Сверла — Геометрические параметры режущей части
ГЕОМЕТРИЧЕСКИЕ ПАРАМЕТРЫ РЕЖУЩЕЙ ЧАСТИ ЗУБА СВЕРЛА. Определение геометрических параметров режущей части производится на основе общих положений кинематики резания. [c.202]Геометрия режущей части сверла. К геометрическим параметрам режущей части сверла относятся угол при вершине сверла, угол наклона винтовой канавки, передний и задний углы, угол наклона поперечного лезвия или лезвия перемычки . (рис. 28, б). [c.73]
Форма заточки и геометрические параметры режущей части сверл по нормали МН 70 65 для обработки легких сплавов Размеры в мм [c.337]
Сверла — Геометрические параметры режущей части 140 — 141, 200—208 [c.566]
Основные размеры, градация диаметров, геометрические параметры режущей части сверл приведены в табл. 3-6. [c.370]
По конструкции различают сверла спиральные, с прямыми канавками, перовые, для глубоких отверстий, для кольцевого сверления, центровочные и специальные комбинированные.
Геометрическими параметрами режущей части свер-,ла являются задний угол а, передний угол у, углы при вершине 2ф и 2фо и угол наклона поперечной кромки ij (рис. 138), Величина заднего угла изменяется вдоль режущей кромки. Наименьшее значение (7—15°) задний угол имеет в наружной поверхности сверла, а наибольшее (20—26°) — около поперечной режущей кромки. Величина переднего угла в разных точках рел [c.241]
Геометрические параметры режущей части сверл цилиндрических полых с выталкивателем для обработки отверстий и пробок имеют профиль, аналогичный профилю зубьев круглых пил для поперечной распиловки древесины. Угловые параметры зубьев и развертка цилиндрической части сверла представлены на рис. 8.
[c.242]
На фиг. 180 приведены геометрические параметры режущей части сверла, предназначенного для обработки чугуна. Угол наклона винтовой канавки принимается равным 20, пластинка же наклонена к оси под углом 6°. Задний угол на периферии по пластинке 10— 12°, а по корпусу 18—20″. Угол при вершине 118—120″. Угол переходной кромки 75° на длине 0,2 диаметра сверла. Важное значение для работоспособности сверла имеет утонение калибрующей части. Оно принимается на длине пластинки для сверл.
Сверла. Основные размеры, геометрические параметры режущей части сверл приведены в табл. 2 — 7. [c.420]
Основные геометрические параметры режущей части сверла для сверления пластмасс (см. рис. 154), мм [c.146]
Геометрические параметры режущей части сверл установлены ГОСТ и рекомендуются для сверл диаметром от 0,25 до 80 мм при обработке стали и чугуна. Формы заточек сверл в зависимости от размера сверла и обрабатываемого материала следует выбирать ио табл. 36.
[c.219]
Своеобразие заточки сверл по коническим поверхностям заключается в том, что сверло относительно конуса заточки надо расположить так, чтобы получить на сверле необходимые величины геометрических параметров режущей части задних углов а, угла наклона поперечной кромки 1(), угла при вершине сверла 2ф. Положение сверла относительно вершины конуса заточки с углом при вершине 2р характеризуется расстоянием I (фиг. 123,а), смещением к осей конуса и сверла [c.229]
В соответствии с режимами резания металлов инструментами из быстрорежущей стали выбираем форму заточки сверл и устанавливаем геометрические параметры режущей части сверла. [c.297]
Устанавливаем геометрические параметры режущей части. Для сверла 013,5 мм [c.306]
На рис. У1-41 приведены элементы конструкции спиральных сверл с коническим и цилиндрическим хвостами. На рис. У1-42 показаны геометрические параметры режущей части сверла, где 1—2
[c.377]
По табл. 8, ч. II для сверла диаметром 9,8 мм геометрические параметры режущей части, в соответствии с ко- [c.383]
Геометрические параметры режущей части сверл для сверления жаропрочных сталей (фиг. 10) [c.247]
Значения геометрических параметров режущей части оказывают влияние на ресурс и стойкость всех видов осевых режущих инструментов (сверл, зенкеров, разверток), а также на точность размеров и шероховатость поверхности обработанных отверстий. Те значения геометрических параметров режущей части, при которых ресурс и стойкость инструмента максимальны и одновременно получаются наилучшие результаты по точности размеров и шероховатости поверхности обработанных отверстий, принято называть оптимальными. Оптимальные значения геометрических параметров, установленные на основе обобщения результатов экспериментальных исследований и передового производственного опыта, приведены в табл.
Геометрические параметры режущих частей сверл [c.482]
Геометрические параметры режущей части сверл Сверла из стали Р9 и Р18 [c.902]
Геометрические параметры режущей части цельных твердосплавных сверл угол при вершине 2ф, задний угол а и передний угол у/ упрочняющей фаски выбираются в зависимости от обрабатываемого материала и его прочности. Рекомендуемые значения углов приведены в табл. 42. [c.195]
Геометрическими параметрами режущей части сверла являются задний угол , передний угол у, углы при вершине 2угол наклона поперечной кромки i > (рис. 16). Величина заднего угла изменяется вдаль режущей кромки. Наименьшее значение (7—15°) задний угол имеет у наружной поверхности сверла, а наибольшее (20—26°) — около поперечной режущей кромки. Величина переднего угла в разных точках режущей кромки неодинакова наибольшее значение (25—30°) угол имеет у наруж-ной-ЛОверхности сверла, а наименьшее — около поперечной кромки, где бн мс жет быть и отрицательным.
Геометрические параметры режущей части сверла состоят из заднего угла а, переднего угла т углов при вершине 2о и угла наклона поперечной кромки сверла Ф (рис. 21). [c.28]
На рис. 261 показаны углы спирального сверла. Передняя поверхность зуба (клина) сверла образуется спиральной канавкой, задняя— боковой поверхностью конуса. Геометрические параметры режущей части сверла показаны на рис. 262 (см. сечение N—Л ). [c.267]
Выполняем рабочий чертеж (рис. 41). Рабочий чертеж должен иметь три проекции (винтовые линии при черчении заменяют прямыми линиями). Форма заточки сверла с геометрическими параметрами режущей части, а также профиль канавочной фрезы вычерчивают отдельно в большом масштабе (см. рис. 41, в). На чертен1б также указывают основные технические требования к сверлу (см. указания на с. 19). [c.128]Геометрические параметры режущей части сверл установлены ГОСТ 2322-43 и рекомендуются для сверления отверстий диаметоом от 0,25 до 80 мм в стали и чугуне.
[c.322]
Геометрические параметры (…°) режущей части сверл для обрабопл [c.430]
На фиг. 432 приведены элементы конструкции винтовых сверл с коническим и цилиндрическим хвостовиком. На фиг. 433, а показаны геометрические параметры режущей части сверла, где 1—2 и 3—4 главные режущие кромки 1—3 лезвие перемычки 2—5 и 4—6 — вспомогательные лезвия круглошлифованных ленточек а — задний угол в точке на режущей кромке в цилиндрическом сечении сверл — передний угол в плоскости, перпендикулярной к режущей кромке ср — главный угол в плане (фиг. 433, б) — угол в плане переходной кромки /о — ширина переходной кро . ки в мм I — угол наклона режущей кромки в град. (фиг. 433, а).
Выбор формы заточки и геометрических параметров режущей части сверла. По табл. 6 (стр. 97) выбирают форму заточки сверла для обработки стали с пределом прочности =68 кг1мм ,.ДХ1 — двойная с подточкой перемычки. [c.82]
Геометрические параметры режущей части сверла (рис. 24) состоят из переднего угла Т (гам1ма), заднего угла а (альфа), угла при вершше 2ф (фи), угла наклона поперечной кромки сверл ijj (пси) и угла наклона винтовой канавки со (омега), указанного на рис. 23.
[c.86]
Геометрические параметры режущей части сверла (рис. 11) состоят из переднего угла у (гамма), заднего угла а (альфа), угла при вершине 2ф (фи), угла наклона поперечной кромки сверл (пен) и угла наклона винтовой канавкп о (омега), указанного на рис. 10. [c.55]
Мо.мент и сила иодачи ири сверлении зависят в основном от геометрических параметров режущей части сверла, диаметра сверла, подачи, охлаждающе-смазывающей жидкости и физикомеханических свойств обрабатываемого материала. [c.165]
Назначение, элементы конструкции и геометрические параметры спирального сверла
Назначение, элементы конструкции и геометрические параметры спирального сверла
Сверла предназначены для получения отверстий в сплошном материале, для рассверливания на больший размер уже имеющихся отверстий, а также для засверливания конусных углублений в сплошном материале. Сверлением обеспечивается 12 ..11-й квалитет точности и шероховатость обработанной поверхности с Ra=80…20 мкм.
