Приступаем к сборке двух осевого ЧПУ станка своими руками.
Сегодня начну цикл статей по сборке двухосевого ЧПУ станка на базе микроконтроллера Arduino своими руками. В данном пособии по сборке двухосевого ЧПУ станка, я расскажу о своём опыте и планах. На живом примере рассмотрим все основные этапы сборки станка от выбора типа будущего ЧПУ до подбора электроники. Таже рассмотрим программную часть от выбора и настройки прошивки до установки и настройки управляющей программы.
Если вы считаете данную тему полезной, пожалуйста, поделитесь данной информацией с другими, чтобы она могла охватить больше людей, которым это может быть интересно.
Почему именно двухосевой ЧПУ станок?
У вас, наверное, возник вопрос, почему я решил сделать цикл статьей именно про двухосевой ЧПУ станок? Дело в том, что данный тип станка самый простой, и стоит он гораздо дешевле, чем небольшой настольный фрезерный станок с ЧПУ.
И для начинающего ЧПУшника я бы рекомендовал начинать знакомство с ЧПУ станками именно с двухосевого. Но, несмотря на это, большая часть полученной информации в данном цикле статьей будет применима и для 3-х осевых станков. Поэтому информация, на мой взгляд, будет полезна как начинающим, так и тем, кто уже начал осваивать данную тему.
Немного о моём опыте по работе с ЧПУ станками.
Разрабатываю и собираю ЧПУ станки на базе Arduino и ESP32 с 2016 года. За это время собрал несколько десятков ЧПУ станков различного назначения, кинематики и размеров. Постоянно провожу консультации по настройке ЧПУ станков. Если у вас есть сложность с настройкой вашего ЧПУ станка, вы можете заказать консультацию у меня на моём сайте.
Насколько примеров моих самодельных ЧПУ станков:
- Самодельный ЧПУ плоттер на Arduino: 4xiDraw;
- ЧПУ плоттер в виде принтера на Arduino своими руками;
- ЧПУ станок для раскраски пасхальных яиц на Arduino.
Своими руками;
- Самодельный ЧПУ фрезерный станок на Arduino с дисплеем;
- Самодельный CNC станок из мебельных направляющих на базе Arduino UNO;
- ЧПУ плоттер на Arduino своими руками;
- Самодельный лазерный гравёр с ЧПУ, в домашних условиях.
И это еще не всё. Больше проектов вы можете посмотреть на сайте. Также есть проекты, которые находятся в стадии разработки или ещё не опубликованы на сайте.
Принимайте участие в корректировке плана публикаций.
У меня есть определённый план статей для данного цикла по сборке двухосевого ЧПУ станка на Arduino, по которому буду постоянно выкладывать новые материалы. Несмотря на это, я жду от вас обратной связи, а именно: что вам интересно, с какими сложностями вы сталкивались. На основе ваших ответов я буду дополнять и корректировать план публикаций.
На сегодня всё. В следующей статье рассмотрим, какие двухосевые ЧПУ станки бывают, а также изучим области их применения.
Понравился статья Приступаем к сборке двух осевого ЧПУ станка своими руками? Не забудь поделиться с друзьями в соц. сетях.
А также подписаться на наш канал на YouTube, вступить в группу Вконтакте, в группу на Facebook.
Спасибо за внимание!
Технологии начинаются с простого!
Чпу выжигатель своими руками Чпу выжигатель своими руками
Home » Pyroprinter блог | Статьи о станке выжигателе ЧПУ » Чпу выжигатель своими руками
При покупке любого станка есть процент людей, которые задаются вопросами сборки его самостоятельно. Также и ЧПУ выжигатель своими руками задумываются собрать.
Но здесь есть ряд нюансов, при которых эта затея может обойтись дороже, чем купить готовый станок. Разберемся почему так получается.
Важный вопрос в том, что если вы решили самостоятельно спроектировать будущий станок, то будьте готовы к дополнительным расходам.
Чаще всего при самостоятельном проектировании процесс выглядит так:
- Вы делаете проект (не важно: в инженерной программе или делаете чертеж) — на это уйдет определенное время;
- После этого заказываете комплектующие.
Срок доставки обычно составляет 2-4 недели в зависимости от самих комплектующих. Большинство деталей можно купить поштучно, но какие-то позиции продаются только пачками или по несколько штук;
- После того, как вы получили нужные запчасти, Вы начинаете сборку. Вот тут есть момент. Если у Вас нет опыта в проектировании станков с ЧПУ, то при сборке окажется, что какие-то детали друг к другу не подходят или какие-то нюансы Вы не учли вовсе. Простой пример: не подошла длина замкнутого ремешка — вместо 120 мм нужно 130 мм (или наоборот). Мелочь, но из-за нее передача работать не будет. В итоге, Вам приходится заказывать новую деталь и ждать еще минимум 2 недели.
