ТВЕРДОСПЛАВНЫЕ ПЛАСТИНЫ ВК8 ООО “Арматон” ⋆
ТВЕРДОСПЛАВНЫЕ ПЛАСТИНЫ ВК8
Твердосплавные пластины для токарных резцов используются для увеличения производительности работ, которые выполняются посредством металлообрабатывающего оборудования. Подобные вещи позволяют сделать применение резца удобнее, это съемные конструкции, и их при поломке или износе можно будет без труда заменить. Для применения сменных инструментов цельные резцы с режущей частью и державкой не подойдут.
Пластины для отрезных либо расточных резцов производятся на основе разных марок твердых сплавов. Это весьма удобно, поскольку позволит вооружиться большим набором режущих элементов, которые будут обрабатывать заготовки из разных элементов.
А еще применение сменных токарных приспособлений для режущего инструмента можно уверенно назвать выгодным решением с экономической точки зрения, поскольку, если случится поломка или износ, не нужно будет менять весь резец целиком, только лишь его режущую часть. Лучше всего применять инструмент, оснащенный сменными твердосплавными пластинами, тогда, когда требуется автоматизировать технологические процессы. Это особенно важно при мелком и среднесерийном производстве разных изделий.
А еще использование сменных твердосплавных пластин, оснащенных механическим креплением, можно значительно повысить срок эксплуатации державки токарного резца, а также не потребуется затачивать и паять режущую его часть. Кроме того, в условиях применения данного инструмента температура и сила резания может снизиться до 40 процентов. Твердые сплавы обладают такими свойствами, что их можно применять для производства пластин, а с их помощью можно обрабатывать металлы при условии изменения режимов резания.
Сменные твердосплавные пластины, устанавливаемые на токарный резец, классифицируются по некоторым параметрам:
типу инструмента — токарные резцы бывают канавочными, фасонными, отрезными, подрезными, расточными и прочими. Под каждый из перечисленных типов потребуется разная форма профиля, которую формируют на стадии производства пластины для резца;
материалу производства — свойства твердосплавных материалов меняются в зависимости от того, в каком количестве в них присутствуют титан, вольфрам и другие материалы. Сменные пластины могут быть сделаны и на основе керамики, их в таком случае применяют в основном с целью обработки жаропрочных сплавов, а еще они актуальны в случаях, когда требуется сделать непрерывную чистовую или получистовую обработку металлических заготовок;
размеру — в зависимости от размера обрабатываемой заготовки с помощью токарного станка нужно выбирать и твердосплавную пластину с требуемыми геометрическими параметрами. Для токарного резца независимо от его типа подбираются изделия соответствующих параметров;
величине заднего угла — этот параметр определяется по марке изделия, от него зависит, насколько чисто будет обработана металлическая заготовка. И чем больше будет задний угол, тем чище будет выполнена обработка поверхности. Пластины с большими задними углами в основном применяются с целью токарной обработки мягких металлов;
классу точности — в настоящее время производители выпускают пластины 5 таких классов. С их помощью можно обрабатывать изделия с разными допусками в зависимости от геометрических параметров заготовки.
Детали из карбида вольфрама (твердого сплава ВК6 и ВК8 ГОСТ3882)
“Вольфрамовые твердые сплавы – двухфазные спеченные металлокерамические материалы на основе карбида вольфрама на Co и Ni связках, получаемые методами порошковой металлургии. При этом содержание металло-связки меняется в достаточно узких пределах от 3 до 15%. Такие твердые сплавы характеризуются высокими значениями физико-механических показателей, таких как теплопроводность, твердость, модуль упругости, ударная прочность, устойчивость к вибрации и т.д. Твердые сплавы существенно более прочны и менее хрупки, нежели традиционные конструкционные керамики, что обуславливает возможность их работы с значительно большими нагрузками, а также обеспечивает их лучшую технологичность и эксплуатационную устойчивость. Твердые сплавы, выпускаемые компанией “”ХИМПРОМ Технология””, ВКН6,8 и ВКК6,8, соответствуют требованиям технических условий ТУ1592-001-68690281-2011. Существует достаточно большое количество видов твердых сплавов в зависимости от содержания основной (керамической) фазы (WC, TiC, TiCN, их смеси и т.

