Плазморез: принцип работы и преимущества
Во многих сферах промышленности и в строительстве применяется оборудование, которое не актуально в быту и в обычной жизни. Один из таких инструментов – плазморез. Для чего он нужен и как работает устройство?
Для начала стоит узнать, что представляет собой плазма. Это – пятое состояние вещества. Например, воздух можно привести в состояние плазмы путем нагрева газа до 300000С. Именно такое вещество используют при плазморезке металлоизделий.
Плазморез позволяет резать быстро и с минимальными погрешностями. Готовые изделия выходят без потеков и неровностей, следов окалины. Резать с использованием плазменного резака можно почти все виды металла – сталь, чугун, алюминий и пр. сплавы. Для кройки подходит сырье в различном состоянии – его нет необходимости очищать от краски или ржавчины.
Плазморез позволяет получить очень ровный и точный рез малого размера без отходов. При этом, деформация обрабатываемого металла настолько незначительна, что никак не сказывается на качестве изделия.
При помощи плазменного резака можно выполнять фигурные резы. Применение такого инструментария полностью безопасно при соблюдении правил эксплуатации.
Плазморез: принцип работы
Разогретый до t 300000С воздух находится в активном, насыщенном ионами, виде, т.е. прекращает быть диэлектриком. Газ проводит ток, благодаря чему металл в зоне обработки расплавляется и происходит его выдув из реза.
Каждый из видов плазморезного оборудования укомплектован плазмотроном (плазменным резаком, который подключается к аппарату посредством кабеля и шланга). Все плазморезы можно подразделить на 2 категории:
- устройства прямого типа подключаются непосредственно к электрической сети;
- аппараты косвенного типа не требуют прямого электропитания и могут использоваться для резки неметаллического сырья.
Качество работы и характеристики плазмотрона напрямую зависят от того, какое сопло используется в конструкции. Чем шире диаметр сопла – тем выше скорость поступления плазмы и нарезки. В большинстве случаев для профессиональной кройки плазмой приобретаются аппараты с соплом диаметром до 3 мм и длиной 9–12 мм.
В качестве электрода в устройстве применяется стержень из гафния, размещенный внутри оборудования.
При проведении резки следует учитывать, что кройка кислородом может привести к окислению металла. Поэтому для повышения качества обработки металла производители могут применять и другие газы, в том числе кислород, водород, гелий.
Плазморезы: классификация
Все плазморезы подразделяют на 2 большие категории:
- трансформаторные – используются для кройки металла, толщина которого до 40 мм;
- инверторные – актуальны при необходимости резки изделий до 30 мм толщиной.
Инверторные плазморезы обладают меньшими габаритами, при этом им присущ высокий КПД и меньшее энергопотребление.
Стоит понимать – при множестве положительных характеристик плазморезы не являются панацеей для кройки металла. Так, подобное оснащение не справится с резкой металла большой толщины (даже серьезные профессиональные модели режут изделия до 100 мм толщиной). К тому же, обработка металлозаготовок на плазморезе требует соблюдения нескольких правил – перпендикулярного размещения сырья (иногда допускается отклонение не более 500), использования в комплекте с плазморезом только одного резака. Если перечисленные исключения не являются актуальными – смело приобретайте оборудование. С ним кройка металла приобретет множество положительных оттенков.
Плазморез. Виды и устройство. Плюсы и минусы. Как выбрать
Плазморез – электрический аппарат для резки металла за счет контролируемого потока плазмы. Широко применяется для фигурного сложного раскроя деталей из листовой стали и прочих металлов, а также обработки их кромок.
Для выполнения плазменной резки требуется оборудование, состоящее из:
- Инвертора.
- Горелки.
- Кабеля массы.
- Баллона со сжатым воздухом или компрессора.
Инвертор плазмореза выполняет преображение переменного электрического тока из сети в постоянный ток. В результате 220В на входе превращаются в 400В с силой тока от 25 до 125А.
