Эксцентриковые шлифмашины » Самоделки Своими Руками – Сделай Сам (чертежи, руководства)
Секреты умельцев /28-мар,2010,15;42 / 39723Пять мифов об эксцентриковых шлифмашинах
Как планета вокруг солнца вращается диск эксцентриковой шлифмашины вокруг своей оси, совершая одновременно колебательные движения по крошечным орбитам. Благодаря такому сложному движению царапины от шлифовального диска располагаются на обрабатываемой поверхности хаотически, взаимно перекрывая друг друга. С каждым переходом к более мелкому абразиву они становятся все менее заметными и сливаются, а поверхность выглядит гладкой и блестящей. Кажется, все ясно, не так ли? Не совсем. На практике возникают бесконечные вопросы, касающиеся эксцентриковых шлифмашин. Как быстро следует ее перемещать? Как сильно ее нужно прижимать? Необходимо включать маши ну, прижимая ее к детали или держа на некотором удалении? Вместо изречения прописных истин , которой может воспользоваться любой мастер (подробности тестирования эксцентриковых шлифмашин
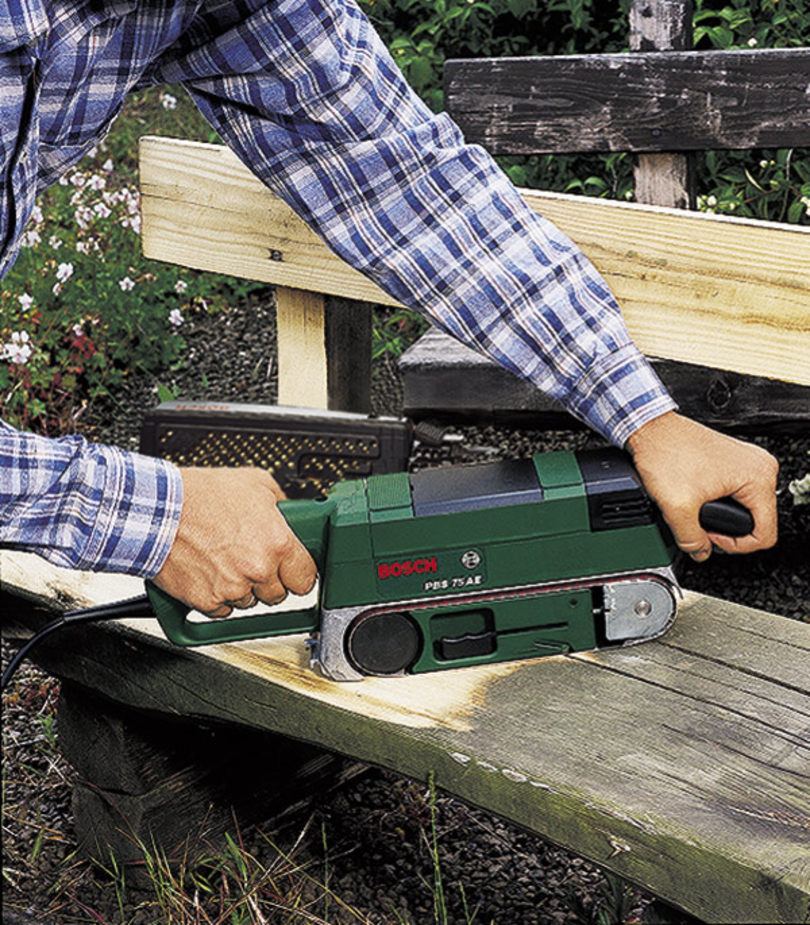
Реальность. Пуск вне детали нисколько не хуже.
Включайте эксцентриковую шлифмашину так, как вам удобнее: на детали или вне ее. Большинство выпускаемых в последнее время моделей имеют встроенную функцию уменьшения числа оборотов диска при работе без нагрузки (электронный тормоз). Это снижает риск появления углублении при включении такой машины вне детали. Тем не менее он не спасет деталь, если опускать на нее шлифовальный диск под наклоном или шлифовать только краем диска. Запуск же машины на детали может привести к появлению нескольких заметных царапин, которые быстро исчезнут после пары проходов (фото А). Гораздо важнее надежно зафиксировать деталь, используя струбцины или специальный антифрикционный коврик, что предотвратит ее сдвиг. Начиная шлифовку, не давите сильно на шлифмашину и не позволяйте ей задерживаться на одном месте.
Неважно, где вы включите шлифмашину Важно, где вы ее выключите. Перед выключением плавно поднимите электроинструмент, и удачное завершение шлифовки вам обеспечено.
Миф 2. При нажиме машина шлифует агрессивнее.
Реальность. Для получения луч шего результата достаточно легкого касания.
При надавливании на инструмент замедляется вращение, что приводит к снижению эффективности и вызывает ускоренный износ подошвы, подшипников, абразивных дисков и застежки-«липучки» для их крепления. Вместо того чтобы быть агрессивнее, инструмент под избыточным нажимом удаляет меньше материала, оставляя при этом грубые царапины (фото В). А на некоторых породах (например, ели Дугласа или американской южной желтой сосне) при сильном нажиме поверхность становится волнистой (фото С). Не давите на шлифмашину, а дайте ей сделать свою работу. Если возникает необходимость более агрессивной шлифовки и для этого требуется прижать инструмент или наклонить его, то это может быть признаком использования слишком мелкого абразива или его затупления.
Миф з. Шлифовка абразивом мельче 120 единиц бесполезна.
Реальность. Для качественной отделки требуется более тонкая шлифовка. Конечно, можно наносить лак слой за слоем чтобы сделать грубо отшлифованную поверхность гладкой, но это увеличивает затраты на отделку. Древесина, отшлифованная абразивом зернистостью грубее 120 единиц, выглядит темнее и испещрена мелкими углублениями; ее текстурный рисунок менее заметен, а грубая поверхность впитывает больше морилки и лака, чем отшлифованная более гладко (фото D). Масляные морилки и проникающие отделочные покрытия делают разницу еще заметнее. Оптимально заканчивать шлифовку абразивом зернистостью 150-220 единиц. При этом обработанная поверхность оказывается достаточно гладкой для хорошего растекания и выравнивания лакового слоя и одновременно достаточно шероховатой для хорошей адгезии.
Независимо от того, насколько гладко требуется отшлифовать древесину, всегда используйте прогрессивный метод шлифовки, переходя последовательно от крупных номеров абразива к более мелким без пропусков. При смене шлифовального диска тщательно удалите пылесосом пыль от шлифовки. Таким образом при дальнейшей обработке частицы более грубого абразива не будут вдавлены в поверхность.
Миф 4. Для ускорения шлифовки нужно быстрее перемещать шлифмашину.
Реальность. На больших поверхностях – тише едешь, дальше будешь. Скорость подачи – это быстрота перемещения инструмента по поверхности детали. Хотя нельзя сказать, что для всех случаев требуется одна и та же скорость подачи, линейное перемещение шлифмашины со скоростью не более 0,3 м/с дает наиболее равно мерный рисунок царапин на обрабатываемой поверхности (фото Е). Можно ли увеличить скорость подачи? Конечно. Но при этом для достижения такого же качества шлифовки потребуются дополнительные проходы, что займет больше времени. При обработке значительных по площади поверхностей (например, шитов) \учше начинать шлифовку с одного угла и вести инструмент вдоль детали от края до края параллельно кромкам, перекрывая след предыдущего прохода наполовину для получения равно мерного покрытия.
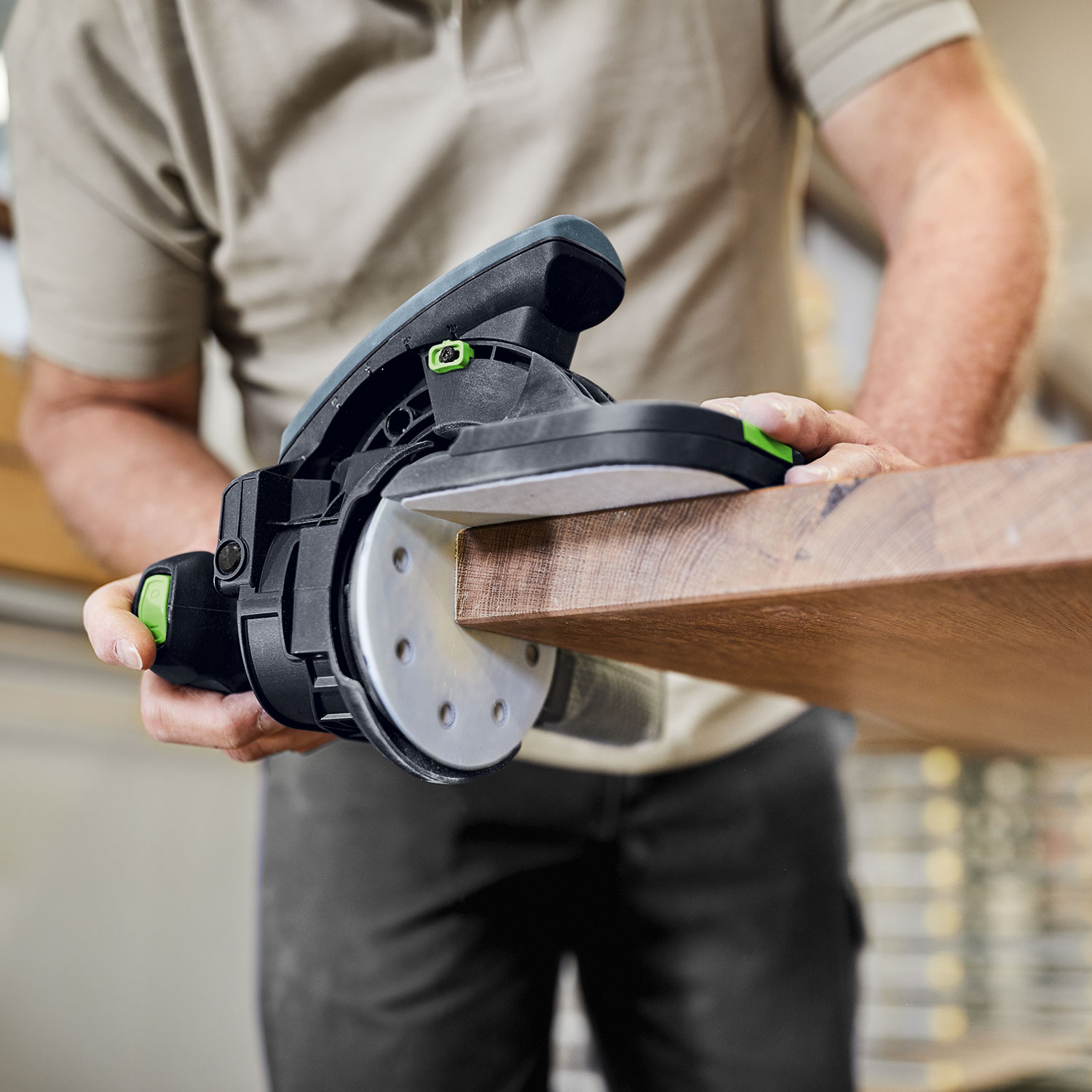
Миф 5. Межслойная шлифовка лака – работа не для шлифмашин.
Реальность. Мы всегда используем для этого эксцентриковую шлиф-машину.
Легкое касание диском, мелкий абразив и отсутствие нагрева поверхно сти – вот три непременных условия успешного применения электрических шлифмашин для шлифовки лаковых покрытий. Однако требуется предельная осторожность, чтобы не прошли фовать тонкий слой покрытия насквозь Мы добивались отличных результатов при межслойной шлифовке полиуре танового лака абразивными дисками с зерном 400 и 600 единиц. Для нитролака можно использовать абразивы на один-два номера крупнее, так как слои прочно соединяются между собой, скрывая следы предыдущей шлифовки. Для обработки криволинейных деталей используйте мягкую сменную подошву, лучше прилегающую к неплоским поверхностям. Следите за нагревом, из-за которого лаковый слой размягчается, что приводит к ускоренному засаливанию абразива. Чтобы не испортить работу, перемещайте шлифмашину без задержек, не нажимая на нее, и очищайте поверхность пылесосом, а затем мягкой тканью.
