Π₯ΠΎΠ»ΠΎΠ΄Π½Π°Ρ ΠΊΠΎΠ²ΠΊΠ° ΠΌΠ΅ΡΠ°Π»Π»Π° Π½Π° Π·Π°ΠΊΠ°Π· Π² ΠΠΎΡΠΊΠ²Π΅
Π ΠΏΡΠΎΠΈΠ·Π²ΠΎΠ΄ΡΡΠ²Π΅
ΠΡ ΠΌΠΎΠΆΠ΅ΡΠ΅ Π·Π°ΠΊΠ°Π·Π°ΡΡ ΡΠΎΠ²Π°Ρ Π½Π° Π·Π°ΠΊΠ°Π· ΠΈΠ»ΠΈ Π²ΡΠ±ΡΠ°ΡΡ Π³ΠΎΡΠΎΠ²ΡΠ΅ ΡΠ°Π·ΠΌΠ΅ΡΡ.
Π₯ΠΎΠ»ΠΎΠ΄Π½Π°Ρ ΠΊΠΎΠ²ΠΊΠ° ΠΏΠΎΠ·Π²ΠΎΠ»ΡΠ΅Ρ ΠΏΡΠΈΠ΄Π°ΡΡ Π½Π΅ΠΎΠ±Ρ ΠΎΠ΄ΠΈΠΌΡΡ ΡΠΎΡΠΌΡ ΠΏΡΡΡΠΊΠ°ΠΌ, ΡΡΡΠ±Π°ΠΌ ΠΈΠ»ΠΈ Π΄ΡΡΠ³ΠΈΠΌ Π·Π°Π³ΠΎΡΠΎΠ²ΠΊΠ°ΠΌ. ΠΠ΅ΡΠ°Π»ΠΈ Ρ ΡΠ°Π·Π½ΡΠΌΠΈ ΠΎΡΠ΅ΡΡΠ°Π½ΠΈΡΠΌΠΈ, ΠΈΠ·ΠΎΠ³Π½ΡΡΡΠ΅ ΠΈ Π²ΠΈΡΡΠ΅, ΡΠ΅Π°Π»ΠΈΠ·ΡΡΡΡΡ ΡΠ°ΡΠ΅ Π²ΡΠ΅Π³ΠΎ Π² ΠΈΠ·Π³ΠΎΡΠΎΠ²Π»Π΅Π½ΠΈΠΈ ΠΊΠΎΠ·ΡΡΡΠΊΠΎΠ², ΠΎΠ³ΡΠ°Π΄, Π²ΠΎΡΠΎΡ, ΡΠ΅ΡΠ΅ΡΠΎΠΊ Π½Π° ΠΎΠΊΠ½Π°. Π¨ΡΡΡΠ½ΡΠ΅ ΡΠ»Π΅ΠΌΠ΅Π½ΡΡ, ΠΏΠΎΠ»ΡΡΠ΅Π½Π½ΡΠ΅ ΠΈΠ· ΠΌΠ΅ΡΠ°Π»Π»Π° Ρ ΠΎΠ»ΠΎΠ΄Π½ΠΎΠΉ ΠΊΠΎΠ²ΠΊΠΎΠΉ, ΡΠΎΠ΅Π΄ΠΈΠ½ΡΡΡΡΡ ΡΠ²Π°ΡΠΊΠΎΠΉ Π² Π³ΠΎΡΠΎΠ²ΡΡ ΠΊΠΎΠΌΠΏΠΎΠ·ΠΈΡΠΈΡ.