К инвертору подключается горелка, которая называется плазмотроном. В ней выполняется возбуждение электрической дуги. На последнюю подается поток воздуха, который сильно разогревается. В результате этого формируется раскаленная плазма. При контакте с практически любыми поверхностями она их прожигает. Температуры плазмы достаточно даже для резки керамики, которая является более термостойкой даже чем сталь.
Скорость истечения плазмы 1500 м/с. Это превосходит возможности обычного газового резака, работающего в сочетании с кислородным баллоном, даже когда давление в том доходит до 10 атм. Таким образом, поток плазмы является более производительным, а главное позволяет получать более чистый рез. Он не выглядит столь оплавленным и неровным как после газового резака. Это естественно и исключает образование большого количества шлака на обратной стороне раскраиваемой заготовки.
Плазморез используется не только на производствах, но и полюбился мастерам в небольших домашних мастерских. Это связано с доступностью данного оборудования. Плазморезы применяются для выполнения раскроя листового металла толщиной 1-100 мм. Конечно, их возможности зависят напрямую от мощности. Бытовые устройства обычно не режут заготовки сечением больше 15-22 мм.
Потоком плазмы можно выполнять сложный раскрой с множеством изломов. То есть, плазморез справляется с такими задачами, которые просто невозможно выполнить обычным абразивным инструментом в силу его особенностей реза.
Плазморезы целесообразно использовать в таких случаях:
- Когда требуется фигурный раскрой металла.
- Для увеличения продуктивности труда.
- Для снижения себестоимости выполнения реза.
Если сравнивать работу плазморезов, к примеру, с УШМ, то чтобы раскроить толстую стальную плиту длиной 1 м потребуется как минимум несколько абразивных отрезных дисков. То есть, себестоимость такой работы будет заключаться как минимум в их покупке. При работе же плазморезом расходные материалы не нужны. По сути, выполняется только потребление электроэнергии, что не так дорого.
В то же время плазморезы превосходят и газовые резаки. Дело в том, что они делают более чистый рез, который если и нужно шлифовать, то это будет менее сложно. Для работы этого аппарата не нужно заправлять баллоны кислородом и пропаном.
ПреимуществаИспользование плазмореза дает много преимуществ в работе. Это не удивительно, так как такое оборудование имеет немало плюсов. К их числу можно отнести:
- Высокая скорость выполнения реза.
- Быстрый прожиг.
- Не сильно греет всю заготовку.
- Высокое качество реза.
- Полная безопасность.
- Простая регулировка.
- Низкие требования к качеству заготовок.
Поток плазмы, выдаваемый плазморезом, имеет рабочую температуру до 20 тыс. градусов, но обычно находится в пределах 8-10 тыс. Это позволяет очень быстро прожигать даже очень толстый металла. К примеру, потоком плазмы можно кроить листовую сталь сечением 25 мм со скоростью 1 м/мин. Никакая болгарка или газовая горелка на такое не способна.
Чтобы прожечь в центре лист металла сечением 15 мм, плазморезу потребуется 2 сек. Это учитывая, что заготовка холодная, поэтому первое время температура с точки воздействия поглощается окружающим материалом. Для сравнения, газовая горелка сделает это не менее, чем за 30 сек.
Поток плазмы прожигает металл быстро, так что срок воздействия в направленную точку небольшой. Это сопровождается тем, что поверхности вокруг разогреваются не сильно. Если пользоваться менее скоростными абразивными инструментами или газовой горелкой, то площадь накала вокруг линии реза намного больше. Когда же обрабатываемая заготовка ранее прошла закалу, то в результате она получит отпуск и станет мягкой. От плазмореза это происходит в меньшей мере. Качества, заданные заготовке в результате предварительной термообработки, после раскроя плазмой практически сохраняются.
