Как своими руками по чертежу с размерами сделать ручной профилегиб
Для равномерной гибки металлического проката с различным профилем сечения применяют профилегиб – станок с устройством из комплекта вальцов. От обычного трубогиба профилегибочный станок отличает возможность делать арочные заготовки из фасонного погонажа металлических профилей, например, тавра, двутавра, швеллера, уголка и других форм. Помимо этого, торцевая поверхность прижимающих вальцов отличается характерным сечением, которое применяется только для определенного вида проката.
…
Оглавление:
Типы профилегибов
По способу осуществления прижима вальцов различают профилегибы:
- гидравлические станки;
- простые ручные приспособления.
По типу передвижения металлического профиля на вальцы профилегиба применяют:
- ручную подачу;
- подачу с электрическим приводом.
Гидравлический прижим обеспечивает прочное закрепление, что дает возможность изгибать профиль значительной толщины.
Принцип работы профилегиба
Работа заключается в механическом воздействии на металл для его холодной деформации. Разные станки воздействуют на профиль при помощи определенной направленности механического усилия:
- Вал для прижимания заготовки движется по направлению сверху вниз. Такое воздействие заложено в основе работы многих гибочных станков, применение силы домкрата в большинстве случаев не требуется.
- Прижимной вал профилегиба работает по направлению снизу вверх, и сила давления действует так же. Этот простой принцип работы применяется в устройствах с применением гидравлического домкрата. Характерно движение серединного вала, а самые боковые валы остаются стационарно неподвижными.
Работа профилегибочного станка по обоим принципам сама по себе является эффективной.
Конструкция самодельного гибочного станка на чертеже
Для изготовления профилегиба своими руками чертежи просто необходимы. Сборка станины и расположение валов нельзя сделать самому «на глазок», так как гибка профиля отличается тем, что нужно выдерживать размер, радиус. В неправильном расположении узлов кроется опасность выпуска бракованных арочных конструкций, которые придется еще раз пропускать через вальцы для исправления.
Помимо неправильного радиуса, есть опасность скручивания профиля, если продвижение заготовки не выровнено в одной плоскости. Как изготовить чертежи можно посмотреть на видео, но актуальным такое копирование будет только в случае:
- если чертежи предназначаются именно для гнутья того вида профиля, что требуется гнуть на самодельном станке, причем даже материал должен совпадать;
- если предлагаемая схема в интернете или другом информационном поле технически совершенна и будет работать, для этого следует досконально разобраться в конструкции или показать чертеж ручного профилегиба специалисту;
- если искомый чертеж содержит описание технологического процесса сборки, а изображения на чертеже имеют все размеры, сечения, диаметры, информацию о расположении узлов и деталей;
- если детали, заготовки и узлы чертежа имеются в свободной продаже, и не возникнет сложностей с их изготовлением или поиском аналогов для самодельного станка.
Изготовление самодельных схем
Чаще всего те мастера, которые изготавливают гибочный станок для профиля своими руками, стараются разработать свои чертежи для работы. При черчении узлов, деталей учитывают вышеизложенные принципы составления схем, а для основы берут готовую конструкцию. При этом проектируют детали и заготовки, которые легко доступны в продаже и без проблем изготавливаются своими руками.
Вальцы или ролики, пропускающие профиль, должны иметь торцевые поверхности, повторяющие сечение профиля, который будет допущен к обработке гнутьем. Для некоторых профилей, например, уголок или усеченный тавр учитывается направление требуемого изгиба, например, в сторону полки или по внутреннему ребру жесткости. Некоторые специалисты при изгибании полого профиля наполняют его сыпучим материалом, песком, концы при этом закрывают заглушками. Эта процедура помогает избежать сминания или разрыва сечения при прохождении через вальцы.
С учетом типажа своего изгибаемого профиля
Рабочие поверхности вальцов, через которые проходит заготовка профиля в процессе изгибания, выполняются своими руками в полном соответствии с сечением проката . Для сложных конфигураций желательно повторить все мельчайшие элементы конструкционных особенностей. Выработаны стандартные формы торцевых поверхностей роликов для:
- трубы круглого или овального сечения, арматуры, прута – в форме желоба по диаметру профиля или круглой канавки по форме изделия;
- квадратной или прямоугольной трубы — в виде правильного сечения соответствующей формы с размерами по внешним габаритам проката;
- уголка для гибки по наружной стороне (когда снаружи арки окажется внутренняя сторона уголка) – торец вальца делается плоским, предусмотрен удерживающий кант в виде борта;
- в предыдущем случае изгибающий и прижимающий элементы должны работать в паре, так, что борт первого четко прижимал металлическую полку к боковой поверхности другого;
- уголка, если гибка осуществляется по внутренней поверхности, тогда удерживающий борт располагается на опорном ролике, а изгибающий имеет плоский торец;
- швеллера, который гнется так же, как и уголок, для него применяется похожая система;
- двутавра – по принципу гладкой торцевой поверхности вальцов, и поперечным сечением, равным по размеру внутреннему габариту профиля, чтобы ролик при пропуске профиля проходил внутри проката.
Последовательность сборки профилегиба с ручной подачей
Этот станок после комплектации и запуска сможет изгибать трубы, у которых диаметр не более 60 мм.
Материалы для работы
Для устройства гибочного станка своими руками понадобятся:
- готовые подшипниковые узлы, в которых подшипники уже запрессованы;
- швеллер № 80;
- сталь полосовая толщиной 5 мм;
- стальной вал с диаметром 70 мм, понадобится три штуки;
- шестерни и цепь ГРМ от классического «жигуленка»;
- стальная арматура гладкого сечения;
- болты диаметром 20, длиной 60 см;
- гайки, болты, гроверные шайбы в ассортименте.
Изготовление станка
Первым этапом своими руками подготавливаем рамные заготовки, для этого из швеллера готовим два куска по 70 см и два – по 20 см, первые относят к продольным, а вторые к поперечным элементам. Торцы двух длинных заготовок отрезаем под углом в 70º. Чтобы разметить место под крепление болтов, прикладывают узлы подшипников к верху длинных кусков швеллера и делают отметки.
По отметкам работают пробойником, чтобы наметить точки сверления, затем дрелью сверлят отверстие насквозь. После этого приступают к изготовлению боковых креплений валов. Размеры крепежных деталей специально не указываются, они принимаются в зависимости от диаметра вала. Чтобы протянуть ось вала через крепление, в нем сверлят отверстие насквозь. Так как прижимной вал будет работать в конструкции с повышенной нагрузкой, то на месте крепления приваривают дополнительные вставки из полосовой стали, чтобы итоговая толщина металла получилась не менее десяти миллиметров.
Чтобы устроить верх прижимного узла своими руками, из остатков швеллера отрезают часть по размеру ширины вала, а его боковые части отпиливают под 45º. Из верха и двух кусков для боковой части делают рамку в виде буквы П для поддерживания вала.
Готовят направляющие полосы, по которым будет двигаться прижимной вал, для этого из швеллера отрезают стойки по полметра высотой, их требуется две штуки. К ним приваривают квадратные пластины из расчета свободного вхождения между стенок швеллера. Отступив от начала 1 сантиметр, делают отверстия для болтов, диаметр которых 12 миллиметров.
Далее формируют узел крепления подвижного вальца. Из пары ранее сделанных боковин и верхнего куска швеллера делают раму, где в процессе сборки вставляется вал. После этого переходят к сборке вертикальных стоек и рамы.
Основание станка собирают сваркой из ранее подготовленных поперечных и продольных заготовок. К нему присоединяют сваркой вертикальные полозья — направляющие, по которым будет осуществляться передвижение прижимного узла. Вверху прижимного устройства находят центр и делают отверстие 22 миллиметра, где будет стоять болт М20. Для свободного вращения болта в отверстии, но без возможности выхода наружу на конце его наваривают два утолщения.
Для направляющих конструируют верхнюю перекладину, отрезают швеллер по размеру, равному расстоянию между рельсами. Прикладывают его к направляющим и сверлят два отверстия по старым, которые уже есть. В центре перекладины делают отверстие, куда поверх приваривают гайку, в которую вставляется болт. Совмещая совпадающие отверстия перекладины и направляющих, крепят болтами верхнюю часть к вертикальным полозьям.
Переходят к креплению подшипниковых узлов поверх рамы на основании со вставленными в них валами. Их крепят чрез совпадающие отверстия с помощью гаек и болтов. Под гайки подкладывают гроверные шайбы.
Шестерни варят к валам, иногда делается более сложная конструкция, состоящая из ступицы, присоединенной сваркой в центре шестеренок под цепь. Диаметр ступицы равен этому размеру у шпинделя вала. Вал протачивается, а в ступице делается наплавленный участок. После этого шестерни ставят на шпиндели и притягивают их гайками – основной и контргайкой.
Ось с шестеренкой для ворота со стороны готовых уже шестеренок приваривают в середине вертикальной направляющей. Стараются расположить ось так, чтобы в цепи присутствовало натяжение, но ее легко было надеть и снять при необходимости. Изготавливая ворот для рук, берут отрезок полосовой стали по длине до 50 см, с одного бока ворота с помощью сварки присоединяют металлическую арматуру, служащую рукояткой. Друга сторона остается для крепления ступицы из трубного обрезка. Его наружный диаметр равен внутреннему диаметру у шестеренок.
