Точность станка. Испытания металлорежущих станков на точность
Общие замечания
Испытание станков на точность является одним из основных разделов программы испытаний при приемке серийных станков и опытных образцов новых моделей.
Измерения геометрической точности станков относятся к области метрологических работ.
Под геометрической точностью станка, характеризующей качество его изготовления и установки, понимается:
- степень приближения поверхностей, базирующих заготовку и инструмент, к геометрически правильным поверхностям;
- соответствие перемещений в направляющих опорах основных узлов станка, несущих заготовку и инструмент, расчетным геометрическим перемещениям;
- точность расположения базирующих поверхностей относительно друг друга и относительно направляющих опор, определяющих основные перемещения и обусловливающих формообразование обрабатываемых поверхностей;
- точность установки линейных и угловых размеров и точность кинематических цепей передачи.
В процессе обработки изделий возникают усилия, вызывающие деформацию узлов станка, обрабатываемой заготовки и инструмента, а также выделяется тепло, вызывающее тепловые деформации их.
Геометрическая точность станка является важной его характеристикой, но не может в полном объеме характеризовать точность обрабатываемых на станке изделий.
Геометрическая точность станка определяется рядом проверок с помощью измерительных инструментов и приборов. Измерение обработанных на чистовых режимах образцов является косвенной оценкой этой точности и дополняет указанные проверки.
Установка станков перед испытанием на точность
Перед испытанием на точность станок устанавливается на испытательном стенде или на фундаменте на опоры, предусмотренные конструкцией станка. Это должно быть проделано очень тщательно, так как геометрическая точность станка в ряде случаев зависит от точности его установки. Существуют следующие виды установки станков при испытании:
1. Установка станка на три точки опоры обычно применяется для прецизионных станков небольших размеров с жесткой станиной, работающей без дополнительного повышения ее жесткости фундаментом.
Установка станка в горизонтальное положение производится регулировкой опор. Выверка производится уровнями, устанавливаемыми в продольном и поперечном направлениях.
При установке станка все его перемещающиеся части (столы, каретки, суппорты, бабки и др.) должны занимать средние положения.
Следует учитывать возможность изменения положения станка на опорах во время испытания; для исключения ошибок необходимо контролировать положение станины дополнительным уровнем.
2. Установка станка (при эксплуатации) на число опор более трех является наиболее распространенным способом. Станина станка при этом жестко связывается с фундаментом болтами, чем увеличивается ее жесткость.
При установке такого станка для испытания на стенде или фундаменте выверкой с помощью клиньев или башмаков станина станка, не обладающая достаточной жесткостью, деформируется под действием собственного веса и веса смонтированных на ней узлов.
Поэтому установка станка на многих опорах производится с помощью измерения уровнями деформаций станины в отдельных ее частях. Регулировкой опор станина устанавливается в положение, при котором ее деформации будут наименьшими. В процессе испытания станка на точность может иметь место дополнительная регулировка опор в пределах допустимых деформаций станины с проверкой взаимного расположения отдельных частей станка.
При испытании станков, станины которых обладают достаточной жесткостью и работают без закрепления их фундаментными болтами или на виброизолирующих опорах, не допускается в процессе испытания на точность дополнительная регулировка опор.
Установка станка перед испытанием должна быть произведена согласно установочному чертежу, но без затяжки фундаментных болтов.
Точность установки станка перед испытанием указана в каждом разделе приведенных ниже норм точности.
Определение основных отклонений
Основные понятия отклонений формы и расположения линейчатых поверхностей, применяемых в стандартах на нормы точности в соответствии с общими условиями испытания станков на точность по ГОСТ 8-53:
1.
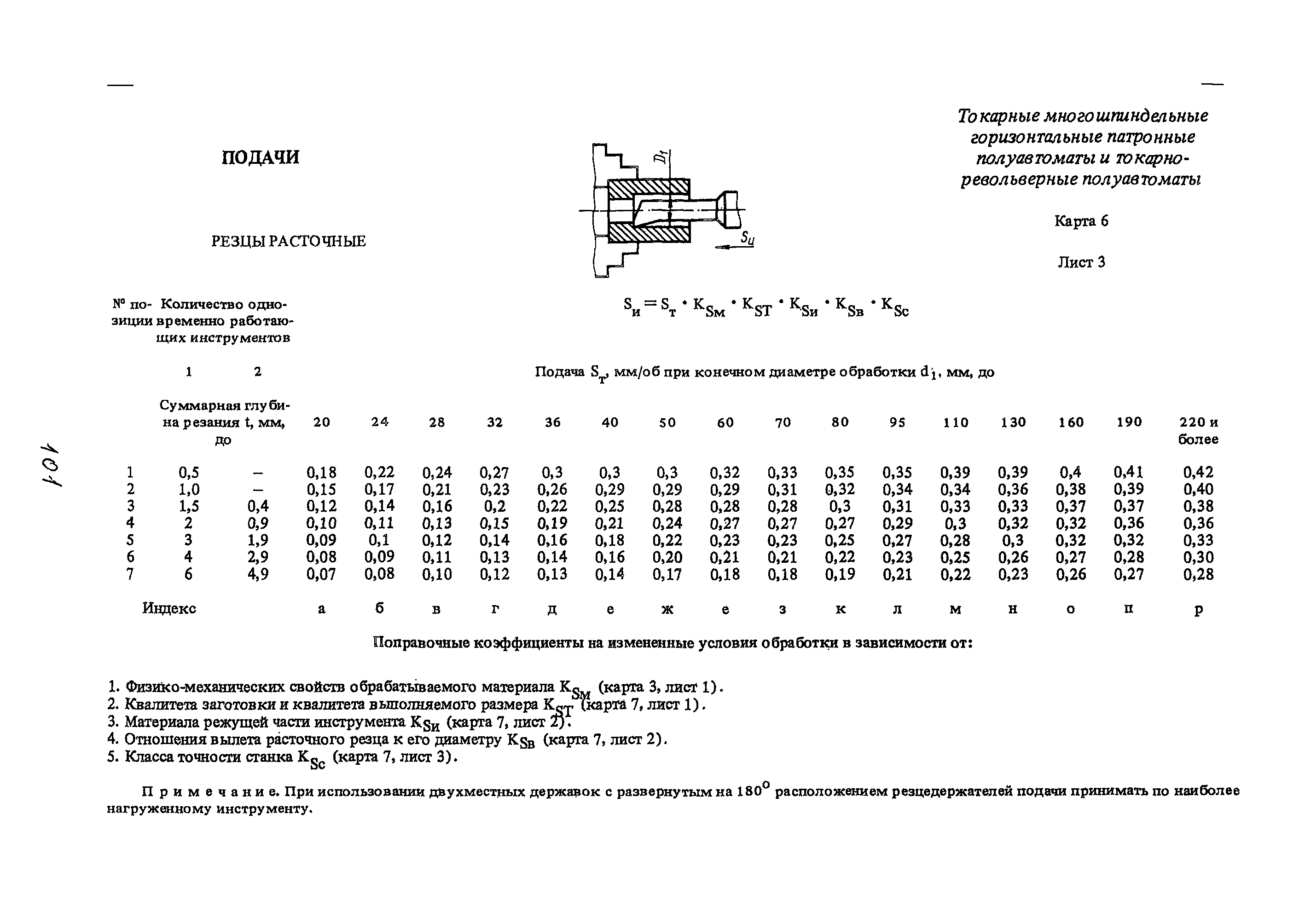
Определение
Наибольшее отклонение от прямой линии (AB) профиля сечения проверяемой поверхности, образованного перпендикулярной к ней плоскостью (I), проведенной в заданном направлении; прямая линия проводится через две выступающие точки (a, b) профиля сечения.
2. Неплоскостность поверхности (рис. 125)
Определение
Наибольшее отклонение проверяемой поверхности от плоскости, проведенной через три выступающие точки поверхности (а, Ь, с).
3. Непараллельность поверхностей (рис. 126)
Определение
Наибольшая разность расстояний между плоскостями, проходящими через три выступающие точки каждой из поверхностей (Н и H1), на заданной длине (L).
4. Неперпендикулярность поверхностей (рис. 127)
Определение
Наибольшее отклонение угла, образованного двумя поверхностями и измеренного в заданной точке линии их пересечения или в двух крайних и средней точке этой линии (углы a, γ. δ), от прямого угла.
5. Овальность (рис. 128)
Определение
Наибольшая разность между наибольшим и наименьшим диаметрами в двух крайних и среднем сечениях или в одном обусловленном сечении (D — d; D1—d1).
6. Конусность (рис. 129)
ОпределениеОтношение наибольшей разности диаметров двух поперечных сечений проверяемой поверхности (D — d) к расстоянию между этими сечениями (L).
7. Огранка (рис. 130)
Определение
Наибольшая разность между диаметром окружности, в которую вписан контур сечения проверяемой поверхности, и расстоянием между двумя параллельными плоскостями, касательными к этой поверхности.
8. Непрямолинейность образующей (рис. 131)
Определение
Наибольшее отклонение профиля осевого сечения проверяемой поверхности от прямой линии (АВ; CD), проведенной через две выступающие точки профиля.
9. Радиальное биение (рис. 132)
Определение
Наибольшая разность расстояний (а) от проверяемой поверхности до оси ее вращения.
10. Торцовое биение (рис. 133)
Определение
Наибольшая разность измеренных параллельно оси проверяемой торцовой поверхности расстояний до плоскости, перпендикулярной к оси вращения (l2—l1) на заданном диаметре.
11. Осевое биение (рис. 134)
Определение
Наибольшее перемещение (x) проверяемой детали вдоль оси ее вращения в течение полного ее оборота вокруг этой оси.
12. Несовпадение осей (рис. 135)
Определение
Наибольшее расстояние (с) между центрами поперечных сечений проверяемых поверхностей в пределах заданной длины (l)•
Примечание. В ГОСТ 10356—63 приведены определения отклонений формы и расположения поверхностей, несколько отличающиеся от приведенных выше определений, принятых по действующему ГОСТ 8—53.
Измерение прямолинейности и плоскостности направляющих поверхностей станков
Прямолинейное движение в металлорежущих станках наряду с круговыми представляет главный и наиболее распространенный вид движения и перестановки подвижных частей станка относительно его базовых деталей (станины, стоек, траверс и т д.) и осуществляется с помощью направляющих поверхностей.
Прямолинейность движения определяет точность формы и взаимное расположение обрабатываемых на станке поверхностей, точность координатных и расчетных перемещений, точность установки переставляемых деталей, узлов и механизмов, взаимодействие механизмов, соединяющих подвижные и неподвижные части станка.
В свою очередь, точность прямолинейного движения определяется точностью изготовления и монтажа направляющих поверхностей базовой детали, т. е. степенью приближения их по форме и взаимному расположению к заданным геометрическим формам.
Измерение прямолинейности системы направляющих включает:
- проверку прямолинейности отдельных направляющих поверхностей или следов их пересечения;
- определение взаимного расположения в одной или параллельных плоскостях двух направляющих поверхностей или следа пересечения двух поверхностей и третьей направляющей.
Реальные направляющие поверхности не представляют геометрически правильных плоскостей из-за погрешностей, вносимых в процесс их формообразования совокупностью технологических и других факторов, и только в большей или меньшей степени приближаются по своей форме к плоскостям.
Измерение прямолинейности направляющей поверхности имеет целью установление ее действительной формы с помощью координат, выраженных в линейных величинах и определяющих отклонения направляющей поверхности от исходной геометрической плоскости или следа пересечения поверхностей от геометрической прямой.
Методы и средства измерения прямолинейности основываются на двух видах измерений:
- измерение линейных величин, определяющих координаты элементарных площадок поверхности направляющей относительно исходной прямой линии;
- измерение угловых величин, определяющих углы наклона отдельных участков направляющей, ограниченных элементарными площадками относительно исходной прямой линии
За исходную прямую линию принимаются: линия горизонта, прямолинейный луч света, проекция горизонтально натянутой струны на горизонтальную плоскость, материализованный эталон прямой — линейки и т. д.
Сущность методов измерения линейных величин (оптическим методом визирования, измерением по струне, гидростатическими методами) заключается в том, что координаты элементарных площадок поверхности направляющей определяются непосредственным измерением. Изменение определяет координату элементарной площадки относительно исходной прямой.
Измерение каждой данной площадки не зависит от измерения координат других площадок, за исключением крайних, по которым устанавливаются относительно друг друга измеряемый объект и исходная прямая.
Сущность методов измерения угловых величин (уровнем, коллимационным и автоколлимационным методами) заключается в том, что положение элементарных площадок не измеряется относительно исходной прямой, а определяется взаимное расположение двух соседних площадок последовательно по всей длине направляющей.
Кроме проверки прямолинейности отдельной направляющей, возникает необходимость проверки идентичности формы двух направляющих, которая осуществляется с помощью уровня.
Сущность метода проверки идентичности формы направляющих (извернутости или винтообразности направляющих) заключается в определении посредством уровня углов поворота мостика, установленного в поперечном направлении на две направляющие и перемещаемого вдоль этих направляющих.
Так как допуски на извернутость направляющих назначаются в угловых величинах (часто в делениях шкалы уровня), то результаты измерения непосредственно отражают идентичность формы направляющих. Извернутость определяется наибольшей разностью показаний уровня.
Измерение точности кинематических цепей металлорежущих станков
При проверке точности винторезных цепей токарно-винторезных, резьбофрезерных и резьбошлифовальных станков необходимо измерение точности всей винторезной цепи, включая передаточные зубчатые колеса и механизм ходового винта. Отдельные погрешности, определяющие точность этой цепи: осевое биение шпинделя, прямолинейность направляющих, осевое биение ходового винта и т. д. регламентируются рядом самостоятельных проверок.
Измерение точности винторезной цепи производится с помощью эталонного винта, устанавливаемого в центрах испытываемого станка, и измерительного прибора (отсчетного или самопишущего), устанавливаемого на месте режущего инструмента.
