Принцип работы плазмореза: устройство, виды, советы по выбору
Содержание
- Устройство и принцип работы плазморезов
- Виды плазморезов
- Виды и классификация плазмотронов
- Как выбрать плазморез и резак
- Где применяют плазменную резку и в чем её преимущества
Плазменная резка — универсальный процесс термической обработки, который подходит для прямолинейного и фигурного раскроя практически любого металла. Это углеродистые и нержавеющие стали, чугун, титан, алюминий, медь и сплавы на их основе. Нужно лишь правильно подобрать оборудование и режимы работы: диаметр сопла резака, ток реза, напряжение и скорость резки с учетом толщины заготовки.
Подробнее о сущности плазменной резки, о том, как устроен и работает плазморез, чем различаются модели оборудования и плазмотроны.
Устройство и принцип работы плазморезов
Система плазменной резки включает в себя трансформаторный или инверторный источник питания, компрессор или баллон со шлангом и регулятором давления для подачи сжатого воздуха и плазменный резак или плазмотрон.
В качестве источника энергии выступает электрическая дуга, которая формируется стенками сопла, стабилизируется плотным потоком плазмообразующего газа и подается в зону резки с помощью наконечника плазмотрона. Дуга горит между электродом с неплавящейся вставкой и заготовкой. Температура плазменного газа может достигать 250000С.
Принцип действия плазмореза основан на локальном нагреве и выдувании расплавленного жидкого металла потоком плазмы — ионизированного и нагретого до сверхвысокой температура газа, переносящего электрическую дугу к заготовке. За счет высокой плотности энергии и концентрации теплоты на малой площади металл быстро плавится. Благодаря высокой кинетической энергии потока плазмы расплав мгновенно удаляется из зоны резки, обеспечивая раскрой заготовки без шлака.
Ключевой элемент плазмореза — резак. Его основные элементы:
- электрододержатель с электродом — как правило, вольфрамовым, легированным оксидами лантана и иттрия;
- камера для образования плазмы и сопло, которое формирует сжатую электрическую дугу;
- изолятор, отделяющий электродный узел от сопла, и завихритель, помогающий стабилизировать сжатую дугу;
- каналы подачи плазмообразующего и защитного газа и система охлаждения электрода и сопла, подвергающихся высокотемпературному воздействию.
При включении плазмотрона между электродом и наконечником образуется вспомогательная или дежурная (пилотная) дуга. Она создает путь для рабочей или основной дуги. Рабочая дуга образуется при контакте вспомогательной дуги с заготовкой. После этого можно начинать резку.
Единый рабочий газ разделяется внутри плазмотрона на плазмообразующий и защитный поток, охлаждающий головку резака.
Виды плазморезов
Аппараты для плазменной резки делят на две основные группы. Это оборудование для ручного раскроя металла и системы для механизированной обработки.
Аппараты для ручной плазменной резки можно разделить на два вида:
- Бытовые. Это портативные модели с ПВ 50-60%, позволяющие работать от однофазной сети и на максимальной выходном токе реза до 60 А. С их помощью можно разрезать металл толщиной до 20 мм.
- Профессиональные. Это мощные аппараты, подключаемые к трехфазной сети и обеспечивающие максимальный рабочий ток реза до 160 А. С ними можно раскраивать заготовки толщиной до 55 мм.
Промышленные системы механизированной плазменной резки имеют диапазон регулировки тока реза от 5 до 800 А. Их используют на тяжелых производствах для работы с деталями толщиной до 90 мм, когда нужны высокая производительность, точность раскроя и чистые кромки.
Виды и классификация плазмотронов
Для работы с плазморезом и решения конкретных задач нужен предназначенный для этого плазменный резак. Плазмотроны различаются конструктивно, техническими характеристиками и технологическими возможностями.
Тип охлаждения
Плазменный резак может иметь воздушное или жидкостное охлаждение. В плазмотронах с воздушным охлаждением электрод и сопло охлаждает защитный газ, который подается по различным каналам: отверстиям в теле элементов или пространству, которое образуется при сопряжении отдельных деталей. Такие резаки используют для бытовых и профессиональных целей.
В плазмотронах с жидкостным охлаждением сопло и электрод резака охлаждает вода, подводимая к поверхностям по системе каналов с замкнутым контуром. Теплоемкость воды выше, чем у воздуха. Жидкостное охлаждение более эффективно и используют его в резаках, предназначенных для резки на высоких токах.
Тип поджига дуги
Поджиг плазменной дуги может быть пневмоконтактным и высокочастотным.
В первом случае при нажатии кнопки плазмотрона происходит замыкание электрода, сопла и заготовки, подача сжатого воздуха и поджиг пилотной дуги. Сжатый воздух поднимает подвижный подпружиненный шток и устанавливает сопло в рабочий режим, при котором основная дуга горит между электродом и заготовкой.