Как сделать ленточно-шлифовальный станок: 6 вариантов конструкции
Финишная обработка деревянных заготовок (например, перед покраской или покрытием лаком) подразумевает шлифовку поверхности мелкой наждачкой.
Для этих целей удобно использовать ленточно-шлифовальный станок. Причем на нем можно обрабатывать не только заготовки из дерева или фанеры, но также и из металла (это может быть сталь, алюминий, латунь или медь).
Вообще, возможности ленточно-шлифовального станка намного шире, чем просто шлифовка. На нем вы можете:
- точить кухонные ножи;
- закруглять острые углы на деревянных и металлических заготовках;
- обтачивать круглые прутки (делать заостренный конец).
В этой статье мы расскажем, как сделать ленточно-шлифовальный станок для мастерской своими руками — рассмотрим 6 вариантов конструкции.
В большинстве случаев приводом обычно служит электродвигатель. Но домашние умельцы предлагают и другие варианты — например, использовать болгарку и дрель, и даже шлифмашину.
Изготавливая самодельный станок для шлифовки, вы не ограничиваете себя — можете самостоятельно определять габариты конструкции и способ ее крепления к столу, а также выбирать подходящие материалы из того, что есть под рукой.
Кстати, ленточные шлифовальные станки могут быть как вертикальными, так и горизонтальными. Мы рассмотрим оба варианта.
Ленточный шлифстанок из мотора от стиралки
Необходимые материалы:
- профильная труба;
- листовой металл;
- строительный уголок;
- деревянный брусок;
- шлифовальная лента;
- резьбовая шпилька;
- мебельный газлифт;
- электромотор от стиральной машины;
- крепеж — болты с гайками.
После того как подготовили все необходимые материалы, можно приступать к работе. Для удобства разобьем весь процесс на несколько основных этапов.
Шаг первый: изготовление приводного и ведомого ролика.
Первым делом необходимо изготовить приводной ролик. Отпиливаем деревянный брусок подходящей длины (чуть больше ширины шлифовальной ленты).
Обтачиваем заготовку — делаем ее круглой. Сверлим в ней продольное отверстие, после чего надеваем на вал двигателя.
После этого надо сделать ролик натяжения (или просто ведомый ролик). Точно также округляем кусок деревянного бруска, и сверлим в нем продольное отверстие.
Дополнительно высверливаем посадочные места под подшипники, и устанавливаем их — запрессовываем киянкой.
Шаг второй: изготовление станины и вертикальной стойки.
Далее необходимо будет «посадить» электродвигатель на основание. Вариантов основания много — мы рассмотрим один из самых простых.
В корпусе двигателя имеются «ушки», в которые вставляем отрезки резьбовой шпильки. На концы шпилек надеваем уголки, фиксируем их гайками.
Отрезаем два куска квадратной профильной трубы. К ним нужно приварить уголки.
К станине привариваем еще один кусок профтрубы, который будет выполнять роль вертикальной стойки.
К верхней части стойки с помощью болта с гайкой крепится подвижный кронштейн, изготовленный из полос металла, который служит для крепления блока натяжения с ведомым роликом.
Шаг третий: изготовление блока натяжения для шлифленты.
Из квадратной профильной трубы, полосы металла и ведомого ролика изготавливается блок натяжения. Потом он крепится к кронштейну на верхней части стойки.
Шаг четвертый: изготовление опорной пластины и рабочего столика.
К стойке необходимо приварить кусок профиля, а к нему — опорную пластину из листового металла. Между креплением опорной пластины и натяжным блоком устанавливается газлифт.
К основанию приваривается кусок профиля, к которому нужно приварить рабочий столик.
Шаг пятый: электромонтажные работы, покраска и сборка.
На последнем этапе останется только выполнить работы по электрической части, потом покрасить все изготовленные детали, и можно переходить к финальной стадии работ — сборке.
Пошаговую инструкцию по изготовлению шлифовального ленточного станка своими руками можно увидеть в авторском видео. Данной идеей поделился автор YouTube канала seby torrisi — берите на заметку.
Самодельная конструкция получилась довольно простой в изготовлении и удобной в использовании. И изготовить ее под силу каждому.
Обратите внимание: нужно предохранять электродвигатель от шлифовальной пыли, иначе он не прослужит и месяца.
Ленточный шлифстанок с регулируемым столом
Необходимые материалы:
- фанера шлифованная;
- фанера ламинированная;
- деревянные бруски;
- резьбовые шпильки;
- крепеж — болты с барашковыми гайками.
Особенность данной конструкции заключается в том, что за основу (в качестве привода) используется шлифовальная машинка.
Это очень удобно, потому что основная часть самодельного шлифстанка уже готова — останется только изготовить станину, стойку и регулируемый столик.
Данной идеей поделился автор YouTube канала Cosel, за что ему огромное спасибо!
Первым делом займемся изготовлением станины. Для этого вырезаем из фанеры две боковых стенки треугольной формы. Соединяем их при помощи перемычки (прямоугольный кусок ламинированной или обычной фанеры).
Из деревянного бруска изготавливаем вертикальную стойку. К корпусу шлифмашинки крепится еще один кусок бруска, чтобы можно было закрепить инструмент на стойке.
Крепим стойку вместе со шлифовальной машинкой к соединительной перемычке станины. Выставляем под прямым углом.
Основная часть работ уже сделана. Теперь останется лишь изготовить регулируемый рабочий столик.
Сначала вырезаем боковые крепления, в которых нужно сделать дугообразные пазы. Крепим боковины к станине шлифстанка.
Из ламинированной фанеры изготавливаем рабочий стол, и прикручиваем его к боковым креплениям.
Таким образом, можно выставить рабочий столик как под углом 90 градусов — перпендикулярно шлифовальной ленте, так и под наклоном (под углом к корпусу).
На последнем этапе прикручиваем к основанию станины резиновые ножки, чтобы в процессе работы шлифстанок уверенно стоял на опорной поверхности. Либо, как вариант, можно сделать деревянные ножки, обработав их на точиле, и приклеив к основанию кусочки резины.
Подробно о том, как изготовить самодельный ленточный шлифовальный станок, вы можете увидеть в видеоролике.
На первый взгляд, конструкция кажется очень простой, но в этом есть свои плюсы:
- изготовить легко;
- работать удобно;
- ломаться здесь нечему.
Да еще и места на столе такая конструкция занимает немного. Но самое главное — не потребуется практически никаких финансовых вложений. Все можно сделать из подручных материалов.
Шлифовальный ленточный станок из электродрели
Необходимые материалы:
- деревянные перила;
- фанера;
- резьбовая шпилька;
- листовой металл;
- подшипники;
- метизы — болты, гайки, шайбы;
- строительный уголок;
- деревянные бруски.
В качестве привода в данном случае будем использовать электродрель. Причем аккумуляторная дрель не подойдет — нужна именно сетевая, со шнуром.
Идеей и своим личным опытом поделился автор YouTube канала Mr Novruz.
Первым делом необходимо будет подготовить заготовки для изготовления станины и роликов (приводного и ведомого, который можно отрегулировать для лучшего натяжения шлифовальной ленты).
От деревянных перил отпиливаем две заготовки, которые будут служить опорными элементами. Основание станка можно сделать из фанеры.
Также из листа фанеры с помощью корончатого сверла по дереву вырезаем круглые детали, которые будут использоваться для изготовления приводного и ведомого роликов.
Отрезки перил прикручиваем к основанию на саморезы. После этого склеиваем два ролика. Сверлим в них отверстия по центру под диаметр вала, а также дополнительно высверливаем посадочные места под подшипники.
С одной из сторон опорных элементов надо просверлить отверстия для резьбовой шпильки, на которой находится приводной ролик.
На другой стороне перил вырезаем два паза — под шпильку с ведомым роликом. Устанавливаем ролики на свои места.
Далее из деревянных брусков изготавливается хомут (крепление) для электродрели. Крепим его к основанию. Устанавливаем дрель. В патроне зажимаем конец резьбовой шпильки, на которой находится приводной ролик.
По бокам опорных элементов (перил) прикручиваем два уголка с отверстиями, в которые устанавливаем крепления для ведомого ролика. Он будет регулировать натяжение шлифленты.
Из листового металла вырезаем пластину подходящего размера. Края пластины можно обработать на точильном станке. Прикручиваем ее сверху опорных элементов.
Сделанный шлифстанок можно использовать в горизонтальном и вертикальном положениях. Во втором случае потребуется прикрутить рабочий опорный столик.
Пошаговая инструкция, как сделать ленточно шлифовальный станок своими руками, показана на видео ниже.
Конструкция получилась довольно бюджетной и простой в сборке. Вместо деревянных перил можно использовать обычные бруски.
Шлифовальный станок из болгарки
Необходимые материалы:
- листовой металл;
- деревянный брусок;
- стальной уголок;
- подшипники;
- болты с гайками;
- пружина.
Основой для изготовления данного шлифстанка послужит болгарка. Все остальные элементы конструкции изготовим из толстого металла и уголка. Но давайте обо всем по порядку.
Шаг первый: изготовление приводного ролика.
Берем деревянный брусок подходящий по размеру, и округляем его на токарном станке. Либо можно использовать уже готовый кругляк из дерева. Отрезаем от него нужным нам кусочек.
Высверливаем по центру заготовки посадочное место под гайку, и запрессовываем ее в отверстие с помощью слесарных тисов или киянкой.
Устанавливаем изготовленный ролик на болгарку, и придаем ему форму бочонка, убирая все лишнее об наждачную бумагу крупной зернистости, закрепленную на доске. Либо можно обработать заготовку на точильном станке.
Шаг второй: изготовление стойки и основания.
Из листового металла вырезаем заготовку требуемой длины и формы. Высверливаем в стойке одно отверстие, и несколько крепежных отверстий, чтобы можно было ее прикрепить к корпусу редуктора УШМ.
Далее изготавливаем основание станины. Для этого нам потребуется два уголка. Отрезаем заготовки подходящей длины, и сверлим в них крепежные отверстия. После этого крепим стойку между уголками, как показано на фото ниже.
Шаг третий: изготовление механизма натяжения шлифовальной ленты.
На следующем этапе приступаем к изготовлению блока натяжения, который состоит из подвижной крепежной пластины и ведомого ролика.
Отрезаем пластину нужной формы и длины. Крепим ее к верхней части стойки. После этого в просверленные отверстия вкручиваем болт с подшипниками (ведомый ролик).
Шаг четвертый: окончательная сборка шлифовального станка.
Крепим к болгарке стойку, после чего на вал редуктора УШМ накручиваем приводной ролик. Между подвижной частью блока натяжения и стойкой устанавливаем возвратную пружину.
Последний этап — изготовление опорной пластины для шлифленты и рабочего столика для удобной работы с заготовками. Красим эти детали, затем крепим к станине. Стойку также надо будет покрасить.
Устанавливаем шлифовальную ленту, после чего можно приступать к работе. Самоделка готова.
Пошаговый процесс изготовления самодельного шлифовального станка можно увидеть в видеоролике ниже.
Конструкция получилась довольно компактной и аккуратной. И самое главное — мы обошлись без использования сварочного аппарата. Идея самоделки принадлежит автору YouTube канала Mistry MakeTool.
Ручной ленточно-шлифовальный станок из болгарки
Необходимые материалы:
- пластмассовый кругляк;
- фанера;
- металл;
- уголок;
- профтруба.
Первым делом из пластмассового кругляка нужно изготовить два ведомых ролика. Потом изготавливаем еще один — приводной, который будет устанавливаться на вал редуктора болгарки.
Из кусочков профильной трубы и металла необходимо изготовить крепление для болгарки. Делаем разметку, сверлим крепежные отверстия.
Далее отрезаем кусок металлического уголка, и привариваем его к одной из сторон крепления для УШМ. Смотрите фото ниже.
К металлическому уголку с помощью болтов крепится площадка, сваренная из двух отрезков прямоугольной профильной трубы.
На следующем этапе изготавливаем механизм натяжения шлифовальной ленты. Устанавливаем его внутри опорной площадки.
Привариваем крепления для установки ручек (шлифстанок в данном случае будет не стационарным, а ручным).
К нижней части площадки приваривается опорная пластина из листового металла, которая не позволит натянутой шлифовальной ленте продавливаться внутрь при шлифовке заготовок.