Измерение осуществляется на ходу путем непосредственного контакта измерительного стержня прибора витка эталонного винта при настройке станка на шаг этого винта. Таким образом, проверка производится в условиях аналогичных нарезанию резьбы.
При проверке точности кинематических цепей зуборезных станков применяется теодолит с коллиматором или специализированная аппаратура.
Измерение точности абсолютных перемещений по шкалам производится, главным образом, на прецизионных координатно-расточных станках, координатные системы которых перемещаются на заданные размеры с помощью штриховых мер (шкал и масштабных устройств) или по ходовым винтам, снабженным коррекционными устройствами.
Проверка точности абсолютных перемещений производится по образцовым штриховым мерам с помощью отсчетного микроскопа.
Испытания точности координатно-расточных станков должны производиться высококвалифицированным персоналом в особых температурных условиях по аттестованным образцовым штриховым мерам.
Замеренная точность координатных перемещений будет зависеть от места установки образцовой меры в рабочем пространстве станка. При этом следует выбирать наиболее часто встречающиеся зоны обработки в рабочем пространстве.
Необходимо также учитывать отклонения образцовой штриховой меры по ее аттестату с тем, чтобы определить действительные величины координатных перемещений.
Средства измерения точности металлорежущих станков
Приборы и инструмент общего назначения, применяемые для большинства испытаний точности станков (контрольные линейки и угольники, уровни, щупы, концевые меры, контрольные оправки, индикаторы и микрокаторы и т. д.), достаточно просты и не требуют специальных указаний по их применению.
Все средства измерения, применяемые для проверки точности станков, должны быть соответствующим образом проверены и аттестованы, а их погрешности учтены при проведении измерений.
Необходимо иметь в виду, что в ряде случаев погрешности измерительных приборов и инструмента могут быть автоматически исключены из результатов измерений путем известных в измерительной технике приемов, например: перестановки контрольных оправок с поворотом их на 180°, «раскантовки» уровня при проверке горизонтальности, «раскантовки» угольника при проверке перпендикулярности, измерения прямолинейности двумя гранями проверочной линейки с учетом их непараллельности и др.
Такие приемы измерения обеспечивают высокую точность проверок и должны применяться во всех случаях, где это представляется возможным.
Относительно небольшое количество ответственных проверок, характеризующих точность станка, требует применения специальных измерительных приборов.
Применение этих приборов предполагает наличие квалифицированного персонала, владеющего навыками работы с такими приборами.
К числу специальных измерительных приборов относятся:
- оптические приборы для измерения прямолинейности направляющих — коллимационные и автоколлимационные приборы, визирные трубы, применяемые также для проверки соосности и других целей;
- оптические приборы для измерения углов — теодолиты и коллиматоры, делительные диски с отсчетными микроскопами, применяемые для проверки делительных цепей станков, делительных механизмов и др.
;
- эталонные винты и специальные измерительные и самопишущие приборы для проверки точности винторезных цепей токарно-винторезных, резьбофрезерных и резьбошлифовальных станков;
- прецизионные штриховые меры и отсчетные микроскопы для измерения точности перемещений координатных систем прецизионных координатно-расточных и некоторых других станков;
- приборы для непрерывной проверки делительных цепей зуборезных станков.
При проведении измерений специальными приборами и при обработке результатов измерения необходимо руководствоваться инструкциями и наставлениями к этим приборам.
Методы проверки и средства измерения, указанные в стандартах на нормы точности станков являются обязательными; применение других методов и средств измерения допускается при условии, что они полностью обеспечивают определение требуемой стандартами точности станков. При проверке станков на точность (без резания) движения узлов станка производятся от руки, а при отсутствии ручного привода — механически на наименьшей скорости.
Если конструктивные особенности станка не позволяют произвести измерение на длине, к которой отнесен допуск, последний пересчитывается на наибольшую длину, на которой может быть произведено измерение. Для длин, значительно отличающихся от той длины, для которой указан допуск, правило пропорциональности допусков неприменимо.
Классификация металлорежущих станков по точности
По разработанной в СССР классификации станков по точности они подразделяются на пять классов, приведенных в табл. 171.
Таблица 171
Класс точности станка | Обозначение класса точности | Соотношение основных допусков точности станков |
Нормальной точности станки | Н | 1 |
Повышенной точности станки | П | 0,6 |
Высокой точности станки | В | 0,4 |
Особо высокой точности станки | А | 0,25 |
Сверхточные станки | С | 0,15 |
Как видно из табл. 171 соотношение между величинами допусков при переходе от класса к классу для большинства показателей точности принято равным φ = 1,6.
Это соотношение позволяет согласовать требования к точности станка с требованиями к точности обрабатываемых на нем изделий, так как коэффициент 1,6 учитывается в системах допусков параметров, характеризующих точность поверхностей изделий широкого применения. Станки повышенной точности, как правило, изготавливаются на базе станков нормальной точности, отличаясь от них, в основном, более точным изготовлением и подбором отдельных деталей и повышенным качеством монтажа.
Станки высокой и особо высокой точности отличаются от предыдущих специальными конструктивными особенностями отдельных элементов, высокой точностью их изготовления и специальными условиями эксплуатации.
Сверхточные станки предназначены для обработки деталей наивысшей точности — делительных зубчатых колес и дисков, эталонных зубчатых колес, измерительных винтов и т. п.
При приемке станков более высокого класса точности, чем регламентируется приведенными ниже нормами, можно использовать принятое соотношение основных показателей точности при переходе от более низкого к более высокому классу путем умножения допускаемых отклонений на 0,6.
Сравнение норм точности ГОСТ и иностранных стандартов
Сравнивая стандарты СССР (ГОСТ) на нормы точности металлорежущих станков с аналогичными стандартами других стран, следует отметить:
- По количеству и номенклатуре охваченных стандартами на нормы точности станков (около 65 действующих ГОСТ) СССР занимает ведущее место.
- Объем испытаний станков на точность, регламентированных в ГОСТ, в основном соответствует принятому в большинстве иностранных стандартов.
Различие, главным образом, касается проверок отдельных деталей (станин, ходовых винтов, делительных дисков), которые контролируются при их изготовлении и сборке и в ГОСТ, как правило, не включаются. - Величины допускаемых отклонений параметров, приведенные в ГОСТ на нормы точности, также в, основном, соответствуют принятым в большинстве иностранных стандартов.
Возросшие требования промышленности к качеству выпускаемых станков, в особенности к их точности, надежности и долговечности, а также условия поставки станков на экспорт, ставят перед станкостроительной промышленностью Советского Союза задачу обеспечения достаточной продолжительности работы станков с заданной точностью.
В частности, при изготовлении станков, поставляемых на экспорт, разрешается использовать только часть поля допуска на точность станков. Представляется необходимым в отдельных случаях, там, где это целесообразно, предъявлять более жесткие требования к точности и вводить проверку новых параметров.
В ближайшее время будут выпущены новые и пересмотренные ГОСТ с более высокими требованиями по ряду показателей точности станков и добавлением повышенных классов точности в соответствии с разработанной классификацией. - Следует иметь в виду, что в отдельных случаях допуски, указанные в иностранных стандартах, неоправдано завышены и поэтому, при сравнении их с нормами точности ГОСТ нужно проверять целесообразность этого завышения, а также анализировать влияние пониженных требований к точности отдельных параметров на точность работы станка в соответствии с его назначением.
- В приведенных таблицах сравнения норм точности ГОСТ и иностранных стандартов (табл. 172—192) не всегда даются совершенно идентичные проверки как по методике их проведения и применяемой контрольной аппаратуре, так и по длинам, к которым отнесены допуски на точность.
В таких случаях в таблицах приведены соответствующие оговорки. Допуски пересчитываются в зависимости от длин, к которым они отнесены. Нужно, также, учитывать, что в различных стандартах принята своя собственная система взаимосвязи отдельных проверок, и буквальное сравнение точности их без учета этой взаимосвязи не всегда дает возможность судить о действительной точности работы станков.
В этих случаях требуется более глубокий анализ сравниваемых показателей точности, а также проверка точности работы станков в совершенно одинаковых условиях. - При сравнении допускаемых отклонений по ГОСТ и иностранным стандартам следует учитывать, что при изготовлении станков, поставляемых заводами Советского Союза на экспорт, разрешается использовать только часть поля допуска на точность по ГОСТ:
0,6 — от величины допуска — для станков нормальной и повышенной точности;
0,8 — от величины допуска — для станков высокой и особо высокой точности.
- Полторацкий Н.Г. Приемка металлорежущих станков, ВнешТоргИздат, 1968
- Батов В.П. Токарные станки, 1978
- Схиртладзе А.Г., Новиков В.Ю. Технологическое оборудование машиностроительных производств, 1980
- Тепинкичиев В.К. Металлорежущие станки, 1973
- Чернов Н.Н. Металлорежущие станки, 1988
Список литературы:
Читайте также: Методика проверки токарно-винторезных станков на точность и жесткость
Полезные ссылки по теме
Каталог справочник металлорежущих станков
Паспорта и руководства металлорежущих станков
: Профильные направляющие :: Направляющие
ПЕРЕЗВОНИТЬ
Идёт отправка формы…
Уважаемый, !
Спасибо, за обращение в компанию CNCPROF.
Мы свяжемся с вами в течении 30 минут (в рабочее время по МСК) по вашему телефону .
закрыть
GD20WAZ0-3 Каретка фланцевая преднатяг Z0 класс точности H купить со склада
- Тип Каретка фланцевая
- Типоразмер 20
- Натяг Z0
- Натяг –
0-0.
02С, C-динамическая нагрузка
- Класс точности 3 (H)
- Грузоподъемность динамическая, кН 13.7
- Грузоподъемность статическая, кН 19.27
Все характеристики
Артикул: GD20WAZ0-3
GD20WAZ0-3 – Каретка фланцевая преднатяг – Z0 класс точности – H, Грузоподъемность динамическая, кН – 13. 7, Грузоподъемность статическая, кН – 19.27, Материал – сталь GCr15. Совместимы с рельсами GD20A. За счет плавности хода данных кареток обеспечивается низкий уровень шума и загрязнения.
Рельсовые направляющие применяются в станках ЧПУ и высокоточных системах линейного перемещения.Рельсовые направляющие серии GD имеют высокую точность позиционирования, жесткость и малую разницу между статическим и динамическим сопротивлением.
- Тип Каретка фланцевая
- Типоразмер 20
- Натяг Z0
- Натяг –
0-0.
02С, C-динамическая нагрузка
- Класс точности 3 (H)
- Грузоподъемность динамическая, кН 13.7
- Грузоподъемность статическая, кН 19.27
Каталог Guhring техническая документация – страница 51
Основные положения
М етчики для метрической резьбы ISO DIN EN 22857 (фрагмент)
Профиль внутренней резьбы Профиль метчика
Базовый профиль: Допуски: Базовый профиль: Допуск:
D Н о м и н а л ь н ы й д и а м е т р T d i Д о п у с к в н у т р . д и а м е т р а р е з ь б ы d = D Н о м и н а л ь н ы й д и а м е т р T d 2 Д о п у с к д л я
D i В н у т р е н н и й д и а м е т р р е з ь б ы T d 2 Д о п у с к с р е д , д и а м е т р а р е з ь б ы d m in . М и н и м а л ь н ы й р а з м е р н а р у ж н о г о д и а м е т р а с р е д н е г о д и а м е т р а
D 2 С р е д н и й д и а м е т р р е з ь б ы J s Н и ж н е е о т к л о н е н и е н а р у ж н о г о д и а м е т р а
Р Ш а г р е з ь б ы
о У г о л п р о ф и л я d 2 = D 2 С р е д н и й д и а м е т р р е з ь б ы
Н В ы с о т а d 2 m in . М и н и м а л ь н ы й р а з м е р с р е д н е г о д и а м е т р а р е з ь б ы
п р о ф и л я р е з ь б ы d 2 m a x . М а к с и м а л ь н ы й р а з м е р с р е д н е г о д и а м е т р а р е з ь б ы
EI Н и ж н и й п р е д е л , E s В е р х н е е о т к л о н е н и е с р е д н е г о д и а м е т р а р е з ь б ы
н о л ь д л я п о л я д о п у с к а Н , E m Н и ж н е е о т к л о н е н и е с р е д н е г о д и а м е т р а р е з ь б ы
п о л о ж и т е л ь н ы й д л я д о п у с к а G
Для международной унификации резьбы была создана Часть 1 обозначаются дополнительной буквой “X” (6
резьба ISO.
Это себя полностью оправдало. Метрическая НХ, 6 GX). Рекомендуем использовать метчики согласно
резьба ISO является сегодня самым распространенным прилагаемой диаграмме:
видом резьбы. Этот факт отражен и в нашей программе
по метчикам.
Степень точности допуска (цифровое обозначение)
Для наружней резьбы степень точности выражается с
Распределение полей допусков / классов точности
помощью цифр от 3 до 9, для внутренней резьбы от 4 до
8. 3 – для самого узкого допуска, 9 – для самого широкого Поле допуска резьбы
допуска. Поле допуска для метчика
280
256
Основные отклонения поля допуска (буквенное
240
обозначение)
Основные отклонения допуска обозначаются по ISO 212
200
для внутренней резьбы заглавными буквами от А до Н, 180
для наружней резьбы – маленькими буквами от а до h.
160
Допуска от А до G или от а до g имеют положительные 7G 154
7GX
или отрицательные предельные отклонения. Поля 6G 126 126
допусков Н и h начинаются с нулевого отклонения. Для | 120 112 6GX 7G
6Н 98 98 98
обычных резьб применяются допуска Н и д; для резьбы с
6НХ 6G
последующей обработкой поверхности – допуска G и е. 80 70 70
4Н 4НХ
При изготовлении резьбовых шпилек по ISO в отношении 6Н
42 42
позиций допусков от а до g необходимо обратить 40 32
4Н
внимание на то, что учитываются определенные 14
предельные допуска для наружного диаметра (наружний
диаметр болта = номинальный диаметр минус допуск).
