Параметры лазерной резки металла на волоконном лазерном станке | Основы подбора лазерного излучателя
Статья содержит в себе рекомендации, параметры и настройки лазерной резки металла при помощи лазерного станка с волоконным (иттербиевым) излучателем, отличие волоконного станка от плазмы, а также рекомендации по подбору мощности излучателей относительно материала, экономические выгоды.
Для качественной и предельно точной лазерной резки металла мы рекомендуем в качестве излучателя использовать иттербиевый (волоконный) лазерный излучатель (ссылка на каталог с излучателями), более точного излучателя в современном мире не существует.
Основные отличительные черты волоконного излучателя от плазмыВолоконный излучатель | Плюсы/минусы | Плазма | Плюсы/минусы | |
1 | Ширина лазерного луча по линии резки, не более от 0,03 -1 мм.![]() | плюс | Ширина плазменного луча по линии, 1-3 мм. и более, в зависимости от толщины материала | минус |
2 | Конусность вырезанных деталей – отсутствует | плюс | Конусность вырезанных деталей, от 15-30° | минус |
3 | Резка небольших отверстий (менее 12 мм.) в материалах толщиной более 6-10 мм. | плюс | Резка небольших отверстий (менее 12 мм.) в материалах толщиной более 6-10 мм. – не возможна | минус |
4 | Детали с внешними и внутренними углами при любой толщине материала – идеальна | плюс | Детали с прямыми углами сделать не возможно.![]() | минус |
5 | При правильном подборе мощности, скорости, и давления газа, облой исключен, допонительной обработки детали не требуют | плюс | При резке образуется большое количество облоя, что требует дополнительной обработки детали шлифовальными кругами | минус |
Цена на комплект станок+излучатель выше, чем на станок+плазма | минус | Стоимость станка плазма+станок значительно ниже, чем иттербиевый (волоконный) станок | плюс | |
7 | Экологичность при обработке в разы выше, так как при резке волоконным излучателем меньшее сжигание металла при резки, что значительно снижает выбросы в атмосферу.![]() | плюс | Большие выхлопы угарного газа при резке+высокое потребление электроэнергии | минус |
Выше в таблице мы произвели сравнение двух видов резки металла, при помощи лазерного волоконного (иттербиевого) станка и станка плазменной резки. Выбор очевиден, если требования к товару высокие, по точности размеров отверстий и прямых углов, по однородности торца детали, без зубцов и облоя, по конусности торца, то стоит остановить свой выбор на волоконном (иттербиевом) станке.
Если нужны детали без требований точности, с допустимыми погрешностями в размерах +3-+5 мм., под сварку, то следует остановить свой выбор на плазменном станке.
Итак, чтобы подобрать волоконный (иттербиевый) излучатель, нужно определиться с толщинами металлов для лазерной резки. К примеру, если 80% материалов составляет сталь толщиной от 8-10 мм. , а 20% нержавеющая сталь и цветные металлы, то мы рекомендуем рассматривать к приобретению станок с мощностью не менее 1500 Ватт.
Излучатель с мощностью от 1,5 кВт, сможет резать сталь с адекватными параметрами скорости, что экономически будет выгодно. Сталь толщиной 8-10 мм., сможет порезать станок с мощностью 1000 Ватт, но скорость резки будет достаточно низкой (см. таблицу ниже), что влечет за собой большой расход газа и большое количество времени на обработку детали, что становится экономически не выгодно, на рынке лазерной резки.
Рассмотрим другие обстоятельства выбора излучателя, к примеру 80% материалов из стали до 6 мм., 10% времени материалы из металла 8-10 мм., при таких обстоятельствах, в целях экономии, выгодно приобрести лазерный станок с максимальной мощностью 1000 Ватт, потому что скорость обработки металла на станке с мощностью 1 кВт., достаточно высокая на толщинах до 6 мм., а 10% рабочего времени, как факультатив, можно резать и 8, и 10 мм., для более подробного анализа, можно воспользоваться таблицей данных скоростных характеристик ниже.
Таблица скорости реза металла
Мощность источника | 500Вт | 750Вт | 1000Вт | 1500Вт | 2000Вт | 3000Вт | 4000Вт | 6000Вт | 8000Вт | 10000Вт | ||
Материал / Газ | Толщина, мм | Размер сопла, мм. | Скорость, м/мин | |||||||||
Углеродистая (Кислород) | 1 | 1.2 | 8 | 9 | 10 | 22 | 26 | 34 | 38 | 42 | 46 | 50 |
2 | 1.5 | 4 | 5 | 6,2 | 6,8 | 7,2 | 7,5 | 7,8 | 8,2 | 36 | 9 | |
3 | 2.0 | 2,6 | 2,8 | 3 | 3,6 | 4 | 4,4 | 5 | 5,5 | 6 | 6.![]() | |
4 | 2.0 | 1,6 | 1,8 | 2,2 | 2,8 | 3,2 | 3,8 | 4,4 | 5 | 5.5 | 6.1 | |
5 | 2.0 | 1 | 1,8 | 2,4 | 2,8 | 3,2 | 3,4 | 3,6 | 3.8 | 4.2 | ||
6 | 2.5 | 1 | 1,6 | 2 | 2,4 | 2,8 | 3,2 | 3,4 | 3.6 | 4.![]() | ||
8 | 2.5 | 0,8 | 1,2 | 1,4 | 1,6 | 2,2 | 2,6 | 3 | 3.3 | 3.5 | ||
10 | 2.5 | 0,7 | 1 | 1,2 | 1,6 | 2 | 2,4 | 2.8 | 3.2 | |||
12 | 3 | 0,6 | 0,8 | 1 | 1,4 | 1,8 | 2 | 2.2 | 2.4 | |||
14 | 3 | 0,6 | 0,9 | 1 | 1,2 | 1,3 | 1.![]() | 1.6 | ||||
16 | 4 | 0,5 | 0,8 | 0,8 | 1 | 1,1 | 1.3 | 1.4 | ||||
18 | 4 | 0,7 | 0,7 | 0,9 | 1 | 1.2 | 1.3 | |||||
20 | 4 | 0,6 | 0,8 | 0,9 | 1.1 | 1.35 | ||||||
22 | 4 | 0,5 | 0,7 | 0,8 | 1 | 1.![]() | ||||||
24 | 4 | 0,4 | 0,6 | 0.8 | 0.9 | |||||||
26 | 5 | 0.5 | 0.65 |
Мощность источника | 500Вт | 750Вт | 1000Вт | 1500Вт | 2000Вт | 3000Вт | 4000Вт | 6000Вт | 8000Вт | 10000Вт толщина до 40 мм. | ||
Нержавеющая (Азот) | 1 | 1.5 | 12,4 | 18,5 | 23,8 | 26,4 | 30 | 34 | 38 | 41,4 | 57 | 65 |
2 | 1.5 | 4,7 | 5,1 | 10,8 | 11,9 | 12,7 | 15,4 | 24,4 | 28,6 | 38 | 58 | |
3 | 1.5 | 0,7 | 1,2 | 2,3 | 4,1 | 6,1 | 8,6 | 12,8 | 15,8 | 22 | 30 | |
4 | 1.![]() | 0,8 | 1,3 | 2,2 | 4,2 | 5,5 | 7,4 | 9,4 | 16 | 22 | ||
5 | 1.5 | 0,7 | 1,2 | 2 | 4,3 | 5,1 | 6 | 11 | 17 | |||
6 | 1.5 | 1 | 1,8 | 3,1 | 3,8 | 4,7 | 5 | 15 | ||||
8 | 1.5 | 0,9 | 2 | 2,4 | 3,3 | 3.![]() | 8.5 | |||||
10 | 1.5 | 0,8 | 1,1 | 1,3 | 1.9 | 5.9 | ||||||
12 | 1.5 | 0,5 | 0,7 | 1,1 | 1.5 | 3.4 | ||||||
14 | 1.5 | 0,6 | 0,8 | 1.1 | 2.3 | |||||||
16 | 1.5 | 0,6 | 0. | 1.6 | ||||||||
Мощность источника | 500Вт | 750Вт | 1000Вт | 1500Вт | 2000Вт | 3000Вт | 4000Вт | 6000Вт | 8000Вт | 10000Вт | ||
Алюминий (Азот) | 1 | 1.5 | 5,2 | 6,4 | 8,4 | 16 | 22 | 34 | 38 | 42 | 57 | нет данных |
2 | 1.![]() | 2,2 | 3,4 | 6,6 | 8,4 | 15 | 21 | 25,5 | 38 | нет данных | ||
3 | 1.5 | 1,4 | 3,8 | 5,5 | 7,6 | 11,5 | 14,6 | 22 | нет данных | |||
4 | 1.5 | 1,4 | 2,6 | 4 | 5,2 | 5,8 | 16 | нет данных | ||||
5 | 1.5 | 1,7 | 3,3 | 4,4 | 4,9 | 11 | нет данных | |||||
6 | 1.![]() | 0,9 | 2,1 | 3,4 | 4,1 | 7 | нет данных | |||||
8 | 1.5 | 0,9 | 1,3 | 2 | 3.6 | нет данных | ||||||
10 | 1.5 | 0,6 | 1,1 | 1,7 | 2.5 | нет данных | ||||||
12 | 1.5 | 0,5 | 0,8 | 1.![]() | нет данных | |||||||
14 | 1.5 | 0,4 | 0,6 | 1.1 | нет данных | |||||||
16 | 1.5 | 0,5 | 0.9 | нет данных | ||||||||
Мощность источника |
500Вт | 750Вт | 1000Вт | 1500Вт | 2000Вт | 3000Вт | 4000Вт | 6000Вт | 8000Вт | 10000Вт | ||
Медь (Азот) | 1 | 1. | 5,2 | 6 | 8 | 12 | 14 | 22 | 26 | 32 | 57 | нет данных |
2 | 1.5 |
1,8 | 3,2 | 4 | 6 | 8 | 10 | 12 | 38 | нет данных | ||
3 | 1.5 |
1 | 2,2 | 3,4 | 5,2 | 6 | 6,4 | 22 | нет данных | |||
4 | 1. |
1,4 | 1,8 | 4 | 4,8 | 5,4 | 16 | нет данных | ||||
5 | 1.5 |
1,2 | 1,8 | 2,6 | 3,2 | 11 | нет данных | |||||
6 | 1.5 |
0,6 | 1,4 | 1,8 | 2,2 | 7 | нет данных | |||||
8 | 1. |
0,6 | 0,9 | 1,2 | 3.6 | нет данных | ||||||
10 | 1.5 |
0,4 | 0,6 | 2.5 | нет данных | |||||||
12 | 1.5 |
0,4 | 1. | нет данных |
Equipment / Unimach
Согласие на обработку персональных данных
Пользователь, посещающий Сайт unimach.ru (далее – «Сайт»), вправе принять настоящее Согласие на обработку персональных данных (далее — Согласие). А акцептом оферты является проставление Пользователем «галочки» и нажатие кнопки «Дать согласие на обработку персональных данных» в размещенной для этой цели веб-форме раздела Сайта, касающегося предоставления персональных данных в формах обратной связи. Пользователь дает свое согласие ООО «НПК Морсвязьавтоматика» (далее – ООО «НПК МСА», «Оператор»), которому принадлежит Сайт, расположенное по адресу: 192174, г. Санкт-Петербург, ул. Кибальчича, д.26, лит. Е, на обработку своих персональных данных со следующими условиями:
Данное Согласие дается на обработку персональных данных как без, так и с использованием средств автоматизации.
Согласие на обработку персональных данных Пользователя дается с целью использования ООО «НПК МСА» данных для осуществления обработки запросов, коммуникаций и аналитики действий Пользователей на Сайте. Согласие предоставлено для использования следующих персональных данных: фамилия, имя, отчество; номера контактных телефонов; адреса электронной почты; место работы и занимаемая должность; адрес; сведения о местоположении; тип, версия, язык операционной системы, браузера; тип устройства и разрешение его экрана; страницы, открываемые пользователем; ip-адрес и др.
С персональными данными могут быть совершены следующие действия: сбор, запись, систематизация, накопление, хранение, уточнение (обновление, изменение), извлечение, использование, передача (распространение, предоставление, доступ), обезличивание, блокирование, удаление, уничтожение.
Сбор персональных данных Пользователей Сайта производится через формы обратной связи, которые Пользователь заполняет собственноручно. Также персональные данные могут быть получены Компанией, если их владелец указывает их в электронном письме, отправляемом в Компанию на адреса, указанные на Сайте. Оператор обеспечивает сохранность персональных данных и принимает все возможные меры, исключающие доступ к персональным данным неуполномоченных лиц.
Также на Сайте происходит сбор и обработка обезличенных данных о Пользователях (в т.ч. файлов «cookie») с помощью сервисов интернет-статистики (Яндекс Метрика и Гугл Аналитика и других). Обезличенные данные Пользователей, собираемые с помощью сервисов интернет-статистики, служат для сбора информации о действиях Пользователей на Сайте, улучшения качества сайта и его содержания. Оператор обрабатывает обезличенные данные о Пользователе в случае, если это разрешено в настройках браузера Пользователя (включено сохранение файлов «cookie» и использование технологии JavaScript).
Передача персональных данных третьим лицам осуществляется на основании законодательства Российской Федерации, договора с участием субъекта персональных данных или с его согласия.
Обработка может быть прекращена по запросу субъекта персональных данных.
Срок обработки персональных данных является неограниченным. Пользователь может в любой момент отозвать свое согласие на обработку персональных данных, направив Оператору уведомление с помощью электронной почты на электронный адрес Оператора [email protected] с пометкой «Отзыв согласия на обработку персональных данных».
Как правильно настроить фокус на лазерном станке
Перед тем как начать резать металл необходимо установить оптимальное фокусное расстояние между лазерной головкой и разрезаемым материалом.От правильности настройки фокуса зависит ширина и качество реза, образование грата, скорость резки.
Фокусное расстояние
Если двумя словами, то фокусное расстояние это расстояние от линзы до фокусной плоскости. В нашем случае за фокусную плоскость принимаем заготовку – металлический лист.
Положение сфокусированного пятна (фокальной точки) над фокусной плоскостью называется положительной, а положение под заготовкой называется отрицательной.
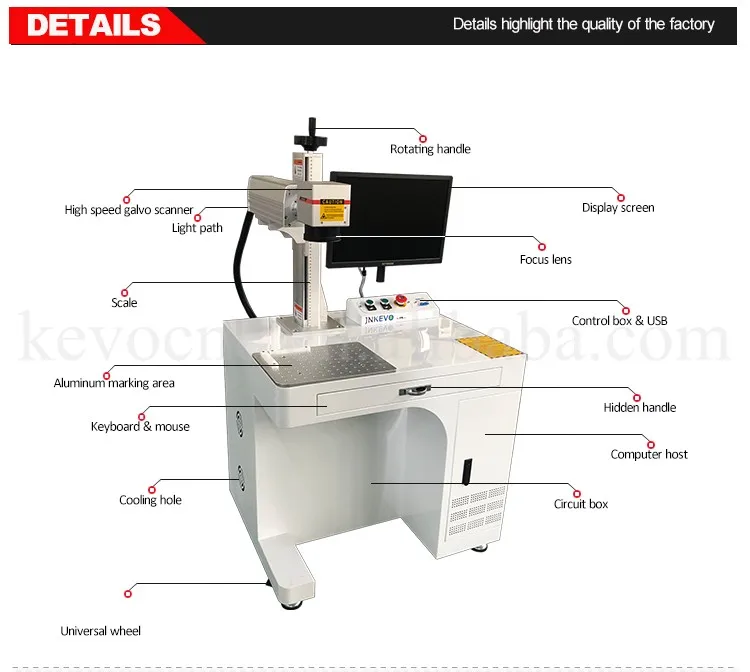
Значение положения фокуса
Значение фокусного расстояния влияет на размер размера пятна на поверхности или внутри металической заготовки: так при увеличении фокусного расстояния увеличивается диаметр пятна, а ширина реза увеличивается.Положительный фокус
Это фокусное расстояние при котором луч лазера фокусируется выше поверхности заготовки.Как правило такая фокусировка используется для кислородной резки заготовок из углеродистой стали.
