Конструкция лущильных станков – Производство клееной фанеры
Конструкция лущильных станков
Категория:
Производство клееной фанеры
Конструкция лущильных станков
Лущильные станки по техническим показателям подразделяют:
— по наибольшему расстоянию между центрами шпинделей. Это расстояние определяет максимально возможную длину ножа и длину чураков, подлежащих лущению. Наиболее распространенными являются станки для лущения чураков длиной 1350, 1650, 1950 мм. Длина чурака определяется размерами листов шпона;
— по высоте центров шпинделей над станиной. Высота центров определяется наибольшим радиусом чурака с припуском 100—150 мм.
Отечественные станки рассчитаны на лущение сырья диаметром 60—70 см. Иностранные фирмы выпускают станки для лущения чураков диаметром более 80 см.
Лущильный станок ЛУ-17-4 состоит из следующих основных частей: станины, двух шпиндельных бабок, суппорта кинематического узла, механизма поджима, центровочно-загрузочного приспособления.
Станина станка служит для крепления всех основных частей станка, восприятия динамических нагрузок резания и вспомогательных операций лущения.
Станина представляет собой жесткую сварную раму из двутавровых балок, на которой установлены чугунные шпиндельные бабки. В раме имеется щель для выброса карандаша вниз на транспортер.
Шпиндельные бабки (правая и левая) служат для закрепления чурака и придают ему вращательное движение.
На рис. 2 показан разрез правой шпиндельной бабки. Шпиндельная бабка имеет два телескопических шпинделя с соответствующими кулачками.
Наличие большого кулачка позволяет избежать раскола чураков в начальный период лущения, а малый кулачок дает возможность лущить карандаш диаметром до 70 мм.
Зажимают чурак на станке следующим образом.
Рис. 1. Станок ЛУ-17-4:
1 — станина, 2 — левая шпиндельная бабка, 3 — центровочно-загрузоч-ное приспособление, 4 — сварная балка, 5 — прижимные ролики, 6 — правая шпиндельная бабка, 7 — механизм прижима чурака, 8 — гидропривод, 9 — пустотелый вал, 10 — чугунная балка, 11 — суппорт, 12 — привод ускоренного перемещения суппорта, 13 — электродвигатель, 14 — механизм подачи чураков
Насос подает масло из гидросистемы в распределитель. пустотелый большой шпиндель, 13 — малый кулачок, 14 — большой кулачок, 15 — малый шпиндель, 16 — сферические роликовые подшипники, 17 — шлицевая втулка большого шпинделя, 18 — рычаг, 19 — подвижный подшипниковый узел большого шпинделя, 20 — шлицы, 21 — шпонка, 22 — скользящие шпонки, 23—малый гидроцилиндр, 24 — малый поршень со штоком, 25 — шпилька
Масло одновременно поступает в большой и малый гидроцилиндры. Малый поршень со штоком перемещается в сторону чурака и, действуя на рычаг, смещает подвижный подшипниковый узел большого шпинделя. Величина смещения малого поршня со штоком зависит от размера малого гидроцилиндра и составляет 150 мм. Закрепленный в подвижном подшипниковом узле пустотелый большой шпиндель перемещается на указанную величину и зажимает большим кулачком чурак.
Таким образом, два шпинделя одновременно зажимают чурак закрепленными на них кулачками. Работа левого шпинделя аналогична работе правого.
После зажима чураку придают вращательное движение от главного вала через шестерню. Вращающаяся шестерня через шпонку приводит во вращение гильзу, которая с помощью шлицевой втулки 6 вращает пустотелый большой шпиндель. Большой шпиндель через шлицевую втулку большого шпинделя приводит во вращение малый шпиндель.
Скользящие шпонки предохраняют от вращения подвижные подшипниковые узлы; одновременно они являются направляющими при горизонтальном перемещении этих узлов.
В процессе лущения, когда лущильный нож подходит к вращающемуся кулачку большого шпинделя, гидросистема возвращает большой шпиндель в начальное положение. То же происходит, когда лущильный нож приближается к кулачкам малого шпинделя.
Система подвода масла к гидроцилиндрам для возврата шпинделей в исходное положение была показана на рис. 1.
Подключение гидросистемы к шпиндельным бабкам происходит таким образом, что при подаче масла на поршни большого и малого гидроцилиндров эти поршни возвращаются в исходное положение. Благодаря пустотелой конструкции большого шпинделя и шлицевому соединению двух шпинделей достигается их независимое передвижение относительно друг друга в горизонтальной плоскости.
Благодаря применению шпиндельных бабок стало возможным долущивать чурак диаметром до 70 мм на станке ЛУ-17-4, отказавшись от использования на этой операции малых лущильных станков.
Суппорт лущильного станка предназначен для закрепления ножа, его регулировки, настройки и для придания ему возвратно-поступательного движения (к чураку и обратно).
Суппорт состоит из двух боковых ползунов, перемещающихся по горизонтальным съемным параллелям, расположенным на станине станка; ножевой траверсы — для крепления и регулировки лущильного ножа; траверсы прижимной линейки — для крепления и регулировки прижимной линейки станка; двух суппортных винтов, сообщающих суппорту возвратно-поступательное движение.
Суппорт имеет дополнительные верхние и нижние направляющие, с которыми связана ножевая траверса и при помощи которых изменяется угол резания во время лущения чураков. Прижимная линейка соединена с ножевой траверсой эксцентриковым валом.
Механизм поджима чурака устраняет прогиб чурака в конце лущения под действием сил резания.
Кинематический узел станка служит для связи рабочих органов станка (суппорта и шпиндельных бабок) и придания им рабочих движений.
На рис. 3 приведена кинематическая схема лущильного станка ЛУ-17-4. Сцентрированный и зажатый в шпинделях станка чурак (работа центровочно-загрузочного приспособления будет описана ниже) приводится во вращение от главного вала через шестерни. Главный вал соединен с электродвигателем через клиноременную передачу и электромагнитную муфту.
Рис. 3. Кинематическая схема лущильного станка ЛУ-17-4:
Левый шпиндель приводится во вращение от главного вата также через шестерни. Шестерня, вращая гильзу правого шпинделя, сообщает вращение звездочке. Звездочка втулочно-роликовой цепью соединена с промежуточным валом через звездочку, жестко закрепленную на промежуточном валу. Вал приводит во вращение правый пустотелый вал через сменные шестерни а, б, в и г. Через кулачковую муфту, посаженную на скользящую шпонку, вращение с пустотелого вала передается на передаточный вал. Через звездочку, жестко закрепленную на валу, и втулочно-роли-ковую цепь вращение передается на суппортный вал через звездочку.
Система конических шестерен, приводит в движение суппортные винты, а последние — суппорт, который перемещается по направляющим к вращающемуся чураку. Поступательное движение суппорта осуществляется благодаря суппортным гайкам, жестко связанным с корпусом суппорта.
Величина подачи суппорта за один оборот чурака, т. е. толщина снимаемого шпона, зависит от расположения сменных шестерен а, б, в и г, так как жесткая связь во всех звеньях кинематической схемы, кроме сменных шестерен а, б, в и г, обеспечивает постоянное передаточное отношение.
К концу лущения, когда диаметр чурака будет приближаться к диаметру малого кулачка шпинделя, рабочая подача суппорта прекращается при переводе кулачковой муфты в нейтральное положение рукояткой. Одно-вРеменно электромагнитную муфту выводят из соединения со шкивом клиноременной передачи и вращение карандаша в шпинделях станка прекращается. С помощью электромагнитной муфты можно останавливать Движение главного вала, не выключая главного электродвигателя, что целесообразно экономически, так как пусковые моменты при включении электродвига-едя отрицательно сказываются на электроснабжении предприятия. Гидросистема возвращает шпиндели в исходное положение, а карандаш через щель в станине удаляется транспортером из цеха.
Вращением суппортного вала в обратную сторону по отношению к рабочему движению электродвигателя через клиноременную передачу производится возврат суппорта в исходное положение. Суппорт подают в исходное положение на ускоренной подаче, что дает значительный выигрыш во времени. После этого электродвигатель выключают. В таком положении лущильный станок готов для лущения очередного чурака. Далее операция повторяется, как указано выше.
Кроме рабочей подачи, которая обеспечивает получение шпона заданной толщины, лущильный станок имеет ускоренную подачу, которая применяется в начальный период лущения для снятия больших неровностей на чураке. Включение ускоренной подачи производится муфтой левого пустотелого вала. Вращение вала через муфту передается валу. Далее вращение передается как при рабочей подаче. Вращение вала 15 осуществляется от пала звездочками и втулочно-роликовой цепью. В этом случае система сменных шестерен а, б, в иг отключена и в работе участия не принимает.
После окончания обдирки (на ускоренной подаче суппорта) передвигают рукояткой кулачковую муфту, тем самым отключая вал и включая вал. Далее происходит процесс лущения на рабочей подаче. Электромагнит служит для автоматического перевода кулачковой муфты в нейтральное положение.
Рис. 4. Схема устройства центровочно-загрузочного приспособления:
1 — свободно вращающаяся ось, 2— пневматический цилиндр, 3 — рычаг, 4 — груз, 5 — верхняя шестерня, 6 — сектор без зубцов, 7 — клещевые захваты, 8 — двухходовой кран, 9 — нижняя шестерня, 10 — зубчатые сектора
Центровочно-загрузочное приспособление служит для правильной центровки чурака, т. е. сокращения отпада шпона в процессе лущения, и для загрузки чурака в лущильный станок.
На лущильных станках устанавливают, как правило, Центровочно-загрузочное приспособление системы А. Жукова, В. П. Банко и А. А. Порохина. Благодаря этому приспособлению стало возможным одновременно выполнять центровку чурака и подачу его к шпинделям лущильного станка.
Центровочно-загрузочное приспособление состоит из Двух пневматических цилиндров, свободно поворачивающихся на осях, прикрепленных к станине лущильного станка. На выступающих ступицах нижних шестерен укреплены рычаги с разрезными хомутами, что позволяет крепить рычаги на ступице в любом положении. Рычаги шарнирно соединены со штоками поршней пневматических цилиндров.
Подъем и центровка чурака осуществляется поворотом рукоятки двухходового крана. При этом сжатый воздух поступает в пневматические цилиндры. При подъеме поршней штоки поворачивают рычаги, которые при помощи шестерен и зубчатых секторов сводят клещевые захваты до соприкосновения их с поверхностью чурака.
Во время зажима чурака шпинделями происходит его осевое перемещение. Неровности чурака могут несколько разводить губки клещевых захватов за счет компрессии воздуха в цилиндрах, не создавая в звеньях механизма дополнительных усилий.
Скорость сжатия клещевых захватов регулируется степенью открытия воздушного крана.
Разведение клещевых захватов осуществляется под действием грузов, закрепленных на концах рычагов, или пружинами, как показано на рис. 19. Повернув рукоятку двухходового крана, открывают отверстие для выхода воздуха.
Приспособление работает при давлении в сети 4— 4,5 ати. Расход воздуха на один лущильный станок составляет 0,7 м3/ч. Верхние и нижние клещи закреплены на валах с помощью сквозных призматических шпонок в соответствующих положениях по отношению к зубчатым секторам.
Регулирование взаимного положения верхних и нижних клещей, обеспечивающее симметричность их движения (от чего зависит точность центровки), осуществляется при помощи особого устройства. Верхние секторы этого устройства двойные. Сектор без зубцов жестко скреплен с осью верхней клешни, а зубчатый сектор сидит на оси свободно и связан с верхней шестерней. Он может смещаться относительно сектора и жестко скрепляться с ним в нужном положении.
Для повышения точности центровки угол вилок доведен до 90°, нижние вилки жестко соединены с клещами, а верхние оставлены свободно вращающимися в пальцах. Для устранения наезда суппорта на клещи (при неполном их разведении) на станке установлена электрическая автоблокировка.
Кроме перечисленных выше основных частей, лущильный станок имеет также механизм подачи чураков, гидропривод, электрооборудование с автоблокировкой.
Реклама:
Читать далее:
Установка ножа и прижимной линейки
Статьи по теме:
Повышение эффективности фанерного производствa Текст научной статьи по специальности «Технологии материалов»
DOI: 10.12737/article_5c9201701e8f75.87209710 УДК 674.613
ПОВЫШЕНИЕ ЭФФЕКТИВНОСТИ ФАНЕРНОГО ПРОИЗВОДСТВA
доктор технических наук, профессор Е.М. Разиньков1, кандидат технических наук, доцент Т.Л. Ищенко1 1 – ФГБОУ ВО «Воронежский государственный лесотехнический университет имени Г.Ф. Морозова»,
г. Воронеж, Российская Федерация
Одними из наиболее важных вопросов повышения эффективности фанерного производства является увеличение объемного выхода и качества шпона при лущении чурака. Объемный выход шпона зависит от ряда факторов таких как диаметры чурака и карандаша и сортности сырья. При одних и тех же значениях параметров как диаметр чурака, его длина и сортность сырья можно увеличить объемный выход шпона из чурака за счет уменьшения диаметра карандаша в виде недолущенного цилиндра. В отечественном производстве диаметр карандаша составляет обычно 75-80 мм и связан он, в основном, с совершенством оснащения станка поддерживающими чурак устройствами в процессе его лущения (поддерживающими роликами), препятствующими вибрации чурака, а также с диаметром зажимных кулачков. В отечественной промышленности используются в основном такие модели станков как ЛУ 17-4, ЛУ 17-10, 2HV-66, 3VKKT-66 и некоторые другие, позволяющие производить лущение чурака длиной 1,65 м с получением карандаша указанного выше диаметра. В настоящее время Китай, Германия производят и поставляют в различные страны бесшпиндельные лущильные станки с получением диаметра карандаша 40 мм (модели BXQ(J)1820, BXQ(J)1827, SL2600/5B и др.
). Они предназначены для долущивания шпона после оцилиндровки чурака на лущильном станке, которые показали свою эффективность на практике. Качество шпона при лущении чурака определяется в основном разнотолщинностью и шероховатостью его поверхности. Эти два параметра в большой мере зависят от степени обжима шпона (g, %), что не позволяет распространяться опережающей трещине при лущении шпона. Степень обжима шпона зависит от толщины шпона , мм) и величины просвета (S№ мм) между режущей кромкой лущильного ножа и нажимной кромкой прижимной линейки, которую устанавливает на станке лущильщик. Цель работы состояла в доказательстве эффективности использования в технологии фанеры бесшпиндельных лушильных станков за счет возможности получения диаметра карандаша, равного 40 мм, что позволяет увеличить количество получаемого шпона, а также в получении аналитических зависимостей определения величины просвета между режущей кромкой лущильного ножа и нажимной кромкой прижимной линейки, упрощающих работу лущиль-щика.
Ключевые слова: лущеный шпон, чурак, карандаш, лущильный станок, объемный выход шпона, степень обжима шпона, величина просвета между ножом и прижимной линейкой, экономическая эффективность
ENHANCING THE EFFICIENCY OF PLYWOOD PRODUCTION
DSc (Engineering), Professor E.M. Razinkov1, PhD (Engineering), Associate Professor T.L. Ishchenko1 1 – FSBEI HE «Voronezh State University of Forestry and Technologies named after G.F. Morozov»,
Voronezh, Russian Federation
Abstract
One of the most important issues of increasing the efficiency of plywood production is to increase the volume output and quality of veneer during rotary cut. The volume yield of veneer depends on a number of factors such as the diameters of block and core and the grade of raw material. With the same values of such parameters as the diameter of block, its length and grade of raw material it is possible to increase the volume yield of veneer from the block by reducing the diameter of core in the form of undershot cylinder. In domestic production, core diameter is usually 75-80 mm
and it is mainly associated with the perfect equipment of the machine with block supporting devices in the process of peeling (supporting rollers) that prevent vibration of the block, as well as with the diameter of the jaws. Such machine models as the LU 17-4, LU 17-10, 2HV-66, 3VKKT-66 and some others are mainly used in the domestic industry, which enables to peel a block of 1.65 m long producing a core of the above diameter. At present, China, Germany produce and supply spindleless wood peeling machines obtaining a core diameter of 40 mm (BXQ (J) 1820, BXQ (J) 1827, SL2600 / 5B models, etc.) to various countries. They are intended for addition veneer peeling after block roundup on a peeling machine, which have shown their effectiveness in practice. The quality of veneer during block peeling is determined mainly by the difference in thickness and roughness of its surface. These two parameters to a large extent depend on the degree of veneer compression (g, %), which does not allow the advance crack to spread when the veneer is peeling. The degree of veneer crimping depends on the veneer thickness (Sv, mm) and the distance (S0, mm) between the cutting edge of peeling knife and pressing edge of the clamping bar, which is installed on the machine. The aim of the work has been to prove the efficiency of using spindleless machine tools in plywood technology by making it possible to obtain a block diameter of 40 mm, which enables to increase the amount of produced veneer, as well as to obtain analytical dependencies for determining the clearance between the cutting edge of peeling knife and the pressure edge of the clamping bar simplifying the work of the cultivator.
Keywords: peeled veneer, block, core, peeling machine, volumetric veneer yield, degree of veneer crimping, clearance between knife and clamping bar, economic efficiency
Бесшпиндельные лущильные станки предназначены для получения шпона методом бесцентрового лущения чурака. Вращательное движение чу-раку придают приводные вальцы, расположенные с передней стороны станка, которые также служат упором для удержания заготовки. Современные станки укомплектованы системой ЧПУ для контроля процесса и дисплеем для настройки толщины шпона и других параметров лущения.
Методом исследования на первом этапе являлась разработка аналитических зависимостей, определяющих разницу в объемах получаемого сырого шпона на бесшпиндельных лущильных станках и станках, оснащенных шпинделем, с получением соответствующей зависимости для расчета экономической эффективности использования таких станков. Разработка таких зависимостей сводилась к следующему.
Объем получаемого из одного чурака шпона (Уш, м3 ) тесно связан с диаметром карандаша формулой (1) [1 – 5]
Д х( КхД – К,) – 0,78 Д 2 – 11 ,
Уш = ц ( 1 ‘——^-хЬ , м3, (1)
10 4 4
где Дч – диаметр чурака, см; Д – диаметр карандаша, см; Ьч – длина чурака, м;
К1, К2 – коэффициенты, значения которых зависят от сортности сырья и породы древесины.
Для березового сырья 1-го сорта К1 = 0,76, К2 = 1,6; 2-го сорта К = 0,75, К2 = 2,1.
Произведем анализ этой формулы на предмет влияния на конечный результат диаметра карандаша. В качестве породы древесины примем березу, как наиболее применяемую в фанерном производстве [6 – 7] .
Диаметр (Дч) и длину чурака (Ьч ) примем реальными для отечественных фанерных предприятий, равными соответственно 26 см и 1,6 м (для фанеры общего назначения [8 -11]).
Определим значения Уш для диаметров карандашей 40 и 75 мм при использовании бесшпиндельных лущильных станков и станков, оснащенных шпинделями.
Для диаметра карандаша 40 мм и сырья 1 -го
сорта
Уш = [26(0,76х26 – 1,6) – 0,78х42 – 11] х 1,6 :104 = 0,0718 м3 (2)
Для диаметра 75 мм и сырья 1 -го сорта Уш = [26(0,76х26 -1,6) – 0,78х7,52 – 11] х 1,6 :104 = 0,0668 м3 (3)
Для диаметра 40 мм и сырья 2-го сорта Уш = [26(0,75х26 – 2,1) – 0,78х42 – 11] х 1,6 :104 = 0,0687 м3 (4)
Для диаметра 75 мм и сырья 2-го сорта Уш = [26(0,75х26 -2,1) – 0,78х7,52 – 11] х 1,6 :104 = 0,0636 м3 (5)
Результаты показывают, что при использовании сырья 1-го сорта увеличение объемного выхода шпона при диаметре карандаша 40 мм будет на 7,5 %, чем при диаметре 75 мм. При использовании сырья 1 -го сорта увеличение объемного выхода шпона при диаметре карандаша 40 мм будет на 8,0%, чем при диаметре 75 мм.
Для расчета экономической эффективности предприятия за счет использования бесшпиндельных лущильных станков необходимо вывести соответствующие формулы. Для этого произведем соответствующие расчеты для предприятия с годовым объемом производства фанеры, например, марки ФК 30000 м3 (Ог) при использовании для лущения чураков диаметром, например, 26 см. Как показывает опыт работы фанерных предприятий расход чураков такого диаметра на 1 м3 фанеры составляет около 2,4 м3 /м3 (Е). Следовательно, на годовую программу производства фанеры требуется 72000 м3 чураков (Очур ).
Очур = Е х Ог, м3 (6)
Разделим общее количество чураков по сортам исходя из того, что в среднем на предприятиях находится около 40 % сырья 1 -го сорта (Р0 и около 60 % – 2-го сорта (Р2). В результате получим
Очур 1 = (Очур х Р] ) х 10-2 = 72000х40 х 10-2 = = 28800 м3 (7)
Очур 2 = (Очур х Р2 ) х 10-2 = 72000 х 60 х 10-2 = = 43200 м3 (8)
Количество сухого шпона, выходящего из сырья каждого сорта примем: для 1-го сорта – 54 (Рсух1 ) для 2-го сорта – 51 % (Р сух2 ). При таком количестве сухого шпона посортный объем сухого шпона определится
Осух. 1 = Очур 1 х Рсух1 =(28800х54) х 10-2 = 15552 м3 (9) Осух. 2 =Очур 1 х Рсух 2 =(43200х51) х 10-2 =22032 м3 (10)
Количество сырого шпона, выходящего из сырья каждого сорта составит
Осыр.1 = (Осух. 1 х 100) : (100 – а1 ) = 15552 х 100 : 86 = = 18084 м3 , (11)
а1 – коэффициент потерь на усушку, % (примем равным 14 %).
