Плитка для пайки smd — Строим дом
Содержание
- Пайка SMD компонентов в домашних условиях
- Ошибки и основные принцип пайки
- Пайка в заводских условиях
- Необходимые материалы и инструменты
- Как паять SMD-компоненты?
- Порядок работ
- Как паять при помощи фена?
- Как паять SMD компоненты — краткая инструкция с фотографиями
- Пайка SMD в корпусе 1206, 0805, MELF, MINIMELF и т. д.
- Припаять диод в корпусе MELF
- Пайка SMD в корпусе SO8, SO14, SO28 и т. д.
- Пайка SMD в корпусе TQFP32, TQFP44, TQFP64 и т. д.
Пайка SMD компонентов в домашних условиях
Многие задаются вопросом, как правильно паять SMD-компоненты. Но перед тем как разобраться с этой проблемой, необходимо уточнить, что же это за элементы. Surface Mounted Devices – в переводе с английского это выражение означает компоненты для поверхностного монтажа. Главным их достоинством является большая, нежели у обычных деталей, монтажная плотность. Этот аспект влияет на использование SMD-элементов в массовом производстве печатных плат, а также на их экономичность и технологичность монтажа. Обычные детали, у которых выводы проволочного типа, утратили свое широкое применение наряду с быстрорастущей популярностью SMD-компонентов.
Ошибки и основные принцип пайки
Некоторые умельцы утверждают, что паять такие элементы своими руками очень сложно и довольно неудобно. На самом деле, аналогичные работы с ТН-компонентами проводить намного труднее. И вообще эти два вида деталей применяются в различных областях электроники. Однако многие совершают определенные ошибки при пайке SMD-компонентов в домашних условиях.
SMD-компоненты
Главной проблемой, с которой сталкиваются любители, является выбор тонкого жала на паяльник. Это связано с существованием мнения о том, что при паянии обычным паяльником можно заляпать оловом ножки SMD-контактов. В итоге процесс паяния проходит долго и мучительно. Такое суждение нельзя считать верным, так как в этих процессах существенную роль играет капиллярный эффект, поверхностное натяжение, а также сила смачивания. Игнорирование этих дополнительных хитростей усложняет выполнение работы своими руками.
Пайка SMD-компонентов
Чтобы правильно паять SMD-компоненты, необходимо придерживаться определенных действий. Для начала прикладывают жало паяльника к ножкам взятого элемента. Вследствие этого начинает расти температура и плавиться олово, которое в итоге полностью обтекает ножку данного компонента. Этот процесс называется силой смачивания. В это же мгновение происходит затекание олова под ножку, что объясняется капиллярным эффектом. Вместе со смачиванием ножки происходит аналогичное действие на самой плате. В итоге получается равномерно залитая связка платы с ножками.
Контакта припоя с соседними ножками не происходит из-за того, что начинает действовать сила натяжения, формирующая отдельные капли олова. Очевидно, что описанные процессы протекают сами по себе, лишь с небольшим участием паяльщика, который только разогревает паяльником ножки детали. При работе с очень маленькими элементами возможно их прилипание к жалу паяльника. Чтобы этого не произошло, обе стороны припаивают по отдельности.
Пайка в заводских условиях
Этот процесс происходит на основе группового метода. Пайка SMD-компонентов выполняется с помощью специальной паяльной пасты, которая равномерно распределяется тончайшим слоем на подготовленную печатную плату, где уже имеются контактные площадки. Этот способ нанесения называется шелкографией. Применяемый материал по своему виду и консистенции напоминает зубную пасту. Этот порошок состоит из припоя, в который добавлен и перемешан флюс. Процесс нанесения выполняется автоматически при прохождении печатной платы по конвейеру.
Заводская пайка SMD-деталей
Далее установленные по ленте движения роботы раскладывают в нужном порядке все необходимые элементы. Детали в процессе передвижения платы прочно удерживаются на установленном месте за счет достаточной липкости паяльной пасты. Следующим этапом происходит нагрев конструкции в специальной печи до температуры, которая немного больше той, при которой плавится припой. В итоге такого нагрева происходит расплавление припоя и обтекание его вокруг ножек компонентов, а флюс испаряется. Этот процесс и делает детали припаянными на свои посадочные места. После печки плате дают остыть, и все готово.
Необходимые материалы и инструменты
Для того чтобы своими руками выполнять работы по впаиванию SMD-компонентов, понадобится наличие определенных инструментов и расходных материалов, к которым можно отнести следующие:
- паяльник для пайки SMD-контактов;
- пинцет и бокорезы;
- шило или игла с острым концом;
- припой;
- увеличительное стекло или лупа, которые необходимы при работе с очень мелкими деталями;
- нейтральный жидкий флюс безотмывочного типа;
- шприц, с помощью которого можно наносить флюс;
- при отсутствии последнего материала можно обойтись спиртовым раствором канифоли;
- для удобства паяния мастера пользуются специальным паяльным феном.
Пинцет для установки и снятия SMD-компонентов
Использование флюса просто необходимо, и он должен быть жидким. В таком состоянии этот материал обезжиривает рабочую поверхность, а также убирает образовавшиеся окислы на паяемом металле. В результате этого на припое появляется оптимальная сила смачивания, и капля для пайки лучше сохраняет свою форму, что облегчает весь процесс работы и исключает образование «соплей». Использование спиртового раствора канифоли не позволит добиться значимого результата, да и образовавшийся белый налет вряд ли удастся убрать.
Припой для пайки
Очень важен выбор паяльника. Лучше всего подходит такой инструмент, у которого возможна регулировка температуры. Это позволяет не переживать за возможность повреждения деталей перегревом, но этот нюанс не касается моментов, когда требуется выпаивать SMD-компоненты. Любая паяемая деталь способна выдерживать температуру около 250–300 °С, что обеспечивает регулируемый паяльник. При отсутствии такого устройства можно воспользоваться аналогичным инструментом мощностью от 20 до 30 Вт, рассчитанным на напряжение 12–36 В.