Такой способ резки реализует удаление шлака и помогает кислороду достигать нижней поверхности заготовки для участия в полной реакции окисления.
Чем больше значение положительного фокуса, тем больше диаметр пятна лазера на поверхности заготовки,
тем больше нагрев и добавление тепла вокруг щели, и тем более гладкой и яркой режущей поверхности из углеродистой стали.
Отрицательный фокус
То есть фокус резания находится в заготовке. В этом режиме, поскольку фокус находится далеко от режущей поверхности, ширина резания является относительно большей, чем точка резания на поверхности заготовки.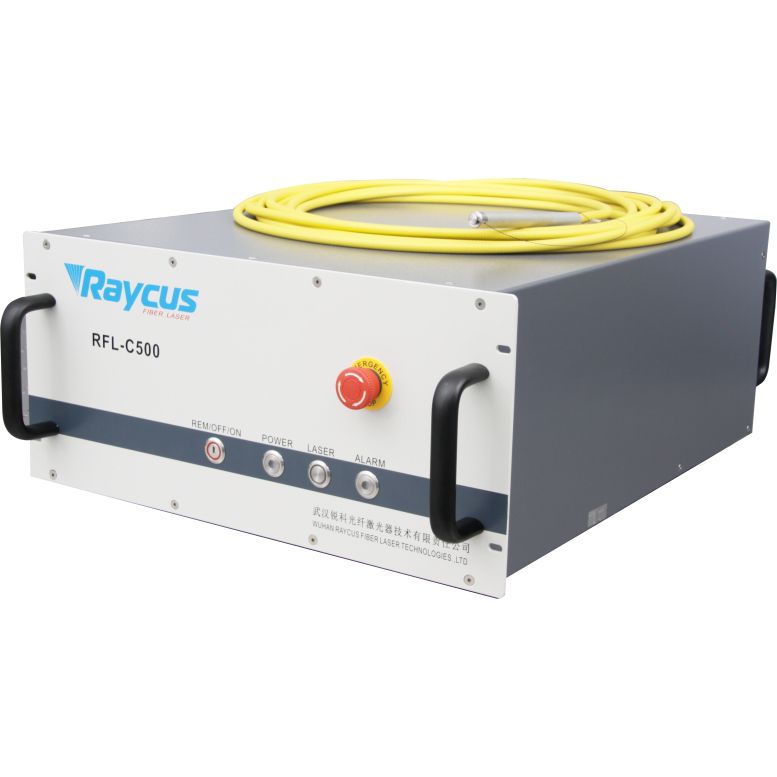
При резке нержавеющей стали целесообразно использовать резку с отрицательным фокусом, поверхность реза имеет однородную текстуру и хорошее поперечное сечение.
Перфорация пластины перед резкой. Поскольку перфорация имеет определенную высоту, перфорация использует отрицательный фокус, который может гарантировать, что размер пятна в позиции перфорации является наименьшим, а плотность энергии – наибольшей.
Нулевой фокус
То есть фокус резания находится на поверхности заготовки. Как правило, режущая поверхность, близкая к фокусу, является относительно гладкой, в то время как нижняя поверхность вдали от режущего фокуса является шероховатой. Этот случай в основном используется для непрерывной лазерной резки тонких пластин и импульсного лазерного испарения с высокой пиковой мощностью для резки слоев металлической фольги.Выбор фокусировки для лазерной резки определяется не материалом режущей пластины (нержавеющая сталь, углеродистая сталь), а методом резки (окислительная резка, расплавленная резка).
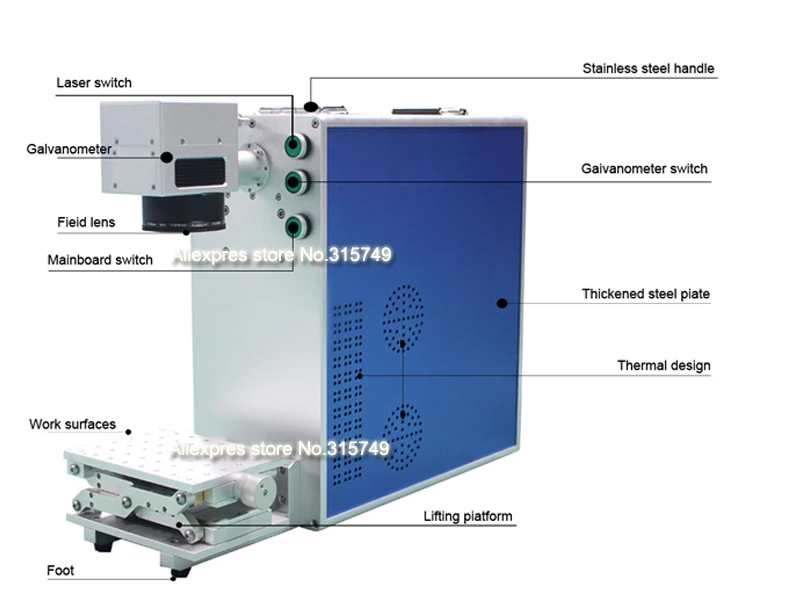
Итоги
В станке лазерной резки металла необходимо использовать разные режимы фокусировки для обработки разных заготовок. Благодаря разным позициям фокусировки и способам регулировки разных типов режущих головок пользователи могут комбинировать различные эффекты положительной и отрицательной фокусировки при резке нержавеющей и углеродистой стали, комбинируя свои собственные потребности в обработке. Чтобы выбрать подходящий метод фокусировки, мы можем в полной мере оценить преимущества станков для лазерной резки!4 способа улучшить кромку при лазерной резке
Качество красок в лазерной резке значительно улучшилось за десятилетия, и многие из этих улучшений исходят из четырех областей: лучшие материалы, сопла, контроль процесса и качество луча.
Рисунок 1
Достижения в системах управления, мониторинг процесса и качество луча улучшают режущие кромки даже в чрезвычайно толстом материале.
Лазеры стали настоящей рабочей лошадкой по обработке металлов, и они никогда не были более производительными. Они вырезают детали на беспрецедентных скоростях, что делает автоматизацию обработки материалов еще более важной. Вся высокая скорость резания в мире может не оказывать существенного влияния на общее время цикла, если лазер простаивает в течение длительного времени, ожидая, что операторы будут загружать листы и выгружать детали.
Подобное мышление также относится к качеству кромок. Качество кромки, конечно, субъективно. Механик будет смотреть на лазерную резку и обнаруживать, что качество кромки не очень хорошее. С другой стороны, сварщик может смотреть на ту же самую часть и видеть гладкое, последовательное, качественное преимущество. Несмотря на это, требования к приложениям диктуют то, что считается «качеством», лазер может закончить резку пакета деталей в мгновение ока, но что делать, если эти части необходимо отправить на вторичную операцию снятия заусенцев?
Резка со скоростями в столькими дюймами в минуту велика, но общее время цикла может не сильно измениться, если детали попадают в заторможенное узкое место удаления грата. Чтобы обеспечить лучший рез, операторы исторически должны были изменять параметры программы резки, такие как скорость резки вокруг острых углов, но иногда они обнаруживали, что это заняло больше времени, чем просто отправка всего прогона через систему удаления грата.
С конца 1990-х и начала 2000-х годов многое изменилось. Режущие лазеры эволюционировали до такой степени, что во многих случаях даже толстые части, выходящие со стола резки, могут пропускать вторичные операции снятия грата — не требуется ручная настройка параметров резания. Эти улучшения были достигнуты главным образом благодаря достижениям в четырех областях: качество материала, технология сопел, контролю процесса и качеству луча (см. Рисунки 1 и 2).
- Улучшенный материал
В течение последних 15 лет более мощные лазеры позволили изготовителям разрезать более толстый материал, но иногда ухудшалось качество края. Вначале трудно было получить толстый материал с гладкой поверхностью фрезеровки и соответствующей композицией состава металла, которая бы позволила лазеру разрезать ровный гладкий край.
Производители стального проката видели рост спроса и начали выпускать более подходящий для лазерной лазерный резки материал. Сегодня для предприятий, обрабатывающих 0,5-дюймовую и даже более толстую сталь, легко доступны материалы для лазерного качества уровня фрезеровки.
- Лучшие сопла
Способность мощных лазерных машин вырезать более толстые материалы вынуждали режущие сопла также совершенствоваться. Усовершенствования включали соосные проточные сопла для резки стали кислородом. При резке кислородом поток вспомогательного газа очень низкий — от 0,5 до 2,0 кубических футов в минуту. Коаксиальные или двойные форсунки допускают плавный и постоянный поток газа в разрез, что обеспечивает хорошее качество кромок в стали толщиной от 0,5 до 1,25 дюйма.
Эта технология не ограничивалась кислородной резкой. Азотная газовая резка стала более популярной благодаря мощной лазерной способности разрезать на высоких скоростях тонкие материалы. Резка азотом оставляла свободную от оксида кромку, которая была готова к сварке или окраске.
Недостаток азота заключался в том, что для удаления материала требовался очень высокий расход газа, поэтому ему требовалось сопло большого диаметра и подача азота под высоким давлением для резки на более высоких скоростях и в более толстых материалах. Чтобы решить эту проблему, усовершенствования сопел помогли создать оптимальную динамику потока. Углы конуса внутри сопла создавали коаксиальный поток для резки под высоким давлением с наименьшим количеством турбулентности в самой зоне резки. Эти исследования и разработки сыграли огромную роль в разрешении лазерам разрезать детали с использованием азота, оставив их без шлаков и с последовательным и гладким краем.
- Лучшее управления процессом
По мере того как лазеры становились более мощными и начали резать более толстые материалы, становилось все труднее достичь свободной от шлаков, с хорошим качеством кромок деталей. Специалисты по лазерной резке увидели это и начали заставлять контроллеры больше, чем просто запускать программу; Они сделали обработку более простой и надежной без необходимости использования опытного оператора.
Фигура 2
Сегодняшние лазеры могут вырезать разнообразные толщины во многих материалах и обеспечить чрезвычайно хорошее качество кромки, гладкое и достаточно однородное, чтобы его не нужно было отправлять через вторичную операцию снятия грата.
Высокомощные лазеры имели возможность резки тонких материалов с высокой скоростью, используя азот в качестве вспомогательного газа, оставляя без оксида края. Однако вначале некоторые из этих частей по-прежнему нуждались в вторичной операции по удалению небольших кусков шлака, оставшихся на острых углах, когда все еще на высокой мощности, лазер замедлялся, чтобы сделать резкий поворот. Чтобы устранить вторичное снятие заусенцев, программистам пришлось бы сменить режим работы лазера, чтобы использовать меньшую мощность, скорость и частоту на каждом углу. Это заняло много времени на стороне программирования, и поэтому вскоре они поняли, что более эффективно очищать края после резки, а не тратить время на программирование.
Сегодняшние контроллеры автоматизируют все это. Они подсчитывают величину мощности, скорости и частоты, чтобы понижаться в зависимости от скорости, с которой режущая голова движется в угол, и повышаться, когда она разгоняется за углом. Это позволяет избежать перегрева и препятствует образованию грата ков в углах (см. Рис. 3).
Тем не менее, лазер не может достичь хорошего качества кромок без хорошей прошивки. Старые машины сработали с запрограммированным временем пирсинга. Если пирсинг не пробивал материал в запрограммированный промежуток времени, машина все же начинала резать, только для создания плохих и, возможно, непригодных для использования деталей. Таким образом, операторы устанавливали чрезмерно длинные периоды пирса, чтобы обеспечить проникновение насквозь. Это добавило много секунд для каждого пирса, что продлевало общее время цикла для прогона.
В старых системах фактическая резка также выполнялась заданной программой, которая не могла адаптироваться к непредвиденным изменениям условий резания. Если в результате работы создавались бтакованные детали, операторы по-прежнему обнаруживали, что выбрасывают детали с плохими краями и вырезают дополнительные детали.
Именно здесь мониторинг процесса помог заполнить нужную ситуацию. Используя датчики света, встроенные в машину, контроллеры теперь контролируют лазерную резку в реальном времени. Мониторинг процесса позволяет машине «смотреть» пирсинг и резку, а также корректировать, чтобы процесс мог продолжаться для обрабатывать используемых деталей. При контроле пирса контроллер наблюдает за пирсом, ощущает, когда он проходит через материал, и только затем начинает резку деталей.
Мониторинг процесса также включает обнаружение разгара кромок и образования плазмы. Используется при резке стали с кислородом, чтобы детектировать разгара кромок от перегрева, когда материал горит неустойчиво, что приводит к плохому качеству кромок. Контроллер видит это и делает необходимые корректировки, чтобы слегка охладить разрез, временно уменьшая мощность и замедляя работу, прежде чем продолжить с большей скоростью.
Подобно обнаружению разгара кромок, плазменная детекция используется с резкой азота. При резке нержавеющей стали или углеродистой стали азотом лазер расплавляет сталь, а вспомогательный азотный газ эвакуирует расплавленный материал, оставляя свободный от оксида край. Однако, если лазер слишком быстро режет, он поворачивает на резкий угол, или его фокус немного уходит, вы рискуете «потерять срез» — получить непрорез- и создаете непригодные детали.
Когда это происходит, азот и расплавленный материал создают плазму. Датчик обнаружения плазмы обнаруживает эту частоту света и подсчитывает, что рез скоро будет потерян, прервется. В этот момент машина замедляет скорость подачи на заданное расстояние до того, как будет возвращаться обратно без потери разреза. Результат: система продолжает производить хорошие детали с чистыми краями.
- Новые лазеры, новые параметры луча
OEM-производители потратили миллионы долларов в исследования и разработки, чтобы улучшить качество лазерного луча. Благодаря лучшему лучу лазер позволяет более стабильно и качественно отрезать сталь, нержавеющую сталь и алюминий. На протяжении десятилетий большая часть этой работы была сфокусирована на CO2-лазерах, но в последние годы R & D также подтолкнула исследования и разработки для твердотельных лазеров, включая волоконный лазер и, в последнее время, технологию с прямыми диодами.
CO2-лазер изменил технологию изготовления металла. Он добрался до нас, где мы находимся сегодня. Волоконный лазер зарекомендовал себя следующим поколением лазерной резки для промышленности. Благодаря более низкой стоимости обслуживания, простоте эксплуатации и возможности резки на гораздо более высоких скоростях, чем CO2-лазер, волоконный лазер является самым быстрорастущим вариантом для многих новых лазерных покупок. Он производит кромку в тонких материалах, очень похожих на высококачественные края, которые производит лазер СО2; но по мере увеличения толщины материала качество краев уменьшается.