Также к станине шлифстанка необходимо будет прикрепить небольшую дощечку из фанеры. Она будет выполнять функцию защитного кожуха — если вдруг наждачка порвется (а такое происходит частенько), то она не зарядит вам по рукам.
Зачищаем и красим все детали конструкции, и приступаем к сборке. Устанавливаем болгарку.
Подробно о том, как сделать ленточный шлифовальный станочек, наглядно показано в авторском видеоролике. Идея изготовления ручной шлифмашины принадлежит автору MaC — fai da te.
Данная конструкция — не самая простая в изготовлении, но разобраться можно. Самоделка отлично пригодится в тех случаях, когда нужно обработать широкие заготовки из дерева или фанеры.
Шлифовальный станок из ленточной шлифмашинки
Представляем вашему вниманию еще один вариант конструкции ленточного наждака, который можно изготовить в условиях домашней мастерской или же в гараже. Основой самодельного станка является шлифовальная машина.
В качестве основания используется лист фанеры — отрезаем кусок требуемого размера (чтобы можно было разместить на нем все необходимые элементы конструкции).
Далее из трех кусочков фанеры изготавливаем упор для шлифмашинки. Инструмент крепится к упорной планке с помощью двух маленьких струбцин.
На следующем этапе необходимо изготовить блок с роликом. Для изготовления крепления используем фанеру. Ролик можно сделать из твердого дерева или кругляка из пластмассы.
Подбираем оптимальное месторасположение крепления с роликом на основании (в зависимости от длины шлифовальной ленты), и крепим его.
Дополнительно нужно прикрепить к основанию отрезок деревянного бруска, и устанавливаем опорную пластину из фанеры.
После этого приступаем к изготовлению рабочего стола. Крепим его к основанию, предварительно прикрутив на саморезы брусочек из дерева или фанеры, чтобы столик был повыше.
Вот, собственно, и все. Основание конструкции обрезаем по размеру, чтобы станок не занимал много места на рабочем верстаке. Для крепления к столу используем болты. Станок можно использовать как по металлу, так и по дереву.
Пошаговый процесс изготовления самодельного станка для шлифовки можно посмотреть в видеоролике ниже. Спасибо всем за внимание.
Оцените запись
[Голосов: 6 Средняя оценка: 5]Мне нравитсяНе нравитсяКак Сделать Шлифмашинку Своими Руками
Как сделать шлифмашинку по дереву своими руками
Как сделать шлифовальную машинку
Когда работа с деревянной поверхностью подходит к окончанию, наступает шаг финальной шлифовки. Чтоб выполнить шлифовку без заусенцев, царапин, прекрасно закруглить острые углы хоть какой детали, нужно пользоваться шлифовальной машинкой по дереву. Такой инструмент поможет выполнить шлифовку мастерски даже новенькому, который в первый раз взял аппарат в руки. При наличии желания сделают шлифовальную машинку без помощи других, используя только средства находящиеся под рукой.
Существующие виды шлифовальных машинок ()
Индустрией выпускаются некоторое количество видов машинок, отличающихся как конструктивно, так и по предназначению. Вот главные там:
- Эксцентриковая или орбитальная, тогда подошва инструмента сразу крутится вокруг собственной оси и по некой орбите. Выходит так, что всякий раз она проходит мало где-то в другом месте, потому царапинки и заусенцы затираются со всеми проходом нашему клиенту остается посильнее и посильнее.
- Вибрационная модель. Тут рабочая подошва производит возвратно-поступательные движения с частотой порядка 20000 движений за минуту. Конкретно путем этих движений и происходит шлифовка.
- Угловая шлифовальная машина, которую еще называют «болгаркой». Посредством этого инструмента проводят грубую обработку деталей, больших бревен и т.п. Для обработки используются абразивные круги нужной зернистости.
- Ленточная шлифовальная машинка, которая обычно употребляется для работ на огромных поверхностях. Конструктивно она представляет из себя валики, приводимые в движение электродвигателем, на которые насажена наждачная лента.
Изготовление ленточной шлифмашинки
своими руками ()Сделать ленточную шлифмашинку без помощи других очень легко, нужно выполнить последующие этапы:
- подобрать подходящие материалы и детали;
- сделать надежную базу для закрепления инструмента;
- установить подходящую столешницу;
- закрепить вертикальные стойки с натяжителем и барабаном;
- смонтировать мотор и барабаны;
- закрепить наждачную ленту.
Чтоб обрабатывать достаточно большие детали и элементы нужно сделать крупную копию серийной шлифмашинки. К примеру, если взять электродвигатель мощностью 2 Квт как еще его называют более мощнейший с частотой вращения ротора 1500 об/мин, то редуктор есть вариант не ставить. Мощности такового мотора вполне хватает, чтоб крутить барабан порядка 20 см в поперечнике и обрабатывать детали около 5 м.
Также используются электронный движок от старенькой стиральной машинки. Станину в данном случае делают из толстого листа железа, подготовив место для установки мотора и кропотливо закрепив его болтами для устранения вибрации. Конструкция таковой машинки это 3.2 барабана, при этом какой-то из них зафиксирован, а 2-ой может натягиваться и крутится на подшипниках вокруг оси. Базу для станка лучше выполнить из металла либо нескольких листов толстой фанеры. Барабаны делают на токарном станке из ДСП. Лента нарезается из полотен наждачной бумаги шириной порядка 20 см и закрепляется на станине. Чем не просто будут размеры стола, тем огромные по размеру детали можно укладывать и обрабатывать затем. Чертежи готовых изделий с легкостью найдете в сети.
Ленточная шлифовальная машина
своими руками.Как сделать ленточную шлифовальную машинку своими руками. ссылка на мотор.
Как
сделать шлифовальную машинку How to make a grinderКак сделать шлифовальную машинку How to make a grinder Я в : Группа в : .
Делаем шлифмашинку из болгарки
Многие могут сказать, что «болгарка» это же и есть угловая шлифовальная машинка, однако тут скрываются некоторые тонкости. Следует иметь ввиду, что УШМ имеет очень высокие обороты и зачастую довольно приличный вес. Чтобы отполировать поверхность болгаркой необходимо иметь немалый опыт в этом деле и пользоваться специальными полировочными дисками и кругами. Шлифовальная машинка имеет намного меньшие обороты двигателя и вес. Для работы заводской шлифовальной машинкой не требуется определенного опыта и сноровки.
Самостоятельно сделать из болгарки хорошую шлифовальную машинку, не уступающую по своим параметрам заводской машинке, можно только путем доработки ее электрической схемы, путем монтажа регулятора на более низкие обороты и путем применения специальных шлифовальных насадок.
Делаем шлифмашинку из дрелиЧтобы превратить обычную, бытовую электрическую дрель в шлифовальную машинку нужно оснастить ее специальной насадкой – рабочим барабаном или специальной опорной тарелкой, в зависимости от поставленной задачи.
Опорная или шлифовальная тарелка представляет собой пластиковую или резиновую основу с наклеенной наждачной бумагой и хвостовиком для зажима в патрон дрели. Тарелки с гибким валом подходят для работы с незакрепленной дрелью, а с жестким лучше применять только для хорошо закрепленной дрели.
Шлифовальные барабаны для бытовой дрели конструктивно представляют собой обычный цилиндр, хвостовик и наклеенную на цилиндр наждачную бумагу. При использовании барабанов рабочая поверхность шлифмашинки располагается параллельно оси вращения.
Делаем орбитальную
шлифмашинкуВ настоящее время сделать орбитальную машинку своими руками можно только из поломанной орбитальной машинки. Связано это со сложным устройством вращения рабочего диска, повторить которое самостоятельно довольно проблематично. Также следует иметь ввиду, что изготовленная специализированной фирмой машинка будет стоить не слишком много, а сделать ее своими руками будет очень сложно и займет много времени.
Делаем шлифмашинку из компьютерного винчестера ()
Любой, отслуживший свое жесткий диск можно переделать в миниатюрную шлифовальную машинку. Для этого необходимо выполнить следующие шаги:
- полностью разобрать винчестер и убрать из корпуса все, что расположено слева от магнитных дисков;
- вырезать рабочий круг из наждачной бумаги, сделать по центру круга отверстие для шпинделя;
- наклеить на вращающийся диск винчестера несколько полосок двустороннего скотча и закрепить на нем наждачную бумагу;
- сделать защитный экран, защищающий глаза от возможного вылета изготовленного наждачного диска;
- подключить готовую конструкцию к блоку питания от компьютера и пользоваться.
Конечно такая конструкция не обладает высокой мощностью, но заточить небольшой нож или ножницы вполне возможно.
Читайте так же
Как сделать шлифленту для ленточной шлифовальной машины
Порвалась шлифлента, а новой нет? Не беда, её можно сделать из обычной наждачной бумаги.
Приложите старую ленту к наждачной бумаге и при помощи ножа отрежьте нужную длину.
При помощи корщётки очистите край наждачки от абразива.
Обильно смажьте клеем ПВА очищенную от абразива полоску.
Нанесите клей на ответную часть наждачки.
Соедините части наждачной бумаги друг с другом при помощи двух досок и струбцин и дайте ленте высохнуть.
Для ускорения процесса схватившуюся ленту можно прогладить утюгом через лист бумаги.
Установите получившуюся ленту на шлифмашинку. Обратите внимание, что на заводской ленте указано направление, как нужно её устанавливать. В случае с самодельной лентой таких подсказок нет, соответственно устанавливать её надо таким образом, чтобы лента не лохматилась во время работы, а прокатывалась по поверхности.
Проверьте работоспособность ленты.
Читайте по теме:
Шлифовальная машинка из HDD диска. Небольшие доработки.
Это так сказать результат. А ниже пред история …
Решил повторить проект шлифовальной машинки с двигателем от HDD уважаемого мной Валеры Перминского .
Скачал любезно предоставленные файлы и сходу на печать.Однако результат удивил. Двигатель от жёсткого диска Samsung отличался посадочным местом от моего HDD Hitachi. Впрочем дело обычное для меня. Готовые STL ки почти всегда чем то не устраивают. Ну а если не устраивает – садимся за самостоятельное проектирование.
Итак корпус. Надо сделать его универсальным под любые HDD движки.
А как? Да просто! Посадочное место делаем отдельной деталью.
Посадочные размеры снимаем с демонтированного двигателя.
Далее печатаем , шлифуем, словом как обычно..
После печати Начинаем сборку. Тут тоже есть нюансы.
Несколько слов об основании для шлифовального диска.. Печатал слоем 0.1 мм со 100% заполнением. Получился тяжёленьким, что даст дополнительный инерционный момент.
Как Вы понимаете, он имеет свои посадочные размеры и это тоже надо учитывать.
После печати не спешите ставить мотор на место. Лучше сразу закрепить диск на роторе на все винты. Потом подключить регулятор для HDD и запустить мотор. Обороты плавно увеличивайте: возможно возникнет вибрация из-за неравномерной посади диска на вал движка. Даже если всё гуд, подшлифуйте диск по внешнему контуру. Это почти токарка. Я добился полного отсутствия вибрации на максимальных оборотах.
За тем наклейте пятачок для фиксации наждачного круга. Брал по ссылке из видеоролика Валерия (смотрите выше)
Потом разбираем и устанавливаем мотор в посадочное кольцо на саморезы и вместе с мотором вклеиваем его на место.
Далее устанавливаем плату регулятора и разъём питания. Последний штрих – нижняя крышка. Приклеил её на несколько точек клеем “Момент-Кристалл”. Так, всегда легко её демонтировать. Но если Вас такой вариант не устраивает легко прихватить на три маленьких самореза.
В принципе всё. Добавил чуток эстетики и универсальности. От себя скажу – вещь очень нужная ! Доволен пополнением в мастерскую.
Исходники для редактирования здесь:
https://3dtoday.ru/3d-models/khobbi/sdelay-sam/slifovalnaya-masinka-iz-hdd-diska
Всем успехов в творчестве.
Можно ли шлифмашинкой полировать авто – АвтоТоп
Как сделать что-то самому, своими руками. сайт домашнего мастера
Как и какую выбрать эксцентриковую шлифмашину. Характеристики, марки и полезные возможности.