Плотно надевают шестерню на ручку, а на ступицу рукоятки напрессовывают, используя для этого тиски, шестеренку для цепи. Для ускорения процесса прессовки шестеренку греют до 120ºС, после чего происходит температурное расширение и увеличивается посадочное отверстие. Остывшие детали суживаются и гарантируют плотное соединение.
Чтобы выполнить прижимной ворот, на окончании болта сверлят отверстие насквозь, куда вставляют обрезок арматуры для изготовления ручки ворота. Установка бокового ворота осуществляется на ранее присоединенную ось, где приварена ступица и затягивается двумя гайками. Цепь натягивается через все имеющиеся шестеренки. После полного окончания устройства гибочного станка его нужно покрасить для замедления окисления металла и предупреждения коррозии.
Что представляет собой профессиональное оборудование
Для изготовления арочных заготовок из более мощного профиля и гибки проката на любые углы, требуется устроить профилегиб прокатного варианта. Он носит название трехроликового. Такой станок показан на фото.
У этой конструкции присутствует на корпусе один центральный изгибающий валец, помимо него есть два опорных ролика. Иногда для этого не нужен корпус, так как крепление вальцов может быть организовано на сконструированной опорной поверхности любого типа или гибка может вестись в горизонтальной плоскости. Стационарно закрепленные опорные ролики не двигаются, перемещается только прижимной валец, на котором есть ручка для вращения во время работы и постепенного поджимания профиля.
Расстояние между шкивами выбирается расчетом приложенного усилия. Если расстояние увеличить, то уменьшится усилие для выгибания проката. При этом увеличится значение минимального радиуса. По технологии при выгибании профиля на концах заготовки остаются «мертвые» куски необработанного профиля. Их длина увеличится при отдалении роликов один от другого.
Материалом для изготовления профилегиба служит в основном металл, но есть и другие варианты. Например, если постоянно приходится иметь дело с мягкими цветными металлами, то самодельные ролики можно сделать даже из дерева, но идеально подходит прочная пластмасса. Но станки со съемными роликами под различное сечение профиля в обязательном порядке делаются из металла, такой вариант будет долго служить и пригодится в разных случаях.
Пресс для отжима сока своими руками
Применяемые виды сварки
Электродуговая сварка
Огромный выбор типов электродов по их номинальным характеристикам и особенности работы ими обеспечивают неоспоримое преимущество перед остальными видами сварки и делают его предпочтительным для данной задачи. Самый лучший шов мы получим в случае применения электродов УОНИ. При работе данными электродами следует учесть их особенности и рекомендации:
- По возможности соединения должны быть выполнены внахлест.
- Для использования данного электрода нужен предварительный опыт работы с ним.
- Перед применением электрод подлежит прокалке в спец. печи на протяжении часа. Температура прокалки 250 С.
- Места соединений изделий должны быть очищены от загрязнений, ржавчины и подготовлены согласно ГОСТу 5264-80.
- Сварщик должен работать короткой дугой средней мощности, постоянным током и обратной полярностью.
- Металлоконструкция сваренная данным электродом не должна использоваться при температуре ниже — 40 С.
Газовая сварка
Данным типом при сварки швеллеров зачастую не пользуются из-за огромной области и температуры нагрева. Данные факторы являться источником образования внутренних напряжений в структуре металла и общих деформаций негативно влияющих на всю металлоконструкцию. Тем не менее газовую сварку часто используют для устранения изъянов готовых конструкций или порезки заготовок с последующим снятием кромок.
Как повысить прочность креплений станка
Многие начинающие мастера изготавливают самодельные приспособления без основания. Это листогибы, которые закрепляются на верстаке с помощью струбцин. При активной работе с таким механизмом крепления будут расшатываться. Мастеру нужно постоянно зажимать крепёжные элементы. Чтобы избавиться от этого недостатка, нужно сделать опорную балку, собрать основание из швеллеров, поставить раскосы из металлических уголков.
На основании нужно сделать рабочий стол. Для этого на конструкцию нужно закрепить лист металла со стопорами, которые будут ограничивать глубину закрепления заготовок.
Ручной рычажный трубогиб
Если вам нет надобности в таком сложном устройстве, а требуется только согнуть стальную круглую трубу небольшого размера, то можно сделать простой рычажный механизм. Он предназначен для гибки труб с тонкими стенами.
Смотрите видео инструкцию по изготовлению.
ТРУБОГИБ ДЛЯ КРУГЛОЙ ТРУБЫ
Мы тоже решили попробовать собрать этот трубогиб своими руками. Нам потребуется: вал с круглым профилем, прижимной ролик, металлический лист на 8 для станины, шпильки, гайки.
Кто-то может сделать данное устройство на глаз, но лучше подготовить чертёж трубогиба или найти подходящий вариант в интернете. Мы решили работать по чертежу.
Чертёж рычажного трубогибаЧертёж вилки рычага
Приступаем к изготовлению:
- Делаем заготовки для вилки. Размер вилки зависит от расстояния между колёсами, точнее от посадочного места трубы, оно должно равняться её диаметру плюс 1–2 мм. Вырезаем из металлического листа и шлифуем:
- станину и крышку для вала;
- упор для станины и небольшую подставку для крышки;
- две прямоугольных пластины, по краям которых делаем отверстия под шпильки.
Нарезаем заготовки
В крышке и станине проделываем отверстия для крепления вала.
Проделываем отверстияГотовые заготовки
Закрепляем упор в тисках, привариваем к его середине станину, а к верху подставку под крышку, шлифуем швы.
Свариваем детали
Продеваем шпильку в отверстие станицы, одеваем вал и сверху накрываем крышкой из металлического листа. С обеих сторон закручиваем гайки.
Устанавливаем вал
Крышку крепим к подставке болтами.
Крепим крышку
С обеих сторон на гайки прикручиваем две прямоугольные заготовки.
Монтируем прямоугольные заготовки
Сверху, между этими пластинами, размещаем ролик, который закрепляем при помощи шпильки и гаек.
Устанавливаем ролик
Две пластины вилки свариваем, разместив между ними заготовку из швеллера.
Свариваем вилку
Прикручиваем ручку из куска металлического профиля.
Подсоединяем ручку
Ну вот, рычажный трубогиб готов, оказалось, что сделать его самостоятельно под силу практически любому домашнему мастеру.
Правила изготовления
Если иметь под рукой необходимый инструментарий и заготовки, подобный станок просто сделать своими руками в домашних условиях. Самые простые конструкции изготавливаются без токарных работ. Для изготовления достаточно иметь алюминиевый двутавр. Также станок легко сделать из задвижки, рельсы и даже из швеллера. Арочный профилегиб может пригодиться даже в быту. На создание такого станка уйдет не более нескольких часов. После оборудование можно будет использовать каждый раз, когда появится необходимость починить конструкцию, где используется гнутый профиль. Самый простой пример – мягкая мебель.
Перед тем как приступать к изготовлению профилегиба, нужно понять, какая конструкция выглядит более привлекательной для пользователя. Обязательно выполняют небольшой чертеж. Готовый можно скачать в интернете. Чем проще выбранная конструкция, тем меньшим функционалом будет обладать станок. Если не планируется налаживать производство по изготовлению гнутого профиля, то такого приспособления будет вполне достаточно. Простота и отсутствие больших финансовых затрат при создании профилегиба позволят быстро приступить к работе.
Чтобы изготовить станок для работы с заготовками диаметром до 2 сантиметров, нет необходимости даже изучать видео с подробной инструкцией. С простым чертежом можно разобраться и самостоятельно. В конструкции такого профилегиба должно быть бетонное основание, несколько зафиксированных штырей. Именно между ними и будет происходить гибка металла.
При отсутствии такого участка его придется сначала создать. Во дворе нужно выбрать место, утрамбовать грунт на нем, а затем насыпать щебня. Перед тем как заливать бетон, щебень выравнивают. Цемент можно заказать, но в небольшом количестве его легче сделать самостоятельно. Делают раствор, используя такие материалы, как песок и цемент в пропорции 4 к 1.
На этапе подготовки в земле закрепляют несколько швеллеров. Вместо них подойдут трубы, диаметр которых должен быть 7 см. Они должны стоять по отношению к поверхности земли под углом в 90 градусов. Между швеллерами сохраняют расстояние 5 сантиметров. Бетонный раствор высыхает в течение нескольких дней.
Изделия из нержавеющей стали также можно сгибать при помощи такого нехитрого станка.Если предполагается делать изделия из заготовок с большим диаметром, чем 2 см, то такое оборудование не поможет. Конструкцию станка придется усовершенствовать
Бетонное основание также будет важной составляющей, но в качестве дополнения потребуется установить два прута. Они обязательно должны быть изготовлены из металла, при этом подбираются элементы с круглым сечением. Пруты играют роль осей, куда помещают ролики
Размер желоба обязан соответствовать тому диаметру, которым обладает сгибаемая труба. Чтобы использовать станок, потребуется установить заготовку между роликами, а один ее конец прочно закрепить. Второй привязывают к лебедке. Именно она должна дать требуемое усилие для сгиба трубы. Лебедка может быть как электрической, так и ручной
Пруты играют роль осей, куда помещают ролики. Размер желоба обязан соответствовать тому диаметру, которым обладает сгибаемая труба. Чтобы использовать станок, потребуется установить заготовку между роликами, а один ее конец прочно закрепить. Второй привязывают к лебедке. Именно она должна дать требуемое усилие для сгиба трубы. Лебедка может быть как электрической, так и ручной.
