Статьи
Перезвоните
мне Отправляя заявку я соглашаюсь с политикой конфиденциальности и правилами обработки персональных данных
Заказать в 1 клик:
Пожалуйста, укажите свои данные и мы перезвоним Вам для уточнения деталей заказа.
Отправляя заявку я соглашаюсь с политикой конфиденциальности и правилами обработки персональных данныхПодъемники
Балансировочные станки
Шиномонтажные станки
Домкраты
Гидравлическое оборудование
Вулканизаторы и борторасширители
Оборудование для замены масла
Компрессоры
Инструменты для автосервиса
-
Ручной инструмент для автосервисов
Оборудование для отвода выхлопных газов
Дополнительное оборудование
Пеногенераторы
Пескоструйные аппараты
Промышленные пылесосы
Главная > О компании > Блог
21.
Балансировочный станок: виды, характеристики, советы по выбору
Читать полностью →
21.11.2022Шиномонтажное оборудование: виды и особенности выбора
Читать полностью →
07.09.2022Рейтинг подкатных домкратов 2т
Читать полностью →
07.09.2022Рейтинг подкатных домкратов
Читать полностью →
11.07.2022Виды автоподъемников
Читать полностью →
05.07.2022Какой подъемник выбрать?
Читать полностью →
27.06.2022Как выбрать компрессор для автосервиса
Читать полностью →
03.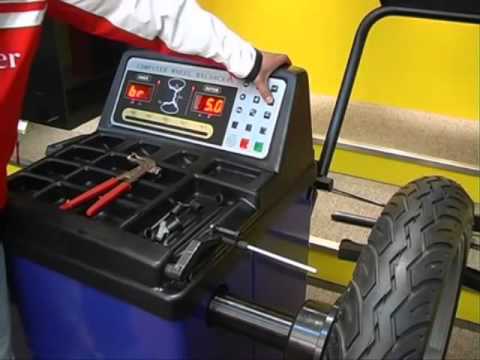
Как выбрать вулканизатор
Читать полностью →
27.05.2022Лучшие гидравлические прессы
Читать полностью →
12.05.2022Виды и особенности пескоструйных аппаратов для автосервиса
Читать полностью →
25.04.2022Рейтинг подъемников
Читать полностью →
13.04.2022Синхронизация двухстоечных подъемников
Читать полностью →
17.02.2022Обзор автомобильных домкратов
Читать полностью →
09.02.2022Читать полностью →
27.
Лучшее шиномонтажное оборудование
Читать полностью →
17.01.2022Лучшие автомобильные домкраты
Читать полностью →
27.12.2021Какое оборудование нужно для автосервиса
Читать полностью →
15.12.2021Виды компрессоров
Читать полностью →
25.11.2021Гидравлический домкрат: устройство и принцип работы
Читать полностью →
17.11.2021Как выбрать домкрат?
Читать полностью →
Подпишитесь и будьте в курсе!
Акции и скидки — ждут!
Калибровка балансировочных станков – Главная
ФБУ “Ростест-Москва”
Тел.: (495) 544-00-00
e-mail: spravka@rostest. ru
www: rostest.ru
КАЛИБРОВКА БАЛАНСИРОВОЧНЫХ СТАНКОВ
тел. (495) 668-28-12 e-mail: [email protected]
Калибровка балансировочного станка | Качественное техническое обслуживание и ремонт автотранспортных средств и, как следствие, их эксплуатационные качества и безопасность могут быть обеспечены только при условии надлежащей поверки тормозных стендов и другого контрольно-диагностического оборудования и средств измерений, задействованных в технологическом процессе. Сотрудники Сектора поверки и испытаний контрольно-диагностического оборудования — метрологи, аттестованные на право поверки и калибровки средств измерений системы автосервиса. |
Сектор создан в 1998 году как структурная единица ФБУ «РОСТЕСТ-МОСКВА» для решения задач по поверке, калибровке и испытаниям измерительного оборудования, предназначенного для диагностирования и ремонта автотранспортных средств.
За годы работы сотрудниками сектора:
- выполнен большой объем работ по испытаниям диагностического оборудования изготовленного такими ведущими зарубежными фирмами производителями, как «Muller Bem», «Hofmann», «Bosch», «Hunter», «Maha» и т. д.
- накоплен огромный опыт работы с этим оборудованием
- создана эталонная база
- сформирован фонд методик поверки и нормативной документации
Все сотрудники сектора аттестованы на право поверки и калибровки диагностического оборудования в рамках области аккредитации и периодически повышают свою квалификацию в соответствии с правилами по метрологии
Клиентами сектора являются заводы такие изготовители АТС, как «АвтоВаз», «Фольксваген», «Вольво» г. Калуга, «Автофрамос» г. Москва, автобусные парки, станции технического обслуживания, пункты технического осмотра.
Мы проводим поверку и калибровку диагностического оборудования на таких крупных фирмах, как «Рольф», «Автомир», «Ника Моторс», «Бизнес Кар» и. т.д.
Наши клиенты понимают, что одним из факторов, влияющих на качество ремонта АТС, является правильная диагностика АТС с помощью оборудования, имеющего соответствующие метрологические характеристики (точность, стабильность, диапазон измерений, чувствительность).
Мы едем к Вам
Сотрудники сектора выполняют метрологические работы по поверке оборудования на базе ФГУ «Ростест–Москва», а также выезжают на поверку стационарного оборудования, расположенного на территории клиента. География оказания метрологических услуг: город Москва и Московская область. Возможны выезды в другие субъекты Российской Федерации, если там отсутствуют аккредитованные метрологические службы.
Передвижные поверочные лаборатории
ЧТОБЫ МЫ ПОНИМАЛИ ДРУГ ДРУГА
Метрология – наука об измерениях Средство измерений – техническое средство, предназначенное для измерений Поверка средств измерений – совокупность операций, выполняемых с целью подтверждения соответствия средств измерений метрологическим требованиям Калибровка средств измерений – совокупность операций, выполняемых в целях определения действительных значений метрологических характеристик средств измерений Погрешность измерений – разность между результатом измерений и истинным значением измеряемой величины | Утверждение типа средств измерений или стандартных образцов – документально оформленное в установленном порядке решение уполномоченного на это федерального органа исполнительной власти о признании соответствия типа средств измерений или стандартных образцов метрологическим и техническим требованиям (характеристикам) на основании результатов испытаний Испытания стандартных образцов или средств измерений в целях утверждения типа – работы по определению метрологических и технических характеристик однотипных стандартных образцов или средств измерений. Единство измерений – состояние измерений, при котором их результаты выражены в допущенных к применению в Российской Федерации единицах величин, а показатели точности измерений не выходят за установленные границы Методика (метод) измерений – совокупность конкретно описанных операций, выполнение которых обеспечивает получение результатов измерений с установленными показателями точности Аттестация методик измерений — исследование и подтверждение соответствия
методик измерений установленным метрологическим требованиям к измерениям.
Включает в себя метрологическую экспертизу комплекта документов по разработке МИ, а также теоретические и экспериментальное исследования для подтверждения соответствия аттестуемой методики требованиям нормативных документов ГСИ. Метрологическая экспертиза – анализ и оценка правильности установления и соблюдения метрологических требований применительно к объекту, подвергаемому экспертизе. Метрологическая экспертиза проводится в обязательном (обязательная метрологическая экспертиза) или добровольном порядке. | Проверка гаражного оборудования — так часто называют комплекс работ по метрологическому обслуживанию ( испытания, поверка и калибровка) средств измерений, используемых на предприятиях автосервиса (стенды для диагностирования тормозных систем, углов установки колес (сход/развал), мощности двигателя и др. Прослеживаемость – свойство эталона единицы величины или средства измерений, заключающееся в документально подтвержденном установлении их связи с государственным первичным эталоном соответствующей единицы величины посредством сличения эталонов единиц величин, поверки, калибровки средств измерений . |
МЕТОД КАЛИБРОВКИ БАЛАНСИРОВОЧНОГО СТАНКА
Заявители претендуют на приоритет в соответствии с 35 U. S.C. § 119 заявки на патент Германии № 10 2018 104 846.7, поданной 2 марта 2018 г. и ускоряется с помощью привода.