Выбираем инструмент – эксцентриковую шлифовальную машину
При использовании эксцентриковой шлифмашины можно шлифовать и полировать древесную породу, металл, органическое стекло и разные лакированные поверхности, в добавок снимать краску с хоть какого материала.
Этот расхожий слух инструмент подходит большинству задач, решаемых в мастерской. Ведь незапятнанная, гладкая поверхность — не только лишь дизайнерский ход, да и серьезное требование неких ремонтов, к примеру подготовки поверхности под расцветку.
KIA Spectra 2008, 101 л. с. — кузовной ремонт
Машины в продаже
Kia Spectra, 2007
Kia Spectra, 2009
Kia Spectra, 2007
Kia Spectra, 2008
Комментарии 134
Слушай а почему ты не стал полировать шлифмашинкой?
Почитал, посмотрел фотки, поплакал и посмеялся))) Учи матчасть, друг) И больше ниииикоогда так не полируй
А как надо? Без сарказма.
как минимум, на данный момент, есть очень много информации для впитывания. На том же forum.car-care.ru/ например. То что сделал автор это жуть просто. Столько, сколько пасты лежит на багажнике, мне хватило бы на всю сторону машины, и эффект был бы куда более блистательней. Опять же! Хочешь результат? Закупайся нормальными материалами и инструментами.
Особенности вибрационных шлифовальных машинок
Соблюдая принцип работы эксцентриковая шлифмашина не совсем отличается от виброшлифмашины или шлифовального круга. Это значит, что совместно с известными движениями виброшлифмашины она делает вращательные движения шлифованного круга. Итог такового метода шлифовки — высочайшая производительность и в особенности гладкая рабочая поверхность.
Секрет хорошего свойства обрабатываемой поверхности заключается в композиции движений, состоящих из вращений и вибраций: вращательное движение обеспечивает снятие материала, а с помощью вибрации создается гладкая поверхность. При всем этом круглая шлифовальная тарелка подвижно крепится к приводному валу и крутится вокруг собственной оси параллельно рабочей поверхности свободно как еще его называют под нажимом. Ведение под нажимом увеличивает производительность снятия стружки, так что конечно делать даже грубые шлифованные работы.
Технические характеристики эксцентриковых шлифмашинок
Значимый параметр, влияющий на производительность, — поперечник окружности вибрации, который именуют также рабочим, шлифованным иначе говоря эксцентриковым ходом. Чем выше ход, тем выше и производительность. Усилие, с которым юзер надавливает на инструмент в свое время работы, тоже оказывает влияние на итог шлифовки.
Следует учитывать, что высочайшая производительность снятия стружки нужна не обязательно. К примеру, во время работы с окрашенными иначе говоря лакированными поверхностями важнее точность. Данные о поперечнике окружности вибрации указывают на то, с какой точностью есть вариант работать.
При незапятанной шлифовке сильный нажим тормозит вращение шлифовальной тарелки, что обеспечивает в особенности неплохой окончательный итог. Основное правило говорит: чем меньше окружность, тем чище шлифовка, и напротив. Таким макаром, маленькая окружность вибрации не просто подходит для незапятанной шлифовки, а большая (в композиции с массивным мотором) — для обработки огромных поверхностей с высочайшей производительностью снятия стружки.
Внимание! Чем выше скорость шлифмашины тем резвее, одновременно грубее обработка поверхности. Массивные инструменты характеризуются высочайшей производительностью.
Тормозная система шлифмашинок.
Эксцентриковые машины неких производителей поначалу помешают на обрабатываем поверхность, а затем включают. Тормоз шлифовальной тарелки, иди, говоря проще, автоматическая система торможения, препятствует образованию бороздок при помещении тарелки на материал, если машина уже включена.
Поперечникы шлифовальных тарелок для эксцентриковых шлифмашинок, составляющие 115, 125 и 150 мм, — самые удобные. Нередко уже в самом заглавии инструмента бывают указание на размер тарелки. Шлифовальные тарелки поперечником 115 и 125 мм в особенности неплохи для обработки вогнуто.выпуклых поверхностей, и дополнительно различных закруглений. Тарелки поперечником 150 мм, напротив, не просто подходят для грубых работ и созданы для огромных плоских поверхностей. В итоге при большенном поперечнике шлифовальной тарелки, зависимо от зернистости шлифовальных кругов и окружности вибрации, производительность шлифовки выше. Если нужна четкая работа в узеньких местах, предпочтительна машина с тарелкой наименьшего поперечника.
Большая часть эксцентриковых шлифовальных машин имеют функцию отвода пыли. Он может выполняться несколькими методами: через подошву, с помощью пылеотвода, по другому с помощью шланга и мешка для сбора пыли. Конечно модели, где конечно отсоединять пылесборник либо поменять его положение.
Технология полировки шлифмашинкой
Работа инструментом во многом сходна с полировкой своими руками, но большая ее часть выполняется автоматически – за этим нужно внимательно следить. Начинается обработка автомобиля с установки нужного полировального круга и разгона аппарата до 1200-1500 об/мин. Затем диск просто прижимается к поверхности кузова и двигается по его плоскости. Процесс требует постоянного контроля:
- Неравномерное давление опаснее, чем сильное (приводит к неравномерному снятию лака).
- Сильное давление опаснее, чем слабое (может стать причиной сильного стирания ЛКП).
Кузов автомобиля нагревается в процессе обработки, поэтому останавливаться на одном месте нельзя. Локальный перегрев может привести к растрескиванию, отслаиванию лака и краски, поэтому нужно тщательно контролировать нагрев. Высокая скорость работы машинки для полировки авто приводит к быстрому забиванию кругов – необходимо периодически менять их, для того чтобы остатки ЛКП не разносились по поверхности авто. Периодически нужно выключать инструмент и внимательно осматривать место обработки, удалять образующуюся пыль салфетками, одновременно с этим смачивая поверхность водой или очищающей жидкостью.
Полировка производится мелкозернистым абразивом, но в качестве такового может вступить даже обычная пыль. По этой причине, а также по причине нагревания автомобиля во время его полирования, следует проводить обработку в закрытом, защищенном от пыли и солнечных лучей помещении. При нагреве выше 90°C, акриловые эмали могут потерять свой блеск окончательно, а при шлифовании авто под солнцем такой нагрев не редкость.
Урок № 24 Орбитальная и эксцентриковая шлифмашины в чем разница. Обзор риски ( малярное дело )
Приветствую, Вас! Сначала рекомендую отличные онлайн магазины. продукты и услуги недорого: Поле.
Российского} автопрома предлагают широкий выбор шлифовальных принадлежностей. Они быть заходить в серийную комплектацию машины либо приобретаться дополнительно. К принадлежностям относят различные крути: абразивные, самоклеящиеся или зажимные, на картонной или тряпичной базе, и дополнительно различной зернистости. Чем меньше зернистость, тем грубее обработка.
Для полировки в эксцентриковых шлифовальных машинах предусмотрены особые полировочные круги. Конечно также особые круги лля обработки древесной породы и покрытия, ватное полотно для снятия ржавчины и грубой грязищи, полотно для втирания полироли, полировальная губка лля втирания воска, особое полотно из войлока для полировки «до блеска» и пр.
Способ крепления расходников.
К подошве эксцентриковых шлифовальных машин укрепляют сменные листы. Крепление их к рабочей плоскости инструмента осуществляется при наличии зажима либо «липучки». Модели с зажимными креплениями дешевле и универсальное, так как сюда проще подобрать расходные материалы. Но крепление на «липучку» скорее и удобнее.
Дополнительные возможности эксцентриковых шлифмашинок.
Некие модели допускают смену подошвы. К примеру, установку подошв поперечником 115 и 125 мм, созданных для различного объема и типа работ.
эргономичность. Некие отечественные изготовители оснащают собственный инструмент особыми вибронакладками на ручки, уменьшающими вибрацию. У массивных моделей на корпусе вам понравятся дополнительная ручка для более комфортной работы. обычно бывают вариации повытрепываться только круглой ручкой сверху и корпусом округленной формы, который можно обхватить одной рукою. Дополнительной ручки у их нет. и возможность ее присоединения не предусмотрена. Ручки имеют форму хомута, дуги либо штанги.
Дополнительные ручки конечно отчасти откидывать (к примеру, при шлифовке по краю поверхности), приводить в разные позиции и кроме того поворачивать вокруг корпуса.
плавный запуск пли поддержание неизменного количества оборотов существенно упрощают работ)’. Можно легко и просто найти количество оборотов и вибраций учитывая материала. В особенности комфортна полноволновая электроника, которая обеспечивает плавную регулировку оборотов. А функция установки малого количества оборотов позволяет обрабатывать термочувствительные материалы.
До того как включить эксцентриковую шлифовальную машину, следует пристально подробно изучить аннотацией производителя.
Для полировки поверхностей лучше использовать модель, снаряженную управляющей электроникой, которая позволяет регулировать частоту колебаний. Что существует, что при таких работах частота колебаний обязана стать меньше, чем при шлифовке. Если юзер будет полировать поверхность на «больших оборотах», перегреется движок как еще его называют повредится обрабатываемый материал.
Лакированные поверхности советуют шлифовать на малой скорости. Они очень чувствительны к высочайшей температуре, для заслуги рационального результата нужно смотреть за тем, чтоб температура не повышалась. Спецы рекомендуют использовать в схожих случаях незапятнанные абразивы и даже не очень очень жать на шлифмашину, чтоб не создавать дополнительное трение.
Для шлифования пластмасс употребляют абразивные круги со степенью зернистости 240 и выше. При обработке поверхностей из металла зернистость абразивного круга желательна двух или больше 600.
Стоит ли игра свеч?
Окружающая среда, поездки за город и не всегда качественное дорожное покрытие приводят к появлению трещин, сколов и царапин на кузове и бамперах. Воздействие прямых солнечных лучей подвергает краску к выцветанию, что приводит к потребности обновления или ремонта лакокрасочного покрытия автомобиля.
Мнений на счет полировки и мелкого ремонта огромное множество, и некоторые считают, что полировка болгаркой автомобиля может привести к ещё худшим результатам. Это мнение можно назвать ошибочным потому, что правильный и точный подход к работе и выбор нужной технологии позволят получить прекрасный результат.
При выборе правильных материалов можно привести к первозданному виду даже самый запущенный авто. Изначально нужно определить фронт работ и выбрать подходящую пасту и полироль, среди которых выделяют несколько типов:
- абразивный и неабразивный — это относится к пасте и полироли;
- силиконовые полироли;
- полироли-восстановители.
Пасты маркируются, для абразивных используются обозначения J3, J6, J7, J10 и М3. Спросом пользуются пасты-полироли. Стоит помнить, что аэрозольный баллон для полировки предназначен для придания окончательного вида и блеска.
При подготовке кузова используется мелкая наждачная бумага Р 2000. Она быстро забивается, поэтому требуется часто смачивать водой поверхность. Такая мелкая наждачная бумага позволит избавиться от глубоких царапин и сколов краски.
Абразивные полироли применяются для снятия потертостей и царапин с лакокрасочного покрытия авто. Обработка таким средством удаляет незначительный слой лака, после чего нужно будет его восстановить. На следующем этапе работы наносится защитный силиконовый полироль. Он заполняет самые мелкие трещины, микроцарапины и придает блеск.
Чтобы не выполнять весь спектр работы вручную, проводится обработка болгаркой автомобиля. При работе используются специальные круги. Машины для шлифовки выбирают эксцентриковые с высокими оборотами биения. Лучше приобретать профессиональный инструмент, например, таких марок как Makita или Bosch.
Выбор
Проф модели созданы для длительной непрерывной работы. Качество материалов, использованных для их производства, надежность узлов и электроники намного выше,
чем у бытовых шлифовальных машин. Инструменты проф класса созданы для многосменной работы в насыщенном режиме, потому в этот список предъявляют более высочайшие эксплуатационные требования. Вы, они чем просто по размеру, а их движок сильнее.
рядового потребителя созданы для работы от варианта к случаю. Они рассчитаны на внедрение за период 20 часов за месяц, обычно имеют наименьшую мощность и вес, более низкую производительность и меньше дополнительных функций. Достоинства бытовых систем — применимая для домашнего мастера иена и удобство в эксплуатации.
