Прижимное устройство для строгального станка
Сначала популярные
Сначала популярные
Сначала популярные
Сначала дешевле
Сначала со скидками
Сначала новинки
9 товаров
Фильтр
9
Купить Купить Купить Купить Купить Купить Купить Купить КупитьNEW Новинка
Купить 230 В NEW Новинка Купить Доставляем по всем регионам РФА
Абакан
Алматы
Анжеро-Судженск
Архангельск
Астрахань
Ачинск
Б
Барнаул
Белгород
Бийск
Благовещенск
Брянск
В
Вологда
Воронеж
Великий Новгород
Великие Луки
Вельск
Владивосток
Владикавказ
Владимир
Волгоград
Волгодонск
Г
Грозный
Е
Екатеринбург
Евпатория
Ж
Жиздра
И
Иркутск
Иваново
Ижевск
Й
Йошкар-ОлаК
Казань
Краснодар
Красноярск
Калининград
Калуга
Канск
Катав-Ивановск
Кемерово
Киров
Королёв
Кострома
Кузнецк
Курск
Кызыл
Л
Липецк
М
Москва и МО
Майкоп
Махачкала
Минск
Мурманск
Н
Новосибирск
Нижний Новгород
Назрань
Нальчик
Нижневартовск
Нижний Тагил
Новоалтайск
Новокузнецк
Новороссийск
Новый Уренгой
О
Омск
Оренбург
Орёл
П
Пермь
Пенза
Петрозаводск
Петропавловск-Камчатский
Псков
Пушкино
Р
Раменское
Ростов-на-Дону
Рязань
С
Санкт-Петербург
Симферополь
Самара
Саранск
Саратов
Севастополь
Серпухов
Смоленск
Сочи
Ставрополь
Стерлитамак
Сургут
Сыктывкар
Т
Тамбов
Тверь
Тольятти
Томск
Тула
Тюмень
У
Ульяновск
Улан-Удэ
Уфа
Х
Хабаровск
Ханты-Мансийск
Ч
Чебоксары
Челябинск
Черкесск
Чита
Э
Элиста
Энгельс
Ю
Южно-Сахалинск
— Оптовые продажи
— Сервисные центры BELMASH
Свернуть
9 идей как сделать фуганок своими руками
Если вам приходится много работать с деревом, то фуганок в мастерской никогда лишним не будет.
Содержание
Фуганок из электрорубанка своими руками
Сделать очень простой настольный вариант фуганка можно самостоятельно. Для этого потребуется электрорубанок, фанера и ДСП.
Сначала необходимо будет отрезать кусок фанеры толщиной 18 мм (размеры — 56х18,4 см). Далее автор делает разметку и на ленточной пиле вырезает небольшой кусок, чтобы можно было «посадить» электрорубанок.
Края фанеры надо будет обрезать под углом. Для основания можно использовать как фанеру, так и ДСП (размеры — 40х25 см, толщина — 18 см). Автор отступает от края основания 8 см, сверлит отверстия и прикручивает потом кусок фанеры.
Основные этапы работ
На следующем этапе автор отрезает кусок ДСП толщиной 8 мм (размеры — 70х18,2 см).
Из нее нужно вырезать кусок прямоугольной формы, чтобы установить рубанок. Затем этот кусок ДСП нужно прикрутить к основанию рубанка, убрав предварительно опорную плиту.
На следующем этапе необходимо прикрутить ДСП с рубанком к основанию. Также надо будет сделать из кусков того же ДСП недостающую часть стола, и тоже прикрутить ее. В итоге получилась ровная рабочая поверхность.
Потом останется только изготовить прижимную планку для заготовок. Для этого автор использует кусок ДСП толщиной 25 мм и кусок фанеры толщиной 10 мм.
Видео
Подробнее о том, как сделать настольный фуганок своими руками из электрорубанка, смотрите в видеоролике на сайте.
Benchtop Jointer making / Free PDFКак сделать фуговальный станок из фанеры и электрорубанка
Если у вас в мастерской нет фуговального станка, но он очень нужен, то можно изготовить его самостоятельно. Для этого потребуется электрорубанок и обрезки фанеры.
Этой интересной идеей поделился с нами автор YouTube канала el Rincon de Vicente.
Конструкция самодельного фуговального станка состоит из следующих элементов:
- станина;
- передний стол;
- задний стол;
- направляющая линейка.
