Методика проверки и испытания токарно-винторезных станков на точность
В статье приводятся методы проверки нормы точности токарных винторезных станков общего назначения с наибольшим диаметром обрабатываемого изделия до 6300 мм и расстоянием между центрами до 20000 мм
Точность установки станка перед испытанием 0,04/1000
Проверка 1. Прямолинейность продольного перемещения суппорта в вертикальной плоскости
Метод проверки
А. На суппорте (ближе к резцедержателю) параллельно направлению его перемещения устанавливается уровень.
Суппорт перемещается в продольном направлении на всю длину хода. Измерения производятся не более чем через 500 мм на станках с длиной хода суппорта до 6000 мм и не более чем через 1000 мм на станках с большей длиной хода суппорта.
Б. Для станков с длиной хода суппорта свыше 6000 мм проверка может производиться с помощью сообщающихся сосудов, один из которых укрепляется на суппорте, другой – рядом со станком.
Допускаемые отклонения:
а) 0,02 мм на 1000 мм длины хода суппорта;
б) На всей длине хода суппорта:
- 0,04 мм – для длины хода до 2000 мм
- 0,06 мм – для длины хода до 4000 мм
- 0,08 мм – для длины хода до 8000 мм
- 0,10 мм – для длины хода до 12000 мм
- 0,12 мм – для длины хода до 16000 мм
- 0,16 мм – для длины хода до 20000 мм
Допускается только выпуклость направляющих станка.
Проверка 2. Перекосы суппорта при его продольном перемещении
Метод проверки
На суппорте (ближе к резцедержателю) перпендикулярно направлению его перемещения устанавливается уровень.
Суппорт перемещается в продольном направлении на всю длину хода.
Измерения производятся не более чем через 500 мм, на станках с длиной хода суппорта до 6000 мм и не более чем через 1000 мм на станках с большей длиной хода суппорта.
При проверке резцедержатель сдвинут к оси центров станка.
Допускаемые отклонения:
а) На 1000 мм длины хода суппорта:
- 0,02/1000 для станков с наибольшим диаметром обработки до 800 мм
- 0,03/1000 для станков с наибольшим диаметром обработки св. 800 мм
б) На всей длине хода суппорта:
для станков с наибольшим диаметром обработки до 800 мм
- 0,03/1000 – для длины хода до 2 000 мм
- 0,04/1000 – для длины хода до 4000 мм
- 0,06/1000 – для длины хода до 8000 мм
- 0,08/1000 – для длины хода до 12000 мм
- 0,10/1000 – для длины хода до 20000 мм
для станков с наибольшим диаметром обработки до 1600 мм:
- 0,04/1000 – для длины хода до 2000 мм
- 0,05/1000 – для длины хода до 4000 мм
- 0,08/1000 – для длины хода до 8000 мм
- 0,10/1000 – для длины хода до 20000 мм
для станков с наибольшим диаметром обработки свыше 1600 мм:
- 0,10/1000 – для длины хода до 16000 мм
- 0,12/1000 – для длины хода до 20000 мм
Проверка 3.

Метод проверки
А. При длине хода суппорта до 3000 мм проверка производится с помощью цилиндрической оправки, закрепляемой между центрами передней и задней бабок, и индикатора.
На суппорте устанавливается индикатор так, чтобы его измерительный стержень касался боковой образующей оправки. Показания индикатора по концам оправки должны быть одинаковыми (это достигается соответствующей установкой задней бабки).
Б. При длине хода суппорта свыше 3000 мм проверка производится с помощью микроскопа, укрепленного на суппорте, и струны, натянутой вдоль направляющих станины.
Ось объектива микроскопа располагается вертикально. Пересечение нитей окулярной пластинки совмещается с боковой образующей струны в начале и в конце хода суппорта.
После достижения указанных условий суппорт перемещается в продольном направлении на всю длину хода.
При проверке резцедержатель сдвинут к оси центров станка.
Погрешность определяется ординатой отклонения траектории от исходной прямой.
Допускаемые отклонения:
а) 0,02 мм на 1000 мм длины хода суппорта;
б) на всей длине хода суппорта:
- 0,03 мм – для длины хода до 2000 мм
- 0,04 мм – для длины хода до 4000 мм
- 0,05 мм – для длины хода до 8000 мм
- 0,06 мм – для длины хода до 12000 мм
- 0,08 мм – для длины хода до 16000 мм
- 0,10 мм – для длины хода до 20000 мм
При перемещении суппорт может иметь отклонение только к оси центров станка
Проверка 4. Параллельность направляющих задней бабки направлению продольного перемещения суппорта
Метод проверки
На суппорте устанавливается индикатор так, чтобы его измерительный стержень касался направляющей задней бабки.
Проверка производится поочередно по каждой направляющей задней бабки – при использовании одного индикатора или по всем направляющим одновременно – при использовании набора индикаторов.
Измерения производятся в плоскостях, перпендикулярных соответствующим направляющим задней бабки.
Суппорт перемещается в продольном направлении на всю длину направляющих задней бабки.
Допускаемые отклонения:
1. Для вертикальных направляющих:
а) 0,03 мм на 1000 мм длины хода суппорта;
б) на всей длине хода суппорта.
- 0,04 мм – для длины хода до 2000 мм
- 0,05 мм – для длины хода до 4000 мм
- 0,06 мм – для длины хода до 8000 мм
- 0,07 мм – для длины хода до 12000 мм
- 0,08 мм – для длины хода до 16000 мм
- 0,10 мм – для длины хода до 20000 мм
2. Для горизонтальных и наклонных направляющих:
а) 0,02 мм на 1000 мм длины хода суппорта;
б) на всей длине хода суппорта:
- 0,025 мм – для длины хода до 2000 мм
- 0,03 мм – для длины хода до 4000 мм
- 0,04 мм – для длины хода до 8000 мм
- 0,05 мм – для длины хода до 12000 мм
- 0,06 мм – для длины хода до 16000 мм
- 0,07 мм – для длины хода до 20000 мм
Проверка 5.

Метод проверки
На станке устанавливается индикатор так, чтобы его измерительный стержень касался центрирующей шейки шпинделя и был перпендикулярен к образующей.
Шпиндель приводят во вращение.
Допускаемые отклонения:
- 0,010 мм – для станков с наибольшим диаметром обработки до 400 мм
- 0,015 мм – для станков с наибольшим диаметром обработки до 800 мм
- 0,020 мм – для станков с наибольшим диаметром обработки до 1600 мм
- 0,030 мм – для станков с наибольшим диаметром обработки до 3200 мм
- 0,040 мм – для станков с наибольшим диаметром обработки до 6300 мм
Примечание Проверка не распространяется на токарные станки с несъемными планшайбами.
Проверка 6. Радиальное биение оси отверстия шпинделя передней бабки
Метод проверки
В отверстие шпинделя передней бабки плотно вставляется цилиндрическая оправка.
На станке устанавливается индикатор так, чтобы его измерительный стержень касался поверхности оправки.
Шпиндель приводят во вращение.
Измерения производятся у торца шпинделя и на расстоянии l=300 мм от него.
Допускаемые отклонения:
а) При измерении у торца шпинделя:
- 0,010 мм – для станков с наибольшим диаметром обработки до 400 мм
- 0,015 мм – для станков с наибольшим диаметром обработки до 800 мм
- 0,020 мм – для станков с наибольшим диаметром обработки до 1600 мм
- 0,030 мм – для станков с наибольшим диаметром обработки до 3200 мм
- 0,040 мм – для станков с наибольшим диаметром обработки до 6300 мм
б) При измерении на расстоянии l=300 мм от торца шпинделя:
- 0,020 мм – для станков с наибольшим диаметром обработки до 400 мм
- 0,025 мм – для станков с наибольшим диаметром обработки до 800 мм
- 0,030 мм – для станков с наибольшим диаметром обработки до 1600 мм
- 0,050 мм – для станков с наибольшим диаметром обработки до 3200 мм
- 0,060 мм – для станков с наибольшим диаметром обработки до 6300 мм
Проверка 7.

Метод проверки
В отверстие шпинделя передней бабки вставляется короткая оправка, торцовая поверхность которой перпендикулярна к ее оси.
На станке устанавливается индикатор так, чтобы его измерительный стержень касался торца оправки у его центра или поверхности шарика, вставленного в центровое отверстие оправки (в этом случае измерительный стержень индикатора плоский).
Шпиндель приводят во вращение.
Проверка производится при затянутых упорных подшипниках.
Допускаемые отклонения:
Допускаемые отклонения:
- 0,010 мм – для станков с наибольшим диаметром обработки до 400 мм
- 0,015 мм – для станков с наибольшим диаметром обработки до 800 мм
- 0,020 мм – для станков с наибольшим диаметром обработки до 1600 мм
- 0,030 мм – для станков с наибольшим диаметром обработки до 3200 мм
- 0,040 мм – для станков с наибольшим диаметром обработки до 6300 мм
Проверка 8.

Метод проверки
На станке устанавливается индикатор так, чтобы его измерительный стержень касался торцовой поверхности буртика шпинделя передней бабки на возможно большем расстоянии от центра.
Шпиндель приводят во вращение.Измерения производятся не менее чем в двух диаметрально противоположных точках одного диаметра (индикатор переставляется).
Погрешность определяется как наибольшая величина показаний индикатора.
Проверка производится при затянутых упорных подшипниках.
Допускаемые отклонения:
Допускаемые отклонения:
- 0,020 мм – для станков с наибольшим диаметром обработки до 400 мм
- 0,025 мм – для станков с наибольшим диаметром обработки до 800 мм
- 0,030 мм – для станков с наибольшим диаметром обработки до 1600 мм
- 0,040 мм – для станков с наибольшим диаметром обработки до 3200 мм
- 0,050 мм – для станков с наибольшим диаметром обработки до 6300 мм
Примечание. Проверка не распространяется на токарные станки с несъемными планшайбами.
Проверка 9. Параллельность оси шпинделя передней бабки направлению продольного перемещения суппорта
Метод проверки
В отверстие шпинделя передней бабки плотно вставляется цилиндрическая оправка.
На суппорте устанавливается индикатор так, чтобы его измерительный стержень касался поверхности оправки:
а) по ее верхней образующей;
б) по ее боковой образующей. Суппорт перемещается вдоль станины.
В каждом разделе проверки измерение производится по двум диаметрально противоположным образующим (при повороте шпинделя на 180°).
Погрешность определяется средней арифметической результатов обоих измерений в данной плоскости.
Допускаемые отклонения:
а) При измерении в вертикальной плоскости:
- 0,030 мм на длине 300 мм – для станков с наибольшим диаметром об работки до 800 мм
- 0,050 мм на длине 300 мм – для станков с наибольшим диаметром об работки до 1600 мм
- 0,060 мм на длине 300 мм – для станков с наибольшим диаметром обработки до 3200 мм
- 0,080 мм на длине 300 мм – для станков с наибольшим диаметром обработки до 6300 мм
б) При измерении в горизонтальной плоскости:
- 0,012 мм на длине 300 мм – для станков с наибольшим диаметром обработки до 400 мм
- 0,015 мм на длине 300 мм – для станков с наибольшим диаметром обработки до 800 мм
- 0,020 мм на длине 300 мм – для станков с наибольшим диаметром обработки до 1600 мм
- 0,025 мм на длине 300 мм – для станков с наибольшим диаметром обработки до 3200 мм
- 0,060 мм на длине 300 мм – для станков с наибольшим диаметром обработки до 6300 мм
Свободный конец оправки может отклоняться только вверх и в сторону резца переднего суппорта.
Проверка 10. Параллельность направления перемещения салазок суппорта оси шпинделя передней бабки
Метод проверки
В отверстие шпинделя передней бабки плотно вставляется цилиндрическая оправка
На салазках суппорта устанавливается индикатор так, чтобы его измерительный стержень касался поверхности оправки по ее боковой образующей.
Поворотная часть суппорта устанавливается в таком положении, чтобы при передвижении салазок показания индикатора по концам оправки были одинаковы. После достижения этого условия индикатор переставляется так, чтобы его измерительный стержень касался поверхности оправки по ее верхней образующей
Салазки суппорта перемещаются вдоль верхних направляющих на всю длину хода.
Допускаемые отклонения:
- 0,03 мм на длине хода салазок до 100 мм
- 0,04 мм на длине хода салазок до 300 мм
- 0,05 мм на длине хода салазок до 500 мм
Проверка 11.

- вращающегося центра, вмонтированного в пиноль;
- вращающегося шпинделя с планшайбой.
Метод проверки
В центровое отверстие задней бабки плотно вставляется цилиндрическая оправка.
На станке устанавливается индикатор так, чтобы его измерительный стержень касался поверхности оправки
Оправка приводится во вращение.
Измерение производится у торца шпинделя (пиноли) и на расстоянии l=300 мм от него.
