Обработка отверстий (сверление, цекование, развертывание и др.) и инструмент
Обработка отверстий – это целый ряд технологических операций, целью которых является доведение геометрических параметров, а также степени шероховатости внутренней поверхности предварительно выполненных отверстий до требуемых значений. Отверстия, которые обрабатываются при помощи таких технологических операций, могут быть предварительно получены в сплошном материале не только при помощи сверления, но также методом литья, продавливания и другими способами.
Обработка высверленного отверстия цилиндрическим зенкером
Конкретный способ и инструмент для обработки отверстий выбираются в соответствии с характеристиками необходимого результата. Различают три способа обработки отверстий – сверление, развертывание и зенкерование. В свою очередь эти методы подразделяются на дополнительные технологические операции, к которым относятся рассверливание, цекование и зенкование.
Чтобы понять особенности каждого из вышеперечисленных способов, стоит рассмотреть их подробнее.
Сверление
Чтобы обрабатывать отверстия, их необходимо предварительно получить, для чего можно использовать различные технологии. Наиболее распространенной из таких технологий является сверление, выполняемое с использованием режущего инструмента, который называется сверлом.
Основные части спирального сверла
При помощи сверл, устанавливаемых в специальных приспособлениях или оборудовании, в сплошном материале можно получать как сквозные, так и глухие отверстия. В зависимости от используемых приспособлений и оборудования сверление может быть:
- ручным, выполняемым посредством механических сверлильных устройств или электро- и пневмодрелей;
- станочным, осуществляемым на специализированном сверлильном оборудовании.
Физика сверления отверстий
Использование ручных сверлильных устройств является целесообразным в тех случаях, когда отверстия, диаметр которых не превышает 12 мм, необходимо получить в заготовках из материалов небольшой и средней твердости.
- конструкционные стали;
- цветные металлы и сплавы;
- сплавы из полимерных материалов.
Если в обрабатываемой детали необходимо выполнить отверстие большего диаметра, а также добиться высокой производительности данного процесса, лучше всего использовать специальные сверлильные станки, которые могут быть настольными и стационарными. Последние в свою очередь подразделяются на вертикально- и радиально-сверлильные.
Рассверливание – тип сверлильной операции – выполняется для того, чтобы увеличить диаметр отверстия, сделанного в обрабатываемой детали ранее. Рассверливание также выполняется при помощи сверл, диаметр которых соответствует требуемым характеристикам готового отверстия.
Физика рассверливания отверстий
Такой способ обработки отверстий нежелательно применять для тех из них, которые были созданы методом литья или посредством пластической деформации материала. Связано это с тем, что участки их внутренней поверхности характеризуются различной твердостью, что является причиной неравномерного распределения нагрузок на ось сверла и, соответственно, приводит к его смещению. Формирование слоя окалины на внутренней поверхности отверстия, созданного с помощью литья, а также концентрация внутренних напряжений в структуре детали, изготовленной методом ковки или штамповки, может стать причиной того, что при рассверливании таких заготовок сверло не только сместится с требуемой траектории, но и сломается.
При выполнении сверления и рассверливания можно получить поверхности, шероховатость которых будет доходить до показателя Rz 80, при этом точность параметров формируемого отверстия будет соответствовать десятому квалитету.
Зенкерование
При помощи зенкерования, выполняемого с использованием специального режущего инструмента, решаются следующие задачи, связанные с обработкой отверстий, полученных методом литья, штамповки, ковки или посредством других технологических операций:
- приведение формы и геометрических параметров имеющегося отверстия в соответствие с требуемыми значениями;
- повышение точности параметров предварительно просверленного отверстия вплоть до восьмого квалитета;
- обработка цилиндрических отверстий для уменьшения степени шероховатости их внутренней поверхности, которая при использовании такой технологической операции может доходить до значения Ra 1,25.
При зенкеровании прикладывается меньшая сила реза, чем при сверлении, и отверстие получается более точное по форме и размерам
Если такой обработке необходимо подвергнуть отверстие небольшого диаметра, то ее можно выполнить на настольных сверлильных станках. Зенкерование отверстий большого диаметра, а также обработка глубоких отверстий выполняются на стационарном оборудовании, устанавливаемом на специальном фундаменте.
Ручное сверлильное оборудование для зенкерования не используется, так как его технические характеристики не позволяют обеспечить требуемую точность и шероховатость поверхности обрабатываемого отверстия. Разновидностями зенкерования являются такие технологические операции, как цекование и зенкование, при выполнении которых используются различные инструменты для обработки отверстий.
Зенкеры конусные по металлу
Специалисты дают следующие рекомендации для тех, кто планирует выполнить зенкерование.
- Зенкерование следует проводить в процессе той же установки детали на станке, при которой осуществлялось сверление отверстия, при этом из параметров обработки меняется только тип используемого инструмента.
- В тех случаях, когда зенкерованию подвергается необработанное отверстие в деталях корпусного типа, необходимо контролировать надежность их фиксации на рабочем столе станка.
- Выбирая величину припуска на зенкерование, надо ориентироваться на специальные таблицы.
- Режимы, на которых выполняется зенкерование, должны быть такими же, как и при осуществлении сверления.
- При зенкеровании должны соблюдаться те же правила охраны труда и техники безопасности, как и при сверлении на слесарно-сверлильном оборудовании.
Зенкование и цекование
При выполнении зенкования используется специальный инструмент – зенковка. При этом обработке подвергается только верхняя часть отверстия. Применяют такую технологическую операцию в тех случаях, когда в данной части отверстия необходимо сформировать углубление для головок крепежных элементов или просто снять с нее фаску.
Чем различаются зенкование и цекование
При выполнении зенкования также придерживаются определенных правил.
- Выполняют такую операцию только после того, как отверстие в детали будет полностью просверлено.
- Сверление и зенкование выполняются за одну установку детали на станке.
- Для зенкования устанавливают небольшие обороты шпинделя (не больше 100 оборотов в минуту) и применяют ручную подачу инструмента.
- В тех случаях, когда зенкование осуществляется цилиндрическим инструментом, диаметр цапфы которого больше диаметра обрабатываемого отверстия, работу выполняют в следующей последовательности: сначала сверлится отверстие, диаметр которого равен диаметру цапфы, выполняется зенкование, затем основное отверстие рассверливается на заданный размер.
Целью такого вида обработки, как цекование, является зачистка поверхностей детали, которые будут соприкасаться с гайками, головками болтов, шайбами и стопорными кольцами. Выполняется данная операция также на станках и при помощи цековки, для установки которой на оборудование применяются оправки.
Развертывание
Процедуре развертывания подвергаются отверстия, которые предварительно были получены в детали при помощи сверления. Обработанный с использованием такой технологической операции элемент может иметь точность, степень которой доходит до шестого квалитета, а также невысокую шероховатость – до Ra 0,63. Развертки делятся на черновые и чистовые, также они могут быть ручными или машинными.
Цилиндрические ручные развертки 24Н8 0150
Рекомендации, которых следует придерживаться при выполнении данного вида обработки, заключаются в следующем.
- Припуски в диаметре обрабатываемого отверстия выбираются по специальным таблицам.
- При использовании ручного инструмента, который вращают только по часовой стрелке, сначала выполняют черновое, а потом чистовое развертывание.
- Обработку стальных деталей выполняют с обязательным использованием СОЖ, чугунных – всухую.
- Машинное развертывание проводят сразу после сверления на станке – с одной установки детали.
- Для контроля качества результата используют специальные калибры.
Slesarnaya 8 Обработка отверстий
1 – лапка; 2 – хвостик; 3 – шейка; 4 – канавка
Рис. 1.18. Приспособления для зажима сверла:
а – трехкулачковый патрон; б – переходная конусная втулка
Сверло с цилиндрическим хвостовиком предварительно закрепляется в специальном патроне (рис. 1.18, а). В том случае, когда конус сверла меньше конуса в шпинделе станка, применяются конусные переходные втулки (рис. 1.18, б). Лапка – концевая часть сверла – служит упором при выбивании сверла из шпинделя станка. При сверлении обрабатываемую деталь закрепляют неподвижно, а сверху сообщают два совместных движения (рис. 1.17): вращательное (по стрелке I) и поступательное, направленное вдоль оси сверла (по стрелке II). Вращательное движение сверла называется главным, а поступательное – движением подачи.
Сверление применяют, когда необходимо получить отверстия невысокой степени точности и невысокого класса шероховатости, например, под крепежные болты и шпильки, а также под нарезание резьбы, развертывание и зенкерование. Если отверстие в детали несквозное, то операция называется засверливанием, а увеличение диаметра отверстия – рассверливанием, или зенкерованием.
В процессе сверления происходит стачивание режущих кромок сверла, и оно становится неработоспособным. Для восстановления режущих свойств сверла его затачивают. Полученный в результате заточки угол при вершине сверла проверяют специальными шаблонами (рис. 1.19). Величина этого угла выбирается в зависимости от обрабатываемого материала (табл. 1.1).
Рис. 1.19. Проверка сверла при заточке по шаблону:
а – шаблон; б – измерение длины режущей кромки;
в – измерение угла при вершине; г – измерение угла заострения;
д – измерение угла наклона поперечной кромки
Таблица 1.
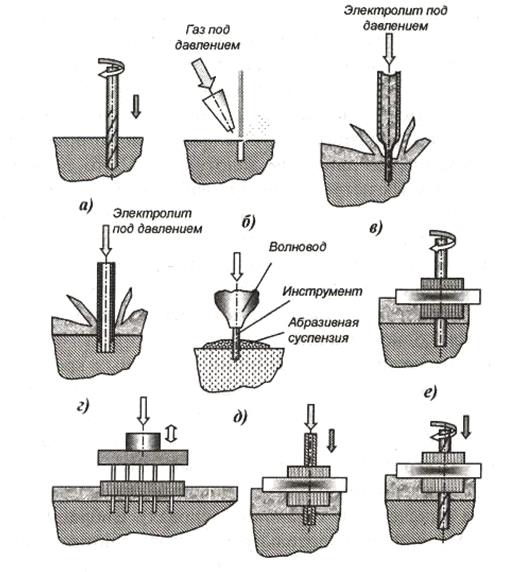
Для уменьшения трения сверло имеет обратную конусность: его диаметр уменьшается по направлению к хвостовику на 0,03…0,12 мм на каждые 100 мм длины.
