технология, контроль, инструмент, методы и способы изготовления
Формирование фасонных поверхностей при токарной обработке происходит путем вращения криволинейных образующих вокруг оси изделий. Образующие могут представлять собой также сочетания линий различного профиля, создающих при вращении определенную конфигурацию детали. Существует несколько способов изготовления и контроля формы изделий с фасонными поверхностями, в том числе с использованием:
- шаблона;
- фасонного инструмента;
- копира;
- сочетанием указанных способов.
При использовании шаблонов подача резца осуществляется как в продольном, так и в поперечном направлении. После срезания определенной толщины слоя к детали прикладывается шаблон для определения размера следующего срезаемого слоя.
Наиболее простым способом получения фасонной поверхности детали является использование резца с режущей кромкой, повторяющей заданную криволинейную образующую.
Применение копира дает возможность получения наиболее точную конфигурацию детали. Иногда на практике приходится использовать комбинацию всех перечисленных способов – чаще всего это касается вытачивания удлиненных изделий с использованием твердосплавного и быстрорежущего инструмента.
Современное станочное оборудование обеспечивает высокую точность обработки заготовок, при этом деталь должна быть надежно закреплена в шпинделе или центрах станка. В случаях, если длина заготовки значительно превышает ее диаметр, применяются добавочные опоры – люнеты. Таким образом, можно значительно увеличить жесткость установки детали, что способствует точности обработки.
Применение на практике резцов с криволинейной конфигурацией ограничивается шириной их режущей части, которая не должна превышать 60 мм. Радиус чугунных и стальных заготовок из чугуна или стали ограничивают 20-ю миллиметрами. В таких случаях важно учитывать, что действующие усилия в зоне резания должны соответствовать общей жесткости всех составляющих системы СИД.
Если необходимо получить радиус обрабатываемой детали, превышающий 20 мм, используют проходные резцы, радиус закругления которых меньше, чем радиус закругления сопрягаемой детали, к примеру, подшипника.
Фасонные резцы:
а – цельный; б – с механическим креплением режущей части; в – дисковый
Обработка проходными резцами
В единичном производстве требования к точности изготовления невелики, поэтому вытачивание на станках фасонных поверхностей выполняется в ручном режиме, а качество исполнения обеспечивается за счет высокой квалификации рабочих. Это объясняется отсутствием автоматических настроек: процесса резания и точность выполнения работы обеспечивает исполнитель, сочетая продольное и поперечное перемещение резца. Для получения практических навыков обработки готовую деталь заданного фасонного профиля устанавливают в шпинделе станка, вдоль которой токарь вручную, используя рукоятки суппорта станка, перемещает резец таким образом, чтобы его режущая часть повторяла контур изделия.
Процесс токарной обработки происходит в двух позициях. Сначала заготовка рукоятки крепится в шпинделе станка за цилиндрическую часть А, выполняется обработка ступенчатой фасонной поверхностью (B, C, D, E) хвостовика. Перед этим на заготовку наносится разметка по длине. Затем деталь переворачивают, закрепляют за обработанный ступенчатый хвостовик и ведут обработку части G детали. Сначала выполняют снятие чернового припуска в несколько проходов, далее – обеспечивают доводку до требуемого размера. Останавливая вращение шпинделя, к неподвижной заготовке несколько раз прикладывают шаблон, измеряют максимальный и минимальный диаметры рукоятки, чтобы за несколько проходов довести ее форму до заданных размеров. В целях ускорения процесса резания продольное перемещение устанавливают в автоматический режим, оставляя ручное управление для поперечного суппорта.
Последовательность обработки фасонной поверхности рукоятки прохладным резцом с применением продольной и поперечной подач:
а – готовая деталь; б, в и г – полуфабрикаты для получения детали; A, B, C, D, E и G – обрабатываемые поверхности
При работе с копиром используют специальное приспособление, в комплекте из копира 5, тяги 3 с пальцем 4. Палец 4, проскальзывая вдоль копира, обеспечивает перемещение тяги, соединенной с суппортом, передвигая его и установленный на нем режущий инструмент в соответствии с контуром копира. Ход суппорта в продольном направлении рекомендуется выполнять в автоматическом режиме, поперечную подачу отключить. Инструмент, повторяя движение тяги, формирует рельеф вращающейся заготовки.
