таблица, формулы расчетов, выбор скорости — как рассчитать глубину, подачу на оборот при точении
25.08.2020
Подготовимся к проведению одной из наиболее распространенных операций. Рассмотрим расчет подачи и режимов резания при токарной обработке. Его важность сложно переоценить, ведь если он проведен правильно, то помогает сделать техпроцесс эффективным, снизить себестоимость производства, повысить качество поверхностей деталей. Когда он выбран оптимально, это самым положительным образом влияет на продолжительность работы и целостность инструментов, что особенно важно в перспективе длительной эксплуатации станков с поддержанием их динамических и кинематических характеристик. И наоборот, если его неверно выбрать и взять не те исходные показатели, ни о каком высоком уровне исполнения продукции говорить не придется, возможно, вы даже столкнетесь с браком.
Режимы резания: что это такое
Это целый комплекс характеристик, задающих условия проведения токарной операции.
В число основных показателей входит глубина, скорость, подача, в список дополнительных – масса объекта, припуски, частота, с которой вращается шпиндель, и в принципе любая характеристика, влияющая на результат обработки. И важно взять те из них, что обеспечат лучшую итоговую точность, шероховатость и экономическую целесообразность.
Есть несколько способов провести расчет режимов резания при точении:
- • аналитический;
- • программный;
- • табличный.
Первый достаточно точный и до появления мощной компьютерной техники считался самым удобным. По нему все вычисления осуществлялись на основании паспортных данных оборудования: мощность двигателя, частоту вращения шпинделя и другие показатели подставляли в уже проверенные эмпирические выражения и получали нужные характеристики.
С разработкой специализированного ПО задача калькуляции существенно упростилась – все операции выполняет машина, быстрее человека и с гораздо меньшей вероятностью совершения ошибок.
Когда под рукой нет компьютера или формул, зато есть опыт, можно определить подходящие критерии на основании нормативных и справочных данных из таблиц. Но для этого необходимо учитывать все изменения значений, даже малейшие, что не всегда удобно в условиях производства.
Особенности определения режимов резания при точении
В первую очередь нужно выбрать глубину обработки, после нее – подачу и скорость. Важно соблюсти именно такую последовательность – в порядке увеличения степени воздействия на инструмент. Сначала вычисляются те характеристики, которые могут лишь минимально изменить износ резца, в конце те, что влияют на ресурс по максимуму.
Параметры следует определять для предельных возможностей оборудования, в обязательном порядке учитывая размеры, металл исполнения, конструкцию инструмента.
Важным пунктом является нахождение подходящей шероховатости. Плюс, правильнее всего взять лезвие под конкретный материал, ведь у того же чугуна одна прочность и твердость, а у алюминия – совсем другая. Не забывайте также, что в процессе происходит нагрев детали и возрастает риск ее деформации.
Выбор режима резания при точении на токарном станке продолжается установлением типа обработки. Какой она будет, черновой или чистовой? Первая грубая, для нее подойдут инструменты, выполненные из твердых сталей и способные выдержать высокую интенсивность техпроцесса. Вторая тонкая, осуществляется на малых оборотах, со снятием минимального слоя металла.
Глубина определяется количеством проходов, за которые убирается припуск. Подача представляет собой расстояние, преодолеваемое кромкой за вращение заготовки, и может быть одного из трех типов:
- • минутная;
- • на зуб;
- • на оборот.
Скорость в значительной степени зависит от того, какая именно операция выполняется, например, при торцевании она должна быть высокой.
Характеристики режимов резания
По мере совершенствования производства даже самые подробные таблицы оказывались все менее удобными: столбцы, колонки, соотношения – на изучение этого и поиск нужного значения уходило огромное количество времени. И это при том, что основные показатели связаны между собой, и уменьшение/увеличение одного из них провоцировало менять остальные.
Установив столь очевидную зависимость, инженеры стали пользоваться аналитическим способом, то есть продумали эмпирические формулы, и начали подставлять в них частоту вращения шпинделя, мощность силового агрегата и подачу и находить нужные характеристики. Ну а развитие компьютеров и появление вычислительного ПО серьезно упростило задачу и защитило итоговые результаты от ошибок человеческого фактора.
Схема расчетов режима резания на токарном станке
Порядок действий следующий:
- • Выбираете, каким инструментом будете пользоваться в данной ситуации; для хрупких материалов подойдет лезвие со сравнительно небольшими показателями прочности, но для твердых – с максимальными.
- • Определяете толщину снимаемого слоя и число проходов, исходя из актуального метода обработки. Здесь важно обеспечить оптимальную точность, чтобы изготовить изделие с минимальными погрешностями геометрических габаритов и поверхностей.
Теперь переходим к рассмотрению конкретных характеристик, играющих важную роль, и к способам их практического нахождения или изменения.
Глубина резания при токарной обработке на станке
Ключевой показатель для обеспечения качества исполнения детали, показывающий, сколько материала нужно убрать за один проход. Общее количество последних вычисляется с учетом следующего соотношения припусков:
- • 60% – черновая;
- • от 20 до 30% – смешанная;
- • от 10 до 20% – чистовая.
Также свою роль играет то, какая форма у заготовки и что за операция выполняется. Например, при торцевании рассматриваемый параметр приравнивается к двойному радиусу предмета, а для цилиндрических деталей он находится так:
k = (D-d)/2, где:
- D и d – диаметры, начальный и итоговый соответственно;
- k – глубина снятия.
Если же изделие плоское, используются обычные линейные значения длины – 2, 1-2 и до 1 мм соответственно. Здесь же есть зависимость от поддерживаемого класса точности: чем он меньше, тем больше нужно совершить подходов для получения результата.
Как определить подачу при точении
Фактически она представляет собой то расстояние, на которое резец передвигается за один оборот, совершаемый заготовкой. Наиболее высока она при черновой обработке, наименее – при чистовой, когда действовать следует аккуратно, и в дело также вступает квалитет шероховатости. В общем случае ее делают максимально возможной (для операции) с учетом ограничивающих факторов, в числе которых:
- • мощность станка;
- • жесткость системы;
- • стойкость и ресурс лезвия.
При фрезеровании отдают предпочтение варианту «на зуб», при зачистке отверстий – рекомендованному для текущего инструмента, в учебных целях – самую распространенную, то есть 0,05-0,5 об/мин.
Формула расчета подачи при точении, связывающая между собой все ее виды, выглядит так:
SM = S*n = SZ*Z*n, где:
n – частота вращения резца,
Z – число зубцов.
Для упрощения вычислений можно брать данные отсюда:
Диаметр, заготовки, мм |
Размер инструмента, мм |
Подача, мм/об, с выбранной глубиной резания, мм |
||||
до 3 |
3-5 |
5-8 |
8-12 |
от 12 |
||
Для стали |
||||||
до 20 |
16х25-25х25 |
0,3-0,4 |
– |
|||
20-40 |
0,4-0,5 |
0,3-0,4 |
– |
|||
40-60 |
16х25-25х40 |
0,5-0,9 |
0,4-0,8 |
0,3-0,7 |
– |
|
60-100 |
0,6-1,2 |
0,5-1,1 |
0,5-0,9 |
0,4-0,8 |
– |
|
100-400 |
0,8-1,3 |
0,7-1,2 |
0,6-1 |
0,5-0,9 |
– |
|
400-500 |
20х30-40х60 |
1,1-1,4 |
1-1,4 |
0,7-1,2 |
0,6-1,2 |
0,4-1,1 |
500-600 |
20х30 |
1,2-1,5 |
1-1,4 |
0,8-1,3 |
0,6-1,3 |
0,4-3,2 |
Для чугуна |
||||||
до 20 |
16х25-25х25 |
– |
||||
20-40 |
0,4-0,5 |
– |
||||
40-60 |
16х25-25х40 |
0,6-0,9 |
0,5-0,8 |
0,4-0,7 |
– |
|
60-100 |
0,8-1,4 |
0,7-1,2 |
0,6-1 |
0,5-0,9 |
– |
|
100-400 |
1-1,3 |
0,9-1,4 |
0,8-1,1 |
0,6-0,9 |
||
400-500 |
20х30-40х60 |
1,3-1,6 |
1,2-1,5 |
1,1-1,3 |
0,8-1 |
0,7-0,9 |
500-600 |
20х30 |
1,5-1,8 |
1,2-1,6 |
1-1,4 |
0,9-1,2 |
0,8-1 |
Если операции осуществляются под серьезными ударными нагрузками, выбранное значение необходимо помножить на 0,85. Если металлом детали является жаропрочная конструкционная сталь, следует ограничиться 1 мм/об.
Расчет скорости резания при токарной обработке
Это показатель с сильнейшим влиянием, зависящий от следующих факторов:
- • тип работы;
- • вид используемого инструмента;
- • материал исполнения заготовки.
Так, торцы отрезаются так быстро, как только возможно, в то время как сверление выполняется уже гораздо медленнее. Для решения стандартных задач параметр можно без труда вычислить, умножив диаметр будущего изделия на число оборотов в минуту и на тт, а затем разделив на поправочный коэффициент в 1000. Для упрощения можно воспользоваться специальным программным обеспечением.
Но если под рукой нет компьютера с установленным ПО или даже калькулятора, есть альтернативный вариант – уже подсчитанная скорость резания при точении из таблицы (ее мы отдельно приведем ниже). Также представим вашему вниманию две формулы – чтобы вы могли воспользоваться любой из них на основе уже имеющихся значений, а после обратили свое внимание на нормированные показатели.
Проверка принятых характеристик
Оборудование необходимо эксплуатировать подходящим образом – это нужно не только для производительности, но и с точки зрения эксплуатации.
Допустим, что вы остановились на каких-то значениях, что предпринять дальше? Прежде чем настраивать по ним станок, необходимо убедиться, что они правильные, так сказать, подтвердить правильность выбора режимов резания при токарной обработке.
Для этого нужно лишь заглянуть в паспорт оборудования и свериться с рекомендованными параметрами. Нормированные показатели должны быть выше тех, что взяли вы. Если это условие не выполняется, следует скорректировать величины, иначе техника вполне может выйти из строя в процессе изготовления деталей.
Какой инструмент использовать
Такой, что обеспечит:
- • необходимую форму и геометрические параметры заготовки;
- • достаточное качество готовой поверхности;
- • технологичность и безопасность процесса выпуска;
- • минимальные энергетические затраты при хорошей производительности;
- • экономичный расход дорогих и/или редких материалов;
- • ремонтопригодность изделия.
Выше мы уже писали, что длина обработки (резания) и подача на оборот при точении зависят лезвия, поэтому его тоже нужно рассмотреть подробнее. Сделаем это прямо сейчас, сгруппировав все разнообразие вариантов по главным признакам и выделив их особенности.
Классификация инструментов
Разделить их можно по трем показателям, каждый из которых оказывает достаточно сильное влияние на результаты проведения операций. Если установить неподходящий, это обернется недостаточной продуктивностью труда, ухудшением точности, повышением износа функциональных узлов или даже нарушением техники безопасности. Поэтому так важно правильно определиться и использовать то, что подходит для станка.
По способу обработки
Чтобы вам было проще выбирать рекомендуемые режимы резания при точении, таблицы составлены для таких разновидностей лезвий:
- • проходные;
- • резьбовые;
- • галтельные;
- • расточные;
- • фасонные;
- • резьбовые;
- • прорезные;
- • подрезные;
- • отрезные.