- Также в ходе сборки оказывается, что Вам нужен определенный инструмент для сборки, которого у Вас могло не оказаться под рукой. Это дополнительные расходы, которые Вы вряд ли сможете предусмотреть заранее.
- После окончательной сборки Вы начинаете тестировать Ваш станок. И на деле оказывается, что печатает он не так, как Вы ожидали.
Появляются разного рода дефекты, полосы, смещения, плохо передаются светлые или средние тона и т.д. На изучение причин и корректировку уйдет еще дополнительное Ваше личное время, пока Вы не получите что-то, чем будете довольны.
Проблема в том, что полный цикл такого изготовления занимает по факту минимум 1 месяц, а по факту около двух. Это учитывая ошибки в проектировании, замену не подошедших комплектующих, отладку и так далее. И нет гарантии, что Вы получите именно тот результат, на который рассчитывали изначально.
Стоит ли собирать ЧПУ выжигатель своими руками?
Вместо потраченного времени на самостоятельную сборку и ожидание, за это время Вы могли уже набить руку на готовом станке и получить первые деньги с продажи портретов. При грамотном подходе разница цене на готовый станок и собранный самостоятельно легко сравняется с деньгами, которые Вы получите от продажи готовых портретов и изделий, сделанных на этом станке за это потраченное на сборку и проектирование время.
Даже собрав ЧПУ выжигатель самостоятельно, нет гарантии, что потратив столько личного времени и денег, Вы останетесь довольны результатом.
Наш опыт сборки станка в единственном экземпляре для собственных нужд
Минус самостоятельной сборки «Ошибки проектирования» мы не просто так написали это в первую очередь. Мы сталкивались с такой проблемой сами, когда хотели сэкономить деньги и собрать лазерный СО2 станок самостоятельно. По факту с учетом ошибок проектирования и различных переделок сумма, которую заплатили за запчасти сравнялась со стоимостью готового аналогичного станка. И это мы не считаем потраченного личного времени и того факта, что станок мог бы раньше функционировать и начать себя окупать.
Такая сборка была бы выгодной, если бы мы планировали производить потом такие станки постоянно. Но так как наша задача была просто один лазерный станок для своих нужд, то это оказалось совершенно не выгодной тратой времени.
Комплекты запчастей для сборки фрезерного станка чпу своими руками на Авито.
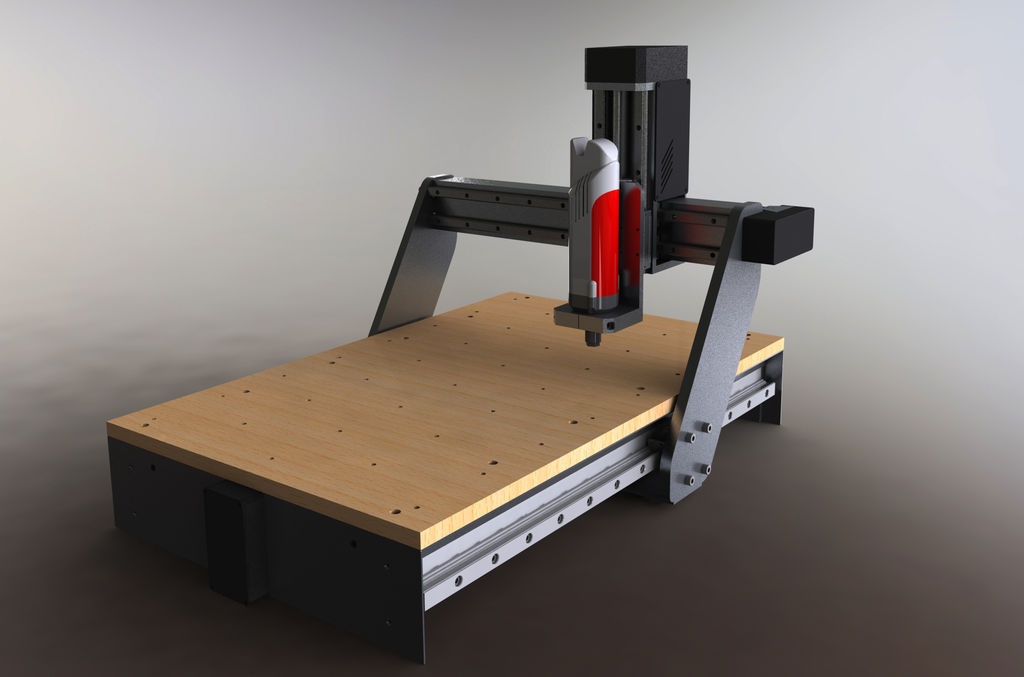
Не зря речь зашла о том, что на самостоятельную разработку станка нужно очень много терпения. На Авито можно найти достаточное количество объявлений о том, что люди продают комплекты заказанных ими запчастей для сборки фрезерных станков с ЧПУ. Их продают люди, которые бросили затею собрать станок самостоятельно, столкнувшись с определенными сложностями. При этом, это не полный комплект — обычно там нет основной рамы и части необходимых деталей. Чаще всего это это сам шпиндель, частотный преобразователь, какие-то элементы механики и электроники. Проблема в том, что фрезерные станки очень индивидуальны, и механика подбирается под определенный проект. К сожалению, нет универсальных комплектов, подходящих для большинства станков.