Обработка фасонных поверхностей по копиру:
1 – резец, 2- рукоятка, 3 – тяга, 4 – палец, 5 – копир
Использование фасонных резцов
Детали небольшой длины целесообразно изготавливать при помощи резцов рабочей кромкой, в точности совпадающий с заданным контуром. Обязательное условие точного выполнения технических параметров резания – передняя поверхность режущего инструмента должна располагаться на уровне линии центров токарного станка. Для затачивания резцов для фасонной обработки ведется используется передняя поверхность, что важно учитывать, если возникнет необходимость их неоднократной установки.
Местом установки призматических радиальных фасонных резцов являются горизонтальная револьверная головка либо поперечный суппорт. Линия режущей кромки фасонного резца должна быть на уровне центра закрепленной в шпинделе или в центрах детали. Размеры задних углов α можно выставить, регулируя положение резца в державке, что достаточно удобно на этапе подготовительных работ.
На металлообрабатывающих производствах предпочтение отдается, как правило, резцам с винтовыми образующими режущих кромок по сравнению с резцами, в которых режущие кромки выполнены в виде кольцевых образующих.
Высокая производительность резцов с винтовой образующей режущей кромки в полной мере используется при их установке в револьверной головке. Для улучшения качества резания используется равномерная подача не более 0,05 мм/об при ширине резца 10…20 мм. Более широкие фасонные резцы (шириной больше 20 мм) рассчитаны на подачу до 0,03 мм/об.
Способы контроля фасонных поверхностей
Основным способом контроля фасонных поверхностей деталей является шаблон, с которым сверяют профиль полученной в результате обработки детали. Если размеры детали имеют отклонения от чертежа, причинами могли стать такие факторы как погрешности при обработке, неточности режущих параметров резца, ошибки в его установке. Возможно также, что отклонения произошли из-за деформаций изделия в процессе обработки – в таком случае следует уменьшить подачу режущего инструмента.
Точение фасонных поверхностей – Ресурс
Фасонная поверхность — поверхность, полученная либо криволинейной образующей, либо сочетанием прямолинейных образующих, которые располагаются под разным наклоном относительно оси детали, либо комбинацией прямолинейных и криволинейных образующих. К ним относятся винтовые канавки, зубья шлицев и шестерен и прочее.
На токарных станках сложную фасонную поверхность можно получить четырьмя способами:
- посредством ручной подачи резца (продольной, поперечной) и подгонкой профиля обрабатываемой поверхности с использованием шаблона;
- при помощи фасонных резцов, которые имеют профиль, аналогичный профилю требуемой детали;
- за счет сочетания вышеперечисленных методов повышается точность и увеличивается производительность обработки деталей.
Разновидности фасонных резцов
Фасонный резец — это инструмент с режущей кромкой, повторяющей профиль обрабатываемой поверхности. Исходя из этого, различают:
- фасонные резцы для вогнутой поверхности — простой и недорогой инструмент, передняя поверхность которого после нескольких переточек становится непригодной для дальнейшей работы. Стачивание пластинки резца негативно сказывается при его установке: за счет уменьшения высоты по центру инструмент становится неподходящим для выполнения последующих работ. Следовательно, фасонные резцы больше всего подойдут при единичном/серийном производстве, когда профиль требуемой поверхности не имеет сложностей;
- призматические фасонные резцы — непростой в плане конструктивного исполнения инструмент. Его передней поверхностью является торец бруска, используемого для изготовления резца. Образование заднего угла обусловлено расположением инструмента в державке под углом. Для его крепления предусмотрен специальный уступ — ласточкин хвост, и винт, обеспечивающий необходимую жесткость;
- дисковые фасонные резцы — их ширина не превышает, как правило, 40 мм (исключение — инструмент до 100 мм).
Для создания требуемого заднего угла передняя поверхность резца размещается на определенную величину ниже его оси. При понижении, составляющем 1/10 диаметра режущего инструмента, задний угол получается приблизительно 12°. В большинстве случаев передний угол составляет 0°. В таком исполнении изготовление резца существенно упрощается, а в процессе работ он не затягивается в обрабатываемую деталь, что способствует улучшению качества обработки.