Вас также могут заинтересовать
Карбид вольфрама является высокоизносостойким материалом, способным работать в агрессивных средах. Свое применение карбид вольфрама нашел в торцовых уплотнениях агрегатов, где присутствует сухое трени
Резцы токарные отрезные с пластинами из твердого сплава, ГОСТ 18885-73. Применяется для отрезки заготовок из прутка и проточки канавок в заготовках на токарных, револьверных станках и станках-автомата
Направляющие из карбида вольфрама и карбида титана Благодаря низкой плотности, высокой износостойкости, устойчивости к окислению и термостойкости, сплавы на основе титана и вольфрама используются в пр
Области применения: • Пары трения (подшипники скольжения) и торцовые уплотнения насосов для перекачки абразивосодержащих и агрессивных жидкостей; • Детали запорной арматуры для газо-
Ножи для деревообработки изготовление, дисковые ножи, роликовые ножи. Ножи из стали и твердых сплавов. Изготовление ножи для деревообработки. Цены и сроки по получении чертежей, эскизов, образцов. Пре
+7 (495) 366-00-24 | |
электронная почта: [email protected] | электронная почта: [email protected] |
![]() В компании Метотехника вы можете купить твердосплавные смеси. Заказ через сайт доступен на странице с ценами. Вы также можете оставить заявку по электронной почте и телефону. Более подробная информация о марках, способах производства и областях применения этих продуктов представлена на этой странице в соответствующих разделах. МаркиВольфрамокобальтовые твердосплавные смеси выпускаются марки ВК. Их основными компонентами являются карбид вольфрама (WC) и кобальт (Co). Карбид обеспечивает твердость и огнеупорность материала, а кобальт служит цементирующим связующим металлом. Еще одной важной группой являются титано-вольфрамовые и титано-танталово-вольфрамовые смеси твердых сплавов, выпускаемые марок ТК и ТТК соответственно. Материалы различаются в зависимости от содержания кобальта. Цифра в конце сорта указывает на его процентный состав. Например, твердый сплав марки ВК8 содержит 8 % кобальта (Со), ВК6 — 6 %, Т30К4 — 4 %, ТТ7К12 — 12 %. Они также включают углерод (C), вольфрам (W), титан (Ti) и тантал (Ta), в зависимости от группы. Химический состав материалов ВК, ТК, ТТК регламентируется техническими условиями 48-19-60-78. ПроизводствоСырьем для производства вольфрамокобальтовой твердосплавной смеси является порошок монокарбида вольфрама (WC) и порошок кобальта (Co). Эти компоненты смешиваются вместе, в результате чего получается твердый сплав в виде порошка. Для изделий марок ТК и ТТК дополнительно применяют порошки монокарбида титана (TiC) и тантала (TaC). Размер частиц, насыпная масса, состояние поставки и механические свойства полуфабрикатов регламентируются техническими условиями 48-19-60-78. ПрименениеСмеси ВК, ТК, ТТК служат сырьем для производства твердых сплавов, поставляемых в виде заготовок и пластин. Например, порошок ВК8 используется для производства одноименного твердого сплава.Методы порошковой металлургии используются для получения полуфабрикатов, описанных выше. Основная технологическая цепочка: формовка -> прессование -> спекание. Твердые сплавы группы ВК активно используются в производстве бурового и режущего инструмента. Из марок ВК8 и ВК6 изготавливают резцы, свёрла, фрезы и другой инструмент, предназначенный для механической обработки заготовок. Твердосплавные плиты марок ВК8, ВК6 применяются также в промышленности. Материалы, относящиеся к группам ТК и ТТК, применяются в основном для изготовления режущего инструмента для различных стадий механической обработки изделий (черновой, получистовой, чистовой токарной, фрезерной, зенкерной и др.).ЦеныДоступные к заказу твердосплавные смеси группы ВК и их цена указаны на странице Стоимость.![]() |
Влияние размера зерна карбида вольфрама в анодном материале ВК8 на формирование слоя легированной стали 35
Реферат
