ООО НПО “ТИТАН” – титан и его сплавы. Прутки, листы, плиты, проволока, трубы — Справка — Резка и мех.обработка
Титан и его сплавы плохо обрабатываются резанием, что обусловлено рядом физико-механических свойств титана. Титановые сплавы отличаются высоким отношением предела текучести к временному сопротивлению разрыва. Это соотношение составляет для титановых сплавов 0,85—0,95, в то время как для сталей оно равно 0,65—0,75. В итоге при механической обработке титановых сплавов возникают большие удельные усилия, что приводит к высоким температурам в зоне резания, обусловленным низкой тепло- и температуропроводностью титана и его сплавов, затрудняющей отвод тепла из зоны резания. Из-за сильной адгезии и высоких температур титан налипает на режущий инструмент, что вызывает значительные силы трения. Налипание и приваривание титана на контактируемые поверхности режущего инструмента приводят также к изменению его геометрических параметров. Отклонение геометрических параметров режущего инструмента от оптимальных их значений приводит к дальнейшему повышению усилий обработки и температуры в зоне резания и износа инструмента.
Трудоемкость механической обработки титановых сплавов в 3—4 раза больше, чем для углеродистых сталей, и в 5—7 раз выше, чем для алюминиевых сплавов.
По данным ММПП “Салют”, коэффициент относительной обрабатываемости по отношению к стали 45 составляет 0,35—0,48 для титана и сплавов ВТ5 и ВТ5-1 и 0,22—0,26 для сплавов ВТ6, ВТ20 и ВТ22. При механической обработке титановых сплавов рекомендуются малые скорости резания при небольших подачах с обильной подачей охлаждающей жидкости. Для обработки титановых сплавов резанием применяют режущий инструмент из более износостойких быстрорежущих сталей, чем для обработки сталей, отдавая предпочтение твердым сплавам. Однако даже при соблюдении всех описанных мероприятий режимы резания, особенно скорости, должны быть снижены по сравнению с обработкой сталей в 3—4 раза для обеспечения приемлемой стойкости инструмента, особенно при обработке на станках с ЧПУ.
Усилия резания и температуры в зоне резания могут быть существенно снижены механоводородной обработкой, включающей в себя наводороживание, механическую обработку и вакуумный отжиг. Легирование титановых сплавов водородом приводит к значительному снижению температур в зоне резания, уменьшению сил резания, повышению стойкости твердосплавного инструмента в 2—10 раз в зависимости от режимов резания и природы сплава. Этот позволяет повысить скорость резания в 1,5—2 раза при сохранении других параметров резания или применять более высокие подачи и глубины резания, не меняя скорости резания.
При высоких температурах, которые развиваются в зоне резания, титановая стружка и обрабатываемая деталь окисляются. Окисление стружки создает проблемы, связанные с её очисткой при вовлечении отходов в плавку и других способах её утилизации. Окисление поверхности обрабатываемых деталей в недопустимой степени может привести к снижению эксплуатационных характеристик.
При изготовлении деталей и конструкций из титановых сплавов применяют все виды механической обработки: точение, фрезерование, сверление, шлифование, полирование.
Важной особенностью механической обработки деталей из титановых сплавов является необходимость обеспечения ресурсных, в особенности усталостных, характеристик, которые в решающей степени обусловлены качеством поверхностного слоя, образующегося после обработки резанием. Вследствие низкой теплопроводности и высокой химической активности обрабатываемого материала применение шлифования как процесса финишной обработки для титановых сплавов ограничено. При шлифовании титановых сплавов легко образуются прижоги, которые существенно снижают усталостную прочность. Кроме того, при шлифовании в поверхностном слое возникают остаточные напряжения растяжения и дефектные структуры, также снижающие усталостную прочность. Поэтому шлифование, если оно используется при обработке деталей из титановых сплавов, должно проводиться при пониженных скоростях и по возможности заменяться лезвийной обработкой либо низкоскоростными методами абразивной обработки, такими, например, как хонингование. Если же применяется шлифование, оно должно выполняться при строго регламентированных режимах с последующим контролем на отсутствие прижогов и сопровождаться упрочнением поверхностным пластическим деформированием (ППД).
Из-за больших усилий резания для механической обработки титана и его сплавов применяют, в основном, станки крупных моделей (ФП-7, ФП-9, ФП-27, ВФЗ-М8 и др.). Наиболее трудоемким процессом при изготовлении деталей является фрезерование. Особенно большие объемы фрезерных работ приходятся на изготовление силовых деталей каркаса самолета: шпангоуты, траверсы, лонжероны, нервюры, балки.