«Сердцем» фуговального станка выступает электрический рубанок — можно использовать как сетевой, так и аккумуляторный инструмент.
Если вы на постоянной основе занимаетесь изготовлением различных изделий из тонколистового металла, то вам может пригодиться гибочный станок с сегментной матрицей.
Пошаговый процесс изготовления и сборки фуговального станка
Сначала необходимо будет изготовить станину фуговального станка. Состоит она из основания и вертикальных стоек.
К внутренней стороне стоек прикручиваются металлические уголки, на которые будет опираться электрический рубанок.
На следующем этапе приступаем к изготовлению переднего и заднего стола. Вырезаем прямоугольные заготовки из фанеры, и крепим их к верхней части станины.
Обратите внимание: передний стол фуговального станка обязательно должен быть подвижным — чтобы можно было регулировать его по высоте.
Для этого используются болты с гайками. Дополнительно нужно установить и закрепить возвратную пружину.
В завершении останется только изготовить направляющую линейку (или как ее еще называют — параллельный упор для заготовок).
Для крепления линейки используются металлические уголки.
После того как все детали изготовлены, можно приступать к сборке и тестированию самодельного фуговального станка.
Видео
В авторском видеоролике ниже можно посмотреть пошаговый процесс сборки фуговального станка из фанеры и электрорубанка (с указанием всех размеров). Спасибо за внимание.
Фуговальный станок из электрорубанка в корпусе из фанеры
На основе электрорубанка можно изготовить компактный фуговальный станок для домашней мастерской. Детали корпуса можно сделать из фанеры.
Первым делом отпиливаем два куска фанеры одинакового размера. В одном из них автор вырезает отверстие, чтобы можно было установить электрорубанок.
А потом с помощью электролобзика аналогичное отверстие вырезаем во второй заготовке.
Советуем также обратить внимание на обзорную статью: как сделать шлифовальную машинку из маленькой болгарки.
Прикладываем электрорубанок к боковым стенкам и отмечаем места сверления крепежных отверстий под болты.
Основные этапы работ
На следующем этапе крепим боковые стенки к основанию (листу фанеры или ДСП), выставив необходимое расстояние между ними.
Далее отпиливаем два кусочка фанеры с ламинированным покрытием. Из них будем делать передний и задний стол фуговального станка.
Прикручиваем к ним металлические крепления. Затем крепим эти две детали к корпусу.
Устанавливаем электрорубанок. Регулируем высоту столов. После этого нужно будет сделать упорную планку (параллельный упор).
Для изготовления упора автор также использует фанеру с ламинированным покрытием. Крепится упорная планка к корпусу фуговального станка с помощью металлических пластин.
Устанавливаем станок на стол, фиксируем струбцинами, и можно работать. При желании можно сделать крепление к столу с помощью болтов.
Видео: фуганок своими руками
Подробно о том, как сделать фуговальный станок из электрорубанка и фанеры, вы можете посмотреть в авторском видеоролике. Идея принадлежит автору YouTube канала Mistry MakeTool.
Make A Benchtop Jointer || DIY Jointer With My Electric PlanerФуговальный станок с приводом от электромотора стиральной машинки
Расскажем, как своими руками изготовить настольный фуговальный станок — для обработки небольших деревянных заготовок.
В качестве привода будет выступать электромотор от стиральной машинки-автомат. Но вы можете взять и другой электрический двигатель.
Своим личным опытом изготовления самодельного фуговального станка поделился с нами автор YouTube канала Handmade Creative Channel.
Основные этапы работПервым делом необходимо будет сделать приводной шкив. Для этого из куска толстой доски вырезаем с помощью кольцевой пилы круг подходящего диаметра.
Устанавливаем его на вал электродвигателя (если нет токарного станка) и обтачиваем. Делаем канавку для ремня.
Из листа ДСП или фанеры и деревянных брусков собираем опорный столик. Размеры — на ваше усмотрение.
На торцы ножек автор решил установить резиновые ножки, чтобы конструкция не скользила по рабочему столу.
Отрезаем две заготовки из металлической полосы, размечаем их и высверливаем крепежные отверстия. Затем крепим их к корпусу электромотора.
На следующем этапе нам потребуется фуговальный станок. Его можно изготовить самостоятельно или же купить в готовом варианте.
С помощью металлических уголков крепим станок к опорной площадке. В нижней части столешницы надо вырезать квадратное «окошко».