Между собой они различаются формой, размерами и исполнением кромок.
По материалу рабочей части
Они бывают:
- инструментальные;
- быстрорежущие;
- минералокерамические;
- твердосплавные – одно-, двух- и трехкарбидные (вольфрамовые, титановольфрамовые и титанотанталовольфрамовые соответственно).
Конкретный вариант подбирается, исходя из твердости поверхности детали – понятно, что он должен быть еще прочнее, чтобы не разрушаться при механическом контакте, а снимать стружку.
По исполнению
Есть один момент, о котором стоит помнить, выбирая любой параметр, например, обороты токарного станка по металлу: таблица составлена сразу для всех видов инструмента. При этом конструкция у него может быть:
- сборная;
- цельная;
-
комбинированная.
У каждого типа свои преимущества. Первый отличается наибольшей ремонтопригодностью, ведь можно заменить лишь один деформированный элемент, а не весь резец. Зато второй гораздо лучше выдерживает повышенные нагрузки, так как равномерно воспринимает все силовые воздействия. Третий же сочетает в себе преимущества двух предыдущих, но стоит дороже всего.
Определяться вам, в зависимости от характера и твердости поверхности, точности снятия слоя, тех геометрических параметров, которые нужно получить в результате.
Формула подачи и режимов резания при токарной обработке
Для вычислений воспользуйтесь следующим выражением:
Vt = n x f (мм/мин), где:
- n – частота вращения;
- f – величина подачи на 1 оборот.
Также есть другие полезные соотношения, например, для нахождения эффективной мощности:
N (э) = (PZ x V)/(1020 x 60), причем:
P (z) – это максимальная нагрузка (тангенциальная сила), и она в свою очередь представлена в виде:
P (z) = 10Ср x t1 x S2 x V3 x Kp
Зная все эти величины, можно определить необходимую производительность станка:
N (п) = N(э)/η,
где η представляет собой заложенный заводом-изготовителем КПД (коэффициент полезного действия) оборудования.
Для выяснения оптимальной скорости резания при токарной обработке таблица необязательна – нужный показатель не составляет труда найти по следующей формуле:
VC = (DC x π x n)/1000 м/мин, где:
- DC – двойной радиус детали;
- n – частота вращения.
Или в качестве альтернативы можно воспользоваться таким соотношением:
- • V = CV/((T1 x t2 x S3) x KV, в котором:
- • T – стойкость инструмента;
- • CV – коэффициент, применяемый как к заготовке, так и к лезвию;
- • 1, 2, 3 – параметры степеней;
- • KV – поправочное значение, зависящее от материала кромки, качества (точности) и особенностей поверхностного слоя.
Опять же, все полученные данные нужно сверить со стандартным рядом, актуальным для имеющегося станка, и убедиться, что они разница между ними не больше 5% и что они не превышают нормированные значения.
Таблица режимов резания при токарной обработке на станке
Материал |
Операция |
Показатели степени |
СР |
|||
Детали |
Лезвия |
n |
x |
y |
||
Сталь конструкционная |
Твердая |
Наружное растачивание |
-0,15 |
1 |
0,75 |
300 |
Прорезание и отрезание |
0 |
0,72 |
0,8 |
408 |
||
Быстрорежущая |
Наружное растачивание |
0 |
1 |
0,75 |
200 |
|
Прорезание и отрезание |
0 |
1 |
1 |
247 |
||
Чугун серый |
Твердый сплав |
Наружное растачивание |
0 |
1 |
0,75 |
92 |
Быстрорежущая сталь |
Прорезание и отрезание |
– |
1 |
1 |
158 |
|
Чугун кованый |
Твердый сплав |
Наружное растачивание |
0 |
1 |
0,75 |
81 |
Прорезание и отрезание |
– |
1 |
1 |
139 |
Теперь вы понимаете, насколько важно верно определить параметры эксплуатации оборудования. Хорошо, что это не будет проблемой теперь, когда вы знаете, как рассчитать режимы резания при токарной обработке. А станок, который эффективно решит любые ваши производственные задачи, вы всегда можете заказать у ижевского производителя – завода «Сармат».
Режимы резания при токарной обработке: расчет, таблица
Точение – один из многофункциональных методов обработки деталей разного типа. Он используется для чистовой и черновой работы с изделиями в процессе выполнения их ремонта или изготовления. Внимательный подход к подбору режимов резанья обеспечивает существенное повышение продуктивности данного процесса.
Что это такое
Под режимом резания чаще всего подразумевают характеристики, которые находят расчетным путем. Это глубина, скорость и подача.
Данные величины являются очень важными. Без них качественно выточить любую деталь просто невозможно.
При расчете режимов работы учитывают и другие характеристики производимых рабочих манипуляций:
- допустимые припуски;
- вес заготовок;
- частота вращения шпинделя станка.
При необходимости учитываются много других характеристик тех элементов, которые влияют на процесс обработки деталей.
Характеристика режимов работы
Расчет операции резания выполняется с использованием специальных справочных и нормативных документов, которых на данный момент существует немало. Необходимо тщательно изучить представленные таблицы и выбрать в них подходящие значения. Правильно выполненный расчет гарантирует высокую эффективность применяемого режима обработки детали и обеспечивает достижение лучшего результата.
Основные виды токарных работ по металлу
Но такой метод расчета является не всегда удачным, особенно в условиях производства, когда нецелесообразно тратить много времени на изучение таблиц с огромным числом значений. Установлено, что все величины режимов резания взаимосвязаны между собой. Если изменить одно значение, закономерно, что все остальные характеристики обработки станут иными.
Поэтому очень часто специалисты предпочитают применять расчетную или аналитическую методику определения режимов резания. Используются специальные эмпирические формулы, при помощи которых определяются все необходимые нормы. Чтобы расчеты по данной методике были абсолютно точными, необходимо знать следующие параметры токарного станка:
- частота вращения шпинделя;
- величины подач;
- мощность.
На современных производствах для выполнения подобных расчетов используют специальное программное обеспечение. Специалисту достаточно ввести известные данные, после чего компьютер выдаст вычисляемые величины. Применение программ для расчетов существенно облегчает работу специалистов и делает производство более эффективным.
Устройство токарного станка
Схема расчетов
Перед выполнением расчетов операции резания необходимо определить, какой тип режущего инструмента будет использоваться в данном случае. При токарной или абразивной обработке хрупких материалов выбирают оснащение с минимальными показателями. Следует не забывать, что во время работы деталь обычно довольно сильно нагревается. Если скорость обработки будет очень высокая, она может деформироваться, что приведет к ее непригодности.
Процесс резания металла
Обязательно учитывается, какая обработка будет осуществляться – чистовая или черновая. В первом случае подбирают рабочие параметры, которые обеспечат максимальную точность. Специалисты обращают внимание и на толщину срезаемого слоя. В зависимости от данной характеристики выбирается количество проходок для выполнения обрезки на специальном оборудовании.
Глубина
Глубина является одним из важнейших параметров для обеспечения качества изготовленных заготовок. Она определяет толщину срезаемого слоя за одну проходку. При выполнении подрезки торца за глубину принимают диаметр детали.
Учитывается количество проходов, что определяется припусками на обработку:
Изменение обрабатываемого диаметра
- 60% на черновую;
- 20–30% на получистовую;
- 10–20% на чистовую.
Для определения глубины обрезки цилиндрических заготовок используется следующая формула:
k=(D-d)/2, где к – глубина обрезки, D – первоначальный диаметр, d – получаемый диаметр.
При определении режимов резания при работе с плоскими деталями вместо диаметров используют длину. Принято считать, что при черновой обработке глубина должна составлять больше 2 мм, получистовой – 1–2 мм, чистовой – меньше 1 мм. Данный параметр зависит от требований к качеству деталей. Чем меньше класс точности, тем больше проходов необходимо выполнить для достижения необходимых свойств изделий.
Схема черновой обработки металла
Подача
Пример построения траектории движения резца
Под подачей подразумевают величину перемещения резца за один оборот заготовки. При выполнении черновой обработки данный параметр может иметь максимально возможные значения. На завершительном этапе работ значение подачи определяется с учетом квалитета шероховатости. Данная характеристика зависит от глубины обрезки и габаритов заготовки. Чем меньше размеры, тем она ниже. При большой толщине срезаемого слоя выбираются минимальные параметры подачи.
Чтобы облегчить работу специалистам, разработаны специальные таблицы. Там указаны значения подачи при разных условиях режима резанья. Для выполнения точных расчетов иногда необходимо знать размер державки резца.
Если резанье выполняется с существенными ударными нагрузками, значения с таблицы необходимо умножать на коэффициент 0,85. При работе с жаропрочной конструкционной сталью подача не должна быть больше 1 мм/об.
Подачи при черновом наружном точении
Скорость
Скорость резания – это один из важнейших показателей, который определяется на этапе расчетов перед выполнением основных работ. Ее значения зависят от проводимых операций. Обычно отрезание торцов происходит при максимально возможной скорости. Сверление или точение имеют совсем иные требования к данному рабочему параметру. Поэтому для качественного выполнения поставленных задач необходимо знать следующее:
Таблица для расчета режимов резания
- тип выполняемой слесарной операции;
- вид применяемого токарного инструмента;
- материал, из которого изготовлена заготовка.
При традиционной токарной обработке скорость определяется путем умножения диаметра заготовки на количество ее оборотов за минуту и на π. Полученное значение необходимо разделить на 1000. Также скорость резанья можно определить, используя стандартные таблицы для режимов резанья.
Проверка выбранных рабочих характеристик
Когда глубина, подача и скорость определены, их необходимо проверить. Полученные рабочие параметры не должны быть больше нормативных значений, которые указаны в паспорте эксплуатируемого токарного станка.
Обязательно необходимо определить мощность оборудования. Для этого силу обрезки умножают на ее скорость и делят на 1000. Полученное значение сравнивают с тем, что указано в паспорте станка. Если рассчитанные по формулам параметры больше, необходимо корректировать глубину, подачу и скорость, чтобы избежать повреждения оборудования и инструментов.
Выбор материала резца при токарной обработке
Какой режущий инструмент использовать
Изготовление деталей на подобных станках осуществляется при помощи специальных токарных резцов. Они должны обеспечивать следующее:
Виды и назначения токарных резцов
- качественную обработку деталей с получением нужной формы и размеров;
- достижение высокого качества обрабатываемой поверхности;
- высокую производительность при минимальных энергетических затратах;
- технологичность в изготовлении;
- ремонтоспособность;
- минимальный расход дорогих материалов для их изготовления.
Токарные резцы классифицируют по разным параметрам. По виду производимых работ они могут быть отрезными, проходными, фасонными, подрезными и т. д. Резцы изготовляются из различных материалов – алмазов, вольфрама, титан-вольфрама и других. В зависимости от конструктивного исполнения данные инструменты бывают цельными, сборными и комбинированными.
Выбор конкретного типа инструмента осуществляется с учетом режимов проводимых рабочих операций, твердости заготовки, геометрических параметров режущей части и других характеристик.