Кромки на вырезанных с помощью плазмореза заготовках получаются достаточно качественными. На них нет таких наплывов и прилипшего шлака, как на деталях, полученных с помощью газового резака. Они достаточно ровные и гладкие, чтобы их сразу использовать по назначению, к примеру, при изготовлении сварных конструкций. Если же поверхность нужно отшлифовать до идеала, то после плазмореза шлифовка происходит не так сложно, так как отсутствуют глубокие рытвины.
Бытовой и полупрофессиональный плазморез не применяет в своей работе горючие газы, подобно газовому резаку или промышленному плазменному. Таким образом, использование такого оборудования не сопровождаться риском взрыва. Также у плазмореза нет обратного удара пламени, как наблюдается у кислородных резаков.
При использовании плазмореза достаточно его просто включить, и если это предусмотрено конструкцией, отрегулировать мощность. Не нужно настраивать давление кислорода и горючего газа. То есть, освоиться с принципом работы аппарата можно за пару минут, и сразу же начать получать навыки работы с ним.
Заготовки, которые подлежат раскрою не обязательно перед работой очищать от ржавчины, старой краски или прочих загрязнений. Плазменная дуга прорезает все, при этом у нее не наблюдаются воздушные хлопки и разбрызгивания жидких горячих капель металла.
НедостаткиПлазморез действительно очень полезное для мастерской оборудование, но его нельзя считать идеальным для выполнения всех работ по раскрою. Существуют задачи, с которыми лучше разобраться другим инструментом. Все дело в некоторых недостатках и ограниченных возможностях данного оборудования.
В целом к минусам плазморезов можно отнести:
- Режет только под прямым углом.
- Не подходит для прогрева заготовок.
- Требует подключения к электросети.
Чтобы рез получился качественным, дуга должна быть направлена перпендикулярно к плоскости заготовки. В противном случае линия реза будет искривленной. Однако дорогие плазморезы могу выполнять и косые резы.
Плазморезы не подходят для того, чтобы греть ими заготовки для повышения их пластичности перед изгибом. С их помощью это сделать реально, но очень сложно, так как существует риск прожечь заготовку. Газовая горелка справляется с такой задачей куда лучше.
Также нельзя забывать, что плазморез работает от электрической сети. Им не получится вырезать металл в месте без электрификации, как это делают газовые резаки. Если устройство используется с компрессором, а не баллоном, то нужно учитывать, что тот также нуждается в электричестве.
Виды плазморезовПлазморезы можно разделить на виды в зависимости от типа:
- Используемого газа.
- Поджига дуги.
- Охлаждения.
В зависимости от типа применяемого газа плазморезы можно разделить на обычные, работающие от сжатого воздуха, а также требующие подключения кислорода, аргона. Прибор на воздухе относится к классу бытовых устройств, которые обычно и применяются частным мастерами. На очищенных газах резка получается быстрее и точнее. Такие устройства применяют на производственном оборудовании.
По типу поджига дуги плазморезы бывают контактные, пневматические и высокочастотные. Они имеют весьма существенные отличия. Так у контактного устройства поджиг дуги происходит только в момент прижатия сопла плазмотрона к поверхности, контактирующей с клеммой массы на инверторе. В результате вспыхивает дуга и происходит рез. У пневматических устройств это случается за счет подачи газа. То есть прикасаться соплом к заготовке не нужно. Это позволяет сохранить ресурс сопла, которое в результате меньше обгорает и пачкается шлаком. Высокочастотный плазморез работает автоматически. Его дуга переходит в режим реза просто при приближении к поверхности. Это происходит за счет ее возбуждения высокочастотным импульсом, между катодом и анодом в сопле.
По типу охлаждения плазморезы можно разделить на воздушные и жидкостные. Первые остывают за счет обдува корпуса инвертора вентилятором. Такой тип охлаждения применяется в бытовых и полупрофессиональных устройствах. Плазморезы с водяным охлаждением это уже профессиональные установки, способные работать значительно дольше без остановок. Они остывают за счет циркуляции внутри охлаждающей жидкости, обычно смеси дистиллированной воды и этилового спирта. В целом для рядового пользователя интересными являются только устройства с воздушным охлаждением. Однако нужно отталкиваться от его эффективности, так как перегревать оборудование нельзя.