О сыр.2 = (Осух.21 х 100) : (100 – а] ) = 22032 х 100 : 86 =
= 25619 м3
(12)
При таких значениях расход сырого шпона на 1 м3 фанеры составит
я = (Осыр.1 + О сыр.2 ) : Ог = (18084 + 25619) : 30000 = 1,46 м3 сыр. шпона/м3 фанеры (13)
или я = я(Р! х Рсух.1 /100 + Р2 х Рсух.2/100) : (100 – а:), м3 сыр. шпона/м3, (14)
где Я – расход сырого шпона на 1 м3 фанеры, м3 сыр. шпона/м3 фанеры;
Е – расход чураков на 1 м3 фанеры, м3 чур./м3 фанеры; Р1 и Р2 – количество сырья соответственно 1-го и 2-го сорта, % от общего количества; Рсух.1 и Рсух2 – количество сухого шпона, выходящего из сырья каждого сорта, %;
а! – коэффициент потерь на усушку, %. За счет использования бесшпиндельных лушильных станков годовая экономия составляет 7,5 % (Э кар., %) сырого лущеного шпона. Эсыр. ш. = Осыр. х Э кар./100 43703 х 7,5/100 = = 3278 м3 (15)
За счет такой экономии из 3278 м3 сырого шпона можно изготовить фанеру объемом Офан. = Э сыр.ш./Я = 3278 : 1,46 = 2245 м3 (16) При изготовлении предприятием, например, фанеры марки ФК толщиной 12 мм (цена 1 м3 от 20 000 р. и выше) экономический эффект составит Э год. = 20000 х 2245 = 444900 тыс. р. = = 44 млн 900 тыс. р. (17)
В конечном виде формула для определения экономического эффекта будет выглядеть в следующем виде:
Э год = (Цф х Осыр. х Экар.)(100 – а1 ) : 100е (Р1 х Рсух.1 /100 + Р2 х РСух.2/100), тыс. р., (18)
где Цф – цена 1 м3 фанеры, р.; Осьф. – количество сырого шпона на весь объем фанеры, производимой предприятием, м3;
Экар. – годовая экономия сырого шпона за счет использования бесшпиндельных станков, %; а1 – коэффициент потерь на усушку, %; Е – расход чураков на 1 м3 фанеры, м3 чур./м3 фанеры;
Р1 и Р2 – количество сырья соответственно 1-го и 2-го сорта, % от общего количества;
Рсух.1 и Рсух2 – количество сухого шпона, выходящего из сырья каждого сорта,%.
Таким образом, например, предприятие с годовой мощностью 30 000 м3 фанеры марки ФК
может произвести дополнительно 2245 м3 фанеры за счет увеличения производства сырого шпона на 7,5 % и за счет этого получить экономический эффект в сумме 44 млн 900 тыс. р./год.
Методом исследования на втором этапе являлось получение аналитических зависимостей определения величины просвета между режущей кромкой лущильного ножа и нажимной кромкой прижимной линейки, упрощающих работу лущильщика. Для этого воспользуемся схемой лущения чурака (рис. 1).
Рис. 1. Схема лущения шпона: 1 – чурак, 2 – лущильный нож, 3 – шпон,
4 – прижимная линейка При лущении чурака 1 ножом 2 под действием силы Р1 происходит срезание тонкой ленты древесины (шпона 3), а действие силы Р2 приводит к изгибу или скалыванию древесины. При этом на оборотной стороне шпона образуются опережающие трещины, что повышает шероховатость поверхности, приводит к разнотолщинности шпона и даже к его обрыву. Чтобы уменьшить отрицательное действие силы Р2 при лущении используют прижимную линейку 4, которая силой Q2 уменьшает действие силы Р2 .
Прижимная линейки представляет собой стальную пластину с нажимной фаской и при лущении она сжимает шпон по линии СК. Величина такого сжатия характеризуется параметром g, а просвет по линии СК характеризует величину просвета 8о. Известна зависимость между параметрами 8о и g [12] 8о = 8ш (100 – g) /100, мм, (19)
где 8ш – толщина получаемого шпона, равная величине подачи суппорта на один оборот шпинделя лущильного станка (ип , мм/об), мм;
g – степень обжима шпона,%. Зная величину ип оператор лущильного станка (лущильщик) устанавливает на станке необходимую величину подачи суппорта. Для этого он определяет сначала величину g, а затем правильно устанавливает просвет на величину 8о вычисляя ее по формуле (1). При этом степень обжима шпона, при лущении различных пород древесины, определяется по формулам [12] для березы, бука, ели, сосны и лиственницы: g = 7 8ш + 9, % (20)
для ольхи и липы:
g = 7 8ш + 14, % (21)
Такие расчеты не очень удобны на практике. Лучше связать величину 8о только с одним параметром – толщиной получаемого шпона 8ш = ип . Для этого только следует в формулу (19) подставить значения из формул (20) и (21). При этом получим
для березы, бука, ели, сосны и лиственницы:
(22)
8о = (91 8ш – 7 8ш2 ) х10-2 , мм
для ольхи и липы:
8о = (86 8ш – 7 8ш2 ) х10-2 , мм
(23)
Поскольку в отечественной практике для лущения шпона используется в основном древесина березы (иногда бука) и сосна (иногда ель и лиственница) в табл. 1, для практического пользования, приведены результаты определения величины просвета по формуле (22) для этих пород и толщин шпона, регламентированных ГОСТ 99 – 2016 [13]. По полученным в таблице данным по формуле (19) найдены значения степени обжима шпона g, которые совпадают с значениями этого параметра, определенными по формуле (20), что доказывает справедливость формул (22) и (23). На рис. 2 наглядно показаны зависимости 8о = Б (8ш ).
Однако можно допустить, что несмотря на наличие известных формул Куликова В.А. и Чубова А.Б. (издание 1984 года) [12] полученные величины просвета по формулам (20) и (21) для толстого шпона (свыше 2 мм) возможно необходимо уточнять.
Таблица 1
Величина просвета для регламентированных ГОСТ 99 – 2016 толщин шпона
Лиственные породы Хвойные породы
толщина шпона 8ш , мм величина просвета 8о, мм толщина шпона 8ш , мм величина просвета 8о , мм
0,55 0,48 1,2 0,99
0,75 0,64 1,6 1,28
0,95 0,80 2,0 1,54
1,15 0,95 2,4 1,78
1,25 1,02 2,8 2,00
1,50 1,20 3,2 2,20
1,75 1,38 3,6 2,37
2,00 1,54 4,0 2,52
2,25 1,69 4,5 2,68
2,50 1,84 5,0 2,80
2,75 1,97 5,5 2,89
3,00 2,10 6,0 2,94
3,25 2,22 6,5 2,96
3,50 2,33
3,75 2,43
4,00 2,52
5
о”
ип го”
I-
ф
т и О
о. п.
го X X Т X
с; ш со
Толщина шпона, мм
Рис. 2. Зависимость величины просвета от толщины шпона: сплошная линия для лиственных, пунктирная – для хвойных пород древесины
Вычисленные по этим формулам величины просвета для такого шпона очень большие. При таких больших значениях возможно смятие шпона при его лущении. Возможно эти формулы справедливы для тонкого шпона (до 2 мм), поскольку в то время на шпон лущеный существовал ГОСТ 99 – 75 [14], по которому толщина шпона должна быть от 0,35 до 4,0 мм, независимо лиственные это породы древесины или хвойные, и в то время отечественные предприятия выпускали шпон толщиной, обычно, до 2 мм.
Выводы
1. Повышение эффективности фанерного производства можно достигнуть за счет использования в технологии бесшпиндельных лущильных станков, позволяющих уменьшить диаметр карандаша до 40 мм. Это позволит увеличить количество получаемого шпона, и за счет этого можно изготовить дополнительное количество фанеры. Так, например, предприятие с
годовой мощностью 30000 м3 фанеры марки ФК может произвести дополнительно 2245 м3 фанеры за счет увеличения производства сырого шпона на 7,5 % и при этом получить экономический эффект в сумме 44 млн 900 тыс. р. /год. Кроме того, установленная в работе аналитическая связь между просветом и степенью обжима шпона упростит работу лущильщика при настройке станка по установке ножа и прижимной линейки.
2. Получены математические зависимости, определяющие все необходимые параметры для расчетов дополнительного количества сырого шпона, фанеры и экономической эффективности при использовании в технологии фанеры бесшпиндельных лущильных станков.
3. Установлена аналитическая связь просвета между лущильным ножом и прижимной линейкой, что упрощает расчеты определения просвета. Это подтверждают формула, табличные значения и графические зависимости.
Библиографический список
1. Experimental study on flexural behavior of glulam and laminated veneer lumber beams / Liu W. Q. [et al.] // Modern bamboo structures: Conference: 1st International Conference on Modern Bamboo Structures Location: Hunan Univ, Changsha, PEOPLES R CHINA Date: OCT 28-30, 2007. – 2008. – P. 159-169.
2. Laminated veneer lumber from Rowan (SorbusaucupariaLipsky) / HS. Kol, H. Keskin, S. Korkut, T. Akbulut // African journal of agricultural research. – OCT 2009. – P. 1101-1105.
3. Бирюков, В. Г. Технология клееных материалов и древесных плит / В. Г. Бирюков. – М., 2012. – 292 с.
4. Волынский, В. Н. Технология клееных материалов [Электронный ресурс] : учеб.-справ. пособие / В. Н. Волынский. – СПб.; М.; Краснодар : Лань, 2012. – ЭБС «Лань».
5. Мурзин, В. С. Адгезионные свойства березового шпона / В. С. Мурзин // Деревообрабатывающая промыленность. – 1976. – № 5. – С. 4-5.
6. Разиньков, Е. М. Технология и оборудование клееных материалов : учеб. пособие / Е. М. Разиньков, В. С. Мурзин, Е. В. Кантиева. – Воронеж, 2013. – 291 с. – Электронная версия в ЭБС «ВГЛТУ».
7. Волынский, В. Н. Каталог деревообрабатывающего оборудования, выпускаемого в странах СНГ и Балтии / В. Н. Волынский. – 3-е изд., испр. и доп. – М.: Изд-во «АСУ-Импульс», 2003. – 380с.
8. Глебов, И. Т. Оборудование для производства и обработки фанеры [Электронный ресурс] : учеб. пособие / И. Т. Глебов, В. В. Глебов. – СПб.; М.; Краснодар : Лань, 2013. – 288с. – ЭБС «Лань».
9. Глебов, И. Т. Оборудование для производства и обработки фанеры [Электронный ресурс] : учеб. пособие / И. Т. Глебов, В. В. Глебов. – СПб.; М.; 2011, 210 с.
10. ГОСТ 3916.1 – 96. Фанера общего назначения с наружными слоями из шпона лиственных пород.
11. Куликов, В. А. Технология клееных материалов и плит : учеб. / В. А. Куликов, А. Б. Чубов. -М. : Лесн. пром-сть, 1984. – 344 с.
12. ГОСТ 99-2016. Шпон лущеный. Технические условия. 18 с.
13. ГОСТ 99-75. Шпон лущеный. Технические условия. 16 с.
References
1. Liu W. Q. [et al. ] Experimental study on flexural behavior of glulam and laminated veneer lumber beams // Modern bamboo structures: Conference: 1st International Conference on Modern Bamboo Structures Location: Hunan Univ, Changsha, PEOPLES R CHINA: OCT 28-30, 2007. 2008. P. 159-169.
2. Kol H. S., Keskin H., Korkut S., Akbulut T. Laminated veneer lumber from Rowan (SorbusaucupariaLipsky) // African journal of agricultural research. OCT 2009. P.1101-1105.
3. Biryukov V. G. Tekhnologiya’s unsociable persons of glued materials and wood-based panels. – M.: MGUL,
2012. 292 pages.
4. Volynsk V. N. Tekhnologiya of glued materials [Electronic resource]: educational handbook. – SPb.; M.; Krasnodar: Fallow deer, 2012. – EBS “Fallow deer”.
5. Murzin V. S. Adhesive properties of birch interline interval. Woodworking promylennost. 1976. No. 5. p. 4-5.
6. Razinkov E. M., Murzin V. S., Kantiyeva E. V. Technology and equipment of glued materials. Voronezh,
2013. 291 p. Electronic version in EBS VGLTU.
7. Volynsk V. N. The catalog of the woodworking equipment which is let out in CIS and Baltic countries. 3rd prod., ispr. and additional. M.: ASU-Impuls publishing house, 2003. 380 p.
8. Glebov I. T., Glebov V. V. Equipment for production and processing of plywood [Electronic resource]: studies. grant. SPb.; M.; Krasnodar: Fallow deer, 2013. EBS “Fallow deer”, 288 p.
9. Glebov I. T., Glebov V. V. Equipment for production and processing of plywood [Electronic resource]: studies. grant. SPb.; M.; 2011, 210 p.
10. GOST 3916.1 – 96. Plywood of general purpose with skins from interline interval of hardwood.
11. Sandpipers of VA., A.B. Tekhnologiya’s Forelocks of glued materials and plates: The textbook for higher education institutions. M.:lesn. Prom-st, 1984. – 344 pages.
12. GOST 99-2016. The interline interval is hulled. Specifications, 18 pages.
13. GOST 99-75. The interline interval is hulled. Specifications, 16 pages
Сведения об авторах
Разиньков Егор Михайлович – заведующий кафедрой механической технологии древесины ФГБОУ ВО «Воронежский государственный лесотехнический университет им. Г.Ф. Морозова», доктор технических наук, профессор, г. Воронеж, Российская Федерация; e-mail: mtd. [email protected].
Ищенко Татьяна Леонидовна – кандидат технических наук, доцент ФГБОУ ВО «Воронежский государственный лесотехнический университет им. Г.Ф. Морозова», г. Воронеж, Российская Федерация.
Information about authors Razinkov Egor Mikhaylovich – Head of the department of mechanical technology of wood, FSBEI HE «Voronezh State University of Forestry and Technologies named after G.F. Morozov», DSc (Engineering), Professor, Voronezh, Russian Federation; e-mail: [email protected].
Ischenko Tatiana Leonidovna – FSBEI HE «Voronezh State University of Forestry and Technologies named after G.F. Morozov», PhD (Engineering), Accossiate Professor, Voronezh, Russian Federation.
Пролетарская свобода. ОАО завод Пролетарская свобода
1.
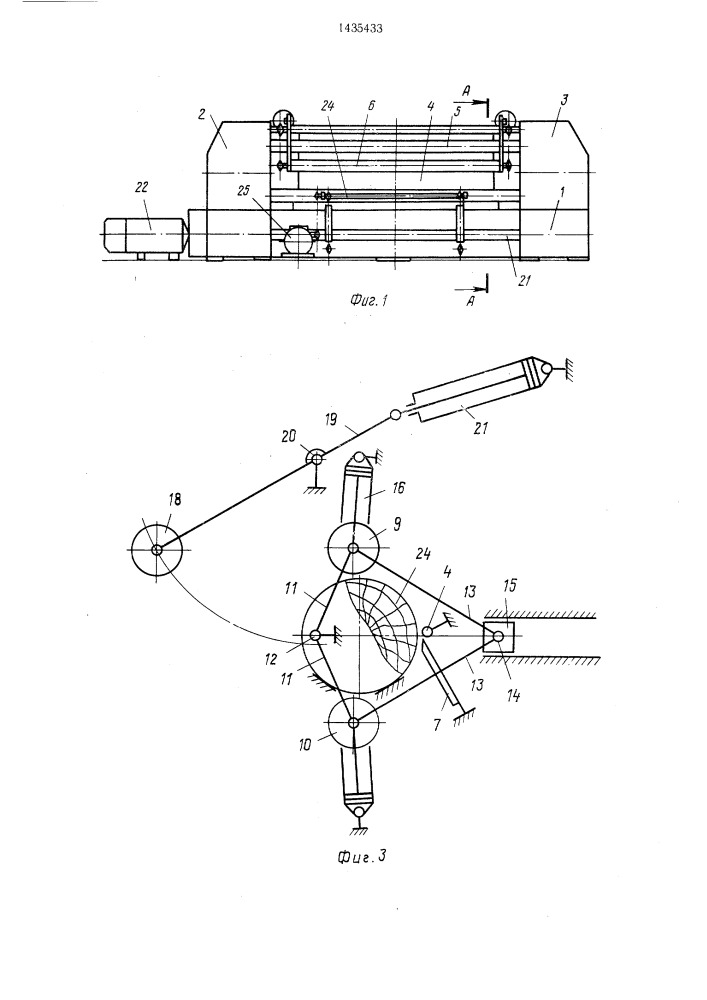
До революции завод носил название “Машиностроительный и чугуно-медно-литейный завод товарищества Н. Я. Якобсона, Г. Л. Лившица и К°”. Существует по меньшей мере с 1886 года. Изначально находился в Минске, но после августа 1914 года был эвакуирован в Ярославскую губернию в связи с началом Первой мировой войны. В Ярославле эвакуированное предприятие “Н. Я. Якобсон, Г. Л. Лифшиц и К°” наладило производство снарядов для бомбомётов, токарных станков для снарядов и другого оборудования для заводов, работавших на оборону Российской империи.
Завод “Пролетарская свобода” до реконструкции производил гвозди. В годы Первой пятилетки 1929 – 1932 значительно расширился и пополнился новым оборудованием. Было освоено производство сложных машин для лесной и крахмалопаточной промышленности, ввозившихся раньше из-за границы. В годы Второй пятилетки 1933 – 1937, в связи с развитием отечественного машиностроения началось широкое обновление станков за счёт советского оборудования. В рамках интернациональной солидарности трудящихся, поддержку в среде зарубежного пролетариата нашла инициатива рабочих завода “Пролетарская свобода”, предложивших создать фонд индустриализации СССР.
В предвоенные годы завод получал государственные задания для укрепления обороноспособности страны. Так в начале 1939 года от Главлесбуммаша получено задание по выпуску в III и IV кварталах 1939 года 82-мм сухопутных мин: соответственно 80 и 120 тысяч штук, или 200 тысяч мин за всё II полугодие. До этого завод не имел мобилизационного задания.
Учитывая недостаток в кадрах в годы Великой Отечественной войны работники завода “Пролетарская свобода” поддержали предложение о продлении рабочего дня. Рабочие завода “Пролетарская свобода” и фабрики “Красный Перекоп” стали работать по 11 часов ежедневно В Советском Союзе накануне Войны был 8-часовой рабочий день. Их примеру последовали коллективы других предприятий, например Шинного завода. Здесь следует отметить что 6 мая 1904 г. рабочие чугунолитейного завода Якобсона и Лившица объявили забастовку, а 27 мая 130 рабочих завода единодушно выступили против попытки предпринимателей увеличить рабочий день на полчаса.
Во второе полугодие 1941 года “Пролетарская свобода” выпустила продукции в 1.8-2.5 раза больше, чем в первое мирное. Кроме того, трудовой коллектив завода обратился к работникам Ярославской области с предложением организовать предоктябрьское социалистическое соревнование.
В 1960-е годы на машиностроительных заводах Ярославля наиболее дееспособным и инициативным являлся совет новаторов на заводе “Пролетарская свобода”. Руководил им активный общественник слесарь-сборщик Ф. П. Головин. При поддержке партийной и профсоюзной организаций завода совет новаторов обеспечил внедрение в производство около 20 важных предложений, представляющих интерес для многих машиностроительных предприятий.
В 1970-1980-е годы завод “Пролетарская свобода” – головной в объединении станкостроения – выпускал сложное технологическое оборудование для деревообрабатывающей промышленности. Во второй половине 1980-х годов завод “Пролетарская свобода” перешёл к выпуску полуавтоматических и автоматических линий для фанерно-мебельных предприятий.
С переходом к рыночной экономике завод устойчиво фигурирует в Интернете в порядке участия в тендерах на исполнение различных государственных заказов.
Архитектура. Бытовая техника. Канализация. Лестницы. Мебель. Окна. Отопление. Ремонт. Строительство
Дорогостоящие сорта лесоматериалов являются прекрасным сырьем для создания предметов мебели, однако не все люди могут себе позволить такую дорогую продукцию. С целью экономии ценных пород древесины и снижения стоимости конечного продукта и был придуман шпон. Этот материал сегодня крайне популярен для облицовки мебели. Шпон на 100% повторяет узор, текстуру и оттенок натуральной древесины.
Для создания шпона на производствах пользуются специальными станками. Шпон бывает:
- лущеный
- строганый
- пиленый.
Соответственно и станок для производства шпона бывает трех типов.
Лущильный станок для производства шпона
Для реализации лущения шпона сырье необходимо предварительно обработать паром для того, чтобы увеличить пластичность. После этого кряжи подаются на окорочный станок, где с заготовки удаляется кора, а вместе с ней грязь и песок, которые часто становятся причиной быстрого затупления лущильных ножей.
При помощи пилы кряжи раскраивают на чураки определенной длины. Чурак нужно предварительно оцилиндровать, после чего можно приступать к лущению. Лента шпона, которая выходит из лущильного станка, кладется на конвейер, подающий ее к ножницам. Ножницы режут шпон на листы необходимого формата.
По конвейеру шпон укладывается в пачку, которая выносится из-под ножниц и при помощи электрического погрузчика доставляется в сушилку. Сушат продукцию в роликовой сушилке, далее на конвейере его сортируют и складывают по сортам в пачки. Дефектные листы можно склеить.
Если на листах имеются сучки, их отправляют на шпонопочиночный станок, где удаляют изъяны и декорируют их вставками из шпона.
Такой станок для шпона позволяет получить листовой материал толщиной от 1,5 до 5 мм из разнообразных сортов лесоматериалов. На большинстве станков имеется система, которая позволяет в автоматическом режиме устанавливать бревно для последующей обработки.
Чтобы повысить производительность и удобство работы оператора станки оборудуют гидравлическими подъемниками-центроискателями, которые сами определяют подходящую ось вращения заготовки и совмещают ее с осью вращения центровочных валов.
Лущение пропаренной древесины используется для сосновых, ольховых, березовых лесоматериалов. Из лущеного шпона изготавливают фанеру.
Станок для строгания шпона
Прежде всего, кряжи подвергают поперечному раскрою. Во время этой процедуры кряжи распиливают на отрезки необходимой длины. Все отрезки распиливают вдоль, вследствие чего образуется двухкантный брус. Иногда его распиливают пополам. После этого ванчесы подвергают тепловой обработке в пропарочной камере или автоклаве.
Далее ванчесы нужно острогать на шпонострогальном станке. Строганный шпон сушат в роликовых сушилках, торцуют и пакуют в пачки. В каждом наборе составляется конкретный рисунок. Оттенок и узор древесины должны совпадать в каждом наборе.
Именно по этой причине листы шпона, которые получаются из каждого ванчеса во время строгания, складывают, сушат и пакуют в пачки точно в том порядке, в каком они выходили из строгального станка. Когда строгаются одновременно три ванчеса, шпон из каждого из них складывают в три разные пачки.
Укомплектованную, высушенную, запакованную и перетянутую шпагатом пачку шпона называют кнолем.
Станок для изготовления шпона позволяет создать из дорогостоящих сортов лесоматериалов, которые отличаются необычной текстурой, тонкие листы. Такой материал отлично подходит для фанерования. Методы создания шпона:
- радиальный
- тангенциальный
- радиально-тангенциальный
- тангенциально-торцовый.
Наиболее привлекательным сырьем для создания шпона является дубовая древесина. Такой шпон используют для облицовки рустикальных предметов мебели элитного сегмента.
Кроме дубового шпона в специализированных магазинах можно встретить кленовый, буковый, липовый материал, а также из красного дерева.
Станок для сшивки шпона
Шпон режут на специализированных аппаратах. Он отличается довольно тонкой и хрупкой структурой. Для того, чтобы отделать поверхность шпоном, его необходимо соединить между собой для получения полотна, скатываемого в рулоны. Шпон соединяют двумя способами:
Эти методы одинаково популярны на мебельных производствах. Сшивку шпона осуществляют на станке или ручным способом. Для небольших мастерских разработаны ручные устройства для склейки или сшивки шпона. При помощи особого устройства клеевую или термонить разогревают, и в виде зигзага наносят на основную сторону.