Тонкости обработки фасонных поверхностей
Чтобы получить заданный профиль обрабатываемой заготовки, следует уделить внимание установке резца: режущая кромка должна располагаться на одном уровне с высотой центров токарного станка. Правильность положения при виде сверху проверяется посредством небольшого треугольника. Одно его ребро следует приложить вдоль оси цилиндрической поверхности заготовки, а другое нужно подвести к боковой стороне резца. При этом между инструментом и угольником не допускается неравномерный просвет.
Правил закрепления фасонных резцов следует придерживаться с особой ответственностью.
Что касается подачи фасонного резца, то она зачастую производится вручную. При этом ее величина зависит:
- от ширины режущего инструмента:
- при 10-20 мм наибольшая подача 0,05 мм/об;
- при 20 мм и выше наибольшая подача 0,03 мм/об;
- от диаметра обрабатываемой детали — чем он меньше, тем меньше подача;
- от расположения обрабатываемого участка заготовки относительно патрона/задней бабки — при минимальном расстоянии рекомендуется выбирать большую подачу, чем при максимальном.
Обработка фасонных деталей в зависимости от подачи
Одновременное действие поперечной и продольной ручной подачи осуществляется в случае точения относительно больших по площади фасонных поверхностей либо при обработке небольшого числа деталей. Если использовать более традиционные способы, то для первого варианта потребовался бы довольно широкий резец, который бы при обработке вызывал серьезные вибрации детали, а для второго варианта изготовление фасонного резца вообще нецелесообразно.
Для снятия припуска используется проходной или чистовой резец. При этом продольные салазки суппорта вручную перемещают влево, а поперечные, вместе с тем, — вперед и назад. Сравнительно малые фасонные поверхности обрабатывают следующим образом: продольная подача осуществляется посредством задействования верхних салазок суппорта, направляющие которого располагаются параллельно центровой линии токарного станка; поперечная — посредством поперечных салазок. В обоих случаях траектория передвижения вершины режущего инструмента будет кривой.
Правильное соблюдение соотношения величин продольной подачи и поперечной при нескольких проходах придаст обрабатываемой заготовке нужную форму. Чтобы качественно выполнять подобную работу требуется определенные навыки и опыт. Квалифицированные токари при обработке сложных поверхностей включают автоматическую продольную подачу, параллельно с ней вручную перемещая поперечный суппорт.
При точении больших партий деталей необходимо автоматизировать сложное движение режущего инструмента. Для того чтобы справиться с этой задачей разрабатываются и изготавливаются копировальные приспособления. Сейчас все более популярными и востребованными становятся так называемые «гидравлические суппорты».
Перейти к списку статей >>
Материалы по теме
Определение, типы, преимущества и недостатки
Что такое токарная обработка? Токарная обработка — это процесс механической обработки, при котором токарный станок используется для вращения металла, в то время как режущий инструмент движется линейно, удаляя металл по диаметру, создавая цилиндрическую форму. Режущий инструмент можно наклонять под разными углами для создания различных форм. Это можно сделать вручную или на токарном станке с ЧПУ. Обработка с ЧПУ обычно используется, когда размеры детали должны быть очень точными.
Что такое поворот?
Токарная обработка — это процесс механической обработки, при котором режущий инструмент перемещается более или менее линейно, в то время как заготовка вращается. Термин «токарная обработка» обычно используется только для создания внешних поверхностей с помощью этого действия резания. Напротив, то же самое существенное режущее действие называется «расточкой» применительно к внутренним поверхностям, таким как отверстия.
Токарная обработка может выполняться вручную на токарном станке, который часто требует постоянного наблюдения со стороны оператора, или на автоматическом токарном станке, который этого не требует. На сегодняшний день наиболее распространенным типом такой автоматизации является числовое программное управление, или ЧПУ.
При точении заготовка (кусок из относительно жесткого материала, такого как дерево) вращается, а режущий инструмент перемещается по одной, двум или даже трем осям движения для получения точных диаметров и глубин. Поворот может быть снаружи цилиндра, чтобы иметь трубчатые компоненты различной геометрии.