При разработке и внедрении технологии механической обработки деталей из титановых сплавов достаточно широко используются малооперационные технологические процессы за счет совмещения нескольких операций в одну при выполнении её на одно- и многоинструментальном оборудовании. Эти технологические операции наиболее целесообразно выполнять на многооперационных станках (обрабатывающих центрах). Так, например, силовые детали из штамповок изготавливают на станках ФП-27С, ФП-17СМН, МА-655А; детали типа “корпус”, “колонка”, “кронштейн” из штамповки и фасонной отливки — на станках МА-655А, Me-12-250, “Горизон”, панели из листа — на станке ВФЗ-М8.
Фрезерование переменных малок при изготовлении деталей типа “нервюра”, “балка”, “траверса” осуществляется несколькими методами:
1) на универсально-фрезерных станках с помощью специальных механических или гидравлических копиров;
2) на гидравлических копирно-фрезерных станках по копирам;
3) на трехкоординатных станках с ЧПУ:
— специальными сборными фрезами с изменяемым в процессе обработки углом;
— фасонными выпуклыми и вогнутыми радиационного профиля фрезами;
— концевыми фрезами с приведением к цилиндрической поверхности путем наклона детали к плоскости стола под определенным углом;

Для механической обработки авиационных материалов в нашей стране разработан ряд станков, соответствующих лучшим мировым образцам, а иногда и не имеющих аналогов в мировой практике:
— продольно-фрезерный трехкоординатный трехшпиндельный станок ВФ-33 с ЧПУ, предназначенный для одновременной обработки тремя шпинделями монорельсов, панелей, балок, нервюр и других деталей легких и тяжелых самолетов;
— продольно-фрезерный четырехкоординатный трехшпиндельный станок 2ФП-242В с двумя подвижными порталами и ЧПУ, предназначенный для обработки крупногабаритных панелей и лонжеронов переменной малкой для широкофюзеляжных и тяжелых самолетов;
— горизонтально-фрезерно-расточный пятнадцати координатный с ЧПУ станок ФРС-1 с подвижной колонной; он предназначен для обработки стыковых поверхностей крыла и центроплана широкофюзеляжных самолетов;
— гибкий производственный комплекс АЛК-250, предназначенный для изготовления прецизионных корпусных деталей гидроагрегатов.
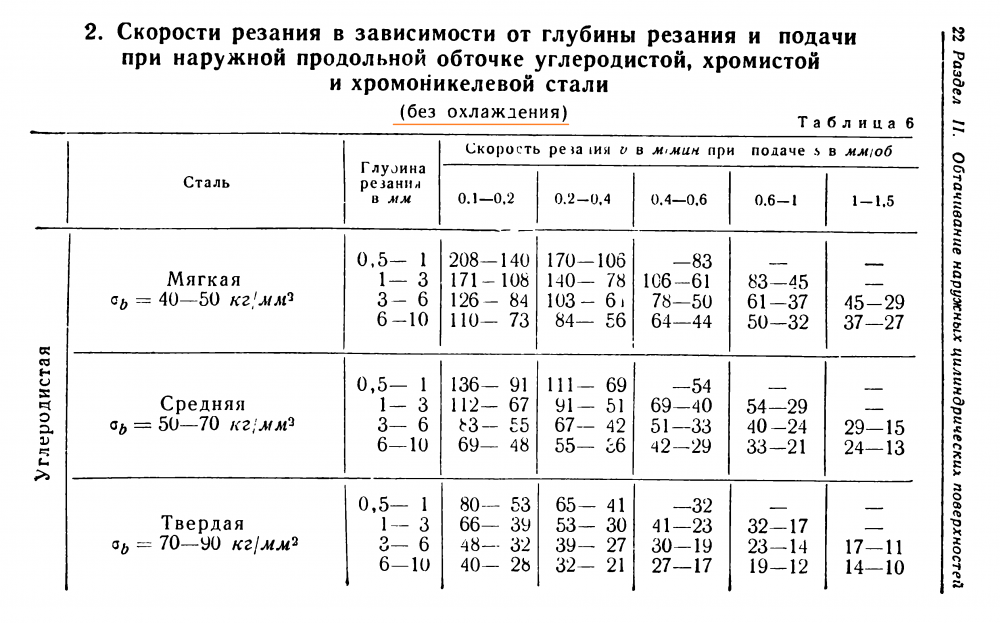
Для обеспечения оптимальных условий резания и высокого качества поверхности деталей следует строго соблюдать геометрические параметры инструмента из быстрорежущих сталей и твердых сплавов.