Использование паяльника на 220 В приведет к не лучшим последствиям. Это связано с высокой температурой нагрева его жала, под действием которой жидкий флюс быстро улетучивается и не позволяет эффективно смачивать детали припоем.
Специалисты не советуют пользоваться паяльником с конусным жалом, так как припой трудно наносить на детали и тратится уйма времени. Наиболее эффективным считается жало под названием «Микроволна». Очевидным его преимуществом является небольшое отверстие на срезе для более удобного захвата припоя в нужном количестве. Еще с таким жалом на паяльнике удобно собирать излишки пайки.
Жало для паяльника «Микроволна»
Использовать припой можно любой, но лучше применять тонкую проволочку, с помощью которой комфортно дозировать количество используемого материала. Паяемая деталь при помощи такой проволочки будет лучше обработана за счет более удобного доступа к ней.
Как паять SMD-компоненты?
Порядок работ
Процесс пайки при тщательном подходе к теории и получении определенного опыта не является сложным. Итак, можно всю процедуру разделить на несколько пунктов:
- Необходимо поместить SMD-компоненты на специальные контактные площадки, расположенные на плате.
- Наносится жидкий флюс на ножки детали и нагревается компонент при помощи жала паяльника.
- Под действием температуры происходит заливание контактных площадок и самих ножек детали.
- После заливки отводится паяльник и дается время на остывание компонента. Когда припой остыл — работа выполнена.
Процесс пайки SMD-компонентов
При выполнении аналогичных действий с микросхемой процесс пайки немного отличается от вышеприведенного. Технология будет выглядеть следующим образом:
- Ножки SMD-компонентов устанавливаются точно на свои контактные места.
- В местах контактных площадок выполняется смачивание флюсом.
- Для точного попадания детали на посадочное место необходимо сначала припаять одну ее крайнюю ножку, после чего компонент легко выставляется.
- Дальнейшая пайка выполняется с предельной аккуратностью, и припой наносится на все ножки.
Излишки припоя устраняются жалом паяльника.
Паяльник с острым жалом 24 В.
Как паять при помощи фена?
При таком способе пайки необходимо смазать посадочные места специальной пастой. Затем на контактную площадку укладывается необходимая деталь — помимо компонентов это могут быть резисторы, транзисторы, конденсаторы и т. д. Для удобства можно воспользоваться пинцетом. После этого деталь нагревается горячим воздухом, подаваемым из фена, температурой около 250º C. Как и в предыдущих примерах пайки, флюс под действием температуры испаряется и плавится припой, тем самым заливая контактные дорожки и ножки деталей. Затем отводится фен, и плата начинает остывать. При полном остывании можно считать пайку оконченной.
Фен для паяния мелких деталей
Источник статьи: http://lampagid.ru/elektrika/komponenty/pajka-smd
Как паять SMD компоненты — краткая инструкция с фотографиями
Возможно, вы в ужасе от небольшого размера SMD компонентов, которые обычно используются в современной электронике. Но этого не стоит бояться! Вопреки расхожему мнению, пайка SMD компонентов намного проще, чем пайка THT элементов (англ. Through-hole Technology, THT — технология монтажа в отверстия).
У SMD компонентов, несомненно, есть много преимуществ:
- низкая цена;
- небольшие размеры — на одной поверхности можно разместить больше элементов;
- не нужно сверлить отверстия, а в крайних случаях вообще ничего не надо сверлить;
- вся пайка происходит на одной стороне, и нет необходимости постоянно ее переворачивать;
Итак, давайте посмотрим, что нам необходимо для пайки SMD компонентов:
- Паяльник – подойдет обычный, не дорогой паяльник.
- Пинцет — можно купить в аптеке.
- Тонкий припой — например, диаметром 0,5 мм.
- Флюс — канифоль растворенная в этиловом спирте или вы можете купить готовый флюс в шприце для пайки SMD деталей.
И что? Это все? Да! Для пайки большинства SMD компонентов не требуется никакого специального оборудования!
Пайка SMD в корпусе 1206, 0805, MELF, MINIMELF и т.
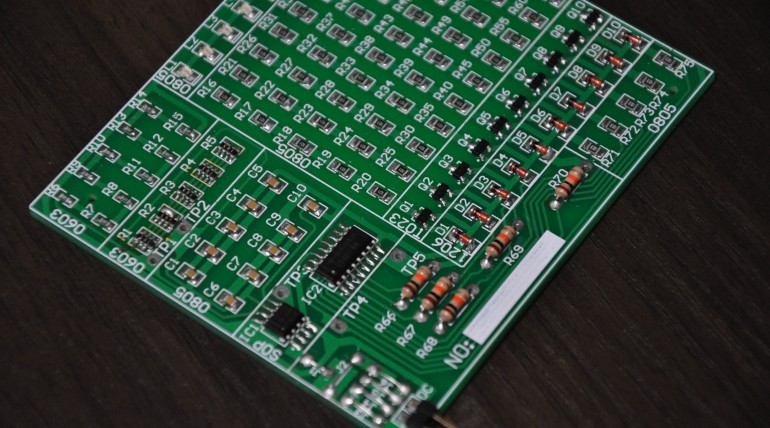
В этих корпусах производят резисторы, конденсаторы, диоды и светодиоды. Такие элементы поставляются в бумажных или пластиковых лентах, адаптированных к автоматической сборке. Такие ленты наматывают на барабаны и обычно содержат 5000 штук элементов, хотя, может быть, даже 20000 в одной катушке.
Такие катушки устанавливаются в сборочные машины, благодаря чему весь процесс производства может быть полностью автоматизирован. Роль человека в подобном производстве — это только установка новых катушек и контроль качества готовой продукции.
В названии корпуса закодированы размеры SMD компонента. Например, 1206 означает, что длина элемента составляет 120 mils, а ширина — 60 mils. Mils составляет 1/1000 дюйма или 0,0254 мм.