Видео по теме: Токарная обработка металла
:: Теоретические положения :: Токарная обработка заготовок :: Основы токарной обработки
Скорость резания – это скорость перемещения точки режущей кромки резца относительно обрабатываемой поверхности.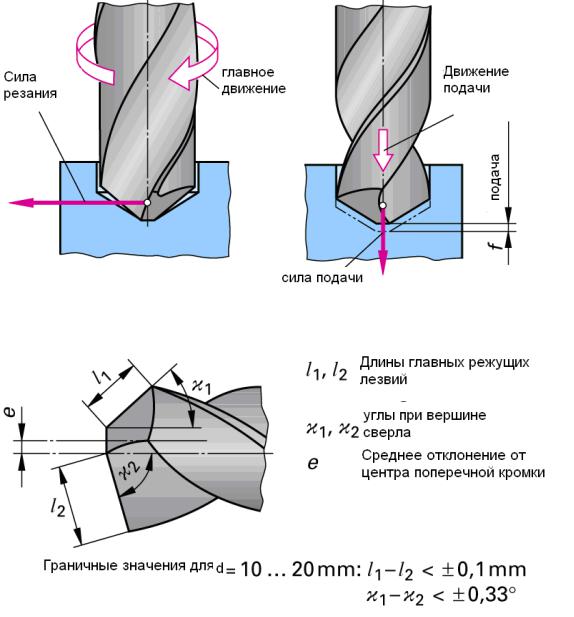
Подача – величина перемещения инструмента в направлении вспомогательного движения за время одного оборота заготовки. При расчетах времени обработки и производительности удобнее пользоваться размерностью подачи в мм/мин.
Глубина резания – толщина слоя металла, удаляемого за один проход инструмента. При точении,
где D – диаметр обрабатываемой поверхности,
d – диаметр обработанной поверхности.
При работе отрезным резцом в режим резания вместо глубины резания t входит ширина резания B (мм). Составляющие режимы резания выбирают в следующей последовательности: глубина резания, величина подачи, скорость резания. Глубину резания и величину подачи стремятся увеличить насколько это допустимо прочностью и жесткостью инструмента и заготовки, мощностью станка, шероховатостью поверхности и другими ограничивающими факторами.
Скорость резания рассчитывают по эмпирическим формулам, учитывающим влияние большого числа факторов, основными из которых являются материал заготовки, материал режущего инструмента, величины подачи и глубины резания, стойкость инструмента (время его работы между переточками), наличие или отсутствие охлаждения.
На практике величины составляющих режима резания колеблются в очень широких пределах: скорость резания от нескольких м/мин до нескольких сот м/мин, величина подачи от сотых долей мм до нескольких мм, глубина резания от сотых долей мм до 10-15 мми более.
При выполнении лабораторной работы режимы резания задаются в технологической карте или указываются преподавателем. По заданным режимам резания необходимо произвести настройку станка – установить с помощью рукояток управления частоту вращения шпинделя – n об/мин и величину подачи S мм/об.
, об/мин
где – заданная скорость резания, м/мин;
D – диаметр обрабатываемой поверхности, мм;
1000 – коэффициент перевода м в мм.
Действительная скорость резания составит:
, м/мин
2. Основные виды токарной обработки и токарных резцов
Основное назначение точения – обработка поверхностей вращения (цилиндрических, конических и фасонных).
Большое разнообразие работ, выполняемых на станках токарной группы, обусловило наличие разнообразных токарных резцов.
Любой токарный резец состоит из рабочей части (головки) и стержня (державки), служащего для закрепления резца в резцедержателе станка.
Различают следующие основные типы токарных работ и токарных резцов.
Точение – обработка наружных поверхностей – выполняется проходными резцами: прямыми 1,2; отогнутыми 3,4; правыми 1,3; левыми 2,4.
Подрезание торца (торцевое точение) выполняют проходным упорным резцом 1, проходным отогнутым резцом 2 или подрезным резцом 3.
Отрезку и подрезание канавок выполняют отрезным резцом .
Растачивание сквозных и глухих предварительно просверленных отверстий большого диаметра осуществляют расточными резцами.
На токарном станке отверстия можно обрабатывать также сверлами, установленными в пиноли задней бабки, с ручной или механической подачей .
Фасонные поверхности обрабатывают специальными фасонными резцами (рис. 2.2, д) с поперечной подачей. Фасонные поверхности обрабатывают также проходными резцами с помощью копировальных устройств.
Обработку конических поверхностей осуществляют, проходными резцами при смещении задней бабки при угле конуса до 8° или с поворотом верхних поворотных салазок суппорта станка.
Нарезание резьбы производят наружными 1 или внутренними 2 резьбовыми резцами, профиль которых соответствует профилю нарезаемой резьбы.
Нарезание наружной резьбы может быть выполнено на токарном станке с помощью специального резьбонарезного инструмента – плашки.
определение способа по таблице для токарной обработки, типовые примеры и задачи как рассчитать параметры, справочники и формулы
25ФевЗначительная часть промышленности – изготовление деталей при помощи металлорежущих агрегатов. За несколько десятилетий технологии сильно видоизменились, но суть остается прежней: снимаются лишние слои до получения элемента с заданными параметрами. Давайте вместе рассмотрим, как рассчитать режимы оптимального резания при грамотной токарной обработке на станке по таблицам.
Содержание статьи:
- Ключевые моменты процесса
- Какие бывают станки
- Основные параметры
- Проверка корректности рабочих параметров
- Способы выбора действия
- Выбор резца
- Как вычислить скорость
Ключевые моменты процесса
Для работы подойдут следующие материалы: металлы, пластики, дерево, минералы. Конечно, для каждого конкретного случая требуется особый инструмент и технологические приемы. Если труд с относительно мягкими из них (пластмасса, алюминий, бронза) обычно не вызывает сложностей, то высоколегированные стали требуют строгого контроля качества заточки. В противном случае происходит быстрый износ режущей кромки. Для увеличения эффективности обязательно использовать эмульсию, обеспечивающую снижение трения и охлаждение рабочей зоны.Кратко опишем процесс:
Деталь закрепляется в патроне или на двух центрах;
В зависимости от необходимых манипуляций выбираются параметры режима резания при токарной обработке;
Предмет устанавливается в правильное положение и проверяется надежность всех фиксаций;
Находим первую точку касания;
Начинаем снимать металл или другой материал;
Контролируем габариты штангенциркулем и микро́метром;
Следует четко понимать, что приемы достаточно разнообразны, и невозможно коротко описать все нюансы. Заготовка может быть величиной от доли миллиметра до нескольких десятков метров. Характеристики изделия кардинально отличаются по твердости и вязкости. Уровень первичной отделки болванки может быть самым разным и иметь внешний слой с другими качествами. Часто нужно сделать сферическую поверхность на маленьком участке. Это накладывает определенные ограничения, так как часть приспособлений не рассчитана на циклические нагрузки.
Какие бывают станки
В зависимости от технологических потребностей применяют разное оборудование. Принято деление на следующие подвиды:
Токарно-винторезный. Это наиболее распространенный агрегат, позволяющий выполнять внушительный спектр работ. Пожалуй, любимым у токарей является К 62 в различных модификациях. Вся группа включает в себя универсальные устройства, отличающиеся степенью автоматизации и габаритами обрабатываемой детали. Большемерные заготовки точатся на ДИП 500. Для обучения специалистов используют модели ТВ-4 или ТВ-16.
- Карусельный аппарат предназначен для придания формы изделиям крупного диаметра.
Внешне он представляет собой стол с патроном значительных размеров, вращающийся в горизонтальной плоскости. Инструмент для рассечения подается сверху и может быть не один. Названием он обязан схожести с детскими аттракционами.
Лобовой. Можно сказать, что это такой же станок, только положенный набок. Это продиктовано технологической целесообразностью при некоторых производствах. Конструкции этой группы не имеют задней бабки и фиксация происходит только благодаря губкам. Основное преимущество – возможность придания изделию конической формы.
- Револьверный незаменим при изготовлении изрядного количества одинаковых деталей из нормированного материала. Например, сгонов из металлической трубы. За счет этого резко повышается эффективность, снижается брак и оптимизируются все процессы. Но у него есть главный недостаток – узкая специализация.
- Автомат продольного точения позволяет синхронизировать движение в двух плоскостях и создавать элементы сложной конфигурации, например, спирали с большим шагом.
Как режущий предмет могут использоваться фрезы и сверла.
- Многошпиндельный автомат применяется для вальцевания элементов сразу несколькими насадками за одну установку. Бывают автоматические и полуавтоматические.
- ЧПУ. Если оснастить любое устройство для обработки металла системой, координирующей порядок, то мы получим центр с числовым программным управлением. При массовом производстве этот комплекс наиболее эффективен.
Способы и правила определения режимов приемлемого резания при точении: формулы
Для разных материалов и необходимой чистоты существуют свои оптимальные системы, включающие в себя скорость подачи, глубину захода и вид заточки.
Многие универсальные токари определяют эти параметры «на глазок». Тем более, они сильно зависят от технических характеристик самого́ станка. При создании программ для ЧПУ и полуавтоматики применяются конкретные математические варианты расчета. За основу берутся качества заготовки (твердость, вязкость, хрупкость, абразивность, подверженность температурным изменениям). Под это разрабатываются инструменты (как правило, несколько для различных технологических приемов). Затем происходит определение режимов идеального резания при умелой токарной обработке на основе жестких правил. Это дает приблизительные показатели, по которым можно назначить оптимальные значения. Более точные данные получаются эмпирическим путем (в процессе стендовых испытаний).
После этого возможно задать для каждой конкретной цели темп вращения шпинделя, интенсивность движения стержня для рассечения и его заглубление.
Название | Формула | Расшифровка |
Частота вращения | n=Vc1000Dc (min/1) | n – оборот в минуту. |
Скорость рассекания | Vc=Dcn1000 (m/min) | V – линейная скорость D – диаметр. |
Подача | Vf=nf(mm/min) | V – подача. f – шаг за 1 оборот. |
Удельный съем материала | Q=Vcapf (см3/min) | Q – объем среза в мин. ар – заглубление. |
Поперечное сечение стружки | A=hb=apf(mm2) | А – площадь сечения |
Основная сила | Fc=Ak01.1h-mo(N) | F – сила резания h – толщина стружки. |
Мощность привода | Pmot=FcVc60000(kW) | Р – минимально необходимая мощность. |
Время | Th=Imfn(min) | Т – конечный результат |
Наиболее распространенное сырьё – сталь и чугун. Вот таблица рекомендованных режимов резания при их токарной обработке:
Обрабатываемый материал в кг/мм2 | Сечение от 0,4 мм c x y | 0,4 – 0,2 c x y | 0,2 – 0,1 c x y |
С 35 45 55 65 75 85 Ч 155 170 190 210 | 88,5 0,28 0,6 61 0,28 0,6 45 0,28 0,6 35 0,28 0,6 28,3 0,28 0,6 23,4 0,28 0,6 32,7 0,2 0,4 28 0,2 0,4 23,2 0,2 0,4 19,5 0,2 0,4 | 106,3 0,28 0,4 73,3 0,28 0,4 54 0,28 0,4 42 0,28 0,4 34 0,28 0,4 28,1 0,28 0,4 35,8 0,2 0,3 30,7 0,2 0,3 25,4 0,2 0,3 21,4 0,2 0,3 | 124,7 0,28 0,3 86 0,28 0,3 63,4 0,28 0,3 49,3 0,28 0,3 39,9 0,28 0,3 33 0,28 0. 42,1 0,2 0,2 36,1 0,2 0,2 29,9 0,2 0,2 25,2 0,2 0,2 |
Основные параметры
Время изготовления детали зависит от трех значений. Они определяют, какое количество металла будет сниматься за определенный период.
На практике предпочтительные величины можно узнать по справочнику режимов оптимального резания для грамотной токарной обработки. Они дают габариты, на которые можно опираться, как на базовые.
