Токарная обработка валов
Токарная обработка валов важный и нужный процесс в обработке металла. В современном машиностроительном производстве для технологической подготовки токарных операций, таких как например, обработка валов на токарном станке на станках с ЧПУ, все шире используются САМ-системы (Computer Aided Manufacturing).
В соответствии с типовой структурой управления станком с ЧПУ с помощью CAM-системы в ней решаются следующие задачи:
- геометрические задачи проектирования формообразующих траекторий движений инструмента и заготовки;
- проектирование элементов технологической операции;
- проверка геометрических расчетов и визуализация процесса обработки;
- формирование управляющей программы (УП) соответственно кодам постпроцессора выбранного станка.
Тем не менее, даже у современных CAM-систем отсутствует модуль, позволяющий в автоматическом режиме рассчитывать режим резания если стоит задача –

Учитывая реальные возможности по управлению всеми компонентами режима резания современных станков, CAM-система должна быть способной к полному использованию таких возможностей. Это означает, что в нее обязательно должен входить модуль, позволяющий в автоматическом режиме проектировать как траектории движений инструмента на черновых операциях по оптимальной глубине резания если выполняется обработка вала на чпу, так и рассчитывать программу управления такими компонентами режима резания как подача и частота вращения шпинделя. Причем, оптимальная глубина резания в сочетании с частотой вращения и подачей должны определяться из решения задачи оптимизации, которая в случае, если токарная обработка валов выполняется на станке с ЧПУ сводится к однокритериальной: найти такое сочетание компонент режима резания, чтобы критерий оптимальности производительность – был максимальным при условии выполнения всех ограничений. Поскольку оптимальное управление проектируется на этапе технологической подготовки производства, то исходные данные для решения задачи оптимизации должны получаться из априорной информации. Другим важным условием является то, что
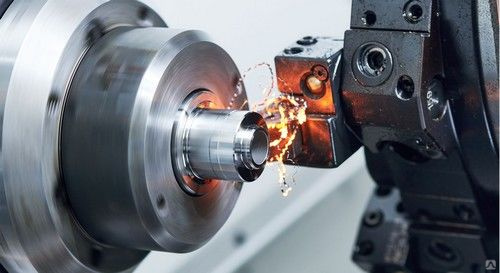
Поскольку реализация запланированных теоретических решений на станках с ЧПУ невозможна без применения САМ-систем, принята концепция создания управляющей программы, ориентированная на применение компьютера. Обработка вала на станке с чпу должна быть смоделирована, структура САМ-системы должна предусматривать процесс резки который проектируется по имеющимся априорным данным и на базе решения задачи расчета траекторий многопроходной обработки. Далее выполняется моделирование процесса точения, во время которого, на каждом его шаге, рассчитываются фактические величины диаметра и глубины резания, которые являются исходными для решения задачи оптимизации и определения оптимальных значений частоты вращения шпинделя и подачи, чтобы
обработка валов на токарных станках с чпу была выполнена оптимальным способом.Следовательно, для решения общей проблемы оптимального управления вначале необходимо установить оптимальную глубину резания на черновых проходах. Для решения такой задачи был разработан алгоритм, который основан на использовании алгоритма решения задачи оптимизации и соответствующей прикладной программы, представленных в работе Петракова Ю.В., Амин Афшара Камбиз “Оптимизация токарной обработки” (сборник Вестник Национального технического университета Украины «КПИ»).
Поскольку обработка ступенчатых валов на токарном станке выполняется наиболее часто с применением схемы точения с использованием инструментальных пластин с главным углом в плане φ>90 0 (рис.1), часть алгоритма, выполняющая расчет допустимой по шероховатости подачи была изменена. По условиям формообразования:
S об ≤ r(1+Sin φ1 + 1/Sin φ1),
поэтому гребешок Rz микронеровностей может образовываться только пересечением дуги окружности радиусом r и линией вспомогательной режущей кромки. Процедура вычисления рассчитывает высоту y профиля гребешка для каждой координаты x с определенным шагом в диапазоне от 0 до x=S об и выбирает максимальную величину. Процедура повторяется с выбранным шагом увеличения подачи Sоб до тех пор, пока y max = Rz.