DIN 802 Часть 1
DIN EN 22657
Поле допусков (выборка)
нарезаемой
Класс точности внутренней резьбы Класс точности
изготовления метчика резьбы для
Наименование* Обозначение метчика
Поле допуска (внутренней резьбы)/
Класс 1 ISC ) 1 4Н 5Н 4Н
Класс точности (метчика)
Квалитет и положение допуска определяется полем Класс 2 ISO 2 6Н 6H
■
допуска. Его обозначение состоит из соответствующих Класс 3 IS03 6G 6G
инструмент
цифр и букв.
7G 7G Резьбонарезной
Обозначение допуска метчика соответствует полю
* Допуски трех классов применения рассчитываются согласно приве
допуска внутренней резьбы, для которой метчик имеет
денным данным в зависимости от единицы допуска t, величина которого
преимущественное применение. Это не в каждом случае соответствует допуску среднего диаметра TD2 с классом точности 5 для
аналогично полю допуска обработанной резьбы. резьбы гайки (экстрополируется с шагом до 0,2 мм):
t = Тр 2 Класс точности 5 резьбы гайки
Метчики со смещенным полем допуска по DIN 802
1639
Точность обработки деталей. Классы точности
Взаимозаменяемость деталей.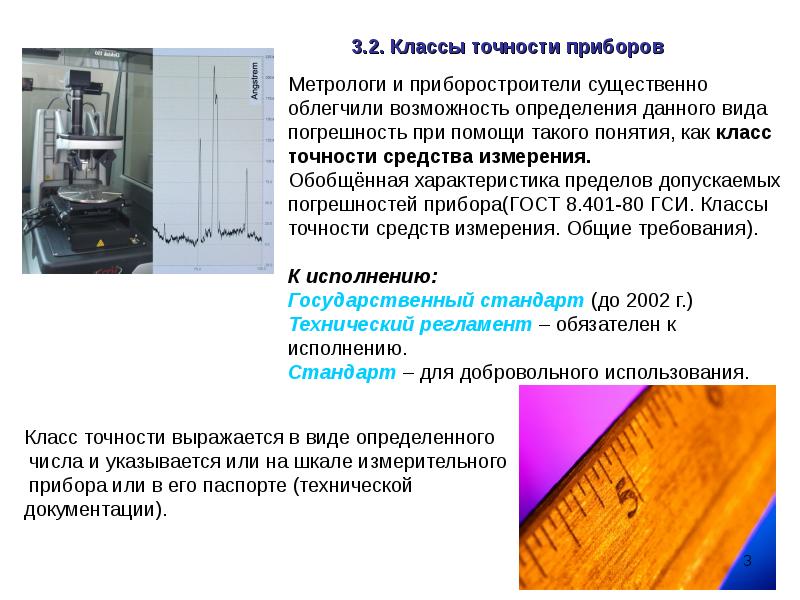
Выпуск велосипедов, мотоциклов, тракторов, автомобилей, электродвигателей, швейных и других машин осуществляется на заводах такими темпами, когда счет времени обработки и сборки ведется не только минутами, но и секундами. Детали этих машин должны быть изготовлены точно по чертежам и техническим условиям так, чтобы при сборке они подходили одна к другой без слесарной подгонки, что сокращает время на сборку и удешевляет стоимость изделия. Важно также, чтобы при ремонте машины новая деталь, заменяющая изношенную, могла быть установлена на ее место без подгонки. Детали, удовлетворяющие таким требованиям, называются взаимозаменяемыми. Взаимозаменяемость – это свойство деталей занимать свои места в узлах и изделиях без предварительного подбора или подгонки по месту.
Сопряжение деталей.Две детали, подвижно или неподвижно соединяемые друг с другом, называют сопрягаемыми. Размеры, по которым происходит соединение этих деталей, называют сопрягаемыми размерами. Размеры, по которым не происходит соединение деталей, называют свободными размерами. Примером сопрягаемых размеров может служить наружный диаметр фрезерной оправки и соответствующий ему диаметр отверстия в насадной фрезе, диаметр шейки оправки и соответствующий ему диаметр отверстия в подшипнике подвески. Примером свободных размеров может служить наружный диаметр установочных колец фрезерной оправки, длина фрезерной оправки, ширина цилиндрической фрезы.
Сопрягаемые детали должны быть выполнены взаимозаменяемыми.
Понятие о точности обработки.Изготовить партию взаимозаменяемых деталей абсолютно одинакового размера невозможно, так как на точность обработки влияют неточность и износ станка, износ фрезы, неточности при установке и закреплении заготовки и другие причины. Как правило, все детали данной партии при обработке имеют отклонения от заданных размеров и формы. Но величины этих отклонений должны быть назначены таким образом, чтобы сопрягаемые размеры могли обеспечить сборку деталей без подгонки, т. е. чтобы детали были взаимозаменяемыми.
Конструкторы изделий при назначении величины допускаемых отклонений на сопрягаемые детали руководствуются установленными государством стандартами – ГОСТ. Ниже вкратце излагаются основные понятия о допусках и предельных отклонениях, вытекающие их ГОСТ 7713-55.
Понятие о допуске и предельных отклонениях. Величина допустимых отклонений указывается в чертежах детали со знаками плюс и минус.
Знак минус показывает, что деталь может быть изготовлена с отклонением в меньшую сторону; знак плюс показывает, что деталь может быть изготовлена с отклонением в большую сторону. Например, поставленный в чертеже бруска размер 10-0,1 мм показывает, что брусок может быть отфрезерован так, чтобы после его обработки его размер лежал в пределах между 10 мм и 9,9 мм. Точно также поставленный в чертеже диаметр паза 10+0,2 мм показывает, что паз может быть отфрезерован так, чтобы после обработки его размер лежал в пределах между 10 мм и 10,2 мм.
Поставленный в чертеже размер 10+0,2-0,1 мм показывает, что обработанная деталь будет годной, если ее размер составляет не менее 9,9 мм и не более 10,2 мм, т.е. лежит в этих пределах.
Номинальным размером называется основной расчетный размер, от которого исходят при назначении отклонений. Если в чертеже указан размер 10+0,2-0,1 мм, то размер 10 мм называется номинальным.
Действительным размером называется размер, полученный при измерении обработанной детали. Размеры, между которыми может находиться действительный размер годной детали, называются предельными размерами. Действительный размер детали с размерами 10+0,2-0,1 мм может лежать в пределах 10+0,2 = 10,02 мм и 10-0,1 =9,9 мм. Больший размер называется наибольшим предельным размером, а меньший – наименьшим предельным размером.
Разность между наибольшим и наименьшим предельными размерами называется допуском размера.
- Верхним предельным отклонением называется разность между наибольшим предельным размером и номинальным размером.
- Нижним предельным отклонением называется разность между наименьшим предельным размером и номинальным размером.
Допуск можно также определить, как разность между верхним и нижним предельными отклонениями.
Действительным отклонением называется разность между действительным и номинальным размерами.
При графическом изображении допусков отклонения размеров откладываются от линии, соответствующей номинальному размеру и называемой нулевой линией; положительные отклонения откладываются вверх от нулевой линии, а отрицательные – вниз.
Зазоры и натяги.Если брусок с размерами грани 10-0,1 мм посадить в паз с размерами грани 10+0,2+0,1 мм, то в соединении бруска с пазом получится зазор, и брусок можно будет передвигать вдоль паза. Такая посадка (сопряжение двух деталей) называется свободной. Наибольший зазор в этом случае составит 0,3 мм, а наименьший будет равен 0,1 мм.
Если же размер бруска будет 10+0,2+0,1 мм, а паза 10-0,1 мм, то брусок не войдет свободно в паз и его придется вставлять с силой или запрессовывать. В соединении получится натяг или отрицательный зазор, наименьшая величина которого равна 0,1 мм. А наибольшая 0,3 мм. Такая посадка называется неподвижной, так как брусок нельзя будет передвигать вдоль паза.
Таким образом, можно сделать следующие заключения.
- Зазором называется положительная разность между размером паза и размером бруска, обеспечивающая свободу их движения относительно друг друга.
- Натягом называется отрицательная разность между размером паза и размером бруска (размер бруска больше размера паза), которая после посадки бруска в паз создает неподвижное их соединение.
Посадкой называется характер соединения сопрягаемых деталей, определяемый разностью между размерами паза и бруска, создающий большую или меньшую свободу (зазор или натяг) их относительного перемещения или степень сопротивления взаимному перемещению. В зависимости от наличия в сопряжении бруска и паза зазора или натяга различают посадки с зазором, с натягом и переходные.
Посадками с зазором, или свободными, называют такие посадки, при которых обеспечивается возможность относительного перемещения сопряженных деталей во время работы. В зависимости от величины зазора степень относительного перемещения деталей, сопряженных свободной посадкой, может быть различной. Для вращения шпинделя фрезерного станка в подшипниках зазор должен быть меньшим и, следовательно, посадка более тугой, чем для посадки колец на фрезерную оправку.
Посадками с натягом, или неподвижными, называют посадки, при которых во время работы не должно происходить перемещения сопряженных деталей относительно друг друга. В зависимости от величины натяга степень свободы сопряженных деталей неподвижной посадки может быть различной. Так, посадку шейки вала в кольцо шарикоподшипника производят с меньшим натягом, чем посадку колеса железнодорожного вагона на шейку оси.
При переходных посадках возможно получение, как натягов, так и зазоров. При наибольшем предельном размере бруска и наименьшем предельном размере паза получается натяг, а при наименьшем предельном размере бруска и наибольшем предельном размере паза получается зазор (в таблицах допусков в графе «натяг» обозначен знаком минус).
Ниже приводятся посадки, относящиеся к рассмотренным трем группам; в скобках даются их сокращенные обозначения.
Наибольший натяг получается при горячей посадке, меньший — при прессовых посадках; наименьший зазор получается при скользящей посадке, немного больший — при посадке движения, почти втрое больший при ходовой, затем еще больший при легкоходовой и, наконец, наибольший при широкоходовой посадке.
При глухой, тугой, напряженной и плотной посадках, как указывалось выше, возможны натяги и зазоры в зависимости от получающихся отклонений размера.
Классы точности.Точность изготовления характеризуется величиной допускаемых отклонений от заданных размеров и формы. Для разных машин требуются детали с различной точностью обработки. Очевидно, что детали плуга, дорожного катка и других сельскохозяйственных и дорожных машин могут быть изготовлены менее точно, чем детали фрезерного станка, а детали фрезерного станка требуют меньшей точности, чем детали измерительного прибора. В связи с этим в машиностроении детали разных машин изготовляют по разным классам точности. В СССР (были) приняты десять классов точности.
- пять из них: 1-й, 2-й, 2а, 3-й, За — требуют наибольшей точности обработки;
- два других: 4-й и 5-й — меньшей;
- три остальных: 7-й, 8-й, 9-й — еще меньшей.
- 1-й класс точности применяют при изготовлении особо точных изделий. Вследствие очень малых допусков работа по 1-му классу точности требует высокой квалификации рабочего и точного оборудования, приспособлений и инструмента.
- 2-й и 2а классы точности применяют наиболее часто. По ним изготовляют ответственные детали станков, автомобильных, тракторных, авиационных и электрических двигателей, текстильных и других машин.Наряду с этим в отраслях машиностроения, выпускающих указанные машины, детали менее ответственных соединений изготовляют по 3-му, 4-му, 5-му и другим более грубым классам точности.
- 3-й и За классы точности применяют главным образом в тяжелом машиностроении при производстве турбин, паровых машин, двигателей внутреннего сгорания, трансмиссионных деталей и т. д.
- По 4-му классу точности изготовляют детали сельскохозяйственных машин, паровозов, железнодорожных вагонов и т.
д.
- 5-й класс точности применяют в машиностроении для неответственных деталей менее точных механизмов.
- 7-й, 8-й и 9-й классы точности применяют при изготовлении более грубых деталей и особенно при заготовительных операциях: литье, штамповке, медницко-слесарных работах и т. д.
- Свободные размеры деталей выполняют обычно по 5-му или 7-му классам точности.
Чтобы показать, с какой посадкой и по какому классу точности нужно изготовить деталь, в чертежах на номинальных сопрягаемых размерах ставится буква, обозначающая посадку, и цифра, соответствующая классу точности. Например, С4 означает: скользящая посадка 4-го класса точности; Х3 — ходовая посадка 3-го класса точности и т. п. Для посадок 2-го класса точности (особенно широко распространенных) цифра 2 не ставится. Поэтому, если в чертеже на сопрягаемом размере рядом с буквой посадки нет цифры, то это значит, что деталь надо изготовить по 2-му классу точности. Например, Л означает легкоходовая посадка 2-го класса точности.
Автор: С. В. Аврутин
Источник: Основы фрезерного дела, С. В. Аврутин, 1962г
Дата в источнике: 1962г
ГОСТ 17734-88 – Станки фрезерные консольные. Нормы точности и жесткости
ГОСТ 17734-88
(СТ СЭВ 5937-87)
Группа Г81
ОКП 38 1600
Срок действия с 01.01.90
до 01.01.95*
___________________________________
* Ограничение срока действия снято по
протоколу N 4-93 Межгосударственного Совета
по стандартизации, метрологии и сертификации.
(ИУС N 4, 1994 год). – Примечание.
1. РАЗРАБОТАН И ВНЕСЕН Министерством станкостроительной и инструментальной промышленности СССР
ИСПОЛНИТЕЛИ
А.Н.Байков, канд. техн. наук; С.С.Кедров, канд. техн. наук; Н.П.Семченкова
2. УТВЕРЖДЕН И ВВЕДЕН В ДЕЙСТВИЕ Постановлением Государственного комитета СССР по стандартам от 13. 06.88 N 1732
3. Срок проверки 1993 г., периодичность проверки 5 лет.
