Обработка внутренних цилиндрических поверхностей – Токарное дело
Обработка внутренних цилиндрических поверхностей
Категория:
Токарное дело
Обработка внутренних цилиндрических поверхностей
Отверстия могут быть сквозные, глухие, нормальные и глубокие длиной свыше пяти диаметров отверстий. В зависимости от вида отверстия, его размеров, точности и параметров шероховатости обработанной поверхности для обработки отверстия применяют сверление, рассверливание, растачивание, зенкерование, развертывание, притирку и раскатывание (развальцовывание).
Рис. 1. Правна заготовки
Рис. 2. Типовые ошибни при заточ-не и установне прорезного и е) отрезного резца
Отверстия диаметром 30—60 мм раскатывают шариковым и роликовым раскатником. При этом диаметр отверстия увеличивается на 0,02—0,03 мм. Головка шарикового раскатника имеет оправку, упорный подшипник и конусные кольцы. Кольцо перемещается вдоль оси оправки и через кольцо поджимается пружиной, сжатие которой .
В зависимости от требований, предъявляемых к точности обработанных отверстий, и их диаметров применяют различные виды инструментов.
Для сверления отверстий при обработке заготовок из материалов средней твердости применяют спиральные сверла с цилиндрическим и коническим хвостовиком; при обработке заготовок из материалов повышенной твердости — твердосплавные цельные сверла или сверла, оснащенные твердосплавными пластинами.
Рис. 187. Протачивание нанавни за один рабочий ход
Рис. 188. Схема обработни широких канавок
При сверлении в заготовках из чугуна отверстий глубиной не более двух-трех диаметров сверла применяют сверло с прямыми канавками. При рассверливании обычно применяют сборные сверла с многогранными неперетачиваемыми пластинами.
При сверлении отверстий сверла устанавливают в пиноль задней бабки или в резцедержатель. При этом используют крепежное приспособление, позволяющее работать как с ручной, так и механической подачей. Сверла с цилиндрическим хвостовиком перед установкой закрепляют в сверлильном патроне, который устанавливают в пиноль задней бабки. Сверла с коническим хвостовиком устанавливают в пиноль задней бабки с помощью переходных втулок, имеющих конус Морзе. При обработке сверла должны быть установлены строго по линии центров.
Рис. 189. Обработка торцовой поверхности и уступов
При обработке отверстия длиной более двух диаметров сначала сверлят его коротким сверлом, а затем длинным. Не допускается сверлить отверстие, имеющее глубину больше длины спиральной канавки сверла. При сверлении глухих отверстий используют шкалу, нанесенную на пиноли задней бабки. При отсутствии рисок на пиноли для определения глубины сверления к пиноли прикладывают масштабную линейку. При сверлении отверстий необходимо использовать СОЖ. При затуплении сверла появляется своеобразный скрежет. Наибольшее изнашивание сверла наблюдается по уголкам ленточки.
Рис. 190. Схема обработки уступов с применением упоров и плавающего центра
Рис. 191. Проверка расположения уступов
Рис. 192.
Рис. 193. Припусни на обработну торцов
Рис. 194. Подрезание торца отогнутым и уступов подрезным резцом
Отверстие диаметром свыше 30 мм обрабатывают за два рабочих хода. Сначала сверлят сверлом d — = 25 мм (рис. 200, ж), а затем рассверливают сверлом требуемого диаметра (рис. 200, з). В отливке или поковке рассверливать отверстие нельзя. Такие отверстия растачивают. Отверстия, глубина которых превышает диаметр сверла в 10 раз и более, сверлят при подводе СОЖ (рис. 200, и).
Растачивают отверстия расточными резцами. Углы заточки расточных резцов выбирают те же, что и у резцов для наружного точения, за исключением задних углов, которые имеют большие значения. Чем меньше диаметр отверстия, тем больше должен быть задний угол а. Вылет резца из резцедержателя делают больше на 5—10 мм глубины растачиваемого отверстия. При растачивании глубину глухого отверстия устанавливают по упору, риске, нониусу (рис. 201, в). При черновом растачивании резец устанавливают несколько ниже осевой линии, при чистовом — несколько выше осевой линии отверстия (рис. 201, г). При креплении тонкостенных втулок в патроне в них могут возникнуть деформации (рис. 202). Искажение формы отверстия можно обнаружить с помощью индикаторного нутромера, имеющего три точки касания (рис. 203).
Рис. 195. Виды отверстий
Рис. 196. Инструменты для обработки отверстий
Зенкеры по сравнению с расточными резцами обладают большой прочностью, поэтому обработку ими можно вести с большей подачей и глубиной резания. Для зенкерования отверстия диаметром до 35 мм применяют зенкеры с тремя режущими кромками и коническим хвостовиком. Для зенкерования отверстий диаметром до 100 мм используют насадные зенкеры, закрепленные на оправке.
При окончательной обработке отверстие развертывают. Развертку устанавливают точно по оси обрабатываемого отверстия. Развертку крепят в шарнирном устройстве. В зависимости от требуемой точности для развертывания применяют одну или несколько разверток (черновую 1 и чистовую 2).
Для получения поверхности отверстий 5 и 6-го квалитета точности при = 0,16…0,05 мм применяют притиры. При этом необходимо, чтобы отверстие предварительно было обработано до 6—8-го квалитета и имело Ra= 1,25…0,2 мм.
Рис. 197. Последовательность применения инструмента для сверления, растачивания и развертывания отверстий
Реклама:
Читать далее:
Обработка наружных и внутренних конических поверхностей
Статьи по теме:
Обработка на токарных станках.

Обтачивание наружных цилиндрических поверхностей выполняют проходными резцами с продольной подачей, гладкие валы, — при установке заготовки в центрах.
Центровые отверстия обрабатывают на токарных, револьверных, сверлильных и двусторонних центровальных станках. Для центрования применяют типовые наборы инструмента — комбинированные центровочные сверла, а также спиральные сверла и конические зенковки.
Центровые отверстия являются, как правило, установочными базами, и поэтому от точности их исполнения зависит и точность обработки остальных поверхностей заготовки.
В полые заготовки после подрезки торца и обработки отверстия с двух сторон вводят пробки или оправки с зацентрованными отверстиями или на кромке отверстия снимают конические фаски, используемые в качестве технологических баз с последующим удалением их при отделочной обработке.
Ступенчатые валы обтачивают по схемам деления припуска на части или деления длины заготовки на части. В первом случае обрабатывают заготовки с меньшей глубиной резания, однако общий путь резца получается большим и резко возрастает То.
Во втором случае припуск с каждой ступени срезается сразу за счет обработки заготовки с большой глубиной резания. При этом Т0 уменьшается, но требуется большая мощность привода станка.
Нежесткие валы рекомендуется обрабатывать упорными проходными резцами, с главным углом в плане j = 90°. При обработке заготовок валов такими резцами радиальная составляющая силы резания Ру = 0, что снижает деформацию заготовок.
Подрезание торцов заготовки выполняют перед обтачиванием наружных поверхностей. Торцы подрезают подрезными резцами с поперечной подачей к центру или от центра заготовки. При подрезании от центра к периферии поверхность торца получается менее шероховатой.
Обтачивание скруглений между ступенями валов – галтелей выполняют проходными резцами с закруглением между режущими кромками по соответствующему
радиусу с продольной или поперечной подачей.
Точение канавок выполняют с поперечной подачей канавочными или фасонными резцами, у которых длина главной режущей кромки равна ширине протачиваемой канавки. Широкие канавки протачивают теми же резцами сначала с поперечной, а затем с продольной подачей.
Обработку отверстий в валах выполняют соответствующими инструментами, закрепляемыми в пиноли задней бабки. На рисунке слева показана схема сверления в заготовке цилиндрического отверстия.
Растачивание внутренних цилиндрических поверхностей выполняют расточными резцами, закрепленными в резцедержателе станка, с продольной подачей.
Гладкие сквозные отверстия растачивают проходными резцами; ступенчатые и глухие — упорными расточными резцами.
Отрезку обработанных деталей выполняют отрезными резцами с поперечной подачей. При отрезке детали резцом с прямой главной режущей кромкой (рисунок слева) разрушается образующаяся шейка и приходится дополнительно подрезать торец готовой детали.
При отрезке детали резцом с наклонной режущей кромкой (рисунок справа) торец получается чистым.
Обтачивание наружных конических поверхностей заготовок осуществляют на токарно-винторезных станках одним из следующих способов.
1. Широкими токарными резцами.
Обтачивают короткие конические поверхности с длиной образующей до 30 мм токарными проходными резцами. Обтачивают с поперечной или продольной подачей. Этот способ можно использовать при снятии фасок с обработанных цилиндрических поверхностей.
2. Поворотом каретки верхнего суппорта.
При обработке конических поверхностей каретку верхнего суппорта повертывают на угол, равный половине угла при вершине обрабатываемого конуса. Обрабатывают с ручной подачей верхнего суппорта под углом к линии центров станка (a). Таким способом обтачивают конические поверхности, длина образующей которых не превышает величины хода каретки верхнего суппорта. Угол конуса обтачиваемой поверхности любой.
3. Смещением корпуса задней бабки в поперечном направлении
.Обрабатываемую заготовку устанавливают на шариковые центры. Корпус задней бабки смещают относительно её основания в направлении,
перпендикулярном к линии центров станка. При этом ось вращения заготовки располагается под углом к линии центров станка, а образующая
конической поверхности — параллельно линии центров станка. Таким образом обтачивают длинные конические поверхности с небольшим углом конуса (2a < 8°) с продольной подачей резца.
4. С помощью конусной линейки
.Коническую поверхность обтачивают с продольной подачей. Скорость продольной подачи складывается со скоростью поперечной подачи, получаемой от ползуна, скользящего по направляющей линейке. Сложение двух движений обеспечивает перемещение резца под углом к линии центров станка. Таким способом обтачивают длинные конические поверхности с углом при вершине конуса до 30—40°.
Обтачивание внутренних конических поверхностей выполняют так же как и наружных, но в основном используют специальные конические зенкеры или развёртки.
Обтачивание фасонных поверхностей с длиной образующей до 40 мм выполняют токарными фасонными резцами. Обтачивают только с
поперечной подачей Sп.
Для обработки на токарно-винторезных станках применяют, как правило, стержневые, призматические или круглые фасонные резцы; резцами остальных видов обтачивают фасонные поверхности на токарных полуавтоматах и автоматах.
Длинные фасонные поверхности обрабатывают проходными резцами с продольной подачей с помощью фасонного копира, устанавливаемого вместо конусной линейки.
Нарезание резьбы на токарно-винторезных станках выполняют резцами, метчиками и плашками. Форма режущих кромок резцов определяется профилем и размерами поперечного сечения нарезаемых резьб. Резец устанавливают на станке по шаблону. Резьбу нарезают с продольной подачей резца Sпр. При нарезании резьбы продольный суппорт получает поступательное движение от ходового винта. Это необходимо для того, чтобы резец получал равномерное поступательное движение, что обеспечивает постоянство шага нарезаемой резьбы.
Методы обработки внутренних цилиндрических поверхностей
Методы обработки внутренних цилиндрических поверхностей [c.68]Виды и методы обработки внутренних цилиндрических поверхностей, достигаемые точность и параметр шероховатости поверхно- [c.68]
Основные методы и виды обработки внутренних цилиндрических поверхностей (отверстий) [c.204]
Обработка внутренних цилиндрических поверхностей. Для окончательной обработки отверстий применяют протягивание и прошивание их выглаживающими протяжками и прошивками, раскатывание многороликовыми раскатками. Методы пластического деформирования более производительны, чем шлифование, и обеспечивают чистоту поверхиости 8—11-го классов. [c.259]
Исследуемыми объектами являлись выпускаемые заводом Калибр рабочие эталоны образцов шероховатости поверхности по ГОСТу 9378—60 — для стальных поверхностей, по ГОСТу 2780—45 — для чугунных поверхностей.

Пределы изменения микрогеометрии при различных методах механической обработки наружных и внутренних цилиндрических поверхностей и плоскостей см. в г. 4. [c.424]
Шлифование относится к числу наиболее производительных методов чистовой обработки. В тяжелом машиностроении оно применяется для обработки наружных и внутренних цилиндрических поверхностей 2—3-го класса точности и выше или же для дости- [c.135]
Металлизированные поверхности по своему внешнему виду и по некоторым свойствам подобны поверхностям литых материалов. Вид и характер поверхности определяются размерами зерен (распылом) и способом подготовки поверхности. Соответственно назначению изделий, могут применяться различные методы обработки металлизационного слоя и последующей термической обработки. Требуемого качества поверхности и точности размеров при обработке металлизированных изделий круглого сечения с учетом структуры металлизационного слоя можно достигнуть токарной обработкой или шлифованием в такой же степени, как и подвергавшихся обработке давлением или литых изделий. Сверление, долбление и строгание металлизационных покрытий применимы лишь при определенных условиях. Металлизация наружных и внутренних цилиндрических поверхностей применяется большей частью для деталей машин, которые перед их использованием должны пройти чистовую токарную обработку или шлифование с соблюдением размеров.
[c.68]
Шлифование методом врезания применяют при обработке коротких отверстий, а также внутренних цилиндрических поверхностей, ограниченных точными торцами или уступами, например роликовых дорожек колец подшипников. Для обеспечения равномерности износа,
[c.247]
Чистовая тонкая обработка методом пластической деформации поверхностного слоя применяется при изготовлении детален из стали. Обработке подвергаются в большинстве случаев наружные и внутренние цилиндрические поверхности при этом придание поверхностным слоям стали чистоты высокого класса (У8—уЮ) сопровождается их упрочнением. [c.275]
Тонкую обработку резцами применяют как метод окончательной отделки наружных и внутренних цилиндрических поверхностей, заменяющий шлифование, и осуществляют при высоких скоростях резания, малых глубинах резания (0,05—0,5 мм) и малых подачах (0,05—0,15 мм/об) на специальных станках. [c.197]
Методы обработки точением наружных и внутренних цилиндрических поверхностей. [c.36]
Вопрос о замене пар различных классов эквивалентными цепями, образованными парами V класса, имеет важное значение не только с точки зрения обобщения теории структуры кинематических цепей и методов их анализа, но и с точки зрения конструктивного оформления элементов кинематических пар. Известно, что наиболее простыми с точки зрения технологической обработки являются пары, элементы которых выполнены по плоскостям или круглым цилиндрическим поверхностям. Более надежными с точки зрения прочности, трения, износа и т. д. являются низшие пары с цилиндрическими или плоскостными элементами. Весьма трудными являются операции технологической обработки шаровых поверхностей, особенно с внутренней шаровой поверхности 11 т. д. Поэтому рассмотрим вопрос о том, какими цепями с парами только V класса могут быть заменены низшие и высшие пары IV, III, II и I классов.
[c.241]
Рассмотрим утверждения, образующие правила выбора средств обработки (станка, инструмента) 1) если необходимо обработать наружную цилиндрическую поверхность и получить шестой класс чистоты, то может быть применена обработка методом чистового точения на токарном станке 2) если необходимо обработать внутренние шлицы и получить поверхность пятого класса чистоты, то может быть применено протягивание, осуществляемое протяжкой и т. п.
[c.9]
Обработка методом врезания. Допуски соответственно для наружной, внутренней цилиндрической и плоской торцовой поверхностей. Номинальная высота кругов, мм. [c.63]
Преимуществом метода являются простота настройки линейки при переходе от обработки цилиндрических поверхностей к обработке конических поверхностей не нужно нарушать наладку станка возможность растачивать внутренние конические поверхности работа с механической подачей суппорта. [c.360]
Доводкой или притиркой называют особый метод окончательной обработки наружных и внутренних, цилиндрических и конических, фасонных и плоских поверхностей детали с целью получения точных размеров и высокой чистоты поверхности или герметичности соединений. [c.169]
По другому методу в качестве заготовки для механической обработки применяют поковки, полученные горячей прошивкой внутренней полости с припусками под дальнейшую механическую обработку цилиндрических поверхностей и торцов (Николаевский
[c. 95]
Основным методом контроля чистоты поверхности режущих инструментов в цеховых условиях является сравнение с образцами чистоты поверхности. Обычные образцы чистоты для контроля режущих инструментов не годятся, поэтому применяются специальные инструментальные образцы, которые имеют четыре вида поверхностей по форме (наружная и внутренняя цилиндрические, плоская и поверхность резьбы) двенадцать видов обработки (точение, строгание, цилиндрическое, торцевое и скоростное фрезерование, круглое и плоское шлифование, заточка, доводка и накатывание резьбы, круглая и плоская доводка) и десять классов чистоты — от 3 до 12-го включительно. [c.355]
Метод обкатки применяют для обработки плоских, наружных и внутренних цилиндрических и фасонных поверхностей осесимметричной формы. Операции обкатывания выполняют на металлорежущих станках токарной, фрезерной, сверлильной групп и др. На рис. 10.30 представлены конструкции шариковых накатных инструментов для обработки наружных цилиндрических и плоских торцовых поверхностей (а) и отверстий (б). Схемы операций обкатки, выполняемые на токарном станке, показаны на рис. 10.31, а, б. В процессе обкатки деталь совершает вращательное движение, державка с шариком совершает поступательное движение — движение подачи, шарик совершает сложное движение. Контактная поверхность перемещается по винтовой линии но поверхности заготовки.
[c.201]
Оно предназначено для обработки внутренних поверхностей цилиндрической или конической формы с прямолинейной образующей. На внутришлифовальных станках используют следующие методы шлифования отверстий с продольной подачей (рис. 13.36, а, б) врезное с поперечной подачей (рис. 13.36, в, г) врезное с дополнительным осциллирующим движением круга (рис. 13.36, в) с планетарным движением шлифовального круга (рис. 13.36, (3). Шлифование с продольной подачей обеспечивает более высокую точность и меньшую шероховатость обработанной поверхности. Врезной метод используют при обработке коротких и глухих отверстий.