В дальнейшем придется учитывать как особенности оборудования (биение, дребезг, мощность, износ), так и отклонения в свойствах материала. Различные партии могут отличаться достаточно сильно, особенно это актуально для рядовых сортов черных металлов. Если в производстве использовать сырье с жестко заданными значениями, то такой процесс может стать экономически невыгодным из-за высокой цены.
Глубина
Это толщина слоя, удаляемая за один проход. На этот параметр влияет свойство поверхности, технические характеристики, качество резца (твердость и угол заточки) и скорость.
Подача
Показывает, на какое расстояние перемещается точка контакта за единицу времени. В универсальных станках рассматриваются её продольный и поперечный виды. Свои особенности есть при изготовлении конусов. Засчет увеличения радиуса заготовки при работе с внешней стороной, нагрузка на инструмент увеличивается, и это необходимо учитывать. У большинства аппаратов предусмотрены разнообразные программы движения от минимальных до резьбовых. На передней панели управления рычагом выставляется одна из функций, обеспечивающая смещение режущей кромки при каждом вращении вала. Это достигается усилием с коробки передач на суппорт (синхронно с вращением переднего шпинделя).
Скорость
По этой формуле понятно, как рассчитать и сделать определение режимов идеального резания при наружном и внутреннем точении.Величины количества оборотов и диаметра заготовки поставлены, как пример. Соответственно, на показатель V влияет расстояние от центра и угловой темп патрона.
Теперь, зная ширину прохода резца и его заглубление, легко понять, какой объем сырья снимается за промежуток времени.
Проверка корректности рабочих параметров
Теоретические данные, полученные с помощью вычислений, способны дать результаты с довольно большими допусками. Чтобы окончательно выбрать оптимальный порядок, необходимо проверить эти выкладки на практике на наличие погрешностей. Отличаться могут как физические свойства материала, так и технические характеристики станка. В жизни не бывает абсолютно одинаковых агрегатов.
Корректировка режима обязательна каждый раз при:
запуске новой серии;
смене оборудования;
замене партии заготовок.
При этом производится пробная обработка с плавным изменением всех рекомендуемых габаритов и выбираются значения, наиболее подходящие для этого случая. Похожие действия нужно повторить и при смене инструмента. Для бесперебойной эксплуатации рекомендуется подобрать норматив с достаточным запасом. Это позволит избежать брака и сэкономить время на переналадку.
Способы выбора действия
Имея на руках марку стали обрабатываемой детали и необходимую степень точности, можно получить предварительные цифры и осуществить расчет режимов для токарных операций.
Приняв первичное решение, нужно произвести пробную точку в рекомендуемых границах. По характеру стружки принимается решение снизить или увеличить вышеназванные основные параметры. В массовых производствах используются инструменты с фиксированной установкой.
После пробного прогона и принятия решения данные заносятся в технологическую карту. Существуют процессы, когда резец испытывает разные нагрузки на одном проходе. Если обрабатывать торцевую поверхность или конус, то порядок обтачивания будет отличаться в зависимости от расстояния до центра. Достаточно сильная разница может быть между черновой и чистовой точкой. Поэтому и приемы тоже различны. В карте обязательно отображаются такие особенности.
Выбор резца
От правильного определения режущего предмета напрямую зависит и скорость, и качество. Иногда для снятия слоя применяются фрезы или абразивные камни.
Расчет режимов для стали 45 или бронзы кардинально отличается. Если обработка сплава меди – задача посильная для начинающего токаря, то высокоуглеродистое железо повышенной прочности требует профильных инструментов и оборудования большого класса точности. К таким изделиям в большинстве случаев предъявляются высокие требования по уровню отделки. Если медный сплав засчет своей пластичности и скользкости прощает небольшую небрежность, то микроскопические отклонения при производстве коленчатого или распределительного вала, деталей коробки скоростей резко снижают срок службы готового продукта и все эксплуатационные характеристики.
Принципиально существует несколько видов режущего механизма, подходящего для разнообразных операций. Они могут быть цельными из твердого сплава, сборными и комбинированными.
По возможностям подразделяются на следующие виды:
Проходной – позволяет эффективно формировать цилиндрическую поверхность по внешнему радиусу;
Расточной – с помощью него точатся внутренние диаметры после сверления;
Отрезной – за счет конструкции способен углубляться в массив на пару сантиметров. Предназначен для отделения и заготовки канавок;
Резьбовой – обладает заниженным профилем.
Дальнейшие модификации применяются для решения нестандартных задач (например, создание профиля с заданным углом).
Острие изготавливается из высокопрочных сплавов с содержанием вольфрама, титана, тантала и т. д. Широкое распространение получили инструменты на основе карбидов. В особо сложных случаях лучше использовать абразивные материалы, где присутствуют корунд, алмаз.
Намного проще обстоит дело с мягким сырьем (бронза, алюминий). Здесь достаточно стали марки Р5М6 или аналогов.
Как вычислить скорость
Насколько быстро резец движется вдоль цилиндрической поверхности, можно легко узнать по количеству оборотов и расстоянию от центра до точки соприкосновения. Интенсивность подачи влияет на это минимально.
Металлообработка — это многогранный процесс, требующий постоянного совершенствования технологий. На рынке периодически появляются новинки, существенно снижающие издержки и уменьшающие сроки изготовления. Например, ленточнопильные станки от производителя «Роста» позволяют снизить себестоимость выпускаемой продукции.
В заключение мы предоставляем вам два видео, из которых будет понятно, как определить типовые режимы резания, как произвести расчет, назначение операций, и как назначить задачи при автоматизированной точке.
Элементы резания при обработке на токарных станках
Обработка металлов резанием сопровождается удалением с поверхности заготовки слоя металла (припуска на обработку) с целью получения из нее детали необходимой формы и размеров с соответствующим качеством обработанных поверхностей.
Для осуществления процесса резания необходимо, чтобы заготовка и режущий инструмент перемещались друг относительно друга.
В металлорежущих станках различают два вида основных движений: главное движение, определяющее скорость отделения стружки, и движения подачи, обеспечивающее непрерывное врезание режущей кромки инструмента в новые слои металла.
При обработке на токарном станке главное движение (вращательное) совершает заготовка (рис. 12), а движение подачи (поступательное) – резец. В результате этих движений резец снимает с обрабатываемой детали припуск на обработку и придает ей необходимую форму и размеры, а также требующуюся чистоту обработанной поверхности.
Обрабатываемой поверхностью называется поверхность детали, с которой снимается стружка.
Обработанной поверхностью называется поверхность, которая получается после обработки, т. е. после снятия стружки.
Поверхностью резания называется поверхность, образуемая на обрабатываемой детали непосредственно главной режущей кромкой резца.
Элементы режима резания. Элементами, характеризующими процесс резания являются: скорость резания, подача и глубина резания.
Скоростью резания при токарной обработке называется величина перемещения в главном движении режущей кромки инструмента относительно обрабатываемой поверхности в единицу времени.
Скорость резания обозначается буквой u и измеряется в метрах в минуту (сокращенно м/мин).
при точении (рис. 13) скорость резания определяеться по формуле
u = π*D*n/1000 м/мин,
где D – диаметр обрабатываемой поверхности, мм;
n – число оборотов детали в минуту.
Подачей называется величина перемещения режущей кромки резца за один оборот обрабатываемой детали (рис. 13). Подача обозначается буквой s и измеряется в миллиметрах за один оборот детали; для краткости принято писать мм/об.
В зависимости от направления, по которому перемещается резец при точении относительно оси центров станка, различают:
продольную подачу – вдоль оси центров;
поперечную подачу – перпендикулярно к оси центров;
наклонную подачу – под углом к оси центров (при обтачивании конической поверхности).
Глубиной резания называют слой металла, снимаемый за один проход резца. Измеряется глубина резания в миллиметрах и обозначается буквой t (см. рис. 13).
При токарной обработке глубина резания определяется как полуразность между диаметром заготовки и диаметром обработанной поверхности, полученной после одного прохода резца, т. е.
t = D-d/2
где D – диаметр заготовки, мм, до прохода резца;
d – диаметр детали, мм после прохода резца.
Кроме глубины резания и подачи, различают еще ширину и толщину среза.
Шириной среза называют расстояние между обрабатываемой и обработанной поверхностью, измеренное по поверхности резания (см. рис. 13). Ширина среза измеряется в меллиметрах и обозначается буквой b.
Зависимость между шириной среза и глубиной резания выражается формулой
b = 1/sin φ
где – φ главный угол в плане главной ружущей кромки.
Толщиной среза называют расстояние между двумя последовательными положениями режущей кромки на один оборот детали, измеряемое перпендикулярно к ширине среза (см. рис. 13).Толщина среза измеряется в миллиметрах и обозначается буквой a. Зависимость толщины среза от величины подачи s и угла в плане φ выражается форумулой
a = s*sin φ
Площадью поперечного сечения среза называют произведение глубины резания t на подачу s или ширины среза b на толщину a.
Площадь поперечного сечения среза обозначается буквой f
и измеряется в квадратных миллиметрах, т. е.
f = t*s = a*b мм2.
На рис.14 показано, что нужно принимать за глубину резания и подачу при различных токарных работах – продольном точении, поперечном точении (протачивании канавки или отрезании), подрезания, продольном растачивании.
При продольном точении в зависимости от соотношения глубины резания и подачи могут быть получены различные сечения реза (рис. 15). Принято считать, что если t>s, то получаются равномерные стружки (рис. 15,а), если t=s, то получаются равнобокие стружки (рис. 15,б), и если s>t, – обратные стружки (рис.15,в)
Режимы резания при токарной обработке
Режимы резания при токарной обработке [c.113]В табл. 19 и 20 указаны геометрия инструмента и режимы резания при токарной обработке некоторых пластмасс. [c.352]
Режимы резания при токарной обработке наружных и торцовых поверхностей [c.113]
Элементы режима резания при токарной обработке рассчитываются по следующим формулам скорость резания (м/мин) [c.204]
Б 8. Режимы резания при токарной обработке пластмасс [c.222]
Режимы резания при токарной обработке резцами из быстрорежущей стали Р18 [c.131] РЕЖИМЫ РЕЗАНИЯ ПРИ ТОКАРНОЙ ОБРАБОТКЕ Подачи при обработке резцами Черновая обработка Наружная продольная обточка [c.

Определение наивыгоднейших режимов резания при токарной обработке 81 [c.81]
В табл. 17 приведены режимы резания при токарной обработке аустенитных нержавеющих сталей. [c.68]
Режимы резания при токарной обработке аустенитных нержавеющих сталей [c.68]
Режимы резания при токарной обработке конструкционных термопластов [c.80]
Параметрами режима резания при токарной обработке являются скорость резания у подача 5 глубина резания 1 (мм), т. е. толщина снимаемого слоя металла за один проход резца. [c.215]
Порядок назначения режимов резания при токарной обработке. [c.206]
Рекомендуемые режимы резания при токарной обработке молибденовых, сплавов указаны в табл. 2.1.9 [c.135]
Режимы резания при токарной обработке молибденового сплава [c.135]
Режимы резания при токарной обработке назначают с учетом материала и геометрических параметров режущей части резца, его конструкции, СОТС, периода стойкости, глубины резания, подачи, скорости резания, усилий и мощности резания, а также основного времени. Разрабатываемые методики.