Свёрла изготовляют из сталей марок Р9, Р18, Р9К10, Р6М5, Р18К5Ф2, У12А, оснащают пластинками из твердых сплавов и композиционных материалов.
При сверлении отверстий диаметр сверла выбирают в зависимости от диаметра крепёжной детали – болта или шпильки (табл. 1.2).
Таблица 1.2 Диаметр сверла при получении отверстия для крепежной детали
Зенкование – это операция обработки цилиндрических или конических углублений и фасок просверленных отверстий под головки болтов, винтов и заклёпок (рис 1.20, а). Режущим инструментом является зенковка. По форме режущей части зенковки делятся на цилиндрические, конические и торцовые (цековки). Все они состоят из рабочей части и хвостовика.
Рис.
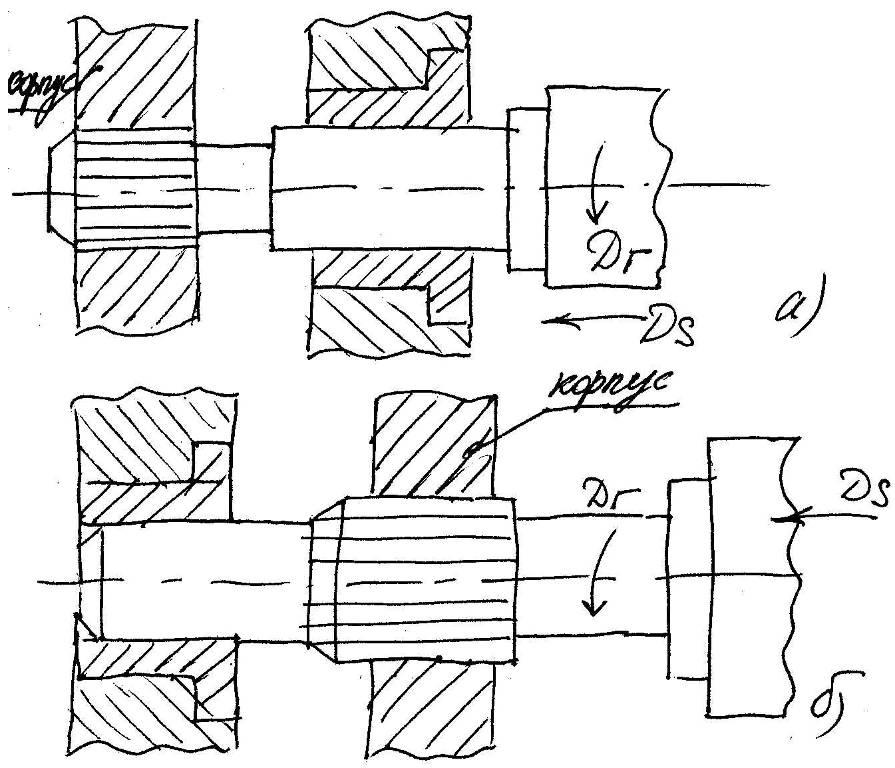
а – зенкование; б – зенкерование; в – развёртывание
Рабочая часть цилиндрической зенковки имеет от 4 до 8 торцовых зубьев и направляющую цапфу, которая входит в просверленное отверстие, что обеспечивает совпадение оси отверстия и образованного зенковкой цилиндрического углубления.
На конической зенковке рабочая часть имеет конус при вершине. Наибольшее распространение получили конические зенковки с углом конуса 30, 60, 90 и 120*.
Цекование производится торцовыми зенковками для зачистки торцовых поверхностей, обработки бобышек под шайбы, упорные кольца, гайки. Для изготовления зенковок используется сталь марок Р9, Р18.
Зенкерование – процесс обработки цилиндрических и конических необработанных отверстий с целью увеличения диаметра, улучшения качества их поверхности, повышения точности (уменьшения конусности, овальности, разбивки). Зенкерование выполняется на сверлильных станках зенкерами (рис. 1.20, б), которые по внешнему виду напоминают сверло и состоят из тех же основных элементов, но имеют большее количество режущих кромок (3–4) и спиральных канавок.
Зенкеры изготовляют из стали марок Р9, Р18, 9ХС, У12А двух типов: цельные диаметром 10…40 мм с длиной рабочей части 80…200 мм и насадные диаметром 32…80 мм с длиной 10…18 мм.
Отверстия, которые после сверления необходимо обрабатывать зенкером, должны иметь меньший диаметр по сравнению с диаметром окончательно обработанного отверстия (табл. 1.3).
Таблица 1.3 Диаметр зенкера с учетом припускаРазвёртывание – обработка отверстий после сверления, зенкерования или расточки для придания им требуемой высокой точности и шероховатости (рис. 1.20, в).
Основным инструментом является развёртка, которая состоит из рабочей части, шейки и хвостовика. В зависимости от формы обрабатываемого отверстия применяют цилиндрические и конические развёртки с 6…12 зубьями. По конструкции развёртки подразделяют на цельные, регулируемые и со вставными зубьями, а по способу применения на ручные и машинные.
При развертывании отверстий вручную применяют развертку с неравномерным распределением зубьев по окружности, что способствует получению менее шероховатой поверхности. Машинные развертки имеют чётное количество равномерно распределенных зубьев. Чем больше зубьев, тем менее шероховатой получается обрабатываемая поверхность.
Цилиндрические и конические развёртки изготовляют из стали марок Р9, 9ХС комплектно. В комплекте из трех развёрток первая – черновая, вторая – переходная, третья – чистовая.
Толщина слоя металла, снимаемого развёрткой, зависит от диаметра отверстия (табл. 1.4).
Таблица 1.4 Припуск на диаметр при развертыванииВиды обработки отверстий в металле и используемый инструмент
Обработка отверстий – это определенный ряд производственных этапов, призванных довести размеры, а также стадию шероховатости внутренней части отверстий до необходимых значений. Отверстия, обрабатываемые при помощи таких производственных операций, могут быть получены в металлоконструкции не только сверлением, но при помощи продавливания, литья и другими методами.
Существуют три метода обработки отверстий – сверление, зенкерование и развертывание. Эти способы подразумевают дополнительные операции, предусматривающие цекование, рассверливание и зенкование.
Методы обработки
Сверление – наиболее распространенный метод, выполняемый с применением режущего приспособления – сверла. При помощи сверла в сплошном материале можно добиться как сквозных, так и глухих отверстий. В зависимости от применяемых инструментов и оборудования сверление может быть:
- ручным – выполняется при помощи механических аппаратов для сверления;
- станочным – производится на специализированном оборудовании для сверления.
Использование ручных устройств для сверления целесообразно, когда диаметр отверстия не больше 12 мм, а получить такой результат необходимо в заготовках из материалов малой и средней плотности: цветные металлы и сплавы; конструкционные стали и сплавы из полимерных составов.
Для того чтобы в детали сделать отверстие большего размера, а также достичь высокой производительности, лучше использовать станки для сверления – настольные или стационарные.
При зенкеровании, выполненном с использованием режущего инструмента, добиваются результатов, связанных с обработкой отверстий, полученных методом литья, штамповки, ковки:
- приведение формы в соответствие с требуемыми значениями;
- повышение точности предварительно просверленного отверстия;
- обработка отверстий для уменьшения шероховатости их внутренней поверхности.
Процессу развертывания подлежат отверстия, полученные в детали при помощи сверления. Данная операция проводится как вручную, так и на станках.
Результат проводимых операций
Результатом данных операций является то, что процесс резания осуществляется вращательными и поступательными движениями режущего инструмента относительно своей оси и приводит к безупречному качеству проделанных отверстий.
Обработка отверстий | Слесарное дело
Обработка отверстий
После выполнения отверстий в сплошном материале производится их обработка для увеличения размеров и снижения шероховатости поверхностей, а также обработка предварительно полученных отверстий (например, литьем, продавливанием и т.п.). Обработка отверстий выполняется несколькими способами, в зависимости от того, какие параметры точности и шероховатости поверхности отверстия заданы чертежом. В соответствии с выбранным способом обработки выбирается и инструмент для ее осуществления. При обработке отверстий различают три основных вида операций: сверление, зенкерование, развертывание и их разновидности: рассверливание, зенкование, цекование.
Сверление
Сверление — это операция по образованию сквозных и глухих отверстий в сплошном материале, выполняемая при помощи режущего инструмента — сверла. Различают сверление ручное — ручными пневматическими и электрическими сверлильными устройствами (дрелями) и сверление на сверлильных станках. Ручные сверлильные устройства используются для получения отверстий диаметром до 12 мм в материалах небольшой и средней твердости (пластмассы, цветные металлы, конструкционные стали и др.). Для сверления и обработки отверстий большего диаметра, повышения производительности труда и качества обработки используют настольные сверлильные и стационарные станки — вертикально-сверлильные и радиально-сверлильные.
Одной из разновидностей сверления является рассверливание — увеличение диаметра отверстия, просверленного ранее. В качестве инструментов для рассверливания отверстий, также как и для сверления, используют сверла. Не рекомендуется рассверливать отверстия, полученные в заготовке методом литья, ковки или штамповки. Такие отверстия имеют различную твердость по поверхности отверстия из-за окалины, образующейся при литье, а также из-за неравномерной концентрации внутренних напряжений в металле на различных участках поверхности отверстий, полученных методом ковки или штамповки. Наличие мест с неравномерной и повышенной твердостью поверхности приводит к изменению радиальных нагрузок на сверло в процессе обработки отверстия, что ведет к смещению его оси, а также является причиной поломки сверла. Обработка отверстий сверлением и рассверливанием позволяет получить точность размеров обработанного отверстия до 10-го квалитета и шероховатость обработанной поверхности до Rz 80.
Зенкерование
Зенкерованием называется операция, связанная с обработкой предварительно просверленных, штампованных, литых или полученных другими методами отверстий с целью придания им более правильной геометрической формы (устранение отклонений от круглости и других дефектов), а также достижения более высокой, по сравнению со сверлением, точности (до 8-го квалитета) и более низкой шероховатости (до Ra 1,25). Зенкерование ведут либо на настольных сверлильных станках (при небольших диаметрах отверстий), либо на стационарном сверлильном оборудовании, устанавливаемом на фундаменте. Ручное сверлильное оборудование для зенкерования не применяется, так как оно не может обеспечить получение требуемых точности и шероховатости поверхности. К разновидностям зенкерования относятся зенкование и цекование.