Технология внутреннего круглого шлифования. Внутреннее круглое шлифование предназначено для обработки внутренних поверхностей цилиндрической или конической формы с прямолинейной образующей. На внутришлифовальных станках отверстия обрабатывают следующими методами шлифованием с продольной подачей (рис. 2.3.2, а, б) врезным шлифованием (рис. 2.3.2, в, г) врезным шлифованием (рис. 2.3.2, в) с дополнительным осциллирующим движением круга шлифованием с планетарным движением шлифовального круга (рис. 2.3.2, д). [c.227]
На специально переоборудованных станках, снабженных не одной, а несколькими парами направляющих роликов на скобе, можио производить обработку одновременно нескольких деталей различными участками движущегося ЭИ. Такой метод обработки в ряде случаев позволяет получить эквидистантные контуры сопрягаемых деталей с более высокой точностью, чем в вышеописанных примерах. Этим способом можно обрабатывать цилиндрические, конические и призматические поверхности различных размеров, а также одновременно несколько деталей по внутреннему и наружному профилю или одну деталь по внутреннему и наружному профилю. На рис. 90 приведены примеры одновременной обработки двух деталей пуансона 2 и матрицы 1 по одному копиру 3 Обработка ведется различными ветвями ЭИ 4, смещенными относительно друг друга с помощью направляющих роликов 5 на величину /, что обеспечивает зазор между пуансоном и матрицей 07 = 01+02 + /. На рис 91 показана схема одновременной обработки детали 1 по внутреннему и наружному контуру. Изменение направления движения ЭИ 2 и его наклон осуществляются четырьмя направляющими роликами 3
[c.121]
На машиностроительных предприятиях для обработки цилиндрических наружных и внутренних поверхностей галтелей и плоскостей деталей применяется метод динамического упрочнения. [c.287]
Возможность работы при шлифовании с малыми глубинами порядка 1—2 мкм и соответственно с малыми силами резания позволяет этим методом легко достигать точности 6-го квалитета. Шлифование обеспечивает шероховатость обработанной поверхности R=0,32- 0,16 мкм. В соответствии с этими особенностями процесс шлифования применяют для окончательной обработки высокоточных деталей, обработки деталей, к которым предъявляются высокие требования в отношении качества поверхности, обработки деталей после закалки, а в некоторых случаях и для черновых операций при работе по твердой корке. На шлифовальных станках могут быть обработаны все виды наружных и внутренних поверхностей — цилиндрические, конические, торцевые, фасонные и винтовые.
[c.377]
Абразивная доводка является методом окончательной обработки деталей, обеспечивающим высокое качество поверхностного слоя, шероховатость поверхности до Ка = 0,01- 0,002 мкм, отклонения размеров и фор.мы обработанных поверхностей до 0,05 — 0,3 мкм. Параметры качества, а также точность плоских, цилиндрических, сферических и фасонных внутренних и наружных поверхностей деталей после доводки выше, чем после тонкого шлифования, суперфиниширования и хонингования.
[c.818]
На токарно-револьверных автоматах производятся в основном следующие операции обтачивание поверхностей цилиндрических, конических и фасонных, центрование, сверление, зенкерование, развертывание и растачивание отверстий, нарезание или накатывание внутренних и наружных резьб, накатывание рифлений, прорезка шлицев, сверление боковых отверстий и другие, так называемые вторые операции. Последнее время новаторы производства на таких автоматах начали выполнять чистовую обработку гладких поверхностей методом накатывания. [c.187]
Этот метод точения широко применяют в авиационной, траК торной и автомобильной промышленности при обработке цилиндрических и конических поверхностей (наружных и внутренних), а также торцовых поверхностей, уступов и др. Чистота обработанных поверхностей получается 8—11-го классов чистоты (см. табл. 4), а точность размеров деталей соответствует 2-му, а иногда и 1-му классу точности. Более высокая точность получается при обработке цветных металлов, так как при обработке сталей и чугунов на точности сказывается износ резца по задней
[c. 165]
Эксцентричными называются детали, имеющие цилиндрические наружные или внутренние поверхности, оси которых параллельны и смещены на определенное расстояние (эксцентриситет). Методы закрепления и обработки таких деталей выбирают в зависимости от их размеров и величины партии. [c.417]
А. Одновитковые индукторы 1) для нагрева наружных поверхностей цилиндрических изделий 2) для нагрева внутренних поверхностей цилиндрических изделий 3) для нагрева плит методом перемещения 4) для нагрева одного зубца шестерни крупного модуля при последовательной обработке зубцов. [c.126]
Шевингование дисковым шевером является простым и эффективным методом, который получил широкое применение для чистовой обработки незакаленных (до твердости HR 30) прямозубых и косозубых цилиндрических колес с внешним и внутренним зацеплением после зубофрезерования” или зубодолбления. Шевингование применяют в целях улучшения качества поверхности зубьев и повышения точности зубчатого зацепления путем исправления погрешности шага, направления зуба, профиля, уменьшения радиального биения и т.

Такой метод применим для получения кольцевых заготовок с наружной цилиндрической и внутренней поверхностью, имеющей профиль, аналогичный приведенным на фиг. 45, б и з. При этом гарантийный припуск на обработку боковых поверхностей может быть, как правило, уменьшен вдвое по сравнению с аналогичными заготовками, отштампованными на Г. К. М. [c.91]
По указанным соображениям, образцовые детали должны представлять собой набор поверхностей разной формы (цилиндрических— наружных и внутренних, плоских), разных классов чистоты, а обработка образцов должна быть произведена способами, применяемыми на данном предприятии. Только в этом случае метод сравнения с образцами может дать результат, близкий к истинному. [c.66]
Механический метод восстановления детали предусматривает установку колец на наружные и внутренние цилиндрические поверхности, цапф на валы, отдельные зубья и сектора на зубчатые колеса и т.д. Для восстановления изношенных деталей используют такхе электроискровое упрочнение и электрохимическую обработку. Для повышения износостойкости и защиты от коррозии весьма эффективны гальванические методы восстановления и защиты деталей.
[c.22]
Более совершенный метод кодирования чертежей тел вращения разработан Горьковским проектно-технологическим институтом (ПТНИИ). Этот метод используется при технологической подготовке производства. Сведения, содержащиеся >в чертеже, делятся на три группы. В первую группу входит информация о наружной и внутренних цилиндрических и торцевых поверхностях (величины диаметров и линейных размеров, сведения о точности и чистоте обработки поверхностей). [c.70]
Высокая точность заготовки позволила при составлении новой технологии установить прогрессивные методы шлифования колец после термической обработки со следующей последовательностью черновое и чистовое бесцентровое шлифование наружной цилиндрической поверхности колец с разрывом потока деталей в зоне шлифования на двух бесцентровошлифовальных станках шлифование отверстия колец (в размер) и донышка (на съем ) одновременно на одном внутришлифовальном станке черновое и чистовое шлифование наружного торца донышка на двух плоскошлифовальных станках с базированием кольца по внутренней поверхности донышка н отверстия. Выбранная последовательность операций без предварительной подготовки торцовых баз позволяет высвободить значительное количество плоскошлифовальных и внутрн-гилифовальных автоматов и сократить стоимость шлифовальной обработки.
[c.291]
Методом круглого шлифования пользуются при обработке наружных цилиндрических и конических поверхностей. Методом плоского шлифования — при обработке плоскостей методом внутреннего шлифования — нри обработке цилиндрических и конических отверстий. Методом бесцентрового шлифования обрабатывают внешние и внутренние поверхности вращения. Фасонные поверхности шлифуют этими методами с подющью фасонных кругов. Для фасонной правки круга устанавливают дополнительный механизм. Кроме того, фасонное шлифование производят на специализированных фасонно-шлифовальных станках. [c.585]
Суперфинишем называется метод особо чистой обработки наружных и внутренних поверхностей мелкозернистыми абразивными брусками, которым сообщается сложное движение. На токарных станках с помощью специальных приспособлений выполняют суперфиниширование как наружных, так и внутренних цилиндрических поверхнсютей.
[c.430]
На 4-мГПЗ создан процесс сверхдоводки (суперфиниш) желобов наружных и внутренних колец прецизионных подшииников, который отличается от распространенного метода суперфи-ниша цилиндрических и конических поверхностей тем, что возвратно-поступательное движение бруска заменено качанием по радиусу желоба кольца. Обработка производится мелкозернистыми брусками на керамической связке. Изделие вращается со скоростью 1—1,5 м сек, число двойных качаний бруска 600 в минуту, амплитуда качания регулируется в широких пределах. Радиальное давление создается пневматически. [c.475]
На рис. 178 показаны схемы образования наружных и внутренних поверхностей, используемые при обработке деталей на автоматах и полуавтоматах, Наружные цилиндрические поверхности получаются продольной подачей. радиальных или тангенциальных проходнш резцов (рис. 178, а), а также поперечным перемещением широких резцов, установленных в поперечных суппортах рис. 178, б). При образовании фасонных поверхностей (рис. 178, в) метод обработки аналогичен. При отрезке j 1 (рис. 178, г) переднюю режущую кромку резца для зачистки торца детали делают скошенной. Перед сверлением отверстия заготовку обычно зацентро-вывают (рис. 178,5). Сверление неглубоких отверстий (/ d) короткими f сверлами большого Диаметра (рис. 178, е) производится без зацентровки
[c.212]
Экономическая точность размеров элементов деталей и параметры шероховатости обработанных поверхностей для основных методов обработки плоских и цилиндрических наружных и внутренних поверхностей приведена в табл. 1.3.1. Табл. 1.3.1 позволяет выбрать методы окончательной обработки поверхностей. Эта же задача выбора метода окончательной обработки поверхностей может бьпъ решена одновременно с установлением последовательности (маршрута) обработки каждого элемента детали с использованием
[c. 81]
Основные элементарные поверхности (цилиндр, плоскость) образуются копированием внутренних эталонов станка направляющих прямолинейного или вращательного движений, шпинделей с точным расположением оси вращения. Размер и расположение этих поверхностей определяются с помощью отсчег-ных устройств, встроенных в станок, или универсальными измерительными свойствами. Винтовые, эвольвентные и иные сложные поверхности образуются с помощью вращательных и поступательных движений. Поверхности одной и той же геометрической формы могут быть обработаны различными способами например, наружная цилиндрическая поверхность может быть получена обтачиванием резцом, 1фуговым фрезерованием, наружньш протягиванием, шлифованием различными методами и т.д. Каждому способу обработки соответствует, как правило, свой тип металлорежущего станка токарный, фрезерный, протяжной, крутаошлифовальный и т.д. и свой вид режущего инструмента резец, фреза, протяжка, шлифовальный круг и т.д. [c.12]
При исследовании трения качения нижним шарам предоставляется возможность свободно перекатываться по чашке, внутренняя поверхность которой может быть выполнена различной формы (например, в форме тора или цилиндрического стакана) [4—6]. В этом случае критериями для характеристики изнашивания служат весовой износ шаров, а также появление и развитие питтинга. Использование четырехшарикового узла трения позволяет быстро определять противопиттинговые свойства смазок. Это обеспечивает возможность эффективного применения методов математической статистики для обработки результатов опытов, что
[c.153]
Зубошевннгованне дисковым шевером является наиболее распространенным и экономичным методом чистовой обработки зубьев незакаленных (с твердостью до ИКС 33) прямозубых и косозубых цилиндрических колес с внешним и внутренним зацеплением после зубофрезерования или зубодолбления. Шевингование применяют для повышения точности зубчатого зацепления, уменьшения параметра шероховатости поверхности на профилях зубьев, снижения уровня шума и т. д. Шевингованием можно повысить точность на одну-две степени. Точность шевингованных зубчатых колес достигает 6 —8-й степени, параметр шероховатости поверхности Ка = 0,8 -ь 2,0 мкм.

А. В Милане, в 1335 г. Б. Нюрнбергский механик П. Хенлейи, в 1510 г. В. X. Гюйгенс воспользовался эффектом изохронности малых колебаний маятника (независимость периода его колебаний от амплитуды), открытым Г. Галилеем. Г. Выдающимся механиком И. П. Кулибиным — Б России и часовым мастером П. Лерца — во Франции (независимо) в целях устранения погрешностей работы часов, связанных с изменениями температуры окружающей среды, было предложено использовать для изготовления маятников биметалл (материал, состоящий из двух металлов). 5. а) Координатно-расточной станок, для финишной обработки отверстий, расположение которых должно быть точно выдержано, а также для прецизионных фрезерных и других точных работ, б) Зубодолбежный полуавтомат, для обработки цилиндрических прямозубых и косозубых колес с наружным и внутренним зацеплением, посредством круглых (зубчатых) долбяков, методом обкатки, в) Многооперацион-ный станок с ЧПУ, для обработки заготовок корпусных деталей на одном рабочем месте с автоматической сменой инструмента, г) Круглошлифовальный станок, для наружного шлифования в центрах заготовок деталей типа тел вращения, д) Вертикально-сверлильный станок, для сверления, зенкерования, зенкования, развертывания отверстий, подрезания торцов изделий и нарезания внутренних резьб метчиками, е) Токарно-револьверный станок, для обработки заготовок с использованием револьверной головки, ж) Радиально-сверлильный станок, для сверления, рассверливания, зенкерования, развертывания, растачивания и нарезания резьб метчиками в крупных деталях, з) Поперечно-строгальный станок, для обработки плоских и фасонных поверхностей сравнительно небольших заготовок, и) Горизонтально-расточной станок, для растачивания отверстий в крупных деталях, а также для фрезерных и других работ, к) Плоскошлифовальный станок, для шлифования периферий круга плоскостей различных заготовок при возвратнопоступательном движении стола и прерывистой поперечной подаче шлифовальной бабки, л) Зубофрезерный полуавтомат, для фрезерования зубьев цилиндрических прямозубых и косозубых шестерен, для обработки червячных колес методом обкатки червячной фрезой,
[c.
146]
Большой недостаток метода кривых нагрева тот, что для многих сплавов трудно или даже невозможно приготовить. СЛ1ИТОК однородного состава. В результате точки линии солидус, опреде пенные по остановкам на кривых нагрева, получаются заниженными. Так, в случае а-и р-фазных сплавов серебра и меди маленькие цилиндрические слитки, отлитые в кокиль, часто имеют зонную ликвацию, благодаря которой наружные и внутренние слои различаются по составу на 1 — 2%. Теоретически, конечно, можно сделать эти слитки однородными по составу путем длительного отжига, однако практически это время слишком велико, и такие образцы непригодны для снятия кривых нагрева, хотя, как было показано выше, они могут быть иногда использованы для исследования методом микроанализа. Обычно ликвация по длине слитка относительно невелика. Поэтому при использовании метода кривых нагрева сначала производят гомогенизацию, затем удаляют тонкий слой металла с поверхности. Эта обработка устраняет необходимость вырезания сердцевины, но не приводит к выравниванию состава снаружи и в середине, если есть сегрегация. Затем сухим чистым резцом стачивают слой толщиной околю
[c.201]
Зубошевингование дисковым шевером является наиболее распространенным и экономичным методом чистовой обработки зубьев незакаленных (с твердостью до 33HRQ прямозубых и косозубых цилиндрических колес с внешним и внутренним зацеплением после зубофрезерования или зубодолбления. Шевингование применяют для повышения точности зубчатого зацепления, уменьшения шероховатости поверхности на профилях зубьев, снижения уровня шума и т.д. [c.664]
Как уже говорилось, при работе золотника в замкнутой системе требуется, чтобы его коэффициент усиления, который пропорционален ширине рабочей щели, не зависел от положения золотника или, другими словами, щели должны быть прямоугольными, с точки зрения изготовления это требование не совсем удачное, так как выполнение прямоугольных отверстий обходится значительно дороже, чем сверление круглых. Тем не менее поддержание постоянным коэффициента усиления важно потому, что практически все золотники имеют прямоугольные рабочие щели. В некоторых случаях, таких, как золотники ХА и Л1Х, описанные в гл. VIII, эти отверстия сверлятся в корпусе золотника, который служит одновременно корпусом и втулкой. Однако в большинстве случаев отверстия выполняются в отдельной втулке, которая затем вставляется в расточку корпуса. Сами отверстия могут быть выфрезе-рованы в стенке втулки снаружи, так что при пересечении этой поверхности с внутренней поверхностью втулки образуется прямоугольное отверстие. По-видимому, этот метод наиболее общий, но точность фрезерования обычно недостаточна для того, чтобы обеспечить допуски, требующиеся в высококачественных золотниках. В этом случае втулка монтируется из нескольких цилиндрических частей (обычно из пяти), имеющих параллельные торцы, причем рабочие щели образуются именно этими торцами. Благодаря тому что плоскошлифовальный станок, обеспечивая высокую точность обработки, позволяет сравнительно легко удовлетворить требования допусков на изготовление, а также благодаря тому, что для окончательной обработки используются абразивные материалы, имеется возможность применять для изготовления втулок твердые материалы.
[c.209]
Обработка токарная поверхностей внутренних – Энциклопедия по машиностроению XXL
Токарные автоматы применяются в крупносерийном и массовом производстве для комплексной обработки наружных и внутренних цилиндрических и резьбовых поверхностей, главным образом при изготовлении деталей из пруткового материала, где благодаря значительным размерам пускаемых в производство партий деталей автоматы могут быть загружены без переналадки в течение нескольких дней в случае недостаточной загрузки и необходимости в частой переналадке целесообразнее применять револьверные станки. В каждом отдельном случае для более правильного с экономической точки зрения решения вопроса, на каких станках — автоматах, полуавтоматах или револьверных — целесообразно вести обработку, необходимо разработать сравнительные варианты технологических провесов обработки детали на том или другом станке и сопоставить полученные техникоэкономические показатели. [c.360]На линии выполняются следующие операции I — полная токарная обработка наружного кольца 2 — черновая токарная обработка внутреннего кольца 3 — чистовая токарная обработка внутреннего кольца 4 — клеймение 5 — магазины задела 5 и 7 — термическая обработка наружного и внутреннего колец 8 — визуальный контроль 9 — плоское шлифование наружного и внутреннего колец (поочередно) а — базового торца б — противоположной поверхности 10 — бесцентровое шлифование наружной поверхности наружного кольца 11 — черновое бесцентровое шлифование дорожки качения наружного кольца 12 — чистовое бесцентровое шлифование дорожки качения наружного кольца 13 — бесцентровая доводка дорожки качения наружного кольца 14 — снятие наката 15 — визуальный контроль 16 — промывка и сушка наружного кольца 17 — автома- [c.

Черновая токарная обработка наружных н внутренних поверхностей барабана [c.22]
Обработка колец шариковых подшипников (табл. 9 и 10). Наиболее распространенными являются подшипники с наружным диаметром 30—160 мм. Программы выпуска этих подшипников таковы, что делают автоматизацию их производства экономичной. В АЛ токарная обработка наружных и внутренних колец ведется на многошпиндельных токарных автоматах. В зависимости от конкретных условий различных заводов существует несколько практически равнозначных вариантов обработки колец одного и того же типа. В табл. 9 и 10 приведены варианты, осуществленные на АЛ, поставленных на подшипниковые заводы. В качестве режущего инструмента при токарной обработке широко используют как твердосплавный инструмент, так и инструмент из быстрорежущей стали. Твердосплавный инструмент используют преимущественно при обработке гладких цилиндрических и торцовых поверхностей, прямых фасок. Скорость резания при этом 100—150 м/мин подача до 0,6 мм/об.
