Как работает плазменная резка?
Что такое плазма?
Чтобы разъяснить принцип действия плазменной резки, сначала нужно ответить на вопрос «Что такое плазма?» Плазма — это четвертое состояние вещества. Обычно мы сталкиваемся только с тремя состояниями вещества: твердым, жидким и газообразным. При поступлении или утрате энергии, например, тепла, вещество может переходить из одного состояния в другое. Например, при поступлении достаточного количества тепла вода переходит из твердого состояния (лед) в жидкое. Если тепла поступит еще больше, она перейдет в газообразное состояние (пар). Если добавить еще больше тепла, пар ионизируется и станет электропроводящим — превратится в плазму. Устройство плазменной резки сможет использовать этот электропроводящий газ для передачи энергии от источника питания к любому материалу-проводнику, что позволяет обеспечить более качественную и быструю резку по сравнению с газовой.
Образование плазменной дуги начинается с пропускания газа, например, кислорода, азота, аргона или даже обычного воздуха, через узкое сопло внутри плазмотрона под высоким давлением.
Составляющие системы плазменной резки
-
Источник питания — источник питания для плазменной резки преобразует одно- или трехфазный переменный ток в постоянный ток напряжением от 200 до 400В. Постоянный ток требуется для поддержания стабильной плазменной дуги на всем протяжении резки. Также источник питания позволяет регулировать силу тока в зависимости от типа и толщины материала.
-
Система поджига дуги — этот контур генерирует переменный ток напряжением около 5000 В и частотой 2 МГц, который образует внутри плазмотрона искру, поджигающую плазменную дугу.
-
Плазмотрон — плазмотрон служит для выравнивания и охлаждения расходных материалов.
Основные расходные материалы для плазменной резки — это электрод, завихритель и сопло. Для повышения качества резки также может потребоваться дополнительный защитный колпачок, а для удержания всех деталей вместе используются внутренний и внешний поджимные колпачки.
Большинство современных систем плазменной резки делятся на традиционные и высокоточные.
В традиционных системах в качестве плазменного газа используется окружающий воздух, а форма плазменной дуги зависит от отверстия сопла. Приблизительная сила тока дуги таких систем составляет примерно 12 000-20 000 ампер на квадратный дюйм. Подобная схема используется во всех системах для ручной резки и некоторых механизированных системах, если это позволяют допуски. | ||
Высокоточные системы плазменной резки (с высокой плотностью тока) используются для особо высококачественной и точной плазменной резки. |
Ручная резка В большинстве систем ручной плазменной резки, например, Tomahawk® Air Plasma, в выключенном состоянии электрод и детали сопла находятся в контакте. При нажатии триггера источник питания начинает вырабатывать постоянный ток, который проходит через это соединение и запускает поток плазменного газа. После того, как плазменный газ (сжатый воздух) достигает достаточного давления, электрод и сопло размыкаются, что приводит к возникновению электрической искры, которая преобразует поток воздуха в струю плазмы. |
Высокоточная плазменная резка
Электрод и сопло внутри плазмотрона для высокоточной резки не соприкасаются и изолированы друг от друга завихрителем, который имеет небольшие вентиляционные отверстия, преобразующие плазменный газ в вихрь. Когда в источник питания поступает команда включения, он начинает подачу постоянного тока с напряжением холостого хода до 400В и начинает предварительную подачу газа через шланг к плазмотрону. Сопло в данный момент подключено к положительному потенциалу источника питания через контур вспомогательной дуги, а электрод — к отрицательному.
После этого система поджига дуги вырабатывает высокочастотную искру, из-за которой плазменный газ ионизируется и становится проводником тока от электрода к соплу. В результате образуется вспомогательная дуга плазмы.
После того, как вспомогательная дуга вступит в контакт с рабочим изделием (заземленному через пластины стола для резки), контур тока перемещается от электрода к рабочему изделию, высокочастотный разряд отключается и включается контур вспомогательной дуги.
После этого источник питания наращивает постоянный ток до выбранной оператором силы тока и меняет предварительную скорость потока газа на оптимальную скорость для данного материала. Также используется вспомогательный поток защитного газа, который подается вне сопла через защитный колпачок.
Форма и диаметр отверстия защитного колпачка заставляют защитный газ еще больше сужать плазменную дугу, что позволяет обеспечить чистую резку с минимальными углами скоса и небольшой шириной линии разреза.
Плазменная сварка – Плазма и газ-резка, сварка, напыление
Требования предъявляемые к плазматронамПри конструировании плазмотронов, предназначенных для различных видов обработки материалов следует учитывать ряд общих требований, предъявляемых к ним:
- Плазмотрон должен обеспечивать многократное надежное зажигание и стабильное горение плазменной дуги в заданном диапазоне рабочих токов и напряжений.
Это требование удовлетворяется при определенных соотношениях между диаметром электрода, сопла, длиной последнего, и зазором между ними, а также при правильном конструктивном решении узла формирования и стабилизации дуги.
- Элементы, наиболее подверженные действию тепла (электрод, сопло), должны выдерживать длительную тепловую нагрузку при максимальной мощности плазмотрона. Это требование выполняется при правильном выборе материала теплонапряженных элементов и си-стемы их охлаждения.
- Электрическая изоляция между электродами и соплом должна быть рассчитана на максимальное напряжение, возникающее на дуговом промежутке при возбуждении дуги и ее обрыве. При возбуждении дуги с помощью осциллятора это напряжение составляет 2-5 кв в диапазоне частот 0,3-1 Мгц.
- Элементы водяных и газовых коммуникаций плазмотрона (шланги, уплотнения, прокладки и пр.) должны выдерживать давление не ниже 10 атм.
- Для обеспечения маневренности плазмотрона подсоединяемые к нему шланги и электрические провода должны быть гибкими и прочными.
- Плазмотрон должен быть технологичным в изготовлении, в ремонте и удобным в эксплуатации. Особо важно обеспечить легкость его разборки и сборки и возможность быстрой замены наиболее часто изнашиваемых деталей (катода и сопла).
- Конструкция плазмотрона должна быть экономичной, т. е. должна предусматривать возможность применения недифицитных материалов для его изготовления и обеспечивать минимальное потребление охлаждающей воды, рабочего газа и минимальные потери тепла.
- Плазмотроны для сварки и наплавки должны обеспечивать надежную защиту шва от вредного воздействия окружающей среды, плазмотроны для напыления — высокие скорость течения и теплосодержание плазменной струи при минимальной ее загрязненности продуктами эрозии электродов, плазмотроны для резки — высокую концентрацию теплового потока плазменной струи. Ручной плазменный резак должен быть легким и удобным в обращении.
- отсутствие любых водо-, электро- или газоподводящих шлангов в рабочем пространстве печи;
- водоохлаждение всех металлических частей;
- защита от излучения всех уплотнений и неметаллических деталей водоохлаждаемыми или термоизоляционными экранами;
- возможность ввода плазмотрона в печную камеру через уплотнение.
В ряде случаев выдвигаются особые требования к системе управления плазмотроном, к способу его охлаждения, к защите от воздействия окружающей среды, к повышенной надежности его в условиях работы на поточной линии и др.
Плазматроны: схемы, классификация
При создании плазмотрона первым шагом является составление схемы его устройства. Исходя из особенностей технологического процесса и условий работы плазмотрона выбираем систему его охлаждения, род тока, плазмообразующую среду, вид и материал электрода, способ стабилизации дуги, перемещения ее электродных пятен и т. д. Различные варианты схем плазмотронов удобнее всего представить в виде классификации (рис.). Данная классификация составлена таким образом, что один из вариантов каждого подраздела является необходимым составным элементом общей схемы плазмотрона любого типа.
В первую очередь все плазмотроны разделяются на две группы по виду дуги (см. рис.): плазмотроны с дугой прямого и косвенного действия (схемы 1 и 2). Различие тепловых свойств обоих типов плазмотронов и области их применения уже рассматривались выше.
рис. 1 Классификация плазмотронов по критериям
По системе охлаждения электрода и сопла плазмотроны также делятся на два основных типа: с воздушным и с водяным охлаждением (схемы 3, 4). Теплоемкость воды намного выше теплоемкости воздуха и других газов. Поэтому наиболее эффективной и распространенной является водяная система охлаждения, при которой допускаются высокие тепловые нагрузки на электрод и сопло, т. е. обеспечивается нормальная работа плазмотрона при больших токах и высокой степени обжатия плазменной дуги. Однако водяное охлаждение несколько усложняет конструкцию плазмотрона, утяжеляет его из-за наличия водоподводящих шлангов и удорожает эксплуатацию плазменной установки. Чистота воды существенно влияет на эффективность теплоотвода. При больших расходах воды плазменную установку целесообразно оснащать циркуляционной системой охлаждения с использованием дистиллированной воды во избежание образования накипи. Система воздушного охлаждения ввиду низкой эффективности применяется реже, главным образом для охлаждения малоамперных плазменных горелок и ручных плазменных резаков, предназначенных для монтажных работ в зимних условиях. В таких резаках рабочий ток обычно не превышает 300-400 а. В обеих системах охлаждающая среда чаще всего проходит последовательно электродный и сопловой узел через изолирующий корпус плазмотрона. При этом существенную роль с точки зрения эффективности охлаждения играет профиль полостей охлаждения, температура и давление поступающей в плазмотрон охлаждающей среды. Основная задача при выборе системы охлаждения состоит в том, чтобы обеспечить максимальную интенсивность отвода тепла стенками сопла, так как чем выше величина теплового потока, отводимого соплом, тем круче температурный градиент газовой прослойки между столбом дуги и стенками канала сопла и, следовательно, тем выше плотность тока и мощность столба дуги.