Влияние размера зерна карбида вольфрама в вольфрам-кобальтовом твердом сплаве, исследовано электроискровое напыление (ЭИЛ) стали 35, ее эрозионная стойкость, прирост массы материала подложки и коэффициент электромассопереноса. Показано, что прессуемая шихта с добавками 0,4 % Cr 3 C 2 –0,4% VC Ингибиторы роста зерен и измельчение в атмосфере спирта и аргона при времени измельчения от 20 до 320 мин использовали при получении новых анодных материалов различной структуры, плотности, пористости, прочности на излом, и размер зерна карбида вольфрама. Приведены результаты эрозионной стойкости и применения полученных новых анодных материалов при ЭИЛ стали 35. При проведении кинетических исследований был определен ряд показателей эффективности формирования легированного слоя с учетом полученных значений дополнительной массы катода, времени ЭСД, удельной поверхности 1 см 2 , а также коэффициент электромассообмена при ЭСД исследуемых анодных материалов. Приведены результаты исследований структуры, толщины, состава легированного слоя, жаростойкости и износостойкости покрытия. Выявлено, что среди созданных новых анодных материалов наилучшую стойкость к окислению покрытия после ЭИЛ при выбранных режимах обработки удалось получить при использовании нового нанодисперсного анодного материала WC8%Co–0,4%Cr 3 C 2 –0,4% VC, средний размер зерна 0,8 мкм WC.
ВВЕДЕНИЕ
Покрытия из карбида вольфрама благодаря своим высоким эксплуатационным характеристикам широко используются в поверхностной инженерии для повышения износостойкости металлических деталей, подвергающихся трибологическим нагрузкам [1, 2]. В настоящее время для получения покрытий из карбида вольфрама применяют различные технологии: газопламенное напыление [1–3], лазерную наплавку [4, 5], гальваническое напыление [1, 6], электроискровое напыление (ЭИЛ) [7, 8]. .
Технология электростатического разряда основана на явлении полярного переноса металла от анода к катоду в процессе воздействия многократных микродуговых разрядов. Благодаря высокой скорости охлаждения материала после прекращения разряда образуется покрытие с исключительно мелкозернистой структурой [9]., 10]. Кроме того, электростатический разряд характеризуется слабым тепловым воздействием на подложку и высокой адгезией сформированного слоя. Однако при напылении материала WC–Co на стальной катод происходит обезуглероживание карбида вольфрама при его взаимодействии с расплавом железа в условиях разряда [11–13]. Высокие скорости охлаждения материала после прекращения разряда способствуют образованию аморфной фазы в покрытиях WC–Co [13]. В номенклатуре инструментальных твердых сплавов WC–Co различают среднезернистые, сверхмелкозернистые и ультрамелкозернистые материалы. В работе [5] показано, что уменьшение размера зерна в порошке WC-12Co улучшает механические свойства газопламенного (ГФО) покрытия. В связи с этим в настоящей работе изучено влияние размера зерна электродных материалов WC–8Co на кинетику электроискрового осаждения, а также на структуру, термостойкость и трибологическое поведение покрытий.
МЕТОДИКА И МАТЕРИАЛЫ
Покрытия наносили на поверхность катодных образцов из стали 35 в виде цилиндра диаметром 12 мм и высотой 10 мм. Для испытаний на циклическую термостойкость были изготовлены образцы – кубы с ребром 6 мм. В качестве анодных материалов для электростатического разряда использовались сплавы ВК8: среднезернистые (ВК8), сверхмелкозернистые (ВК8ОМ) и ультрамелкозернистые (ВК8УМ). Электродные материалы (табл. 1) были изготовлены по традиционной технологии порошковой металлургии. Порошки карбида вольфрама крупнозернистые (КГТК, марка ВК3, чистота 99,9%), нанодисперсный карбид вольфрама Hongwu (80–100 нм) и кобальт (Kokkola, чистота 99,9%). При получении электродного материала №. 0, 3 и 4 (табл. 1) в качестве ингибиторов роста зерен использовали порошки карбида хрома в соотношении 0,4 % Cr 3 C 2 (Донецкий завод химических реактивов, чистота 99,9 %) и 0,4 % карбида ванадия. ВК (ЗАО «Вектон», чистота 99,9%). Гранулирование смесей для получения среднезернистых и субмикронных сплавов проводили после смешения с раствором каучука в бензине концентрацией 1 мас. %. Сырье для прессования смешивали и измельчали в планетарной мельнице Retsch PM400 в атмосфере спирта и аргона при 250 мин –1 и время измельчения от 20 до 320 мин. Соотношение масс мелющих тел к обрабатываемому материалу 10 : 1.