Рис.1. Схема обработки (а) и образование шероховатости поверхности (б)
Обработка валов на токарных станках с чпу должна происходить с оптимальной глубиной резания на черновых проходах, это значение, при котором, с оптимальными частотой вращения шпинделя и продольной подачей, производительность, оцениваемая по скорости срезания припуска, будет максимальным. При выполнении таких исследований было установлено, что всегда имеется определенное сочетание глубины резания подачи и частоты вращения, полученное из решения задачи оптимизации, которое обеспечивает максимум принятого критерия.
В таблице 1 представлены результаты исследований по определению оптимального режима резания, когда выполняется черновая обработка валов на токарном станке. Сталь 30 инструментом Т5К10 с радиусом при вершине r=0,2 мм и углами в плане φ=95 градусов, φ1=5 градусов на токарном станке 1К62Ф2.
Таблица 1. Зависимость оптимального режима от глубины резания
Результаты исследований в графической форме представлены на рис.2. Видно, что гипотеза о наличии экстремума режима резания при черновой обработке от заданной глубины резания полностью подтвердилась. Для условий эксперимента режим резания H=2,5 мм, S м=425 мм/мин и n=648 об/мин обеспечивает максимальную скорость снятия припуска, объем которого при постоянном диаметре оценивается по площади поперечного сечения срезаемого слоя. Следовательно, такой режим является оптимальным для черновой обработки.
Рис.2. Графики зависимости критерия оптимальности от глубины резания для черновой и чистовой обработки
Токарная обработка валов с оптимальным режимом резания для чистовых проходов оценивается по скорости формообразования, т. е. по величине Sм минутной подачи и зависит от припуска.
Обработка ступенчатых валов на токарном станке выполняется в соответствии с принятой концепцией, модуль оптимизации САМ-системы построен по алгоритму, укрупненная блок-схема которого представлена на рис.3.
Рис.3. Блок-схема алгоритма модуля оптимизации
Модуль оптимизации предусматривает предварительный расчет по встроенной процедуре определения оптимального режима резания на черновых проходах в зависимости от введенных исходных данных. Процедура в автоматическом цикле находит максимум целевой функции Sм*H и определяет, таким образом, глубину резания. Далее, вычисляется необходимое количество проходов и выполняется формирование траекторий движения инструмента как эквидистант к контуру детали. Для этого используется специальная процедура, предусматривающая построение технологической эквидистанты, с достраиванием траектории движения на углах контура по дуге окружности.
Обработка вала на чпу при первом проходе и далее в некоторых местах обработки непостоянна, глубина резания может отличаться от расчетной, при моделировании процесса обработки предусмотрено постоянное обращение к процедуре оптимизации, которая вычисляет оптимальный режим резания для фактической глубины резания. Все расчетные данные (координаты траектории, частота вращения шпинделя и продольная подача) используются для формирования управляющей программы в G-кодах.
Поскольку модуль рассчитан и на автономное использование при технологической подготовке программ для токарных станков с ЧПУ, в него включен интерфейс, выполняющий функции CAD-системы (
рис.4).Рис.4. Графический интерфейс модуля оптимизации
В левом углу задаются геометрические параметры детали, справа выбирается вид заготовки и вводятся ее геометрические размеры. После нажатия кнопок «Применить», изображения контура детали и заготовки появляются в графическом окне, там же обозначены номера участков детали.
Следует отметить, что для использования в дальнейших расчетах универсальных процедур, контуры детали и заготовки представляются дискретными геометрическими моделями в виде цифровых массивов.
При нажатии кнопки «Фрезерно-центровальная операция» выполняется соответствующая перестройка массива контура заготовки показано пунктирной линией на рис.4.