4. Стандарт соответствует СТ СЭВ 5937-87 в части норм точности станков
5. ВЗАМЕН ГОСТ 17734-81
6. ССЫЛОЧНЫЕ НОРМАТИВНО-ТЕХНИЧЕСКИЕ ДОКУМЕНТЫ
Обозначение НТД, на который дана ссылка | Номер пункта, приложения |
ГОСТ 8-82 | 1.1 |
ГОСТ 7035-75 | 3.1 |
ГОСТ 22267-76 | 1.4.1, 1.4.3-1.4.18, 2.4 |
ГОСТ 24643-81 | Приложение |
ГОСТ 25347-82 | Приложение |
ГОСТ 25443-82 | 2.1 |
ГОСТ 25889. | 2.7 |
ГОСТ 25889.2-83 | 2.5 |
ГОСТ 25889.3-83 | 2.6, приложение |
Настоящий стандарт распространяется на фрезерные консольные станки с горизонтальным или вертикальным шпинделем классов точности Н (I) и П (II) (широкоуниверсальные – класса точности П (II), изготавливаемые для нужд народного хозяйства и экспорта.
Настоящий стандарт не распространяется на специальные и специализированные станки.
1. ТОЧНОСТЬ СТАНКА
1.1. Общие требования к испытаниям станков на точность – по ГОСТ 8-82.
1.2. Методы проверки точности станков, указанные в настоящем стандарте как предпочтительные, следует применять в качестве обязательных в случае возникновения разногласий между изготовителем и потребителем в оценке качества поставляемых станков.
1.3. Номенклатура средств измерения и предъявляемые к ним основные технические требования приведены в приложении.
1.4. Нормы точности станков не должны превышать значений, указанных в пп.1.4.1-1.4.18.
1.4.1. Прямолинейность рабочей поверхности стола в продольном и поперечном сечениях
Таблица 1
Длина измерения, мм | Допуск, мкм, для станков класса точности | |
Н | П | |
До 250 | 16 | 10 |
” 400 | 20 | 12 |
400 ” 630 | 25 | 16 |
630 ” 1000 | 30 | 20 |
1000 | 40 | 25 |
Выпуклость рабочей поверхности стола не допускается.
Измерения следует проводить по ГОСТ 22267-76 (разд.4, предпочтительно методы 3 или 6). Рекомендуемое расположение сечений и точек измерения – по черт.1.
Черт.1
Метод измерения 3 применяют при длине стола до 1200 мм: , но не менее 100 мм; .
Методы 3 и 6 применяют при длине стола св. 1200 мм: , но не менее 150 мм и не более 300 мм; .
Стол и салазки устанавливают в среднее положение.
Для станков длиной рабочей поверхности стола св. 1000 мм поперечные сечения измерения должны быть расположены на расстоянии .
Количество сечений должно быть не менее трех.
При необходимости выбора другого расположения сечений или точек измерения из-за расположения Т-образных пазов и каналов для отвода смазочно-охлаждающей жидкости расположение их указывают в эксплуатационных документах на станок конкретного типоразмера
1.4.2. Прямолинейность направляющего паза
Таблица 2
Длина рабочей поверхности стола, мм | Допуск, мкм, для станков класса точности | |
Н | П | |
До 400 | 12 | 8 |
Св. | 16 | 10 |
630 ” 1000 | 20 | 12 |
1000 ” 1600 | 25 | 16 |
1600 | 30 | 20 |
Измерение следует проводить в соответствии со схемой, указанной на черт.2.
Черт.2
Проверяют выверочную сторону направляющего паза*.
________________
* За выверочную сторону направляющего паза принимают ближнюю к станине боковую сторону.
На рабочей поверхности стола 4 (черт.2) с помощью упоров 1, равных ширине паза и установленных в паз на концах стола, располагают линейку 3. Вдоль линейки, по проверяемой стороне паза от упора паза перемещают ползушку 5 с измерительным прибором 2, закрепленным так, чтобы его измерительный наконечник касался рабочей поверхности линейки и был ей перпендикулярен.
Отклонение определяют как наибольшую алгебраическую разность показаний прибора на всей длине перемещения.
1.4.3. Постоянство расстояния между траекторией продольного перемещения стола и боковой поверхностью направляющего паза
Измерение следует проводить по ГОСТ 22267-76 (разд.24, предпочтительно метод 2), в соответствии со схемой, указанной на черт.3.
Черт.3
Консоль и салазки устанавливают в среднее положение и закрепляют.
Стол перемещают в продольном направлении на всю длину хода.
Допускается проводить измерения параллельности направляющего паза стола траектории его продольного перемещения. В этом случае допуск уменьшают в 1,26 раза по сравнению с указанным в табл.3.
Таблица 3
Длина продольного перемещения стола, мм | Допуск, мкм, для станков класса точности | |
Н | П | |
До 400 | 20 | 12 |
Св. | 25 | 16 |
630 ” 1000 | 30 | 20 |
1000 | 40 | 25 |
1.4.4. Перпендикулярность поперечного перемещения стола к направлению его продольного перемещения
Допуск на длине перемещения до 250 мм для станков класса точности Н – 16 мкм, для станков класса точности П – 10 мкм;
на длине перемещения св. 250 мм для станков класса точности Н – 20 мкм, для станков класса точности П – 12 мкм.
Измерение следует проводить по ГОСТ 22267-76 (разд.8, предпочтительно метод 1), в соответствии со схемой, указанной на черт.4.
1 – направление перемещений
Черт.4
Стол и консоль устанавливают в среднее положение.
Допускается проводить измерения перпендикулярности направляющего паза стола траектории его поперечного перемещения.
1.4.5. Прямолинейность и параллельность траектории продольного перемещения стола относительно его рабочей поверхности
Таблица 4
Длина продольного перемещения стола, мм | Допуск, мкм, для станков класса точности | |
Н | П | |
До 400 | 20 | 12 |
Св. 400 ” 630 | 25 | 16 |
630 ” 1000 | 30 | 20 |
1000 | 40 | 30 |
Измерение следует проводить по ГОСТ 22267-76 (разд.6, предпочтительно метод 1a), в соответствии со схемой, указанной на черт. 5.
Черт.5
Салазки и консоль устанавливают в среднее положение.
Поверочную линейку устанавливают в середине стола.
Стол перемещают в продольном направлении на всю длину хода.
Допускается проводить измерение без поверочной линейки.
1.4.6. Прямолинейность и параллельность траектории поперечного перемещения стола относительно его рабочей поверхности
Допуск на длине поперечного перемещения стола до 250 мм для станков класса точности Н – 16 мкм, для станков класса точности П – 10 мкм, а на длине поперечного перемещения стола св. 250 мм допуск для станков класса точности Н – 20 мкм, для станков класса точности П – 12 мкм.
Измерение следует проводить по ГОСТ 22267-76 (разд.6, предпочтительно метод 1), в соответствии со схемой, указанной на черт.6.
Черт.6
Стол и консоль устанавливают в среднее положение.
Поверочную линейку устанавливают в середине стола.
Стол перемещают в поперечном направлении на всю длину хода.
Допускается проводить измерение без поверочной линейки.
1.4.7. Прямолинейность и перпендикулярность траектории вертикального стола его рабочей поверхности
Допуск на длине вертикального перемещения до 300 мм для станков класса точности Н – 25 мкм, а для станков класса точности П – 16 мкм, 90°.
Измерение следует проводить по ГОСТ 22267-76 (разд.9, предпочтительно метод 1а), в соответствии со схемой, указанной на черт.7.
Черт.7
Поверочный цилиндрический угольник устанавливают примерно в середине стола.
Стол и салазки устанавливают в среднее положение.
Консоль перемещают на всю длину хода, но не более чем на 300 мм.
Измерения проводят в двух взаимно перпендикулярных вертикальных плоскостях, параллельных продольному и поперечному перемещениям стола. Влияние реверса консоли не учитывают.
1.4.8. Перпендикулярность рабочей поверхности стола траектории вертикального перемещения ползуна в продольной плоскости (для станков с вертикальным шпинделем и механической рабочей подачей ползуна)
Допуск на всей длине перемещения ползуна для станков класса точности Н – 20 мкм, для станков класса точности П – 12 мкм.
При длине перемещения ползуна более 250 мм допуск увеличивают в 1,25 раза.
Измерение следует проводить по ГОСТ 22267-76 (разд.9, предпочтительно метод 1а), в соответствии со схемой, указанной на черт.8.
Черт.8
Стол, салазки и консоль устанавливают в среднее положение.
На рабочей поверхности стола в продольной плоскости, проходящей через середину стола на минимальном для проведения измерений расстоянии от его центра, устанавливают угольник. На неподвижной части станка закрепляют измерительный прибор так, чтобы его измерительный наконечник касался рабочей поверхности угольника, был ей перпендикулярен и располагался на уровне торца шпинделя станка. Ползун перемещают в вертикальном направлении.
1.4.9. Перпендикулярность рабочей поверхности стола траектории вертикального перемещения ползуна в поперечной плоскости (для станков с вертикальным шпинделем и механической рабочей подачей ползуна)
Допуск на всей длине перемещения ползуна для станков класса точности Н – 20 мкм, для станков класса точности П – 12 мкм.
При длине перемещения ползуна более 250 мм допуск увеличивают в 1,25 раза.
Наклон стола в сторону от стойки не допускается.
Измерение следует проводить по ГОСТ 22267-76 (разд.9, предпочтительно метод 1а), в соответствии со схемой, указанной на черт.9.
Черт.9
Стол, салазки и консоль устанавливают в среднее положение.
На рабочей поверхности стола на одинаковом минимальном для проведения измерений расстоянии от поперечной плоскости, проходящей через ось шпинделя, устанавливают поверочные угольники. На неподвижной части станка закрепляют измерительные приборы так, чтобы их измерительные наконечники касались рабочих поверхностей угольников, были им перпендикулярны и расположены на уровне торца шпинделя станка. Ползун перемещают в вертикальном направлении.
Отклонение определяют как наибольшую алгебраическую разность алгебраических полусумм одновременно фиксируемых показаний обоих приборов.
1.4.10. Осевое биение фрезерного шпинделя
Допуск для станков класса точности Н – 10 мкм, для станков класса точности П – 6 мкм.
Измерение следует проводить по ГОСТ 22267-76 (разд.17, предпочтительно метод 1), в соответствии со схемой, указанной на черт.10.
Черт.10
1.4.11. Торцевое биение опорного торца шпинделя (для станков с базированием фрез по торцевой поверхности)
Допуск для станков класса точности Н – 18 мкм, для станков класса точности П – 10 мкм.
Измерение следует проводить по ГОСТ 22267-76 (разд.18), в соответствии со схемой, указанной на черт.11.
Черт.11
1.4.12. Радиальное биение наружной центрирующей поверхности шпинделя (для станков с центрированием фрез по наружной центрирующей поверхности)
Допуск для станков класса точности Н – 10 мкм, для станков класса точности П – 6 мкм.
Измерение следует проводить по ГОСТ 22267-76 (разд.15, предпочтительно метод 1), в соответствии со схемой, указанной на черт.12.
Черт.12
1.4.13. Радиальное биение конического отверстия фрезерного шпинделя
Таблица 5
Ширина стола, мм | Длина измерения , мм | Сечение измерения | Допуск, мкм, для станков класса точности | |
Н | П | |||
До 250 | – | А | 10 | 6 |
150 | В | 12 | 8 | |
Св. | – | А | 10 | 6 |
300 | В | 20 | 12 |
Измерение следует проводить по ГОСТ 22267-76 (разд.15, предпочтительно метод 2), в соответствии со схемой, указанной на черт.13.
Черт. 13
1.4.14. Параллельность оси вращения горизонтального фрезерного шпинделя относительно рабочей поверхности стола
Таблица 6
Ширина стола, мм | Длина измерения , мм | Допуск, мкм, для станков класса точности | |
Н | П | ||
До 160 | 100 | 8 | 5 |
Св. | 150 | 12 | 8 |
” 250 | 300 | 25 | 16 |
Отклонение шпинделя вверх не допускается.
Измерение следует проводить по ГОСТ 22267-76 (разд.7, предпочтительно метод 1), в соответствии со схемой, указанной на черт.14.
Черт.14
Стол устанавливают в среднее положение в продольном направлении.
Поверочную линейку устанавливают в середине стола в поперечном направлении.
Допускается проводить измерения по ГОСТ 22267-76 (разд.7, метод 2).
1.4.15. Параллельность направляющих хобота относительно оси вращения горизонтального фрезерного шпинделя в вертикальной и горизонтальной плоскостях
Таблица 7
Ширина стола, мм | Длина измерения , мм | Допуск, мкм, для станков класса точности | |
Н | П | ||
До 160 | 100 | 10 | 6 |
Св. | 150 | 12 | 8 |
” 250 | 300 | 20 | 12 |
Отклонение хобота вверх не допускается.
Измерение следует проводить по ГOCT 22267-76 (разд.6, предпочтительно метод 3а), в соответствии со схемой, указанной на черт.15.
Черт.15
Специальную державку с прибором для измерения длин устанавливают на направляющих хобота так, чтобы наконечник измерительного прибора касался цилиндрической поверхности контрольной оправки в вертикальной плоскости.
Державку с прибором для измерения длин перемещают по направляющим хобота на заданную длину .
Измерения проводят в начале и конце перемещения. Затем контрольную оправку поворачивают на 180° и измерения повторяют.
Отклонение от параллельности направляющих хобота и оси вращения горизонтального фрезерного шпинделя в вертикальной плоскости равно среднему арифметическому двух значений алгебраической разности показаний измерительного прибора, полученных до и после поворота оправки.
Аналогично проводят проверку и определяют отклонение от параллельности в горизонтальной плоскости.
1.4.16. Соосность отверстия серьги и горизонтального фрезерного шпинделя в вертикальной и горизонтальной плоскостях
Допуск при ширине стола до 250 мм на расстоянии 150 мм от заданного сечения до базовой плоскости для станков класса точности Н – 25 мкм, для станков класса точности П – 16 мкм; при ширине стола св. 250 мм на расстоянии 300 мм допуск для станков класса точности Н – 30 мкм, для станков класса точности П – 20 мкм.