[c.262]
Обработка колец железнодорожных подшипников (табл. И и 12). Токарная обработка наружных и внутренних колец выполняется на одношпиндельных токарных гидрокопировальных автоматах резцами, оснащенными твердым сплавом. Скорость резания до 100 м/мин подача 0,2—0,8 мм/об в зависимости от вида обрабатываемых поверхностей и выполняемой операции. Особенностью токарной обработки наружных колец является чистовое точение трех торцов одновременно. Операция введена с целью обеспечения равномерного и минимального припуска при шлифовании этих торцов. [c.263]
Во многих случаях это обычные универсальные станки со специальными наладками. Применяются для обработки круговых цилиндрических поверхностей, наружных или внутренних винтовых поверхностей постоянного шага, особенно, когда шаг их чрезмерно велик для обработки на токарном станке. Главное движение обычно осуществляется изделием, установленным на столе, или в специальных случаях инструментом скорость настраиваемого движения подачи сохраняется постоянной.
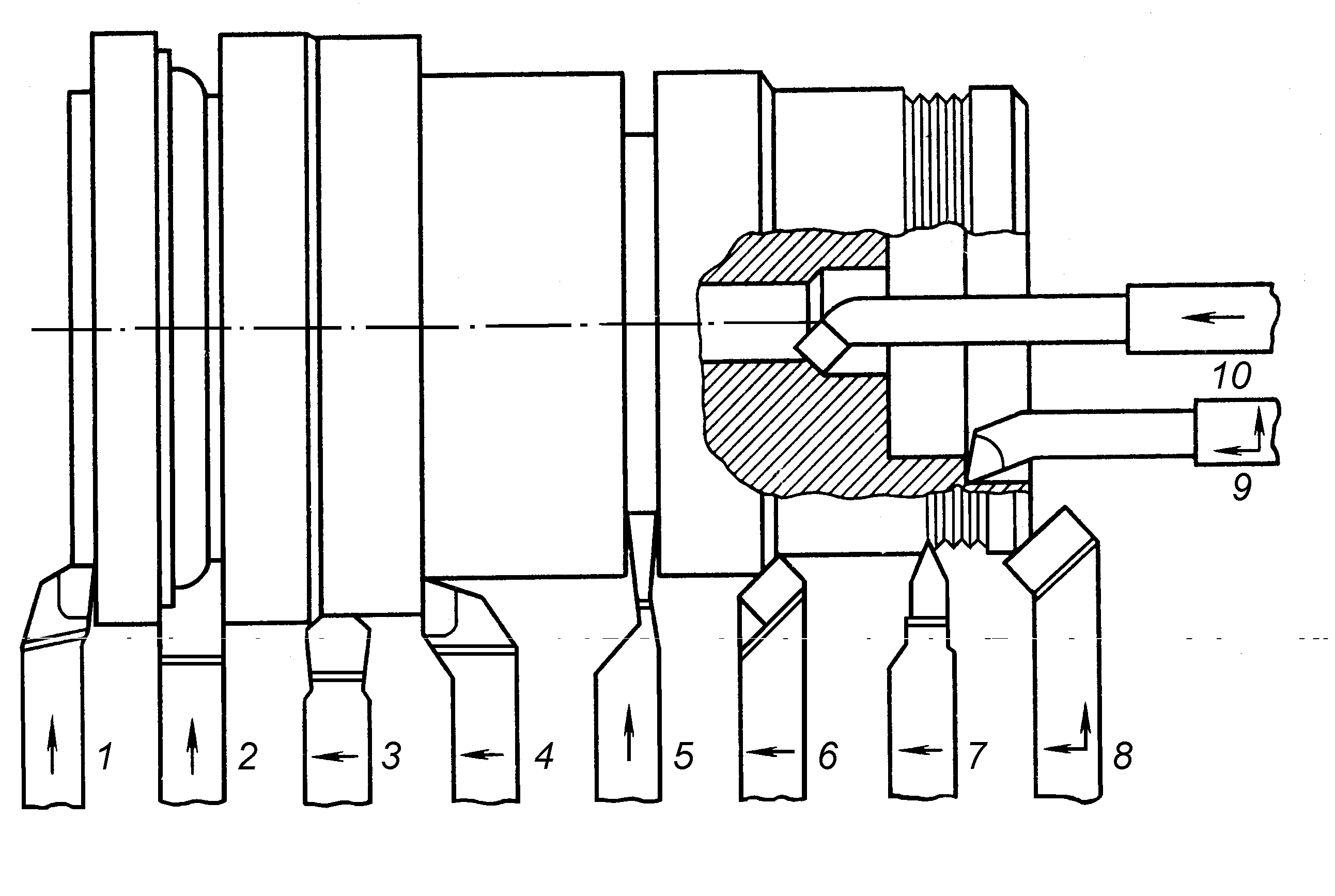
На токарных станках с ЧПУ последовательность переходов обработки следующая а) предварительная (черновая) обработка основных участков поверхностей детали подрезка торцов, центрование перед сверлением отверстий диаметром до 20 мм, сверление (если используются два сверла, то вначале сверлом большего диаметра), рассверливание отверстий, точение (получистовая обработка) наружных поверхностей, а затем растачивание внутренних поверхностей б) обработка дополнительных участков поверхностей детали (кроме канавок для выхода шлифовального круга, резьбы и т. п.) в тех случаях, когда черновая и чистовая обработки внутренних поверхностей проводятся одним резцом, все дополнительные участки обрабатывают после чистовой обработки в) окончательная (чистовая) обработка основных участков поверхности детали, сначала внутренних, потом наружных г) обработка дополнительных участков поверхностей детали, не требующих черновой обработки сначала в отверстиях или на торцах, затем на наружной поверхности.
[c.237]
При рассмотрении технологии следует остановиться на особенностях выполнения токарной черновой и чистовой операций и на замерах конических поверхностей. Обработка наружных и внутренних конических поверхностей выполняется на токарных стан-21 323 [c.323]
В качестве примера рассмотрим технологический процесс восстановления гильз цилиндров двигателей СМД-14. Процесс содержит следующие операции мойку, очистку, дефектацию, токарную обработку наружной поверхности, термопластическое обжатие, очистку, обезжиривание поверхности, металлизацию посадочных поясков, шлифование посадочных поясков, расточку внутренней поверхности, протачивание бурта гильзы, чистовое и окончательное шлифование посадочных поясков, предварительное чистовое и окончательное хонингование внутренней поверхности, мойку, очистку, выходной контроль, консервацию и упаковку. Схема расположения технологического оборудования и оснастки на участке восстановления гильз цилиндров показана на рис. 83 перечень технологического обо-
[c.428]
Точение является основным способом обработки поверхностей тел вращения (см. рис. 31.2, а). Процесс резания осуществляется на токарных станках при вращении обрабатываемой заготовки (главное движение) и перемещении резца (движение подачи). С помощью точения выполняют операции обтачивание — обработку наружных поверхностей растачивание — обработку внутренних поверхностей подрезание — обработку торцевых поверхностей резку — разрезание заготовки на части резьбонарезание — нарезание резьбы. [c.585]
Станки токарной группы составляют значительную долю станочного парка. Она включает в себя девять типов (см. табл. 1.1) станков, различающихся по назначению, компоновке, степени автоматизации и другим признакам. Токарные станки предназначены главным образом для обработки наружных и внутренних цилиндрических, конических и фасонных поверхностей, нарезания резьбы и обработки торцовых поверхностей деталей типа тел вращения с помощью разнообразных резцов, сверл, зенкеров, разверток, метчиков и плашек.
[c.133]
Число операций при токарной обработке и их последовательность зависят от конфигурации, точности и качества поверхностей обрабатываемых заготовок. Ориентировочные данные по точности обработки наружных и внутренних поверхностей на станках токарной группы приведены в табл. 15 и 16. Основные способы креп- [c.302]
Для обработки криволинейных поверхностей тел вращения длиной до 100 мм применяют фасонный инструмент, профиль которого соответствует профилю обрабатываемой поверхности. Фасонными резцами могут обрабатываться как наружные, так и внутренние фасонные поверхности. В зависимости от направления подачи резцы делятся на радиальные, подача которых направлена по радиусу обрабатываемой детали тангенциальные, подача которых направлена по касательной к образующей обрабатываемой детали. Точность поверхностей, обработанных радиальными резцами, зависит от точности выключения подачи, а обработанных тангенциальными резцами от точности установки резца.
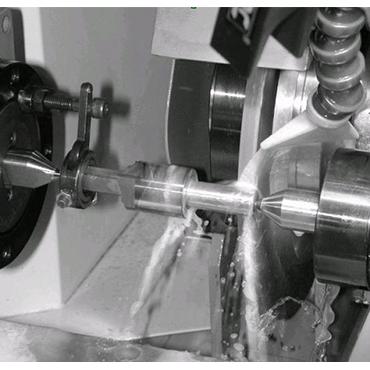
III — линия токарной обработки наружных и внутренних колец IV — линия шлифования наружных поверхностей наружных колец У — то же, внутренних колец [c.512]
При бесцентровом внутреннем шлифовании отверстий может быть достигнута точность размера диаметра до 0,007 мм, по конусности, овальности и эксцентричности — до 0,002 мм. Перпендикулярность оси отверстия к торцу детали будет соблюдена в той же мере, в какой она была достигнута при обработке наружной поверхности и торца на токарных станках. [c.143]
Технологический маршрут. Изготовление наружного и внутреннего колец шарикоподшипников начинается с обработки наружных и внутренних поверхностей одновременно двух заготовок на токарных автоматах пруткового типа (двухшпиндельных — для наружных и шестишпиндельных — для внутренних колец), после чего производят клеймение и термообработку.
[c.455]
Токарная обработка наружных и внутренних поверхностей [c.458]
Токарная обработка наружных и внутренних поверхностей одновременно на двух заготовках [c.340]
После первых пяти операций получают высококачественную заготовку с припуском по наружному и внутреннему диаметрам кольца 0,2 мм. При применении этой заготовки отпадает необходимость в токарной обработке наружной и внутренней цилиндрической поверхности кольца. По высоте заготовка имеет припуск 2 м.ч. При черновом подрезании торца заготовки срезают большую часть припуска на высоту заготовки—1,3 мм. Подрезание дна и узкого торца производят с одной установки, что обеспечивает требуемую точность расположения поверхностей. [c.364]
Станки токарной группы предназначаются для обработки наружных и внутренних поверхностей вращения (цилиндрических, конических и фасонных), подрезания торцов, нарезания резьбы и некоторых других работ. Основным видом режущего инструмента для токарных станков являются резцы. Для обработки отверстий используют также сверла, зенкеры, развертки и др. Для нарезания резьбы применяют метчики и плашки.
[c.534]
Число операций при токарной обработке и их последовательность зависят от конфигурации, точности и качества поверхностей обрабатываемых заготовок. Ориентировочные данные по точности обработки наружных и внутренних поверхностей на станках токарной группы приведены в табл. 15 и 16. Основные способы крепления инструмента при растачивании отверстий на токарных станках даны в табл. 17. [c.332]
Использование режима диалога с ЭВМ для проектирования станочных операций обработки. Проектирование технологических процессов механической обработки связано с большим количеством трудноформализуемых логических действий. Особенно большие трудности возникают при проектировании станочных операций обработки деталей на многошпиндельном и многопозиционном оборудовании. Например, анализ инструментальной наладки токарно-револьверного автомата (рис. 3.10, а) показывает, что время обработки наружных поверхностей деталей больше, чем время обработки их внутренних поверхностей. Поиск оптимального варианта приводит к решению совместить переходы обработки поверхностей проходным и канавочиым резцами в один сложный инструментальный переход, выполняемый фасонным резцом (рис. 3.10,6). Принять такое решение технологу-проектировщику, работающему с ЭВМ в пакетном режи- [c.116]
На рис. 141 показаны примеры изменения конструкций для облегчения обработки труднодоступных поверхностей. Обработку внутренней полости т корпуса запорного клапана (вид 7) можно упростить, увеличив диаметр нарезной части корпуса (вид 2). В эюм случае токарную обработку можно заменить сверлением или зеикерование.м. [c.122]
На фиг. 627, а изображена вилка механизма блокировки автоматического включения фрикциона шестишпиндельного токарного автомата, тре-бующ,ая обработки наружных и внутренних поверхностей с обеспечением , при этом точных размеров. Наиболее затруднительна здесь обработка внутреннего паза шириной 40 ° мм, которая требует применения фрезы большого диаметра либо подрезки внутренних торцов при сверлении или расточке отверстий в ушках вилки. [c.606]
Автоматическая линия МЕ436Л1А состоит из восьми шестишпиндельных токарных автоматов 4, объединенных транспортной системой. На автоматической линии выполняется одна технологическая операция — токарная обработка наружных и внутренних поверхностей гильзы со стороны узкого торца. С конвейера-загружателя / гильзы автоматически, по мере освобождения трассы транспортирования от гильз, направляются через приводной конвейер 2 на конвейер-распределитель 7. В случае переполнения конвейера-распределителя 7 гильзы направляются в магазин 3. При отсутствии гильз на конвейере 2 гильзы выдаются на конвейер-распределитель из магазина 5 магазин 3 таким образом регулирует равномерность поступления гильз. По командам токарных автоматов конвейер-распределитель 7 выдает гильзы на поперечные конвейеры 6, с которых гильзы с помощью загружателей 5 подаются в загрузочную зону токарных автоматов. Обработанные гильзы с помощью загружателей 5 опускаются и поступают на нижнюю ветвь поперечных приводных конвейеров 6, а затем на нижнюю отводящую ветвь конвейера-распределителя 7 и направляются через подъемник 9 в транспортную систему автоматической линии МЕ437Л1А. [c.114]
Автоматическая линия МЕ437Л1А состоит из восьми шестишпиндельных токарных автоматов 12, моечного автомата 15. На автоматической линии осуществляется токарная обработка наружных и внутренних поверхностей гильзы со стороны широкого торца и промывка гильзы от прилипшей стружки. Заготовки, поступившие из автоматической линии мод. МЕ4361Л1 А, направляются конвейером-распределителем 11 к токарным автоматам 12. При переполнении транспортера-распределителя 11 гильзы направляются в магазин 10 и выдаются из него при перерывах в поступлении гильз с автоматической линии МЕ436Л1А. Подача гильз к каждому токарному автомату 12 и отвод гильз осуществляется поперечным конвейером 14 и загружателем 13. После токарной обработки гильзы направляются конвейером-распределителем и и поперечным конвейером 18 в моечную машину 15. После промывки гильзы поступают на конвейер 16. С конвейера 16 гильзы вручную снимают и загружают в кассеты для отправки на операцию искусственного старения. После искусственного старения гильзы загружают на конвейер 17, далее они направляются конвейером 17 в магазин 19. [c.116]
Автоматическая линия МЕ439Л1 состоит из восьми шестишпиндельных токарных автоматов 20 и транспортной системы. На автоматической линии выполняется одна технологическая операция — чистовая токарная обработка наружных и внутренних поверхностей со стороны узкого торца. Из магазина 19 заготовки конвейером-распределителем 23 направляются на поперечные конвейеры 22 и загружате-лями 21 подаются к токарным автоматам 20. После токарной обработки гильзы по нижней отводящей трассе конвейера 23 направляются к подъемнику 24 и далее в транспортную систему автоматической линии МЕ440Л4. [c.116]
Мировое станкостроение в последней трети XIX в. располагало пятью основными типами металлорежущих станков. Преобладающую часть станочного парка составляли ток арные станки, которые применяли для обработки наружных и внутренних поверхностей тел вращения. На токарных станках обтачивали гладкие и ступенчатые валы, конусы, шары, различные фасонные поверхности, растачивали цилиндры, отверстия, нарезали резьбу. Вторую многочисленную группу составляли сверлильные станки, предназначавшиеся для сверления и обработки отверстий, а также для расточки и нарезки резьбы. Строгальные станки, подразделявшиеся на горизонтальные и вертикальные (долбежные), служили для обработки плоских поверхностей изделий. Расширялось использование фрезерных станков для обработки наружных и внутренних поверхностей особенно точных деталей, а также для получения изделий фасонной конфигурации. Наконец, пятую группу металлообрабатывающего оборудования составляли шлифовальные станки, на которых проводили чистовую обработку деталей различной формы с помощью абразивных материалов и инструментов. [c.20]
Определение точности линейного технологического процесса. Исследование точности линейных динамических технологических процессов базируется на теории линейных преобразований случайных функций. Действительно, любой технологический объект можно рассматривать как процесс, преобразующий входную случайную переменную X (s) в выходную переменную Y (t). Например, для процесса токарной обработки имеем преобразование внутренних и наружных диаметров и длин заготовки, которые представляют собой входные случайные функции X (s), в измененные внутренние и наружные диаметры и длины деталей, которые представляют собой выходную случайную функцию Y (t) [в общем случае X (s) и Y (t) являются векторами]. Аналогично для процесса наружного шлифования круглой поверхности имеем преобразования наружного диаметра до шлифования X (s) в шлифованный диаметр Y (t) для процесса термической обработки до выполнения операции диаметр характеризуется случайной функцией X (s), а после обработки преобразуется в случайную функцию У ( ) и т. д. [c.347]
К токарным относится большая группа станков, предназначенных в основном для обработки поверхностей вращения, соосных оси шпинделя (цилиндрических, конических, фасонных, винтовых, а также торцовых). Для обработки наружных поверхностей деталей типа валов применяют как центровые, так и бесцентровые токарные станки. Концентрические поверхности деталей типа втулок и колец обрабатывают на токарно-центровых и патронных токарных станках. Детали типа дисков (со значительными по размеру торцовыми поверхностями) обрабатывают на лобото-карных станках, которые занимают меньшую площадь, чем центровые станки, и лучше приспособлены для обработки наружных и внутренних торцовых поверхностей детали. Лобо-токарные станки имеют устройства для поддержания постоянной скорости резания, а также устройства для нарезания торцовых резьб (спиралей). [c.224]
В конструкциях токарных станков с ЧПУ используют револьверные головки четырех – двенадцатипозиционные. В каждой позиции головки можно устанавливать по два инструмента для параллельной обработки наружной и внутренней поверхностей заготовки. Инструментальные магазины (вместимостью по 8. .. 20 инструментов) в токарных станках с ЧПУ используют редко. Использование инструментальных магазинов с большим числом [c.348]
Обработка заготовок на патронноцентровом токарном станке с ЧПУ (мод. 16К20ФЗС5). Станок предназначен для обработки наружных и внутренних поверхностей заготовок типа тел вращения со ступенчатым или криволинейным фасонным профилем за один или несколько проходов в замкнутом полуавтоматическом цикле, а также для нарезания резьб. Число используемых инструментов – 6. [c.357]
Станок предназначен для токарной обработки наружных и внутренних поверхностей заготовок типа тел вращения со ступенчатым или криволинейным профилем, а также для нарезания резьб. Обработка происходит за один или несколько проходов в замкнутом полуавтоматическом цикле. Установка заготовок осуществляется в патроне, а длинномерных заготовок — в центрах. Станок разработан на базе токарного станка 16К20 и имеет традиционную для токарных станков компоновку. [c.80]
Токарные станки предназначены для обработки валов, втулок, дисков, фланцев и др. Станки делят на универсальные (общего назначения) и специализированные. Универсальные станки подрезделяют на токарно-винторезные и токарные. На токарновинторезных станках выполняют обработку наружных и внутренних цилиндрических, конических, фасонных и торцовых поверхностей нарезание наружных и внутренних резьб отрезку торцов, прорезку канавок, сверление, зенкерование и развертывание отверстий. На токарных станках выполняют указанные выше операции за исключением нарезания резьб резцами. На специализированных токарных станках выполняют технологические операции для определенного типа деталей, например, дисков, фланцев, втулок и т. п. В инструментальном производстве токарную обработку стержневого, насадного (втулочного) и дискового инструмента в мелкосерийном производстве производят на токарных станках общего назначения. При изготовлении специального инструмента (долбяков, шеверов, протяжек, корпусов сборного инструмента) эффективно применяют станки с ЧПУ. В серийном и массовом производстве токарную обработку производят на гидрокопировальных станках общего назначения, многорезцовых, револьверных станках, одношпиндельных и многошпиндельных автоматах и полуавтоматах, а также на высокоавтоматизированных специализированных станках. [c.103]
Высокой жесткостью и виброустойчивостью обладает новая компоновка токарного станка 16К20ФЗС5 е ЧПУ. Станок предназначен для токарной обработки наружных и внутренних поверхностей деталей типа тел вращения со ступенчатыми и криволинейными профилями различной сложности за один или несколько проходов в автоматическом цикле, имеет автоматическую смену инструмента с помощью шестипозиционной резцовой головки. Главной особенностью станка является нормализация основных узлов (см. рис. 77). Главный привод включает автоматическую коробку скоростей и редуктор. Передачи винт—гайка качения совместно с беззазорными редукторами служат составными частями приводов поперечной и продольной подач. [c.118]
На рис. 60 схематически показано гидрокопировальное устройство 1КСТ-1, разработанное на заводе им. С. Орджоникидзе для токарных универсальных станков. Этот самодействующий узел позволяет автоматизировать весь цикл обработки наружных и внутренних ступенчатых поверхностей, а также контурных изделий. [c.86]
На фиг. 525, а изображена вилка механизма блокировки автоматического включения фрикциона шестиигниндельного токарного автомата, требующая обработки наружных и внутренних поверхностей с обеспечением нри этом точных размеров. Наиболее затруднительна здесь обработка внутреннего [c.656]
Изготовление наружного и внутреннего колец роликопод-шипников начинается с обработки наружных и внутренних поверхностей на двухблочных восьмишпиндельных токарных автоматах с двух сторон. Внутреннее кольцо сложнее наружного, поэтому после этой операции обработка роликовой дорожки во внутреннем кольце завершается на одношпиндельном трехсуппортном автомате. После этой операции производят клеймение и термическую обработку по той же схеме, что и для наружных и внутренних колец шарикоподшипников, а затем шлифование торцов. [c.455]
На линии выполняются следующие операции 1 — полная токарная обработка наружного кольца 2 — черновая токарная обработка внутреннего кольца 3 — чистовая токарная обработка внутреннего кольца 4 — клеймение 5 — хранение в магазинах 6 и 7 — термическая обработка наружного и внутреннего колец 8 — визуальный контроль 9 — плоское шлифование наружного и внутреннего колец (поочередно) а — базового торца б — противоположной поверхностп 10— бесцентровое шлифование наружной поверхности наружного кольца II — черновое бесцентровое шлифование дорожки качения наружного кольца 12 — чистовое бесцентровое [c.140]
Токарные, патронные, вертикальные полуавтоматы мод. 1723ФЗ, 1734ФЗ и 1751ФЗ (табл. 3, рис. 6) предназначены для черновой и чистовой обработки наружных и внутренних поверхностей деталей с прямолинейными образующими типа дисков, сепараторов, фланцев, зубчатых колес, стаканов и т. д. с креплением их в патроне и с автоматической сме- [c.70]
Токарная обработка наружных и внутренних поверхностей заготовок колец шарикоподш ипников производится на токарных автоматах пруткового типа. [c.338]
Черновую и чистовую токарную обработку наружных и внутренних поверхностей заготовки ротора выполняют за три операции на трех вертикальных токарных многорезцовых автоматах Ш734А (фиг. 45). После первой и второй операций производят поворот обрабатывае.мой детали на 180 с помощью кантователя. Токарные автоматы для первой и второй операций и leют правый и левый суппорты, а для третьей операции, кроме того, и вертикальный расточной шпиндель (мод. Ш734). [c.370]
Лабораторная работа по теме: “Обработка внутренних цилиндрических поверхностей” | Методическая разработка по теме:
Государственное бюджетное профессиональное образовательное учреждение
«Сормовский механический техникум
им. Героя Советского Союза П.А.Семенова»
МЕТОДИЧЕСКИЕ УКАЗАНИЯ
По выполнению лабораторной работы
по теме: Обработка внутренних цилиндрических поверхностей
ПМ 02. «Обработка деталей на металлорежущих станках различного типа »(сверлильных, токарных, фрезерных, копировальных, шпоночных и шлифовальных)
МДК 02.01. «Технология обработки на металлорежущих станках»
профессия : « Станочник» (металлообработка)
РАЗРАБОТАЛ:
преподаватель Козлянкина Т.Ю.