Точение кованых заготовок осуществляется резцами с пластинками из твердого сплава ВК8. При обработке по газонасыщенной корке рекомендуют следующие геометрические параметры резцов: передний угол γ=0°; задний угол α = 12°; главный угол в плане
При чистовом и получистовом непрерывном точении применяют инструмент из твердых сплавов ВК4, ВК6, ВКбм, ВК8 и др. при подаче s = 0,1 — 1,0 мм/об, скорости резания v = 40 — 100 мм/мин и глубине резания t = 1 — 10 мм. Возможно также применение инструмента из быстрорежущей стали (Р9К5, Р6М5К5, Р9М4К8). Рекомендуемые геометрические параметры резцов из быстрорежущей стали: задний угол α = 10°, φ = 15°, радиус при вершине r = 1 мм. Режимы резания при точении титана v = 24 — 30 м/мин, s t = 0,5 — 3 мм.
Фрезерование титана и его сплавов затруднено из-за налипания титана на зубья фрезы и их выкрашивания. Для рабочих частей фрез применяют твердые сплавы ВК4, ВК6М, ВК8 и быстрорежущие стали Р8МЗК6С, Р9К5, Р9К10, Р6М5К5, Р9М4К8. При фрезеровании титана фрезами с пластинками из сплаваВК6М рекомендуют следующие режимы резания: s = 0,08 — 0,12 мм/зуб, v = 80 — 100 м/мин, t = 2 — 4 мм.
Сверление титана и его сплавов также осуществляется с трудом из-за налипания стружки титана на рабочие поверхности инструмента и ее скопления в отводящих канавках сверла, что приводит к сильному повышению сопротивления резания и быстрому износу сверл. Поэтому при сверлении глубоких отверстий необходимо периодически выводить инструмент для очистки его от стружки. Для сверления применяют инструмент из быстрорежущих сталей Р9К5, Р9К10, Р18Ф2, Р9Ф5, Р6М5К5, Р9М4К8, Р12Ф2К8МЗ и твердого сплава ВК8. Рекомендуемые геометрические параметры сверл:
Для увеличения производительности механической обработки титановых сплавов резанием и повышения стойкости режущего инструмента применяют галлоидосодержащие смазывающе-охлаждающие жидкости типа РЗ СОЖ-8. Охлаждение обрабатываемых деталей осуществляют методом обильного полива. Использование галлоидосодержащих жидкостей при механической обработке приводит к образованию на поверхности титановых деталей солевой корки, которая при повышенных температурах и одновременном действии напряжений вызывает солевую коррозию. Поэтому детали, обрабатываемые с применением РЗ СОЖ-8, после механической обработки подвергают облагораживающему травлению со снятием поверхностного слоя толщиной 0,005—0,010 мм. При сборочных и механосборочных операциях не допускают применения РЗ СОЖ-8.
Обрабатываемость титановых сплавов резанием существенно зависит от их химического и фазового состава, типа и параметров микроструктуры. Наиболее трудно обрабатываются резанием титановые полуфабрикаты и детали с грубой пластинчатой структурой. Такую структуру имеют, в частности, фасонные отливки. Кроме того, фасонное литье из титана и его сплавов имеет на поверхности газонасыщенную корку, которая сильно изнашивает инструмент.
Шлифование титановых деталей связано с определенными трудностями, что обусловлено высокой склонностью к контактному схватыванию при трении. Относительно тонкая оксидная пленка на титане легко разрушается при трении под воздействием высоких удельных нагрузок в точках контакта из-за более высокой пластичности титана по сравнению с оксидной пленкой. При трении в точках контакта двух поверхностей происходит активный перенос обрабатываемого материала на инструмент — “схватывание”. Этому способствуют и другие свойства титана: повышенная упругая деформация из-за сравнительно низкого модуля упругости, более низкая теплопроводность. Благодаря выделению теплоты трущаяся поверхность обогащается газами из окружающей среды и происходит образование оксидных пленок, что повышает прочность поверхностного слоя.
При обработке титановых сплавов применяют шлифование абразивными кругами и ленточное шлифование. Для титановых сплавов наибольшее распространение в промышленности получили абразивные круги из зеленого карбида кремния, обладающего большими твердостью и хрупкостью, стабильностью физико-механических свойств и более высокой абразивной способностью, чем черный карбид кремния.
Основным способом окончательной обработки сложных криволинейных поверхностей деталей из титановых сплавов является ленточное шлифование. К преимуществам применения абразивных лент при формообразовании сложных фасонных поверхностей относится возможность обработки с линейным или поверхностным контактом между инструментом и обрабатываемой поверхностью, что значительно сокращает число формообразующих движений станка.
Обработку деталей с линейным контактом осуществляют методом обкатки. При обработке деталей методом обкатки форма инструмента сопряжена с формой обрабатываемой поверхности детали. Формообразование обрабатываемой поверхности происходит путем обкатки детали по заданной траектории вокруг.