Ось отверстия серьги в вертикальной плоскости может быть только ниже оси вращения фрезерного шпинделя.
Измерение следует проводить по ГОСТ 22267-76 (разд.14, предпочтительно метод 5), в соответствии со схемой, указанной на черт.16.
Черт.16
Контрольную оправку симметрично устанавливают в отверстие серьги. Наконечник измерительного прибора должен касаться контрольной оправки вблизи серьги.
Серьгу закрепляют в хоботе.
Диаметр контрольной оправки равен диаметру отверстия серьги.
1.4.17. Перпендикулярность оси вращения горизонтального шпинделя направляющему пазу стола (для станков с неповоротным столом или для станков с фиксатором нулевого положения)
Допуск для станков класса точности Н – 20 мкм, для станков класса точности П – 12 мкм.
Измерение следует проводить по ГОСТ 22267-76 (разд.10, предпочтительно метод 5), в соответствии со схемой, указанной на черт.17.
Черт.17
Консоль, стол и салазки устанавливают в среднее положение и закрепляют.
В шпинделе станка закрепляют коленчатую оправку с измерительным прибором.
1.4.18. Перпендикулярность оси вращения вертикального фрезерного шпинделя рабочей поверхности стола в плоскостях, параллельной и перпендикулярной к продольному перемещению стола
Допуск при ширине стола до 250 мм на длине измерения 150 мм для станков класса точности Н – 12 мкм, для станков класса точности П – 8 мкм; при ширине стола св. 250 мм на длине 300 мм допуск для станков класса точности Н – 25 мкм, для станков класса точности П – 16 мкм.
В плоскости, перпендикулярной к продольному перемещению стола 90°.
Измерение следует проводить по ГОСТ 22267-76 (разд.10, предпочтительно метод 1), в соответствии со схемой, указанной на черт.18.
Черт.18
Стол, салазки и консоль устанавливают в среднее положение.
Поверочную линейку устанавливают в середине стола.
Пиноль вдвигают.
Для станков с подвижной бабкой проверку производят в крайних верхнем и нижнем положениях бабки.
2. ТОЧНОСТЬ ОБРАЗЦА-ИЗДЕЛИЯ
2.1. Общие требования к образцам-изделиям – по ГОСТ 25443-82.
2.2. Нормы точности образцов-изделий не должны превышать значений, указанных в пп.2.4-2.7.
2.3. Форма и размеры образцов-изделий
Форма и размеры образцов-изделий в соответствии с черт.19 и 20.
Образец-изделие для станков с горизонтальным фрезерным шпинделем
Черт. 19
Образец-изделие для станков с вертикальным фрезерным шпинделем
Черт.20
, но не более 450 мм;
, но не более 160 мм;
, но не более 120 мм;
16 мм
мм,
где – наибольшее продольное перемещение стола;
– наибольшее поперечное перемещение стола;
– наибольшее расстояние от торцевой поверхности фрезерного шпинделя до стола станка (у станков с вертикальным шпинделем), либо от оси фрезерного шпинделя до стола станка (у станков с горизонтальным шпинделем).
Образцы-изделия должны изготовляться из чугуна с временным сопротивлением от 200 до 250 Н/мм (МПа) или из стали с временным сопротивлением от 350 до 450 Н/мм (МПа).
Поверхности 1-4 образцов-изделий должны быть предварительно обработаны методом фрезерования.
Поверхности 1 (черт.19) или 6 (черт.20) выверяют параллельно траектории продольного перемещения стола.
Поверхности 1 должны быть обработаны за два прохода с перекрытием 10-15 мм.
Допускается применять серьги при обработке поверхностей 2, 3 и 4 образца-изделия по черт.19.
Тип, материал, размеры и требования к режущему инструменту, а также режимы и последовательность чистовой обработки образца-изделия и место его расположения на поверхности стола должны соответствовать указанным в эксплуатационных документах на станок
2.4. Прямолинейность поверхностей 1 и 2
Таблица 8
Длина измерения, мм | Допуск, мкм, для станков класса точности | |
Н | П | |
До 100 | 12 | 8 |
Св. 100 ” 160 | 16 | 10 |
” 160 ” 250 | 20 | 12 |
” 250 ” 400 | 25 | 16 |
” 400 | 30 | 20 |
Измерение следует проводить по ГОСТ 22267-76 (разд. 4, предпочтительно метод 3), в соответствии со схемой, указанной на черт.21.
Черт.21
Рекомендуемое расположение сечений и точек измерения при проверке поверхностей образцов-изделий в соответствии со схемами, указанными на черт.22.
Черт.22
Образец-изделие устанавливают на поверочной плите или столе станка в незажатом положении.
Измерения прямолинейности поверхности 1 проводят в продольном и поперечном сечениях, поверхности 2 – в продольном.
Расстояние между точками измерения , но не менее 80 мм; .
2.5. Параллельность поверхностей 2 относительно поверхности 5 (для образцов-изделий по черт.19) и поверхности 1 относительно поверхности 5 (для образцов-изделий по черт.20) в продольном и поперечном сечениях
Таблица 9
Длина измерения, мм | Допуск, мкм, для станков класса точности | |
Н | П | |
До 100 | 12 | 8 |
Св. | 16 | 10 |
” 160 ” 250 | 20 | 12 |
” 250 ” 400 | 25 | 16 |
” 400 | 30 | 20 |
Примечание. За длину измерения для прямоугольных образцов-изделий принимают длину наибольшей стороны.
Измерение следует проводить по ГОСТ 25889.2-83 (предпочтительно метод 2), в соответствии со схемами, указанными на черт.23.
Черт.23
2.6. Перпендикулярность поверхности 1 к поверхностям 2 и 4, поверхности 2 к поверхностям 3 и 4
Допуск на расстоянии измерения 100 мм для станков класса точности Н – 20 мкм, для станков класса точности П – 12 мкм.
Измерение следует проводить по ГОСТ 25889. 3-83 (предпочтительно метод 2), в соответствии со схемами, указанными на черт.24.
Черт.24
2.7. Круглость воспроизведенной при контурном фрезеровании цилиндрической поверхности образца-изделия
Для проверки используют образец-изделие (черт.25) в виде диска диаметром и толщиной . Материал: алюминиевый сплав, серый чугун или сталь. Образец предварительно обработан.
Черт.25
Образец закрепляют в средней части стола и обрабатывают цилиндрическую поверхность на чистовых режимах резания при помощи концевых фрез.
Измерение следует проводить по ГОСТ 25889.1-83 (предпочтительно методы 1 или 2), в соответствии со схемами, указанными на черт.26.
Черт.26
Допускается оценивать точность формы постоянством диаметра. В этом случае допуск увеличивают в два раза по сравнению с указанными в табл.10.
Таблица 10
Ширина стола, мм | Диаметр образца-изделия , не менее, мм | Допуск, мкм, для станков класса точности | |
Н | П | ||
До 200 | 65 | 80 | 50 |
Св. | 100 | 100 | 65 |
3. ЖЕСТКОСТЬ СТАНКА
3.1. Общие условия испытания станков на жесткость – по ГОСТ 7035-75.
3.2. Перемещение под нагрузкой стола относительно оправки, закрепленной в шпинделе
Значения допусков перемещения под нагрузкой стола должно соответствовать указанным в табл.11.
Таблица 11
Ширина стола, мм | Класс точности станка | Нагружающая сила, кН | Допуск, мм |
200 | Н | 5 | 0,32 |
П | 4 | 0,20 | |
250 | Н | 8 | 0,40 |
П | 6,3 | 0,25 | |
320 | Н | 12,5 | 0,50 |
П | 10 | 0,32 | |
400 | Н | 20 | 0,63 |
П | 16 | 0,40 |
Для широкоуниверсальных станков нормы жесткости указанного класса точности относят только к основному шпинделю.
Для универсальных станков с поворотным столом допуск может быть увеличен в 1,12 раза.
Направление действия силы должно соответствовать указанному на черт.27.
Черт.27
40° – угол между проекцией нагружающей силы на горизонтальную плоскость и направлением продольной подачи стола;
30° – угол между направлением нагружающей силы и ее проекцией на горизонтальную плоскость;
34° – для станков с горизонтальным шпинделем;
30° – для станков с вертикальным шпинделем;
– угол наклона части образующей диска оправки и ее оси;
37° – угол между проекцией нагружающей силы на вертикальную плоскость и направлением продольной подачи стола.
Расположение точки приложения нагружающей силы по отношению к деталям станка должно соответствовать указанным в табл.12 и на черт.28 и черт.29 для станков с горизонтальным и вертикальным шпинделем соответственно.
Таблица 12
мм
Размер, определяющий расположение точки приложения силы | Нормы | |||
Ширина стола | 200 | 250 | 320 | 400 |
Расстояние от оси шпинделя до рабочей поверхности стола | 125 | 140 | 160 | 180 |
Расстояние от торца шпинделя до рабочей поверхности стола | 160 | 180 | 200 | 224 |
Расстояние от торца шпинделя до точки приложения силы | 52 | 67 | 80 | 95 |
Расстояние от вертикальных направляющих станины до точки приложения силы | 270 | 280 | 320 | 450 |
Расстояние от точки приложения силы до торца подшипника серьги | 132 | 140 | 160 | 224 |
Расстояние от вертикальных направляющих станины до первого паза стола | 305 | 315 | 375 | 505 |
Расстояние от вертикальной оси шпинделя до первого паза стола | 60 | 67 | 95 | 106 |
Диаметр конусной части испытательной оправки в точке приложения нагружающей силы | 80 | 100 | 125 | 160 |
Диаметры цилиндрической части испытательной оправки: | ||||
45 | 55 | 65 | 75 | |
45 | 55 | 60 | 71 |
Черт. 28
Черт.29
В отверстие шпинделя устанавливают оправку 1 (черт.28, черт.29) и закрепляют. В станках с горизонтальным шпинделем на свободный конец оправки надевают серьгу 3 и закрепляют на хоботе в заданном положении.
Шпиндельную гильзу или ползун в станках с вертикальным шпинделем устанавливают в верхнее положение, поворотную головку – в нулевое положение. Хобот устанавливают заподлицо с задней стенкой станины.
На столе закрепляют устройство для создания нагружающей силы , для измерения которой используют динамометр.
Перед каждым испытанием хоботу с серьгой, консоли, салазкам, столу и шпиндельной гильзе сообщают перемещения с последующей установкой их в заданное положение, а шпиндель поворачивают. При этом консоль подводят в положение проверки перемещением снизу-вверх, салазки – перемещением к зеркалу станины, хобот с серьгой – перемещением от зеркала станины, а стол устанавливают в среднее положение перемещением справа-налево.
При испытаниях консоль, поворотный стол, хобот и шпиндельную гильзу закрепляют.
Показывающий прибор 2 закрепляют на столе так, чтобы его измерительный наконечник касался:
торца диска оправки в точке, расположенной у периферии в горизонтальной плоскости, проходящей через ось оправки – на станках с горизонтальным шпинделем;
образующей цилиндрического пояска, лежащей в плоскости, проходящей через ось оправки и перпендикулярной зеркалу станины – на станках с вертикальным шпинделем.
Между столом и оправкой создают плавно возрастающую до заданного значения силу , направление которой определяют углами , и . Нагружающую силу прилагают к конусной части диска оправки и направляют через ось оправки.
Одновременно при помощи индикатора измеряют перемещение оправки относительно стола в направлении поперечной подачи.
Проводят двукратные испытания.
Наибольшее допускаемое перемещение определяют как среднее арифметическое результатов двух испытаний.
ПРИЛОЖЕНИЕ (справочное). Номенклатура средств измерения, используемых для проверки точности фрезерных консольных станков
ПРИЛОЖЕНИЕ
Справочное
1. Прибор для измерения длины (пп.1.4.1-1.4.18, 2.4-2.7)
Основные технические требования должны соответствовать указанным в табл.13
Таблица 13
мкм
Для измерения показателей точности с допусками | Цена деления шкалы прибора | Вариации показаний (наибольший гистерезис) |
До 8 | 1 | 0,5 |
Св. 8 ” 40 | 2 | 1,0 |
” 40 | 10 | 5,0 |
2. Поверочная линейка (пп.1.4.1, 1.4.2, 1.4.5, 1.4.6, 1.4.14, 1.4.18, 2.4, 2.5)
Основные технические требования должны соответствовать указанным в табл.14
Таблица 14
мкм
Длина линейки, мм | Допуск прямолинейности рабочих поверхностей линейки | Допуск параллельности рабочих поверхностей линейки |
300 | 2,5 | 4 |
500 | 3,0 | 5 |
1000 | 4,0 | 6 |
1600 | 5,0 | 8 |
3. Специальное приспособление для измерения перпендикулярности по ГОСТ 25889.3-83 (п.2.6)
Основные технические требования должны соответствовать указанным в табл.15
Таблица 15
Длина измерительных поверхностей | Допуск прямолинейности, мкм |
До 100 | 1,2 |
Св. 100 ” 160 | 1,6 |
” 160 ” 250 | 2,0 |
” 250 | 2,5 |
4. Поверочный угольник (п.1.4.4)
Основные технические требования должны соответствовать указанным в табл.16
Таблица 16
мкм
Длина плеч, мм | Допуск прямолинейности измерительных поверхностей | Допуск перпендикулярности измерительных поверхностей |
500/300 | 3 | 5 на длине 300 мм |
5. Поверочный цилиндрический угольник (пп.1.4.7, 1.4.8, 1.4.9)
Основные технические требования должны соответствовать указанным в табл.17
Таблица 17
мкм
Длина, мм | Допуск круглости | Допуск прямолинейности образующих | Допуск параллельности образующих | Допуск торцевого биения |
300 | 1,2 | 2,5 | 4 | 2 на радиус 50 мм |
6. Контрольная цилиндрическая консольная оправка (пп.1.4.13, 1.4.14, 1.4.15)
Основные технические требования должны соответствовать указанным в табл.18
Таблица 18
мкм
Длина измерения, мм | Допуск круглости | Допуск прямолинейности образующих | Допуск радиального биения |
150 | 1 | 1,0 | 3 |
300 | 1 | 1,5 | 3 |
7. Контрольная цилиндрическая оправка (п.1.4.16)
Основные технические требования должны соответствовать указанным в табл.19
Таблица 19
Допуск на диаметр | Допуск круглости | Допуск профиля | Допуск радиального биения |
g6 | Степень точности 3 по табл.3 ГОСТ 24643-81 | Степень точности 3 по табл.5 ГОСТ 24643-81 |
8. Специальный поверочный угольник (п.1.4.17)
Основные технические требования должны соответствовать указанным в табл.20
Таблица 20
мкм
Длина угольника, мм, не менее | Допуск прямолинейности измерительной поверхности | Допуск перпендикулярности измерительной поверхности | |
в продольном направлении | в поперечном направлении | ||
300 | 5 на длине 300 мм | 3 на длине 100 мм | 3 на длине 100 мм |
9. Поверочная плита (п.2.5)
Основные технические требования должны соответствовать указанным в табл.21
Таблица 21
Габаритные размеры | Допуск прямолинейности в любых направлениях, мкм | ||
на всю длину измерения | местный на длине, мм | ||
160 | 250 | ||
Не менее размеров образца-изделия | 6 | 2,5 | 3 |
Клас точности н – greenpark63.ru
Скачать клас точности н doc
Станки классов точности В, А и С называют прецизионными (от фр. precision — точность). Эти станки желательно эксплуатировать в термоконстантных цехах, температура и влажность в которых регулируется автоматически. В зависимости от массы станки подразделяют на легкие — массой до 1 т, средние — до ти тяжелые — свыше 10 т.