Деталь, подлежащая токарной обработке, может называться “точеной деталью” или “обработанной деталью”. Для получения дополнительной информации см. нашу статью о типах процессов обработки.
Какие инструменты используются в процессе токарной обработки?
Инструменты, используемые в процессе токарной обработки, включают одноточечные режущие инструменты для удаления материала с вращающейся заготовки и токарный станок или токарный станок. Конструкция токарного инструмента варьируется в зависимости от конкретного применения.
В процессе токарной обработки с ЧПУ также используются токарные станки с ЧПУ или токарные станки. Типы токарных станков, используемых для токарной обработки, включают токарные станки с револьверной головкой, токарные станки с двигателем и токарные станки специального назначения. Токарные станки могут быть ручными или с ЧПУ.
Какие материалы используются для токарной обработки?
Материалы, используемые для токарной обработки, в основном металлы. Эти металлы включают легированную сталь, углеродистую сталь, чугун, нержавеющую сталь, алюминий, медь, магний и цинк. Однако этот процесс также может обрабатывать пластмассовые детали и работать с другими материалами, такими как керамика, композиты, термопласты и реактопласты.
Как работает процесс токарной обработки?
Процесс токарной обработки работает на токарном станке, перемещающем режущий инструмент линейным движением вдоль поверхности вращающейся заготовки, удаляя материал по окружности до тех пор, пока не будет достигнут желаемый диаметр, для обработки цилиндрических деталей с внешними и внутренними элементами, такими как пазы, конусы и резьба.
Токарная обработка использует одноточечные режущие инструменты для удаления материала с вращающейся заготовки. Конструкция токарного инструмента зависит от его применения: доступны инструменты для черновой, чистовой обработки, торцевания, нарезания резьбы, отрезки, формовки, подрезки и обработки канавок.
Какие изделия изготавливаются с помощью токарной обработки?
При токарной обработке получают вращающиеся, как правило, осесимметричные детали со многими элементами, такими как отверстия, канавки, резьба, конусность, ступени различного диаметра и даже контурные поверхности. Изделия, изготовленные полностью путем токарной обработки, часто включают компоненты, используемые в ограниченном количестве, особенно для прототипов, такие как изготовленные по индивидуальному заказу валы и крепежные детали.
Токарная обработка также часто используется в качестве вторичного процесса для добавления или улучшения характеристик деталей, изготовленных другим методом.
Некоторыми примерами изделий, изготовленных с помощью токарной обработки, являются распределительные валы, коленчатые валы, бейсбольные биты, миски, кии, вывески, музыкальные инструменты и ножки столов и стульев.
Какие бывают токарные процессы?
Прямолинейное точение, также известное как цилиндрическое точение, уменьшает рабочий диаметр равномерным движением, чтобы предотвратить изменение рабочего диаметра резания. Прямое точение часто считается «черновой» операцией, при которой удаляется большое количество материала перед прецизионной резкой.
Коническая токарная обработка позволяет получить цилиндрическую форму с постепенно уменьшающимся диаметром.
Генерация сфер происходит, когда программа создает форму вокруг фиксированной оси вращения или когда специальный полукруглый инструмент используется для уменьшения диаметра до нуля для создания идеальной сферы.
Нарезание канавок выполняется, когда фасонный инструмент вдавливается в выемку компонента, образуя узкую полость.
Разделитель используется для глубокой выемки в компоненте, чтобы отделить готовую деталь от исходной детали.
Накатка выполняется путем вырезания зубчатого рисунка на материале. Накатка обычно выполняется с материалами, которые требуют дополнительного сцепления.
Нарезание резьбы осуществляется путем нарезания спиральной траектории для создания канавок, которые можно вкручивать в другие предметы.
Каковы преимущества процесса токарной обработки?
Преимущества процесса токарной обработки:
1. Все материалы взаимозаменяемы.
Хотя токарная обработка в основном используется для обработки металлов, при токарной обработке можно использовать любой материал, в том числе дерево и пластик. Это делает поворот очень гибким процессом.
2. Переносимость отличная.