Следующий интерфейс (
Рис. 5. Интерфейс ввода технологических параметров
При нажатии кнопки «Применить данные» появляется графическое окно анимации процесса обработки. На рис.6 показано такое окно в исходном положении для условий рассматриваемого примера.
При нажатии кнопки «Черновая обработка» выполняется моделирование процесса точения, результаты которого в определенном масштабе выводятся в окно анимации. Моделирование выполняется с заданным шагом (0,1 мм), предусматривает, что обработка валов на токарном станке будет производится только после вычисления фактической глубины резания и обращения к процедурам определения оптимизации значений подачи и частоты вращения шпинделя на каждом шаге. Вычисление фактической глубины резания производится специальной процедурой сравнения цифровых массивов текущей траектории движения резца и контура заготовки, сформированного на предыдущем проходе. Резец выполняет движение по траекториям, сформированным на предыдущих этапах работы модуля.
Рис.6А. Состояние графического окна в начале процесса моделирования
Таким образом, во время моделирования создаются массивы данных, представляющие траектории движения инструмента (координаты X и Y), а также привязанные к ним значения подачи и частоты вращения шпинделя.
В конце моделирования деталь 1 приобретает заданную вначале проектирования форму, резец 2 занимает исходное положение а в графическом окне появляются рассчитанные траектории движения на черновой обработке (линии 3) и на чистовой обработке (линия 4). Там же афишируется расчетное время обработки на этих переходах или операциях, это особенно важно если происходит обработка длинного вала на токарном станке.
Рис. 6Б. Состояние графического окна в начале процесса моделирования
Для визуальной проверки результатов моделирования и генерирования управляющей программы в G-кодах используется следующий интерфейс модуля оптимизации. В графическом окне интерфейса (рис. 7) можно представлять графики управления подачей и частотой вращения шпинделя как на черновых так и на чистовом проходах. Причем в зависимости от номера прохода, который выбирается в окне «номер прохода», можно наблюдать управляющие воздействия на любом проходе процесса обработки.
В качестве графического окна представления использован компонент Chart (Среда программирования Delphi), что позволяет проводить увеличение масштаба любого участка графиков и, таким образом, оценивать значения управляющих воздействий.
На рис.7 линией 1 обозначен закон управления подачей, а линией 2 частотой вращения шпинделя. Оба закона привязаны к длине траектории и поэтому, в сочетании с цифровыми массивами координат, являются исходной базой данных для генерирования управляющей программы.
Уменьшение подачи в зонах А и Б объясняется тем, что обработка вала на чпу производится с особенностями точения торцевых участков контура детали, где глубина резания значительно возрастает из-за смены направления подачи и геометрии главного угла в плане резца. На такие возмущения программа успешно среагировала, выбрав (согласно алгоритму) соответствующие изменения управляющих воздействий.
Рис.7. Интерфейс представления графиков управлений (7-ой черновой проход)
Законы управления на чистовом проходе также представлены в функции координаты длины траектории инструмента (рис.8). Постоянство частоты вращения на всех участках контура детали (линия 1) обусловлено конструктивными ограничениями выбранного станка (смотри рис.5), а изменение подачи разными требованиями по шероховатости обработки, назначенными при проектировании чертежа детали (смотри рис.4).
В заключение следует отметить, что аналогичным образом решается задача проектирования оптимального управления и при выборе заготовки в виде штамповки или литья (смотри рис.4). При этом в исходных данных назначается литейные (штамповочные) уклоны и величина припуска. Припуск по умолчанию принимается эквидистантный, а формирование его цифрового массива, представляющего дискретную геометрическую модель, выполняется процедурой расчета эквидистанты, которая используется и для определения траекторий на черновой обработке.
Выводы.