Выбирая плазморез следует обратить внимание на такие важные параметры:
- Максимальная толщина чистовой и черновой резки.
- Длина шланг пакета.
- Требуемая мощность компрессора.
- Продолжительность работы без перерыва.
При выборе нужно учитывать, что рекомендуемая максимальная толщина реза указывается в двух значениях. Первое определяет сечение, при котором кромки после резки не нужно будет обрабатывать. Второй параметр толщины является максимальным пределом, но при такой обработке рез будет иметь дефекты.
Похожие темы:
- Осцилляторы. Виды и устройство. Работа и применение. Особенности
- Инверторные сварочные аппараты. Как выбрать. Типы и работа
- Сварочный аппарат (Часть 1). Типы и особенности. Сварка. Дуга. Применение
- Сварочный аппарат (Часть 2). Виды и особенности. Применение. Как выбрать
- Качество плазменной резки. От чего зависит и особенности
- Электроэрозионная обработка. Применение и особенности
10 основных преимуществ плазменной резки
Плазменный резак является одним из наиболее точно настроенных, широко используемых, эффективных и универсальных инструментов для легкой резки даже тяжелых и толстых материалов. Это инструмент, который можно использовать для различных материалов и проектов, помогая безопасно резать металлы, которые иначе было бы невозможно разрезать. Продолжайте читать, чтобы узнать, что такое плазменная резка и основные преимущества работы с нами над вашим следующим проектом.
Что такое плазменная резка?
Плазменная резка — это процесс, используемый для резки стали, нержавеющей стали и алюминия с помощью плазменной горелки. Проще говоря, газ выдувается с высокой скоростью из сопла, в то время как электрическая дуга плавит металл, а сжатый воздух выдувает расплавленный металл. Это оставляет более чистый рез, чем резка кислородно-ацетиленовой горелкой.
Tampa Steel & Supply предоставляет эту услугу при толщине до полдюйма. Свяжитесь с нами сегодня, чтобы узнать, можем ли мы помочь вам с этой услугой.
Для чего используется плазменный резак?
Плазменные резаки можно использовать по-разному, и наша компания будет рада вам помочь. Плазменная резка часто используется для различных работ по изготовлению металлов, например, в строительстве. Однако его также можно использовать в декоративных целях, когда художники и дизайнеры полагаются на этот инструмент, чтобы воплотить свое видение в жизнь. Скульптуры и знаки нуждаются в плазменной резке, чтобы получить гладкую и профессиональную отделку, которая в противном случае была бы невозможна.
Различные типы плазменных резаков могут работать с легкими и тяжелыми металлами, обрезая лишний материал, который не нужен для проекта. Эти резаки также могут резать металлы, проводящие электричество, такие как алюминий и сталь. Точность этого процесса означает, что он очень универсальный вариант практически для любого проекта, связанного с металлом или сталью, поэтому он так популярен на протяжении многих лет.
10 основных преимуществ плазменной резки
Вот список десяти основных преимуществ плазменной резки металлических материалов:
1. Больше универсальности
Плазменная резка может выполняться на различных типах металла. Он использует электрическую дугу для резки любого проводящего металла, такого как сталь, железо, медь, латунь, алюминий, нержавеющая сталь и другие прочные материалы. Плазменная резка также позволяет резать различные материалы, уложенные друг на друга, с максимальной скоростью резки. Такие методы, как Oxyfuel, не могут повторить это, поэтому это один из лучших вариантов для различных работ по металлу. Разрезы, которые может создать плазменный резак, также универсальны, что позволяет вам воплотить в жизнь свое видение произведения искусства или проекта.
2. Простота использования
Плазменные резаки портативны, и вы можете легко перемещать их туда, куда вам нужно. Некоторые бренды настолько портативны, что с ними может легко справиться только один человек. Пока оператор плазменной резки хорошо обучен, это очень безопасное и надежное решение для резки металла.