Точение можно использовать для изготовления деталей с чрезвычайно высокими допусками. Из-за высоких допусков и чистоты поверхности, которую может предложить токарная обработка, этот процесс часто используется для добавления точных вращательных элементов к детали, основная форма которой уже сформирована другим методом.
3. Время выполнения короткое.
Токарная обработка занимает мало времени. Время выполнения — это время между моментом, когда клиент размещает заказ, и моментом, когда клиент получает окончательную доставку. Поскольку токарная обработка является быстрым процессом, время выполнения заказа короткое.
4. Нет необходимости в высококвалифицированном операторе.
Токарная обработка не требует высокой квалификации оператора станка. Чтобы работать на токарном станке с ЧПУ, машинист должен выполнить определенный объем курсовой работы и получить сертификат от аккредитованной организации по обучению в промышленности.
5. Скорость удаления материала регулируется.
Еще одним преимуществом токарной обработки является возможность регулировки скорости удаления материала. Токарные станки могут работать с разной скоростью в зависимости от обрабатываемого материала или желаемого конечного продукта.
Каковы недостатки процесса токарной обработки?
Недостатки процесса токарной обработки следующие:
1. Разрешены только вращающиеся компоненты.
Поскольку токарная обработка требует вращения заготовки, можно поворачивать только вращающиеся компоненты. Это означает, что размер деталей, которые можно создать с помощью токарной обработки, ограничен.
2. Детали могут потребовать многих процедур и машин.
Токарная обработка может оказаться единственным процессом, используемым для создания детали. Он часто используется в сочетании с другими процедурами, что означает, что для производства конечного продукта требуется более одной машины.
3.
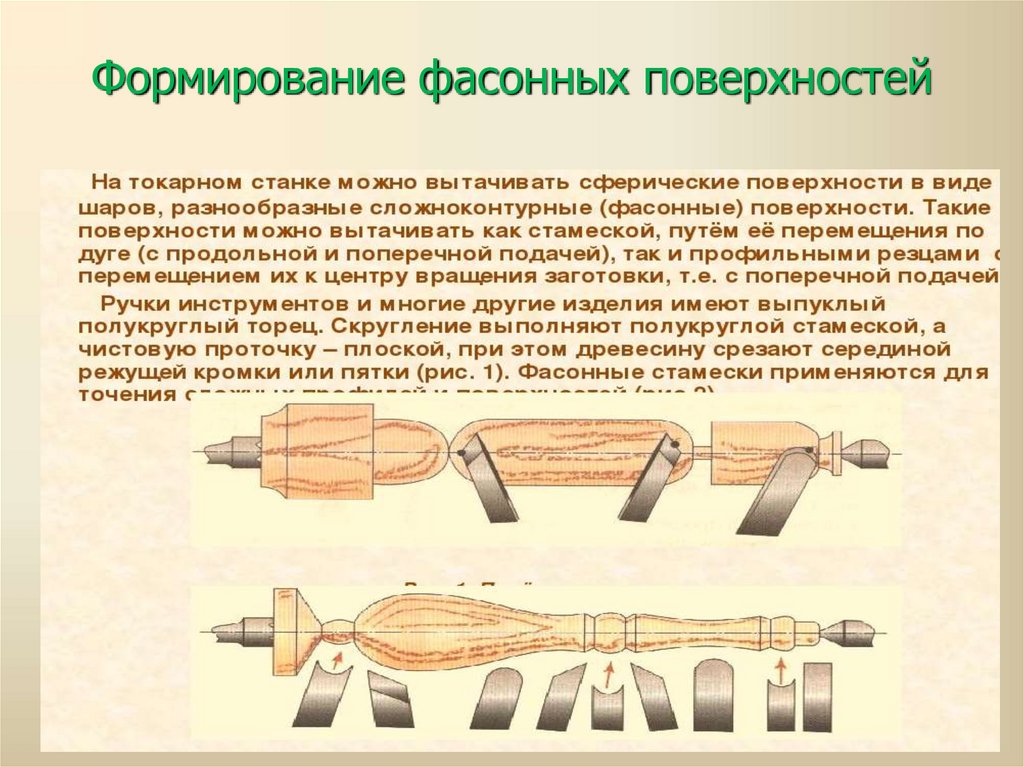
Токарные станки могут быть дорогими, особенно с ЧПУ. Кроме того, токарная обработка требует дополнительных приспособлений и приспособлений, что увеличивает стоимость оборудования.
