Станина служит для крепления на ней всех узлов станка. Имеет две тумбы и направляющие, по которым перемещается каретка суппорта и задняя бабка.
Передняя бабка– представляет собой коробку скоростей неподвижно закрепленную на станке. Важная часть передней бабки- шпиндель– пустотелый вал, установленный на подшипниках.
Задняя бабка– предназначена для крепления правого конца длинных заготовок, а также установки переходных конических втулок при обработке отверстий для крепления сверл, зенкеров, разверток.
Коробка подач – предназначена для получения различных по величине подач. Механизмы коробки подач получают движение от шпинделя станка.
Суппорт с фартуком
Станина станка имеет рамную конструкцию, что позволяет увеличить виброустойчивость станка и точность обработки. В подшипниковых опорах применены подшипники особо высокой точности. Поэтому жесткость шпиндельного узла увеличена на 30% в сравнении со станком мод 1К62. Это снизило дробление наиболее распространенных режимов резания и позволяет вести обработку заготовок с большими силами резания (силовое точение) и наиболее полно использовать мощность привода (скоростное точение).
На станке мод. 16К20 можно обрабатывать заготовки как из незакаленных так и закаленных сталей, а также из труднообрабатываемых материалов.
Технические характеристики станка мод. 16к20
Наибольший диаметр заготовки над станиной – 400 мм.
Высота центров – 200 мм.; наибольший диаметр обрабатываемого прутка, проходящего через отверстие шпинделя – 50 мм.; величины скоростей вращения шпинделя, мин-1: 12,5; 16; 20, 25, 31,5; 40, 50, 63, 80, 100, 125, 160, 200, 250, 315, 400, 500, 630, 800, 1000, 1250, 1600.
Продольная подача, мм/об: 0,051; 0,06; 0,075; 0,09; 0,1; 0,125; 0,15; 0,175; 0,2; 0,25; 0,2; 0,35; 0,44 0,5; 0,6; 0,74 0,8; 1,0; 1,2; 1,4; 1,6; 2,0; 2,4; 2,8.
Поперечная подача, мм/об: 0,25; 0,03; 0,0375; 0,045; 0,05; 0,0625; 0,075; 0,0875; 0,1; 0,125; 0,15; 0,175; 0,2; 0,25; 0,3; 0,35; 0,4; 0,5; 0,6; 0,7; 0,8; 1,0; 1,2; 1,4.
Пределы шагов нарезаемых резьб: метрической, мм. – 0,5…112; дюймовой, число ниток на 1” – 0,5…56; модульной, мм – (0,5…112)π; питчевой – р=56-95 питча.
Габаритные размеры станка: (2505-3795)х1190х1500 мм.
Приложение 2 – Определение шага резьб
Шаг дюймовой резьбы:
,
где n – число ниток на 1″.
Шаг модульной резьбы:
t=π•m,
где m – модуль нарезаемой резьбы.
Шаг питчевой резьбы:
,
где p – число питчей (т. е. число зубьев зубчатого колеса, приходящихся на один дюйм диаметра его начальной окружности). Питч является расчетной величиной зубчатых зацеплений, принятый в странах, сохранивших измерение длин в дюймах.
Уравнения цепи подач при: продольной подаче :
Sпр.под=1об.шп.• Uconst • Upм
• Uгит • Uк.п • Uм • Uр.м. • Uф • nmzp.k , мм/об;поперечной подаче:
Sпоп.под=1об.шп.• Uconst • Upм • Uгит • Uк.п • Uм • Uр.м. • Uф • tх.в.пп , мм/об;
нарезаемой резьбы:
Sн.р=1об.шп.• Uз.ув.ш • Upм • Uгит • Uк.п • Uм • Uр.м. • tх.в. , мм
где Uconst, Uз.ув.ш , Upм , Uгит , Uк.п , Uр.м. , Uм ,Uф – соответственно передаточное число постоянной передачи, звена увеличения шага, реверсивного механизма, гитары сменных колес, механизма коробки подач, распределительного механизма, множительного механизма, механизма фартука.
Приложение 3- Уравнение кинематической цепи и значение ременной части передаточного отношения коробки скоростей
№ п/п | Кинематическое уравнение переменной части передаточного отношения коробки скоростей станка 16К20 | Значение переменной части передаточного отношения | |
0,015 | |||
0,02 | |||
0,025 | |||
0,03 | |||
0,04 | |||
0,05 | |||
0,06 | |||
0,08 | |||
0,1 | |||
0,13 | |||
0,16 | |||
0,21 | |||
0,25 | |||
0,40 | |||
0,51 | |||
0,62 | |||
0,65 | |||
0,79 | |||
0,82 | |||
1,01 | |||
1,63 | |||
2,06 |
Приложение 4-Условные обозначения основных передач и механизмов металлорежущих станков
Наименование | Обозначение | Наименование | Обозначение |
Вал, ось, стержень Конец шпинделя для центровых работ Конец шпинделя для патроновых работ Ходовый винт для передачи движения Радиальный подшипник без уточнения типа Радиальный подшипник скольжения Радиальный подшипник качения Глухое жесткое соединение двух соосных валов Эластичное соединение двух валов | Телескопическое соединение валов Кулачковая односторонняя муфта сцепления Фрикционная односторонняя дисковая муфта Фрикционная односторонняя электромагнитная муфта Глухое, неподвижное соединение детали с валом Свободное для вращения соединение детали с валом Подвижное вдоль оси соединение детали с валом Соединение детали с валом посредством вытяжной шпонки Общее обозначение электродвигателя |
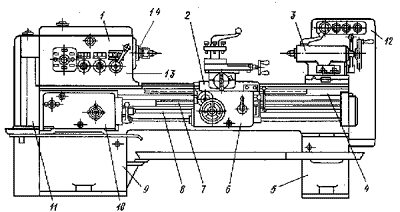
Сборочные единицы (узлы) и механизмы токарно-винторезного станка: 1 – передняя бабка, 2 – суппорт, 3 – задняя бабка, 4 – станина, 5 и 9 – тумбы, 6 – фартук, 7 – ходовой винт, 8 – ходовой валик, 10 – коробка подач, 11 – гитары сменных шестерен, 12 – электро -пусковая аппаратура, 13 – коробка скоростей, 14 – шпиндель.
Токарно-винторезные станки предназначены для обработки, включая нарезание резьбы, единичных деталей и малых групп деталей. Однако бывают станки без ходового винта. На таких станках можно выполнять все виды токарных работ, кроме нарезания резьбы резцом. Техническими параметрами, по которым классифицируют токарно-винторезные станки, являются наибольший диаметр D обрабатываемой заготовки (детали) или высота Центров над станиной (равная 0,5 D), наибольшая длина L обрабатываемой заготовки (детали) и масса станка. Ряд наибольших диаметров обработки для токарно-винторезных станков имеет вид: D = 100, 125, 160, 200, 250, 320, 400, 500, 630, 800, 1000, 1250, 1600, 2000 и далее до 4000 мм. Наибольшая длина L обрабатываемой детали определяется расстоянием между центрами станка. Выпускаемые станки при одном и том же значении D могут иметь различные значения L. По массе токарные станки делятся на легкие – до 500 кг (D = 100 – 200 мм), средние – до 4 т (D = 250 – 500 мм), крупные – до 15 т (D = 630 – 1250 мм) и тяжелые – до 400 т (D = 1600 – 4000 мм). Легкие токарные станки применяются в инструментальном производстве, приборостроении, часовой промышленности, в экспериментальных и опытных цехах предприятий. Эти станки выпускаются как с механической подачей, так и без нее. На средних станках производится 70 – 80% общего объема токарных работ. Эти станки предназначены для чистовой и получистовой обработки, а также для нарезания резьб разных типов и характеризуются высокой жесткостью, достаточной мощностью и широким диапазоном частот вращения шпинделя и подач инструмента, что позволяет обрабатывать детали на экономичных режимах с применением современных прогрессивных инструментов из твердых сплавов и сверхтвердых материалов. Средние станки оснащаются различными приспособлениями, расширяющими их технологические возможности, облегчающими труд рабочего и позволяющими повысить качество обработки, и имеют достаточно высокий уровень автоматизации. Крупные и тяжелые токарные станки применяются в основном в тяжелом и энергетическом машиностроении, а также в других отраслях для обработки валков прокатных станов, железнодорожных колесных пар, роторов турбин и др. Все сборочные единицы (узлы) и механизмы токарно-винторезных станков имеют одинаковое название, назначение и расположение. Смотри рисунок вверху.
16К20 Характеристики станка 16К20 завода “Красный пролетарий”
.
Типичный токарно-винторезный станок завода “Красный пролетарий” показан на рисунке внизу.