3. Быстрая резка
Если вы сравните скорость резки плазменной резки с любыми режущими инструментами, вы обнаружите, что плазменная резка является победителем, поскольку она экономит время и намного проще, чем другое режущее оборудование. Плазменный резак выполняет работу за четверть времени по сравнению с любым другим режущим инструментом. Этот инструмент не требует предварительного нагрева перед резкой. Таким образом, это экономит время резки, помогая вам завершить проект в кратчайшие сроки.
4.
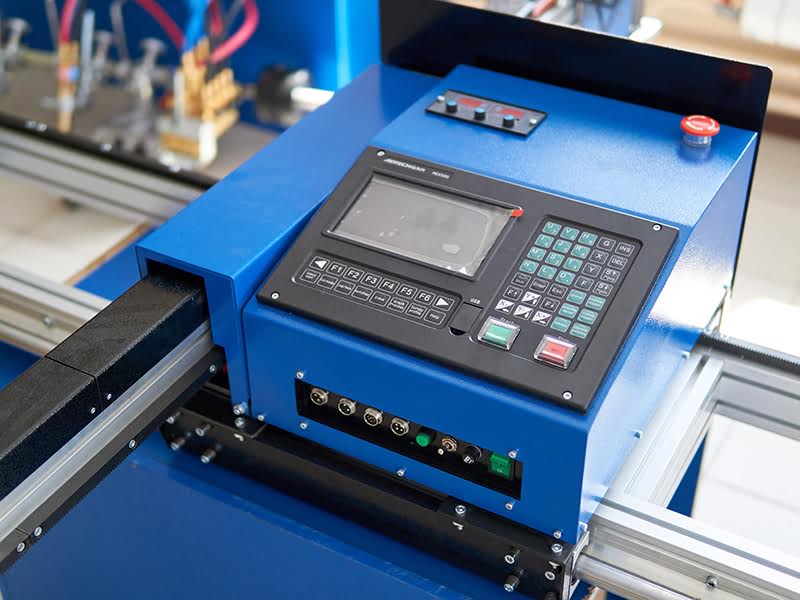
Для действительно чистого реза требуется опытный оператор с твердой рукой. Прецизионная или точная резка является одним из основных преимуществ плазменного резака, особенно когда речь идет о резке листового металла различной формы или под разными углами. Обсуждая вопрос о том, что такое плазменная резка, вы обнаружите, что это одно из главных преимуществ данного вида работ.
5. Низкая цена
Плазменная резка позволяет выполнять резку быстрее и с меньшими потерями, кроме того, очень мало потерь из-за производственных травм. Это означает, что цена для конечного пользователя снижается, поэтому этот процесс является более рентабельным, чем другие методы резки.
6. Пронзающая скорость
Вот где плазма действительно сияет по сравнению с кислородным топливом. Многие операции по резке требуют внутреннего прокалывания. При прокалывании металла толщиной 15 мм с помощью Oxyfuel его необходимо сначала нагреть примерно до 1000 градусов по Цельсию, что занимает более 30 секунд. Поскольку плазме не нужен этот шаг, она может сделать тот же прожиг менее чем за две секунды. Меньше времени — меньше денег, взимаемых с конечного пользователя.
7. Безопасность
Поскольку в этом процессе резки используется НЕ легковоспламеняющийся газ, этот метод является более безопасным, чем другие процессы. Мы всегда рекомендуем работать с нашей командой профессионалов, которые обеспечат безопасную и точную резку вашего металла.
8. Подходит для различных толщин
Наша команда предлагает плазменную резку металлов толщиной до полдюйма. Это означает, что мы можем работать над различными проектами, и по сравнению с другими вариантами резки металла мы можем работать с гораздо более толстым куском металла.