Как сделать столярные тиски самостоятельно
Для работы с металлическими деталями и заготовками используются слесарные тиски. Если же возникает потребность в обработке деревянных заготовок, то для таких целей слесарные тиски подходят меньше всего, так как они имеют некоторые недостатки. Фиксируемые детали могут деформироваться, поэтому для работы с деревообрабатывающими материалами рекомендуется пользоваться слесарными тисками. Покупать их специально для работы с деревом совсем не обязательно. Для таких случаев можно сделать столярные тиски своими руками. Инструкцию по изготовлению рассмотрим подробно.
Столярные тиски делаются из дерева, что является преимуществом при их изготовлении. При работе с деревом исключается необходимость применения сварочного аппарата. Для сверления отверстий используется дрель, а для отрезания деталей будущего инструмента, применяется ручная ножовка, лобзик или болгарка с диском по дереву.
Первым делом подготовим винт. Для этого отрезаем необходимую длину шпильки
На шпильку накручивается с одной стороны гайка
Используя водопроводный тройник, следует надеть его центральным отверстием на шпильку
Причем важно соблюдать, чтобы шпилька не выступала за грани двух параллельных отверстий тройника. Просверлить по центру тройника отверстие для установки болта под ключ на «10»
Сверлить необходимо тройник вместе со шпилькой
В полученное отверстие установить болт под ключ на «10». Таким способом изготавливается рукоятка для будущего инструмента
Далее переходим к изготовлению губок тисков. Для этого из доски, толщиной не менее 6 см, следует отрезать необходимую длину — 20-30 см
Две доски должны получиться одинакового по длине размера. Именно эти доски будут выступать в качестве фиксирующих губок
По центру обеих досок требуется просверлить центральные отверстия, через которые будет проходить шпилька
Просверливаем дополнительные отверстия по бокам обеих досок, которые нужны для направляющих
В одной доске на центральном отверстии нужно сделать паз для размещения гайки
Теперь завинчивается гайка и насаживается шайба на шпильку со стороны, где имеется сквозное отверстие
Устанавливаем шпильку в центральное отверстие доски с пазом
С другой стороны шпильки устанавливается шайба, и насаживается тройник, фиксирующийся болтом
Гайку с обратной стороны доски следует затянуть, утопив ее в пазу. Чтобы предотвратить в будущем вращение этой гайки, ее необходимо соединить со шпилькой. Для этого можно воспользоваться сваркой, но альтернативный способ — применить дрель. При помощи дрели сверлится отверстие в гайке, насаженной на шпильку, посредством которого обеспечивается жесткая фиксация двух деталей
Используя соответствующего диаметра болт, необходимо его забить в отверстие, сделанное в предыдущем пункте
Собираем конструкцию, получая в итоге подвижную губку тисков
Используем два металлических стержня, которые необходимо установить в боковые отверстия доски
К столу или верстаку присоединяется вторая доска, которая будет играть роль неподвижной губки столярных тисков. Для этого фиксируем доску струбциной к столу, после чего сверлим отверстия в конструкции стола
Приступаем к сборке конструкции. Для этого необходимо соединить две части, используя широкую гайку. После накручивания гайки на шпильку, необходимо обвести ее грани по периметру
По полученной разметке необходимо вырубить паз, воспользовавшись стамеской. Это необходимо для того, чтобы зафиксировать гайку в губках тисков
Утапливаем гайку в конструкцию губки
Получается практически готовые столярные тиски, на которых не хватает только рукоятки. Сделать ее можно из деревянной трубки соответствующего диаметра. После этого собираем инструмент
Чтобы направляющие свободно перемещались в неподвижной губке, следует изготовить стальные втулки, и установить их внутрь отверстий. Неподвижная губка фиксируется к поверхности стола посредством саморезов. Причем к этому делу нужно отнестись ответственно. Предварительно следует просверлить отверстия, а также сделать пазы для шляпок саморезов. Ведь поверхность доски является рабочей частью столярных тисков, поэтому любые выступы на ней и прочие дефекты негативно отразятся на качестве обрабатываемых заготовок.
Вот таким вот несложным способом можно изготовить в домашних условиях столярные тиски. Причем для их изготовления не понадобится покупать материалы, так как все самое необходимое наверняка имеется в распоряжении у каждого домашнего мастера.
Шаг 5: Финальные штрихи
Если гибочный станок правильно собран и отрегулирован, то он будет отлично справляться со своей задачей. Вам, конечно, придется немного потренироваться. Станок должен крепиться к какому-либо жесткому основанию: подойдет, например, крепкая скамейка.
Создавать давление домкратом нужно постепенно, начиная с небольшого усилия. Примерно, четверть оборота винта домкрата будет достаточно.
Из-за особенностей станка, при гибке, кольцо получается с прямыми концами. Это можно исправить, предварительно согнув концы. Можно прокатать кольцо с запасом, чтобы не загнутые концы пересекались, затем оба конца обрезаются в одном месте и свариваются между собой.
Изготавливаемые с помощью этого станка кольца получаются не идеально круглыми. Молоток поможет вам справиться с этой проблемой. Повторная прокатка кольца также может помочь исправить кривизну.
Рассказываю как сделать какую-либо вещь с пошаговыми фото и видео инструкциями.
Арматурные стержни различных профилей, диаметров и классов прочности – металлоизделия, необходимые при возведении монолитных и монолитно-сборных фундаментов. Арматура повышает устойчивость бетонных конструкций к растягивающим нагрузкам. Для усиления угловых бетонных элементов в соответствии с нормативной документацией необходимо применять только гнутые стержни.
Столярные
Столярные тиски Моксона придуманы для странствующих столяров и плотников. В Европе, США и Канаде это довольно-таки востребованная специальность: при тамошних ценах на пиломатериалы многие заказчики требуют, чтобы мастер работал при них по месту и малейшие обрезки, вплоть до опилок и стружки, оставлял хозяину. Пару тисков Моксона, что дает возможность работать с длинномерными материалами, можно возить в багажнике автомобиля, на велосипеде, скутере и носить с собой в сумке. Находку сразу оценили и любители – тиски Моксона позволяют быстро и обратимо превратить любой более-менее прочный стол в столярный верстак.
Внешний вид и способ крепления мобильных столярных тисков Моксона показаны слева и в центре на рис. Справа – устройство их любительского варианта для крепления к столу наглухо.
Внешний вид, крепление в рабочем положении и устройство столярных тисков Моксона
Тиски Моксона породили множество модификаций. Чертежи одной из них, очень простых и удобных столярных тисков всего из 3-х досок и пары струбцин, приведены на рис. далее. Правда, на самом деле понадобятся еще 2 короткие струбцины, для крепления тисков к столу. Лишние 4 струбцины (тоже не очень дешевое удовольствие в наше время) любителю могут оказаться накладны. Но для столяра – ИП-индивидуала, работающего по вызову такие тиски находка, их разобранными можно носить с собой в обычной вещевой сумке.
Чертежи самодельных простых столярных тисков
Последовательность изготовления своими руками пресса из домкрата
Перед тем как сделать своими руками пресс, необходимо подготовить сварочный аппарат, электроды, болгарку, дрель и сверла. Для финишной обработки металлических элементов конструкции от заусениц понадобится шлифовальная машинка. На первом этапе собирается рама для пресса. От ее прочности и надежности зависит качество и эффективность рабочего процесса. В станине будет расположен рабочий цилиндр (в виде домкрата) и обрабатываемая заготовка.
Для изготовления основания установки, рассчитанной на давление до 5 тонн, необходим швеллер типоразмера 8П.
Материал для станины, ее конструктивное исполнение и вариант сборки определяются исходя из воспринимаемого давления домкрата. Согласно чертежу пресса своими руками, основа устройства представлена П-образной прямоугольной рамой из швеллера или сварного стального уголка. Основное усилие будет сосредоточено в центральной части горизонтальных перекладин. Достичь максимально возможной устойчивости конструкции получится путем ее приваривания к основанию металлической пластины толщиной 08-1,2 см.
Для изготовления станины установки, рассчитанной на усилие до 5 тонн, понадобится швеллер типоразмера 8П и два горячекатаных уголка размером 50х50 мм, которые соединены цельным сварным швом либо связаны прутьями через каждые 25 см. Если инструмент будет воспринимать усилие до 10 тонн, для станины требуется швеллер 10П и спаренные уголки размером 63х7 мм. Для изготовления пресса с необходимым усилием сжатия 15 тонн и выше следует использовать швеллер 14П и спаренный уголок размером 75х8 мм.
Обратите внимание! Станина из вышеуказанного металлопроката будет иметь десятикратный запас прочности, что будет способствовать нормальной работе устройства – без разрушения рамы
Области применения
Опираясь на видео и фото инструкции, представленные пошаговые руководства, собрать конструкцию не сложно. Другой вопрос — зачем вообще вам может потребоваться подобный механизм.
Самодельные прессы могут оказаться полезными для:
- Приготовления соков из овощей, фруктов;
- Самостоятельного изготовления масла прессом;
- Запрессовки и выпрессовки подшипников, сайлентблоков;
- Формирования заготовок по матрицам;
- Выпрямления погнутых элементов;
- Сгибания прочных изделий из металла и пр.
