Обработка наружных цилиндрических поверхностей – Токарное дело
Обработка наружных цилиндрических поверхностей Категория: Токарное дело Обработка наружных цилиндрических поверхностей Если вращать прямоугольник АБСД вокруг оси АД, получим цилиндрическую поверхность. Любая точка на поверхности цилиндра одинаково удалена от оси АД, которую называют осью цилиндра. В зависимости от требований, предъявляемых к точности обработки и параметрам шероховатости обработанной поверхности, различают черновое» получистовое, чистовое и тонкое (алмазное) обтачивание. В зависимости от длины заготовки обтачивание производят в патроне без поджатия центром, если 1,5, в патроне с поджатием задним центром, если L/d 1,5, в патроне с неподвижным люнетом, если L/d> >12. Если L/d< 12, обтачивание в центрах производят без люнета. Частоту вращения заготовки и подачу инструмента назначают в зависимости от глубины резания, материала заготовки и инструмента. Частоту вращения и подачу устанавливают посредством рукояток, расположенных на передней стороне коробки скоростей и подач. При продольном точении в патроне соблюдают следующую последовательность. Устанавливают трехкулачко-вый самоцентрирующий патрон на шпиндель. Закрепляют резцы для черновой и чистовой обработки в резцедержателе так, чтобы их вершины совпадали с линией центра станка. Зажимают заготовку в патроне. Устанавливают на станке 1К62 требуемую частоту вращения и подаче рукоятками. Закрепляют в патроне заготовку и проверяют ее биение. Включают станок и подводят резец к заготовке до соприкосновения с ее поверхностью для определения толщины срезаемой стружки. Отводят резец вправо от торца заготовки и по лимбу устанавливают глубину резания. Включают продольную подачу, протачивают заготовку на длине 5—10 мм и отводят резец. Выключают станок и измеряют штангенциркулем обточенный диаметр. Рис. 173. Крепление энсцентриновых заготовон Рис. 174. Установка нопенчатого вала на токарном станне Рис. 175. Установка нопенчатого вала в центросместитепе и эксцентрических деталей в центрах При обтачивании заготовки в центрах необходимо проделать следующее. ![]() 4. Закрепить резец в резцедержателе по линии центров. 5. Установить заготовку с хомутиком в центрах и резец под углом 90° к оси центров станка. 6. Для определения правильности установки заготовки и резца обработать поверхность на длине 3—5 мм и отвести резец. Затем установить требуемый размер заготовки. Включить станок, проточить заготовку на длине 10—15 мм. Выключить рукоятку подачи и отвести резец за торец заготовки. Измерить штангенциркулем диаметр обточенной части заготовки и при необходимости внести коррекцию. Включить станок и рукоятку подачи, обточить заготовку на заданную длину. Выключить рукоятку подачи, отвести резец и выключить станок. Измерить обработанный диаметр заготовки микрометром и при необходимости обточить снова. Рис. 176. Центрование заготовок Рис. 177.Инструменты и приспособления для разметни и сверления центрового отверстия Рис. Рис. 179. Схемы применения центров и люнетов в зависимости от длины заготовки Взять левой рукой заготовку, правой рукой отвести задний центр и снять заготовку со станка. Открепить хомутики и закрепить его на обработанной поверхности заготовки через разрезную втулку. Установить заготовку в центрах станка. Подвести резец на заданный размер по лимбу, включив подачу, проточить необработанную поверхность заготовки. Выключить станок и измерить диаметр обработанной поверхности. Снять деталь со станка, затем с детали хомутик и разрезную втулку. Для установки резца на требуемую глубину на винте поперечной и продольной подачи установлены лимбы, на которых нанесены деления. При касании резца поверхности заготовки лимб устанавливают на нулевую отметку. На большинстве станков лимб имеет 100 делений. При шаге Р — 5 мм винта поперечной подачи и полном обороте лимба резец перемещается на длину 5 мм. Следовательно, при перемещении лимба на одно деление резец переместится на 5/100 = 0,05 мм, а диаметр обработанной поверхности уменьшится на 0,1 мм. Рис. 180. Последовательность действий при продольном точении Продольный и поперечный зазор в суппорте устраняют, перемещая подвижные гайки 2 в осевом направлении гайкой и винтами. Для безопасной работы на токарном станке необходимо учесть следующее. При наружном обтачивании выполняют отрезку заготовок и протачивание наружных канавок. Большое влияние на отрезку заготовок оказывает правильность заточки и установки отрезного резца. На рис. 186 показаны примеры неправильной заточки и установки резцов относительно линии центров: у резца отсутствуют вспомогательный угол и задние вспомогательные углы ой и а2, что приводит к поломке резца; большие задние и передние углы , что тоже приводит к поломке резца; затачивание резца с завалом боковых поверхностей относительно оси резца приводит к затуплению резца; установка резца ниже или выше центра приводит к поломке резца; установка резцов под углом к оси центров приводит к выпуклости или вогнутости торцов детали. Широкие канавки обрабатывают за несколько рабочих ходов, если ширина с резца меньше ширины h канавки. Сначала прорезают правую часть канавки с припуском Д на глубину канавки. Рис. 181. Последовательность обработни заготовни в центрах Рис. 182. Лимбы для установни глубины резания Рис. 183. Устранение продольного и поперечного зазора суппорта Реклама:Читать далее:Обработка торцовых поверхностей
Статьи по теме:
Главная → Справочник → Статьи → Блог → Форум |
1.