Сегодня станки для сшивки шпона представляют собой небольшие аппараты, функционирующие в автономном режиме. Управление такой машиной осуществляет один специалист. Вся работа на них производится четко, качественно и достаточно быстро.
Ручная сшивка встречается все реже, главным образом, в антикварных, реставрационных и авторских мастерских.
Источник: http://wood-prom.ru/clauses/promyshlennoe-oborudovanie/stanok-dlya-shpona
Как делают фанеру: подготовка бревен, оцилиндровка и лущение, нарезка на листы, сушка в прессе, обрезка, сортировка и складирование
Все фото из статьи
Тема этой статьи – изготовление фанеры. Мы познакомимся с полным циклом ее производства – от окорки древесных стволов, до отгрузки готового материала на склад. Кроме того, мы выясним, можно ли производить фанеру в домашних условиях.
Одна из стадий производства – подача бревен в лущильный станок.
Производственный цикл
Он состоит из нескольких этапов:
На некоторых этапах стоит остановиться чуть подробнее.
Подготовка бревен
Из чего делается фанера при полном цикле производства?
- Из стволов хвойных и лиственных деревьев;
- Из связующего – клеев на основе искусственных смол.
Наиболее типичный материал фанеры – сосна и береза. Несколько реже применяются пихта, лиственница, кедр, ель, тополь, ольха, липа, осина и бук.
Обратите внимание: хвойная и лиственная фанера заметно различается механической прочностью и производится по разным ГОСТ – 3919.1-96 и 3919.2-96 соответственно.
Спиленные и лишенные сучьев бревна окоряются (очищаются от коры) и нарезаются вручную или на торцовочном станке на отрезки одинаковой длины. В зимнее время стволы предварительно выдерживаются в ванне с теплой водой для придания замерзшей древесине необходимой пластичности.
Окорка ствола.
Оцилиндровка и лущение
Как правило, эти две операции выполняются на одном станке. Вначале заготовке придается цилиндрическая форма; затем с нее по сужающейся спирали снимается слой древесины толщиной около миллиметра. Оставшийся черенок в производстве не используется.
Нарезка на листы
Она сопровождается сортировкой материала. Дефектные участки листов вырезаются; полосы небольшой (менее 1,5 м) ширины могут быть использованы для склейки в целый лист.
Нарезка шпона на листы и первичная сортировка.
Затем шпон проходит клеевальцы, где он промазывается связующим.
Справка: в производстве фанеры ФК используется карбамидоформальдегидная смола.
Так называемая техническая фанера ФСФ склеивается фенолформальдегидными смолами, что позволяет отнести это производство к категории вредных.
Сушка в прессе
Для сушки листов используется гидравлический пресс с прогревом плит перегретым паром. Типичная температура сушки около 200 градусов. Продолжительность этой части цикла составляет от 30 минут до 2 часов в зависимости от толщины листа.
Сушка осуществляется при интенсивной принудительной вентиляции помещения: как уже говорилось, формальдегиды отнюдь не полезны для здоровья.
Выгрузка из пресса.
Обрезка
Просушенный лист представляет собой неопрятный сэндвич с неровными кромками. Чтобы превратиться в готовое для продажи изделие, он проходит обрезку на распиловочном станке.
Обратите внимание: согласно требованиям ГОСТ, кромки листа должны быть строго перпендикулярны друг другу.
Косина может составлять не более 2 мм на погонный метр.
Сортировка
Качество фанеры определяется визуально и, в зависимости от внешнего вида поверхности, позволяет отнести ее к одному из сортов – от элитного до четвертого.
К основным дефектам относятся:
- Живые и выпадающие сучки;
- Разошедшиеся и неразошедшиеся трещины;
- Здоровые и болезненные изменения цвета.
Цена листа в зависимости от сорта может различаться в два раза и более.
Особо стоит отметить два факта:
- Для материала сорта Е (Элита) недопустимы даже резкие переходы цвета и существенные изменения структуры поверхностного слоя шпона;
Фото позволяет оценить разницу между элитным и прочими сортами.
- Расслоение шпона сразу отправляет лист в брак вне зависимости от сорта.
Складирование
Установленная вертикально или под наклоном фанерная плита способна деформироваться под собственным весом благодаря текучести связывающих слои шпона смол.
Кроме того: ферментация может изменить цвет верхнего слоя на ярком солнечном свету.
Именно поэтому содержащаяся в отечественных стандартах инструкция по складированию листов предписывает хранить их строго определенным образом:
- в закрытом помещении с постоянной влажностью;
- защищенными от прямых солнечных лучей;
- в горизонтальном положении, уложенными на поддоны или подкладки.
Складирование материала.
Особый случай
Чтобы избежать путаницы в терминологии, стоит объяснить одну тонкость. Вопреки названию, перфорированная фанера не имеет к слоистому материалу из шпона никакого отношения.
Так называется лист ХДФ (древесноволокнистая плита высокой плотности, она же – прессованный оргалит) с проделанными в нем через равные промежутки отверстиями. Материал используется при оформлении витрин, в качестве филенок шкафных и внутренних дверей и т.д.
Перфорированный ХДФ.
Очумелые ручки
Может ли обычная фанера производиться в условиях небольшой частной мастерской? По полному циклу – едва ли, слишком габаритное оборудование требуется для распаривания, окорки стволов и лущения шпона. А вот склеивать шпон в готовые листы в домашних условиях вполне возможно.
Зачем это нужно? Например, для производства так называемой инженерной паркетной доски, состоящей из фанеры ФК с наклеенным на нее слоем шпона из древесины твердых пород.
Самый очевидный способ наладить кустарное производство – купить клеевальцы и пресс, благо оборудование для производства фанеры б у вполне доступно по стоимости. Однако если фанера своими руками будет производиться не на продажу, а исключительно ради ремонта в собственном доме, оно просто не окупится.
План «Б» состоит в холодной склейке шпона с готовым фанерным листом:
Оклейка фанеры шпоном благородных пород.
- И уложенный на ровное основание лист, и тыльная сторона шпона промазываются клеем ПВА;
- Шпон укладывается на поверхность листа и разглаживается;
- Заготовка придавливается листом толстой (22 – 27 мм) фанеры и пригружается весом 300 – 400 кг, максимально равномерно распределенным по всей поверхности.
Полная просушка клея займет около суток. По прошествии этого времени лист нарезается на доски нужного размера на обычной стационарной циркулярке. Затем фрезерный станок или ручной фрезер для дерева с направляющей используется для снятия фаски глубиной около миллиметра.
Внешний вид получившегося материала не уступит покупному паркету.
Обратите внимание: по понятным причинам изготовленный таким образом паркет можно укладывать только на клей.
В отсутствие кликовых замков о плавающей укладке речь не идет.
Заключение
Источник: https://rubankom.com/materialy/proizvodnye/fanera/1917-kak-delayut-faneru
Pereosnastka.ru
Конструкция лущильных станков
К атегория:
Производство клееной фанеры
Конструкция лущильных станков
Лущильные станки по техническим показателям подразделяют:- по наибольшему расстоянию между центрами шпинделей. Это расстояние определяет максимально возможную длину ножа и длину чураков, подлежащих лущению.
Наиболее распространенными являются станки для лущения чураков длиной 1350, 1650, 1950 мм. Длина чурака определяется размерами листов шпона;
По высоте центров шпинделей над станиной.
Высота центров определяется наибольшим радиусом чурака с припуском 100-150 мм.
Отечественные станки рассчитаны на лущение сырья диаметром 60-70 см. Иностранные фирмы выпускают станки для лущения чураков диаметром более 80 см.
Лущильный станок ЛУ-17-4 состоит из следующих основных частей: станины, двух шпиндельных бабок, суппорта кинематического узла, механизма поджима, центровочно-загрузочного приспособления.
Станина станка служит для крепления всех основных частей станка, восприятия динамических нагрузок резания и вспомогательных операций лущения.
Станина представляет собой жесткую сварную раму из двутавровых балок, на которой установлены чугунные шпиндельные бабки. В раме имеется щель для выброса карандаша вниз на транспортер.
Шпиндельные бабки (правая и левая) служат для закрепления чурака и придают ему вращательное движение.
На рис. 2 показан разрез правой шпиндельной бабки. Шпиндельная бабка имеет два телескопических шпинделя с соответствующими кулачками.
Наличие большого кулачка позволяет избежать раскола чураков в начальный период лущения, а малый кулачок дает возможность лущить карандаш диаметром до 70 мм.
Зажимают чурак на станке следующим образом.
Рис. 1. Станок ЛУ-17-4:
1 – станина, 2 – левая шпиндельная бабка, 3 – центровочно-загрузоч-ное приспособление, 4 – сварная балка, 5 – прижимные ролики, 6 – правая шпиндельная бабка, 7 – механизм прижима чурака, 8 – гидропривод, 9 – пустотелый вал, 10 – чугунная балка, 11 – суппорт, 12 – привод ускоренного перемещения суппорта, 13 – электродвигатель, 14 – механизм подачи чураков
Насос подает масло из гидросистемы в распределитель. Поршень под давлением перемещает шток в большом гидроцилиндре на величину до 150 мм. Шток поршня, жестко связанный с подвижным подшипниковым узлом малого шпинделя, перемещается также на длину гидроцилиндра. На подшипниковом узле малого шпинделя закреплен малый шпиндель. Последний, свободно перемещаясь внутри пустотелого большого шпинделя, кулачком зажимает чурак.
Разрез правой шпиндельной бабки станка ЛУ-17-4:
1 – поршень, 2 – большой гидроцилиндр, 3 – шток поршня, 4 – подвижной подшипниковый узел малого шпинделя, 5 – корпус, 6 – шли-цевая втулка, 7- шпонка шестерни, 8 – шестерня, 9- шпонка звездочки, 10 – звездочка, 11 – гнльза, 12-пустотелый большой шпиндель, 13 – малый кулачок, 14 – большой кулачок, 15 – малый шпиндель, 16 – сферические роликовые подшипники, 17 – шлицевая втулка большого шпинделя, 18 – рычаг, 19 – подвижный подшипниковый узел большого шпинделя, 20 – шлицы, 21 – шпонка, 22 – скользящие шпонки, 23-малый гидроцилиндр, 24 – малый поршень со штоком, 25 – шпилька
Масло одновременно поступает в большой и малый гидроцилиндры. Малый поршень со штоком перемещается в сторону чурака и, действуя на рычаг, смещает подвижный подшипниковый узел большого шпинделя. Величина смещения малого поршня со штоком зависит от размера малого гидроцилиндра и составляет 150 мм. Закрепленный в подвижном подшипниковом узле пустотелый большой шпиндель перемещается на указанную величину и зажимает большим кулачком чурак.
Таким образом, два шпинделя одновременно зажимают чурак закрепленными на них кулачками. Работа левого шпинделя аналогична работе правого.
После зажима чураку придают вращательное движение от главного вала через шестерню. Вращающаяся шестерня через шпонку приводит во вращение гильзу, которая с помощью шлицевой втулки 6 вращает пустотелый большой шпиндель. Большой шпиндель через шлицевую втулку большого шпинделя приводит во вращение малый шпиндель.
Скользящие шпонки предохраняют от вращения подвижные подшипниковые узлы; одновременно они являются направляющими при горизонтальном перемещении этих узлов.
В процессе лущения, когда лущильный нож подходит к вращающемуся кулачку большого шпинделя, гидросистема возвращает большой шпиндель в начальное положение. То же происходит, когда лущильный нож приближается к кулачкам малого шпинделя.
Система подвода масла к гидроцилиндрам для возврата шпинделей в исходное положение была показана на рис. 1.
Подключение гидросистемы к шпиндельным бабкам происходит таким образом, что при подаче масла на поршни большого и малого гидроцилиндров эти поршни возвращаются в исходное положение. Благодаря пустотелой конструкции большого шпинделя и шлицевому соединению двух шпинделей достигается их независимое передвижение относительно друг друга в горизонтальной плоскости.
Благодаря применению шпиндельных бабок стало возможным долущивать чурак диаметром до 70 мм на станке ЛУ-17-4, отказавшись от использования на этой операции малых лущильных станков.
Суппорт лущильного станка предназначен для закрепления ножа, его регулировки, настройки и для придания ему возвратно-поступательного движения (к чураку и обратно).
Суппорт состоит из двух боковых ползунов, перемещающихся по горизонтальным съемным параллелям, расположенным на станине станка; ножевой траверсы – для крепления и регулировки лущильного ножа; траверсы прижимной линейки – для крепления и регулировки прижимной линейки станка; двух суппортных винтов, сообщающих суппорту возвратно-поступательное движение.
Суппорт имеет дополнительные верхние и нижние направляющие, с которыми связана ножевая траверса и при помощи которых изменяется угол резания во время лущения чураков. Прижимная линейка соединена с ножевой траверсой эксцентриковым валом.
Механизм поджима чурака устраняет прогиб чурака в конце лущения под действием сил резания.
Этот механизм состоит из чугунной балки, закрепленной на пустотелом валу, двух пар прижимных роликов, гидроцилиндра перемещения роликов, смонтированного на стальной сварной балке, соединяющей обе бабки станка, а также устройства для регулировки синхронности перемещения ножа и прижимных роликов. Блок прижимных роликов шарнирно соединен с балкой и со штоком гидроцилиндра. Цапфы пустотелого вала установлены в подшипниках, корпуса которых прикреплены к бабкам станка.
Кинематический узел станка служит для связи рабочих органов станка (суппорта и шпиндельных бабок) и придания им рабочих движений.
На рис. 3 приведена кинематическая схема лущильного станка ЛУ-17-4. Сцентрированный и зажатый в шпинделях станка чурак (работа центровочно-загрузочного приспособления будет описана ниже) приводится во вращение от главного вала через шестерни. Главный вал соединен с электродвигателем через клиноременную передачу и электромагнитную муфту.
Кинематическая схема лущильного станка ЛУ-17-4:
1 – главный электродвигатель, 2 и 22 – клиноременная передача, 3 – электромагнитная муфта, 4, 5, 6 – шестерни, 7 – главный вал, 8, 9, 10, 16, 17, 18 – звездочки, 11 – промежуточный вал, 12-правый пустотелый вал, 13 – кулачковая муфта, 14 – передаточный вал, 15 – левый пустотелый вал, 19, 20 – конические шестерни, 21 – суппортный вал, 23 – электродвигатель ускоренного подвода и отвода суппорта, 24 – суппортные винты, 25 – поршни гидроцилиндра следящей системы, 26 – пневмоцилиндры центровки чураков, 27 – механизм подачи чураков, 28 – рукоятка переключения ускоренной и рабочей подачи суппорта, 29 – электромагнит; а, б, в, г – сменные шестерни набора толщин шпона
Левый шпиндель приводится во вращение от главного вата также через шестерни. Шестерня, вращая гильзу правого шпинделя, сообщает вращение звездочке. Звездочка втулочно-роликовой цепью соединена с промежуточным валом через звездочку, жестко закрепленную на промежуточном валу.
Вал приводит во вращение правый пустотелый вал через сменные шестерни а, б, в и г. Через кулачковую муфту, посаженную на скользящую шпонку, вращение с пустотелого вала передается на передаточный вал.
Через звездочку, жестко закрепленную на валу, и втулочно-роли-ковую цепь вращение передается на суппортный вал через звездочку.
Система конических шестерен, приводит в движение суппортные винты, а последние – суппорт, который перемещается по направляющим к вращающемуся чураку. Поступательное движение суппорта осуществляется благодаря суппортным гайкам, жестко связанным с корпусом суппорта.
Величина подачи суппорта за один оборот чурака, т. е.
толщина снимаемого шпона, зависит от расположения сменных шестерен а, б, в и г, так как жесткая связь во всех звеньях кинематической схемы, кроме сменных шестерен а, б, в и г, обеспечивает постоянное передаточное отношение.
Из таблицы видно, что изменение толщины шпона от 0,2 до 3,2 мм достигается в основном сменой шестерни а при взаимном расположении блок-шестерен (б – в) в двух положениях.
К концу лущения, когда диаметр чурака будет приближаться к диаметру малого кулачка шпинделя, рабочая подача суппорта прекращается при переводе кулачковой муфты в нейтральное положение рукояткой. Одно-вРеменно электромагнитную муфту выводят из соединения со шкивом клиноременной передачи и вращение карандаша в шпинделях станка прекращается.
С помощью электромагнитной муфты можно останавливать Движение главного вала, не выключая главного электродвигателя, что целесообразно экономически, так как пусковые моменты при включении электродвига-едя отрицательно сказываются на электроснабжении предприятия.
Гидросистема возвращает шпиндели в исходное положение, а карандаш через щель в станине удаляется транспортером из цеха.
Вращением суппортного вала в обратную сторону по отношению к рабочему движению электродвигателя через клиноременную передачу производится возврат суппорта в исходное положение. Суппорт подают в исходное положение на ускоренной подаче, что дает значительный выигрыш во времени. После этого электродвигатель выключают. В таком положении лущильный станок готов для лущения очередного чурака. Далее операция повторяется, как указано выше.
Кроме рабочей подачи, которая обеспечивает получение шпона заданной толщины, лущильный станок имеет ускоренную подачу, которая применяется в начальный период лущения для снятия больших неровностей на чураке.
Включение ускоренной подачи производится муфтой левого пустотелого вала. Вращение вала через муфту передается валу. Далее вращение передается как при рабочей подаче. Вращение вала 15 осуществляется от пала звездочками и втулочно-роликовой цепью.
В этом случае система сменных шестерен а, б, в иг отключена и в работе участия не принимает.
После окончания обдирки (на ускоренной подаче суппорта) передвигают рукояткой кулачковую муфту, тем самым отключая вал и включая вал. Далее происходит процесс лущения на рабочей подаче. Электромагнит служит для автоматического перевода кулачковой муфты в нейтральное положение.
Рис. 4. Схема устройства центровочно-загрузочного приспособления:
1 – свободно вращающаяся ось, 2- пневматический цилиндр, 3 – рычаг, 4 – груз, 5 – верхняя шестерня, 6 – сектор без зубцов, 7 – клещевые захваты, 8 – двухходовой кран, 9 – нижняя шестерня, 10 – зубчатые сектора
Центровочно-загрузочное приспособление служит для правильной центровки чурака, т. е. сокращения отпада шпона в процессе лущения, и для загрузки чурака в лущильный станок.
На лущильных станках устанавливают, как правило, Центровочно-загрузочное приспособление системы А. Жукова, В. П. Банко и А. А. Порохина. Благодаря этому приспособлению стало возможным одновременно выполнять центровку чурака и подачу его к шпинделям лущильного станка.
Центровочно-загрузочное приспособление состоит из Двух пневматических цилиндров, свободно поворачивающихся на осях, прикрепленных к станине лущильного станка. На выступающих ступицах нижних шестерен укреплены рычаги с разрезными хомутами, что позволяет крепить рычаги на ступице в любом положении. Рычаги шарнирно соединены со штоками поршней пневматических цилиндров.
Подъем и центровка чурака осуществляется поворотом рукоятки двухходового крана. При этом сжатый воздух поступает в пневматические цилиндры. При подъеме поршней штоки поворачивают рычаги, которые при помощи шестерен и зубчатых секторов сводят клещевые захваты до соприкосновения их с поверхностью чурака.
Во время зажима чурака шпинделями происходит его осевое перемещение. Неровности чурака могут несколько разводить губки клещевых захватов за счет компрессии воздуха в цилиндрах, не создавая в звеньях механизма дополнительных усилий.
Скорость сжатия клещевых захватов регулируется степенью открытия воздушного крана.
Разведение клещевых захватов осуществляется под действием грузов, закрепленных на концах рычагов, или пружинами, как показано на рис. 19. Повернув рукоятку двухходового крана, открывают отверстие для выхода воздуха.
Приспособление работает при давлении в сети 4- 4,5 ати. Расход воздуха на один лущильный станок составляет 0,7 м3/ч. Верхние и нижние клещи закреплены на валах с помощью сквозных призматических шпонок в соответствующих положениях по отношению к зубчатым секторам.
Регулирование взаимного положения верхних и нижних клещей, обеспечивающее симметричность их движения (от чего зависит точность центровки), осуществляется при помощи особого устройства. Верхние секторы этого устройства двойные. Сектор без зубцов жестко скреплен с осью верхней клешни, а зубчатый сектор сидит на оси свободно и связан с верхней шестерней. Он может смещаться относительно сектора и жестко скрепляться с ним в нужном положении.
Для повышения точности центровки угол вилок доведен до 90°, нижние вилки жестко соединены с клещами, а верхние оставлены свободно вращающимися в пальцах. Для устранения наезда суппорта на клещи (при неполном их разведении) на станке установлена электрическая автоблокировка.
Кроме перечисленных выше основных частей, лущильный станок имеет также механизм подачи чураков, гидропривод, электрооборудование с автоблокировкой.
Но при многих достоинствах у традиционных лущильных станков есть и серьезные недостатки конструкции, связанные с необходимостью использования кулачков, которые вонзаются в торцы чураков и заставляют их вращаться. Нередко чурак проворачивается в кулачках и дальнейшее лущение становится невозможным. Как правило, это происходит из-за сердцевинной гнили, особенно часто встречающейся в осиновых чураках. В результате получаются так называемые провертыши – чураки большого диаметра, непригодные для дальнейшей обработки на лущильном станке.
Еще один недостаток традиционной техники лущения – потери древесины в виде остатков от лущения, так называемых карандашей. Диаметр «карандаша» зависит от диаметра внутренних кулачков станка и длины чурака. При длине чурака 1,6 м диаметр «карандаша» обычно 75 мм, а при длине 2,5 м – до 100 мм. Потери древесины составляют 10-12% объема чурака.
Рис. 1. Схема бесшпиндельного лущильного станка
Желание избавиться от этих недостатков привело конструкторов оборудования к идее бесшпиндельного лущильного станка. Впервые, вероятно, эта идея была реализована фирмой Raute (Финляндия) еще в 1990-е годы (рис. 1) в станках для лущения чураков максимальным диаметром 400 мм и длиной 1,7 и 2,8 м.
Вращение чураков в станке осуществлялось за счет приводных рифленых роликов, расположенных под углом 120° друг к другу. Верхний валец служил одновременно прижимной линейкой, а нижние перемещались прямолинейно по мере уменьшения диаметра чурака. Каждый валец оснащен индивидуальным гидроприводом. В процессе лущения ножевой суппорт немного поворачивался относительно чурака, что обеспечивало оптимальные параметры лущения чурака до диаметра карандаша 50 мм. Положение валов, толщина шпона и угол резания регулировались микро-ЭВМ. Диаметр чурака измерялся до его подачи в станок для определения просвета между валами.