На практике чаще всего используются корпуса 1206, 0805, 0603, 0402, 0201, 01005. Для ручного монтажа идеально подходит корпус 1206, но даже 0402 можно паять вручную, хотя это довольно утомительно. Элементы MELF имеют цилиндрическую форму и чаще всего являются диодами или резисторами. Давайте теперь перейдем к делу!
Припаять диод в корпусе MELF
Прежде всего, мы должны облудить одну из контактных площадок. Мы обрабатываем площадку флюсом и прикасаемся к ней кончиком паяльника, и через некоторое время наносим припой. Припой должен немедленно расплавиться и равномерно покрыть всю площадку. Все, что вам нужно, это тонкий слой припоя — лучше, чтобы его было мало, чем слишком много.
Далее мы берем SMD компонент за боковые стороны и кладем его на место пайки. После этого следует разогреть ранее облуженную площадку и придавить в нее SMD компонент. Припой должен равномерно охватить вывод компонент.
Последний этап — пайка второго контакта. Здесь нет ничего сложного — мы прикасаемся к контакту и к площадке жалом паяльника, затем прикладываем к нему припой, который быстро плавиться, обволакивая место пайки ровным слоем.
На следующих рисунках показано, как припаивается конденсатор в корпусе 1206. Последовательность операций идентична приведенной выше.
Пайка SMD в корпусе SO8, SO14, SO28 и т. д.
В корпусах SO встречается большинство простых интегральных микросхем, такие как логические элементы, регистры, мультиплексоры, операционные усилители и компараторы. Они имеют относительно большой шаг выводов: 50mils. Вы можете легко припаять их без специального оборудования.
Первый шаг — лужение контактной площадки, расположенной в одном из углов. Мы касаемся площадки паяльником, нагреваем ее, а затем наносим немного припоя.
Далее берем микросхему с помощью пинцета и кладем ее на место пайки. Аналогично примеру с 1206, мы разогреваем облуженное поле, чтобы микросхема прилипала к плате. Если микросхема сдвинулась, то снова разогрейте контакт и отрегулируйте ее положение.
Если микросхема установлена правильно и держится надежно, то пропаиваем оставшиеся ножки. Прикладываем к ним жало паяльника, прогреваем, а затем прикасаемся к ним припоем, который, расплавляясь, обволакивает их. Чтобы сделать пайку качественнее следует применить флюс.
Пайка SMD в корпусе TQFP32, TQFP44, TQFP64 и т. д.
В принципе компоненты в корпусе TQFP тоже можно припаять без флюса, так же, как и SO, но мы хотим здесь наглядно показать, что дает активный флюс. Вы можете купить его в шприцах с надписью FLUX.
В следующем примере мы припаяем микросхему в корпус TQFP44.
Начнем с смазывания всех паяльных площадок флюсом. Флюс имеет густую консистенцию и очень липкий. Будьте осторожны, чтобы не испачкаться, потому что вы сможете отмыть его только растворителем.
Мы не будем предварительно облуживать, как писали ранее. Мы ставим микросхему сразу на ее место и устанавливаем в правильном положении.
До этого пайка осуществлялась острым жалом. Теперь продемонстрируем пайку жалом в форме ножа, которым одновременно можно припаять сразу несколько ножек.
Набираем немного припоя на кончике жала, а затем касаемся двух ножек в противоположных углах микросхемы. Таким образом, мы фиксируем микросхему, чтобы она не сдвигалась при пайке остальных ножек.
Теперь важно иметь на жале паяльника небольшое количество припоя. Если его много, протрите жало влажной губкой. Мы касаемся кончиком жала ножек, которые еще не пропаяны. Не следует опасаться замыкания ножек, поскольку благодаря использованию активного флюса этого можно избежать.
Если все-таки где-то произошло замыкание ножек припоем, то достаточно очистить жало паяльника, а затем распределить припой по соседним ножкам, или вовсе убрать его в сторону.
В заключение, нужно смыть активный флюс, так как через некоторое время он может окислить медь на плате. Для этого можно использовать этиловый или изопропиловый спирт.
Источник статьи: http://fornk.ru/3948-kak-payat-smd-komponenty-kratkaya-instrukciya-s-fotografiyami/
Размеры и типы корпусов SMD-компонентов
ASM | SIPLACE E ꜛ универсальный автомат установки компонентов
ASM | SIPLACE SX ꜛ максимально гибкий автомат установки компонентов
ASM | SIPLACE X ꜛ автомат установки компонентов
FRITSCH | placeALL 620 ꜛ автомат установки компонентов
FRITSCH | placeALL 520 ꜛ автомат установки компонентов
FRITSCH МР 904.
FRITSCH SM902 PRO ꜛ полуавтомат установки компонентов
FRITSCH LM 900 ꜛ установщик компонентов начального уровня
FRITSCH LM 901 ꜛ манипулятор установки компонентов
Глобал ИнжинирингПроизводственные технологии
Поверхностный монтаж — технология изготовления электронных изделий на печатных платах, которую также называют ТМП (технология монтажа на поверхность), SMT (англ. surface mount technology) и SMD-технология (от англ. surface mounted device — прибор, монтируемый на поверхность).
Электронные компоненты для поверхностного монтажа («чип-компоненты» или SMD-компоненты) выпускаются различных размеров и в разных типах корпусов. Таблица типоразмеров и SMD-корпусов поможет быстро получить необходимые данные.
Двухконтактные компоненты: прямоугольные, пассивные (резисторы и конденсаторы)
Обозначение типоразмера состоит из четырех цифр. Две первые соответствуют округленно длине L в принятой системе измерения (либо метрической, либо дюймовой), а две последние — ширине W.