Это многозадачное устройство, которое может оказаться полезным в быту.
Для некоторых операций домашнему мастеру может потребоваться пресс со значительным усилием сжатия, но приобретение оборудования такого класса будет совершенно неоправданным.
Делаем электромеханический трубогиб
Мы решили рассказать вам, как изготовить электромеханическую модель трубогиба. Такое оборудование способно справиться с любым объёмом работ, при этом не придётся прикладывать физическую силу.
Для изучения, представляем две версии инструкции как изготовить трубогибочный станок для круглых труб своими руками. Если после ознакомления текстового руководства возникнут вопросы, рекомендуем смотреть так же и видео материалы.
Как сделать трубогиб без сварки и токарки. Размеры, чертежи, нюансы The pipe bender
Устройство состоит из трёх рабочих органов — одного нажимного и двух опорных валиков, поэтому его ещё называют трёхваловым прокатным станком. Это один из самых сложных гибочных механизмов, который можно собрать своими руками, но мы решили начать именно с него. Если он у нас получится, то сделать более простые виды трубогибов нам не составит труда.
Итак, устройство мы будем делать из: 204-ых подшипников, стабилизатора поперечной устойчивости от автомобиля «Ваз», гаек, шпилек, обрезков труб (20 на 40 с толщиной 2 мм, 15 на 15 на 1,5 мм; 80 — 80 — 5 мм), металлического листа толщиной 3 мм.
Для сборки электрического гибочного станка мы воспользовались следующими чертежами.
Схема прокатного станкаСхема валаЧертёж вилкиОпоры для подшипниковЧертёж щекиСхема прижимного винта
Переходим к работе, пошаговая подробная инструкция выглядит следующим образом:
Подготавливаем станину — для этого понадобится два отрезка арматуры или профиля одного размера, на верхней стенке которых мы делаем по 4 отверстия для наших шпилек.
Детали для станины
Из металлического листа вырезаем две боковые стенки конструкции, проделываем в заготовках отверстия для их крепления к станине и установки вальцов, а также большое окошко для подвижного валика. Отверстия следует проделывать сразу в двух заготовках, чтобы они совпадали.
Вырезаем боковины
Берём стабилизатор поперечного сечения от жигулей, протачиваем его под головку 19, это позволит вращать вал шуроповёртом. На него будет одеваться подшипник с диаметром 20 мм.
Делаем проточки на стабилизатореОдеваем подшипник
Приступаем к изготовлению прижимного механизма из винта и куска швеллера, размер которого должен быть чуть меньше, чем расстояние между боковыми стенками конструкции, чтобы заготовка свободно ходила в нем. В швеллере проделываем отверстие, равное размеру винта, куда привариваем гайку. После чего вкручиваем винт и снизу фиксируем гайкой. Сверху в винте просверливаем отверстие, в него вставляем шпильку, которая будет служить рукояткой.
Привариваем гайкуВставляем винт
На вал одеваем два подшипника, фиксируем шайбами. Заготовка устанавливается на швеллер, в котором предварительно мы проделали отверстия для прижимного винта и боковые для крепления.
Собираем прижимной вал
Приступаем к сбору приспособления:
- вставляем шпильки в отверстия одной боковой стенки и фиксируем их гайками;
- средние шпильки — это наши входной и выходной ролики, они наборные, размер зависит от комплектации подшипниками под различные задачи;
Вставляем шпильки-ролики
на нижние шпильки одеваем шайбы, а затем устанавливаем две заготовки из профиля, которые будут служить основанием нашего станка;
Устанавливаем профильное основание
прижимной вал размещаем в середине конструкции, протолкнув винт в отверстие, он должен располагаться точно по центру между роликами, а между винтом и щеками устанавливаем прокладки из металлической пластины;
Размещаем прижимной вал
прижимной винт прикручиваем к швеллеру вала гайкой;
Прикручиваем прижимной винт
накрываем конструкцию второй боковиной и закручиваем гайки.
Одеваем стенку
Станок готов, остаётся на заточенную сторону вала одеть головку, а затем с помощью шуруповёрта привести в действие устройство. Это универсальный станок-кольцевик, используя его вы сможете изгибать не только круглые, но и профильные трубы, достаточно только поменять насадки на роликах.
Основное назначение профилегиба
Сейчас профилегиб широко используется при изготовлении алюминиевых, медных, стальных и ПВХ труб, а также для прокладывания систем водо- и газоснабжения, и при прокладке кабелей. Профилегиб применяется для гибки разных заготовок:
- цельных заготовок квадратного и прямоугольного сечения;
- балок;
- уголков;
- труб;
- двутавров;
- швеллеров;
- металлических прутков и т. д.
Когда металл нужно выгнуть под необходимым углом, то, как правило, применяют ручной самодельный профилегиб. Этот станок дает возможность выгибать своими руками металлический профиль с помощью холодного проката без нагревания изделия. При этом профилегибочные станки дают возможность создавать изделия с симметричными или несимметричными контурами знакопеременной или одинарной кривизны.
Основным преимуществом профилегибов является изгиб за один прокат. При этом можно обрабатывать стальные профили в вертикальной и горизонтальной плоскости, делать из заготовок окружности или спирали. Станки дают возможность выполнять замкнутые и открытые контуры, а также контуры, имеющие плавный переход.
Сейчас профилегибы пользуются огромной популярностью во многих строительных сферах: морской, энергетической, спортивной, электрической, автомобильной, мебельной, нефтехимической промышленности. Процесс изгибания проходит по радиусу и имеет два основных этапа: изделие прокатывается между валиками с одновременным прижимом боковых валиков или верхнего ролика.
Конструкция профилегибочного станка
обрабатывать любые изделия
Выделяют четыре вида систем профилегибов. Конструкция с верхним подвижным валиком является самым простым видом в плане работы механики, в этом случае перемещается только верхний валик. Устройство этого механизма может отличаться:
- гидравлический ролик – управляется гидросистемой непосредственно верхнего ролика;
- верхний ручной ролик – управляется с помощью редуктора.
Это положение роликов позволяет рассчитать возможный радиус для изгибания деталей с минимальными погрешностями на упружнения металла или небольшим градиентом во время деформации профиля. Эти чертежи профилегиба своими руками являются сегодня самыми популярными.
Станки с левым роликом более удобней для завивки спиралей, они дают возможность производить аналогичные функции, как и вышеописанные профилегибы, с отличием только в механизме привода бокового валика. Модели оборудованы ЧПУ, то есть, контролируют градиент изгибания: выгибают изделие с исходного чертежа, либо управляются с предустановленными функциями.
Станки с нижними роликами применяются, в первую очередь, для гибки больших профилей, так как усилие гибки равномерно распределяется на два нижних вала, а механизм привода полностью гидравлический. У каждого ролика находится свой контроллер месторасположения, для сохранения возможности изготовления спиралей. Этот механизм считается самым используемым, так как валики вращаются по сегменту окружности.
Станки, где все ролики подвижные, имеют наиболее сложный механизм, и включают в себя все преимущества вышеописанных станков. Эти профилегибы могут выполнять работу, которую делают по отдельности предыдущие устройства.
Принцип работы профилегибочного станка
механических и электрических элементов
Перед первым запуском ролики чистятся от консервирующей смазки при помощи сухой ткани, а также проверяется соответствие напряжения сети с необходимым для профилегиба. Затем аппарат обкатывается в холостом режиме в течение получаса. Если появляются отклонения от нормального режима, то профилегиб останавливают и убирают неисправности.
Заготовки чистят от смазки и проверяют упругость металла, которая обязана быть одинаковой по всей длине изделия. Затем валики настраивают для обработки детали в следующей последовательности:
- гайки крепления прижимных и опорных валиков откручивают ключом;
- устанавливают ролики на валы со шпонкой и крепят с помощью гаек;
- при помощи рукоятки поднимают вверх прижимной валик;
- деталь зажимают между роликами;
- после под высоким давлением между валами проходит прокатка.
Уровень кривизны задается при помощи опускания и поднятия верхнего вала. В ручном станке механизм работает с помощью рычага, который перемещает оператор. Электрический профилегиб работает за счет электродвигателя.
Механика материалов: изгиб – нормальное напряжение » Механика гибких конструкций
исследования
человек
курсы
блог
Моменты площади
Чтобы рассчитать напряжение (и, следовательно, деформацию), вызванное изгибом, нам нужно понять, где находится нейтральная ось балки, и как рассчитать второй момент площади для данного поперечного сечения.
Начнем с того, что представим себе произвольное поперечное сечение — что-то не круглое, не прямоугольное и т. д.
На изображении выше произвольная форма имеет площадь, обозначенную A . Мы можем посмотреть на небольшую дифференциальную область дА , которая существует на расстоянии x и y от начала координат. Мы можем посмотреть на первый момент площади в каждом направлении по следующим формулам:
Первый момент площади — это интеграл длины по площади — это означает, что он будет иметь единицы длины в кубе [L 3 ]. Это важно, потому что помогает нам найти центр тяжести объекта. Центроид определяется как “среднее x (или y ) позиции области”. Математически это утверждение выглядит так:
Крайняя правая часть приведенных выше уравнений будет очень полезна в этом курсе — она позволяет нам разбить сложную фигуру на простые формы с известными площадями и известным расположением центроидов. В большинстве инженерных сооружений есть хотя бы одна ось симметрии — и это позволяет значительно упростить нахождение центроида. Центроид должен располагаться на оси симметрии . Например:
Для поперечного сечения слева мы знаем, что центроид должен лежать на оси симметрии, поэтому нам нужно найти только центроид вдоль оси y . Поперечное сечение справа еще проще — поскольку центроид должен совпадать с осями симметрии, он должен быть в центре объекта.