Общий вид и размещение органов управления токарно-винторезного станка мод. 16К20:
Рукоятки управления: 2 – сблокированная управление, 3,5,6 – установки подачи или шага нарезаемой резьбы, 7, 12 – управления частотой вращения шпинделя, 10 – установки нормального и увеличенного шага резьбы и для нарезания многозаходных резьб, 11 – изменения направления нареза-ния резьбы (лево- или правозаходной), 17 – перемещения верхних салазок, 18 – фиксации пиноли, 20 – фиксации задней бабки, 21 – штурвал перемещения пиноли, 23 – включения ускоренных перемещений суппорта, 24 – включения и выключения гайки ходового винта, 25 – управления изменением направления вращения шпинделя и его остановкой, 26 – включения и выключения подачи, 28 – поперечного перемещения салазок, 29 – включения продольной автоматической подачи, 27 – кнопка включения и выключения главного электродвигателя, 31 – продольного перемещения салазок; Узлы станка: 1 – станина, 4 – коробка подач, 8 – кожух ременной передачи главного привода, 9 – передняя бабка с главным приводом, 13 – электрошкаф, 14 – экран, 15 – защитный щиток, 16 – верхние салазки, 19 – задняя бабка, 22 – суппорт продольного перемещения, 30 – фартук, 32 – ходовой винт, 33 – направляющие станины.
Механизм подач и коробка скоростей 16К20 токарного станка.

Главный привод станка. В передней бабке размещены коробка скоростей и шпиндель, которые приводят во вращение обрабатываемую деталь при выбранных глубине резания и подаче. На рисунке показано устройство коробки скоростей, которая работает следующим образом. Заготовка зажимается в кулачковом патроне, который крепится к фланцу шпинделя 13. Вращение от электродвигателя 1 через ременную передачу 2 и муфту включения 3 передается на вал 5.
Блок из трех шестерен 7, 8 и 9, расположенный на валу 5, с помощью реечной передачи связан с рукояткой 17. Этой рукояткой блок шестерен вводится в зацепление с зубчатым колесом 4 (или 10, или 11), жестко закрепленным на валу 6. Колеса 4 и 12 сопряжены соответственно с колесами 15 и 16, которые передают крутящий момент шпинделю через зубчатую муфту 14, соединенную с рукояткой 18. Если муфта передвинута вправо, то шпиндель получает вращение через зубчатое колесо 16, а если влево – через зубчатое колесо 15. Таким образом коробка скоростей обеспечивает шесть ступеней частоты вращения шпинделя. Механизм подач. Связь шпинделя и суппорта станка для обеспечения оптимального режима резания осуществляется с помощью механизма подач, состоящего из реверсирующего устройства (трензеля) и гитары, которые осуществляют изменение направления и скорости перемещения суппорта.

Привод этого механизма осуществляется от коробки скоростей через трензель (смотри рисунок справа), который состоит из четырех зубчатых колес а, б, в, г, связанных с рукояткой 19, переключением которой осуществляется реверс (т. е. изменение направления вращения) вала 20 (приводного вала суппорта). Позиции а, б, в, г, 19 и 20 (см. рисунки). При крайнем нижнем положении рукоятки 19 (положение А) зубчатые колеса а, б, в, г соединены последовательно и направление вращения вала 20 совпадает с направлением вращения шпинделя. При верхнем положении рукоятки 19 (положение В) соединены только зубчатые колеса а, в, г и направление вращения вала 20 изменяется на противоположное. В среднем положении рукоятки 19 (положение Б) зубчатые колеса б и в не соединяются с зубчатым колесом а и вал 20 не вращается.

С помощью гитары устанавливают (настраивают) зубчатые колеса с определенным передаточным отношением, обеспечивающим необходимое перемещение суппорта на один оборот шпинделя. Расстояние L между валами 1 и 2 является постоянным. На валу 2 свободно установлен приклон 3 гитары, закрепленный болтом 4. Ось 5 промежуточных колес вис можно перемещать по радиальному пазу, тем самым изменяя расстояние А между центрами колес c и d. Дуговой паз приклона 3 позволяет регулировать размер В.
Коробка подач.

Назначение коробки подач – изменять скорости вращения ходового винта и ходового вала, чем достигается перемещение суппорта с выбранной скоростью в продольном и поперечном направлениях. Вал 14 в подшипниках 15 (сотри рисунок) коробки подач получает вращение от зубчатых колес гитары; вместе с ним вращается и имеет возможность перемещаться вдоль него зубчатое колесо П с рычагом 10. На одном конце рычага 10 вращается (на оси) зубчатое колесо 12, сопряженное с зубчатым колесом 11, а на другом – рукоятка 9, с помощью которой рычаг 10 перемещается вдоль вала 14 и может занимать любое из десяти положений (по числу зубчатых колес в механизме 1 Нортона). В каждом из таких положений рычаг 10 поворачивается и удерживается штифтом 9, который входит в соответствующие отверстия на передней стенке 7 коробки подач. При этом зубчатое колесо 12 входит в зацепление с соответствующим зубчатым колесом 13 механизма 1, в результате чего устанавливается выбранное число оборотов вала 2. Вместе с валом 2 вращается зубчатое колесо 3, которое можно перемещать вдоль него рукояткой. При перемещении вправо зубчатое колесо 3 посредством кулачковой муфты 4 соединяется с ходовым винтом 5 и передает ему вращательное движение, а при перемещении влево – входит в зацепление с зубчатым колесом 8 и передает вращательное движение ходовому валу 6.
Суппорт

Суппорт предназначен для перемещения во время обработки режущего инструмента, закрепленного в резцедержателе. Он состоит из нижних салазок (продольного суппорта) 1, которые перемещаются по направляющим станины с помощью рукоятки 15 и обеспечивают перемещение резца вдоль заготовки. На нижних салазках по направляющим 12 перемещаются поперечные салазки (поперечный суппорт) 3, которые обеспечивают перемещение резца перпендикулярно оси вращения заготовки (детали). На поперечных салазках 3 расположена поворотная плита 4, которая закрепляется гайкой 10. По направляющим 5 поворотной плиты 4 перемещаются (с помощью рукоятки 13) верхние салазки 11, которые вместе с плитой 4 могут поворачиваться в горизонтальной плоскости относительно поперечных салазок и обеспечивать перемещение резца под углом к оси вращения заготовки (детали). Резцедержатель (резцовая головка) 6 с болтами 8 крепится к верхним салазкам с помощью рукоятки 9, которая перемещается по винту 7. Привод перемещения суппорта производится от ходового винта 2, от ходового вала, расположенного под ходовым винтом, или вручную. Включение автоматических подач производится рукояткой 14. Устройство поперечного суппорта показано на рисунке внизу. По направляющим продольного суппорта 1 ходовым винтом 12, оснащенным рукояткой 10, перемещаются салазки поперечного суппорта. Ходовой винт 12 закреплен одним концом в продольном суппорте 1, а другим – связан с гайкой (состоящей из двух частей 15 и 13 и клина 14), которая крепится к поперечным салазкам 9. Затягивая винт 16, раздвигают (клином 14) гайки 15 и 13, благодаря чему. выбирается зазор между ходовым винтом 12 и гайкой 15. Величину перемещения поперечного суппорта определяют по лимбу 11. К поперечному суппорту крепится (гайками 7) поворотная плита 8, вместе с которой поворачиваются верхние салазки 6 и резцедержатель 5. На некоторых станках на поперечных салазках 9 устанавливается задний резцедержатель 2 для проточки канавок, отрезки и других работ, которые могут быть выполнены перемещением поперечного суппорта, а также кронштейн 3 с щитком 4, защищающим рабочего от попадания стружки и смазочно-охлаждающей жидкости.