высшая категория
Н.Новгород
2016г.
Введение
Методические указания по лабораторной работе по теме «Обработка внутренних цилиндрических поверхностей» по дисциплине «Технология обработки на металлорежущих станках» по специальности «Станочник» составлены в соответствии с ПМ02 «Обработка деталей на металлорежущих станках различного вида и типа» (сверлильных, токарных, фрезерных, копировальных, шпоночных и шлифовальных)
Лабораторная работа по теме «Обработка внутренних цилиндрических поверхностей» выполняется 4часа и включает: тему, цели работы, задание, необходимое оборудование и инструменты, ход работы, пояснение к выполнению работы, содержание отчета, контрольные вопросы по данной теме. Лабораторная работа является составной частью комплексной программы обучения обучающихся к их дальнейшей производственной деятельности.
Лабораторная работа – имеет своей целью закрепление и углубление знаний, полученных студентами в процессе теоретического обучения, приобретение необходимых умений, навыков и опыта практического выполнения работы по обработке отверстий, проводится для овладения обучающимися навыков самостоятельной работы, проверки полученных знаний и профессиональной готовности будущего специалиста к самостоятельной трудовой деятельности и применения приобретенных навыков на практике
Для контроля и наиболее полного закрепления изученного материала обучающиеся выполняют отчет, по каждой лабораторной работе выполненный в соответствии с методическими указаниями
Лабораторная работа
Тема: Обработка внутренних цилиндрических поверхностей
1.Цель работы: Ознакомится с технологическим процессом обработки отверстий режимами резания и технологической оснасткой
2.Краткая теоретическая часть
Сверление отверстий на токарном станке
При сверлении на токарном станке сверло, закрепленное в пиноли задней бабки, подают к детали, закрепленной в патроне, вручную — вращением маховика. Применение каких-либо дополнительных рычагов не допускается. Максимальный диаметр сверления для станков 1К62 и 16К20 — 25 мм по стали и 28 мм по чугуну. Чтобы сверло не уходило от горизонтальной оси в начале сверления, торец заготовки предварительно центруют коротким сверлом
Важно, чтобы перед сверлением торец заготовки был подрезан, т. е. был перпендикулярен оси. Отверстия большого диаметра (30 мм и более) обрабатывают последователю двумя сверлами: вначале сверлом меньшего диаметра, затем рассверливают на больший диаметр. Рассверливание обеспечивает точность до 12-го квалитета и шероховатость поверхности не выше 4-го класса.
Элементы режима резания при сверлении.
Глубиной Р е з а н и я является половина диаметра сверла.
t= D
2
При рассверливании глубина резания — это полуразность диаметров до и после обработки (мм): t= D-d
2
Величина подачи («п о д а ч а»)при сверлении — это путь сверла, пройденный за один оборот заготовки Ѕ мм/об.
Скорость резания V м\мин при сверлении зависит от диаметра сверла и частоты вращения заготовки n об/мин.
3.Оснащение
Оборудование:
- Токарно-винторезный станок 16К20
Приспособления:
- 3-х кулачковый самоцентрирующий патрон
- переходные втулки
- сверлильный патрон
Режущий инструмент:
- резец проходной отогнутый
- резец отрезной
- центровочное сверло
- сверло
- зенковка
Измерительный инструмент:
4.Время выполнения: – 4часа
5.Задание:
1) изучить технологическую документацию по рассматриваемой операции
2) выполнить определенную операцию на токарном станке
3) составить отчет
6.Порядок выполнения работы:
1) изучить теоретическую часть
2) выполнить графическую часть работы : эскиз (операции, эскизы или рисунки, иллюстрирующие отдельные приемы)
3) заполнить данными учебную карту
4) произвести обработку и контроль данной детали
7.Содержание отчета
1) тема и цель работы
2) задание, оснащение
3) эскиз детали
4) заполненная учебная карта
5) ответы на контрольные вопросы
6) выводы
8.Контрольные вопросы
1) Чему равен угол при вершине сверла 2φ при обработке сталей
2) С помощью чего крепятся сверла с коническим хвостовиком в пиноле задней бабки
3) Каким измерительным инструментом можно проверить отверстие при массовом производстве
9.Литература
1. Багдасарова Т.А. Токарь-универсал : учеб. пособие для нач. проф. об-разования / Т. А. Багдасарова. — М.: Изд. центр «Академия», 2004. — 288 с.
2. Белецкий Д.Г. Справочник токаря-универсала / Д. Г. Белецкий, В.Г.Моисеев, М.Г. Шеметов ; под ред. М.Г. Шеметова. — М. : Машино-строение, 1987. — 560 с.
3. ВереинаЛ.И. Справочник токаря :учеб. пособие для нач. проф. образо-вания / Л. И. Вереина. — М.: Изд. центр «Академия», 2004. — 448 с.
Учебная карта
Тема: Обработка внутренних цилиндрических поверхностей
Подготовка к выполнению операции
- Ознакомление с чертежом.
1 .Требования к форме поверхностей _________________________________
2. Размеры: заготовки
диаметр _________________________________________________________
длина ___________________________________________________________
3. Чистота обработки ______________________________________________
4. Класс точности__________________________________________________
5. Марка обрабатываемого материал__________________________________
II. Организация рабочего места.
1. Получить чертеж, инструмент, заготовки, принадлежности и вспомогательные материалы.
2. Расположить на рабочем месте по правилам, изученным по предыдущим картам. Убрать посторонние предметы.
III. Характеристика оборудования.
1. Тип ____________________________________________________________
2. Цена деления лимба пиноли задней бабки____________________________.
3..Места ручной смазки______________________________________________
IV. Характеристика режущего инструмента(сверла)
1. Вид и материал _________________________________________________
2. Величина угла заточки____________________________________________
V Характеристика измерительного инструмента.. (отверстия)
1. Название ________________________________________________________
2. Точность_________________________________________________________
3. Предел измерения_________________________________________________
. VI. Последовательность обработки данной детали:
УстановА: Установить и закрепить заготовку в 3-х кулачковом патроне
1._________________________________________________________________
2._________________________________________________________________
3.__________________________________________________________________
Подготовка станка к работе
Наладка станка:
1. Проверить исправность станка. Смазать трущиеся части станка.
2. Установить заготовку в патроне с минимально допустимом вылетом, выверить и устранить биение, закрепить заготовку окончательно . Нанести риску на длину обработки . Ручку перебора – в нейтральное положение
3. Установить необходимый режущий инструмент вершина резца
устанавливается точно по линии центров станка;
4. Установить заданное число оборотов шпинделя
Выполнение операции
I.Получение формы и исходного размера при подрезании торца или уступа.
1. Включить вращение шпинделя. Вершина резца должна находиться в 3 -5 мм от поверхности подрезаемого торца
2. Медленным продольным перемещением суппорта произвести касание вершиной резца поверхности торца.
3. Отвести резец в поперечном направлении наружного диаметра и выключить вращение шпинделя.
4. Установить резец на заданную глубину резания по лимбу фартука или верхнего суппорта. Лимб – в нулевое положение.
Первый проход
2. получение заданных размеров
1. включить вращение шпинделя.
2. подавать резец равномерно ручной подачей в заданном направлении на длину обработки. Добиться одинаковой чистоты обработки на всей поверхности
3. отвести резец от поверхности: при обтачивании – в поперечном направлениях – в исходное положение.
4. включить вращение шпинделя. Произвести промежуточный контроль: проверить прямолинейность, перпендикулярность, размеры и чистоту обработанной поверхности. Недостаточная чистота получается при большой или неравномерной подаче резца, неправильной его заточке и недостаточном креплении.
Последующие проходы
1. проверить, состояние резца. При обнаружении отклонений-затупился, раскрошился – заправить. Уточнить установку резца по центру.
2. установить резец на заданную глубину резания
3. обработать поверхности окончательно до заданного размера.
Сверление отверстия
- установить сверлильный патрон в пиноль задней бабки
- подвести к торцевой поверхности не касаясь её.
- закрепить заднюю бабку на станине станка с помощью рычага
- включить вращение шпинделя
- подавать пиноль задней бабки в ручную с помощью маховика на 5-7мм углубиться в металл.
- отвести пиноль с центровым сверлом .
- открепить заднюю бабку и отвести на исходную позицию.
- установить сверло с помощью переходных втулок в пиноль задней бабки
- подвести к торцевой поверхности не касаясь её.
- закрепить заднюю бабку на станине станка с помощью рычага
- включить вращение шпинделя
- подавать пиноль задней бабки в ручную с помощью маховика на заданную глубину периодически выводя сверло из отверстия
- отвести пиноль с сверлом
- открепить заднюю бабку и отвести на исходную позицию
- выключить вращение шпинделя
3.контроль детали.
1. измерить деталь и сравнить с заданными размерами
2. сравнить с эталоном чистоту обработанных поверхностей.
3. предъявить деталь преподавателю.
6.3
√
Неуказанные предельные отклонения размеров h24 h24 JT/2
Варианты | А | Б | В |
1 | 26 | 12 | 35 |
2 | 22 | 11 | 40 |
3 | 18 | 9 | 30 |
4 | 30 | 15 | 25 |
5 | 32 | 16 | 36 |
Токарная обработка. Обработка металла. Изготовление металлоизделий на заказ.
Токарная обработка металла – это механическая обработка деталей вращения, в ходе которой для получения необходимых заказчику параметров металлического изделия (формы и размеров изготовленной детали, чистоты поверхности и других характеристик) с поверхности заготовки путем резания или точения удаляются излишки металла. Среди основных операций точения металла выделяют:
- Обтачивание т.е. обработку наружных поверхностей
- Растачивание т.е. обработку внутренних поверхностей.
- Подрезание т.е. обработку плоских торцевых поверхностей.
- Резку т.е. разделение заготовки на части или отделение готовой детали от заготовки.
Точение применяется при изготовления деталей типа тел вращения (валов, дисков, осей, пальцев, цапф, фланцев, колец, втулок, гаек, муфт и др.)
Обработка металла в Санкт-Петербурге производится специалистами Группы Компаний “ЛИГ” на специальном металлорежущем оборудовании – токарных станках и комплексах. Токарные станки быть:
- универсальные;
- специальные;
- специализированные.
Для срезания слоя металла применяется особый режущий инструмент, например: резцы, метчики, плашки. Заготовки, которые мы применяем в процессе производства металлоизделий на заказ – это прокат из стали или цветных металлов различного профиля (прутки, трубы поковки, отливки, штамповки).
В зависимости от способа установки заготовки или детали на токарных станках обработка может быть осуществлена:
- в центрах;
- в патроне;
- на планшайбе.
Токарная обработка металла применяется для выполнения следующих работ:
- обработка наружных цилиндрических и конических поверхностей;
- обработка внутренних цилиндрических и конических поверхностей;
- обработка торцов и уступов;
- вытачивание канавок;
- отрезка заготовки;
- сверление, зенкерование и развертывание отверстий;
- нарезание внутренней и наружной резьбы;
- обработка фасонных поверхностей;
- накатывание рифлений.
На качество металлообработки влияют несколько факторов:
- Квалификация персонала.
- Состояние оборудования.
- Наличие и качество технологической оснастки .
- Качество металлорежущего инструмента.
Подразделение Группы Компаний «ЛИГ» в настоящий момент имеет Сертификат качества ISO 9001:2008 – это означает что, мы отслеживаем качество изготавливаемых нами деталей на всех этапах производимых нами работ.
Производство Группы Компаний«ЛИГ» основано на применении собственного оборудования – универсальных станков повышенной точности. Мы используем технологическую оснастку и металлорежущий инструмент ведущих производителей. На нашем предприятии работают высококвалифицированные специалисты, имеющие многолетний опыт работ. Это позволяет выполнять практически все виды токарных работ на заказ, при этом мы гарантируем высокое качество изготовления. Токарные работы по металлу на заказ могут потребоваться предприятиям, которым необходимо изготовление пальцев, шкивов, осей, болтов, втулок, колец, гаек, а также различных деталей машин, механизмов. Мы изготавливаем детали на токарных станках по образцу или чертежам заказчика. Производим механическую обработку как поштучно, так и для промышленных целей.
Порядок выполнения токарной обработки
Процесс обработки металла на токарном оборудовании подразделяется на 2 этапа:
первичная обработка металла;
финишная обработка металла.
При первичной обработке из заготовки вытачивается деталь нужной формы. При этом погрешность по размерам зависит от глубины резания и регламентируется ГОСТом. При данном виде обработки допускается несоблюдение точности токарной обработки.
Финишная обработка заключается в придании детали окончательных форм и размеров детали с необходимыми параметрами шероховатости.
Цена токарной обработки
На цену токарной обработки оказывает влияние несколько факторов. К ним относится:
- стоимость закупки материала для проведения токарных работ;
- характеристика материала выбранного для изготовления детали, особенности его обработки;
- особенности производимых работ, их сложности;
- наличие необходимого оборудования, инструмента и оснастки;
- размер партии изготовления;
- сроки изготовления.
Снизить цену позволяет размещение заказа не через посредников, а напрямую на предприятия занимающиеся металлобработкой. Нашим клиентам мы предлагаем конкурентные цены и высокое качество работ.
Для правильного расчета стоимости и сроков выполнения Вашего заказа необходимо связаться с нашими специалистами предоставить чертеж или образец детали. В заявке на выполнение токарных работ необходимо указать материал, из которого будет изготавливаться деталь, параметры получаемого изделия (габаритные размеры, точность изготовления, шероховатость поверхности и т.д.), требуемое количество изделий. Произвести заказ на металлообработку вы можете при помощи формы на нашем сайте.