Наибольшее распространение в промышленности получили спиральные сверла из быстрорежущей стали с цилиндрическим хвостовиком (диаметры от 0,1 до 20 мм) и коническим хвостовиком (диаметры от 6 до 80 мм). Основные размеры сверл, такие, как диаметр сверла, длина рабочей части, размеры хвостовика, а также параметры точности, стандартизированы. Спиральное сверло состоит из рабочей части l1 (рис. 1.22), шейки l3 хвостовика l4 с лапкой l5 на конце. Непосредственно работу резания выполняет режущая часть /„. Остальной участок l2 рабочей части служит для вывода стружки, направления сверла в работе и резервом для переточек сверла. Поэтому часть l2 получила название направляющей части, иногда ее называют калибрующей.
Хвостовик l4 служит для закрепления сверла непосредственно в коническом гнезде шпинделя станка или в гнезде переходной втулки. Цилиндрические хвостовики закрепляются в специальных цанговых или трехкулачковых самоцентрирующихся патронах Момент резания передается силами трения, возникающими на поверхностях хвостовика. Лапка l5 предназначена для выбивания сверла из гнезда шпинделя станка или переходной втулки, а шейка l3 — для выхода шлифовального круга при шлифовании хвостовика и рабочей части.
Рабочая часть сверла состоит из двух перьев (зубьев) 4, двух винтовых канавок 2 и сердцевины 1, диаметр которой dc в сторону хвостовика несколько увеличивается для повышения прочности и жесткости сверла. Каждое перо сверла представляет собой режущий клин и имеет переднюю поверхность 9, заднюю главную поверхность 8 и заднюю вспомогательную поверхность 5, которая является частью наружной цилиндрической поверхности сверла, оставшейся после образования спинки 7, и называется круглошлифованной ленточкой. Спинка пера 7 также имеет цилиндрическую форму, но ее диаметр меньше диаметра сверла D. Занижение спинки необходимо для уменьшения трения при направлении сверла цилиндрическом поверхностью D но уже обработанной части отверстия. В результате роль направляющей поверхности выполняет узкая круглошлифованная ленточка 5.
В соответствии с рабочими поверхностями у сверла различают две главные режущие кромки 3, две вспомогательные режущие кромки 10 и поперечную режущую
кромку б на стыке двух задних поверхностей 8.
В статической системе координат основной плоскостью является осевая плоскость сверла, проходящая через рассматриваемую точку главной режущей кромки, так как она перпендикулярна к вектору скорости резания в этой точке. Плоскостью резания является плоскость, перпендикулярная к основной и проходящая через главную режущую кромку. Поэтому углы заточки сверла рассматриваются и определяются так же, как и у резца, который пунктиром наложен на сверло с совмещением рабочих поверхностей, главных и вспомогательных режущих кромок (рис. 1.23).
Как и у резца, у каждого пера сверла различают главный φ и вспомогательный φ1 углы в плане, угол наклона главной режущей кромки λ, но измеренный в проекции на плоскость, перпендикулярную оси сверла, передний угол у и задний угол в нормальной секущей плоскости. Удвоенное значение угла в плане, угол 2φ, называют углом при вершине сверла.
Особенности конструкции и условий работы сверла вносят некоторые отличия в геометрию его режущей части по сравнению с резцом, В связи с наличием поперечной кромки дополнительно появляется угол ψ положения этой кромки, зависящий от значений задних углов αN a также задний αп и сильно отрицательный передний γп углы поперечной режущей кромки (см. рис. 1.23). Задний вспомогательный угол равен нулю, так как задняя вспомогательная поверхность — часть цилиндра диаметром D. Угол φ1 предназначенный для уменьшения трения об обработанную поверхность, очень малый (1—2’) и образуется за счет обратной конусности рабочей части, т. е. за счет небольшого уменьшения диаметра сверла в сторону хвостовика. Главный задний угол а задается в плоскости О-О (см. рис. 1.23), параллельной оси и перпендикулярной к основной плоскости. Для резца он является поперечным задним углом. Поперечный передний угол резца является углом наклона со винтовой стружечной канавки сверла.
Передний и задний углы не постоянны вдоль главной режущей кромки от периферии к цен гру сверла передний угол уменьшается, а задний увеличивается. Указанный характер изменения заднего угла обеспечивается формой заточки задних поверхностей, а переднего — обусловливается способом изготовления винтовой стружечной канавки сверла. При постоянном шаге канавки угол ее наклона со, являющийся продольным передним углом сверла, при приближении к центру сверла уменьшается. В процессе работы интенсивность изменения рабочих углов несколько меньше, чем статических, так как αРx = αx — μx (см. рис. 1.23), γPx = γx+μx, a μx=arctg(S7/πDx) при приближении к оси сверла растет (см. рис. 1.23). Но тем не менее кинематические, или рабочие, углы сверла не постоянны вдоль режущей кромки, а поэтому не оптимальны, что является большим недостатком геометрии сверла.
Характер изменения статического переднего угла определяется формулой.
Пересчет заднего угла из одной секущей плоскости в другую производится но формуле:
Смотрите также
Геометрические параметры сверла. — Студопедия
Ðj– главный угол в плане – это угол в основной плоскости между плоскостью резания и рабочей плоскостью, влияет на толщину и ширину срезаемого слоя, условия теплоотвода, прочность режущей части сверла, назначают в зависимости от обрабатываемого материала.
Ð2j – угол при вершине – это угол между главными режущими кромками, Ð2j =60о…140о. Для сверления пластичных материалов берут большие значения, чем для хрупких, например:
– стали Ð2j ≈ 116о…118о
– чугуны Ð2j ≈ 118о…120о
– алюминий Ð2j ≈ 140о
– мрамор Ð2j ≈ 80о
Ðj1 – вспомогательный угол в плане – это угол между проекцией вспомогательной режущей кромки (кромки ленточки) на основную плоскость сверла, и рабочей плоскостью. Ðj1≤ 10/, но может быть равен 1-3о
tg j1 =
где l – длина направляющей части сверла.
Ðw – угол наклона винтовой канавки – это угол, заключенный между осью сверла и развернутой винтовой линией стружечной канавки. Наклон винтовой канавки – это наклон передней поверхности сверла в продольном направлении. В разных точках главной режущей кромки он неодинаков, чем ближе к оси сверла, тем меньше Ðw. Назначается конструктивно в зависимости от диаметра сверла в пределах от 15о до 60о
где ωх – угол наклона винтовой канавки в конкретной точке режущей кромки.
ω = 55-60о для шнековых сверл.
Ða1 – вспомогательный задний угол – измеряется в плоскости, нормальной к вспомогательной режущей кромке (кроме ленточки). a1=0,так как вспомогательная задняя поверхность очерчена поверхностью цилиндра. (рис.2.4, сечение N1 – N1)/
Ðl – угол наклона главной режущей кромки – это угол между режущей кромкой и радиусом, проведенным через точку режущей кромки.
Ðy – угол наклона перемычки (поперечного лезвия, поперечной режущей кромки) – это угол между проекциями поперечной и одной из главных режущих кромок на плоскость, перпендикулярную к оси сверла. Обычно Ðy = 50…55о . Угол резания d у перемычки больше 90о, а, следовательно, металл не режется, а скоблится.
Ðg – главный передний угол – это угол между касательной к передней поверхности сверла в рассматриваемой точке главной режущей кромки и нормалью к этой же точке к поверхности вращения, образованной при вращении режущего лезвия вокруг оси сверла. В каждой точке режущей кромки Ðg, является величиной переменной.
g = max на периферии сверла. В плоскости параллельной оси сверла (О-О) Ðw=Ðjgmax»25…30о
g = min у вершины сверла. На поперечной режущей кромке Ðg имеет отрицательное значение, что создает угол резания больше 90о , а, следовательно, и тяжелые условия резания.
Такое резкое уменьшение угла g вдоль всей длины режущей кромки является большим недостатком сверла, так как это вызывает более сложные условия образования стружки.
На периферии сверла, где наибольшая скорость и наибольшее тепловыделение, необходимо было бы иметь и большее тело зуба сверла. Большой угол Ðg уменьшает Ðb, это приводит к более быстрому нагреву этой части сверла, а, следовательно, и к наибольшему износу. На периферии сверла: tgg = tgw / sinj.
В любой точке режущей кромки: tggх = tgwх / sinj = Dx· tgw / D·sin j
Ða – главный задний угол – это угол между касательной к задней поверхности в рассматриваемой точке режущей кромки и плоскостью резания. В процессе резания истинное значение Ða уменьшается так как действительной траекторией точки, лежащей на главном режущем лезвии, будет не окружность, а винтовая линия с шагом равным величине подачи (рис3).
Рисунок 3 – Поверхности при сверлении
Поверхность резания представляет собой винтовую поверхность. Поэтому действительный задний угол aд определяется касательными к этой винтовой и задней поверхностям в рассматриваемой точке. С приближением к оси сверла aд уменьшается . чтобы обеспечить достаточную величину Ða в процессе резания у точек режущего лезвия, расположенных ближе к оси сверла, задняя его поверхность затачивается так, что на периферии Ða имеет min значение (Ða=8-14о), а по мере приближения к оси сверла он увеличивается (Ða=20-27о). Такая заточка сверл обеспечивается конструкцией и кинематикой заточных станков. Так как Ðg > Ða у периферии сверла, а у сердцевины наоборот Ða > Ðg, то Ðb остается для всех точек режущего лезвия более или менее постоянным.
f – ширина ленточки (фаски) –принимается в зависимости от размеров и конструкции сверла.