Дальше устанавливаем на опорную поверхность электродвигатель. Соединяем приводной вал с ведомым валом на фуговальном станке.
Край электромотора дополнительно фиксируем с помощью пружины — таким образом будет обеспечена необходимая натяжка ремня.
В завершении останется только изготовить и установить на стол блок управления с кнопками включения и выключения. В данном случае используется корпус, изготовленный из пластиковой канализационной трубы.
ВидеоПодробно о том, как сделать фуговальный станок с приводом от электромотора стиральной машинки, вы можете посмотреть в авторском видеоролике ниже.
Amazing DIY Idea Using Old Washing Machine MotorКак сделать фуганок из ручного электрического рубанка
В данном обзоре рассмотрим процесс изготовления самодельного фуганка для обработки деревянных заготовок (досок, брусков, реек и т.д.). За основу самоделки используется ручной электрорубанок.
В первую очередь необходимо изготовить две боковых стенки станины. Автор отпилил два куска фанеры подходящего размера, склеил их вместе, после чего лобзиком вырезал в них технологические отверстия.
Далее вырезаются две торцевые стенки с отверстиями, и собирается станина фуганка — для крепления заготовок используются болты с гайками.
Возможно, вам также интересно будет прочитать статью: как изготовить настольные ножницы для резки тонколистового металла.
Основные этапы работ
На следующем этапе к станине крепится электролобзик. В корпусе инструмента мастер установил мебельные гайки, после чего прикрепил его к станине болтами. Фиксируется рубанок барашковыми гайками.
После этого необходимо вырезать две металлических пластины (из алюминия). Крепятся они к верхней части станины по обе стороны электрорубанка. Они выступают в качестве рабочего стола.
Еще одним важным элементом конструкции является параллельный упор. Изготовить его можно из фанеры и алюминиевых пластин. Крепим его к станине.
Что касается вариантов крепления, то самодельный фуганок можно закрепить к верстаку или же просто зажать в столярных тисках.
Подробно о том, как сделать фуганок из ручного электрорубанка, показано в авторском видеоролике. Идеей поделился автор YouTube канала Woodman.
Мини фуговальный станок из электрорубанка и профильных труб
Из обычного электрического рубанка можно изготовить удобный в работе мини фуговальный станок. И в данном обзоре автор показывает, как это сделать.
Станок подойдет для обработки небольших заготовок. Сначала необходимо будет отрезать заготовки из профильной трубы (по размерам электрорубанка).
После этого автор сваривает первые четыре детали. Для этого к четырем отрезкам профиля (по краям) привариваются «коротыши» — четыре заготовки меньшей длины.
Основные этапы работ
На следующем этапе в четырех стойках нужно просверлить отверстия. Затем аналогичные по диаметру отверстия надо будет просверлить в самом корпусе электрорубанка.
Прикручиваем ножки к электрическому рубанку. Для этого потребуется две резьбовых шпильки и гайки.
Далее вырезаем прямоугольную пластину из листового металла. По краям сверлим крепежные отверстия. Затем привариваем к ней ножки.
После этого автор отрезаем кусок металлической полосы и приваривает его к двум отрезкам квадрата, которые вставляются в стойки. В результате получился параллельный упор.
В завершении останется только зачистить сварные швы и покрасить детали. Потом приступаем к финальной сборке.
Видео
Подробно о том, как сделать мини фуговальный станок из электрорубанка, можно посмотреть на видео ниже. Как вам такая самоделка?
Simple Homemade hand planer stand.Настольный фуговальный станок с деревянной рамой
Для изготовления качественной мебели и других изделий или поделок из дерева часто требуются различные деревообрабатывающие станки.
И многие домашние умельцы, чтобы сэкономить, собирают такие станки своими руками.
В данном обзоре мы расскажем, как изготовить настольный фуговальный станок из электрорубанка.
Советуем также прочитать: как сделать стул-кресло (дачный вариант) на скорую руку.
Приступаем к работе
Для изготовления основания фуговального станка мастер использует куски МДФ. Но вы можете использовать фанеры или щиты, склеенные из досок.
По центру основания необходимо просверлить отверстие. Отрезаем небольшой кусок шпильки и привариваем к ней кусок стального кругляка.
Вставляем деталь в просверленное отверстие и фиксируем гайкой.
Автор делает посадочное место для гайки, чтобы утопить ее заподлицо с рабочей поверхностью.