ОБРАБОТКА НАРУЖНЫХ ЦИЛИНДРИЧЕСКИХ И ТОРЦОВЫХ ПОВЕРХНОСТЕЙ
§ 1. Общие сведения1. Виды наружных поверхностей. По форме наружные поверхности цилиндрических деталей могут быть разделены на цилиндрические, торцовые, уступы, канавки, фаски (рис. 25).
Цилиндрические поверхности 1 получаются вращением прямой линии (образующей) вокруг параллельной ей линии, называемой осью цилиндра. В продольном сечении такие поверхности прямолинейны, в поперечном — имеют форму окружности.
Крайние плоские поверхности 2, перпендикулярные к оси детали, называют торцами.
Переходные плоские поверхности 5 между цилиндрическими участками, перпендикулярно расположенные к оси детали, принято называть уступами.
Занижения 4, выполненные по окружности цилиндрической или торцовой поверхности, называются канавками.
Фасками называются небольшие скосы 3 на кромках детали.
2. Способы установки заготовок на станке. При токарной обработке наиболее часто применяются четыре основных способа установки заготовок на станке: в патроне, в патроне и заднем центре, в центрах и на оправках.
В патроне 1 (рис. 26, а) устанавливают короткие заготовки с длиной выступающей части l из кулачков до 2—3 диаметра d.
Для повышения жесткости более длинные заготовки устанавливают в патроне 1 и заднем центре 2 (рис. 26, б).
Установку в центрах (рис. 26, в) применяют в основном для чистового обтачивания длинных валов, когда необходимо выдержать строгую соосность обрабатываемых поверхностей, а также в случаях последующей обработки детали на других станках с такой же установкой. Заготовку опирают центровыми отверстиями на передний 4 и задний 2 центры, а вращение от шпинделя к ней передается поводковым патроном 1 и хомутиком 3.
Установка на оправке 1 (рис. 26, г) используется для обработки наружных поверхностей, когда заготовка имеет ранее обработанное отверстие (см. гл. IV).
§ 2. Обработка цилиндрических поверхностей
1. Обтачивание гладких поверхностей. Технические требования. При обработке цилиндрической поверхности токарь должен выдержать ее размеры (диаметр, длину), правильную форму и требуемую чистоту..
Точность размеров ограничивается допустимыми отклонениями, проставляемыми на чертеже. Размеры без допусков должны
выполняться по 7-му или реже 8—9-му классам точности. В этом случае на наружные размеры допустимые отклонения устанавливаются на минус от номинального размера, на внутренние-—на плюс.
Точность цилиндрической формы определяется отклонениями цилиндра в продольном направлении — конусообразностью, бочкообразностью, седлообразностью и в поперечном — овальностью (рис. 38). Первые три погрешности характеризуются разностью диаметров обработанной поверхности по краям и в середине, четвертая — разностью диаметров одного сечения во взаимно перпендикулярных направлениях. Если на чертеже отсутствуют указания точности формы поверхности, то ее погрешности не должны превышать допуска на диаметр.
Чистота обработки характеризуется степенью шероховатости поверхности, остающейся на ней. после точения. Допустимая шероховатость обозначается на чертеже треугольником, справа от которого проставляется число, соответствующее классу чистоты.
Например, V.5 означает пятый класс чистоты.
Точность обработки должна соответствовать техническим требованиям рабочего чертежа. При этом следует учитывать, что нормально достижимая точность обтачивания на токарных станках составляет 3—4-й класс и чистота до 7-го класса. Поверхности более высокой точности и чистоты обычно обрабатывают точением предварительно с припуском 0,3—0,6 мм на диаметр для последующего шлифования.
Применяемые резцы. Обтачивание наружных поверхностей выполняют проходными резцами (рис. 39). По форме они делятся на прямые а, отогнутые б и упорные в.
Первые два типа резцов преимущественно применяют для обработки жестких деталей; ими можно обтачивать, снимать фаски, а отогнутыми и подрезать торцы. Наибольшее распространение в токарной практике получили упорные резцы, которые, кроме указанных работ, позволяют подрезать уступы. Эти резцы особенно рекомендуются для обтачивания нежестких валов, так как они создают наименьший по сравнению с другими резцами поперечный прогиб детали.
Проходные резцы имеют различную стойкость (время непосредственной работы от заточки до переточки). При равных условиях наименее стойки упорные резцы, так как их острая вершина менее прочна и быстрее нагревается. Эту особенность упорных резцов следует учитывать при назначении режимов резания.
При универсальных работах проходные резцы с различным радиусом закругления вершины применяют как для чернового, так и чистового точения. У черновых резцов вершину закругляют радиусом r=0,5—I мм, у чистовых- r = 1,5—2 мм. С увеличением радиуса закругления вершины чистота обработки улучшается.
Для выполнения только чистового обтачивания рекомендуется применять чистовые двусторонние резцы (рис. 39, г) с увеличенным радиусом закругления вершины г=2—5 мм, ими можно работать с продольной подачей в обе стороны.
Установка резцов на станке. Резцы должны быть правильно установлены и прочно закреплены в резцедержателе суппорта. Первое условие определяется положением резца относительно оси центров станка. Резцы для наружного точения устанавливаются так, чтобы вершина их находилась на уровне оси центров. В некоторых случаях, например при черновом обтачивании и обработке нежестких валов, рекомендуется выполнять такую установку выше линии центров на 0,01—0,03 диаметра детали.
Высоту установки резца регулируют стальными подкладками 1 (рис. 40, а), обычно не более чем двумя. При этом размеры подкладок должны обеспечивать устойчивое положение резца по всей опорной поверхности. Токарь должен иметь набор таких подкладок разной толщины для компенсации уменьшения высоты резца по мере переточки.
Установку резца по высоте проверяют совмещением вершин резца и одного из центров или пробной подрезкой торца заготовки.
В последнем случае при правильной установке резца в центре торца заготовки не должна оставаться бобышка.
Закрепление резца должно быть прочное, не менее чем двумя винтами. Для повышения жесткости крепления вылет резца из резцедержателя устанавливают наименьшим, не более 1,5 высоты стержня. Кроме того, резец располагают перпендикулярно к оси обрабатываемой детали (рис. 40, б).
Приемы обтачивания. Чтобы получить необходимый диаметр обрабатываемой поверхности, резец устанавливают на глубину резания. Для этого его подводят до касания с поверхностью вращающейся заготовки. Когда появится слабо заметная риска, резец отводят вправо за торец заготовки, лимб поперечной подачи устанавливают на нуль и подают суппорт поперечно вперед на требуемый размер по лимбу. Механическую продольную подачу включают после того, как резец врежется в металл ручным перемещением суппорта.
Установку резца на точный размер выполняют аналогично пробным обтачиванием конца заготовки на длину 3—5 мм. По результатам измерения диаметра полученной поверхности штангенциркулем (рис. 41, а) или при более высокой точности — микрометром (рис. 41, б) резец подают на окончательный размер по лимбу. Когда требуемый размер достигнут, лимбовое кольцо устанавливают на нуль для возможности обработки всех последующих деталей из партии без пробных отсчетов.
Длину обтачивания выдерживают разметкой заготовки или по лимбу продольной подачи. В первом случае на заготовке протачивают риску на определенном расстоянии от торца, расположение
которой устанавливают линейкой (рис. 42) или штангенциркулем. При пользовании для этой цели лимбом продольной подачи резей подводят к торцу заготовки, устанавливают лимб на нуль и руч-
ным продольным перемещением суппорта врезаются в металл. Затем включают продольную подачу и выполняют обтачивание. Подачу выключают, не доходя 2—3 мм до требуемого размера длины. Оставшуюся часть обрабатывают ручным перемещением суппорта.
Чистоту обработки определяют сравнением поверхности детали с эталонами чистоты 2 (рис. 43).
Особенности пользования лимбами. Подавая резец на глубину резания по лимбу поперечной подачи, следует иметь в виду, что он перемещается по радиусу к оси детали. Следовательно, диаметр последней после обтачивания уменьшается на величину, вдвое большую глубины резания. Например, если заготовку диаметром 30 мм надо обточить до диаметра 27 мм, т. е. уменьшить диаметр на 3 мм, то резец следует переместить поперечно на 1,5 мм.
Чтобы определить необходимый поворот лимба, следует разделить глубину резания на цену его деления.
Ценой деления называется величина перемещения резца, соответствующая повороту лимба на одно деление. Допустим, требуется подать резец на глубину резания 1,5 мм при цене деления лимба 0,05 мм. Число делений поворота лимба будет равно 1,5 : 0,05 = = 30.
Некоторые станки имеют лимбы поперечной подачи, цена деления которых указывается «на диаметр». В таком случае величину поворота лимба определяют делением разности диаметров заготовки до и после обтачивания на цену деления. Например, заготовка диаметром 25 мм обтачивается до диаметра 20 мм при цене деления лимба 0,05 на диаметр. Число делений, на которое потребуется повернуть лимб, будет равно (25—20): 0,05=100.
При пользовании лимбами необходимо учитывать наличие и величину люфта (зазора) в передачах движения суппорта. Если, например, выдвинутый вперед суппорт отводить назад, то при некоторой части оборота маховичка ручной подачи он будет стоять на месте. Это и характеризует величину люфта в передаче. Поэтому во время отсчетов размеров на станке маховичок ручной подачи необходимо плавно поворачивать только в одну сторону (рис. 44, а). Если допущена ошибка и лимб повернут на большее число делений, чем требуется, то маховичок поворачивают в обратную сторону на величину немного больше люфта (примерно 0,5—1 оборота), а затем, вращая в прежнем направлении, доводят лимб до нужного деления (рис. 44, б). Так же поступают, когда надо отвести резец от поверхности детали на определенный размер. Для этого суппорт отводят на величину, больше необходимой, а затем, подавая его к детали, доводят лимб до необходимого} деления.
Автор – nastia19071991
Токарная обработка – Производственные процессы 4-5
После завершения этого раздела вы сможете:
• Опишите черновое и чистовое точение.
• Опишите поворотный уступ.
• Опишите торцевой пропил.
• Объясните, как настроить центровочное / точечное сверление.
• Объясните, как настроить на растачивание.
• Объясните, как настроить накатку.
• Правильно настройте деталь для отрезки / обработки канавок.
• Определите расчет конуса.
• Правильно установите заготовку в 4-кулачковый патрон.
Заготовку обычно обрабатывают на токарном станке по двум причинам: чтобы отрезать ее по размеру и получить истинный диаметр. Работа, которая должна быть обрезана по размеру и иметь одинаковый диаметр по всей длине заготовки, включает операцию параллельного точения. Многие факторы определяют количество материалов, которые можно удалить на токарном станке. Диаметр необходимо обрезать за два прохода: черновой и чистовой.
Чтобы иметь одинаковый диаметр на каждом конце заготовки, центры токарного станка должны быть на одной линии.
Процедура:
1. Установите составной упор на 30 градусов.
2. Установите инструмент для черновой или чистовой обработки. Используйте правосторонний токарный инструмент, если подайте седло в направлении передней бабки.
3. Переместите резцедержатель к левой стороне составной опоры и установите резцедержатель в центр правой высоты.
4. Настройте токарный станок на правильную скорость и подачу в соответствии с диаметром и типом разрезаемого материала.
5. Запустите токарный станок и сделайте легкий рез.005 дюйма и 0,250 дюйма длиной на правом конце заготовки.
6. Остановите токарный станок, но не перемещайте рукоятку винта поперечной подачи.
7. Переместите режущий инструмент к концу заготовки (вправо), поворачивая маховик каретки.
8. Измерьте работу и рассчитайте количество удаляемого материала.
9. Поверните градуированную манжету на половину удаляемого материала. Например, если нужно удалить 0,060 дюйма, необходимо завернуть градуированное кольцо.030 дюймов, так как срез снимается по окружности заготовки.
10. Помните, что , на каждую тысячную глубину резания диаметр ложи уменьшается на две тысячных.
Операция чернового точения используется для удаления как можно большего количества металла в кратчайшие сроки. В этой операции не важны точность и чистота поверхности. Поэтому рекомендуется максимальная глубина 0,030 дюйма и подача от 0,020 до 0,030 дюйма. Заготовку обычно подвергают черновой обработке с точностью до прибл.030 дюймов готового размера за несколько разрезов, насколько это возможно.
Процедура:
1. Установите токарный станок на правильную скорость и скорость подачи в соответствии с типом и размером разрезаемого материала.
2. Отрегулируйте быстродействующий редуктор на подачу от 0,010 до 0,030 дюйма, в зависимости от глубины резания и состояния машины.
3. Например: .010
4. Переместите резцедержатель с левой стороны компаундной опоры и установите насадку на правую высоту до центра.
5. Надежно затяните резцедержатель, чтобы резцедержатель не смещался во время обработки.
6. Сделайте легкий пробный надрез на правом конце заготовки на длину около 0,250 дюйма.
7. Измерьте заготовку и отрегулируйте насадку на нужную глубину резания.
8. Отрежьте примерно 0,25 дюйма, остановите токарный станок и проверьте диаметр на размер. Диаметр должен быть примерно на 0,030 дюйма над финишной стороной.
9. При необходимости отрегулируйте глубину резания.
Чистовое точение на токарном станке, которое следует за черновым точением, обеспечивает гладкую поверхность и вырезает заготовку до точного размера. Такие факторы, как состояние режущего инструмента, жесткость станка и заготовки, скорость и скорость подачи токарного станка, могут повлиять на тип обработанной поверхности.
Процедура:
1. Убедитесь, что на режущей кромке насадки нет зазубрин, ожогов и т. Д. Перед чистовой резкой рекомендуется установить режущую кромку в исходное положение.
2. Установите токарный станок на рекомендованные скорость и скорость подачи. Используемая скорость подачи зависит от требуемой шероховатости поверхности.
3. Сделайте легкий пробный пропил длиной около 0,250 дюйма с правой стороны заготовки, чтобы получить истинный диаметр, установите режущий инструмент на диаметр и установите градуированное кольцо на нужный диаметр.
4. Остановите токарный станок, измерьте диаметр.
5. Установите глубину резания на половину количества удаляемого материала.
6.Отрежьте до 0,250 дюйма, остановите токарный станок и проверьте диаметр.
7. При необходимости отрегулируйте глубину резания и доведите диаметр до конца. Чтобы получить максимально возможный диаметр, доведите обрабатываемую деталь до необходимого размера. Если необходимо обработать диаметр пленкой или полировкой, никогда не оставляйте для этой операции более 0,002–0,003 дюйма.
При точении детали более одного диаметра. Изменение диаметра или шага называется уступом.
Три распространенных типа плеча:
1.Площадь
2. Уголок скругленный
3. Уголок конический
Процедура:
1. Установив деталь на токарном станке, определите положение уступа от готового конца детали. В случае скругленных уступов – всей длины, достаточной для формирования правильного радиуса на готовом уступе.
2. Поместите острие насадки на эту отметку и прорежьте небольшую канавку по окружности, чтобы обозначить длину.
3.С помощью насадки для токарного инструмента выполните черновую и чистовую обработку заготовки примерно на 0,063 дюйма необходимой длины.
4. Установите торцевой инструмент. Нарежьте мелом небольшой диаметр заготовки и поднимите режущий инструмент до тех пор, пока он не удалит отметку от мела.
5. Запишите показания на градуированной манжете рукоятки поперечной подачи.
6. Лицом выровняйте заплечик, обрезая его до линии, используя ручную подачу.
7. Для последовательных резов верните рукоятку поперечной подачи в то же положение градуированной манжеты.
Если требуется скругленный угол, для чистовой обработки уступа используется фреза с таким же радиусом. Угловые или скошенные кромки могут быть получены путем установки режущей кромки насадки инструмента на желаемый угол фаски и подачи ее к заплечику или путем установки составной опоры на желаемый угол.
Обрабатываемые детали обычно режутся немного длиннее, чем требуется, и выравниваются до нужной длины. Облицовка – это операция обработки торцов квадрата заготовки его осью.Чтобы получить плоскую квадратную поверхность при облицовке, токарный станок может быть настоящим.
Назначение облицовки:
• Для получения истинно плоской поверхности, перпендикулярной оси заготовок.
• Обеспечение точной поверхности для проведения измерений.
• Для обрезки заготовок нужной длины.
Рисунок 1. Операция перед лицом
Процедура:
1. Переместите резцедержатель к левой стороне составной опоры и установите правую торцевую насадку на правую высоту центральной точки токарного станка.Для точной торцевой поверхности упор можно установить под углом 30 градусов.
2. Установите заготовку в патрон лицевой стороной. Используйте центр линии в хвосте или прямую линейку, если необходимо для истинности.
3. Вставьте торцевой инструмент.
4. Расположите инструмент на некотором расстоянии от детали.
5. Установите фрезу для торцевания влево под углом 15-20 градусов. Острие насадки должно быть ближе всего к заготовке, а сбоку должно быть оставлено пространство.
6. Настройте токарный станок на правильную скорость и подачу в соответствии с диаметром и типом разрезаемого материала.
7. Перед включением станка проверните шпиндель вручную, чтобы убедиться, что детали не мешают вращению шпинделя.
8. Запустите токарный станок и поднесите резец ad как можно ближе к центру токарного станка.
9. Переместите каретку влево с помощью маховика, пока не начнется резка.
10. Вставьте насадку для режущего инструмента внутрь к центру, поворачивая рукоятку поперечной подачи. Если для подачи режущего инструмента используется поперечная подача с механической подачей, каретка должна быть заблокирована в этом положении.
11. Повторяйте процедуры 6,7 и 8, пока заготовка не будет обрезана до нужной длины. 12. После облицовки на заготовке останется острая кромка, которую следует сломать напильником.
СверлоSpotting Tool используется для выполнения неглубокого V-образного отверстия в центре заготовки. Предоставляет руководство по выполнению упражнения. Отверстие можно обнаружить быстро и достаточно точно с помощью центрирующего сверла. Для максимальной точности следует использовать насадку для инструмента для определения отметок.
Рисунок 2: Инструмент Центр / Точечный
Процедура:
1.Закрепите заготовку в патроне.
2. Установите сверлильный патрон в заднюю бабку.
3. Убедитесь, что хвостовик сверлильного патрона надежно закреплен в задней бабке.
4. Переместите заднюю бабку в желаемое положение и зафиксируйте ее.
5. Перед включением станка проверните шпиндель вручную, чтобы убедиться, что детали не мешают вращению шпинделя.
6. Настройте скорость токарного станка на скорость, соответствующую типу материала для точечного или центровочного сверления.
7.Начните отверстие с помощью центрирующего сверла. 8. Найдите отверстие с помощью коронки или сверла для центрирования.