- 1. Впервые доказано, что черновая обработка валов на токарном станке зависит от глубины резания, причем зависимость носит экстремальный характер. Предложен алгоритм автоматического поиска экстремума по глубине резания и формирования траекторий движения резца на черновых проходах.
- 2. Впервые разработан модуль САМ-системы управления токарной обработкой ступенчатых валов, не требующий от технолога задания параметров режима резания и выбора траекторий движения.
- 3. Разработанный модуль в автоматическом режиме определяет частоту вращения шпинделя и продольную подачу, которые обеспечивают минимально возможное время обработки и генерирует управляющую программу для станка с ЧПУ.
- 4. Рассчитывая управляющую программу согласно принятой концепции, разработанный модуль автоматически обеспечивает работу станка на максимально допустимых режимах и, тем самым токарная обработка валов, обеспечена стабилизацией условий обработки на черновых проходах, и решены одновременно две важнейшие задачи управления: стабилизация и оптимизация.
A design technique technological operations of lathe treatment, oriented to the use of CAM-system for machine-tools with CNC, is offered. The module of optimization of sharpening process, intended for building in CAM-system and capable in the automatic mode to expect the optimum laws of cutting process control, is presented.
Рис.8. Интерфейс представления графиков управлений на чистовом проходе
Статьи по станкам ЧПУ
Более 1000 статей о станках и инструментах, методах обработки металлов на станках с ЧПУ.
Предыдущая статья
Следующая статья
Токарная обработка с ЧПУ – процессы, операции и оборудование часть 1
Токарная обработка с ЧПУ является одним из основных методов производства цилиндрических деталей с различными контурами.
В машиностроении нельзя обойти валы для передачи энергии от двигателя к движущимся частям. Валы, конечно, требуют точения.
Но токарные станки с ЧПУ находят широкое применение в различных отраслях промышленности для изготовления обычно осесимметричных деталей.
Что такое токарная обработка?
Токарная обработка – это процесс субтрактивной обработки, который использует режущий инструмент для удаления материала для создания цилиндрических деталей. Сам инструмент перемещается вдоль оси обрабатываемой детали во время ее вращения, создавая спиральную траекторию движения инструмента.
Термин токарная обработка относится к производству деталей путем резки на внешней поверхности. Противоположностью токарной обработки является растачивание, при котором токарные станки используются, например, для создания полых деталей.
Токарный станок по металлу исторически является одним из первых станков для производства деталей полуавтоматическим способом. Сегодня большинство компаний предоставляют услуги токарной обработки с ЧПУ. Это означает, что процесс в значительной степени автоматизирован от начала до конца.
ЧПУ означает числовое программное управление, что означает, что компьютеризированные системы берут на себя управление оборудованием. Входной сигнал – цифровой код. Это контролирует все движения инструмента и скорость вращения, а также другие вспомогательные действия, такие как использование охлаждающей жидкости.
Токарный процесс с ЧПУ:
Из чего на самом деле состоит процесс токарной обработке на станке с ЧПУ? Хотя сама вырезка довольно проста, мы рассмотрим здесь всю последовательность, которая фактически начинается с создания файла САПР.
Шаги процесса:
- Создание цифрового представления детали в САПР;
- Создание кода обработки из файлов САПР;
- Настройка токарного станка с ЧПУ;
- Изготовление токарных деталей.
CAD-дизайн и G-код:
Первые 2 шага можно рассматривать как отдельные или идущие рука об руку. Один из способов – просто использовать программу САПР для создания файлов и отправки их в производство. Затем инженер-технолог создаст Gкод и Mкод для обработки.
cad-cam для токарных операций
Другой способ – просто использовать программное обеспечение CAD-CAM, которое позволяет инженеру-конструктору проверить возможность производства детали. Мощные инструменты моделирования могут визуализировать весь процесс от сырья до конечного продукта, даже используя исходные данные, касающиеся требований к отделке.
Наконец, есть также ручной способ создания кода. Например, вы не можете автоматически сгенерировать код из 2D-чертежа, у вас есть 2 варианта: либо написать код вручную, либо сначала создать 3D-модель.