Основные правила зенкерования отверстий:
• сверление и зенкерование отверстий необходимо производить с одной установки детали (заготовки) на станке, т. е. меняя только обрабатывающий инструмент;
• при зенкеровании необработанных отверстий в корпусных деталях особое внимание следует обращать на надежность установки и прочность закрепления детали;
• необходимо точно соблюдать величину припуска на зенкерование, руководствуясь соответствующей таблицей;
• зенкерование следует производить на тех же режимах, что и сверление;
• необходимо соблюдать те же правила охраны труда, что и при сверлении.
Зенкование
Зенкование — это обработка на вершине просверленных отверстий цилиндрических или конических углублений под головки винтов и заклепок, а также фасок. Операция выполняется при помощи специального инструмента — зенковки.
Основные правила зенкования отверстий:
• необходимо соблюдать правильную последовательность зенкования отверстий: вначале просверлить отверстие, а потом осуществить его зенкование;
• сверление отверстия и его зенкование следует производить с одной установки заготовки (детали), сменяя только инструмент;
• зенкование следует выполнять при ручной подаче зенковки и малой частоте вращения шпинделя (не более 100 об/мин) с применением эмульсии, глубину зенкования надо проверять штангенциркулем или линейкой станка;
• при зенковании отверстий цилиндрической зенковкой, когда диаметр цапфы больше диаметра отверстия, необходимо вначале просверлить отверстие по диаметру цапфы, а затем зенковать отверстие. Заключительная операция — рассверливание отверстия на заданный размер.
Цекование — это операция по зачистке торцевых поверхностей при обработке бобышек под шайбы, гайки, стопорные кольца. Операция производится с помощью специального инструмента — це- ковки, которая устанавливается на специальных оправках.
Развертывание
Развертывание — это операция по обработке ранее просверленных отверстий с высокой степенью точности (до 6-го квалитета) и малой шероховатостью (до Ra 0,63). Обработка развертыванием выполняется после предварительного сверления, рассверливания и зенкерования отверстия развертками, которые подразделяются на черновые и чистовые, ручные и машинные. Осуществляется развертывание как вручную, так и на станках, как правило, стационарных. Конструкция инструмента выбирается в зависимости от применяемого метода обработки.
Основные правила развертывания отверстий:
• необходимо точно соблюдать величину припуска на развертывание, руководствуясь соответствующей таблицей;
• ручное развертывание следует выполнять в два приема: вначале черновое, а затем чистовое;
• в процессе развертывания отверстия в стальной заготовке необходимо обильно смазывать обрабатываемую поверхность эмульсией или минеральным маслом, чугунные заготовки следует развертывать всухую;
• ручное развертывание следует осуществлять только по часовой стрелке во избежание задиров стенок отверстия стружкой;
• в процессе обработки следует периодически очищать развертку от стружки;
• точность обработки развернутых отверстий следует проверять калибрами: цилиндрических — проходным и непроходным; конических — по предельным рискам на калибре. Развернутое коническое отверстие допускается проверять контрольным штифтом «на карандаш»;
• сверление и развертывание отверстий на сверлильном станке машинной разверткой необходимо производить с одной установки заготовки, меняя только обрабатывающий инструмент.
Технология обработки цилиндрических отверстий
Рекомендуем приобрести:
Установки для автоматической сварки продольных швов обечаек – в наличии на складе!
Высокая производительность, удобство, простота в управлении и надежность в эксплуатации.
Сварочные экраны и защитные шторки – в наличии на складе!
Защита от излучения при сварке и резке. Большой выбор.
Доставка по всей России!
На токарных станках обработка цилиндрических отверстий производится сверлами, зенкерами, развертками и расточными оправками с закрепленными в них резцами.
Сверление
Главное движение резания при сверлении — вращательное, оно выполняется заготовкой; движение подачи — поступательное, выполняется инструментом.
Сверла с коническими хвостовиками устанавливают непосредственно в конусное отверстие пиноли задней бабки, а если размеры конусов не совпадают, то используют переходные втулки.
Для крепления сверл с цилиндрическими хвостовиками (диаметром до 16 мм) применяют сверлильные кулачковые патроны, которые устанавливают в пиноли задней бабки.
Перед сверлением отверстий заднюю бабку перемещают по станине на такое расстояние от заготовки, чтобы сверление можно было производить на требуемую глубину при минимальном выдвижении пиноли из корпуса задней бабки. Перед началом сверления заготовку приводят во вращение включением шпинделя.
Сверло плавно (без удара) подводят вручную (вращением маховика задней бабки) к торцу заготовки и производят сверление на небольшую глубину (надсверливают). Затем отводят инструмент, останавливают заготовку и проверяют точность расположения отверстия. Для того чтобы сверло не сместилось, предварительно производят центрование заготовки коротким спиральным сверлом большого диаметра или специальным центровочным сверлом с углом при вершине 90°. Благодаря этому в начале сверления поперечная кромка сверла не работает, что уменьшает смещение сверла относительно оси вращения заготовки. Для замены сверла маховик задней бабки поворачивают до тех пор, пока пиноль не займет в корпусе бабки крайнее правое положение, в результате чего сверло выталкивается винтом из пиноли. Затем в пиноль устанавливают нужное сверло.
При сверлении отверстия, глубина которого больше его диаметра, сверло (также как при работе на сверлильных станках), периодически выводят из обрабатываемого отверстия и очищают канавки сверла и отверстие заготовки от накопившейся стружки.
При ручном управлении станком трудно обеспечить постоянную скорость движения подачи. Для стабилизации скорости подачи используют различные устройства. Для механической подачи сверла его закрепляют в резцедержателе. Сверло 1 с цилиндрическим хвостовиком (рис. 4.29, а) с помощью прокладок 2 и 3 устанавливают в резцедержателе так, чтобы ось сверла совпадала с линией центров. Сверло 1 с коническим хвостовиком (рис. 4.29, б) устанавливают в державке 2, которую крепят в резцедержателе.
После выверки совпадения оси сверла с линией центров суппорт со сверлом вручную подводят к торцу заготовки и обрабатывают пробное отверстие минимальной глубины, а затем включают механическую подачу суппорта. При сверлении напроход перед выходом сверла из заготовки скорость механической подачи значительно уменьшают или отключают подачу и заканчивают обработку вручную.
При сверлении отверстий диаметром 5…30 мм скорость подачи S0 = 0,1 …0,3 мм/об для стальных деталей и S0 = 0,2. ..0,6 мм/об для чугунных деталей.
Для получения более точных отверстий и для уменьшения увода сверла от оси детали используют рассверливание, т. е. сверление отверстия в несколько приемов. При сверлении отверстий большого диаметра (свыше 30 мм) также прибегают к рассверливанию для уменьшения осевого усилия. Режимы резания при рассверливании отверстий те же, что и при сверлении.
Зенкерование
Зенкером обрабатывают отверстия, предварительно штампованные, литые или просверленные. Зенкерование может быть как предварительной (перед развертыванием), так и окончательной обработкой. Кроме обработки отверстий, зенкеры применяются иногда для обработки торцовых поверхностей заготовок.
Для повышения точности зенкерования (особенно при обработке литых или штампованных глубоких отверстий) рекомендуется предварительно расточить (резцом) отверстие до диаметра, равного диаметру зенкера, на глубину, примерно равную половине длины рабочей части зенкера.
Зенкеры, как и сверла, устанавливают на токарных станках чаще всего в задней бабке или револьверной головке.
Развертывание
Для получения на токарных станках отверстий высокой точности и заданного качества обрабатываемой поверхности применяют развертывание.
При работе чистовыми развертками на токарных и токарно-револьверных станках применяют качающиеся оправки, которые компенсируют несовпадение оси отверстия с осью развертки. Для того чтобы обеспечить высокое качество обработки, сверление, зенкерование (или растачивание) и развертывание отверстия производят за одну установку заготовки в патроне станка.
Выбор режимов резания при обработке цилиндрических отверстий стержневыми инструментами на токарных станках производят по тем же таблицам справочника, что и при обработке на сверлильных станках. Однако, учитывая малую жесткость крепления стержневых инструментов на станках токарной группы, расчетные значения режимов на практике уменьшают.
Растачивание
Если диаметр отверстия превышает диаметр стандартных сверл или зенкеров, то такое отверстие растачивают. Растачивание применяют также при обработке отверстий с неравномерным припуском или с непрямолинейной образующей.
В зависимости от назначения различают токарные расточные резцы для обработки сквозных и глубоких отверстий. У токарных расточных стержневых резцов консольная часть выполнена круглой, а стержень для крепления резцов — квадратным; такими резцами можно растачивать отверстия диаметром 30…65 мм. Для повышения виброустойчивости режущая кромка резцов выполнена по оси стержня.
На токарно-револьверных станках применяют расточные резцы круглого сечения, которые крепятся в специальных оправках-державках (рис. 4.30).
Форма передней поверхности и все углы у расточных резцов (за исключением заднего) принимаются такими же, как и у проходных, применяемых при наружном точении. Углы резания у расточных резцов можно изменять путем установки режущей кромки резцов относительно продольной оси детали (выше или ниже оси).
При растачивании резец находится в более тяжелых условиях, чем при наружном продольном точении, так как ухудшаются условия для отвода стружки, подвода СОЖ и отвода тепла.
Расточный резец по сравнению с токарным имеет меньшую площадь сечения державки и больший вылет, что обусловливает отжим резца и способствует возникновению вибраций; поэтому при растачивании, как правило, снимается стружка меньшего размера и снижается скорость резания.
При черновом растачивании стали принимают глубину резания до 3 мм; продольную подачу — 0,08…0,2 мм/об; скорость резания — около 25 м/мин для резцов из быстрорежущей стали и 50… 100 м/мин для твердосплавных резцов.
При чистовом растачивании глубина резания не превышает 1 мм, продольная подача — 0,05…0,1 мм/об, скорость резания — 40… 80 м/мин для резцов из быстрорежущей стали и 150… 200 м/мин для твердосплавных резцов.