При калибровке балансировочного станка при серийном производстве мастер-деталь, например, мастер-ротор, изготавливается из серийной детали, что позволяет наложить известные контрольные дисбалансы. Используя этот мастер, процесс балансировки калибруется в смысле регулировки, путем прикрепления контрольного груза в каждом случае для каждой дисбалансированной плоскости и измерения вибрации. Кроме того, вибрация ротора измеряется без контрольных грузов. По различиям можно определить влияние дисбаланса на колебания.
Получаемая при этом матрица коэффициентов влияния сохраняется в измерительном устройстве и впоследствии используется для измерения дисбаланса каждой дополнительной детали. Процедура коэффициента влияния часто используется в связи с роторами с упругим валом; однако его также можно использовать при балансировке жестких роторов. В случае жестких роторов величина матрицы коэффициентов влияния просто меньше, и используется только фиксированная скорость вращения.
{стрелка вправо над (s)} – вектор параметра вибрации измерительного участка длиной M, количество точек измерения. Измерение с использованием датчика или измерение с заданной фиксированной скоростью вращения или интервалом скорости вращения обычно обозначается как точка измерения. Если используется несколько датчиков или несколько скоростей вращения, M является произведением количества датчиков и количества точек отбора проб.
Дисбаланс самолетов хранится в векторе дисбаланса {стрелка вправо над (u)}. Длина вектора равна P, количеству плоскостей дисбаланса.
Предполагая линейное поведение передачи дисбалансов при измеренных вибрациях, система может быть выражена в виде системы линейных уравнений:
{стрелка вправо над (s)}=K{стрелка вправо над (u)}
K в данном случае это матрица коэффициентов влияния или калибровочная матрица. Он имеет размерность M×P.
Оба элемента вектора вибрации {стрелка вправо над (s)}, а также вектор дисбаланса и матрица коэффициентов влияния являются комплексными числами. Что касается параметров вибрации, то они относятся к амплитуде и фазе первого порядка датчика скорости вращения; что касается значений дисбаланса, они относятся к величине и углу дисбаланса ротора.
Калибровочная матрица K определяется в процессе калибровки посредством эталонной калибровки с использованием тестовых дисбалансов.
Когда известна матрица K, можно вычислить вектор дисбаланса из каждого цикла измерений (включая новые детали той же конструкции) из вектора значений вибрации. Это делается путем решения системы линейных уравнений, если К является квадратичной матрицей, или путем вычисления линейной поправки, если К имеет больше строк, чем столбцов, другими словами, является переопределенной.
Известные процедуры калибровки, использующие мастер-детали, могут содержать ошибки, которые впоследствии влияют на весь производственный процесс. Результатом является излишне плохая коррекция дисбаланса.
Таким образом, изобретение решает проблему обеспечения альтернативной калибровки балансировочного станка.
Задача согласно изобретению достигается за счет предоставления способа калибровки балансировочного станка на корректирующем прогоне k, в котором корректируемый ротор устанавливается с возможностью вращения в подшипниках и ускоряется с помощью привода, включающий следующие этапы :
- а. в котором по крайней мере один измерительный датчик определяет первоначальную вибрацию ротора перед коррекцией дисбаланса и передает эту вибрацию на устройство оценки, которое сохраняет измеренное значение в виде вектора вибрации {стрелка вправо над (s)} 0 ,
- б. в котором устранен дисбаланс ротора,
- c. в котором остаточная вибрация ротора измеряется измерительным датчиком, передается в блок обработки и сохраняется в виде вектора вибрации {стрелка вправо над (s)} 1 ,
- d. в котором разница δ{стрелка вправо над (s)}={стрелка вправо над (s)} 1 -{стрелка вправо над (s)} 0 и скорректированный дисбаланс для прогона коррекции k сохраняется как δ {стрелка вправо над (s)} k и {стрелка вправо над (u)} k блоком оценки,
- e.