Допускаемые отклонения:
а) При измерении у торца пиноли
- 0,02 мм – для станков с наибольшим диаметром обработки до 1600 мм
- 0,03 мм – для станков с наибольшим диаметром обработки до 3200 мм
- 0,04 мм – для станков с наибольшим диаметром обработки до 6300 мм
б) При измерении на расстоянии l=300 мм от торца пиноли:
- 0,03 мм – для станков с наибольшим диаметром обработки до 1600 мм
- 0,05 мм – для станков с наибольшим диаметром обработки до 3200 мм
- 0,06 мм – для станков с наибольшим диаметром обработки до 6300 мм
Проверка 12.

Метод проверки
В отверстие шпинделя задней бабки (пиноли) плотно вставляется цилиндрическая оправка.
На суппорте устанавливается индикатор так, чтобы его измерительный стержень касался поверхности оправки:
а) по ее верхней образующей;
б) по ее боковой образующей. Суппорт перемещается вдоль станины.
В каждом разделе проверки измерение отклонения производится по двум диаметрально противоположным образующим (для чего оправка переставляется в отверстии пиноли, а в случае вращающейся пиноли – поворачивается на 180°).
Погрешность определяется средней арифметической результатов обоих измерений в данной плоскости.
Допускаемые отклонения:
- 0,03 мм на длине 300 мм – для станков с наибольшим диаметром обработки до 800 мм
- 0,04 мм на длине 300 мм – для станков с наибольшим диаметром обработки до 1600 мм
- 0,05 мм на длине 300 мм – для станков с наибольшим диаметром обработки до 3200 мм
- 0,06 мм на длине 300 мм – для станков с наибольшим диаметром обработки до 6300 мм
Свободный конец оправки может отклоняться только вверх и в сторону резца переднего суппорта
Проверка 13.

Метод проверки
Пиноль вдвигается в заднюю бабку и зажимается.
На суппорте устанавливается индикатор так, чтобы его измерительный стержень касался поверхности пиноли в точках, расположенных на ее верхней образующей и на ее боковой образующей.
Пиноль освобождается, выдвигается на половину максимального выдвижения и снова зажимается.
Суппорт перемещается в продольном направлении так, чтобы измерительный стержень индикатора снова коснулся образующей пиноли в той же точке, что и при первоначальной установке.
Погрешность определяется алгебраической разностью показаний индикатора.
Допускаемые отклонения:
а) При измерении в вертикальной плоскости:
- 0,03 мм на длине 100 мм – для станков с наибольшим диаметром обработки до 800 мм
- 0,04 мм на длине 100 мм – для станков с наибольшим диаметром обработки до 1600 мм
- 0,06 мм на длине 300 мм – для станков с наибольшим диаметром обработки до 3200 мм
- 0,08 мм на длине 300 мм – для станков с наибольшим диаметром обработки до 6300 мм
б) При измерении в горизонтальной плоскости:
- 0,01 мм на длине 100 мм – для станков с наибольшим диаметром обработки до 400 мм
- 0,012 мм на длине 100 мм – для станков с наибольшим диаметром обработки до 800 мм
- 0,015 мм на длине 100 мм – для станков с наибольшим диаметром обработки до 1600 мм
- 0,03 мм на длине 300 мм – для станков с наибольшим диаметром обработки до 3200 мм
- 0,04 мм на длине 300 мм – для станков с наибольшим диаметром обработки до 6300 мм
При выдвижении конец пиноли может отклоняться только вверх и в сторону резца переднего суппорта.
Проверка 14. Расположение осей отверстий шпинделя передней бабки и пиноли на одинаковой высоте над направляющими станины для суппорта
Метод проверки
1. Задняя бабка с полностью вдвинутой пинолью устанавливается примерно на 1/4 наибольшего расстояния между центрами.
В отверстие шпинделя передней бабки и пиноли плотно вставляются оправки, имеющие на конце цилиндрические шейки одинакового диаметра.
На суппорте устанавливается индикатор так, чтобы его измерительный стержень касался поверхности шейки одной из оправок у ее верх ней образующей.
Верхняя часть суппорта перемещается в поперечном направлений вперед и назад для определения наибольшего показания индикатора. Затем, без изменения положения индикатора на суппорте, такое же измерение производится по шейке второй оправки.
Погрешность определяется алгебраической разностью наибольших показаний индикатора в обоих измерениях
2. Для станков с длиной хода суппорта до 6000 мм проверку можно производить следующим методом.
Между центрами передней и задней бабок зажимается цилиндрическая оправка, длина которой приблизительно равна удвоенной длине каретки.
На суппорте устанавливается индикатор так, чтобы его измерительный стержень касался поверхности оправки по ее верхней образующей.
Верхняя часть суппорта перемещается в поперечном направлении вперед и назад для определения наибольшего показания индикатора.
Измерения производятся у обоих концов оправки, приблизительно на одинаковых расстояниях от центра.
Погрешность определяется алгебраической разностью наибольших показаний индикатора в обоих измерениях.
Допускаемые отклонения:
- 0,06 мм – для станков с наибольшим диаметром обработки до 400 мм
- 0,10 мм – для станков с наибольшим диаметром обработки до 800 мм
- 0,16 мм – для станков с наибольшим диаметром обработки до 1600 мм
- 0,25 мм – для станков с наибольшим диаметром обработки до 3200 мм
- 0,40 мм – для станков с наибольшим диаметром обработки до 6300 мм
Ось отверстия пиноли может быть только выше оси отверстия шпинделя передней бабки.
Проверка 15. Параллельность продольного перемещения заднего суппорта продольному перемещению суппорта
Метод проверки
На заднем суппорте устанавливается индикатор так, чтобы его измерительный стержень касался вертикальной продольной грани жесткого упора, закрепленного на переднем суппорте с внутренней стороны.
Передний и задний суппорты одновременно перемещаются в про дольном направлении на всю длину хода заднего суппорта.
Допускаемые отклонения:
а) 0,02 мм на 1000 мм длины хода суппортов;
б) на всей длине хода суппортов:
- 0,03 мм – для длины хода до 2000 мм
- 0,04 мм – для длины хода до 4000 мм
- 0,05 мм – для длины хода до 8000 мм
- 0,06 мм – для длины хода до 12000 мм
Проверка 16. Осевое биение ходового винта
Метод проверки
Индикатор устанавливается так, чтобы его измерительный стержень касался торца винта у его центра или поверхности шарика, вставленного в центровое отверстие винта (в этом случае измерительный стержень индикатора плоский).
Винт, нагруженный в осевом направлении, приводится во вращение.
Проверка производится как при правом, так и при левом вращении винта (при соответствующих направлениях осевой нагрузки, создаваемой рабочим давлением между винтом и гайкой при продольном перемещении суппорта).
Допускаемые отклонения:
- 0,010 мм – для станков с наибольшим диаметром обработки до 400 мм
- 0,015 мм – для станков с наибольшим диаметром обработки до 800 мм
- 0,020 мм – для станков с наибольшим диаметром обработки до 1600 мм
- 0,025 мм – для станков с наибольшим диаметром обработки до 3200 мм
- 0,030 мм – для станков с наибольшим диаметром обработки до 6300 мм
Проверка 17. Точность передаточной цепи от шпинделя к ходовому винту без участия коробки подач (см. примеч. 2)
Метод проверки
Между центрами передней и задней бабок укрепляется эталонный винт с точной гайкой, плотно навернутой или снабженной устройством для выбирания люфта.
Гайка закрепляется так, чтобы она могла только перемещаться вдоль винта, но не поворачиваться.
На каретке устанавливается индикатор так, чтобы измерительный стержень упирался в торец гайки. Ходовому винту сообщается вращение от шпинделя с передачей, равной отношению шага эталонного винта к шагу ходового винта.
Накопленная ошибка определяется как наибольшая алгебраическая разность показаний индикатора между любыми двумя точками, расположенными по резьбе эталонного винта в пределах заданной длины 100 и 300 мм
Допускается непосредственное касание измерительного стержня индикатора боковой стороны профиля резьбы эталонного винта.
Допускаемые отклонения:
а) Накопленная погрешность передаточной цепи при проверке эта лонным винтом:
- 0,03 мм на длине 100 мм – для станков с наибольшим диаметром обработки до 400 мм
- 0,035 мм на длине 100 мм – для станков с наибольшим диаметром обработки до 800 мм
- 0,04 мм на длине 100 мм – для станков с наибольшим диаметром обработки до 1600 мм
- 0,05 мм на длине 100 мм – для станков с наибольшим диаметром обработки до 3200 мм
- 0,06 мм на длине 100 мм – для станков с наибольшим диаметром обработки до 6300 мм
- 0,04 мм на длине 300 мм – для станков с наибольшим диаметром обработки до 400 мм
- 0,05 мм на длине 300 мм – для станков с наибольшим диаметром обработки до 800 мм
- 0,06 мм на длине 300 мм – для станков с наибольшим диаметром обработки до 1600 мм
- 0,07 мм на длине 300 мм – для станков с наибольшим диаметром обработки до 3200 мм
- 0,08 мм на длине 300 мм – для станков с наибольшим диаметром обработки до 6300 мм
б) Накопленная ошибка шага при проверке нарезанной резьбы:
- 0,035 мм на длине 100 мм – для станков с наибольшим диаметром обработки до 400 мм
- 0,040 мм на длине 100 мм – для станков с наибольшим диаметром обработки до 800 мм
- 0,050 мм на длине 100 мм – для станков с наибольшим диаметром обработки до 1600 мм
- 0,060 мм на длине 100 мм – для станков с наибольшим диаметром обработки до 3200 мм
- 0,070 мм на длине 100 мм – для станков с наибольшим диаметром обработки до 6300 мм
- 0,050 мм на длине 300 мм – для станков с наибольшим диаметром обработки до 400 мм
- 0,060 мм на длине 300 мм – для станков с наибольшим диаметром обработки до 800 мм
- 0,070 мм на длине 300 мм – для станков с наибольшим диаметром обработки до 1600 мм
- 0,080 мм на длине 300 мм – для станков с наибольшим диаметром обработки до 3200 мм
- 0,100 мм на длине 300 мм – для станков с наибольшим диаметром обработки до 6300 мм
Примечания.
1. При отсутствии эталонного винта с гайкой проверка может быть заменена проверкой накопленной ошибки шага резьбы, нарезанной на станке. На стальном валике, диаметр которого примерно равен диаметру ходового винта, нарезается однозаходная трапецеидальная резьба с шагом, близким к шагу ходового винта станка. Шаг нарезанной резьбы проверяется с помощью специального прибора.
2. В случае невозможности прямого соединения (через гитару) шпинделя и ходового винта, проверка производится при участии коробки передач. Допуски при этом на 25% больше указанных.
Проверка 18. Проверка станка на точность обработки. Проверяется правильность геометрической формы наружной цилиндрической поверхности образца после его чистовой обработки на станке (отсутствие: а – овальности, б – конусности).
Метод проверки
Стальной или чугунный валик (или планшайба для станков с наибольшим диаметром обрабатываемого изделия свыше 800 мм) обрабатывается при закреплении в патроне или в коническом, отверстии шпинделя (без задней бабки). Диаметр валика (планшайбы) должен быть не менее 1/8 наибольшего диаметра обрабатываемого изделия и не более 300 мм – для станков с наибольшим диаметром обрабатываемого изделия свыше 1600 мм.
Длина образца должна быть равна трем его диаметрам, но не более 500 мм.
После чистовой обточки образец измеряется пассаметром или микрометром.
Примечание.
При использовании в качестве образца планшайбы необходимо предусмотреть отверстие для ее облегчения.
Допускаемые отклонения:
а) При проверке овальности:
- 0,010 мм на длине 100 мм – для станков с наибольшим диаметром обработки до 400 мм
- 0,015 мм на длине 300 мм – для станков с наибольшим диаметром обработки до 800 мм
- 0,020 мм на длине 300 мм – для станков с наибольшим диаметром обработки до 1600 мм
- 0,030 мм на длине 300 мм – для станков с наибольшим диаметром обработки до 3200 мм
- 0,040 мм на длине 300 мм – для станков с наибольшим диаметром обработки до 6300 мм
б) При проверке конусности:
- 0,010 мм на длине 100 мм – для станков с наибольшим диаметром обработки до 400 мм
- 0,030 мм на длине 300 мм – для станков с наибольшим диаметром обработки до 800 мм
- 0,040 мм на длине 300 мм – для станков с наибольшим диаметром обработки до 1600 мм
- 0,050 мм на длине 300 мм – для станков с наибольшим диаметром обработки до 3200 мм
- 0,060 мм на длине 300 мм – для станков с наибольшим диаметром обработки до 6300 мм
Проверка 19.