Следует смотреть на гарантию производителя и наличие сервисных центров, в каких есть вариант починить инструмент как еще его называют произвести техно профилактику. Непременно обусловьтесь с объемами и специфичностью работ, которые предстоит делать. Если инвентарем подразумевают работать что ни день, лучше приобрести модель проф класса.
Бытовой инструмент не управится с непосильными задачками и выйдет из строя ранее времени. При этом гарантия на такую машину распространяться не будет (если в сервисе выяснится, что инструмент использовали с превышением рекомендуемого производителем режима). Объемы выполняемых работ оказывают влияние на многофункциональные особенности инструмента.
Популярные марки и производители вибрационных шлифовальных машинок
- DeWALT
- Black Decker
- Bosch
- Hitachi
- Makita
- Skil
- Metabo
- AEG
Выводы:
- При помощи неких моделей конечно шлифовать бетон
- Большая часть систем управятся с металлическими поверхностями
- Самая нужная работа-зачистка и полировка дерева
- Марка расходного материала – залог долговечности и производительности
- Если позволяет поперечник отводящей трубы, ее конечно соединить при помощи пылесоса
- Пыль может отводиться в приемник, который просто разобрать и почистить
Источник
Зачем полировать?
Полировка может понадобиться не только при появлении незначительных повреждений или царапин. При помощи абразивных паст и средств для полировки кузов автомобиля возможно содержать практически в первозданном виде. Панель приборов, фары и бампера полировка позволит поддерживать в идеальном состоянии. Главное выбирать нужный вид средства при определенной работе.
Абразивы постепенно удаляют верхние покрытия лака и краски, постоянная полировка приведет к обратному результату. Если нет необходимости в обработке кузова автомобиля, не нужно злоупотреблять абразивной полировкой. Это может привести к полному удалению лакокрасочного покрытия, вплоть до металла, в таком случае потребуются более дорогостоящие процедуры по восстановлению краски, нанесению лака и завершающей полировке.
Методы шлифования | Мокрое или сухое
Одни и те же абразивы при работе «на сухую» и «на мокрую» всегда отличаются по своей агрессивности, кроме того, нередко бывает, что указанная зернистость не соответствует действительности. Если мы возьмем, к примеру, круг P400 от sia и лист от того же бренда и той же градации, которым будем работать «на мокрую», то получим совершенно разные результаты — мокрая обработка будет значительно грубее. Именно для этих целей мы и затеяли наш эксперимент: часто для достижения нужного результата достаточно обработки шлифмашинкой с 400-м кругом. По нашему опыту, при обработке поверхности с водой (ручным способом) глубина риски возрастает примерно в 2 раза. То есть сухая машинная обработка 400-м кругом сопоставима с мокрой шлифовкой листом P800 вручную. Если мы обработаем деталь, скажем, кругом P240, то результат будет как от мокрой ручной обработки листом градации P400–500. Важно отметить, что если мы будем шлифовать одной и той же градацией одним и тем же способом (допустим, шлифмашинкой, которая дает более стабильные показатели), но в одном случае «на сухую», а в другом — с увлажнением, то мы получим разницу в глубине риски примерно в 1,5 раза, где риска с увлажнением будет грубее.
Отдельный акцент стоит сделать на выборе шлифмашинок для разных работ. Если мы проводим финишную подготовку детали перед покраской, то лучше выбирать шлифмашинку с ходом эксцентрика 2,5–3 мм; если это подготовка под грунт, — можно использовать эксцентрик 5 мм; если нам необходимо вообще полностью снять покрытие, — выбирать стоит машинку с еще большим ходом эксцентрика (минимум 9 мм).
Как мы выяснили, удобнее, быстрее и эффективнее обрабатывать деталь с помощью шлифмашинки «на сухую» — этот метод в авторемонте уже давно стал наиболее популярным. Но, конечно, не всегда есть возможность зашлифовать деталь полностью машинкой. К примеру, основные участки бампера мы уже прошли шлифмашинкой и остальные нужно обработать вручную. Как это сделать проще всего? Допустим, мы не хотим использовать воду, поэтому с машинки снимаем кружок и вручную начинаем им обрабатывать труднодоступные участки. Но так как на машинке 400-й абразив — это одно дело, а при обработке этим же абразивом вручную результат получается значительно грубее. Поэтому после того, как вся шагрень будет спилена, берем двухстороннюю губку sia Ultrafine (синего цвета) и дошлифовываем эти же участки. Важно, что зерно губки должно быть мельче, чем на машинке: например, ориентировочная градация синей губки от sia составляет примерно P800 и зависит от степени нажатия.
Как правило, кто привык дорабатывать сложные участки «на сухую», уже не вспоминает про мокрую обработку. Есть, впрочем, мастера, которые панически не принимают полностью «сухой» метод и утверждают, что с водой им проще работать. Но такой способ все же значительно энергозатратнее: деталь надо просушить, пройтись обезжиривателями на водно-спиртовой основе, чтобы убрать примеси, содержащиеся в воде… В свою очередь, «на сухую» гораздо проще контролировать результат, который при обработке «на мокрую» можно увидеть только после очистки и сушки обработанного участка.
Как сделать шлифовальный станок
Чтобы приступить к работе над этой шлифовальной машиной, я нашел подходящий двигатель. Это отстойный насос в виде пьедестала (показан ниже), и они очень распространены. Часто сам насос изнашивается и выбрасывается, но двигатель по-прежнему работает нормально. Даже новые, они часто невероятно недороги, так что о продаже их не исключено.
У меня 1/3 л.с. и 1725 об / мин. Размер и скорость важны, так как этой шлифовальной машине действительно не нужен очень мощный двигатель, и она не будет столь же эффективной для шлифования дерева с помощью более быстрого.
Общая длина 8-1 / 2 ″ (216 мм), диаметр корпуса и длина корпуса 5-3 / 4 ″ (146 мм). Вал имеет 1/2 дюйма (12,7 мм) и длину 1-1 / 4 дюйма (32 мм). Часть на передней части двигателя, которая была прикреплена к трубе основания, имеет диаметр 1-7 / 8 ″ (48 мм) и длину 1 ″ (25 мм). На задней крышке имеется круглый выступ диаметром 1-3 / 4 ″ (44 мм) и длиной 3/8 ″ (10 мм):
Вал вращается против часовой стрелки, если смотреть спереди. Это типично для этих двигателей, но лучше подтвердить это перед фиксацией, так как их очень сложно отменить.
Подключение не должно быть сложным. Здесь я на самом деле прикрепил металлическую электрическую коробку к торцевой крышке шнура питания и переключателя:
Я использовал маленькие винты для листового металла, чтобы прикрепить коробку, и для этого снял торцевую крышку с двигателя. Если ваш двигатель поставляется с более длинным шнуром, имеет смысл установить переключатель отдельно, а не делать это. Провода у меня были очень короткими, и лучше всего было установить коробку на двигатель.
Что касается вырезания деталей, то шлифовальный станок спроектирован так, чтобы он был изготовлен из фанеры 1/2 ″ (13 мм) исключительно для того, чтобы максимально упростить сборку. Я использовал балтийскую березу, но подойдет и любая мебельная фанера хорошего качества. Хотя это возможно, я не рекомендую использовать для этого МДФ или ДСП.
Здесь я вырезаю основную стойку и делаю упор для выемки наверху:
Затем я закончил пропил своей ленточной пилой , но также подойдет лобзик или ручная пила.
У этой детали также есть выемка наверху со скошенными сторонами (в плане изменена на одну сторону под углом), и я отметил это, используя размеры на плане, прежде чем вырезать на ленточной пиле:
Эта выемка предназначена для узла кронштейна верхнего колеса и позволяет ему перемещаться для регулировки трекинга и натяжения ремня.
Основная стойка имеет два положения для гаек, и я сверляю неглубокие зенковки с помощью долота Форстнера 3/4 ″ (19 мм):
Затем просверлите отверстие сверлом 5/16 ″ (8 мм):
Есть пять мест, где t-образные гайки используются таким же образом, с мелкой цековкой перед сквозным отверстием.
Разделитель – это передний монтажный кронштейн для двигателя, и для него требуется отверстие, соответствующее носу. У меня 1-7 / 8 ″ (48 мм), я просверлил самый близкий к нему размер, а затем зашлифовал отверстие, чтобы оно соответствовало:
Если у вас есть двигатель, у которого нет этого удлинителя носовой части или к нему уже прикреплен монтажный кронштейн, вам придется придумать другой способ его крепления. Главное, чтобы вал был в нужном месте и мотор держался надежно.
В нижней крышке диска есть круговой вырез, который чуть больше нижнего колеса, и я использую свой компактный циркуль, чтобы нарисовать эту дугу:
У меня есть кусок фанеры той же толщины, чтобы выдвинуть точку поворота за пределы детали, и радиус, который я установил компасом, совпадает с точками, отмеченными на детали на чертежах.
Также необходимо отверстие для плотного прилегания к шлангу пылесоса, используемому для сбора пыли:
Если вы думаете, что будете часто шлифовать диск под углом, возможно, лучше будет найти отверстие для сбора пыли на передней панели шлифовальной машины. Как бы то ни было, при наклоне дискового стола шланг будет мешать. Я очень и очень редко меняю дисковый стол с 90 градусов, поэтому шланг здесь лучше всего подходит для меня.
Колеса сделаны из трех слоев фанеры, заготовки я вырезал квадратной формы и немного увеличенного размера.Точки поворота для верхних колес будут подшипниками, используемыми для верхнего колеса, и я просверлил их после разметки центров:
Это ступенчатое отверстие, в котором просверлено отверстие 7/8 ″ (22 мм), соответствующее толщине подшипника:
Я буду использовать фрезер с круглым зажимом, чтобы вырезать их, и для этого использовал двусторонний скотч, чтобы проделать отверстия в заготовках на обрезной фанере:
Вот круглый зажим – просто стержень с резьбой, ввинченный в основание фрезы, и шарнирный блок с вставленным хвостовиком сверла 3/8 дюйма.Бита подходит к используемым подшипникам:
Резка выполняется в три прохода, с каждым углублением:
Этот метод позволяет получить почти идеальные колесные заготовки, поскольку он вращается на подшипнике, который будет использоваться в готовом колесе.
Заготовки нижнего колеса изготавливаются таким же образом, за исключением того, что вместо отверстия для подшипника требуется только поворотное отверстие 3/8 ″, чтобы в него поместился хвостовик сверла. Необходимо вырезать две нижние заготовки, чтобы очистить шкив, и мне действительно следовало нарисовать этот круг перед сверлением отверстия для шарнира:
Я лобзиком вырезал середину:
А потом исправил это с помощью этого простого приспособления на шпиндельной шлифовальной машине:
Эта деталь не является строго необходимой, так как балансировка для таких маленьких колес не представляет большой проблемы.Я более или менее сделал это просто для того, чтобы показать эту простую приспособление для создания концентрической внутренней окружности.
Готовых колесных заготовок:
Разметка кронштейна верхнего колеса:
И вырезать:
Я снова использовал ленточную пилу и внимательно следил за линиями. Порезы должны быть хорошими, но здесь есть некоторая терпимость.
Стол для наклона ремня нуждается в частичном скосе, и я сделал это от руки на настольной пиле, просто откусив угол, пока он не приблизился:
Важно помнить, что не каждый разрез должен быть идеальным, особенно такой, который предназначен только для очистки.
Все детали из фанеры вырезаны, просверлены и готовы к сборке:
ПРИМЕЧАНИЕ : На плане, на котором подробно описана стойка, отсутствуют два размера, которые показаны здесь:
Поскольку они должны высохнуть в течение ночи, я сделал ручки и сделал ручки из квадратной сосны размером 1 дюйм (25 мм):
Я обрезал стержни с резьбой до нужной длины и отшлифовал плоское пятно на конце, которое приклеивается к ручке:
Плоское пятно фиксирует стержень в ручке и помогает предотвратить его проворачивание после схватывания клея.
Затем использовал строительный полиуретановый клей для приклеивания шпилек в:
Затем я собрал колеса, используя обычный столярный клей. Перед зажимом убедился, что заготовки выровнены точно:
Я использовал гвоздодер со штифтом, чтобы удерживать детали на одном уровне и не позволять им скользить во время зажима. Другой вариант – шурупы – перед приклеиванием просверлите пилотные отверстия, и тогда шурупы тоже будут зажимать.