в котором из данных измерений определяется матрица калибровки процесса K путем решения системы уравнений S=UK T или с использованием начальной вибрации {стрелка вправо над (s)} 0 и/или вектора дисбаланса { стрелка вправо над (u)}, можно выбрать уже существующую матрицу калибровки процесса и
- f. в котором матрица калибровки процесса сохраняется в соответствии с этапом e в качестве матрицы калибровки в блоке оценки и используется для вычисления неизвестного вектора дисбаланса ротора.
Таким образом, балансировочный станок калибруется во время корректирующего прогона, поэтому нет необходимости в отдельном калибровочном прогоне с использованием эталонной детали. Кроме того, калибровку балансировочного станка можно выполнять в любой корректировке или в определенные моменты времени. Ротор по смыслу изобретения представляет собой вращающееся тело. Метод может быть применен к различным балансировочным машинам, которые используются для балансировки различных тел вращения (например, валов, роторов турбокомпрессоров и т. д.). Одним из преимуществ способа согласно изобретению является то, что для каждого ротора требуется, в частности, только два измерения, а именно одно до и одно после коррекции, даже если ротор имеет более одной неуравновешенной плоскости.
Для измерения балансируемого ротора используется, в частности, доступная в настоящее время матрица калибровки процесса, в которой данные измерения ротора могут использоваться для улучшения матрицы калибровки процесса.
Этот метод оказывается особенно выгодным, поскольку он применяется, в частности, когда калибровка с использованием эталона либо относительно очень подвержена ошибкам, либо коррекция не может точно следовать спецификации дисбаланса, и возникает систематическая ошибка (например, глубина сверления, угол ошибка).
Матрица калибровки процесса может быть определена с помощью системы уравнений S=UK T и сохранена как матрица калибровки в блоке обработки, чтобы при балансировке дополнительных роторов можно было бы использовать эту матрицу калибровки для расчета вектора дисбаланса. Однако можно также прибегнуть к уже существующей матрице калибровки процесса. В связи с этим предпочтительно, чтобы параметры (например, исходные вибрации, дисбаланс, величина геометрической погрешности, например, люфта подшипника и т. д.) балансируемого ротора совпадали с параметрами роторов, при измерении которых данных была создана сохраненная матрица калибровки процесса.
Предпочтительно, чтобы для каждого шага балансировки матрица S содержала строку, имеющую транспонированный вектор колебаний Sk=δ{стрелка вправо над (s)} k T для шага k, и чтобы матрица U содержала в каждой строке транспонированный вектор дисбаланса Uk={стрелка вправо над (u)} k T этапа k, а матрица калибровки процесса рассчитывается путем транспонирования K T , при этом для расчета калибровки процесса используется множество уже сбалансированных роторов. матрица K с помощью системы уравнений S=UK Т . Система уравнений S=UK T может быть решена с помощью процедуры оптимизации, в частности, с помощью процедуры вычисления линейной поправки. Преимущественно данные измерений используются для роторов, которые имеют по существу аналогичные или даже идентичные параметры с параметрами балансируемого ротора.
Одна конструкция предусматривает, что уже отбалансированные роторы объединяются в группы на основе их начальной вибрации {стрелка вправо над (s)} 0 и/или их вектора дисбаланса {стрелка вправо над (u)}, а также на основе их начальных вибраций и/или векторов дисбаланса рассчитывается калибровочная матрица кластерного процесса, в частности, путем решения системы уравнений S=UK T , и используется как уже существующая матрица калибровки процесса, при этом матрица калибровки кластерного процесса выбирается как уже существующая матрица калибровки процесса, которая содержит роторы, чьи начальные векторы колебаний и/или дисбаланса по меньшей мере аналогичны начальный вектор вибрации и/или дисбаланса балансируемого ротора. Также может быть выгодно, чтобы вместо начальных вибраций {стрелка вправо над (s)} 0 векторы дисбаланса использовались для расчета матрицы калибровки кластерного процесса. Можно выбрать любой размер кластера. Также можно использовать дополнительные параметры ротора для формирования кластеров.