Далее нам потребуются деревянные брусочки. Делаем разметку, и сверлим в них отверстия. Делаем потай под шляпки саморезов.
После этого собираем из подготовленных заготовок четыре детали (смотрите на фото ниже).
Прикручиваем детали к основанию станка. К ним прикручиваем кусок обрезной доски. Также автор прикручивает к доске возвратную пружину.
Чтобы поднять доску на нужную высоту, автор использует винт, установленный ранее.
Сборка фуговального станка
На следующем этапе автор отпиливает еще четыре бруска и сверлит в них по два отверстия.
Получившиеся стойки прикручиваем к рабочей поверхности. Отрезаем два куска круглой трубы в отверстия в стойках.
Затем устанавливаем электрорубанок. Самоделка готова!
Как сделать мобильный фуговальный станок своими руками
В данном обзоре автор YouTube канала «ІГОР АНДРЕЙЧУК» поделится своим опытом изготовления фуговального станка.
Особенность конструкции — простота и мобильность.
Фуговальный станок можно вывезти из мастерской на улицу, что очень удобно, не нужно таскать пиломатериалы с улицы в помещение.
Советуем вам также прочитать: как изготовить простенький самодельный сверлильный станок из дрели.
Основные этапы работ
Первым делом необходимо будет изготовить станину фуговального станка. Для этого автор использует металлический уголок. В нижней части крепятся две оси с колесами.
Ножевой вал автор использует заводской. Если повезет, можно найти его на металлоприемке. На вал с двух сторон надеваются корпусные подшипники.
После этого устанавливаем вал на станину: делаем разметку, и сверлим отверстия для крепления корпусных подшипников.
Рабочий стол состоит из двух частей — переднего и заднего стола. Под передним столом находится подъемный механизм.
Далее нам потребуется электродвигатель.
На вал двигателя крепится шкив из алюминия (можно сделать его самостоятельно: отлить болванку из алюминия, после чего обточить на токарном станке).
Второй шкив надеваем на ножевой вал. Потом соединяем оба шкива с помощью ремня.
Красим все элементы конструкции, и приступаем к сборке. На станину крепим ножевой вал, потом устанавливаем задний стол и передний стол с подъемным механизмом. Крепим к станине электродвигатель.
Видео: передвижной фуганок своими руками
Подробный процесс изготовления фуговального станка смотрите на видео ниже. Идеей поделился автор YouTube канала «ІГОР АНДРЕЙЧУК».
Самодельный прижим для фуговального станка
Чтобы облегчить и ускорить процесс строгания досок на фуговальном станке, можно изготовить и установить самодельный прижим для обрабатываемых заготовок. С этим приспособлением повысится и безопасность работ.
Эту интересную идею мы подсмотрели у автора YouTube канала «ІГОР АНДРЕЙЧУК». Рекомендуем взять на заметку!
Необходимые материалы:
- резиновые валы;
- строительный уголок из стали;
- подшипники;
- круглая труба;
- профильная труба.
Чтобы изготовить самодельный прижим, потребуются сварочный аппарат, электрическая дрель, а также углошлифовальная машина (болгарка).
Резиновые валы можно демонтировать со старой стиральной машины. На металлоприемке такого добра хоть пруд пруди.
Укорачиваем валы до требуемой длины.
Надеваем на них подшипники в корпусе. Корпус можно сделать из круглой трубы.
К корпусным подшипникам необходимо будет приварить два отрезка уголка, выставив их параллельно друг другу (смотрите фото ниже).
На следующем этапе из отрезков строительного уголка свариваем стойку с перекладиной. В основании сверлим отверстия для крепления к неподвижному столу фуговального станка.
Из стальной круглой трубы изготавливаем раму прижима.
Привариваем ее к рамке с валами и с помощью подвижных креплений крепим к стойке. Из профильной трубы изготавливаем упор.
В завершении останется только зачистить сварные швы и покрасить самодельную конструкцию. Крепим ее к столу фуговального станка.
Отличная вещь! Обязательно сделаю себе
50.94%
Требует доработки
35.85%
Ерунда полная! Лучше купить готовые приспособы
13.21%
Проголосовало: 53
Пошаговый процесс изготовления, а также тест самодельного прижима для фуговального станка, показан в авторском видеоролике ниже. Спасибо за внимание.
Приспособление для фугования из ручного фрезера
Далеко не все домашние мастерские достаточно просторны для того, чтобы установить в них широкоформатные станки. Поэтому иногда приходится обходиться разными самодельными приспособлениями.