Чистовая обработка отверстий
На данный момент сложно себе представить какие-либо сложные детали, габаритные узлы, выпускаемый продукт без применения в нем различных отверстий. Мировая промышленность стремится к оптимизации процессов производства, в связи с чем заготовки становятся все более близкими к конечной форме (без лишнего перевода материала в стружку). Применение аддитивных технологий (3D печать и т. п.) за последние 5 лет выросло в 30 раз (продажи промышленных 3D принтеров выросли с 219 168 в 2015 г. до 6 700 000 шт за первый квартал 2020 г).
Следует оставаться объективным и отметить, что на данный момент точность, достижимая при моделировании на 3D принтерах, недостаточна для формирования функциональных поверхностей. В связи с этим перечислим принципиальные возможности увеличить диаметр имеющегося отверстия : рассверливание, растачивание невращающимся инструментом (обычным резцом/державкой), растачивание вращающимся инструментом, зенкером, разверткой, фрезерованием по винтовой интерполяции и др. Не все эти способы позволяют получить требуемое отверстие с нужными техническими характеристиками (допуск, эллипсность, шероховатость и т. д.).
Ниже опишем стандартные методы именно чистовой обработки отверстий и присущие им характеристики.
1. Сверление.
Сверла, выполненные по ГОСТу и сверла HSS (быстрорежущие) позволяют получить отверстие IT11-13 (11-13 квалитет), шероховатость Rz=20-80мкм. Применение высокопроизводительных (как правило импортных) твердосплавных сверл позволяет добиться отверстия IT9-10.
Существуют специальные твердосплавные сверла для обработки прецизионных отверстий (ружейные, пушечные и схожие с ними конструкции) —отверстие IT8-9.
Сверление, как правило, относят к предварительной операции обработки.
2. Зенкерование.
Зенкер — многозубый лезвийный инструмент для повышения точности формы и направления оси цилиндрических отверстий. Часто применяется в виде промежуточного инструмента между сверлом и разверткой (позволяет продлить срок службы последней. Зенкера по ГОСТу и различные быстрорежущие позволяют получить 10-12 квалитет. Высокопроизводительные и импортные твердосплавные зенкера позволяют получить отверстие IT 7, Rz=20-50 мкм. В современной механообработке применяются редко.
3. Развертывание отверстий.
Развертка — это осевой многолезвийный режущий инструмент для повышения точности формы и размеров отверстия, снижения шероховатости обработанной поверхности. Развертки по ГОСТу позволяют добиться 6-12 квалитет, Rz=20-40 мкм. Повышение чистоты и точности отверстия достигается за счет одновременного резания несколькими режущими кромками. Благодаря большому числу режущих кромок и минимальному припуску улучшается центрирование и снижаются силы, вызывающие осевое отклонение. Развертка исправляет форму отверстия, но, как правило, не может исправить направление его оси (слишком маленький припуск).
Развертки высокопроизводительные твердосплавные позволяют получить отверстия вплоть до 5 квалитета. Применение неравномерного шага позволяет добиться погрешности на форму отверстия 1-2 мкм. Диапазон шероховатости для твердосплавных разверток составляет Rz=2-15 мкм
Преимущества: высокое качество отверстия при большой минутной подаче, возможность применения в массовом производстве.
Целесообразность применения: крупная серия деталей, мелкий диаметр, производительность.
4. Растачивание вращающимся инструментом:
Процесс чистового растачивания позволяет добиться отверстий IT6-9 . Сложность данного вида инструмента привела к появлению целых «расточных систем». На данный момент существуют системы, совмещающие механическую и электронную регулировку непосредственно в шпинделе станка («аналог и цифра»). Большое разнообразие систем условно можно разделить на многолезвийные и однолезвийные расточные системы. Многолезвийное растачивание: черновая расточка, класс точности по IT9 и более. Применяется когда главный критерий — скорость съема металла.
Однолезвийные расточные системы – качество отверстия по IT6, возможность регулировки с точностью до 0,002мм (2 микрона). Позволяет обрабатывать малые диаметры (как правило от 5мм). Может сочетать механическую регулировку с цифровым дисплеем.
Процесс растачивания выполняется на обрабатывающих центрах и горизонтально-расточных станках, вращающийся инструмент работает с осевой подачей.
При выборе расточных систем и назначении режимов резания обязательно необходимо учитывать мощность оборудования. В формуле приведена связь крутящего момента Мс (Нм) , потребляемой мощности оборудования Pc (кВт), частоты вращения шпинделя n (об/мин)
Целесообразность применения: универсальность (одна расточная система «перекрывает» большую номенклатуру деталей), жесткий допуск, большой диапазон диаметров (приблизительно 6мм — 1000мм), возможность обработки отверстий с эллипсностью (до определенного момента), низкая стоимость расходника (самого режущего элемента), так же системы выдерживают ошибки позиционирования (неточность до 0,01мм),
Выводы: при выборе метода чистовой обработки отверстия следует учесть, в первую очередь, предъявляемые к нему требования (допуск, квалитет, шероховатость, соосность и т. д.), конструктивные особенности детали, специфику производства (серийность или универсальность), возможности оборудования.
Список литературы:
1) Фельдштейн Е.Ф. «Обработка материалов и инструмент»
2) Рыжкин А. А. «Обработка материалов резанием»
3) Технические справочники компаний-производителей инструмента
Обработка отверстий
Диаметр отверстия, мм | Заготовка под отверстие | Квалитет | ||
7…8 | 9…10 | 11 | ||
До 10 | Сплошной материал | Сверление и развертывание полу-чистовое и чистовое | Сверление, развертывание | Сверление |
От 10 до 30 | Сплошной материал | Сверление, зенкерование или растачивание, развертывание полу-чистовое и чистовое | Сверление, растачивание или зенкерование, развертывание | Сверление,зенкерованиеилиразвертывание |
Отлитое или прошитое отверстие с припуском до 4мм на диаметр | Растачивание или зенкерование, развертывание полу-чистовое и чистовое | Растачивание, или зенкерование, развертывание | Растачивание, или зенкерование | |
Отлитое или прошитое отверстие с припуском свыше 4мм на диаметр | Растачивание или зенкерование черновое, зенкерование или растачивание полу-чистовое, развертывание чистовое | Растачивание или зенкерование черновое, развертывание | Растачивание или зенкерование черновое, зенкерование или растачивание чистовое | |
От 30 до 100 | Сплошной материал | Сверление, рассверливание, зенкерование или (вместо рассверливания и зенкерования) растачивание черновое, развертывание полу-чистовое и чистовое | Сверление, рассверливание, зенкерование или (вместо рассверливания и зенкерования) растачивание, развертывание | Сверление, рассверливание или (вместо рассверливания) растачивание |
Отлитое или прошитое отверстие с припуском до 6мм на диаметр | Растачивание или зенкерование, развертывание полу-чистовое и чистовое | Растачивание или зенкерование, развертывание | Растачивание или зенкерование | |
Отлитое или прошитое отверстие с припуском свыше 6мм на диаметр | Растачивание или зенкерование черновое, зенкерование и растачивание полу-чистовое, развертывание чистовое | Растачивание или зенкерование черновое, растачивание или зенкерование полу-чистовое, развертывание | Растачивание или зенкерование полу-чистовое | |
Свыше 100 | Отлитое или прошитео отверстие с припуском свыше 6мм на диаметр | Растачивание черновое, растачивание полу-чистовое, растачивание чистовое и развертывание специальной разверткой | Растачивание черновое, растачивание полу-чистовое, растачивание чистовое или применение специальной развертки | Растачивание черновое, растачивание чистовое |
Обработка отверстий – сверление и развертывание
Обработка отверстий в деталях втулочного и дискового класса играет важную роль. Когда мы обращаем внимание на общие технологические процессы этих деталей, в случае классических технологических процессов используется общий технологический процесс деталей гильзового класса с отверстиями. Ниже представлены избранные задачи обработки отверстий. Информация о черновой обработке отверстий приведена в статье под тем же названием: Черновая обработка отверстий.В статье Конструкционный чертеж и технология. В разделе «Как читать» обсуждались основы чтения технического чертежа с точки зрения технолога. На рисунке 1 показан пример конструкции рукава. Выбор производственного оборудования, включая станки, производственные технологии и конкретные методы обработки, зависит от условий использования и требований к качеству (точность геометрических размеров, шероховатость поверхности и твердость поверхностного слоя). С технологической точки зрения методы обработки отверстий (сверление, сверление, развёртывание, растачивание, шлифование, электроэрозионное сверление) характеризуются значительно лучшими качественными эффектами, чем обработка цилиндрических наружных поверхностей.
В этой статье рассматриваются вопросы, связанные с бурением и расширением.
Рис. 1. Пример конструкции детали гильзы класса.
На рисунке 1 видно, что отверстие Ø40H8 является основой для допуска радиального биения внешней поверхности Ø50h6. Отверстие должно быть обработано с классом точности 8, а внешняя поверхность – с классом точности 6.
отверстий
Отверстия есть почти во всех конструкциях деталей машин и устройств, независимо от класса деталей. Мы выделяем следующие критерии разделения на типы отверстий.Большинство из них обычно классифицируют одновременно на несколько типов.
- Качественный критерий (точность геометрических размеров и шероховатости поверхности): неточные, точные и очень точные отверстия. Отверстия для крепления шурупов не требуют высокой точности и выполняются мастерским классом точности (IT14-15).
- Критерий обработки цельного материала или предварительно проделанных отверстий в заготовке (рисунок 2). Готовые отверстия в отливках или поковках характеризуются неровной поверхностью с высокой шероховатостью, что способствует более быстрому износу спиральных сверл.
Рекомендуется сначала обработать этот тип отверстий битами с режущими пластинами или расточить.
- Критерий сквозных и глухих отверстий. Обработка сквозных отверстий проще, чем глухих. Для последнего необходимо обеспечить эффективный отвод стружки. Необходимо использовать сверла с внутренними каналами подачи охлаждающей жидкости. Внешняя подача СОЖ через отверстия глубиной более 30 мм вообще не работает с точки зрения снижения температуры в зоне резания.
- Критерий длины отверстия: нормальные и длинные отверстия.
- Критерий диаметра: очень маленькие и очень большие отверстия.
