменные пластины, расположенные по периферии корпуса фрезы. Огибающая прорезей, сделанных каждой пластиной, дает полуфабрикатную боковую поверхность и завершает фрезерованную корневую форму с выступом.
Рисунок 6: Инструмент для зарезки со сменными пластинами полной формы Выбор зарезки поверх зубофрезеровки
Если доступны отдельные индексирующие станки, будь то специальные зубофрезерные станки или оборудование с ЧПУ с возможностью точного индексирования, возможно зарезание / зубофрезерование.
При выборе зубофрезерования или зарезки необходимо учитывать следующие факторы:
- Число зубьев шестерни . У шестерен и шестерен с небольшим количеством зубьев (с учетом их модуля или размера DP) зазор между зубьями увеличивается по мере уменьшения дуги делительной окружности. Длина хорды зацепления червячного инструмента будет меньше, чем у шестерни большего диаметра с большим количеством зубьев и большей дугой делительной окружности. Это означает, что меньше зубьев фрезы задействовано для создания необходимого зазора.Это ограничивает подачу варочной панели, так как зубья варочной панели быстро перегружаются. Разрезание может завершать форму за один или несколько проходов, в зависимости от жесткости машины и настройки, мощности и крутящего момента. Время индексации фрезы от одного промежутка зуба к другому сокращается вместе с количеством зубьев. Это работает в пользу продолжительности цикла измельчения.
- Требования к филе корня . Филе корня образуются в процессе зубофрезерования и несколько ограничены из-за ранее описанной трохоидальной петли.
Если при последующей операции требуется шлифовка, стачивание или хонингование боковых сторон, то необходим соответствующий припуск в области корня. Степень гибкости важна. Зубцевание может создать настоящий поднутрение, как показано на рис. 3. Зарезание приведет к прямому рельефу в корне. Это предпочтительно во многих случаях из-за увеличения толщины поперечного сечения зуба в области корня ниже начала активного профиля. При малозубчатых шестернях трохиодальная петля может образовывать очень большой подрез при зубофрезеровании.В таких случаях для прочности предпочтительнее зарезание. - Только с обычным оборудованием с ЧПУ. Если в наличии нет зубофрезерного станка, но есть станок с ЧПУ с возможностью индексации, часто хорошим вариантом является зарезка. Здесь необходимо учитывать, что станок имеет очень качественный индексирующий стол (4-я или 5-я оси), который может обеспечить допуски погрешности расстояния между зубьями в соответствии с требованиями. Современные многоцелевые токарно-фрезерные станки набирают популярность и обладают огромным потенциалом.Также необходимо учитывать мощность на шпинделе и жесткость. Необходимо учитывать качественные интерфейсы между инструментом и шпинделем. Конус № 50 ISO, Coromant Capto или HSK – хорошие варианты интерфейса между шпинделем и инструментом для повышения точности и жесткости. Станки с ЧПУ не будут иметь подвесной оправки, как у традиционных зуборезных станков; поэтому может потребоваться выполнить несколько проходов для уменьшения усилий. С другой стороны, шлицевое фрезерование обычно гораздо менее требовательно, поскольку общая глубина часто составляет половину одного и того же размера шестерни.При шлицевом фрезеровании время цикла часто на 50 процентов меньше, чем при традиционном горизонтальном фрезеровании HSS, особенно если выбранный станок с ЧПУ имеет высокую скорость ускоренного хода. Это может быть меньше одной секунды на зуб.
Рис. 7: Полуфабрикаты, зуборезные фрезы с тангенциальной пластиной Комбинация зарезки и зубофрезерования
Инструменты для резки и зубофрезерования можно комбинировать на одном станке. Многие современные зубофрезерные станки имеют функцию управления, позволяющую резаку, установленному на той же оправке, что и варочная панель, выполнять единичную индексацию и черновую или получистовую обработку промежутков между зубьями.Затем фрезерная головка может сместиться – без потери положения зуба на заготовке и расположения червячной фрезы – для завершения фрезерования зубчатой передачи. Этот метод полезен при использовании резца со сменными пластинами из твердого сплава для удаления большей части заготовки, когда рабочий материал труден и трудно обрабатывать с помощью традиционной фрезы из быстрорежущей стали. Инструмент для варочной поверхности обрабатывает шестерню только за счет удаления минимального количества материала. Длину варочной панели можно уменьшить, а время между переточками можно увеличить. (См. Рисунок 11.)
Определение толщины стружки при зарезке
Наиболее важным фактором при правильном применении зубофрезерных фрез является определение толщины стружки. Поскольку дуга зацепления зуборезной фрезы обычно очень короткая, часть фрезы, задействованная в работе, очень мала по отношению к общей окружности (см. Рисунок 12). Скорость подачи при фрезеровании часто выражается в единицах подачи на зуб. Из-за этой небольшой дуги зацепления фактическая толщина стружки будет значительно меньше подачи на зуб.
Рис. 8: Чистовая, дуплексная, тангенциальная зубофрезерная фреза При этом необходимо рассчитать фактическую толщину стружки. Фактическая толщина стружки обозначается как H ex . Необходимо определить расчет коэффициента модификации fz. Этот коэффициент указывается как множитель фактической подачи на зуб, обозначаемый как f z . Первым делом нужно определить диаметр фрезы, или D c . Затем определите фактическую всю глубину пространства между зубьями или глубину фрезерования (если требуется несколько проходов), которая обозначается как A e .Конечно, правильное значение H ex должно определяться в соответствии с рекомендациями производителя инструмента.