Может быть предпочтительным, чтобы матрица калибровки кластерного процесса интерполировалась из выбранных матриц калибровки кластерного процесса и использовалась в качестве уже существующей матрицы калибровки процесса. При наличии дополнительных калибровочных матриц кластерного процесса и балансируемого ротора с параметрами, не позволяющими однозначно выбрать калибровочную матрицу кластерного процесса, новая калибровочная матрица кластерного процесса может быть интерполирована из уже имеющихся калибровочных матриц кластерного процесса, а именно с использованием данных ротора, которые по существу идентичны исходному вектору вибрации и/или дисбаланса балансируемого ротора.
Предпочтительно, калибровка может выполняться либо один раз для определенного количества роторов, либо обновляться при каждом запуске балансировочного станка. Таким образом, калибровку можно улучшать при каждом запуске.
Вариант осуществления настоящего изобретения показан на прилагаемом чертеже и будет описан более подробно ниже. На чертеже
РИС. 1 показан ротор, установленный на балансировочном станке.
РИС. 1 схематически изображен балансировочный станок, в котором ведомый ротор 1 устанавливается в подшипники 2 . Подшипники 2 могут быть мягкими или жесткими. Вибрации ротора 1 можно рассчитать по значениям измерения измерительного датчика 3 (например, датчика вибрации). Записанные значения измерений подаются на устройство оценки 4 . Могут быть предусмотрены дополнительные датчики, такие как, например, датчики скорости вращения и угловые датчики. Измерительный датчик 3 , выполненный в виде датчика вибрации, может измерять вибрации, например, на подшипниковых опорах, непосредственно на роторе или на корпусе. Положение измерительного датчика 3 не критично при выполнении этой процедуры. Количество датчиков также может быть адаптировано к применению в каждом конкретном случае.
Привод устройства для измерения дисбаланса разгоняет ротор 1 до соответствующей скорости вращения, при этом приводом также можно управлять таким образом, что можно задавать фиксированные скорости вращения для балансировки. Записываемые значения измерений также могут быть записаны в обычном рабочем режиме, так что, например, при запуске ротора 1 при заданной балансировочной частоте вращения значения измерений записываются и передаются на устройство оценки 4 . Ротор 1 также можно разогнать до рабочей скорости вращения.
В способе согласно изобретению вместо калибровочного прогона с использованием специального эталона выполняется технологическая калибровка, при которой калибровка происходит во время фактической балансировки ротора 1 , с использованием балансировочного прогона, другими словами корректирующий прогон, как калибровочный прогон. В этом смысле способ согласно изобретению можно также назвать калибровкой процесса. Калибровку можно использовать для последующих роторов. Ротор, используемый для калибровки, может выиграть от калибровки процесса при измерении дисбаланса после коррекции.
В способе согласно изобретению вектор вибрации измеряется для шага коррекции перед коррекцией с использованием подходящего измерительного датчика 3 и сохраняется как {стрелка вправо над (s)} 0 устройством оценки 4 . Дисбаланс рассчитывается с использованием действующей на данный момент калибровки балансировочного станка, т. е. с использованием калибровки, которая уже сохранена в балансировочном станке. В начале производства еще нет предварительных шагов балансировки, которые можно использовать для расчета калибровки. Первую калибровку и, следовательно, расчет дисбаланса можно выполнить с помощью эталонной калибровки. В качестве альтернативы можно провести тестовые процессы балансировки, не зная фактического дисбаланса. Все дополнительные калибровки выполняются с использованием способа согласно изобретению.
Рассчитанный дисбаланс {стрелка вправо над (u)} корректируется на роторе 1 , и вибрация снова измеряется как остаточная вибрация и сохраняется как {стрелка вправо над (s)} 1 . Разница δ{стрелка вправо над (s)}={стрелка вправо над (s)} 1 -{стрелка вправо над (s)} 0 и скорректированный дисбаланс для прогона коррекции k сохраняется как δ{стрелка вправо над (s)} k и {стрелка вправо над (u)} k , при этом прогон или этап коррекции может содержать либо тот же, либо новый ротор. Для расчета матрицы калибровки процесса K необходимо решить систему уравнений S=UK Т . Для каждого шага балансировки матрица S, таким образом, содержит линию с транспонированным вектором колебаний шага k, где Sk=δ{стрелка вправо над (s)} k T . Соответственно, матрица U содержит в каждой строке транспонированный вектор дисбаланса шага U k = {стрелка вправо над (u)} k T .