Рис. 2. Пример предварительно проделанных отверстий в заготовках (отливках).
Бурение
Обработка отверстий обычно связана со сверлением. Этот вид обработки рассматривается в первую очередь как черновая. Об этом также свидетельствует достижимая точность (классы точности IT11-12) и шероховатость поверхности (Ra20-Ra5). Достижимые параметры качества для этого и других методов обработки представлены в статье «Качество в технологии изготовления».Однако следует помнить, что этот тип компиляции был разработан много лет назад.
Сегодня обработка отверстий осуществляется сверлами (твердосплавными, со сменными пластинами или с припаянными твердосплавными пластинами – рис. 3). Различные инструменты обеспечивают разную точность обработки. Монолитные инструменты обычно обеспечивают лучшую точность и меньшую шероховатость обработанной поверхности отверстия.
Рис.3. Пример монолитного сверла вверху (CoroDrill 860) и со сменной пластиной внизу CoroDill 870 (фото любезно предоставлено SANDVIK Coromant).
Современные сверла, такие как CoroDrill от SANDVIK Coromant (рис. 3 и 4), позволяют выполнять одну операцию сверления без необходимости сверлить направляющее отверстие (сверление и повторное растачивание).
Рис.4. Инструмент CoroDrill 880 от SANDVIK Coromant для сверления или растачивания (фото любезно предоставлено SANDVIK Coromant).
Другой пример сверла со сменными пластинами – CoroDrill 880 от SANDVIK Coromant для общего сверления (рис. 4), предназначенное для обработки отверстий среднего и большого диаметра со средним допуском, включая глухие отверстия, требующие плоского дна.Правильная конфигурация CoroDrill 880 с использованием специальной режущей пластины позволяет растачивать.
Семейство сменных пластинCoroDrill предназначено для обработки широкого спектра материалов и обеспечивает точность класса IT12-13 и шероховатость поверхности в диапазоне от Ra1 до Ra5. Это связано с тем, что это складные инструменты с использованием режущих пластин.
Sandvik Coromant предлагает широкий ассортимент сверл со сменными пластинами (CoroDrill 880, 881, Coromant U, T-Max® U для пакетов и трепанирования), которые позволяют экономичную обработку, когда снижение затрат на обработку считалось критически важным.
Твердосплавные монолитные сверлаCoroDrill Delta-C позволяют обрабатывать отверстия с точностью до класса IT5-10. Сверла CoroDrill Delta-C должны работать на более низких скоростях резания, но с более высокой скоростью подачи, чем сверла CoroDrill.
Точечное бурение
Точечное сверление используется при обработке отверстия в полном материале заготовки. При точечном сверлении делается выемка по оси планируемого отверстия. При выполнении этой процедуры на токарном станке точечное сверление обычно выполняется по оси заготовки.Современные станки с ЧПУ с числовым программным управлением и высокой жесткостью, обеспечивающие определенную точность позиционирования, позволяют отказаться от точечного сверления.
Кроме того, сверло для точечного сверления должно иметь угол конуса в диапазоне 90 ° ÷ 100 °, что улучшает положение сверла при входе в материал. Преимущество использования точечного сверления заключается в том, что вы можете отказаться от токарной обработки торца детали.
Точность обработки
При классическом подходе для получения точного отверстия (класс точности IT6 ÷ 8) необходимо выполнить операцию, состоящую минимум из 4 операций: точечное сверление, сверление, черновое и чистовое растачивание.Для отверстий диаметром до Ø8, как правило, применяют сверло и чистовую развертку. В свою очередь, для отверстий диаметром от Ø16 до Ø50 в классах IT11 и IT 12 с отклонениями в пределах от 0,11 до 0,25 вместо чернового растачивания выполняется фасонное растачивание. Это приводит к улучшенному выравниванию отверстий. Если требуется низкая шероховатость, рекомендуется использовать развертку для предварительной чистовой обработки. Эти виды инструментов изготавливаются на заказ, т.е. их экономическое использование ограничивается серийным производством. Имеющиеся в продаже инструменты и технологическое оборудование следует использовать в штучном и мелкосерийном производстве.
Во многих случаях до сих пор используется этот тип технологической конфигурации операции. Современные инструменты, как монолитные, так и со сменными режущими пластинами, а также конструкции станков с высокой жесткостью существенно влияют на возможность обработки точных отверстий. Благодаря этому сокращается количество необходимых обработок для достижения требуемых показателей качества.
Параметры обработки
На точность обработки влияет не только конструкция инструмента, но и параметры обработки:
Скорость резания vc [м / мин] имеет решающее значение для стойкости инструмента.По мере увеличения скорости резания увеличивается температура и скорость износа задней поверхности инструмента. В случае мягких материалов, обработка которых обычно характеризуется появлением ленточной стружки, более высокая скорость резания способствует более благоприятному стружкообразованию.
Подача fn [мм / об] влияет на качество поверхности, допуск отверстия и прямолинейность. Величина подачи также влияет на формирование стружки. Высокая рабочая подача во время сверления означает сокращение основного времени, но также меньший износ на каждый метр обработанного отверстия, но в то же время вероятность KSO (катастрофического затупления лезвия) увеличивается из-за поломки пластины или сверла (Рисунок 4).
На рис. 5 показано сверло из инструментальной стали из быстрорежущей стали, используемое для сверления отверстий в конструкционной стали. Неправильные параметры обработки, в том числе слишком высокая подача, привели к поломке сверла в нескольких местах.
Рис.5. Пример сломанного сверла из быстрорежущей стали. Он сломался, проделав дыру в конструкционной стали.
Стружка и охлаждающая жидкость
Удаление стружки играет важную роль и должно быть обеспечено. Блокирование стружки и медленное удаление стружки влияют на качество отверстия и стойкость инструмента.Правильное стружкообразование в первую очередь предполагает их без осложнений. Согласно [2], хороший способ проверить правильность удаления стружки – на слух. Ровный звук означает, что процесс удаления стружки происходит правильно. Прерывистый звук означает, что стружка заблокирована в канавках инструмента.
На рис. 6 показано твердосплавное сверло SANDVIK CoroDrill® 460 и влияние неправильно выбранных параметров обработки, которые привели к появлению царапин на поверхности обработанного отверстия в его начальной части (на половине длины сквозного отверстия).Этому могла способствовать неправильная подача охлаждающей жидкости извне. Удаление стружки было сочтено правильным, хотя поверхность обработанного отверстия предполагает проблемы с надлежащим отводом стружки во время обработки. Заготовка представляла собой алюминиевый куб PA6. Этот тип материала плохо удаляет стружку.
Рис.6. Пример неправильно подобранных параметров обработки и подачи СОЖ.
Повреждение поверхности отверстий (Рисунок 6) может указывать на отсутствие стабильности на начальном этапе обработки.Условие правильной работы отверстия:
- использование резцедержателя с минимальным радиальным биением;
- правильная установка инструмента в держателе;
- правильно (надежно) закрепить заготовку;
- обеспечивает направление сверла.
Расточка
Растачивание отлично подходит для мелкосерийного производства в штучном, мелкосерийном и серийном производстве. В серийном производстве протяжка по-прежнему используется в качестве отделки в обоснованных случаях. Если конструкция отверстия не содержит канавок, расширение является предпочтительным вариантом, а не протяжкой.Для протяжки необходимо спроектировать и изготовить протяжку.
Растачивание – это чистовая обработка многолезвийными инструментами. Примером современной развертки со сменными режущими пластинами является инструмент от SANDVIK CoroReamer 830 (рис. 7). Как видно на рис. 7, развертка Cororeamer 830 представляет собой модульный инструмент со сменной головкой. Замену головки в этой развертке можно выполнить на станке, не снимая этот инструмент. Сменная головка закреплена в оправке с конической поверхностью, что обеспечивает требуемую повторяемость концентричности с биением до 3 мкм.В пазах головки мы видим каналы, подающие СОЖ непосредственно в зону резания (снижение температуры в зоне резания и удаление стружки).
Рис.7. Развертка CoroReamer 830 от SANDVIK Coromant (фото любезно предоставлено SANDVIK Coromant).
SANDVIK CoroReamer 830, показанный на рис. 7, допускает отверстия с допуском H7. Основное назначение развертки – обработка стали и чугуна. Ограничением этого инструмента является возможность обработки только сквозных отверстий. Ассортимент SANDVIK Coromant также включает монолитные развертки (рис. 8).CoroReamer 435 и 835, которые также обеспечивают точность отверстий с IT7. Развертки с прямыми канавками предназначены для обработки глухих отверстий, а с винтовыми канавками – для сквозных отверстий.
Рис.8. Развертки CoroReamer 435 и 835 (фото любезно предоставлено SANDVIK Coromant)
Сводка
Возвращаясь к конструкции рукава на рисунке 1, давайте определим, как мы можем проделать отверстия в этом рукаве. Речь идет о сквозных отверстиях, выполненных с классом точности 8 (H8). Отверстия изначально делались в отливке или поковке, в зависимости от используемого материала.Следует помнить, что в случае втулок на первой операции технологического процесса мы можем подготовить отверстие, если нет обоснованных противопоказаний (высокая гладкость поверхности, шпоночные пазы, поперечные отверстия). У нас есть несколько вариантов на выбор. Первый из них – это обработка отверстия почти до Ø40H8 путем растачивания и выполнения технологической канавки. При следующей обработке отверстие доводится растачиванием (готовится отдельная статья). Второй вариант из-за диаметра – это использование предварительной обработки сверла со сменными режущими пластинами с последующим выполнением операций резания, развертывания или растачивания.
Окончательный выбор методов обработки зависит от их текущей доступности, и цель состоит в достижении требуемых параметров качества (точности геометрических размеров и шероховатости поверхности). Требуемая шероховатость поверхности может потребовать чистового растачивания или шлифования. Для анализируемой втулки чистовое растачивание должно обеспечить требуемую шероховатость поверхности Ra0,63.
Средла
- Feld M., Podstawy projektowania processów technologicznych typowych części maszyn, WNT 2000
- SANDVIK Coromant, Руководство по обработке, SANDVIK 2010
- Информационные материалы компании Systemy i Technologie Mechaniczne Sp.z o.o.