4. Значительный износ инструмента.
Повторяющееся точение означает, что режущий инструмент подвержен значительному износу.
5. Создает значительное количество брака.
Как и в большинстве процессов механической обработки, при токарной обработке образуется металлолом. Кусочки металла, полученные в результате токарных операций, известны в Северной Америке как стружка, а в некоторых регионах их можно назвать токарной обработкой.
Резюме
В этой статье представлена токарная обработка при механической обработке, объясняется, что это такое, и обсуждается, когда лучше всего использовать этот процесс при механической обработке. Чтобы узнать больше о токарной обработке, свяжитесь с представителем Xometry.
Xometry предоставляет широкий спектр производственных возможностей, включая обработку с ЧПУ и другие дополнительные услуги для всех ваших потребностей в прототипировании и производстве. Посетите наш веб-сайт, чтобы узнать больше или запросить бесплатное предложение без каких-либо обязательств.
Заявление об отказе от ответственности
Содержание, представленное на этой веб-странице, предназначено только для информационных целей. Xometry не делает никаких заявлений и не дает никаких гарантий, явных или подразумеваемых, в отношении точности, полноты или достоверности информации. Любые рабочие параметры, геометрические допуски, особенности конструкции, качество и типы материалов или процессов не должны рассматриваться как представляющие то, что будет поставляться сторонними поставщиками или производителями через сеть Xometry. Покупатели, которым нужны расценки на детали, несут ответственность за определение конкретных требований к этим частям. Пожалуйста, ознакомьтесь с нашими условиями для получения дополнительной информации.
Команда Xometry
Эта статья была написана различными участниками Xometry. Xometry — это ведущий ресурс по производству с помощью станков с ЧПУ, изготовления листового металла, 3D-печати, литья под давлением, литья уретана и многого другого.
Калькулятор шероховатости поверхности для токарной обработки
Несоответствия шероховатости поверхности Сокращенный срок службы режущих наконечников Добавление процесса шлифования с помощью другой машины
Superoll — это полная линейка инструментов для полировки валиком, которые обеспечивают более гладкую поверхность за счет сжатия поверхности без удаления материала.
Изучить примеры из практики
См. примеры из практики
Эти закаленные и тщательно отполированные инструменты интегрируются в обрабатывающие центры, чтобы исключить вторичные процессы, такие как шлифование и хонингование, без удаления материала.
Идеально подходит для обработки с более коротким временем цикла для повышения производительности и снижения затрат.
Шероховатость поверхности – это мелкие геометрические неровности на поверхности объекта. При токарной обработке это относится к высоте пиков и впадин, образованных за счет передачи формы вершины резания.
F: Подача за один оборот (мм/об)
R: Размер вершины R режущей кромки (мм)
Однако соответствует ли фактическая шероховатость поверхности теоретической шероховатости на вашем производственном участке?
Давайте рассмотрим причины, по которым они могут не совпадать
Почему фактическая шероховатость поверхности не соответствует теоретической шероховатости:
ПРИЧИНА 1: Нарост на кромке ухудшает шероховатость поверхности.
Обработка в неподходящих условиях приводит к образованию наростов на конце режущей кромки.
В результате обработанная поверхность не имеет правильной формы и отклоняется от теоретической формы.
Данные измерения свойств поверхности — обработано
режущим наконечником с наростом.
«Нарост на кромке» — это явление, при котором крошечная часть заготовки прилипает к кромке режущей кромки во время резания и изменяет форму режущей кромки. Чем медленнее скорость подачи, тем лучше шероховатость поверхности, но тем больше вероятность того, что произойдет прилипание. Таким образом, потребуется обработка с высокой скоростью вращения.
Почему фактическая шероховатость поверхности не соответствует теоретической шероховатости:
ПРИЧИНА 1: Нарост на кромке ухудшает шероховатость поверхности.