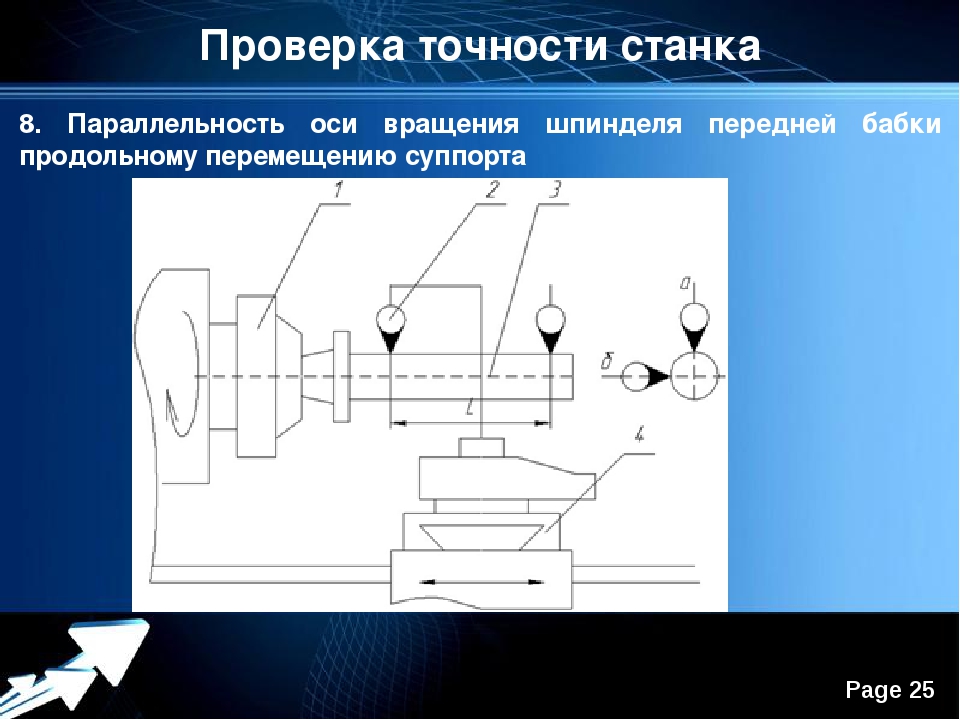
Метод проверки
У стальной или чугунной планшайбы диаметром не менее 1/2 наибольшего диаметра обрабатываемого изделия не более 1000 мм – для станков с наибольшим диаметром обрабатываемого изделия свыше 1600 мм обтачивается торцовая поверхность.
Допускается обточка не всей торцовой поверхности, а отдельных концентричных поясков – не менее трех у периферии, в середине и у центра.
Проверка производится одним из следующих методов:
1. К поверхности планшайбы или к двум установленным у ее периферии калиброванным плиткам одинаковой высоты проверочной гранью прикладывается линейка.
Щупом и плитками измеряется просвет между гранью линейки и обработанной поверхностью
2. На суппорте станка устанавливается индикатор так, чтобы его измерительный стержень касался проверяемой поверхности.
Верхняя часть суппорта перемещается в поперечном направлении на длину, равную диаметру образца.
Погрешность определяется половиной разности показаний индикатора.
Допускаемые отклонения:
- 0,015 мм – на диаметре образца 200 мм
- 0,020 мм – на диаметре образца 300 мм
- 0,025 мм – на диаметре образца 400 мм
- 0,030 мм – на диаметре образца 500 мм
- 0,040 мм – на диаметре образца 600 мм
- 0,050 мм – на диаметре образца 700 мм
- 0,060 мм – на диаметре образца 800 мм
- 0,070 мм – на диаметре образца 900 мм
- 0,080 мм – на диаметре образца 1000 мм
Допускается только вогнутость обтачиваемой поверхности образца. Примечание. Приведенные выше нормы точности – по ГОСТ 42-56.
- Полторацкий Н.Г. Приемка металлорежущих станков, ВнешТоргИздат, 1968
- Батов В.П. Токарные станки, 1978
- Схиртладзе А.Г., Новиков В.Ю. Технологическое оборудование машиностроительных производств, 1980
- Тепинкичиев В.К. Металлорежущие станки, 1973
- Чернов Н.Н. Металлорежущие станки, 1988
Список литературы:
Читайте также: Точность станка. Испытания металлорежущих станков на точность
Полезные ссылки по теме
Каталог справочник токарных станков
Паспорта и руководства токарных станков
Проверка токарного станка на точность
При проверке токарного станка на точность в основном проверяют направляющие станины, биение шпинделя и ходовой винт. [c.240]На рис. 382 показаны некоторые схемы проверки токарного станка на точность. Шпиндели проверяют на осевое и радиальное биение при помош.и [c.458]
На заводе-изготовителе станок получает акт о приемке после прохождения проверки на точность. Такие проверки проводятся также после среднего и капитального ремонтов станка. Нормы точности каждого типа станка указаны в ГОСТ 42—56, которым руководствуются при проверке станков на точность. Ниже приведены основные проверки токарного станка на точность. Проверка радиального биения центрирующей шейки шпинделя передней бабки (рис. 202, а). Допускаемое биение для станков с наибольшим диаметром обрабатываемой заготовки 400 мм составляет 0,015 мм. Проверку осуществляют индикатором, установленным на направляющих станины. Измерительный штифт индикатора должен касаться центрирующей шейки, шпиндель вращается со скоростью 10—20 об мин. [c.138]
При проверке токарного станка на точность контролируют. направляющие станины, биение шпинделя и зазор ходового винта. [c.65]
Нарисуйте схемы, поясняющие основные методы проверки токарного станка на точность. [c.72]
ОСНОВНЫЕ ПРОВЕРКИ ТОКАРНОГО СТАНКА НА ТОЧНОСТЬ [c.108]
Ниже приведены основные проверки токарного станка на точность. [c.108]
Проверка токарного станка на точность [c.13]
ПРОВЕРКА ТОКАРНОГО СТАНКА НА ТОЧНОСТЬ [c.13]
Проверка токарных станков на точность (методы проверки и нормы точности для станков наиболее распространенных габаритов) [c.14]
Рис, 214, Проверка токарного станка на геометрическую точность [c.303]
Методы проверки этих параметров могут быть хорошо показаны на примере методов проверки токарного станка по ГОСТ 42-40, который предусматривает также проверку станка по точности обработки детали. Ниже для примера приводим выдержку характерных технических условий и методов их проверки. [c.625]
Проверка токарно-карусельных станков на точность [c.76]
ПРОВЕРКА ТОКАРНО-ВИНТОРЕЗНОГО СТАНКА НА ТОЧНОСТЬ [c.238]
Испытание станка на точность. Как и всякие другие металлорежущие станки, токарно-револьверные станки подлежат испытанию на точность при приемке их на заводе-изготовителе. Результаты проверки по всем предусмотренным параметрам заносятся в паспорт, который является частью технической документации. [c.151]
Для этого при проверке токарного станка в работе на точность геометрической формы цилиндрической поверхности обрабатывают цилиндрический образец с 2—3 поясками. Обеспечение плоскостности торца контролируется обработкой диска. После обработки замеряются размеры полученных деталей. Допускаемые погрешности диаметра в поперечном сечении и величина неплоскостности приводятся в табл. 154. [c.265]
При испытании станка на точность, во-первых, проверяют точность работы отдельных механизмов или точность изготовления элементов станка безотносительно к другим его узлам и элементам. Сюда относится точность вращения (биение) шпинделей, прямолинейность или плоскостность направляющих или поверхностей столов, прямолинейность перемещения суппорта или стола, точность ходового винта станка и др. Во-вторых, проверяют правильность взаимного положения и движения узлов и элементов станка. К этим проверкам относится параллельность или перпендикулярность основных направляющих или поверхностей столов и осей шпинделей, например параллельность оси шпинделя токарного станка и направляющих суппорта или перпендикулярность оси шпинделя координатно-расточного станка плоскости его стола. Сюда же относятся соосность или параллельность шпинделей, например параллельность шпинделя изделия и шлифовального шпинделя во внутришлифовальных станках или соосность шпинделя токарного станка и пиноли задней бабки. [c.378]
Специальные приборы применяются для определения суммарной погрешности отдельных механизмов станка, непосредственно влияющих на точность обработки. Такими устройствами пользуются для проверки механизмов цепи деления, механизмов для осуществления точных конечных перемещений и т. п. На фиг. 2 приведён прибор системы Д. И. Писарева для определения суммарной ошибки винторезной цепи токарного станка. [c.670]
Карта проверки на точность Токарные станки общего назначения (нормы по ГОСТ 42-40) [c.710]
В заключение следует отметить, что опытная проверка использования инструкции, проведенная на 12 ленинградских заводах (свыше, чем на 40 автоматах, револьверных и токарных станках), вскрыла неудовлетворительное качество капитального и, особенно, среднего ремонта станков. Около 45% отремонтированных станков по технологической точности оказались не удовлетворительными, а, в ряде случаев, эта точность после ремонта понизилась . Нами признавался результат ремонта удовлетворительным, если рассеяние (5) линейных размеров уменьшилось не менее чем на 25%, а отклонения формы и расположения (. 1) — на 40% и более. [c.346]
Проверка суммарной ошибки шага ходовых винтов 3 и 4-го классов может производиться на токарных станках, имеющих ходовой винт 1 или 2-го класса точности (рис. 63, е). Проверяемый ходовой винт 5 с навернутыми на него двумя гайками 2 а 3, между которыми поставлена распорная пружина 8, устанавливается в центрах станка. Гайки от проворота удерживаются сухарями 6 державки 7, закрепленной в суппорте станка. В державке закреплены два индикатора 1 я 4, которые своими мерительными наконечниками упираются в торцы гаек 2 я 3. При пуске станка синхронно вращаются ходовой винт станка и измеряемый винт, гайки с державкой перемещаются. Отставание или опережение гаек от суппорта фиксируется индикаторами. При изменении направления вращения винтов индикатор 1 измеряет суммарную ошибку шага винта по левой стороне профиля, а индикатор 4 — по правой стороне профиля. [c.125]
Одной из задач ремонтной службы является сокращение простоев оборудования в ремонте. Поэтому мастер участка должен следить, чтобы проверка оборудования на точность, осмотры, промывка и смена масла выполнялись в нерабочее время. При малом ремонте допускается простой оборудования в пределах 0,25, при среднем ремонте — 0,6 и при капитальном — до 1 рабочего дня на каждую единицу ремонтосложности. Так, время простоя токарно-револьверного станка (12-я группа ремонтосложности) в ремонте не должно превышать при малом ремонте— 3, при среднем —7,2 дня и при капитальном — 12 дней. Однако ввиду недостаточной технической и материальной подготовки и неудовлетворительной организации ремонтных работ оборудование нередко выходит из строя на значительно большее время, что нарушает бесперебойность осуществления производственного процесса на участке. [c.30]
Естественно, что первой задачей обеспечения прочности проектируемой конструкции является получение гарантии против ее разрушения при действии на нее определенных внешних сил. Однако в большинстве случаев приходится считаться не только с опасностью разрушения, но и с величиной деформаций и их характером. Чрезмерные деформации могут совершенно изменить условия работы конструкции и исключить возможность выполнения ею своего назначения в полной мере. Так, например, при большой деформации суппорта токарного станка невозможно обеспечить необходимую точность обработки детали, вытачиваемой на этом станке. Большие деформации конструкций моста делают невозможным пропуск нагрузки с нормальной скоростью, в результате чего приходится ограничивать скорость движения по мосту. Таким образом, вопрос о проверке прочности следует рассматривать в более широком смысле, понимая под его решением обеспечение не только прочности против разрушения, но и определенной величины и характера деформаций. Для этого, очевидно, необходимо знать не только обстоятельства, связанные с разрушением тел, но и иметь представление о всем процессе деформирования. [c.12]
Установка в патронах. Проверка новых патронов (табл. 33) производится на токарных станках, отвечающих весьма жестким требованиям точности, при зажиме закаленных шлифованных контрольных оправок и колец. Погрешности установки заготовок в патронах в цеховых условиях значительно больше, так как они опре- [c.53]
Должен знать устройство и правила проверки на точность универсальных токарных станков правила управления крупными станками, обслуживаемыми совместно с токарем более высокой квалификации условную сигнализацию устройство и условия применения универсальных и специальных приспособлений геометрию и правила заточки режущего инструмента, изготовленного из инструментальной стали или оснащенного пластинками твердого сплава назначение и способ применения точных контрольно-измерительных инструментов и приборов допуски и посадки, классы точности и чистоты обработки основные свойства обрабатываемых материалов. [c.320]
Индикаторы предназначены для проверки на точность узлов токарного станка, установки предварительно обработанных деталей, проверки биения, овальности, конусности цилиндрических поверхностей. В сочетании с нутромерами, глубиномерами и другими инструментами они используются для измерения внутренних и наружных размеров, параллельности, плоскостности и т. д. [c.105]
Поверхность крышки насоса восстанавливают шлифованием на плоскошлифовальном станке. Износ в корпусе гнезда под шестерни устраняют обработкой в специальном приспособлении на токарном станке. Вначале обрабатывают внутреннюю поверхность на глубину не более 2 мм, а затем подрезают торцовую поверхность, обеспечивая заданную по техническим условиям глубину гнезда. Проверка точности обработки производится индикаторным устройством. [c.230]
Токарно-револьверные станки с преселективным гидравлическим управлением представляют сложную конструкцию, поэтому к обслуживающему персоналу — рабочим-револьверщикам, наладчикам — предъявляют повышенные требования. Станки подвергаются периодической проверке на точность в соответствии с ГОСТом 17—59. Срок службы станка зависит от качественной смазки и заполнения ею гидравлической системы. Масло не должно образовывать осадки, которые загрязняют маслопроводную систему и вызывают коррозию на деталях гидросистемы. Для смазки и заполнения гидросистемы применяется масло индустриальное 20 ГОСТ 1707—51. В процессе работы станка возможно, что некоторые его механизмы теряют первоначальную наладочную точность, поэтому получаемые детали в процессе обработки не соответствуют требованиям точности, предъявляемым к ним. Потеря станком первоначальной наладочной точности может быть из-за выхода из строя некоторых механизмов, износа деталей или некачественной наладки станка. [c.118]