В данном обзоре предлагаем вашему вниманию приспособу для фугования больших заготовок, сделанную из ручного Фрезера. Основной материал — фанера.
В первую очередь надо будет напилить на циркулярной пиле 12 заготовок прямоугольной формы. И к шести заготовкам нужно будет приклеить 6 небольших брусочков.
Основные этапы работ
На следующем этапе нужно будет вырезать в заготовках пазы, и соединить их с помощью квадратного брусочка. В итоге должны получиться шесть опорных стоек.
Сами стойки будут фиксироваться к верстаку. Для этого в столе и стойках нужно просверлить отверстия. Что прикрепить стойки к верстаку, автор использует длинные болты.
Затем опорные стойки крепятся к верстаку. Благодаря наличию пазов, их можно зафиксировать на нужной высоте. В сами стойки вставляется длинный уровень. На одну сторону верстака требуется по три стойки.
На последнем этапе из кусков фанеры изготавливается короб прямоугольной формы. С одного из торцов нужно вырезать с помощью кольцевой пилы полукруглое отверстие (под ручку фрезера).
Теперь останется только выбрать в коробе продольный паз для фрезы, и можно приступать к окончательной сборке данного приспособления.
Видео
Подробный процесс изготовления приспособы для фугования из ручного Фрезера смотрите в видеоролике на сайте.
Adjustable Router Sled HomemadeАндрей Васильев
Задать вопрос
Быстрые самодельные зажимы — маленькие и большие [с видео]
В этом посте я делюсь своей любимой конструкцией самодельных зажимов. Их можно сделать очень большими или очень маленькими в соответствии с вашими потребностями.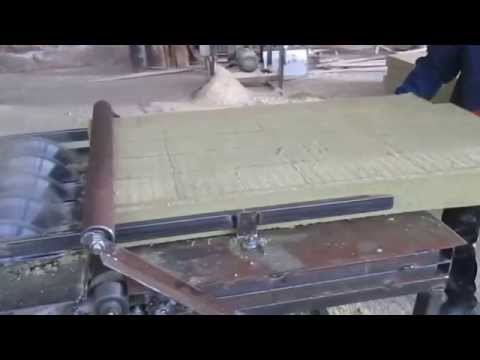
Далее мы также включаем короткий видеофрагмент из нашей последней серии, где я подробно объясняю, как работают зажимы.
Я только что сидел и смотрел на дно пустого чайника.
И я задумался. Не могу вспомнить, когда в последний раз что-то покупал. Я не имею в виду счет или что-то в этом роде, просто то, что я действительно хотел. Возможно, это были излишки ботинок, я думаю, они стоили 20 фунтов.
Это не потому, что я не ценю ценность или я тайтовый. Если честно, то скорее наоборот. Я действительно могу оценить изделия ручной работы и их стоимость. И если есть что-то, что мне действительно нужно или нужно, я с удовольствием потрачу. Обычно я из тех, кто «купи хорошо, купи правильно и сделай это один раз».
Дело в том, что мне не нравится иметь много вещей.
А может быть, этот «старичок» присаживается ко мне чуть раньше.
Так или иначе, я снова наполнил чайник, так что проблема решена.
Это все, что нужно сказать о том, что когда дело доходит до быстрого удовольствия от покупки чего-то нового, одна вещь, которая никогда даже не попадет в список, — это зажим.
Они довольно дорогие и обычно их нужно много.
Держу пари, я мог бы предоставить кому-нибудь полный стартовый набор хороших ручных инструментов по цене полного набора зажимов.
И я гарантирую, что даже с зажимами следующая работа, которую вы начнете, не будет достаточно длинной. На самом деле, вы могли бы построить целый чертов верстак с дорогими деревянными тисками по цене набора зажимов.
Но дело не в цене. Скорее они просто тупые.
И именно поэтому у меня самый дрянной набор зажимов, который вы, вероятно, найдете в любой профессиональной мастерской.
Я хотел показать вам один из многих моих способов обхода отсутствия хороших зажимов.
Это действительно отличная конструкция зажима, которую вы можете сделать сами, когда вам это нужно.
Я обнаружил, что они работают настолько хорошо, что мне никогда не хотелось и не нуждались в «правильных» зажимах.
Этот простой зажим представляет собой кусок палки с блоком, привинченным к каждому концу.