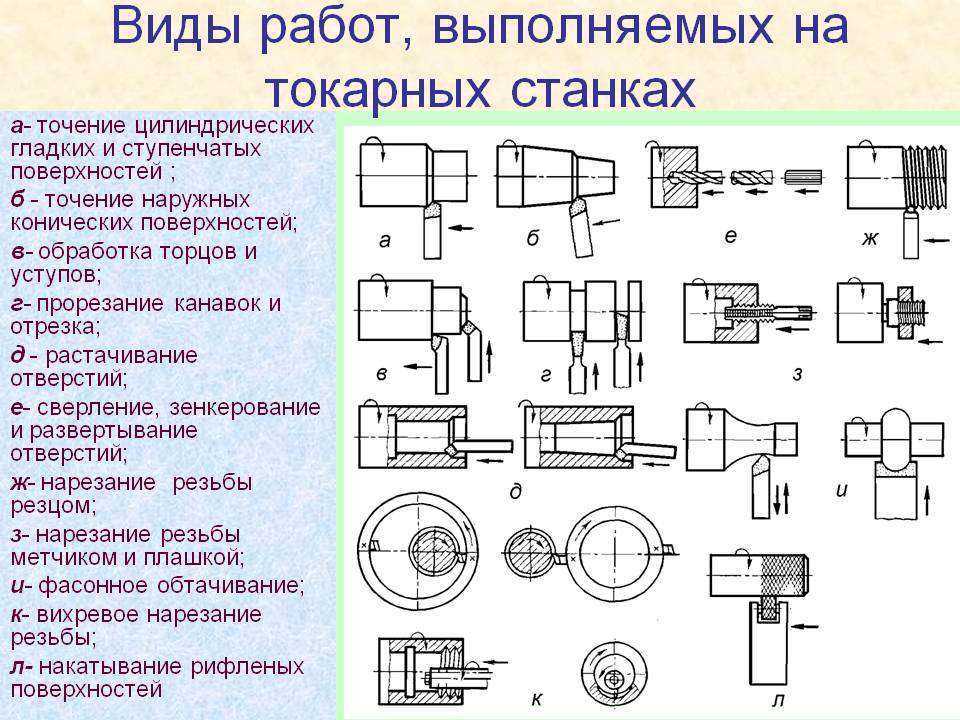
Детали, имеющие форму тел вращения, можно разделить на валы, втулки и диски. Однако наиболее характерным видом деталей тел вращения, состоящих из сочетания наружных поверхностей (цилиндрических, конических, сложной формы), является вал. Валы могут быть изготовлены из проката, поковок, штампованных заготовок и отливок. По форме валы бывают: гладкие, ступенчатые, эксцентриковые, коленчатые. По размерам – мелкие (длиной до 200 мм), средние (длиной от 200 до 1000 мм) и крупные (длиной более 1000 мм). Перед механической обработкой заготовки валов (например, прокат) подвергают правке и резке на мерные заготовки и выполнению центровых отверстий.
Обработку
наружных поверхностей вращения лезвийным
инструментом (точение) производят на
станках токарной группы: токарно-винторезных,
гидрокопировальных, токарно-револьверных,
многорезцовых, токарно-карусельных,
лоботокарных, одно- и многошпиндельных
токарных полуавтоматах и автоматах.
Заготовки устанавливают в центрах станка или патронах различных типов: 3-кулачковых, самоцентрирующих, цанговых и др.