Система уравнений содержит в правой части матрицу U, а также матрицу K T в качестве неизвестной и может решаться отдельно для каждого столбца S и K Т . Поскольку в системе уравнений обычно больше строк, чем столбцов (используется больше шагов балансировки или роторов 1 , чем несбалансированных плоскостей), она является переопределенной и может быть решена с помощью процедуры оптимизации, такой как метод расчета линейной коррекции. Затем определяется матрица калибровки процесса путем транспонирования K T .
Несмотря на то, что при обычной калибровке с использованием ротора 1 для P плоскостей требуются калибровочные прогоны P+1, способ согласно изобретению также работает с использованием одного шага коррекции на ротор 1 независимо от количества самолетов. Это одно из преимуществ метода, потому что в последовательных процессах важна короткая частота цикла, и поэтому часто требуется иметь только один шаг коррекции. Было показано, что при использовании способа согласно изобретению может быть достигнута короткая скорость цикла.
В этом методе матрица калибровки процесса используется для расчета дисбаланса с использованием процедуры коэффициента влияния. В этом контексте следует отметить, что процедура определения коэффициента влияния часто используется для роторов с упругим валом. Однако процедуру определения коэффициента влияния можно рассматривать как общую процедуру, используемую при балансировке как жестких, так и упругих по валу роторов. Что касается жестких роторов, размер матрицы коэффициентов влияния, которая также называется матрицей калибровки процесса в значении изобретения, просто меньше, и используется только фиксированная скорость вращения. В качестве альтернативы для расчета дисбаланса можно использовать другую процедуру оптимизации.
Поскольку при калибровке процесса используется большое количество роторов 1 , можно получить хорошие результаты измерений, несмотря на большое количество ошибок. Ошибки рассеяния уменьшаются при решении переопределенной системы уравнений, и определяется только систематическое поведение передачи ротора 1 . Это большое преимущество по сравнению с использованием одного главного ротора, который из-за своих индивидуальных свойств подшипника не должен быть репрезентативным для разнообразия производства, поэтому нельзя гарантировать точную и безошибочную калибровку.
Калибровка процесса может выполняться однократно для определенного набора роторов 1 или шагов коррекции, либо обновляться постоянно. Шаги а. к д. Методика определения данных измерений и расчета технологической калибровочной матрицы K может быть повторена с использованием n-роторов. В этом типе обновленной калибровки всегда используется определенное количество предыдущих измерений (например, последние 200 роторов). Таким образом, можно гарантировать, что калибровка учитывает медленные изменения в процессе (например, износ инструмента или модификации на предшествующем этапе производства). В отношении выбора шагов могут быть определены дополнительные правила, например, что должны использоваться только детали, входные параметры которых находятся в определенных пределах. Таким образом, например, можно исключить особенно малые поправочные дисбалансы, диапазон неопределенности которых больше, чем их польза. Если обновление происходит автоматически без вмешательства оператора, то этот процесс можно назвать «самообучением».
При последовательной балансировке корпусных групп турбокомпрессора было показано, что поведение вибрации нелинейным образом зависит от входных дисбалансов, в результате чего возникают систематические ошибки балансировки в зависимости от величины входные колебания. При использовании входных данных с различными амплитудами получаются различные калибровочные матрицы. Систематические ошибки коррекции увеличиваются, особенно при больших начальных дисбалансах. В связи с этим оказалось выгодным, что роторы организованы в группы в соответствии с их начальной вибрацией {стрелка вправо над (s)} 0 и/или их вектор дисбаланса {стрелка вправо над (u)}, и их начальные колебания и/или векторы дисбаланса образуют калибровочную матрицу кластерного процесса, которая используется в качестве уже имеющейся калибровочной матрицы процесса. Это означает, что можно использовать уже существующие матрицы калибровки процесса. С помощью исходной вибрации в исходном состоянии, например, решают, для какой калибровки может быть использован соответствующий прогон, т.е. какая матрица калибровки кластерного процесса выбрана или предпочтительна матрица калибровки текущего процесса. При расчете дисбаланса сохраненные матрицы калибровки процесса выбираются с использованием величины исходных вибраций.