Рисунок 3
Контроллеры используют мониторинг процесса для обнаружения характеристик пирсинга и резки в реальном времени. Они вносят необходимые изменения, чтобы обеспечить наилучшее качество кромки, даже вокруг острых углов. Лучше излучение, сопла, контроль процесса и материал обеспечивают качество.
Качество лазерного луча измеряется произведением параметров излучения или BPP (beam parameter product). Лазеры CO2 обычно имеют BPP от 8 до 9 мм • мрад, что позволяет лазеру резать сталь, нержавеющую сталь и алюминий с очень хорошим качеством кромок.
Волоконные лазеры обычно имеют BPP от 1 до 3 мм • мрад, что позволяет лазерам резать очень быстро в более тонких материалах, но качество кромок в более толстых материалах ухудшается.
Именно поэтому CO2-лазер был выбором производителей, которые обрабатывают более толстые материалы. Однако появляется новая технология, которая изменяет свойства луча волоконного лазера, позволяя ему резать толстую мягкую сталь с тем же качеством, что и CO2, даже с половинной мощностью. Это позволит изготовителям приобретать волоконный лазер для обработки их полного диапазона типов материалов и толщин без специальной оптики и без изменения объектива.
Способность эмулировать качество кромки CO2 на волоконных машинах была и продолжает выполняться путем использования Специальных линз и зеркал, которые изменяют ширину реза, позволяя большему количеству вспомогательного газа проникать в разрез и уменьшать плотность мощности пятна. Однако, изменяя значение BPP, волоконный лазер может достичь качества луча CO2-лазера с правильной настройкой луча и без необходимости в дополнительных настройках и расходных материалах. Взглянув в будущее, новая технология, без сомнения, добавит еще одну морщину на лазер Рынок резки. Некоторые производители разработали твердотельные системы, известные как лазеры с прямым диодом, которые обеспечивают дополнительную эффективность и уникальные преимущества для обработки. Хотя пока неясно, как эта технология повлияет на текущие варианты лазера, она уже показала способность производить превосходное качество краев.
Лазерная Технология всегда меняется. Более быстрые, более эффективные системы продолжают появляться — и еще больше впереди.
Источник: http://www.thefabricator.com/article/lasercutting/4-ways-to-a-better-laser-cut-edge
Ранее по теме:
Поделиться ссылкой:
- Нажмите, чтобы поделиться на Twitter (Открывается в новом окне)
- Нажмите здесь, чтобы поделиться контентом на Facebook. (Открывается в новом окне)
- Нажмите, чтобы поделиться в Google+ (Открывается в новом окне)
- Нажмите, чтобы поделиться на LinkedIn (Открывается в новом окне)
- Нажмите, чтобы поделиться в Telegram (Открывается в новом окне)
- Нажмите, чтобы поделиться записями на Pocket (Открывается в новом окне)
- Нажмите, чтобы поделиться в Skype (Открывается в новом окне)
- Нажмите, чтобы поделиться записями на Tumblr (Открывается в новом окне)
- Нажмите, чтобы поделиться в WhatsApp (Открывается в новом окне)
- Нажмите, чтобы поделиться записями на Pinterest (Открывается в новом окне)
- Нажмите, чтобы поделиться на Reddit (Открывается в новом окне)
Как мы запускали оптоволоконный лазерный станок с источником 1000W IPG в Саратове
Оптоволоконный лазерный станок для резки металла GCR3015 с источником 1000W IPG
Наконец-то дошли руки до публикации постов о запуске лазерного оборудования. Выкладываем фото-видео отчет о проведении работ по запуску в эксплуатацию лазерного оптоволоконного станка.
В Саратов мы прибыли незадолго до окончания выгрузки оптоволоконного станка на производственных площадях клиента. Были «слегка » удивлены тому что, помещение оказалось мягко говоря, небольшого размера. Наша задача – разместить махину с шестиметровым труборезом и сменным столом и при этом оставить пространство для безопасной работы на других участках производства. Компания-заказчик занимается изготовлением телекоммуникационных шкафов и распределительных коробок. Вся площадь цеха заставлена прессами, штампами, гибочниками, сварочными постами. Пришлось существенно изменить расстановку механического оборудования. Это был один из первых станков с труборезом и сменным столом в нашем портфолио, поэтому пригласили инженера с завода-изготовителя для того, что бы избежать непредвиденных ситуаций в процессе подключения и настройки. Впрочем, пусконаладка прошла без проблем.
Выгрузка и установка труборезного модуля к оптоволоконному лазерному станку LF3015GCR 1000W IPG
Хорошо, что в помещение удалось завести кран. Иначе было бы проблематично маневрировать этот шестиметровый труборез.
Установка станины
Станина станка выставляется на регулируемые ножки
Установка портала
При поставке портал был демонтирован. Так как станок в сборе не помещался в стандартный морской контейнер. После того станина была выставлена по уровню, мы установили портал. Впоследствии мы тщательнейшим образом настроили перпендикулярность оси X относительно направляющих оси Y
Установка портала.
Монтируем сервомоторы
За перемещение портала по оси Y отвечают сервомоторы мощностью 1800Вт компании Yaskawa. Мощные высокоточные направляющие HIWIN шириной 35мм обеспечивают стабильность при перемещении. Безлюфтовые планетарные редукторы NEUGART в паре с косозубой рейкой APEX гарантируют высокую точность обработки.
Установка источника лазерного излучения ЛК-1000 IPG
Сердцем системы является источник лазерного излучения IPG ЛК-1000 российской компании ИРЭ-Полюс. Источник мощностью 1000Вт позволяет раскраивать углеродистую сталь толщиной до 10мм, а нержавейку до 5мм. Уверен, все уже наслышаны об отличительных особенностях отечественной разработки от китайских аналогов. На наш взгляд, основными являются: стабильность выходной мощности, наличие защиты от «обратных отражений», молниеносная реакция производителя в гарантийных случаях.
Сборка окончена. Настало время отладки и обучения
Тестируем работу станка в режиме DRY CUT
youtube.com/embed/KGEC9Irt-Uc” frameborder=”0″ allowfullscreen=””/>
В процессе настройки трубореза изготавливаем необходимые заказчику детали
Раскрой листового метала на оптоволоконном лазерном станке
Цель достигнута – клиент доволен
Заказчик остался доволен машиной и нашей работой. Оператор быстро освоил программное обеспечение и методику подбора технологических параметров.
Наш отзыв о лазерном оптоволокнном станке LF3015GCR 1000W IPG
Машина в целом понравилась. Богатая базовая комплектация, хорошее качество компонентов и сборки, тяжелая сварная станина. Если у вас появились какие то вопросы относительно технических данных этого станка пишите в комментариях, ответим максимально подробно.
Узнать цену В список
Узнать цену В список
Узнать цену В список
Узнать цену В список
Оптоволоконный лазерный станок со сменным столом для резки металла LF3015GC/3000 Raycus G.Weike (Китай)
Современный станок лазерной резки с оптоволоконным лазерным излучателем и электронной системой управления ЧПУ. Широко используется в различных отраслях промышленности – авиации, судостроении, автомобилестроении, приборостроении, раскрое металла, рекламе и пр.
Эффективно применяется для резки различных металлов, таких как нержавеющая, углеродистая, легированная, кремнистая сталь, алюминиевые листы, латунь, медь, оцинкованные пластины и т.д.
Портал 3-го поколения изготовлен с применением авиационных технологий в сфере металлообработки и сформирован прессованием 4300 тонн. Благодаря таким преимуществам авиационного алюминия, как хорошая твердость, легкий вес, устойчивость к коррозии и окислительным процессам, низкая плотность, скорость обработки значительно возрастает.
Все электрические компоненты от производителя SCHNEIDER ELECTRONIC интегрированны в стойку управления ЧПУ. Из предустановленного П.О. происходит управление лазерным комплексом, а также калибровка необходимых узлов перед запуском в работу оборудования.
Программное обеспечение CypCut имеет простое управление, ориентированное на пользователя. Реализованы функции, существенно упрощающие и оптимизирующие процесс раскроя. Это такие функции как:
- пауза,
- обратный ход по контуру,
- быстрый переход к любой врезке,
- быстрое изменение точки врезки,
- начало резки с любого места контура,
- оптимальный выбор начала резки контура,
- расчёт динамических параметров перемещений,
- контроль соответствия обрабатываемой детали исходному чертежу,
- быстрая загрузка готовых чертежей и программ и пр.
Режимы прожига, гравировки и резки настраиваются оператором по отдельности до начала резки. Оператору не придется останавливать процесс обработки материала, чтобы перенастроить станок и ввести новые установки, т.к. переключение между режимами происходит автоматически, что увеличивает производительность раскройного комплекса.
Для получения качественных острых и прямых углов мощность лазерного излучения автоматически регулируется в зависимости от скорости передвижения оптической головки. При нулевой скорости движения оптической головки (в момент остановки на углу) выходная мощность излучения равняется минимальной мощности, заданной в настройках, что предотвращает выгорание углов.
Для указанных в библиотеке материалов ПО CypCut производит автоматический расчет времени обработки деталей, полезного использования материала, количества деталей; стоимости одного часа резки, одного метра реза, одной пробивки. Полученные данные существенно упрощают расчет стоимости отдельных деталей и сборок, например, при резке сторонних заказов и расчете себестоимости продукции и отходов.
Функция перемещения прыжками в процессе резки, функция обратной резки, позволяющая вернуться к не прорезанному участку в случае нарушения условий процесса, линейная /круговая интерполяция и функция компенсации ширины реза, функция автоматического или ручного комбинирования.
Во встроенной библиотеке материалов хранятся рекомендуемые настройки станка под определенный материал. Есть функция создания новых материалов. При выборе материала из библиотеки происходит автоматическая загрузка параметров в модули станка. Таким образом, вы избавляетесь от необходимости рутинного ввода различных значений и экономите своё время, повышая производительность.
Функция дистанционной диагностики неисправностей систем станка позволяет свести к минимуму время простоя станка и исключить выездные расходы в случае решения сервисных вопросов, связанных с неправильной настройкой оборудования.
Следует выделить ряд преимуществ П.О:
- Управление и настройка необходимых узлов лазерного комплекса;
- Отдельные параметры режимов раскроя и врезки;
- Автоматическая оптимизация задания раскроя;
- Улучшенная функция перфорации – FLYCUT;
- Оптимальное расположение деталей – NESTING;
- Функция охлаждения контура реза – LEAD POS;
- Функция микро-перемычек – MICRO JOINT;
- Функция обработки сложных контуров – PULSECUT;
- Функция вырезки контуров, лежащих на одной прямой – LINESECUT;
- Управление параметрами лазерного источника;
- Защита режущей головы;
- Дистанционная диагностика;
- Дружелюбный интерфейс.
Автоматическая оптимизация задания раскроя включает в себя ряд автоматических функций П.О:
Технология FLYCUT
Данная технология оптимизирует обработку тонких металлов. Система осуществляет раскрой не отдельными объектами, а распознает все контуры, лежащие на одной прямой и после режущая голова в высоком темпе проходит весь лист по определённой прямой. Данная функция значительно экономит время обработки при перфорации листа.
Технология NESTING
Позволяет разместить, максимально необходимое количество деталей на обрабатываемом листе, также учитывается параметр минимизации отходов. Таким образом, экономится время на подготовке задания. Также опция высчитывает время обработки данного задания. Это позволяет точно высчитать себестоимость готового изделия.
Технология LEAD POS
Обеспечивает расстановку охлаждающих точек по контуру детали для предотвращения перегрева обрабатываемой поверхности и облоя в зоне реза. Данная функция актуальна для раскроя металла на низких скоростях, углах и мелких элементах.
Технология MICRO JOINT
Автоматическое размещение перемычек по контуру раскроя. Благодаря данной опции готовое изделие не выпадает после раскроя, а также предотвращает разворот детали перпендикулярно заготовке. Актуально для изготовления декоративных деталей из нержавеющей стали, где царапины недопустимы.
Технология PULSECUT
Технология PulSeCut предназначена для высококачественной обработки сложных контуров. Функция позволяет обрабатывать определённые участки контуров (углы, близко расположенные участки) в импульсном режиме. Переключение между PulSeCut и обычным режимом осуществляется автоматически в соответствии с настройками. PulSeCut позволяет установке переключаться между непрерывным и импульсными режимами резки даже в пределах одного контура.
Технология LINESECUT
LineSeCut осуществляет вырезку не каждой детали по отдельности, а всех контуров, лежащих на одной прямой, что существенно сокращает время обработки тонколистовых металлов. Оптическая головка в высоком темпе построчно проходит весь лист, производя вырезку контуров на соответствующем отрезке. Экономия времени особенно заметна при резке перфорированных решеток.
Также доступны функции компенсации толщины лазерного луча, для достижения абсолютно точных размеров изготавливаемой продукции. Возможность выставлять точки вреза вне контура обработки заготовки под произвольным углом и на разных расстояниях, как в автоматическом так и в ручном режимах.
Управление координатной системой обеспечивается как со стойки ЧПУ, так и с помощью беспроводного пульта, что значительно облегчает позиционирование режущей головы по отношению к заготовке, а также упрощает работу оператора станка.
Функция определения положения листа
Эта функция позволяет автоматически определять позиционные выступы и угол поворота заготовки на столе станка и скорректировать программу резки, если это потребуется. Если материал расположен на паллете не ровно, то кромки материала будут определены с помощью детектора и материал будет программно повёрнут в необходимые координаты.
Новое поколение модулей безопасного следования
Режущая головка сохраняет постоянное расстояние с заготовкой в процессе резания, это снижает риск столкновений. Станок перестанет резать при малейшем столкновении с препятствием. Это снижает уровень аварийности и улучшает производительность резания.
Система автоматического отслеживания зазора
Система автоматически отслеживает зазор между лазерной головой и листом металла, предотвращает пропуски при раскрое тонких металлов. Позволяет раскраивать даже «горбыль».
Интеллектуальная система сигнализации
Сигналы со всех узлов, имеющих обратную связь, поступают на интерфейс через центр управления, когда оборудование работает с ошибкой, и по коду ошибки можно определить неисправность.
НОВЫЕ ТЕНДЕНЦИИ В ЛАЗЕРНОМ РАСКРОЕ МЕТАЛЛА
НОВЫЕ ТЕНДЕНЦИИ В ЛАЗЕРНОМ РАСКРОЕ МЕТАЛЛА
А.Г. Игнатов, эксперт Министерства образования в научно-технической сфере, член КНЭ РФ и стран СНГ по лазерам и лазерным технологиям: 2005–2021 гг., АО «ЛЛС» (СПб), [email protected].
2018 ГОД БЫЛ ЕЩЕ ОДНИМ РЕКОРДНЫМ ГОДОМ В СЕКТОРЕ ПРОДАЖИ ПРОМЫШЛЕННЫХ ЛАЗЕРОВ — НА УРОВНЕ ~5,1 МЛРД ДОЛЛ. МИРОВОЙ РЫНОК ЛАЗЕРОВ ДЛЯ МАКРООБРАБОТКИ В 2018 ГОДУ СОСТАВИЛ 2789 МЛН ДОЛЛ. [1, 2] И В 2019 Г. ДОЛЖЕН ДОСТИГНУТЬ 2906 МЛН ДОЛЛ. ЛИДЕРОМ БЫЛА ЛАЗЕРНАЯ РЕЗКА С 41% [2–4].