рис. 2 Классификация плазмотронов по методам стабилизации дуги
Плазмотроны можно классифицировать и по способу стабилизации дуги. Система стабилизации дуги, обеспечивающая сжатие столба и строгую фиксацию его по оси электрода и сопла плазмотрона, является наиболее важным элементом плазмотрона. Существуют три вида стабилизации дуги: газовая, водяная и магнитная. Наиболее простой и распространенной является газовая стабилизация, при которой наружный холодный слой рабочего плазмообразующего газа, омывая стенки столба дуги, охлаждает и сжимает его. При этом в зависимости от способа подачи газа (вдоль или перпендикулярно оси столба) газовая стабилизация может быть аксиальной или вихревой (схемы 5, 6). Наибольшее обжатие дуги достигается при вихревой ее стабилизации, поэтому этот способ используется главным образом в плазмотронах для резки и напыления. При аксиальной стабилизации поток газа, обдувающего столб дуги, имеет более спокойный, ламинарный характер, что обеспечивает лучшие условия защиты нагреваемого изделия от воздействия окружающей среды. Поэтому аксиальная стабилизация применяется в плазмотронах для сварки и наплавки. Иногда применяют двойную стабилизацию дуги (схема 7), при которой сочетается аксиальная подача газа через первичное и вихревая подача через вторичное сопло или наоборот. Столб дуги можно стабилизировать, омывая его водяной струей (схема 8). Образуемый из струи водяной пар служит плазмообразующей средой. При водяной стабилизации можно достигнуть наиболее высокой степени сжатия и температуры столба дуги до 50 000 °К. Однако присутствие паров воды вблизи катодной области приводит к интенсивному сгоранию электродов из любых материалов. В плазмотронах с водяной стабилизацией, предназначенных для резки, используется графитовый электрод, автоматически перемещаемый по мере его сгорания. Плазмотроны с водяной стабилизацией отличаются сложностью конструкции, малой надежностью системы автоматического регулирования подачи электрода и сложностью способов возбуждения дуги. Магнитная стабилизация (схема 9), при которой создается продольное магнитное поле, сжимающее столб дуги, менее эффективно, чем газовая и водяная.
Кроме того, надетый на сопло соленоид усложняет конструкцию плазмотрона. Преимущество способа магнитной стабилизации состоит в возможности регулирования степени сжатия столба дуги независимо от расхода рабочего газа, в то время как при газовой и водяной стабилизации рабочий газ является одновременно плазмообразующим и стабилизирующим. На практике наложение продольного магнитного поля применяется не столько для стабилизации дуги, сколько для вращения ее анодного пятна по внутренним стенкам сопла с целью повышения стойкости последнего. Например, в плазмотронах, применяемых для напыления, магнитное вращение анодного пятна газовихревым способом позволяет значительно снизить эрозию сопла и, следовательно, загрязненность плазменной струи.
Классификация плазмотронов по виду электрода
По виду электрода-катода плазмотроны постоянного тока можно разделить на две группы: плазмотроны со стержневым и плазмотроны с распределенным катодом.В плазмотронах со стержневым катодом, катодное пятно фиксируется на торце электрода, а в плазмотронах с распределенным катодом — интенсивно перемещается с помощью газовихревого или магнитного вращения по развитой поверхности электрода.
В плазмотронах для обработки металлов применяются в основном стержневые катоды, подразделяемые на три основных вида: расходуемый, газозащищенный и пленкозащитный (схемы 1, 2, 3).
Расходуемый, чаще всего графитовый, электрод был показан в схеме плазмотрона с водяной стабилизацией. Несмотря на то, что графит обладает высокой температурой плавления, при нагревании до этой температуры он не плавится, а возгоняется, чем и обусловлен его повышенный расход.
Газозащищенный вольфрамовый электрод — самый распространенный из всех видов электродов. При работе в инертной (аргон, гелий) и восстановительной (азот, водород) средах катод из тугоплавкого вольфрамового стержня при нагрузке 15-20 а/мм2 практически не расходуется. Вольфрамовый катод по сравнению с графитовым значительно прочнее и обладает во много раз большей электропроводностью.
Для улучшения условий работы катоды дуговых плазмотронов изготовляют из вольфрама с небольшой добавкой окиси тория или лантана (1,5-2%). Существует мнение, что торированные вольфрамовые электроды обладают некоторой радиационной способностью, поэтому в последнее время чаще используются лантанированные вольфрамовые электроды. Примеси окиси тория или лантана повышают эмиссионные свойства вольфрамового катода (работа выхода электронов понижается с 4,5 до 2,63 эв), что обеспечивает лучшие условия зажигания, более высокую допустимую плотность тока и устойчивость горения дуги. Кроме того, вольфрам с указанными добавками имеет температуру рекристаллизации на 600° К выше, чем чистый вольфрам и, следовательно, сохраняет волокнистое строение и пластичность до более высокой температуры. Однако стойкость вольфрамового электрода при добавлении кислорода к газовой среде в связи с образованием летучих соединений резко снижается. Например, в плазмотронах, применяемых для резки, при использовании технического азота, содержащего 3-5% О2, на вольфрамовом катоде через 2-3 ч работы при токе 300-400 а образуется кратер, смещение центра которого относительно оси сопла вызывает соответствующее смещение столба дуги и приводит к явлению двойного дугообразования. Поэтому при работе с кислородосодержащей плазмообразующей средой в первичное сопло подается аргон, защищающий вольфрамовый электрод от воздействия рабочего кислородосодержащего газа, подаваемого во вторичное сопло.
Система с двойным газовым потоком имеет существенные недостатки. При использовании дешевого рабочего газа, например воздуха, все же остается необходимость в использовании дефицитного аргона. При этом усложняется конструкция плазмотрона и ухудшается нагрев рабочего газа, так как наиболее эффективно газ нагревается вблизи катодной области. Сравнительно недавно появился новый вид катода — пленкозащитный стержневой катод, обладающий высокой стойкостью в газах, содержащих кислород (в воздухе, углекислом газе, техническом азоте). Он представляет собой стержень из циркония или его сплавов, запрессованный в медной обойме. Механизм работы такого электрода должен быть еще детально изучен, но можно уже считать установленным, что достаточно высокая термостойкость циркония, имеющего относительно низкую температуру плавления (2125° К), в значительной мере обусловлена образованием стойкой тугоплавкой пленки из его окислов и нитридов, защищающей чистый цирконий от испарения. Тугоплавкие соединения, образующие пленку, при обычных температурах являются диэлектриками, а при температурах, близких к температуре плавления (3200° К), теряют свои диэлектрические свойства и становятся проводниками с ионной проводимостью (σ >= 1 ом-1*см-1).
Таким образом, стойкость циркониевого катода определяется его термохимическим взаимодействием с плазмообразующей средой. Не-обходимыми условиями, обеспечивающими высокую стойкость катода, является наличие в составе газовой среды кислорода и азота, а также такая интенсивность его охлаждения, при которой температура катодного пятна не превышала бы температуру разложения туго-плавких соединений. Эрозия циркониевого катода резко повышается при большем процентном содержании кислорода, чем в воздухе (более 20%) и особенно при наличии в газовой среде водорода. Особо важное значение с точки зрения повышения стойкости циркониевого катода имеет его конструкция и система охлаждения. В настоящее время в плазмотронах для воздушно-плазменной резки достигнута вполне удовлетворительная стойкость циркониевого катода при работе на токах до 400 а. Применение пленкозащитного электрода в плазмотронах переменного тока исключается ввиду его активного разрушения в полупериоды обратной полярности. Особенностью работы циркониевой вставки является постепенное углубление ее нижнего основания в медную обойму по мере эрозии.
Циркониевая вставка расходуется главным образом при включении дуги, очевидно, вследствие разрушения пленки от термоудара. При определенном углублении нижней поверхности вставки последующее зажигание дуги осуществляется с медной обоймы, поэтому для перемещения катодного пятна на циркониевую вставку и для жесткой фиксации его необходимо применять газовихревую или магнитную стабилизацию дуги, обеспечивающую строгую соосность столба дуги с электродом и соплом плазмотрона. При использовании циркониевого электрода допускается большая плотность тока, достигающая 80-100 а/мм2, чем при использовании вольфрамового электрода. При работе плазмотрона с окислительной плазмообразующей средой на больших токах (1000 а и выше) используются разнообразные виды распределенных катодов, наиболее распространенными из которых являются полый, дисковый и кольцевой (схемы 4, 5 и 6). Недостатками распределенных катодов являются сложность их конструкции, трудность равномерного перемещения катодного пятна по всей поверхности электрода, низкая стабильность горения дуги, возрастание напряжения прикатодной области дуги и связанное с этим увеличение потерь мощности в электроде.
Поэтому в плазмотронах для обработки металлов распределенные катоды не нашли практического применения. Существует классификация плазмотронов и по плазмообразующей среде. Состав плазмообразующей среды диктуется технологическим процессом и в свою очередь является определяющим фактором при выборе схемы плазмотрона.
По химическому воздействию на обрабатываемое изделие и электроды плазмотрона все плазмообразующие среды можно разделить на три большие группы: инертная, восстановительная и окислительная. Физические свойства и оценка роли каждого из плазмообразующих газов уже рассматривались выше.
Классификация плазмотронов по роду тока
По роду тока плазмотроны отличаются наибольшим разнообразием вариантов. Поэтому рассмотрим лишь основные из них. Подавляющее большинство плазмотронов для обработки металлов выполняется на постоянном токе прямой полярности (схема 1). Это объясняется, прежде всего, физической особенностью дуги, заключающейся в том, что на аноде дуги выделяется большее количество тепла, чем на катоде. Тепловая мощность, выделяемая в электроде плазмотрона, в отличие от плавящегося электрода сварочной дуги является не только бесполезной, но и вредной. Наименьшую тепловую нагрузку несет электрод, являющийся катодом. Достаточно отметить, что предельно допустимая токовая нагрузка на лантанированный вольфрамовый электрод на переменном токе примерно в два раза, а на обратной полярности при использовании постоянного тока в десять раз ниже, чем на прямой полярности. Поэтому плазмотроны постоянного тока имеют наиболее высокий коэффициент полезного использования мощности. Столб интенсивно сжатой дуги должен быть жестко стабилизирован по оси электрода и сопла плазмотрона. При смене полярности электрода эта стабилизация нарушается, поэтому дугу переменного тока сжать труднее, чем дугу постоянного тока.
Важным преимуществом плазмотронов постоянного тока по сравнению с плазмотронами переменного тока является большая стабильность горения дуги. Прохождение тока через нуль может вызвать погасание дуги, поэтому обычно напряжение холостого хода источника питания переменным током не менее чем вдвое превышает рабочее напряжение дуги. При питании плазмотронов постоянным током можно достичь отношения uд/uxx равного 0,8-0,9. Следовательно, при одинаковой мощности дуги установленная мощность и габариты источника постоянного тока меньше, чем мощность и габариты источника переменного тока. Кроме того, источник постоянного тока обеспечивает равномерную загрузку трехфазной сети. Существовавшая раньше проблема выпрямления постоянного тока в настоящее время практически решена благодаря созданию и широкому выпуску электропромышленностью мощных малогабаритных полупроводниковых вентилей. Первоначальные затраты и расходы на эксплуатацию плазменных установок переменного и постоянного тока приблизительно равны. Поэтому с учетом перечисленных выше преимуществ для большинства процессов обработки материалов целесообразно применять плазмотроны постоянного тока. Плазмотроны переменного тока применяются в ряде случаев в силу технологических требований процесса. Например, плазменную сварку алюминиевых сплавов необходимо вести на переменном токе, так как в периоды обратной полярности за счет действия эффекта катодного распыления разрушается тугоплавкая пленка окиси алюминия, препятствующая нормальному процессу сплавления металла.