Образцы прессовали под давлением 250 МПа. Образцы спекали в трубчатой печи CarboliteSTF в вакууме в течение 1 ч при относительно низкой температуре 1390 °С, что позволило ограничить рост зерен электродных материалов. Для исследования использовались полученные образцы твердых сплавов разного состава. Размер полученных образцов анодных материалов (20 х 6,5 х 5,25 мм) и метод определения прочности соответствовали ИСО 3327-82. Прочность определяли на испытательном прессе ИП-250. В качестве генератора импульсов при формировании легированного слоя (АЛ) методом электроискрового напыления (ЭИЛ) использовалась установка Института материаловедения (ИМЭСД) со следующими режимами обработки: длительность разрядных импульсов t d = 20 мкс, цикл пористости t p = 80%, частота импульсов электрического разряда f = 500 Гц, импульсный ток 180 А при 40 В.
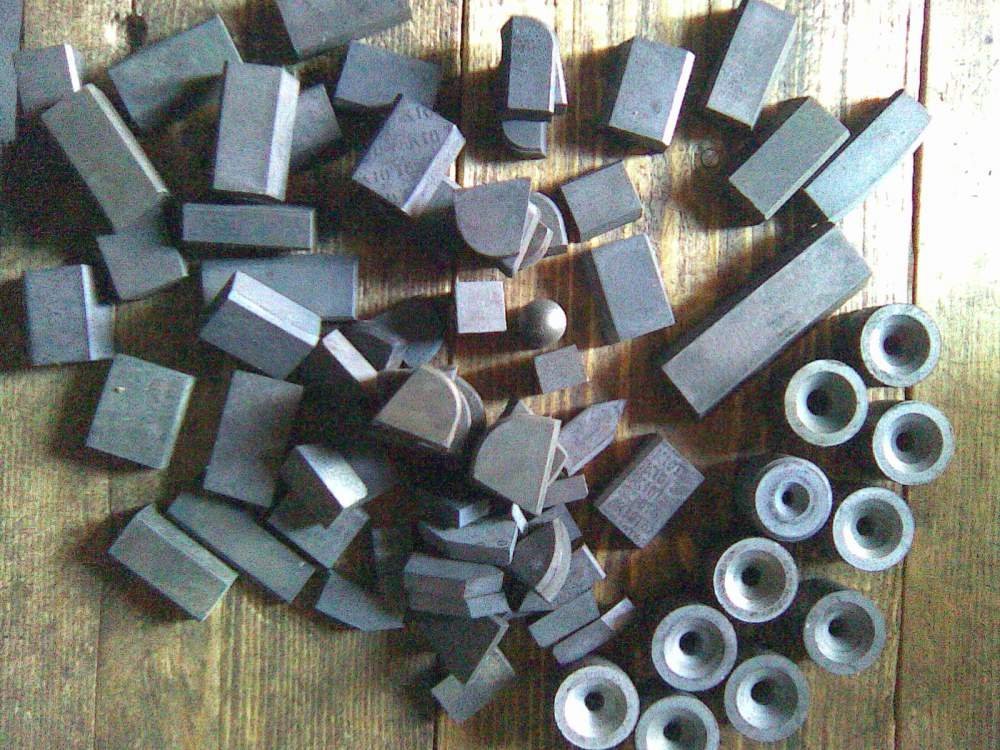
РЕЗУЛЬТАТЫ И ИХ ОБСУЖДЕНИЕ
Общий вид шлифов полученного анодного материала №. 0, 1, 4 и 5 (рис. 1) видно, что карбидная фаза обр. 0 имеет более мелкозернистую структуру (0,18 мкм) с пористостью 2,0% по сравнению с другими, например, №. 1 (1,16 мкм) с пористостью 2,5% и № 1. 5 (со средней зернистостью 1,07 мкм), отличающийся наибольшей плотностью (14,65 г/см 3 ) и наименьшей пористостью.