Какие еще минусы при сборке самостоятельно:
- ошибки проектирования
- неизвестный уровень производительности в сравнении с заводским аналогом. Довольно сложно из подручных материалов и подручного инструмента создать станок с высокой мощностью
- точный подбор комплектующих: выливается или в запчасти, которые не пригодились или использование того что есть или того что купили
- не забывайте о том, что производитель закупает запчасти и комплектующие по цене, значительно отличающейся от той, которую Вам придется заплатить, покупая то же самое в розницу
- покупка инструмента, который пригодится на 3-5 минут для сборки станка
- уровень безопасности самодельных станков, к сожалению, сильно ниже заводских станков
- ошибки при подсоединении могут быть фатальны для электроники станка
- Вы можете столкнуться с нехваткой знаний и опыта к примеру пайки проводов
- не на станок, не на комплектующие не будет действовать гарантия
20 лет опыта по работе со станками ЧПУ
Очень большой вклад в развитие Пиропринтера внес Юрий Горбачев, благодаря его компетенции. Он начинал работать с ЧПУ еще в 90-х годах. Для понимания, тогда не было программного обеспечения в открытом доступе. Сами ЧПУ станки (преимущественно фрезерные и токарные) были зарубежными и продавались в комплекте с программами и были не доступны для обычных людей. Такое оборудование могли себе позволить только крупные корпорации или оборонные заводы. Для понимания, общеизвестная сейчас программа для фрезерных станков Mach4 была выпущена в 1990году. В свободный доступ вышла существенно позже.
Юрию пришлось изучить 6 языков программирования и писать программы для ЧПУ самостоятельно. Поэтому программа Пиропринтер имеет ядро, написанное с нуля. Благодаря оптимизированным алгоритмам кода, это позволило электронике станка работать на большой частоте, что создает существенное преимущество — станок выдает намного большее число оттенков серого цвета при той же скорости, чем более старые версии станка. Это позволило существенно поднять скорость выжигания.
В версии Пиропринтер 3 и Пиропринетр Х мы поменяли процессор. Теперь мы используем 32 битный процессор STM, что позволило существенно увеличить скорость работы станка, а также добавить карту памяти и вайфай модуль. Теперь станок Пиропринтер Х работает как два станка Пиропринтер 2.
На разработку последней версии у Юрия ушло 2 года это не смотря на большой опыт работы со станками ЧПУ и в проектировании станков.
Какое оборудование мы используем для производства Пиропринтера
Использование ЧПУ и 4-й оси для изготовления ножей
Изготовление ножей — популярное искусство среди владельцев Tormach. Несколько лет назад братья Гримсмо обратили внимание на то, как легко малый бизнес может начать производить качественные ножи, имея доступ к оборудованию Tormach.
Сейчас новое поколение производителей ножей берет в свои руки ЧПУ на станках Tormach и делает красивые детали. Джейсон Ван Кэмп начал заниматься ЧПУ, когда хотел модифицировать некоторые ножи для повседневного ношения. После ряда успешных модификаций он занялся изготовлением собственных ножей и запустил VC Edge.
«За годы коллекционирования ножей я пришел к пониманию, что важно не просто иметь инструмент, который может резать, вы можете получить один из них очень дешево практически в любом месте, но важно то, как вы себя чувствуете, имея/держать /используй его, — объяснил Ван Кэмп. «Это очень похоже на причины, по которым люди любят дорогие часы, модные машины или красивую обувь: если это то, что вы используете на регулярной основе, гораздо приятнее делать это с искусно сделанным инструментом».