Вертикальная сборка состоит из трех слоев, которые склеиваются и зажимаются следующим образом:
После высыхания (на следующий день) установил t-гайки:
Колеса и верхний кронштейн колеса в сборе после сушки в течение ночи:
Может возникнуть соблазн поторопиться с некоторыми деталями, но я рекомендую дать этим важным узлам как минимум 8 часов, чтобы они полностью высохли, прежде чем снимать зажимы.Это может занять много времени, чтобы клей, находящийся внутри стыка, полностью высох и достиг нужной прочности. Если вы хотите ускорить процесс, лучше всего подойдет эпоксидная смола с быстрым схватыванием, или вы можете добавить винты, чтобы постоянно удерживать детали вместе.
Пока клей высыхал на узлах, я установил шкив на вал двигателя и выровнял поверхность:
Я прижал его к куску 2 × 8 с помощью самодельного зажима для ремня и установил фанерный упор для долота 1/4 дюйма, который использовал для работы.Это не заняло много времени, и видео внизу страницы показывает процесс.
Чтобы закрепить нижнее колесо, я начал с того, что прижал его очень близко к шкиву с помощью двустороннего скотча. Опять же, видео-удар показывает это вживую и лично. После того, как колесо было правильно отцентрировано, я просверлил отверстия, чтобы отметить места отверстий для винтов на шкиве. Затем я мог снять колесо и сверлить отверстия:
Четыре винта удерживают колесо на шкиве, и я обнаружил, что это лучший и самый надежный способ соединения такого типа.Шкив в основном действует как монтажный фланец для нижнего колеса.
Если колесо не отцентрировано идеально (мое было достаточно близко), вы можете исправить это, отключив лишнее, как на токарном станке. Я делал это в своей предыдущей ленточно-шлифовальной машине проекта .
ПРИМЕЧАНИЕ. Планируется использовать винты 1-1 / 4 ″ для крепления нижнего колеса, но на самом деле это винты 1 ″, как указано в списке материалов.
Основная сборка начинается с прикрепления стойки к основанию, и здесь я отметил точное местоположение:
Я использовал 5-минутную эпоксидную смолу, чтобы приклеить стойку к основанию и дать ей застыть, пока я обедал.Когда эпоксидная смола высохла, я мог затем просверлить и завинтить винты снизу, и мне не нужно было беспокоиться о ее движении:
Обратите внимание на ориентацию основания во время сборки. Я пометил «назад» на своем, и это соответствует плану.
Мне пришлось надрезать задний кронштейн двигателя, чтобы выключить выключатель питания:
У моего двигателя есть эта крышка подшипника на задней стороне, которая выступает, но если у вас нет, вам нужно будет придумать другой способ поддержки задней части двигателя.Одна из возможностей – ввернуть винты прямо в заднюю крышку двигателя, если они достаточно короткие, чтобы ни во что не попасть. Лучше всего использовать большие хомуты для шлангов, которые оборачивают корпус двигателя и прижимают его к фанерной полосе под ним. Затем полосу можно прикрутить к разделителю спереди и к заднему кронштейну двигателя сзади.
Шлифовальная машинка разработана для мотора, который у меня есть (который очень распространен), и вам, возможно, придется внести некоторые изменения в некоторые детали, если вы используете другую модель.Имейте это в виду, работая над этой частью сборки:
Чтобы стабилизировать двигатель и предотвратить его вращение, я приклеил два блока между разделителем и передней частью двигателя:
Позже я изменил это на лучшее решение, но решил показать его здесь для протокола. Эта сборка была прототипом, и по ходу я работал над некоторыми проблемами и трудностями.
Плита прикручена к разделителю, и он должен совпадать с передней частью колеса и не касаться его.При необходимости внесите изменения:
Я сделал пластину из стали, но алюминий – тоже хороший вариант. При необходимости его можно сделать выше.
Трекинговый кронштейн приклеивается и привинчивается к стойке в сборе:
Это еще одна деталь, у которой сзади есть Т-образная гайка, которую я установил перед закреплением кронштейна.
Затем крепится лицевая панель, и самое время поговорить о клее. Разделитель, задний кронштейн двигателя и передняя панель крепятся без клея, так как вам может потребоваться взять шлифовальный станок для обслуживания:
Я также установил ремень на этой фотографии, чтобы проверить длину и посмотреть на верхнее крепление.Оказалось, что была проблема с моей первоначальной концепцией «безаппаратного» шарнира для верхнего кронштейна колеса, но я попробовал несколько вещей и нашел простое решение.
Кстати о проблемах, мое первоначальное место для ручки регулировки натяжения было немного не так:
Переместил и планы обновились.
Исправление проблемы с кронштейном верхнего колеса заключалось в добавлении двух блоков вверху, чтобы построить его:
Опять же, это было изменено в планах по исправлению проблемы.
Я сделал пластины из листового металла для контактных точек ручки трекинга и натяжения на узле кронштейна верхнего колеса. Я скрепил их двусторонним скотчем:
Еще одна небольшая проблема в моем первоначальном дизайне заключалась в расположении винтов с правой стороны нижней крышки колеса. Длину этой части (а также стола с дисками) необходимо отрегулировать после сборки основной части шлифовальной машины. Фанера разной толщины может привести к тому, что эти детали получатся слишком длинными, и их придется подрезать.Я переместил винты дальше на панели, и вы должны обрезать правую сторону, чтобы отрегулировать длину:
Дисковый стол в сборе после отрезания его до нужной длины:
Стол для наклона ремня использует для работы стыковой шарнир, который крепится шурупами 1/2 ″. У меня их не было, поэтому кончики моих винтов торчали, и мне пришлось отпилить их заподлицо:
Наклейка на блоке крепления стойки… неправильно – скос должен быть обращен в другую сторону:
На самом деле, лучше оставить квадрат квадратным и при необходимости выровнять только угол.Как выяснилось у меня, стол полностью опускался до 45 градусов без ударов:
Стойка крепится к блоку стойки с помощью одного винта и шайбы. Винт затягивается, затем слегка ослабляется, чтобы дать стойке возможность работать:
Установив верхнее колесо, натянув и затянув ремень, я отшлифовал небольшую коронку на верхнем колесе с помощью одного из моих шлифовальных файлов :
Я показываю это на видео сборки внизу этой страницы.Колесу не нужна корона, чтобы оно могло правильно двигаться.
Также подправил переднюю грань нижнего колеса, так как к нему будет крепиться шлифовальный диск:
Это также видно на видео. Позже я нанесла несколько слоев полиуретана, чтобы улучшить поверхность самоклеящегося диска.
На этом фото также виден небольшой скос на внутренней стороне нижней крышки диска. Я сделал это, чтобы улучшить сбор пыли с диска.
Теперь перейдем к усовершенствованному способу удержания двигателя в неподвижном состоянии. Сначала я вырезал блоки, которые я склеил, с помощью самодельной пилы «ласточкин хвост» :
Затем я прикрутил кусок фанеры между двигателем и разделителем и частично просверлил отверстие в носовой части двигателя:
2-дюймовый шуруп для дерева, вбитый внутрь, фиксирует двигатель на месте намного лучше, чем два блока:
Фанерный блок просто прикручивается двумя винтами 1 ″ через разделитель:
Не обязательно, но из-за этого машина выглядит круче. Я просверлил четыре отверстия в верхнем колесе и снял фаски с краев на моем фрезерном столе :
Кроме того, когда я переустанавливал верхнее колесо, я нанес немного полиуретанового строительного клея на конец стержня с резьбой перед тем, как навинтить внешнюю гайку.Это предотвратит развинчивание гайки.
Лучшим выбором для переключателя является более старый тип переключателя, чем эта модель Decora. Я сделал фанерный кожух, чтобы было труднее случайно включить шлифовальный станок, и приклеил его на пластиковую пластину:
Я снова разобрал шлифовальную машинку и покрыл все детали двумя слоями полиуретана, чтобы она хорошо выглядела и защищалась от влаги. Я дал ему высохнуть в течение целого дня, прежде чем снова собрать:
Если вы заинтересованы в создании одного из них для себя, доступны планы:
В планах изображен стенд.
Сделал видео сборку этой шлифовальной машины:
Как сделать идеальный шлифовальный блок
Когда дело доходит до шлифования, правила просты. Когда вы имеете дело с кривыми и мягкими краями, вы можете использовать контуры руки, чтобы скопировать наждачную бумагу и естественным образом имитировать форму. Но когда дело доходит до плоской поверхности: никогда не шлифуйте без шлифовального блока. Благодаря этому бумага останется ровной, а значит, и ваш окончательный проект останется плоским.
У меня была дурная привычка резать новую каждый раз, когда я приходил к завершению проекта, что иногда означало, что я шел против моего здравого смысла и игнорировал правило шлифовального блока при работе с плоскими панелями и столешницами. (Знаю, знаю.) Итак, я решил потратить час и создать блок, который я буду рад использовать каждый раз. Тот, который удобен, обеспечивает отличную отделку и наилучшим образом использует мою наждачную бумагу, сводя к минимуму отходы.
Примечание: сделать два или три из них так же легко, как и один, поэтому мы рекомендуем создать несколько из них за один раз, чтобы они были всегда под рукой.
Шаг первый: Определите размер наждачной бумаги.
Никто не использует сразу весь лист наждачной бумаги. Итак, размер вашего блока должен быть как можно более экономичным. Размер стандартного листа наждачной бумаги составляет 9 × 11 дюймов, и чтобы сделать блок, который поместится в руке, лучше всего разделить его на четыре части (один горизонтальный сгиб, один вертикальный) или шесть (два горизонтальных сгиба для создания трети , одна вертикаль).
Мой блок разработан для использования шести частей, что делает блок более удобным для удержания.Я начал с того, что сложил лист пополам на стороне 11 дюймов, как букву.
Затем я положил линейку на складки и разорвал ее на части. Вы можете использовать здесь ножницы или нож, но вы просто стучите лезвиями. Как только они составили тройки, я сложил каждую пополам и снова разорвал. Шесть более-менее ровных штук.
Шаг второй: Отрежьте блок до нужного размера.
Сам блок строится из строительного бруса «вдвое». Здесь, на северо-западе, это может быть могучая ель Дугласа, но там, где вы живете, это может быть сосна или даже белая древесина.Я использовал имеющийся у меня обрезок размером 2 × 10, у которого были хорошие прямые волокна по краям, которые я мог обрезать с одного конца, чтобы получить по существу распиленный материал на четверть. К тому времени, когда его начали гладко, он оказался чуть севернее 1 1/4 дюйма в толщину.
Затем я разрезаю полоску так, чтобы обрезки наждачной бумаги наматывались на 1/4 дюйма с каждой стороны, что позволяло легко удерживать бумагу во время использования. Моя окончательная ширина составила 2 7/8 дюйма.
Затем я разрезал полосу на несколько блоков по 4 дюйма.
Окончательный размер блока = 1 5/16 ″ толщиной x 2 7/8 ″ шириной x 4 ″ длиной .По краям есть хорошая ровная полоса излишков бумаги толщиной 1/4 дюйма.
Шаг 3: Сформируйте блок.
Чтобы сделать его более удобным в использовании, я прикрепил блок к своему рабочему столу, а затем сделал широкую фаску 45 ° по верхним краям. Я сделал это с помощью маршрутизатора, но вы можете использовать ручной рубанок или даже пилу, если будете осторожны.
После того, как начальные грани были вырезаны, я зачистил все острые углы и края наждачной бумагой.
Шаг четвертый: Добавьте пробку.
Последний шаг – прикрепить пробку к нижней части блока. Это позволяет блоку размещать невидимые гребни, впадины и пики в древесине. Вы не можете их сейчас увидеть, но они значительно улучшат качество вашей окончательной отделки.
У меня есть рулон пробки толщиной 3/32 дюйма, который я использую для множества проектов, так что я просто использовал его. Но вы можете купить пробку толщиной 1/8 дюйма в магазине товаров для рукоделия или на Amazon. Вы также можете использовать пробковую бумажную подкладку для полок Con-Tact, которая имеет клейкую основу.