Рис. 1.Общий вид срезов поверхности полученного анодного материала №№. 0, 1, 3, 5.
Увеличить
На рис. 2 представлены NURBS-кривые кинетики процесса ЭИЛ при t = 5 мин стали 35 при t р / t d = 80/20 с № анодных материалов 0, 1, 2, 3, 4 и 5: суммарная эрозия электрода (ΣΔ c ), суммарный коэффициент усиления катода (ΣΔ c ) и средний суммарный коэффициент электромассопереноса (Σ K t ). Значения эрозии исследуемых анодных материалов достигали значений ΣΔ a (5 мин) = 136–248 г × 10 –4 (рис. 2а). В соответствии с полученным рядом эрозионной стойкости материалов анода (1*): (0) → (1) → (4) → (5) → (3) → (2) № материала анода. 2 и 3 отличаются наибольшей эрозионной стойкостью (ΣΔ а (5 мин) = 136 и 143 г × 10 –4 соответственно). При повышении прочности материалов электродов выше 1100 МПа их эрозия стала уменьшаться (рис. 2г).
NURBS-кривые кинетики процесса ЭИЛ стали 35 с режимами t p / t d = 20/80 с № материала анода. 0, 1, 2, 3, 4, 5: а — полная эрозия анода; (б) общий привес катода; (в) общий коэффициент массообмена; (г) зависимость общей эрозии материала анода от предела прочности.
Увеличить
Все кривые набора массы катода (рис. 2б) при формировании АС относятся к классу кривых Лазаренко [14]. Значения массопереноса для исследуемых анодных материалов при ЭИЛ удельной поверхности 1 см 2 при t ЭСР = 5 мин наблюдались в пределах 36–727 × 10 –4 г. Полученный ряд прироста массы катода для исследуемых материалов анода (2*): (4) → (2) → (3) → (1) → (5) → (0) показал, что выбранные условия ЭСД обеспечивают вес прирост ΣΔ c (5 мин) = 36–84 г × 10 –4 .
При этом был получен следующий ряд средних значений коэффициента массообмена (Σ К t , %) исследуемых анодных материалов (3*): (1) → (2) → (3 ) → (4) → (5) → (0), что имеет низкие значения для выбранного режима ПАЗ (Σ К р = 27–42%).
С учетом полученных значений прироста массы катода, времени t ЭСД , удельной поверхности 1 см 2 , а также коэффициента электромассообмена при ЭИЛ исследуемых анодных материалов и режимов обработки, выявлен ряд γ эфф.ф.АЛ показателя эффективности образования АС [15]:
$${{\gamma }_{{{\text{эф}}{\text {.f}}{\text{.AL}}}}} = \Sigma {{\Delta}_{{\text{c}}}}{{t}_{{{\text{ESD}}} }}\Sigma {{K}_{{\text{t}}}};\,\,{\text{где:}}\,\,\Sigma {{K}_{{\text{t}} }}} = {{\ Sigma {{\ Delta} _ {{\ text {c}}}}} \ mathord {\ left / {\ vphantom {{\ Sigma {{\ Delta} _ {{\ text {c }}}}} {\Sigma {{\Delta}_{{\text{a}}}}}}} \right. \ kern-0em} {\ Sigma {{\ Delta } _ {{\ text {a}}}}}}. $ $
В соответствии с этим рядом индекса эффективности (4*): (4) → (3) → (2) → (5) → (1) → (0) формирование АЛ при использовании режима обработки является лучше всего подходит для анодного материала №. 1 и 0.