Резцедержатель, фартук и разъемная гайка



Устройство резцедержателя показано на рисунке сверху. В центрирующей расточке верхних салазок 5 установлена коническая оправка 3 с резьбовым концом. На конусе оправки установлена четырехсторонняя резцовая головка 6. При вращении рукоятки 4 головка 2 перемещается вниз по резьбе конической оправки 3 и через шайбу 1 и упорный подшипник обеспечивает жесткую посадку резцовой головки 6 на конической поверхности оправки 3. От поворота при закреплении резцовая головка удерживается шариком, который заклинивается между поверхностями, образованными пазом на основании конической оправки 3 и отверстием в резцовой головке 6. При необходимости сменить позицию инструмента рукоятку 4 поворачивают против часовой стрелки. При этом головка 2 поворачивается и перемещается вверх по резьбе конической оправки 3, снимая усилие затяжки резцовой головки 6 на конусе конической оправки 3. Одновременно головка 2 поворачивает резцовую головку 6 посредством тормозных колодок, фрикционно связанных с поверхностью расточки головки 2 и соединенных с резцовой головкой 6 штифтами 7. При этом шарик, расположенный у основания конической оправки 3, не препятствует повороту резцовой головки, так как он утапливается в отверстие, сжимая пружину. Если в процессе работы рукоятка 4 (в зажатом положении) стала останавливаться в неудобном положении, то, изменяя толщину шайбы 1, можно установить ее в удобное для рабочего положение. Продольное и поперечное перемещение салазок суппорта производится через фартук 2 (смотри рисунок справа), который крепится к нижней поверхности продольного суппорта 1. Ручная продольная подача производится маховиком, который через зубчатую передачу сообщает вращение зубчатому колесу 4, катящемуся по рейке 3, закрепленной на станине 5 станка, и перемещает продольный суппорт вместе с поперечным суппортом и фартуком 2. Продольная подача суппорта 1 от ходового винта 2 производится включением разъемной гайки рукояткой 14 (смотри рисунок слева). Разъемная гайка состоит из двух частей (1 и 2), которые перемещаются по направляющим А при повороте рукоятки 5. При этом диск 4 посредством прорезей В, расположенных эксцентрично, перемещает пальцы 3, в результате чего обе части гайки сдвигаются или раздвигаются. Если обе части гайки охватывают ходовой винт, то производится продольная подача (перемещение) суппорта; если они раздвинуты, то подача отключается.
Задняя бабка 16К20
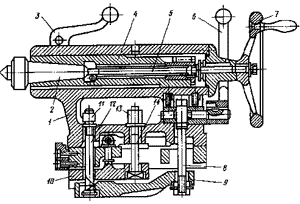
Устройство задней бабки показано на рисунке. В корпусе 1 (при вращении винта 5 маховиком 7) перемещается пиноль 4, закрепляемая рукояткой 3. В пиноли устанавливается центр 2 с коническим хвостовиком (или инструмент). Задняя бабка перемещается по направляющим станка вручную или с помощью продольного суппорта. В рабочем неподвижном положении задняя бабка фиксируется рукояткой 6, которая соединена с тягой 8 и рычагом 9. Сила прижима рычага 9 тягой 8 к станине регулируется гайкой 11 и винтом 12. Более жесткое крепление задней бабки производится с помощью гайки 13 и винта 14, который прижимает к станине рычаг 10.
Другие статьи по теме:
Московский станкостроительный завод, решил начать разработку и производство новых токарных станков в 1930 году. Им стал ДИП 200, а за прототип взяли немецкую фирму с их моделью VDF.
Уже весной 32 года, компания начинает подготовку выпуска первых партий. К завершению того же года, фирма выпустила порядка двадцати пяти экземпляров.
Краткая история серии
Еще два года спустя, в 1934 году, происходит запуск производства таких моделей, как ДИП-300, ДИП-400, ДИП-500.
К 1937 году разрабатывают специальные типажи по номенклатуре и размерам. Принимают единую систему условных обозначений. Таким образом, первый выпущенный заводом станок получил название 1Д62, но аббревиатуру ДИП – 20 сохранили.
1940 год ознаменовался созданием станка 162К 26А, как одного из версий ДИП-200.
Затем выпускают разные модернизированные станки, и в 48 году XX века, появляется легендарный 1А62. Модели выпускались по крупносерийному тиражу.
И, наконец в 1971 году, изготавливается первый опытный образец станка 16 к 20. Станок даже получил золотую медаль на ярмарке в 72 году.
С 1972 по 1973 года производят реконструкцию на заводе, связано это с масштабным выпуском новых моделей 16К20. Компания занимается освоением серийного производства этой модели и вот в конце 1973 года месячный оборот производства достигает 1 тыс. экземпляров. Экспортируется порядка 10% от общего числа.
Затем появились различные модификации модели 16 к 20, среди которых 16 К 25, 16 К2 0М, 16 К2 0П, 16 К 20В, 16 К 20Г, 16 К 20К, 16К20Ф1, 16К20ПФ1, 16К20ВФ1 и другие. Все они были основаны на базовых стандартах модели 16 к 20.
1988 год ознаменует прекращение производства станков этой модели. Его сменила серия МК.
Назначение и область применения токарно-винторезного станка по металлу
Предназначение токарно-винторезного станка 16 к 20, обработка поверхностей с цилиндрической, конической формой. И нарезка резьбы.
При обработке заготовок, станок использует развертку, зенкер, сверла, резцы. Универсальная модель 16 к 20 считается самой удачной в серии средне размерных станков.
Основные разновидности и расшифровка модификаций
Данная модель имеет четыре разновидности, но общую кинематическую схему при этом:
- 16К20 – стандартная токарно-винторезная модель;
- 16К20П- станок токарно-винторезный с повышенной точностью;
- 16К20Г- станок токарно-винторезный имеет нормальную точность и выемку в станине;
- 16К25 – облегченная модель токарно-винторезного станка с высотой центров 250 мм.
Цифры и буквы в наименовании станка обозначают следующее:
- Цифра «1» указывает на соответствующую группу, к которой принадлежит станок (это универсальная токарно-винторезная модель, по общепринятой российской классификации ЭНИМС).
- Цифра «6» — описывает подгруппу (токарно-винторезную в этом случае).
- Буква «К» это расшифровка завода, изготовившего станок, и обозначение поколения.
- Цифра «20» показывает высоту центра в 220 мм.
Технические характеристики
Основные параметры станка
- С наибольшим диаметром обработки станины — 400 мм.
- С наибольшим диаметром обработки суппорта — 220 мм.
- Расстояние между центрами -1500 мм.
- Отверстие шпинделя — 51 мм.
- Скорость шпинделя — 12,5–1600 об / мин 24 шага.
- Источник питания — 415 вольт / 50 Гц / 3 фазы.
- Сверхмощный токарно-винторезный станок.
- Изготовлено в России.
- Цельная литая основа.
- Пневматический плавающий хвостовой запас.
- Седельная смазка.
- Метрическая конфигурация.
- Галогенная рабочая лампа.
- Резерв для механической защиты патрона.
- Защита задней бабки, ходового винта и подающего вала.
- Система охлаждения.
Шпиндель
Выступает в качестве пустотелого, многоступенчатого вала, изготовленного из стали, с термической обработкой для увеличения стойкости.
Шпиндель имеет стальную конструкцию и продольное отверстие внутри, оно пропускает заготовку. Сам шпиндель вращается за счет специализированных прецизионных подшипников. Они износостойки и точны в изготовлении, не требуют частого техобслуживания.
Суппорт и подачи
Это часть станка, используемая для удержания инструмента и позволяющая производить продольное и поперечное перемещение инструмента.
Этот блок станка очень жесткий, что снижает вероятность ошибок, вызванных упругой деформацией системы скольжения во время резки.
Резцовые салазки
Салазки нужны для настройки попадания резьбы, они ездят по продольному направлению. На них закрепляют резцовую головку.
Задняя бабка
Используется для зажима вращающегося режущего инструмента и в качестве дополнительной опоры, применяется с вращающимися и не вращающимися центрами при жесткой резке.
Электрооборудование
Благодаря электрооборудованию, обеспечивается максимальная защита работника, ограждая его от удара электрического тока. А сам агрегат от получения повреждений.
Из чего состоит электрооборудование:
- Основного электродвигателя.
- Электродвигателя, перемещающего суппорт и каретку.
- Электронасоса с системой СОЖ.
- Системы автоматического выключения.
- Предохранителей.
- Теплового реле.
- Заземления.
- Микропереключателя.
Габариты и масса
Размер (Д х Д х В) — 3200 мм х 1300мм х 1900мм;
Вес (приблизительно) — 3000 кг.
Общая конструкция и принцип работы
Конструкция токарно-винторезного станка представляет собой крупный агрегат, состоящий из большого числа составных элементов, куда входит электрооборудование, суппорты, коробку подач, шпиндель и заднюю бабку.
Важно!
Конструкция предусматривает наличие целого ряда защитных элементов, блокирующие и ограждающие, обеспечивая безопасность взаимодействия с устройством.
Работает по принципу универсального токарного станка, выполняющего ряд различных работ, и некоторые нестандартные операции с использованием дополнительного оборудования, например, нарезание резьбы, сверления и т. п.
Фото и описание устройства станка
Ниже будут представлены схематичные изображения наиболее важных компонентов станка и краткое описание к ним.
Общий вид
Чертеж
На чертеже изображена рабочая зона станка, расположение и расстояние всех значимых частей оборудования.
Расположение органов управления
На схеме под цифрами обозначено расположение следующих органов управления:
- Рукоятки, устанавливающей величину подачи, и резьбу.
- Рукоятки, отвечающей за вид работы: подачу и тип резьбы.
- Рукоятки, устанавливающей число по оборотам шпинделя.