При плазменной плавке в случае параллельной работы нескольких мощных плазмотронов постоянного тока на общую ванну-анод возникает трудноустранимое магнитное взаимодействие между дугами. Поэтому в этих условиях могут быть использованы плазмотроны переменного тока. В этом случае целесообразно использовать плазмотроны в количестве, кратном трем, что обеспечивает равномерную загрузку трехфазной сети. Рассмотрим три основные схемы плазмотронов переменного тока. На схемах 2 и 3 плазмотроны питаются от однофазного трансформатора. В схеме 3 осуществлена вентильная коммутация тока таким образом, что электрод функционирует только как катод (в полупериод прямой полярности), а сопло — как анод (в полупериод обратной полярности). При такой схеме обеспечивается большая стойкость вольфрамового электрода. Однако с увеличением тока ухудшаются условия работы сопла, а при работе на токах ниже определенного предела (~150 а) нарушается стабильность горения дуги. На схеме 4 плазмотрон питается от трехфазного трансформатора. В этом случае обеспечивается высокая стабильность горения дуги, однако электроды и сопло находятся в сравнительно тяжелых условиях работы. Кроме того, значительно усложняется конструкция плазмотрона. В целях повышения стабильности горения дуги переменного тока некоторые плазмотроны выполняют комбинированными. В этом случае основную дугу переменного тока прямого действия стабилизируют вспомогательной маломощной дугой постоянного тока, горящей либо между электродом и соплом (схема 5), либо между двумя соплами (схема 6), одно из которых (катод) является формирующим. Второе сопло (анод) выполняется с большим внутренним диаметром. Благодаря этому оно подвержено меньшему тепловому воздействию столба основной дуги.
Наряду с дуговыми плазмотронами, работающими на переменном токе промышленной частоты, за последнее время были разработаны высокочастотные (ВЧ) и сверхвысокочастотные (СВЧ) плазмотроны [7, 8]. Принцип работы высокочастотного индуктивного или безэлектродного плазмотрона (схема 7) заключается в нагреве газа до состояния плазмы в электромагнитном поле индуктора. Для этого в полость индуктора, питаемого от высокочастотного генератора (частотой 1-40 Мгц, напряжением до 10 кв и мощностью до 50 кВт), помещается трубка из термостойкого изолирующего материала, например, кварца. В трубку подается плазмообразующий газ и кратковременно вводится металлический или графитовый пруток. Последний раскаляется под действием поля индуктора и вызывает нагрев и первоначальную ио-низацию окружающего газа. Когда электропроводность газа возрастает до определенной величины, начинается интенсивный его нагрев и ионизация вихревыми токами, создаваемыми полем индуктора. После развития самостоятельного кольцевого разряда пруток удаляется из полости трубки. Продуваемый через трубку газ, проходя через кольцевой разряд, нагревается и истекает в виде плазменной струи, температура которой достигает 15 000-20 000° К, а скорость истечения в десятки раз меньше, чем скорость истечения плазменной струи дуговых плазмотронов. Высокочастотная энергия сравнительно дорога, высокочастотные генераторы сложны и имеют ограниченную мощность.
Поэтому очень чистый (ввиду отсутствия электродов) и мягкий факел индукционного плазмотрона нашел применение для обработки особо чистых тугоплавких порошковых материалов, выращивания монокристаллов и других специальных процессов, не требующих высокой производительности.
В сверхвысокочастотных (СВЧ), или электронных плазмотронах, газ также нагревается электромагнитным полем, создаваемым электродом-излучателем (схема 8). Плазменный высокочастотный факел возникает у электрода при остроконечной форме электрода и высокой напряженности поля вблизи него. В высоковольтном и сверхвысокочастотном электрическом поле свободные электроны ускоряются и приобретают такую кинетическую энергию, что при столкновении с частицами газа вызывают их диссоциацию и ионизацию. Электрод плазмотрона подключен к магнетронному генератору частотой 2000-3000 Мгц и мощностью 2-5 кет. Плазменный факел электронного плазмотрона интересен тем, что в нем нет термического равновесия: температура электронов на порядок выше температуры ионов и свободных атомов. Например, при температуре факела 3500° К электронная температура достигает 35 000° К. Такая высокая температура электронов позволяет проводить в плазменной струе химические реакции синтеза некоторых специальных материалов.
Инвертор для плазменной резки РЕСАНТА ИПР-40
Описание:
Инверторный плазменный резак Ресанта ИПР 40 предназначен для качественной резки листового металла с минимальным деформированием. Плавная регулировка сварочного тока позволяет точно выставить необходимый режим работы. Автоматическая система поджига дуги с 5-секундным интервалом. На передней панели предусмотрен манометр, который позволяет вести визуальный контроль рабочих параметров. Резак требует подключения к источнику сжатого воздуха.
Параметры сети: 230 В / 50 Гц / 30 A (макс.)
Рабочий цикл: 40 A – 35%, 30 A – 60%, 20 A – 100%
Плата управления: IGBT Inverter
Давление воздуха: 0. 4~0.5 MPA
Режущая способность: 12мм Сталь; 7мм Нержавейка; 6мм Алюминий
Система поджига дуги: Автостарт (с 5-секундным интервалом)
Особенности
– Удобная транспортировка. С помощью рукоятки на крышке аппарата удобно переносить. Специальные петли позволяют крепить к ним плечевой ремень.
– Прост в управлении. Панель управления оснащена манометром для контроля давления, регулятором тока, а также индикаторами.
– Эффективное охлаждение. Вентиляционные отверстия на корпусе дают выход теплого воздуха, что предотвращает перегрев.
– Легкость в работе. С помощью клавиши включения на горелке можно выполнять операции одной рукой.
Преимущества
– Защита от перегрева.
– Удобная транспортировка.
– Высокий КПД.
– Прочный корпус.
– Четкая и ровная линия реза.
Основные характеристики:
Диапазон регулирования тока реза, А | 15 — 40 |
Инверторная технология | Да |
Мощность, Вт | 6600 |
Наличие сетевой вилки | Да |
Плазменная резка | Да |
Тип расположения | Плазменной резки |
Тип горелки | Несъемная |
Чтобы купить инвертор для плазменной резки РЕСАНТА ИПР-40 просто добавьте товар в корзину и оформите заказ, выбрав предпочитаемый способ оплаты и доставки. После оформления заказа наш менеджер свяжется с вами для подтверждения.
Преимущества плазменной резки над газопламенной (кислородной)
Преимущества плазменной резки над газопламенной (кислородной)Плазменная резка металла активно вытесняет резку с использованием газа, например кислорода. Это связано со многими причинами, главные из которых: она намного проще в работе и к тому же продуктивнее. Для того чтобы ответить на вопрос, чем именно первый тип резки лучше второго, обратимся к самой природе получаемой дуги.
Технология резки металла плазмой
Плазменная дуга отличается от обычной электрической, образуемой в процессе сварки. Если сварочная дуга образуется в среде защитного газа (СО2, аргон, смесь и т.д.), то для получения второй нужен сжатый воздух. Так, в результате ионизации воздуха и возникновения электрического разряда образуется плазма. Она более энергоемкая и горячая. Температура достигает 22 тысяч градусов Цельсия. Это позволяет разрезать металл толщиной до 50 мм. Сжатый воздух, используемый в процессе резки, выдувает расплавленный металл и в результате мы получаем кромку очень высокого качества. Она практически готова к дальнейшей сварке.
Основные преимущества использования аппаратов плазменной резки
1) Квалификация работника. Резка металла плазмой намного проще по своей работе. Резчику нужно всего лишь разжечь дугу и вести резак в нужном направлении. Резка кислородом намного сложнее и она требует определенной квалификации сотрудника. Более того, при использовании газопламенной резки вашему работнику нужны корочки газорезчика. При использовании плазмореза никаких корочек не требуется и к работе можно привлекать специалистов с меньшим опытом, а это экономия на фонде оплаты труда.
2) Плазменная резка более безопасная, т.к. в работе не используются горючие газы. Для работы аппарата нужен только сжатый воздух Вам не придется иметь дело с такими газами, как ацетилен (при резке кислородом). Как известно, ацетилен очень нестабильный и легко воспламеняемый газ. А это лишние риски.
3) Простота процесса резки. Если говорить о резке газом, то в данном процессе очень много тонкостей. Резчику необходимо регулировать подачу газа, соблюдать определенный интервал между изделием и горелкой. И вообще постоянно наблюдать за происходящим процессом и в случае каких-то отклонений оперативно переключать рабочие параметры. Плазменный резак работает в контакте с деталью, и на всем промежутке резки аппарат держит одни показатели.
4) Универсальность. Аппарат плазменной резки можно использовать для резки любых металлов (сталь, алюминий, медь, нержавейка и др.). Газопламенная резка ограничена используемыми газами. Для каждого металла – свой газ.
5) Качество плазменной резки выше. При резке данным способом меньшая площадь металла подвергается нагреву, в результате образуется намного меньше окалин и край реза получается более качественным.
6) Более высокая производительность и экономичность. Если говорить о кислородной резке, то она требует значительно больше временных ресурсов. Зачастую, еще до процесса резки необходимо нагреть металл и только потом резать. Более того, практически всегда необходима доработка среза: нужно удалять остатки расплавленного металла. Скорость и качество плазменной резки на порядок выше. Это делает данное оборудование не только более производительным, но и более экономичным. Если говорить об экономическом аспекте, то несмотря на то, что резаки для газопламенной резки намного дешевле,в повседневном использовании они требуют больше затрат, например, постоянного приобретения газа. Если рассматривать длительный период времени с учетом расходов на текущее содержание и эффективность работы, то кислородная резка значительно уступает.
Несмотря на все перечисленные преимущества, у плазморезов есть один существенный нюанс. Используемый в работе воздух должен быть сухим. Наличие лишней влаги может сказаться на качестве работы аппарата. Для стабильной работы часто используются специальные осушители и влагоуловителя. Поэтому, если вы задумываетесь о приобретении такого аппарата, позаботьтесь о наличии воздуха нужного качества без влаги.
Перейти в каталог “Аппараты для плазменной резки металла”
7 преимуществ плазменной резки перед кислородной
Плазменная резка стремительно завоёвывает популярность среди предприятий самой разной направленности. Технология плазменной резки металлов основана на создании плазмы посредством электрического разряда в газовой среде и пригодна для обработки металлов толщиной до 50 мм.
Ближайшим конкурентом плазмы является кислородная резка металлов, и она действительно даёт возможность получения хороших результатов (например, если нужно обработать очень толстые листы низкоуглеродистой стали). Однако более универсальным, высокоскоростным и качественным способом резки считаются именно плазменные системы, и в этой статье мы расскажем, в чём же заключаются их основные преимущества.