Во втором случае поджиг происходит без пилотной дуги, при помощи высокочастотного осциллятора в плазморезе. При нажатии кнопки плазмореза осциллятор подает импульс на электрод. Касаться заготовки не нужно, для поджига рабочей дуги достаточно поднести резак близко к поверхности.
Тип используемого газа
В качестве плазмообразующей и защитной среды используют не только сжатый воздух, но и другие газы и газовые смеси. Выбор зависит от особенностей технологического процесса, требований к качеству реза и обрабатываемого материала.
Существуют плазменные резаки, рассчитанные на работу одним газом, и двухгазовые модели, позволяющие использовать один газ в качестве плазмообразующего и другой для защиты зоны резки.
Применяемые газы и комбинации:
- Сжатый воздух. Универсальное решение и оптимальный выбор по качеству, экономичности и скорости раскроя углеродистой стали и сплавов, нержавейки и алюминия.
- Азот. Продлевает срок службы электрода и других деталей резака и обеспечивает чистый рез нержавеющей стали и цветных металлов, но скорость раскроя ниже, чем воздушной плазмой.
- Аргоно-водородная плазма и азот. Комбинацию используют для резки нержавейки и алюминия большой толщины, строжки стали, если нужна чистая кромка для хорошей свариваемости.
- Кислород. Подходит для высокоточной резки конструкционных сталей, когда необходимо получить идеальную кромку без грата, уменьшить угол и увеличить скорость раскроя.
- Водородно-азотная плазма и сжатый воздух.
Комбинацию применяют исключительно для раскроя алюминиевых заготовок, чтобы повысить скорость и увеличить толщину металла.
Тип резки
Как и плазморезы, резаки различаются допустимой нагрузкой по току и ПН. Их разделяют на две группы:
- Для ручной резки. Используют сжатый воздух, предназначены для резки на токах до 60-80 А и раскроя металла толщиной до 20-25 мм.
- Для механизированной и автоматической резки. Могут использовать не только сжатый воздух, но и другие газы и смеси, и иметь водяное охлаждение, предназначены для резки на токах от 100 А.
Есть универсальные резаки, работающие на сжатом воздухе, азоте, смесях и токах до 300 А, которые можно использовать для ручной и механизированной резки.
Как выбрать плазморез и резак
Чтобы выбрать плазморез, нужно учитывать диапазон толщин металла, с которыми вы планируете работать, решаемые задачи и условия эксплуатации. Отталкивайтесь от таких характеристик, как:
- Диапазон тока реза.
Для примерного расчета можно использовать зависимость 4 А на 1 мм углеродистой стали и 5-6 А на 1 мм алюминия и нержавейки.
- Продолжительность включения. От неё зависит, сможете ли вы раскраивать металл или вырезать деталь, не прерывая рабочий цикл.
- Параметры сети и потребляемая мощность. Плазморезы могут работать от бытовой однофазной и трехфазной сети, которая должна выдерживать планируемую нагрузку.
При выборе резака обращайте внимание на то, какой диапазон тока реза у плазмореза, с каким газом вы будете работать и с какими толщинами металла.
Важно! Производители могут указывать в характеристиках резака только максимальную толщину металла для разделительного реза или максимальную и рекомендуемую толщину, т.е. такую, при которой выполняется качественная чистовая резка. Разделительный рез отличает меньшая точность деталей, шероховатость кромки, наличие грата и сильного оплавления.
Если производитель не указал рекомендуемую толщину, вы можете рассчитать её сами. Нужно отнять от максимальной примерно 30%.
Для подбора плазмореза и сопла резака можно воспользоваться таблицей с примерными значениями
Металл |
Толщина заготовки, мм |
Ток реза, А |
Диаметр сопла, мм |
Углеродистые стали |
до 5 |
20-35 |
1,1 |
5-10 |
40-50 |
1,1-1,4 |
|
10-15 |
50-65 |
1,4 |
|
15-20 |
65-90 |
1,7 |
|
20-30 |
90-100 |
1,9 |
|
Нержавейка |
до 5 |
20-40 |
1,1 |
5-10 |
40-60 |
1,4-1,7 |
|
10-15 |
60-80 |
1,7 |
|
15-20 |
80-90 |
1,9 |
|
Алюминий и сплавы |
2-10 |
20-40 |
1,4 |
10-20 |
40-75 |
1,7 |
|
20-25 |
75-100 |
1,9 |
|
25-40 |
100-150 |
1,9-3 |
|
Медь |
10 |
300 |
3 |
20 |
|||
30 |
|||
40 |
Где применяют плазменную резку и в чем её преимущества
Плазменную резку металла используют при кузовных работах, в строительстве и ремонте для раскроя листового металла и профилей для монтажа сварных и сборных конструкций, при устройстве систем вентиляции, на мелком и крупном производстве.