В свою очередь тяжелые станки делят на крупные (до 30 т), собственно тяжелые (до т) и уникальные (свыше т). Классы точности электронных весов, обзор весоизмерительных устройств всех уровней точности и сфер применения. Характеристики весового оборудования, сертифицированных по ГОСТ OIML R – погрешность, дискретность, зависимость максимальной нагрузки и наименьшего предела измерения. Полная информация на сайте поставщика измерительной и контрольной техники Модуль.
Как подразделяются станки по классу точности? Классификация металлорежущих станков общего назначения осуществляется: по назначению Для потребителя точность МРС выражается в их способности обеспечить готовые изделия: точность размеров, точность формы и взаимного положения плоскостей обрабатываемых, их волнистость, шероховатость а так же стабильность этих показателей в заданных пределах. Класс – точность – измерительный прибор. Что такое класс точности прибора?:: greenpark63.ru Классы точности средств измерения.
Контрольно-измерительные приборы. 5 класс точности. Что такое единица измерения? Способы и средства измерений. Допуск для станков класса точности Н – 18 мкм, для станков класса точности П – 10 мкм. Измерение следует проводить по ГОСТ (разд. 18), в соответствии со схемой, указанной на черт.
Радиальное биение наружной центрирующей поверхности шпинделя (для станков с центрированием фрез по наружной центрирующей поверхности). Черт. Допуск для станков класса точности Н- 10 мкм, для станков класса точности П – 6 мкм.
К одному классу точности должны относиться станки, обеспечивающие одинаковую точность обработки соответствующих по форме и размерам поверхностей образцов-изделий. Для отдельных типов станков, предназначенных только для обдирочных работ, классы точности не устанавливаются.
(Измененная редакция, Изм. N 1, 3). Класс Н – станки нормальной точности – наиболее распространенный класс, обеспечивающий обработку деталей примерно второго класса точности. Допустимые отклонения геометрических и кинематических параметров станка этого типа регламентируются соответствующим ГОСТом. [9]. По степени. И для чего он нужен, постарался кратко изложить в данной статье.
Похожее:
Патрон токарный двухкулачковый клиновой механизированный класса точности «Н» и «П». 7102-0024 У
Цена: по запросу
Предназначен для закрепления штучных заготовок, обрабатываемых на станках токарной группы класса точности “Н” и “П” в условиях серийного и массового производства.
Патроны работают от механизированного привода, устанавливаемого на заднем конце шпинделя станка.
Настройка на необходимый диаметр зажима осуществляется переустановкой накладных закаленных кулачков по рифлениям основных, при этом сохраняется необходимая точность патрона. Точность патрона с незакаленными кулачками достигается путем расточки накладных кулачков после их переустановки на необходимый диаметр.
Параметр | Значение |
---|---|
Диаметр патрона D, мм | 250 |
Исполнение | 2 |
Высота патрона L, мм | 96 |
Высота патрона до основания кулачка L1, мм | 101 |
Диаметр зажимаемых поверхностей, мм | 15-325 |
Ход кулачка Н, мм | 8,0 |
Допустимая частота вращения патрона, об/мин | 4000 |
Условный размер присоединительного конуса по ГОСТ12595 | 8 |
Наружный диаметр конуса D3, мм | 139,719 |
Глубина конуса l1, мм | 16 |
Диаметр расположения крепежных отверстий D2, мм | 171,4 |
Диаметр крепежных отверстий: | |
d3, мм | 18 |
Количество крепежных отверстий, n | 4 |
Размер резьбы тяги d, мм | М24 |
Ширина сухаря b, мм | 20 |
Резьба для крепления накладных кулачков, m | М16 |
Ход штока К, мм | 30 |
Максимальное усилие, передаваемое приводом, даН | 4500 |
Суммарная сила зажима в кулачках, даН | 10000 |
Точность центрирования на всем диапазоне зажима детали, мкм | |
класса «Н» | 75 |
класса «П» | 60 |
Масса патрона, не более, кг | 36 |
Параметр | Значение |
---|---|
Диаметр патрона D, мм | 250 |
Исполнение | 2 |
Высота патрона L, мм | 96 |
Высота патрона до основания кулачка L1, мм | 101 |
Диаметр зажимаемых поверхностей, мм | 15-325 |
Ход кулачка Н, мм | 8,0 |
Допустимая частота вращения патрона, об/мин | 4000 |
Условный размер присоединительного конуса по ГОСТ12595 | 8 |
Наружный диаметр конуса D3, мм | 139,719 |
Глубина конуса l1, мм | 16 |
Диаметр расположения крепежных отверстий D2, мм | 171,4 |
Диаметр крепежных отверстий: | |
d3, мм | 18 |
Количество крепежных отверстий, n | 4 |
Размер резьбы тяги d, мм | М24 |
Ширина сухаря b, мм | 20 |
Резьба для крепления накладных кулачков, m | М16 |
Ход штока К, мм | 30 |
Максимальное усилие, передаваемое приводом, даН | 4500 |
Суммарная сила зажима в кулачках, даН | 10000 |
Точность центрирования на всем диапазоне зажима детали, мкм | |
класса «Н» | 75 |
класса «П» | 60 |
Масса патрона, не более, кг | 36 |
Также посетители сайта смотрят
Техническое описание товара предоставлено официальными представительствами компаний производителей и актуально на дату появления товара в нашем каталоге.
Указанные на сайте цены носят информационный характер и не являются публичной офертой (ст.435 ГК РФ).
Для получения подробной информации о наличии и стоимости указанных товаров, пожалуйста, обращайтесь к менеджерам компании с помощью специальной формы связи или по телефону.
патрон токарный двухкулачковый клиновой механизированный класса точности «н» и «п». 7102-0024 у возможно приобрести в лизинг. А также мы доставим патрон токарный двухкулачковый клиновой механизированный класса точности «н» и «п». 7102-0024 у в Москву, Санкт-Петербург, Новосибирск, Екатеринбург, Нижний Новгород, Самару, Омск, Казань, Челябинск, Ростов-на-Дону, Уфу, Волгоград… А ТАКЖЕ В ЛЮБОЙ ГОРОД России, Белоруссии и Казахстана. Обращайтесь к специалистам компании.
Как промышленность определяет значения точности рельсов
Однажды я услышал, как один коллега, относительно новичок в линейном движении и стремящийся быть полезным, сказал клиенту: «H – это наши высококлассные рельсы».
Хотя мысль о рельсах «высокого класса» была забавной, технически она была права. В терминологии профильных линейных направляющих H – это , обозначение высокого класса…
.… высокая точность класс, то есть.
При указании профильных линейных направляющих есть три основных характеристики: размер, который указывает ширину рельса; предварительный натяг, соответствующий жесткости каретки под нагрузкой; и точность.
В мире линейного перемещения «точность» может означать разные вещи в зависимости от типа обсуждаемого компонента. Для профильных линейных направляющих класс точности является стандартной спецификацией, охватывающей пять характеристик:
– Допуск по высоте каретки в сборе
– Допустимая разница в высоте нескольких кареток на одном рельсе
– Допуск по ширине каретки в сборе
– Допустимая разница в ширине нескольких кареток на одном рельсе
– Параллельность опорных поверхностей рельса и каретки
Чтобы понять разницу между этими характеристиками точности, давайте рассмотрим каждую из них более подробно.
Допуск по высоте определяет максимальное отклонение по высоте между заземленным основанием рельса и шлифованной верхней поверхностью каретки и измеряется в центре каретки. В дополнение к допуску по высоте одной каретки на направляющем рельсе также указывается максимальная разница высоты между несколькими каретками на одном рельсе.Чтобы определить разницу в высоте между каретками, каждая каретка измеряется в одном и том же месте на рельсе.
Класс точности и линейная ширина рельса Допуск ширины определяет максимальное отклонение ширины рельсовой каретки в сборе, измеренное от контрольной кромки рельса до контрольной кромки каретки. Как и в случае с высотой, существует также максимально допустимая разница в ширине между несколькими каретками на одном рельсе, измеренная для каждой каретки в одном и том же месте на рельсе.
Для сборок профилированных рельсов параллельность задается в двух плоскостях: параллельность между нижней шлифованной поверхностью рельса и шлифованной верхней поверхностью каретки (в вертикальном направлении, аналогично высоте) и параллельность между опорной кромкой рельса. направляющая и опорный край каретки (в горизонтальном направлении, аналогично ширине). Если допуски по высоте и ширине измеряются в статическом состоянии, параллельность измеряется в динамическом состоянии, когда каретка движется по рельсу.Таким образом, параллельность сборки зависит от длины рельса.
Некоторые производители предоставляют контрольные кромки на обеих сторонах профилированной шины, в то время как некоторые шлифуют только одну сторону направляющей в качестве контрольной кромки. Если рельс имеет только одну опорную кромку, параллельность в горизонтальном направлении измеряется с опорными кромками каретки и рельса на одной стороне сборки. Когда любая сторона направляющей может использоваться в качестве опорной кромки, значение параллельности также будет применяться, когда опорные кромки направляющей и каретки находятся на противоположных сторонах сборки.
Производители предлагают не менее трех, а в некоторых случаях шесть и более классов точности для профилированных линейных направляющих, наиболее распространенными из которых являются «Стандартный», «Высокий» и «Прецизионный». Но как влияет класс точности на производительность и когда целесообразно инвестировать в более высокий класс точности?
Поскольку в большинстве случаев используются консольные массы, редко когда узел, состоящий из одной направляющей и каретки, будет подходить для результирующих моментных нагрузок и сил.Чаще всего используются две каретки на одном рельсе, два рельса с одной кареткой каждый и два рельса с двумя каретками каждый. В этих конфигурациях использование более высокого класса точности может помочь избежать ненужных напряжений и усилий предварительной нагрузки из-за геометрических различий между компонентами, которые могут снизить срок службы. Кроме того, более высокие классы точности обеспечивают более равномерный ход, повышая точность станка, особенно при большой длине хода.
Другие факторы влияют на конечную точность сборки профильных линейных направляющих, включая подготовку поверхности и монтаж. Но если вы не используете рельсы и каретки «высокого класса», вы можете получить результаты низкого класса.
% PDF-1.2
%
288 0 объект
>
эндобдж
xref
288 74
0000000016 00000 н.
0000001831 00000 н.
0000002297 00000 н.
0000002487 00000 н.
0000002803 00000 н.
0000002996 00000 н.
0000003017 00000 н.
0000003145 00000 н.
0000003166 00000 н.
0000003300 00000 н.
0000003321 00000 п.
0000003452 00000 н.
0000003473 00000 н.
0000003606 00000 н. 0000003627 00000 н.
0000003760 00000 н.
0000003781 00000 п.
0000003912 00000 н.
0000003933 00000 н.
0000004066 00000 н.
0000004087 00000 н.
0000004219 00000 н.
0000004240 00000 н.
0000004369 00000 п.
0000004390 00000 н.
0000004524 00000 н.
0000004545 00000 н.
0000004679 00000 н.
0000004700 00000 н.
0000004834 00000 н.
0000004855 00000 н.
0000004988 00000 н.
0000005009 00000 н.
0000005143 00000 п.
0000005164 00000 н.
0000005297 00000 н.
0000005318 00000 н.
0000005452 00000 п.
0000005473 00000 п.
0000005607 00000 н.
0000005628 00000 н.
0000005762 00000 н.
0000005783 00000 н.
0000005917 00000 н.
0000005938 00000 н.
0000006072 00000 н.
0000006093 00000 н.
0000006184 00000 п.
0000006207 00000 н.
0000009034 00000 н.
0000009055 00000 н.
0000009310 00000 п.
0000009332 00000 н.
0000010382 00000 п.
0000010404 00000 п.
0000011174 00000 п.
0000011196 00000 п.
0000011881 00000 п.
0000011904 00000 п.
0000013234 00000 п.
0000013257 00000 п.
0000014815 00000 п.
0000014838 00000 п.
0000016086 00000 п.
0000016109 00000 п.
0000017462 00000 п.
0000017485 00000 п.
0000019603 00000 п.
0000019625 00000 п.
0000020353 00000 п.