ΠΡΠΎΡΡΠΎΡΠ° ΡΠ΅Ρ Π½ΠΎΠ»ΠΎΠ³ΠΈΠΈ ΠΏΠΎΠ·Π²ΠΎΠ»ΡΠ΅Ρ Π²ΡΠΏΠΎΠ»Π½ΠΈΡΡ ΠΎΠ±ΡΠ΅ΠΌΠ½ΡΠ΅ ΠΊΠΎΠΌΠΏΠΎΠ·ΠΈΡΠΈΠΈ, Π½Π΅ΠΎΠ±ΡΡΠ½ΡΠ΅ ΡΠ·ΠΎΡΡ, ΠΎΠ±Π»Π°Π΄Π°Ρ ΠΌΠΈΠ½ΠΈΠΌΠ°Π»ΡΠ½ΡΠΌΠΈ Π½Π°Π²ΡΠΊΠ°ΠΌΠΈ ΡΠ°Π±ΠΎΡΡ Ρ ΠΌΠ΅ΡΠ°Π»Π»ΠΎΠΌ. ΠΠΎΠ»ΡΡΠΎΠ΅ ΠΏΡΠ΅ΠΈΠΌΡΡΠ΅ΡΡΠ²ΠΎ β Π²ΠΎΠ·ΠΌΠΎΠΆΠ½ΠΎΡΡΡ ΠΏΡΠΈΠΌΠ΅Π½Π΅Π½ΠΈΡ Π³ΠΎΡΠΎΠ²ΡΡ Π·Π°Π³ΠΎΡΠΎΠ²ΠΎΠΊ. Π£Π»ΠΈΡΠΊΠΈ, Π·Π°Π²ΠΈΡΡΡΠΊΠΈ, Π²ΠΈΠ½ΡΠΎΠ²ΠΎΠΉ ΠΏΡΠΎΡΠΈΠ»Ρ, ΡΠΎΠ·Π΅ΡΠΊΠΈ ΡΡΠ°Π½Π΄Π°ΡΡΠ½ΡΡ ΡΠ°Π·ΠΌΠ΅ΡΠΎΠ² ΠΈΡΠΏΠΎΠ»ΡΠ·ΡΡΡΡΡ Π΄Π»Ρ ΡΠΎΠ·Π΄Π°Π½ΠΈΡ ΠΊΠ°ΠΊ Π΅Π΄ΠΈΠ½ΠΈΡΠ½ΡΡ ΠΈΠ·Π΄Π΅Π»ΠΈΠΉ, ΡΠ°ΠΊ ΠΈ Π΄Π»Ρ Π²ΡΠΏΠΎΠ»Π½Π΅Π½ΠΈΡ ΡΠ°Π±Π»ΠΎΠ½Π½ΡΡ ΡΠ°Π±ΠΎΡ, ΠΎΠ΄ΠΈΠ½Π°ΠΊΠΎΠ²ΡΠ΅ ΠΏΡΠΎΠ»Π΅ΡΡ ΠΎΠ³ΡΠ°ΠΆΠ΄Π΅Π½ΠΈΠΉ.
Π’Π΅Ρ Π½ΠΎΠ»ΠΎΠ³ΠΈΡ Ρ ΠΎΠ»ΠΎΠ΄Π½ΠΎΠΉ ΠΊΠΎΠ²ΠΊΠΈ
ΠΠΎΠ»ΡΡΠΈΡΡ Π³ΠΎΡΠΎΠ²ΡΠΉ ΡΠ»Π΅ΠΌΠ΅Π½Ρ ΠΌΠΎΠΆΠ½ΠΎ, Π²ΡΠΏΠΎΠ»Π½ΠΈΠ² Π½Π΅ΡΠΊΠΎΠ»ΡΠΊΠΎ ΡΠ΅Ρ
Π½ΠΎΠ»ΠΎΠ³ΠΈΡΠ΅ΡΠΊΠΈΡ
ΠΏΡΠΎΡΠ΅ΡΡΠΎΠ². ΠΠ»Π°Π²Π½ΡΠΌ ΡΡΠ°ΠΏΠΎΠΌ ΡΡΠΈΡΠ°Π΅ΡΡΡ ΠΏΡΠΈΠ΄Π°Π½ΠΈΠ΅ Π·Π°Π³ΠΎΡΠΎΠ²ΠΊΠ΅ Π½Π΅ΠΎΠ±Ρ
ΠΎΠ΄ΠΈΠΌΠΎΠΉ ΡΠΎΡΠΌΡ Ρ ΠΏΠΎΠΌΠΎΡΡΡ ΠΎΠ±ΠΎΡΡΠ΄ΠΎΠ²Π°Π½ΠΈΡ, ΠΊΠΎΡΠΎΡΠΎΠ΅ ΠΏΠΎΠ΄ Π΄Π°Π²Π»Π΅Π½ΠΈΠ΅ΠΌ ΠΏΡΠ΅ΡΡΡΠ΅Ρ, ΠΈΠ·Π³ΠΈΠ±Π°Π΅Ρ, ΠΏΡΠ΅ΠΎΠ±ΡΠ°Π·ΡΠ΅Ρ ΠΌΠ΅ΡΠ°Π»Π». ΠΠ·Π³ΠΎΡΠΎΠ²Π»Π΅Π½Π½ΡΠ΅ ΡΠ°ΠΊΠΈΠΌ ΡΠΏΠΎΡΠΎΠ±ΠΎΠΌ Π΄Π΅ΡΠ°Π»ΠΈ Π½Π΅ ΡΠ»ΠΎΠΌΠ°ΡΡ, Π° ΡΡΠΎΠΊ ΡΠΊΡΠΏΠ»ΡΠ°ΡΠ°ΡΠΈΠΈ, Π΅ΡΠ»ΠΈ ΡΡΠ°Π²Π½ΠΈΠ²Π°ΡΡ Ρ Π»ΠΈΡΡΠ΅ΠΌ ΠΈΠ»ΠΈ ΡΡΠ°ΠΌΠΏΠΎΠ²ΠΊΠΎΠΉ, Π½Π°ΠΌΠ½ΠΎΠ³ΠΎ Π±ΠΎΠ»ΡΡΠ΅. Π₯ΠΎΠ»ΠΎΠ΄Π½Π°Ρ ΠΊΠΎΠ²ΠΊΠ° ΠΌΠ΅ΡΠ°Π»Π»ΠΈΡΠ΅ΡΠΊΠΈΡ
ΠΈΠ·Π΄Π΅Π»ΠΈΠΉ ΠΈΡΠΏΠΎΠ»ΡΠ·ΡΠ΅Ρ Π½Π΅ΡΠΊΠΎΠ»ΡΠΊΠΎ Π²ΠΈΠ΄ΠΎΠ² ΠΎΠ±ΡΠ°Π±ΠΎΡΠΊΠΈ:
- ΠΏΡΠΎΠΊΠ°Ρ;
- ΠΊΠΎΠ²ΠΊΠ°;
- Π³ΠΈΠ±ΠΊΠ°;
- ΡΡΠ°ΠΌΠΏΠΎΠ²ΠΊΠ°;
- ΡΠΊΡΡΡΠΈΠ²Π°Π½ΠΈΠ΅.
ΠΡΠΈΠΌΠ΅Π½ΡΠ΅ΠΌΡΠ΅ ΠΌΠ΅ΡΠΎΠ΄Ρ ΠΎΠ±ΡΠ°Π±ΠΎΡΠΊΠΈ Π·Π°Π²ΠΈΡΡΡ ΠΎΡ Π²ΠΈΠ΄Π° ΠΈ ΡΠΎΡΠΌΡ ΠΌΠ΅ΡΠ°Π»Π»ΠΎΠΏΡΠΎΠΊΠ°ΡΠ°. ΠΠ΄Π΅ΡΡ ΡΡΠΎΠΈΡ ΠΎΡΠΌΠ΅ΡΠΈΡΡ, ΡΠ΅ΠΌ ΠΎΡΠ»ΠΈΡΠ°Π΅ΡΡΡ Π³ΠΎΡΡΡΠ°Ρ ΠΊΠΎΠ²ΠΊΠ° ΠΎΡ Ρ ΠΎΠ»ΠΎΠ΄Π½ΠΎΠ³ΠΎ ΠΌΠ΅ΡΠΎΠ΄Π° ΠΎΠ±ΡΠ°Π±ΠΎΡΠΊΠΈ ΠΌΠ΅ΡΠ°Π»Π»ΠΈΡΠ΅ΡΠΊΠΈΡ ΠΈΠ·Π΄Π΅Π»ΠΈΠΉ. ΠΠ°Π³ΡΠ΅Π² Π·Π°Π³ΠΎΡΠΎΠ²ΠΊΠΈ ΠΌΠ΅Π½ΡΠ΅Ρ ΡΡΡΡΠΊΡΡΡΡ ΠΌΠ΅ΡΠ°Π»Π»Π°, ΠΏΠΎΡΡΠΎΠΌΡ Π·Π°Π³ΠΎΡΠΎΠ²ΠΊΠ° ΡΡΠ°Π½ΠΎΠ²ΠΈΡΡΡ ΠΏΠ»Π°ΡΡΠΈΡΠ½Π΅Π΅, Π»Π΅Π³ΠΊΠΎ ΠΏΡΠΈΠ½ΠΈΠΌΠ°Π΅Ρ Π½ΡΠΆΠ½ΡΡ ΡΠΎΡΠΌΡ. Π₯ΠΎΠ»ΠΎΠ΄Π½Π°Ρ ΠΊΠΎΠ²ΠΊΠ° Π½Π΅ ΠΏΡΠ΅Π΄ΡΡΠΌΠ°ΡΡΠΈΠ²Π°Π΅Ρ Π½Π°Π³ΡΠ΅Π² ΠΌΠ΅ΡΠ°Π»Π»Π°, ΡΡΡΡΠΊΡΡΡΠ° Π½Π΅ ΠΌΠ΅Π½ΡΠ΅ΡΡΡ. ΠΠΎΡΡΠΎΠΌΡ Π΄Π»Ρ ΠΏΠΎΠ»ΡΡΠ΅Π½ΠΈΡ Π΄Π΅ΡΠ°Π»ΠΈ Π½ΡΠΆΠ½ΠΎΠΉ ΡΠΎΡΠΌΡ ΠΏΡΠΈΡ ΠΎΠ΄ΠΈΡΡΡ ΠΏΡΠΈΠΊΠ»Π°Π΄ΡΠ²Π°ΡΡ Π±ΠΎΠ»ΡΡΠ΅ ΡΡΠΈΠ»ΠΈΠΉ.