Сдача комплекта по нормам точности, устранение дефектов. Для прецизионных станков после испытания шпиндельного комплекта и проверки норм точности производится разборка корпуса шпиндельного комплекта, т. е. вынимаются валы и шпиндель, производится контроль всех элементов (проверяется наличие задиров и трещин, величина пятна контакта и т. д.), а также промывка всех деталей и корпуса шпиндельного узла сборка шпиндельного комплекта, обкатка и окончательная сдача по нормам точности. Точность шпиндельного комплекта токарного станка в наибольшей степени зависит от правильной сборки и точности регулировки шпиндельных подшипников, от точности изготовления ответственных деталей, от точности балансировки основных деталей как отдельно, так и в сборе их с другими деталями. Поэтому на первом этапе необходимо оценить точность ответственных деталей шпиндельного комплекта и точность шпиндельных подшипников. [c.253]
При испытании на точность токарного станка общего назначения проверке согласно ГОСТу 42—56 подлежат следующие параметры прямолинейность продольного перемещения суппорта в горизонтальной плоскости правильность расположения осей отверстий шпинделя передней бабки и пиноли на одинаковой высоте над направляющими станины для суппорта величина радиального биения центрирующей шейки и оси отверстия шпинделя передней бабки параллельность оси отверстия шпинделя передней бабки направлению продольного перемещения суппорта и ряд других. [c.246]
Приспособление своим конусным хвостовиком или через переходную конусную втулку закрепляют в конусном отверстии шпинделя. Индикатор устанавливают на поперечные салазки и подводят к одному из концов линейки приспособления. При медленном вращении шпинделя (от руки) замечают максимальное отклонение стрелки. С помощью винтов устраняют биение образующей линейки. Этим устанавливают ее перпендикулярно оси вращения шпинделя с точностью 5 мкм и создают базу для проверки расположения различных узлов станка. Затем поперечные салазки перемещают к противоположному концу приспособления и засекают максимальное отклонение стрелки индикатора при медленном вращении шпинделя (от руки). Разность показаний индикатора на обоих концах линейки соответствует величине перпендикулярности направления движения салазок суппорта к оси шпинделя на длине линейки, что характеризует плоскостность проточки торца на диаметре, в два раза превышающем длину линейки. Такая проверка обычно заменяет трудоемкую проверку плоскости методом обработки торца на токарном станке и др [c.44]
Под наладкой токарно-револьверного станка понимается ряд мероприятий, выполняемых для того, чтобы на станке можно было обрабатывать заданные заготовки с требуемой чистотой, точностью и производительностью. В наладку станка на выполнение заданной работы входит установка закрепляющего обрабатываемую заготовку устройства (патрона, оправки и т. п.) установка державок для закрепления обрабатывающих инструментов, установка режущих инструментов установка упоров для обрабатываемого пруткового материала и режущих инструментов установка рукояток коробки скоростей и коробки подач для получения соответствующих требуемой скорости и требуемой подачи смазка станка перед его пуском подвод смазочно-охлаждающей жидкости сразу после начала резания выполнение двух-трех деталей и проверка их по соответствующим калибрам и шаблонам. [c.108]
Проверка параллельности оси шпинделя передней бабки направлению продольного перемещения суппорта (рис. 202, в). Допускаемое отклонение в вертикальной плоскости 0,030 М.Н, а в горизонтальной плоскости 0,015 мм на длине 300 мм. В отверстие шпинделя плотно вставляют точную закаленную и шлифованную цилиндрическую оправку, а на суппорте устанавливают индикатор так, чтобы его измерительный штифт касался поверхности оправки. Суппорт перемещают вдоль станины. Для токарных станков предусмотрено 18—25 различных проверок. Эти проверки производятся ОТ К. Токарю приходится проверять станок только в случаях появления брака деталей без технологических причин, Ему нужно убедиться, не является ли причиной брака неточность станка. Иногда токарю нужно проверить, может ли станок обеспечить заданную в чертеже детали точность. Б этих случаях проверка производится как при приемке станка, но [c.138]
При проверке токарных станков определяют точность вращения шпинделя (радиальное и осевое биение) (рис. 18.2). У зубо-и резьбообрабатывающих станков проверяют кинематическую точность. Для этого кинематометром контролируют согласованность движений (постоянство отношений скоростей) конечных звеньев винторезной или другой цепи. Предусмотрена комплексная проверка станка на точность обработки. На рис. 18.3 приведена схема кинематической проверки цепи обката зубофрезерного станка кинематометром КН-7У. Прибор имеет фотодатчик /, закрепляемый на столе станка, магнитоэлектрический датчик,установленный на шпинделе фрезы, электронный делитель 3 для настройки прибора на передаточные отношения, фазометр 4 и самописец 5. Датчики 1 II 2 преобразуют углы поворота фрезы и стола в электрические импульсы. [c.413]
Для токарных станков предусмотрено 25 различных проверок. Эти проверки производятся отделом технического контроля (ОТК). Токарь проверяет станок на точность только в случаях появления брака деталей, когда нужно убедичьси, нс является ли пртикоЯ брака неточность станка. [c.108]
Наилучшие результаты выверки длинных составных станин в горизонтальной и вертикальной плоскости могут быть достигнуты при помощи оптических методов измерения (зрител ной трубой с коллиматором или автоколлиматором). Технически достижимая точность измерения–0,02 мм на 1000 мм длины. Одна из принципиальных схем оптической проверки показана на фиг. 8. При выверке станины токарного станка подвижный элемент оптической системы размещают на подвижном мостике, скользящем по направляющим станины. [c.406]
Для проверки правильности решения поставленной задачи система была исследована на электронной модели МНБ-1. Исследования показали, что применение инвариантного до е регулятора повышает точность работы ССПУ токарным станком примерно на 50%. [c.159]
Токарь 5-г о разряда. Обработка деталей средней сложности по 2-му и 3-му классам точности на токарных станках различных моделей. Обтачивание и растачивание цилиндрических, конических и эксцентрических поверхностей. Нарезание наружных и внутренних остроугольных прямоугольных и трапецоидаль-ных однозаходных резьб. Глубокое сверление и чистовая обработка отверстий. Обработка точных фасонных выпуклых Т1 вогнутых поверхностей с применением шаблонов и приспособлений. Установление наивыгоднейшего режима резания, сообразуясь с инструментом и обрабатываемым материалом или по технологической карте. Подсчет и подбор шестёрен для нарезки резьбы и обточки конусов. Правильное применение режущего и мерительного инструмента, проверка правильности показаний мерительного инструмента. Заправка и заточка режущего инструмента средней сложности по шаблонам и угломеру. Выполнение работ по чертежам и эскизам средней сложности. Пользование паспортом станка и таблицами для нарезания резьбы. Определение причин ненормальной работы станка и предупреждение брака. Устранение мелких неисправностей станка и его регулировка, не требующие разборки. [c.101]
Стальная поковка стержня шатуна поступает на разметочную плиту для проверки ее размеров и разметки центров на торцах. Затем заготовку зацентровывают и передают на токарный станок для обтачивания средней цилиндрической части стержня и всей поверхности вращения верхней головки и подошвы, а также для подрезания поверхности Ь подошвы стержня. После обработки на токарном станке стержень снова размечают для обработки плоскостей е верхней головки и плоскостей I нижней части шатуна. Эти плоскости обрабатывают на фрезерном или строгальном станке, после чего, в зависимости от размера детали, характера производства и предъявляемых требований в отношении точности, тем или ЯНЫ1М способом (на сверлильном или расточном станке по разметке [c.215]
Рассмотрим в качестве примера повышение точности геометрической формы валов в продольном сечении при обработке деталей на универсальном токарном станке 1А62, оснащенном САУ упругими перемещениями путем регулирования величины продольной подачи. Как было установлено экспериментальными исследованиями, при обработке на указанном станке резцом с главным углом в плане ф = 45° между эквивалентной силой Рд и радиальной составляющей Ру силы резания существует пропорциональная зависимость. В связи с этим изменение величины упругого перемещения по программе осуществлялось посредством изменения силы Ру. Для расчета программы сначала нужно обработать одну деталь с Ру = onst, причем для получения наивысшей производительности обработку первой детали следует производить с Ру шах = onst, где величина Ру ах выбирается из расчета прочности звеньев системы СПИД с проверкой по мощности привода станка. Чтобы эта деталь не попала в брак, у нее на второй проход оставляется припуск, равный 0,2—0,3 мм. [c.236]
Эксплуатационные качества токарных патронов характеризуются точностью, жесткостью, прочностью и износостойкостью. Проверка эксплуатационных качеств стаг1дартных патронов проводится по ГОСТу 1654—47, а нормализованных — по заводским нормалям или по аналогии со стандартными. Для револьверных станков и автоматов используют цанговые патроны. Размеры цанг стандартизованы (ГОСТ 2876—45). Цанговые патроны применяют только для калиброванного материала. Усилия зажима в патронах приведены в табл. 49. Полые заготовки для обработки наружной поверхности, после того как обработана внутренняя, устанавливают на оправки (табл. 50). Рабочие схемы обточки наружных гладких, ступенчатых, конических, сферических и фасонных поверхностей приведены в табл. 51. [c.587]
4. Исследования и разработка методов и средств диагностики автоматизированного технологического оборудования и металлорежущих станков с ЧПУ.
4. Исследования и разработка методов и средств диагностики автоматизированного технологического оборудования и металлорежущих станков с ЧПУ.Широкое применение компьютеров, методов, средств неразрушающего контроля и технической диагностики, развитого программного обеспечения позволило перейти к решению задач нового вида, связанных с мониторингом и прогнозированием технического состояния механизмов, узлов и систем металлорежущих станков разного вида. Для этого в ИМАШ применяются компьютеризированные приборные комплексы, оснащенные датчиками, специальным программным обеспечением, включающим алгоритмы искусственного интеллекта, средствами автоматического сбора и обработки информации. В ряде случаев такие комплексы включают интеллектуальные датчики и телемеханические средства управления процессом диагностирования объекта, в том числе и с помощью радиоаппаратуры.
Исследования различного автоматического оборудования проводились на предприятиях станкостроительной, автомобильной, оборонной, судостроительной, приборостроительной и других отраслях промышленности. Эти исследования включали неразрушающий контроль и диагностику по параметрам: жесткостным, движения, временным, точности, температуре, а также вибродиагностику и виброустойчивость при резании, квалиметрическую и экологическую диагностику.
Диагностировались одно- и многошпиндельные токарные автоматы, станки с ЧПУ, обрабатывающие центры, агрегатные станки и автоматические линии разного назначения: сборочные, сварочные, литейные, упаковочного оборудования и промышленные роботы.
Исследование и диагностирование оборудования проводились на всех этапах жизненного цикла: при проектировании, моделировании и расчете, при стендовых испытаниях, при эксплуатации в производственных условиях, при модернизации, до и после ремонта.
На основании проведенных исследований были разработаны методики диагностирования станков и программы, в которых содержится большое количество основных дефектов узлов станков и инструмента, представляющих потенциальную опасность отказов этого оборудования.
Использование методов диагностирования и аппаратно-программных средств показано на примере методики ИМАШ для диагностирования шпиндельных узлов станков. Эта методика предназначена для диагностирования шпиндельных узлов с опорами на подшипниках качения, которые применяются в конструкциях станков разного назначения: обрабатывающих центров, агрегатных расточных, фрезерных и т.д. среднего типоразмера.