1. Лучшее качество резки
Разрезы, которые выполняются с помощью аппарата плазменной резки, всегда отличаются меньшей степенью образования окалины, меньшим изгибом и меньшей областью нагрева. Малая ширина реза по данной технологии обеспечивается за счёт высокой концентрации энергии в зоне реза и составляет не более 2,5 мм для заготовки шириной 20 мм.
Так как плазменная резка обеспечивает отсутствие деформации даже на тонких листовых заготовках и позволяет получить хорошее качество кромок, без наплывов и грата, с её помощью становится возможным применять экономичные схемы раскроя и осуществлять сварку металлических конструкций без механической обработки.
2. Больше деталей за единицу времени
Благодаря значительному превосходству станков плазменной резки в скорости, такие системы, безусловно, выигрывают с точки зрения производительности у кислородных систем, даже если не учитывать время, которое необходимо для предварительного нагрева кислородного станка и операций вторичной обработки, которые потребуются в случае использования данной технологии.
Высокая производительность плазменной резки обеспечивается не только за счёт большой скорости обработки металлов разной толщины и короткого времени прожига, но также благодаря быстрому отключению резака.
3. Снижение затрат на производство
Стоимость плазменной резки в пересчёте на количество заготовок за единицу времени будет ниже, по сравнению с кислородной резкой, так как эксплуатационные затраты равномерно распределяются между большим количеством изготавливаемых за час деталей, а операции по вторичной обработке либо совсем не нужны, либо занимают меньше времени.
Длительный срок службы расходников, высокая производительность и достойное качество резки также вносят свой вклад в минимизацию удельных затрат по сравнению с технологией кислородной резки. Благодаря современным разработкам, затраты на производственный процесс по технологии плазменной резки удаётся снизить практически в два раза.
4. Высокая рентабельность
Плазменная резка является на сегодняшний день одним из самых рентабельных способов термического раскроя. Повышение прибыли при использовании станков плазменной резки обеспечивается за счёт снижения эксплуатационных затрат и увеличенной производительности, а также благодаря минимизации или даже полному исключению операций вторичной обработки.
5. Простота в эксплуатации
Данное преимущество плазменной резки достигается за счёт отсутствия необходимости регулировать подачу газа и управлять химической реакцией горения. Аппарат плазменной резки металлов разработан для контактной резки листов, поэтому при его использовании не нужно прилагать усилия для поддержания расстояния между резаком и заготовкой.
Оптимизированные параметры резки автоматизированных плазменных систем можно вводить и контролировать одним действием, что ещё более упрощает эксплуатацию оборудования. Благодаря возможности осуществления контактной резки и отсутствию необходимости регулировки подачи газа, ручные системы плазменной резки требуют меньше времени для изучения, значит, персонал предприятия сможет быстрее приступить к работе.
6. Повышенная гибкость
Плазменная технология может применяться для резки любых металлов, которые проводят ток, включая низкоуглеродистую сталь, алюминий, нержавейку, медь и большинство других разновидностей металла. В отличие от плазмы, технология кислородной резки связана с протеканием химической реакции между кислородом и железом, поэтому она используется только для обработки низкоуглеродистой (мягкой) стали.
Гибкость и универсальность плазменной резки имеет и другие аспекты. Так, по данной технологии возможна резка вручную, резка по направляющей и с применением трубореза, а также резка на удобном координатном столе. Кроме того, плазменные системы можно использовать для строжки, разметки и разрезания окрашенного, ржавого и даже многослойного металла, листы которого наложены друг на друга. Плазма даёт возможность выполнять как обычную резку, так и резку металлической решётки со скосом, что сложно выполнить с помощью кислородной резки.
7. Улучшенная безопасность
Для работы систем плазменной резки используется только сжатый воздух, в отличие от кислородной резки, в работе которой применяется смесь кислорода с топливным газом (ацетиленом, пропаном, пропиленом и природным газом). Среди этих соединений самым популярным является ацетилен, обеспечивающий более горячее пламя и снижающий время прожига. Однако, при этом ацетилен – это нестабильный и легко воспламеняющийся газ, чувствительный даже к статическому электричеству, не говоря уж о повышенном давлении и температуре. В таких условиях работа на оборудовании кислородной резки уже не может считаться полностью безопасной.
В заключение предлагаем посмотреть видео, в котором все преимущества плазменной резки перед кислородной наглядно иллюстрируются и поэтому становятся более понятными:
История и хронология эволюции плазменной резки
Компании, которые занимаются производством и обработкой металлов, даже и не подозревают, какая длинная и интересная история у плазменной резки. Эта технология начала развиваться еще во второй половине 1950-х годов. Сегодня сварочные аппараты и устройства для резки металла позволяют изготовить изделие любой формы и сложности.
Исторические сведения
В 1950-х годах инженеры компании Union Carbide Corp. изобрели плазменную резку. Хотя ее история началась гораздо раньше: в 1929 американские физики И. Ленгмур и Л. Тонко изучали ионизированные газы в газоразрядной трубке. Именно они и открыли материю, которую назвали четвертым состоянием вещества – плазму. Она входит в состав практически всех тел во Вселенной: звезд, туманностей, других космических объектов.
А с 1950-х плазму начали применять для обработки металлов. Сегодня именно эта технология позволяет изготавливать изделия с идеально гладкими краями. С помощью плазменных аппаратов можно вырезать настолько маленькие отверстия, что их диаметр не превышает размеров крепежных элементов – болтов, саморезов.
Главные инженерные прорывы
В истории эволюции плазменной резки было несколько важных дат и событий:
- 1963 – воздушная технология;
- 1965 – водная защита;
- 1977 – подводная технология;
- 1983 – резка с подачей кислорода;
- 1999 – струйная технология;
- 2006 – портативная установка резки.
Воздушная плазменная резка, открытая в 1963 году, позволила ускорить процедуру, но при этом поверхность металла сильно окислялась. А процесс с впрыскиванием воды сократил количество окалины. Инженеры работали над созданием водяного глушителя и создала технологию подводной резки.
Позже стали использовать кислород в качестве режущего газа, что существенно снизило окисляемость металлов. В 1987 был представлен резак с контактным пуском. А в 1990 появилась плазменная система, которая может обрабатывать металл под водой на глубине 4-5 м.
В 1999 инженеры создали коаксиальную струйную технологию. В результате во время резки поток газа стал поступать в плазменную дугу по общей оси. Это позволило резать толстые металлы на большой скорости. А в начале 2000-х были представлены портативные сварочные полуавтоматы .
Основы плазменной резки − все про сварочное оборудование и сварку
С течением времени оборудование для плазменной резки сильно усовершенствовалось.
Плазменная резка – это процесс, при котором в столб дуги постоянно подается не ионизированный газ. Благодаря энергии дуги этот газ нагревается, ионизируется и превращается в плазменную струю. В современном оборудовании плазменная дуга дополнительно сжимается вихревым потоком газа, поэтому создается очень интенсивный и концентрированный источник тепловой энергии, который превосходно подходит для резки металлов. Хотя технология плазменной резки и кажется сложной, сам процесс нетрудно изучить и выполнить.
Преимущества плазменной резки
До появления плазменной резки для разделки стали был очень популярен способ газовой резки, В настоящее время все больше отдается предпочтение плазменной резке, так как она имеет много преимуществ. Плазмой металл режется быстрее, чем кислородом, не требуется предварительный подогрев металла, ширина разреза очень небольшая, а также, меньше зона термического влияния, поэтому разрезаемый металл не деформируется, не закаливается.
Способ плазменной резки можно использовать для большинства металлов (газовой резкой нельзя резать нержавеющую сталь, алюминий, медь). Кроме того, плазменная резка более чистый, дешевый и удобный способ резки металла, так как для плазменной резки используются в качестве исходных материалов воздух и электричество.
Правильно подключенное оборудование плазменной резки более безопасно, чем оборудование газовой резки, так как в этом случае в горелке не возникает опасность обратного удара пламени.
Способ плазменной резки превосходно подходит для проплавления отверстий, так как сжатая плазменная дуга концентрированно нагревает и плавит металл в месте разреза и в то же время интенсивно, благодаря воздействию скоростного потока газа, удаляет расплавленный металл. Кроме того, для плазменного проплавления отверстий не требуется предварительный прогрев металла, способом плазменной резки легче резать разнородные металлы.
Область применения плазменной резки
Способом плазменной резки можно резать любой электропроводящий материал.
Способом плазменной резки можно резать металлы разнообразной толщины. В зависимости от мощности аппарата плазменной резки можно разрезать как алюминий, так и нержавеющую или углеродистую сталь, а также титан толщиной несколько сантиметров.
Подготовка плазменной резки к работе
При подготовке оборудования к работе в аппарат плазменной резки подается сжатый воздух. Возможны три источника сжатого воздуха: баллоны сжатого воздуха, подключение к имеющейся на заводе системе сжатого воздуха или небольшой воздушный компрессор. Большинство аппаратов плазменной резки имеют регулятор, необходимый для подачи и распределения потока воздуха в системе.При подборе необходимого тока и скорости резки лучше всего выполнить несколько разрезов при более высоком токе. Затем, при необходимости, в зависимости от скорости резки, можно уменьшать ток.

Резку начинают, располагая плазматрон как можно ближе к краю разрезаемого основного металла. Нажмите кнопку выключателя плазматрона – зажжется дежурная дуга, а затем режущая дуга. После зажигания режущей дуги медленно двигайте плазматрон вдоль планируемой линии разреза.
Регулируйте скорость движения так, чтобы искры были видны с обратной стороны листа металла. Дуга должна быть направлена вниз и под прямым углом к поверхности разрезаемого металла. Если на обратной стороне металлического листа не видно искр, это значит, что металл не прорезан насквозь. Это может происходить из-за слишком большой скорости движения, недостаточного тока или из-за того, что струя плазмы направлена не под прямым углом к поверхности разрезаемого металла.

По окончании резки слегка наклоните плазматрон в сторону конца разреза или временно остановитесь, чтобы закончить резку. После того, как вы отпустили кнопку выключателя на плазматроне, некоторое время будет подаваться воздух для охлаждения его нагревающихся частей, и в случае необходимости резку можно снова возобновить.
Строжка плазменной дугой
Операцию строжки можно выполнить, когда угол наклона плазматрона в среднем составляет 40 градусов. Нажмите кнопку выключателя плазматрона, чтобы зажечь дежурную, а затем и режущую дугу. В начале строжки поддерживайте как можно более короткую длину горящей плазменной дуги. Затем длину дуги и скорость прохода можно изменять в зависимости от надобности. Не делайте слишком глубокую строжку, лучше выполнить несколько проходов. После того, как вы отпустили кнопку выключателя на плазматроне, некоторое время будет подаваться сжатый воздух для охлаждения, и в случае необходимости строжку можно снова возобновить.Проплавление отверстий плазменной дугой
Проплавить отверстие при угле наклона плазматрона 40 градусов.