[c.169]
Цель работы, экспериментально установить закономерности износа резца от пути резания и режимов резания при токарной обработке заготовок на настроенных станках. [c.28]
Построить графики зависимостей высоты микро неровностей от режимов резания при токарной обработке [c.53]
Приведем порядок и метод определения режима резания при многоинструментной обработке на одношпиндельных токарных полуавтоматах и на многошпиндельных полуавтоматах последовательного действия. К числу первых из названных станков относится, например, токарный многорезцовый полуавтомат модели 1721, к числу вторых — токарный шестишпиндельный полуавтомат завода Красный пролетарий модели 1272. [c.141]
Нормативы по режимам резания при многоинструментальной обработке (токарные полуавтоматы . М., Машгиз, 1955.
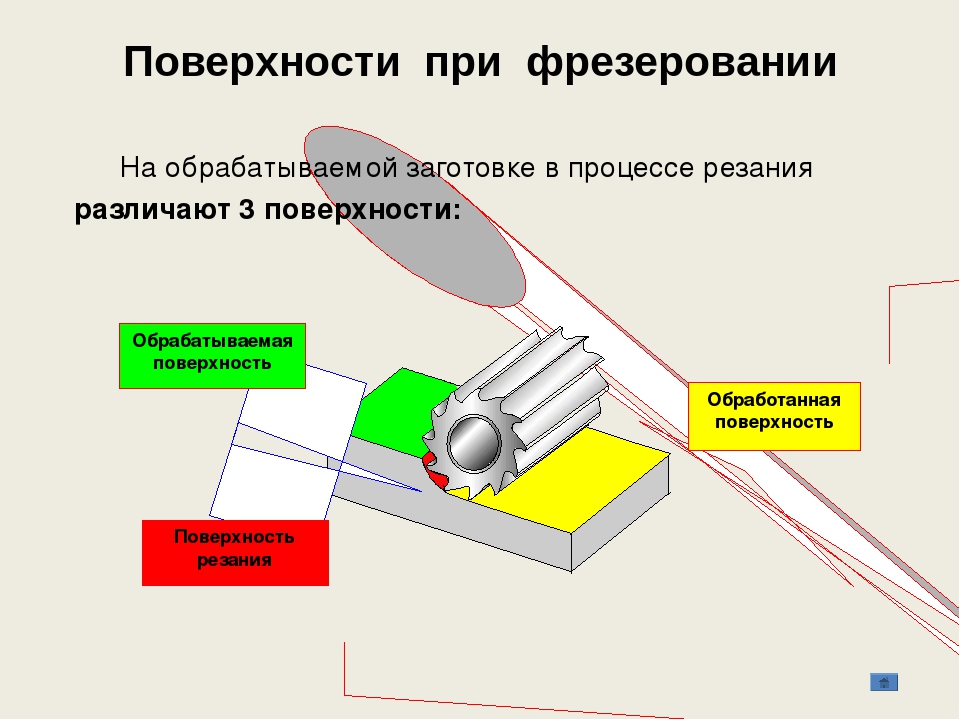
Пример применения метода регулярного поиска для определения оптимальных режимов резания при обработке ступенчатых валов на токарном гидрокопировальном полуавтомате (рис, 3.55). Задаются исходные данные (размеры и материалы детали, режущий инструмент, глубина резания, жесткость узлов станка, цикловые и внецикловые потери времени работы оборудования) требуется найти режим обработки (sj, п,), удовлетворяющий условиям по точности обработки шероховатости поверхности [c.136]
При назначении режимов глубина резания обычно устанавливается максимальной, чаще всего весь припуск снимается за один проход. Для увеличения производительности стремятся брать максимальную подачу, если она не лимитируется требованиями к шероховатости поверхности. Определение наиболее выгодного режима, поэтому, часто, особенно при токарной обработке, сводится к необходимости оптимизировать скорость резания. Именно она оказывает наибольшее влияние на себестоимость и время обработки.
[c.46]
СВЕДЕНИЯ ПО ТЕХНОЛОГИИ ТОКАРНОЙ ОБРАБОТКИ 68. Режимы резания при точении пластмасс [c.311]
Бронза — Режимы резания при обработке токарной 291 [c.748]
Режимы резания при обработке токарной 291, 296, 298, 302, 304 [c.761]
Режимы резания и геометрия резцов при токарной обработке органического стекла приводятся в табл. 15. [c.707]
Режимы резания, рекомендуемые при токарной обработке, приведены в табл. 32—61. [c.50]
Используют также различные методы поиска, исключающие полный перебор (например, регулярного поиска для определения оптимальных режимов резания при обработке ступенчатых валов на токарном гидрокопировальном полуавтомате). Задают исходные данные (размеры и материал детали, режущий инструмент, глубину резания, жесткость узлов станка, цикловые и внецикловые потери времени работы оборудования). Требуется найти режим обработки удовлетворяющий условиям по точности обработки, шероховатости поверхности, мощности, расходуемой на резание, кинематике станка и приводящий целевую функцию к максимуму. [c.221]
Точение. Резание резцами производится с выбранной скоростью движения подачи при определенной глубине резания и с допустимой (оптимальной) скоростью резания. Режимы резания — это совокупность указанных величин. При выборе режимов точения целесообразно использовать материалы справочника Режимы резания металлов [24], а именно Общие указания по расчету режимов резания (с. 7…8), условные обозначения величин, относящихся ко всем разделам справочника (с. 9… 10), а также материалы, приведенные в разд. 1 Режимы резания на токарных станках , ссылки на которые будут даны при выборе режимов резания. В карте Т-1 разд. I на листах 1… 3 подразд. Токарные станки изложена Методика расчета режимов резания при обработке на одношпиндельных токарных станках (с. 11… 13). [c.58]
В машиностроении большинство деталей получает окончательные формы и габаритные размеры в результате механической обработки заготовки резанием, которое осуществляется путем последовательного удаления режущим инструментом с поверхности заготовки тонких слоев материала в виде стружки. Схема работы резца, его элементы и геометрия, а также режимы резания при точении и других видах токарной обработки приведены в гл. 2. [c.141]
Выбор режимов резания при обработке цилиндрических отверстий стержневыми инструментами на токарных станках производят по тем же таблицам справочника [24], что и при обработке на сверлильных станках (см. гл. 2). Однако, учитывая малую жесткость крепления стержневых инструментов на станках токарной группы, расчетные значения режимов на практике уменьшают. [c.160]
Примечание. По варианту И обработку вели с соблюдением заданных режимов резания, а по варианту П1 при токарной обработке не соблюдали режимов резания. [c.285]
На сопротивление усталости образцов при токарной обработке могут оказывать существенное влияние режимы течения (подача, глубина резания, скорость резания, износ резца и т. д.) [15 40, 48, 82]. Особенно резкое влияние режимы точения оказывают на выносливость. титановых сплавов (табл. 3, 4, 5) [40]. Испытания на усталость производили на машине НУ на базе 5-10 циклов. [c.146]
Принципы и порядок назначения элементов режима резания при строгании те же, что и при токарной обработке. 1. Определяют глубину резания в зависимости от припуска на об а- Сотку (см. стр. 158). 2. Выбирают подачу, максимально допустимую по технологическим требованиям. [c.220]
Принципы и порядок назначения элементов режима резання ри строганин те же, что и при токарной обработке. [c.183]
Отделочная токарная обработка имеет ряд особенностей, отличающих ее от чернового и межоперационного точения, поэтому рекомендуемые режимы резания при тонком (алмазном) точении на быстроходных токарных станках повышенной точности и расточных станках приведены отдельно в табл. 19. [c.369]
Оптимизация режимов резания при токарной обработке (ЕХАРТ 2) [c.157]
ОПРЕДЕЛЕНИЕ НАИВЫГОДНЕИШИХ РЕЖИМОВ РЕЗАНИЯ ПРИ ТОКАРНОЙ ОБРАБОТКЕ [c.79]
Токарная обработка концов коленчатого вала. Черновое и чистовое обтачивание концов вала проводят на гидрокопировальных автоматах с многорезцовой наладкой. При этом обработка концов из-за низкой жесткости вала и больших съемов — раздельная (отдельно передний, отдельно задний конец вала). Базирование вала при черновой обработке осуществляется в центрах с приводом поводковым патроном за необработанный конец, при чистовой — с установкой люнета под среднюю коренную шейку. Режимы резания при черновом обтачивании с/рез = 60-7-85 м/мин s = = 0,4-j-0,6 мм/об при чистовом обтачивании Црез до 130 м/мин, S = = 0,2- 0,4 мм/об. При обработке используются резцы с пластинами из твердого сплава Т5КЮ и Т14К5. [c.76]
Ниобий хороню обрабатывается резанием. Рекомендуемые режимы при токарной обработке и = 18 м1мин, Sq,epn = 0,2ч-0,3 мм1об, Squ m не более 0,125 мм/об. Параметры инструмента радиус закругления резца 0,5 мм, задний угол в плане 10—20°, боковой и концевой зазор 5°, боковой скос 15°, угол резания 30° [5]. [c.414]
Результаты этих исследований 18] показаны на диаграмме фиг. 78, на которой даны пределы усталости a i кПмм (на базе 50 10 циклов) нормализованной стали 45 в воздухе и соленой воде (3%-ный раствор Na l), в зависимости от скоросги резания v м/мин и подачи S мм/об, примененных при токарной обработке образцов диаметром 20 мм. На этой же диаграмме приведена также зависимость предела усталости образцов той же стали, шлифованных после токарной обработки при соответствующих режимах резания, которая показывает влияние режимов резания той обработки, которая предшествовала финишной. Чистота поверхности токарно-обработанных образцов была равна 5-му классу, шлифованных — 9-му. [c.147]
описание, особенности выбора и технология
Для того чтобы обычную заготовку превратить в подходящую деталь для механизма, используют токарные, фрезерные, шлифовальные и прочие станки. Если фрезерные необходимы для изготовления более сложных деталей, например, зубчатых колес, нарезания шлицов, то токарные применяются для создания более простых деталей и придания им необходимой формы (конус, цилиндр, сфера). Режимы резания при токарной обработке очень важны, поскольку, например, для ломкого металла необходимо использовать меньшую скорость вращения шпинделя, чем для прочного.
Особенности токарной обработки
Для того чтобы выточить определённую деталь на токарном станке, как правило, используют резцы. Они бывают самых различных модификаций и классифицируются по виду обработки, направлению подачи и форме головки. Кроме того, резцы выполняются из различных материалов: легированная сталь, углеродистая, инструментальная, быстрорежущая, вольфрам, твердый сплав.
Выбор того или иного зависит от материала обрабатываемой детали, её формы и способа обтачивания. Режимы резания при токарной обработке обязательно учитывают эти все нюансы. При точении обрабатываемая деталь закрепляется в шпинделе, он выполняет главные вращательные движения. В суппорте устанавливается инструмент для обработки, и движения подачи совершаются непосредственно им. В зависимости от используемого станка можно обрабатывать как очень мелкие детали, так и крупные.
Основные элементы
Какие элементы режимов резания при токарной обработке могут быть использованы? Несмотря на то что точение – это не всегда очень легкая операция, основные его элементы – это скорость, подача, глубина, ширина и толщина. Все эти показатели зависят в первую очередь от материала обрабатываемой детали и размера. Для очень маленьких деталей, например, скорость резания выбирают наименьшую, поскольку даже 0,05 миллиметров, которые случайно срезали, могут привести к браку всей детали.