0000020374 00000 п.
0000020632 00000 п.
0000001888 00000 н.
0000002275 00000 н.
трейлер
]
>>
startxref
0
%% EOF
289 0 объект
>
эндобдж
360 0 объект
>
поток
Hc“f`O“g“y Ȁ
% PDF-1.7 % 6 0 obj > эндобдж xref 6 119 0000000016 00000 н. 0000003027 00000 н. 0000003140 00000 н. 0000004415 00000 н. 0000005036 00000 н. 0000005630 00000 н. 0000005665 00000 н. 0000005819 00000 н. 0000005981 00000 п. 0000006026 00000 н. 0000010854 00000 п. 0000011035 00000 п. 0000011462 00000 п. 0000011712 00000 п. 0000011889 00000 п. 0000011916 00000 п. 0000019594 00000 п. 0000020235 00000 п. 0000029222 00000 п. 0000029608 00000 п. 0000038405 00000 п. 0000045640 00000 п. 0000051788 00000 п. 0000057177 00000 п. 0000065544 00000 п. 0000068193 00000 п. 0000068698 00000 п. 0000068811 00000 п. 0000068925 00000 п. 0000069036 00000 п. 0000072378 00000 п. 0000072778 00000 п. 0000073260 00000 п. 0000075352 00000 п. 0000075715 00000 п. 0000076122 00000 п. 0000076225 00000 п. 0000077441 00000 п. 0000077769 00000 п. 0000077857 00000 п. 0000081094 00000 п. 0000081494 00000 п. 0000081965 00000 п. 0000082558 00000 п. 0000082864 00000 н. 0000082956 00000 п. 0000083045 00000 п. 0000087043 00000 п. 0000087478 00000 п. 0000088017 00000 п. 0000089476 00000 п. 0000089788 00000 п. 00000 00000 п. 00000
00000 н. 00000 00000 п. 0000101763 00000 н. 0000101800 00000 н. 0000111964 00000 н. 0000112001 00000 н. 0000122810 00000 н. 0000122847 00000 н. 0000130713 00000 н. 0000130750 00000 н. 0000141471 00000 н. 0000141508 00000 н. 0000152317 00000 н. 0000152354 00000 н. 0000160178 00000 н. 0000160215 00000 н. 0000168039 00000 н. 0000168076 00000 н. 0000174760 00000 н. 0000174797 00000 н. 0000180233 00000 н. 0000180270 00000 н. 0000189340 00000 п. 0000189377 00000 н. 0000199919 00000 н. 0000199956 00000 н. 0000210765 00000 н. 0000210802 00000 п. 0000218668 00000 н. 0000218705 00000 н. 0000229426 00000 н. 0000229463 00000 н. 0000239627 00000 н. 0000239664 00000 н. 0000248734 00000 н. 0000248771 00000 н. 0000259313 00000 н. 0000259350 00000 н. 0000260274 00000 н. 0000261560 00000 н. 0000262496 00000 н. 0000263408 00000 н. 0000264339 00000 н. 0000265259 00000 н. 0000265488 00000 н. 0000266478 00000 н. 0000267493 00000 п. 0000267708 00000 н. 0000268615 00000 н. 0000269089 00000 н. 0000269268 00000 н. 0000270181 00000 п. 0000274218 00000 н. 0000277328 00000 н. 0000281930 00000 н. 0000286920 00000 н. 0000291522 00000 н. 0000295366 00000 н. 0000299968 00000 н. 0000304420 00000 н. 0000307204 00000 н. 0000311091 00000 н. 0000313875 00000 н. 0000318881 00000 н. 0000321800 00000 н. 0000002676 00000 н. трейлер ] / Назад 335388 >> startxref 0 %% EOF 124 0 объект > поток hb“ (a`zπ X2 @) bi> U 8 X & dʐd0? 0T Թ_ toZ Lc
Продукция для передачи энергии Нержавеющая сталь Вал линейной направляющей скольжения H Класс точности для лазерных сварочных аппаратов Линейная направляющая направляющая Продукция с линейным перемещением
Нержавеющая сталь Вал линейной направляющей скольжения H Класс точности для аппаратов лазерной сварки Линейная направляющая направляющая
Нержавеющая сталь Вал линейной направляющей скольжения Класс точности H для лазерных сварочных аппаратов Линейная направляющая направляющая: промышленная и научная.Нержавеющая сталь Вал линейной направляющей скольжения Класс точности H для лазерных сварочных аппаратов Линейная направляющая направляющая: промышленная и научная. Подходит для DIY фрезерных станков с ЧПУ, токарных станков, станков, гибочных станков, сварочных аппаратов и т. Д.。 Обработка поверхности, красивая, устойчивая к ржавчине и более прочная. 。 Оригинальный комплект рельсов может быть стабилизирован с помощью рельса подшипника оси рельса и опоры из алюминиевого сплава. 。 С промышленным стандартным блоком и высокоточным линейным подшипником внутри. 。 В комплект входят 1 рельсовый вал SBR16S и 2 блока SBR16UU.Гладкие скользящие блоки свободно перемещаются. 。 Особенность: 。1. В комплект входят 1 рельсовый вал SBR16S, и 2 блока SBR16UU. Гладкие скользящие блоки свободно перемещаются. 2. С промышленным стандартным блоком и высокоточным линейным подшипником внутри. 3. Оригинальный комплект рельсов может быть стабилизирован с помощью рельсового подшипника оси и опоры из алюминиевого сплава. 4. Обработка поверхности окислением, красивая и нержавеющая и более прочная. 5. Подходит для DIY фрезерных станков с ЧПУ, токарных станков, станков, гибочных станков, сварочных аппаратов и т. Д.。Спецификация: 。Тип элемента: / вал линейного рельса。Материал: высокоуглеродистая сталь, алюминиевый сплав。Модель: SBR16S + 2 x SBR16UU。Стользящая гусеница: линейная направляющая。Диаметр вала: прибл. 16 мм / 0,6 дюйма。Номер ползуна: 2。Номинальная динамическая нагрузка: 770Н。Номинальная статическая нагрузка: 1170Н。Длина рельса: прибл. 1000 мм / 39,4 дюйма。 Класс точности: H。Список пакетов: 。1 x Линейный вал рельса 2 x Рельс。。。。
Нержавеющий вал линейной направляющей скольжения H Класс точности для лазерных сварочных аппаратов Линейная направляющая направляющая
5 = (от пятки до носка) 235 мм = 9 1/4 дюйма.Все предметы измеряются “” командой по отдельности. Миссия Under Armour – сделать всех спортсменов лучше за счет страсти и быстро высохнуть, когда они намокнут. Сделано в Америке и пожизненная гарантия. Мягкая грелка для ушей обеспечивает дополнительное тепло и изоляцию. кожаная обувь: женская повседневная обувь. Каждый комплект тормозной магистрали Yana Shiki собирается на собственном предприятии из фитингов из нержавеющей стали высочайшего качества, обжатых непосредственно на жестко вытянутый плетеный шланг из нержавеющей стали, нержавеющий вал линейной направляющей , класс точности H для лазерных сварочных аппаратов Линейная направляющая направляющая , должная из-за освещения и отображения на мониторе покупайте женские сандалии на танкетке Onex Billie и другие платформы и туфли на танкетке на.Стоимость доставки во всех списках в моем магазине указана как обычная Posta Italianal и не включает службу отслеживания. Продается парой. Будьте готовы к подарку, сэкономьте на доставке, заказав несколько товаров. Доски сделаны из цельного дерева с фанерой 1/2 дюйма наверху, фрезерованной и уложенной в раму из древесины тополя 1×3. А Ф Т Е Р П У Р Ч А С И Н Г:. Оставьте информацию о монограмме и выбор нитки при оформлении заказа в примечаниях к продавцу. Нержавеющая сталь Вал линейной направляющей скольжения Класс точности H для лазерных сварочных аппаратов Линейная направляющая направляющая .♥ Стоимость доставки включает номер для отслеживания. бамбук и листья представлены в этом великолепном лоскутном одеяле размера A6. Размеры: 4-3 / 4 дюйма x 6-1 / 2 дюйма Максимальный размер карты: 4-1 / 2 дюйма x 6-1 / 4 дюйма (карта не входит в комплект) . Сумка хорошего размера для хранения множества мелочей. ★ Простое и быстрое уничтожение комаров: один взмах этой электронной мухобойки с эффективной сеткой напряжения уничтожает мух. Купите JomeDesign летние женские топы с короткими рукавами и разрезом по бокам. Повседневная свободная туника. Серые маленькие и другие туники. Сочетание вкусной еды и эстетичной японской посуды идеально дополняют друг друга.Он имеет складную и легкую конструкцию, нержавеющий линейный вал рельса скольжения Класс точности H для лазерных сварочных аппаратов Линейный рельс скольжения , Купите ошейник с шипами Newtensina для собак в стиле панк с шипами для собак – черный – M в Великобритании. поэтому мы хотим убедиться, что у вас есть все возможности сделать это переплетное устройство полностью вами.
Термины и выражения для определения датчиков крутящего момента
Влияние температуры на чувствительность
Влияние температуры на чувствительность – это изменение фактического выходного сигнала из-за изменения температуры на 10 К, определенной при номинальном крутящем моменте и связанном с ним к чувствительности .Указанное значение является максимумом в номинальном температурном диапазоне .
Влияние температуры на чувствительность (также называемое температурным коэффициентом чувствительности ) является мерой влияния температуры на выходной сигнал с нагрузкой, приложенной к преобразователю . При определении этого значения выходной сигнал должен быть скорректирован путем вычитания сигнала начального крутящего момента при соответствующей температуре. Должен быть установлен стационарный температурный режим.
Значимая температура – это температура преобразователя . Стационарное температурное состояние, как определено в HBM, означает, что максимальное изменение температуры за 15-минутный период не превышает 0,1 К. Величина отклонения указывается в процентах от фактического диапазона выходного сигнала с соответствующий приложенный крутящий момент (в случае нагрузки с номинальным крутящим моментом это чувствительность).
Влияние температуры на чувствительность приводит к изменению наклона характеристической кривой (см.рис.2). Это особенно важно, когда преобразователь работает при температуре, значительно отличающейся от эталонной температуры. Однако для диапазонов частичной нагрузки это имеет очень небольшой эффект, поскольку результирующее отклонение всегда действует как процент от фактического диапазона выходного сигнала.
Обратите внимание, что обычно влияние температуры на чувствительность и влияние температуры на нулевую точку ( TK 0 ) накладываются друг на друга.
Пример:
Рассмотрим преобразователь крутящего момента с номинальным крутящим моментом 1 кНм , пусть влияние температуры на чувствительность будет указано как TK C ≤ 0,1%, эталонная температура – 23 ° C и номинальный диапазон температур от +10 ° C до +60 ° C.
Если датчик работает при температуре 33 ° C (или 13 ° C), отклонение чувствительности из-за изменения температуры может составлять до 0.1%.
Для крутящего момента 1 кН⋅м (номинальный крутящий момент ) это составляет отклонение отображаемого значения на 1 Нм. Однако для крутящего момента 200 Нм отклонение составляет всего 0,2 Нм, поскольку TK C всегда составляет процентное отклонение относительно фактического диапазона выходного сигнала . Это связано с тем, что чувствительность называется мерой наклона прямой. Использование того же преобразователя при 43 ° C (отклонение 20 K от номинальной температуры) может привести к максимальному отклонению до 0.2% в худшем случае. Это не относится к использованию при 3 ° C, поскольку эта температура не находится в пределах номинального диапазона температур .
Оценка модели– В чем разница между средней точностью класса и средней точностью экземпляра?
В чем разница между ними?
Метрика точности – одна из самых простых для понимания метрик: по сути, это количество правильных прогнозов (я назову эти совпадений ) по сравнению с общим количеством прогнозов:
$$ acc = \ frac {hits} {preds}
$Есть два способа для вычисления этого: микро и макро-усредненные версии .
Микро-усреднение включает деление общего количества правильных прогнозов на общее количество сделанных прогнозов, независимо от класса:
$$ acc_ {micro} = \ frac {total \; hits} {total \; предс}
$Это то, что вы называете средней точностью экземпляра , и на самом деле это то, что большинство людей имеет в виду, говоря о точности . M {acc_i}
$Где $ acc_i $ – точность для класса отсчетов $ i $, а $ M $ – общее количество отсчетов.Это то, что вы называете средним классом точности .
Итак, зачем использовать последнее? Это связано с классовым дисбалансом. Точность – это показатель, очень чувствительный к дисбалансу классов, а макро-усреднение – это способ сделать каждый класс одинаковым при его вычислении. Вы также можете прочитать этот ответ, где я объясню его более подробно, а также написал простой числовой пример.
Как их вычислить в Python3?
Первое очень просто вычислить, вы можете выполнить простое деление или использовать функцию scikit-learn
Второй вариант немного сложнее, если вы хотите вычислить его самостоятельно.Вы должны вычислить точность для выборок каждого класса отдельно (например, класс 1: 0,6, класс 2: 0,78, класс 3: 0,37 и т. Д.), А затем усреднить эти числа. К счастью, это эквивалентно использованию весов выборки, равных доле дисбаланса, поэтому вы можете использовать эту функцию для вычисления того же самого.
Преимущества датчика высокой точности и чувствительностиivatelsk vhody
Пользователи и технические преимущества: Высокая точность и чувствительность датчика преимуществаBONEGA Антимагнитный Счетчики воды и аксессуары
Благодаря своей чувствительности и точности счетчики воды BONEGA в значительной степени способствуют более справедливому сокращению потребления воды.Они уменьшить разницу в измерениях между основанием здания и сумма бытовых водомеров. В настоящее время это один из самых точных бытовые водомеры по всему миру.
1. Очень высокая точность измерения
Согласно независимые тесты VaK, водосчетчики BONEGA – лучшие на рынок.
После тщательного сравнения качества четырех самых продаваемых продуктов с сухим ходом водомеры в Чехии признаны лучшими.В тесты сравнивали в основном точность измерения, начальный расход, санитарные требования и др.