Следующее видео представляет собой короткий фрагмент, взятый из нашей сборки Nest of Tables.
Здесь я расскажу немного больше о моих «самодельных» зажимах, а также о том, почему они были так полезны для склеивания этого маленького столика, который был деликатным и неудобным из-за того, как важно было держать все параллельно и прямоугольно:
Чтобы сделать зажимы, я оставляю пространство между блоками примерно на дюйм шире, чем то, что зажимается.
И затем клин грубой резки действует, чтобы обеспечить зажимное усилие.
Клин не обязательно должен быть точным, так как блок может вращаться на одном винте.
В зависимости от того, что вы зажимаете, вы можете усилить клин рукой или сильно ударить его молотком, если вам нужно немного больше.
Вы можете сделать их более прочными или легкими по мере необходимости, и я обычно после этого держу латы, поэтому у меня всегда есть много зажимов под рукой.
Палка с прорезью – самая полезная вещь в любой мастерской!
Конечно, при необходимости его стоит усилить шурупом большего калибра.
Эти хомуты можно сделать даже красивыми.
Нанесите воском массу реек, чтобы предотвратить прилипание клея, и просверлите множество предварительно просверленных отверстий по всей их длине. Затем просто прикрутите блоки на место по мере необходимости. Заполните коробку несколькими дюжинами клиньев, и все готово.
Конечно, я знаю многих людей, которые построили очень хорошие рабочие зажимы, но для меня на этом этапе я бы предпочел просто купить их.
Ничто из этого не означает, что вам не нужно покупать зажимы. Мне нравится иметь несколько быстрых захватов ногами по верстаку. Но когда дело доходит до нехватки или правильного размера, то это быстрый выход из тюрьмы.
И после долгой работы наша сборка Nest of Tables завершена!
В общей сложности более 8 часов полной серии предлагает множество советов и подсказок, поскольку мы решаем довольно уникальные задачи этой действительно точной сборки.
Посмотреть трейлер сериала и узнать подробности можно ЗДЕСЬ.
Как сделать деревянную скобу для перекладины
Посмотреть планы этого проекта $9
К этому моменту я уже потерял счет тому, сколько различных деревянных скоб я спроектировал и изготовил за эти годы. Некоторые из них были успешными, а другие… ну, не такими успешными. Но все они были частью учебного процесса. Без этих более ранних версий и знаний, которые я получил при их создании и использовании, сомнительно, что я смог бы представить сегодня то, что я считаю лучшим, что я сделал до сих пор. Он берет все, чему я научился у предыдущих, и так или иначе применяет это к этому дизайну. Что работает, а что нет.
Как и большинство вещей, которые я делаю, все началось с идеи, которую я грубо набросал на бумаге, затем немного усовершенствовал в SketchUp, прежде чем создать прототип. При создании прототипа я придумал способы его дальнейшего улучшения и опробовал их, прежде чем приступить к окончательному дизайну. В этом преимущество создания прототипа и сокращения дизайна для его усовершенствования; Минус в том, что это занимает намного больше времени.
Для начала я нарезал бруски для шести новых хомутов из ясеня до нужного размера и обстрогал их до гладкости:
Ясень — хороший выбор для барной стойки — это очень прочная и жесткая древесина твердых пород, которая не изгибается. Доска, из которой я их вырезал (один лист размером 4/4 x 6″ x 8 футов), была прямоволокнистой и без дефектов, поэтому эти бруски должны выдерживать интенсивное использование без поломок. При цене 2,80 доллара за досковый фут, которую я заплатил за золу у своего местного поставщика, стоимость брусков составила 11,20 доллара. Неплохо для шести зажимов.
Что касается других пород дерева, то любые твердые породы твердой древесины (например, клен, дуб, гикори) подойдут. Я бы избегал мягких пород дерева, так как они, как правило, не имеют достаточной жесткости, чтобы противостоять изгибающему усилию, а зубья пилы, которые будут прорезаны в бруске, могут преждевременно изнашиваться.
Говоря о выемках для зубьев пилы, я сделал довольно простое приспособление, чтобы сделать это с помощью фрезерного станка . Первый шаг состоял в том, чтобы вырезать кусок дерева с наклоном 10 градусов на каждом конце. Я использовал широкий упор, прикрепленный к моей торцовочной пиле, и сделал разрез, установив пилу под углом 10 градусов:
Затем я мог обрезать его до окончательного размера на настольной пиле и отрезать две части по длине. Есть подробности по изготовлению этого приспособления в планах по этому проекту, а я сделал видео во время его создания.