Черновую обработку ступенчатых валов выполняют по разным вариантам (рис. 2). Схема с наименьшей продолжительностью обработки считается предпочтительной.
Удаляя припуск, исходят из соображений последовательного уменьшения жесткости вала, т.е. ступени меньшего диаметра обрабатывают в последнюю очередь. При черновом точении точность обработки достигает 14-го квалитета, а шероховатость Rz = 40…80 мкм).
Рис. 2. Схемы обтачивания ступенчатого вала: 1–4 – номера переходов; А, Б, В – ступени вала |
При черновом наружном точении обработку производят с большой глубиной резания (

Получистовое точение обеспечивает точность обработки 9–12-го квалитета и шероховатость поверхности Rz = 10…20 мкм.
При получистовом точении обработку производят с глубиной резания t, равной 3–6 мм на сторону, продольной подачей S = 0,2–0,5 мм/об и скоростях резания от 100 до 140 м/мин (при обработке резцами, снабженными пластинами из твердого сплава типа Т15К6). В качестве СОЖ применяют эмульсию.
Чистовое
точение обеспечивает
точность обработки 7–8-го квалитета
и шероховатость поверхности
Ra = 1,25…2,5 мкм.
При чистовом точении устанавливают
глубину резания порядка 0,15–1,5 мм на
сторону, продольную подачу от 0,05 до 0,15
мм/об и скорость резания порядка 150 м/мин
(при работе резцами с пластинами
из твердого сплава типа Т30К4, ВК2 или
ВК3). В качестве СОЖ применяют эмульсию.
Тонкое (алмазное) точение – это отделочный метод обработки. При наружном точении алмазными (эльборовыми) резцами цветных сплавов достигается точность 5–6-го квалитета и шероховатость поверхности Ra = 0,16…0,32 мкм. Обработку производят на режимах: глубина резания t = 0,05…0,1 мм, продольная подача S = 0,01…0,03 мм/об, скорость резания V = 300…3000 м/мин. Алмазное точение, как правило, производят без применения СОЖ, так как при этом методе обработки смазочно-охлаждающей технологической средой (СОТС) является воздух. Для алмазного точения должны применяться станки особо высокой точности и жесткости.
В
качестве инструмента при тонком точении
сталей можно использовать широкие
резцы, оснащенные пластинами из твердого
сплава Т30К4, а для обработки чугунов –
резцы с пластинками из твердого
сплава ВК2 или ВК3. Передние и задние
поверхности режущих пластин должны
быть доведены до шероховатости поверхности
Ra = 0,02…0,04
мкм.
Тонкое точение резцами с твердосплавными пластинами производят при глубине резания t = 0,05…0,15 мм, продольной подаче S = 0,01…0,05 мм/об и скорости резания V = 200…350 м/мин. При этом достигается точность 6–7-го квалитета и шероховатость поверхности Ra = 0,32…0,63 мкм. В качестве СОЖ обычно применяют эмульсию.
В табл.1 приведены значения экономической точности и шероховатости поверхности при точении и подрезке торцов деталей из разных материалов.
Таблица 1
Значения экономической точности и шероховатости поверхности при наружном точении и подрезке торцов
Вид обработки | Шероховатость поверхности, мкм | Точность (квалитет) | ||||
Неметаллические | Сплавы на основе Mg и Al | Латунь, бронза | Сталь | |||
Наруж-ное точение | Черновое | — | Rz = 40…80 | Rz = 40…80 | Rz = 40…80 | 12–14 |
Получистовое | — | Rz = 5…10 | Rz = 5…10 | Rz = 10…20 | 9–12 | |
Чистовое | Ra = 5…10 | Ra = 1,25 | Ra = 1,25 | Ra = 1,25…2,5 | 7–8 | |
Тонкое | — | Ra = 0,3 | Ra = 0,3 | Ra = 1,2…0,3 | 5–7 | |
Подрезка торцов | Черновая | — | Rz = 40…80 | Rz = 40…80 | Rz = 40…80 | 13–14 |
Получистовая | — | Rz = 10…20 | Rz = 10…20 | Rz = 10…20 | 11–12 | |
Чистовая | Ra = 2,5…10 | Ra = 1,2…2,5 | Ra = 1,2…2,5 | Ra = 1,2…2,5 | 7–9 | |
Тонкая | — | Ra = 0,6 | Ra= 0,6 | Ra = 0,6 | 6–7 |
При
обработке длинных маложестких валов
применяют неподвижные (рис. 1,а)
и подвижные люнеты (рис.1,б).