ΠΠ°ΠΆΠ½ΠΎ, ΡΡΠΎ ΠΏΡΠΈ ΡΠΊΡΡΡΠΈΠ²Π°Π½ΠΈΠΈ ΠΈΠ»ΠΈ Π³ΠΈΠ±ΠΊΠ΅ ΡΠΎΠΏΡΠΎΡΠΈΠ²Π»Π΅Π½ΠΈΠ΅ Π²Π΅ΡΡ
Π½Π΅Π³ΠΎ ΡΠ»ΠΎΡ ΠΌΠ°ΡΠ΅ΡΠΈΠ°Π»Π° ΡΠ²Π΅Π»ΠΈΡΠΈΠ²Π°Π΅ΡΡΡ ΠΈΠ·-Π·Π° ΠΆΠ΅ΡΡΠΊΠΎΡΡΠΈ ΡΠΎΡΠΌΡ Π·Π°Π³ΠΎΡΠΎΠ²ΠΊΠΈ. Π ΡΠ΅ΡΠ΄ΡΠ΅Π²ΠΈΠ½Π°, ΠΎΡΠ»ΠΈΡΠ°ΡΡΠ°ΡΡΡ Π²ΡΡΠΎΠΊΠΎΠΉ Π²ΡΠ·ΠΊΠΎΡΡΡΡ, ΡΠΏΠΎΡΠΎΠ±Π½Π° ΠΏΡΠΈΠ½ΡΡΡ Π½ΡΠΆΠ½ΡΡ ΡΠΎΡΠΌΡ, ΡΠΎΠ»ΡΠΊΠΎ ΠΏΡΠ΅ΠΎΠ΄ΠΎΠ»Π΅Π² ΡΠΈΠ»Ρ ΡΠΎΠΏΡΠΎΡΠΈΠ²Π»Π΅Π½ΠΈΡ ΠΏΠΎΠ²Π΅ΡΡ
Π½ΠΎΡΡΠ½ΠΎΠ³ΠΎ ΡΠ»ΠΎΡ. ΠΠΎΡΡΠΎΠΌΡ Π²ΡΠΏΠΎΠ»Π½ΠΈΡΡ ΠΎΠΏΡΠ΅Π΄Π΅Π»Π΅Π½Π½ΡΡ ΠΊΠΎΠ²ΠΊΡ Π½Π΅Π²ΠΎΠ·ΠΌΠΎΠΆΠ½ΠΎ Ρ ΠΏΠΎΠΌΠΎΡΡΡ ΠΎΠ±ΡΡΠ½ΠΎΠ³ΠΎ ΠΌΠΎΠ»ΠΎΡΠΊΠ°. ΠΠ»Ρ Π²ΡΠΏΠΎΠ»Π½Π΅Π½ΠΈΡ ΡΠ°ΠΊΠΈΡ
ΡΠ°Π±ΠΎΡ ΠΏΠΎΡΡΠ΅Π±ΡΡΡΡΡ ΡΠΏΠ΅ΡΠΈΠ°Π»ΡΠ½ΡΠ΅ ΠΏΡΠΈΡΠΏΠΎΡΠΎΠ±Π»Π΅Π½ΠΈΡ.