Рис. 3. Сверло
Процедура:
1. Установите сверлильный патрон в заднюю бабку.
2. Закрепите заготовку в патроне.
3. Проверьте центр инструментария и убедитесь, что он выровнен.
4. Убедитесь, что хвостовик сверлильного патрона надежно закреплен в задней бабке.
5. Переместите заднюю бабку в желаемое положение и зафиксируйте ее.
6. Перед включением станка проверните шпиндель вручную, чтобы убедиться, что детали не мешают вращению шпинделя.
7. Начните отверстие, используя насадку для центрирования или центрирования.
8. При использовании центрирующего сверла всегда используйте вместе с ним смазочно-охлаждающую жидкость.
9. Центровочное сверло не режет так легко, как сверло, поскольку оно имеет мелкие канавки для дополнительной жесткости.
10. Просверлите конус полностью, чтобы образовалась воронка для ввода сверла.
11. Установите сверло в шпиндель задней бабки, в сверлильный патрон или в держатель сверла.
12. Установите на токарном станке скорость, соответствующую типу сверлимого материала.
13. Запустите токарный станок и просверлите на желаемую глубину в соответствии с чертежом, применяя смазочно-охлаждающую жидкость.
14. Чтобы измерить глубину отверстия, используйте градуировку на шпинделе задней бабки или используйте стальную линейку для измерения глубины.
15. Используйте сверло для удаления стружки и измерения глубины отверстия.
16. При сверлении снимите материал сверла максимум на один или два диаметра сверла перед откаткой, удалением стружки и повторным нанесением смазочно-охлаждающей жидкости.
17. Если сверло скрипит относительно ложи, нанесите еще смазочно-охлаждающей жидкости.
18. Чтобы снять сверлильный патрон с задней бабки, потяните его назад примерно на четверть оборота больше, чем он может легко вынуть.
19. Используйте шпильку, чтобы выдавить патрон из цанги.
Растачивание – это операция по увеличению и точной чистовой обработке отверстий.Обработка отверстия путем удаления материала с внутренних поверхностей с помощью одноточечной фрезы. Отверстия особого диаметра, для которых нет сверл, могут быть произведены путем растачивания.
При растачивании используется одноточечный режущий инструмент для увеличения отверстия. Эта операция обеспечивает более точное и концентрическое отверстие, чем сверление.
Поскольку фреза выступает из станка из расточной оправки, инструмент не имеет такой хорошей опоры, что может привести к вибрации. Чем глубже занудная операция, тем хуже болтовня.Чтобы исправить это:
1. Уменьшите скорость шпинделя.
2. Увеличьте подачу.
3. Нанесите больше СОЖ.
4. Уменьшите вылет расточной оправки.
5. Отшлифуйте меньший радиус на вершине инструмента.
Процедура:
1. Установите заготовку в патрон.
2. Выровняйте, сделайте отметку и просверлите отверстие в заготовке.
3. Проверьте, достаточно ли зазора расточной оправки.
- Если отверстие слишком маленькое для расточной оправки, стружка застрянет во время обработки и сместит оправу со смещением.
4. Убедитесь, что острие расточного инструмента является единственной частью фрезы, которая контактирует с внутренней поверхностью заготовки.
5. Если угол не обеспечивает достаточного зазора на концах, замените фрезу на фрезу с более острым углом.
6. Расположите расточную оправку так, чтобы острие фрезы находилось на средней линии ложи.
7. Инструмент, расположенный не на одной линии с центром заготовки, будет тянуться по поверхности заготовки, даже если имеется достаточный угол снятия торца.
8. Выберите расточную оправку как можно большего размера и сделайте так, чтобы она выходила за пределы держателя ровно настолько, чтобы обеспечить глубину просверливаемого отверстия.
9. Установите держатель и планку расточного инструмента с помощью насадки для фрезерного инструмента с левой стороны стойки инструмента и поворачивайте заготовку.
10. Установите сверло расточного инструмента по центру.
- Примечание. В зависимости от жесткости установки насадка для расточного инструмента будет иметь тенденцию подпрыгивать вниз при приложении давления к режущей кромке.Путем установки насадки расточного инструмента немного выше центра, была произведена компенсация для направленной вниз пружины, и резец фактически будет позиционироваться точно по центру заготовки во время операций обработки.
11. Установите токарный станок на правильную скорость резания и подачу. а. Примечание: для скорости подачи выберите среднюю скорость подачи.
12. Нанесите смазку на отверстие перед включением машины.
13. Включите станок и вставьте инструмент в предварительно просверленное отверстие.
14.Запустите токарный станок и медленно приведите расточной инструмент, пока он не коснется внутреннего диаметра отверстия.
15. Возьмите легкий разрез (около 0,003 дюйма) и длиной примерно -375 мм.
16. Остановите токарный станок и измерьте диаметр отверстия телескопическим калибром или внутренним микрометром.
17. После измерения отверстия определите количество материала, которое нужно удалить из отверстия. Оставьте около 0,020 на чистовой надрез.
18. Запустите токарный станок и выполните черновой рез.
19. Вставьте расточную оправку в заготовку, взлетая примерно.020 на каждом проходе.
20. Вытащите расточную оправку, как только будет достигнута желаемая глубина.
21. Повторяйте шаги 19 и 20, пока не получите желаемый диаметр внутреннего отверстия.
22. После завершения черновой обработки остановите токарный станок и выньте сверло из отверстия, не перемещая рукоятку поперечной подачи.
23. Установите глубину чистового пропила и просверлите отверстие нужного размера. Для получения хорошего качества поверхности рекомендуется небольшая скорость подачи.
24.На последнем проходе остановитесь на желаемой глубине и верните фрезу к центру ложи. Это будет лицом к задней части отверстия.
25. Выньте расточную оправку из станка и остановите станок.
Рисунок 4. Расточка на токарном станке
1. Накатка – это выпуклый отпечаток на поверхности детали, созданный двумя закаленными валками.
2. Накатки обычно бывают двух видов: ромбовидные или прямые.
3. Обычные рисунки накатки бывают мелкими, средними или грубыми.
4. Ромбовидный узор образован правой и левой спиралями, установленными в самоцентрирующейся головке.
5. Используется для улучшения внешнего вида детали и обеспечения хорошей поверхности захвата для рычагов и ручек инструментов.
6. Обычные формы накатки бывают мелкие, средние или грубые.
7. Прямой узор, образованный двумя прямыми валками, используется для увеличения размера детали для прессовой посадки в легких условиях.
8. Используются три основных типа державок для накатки: держатель шарнирного соединения, держатель поворотной головки и держатель поворотной головки.
9. Накатка лучше всего подходит для деталей, установленных между центрами.
10. Накатки не режут, а вытесняют металл под высоким давлением.
11. Смазка более важна, чем охлаждение, поэтому можно использовать смазочно-охлаждающую жидкость или смазочное масло.
12. Для накатки используются низкие скорости (примерно такие же, как для нарезания резьбы) и подача от 0,010 до 0,020 дюйма.
13. Накатки должны быть отцентрированы на заготовке вертикально, а резцедержатель должен располагаться под углом к заготовке.
14. На мягком металле примерно на половину глубины следует начать накатку и проверить рисунок.
15. Для завершения накатки на тонкой заготовке может потребоваться несколько проходов, поскольку инструмент имеет тенденцию отталкивать ее от накатки.
16. Накатки следует очищать проволочной щеткой между проходами.
Рисунок 5. Накатка
Процедура:
1. Установите накатной инструмент в держатель инструмента и отрегулируйте его по точной средней линии шпинделя токарного станка.
2. Установите и закрепите инструмент для накатки под углом 90 градусов к поверхности накатки.
3. Переместите каретку токарного станка рукой и найдите участок на заготовке, который нужно накатать.
4. Поверните накатную головку, чтобы установить правильные накатки.
5. Поместите накатку на правый край заготовки так, чтобы половина накатки касалась правого края заготовки.
6. Нанесите на работу смазочно-охлаждающую жидкость.
7. Поверните шпиндель примерно на 100 об / мин и используйте маховик поперечной подачи, чтобы ввести накатной инструмент в работу.Это должно быть примерно 0,030 дюйма, или до тех пор, пока накатки не сойдутся и не образуют хороший узор.
8. Включите механическую подачу токарного станка, чтобы переместить каретку к передней бабке со скоростью подачи от 0,010 до 0,020 дюйма за оборот.
9. Нанесите масло по мере необходимости и смажьте рифленую поверхность жесткой щеткой, чтобы удалить стружку с накатки.
10. Когда накатки достигнут конца области накатки, измените направление подачи в направлении подачи каретки и подайте накатки на изделие еще на 0,005-0,0.010 дюймов.
11. Продолжайте накатывать вперед и назад, пока не появится острый ромб.
Назначение отрезки и обработки канавок:
Бывают случаи, когда вы можете вырезать деталь с конца заготовки или вы можете сделать канавку в заготовке.
Обработка канавок, обычно называемая выемкой, подрезкой или шейкой, часто выполняется в конце резьбы, чтобы обеспечить полный ход гайки до заплечика или края заплечика для обеспечения надлежащей посадки сопрягаемых деталей.Существует три типа канавок: квадратные, круглые и U-образные.
Закругленные канавки обычно используются там, где деталь подвергается деформации и где квадратный угол может привести к растрескиванию металла.
Процедура:
1. Выберите насадку с желаемым размером и формой канавки.
2. Отметьте расположение канавки.
3. Установите токарный станок на половину скорости вращения.
4. Установите заготовку в токарный станок.
5. Установите инструментальную коронку на центральную высоту.
6. Медленно введите насадку в заготовку, используя рукоятку поперечной подачи.
7. Нанесите большое количество смазочно-охлаждающей жидкости на острие режущего инструмента. Чтобы резка не слепила канавку. Если появляется вибрация, уменьшите скорость шпинделя.
8. Остановите токарный станок и проверьте глубину канавки.
9. Повторяйте процедуры 6-7 до тех пор, пока работа не будет обрезана на нужную глубину.
Рисунок 6. Нарезание канавки
Отрезной инструмент, часто называемый отрезным инструментом, используется для резки заготовки.Есть три типа инструментов для пробора. Инструмент для отрезки состоит из прямого держателя, чаще всего используются вставные лезвия со смещением влево и вправо.
Существуют две распространенные проблемы при отрезке, дребезжании и прижатии. Дребезжание возникает, когда инструмент удерживается недостаточно прочно; любой люфт в инструменте, держателе или любой части самого токарного станка делает резку трудной, неровной и часто невозможно. Прижатие означает, что инструмент имеет тенденцию врезаться в заготовку, а может вылезти за верхнюю часть режущей кромки.Обычно это отламывает насадку или повреждает заготовку. Прижимание обычно возникает, когда отрезной инструмент установлен слишком высоко или слишком низко.
• Отрезные инструменты уже, но глубже токарных. Отрезные инструменты используются для создания узких бороздок и отрезания частей заготовки.
• При установке отрезного инструмента резцедержатель не должен выходить за пределы обрабатываемой детали.
• Убедитесь, что отрезной инструмент перпендикулярен оси вращения.
• Убедитесь, что кончик инструмента находится на той же высоте, что и центр ложи.В этом может помочь удерживание инструмента напротив лицевой стороны детали.
• Установите высоту инструмента, приложите его к торцу детали и зафиксируйте инструмент на месте. Не забывайте применять смазочно-охлаждающую жидкость, особенно при выполнении глубоких надрезов.
Рисунок 7. Разделение
Процедура:
1. Установите заготовку в патрон так, чтобы отрезанная деталь была как можно ближе к патрону.
2. Установите отрезной инструмент с левой стороны компаундной опоры, установив режущую кромку по центру.
3. Поместите держатель как можно ближе к стойке инструмента, чтобы предотвратить вибрацию и дребезжание.
4. Отрегулируйте насадку. Насадка для инструмента должна выходить из держателя на расстояние, составляющее немногим более половины диаметра заготовки. Отрегулируйте число оборотов в минуту (об / мин) примерно на ⅔ скорости вращения.
5. Отметьте место разреза.
6. Установите режущий инструмент на место.
7. Запустите токарный станок и медленно вручную введите отрезной инструмент в заготовку.Возьмитесь за рукоятку поперечной подачи обеими руками, чтобы подавать равномерно и равномерно. Нанесите большое количество смазочно-охлаждающей жидкости.
8. Когда размер заготовки составляет около дюйма, рекомендуется немного сдвинуть отрезной инструмент в сторону. При этом боковом движении срежьте немного шире, чтобы предотвратить заклинивание инструмента.
9. Во избежание дребезга держите режущий инструмент и равномерно наносите смазочно-охлаждающую жидкость во время работы. Подавайте медленно, когда деталь почти отрезана.
10. Продолжайте продвигать инструмент, пока он не достигнет центра заготовки.Когда вы приближаетесь, заготовка подвешивается на тонком металлическом стержне.
11. Конец заготовки, который вы отрезаете, обычно будет иметь довольно грубую отделку и небольшой металлический стержень, выступающий из конца. См. Рисунок 19 ниже.
12. Последний шаг – установка этой детали в патрон и выполнение торцевого разреза для очистки конца. Одна из проблем на этом этапе заключается в том, что кулачки патрона могут испортить готовую заготовку. Если вы внимательно посмотрите на рисунок 20 ниже, вы действительно сможете увидеть отпечаток кулачков патрона.Чтобы избежать этого, вы можете обернуть заготовку тонкой полоской бумаги эмори или аналогичным защитным материалом, прежде чем зажимать ее.
Рисунок 8. Отрезка заготовки Рисунок 9. Готовая заготовка
Для получения параллельного диаметра при обработке между центрами важно, чтобы два токарных центра находились на одной линии друг с другом и точно совпадали с центральной линией токарного станка. Если центр не выровнен, обрабатываемая деталь будет конической.
Центры токарного станка можно выровнять тремя способами:
1. Совместив центральные линии на задней части задней бабки друг с другом. Это только визуальная проверка и поэтому не является точной.
2. Метод пробной резки, при котором с каждого конца детали делается небольшой надрез, а диаметр измеряется микрометром.
3. Выровняйте центры с помощью индикатора часового типа.
Метод 1. Выровнять центры путем регулировки задней бабки.
Процедура:
1.Ослабьте зажим задней бабки или рычаг.
2. Ослабьте один из регулировочных винтов с левой или правой стороны, в зависимости от направления перемещения задней бабки. Затяните другой регулировочный винт до тех пор, пока линия на верхней половине задней бабки точно не совпадет с линией на нижней половине.
3. Затяните ослабленный регулировочный винт, чтобы зафиксировать обе половины задней бабки на месте.
4. Зафиксируйте зажимную гайку или рычаг задней бабки.
Метод 2. Выровнять центр методом следа.
Процедура:
1. Сделайте легкий пропил приблизительно 0,010 до истинного диаметра из секции A на конце задней бабки длиной 0,250 дюйма.
2. Остановите подачу и отметьте показания на градуированной манжете рукоятки поперечной подачи.
3. Переместите режущий инструмент ближе к концу передней бабки.
4. Поднесите режущий инструмент к той же настройке воротника, что и в шаге 1 (Раздел A).
5. Верните режущий инструмент к той же настройке воротника, что и на шаге 1.(Раздел A)
6. Отрежьте отрезок 0,250 в секции B и остановите токарный станок.
7. Измерьте оба диаметра микрометром.
8. Если оба диаметра не одинакового размера, отрегулируйте заднюю бабку по направлению к режущему инструменту или от него на половину разницы между двумя показаниями.
9. Сделайте еще один легкий пропил на участках A и B. Измерьте эти диаметры и при необходимости отрегулируйте заднюю бабку.
Метод 3. Выравнивание центров с помощью индикатора часового типа.
Процедура:
1. Очистите токарный станок и рабочие центры и установите циферблатный индикатор.
2. Плотно отрегулируйте испытательную планку между центрами и затяните зажим шпинделя задней бабки.
3. Установите циферблатный индикатор на резцедержатель или каретку токарного станка. Убедитесь, что плунжер индикатора расположен параллельно станине токарного станка, а точка контакта установлена по центру.
4. Отрегулируйте поперечный суппорт так, чтобы индикатор показывал около 0,025 дюйма на конце задней бабки.
5. Переместите каретку рукой так, чтобы индикатор проверки совпадал с диаметром на конце передней бабки, и отметьте показания индикатора проверки.
6. Если показания обоих индикаторов теста не совпадают. Отрегулируйте заднюю бабку с помощью регулировочного винта, пока индикатор не будет регистрировать одинаковые показания на обоих концах.
Для расчета конусности на фут (tpf). Необходимо знать длину конуса, большой и малый диаметр.
Рисунок 10. Основная часть дюймового конуса
Формула:
Tpf = ((D-d) / длина конуса) x 12
Пример:
Tpf = ((1.25 – 1) / 3) x 12 = (0,25 / 3) x 12 = 1 дюйм
При вычислении смещения задней бабки должны быть известны конус на фут и общая длина заготовки.
Рисунок 11. Размер заготовки с конусом
Формула:
Смещение задней бабки = (tpf x общая длина заготовки) / 24
Пример:
1. Найдите tpf:
tpf = ((1,125 – 1) x 12) / 3 = (0,125 x 12) / 3 = 0,50 дюйма
2. Найдите смещение задней бабки:
Смещение задней бабки = (.5 x 6) / 24 = 3/24 = 0,125 дюйма
В некоторых случаях, когда нет необходимости определять конусность на фут, можно использовать следующую упрощенную формулу.
Формула:
Смещение задней бабки = (OL / TL) x ((D-d) / 2)
OL = Общая длина заготовки
TL = длина конической части
D = конец большого диаметра
d = конец малого диаметра
Пример:
Смещение задней бабки = (6/3) x ((1.125-1) / 2) =.125
Использование резиновой опоры для получения коротких или крутых конусов. Насадку следует вводить вручную, используя рукоятку подачи сложного упора.
Процедура:
1. Обратитесь к чертежу, чтобы узнать величину требуемого конуса в градусах.
2. Ослабьте стопорные винты составной опоры.
3. Поверните составную опору на желаемый угол. (См. Первое изображение)
4. Затяните стопорные винты составной опоры.
5. Отрегулируйте насадку по центру и подайте насадку для режущего инструмента, используя винт подачи компаундной опоры.
6. Проверьте размер и размер конуса.
Рис. 12. Операция точения конуса
1. Циферблат или контрольный индикатор следует использовать всякий раз, когда обрабатываемый диаметр должен быть выровнен с точностью до тысячных долей дюйма.
2. Порядок действий:
3. Вставьте заготовку в 4-кулачковый патрон и приблизительно выровняйте ее с помощью мела или поверхностного щупа.
4. Установите индикатор в резцедержатель токарного станка.
5.Установите индикаторный шпиндель в горизонтальное положение, установив точку контакта на центральную высоту.