Как безопасно работать с оборудованием плазменной резки
При работе с оборудованием плазменной резки необходимо жестко придерживаться правил техники безопасности, так как, выполняя плазменную резку, мы имеем большое количество представляющих опасность факторов: высокое напряжение, температура, ультрафиолетовое излучение и расплавленный металл. Необходимо носить одежду сварщика, иметь сварочный щиток со стеклами соответствующей степени затемнения.
Перед началом резки осмотрите защитный щиток, сопло и электрод, не начинайте работу, если сопло или электрод недостаточно закреплены.
Не стучите плазматроном, стараясь удалить брызги металла, так как можете его повредить.
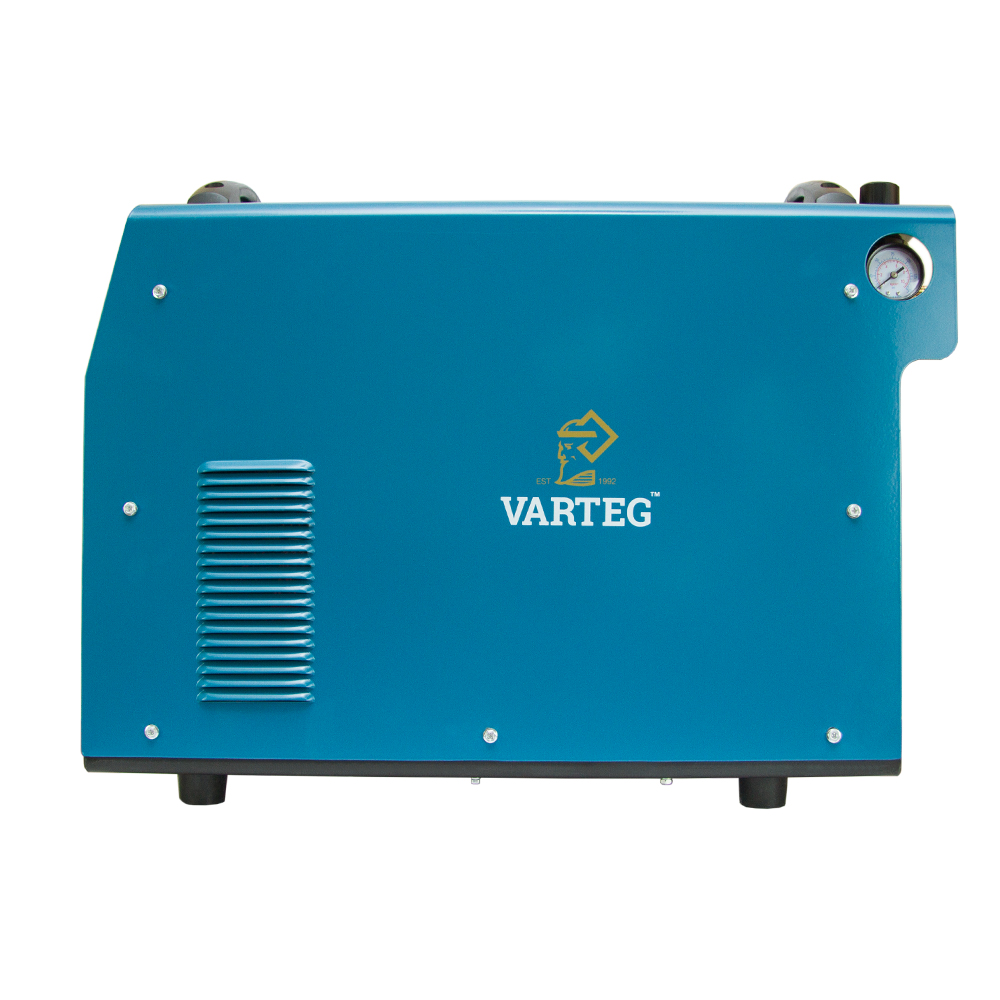
Правильно эксплуатируя и обслуживая аппарат плазменной резки, вы сможете выполнять резку с высокой скоростью, качественно и чисто.
Основные параметры плазменной резки
Важными параметрами плазменной резки считаются: факельный зазор (между соплом и листом), состав плазмообразующего газа, скорость резки, сила тока плазменной дуги. Скорость резки будет зависеть от силы тока и зазора между соплом и листом.При ручной плазменной резке в качестве газа используется воздух. Для автоматической плазменной резки применяется двойной газ: листы до 25 мм режутся азотом и водяным туманом, а более 25 мм – водородом или аргоном в сочетании с азотом или двуокисью углерода. В процессе плазменной резки важен не только используемый газ, но и давление, образующееся в течение резки (чем выше, тем хуже), это повлияет на качество процесса и срок службы электрода и сопла.
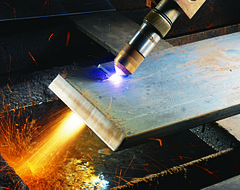
На длительность эксплуатации электрода и сопла напрямую влияет также ток дуги. Для определенного комплекта электрод-сопло установлен свое номинальное значение тока. Если нужно увеличить ток, то следует брать сопло большего диаметра.
Факельный зазор, т.е. расстояние между соплом и листом, должен быть постоянным. Только в этом случае можно получить качественный рез. Если уменьшить зазор, то это приведет к сгоранию сопла и электрода. Особенно быстро сгорит сопло при контакте с листом.
Скорость плазменной резки влияет на качество реза, а также на образование шлака и легкость его удаления. На качество и точность резки решающее влияние оказывают ширина реза и угол наклона кромок. Эти параметры определяются током дуги, расходом газа и скоростью движения плазмотрона. Ширина реза определяется диаметром выходного отверстия сопла и током дуги. Чтобы оценить ширину, следует увеличить диаметр сопла в 1,5 раза. Широкий рез может получиться при частичном разрушении электрода, большом факельном зазоре (расстоянии между соплом и листом), высоком токе дуги, малой скорости резки.

Устройство плазменных резаков
Плазменный резак, называемый также плазмотроном или плазменной горелкой, предназначен для образования плазмы при резке металла. Плазмотроны предназначаются как для ручной, так и механизированной плазменной резки.В комплект резака входят следующие узлы: сопло, электродержатель с электродом, дуговая камера, изолятор, который разделяет электродный и сопловый узлы, системы водо- и газоснабжения.
Устройство резака для плазменной резки будет зависеть от рабочей среды, зажигания среды, системы охлаждения и пр. Самые простые виды плазмотронов – для инертных и восстановительных газов. Плазмотроны с водяной и магнитной стабилизацией используются редко.
Резаки с газожидкостной стабилизацией дуги комплектуются системой каналов для подачи воды в столб дуги в сопловом узле. Для стабилизации дуги при плазменной резке используются двухфазные газожидкостные потоки, которые вводятся по схеме двухпоточного плазмотрона. Такой способ стабилизации повышает режущие свойства плазменной дуги, а за счет подачи жидкости в формирующее сопло улучшается его охлаждение.

Также активно используются плазмотроны с водяной завесой и газожидкостной системой охлаждения. Они также укомплектованы системой водяных каналов, которые создают завесу вокруг дуги. Вода охлаждает кромку металла и улучшает условия и качество плазменной резки таким плазмотроном.
Сопло плазменного резака формирует дугу, разрезающую металл. На свойства дуги будут влиять форма и размеры соплового канала. Уменьшая диаметр сопла и увеличивая его длину, вы получаете поток плазмы высокой скорости и отличные условия плазменной резки.
Плазменная резка зимой
В зимний период при минусовых температурах отличной альтернативой газо-кислородной резке становится плазменная резка. Этот вид резки металла не требует заправки, аттестации, доставки большого количества комплектующих. Для плазменной резки нужна лишь электроэнергия и периодическая смена комплекта сопел и электродов.Для плазменной резки при низких температурах плазмотрон должен иметь воздушное охлаждение.

Аппараты плазменной резки с воздушным охлаждением плазмотрона режут металл толщиной до 55 мм. Но не весь металл имеет подобную толщину, иногда требуется плазмотрон для более плотного листа. Аппараты могут комплектуются кабель-шланговыми пакетами до 30 м – это позволит осуществлять плазменную резку на морозе, не вынося само оборудование из теплого помещения.
Машины для плазменной резки
Плазменная резка может быть как ручной, так и механизированной. В комплект оборудования для механизированной резки входят плазменная горелка (плазмотрон), источник энергии, система управления процессом резки, устройство для перемещения установки.Машины для плазменной резки могут быть стационарными и передвижными, одно-, двух- и многоместными, портального, портально-консольного и шарнирного типа, с фотоэлектронным, магнитным или числовым управлением.

На машинах для плазменной резки портального типа лист располагается под ходовой частью – порталом. На портально-консольных машинах лист находится под консолью, а на портале располагается копировальное устройство. На консоли находятся плазмотрон и суппорт. Шарнирные машины размещают лист под шарнирной рамой. В комплект такого устройства также входят суппорт, копирующий механизм и собственно плазмотрон.
При фотоэлектронном управлении машиной для плазменной резки фотокопировальное устройство отслеживает контур чертежа. Плазмотрон режет лист четко по контуру, повторяя за фотоэлементом.
Электромагнитное управление плазменной резкой используется в шарнирных машинах. Копиром является ранее вырезанная деталь. Копировальная машина комплектуется электродвигателем, редуктором, электромагнитом и металлическим стержнем. Под действием магнита стержень прижимается к копиру и обводит его по контуру. За стержнем движется и плазматрон.
Программное управление процессом резки позволяет получать комплект деталей нужного контура, а также заранее программировать плазматрон на выполнение определенной задаче по резке в зависимости от толщины металла, вида реза и пр.

Станки для плазменной резки с плазматронами различаются также по виду обрабатываемой продукции. Это может быть прокат, листовой или профильный, трубы. От вида разрезаемой продукции зависит комплектация того или иного станка.
Плазмотрон с медным полым электродом для плазменной резки
Ресурс работы электрода при плазменной резке особо актуален, когда дело имеешь с толстым металлом. Для решения этой проблемы существует плазмотрон с полым медным внутренним электродом, оснащенный резьбовой нарезкой. При разработке плазмотрона за основу брались теоретические и экспериментальные исследования. За основу бралась модель непрерывно движущегося пятна привязки дуги по поверхности электрода. В каждом макро пятне есть микро пятна, которые передвигаются по поверхности разогретого электрода. Для расчета эрозии электрода высчитывают время нагрева электрода до плавления, кипения и испарения, а также принимают плотность тока в микро пятне.Уменьшение плотности тока в микро пятне приводит к уменьшению эрозии электрода плазмотрона.