- Рукоятки, устанавливающей увеличенный шаг резьбы.
- Вводного автоматического выключателя.
- Сигнальной лампы.
- Выключателя насоса.
- Указателя нагрузок.
- Рукоятки, регулирующую правую и леву резьбу.
- Рукоятки, устанавливающей ряд чисел оборота.
- Рукоятки, регулирующей фрикционную муфту в главном приводе.
- Выключателя освещения рабочего места.
- Рукоятки, поворачивающую и закрепляющую индексируемую резцовую головку.
- Рукоятки, перемещающей резцовые салазки.
- Рукоятки, крепящие заднюю бабку к корпусу станины.
- Маховика, перемещающего заднюю бабку.
- Рукоятки, регулирующей фрикционную муфту.
- Рукоятку, выключающую и включающую ходовой винт.
- Рукоятку, управляющую механическим перемещением каретки и салазок.
- Кнопочной станции, включающей и выключающей электродвигатель.
- Рукоятку, перемещающую поперечную салазку суппорта.
- Маховика, устанавливающего ручное перемещение каретки.
- Кнопку, направляющую каретку и поперечные салазки.
- Рукоятку, устанавливающую подачу и шаг для резьбы.
Кинематическая схема
Кинематическую схему используют для того, чтобы понять связь и взаимодействие между основными элементами станка.
Шпиндельная бабка
Шпиндельная бабка может устанавливать числа в 4 ряда, по двум рядам с пределами 40, 50 и 160 об/мин, по двум рядам с пределами 200, 630 и 500.
Коробка подач
Обеспечивает перемещение резца и инструмента на направляющих станка с заданной скоростью. Эта часть используется для установки постоянной скорости подачи при резке или других работах.
С редуктором внутри, состоящим из переключаемой зубчатой передачи. На нее, с использованием входного вала, идет крутящий момент от шпиндельного узла. С ходовым винтом, валом на коробке подач.
Фартук
Фартук – деталь, отвечающая за точность подачи в суппорт. Имеет механизмы, ограждающие и обеспечивающие надежность с безопасностью во время работы.
Фартук располагается в корпусе, рядом с каретой суппорта. Обеспечивает вращательные движения ходового винта и передает их суппорту.
Суппорт
Представляет собой узел, крепящий инструмент в ручном или автоматическом режиме. Суппорт содержит резцедержатель и салазки.
Задняя бабка
Если при отведении рукоятки 19, не обеспечивается достаточный прижим задней бабки, необходимо изменить регулировку винтов 26 и 33, чтобы изменить прижимную планку.
Если нужно установить заднюю бабку поперечно шпинделю, нужно совместить винты 41 с плоской поверхностью А.
Схема электрическая принципиальная
Электродвигатель запускает кнопкой s4 и выключается кнопкой s3
Инструкция по первому запуску и эксплуатации
Перед первым запуском, нужно проверить внешние параметры надежности, устойчивость установки агрегата. Закончив осмотр, стоит выключить питание для каждого электродвигателя и используя вводный автоматический выключатель F1 в цеховую сеть.
Все блокировочные устройства должны соответствовать данным, указанным в инструкции:
- Главный привод вращается против часовой стрелки в сторону вала.
- Электронасос вращается согласно указанной схеме на корпусе.
- Гидроэлектростанция вращается в сторону вентилятора, по часовой стрелке.
- Электродвигатель быстрого перемещения вращается по часовой стрелке.
Важно!
Проверьте срабатывание магнитного пускателя и реле. После проверки правильности работы каждого электроаппарата, присоедините прежде выключенные провода. После полной проверки электродвигателя, можно приступать к работе.
Правила эксплуатации и ухода, паспорт станка
- Предназначение станков использование в малосерийном и единичном производстве.
- Температуру в цеху, стоит поддерживать на уровне 30 градусов.
- Контроль влажности не больше 80%.
- Сохранение качества и долговечность работы агрегата напрямую зависит от условий эксплуатации, недопустимо накопление пыли, появления оскалин.
- Чугунные детали, вызывают повышенный износ трущейся части, во время обработки требуется тщательное удаление стружки и пыли.
- Своевременно смазываются движущие части.
- Устройство, оставленное на длительный период, должно быть, накрыто.
Скачать бесплатно паспорт токарно-винторезного станка 16К20 в pdf-формате можно по ссылке: Паспорт 16К20
Современные аналоги
Уже упоминалось, что завод прекратил производство модели 16 к 20, поэтому актуален подбор станков с аналогичными характеристиками. Зарубежные производители славятся агрегатами D420x1000, Proma SPC-900PA, Jet GH-1640ZX DRO.
Белорусские аналоги, выпускаемые на Гомельском заводе, предлагают 16ВТ20П-21. Еще можно отметить модели TRENS, от Словацкого производителя SN 50 С и SN 500 SA.
Они имеют современную конструкцию и качественные немецкие комплектующие, с относительно небольшой стоимостью за свои характеристики.
Цены на товары других производителей начинаются от полутора миллиона до двух, без расчета доставки и установки агрегатов.
Кинематическая схема токарного станка 16К20
Кинематическая схема (рис. 1.) приведена для понимания связей и взаимодействия основных элементов станка 16К20. На выносках проставлены числа зубьев (z) шестерен (звездочкой обозначено число заходов червяка).
Рис. 1. Кинематическая схема токарного станка 16К20
Кинематическая схема – описание
От электродвигателя Д1 через клиноременную передачу 148/268 вращение передается на входной вал II коробки передач станка. Муфта М1 на этом валу позволяет получить через двойной блок зубчатых колес 56/34 или 51/39 прямое вращение вала III или через зубчатые колеса 50/21 и 36/38 — обратное вращение. Через блок зубчатых колес 29/47, 21 /55 или 38/38 вал IV получает шесть частот вращения в прямом направлении (соответствует вращению шпинделя против часовой стрелки) и три частоты вращения в обратном. С вала IV’ через двойной блок зубчатых колес 60/48 или 30/60 шпиндель VII получает двенадцать высоких частот вращения (либо шесть в обратном направлении).
Двенадцать низких частот вращения шпинделя передаются через валы IV и VI перебора с помощью двойного блока зубчатых колес 45/45 или 15/60 и зубчатых передач 18/72 и 30/60. Для включения этой цепи зубчатое колесо z=60 двойного блока сцепляется с зубчатым колесом z=30 вала VI.
На высоких частотах вращения шпинделя группа зубчатых колес на валах V и VI не участвует в передаче мощности от двигателя на шпиндель, что повышает динамические свойства привода главного движения, т. е. уменьшается время разгона шпинделя и его торможения, уменьшаются вибрации и повышается долговечность станка. Всего на шпиндель передается 22 частоты вращения, так как две частоты совпадают.
Частота вращения шпинделя, об/мин:
Аналогично могут быть определены другие промежуточные частоты вращения. Перемещение суппорта при нарезании резьбы, при продольной или поперечной подаче осуществляется по кинематической цепи механизма подач. От шпинделя VII вращение передается валу VIII через зубчатые колеса 60/60. Для увеличения шага нарезаемой резьбы или подачи используется звено увеличения шага: вращение снимается с вала IV через зубчатые колеса 45/45, что позволяет увеличить подачу (или шаг нарезаемой резьбы) в 4 или 16 раз. Далее через колеса 30/45 или цепочку реверса 30/25/45, гитару сменных зубчатых колес a/b и c/d вращение передается на приемный вал Х коробки подач.
Через колеса 28/38 и зубчатые передачи 28/28, 28/35, 30/25 или 42/30 вал ХII и через муфту М4 вал XIII получают четыре частоты вращения, используемые при нарезании метрических и модульных резьб. Дюймовые резьбы нарезаются через кинематическую цепь 28/38, муфту М3 и колеса 30/33. Вращение выходному валу ХV передается через различные комбинации включения зубчатых колес на валах XIII, XIV и ХV.
Настройка коробки подач на выбранную подачу или шаг нарезаемой резьбы производится перемещением блока зубчатых колес z=18 и z=28 и включением муфт М2, М3, М4 и М5. Муфта М5 передает вращение на ходовой винт XIX для нарезания резьб, а при отключенной муфте М5 через зубчатые колеса 23/40, 24/39, муфту обгона М6 и колеса 28/35 — на ходовой валик XVI для работы с продольной и поперечной подачами.
С ходового валика XVI зубчатыми колесами 30/32/32/30 через муфту М7, червячную передачу 4/21 вращение сообщается зубчатому колесу z=36. Продольное перемещение суппорта осуществляется через зубчатые колеса z=41, муфты М8 или М9, зубчатые передачи 17/66 на реечную шестерню 10. Для поперечного перемещения суппорта вращение от колеса z=36 передается через зубчатые колеса z=36, муфты М10 или М11, зубчатые передачи 34/29/16 на винт поперечных салазок ХXI с шагом 5 мм.