Технология бесшпиндельного лущения шпона в Европе по какой-то причине не получила развития, но широко распространилась в азиатских странах. В Юго-Восточной Азии на многих предприятиях применяют бесшпиндельное лущение тонкомерного сырья и долущивание карандашей. Обычно лущильная линия состоит из окорочно-оцилиндровочного станка, бесшпиндельного лущильного станка с роторными ножницами.
Рис. 2. Линия лущения шпона RD2800 Raute
В окорочно-оцилиндровочном станке чурак зажимается тремя приводными зубчатыми роликами и приводится во вращение. Нож, аналогичный лущильному, удаляет кору и неровности, придает чураку цилиндрическую форму. Начальный диаметр чурака – до 500 мм, после оцилиндровки – не более 360 мм.
Передающий конвейер выравнивает чураки и подает их на бесшпиндельный лущильный станок, оснащенный тремя приводными роликами с мелкой насечкой и лущильным ножом. Максимальный диаметр чурака – 360 мм. Диаметр карандаша – 30-40 мм в зависимости от модели станка. Толщина получаемого шпона – от 1,0 до 3,0 мм. Линейная скорость лущения – 40 м/мин. После лущения шпон поступает на роторные ножницы, где в автоматическом режиме рубится на форматные листы.
Технология лущения тонкомерных чураков будет интересна российским предприятиям, которым приходится работать в наших непростых условиях. Китайские лущильные станки работают и в России, например на фанерном заводе «ИнвестФорэст» в пгт Суслонгер в Республике Марий Эл, на Уфимском фанерно-плитном комбинате, на заводе «Сатис-Мебель» под Нижним Новгородом.
Последнее предложение фирмы Weihai Hanvy из Китая – линия HVPL1326 с окорочно-оцилиндровочным станком и бесшпиндельным лущильным станком с ЧПУ Siemens HXQ2700 и электроникой от фирмы Scheider. Новый станок для бесшпиндельного лущения предназначен для обработки чураков длиной 2,6 м и максимальным диаметром 500 мм. Диаметр карандаша – 40 мм, скорость лущения – 40-100 м/мин. В станке предусмотрено изменение угла наклона ножа в ходе лущения, пневматическое крепление инструмента и автоматическое регулирование толщины шпона.
Рис. 3. Бесшпиндельный лущильный станок D1700 G26 и схема его работы
Фирма Raute не оставила идею создания бесшпиндельного лущильного станка и разработала линии RD1400, RD1700 (рис. 3) и RD2800, в составе каждой из которых четыре агрегата с необходимыми транспортным связями: окорочно-оцилиндровочный станок, лущильный станок, роторные ножницы и вакуумный укладчик шпона (рис. 2).
Сырье (чураки заданной длины) подается на поперечный конвейер с дозирующими упорами. В процессе окорки и оцилиндровки чураки приобретают необходимую для лущения цилиндрическую форму и передаются на лущильный станок при помощи еще одного поперечного конвейера.
Рис. 4. Схема зоны лущения с прижимным роликом
Кинематическая схема станка претерпела принципиальные изменения в сравнении с предыдущими моделями. Чурак подается в станок сверху, затем поджимается к двум приводным роликам с мелкой насечкой, которые установлены на едином суппорте. В окорочно-оцилиндровочном станке подача роликового суппорта гидравлическая, а в лущильном станке – электромеханическая. Третий ролик находится на неподвижном суппорте с лущильным ножом и играет роль прижимной линейки (рис. 4).
Чурак в станке самоцентрируется по трем точкам. При подаче роликового суппорта вперед чурак поджимается к ножевому суппорту, и выполняется лущение шпона. Толщина шпона задается с пульта управления установкой зазора между ножом и прижимным роликом, в ходе лущения угол резания автоматически меняется для обеспечения оптимальных параметров лущения (рис. 5).
В цепочке за лущильным станком установлены роторные ножницы для рубки шпона. Они подрубают передний край ленты шпона, разделяя форматный шпон и отходы. Передняя кромка листа шпона распознается при помощи фотоэлементов. Далее прохождение шпона по цепочке контролируется с помощью импульсного кодирующего устройства. Рубка выполняется при вращении ножа, расположенного над нижним резиновым роликом. На ножевом вале установлены три ножа. Автономный датчик системы распознавания контролирует пуск и остановку рубки шпона.
Рис. 5. Изменение угла резания в ходе лущения чурака
За ножницами расположен выходной конвейер с типпельным устройством для отсекания от потока кусков и неформатного шпона. Распознавание осуществляется при помощи фотоэлементов. Далее прохождение шпона по линии контролируется с помощью импульсного кодирующего устройства.
На ножевом валу установлены три ножа. Рубка шпона выполняется при вращении ножа, расположенного над нижним резиновым роликом. Автономный датчик системы распознавания контролирует пуск и остановку процесса рубки шпона.
После ножниц расположен выходной конвейер с типпельным устройством для отсекания кусков и неформатного шпона от потока. Распознавание осуществляется при помощи фотоэлементов, установленных перед типпелем. Форматные листы шпона укладываются стопоукладчиком на подъемник (в базовой модели могут быть один или два подъемника). Управление высотой укладки контролируется фотоэлементом. Полная стопа шпона выкатывается из стопоукладчика при помощи неприводного рольганга. Под линией находится поперечный конвейер необходимой длины для удаления отходов.
Линия RauteLite предназначена для лущения чураков из мягких и твердых пород древесины длиной 3/4/5/6/8 футов (0,9-2,4 м) и диаметром 120-350 мм. После оцилиндровки диаметр чурака может быть 80-300 мм, диаметр карандаша – 30-35 мм. На линии можно получать качественный шпон толщиной 1,2-2,2 мм c разнотолщинностью ±0,1 миллиметра.
Особо следует отметить, что в состав линии лущения входит система OPG (Optimum Peeling Geometry), с помощью которой посредством сервоконтроля достигается синхронизация скорости подачи роликов, изменение величины зазора между ножом и прижимным роликом, изменение заднего угла ножа в процессе лущения. Эта система осуществляет тотальный контроль всех параметров процесса – с момента начала лущения до удаления карандаша, что позволяет обеспечить высокую стабильность толщины шпона.
Подобные линии вряд ли полностью заменят традиционные лущильные станки, но могут занять свою нишу в линейке оборудования для производства лущеного шпона из маломерного сырья и долущивания карандашей. По расчетам автора, уменьшение диаметра карандаша с 75 до 35 мм позволяет увеличить выход шпона на 7,6% (при среднем диаметре чурака 240 мм), поэтому у подобной техники хорошие перспективы при долущивании карандашей и провертышей.
При выполнении этой задачи в линию уже не нужно включать окорочно-лущильный станок. Именно такую укороченную линию фирма Raute поставила на комбинат «СВЕЗА Кострома», в конце 2017 года линия была пущена.
Владимир ВОЛЫНСКИЙ
Все фото из статьи
Тема этой статьи – изготовление фанеры. Мы познакомимся с полным циклом ее производства – от окорки древесных стволов, до отгрузки готового материала на склад. Кроме того, мы выясним, можно ли производить фанеру в домашних условиях.
Одна из стадий производства – подача бревен в лущильный станок.
Производственный цикл
Он состоит из нескольких этапов:
На некоторых этапах стоит остановиться чуть подробнее.
Подготовка бревен
Из чего делается фанера при полном цикле производства?
- Из стволов хвойных и лиственных деревьев;
- Из связующего – клеев на основе искусственных смол.
Наиболее типичный материал фанеры – сосна и береза. Несколько реже применяются пихта, лиственница, кедр, ель, тополь, ольха, липа, осина и бук.
Обратите внимание: хвойная и лиственная фанера заметно различается механической прочностью и производится по разным ГОСТ – 3919.1-96 и 3919.2-96 соответственно.
Спиленные и лишенные сучьев бревна окоряются (очищаются от коры) и нарезаются вручную или на торцовочном станке на отрезки одинаковой длины. В зимнее время стволы предварительно выдерживаются в ванне с теплой водой для придания замерзшей древесине необходимой пластичности.
Окорка ствола.
Оцилиндровка и лущение
Как правило, эти две операции выполняются на одном станке.
Вначале заготовке придается цилиндрическая форма; затем с нее по сужающейся спирали снимается слой древесины толщиной около миллиметра. Оставшийся черенок в производстве не используется.
Нарезка на листы
Она сопровождается сортировкой материала. Дефектные участки листов вырезаются; полосы небольшой (менее 1,5 м) ширины могут быть использованы для склейки в целый лист.
Нарезка шпона на листы и первичная сортировка.
Затем шпон проходит клеевальцы, где он промазывается связующим.
Справка: в производстве фанеры ФК используется карбамидоформальдегидная смола.
Так называемая техническая фанера ФСФ склеивается фенолформальдегидными смолами, что позволяет отнести это производство к категории вредных.
Сушка в прессе
Для сушки листов используется гидравлический пресс с прогревом плит перегретым паром.
Типичная температура сушки около 200 градусов.
Продолжительность этой части цикла составляет от 30 минут до 2 часов в зависимости от толщины листа.
Сушка осуществляется при интенсивной принудительной вентиляции помещения: как уже говорилось, формальдегиды отнюдь не полезны для здоровья.
Выгрузка из пресса.
Обрезка
Просушенный лист представляет собой неопрятный сэндвич с неровными кромками. Чтобы превратиться в готовое для продажи изделие, он проходит обрезку на распиловочном станке.
Обратите внимание: согласно требованиям ГОСТ, кромки листа должны быть строго перпендикулярны друг другу.
Косина может составлять не более 2 мм на погонный метр.
Сортировка
Качество фанеры определяется визуально и, в зависимости от внешнего вида поверхности, позволяет отнести ее к одному из сортов – от элитного до четвертого.
К основным дефектам относятся:
- Живые и выпадающие сучки;
- Разошедшиеся и неразошедшиеся трещины;
- Здоровые и болезненные изменения цвета.
Цена листа в зависимости от сорта может различаться в два раза и более.
Особо стоит отметить два факта:
- Для материала сорта Е (Элита) недопустимы даже резкие переходы цвета и существенные изменения структуры поверхностного слоя шпона;
Фото позволяет оценить разницу между элитным и прочими сортами.
- Расслоение шпона сразу отправляет лист в брак вне зависимости от сорта.
Складирование
Установленная вертикально или под наклоном фанерная плита способна деформироваться под собственным весом благодаря текучести связывающих слои шпона смол.
Кроме того: ферментация может изменить цвет верхнего слоя на ярком солнечном свету.
Именно поэтому содержащаяся в отечественных стандартах инструкция по складированию листов предписывает хранить их строго определенным образом:
- в закрытом помещении с постоянной влажностью;
- защищенными от прямых солнечных лучей;
- в горизонтальном положении, уложенными на поддоны или подкладки.
Складирование материала.
Особый случай
Чтобы избежать путаницы в терминологии, стоит объяснить одну тонкость. Вопреки названию, перфорированная фанера не имеет к слоистому материалу из шпона никакого отношения.
Так называется лист ХДФ (древесноволокнистая плита высокой плотности, она же – прессованный оргалит) с проделанными в нем через равные промежутки отверстиями. Материал используется при оформлении витрин, в качестве филенок шкафных и внутренних дверей и т.д.
Перфорированный ХДФ.
Очумелые ручки
Может ли обычная фанера производиться в условиях небольшой частной мастерской? По полному циклу – едва ли, слишком габаритное оборудование требуется для распаривания, окорки стволов и лущения шпона. А вот склеивать шпон в готовые листы в домашних условиях вполне возможно.
Зачем это нужно? Например, для производства так называемой инженерной паркетной доски, состоящей из фанеры ФК с наклеенным на нее слоем шпона из древесины твердых пород.
Самый очевидный способ наладить кустарное производство – купить клеевальцы и пресс, благо оборудование для производства фанеры б у вполне доступно по стоимости. Однако если фанера своими руками будет производиться не на продажу, а исключительно ради ремонта в собственном доме, оно просто не окупится.
План «Б» состоит в холодной склейке шпона с готовым фанерным листом:
Оклейка фанеры шпоном благородных пород.
- И уложенный на ровное основание лист, и тыльная сторона шпона промазываются клеем ПВА;
- Шпон укладывается на поверхность листа и разглаживается;
- Заготовка придавливается листом толстой (22 – 27 мм) фанеры и пригружается весом 300 – 400 кг, максимально равномерно распределенным по всей поверхности.
Полная просушка клея займет около суток.
По прошествии этого времени лист нарезается на доски нужного размера на обычной стационарной циркулярке.
Затем фрезерный станок или ручной фрезер для дерева с направляющей используется для снятия фаски глубиной около миллиметра.
Внешний вид получившегося материала не уступит покупному паркету.
Обратите внимание: по понятным причинам изготовленный таким образом паркет можно укладывать только на клей.
В отсутствие кликовых замков о плавающей укладке речь не идет.
Заключение
Источник: https://rubankom.com/materialy/proizvodnye/fanera/1917-kak-delayut-faneru
Станок для шпона
Дорогостоящие сорта лесоматериалов являются прекрасным сырьем для создания предметов мебели, однако не все люди могут себе позволить такую дорогую продукцию.
С целью экономии ценных пород древесины и снижения стоимости конечного продукта и был придуман шпон. Этот материал сегодня крайне популярен для облицовки мебели.
Шпон на 100% повторяет узор, текстуру и оттенок натуральной древесины.
Для создания шпона на производствах пользуются специальными станками. Шпон бывает:
- лущеный
- строганый
- пиленый.
Соответственно и станок для производства шпона бывает трех типов.
Лущильный станок для производства шпона
Для реализации лущения шпона сырье необходимо предварительно обработать паром для того, чтобы увеличить пластичность.
После этого кряжи подаются на окорочный станок, где с заготовки удаляется кора, а вместе с ней грязь и песок, которые часто становятся причиной быстрого затупления лущильных ножей.
При помощи пилы кряжи раскраивают на чураки определенной длины. Чурак нужно предварительно оцилиндровать, после чего можно приступать к лущению.
Лента шпона, которая выходит из лущильного станка, кладется на конвейер, подающий ее к ножницам. Ножницы режут шпон на листы необходимого формата.
По конвейеру шпон укладывается в пачку, которая выносится из-под ножниц и при помощи электрического погрузчика доставляется в сушилку.
Сушат продукцию в роликовой сушилке, далее на конвейере его сортируют и складывают по сортам в пачки. Дефектные листы можно склеить. Если на листах имеются сучки, их отправляют на шпонопочиночный станок, где удаляют изъяны и декорируют их вставками из шпона.
Такой станок для шпона позволяет получить листовой материал толщиной от 1,5 до 5 мм из разнообразных сортов лесоматериалов.
На большинстве станков имеется система, которая позволяет в автоматическом режиме устанавливать бревно для последующей обработки.
Чтобы повысить производительность и удобство работы оператора станки оборудуют гидравлическими подъемниками-центроискателями, которые сами определяют подходящую ось вращения заготовки и совмещают ее с осью вращения центровочных валов.
Лущение пропаренной древесины используется для сосновых, ольховых, березовых лесоматериалов. Из лущеного шпона изготавливают фанеру.
Станок для строгания шпона
Прежде всего, кряжи подвергают поперечному раскрою. Во время этой процедуры кряжи распиливают на отрезки необходимой длины.
Все отрезки распиливают вдоль, вследствие чего образуется двухкантный брус. Иногда его распиливают пополам.
После этого ванчесы подвергают тепловой обработке в пропарочной камере или автоклаве.
Оттенок и узор древесины должны совпадать в каждом наборе.
Именно по этой причине листы шпона, которые получаются из каждого ванчеса во время строгания, складывают, сушат и пакуют в пачки точно в том порядке, в каком они выходили из строгального станка.
Когда строгаются одновременно три ванчеса, шпон из каждого из них складывают в три разные пачки. Укомплектованную, высушенную, запакованную и перетянутую шпагатом пачку шпона называют кнолем.
Станок для изготовления шпона позволяет создать из дорогостоящих сортов лесоматериалов, которые отличаются необычной текстурой, тонкие листы. Такой материал отлично подходит для фанерования. Методы создания шпона:
- радиальный
- тангенциальный
- радиально-тангенциальный
- тангенциально-торцовый.
Наиболее привлекательным сырьем для создания шпона является дубовая древесина. Такой шпон используют для облицовки рустикальных предметов мебели элитного сегмента.
Кроме дубового шпона в специализированных магазинах можно встретить кленовый, буковый, липовый материал, а также из красного дерева.
Станок для сшивки шпона
Шпон режут на специализированных аппаратах. Он отличается довольно тонкой и хрупкой структурой.
Для того, чтобы отделать поверхность шпоном, его необходимо соединить между собой для получения полотна, скатываемого в рулоны.
Шпон соединяют двумя способами:
Эти методы одинаково популярны на мебельных производствах. Сшивку шпона осуществляют на станке или ручным способом.
Для небольших мастерских разработаны ручные устройства для склейки или сшивки шпона.
При помощи особого устройства клеевую или термонить разогревают, и в виде зигзага наносят на основную сторону.
Сегодня станки для сшивки шпона представляют собой небольшие аппараты, функционирующие в автономном режиме. Управление такой машиной осуществляет один специалист. Вся работа на них производится четко, качественно и достаточно быстро.
Ручная сшивка встречается все реже, главным образом, в антикварных, реставрационных и авторских мастерских.
При постройке моделей часто приходится применять шпон различной толщины. Обычно нужную толщину получают шлифованием с помощью грибка с наклеенной на торце шкуркой, вставленного в патрон сверлильного станка. Такой способ самый доступный, но он имеет ряд недостатков: низкая производительность, невозможность обработать шпон толщиной менее 0,5 мм, поскольку из-за вращения грибка шпон вырывается из рук и ломается, и, наконец, основной недостаток – это большая загрязнённость воздуха древесной пылью. Обработать больше трёх-четырёх пластин не удаётся даже в респираторе.
Всех этих недостатков лишён сконструированный мной шлифовальный станок, работающий по принципу встречного фрезерования. Он был изготовлен (за исключением сварочных работ) в условиях авиамодельной лаборатории. В его конструкции отсутствуют дефицитные детали и материалы.
Все узлы станка крепятся на основании, представляющем собой параллелепипед размерами 200x265x340 мм, сваренный из стальных уголков 40x40x4 мм. К основанию привариваются, кроме того, два кронштейна, изготовленные из швеллера № 8, для крепления корпусов подшипников барабана.
Барабан (основной рабочий орган) и его шкив – литые. В качестве материала использован алюминиевый сплав АЛ-25, из которого сделаны поршни автомобильных двигателей. Поршни расплавляются в муфельной печке, а затем отливаются в песчаную форму. Отверстия в барабане под поворотный болт-зажим шкурки и противовесный болт должны быть просверлены симметрично относительно его оси. Кстати, масса у первого (вместе с «собачкой» фиксатором) и масса второго должны быть равные. В противном случае в результате дисбаланса возникнет вибрация, которая приведёт к преждевременному износу подшипников и отразится на работоспособности станка.
Корпуса подшипников выполнены сварными. Окончательный размер под подшипники в корпусах растачивается после сварки. Барабан приводится во вращение при помощи клиноремён-ной передачи от электродвигателя мощностью не менее 300 Вт, с числом оборотов в минуту от трёх до пяти тысяч, с достаточно большим пусковым моментом, так как барабан имеет довольно приличную массу, несмотря на то, что он выполнен из алюминиевого сплава. Этому требованию отвечают коллекторные электродвигатели. Я использовал на станке мотор от бытового электрополотёра.
Принципиально важным в предлагаемой мною конструкции шлифовального станка является наличие системы отсоса загрязнённого опилками и древесной пылью воздуха. Эта система делает станок экологически чистым и более «комфортабельным» при работе, так как позволяет обойтись без респиратора. Для отсоса опилок использован центробежный вентилятор-нагнетатель системы отопления салона автомобиля, который устанавливается на резьбовом конце оси барабана. Такой «пылесос» по производительности не уступает бытовому агрегату.
Кожух вентилятора крепится к кронштейну подшипника при помощи винтов-барашков, позволяющих быстро снимать его, когда возникает необходимость заменить износившуюся шкурку. На нагнетательный патрубок надевается мешочек из плотной ткани для сбора опилок. Всасывающее отверстие кожуха вентилятора соединяется с полостью кожуха барабана при помощи патрубка. Патрубок выклеивается из стеклоткани на пенопластовой болванке, которая затем выплавляется ацетоном. Полость кожуха барабана образована двумя концентрическими оболочками,приваренными к торцевым пластинам-фланцам. Внутренняя из них может быть приварена прерывистым швом, а наружная – обязательно сплошным, во избежание потерь давления. Расстояние между оболочками выбирается из условия равенства площади всасывающего отверстия кожуха вентилятора площади двух щелей, образуемых оболочками. В переднюю щель всасываются опилки, выбрасываемые барабаном при шлифовке, а в заднюю – опилки, которые захватываются шкуркой и выбрасываются центробежной силой барабана.
Кожухи барабана и ременной передачи и обшивка основания станка изготовлены из стального листа толщиной 1,5 мм. Ось барабана выточена из стали 30, а остальные детали – из стали 10.
Операция по заправке шкурки проста и достаточно наглядно показана на рисунке. Натяжка шкурки осуществляется при помощи рычага-«собачки»,надетого на квадратную часть поворотного болта-зажима шкурки и фиксирующегося в одном из пяти положений.
Стол изготавливается из стального листа толщиной 10 мм и имеет размеры 180×350 мм. Его рабочая поверхность должна быть ровной, по возможности отшлифованной на плоскошлифовальном станке. Стол, шарнирно закреплённый на основании, поднимается и опускается при помощи регулировочного болта, что даёт возможность получать шпон толщиной от 0,3 до 30 мм. Необходимый размер устанавливается по линейке, привинченной к основанию. Линейка градуируется при помощи мерных брусков, зажимаемых между барабаном и столом.
О неплохой производительности станка красноречиво свидетельствует тот факт, что за один проход можно снимать «стружку» толщиной до 1,5 мм.
Дорогостоящие сорта лесоматериалов являются прекрасным сырьем для создания предметов мебели, однако не все люди могут себе позволить такую дорогую продукцию. С целью экономии ценных пород древесины и снижения стоимости конечного продукта и был придуман шпон. Этот материал сегодня крайне популярен для облицовки мебели. Шпон на 100% повторяет узор, текстуру и оттенок натуральной древесины.
Для создания шпона на производствах пользуются специальными станками. Шпон бывает:
- лущеный
- строганый
- пиленый.
Соответственно и станок для производства шпона бывает трех типов.