Формула для f z , коэффициент модификации:
Уравнение 1
Примером может служить фреза диаметром 8 дюймов, D c = 8
Однопроходное фрезерование до глубины зазора между зубьями 0,7 дюйма, A e = 0,7
Таким образом, fz , коэффициент модификации = 5.7143 / 3,229 = 1,769
Следовательно, если требуется H ex из 0,008, то f z из 0,008 x 1,769 = 0,014.
Рисунок 9: Инструмент для зарезки шлицевых шлицев Утончение стружки на боковой поверхности по сравнению с корнем
Предыдущий раздел о толщине стружки относится к корневой зоне. В корневой зоне рассчитывается максимальная толщина стружки. Стружка, образующаяся на боковой поверхности зуба, намного тоньше. Простой способ взглянуть на это – рассмотреть базовую V-образную форму стойки.В случае редуктора с углом сжатия 20 градусов вы просто берете тангенс угла 20 градусов, что составляет 0,364. Используя этот коэффициент, толщина стружки, рассчитанная на основе корня 0,008, будет умножена на 0,364. Это будет означать, что толщина боковой стружки составляет около 0,003 дюйма.
Поскольку боковые поверхности не имеют прямой V-образной формы (за исключением фрезерования прямой зубчатой рейки) с типичной конструкцией эвольвентной кривой, нецелесообразно рассчитывать точную толщину стружки на боковой поверхности. Этот метод использования тангенса угла давления приемлем для целей планирования процесса.Этот фактор более тонкой стружки на боковой поверхности также является причиной более легкой подготовки режущей кромки на боковых пластинах. Слишком большая заточка кромки может привести к трению и смазыванию металла из-за слишком большого давления и недостаточного срезающего действия.
Рис. 10: Различные профили пластин для шлицев одинакового размера с 45, 39 и 32 зубьями По этой причине, когда инструменты изготавливаются с отдельными корневыми и боковыми пластинами, конструкторы часто увеличивают количество корневых пластин по сравнению с боковыми пластинами. Отношение корней к боковым сторонам составляет 2: 1 и 3: 1.Корневые пластины производят примерно в три раза больше работы, чем боковые пластины, поэтому эта концепция имеет смысл для балансировки износа инструмента всех задействованных пластин.
Полноразмерный разрыв
Возвращаясь к Рисунку 6, полноразмерные режущие инструменты во многих случаях имеют свои достоинства. При полном зарезании твердосплавные пластины шлифуются по всей форме производимого пространства зуба (корень и боковые поверхности). Это наиболее точный вариант благодаря универсальной конструкции. В случае отдельных пластин с корнем, левой и правой боковыми поверхностями каждая пластина имеет допуск, плюс гнезда под пластину в корпусе инструмента имеют допуски; следовательно, наложение больше, чем у полноразмерной вставки, где требуются одна вставка и один карман.
Рис. 11: Комбинация зубофрезеровки и зарезки Еще одним преимуществом полноформатной конструкции является простота и эффективность удаления стружки. Конструкции тангенциальных пластин с множеством различных корневых и боковых пластин создают различные образования стружки, которые изгибаются в разных направлениях. Прогнозирование этих схем формирования стружки и последующего удаления стружки может оказаться сложной задачей даже для самых опытных разработчиков инструментов. Иногда встречается смазывание стружки и повторная резка. Цельнозубчатые фрезы имеют до двух раз более эффективные зубья, чем тангенциальные фрезы; следовательно, они более производительны.
Незначительным недостатком полноразмерной конструкции является то, что отношение корневой части к боковой поверхности составляет 1: 1, что, как упоминалось в предыдущем разделе, не является идеальным балансом для износа инструмента. Улучшения производительности, качества и удаления стружки обычно перевешивают эти проблемы. По мере увеличения зубчатого модуля или размера DP размер требуемого размера твердосплавной заготовки становится больше, и в конечном итоге его производство становится непрактичным как с технической, так и с экономической точки зрения.
Если требования AGMA, DIN или другие требования к качеству зубчатой передачи вызывают озабоченность у разработчика инструмента или инженера-технолога, следует рассмотреть вариант полной формы.
Фрезерование с подъемом и обычным фрезерованием
Распространенной передовой практикой фрезерования является использование подъемного фрезерования для зарезания зубчатых колес. Иногда используется другой процесс, обычно называемый обычным измельчением. Визуализация этих двух методов показана на рисунке 13.
Рис. 12: Малая дуга зацепления Фрезерование с подъемом позволяет режущей пластине входить в работу с некоторым немедленным стружкообразованием и выходить из зоны резания без толщины стружки.Поскольку карбид лучше всего работает при сжимающей нагрузке, этот метод доказал свою лучшую стойкость инструмента. Разгрузка на выходе менее опасна для инструмента, так как выходной удар минимален.
При обычном фрезеровании инструмент входит в резку без толщины стружки, а затем постепенно формирует стружку по мере продвижения в работу. Он выходит из резания с некоторой толщиной стружки, поэтому разгрузка происходит внезапно и отрицательно сказывается на стойкости инструмента. Кроме того, трение при входе инструмента в работу вызывает большее тепловыделение и тепловой эффект.При использовании этого метода также значительно увеличивается давление инструмента. Одним из ощутимых преимуществ является то, что качество обработки поверхности обычно лучше при обычном фрезеровании из-за сжимающего и полирующего действия, когда инструмент начинает формировать стружку. Лабораторные исследования Sandvik Coromant показали снижение Ra на 20–30% при использовании обычного фрезерования по сравнению с резанием с подъемом.