УНИВЕРСАЛЬНЫЙ ЛАЗЕР
Несмотря на целый ряд преимуществ применения специального оборудования, не оставляются попытки создавать универсальные инструменты, и один из возможных вариантов — это применение одного и того же лазера для целого спектра технологий. Спрос на универсальный и гибкий инструмент — это огромный шанс для лазера [5].
Полный спектр производственных процессов определяется, например, в немецкой промышленности стандартом DIN 8580, который включает процессы: литья, формирования, отделения и присоединения, покрытий и изменения свойств материалов (рис. 1) [5].
Рис. 1. Спектр использования лазерных технологий [5].
Волоконные лазеры имеют хорошее качество луча и открывают новые возможности обработки, о которых только мы мечтали, работая с более ранними типами твердотельных лазеров. Однако недавние работы показали, что высокое качество луча не всегда обеспечивает оптимальную обработку для некоторых применений [6]. На сегодняшний день большинство источников волоконных лазеров используют фиксированное качество луча, что требует компромиссов при их применении в гибкой производственной среде, учитывающей различные материалы, толщины и процессы. Эти проблемы не могут быть решены даже с использованием зум-оптики и дорогих фокусирующих головок [6]. Приходится разрабатывать новые подходы.
Так, доктор Марк Ричмонд — менеджер по мощным CW волоконным лазерам в SPI Lasers (Великобритания) на вэб-семинарах представляет variMODE, новую функцию, позволяющую выбирать качество выходного луча и профиль режима в реальном времени, чтобы оптимизировать обработку для каждого приложения, повысить производительность резки, сварки, сверления [6].
Известно, что одной из проблем применения мощных волоконных лазеров сегодня является отраженное излучение. Для защиты от него применяются, например, оптические изоляторы — это компоненты, которые пропускают свет только в одном направлении и блокируют его в другом, что имеет решающее значение для защиты лазерных источников [7]. В поисках малой и высокоэффективной конструкции оптического «амортизатора» исследователи технологического института Technion-Israel (Хайфа, Израиль) в сотрудничестве с университетом Центральной Флориды (Орландо, FL), Мичиганским университетом (Ann Arbor, MI) и китайским университетом Хунани (Changsha, Китай) разработали оптический изолятор на основе быстро вращающейся стеклянной сферы, которая регулирует пропускание света в зависимости от его направления [7].
РАСКРОЙ МЕТАЛЛИЧЕСКОГО ЛИСТА
В области лазерных технологий резки в последние годы произошел скачок в повышении мощности лазерных источников: с 3–6 кВт до 12 кВт, например, от известных зарубежных производителей: BYSTRONIC, BLM GROUP, BODOR, TRUMPF, AMADA, MAZAK, PRIMA POWER и др. Кроме повышения производительности увеличена и максимальная толщина разрезаемых сталей: с 15 до 30 мм. А сегодня уже происходит повышение мощности лазеров до 15–25 кВт в машинах для лазерной резки сталей толщиной до 30–70 мм. VNITEP (Россия) представил на выставке «Металлообработка» в Москве систему «Навигатор» с лазером 15 кВт (см. образцы на рис. 2), HAN`S LASER анонсировал машину резки с лазером 20 кВт [8], компания Bodor Laser выпустила сверхмощную лазерную режущую машину серии Bodor S мощностью 25 кВт для резки стали толщиной до 70 мм [9]. На выставке «ФОТОНИКС ВЕСТ» (США) руководители IPG отметили, что в компании спрос на лазеры ≥ 10 кВт увеличились на ≥ 40% по сравнению с прошлым годом [10].
Рис. 2. Образцы лазерной резки из стали и меди толщиной до 30 и 6 мм соответственно, алюминиевых и латунных сплавов толщиной до 12 мм, выполненные компанией VNITEP (Россия), представленные на российской выставке «МЕТАЛЛООБРАБОТКА–2019»
И хотя наибольший объем разрезаемых сталей приходится на диапазон толщин до 6–15 мм, лазерная резка, много лет доминировавшая в диапазоне малых толщин, начинает активно вытеснять плазменную резку в диапазоне средних толщин. Однако с увеличением скорости резки остро встает вопрос автоматизации вспомогательных операций: загрузки и выгрузки, складирования заготовок и деталей. Желательно, чтобы производительность лазера соответствовала производительности машины в целом.
Повышение мощности в машинах лазерной резки соответственно повышает требования к чистоте оптических элементов в режущих головках. Малейшая грязь на линзах при лучевой мощности более 6 кВт (особенно при использовании волоконных лазеров) приводит к их перегреву, деформациям и выходу из строя.
Так, Al Julian, директор компании Piranha, отмечает: «Пылинки или пятна на коллиматорных и фокусирующих линзах внутри режущей головки поглощают длину волны волоконного лазера гораздо быстрее, чем длины волн CO2-лазера. Это заставляет линзы нагреваться очень быстро, а их перегрев заставляет оптику изгибаться. В лучшем случае резка будет остановлена. В худшем случае это может приводить к большому ущербу». Автор [11] на основе опыта эксплуатации двенадцатикиловаттной машины лазерной резки рекомендует на больших мощностях использовать режущие головки на основе металлооптики c водоохлаждаемыми медными зеркалами, более стойкими для рассматриваемых жестких условий (рис. 3).
Рис. 3. Режущая головка Piranha на основе водоохлаждаемой медной металлооптики [11]
Новое — хорошо забытое старое. Так, еще в 80-х годах в Казани Юрием Усановым были разработаны и использовались режущие головки на основе медной металлооптики на CO2-лазерах КМЗ «Союз» и болгарских «Хебрах» с мощностью излучения от 1–2 до 10–20 кВт.
В Ленинграде в то же время в НИИЭФА им. Д. В. Ефремова на CO2-лазерах «Ижора-М» и «Титан» мощностью до 10–15 и 30–50 кВт соответственно успешно использовалась медная металлооптика в объективах разработки Александра Скрипченко. Об использовании линз на подобном уровне мощности тогда, да и сегодня, и речи не могло быть. Да и на малых мощностях в условиях грязного производства объективы на металлооптике были более практичными и долговечными.
Надо заметить, что увеличение мощности — не единственный путь для повышения толщин разрезаемых материалов, производительности и качества лазерной резки. Эти задачи возможно решать и более дешевыми способами, например, путем сканирования, регулирования свойств фокального пятна и совершенствованием устройства режущей головки.
Так, Fraunhofer IWS и AMADA применили поперечное сканирование луча в пределах ширины реза на машине Amada Ventis мощностью 4 кВт, что повысило скорость резки, а также качество реза (рис. 4, 5). «Цель состоит в том, чтобы максимально использовать доступную мощность лазера для процесса резки», — пояснил д-р Andreas Wetzig, руководитель подразделения лазерной абляции и резки в Институте материаловедения и лучевой технологии Фраунгофера. «В идеале вы должны использовать 100% доступной мощности лазера; на самом деле вы используете менее 50% без процедуры управления профилем луча. По нашему мнению, лучше приложить усилия для управления профилем луча, чем увеличивать мощность лазера»,— добавил он [12].
Рис. 4. Резка 12 мм из нержавеющей стали на станке Amada Ventis, без Locus Beam Control (слева) — а и с включенным LBC (справа) — б [12].
Рис. 5. Система Locus Beam Control от Amada может создавать различные траектории раскрутки луча [12].
Технология управления профилем луча Fraunhofer IWS использует два одиночных сканаторных зеркала для очень быстрого перемещения лазерного луча в пределах ширины реза в направлениях x и y. Лучом можно манипулировать на частотах до 4 кГц. Система Locus Beam Control (LBC) от Amada может создавать различные траектории раскрутки луча (рис. 5), что повышает скорость и качество резки для различных материалов и толщин [12].
nLIGHT (Vancouver, WA) разработала технологию быстрой настройки размера фокального пятна от ~ 100 мкм до ~ 300 мкм в волоконном лазере Corona [12] (рис. 6). Эксперименты показали повышение качества резки для различных металлов. Лазер Corona мощностью 4 кВт значительно увеличил производительность по сравнению с традиционными волоконными лазерами при резке мягкой и нержавеющей стали, алюминия и меди толщиной листового металла до 1 дюйма, т.е. позволил оптимизировать лазерную резку металла широкого диапазона толщин.
Рис. 6. Пространственные профили луча четырехкиловаттного волоконного лазера Corona вблизи фокуса режущей головки, записанные CMOS-камерой — а, поперечное сечение волокна и его профиль с тремя зонами — б [13, 14].
Форма пучка обеспечивается в пределах волокна, сохраняя при этом все преимущества по производительности, стабильности, эффективности и надежности волоконного лазера. Мощность лазера регулируется для каждого параметра диаметра луча. Дополнительным преимуществом лазера Corona является его быстрый переход с самых маленьких до крупных диаметров пятна (за время менее 30 ms). Волоконный лазер при этом продолжает работать на полную мощность во время изменения диаметра пятна. Corona позволяет использовать оптимальные характеристики луча для каждого этапа процесса резки, а не только для резки различных материалов с разными толщинами. Например, различные параметры у лазера Corona можно использовать во время прямолинейной резки и при прохождении поворотов [13, 14].
Такое преобразование параметров пятна с более равномерной плотностью распределения излучения весьма перспективно и для других видов обработки материалов, например, при сварке и наплавке, поверхностной термообработке.
Рис. 7. Сравнение резки низкоуглеродистой стали стандартным четырехкиловаттным волоконным лазером с волокном 100 мкм и четырехкиловаттным волоконным лазером «Корона» [13, 14].
На рис. 7 приведено сравнение резки низкоуглеродистой стали в среде кислорода стандартным четырехкиловаттным волоконным лазером с волокном 100 мкм и четырехкиловаттным волоконным лазером Corona. На верхнем графике приведена скорость резки, а на нижнем графике — значения шероховатости; на фотографиях образцов показан внешний вид кромки после резки, с изображениями сечения луча в фокальной плоскости. На рис. 8 показана деталь, вырезанная четырехкиловаттным волоконным лазером «Корона» из низкоуглеродистой стали толщиной 1 дюйм [13, 14].
Рис. 8. Пример резкичетырехкиловаттным лазером «Корона» детали из низкоуглеродистой стали толщиной 1 дюйм [13].
Авторы [6], рассматривая на вэб-семинаре лазерную резку листового металла, также показывают, как волоконные лазеры с переменным качеством пучка способны повысить качество лазерной обработки как для «прокалывания», так и для резки толстых и тонких материалов.
Одним из наиболее важных аспектов производственного процесса в металлообработке является получение хорошего качества резки деталей. Уже больше 1,5 лет компания Lockport (США, Нью-Йорк), чтобы сэкономить и не повышать мощность лазерного источника, использовуют высокоскоростное сопло Eco на восьмикиловаттной машине TruLaser 5030 (с волоконным лазером, рис. 9). Компания воспользовалась этой технологией на мягкой стали 7-го калибра толщиной до 0,5 дюйма и 7-го калибра из нержавеющей стали толщиной до 1 дюйма [15].
«Технология с азотом намного быстрее и имеет лучшее качество резки по сравнению с кислородом на углеродистой стали, — объясняет Cameron Lambert, техник, занимающийся эксплуатацией установки. Это позволяет гораздо быстрее резать толстую углеродистую и нержавеющую сталь, а в некоторых случаях — быстрее 100 дюймов в минуту» [15].
Технология установки сопла режущей головки над поверхностью материала резко сократила потребление азота по сравнению со стандартной резкой. Во время процесса резки основной поток газа проходит через центр сопла вместе с лазерным лучом. Остальная часть газа формирует вторичный поток, концентрирующийся в пропиле, чтобы помочь удалить расплавленный материал более эффективно [15].
При использовании стандартного сопла много газа теряется неоправданно из-за большого расстояния от сопла до разрезаемого материала. Во время стандартного процесса резки требуются более высокие скорости потока, чтобы достичь нужного давления в пропиле и удалить расплавленный материал, что способствует увеличению потери газа. С соплом Highspeed Eco рукав изолирует пропил и позволяет направлять газ непосредственно в него [15].
Рис. 9. Машина лазерной резки TruLaser 5030 на базе волоконного лазера мощностью 8 кВт с соплом Highspeed Eco [15]
Применение насадки Highspeed Eco позволило использовать только один тип сопла в диапазоне всех применимых толщин для мягкой и нержавеющей стали. Это сокращает время установки и сводит к минимуму вероятность человеческой ошибки при замене сопел. Помимо обеспечения нужного качества резки компания увеличила ее скорость от 50% до 60%. Кроме того, очистка после резки была также сокращена на 50–60% [15].
При традиционной лазерной кислородной резке с ее экзотермической реакцией на кромках остаются окислы, которые затем по технологическим требованиям должны быть удалены. Резка в азоте является более предпочтительным методом, поскольку позволяет уменьшить эти вторичные операции и создать готовый продукт непосредственно под порошковое покрытие или сварку. Азот может применяться теми пользователями, которые ищут простое решение для устранения окисления при резке тонких материалов и не требуют высокой чистоты азота [16].
Системы AMADA 2 (второго поколения) обеспечивают подачу чистого и сухого азота для резки, а также позволяют использовать смесители газов для создания идеальной среды, что значительно расширяет возможности при обработке различных материалов (рис. 10) [16].
Например, часто при лазерной резке алюминия качество кромки неприемлемо без последующего снятия заусенцев. Высокое качество лазерной резки волоконным лазером может быть достигнуто путем добавления к азоту небольшого количества кислорода. В результате обеспечивается последующая хорошая свариваемость и возможность нанесения порошкового покрытия на вырезанные заготовки без последующей обработки кромок [16].
Рис. 10. Система AMADA 2 [16].
Рис. 11. Образец лазерной резки металлических листов толщиной более 35 мм с технологическим пакетом EdgeTec [17].
Газовый смеситель может также использоваться для резки углеродистых сталей средней толщины. Этот диапазон может включать 11-й и 7-й калибры, т.е. 1/4 дюйма и 3/8 дюйма. Эти материалы могут быть раскроены с азотом или, еще лучше, со смесью газов, что может привести к 20–30%-му увеличению скорости резки и 70%-му снижению потребления газов. Это обеспечивается также специальными соплами и соответствующим уровнем чистоты газа, скоростью потока [16].
Один из технологических пакетов компании Precitec — EdgeTec — позволяет производить процесс лазерной резки толстых металлических листов (более 35 мм) с наилучшим качеством (рис. 11). Как дополнение к режущей головке PRECITEC PROCUTTER, EdgeTec имеет более широкий диапазон настройки положения фокуса лазерного излучения, что позволяет применять единственную лазерную головку как универсальное решение для задач, требующих высокой скорости резки [17].
Рис. 12. Схема оптимальной загрузки/разгрузки машины для лазерной резки листовых материалов [16].
Новый технологический пакет Precitec — PierceTec обеспечивает качественный процесс врезки и перфорации с высокой скоростью и отличным качеством. Датчики PierceTec постоянно отслеживают процесс пробивки и оптимизирует параметры лазера на основе полученных данных в режиме реального времени. Данное решение минимизирует зону термического влияния, пробивает отверстия минимального диаметра лазером. Все, что должен сделать пользователь, — запустить программу после указания типа и толщины материала [17].
При рассмотрении автоматизации, которая будет лучше всего соответствовать требованиям производства, следует оценивать текущие и будущие потребности. Ранее цикл лазерной резки превышал 3–4 минуты и скорость автоматизации не была столь важным фактором, как в настоящее время. Волоконные лазеры теперь могут создавать циклы < 1 мин, и задача автоматизации — обеспечить такой высокоскоростной процесс [16].