Отличительной особенностью методики ИМАШ от зарубежных и отечественных методических разработок (компании Брюль и Къер, SKF CMAK 300-SL, Диамех-2000, ВИЭМ и другие) является комплексный подход к диагностике, основанный на контроле и анализе всех основные параметров ШУ; использование эвристических интеллектуальных алгоритмов и программ на основе «деревьев отказов», раскрывающих причинно-следственные связи физических явлений и отказов; оценка качества изготовления, сборки и ремонта ШУ на основе обобщенного квалиметрического показателя, представляющего свертку количественных оценок каждого диагностического параметра шпиндельного узла.
Процедуры контроля диагностических параметров шпиндельных узлов, которые совместно с методами расчета и диагностирования составляют комплексную методику, позволяющую разработать технологию диагностирования для каждого конкретного шпиндельного узла с учетом его конструктивных особенностей и назначения.
Разработанный в ИМАШ комплексный подход к диагностированию реализован в виде методики, состоящей из набора автоматизированных процедур. Каждая процедура включает в себя контроль диагностических параметров, их методы расчета и диагностирования. В настоящее время этот инструментарий позволяет диагностировать шпиндельные узлы с опорами на подшипниках качения, которые широко применяются в конструкциях обрабатывающих центров, агрегатных, расточных, фрезерных и других станках среднего типоразмера. Комплексная методика ИМАШ позволяет разработать технологию диагностирования для каждого конкретного ШУ с учетом его конструктивных особенностей и назначения; причем диагностирование с использованием данной методики может проводиться и на этапе изготовления и ремонта шпиндельного узла, и на этапе его эксплуатации.
Перечень контролируемых диагностических параметров, охватываемых методикой ИМАШ, приведен на Рис. 4.1.
Рис. 4.1 – Диагностические параметры шпиндельного узла
Для исследования и разработки процедур контроля диагностических параметров шпиндельного узла изготовлен испытательный стенд, состоящий из стендовой установки (в виде малогабаритного токарного станка) (Рис. 4.2) и аппаратно-программного комплекса.
Рис. 4.2 – Стендовая установка
Рис. 4.3 – Блок-схема аппаратной части комплекса: 1 – плата элементов схемы аналогового датчика, 2 – блок питания аналоговых датчиков, 3 – источник питания, 4 – аналого-цифровой преобразователь, 5 – персональный компьютер, 6 – принтер, 7 – конвертор USB, 8 – электронные блоки цифровых датчиков.
Основой аппаратной части аппаратно-программного комплекса является система сбора данных ССД-01 ИМАШ с набором датчиков и измерительных приборов (Рис. 4.4), вторичных блоков преобразования сигналов и портативным компьютером (Рис. 4.3). Все датчики через блоки-преобразователи (АЦП) с USB-интерфейсом подключены к компьютеру, оснащенному комплектом специализированных программных средств.
Особенностью аппаратной части комплекса является возможность использования датчиков разного вида – аналоговых, цифровых и интеллектуальных с интерфейсом USB.
Комплект программ условно делится на две части: одна из них предназначена для предварительной обработки поступающих с датчиков сигналов, другая – обеспечивает диагностику ШУ на основе необходимых расчетных процедур. Комплекс программ написан на языках С++ и VBA, а его программный интерфейс создавался исходя из удобства работы пользователя-инженера.
Рис. 4.4 – Измерительные приборы и датчики
Далее представлены примеры автоматизированных процедур для измерения диагностических параметров ШУ.
Измерение радиального биения шпинделя
В самоцентрирующийся трехкулачковый патрон зажимается деталь-заготовка с небольшим вылетом на длину 50-60 мм и обтачивается для подготовки базовой поверхности контроля осевого биения, т.е. получается очищенная от биения базовая поверхность.
Рис.4.5 – Схема измерения биения шпинделя
Рис.4.6 – Измерение биения шпинделя
После измерения микроперемещений шпинделя за один оборот строится “График биения” (Рис. 4.7).
Рис. 4.7 – Радиальное биение шпиндельного узла
Можно провести несколько аналогичных экспериментов, и получить обобщенную картину биения шпиндельного узла (Рис. 4.8). На графике показаны значения биения шпинделя при пяти оборотах.
Рис.4.8 – График биения шпинделя при 5-ти оборотах
Измерение температуры шпиндельного узла
Температура измеряется с помощью ручного прибора AR37 в той области, которую подсвечивает встроенная в данном приборе лазерная указка (Рис. 4.9). Измерения проводятся при холостом вращении и под осевой нагрузкой в зоне передней опоры шпинделя.
Рис. 4.9 – Измерение температуры передней опоры шпиндельного узла
По полученным с помощью периодически выполненных измерений данным строится график температурной характеристики шпиндельного узла (Рис. 4.10).
Рис. 4.10 – Температурная характеристика ШУ
1- перегрев; 2, 3 – допустимый нагрев
Измерение жесткостных параметров шпинделя
Рис. 4.11 – Схема измерения жесткостных параметров шпинделя
Сила нагружения ШУ создается с помощью рычага и набора тарированных грузов и контролируется с помощью датчика силы ДСТ5.2 с цифровым табло PSF-2R2. Смещение фланца шпинделя измеряется датчиком М-022-02. (Рис. 4.12).
Рис. 4.12 – Измерение жесткостных параметров шпинделя
По полученным данным строится график смещения шпинделя в зависимости от приложенной силы и рассчитывается податливость ШУ (Рис. 4.13).
Рис.4.13 – График смещения шпинделя при нагружении радиальной силой
Полученные данные сравниваются с значениями, рассчитанными с помощью программы «Податливость шпиндельного узла», которая позволяет проводить диагностические проверки и оценивать состояние шпиндельного узла по параметрам податливость/жесткость.
Измерение вибрации на холостом ходуРис. 4.14 – Схема измерения вибрации
Схема размещения датчиков при измерении параметров вибрации показана на Рис. 4.14 Датчик виброускорения ВД06А устанавливается на верхнюю часть корпуса шпиндельного узла в контрольной точке у передней опоры и подключается к виброанализатору ВИБРАН-2.1, который подсоединяется к компьютеру через USB-интерфейс (Рис. 4.15).
Аналогичным образом проводится измерение параметров вибрации у задней опоры шпинделя.
Рис. 4.15 – Измерение вибрации на холостом ходу
Обработанные программой данные представляются в виде графиков временного сигнала и частотного спектра (Рис. 4.16 и Рис. 4.17).
Рис. 4. 16 – График временного сигнала вибрации
Рис. 4. 17 – График частотного спектра
Измерение вибрации шпиндельного узла под нагрузкой
Внешний вид установки показан на Рис. 4.18. Схемы измерения вибрации шпиндельного узла под нагрузкой представлена на Рис. 4.19.
При измерениях в шпиндель устанавливается вращающийся центр. Датчик виброускорения ВД06А устанавливается на верхнюю часть корпуса у передней опоры шпиндельного узла и подключается к виброанализатору ВИБРАН-2.1. Виброанализатор подключается к компьютеру через разъем USB.
При нагружении радиальная сила создается с помощью механизма поперечной подачи 4 каретки станка (Рис. 4.19а). Датчик силы устанавливается с помощью специальной оснастки в резцедержку каретки.
При нагружении шпинделя осевой силой датчик силы устанавливается между зажимным приспособлением (задней бабкой) 4 стенда и вращающимся центром 5, зажимается, передавая заданную осевую силу на вращающийся шпиндель (Рис. Рис. 4.19б).
Рис. 4.18 – Измерение вибрации шпиндельного узла под нагрузкой
Схемы измерение уровня вибрации ШУ при нагружении радиальной и осевой силой представлены на рис. 4.19 (а,б).
Рис. 4.19а – Схема измерение вибрации при нагружении шпинделя радиальной силой
1 – датчик вибрации; 2 – шпиндель; 3 – вращающийся центр; 4 – механизм поперечной подачи каретки; 5 – суппорт станка; 6 – датчик угловой скорости; 7 – кронштейн; 8 – призма; 9 – датчик силы.
Рис. 4.19б – Схема измерение вибрации при нагружении шпинделя осевой силой
Предлагаемые методика и процедуры диагностики разработаны с учетом их применения как для производственных условий (цеховых проверок) и мониторинга в условиях действующего производства, так и для испытаний ШУ на специальном стенде, на котором проводится обкатка и контроль качества ШУ после ремонта.
Эта методика успешно применялась при диагностировании шпиндельных узлов различных моделей станков с ЧПУ на машиностроительных и станкостроительных предприятиях.
Проверка токарных станков на точность: ГОСТ, видео
Малярный валик — инструмент, помогающий ускорить процесс окрашивания стен, потолка, пола. Но достигнуть идеального результата равномерно окрашенных стен без подтеков и полос достаточно сложно, если не знать некоторых секретов и тонкостей процесса.
Опытные мастера отмечают несколько моментов, принимая во внимание которые можно получить идеально окрашенные поверхности без полос
Renault Duster против Mercedes-Benz ML Оффроуд Батл. Кроссовер, внедорожник 2017
Малярный инструмент отличатся по размеру и материалу изготовления мягкой части (шубки), подробнее https://laksavto.com.ua. Так, чем больше окрашиваемая поверхность, тем шире валик необходимо использовать (максимальный размер 30 см).
Не точность станка после ремонта
В зависимости от используемой краски подбирается определенный тип «шубки» валика. Инструмент с поролоновой мягкой частью идеально подходит для окрашивания водно-дисперсионными составами. Не стоит использовать данный инструмент для эмульсионной краски (в процессе нанесения краска насыщается воздухом, после чего ложится на стену неровными полосами).
1А240-6 — Автомат токарный горизонтальный прутковый
Получить равномерно окрашенную масляными или эмульсионными красками стену, потолок, поможет валик с велюровой мягкой частью.
Также от типа окрашиваемой поверхности подбирается длина ворса шубки валика. Для гладко оштукатуренных стен идеальный вариант — 6мм, для структурных обоев — 15мм, для кирпичных стен или блоков бетона хорошо подходит инструмент с ворсом не менее 19 мм.
Секрет: независимо от того из какого материала выполнена мягкая часть валика, перед первым использованием инструмент обязательно замачивают на несколько часов в воде, а затем хорошенько просушивают.
Чтобы избежать негативных последствий коррозии современному водителю нужно позаботиться о защите кузовной части машины. А лучший способ защиты – это его покраска, такая как на сайте http://www.77professional.ru/okraska-avtomobilya. К тому же покрашенный автомобиль – это очень красиво и роскошно, смотрите на сайте https://laksavto.com.ua. Однако, довольно часто кузов машины покрывается мелкими царапинами, причиной которых могут служить различные факторы: неудачная парковка, дорожно-транспортное происшествие, кто-то зацепил. В целом же, время берет свое и меняет окрас авто под воздействием моющего средства и влияний погоды (солнце, дождь, снег, град). Весь этот перечень неприятностей решается покраской машины. Если же Вы, конечно, желаете получения качественного и максимального результата, тогда лучше не браться за работу своими руками. Для таких случаев предусмотрена покраска автомобиля ведущими специалистами своего дела с многолетним стажем и опытом работы.
Защита кузовной части
Во все времена коррозия являлась главным врагом всех автомобилистов. В связи с тем, что не придумали еще способ и средства от появления ржавчины, то лучше своевременная реакция на предотвращение подобной ситуации.
Профессиональные работники проведут необходимые операции, устранив коррозию и другие дефекты, до начала покраски автомобиля.
Почему лучше остановить свой выбор на профессиональной покраске авто?
Для проведения покраски машины, желательно иметь не только некие знания, умения и силы, но и творческий подход. В начале, автомаляром подбирается нужный цветовой оттенок. Не надо переживать по поводу сходства цвета, в случае покраски некоторых деталей, к примеру, дверь. Каждая машина имеет специальную бирку с номером краски, мастер без труда получит такой же цвет. Шпаклевать и грунтовать также нужно с особым вниманием, правильность ее нанесения и шлифовальные работы – будут означать удачную и ровную поверхность на кузове.
Немаловажное значение придается помещению, в котором производится покраска и подсушка машины. Без наличия вытяжек и изоляций от внешней среды, конечный результат не порадует владельца авто. По этой причине красить машину в специальной камере. Любая, даже небольшая соринка или волос бросится при проверке качества покраски. Такая работа будет признана бракованной. Лучший выбор для Вас – предоставление этих действий мастеру, который сделает покраску высококачественно и с гарантией.
Говоря о точности токарного станка имеется ввиду соответствие данных паспорта оборудования следующим параметрам:
перемещение тех элементов, на которых располагается заготовка;
расположение тех поверхностей, с помощью которых базируется инструмент или заготовка;
форма базовых поверхностей.
После окончательной сборки и проверки на заводе, а также после ремонтов станки получают акт о приемке, и только после этого, вводятся в эксплуатацию.
Требования к точности указываются в паспорте станков.