Преимущества технологии:
- простота процесса, особенно с использованием мобильных инверторов и работе с сжатым воздухом;
- высокая скорость раскроя, благодаря которой тепловложение в металл небольшое, деформации минимальны, а кромки чистые;
- экономичность, которая обусловлена производительностью, использованием сжатого воздуха и отсутствием необходимости зачищать поверхность.
Возможности аппаратов можно расширить. Если установить на резак специальное сопло, то можно выполнять и быструю, точную плазменную строжку.
Принцип плазменной резки. Работа на плазменной резке.
2.1 Нечто большее, чем просто одно из состояний вещества?
Как правильно понимать источники плазменной резки? Плазма представляет собой нагретый до высокой температуры газ, обладающий электропроводимостью, который состоит из положительно и отрицательно заряженных частиц, а также возбужденных и нейтральных атомов и молекул. Между процессами диссоциации, ионизации и рекомбинации, присущими плазменному состоянию, устанавливается динамический баланс. В результате плазма электрически нейтральна. В физике плазму часто называют четвёртым состоянием вещества. В природе плазменное состояние вещества, обусловленное высокими температурами, имеет место внутри солнца и других звёзд. Молния также является примером перехода вещества в плазменное состояние, происходящий под действием сил электрического поля большой величины.
Рисунок 1: Плазма — четвертое состояние вещества |
Для того чтобы создать плазму для технических потребностей, газ либо сильно разогревается с помощью источника тепла, либо подвергается действию сильного электрического поля, так чтобы перевести его в ионизированное состояние.
2.2 Принцип плазменной резки
Плазменная резка – это процесс термической резки, при котором плазменная дуга обжимается, проходя через сопло. Дуга прямого действия, которая возникает, когда электрический ток протекает от неплавящегося электрода (катода) на изделие (анод), используется для резки материалов, обладающих электрической проводимостью. Эта форма плазменной резки является наиболее часто используемой. В случае дуги косвенного действия, она создаётся между электродом и соплом. Даже если используется режущий газ, в состав которого входит кислород, тепловой эффект плазменной дуги преобладает. Таким образом, данный метод не рассматривается как процесс кислородной резки, а скорее как резка путём плавки.
Плазменные газы в дуге частично подвергаются диссоциации и ионизации, что делает их электропроводящими. Благодаря высокой плотности энергии и температуре плазма расширяется и движется по направлению к изделию со скоростью, которая в три раза превышает скорость звука.
Благодаря рекомбинации атомов и молекул на поверхности изделия потреблённая энергия сразу же высвобождается и усиливает тепловой эффект воздействия плазменной дуги на изделие. В плазменной дуге температура доходит до 30 000 К. В сочетании с высокой кинетической энергией плазменного газа такая температура обеспечивает чрезвычайно высокую скорость резки всех материалов, обладающих электрической проводимостью, которая зависит от толщины материала.
Для начала процесса резки в первую очередь зажигается пилотная дуга между соплом и электродом путём подачи высокого напряжения. Эта низкоэнергетическая пилотная дуга подготавливает пространство между плазменным резаком и изделием, вызывая частичную ионизацию. Когда пилотная дуга контактирует с изделием (резка с лёта), благодаря автоматическому увеличению мощности зажигается основная плазменная дуга.
Рисунок 2: Принцип плазменной резки с помощью дуги прямого действия |
Металлический материал плавится и частично испаряется благодаря тепловой энергии дуги и плазменного газа. Расплавленный металл выдувается из реза под действием кинетической энергии плазменного газа. В отличие от кислородной резки, при которой около 70% тепловой энергии вырабатывается благодаря сгоранию железа, в процессе плазменной резки энергия, требующаяся, для того чтобы расплавить материал в резе создаётся только под действием электричества.
Выбор используемого плазменного газа зависит от того, какой материал требуется разрезать. Например, одноатомный газ аргон и/или двухатомные газы, такие как водород, азот, кислород и смеси этих газов, а также очищенный воздух, используются в качестве плазменного газа и режущего газа.
Резаки могут иметь как водяное, так и газовое охлаждение. В зависимости от того, где используются процессы плазменной резки, различают процессы, выполняемые над водой и на ней, а также такие, которые производятся под поверхностью воды.
2.3 Оборудование для плазменной резки
2.3.1 Источник питания для плазменной резки
Источник питания для плазменной резки подаёт рабочее напряжение и ток резки для основной и вспомогательной дуги. Напряжение источника питания для плазменной резки без нагрузки находится в диапазоне между 240 и 400 В. В состав источника питания входит система зажигания пилотной дуги (вспомогательной плазменной дуги), назначение которой состоит в возбуждении основной плазменной дуги. Для того чтобы это выполнить сначала зажигают плазменную дугу косвенного действия, используя импульсы высокого напряжения. Назначение данной дуги состоит в ионизации пространства между соплом и изделием, что позволяет возбудить основную плазменную дугу.