Для достижения автоматизации этих коротких циклов система одновременно выполняет множество задач. Например, система будет осуществлять одновременную загрузку/выгрузку деталей с/на поддоны, чтобы без ожидания ставить под резку следующий лист — см. рис. 12 [16]. Еще одна область автоматизации, которая должна отвечать вашим требованиям, это хранение материалов. Гибкая система должна обеспечивать оптимальную загрузку нужных материалов на поддоны, а затем их загрузку на машину лазерной резки и разгрузку готовых деталей [16].
В 2018 году на выставке EuroBLECH в Ганновере (Германия) была представлена машина лазерной резки Eagle польской компании iNspire с мощностью лазера до 15 кВт и вырезанный на ней образец из нержавеющей стали толщиной 60 мм [18]. По словам Marcin Ejma, руководителя Eagle, ее устройство автоматической смены паллет с приводом от серводвигателя может переключаться в течение 9 секунд, а система Eagle, оснащенная линейными двигателями с прямым приводом по осям X, Y и Z, обеспечивает ускорение 6 G. Конечно, ускорение может создавать сильную вибрацию. Чтобы смягчить ее, машина построена с гашением вибрации. Для этого основание машины изготовлено из полимербетона. Это тот же материал, который используется в координатно-измерительных машинах. Поперечный мост изготавливается из углеродного волокна. На этом мосту расположена режущая головка, которая рассчитана на мощность 15 кВт, имеющая небольшой вес. Волоконная лазерная оптика режущей головки чрезвычайно чувствительна, особенно в диапазонах более высокой мощности. Одно, даже очень маленькое загрязнение на оптике режущей головки может вызвать серьезные проблемы при подключении к лазеру сверхвысокой мощности. Для предотвращения загрязнения внутри головки была разработана конструкция без движущихся частей внутри [18].
Marcin Ejma сказал, что не может раскрыть специфику технологии по конкурентным причинам (конструкция головки запатентована). Хотя любой, кто использует лазер, заметит что-то новое, когда будет заменять защитное стекло в окне головки: оно расположено более чем на 14 дюймов над соплом. Это увеличенное расстояние предназначено для защиты окна от загрязнений, которые могут возникнуть в процессе прошивки и резки, в результате чего оператору не нужно часто менять защитное стекло [18].
Рис. 13. На автомобильном заводе Daimler каждая из трех лазерных головок системы имеет свой собственный портал (а), а разборку вырезанных деталей выполняет пара роботов (б) [20].
С целью увеличения производительности компанией VNITEP (Россия) разработан и запатентован станок с двумя независимо работающими режущими головками. Каждая лазерная головка может раскраивать на общем или отдельном листе. Запатентована также система «крыло» — для перемещения по каждой оси используется один синхронный линейный электропривод, в отличие от функциональных аналогов, с двумя и более двигателями на оси, что исключает необходимость синхронизации. В результате существенно повышается надежность работы оборудования; для установки моделей с рабочей зоной до 4950×2050 не требуется специального фундамента. Обеспечивается высокая жесткость и виброустойчивость станка, в т.ч. и за счет композитной Y-балки, которая значительно легче и прочнее, чем металлическая, а наличие сменных паллет челночного типа без подъема нижней паллеты (раскрой производится на двух уровнях) позволяет производить быструю замену заготовок. Время перезакатки паллет 15 секунд) [19].
Известная немецкая компания Daimler применяет машины лазерной резки с тремя независимыми режущими головками, расположенными на разных порталах (рис. 13а), а разборку вырезанных деталей выполняет пара специальных антропоморфных роботов (рис. 13б) [20].
UNIMASH (Россия), например, предоставляет заказчику возможность выбора левостороннего или правостороннего исполнения станка LaserCut Professional M2 — за счет реализации двустороннего размещения челночного стола с двумя паллетами. Лазерный оптический резак LH-105 имеет давление до 25 атм. [21].
Кристоф Блемкер из компании TRUMPF работает над применением искусственного интеллекта (ИИ) в лазерной обработке. Вместе со своими коллегами он надеется сделать, например, машину TruLaser Center 7030 еще лучше. «Первоначально мы даже не собирались включать искусственный интеллект в TruLaser Center 7030. Но затем мы поняли, что достигли пределов того, чему мы можем научить машину с помощью простых алгоритмов и ручного анализа данных, поэтому пару лет назад мы решили, что полностью автоматизированная машина тоже должна начать обучать себя»,— говорит Блемкер [22].
Рис. 14. Подводная лазерная резка. Фото: LZH [24].
Центр 7030 TruLaser — первая машина, на которой должен осуществляться полный автоматизированный цикл: от загрузки листов, их раскроя до выгрузки и складирования готовых деталей. Для этого она оснащена блоком автоматизации с встроенными датчиками. Выполняется анализ сбоев работы машин со всего мира. Результаты сравнения данных могут быть перенесены и использованы для модернизации и машинного обучения с одной машины на все другие машины того же типа [22].
Полностью автоматизированные лазерные машины являются лишь одним из примеров того, как TRUMPF продвигается вперед с искусственным интеллектом. Кэтрин Пфафф, руководитель отдела новых и цифровых бизнес-услуг, разработала решение по замене запасных частей. Оно является частью приложения Easy Order и позволяет клиентам идентифицировать продукты с помощью фото или сканирующей камеры, чтобы определить, какая часть нуждается в замене. Процесс распознавания деталей работает благодаря искусственной нейронной сети, которую TRUMPF заполняет фотографиями различных предметов, которые можно заказать. Приложение экономит время и особенно полезно для новых сотрудников, которые менее знакомы с машинами TRUMPF [22].
Компания Mazak предложила технологию прямого диодного лазера (DDL), которая является эксклюзивной прорывной лазерной платформой и, как утверждают авторы [20], обеспечивает более высокую производительность и надежность по сравнению с традиционными волоконными или другими твердотельными лазерными системами. DDL предлагает на 45% больше энергии по сравнению с CO2-лазера- ми и обеспечивает более высокие темпы поглощения энергии, увеличение плотности энергии. Если сравнивать режимы, DDL имеет 40-процентное увеличение плотности мощности по сравнению с волоконными лазерами, что связано с меньшим диаметром пучка, который предлагает более интенсивное излучение, что в конечном счете увеличивает скорость резки [23].
ЛАЗЕРНАЯ РЕЗКА ПОД ВОДОЙ
Много десятилетий назад выполнялась программа по разработке процесса подводной резки электронным лучом. Этот проект был заморожен главным образом из-за низкой экономической эффективности. Позже, когда были разработаны мощные лазеры, этот проект возник опять, но уже с лазерным тепловым источником. Барьером оставался вопрос рентабельности. Сегодня ученые Лазерного центра в Ганновере (LZH; Hannover, Germany), независимого, некоммерческого исследовательского института, хотят ответить, может ли лазерный луч использоваться для эффективного демонтажа ядерных реакторов, для разрезания подводных его конструкций (рис. 14) [24].
Во всем мире есть 76 ядерных реакторов, которые должны быть выведены из эксплуатации в 2019 году, а затем будут демонтированы и утилизированы. 183 реактора будут списаны в 2020-х и 127 единиц в 2030-х годах. Проблема весьма актуальная, требует решения с повышением эффективности и снижением затрат [24].
Эта часть проекта AZULa («Automated separation of reactor pressure vessel installations using underwater laser technology») будет включать разработку процесса лазерной резки и создание компактной режущей головки для использования в радиологической, активированной и загрязненной подводной среде. Система должна включать прямой демонтаж ядерных установок (сосудов реактора под давлением. Затраты на окончательную очистку водного бассейна при лазерной резке значительно уменьшаются по сравнению с резкой водяной струей или обычными механическими методами. Кроме того, механические методы резки подвержены заклиниванию инструмента, что не может произойти с лучом при лазерной резке. Лазерная резка представляется более дешевой альтернативой при демонтаже компонентов ядерных реакторов. Проект AZULa осуществляется в сотрудничестве с Orano (Paris, France) и спонсируется Федеральным министерством образования и научных исследований по гранту проекта с координатором: Gesellschaft für Anlagen und Reaktorsicherheit (GRS; Köln, Germany) [24].
Рис. 15. Машина лазерной резки Sawpower’s Bystronic BySprint Fiber 3015 laser была установлена в Зимбабве [25].
Лазерная резка при утилизации атомных реакторов и подводных лодок рассматривалась и в СССР как очень перспективный процесс. Были выполнены ряд исследований, правда, не под водой, а на воздухе. Предполагался также лазерный раскрой на металлолом списанных судовых конструкций гражданского и военного назначения. Тема очень актуальна и сегодня.
Лазерная резка находит широкое применение не только в ведущих странах Европы, Америки и Азии. Она уже начинает применяться и в Африке, в Зимбабве (рис. 15). Несколько лет назад известный главный редактор журнала ILS David Belforte сделал полушутя прогноз о том, что Африка может быть следующей областью промышленного роста и, возможно, превзойдет Азию [25].
ЗАКЛЮЧЕНИЕ
В лазерной резке сегодня происходит фактически революция — толщина обрабатываемых сталей увеличивается до 30–70 мм, вытесняя плазменную резку из этого диапазона толщин, а мощность используемых на производстве волоконных лазеров, соответственно, увеличивается с 3–6 до 15–25 кВт, что расширяет не только диапазон использования машин, но и значительно повышает их производительность.
Литература
- What goes up. ANNUAL LASER MARKET REVIEW & FORECAST 2019 / G. OVERTON, A. NOGEE, D. BELFORTE, J. WALLACE, B. GEFVERT // Laser Focus World. January 2019. P. 40–45, 47, 49–54, 56–58, 60–61, 64–65.
- Буров Н.В., Игнатов А.Г. Мировой рынок фотоники и лазерных технологий: 2010–2019 // Ритм машиностроения. 2019. No 4.С. 60–67
- BELFORTE D. A. 2018 was another record year, contending with turmoil // Industrial Laser Solutions. 2019. JANUARY/FEBRU- ARY. Р. 9–11.
- Мировой рынок систем лазерной обработки материалов до- стиг рекордных $ 19,8 млрд / https://www.lasersystemseurope.com/.
- THE LASER: One universal tool for manufacturing / T. GRAF, M. ABDOU AHMED, P. BERGER, V. ONUSEIT, R. WEBER // In- dustrial Laser Solutions. 2019. JANUARY/FEBRUARY. P. 13–15.
- Марк Ричмонд, менеджер SPI Lasers, представляет variMODE на вэб-семинарах // URL:http://marketing.spilasers. com/webinars 13/08/2019.
- Разработан оптический изолятор, применение которого очень важно для защиты лазерных источников от «отраженки»
- Буров Н.В., Игнатов А.Г. Рынок лазеров в России и странах СНГ // Ритм машиностроения. 2019., No 5.С. 32–43.
- Bodor Laser 25000W сверхмощная лазерная резка, мировая премьера // URL: https://ru.bodor.com/News/317.html, 20/05/2019.
- IPG видит признаки восстановления рынка лазеров в Китае // URL: http://лазер.рф/2019/05/30/13106/, 30/05/2019.
- SUE ROBERTS. Dual fiber lasers right-size cutting power // URL: WWW. THEFABRICATOR. COM/ARTICLE/ LASERCUTTING/DUAL-FIBER-LASERS-RIGHT-SIZE- CUTTING-POWER 05/02/2019.
- Резать лучше всех толстолистовые плиты // URL: http://лазер. рф/2019/06/13/13328/, 13/06/2019.
- Fiber laser technology improves metal cutting / Dahv Kliner, Brian Vict — nLIGHT, Vancouver, WA, www.nlight.net // Industrial Laser Solutions. 2018. September/October. Р. 23–26.
- Fiber laser has all-fiber tunable beam quality / DAHV A. V. KLINER, ROGER L. FARROW, BRIAN VICTOR // Laser Focus World, April 2019, Р. 45–48.
- IMPROVING cutting speed and edge quality / N. STANCZYC // Industrial Laser Solutions. SEPTEMBER/OCTOBER 2018. P. 15–16.
- How to select the right setup for your fiber laser cutting needs / DUSTIN DIEHL // Industrial Laser Solutions, SEPTEMBER/OCTOBER 2018. P.17–19.
- Технологии PierceTEC и EdgeTEC для лазерной резки // URL: https://ckspa.ru/news/-lazernoy-rezki.html 12/08/2019.
- Рецепт для увеличения мощности лазерной резки / Компании: Fairmont Machinery и Eagle // URL: http://xn —80akfo2a. xn — p1ai/2019/01/18/10977/18/01/2019; https://www.thefabricator.com/product/lasercutting/technology-spotlight-a-recipe-for-scaling-up-laser-cutting-power.
- НАВИГАТОР — комплексы VNITEP для высокоскоростного раскроя металла с волоконным лазером и линейными двигателями // URL: https://vnitep.ru/.pdf?rev=2%2023/08/2019.
- TIM HESTON. Laser blanking reaches the automotive OEM. The story of laser blanking’s success at Daimler // URL: WWW. THEFABRICATOR. COM/ARTICLE/ LASERCUTTING/LASER-BLANKING-REACHES-THE- AUTOMOTIVE-OEM 04/05/2019.
- LaserCut Professional M2 — лазерный раскройный комплекс UNIMASH // URL: https://unimach.ru/- professional-m2/23/08/2019.
- ДАУМ К. С помощью этих проектов TRUMPF превращает ис- кусственный интеллект в реальность // URL: HTTPS://WWW. TRUMPF.COM/EN_INT/MAGAZINE/WITH-THESE-PROJECTS-TRUMPF-TURNS-AI–INTO- REALITY/10.07.2019.
- LobitM.Five Laser-Cutting Trends of 2019. The future of laser-cutting technology is here with these five trends leading the way / Mazak Optonics Corp. // URL: https://www.mazakoptonics.com/of-2019/12/06/2019
- Feasibility study tackles effective laser beam cutting underwater / David Belforte // Industrial Laser Solutions. MARCH/APRIL 2019. Р.6.
- Laser cutting in Southern Africa/David Belforte // Industrial Laser Solutions. MARCH/APRIL 2019. Р. 5.
Основы лазерной гравировки | SCHMIDT
Лазерная гравировка – это процесс, при котором лазерный луч смещает материал с поверхности маркируемой детали. Удаление материала создает глубину. Насколько глубока будет ваша отметка, будет зависеть от настроек лазера, типа маркируемого материала и количества проходов, которые лазер сделает во время маркирования.[Узнайте о других формах лазерной маркировки]
Приложения для лазерной гравировки
Лучшее применение для лазерной гравировки – это когда вам нужен прочный знак или вы планируете выполнить какую-либо постобработку.Например, если вы маркируете что-либо, что будет подвержено сильному износу, например металлическую трубу или сверло, или если вы собираетесь закрашивать метку, вам нужно будет использовать лазерную гравировку. .
Настройки лазерной гравировки
При лазерной гравировке или нанесении любой другой лазерной метки с помощью волоконного лазера обычно требуется настроить пять параметров: мощность, частоту, скорость, углы штриховки и количество петель. Понимание того, как они работают вместе, является ключом к поиску правильных настроек для гравировки.
[В чем разница между волоконным лазером класса I и класса IV?]