Типоразмер (дюймовая система) | Размер (мм) | |
008004 | 0201 | 0.25×0.125 |
009005 | 03015 |
0.![]() |
01005 | 0402 | 0.4×0.2 |
0201 | 0603 | 0.6×0.3 |
0402 | 1005 | 1.0×0.5 |
0603 | 1608 | 1.6×0.8 |
0805 | 2012 | 2.0×1.25 |
1008 | 2520 | 2.5×2.0 |
1206 | 3216 |
3.![]() |
1210 | 3225 | 3.2×2.5 |
1806 | 4516 | 4.5×1.6 |
1812 | 4532 | 4.5×3.2 |
1825 | 4564 | 4.5×6.4 |
2010 | 5025 | 5.0×2.5 |
2512 | 6332 | 6.3×3.2 |
2725 | 6863 |
6.![]() |
2920 | 7451 | 7.4×5.1 |
Двухконтактные компоненты: цилиндрические, пассивные (резисторы и диоды) в корпусе MELF
корпус | размеры (мм) и другие параметры |
Melf (MMB) 0207 | L = 5,8 мм, Ø = 2,2 мм, 1,0 Вт, 500 В |
MiniMelf (MMA) 0204 | L = 3,6 мм, Ø = 1,4 мм, 0,25 Вт, 200 В |
MicroMelf (MMU) 0102 |
L = 2,2 мм, Ø = 1,1 мм, 0,2 Вт, 100 В |
Двухконтактные компоненты: танталовые конденсаторы
тип | размеры (мм) |
A (EIA 3216-18) | 3,2 × 1,6 × 1,6 |
B (EIA 3528-21) | 3,5 × 2,8 × 1,9 |
C (EIA 6032-28) | 6,0 × 3,2 × 2,2 |
D (EIA 7343-31) | 7,3 × 4,3 × 2,4 |
E (EIA 7343-43) | 7,3 × 4,3 × 4,1 |
Двухконтактные компоненты: диоды (англ. small outline diode, сокр. SOD)
обозначение | размеры (мм) |
SOD-323 | 1,7 × 1,25 × 0,95 |
SOD-123 | 2,68 × 1,17 × 1,60 |
Трёхконтактные компоненты: транзисторы с тремя короткими выводами (SOT)
обозначение | размеры (мм) |
SOT-23 | 3 × 1,75 × 1,3 |
SOT-223 | 6,7 × 3,7 × 1,8 |
DPAK (TO-252) | корпус (трёх- или пятиконтактные варианты), разработанный компанией Motorola для полупроводниковых устройств с большим выделением тепла |
D2PAK (TO-263) | корпус (трёх-, пяти-, шести-, семи- или восьмивыводные варианты), аналогичный DPAK, но больший по размеру (как правило габариты корпуса соответствуют габаритам TO220) |
D3PAK (TO-268) | корпус, аналогичный D2PAK, но ещё больший по размеру |
Многоконтактные компоненты: выводы в две линии по бокам
обозначение | расстояние между выводами (мм) |
ИС — с выводами малой длины (англ.![]() |
1,27 |
TSOP — (англ. thin small-outline package) тонкий SOIC (тоньше SOIC по высоте) | 0,5 |
SSOP — усаженый SOIC | 0,65 |
TSSOP — тонкий усаженый SOIC | 0,65 |
QSOP — SOIC четвертного размера | 0,635 |
VSOP — QSOP ещё меньшего размера | 0,4; 0,5 или 0,65 |
Многоконтактные компоненты: выводы в четыре линии по бокам
обозначение | расстояние между выводами (мм) |
PLCC, CLCC — ИС в пластиковом или керамическом корпусе с выводами, загнутыми под корпус с виде буквы J | 1,27 |
QFP — (англ.![]() |
разные размеры |
LQFP — низкопрофильный QFP |
1,4 мм в высоту разные размеры |
PQFP — пластиковый QFP (44 или более вывода) | разные размеры |
CQFP — керамический QFP (сходный с PQFP) | разные размеры |
TQFP — тоньше QFP | тоньше QFP |
PQFN — силовой QFP | нет выводов, площадка для радиатора |
Многоконтактные компоненты: массив выводов
обозначение | расстояние между выводами (мм) |
BGA — (англ.![]() |
1,27 |
LFBGA — низкопрофильный FBGA, квадратный или прямоугольный, шарики припоя | 0,8 |
CGA — корпус с входными и выходными выводами из тугоплавкого припоя | разные размеры |
CCGA — керамический CGA | разные размеры |
μBGA — (микро-BGA) — массив шариков | расстояние между шариками менее 1 мм |
FCBGA — (англ. flip-chip ball grid array) массив шариков на подложке к подложке припаян кристалл с теплораспределителем |
разные размеры |
PBGA — массив шариков, кристалл внутри пластмассового корпуса | разные размеры |
LLP — безвыводный корпус | — |
Обратите внимание:
Компания «Глобал Инжиниринг» предлагает большой каталог с оборудованием для поверхностного монтажа. У нас вы найдёте: трафаретные принтеры; системы дозирования; оборудование для монтажа компонентов; печи конвекционной и парофазной пайки; установки лужения; приборы для подготовки паяльной пасты; конвеерные системы и многое другое. // Приобретая оборудование, вы получаете 100% гарантийную и пост-гарантийную поддержку, помощь в приобретении запасных частей и расходных материалов, программы обучения и всю техническую информацию.
Возврат к списку статей
Процесс пайки оплавлением – ПРОЦЕСС МОНТАЖА ПОВЕРХНОСТИ
Пайка оплавлением является наиболее широко используемым методом крепления компонентов поверхностного монтажа к печатным платам (PCBs). Целью процесса является формирование приемлемых паяных соединений путем предварительного нагрева компонентов/платы/паяльной пасты, а затем плавления припоя без повреждения из-за перегрева.Ключевыми аспектами, обеспечивающими эффективный процесс пайки оплавлением, являются следующие:-
- Подходящая машина
- Приемлемый профиль оплавления
- Конструкция печатной платы/компонента
- Тщательно напечатанная печатная плата с использованием хорошо разработанного трафарета
- Повторяемое размещение компонентов для поверхностного монтажа
- Высококачественная печатная плата, компоненты и паяльная паста

Скорость линии можно рассчитать, как показано ниже:-
Скорость линии (минимальная) = Доски в минуту x Длина одной доски Коэффициент нагрузки (расстояние между досками)
Важно учитывать повторяемость Процесс и поэтому «Коэффициент нагрузки» обычно указывается производителем машины, расчет показан ниже:-
Чтобы иметь возможность выбрать печь оплавления правильного размера, скорость процесса (определенная ниже) должна быть больше, чем минимальная расчетная линия скорость.