Рисунок 13: Фрезерование с подъемом и обычное фрезерование Фрезерование со смазочно-охлаждающей жидкостью и сухое резание
Лучшая практика фрезерования твердосплавными инструментами – это, за некоторыми исключениями, резание всухую.При резке жидкостью твердосплавный инструмент подвергнется термическому удару при выходе из резания. Эффект теплового удара обычно отрицательно сказывается на стойкости инструмента. Пример этого механизма разрушения показан на рисунке 14. Здесь повторяющиеся циклы нагрева и охлаждения в конечном итоге приводят к перпендикулярным краевым трещинам, которые в конечном итоге позволяют материалу вставки высвободиться, что приводит к быстрому разрушению. Водорастворимые смазочно-охлаждающие жидкости оказывают наиболее вредное воздействие на тепловой удар, поскольку вода быстро охлаждает инструмент. Смазочно-охлаждающие жидкости также обладают значительным охлаждающим эффектом, но они не удаляют БТЕ так быстро, как вода.Поэтому они несколько лучше воды по стойкости инструмента. Конечно, при использовании жидкостей как на нефтяной, так и на водной основе возникают экологические издержки, и цель должна заключаться в их устранении, когда это возможно.
Применение сжатого производственного воздуха или даже вихревое охлаждение сжатого воздуха может способствовать удалению стружки и охлаждению инструмента и работы. Пример этого метода охлаждения показан на рисунке 15. Это проверенный метод охлаждения. Устранение тепловыделения и удаление стружки – основная причина, по которой все еще используются смазочно-охлаждающие жидкости.
Рисунок 14: Термическое растрескивание Инструменты могут иметь внутренние воздушные каналы, как показано на Рисунке 16. Такая конструкция способствует удалению стружки и охлаждению инструмента. Однако такие функции значительно увеличивают сложность и стоимость инструмента. Этот метод подачи внутреннего воздуха следует тщательно продумать, так как необходимы модификации шпинделя и оправки станка, а также стоимость инструмента и проблемы сложности прохождения воздуха через инструмент. При правильной конструкции инструмента для свободного отвода стружки в сочетании с правильной стратегией резания, вероятно, можно избежать внутренних воздушных отверстий.
Рисунок 15: Система охлаждения сжатым воздухом Vortex Сила резания
Требования к мощности и крутящему моменту должны быть определены для эффективного применения зубофрезерных фрез для стабильного процесса обработки. Чтобы правильно оценить усилия обработки, необходимо определить площадь поперечного сечения стружки и удельную силу резания для данного материала. Вычислить точную площадь поперечного сечения для данного пространства зуба довольно сложно, и лучше всего это сделать с помощью компьютерного программного обеспечения, способного создать точный профиль боковой поверхности и конфигурацию корня.Подобные расчеты выходят за рамки данной статьи. Вместо этого цель состоит в том, чтобы найти близкое, пригодное для использования приближение. Для этого можно изучить базовую конфигурацию стойки (V-образную форму) для заданного угла давления без сложного профиля эвольвентной кривой на боковых сторонах. Примечание. При использовании этого метода оценки для фрезерных шестерен или шестерен с малым числом зубьев, как обсуждалось ранее, зазор будет открываться по мере уменьшения делительной окружности. В таких случаях может потребоваться дополнить результаты расчета силы в сторону высоких значений.
Первым шагом в вычислении поперечного сечения микросхемы является определение базовой стойки. (См. Рисунок 17.)
Рисунок 16: Зубофрезерная фреза с внутренним воздухом Номенклатура
- H = Общая глубина зазора между зубьями (мм)
- a = Угол давления (градусы)
- V = Смещение боковой поверхности от основания (мм)
- B = толщина стружки на боковой поверхности (мм)
- D = Ширина корня (мм)
- A = Площадь зуба (мм 2 )
- f z = Подача на зуб (мм)
- h ex = Максимальная толщина стружки (мм)
- h м = Средняя толщина стружки (мм)
- v c = Скорость резания (м / мин.)
- M c = крутящий момент (Нм)
- P c = Полезная мощность (кВт)
- a e = рабочее зацепление (мм)
- D c = Диаметр фрезы (мм)
- k c1 = Удельная сила резания для данного материала (Н / мм 2 )
- м c = коэффициент удельного увеличения силы резания относительно толщины стружки
- kc = Удельная сила резания при м c с учетом
- n =
об / мин- z c = Общее количество эффективных зубьев фрезы
- M n = Размер модуля (мм)
- v f = Скорость подачи (мм / мин.)
Рисунок 17: Базовая конфигурация стойки В следующем примере показано, как рассчитать мощность и силы резания. Первым шагом является определение частоты вращения фрезы ( n ) на основе рекомендованной скорости резания ( v c ).
Формула:
Уравнение 2
Для этого примера:
Затем необходимо определить v f (подача мм / мин). Формула:
Уравнение 3
В этом примере мы предполагаем, что:
Далее необходимо определить k c .Формула:
Уравнение 4
В этом примере мы используем:
Этот коэффициент доступен в разделах материалов каталогов Sandvik Coromant и в технической литературе в печатном и электронном виде. (См. Рисунок 18.)