На рис. 3 представлены результаты рентгенофазового анализа электроискровых покрытий. Отсюда следует, что состав покрытия №. 0 и 1 преобладают фазы субкарбида вольфрама (W 6 C 2,54 ) и β-карбида вольфрама (WC 1 – x ). Рентгеноструктурный анализ образцов № 0 и 1 показали смещение отражений W 6 C 2,45 в сторону больших углов, т. е. межплоскостные расстояния в решетке этой фазы были меньше по сравнению со штатной картотекой ПДФ-2. На дифрактограммах покрытия №. 4 и 5 наблюдается широкое гало в области углов 2θ = 35°–50° без резких брэгговских отражений. Это свидетельствует о преобладании аморфной фазы в составе покрытий. Рефлексы фазы карбида вольфрама αWC в спектрах образцов не обнаружены. Таким образом, карбид вольфрама при электроискровом переносе на подложку полностью разрушался.
Рентгенограммы покрытий.
Изображение в натуральную величину
Изображения поперечного сечения покрытий образцов №. 0 и 1 в обратно рассеянных электронах (рис. 4а, 4г) показали, что в структуре покрытий, образующихся в результате газовыделения в условиях разряда, наблюдаются поры. На границе АС и подложки продольных трещин не наблюдалось, что может свидетельствовать о хорошей адгезии покрытия к стальной основе. Энергодисперсионный анализ показал равномерное распределение элементов (Fe, W, C, Co) по сечению покрытия (рис. 4б, 4д). Концентрация железа в составе покрытия достигала 30–50 ат. %, что свидетельствует об интенсивном конвективном перемешивании переносимого материала анода со стальной подложкой при ЭИЛ. Размер переходной зоны был небольшим (1,5–3 мкм).
Рис. 4. РЭМ-изображения поперечного сечения покрытия №. (а, в) 0 и (г, е) 1 при увеличениях (а, г) 5000х и (в, е) 20 000х, а также распределение элементов по толщине покрытия, согласно (б , д) данные энергодисперсионного анализа.
Увеличить
В микроструктуре покрытий наблюдаются равноосные кристаллиты, более обогащенные вольфрамом по сравнению с окружающей аморфной матрицей (рис. 4в, 4е). Размер кристаллитов для покрытия нет. 0 составила 0,17 ± 0,04 мкм, что значительно меньше, чем для покрытия № 0. 1 (0,5 ± 0,3 мкм). Средняя толщина покрытий различалась незначительно и составляла 12–15 мкм.
Как известно, аморфные материалы на основе железа характеризуются некоторым повышением физико-химических и эксплуатационных свойств за счет увеличения растворимости легирующих элементов в твердых растворах, дробления структурных составляющих, образования метастабильных кристаллических и аморфных фаз . На рис. 5а представлена кинетика изменения массы образцов с покрытиями и стали 35 при температуре 700°С и выдержке в течение 100 ч. Увеличение массы образцов связано с фиксацией кислорода на поверхности образцов в виде оксида железа в модификации гематита [16]. За 100 ч испытаний образцы с покрытиями окислялись в 3–12 раз меньше, чем непокрытая сталь из-за ограниченного контакта с кислородом. Для образцов №. 4 и 5 с преобладанием аморфной фазы ожидалась повышенная жаростойкость по сравнению с другими образцами. Однако проведенные испытания позволяют сделать вывод, что аморфизация системы Fe–W–C–Co не приводит к повышению жаростойкости. На рис. 5б представлены рентгенограммы поверхности покрытий после испытания на термостойкость. Гематит (Fe 2 O 3 ) преобладал в составе накипи, а магнетит (Fe 3 O 4 ) формировался в прилегающем к покрытию слое за счет затрудненной диффузии кислорода. Наилучшую жаростойкость продемонстрировало покрытие, полученное с использованием ультрамелкозернистого электрода.
Циклическая жаростойкость покрытий из стали 35 при температуре 700°С.