Шлифование методом обкатки, например лопаток компрессора ГТД, производят абразивными кругами (сопряженное шлифование) или широкой абразивной лентой на станках ХШ-185, ХШ-186, MB-885, 381ЗД. При соответствующем подборе ширины ленты одновременно шлифуется вся обрабатываемая поверхность с одной стороны. Этот метод отличается высокой производительностью, и его широко применяют в промышленности при шлифовании деталей небольших размеров. Для лопаток с длиной пера более 120 мм наиболее рациональным является строчечный метод обработки узкой абразивной лентой, позволяющий достигать большой точности. Строчечный метод шлифования применяется в станках 4ШСЛ-7, ЛШ-1, ЛШ1А, ЛШ2. Обработку на них производят продольными строчками, причем направление подачи детали перпендикулярно плоскости перемещения абразивной ленты.
Продольная подача детали s осуществляется за счет возвратно-поступательного перемещения стола станка. Дискретное вращение заготовки вокруг оси обеспечивает круговую подачу s . При обработке на станке ЛШ-1 устанавливается определенная сила контактного давления Р между обрабатываемой заготовкой и абразивной лентой, которая регулируется компенсирующими пружинами.
Сложной операцией является шлифование пересекающихся поверхностей деталей, сопряженных по радиусу (например, поверхностей прикомлевых участков лопаток компрессора), которое выполняют методами обкатки и копирования. При формообразовании поверхностей методом копирования рабочие поверхности контактного копира должны быть эквидистантны на толщину абразивной ленты обрабатываемым поверхностям. Ширина ленты может превышать ширину обрабатываемой поверхности или составлять часть ее. В последнем случае формообразование радиусных участков производится поперечным движением лент относительно детали. В промышленности по этому принципу работает много станков: ЗЛШ-5 (ЗЛШ-52), ЗЛШ-9 (ЗЛШ-91) и др. Обрабатываемая деталь подается по нормали к поверхности на врезание под действием силы 50—100 Н к контактному копиру, который огибает абразивная бесконечная лента. Сила натяжения ленты составляет 10—30 Н на 10 мм ширины ленты. При обработке поверхностей с малым радиусом сопряжений стойкость лент существенно уменьшается.
До последнего времени полагали, что шлифовать титановые сплавы алмазными кругами неэффективно из-за химического сродства титана и углерода, что приводит к сильному изнашиванию режущих кромок алмазных зерен и последующему засаливанию поверхности инструмента. К тому же при алмазном шлифовании в поверхностном слое формируются остаточные растягивающие напряжения. К настоящему времени удалось создать алмазные круги на специальных металлических связках, которые синхронизировали процесс сглаживания режущих кромок зерен с их выкрашиванием из связки и обновлением рабочей поверхности инструмента, т.е. обеспечили самозатачивание алмазного круга. Алмазное шлифование успешно применяется на ММПП “Салют” при шлифовании пера лопаток компрессора.
Разновидностью алмазного шлифования является обработка детали с наложением постоянного тока. Шлифование осуществляют в электролите, при этом алмазный круг служит анодом . Анодное растворение связки круга и титана на поверхности круга позволяет поддерживать постоянные режущие свойства круга. Электрохимическое алмазное шлифование, как правило, формирует в поверхностном слое обрабатываемой детали благоприятные сжимающие напряжения.
Советы по токарной обработке титана
Обработка титана часто обсуждается применительно к фрезерованию, но о токарной обработке титана имеется не так много информации. Хотя большинство титановых изделий обычно обрабатывается фрезерованием, нередко этот экзотический материал подвергается токарной обработке.
Токарная обработка титана часто используется для изготовления фланцев или труб, которые будут использоваться в агрессивных средах. Он также используется для изготовления прочных, легких деталей, которые должны выдерживать нагрузку, и в деталях турбин.
В этой статье я поделюсь некоторыми советами, которые помогут вам успешно обрабатывать титан на токарном станке.
Примечание: данная статья является переводом
Совет №1: Титан двигается
Поскольку одно из наиболее типичных применений титана связано с облегчением веса, очень часто можно встретить очень тонкие титановые детали.
При обработке титана вы сразу же обнаружите одну вещь: он не сидит на месте. Очень редко удается использовать подход “грубо, чисто, грубо, чисто” при обработке всех сторон детали. Он значительно деформируется при удалении материала.
Возможно, вам уже знакомы некоторые из этих проблем, особенно если вы имели дело с тонким алюминием или нержавеющей сталью. Однако для титана следует ожидать еще большего коробления.
Тонкие титановые детали обычно необходимо зачистить с обеих сторон, затем разжать и обработать. Медленно подходите к готовым размерам, чтобы убедиться, что вы можете удерживать жесткие допуски.