6. Поднесите индикаторную точку к диаметру заготовки так, чтобы она показывала около 0,020, и проверните шпиндель токарного станка вручную.
7. Во время вращения токарного станка обратите внимание на самое высокое и самое низкое показания на циферблатном индикаторе.
8. Слегка ослабьте зажимной зажим патрона при самом низком показании и затяните зажим при высоком показании до тех пор, пока работа не переместится на половину разницы между двумя показаниями индикатора.
Сторона 1. Левая и правая сторона
9. Продолжайте регулировать только эти две противоположные губки, пока индикатор не зарегистрирует их на обеих губках. Не обращайте внимания на показания индикатора работы между этими двумя губками.
10. Отрегулируйте другой набор противоположных кулачков таким же образом, пока индикатор не покажет то же самое в любой точке окружности заготовки.
Сторона 2. Левая и правая сторона
11. Равномерно затяните все кулачки, чтобы надежно закрепить заготовку.
12.Проверните шпиндель токарного станка вручную и еще раз проверьте показания индикатора.
1. Под каким углом устанавливается составной упор?
2. Объясните разницу между черновым и чистовым точением.
3. Следует ли устанавливать острие инструмента над или по центру оси шпинделя при выполнении торцевого пропила?
4. Какова цель облицовки?
5. Почему мы просверливаем деталь точечным сверлением?
6. С какой целью надоедать?
7. Назовите три типа отрезных инструментов.
8. Назовите три метода выравнивания центров токарного станка.
9. Рассчитайте смещение для конуса, если D = 2, d = 1, OL = 6 и TL = 3. Формула:
Смещение = (OL x (D-d)) / (2 x TL)
10. Опишите производителя конуса.
Различные типы операций обработки и процесс обработки
Во время изготовления детали для удаления излишков материала требуются различные операции и процессы обработки. Эти операции обычно являются механическими и включают в себя режущие инструменты, абразивные круги, диски и т. Д.Операции механической обработки могут выполняться на фасонных прокатных станах, таких как пруток и плоские поверхности, или они могут выполняться на деталях, изготовленных с помощью предыдущих методов производства, таких как литье или сварка. С недавним развитием аддитивного производства, обработка в последнее время была названа «субтрактивным» процессом, описывающим удаление материала для изготовления готовой детали.
Различные типы операций обработки
Два основных процесса обработки – токарная и фрезерная – описаны ниже.Другие процессы иногда совпадают с этими процессами или выполняются с помощью автономного оборудования. Например, сверло может быть установлено на токарном станке, используемом для токарной обработки, или зажато в сверлильном станке. Когда-то можно было различать токарную обработку, при которой деталь вращается, и фрезерование, при которой вращается инструмент. Это несколько размылось с появлением обрабатывающих центров и токарных центров, которые способны выполнять все операции отдельных станков на одном станке.
Токарная
Токарная обработка – это процесс обработки на токарном станке; токарный станок раскручивает заготовку, когда режущие инструменты перемещаются по ней. Режущие инструменты работают по двум осям движения, создавая пропилы с точной глубиной и шириной. Существуют токарные станки двух различных типов: традиционные ручные и автоматизированные с числовым программным управлением (ЧПУ).
Токарная обработка может выполняться как на внешней, так и на внутренней стороне материала. Когда выполняется изнутри, это называется «растачиванием» – этот метод (который может быть горизонтальным или вертикальным в зависимости от ориентации шпинделя) чаще всего применяется для создания трубчатых компонентов.Другая часть процесса токарной обработки называется «торцеванием» и происходит, когда режущий инструмент перемещается через конец заготовки – обычно это выполняется на первом и последнем этапах токарной обработки. Торцевание может применяться только в том случае, если токарный станок имеет приспособленный поперечный суппорт. Используется для создания базы на лицевой поверхности отливки или заготовки, которая перпендикулярна оси вращения.
Токарные станки обычно относятся к одному из трех различных подтипов: токарно-револьверные станки, токарные станки для двигателей и токарные станки специального назначения.Токарные станки для двигателей – это наиболее распространенный тип, который используется обычными машинистами или любителями. Токарные станки с револьверной головкой и токарные станки специального назначения чаще используются в тех случаях, когда требуется многократное изготовление деталей. Токарно-револьверный станок оснащен держателем инструмента, который позволяет станку последовательно выполнять ряд операций резания без вмешательства оператора. К специальным токарным станкам относятся, например, токарные станки для дисков и барабанов, которые автомобильный гараж может использовать для обтачивания поверхностей компонентов тормозов.
Фрезерно-токарные центрыс ЧПУ сочетают в себе головную и заднюю бабки традиционных токарных станков с дополнительными осями шпинделя, чтобы обеспечить эффективную обработку деталей с симметрией вращения (например, крыльчатки насоса) в сочетании со способностью фрезы создавать сложные детали. Сложные кривые можно создавать, вращая заготовку по дуге, когда фреза движется по отдельной траектории. Этот процесс известен как 5-осевая обработка.
Сверление / растачивание / развёртывание
Сверление позволяет получать цилиндрические отверстия в твердых материалах с использованием сверл – это один из наиболее важных процессов обработки, поскольку создаваемые отверстия часто предназначены для облегчения сборки.Часто используется сверлильный станок, но биты также можно вставлять в токарные станки. В большинстве производственных операций сверление является предварительным этапом изготовления готовых отверстий, отверстий, которые затем нарезают, разматывают, растачивают и т. Д. Для создания отверстий с резьбой или для приведения размеров отверстий в допустимые допуски. Сверла обычно прорезают отверстия, превышающие их номинальный размер, и отверстия, которые не обязательно прямые или круглые из-за гибкости сверла и его тенденции идти по пути наименьшего сопротивления.По этой причине сверление обычно выполняется с меньшим размером, а за ним следует другая операция механической обработки, которая доводит отверстие до его конечного размера.
Используемые сверла имеют два спиральных канала, идущих вверх по валу сверла. Известный как «рифление», он выносит стружку или стружку из отверстия по мере продвижения сверла в материал. Для каждого типа материала есть рекомендованная скорость сверления и подача.
Хотя сверление и растачивание часто путают, растачивание используется для уточнения размеров и точности просверленного отверстия.Сверлильные станки бывают нескольких вариантов в зависимости от объема работы. Вертикально-расточный станок используется для обработки очень больших и тяжелых отливок, когда деталь вращается, а расточная оправка остается неподвижной. Горизонтально-расточные станки и координатно-расточные станки удерживают рабочую поверхность в неподвижном состоянии и вращают режущий инструмент. Растачивание также производится на токарном станке или в обрабатывающем центре. Расточный резец обычно использует одну точку для обработки стороны отверстия, что позволяет инструменту действовать более жестко, чем сверло. Отверстия в отливках обычно завершаются растачиванием.
Машинные и ручные развертки также используются для чистовой обработки отверстий, часто с большей шероховатостью поверхности, чем можно получить только путем растачивания. Стандартные развертки доступны с шагом 1/64 дюйма. Развертки бывают с прямыми или спиральными канавками и режут по периферии, удаляя только 0,004–0,008 дюйма отверстия. Развертка выполняется на тех же станках, что и расточка, а иногда и на сверлильном станке.
Фрезерный
При фрезеровании для удаления материала используются вращающиеся фрезы, в отличие от токарных операций, когда инструмент не вращается.Традиционные фрезерные станки оснащены подвижными столами, на которых устанавливаются детали. На этих станках режущие инструменты неподвижны, а стол перемещает материал так, чтобы можно было делать желаемые разрезы. В других типах фрезерных станков в качестве подвижных инструментов используются как стол, так и режущие инструменты.
Двумя основными операциями фрезерования являются фрезерование слябов и торцевое фрезерование. При фрезеровании слябов периферийные кромки фрезы используются для выполнения плоских надрезов по поверхности заготовки.Шпоночные пазы в валах можно вырезать с помощью аналогичной фрезы, но более узкой, чем обычная фреза для плит. Торцевые фрезы вместо этого используют конец фрезы. Доступны специальные фрезы для различных задач, например, фрезы со сферическим концом, которые можно использовать для фрезерования карманов с изогнутыми стенками.
Некоторые операции, которые может выполнять фрезерный станок, включают строгание, резку, шлифование, фрезерование, вырубку и т. Д., Что делает фрезерный станок одним из наиболее гибких единиц оборудования в механическом цехе.
Существует четыре типа фрезерных станков – ручные фрезерные станки, плоские фрезерные станки, универсальные фрезерные станки и универсальные фрезерные станки – и они имеют либо горизонтальные фрезы, либо фрезы, установленные на вертикальной оси. Как и ожидалось, универсальный фрезерный станок позволяет монтировать как вертикально, так и горизонтально режущие инструменты, что делает его одним из самых сложных и универсальных фрезерных станков на рынке.
Как и токарные центры, фрезерные станки, способные производить серию операций на детали без вмешательства оператора, являются обычным явлением и часто называются просто вертикальными или горизонтальными обрабатывающими центрами.Они неизменно основаны на ЧПУ.
Шлифовальный
Шлифование используется для удаления небольшого количества материала как с плоских поверхностей, так и с цилиндрических форм. Плоскошлифовальные станки совершают возвратно-поступательные движения на столе, подавая его в шлифовальный круг. Глубина, на которую режет круг, обычно составляет от 0,00025 до 0,001 дюйма. Цилиндрические шлифовальные машины устанавливают заготовку по центрам и вращают ее, одновременно прикладывая к ней периферию вращающегося абразивного круга. Бесцентровое шлифование используется для производства мелких деталей в больших объемах, где шлифованная поверхность не имеет отношения к какой-либо другой поверхности, кроме как в целом.Шлифованные поверхности 200-500 мин. среднеквадратичное значение обычно считается приемлемым для многих приложений и является отправной точкой для дальнейших чистовых операций, включая притирку, хонингование и суперфиниширование.
Строгание
Строгание используется, прежде всего, для обработки больших плоских поверхностей, особенно тех, которые будут обработаны скребком, например направляющих станков. Мелкие детали, собранные вместе в приспособление, также экономично обрабатываются.
Пиление
Распиловка металлов обычно выполняется на отрезных станках для получения более коротких отрезков из прутков, экструдированных профилей и т. Д.Распространены вертикальные и горизонтальные ленточные пилы, в которых используются непрерывные петли из зубчатых лент для долбления материала. Скорость ленты варьируется в зависимости от материала с некоторыми жаропрочными сплавами, требующими медленных 30 футов в минуту, в то время как более мягкие материалы, такие как резка алюминия со скоростью 1000 футов в минуту или более. К другим отрезным станкам относятся механические ножовки, пилы с абразивным кругом и дисковые пилы.
Протяжка
Протяжка используется для изготовления квадратных отверстий, шпоночных пазов, шлицевых отверстий и т. Д.Протяжка состоит из множества зубцов, расположенных последовательно, почти как напильник, но каждый последующий зуб немного больше, чем каждый предыдущий зуб. Протяжка протягивается или проталкивается через подготовленное направляющее отверстие (или выходит за пределы поверхности) и делает серию все более глубоких надрезов. Протяжка с выталкиванием часто выполняется на станках с вертикальным прессом. Протяжка с вытяжкой часто выполняется с помощью вертикальных или горизонтальных машин, которые во многих случаях имеют гидравлический привод. Скорость резания варьируется от 5 футов в минуту для высокопрочных металлов до 50 футов в минуту для более мягких металлов.
ECM / EDM
Это немеханические формы удаления материала с использованием эрозионных искр или химикатов. Электроэрозионная обработка использует искру, передаваемую через диэлектрическую жидкость от электрода к поверхности токопроводящей детали. Этим методом можно обрабатывать очень мелкие детали, включая отверстия малого диаметра, полости штампа и т. Д. На скорость разряда обычно влияет не твердость, а тепловые свойства и проводимость металла.
Электрохимическая обработка – это процесс обратного гальванического покрытия, позволяющий получать отверстия без заусенцев с высоким качеством поверхности.Это процесс холодной обработки, который не вызывает термических напряжений в заготовке.
Сводка
В этой статье представлен краткий обзор операций и процессов обработки. Для получения дополнительной информации о сопутствующих продуктах обратитесь к другим нашим руководствам или посетите платформу Thomas Supplier Discovery Platform, чтобы найти потенциальные источники поставок или просмотреть подробную информацию о конкретных продуктах.
Прочие изделия для обработки
Больше от Custom Manufacturing & Fabricating
Универсальный токарный станок, конструкция и возможная обработка – основы
История токарного станка восходит к 4000 г. до н.э.к так называемым струнным сверлам. В средние века водяное колесо использовалось в качестве источника энергии. Леонардо да Винчи считается создателем прототипов различных современных технологических станков, в том числе токарных.
На протяжении веков технология изготовления не претерпела серьезных изменений. Технологическое развитие было медленным процессом. Во второй половине XIX века Джон Уилкинсон построил прецизионный расточной станок с паровым цилиндром. В тот же период И.А. Нартоу и Генри Модслей представили механические инструменты для поддержки кареток в портативных режущих машинах. Токарные станки – основная группа станков для обработки цилиндрических (вращающихся) наружных и внутренних поверхностей. Развитие станков, в том числе токарных, является примером качественного характера технического прогресса.
В случае токарных станков формирование обработанных поверхностей происходит путем передачи основного вращательного движения шпинделем на заготовку и прямолинейного движения подачи инструмента.
Станок токарный обычный – строительный
На рис. 1 описана основная сборка и компоненты кинематической системы обычного токарного станка. В случае обычных станков у нас нет плавного изменения скорости вращения главного привода или подающего инструмента.
Рис. 1. Станок токарный универсальный универсальный – описание основных узлов и частей кинематической системы.
Стоит присмотреться к деталям конструкции обычного универсального токарного станка.На рис. 2 показан трехкулачковый патрон, прикрепленный к шпинделю токарного станка при обращении с валом как с заготовкой. Фиксация и зажим самоцентрирующихся трехкулачковых патронов производятся одновременно. Зажимные губки центрируют заготовку и обеспечивают зажимное усилие. При установке объекта оператор должен подтягивать каждую из губок отдельно, несмотря на их одновременное зажатие.
Рис. 2. Самоцентрирующийся трехкулачковый патрон – обычный токарный станок.
На рис. 3 показано сквозное отверстие в трехкулачковом патроне, шпинделе и всей передней бабке, которая используется для подачи длинных прутков в качестве заготовок.
Рис. 3. Самоцентрирующийся трехкулачковый патрон – отверстие для транспортировки длинного прутка в качестве заготовки.
На рис. 4 показаны детали узла держателя (каретки) инструмента, который состоит из продольного суппорта, поперечного суппорта, суппорта инструмента, держателя инструмента и корпуса держателя.
Рис. 4. Инструментальный суппорт (каретка) обычного универсального токарного станка.
В представленном решении (рис. 4) резцедержатель позволяет использовать 4 инструмента (токарные ножи, а также устройство для накатки – холодная пластическая обработка, придавая поверхности специфическую текстуру).На рис. 5 показан крупный план державки инструмента.
Рис. 5. Держатель инструмента с 2. установленными токарными ножами.
Каретка инструмента благодаря продольным суппортам скользит вдоль оси шпинделя по линейным направляющим (рисунки 6 и 7). Таким же образом перемещайте заднюю бабку вручную. Пути являются неотъемлемой частью станины токарного станка. Их обработка – сложная задача, потому что необходимо поддерживать их взаимный параллелизм. Обработка путей по функциональным причинам должна быть гладкой (фрезерование, суперфиниширование).
Рис. 6. Деталь продольных салазок на линейном скользящем пути.
Рис. 7. Линейные направляющие на станине токарного станка.
С точки зрения технолога, мы смотрим на станок спереди, с точки зрения оператора. Для обычных токарных станков, таких как универсальный токарный станок с центром, обсуждаемый здесь, шпиндель (главный привод находится слева) и задняя бабка справа (рисунок 8).
Рис. 8. Задняя бабка.
На рисунке 9 показаны ходовой винт (вверху) и ведущий (подающий) вал (внизу).Ходовой винт используется только для нарезания резьбы, что способствует его долговечности. Кинематическая связь ходового винта с главным приводом имеет точность, необходимую для нарезания резьбы. Приводной вал служит для обеспечения направления и осуществления рабочей подачи заданной величины.
Рис. 9. Ходовой винт и подающий вал универсального токарного станка.
Значения частоты вращения и подачи обработки
Настройка скорости вращения и рабочей подачи заключается в установке значений из доступного диапазона постоянных значений – e.г. для частоты вращения главного привода это могут быть следующие значения: 18; 28; 71; 90; 710; 1120. Конкретное значение выбирается установкой положения шестерен в коробках передач. Имея в своем распоряжении определенные передачи и возможные их комбинации в 2 или 3 передачи, мы можем добиться постепенного изменения значений. На рисунке 10 показана лицевая сторона передней бабки с тремя переключателями направления движения и выбора конкретной скорости главного привода.
Значения постепенного изменения параметров, в том числе скорости вращения главного привода, определялись станками по металлу стандарта PN-62 / M-03150.Скорости шпинделя, которые были сняты с производства в январе 2001 года и не были заменены никаким новым стандартом. Это связано, в частности, с тем, что технические стандарты, за исключением стандартов OHS, больше не применяются. Значения скорости вращения для этого стандарта взяты из серии Renard R20.
Рис. 10. Лицевая панель передней бабки с рычагами переключения передач для задания направления и скорости вращения главного привода.
Аналогичным образом постепенно определяются значения рабочих подач (рис.11). Привод на загрузочную коробку передается через подающий вал.
Рис. 11. Коробка подачи на обычном универсальном токарном станке.
На первом этапе выбор параметров обработки состоит в выборе скорости резания. В случае обычных токарных и фрезерных станков с градуированными значениями скоростей вращения главных приводов, после определения скорости резания по классической формуле для скорости резания v c , значение частоты вращения n главного привода определен.Затем значение частоты вращения n сравнивается с имеющимися значениями на данном станке. В случае несовместимости сравниваемых значений, обычно, скорость n от станка следует выбирать наиболее близкую к определяемой n, но меньшую по величине. Скорость резания необходимо пересчитать.
По сравнению со станками с ЧПУ, градация скорости вращения и скорости подачи является ограничением и даже может считаться недостатком. Однако давайте вспомним, что это эффект технологических возможностей, появившихся несколько десятилетий назад, когда такие концепции, как числовое управление, были совершенно чужды, даже за пределами горизонта восприятия будущего.Тогда только решения с использованием кинематических цепей могли обеспечить любую возможность выбора скорости вращения и скорости подачи.