Плазмотрон с медным полым электродом в связи с рядом его особенностей комплектуется источником питания с более высоким напряжением холостого хода. Увеличения напряжения дуги приводит к росту мощности плазмотрона, что благоприятно влияет на резку. С медным полым электродом плазмотрон может работать и на нейтральных, и на кислородсодержащих газах.
Такого рода плазмотрон состоит из катодного и соплового узлов, которые разделены вихревой камерой, куда подается газ. Узел катода – это медный полый электрод, запрессованный в корпус.

На мощность плазмотрона влияет увеличение тока дуги, а также изменение расстояние между срезом сопла и изделием. При силе тока на дуге 400 А и толщине металла до 80 мм стойкость сопла и внутреннего электрода плазмотрона составит 120-150 часов.
Факторы, определяющие качество плазменной резки
Иногда можно встретить мнения о недостаточном качестве плазменной резки металлов. Но они однозначно ошибочны и связаны с отсутствием опыта человека в этой сфере.Плазменная резка способна справится с широким ассортиментом металлов и сплавов. Благодаря высокой температуре луча плазмотрона, плазменный резак разрежет и титан.
Комплектующие и оборудования для плазменной резки недорогие в сравнении с той же лазерной резкой. К тому же комплект сопел и электродов для резки не занимает много места.
Основных факторов, которые влияют на качество плазменной резки всего пять. Во-первых, это техническое состояние оборудования.

И последний, но не менее важный показатель – контроль за состоянием электрода и сопла. Состояние этих небольших, но очень важных комплектующих аппарата для плазменной резки способно определить исход процесса.
Плазмотрон высокой мощности, обеспечивающий высокую концентрацию энергии в месте реза, гарантирует малую ширину реза, отличное качество кромок и отсутствие коробления. На качество реза также важное влияние оказывает скорость перемещения плазмотрона. Правильно выбранная скорость плазмотрона обеспечит узкий, шириной не более двойного диаметра сопла, рез, гладкие поверхности и отсутствие скруглений.

Технология, типы, комплектующие
Плазменная резка разрезает металл за счет теплоты, которая выделяется сжатой плазменной дугой. А получается плазменная дуга в специальном устройстве – плазмотроне в результате сжатия и вдувания в нее плазмообразующего газа.Различают плазменно-дуговую резку и резку плазменной дугой. При первом типе резки дуга образуется между электродом и слоем металла. Разрезает металл энергия одного из приэлектродных пятен дуги, плазмы столба и факела.
При резке плазменной дугой дуга горит между электродом и наконечником плазмотрона, металл же не входит в электрическую цепь. Часть плазмы дуги выносится из плазмотрона в виде струи, которой и режется металл.
В плазмотроне находится цилиндрическая дуговая камера с выходным каналом, который формирует сжатую плазменную дугу. Такое комплектующее как электрод располагается в тыльной части этой камеры. Обычно возбуждение дуги между электродом и металлом затруднительно. Поэтому зажигается дежурная дуга между электродом и плазмотроном.
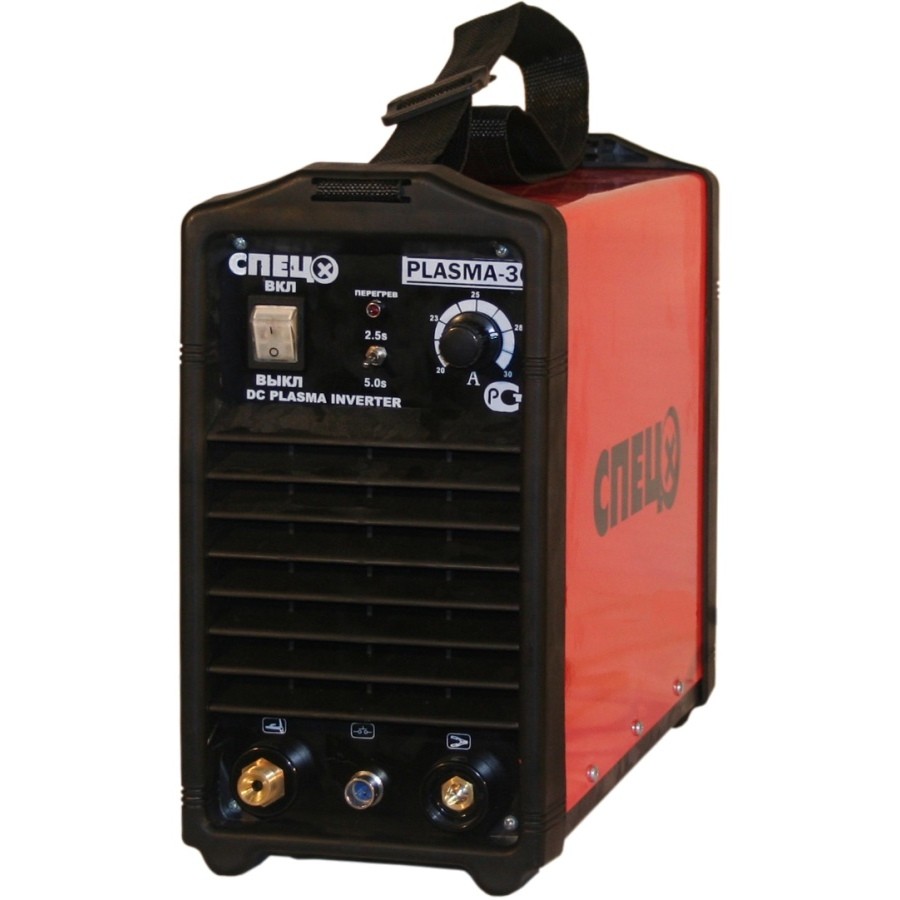
В дуговую камеру плазмотрона подается плазмообразующий газ, который под действием тепла дуги нагревается, увеличивается в объеме и истекает из сопла со скоростью 2-3 км/с.
Электроды, важнейшие комплектующие аппаратов и машин для плазменной резки, изготавливаются из вольфрама, меди, гафния и прочих металлов. Не менее важные комплектующие сопла выбираются медные и медные с вольфрамовой вставкой. Комплект электрод-сопло наряду с плазмотроном являются важнейшими составляющим устройств для плазменной резки, от качества которых зависит исход резки. На процесс резки и характеристики основных узлов плазмотрона влияет состав плазмообразующего газа. Наряду с комплектующими плазменного резака, плазмообразующая среда определяет количество тепла, которое будет выделяться в процессе, поскольку при определенной геометрии сопла и токе именно состав среды будет определять напряженность поля столба дуги внутри и снаружи сопла.

Инъекция плазмы, обогащенной тромбоцитами (PRP): как это работает
В последние годы врачи узнали, что организм обладает способностью к самовосстановлению. Плазмотерапия с высоким содержанием тромбоцитов – это форма регенеративной медицины, которая может использовать эти способности и усилить естественные факторы роста, которые ваше тело использует для заживления тканей.
Что такое плазма и что такое тромбоциты?
Плазма – жидкая часть цельной крови. Он состоит в основном из воды и белков и обеспечивает среду для циркуляции красных кровяных телец, лейкоцитов и тромбоцитов в организме.Тромбоциты, также называемые тромбоцитами, представляют собой клетки крови, которые вызывают образование тромбов и другие необходимые функции заживления роста.
Активация тромбоцитов играет ключевую роль в естественном процессе заживления организма.
Что такое плазма, обогащенная тромбоцитами (PRP) и что такое инъекции PRP?
Терапия с использованием обогащенной тромбоцитами плазмы (PRP) использует инъекции концентрации собственных тромбоцитов пациента для ускорения заживления поврежденных сухожилий, связок, мышц и суставов. Таким образом, инъекции PRP используют собственную систему исцеления каждого отдельного пациента для улучшения опорно-двигательного аппарата.
PRP нужно взять от одной до нескольких пробирок с вашей собственной кровью и пропустить ее через центрифугу для концентрирования тромбоцитов. Затем эти активированные тромбоциты вводятся прямо в поврежденную или больную ткань. Это высвобождает факторы роста, которые стимулируют и увеличивают количество репаративных клеток, которые производит ваше тело.
Иногда для направления инъекции используется ультразвуковая визуализация. На фотографиях ниже показана инъекция PRP в разорванное сухожилие пациента.Слева показано ультразвуковое руководство, справа – инъекция.
Видео: Как работают инъекции богатой тромбоцитами плазмы?
В этом видео врач спортивной медицины HSS Брайан Д. Халперн обсуждает и демонстрирует инъекции PRP.
Плазма, богатая тромбоцитами, значительно улучшает процесс заживления, и использование PRP инъекции при боли в плече, вызванной разрывами вращающей манжеты, при разрывах ахиллова сухожилия и других травмах мягких тканей, становится все более распространенным.
PRP улучшает функцию и уменьшает боль у людей с тендинитом или хроническими состояниями тендиноза, такими как теннисный локоть или локоть игрока в гольф.
Некоторые из ключевых преимуществ инъекций PRP заключаются в том, что они могут снизить потребность в противовоспалительных или более сильных лекарствах, таких как опиоиды. Кроме того, побочные эффекты инъекций PRP очень ограничены, потому что, поскольку инъекции создаются из вашей собственной крови, ваше тело не будет их отвергать или отрицательно реагировать на них.Узнайте больше об инъекциях PRP из статей и других материалов ниже или найдите лучшего врача, который выполняет инъекции PRP в HSS в соответствии с вашим конкретным состоянием и страховкой.
Назад в игру Истории пациентов
Что такое космическая плазма? | UCL Кафедра физики космоса и климата
Вселенная состоит из космической плазмы, четвертого состояния материи.
Вселенная состоит из космической плазмы. Плазма – это слово, относящееся к четвертому состоянию материи (твердое, жидкое, газовое, плазменное). Плазма – это настолько горячий газ, что некоторые или все составляющие его атомы расщепляются на электроны и ионы, которые могут двигаться независимо друг от друга. Поскольку они состоят из электрически заряженных частиц, на плазму могут сильно влиять электростатические и электромагнитные поля и силы, что может привести к очень сложному и интересному поведению.
Плазма встречается по всей Солнечной системе и за ее пределами: в солнечной короне и солнечном ветре, в магнитосфере Земли и других планет, в хвостах комет, в межзвездных и межгалактических средах и в аккреционных дисках. вокруг черных дыр. Здесь, на Земле, также есть плазма, от внутренней части термоядерного реактора до пламени свечи.