Средняя толщина стружки, или h м , определяется по формуле:
Уравнение 5
В этом примере мы используем полную глубину ( H ) 36 мм. Мы предполагаем однопроходную операцию, поэтому a e = H и f z (подача на зуб в мм) 0.04 мм:
Уменьшено до:
Это может быть уменьшено до:
Таким образом, для удельной силы резания мы имеем k c = 1900 / (0,130,25) = 3188,93
Далее необходимо определить площадь зубного промежутка. Возвращаясь к рисунку 17, мы должны сначала определить C . Формула для этого:
Уравнение 6
В этом примере предполагается размер модуля: M n = 16 и a = 20:
Далее, из рисунка 17 необходимо определить D .Формула:
Уравнение 7
В этом примере:
Опять же из рисунка 17 необходимо определить V . Формула:
Уравнение 8
В этом примере:
Далее, из рисунка 17 необходимо определить A , поэтому формула:
Уравнение 9
В этом примере это:
Выполнив эти шаги, мы можем рассчитать мощность на шпинделе, или P c .Формула:
Уравнение 10
В этом примере:
Следующий важный расчет – крутящий момент, или M c . Формула для этого расчета:
Уравнение 11
В этом примере:
Таким образом, модульная фреза 16 мм, диаметром 350 мм с восемью эффективными зубьями, работающая со скоростью 180 м / мин. скорость резки, подача со скоростью 524 мм / мин. Скорость подачи, резка нормальной низколегированной стали с твердостью 300 BHN потребует приблизительно 24 кВт на шпинделе с требованием крутящего момента 1392 Нм.
Можно написать простую компьютерную программу для работы с электронными таблицами, чтобы автоматизировать эти вычисления, чтобы сэкономить время и предотвратить ошибки вычислений. Это очень поможет инженеру-производителю зубчатых колес при планировании процесса. Та же самая таблица может быть интегрирована с расчетами времени цикла.
Рисунок 18: Информация от Sandvik Coromant с конкретными характеристиками силы резания Заключение
Зубофрезерование или зарезание зубцов при обработке зубчатых колес – это хорошо зарекомендовавший себя, эффективный и стабильный метод изготовления зубчатых колес.Возможности повышения производительности, снижения затрат и создания качественных шестерен очевидны. Помощь квалифицированных поставщиков инструментов поможет направить инженера в правильном направлении. Новые концепции инструментов, прогрессивные концепции станков, методы термообработки и материалы для зубчатых колес постоянно меняют производственную среду. И новое поколение профессионалов в области оборудования, приходящих на рабочее место, привносит свежие идеи и готовность использовать новые методы от молодых инженеров, которые руководят технологическим сдвигом.
Наряду с этими факторами, все больше и больше используются многозадачные станки с ЧПУ для изготовления зубчатых колес. У производства зубчатых колес светлое будущее, и ближайшие годы станут захватывающим временем для тех, кто работает в этой отрасли.
Список литературы
- Антониадис, А., Видакис, Н., и Билалис, Н. «Исследование усталостного разрушения твердосплавных инструментов при зубофрезеровании, Часть 1: Моделирование зубофрезерования с помощью МКЭ и вычислительная интерпретация экспериментальных результатов.”Журнал производственной науки и техники, ASME, Vol. 124, ноябрь 2002 г.
- Антониадис А., Видакис Н. и Билалис Н. «Исследование усталостного разрушения твердосплавных инструментов при зубофрезеровании, Часть 2: Влияние параметров резания на уровень напряжений инструмента – количественный параметрический анализ». Журнал производственной науки и техники, ASME, Vol. 124, ноябрь 2002 г.
- Исаков Эдмунд, канд. «Расчетная сила», Разработка режущего инструмента – Плюс, Вып. 64, выпуск 5, май 2012 г.
- «Техническое руководство Sandvik Coromant – токарная обработка, фрезерование, сверление, растачивание, крепление инструмента». AB Sandvik Coromant, 2010.
- Абуд, Али М. «Динамический анализ режущих сил при зубофрезеровании». Школа механики и системотехники, Университет Ньюкасл-апон-Тайн, Великобритания, декабрь 2002 г.
* Напечатано с разрешения правообладателя, Американской ассоциации производителей оборудования, 1001 N. Fairfax Street, Suite 500, Alexandria, Virginia 22314. Заявления, представленные в этом документе, принадлежат авторам и могут не отражать позицию или мнение Американская ассоциация производителей шестерен (AGMA).Этот документ был представлен в октябре 2015 года на осеннем техническом совещании AGMA в Детройте, штат Мичиган. 15ФТМ11.
Специально разработанные фрезы для выпуклостей
Код продукта: MXCMC 05
Доступная модель / тип
Материал: HSS M2; M35; ASP 2030
Покрытия доступны по запросу
Приложения
Для вырезания истинного радиуса вогнутости
Особенности
Мы используем сырье высшего качества, и наши продукты известны своей превосходной производительностью и оптимальным качеством.
Краткое описание продукции
Фрезы производятся с использованием новейших и превосходных легированных сталей и качественной стали, которая обеспечивает высокую рабочую твердость при рабочих условиях около 600 градусов по Цельсию. Они имеют коррозионно-стойкое покрытие, а также доступны в форме прямых зубьев, которые подходят как для легких, так и для тяжелых операций с глубокими пазами. На протяжении многих лет выпуклые фрезы широко использовались для фрезерования поверхностей компонентов и изготовления профилей и компонентов.Выпуклые фрезы бывают с зубьями на периферийной поверхности или с боковыми сторонами, либо с их комбинацией.
Фрезы выпуклые Quaity
Maxwell предлагает широкий ассортимент высококачественных выпуклых фрез, которые используются для фрезерования различных материалов поверхности. У нас есть выпуклые фрезы различных размеров от 10 до 100 мм в диаметре. Самое главное, что наши фрезы применимы в разных секторах и служат разным целям.
Креативный дизайн
Наши выпуклые фрезы специально разработаны для обеспечения прецизионной резки любой формы, какой бы сложной она ни была, а также обеспечивают жизненно важную поддержку для пользователей в поддержании правильного угла резания.Мы производим выпуклые фрезы, которые соответствуют стандартам прецизионной конструкции для обеспечения оптимальной производительности. Мы также специализируемся на предоставлении уникальных и комплексных фрез для выпуклых фрез, которые могут быть адаптированы в соответствии с требованиями наших клиентов. Благодаря своим уникальным характеристикам, таким как более длительный срок службы, стойкость к истиранию и коррозионная стойкость, наши фрезы для выпуклой резки стали известны потребителям, которые ценят качество и простоту эксплуатации. Это сделало наши выпуклые фрезы востребованными во всем мире.