Фреза
Рисунок 5 – Геометрические параметры режущей части цилиндрической фрезы
Элементы зуба фрезы.
1 – передняя поверхность – поверхность по которой сходит стружка.
2 – главная задняя поверхность.
3 – вспомогательная задняя поверхность.
f – ширина главной задней поверхности.
4 – главная режущая кромка ( у цилиндрических фрез отсутствует).
5 – вспомогательные режущие кромки.
6 – вершины.
7 – канавка – выемка для отвода стружки, ограничивается передней поверхностью и спинкой другого зуба. Канавки бывают прямые и винтовые.
8 – спинка зуба – это поверхность, смежная с задней поверхностью одного зуба и передней поверхностью другого зуба.
Главная режущая кромка у цилиндрических фрез может быть прямолинейной (по образующей цилиндра), наклонной к образующей цилиндра и винтовой.
Ðg – главный передний угол – это угол между передней поверхностью и основной плоскостью, проходящей через ось фрезы и рассматриваемую точку режущей кромки.
Ða – главный задний угол – это угол между касательной к задней поверхности фрезы и плоскостью резания.
Ðw – угол наклона винтовой канавки – бывает только у цилиндрических косозубых фрез, он создает благоприятные условия врезания и равномерности фрезерования.
tт – окружной шаг фрезы в торцовой плоскости (длина дуги по торцу фрезы между двумя соседними зубьями).
Ход выполнения работы:
1. Выполнить эскиз сверла в проекциях с необходимыми сечениями, на которых показать буквами размеры и обозначить все углы сверла (см. рис.1, рис.2)
2. Измерить конструктивные параметры сверла и занести их в протокол (таблица 1).
3. Выполнить необходимые расчеты, записать формулы:
Ðj+Ðe+Ðj = 180о; Ðe = Ð2j; Ðj = (180-Ð2j) / 2;
tg j1 = ; .
Таблица 1 – Результаты измерения сверла
Наименование инструмента | Длина рабочей части, мм | Длина режущей части, мм | Длина шейки, мм | Длина хвостовика, мм | Длина лапки, мм | Длина сверла, мм | Диаметр сверла | Ширина ленточки, f, мм | Угол наклона винтовой канавки, ω, град | Угол наклона поперечной кромки, ψ, град | Угол между режущими кромками, 2φ, град | Шаг винтовой линии, Н, мм | Главный угол в плане, φ, град | Вспомогательный угол в плане, φ1, град | Передний угол, γ, град | |
У хвостовика, Д1, мм | У режущей части, Д, мм | |||||||||||||||
4. Выполнить эскиз фрезы в проекциях с необходимыми сечениями. На эскизе показать габаритные размеры и обозначить углы фрезы (рис. 5)
5. Измерить углы фрезы и записать их величину в таблицу 2 протокола.
Таблица 2 – Результаты измерения фрезы
Наименование инструмента | Материал режущей части | Размеры фрезы, мм | Число зубьев, Z | Угол наклона винтовой канавки, ω, град | Шаг винтовой канавки, Н, мм | Углы фрезы в торцовой плоскости, град | Окружной шаг фрезы, tт, град | Шаг зубьев фрезы в нормальной плоскости, tN, град | Осевой шаг зубьев фрезы, to, град | |||||
D | L | d | γт | α | βт | δт | ||||||||
6. Записать расчетные формулы, выполнить необходимые расчеты:
Окружной шаг фрезы в торцовой плоскости: ,
где D – диаметр фрезы; Z – число зубьв фрезы.
Шаг зубьев фрезы в нормальном сечении.
Осевой шаг зубьев фрезы:
Шаг винтовой канавки зуба фрезы:
7. Вывод по лабораторной работе.
Геометрический параметр – сверло – Большая Энциклопедия Нефти и Газа, статья, страница 1
Геометрический параметр – сверло
Cтраница 1
Геометрические параметры сверла определяют условия его работы. Передний угол у измеряют в главной секущей плоскости / / – / /, перпендикулярной к главной режущей кромке. Задний угол а измеряют в плоскости / – /, параллельной оси сверла. [1]
Геометрические параметры сверла рассматриваются на его режущей части. [2]
Геометрические параметры сверл аналогичны стандартным.
[4]
Геометрические параметры сверл несколько отличаются от обычных. [5]
Геометрические параметры сверл, заточенных по плоскости, взаимосвязаны; поперечная кромка прямолинейна и перпендикулярна к оси сверла. [7]
Геометрические параметры сверла определяют условия его работы. Передний угол у измеряют в главной секущей плоскости IJ-II, перпендикулярной к главной режущей кромке. Задний угол а измеряют в плоскости / – /, параллельной оси сверла. Передний и задний углы в различных точках главной режущей кромки различны. У наружной поверхности сверла угол у наибольший, а угол а наименьший; ближе к оси – наоборот. Угол при вершине сверла 2ф измеряют между главными режущими кромками; его значение различно в зависимости от обрабатываемого материала. Угол наклона поперечной режущей кромки ] i измеряют между проекциями главной и поперечной режущих кромок на плоскость, перпендикулярную к оси сверла. Угол наклона винтовой канавки в) измеряют по наружному диаметру. С увеличением угла со увеличивается передний угол у; при этом облегчается процесс резания и улучшается выход стружки. Рекомендуемые геометрические параметры сверла приведены в справочной литературе.
[8]
Геометрические параметры сверла определяют условия его работы. Передний угол у измеряют в главной секущей плоскости II-II, перпендикулярной главной режущей кромке. Задний угол а измеряют в плоскости I-I, параллельной оси сверла. Передний и задний углы в различных точках главной режущей кромки различны. У наружной поверхности сверла угол у наибольший, а угол а наименьший. [10]
Особенность геометрических параметров сверл заключается в том, что они влияют не только на шероховатость и качество обработанной поверхности, способность выводить стружку и противостоять изнашиванию, но и на диаметр полученного отверстия, т. е. на его точность.
[11]
Определение геометрических параметров сверла при I способе задания задней поверхности не встречает особых трудностей. Рассмотрим несколько примеров II способа расчета. [13]
В табл. 26 приведены рекомендуемые геометрические параметры сверл для сверления отдельных марок пластмасс различных групп обрабатываемости. [14]
Страницы: 1 2 3
Металлорежущий инструмент и инструментальная оснастка / Cutting tools and tooling system GUHRING |
Каталог GUHRING 2012 Общий Инструмент Оснастка (Всего 1669 стр. | ||||||||
1581 Каталог GUHRING 2012 Режущий инструмент и инструментальная оснастка Стр.1610 | ||||||||
Геометрические параметры сверла спирального с цилиндрическим или коническим хвостовиками Геометрия режущей части инструмента Углы при резании Геометрические параметры сверла спирального с цилиндрическим или коническим хвостовиками Геометрия режущей части инструмента Углы при резании _ Длина главной режущей кромкк Перемычка Угол перемычки Главная режущая кромка Поперечная кромка Сечение А-А Режущий клин мка Стружечная канавка Передняя по- Вспом. Ширина ленточки верхность кромка стружечной канавки Описание основных элементов Перо сверла (спинка + ленточка) Исполнение вспомогательной кромки стружечной канавки Выноска X з.. з. заостренная с фаской скругленная 1610 GUHRING Сверла Основные положения Стружечная Длина стружечной канавки Лапка DIN 18- (по DIN 1809) Корпус Ось Цилиндр. | ||||||||
См.также / See also : | ||||||||
Сверла Конструкция / Parts of a drill | ||||||||
Технология сверления металла / Drill a hole in metal | Обработка глубоких отверстий / Deep hole drilling | |||||||
Расчет режимов резания при сверлении / Formulas for drilling | Диаметр под резьбу / Tap drill sizes | |||||||
Перевод дюймов в мм / Inches to mm Conversion table | Оснастка для сверлильных и фрезерных станков / Tool holders for drilling and milling | |||||||
Каталог GUHRING 2012 Общий Инструмент Оснастка (Всего 1669 стр.![]() | ||||||||
| 1578 Хвостовики инструментов для металлообработки на современных станках Хвостовик HSK Обзор разных исполнений Формы A B C D E F ISO 12164-1 DIN 69893 | 1579 Перевод дюймов в миллиметры Таблица справочная конвертации от 1/64 дюйма до 11 63/64 дюйма В том числе и десятичные доли дюйма и общепринятые размеры | 1580 Немецкие марки стали Новые и станрые обозначения обрабатываемых материалов Выборочная переходная таблица Нержавейка Конструкционная и жаростойкая сталь | 1582 Формы заточки спиральных сверл по DIN 1412 A B C D E Наглядные иллюстрации Производственные допуски на сверлильный инструмент согласно DIN 286 Таблица | 1583 | 1584 | ||
Каталоги инструмента GUHRING | ||||||||
| ||||||||
Каталог GUHRING 2016 Металлорежущий инструмент Сверла (англ.яз. / ENG) (910 страниц) | Каталог GUHRING 2016 Режущий инструмент для обработки резьбы (англ. ![]() (878 страниц) | |||||||
Каталог GUHRING 2012 Общий Инструмент Оснастка (1669 страниц) | ||||||||
Каталог GUHRING 2012 Инструментальная оснастка (216 страниц) | Каталог GUHRING 2010 Металлорежущий резьбовой инструмент (492 страниц) | Каталог GUHRING 2009 Режущий инструмент и оснастка (1482 страницы) | ||||||
Каталоги инструмента и оснастки для металлообработки на станках / | ||||||||
— — |
Конструкция, геометрические параметры спиральных сверл и их заточка.