На самом деле, возможно, имеет смысл попробовать провести цикл термообработки для снятия напряжения между черновой и чистовой обработкой. Это особенно удобно, если вы удаляете большое количество материала и требуется точность.
Обычно плоскостность очень сложна, если допуски жесткие. Поскольку деталь деформируется при повороте, отверстия также могут деформироваться так, что они становятся некруглыми и могут вмещать только штифты меньшего размера.
Cовет: не снимайте большое количество материала после достижения окончательных размеров; титан деформируется как сумасшедший. Сначала сделайте черновую обработку и потихоньку подбирайтесь к жестким допускам.
Совет профессионала: Использование чистового инструмента с малым радиусом носика (например, около .008″) может означать более длительный цикл чистовой обработки, но меньшее давление резания и меньший нагрев могут означать меньшее коробление при точной чистовой обработке.
Совет №2: Титан изолирует
Тепло от титана быстро не рассеивается. На самом деле, по сравнению с большинством других металлов, титан является скорее теплоизолятором, чем проводником.
Что это означает для токарной обработки?
Стружка не отводит тепло, как это происходит со сталью или алюминием.
На самом деле, если вы дадите агрессивную нагрузку, ваш резец быстро сгорит. Ваш инструмент – это то, что примет на себя большую часть тепла от резки. Ключ к успешному точению титана заключается в том, чтобы максимально снизить нагрев.
Вот как это проявляется при обработке титана:
- Используйте резцы, предназначенные для титана, которые обычно намного острее, чем те, которые вы бы использовали для стали. Такие резцы лучше режут и не выделяют столько тепла. Фрезы с отрицательным углом наклона или с закругленными режущими кромками не подходят для обработки титана;
- Используйте прореживание стружки. Если это вообще возможно, используйте вставки которые уменьшают размер стружки. Круглые вставки могут хорошо работать, как и при использовании 110-градусного угла вставки CNMG вместо 80-градусной стороны, когда это возможно;
- Хорошая подача охлаждающей жидкости имеет решающее значение! Тепло будет попадать в резак, и только охлаждающая жидкость предотвратит преждевременное выгорание твердого сплава.
Мало того, что охлаждающая жидкость должна быть сильно направлена в разрез, вам, вероятно, также понадобится более концентрированная смесь, чтобы получить необходимую смазывающую способность. Это подходящее время для того, чтобы поговорить с вашим торговым представителем охлаждающей жидкости, чтобы узнать, что они рекомендуют;
- Не нажимайте на обороты. Обычный SFPM для титана обычно составляет около 150 или около того, и вы можете получить немного больше для чистовой обработки, если ваш сплав позволяет это. Иногда даже изменение скорости вращения на 10% может привести к катастрофическому отказу фрезы, которая прослужила бы целый час. Титан неумолим;
- Нагрузка стружки важна, но не так важна, как число оборотов. Вы просто не сможете оттолкнуть 6- и 9-гранники толщиной .040″, как это можно сделать со сталью, но вы можете сделать это лучше, чем многие думают. Одно исследование показало, что изменение нагрузки на стружку от .002″ до .020″ привело к изменению температуры реза на 300 градусов по Фаренгейту.
Если вы пытаетесь достичь максимальной производительности, увеличивайте подачу, а не скорость.
Совет №3: Титан съедает твердый сплав заживо
Титан является абразивным материалом для резки, и твердый сплав испытывает на себе его воздействие.
К распространенным проблемам относятся сколы и износ насечек на “коже” реза. Геометрия и марка пластины могут оказать огромное влияние на срок службы инструмента и стабильность процесса. Например, рассмотрите возможность использования пластины WNMG вместо CNMG.
Представители инструментальной промышленности обычно всегда хотят продемонстрировать свои новейшие и лучшие марки твердых сплавов для титана. Я бы настоятельно рекомендовал брать все бесплатные изделия, которые они готовы раздать, чтобы проверить, действительно ли это имеет значение.
Помимо правильного выбора резцов, есть несколько методов программирования, которые помогут вам продлить срок службы ваших инструментов.
Поскольку износ насечки – явление очень распространенное, попробуйте варьировать глубину резания, чтобы распределить его. Закапывайте фрезу, пока есть запас, и уменьшайте глубину реза по мере истончения заготовки.
Инструменты также не любят, когда их зарывают в углах. Даже при точении программирование интерполяции дуги и использование инструмента с меньшим радиусом наконечника, скорее всего, увеличат срок службы инструмента, чем полное погружение инструмента на одном шаге. Это особенно важно для отделки траекторий движения инструмента.
Исследования по токарной обработке титана:
Многие производители оснастки демонстрируют свои собственные исследования о том, насколько им удалось повысить срок службы и эффективность инструмента с помощью новейших разработок. Честно говоря, трудно отделить маркетинговый ход от правды.