Собрав приспособление, я настроил его, чтобы сделать первую выемку. Для этого направляющая планка должна быть обрезана, как показано здесь, чтобы она располагалась поверх планки:
Для этого я использовал шлифовальный напильник . Этот стержень используется только для первого надреза и будет заменен на другой, который не был обрезан для остальных надрезов.
Вот первый. Они не должны быть глубокими, чтобы зажим мог захватить их. Это одна из вещей, которые я узнал из других сборок:
В идеале выемка должна иметь глубину 1/16″ в самой нижней точке и не глубже. Чтобы сделать разрез, мой фрезерный станок был оснащен прямой фрезой 1/2 дюйма и направляющей втулкой 5/8 дюйма, чтобы перемещаться в зажимном приспособлении.
Для остальных пропилов узкая планка садится в предыдущий паз и задает расстояние для следующего. Чтобы изменить расстояние, все, что вам нужно сделать, это изменить ширину узкой планки и глубину резания на фрезерном станке:
Когда планки готовы, я перешел к изготовлению двух частей, которые будут неподвижной губкой. . Я решил сделать их из вишни для разнообразия внешнего вида, но можно было бы использовать и ясень. Две половинки фиксированной челюсти подходят к стержню, и для этого я сделал серию пропилов на настольной пиле, используя свой мини-салазки для настольной пилы . Сначала я сделал образец, чтобы убедиться, что он идеально подходит, и вот что я делаю здесь:
Мне нравится!
Некоторые не видят смысла в изготовлении собственных зажимов, но я категорически не согласен. Если вы только начинаете, это не только дает вам мощный инструмент, который вы можете использовать в течение многих лет, но также дает вам столь необходимый опыт создания точных вырезов для создания столярных изделий, которые вы позже будете использовать для более «важных» проектов, таких как мебель.
Когда образец был готов и хорошо подогнан, я мог вырезать детали, а затем приклеить их к концам стержней:
Я использовал самодельные зажимы, чтобы зажать зажим – просто обрезки 1/2″ фанеры и 3 ″ винты. Альтернативный способ сделать это — просто привинтить эти части вместе прямо на стержне. Винты скрепят детали, а также добавят прочности соединениям.
Чтобы проиллюстрировать это, я сделал это с одним из моих брусков, который уже был склеен:
Я расположил винты со смещением относительно друг друга, как показано, и просверлил направляющее отверстие и зенковку для винтов #8 x 1-1/4″, которые я использовал. Перед нанесением клея лучше выровнять детали и просверлить направляющие отверстия и зенковки. Это предотвратит скольжение деталей и обеспечит лучшую точность.
Все шесть моих после того, как клей высохнет и отшлифуется до гладкости:
Затем я начал работу над подвижной челюстью, вырезав детали для зажимной площадки. Он имеет L-образную форму и сделан из двух кусков ясеня, соединенных уздечным соединением. Первые разрезы были на вертикальной части. Обратите внимание на цековку на конце ходового винта:
Чтобы аккуратно выполнить эти разрезы, я быстро сделал простую направляющую, которая надевается на упор для настольной пилы соединение уздечки:
Затем я вырезал другую часть, нижнюю часть буквы «L»:
Еще раз я сделал образцы, прежде чем делать какие-либо из этих разрезов в реальных частях. Плотная посадка важна для максимальной прочности в этом суставе.
Для склеивания я использовал полиуретановый строительный клей. У него более длительное открытое время и гораздо лучшие свойства заполнения зазоров, чем у обычного столярного клея. Его также не нужно зажимать, чтобы получить красивое плотное соединение, подобное этому:
Далее, вероятно, самая сложная часть для этих зажимов. Я называю его винтовым блоком, так как в нем находится Т-образная гайка, в которую ввинчивается ходовой винт. Я придал ей базовую форму перед тем, как просверлить зенковку для Т-образной гайки:
Затем просверлил отверстие для ходового винта и установил Т-образную гайку. Важно всегда отмечать и просверливать отверстия для хвостовиков на этих Т-образных гайках, прежде чем вкручивать их, так как хвостовики будут раскалывать древесину на такой небольшой части. Чтобы удержать его там, чтобы он не мог вывернуться, я вкрутил небольшой винт, выступающий над фланцем:
Затем я вырезал пластины защелки из алюминия 1/8″, используя большие салазки для настольной пилы . Для этого я вставил в пилу лезвие для резки металла. Несмотря на то, что обычный деревообрабатывающий диск с твердосплавными зубьями справится с этим алюминием, я бы не рекомендовал это делать. Угол зацепа на зубьях слишком агрессивен, особенно для таких мелких деталей. Также настоятельно рекомендуется использовать сани, как я сделал здесь. Алюминий прилипает к зубьям лезвия, делая эти мелкие детали потенциально смертельными снарядами, если их отбросить назад после зажатия между лезвием и ограждением:
И помните, если осторожность исходит от меня, на нее можно рассчитывать — я не преувеличиваю риски.