ΠΠ»Π°Π²Π½Π°Ρ ΠΎΡΠΎΠ±Π΅Π½Π½ΠΎΡΡΡ ΡΠ΅Ρ Π½ΠΎΠ»ΠΎΠ³ΠΈΠΈ β ΠΏΠΎΠ»ΡΡΠΈΡΡ ΠΎΠ΄Π½Ρ ΡΠΎΡΠΌΡ ΠΌΠΎΠΆΠ½ΠΎ ΠΈΡΠΏΠΎΠ»ΡΠ·ΡΡ ΡΠΎΠ»ΡΠΊΠΎ ΠΎΠ΄ΠΈΠ½ Π²ΠΈΠ΄ ΠΏΡΠΈΡΠΏΠΎΡΠΎΠ±Π»Π΅Π½ΠΈΡ.
ΠΡΠ΅ ΠΏΡΠΈΡΠΏΠΎΡΠΎΠ±Π»Π΅Π½ΠΈΡ Π΄Π»Ρ ΡΡΠΎΠΉ ΡΠ΅Ρ Π½ΠΎΠ»ΠΎΠ³ΠΈΠΈ β ΡΡΠΎ ΡΠΏΠ΅ΡΠΈΠ°Π»ΡΠ½ΡΠΉ ΠΈΠ½ΡΡΡΡΠΌΠ΅Π½Ρ:
- Π³ΠΈΠ±ΠΊΠ° ΠΏΠΎΠ»ΠΎΡΡ ΠΈΠ»ΠΈ ΠΏΡΠΎΡΠΈΠ»Ρ Π² Π·Π°Π²ΠΈΡΠΎΠΊ Π²ΡΠΏΠΎΠ»Π½ΡΠ΅ΡΡΡ Π½Π° ΡΡΠ°Π½ΠΊΠ΅-ΡΠ»ΠΈΡΠΊΠ΅;
- ΠΈΠ·Π³ΠΎΡΠΎΠ²Π»Π΅Π½ΠΈΠ΅ Π»Π΅ΠΏΠ΅ΡΡΠΊΠΎΠ² ΠΈΠ»ΠΈ ΡΠΎΠ·Π΅ΡΠΎΠΊ Ρ ΠΏΠΎΠΌΠΎΡΡΡ ΡΡΠ°ΠΌΠΏΠΎΠ²ΠΊΠΈ ΡΠΎΠ·Π΄Π°Π΅ΡΡΡ ΠΏΡΠ΅ΡΡΠΎΠΌ ΠΈ ΠΏΡΠ°Π½ΡΠΎΠ½Π°ΠΌΠΈ;
- ΠΏΠΎΠ»ΠΎΡΠ°, ΠΊΠ²Π°Π΄ΡΠ°Ρ, ΡΡΡΠ±Ρ ΡΠΊΡΡΡΠΈΠ²Π°ΡΡΡΡ Π½Π° ΡΠΎΡΡΠΈΠΎΠ½Π΅;
- ΠΊΠΎΠ²ΠΊΠ° Π΄Π΅Π»Π°Π΅ΡΡΡ Ρ ΠΈΡΠΏΠΎΠ»ΡΠ·ΠΎΠ²Π°Π½ΠΈΠ΅ΠΌ Π½Π°ΠΊΠΎΠ²Π°Π»ΡΠ½ΠΈ ΠΈΠ»ΠΈ Π³ΠΈΠ΄ΡΠ°Π²Π»ΠΈΡΠ΅ΡΠΊΠΎΠ³ΠΎ ΠΏΡΠ΅ΡΡΠ°;
- Π΄Π»Ρ ΠΏΡΠΎΠΊΠ°ΡΠ° ΠΏΡΠΈΠΌΠ΅Π½ΡΡΡ ΡΠ°Π·Π½ΠΎΠ³ΠΎ Π΄ΠΈΠ°ΠΌΠ΅ΡΡΠ° ΠΈ ΠΏΡΠΎΡΠΈΠ»Ρ Π²Π°Π»ΡΡΡ.