Что бы вы ни использовали, сначала сделайте негабаритный. Нанесите тонкий слой желтого столярного клея на обе поверхности, дайте ему стать немного липким, затем сложите клеевые стороны вместе. Зажмите или установите что-нибудь тяжелое на блок, чтобы обеспечить полный контакт.
После высыхания клея используйте стороны блока в качестве направляющих, чтобы обрезать пробку до нужного размера.
Если можете, разрежьте пробку с небольшим скосом, чтобы немного облегчить острые края, затем используйте наждачную бумагу, чтобы немного скруглить все вокруг.
Для использования оберните кусок наждачной бумаги вокруг дна и держите его за края. Тогда просто отшлифуйте!
Эта вещь очень удобна в использовании, лучше всего использует лист наждачной бумаги и помогает создать гладкую поверхность. Это делает шлифование по-настоящему увлекательным! Ну, почти.
Информационный центр изготовителя ножей своими руками: 12-дюймовый дисковый шлифовальный станок
Самодельный 12-дюймовый дисковый шлифовальный станок
Одна из вещей, которые я чаще всего использую в магазине, – это маленькая дисковая шлифовальная машина на моей комбинированной ленточной шлифовальной машине 4×36 дюймов / 7 дюймов.Он довольно легкий, и когда я увидел на YouTube несколько примеров того, как другие делали 12-дюймовую деревянную заготовку, я задумался о своих записках и подумал, не смогу ли я собрать что-нибудь по дешевке.Мотор
Я купил на гаражной распродаже двигатель мощностью 1/2 лошадиные силы 1750 об / мин за 5 долларов. Вал 5/8 “, и мне придется что-то установить для установки диска. Кража за 5 долларов, но тогда и продавец, и я никогда не знали, работает ли он в то время. Это работает! пусковой конденсатор приводит к вращению двигателя против часовой стрелки (если смотреть на вал).
Диск
Я купил кусок алюминия толщиной 1/4 дюйма в металлическом супермаркете. Это, вероятно, будет самый дорогой элемент в сборке. Я сократил его до 12-1 / 2 x 12-1 / 2 дюйма с помощью лобзик. Я использовал малярный скотч и хорошо зажал кусок перед резкой. Это медленно, но выполнимо. Я нашел примерную центральную точку.
Пробили ямочку на перекрестке.
Затем, используя штангенциркуль, установленный на 6 дюймов, я поцарапал круг. Затем я прошел по кругу фломастером.
На портативной ленточной пиле вырезал круг. Это было сделано в 8 небольших разделах. Я остаюсь за линией, так как буду исправлять круг после того, как он будет установлен.
Вуаля! Круг диаметром 12-1 / 8 дюйма из алюминия толщиной 1/4 дюйма.
Я нашел этот шкив с плоской гранью. Он имеет отверстие 5/8 дюйма (соответствует валу двигателя), имеет установочный винт и имеет внешний диаметр около 3 дюймов.
Для крепления шкива я использовал четыре крепежных винта 10-24 с плоской головкой.
Я поставил шкив прямо по центру и просверлил одно отверстие.Винт и гайка помогут удерживать его на месте при сверлении других отверстий.
На лицевой стороне отверстия утоплены со стандартной зенковкой 82 °. Идея здесь в том, что никакая часть головки винта не находится над поверхностью. Постарайтесь, чтобы они были идеально промытыми.
Я использовал немного лака для ногтей для фиксации резьбы крепежных винтов, чтобы гайки не ослабли.
Теперь двигатель и диск в хорошем состоянии, пришло время построить раму для крепления двигателя и возможность крепления на столе.
Рама
В куче металлолома у меня есть утилизированный канал размером 1-1 / 2 дюйма. Он используется как подпорка для больших картонных транспортировочных коробок, чтобы они оставались жесткими. Он сложен 18 калибра, так что это не самая сильная вещь, но когда он скреплен паутиной, это будет довольно сильным.Базовая рама имеет размеры 13 дюймов x 12-1 / 4 дюйма. 12-1 / 4 дюйма должны приблизить нас к диаметру диска, чтобы мы могли добавить пару вертикальных опор для удержания стола. Мотор необходимо поднять на 3 дюйма от верстака, чтобы диск вращался свободно. О да, он выглядит как Франкштейн, но будет работать нормально. Я приварил 4 болта 1/4 “NC x 1/2” к нижней стороне крепления двигателя. Пространство 3 x 5 дюймов по центрам. Мотор и диск туда поместились. Теперь наметим вертикали для поддержки стола. Я хочу, чтобы стол можно было регулировать примерно на 50 °.(От + 5 ° до -45 °) Повторно используя пластину 3/16 “x 3”, я сделал эти две вертикальные опоры для каждого конца стола. Я просверлил и приварил гайку 5/16 дюйма NC к каждому из них. Другие отверстия подходят для стержня с резьбой 5/16 дюйма для поддержки и точной регулировки. Я приварил опору к раме и установил стержень с резьбой 5/16 дюйма, который работал как ферма.
Другой вид с установленной фермой. Гайки можно отрегулировать для создания некоторого внешнего натяжения на вертикальной опоре. Когда мы затягиваем стол, он не сгибает опоры друг к другу.
Это фотография штока с двигателем и диском на месте.
Вот, после некоторого количества ржавой краски Royal Blue, мы готовы приступить к окончательной сборке.
Стол
Что касается стола, я имел в виду две вещи – регулируемый угол и легкий Удалить.При снятии стола необходимо сменить наждачную бумагу. Для того, чтобы стол раскачивался, мне нужно установить шарнир в правильном месте. Я поиграл в AutoCAD, чтобы увидеть, где должна располагаться точка поворота. Я решил, что мертвая точка на диске будет хорошей.
стол можно сделать из чего угодно плоского. Я выбрал сталь 3/16 дюйма,
купил для какой-то другой цели и сократил его до 16 x 8 дюймов.
Выровняйте выемку, пытаясь получить красивую прямую линию. Он будет проходить параллельно лицевой стороне диска, так что все, кроме прямой линии, будет смотреться в стороне.
Это должен сделать хороший большой стол для работы.
Я вырезал два куска 5-1 / 2 дюйма из угла 1-1 / 2 дюйма для крепления стола. Это позволит нам надежно затянуть стол, не сгибая его.
В каждом углу просверлены два отверстия диаметром 11/32 дюйма, чтобы пропустить звездочку или ручку с резьбой.
Проверка диапазона угла наклона стола.Выглядит неплохо.
Капюшон
К Я выбрал для работы что-нибудь более простое, чем сталь. я у меня была фанера 1/2 дюйма, и я разрезал ее на 12-5 / 8 дюймов на 12-5 / 8 дюймов. Я просверлил 3/4 дюйма отверстие в центре нарисовало дугу радиусом 6,25 дюйма. Это даст красивая круглая кривая. Я разрезал на ленточной пиле и зачистил на шлифовальной машине. Из дно я вырезал до дырочки, чтобы она скользила по мотору вал.
Контрольная установка на валу двигателя.
Вырезаю полукруг, снова 6.Радиус 25 дюймов из обрезков фанеры 3/4 дюйма. Другой разрез с радиусом около 4 дюймов дает изогнутую полосу шириной около 2 дюймов. Я разрезал это на «клинья».Клинья просверливаются, приклеиваются и прикручиваются по радиусу вытяжки.
Когда клей высохнет, я отрезаю полоску ДВП толщиной 1/8 дюйма шириной 2-3 / 8 дюйма и длиной 19 дюймов. Она приклеивается и прикручивается. Начиная с одной полосы и работая по кривой. Любые небольшие излишки обрезаются. под чистовую отделку.
Я использовал несколько шурупов с полукруглой головкой №10 для крепления вытяжки.
Это установленная вытяжка и стол.
Электрооборудование
Электрооборудование – это основная коммутируемая цепь. Я включил несколько фотографий, чтобы показать, что я сделал, но если вы в безопасности, дерзайте! Соедините белые провода вместе. Затем подключите зеленые провода. Добавьте новый кусок зеленого провода, скажем 4 дюйма, для соединения двигателя.Свяжите их проволочными гайками.
Обожмите несколько наконечников на черных проводах и подключите их к переключателю.
Установите выключатель в коробку 1110 и наденьте на него пластину. Я сделал несколько красных и зеленых прямоугольников из дюралейбеля и красных и зеленых фломастеров.
Завершение
Я вырезал из этикеток форму стрелки. Наклеил на капюшон.
Готовим стол.
Я собираюсь обшить нижнюю часть стола листовым металлом и добавить насадку для вакуумного шланга.
Здесь вы можете увидеть стол, затянутый болтами.
Клиренс близок к 90 градусам. Если диск с наждачной бумагой не приклеен должным образом, он продолжает вращаться. Эта штука действительно полезная. Я сделал несколько видеороликов, которые выложу на YouTube.
Ведомость материалов
Мотор: $ 5
Алюминий: 27 9000 долларов США. Шкив: $ 6
Винты: 2,50 $
Сталь: $ 12
Разное (кабельные стяжки, шурупы, краска): 5
долларов США. Электрическая коробка и плита переключателя: 5 долларов США.99
Шнур: 5 $
Коммутатор: 1,99 доллара США
Пластиковая втулка 1/2 дюйма: 0,49 долл. США
Текущий итог: около 71,00 долл. США
Самодельная дисковая шлифовальная машина Джона Хейса
Самодельная дисковая шлифовальная машина Джона Хейса Джон Хейс прислал мне несколько фотографий своей самодельной шлифовальной машины.
Иоанн пишет:
“Я построил большую часть этого вчера днем.
Я много подумал над деталями сборки перед тем, как начать и сделал некоторые элементарные рисунки с помощью SketchUp.
Это один из моторов для беговой дорожки мощностью 1 л.с., который я купил в Princess Auto.
Биение будет самым большим препятствием для этого типа шлифовальной машины, и Имея это в виду, я подумал, что небольшая гибкость тарелки может быть необходимым – поскольку объекты необходимо прижать к диску для шлифования, гибкость компенсирует любое незначительное биение. Маленький шкив служил это и сделал прочное соединение с валом (болтовое соединение, с эпоксидной смолой для нитеводитель). Я отфрезеровал поверхность шкива как можно более плоской, чтобы попытаться уменьшить количество биений, передаваемых на большой диск.
Между креплением двигателя и готовым агрегатом произошли некоторые пробы и ошибки. Сначала я использовал фанеру из балтийской березы 3/4 дюйма для тарелки и установил ее, Я мог «выточить» любой выбег от забоя. Не хорошая идея. Я никак не мог получить эту отфрезерованную плоскую поверхность с обеих сторон, а затем выбросить ее и переключить к меламину. Выбег с установленным диском составлял ~ 1/32 на ободе. Я довел это почти до нуля, приклеив диск клочком бумаги – один слой имел значение.Я покрыл край тарелки силиконом герметик, чтобы защитить его от влаги.
Я полагаю, что лучшим способом было бы установить шкив подальше назад. на валу, чтобы разместить вспомогательный диск меньшего размера, который может быть больше надежно фрезерованная квартира. Скажем, 6 дюймов фанера из балтийской березы, с прикрепленным блюдом. к этому. Я действительно могу внести это изменение, когда придет время для нового шлифовальный диск. На данный момент агрегат работает отлично.
Защитный кожух, покрывающий диск, сделан из деревянных кусков толщиной 3/8 дюйма, 1/2 дюйма. шириной, обрезанной под углом 4 градуса и приклеенной вокруг обода.Прошло 40 штук, длиной 2,5 дюйма.
Первоначально я собирался использовать листовой металл, но подумал, что так будет лучше.
Цапфы наклона я сделал на ходу, не зная наверняка, будет работать хорошо или нет. К счастью, они это сделали.
Вырезание паза для ручки фиксатора цапфы для цапфы стола штук на столе маршрутизатора. Использование хвостовика сверла в качестве центрального штифта для поворота детали во время фрезерования.
Две дуги, проложенные в фанере, образуют точный полукруг для неподвижной части цапф.
Затем полукруг разрезают на две четверти дуги.
Я прикрепил угол наклона к столу. Это та, что прилагалась к моей настольной пиле Makita (та, которую я выбросил, чтобы построить новый). На нем эти губы которые зафиксируют его на треке. Вместо того, чтобы отталкивать их, я сделал трек, чтобы принять их.