3. КОНСТРУКЦИЯ, ГЕОМЕТРИЧЕСКИЕ ПАРАМЕТРЫ СПИРАЛЬНЫХ СВЕРЛ И ИХ ЗАТОЧКА
Спиральное сверло (рис. 96) состоит из рабочей части, шейки и хвостовика.
На рабочей частисверла профрезерованы две спиральные (винтовые) канавки, образующие два рабочих зуба (пера). Рабочая часть включает в себя режущую и цилиндрическую (направляющую) части с двумя ленточками, обеспечивающими направление и центрирование сверла в отверстии.
ляется в коническом отверстии шпинделя или в переходной конической втулке.
Лапкау сверл с коническим хвостовиком не позволяет сверлу провертываться в шпинделе и служит упором при выбивании сверла из гнезда. Основные углы сверла показаны на рис. 97.
1. Передний угол уизмеряется в плоскости, перпендикулярной к главной режущей кромке (плоскость //—//). Он образуется касательной АМк передней поверхности в точке Л на режущей кромке и линией АК,перпендикулярной к поверхности резания в той же точке.
В различных точках режущей кромки передний угол имеет разные значения. Если у периферии сверла на наружном диаметре он имеет наибольшую величину (25—30°), то по мере приближения к вершине сверла уменьшается до величины, близкой к нулю.
2. Задний угол а измеряется в плоскости /—/, касательной к цилиндрической поверхности, ось которой совпадает с бсью сверла. Он образуется касательной к задней поверхности в рассматриваемой точке Л на режущей кромке и касательной в той же точке к поверхности резания. Задние углы у сверла различны для разных сечений по диаметру сверла. У периферии они меньше (6—8 ), а у перемычки достигают 30°.
3. Угол наклона поперечной кромки ф образуется между проекциями поперечной кромки (рис. 98) и главными режушшми кромками на плоскость, перпендикулярную к оси сверла.
В целях повышения стойкости сверл диаметром до 12 мм’и выше применяют двойную заточку сверл, при этом режущие кромки имеют форму ломаной линии (рис. 98). Основной угол 2ф = 116—118° (для сталей и чугунов), а на участке ? = = (0,18—0,22) Dмм затачивается второй угол при вершине сверла 2(ро — 70—75°.
Стойкость сверл с двойной заточкой примерно в 2 раза выше стойкости обычных сверл. Это значит, что скорость резания при работе сверлами с двойной заточкой может быть принята на 15% большей, чем рекомендуется в таблицах нормативов для обычных сверл.
4. Угол наклона винтовой канавки cd — угол, заключенный между направлением оси сверла и касательной к ленточке. Величина этого угла колеблется в пределах от 18 до 30°. Для сверл малых диаметров (от 0,25 до 3 мм) угол со = 18—25°, для сверл диаметром от 10 мм и выше со = 30°.
5. Угол при вершине сверла 2ср — угол, заключенный между режущими кромками.
Рис. 96. Спиральное сверло.
Режущая частьрасполагает двумя главными режущими кромками, образованными пересечением передних и задних поверхностей и выполняющими основную работу резания, а также поперечной кромкой (на перемычке сверла).
Рис. 97. Геометрия спирального сверла.
Шейка сверла— промежуточная часть, соединяющая рабочую часть сверла с хвостовиком.
Хвостовикслужит для закрепления сверла в шпинделе станка или патроне и для передачи крутящего момента от шпинделя. У сверла небольшого диаметра хвостовик имеет форму цилиндра и закрепляется в специальном патроне; у сверла большого диаметра — коническую форму и закреп-
Геометрии спиральных сверл | Железная лаборатория
При сверлении можно получить отверстия 4-5-го классов точности с шероховатостью поверхности v 3 — v 5. Сверло является более сложным инструментом, чем резец. Оно имеет пять лезвий: два главных ab и cd, два вспомогательных перемычки ас. Вспомогательные лезвия представляют собой винтовую кромку, идущую вдоль всей рабочей поверхности сверла. Передняя поверхность сверла винтовая. Задняя поверхность, в зависимости от способа заточки, может быть конической, винтовой, цилиндрической или плоской. В главной секущей плоскости сверло имеет форму резца с присущими ему геометрическими параметрами.
Геометрические параметры режущей части сверла.
Увеличение крутящегося момента особенно нежелательно для сверл малого диаметра. Величина угла 2ср зависит от свойств обрабатываемого материала. При обработке хрупких материалов выбирают меньшие значения этого угла, а при обработке вязких материалов — более высокие:
Угол наклона перемычки φ обычно принимается равным 55°, вспомогательный задний угол аг = 0°, угол резания лезвия перемычки больше 90°, в результате чего лезвие не режет, а скоблит.
Угол наклона главного лезвия для сверл определяют так же, как и для резцов. Его измеряют в плоскости резания между главным лезвием АС и нормалью к вектору скорости резания AN.
Определение угла сверла.
Таким образом, угол наклона главного лезвия заметно изменяется вдоль длины лезвия.
Задний угол обычно задается в цилиндрическом сечении, концентричном оси сверла, т. е. в плоскости Б-Б.
Задний угол также является переменным вдоль лезвия и изменяется примерно в пределах 20°. Причем, меньшие его значения будут на периферии сверла, а большие — у центра.
Таким образом, величины углов сверла у, а, со и X значительно изменяются на различных участках главного лезвия. В результате этого сверло работает в тяжелых условиях, что вызывает интенсивный его износ. Поэтому меры, направленные на улучшение геометрии и конструкции сверла, имеют большое практическое значение.
Величина переднего угла зависит от величины угла наклона винтовой канавки со, поэтому угол со является исходным параметром при изготовлении сверл. Силы резания, сход стружки, прочность и стойкость сверла также зависят от величины этого угла. С его увеличением уменьшается степень пластической деформации и трение на передней поверхности, так как увеличивается передний угол. С возрастанием угла со выше допустимого до определенного предела ухудшается сход стружки. В этом случае увеличивается путь движения стружки, она может упираться в противоположную стенку канавки, что увеличивает трение и температуру на передней поверхности. Кроме того, при больших значениях угла со величина угла заострения сравнительно небольшая, поэтому прочность и стойкость сверла снижаются. Угол со для быстродействующих сверл в зависимости от свойств обрабатываемого материала находится в пределах 10-40°.
Задний угол у периферии сверла принимается равным 8-14% а у вершины — 25-35° (большие значения задних углов имеют сверла малых размеров, а меньшие — сверла больших размеров). Передний угол, как указывалось, изменяется в обратном направлении: у вершины сверла он меньше, а на периферии — больше. Такой характер измерения углов у и а обеспечивает в некоторой мере равенство углов заострения различных точек лезвия сверла, что благоприятно влияет на его стойкость.
Углы заточки твердосплавных сверл образуются только по длине пластинки. За пластинкой идет винтовая канавка, угол наклона которой принимается равным 15-20°. При сверлении легких металлов угол увеличивается до 45°.
Передний угол для сверл, оснащенных твердым сплавом, принимается для стали и чугуна твердостью НВ 1960 МПа — 0-7°;
Величины статических углов сверла в процессе резания изменяются незначительно. Например, при D = 10 • 10~3 м и s = 0,2 х 10-3 м/об углы у и а на периферийной точке лезвия сверла изменяются всего лишь на несколько минут.
Силы резания и крутящий момент при сверлении.
загрузка…
материалов | Бесплатный полнотекстовый | Минимизация заусенцев при сверлении за счет изменения геометрии сверла
1. Введение
Быстрое развитие промышленности влечет за собой необходимость использования новых типов материалов и улучшения методов их обработки. Благодаря своим особым свойствам, титановые сплавы, особенно сплав Ti-6Al-4V, становятся все более популярными. Их наиболее важными характеристиками являются хорошая коррозионная стойкость, биосовместимость и отличное соотношение прочности и веса. Благодаря этим свойствам они используются, например, в авиационной, химической, автомобильной, военной и космической отраслях, а также в медицине (имплантологии) [1,2].С другой стороны, у таких материалов есть существенный недостаток – их обработка вызывает множество трудностей. Это связано с их очень хорошими механическими свойствами, низкой теплопроводностью и высокой химической реакционной способностью.