Изображение в натуральную величину
Средняя твердость покрытий колебалась от 6,4 до 9.3 (рис. 6а). Твердость стали 35 составила 2,6 ± 0,6 ГПа. Наибольшей твердостью обладало аморфное покрытие, нанесенное из стандартного твердого сплава ВК8. Средний коэффициент трения покрытий колебался от 0,76 до 0,86 (рис. 6б). Коэффициент трения покрытий был выше, чем у стали 35 (0,73), за счет абразивного износа контртела более твердыми покрытиями. Коэффициент трения покрытий хорошо коррелирует с их твердостью; таким образом, наименее твердого покрытия нет. 4 показал самый низкий коэффициент трения. Несмотря на более высокие коэффициенты трения покрытий WC–Co, скорость их изнашивания была в 5–10 раз ниже по сравнению со сталью 35 без покрытия (рис. 6в). В то же время покрытие, сформированное электродным материалом №. 1 имеет самые низкие значения износа. Высокий уровень шума в случае стали 35 и наименее твердое покрытие отсутствуют. 4 предполагает периодическое отложение и отслоение материала, переносимого между трущимися поверхностями, и может быть связано с окислительным механизмом изнашивания.
(а) Микротвердость, (б) коэффициент трения и (в) скорость изнашивания покрытий по сравнению со сталью 35.
Увеличенное изображение
ВЫВОДЫ ингибиторов роста зерен (0,4 % Cr
3 C 2 и 0,4 % VC) и времени измельчения (40–320 мин), изменение размера зерна карбида вольфрама (0,18–1,16 мкм), плотности (14–14,65 г/см 3 ), пористость (0,0–4,4%), структура и прочность на излом (947–1296 МПа).(2) При ЭСД стали 35 для полученных анодных материалов выявлен ряд эрозионной стойкости, привеса катода, коэффициента массоотдачи и показателя эффективности формирования АС. Показана закономерность повышения эрозионной стойкости электродных материалов с ростом их сопротивления разрушению, которая начинает сказываться при σ ≥ 1100 МПа.
(3) АЛ не имеют четкой границы с подложкой и продольных трещин, что свидетельствует о хорошей его адгезии к стали 35. В АЛ наблюдаются равноосные кристаллиты, размер которых был значительно меньше (0,17 мкм) при использовании ультрамелкозернистого электрода, чем в случае мелкозернистого электрода (0,5 мкм). Средняя толщина покрытий составляла от 12 до 15 мкм.
(4) При 700°С и выдержке в течение 100 ч образцы с покрытиями окислялись в 3–12 раз меньше, чем без покрытия, из-за ограниченного контакта с кислородом. Покрытия с преобладанием кристаллических фаз (W 6 C 2,54 и WC 1 – x ) не уступали по термостойкости аморфным образцам. Наилучшая термостойкость получена при ЭИЛ с ультрамелкозернистым материалом анода.
(5) ЭСД стали 35 с новыми материалами анода повышает ее износостойкость в пять-десять раз, причем самые высокие значения износостойкости были получены при использовании среднезернистого материала анода.
ЛИТЕРАТУРА
Ляшенко Б.А., Подчерняева И.А., Коневцов Л.А., Козырь А.В. и др., Материалогия покрытий титановых сплавов методами физикохимии и элек троискового легирования: монография в 2 гл. (Материалогия покрытий из титановых сплавов методами физико-химии и электроискрового легирования: Монография в 2-х частях), Ч.
Вашиштха, Н., Хатиркар, Р.К., и Сапате, С.Г., Трибологическое поведение напыленных покрытий WC-12Co, WC-10Co-4Cr и Cr3C2-25NiCr HVOF, Tribol. Междунар., 2017, том. 105, с. 55.
Артикул Google Scholar
Комаров П., Йех Д., Ткаченко С., Сламечка К., Дворжак К., Челко Л. Смачиваемость износостойких керамических покрытий WC–Co–Cr производства HVOF: Роль химического состава и шероховатости поверхности, Дж. Терм. Spray Techn., 2021, vol. 30, с. 285.