Он купил 1100MX (с 4-й осью microARC) и использует его для создания своих высококачественных сверхлегких карманных ножей. Его нож с 3,6-дюймовым лезвием, известный как «Интерфейс», весит всего 1,7 унции благодаря уникальному дизайну корпуса Ван Кэмпа из углеродного волокна.
«Я давно присматривался к мельницам Tormach, изучая обработку с ЧПУ, из-за более разумной цены по сравнению с другими и окружающим их сообществом. Первым соображением была площадь основания машины и общий размер. Мне нужно было, чтобы он поместился в обычном гараже и использовал обычное однофазное электричество 240 В».
В июле 2020 года Ван Кэмпу был доставлен 1100MX, и он приступил к работе.
4-я ось для изготовления ножей?
Большинство производителей ножей используют станки с ЧПУ для создания нестандартных деталей для своих ножей, а поскольку карманные ножи, как правило, должны помещаться в вашем кармане, детали обычно довольно плоские. Ван Кэмп купил 4-ю ось microARC со своим 1100MX, что может показаться необычным для производителя ножей.
«В настоящее время я использую ось microARC 4 th в качестве позиционера для установки на поддонах на надгробии. Это позволяет мне изготавливать гораздо больше деталей за один цикл и дольше обрабатывать их без присмотра. В противном случае мне пришлось бы нянчиться с машиной, пока она делает всего несколько деталей за раз».
С помощью microARC на своем 1100MX Ван Кэмп смог создать более автоматизированный и эффективный процесс изготовления своих ножей. Укладка на поддоны — это способ обеспечить быструю загрузку и разгрузку деталей, чтобы он мог позволить машине вернуться к работе, а затем добавление 4-й оси означает, что он может иметь несколько установок на машине одновременно, что освобождает его для выполнения большего количества операций. практические задачи и вести свой бизнес.
Он продолжил: «Одним из других основных преимуществ использования 4-й оси является внешнее контурирование нескольких частей ножа. Это требует использования небольших шаровых концевых фрез, и я могу использовать microARC для наклона паллеты для контурной обработки. Затем я могу надежно вернуться в плоское состояние, когда этого потребует следующая операция. Это означает, что я использую большую часть режущего инструмента, а не только его кончик. В результате я получаю лучшее качество поверхности и гораздо более долговечные инструменты, чем раньше».
MicroARC не только повышает эффективность настройки, но и экономит деньги Van Camp на оснастке, а также создает более привлекательную деталь!
Изготовление ножей с ЧПУ
Ножи бывают разных материалов и конструкций. Ножи Van Camp требуют тщательного рассмотрения материалов и разработки, чтобы сделать их достаточно прочными для повседневного использования, оставаясь при этом легкими и эстетически привлекательными.
«Изготовление этих ножей требует необычайной обработки, чтобы снять достаточно материала. Например, одна отдельная карманная клипса будет работать на станке с ЧПУ целый час», — пояснил он. «Мне больше всего нравится использовать титан и углеродное волокно, но я также использую множество других материалов, таких как алюминий, сталь, стабилизированный древесный кап и бронзу. В основном все, что вы можете разрезать с помощью твердосплавной концевой фрезы, так что ограничений не так много».
Ван Кэмп выбрал 1100MX для рабочей зоны и шпинделя 10k, но он также доволен допусками, которые он может выдерживать. «Накопление допусков может стать проблемой при изготовлении ножей, если вы не будете осторожны, а допуски на многих частях моих ножей очень жесткие».
Несмотря на то, что в его мастерской происходит определенная ручная отделка, Ван Кэмп также является поклонником «чисто обработанных» деталей, если они сделаны правильно. «Я часто оставляю этот финиш там, где могу. Чем лучше детали отрываются от станка, с точки зрения точности и внешнего вида, тем меньше работы нужно выполнять после».
Ван Кэмп документирует свои процессы изготовления ножей на YouTube и в Instagram, а также активно продает свои ножи на веб-сайте VC Edge.
Opendesk — автокоррекция для ваших рук
Представьте себе ручной инструмент, который компенсирует ваши ошибки при резке сложных деталей. Почему бы не искоренить ошибки вообще?
Мы встречаемся с нашими друзьями из Shaper Tools, которые только что выпустили ручной инструмент, который превратит любого в профессионального мастера — Shaper Origin.
Мы уже давно присматриваемся к этому стартапу из Сан-Франциско, и я уверен, что мы не одиноки. Origin — чрезвычайно захватывающая перспектива для всех, кто когда-либо испытывал желание что-то сделать, но хочет, чтобы этот опыт был немного более увлекательным, чем игра на 3D-принтере. Это огромный шаг к автономизации цифрового производства. Автоматизация с человеческим прикосновением, которая в конечном итоге заставляет вас чувствовать себя ремесленником, а не оператором станка.