Рисунок 3: Пример установки для плазменной резки |
Источники питания для плазменной резки либо имеют круто падающую кривую вольтамперной характеристики (рис. 6), либо постоянную токовую характеристику (рис. 7), в связи с чем при удлинении дуги мощность резки изменяется незначительно или остаётся неизменной.
Рис.6: Источник питания для плазменной резки с крутоубывающей (крутопадающей характеристикой) кривой напряжения и тока | Рис.7: Источник питания для плазменной резки с постояноой токовой характеристикой (вертикальнок падение) |
2.

Повышение эффективности плазменной резки в большой степени зависит от конструкции плазменного резака. Чем плотнее плазменная дуга обжимается, тем выше скорость резки и качество кромки реза.
Важнейшими деталями плазменного резака являются плазменное сопло и электрод. Как плазменное сопло, так и электрод являются быстроизнашивающимися деталями. Неправильный подбор, либо неверное использование сопла или электрода могут значительно сократить срок их службы и повредить резак.
Срок службы электрода в значительной степени определяется силой тока резки, количеством зажиганий, а также типом используемого плазменного газа. Кроме того, управление газом и мощностью вначале и в конце резки, а также рассеяние тепла от электрода также играет ключевую роль. Обычно используются электроды стержневой формы из вольфрама, а также имеющие форму пальца из циркония или гафния, которые можно сделать заострёнными или плоскими. Ввиду того, что они подвержены эрозии, электроды из вольфрама могут применяться только с инертными плазменными газами и их смесями, а также с газами с низкой реакционной способностью и восстановительными плазменными газами. При использовании чистого кислорода, либо плазменных газов, в состав которых входит кислород, электроды будут служить значительно дольше, если они будут изготовлены из циркония или гафния. Эти материалы естественным образом формируют защитный слой, плавящийся при более высокой температуре (табл. 1), и, к тому же, они заключены в основную оболочку, обладающую очень большой теплопроводностью, которая интенсивно охлаждается. Если в плазменной резке используется кислород, увеличения срока службы электрода можно добиться, подавая два газа: процесс зажигания проводится с использованием газа с низкой окислительной способностью, а сам процесс резки с использованием кислорода.
Ключевые факторы, влияющие на срок службы сопла:
- диаметр на выходе сопла
- масса и теплопроводность материала сопла
- выход (произведение силы тока резания на напряжение резания)
- время действия плазменной дуги
- количество зажиганий
- последовательность прожигания отверстий
- и интенсивность охлаждения.
Водяное охлаждение является более интенсивным. Воздушное охлаждение требует большего количества газа.
Таблица 1: Типовые величины для расходных деталей, применяемых с плазменными резаками
Материал | Усл. | Температура | Используемый | Теплопроводность |
Вольфрам | W | ≈ 3400 | Ar | ≈ 174 |
Оксид вольфрама | WO3 | ≈ 1473 | Ar/H2 | |
Цирконий | Zr | ≈ 1852 | O2 | ≈ 22 |
Оксид циркония | ZrO2 | ≈ 2700 | Воздух | ≈ 2,5 |
Нитрид циркония | ZrN | ≈ 2982 | ||
Гафний | Hf | ≈ 2227 | ||
Оксид гафния | HfO2 | 1700 | O2 | |
Нитрид гафния | HfN | 3305 | Воздух | ≈ 29 |
Медь | Cu | 1083 | ||
Оксид меди | Cu2O | 1235 | Все | ≈ 400 |
Серебро | Ag | 961 | Все | ≈ 429 |
(Источник: информационный листок DVS 2107)
2.