Теперь, когда мы знаем, как найти центр тяжести, мы можем обратить внимание на второй момент площади. Как вы, возможно, помните из предыдущего раздела о кручении, это определяется как:
И, наконец, иногда нам нужно будет определить второй момент площади относительно произвольной оси x или y , которая не соответствует центроиду. В этом случае мы можем использовать теорему о параллельных осях для его вычисления. В этом случае мы используем второй момент площади относительно центроида плюс термин, который включает расстояния между двумя осями.
Это уравнение называется теоремой о параллельных осях . Это будет очень полезно на протяжении всего курса. Как описано во вступительном видео к этому разделу, вычисление второго момента площади простой формы может быть простым. Для более сложных форм нам потребуется вычислить I путем вычисления отдельных I для каждой простой формы и объединения их вместе с использованием теоремы о параллельных осях.
Поперечная нагрузка относится к силам, которые перпендикулярны длинной оси конструкции. Эти поперечных нагрузок вызовут изгибающий момент M , который вызывает нормальное напряжение , и поперечную силу V , которая вызывает касательное напряжение . Эти силы могут и будут варьироваться по длине балки, и мы будем использовать диаграммы сдвига и момента (диаграмма VM) для извлечения наиболее подходящих значений. Построение этих диаграмм должно быть вам знакомо по статике , но мы рассмотрим их здесь. При исследовании балки с поперечной нагрузкой необходимо учитывать два важных момента:
- Как балка нагружена?
- точечная нагрузка, распределенная нагрузка (равномерная или переменная), комбинация нагрузок…
- Как балка поддерживается?
- свободно опертый, консольный, нависающий, статически неопределимый…
Знание нагрузок и опор позволит вам начертить качественную диаграмму V-M, а затем статический анализ свободного тела поможет вам определить количественное описание кривых. Начнем с того, что вспомним наши соглашений о знаках .
Эти соглашения о знаках должны быть знакомы. Если сдвиг вызывает вращение против часовой стрелки, он положительный. Если момент изгибает луч таким образом, что луч изгибается в «улыбку» или U-образную форму, он положительный. Лучший способ вспомнить эти диаграммы — это проработать пример. Начните с этой консольной балки — отсюда вы можете переходить к более сложным нагрузкам.
Нормальное напряжение при изгибе Во многом изгиб и кручение очень похожи. Изгиб возникает из-за приложенной пары или изгибающего момента M . Как и при кручении, при чистом изгибе в материале есть ось, на которой напряжение и деформация равны нулю. Это называется нейтральной осью . И, как и при кручении, напряжение уже не одинаково по сечению конструкции — оно меняется. Давайте начнем с того, что рассмотрим момент о z – ось изгибает конструкцию. В данном случае мы не будем ограничиваться круглыми сечениями – на рисунке ниже рассмотрим призматическое сечение.
Прежде чем мы углубимся в математику изгиба, давайте попробуем понять его концептуально. Возможно, лучший способ увидеть, что происходит, — наложить изогнутую балку поверх оригинальной прямой балки.
Теперь вы можете заметить, что нижняя поверхность луча стала длиннее, а верхняя поверхность луча стала короче. Также по центру луча длина вообще не изменилась – соответствует нейтральной оси. Повторяя это язык этого класса, мы можем сказать, что нижняя поверхность находится под напряжением, а верхняя поверхность находится под сжатием. Кое-что, что является немного более тонким, но все еще можно наблюдать из наложенного выше изображения, заключается в том, что смещение луча изменяется линейно сверху вниз, проходя через ноль на нейтральной оси. Помните, это именно то, что мы видели и при кручении — напряжение линейно менялось от центра к центру. Мы можем посмотреть на это распределение напряжений по поперечному сечению балки немного более явно:
Теперь мы можем найти математическую связь между приложенным моментом и напряжением внутри балки. Мы уже упоминали, что балка деформируется линейно от одного края к другому — это означает, что деформация в направлении x увеличивается линейно с расстоянием вдоль оси y- (или по толщине балки). Таким образом, деформация будет максимальной при растяжении при y = -c (поскольку y=0 находится на нейтральной оси, в данном случае в центре балки), и будет максимальной при сжатии при y=c . Мы можем записать это математически следующим образом:
Теперь это говорит нам кое-что о деформации, что мы можем сказать о максимальных значениях напряжения? Начнем с умножения обеих частей уравнения на E , модуль упругости Юнга. Теперь наше уравнение выглядит так:
Используя закон Гука, мы можем связать эти величины с фигурными скобками под ними с напряжением в направлении x и максимальным напряжением. Что дает нам это уравнение для напряжения в направлении x-:
Наш последний шаг в этом процессе — понять, как изгибающий момент связан с напряжением. Для этого вспомним, что момент — это произведение силы на расстояние. Если мы можем представить себе, что смотрим только на очень маленький элемент в луче, дифференциальный элемент, то мы можем записать это математически как:
Поскольку в нашем уравнении есть дифференциалы, мы можем определить момент M , действующий по площади поперечного сечения балки, путем интегрирования обеих частей уравнения. И если мы вспомним наше определение напряжения как силы на единицу площади, мы можем написать:
Последний член в последнем уравнении — интеграл по y в квадрате — представляет второй момент площади относительно оси z (из-за того, как мы определили наши координаты). В декартовых координатах этот второй момент площади обозначается I (в цилиндрических координатах, помните, обозначался J ). Теперь мы можем, наконец, записать наше уравнение для максимального напряжения и, следовательно, напряжения в любой точке вдоль оси y , как:
Важно отметить, что нижние индексы в этом уравнении и направление вдоль поперечного сечения (здесь оно измеряется вдоль y ) будут меняться в зависимости от характера проблемы, то есть направления момента — по какой оси находится луч. сгибаясь? Мы основывали наши обозначения на изображении изогнутой балки на первом изображении этого урока.
Помните, в начале раздела я упомянул, что изгиб и кручение на самом деле очень похожи? На самом деле мы очень ясно видим это в последнем уравнении. В обоих случаях напряжение (нормальное для изгиба и сдвиговое для кручения) равно пар/момент ( M для изгиба и T для кручения), умноженных на положение вдоль поперечного сечения. , , потому что напряжение неравномерно по поперечному сечению (с декартовыми координатами для изгиба и цилиндрическими координатами для кручения), все делится на второй момент площади поперечного сечения.
На этом уроке мы узнали о моментах площади и диаграммах момента сдвига . Из первого момента площади поперечного сечения мы можем вычислить центроид . Мы узнали, как вычислить секундный момент площади в декартовых и полярных координатах, и мы узнали, как теорема о параллельных осях позволяет нам вычислить второй момент площади относительно центра тяжести объекта — это полезно для разбиения сложного поперечного сечения на несколько простых фигур и объединение их вместе. Мы пересмотрели концепцию 9Диаграммы сдвига и момента 0015 из статики. Эти диаграммы будут необходимы для определения максимальной силы сдвига и изгибающего момента вдоль сложно нагруженной балки, что, в свою очередь, потребуется для расчета напряжений и прогнозирования разрушения. Наконец, мы узнали о нормальном напряжении от изгиба балки. И напряжение, и деформация изменяются по поперечному сечению балки, при этом одна поверхность растягивается, а другая сжимается. Плоскость, проходящая через центр тяжести, образует нейтральную ось — вдоль нейтральной оси нет напряжений или деформаций. Напряжение является функцией приложенного момента и второго момента площади относительно оси, вокруг которой находится момент.
Этот материал основан на работе, поддержанной Национальным научным фондом в рамках гранта № 1454153. Любые мнения, выводы, заключения или рекомендации, выраженные в этом материале, принадлежат авторам и не обязательно отражают точку зрения Национальный научный фонд.
ЧЕРТЕЖИ СТАЛЬНЫХ КОНСТРУКЦИЙ – АРХИТЕКТУРНЫЕ ТЕХНОЛОГИИ
КОНСТРУКЦИОННЫЕ ФОРМЫ И ЭЛЕМЕНТЫ
Различные конструкционные элементы используются для изготовления самых разных форм и размеров поперечного сечения. Многие формы показаны на рис. 7-1. Эти символы составлены из части 4 военного стандарта 18B (MIL-STD-18B) и информации Американского общества инженеров-строителей (ASCE). В следующих параграфах объясняются общие конструктивные формы, используемые в строительных материалах, и общие конструктивные элементы, изготовленные в этих формах.
Формы
Три наиболее распространенных типа элементов конструкции: W-образная (широкая полка), S-образная (двутавровая балка американского стандарта) и C-образная (американский стандартный швеллер). Эти три типа идентифицируются по номинальной глубине в дюймах вдоль стенки и весу на фут длины в фунтах. Например, W 12 x 27 указывает на W-образную форму (широкий фланец) со стенкой глубиной 12 дюймов и весом 27 фунтов на погонный фут.