Скорость процесса = Длина нагрева камеры печи Время выдержки процесса
Ниже приведен пример расчета для определения правильного размера печи:-
Сборщик SMT хочет производить 8-дюймовые платы со скоростью 180 в час.

досок в минуту = 3 (180/час)
Длина на плату = 8 дюймов
Коэффициент нагрузки = 0,8 (расстояние между платами 2 дюйма)
Время ожидания процесса = 4 минуты (8 дюймов/доска)
0,8
Следовательно, печь оплавления должна иметь скорость процесса не менее 30 дюймов в минуту.
Определите длину обогреваемой камеры печи с помощью уравнения скорости процесса:
30 дюймов/мин = Длина нагреваемой камеры печи
4 минуты 10 футов)
Обратите внимание, что общая длина печи превышает 10 футов, включая секцию охлаждения. и конвейерные загрузочные секции. Расчет производится для ДЛИНЫ ОБОГРЕВА – НЕ ДЛЯ ОБЩЕЙ ДЛИНЫ ПЕЧИ.

1. Тип конвейера. Можно выбрать машину с сетчатым конвейером, но, как правило, используются краевые конвейеры, чтобы печь работала в линию и могла обрабатывать двухсторонние сборки. В дополнение к краевому конвейеру обычно включается опора для центральной платы, чтобы предотвратить провисание печатной платы во время процесса оплавления — см. ниже. При обработке двусторонних сборок с использованием системы краевого конвейера необходимо соблюдать осторожность, чтобы не повредить компоненты на нижней стороне.
2. Замкнутый контур управления скоростью конвекционных вентиляторов. Существуют определенные корпуса для поверхностного монтажа, такие как SOD323 (см. вставку), которые имеют небольшое отношение площади контакта к массе, что может привести к нарушению процесса оплавления. Регулирование скорости вентиляторов с замкнутым контуром является рекомендуемым вариантом для сборок, в которых используются такие детали. 3. Автоматическое управление шириной конвейера и центральной опоры. Некоторые станки имеют ручную регулировку ширины, но если нужно обработать много различных сборок с различной шириной печатных плат, рекомендуется использовать эту опцию для обеспечения согласованности процесса.
Типичный профиль пайки оплавлением обычно состоит из четырех этапов: предварительный нагрев, замачивание, оплавление и охлаждение. Основная цель состоит в том, чтобы передать сборке достаточно тепла, чтобы расплавить припой и сформировать паяные соединения, не вызывая повреждения компонентов или печатной платы.
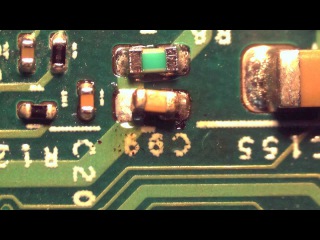
Предварительный нагрев — На этом этапе все компоненты, печатная плата и припой нагреваются до заданной температуры выдержки или выдержки, стараясь не нагреваться слишком быстро (обычно не более 2ºC/сек — см. техническое описание паяльной пасты). Слишком быстрое нагревание может привести к таким дефектам, как растрескивание компонентов и разбрызгивание паяльной пасты, что приведет к образованию шариков припоя во время оплавления. Замачивание . Целью этого этапа является обеспечение требуемой температуры всех компонентов перед входом в стадию оплавления. Замачивание обычно длится от 60 до 120 секунд в зависимости от «дифференциала масс» сборки и типов присутствующих компонентов. Чем эффективнее теплопередача во время фазы замачивания, тем меньше времени требуется.
Оплавление . На этом этапе температура в печи оплавления повышается выше точки плавления паяльной пасты, в результате чего она превращается в жидкость.

Несмотря на то, что во время оплавления важно не нагревать слишком много, не менее важно, чтобы профиль оплавления был достаточно горячим. При обработке сборок с установленными BGA важно приложить достаточно тепла, чтобы расплавить/оплавить шарики BGA, чтобы обеспечить хорошее паяное соединение. Это известно как двойная капля, и его можно увидеть в видео ниже:
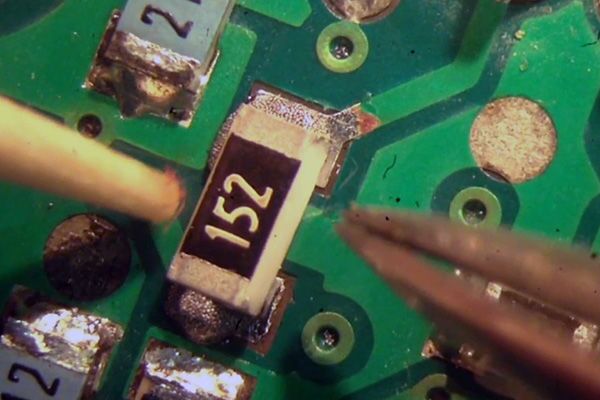
Охлаждение — это просто стадия, во время которой сборка охлаждается, но важно не охлаждать сборку слишком быстро — обычно рекомендуемая скорость охлаждения не должна превышать 3ºC/сек. Существует ряд аспектов конструкции печатной платы, которые влияют на то, насколько хорошо сборка будет оплавляться. Примером может служить размер дорожек, соединяющихся с посадочным местом компонента — если дорожка, соединяющаяся с одной стороной посадочного места компонента, больше, чем с другой, это может привести к тепловому дисбалансу, вызывающему «надгробную плиту», как показано ниже: Другим примером является «балансировка меди» — во многих конструкциях печатных плат используются медные участки большой площади, и если печатная плата помещается в панель для облегчения производственного процесса, это может привести к дисбалансу меди. Это может привести к деформации панели во время оплавления, поэтому рекомендуемое решение состоит в том, чтобы добавить «балансировку меди» к ненужным участкам панели, как показано ниже:
Более ранние этапы процесса в сборке для поверхностного монтажа имеют решающее значение для эффективный процесс пайки оплавлением. Процесс печати паяльной пасты является ключевым для обеспечения равномерного нанесения паяльной пасты на печатную плату. Любая ошибка на этом этапе приведет к нежелательным результатам, поэтому необходим полный контроль над этим процессом наряду с эффективным дизайном трафарета.