В пластине должно быть отверстие, чтобы ее можно было привинтить к винтовому блоку:
И конец пластины должен совпадать с углом на деревянном блоке. На моем я вырезал оба одновременно, установив торцовочную пилу на 10 градусов. Я использовал простое приспособление, закрепленное на пиле, чтобы точно удерживать детали во время резки. Это можно увидеть на видео внизу этой статьи.
Еще одна вещь, которую нужно сделать с пластиной, это подпилить небольшой задний скос, чтобы она лучше совпадала с прорезью в стержне:
Вот как это должно выглядеть с винтовым блоком и прижимной пластиной на месте планка:
Пластина защелки идеально входит в паз пилы. Если вы делаете это и обнаруживаете, что ваш не подходит, вы всегда можете сделать нижнюю часть зажимной площадки тоньше, чтобы отрегулировать ее. Точно так же, если он слишком длинный, вы всегда можете укоротить пластину защелки и винтовой блок.
Пришло время сделать другую очень важную часть подвижной челюсти, нижний блок с деревянной пружиной:
Я использовал ясень для блока и клен для пружины. Клен более устойчив, чем ясень или вишня, так что это лучший выбор для этого. Пружина должна быть изготовлена из очень прямоволокнистой древесины, иначе она может сломаться. Заменить пружину в готовом хомуте можно, но это непростая задача. Я использовал эпоксидную смолу, чтобы приклеить пружину к блоку для максимальной прочности. Для этого также подойдет обычный столярный клей.
****ПРИМЕЧАНИЕ: На плане отсутствует размер нижнего блока:
Мои ручки были сделаны из вишни, но это часть, для которой вы можете использовать мягкую древесину, если хотите. В конце необходимо просверлить отверстие диаметром 3/8″ для ходового винта с резьбой, и я держу деталь вертикально в тисках для сверлильного станка:
Затем я закончил формование, в основном с помощью ленточной шлифовальной машины . платформа :
Резьбовые стержни обрезаны по длине, и я отшлифовал плоское место возле конца, которое будет вставлено в рукоятку при вклеивании:
Стержень должен выступать на 4″, а 2″ вклеены в ручку:
Я сделал фиксаторы из ясеня:
Я просверлил отверстия сверлом 3/8″, затем немного рассверлил их ступенчатым сверлом.
Сборка подвижной челюсти начинается с вкручивания ходового винта в блок винтов, затем надевания фиксатора перед приклеиванием гайки к концу:
Я использовал эпоксидную смолу и перед приклеиванием гайки убедился, что детали чистые. на месте на конце ходового винта. Есть и другие способы закрепить гайку, например, слегка сплющить конец стержня для посадки с натягом или просверлить отверстие для штифта.
Далее прижимная площадка приклеивается к фиксатору и зажимается. Перед этим в расточенное отверстие вставили 3/16-дюймовую шайбу крыла и нанесли небольшое количество вазелина на конец ходового винта для смазки:
Ожидание высыхания клея компенсирует большую часть время, необходимое для создания этих зажимов, поэтому разумно запланировать другие операции, пока это происходит. Здесь я обрезал и выстрогал стороны подвижной челюсти, ожидая, пока высохнет клей на фиксаторе:
Я снова сделал их из вишни и обрезал их до нужной длины на моей торцовочной пиле с упором, установленным на 5″.
Их можно склеивать и зажимать, но у меня нет под рукой достаточного количества зажимов, чтобы сделать шесть штук одновременно. Поэтому вместо этого я просверлил зенкеры перед тем, как просверлить направляющие отверстия для винтов № 6, которые я использовал для этого:
Достаточно всего четырех стратегически расположенных.