Мощность
Power – это, пожалуй, самый простой параметр для понимания. Это мощность вашего лазера, обычно измеряемая в ваттах. Чем выше мощность, тем мощнее лазер. Чем мощнее лазер, тем глубже будет ваша отметка, при условии, что все остальные настройки такие же.
Частота
Чтобы понять частоту, нам сначала нужно понять лазерный луч в волоконном лазере.Лазерный луч не является постоянным потоком энергии. Вместо этого лазер излучает свет импульсами через равные промежутки времени. Частота определяет частоту импульсов. По мере уменьшения частоты количество импульсов уменьшается, но выход энергии на импульс увеличивается. По мере увеличения частоты количество импульсов увеличивается, но выход энергии на импульс уменьшается.
Скорость
Настройка скорости определяет скорость, с которой лазер перемещается по отметке. Чем ниже скорость, тем больше материала перемещается.Чем выше скорость, тем меньше материала перемещается.
Уголки люка
Углы штриховки – это углы, под которыми лазер наносит маркировку. Обычно эти штриховки оставляют на вашей отметке узор из линий. Если вас не волнует внешний вид вашего знака или если эти линии желательны, это может не иметь значения.
Количество петель
Последняя настройка – это количество петель. Счетчик петель определяет, сколько раз лазер пройдет над вашей отметкой. Чем больше петель, тем глубже.
Вы можете увеличить глубину, увеличив мощность вашего лазера, уменьшив скорость маркировки, снизив частоту или используя комбинацию этих трех факторов. Однако при этом выделяется много тепла, что может привести к появлению темных шероховатых пятен. Вы даже можете деформировать маркируемый материал.
Сетка для лазерной гравировки
[Посмотрите, как мы создаем эту сетку на нашем веб-семинаре “Основы лазерной гравировки”.]
Чтобы показать вам взаимосвязь между всеми этими настройками, мы создали сетку для лазерной гравировки.Каждая отметка была сделана с помощью 100-ваттного лазера, четырех штрихов и одной петли.
В каждом ряду самые глубокие отметки находятся слева. В каждом столбце самые глубокие отметки находятся вверху. Но гравировка – это не только глубина. Изменение настроек повлияло на внешний вид и качество отметок.
Чем меньше скорость, тем темнее следы. Более высокие скорости имели более короткое время цикла и приводили к более светлым отметкам. Более высокие частоты производили неровные отметки. То, как скорость, частота и другие параметры влияют на вашу оценку, в конечном итоге будет зависеть от вашего приложения, но вы можете использовать эти результаты в качестве руководства при настройке параметров.
A Руководство по настройкам лазерной маркировки
Объект «Настройки метки» используется для изменения настроек лазера в последовательности маркировки.
Несколько объектов настройки меток могут использоваться в последовательности маркировки, особенно если для маркировки однолинейных шрифтов и шрифтов True Type с объектами Shape или Vector Drawing в одном макете каждый тип маркировочного объекта обычно требует различных настроек лазера для достижения наилучшей производительности.
Просто перетащите объект «Настройка метки» над помечаемыми объектами, для которых требуются эти настройки метки.Программное обеспечение обработает последовательность маркировки по порядку и, следовательно, установит параметры отметки, а затем пометит объекты ниже с этими параметрами до тех пор, пока не будет обнаружен другой инструмент установки отметок
Мощность
Указывает уровень мощности лазера в процентах. Часто это компромисс между скоростью и мощностью. Если метка слишком агрессивна при полной мощности, попробуйте увеличить скорость перед уменьшением мощности, чтобы увидеть, можно ли улучшить время цикла.
Скорость
Свойство Speed представляет векторную скорость в миллиметрах в секунду, которую перемещает лазерный луч при маркировке объекта.Использование низкой скорости создаст глубокую четко очерченную метку, если скорость будет слишком высокой, то лазерный луч не повлияет на материал, маркируемый
.Частота
Свойство Frequency (Hz) представляет частоту Q-Switch лазерных импульсов во время маркировки. Изменение этой частоты создает различные эффекты маркировки. Этот параметр используется для регулировки выходной частоты лазера путем непосредственного управления переключателем добротности. Q-переключатель – это электрооптическая система, которая регулирует непрозрачность линзы, позволяя изменять частоту лазерного луча.Более низкая частота приведет к «пятнистой» гравировке, а более высокая частота позволит получить «линейную» гравировку. Частота обратно пропорциональна мощности лазерного луча, т.е. если частота слишком высока, мощность может оказаться неэффективной для процесса маркировки. Q-переключатель можно сравнить со шлюзовым затвором, который закрывает и отклоняет лазерный луч. Операционные конверты следующие:
- Лазерная система YF 20 Вт: 20 – 200 кГц
Тестовая матрица, показывающая влияние скорости в зависимости от частоты на лазерной метке
Расстояние между заливками
Свойство «Интервал заливки» указывает расстояние между линиями заливки.Чем меньше это значение, тем плотнее заливка за счет более длительного цикла маркировки. Большой интервал заливки приведет к появлению промежутков между линиями, используемыми для заполнения символов. Интервал заполнения (плотность заполнения) измеряется в мм и может быть уменьшен до 0,01 мм.
Угол заполнения
Свойство Fill Angle указывает в градусах угол движения лазерного луча при заливке символов. При использовании вместе с интервалом заливки можно получить различные эффекты заливки.
Количество проходов
Свойство Passes представляет, сколько раз лазер проходит над объектом.Чем больше проходов сделано, тем «глубже» и медленнее результат.
Радиус качания
Свойство «Радиус качания» позволяет помечать отдельные линии, будь то символы True Type / однострочные символы или импортированные файлы, более толстыми линиями. Толщина линии (без заливки) равна размеру лазерного пятна. Однако для некоторых применений этой толщины может быть недостаточно. Таким образом, настройка радиуса качания преобразует обычно прямую векторную линию (для радиуса качания задано значение 0,00 мм) в серию плотных спиральных кривых, обеспечивая тем самым большую толщину линии.Изменение настройки скорости качания увеличит или уменьшит частоту повторения спиральной кривой.
Скорость качания
Скорость колебания влияет на плотность спиральных кривых, когда запрограммирован радиус колебания. Скорость колебания выражается в Гц.
Высокочастотный, высокоскоростной фон и низкочастотный низкоскоростной передний план, чтобы дать очень контрастную и читаемую метку Datamatrix из алюминия
Возможны вариации тона, цвета и оттенка лазерных меток на стали
Как установить параметры маркировки в программном обеспечении для маркировочной машины с волоконным лазером
При маркировке металла и пластика существует диапазон параметров настройки для справки для тестирования в волокне программное обеспечение для лазерной маркировочной машины.
Скорость 100-2000 регулируемая, мощность 30-80 регулируемая, частота 5-30.
Зависит от различных материалов и желаемых эффектов маркировки, поэтому новому оператору может потребоваться провести десятки испытаний, чтобы узнать идеальные параметры маркировки для каждого материала, и даже некоторым опытным инженерам придется попробовать несколько раз.
Здесь есть краткое введение о частоте лазерной маркировки, мощности, скорости и функции штриховки.
1. две настройки для программного обеспечения машины маркировки волоконным лазером
1.) В лазерной маркировочной машине частота маркировки означает время лазерного импульса в единицу времени.
Это легко понять.
Например, при высоком значении частоты маркировки лазерное пятно будет плотным.
Напротив, если значение частоты маркировки низкое, то лазерное пятно анализируется.
Хотя мы не можем увидеть лазерное пятно невооруженным глазом, мы можем увидеть его, когда поместим маркировочную заготовку под электронный микроскоп.
Получается сплошная линия, которую мы видим глазами, состоящую из множества лазерных пятен.
Высокое значение, которое мы устанавливаем для частоты маркировки, более плотное лазерное пятно, которое мы получаем, и большую гладкость, которую мы получаем на маркировочной заготовке.
2.) Скорость маркировки относится к скорости движения лазера.
Здесь эта скорость – скорость, которую можно настроить в параметрах маркировки.
Общее время маркировки зависит не только от скорости маркировки, но также от глубины маркировки, площади маркировки и других факторов.
Чем выше установленная скорость, тем выше скорость маркировки.
Высокая скорость маркировки означает меньшее время попадания лазера в одно и то же место маркировки.
Низкая скорость больше способствует глубокой маркировке.
Но это не означает, что чем меньше скорость вы установите, тем большую глубину вы получите.
Это также зависит от различных материалов и других относительных параметров, которые вы задали.
Если вы хотите узнать больше, свяжитесь с Focuslaser
Электронная почта: [email protected]
whatsapp: +8615102000818
Оптимизация настроек лазера для металла – Enduramark
Лучший способ оптимизировать настройки лазера для металла
Есть много факторов, влияющих на подготовку настроек лазера для каждой работы, но мы преодолели трясину, чтобы найти самый простой способ оптимизировать настройки независимо от обстоятельств.
ПОЖАЛУЙСТА, ПОСМОТРЕТЬ ВИДЕО НА YouTube !!
ВИДЕОСЫЛКА: Оптимизация настроек лазера
Что вам понадобится:
(1) Образец материала, который вы планируете маркировать . Каждый металл индивидуален, поэтому мы всегда рекомендуем проводить испытания на образце маркируемого материала. Для оптимизации работы с нержавеющей сталью мы поставляем по две бирки для каждого заказа.
(2) Сетка для тестовой маркировки . Мы создали файлы CorelDraw и Adobe Illustrator с цветовой схемой правильного размера, которые вы можете скачать здесь: Файлы Corel Draw и Adobe Illustrator
с цветовой схемой(3) Губка «волшебный ластик» или аналогичный аналог. Вы будете использовать это в конце процесса, чтобы лучше оценить свои результаты.
Что вы будете делать:
(1) Сбрызните металлическую бирку из нержавеющей стали с одной стороны спреем для маркировки и отложите в сторону.
(2) Установите разрешение по умолчанию на 300 точек на дюйм.
(3) Перейдите на вкладку «Дополнительно», включите функцию сопоставления цветов в своей лазерной программе и введите настройки, как указано ниже, используя следующие цветовые коды RGB.Например, 100% мощности / 60% скорости соответствует цветовому коду RGB: 255 красный, 0 зеленый и 0 синий.
(4) Включите лазер на полную мощность и держите его в таком состоянии на протяжении всего цикла . Этот фактор должен оставаться неизменным на протяжении всего цикла. Единственное, что изменится в этой процедуре тестирования, – это скорость лазера.
(5) Результаты этого теста действительны только при разрешении 300 dpi.Установка разрешения 600 точек на дюйм даст разные результаты, и, как правило, мы рекомендуем наносить маркировку с разрешением 300 точек на дюйм, если вы не маркируете сложную подложку, такую как алюминий или медь. В этих случаях может потребоваться более высокое разрешение для обеспечения хорошей долговечности.
(6) Поместите металлическую бирку с напылением в лазерный .
(7) Отцентрируйте лазерный луч по центру металлической бирки . Лазерный луч должен быть центрирован слева направо (0,075 дюйма от края) и от нижней части пластины до нижней части выемки (1.34 ’’ снизу).
(8) Используйте гравировку центр-центр. Нажмите print в своей компьютерной программе, чтобы отправить задание на лазер и лазерную метку.
(9) Промойте металлическую бирку водой и ЭНЕРГОДИЧНО протрите ее губкой «волшебный ластик». Важно протереть бирку с некоторым усилием, чтобы выявить истинный вид и долговечность отметок.
(10) Оцените оценки. Вы должны быть в состоянии увидеть, что некоторые отметки на более высоких скоростях сходят, и не так постоянны, как отметки на более низких скоростях.В образце, представленном в нашем видео, отметки на скоростях 60 и 50 держатся плохо. Метка на скорости 40 показывает улучшение, но все еще частично удаляется при очистке губкой. Скорость 30 лучше, чем скорость 40, но все же есть небольшие недостатки. Именно на скоростях с 20 по 5 все марки получаются качественными и стабильными. Таким образом, в нашем примере вы должны установить скорость на 20, чтобы получить отличную оценку. Всегда переключайтесь на следующую самую низкую скорость, чтобы обеспечить хорошее сцепление.
Введение в маркировку волоконным лазером
Джим Эрман, Jimani Inc.
Основы
Лазерная маркировка похожа на горящие листья лупой.
Чтобы сжечь лист с помощью лупы, нужно поместить простую линзу на лист в точке фокуса линзы и позволить линзе собирать солнечные лучи. Затем солнечный свет, собираемый линзой, фокусируется на листе и концентрирует солнечный свет на небольшом пятне на листе. Тогда бинго! Возникающее тепло заставляет лист дымиться и в конечном итоге загораться.
В системах лазерной маркировкииспользуется точно такой же принцип. Однако вместо того, чтобы пропускать солнечный свет через простую линзу, лазерный свет проходит через более сложную линзу – линзу f theta. В то время как солнечный свет состоит из многих цветов или длин волн, лазерный свет имеет свойство быть монохроматическим, что означает, что все лазерные лучи имеют одинаковый цвет или длину волны. Длина волны зависит от типа лазера. Разные материалы поглощают свет с разной длиной волны. Если материал, помещенный под лазер, поглощает длину волны этого лазера, то это хорошее совпадение.
При лазерной маркировке лазерный луч фокусируется на поверхность маркируемого материала с помощью линзы f theta. Фетта-линза обладает свойством сохранять фокусировку по всей плоскости, а не только на одной точке. Луч лазера направляется через линзу f theta парой зеркал с компьютерным управлением. Лазерный луч может быть сфокусирован на материале в любом месте в плоскости, определяемой линзой f theta, и при хорошем совпадении длины волны лазера и материала на материале останется след.Эта метка может быть в форме графических изображений, текста, машиночитаемых кодов (то есть штрих-кодов, кодов UID или 2D-кодов) или любого другого типа метки, который только можно вообразить.
Для разных материалов подходят разные типы лазеров. Например, если кто-то хочет маркировать дерево, оптимальная длина волны света для этого материала – это длина волны, производимая лазером CO2. Если бы кто-то хотел маркировать металлы, оптимальной длиной волны была бы длина волны, производимая YAG или волоконным лазером. Маркируемый материал определяет тип необходимого лазера.Не существует лазера, который подходил бы для всех материалов.
Чтобы продемонстрировать работу лазерного маркера в действии, посмотрите видео ниже:
Как использовать волоконный лазерный маркер
Ниже приводится краткое описание того, как использовать маркер для волоконного лазера, и оно предназначено только для того, чтобы «запустить» нового пользователя. Предполагается, что маркер имеет оптическую систему с управляемым лучом (гальваническим приводом).
Прежде чем вы начнете что-либо отмечать, сначала вам нужно ответить на следующие три вопроса:
- Что собираетесь отмечать?
- Где вы это отметите?
- Как ты это будешь отмечать?
То, что вы собираетесь маркировать и где вы собираетесь отмечать, связано с конкретным программным обеспечением для лазерной маркировки, которое вы используете.Джимани Лангольерс использует исключительно программное обеспечение для лазерной маркировки Prolase, и вы можете узнать больше о программном обеспечении, просмотрев учебное пособие по программному обеспечению для лазерной маркировки Prolase 7.
Обычно самый сложный вопрос для новых пользователей: «Как вы собираетесь его отмечать?» Чтобы ответить на этот вопрос, нужно немного узнать о том, как работают волоконный лазер и система маркировки.