9. Создание разнообразных форм
Независимо от того, по какой причине вы решили изучить вопрос о том, что такое плазменная резка, вы обнаружите, что с помощью этого инструмента можно создать практически любую форму или линию, которые только можно вообразить. Наша команда может создавать прямые линии, кривые и сложные формы, которые иначе было бы невозможно сделать. Точный луч обеспечит высокую точность независимо от того, насколько сложным для нас является ваш проект.
10. Энергоэффективный процесс
При поиске способов повышения энергоэффективности ваших проектов вы обнаружите, что плазменная резка — это путь вперед. Это более устойчивое решение, чем другие варианты, поэтому мы видим больше компаний, чем когда-либо прежде, склоняющихся к использованию этой услуги.
Посетите Tampa Steel and Supply для получения качественной стали и поставок металла
Вам нужны поставки и обработка стали? Не ищите ничего, кроме профессионалов Tampa Steel and Supply. У нас есть обширный список металлопродукции для любого проекта, который вам нужен. Мы гордимся тем, что обслуживаем наших клиентов почти четыре десятилетия, и готовы помочь вам с вашими потребностями в стали. Есть вопросы? Позвоните нам сегодня, чтобы узнать больше, или зайдите в наш прекрасный выставочный зал в Тампе.
Запросите предложение онлайн
Или позвоните в Tampa Steel & Supply по телефону (813) 241-2801
Типы газов для плазменной резки и их преимущества
12 90 марта 2003 г.
Типы газов для плазменной резки и их преимущества
Mac-Tech Inc.2021-03-12T10:28:51-06:00
Автор Mac-Tech Inc. Статьи Комментарии отключены о типах газов для плазменной резки и их преимуществах
При проведении исследований оператор или владелец может столкнуться с ошеломляющим набором газовых вариантов. Многие производители выбирают системы плазменной резки с возможностью работы с двумя или несколькими газами. Это означает, что различные плазменные и защитные газы могут использоваться для различных целей. Плазменная горелка — это просто сильно заряженный ион, который прожигает электрически заряженные основания, такие как металлические пластины.
Аппарат плазменной сварки использует различные виды газов для разрыва металлов. Газ плазменной резки передает электрическую дугу, чтобы расколоть толстый металлический кусок. В большинстве плазменных систем в сварочных процессах одновременно используется несколько газов. Таким образом, в большинстве плазменных резаков используется смесь газов для повышения теплоемкости.
Продолжайте читать, чтобы изучить типы газов для плазменной резки и их преимущества, а также дать оптимальные рекомендации по резке трех наиболее распространенных типов материалов: низкоуглеродистой стали, нержавеющей стали и алюминия.
Категории газа
Ниже приведены основные типы газа, используемые для операций плазменной резки. Как правило, газы для плазменной резки соответствуют этим основным категориям.
- Контроль топлива . Плазменная резка требует идеальных условий для эффективной работы. То, как работает плазменный резак, позволяет определенным компонентам соблюдать некоторые условия, чтобы облегчить ускоренную струю плазменной горелки.
Управление топливом отличается тем, что оно ведет к плазменной головке. Он также регулирует нагрев вокруг сопла защиты резака. Эта конфигурация гарантирует, что пламя реза загорится только после правильной настройки плазменной головки.
- Топливо для плазменной резки . Топливо для плазменной резки предлагает как базовые, так и высокотехнологичные модели с разным уровнем нагрева. Первый этап происходит при слабом воспламенении, затем на стадии резания протекает больше мощности. В этих двух стадиях участвуют несколько газов.
- Завихритель топлива . Во время процесса плазменной резки материалы могут искривляться или сворачиваться из-за сильного нагрева. Эта реакция делает резку менее точной. Чтобы предотвратить эти деформации и дефекты, производители используют вихревое топливо.