Ускоренные продольные или поперечные перемещения суппорта осуществляются от двигателя Д2, связанного с ходовым валиком клиноременной передачей 85/127. Муфта обгона М6 не препятствует быстрому вращению валика от включенных зубчатых колес в коробке подач.
Направление подачи и быстрых перемещений суппорта определяется включением одной из четырех муфт М8…М11, управляемых одной рукояткой. Для включения необходимой подачи рукоятку наклоняют в соответствующую сторону, а нажимом кнопки на торце рукоятки включают двигатель быстрых перемещений.
В некоторых модификациях станка 16К20 подача верхнего суппорта также механизирована: от зубчатого колеса z=29 вращение снимается колесом 18 на вал ХХ и через зубчатые передачи 20/20, 20/23/30/28/30 и 20/20 передается на ходовой винт ХХII верхнего суппорта.
Источник: ТОКАРНЫЕ СТАНКИ И РАБОТА НА НИХ Тишенина Т.И. Федоров В.Б.
Схемы и чертежи | 16К20 Токарный станок
Кинематическая схема — Шпиндельная бабка 16К20 (коробка скоростей):
(кликните для увеличения)Шпиндельная бабка на токарных станках — это специальный узел для размещения шпинделя, а так же механизма его привода. Шпиндельная бабка выполняет три основных функции:
— вращение шпинделя;
— продольная подача;
— зажим обрабатываемой детали.
Кинематическая схема — Задняя бабка 16К20
(кликните для увеличения)На токарно-винторезных станках задняя бабка используется для установки сверла, развёртки, метчика либо иных инструментов, а так же для поддержания другого конца обрабатываемых деталей.
Кинематическая схема — Суппорт 16К20:
(кликните для увеличения)Суппорт 16К20 предназначен для перемещения резцедержателя с резцом в продольном, поперечном и наклонном к оси агрегата направлениях.
Кинематическая схема — Коробка подач 16К20
(кликните для увеличения)На рисунке представлен подробный чертёж коробки подач токарного станка 16К20. Она предназначена для передачи вращения ходовому винту устройства либо ходовому валу. Так же, с помощью коробки подач, можно изменять число оборотов вращения вала.
Разрез Б-Б:
(кликните для увеличения)Разрез Г-Г:
(кликните для увеличения)ВНИМАНИЕ! Номера в схемах узлов полностью соответствуют с номером по кинематике. С помощью этого номера Вы сможете быстро найти нужную Вам деталь.
(кликните для увеличения)На рисунке представлена подробная кинематическая схема токарно-винторезного станка 16К20, 16К20М, 16К20Г, 16К20Ф1. Она используется для графического отображения взаимосзвязей основных механизмов и элементов агрегата. На схеме цифрой «1» отмечен суппорт с механическим перемещением резцовых салазок. На сносках отмечены числа зубьев (z) шестерен. При этом звёздочкой показано число заходов червяка.
Токарно-винторезные станки относят к группе универсальных станков, предназначенных для эксплуатации в условиях единичного и мелкосерийного производств. Эти станки имеют практически однотипную компоновку, примером которой может служить компоновка узлов и частей станка модели 16К20 (рис. 1.10).
Рис. 1.10. Общий вид токарно-винторезного станка модели 16К20
Модель станка содержит краткую информацию о самом станке. Первая цифра в соответствии с национальной классификацией металлообрабатывающего оборудования, приведённой в приложении 1, указывает на номер группы, к которой принадлежит станок. Цифра «1» в модели станка 16К20 говорит о том, что данный станок относят к станкам токарной группы. Вторая цифра модели характеризует номер типа станка в рамках группы. Соответственно данным таблицы приложения 1 станок 16К20 принадлежит к шестому типу станков токарной группы — токарным и токарно-винторезным станкам. Буква между цифрами (в модели станка 16К20 буква «К») указывает на то, что станок по отношению к предыдущей модели станков данных группы и типа модернизирован. Последние две цифры модели в виде числа «20» характеризуют высоту расположения оси шпинделя над направляющими станины (высоту центров) равную 200 мм. Это означает, что диаметр заготовки, обрабатываемой на станке 16К20, не может превышать 400 мм.
Основными частями станка являются станина 1, передняя бабка 4, шпиндель 5, суппорт 12, фартук 6, коробка подач 3, гитара сменных зубчатых колёс 2, задняя бабка 13, механизм быстрого перемещения суппорта 16.
Станина 1 установлена на левой 18 и правой тумбах 17 и служит для монтажа на ней основных узлов и частей станка. Станина снабжена направляющими, по которым перемещаются суппорт и задняя бабка.
Передняя бабка 4 предназначена для размещения в ней коробки скоростей, с помощью которой изменяют частоту и направление вращения шпинделя 5.
На правый конец шпинделя, являющегося пустотелым валом, устанавливают различные приспособления для закрепления заготовки. На рисунке 1.10 таким приспособлением является трёхкулачковый самоцентрирующий патрон.
Суппорт 12 станка состоит из продольных 7 и поперечных 8 салазок, верхнего суппорта 10 и четырёхпозиционного поворотного резцедержателя 9. В резцедержателе устанавливают и закрепляют резцы, которым вместе с суппортом сообщают движения продольной и (или) поперечной подач.
Коробка подач 3 предназначена для изменения скоростей продольного и поперечного движений подачи суппорта, с которым она соединена с помощью ходового винта 14 и ходового вала 15. Передачу вращательного движения выходного вала коробки подач к механизмам суппорта через ходовой винт используют только при нарезании резьб. Для выполнения всех других видов токарных работ движение от коробки подач к суппорту поступает через ходовой вал.
Гитара сменных зубчатых колёс 2 является звеном передачи движения от шпинделя станка к коробке подач и настраивается при нарезании точных резьб. Заменяя одни зубчатые колёса гитары другими, можно изменять величину подачи суппорта.
Фартук 6 предназначен для размещения в нём механизмов, обеспечивающих преобразование вращательного движения ходового вала 15 или ходового винта 14 в прямолинейное поступательное движение суппорта.
Заднюю бабку 13 используют в качестве дополнительной опоры заготовки при изготовлении валов с отношением длины к диаметру заготовки более четырёх, а также для закрепления свёрл, зенкеров, развёрток, метчиков и плашек. Этим инструментам, устанавливаемым в выдвигаемую пиноль задней бабки 11, вращением маховичка с рукояткой Р1 (см. рис. 1.10) сообщают движение подачи при обработке отверстий, расположенных по оси вращения заготовки.
Привод быстрого перемещения суппорта 16 применяется для сокращения непроизводительных затрат времени на вспомогательные передвижения суппорта. Механизм привода состоит из электродвигателя, вмонтированного в заднюю стойку станины, и клиноременной передачи, с помощью которой передаётся вращение на ходовой вал.
Токарные приспособления
Для установки и закрепления заготовок на токарных станках используют различные приспособления (рис. 1.11).
Рис. 1.11. Приспособления к токарным станкам:
а) — трёхкулачковый самоцентрирующий патрон; б) — центр обыкновенный; в) — центр вращающийся; г) — поводковый патрон; д) — люнет неподвижный
К основным типам приспособлений относят: двух‒, трёх‒ и четырёхкулачковые патроны, цанговые и поводковые (рис. 1.11, г) патроны, центры (рис. 1.11, б, в), люнеты. Патроны закрепляют на шпинделе станка, а центры устанавливают в пиноли задней бабки или в отверстии шпинделя станка.
Кулачковые патроны подразделяют на самоцентрирующие, обеспечивающие при закреплении заготовки, имеющей цилиндрическую поверхность (наружную или внутреннюю), совпадение её оси с осью центров станка, и простые, не реализующие эту функцию.
Самоцентрирующие патроны в большинстве случаев изготавливают трёхкулачковыми (рис. 1.11, а) и реже — двухкулачковыми. Патроны этого типа удобны в работе, так как все кулачки, закрепляющие заготовку, перемещаются по радиальным пазам к центру или от центра одновременно и синхронно друг с другом. При использовании самоцентрирующих патронов значительно сокращается время на закрепление заготовки.
Простые (не самоцентрирующие) патроны изготовляют обычно четырёхкулачковыми. Каждый кулачок в них перемещается своим винтом независимо от остальных. Это позволяет устанавливать и закреплять в патронах заготовки цилиндрической и не цилиндрической форм.
При обработке на токарных станках длинных и нежёстких заготовок применяют люнеты. Люнеты подразделяют на неподвижные (рис. 11.1, д), закрепляемые на станине станка, и подвижные, устанавливаемые на суппорт. Неподвижный люнет при обработке заготовки не меняет своего положения относительно станка. Подвижный люнет, используемый при продольном точении, перемещается вместе с суппортом. Обработку заготовок несимметричных форм осуществляют с использованием планшайб, угольников, оправок и других различных специальных приспособлений.