Для реализации лущения шпона сырье необходимо предварительно обработать паром для того, чтобы увеличить пластичность. После этого кряжи подаются на окорочный станок, где с заготовки удаляется кора, а вместе с ней грязь и песок, которые часто становятся причиной быстрого затупления лущильных ножей. При помощи пилы кряжи раскраивают на чураки определенной длины. Чурак нужно предварительно оцилиндровать, после чего можно приступать к лущению. Лента шпона, которая выходит из лущильного станка, кладется на конвейер, подающий ее к ножницам. Ножницы режут шпон на листы необходимого формата. По конвейеру шпон укладывается в пачку, которая выносится из-под ножниц и при помощи электрического погрузчика доставляется в сушилку. Сушат продукцию в роликовой сушилке, далее на конвейере его сортируют и складывают по сортам в пачки. Дефектные листы можно склеить. Если на листах имеются сучки, их отправляют на шпонопочиночный станок, где удаляют изъяны и декорируют их вставками из шпона.
Такой станок для шпона позволяет получить листовой материал толщиной от 1,5 до 5 мм из разнообразных сортов лесоматериалов. На большинстве станков имеется система, которая позволяет в автоматическом режиме устанавливать бревно для последующей обработки.
Чтобы повысить производительность и удобство работы оператора станки оборудуют гидравлическими подъемниками-центроискателями, которые сами определяют подходящую ось вращения заготовки и совмещают ее с осью вращения центровочных валов.
Лущение пропаренной древесины используется для сосновых, ольховых, березовых лесоматериалов. Из лущеного шпона изготавливают фанеру.
Прежде всего, кряжи подвергают поперечному раскрою. Во время этой процедуры кряжи распиливают на отрезки необходимой длины. Все отрезки распиливают вдоль, вследствие чего образуется двухкантный брус. Иногда его распиливают пополам. После этого ванчесы подвергают тепловой обработке в пропарочной камере или автоклаве.
Далее ванчесы нужно острогать на шпонострогальном станке. Строганный шпон сушат в роликовых сушилках, торцуют и пакуют в пачки. В каждом наборе составляется конкретный рисунок. Оттенок и узор древесины должны совпадать в каждом наборе. Именно по этой причине листы шпона, которые получаются из каждого ванчеса во время строгания, складывают, сушат и пакуют в пачки точно в том порядке, в каком они выходили из строгального станка. Когда строгаются одновременно три ванчеса, шпон из каждого из них складывают в три разные пачки. Укомплектованную, высушенную, запакованную и перетянутую шпагатом пачку шпона называют кнолем.
Станок для изготовления шпона позволяет создать из дорогостоящих сортов лесоматериалов, которые отличаются необычной текстурой, тонкие листы. Такой материал отлично подходит для фанерования. Методы создания шпона:
- радиальный
- тангенциальный
- радиально-тангенциальный
- тангенциально-торцовый.
Наиболее привлекательным сырьем для создания шпона является дубовая древесина. Такой шпон используют для облицовки рустикальных предметов мебели элитного сегмента.
Кроме дубового шпона в специализированных магазинах можно встретить кленовый, буковый, липовый материал, а также из красного дерева.
Шпон режут на специализированных аппаратах. Он отличается довольно тонкой и хрупкой структурой. Для того, чтобы отделать поверхность шпоном, его необходимо соединить между собой для получения полотна, скатываемого в рулоны. Шпон соединяют двумя способами:
- склейка
- сшивка.
Эти методы одинаково популярны на мебельных производствах. Сшивку шпона осуществляют на станке или ручным способом. Для небольших мастерских разработаны ручные устройства для склейки или сшивки шпона. При помощи особого устройства клеевую или термонить разогревают, и в виде зигзага наносят на основную сторону.
Сегодня станки для сшивки шпона представляют собой небольшие аппараты, функционирующие в автономном режиме. Управление такой машиной осуществляет один специалист. Вся работа на них производится четко, качественно и достаточно быстро.
Ручная сшивка встречается все реже, главным образом, в антикварных, реставрационных и авторских мастерских.
Копировальные станки очень помогают в создании конкретной детали по шаблону для партий небольшого объема. Копировально-фрезерный станок применяют как на предприятиях, занимающихся производством продукции для крупных оптовых клиентов, так и в мелких мастерских, а также для бытого использования. Промышленные станки способны создавать изделия почти в неограниченном количестве. Однако в этой статье мы расскажем о том, как сделать копировально-фрезерный станок своими руками для мелкосерийного мебельного производства.
Лущильный станок своими руками. Какие существуют способы изготовления шпона в домашних условиях? Изготовление пиленого шпона
Дорогостоящие сорта лесоматериалов являются прекрасным сырьем для создания предметов мебели, однако не все люди могут себе позволить такую дорогую продукцию. С целью экономии ценных пород древесины и снижения стоимости конечного продукта и был придуман шпон. Этот материал сегодня крайне популярен для облицовки мебели. Шпон на 100% повторяет узор, текстуру и оттенок натуральной древесины.
Для создания шпона на производствах пользуются специальными станками. Шпон бывает:
- лущеный
- строганый
- пиленый.
Соответственно и станок для производства шпона бывает трех типов.
Лущильный станок для производства шпона
Для реализации лущения шпона сырье необходимо предварительно обработать паром для того, чтобы увеличить пластичность. После этого кряжи подаются на окорочный станок, где с заготовки удаляется кора, а вместе с ней грязь и песок, которые часто становятся причиной быстрого затупления лущильных ножей.
При помощи пилы кряжи раскраивают на чураки определенной длины. Чурак нужно предварительно оцилиндровать, после чего можно приступать к лущению. Лента шпона, которая выходит из лущильного станка, кладется на конвейер, подающий ее к ножницам. Ножницы режут шпон на листы необходимого формата.
По конвейеру шпон укладывается в пачку, которая выносится из-под ножниц и при помощи электрического погрузчика доставляется в сушилку. Сушат продукцию в роликовой сушилке, далее на конвейере его сортируют и складывают по сортам в пачки. Дефектные листы можно склеить.
Если на листах имеются сучки, их отправляют на шпонопочиночный станок, где удаляют изъяны и декорируют их вставками из шпона.
Такой станок для шпона позволяет получить листовой материал толщиной от 1,5 до 5 мм из разнообразных сортов лесоматериалов. На большинстве станков имеется система, которая позволяет в автоматическом режиме устанавливать бревно для последующей обработки.
Чтобы повысить производительность и удобство работы оператора станки оборудуют гидравлическими подъемниками-центроискателями, которые сами определяют подходящую ось вращения заготовки и совмещают ее с осью вращения центровочных валов.
Лущение пропаренной древесины используется для сосновых, ольховых, березовых лесоматериалов. Из лущеного шпона изготавливают фанеру.
Станок для строгания шпона
Прежде всего, кряжи подвергают поперечному раскрою. Во время этой процедуры кряжи распиливают на отрезки необходимой длины. Все отрезки распиливают вдоль, вследствие чего образуется двухкантный брус. Иногда его распиливают пополам. После этого ванчесы подвергают тепловой обработке в пропарочной камере или автоклаве.
Далее ванчесы нужно острогать на шпонострогальном станке. Строганный шпон сушат в роликовых сушилках, торцуют и пакуют в пачки. В каждом наборе составляется конкретный рисунок. Оттенок и узор древесины должны совпадать в каждом наборе.
Именно по этой причине листы шпона, которые получаются из каждого ванчеса во время строгания, складывают, сушат и пакуют в пачки точно в том порядке, в каком они выходили из строгального станка. Когда строгаются одновременно три ванчеса, шпон из каждого из них складывают в три разные пачки.
Укомплектованную, высушенную, запакованную и перетянутую шпагатом пачку шпона называют кнолем.
Станок для изготовления шпона позволяет создать из дорогостоящих сортов лесоматериалов, которые отличаются необычной текстурой, тонкие листы. Такой материал отлично подходит для фанерования. Методы создания шпона:
- радиальный
- тангенциальный
- радиально-тангенциальный
- тангенциально-торцовый.
Наиболее привлекательным сырьем для создания шпона является дубовая древесина. Такой шпон используют для облицовки рустикальных предметов мебели элитного сегмента.
Кроме дубового шпона в специализированных магазинах можно встретить кленовый, буковый, липовый материал, а также из красного дерева.
Станок для сшивки шпона
Шпон режут на специализированных аппаратах. Он отличается довольно тонкой и хрупкой структурой. Для того, чтобы отделать поверхность шпоном, его необходимо соединить между собой для получения полотна, скатываемого в рулоны. Шпон соединяют двумя способами:
Эти методы одинаково популярны на мебельных производствах. Сшивку шпона осуществляют на станке или ручным способом. Для небольших мастерских разработаны ручные устройства для склейки или сшивки шпона. При помощи особого устройства клеевую или термонить разогревают, и в виде зигзага наносят на основную сторону.
Сегодня станки для сшивки шпона представляют собой небольшие аппараты, функционирующие в автономном режиме. Управление такой машиной осуществляет один специалист. Вся работа на них производится четко, качественно и достаточно быстро.
Ручная сшивка встречается все реже, главным образом, в антикварных, реставрационных и авторских мастерских.
Источник: http://wood-prom.ru/clauses/promyshlennoe-oborudovanie/stanok-dlya-shpona
Как делают фанеру: подготовка бревен, оцилиндровка и лущение, нарезка на листы, сушка в прессе, обрезка, сортировка и складирование
Все фото из статьи
Тема этой статьи – изготовление фанеры. Мы познакомимся с полным циклом ее производства – от окорки древесных стволов, до отгрузки готового материала на склад. Кроме того, мы выясним, можно ли производить фанеру в домашних условиях.
Одна из стадий производства – подача бревен в лущильный станок.
Производственный цикл
Он состоит из нескольких этапов:
На некоторых этапах стоит остановиться чуть подробнее.
Подготовка бревен
Из чего делается фанера при полном цикле производства?
- Из стволов хвойных и лиственных деревьев;
- Из связующего – клеев на основе искусственных смол.
Наиболее типичный материал фанеры – сосна и береза. Несколько реже применяются пихта, лиственница, кедр, ель, тополь, ольха, липа, осина и бук.
Обратите внимание: хвойная и лиственная фанера заметно различается механической прочностью и производится по разным ГОСТ – 3919.1-96 и 3919.2-96 соответственно.
Спиленные и лишенные сучьев бревна окоряются (очищаются от коры) и нарезаются вручную или на торцовочном станке на отрезки одинаковой длины. В зимнее время стволы предварительно выдерживаются в ванне с теплой водой для придания замерзшей древесине необходимой пластичности.
Окорка ствола.
Оцилиндровка и лущение
Как правило, эти две операции выполняются на одном станке. Вначале заготовке придается цилиндрическая форма; затем с нее по сужающейся спирали снимается слой древесины толщиной около миллиметра. Оставшийся черенок в производстве не используется.
Нарезка на листы
Она сопровождается сортировкой материала. Дефектные участки листов вырезаются; полосы небольшой (менее 1,5 м) ширины могут быть использованы для склейки в целый лист.
Нарезка шпона на листы и первичная сортировка.
Затем шпон проходит клеевальцы, где он промазывается связующим.
Справка: в производстве фанеры ФК используется карбамидоформальдегидная смола.
Так называемая техническая фанера ФСФ склеивается фенолформальдегидными смолами, что позволяет отнести это производство к категории вредных.
Сушка в прессе
Для сушки листов используется гидравлический пресс с прогревом плит перегретым паром. Типичная температура сушки около 200 градусов. Продолжительность этой части цикла составляет от 30 минут до 2 часов в зависимости от толщины листа.
Сушка осуществляется при интенсивной принудительной вентиляции помещения: как уже говорилось, формальдегиды отнюдь не полезны для здоровья.
Выгрузка из пресса.
Обрезка
Просушенный лист представляет собой неопрятный сэндвич с неровными кромками. Чтобы превратиться в готовое для продажи изделие, он проходит обрезку на распиловочном станке.
Обратите внимание: согласно требованиям ГОСТ, кромки листа должны быть строго перпендикулярны друг другу.
Косина может составлять не более 2 мм на погонный метр.
Сортировка
Качество фанеры определяется визуально и, в зависимости от внешнего вида поверхности, позволяет отнести ее к одному из сортов – от элитного до четвертого.
К основным дефектам относятся:
- Живые и выпадающие сучки;
- Разошедшиеся и неразошедшиеся трещины;
- Здоровые и болезненные изменения цвета.
Цена листа в зависимости от сорта может различаться в два раза и более.
Особо стоит отметить два факта:
- Для материала сорта Е (Элита) недопустимы даже резкие переходы цвета и существенные изменения структуры поверхностного слоя шпона;
Фото позволяет оценить разницу между элитным и прочими сортами.
- Расслоение шпона сразу отправляет лист в брак вне зависимости от сорта.
Складирование
Установленная вертикально или под наклоном фанерная плита способна деформироваться под собственным весом благодаря текучести связывающих слои шпона смол.
Кроме того: ферментация может изменить цвет верхнего слоя на ярком солнечном свету.
Именно поэтому содержащаяся в отечественных стандартах инструкция по складированию листов предписывает хранить их строго определенным образом:
- в закрытом помещении с постоянной влажностью;
- защищенными от прямых солнечных лучей;
- в горизонтальном положении, уложенными на поддоны или подкладки.
Складирование материала.
Особый случай
Чтобы избежать путаницы в терминологии, стоит объяснить одну тонкость. Вопреки названию, перфорированная фанера не имеет к слоистому материалу из шпона никакого отношения.
Так называется лист ХДФ (древесноволокнистая плита высокой плотности, она же – прессованный оргалит) с проделанными в нем через равные промежутки отверстиями. Материал используется при оформлении витрин, в качестве филенок шкафных и внутренних дверей и т.д.
Перфорированный ХДФ.
Очумелые ручки
Может ли обычная фанера производиться в условиях небольшой частной мастерской? По полному циклу – едва ли, слишком габаритное оборудование требуется для распаривания, окорки стволов и лущения шпона. А вот склеивать шпон в готовые листы в домашних условиях вполне возможно.
Зачем это нужно? Например, для производства так называемой инженерной паркетной доски, состоящей из фанеры ФК с наклеенным на нее слоем шпона из древесины твердых пород.
Самый очевидный способ наладить кустарное производство – купить клеевальцы и пресс, благо оборудование для производства фанеры б у вполне доступно по стоимости. Однако если фанера своими руками будет производиться не на продажу, а исключительно ради ремонта в собственном доме, оно просто не окупится.
План «Б» состоит в холодной склейке шпона с готовым фанерным листом:
Оклейка фанеры шпоном благородных пород.
- И уложенный на ровное основание лист, и тыльная сторона шпона промазываются клеем ПВА;
- Шпон укладывается на поверхность листа и разглаживается;
- Заготовка придавливается листом толстой (22 – 27 мм) фанеры и пригружается весом 300 – 400 кг, максимально равномерно распределенным по всей поверхности.
Полная просушка клея займет около суток. По прошествии этого времени лист нарезается на доски нужного размера на обычной стационарной циркулярке. Затем фрезерный станок или ручной фрезер для дерева с направляющей используется для снятия фаски глубиной около миллиметра.
Внешний вид получившегося материала не уступит покупному паркету.
Обратите внимание: по понятным причинам изготовленный таким образом паркет можно укладывать только на клей.
В отсутствие кликовых замков о плавающей укладке речь не идет.
Заключение
Источник: https://rubankom.com/materialy/proizvodnye/fanera/1917-kak-delayut-faneru
Pereosnastka.ru
Конструкция лущильных станков
К атегория:
Производство клееной фанеры
Конструкция лущильных станков
Лущильные станки по техническим показателям подразделяют:- по наибольшему расстоянию между центрами шпинделей. Это расстояние определяет максимально возможную длину ножа и длину чураков, подлежащих лущению.
Наиболее распространенными являются станки для лущения чураков длиной 1350, 1650, 1950 мм. Длина чурака определяется размерами листов шпона;
По высоте центров шпинделей над станиной.
Высота центров определяется наибольшим радиусом чурака с припуском 100-150 мм.
Отечественные станки рассчитаны на лущение сырья диаметром 60-70 см. Иностранные фирмы выпускают станки для лущения чураков диаметром более 80 см.
Лущильный станок ЛУ-17-4 состоит из следующих основных частей: станины, двух шпиндельных бабок, суппорта кинематического узла, механизма поджима, центровочно-загрузочного приспособления.
Станина станка служит для крепления всех основных частей станка, восприятия динамических нагрузок резания и вспомогательных операций лущения.
Станина представляет собой жесткую сварную раму из двутавровых балок, на которой установлены чугунные шпиндельные бабки. В раме имеется щель для выброса карандаша вниз на транспортер.
Шпиндельные бабки (правая и левая) служат для закрепления чурака и придают ему вращательное движение.
На рис. 2 показан разрез правой шпиндельной бабки. Шпиндельная бабка имеет два телескопических шпинделя с соответствующими кулачками.
Наличие большого кулачка позволяет избежать раскола чураков в начальный период лущения, а малый кулачок дает возможность лущить карандаш диаметром до 70 мм.
Зажимают чурак на станке следующим образом.
Рис. 1. Станок ЛУ-17-4:
1 – станина, 2 – левая шпиндельная бабка, 3 – центровочно-загрузоч-ное приспособление, 4 – сварная балка, 5 – прижимные ролики, 6 – правая шпиндельная бабка, 7 – механизм прижима чурака, 8 – гидропривод, 9 – пустотелый вал, 10 – чугунная балка, 11 – суппорт, 12 – привод ускоренного перемещения суппорта, 13 – электродвигатель, 14 – механизм подачи чураков
Насос подает масло из гидросистемы в распределитель. Поршень под давлением перемещает шток в большом гидроцилиндре на величину до 150 мм. Шток поршня, жестко связанный с подвижным подшипниковым узлом малого шпинделя, перемещается также на длину гидроцилиндра. На подшипниковом узле малого шпинделя закреплен малый шпиндель. Последний, свободно перемещаясь внутри пустотелого большого шпинделя, кулачком зажимает чурак.
Разрез правой шпиндельной бабки станка ЛУ-17-4:
1 – поршень, 2 – большой гидроцилиндр, 3 – шток поршня, 4 – подвижной подшипниковый узел малого шпинделя, 5 – корпус, 6 – шли-цевая втулка, 7- шпонка шестерни, 8 – шестерня, 9- шпонка звездочки, 10 – звездочка, 11 – гнльза, 12-пустотелый большой шпиндель, 13 – малый кулачок, 14 – большой кулачок, 15 – малый шпиндель, 16 – сферические роликовые подшипники, 17 – шлицевая втулка большого шпинделя, 18 – рычаг, 19 – подвижный подшипниковый узел большого шпинделя, 20 – шлицы, 21 – шпонка, 22 – скользящие шпонки, 23-малый гидроцилиндр, 24 – малый поршень со штоком, 25 – шпилька
Масло одновременно поступает в большой и малый гидроцилиндры. Малый поршень со штоком перемещается в сторону чурака и, действуя на рычаг, смещает подвижный подшипниковый узел большого шпинделя. Величина смещения малого поршня со штоком зависит от размера малого гидроцилиндра и составляет 150 мм. Закрепленный в подвижном подшипниковом узле пустотелый большой шпиндель перемещается на указанную величину и зажимает большим кулачком чурак.
Таким образом, два шпинделя одновременно зажимают чурак закрепленными на них кулачками. Работа левого шпинделя аналогична работе правого.
После зажима чураку придают вращательное движение от главного вала через шестерню. Вращающаяся шестерня через шпонку приводит во вращение гильзу, которая с помощью шлицевой втулки 6 вращает пустотелый большой шпиндель. Большой шпиндель через шлицевую втулку большого шпинделя приводит во вращение малый шпиндель.
Скользящие шпонки предохраняют от вращения подвижные подшипниковые узлы; одновременно они являются направляющими при горизонтальном перемещении этих узлов.
В процессе лущения, когда лущильный нож подходит к вращающемуся кулачку большого шпинделя, гидросистема возвращает большой шпиндель в начальное положение. То же происходит, когда лущильный нож приближается к кулачкам малого шпинделя.
Система подвода масла к гидроцилиндрам для возврата шпинделей в исходное положение была показана на рис. 1.
Подключение гидросистемы к шпиндельным бабкам происходит таким образом, что при подаче масла на поршни большого и малого гидроцилиндров эти поршни возвращаются в исходное положение. Благодаря пустотелой конструкции большого шпинделя и шлицевому соединению двух шпинделей достигается их независимое передвижение относительно друг друга в горизонтальной плоскости.
Благодаря применению шпиндельных бабок стало возможным долущивать чурак диаметром до 70 мм на станке ЛУ-17-4, отказавшись от использования на этой операции малых лущильных станков.
Суппорт лущильного станка предназначен для закрепления ножа, его регулировки, настройки и для придания ему возвратно-поступательного движения (к чураку и обратно).
Суппорт состоит из двух боковых ползунов, перемещающихся по горизонтальным съемным параллелям, расположенным на станине станка; ножевой траверсы – для крепления и регулировки лущильного ножа; траверсы прижимной линейки – для крепления и регулировки прижимной линейки станка; двух суппортных винтов, сообщающих суппорту возвратно-поступательное движение.
Суппорт имеет дополнительные верхние и нижние направляющие, с которыми связана ножевая траверса и при помощи которых изменяется угол резания во время лущения чураков. Прижимная линейка соединена с ножевой траверсой эксцентриковым валом.
Механизм поджима чурака устраняет прогиб чурака в конце лущения под действием сил резания.
Этот механизм состоит из чугунной балки, закрепленной на пустотелом валу, двух пар прижимных роликов, гидроцилиндра перемещения роликов, смонтированного на стальной сварной балке, соединяющей обе бабки станка, а также устройства для регулировки синхронности перемещения ножа и прижимных роликов. Блок прижимных роликов шарнирно соединен с балкой и со штоком гидроцилиндра. Цапфы пустотелого вала установлены в подшипниках, корпуса которых прикреплены к бабкам станка.
Кинематический узел станка служит для связи рабочих органов станка (суппорта и шпиндельных бабок) и придания им рабочих движений.
На рис. 3 приведена кинематическая схема лущильного станка ЛУ-17-4. Сцентрированный и зажатый в шпинделях станка чурак (работа центровочно-загрузочного приспособления будет описана ниже) приводится во вращение от главного вала через шестерни. Главный вал соединен с электродвигателем через клиноременную передачу и электромагнитную муфту.
Кинематическая схема лущильного станка ЛУ-17-4:
1 – главный электродвигатель, 2 и 22 – клиноременная передача, 3 – электромагнитная муфта, 4, 5, 6 – шестерни, 7 – главный вал, 8, 9, 10, 16, 17, 18 – звездочки, 11 – промежуточный вал, 12-правый пустотелый вал, 13 – кулачковая муфта, 14 – передаточный вал, 15 – левый пустотелый вал, 19, 20 – конические шестерни, 21 – суппортный вал, 23 – электродвигатель ускоренного подвода и отвода суппорта, 24 – суппортные винты, 25 – поршни гидроцилиндра следящей системы, 26 – пневмоцилиндры центровки чураков, 27 – механизм подачи чураков, 28 – рукоятка переключения ускоренной и рабочей подачи суппорта, 29 – электромагнит; а, б, в, г – сменные шестерни набора толщин шпона
Левый шпиндель приводится во вращение от главного вата также через шестерни. Шестерня, вращая гильзу правого шпинделя, сообщает вращение звездочке. Звездочка втулочно-роликовой цепью соединена с промежуточным валом через звездочку, жестко закрепленную на промежуточном валу.