Разновидности плазмообразующих газов
Воздух
Воздух является наиболее универсальным плазмообразующим газом; он обеспечивает хорошее качество и скорость резки нержавеющей стали, низкоуглеродистой стали и алюминия. Воздух также снижает затраты, поскольку нет необходимости покупать газы. Однако воздух не свободен. Воздух в цеху необходимо очищать от таких загрязнений, как твердые частицы, масляный туман и влага. Лучшим решением для воздушно-плазменных систем является специальный воздушный компрессор хорошего размера, рефрижераторный осушитель и набор фильтров для удаления загрязняющих веществ.
Свариваемость режущей кромки является проблемой при использовании воздушной плазмы. Воздушной плазмой происходит некоторое азотирование и окисление поверхности реза, что может вызвать пористость сварных швов. Air является хорошим вариантом для многих мастерских благодаря своей универсальности, хорошей скорости, низкому уровню окалины и сроку службы деталей до 600 пусков.
Кислород
Кислород стал стандартом в отрасли для резки низкоуглеродистой стали, поскольку он обеспечивает наилучшее, чистое качество резки и самую высокую скорость резки по сравнению с любым другим плазмообразующим газом. Однако плазменная резка алюминиевой пластины или пластины из нержавеющей стали с кислородным плазменным газом не рекомендуется. Недостатками кислорода являются стоимость газа и срок службы расходных частей. Однако в современных плазменно-кислородных плазменных системах используются инертные пусковые газы, такие как азот, для достижения срока службы деталей, аналогичного азотным или воздушным системам. Эти системы имеют срок службы деталей в диапазоне 800-1500 пусков. Сокращение вторичных операций обычно компенсирует повышенные затраты на расходные материалы и газ для удаления окалины и выпрямления скошенных деталей. Воздушный экран обычно используется с кислородной плазмой.
Азот
Азот использовался в большинстве ранних процессов плазменной резки. Это по-прежнему лучший выбор, если вы режете много нержавеющей стали или алюминия. Качество резки и срок службы деталей превосходны (в среднем более 1000 запусков). Однако при работе с более толстыми материалами при исчерпании возможностей вашей плазменной системы переключитесь на ардон-водород.
В общем, воздух является лучшим вторичным газом при использовании азотной плазмы. . CO2 также работает хорошо, немного улучшая отделку, скорость резки и срок службы деталей по сравнению с использованием воздуха. Но CO2 стоит дороже, чем воздух, и требует нескольких газовых баллонов с коллектором или объемной системы для обеспечения адекватного потока. Вода является отличным вторичным по отношению к использовать с азотной плазмой, если это позволяет система. Использование при резке нержавеющей стали или алюминия позволяет получить гладкую и блестящую поверхность реза. Вторичная вода требует наличия грунтовых вод, чтобы избежать утечки.
Аргоно-водородная
Аргон-водородная плазма является предпочтительной плазмой для резки толстой нержавеющей стали и алюминия (более 0,5 дюйма). В смеси обычно используется 35% водорода и 65% аргона. Водород аргона является самым горячим горящим плазменным газом и обеспечивает наибольшую режущую способность.
Аргон-водород используется в горелках с впрыском воды до 1000 ампер для резки нержавеющей стали диаметром до 6 дюймов. Аргон-водород обеспечивает прямой рез и гладкую, почти полированную поверхность нержавеющей стали в многогазовых горелках. Вдоль верхней или нижней кромки могут образоваться неровные окалины. Азот обычно используется в качестве защитного газа с аргоном и водородом. Недостатком этой установки является расход.
Четыре эмпирических правила, которые необходимо учитывать
Выбор наилучшего газа зависит от трех основных соображений: качества резки, производительности и экономичности.
- Мягкая сталь . Для низкоуглеродистой стали используйте кислородную плазму и воздушную защиту для получения чистого, ровного качества резки, минимального количества окалины, минимальной доработки, отличной свариваемости и превосходной производительности.
- Толщина менее 0,5 дюйма . Для наилучшего качества резки нержавеющей стали и алюминия размером менее 0,5 дюйма используйте азотную плазму и вторичную воздушную среду для правильного баланса качества резки и доступности.