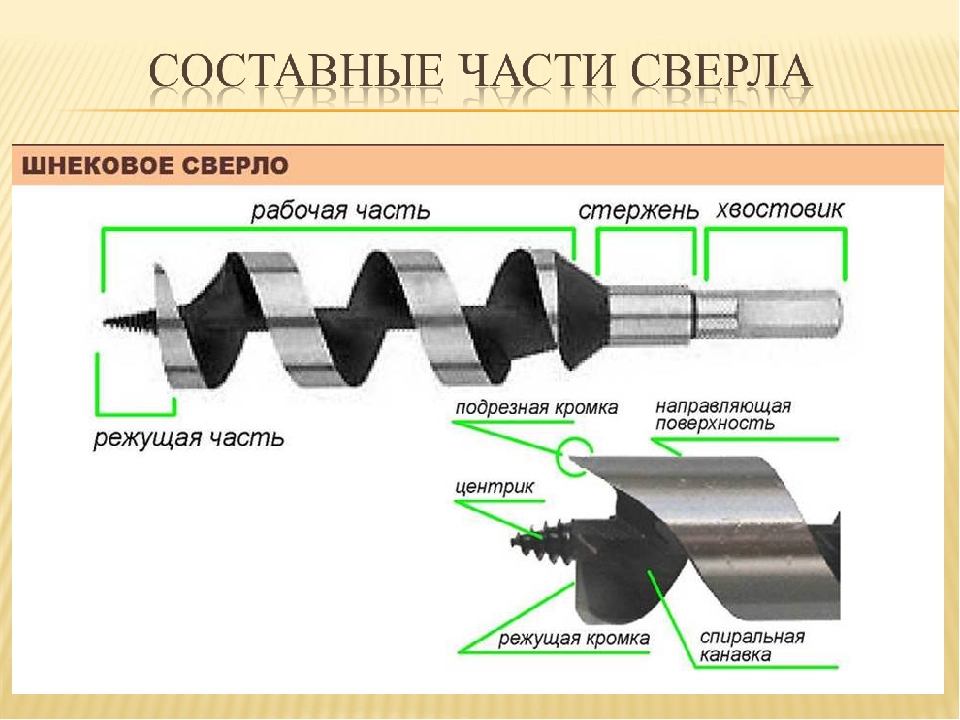



3. Результаты и анализ
Полученные результаты – высота заусенца h в зависимости от формы используемого инструмента (l 3 , κ 2 ) и подачи f – сведены в Таблицу 5 и представлены на Рисунке 8.Для обработки результатов использовался метод ANOVA. Дисперсионный анализ показан в Таблице 6, а зависимость высоты заусенца h от подачи f, длины l 3 и угла фаски κ 2 показана на Рисунке 9. Также были определены взаимодействия между тестируемыми факторами. Как видно на рисунке 10, влияние длины фаски l 3 и угла κ 2 на высоту заусенца наибольшее при высоких скоростях подачи.
h = 461 + 2269 · f2 + 88,7 · l32 + 0,427 · κ22−455 · f − 336 · l3−8,3 · κ2
(1)
Среди протестированных геометрий сверла оптимальным оказался вариант с длиной фаски l 3 = 2 мм и углом κ 2 = 10 °. В дальнейшей части работы сравнивали средние значения высоты заусенцев для заводского сверла и сверла, модифицированного описанным выше способом.Кроме того, значения осевой силы резания (F f ) для различных подач сравнивались между этими двумя геометриями сверла. Результаты этих измерений представлены в Таблице 7. Исследования показали, что изменение позволило значительно уменьшить размер заусенцев (Рисунок 11). Полученные результаты соответствуют моделям, представленным Rana et al. [12] и Mittal et al.
Видно, что чем выше подача, тем меньше относительный эффект. После применения модификации сверла для f = 0.20 мм / об высота заусенца была меньше на 10%, а при f = 0,08 мм / об – на 22%. Относительное изменение размера заусенцев в зависимости от подачи для крайних значений этого параметра (f = 0,08–0,20 мм / об) составило 9% для заводского сверла и 20% для модифицированного сверла.
Как видно на Рисунке 12, для всех значений скорости подачи сила резания была значительно ниже при сверлении модифицированным сверлом (приблизительно 22–23%). Данные, представленные на рисунках 11 и 12, доказывают, что с увеличением подачи увеличивается и сила резания, и высота заусенцев.Для обеих геометрий сверла можно отметить положительную корреляцию между осевым усилием сверления F f и высотой заусенца h (Рисунок 13). В каждом случае процесс сверления регистрировался с помощью высокоскоростной камеры. При использовании заводского сверла, независимо от используемой подачи, образовывались заглушки, которые впоследствии приходилось снимать с края отверстия механически.
4. Выводы
Новшеством, представленной в статье, является предложенный метод минимизации заусенцев путем изменения геометрии твердосплавного сверла, работающего в титановом сплаве. Внедренные модификации (длина фаски 2 мм, угол фаски 10 °) привели к относительно большому уменьшению размеров заусенцев и полному устранению явления образования шапки сверла. В зависимости от величины подачи высота заусенцев уменьшалась в диапазоне от 10 до 22%. Таким образом, отпала необходимость механического снятия колпачков и дополнительных операций по уменьшению размеров заусенцев.Изменение геометрии сверла, которое является технологически простым и недорогим решением, оказалось эффективным. Использование в промышленности за счет сокращения количества инструментов, операций и потребляемой энергии может иметь положительный эффект с точки зрения снижения затрат и воздействия на окружающую среду.
Исследования показали, что размер заусенцев зависит от величины подачи. Процесс сверления модифицированным сверлом кажется более чувствительным к изменению этого параметра. Для оригинального сверла было изменение высоты заусенца на 9% между крайними значениями испытанной подачи (0.08–0,20 мм / об). Для модифицированного сверла он составил 22% соответственно. Исходя из этих результатов, можно ожидать, что при более высоких кормлениях эффект будет уменьшаться и даже может стать отрицательным. Затем можно дополнительно оптимизировать форму сверла, чтобы увеличить эффект минимизации размера заусенцев. Желательным решением является получение максимально возможного эффекта при относительно высоких скоростях подачи, чтобы обеспечить, помимо удовлетворительного качества кромки отверстия, высокую эффективность обработки.
Сила резания уменьшилась при использовании модифицированного сверла (22–23% в зависимости от величины подачи), что может положительно сказаться на стойкости инструмента. Наличие корреляции между силой резания и размером заусенцев позволяет путем измерения этой силы в процессе сверления оценить размер заусенцев в реальном времени. После надлежащей проверки, состоящей в определении взаимосвязи между высотой заусенца и силой резания для данного материала, инструмента и параметров резания, такое решение может стать обычным методом управления производственным процессом.
На следующем этапе работы также желательно построить кривые износа для обоих инструментов.Сравнение их ресурса позволит оценить производственный потенциал модифицированного бура. Учитывая, что силы резания уменьшились после модификации сверла, можно надеяться, что срок его службы будет удовлетворительным или даже лучше, чем у исходного сверла.
Ограничением для эксперимента были тип используемого инструмента и материала. Дальнейший ход этого исследования должен включать изучение влияния предлагаемой модификации на другие типы сверл (геометрия, материал, покрытие), чтобы сделать более общие выводы о влиянии, которое дает применение фаски. Аналогичные испытания следует проводить и для других труднообрабатываемых материалов, чтобы проверить влияние твердости, адгезии и т. Д. На явление образования заусенцев и эффективность операции снятия фаски. Информация, полученная в результате таких экспериментов, на практике позволит более широкий выбор материала в зависимости от области применения и допустимого размера заусенцев.
Огромный скачок вперед в сверлении стали
Новая инновационная концепция режущего инструмента повышает производительность сверления в стали.
Надежный и эффективный процесс обработки отверстий имеет жизненно важное значение в современной механической обработке. Когда речь идет о большом количестве отверстий, производительность является важным фактором конкурентоспособного производства. Современное высокопроизводительное сверло должно обеспечивать сочетание высокой скорости проходки, предсказуемой стойкости инструмента и давать стабильные результаты. Преданность делу – это превыше всего умения свести к минимуму общие затраты на просверливание отверстия.
ЧТО НУЖНО, ЧТОБЫ ДРЕЛЬ БЫЛА ДЕЙСТВИТЕЛЬНО ЭФФЕКТИВНОЙ СЕГОДНЯ?
Особое внимание уделяется материалу заготовки, более высокой скорости резания и скорости проплавления.Важнейшие свойства включают постоянное выполнение отверстий в узком диапазоне допусков, характерных для большого количества типов отверстий, и поддержание безопасности обработки на протяжении длительного срока службы инструмента. Также важно: возможность легко работать с самого начала с возможностью оптимизации.
Сверло с такими возможностями откроет новые возможности для повышения уровня производительности, особенно на современных машинах с высокими техническими характеристиками. Однако сверло должно также обладать универсальностью, чтобы дать любому станку (с допустимой скоростью вращения шпинделя) возможность использовать потенциал более высокой скорости резания.