Обрабатывая полые валы с контролируемой
разностенностью стенки, используют
кольцевые (вертлюжные) люнеты.
Люнеты служат дополнительной опорой, испытывающей нагрузки. Подвижный люнет, следуя за резцом, воспринимает силу резания. Обрабатываемая поверхность опирается на кулачки люнета. В тех случаях, когда следует обеспечить соосность обтачиваемой поверхности с ранее обработанной, кулачки люнета устанавливают впереди резца, то есть на ранее обработанную поверхность.
Рис. 3.2. Люнеты: а – с роликовыми опорами; б – подвижный люнет-виброгаситель
При
скоростном резании кулачки создают
значительное трение. Чтобы уменьшить
трение, применяют люнеты
с роликовыми опорами (см. рис. 3.2, а).
При скоростном точении часто возникают
вибрации, которые увеличивают шероховатость
поверхности и снижают точность обработки.
Для устранения вибраций используют
люнеты с виброгасителем (см. рис.1,б).
Тарельчатые пружины, помещенные в
корпусе виброгасителя, поглощают
вибрации детали.
При высоких скоростях резания стружка имеет сливную форму и сходит из-под резца непрерывной лентой. Такая стружка весьма опасна, так как может явиться причиной травматизма (порезов и (или) ожогов). Для размельчения такой стружки применяют специальные устройства – стружколоматели.
В массовом и крупносерийном производствах обработку валов часто производят на многорезцовых станках, которые имеют два суппорта – передний и задний. Передний суппорт служит для точения. Задний суппорт, совершающий поперечное движение, предназначен для подрезки торцов и прорезания канавок. Резцы настраивают так, чтобы обработка всех участков заканчивалась одновременно. Многорезцовое обтачивание выполняют тремя способами.
Первый
способ – деление общего припуска по
глубине. При этом способе припуск на
одной из ступеней снимается последовательно
несколькими резцами, и передний суппорт
совершает путь L,
равный сумме обрабатываемых ступеней L = l1 + l2 + l3 (рис. 2,а).
Второй способ – деление длины заготовки на несколько участков (рис. 3.3, б). Применяется, когда максимальный припуск может быть удален резцами за один проход. При такой схеме обработки длина хода резца l = L/n, где n – количество ступеней.
Рис. 2. Способы обработки ступенчатого вала на многорезцовом станке: а – способ деления припуска; б – способ деления длины обработки вала; в – способ деления длины максимальной ступени |
Третий способ – деление максимальной ступени вала (рис. 2, в). Более длинная ступень l1 протачивается несколькими резцами, установленными на одинаковую глубину съема.
Установка
резцов производится либо по обработанной
заготовке, либо по специальному эталону.
Многорезцовую обработку применяют, как правило, на предварительных операциях. Чистовое точение можно выполнять на гидрокопировальных станках 1708, 1Н713, 1Б732 и др., имеющих два суппорта, расположенных в вертикальной плоскости, что позволяет облегчить сход стружки из зоны резания. Точение по копиру осуществляется одним резцом, расположенным на верхнем суппорте. Подрезка торцов осуществляется резцами, расположенными в нижнем суппорте. Точение на многорезцовых станках осуществляется со скоростью резания 30–50 м/мин, а чистовое точение на гидрокопировальных станках – со скоростью резания 150–200 м/мин. В качестве СОЖ обычно применяют эмульсию.
В серийном и мелкосерийном производствах валы обрабатывают на станках с числовым программным управлением или ручным управлением.
В единичном производстве обработку валов обычно осуществляют на универсальном оборудовании с ручным управлением.
Прецизионная обработка наружных цилиндрических поверхностей стали EN8 методом электрохимического хонингования (ЭХО) с использованием технологии OFAT
- title={Прецизионная отделка наружных цилиндрических поверхностей стали EN8 методом электрохимического хонингования (ЭХО) с использованием технологии OFAT},
автор={П.