Если вам понравилась статья, то ставьте лайк, делитесь ею со своими друзьями и оставляйте комментарии!
Советы по токарной обработке титана – сделайте его из металла
Обработка титана часто обсуждается при фрезеровании, но доступной информации о токарной обработке титана не так много. Хотя большая часть титана обычно обрабатывается фрезерованием, этот экзотический материал нередко подвергают токарной обработке.
Токарная обработка титана часто используется для изготовления фланцев или труб, которые будут использоваться в агрессивных средах. Он также используется для изготовления прочных и легких деталей, которые должны выдерживать нагрузку, а также в деталях турбин.
В этой статье я поделюсь некоторыми найденными мною советами, которые помогут вам успешно обрабатывать титан на токарном станке.
Table of Contents
Совет № 1: Титан движется
Поскольку одно из наиболее распространенных применений титана связано с облегчением веса, очень часто можно найти очень тонкие детали из титана.
При обработке титана вы сразу же обнаружите, что он не стоит на месте. Очень редко вы сможете использовать черновой, чистовой, черновой, чистовой подход, когда обрабатываете все стороны детали. Он значительно деформируется, когда вы снимаете запас.
Возможно, вам уже знакомы некоторые из этих проблем, особенно если вы имели дело с тонким алюминием или нержавеющей сталью. Однако для титана ожидайте еще большей деформации.
Тонкие детали из титана обычно требуют черновой обработки с обеих сторон, затем разжима и окончательной обработки. Сползайте на готовые размеры, чтобы гарантировать, что вы можете выдержать жесткие допуски.
На самом деле, возможно, имеет смысл попробовать цикл термообработки для снятия напряжения между черновой и чистовой обработкой. Это особенно удобно, если вы снимаете большое количество материала и требуется точность.
Обычно плоскостность является очень сложной задачей, если допуски жесткие. Поскольку деталь деформируется при повороте, отверстия также могут деформироваться так, что они станут некруглыми и могут вместить только штифты меньшего размера.
Подводя итог этому совету: не удаляйте большое количество материала после достижения окончательных размеров; титан деформируется как сумасшедший. Сначала сделайте черновую обработку, а затем постепенно увеличивайте допуски.
Совет для профессионалов: Использование инструмента для чистовой обработки с малым радиусом при вершине (например, около 0,008″) может означать более длительный цикл чистовой обработки, но меньшее давление резки и меньший нагрев могут означать меньшую деформацию при прецизионных чистовых резах.
Совет № 2. Титан обеспечивает изоляцию
Титан не рассеивает тепло быстро. На самом деле, по сравнению с большинством других металлов, титан является скорее теплоизолятором, чем проводником.
Что это значит для токарной обработки?
Чипсы не отводят тепло, как сталь или алюминий.
На самом деле, если вы возьмете агрессивную нагрузку на стружку, ваш карбид быстро сгорит. Ваш инструмент — это то, что примет на себя большую часть тепла от резки. Ключ к успешному точению титана заключается в максимально возможном снижении нагрева.
Вот как это относится к точению титана:
- Используйте пластины, предназначенные для титана , которые обычно намного острее, чем те, которые вы используете для стали.
Это означает, что они лучше режут и не выделяют столько тепла. Отрицательный передний угол или закругленные режущие кромки не будут хорошо работать с титаном.
- Используйте истончение стружки. По возможности используйте пластину с геометрией, уменьшающей толщину стружки. Круглые пластины могут работать хорошо, то же самое с использованием 110-градусного угла пластины CNMG вместо 80-градусной стороны, когда это возможно.
- Хорошая подача охлаждающей жидкости имеет решающее значение! Тепло будет передаваться вашему резцу, и только охлаждающая жидкость не позволит вашему карбиду преждевременно сгореть. Мало того, что ваша охлаждающая жидкость должна быть сильно направлена в разрез, вам, вероятно, также понадобится более концентрированная смесь, чтобы получить необходимую смазывающую способность. Поговорите с торговым представителем охлаждающей жидкости с пользой для себя, чтобы узнать, что они порекомендуют.
- Не повышайте обороты.
Обычный SFPM для титана обычно составляет около 150 или около того, и вы можете получить немного больше для чистовой обработки, если это позволяет ваша марка пластины. Это тот, который обычно не прощает. Иногда даже 10-процентное изменение оборотов может привести к катастрофическому отказу фрезы, которая проработала бы час. Титан неумолим.
- Нагрузка на стружку важна, но не так важна, как число оборотов в минуту . Вы просто не можете оттолкнуть эти шестерки и девятки толщиной 0,040 дюйма, как со сталью, но вы можете добиться большего, чем думает большинство людей. Одно исследование показало, что изменение толщины стружки от 0,002″ до 0,020″ привело к изменению температуры реза всего на 300 градусов по Фаренгейту. Если вы пытаетесь максимально увеличить свою производительность, увеличивайте подачу, а не скорость.