Устройство токарно-винторезного станка 16К20
Сборочные единицы (узлы) и механизмы токарно-винторезного станка:
|
Токарно-винторезные станки предназначены для обработки, включая нарезание резьбы, единичных деталей и малых групп деталей. Однако бывают станки без ходового винта. На таких станках можно выполнять все виды токарных работ, кроме нарезания резьбы резцом. Техническими параметрами, по которым классифицируют токарно-винторезные станки, являются наибольший диаметр D обрабатываемой заготовки (детали) или высота центров над станиной (равная 0,5 D), наибольшая длина L обрабатываемой заготовки (детали) и масса станка. Ряд наибольших диаметров обработки для токарно-винторезных станков имеет вид: D = 100, 125, 160, 200, 250, 320, 400, 500, 630, 800, 1000, 1250, 1600, 2000 и далее до 4000 мм. Наибольшая длина L обрабатываемой детали определяется расстоянием между центрами станка. Выпускаемые станки при одном и том же значении D могут иметь различные значения L. По массе токарные станки делятся на легкие – до 500 кг (D = 100 – 200 мм), средние – до 4 т (D = 250 – 500 мм), крупные – до 15 т (D = 630 – 1250 мм) и тяжелые – до 400 т (D = 1600 – 4000 мм). Легкие токарные станки применяются в инструментальном производстве, приборостроении, часовой промышленности, в экспериментальных и опытных цехах предприятий. Эти станки выпускаются как с механической подачей, так и без нее. На средних станках производится 70 – 80% общего объема токарных работ. Эти станки предназначены для чистовой и получистовой обработки, а также для нарезания резьб разных типов и характеризуются высокой жесткостью, достаточной мощностью и широким диапазоном частот вращения шпинделя и подач инструмента, что позволяет обрабатывать детали на экономичных режимах с применением современных прогрессивных инструментов из твердых сплавов и сверхтвердых материалов. Средние станки оснащаются различными приспособлениями, расширяющими их технологические возможности, облегчающими труд рабочего и позволяющими повысить качество обработки, и имеют достаточно высокий уровень автоматизации. Тяжелые токарные станки применяются в основном в тяжелом и энергетическом машиностроении, а также в других отраслях для обработки валков прокатных станов (вальце-токарные станки, вальце-фрезерные станки), железнодорожных колесных пар (колесо-токарные станки), роторов турбин и др.
Смотри рисунок вверху.
16К20 Характеристики станка 16К20 завода “Красный пролетарий”.Типичный токарно-винторезный станок 16К20 завода “Красный пролетарий” показан на рисунке внизу. 16К20 Характеристики станка 16К20 завода “Красный пролетарий”.
Общий вид и размещение органов управления токарно-винторезного станка мод. 16К20: Рукоятки управления: 2 – сблокированная управление, 3,5,6 – установки подачи или шага нарезаемой резьбы, 7, 12 – управления частотой вращения шпинделя, 10 – установки нормального и увеличенного шага резьбы и для нарезания многозаходных резьб, 11 – изменения направления нареза-ния резьбы (лево- или правозаходной), 17 – перемещения верхних салазок, 18 – фиксации пиноли, 20 – фиксации задней бабки, 21 – штурвал перемещения пиноли, 23 – включения ускоренных перемещений суппорта, 24 – включения и выключения гайки ходового винта, 25 – управления изменением направления вращения шпинделя и его остановкой, 26 – включения и выключения подачи, 28 – поперечного перемещения салазок, 29 – включения продольной автоматической подачи, 27 – кнопка включения и выключения главного электродвигателя, 31 – продольного перемещения салазок; Узлы станка: 1 – станина, 4 – коробка подач, 8 – кожух ременной передачи главного привода, 9 – передняя бабка с главным приводом, 13 – электрошкаф, 14 – экран, 15 – защитный щиток, 16 – верхние салазки, 19 – задняя бабка, 22 – суппорт продольного перемещения, 30 – фартук, 32 – ходовой винт, 33 – направляющие станины.
Механизм подач и коробка скоростей 16К20 токарного станка.
Главный привод станка. В передней бабке размещены коробка скоростей и шпиндель, которые приводят во вращение обрабатываемую деталь при выбранных глубине резания и подаче. На рисунке показано устройство коробки скоростей, которая работает следующим образом. Заготовка зажимается в кулачковом патроне, который крепится к фланцу шпинделя 13. Вращение от электродвигателя 1 через ременную передачу 2 и муфту включения 3 передается на вал 5. Блок из трех шестерен 7, 8 и 9, расположенный на валу 5, с помощью реечной передачи связан с рукояткой 17. Этой рукояткой блок шестерен вводится в зацепление с зубчатым колесом 4 (или 10, или 11), жестко закрепленным на валу 6. Колеса 4 и 12 сопряжены соответственно с колесами 15 и 16, которые передают крутящий момент шпинделю через зубчатую муфту 14, соединенную с рукояткой 18. Если муфта передвинута вправо, то шпиндель получает вращение через зубчатое колесо 16, а если влево – через зубчатое колесо 15. Таким образом коробка скоростей обеспечивает шесть ступеней частоты вращения шпинделя. Механизм подач. Связь шпинделя и суппорта станка для обеспечения оптимального режима резания осуществляется с помощью механизма подач, состоящего из реверсирующего устройства (трензеля) и гитары, которые осуществляют изменение направления и скорости перемещения суппорта.
Привод этого механизма осуществляется от коробки скоростей через трензель (смотри рисунок справа), который состоит из четырех зубчатых колес а, б, в, г, связанных с рукояткой 19, переключением которой осуществляется реверс (т. е. изменение направления вращения) вала 20 (приводного вала суппорта). Позиции а, б, в, г, 19 и 20 (см. рисунки). При крайнем нижнем положении рукоятки 19 (положение А) зубчатые колеса а, б, в, г соединены последовательно и направление вращения вала 20 совпадает с направлением вращения шпинделя. При верхнем положении рукоятки 19 (положение В) соединены только зубчатые колеса а, в, г и направление вращения вала 20 изменяется на противоположное. В среднем положении рукоятки 19 (положение Б) зубчатые колеса б и в не соединяются с зубчатым колесом а и вал 20 не вращается.
С помощью гитары устанавливают (настраивают) зубчатые колеса с определенным передаточным отношением, обеспечивающим необходимое перемещение суппорта на один оборот шпинделя. Расстояние L между валами 1 и 2 является постоянным. На валу 2 свободно установлен приклон 3 гитары, закрепленный болтом 4. Ось 5 промежуточных колес вис можно перемещать по радиальному пазу, тем самым изменяя расстояние А между центрами колес c и d. Дуговой паз приклона 3 позволяет регулировать размер В.
Коробка подач токарного станк 16К20.
Назначение коробки подач – изменять скорости вращения ходового винта и ходового вала, чем достигается перемещение суппорта с выбранной скоростью в продольном и поперечном направлениях. Вал 14 в подшипниках 15 (сотри рисунок) коробки подач получает вращение от зубчатых колес гитары; вместе с ним вращается и имеет возможность перемещаться вдоль него зубчатое колесо П с рычагом 10. На одном конце рычага 10 вращается (на оси) зубчатое колесо 12, сопряженное с зубчатым колесом 11, а на другом – рукоятка 9, с помощью которой рычаг 10 перемещается вдоль вала 14 и может занимать любое из десяти положений (по числу зубчатых колес в механизме 1 Нортона). В каждом из таких положений рычаг 10 поворачивается и удерживается штифтом 9, который входит в соответствующие отверстия на передней стенке 7 коробки подач. При этом зубчатое колесо 12 входит в зацепление с соответствующим зубчатым колесом 13 механизма 1, в результате чего устанавливается выбранное число оборотов вала 2. Вместе с валом 2 вращается зубчатое колесо 3, которое можно перемещать вдоль него рукояткой. При перемещении вправо зубчатое колесо 3 посредством кулачковой муфты 4 соединяется с ходовым винтом 5 и передает ему вращательное движение, а при перемещении влево – входит в зацепление с зубчатым колесом 8 и передает вращательное движение ходовому валу 6.