В Группе физики космической плазмы мы изучаем плазму в магнитосфере Земли и солнечный ветер, а также то, что происходит, когда они взаимодействуют.
- Магнитосфера
- Земля имеет магнитное поле, которое создается электрическими токами, протекающими в ее жидком внешнем ядре. Его можно обнаружить с помощью простого магнитного компаса: в Великобритании компас указывает на север, если вы держите его горизонтально, и в землю, если вы держите его вертикально. Если бы вы провели этот эксперимент во многих точках на поверхности Земли, вы бы обнаружили, что магнитное поле Земли похоже на магнитное поле стержневого магнита – магнитного диполя. Магнитное поле Земли простирается далеко в космос, где оно встречается с магнитным диполем. межпланетное магнитное поле, которое переносится по всей солнечной системе солнечным ветром, порывистый поток плазмы, который течет через солнечную систему с типичной скоростью 450 км / с.Солнечный ветер отклоняется вокруг магнитного поля Земли, которое сжимает магнитное поле Земли на стороне, обращенной к Солнцу, и образует длинный хвост на стороне, направленной от Солнца. Область космоса, содержащая магнитное поле Земли, называется магнитосферой
- Плазма в магнитосфере
Несмотря на то, что многие думают, космос на самом деле не пуст, и магнитосфера Земли не исключение! Магнитосфера заполнена плазмой самых разных температур и плотностей, хотя большая часть ее слишком разрежена, чтобы ее можно было увидеть невооруженным глазом или даже в телескоп.
Воздух на уровне моря содержит 100000000000000000000 частиц на кубический сантиметр и имеет температуру 20 градусов Цельсия. Самая плотная и самая холодная часть магнитосферы, плазмосфера имеет от 10 до 10000 частиц на кубический сантиметр и температуру 58000 градусов Цельсия – выше, чем поверхность Солнца!
Заполнитель виджета YouTubeОдна из величайших загадок магнитосферы заключается в том, как вся эта различная плазма создается только из этих двух отправных точек.
- Магнитосфера и полярное сияние
- Именно благодаря магнитосфере на нашей планете есть впечатляющие северное и южное сияние – северное и южное сияние, которые часто можно увидеть ночью возле полярных и антарктических кругов. Полярное сияние вызывается электронами из магнитосферы, которые ускоряются вдоль магнитного поля Земли в верхние слои атмосферы, где они сталкиваются с атмосферными частицами на высотах от 100 до 200 км.Самый яркий цвет полярного сияния, зеленый, вызван ударами электронов атомов кислорода в атмосфере.
Изображения из космоса показали нам, что полярные сияния образуют овалы с центром вокруг магнитных полюсов Земли. Радиус этих овалов увеличивается, и полярные сияния перемещаются в более низкие широты, когда магнитосфера Земли сильно подвержена влиянию солнечного ветра или поглощается выбросом корональной массы, массивным взрывом солнечной плазмы и магнитного поля, которое проходит через солнечную систему, часто на скоростях, намного превышающих нормальный солнечный ветер.
Заполнитель виджета YouTube https://www.youtube.com/watch? V = AuAzTF1GGhg
Заполнитель виджета Vimeo https://vimeo.com/21294655
Во время самых сильных событий северный овал может достигать как Великобритания. Подпишитесь на aurorawatch, чтобы получать уведомления, когда вы можете увидеть северное сияние в Великобритании!
- Космическая погода: эффекты в космосе
- Космическая погода – это название, которое мы даем влиянию взаимодействия между Солнцем и Землей на наши технологии и общество.
Магнитосфера действует как защитный экран, не позволяя большей части излучения солнечных энергетических частиц от солнечных вспышек и космических лучей из более широкой галактики и за ее пределами достичь Земли. Несмотря на то, что она хорошо защищает нас, магнитосфера не совсем безобидная. Он является домом для опасных радиационных поясов, областей космоса, заполненных высокоэнергетическими протонами и электронами, которые вредны для космонавтов и могут повредить космические корабли. Радиационные пояса намного более опасны в часы и дни после того, как магнитосфера подверглась воздействию коронального выброса массы или подверглась воздействию особенно сильного солнечного ветра.Орбита группировки GPS и геосинхронная орбита, где расположено подавляющее большинство спутников связи, находятся во внешнем радиационном поясе, что делает их уязвимыми во время некоторых явлений космической погоды.
- Космическая погода: Влияние на землю
- Космическая погода и динамика магнитосферы также могут влиять на поверхность Земли и нашу атмосферу.
Во время космической погоды поток заряженных частиц, сталкивающихся с верхними слоями атмосферы, превышает обычный.Это может незаметно изменить условия в ионосфере и создать помехи для радио- и спутниковой связи. Эти повышенные потоки частиц наиболее сильны на полюсах, поэтому они также могут привести к отклонению трансполярных рейсов. Космические погодные явления также могут создавать помехи для электросетей. Взаимодействие между солнечным ветром и магнитосферой Земли может заставить магнитное поле Земли колебаться. Колеблющиеся магнитные поля могут генерировать электрические токи, которые в случае магнитного поля Земли могут течь в электрических сетях.Если это происходит без предупреждения, дополнительный ток может иногда перегрузить сети, как это произошло в Квебеке в 1989 году.
Только правильно понимая магнитосферу и то, как она взаимодействует с солнечным ветром, мы можем точно предсказать и смягчить последствия космической погоды. на наше общество.
инъекций плазмы, обогащенной тромбоцитами | Johns Hopkins Medicine
Инъекции обогащенной тромбоцитами плазмы (PRP) становятся все более популярными при различных заболеваниях, от спортивных травм до выпадения волос. В процессе лечения используются собственные клетки крови пациента, чтобы ускорить заживление в определенной области.
Что такое плазма, обогащенная тромбоцитами?
Плазма, богатая тромбоцитами, состоит из двух элементов: плазмы, или жидкой части крови, и тромбоцитов, типа клеток крови, которые играют важную роль в заживлении всего организма. Тромбоциты хорошо известны своей способностью к свертыванию, но они также содержат факторы роста, которые могут запускать размножение клеток и стимулировать регенерацию или заживление тканей в обработанной области.Плазма, богатая тромбоцитами, – это просто кровь, которая содержит больше тромбоцитов, чем обычно.
Для создания плазмы, обогащенной тромбоцитами, врачи берут образец крови у пациента и помещают его в устройство, называемое центрифугой, которое быстро вращает образец, отделяя другие компоненты крови от тромбоцитов и концентрируя их в плазме.
Что такое инъекция PRP?
После создания богатой тромбоцитами плазмы из образца крови пациента этот раствор вводится в целевую область, например, в поврежденное колено или сухожилие. В некоторых случаях врач может использовать ультразвук для проведения инъекции. Идея состоит в том, чтобы увеличить концентрацию определенных биопротеинов или гормонов, называемых факторами роста, в определенной области, чтобы ускорить процесс заживления.
Механизм инъекций PRP до конца не изучен. Исследования показывают, что повышенная концентрация факторов роста в плазме, богатой тромбоцитами, может стимулировать или ускорять процесс заживления, сокращая время заживления травм, уменьшая боль и даже способствуя росту волос.
Для чего используется лечение PRP?
инъекций PRP используются для лечения целого ряда состояний *, от скелетно-мышечной боли и травм до косметических процедур.
Травмы сухожилий, связок, мышц и суставов
Инъекции PRP могут помочь при различных травмах и состояниях опорно-двигательного аппарата. Например, хронические травмы сухожилий, такие как теннисный локоть или колено прыгуна, часто требуют длительного времени для заживления, поэтому добавление инъекций PRP к режиму лечения может помочь стимулировать процесс заживления, уменьшить боль и позволить быстрее вернуться к физической активности.
Послеоперационное заживление
Клиницисты впервые использовали PRP для ускорения заживления после челюстных или пластических операций. Теперь послеоперационные инъекции PRP расширились, чтобы помочь заживить мышцы, сухожилия и связки, поскольку процедуры на этих тканях, как известно, имеют длительное время восстановления.
Остеоартроз
Ранние исследования показывают, что инъекции PRP могут помочь в лечении боли и скованности при остеоартрите, изменяя среду суставов и уменьшая воспаление, но исследования продолжают расти.
Выпадение волос
ИнъекцииPRP могут быть эффективными при лечении облысения по мужскому типу, как для предотвращения выпадения волос, так и для стимулирования роста новых волос. PRP также может помочь в стимуляции роста волос после пересадки волос.
Омоложение кожи
Инъекции PRP иногда используются как средство против старения, но мало доказательств того, что PRP уменьшает морщины и другие признаки старения.
Риски и побочные эффекты терапии PRP
Инъекция PRP – это процедура с низким уровнем риска и обычно не вызывает серьезных побочных эффектов.Процедура включает забор крови, поэтому вам следует убедиться, что вы достаточно увлажнены и поели заранее, чтобы не было головокружения. После процедуры у вас могут появиться болезненные ощущения и синяки в месте укола.
Поскольку инъекции PRP состоят из ваших собственных клеток и плазмы, риск аллергической реакции намного ниже, чем при использовании других инъекционных препаратов, таких как кортикостероиды. Менее распространенные риски инъекций PRP включают:
- Кровотечение
- Повреждение тканей
- Инфекция
- Травмы нервов
Если вы подумываете об инъекциях PRP, обязательно обсудите со своим врачом все преимущества и риски.
* Исследования различных приложений PRP перспективны и быстро растут. Хотя оборудование, используемое для производства PRP, и сами инъекции были одобрены FDA, эта процедура считается исследовательской и не была официально одобрена FDA для большинства применений. Поскольку PRP – это вещество, полученное из собственной крови, оно не считается лекарством. Разрешение FDA означает, что врачи могут назначать и применять PRP, если они считают, что это отвечает интересам пациента.Однако отсутствие одобрения FDA означает, что лечение PRP может не покрываться страховкой.
Терапевтический обмен плазмы | Терапевтический аферез
Терапевтический обмен плазмы: чего ожидать
Во время этой терапии небольшие количества крови постепенно удаляются через введенную иглу или катетер центральной линии и циркулируют через машину, которая разделяет кровь на эритроциты, лейкоциты, тромбоциты и плазма.
Плазменная часть крови удаляется и заменяется заменителем плазмы, а затем добавляется обратно к клеткам (эритроцитам, лейкоцитам и тромбоцитам) и, наконец, возвращается через внутривенный или центральный венозный катетер.Удаленная плазма выбрасывается.
Одна процедура обычно удаляет от 65% до 70% болезнетворных белков (антител) в плазме. Обычно для улучшения клинического состояния требуется несколько процедур.
Плазмаферез – безопасная процедура с некоторыми возможными побочными эффектами.