Вал приводит во вращение правый пустотелый вал через сменные шестерни а, б, в и г. Через кулачковую муфту, посаженную на скользящую шпонку, вращение с пустотелого вала передается на передаточный вал.
Через звездочку, жестко закрепленную на валу, и втулочно-роли-ковую цепь вращение передается на суппортный вал через звездочку.
Система конических шестерен, приводит в движение суппортные винты, а последние – суппорт, который перемещается по направляющим к вращающемуся чураку. Поступательное движение суппорта осуществляется благодаря суппортным гайкам, жестко связанным с корпусом суппорта.
Величина подачи суппорта за один оборот чурака, т. е.
толщина снимаемого шпона, зависит от расположения сменных шестерен а, б, в и г, так как жесткая связь во всех звеньях кинематической схемы, кроме сменных шестерен а, б, в и г, обеспечивает постоянное передаточное отношение.
Из таблицы видно, что изменение толщины шпона от 0,2 до 3,2 мм достигается в основном сменой шестерни а при взаимном расположении блок-шестерен (б – в) в двух положениях.
К концу лущения, когда диаметр чурака будет приближаться к диаметру малого кулачка шпинделя, рабочая подача суппорта прекращается при переводе кулачковой муфты в нейтральное положение рукояткой. Одно-вРеменно электромагнитную муфту выводят из соединения со шкивом клиноременной передачи и вращение карандаша в шпинделях станка прекращается.
С помощью электромагнитной муфты можно останавливать Движение главного вала, не выключая главного электродвигателя, что целесообразно экономически, так как пусковые моменты при включении электродвига-едя отрицательно сказываются на электроснабжении предприятия.
Гидросистема возвращает шпиндели в исходное положение, а карандаш через щель в станине удаляется транспортером из цеха.
Вращением суппортного вала в обратную сторону по отношению к рабочему движению электродвигателя через клиноременную передачу производится возврат суппорта в исходное положение. Суппорт подают в исходное положение на ускоренной подаче, что дает значительный выигрыш во времени. После этого электродвигатель выключают. В таком положении лущильный станок готов для лущения очередного чурака. Далее операция повторяется, как указано выше.
Кроме рабочей подачи, которая обеспечивает получение шпона заданной толщины, лущильный станок имеет ускоренную подачу, которая применяется в начальный период лущения для снятия больших неровностей на чураке.
Включение ускоренной подачи производится муфтой левого пустотелого вала. Вращение вала через муфту передается валу. Далее вращение передается как при рабочей подаче. Вращение вала 15 осуществляется от пала звездочками и втулочно-роликовой цепью.
В этом случае система сменных шестерен а, б, в иг отключена и в работе участия не принимает.
После окончания обдирки (на ускоренной подаче суппорта) передвигают рукояткой кулачковую муфту, тем самым отключая вал и включая вал. Далее происходит процесс лущения на рабочей подаче. Электромагнит служит для автоматического перевода кулачковой муфты в нейтральное положение.
Рис. 4. Схема устройства центровочно-загрузочного приспособления:
1 – свободно вращающаяся ось, 2- пневматический цилиндр, 3 – рычаг, 4 – груз, 5 – верхняя шестерня, 6 – сектор без зубцов, 7 – клещевые захваты, 8 – двухходовой кран, 9 – нижняя шестерня, 10 – зубчатые сектора
Центровочно-загрузочное приспособление служит для правильной центровки чурака, т. е. сокращения отпада шпона в процессе лущения, и для загрузки чурака в лущильный станок.
На лущильных станках устанавливают, как правило, Центровочно-загрузочное приспособление системы А. Жукова, В. П. Банко и А. А. Порохина. Благодаря этому приспособлению стало возможным одновременно выполнять центровку чурака и подачу его к шпинделям лущильного станка.
Центровочно-загрузочное приспособление состоит из Двух пневматических цилиндров, свободно поворачивающихся на осях, прикрепленных к станине лущильного станка. На выступающих ступицах нижних шестерен укреплены рычаги с разрезными хомутами, что позволяет крепить рычаги на ступице в любом положении. Рычаги шарнирно соединены со штоками поршней пневматических цилиндров.
Подъем и центровка чурака осуществляется поворотом рукоятки двухходового крана. При этом сжатый воздух поступает в пневматические цилиндры. При подъеме поршней штоки поворачивают рычаги, которые при помощи шестерен и зубчатых секторов сводят клещевые захваты до соприкосновения их с поверхностью чурака.
Во время зажима чурака шпинделями происходит его осевое перемещение. Неровности чурака могут несколько разводить губки клещевых захватов за счет компрессии воздуха в цилиндрах, не создавая в звеньях механизма дополнительных усилий.
Скорость сжатия клещевых захватов регулируется степенью открытия воздушного крана.
Разведение клещевых захватов осуществляется под действием грузов, закрепленных на концах рычагов, или пружинами, как показано на рис. 19. Повернув рукоятку двухходового крана, открывают отверстие для выхода воздуха.
Приспособление работает при давлении в сети 4- 4,5 ати. Расход воздуха на один лущильный станок составляет 0,7 м3/ч. Верхние и нижние клещи закреплены на валах с помощью сквозных призматических шпонок в соответствующих положениях по отношению к зубчатым секторам.
Регулирование взаимного положения верхних и нижних клещей, обеспечивающее симметричность их движения (от чего зависит точность центровки), осуществляется при помощи особого устройства. Верхние секторы этого устройства двойные. Сектор без зубцов жестко скреплен с осью верхней клешни, а зубчатый сектор сидит на оси свободно и связан с верхней шестерней. Он может смещаться относительно сектора и жестко скрепляться с ним в нужном положении.
Для повышения точности центровки угол вилок доведен до 90°, нижние вилки жестко соединены с клещами, а верхние оставлены свободно вращающимися в пальцах. Для устранения наезда суппорта на клещи (при неполном их разведении) на станке установлена электрическая автоблокировка.
Кроме перечисленных выше основных частей, лущильный станок имеет также механизм подачи чураков, гидропривод, электрооборудование с автоблокировкой.
Шпонирование деревянной основы, еще называют фанерованием. Шпонирование, как собственно говоря, фанерование, подразумевает под собой приклеивание тонких пластин дерева, шпона, на деревянную основу. Основа это столы, двери, шкафы, стены и прочие деревянные поверхности. Более подробно, о том, какие виды фанерования существуют, зачем это делать и как производить шпонирование своими руками, расскажем в статье.
Для чего шпонируют мебель
Шпон – это тонкая пластина древесины, как правило, ценных пород. Используют шпон, для того, чтобы обычное, недорогое дерево, стало по всем внешним признакам, ценной, дорогой породой.
Вследствие этого, цена на шпонированную мебель, в разы ниже, чем на массив дерева ценных пород. А внешний вид практически ничем не уступает второму.
Кроме выгоды в стоимости, использование шпона, дает широкие возможности для дизайна. Им же можно обклеить старую мебель, тем самым вдохнуть в нее вторую жизнь.
Какие бывают виды шпонирования
Основными видами шпонирования или фанерования, являются три вида. А именно, горячее, холодное и мембранное шпонирование.
Самым доступным методом, для домашнего использования, является метод горячего шпонирования. Тут шпон приклеивается к основе клеящим составом.
Остальные два вида шпонирования -холодное и мембранное, требует специальных станков и других производственных мощностей. Так, холодное шпонирование это прессование шпона к основе. Для этого используются прессовальные аппараты или винтовые ваймы.
Мембранное шпонирование производится на сложных рельефных поверхностях. И базируется на вакуумном соединении гладких и рельефных плит и шпона
Процесс шпонирования своими руками
Как мы уже говорили ранее, самым доступным способом, для домашнего использования, является горячее фанерование. Для работы вам понадобятся следующие основные материалы и инструменты из списка:
- Основа для шпонирования
- Шпон из дерева
- Нож фанерный
- ПВА клей
- Чистый лист бумаги
- Валик или деревянный брусок, для затирки шпона
- Наждачка
- Утюг, чем тяжелее, тем лучше
- Резак
Подготовительные работы
Прежде, чем приступить к шпонированию, нужно, в первую очередь, подготовить шпон. Шпон натурального происхождения, часто скручивают в рулон. Шпон, также может быть покоробленным и так далее.
Чтобы придать шпону правильное положение, смочите его увлажненной водой, губкой, и положите между двумя листами фанеры. А чтобы ушла лишняя влага, проложите между фанерой и шпоном, с обеих сторон шпона, упаковочную бумагу.
Чаще всего, для отделки мебели применяют строганный шпон. Это узкие, но длинные листы. Ширина строганного шпона, как правило, не шире 30 сантиметров.
Поэтому, после выравнивания и удаления лишней влаги с поверхности шпона, нарезаем листы, необходимой длины. Если, для примера, вы хотите обклеить стол, то шпон должен слегка выступать ха края основы. Лишнее, по окончании процесса шпонирования, можно будет срезать или зашкурить.
Кстати, не режьте шпон ножом или ножницами. Шпон может растрескаться и режется от неровно этими приспособлениями. Для резки шпона используйте фанерный нож или строгальный станок.
Склеивание шпона и основы
Клей ПВА наносим на шпон и на основу. На основе промазываем участок основы. Лучше всего, клеем промазывать дважды. Первый слой клея сушим почти до полного высыхания, чтобы клей практически перестал липнуть. Второй слой просушиваем до отлипа.
Следующим этапом, разогреваем утюг до 50 градусов. Это, примерно, средняя температура на утюга. И через лист белой бумаги утюжим шпон. После прохода утюгом, сразу же начинаем притирать валиком или бруском, шпон и основу.
Лущильный станок был изобретен еще в конце XIX века. Без этого оборудования сегодня просто невозможно представить производство фанеры и изготовление спичек. За прошедшие сто с лишним лет было создано немало конструкций и модификаций станков, но принцип остался прежним: срезание с коротких бревен-чураков тонкой ленты древесины.Но при многих достоинствах у традиционных лущильных станков есть и серьезные недостатки конструкции, связанные с необходимостью использования кулачков, которые вонзаются в торцы чураков и заставляют их вращаться. Нередко чурак проворачивается в кулачках и дальнейшее лущение становится невозможным. Как правило, это происходит из-за сердцевинной гнили, особенно часто встречающейся в осиновых чураках. В результате получаются так называемые провертыши – чураки большого диаметра, непригодные для дальнейшей обработки на лущильном станке.
Еще один недостаток традиционной техники лущения – потери древесины в виде остатков от лущения, так называемых карандашей. Диаметр «карандаша» зависит от диаметра внутренних кулачков станка и длины чурака. При длине чурака 1,6 м диаметр «карандаша» обычно 75 мм, а при длине 2,5 м – до 100 мм. Потери древесины составляют 10-12% объема чурака.
Рис. 1. Схема бесшпиндельного лущильного станка
Желание избавиться от этих недостатков привело конструкторов оборудования к идее бесшпиндельного лущильного станка. Впервые, вероятно, эта идея была реализована фирмой Raute (Финляндия) еще в 1990-е годы (рис. 1) в станках для лущения чураков максимальным диаметром 400 мм и длиной 1,7 и 2,8 м.
Вращение чураков в станке осуществлялось за счет приводных рифленых роликов, расположенных под углом 120° друг к другу. Верхний валец служил одновременно прижимной линейкой, а нижние перемещались прямолинейно по мере уменьшения диаметра чурака. Каждый валец оснащен индивидуальным гидроприводом. В процессе лущения ножевой суппорт немного поворачивался относительно чурака, что обеспечивало оптимальные параметры лущения чурака до диаметра карандаша 50 мм. Положение валов, толщина шпона и угол резания регулировались микро-ЭВМ. Диаметр чурака измерялся до его подачи в станок для определения просвета между валами.
Технология бесшпиндельного лущения шпона в Европе по какой-то причине не получила развития, но широко распространилась в азиатских странах. В Юго-Восточной Азии на многих предприятиях применяют бесшпиндельное лущение тонкомерного сырья и долущивание карандашей. Обычно лущильная линия состоит из окорочно-оцилиндровочного станка, бесшпиндельного лущильного станка с роторными ножницами.
Рис. 2. Линия лущения шпона RD2800 Raute
В окорочно-оцилиндровочном станке чурак зажимается тремя приводными зубчатыми роликами и приводится во вращение. Нож, аналогичный лущильному, удаляет кору и неровности, придает чураку цилиндрическую форму. Начальный диаметр чурака – до 500 мм, после оцилиндровки – не более 360 мм.
Передающий конвейер выравнивает чураки и подает их на бесшпиндельный лущильный станок, оснащенный тремя приводными роликами с мелкой насечкой и лущильным ножом. Максимальный диаметр чурака – 360 мм. Диаметр карандаша – 30-40 мм в зависимости от модели станка. Толщина получаемого шпона – от 1,0 до 3,0 мм. Линейная скорость лущения – 40 м/мин. После лущения шпон поступает на роторные ножницы, где в автоматическом режиме рубится на форматные листы.
Технология лущения тонкомерных чураков будет интересна российским предприятиям, которым приходится работать в наших непростых условиях. Китайские лущильные станки работают и в России, например на фанерном заводе «ИнвестФорэст» в пгт Суслонгер в Республике Марий Эл, на Уфимском фанерно-плитном комбинате, на заводе «Сатис-Мебель» под Нижним Новгородом.
Последнее предложение фирмы Weihai Hanvy из Китая – линия HVPL1326 с окорочно-оцилиндровочным станком и бесшпиндельным лущильным станком с ЧПУ Siemens HXQ2700 и электроникой от фирмы Scheider. Новый станок для бесшпиндельного лущения предназначен для обработки чураков длиной 2,6 м и максимальным диаметром 500 мм. Диаметр карандаша – 40 мм, скорость лущения – 40-100 м/мин. В станке предусмотрено изменение угла наклона ножа в ходе лущения, пневматическое крепление инструмента и автоматическое регулирование толщины шпона.
Рис. 3. Бесшпиндельный лущильный станок D1700 G26 и схема его работы
Фирма Raute не оставила идею создания бесшпиндельного лущильного станка и разработала линии RD1400, RD1700 (рис. 3) и RD2800, в составе каждой из которых четыре агрегата с необходимыми транспортным связями: окорочно-оцилиндровочный станок, лущильный станок, роторные ножницы и вакуумный укладчик шпона (рис. 2).
Сырье (чураки заданной длины) подается на поперечный конвейер с дозирующими упорами. В процессе окорки и оцилиндровки чураки приобретают необходимую для лущения цилиндрическую форму и передаются на лущильный станок при помощи еще одного поперечного конвейера.
Рис. 4. Схема зоны лущения с прижимным роликом
Кинематическая схема станка претерпела принципиальные изменения в сравнении с предыдущими моделями. Чурак подается в станок сверху, затем поджимается к двум приводным роликам с мелкой насечкой, которые установлены на едином суппорте. В окорочно-оцилиндровочном станке подача роликового суппорта гидравлическая, а в лущильном станке – электромеханическая. Третий ролик находится на неподвижном суппорте с лущильным ножом и играет роль прижимной линейки (рис. 4).
Чурак в станке самоцентрируется по трем точкам. При подаче роликового суппорта вперед чурак поджимается к ножевому суппорту, и выполняется лущение шпона. Толщина шпона задается с пульта управления установкой зазора между ножом и прижимным роликом, в ходе лущения угол резания автоматически меняется для обеспечения оптимальных параметров лущения (рис. 5).
В цепочке за лущильным станком установлены роторные ножницы для рубки шпона. Они подрубают передний край ленты шпона, разделяя форматный шпон и отходы. Передняя кромка листа шпона распознается при помощи фотоэлементов. Далее прохождение шпона по цепочке контролируется с помощью импульсного кодирующего устройства. Рубка выполняется при вращении ножа, расположенного над нижним резиновым роликом. На ножевом вале установлены три ножа. Автономный датчик системы распознавания контролирует пуск и остановку рубки шпона.
Рис. 5. Изменение угла резания в ходе лущения чурака
За ножницами расположен выходной конвейер с типпельным устройством для отсекания от потока кусков и неформатного шпона. Распознавание осуществляется при помощи фотоэлементов. Далее прохождение шпона по линии контролируется с помощью импульсного кодирующего устройства.
На ножевом валу установлены три ножа. Рубка шпона выполняется при вращении ножа, расположенного над нижним резиновым роликом. Автономный датчик системы распознавания контролирует пуск и остановку процесса рубки шпона.
После ножниц расположен выходной конвейер с типпельным устройством для отсекания кусков и неформатного шпона от потока. Распознавание осуществляется при помощи фотоэлементов, установленных перед типпелем. Форматные листы шпона укладываются стопоукладчиком на подъемник (в базовой модели могут быть один или два подъемника). Управление высотой укладки контролируется фотоэлементом. Полная стопа шпона выкатывается из стопоукладчика при помощи неприводного рольганга. Под линией находится поперечный конвейер необходимой длины для удаления отходов.
Линия RauteLite предназначена для лущения чураков из мягких и твердых пород древесины длиной 3/4/5/6/8 футов (0,9-2,4 м) и диаметром 120-350 мм. После оцилиндровки диаметр чурака может быть 80-300 мм, диаметр карандаша – 30-35 мм. На линии можно получать качественный шпон толщиной 1,2-2,2 мм c разнотолщинностью ±0,1 миллиметра.
Особо следует отметить, что в состав линии лущения входит система OPG (Optimum Peeling Geometry), с помощью которой посредством сервоконтроля достигается синхронизация скорости подачи роликов, изменение величины зазора между ножом и прижимным роликом, изменение заднего угла ножа в процессе лущения. Эта система осуществляет тотальный контроль всех параметров процесса – с момента начала лущения до удаления карандаша, что позволяет обеспечить высокую стабильность толщины шпона.
Подобные линии вряд ли полностью заменят традиционные лущильные станки, но могут занять свою нишу в линейке оборудования для производства лущеного шпона из маломерного сырья и долущивания карандашей. По расчетам автора, уменьшение диаметра карандаша с 75 до 35 мм позволяет увеличить выход шпона на 7,6% (при среднем диаметре чурака 240 мм), поэтому у подобной техники хорошие перспективы при долущивании карандашей и провертышей.
При выполнении этой задачи в линию уже не нужно включать окорочно-лущильный станок. Именно такую укороченную линию фирма Raute поставила на комбинат «СВЕЗА Кострома», в конце 2017 года линия была пущена.
Владимир ВОЛЫНСКИЙ
Все фото из статьи
Тема этой статьи – изготовление фанеры. Мы познакомимся с полным циклом ее производства – от окорки древесных стволов, до отгрузки готового материала на склад. Кроме того, мы выясним, можно ли производить фанеру в домашних условиях.
Одна из стадий производства – подача бревен в лущильный станок.
Производственный цикл
Он состоит из нескольких этапов:
На некоторых этапах стоит остановиться чуть подробнее.
Подготовка бревен
Из чего делается фанера при полном цикле производства?
- Из стволов хвойных и лиственных деревьев;
- Из связующего – клеев на основе искусственных смол.
Наиболее типичный материал фанеры – сосна и береза. Несколько реже применяются пихта, лиственница, кедр, ель, тополь, ольха, липа, осина и бук.
Обратите внимание: хвойная и лиственная фанера заметно различается механической прочностью и производится по разным ГОСТ – 3919.1-96 и 3919.2-96 соответственно.
Спиленные и лишенные сучьев бревна окоряются (очищаются от коры) и нарезаются вручную или на торцовочном станке на отрезки одинаковой длины. В зимнее время стволы предварительно выдерживаются в ванне с теплой водой для придания замерзшей древесине необходимой пластичности.
Окорка ствола.
Оцилиндровка и лущение
Как правило, эти две операции выполняются на одном станке.
Вначале заготовке придается цилиндрическая форма; затем с нее по сужающейся спирали снимается слой древесины толщиной около миллиметра. Оставшийся черенок в производстве не используется.
Нарезка на листы
Она сопровождается сортировкой материала. Дефектные участки листов вырезаются; полосы небольшой (менее 1,5 м) ширины могут быть использованы для склейки в целый лист.
Нарезка шпона на листы и первичная сортировка.
Затем шпон проходит клеевальцы, где он промазывается связующим.
Справка: в производстве фанеры ФК используется карбамидоформальдегидная смола.
Так называемая техническая фанера ФСФ склеивается фенолформальдегидными смолами, что позволяет отнести это производство к категории вредных.
Сушка в прессе
Для сушки листов используется гидравлический пресс с прогревом плит перегретым паром.
Типичная температура сушки около 200 градусов.
Продолжительность этой части цикла составляет от 30 минут до 2 часов в зависимости от толщины листа.
Сушка осуществляется при интенсивной принудительной вентиляции помещения: как уже говорилось, формальдегиды отнюдь не полезны для здоровья.
Выгрузка из пресса.
Обрезка
Просушенный лист представляет собой неопрятный сэндвич с неровными кромками. Чтобы превратиться в готовое для продажи изделие, он проходит обрезку на распиловочном станке.
Обратите внимание: согласно требованиям ГОСТ, кромки листа должны быть строго перпендикулярны друг другу.
Косина может составлять не более 2 мм на погонный метр.
Сортировка
Качество фанеры определяется визуально и, в зависимости от внешнего вида поверхности, позволяет отнести ее к одному из сортов – от элитного до четвертого.
К основным дефектам относятся:
- Живые и выпадающие сучки;
- Разошедшиеся и неразошедшиеся трещины;
- Здоровые и болезненные изменения цвета.
Цена листа в зависимости от сорта может различаться в два раза и более.
Особо стоит отметить два факта:
- Для материала сорта Е (Элита) недопустимы даже резкие переходы цвета и существенные изменения структуры поверхностного слоя шпона;
Фото позволяет оценить разницу между элитным и прочими сортами.
- Расслоение шпона сразу отправляет лист в брак вне зависимости от сорта.
Складирование
Установленная вертикально или под наклоном фанерная плита способна деформироваться под собственным весом благодаря текучести связывающих слои шпона смол.
Кроме того: ферментация может изменить цвет верхнего слоя на ярком солнечном свету.
Именно поэтому содержащаяся в отечественных стандартах инструкция по складированию листов предписывает хранить их строго определенным образом:
- в закрытом помещении с постоянной влажностью;
- защищенными от прямых солнечных лучей;
- в горизонтальном положении, уложенными на поддоны или подкладки.
Складирование материала.