Артикул Google Scholar
Maurizi Enrici, T., Dedry, O., Boschini, F., Tchuindjang, J.T., и Mertens, A., Микроструктурные и термические характеристики композитных покрытий 316L + WC, полученных лазерной наплавкой, Adv. англ. мат.,
2020, вып.22, с. 2000291.
Артикул Google Scholar
Zhang, J., Lei, J., Gu, Z., Tantai, F., Tian, H., Han, J. и Fang, Y., Влияние содержания WC-12Co на износ и электрохимическую коррозию свойства композиционных покрытий Ni–Cu/WC–12Co, нанесенных методом лазерной наплавки, Surf. Пальто. техн., 2020, вып. 393, с. 125807.
Артикул Google Scholar
Ахмадие С., Расули А. и Хоссейни М.Г. Исследование коррозии и износа композиционных покрытий Ni–W–B/WC, гальванопокрытий методом импульсного осаждения, Доп. англ. мат., 2020, вып. 22, с. 2000426.
Артикул Google Scholar
Ляшенко Б.А., Подчерняева И.А., Коневцов Л.А., Козырь А.В., Коваленко С.В., Каминский А.В.,
(Материалогия покрытий титановыми сплавами методами физико-химии и электроискрового легирования: Монография в 2-х частях), Часть 2: ЭИЛ-покрытие (ESA Coatings), Хабаровск: Тихоокеан. Гос. унив., 2020.
Салмалийан М., Малек Гани Ф. и Эбрахимния М. Влияние параметров процесса электроискрового напыления на покрытие WC–Co на стали h23, Surf. Пальто. техн., 2017, т. 1, с. 321, с. 81.
Артикул Google Scholar
Шафей Х., Салехи М. и Бахрами А. Изготовление, определение микроструктуры и оценка механических свойств Ti/TiB/TiB 2 Композиционные покрытия, нанесенные на сплав Ti 6 Al 4 V методом электроискрового напыления, Ceram. Междунар. , 2020, том. 46, с. 15276.
Артикул Google Scholar
Чжао, Х., Гао, К., Ву, X.Y., Сюй, Б.
, Лу, Ю.Дж. и Чжу, Л.К., Новый метод изготовления композитных покрытий с помощью электроискрового порошкового осаждения с ультразвуковой поддержкой, Керам. Int., 2019, vol. 45, с. 22528.
Артикул Google Scholar
Николенко С.В., Бурков А.А., Дворник М.И., Зайцев А.В., Суй Н.А. Влияние параметров электроискрового разряда на физико-химические характеристики поверхности стали 45 после ЭИЛ электродов на основе WC– 8%Co с добавками карбида хрома, Surf. англ. заявл. Электрохим. , 2019, том. 55, с. 251.
Артикул Google Scholar
Wang, R.J., Qian, Y.Y., and Liu, J., Исследование поведения поверхности раздела покрытия WC92-Co8, полученного электроискровым осаждением, Appl. Серф. науч. , 2005, том. 240, вып. 1–4, с. 42. https://doi.org/10.1016/j.apsusc.2004.05.299
Статья Google Scholar
Замулаева Е.
И., Левашов Е.А., Кудряшов А.Е., Вакаев П.В., Петржик М.И. Электроискровые покрытия, нанесенные на подложку из армко-железа с нано- и микроструктурированными WC-Co-электродами: процесс осаждения, структура и свойства , Прибой. Пальто. техн., 2008, т. 1, с. 202, с. 3715.
Артикул Google Scholar
Верхотуров А.Д., Гордиенко П.С., Достовалов В.А., Коневцов Л.А., Панин Е.С., Достовалов Д.В., Высокоэнергетическое локальное воздействие на вольфрамсодержащие материалы и металлик (высокоэнергетическое локальное воздействие на Вольфрамсодержащие материалы и металлы // Владивосток: Дальневост. Кормили. ун-та, 2012, с. 472.
Иванов В.И. 2. Коневцов Л.А. Методические аспекты применения электроискрового легирования. Часть 2. Разработка методологии исследования, критериев и показателей эффективности, Тех. Сервис Машин, 2020, вып. 141, нет. 4, с. 100.
Артикул Google Scholar
Бурков А.