Кроме того, очень важными показателями, от которых зависит выбор режимов резания при токарной обработке, являются этапы, на которых она производится. Рассмотрим основные элементы и этапы металлорезания более детально.
Черновая, получистовая и чистовая обработка
Превращение заготовки в необходимую деталь – сложный и трудоемкий процесс. Он делится на определенные этапы: черновую, получистовую и чистовую обработку. Если деталь несложная, то промежуточный (получистовой) этап, как правило, не учитывается. На первом этапе (черновом) деталям придают необходимую форму и примерные размеры. При этом обязательно оставляют припуски на последующие этапы. Например, дана заготовка: D=70 мм и L= 115 мм. Из неё необходимо выточить деталь, первым размером которой будет D1 = 65 мм, L1 = 80 мм, а вторым – D2= 40 мм, L2= 20 мм.
Черновая обработка будет заключаться в следующем:
- Подрезать торец на 14 мм.
- Проточить диаметр по всей длине на 66 мм
- Проточить второй диаметр D2= 41 мм на длину 20 мм.
На этом этапе мы видим, что деталь была обработана не полностью, но максимально приближена к её форме и размеру. А припуск на общую длину и на каждый из диаметров составил по 1 мм.
Чистовая обработка данной детали будет заключаться в следующем:
- Выполнить чистовое подрезание торца с необходимой шероховатостью.
- Проточить по длине 80 мм в диаметр 65 мм.
- Выполнить чистовое точение по длине 20 мм в диаметр 40 мм.
Как мы видим, чистовая обработка требует максимальной точности, по этой причине и скорость резания в ней будет меньше.
С чего начать расчет
Для того чтобы рассчитать режим резания, в первую очередь необходимо выбрать материал резца. Он будет зависеть от материала обрабатываемой детали, вида и этапа обработки. Кроме того, более практичными считаются резцы, в которых режущая часть съёмная. Иными словами, необходимо подобрать лишь материал режущей кромки и закрепить её в режущий инструмент. Самым выгодным режимом считается тот, при котором затраты на изготавливаемую деталь будут наименьшими. Соответственно, если выбрать не тот режущий инструмент, он, скорее всего, сломается, а это принесет убытки. Так как же определить необходимый инструмент и режимы резания при токарной обработке? Таблица, представленная ниже, поможет выбрать оптимальный резец.
Толщина срезаемого слоя
Как уже говорилось ранее, каждый из этапов обработки требует той или иной точности. Очень важными эти показатели являются именно при вычислении толщины срезаемого слоя. Режимы резания при токарной обработке гарантируют подбор самых оптимальных значений для вытачивания деталей. Если же ними пренебречь и не выполнить расчет, то можно сломать как режущий инструмент, так и саму деталь.
Итак, в первую очередь необходимо выбрать толщину срезаемого слоя. Когда резец проходит по металлу, он срезает определенную его часть. Толщина или глубина резания (t) – это расстояние, которое будет снимать резец за один проход. Важно учитывать, что для каждой последующей обработки необходимо выполнять расчет режима резания. Например, следует выполнить наружное точение детали D= 33,5 мм на диаметр D1=30,2 мм и внутренне растачивание отверстия d = 3,2 мм на d2 = 2 мм.
Для каждой из операций расчет режимов резания при токарной обработке будет индивидуальным. Для того чтобы рассчитать глубину резания, необходимо из диаметра после обработки вычесть диаметр заготовки и разделить на два. На нашем примере получится:
t = (33,5 – 30,2) / 2 = 1,65 мм
Если диаметры имеют слишком большую разницу, например 40 мм, то, как правило, её необходимо разделить на 2, и полученное число будет количеством проходов, а глубина будет соответствовать двум миллиметрам. При черновом точении можно выбирать глубину резания от 1 до 3 мм, а при чистовом – от 0,5 до 1 мм. Если же выполняется подрезание торцевой поверхности, то толщина снимаемого материала и будет глубиной резания.
Назначение величины подачи
Расчет режимов резания при токарной обработке невозможно представить без величины перемещения режущего инструмента за один оборот детали – подачи (S). Её выбор зависит от требуемой шероховатости и степени точности обрабатываемой детали, если это чистовая обработка. При черновой допустимо использовать максимальную подачу, исходя из прочности материала и жесткости её установки. Выбрать необходимую подачу можно при помощи таблицы ниже.
После того как S была выбрана, её необходимо уточнить в паспорте станка.
Скорость резания
Очень важными значениями, влияющими на режимы резания при токарной обработке, являются скорость резания (v) и частота вращения шпинделя (n). Для того чтобы вычислить первую величину используют формулу:
V = (π х D х n) / 1000,
где π – число Пи равное 3,12;
D – максимальный диаметр детали;
n – частота вращения шпинделя.
Если последняя величина остается неизменной, то скорость вращения будет тем больше, чем больше диаметр заготовки. Данная формула подходит, если известна скорость вращения шпинделя, в противном случае необходимо использовать формулу:
v = (Cv х Kv)/ (Tm х t х S),
где t и S – уже рассчитанная глубина резания и подача, а Cv, Kv, T – коэффициенты, зависящие от механических свойств и структуры материала. Их значения можно взять в таблицах режимов резания.
Калькулятор режимов резания
Кто же может помочь выполнить расчет режимов резания при токарной обработке? Онлайн-программы на многих интернет-ресурсах справляются с данной задачей не хуже человека.
Существует возможность использовать утилиты как на стационарном компьютере, так и на телефоне. Они очень удобные и не требуют особых навыков. В поля необходимо ввести требуемые значения: подачу, глубину резания, материал заготовки и режущего инструмента, а также все необходимые размеры. Это позволит получить комплексный и быстрый расчет всех необходимых данных.
Страница не найдена | MIT
Перейти к содержанию ↓- Образование
- Исследовательская работа
- Инновации
- Прием + помощь
- Студенческая жизнь
- Новости
- Выпускников
- О Массачусетском технологическом институте
- Подробнее ↓
- Прием + помощь
- Студенческая жизнь
- Новости
- Выпускников
- О Массачусетском технологическом институте
Попробуйте поискать что-нибудь еще! Что вы ищете? Увидеть больше результатов
Предложения или отзывы?
Существуют правила и принципы скорости резания и Р.ВЕЧЕРА. расчеты, которые применимы ко всем операциям по резке металла. Рабочая скорость для резки всех металлов операций зависит от материала режущего инструмента и твердости материал для резки. В этом разделе мы сконцентрируемся на скорости резки для одноточечный инструмент.
Какое колесо проехало дальше? Колесо большего размера проехало дальше, потому что оно имеет большую окружность и большую площадь поверхности.Скорости резки работают на тот же принцип. Если две круглые детали разного размера вращаются одновременно оборотов в минуту (об / мин), более крупная деталь имеет большую поверхностную скорость. Скорость поверхности измеряется в поверхностных футах в минуту (SFPM). Все скорости резания работать по принципу наземной съемки. Опять же, скорость резания в первую очередь зависит от тип материала, который вы режете, и тип режущего инструмента, который вы используете. Твердость рабочего материала во многом зависит от рекомендованной скорость резки.Чем тверже обрабатываемый материал, тем меньше скорость резания. В Чем мягче обрабатываемый материал, тем выше рекомендуемая скорость резания (Рисунок 2). Твердость материала режущего инструмента во многом зависит от рекомендуемая скорость резания. Чем тверже материал режущего инструмента, тем быстрее скорость резания (рисунок 3). Чем мягче материал режущего инструмента, тем медленнее рекомендуемая скорость резания. Глубина резания и скорость подачи также влияют на скорость резания, но не в такой степени, как тяжелая работа. Эти три фактора, сокращающие скорость, скорость подачи и глубина резания известны как режимы резания. Резка условия определяются рейтингом обрабатываемости. Обрабатываемость – это сравнение материалов по обрабатываемости. От обрабатываемости рейтинги, мы можем получить рекомендуемые скорости резания.Рекомендуемые скорости резания: приведены в таблицах. Эти диаграммы можно найти в вашем справочнике Machinerys , учебник или таблицу, которую дал вам продавец инструментов. В таблице 4 вы найдите типичную таблицу рекомендуемых скоростей резания. Таблица 4. Рекомендуемые скорости резания в футах в минуту
Станок токарный R.P.M. должен быть установлен так, чтобы режущий инструмент с одной точкой работает с правильной скоростью резания. Чтобы установить правильную скорость, нам нужно рассчитайте правильную настройку оборотов в минуту или оборотов в минуту.Мы заявили ранее скорость резания или скорость резания будут изменяться в зависимости от размера детали. Так чтобы поддерживать одинаковую поверхностную скорость для каждой размерной детали, мы должны использовать формулу, которая включает диаметр детали для расчета правильного числа оборотов в минуту для поддержания надлежащая съемка поверхности.
Скорость вращения зависит от скорости резания и диаметра часть.Настройка числа оборотов будет меняться в зависимости от диаметра детали. Поскольку диаметр детали становится меньше, частота вращения должна увеличиваться, чтобы поддерживать рекомендованный поверхностные кадры. Снова возьмем случай с колесом. Думайте о детали как о колесе и скорость резания как расстояние. Более крупное колесо (деталь) нужно будет повернуть меньше оборотов в минуту, чтобы преодолеть такое же расстояние за такое же количество время, чем меньшее колесо (деталь). Таким образом, чтобы поддерживать рекомендуемую резку скорости, детали большего диаметра должны работать на более медленных скоростях, чем детали меньшего диаметра. часть диаметра. Токарный станок необходимо настроить так, чтобы деталь работала правильно. надводная скорость. Настройки скорости шпинделя на токарном станке выполняются в об / мин. К рассчитать правильную частоту вращения для инструмента и заготовки, мы должны использовать следующая формула: Эта упрощенная версия формулы числа оборотов в минуту является наиболее распространенной формулой, используемой в механические цеха. Эту формулу числа оборотов в минуту можно использовать для других операций обработки как хорошо. Давайте применим эту формулу при вычислении числа оборотов в минуту для обработки. пример ниже.Используйте таблицы рекомендуемых скоростей резания в Таблице 4. Необходимо выполнить резку с помощью инструмента из быстрорежущей стали (HSS) диаметром 2 дюйма. кусок стали 1018 с твердостью по Бриннелю 200. Рассчитайте настройку числа оборотов в минуту на выполнить этот разрез.
Так как доступные настройки скорости шпинделя обычно не бесконечно переменной, машина не может быть точно настроена на расчетную настройку оборотов.При выборе используемой скорости необходимо принять определенное решение. Попытайтесь добраться до скорость, которая ближе всего к расчетным оборотам в минуту, но если вы не можете, примите во внимание эти условия. Черновая или чистовая обработка? Если вы делаете черновую обработку, действуйте медленнее. Если вы заканчиваете, иди быстрее. Какая у вас глубина резания? Если это глубокий порез, иди на более медленную настройку оборотов. Настройка очень жесткая? Медленнее для установок, которые не хватает жесткости. Вы используете охлаждающую жидкость? Вы можете перейти на более быстрая из двух настроек, если вы используете охлаждающую жидкость.Самый большой показатель скорости резания – это цвет стружки. При использовании резака для быстрорежущей стали микросхемы никогда не должны становиться коричневыми или синими. Фишки соломенного цвета указывают, что вы находитесь на максимальной скорости резки для вашей резки условия. При использовании карбида цвета стружки могут варьироваться от янтарного до синего, но никогда не черный. Темно-фиолетовый цвет будет указывать на то, что вы находитесь на максимальном уровне. условий резки. Режущие инструменты из твердого сплава покрываются гораздо большими подробно в других разделах ваших учебных материалов. Давайте попробуем еще примеры. Надрезать токарным инструментом (HSS) на куске диаметром 0,75 дюйма из 1045 сталь с твердостью по бриннелю 300. Рассчитайте значение числа оборотов в минуту, чтобы выполнить это резать.