Виды поперечного сечения W-, S- и C-образных форм показаны на Рисунке 7-2. Отличие W-образной формы от S-образной заключается в конструкции внутренних поверхностей фланца. W-образная форма имеет параллельные внутренние и внешние поверхности фланцев с постоянной толщиной, а S-образная форма имеет наклон приблизительно 17 градусов на внутренних поверхностях фланцев. С-образная форма похожа на S-образную тем, что ее внутренняя поверхность фланца также наклонена примерно на 17 градусов.
W-образная форма
W-образная форма представляет собой конструктивный элемент, поперечное сечение которого образует букву H, и является наиболее широко используемым конструктивным элементом. Он устроен так, что его полки обеспечивают прочность в горизонтальной плоскости, а стенка придает прочность в вертикальной плоскости. W-образные формы используются в качестве балок, колонн и элементов ферм, а также в других несущих конструкциях.
Несущая свая
Несущая свая (HP-форма) почти идентична W-образной. Единственное отличие состоит в том, что толщина полки и толщина стенки несущей сваи равны, тогда как W-образная форма имеет разную толщину стенки и полки.
S-образная форма
S-образная форма (двутавровая балка американского стандарта) отличается тем, что ее поперечное сечение имеет форму буквы I. S-образные формы используются реже, чем W-образные, поскольку S-образные формы обладают меньшей прочностью и менее адаптируемы, чем W-образные.
С-образная форма
С-образная форма (швеллер американского стандарта) имеет поперечное сечение, несколько похожее на букву С. Это особенно полезно в местах, где требуется одна плоская поверхность без выступающих фланцев с одной стороны. С-образная форма не очень эффективна для балки или колонны, когда используется отдельно. Однако эффективные сборные элементы могут быть изготовлены из швеллеров, собранных вместе с другими структурными формами и соединенных заклепками или сваркой.
Каналы
Поперечное сечение канала похоже на квадратную букву C. Каналы идентифицируются по их номинальной глубине и весу на фут. Например, обозначение канала C9 x 13,4 по американскому стандарту на рис. 7-1 показывает номинальную глубину 9 дюймов и вес 13,4 фунта на погонный фут. Швеллеры в основном используются в местах, где одна плоская поверхность без выступающих фланцев на стороне требуется. Однако канал не очень эффективен в качестве луча или столбца, когда используется отдельно. Но каналы могут быть собраны вместе с другими конструктивными формами и соединены заклепками или сваркой, чтобы сформировать эффективные составные элементы.
Уголки
Угол (рис. 7-3) представляет собой конструктивную форму, поперечное сечение которой напоминает букву L. Обычно используются два типа: равнополочный угол и неравнополочный угол. Угол определяется размером и толщиной его ножек, например, угол 6 дюймов на 4 дюйма на 1/2 дюйма. Размер ног должен быть получен путем измерения по внешней стороне задней части ног. Когда угол имеет неравные стороны, сначала указывается размер более широкой стороны, как на Рисунке 7-3 — Углы. пример только что привел. Третье измерение относится к толщине ножек, которые всегда имеют одинаковую толщину. Уголки могут использоваться в комбинации из двух или четырех элементов для формирования основных элементов. Один угол также может использоваться для соединения основных частей вместе.
Пластины
Как правило, основное, что нужно помнить о пластинах, это то, что они имеют ширину более 8 дюймов и толщину 1/4 дюйма или более. Пластины обычно используются в качестве соединений между другими конструктивными элементами или в качестве составных частей сборных конструктивных элементов. Пластины, нарезанные по определенным размерам, могут иметь ширину от 8 дюймов до 120 дюймов и более и различную толщину. Края этих листов могут быть обрезаны ножницами (листы со сдвигом) или прокатаны под прямым углом (листы универсального проката).
Часто листы обозначаются по их толщине и ширине в дюймах, например, лист 1/2 дюйма x 24 дюйма. Длина во всех случаях указывается в дюймах. Обратите внимание на рис. 7-4, что 1 кубический фут стали весит 490 фунтов. Этот вес, разделенный на 12, равняется 40,8, что является весом (в фунтах) стальной пластины площадью 1 квадратный фут и толщиной 1 дюйм. Дробная часть обычно отбрасывается, а 1-дюймовая тарелка называется 40-фунтовой тарелкой. На практике вы можете услышать, что плита упоминается по ее приблизительному весу на квадратный фут для определенной толщины. Примером может служить 20-фунтовая тарелка, что означает 1/2-дюймовую тарелку.
Обозначения, обычно используемые для плоского проката, были установлены Американским институтом чугуна и стали (AISI). Плоская сталь обозначается как пруток, полоса, лист или плита в зависимости от толщины материала, ширины материала и (в некоторой степени) процесса прокатки, которому он подвергался.
Тройники
Строительный тройник изготавливается путем разрезания стандартной двутавровой или двутавровой балки по центру ее стенки с образованием двух Т-образных профилей из каждой балки. При определении размеров перед символом структурного тройника ставятся буквы ST. Например, обозначение ST 5 WF 10,5 означает, что тройник имеет номинальную глубину 5 дюймов, широкий фланец и весит 10,5 фунтов на погонный фут. Катаный тройник представляет собой изготовленную форму. В обозначении размеров перед символом катаного тройника ставится буква Т. Размер Т 4 х 3 х 9.2 означает, что прокатанный Т имеет 4-дюймовый фланец, номинальную глубину 3 дюйма и вес 9,2 фунта на погонный фут.
Zee
Эти формы различаются по глубине, ширине полки и весу на погонный фут. Следовательно, Z 6 x 3 1/2 x 15,7 означает, что зи имеет глубину 6 дюймов, фланец 3 1/2 дюйма и весит 15,7 фунтов на погонный фут.
Плоский стержень
Структурная форма, называемая стержнем, имеет ширину 8 дюймов или меньше и толщину более 3/16 дюйма. Кромки прутков обычно завальцованы под прямым углом, как универсальные прокатные плиты. Размеры выражаются так же, как и для пластин, например, бар 6 дюймов на 1/2 дюйма. Стержни доступны в различных формах поперечного сечения – круглые, шестиугольные, восьмиугольные, квадратные и плоские. Четыре различных формы показаны на рис. 7-5. Как квадраты, так и круглые обычно используются в качестве элементов жесткости легких конструкций. Их размеры в дюймах относятся к стороне квадрата или диаметру круга.
Колонны
Как правило, для колонн используются элементы с широкими полками, как можно более квадратные в поперечном сечении, но иногда используются трубы большого диаметра, даже если трубные колонны могут создавать трудности с соединением при креплении других элементов (рис. 7). -6). Колонны также могут быть изготовлены путем сварки или соединения болтами ряда других профилей проката, обычно уголков и пластин (рис. 7-7).
Балки
Балки — это основные горизонтальные элементы конструкции стального каркаса. Они соединяются от колонны к колонне и обычно соединяются сверху колонн с помощью накладок (подшипники) (рис. 7-8). Альтернативным методом является сидячее соединение (рис. 7-9). Балка крепится к полке колонны с помощью уголков, при этом одна нога проходит вдоль полки балки, а другая напротив колонны. Функция балок заключается в поддержке балок межэтажного перекрытия.
Элементы
Основными частями конструкции являются несущие элементы. Они поддерживают и передают нагрузки на конструкцию, оставаясь при этом равными друг другу. Места, где элементы соединяются с другими элементами, называются соединениями. Общая сумма нагрузок, воспринимаемых элементами конструкции в конкретный момент времени, равна общей статической нагрузке плюс общая временная нагрузка.
Общая статическая нагрузка — это общий вес конструкции, который постепенно увеличивается по мере подъема конструкции и остается постоянным после ее завершения. Общая динамическая нагрузка — это общий вес подвижных объектов, таких как люди, мебель и движение по мосту, которые конструкция поддерживает в определенный момент.
Базовая система – стойка и балка (каркасная рама) и пространственные рамы.
2. Преимущества конструкции со стальным каркасом:
1. Можно строить очень высокие и широкие (самые высокие здания в мире)
2. Легкий и прочный (намного легче и прочнее, чем бетон)
3. Сборный – каркас быстро собирается
4. Точный и предсказуемость (отличный контроль качества)
3. Недостатки конструкции со стальным каркасом:
1. Сталь — дорогой материал (гораздо дороже кирпичной кладки или бетона)
2. Каркасы неустойчивы
3. Требуется противопожарная защита
4. Требуется отдельная “обшивка” (стены и полы)
4. Методы стабилизации зданий со стальным каркасом:
1. Жесткое ядро - обычно достигается за счет внутренней кладки (или бетона) лестничных башен и лифтовых шахт, создающих вертикальное жесткое ядро, противодействующее деформациям и кручению здания под действием внешних боковых сил.
2. Диагональные распорки — добавление диагональных распорок «X» или «K», которые противостоят боковым нагрузкам. Проблемы – могут мешать внешние окна.
3. Устойчивые к моменту соединения балки с колонной. Обычно выполняются путем изготовления дополнительных соединительных уголков, сварных швов и болтов, которые значительно повышают жесткость соединения. Проблемы – крайне трудоемкие и дорогие.