Нравится:
Нравится Загрузка …
СвязанныеОбработка отверстий
Инструменты PRAMET Tools для обработки отверстий традиционно содержат инструменты со сменными режущими пластинами, конструкция которых была адаптирована для достижения большей прочности инструмента. Мы также можем предложить вам цельные сверла, которые относятся к очень производительным инструментам. Также мы разместили в ассортименте инструменты для растачивания; в него входят расточные инструменты для отверстий от 6 мм до 500 мм.
С июля 2014 года компания PRAMET Tools является дистрибьютором инструментов DORMER. Ассортимент инструментов DORMER значительно расширил ассортимент инструментов не только для обработки отверстий.
Ассортимент сверл со сменными сверлами предлагает инструменты широкого выбора диаметров для глубины сверления от 2D до 5D. Сверла можно использовать как вращающийся или стационарный инструмент. Сверла однолезвийные и могут работать вне оси. Размер просверленного отверстия можно регулировать в пределах -0.От 2 до +0,5 мм с помощью инструмента со смещением от центра. Сверла без проблем работают даже в нестабильных условиях прерывистого резания.
Вы не должны пропустить
Каждая квадратная сверлильная пластина имеет 4 режущих кромки. Их полная применимость достигается разной геометрией и классом внутренней и внешней вставки. Внутренняя пластина, которая должна резать в середине сверла при нулевой скорости резания, изготовлена из прочного сплава с очень прочным стружколомом. С другой стороны, внешняя пластина является износостойкой и позволяет увеличить скорость резания на периферии инструмента до двукратной скорости по сравнению со сплошными сверлами.Таким образом, правильный выбор сплава для периферийных пластин может обеспечить высокую производительность и долговечность инструмента.
перейти на e-Cat >>
Стандартный ассортимент массивных сверл охватывает все основные области бурения. Помимо обычных инструментов, есть еще ступенчатые сверла под резьбу, которые просверливают отверстие, включая снятие фаски. Имеется набор фасок с разными углами острия для снятия фаски.
Не пропустите
Абсолютным лидером среди массивных сверл из твердого сплава является линейка 308FA.Не только из-за его длины и цветового оттенка покрытия. Это четырехгранные цельные сверла с полированной спиралью, обеспечивающие высокую точность просверленных отверстий и качество их поверхности. Параметры и производительность этой линейки сверл удовлетворят даже самого требовательного покупателя.
Предложение сплошных сверл дополнено линией для сверления коррозионно-стойких сталей (группа материалов M), которая подходит для мягких сталей, труднообрабатываемых материалов (группа S) и легкообрабатываемых сплавов цветные металлы (группа N).
перейти на e-Cat >>
PRAMET Tools предлагает полный ассортимент модульных расточных инструментов – PINZBOHR для отверстий диаметром от 8 до 500 мм. Имеется полный набор наиболее часто используемых типов зажимных оправок – DIN 69871, MAS BT (JIS B 6339), DIN 2080, HSK, MORSE и WELDON (DIN 1835), включая удлинители и редукторы.
Вы не должны пропустить
В предложении 12 двухкромочных черновых головок для чернового растачивания.Они способны покрывать отверстия размером от 24 до 500 мм в пределах поля допуска IT9. Головки для чернового растачивания изготавливаются со встроенными посадочными местами диаметром от 22 мм до 54 мм и кассетной конструкцией от диаметра от 68 мм до 500 мм.
В предложении 12 однолезвийных расточных головок для чистовых операций. Они имеют микрометровый винт с точностью регулировки 0,002 мм. Эти головки покрывают одинаковую область применения от 24 до 500 мм и предназначены для растачивания отверстий в пределах допуска IT8.
Мы поставляем очень стабильные микроголовки от 8 до 38 мм для самых маленьких диаметров. Они определены для растачивания в пределах допуска IT6. Головки позволяют зажимать расточные штанги с различными размерами штанг из инструментальной стали и спеченного карбида.
перейти на e-Cat >>
Каждый год мы запускаем сотни новых продуктов, но они не всегда соответствуют вашим требованиям. Поэтому мы готовы проектировать и производить специальные инструменты для обработки сложных приложений, а также инструменты для достижения более быстрого цикла обработки.Скомпилируем для вас комплексное решение.
Что вы можете ожидать от нас:
– быстрый ответ на ваш запрос
– простой заказ
– поставка в согласованный срок
– полная информация о строительном инструменте
перейти на e-Cat >>
Masters of the Small Отверстие
В 1937 году Джон Куплер работал на текстильном заводе и придумал лучший способ делать сверла, которые могли бы проделывать очень маленькие отверстия, используемые при производстве фильер, используемых в процессе экструзии волокна.Результатом новаторства г-на Куплера стало основание компании National Jet Co. (ЛаВейл, Мэриленд).
С самого начала спрос на производственные мощности компании по производству малых отверстий был высоким. Буквально и образно узкая ниша, ее специализированная направленность вывела компанию на глобальную позицию в качестве ведущего поставщика для изготовления микроотверстий, используемых в приложениях с прецизионным потоком, и, как следствие, открыла дополнительные, более традиционные производственные возможности. .
Помимо разработки и производства сверл для сверления отверстий, Mr.Куплер построил станки для изготовления небольших отверстий. Это ручные станки, и сегодня цех использует их для разработки прототипов новых инструментов и производства ограниченных партий.
Уровень квалификации оператора на этих машинах достаточно высок. Чтобы сделать отверстия размером 0,001 дюйма с помощью микроскопа на ручном станке, требуется ловкое прикосновение. Подающий рычаг по оси Z для этих станков сбалансирован до такой степени, что его чувствительность позволяет оператору «чувствовать» затупление сверла.
Нашим хозяином посещения магазина National Jet был Чак Кондор, менеджер по продажам компании.Он и Бен Одом, генеральный менеджер компании, наблюдали за эволюцией бизнеса от специализированного поставщика микроотверстий до контрактного механического цеха с полным спектром услуг, который хорошо справляется с производством мелких отверстий.
«В течение многих лет наша способность проделывать микроотверстия привлекала внимание к работе в цехе, – говорит г-н Кондор. «Клиенты, часто из других магазинов, отправляли в National Jet детали для обработки отверстий, необходимых для завершения заготовки. За последнее десятилетие мы добавили возможность предоставлять полный комплекс услуг по механической обработке, что позволило нам получить рабочие места, которые мы производим в комплекте.Для наших клиентов имеет смысл иметь дело с одним источником ».
Компания, в которой работают 26 сотрудников, расширила свои возможности по изготовлению микроотверстий с помощью вертикальных и горизонтальных обрабатывающих центров с ЧПУ, электроэрозионных станков и токарных станков с ЧПУ, что обеспечивает дополнительные возможности обработки. Г-н Кондор говорит, что даже работы, которые выполняются машинами National Jet, почти всегда включают в себя небольшие отверстия в геометрии детали. Это специальность компании.
Поток должен идти
В соответствии с корнями компании в производстве волоконных фильер, многие работы, выполняемые National Jet, требуют точных и повторяемых отверстий, контролирующих расход жидкостей или газов.Он по-прежнему выполняет много работы для промышленности по производству волокна, в том числе для экструзионных головок.
«Мы проделали большую работу по производству сопел для индустрии 3D-печати, и медицина является еще одной важной клиентской базой», – говорит г-н Кондор. «Мы хорошо справляемся с любыми приложениями, в которых требуется точное управление потоком».
Ключом к успешному производству этих деталей с малым отверстием, зависящих от расхода, является то, что они не должны иметь заусенцев. Микроскопы усеивают цех на рабочих местах, где проводится 100-процентный осмотр просверленных отверстий в поисках заусенцев.
Любые заусенцы на пути потока, создаваемые National Jet, могут отрицательно отклонить жидкость или газ и препятствовать их постоянному отложению. Например, сопла для струйной печати чувствительны к заусенцам. «Например, если на пути сопла для струйной печати есть заусенец, чернила будут« изгибаться »и не попадут туда, куда они нацелены», – говорит г-н Кондор.
«Поскольку мы изготавливаем собственные сверла с допуском от +0,0000 до -0,0001 дюйма, – говорит г-н Кондор, – иногда мы можем разработать геометрию, которая снижает образование заусенцев.Однако по большей части мы должны обнаруживать и удалять заусенцы с мелких деталей, которые мы производим. Удаление заусенцев – трудоемкий процесс, но он имеет решающее значение для нашего успеха. В дополнение к микроскопам у нас есть оптические датчики, некоторые из которых довольно сложные, чтобы помочь «увидеть» заусенцы, чтобы их можно было удалить. У нас в этом цехе допуск без заусенцев ».
Основным материалом для текстильных фильер и экструзионных головок является закаленная нержавеющая сталь 17-4, как правило, с круглым или прямоугольным основанием. Обладая возможностями обрабатывающего центра, National Jet может обрабатывать основания и добавлять микроотверстия для выполнения работы.Эти штампы могут иметь несколько или тысячи микроотверстий в зависимости от области применения штампа.
Маленький, для одного человека
У каждой компании любого возраста есть своя история. После 82 лет работы в бизнесе National Jet не исключение. Одна история, которую мне рассказали во время моего визита, связана с основателем компании Джоном Куплером.
Несколько лет назад, спустя много лет после того, как г-н Куплер обосновался в сфере микробурения, заграничный производитель сверл прислал ему одно из своих сверл, которое рекламировалось как «самое маленькое в мире», с вопросом, может ли он сделать сверло такого маленького размера.Мистер Куплер ответил, просверлив отверстие в самом маленьком сверле в мире и вернув его отправителю. Достаточно сказано!
Для National Jet диапазон размеров малых рабочих отверстий составляет от 0,001 до 0,02 дюйма. Они могут делать отверстия меньшего размера, но этот диапазон удобен для обеспечения стабильности производства.
Технологии сверления, разработанные компанией на ручных станках, переносятся на станки с ЧПУ, используемые в производстве. Процедуры клевания используются почти для каждой операции сверления небольших отверстий и выполняются «мокрым» с использованием легкого смазочно-охлаждающего масла.Программное обеспечение CAM, используемое на станках с ЧПУ, запрограммировано так, чтобы имитировать методы микро-сверления, используемые на ручных станках, а на некоторых работах, например, швейцарский станок можно настроить для работы без присмотра.