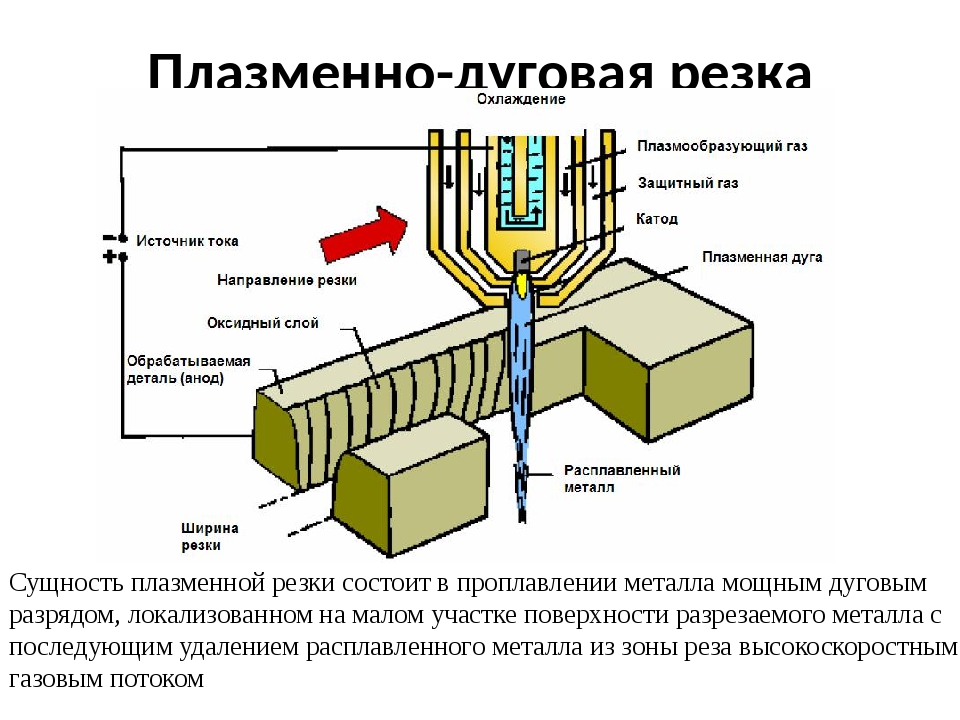
При плазменной резке с помощью плазменной дуги прямого действия разрезаемый материал должен обладать электрической проводимостью, так как изделие является частью электрической цепи. Заземление подсоединённого изделия должно проектироваться таким образом, чтобы обеспечивалось непрерывное прохождение тока.
2.3.4 Подаваемый газ
Системы плазменной резки работают с инертными, восстановительными газами или с газами с низкой реакционной способностью, а также с химически активными газами и их смесями. Подробное описание систем подачи газа и информация по выбору газов, а также рекомендации по качеству применяемого газа приведены в главе 4.
2.3.5 Системы циркуляции охладителя
Поскольку плазменная резка сопряжена с большими тепловыми нагрузками, необходимо эффективное охлаждение. Различают интегрированные и внешние контуры циркуляции водяного охлаждения и газового охлаждения. Резаки, работающие с током около 100 ампер и более, обычно охлаждаются водой.
2.3.6 Система воспроизведения
Требования, относящиеся к точности воспроизведения, а также эксплуатационные характеристики систем воспроизведения устанавливаются стандартом ISO 8206.
2.3.7 Стол для резки и система вытяжки
Столы для плазменной резки служат стабильной основой для расположения металлического листа, который требуется разрезать. Размеры стола зависят от размера, толщины и массы листа металла. Выделения, которые сопровождают процесс резки можно значительно уменьшить, используя плазменный резак в сочетании с вытяжной системой для удаления дыма и пыли, либо с водяным бассейном.
Что такое плазменная резка? Принцип работы и его преимущества
Существует несколько преимуществ плазменной резки как метода изготовления металла по сравнению с другими. Эти преимущества включают экономическую эффективность, более широкий диапазон резки металла, высокую точность и повторяемость.
Что такое плазменная резка? Как работает этот процесс? Какой газ идеально подходит для использования в этом процессе? С какими материалами работают плазменные резаки? Мы подробно ответим на эти вопросы и предоставим вам другую важную информацию о плазменной резке.
Плазменная резка — это процесс изготовления металла, в котором используются ионизированные газы, нагретые до температуры выше 20 000 0 C, для плавления металлических материалов. Этот газ, выбрасываемый под высоким давлением, расплавляет материал и удаляет его из разреза.
Важно отметить, что этот процесс работает только с электропроводящими материалами, такими как нержавеющая сталь, медь, алюминий и другие металлы. Другими словами, плазменная резка не может резать камень, бумагу, стекло и другие плохие проводники электричества.
Этот метод не имеет себе равных по экономичности, когда речь идет о резке толстых металлов. Кроме того, он универсален и требует низких затрат на обслуживание инструмента. Он также обладает высокой точностью резки, что делает его идеальным для резки деталей со сложной геометрией.
Кратко познакомившись с тем, что такое плазменная резка, давайте узнаем немного об ее истории.
Процесс плазменной резки существует с 1957 года. Он начался как расширение процесса GTAW (дуговая сварка вольфрамовым электродом). Первоначально его основным применением была резка стальных и алюминиевых пластин толщиной от половины дюйма до шести дюймов.
Плазменные резаки, использовавшиеся в ту эпоху, были непредсказуемы и не обладали точностью, присущей современным резакам. Кроме того, используемые электроды и сопла быстро выходили из строя из-за воздействия тепла во время процесса. Замена сопла и электродов часто делала плазменную резку в то время дорогой.
Конец 1960-хОднако в конце 1960-х и начале 1970-х годов в этой технике произошел прорыв, когда инженеры создали двухпоточную горелку. Этот резак помог увеличить срок службы электродов и сопел, а также повысить качество и точность резки.
1970-е годы Инженеры использовали 1970-е годы для контроля паров и дыма, первоначально возникающих в процессе резки, с помощью водяного глушителя и стола. Они также разработали более совершенные сопла, которые помогли повысить точность дуги, предоставив операторам и машинистам возможность тонкой настройки.