4. Стены жесткости – Наружные (или внутренние) стены, построенные из кирпичной кладки или бетона, которые действуют как вертикальная консольная балка, воспринимающая боковые нагрузки. Проблемы – могут мешать наружные окна, трудоемкий, тяжелый.
5. Основные профили из конструкционной стали (горячекатаные):
Как правило, конструкционная сталь изготавливается в процессе горячей прокатки под несколькими обозначениями ASTM, наиболее распространенным из которых является A36. Эта сталь имеет минимальный предел текучести 36 тысяч фунтов на квадратный дюйм и минимальное предельное (разрушающее) напряжение 58 тысяч фунтов на квадратный дюйм. Доступны многие другие марки, с пределом текучести A572 – 50 KSI в качестве выбора для более высокой прочности. Новая марка стали A992 недавно заменила A572 и A36 (для профилей W) в качестве стандартной марки стали. Как и A572, он также имеет предел текучести 50 KSI.
1. Широкая полка — типичная «двутавровая балка», используемая в строительстве. Пример — W18x35, где «W» = широкая полка, 18 = номинальная глубина элемента в дюймах и 35 = вес балки в фунтах на погонный фут. Используется для балок, колонн, свай, распорок и других тяжелых применений.
2. Углы – равнополочные или неравнополочные. Пример — L4 x 3 x 1/4, где 4 и 3 — фактические размеры полки в дюймах, а 1/4 = толщина уголка в дюймах. Используется для перемычек, раскосов, составных балок и колонн, вторичного каркаса и других легких применений.
3. Стальные швеллеры – эти элементы в форме буквы «С» используются для балок, сборных колонн, распорок, вторичного каркаса и других применений с легкими и средними нагрузками. Примером канала является C10x30, где «C» обозначает канал, 10 — фактическая высота канала в дюймах, а 30 — фунты на погонный фут.
4. Стальная труба. Круглая труба чаще всего используется для колонн. Выпускается в трех категориях в зависимости от диаметра и толщины стенки: «стандартный вес», «сверхпрочный» и «двойной сверхпрочный». Двойная сверхпрочная труба является самой прочной, потому что у нее самые толстые стенки. Пример — труба стандартного веса диаметром 4 дюйма
5. Трубчатая сталь – эти квадратные или прямоугольные сечения чаще всего используются в качестве колонн, но также могут использоваться в качестве балок, распорок или других применений. Типичным примером является TS6x4x1/4, где TS = трубная сталь, 6 и 4 — фактическая ширина и глубина в дюймах, а 1/4 — толщина стенки в дюймах.
С 2003 года трубная сталь теперь называется Американским институтом стальных конструкций «полым конструкционным сечением» (HSS). Типичное обозначение HSS6x4x1/4.
6. Пластины – плоские куски стали, нарезанные по размеру. Обычно в диапазоне от 1/8 дюйма до 6 дюймов. Используется в качестве опорных плит колонн, составных балок и колонн (т. е. пластинчатых ферм), соединительных деталей (т. е. косынок, сварных пластин и т. д.) и любого другого применения, где требуются детали определенного размера. Пример – PL 6x4x3/8, где 6 и 4 – длина и ширина листа в дюймах, а 3/8 – толщина листа в дюймах.
7. Вырезанные секции. Обычно это секции с широкими полками, которые разрезаются пополам, образуя Т-образную секцию. Используется для перемычек, балок, раскосов и колонн. Пример – WT7x19 представляет собой секцию, вырезанную из широкой полки W14x38.
6. Заклепки – Обычно больше не используются по таким причинам, как низкая прочность, безопасность и плохой контроль качества.
1. Болты – бывают двух видов – из углеродистой стали и высокопрочные. Болты из углеродистой стали получают свою прочность за счет сдвига (или растяжения) только вдоль стержня болта. Наиболее распространенное обозначение ASTM для болтов из углеродистой стали, используемых в конструкциях, – A307. Эти болты не могут нести ту же нагрузку, что и высокопрочные болты, и используются для легких условий эксплуатации, таких как анкерные болты. Высокопрочные болты получают свою прочность не только за счет сдвига и растяжения вдоль вала, но и за счет сил трения, возникающих при натяжении гайки до заданного уровня. Самый распространенный ASTM
2. Сварка. Сварка осуществляется путем механического соединения стали путем нагревания электродов в расплавленном состоянии, которое образует одно целое из двух. Создает чрезвычайно жесткие соединения. Наиболее распространенным типом сварки, используемым для строительных конструкций, является «угловой» шов, который соединяет детали под прямым углом. Обычно соединительные уголки к балкам и колоннам приваривают в цеху, а затем скрепляют их болтами в полевых условиях на стройплощадке.
7. Стальной настил: стальной настил
относится к одному из нескольких основных типов. Весь настил холоднокатаный и продается толщиной от 16 (самая тяжелая) до 28 (самая легкая).
1. Настил крыши – обычно доступен высотой 1½ дюйма и 3 дюйма и толщиной от 16 до 22 калибров. Настил крыши характеризуется тем, что верхняя канавка намного шире, чем нижняя, что обеспечивает максимально возможную плоскую поверхность для несущих ненесущих компонентов здания, таких как жесткая изоляция. Ширина нижней канавки варьируется, и доступны различные профили, такие как «узкое ребро», «промежуточное ребро» и «широкое ребро».
2. Настил пола (некомпозитный) — используемый для полов, этот тип настила имеет верхнюю и нижнюю канавки примерно одинаковой длины и действует как форма для бетона. Типичные доступные высоты: 9/16″, 1″, 1 5/16″, 1½”, 2″ и 3″. Бетон, помещенный в настил, обычно армируется сварной проволочной тканью.
3. Настил пола (композитный) — Подобно настилу пола из некомпозитного материала, этот настил обычно имеет дополнительные перфорации в настиле для «сцепления» с бетоном. Эта палуба действует как часть структурной системы со стальными балками. Настил помещается поверх стальной балки, и стальные «шпильки» привариваются через настил и к верхней полке балки. После того, как бетон уложен и отвержден, он захватывает срезные шпильки и взаимодействует со стальной балкой, значительно увеличивая несущую способность одной только стальной балки.
8. Стальные балки (стержневые балки):
Эти легкие «фермы» с открытой стенкой производятся различными компаниями (такими как Vulcraft), чтобы обеспечить максимально легкую альтернативу балкам. Они используются чаще всего для сборки крыши. Типичная стальная балка показана ниже:
Элементы легкого стального каркаса используются для каркаса стен, перекрытий, балок и перемычек — всего, для чего используются обычные деревянные каркасные элементы. Строительные нормы и правила большинства штатов предписывают использовать негорючие конструкции для объектов определенного типа, а элементы деревянного каркаса использовать НЕЛЬЗЯ. Эти легкие элементы представляют собой холоднокатаные (аналогичные стальному настилу) изделия из листового металла, которые доступны от различных производителей в виде элементов «С» в калибрах, обычно от 12 до 26 калибров.

10. Противопожарная защита:
Все стальные конструкции должны быть защищены от огня в соответствии с государственными и местными строительными нормами. Хотя для фактического плавления стали требуется очень значительное количество тепла, она теряет большую часть своей прочности при температурах выше 7000 F. Обычно существуют две основные категории огнезащиты – термическая и абсорбционная.
1. Тепловая противопожарная защита – замедляет прохождение тепла через сталь. Используемые методы включают изоляцию и вспучивающуюся краску.
2. Абсорбционная противопожарная защита – поглощает тепло. Используемые методы включают покрытие стальных элементов бетоном, гипсом (напылением) и сложные методы, такие как заполненные жидкостью камеры (обычно оборачиваются вокруг колонн).
СВАРНЫЕ И КЛЕПНЫЕ СТАЛЬНЫЕ КОНСТРУКЦИИ
В следующих параграфах обсуждаются сварные и клепаные стальные конструкции и приводятся примеры обоих методов изготовления ферм.

Сварные стальные конструкции
Как правило, сварные соединения имеют рамку или посадку точно так же, как и клепаные соединения, которые мы обсудим позже. Однако сварные соединения более гибкие. Отверстия, используемые для соединения деталей болтами или штифтами во время сварки, обычно просверливаются в производственной мастерской. Балки обычно не привариваются непосредственно к колоннам. Процедура обеспечивает жесткое соединение и приводит к сильному изгибу, который нагружает балку, чему должны сопротивляться как балка, так и сварной шов.
Обозначение сварки
Чертежи содержат специальные обозначения для указания места сварки, типа соединения, а также размера и количества металла сварного шва, который должен быть наплавлен в соединении. Американское общество сварщиков (AWS) стандартизировало их. Сварщик увидит их всякий раз, когда он или она выполняет сварочное задание из набора распечаток, поэтому вам необходимо ознакомиться со всеми элементами стандартного символа сварки, а также с расположением и значением основных символов сварки.
Стандартный символ сварки (рис. 7-15): контрольная линия + стрелка + хвост.
Линия отсчета является основой. На него наносятся символы сварки, размеры и другие данные. Стрелка соединяет контрольную линию с соединением или областью, подлежащей сварке. Направление стрелки не имеет отношения к значению опорной линии. Конец символа сварки используется только при необходимости для включения информации о процессе, спецификации или другой справочной информации.
Обозначения типов сварных швов
Обозначения сварных швов относятся к обозначениям для определенного типа сварного шва, такого как угловой шов, паз, стык, наплавка, пробка или паз.