Выполнение измерения для выявления погрешностей следует производить регулярно в соответствии с нормативами ГОСТ.
Скачать ГОСТ 8-82 «Станки металлорежущие. Общие требования к испытаниям на точность»
Скачать ГОСТ 18097-93 «Станки токарно-винторезные и токарные. Основные размеры. Нормы точности».
В процессе использования токарного оборудования происходит износ его деталей, т.к. при обработке изделий появляются силы, которые производят различные деформации. При работе станок нагревается и под воздействием температуры образуются тепловые деформации. Все эти дефекты оказывают отрицательное влияние на качество обрабатываемых деталей. И для того чтобы восстановить паспортные показатели станка периодически следует ремонтировать изношенные детали.
Качественное испытание токарных станков в соответствии с государственным стандартом во многом зависит от того, насколько правильно он установлен на испытательном стенде. Установка на стенд должна происходить строго, соблюдая установочный чертеж. Самым распространенным методом, является установка на количество опор более 3-х. Отметим, что все двигающиеся части проверяемого станка должны находится в средних положениях.
Геометрическая точность токарного станка характеризует качество изготовления деталей, поэтому установка заготовки должна осуществляться на геометрическую правильную поверхность.
Для определения степени износа нужно установить линейку поочередно на каждую из направляющих станины. После этого, щупом определяется расстояние между направляющими и контрольной линейкой. Допустимое значение такого износа согласно государственного стандарта не должно превышать 0,02 мм.
Не мало важным фактором является соответствие горизонтальности направляющих станины. Определить ее можно с помощью перемещения специального уровня вдоль поверхности направляющих, который покажет значение имеющегося отклонения. Предельно допустимое отклонение по ГОСТ не может превышать значение 0,05 мм. А параллельность между направляющими станины для упорной (задней бабки) и каретки можно проверить с помощью специального измерительного индикатора. Его необходимо закрепить на каретке с суппортом и с помощью перемещения каретки выявить величину отклонения.
Также точность токарного станка поможет определить биение вращающегося шпинделя, в который крепится заготовка. Обязательно при этом соблюдать параллельность между осью шпинделя и направляющими станины. Во время проверки в отверстие вала устанавливают специальную контрольную оправку и на протяжении всей ее длины проверяют ее на биение.
Проверка параллельности оси шпинделя направляющим станины: а — индикатор закреплен в вертикальной плоскости; б — индикатор закреплен в горизонтальной плоскости
Осуществляя технологическую проверку на точность стоит обратить внимание также и на вращение шеек вращающегося вала. Биение при их вращении — не допустимо. В резцовой головке необходимо закрепить индикатор, затем уперев его штифт в шейке шпинделя произвести измерения. По ГОСТ значение не должно превышать 0,01 мм. Не допустимым будет при вращении шпинделя, чтобы он отклонялся от оси.
Проверка биения шпинделя: а — проверка биения шейки шпинделя; б — проверка осевого перемещения шпинделя; в — проверка биения переднего центра
Также одним из важных измерений при проверке токарного станка на точность является определение точности шага ходового винта. Величина отклонения в соответствии с ГОСТ определяется с помощью следующей методики:
в центры передней и задней бабки устанавливают резьбовую оправку;
на эту оправку накручивают гайку в форме цилиндра и имеющую паз;
в паз этой цилиндрической гайки устанавливается шарик державки;
индикатор, закрепленный в державке, упирается в торцевую часть цилиндрической гайки;
токарный станок настраивается на шаг резьбы;
индикатор определяет отклонения.
Проверка точности шага ходового винта
Основные погрешности формы обрабатываемых заготовок:
непрямолинейность;
конуснообразность;
отсутствие параллельности;
некруглость;
неконцентричность.
Инструмент, применяемые при испытаниях:
контрольная линейка;
уровень;
щуп;
угольник;
измерительный индикатор;
резьбовая оправка;
контрольная оправка;
цилиндрическая гайка;
державка.
При выполнении измерений следует использовать только те инструменты, которые прошли метрологическую поверку с учтенной погрешностью.
Если вы нашли ошибку, пожалуйста, выделите фрагмент текста и нажмите Ctrl+Enter.
(PDF) Оборудование и методика экспериментального определения статической жесткости токарных станков для двигателей
191
7130
05610
400
Y
F
K
xy
Py
===
== ,
(9)
, где P обозначает направление плоской силы
Fxy.
4. ЗАКЛЮЧЕНИЕ
Определение статической жесткости токарных станков MSA
и претензий на каретку для конкретной рабочей среды
, которая относится к структуре
TMS, справочным материалам, состояниям системы, нагрузкам и деформациям
.
В данной статье представлено несколько схем для
измерения нагрузок и деформаций TMS, вместе
с двумя конструкциями экспериментального стенда
, которые могут быть использованы для измерения жесткости
MSA и каретки токарных станков. Также в статье представлены несколько конструкций испытательного стержня
, который используется на экспериментальном стенде
.
Предложенные схемы и разработанный экспериментальный стенд
могут быть использованы для измерения жесткости других деталей токарных станков
или других типов ТМС
(на фрезерных станках, шлифовальных станках и т. Д.)).
Как показывают экспериментальные данные, жесткость
каретки токарного станка ниже, чем жесткость
MSA токарного станка. Этот результат является прямым следствием
большего количества фиксированных и подвижных шарниров
, которые используются в конструкции узла каретки
по сравнению с MSA.
ПОДТВЕРЖДЕНИЕ
Работа Иону-Габриэля Гионеа была
профинансирована Секторной операционной программой
Развитие человеческих ресурсов на 2007-2013 годы
Министерства европейских фондов через Финансовое соглашение
POSDRU / 159/159/159/159/159/159/159/
.5 / S / 138963.
5. ССЫЛКИ
[1] Weck, M., Werkzeugmaschinen, Band 4,
Messtehnische Untersuchung, VDI-Verlag
GmbH, Dusseldorf, 1990.
[2] Weck, M. et al. для определения статической жесткости станков
, Mechanik,
4 (1989), стр. 125-129.
[3] Тонойу С., Вклад в исследование
жесткости технологической производственной системы,
Кандидатская диссертация в университете «Политехника»
Бухарест, 1999.
[4] Георге, М., Тонойу, С., Основы
нагрузок, деформаций, жесткости и податливости
технологических систем, Труды Международной конференции
по достижениям в области
материалов и технологий обработки, 2003 ,
с. 1662-1665.
[5] Prakosa, T., Wibowo, A., Ilhamsyah, R.,
Оптимизация статической и динамической жесткости вала шпинделя станков
для улучшения качества обрабатываемой продукции
, журнал KONES
Powertrain and Transport , 20, 4 (2013), с.
363-370.
[6] Пауло Давим, Дж. Традиционная обработка
Процессы – научно-исследовательские достижения, Springer-
Verlag, Berlin-Heidelberg, 2015.
[7] Таскесен, А., Менди, Ф., Кисиоглу, Ю. ., Kulekci,
MK, Анализ деформации расточных стержней
с использованием аналитических подходов и методов конечных элементов,
Journal of Mechanical Engineering, 52, 3 (2006),
pp. 161-169.
[8] Попеску, И., Тоною, С., Статическая жесткость токарного инструмента
, Научный бюллетень «Политехники»
Университет Бухареста, 72, 2 (2010), стр.
115-122.
[9] Денкена, Б., Холлманн, Ф., Process Machine
Взаимодействия – прогнозирование и манипуляции
взаимодействий между производственными процессами
и конструкциями станков, Springer-Verlag,
Berlin-Heidelberg, 2013.
[10] Тоною, С., Катана, М., Тарба, К., Дизайн
и тестирование улучшенных испытательных стержней для
Измерение жесткости шпинделей обычных токарных станков
, Труды 7-й Международной конференции
по передовым производственным технологиям
, Бухарест, 2014, стр. 645-650.
[11] Дарбинян В.Л., Есаян П.М., Жесткость
токарной каретки с ЧПУ, Советский журнал
Технические исследования, Том 1, Выпуск 9,
с.86-88, 1981.
[12] Ямазаки, Т., Мацубара, А., Фудзита, Т.,
Мураки, Т., Асано, К., Кавасима, К.,
Измерение жесткости шпинделя с помощью Использование магнитного погрузчика
, Труды 5-й Международной конференции
по передовому производству
в 21 веке, Осака, Япония, Журнал
Advanced Mechanical Design Systems And
Manufacturing, Том 4, Выпуск 5, стр. 985 –
994, 2010.
01. Как проверить точность вашего токарного станка >> Блог
01. Как проверить точность вашего токарного станка
ТАМ – старая поговорка, что плохой рабочий винит свои инструменты; наоборот, хороший рабочий – это тот, кто знает, как правильно использовать свои инструменты. Мы не предлагаем объяснять, как исправить неточный токарный станок, а только чтобы показать, как его следует проверять на наличие неисправностей, что, в конце концов, является важным предварительным условием для принятия решения что-то с этим делать.Теперь можно подумать, что самый быстрый способ проверить токарный станок на истинность – это проверить проделанную работу, но любой, кто пробовал этот способ, согласится, что это медленный и ненадежный. Редко осознается, насколько пружинит сама работа, даже при самых легких порезах. Например, если передняя бабка отрегулирована так, чтобы повернуть параллельно кусок стержня, удерживаемого в патроне, цилиндр, просверленный сразу после этого, окажется наиболее необъяснимо большим на заднем конце. Ошибка может быть небольшой, если оправка жесткая, а работа жесткая, но она все равно будет там, и неоднократные попытки добиться правильного результата с помощью этого метода обычно заканчиваются тем, что несчастный владелец желает, чтобы он ушел хорошо. в одиночестве.Чтобы получить максимальную производительность от вашего токарного станка, вам необходимо проверить точность его рабочих частей. Современные токарные станки имеют встроенную точность, но могут быть некоторые детали, которые не являются точными или правильно выровнены. Некоторые из этих проблем могут быть легко устранены, а некоторые требуют дополнительной работы, но, описывая каждую из этих проблем, мы все время указываем, какие отклонения допустимы (допуск) и на какие операции эти ошибки могут повлиять. Так вы сможете решить, нужно ли вам решать проблему.Например, Fox, если вы никогда не сверлите с задней бабки или не используете заднюю бабку для стабильной работы, удерживаемой в патроне, то совмещение центров головки и хвоста не очень важно.
Прежде чем приступить к работе с токарным станком, уместно сказать несколько слов о безопасности в мастерской. В промышленной среде многие виды деятельности, связанные со станками, регулируются законодательством, направленным на улучшение здоровья и безопасности. Один из восхитительных аспектов семинара заключается в том, чтобы «убежать» от мирских забот извне, и поэтому в наших занятиях досугом большая часть такого законодательства не применяется, и ответственность за безопасность как нас самих, так и наших посетителей во многом лежит на нас. своими руками.Разумный подход к безопасным методам работы включает, во-первых, оценку факторов, которые могут привести к травмам (и те части тела, которые подвержены риску), и, во-вторых, здравый смысл в отношении работы с этими факторами.
Пальцы и руки
В то время как небольшой станок, такой как настольный токарный станок, имеет гораздо меньшую мощность, чем тяжелый промышленный токарный станок с двигателем. Но инерции патрона и рабочего вращения на максимальной скорости, безусловно, будет достаточно, чтобы нанести серьезный ущерб неправильно установленному пальцу.Еще одна из частых травм – это порезы от острых краев, которыми могут быть инструменты, работа или стружка. Ленты из стружки могут выглядеть как кусочки рождественского украшения, но думайте о них как о длинных тонких рваных лезвиях бритвы. Поэтому при очистке от стружки не пользуйтесь пальцами.
Глаза
Из некоторых материалов, особенно из латуни, образуется стружка, которая уходит небольшими иголками с большой скоростью. Если вам не повезло, что часть этого попала в глаз, то это почти наверняка поездка в больницу, где (не намагничивая) она будет удалена вручную.Защитные очки дешевы и предотвратят это. Их также следует носить при заточке инструментов на верстаке.
Ноги
На машиностроительном заводе вы можете носить защитные ботинки или обувь, рассчитанную на то, чтобы вы могли проехать на машине по ноге, не повредив пальцы ног. В нашей любительской мастерской большая часть того, с чем мы работаем, будет, возможно, не слишком тяжелой. Но фунт или полкилограмма, упавший с высоты скамьи, вызовет изрядное количество синяков, поэтому кроссовки или сандалии с открытым носком могут быть не идеальной обувью.Наша версия закона Мерфи также гласит, что если вы уроните на ногу предмет с острой кромкой, он упадет острой стороной вниз.
Волосы
Длинные волосы могут быть захвачены вращающимся стержнем и намотаны, что может привести к травме головы или лица. Соберите волосы назад или используйте сетку.