Универсальное сверло недостаточно конкурентоспособно, чтобы полностью оптимизировать производство множества отверстий одинакового диаметра. Современные производственные требования требуют современной концепции сверления, специально разработанной для решения этой конкретной задачи: от режущей кромки до конструкции канавок. Хотя спиральное сверло может показаться простым решением, оно не сравнится по характеристикам с недавно разработанными твердосплавными сверлами.
КАКАЯ ОБЛАСТЬ ПРИМЕНЕНИЯ ВОПРОСЫ?
Область просверливания отверстий в стали, подходящая для улучшения с помощью стандартного твердосплавного сверла, – это диапазон диаметров 0.От 118 до 0,787 дюйма, глубина сверления в 3-8 раз больше диаметра. Многие отверстия в этом диапазоне имеют допуски отверстий IT 8-9, шероховатость поверхности Ra 0,8-1,8 микрон (в зависимости от материала и области применения), пределы прямолинейности 0,003-0,005 дюйма на просверленное 3,937 дюйма и требования к минимальному проникновению. и выход-заусенец.
В дополнение к прямым отверстиям на плоской горизонтальной поверхности входа / выхода сверло не должно иметь ограничений при работе с большинством конфигураций отверстий, таких как наклонные поверхности входа / выхода, выпуклые или вогнутые поверхности, отверстия, требующие фаски, и отверстия с поперечным проходом . Преданность материалам в области ISO-P требует универсальности для эффективной обработки всех типов сталей, от низкоуглеродистых, нелегированных, высокоуглеродистых и высоколегированных сталей до стальных отливок с твердостью от 125 до 350 HB.
Более высокая скорость проходки и большая длина пробуренных отверстий обеспечивают реальные преимущества при серийном производстве компонентов во многих отраслях промышленности. Устанавливается новый ориентир: повышение производительности на 100+ процентов. Механические цеха могут использовать новые твердосплавные сверла с более высокими показателями проникновения и повышенной долговечностью, чтобы устранить узкие места в производстве, вызванные устаревшими возможностями сверления.
Даже если узкое место не очевидно, новое высокопроизводительное сверло поможет сократить общее время обработки компонентов, упростит проблемы с настройкой, устранит множественные остановки для смены инструмента и приведет к низкому контролю или ранее невозможной обработке без участия человека. Экономия инструмента может быть улучшена за счет ремонта оборудования. В различных производственных условиях эффективность сверла, более высокая скорость и меньшие силы резания позволяют максимально использовать машину.
Доброжелательный характер инструмента помогает уменьшить количество неэффективных или неудовлетворительных применений в пределах его основной области применения, даже если они используются немного неправильно.Однако это сверло было разработано для более высоких скоростей резания – чтобы быть самым быстрым и надежным сверлом для стали. Он не предназначен для работы на низких скоростях резания, где низкая производительность может привести к другим проблемам.
ЧТО ТАКОЕ УНИКАЛЬНАЯ НОВАЯ КОНЦЕПЦИЯ ДРЕЛЯ?
CoroDrill 860 – результат передовых и обширных исследований и разработок. Успех уникальной концепции обусловлен новым прогрессом в разработке инструментов, процессах производства инструментов, взаимодействии между дисциплинами разработки и реальных производственных приложениях.
В начале разработки, сверление низкоуглеродистой и низколегированной стали было использовано для создания основы для этой совершенно новой геометрии сверла, предназначенной для области применения ISO-P. После первоначальных опытно-конструкторских работ, полевых испытаний и взаимодействия с различными производственными компаниями была проведена цепочка оптимизаций различных геометрических параметров и канавок сверла. По мере продолжения работы в процессы разработки вводились легированная сталь, углеродистая сталь, стальные отливки и высоколегированные стали с повышенной твердостью и другими требованиями к структуре материала.
Во время и после этого обмена между опытно-конструкторскими работами и испытаниями отверстий в многочисленных механических цехах были установлены значения параметров звукового резания для реалистичных рекомендаций по повышению производительности инструмента. При установлении параметров сверления и уровней данных резания также была сформирована основа для разработки размера программы диаметров сверл, длин и возможностей отверстий, а также указаний на предсказуемые результаты.
ЧЕМ НОВАЯ СВЕРЛА ОТЛИЧАЕТСЯ ОТ СУЩЕСТВУЮЩИХ КОНЦЕПЦИЙ?
Геометрия острия сверла уникальна благодаря новому инновационному дизайну, обеспечивающему заметно более эффективное и плавное резание. Меньшие силы резания способствуют увеличению срока службы инструмента. Это за счет увеличения контролируемого развития износа, а не более разрушительного и быстрого износа. Идеальное стружкообразование также было основной целью, где расширенное моделирование стружкообразования было лишь одним из средств, используемых для определения геометрии острия.Совершенно новая режущая кромка является результатом разработок и обширных испытаний, в ходе которых разработки как макро-, так и микрогеометрии внесли свой вклад в создание новой вершины сверла.
Новый дизайн угловых кромок был разработан для обеспечения высокой безопасности, что привело к устранению тенденции к скалыванию кромок. Микрогеометрия претерпела значительные изменения, где, например, форма и размер закругления кромок и даже процесс на режущих кромках являются совершенно новыми разработками.Более контролируемое закругление кромок способствует минимизации сил резания и снижению тепловыделения на кромке и, следовательно, степени износа инструмента.
В дополнение к улучшенному режущему эффекту, покрытие для закругления кромок было оптимизировано для улучшения сцепления с материалом. Подложка твердосплавного сверла также была разработана для обеспечения надлежащей ударной вязкости для сверл различного диаметра и надежного обеспечения более высоких скоростей резания стали.
В дополнение к уникальной геометрии острия сверла были полностью переработаны буровые канавки.Запатентованная последовательность канавок играет жизненно важную роль в эвакуации стружки. Эффективное и беспроблемное удаление стружки из материалов с короткой и длинной стружкой достигается для обеспечения требуемой безопасности при более высоких скоростях обработки, которые встречаются по всей области стали.
Процессы нанесения покрытия и постобработки для производства сверл были разработаны с использованием новой технологии, способствующей повышению их производительности и результатов. Оптимальная форма, текстура поверхности и блеск канавок в сочетании с увеличивающимся размером более длинных сверл обеспечивают значительно улучшенный отвод стружки из зоны обработки и самого сверла.
Новые инновации такого масштаба в буровой технике встречаются нечасто. Эта новая концепция является результатом нового подхода, обширных исследований и разработок, а также сотрудничества в производстве, что привело к огромному прогрессу в технологии изготовления отверстий. Доказано, что это новое поколение твердосплавных сверл. Это сверло для обработки стали, где в производстве установлены высокие стандарты конкурентоспособности и где приоритетным параметром обработки является более низкая стоимость отверстия.
Исследование влияния параметров и коэффициента гибкости стружки на качество процесса сверления стали AISI 1050
Отношение гибкости стружки является важным параметром в теоретических и применимых операциях обработки. В операциях предварительного сверления стального сплава AISI 1050 использовались сверла из быстрорежущей стали, а также влияние выбранных параметров на коэффициент гибкости стружки, а также влияние коэффициента гибкости стружки на осевое усилие, шероховатость поверхности, расслоение просверленных отверстий, износ инструмента. , и морфология чипа.Основными параметрами, влияющими на коэффициент гибкости стружки, были скорость подачи и угол при вершине, в то время как скорость шпинделя была слишком мала, чтобы ею можно было пренебречь. С увеличением степени гибкости стружки сила осевого напора и износ инструмента уменьшались, что приводило к соответствующей морфологии стружки, но при этом увеличивалась шероховатость поверхности. Однако коэффициент гибкости стружки не повлиял на расслоение просверленного отверстия.
1. Введение
Процесс сверления – это метод резки металла, при котором обрабатываются металлические детали требуемой геометрии и размеров в производственной зоне [1]. Этот метод производства занимает важное место, поскольку он используется около 33% среди традиционных методов производства [2]. В процессе бурения исследователи провели множество работ после завершения сложных операций и производственных процессов, чтобы получить требуемую высочайшую чувствительность и лучшее качество [3]. Многие параметры, такие как угол при вершине сверла, материал, используемый для бурения, и свойства бурового оборудования влияют на процесс бурения. Оснащение инструмента влияет на размер просверленного отверстия, износ инструмента, качество поверхности и длину стружки и, следовательно, на морфологию стружки [4].При увеличении скорости подачи качество поверхности изменяется обратно пропорционально, иными словами, увеличивается шероховатость поверхности. Поскольку сила тяги и износ инструмента уменьшаются при высоких скоростях шпинделя и углах вершины сверла, значения шероховатости поверхности уменьшаются; таким образом улучшается качество поверхности. Однако температура процесса и расслоение просверленного отверстия увеличиваются при высоких скоростях шпинделя и углах острия сверла [5].
Размер расслоения пробуренной скважины зависит от силы тяги и скорости подачи в процессе бурения [6, 7].Кроме того, сила тяги увеличивает расслоение просверленного отверстия и износ инструмента [8]. По мере увеличения количества просверленных отверстий увеличивается и степень износа инструмента [9]. Поскольку высота стружки и сила тяги увеличиваются из-за увеличения скорости подачи, высота стружки и сила тяги уменьшаются с увеличением скорости шпинделя [10, 11].