Даже мощные программы CAM не всегда могут сделать все точно, поэтому рекомендуется проверить закодированные инструкции.
Настройка токарного станка:
Далее идет настройка машины. Здесь роль оператора станка становится очевидной. Хотя современные токарные станки с ЧПУ выполняют большую часть работы автоматически, оператор по-прежнему играет жизненно важную роль.
Шаги по настройке токарного центра с ЧПУ:
- Убедитесь, что питание отключено. Обработка с ЧПУ может быть опасной, поэтому необходима особая осторожность, и проверка выключателя питания является основой для этого;
- Закрепление детали в патроне. Патрон удерживает деталь на протяжении всего процесса. Неправильная загрузка может представлять опасность, а также привести к получению готовой детали неправильных размеров;
- Загрузка револьверной головки. Токарная обработка состоит из множества этапов, поэтому убедитесь, что вы выбрали правильный инструмент для определенной отделки. Револьверная головка может одновременно удерживать множество инструментов для бесперебойной работы от начала до конца;
- Калибровка. И инструмент, и деталь должны быть правильно настроены. Если что-то не так, результат не будет соответствовать требованиям;
- Загрузите программу. Последний шаг перед нажатием кнопки пуска – это загрузка кода в станок с ЧПУ.
Револьверная головка станка ЧПУ.
Производство деталей:
Самый простой способ понять суть производства – это просто посмотреть видео выше. Сырье, как видно, не является круглым бруском, что является наиболее распространенным вариантом. Скорее всего, шестигранный профиль – это более эффективный способ избежать фрезерования с ЧПУ в дальнейшем.
В зависимости от сложности детали может потребоваться один или несколько циклов. Расчеты времени цикла определяют конечное затраченное время, необходимое для расчета затрат.
Время цикла токарной обработки включает:
- Время загрузки. Мы уже описали это как часть установки, но цикл может потребовать другого способа загрузки детали в оборудование;
- Время резки. Время, необходимое для этого, зависит от глубины резания и скорости подачи;
- Время простоя. Время простоя относится ко всему, что не относится к резке, например, к перемещению инструментов к детали и от детали, изменению настроек токарного станка и т.
д.;
- Срок службы инструмента. Хотя каждый цикл не приводит к полному износу инструмента, время резания будет учитываться по сравнению с общим сроком службы инструмента, чтобы включить его в окончательную стоимость.
Параметры токарной обработки:
Параметры токарной обработки с ЧПУ зависят от различных аспектов. К ним относятся материал детали и инструмента, размер инструмента, требования к отделке и т. д.
Основные параметры токарной обработки с ЧПУ:
- Скорость вращения шпинделя. Единица измерения – это обороты в минуту (об/мин), и она показывает скорость вращения шпинделя (N), а значит, и заготовки. Скорость вращения шпинделя находится в прямой зависимости от скорости резания, которая также учитывает диаметр. Поэтому скорость вращения шпинделя должна изменяться, чтобы поддерживать постоянную скорость резания при значительном изменении диаметра.
- Диаметр заготовки. Как уже говорилось, это играет важную роль в достижении правильной скорости резания.
Обозначается символом D, а единица измерения – мм.
- Скорость резания. Уравнение для расчета скорости резания: V =πDN/1000. Он показывает относительную скорость заготовки относительно режущего инструмента.
- Скорость подачи. Единица измерения – мм/об, символ – с. Подача резания показывает расстояние, на которое режущий инструмент перемещается за один оборот заготовки. Расстояние измеряется в осевом направлении.
- Осевая глубина реза. Довольно очевидно, так как он показывает глубину разреза в осевом направлении. Это основной параметр для облицовочных операций. Более высокая скорость подачи оказывает большее давление на режущий инструмент, сокращая его срок службы.