Символ сварки (Рисунок 7-16) является лишь частью информации, необходимой для обозначения сварки. При использовании для распространения информации термин «символ сварки» относится к общему символу, который включает в себя все символы сварки, необходимые для указания требуемых сварных швов.
Наложение символа сварного шва на контрольную линию показано на рис. 7-17. Обратите внимание, что вертикальная сторона символа сварки показана слева от наклонной или изогнутой стороны символа. Независимо от того, относится ли символ к угловому, фасочному, J-образному или развальцовочному шву, вертикальная сторона всегда рисуется влево. Значение положения символа сварки на опорной линии показано на рис. 7-18.
Когда необходимо скосить только одну кромку соединения, необходимо показать, какой элемент должен быть скошен (Рисунок 7-19). Когда указан такой стык, стрелка символа сварки указывает с определенным разрывом на деталь, подлежащую скосу. Другие символы сварки могут быть добавлены к символу сварки по мере необходимости для передачи всей информации, необходимой для сварки.
Однако, независимо от направления стрелки, вся информация, нанесенная на опорную линию символа сварки, читается слева направо. Список символов сварки показан на рис. 7-20.

Дополнительный
Помимо основных символов сварки, символ сварки может включать дополнительные символы (Рисунок 7-22). Контурные символы показывают, как должно быть сформировано лицо; символы отделки указывают метод, используемый для формирования контура.
Символ отделки (если он используется) показывает метод отделки, C обозначает скалывание, M означает механическую обработку, а G обозначает шлифовку, а не степень отделки. Как символы контура и отделки применяются к символу сварки, показано на Рис. 7-23. Этот символ указывает на то, что сварной шов должен быть зачищен заподлицо. Также обратите внимание, что символы размещаются с той же стороны от базовой линии, что и символ сварного шва.
Другим дополнительным символом является символ сварки по всему периметру. Когда этот символ помещается на символ сварки, сварные швы должны продолжаться по всему стыку.
Еще один символ на Рисунке 7-22 — это символ монтажной сварки, черный флажок, указывающий на конец символа сварки. Для сварных швов, которые не могут быть выполнены в цеху из-за размера, транспортировки, конструктивных особенностей или по другим причинам, этот символ указывает сварщику выполнить сварку в полевых условиях, которая может выполняться «на месте» или на месте.
Сварные стальные фермы
Чертеж типичной сварной стальной фермы показан на рис. 7-24. Когда вы интерпретируете символы сварки, вы увидите, что большинство из них показывают, что конструкционные углы будут сварены угловым швом. Скругление будет иметь радиус 1/4 дюйма (толщину) с обеих сторон и будет проходить вдоль угла на протяжении 4 дюймов.
Сварные стальные фермы
Чертеж типичной сварной стальной фермы показан на рис. 7-24. Когда вы интерпретируете символы сварки, вы увидите, что большинство из них показывают, что конструкционные углы будут сварены угловым швом. Скругление будет иметь радиус 1/4 дюйма (толщину) с обеих сторон и будет проходить вдоль угла на протяжении 4 дюймов.
Элементы стальных конструкций клепаются в цехе, где они изготавливаются, в объеме, допускаемом условиями отгрузки.

Посмотрите на производственный чертеж клепаной стальной фермы крыши на рис. 7-25. На первый взгляд он кажется загроможденным и трудночитаемым. Это вызвано тем, что на чертеже необходимо указать множество размеров и других соответствующих фактов, но вы сможете прочитать его, как только поймете, что ищете, как мы объясним в следующих параграфах.
Верхний пояс состоит из двух углов, обозначенных спецификацией 2L 4 x 3 1/2 x 5/16 x 16´-5 1/2″. Это означает, что хорда составляет 4 дюйма на 3 1/2 дюйма на 5/16 дюйма толщиной и 16 футов 5 1/2 дюйма длиной.0216 Верхний пояс также имеет спецификацию IL 4 x 3 x 3/8 x 7(e). Это означает, что к нему прикреплено пять зажимных уголков, и каждый из них представляет собой угол размером 4 дюйма на 3 дюйма, толщиной 3/8 дюйма и длиной 7 дюймов.
Косынка (а) в левом нижнем углу вида имеет маркировку PL 8 x 3/8 x 1´-5 (a).
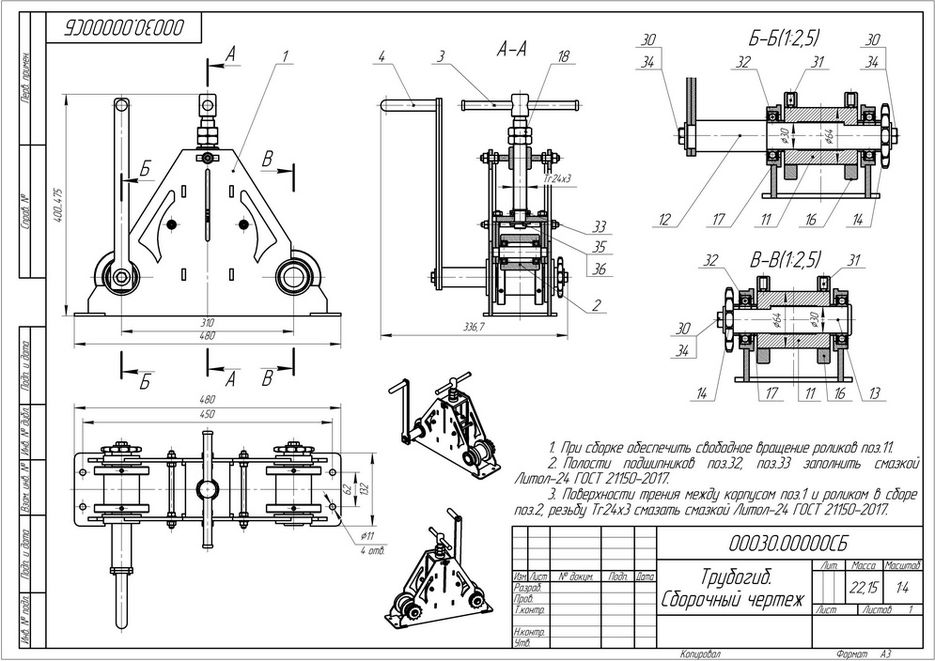
Нижний пояс состоит из двух уголков 2 1/2 дюйма на 2 дюйма на 5/16 дюйма на 10 футов 3 7/16 дюйма, которые соединены с косынками А и В, и еще двух уголков 2 1/2 дюйма на 2 дюйма на 1/4 дюйма на 10 футов 4 1/8 дюйма, которые соединяются с косынкой B и продолжаются до другой половины фермы. Еще два уголка соединены с косынками С и В на верхнем и нижнем поясах; они 2 1/2 дюйма на 2 дюйма на 1/4 дюйма на 2 фута 10 1/2 дюйма. Другой элемент между верхним и нижним поясами, соединенный с косынкой B и косынкой D, состоит из двух уголков 2 1/2 дюйма на 2 дюйма на 1/4 дюйма на 8 футов 5 дюймов.
Рисунок 7-27 — Размеры клепаной стальной фермы.
На рис. 7-26 та же ферма показана только с названиями некоторых элементов и размерами косынок (A, C и D) между углами.
На рис. 7-27 та же ферма показана только с некоторыми необходимыми размерами, чтобы упростить чтение полного рабочего чертежа конструкции.
Большая часть заклепок будет забита в цехе, за исключением пяти заклепок в косынке прогона d и двух показанных заклепок, соединяющих центральную часть нижнего пояса, который соединяется с косынкой b. Эти семь заклепок будут вбиты на стройплощадке. Условные обозначения заклепок, забиваемых в цеху и в полевых условиях, показаны на рис. 7-28.
ЧЕРТЕЖИ МЕТАЛЛИЧЕСКИХ КОНСТРУКЦИЙ
Чертежи, используемые для изготовления и монтажа стальных конструкций, обычно состоят из группы различных типов чертежей, таких как компоновочные, общие, производственные, монтажные и монтажные. Эти чертежи описаны в следующих параграфах.
Компоновочные чертежи
Компоновочные чертежи также называются общими планами и чертежами профилей. Они предоставляют необходимую информацию о местоположении, выравнивании и высоте конструкции и ее основных частей относительно земли на площадке. Они также предоставляют другие важные сведения, такие как характер подстилающего грунта или расположение прилегающих сооружений и дорог. Эти чертежи дополняются инструкциями и информацией, известной как письменные спецификации.
Общие планы
Общие планы содержат информацию о размерах, материале и составе всех основных элементов конструкции, их взаимном расположении и способе соединения, а также крепления других частей конструкции. Количество поставляемых чертежей общего плана определяется такими факторами, как размер и характер сооружения, сложность операций. Общие планы состоят из видов в плане, фасадов и разрезов сооружения и его различных частей. Объем необходимой информации определяет количество и расположение секций и фасадов.
Производственные чертежи
Производственные чертежи или заводские чертежи содержат необходимую информацию о размере, форме, материале и положениях для соединений и креплений для каждого элемента. Эта информация достаточно подробна, чтобы можно было заказать материал для соответствующего элемента и изготовить его в магазине или на верфи. Составные части элементов показаны на производственном чертеже, а также размеры и монтажные метки.