Компания накопила обширную базу данных подачи и скорости режущего инструмента, которая является отправной точкой для большинства приложений. «За прошедшие годы мы обнаружили, что при консервативных скоростях подачи и скорости мы можем добиться успеха в большинстве наших операций по микробурению», – говорит г-н Кондор.
По словам г.Кондор, глубина резания обычно является ограничивающим фактором при сверлении небольших отверстий. Чтобы выдержать допуск в диапазоне диаметров 0,001 дюйма, соотношение длины к диаметру 7: 1 является надежной ставкой для микродрели, которую National Jet использует в производственных объемах.
EDM в соответствии с планом B
National Jet производит микроотверстия с помощью сверления, если это возможно. Как правило, процесс сверления происходит быстрее, и инструменты можно адаптировать к станкам цеха, включая токарные станки швейцарского типа и обрабатывающие центры.
Однако есть некоторые рабочие места, которые National Jet нашла благодаря опыту, которые могут быть лучше выполнены с использованием EDM. Некоторые микроотверстия не могут быть изготовлены другим способом.
EDM – это бесконтактный процесс удаления микроскопических «стружек» с заготовки с помощью электрической искры для эрозии металла. Проволока и трамбовка (штамповка) – это два типа электроэрозионных станков, и National Jet использует их в некоторых своих приложениях для изготовления микроотверстий.
Вероятно, самым большим преимуществом EDM перед сверлением микроотверстий является отсутствие заусенцев.«В случаях, когда геометрия детали слишком сложна, чтобы обеспечить доступ для удаления заусенцев, мы обработаем микроотверстия электроэрозионной обработкой, чтобы избежать образования заусенцев», – говорит г-н Кондор.
Электрод или проволока EDM могут производить отверстия диаметром 0,001 дюйма. Поскольку процесс EDM разрушает обрабатываемый материал, необходимы расчеты, чтобы учесть зазор между электродом и деталью.
Один из примеров, который приводит г-н Кондор, заключается в том, что для отверстия диаметром 0,0068 дюйма электрод EDM может быть изготовлен в соответствии со спецификацией 0.0062 дюйма для зазора стружки и поддержания зазора электрической дуги. Затем выполняются пробные разрезы для определения оптимального диаметра, которые регулируются в большую или меньшую сторону, чтобы соответствовать окончательной спецификации допуска.
Еще одно применение, которое National Jet использует EDM для обработки небольших отверстий, – это закаленный материал. «Мы делаем много стержней для штампов, которые мы производим», – говорит г-н Кондор. «Они могут быть 40 и выше по шкале Роквелла и быстро прожигают режущие инструменты. Электроэрозионная обработка этих твердых материалов более рентабельна.”
Поскольку многие микроотверстия, создаваемые National Jet, чувствительны к потоку материала, в некоторых приложениях требуется, чтобы отверстие было очень гладким. Сверление может оставлять микроскопические следы в отверстии, которых нет на EDM. EDM обычно обеспечивает внутреннюю поверхность отверстия без зазубрин, что является предпочтительным для некоторых применений.
Фигурные отверстия
В дополнение к опыту в области сверления микроотверстий, National Jet специализируется на вырезании профильных отверстий. «Они производятся с использованием EDM», – сказал г-н.Кондор говорит. «Мы сами вырезаем электроды для этих отверстий и сжигаем их на наших собственных трамбовочных станках, созданных специально для этих целей».
Одним из примеров является трехуровневое Y-образное отверстие, которое функционирует как фильеры для штампа, используемого в ковровой промышленности. Основания обрабатываются на обрабатывающих центрах цеха, а затем устанавливаются на штамповочные грузила компании. Некоторые из штампов имеют по 300 таких отверстий.
Технические характеристики этих электродов имеют решающее значение. Кондор объясняет, что одно такое Y-образное отверстие может иметь размер, равный нулю ширины ножек.006 дюймов, длина ножек может составлять 0,020 дюйма, а глубина также может составлять 0,020 дюйма.
Глубина электрода является наиболее важным размером для отверстия этой формы. Поскольку размер электрода немного занижен, делаются пробные надрезы, чтобы привести электрод к его оптимальному размеру для обеспечения требуемых допусков и чистоты поверхности.
Электроды восстанавливают после прорезания каждого отверстия. После того, как машины настроены, они автоматически производят отверстия для штампов, что позволяет работать без участия человека.
Сотрудничество
Благодаря накопленному опыту в области обработки малых отверстий и расширению общих возможностей обработки, National Jet все чаще просят проконсультироваться со своими клиентами. Некоторых заказчиков просят предложить изменения в конструкции, которые позволят более эффективно производить детали заказчика без ущерба для их функциональности.
Компания построила свой бизнес, используя свою нишу высококачественной специальной обработки небольших отверстий, чтобы предложить клиенту больше, чем он считал нужным или мог получить от механического цеха.Это хорошее место для производства, и семейная культура этой компании направлена на поддержание этого.
National Jet Co. / 301-729-2300 / najet.com
Как использовать расширенные услуги ЧПУ Методы обработки отверстий
Отправлено в августе. 12-е, 2019, | Автор: WayKen Project Manager
Производство отверстий в значительной степени недооценивается, потому что большинство отверстий, которые мы делаем, имеют тривиальную точность, небольшую глубину и предназначены только для болтов.Тем не менее, современные высокотехнологичные отрасли промышленности (особенно аэрокосмическая и автомобильная) приходят на рынок услуг с ЧПУ с требованиями изготовления деталей с очень точными или глубокими отверстиями или с очень точным расположением отверстий. Помимо передовых услуг обработки с ЧПУ, такие требования требуют особых методов и тщательного планирования.
Проблемы с обработкой отверстий
Процесс изготовления отверстия на самом деле довольно сложный с производственной точки зрения.Инструмент и заготовка могут быть легко перегреты, потому что трудно нанести охлаждающую жидкость в отверстие, процесс не виден машинисту, поэтому он может полагаться только на информацию о станке и должен резать вслепую, проведение измерений затруднено, особенно в отверстиях с малые диаметры. И это лишь некоторые проблемы с изготовлением отверстий. Таким образом, чтобы делать точные отверстия, службы ЧПУ всегда разрабатывают и улучшают стратегии обработки, они изобретают новые инструменты и инструменты для удовлетворения требований клиента.
Глубокое сверление
Ну, сверление само по себе является обычным процессом, и в сверлении коротких отверстий нет ничего интересного, но чем глубже отверстие, тем сложнее удерживать его ось прямо во время бурения. Это связано с тем, что более длинное сверло менее жесткое, поскольку оно имеет две режущие кромки, которые нельзя сделать одинаковой длины. Таким образом, сила резания сторон сверла различна, и сверло обычно отклоняется от прямой оси и делает отверстие однобоким.Это неприемлемо для высокоточных деталей с ЧПУ.
Вот почему было изобретено ружейное сверление. как следует из названия, он был впервые использован для производства длинномерного ружья, для которого основным требованием было наличие длинного, но точного отверстия. Тем не менее, с развитием производственных технологий, другие отрасли стали применять ружейное бурение в своих целях. Основное отличие этой стратегии – это инструмент. Пистолетное сверло имеет одну режущую кромку, поэтому оно не отклоняется от своего курса, как обычное сверло.Он имеет большую канавку для удаления стружки, которая также служит каналом охлаждения. Охлаждающая жидкость прокачивается через канавку под высоким давлением, удаляет стружку и намного лучше охлаждает сверло. Обратной стороной этого метода является то, что это сверло нельзя установить на обычный фрезерный центр с ЧПУ, для этого требуется дополнительная оснастка.
Станкис ЧПУ используют ружейные сверла в самых крайних случаях, но в основном они стараются придерживаться универсальных инструментов, поэтому существуют определенные стратегии, которые позволяют сверлить глубокие отверстия простыми сверлами.Во-первых, длина отверстия делится на сегменты глубиной около 3-4 диаметров отверстия. Каждый раз, когда сверло достигает конца сегмента, оно выбрасывается, чтобы дать заготовке и инструменту остыть и удалить всю стружку из отверстия.
Высокоточная обработка отверстий
Чтобы сделать точное отверстие, сверление с ЧПУ обычно выполняется несколькими инструментами, первый из которых значительно меньше диаметра отверстия и увеличивается со следующим инструментом.Это сделано для уменьшения силы резания и, следовательно, отклонения оси по указанной выше причине. Кроме того, последовательные методы часто отличаются от простого сверления:
Колонковое бурение проводится сразу после бурения. У корончатого сверла три режущих кромки вместо одной, что делает его более устойчивым. Корончатые сверла обычно обрабатывают пропил глубиной всего 0,5 мм, но их абсолютным преимуществом является возможность корректировки оси.
Развертка. Если вашему клиенту требуется отверстие с допуском до IT6 и очень гладкой поверхностью, вы берете развертку и делаете подачу обработки чрезвычайно низкой.Развертка – это инструмент с множеством длинных режущих кромок, расположенных по бокам инструмента. У него есть передние режущие лезвия, но они очень маленькие, поэтому глубина резания при развертывании составляет около 0,1-0,05 мм. Благодаря этому и высочайшей точности режущих кромок при расширении получаются большие отверстия. Для отверстий меньшего размера расширение выполняется вручную.
Хонингование – это абразивный процесс, но его можно выполнять на станке с ЧПУ, однако специальные хонинговальные станки определенно лучше. Хонингование – это расширитель с абразивными досками вместо режущих лезвий.Еще одно отличие состоит в том, что доски можно подогнать под нужный диаметр. Хонок вставляется в отверстие, и он вращается вокруг своей оси, пока доски шлифуют материал. Как только хон выходит, направление вращения меняется на противоположное. В результате на поверхности отверстия появляются перекрещенные микроскопические канавки, которые делают смазку намного более эффективной.
Стратегии нарезания резьбы
Для многих отверстий требуется резьба, которая состоит из сложных тонких поверхностей и на самом деле довольно трудно обрабатывать.Существует несколько способов нарезания резьбы, но перед этим абсолютно необходимо выполнить зенкование или зенкование. Эти два процесса создают коническую или цилиндрическую канавку на входе в отверстие. Это позволяет резьбонарезному инструменту входить правильно и в дальнейшем помогает при сборке реальных деталей. Итак, вот несколько стратегий многопоточности.