До TPE
Перед процедурой мы рекомендуем пациентам в течение нескольких дней пить большое количество негазированных безалкогольных напитков. Мы также рекомендуем поесть перед запланированной процедурой.
Во время TPE
При установке внутривенных катетеров (ВВ) руки пациентов подпирают подушками, и их просят сжать кулак, чтобы улучшить кровоток. Пациенты могут испытывать синяки или дискомфорт в месте установки капельниц. Если вместо этого используется катетер или порт большего размера, пациенты могут свободно пользоваться руками во время процедуры.
Процедура обычно длится два-три часа, но может быть короче или дольше в зависимости от множества факторов.
После начала процедуры пациенты могут испытывать легкое онемение, покалывание, головокружение или тошноту. Сотрудник по аферезу, специализирующийся на данной процедуре, будет находиться с пациентом в течение всего лечения. Пациенты должны сообщать медсестре о любых побочных эффектах или симптомах, которые они испытывают.
После TPE
После завершения процедуры пациенты могут чувствовать усталость до конца дня. После процедуры рекомендуем пить много жидкости. Мы также рекомендуем пациентам попросить кого-нибудь из членов семьи или друга отвезти их домой.
Сандианские национальные лаборатории: Центр исследования плазмы
Введение
ЗАЯВЛЕНИЕ О МИССИИ
Постоянно служить сообществу разработчиков низкотемпературной плазмы, предоставляя им доступ к возможностям и опыту мирового класса, которые позволят им добиваться своих целей и продвигать науку о плазме.
О КОМПАНИИ
Центр исследования низкотемпературной плазмы (PRF) в Сандии предлагает сотрудникам доступ к передовым диагностическим и вычислительным возможностям и опыту, необходимым для постановки и проведения экспериментов и анализа данных, полученных в ходе совместной работы.Исследовательские возможности и опыт применимы для исследования большого разнообразия низкотемпературной плазмы в широком диапазоне условий, таких как: переходное к установившемуся, от низкого давления без столкновений к высокому давлению, от неравновесного к тепловому, с применением и без РЧ, импульсные или постоянные электрические и магнитные поля. Эти возможности включают:
- Оптический допрос видов с помощью непрерывных, наносекундных, пикосекундных и фемтосекундных лазерных систем для лазерно-индуцированной флуоресценции, двухфотонной лазерной флуоресценции, лазерной флуоресценции, индуцированной столкновениями, одномерного рамановского изображения, 2D CARS, томографического PIV, томсоновского рассеяния, электрического индуцированная полем генерация второй гармоники, многофотонная ионизация и микроволновое рассеяние
- Диагностика наночастиц в плазме и газовой фазе на месте (визуализация и распределение по размерам, химический состав, измерения заряда, скорости)
- Высокоскоростное и многомерное отображение динамических и стохастических сред с помощью высокоскоростных камер (частота кадров до 1 MFPS), усиленных камер со стробированием (ворота <200 пс) и кадрирующих камер (1 BFPS)
- Спектроскопические инструменты, охватывающие вакуумный ультрафиолет (ВУФ) через видимый и дальний ИК-диапазон (FTIR), а также масс-спектроскопию высокого разрешения.
- Крупная инфраструктура оборудования для создания или включения широкого диапазона источников плазмы и условий эксплуатации
- Измерение свойств плазменной поверхностной зарядки и вторичной электронной эмиссии материалов, облицованных плазмой
- Массивно-параллельная ES и EM PIC-DSMC, а также возможности гибридного и жидкостного моделирования в стадии разработки для многомодовых плазменных систем высокого давления и бесстолкновений с неравновесными химическими и фотонными процессами
- Поддержка аналитической теории для плазменных экспериментов, моделирования и оптических расчетов
- Поддержка квантово-химических расчетов, относящихся к взаимодействиям плазмы с материалом и синтезу наночастиц
Сотрудничество будет отбираться посредством ежегодного процесса подачи и рассмотрения предложений.При выборе будут учитываться научная и техническая ценность, уместность предложенных методов или подхода, а также осуществимость и доступность ресурсов объекта.
Исследователям настоятельно рекомендуется обсудить свои идеи с учеными учреждения до подачи заявки.
Конкурс предложений состоится в октябре (сразу после GEC), а крайний срок подачи предложений – в декабре. В материалах будет использоваться общий шаблон, который можно отправить в одно или оба принимающих учреждения.
Плазма
Плазма получается путем отделения жидкой части крови от клетки. Одна единица плазмы – это плазма, взятая из единицы целого кровь. Плазма замораживается быстро после сдачи крови, обычно в течение 8-24 часов. часов сбора, чтобы сохранить факторы свертывания крови. Замороженная плазма можно хранить до одного года и разморозить незадолго до использования. Замороженный плазма содержит все факторы свертывания крови, близкие к норме концентрации. Размороженную плазму можно переливать в течение 5 дней после оттаивание и содержит несколько пониженные уровни фактора V (66 +/- 9%) и пониженные уровни фактора VIII (41 +/- 8%) .Плазма не содержит эритроцитов, лейкоцитов и тромбоцитов, а в целом должен быть ABO-совместимым с эритроцитами реципиента. Rh фактор не нужно учитывать. Поскольку жизнеспособных лейкоцитов нет, плазма не несет риска передачи цитомегаловируса (CMV) или реакции «трансплантат против хозяина» (GVHD) .Переливание плазмы показано пациентам с задокументированным дефицит фактора свертывания крови и активное кровотечение, или кто собирается пройти инвазивную процедуру.Недостатки могут быть врожденными или приобретенный вторично по отношению к заболеванию печени, диссеминированный внутрисосудистый коагуляция (DIC) , или гемодилюция после массивного переливания с эритроцитами и кристаллоидными / коллоидными растворами. Кроме того, Переливание плазмы показано при лечении тромботических тромбоцитопеническая пурпура (ТТР) , обычно в сочетании с плазмообменом.
Плазма не должна использоваться при дефиците фактора свертывания крови. какой доступен более безопасный продукт, i.е. фактор VIII и IX концентраты для лечения гемофилии A и B соответственно. Также плазма не следует использовать для отмены варфарина (кумадин) антикоагулянт. Этого можно безопасно достичь, давая витамин К или проведение варфарина за два-три дня до запланированной процедуры. Стремительный отмена антикоагуляции варфарина при опасном для жизни кровотечении может достигается с помощью Kcentra®, 4-факторного концентрата протромбинового комплекса (PCC) .
Плазму нельзя использовать для увеличения объема, за исключением случаев, когда у пациента также имеется выраженная коагулопатия и кровотечение.
Дозировка
Объем одной единицы плазмы составляет 200-250 мл. Начальный Рекомендуемая доза для взрослых составляет 10 мл / кг, а для взрослых – 10-15 мл / кг. педиатрические пациенты.
Пример: пациент 70 кг x 10 мл / кг = 700 мл (округлить до ближайших 200 мл) = 800 мл = 4 единицы плазмы.
В случае сомнений рекомендуется консультация гематолога или банка крови относительно дозы плазмы.
Влияние инъекций обогащенной тромбоцитами плазмы по сравнению с плацебо на симптомы и функцию голеностопного сустава у пациентов с остеоартритом голеностопного сустава: рандомизированное клиническое испытание | Гериатрия | JAMA
Ключевые моментыВопрос Улучшают ли внутрисуставные инъекции богатой тромбоцитами плазмы симптомы и функцию голеностопного сустава у пациентов с остеоартритом голеностопного сустава?
Выводы В этом рандомизированном клиническом исследовании с участием 100 пациентов лечение двумя внутрисуставными инъекциями плазмы, богатой тромбоцитами, по сравнению с инъекциями плацебо с физиологическим раствором привело к среднему изменению в шкале Американского общества ортопедов стопы и голеностопного сустава (диапазон от 0 до 100; более высокие баллы указывают на меньше боли и лучше функционирование) 10 против 11 баллов за 26 недель; разница между группами не была статистически значимой.
Значение Эти данные не подтверждают использование инъекций богатой тромбоцитами плазмы пациентам с остеоартритом голеностопного сустава.
Важность Приблизительно 3,4% взрослых страдают остеоартрозом голеностопного сустава (тибиоталарного), а среди более молодых пациентов остеоартрит голеностопного сустава встречается чаще, чем остеоартрит коленного и тазобедренного суставов. Существует мало эффективных нехирургических вмешательств, но инъекции обогащенной тромбоцитами плазмы (PRP) широко используются, с некоторыми доказательствами эффективности при остеоартрите коленного сустава.
Объектив Определить влияние инъекций PRP на симптомы и функцию у пациентов с остеоартритом голеностопного сустава.
Дизайн, обстановка и участники Многоцентровое, блочно-рандомизированное, двойное слепое, плацебо-контролируемое клиническое исследование, проведенное в 6 центрах в Нидерландах, включало 100 пациентов с болью более 40 баллов по визуальной аналоговой шкале (диапазон 0–100) и сужением пространства тибиоталарного сустава. Набор начался 24 августа 2018 г., а последующее наблюдение было завершено 3 декабря 2020 г.
Вмешательства Пациенты были случайным образом распределены (1: 1) для получения 2 внутрисуставных инъекций под контролем УЗИ либо PRP (n = 48), либо плацебо (физиологический раствор; n = 52).
Основные результаты и мероприятия Первичным результатом была подтвержденная оценка Американского общества ортопедов стопы и голеностопного сустава (диапазон от 0 до 100; более высокие баллы указывают на уменьшение боли и улучшение функции; минимальная клинически значимая разница, 12 баллов) в течение 26 недель.
Результаты Среди 100 рандомизированных пациентов (средний возраст 56 лет; 45 [45%] женщин) ни один пациент не был потерян для последующего наблюдения по первичному результату.По сравнению с исходными значениями, средний балл Американского ортопедического общества стопы и голеностопного сустава улучшился на 10 баллов в группе PRP (с 63 до 73 баллов [95% ДИ, 6–14]; P <0,001) и на 11 баллов в группе PRP. группа плацебо (от 64 до 75 баллов [95% ДИ, 7-15]; P <0,001). Скорректированная разница между группами за 26 недель составила -1 ([95% ДИ, от –6 до 3]; P = 0,56). В группе плацебо было зарегистрировано одно серьезное нежелательное явление, не связанное с вмешательством; было 13 других нежелательных явлений в группе PRP и 8 в группе плацебо.
Выводы и значимость У пациентов с остеоартритом голеностопного сустава внутрисуставные инъекции PRP по сравнению с инъекциями плацебо не привели к значительному улучшению симптомов и функции голеностопного сустава в течение 26 недель. Результаты этого исследования не подтверждают использование инъекций PRP при остеоартрите голеностопного сустава.
Регистрация проб Реестр испытаний в Нидерландах: NTR7261
.