Сверло диаметром 1 дюйм (HSS) используется на куске диаметром 4 дюйма из стали 1012 с твердость по бриннелю 100.Рассчитайте настройку числа оборотов для выполнения этого сверления. операция.
Обратите внимание, что в R.P.M. расчет, мы использовали диаметр сверла, а не заготовка. Это было сделано потому, что резка происходит на диаметре сверло, а не по внешнему диаметру заготовки. Токарная операция должна выполняться на 3,00-дюймовом куске из легированной стали 4140. с твердостью по бриннелю 200. Необходимо использовать твердосплавный токарный инструмент. Рассчитать настройку оборотов для выполнения этой резки. ( ср. fpm) Диаметр детали = 3,00 Вверх |
Рекомендации по токарной обработке пластика | Таблица скоростей и подачи
Указания по токарению
Токарная обработка – это распространенный метод обработки пластмасс.В этом процессе пластиковая деталь удерживается на токарном станке и вращается против режущего инструмента. Ниже приведены рекомендации по токарной обработке пластмасс с несколькими характеристиками.
Для точения рекомендуются твердосплавные пластины с чистым покрытием класса C-2. Полированные верхние поверхности помогут уменьшить скопление материала и улучшить качество обработки поверхности. Режущие кромки должны иметь большие задние углы и отрицательный задний передний край, чтобы минимизировать трение. Черновой рез должен выполняться со скоростью подачи 0,015 IPR, а чистовой проход должен выполняться со скоростью подачи 0.005 IPR или меньше.
Дополнительную информацию см. В нашем Руководстве по обработке пластмасс. Нужна помощь в обработке пластика? Спросите эксперта по пластмассам.
Особые меры: █ Разогрейте материал до 250 ° F █ Осторожно при использовании охлаждающих жидкостей, подверженных растрескиванию под напряжением █ Используйте инструменты с твердосплавными напайками
Радиус при вершине r должен быть не менее 0,5 мм
Материал | α Зазор | ϒ Грабли | X Сторона | V Резка | S Корм |
---|---|---|---|---|---|
АБС | 5–15 | 25–30 | 15 | 650–1640 | 0.008 – 0,020 |
Ацеталь (сополимер) | 6–8 | 0–5 | 45–60 | 980 – 1960 | 0,004 – 0,015 |
Ацеталь (гомополимер) | 6–8 | 0–5 | 45–60 | 980 – 1960 | 0,004 – 0,015 |
Норил | 5–10 | 6–8 | 45–60 | 980 | 0.004 – 0,020 |
Нейлон 6 | 6–10 | 0–5 | 45–60 | 920–1640 | 0,004 – 0,020 |
PAI | 2–5 | 0–5 | 7–10 | 320–390 | 0,002 – 0,003 |
PBT | 5–10 | 0–5 | 45–60 | 980–1300 | 0.008 – 0,015 |
PEEK | 6–8 | 0–5 | 45–60 | 920–1640 | 0,004 – 0,020 |
ПЭТ | 5–10 | 0–5 | 45–60 | 980–1300 | 0,008 – 0,015 |
Поликарбонат | 5–10 | 6–8 | 45–60 | 980 | 0.004 – 0,020 |
Полиэтилен | 6–10 | 0–5 | 45–60 | 920–1640 | 0,004 – 0,20 |
Полипропилен (гомополимер) | 6–10 | 0–5 | 45–60 | 920–1640 | 0,004 – 0,020 |
Полисульфон | 6 | 0 | 45–60 | 1140–1300 | 0.004 – 0,012 |
PPS | 6–8 | 0–5 | 45–60 | 920–1640 | 0,004 – 0,020 |
ПТФЭ | 10 | 5–8 | 10 | 490–1640 | 0,004 – 0,012 |
ПВДФ | 10 | 5–8 | 10 | 490–1640 | 0.004 – 0,012 |
PPSU (Radel® R) | 6 | 0 | 45–60 | 1140–1300 | 0,004 – 0,012 |
Ultem® | 6 | 0 | 45–60 | 1140–1300 | 0,004 – 0,012 |
DuPont ™ Vespel® Полиимид | 2–5 | 0–5 | 7–10 | 320–390 | 0.0200 – 0,010 |
(PDF) Влияние скорости резания и скорости подачи на скорость износа инструмента и шероховатость поверхности в процессе токарной обработки
International Journal of Engineering Trends and Technology (IJETT) – Volume22 Number 4- April 2015
ISSN: 2231-5381 http: //www.ijettjournal.org Страница 173
Влияние скорости резания и скорости подачи на инструмент
Скорость износа и шероховатость поверхности в токарном станке
Процесс токарной обработки
Олугбоджи Олувафеми Айодеджи1, Мэтью Сандей Аболарин2, Джия Джонатан Йиса3, Попула Соломон Олаолува ,
Аджани Клемент Кехинде5
Кафедра машиностроения, Школа инженерии и инженерных технологий,
Федеральный технологический университет, П.M.B 65, Минна, Нигерия,
Резюме. Механическая обработка является важной частью производственного процесса в
обрабатывающих отраслях. Операция Тьюринга была выполнена на мягкой стали
для изготовления валов различного диаметра. Условия
,, применяемые во время токарной операции, включают изменение
скорости резания и скорости подачи при сохранении других переменных
резания, таких как глубина резания, постоянной. Результаты подтверждают, что увеличение скорости резания на
,приводит к снижению стойкости инструмента, увеличение скорости подачи на
,также влияет на качество получаемой поверхности.
Ключевые слова: микроструктура, скорость подачи, скорость резания, стойкость инструмента,
глубина резания.
I. ВВЕДЕНИЕ
Токарная обработка – это форма операции механической обработки, процесс удаления
, который используется для создания вращающихся деталей путем удаления нежелательного материала
и требует токарного станка
или токарного станка и режущего инструмента. Заготовка представляет собой формованный материал до
, который прикреплен к приспособлению, которое само по себе
прикреплено к токарному станку и позволяет вращаться с высокой скоростью
.Резак обычно представляет собой одноточечный режущий инструмент, который
также прикреплен к станку, хотя некоторые операции
требуют использования многоточечных инструментов. Режущий инструмент подается во вращающуюся заготовку
и срезает материал в виде мелких стружек
, чтобы создать желаемую форму. Исследование процесса резки металла
, как правило, очень сложно из-за сложности
, возникающей из-за множества задействованных переменных.Переменные
,– это переменные основных величин, участвующих в процессе
, таких как заготовка, инструмент и станок. Другие
переменные с точки зрения состава и геометрии инструмента также учитываются
, а параметры заготовки включают ее диаметр
, условия зажима и микроструктуру. Станок
переменные инструмента включают скорость шпинделя, тепловое расширение,
подачи, смазку, силы резания, мощность и вибрацию.Другие значения
включают скорость резания, глубину резания, качество поверхности и скорость удаления металла
[1].
Исследования в области резки металлов широко изучались [2], [3],
после появления первых станков. Срок службы инструмента – это период времени
, в течение которого инструмент может правильно обработать, прежде чем
потребуется переточка или замена. Это зависит от типа материала
, из которого изготовлен инструмент, а также от состояния
резания.
Сталь представляет собой сплав железа и углерода и на сегодняшний день является наиболее важным, многофункциональным и наиболее адаптируемым материалом, используемым
в производственных процессах для производства линий электропередач
опор, трубопроводов природного газа, станки и т. д., и он
имеет низкие производственные затраты по сравнению с другими материалами типа
. Сталь подвергается различным процессам, таким как процесс резки металла
, чтобы получить конечный продукт [4].Процессы резки металла
– это промышленные процессы, в которых металлическим деталям придают форму или удаляют
ненужные материалы. При изучении резки металла.
Значительное улучшение качества продукции может быть достигнуто
за счет оптимизации параметров резки, и это также обеспечивает низкую стоимость производства
. Качество продукции зависит от шероховатости поверхности
. Углеродистая сталь – это металлический сплав, состоящий из двух элементов
: железа и углерода.Возможность использования углеродистой стали
зависит от того, подходят ли их свойства
(растяжение, текучесть и усталость, прочность, ударопрочность, необходимость термообработки
,и т. Д.) Для используемых деталей [5].
Токарные станки обычно считаются самыми старыми станками.
Токарный станок – это станок, работа которого поддерживается таким образом, что он может
вращаться вокруг оси, в то время как режущий инструмент перемещает часть
работы от одного конца до другого, тем самым заставляя его
требуемой формы с помощью удаление ставок, именуемых фишками.Типичные операции, выполняемые на токарном станке
: торцовые, параллельные
токарная обработка, накатка, нарезание резьбы, сверление, развёртывание и растачивание и
растачивание. Различные части токарного станка:
Шпиндель, который может удерживать различные приспособления для удержания заготовок
, такие как трехкулачковые патроны, цанги и центры
.
Станина, тяжелая прочная отливка, сделанная для поддержки рабочих частей токарного станка
.
Передняя бабка, крепится с левой стороны станины.
Задняя бабка состоит из двух частей. Верхнюю половину
можно отрегулировать на основании с помощью двух регулировочных винтов для
, совмещая заднюю бабку и центр передней бабки для параллельного точения
.
Основная цель исследований в области металлообработки заключалась в том, чтобы
разработать методы прогнозирования стойкости инструмента с учетом
механизма отказа инструмента и анализа скорости резания. Следовательно, быстрорежущие стали
были постепенно заменены литыми сплавами, карбидами
, керамикой и цементитом для повышения производительности [6].
Методы резания, используемые в токарном станке, представляют собой ортогональную резку
, когда режущая кромка инструмента находится на
перпендикулярно направлению относительного движения и наклонная
резка, при которой режущая кромка инструмента наклонена под меньшим углом
, чем 900 в направлении движения инструмента [1].
Что такое подача при обработке? Единица, значение, эффекты и выбор
Обработка – это, по сути, один процесс удаления материала, при котором излишки материала постепенно удаляются с заготовки в виде стружки путем подачи режущего инструмента к заготовке.Для плавного удаления материала необходимо обеспечить три относительных движения между инструментом и заготовкой. К таким движениям относятся скорость резания (или скорость резания), скорость подачи и глубина резания. Поскольку эти три параметра присущи любому традиционному процессу обработки, их также называют параметрами резания.
Подача – это один из параметров резания, который обеспечивает перемещение инструмента относительно заготовки для покрытия всей обрабатываемой поверхности. Обычно его передают в направлении, перпендикулярном скорости резания; однако угол между вектором скорости резания и вектором подачи также может отклоняться от 90º.Следующая схематическая диаграмма для прямой токарной обработки показывает направление подачи в сочетании со скоростью и глубиной резания.
Схематическое изображение скорости резания, подачи и глубины резания при токарной обработке.В различных операциях обработки используются разные единицы измерения, чтобы выразить скорость подачи наиболее подходящим образом, особенно для этого процесса. В приведенном ниже списке показаны общие единицы скорости подачи, используемые в различных операциях обработки. Независимо от единицы, цель скорости подачи остается неизменной, как обсуждалось ранее.