Высокая производительность и долговечность
Maxwell известна производством выпуклых фрез, которые известны своей высокой производительностью и длительным сроком службы. Наши выпуклые фрезы из быстрорежущей стали облегчают фрезерование сложных, но выдающихся полукругов на любом типе материала с радиусом 200 мм. Мы зарекомендовали себя как один из известных и наиболее уважаемых производителей и поставщиков выпуклых фрез по всему миру.
Благодаря команде профессионалов компания Maxwell зарекомендовала себя как ведущий производитель и поставщик обширного и широкого ассортимента превосходных выпуклых фрез, изготовленных с использованием лучших доступных материалов и лучших технологий.На наш широкий ассортимент выпуклых фрез предоставляются следующие гарантии:
- Качественные продукты с хорошим соотношением цены и качества
- Долгая жизнь
- Постоянство качества
- Прочность
- Надежность
В дополнение к вышесказанному, производимые нами выпуклые фрезы обладают высокими термостойкими характеристиками, что позволяет использовать меньше тепла при резке даже самых твердых поверхностей.
Итак, на что следует обратить внимание при покупке идеальной выпуклой фрезы? Для начала, идеальная фреза должна быть достаточно большой, чтобы хватить на всю рабочую поверхность, чтобы работу можно было выполнять быстро и быстро.В то же время вы также должны учитывать, что выпуклая фреза с фрезой малого диаметра будет проходить по поверхности за значительно более короткое время, чем фреза с фрезой большого диаметра, которая подается с той же скоростью.