- Радиальная глубина реза. В отличие от осевого реза, она показывает глубину резания перпендикулярно оси. Опять же, более низкие скорости подачи помогают продлить срок службы инструментов и обеспечить лучшую чистовую обработку.
Основные части токарного станка с ЧПУ:
Теперь давайте рассмотрим на основные компоненты токарного центра.
Передняя бабка
Передняя бабка токарного станка с ЧПУ составляет переднюю часть станка. Именно здесь приводной двигатель находится вдоль механизмов, приводящих в действие шпиндель. Патрон или цанга крепятся к шпинделю. Любой из них, в свою очередь, удерживает заготовку во время токарной операции.
Патрон и цанга
Патрон захватывает обрабатываемую деталь своими губками. Он крепится непосредственно к шпинделю, но является сменным, поэтому можно обрабатывать детали разного размера. Цанга – это в основном уменьшенная версия патрона. Размер детали, подходящей для цанг, составляет до 60 мм. Они обеспечивают лучшее сцепление с мелкими деталями.
Задняя бабка
Другой конец токарного центра с ЧПУ. Задняя бабка крепится непосредственно к станине и предназначена для поддержки более длинных заготовок. Пиноль задней бабки обеспечивает поддержку за счет гидравлической силы.
Движущая сила по-прежнему идёт от шпинделя, а задняя бабка просто движется вместе с деталью. Использование задней бабки не подходит при необходимости торцевого точения, так как она будет мешать.
Станина токарного станка
Станина – это просто опорная плита, которая опирается на стол, поддерживая другие части машины. Каретка движется по станине, которая подвергается термообработке, чтобы выдерживать воздействие механической обработки.
Каретка
Каретка опирается на пути скольжения вдоль вращающейся заготовки. Она удерживает инструменты, позволяя протекать процессу резки.
Башня
Новые машины обычно поставляются с башней, которая заменяет каретку. Она может держать больше инструментов одновременно, что делает переключение с одной операции на другую менее трудоемким.
Вращающиеся инструменты на станке с ЧПУ
Обрабатывающие центры с ЧПУ могут поставляться с вращающимися инструментами. В то время как одноточечные режущие инструменты подходят для большинства токарных операций, к вращающимся инструментам относятся фрезы, сверла и другие инструменты, которые имеют собственный привод. Это позволяет создавать шпоночные пазы или отверстия, перпендикулярные оси детали, без использования какого-либо другого оборудования в процессе.
Панель управления
Здесь вступает в действие числовое программное управление. Мозг токарных станков с ЧПУ находится прямо за панелью. Сама панель позволяет оператору настроить программу и запустить ее.
Если вам понравился данная статья, то поделитесь её со своими друзьями, оставляйте комментарии и ставьте лайк!
Типы валов, функции, технологический маршрут, токарные проблемы и решения | Dajin Precision
Руководство по обработке прецизионных валов с ЧПУ: типы валов, функции, маршрут обработки, токарные проблемы и решения | Dajin Precision
2020/02/17 18:06:57
Обрабатывающий вал с ЧПУ является важным компонентом целого ряда оборудования. Dajinprecision.com является профессиональной компанией China Precision Shaft Machineing , предлагающей прочные и дешевые токарные валы . Сегодня мы представим определение валов, функции, типы, способ обработки, а также проблемы, причины и решения при токарной обработке валов с ЧПУ.
Что такое валы?
Валы являются одной из наиболее типичных деталей машин, относится к вращающемуся элементу, длина которого больше диаметра, поперечное сечение обычно круглое, обработанная поверхность обычно имеет внутреннюю и внешнюю цилиндрическую поверхность, коническую поверхность, резьбу, шлицы, паз и поперечное отверстие.
Для чего используются валы?
Детали вала в основном используются для поддержки деталей трансмиссии, передачи мощности от одной детали к другой и крутящего момента. На него часто монтируют шестерни и шкивы.
Какие бывают типы валов?