Одежда общего назначения
Галстук представляет такую же опасность, как и длинные волосы.Желательно снять его или хотя бы убедиться, что он заправлен под свитер. Также не рекомендуется использовать свободные рукава. Открытые воротники могут стать проблемой при обработке на высокой скорости. Попадание горячей стружки внутрь шеи может быть болезненным и может вызвать непроизвольное движение, что приводит к вторичному риску.
Электробезопасность
Если вы приобрели новый токарный станок, то все должно быть в порядке. Если подержанный, то, возможно, стоит проверить, что вилка, кабель и соединения в хорошем состоянии.Если вы используете удлинительный кабель, проложите его так, чтобы не зацепиться за него. Подключение через устройство защиты от утечки на землю или защитного отключения является разумной мерой предосторожности. В промышленных процессах обработки часто широко используется СОЖ на водной основе для ускорения резки. Понятно, что вода и электричество (особенно при сетевом напряжении) не устраивают соратников. Более безопасным вариантом будет использование запатентованных режущих смесей. Самая важная проверка токарного станка, без сомнения, заключается в точности работы и способе ее изготовления – квалифицированный оператор может преодолеть существенные элементарные неточности.Даже если работа носит относительно простой характер, существует достаточно возможностей для ошибок – при условии, что есть достаточные вариации для проверки всех аспектов согласования. Это означает, что токарный станок может быть точным для одного вида работ, но не для другого, и опыт его использования может указать, где ожидать ошибок, хотя причина, по которой они не всегда могут быть очевидны сразу. Однако существуют различные простые тесты, которые в значительной степени заменяют «опыт работы» и могут быть полезны для обнаружения ошибок, для исправления машины (если возможно) или в некоторых случаях для настройки.
Простой, но важный тест, фото A , – это соединение центров передней и задней бабок. Когда фиксированный центр заметно опускается, указывается износ нижней стороны задней бабки и, возможно, самой станины. Влияние на межцентровое точение может быть небольшим или отсутствовать, но необходимо соблюдать осторожность при использовании центровочных сверл или расточных фрез из задней бабки – степень «подъема» тогда необходима для центрирования инструментов.Такой же эффект достигается и при поддержке зажимного приспособления от задней бабки. Это испытание следует проводить с закрытым стволом и хорошо выдвинутым стволом. Подобную ошибку вбок часто можно исправить, отрегулировав заднюю бабку. Более суровое испытание того же типа, фото B , может быть выполнено с индикатором, который может быть циферблатным или одной из небольших недорогих разновидностей. Индикатор устанавливается в патроне или на приводной пластине так, чтобы его плунжерный подшипник находился в неподвижном центре. Затем шпиндель токарного станка поворачивают, когда устойчивые показания показывают идеальное выравнивание, используя маленькое зеркало, чтобы увидеть инструмент вверх ногами и сзади.Если есть отклонения в показаниях, как это бывает практически всегда, можно увидеть, в каком направлении (вертикальном или боковом) они возникают, и задняя бабка отрегулирована для исправления боковой ошибки. Испытание «живого центра» для проверки истины, фото B , может быть выполнено из одного, обычно находящегося в шпинделе, и из других с таким же конусом с индикатором, установленным на опоре скольжения. Иногда это может показать, что сами центры не соответствуют действительности; и при использовании может быть целесообразно держать их в одном положении – шпиндель или маркировка задней бабки для установки определенным образом.
Общее выравнивание
Испытание на общее совмещение передней бабки и задней бабки для межцентрового точения может быть выполнено с использованием оправки, фото C . Можно использовать любой подходящий кусок стержня, тщательно отцентрировать, уменьшить его длину и повернуть концы одинакового размера. Инструмент, установленный на опоре скольжения, можно приблизить к одному диаметру, оставив небольшой зазор, затем проверить зазор на другом диаметре, лист белой бумаги на станине обеспечивает светлый фон, на котором можно увидеть зазоры.Наконец, инструмент можно настроить так, чтобы он слегка касался диаметров при перемещении по седлу. Это помогает разумно настроить токарный станок перед началом работы, а в качестве альтернативы инструменту можно использовать индикатор. Лицевая панель может быть проверена правилом , фото D , и при установке на шпиндель и вращении проверяется на раскачивание торца. Если патрон обработан правильно, можно провести испытание лицевой панели на совмещение поперечных салазок в два этапа, фото E и F , с помощью инструмента или индикатора.При тестировании вдоль ближней стороны по линии X-X1 на фото выше не может быть никаких ошибок, если лицевая панель была обработана на токарном станке, поскольку совмещение соответствует поперечному суппорту. Однако при тестировании на дальней стороне, на линии X2-X3, любая ошибка удваивается и ее можно легко увидеть. Установку верхнего суппорта можно проверить как фото G , индикатор на оправке и закругленный стержень на опоре скольжения. Когда ползун не выровнен, движение происходит вдоль, например, X4-X5, и при проверке с помощью траверсы седла отображаются вариации, тогда как при истинной настройке показания будут одинаковыми.
7 вещей, которые вы должны знать о токарных станках швейцарского типа
Швейцарские часовые механизмы долгое время считались эталоном точности изготовления, точного хронометража и надежности. Даже в наш век цифровых технологий швейцарские часы марки Marque продаются по очень высокой цене и становятся символом успеха их владельцами.
Для изготовления этих компонентов часов с соблюдением строгих допусков требуются высокоточные режущие станки. Не удовлетворившись существующей технологией, швейцарские станкостроители изобрели токарный станок в швейцарском стиле, чтобы удовлетворить свои потребности.Сегодня швейцарские токарные центры также производят высокоточные крупносерийные детали для медицинских изделий, зубных имплантатов, аэрокосмической и авиационной техники, измерительных приборов и многих других приложений.
Стоит ли вам рассмотреть возможность добавления в свой цех токарного станка швейцарского типа? Если вы хотите обеспечить длительные производственные циклы высокоточных деталей, особенно небольших диаметров, то станок швейцарского типа может стать хорошей инвестицией. Как и при любом решении о покупке, чем больше вы знаете о том, как работают токарные станки швейцарского типа и как они устроены, тем лучше вы будете оснащены, чтобы сделать осознанный выбор.Вот 7 вещей, которые вы должны знать о станках швейцарского типа:
1. Основное отличие традиционных токарных станков от станков швейцарского типа заключается в том, что первый имеет фиксированную переднюю бабку, которая удерживает вращающуюся заготовку, когда режущий инструмент перемещается для обработки внешнего диаметра. С другой стороны, в станке швейцарского типа используется скользящая бабка, которая подает пруток через направляющую втулку по оси Z мимо неподвижного режущего инструмента. Такая конфигурация означает, что режущий инструмент всегда входит в контакт с прутковой заготовкой рядом со втулкой, обеспечивая, таким образом, максимальную поддержку и, следовательно, уменьшая вибрацию и отклонение инструмента.В результате хорошо спроектированный и изготовленный токарный станок в швейцарском стиле позволяет удерживать даже длинные и тонкие заготовки с более жесткими допусками и, при необходимости, обеспечивает резкое точение.
2. Некоторые токарные станки швейцарского типа включают вспомогательный шпиндель для дополнительных операций обработки, таких как сверление и растачивание. Такая универсальность устраняет необходимость перемещать деталь с одного станка на другой, сокращая тем самым общее время производства, затраты на рабочую силу, ошибки оператора и время простоя шпинделя.
3. Направляющая втулка и шпиндель лежат в основе способности токарного станка Swiss-Style выдерживать жесткие допуски.Поскольку шпиндель полый, критически важно, чтобы материал шпинделя обеспечивал оптимальную степень жесткости. Например, швейцарский производитель станков Nomura использует хромомолибденовую сталь SCM415 для своих шпинделей. После точной обработки внешняя часть шпинделя подвергается термообработке для повышения прочности, а внутренняя часть обрабатывается до различной степени твердости. Этот запатентованный процесс позволяет шпинделю сохранять большую прочность, точность и стабильность.
4. Хотя токарные станки швейцарского типа по своей конструкции обеспечивают более стабильную среду резания, пруток редко бывает идеально прямым или круглым и может создавать вибрации, влияющие на точность и износ инструмента.Токарные станки швейцарского типа, не использующие ременной привод, обычно создают меньше вибрации и, следовательно, более стабильны и точны. Скользящая бабка также должна двигаться плавно и точно. Использование линейной направляющей с предварительно нагруженными роликовыми подушками помогает достичь этого точного движения, в то время как механизм скольжения поглощает большую часть гармонической вибрации, создаваемой высокоскоростным вращением прутка.
Пример полностью встроенного шпинделя, для которого не требуется ременной привод.
5. Направляющие поверхности станка швейцарского типа должны быть как можно более гладкими и плоскими для повышения устойчивости и дальнейшего снижения воздействия вибрации. Какими бы мощными ни были устройства для зачистки, ничто не сравнится с точностью ручной очистки, выполняемой опытным мастером. Обработанная вручную поверхность станка может обеспечить сверхточную поверхность с субмикронными неровностями менее 0,0001 мм.
Очистка вручную обеспечивает исключительную ровность и гладкость.
6. Другие детали, на которые следует обратить внимание, – это сверхмощные шарико-винтовые пары большего размера на каждой оси для более эффективной передачи мощности от двигателя к передней бабке, держатели инструментов, направляемые салазками в форме ласточкина хвоста, которые перемещаются на тонкой масляной пленке, и использование структурно стабильных материалов, таких как чугун, для основных компонентов. Поскольку эти типы шарико-винтовых пар и суппортов уменьшают влияние инерции, машины прослужат дольше и требуют меньшего обслуживания, что увеличивает рентабельность инвестиций.
7. Чтобы оптимизировать производительность ваших станков в швейцарском стиле, правильный автоматический податчик прутка может обеспечить непрерывную, автоматическую работу и даже работу без отключения света. Они также обеспечивают дополнительную материальную поддержку для дальнейшего снижения вибрации и защиты операторов от открытого прутка, вращающегося на высоких скоростях.
Легко доступное техническое обслуживание, запасные части, обучение и постоянная поддержка клиентов также являются важными факторами при выборе токарного станка в швейцарском стиле.Работа с правильным поставщиком может снизить реальную стоимость владения и обеспечить максимальную рентабельность инвестиций.
Хотите узнать больше? Специалисты по механической обработке в швейцарском стиле в NomuraSwiss ответят на все ваши вопросы, окажут помощь в применении и помогут найти идеально подходящий станок.
Обработка с ЧПУ по сравнению с традиционной обработкой
Промышленность прецизионного производства в значительной степени полагается на обработку с числовым программным управлением (ЧПУ), включая операции, в которых когда-то использовалось оборудование, управляемое инженерами, такое как фрезерные станки, формовочные станки, вертикальные фрезерные станки и токарные станки.Производители во многих отраслях промышленности выбирают обработку с ЧПУ, поскольку она обеспечивает эффективную, целесообразную и точную производственную мощность, идеально подходящую для создания большого количества изделий, обычно производимых на шлифовальном станке, фрезерном станке, токарном станке или формовочном станке.
При ручной токарной обработке на каждом станке должен быть квалифицированный специалист, тогда как при обработке с ЧПУ один квалифицированный специалист может управлять несколькими станками. Обработка с ЧПУ позволяет производить широкий спектр металлических компонентов, используемых во многих отраслях промышленности, благодаря их точной, последовательной и сложной резке.Некоторые примеры этих отраслей: аэрокосмическая, автомобильная, электроника, огнестрельное оружие, гостиничный бизнес, производство, металлообработка, военная промышленность, производство и транспорт. Первые станки с ЧПУ были разработаны механиками ВВС США в 1940-х годах. Эти ранние машины использовали технологию перфорированной бумаги в качестве драйвера, который превратился в сегодняшнее цифровое программное обеспечение. Обработка с ЧПУ стала популярной из-за ее способности получать подробные и точные результаты в больших количествах с помощью компьютеров.
Компьютерное числовое управлениеотличается от обычных ПК, потому что программное обеспечение, используемое для управления станком, специально настроено и запрограммировано с G-кодом, который является специфическим для ЧПУ, что позволяет точно контролировать скорость, местоположение, координацию и скорость подачи.Один человек может делегировать машинную работу, которая была бы эквивалентна множеству операторов на токарных, шлифовальных, фрезерных, фрезерных и формовочных станках, что не всегда эффективно выполняет человек-оператор и обычное оборудование. В производственной сфере обработка с ЧПУ очень полезна, поскольку в этой отрасли требуется большое количество металлических и пластмассовых деталей, часто сложной формы. Различные типы станков с ЧПУ имеют преимущество в виде нескольких осей, которые могут регулироваться под сложными углами и помогают управлять труднообрабатываемыми материалами.