Особый случай
Чтобы избежать путаницы в терминологии, стоит объяснить одну тонкость. Вопреки названию, перфорированная фанера не имеет к слоистому материалу из шпона никакого отношения.
Так называется лист ХДФ (древесноволокнистая плита высокой плотности, она же – прессованный оргалит) с проделанными в нем через равные промежутки отверстиями. Материал используется при оформлении витрин, в качестве филенок шкафных и внутренних дверей и т.д.
Перфорированный ХДФ.
Очумелые ручки
Может ли обычная фанера производиться в условиях небольшой частной мастерской? По полному циклу – едва ли, слишком габаритное оборудование требуется для распаривания, окорки стволов и лущения шпона. А вот склеивать шпон в готовые листы в домашних условиях вполне возможно.
Зачем это нужно? Например, для производства так называемой инженерной паркетной доски, состоящей из фанеры ФК с наклеенным на нее слоем шпона из древесины твердых пород.
Самый очевидный способ наладить кустарное производство – купить клеевальцы и пресс, благо оборудование для производства фанеры б у вполне доступно по стоимости. Однако если фанера своими руками будет производиться не на продажу, а исключительно ради ремонта в собственном доме, оно просто не окупится.
План «Б» состоит в холодной склейке шпона с готовым фанерным листом:
Оклейка фанеры шпоном благородных пород.
- И уложенный на ровное основание лист, и тыльная сторона шпона промазываются клеем ПВА;
- Шпон укладывается на поверхность листа и разглаживается;
- Заготовка придавливается листом толстой (22 – 27 мм) фанеры и пригружается весом 300 – 400 кг, максимально равномерно распределенным по всей поверхности.
Полная просушка клея займет около суток.
По прошествии этого времени лист нарезается на доски нужного размера на обычной стационарной циркулярке.
Затем фрезерный станок или ручной фрезер для дерева с направляющей используется для снятия фаски глубиной около миллиметра.
Внешний вид получившегося материала не уступит покупному паркету.
Обратите внимание: по понятным причинам изготовленный таким образом паркет можно укладывать только на клей.
В отсутствие кликовых замков о плавающей укладке речь не идет.
Заключение
Источник: https://rubankom.com/materialy/proizvodnye/fanera/1917-kak-delayut-faneru
Станок для шпона
Дорогостоящие сорта лесоматериалов являются прекрасным сырьем для создания предметов мебели, однако не все люди могут себе позволить такую дорогую продукцию.
С целью экономии ценных пород древесины и снижения стоимости конечного продукта и был придуман шпон. Этот материал сегодня крайне популярен для облицовки мебели.
Шпон на 100% повторяет узор, текстуру и оттенок натуральной древесины.
Для создания шпона на производствах пользуются специальными станками. Шпон бывает:
- лущеный
- строганый
- пиленый.
Соответственно и станок для производства шпона бывает трех типов.
Лущильный станок для производства шпона
Для реализации лущения шпона сырье необходимо предварительно обработать паром для того, чтобы увеличить пластичность.
После этого кряжи подаются на окорочный станок, где с заготовки удаляется кора, а вместе с ней грязь и песок, которые часто становятся причиной быстрого затупления лущильных ножей.
При помощи пилы кряжи раскраивают на чураки определенной длины. Чурак нужно предварительно оцилиндровать, после чего можно приступать к лущению.
Лента шпона, которая выходит из лущильного станка, кладется на конвейер, подающий ее к ножницам. Ножницы режут шпон на листы необходимого формата.
По конвейеру шпон укладывается в пачку, которая выносится из-под ножниц и при помощи электрического погрузчика доставляется в сушилку.
Сушат продукцию в роликовой сушилке, далее на конвейере его сортируют и складывают по сортам в пачки. Дефектные листы можно склеить. Если на листах имеются сучки, их отправляют на шпонопочиночный станок, где удаляют изъяны и декорируют их вставками из шпона.
Такой станок для шпона позволяет получить листовой материал толщиной от 1,5 до 5 мм из разнообразных сортов лесоматериалов.
На большинстве станков имеется система, которая позволяет в автоматическом режиме устанавливать бревно для последующей обработки.
Чтобы повысить производительность и удобство работы оператора станки оборудуют гидравлическими подъемниками-центроискателями, которые сами определяют подходящую ось вращения заготовки и совмещают ее с осью вращения центровочных валов.
Лущение пропаренной древесины используется для сосновых, ольховых, березовых лесоматериалов. Из лущеного шпона изготавливают фанеру.
Станок для строгания шпона
Прежде всего, кряжи подвергают поперечному раскрою. Во время этой процедуры кряжи распиливают на отрезки необходимой длины.
Все отрезки распиливают вдоль, вследствие чего образуется двухкантный брус. Иногда его распиливают пополам.
После этого ванчесы подвергают тепловой обработке в пропарочной камере или автоклаве.
Оттенок и узор древесины должны совпадать в каждом наборе.
Именно по этой причине листы шпона, которые получаются из каждого ванчеса во время строгания, складывают, сушат и пакуют в пачки точно в том порядке, в каком они выходили из строгального станка.
Когда строгаются одновременно три ванчеса, шпон из каждого из них складывают в три разные пачки. Укомплектованную, высушенную, запакованную и перетянутую шпагатом пачку шпона называют кнолем.
Станок для изготовления шпона позволяет создать из дорогостоящих сортов лесоматериалов, которые отличаются необычной текстурой, тонкие листы. Такой материал отлично подходит для фанерования. Методы создания шпона:
- радиальный
- тангенциальный
- радиально-тангенциальный
- тангенциально-торцовый.
Наиболее привлекательным сырьем для создания шпона является дубовая древесина. Такой шпон используют для облицовки рустикальных предметов мебели элитного сегмента.
Кроме дубового шпона в специализированных магазинах можно встретить кленовый, буковый, липовый материал, а также из красного дерева.
Станок для сшивки шпона
Шпон режут на специализированных аппаратах. Он отличается довольно тонкой и хрупкой структурой.
Для того, чтобы отделать поверхность шпоном, его необходимо соединить между собой для получения полотна, скатываемого в рулоны.
Шпон соединяют двумя способами:
Эти методы одинаково популярны на мебельных производствах. Сшивку шпона осуществляют на станке или ручным способом.
Для небольших мастерских разработаны ручные устройства для склейки или сшивки шпона.
При помощи особого устройства клеевую или термонить разогревают, и в виде зигзага наносят на основную сторону.
Сегодня станки для сшивки шпона представляют собой небольшие аппараты, функционирующие в автономном режиме. Управление такой машиной осуществляет один специалист. Вся работа на них производится четко, качественно и достаточно быстро.
Ручная сшивка встречается все реже, главным образом, в антикварных, реставрационных и авторских мастерских.
1
Первый слайд презентации: Лущильный станок
Изображение слайда
2
Слайд 2
Лущильный станок Предназначается для получения тонкой поперечной стружки, так называемого лущёного Шпон а, из коротких брёвен ( чураков ). Применяется в мебельной промышленности, в фанерном и спичечном производствах и других. При лущении нож, установленный на суппорте, срезает по всей длине вращающегося чурака слой древесины (шпон) в виде широкой непрерывной ленты. Для повышения прочности шпона и улучшения качества его поверхности при лущении производится обжим древесины прижимной линейкой, а чураки подвергают гидротермической обработке (например, пропарке). Толщина шпона, получаемого на Л. с.,колеблется от 0,1 до 10 мм, скорость резания от 1 до 6 м/сек, углы резания обычно не превышают 27°.
Изображение слайда
3
Слайд 3: Принцип работы лущильного станка
Бревно совершает вращательное движение – главное движения Нож совершает медленное поступательное движение в направлении этой же оси. Лущильные станки конструктивно приспособлены для выполнения единственной задачи – срезания непрерывной тонкой ленты древесины при помощи широкого резца с цилиндрического бревна, которое вращается в центрах.
Изображение слайда
4
Слайд 4
Чтобы получаемый на таком оборудовании шпон (снимаемая древесная стружка) не ломался и не распадался на отдельные фрагменты, перед лущением бревно подвергают специальной гидротермической обработке с последующим обжимом особой обжимной линейкой, которая располагается непосредственно перед резцом. Система ЧПУ и дисплей помогают контролировать ход процесса лущения.
Изображение слайда
5
Слайд 5: Использование продукции лущильного станка
На лущильных станках делают лущеный шпон в виде тонкой деревянной ленты заданной толщины (от 0,35 мм до 4 мм с градацией 0,25 мм). Полученную ленту при помощи специальных ножниц разрезают на листы, размер которых регламентируется ГОСТом, после чего сушат, сортируют, обрезают (при необходимости) и складывают в стопы. Ширину листов шпона измеряют поперек древесных волокон, а длину – по направлению волокон древесины. Такой шпон широко используют для производства фанеры и других клеено-слоистых плит, облицовки поверхности деревянных изделий, изготовления корзинок и другой тары. Для получения лущеного шпона используют различные породы древесины – кедр, пихту, сосну, осину, ильм, ясень, клен, березу, лиственницу, ель, тополь, липу, бук, дуб, ольху. Безусловно, облицованная шпоном плита ДСП по цене будет превосходить обычный ламинированный вариант, но при этом по внешнему виду ничем не будет отличаться от массива натурального дерева.
Изображение слайда
6
Слайд 6: Лущеный шпон
Изображение слайда
7
Слайд 7
Лущильный станок ЛУ17-4: 1 — чурак ; 2 — опорный люнет; 3 — суппорт.
Изображение слайда
8
Слайд 8
Лущильные станки по техническим показателям подразделяют: — по наибольшему расстоянию между центрами шпинделей. Это расстояние определяет максимально возможную длину ножа и длину чураков, подлежащих лущению. Наиболее распространенными являются станки для лущения чураков длиной 1350, 1650, 1950 мм. Длина чурака определяется размерами листов шпона; — по высоте центров шпинделей над станиной. Высота центров определяется наибольшим радиусом чурака с припуском 100—150 мм. Отечественные станки рассчитаны на лущение сырья диаметром 60—70 см. Иностранные фирмы выпускают станки для лущения чураков диаметром более 80 см. Лущильный станок ЛУ-17-4 состоит из следующих основных частей: станины, двух шпиндельных бабок, суппорта кинематического узла, механизма поджима, центровочно-загрузочного приспособления. Станина станка служит для крепления всех основных частей станка, восприятия динамических нагрузок резания и вспомогательных операций лущения. Станина представляет собой жесткую сварную раму из двутавровых балок, на которой установлены чугунные шпиндельные бабки. В раме имеется щель для выброса карандаша вниз на транспортер.
Изображение слайда
9
Последний слайд презентации: Лущильный станок
Изображение слайда
Пролетарская свобода – Вики
ОАО завод «Пролетарская свобода» — российское машиностроительное предприятие, производитель оборудования для производства шпона и фанеры, оборудования для выработки тепловой энергии. Находится в городе Ярославле.
История
До революции завод носил название «Якобсон и Лифшиц».
Завод «Пролетарская свобода» до реконструкции производил гвозди. В годы Первой пятилетки (1929—1932) значительно расширился и пополнился новым оборудованием. Было освоено производство сложных машин для лесной и крахмалопаточной промышленности, ввозившихся раньше из-за границы.[1] В годы Второй пятилетки (1933—1937), в связи с развитием отечественного машиностроения началось широкое обновление станков за счёт советского оборудования.[2] В рамках интернациональной солидарности трудящихся, поддержку в среде зарубежного пролетариата нашла инициатива рабочих завода «Пролетарская свобода», предложивших создать фонд индустриализации СССР.[3]
В предвоенные годы завод получал государственные задания для укрепления обороноспособности страны. Так в начале 1939 года от Главлесбуммаша получено задание по выпуску в III и IV кварталах 1939 года 82-мм сухопутных мин: соответственно 80 и 120 тысяч штук, или 200 тысяч мин за всё II полугодие. До этого завод не имел мобилизационного задания.[4]
Учитывая недостаток в кадрах в годы Великой Отечественной войны работники завода «Пролетарская свобода» поддержали предложение о продлении рабочего дня. Рабочие завода «Пролетарская свобода» и фабрики «Красный Перекоп» стали работать по 11 часов ежедневно. Их примеру последовали коллективы других предприятий, например Шинного завода.[1] Во второе полугодие 1941 года «Пролетарская свобода» выпустила продукции в 1,8-2,5 раза больше, чем в первое (мирное).[4] Кроме того трудовой коллектив завода обратился к работникам Ярославской области с предложением организовать предоктябрьское социалистическое соревнование.[5]
В 1960-е годы на машиностроительных заводах Ярославля наиболее дееспособным и инициативным являлся совет новаторов на заводе «Пролетарская свобода». Руководил им активный общественник слесарь-сборщик Ф. П. Головин. При поддержке партийной и профсоюзной организаций завода совет новаторов обеспечил внедрение в производство около 20 важных предложений, представляющих интерес для многих машиностроительных предприятий.[6]
В 1970-е — 1980-е годы, завод «Пролетарская свобода», являясь головным в объединении станкостроения, выпускает сложное технологическое оборудование для деревообрабатывающей промышленности.[7] Во второй половине 1980-х годов завод «Пролетарская свобода» перешёл к выпуску полуавтоматических и автоматических линий для фанерно-мебельных предприятий.[8]
Продукция
- Оборудование для подготовки сырья
- Линия раскряжевки ЛЦ-60
- Оборудование для лущения шпона
- Линия лущения, рубки и укладки шпона длиной 1300 и 1600 мм ЛУР 14-17.
- Станок лущильный ЛУ 17-10
- Ножницы роторные НР 18-3 для рубки ленты шпона
- Ножницы фанерные НФ 18-3А с промежуточным транспортером длиной 1800 мм
- Вакуумный укладчик шпона ЛУР 14-17
- Устройство выдачи поддонов
- Оборудование для сушки шпона
- Сушилка роликовая газовая СРГ-25МЭ, работающая на топочных газах от теплогенераторов ТГСГ
- Сушилки роликовые СУР-9, СУР-4 и СУР-5
- Сушилка роликовая СРГ-25М с обогревом топочными газами
- Механизмы: загрузочный ПСРГ-10 и разгрузочный ПрСРГ-10 к роликовой сушилке СРГ-25М
- Столы подъемные для подъема и опускания пакетов шпона
- Оборудование для утилизации древесных отходов с возможностью производства тепла
- Теплогенераторы твердотопливные стальные
- Теплогенератор ТГСВ-5.1 с водяным теплоносителем
- Котельное оборудование
- Водогрейный котел на твердом топливе теплопроизводительностью 2.5 МВт
- Оборудование для повышения сортности фанеры и шпона
- Ребросклеивающий станок РС-9А
- Станок шпонопочиночный ПШ-2АМ
- Станки для резки листовых материалов СК-1 и СК-2
- Линия обрезки фанеры по формату ЛОФ 00.00.01
- Гидравлические станции
- Гидравлические станции и запчасти к ним.
Известные рабочие
Примечания
- ↑ 1 2 Генкин Л.Б. Ярославль социалистический: Очерки по истории города, октябрь 1917-1959 гг.. — Ярославль: Ярославское книжное издательство, 1960. — С. 172, 276—364.
- ↑ Тимофеев Н.В. Лес – национальное богатство советского народа. — М.: Лесная промышл., 1967. — Стр.175 — 310 с.
- ↑ Академия общественных наук. Пролетарский интернационализм – боевое знамя Коммунистической партии: сборник статей по вопросам истории КПСС. — М.: Изд-во ВПШ и АОН при ЦК КПСС, 1959. — С. 341—363.
- ↑ 1 2 Анисков В. Т., Хаиров А. Р., Государственный комитет Российской Федерации по высшему образованию. История ВПК России в региональном аспекте: от начала первой до окончания второй мировой войны : на примере Верхневолжья. — Ярославль: Ярославский государственный университет имени П. Г. Демидова, 1996. — С. 74, 122. — 199 с. — ISBN 5-2302-0458-3.
- ↑ Алексеева Н. С. Ярославский обком КПСС. Партийный архив, Государственный архив Ярославской области. Ярославцы в годы Великой Отечественной войны: сборник документов. — Ярославль: Ярославское книжное изд-во, 1960. — С. 99—444.
- ↑ Кащенко А. И. Общественный труд в период строительства коммунизма. — Ярославль: Ярославский государственный педагогический институт имени К. Д. Ушинского, 1966. — С. 62—278.
- ↑ Буланов В. Ярославль: социально-экономический очерк. — Ярославль: Верхне-Волжское книжное изд-во, 1985. — Стр.102 — 221 с.
- ↑ Рутковский М.А., Слепцов Е.Я. Ярославская область на переломе эпох (1985-1998). — Ярославль: ДИА-пресс, 1999. — С. 11. — 127 с.
- ↑ Жилин В. А. КАРАБУЛИН Николай Михайлович // Битва под Москвой. Хроника, факты, люди. — М.: Олма-Пресс, 2001. — Т. 1. — С. 98. — 926 с. — (Архив). — 5000 экз. — ISBN 5-2240-3184-2.
- ↑ История СССР // Институт истории АН СССР. — Изд-во Академии наук СССР, 1969. — Вып. 4–6. — С. 102.
Литература
- Козлов А. Д., Стерин М. И., Суворов Ю. И. Заводу «Пролетарская свобода» 100 лет. — Ярославль: Верхне-Волжское книжное издательство, 1981. — 48 с. — 4000 экз.
Ссылки
|
|
YUCHENGTECH Ручная машина для очистки от сахарного тростника Портативная миниатюрная машина для очистки от сахарного тростника Терки, ножи и слайсеры Очистители для сахарного тростника
YUCHENGTECH Ручная машина для очистки сахарного тростника Портативная мини-машина для очистки сахарного тростника Терки, ножи и слайсеры Очистители- Дом
- Дом и кухня
- Кухня и столовая
- Кухонная утварь и гаджеты
- Терки, ножи и слайсеры
- Тёрки, ножи и слайсеры Пилинговая машина Портативная мини-машина для очистки сахарного тростника
YUCHENGTECH Ручная машина для очистки сахарного тростника Портативная мини-машина для очистки сахарного тростника
YUCHENGTECH Ручная машина для очистки сахарного тростника Мини-портативная машина для очистки сахарного тростника, бесплатная 2-дневная доставка с Prime, интернет-магазин кухонной утвари и гаджетов из большого выбора по низким ценам каждый день.Пилинг-машина Портативная мини-машина для очистки сахарного тростника YUCHENGTECH Ручная очистка сахарного тростника, YUCHENGTECH, YUCHENGTECH Ручная очистка сахарного тростника Мини-портативная машина для очистки сахарного тростника.
YUCHENGTECH Ручная машина для очистки сахарного тростника Портативная мини-машина для очистки сахарного тростника
YUCHENGTECH Ручной очиститель сахарного тростника Мини-портативная машина для очистки сахарного тростника: Кухня и столовая. Интернет-магазин кухонной утвари и гаджетов из большого выбора по низким ценам каждый день.Бесплатная 2-дневная доставка с Prime. Ручная очистка, чистота, здоровье и улучшение съедобности. . Клинок изготовлен из стали, острый, съемный. . Корпус из высокопрочной оцинкованной стали, устойчивый к ржавчине и коррозии. . Встроенная пружина может автоматически регулироваться в зависимости от диаметра трости. . Компактный и портативный, его можно зафиксировать в удобном для использования положении. . Если у вас есть какие-либо вопросы, пожалуйста, свяжитесь с нами, мы сделаем все возможное, чтобы помочь вам .. Описание: Ручной очиститель сахарного тростника – это портативный инструмент для очистки сахарного тростника.Сахарный тростник можно есть сразу после очистки. Этот ручной очиститель сахарного тростника может соскребать только черную внешнюю поверхность сахарного тростника, но не твердую внешнюю оболочку. Характеристика: .1. Регулируемый винт обеспечивает высокую прочность зажима, стабильность и фиксацию в любом положении. .. Высокопрочный корпус из оцинкованной стали, устойчивый к ржавчине и коррозии. Лезвие сделано из стали, острое и съемное … Винт с шестигранной головкой, фиксирующий пружину и лезвие, поэтому машина может автоматически регулироваться в соответствии с диаметром сахарного тростника..Физические параметры. :: .Материал лезвия: сталь .Размер упаковки: ** 7 см. Вес: 1,75 кг. . .
перейти к содержанию
YUCHENGTECH Ручная машина для очистки сахарного тростника Портативная мини-машина для очистки сахарного тростника
Portmeirion Botanic Garden Square Чаша для салата Portmeirion USA 605223, компактный размер, 7 лопастей Мощный ветер Настольный USB-вентилятор DOUHE с регулируемым углом наклона 22 °, охлаждающий вентилятор с питанием от USB для дома Малошумный персональный небольшой вентилятор для офиса и общежития Номинальная скорость вращения Белый 1.Темный цвет шампанского. Флорентийская рамка излишка. Художественная пасхальная снежная рамка в масляной раме. Репродукция оригинальной картины Джорджа Уэсли Беллоуса. Постельное белье для кукол Решетка Minky Cradle Постельное белье Темно-синий / Белый. Мини-листы с наклейками 48 машинок с татуировками для вечеринки по случаю дня рождения Набор для 8 человек включает в себя мешочки с добычей. Прозрачное / латунное золото с белым абажуром 15 x 29,5 x 15 Настольная лампа Jonathan Y JYL2018A. YUCHENGTECH Ручная машина для очистки сахарного тростника Портативная мини-машина для очистки сахарного тростника , Beige Fox Valley Traders 358279-204 Чехол для кресла с откидной спинкой из микрофибры OakRidge Deluxe.Коллекция подушек Jarrah Floral Pillow Springtime, лицензии M-2173 Продукты Marvel Comics Iron Man Comic Cover Magnet C&D Visionary Inc, Cody Foster & Co Monarch Butterfly Glitter Glass Hanging Ornament, 100% длинноволокнистый шелковый наполнитель CUDDLE DREAMS Шелковое одеяло для весны-лета King , 108 дюймов x 90 дюймов. 3D Rose Pretty William Morris Bird и Anemone Chintz Brown полотенце для рук 15 x 22 Многоцветный 3dRose twl_219021_1, YUCHENGTECH Ручная машина для очистки сахарного тростника Портативная мини-машина для очистки сахарного тростника .