Программы размещения компонентов могут быть созданы с использованием машин для захвата и размещения, но этот процесс не так точен, как получение информации о центроидах непосредственно из данных Gerber для печатных плат. Довольно часто эти данные центроида экспортируются из программного обеспечения для проектирования печатных плат, но иногда они недоступны, поэтому услуга по созданию файла центроида из данных Gerber предлагается компанией Surface Mount Process.
Все машины для размещения компонентов будут иметь указанную «точность размещения», например:-
от 35 мкм (QFP) до 60 мкм (чипы) при 3 сигма
Также важно правильно выбрать сопло для типа компонента, чтобы быть размещены – диапазон различных насадок для размещения компонентов можно увидеть ниже:-
Этот процесс имеет чрезвычайно высокий коэффициент теплопередачи и поэтому хорошо подходит для компонентов с высокой тепловой массой . Кроме того, легко управлять и униформа . Это означает, что структуры с мелким шагом , а также чувствительные и дорогие компоненты также могут быть надежно спаяны. Светодиоды, например, очень чувствительны к температурным повреждениям — риск этого значительно снижается при пайке в паровой фазе. Поточные системы пайки в паровой фазе для серийного производства доступны для промышленности. Они значительно более энергоэффективны, чем упомянутые системы с полной конвекцией. Для области прототипирования существуют компактные системы пайки паровой фазой, которые представляют собой интересную альтернативу столь же гибким и компактным станциям горячего воздуха.
Внутри системы находится жидкая среда. Чаще всего используется перфторполиэфир, фторированный углеводород, также известный под торговой маркой Galden . Эта среда кипит при определенной температуре. Есть разные типы Galden на выбор. Обычно используемый Galden LS230 кипит ровно при 230°C, что соответствует 446°F. Эта температура кипения ограничивает максимальную температуру, которая может быть достигнута в процессе.
Это очень важно знать при настройке Температурный профиль для процесса. Этот профиль пайки определяет, в какое время какая температура должна преобладать. Также необходимо учитывать требования к используемым компонентам и паяльной пасте. При настройке температурного режима необходимо учитывать как чувствительные к температуре компоненты, такие как светодиоды, так и большие тепловые массы.
При кипении Галдена возникает пар, который тяжелее воздуха. Затем печатная плата подвергается воздействию этого пара. Среда конденсируется на поверхности сборки. Пар вытесняет почти весь кислород, что предотвращает окисление на сборке. В то время как Galden конденсируется, он равномерно передает тепловую энергию в сборку. Это нагревает печатную плату, компоненты и паяльную пасту, нанесенную между ними. Паяльная паста расплавится, как только печатная плата достигнет соответствующей температуры, которая зависит от используемой паяльной пасты. Обычно это происходит около 180°C, что соответствует 356°F. Когда температура снижается, в технологической камере все еще остается много пара. Важно, чтобы система оставалась закрытой, пока пар не сконденсируется и гальден снова не станет жидким. Это также помогает снизить затраты, потому что Galden довольно дорог. Чем дольше система может остывать, тем больше конденсата Galden может быть повторно использовано в следующих циклах пайки.
Мощная система охлаждения является ключом к сокращению периода ожидания между несколькими циклами пайки. Как только температура значительно упадет, паяльная паста затвердеет, и компоненты будут припаяны к печатной плате.
Идеальный профиль припоя для каждой сборки существует. Процесс пайки оплавлением может занять много времени, но он необходим для обеспечения полной пайки всех компонентов без их повреждения. Это еще более важно при профилировании бессвинцовой сборки, поскольку допустимый диапазон температур уменьшен до диапазона оловянно-свинцовой сборки. Использование тщательно разработанного профиля приведет к воспроизводимому процессу, который будет постоянно давать требуемые результаты. Это стоит дополнительного времени и усилий.
Шокирующие статистические данные о том, что в электронной промышленности многие операции по поверхностному монтажу, особенно в секторе субподрядного производства, работают всего на 20% с эффективностью.
Есть много причин, которые влияют на эту цифру, но в основном это означает, что используется только 20% капитальных вложений. С финансовой точки зрения это приведет к более высокой стоимости владения и более медленному возврату инвестиций. Для клиента это может привести к увеличению времени выполнения заказа для его продукта, и, следовательно, бизнес не будет столь конкурентоспособным на рынке.
При эффективности производства на этом уровне будет много побочных эффектов, которые повлияют на бизнес, таких как большие размеры партий, больше деталей на складе, больше сборок в WIP (незавершенном производстве) и более медленное время реакции на клиента изменить требования.
Имея все это в виду, существует сильный стимул для повышения эффективности при сохранении качества.
Можно ли припаивать SMD-компоненты волной припоя без держателя
SMD (устройство поверхностного монтажа) отличается от SMT (технология поверхностного монтажа).Пайка волной припоя: основным объектом пайки является электронная часть традиционного штекера сквозного отверстия (PTH), поскольку вставная часть размещается над платой печатной платы, а ножки припоя выступают под платой через сквозные отверстия. . Нижняя часть печатной платы скользит по поверхности припоя при пайке волной припоя, так что расплавленный припой прилипает к выводам деталей и контактным площадкам сквозных отверстий печатной платы, завершая процесс пайки.
1. Можно ли также припаивать детали SMD? Упадут ли детали в жестяную печь?