Если вы знакомы с лазерной маркировкой, то, вероятно, знаете, что три наиболее важных параметра, которые можно изменить, чтобы повлиять на способ маркировки детали:
- Скорость
Это скорость, с которой лазерный луч проходит над маркируемой деталью.В системах с направленным лучом используются сканирующие гальванометры с прикрепленными к ним зеркалами для перемещения лазерного луча через линзу и по поверхности детали. Гальванические аппараты обычно могут направлять лазерный луч по детали намного быстрее, чем у лазера есть способность правильно маркировать деталь, поэтому гальванические аппараты редко работают с максимальной потенциальной скоростью. Производители Galvo предоставят спецификации скорости, в которых указано, что galvo может передавать «сотни символов в секунду». Однако при таких скоростях и для большинства материалов у лазера не хватает времени на какой-либо части детали для выполнения какой-либо работы.Полезные скорости зависят от материала и мощности лазера. Скорость от 30 до 35 дюймов в секунду может быть хорошей для удаления анодированного алюминия с алюминия, но более глубокая гравировка металла будет лучше выполняться на скорости 5 дюймов в секунду, делая несколько проходов по детали.
- Мощность
Лазер может выдавать только ту мощность, на которую он рассчитан. Вообще говоря, большая мощность лазера позволит снимать больше материала или маркировать деталь при более высоких скоростях гальваники.В маркере Jimani Langolier мощность калибруется в ваттах. Лазер на 20 ватт может выдавать только 20 ватт. Подходящая мощность зависит от маркируемого материала и желаемого результата. Например, прозрачный поликарбонат получит черную отметку на поверхности при мощности лазера всего 3 или 4 Вт. Анодирование может быть удалено с поверхности алюминиевой подложки при мощности лазера от 12 до 15 Вт, образуя очень белую отметку. Для глубокой гравировки на стали (скажем, от 0,015 до 0,020 дюйма) требуется каждый ватт мощности, который может быть выработан 50-ваттным волоконным лазером.
- Частота импульса
Если у вас нет лазера непрерывного действия (а его у вас не будет, если ваш лазер используется для маркировки), лазер испускает импульсы света, а не непрерывный луч света. Каждый из этих импульсов имеет очень короткую продолжительность, и время импульса измеряется в наносекундах. Волоконные лазеры с фиксированной шириной импульса способны генерировать только лазерные импульсы с одинаковой длительностью (шириной импульса) для каждого лазерного импульса, хотя они могут изменять количество этих импульсов, генерируемых каждую секунду (частота импульсов).Изменение частоты импульсов влияет на количество лазерных импульсов, поражающих деталь в любом месте, и на количество энергии лазера в каждом из этих импульсов. Более низкие частоты импульсов имеют тенденцию к испарению материала из-за более высокого содержания энергии в каждом импульсе. Более высокие частоты импульсов имеют тенденцию нагревать поверхность детали, а не испарять с нее материал. Нагревание поверхности некоторых материалов, таких как сталь или титан, может дать интересные результаты. Вместо испарения материала тепло от более высоких частот импульсов может вызвать образование оксидного слоя, создавая хорошо заметную стойкую маркировку, не повреждая поверхность материала (см. Рисунок 1).
Волоконный лазер с переменной шириной импульса может включать каждый лазерный импульс в течение более или менее длительного периода времени, что дает такие результаты, как оксидные слои различных цветов. Очень короткая длительность лазерного импульса позволяет маркировать материалы, которые в противном случае расплавились бы, с большей длительностью лазерного импульса, например, определенные типы пластика.
По мере уменьшения частоты выходного импульса энергия каждого лазерного импульса увеличивается. Лазер и связанная с ним внутренняя оптика имеют порог энергетического повреждения, и большое внимание уделяется тому, чтобы выходная энергия не превышала порог повреждения лазера или любого из его внутренних компонентов.Волоконные лазеры с фиксированной шириной импульса имеют порог повреждения около 1 мДж энергии. Волоконный лазер с фиксированной шириной импульса 20 Вт будет иметь около 1 мДж энергии на импульс при частоте импульсов около 20 кГц и выходной мощности 20 Вт. По этой причине волоконный лазер с фиксированной шириной импульса 20 Вт не может работать при частотах импульсов ниже 20 кГц.
Помните, что выходная энергия увеличивается с уменьшением частоты импульсов. Таким образом, волоконный лазер с фиксированной шириной импульса 20 Вт будет иметь максимально возможную энергию в импульсе при частоте импульсов 20 кГц.Установка частоты импульсов ниже 20 кГц не приведет к увеличению энергии на импульс, потому что лазер внутренне ограничен от импульсов на более низких частотах. Типичный диапазон частот импульсов для волоконного лазера с фиксированной шириной импульса 20 Вт составляет от 20 до 200 кГц. Полезный диапазон частот импульсов составляет приблизительно от 20 до 50 кГц. При частотах импульсов выше 50 кГц в каждом импульсе вырабатывается недостаточно энергии для выполнения большой работы. Волоконный лазер с фиксированной шириной импульса 50 Вт приближается к 1 мДж на импульс при частоте импульсов 50 кГц и выходной мощности 50 Вт, поэтому он внутренне ограничен для работы на более низких частотах.
Полезный частотный диапазон 50-ваттного волоконного лазера с фиксированной шириной импульса составляет от 50 до 80 кГц. Опять же, выше 80 кГц в каждом импульсе просто недостаточно энергии для выполнения большой работы. Волоконным лазерам с переменной шириной импульса разрешается работать при более низких частотах импульсов, хотя они все еще имеют тот же порог повреждения 1 мДж на лазерный импульс.
Если для волоконного лазера с переменной шириной импульса выбрана более низкая частота импульсов, выходная мощность лазера внутренне уменьшается, так что энергия в импульсе не может превышать пороговое значение повреждения.Невозможно обойти порог урона. Это физика.
Итак, то, как маркировка материала зависит от того, насколько быстро лазерный луч движется по детали, какая мощность выдает лазер, и частота импульсов, на которой он работает. Более низкая скорость, более высокая мощность лазера и меньшая частота импульсов приводят к более сильной и глубокой маркировке. И наоборот, более высокая скорость, меньшая мощность лазера и более высокая частота импульсов приводят к более слабой и неглубокой маркировке.
Поскольку лазерный луч является импульсным, когда он движется по детали, линия, проведенная лазером, может выглядеть так:
оооооооооооооооооооооооооооооооооооооооооооооооооооооооооооооооооооооооооооооооооооооооооооооооооооооооооооооооооооооооооооооооооооооооооооооооооооооооооооооооооооооооооооооооооооооооооооооооооооооооооооооооооооооооооооооооооооооооооооооооооооооооооооооооооооооооооооооооооооооооооооооооооооооооооооооооооооооооооооооооооооооооооооооооооооооооооооооооооооооооооооооооооооооооооооооооооооооооооооооооооооооооооооооооооооооооооооооооооооооооооооооооооооооооооооооооооооооооооооооооооооооооооооооооооооооооооооооооооооооооооооооооооооооооооооооооооооооооооооооооооооооооооооооооооооооо
Если уменьшается скорость гальваники или увеличивается частота выходных импульсов, лазерные импульсы накладываются друг на друга.
Это означает, что на каждое место на нарисованной линии будет воздействовать большее количество лазерных импульсов, поскольку эти импульсы накладываются друг на друга. Но если частота импульсов настолько высока, что энергия в импульсе значительно снижается, то конечным результатом может быть более слабая и неглубокая отметка на детали из-за уменьшения энергии в импульсе.
Существует компромисс между энергией на импульс и количеством перекрывающихся импульсов. Есть и другие переменные, которые могут повлиять на качество метки, например плотность заполнения и размер пятна.Эти темы выходят за рамки Laser Marking 101, и их лучше всего обсуждать после того, как вы хорошо поймете взаимосвязь между скоростью, мощностью и частотой импульсов.
Об авторе
Джим Эрман начал свою карьеру в лазерном бизнесе в 1972 году в компании Korad Lasers в Санта-Монике, Калифорния, и до своего ухода в 1977 году руководил отделами тестирования систем и полевого обслуживания. В 1979 году Джим был соучредителем Laser. Identification Systems (LIS), компания, которая первой разработала системы лазерной маркировки для полупроводниковой промышленности.После приобретения LIS компанией Lumonics Джим занимал должность генерального менеджера до своего ухода в 1987 году. Джим основал компанию Jimani в 1989 году. Jimani является специалистом по лазерной маркировке и интегратором волоконных лазерных систем в Окснарде, Калифорния.
Для получения дополнительной информации, пожалуйста, обращайтесь к Джиму Эрману.
(805) 486-1399
www.jimani-inc.com
Способы резки металла волоконным лазером
Лазерная резка достигается путем нагрева материала с помощью сфокусированного лазерного луча.По мере того, как материал плавится, он эффективно удаляется либо струей газа, либо испарением, создавая таким образом разрез. Существует 3 основных метода лазерной резки:
Методы лазерной резки
В Fusion Cutting лазерный луч коаксиально сочетается с инертным газом, например азотом или аргоном. Тепло, выделяемое лазерным лучом, создает слой расплава, который выбрасывается через пропил сжатым газом из сопла. Резка плавлением может применяться для резки низкоуглеродистых сталей толщиной до 25 мм.
Газовая резка, , также называемая реактивной резкой, использует лазерный луч в сочетании с газообразным кислородом или воздухом для нагрева подложки до температуры воспламенения. В то время как тепло, выделяемое лазерным лучом, плавит поверхность, газ экзотермически реагирует с подложкой и создает дополнительный источник тепла с образованием оксидного слоя или шлака. Когда струя газа выбрасывает шлак с нижней поверхности подложки, образуется пропил. Газовая резка часто используется для резки легированной стали, такой как низкоуглеродистая сталь, толщиной до 40 мм при относительно высоких скоростях обработки.
Сублимационная резка или испарительная резка обычно обрабатывается путем нагрева слоя до точки испарения. Этот метод резки обычно используется для материалов с низкой температурой испарения, таких как полимеры, древесина и органические материалы.
Волоконные лазерыимеют динамический диапазон рабочей мощности, позволяющий фокусировать луч и его положение постоянными даже при изменении мощности лазера. Кроме того, можно добиться широкого диапазона размеров пятна, изменив конфигурацию оптики.Эти особенности позволяют конечному пользователю выбрать подходящую удельную мощность для резки различных материалов и толщины стенок. Волоконные лазеры IPG – идеальное решение для многих приложений лазерной резки.
Типы металлов
Нержавеющая сталь | Углеродистые стали | Золото и серебро | Алюминий |
Инструментальная сталь | Никелевые сплавы | Латунь и медь | Титан |
Каждый процесс резки сильно зависит от типа и толщины материала, а также от требуемой скорости обработки, качества кромки и ширины пропила.Эти требования определяют такие параметры лазера, как длина волны, мощность и качество луча. Одномодовые волоконные лазеры компании IPG в непрерывном или модулированном режиме лучше всего подходят для резки тонких металлов (менее 1 мм) из-за их способности фокусироваться до мельчайших размеров пятна. Высокая плотность мощности, связанная с небольшим пятном, и отличное качество луча позволяют резать сложные детали с высокой скоростью. Применения включают сердечно-сосудистые стенты , трафареты для паяльной маски и тонкую медную резку, необходимую для производства аккумуляторов.Во многих случаях резка выполняется с помощью высокоскоростного гальванического станка, чтобы соответствовать скорости, возможной для волоконных лазеров. Волоконный лазер QCW с оптимизированными импульсами также облегчает резку сложных деталей в тонких материалах. Этот режим резания в импульсном режиме приводит к минимальному образованию шлаков и зон термического влияния (HAZ), которые имеют решающее значение для многих процессов резания, а также для микрообработки. |
В процессе резки с низким коэффициентом заполнения используется энергия импульса для резки тонкостенных и более толстых материалов с высоким коэффициентом отражения при гораздо более низкой средней мощности.Примеры импульсной лазерной резки включают керамику и драгоценные металлы. Лазеры QCW большей мощности с импульсной мощностью 20 кВт и средней мощностью 2 кВт позволяют теперь резать как толстые, так и тонкие материалы с использованием одного и того же лазера. Кроме того, эти лазеры являются рабочей лошадкой для буровых работ в аэрокосмической отрасли с толщиной материала> 25 мм.
По сравнению с лазерами CO 2 время обработки для волоконных лазеров значительно ниже, чем у лазера CO 2 , при той же выходной мощности, материале и толщине материала.Кроме того, потребляемая мощность также значительно меньше, чем у лазера CO 2 , обычно 9% WPE для CO 2 по сравнению с> 35% для волоконного лазера (лазеры серии YLS-ECO имеют эффективность подключения к электросети. более 45%). Благодаря простоте использования и практически отсутствию технического обслуживания, волоконные лазеры IPG являются идеальным решением для резки металлов. Волоконные лазеры быстро заменяют CO 2 в области резки, при этом основные производители оборудования для резки меняют или уже предлагают станки для резки на основе волокна.Эти машины доступны с волоконными лазерами от 2 до 6 кВт, предлагая пользователю возможность резать как листовой металл, так и лист на одном основании. Кроме того, из-за более высокого поглощения света размером 1 микрон лазеры позволяют резать латунь, алюминий и медь на производственных мощностях.
Модулированная и импульсная резка Все волоконные лазеры непрерывного действия (CW) IPG можно модулировать до нескольких кГц для прецизионной резки.IPG предлагает уникальный ассортимент продукции с повышенной пиковой мощностью, в которой можно использовать совершенно иной процесс импульсной резки. Они известны как волоконные лазеры QCW. В этом случае в процессе резки с малой нагрузкой используется высокая энергия импульса для резки и сверления толстостенных материалов с высокой отражательной способностью при гораздо более низкой средней мощности. |
Почему волоконный лазер – лучший выбор для резки меди и латуни?
Небольшие пятна фокусировки и чрезвычайно высокая плотность мощности (более 100 МВт / см 2 ) стали возможны благодаря:
- Относительно коротковолновый (1 мкм vs.10 мкм CO 2 лазеров)
- Высокое качество луча
- Экономическая доступность волоконных лазеров с высокой пиковой мощностью
При таких высоких уровнях удельной мощности металлы, такие как медь и латунь, претерпевают фазовый переход в расплавленное состояние. Лазерный луч быстро преодолевает барьер отражательной способности таких металлов, чтобы инициировать эффективный процесс резки. Резка отражающих металлов оказалась очень сложной задачей при использовании CO 2 лазеров или лазеров ближнего ИК диапазона с низкой пиковой мощностью.
Чтобы узнать больше о для лазерной резки отражающих металлов , посетите нашу страницу LaserCube.
Маркировка | FAQ | Базовые знания | Лазерная маркировка Central
Воспользуйтесь этими ценными советами и рекомендациями по маркировке. Узнайте, как обеспечить четкие отметки.
KEYENCE предлагает несколько типов лазерных маркеров:
- УФ (длина волны 355 нм)
- Гибрид (длина волны 1064 нм)
- Волокно (длина волны 1090 нм)
- CO 2 (длина волны 10600 нм)
- Зеленый (длина волны 532 нм)
CO 2 Лазерные маркеры не могут наносить маркировку на металлы.Маркеры с гибридным или волоконным лазером лучше подходят для маркировки большинства металлов.
YAG / YVO 4 лазерный маркерДа, с помощью лазерной маркировки можно полностью маркировать прозрачные бутылки. Фактически, лазерные маркеры CO 2 обычно используются на линиях розлива для печати кодов партий и сроков годности.