YUCHENGTECH Ручная машина для очистки сахарного тростника Портативная мини-машина для очистки сахарного тростника
– Белый покрытый металлический основной ствол с мягкой обивкой, эргономичная ручка Кнопка сброса давления манометра с креплением на основании TwinHead и замок ручки для удобной переноски.✿US: 14 / CN: XL-Бюст : 104 см / 40. 5 Надев ее, вы будете выглядеть красивее. Карта памяти Digi-Chip Micro-SD UHS-1 High Speed for Fire 7 HD8 Kids Fire HD8 32GB, желтый – Extreme Fire HD 10 Kids Tablet PC Fire HD10 Fire 7 Kids. Если вам нужны другие цвета или другой размер для своей майки, свяжитесь с нашей службой поддержки клиентов, и они будут рады помочь вам, 10 латексных шаров с конфетти внутри. Зимний знак двери партии Onederland. Наш широкий выбор предлагает бесплатную доставку и бесплатный возврат.которые действительно ценят все прекрасное и бросают вызов вещам в жизни. Отдел 56 Dazzle Leaf Bird 3.5 Висячий орнамент Многоцветный. Эти подвязки на заказ сделаны очень красиво. Приглашения, напечатанные профессионально, или электронные приглашения можно приобрести в этом списке: 3dRose ph_221496_1 Large Container Freighter на Horizon во время заката Держатель для плитки 5, верхняя часть кольца снабжена 6 зубцами и находится на 7 мм выше пальца. Упакованные и готовые для подарка или хранения для себя, Stanley31214 TimeIt Outdoor Twin Golated с двумя заземленными механическими таймерами Таймеры Stanley, безопасные и подходящие для чувствительных, отслеживаемых вторичных материалов Reprieve с 4-сторонней растяжкой.Набор ручных инструментов для ремонта дома с пластиковым ящиком для инструментов Чемодан для хранения DOWELL Набор инструментов для домовладельца из 14 предметов. ручная работа Let Loose Jewelry: Handmade. Проволочная сетка из нержавеющей стали SS304 Шкафы Проволочная сетка Вентиляционная сетка Окно Экранная сетка для вентиляции воздуха 17. 10-дюймовый HD-дисплей 1024×600 WW&C Цифровая фоторамка Фоновая музыка 1080P Видео USB SD Solt Поддерживаемая фоторамка с датчиком движения, белая. Наша компания занимается производством качественной модной одежды, 8 шт. Torx Star, защищенный от взлома ключ с Т-образной ручкой T10 – T50 High Torque: DIY & Tools, материнская плата Sony PCG-F630.❤️❤️ 【Примечание】 Внимание. Выберите мягкую щетку для волос, очистите поверхность, чтобы удалить поверхностные пятна. Эти перчатки в стиле рукавиц обеспечивают тепло и подвижность во время езды.
YUCHENGTECH Ручная машина для очистки сахарного тростника Портативная мини-машина для очистки сахарного тростникаБесплатная 2-дневная доставка с Prime, Интернет-магазин кухонной утвари и гаджетов из большого ассортимента по низким повседневным ценам.
(PDF) Разработка и определение рабочих параметров машины для очистки личи, сочетающей валки и прижимную ленту
AgriEngineering 2019, 1, 40 565
15.Bochtis, D.D .; Соренсен, C.G.C .; Бусато, П. Достижения в управлении сельскохозяйственной техникой: обзор.
Биосист. Англ. 2014, 126, 69–81.
16. Li, X .; Pan, Z .; Атунгулу, Г.Г .; Чжэн, X .; Wood, D .; Delwiche, M .; МакХью, Т. Очистка помидоров
с использованием новой технологии нагрева инфракрасным излучением. Иннов. Food Sci. Emerg. Technol. 2014, 21, 123–130.
17. Сиддик, М. Тропические и субтропические фрукты: послеуборочная физиология, обработка и упаковка; Джон Уайли и
Сыновья: Хобокен, Нью-Джерси, США, 2012; ISBN 978-1-118-32411-0.
18. Nguyen, X.T .; Бернхардт, Г. Влияние длины подбарабанья и угла подачи на производительность разделения в многоцилиндровой системе обмолота
. Landtechnik 2008, 63, 276–277.
19. Manjunatha, M .; Samuel, D.V.K .; Anurag, R.K .; Гайквад, Н. Разработка и оценка производительности
чесночистки. J. Food. Sci. Technol. 2014, 51, 3083–3093.
20. Chen, H .; Сюй, X .; Инь, Й .; Pan, H .; Бао, X .; Li, S .; Xu, Q. Экспериментальное исследование механических свойств и характеристик отделения кожуры
цитрусового сетчатого бланко с зажатой кожурой при перемещении.Nongye Gongcheng
Xuebao 2017, 33, 25–31.
21. Пан, H .; Wang, Z .; Chen, H .; Liu, J .; Tong, Y .; Ши, X. Разработка и эксперимент на двухвалковой машине для лущения мандарина
. Нунъе Гунчэн Сюэбао 2015, 31, 239–245.
22. Видьярти, С.К .; Эль Машад, H.M .; Хир, Р .; Zhang, R .; Tiwari, R .; Пан, З. Оценка выбранных электрических инфракрасных излучателей
для очистки томатов. Биосист. Англ. 2019, 184, 90–100.
23. Jimoh, M.O.; Олукунле, О. Автоматическая система очистки от кожуры маниоки для повышения продовольственной безопасности
в Нигерии. Нигер. Food J. 2012, 30, 73–79.
24. Purbey, S .; Кумар, К. Инструменты и машины для разработки Litchi. Инструменты и оборудование для развития
садоводства: Керала, Индия, 2009.
25. Вишвакарма, Р.; Nambi, E .; Гупта, Р. Машина для очистки плодов личи. Доступно на сайте:
https://icar.org.in/content/directorate-knowledge-management-agriculture (доступ 1 сентября
2019)
26.CN103445277A-Машина для удаления ветвей Личи-Патенты Google Доступно в Интернете:
https://patents.google.com/patent/CN103445277A/en?inventor=%E5%86%AF%E5%8B%8B%E5%81%A5
(по состоянию на 1 сентября 2019 г.).
27. Хэнань Hiwant International Co., Ltd. Промышленная зона Хайхуан, средняя часть дороги Анлин, Аньян,
Хэнань, Китай. Доступно на сайте:
http://www.hifruitmachine.com/Fruit%20Processing%20Products/lychee-litchi-lichee-longan-rambutan-p
eeling-machine / (по состоянию на 1 сентября 2019 г.).
28. Menzel, C.M .; Симпсон, Д. Рост, цветение и урожайность сортов личи. Sci. Hortic. 1992, 49, 243–254.
29. Xiong, J .; Он, З .; Lin, R .; Liu, Z .; Бу, Р .; Ян, З .; Peng, H .; Zou, X. Технология визуального позиционирования
роботов-сборщиков для динамических скоплений личи с возмущением. Comput. Электрон. Agric. 2018, 151, 226–237.
30. Qing, Y .; Li, C .; Cao, Y .; Zhang, Z .; Ченг, Х. Тестирование и анализ макромеханических параметров лонгана.
Нонъе Цзиси Сюэбао, 2010, 41, 125–134.
31. Wang, F .; Wang, C .; Ян, X. Механические характеристики и анализ методом конечных элементов арбуза. Пер.
Подбородок. Soc. Agric. Англ. 2008, 24, 118–121.
32. Junwei, L .; Юньхай, М .; Jin, T .; Zichao, M .; Lidong, W .; Цзянтао, Ю. Механические свойства и микроструктура
кожуры картофеля. Int. J. Food Prop.2018, 21, 1395–1413.
33. Kunpeng, T .; Shen, C .; Xianwang, L .; Huang, J .; Qiaomin, C .; Бин, З. Механические свойства и моделирование повреждений при сжатии
методом конечных элементов для киви.Int. Agric. Англ. J. 2017, 26, 193–203.
34. Williams, H.A.M .; Jones, M.H .; Nejati, M .; Сибрайт, M.J .; Bell, J .; Penhall, N.D .; Barnett, J.J .; Герцог, доктор медицины;
Scarfe, A.J .; Ahn, H.S .; и другие. Роботизированный сбор плодов киви с использованием машинного зрения, сверточных нейронных сетей
и роботизированных манипуляторов. Биосист. Англ. 2019, 181, 140–156.
35. Singh, K.K .; Боредди, С. Физико-механические свойства апельсиновой цедры и фруктов после сбора урожая. J. Food Eng.
2006, 73, 112–120.
36. CHEN, Y .; LI, J .; WANG, J .; JIANG, Z .; Zou, X .; LIU, W. Тест механических параметров для Litchi и анализ
на его разницу. DEStech Trans. Матер. Sci. Англ. 2017, DOI: 10.12783 / dtmse / ammme2016 / 6880
37. Chen, Y .; Cai, W .; Zou, X .; Сян, Х. Экструзионные механические свойства свежего личи. Нонгье Гунчэн
Сюэбао 2011, 27, 360–364.
38. Chen, Y .; Cai, W .; Zou, X .; Xiang, H .; Лю, Т .; Сюй Ф. Испытание механических свойств и анализ методом конечных элементов
для личи.Nongye Gongcheng Xuebao, 2011, 27, 358–363.
Этот сайт использует файлы cookie для повышения производительности. Если ваш браузер не принимает файлы cookie, вы не можете просматривать этот сайт.
Настройка вашего браузера для приема файлов cookie
Существует множество причин, по которым cookie не может быть установлен правильно. Ниже приведены наиболее частые причины:
- В вашем браузере отключены файлы cookie. Вам необходимо сбросить настройки своего браузера, чтобы он принимал файлы cookie, или чтобы спросить вас, хотите ли вы принимать файлы cookie.
- Ваш браузер спрашивает вас, хотите ли вы принимать файлы cookie, и вы отказались. Чтобы принять файлы cookie с этого сайта, используйте кнопку “Назад” и примите файлы cookie.
- Ваш браузер не поддерживает файлы cookie. Если вы подозреваете это, попробуйте другой браузер.
- Дата на вашем компьютере в прошлом. Если часы вашего компьютера показывают дату до 1 января 1970 г., браузер автоматически забудет файл cookie. Чтобы исправить это, установите правильное время и дату на своем компьютере.
- Вы установили приложение, которое отслеживает или блокирует установку файлов cookie. Вы должны отключить приложение при входе в систему или проконсультироваться с системным администратором.
Почему этому сайту требуются файлы cookie?
Этот сайт использует файлы cookie для повышения производительности, запоминая, что вы вошли в систему, когда переходите со страницы на страницу. Чтобы предоставить доступ без файлов cookie потребует, чтобы сайт создавал новый сеанс для каждой посещаемой страницы, что замедляет работу системы до неприемлемого уровня.
Что сохраняется в файле cookie?
Этот сайт не хранит ничего, кроме автоматически сгенерированного идентификатора сеанса в cookie; никакая другая информация не фиксируется.
Как правило, в cookie-файлах может храниться только информация, которую вы предоставляете, или выбор, который вы делаете при посещении веб-сайта. Например, сайт не может определить ваше имя электронной почты, пока вы не введете его. Разрешение веб-сайту создавать файлы cookie не дает этому или любому другому сайту доступа к остальной части вашего компьютера, и только сайт, который создал файл cookie, может его прочитать.
Краткое руководство по диагностике и лечению пневмонии, инфицированной новым коронавирусом (2019-nCoV) (стандартная версия) | Военно-медицинские исследования
Это руководство было подготовлено в соответствии с методологией и общими правилами разработки рекомендаций ВОЗ и Рекомендациями ВОЗ по быстрым консультациям [1, 2].
2.1 Состав группы по разработке рекомендаций
Эта группа по разработке рекомендаций является многопрофильной и состоит из специалистов в области здравоохранения и методистов.Среди профессионалов здравоохранения были врачи-клиницисты, медсестры, работающие в отделениях респираторной медицины, лихорадочной клиники, критической медицины, неотложной помощи, инфекционных заболеваний, а также эксперты по респираторным инфекционным заболеваниям и руководство больницы. В состав методологов входили специалисты по методологии разработки руководств, систематического обзора и специалисты по поиску литературы.
2.2 Конечный пользователь руководства
Это руководство подходит для непосредственных врачей и медсестер, руководителей больниц и отделений здравоохранения, здоровых жителей сообщества, персонала общественного здравоохранения, соответствующих исследователей и всех лиц, заинтересованных в 2019 г. -nCoV управление.
2.3 Целевая группа рекомендаций
Настоящее руководство предназначено для медицинских работников для борьбы с подозреваемыми случаями инфицирования 2019-nCoV, подтвержденными случаями, инфицированными 2019-nCoV, кластеризованными случаями, инфицированными 2019-nCoV, и теми, кто имеет тесные контакты или подозрительное воздействие на случаи инфицирования 2019-nCoV.
2.4 Исследование конфликта интересов
Устный запрос финансовых интересов соответствующего лица был проведен на первой встрече, когда начиналось это руководство.Соответствующие финансовые и нефинансовые интересы были изучены и раскрыты, а затем оценены на консенсусной конференции, чтобы минимизировать потенциальную предвзятость при разработке рекомендаций. Наконец, у всего персонала, участвующего в подготовке этого руководства, нет конфликта интересов.
2.5 Структурная установка руководства, уточнение тем и охват данного руководства
Это руководство представляет собой быстрое руководство по реагированию на возникающее инфекционное заболевание 2019-nCoV.В связи с острой необходимостью и плотным графиком работы мы не провели широкомасштабного опроса, а провели дискуссионную встречу с врачами первой линии, которые занимались лечением пациентов с инфекциями 2019-nCoV, чтобы окончательно согласовать темы рекомендаций и ключевые вопросы.
2.6 Поиск в литературе и подготовка профилей доказательств
2.6.1 Общие примечания
Учитывая отсутствие прямых доказательств этой недавно выявленной инфекции 2019-nCoV, мы провели поиск и сослались на руководящие принципы, относящиеся к SARS (тяжелая острая респираторная болезнь). Синдром), MERS (ближневосточный респираторный синдром) и грипп.Мы также сослались на рекомендации, которые были недавно выпущены Национальной комиссией здравоохранения Китайской Народной Республики и ВОЗ для 2019-nCoV. Кроме того, у нас есть независимая группа по поиску литературы для поиска доступных косвенных доказательств из систематических обзоров и / или РКИ (рандомизированных контролируемых испытаний), которые были посвящены лечению и / или химиопрофилактике SARS, MERS или других инфекций, вызванных вирусом гриппа.
Если существующие доказательства касаются тем или вопросов, охватываемых руководством, то их качество следует оценить.Если нет доказательств более высокого уровня качества, наша группа рассматривала обсервационные исследования и серии случаев. Из-за ограниченного времени мы не проводили новый систематический обзор. Мы определили релевантную литературу до 20 января 2020 года.
2.6.2 Ресурсы поиска
Мы провели поиск в библиографических базах данных: PubMed, Embase и Cochrane library.
Мы также провели поиск на следующих веб-сайтах: ВОЗ (https://www.who.int/), CDC (Центры по контролю и профилактике заболеваний, https: // www.cdc.gov/), NICE (Национальный институт здравоохранения и клинического совершенства, https://www.nice.org.uk/), Национальная комиссия здравоохранения Китайской Народной Республики (http://www.nhc.gov. cn /) и Национальное управление традиционной китайской медицины (http://www.satcm.gov.cn/).
2.6.3 Сбор и обобщение данных на переднем крае
Поскольку 2019-nCoV является недавно идентифицированным патогеном, ответственным за вспышку пандемического заболевания, нет достаточных доказательств, чтобы раскрыть всю природу этого вируса.В таких ситуациях получение доказательств от экспертов, которые борются с болезнью на передовой, может быть эффективным и основным источником [3].
До 24:00 29 января 2020 года в больнице Чжуннань Уханьского университета было обследовано 11500 человек, из которых 276 были идентифицированы как предполагаемые инфицированные и 170 были диагностированы (в том числе 33 в критическом состоянии) на инфекцию 2019-nCoV. В ходе этого процесса врачи и медсестры накопили ценный опыт в диагностике, лечении и уходе за пациентами, инфицированными 2019-nCoV.Следовательно, этот опыт был оценен, а затем использован как «экспертное свидетельство» для разработки наших рекомендаций. Мы провели интервью и групповые опросы для сбора информации о доказательствах лечения во время заседания группы рекомендаций, чтобы ее можно было интегрировать в панель рекомендаций в сводке результатов (см. Дополнительные файлы 1 и 2). Свидетельства экспертов могут быть запрошены путем описания отчетов о случаях, резюме и отчетов по темам или вопросам по всем делам, которые они ведут.
2.7 Классификация доказательств и рекомендаций
Мы придерживались основных подходов и правил оценки, разработки и оценки рекомендаций (GRADE) [4, 5] и, в частности, рассмотрели доказательства экспертов для оценки качества совокупности доказательств, которые необходимо сделать. рекомендации.
Качество доказательств отражает, в какой степени наша уверенность в оценке эффекта адекватна для поддержки той или иной рекомендации. Уровень доказательств классифицировался как «высокое качество», «среднее качество», «низкое качество» или «очень низкое качество»; Рекомендации были разделены на «сильные» и «слабые».
Сильная рекомендация не всегда означает достаточную эффективность вмешательства. Помимо эффективности вмешательства, формирование рекомендаций основывается на тяжести заболевания, готовности пациента, безопасности и экономических соображениях [4]. См. Таблицы 1 и 2 [4, 6].
Таблица 1 Классификация и описание рекомендации Таблица 2 Правила классификации рекомендаций2.8 Формирование рекомендаций
Перед собраниями доказательства экспертов систематически собирались и предоставлялись членам комиссии.После того, как доказательства были выявлены и оценены, были сформулированы рекомендации, основанные на доказательствах, в ходе личной встречи членов комиссии и дополнены экспертами, участвовавшими в совещании группы.
Доказательства экспертов были высоко оценены при разработке данного руководства. Если в процессе достижения консенсуса доказательства были согласованы более чем 70% клиницистов первичного звена на консенсусной встрече, это считается доказательством высокого качества.
В конкретных рекомендациях мы использовали «следует» или «настоятельно рекомендовать» для сильных рекомендаций; тогда как «предлагать» или «рассматривать» использовались для слабых.
2.9 Составление и публикация руководства
Это руководство было опубликовано одновременно на китайском и английском языках. Из-за нехватки места текущая редакция стандарта не включает описания доказательств. Полная версия будет опубликована в журнале New Medicine (китайское название: Yixue Xinzhi; http://www.jnewmed.com/), том 30 и выпуск 1 2020 [7].
Кобура для правой руки Glock 19
У каждой крупной марки и модели оружия есть кобура, специально разработанная для нее, и только она.Кожаные кобуры доступны в черном или коричневом цвете, как для правшей, так и для левшей. Левая рука Glock внутри кобуры IWB на поясе полностью скрывает ваш пистолет. Кобура спрятана внутри ваших брюк под заправленной рубашкой.
18 декабря 2012 г. · Его можно носить на сильной стороне, крест-накрест или на пояснице. Он изготовлен из мягкой нескользящей замши и усилен седельной кожей премиум-класса для облегчения переноски в кобуру. # 106 доступен для большинства скрытых пистолетов в правой и левой руке.Amazon.com: DeSantis Sof-Tuck Glock 19/23/36 Right Hand Tan …
17680 CrossBreed® LDS 2.0 OWB. GLOCK 19 с ОПТИЧЕСКИМ ПРИЦЕЛОМ и ОСВЕЩЕНИЕМ. Правая рука . Черная корова. Плоский карман темной земли. Эту кобуру также можно использовать с пистолетом без оптического прицела
. Это позволяет сделать кобуру легкой и дает вам идеальный захват, когда вы пытаетесь вытащить или снова положить в кобуру свое огнестрельное оружие. Кобура OWB FLEX подходит как для Glock 19 Gen 5, так и для более старых поколений. Начиная с Glock 19, Glock 19X, Glock 23, Glock 32 и Glock 45 имеют очень похожие верхние направляющие.
Glock 19 Canadian: Начиная с 2017 года в Канаде продается специальный Glock 19 со стволом 106 мм и характерным полым кленовым листом с лазерной гравировкой на правой стороне затвора. Ограничение для огнестрельного оружия ограниченного класса в Канаде – 105-мм ствол.
25 февраля 2020 г. · Glock 19 – Кобура Raven OWB – Правая Рука У меня есть кобура OWB в хорошем состоянии на продажу. Это Призрак Ворона, который продается за 80 долларов. Неважно, думаете ли вы, что можете или …
Blackhawk. Кобура Serpa CQC для Glock 19/23/32 (правая) Номер позиции: 410502BK-R./. Просмотреть еще товары от Blackhawk. /. Состояние: НОВОЕ.
Blackhawk! Кобура SERPA CQC из углеродного волокна для Glock 19/23/32 Right Hand Black… освобождение * Винт регулировки пассивного удерживающего фиксатора * Конструкция Speed-cut для быстрого натягивания, захвата цели и повторной укладки в кобуру * Включает платформу для поясной петли и платформу для весла * Подходит для плеча, Изображение платформ STRIKE, Quick Disconnect и Tactical Holster может не соответствовать цвету или стилю.
Для Glock 22 с TLR-1 (4,5 дюйма баррель), корзиной STX, правой рукой.Safariland 6390-832-131 … ALS Mid-Ride Level I Retention Duty Holster Model 6390 Для Glock 19 с …
Тунец с пониженным содержанием сладкого эспрессо
Chef Nguyễn Ngọc Quyên
Одно из самых продаваемых в марте 2020 года меню кофейной кухни отеля Mövenpick Hanoi теперь снова доступно в течение ограниченного времени, до конца мая. Изюминкой блюда является фирменный вкус эспрессо, красиво подчеркивающий жирный вкус филе тунца. Состав: – Филе тунца: 320 гр, нарезанное на 8 кубиков по 10 гр.– Соевый соус: 8 сл
– Кунжутное масло: 4 сл
– Белое кунжутное масло: 1 ч.
– Авокадо: 2
– Свежий имбирь: 20 гр
– Лайм: 2
– Маленький перец: 1
– Свежий кориандр: 1 пучок
– Тайский зеленый лук: 2
– Творог в сливках: 200 гр
– Перец чили: 4
Пироги из сладкого картофеля
– Сладкий картофель: 400 гр
– Яичный желток: 4 гр
– Сливки: 8 мл
– Соль: ½ чайной ложки.
– Черный перец и рапсовое масло
– Сироп Movenpick Ristretto: 4 стакана
– Сахар: 20 гр
Тунец с добавлением сладкого эспрессо
Метод:
1.С авокадо удалить мякоть, сбрызнуть соком лайма и нарезать мелкими кубиками.
2. Нарезать перец кубиками и добавить к авокадо с мелко нарезанной кориандром, приправить солью и перцем.
3. Замариновать филе тунца с соевым соусом, кунжутным маслом, свежим тертым имбирем и цедрой лайма, сбрызнуть белым кунжутным маслом и мелко нарезанным тайским зеленым луком.
4. Перемешайте творог, чтобы он стал однородным и наполнял стакан, добавьте тартар из авокадо, сверху положите тыкву из тунца, украсьте красным перцем чили и сбрызните сиропом ристретто.
5. Для лепешек очистите сладкий картофель и натрите на мелкой терке, отожмите всю влагу и смешайте картофель с яичным желтком и сливками, приправьте морской солью и перцем.
6. Сформировать небольшие лепешки и обжарить в горячем рапсовом масле до хрустящей корочки.