По характеристикам конструкции и формы валы можно разделить на гладкие валы, ступенчатые валы, полые валы и валы специальной формы (включая коленчатый вал, распределительный вал, эксцентриковый вал и поперечный вал). Например, наш станок с ЧПУ для токарной обработки Эксцентриковый полый вал представляет собой как полый вал, так и эксцентриковый вал.
По соотношению длины и диаметра вал можно разделить на жесткий вал (длина / диаметр < 15), гибкий вал и тонкий вал (длина / диаметр > 15).
Общий технологический маршрут и технологии обработки вала с ЧПУ
Основной поверхностью прецизионных деталей вала является поверхность внешнего круга. Требования к точности внутреннего отверстия полого вала не очень высоки, в то время как точность вторичной поверхности резьбы и шлица на прецизионном шпинделе должна быть высокой. Таким образом, маршрут обработки деталей вала в основном учитывает последовательность обработки внешнего круга и разумно добавляет обработку вторичной поверхности. Маршрут производства и обработки Валы для обработки с ЧПУ с различной точностью и материалами, как показано ниже.
1. Валы из науглероженной стали: подготовка материала -> ковка -> нормализация -> просверливание верхнего отверстия -> черновое точение -> получистовое точение, чистовая обработка -> науглероживание, закалка, низкотемпературный отпуск -> черновое шлифование -> вторичное обработка поверхности -> тонкое шлифование
2. Валы из прецизионной закаленной и отпущенной стали: подготовка материала -> ковка -> нормализация (отжиг) -> сверление верхнего отверстия -> черновое точение -> закалка и отпуск -> получистовое точение , чистовая обработка -> закалка поверхности, отпуск -> черновая шлифовка -> вторичная обработка поверхности -> тонкая шлифовка
3. Прецизионное азотирование стальных деталей вала: подготовка материала -> ковка -> нормализация (отжиг) -> сверление верхнего отверстия -> черновая токарная обработка -> закалка и отпуск -> получистовая токарная обработка, чистовая обработка -> низкотемпературное старение -> черновое шлифование -> азотирование -> вторичная обработка поверхности -> тонкое шлифование -> чистовая обработка
4. Полностью закаленные детали вала: подготовка материала -> ковка -> нормализация (отжиг) -> сверление верхнего отверстия -> черновое точение -> закалка и отпуск -> получистовое точение, чистовая обработка -> вторичная обработка поверхности -> интегральная закалка -> черновое шлифование -> низкотемпературное старение -> тонкое шлифование
5. Общие прецизионные детали вала: примените шлифовку, так как окончательный процесс может гарантировать качество
Проблемы обработки, причины и решения точения вала с ЧПУ
1. Точность размеров не соответствует требованиям
Причины: неправильный чертеж; неправильное использование циферблата; нет пробной резки; неточное измерение; режущий тепловой эффект; и т.д.
Решения: четко ознакомьтесь с требованиями к размерам чертежа деталей; правильно пользоваться циферблатом; провести пробную резку; проверьте и отрегулируйте нулевое положение и правильно измерьте; не измеряйте, когда температура детали высокая, используйте смазочно-охлаждающую жидкость для снижения температуры.
2. Изготовить конус
Причины: токарный резец постепенно изнашивается посередине; вылет заготовки длинный, когда она зажата, а передний конец отодвигается из-за силы резания при токарной обработке; при использовании патрона для зажима продольной подачи при токарной обработке направляющая станины станка не параллельна оси шпинделя станка
Решения: выберите соответствующий материал режущего инструмента или уменьшите скорость резания; максимально уменьшите длину заготовки или используйте заднюю центральную опору на другом конце для увеличения жесткости зажима; отрегулировать параллельность шпинделя токарного станка и направляющей
3. Неквалифицированная круглость
Причины: слишком большой зазор шпинделя токарного станка; припуск на заготовку неравномерен, слишком большая обратная подача инструмента в процессе резания и т. д.