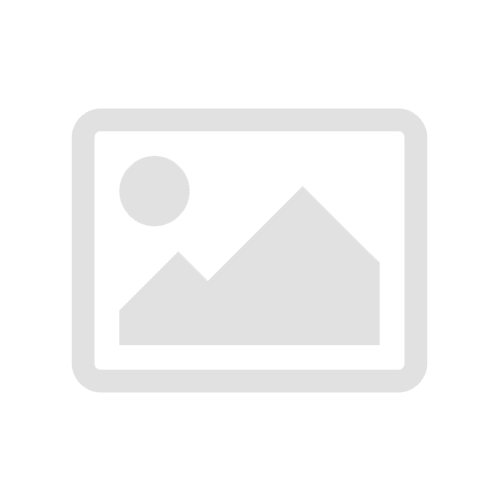








• Концевые фрезы режут материал как по периферии, так и по торцу, одновременно создавая напряжение, поскольку инструмент удерживается только на шпинделе.
• Фрезы используются в таких приложениях фрезерования, как профильное фрезерование, трассировочное фрезерование, торцевое фрезерование, врезание.

• С центрированием и без центрирования.
• Также доступны концевые фрезы с резьбой.
• COBALT STEEL подходят для использования с более прочными материалами и для всех тяжелых условий эксплуатации, где требуется увеличенная глубина резания.Добавление кобальта дает оптимальную твердость и ударную вязкость, улучшая, таким образом, режущие характеристики.