- Токарная обработка – мм / об, на режущем инструменте.
- Фрезерование — мм / зуб, нанесенное на режущий инструмент.
- Сверление — мм / об, нанесенное на режущий инструмент.
- Формовка – мм / ход, нанесенная на рабочий стол (заготовку).
- Строгание — мм / ход, применяемое к режущему инструменту.
- Прорезание пазов — мм / об, нанесенное на рабочий стол (заготовку).
- Обработка канавок – мм / об, нанесенная на режущий инструмент.
- Накатка – мм / об, нанесенная на режущий инструмент.
Поскольку подача является одним из трех параметров резания, ее значение необходимо тщательно выбирать перед фактической операцией обработки.Неправильная скорость подачи может привести к неточности обработки и, как следствие, к производству бракованных деталей. Скорость подачи влияет на производительность обработки во многих отношениях – от качества поверхности до стойкости инструмента, как обсуждается ниже. Для получения дополнительной информации вы также можете прочитать влияние скорости подачи на производительность обработки.
- Более высокая скорость подачи указывает на более высокую скорость съема материала (MRR), поскольку MRR прямо пропорциональна скорости подачи. Таким образом, производительность может быть увеличена за счет более высокой скорости подачи.
- Однако более высокая скорость подачи приводит к плохой чистоте поверхности.Следы гребешков и, следовательно, шероховатость поверхности будут выше. Для получения гладкой поверхности следует использовать меньшую скорость подачи.
- Высокая подача также ускоряет износ инструмента и, как следствие, снижает его стойкость.
Значение скорости подачи влияет на производительность и экономичность обработки, поэтому всегда желательно оптимальное значение. Ниже приведены типичные значения скорости подачи для нескольких обычных операций механической обработки.
- Подача при прямом точении — 0,01 – 0.1 мм / оборот для чистового пропила; 0,05 – 0,5 мм / оборот для черновой резки.
- Подача при точении резьбы – равна шагу или шагу (для многозаходной резьбы) резьбы (обычно 0,5 или 1,0 мм / об).
- Подача при сверлении – должна быть очень низкой, иначе инструмент может сломаться из-за забивания стружкой. Типичное значение составляет 0,01–0,05 мм / об.
- Подача при фрезеровании – обычно 0,05–0,10 мм / об.
- Подача при накатке – 0,5 – 1,0 мм / об (скорость резания обычно очень мала при накатке, но скорость подачи очень высока).
Перед обработкой выбор оптимальной скорости подачи имеет решающее значение, поскольку параметр процесса влияет на ряд факторов. Оптимизация может помочь найти подходящий диапазон для скорости подачи для обработки конкретного материала в определенных условиях и среде резания. Однако учесть все возможные факторы иногда бывает сложно, и поэтому в механическом цехе его значение обычно выбирается из практического опыта. В следующей таблице показано влияние неправильной скорости подачи на производительность обработки.
Влияние слишком высокой подачи | Влияние слишком низкой подачи |
---|---|
Высокая шероховатость поверхности (плохая обработка поверхности) | Недостаточное использование станков |
Чрезмерный износ инструмента и высокая вероятность катастрофического отказа инструмента. Таким образом снижается стойкость инструмента | Низкая скорость съема материала (MRR) |
Более длительный простой из-за частой смены инструмента и, как следствие, высокая стоимость производства | Снижение производительности и, как следствие, увеличение времени обработки и производственных затрат |
Больше отклонения стружки от ортогональной плоскости | Более широкий бор |
Прерывистое стружкообразование | |
Высокая температура резания и выжигание стружки | |
Высокая тенденция к образованию наростов (BUE) | |
Высокое усилие резания и риск вибрации |
Существует большое количество факторов, которые следует учитывать при выборе оптимального значения скорости подачи, как описано ниже.Обратите внимание, что следующий список – это лишь некоторые из таких факторов, которые необходимо учитывать при выборе значения скорости подачи.
Требования к чистоте поверхности — Более низкая подача обеспечивает хорошее качество поверхности. Таким образом, если операция является черновой, можно рассмотреть более высокое значение. Например, для чернового точения можно взять подачу 0,1 – 0,3 мм / об; тогда как для чистового прохода можно рассматривать 0,01–0,05 мм / об.
Требования к производительности — В случае более высоких требований к производительности скорость подачи можно увеличить, если можно пожертвовать качеством поверхности.В противном случае скорость резания (об / мин) может быть увеличена без изменения скорости подачи.
Допустимая скорость подачи —Механические инструменты имеют максимальный и минимальный предел скорости подачи, за пределами которого выбор не разрешен. Опять же, обычные станки могут иметь только несколько вариантов скорости подачи в этом диапазоне.
Геометрия режущего инструмента — Помимо скорости подачи, геометрия инструмента также влияет на качество поверхности. Итак, если позволяет геометрия, можно выбрать более высокое значение.
Возможности станка — Более высокая скорость подачи вызывает большую силу резания и вибрацию.Скорость подачи следует выбирать в зависимости от способности станка поглощать и передавать такие силы и вибрации.
- Книга: Обработка и станки А. Б. Чаттопадхая (Wiley).
- Книга: Обработка металлов: теория и практика А. Бхаттачарьи (Новое центральное книжное агентство).
Мы не можем найти эту страницу
(* {{l10n_strings.REQUIRED_FIELD}})
{{l10n_strings.CREATE_NEW_COLLECTION}} *
{{l10n_strings.ADD_COLLECTION_DESCRIPTION}}
{{l10n_strings.COLLECTION_DESCRIPTION}} {{addToCollection.description.length}} / 500 {{l10n_strings.TAGS}} {{$ item}} {{l10n_strings.PRODUCTS}} {{l10n_strings.DRAG_TEXT}}{{l10n_strings.DRAG_TEXT_HELP}}
{{l10n_strings.LANGUAGE}} {{$ select.selected.display}}{{article.content_lang.display}}
{{l10n_strings.AUTHOR}}{{l10n_strings.AUTHOR_TOOLTIP_TEXT}}
{{$ select.selected.display}} {{l10n_strings.CREATE_AND_ADD_TO_COLLECTION_MODAL_BUTTON}} {{l10n_strings.CREATE_A_COLLECTION_ERROR}}3 критических фактора скорости поворота и подачи
Многие факторы играют важную роль при определении правильной скорости и подачи, а также стратегии глубины резания для токарных операций.Хотя три из этих факторов – те, которые мы сочли одними из самых важных – перечислены ниже, обратите внимание, что есть много других соображений, которые не перечислены, но также важны. Например, безопасность всегда должна быть в центре внимания любой операции механической обработки, поскольку неправильные параметры режущего инструмента могут привести к проверке пределов возможностей станка, что приведет к аварии, которая потенциально может привести к серьезным телесным повреждениям.
Состояние, тип, возможности и настройка станка, как и выбор токарного инструмента и державки, очень важны для успешного токарного станка в целом.
Скорость поворота и коэффициент подачи 1: Состояние машины
Состояние вашего станка всегда следует учитывать перед началом операции обработки на токарном станке. Старые станки, которые использовались для производственных операций, где обрабатывались твердые или абразивные материалы, как правило, имеют большой люфт или износ механических частей станка. Это может привести к получению менее чем оптимального результата и может потребовать, чтобы параметры скорости и подачи, рекомендованные производителем инструмента, нужно было немного вернуть назад, чтобы не работать на станке более агрессивно, чем он может справиться.
Фактор 2: Тип машины и возможности
Прежде чем устанавливать скорость вращения и подачу, необходимо понять тип станка и его возможности. Станки программируются по-разному, в зависимости от типа используемого токарного центра: токарный станок с ЧПУ или ручной токарный станок.
Токарные станки с ЧПУ
На станках этого типа деталь и инструмент могут приводиться в движение.
Токарные обрабатывающие центры с ЧПУможно запрограммировать как G96 (постоянная площадь поверхности) или G97 (постоянная частота вращения).Для этого типа машины максимально допустимая частота вращения может быть запрограммирована с помощью G50 с командой S. Например, ввод G50 S3000 в вашу программу ЧПУ ограничит максимальное число оборотов до 3000. Кроме того, в токарных центрах с ЧПУ скорость подачи программируется и может быть изменена в различных положениях или местах в программе обработки детали.
Ручной токарный токарный центр
На станках этого типа движется только деталь, а инструмент остается неподвижным.
Для ручных токарных обрабатывающих центров параметры программируются немного иначе.Здесь скорость шпинделя устанавливается на постоянное значение об / мин и обычно остается неизменным на протяжении всей операции обработки. Очевидно, это возлагает на машиниста больше ответственности за правильную скорость, так как операция может быстро сорваться, если параметры скорости вращения не оптимальны для работы. Однако, как и в случае с токарно-токарными станками с ЧПУ, критически важно понимать мощность вашего станка и максимальную скорость подачи.
Фактор 3: Настройка машины
Чрезмерный вылет инструмента. Цифровое изображение, автоматизация Hass. https: // www.haascnc.com/service/troubleshooting-and-how-to/troubleshooting/lathe-chatter—troubleshooting.htmlУсловия обработки
При учете наладки вашего станка необходимо учитывать условия обработки. Ниже приведены некоторые идеальные условия, к которым следует стремиться, а также некоторые неоптимальные условия обработки, которых следует избегать для набора правильных скоростей вращения и подачи.
Идеальные условия обработки для токарной обработки
- Зажим заготовки или приспособление находится в оптимальном состоянии, а вылет заготовки минимизирован для повышения жесткости.
- Имеются системы подачи охлаждающей жидкости, которые помогают удалять стружку с детали и помогают контролировать тепловыделение.
Неоптимальные условия обработки для токарной обработки
- Использование токарных инструментов, которые увеличены для достижения цели, когда в этом нет необходимости, что приводит к увеличению отклонения инструмента и ухудшению жесткости операций обработки.
- Зажим или фиксация заготовки изношены, неэффективны и находятся в плохом состоянии.
- Системы подачи охлаждающей жидкости отсутствуют или неэффективны.
- На машине нет ограждений или кожухов, что создает проблемы с безопасностью.
Выбор режущего инструмента и держателя инструмента
Как всегда, выбор режущего инструмента и державки имеет решающее значение. Не все производители токарных инструментов одинаковы. Лучшие машинисты устанавливают давние отношения с производителями инструментов и могут полагаться на их отзывы и рекомендации.Например, Micro 100 производит токарные инструменты высочайшего качества в отрасли уже более 50 лет. Кроме того, его предложение держателей инструмента включает в себя несколько уникальных стилей, что позволяет машинистам определять продукт, который им лучше всего подходит.
Pro Совет: обязательно принимайте во внимание мощность машины и максимальную скорость подачи при определении рабочих параметров.
Бонус: Общая терминология приложений скорости вращения и подачи
Vc = скорость резания
n = скорость шпинделя
Ap = глубина резания
Q = Скорость съема металла
G94 Скорость подачи IPM (дюймы в минуту)
G95 Скорость подачи IPR (дюймы на оборот)
G96 CSS (постоянная скорость движения)
G97 Постоянная частота вращения (оборотов в минуту)
Команда инженеровHarvey Performance Company работает вместе над тем, чтобы каждая ваша задача обработки – от выбора инструмента и поддержки приложений до разработки идеального индивидуального инструмента для вашей следующей работы – была решена с помощью продуманного комплексного решения.