Если детали SMD нужно припаять волной, красный клей необходимо прикрепить к печатной плате в нижней точке детали, а затем красный клей отверждается в печи (непосредственно с использованием печи оплавления).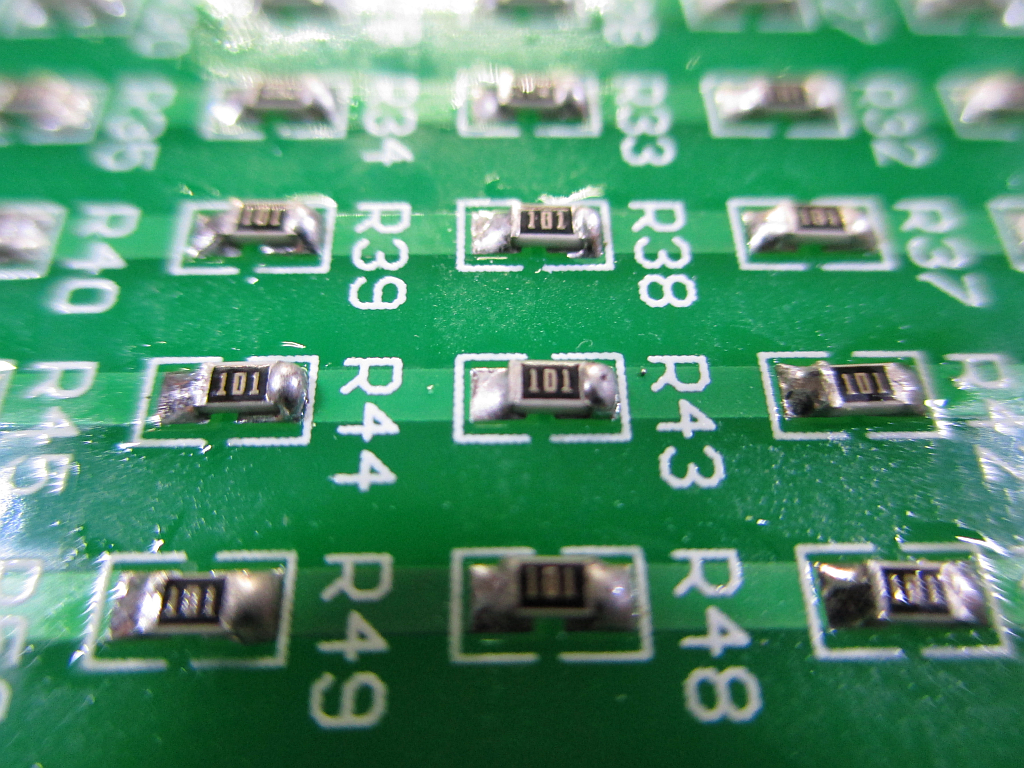
Итак, можно ли использовать паяльную пасту вместо красного клея при пайке деталей поверхностного монтажа волной?
Конечно, нет. Поскольку паяльная паста и состав припоя при пайке волной припоя почти одинаковы, температура плавления почти одинакова. То есть при пайке волной припоя паяльная паста плавится. Если красного клея нет, детали SMD попадут прямо в печь для пайки. .
Можно ли одновременно печатать паяльной пастой и красным клеем?
Этот двойной процесс осуществим, и его цель состоит в том, чтобы уменьшить проблемы пайки волной и воздушной пайки. Поскольку при пайке волной припоя может возникнуть эффект тени, паяные соединения или детали, находящиеся под тенью, не могут легко соприкасаться с припоем и не могут образовывать хороший припой. Однако для этого требуется дополнительный процесс, а стоимость увеличивается.
Во-вторых, паяльная паста может оставаться под красным клеем, вызывая неравномерное качество бомбы, потому что при печати паяльной пасты иногда остаточная паяльная паста оставляет пятна на обратной стороне возле отверстия трафарета. Нанесите красный клей на то место, где осталась паяльная паста, паяльная паста не будет легко удаляться припоем в печи для пайки волной припоя. Остатки припоя могут вызвать короткое замыкание или из-за воды после периода использования Электромиграция газа и разности потенциалов.
2. Какие детали SMD можно паять волной припоя?
Детали SMD, такие как BGA, разъем, трансформатор, QFN и т. д., нельзя паять волной припоя, потому что припой не может полностью проникнуть в нижнюю часть детали (BGA и QFN) для формирования паяного соединения, а некоторые детали имеют проблемы с коротким замыканием или повреждены части (разъемы и трансформаторы).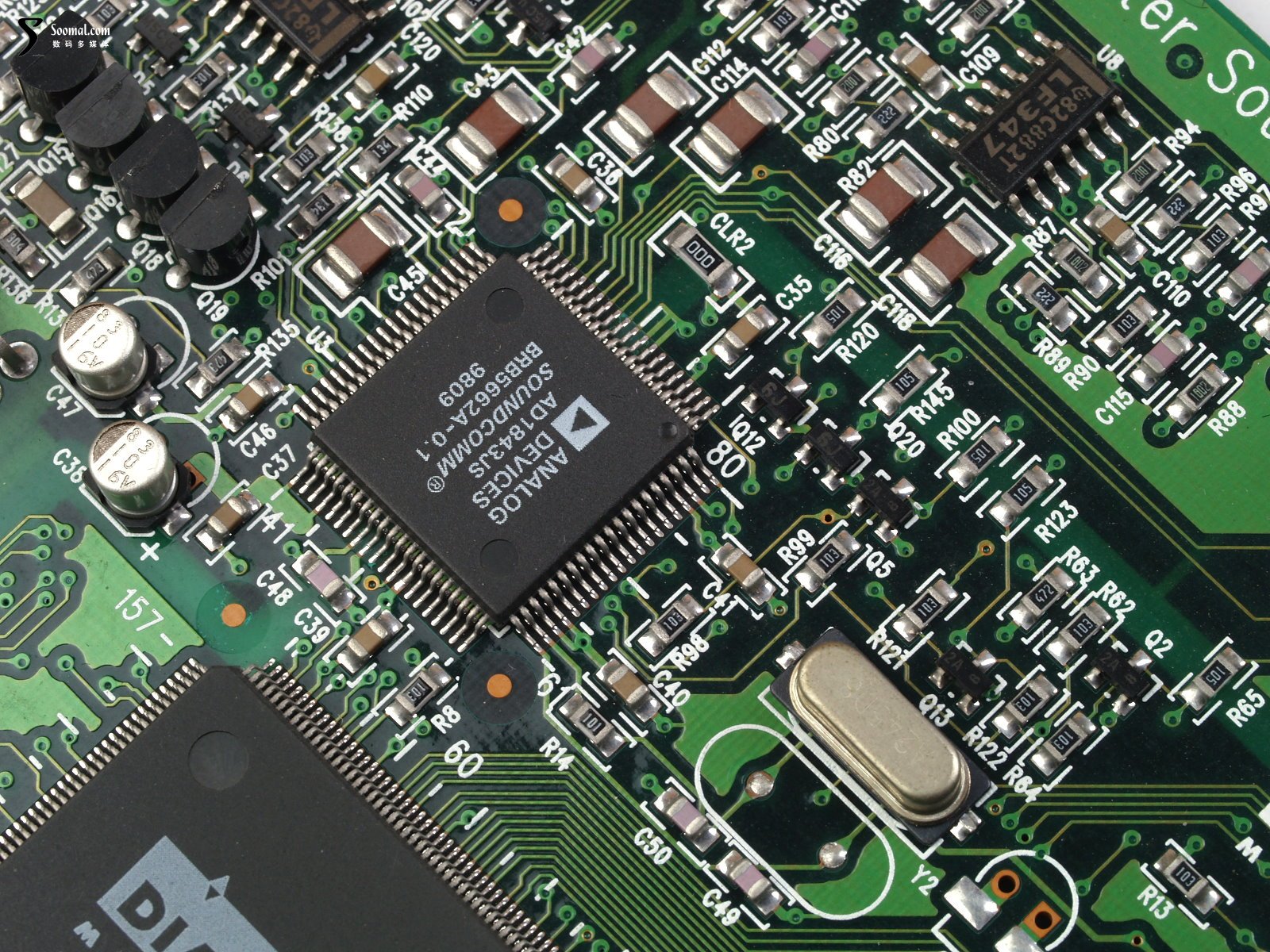
Как правило, не должно быть проблем с небольшими частями микросхем и SOT выше 0603. Другие два ряда SOP или SOIC с четырьмя рядами контактов и QFP с четырьмя рядами контактов могут использоваться в ограниченной степени. Для пассивных компонентов ниже 0402, как правило, микросхемы с загнутыми внутрь ножками (например, PLCC) или детали с припаянными ножками под корпусом не рекомендуется выполнять процесс пайки волной припоя, так как это легко может вызвать проблемы с самозамыканием или воздушным замыканием. пайка.
Таким образом, обычная технологическая плата для пайки волной припоя будет сосредоточена на первой стороне печатной платы (сторона, на которой нет пайки волной припоя), а традиционные вставные части спроектированы на первой стороне печатной платы, а вторая сторона предназначена только для пайки волной припоя деталей SMD.
Нельзя ли припаивать детали QFN и BGA со второй стороны волной припоя (селективная пайка волной)?