Кроме того, скорость подачи является важным параметром, влияющим на качество процесса и шероховатость поверхности, больше, чем скорость шпинделя в процессе сверления [12–20].При достаточном увеличении силы тяги в процессе сверления толщина стенки сверла и угол спуска увеличиваются; в противном случае уменьшаются угол острия сверла и винтовой угол [21, 22]. Однако с увеличением скорости подачи и угла при вершине сила тяги и шероховатость поверхности увеличиваются [23]. В процессе сверления вибрация, износ инструмента и условия сухого процесса вызывают изменения диаметра просверленного отверстия [24]. При низких скоростях резания и подаче, благодаря наличию требуемой морфологии стружки, достигаются лучшие характеристики в процессах сверления.Кроме того, угол при вершине инструмента не оказывает существенного влияния на температуру процесса [25]. В процессе обработки получается прерывистая стружка короткой формы из-за прерывистой пластической деформации при низких оборотах шпинделя. При увеличении угла острия сверла и скорости шпинделя сила тяги, возникающая в результате приложения давления на материал заготовки острием сверла, уменьшается. Толщина стружки значительно меняется по всей режущей кромке в течение цикла сверла [26].При увеличении условий резания морфология структуры стружки меняется от пластичной к хрупкой. С увеличением скорости подачи увеличивается высота стружки, а также увеличивается сила тяги, расслоение просверленного отверстия, шероховатость поверхности и износ инструмента [11]. Коническая режущая кромка, начинающаяся от острия сверла, вызывает изменения силы резания по всей режущей кромке сверла [27].
Поскольку коническая геометрия формируется углом при вершине сверла, основная особенность процесса сверления показывает отличия по всей режущей кромке.В то время как скорость подачи достигает максимального отношения на крайнем диаметре сверла, она приближается к нулевому значению по направлению к острой оси сверла, где она составляет сердцевину сверла из-за уменьшения диаметра [28].
Отношение гибкости стружки – это отношение глубины резания к скорости подачи, которое является важным параметром, влияющим на результаты обработки. Поэтому исследование коэффициента гибкости чипа является основным явлением. Кроме того, целью данного исследования является изучение влияния коэффициента гибкости стружки на процесс предварительного сверления.В литературе он определяется как отношение глубины резания к скорости подачи, что является важным параметром при операциях механической обработки. В процессах сверления из-за того, что глубина стружки зависит от диаметра просверленного отверстия и острия сверла, коэффициент гибкости стружки рассчитывался как отношение квадрата скорости подачи к площади контакта стружки инструмента. Учитывая геометрию острия сверла, площадь стружки была рассчитана математически в зависимости от угла острия сверла.Площадь стружки рассчитывалась путем пересечения этих двух измеренных геометрических размеров. В ходе исследования исследовалось влияние угла острия сверла, скорости шпинделя и скорости подачи на коэффициент гибкости стружки. Кроме того, с помощью рассчитанной площади стружки из этого исследования были рассчитаны теоретические коэффициенты гибкости стружки.
2. Процедура эксперимента
Эксперименты проводились на вертикальном фрезерном станке с ЧПУ Mazak с ЧПУ, который является моделью NEXUS 510 C-II, как показано на рисунке 1.Образцы из легированной стали AISI 1050 были приготовлены с размерами 100 × 100 × 15 мм 3 . Перед экспериментом образцы предварительно просверливали диаметром 5 мм. Расстояние между центрами просверленных отверстий на образцах составляло 20 мм. Химические компоненты и механические характеристики легированной стали AISI 1050 показаны в таблице 1. Во время процесса сверления сила тяги измерялась динамометром Kistler 5233A в единицах Ньютона.
С помощью глубинного микрометра расслоение просверленного отверстия было измерено как µ м в 4 различных точках, что составляет 5 мм в глубину, и было принято во внимание среднее арифметическое этих значений. В ходе экспериментального исследования было выбрано 4 различных значения угла при вершине сверла: 100 °, 118 °, 136 ° и 154 °. Острия сверла шлифовали под выбранными углами при вершине с помощью шлифовального станка, как показано на Рисунке 2 (а). Фотографии шлифованных точек сверла также можно увидеть на Рисунке 2 (б).Геометрические свойства вершин сверла из быстрорежущей стали показаны в таблице 2.
3.![]() 3.1. Геометрия анализа стружкиДлина режущей кромки формируется в зависимости от угла вершины сверла во время процесса сверления. Следовательно, геометрия сверла жизненно важна для процессов сверления из-за изменения скорости резания и различий по всей режущей кромке. Скорость резания достигает максимального отношения на крайнем диаметре сверла, и она уменьшается и приближается к нулю по направлению к оси сверла, где сверло составляет керн [28].Угол вершины сверла имеет важное влияние на длину режущей кромки в процессе сверления. Геометрия острия сверла показана на рисунке 3. На этом рисунке Ø d o – это диаметр предварительно просверленного отверстия в образце заготовки перед экспериментальными процессами. Эффективные силы на 1-й и 2-й режущих кромках сверла были показаны соответственно как F t1 и F t2 тангенциальные силы, F z1 и F z2 силы тяги, и F y1 и F y2 радиальные силы в направлении вращения. В этом экспериментальном исследовании, чтобы исключить влияние керна сверла, были предварительно просверлены отверстия диаметром 5 мм.Размеры режущих кромок сверл, используемых в экспериментальных процессах сверления, в которых излишки не были предварительно просверлены, рассчитываются, как показано в (1), в зависимости от геометрии наконечника сверла, как показано на рисунке 4. в зависимости от диаметра предварительного сверления и угла при вершине сверла: Высота необрезанной стружки () может быть рассчитана на основе скорости подачи () и угла при вершине () с помощью (2) в соответствии с геометрией острия сверла, как показано на рисунке 4. В этом экспериментальном исследовании, поскольку излишки были предварительно просверлены диаметром 5 мм , влиятельные значения ширины и высоты стружки были показаны с помощью и, соответственно. В этих условиях эффективная площадь стружки () и ширина стружки (), в зависимости от высоты стружки (), могут быть рассчитаны в соответствии со следующим уравнением: В этом экспериментальном исследовании были выбраны 4 различных угла острия сверла. . Они были представлены символами Φ 1 , Φ 2 , Φ 3 и Φ 4 , и они были выбраны как 100 °, 118 °, 136 ° и 154 ° соответственно. В соответствии с геометрией острия сверла, длиной режущей кромки без предварительного просверленного отверстия () и длиной режущей кромки с предварительно просверленным отверстием (), другими словами, значениями ширины неразрезанной стружки () и (), показали различия в зависимости от изменения угла при вершине сверла. При расчете коэффициента гибкости стружки значения ширины стружки (), высоты стружки () и площади стружки () учитывались в операциях предварительного сверления в зависимости от углов вершины сверла с использованием (1) – ( 4). 3.2. Анализ коэффициента гибкости стружкиКоэффициент гибкости стружки является важным параметром, когда учитывается скорость подачи глубины резания в расширенном законе скорости резания. Это соотношение называется «фактором гибкости стружки» или «морфологией стружки».Для одной и той же площади контакта стружки коэффициент гибкости стружки высокий при выбранной большей глубине стружки, тогда как он низкий при меньшей выбранной глубине резания стружки. Производители исследуют влияние глубины резания и скорости подачи на коэффициент гибкости стружки одновременно в реальных применимых операциях обработки. Оптимальный коэффициент гибкости стружки составляет 5: 1 согласно результатам, приведенным в литературе. Однако это значение (5: 1) недействительно для токарных операций, потому что выбранные скорости подачи больше, чем выбранные глубины резания. Как видно из следующего уравнения, коэффициент гибкости стружки () можно определить как отношение глубины резания () к скорости подачи ( ): При рассмотрении общего решения (5) и (6) коэффициент гибкости стружки () можно рассчитать как отношение площади контакта стружки () к квадрату скорости подачи (): 4.Результаты и обсуждение4.1. Влияние выбранных параметров на коэффициент гибкости стружки Коэффициент гибкости стружки – это рабочий параметр, принятый исследователями, работающими в области механической обработки. Этот параметр демонстрируется как отношение выбранной глубины стружки () к скорости подачи () [30]. Подача – важный результат в производственной операции механической обработки, и это самый важный параметр, определяющий качество операции. В этом исследовании площади микросхем были исследованы как расчетные (теоретические) площади микросхем. Расчетные (теоретические) площади стружки были рассчитаны с использованием (2) – (4) и в зависимости от геометрии острия сверла, как показано на Рисунке 3. Было исследовано, что влияние параметров следует рассчитывать по коэффициентам гибкости стружки в Рис. Влияние скорости вращения шпинделя на теоретический коэффициент гибкости стружки должно быть нулевым в соответствии с (6) и (7). При этом делается вывод, что геометрические и математические уравнения, обеспечивающие доверительные результаты, теоретически зависят от выбранных параметров.