Совет № 3. Титан съедает карбид заживо
Титан является абразивным материалом для резки, а карбид терпит от него абсолютное поражение.
Распространенные проблемы включают выкрашивание и износ на «коже» разреза. Геометрия пластины и сплав могут иметь огромное влияние на стойкость инструмента и стабильность процесса. Например, рассмотрите возможность использования вставки WNMG вместо вставки CNMG.
Торговые представители обычно всегда хотят продемонстрировать свои новейшие и лучшие сплавы карбида для титана. Я настоятельно рекомендую взять все бесплатные подарки, которые они готовы раздать, чтобы проверить, действительно ли они имеют значение.
Помимо правильного выбора фрезы, существует несколько методов программирования, которые могут помочь вам увеличить срок службы ваших инструментов.
Так как насечки очень распространены, попробуйте изменить глубину резания, чтобы распределить их. Закапывайте фрезу, пока есть запас, и уменьшайте глубину резания по мере утончения заготовки.
Инструменты тоже не любят зарываться в углы. Даже для токарной обработки программирование дуговой интерполяции и использование инструмента с меньшим радиусом вершины, скорее всего, продлит срок службы инструмента, чем полное заглубление инструмента на шаг. Это особенно важно для чистовой обработки траекторий.
Титановые токарные исследования
Многие производители инструментов продемонстрируют свои собственные исследования того, насколько они смогли улучшить срок службы и эффективность инструмента с помощью новейших и лучших разработок. Честно говоря, довольно сложно отделить то, что просто является маркетингом, от того, что законно.
Компания TechSolve провела действительно интересное исследование, в ходе которого они протестировали различные покрытия, подачи и скорости при токарной обработке титана. Если вы хотите углубиться в сорняки на эту тему, я настоятельно рекомендую прочитать ее. Вы можете найти копию их тестов и результатов здесь.
Если вам нужны заметки Клиффа вместо глубокого погружения, вот некоторые из основных выводов:
- Суперобработанные кромки инструмента (подобные тому, что вы можете получить от Microtek MMP) привели к удвоению срока службы инструмента. Это процесс, который дает чрезвычайно гладкую режущую поверхность, что снижает трение.
- Скорость резания оказала огромное влияние на стойкость инструмента, особенно по сравнению с нагрузкой на стружку. Изменение с 20 до 150 SFM привело к разнице примерно в 900 градусов по Фаренгейту против всего лишь 300 градусов по Фаренгейту при изменении загрузки стружки с 0,002″ до 0,020″.
- Большое количество охлаждающей жидкости имело большое значение для большинства режущих инструментов.
- Необходимы острые режущие инструменты, а поломка инструмента происходит очень быстро, как только на инструменте появляются признаки износа. Они отображали изображения каждого режущего инструмента после каждого
Если вы только начинаете обрабатывать титан и хотите получить практические советы по фрезерованию, обязательно ознакомьтесь с моим руководством о том, как обрабатывать его как профессионал.
Резка титана на токарном станке | Главная Форум машинистов моделей двигателей
В 45
Известный член
- #1
У меня есть несколько титановых болтов диаметром 5/8 дюйма. Насколько сложно будет вырезать их на токарном мини-станке или фрезерном станке? Просто хочу сделать что-нибудь из материала, но мне любопытно, как он будет резаться. болты авиационного класса. Подойдет ли быстрорежущая сталь или карбид?0120 Еще раз спасибо,
В 45
Машином Том
Старший член
- #2
Я резал обоими, но карбид намного лучше. Если HSS должен быть свежим, острым, ударьте по Ti слегка тупым битом, и он затвердеет до того, как будет произнесено слово Oh’xx. Будьте осторожны при сверлении по той же причине, затачивайте сверло перед использованием, а не после того, как оно перестало сверлить.
Он будет работать очень хорошо со скоростью, карбидом, смазкой. а. Деталь 1/2″ D при 2K+ будет выглядеть так, как если бы она была отшлифована. Стружка раскалится до ярко-красного цвета. НЕ останавливайтесь во время резки, сверло прилипнет и затвердеет.
Стружка Mke
рейка60
Известный член
- #3
Для обработки титана требуется низкая скорость резания, высокая подача, подача СОЖ и очень острые инструменты.
Никогда не позволяйте инструменту останавливаться.
Титан сразу затвердеет, если вы позволите инструменту тереться о него, не разрезая.
Будьте осторожны с этими тонкими стружками.
Если срез не залить охлаждающей жидкостью, эти тонкие стрингеры могут загореться металлическим пожаром, который очень трудно потушить.