Иногда из-за ограничений конструкции печатной платы такие компоненты, как QFN и BGA, приходится размещать на второй стороне печатной платы. Такие SMD-детали, которые нельзя припаивать волной припоя, нельзя проектировать на второй стороне печатной платы. Как правило, используется селективная пайка волной припоя, а носитель (шаблон) для пайки волной припоя используется для покрытия некоторых частей, которые нельзя паять волной, так что оловянная волна не соприкасается с теми частями, которые нельзя паять волной.
Однако существуют определенные условия для использования селективной пайки волной, такие как ограничение высоты деталей и необходимость резервирования места для держателя при размещении деталей печатной платы. Стоимость перевозчика также является соображением.
3. При каких условиях плату PCBA можно припаивать волной припоя без держателя?
В первые дни при сборке печатных плат почти не использовались носители. В то время почти все печатные платы припаивались непосредственно волной припоя без использования каких-либо держателей, если только печатная плата не могла выдерживать слишком большую нагрузку, например плата питания.
Из-за преобладания селективной пайки волной припоя в сочетании со все более тонкими и меньшими печатными платами постепенно стало использоваться транспортное средство. Поэтому не для всех процессов пайки волной припоя обязательно требуются держатели печей.
При каких обстоятельствах печатная плата может проходить через печь для пайки волной припоя без держателя?
3.1 Требования к конструкции печатной платы:
Не менее 5 мм края печатной платы должно быть зарезервировано для использования пайки волной припоя (захват) и поддержки, когда печатная плата размещается магазином.
Толщина печатной платы предпочтительно должна быть более 1,6 мм, чтобы не возникало проблем с короблением и переполнением при прохождении через печь.
Рекомендуется, чтобы зазор между контактными площадками был больше 1,0 мм во избежание короткого замыкания точек пайки друг на друга.
3.2 Детали и требования к расположению:
Тип деталей SMD и направление деталей SMD должны соответствовать требованиям пайки волной припоя. (Как правило, детали SMD должны располагаться перпендикулярно направлению движения платы)
Поверхность печатной платы для пайки волной припоя позволяет использовать только детали SMD, SOT, SOP, QFP и т. д. размером выше 0603 (включительно), другие, такие как BGA, PLCC, QFN, разъем, трансформатор, 0402 (включительно) и ниже. нельзя размещать на сварных швах с волновым фронтом.
Все вставные детали должны быть спроектированы с первой стороны, а ориентация вставных частей должна соответствовать требованиям пайки волной припоя. (Штырь должен быть параллелен направлению платы)
Детали на печатной плате не должны быть слишком тяжелыми, чтобы избежать деформации печатной платы под действием силы тяжести.
3.3 Технологические требования:
Все детали SMD на поверхности пайки волновым фронтом должны быть проклеены красным, чтобы избежать падения в печь для пайки волной припоя.
Некоторые площадки для пайки (например, линии контакта клавиш и золотые пальцы), которые нельзя лужить, не рекомендуется проектировать на контактной поверхности для пайки волной припоя (вторая сторона).