Для сверления метчиком используется один инструмент, который напоминает болт, но имеет канавки для удаления стружки и длинную коническую область спереди для постепенного увеличения глубины резания.Подача обработки при нарезании резьбы с конусом (и с любой резьбой в этом отношении) такая же, как и шаг винта. Метчик медленно вставляется в отверстие, где каждая из его спиральных режущих кромок постепенно отрезает кусок материала, чтобы сформировать резьбу. Небольшие отверстия обрабатываются вручную, и в этом случае процесс отверстия напоминает завинчивание болта различной степени затяжки. Сверло для метчика необходимо извлекать с большой осторожностью, так же как оно было вставлено. Если вы забудете об этом и попытаетесь извлечь сверло для метчика, не отвинчивая его, вы можете сломать его, и вам придется извлекать его с помощью электроэрозионной обработки.
Фрезерование резьбы дает лучшие результаты, потому что температура процесса ниже и гораздо легче наносить охлаждающую жидкость. Специальная фреза, которая на 30-40% меньше диаметра отверстия, движется по спирали по траектории канавок сверла и вращается вокруг своей оси для эффективного резания. Минимальный диаметр отверстия зависит от минимального диаметра фрезы.
Другая стратегия называется растачиванием резьбы. На самом деле это то же самое, что и токарная обработка в отношении установки детали и основных движений, но инструмент изготовлен так, чтобы копировать форму канавки резьбы.Итак, он подается с шагом винта в отверстие детали и нарезает спиральные поверхности резьбы. Важно отметить, что растачивание отлично подходит для больших отверстий, но не позволяет обрабатывать отверстия меньше 20 мм.
Свяжитесь с нами-Wayken, чтобы узнать, как прецизионная обработка с ЧПУ позволяет проектировать отверстия в деталях для вашего проекта.
Непрерывная обработка чистовых отверстий Все образцы обработки Электроэрозионные станки для чистовых отверстий
|
|
Обработка отверстий в 2 и 3 осях CAM Часть 2: Параметры резания
Добро пожаловать в нашу серию из 4 частей по обработке отверстий в 2- и 3-осевом CAM с использованием подключаемых модулей CAM от MecSoft.Полное руководство из 4 частей доступно всем подписчикам AMS как часть вашего пакета самообучения CAMJam. См. Как загрузить ваши учебные материалы CAMJam для получения информации о CAMJam и о том, как воспользоваться преимуществами подписки на AMS!
Во второй части нашей серии статей мы исследуем параметры вырезания отверстий, доступные для каждой операции отверстия. Вы узнаете о свойствах кода постоянного цикла каждого типа отверстия и параметрах резания двух стратегий траектории 2-осевого фрезерования, которые используются исключительно для вырезания отверстий.Это 2-осевая обработка отверстий и профилирование 2-х осевых отверстий. В этот раздел также включены правила сортировки отверстий.
В эту серию включены следующие 4 статьи блога:
- Обработка отверстий в 2 и 3 осях CAM Часть 1: Выбор геометрии
- Обработка отверстий в 2 и 3 осях CAM Часть 2: Параметры резания
- Обработка отверстий в 2 и 3 осях CAM Часть 3: Автоматизация программ
- Обработка отверстий в 2 и 3 осях CAM Часть 4: Управление выходом
В каждом диалоговом окне операции с отверстием есть вкладка «Параметры резки», которая содержит все параметры цикла, необходимые для определения отверстия.Например, диалоговое окно Drill operation включает меню выбора Drill Type, которое позволяет вам определить тип определяемого цикла сверления. Для сверления меню включает в себя стандартное сверление, глубокое сверло, сверло для удаления стружки, сверло с зенковкой, а также четыре определяемых пользователем цикла сверления. Параметры стандартного цикла и параметры фрезерования отверстий обсуждаются в отдельном разделе ниже.
Стандартное сверло | Сверло Deep & Peck | Сверло с зенковкой |
В таблицах ниже перечислены параметры постоянного цикла, поддерживаемые каждым типом отверстия.Вы заметите, что некоторые параметры включают или отключают другие параметры. Например, для типа «Сверло зенковки» параметр «Диаметр зенковки» включен, а «Глубина» отключен.
Параметры резки цикла сверленияПример G-кодов:
G81X1.2374Y1.2374Z-0.6443R0.25F10.
G82P0X1.2374Y1.2374Z-0.1443R0.25F10.
G83X1.2374Y1.2374Z-0.6443R0.25Q0.1F10.
G73X1.2374Y1.2374Z-0.6443R0.25F10.Q0.1
Пример G-кодов:
G84X1.2374Y1.2374Z-0.5R0.1F300.
G84X1.2374Y1.2374Z-0.5R0.1Q0.1F14.667
Пример G-кодов:
G85X1.2374Y1.2374Z-0.5R0.1F14.667
G86X0.750Y-0.750Z-0.500R0.100F14.7
G87X0.750Y0.750Z-0.500R0.100F14.7
Пример G-кодов:
G77X1.2374Y1.2374Z-0.5R0.1F14.667
Фрезерование отверстийДля больших отверстий вы можете выбрать одну из стратегий траектории 2-осевого фрезерования, которая специально разработана для вырезания круглых отверстий и карманов с использованием фрезерных режущих инструментов.К ним относятся 2-осевая обработка отверстий и профилирование 2-х осевых отверстий. Здесь следует отметить, что это не циклы постоянных отверстий. Это 2-х осевые траектории фрезерования, которые обеспечивают линейное, дуговое и спиральное движение. Обработка отверстий сочетает в себе спиральное движение входа со спиральным движением резания на каждом уровне резания. Профилирование отверстия – это движение по спирали в сочетании с движением входа и выхода.
Пример прорезания карманов | Пример профилирования отверстия |
В дополнение к параметрам «Местоположение геометрии реза» дополнительные параметры реза включают в себя общий допуск (t), глубину отверстия (H), диаметр отверстия (D), направление реза и шаг по спирали.Обработка отверстий также включает в себя Stepdown (Dz), Stepover (S) и возможность добавления прохода очистки на каждом уровне резки. Обе эти операции позволяют дополнительно создавать полные спиральные движения на 360 градусов и выводить каждую спираль индивидуально в опубликованном G-коде. Параметры резки для каждого типа операции перечислены ниже.
Параметры резания для прорезания карманов | Параметры резания для прорезания карманов |
Если вам нужно обработать много отверстий за одну операцию, вы можете воспользоваться вкладкой «Сортировка» в диалоговом окне каждой операции отверстия.Это позволяет выполнять сортировку отверстий по минимальному расстоянию и сортировку по направлению отверстий. В Сортировке по минимальному расстоянию вы можете указать начальное положение, такое как нижний левый, верхний правый и т. Д. Программа рассчитает последовательность обработки отверстий на основе расстояния между отверстиями.
Если у вас много отверстий на близком рисунке, эта опция сведет время обработки к минимуму. Если у вас много отверстий в нескольких рисунках, вы можете использовать параметр «Сортировка по направлению». Это позволяет вам указать первичное и вторичное направление, а также шаблон обхода (т.е., зиг или зигзаг). Вкладка «Сортировка» также доступна для всех диалоговых окон «Отверстие», а также для многих других операций фрезерования.
Вкладка Правила сортировки отверстий (сортировка не выбрана)
Нет выбора сортировки на вкладке сортировки
Вкладка Правила сортировки отверстий (выбрано минимальное расстояние)
Минимальное расстояние / верхний левый угол, выбранный на вкладке сортировки
Вкладка «Правила сортировки отверстий» (выбрано направление)
Направленная сортировка, по убыванию, зигзаг, выбранный на вкладке сортировки
Для дополнительной информации:Вот список статей из этой серии:
- Обработка отверстий в 2 и 3 осях CAM Часть 1: Выбор геометрии
- Обработка отверстий в 2 и 3 осях CAM Часть 2: Параметры резания
- Обработка отверстий в 2 и 3 осях CAM Часть 3: Автоматизация программ
- Обработка отверстий в 2 и 3 осях CAM Часть 4: Управление выходом
Дон ЛаКурс (Don LaCourse) – разработчик приложений в MecSoft Corporation.Дон обладает более чем 20-летним опытом работы в CAD / CAM-технологиях как в автомобилестроении, так и в проектировании пресс-форм. Дон также имеет обширный опыт в документировании продуктов CAD / CAM и активно участвует в написании интерактивной справки, а также в создании учебных пособий по продуктам MecSoft.
Обработка высокоскоростных отверстий (HSH)
СОВРЕМЕННЫЕ ПОГРУЖНЫЕ ВЫСОКОСКОРОСТНЫЕ ОБОРУДОВАНИЯ ДЛЯ АЭРОКОСМИЧЕСКОЙ И IGT ПРОМЫШЛЕННОСТИ
Высокоскоростная электроэрозионная обработка отверстий – это уникальный способ быстрого и экономичного создания точных отверстий в проводящих материалах независимо от их формы или твердости.Это достигается за счет использования процесса эрозии материала через электрическую искру, прыгающую через зазор между вращающимся электродом и заготовкой. Эта эрозия материала выполняется, когда диэлектрическая жидкость проходит через полый электрод под высоким давлением, чтобы охладить заготовку и удалить эродированный материал. Помимо круглых отверстий, этот процесс позволяет нам создавать формы диффузоров вокруг отверстий, что повышает эффективность охлаждения компонентов газотурбинного двигателя.
Возможности и технологии:
- Способен сверлить «отверстия вне прямой видимости» с использованием запатентованных технологий.
- Используйте технику «мягкого выравнивания», которая устраняет необходимость в гнезде твердых точек, что обеспечивает полный доступ к заготовке.
- Размеры отверстий от 0,008 дюйма (0,2 мм) до 0,236 дюйма (6 мм)
- Усовершенствованное обнаружение прорыва для предотвращения обратного удара при быстром сверлении отверстий в полых полостях. Обнаружение происходит в течение 1 секунды или 0.040 ”(1 мм)
- Система подъема и опускания рабочего резервуара для более быстрого отвода диэлектрика и сокращения времени цикла.
- Устройство автоматической смены инструмента (ATC) обеспечивает автоматическую работу станка и быструю замену электродов менее чем за 30 секунд.