Судхакар Рао, П. К. Джайн и Дхирендра Кумар Двиведи}, journal={Материалы сегодня: Материалы}, год = {2015}, объем = {2}, страницы={3220-3229} }
- P. S. S. Rao, P. Jain, D. K. Dwivedi
- Опубликовано 2015
- Материаловая наука
- Материалы сегодня: Материалы
Просмотр через издатель
Оптимизация ключевых параметров процесса на электро -химическом веществе (Ech). Поверхности титанового сплава Ti 6Al 4V
- P. S. Rao, P. Jain, D. K. Dwivedi
Материаловедение
- 2017
ЭЛЕКТРОХИМИЧЕСКАЯ ОБРАБОТКА (ECH)0023
- Sudhakar Rao, P. Jain, D.K. Dwivedi
Материаловедение
- 2016
Электрохимическое хонингование — это процесс прецизионной механической обработки труднообрабатываемых материалов и придания формы поверхностям произвольной формы с помощью процесса ECM. с комбинированным механическим хонингованием. В ECH,…
Последние достижения в электроэрозионной обработке композиционных материалов с металлической матрицей
- Мумтаз Ризви, П.
Судхакар Рао, М. Ю. Хан
Materials Science
- 2020
A Study of Electrochemical Machining of Ti-6Al-4V in NaNO3 solution
- Hansong Li, Chuanping Gao, Guoqian Wang, N. Qu, Di Zhu
Materials Science
Научные отчеты
- 2016
Результаты экспериментов показывают, что при соответствующих технологических параметрах в 10% растворе NaNO3 можно получать высококачественные отверстия, и этот сплав используется во многих отраслях промышленности, включая авиацию, автомобилестроение и медицину оборудование.
Смешанная порошковая электроэрозионная обработка (PM-EDM): методологический обзор
- Mohd. Yunus Khan, P. Sudhakar Rao, B. S. Pabla
Материалисные науки
- 2020
Проектные соображения для соединительного стержня
- B. Sriharsha, P. S. Rao
Engineering
- 202020777777777777102020202020202 один из ключевых компонентов двигателя, который соединяет поршень с коленчатым валом и преобразует возвратно-поступательное движение поршня во вращение коленчатого вала.
Шатун должен быть…
International Journal of Innovative Technology and Exploring Engineering (IJITEE)
- R. Alnanih
Business, Computer Science
- 2019
Инженерный подход, основанный на моделях, ориентирован на общий метамодель построения общего репозитория страховые компании качества, иллюстрированные CMMI.
ПОКАЗАНЫ 1-10 ИЗ 10 ССЫЛОК
Оптимизация шероховатости поверхности и MRR при электрохимической обработке инструментальной стали EN31 с использованием подхода Грея-Тагучи
- Милан Кумар Дас, Каушик Кумар, Т. Барман, P. Sahoo
Материалогические науки
- 2014
Разработка модели ANN для предсказания шероховатости поверхности во время криогенной операции
- .. K.K.
Материаловедение, машиностроение
- 2013
Эта исследовательская работа посвящена передовой технологии производства, которая может быть достигнута за счет улучшения параметров обработки за счет криогенного охлаждения вместо обычного охлаждения…
Экспериментальные исследования по электрохимическому хонингованию
- A.
Dubey
Материаловедение
- 2008
Электрохимическое хонингование (ЭХО) представляет собой гибрид традиционной технологии электрохимической обработки и хонингования, основанный на принципах прецизионной электрохимической обработки, основанной на принципах шлифования с помощью микрошлифования. обеспечить…
Электрохимическое хонингование зубчатых колес — новый метод чистовой обработки зубчатых колес
- Чен Чи-пин, Л. Цзянь, Вэй Го-Чань, Ван Чао-Бин, В. Цзянь, Р. Леви
Инженерия, материаловедение
- 1981
Анализ топологии поверхности при сухой обработке стали EN-8
- Сунил Дж. Райкар, Д. Д’Аддона, Д. Крамар
4
10 Материаловедение 4 19090041
- 2014
Электрохимические отходы управляемого полета
- W. Guo-Qiang, Wang Zhao-Bing, Chen Chi-Ping
Материалоте Электрохимическое хонингование в полевых условиях)
- Fengbao He, Wei Zhang, K.
Nezu
Материаловедение
- 2000
В данной статье представлен новый рабочий метод управляемого электрохимического хонингования (ЭХО) зубчатых колес следующим образом. Катод в форме зубчатого колеса, который входит в зацепление с зубчатым колесом заготовки во время обработки, выявляется как…
Характеристика поверхности обработанной электрическим разрядом поверхности быстрорежущей стали
- К. Маннан, А. Кришнайах, Шива Прасад Арикатла
Материаловедение
- 2013
В этом проекте было проведено всестороннее исследование характеристик поверхности обработанной электрическим разрядом поверхности заготовки из быстрорежущей стали. Электроэрозионные испытания детали из быстрорежущей стали…
Исследование поведения ECH конических зубчатых колес в зависимости от времени
- J. P. Misra, P. Jain, D. K. Dwivedi, N. Mehta
Инженерное дело, бизнес
- 20011 Нетрадиционные производственные процессы
- Г.