Условия обработки
Рабочее произведение: φ30 SCM440
Резжая Наконец: карбид/нос r 0,4
Охлаждающая жидкость: не используется
Периферийная скорость: 50 -250 м/мин
. Поправо Величина резки: 0,4 мм *Фиксированная
Почему фактическая шероховатость поверхности не соответствует теоретической шероховатости:
ПРИЧИНА 2: Износ режущего наконечника.
Шероховатость поверхности постепенно ухудшается из-за износа режущего наконечника.
Таким образом, при стремлении к Rz 3.2 в массовом производстве — при условии, что он будет постепенно ухудшаться — подходящая скорость подачи будет 0,07 мм/об, а затем необходимая окружная скорость составит 450 мм/мин (4775 об/мин).
Однако, если скорость резания (окружная скорость) выше, срок службы инструмента значительно сократится из-за повышения температуры резания. Кроме того, замедление подачи увеличивает износ задней поверхности, что приводит к сокращению срока службы инструмента.
Калькулятор шероховатости поверхности →
Введите свои значения в калькулятор ниже, чтобы определить Rz и Ra. ПРИМЕЧАНИЕ. В качестве ориентира или простого преобразования, хотя и с меньшей точностью, мы конвертируем Rz в Ra путем деления на 4.
Проблемы и решения
Изучите реальные примеры того, как Superoll может упростить и улучшить ваш процесс.
Пример первого случая:
Автоматизация нестабильных работ
Проблема
Заготовка слишком длинная для высокоскоростной обработки. Вибрации на высокой скорости привели к неравномерной отделке и шероховатости поверхности.
Обычный способ
Точность размеров достигается только за счет обработки на низкой скорости. Но ручная обработка наждачной бумагой требовалась для соответствия требованиям к шероховатости поверхности, а однородность отсутствует, поскольку ручная обработка зависит от рабочего.
С Superoll
Без опасных отходов. Процесс полностью автоматизирован, что обеспечивает равномерную отделку каждый раз. Стабильная шероховатость поверхности. Сокращение времени цикла.
Второй пример:
Снижение частоты замены режущих наконечников
Проблема
Проблема: Срок службы режущего наконечника был значительно короче из-за шероховатости поверхности
Обычный способ
Режущий наконечник необходимо было часто заменять из-за шероховатой текстуры поверхности.
С Superoll
Поскольку Superoll использует сжатие вместо резки, срок службы инструмента увеличивается в четыре раза по сравнению с обычными режущими наконечниками. Это экономит время и деньги.
Пример третьего случая:
Оптимизация условий обработки коленчатых валов
Проблема
Низкая скорость вращения необходима для поддержания баланса в процессе обработки.
Обычный способ
Необходимая низкая скорость вращения потребовала отдельного этапа шлифования и покупки дорогостоящего вторичного станка.
С Superoll
Стабильность поверхности достигается без использования вспомогательной машины.
Пример четвертого случая:
Объединение процесса механической обработки и шлифования
Проблема
Низкоскоростная обработка приводит к наростам на кромках. Нарост на кромке приводит к царапинам.
Обычный способ
Необходим визуальный осмотр всех частей.
С Superoll
Позволяет выполнять обработку на высокой окружной скорости с быстрой подачей. Это не создает образования краев. Нет наростов на кромках = нет царапин = нет необходимости в осмотре. Экономия времени и трудозатрат.
Сравнение традиционных методов с использованием Superoll на вашем токарном станке
Черновая обработка + Обработка размеров + Обработка поверхности
Токарная обработка традиционным способом
Введите текст здесь! Текстовый элемент предназначен для длинной копии, которая потенциально может включать несколько абзацев.
Токарная обработка с помощью Superoll
Использование Superoll позволяет достичь прецизионной точности размеров и шероховатости поверхности ТОЛЬКО при подключении вашего токарного станка!
Поговорите с экспертом
Часто задаваемые вопросы
Вопросы
Однороликовый Superoll можно прикрепить к имеющейся револьверной головке токарного станка с ЧПУ или ЧПУ.
Superoll не является режущим инструментом, он служит для выглаживания заготовки сжатием (пластической деформацией).