1980-е годы были периодом экспериментов для инженеров, когда они разработали и внедрили несколько новых функций. Эти функции включают плазменные резаки на основе кислорода и обеспечивают лучший контроль резки за счет различных уровней мощности. Они также сосредоточились на портативности блока плазменной резки, сделав его более эргономичным.
С 1990-х годов по настоящее времяК 1990-м годам плазменные резаки высокого разрешения появились на рынке благодаря использованию долговечных кислородных процессов. Эти долговечные кислородные процессы в сочетании с новой системой сопел дали плазменным резакам той эпохи возможность в четыре раза увеличить плотность энергии по сравнению с предыдущими периодами.
С 1990-х годов по сегодняшний день в центре внимания инженеров находятся варианты питания и управления, а также повышение эффективности. Они также повысили точность плазменных резаков: сегодня модели предлагают более острые края и точные разрезы. Портативность и автоматизация — другие аспекты плазменного резака, которые инженеры значительно улучшили по мере того, как в обращении появилось больше портативных устройств.
Теперь, когда мы знаем, как развивалась плазменная резка, как она работает?
Как работает плазменная резкаПроцесс плазменной резки включает использование тепла для плавления металла вместо механической резки. Плазменные резаки работают, посылая электрическую дугу через газ. Затем этот газ проходит через суженное отверстие (сопло). Ограниченное отверстие заставляет газы проталкиваться через него с высокой скоростью, образуя плазму. Резка заготовки влечет за собой контакт режущего наконечника плазменного резака с заготовкой. Также обратите внимание, что из-за проводимости плазмы необходимо соединить заготовку с землей через режущий стол.
Не все системы плазменной резки работают одинаково. Однако существует три типа процессов резки.
- Высокочастотный контакт : Это малобюджетная форма. Также из-за риска помех современному оборудованию из-за его высокой частоты этот процесс недоступен для плазменных резаков с ЧПУ. Высокочастотная контактная резка включает использование высокочастотной искры и высокого напряжения — искра образуется, когда плазменная горелка соприкасается с разрезаемым металлом. Контакт замыкает цепь, инициирует искру и создает плазму, используемую для резки.
- Пилотная дуга: В этом процессе резки искра возникает внутри резака за счет комбинации слаботочной цепи и высокого напряжения. Эта искра способствует созданию вспомогательной дуги, небольшого количества плазмы. При соприкосновении с заготовкой плазменный резак создает режущую дугу, которая позволяет машинисту или оператору начать процесс резки.
- Подпружиненная головка плазменной горелки: Чтобы создать короткое замыкание, операторы прижимают резак к заготовке.
При возникновении короткого замыкания начинает течь ток. Для создания вспомогательной дуги операторы сбрасывают давление.
Тип газа, используемого в процессе, зависит от метода резки, режущего материала и толщины. Помимо обеспечения формирования плазменной струи, используемый газ также должен способствовать удалению расплавленного материала и оксида из реза. Наиболее распространенные газы, используемые для плазменной резки, включают:
АргонАргон — инертный газ, и его плазменная дуга стабильна. Стабильность означает, что этот газ почти не реагирует с любым металлом при высоких температурах. Электроды и сопла, используемые для резки аргоном, часто имеют более длительный срок службы, чем те, которые используются с другими газами.
Газ аргон имеет ограничения при резке из-за его низкой плазменной дуги и энтальпии. Кроме того, при резке с использованием аргона в среде с защитой от аргона неизбежно возникнут проблемы со шлаком. Это в первую очередь связано с тем, что поверхностное натяжение расплавленного металла примерно на 30% выше, чем в азотной среде. Эти проблемы являются одной из причин, по которой аргон редко используется для плазменной резки.
Азот имеет лучшую стабильность плазменной дуги и более высокую энергию струи, чем аргон, особенно при более высоком напряжении питания. Кроме того, он образует минимальное количество шлака на нижних краях разреза даже при резке таких металлов, как сплавы на основе никеля и нержавеющая сталь с высокой вязкостью.
Газообразный азот работает как самостоятельный газ или в сочетании с другими газами. Это также облегчает высокоскоростную резку углеродистой стали.
Воздух Воздух содержит 78 % азота и 21 % кислорода по объему, что делает его подходящим газом для плазменной резки. Кислородная составляющая воздуха делает его одним из самых быстрых газов, используемых при резке низкоуглеродистой стали. Кроме того, поскольку воздух повсюду, это экономичный газ для работы.
С другой стороны, электрод и сопло, используемые для этого процесса, обычно имеют короткий срок службы, что увеличивает затраты на резку и снижает эффективность. Кроме того, использование воздуха в качестве автономного газа проблематично, так как это приводит к зависанию шлака и снижению окисления.