МашиныBasic имеют режущий инструмент, работающий по осям x и y, каждый из которых работает независимо и одновременно. У современных станков может быть до пяти осей, которые работают одинаково и способны поворачивать и переворачивать деталь. Станки с ЧПУ могут автоматизировать работы, требующие нескольких разрезов. Фрезерный станок или шпиндель поворачивает режущий инструмент, который напоминает сверло, и режет материал, в то время как настоящее сверло режет только кончик. Программирование на станках с ЧПУ включает в себя все точные, высокоскоростные движения, необходимые для изготовления объекта, и позволяет выполнять детальную настройку.Обработка с ЧПУ становится все более популярной для изготовления металлических и пластмассовых деталей, поскольку она позволяет производителю изготавливать сложные формы, которые практически невозможно создать вручную. Многие отрасли промышленности обращают внимание на преимущества обработки с ЧПУ для производственных решений, включающих металл и пластик, а также любое количество процессов обработки, которые могут им понадобиться.
КакЧПУ, так и обычные станки начинают с необработанного куска металла или пластика и превращают его в деталь. Основное различие между двумя станками – автоматизация ЧПУ по сравнению с ручным характером обычных.Скорость, производительность и точность – вот некоторые из основных преимуществ обработки с ЧПУ по сравнению с традиционной обработкой. Квалифицированный сотрудник программирует программное обеспечение для резки деталей на станке с ЧПУ, в то время как в обычном случае сотрудник настраивает станок и шестерни и управляет ими. Обычный стоит меньше и обычно используется для небольших проектов. ЧПУ используется для больших объемов и не так рентабельно для небольших проектов. Станок с ЧПУ использует три инструмента для резки деталей, в то время как обычным станкам требуется пять инструментов и больше времени для выполнения работы.Для большинства видов обработки доступны обычные технологии и технологии ЧПУ. Некоторые из них включают в себя сверла – биты вращаются для контакта с материалом, токарные станки – блок материала движется против сверла, обычно в боковом движении, и фрезерные станки – вращающиеся режущие инструменты удаляют материал из заготовки. Новые технологии обработки с ЧПУ включают менее распространенные типы, такие как электрическая / химическая, когда блок материала разрезается с использованием определенного вида обработки, такого как электронно-лучевые, электрохимические, электрические разряды, фотохимические и ультразвуковые.Менее распространенные методы обработки с ЧПУ включают режущие среды, такие как лазеры, кислородно-топливная, плазменная и водяная струи.
Программное обеспечение автоматизированного проектирования (САПР) используется при обработке с ЧПУ для создания двух- или трехмерной модели готовой детали. Изображение прототипа этого компонента вводится в программное обеспечение, которое работает через компьютер, чтобы направлять инструменты механической обработки для производства элементов, идентичных модели. После того, как компьютер загрузил новое изображение для обработки с ЧПУ, он может многократно извлекать эту модель, чтобы произвести больше элемента.Это разработано для достижения точности обработки в пределах .0001.
Традиционные и нетрадиционные методы обработки с ЧПУ используются для множества работ, которые могут включать в себя различные материалы, такие как:
Алюминий
Латунь
Медь
Пена
Стекловолокно
Пластик
Полипропилен
Сталь
Титан
Дерево
Это 20 операций по резке, которые часто выполняются с помощью станков с ЧПУ:
Отверстие
Контур
Насечка
Сверло
Гравировка
Лицевая сторона
Отшлифовать
Паз
Накатка
Токарный станок
Фрезеровка
Пуансон
Срез
Форма
Штамп
Метчик
Текстура
Резьба
Поворот
Сварка
Преимущества обработки с ЧПУ
Прецизионные компоненты: Цифровой шаблон и автономная обработка ЧПУ практически исключают человеческий фактор и обеспечивают точность в пределах 1/1000.
Надежная выносливость: станки с ЧПУ работают круглосуточно каждый день и предназначены только для ремонта или технического обслуживания.
Высокая производительность и масштабируемость: после того, как проектные параметры и спецификации были введены в станок с ЧПУ, он постоянно выполняет огромные объемы и обеспечивает гибкую масштабируемость.
Больше возможностей: при использовании в тандеме с передовым программным обеспечением для проектирования станки с ЧПУ создают выходные данные, которые невозможно воспроизвести на ручных станках. Даже самые одаренные инженеры не могут использовать обычные станки вплоть до станков с ЧПУ из-за передового программного обеспечения, которое они используют.Эти машины могут производить любой необходимый размер, форму или текстуру.
Меньше труда: обработка с ЧПУ требует меньшего количества персонала для выполнения производственных задач. Один опытный оператор может запустить несколько автономных станков с ЧПУ, в то время как другой программист может загрузить их с проектами. Для станков с ручным управлением требуется как минимум один опытный оператор на каждую машину и супервизор. То, что вы можете сэкономить на рабочей силе, можно передать клиентам.
Единый продукт: когда вы используете станки с ЧПУ вместо обычных станков, ваши выходные данные с ЧПУ точно совпадают.Даже самые талантливые станочные операторы, работающие на традиционных машинах, их продукция будет очень незначительно. Безупречные детали всегда гарантируются станками с ЧПУ.
Низкие затраты: станки с ЧПУ имеют высокую скорость, более эффективны, точны и требуют меньше рабочих часов. Экономия денег или получение большего дохода – одно из популярных преимуществ обработки с ЧПУ.
Меньше головной боли: ручные станки служат многим отличным целям, но когда ваш оператор отсутствует или ваш персонал не выполняет своих ожиданий, вы не сможете производить столько, сколько вы бы использовали на станке с ЧПУ.
Повышенная безопасность: несмотря на то, что станки с ЧПУ по-прежнему требуют использования операторов, они находятся на некотором расстоянии от острых инструментов. Операторы традиционных ручных токарных станков, сверл и пуансонов непосредственно контактируют с инструментом.
Сохранение дизайна: после того, как проект был загружен в программное обеспечение станка с ЧПУ и был создан идеальный прототип, программа может легко извлечь проект и создать объект заново.
Низкие эксплуатационные расходы: программное обеспечение на основе G-кода будет автоматически обновляться при необходимости, и станки с ЧПУ обычно не требуют особого обслуживания, кроме замены режущих инструментов с надлежащими интервалами.Ни одно регулярное обслуживание не требует профессионального обслуживания.
Универсальность: обработка с ЧПУ позволяет создавать практически любые компоненты. Некоторые модели включают специальные функции и аксессуары, которые еще больше ускоряют и упрощают производственный процесс.
Использование станков с ЧПУ дает множество преимуществ, и в Sheldon Precision мы используем только лучшие станки, чтобы гарантировать, что ваш продукт изготовлен с максимально возможным качеством. Свяжитесь с нами сегодня, чтобы узнать цену на https://sheldonprecision.com/request-a-quote/
Статья адаптирована из: https: // www.fairlawntool.com/blog/advantages-cnc-machines/
Достижение допуска меньше точности: ЧПУ | Блоги
Точность позиционирования, повторяемость – достижение допуска меньше точности
Вот вопрос:
Токарный станок с ЧПУ имеет точность позиционирования 0,010 мм и повторяемость 0,002 мм. Можно ли на этом станке обработать диаметр с допуском +/- 0,006 мм?
Ответ:
Да.
С поз. с точностью до 10 микрон, команда X100.0 заставит инструмент перейти в любое место между X99.990 и X100.010. Однако он будет повторять эту ошибку в пределах 2 микрон каждый раз.
Предположим, что в первой части он идет до X100.07 – вне нашего диапазона допуска. Последующие части будут в диапазоне от X100.05 до X100.09. Так что просто проверьте диаметр. на первой части и точно настройте смещение, чтобы получить диам. Поскольку повторяемость составляет 2 микрона, последующие детали будут находиться в пределах 100 +/- 2 микрон.
По сути, этот токарный станок с ЧПУ делает ошибку при позиционировании, но он делает ошибку достаточно постоянно, что является поведением. «Ошибка» – это точность позиционирования. «Последовательность» – это повторяемость. Эта машина совершает ошибку с высокой степенью согласованности, достаточно высокой, чтобы мы могли добиться жестких допусков на детали. Это касается любых станков – токарных, обрабатывающих, шлифовальных и т.д.
Идея этого поста взята из вопроса, который г-н Вирендра Патил из Shree Spherotec Pvt Ltd задал в предыдущем посте.Он также подтвердил логику с помощью лазерного измерения.
Программное обеспечение CAD / CAM, моделирование программ с ЧПУ, мониторинг станков, программное обеспечение для обучения ЧПУ
Мой любимый серьезный паб
Пекос в Бангалоре – это то место, куда я иду, когда хочу немного хорошей еды и много разливного пива. Здесь представлено около 5 сортов пива и обширное меню с необычными блюдами. Играет музыка 70-х. Большой разброс для хищников, не для травоядных.У блюд есть названия, которые точно скажут вам, что они из себя представляют, а не причудливые названия. Ничего подобного «Курица 65», повсеместно распространенная по всей Индии (и никто не знает, что такое 65 – может быть, возраст курицы, когда она достигла Лотосных стоп Господа?). У вас также есть доса и паротта, которые можно сочетать с тем, что вы едите. В следующий раз мне стоит попробовать соединить паротту и пиво – окунуть первое в последнее, как печенье в чай. Паротта – это пушистая малабарская паротта из Кералы, а не парата в Пенджабе.
Старое отделение Pecos находится у Brigade Rd, а новое – на Church St. На улице Church St есть настоящая боковая панель микроавтобуса (я думаю, что это Bajaj Matador), прикрепленная к стене с колесами. Другие могут подумать, что это банально, но мне это нравится, и я думаю, что это придает этому месту характер.
Все в Pecos остается неизменным на протяжении десятилетий, и менеджменту наплевать на изменение тенденций в оформлении, музыке, еде или выпивке.Их позиция “Вот и все, люди, оставьте это” работает на них. Он популярен среди людей разных поколений, и часто рядом с ним слоняются моя 21-летняя дочь и 57-летняя Я (первая в полной мере использует свой недавно приобретенный «Агент 007: Лицензия на выпивку»).
В 1 пинте (ваш обычный размер кружки) разливного пива 180 калорий, а это значит, что мне потребовалось 1,5 часа езды на велосипеде на следующий день, чтобы сжечь 4 кружки, которые у меня были в тот день. Я где-то читал, что сон сжигает 60 кал / час. В следующий раз я буду спать по 3 часа на каждую кружку, по 12 часов на 4 кружки.Почему я не подумал об этой простой программе похудания раньше?
Примечание: Используя линейку, проверьте, что вся длина обточенной области сужается (рис. 1).Не должно быть любое открытое пространство вдоль прямой кромки, если вся длина сужается. Если весь длина не сужается, люфт в насадке конуса остается. Попробуйте запустить сделайте резку дальше, чтобы уменьшить люфт. Метод проб и ошибок конусности Регулировка навесного оборудования приемлема, если у вас есть много лишнего материала для работы с участием.
Перемещайте каретку до тех пор, пока показания оси X не начнут показывать постоянную величину. путешествия. Сбросьте оба дисплея осей на ноль. Переместите каретку 1.00 дюймов. Обратите внимание на ось X координата диаметра. Когда конусный стержень установлен правильно, показание диаметра оси X превышает ход каретки на один дюйм должен соответствовать требуемому конусу на дюйм. Верх |
Торнос | Торнос
Швейцарский производитель станков
Tornos использует ряд технологий обработки с возможностью удаления стружки для производства деталей, требующих высочайшей точности и качества.
Станки Tornos могут предложить вам решение, гарантированно соответствующее вашим потребностям, будь то обработка простых или очень сложных деталей малыми или большими партиями!
MultiSwiss
Tornos представляет два новых варианта MultiSwiss – MultiSwiss 8×26 и MultiSwiss 6×32, основанные на философии и технологии, которые оказались столь успешными на MultiSwiss 6×14 и MultiSwiss 6×16. Эти станки представляют собой отход от обычных многошпиндельных станков, обеспечивая связь между многошпиндельными и одношпиндельными токарными станками.Встроенная технология станков означает, что они могут обеспечивать время цикла, равное времени цикла многошпиндельных токарных станков с кулачковым приводом.
Узнать больше
SwissNano 7: Сверхкомпактность для большей производительности на квадратный метр
Благодаря компактным размерам и продуманному дизайну, линейка SwissNano может максимизировать производительность любой мастерской на квадратный метр. На площади менее 80 кв.м можно установить 10 машин!
Узнать больше
Опыт SwissNano
Наш ассортимент
Наши машины покрывают от 1 мм до 36 мм.Быстрая установка, быстрое переключение и простота использования, наша технология представляет собой разумное вложение. Приглашаем вас ознакомиться с нашим ассортиментом.
Узнать больше
Сервис
В Tornos мы понимаем, что нашим клиентам необходимо поддерживать высочайший уровень производительности. Наши инженеры обучены обеспечивать бескомпромиссное обслуживание и поддержку клиентов.
Узнать больше
Социальные сети
Посетите наше сообщество на этой странице.
.