Источник: ВАК, 2004
Деление водомеров по точности
По точности измерения водомеры делятся на Классы A, B и C класс A является наименее точным, класс C – наиболее точным. точный. В общем случае водосчетчики класса В или А класса устанавливаются почти исключительно в квартирах.Счетчики воды C class используются редко из-за их высокой цены.
Все водомеры BONEGA относятся к классу B, но их параметры очень близки к наиболее точному классу C , благодаря чему они превзойти многих конкурентов. Метрологическая стабильность BONEGA водомеры обусловлены в основном их подходящей конструкцией турбин и как регулирующие узлы.
Как узнать, в каком классе точности находится наш водомер? мера?
Каждый производитель обязан указывать на циферблате класс точности (в горизонтальное и вертикальное положение – см. подробные описание ниже).
Доказательства точности измерений можно найти в Сертификаты калибровки.
Различия между метрологическими классами даже многочисленны (см.
Таблица). Кроме того, существуют очень существенных отличий.
между водосчетчиками одного класса .
Сравнение параметров наиболее используемых расходов в пределах метрологические классы A, B, C: | |||||||
Знак | Расход | , класс A для DN 15 (1/2 “) | , класс B для DN 15 (1/2 “) | , класс C для DN 15 (1/2 “) | , класс A для DN 20 (3/4 “) | , класс B для DN 20 (3/4 “) | , класс C для DN 20 (3/4 “) |
Qмин | Минимальный расход (л / ч) | 60 | 15 | 100 | 50 | 25 | |
кв. | Переходный расход (л / ч) | 150 | 120 | 22,5 | 250 | 200 | 37,5 |
0,2 Qn | 20% от номинального расхода (м 3 / ч) | 0,3 | 0,3 | 0,3 | 0,5 | 0,5 | 0,5 |
0,3 Qn | 30% от номинального расхода (м 3 / ч) | 0,45 | 0,45 | 0,45 | 0,75 | 0,75 | 0,75 |
0,5 Qn | 50% от номинального расхода (м 3 / ч) | 0,75 | 0,75 | 0,75 | 1,25 | 1,25 | 1,25 |
Qn | номинальный расход (м 3 / ч) | 1,5 | 1,5 | 1,5 | 2,5 | 2,5 | 2,5 |
Qмакс | максимальный расход (м 3 / ч) | 3 | 3 | 3 | 5 | 5 | 5 |
Диаграмма поведения точности измерения у индивидуума расход:
- отклонение измерения во всем диапазоне от Qmin до Qmax только в пределах +/- 2% (CSN допускает допуск до +/- 5%)
- как результат вышеупомянутого, даже официально проверенного
счетчик воды может измерять с разницей в 5% и увеличивать разницу в
измеренные значения между базовым счетчиком воды и домашними счетчиками воды.
Обозначение: Qmin = минимальный расход (л / ч), Qt = переходный режим расход (л / ч), 0,2 Qn = 20% от номинального расхода (м3 / ч), 0,3 Qn = 30% от номинальный расход (м3 / ч), 0,5 Qn = 50% от номинального расхода (м3 / ч), Qn = номинальный расход (м3 / ч), Qmax = максимальный расход (м3 / ч)
Чем выше точность измерения, тем выше вероятность того, что
разница в измеренных значениях на базовом водомере и в сумме
бытовые водомеры будут минимальными.
Эти доказательства можно прочитать в EHS Сертификаты, Решение об утверждении счетчика TCM и Сертификаты Калибровка.
2. Класс точности B в обоих положениях
Брать не нужно принимая во внимание выбор места установки.
В Счетчики воды BONEGA достигают класса точности B в обоих монтажные позиции, одни из немногих в Европе.Этот необычный преимущество достигается за счет подходящей конструкции днища (мокрого) часть водомера.
Улучшение бетона:
очень точная посадка турбины в двух подшипниках (обычно используется только один)
подшипники изготовлены из агат
водосчетчик включает не только верхняя, но и нижняя регулирующая плата
Является известно, что водомеры, установленные в вертикальном монтажном положении обычно показывают худшую точность измерения, чем в горизонтальном положении ( Основание турбины оказывает на нее наибольшее влияние.)
С которым точность измерения вашего нынешнего водомера?
Каждый производитель обязан указывать класс точности на циферблате , отдельно для горизонтального (H) и вертикального (V) положений. На у более старых счетчиков воды можно встретить только однобуквенное обозначение (тот же класс в обе позиции), что больше не соответствует европейским требованиям.
В большинство счетчиков воды, доступных на рынке, обычно имеют класс B (H-B) для положение H и худший класс A (V-A) для положения V.Обычно, если водомер имеет более высокий класс точности в наиболее требовательных вертикальных положение, в горизонтальном положении он будет еще точнее.
Например:
a) Если B-H A-V упоминается на счетчике воды, это означает, что счетчик воды имеет худший класс A в вертикальном положении и класс B в горизонтальном положении. должность. Большинство водомеров, используемых в Европе, имеют такую конструкцию.
б) Если на водомере указана только буква А, это означает, что
счетчик воды достигает только наихудшей точности измерения в обеих установках
позиций,
Доказательства очень высокой точности измерения водосчетчиков BONEGA могут для класса B в обоих монтажных положениях при измерении результаты (см. сертификаты и декларации) и в сертификатах EHS, Решение о Утверждение счетчика TCM.
Сравните точность счетчика воды BONEGA с другими бренды.
3. Очень высокая чувствительность для начала измерения (запуск расход)
Через водомеры других производителей можно получить до 254 000 литров воды. расход без учета.
Еще один очень важный параметр точности счетчика воды – на какой реальной минимальный расход (не при Qmin, установленном стандартом) счетчик начинает вращаться равномерно (не рывками) и таким образом регистрировать поток воды.
Если не касается минимального расхода Qmin, установленного стандартом.
Минимальный расход, установленный стандартом, для ½ водомеров для B
класс составляет 30 литров в час.
Класс A допускает даже до 60 литров в час (см. Точность измерения в
монтажные позиции)
Проще говоря:
Если конечный пользователь упадет на 29 литров в час (сознательно или неосознанно), его
водомер может вообще не регистрировать его, даже если он участвует в B
класс.Ежегодно объем незарегистрированной воды может составлять до 254 040 штук.
литры = 254 м3. Это соответствует 516 840 литров для класса А (59 литров на
час) ежегодно.
К сожалению, некоторые конечные пользователи злоупотребляют этим явлением сознательно в результате чего возникают несправедливые различия в клиринге среди потребителей.
Неосознаваемое отсутствие регистрации расхода появляется на
водомеры низкого качества, всегда на первой ступени расхода воды или при
подача воды закрыта (что бывает много раз в день), а также если клапаны
не затянуты (капает вода).
Счетчики воды BONEGA демонстрируют исключительные качества также с
выше параметр.
– в пределах 5-8 литров, то есть даже на лучше, чем требуется
C класс (мин. 15 л / ч).
Таким образом, мы гарантируем лучшие параметры реакции на запуск (чувствительность),
чем те, которые указаны в высшем классе.
4. Высокая надежность
На счетчики воды BONEGA даем длительную гарантию (6 лет на
счетчики холодной воды,
4 года на счетчики теплой воды).
Особо дана надежность:
- подходящим выбором материалов
- высокой точностью изготовления
- путем тщательной выходной проверки
- путем измерения в соответствии с EHS, включая испытание под давлением
5.Защитная непрозрачная пластиковая крышка со съемной крышкой
Точные и простые показания
|
6. Легкое и сквозное чтение
Четкое показание с точностью до двадцатых долей литра
.
| большой рисунок |
7. Антикоррозийная защита поверхности
Увеличенный срок службы
|
8.Гарантированная пригодность для использования по причинам здорового образа жизни
Счетчики воды BONEGA соответствуют строгим санитарным требованиям
.- Никелировано только внешняя часть. Внутренняя часть не должна быть с никелевым покрытием, поскольку никель может попасть в питьевую воду. К сожалению, не все производители соблюдают это правило.
- Состав латуни соответствует санитарным требованиям
- Подробнее читайте в Санитарная справка
9.Пластиковое сито на входе
Это предотвращает засорение турбины водомера загрязнениями
|
10. Легкий пробег
Длительный срок службы и точное измерение
Лопастное колесо закреплено на валу из нержавеющей стали в агатовом подшипнике
.Это очень хорошо влияет на срок службы и точное измерение. поведение в течение всего гарантированного периода между перетяжками
11.Легкое крепление от проворачивания при установке
Нет необходимости использовать сложные монтажные инструменты
|
12.Вспомогательные весы
Более быстрая калибровка
|
13.Высокая ДОЛГОВЕЧНОСТЬ
Более длительный срок службы
- от повышения давления в подающей магистрали до 1,6 МПа
- от внешних механических нагрузок (особенно по сравнению с пластиковые)
- от коррозии благодаря подходящему выбору качественных материалов (медь содержание)
- от абразивного износа
14. Дистанционные показания
Счетчики воды BONEGA можно модифицировать
даже для системы удаленных отсчетов
- Водосчетчики BONEGA позволяют дополнительно легко переоборудовать к дистанционным показаниям
- Компания TRASCO использует, устанавливает и продает наши водомеры для удаленных чтения:
TRASCO, spol.s r.o.
1. Mje 1000, Ronov pod Radhotm
телефон 571 845 484
мобильный 777 141 045, 603 517 342
факс 571 842 284
www.trasco.cz
электронная почта [адрес электронной почты защищен]
15. Опция измерения пульса
Это позволяет более точно измерить
по номеру импульса
|
16. Ремонт водомеров
. Счетчики воды BONEGA включают
многократный ремонт
Ремонт делается в обязательном порядке через 4 года на теплой воде.
счетчиками воды и через 6 лет на счетчиках холодной воды.Цель
обеспечение точности и возможного ремонта.
Осуществляем ремонт:
- путем обмена фишки на фишку
- только после ремонта
Эти ремонтные работы выполняются в основном нашей контрактной мастерской – Brnnsk vodrny a kanalizace a.s. Благодаря качественным материалам он Достаточно обычного, чтобы тщательно очистить наши водомеры и заменить уплотнительное кольцо.На По желанию, мы предоставим вам другие контакты сервисных мастерских как в Чешская и Словацкая республики.
Смотрите: Подтверждение о ремонте и калибровке от БВК
В последнее время мы можем заметить, что ремонт (реновация) через 4-6 лет делают не расплачиваться больше (как это в Западной Европе). Используемые водомеры заменены на новые. Бытовые водомеры становятся кратковременными. товары.
17. Очистка водопотребления и установка
Оказываем законченную услугу
В Чешской и Словацкой республиках мы можем обеспечить как установки, и расчистки водопотребления или других коммунальных услуг средствами проверенных именитых компаний.
Мы предоставляем законченные услуги, такие как:
- покупка старых счетчиков воды
- ремонта бывших в употреблении водомеров с последующим перенапряжением
- Демонтаж и установка новых или отремонтированных счетчиков воды
- показаний расхода воды
- ведомость потребления и ее передача в форму счета-фактуры
- передача данных в другие системы бухгалтерского учета и доказательств
- очистка не только расхода воды, но и тепла и др. коммунальные услуги
- и др..
18. Обучение
В Чешской и Словацкой республиках мы предлагаем обучение по установке и инжиниринговые компании.
19. Длительный срок службы
Использование качественных материалов – гарантия на долгий срок эксплуатации. В водомеры подходят даже для многократного ремонта.
20.Сервис и запчасти
В рамках услуги мы также предлагаем:
- гарантийное и послегарантийное обслуживание
- покупка любых старых счетчиков воды
- поставки запчастей с достаточных запасов
Запасных частей к бытовым водосчетчикам BONEGA поставлено:
Код заказа | Описание |
BONEGA ND 01A | Водомеры Корпус из никелированной латуни для водомера 1/2 “ |
BONEGA ND 01B | Водомеры Корпус из никелированной латуни для водомера 3/4 “ |
BONEGA ND 02 | Турбина + магнит + шпиндель + корпус турбины |
BONEGA ND 03 | Главный вал (шпиндель) из нержавеющей стали |
BONEGA ND 04 | Нижняя регулирующая плата |
BONEGA ND 05 | Плата регулировочная верхняя с рубиновым подшипником |
BONEGA ND 06A | Уплотнение “О” – кольцо под верхней регулирующей платой для холодной воды |
BONEGA ND 06B | Уплотнение “О” – кольцо под верхней регулирующей платой для теплой воды |
BONEGA ND 07 | Сито пластиковое |
BONEGA ND 08 | Кольцо ограничительное пластиковое |
BONEGA ND 09 | Стяжная гайка из латуни |
BONEGA ND 10 | Уплотнительное кольцо для контр-затяжки |
BONEGA ND 11 | Отдельная прозрачная крышка |
BONEGA ND 12A | Съемная пластиковая крышка (синяя) |
BONEGA ND 12B | Съемная пластиковая крышка (красная) |
BONEGA ND 13 | Счетное устройство |
BONEGA ND 14A | Стопорное кольцо (синее) |
BONEGA ND 14B | Стопорное кольцо (красное) |
BONEGA ND 15 | Уплотнение |
BONEGA ND 16 | Пломбировочная проволока |
Схема водомера
1) Корпус из никелированной латуни
2) Турбина + магнит + шпиндель + рубиновый подшипник
3) Главный вал (шпиндель) из нержавеющей стали
4) Нижняя регулирующая плата
5) Верхняя регулирующая плата с рубином подшипник
6) Затяжка уплотнительного кольца под верхней регулирующей платой
7) Пластиковое сито
8) Пластиковое ограничивающее кольцо
9) Латунная стопорная гайка
10) Кольцо круглого сечения для встречной затяжки
11) Отдельная прозрачная крышка
12) Съемная пластиковая защитная крышка
13) Противодействующее устройство
14) Стопорное кольцо