КислородКак и воздух, кислород увеличивает скорость резки низкоуглеродистой стали. Использование высокоэнергетической плазменной дуговой резки и высокой температуры кислорода увеличивает ее скорость. Однако для использования кислорода лучше всего сочетать его с электродами, устойчивыми к высоким температурам и окислению.
Водород Водород часто используется в качестве вспомогательного газа для смешивания с другими газами для плазменной резки. Одной из наиболее распространенных комбинаций является водород и аргон, который производит один из самых мощных газов при плазменной резке.
Смешивание аргона с водородом значительно увеличивает напряжение дуги, энтальпию и режущую способность струи аргоновой плазмы. Режущая эффективность этой комбинации также увеличивается при сжатии струей воды.
При плазменной резке обычно используются несколько газов. В таблице ниже показаны эти газы, разрезаемые материалы и преимущества газа по отношению к материалу.
16Толщина материала | Плазменный газ | Вторичный газ | Замечание | |||
Структурная сталь от 0,5 до 8 мм | кислород | кислород или кислород/ азот или азота | Без серда. 50 мм | Кислород | Кислород/азот или азот или воздух | Без заусенцев до 20 мм, поверхность разреза выглядит гладкой, допуск на прямоугольность до 25 мм, аналогично лазерной резке |
Высоколегированная сталь от 5 до 45 мм | Аргон/водород/азот | Азот или азот/водород | Без заусенцев до 20 мм, гладкие резы, плохая устойчивость к прямоугольности | |||
Сжатый воздух | Азот или азот/водород | Резка без заусенцев, поверхность может быть шероховатой или зернистой, что позволяет выполнять почти вертикальную резку | ||||
Алюминий от 5 до 40 мм | Аргон/водород/азот | Азот или азот/водород | Без заусенцев до 20 мм, зернистая или шероховатая поверхность, позволяет резать почти вертикально Это в первую очередь потому, что этот процесс может разрезать любой проводящий материал.![]() Алюминий обладает электропроводностью, что делает плазменную резку идеальным процессом для его изготовления. Кроме того, этот процесс дает преимущества при работе с более толстыми металлами по сравнению с другими методами изготовления алюминия, такими как лазерная резка. Он может резать алюминий толщиной до 160 мм. Кроме того, производство алюминия с помощью плазменной резки более рентабельно из-за более низких эксплуатационных расходов и затрат на оборудование. Мягкая стальМягкая сталь — это тип стали с низким содержанием углерода, обычно не более 2,1%. Это одна из наиболее часто используемых форм стали из-за ее свойств, которые подходят для многих целей. Кроме того, мягкая сталь недорога в приобретении, и ее свойства, такие как высокая ударная вязкость, свариваемость и пластичность. Нержавеющая сталь Нержавеющая сталь представляет собой сплав железа, устойчивый к коррозии и ржавчине. Латунь — еще один металл, который легко изготавливается с помощью плазменной резки. Это связано с его высокой проводимостью. Однако при изготовлении латуни этим методом лучше всего это делать в хорошо проветриваемых помещениях. Это связано с тем, что латунь содержит цинк, а вдыхание паров, содержащих горящий цинк, вредно для здоровья. Медь Медь обладает тепло- и электропроводностью всех материалов, кроме драгоценных металлов. Важные качества этого металла включают в себя; коррозионная стойкость, высокая пластичность и свариваемость. Эти свойства, в том числе высокая проводимость, делают медь идеальным металлом для плазменной резки. Однако, как и латунь, этот металл важно резать в местах с хорошей вентиляцией. Этот металл популярен благодаря своей низкой стоимости и пластичности. В незначительных количествах он содержит такие элементы, как марганец, сера, фосфор и кремний. Чугун обладает высокой электропроводностью, высокой прочностью на сжатие и низкой температурой плавления, что делает его идеальным для плазменной резки. Преимущества плазменной резкиСуществует несколько преимуществ использования плазменной резки для изготовления металлов по сравнению с другими методами, начиная от экономической эффективности и заканчивая более высокой производительностью и лучшим качеством резки. Вот некоторые другие преимущества. Высокое качество резки По сравнению с другими процессами обработки металлов, такими как газовая резка или гидроабразивная резка , резка плазменными резаками обеспечивает более высокое качество резки металлов. Это связано с отсутствием остаточной накипи на кромке реза металла и меньшей площадью околошовной зоны. Этот процесс позволяет резать любой проводящий электричество металл, что делает его очень универсальным. Он может легко резать такие металлы, как алюминий и высоколегированную сталь средней и большой толщины. Он отлично подходит для нарезания канавок, строгания или маркировки металлов. Кроме того, этот процесс позволяет резать металлы в воде с пониженным уровнем шума. Высокая скоростьПлазменная резка в 100 раз быстрее лазерной и примерно в 10 раз быстрее кислородной. Другими словами, он повышает производительность и сокращает время, затрачиваемое на изготовление металла, по сравнению с другими методами. Более высокая точность и повторяемость Вырезанные детали имеют более высокую точность и качество поверхности благодаря нагреву в процессе. Кроме того, скорость изготовления улучшает воспроизводимость при одновременном сокращении времени, затрачиваемого на механическую обработку металлов. Вы хотите производить металл с помощью плазменной резки? Зачем подвергать себя риску, связанному с процессом, если вы можете передать его более умелым рукам, таким как RapidDirect? RapidDirect — одна из лучших компаний по плазменной резке в мире, предлагающая широкий спектр Услуги по плазменной резке . Наши передовые плазменные резаки могут резать широкий спектр металлов толщиной до 15 мм. Компания RapidDirect гордится тем, что производит детали для плазменной резки с высокой точностью и постоянством, используемые в различных отраслях промышленности. Итак, зачем ждать? Свяжитесь с RapidDirect, чтобы получить детали для плазменной резки уже сегодня. Попробуйте RapidDirect прямо сейчас! Вся информация и загрузки защищены и конфиденциальны. Недостатки плазменной резкиНесмотря на то, что обработка металлов с помощью плазменной резки имеет множество преимуществ, существуют и недостатки.