Наибольшее значение теоретического коэффициента гибкости чипа составило 84, а наименьшее – 7,72. 4.2. Влияние коэффициента гибкости стружки на осевую силуВо время буровых работ осевая сила является одним из важных факторов, определяющих качество процесса и предоставляющих информацию о результатах. Если во время работы сила тяги мала, это означает, что качество работы высокое. На Рисунке 5 видно, что сила тяги уменьшалась, когда коэффициент гибкости стружки увеличивался.С другой стороны, также было замечено, что коэффициент гибкости стружки уменьшался параллельно с силой осевого давления, когда угол острия сверла увеличивался для теоретического коэффициента гибкости стружки. Однако с увеличением теоретического коэффициента гибкости стружки наблюдалось уменьшение осевой силы. Как показано на рисунке 5, самые низкие значения осевой силы были получены как 274,70 и 292,09 Н при теоретическом коэффициенте гибкости стружки 84. Однако скорость шпинделя не влияла на теоретический коэффициент гибкости стружки в зависимости от геометрии сверла. 4.3. Влияние коэффициента гибкости стружки на шероховатость поверхностиПоскольку коэффициент гибкости стружки напрямую зависит от скорости подачи, наиболее эффективного параметра шероховатости поверхности, таким образом, коэффициент гибкости стружки является наиболее влиятельным параметром шероховатости поверхности. Согласно графику на рисунке 6, когда коэффициент гибкости стружки увеличивался, значения шероховатости поверхности также увеличивались, но качество поверхности снижалось. При максимальном (60–80) и самом низком (7–20) значениях коэффициента гибкости стружки максимальное и минимальное значения шероховатости поверхности составили 4,50 µ м и 1,6 µ м, соответственно, как показано на рисунке 6. 4.4. Влияние коэффициента гибкости стружки на расслоение просверленных отверстий В связи с тем, что расслоение просверленных отверстий в операциях сверления в основном зависит от движений инструмента и взаимодействия между инструментом и заготовкой, стружка не сильно влияет на него. 4.5. Влияние расчетного коэффициента гибкости стружки на морфологию стружкиПри сверлении морфология является наиболее важным маркером, влияющим на качество операции.В этом исследовании было продемонстрировано влияние коэффициента гибкости стружки на морфологию стружки, как показано на рисунках 8 (a) –8 (c), для выбора скорости подачи 0,025, 0,050 и 0,075 мм / об соответственно. Как показано на Рисунке 8 (а), при скорости подачи 0,025 мм / об с увеличением угла острия сверла морфология стружки изменилась с хрупкой и короткой формы на сплошную. При получении требуемой пластичной формы, длинной и непрерывной морфологии стружки с увеличением угла при вершине, при скорости подачи 0,025 мм / об при механической обработке износ инструмента также снизился. Кроме того, с увеличением угла острия сверла уменьшалась гибкость стружки. Сплошная, длинная и пластичная морфология стружки с уменьшающимся коэффициентом гибкости стружки была получена при выбранных углах острия сверла 136 ° и 154 °.Как показано на Рисунке 8 (b), уменьшение степени гибкости стружки при скорости подачи 0,050 мм / об было получено только при угле острия сверла 154 °. Но морфология сплошной, длинной и вязкой стружки была получена и с другими углами острия сверла. На рисунке 8 (c), хотя коэффициент гибкости стружки увеличился при скорости подачи 0,075 мм / об и скорости шпинделя 800 об / мин, значение этого отношения уменьшилось из-за увеличения скорости шпинделя. Здесь наблюдались положительные эффекты, когда скорость подачи и скорость шпинделя одновременно менялись друг с другом. 4.6. Влияние расчетного коэффициента гибкости стружки на износ инструментаИзнос инструмента является важным показателем стойкости инструмента при обработке.Меньший износ инструмента увеличивает срок его службы. Влияние угла при вершине сверла, скорости шпинделя и скорости подачи на износ инструмента показано на Рисунке 9 для операций предварительного сверления. При скорости подачи 0,025 мм / об с увеличением угла острия сверла расчетный коэффициент гибкости стружки линейно уменьшался. Кроме того, величина износа инструмента уменьшилась, как показано на Рисунке 9 (а). При скорости подачи 0,050 мм / об износ инструмента увеличивался при более высоких скоростях шпинделя, таких как 1200 и 1600 об / мин, но при меньших углах вершины сверла он уменьшался до 100 ° и 118 °. При увеличении скорости подачи до 0,075 мм / об износ инструмента увеличивался только при более низкой скорости шпинделя и угле при вершине 100 °; с увеличением угла при вершине степень износа режущей кромки инструмента увеличивалась при частоте вращения шпинделя 1600 об / мин. 5. Выводы В операциях предварительного сверления стального сплава AISI 1050 использовались сверла из быстрорежущей стали, и влияние выбранных параметров на коэффициент гибкости стружки, а также влияние коэффициента гибкости стружки на осевое усилие, поверхность были исследованы шероховатость, расслоение просверленного отверстия, износ инструмента и морфология стружки. Основными параметрами, влияющими на коэффициент гибкости стружки, были скорость подачи и угол вершины сверла, но влияние скорости шпинделя было слишком маленьким, чтобы им можно было пренебречь; с уменьшением степени гибкости стружки уменьшались осевая сила и износ инструмента, а также морфология удаляемой стружки изменялась с более короткой, хрупкой и зазубренной на сплошную, пластичную и без зазубрин.Кроме того, с увеличением расчетного коэффициента гибкости стружки побочно увеличивалась шероховатость поверхности. Однако коэффициент гибкости стружки не имел какого-либо важного влияния на расслоение отверстий, которое следовало бы принимать во внимание. Кроме того, с изменением угла при вершине от 100 ° до 154 ° коэффициент гибкости стружки уменьшился с 84 до 7, степень износа инструмента уменьшилась, а морфология удаленной стружки изменилась с хрупкой, более короткой и зубчатой формы, что нежелательно. от формы стружки до непрерывной, более длинной пластичной и без зубчатой формы, наиболее желаемой формы стружки при обработке. Доступность данныхДанные, использованные для подтверждения результатов этого исследования, включены в статью. Конфликт интересовАвторы заявляют об отсутствии конфликта интересов. Износ сверл при измерении сопротивления сверлению древесины Лесная служба США Министерство сельского хозяйства США
Показать больше Меньше https://www.fs.usda.gov/treesearch/pubs/56759 Исследование влияния геометрических параметров спирального сверла на производительность сверления нержавеющей стали[1] ИКС.Ф. Чжоу, Ф. Фанг, J.Q. Цзян. Инструментальная инженерия Vol. 42 (2008), стр.29 (на китайском языке). [2] X.B. Ван, Х. Лэй. Инструментальная инженерия Vol.33 (1999), стр.11 (на китайском языке). [3] Л.С. Сюн, Х. Ши, Ю. Чен. Инструментальная инженерия, Vol. 39 (2005), стр.11 (на китайском языке). [4] H.C. Чьян К.Ф. Эманн. Jour. Англ. Manuf. Vol. 216 (2002), стр.61. [5] Ю.Ф. Цай. Диаграмма обычного спирального сверла и сверла Ni Fu-zhi, Machinery Industry Press, Пекин (2008), в печати. [6] Ю.М. Лу, W.Y. Чен. Китай Машиностроение Vol. 11 (2000), стр.292 (на китайском языке). [7] Ю.Д. Чен, Х. Цзян. Машинный дизайн Vol.17 (2000), стр.25 (на китайском языке). [8] П. Чжан. Инженер-механик Том. 12 (2007), с.147 (на китайском языке). [9] ГРАММ.Л. Ма, Q.X. Цао. Журнал Хэнаньского машиностроительного и электротехнического колледжа, том. 10 (2002), стр. 39 (на китайском языке). Зависимость удельной механической энергии от глубины резания при резке и бурении горных пород (Журнальная статья) Экспериментальное исследование механизмов и стратегий сверления гибридных штабелей углепластика / титана% PDF-1.4 % 1 0 объект > эндобдж 11 0 объект /Заголовок /Предмет / Автор /Режиссер / Ключевые слова / CreationDate (D: 20210222144418-00’00 ‘) / CrossMarkDomains # 5B1 # 5D (sciencedirect.com) / CrossMarkDomains # 5B2 # 5D (elsevier.com) / CrossmarkDomainExclusive (истина) / CrossmarkMajorVersionDate (23 апреля 2010 г.) / ElsevierWebPDFS Технические характеристики (6.5) / ModDate (D: 20191218120656 + 01’00 ‘) / В ловушке / Ложь / doi (10.1016 / j.compstruct.2016.07.025) / роботы (noindex) >> эндобдж 2 0 obj > эндобдж 3 0 obj > эндобдж 4 0 объект > эндобдж 5 0 obj > эндобдж 6 0 obj > эндобдж 7 0 объект > эндобдж 8 0 объект > транслировать приложение / pdfdoi: 10.1016 / j.compstruct.2016.07.025 |