• ВЫСОКОСКОРОСТНАЯ СТАЛЬ демонстрирует исключительные результаты при обработке низкоуглеродистой, легированной и инструментальной стали и является превосходным инструментом для чистовой обработки, используемым в производственных процессах.
• Также доступны нестандартные длины и размеры в мм.
(a) ВЫСОКОСКОРОСТНАЯ СТАЛЬ (HSS)
(1) Качество M2 (Single H)
(1) Качество M-35 (5% кобальта) (двойной H)
(2) Качество M42 (8% кобальта) (Triple H)
Код товара No.
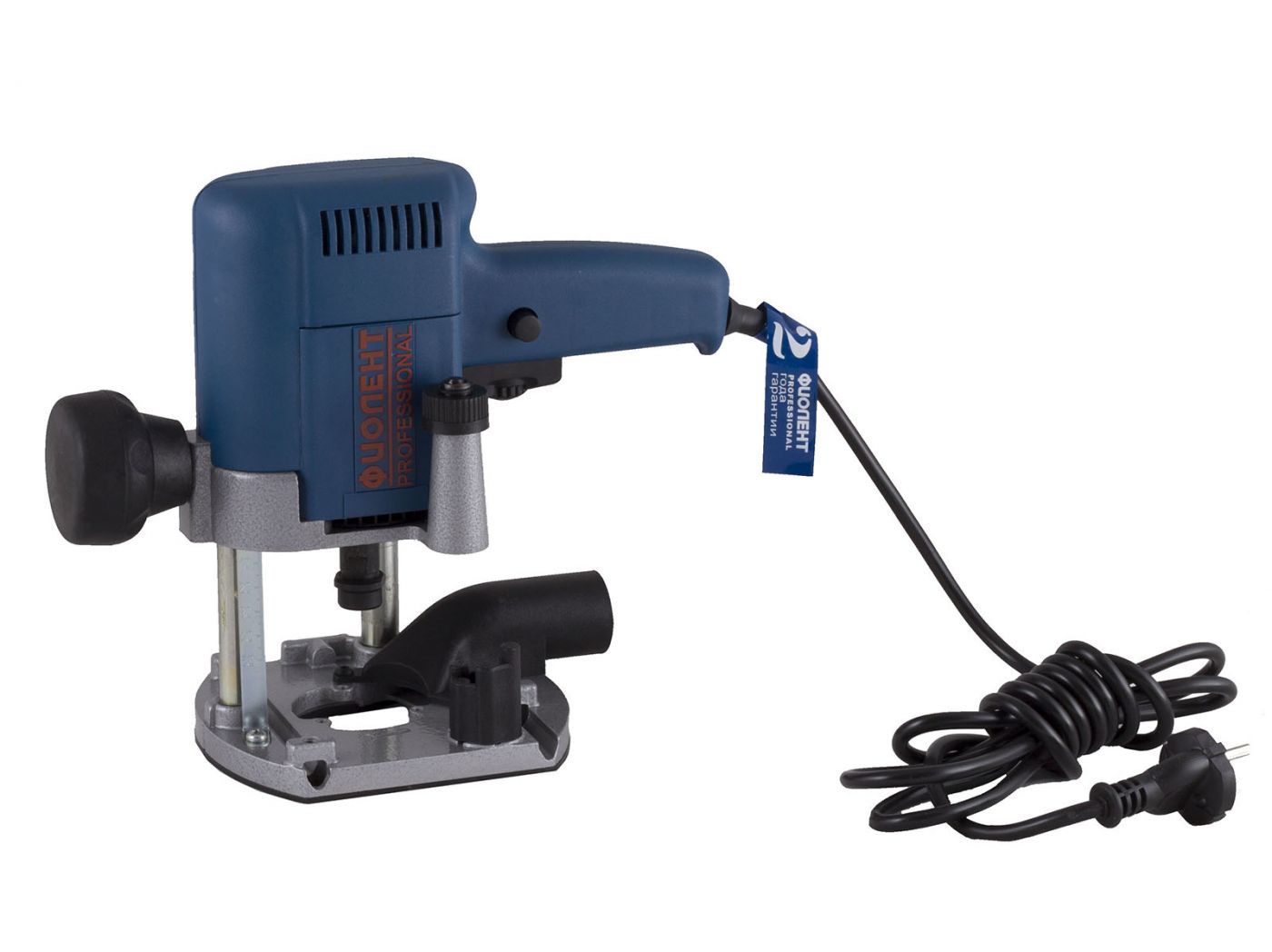
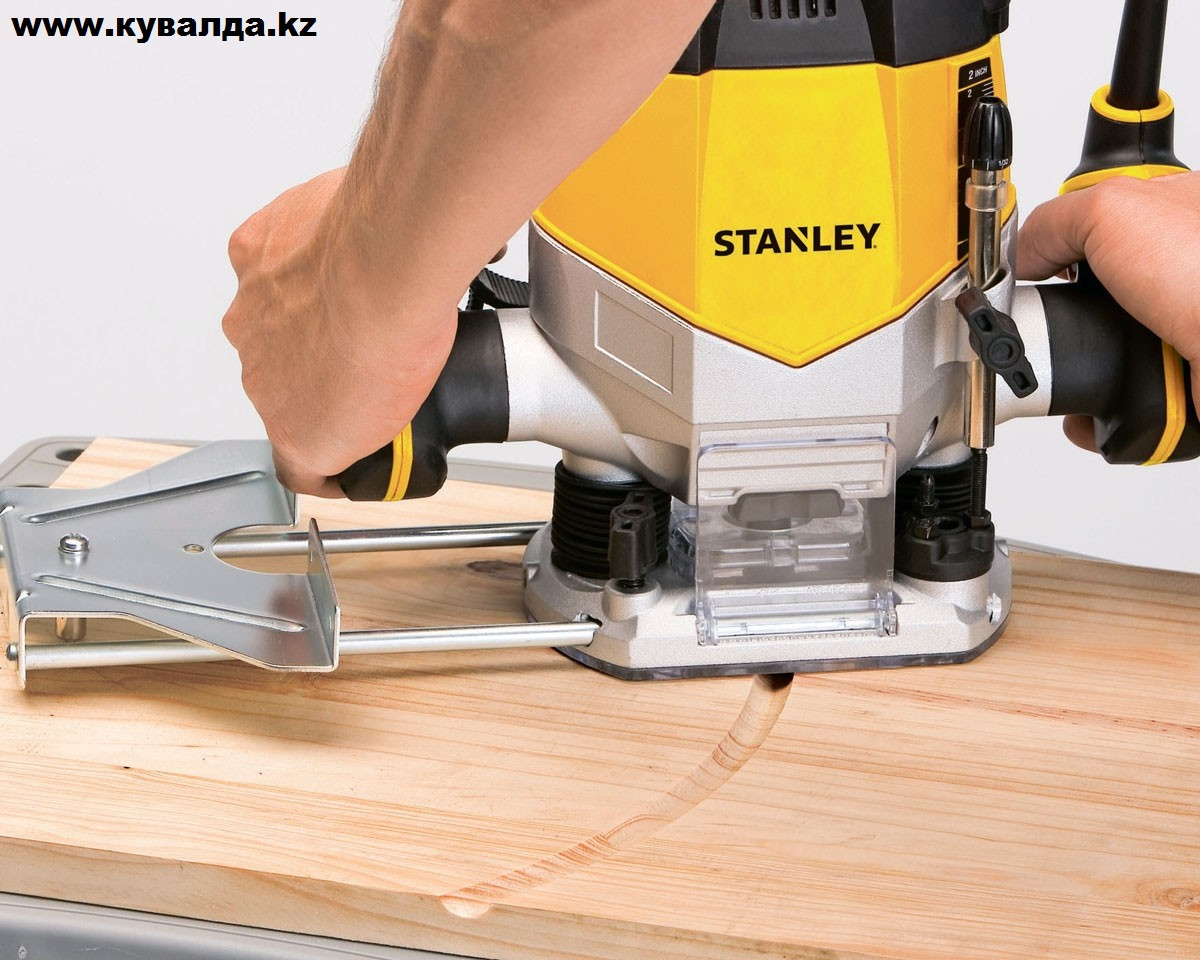



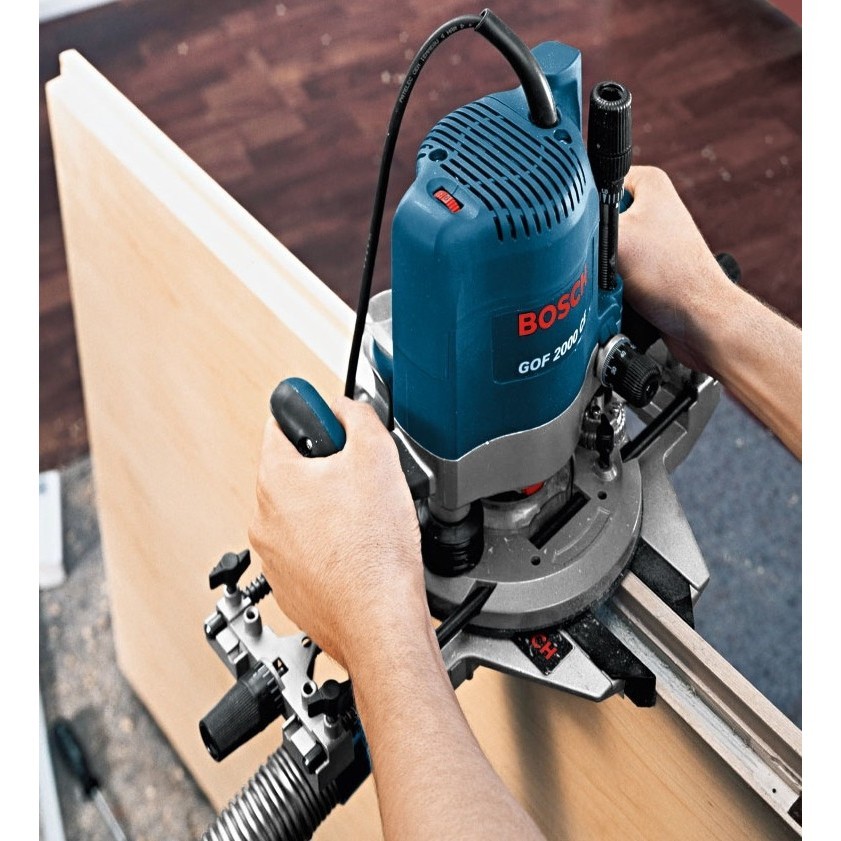
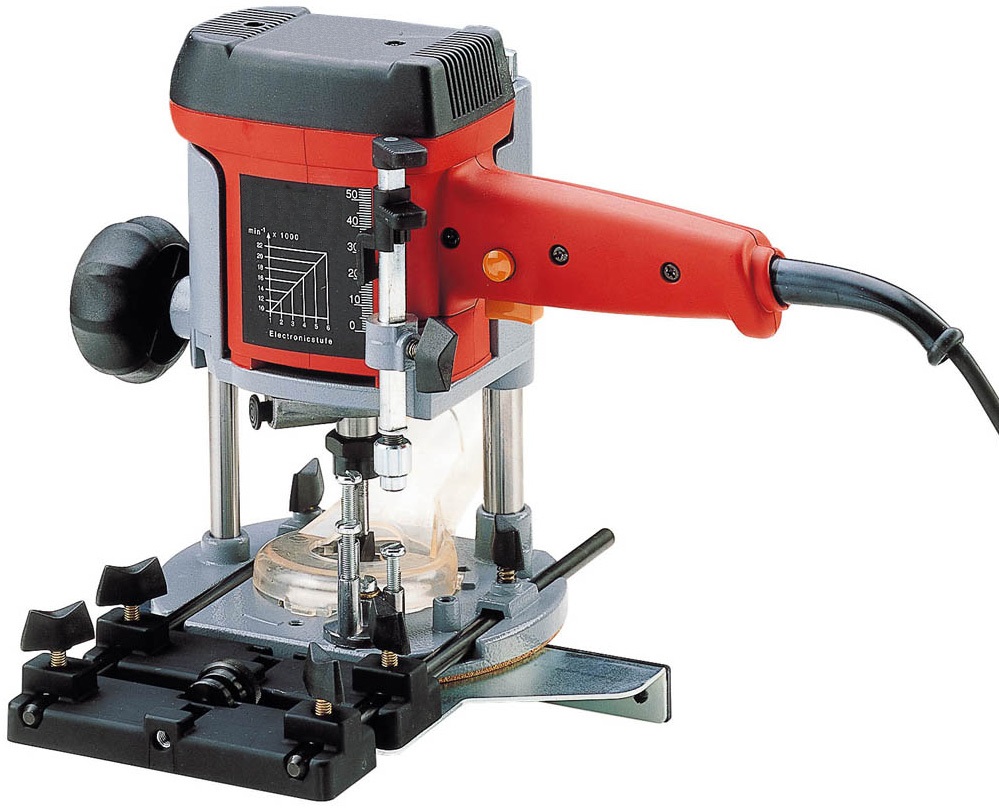
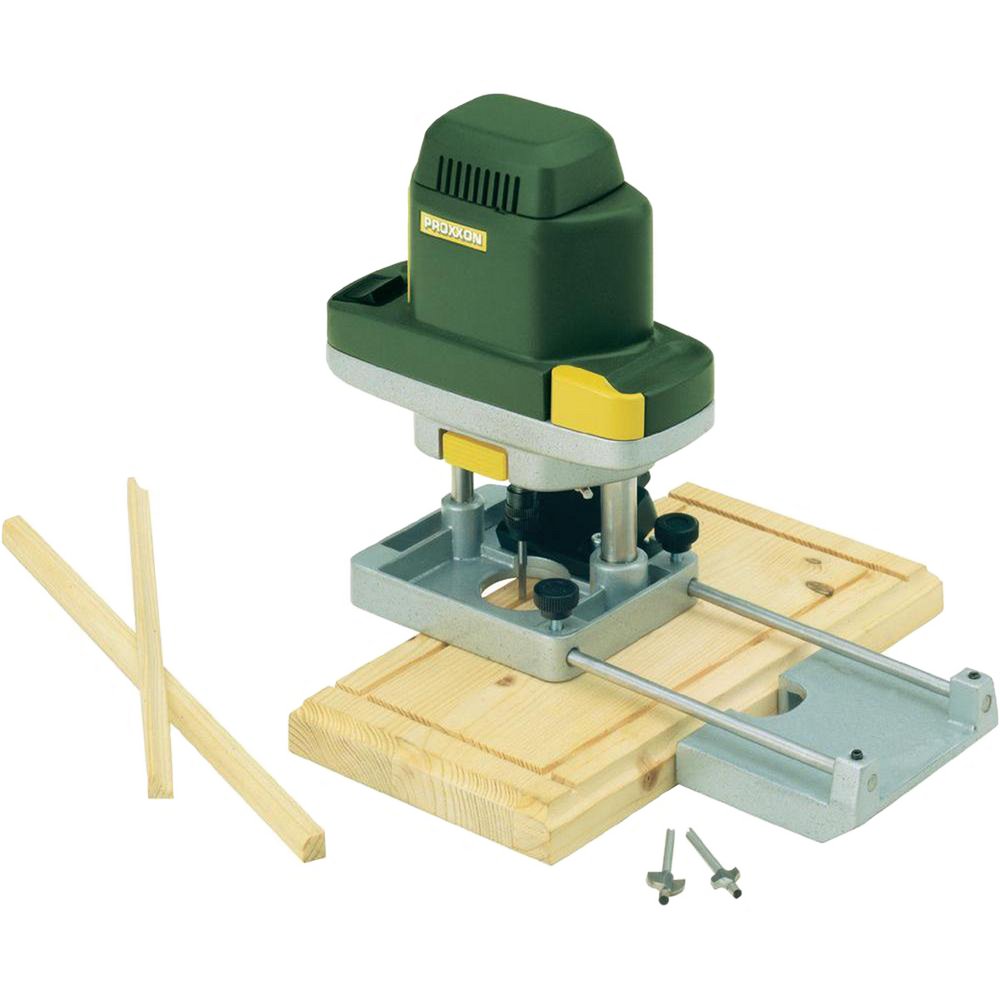

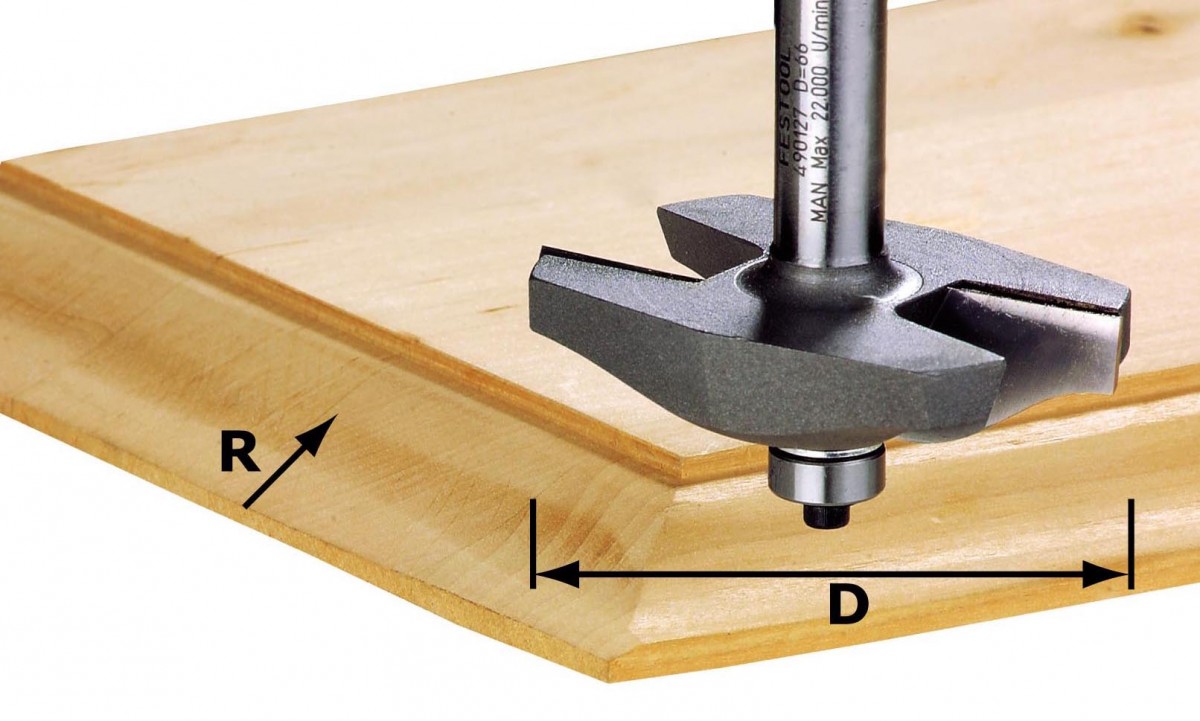

Покрытия доступны по запросу