Хорошо работает, подходит для настройки под углом или под углом 90 градусов. При наклоне стола можно получить довольно точную составную торцовку. при необходимости обработать тонкой обрезной заготовкой – намного безопаснее, чем пытаться резать ее на отрезной пиле.
Джон Хейс с тех пор начал создавать свой собственный сайт с более подробной информацией об этой дисковой шлифовальной машине
Джон также выпустил видео на YouTube, демонстрирующее шлифовальный станок.
Начиная с 2:20 вы можете увидеть, как он работает.
И еще одно видео о шлифовальной станции, созданной для дисковой шлифовальной машины.
Создание луковой шлифовальной машины | Гильдия плотников Америки
Этот крутой инструмент отлично подходит для шлифования этих неправильных форм или очистки закругленных углов: там, где вам нужна управляемая комбинация руки и глаза, чтобы добиться нужного результата.Он состоит из пяти полос белого дуба толщиной 1/8 дюйма и имеет простую клиновую систему фиксации. Вам не потребуется никакого оборудования, просто отрезайте полоску одной из ваших старых шлифовальных лент размером 3 x 21 дюйма.
Я покажу вам, как сделать простую форму для гибки, которая прижимает склеенные полосы вместе самодельными клиньями, так что вам не нужно использовать один деревянный зажим. Просто следуйте инструкциям на фото и получите нужные вам размеры по чертежам.
Щелкните здесь, чтобы загрузить чертежи в формате PDF.
Изготовьте форму для гибки из фанеры 3/4 дюйма. Отрежьте гибкую деревянную планку на настольной пиле, а затем натяните ее вокруг гвоздей и между ними, чтобы размеры были такими, как показано. Это не часть круга. Левый и правый концы кривой более сглаживаются. Эта форма лучше всего подходит для удержания клиньев шлифовальной ленты на месте.
Вырежьте фигуру из фанеры ленточной пилой или лобзиком, затем обведите и вырежьте еще две части. Обозначьте правую и левую стороны каждой детали на случай, если кривая не совсем симметрична.
Склейте формы из фанеры ¾ ”и скрепите их друг с другом с помощью шурупов с обеих сторон.
Временно прикрутите изогнутые склеенные опалубки к листу фанеры размером 7 x 19-1 / 4 дюйма, как показано на рисунке. Проведите две линии вдоль кривой. Первые 3/4 дюйма – это зазор, необходимый для ламинирования. Разметка 1-1 / 8 дюйма предназначена для выравнивания центров штифтов диаметром 3/4 дюйма.
Удалите изогнутые части формы для гибки, чтобы у вас было немного больше места для локтей для размещения центров отверстий для длинных дюбелей в опорной плите.Обратитесь к чертежу, чтобы точно определить расположение отверстий. Если у вас есть сверлильный станок, он лучше всего подойдет для получения прямых перпендикулярных отверстий. Если вы используете ручную дрель, постарайтесь выпрямить их. Дайте клею застыть на ночь, а затем навсегда прикрутите изогнутую деталь к подложке.
Равномерно разорвите полоски длиной 24 дюйма на вашей настольной пиле. Я перевернул перьевую доску и зафиксировал ее на месте, чтобы можно было оторвать кусок, затем прижал бланк к краю перьевой доски и сдвинул забор до противоположного края, зафиксировал его и сделал следующий разрыв.Эта система дает точные разрывы, не пытаясь зажать их между лезвием и ограждением.
Возьмите полоски и испытайте их на форме. Чтобы согнуть и вставить полоски, потребуется немного тонкости. Возможно, вам будет полезно прикрутить всю форму к скамейке, чтобы она не двигалась. Когда вы освоитесь, нанесите клей между слоями и нанесите их на форму. Примечание: обязательно нанесите на форму растительное масло или восковую пасту, чтобы просачивающийся клей не приклеил ламинат к вашей форме навсегда!
Молотком постучите приклеенными пластинами по основанию формы.Используйте кусок дерева, если вам нужно еще раз постучать, чтобы выровнять полосы.
Забейте самодельные клинья между дюбелями и приклеенными полосами, чтобы прижать их к изгибу. Идея состоит в том, чтобы закрыть пустоты между слоями для прочной связи. Как только вы закрепите ламинат, подождите до следующего дня, чтобы удалить клинья. и обрезать концы ламелей ровно по краю формы. Примечание: если вы попытаетесь удалить его через час или два, давление в древесине разорвет ламинат.
После обрезки рамы по длине и снятия ее с форм отшлифуйте обе стороны заподлицо. Затем отрежьте клиновые анкеры до размеров, указанных на чертеже, приклейте и закрепите их на раме. Если анкеры не прилегают к раме заподлицо, нанесите на раму очень неглубокую плоскую поверхность, чтобы обеспечить максимальное сцепление с поверхностью клеевого соединения.
После того, как клей затвердеет для клиновых анкеров, просверлите отверстие в центре контактной площадки, затем приклейте и вбейте дюбель 3/8 дюйма через анкер в раму.Распилите дюбель с обеих сторон заподлицо. Дайте клею высохнуть. Дюбель является необходимой частью анкера, чтобы придать ему прочность и удерживающую способность под воздействием клина, удерживающего шлифовальную ленту.
Обрежьте клинья, как показано на рисунке. Возможно, вам придется отрегулировать их, чтобы они соответствовали друг другу. Я приклеил к клину кусок наждачной бумаги, чтобы усилить трение с анкером. Зернистость 150 кажется лучшей. Разрежьте шлифовальную ленту (разрез на обратной стороне ленты) пополам в поперечном направлении, затем отметьте и разорвите полоску до ширины 1-1 / 4 дюйма.Возможно, вам придется немного обрезать длину, чтобы она соответствовала вашей оправе. Вы же не хотите, чтобы полоса полностью заходила на якоря. Сделайте это немного застенчивым с обеих сторон.
Когда вы забиваете клинья в анкеры, чтобы зафиксировать ремень, постучите по ним молотком, чтобы надежно закрепить ремень. Шлифовальный станок отлично работает, как показано на рисунке, и даже лучше, когда вы зажимаете заготовку на верстаке, чтобы вы могли управлять шлифовальной машиной двумя руками.
Самодельный барабанный шлифовальный станок своими руками – WOODBREW
Двигатель должен быть уже внутри коробки, а сторона шкива должна выходить из отверстия.Ставим мотор на обрезной кусок доски, который на шарнире крепим к коробке. Таким образом, часть веса двигателя может ослабить ремень, и его будет немного легче надеть. Мы использовали вентиляторный двигатель, просто старый, который у нас лежал, и он мощностью 1/2 л.с., что достаточно для этой установки.
Отрежьте вал доступаТеперь, когда барабан готов и установлен на место, вы можете отрезать вал доступа. Делайте то, что мы делали в видео, только если вам очень удобно: мы включили станок и использовали ручную пилу для резки металла, чтобы медленно отрезать доступ.На противоположной стороне у вас тоже может быть немного осталось, у нас было достаточно места, чтобы использовать нашу портативную ленточную пилу для этой стороны. Все, что работает лучше всего!
Подъемный механизмЯ не знаю, насколько хорошо я могу объяснить, как работает настольный подъемник, поэтому я посоветую вам обратиться к видео для этой части. Это начинается в 7:40.
Изготовление и установка кожухов барабана и ремняМы сделали кожух барабана из МДФ таким образом, чтобы он сидел на болтах опорного блока и никогда не касался наждачной бумаги.Мы также просверлили небольшую прорезь на стороне, противоположной двигателю, чтобы болт мог перемещаться вверх и вниз внутри, когда ручка снаружи ослаблена. Это необходимо для того, чтобы вы могли регулировать толщину материала при шлифовании и сохранять пылеуловитель A1. Крышка ремня также сделана из МДФ, и мы добавили только одну петлю, чтобы вы могли открывать и закрывать ее, когда вам нужно залезть внутрь, чтобы закрепить ремень или заменить его и т. Д.
Наждачная бумагаМы нанесите на барабан наждачную бумагу зернистостью 80 и 120.Мы не планируем когда-либо вставлять сюда целую 18-дюймовую доску, поэтому мы можем легко переключаться между наждачной бумагой с зернистостью 80 и 120, не снимая и не снимая бумагу снова. Наждачная бумага помещается в канавку в барабане. , затем привинчивают небольшой кусок дерева со скошенной кромкой, чтобы удерживать оба конца бумаги на месте.
Как построить шлифовальный станок, чтобы сделать вашу ленточную шлифовальную машину настольным инструментом
При нынешнем экономическом положении все больше и больше плотников стремятся максимально эффективно использовать инструменты, которые у них уже есть, поэтому я создал это простое базовое приспособление, которое превращает стандартную переносную ленточную шлифовальную машину в небольшую горизонтальную настольный шлифовальный станок.
Приспособление простое в сборке и позволяет использовать шлифовальный станок для точной обработки, обрезки и шлифовки мелких деталей.
Используйте квадратную линейку, чтобы убедиться, что шлифовальный станок полностью выровнен, если это не поможет, сэкономьте немного древесных отходов, чтобы подпереть конец, пока он не выровняется. Чтобы построить приспособление, сначала вырежьте опорную пластину из фанеры или МДФ толщиной 1/2 или 3/4 дюйма, которая имеет ширину на 14 дюймов и на 6-8 дюймов длиннее, чем длина вашей ленточной шлифовальной машины.
Важно отметить, что мы предоставляем реальные размеры моего приспособления, но вам нужно будет отрегулировать их, чтобы они соответствовали вашей шлифовальной машине.
Установите шлифовальную машину на опорную плиту так, чтобы открытая сторона ременных роликов была обращена вверх, и расположите ленточный валик (плоская поверхность под рабочей частью полотна) параллельно длинному краю основания.
Некоторые шлифовальные машины, такие как эта модель DeWalt, имеют съемные ручки или другие детали, через которые вы можете пропустить часть приспособления, чтобы закрепить шлифовальный станок на остальной части основания. Теперь выровняйте поверхность валика к опорной плите, используя при необходимости распорки, клинья или прокладки под корпусом шлифовальной машины.Закрепите шлифовальный станок на опорной плите, используя любые резьбовые точки крепления, которые могут быть у шлифовального станка, например, съемную переднюю ручку или отверстия для крепления принадлежностей.
Сделайте кронштейны из обрезков фанеры в соответствии с положением монтажных отверстий, прикрутите их к шлифовальной машине, затем приклейте к основанию. Для обеспечения максимальной устойчивости закрепите шлифовальную машинку как минимум в двух местах: спереди и сзади или рядом с ним.
После того, как вы склеили ножки и основание крепления, используйте гвоздодер для фиксации стыков.Вырежьте угловой рабочий стол приспособления из фанеры или МДФ шириной 8 дюймов и примерно на 2 дюйма короче основания. Если хотите, проткните паз под углом в столешнице, используя либо прямую фрезу в фрезере, либо лезвие дадо в настольной пиле. Этот паз позволяет использовать обычный калибр для резки под углом или другие приспособления или приспособления с направляющими под углом для точного шлифования квадратных или угловых кромок.
Стол сконструирован так, чтобы он располагался выше в задней части шлифовальной машины: он снижает вибрацию во время шлифования и более равномерно распределяет износ по ленте.Размер опор стола должен быть таким, чтобы верх стола был немного ниже нижнего края ремня на нижнем конце и на 1–1⁄2 дюйма ниже верхнего края ремня на верхнем конце. Приклейте и прикрутите опоры к нижней стороне стола. Затем прикрутите опоры стола к основанию снизу, оставив минимальный зазор между ремнем и столом.
В целях безопасности навинтите стопорный блок на конец шлифовального стола, чтобы предотвратить слишком сильное оттягивание детали шлифовальной машиной. Наконец, прикрутите небольшой стопорный блок к столу рядом с задним концом ремня, чтобы мелкие детали не отбрасывались с поверхности стола под действием ходовой шлифовальной машины.. Перед использованием ленточной шлифовальной машины закрепите опорную пластину на столе. Используйте фиксатор спускового крючка ленточной шлифовальной машины, чтобы инструмент оставался включенным во время шлифования.