Для выбора входного значения необходимо вычислить скалярное (или многомерное) значение выбора по уровню вибрации. Это может быть величина дисбаланса, например, с использованием усредненной матрицы калибровки процесса или максимальное количество вибрации. Чтобы выбрать матрицу калибровки процесса для расчета дисбаланса, можно либо выбрать матрицу калибровки кластерного процесса соответствующего кластера, либо можно интерполировать матрицу калибровки отдельного процесса из доступной матрицы калибровки кластерного процесса.
Исследование по калибровке динамического балансировочного станка для разделения вибрации системы разделения
Главная Ключевые инженерные материалы Ключевые инженерные материалы Vol. 613 Исследование калибровки динамической балансировки…
Предварительный просмотр статьи
Резюме:
Минимально достижимый коэффициент остаточного дисбаланса e mar является показателем для оценки балансировочной способности динамической балансировочной машины. Когда е март , как ожидается, достигнет уровня 0,1 мкм или выше, чтобы использовать потенциал исключительно из-за конструкции цепей формирования сигнала или алгоритм цифровой обработки сигналов не может полностью решить проблемы, не менее важное значение следует уделять устранению влияния собственных машин. интерференционная вибрация. К сожалению, по сравнению с большими усилиями по исследованию и внедрению схем и алгоритмов извлечения сигналов дисбаланса, последним уделяется мало внимания. В этой статье предлагается подход к разделению интерференционных вибраций, основанный на многоточечной калибровке циркуляции испытательной массы, с целью улучшения общих характеристик балансировочного станка. Система измерения динамического балансировочного станка, состоящая из вибрационного механизма, датчика вибрации. , схемы формирования сигнала и модуль цифровой обработки сигналов, в котором вибрационный механизм расположен на переднем конце и имеет большое значение. В текущей конструкции динамической балансировочной машины существует гипотеза о том, что вибрационный механизм вибрирует в виде простых гармонических колебаний, вызванных дисбалансом испытуемой вращающейся детали, а амплитуда и начальная фаза этой вибрации связаны только с величина и угловое положение дисбаланса.
Однако в практической балансировочной машине дисбаланс приводных устройств, коаксиальная ошибка муфты или вибрация приводного ремня вызывают дополнительные вибрации вибрационного механизма. Имея ту же частоту или близкую к частоте неуравновешенной вибрации, эти интерференционные вибрации трудно удалить с помощью схем формирования сигнала или подхода цифровой обработки сигналов. метод точечного измерения и комплексной калибровки. Принцип метода будет представлен и подробно проанализирован в статье. На основе векторной операции и аппроксимации по методу наименьших квадратов реакции неуравновешенной вибрации с полученными составными колебаниями интерференционная вибрация может быть в достаточной степени отделена. Проведено исследование экспериментов на динамической балансировочной машине с жесткими подшипниками, и результаты экспериментов демонстрируют возможность реализации указанного метода.
Доступ через ваше учреждение
Вас также могут заинтересовать эти электронные книги
Предварительный просмотр
* – Автор, ответственный за переписку
использованная литература
[1]
ЛЮ Цзянь, Исследование метода калибровки и системной компенсации ошибок балансировочных станков, Модульный станок и технология автоматического производства, Том. 4, (2004).
[2] Ци Вэй, Исследование по извлечению сигнала вибрации дисбаланса на основе МУЗЫКИ, Китайский журнал научных инструментов, Vol. 33(6), стр. 1240-1246, (2012).
[3] Кокс М. Г. Численная оценка B-сплайнов, Journal of Applied Mathematics, Vol. 10(2), стр. 13549, (1972).
[4]
Сучилин В.А. Повышение точности интерполяции цифровых сигналов с помощью дискретного преобразования Фурье // Телекоммуникации и радиотехника.