Плазменная резка — это процесс, который включает использование четвертой стадии материала для резки проводящих металлов. Чтобы получить максимальную отдачу от плазменной резки как процесса производства металла, вам нужен RapidDirect. Мы предлагаем одну из лучших услуг плазменной резки в мире, а также предоставляем другие услуги по резке, такие как гидроабразивная резка и лазерная резка. Кроме того, у нас одни из самых быстрых сроков поставки при конкурентоспособных ценах. Хотите работать с нами? Просто загрузите свой дизайн на нашу онлайн-платформу , чтобы мгновенно рассчитать стоимость! Как работают плазменные резаки? Невероятная прочность металла сделала его идеальным материалом для изготовления многих вещей, от которых мы все зависим как в производстве, так и в нашей повседневной жизни. Однако его сила может также удвоиться как слабость, потому что его нелегко формовать, резать или манипулировать. Плазменные резаки призваны помочь в решении этой задачи. Что такое плазменный резак?Плазменный резак посылает электрическую дугу через газ, проходя через суженное отверстие. Используя сильное тепло, плазменные резаки повышают температуру газа и переводят его в четвертое состояние материи, называемое плазмой. В сочетании с совместимым плазменным резаком этот инструмент может проходить через такие металлы, как сталь, алюминий, латунь и медь, практически без сопротивления. Этот острый процесс сварки позволяет получить более четкие, четкие линии и более прочную конструкцию. Совершенствование производственного процессаПлазменные резаки необходимы в обрабатывающей промышленности, от строительных компаний и автомастерских до слесарей. По мере развития технологий менялись и дизайн, и возможности этого инструмента. Плазменные резаки и горелки обычно делятся на две категории: ручные и машинные. Ручные резаки универсальны и часто портативны, что делает сварочные работы более удобными. Они обеспечивают высокую силу тока при резке, но обычно используются при обработке легких металлов для обрезки лишнего материала. С другой стороны, механизированные плазменные резаки используются для крупномасштабных работ. Они включают в себя больше функций и используются вместе с раскройными столами. Эти системы не могут быть легко перемещены, так как для их работы требуется более мощный источник питания. Выбор между механизированным или ручным резаком зависит от размера, формы и толщины материала, который необходимо разрезать. Столы для резки с ЧПУ включают программное обеспечение, которое можно запрограммировать для выполнения сложных конструкций. Газокислородная горелка, вариант Машины для газокислородной резки также используются в механической обработке и производстве для резки твердых материалов. Эти машины работают с использованием пламени кислорода / топливного газа для предварительного нагрева стали до температуры воспламенения. Затем на металл направляется мощная струя кислорода, вызывая химическую реакцию с образованием оксида железа, также известного как шлак. Затем струя удаляет шлак из разреза. Ручные резаки, также называемые газокислородными резаками, также используются для резки твердых материалов, таких как металл, и используются чаще, чем режущие машины. Резаки используются для резки толстой стали и нержавеющей стали и хорошо подходят для работ по сносу. Engineering.com отмечает, что в некоторых случаях предпочтение отдается кислородному топливу. Он не требует сжатого воздуха или источника электроэнергии, что делает эти фонари очень портативными. Кроме того, кислородно-топливные горелки легче режут более толстые стальные детали, чем плазменные. Обычный ручной газокислородный резак может резать листы толщиной до 12 дюймов. Однако он может резать только сталь и другие черные металлы, потому что он основан на окислении. Плазменные резаки, тем временем, могут резать материалы быстрее, чем кислородно-топливные горелки. Они также не используют газ или открытое пламя, что делает их потенциально более безопасными. Каждый тип имеет свои преимущества для определенных видов работ. |