Суппорт токарного станка 16К20
Суппорт предназначен для перемещения во время обработки режущего инструмента, закрепленного в резцедержателе. Он состоит из нижних салазок (продольного суппорта) 1, которые перемещаются по направляющим станины с помощью рукоятки 15 и обеспечивают перемещение резца вдоль заготовки. На нижних салазках по направляющим 12 перемещаются поперечные салазки (поперечный суппорт) 3, которые обеспечивают перемещение резца перпендикулярно оси вращения заготовки (детали). На поперечных салазках 3 расположена поворотная плита 4, которая закрепляется гайкой 10. По направляющим 5 поворотной плиты 4 перемещаются (с помощью рукоятки 13) верхние салазки 11, которые вместе с плитой 4 могут поворачиваться в горизонтальной плоскости относительно поперечных салазок и обеспечивать перемещение резца под углом к оси вращения заготовки (детали). Резцедержатель (резцовая головка) 6 с болтами 8 крепится к верхним салазкам с помощью рукоятки 9, которая перемещается по винту 7. Привод перемещения суппортапроизводится от ходового винта 2, от ходового вала, расположенного под ходовым винтом, или вручную. Включение автоматических подач производится рукояткой 14. Устройство поперечного суппорта показано на рисунке внизу. По направляющим продольного суппорта 1 ходовым винтом 12, оснащенным рукояткой 10, перемещаются салазки поперечного суппорта. Ходовой винт 12 закреплен одним концом в продольном суппорте 1, а другим – связан с гайкой (состоящей из двух частей 15 и 13 и клина 14), которая крепится к поперечным салазкам 9. Затягивая винт 16, раздвигают (клином 14) гайки 15 и 13, благодаря чему. выбирается зазор между ходовым винтом 12 и гайкой 15. Величину перемещения поперечного суппорта определяют по лимбу 11. К поперечному суппорту крепится (гайками 7) поворотная плита 8, вместе с которой поворачиваются верхние салазки 6 и резцедержатель 5. На некоторых станках на поперечных салазках 9 устанавливается задний резцедержатель 2 для проточки канавок, отрезки и других работ, которые могут быть выполнены перемещением поперечного суппорта, а также кронштейн 3 с щитком 4, защищающим рабочего от попадания стружки и смазочно-охлаждающей жидкости.
Резцедержатель, фартук и разъемная гайка токарного станка 16К20
Устройство резцедержателя показано на рисунке сверху. В центрирующей расточке верхних салазок 5 установлена коническая оправка 3 с резьбовым концом. На конусе оправки установлена четырехсторонняя резцовая головка 6. При вращении рукоятки 4 головка 2 перемещается вниз по резьбе конической оправки 3 и через шайбу 1 и упорный подшипник обеспечивает жесткую посадку резцовой головки 6 на конической поверхности оправки 3. От поворота при закреплении резцовая головка удерживается шариком, который заклинивается между поверхностями, образованными пазом на основании конической оправки 3 и отверстием в резцовой головке 6. При необходимости сменить позицию инструмента рукоятку 4 поворачивают против часовой стрелки. При этом головка 2 поворачивается и перемещается вверх по резьбе конической оправки 3, снимая усилие затяжки резцовой головки 6 на конусе конической оправки 3. Одновременно головка 2 поворачивает резцовую головку 6 посредством тормозных колодок, фрикционно связанных с поверхностью расточки головки 2 и соединенных с резцовой головкой 6 штифтами 7. При этом шарик, расположенный у основания конической оправки 3, не препятствует повороту резцовой головки, так как он утапливается в отверстие, сжимая пружину. Если в процессе работы рукоятка 4 (в зажатом положении) стала останавливаться в неудобном положении, то, изменяя толщину шайбы 1, можно установить ее в удобное для рабочего положение. Продольное и поперечное перемещение салазок суппорта производится через фартук 2 (смотри рисунок справа), который крепится к нижней поверхности продольного суппорта 1. Ручная продольная подача производится маховиком, который через зубчатую передачу сообщает вращение зубчатому колесу 4, катящемуся по рейке 3, закрепленной на станине 5 станка, и перемещает продольный суппорт вместе с поперечным суппортом и фартуком 2. Продольная подачасуппорта 1 от ходового винта 2 производится включением разъемной гайки рукояткой 14 (смотри рисунок слева). Разъемная гайка состоит из двух частей (1 и 2), которые перемещаются по направляющим А при повороте рукоятки 5. При этом диск 4 посредством прорезей В, расположенных эксцентрично, перемещает пальцы 3, в результате чего обе части гайки сдвигаются или раздвигаются. Если обе части гайки охватывают ходовой винт, то производится продольная подача (перемещение) суппорта; если они раздвинуты, то подача отключается.
Задняя бабка 16К20
Устройство задней бабки показано на рисунке. В корпусе 1 (при вращении винта 5 маховиком 7) перемещается пиноль 4, закрепляемая рукояткой 3. В пиноли устанавливается центр 2 с коническим хвостовиком (или инструмент). Задняя бабка перемещается по направляющим станка вручную или с помощью продольного суппорта. В рабочем неподвижном положении задняя бабка фиксируется рукояткой 6, которая соединена с тягой 8 и рычагом 9. Сила прижима рычага 9 тягой 8 к станине регулируется гайкой 11 и винтом 12. Более жесткое крепление задней бабки производится с помощью гайки 13 и винта 14, который прижимает к станине рычаг 10.
характеристики, схемы, описание и отзывы
Токарный станок 16К20 относится к категории режущих устройств. Его выпуск был установлен на заводе “Красный пролетарий” в 1973 году. Некоторые детали поставлялись Гомельским комбинатом комплектующих для машин. Современным аналогом рассматриваемой машины является блок GS526U. Основной сферой применения устройства является промышленное производство, в частном хозяйстве оно неактуально из-за его высокой стоимости и довольно внушительных габаритов.
Характеристики токарного станка 16K20
В рассматриваемом оборудовании используется резка в прямом направлении (метрическая, модульная, шаговая, дюймовая конфигурация) и некоторые другие токарные операции. Этот агрегат широко использовался в промышленности постсоветских стран. С момента выпуска модель была снята в 1989 году, но на современном рынке можно найти идентичную китайскую копию с такой же табличкой.
Основные параметры токарного станка 16K20:
- Класс точности H.
- Максимальный диаметр заготовки составляет 50 мм.
- Аналогичный показатель поворота составляет 220 мм.
- Длина обслуживаемого продукта максимальная – 2 метра.
- Пределы поперечной / продольной подачи – 1,4 / 2,8 мм / об.
- Номинальная мощность основного электродвигателя составляет 11 кВт.
- Длина / ширина / высота машины составляет 2,5 (3,79) / 1,19 / 1,5 м. Длина зависит от модификации.
- Вес оборудования с комплектным оборудованием составляет 3,6 тонны.
Управление и оборудование
Токарный станок 16К20 относится к дорогостоящему оборудованию и требует соответствующего ухода.Для начала давайте познакомимся с его руководством. Маховики и переключатели управляются в ручном режиме. Блок дополнительно оснащен центральным держателем инструмента, с помощью которого обрабатываются отверстия для механической и ручной подачи. В этом случае задняя бабка не участвует.
При перемещении регулируемых салазок ось режущего инструмента и шпиндель взаимосвязаны. Перед началом обработки необходимо вдвинуть козырек в кронштейн до упора. Ручка поперечного ползуна служит для регулировки положения оси резака.
Токарные станки по металлу 16К20 оснащены жестким упором микрометрического типа, отвечающим за продольное перемещение. По запросу мы предлагаем устройство с верхним заносом и механическим ходом. Кроме того, устройство предназначено для многопроходной нарезки резьбы и обработки многогранных деталей. Этот блок включает в себя опору для гидрокопии, коническую линейку и держатель инструмента.
Основание монолитного оборудования имеет коробчатую форму с подогреваемыми направляющими для шлифования. Коробка дополнительно служит для сборки стружки, а также является контейнером, отвечающим за охлаждение рабочей жидкости.
Неисправности
В некоторых случаях проводится ремонт или замена отдельных частей токарного станка 16K20. Чаще всего ремонт проводится в части шлифовки рамы, замены подшипников или коробки передач фрикционной муфты. В аналогичном блоке контроля передач чаще меняются зубчатые передачи и подшипники.
Крепление фартука заключается в замене маточных гаек, подшипников, полировочных направляющих. При поиске неисправностей в суппортах меняются винты, гайки, клинья с последующим шлифованием направляющих элементов.Если необходимо восстановить работоспособность задней бабки, обычно заменяют гусиное перо, растирают рабочие отверстия, выполняют соскоб направляющих деталей. Капитальный ремонт также включает замену электрического наполнения, проверку точности и геометрии агрегата, установку системы охлаждения.
Ремонт токарных станков 16K20
Подготовительный процесс включает в себя проверку оборудования на холостых оборотах. Это позволяет идентифицировать моменты шума и вибрации в разных положениях шпинделя. На этом этапе можно обработать прототип, чтобы определить состояние опор.Такое манипулирование является обязательным, так как позволяет обнаруживать дефекты, которые практически не заметны при эксплуатации.