Shaper Origin — уникальный инструмент. Благодаря проекционному дисплею вы можете разместить рисунок в любом месте на заготовке. По запросу фрезер начнет резку материала. Используя дисплей, пользователь следует по направляемому пути, смутно отслеживая рисунок. По мере того, как пользователь проводит трассировку, Shaper постоянно корректирует положение фрезы, переводя расплывчатую трассировку в точную траекторию движения инструмента. В результате получается опыт, не похожий ни на что другое.
Shaper Origin легко справляется со стулом Edie.
Что нас больше всего восхищает в Origin, так это его влияние на доступность производства. Поскольку так много файлов дизайна доступно открыто по лицензиям Creative Commons, для нас важно, чтобы производители хобби имели возможность пользоваться ресурсами, которыми мы делимся. Фрезерные станки с ЧПУ стоят более 8000 фунтов стерлингов (как минимум), весят более одной тонны и занимают не менее двух квадратных метров — не самый доступный инструмент для любителя. Поскольку Shaper Origin стоил около 1500 долларов во время кампании предварительного заказа и весил меньше, чем ваш средний бытовой пылесос, барьер для входа значительно снизился. Любой, у кого есть плоская поверхность, запасной материал и горячее желание сделать, может иметь его. Это вдохнуло новую жизнь во фразу «сделай сам». Мы надеемся, что Origin даст возможность новой волне любителей загружать и создавать проекты Opendesk в своем домашнем гараже или садовом сарае.
В дополнение к более важным вещам, Origin занимается оригинальным Studio Desk.
Джо Хебенстрейт
Сразу после того, как я получу свою! Сначала мы запускаем в США и будем расширяться на международном уровне, как только сможем.
Opendesk: С чего все началось? Момент лампочки..
Joe Hebenstreit: В 2011 году, находясь в отпуске после получения докторской степени в Массачусетском технологическом институте, соучредитель Алек Риверс попытался заняться деревообработкой, используя ручные инструменты, которые он унаследовал от своего дедушки. Он быстро обнаружил, что наличие инструментов не делает его изготовителем — ему все еще не хватало многолетнего опыта, необходимого для того, чтобы получить инструменты и свои руки для производства чего-то, чем он мог бы гордиться.
Опендеск:
Тогда и сейчас — подведем итоги путешествия Origin и команды.
Джо Хебенстрейт:
Вернувшись в Массачусетский технологический институт со своим одноосным прототипом в руках, Алек был представлен Илану Мойеру, одному из самых опытных разработчиков цифровых инструментов в Массачусетском технологическом институте. Работая вместе, пара превратила одноосный станок в двухосный, который впоследствии стал Shaper Origin.
После Массачусетского технологического института Алек и Илан создали компанию на основе разработанной ими базовой технологии «Tool GPS», привлекли первоначальное финансирование и переехали в Калифорнию.
В прошлом году мы построили 10 полнофункциональных прототипов и довели их до предела в ходе бета-тестирования как в магазине, так и с реальными пользователями в полевых условиях. Это прототипы, которые вы видите во многих наших видео. Это реальное тестирование дало ценную информацию, и эти знания были направлены на повышение надежности, производительности, удобства использования и технологичности Origin. Спустя 5 с лишним лет разработки и тысячи часов тестирования мы очень рады начать производство с Origin.
Опендеск:
Автономия против автоматизации. Чем Shaper Origin отличается от инструментов цифрового производства.
Джо Хебенстрейт:
Происхождение отличается на нескольких уровнях. Во-первых: это легко. Origin интуитивно понятен — вам не нужно быть опытным оператором ЧПУ. Наша цель — сделать Origin машиной, к которой вы беретесь в первую очередь, когда хотите что-то сделать. Благодаря расширенному представлению о заготовке и таким функциям, как изменение траектории резания на инструменте и регулировка смещения долота, можно легко изменять дизайн или подгонку между деталями по ходу работы. Следующее — размер кровати или конверта… или их отсутствие. Origin может браться за большие и маленькие проекты — мы думаем об этом как о машине с «бесконечным конвертом». Он также портативный и, следовательно, полностью портативный, что позволяет вам брать инструмент с материалами, а не перетаскивать их в фиксированное место. По сравнению с другими цифровыми инструментами для производства, такими как лазерные резаки или 3D-принтеры, Origin может работать с огромным диапазоном и толщиной материалов.