Ф. Бенедикт
Материаловедение
- 1987
Эта книга представляет собой удобный единый источник информации о передовых процессах механической обработки, формирования материалов и соединения. В нем описаны доступные технологии, в которых используются такие инструменты, как высокоскоростные…
Испытания наружных цилиндрических поверхностей деталей автомобилей после обработки широким выглаживанием
Главная Основные технические материалы Основные технические материалы Vol. 746 Испытания наружных цилиндрических поверхностей автомобилей…
Предварительный просмотр статьи
Аннотация:
В Российской Федерации разработана сверхпроизводительная технология поверхностной пластической деформации, получившая название широкое выглаживание (WB). Механика новой технологии WB отличается от классических технологий SPD (прокатка или воронение). Например, приложенное усилие при обработке выглаживания составляет 150-300 Н, ВО 2500-5000 Н, что обусловлено условием реализации процесса в серийном производстве с ограниченным временем обработки (3-4 оборота заготовки).
WB также имеет высокую степень деформации из-за многократного прохода деформации. Потребность в разработке методики испытаний «Детали сальниковой шейки автомобиля ВАЗ, обработанные различными методами» была вызвана тем, что проведенные ранее стендовые испытания не воспроизводят реальную поверхность шеек валов, работающих в паре с манжетными уплотнениями. Также отсутствовала методика измерения величины износа шейки сальника и определялась максимальная величина канавки износа 1,0 мм. Испытывались образцы, воспроизводящие сальниковую шейку в двух наиболее ответственных деталях: фланец крепления карданного вала к приводному валу коробки передач из стали 40 и коленчатый вал из высокопрочного чугуна 75-50-03 автомобиля ВАЗ. Результаты испытаний образцов из стали 40 показали параметр шероховатости поверхности Ra = 0,06 мкм после воронения и Ra = 0,28 мкм после полирования. Результаты испытаний были измерены на профилографе и были получены следующие данные: ширина канавок износа составила 936 мкм с воронением и 1152 мкм с полировкой, глубина составила 2,16 и 4,94 мкм соответственно.
Размер площади поперечного сечения канавки образца при износе с воронением – 1090 мкм 2 , с полированием – 2848 мкм 2 .
Доступ через ваше учреждение
Вас также могут заинтересовать эти электронные книги
Предварительный просмотр
* – Автор, ответственный за переписку
использованная литература
[1] Ю.Г. Schneider, Служебные характеристики заготовок с регулярным микрорельефом, J.
Prec. англ. 6(4) 32 (1984).
[2] Шероховатость поверхности. Параметры и характеристики, ГОСТ 2789-73, информация на: www. нтцэксперт. ru/documents/docs/gs_03. док.
[3] X. Yin, K. Komvopoulos Анализ пластичности линии скольжения трения скольжения шероховатых поверхностей, демонстрирующих самоаффинное (фрактальное) поведение, Journal of the Mechanics and Physics of Solids, 60 (3) (2012). DOI: 10. 1016/j. jmps. 2011. 10. 008.
DOI: 10.1016/j.jmps.2011.10.008
[4] Л.
Хигеманн, К. Ведделинг, Н.Б. Халифа, А. Э. Теккая, Аналитическое прогнозирование шероховатости после шарикового полирования поверхностей с термическим покрытием, Procedia Engineering, 81 (2014) 1921-1926. ISSN 1877-7058. DOI: 10. 1016/j. проангл. 2014. 10. 257.
DOI: 10.1016/j.proeng.2014.10.257
[5] Поверхности правильной микроформы. Классификация, параметры и характеристики, ГОСТ 24773-81, информация на сайте: http: /vsegost. com/Каталог/30/30256. штмл.
[6] С.Н. Григорьев, Н.М. Бобровский, И.Н. Бобровский, П.А. Мельников А.А., Лукьянов, Экологические аспекты технологии пластической деформации зеленых поверхностей автомобильных деталей, Серия конференций ИОП: Науки о Земле и окружающей среде, 50 (2017) 012015.
- Г.
- Fengbao He, Wei Zhang, K.