Решения: проверьте зазор шпинделя перед точением и правильно отрегулируйте его. Если подшипник главного вала сильно изношен, замените подшипник; провести чистовую токарную обработку после получистовой токарной обработки
4. Неквалифицированная шероховатость поверхности
Причины: низкая жесткость станка, вибрация, вызванная разбалансировкой деталей трансмиссии или слишком ослабленным шпинделем; неразумные геометрические параметры токарного инструмента; неправильный выбор количества резки и т. д.
Решения: отрегулировать зазор каждой части станка, устранить или предотвратить вибрацию станка; подобрать разумные геометрические параметры; подача не должна быть слишком большой, припуск на чистовую обработку и скорость резания должны быть соответствующими
Прототипы и производство Токарная обработка с ЧПУ | Токарная обработка средних и больших валов
Запрос цен
Jerpbak-Bayless обрабатывает различные средние и большие валы и регулярно нарезает уникальные формы резьбы, на которые способны немногие другие. На наших многочисленных токарных станках с ЧПУ у нас есть возможности от 20-дюймового поворота с межосевым расстоянием 60 дюймов до 40-дюймового поворота с межосевым расстоянием 200 дюймов.
Возможности нашего современного токарного центра включают:
- Глубокое сверление
- 5-осевой токарно-фрезерный станок
- Проходные люнеты
- Большие сквозные отверстия шпинделя для удлиненных деталей
Благодаря нашему инновационному токарному оборудованию с ЧПУ компания Jerpbak-Bayless может выдерживать допуски точности +/-0,0005″, чтобы удовлетворить ваши самые экстремальные требования к токарной обработке. Мы также предлагаем ряд токарных станков с длинной станиной, которые могут выполнять множество второстепенных операций, чтобы обеспечить эффективность вашей работы. Узнайте больше о нашей дополнительной специальной обработке и дополнительных операциях.
5-осевая обработка
Токарно-фрезерное оборудование Jerpbak-Bayless дает нам возможность обрабатывать несколько элементов за один установ. Эти дополнительные оси движения обеспечивают более жесткие допуски между элементами, снижая затраты, связанные с обработкой более сложных деталей. Это позволяет нам преобразовывать заготовку в готовую деталь за значительно меньшее количество шагов. 5-осевая обработка устраняет риск несоответствий, связанных с несколькими настройками. Детали, которые ранее требовали шести установок, могут быть изготовлены всего за одну, что сокращает время доставки и затраты.
Applications
Jerpbak-Bayless успешно помогает широкому кругу отраслей благодаря расширенным возможностям обслуживания.
Наша передовая технология токарной обработки с ЧПУ может использоваться для широкого спектра применений, включая, помимо прочего:
- Насосы, приводные, шлицевые, шпоночные и осевые валы
- Резьбовые валы
- Стяжки
Мы приглашаем вас узнать больше о наших инновационных возможностях обработки. Запросите предложение сегодня о наших превосходных услугах по токарной обработке с ЧПУ или любых наших дополнительных услугах.
Технические характеристики
- Объем производства
от 1 до 1000 шт.
- Список токарного оборудования с ЧПУ
36×167″, диаметр шпинделя 9,5”, сквозное отверстие, люнет, двойной патрон
44×200”, подача СОЖ под высоким давлением, широкие возможности растачивания
18×60”, сквозное отверстие шпинделя, люнет
30×86”, диаметр 4,5”, сквозное отверстие, люнет
29,5×120”, диаметр 7,1”, сквозное отверстие, люнет
30×86”, диаметр 6,5”, сквозное отверстие, люнет, подача СОЖ под высоким давлением
30×62”, сквозное отверстие шпинделя диаметром 4,0”, подача СОЖ под высоким давлением
- Доступные размеры детали
Детали неограниченной длины
- Доступные внешние диаметры
1,5″ до 34″, обычный диапазон
- Доступный допуск
Обычно до +/-.