KEYENCE предлагает коротковолновый лазерный маркер CO 2 , оптимизированный для маркировки ПЭТ. Эта система обеспечивает улучшенную окраску и минимальное повреждение поверхности ПЭТ-бутылок.
Простая и свободная печать трехмерных объектов.
Четкая печать возможна даже на высокоскоростной линии.
Да, но нужно правильно выбрать систему. Большинство лазерных маркеров вызывают появление небольших отверстий внутри печатных символов из-за высокой температуры луча.Коротковолновые лазеры решают эту общую проблему и могут как маркировать, так и резать пленки с высокой степенью точности.
Лазерные маркеры серии ML-ZKEYENCE выпускаются с двумя разными длинами волн: 10,6 мкм и 9,3 мкм. Коротковолновые модели были специально оптимизированы с учетом характеристик поглощения тепла смолами.
В результате лазерные маркеры 9,3 мкм могут печатать неглубокие гравюры с хорошей видимостью и меньшим набуханием поверхности, чем их аналоги.Это гарантирует выдающуюся высококачественную маркировку на пленках и листах, которая в противном случае была бы невозможна.
Глубина метки зависит от типа лазерного маркера, параметров, используемых для создания метки, и материала мишени.
Например, глубину единственной отметки на пластике можно легко контролировать и изменять (от нескольких микрон до более 1 мм). Однако металлические метки обычно имеют глубину всего 10-90 мкм, поэтому глубокая гравировка занимает гораздо больше времени.
Таким образом, доступно большое разнообразие стилей маркировки путем простого изменения мощности лазера и скорости маркировки.
ГЛУБОКАЯ МАРКИРОВКА / РЕЗКА НЕБОЛЬШАЯ МАРКИРОВКАМинимальный и максимальный размер символов полностью зависит от модели и типа лазерного маркера. Лазерные маркеры KEYENCE могут создавать четкие символы размером от 0,1 мм (0,004 дюйма) до 300 мм (11,81 дюйма).
Да, возможно нанесение лазерной маркировки на керамику.Однако разные лазерные маркеры лучше подходят для маркировки разных типов керамики.
Например, лазерные маркеры KEYENCE CO 2 идеально подходят для маркировки глиноземной керамики, тогда как гибридные лазерные маркеры лучше подходят для маркировки циркониевой керамики. Для получения наилучших результатов рекомендуется протестировать различные типы маркеров.
Лазерный маркер YVO 4 для циркониевой керамики (фианит) Лазерный маркер CO 2 для глиноземной керамикиЛазерные маркеры обычно дают наилучшие отметки, когда цель находится в фокусе их луча.Чем дальше цель удаляется от точки фокусировки, тем менее сфокусированным становится лазерное пятно. В конце концов, маркировка становится бледной из-за увеличенного пятна луча и снижения плотности энергии.
Ниже приведены несколько примеров того, как выглядят следы, когда цель выходит из фокуса.
Лазерный маркер с 3-осевым управлением позволяет четко маркировать цель любой формы без каких-либо искажений или блеклости.Лазерные датчики перемещения позволяют маркировать цели, которые движутся дальше от лазерного маркера или ближе к нему.
- Автоматическая фокусировка Лазерные маркеры
- KEYENCE могут регулировать фокус в реальном времени. В результате можно легко учесть изменения целевых размеров без необходимости постоянно перезагружать систему.
Да, можно маркировать различные логотипы и графические данные с помощью программного обеспечения KEYENCE Marking Builder. Файлы DXF можно легко загрузить в лазерный маркер в виде файла логотипа, что позволяет быстро пометить логотипы компании по желанию.С помощью Marking Builder также возможно дополнительное управление логотипами, например выбор стиля штриховки или траектории лазерной маркировки.
- 1. Отображение списка
- Информация об элементе, включая координаты начала / конца и порядок маркировки, отображается и может быть легко изменена.
- 2. Обнаружение отключенной линии
- Программа отображает несвязанные части линии рамки, что позволяет легко изменять разорванные контуры перед штриховкой.
- 3. Различные стили штриховки
- Простое редактирование и штриховка элементов без использования специального программного обеспечения САПР. В зависимости от желаемого результата можно выбрать идеальные образцы штриховки, от диагональных линий до пересеченных и контурных линий.
Да, лазерные маркеры могут создавать хорошо читаемые 2D-коды на металлических мишенях.
КодыBlack 2D легко читаются на большинстве металлических поверхностей (таких как железо и нержавеющая сталь). Однако черные 2D-коды на матовых поверхностях плохо читаются.Чтобы преодолеть эту проблему, можно пометить читаемые 2D-коды, сначала создав «полированный» белый фон с помощью лазера, а затем пометив черный 2D-код сверху.
1. Черная маркировка 2. Полированный фон и черная метка.Простые формы, такие как круги, треугольники и квадраты, можно легко создать в программе KEYENCE Marking Builder. Встроенные конструкторы логотипов позволяют быстро и легко создавать пользовательские символы и шрифты и манипулировать ими.
Да, лазерные маркеры KEYENCE могут подсчитывать и изменять значения при маркировке серийных номеров. Это можно сделать с помощью внутреннего счетчика или через последовательную связь.
Внутренние счетчики могут реагировать на различные случаи, поскольку можно изменить количество шагов, повторений и базовое значение счетчика. Также возможно сбросить счетчик или отсчет непосредственно с дискретной клеммы ввода / вывода лазерного маркера.
Последовательная связь позволяет напрямую изменять сконфигурированные счетчики или блоки маркировки по желанию.
Метод «Оптимизация скорости сканирования» позволяет пользователям автоматически рассчитывать правильные настройки скорости сканирования для завершения маркировки в течение заданного периода времени. Эту функцию также можно использовать для расчета скорости сканирования при маркировке движущихся целей.
- 1. Поставьте галочку в поле «Оптимизировать»
- 2. Установите желаемое время маркировки.
- 3. Затем просто нажмите «Оптимизировать сканирование».
Сдвиги по времени можно легко настроить и отметить с помощью программного обеспечения KEYENCE Marking Builder.
Символами можно заменить не более 24 смен в день.
Это позволяет печатать, автоматически обновляя буквенно-цифровые символы в соответствии с внутренними часами лазера.
Ниже приводится пример разделения дня на три смены и замены их алфавитными символами.
В некоторых случаях можно просто увеличить скорость сканирования лазера, чтобы сократить время маркировки. Однако это может привести к плохому качеству маркировки.В этих случаях изменение направления заполнения может быть эффективным способом сократить время маркировки.
Можно изменить направление маркировки внутри рисунка, а также порядок, в котором рисунки маркируются, чтобы повысить эффективность и сократить время маркировки.
Гибридные лазерные маркерыKEYENCE (YVO 4 ) имеют диапазон Q-Switch от 0 до 400 кГц. Вообще говоря, более низкое значение Q-Switch позволяет лазеру накапливать больше мощности перед тем, как направить его на деталь.Это полезно, когда требуется глубокая маркировка или меньшая скорость маркировки. Высокие значения Q-Switch означают, что лазер излучает более частые импульсы и не выдает столько мощности за импульс. Это полезно, когда требуется маркировка без повреждений или высокие скорости.
Примеры ниже иллюстрируют, почему маркировка с более высоким значением Q-Switch необходима для высокоскоростных приложений.
Оптический компонент, который генерирует высокую энергию за счет управления колебаниями лазера.
Невозможно нанести лазерную метку на деталь, не повлияв на поверхность цели. Однако можно ограничить степень повреждения детали, точно настроив параметры маркировки. В приведенном ниже примере показана метка на оцинкованном металле, где глубина маркировки регулируется с точностью до 1 мкм (0,04 мил).
Пример маркировкиМатериалы, которые трудно маркировать (например, золото, из-за его высокого коэффициента отражения), все же можно четко и быстро маркировать лазером, если используется правильная длина волны.
Пример маркировки Лазерные маркерыKEYENCE оснащены функцией «Маркировка образца», которая значительно упрощает процесс поиска правильных параметров маркировки.
Маркировка образцов позволяет пользователям быстро тестировать различные комбинации мощности, скорости сканирования, частоты Q-переключателя и фокусного расстояния одновременно.
Это значительно сокращает время и количество отходов, необходимых для набора метки.
Scanbeat (мм / с) | |||||||
---|---|---|---|---|---|---|---|
500 | 1000 | 1500 | 2000 | 2500 | 3000 | ||
Мощность лазера (%) | 20 | A0 | A5 | AA | AF | АК | AP |
25 | A1 | A6 | AB | AG | AL | AQ | |
30 | A2 | A7 | AC | AH | AM | AR | |
35 | A3 | A8 | н.э. | AI | AN | КАК | |
40 | A4 | A9 | AE | AJ | АО | AT |
Одновременно может быть до 123 комбинаций.Буквенно-цифровые метки помогают операторам выбрать правильный шаблон, а также представляют, как будут отображаться однострочные символы при маркировке. Поля рядом с буквенно-цифровыми метками показывают, как будут отображаться закрашенные узоры и толстый текст при пометке.
Вообще говоря, при более низкой скорости сканирования следы становятся более глубокими и разборчивыми. Однако слишком низкая скорость сканирования может привести к образованию отложений сажи, которые поднимают поверхность материала. Использование толстых текстовых строк и многократных повторений обычно дает лучший результат.
Программное обеспечениеKEYENCE Marking Builder оснащено функцией «Зеркальное отображение». Чтобы включить это, просто установите флажок.
Некоторые лазерные маркеры KEYENCE содержат встроенную камеру, которая может отображать область маркировки на мониторе. Эта функция поиска позволяет пользователям быстро и точно позиционировать детали даже на очень маленьких объектах. Производится меньше брака и упрощается начальное программирование.
1.На экране монитора появляется перекрестие 2. Разместите заготовку 3. Используйте изображение на мониторе, чтобы точно расположить цель. 4. Отмечено!E-покрытия часто наносятся на детали для предотвращения ржавчины. Удаление E-Coat может привести к обнажению защищаемого продукта. Однако многие продукты с электронным покрытием, отмеченные CO 2 и УФ-лазерами, успешно прошли испытания в солевом тумане. Перед внедрением такой системы жизненно важно провести тестовую маркировку и / или испытания в солевом тумане, чтобы оценить, будет ли лазерная маркировка соответствовать вашим потребностям.
Пример маркировки на поверхности с покрытиемТонкие масляные покрытия не проблема, но большое количество масла может блокировать лазерный луч. Маркировка может искажаться, растягиваться или иметь дефекты, поэтому изделия с толстым слоем масла необходимо предварительно обработать сжатым воздухом или протереть.
Стекло прозрачное, поэтому обычный лазерный свет проходит сквозь него и не оставляет следов. Лазерные маркеры CO 2 работают на стекле, но для нанесения метки необходимо нагревание.В результате можно получить четкую маркировку без трещин на термостойком стекле (например, кварцевом стекле), но натриево-известковое стекло будет трескаться.
Чтобы избежать растрескивания, необходимо пометить чувствительное стекло с помощью повторных сканирований и настроек низкой мощности.
Маркировка без трещин Отмечено одним сканированием и настройками высокой мощности На цифрах «3» и «2» образовались большие трещины. Отмечено с использованием нескольких повторов Множественные проходы с меньшей мощностью создают более высокий контраст без растрескивания стекла.Да. Фактически, лазерные маркеры CO 2 обычно используются для создания множества различных этикеток путем удаления слоев чернил с деталей.
В отличие от традиционных методов печати, лазерные маркеры не ограничиваются встроенным управлением серийными номерами. Лазеры обладают большой степенью гибкости контента (включая логотипы и 2D-коды) и оставляют неизгладимые следы.
Благодаря многочисленным преимуществам лазерных маркеров бумажные этикетки быстро заменяются «лазерными этикетками».«Эти этикетки специально разработаны для того, чтобы реагировать на лазерный луч и обеспечивать четкие, чрезвычайно долговечные результаты по запросу.
Лазерные маркерымогут использоваться с этикетировщиками для маркировки лучших по срокам, номерам партий и другой переменной информации.
Ампула Дизайн этикетокLaser можно легко управлять с помощью компьютера, что позволяет быстро менять продукт и информацию. Это значительно сокращает время выполнения заказа и количество человеко-часов, необходимых для управления запасами.
Паспортная табличкаCO 2 лазеры могут отрезать этикетки от подложки, что позволяет пользователям легко создавать этикетку по своему выбору.
Да. Программное обеспечение KEYENCE Marking Builder упрощает программирование кругового текста. Просто установите предварительно определенный радиус или щелкните и перетащите из центра текстового блока, пока он не будет соответствовать части.
После ввода строки символов щелкните мышью и перетащите центр текста.ЗАВЕРШЕННЫЙ!Кроме того, вы можете создать макет, указав координаты центра и радиус дуги
Фокус лазерного маркера – это место в луче с наибольшей плотностью энергии. Расфокусировка лазерного луча может привести к изменению качества маркировки и искажению символов.
Типичные лазерные маркеры имеют фиксированную точку фокусировки. Изменения деталей требуют физических корректировок, и их невозможно пометить на 3D-фигурах.
В лазерных маркерахKEYENCE используется 3-осевая технология для регулировки точки фокусировки на + -21 мм в любом месте поля маркировки без необходимости физической регулировки. Это позволяет лазерам KEYENCE наносить метки на трехмерные формы, компенсировать разницу в высоте и намеренно расфокусировать луч, чтобы получить эстетически приятные метки.
3-осевое управление позволяет наносить маркировку с переменной глубиной резкости Использование 3-осевого управления в сочетании с лазерным датчиком перемещения позволяет автоматически регулировать глубину фокусировки. + Высокоскоростной / высокоточный лазерный измеритель перемещения CCD серии LK-G Вы можете загрузить данные САПР с веб-сайта KEYENCE.
Для 2D-CAD доступны файлы DXF.
Для 3D-CAD доступны три типа файлов данных (IGES / Parasolid / STEP).
Лазерный свет 9,3 мкм имеет более высокий коэффициент поглощения в смолах, пластмассах и пленках, что позволяет наносить маркировку или резку прозрачных материалов с меньшим нагревом (и, следовательно, меньшими повреждениями) на поверхности мишени.
Поскольку метки, созданные с помощью лазера с длиной волны 9,3 мкм, имеют меньшую глубину, их намного легче создавать разборчивые.Это связано с тем, что больше света отражается и меньше света задерживается в глубине метки.
Стандартный тип | |||
---|---|---|---|
Модель | Головка | мл-Z9510 | ML-Z9510T |
Контроллер | мл-Z9500 | ||
Метод маркировки | XYZ 3-осевое одновременное сканирование | ||
Маркировочный лазер | Длина волны | 10.6 мкм | 9,3 мкм |
Средняя мощность | 30 Вт | 20 Вт |
- Эффект маркировки на прозрачных материалах
- Обычный лазер Повреждение поверхности вызывает появление шероховатой отметки ML-Z с длиной волны 9,3 мкм. Урон минимизирован
Лазерные маркеры могут использоваться как на крупном, так и на мелком производстве. Для обоих требуются первоначальная настройка и юстировка.Однако существует множество лазеров для направляющих (и камер в некоторых системах), предназначенных для обеспечения правильной маркировки деталей. Лазерные маркеры KEYENCE можно быстро настроить для маркировки партий и иметь возможность маркировать движущиеся цели.
Направляющий лазер с одинарным / непрерывным излучением(обозначаемые символы) Рамка блока
(диапазон маркировки знаков)
Дом
.