Рик
В 45
Известный член
- #4
Сначала я попробовал это на своем фрезерном станке… просто обрезал конец резьбой… скорость была 450 об/мин, и резал довольно хорошо. Я не знал, что TI будет флеймить!! Я знаю, что магний делает это легко. Спасибо за совет. У меня нет залива, но мой распылитель выдает много охлаждающей жидкости, пока я продолжаю выдавливать. Просто пытаюсь узнавать что-то новое каждый раз, когда иду в свой маленький магазинчик в подвале.
Еще раз спасибо… V45
брет4
Известный член
- #5
Я режу ти каждый день на работе. Как уже упоминалось, необходим острый резак, иначе вы зажжете огонь на тонкой стружке. Тяжелая щепа не горит легко. Мне нравится инструмент с радиусом на нем. Небольшой токарный станок вроде вашего, я бы сказал, с радиусом от 0,005 до 0,015. Не используйте острие инструмента. Жара его быстро притупит. Скорость подачи 0,003 на оборот является правильной. Инструменты из быстрорежущей стали могут работать, но для большого количества токарных работ лучше всего подходят твердосплавные. Просто держите их острыми.
При сверлении я считаю, что хорошо работают кобальтовые сверла. Если вы используете новые сверла из быстрорежущей стали, мне нравится затачивать их вручную, чтобы острие немного смещалось от центра. Это позволяет немного уменьшить размер сверла. Если этого не сделать, сверло может сгореть и расплавиться. Всегда используйте большое количество охлаждающей жидкости при сверлении.
Нажимать на ti сложнее, чем на что-либо еще, что вы пытаетесь нажать. Для отвода ti изготавливаются специальные метчики. Вы можете нарезать ti метчиками из быстрорежущей стали, сточив часть резьбы так, чтобы на диаметре метчика осталось около 1/4 резьбы. Затем отшлифуйте канавки, чтобы поверхность резьбы была плоской. Могу выложить фото, если есть интерес. Это как-то трудно объяснить.
Брет
Вудстер
Младший член
- #6
Раньше я делал эти детали на токарном станке с ЧПУ, используя инструмент HSS для нарезания резьбы! Шаг 4 мм, площадка 1 мм, прямая сторона, параллельность 11 мм, затем увеличение диаметра на 2 радиуса – радиус 136,5 мм внизу, радиус 85 мм вверху. Потребовалось 3 дня, чтобы запрограммировать в режиме онлайн, а не с помощью CAD / CAM, проработав каждую траекторию резания инструмента, чтобы инструмент постоянно резал с 5 строками G-кода на рез. Обрезать нить заняло около 30 минут!!
Вудстер
дман
Известный член
- #7
ti не слишком сложно на токарном станке. вы получаете довольно непрерывный рез на токарном станке, просто убедитесь, что ваш инструмент острый, на токарном станке также не нужна охлаждающая жидкость, но это помогает. на мельнице у вас есть некоторые проблемы. он затвердевает, а чипсы легко воспламеняются. лучше всего стричь его агрессивно и делать лазающие срезы. это может быть проблемой на ручной мельнице, потому что стол может прыгать. Причина в том, что титан на удивление губчатый и будет сжиматься под режущей кромкой, и трудно начать каждую стружку. попутное фрезерование помещает режущую кромку в свежий недеформационно упрочненный материал и придает ему более крутой угол атаки. он лучше вгрызается в материал. чем больше перешаг или меньше концевая фреза (в пределах разумного), тем лучше. Я пытаюсь получить 1/3 диаметра фрезы с превышением. это также может быть трудно сделать прикарманивание. это тяжело на углах концевой фрезы, и они легко скалываются, усугубляя проблемы с наклепом. вы можете использовать небольшой радиус на концевой фрезе, чтобы усилить углы.
не используйте черновые концевые фрезы, и это может помочь получить концевые фрезы из твердого сплава или с высоким содержанием кобальта из быстрорежущей стали с большим углом наклона спирали для более плавного резания и лучшего выброса чашки. фрезы с 3 канавками под углом 60 градусов работают нормально для удаления стружки и выброса стружки, но углы слабы. Я считаю, что 5-зубая фреза также хорошо работает, а может быть и 6-зубая, если у нее хороший зазор от стружки. это балансирование, чтобы получить правильное количество канавок и зазор для стружки, чтобы резать его хорошо. как кто-то сказал ранее, не останавливайтесь на резаке. не бойтесь продвигать его, просто идите в устойчивом темпе. это как резать алюминий в замедленной съемке. та же толщина стружки, но 1/10 об/мин/поверхность фут/мин и, следовательно, 1/10 дюйм/мин скорости подачи.