Шлифование – это очистка всех выступающих кромок и отверстий на поверхности сердечника станка. Рама крепится на столе, фиксируясь на внутренних углах. На этом этапе необходимо точно проверить параллельное расположение узла относительно поверхности рабочего места. Это может быть сделано с помощью уровня здания. Рама фиксируется с помощью прокладок и винтов с отклонением 0.05 мм.
Извлечение направляющих элементов
Некоторые заводы проводят закалочные машины методом прокатки. В некоторых случаях дополнительно используется упрочнение, что повышает устойчивость деталей к износу. Способ ремонта выбирается исходя из степени твердости направляющих деталей и имеющейся ремонтной базы.
Наиболее популярными способами восстановления направляющих являются следующие опции:
- Строгание.
- Scaring.
- Шлифовка.
Отпугивание относится к наиболее трудоемкому процессу ремонта, даже с минимальным износом. В большинстве случаев такая манипуляция осуществляется механически, что дает определенный экономический эффект.
Шлифование обеспечивает высокую чистоту и точность обработки. Этот метод оптимален при работе с закаленными поверхностями. Шлифование позволяет увеличить производительность в несколько раз, по сравнению с операцией соскабливания. При работе с закаленными направляющими элементами потребуется дополнительная чистовая отделка.
Отзывы и цены
Токарный станок по металлу 16К20, цена на который начинается от 850 тыс. Руб. Пришла на смену устаревшей версии 1К62. Новое оборудование имеет лучшие характеристики. Пользователи среди качественных параметров оборудования выделяют следующие параметры:
- Долгий срок службы.
- Надежность.
- Точность обработки.
- Высокая производительность.
- Безопасность труда.
- Простота и удобство обслуживания.
Маркировка
Рассматриваемая машина обрабатывает ориентированные конические, цилиндрические и нестандартные поверхности. Пользователи отмечают универсальность оборудования, так как базы могут быть внешнего и внутреннего типа. Кроме того, агрегат служит для нарезания различных типов нитей. Также владельцы отмечают возможность использования станка для обработки торцевых поверхностей с помощью резцов, сверл, зенковок, метчиков и штампов.
При покупке описанного оборудования, пожалуйста, обращайте внимание на буквенно-цифровой код в названии модели.В индексе указывается, что токарный станок – это станок, цифра 6 – способность выполнять операции резания винта. Буква «К» в названии агрегата относится к поколению станков, последняя цифра обозначает максимальную высоту центров (220 мм). Наличие в названии буквы «Р» свидетельствует о повышенной точности устройства.
Наконец,
Токарный станок 16K20, обзоры которого приведены выше, относится к высокоточному оборудованию. Тем не менее время от времени, как и любая техника, она требует ремонта.Чаще всего самовосстановление заключается в замене изношенных деталей или шлифовке выбоин и острых краев. Капитальный ремонт и более серьезные ремонтные работы должны быть поручены мастеру. Необходимо проверить каретку, фартук и направляющие элементы после ремонта по уровню. В противном случае точность обработки может быть существенно снижена.
р >> ,Лучшие Продажи Токарный Инструмент С ЧПУ 93 Градусов MTJNR1616h26 MTJNR2020K16 MTJNL2020K16 MTJNR2020K16 Токарный Инструмент Доступ
Советы по покупке
1.Картина :
- Фотографии, представленные в нашем магазине, сделаны настоящими продуктами. Из-за разного освещения или из-за проблем с камерой цвет упаковки немного отличается, это будет нормально.
2. Оплата:
- Когда вы используете ESCROW в качестве оплаты, она будет надежно депонирована, мы также принимаем кредитные карты, T / T и т. Д.
- После того, как вы подтвердите доставку, деньги будут выплачены нам.
- Если у вас возникли проблемы с оплатой, пожалуйста, свяжитесь с нами как можно скорее.
3. возврат:
- 100% гарантия возврата денег на каждый товар. Пожалуйста, свяжитесь с нами в течение 24 часов после получения товара.
- Если у вас есть какие-либо вопросы о товаре, мы вернем оплату после получения товара в первоначальном состоянии.
4. Доставка:
- EMS: 5-15 дней по всему миру быстро, стоимость нормальная
- TNT: 5-15 дней по всему миру Быстро, дорого
- Воздушная Почта Столба кита: 15-60 дней по всему миру, длительный срок поставки, но низкая стоимость
5.Обратная связь :
- Ваше удовлетворение и положительные отзывы очень важны для нас. Пожалуйста, оставьте положительный отзыв и 5 звезд, если вы удовлетворены нашими товарами и услугами.
- Если у вас возникли проблемы с нашими товарами или услугами, пожалуйста, сначала свяжитесь с нами.
- Мы быстро решим проблемы и пообещаем вам 100% хорошие товары и услуги.
- Примечание:
- Из-за другой модели токарного инструмента, форма также немного отличается, после того, как вы получите действительно продукты, он будет не такой формы с изображениями, которые мы показали в нашем магазине, пожалуйста, свяжитесь с нами, прежде чем сделать заказ, спасибо.
Cld-20 Dmtg по конкурентоспособной цене
CLD-20 DMTG Токарный станок с ЧПУ по конкурентоспособной цене
Описание Токарный станок с ЧПУ по конкурентоспособной цене
1.Новая новая серия CL с наклонной станиной с ЧПУ с 9000 железная структура закаленной (50-52HRC) подземной гарантируют высокую точность и стабильность.
2. Станина станка изготовлена из термостабилизированного чугуна .
3. Доступна различная конфигурация со шпинделями от ASA 5 “до ASA 15”, мощностью до 30 кВт и длиной поворота до 3000 мм. Широкий спектр опций и принадлежностей позволяет широко использовать станок для очень точного и надежного обработка.
Основные характеристики DMTG Токарный станок с ЧПУ
1. Конструкция с высокой жесткостью конструкции :
с цельным литьем, машина имеет большую загрузочную секцию, поэтому она имеет хорошую жесткость и амортизацию, что обеспечивает высокую точность работы.
2. Высокая эффективность и низкий уровень шума:
с серводвигателем переменного тока и эффективной передачей клинового ремня, машина может избежать шума.
3. Главный шпиндель с высокой скоростью и жесткостью :
с прецизионными высокоскоростными наборами шпинделей NSK, усилием затяжки и хорошей поддержкой расстояния, шпиндель обладает высокой жесткостью и скоростью.
4. Подставка для ножей с высокой надежностью :
Гидравлический упор для ножей высокой жесткости обладает высокой надежностью и точностью повторения местоположения.
5. Машина разработана:
с шарико-винтовой передачей, пластиковые наклейки; Обладает высокой эффективностью вождения и точностью, устойчивым движением ножа.
6. Автоматическая централизованная система смазки:
Направляющий канал и шариковый винт могут смазываться непрерывно и эффективно.
7. Полная защита уплотнения :
без утечки охлаждающей жидкости, машина может обеспечить безопасную и комфортную рабочую среду.
8. Система охлаждения хладагента для удаления :
система охлаждения хладагента имеет отдельное оборудование для удаления цепей с судна и насос охлаждающей жидкости с большим расходом.
Технические параметры Токарный станок с ЧПУ по конкурентоспособной цене
Индекс | Блок | CL15 | CLD-15 | 901 мм | 400 | φ400 φ440 | ||
Максимальный диаметр резки (вал / диск) | мм 165/200 | φ165 φ260 | ||||||
Максимальная длина реза | мм 250/330 | 400 | 450 | |||||
Размер патрона | ” | 6 | 6 “ | 8″ | ||||
Форма шпинделя | ISOA2-5 | ISO A201 901-5 A2 6 | ||||||
Диапазон частоты вращения шпинделя | об / мин | 50-5000 | 50-3500 | 45-3000 | ||||
Ser шпинделя vo мощность двигателя | k w | Stepless 5.5 / 7.5 FANUCα6 / 10000i | 5.5 / 7.5 (DALIAN) | 11/15 (GUANGZHOU) | ||||
Диаметр сквозного отверстия шпинделя | мм | 46 | 46 | 901 901 901 934 901 9 9 9 9 9 9 9 9 9 9 934 901 9 мм | X 120 Z 260/340 | 360/410 | 400/460 | |
Скорость быстрого перемещения (X / Z) | м / мин | 15/18 | 15/18 | 16 / 20 | ||||
Размер машины (Д * Ш * В) | мм | 2335 * 2660 * 1850 (с удалением задней стружки) | 2670 × 1500 × 1850 | 3165 * 1655 * 1760 | ||||
3635 * 1460 * 1850 (с удалением боковой стружки) | ||||||||
Масса нетто машины | кг | 3300 | 2900 | 3900 |
DMTC Packagin г
,