Примеры возможной обработки на универсальном токарном станке
На обычном универсальном токарном станке можно выполнять ряд различных обработок (рисунки 11.1; 11.2 и 11.3):
- поворот внешней цилиндрической поверхности – рис. 12.1.a;
- внешнее торцевое точение (торцевое точение) – рис. 12.1.b;
- поворотный конус (повернутый продольный суппорт) – рис.12.1.c;
- расточка внутренней цилиндрической поверхности (просверливание отверстия) – рис. 12.1.d;
- профилирование – форма обрабатываемой поверхности зависит от очертания режущей кромки – рис. 12.2.e;
- точение резьбы – рисунок 12.2.f;
- обработка паза (отрезка) – рисунок 12.2.g;
- сверление по оси шпинделя и заготовки – сверло устанавливается в задней бабке – рис. 12.2.h;
- накатка – создание определенной текстуры (канавок) на обработанной поверхности с помощью холодной обработки – полирование (я встречал термин «замес») – рис.12.3.i.
Рис. 12.1. Пример возможной обработки на обычном универсальном токарном станке – а) токарная обработка цилиндров; б.) торцевое точение; в.) поворот конуса; г) растачивание отверстия.
Рис. 12.2. Пример возможной обработки на обычном универсальном токарном станке – д.) Профилирование; е.) точение резьбы; ж.) обработка паза – отрезка; з.) сверление оси шпинделя и заготовки.
Рис. 12.3. Пример возможной обработки на обычном универсальном токарном станке – i.) накатка.
Обработка резьбы
Есть несколько способов нарезания резьбы на токарном станке. Один из них – использование ножей с режущими пластинами, предназначенными для определенного типа резьбы. Можно использовать резьбонарезной штамп для обработки внешней резьбы и метчики для внутренней резьбы. Здесь следует подчеркнуть, что обсуждается тема нарезания резьбы на цилиндрических поверхностях, расположенных на оси шпинделя.
При резьбонарезании мы используем ходовой винт, чтобы обеспечить необходимую точность кинематической связи между вращательным движением заготовки и движением подачи инструмента.Подача выражается в выбранных единицах, обычно в [мм] на оборот [мм / оборот] в случае нарезания резьбы, это ровно 1 шаг резьбы на оборот, что требует точности.
Накатка
Накатка как метод обработки редко упоминается в контексте использования на токарных станках. Накатка – это метод холодной обработки прессованием (полирование). Метод позволяет получить на обработанной поверхности специфическую текстуру. Эта текстура представляет собой наложение рисунка на так называемые накатные ролики – узорчатые ролики.Рифленая поверхность обеспечивает более надежный захват для пользователя. Этот тип текстуры применяется к различным типам устройств – например, на рукоятке моделировочного ножа (рис. 13).
Рис. 13. Пример рифленой поверхности – рукоятка моделировочного ножа.
Рис. 14. Размеры, характерные для обычного универсального токарного станка.
Характерные размеры для токарного станка
Каждая технологическая машина характеризуется параметрами, определяющими ее технологические возможности (рис.14). В случае обычного универсального токарного станка это:
- l – межосевое расстояние – особенно важно для центровых токарных станков;
- d1 – наибольший допустимый диаметр точения над станиной токарного станка;
- d2 – наибольший допустимый диаметр точения над суппортом;
- d3 – наибольший допустимый диаметр стержня, проходящего через шпиндель и канал в узле передней бабки;
- lc – максимально возможная длина точения.
Источники
- Падеревский К., Обрабярки, ВСиП 1993
- Erbel J. (ред.), Encyklopedia technik wytwarzania stosowanych w przemyśle maszynowym, tom II. Obróbka skrawaniem. Monta, OWPW 1993
- Erbel S., Kuczyński K., Marciniak Z., Techniki wytwarzania. Obróbka plastyczna, PWN 1981
- Notatki własne autora.
- Radełka tokarskie – Artykuły Techniczne
- Wsparcie ZAiOS Instytut Technik Wytwarzania na Wydziale Inżynierii Produkcji , Politechnika Warszawska
Нравится:
Нравится Загрузка…
СвязанныеТехническая информация | Pretech ・ N Co., Ltd. Обработка ・ Токарный станок ・ Фрезерование ・ Круглое шлифование ・ Внутреннее шлифование ・ Плоское шлифование, Различная обработка металлов и дизайн, Сборка станков
Особенности Pretech N
Интегрированная система производства и поставки за счет высоких технологий обработки
- Передовые технологии обработки
Мы будем отвечать потребностям обработки различных металлов на высоком уровне, добавляя новые технологии и идеи к нашему опыту, который накапливался на протяжении многих лет.У нас много достижений в прецизионной обработке микронных единиц и обработке сложных форм.
- Интегрированная производственная система
Последовательно переходя от проектирования промышленного оборудования к сборке, мы сокращаем расходы и способствуем быстрой доставке. Гибко реагируем на индивидуальные заказы от обработки до сборки.
- Надежная доставка
Мы доставляем продукцию высокого качества в срок.Каждый производственный процесс строго контролируется, даже «обычные вещи, которые принимаются как должное» для создания быстрой и надежной производственной системы.
Мы доставляем продукцию высокого качества в обещанный срок. Наша система управления сроками поставки и контроля качества основана на массовом производстве автомобильных запчастей.
Основной бизнес
Комплексная поддержка от проектирования промышленных машин до сборки
Мы сделаем промышленное оборудование более простым и безопасным в использовании, что поможет увеличить производственные мощности и сэкономить рабочую силу.
Нам можно доверить дизайн, а можем изготовить по чертежам заказчика.
До сих пор промышленные машины Pretech N использовались на различных предприятиях, таких как производство пищевых продуктов, полиграфия, медицинское оборудование и запчасти для самолетов.
- Универсальная поддержка от проектирования до закупки и сборки.
- У нас есть опыт производства широкого спектра промышленного оборудования.
Прецизионная обработка металлических деталей различными способами резки и шлифования
- Поддерживается совместимая токарная обработка, а также обработка MC, токарная обработка и одновременная обработка сложных форм по 5 осям.
- Совместим с различными материалами, включая железо, алюминий и нержавеющую сталь.
- Поскольку на предприятии установлены различные шлифовальные станки (цилиндрические, с внутренней поверхностью, с плоской поверхностью), можно за одну остановку удовлетворить требования к точности в диапазоне мкм.
Производство автомобильных запчастей
По запросу одного из ведущих японских производителей приборов и датчиков мы собираем детали для бортовых счетчиков, в основном мотоциклов, и датчиков скорости.
Строгий контроль качества осуществляется в процессе обработки, изготовления, проверки и доставки деталей, и мы заслужили высокий уровень доверия, поставляя высококачественную продукцию вовремя на протяжении многих лет.
- Поддерживает высококачественную и своевременную доставку для различных типов мелкосерийного производства, для которых требуются возможности управления.
- Оснащенный оборудованием для впрыскивания двухкомпонентной смеси эпоксидных смол и термореактивного материала, мы можем удовлетворить потребности в заполнении формовочного агента.
Используя накопленные ресурсы и производственные технологии в нашем базовом городе Нагаока, мы можем доставлять продукцию от чертежей до готовых деталей – от заготовки материалов до термообработки, резки, токарной обработки и обработки поверхности.
Мы можем гибко реагировать на использование отдельных процессов, таких как запросы на резку только поставляемых материалов или измельчение только обработанных продуктов.
Как спроектировать для токарной обработки с ЧПУ
Есть концепция дизайна следующего лучшего корпуса объектива камеры? Как насчет революционного приводного вала для газонокосилки с фрезерованными лесками и резьбовыми отверстиями? Скорее всего, мы сможем доставить перевернутый прототип с такой геометрией.
Токарная обработка таких деталей дает ряд преимуществ по сравнению с фрезерованием. Как предполагалось ранее, большое отношение длины к диаметру на поршнях и валах вызывает у операторов мельниц расстройство желудка. А вот повернуть набор подсвечников к 60-летию тети Марты на токарном станке совсем несложно.
Примеры на каждый день
Если вы все еще не уверены, какие детали подходят для токарного станка, подумайте о нескольких предметах домашнего обихода. Например, пинтовое стекло с его гладкой, правильной формой и длиной, в несколько раз превышающей внешний диаметр, представляет собой несложное упражнение на токарном станке.На обрабатывающем центре все иначе. А кофейную чашку с ее выступающей ручкой и отверстием для пальцев невозможно повернуть.
Те 3 фунта. пылящиеся в туалете гантели можно было довольно легко повернуть на токарном станке. Широкую и относительно глубокую выемку, в которой ваша рука сжимает пруток, можно повернуть с помощью простой процедуры нарезания канавок, а вырезать на фрезерном станке было бы убийственно.
Маленькое блюдце для чашки могло быть любым. Интерполяция концентрических выступов и криволинейных поверхностей в равной степени возможна на фрезерном или токарном станке, для чего не требуется ничего, кроме точного G-кода и подходящей фрезы.Тем не менее, почти наверняка будет быстрее перевернуть блюдце и гораздо эффективнее с точки зрения использования материалов.
Как насчет зазубрины для спринклера? V-образные канавки потребуют специальной фрезы на обрабатывающем центре, тогда как токарный станок может использовать стандартный токарный инструмент. То же самое можно сказать и о сменном колесе для гриля для барбекю, хотя фрезерование этих маленьких вырезов в форме магнитного колеса на поверхности на большинстве токарных станков было бы затруднительно или совершенно невозможно.
Банки для супа и солонки, бутылки с водой и цветочные горшки – вот что такое токарные станки.Пакеты для молока и рамы для картин? Не так много. Protolabs предлагает различные материалы для работы, такие как алюминий, латунь, низкоуглеродистая сталь, нержавеющая сталь, стальной сплав и титан.
Возможности токарного станка
По размеру мы будем работать с деталями диаметром до 2,95 дюйма (75 мм), длиной 9 дюймов (228 мм) и такими маленькими, как диаметр 0,03 дюйма (4 мм) и длиной 0,060 дюйма (1,5 мм). Острые конические наконечники допустимы, если угол больше 30 градусов. Никаких обещаний по поводу прототипов шариковой ручки или моделей соломинок из-под газировки.
Как упоминалось ранее, наши новые токарные станки могут фрезеровать. Сверление бокового отверстия или фрезерование плоскости вполне по силам, если эта деталь параллельна или перпендикулярна длинной оси детали. Нет угловых отверстий, извините. Любые фрезерованные канавки должны быть шире 0,047 дюйма (1,2 мм), но поскольку все наши токарные станки оснащены осью Y, мы можем обрабатывать пазы или отверстия со смещением от центра (в пределах разумного).
Вам нужно выгравировать название вашей компании на деталях? Лучше всего поднятый текст, но мы можем обработать практически любые буквы, если ширина строки и расстояние между символами не менее 0.020 дюймов (0,5 мм) в поперечнике. Маленькие дырочки нас не пугают, как и нитки. Фактически, мы просверливаем радиальные отверстия до 0,08 дюйма (2 мм) и осевые отверстия вдвое меньше. Точно так же мы поддерживаем ряд внутренних и внешних UNC, UNF и метрических резьб.
Если вы ранее пользовались нашими услугами по механической обработке, вы можете обнаружить, что точеные поверхности более гладкие и круглые, чем их фрезерованные аналоги. На фрезерованных элементах могут быть видимые следы инструмента, но мы можем обработать эти поверхности дробеструйной очисткой, чтобы придать им матовый вид и сбить любые мелкие заусенцы, оставшиеся после процесса обработки.
Как и все обработанные детали, процесс начинается с ввода вашей CAD-модели в нашу автоматизированную систему расценок. Наше программное обеспечение определит лучший метод обработки (фрезерование или токарная обработка) для каждого материала. Однако это решение иногда может быть отменено при настройке расценки. Каждый процесс имеет разные возможности для создания желаемых функций и многопоточности; ценообразование также варьируется между двумя процессами. Когда вы настраиваете расценки, после взвешивания этих факторов выберите процесс обработки, который лучше всего соответствует вашим потребностям.Если деталь не подходит для токарной обработки из определенного материала, эта опция не будет доступна в расценках на этот материал.
За прошедшие годы мы обнаружили, что изготовление круглых деталей из квадратной или прямоугольной заготовки может оставлять желать лучшего. Фрезерование квадратных углов, чтобы добраться до круглой детали под ними, занимает больше времени, чем обработка прутковой заготовки. Это также приводит к увеличению количества материальных отходов. Превращение этих деталей в станок, предназначенный для такой работы, несомненно, будет беспроигрышным для всех.Чтобы узнать больше о превращении в Protolabs, посетите нашу страницу процессов и рекомендаций или загрузите свою деталь сейчас, чтобы узнать, соответствует ли она требованиям.
Объяснение твердого точения и шлифования
Твердое точение и шлифование
У вас есть конкретное приложение, которое может потребовать шлифования с ЧПУ или чистового точения? Не уверены, какой процесс лучше всего? До появления твердого точения в 90-х годах круглое шлифование высокоточных заготовок было отраслевым стандартом. Однако твердое точение стало широко распространенным с момента его появления и заменило многие процессы шлифования во всем мире.Тем не менее, оба процесса принципиально надежны, но отличаются друг от друга, и какой метод лучше всего подходит, зависит от обрабатываемой детали и количества деталей в производственном цикле.
Преимущества твердого точения.
Твердое точение – идеальный процесс для деталей сложной формы, требующих сочетания внешней и внутренней обработки. Часто все операции можно выполнить за один зажим. Сложные геометрические формы могут быть точно созданы путем позиционирования и резки с ЧПУ с пластиной из CBN.В процессе шлифования каждый контур должен создаваться шлифовальным кругом особой формы, который требует регулярной правки. Кроме того, процесс жесткого точения легче настроить и переключить, часто в течение 1/2 часа. Это делает твердое точение особенно выгодным для малых и средних производств самых разных типов заготовок.
Преимущества шлифования
Шлифование – это более известный процесс. Большинство заготовок можно шлифовать независимо от их формы.С другой стороны, резкое точение имеет геометрические ограничения, как в случае с длинными и тонкими деталями. Широкие поверхности можно эффективно обработать, часто с помощью одной врезной шлифовки. Кроме того, шлифованием достигается чистота поверхности без витков, которая часто требуется для диаметров уплотнения. Специальное цилиндрическое шлифование по внутреннему и внешнему диаметру также незаменимо при больших объемах обработки. Различия в материалах и вариации твердости в одной и той же детали также могут быть проблематичными для твердого точения.
Преимущества сочетания твердого точения и шлифования
Итак, вы в настоящее время шлифуете все свои заготовки, но понимаете, что чистовое твердое точение может дать некоторые реальные преимущества? В этом случае гибридный станок, такой как MikroTurnGrind 1000, который сочетает в себе твердое точение и чистовое шлифование на одном станке, может стать решением вашей проблемы. Это позволит вам применить наиболее подходящий процесс для каждой обрабатываемой поверхности в одной установке без необходимости использования нескольких станков.
Подходит ли мое приложение для твердого точения?
Позвольте нам просмотреть ваши чертежи деталей, и мы с радостью сообщим вам, подходит ли это для ваших деталей. При необходимости мы можем предоставить вам предложение по оборудованию и исследование продолжительности цикла. Не стесняйтесь обращаться, заполнив контактную форму. Или свяжитесь с нами напрямую по адресу [email protected] или по телефону (011) +31 23 512 4900.
Производители и поставщики токарных станков с ЧПУ с внутренним цилиндром и конической поверхностью – Заводская цена
Цилиндрический шлифовальный станок с ЧПУ, мы поставляем MK1332, MK1632, MK1320, MK1620.Эта машина использует немецкую Siemens или известную отечественную систему ЧПУ для достижения цикла автоматических шлифовальных работ. Механизм перемещения рабочего стола использует серводвигатель переменного тока для непосредственного привода пары шарико-винтовых пар, направляющая консоли управления принимает скользящая направляющая из липкого пластика. Измерительная система может быть оснащена измерительным прибором в соответствии с требованиями заказчика для выполнения осевого позиционирования и радиального онлайн-измерения заготовки, а также связана с системой ЧПУ станков для завершения автоматического цикла шлифования заготовки.
ЗапросЧат сейчас
Придерживаясь концепции «Создавать товары высокого качества и заводить хороших друзей с людьми сегодня со всего мира», мы постоянно вызываем интерес покупателей в первую очередь к станкам для шлифования подшипников, бывшим в употреблении шлифовальным станкам, станкам для наружного круглого шлифования с ЧПУ. В будущем наша компания продолжит преодолевать трудности, использовать потенциал и постоянно обновляться с решимостью. Мы будем предоставлять лучшие системные решения и услуги для максимального удовлетворения потребностей пользователей с уважением к личности, прежде всего с клиентом, и стремлением к совершенству в качестве убеждения.Если вы ищете высокоточный круглошлифовальный станок с ЧПУ, обращайтесь к нашей фабрике, чтобы узнать цену и коммерческое предложение. Как один из профессиональных производителей и поставщиков шлифовальных станков в Китае, мы также предлагаем индивидуальные услуги. Не стесняйтесь покупать дешевую машину китайского производства на складе у нас.
Номер модели: MK1332
Объект обработки: заготовка
Автоматическая Оценка: Автоматическая
Сертификация: ISO 9001
Скорость перемещения рабочего стола: 0 90-8258
Код HS: 8460
0
Тип: Цилиндрический шлифовальный станок
Режим управления: ЧПУ
- Высокая точность Максимум.вес заготовки: 100/150/200 кг
Торговая марка: changyi
Происхождение: Китай
Наибольший размер шлифовального круга: φ600x (75) xφ305 мм
Описание продукта
Высокоточный цилиндрический шлифовальный станок с ЧПУ (MK1332)
Этот станок оснащен автоматическая количественная смазка для обеспечения смазки направляющей и винтовой штанги.
Система охлаждения имеет конструкцию с независимой охлаждающей промывкой и оснащена независимым резервуаром для охлаждающей воды для обеспечения качества измельчения.
Регулирование частоты передней бабки осуществляется электродвигателем переменного тока с бесступенчатым регулированием. он может адаптироваться к шлифованию различных заготовок.
Наружный диаметр шлифовального круга: φ8-320 мм
Расстояние до центра: 1000/1500/2000 мм
Вес самой большой заготовки: 100/150/200 кг
Наибольший размер шлифовального круга: φ8-320 мм
Всего мощность станков: 20кВт
WUXI CHANGYI MACHINE TOOLS CO., LTD.
Адрес: Hengxin Road No.5, промышленный парк Qianqiao Hengyuanxiang, город Уси, Цзянсу,
Контактное лицо: Ms.zeng
Мобильный: + 86-15852736128 / 13506159949
Телефон: + 86-510-83291139
Факс: + 86-510-83273338
Электронная почта: export_changyi @ 126.com
Интернет: http://www.changyigrinder.com/
Наша компания имеет профессиональную команду технического менеджмента, богатый производственный опыт, совершенную систему управления и является одним из лучших китайских производителей токарных станков с ЧПУ для обработки внутренних цилиндров и конических поверхностей.