ΠΡΠ΅ΠΈΠΌΡΡΠ΅ΡΡΠ²Π°
Π’Π΅Ρ Π½ΠΎΠ»ΠΎΠ³ΠΈΡ ΠΎΠ±Π»Π°Π΄Π°Π΅Ρ ΡΠ»Π΅Π΄ΡΡΡΠΈΠΌΠΈ ΠΏΡΠ΅ΠΈΠΌΡΡΠ΅ΡΡΠ²Π°ΠΌΠΈ:
- Π²ΡΡΠΎΠΊΠ°Ρ ΠΏΡΠΎΠΈΠ·Π²ΠΎΠ΄ΠΈΡΠ΅Π»ΡΠ½ΠΎΡΡΡ ΠΏΡΠΈ ΠΌΠ°Π»ΠΎΠΉ ΡΡΡΠ΄ΠΎΠ΅ΠΌΠΊΠΎΡΡΠΈ;
- Π½ΠΈΠ·ΠΊΠ°Ρ ΡΠ½Π΅ΡΠ³ΠΎΠ΅ΠΌΠΊΠΎΡΡΡ;
- Π»Π΅Π³ΠΊΠΎΡΡΡ ΠΎΡΠ²ΠΎΠ΅Π½ΠΈΡ ΡΠ΅Ρ Π½ΠΎΠ»ΠΎΠ³ΠΈΠΈ;
- Π²ΡΡΠΎΠΊΠ°Ρ ΠΏΠΎΠ²ΡΠΎΡΡΠ΅ΠΌΠΎΡΡΡ ΡΠ΅ΡΠΈΠΉΠ½ΡΡ Π΄Π΅ΡΠ°Π»Π΅ΠΉ;
- ΠΏΠΎΠ·Π²ΠΎΠ»ΡΠ΅Ρ ΡΠΎΡΠ΅ΡΠ°ΡΡ ΠΎΡΠ½ΠΎΠ²Π½ΡΠ΅ ΡΠ»Π΅ΠΌΠ΅Π½ΡΡ Π΄Π»Ρ Π²ΡΠΏΠΎΠ»Π½Π΅Π½ΠΈΡ ΡΠ½ΠΈΠΊΠ°Π»ΡΠ½ΡΡ
ΡΠ·ΠΎΡΠΎΠ², ΠΎΡΠ½Π°ΠΌΠ΅Π½ΡΠΎΠ² ΠΈ ΠΊΠΎΠ½ΡΡΡΡΠΊΡΠΈΠΉ.
ΠΠ±ΡΠ°Π±ΠΎΡΠΊΠ° ΠΈΠΌΠ΅Π΅Ρ ΡΠ»Π΅Π΄ΡΡΡΠΈΠ΅ ΠΎΡΠΎΠ±Π΅Π½Π½ΠΎΡΡΠΈ:
- Π·Π°Π³ΠΎΡΠΎΠ²ΠΊΠΈ Π½Π΅ Π½Π°Π΄ΠΎ ΠΏΡΠ΅Π΄Π²Π°ΡΠΈΡΠ΅Π»ΡΠ½ΠΎ Π½Π°Π³ΡΠ΅Π²Π°ΡΡ Π΄ΠΎ Π²ΡΡΠΎΠΊΠΈΡ ΡΠ΅ΠΌΠΏΠ΅ΡΠ°ΡΡΡ;
- ΠΏΠΎΠ²Π΅ΡΡ Π½ΠΎΡΡΡ ΠΈΠ·Π΄Π΅Π»ΠΈΠΉ ΠΏΡΠΎΡΠ½Π΅Π΅, ΡΠ΅ΠΌ ΠΏΡΠΈ ΠΏΡΠΎΠΈΠ·Π²ΠΎΠ΄ΡΡΠ²Π΅ ΡΠ»Π΅ΠΌΠ΅Π½ΡΠΎΠ² Π³ΠΎΡΡΡΠΈΠΌ ΠΌΠ΅ΡΠΎΠ΄ΠΎΠΌ;
- ΠΎΠ±Π΅ΡΠΏΠ΅ΡΠΈΠ²Π°Π΅Ρ ΡΠΎΡΠ½ΡΡ ΠΏΠΎΠ΄Π³ΠΎΠ½ΠΊΡ, Π²ΡΡΠΎΠΊΠΎΡΠΎΡΠ½ΡΡ ΠΎΠ±ΡΠ°Π±ΠΎΡΠΊΡ;
- ΡΠ»Π΅ΠΌΠ΅Π½ΡΡ Π½Π΅ Π½Π°Π΄ΠΎ Π΄ΠΎΠΏΠΎΠ»Π½ΠΈΡΠ΅Π»ΡΠ½ΠΎ ΠΎΠ±ΡΠ°Π±Π°ΡΡΠ²Π°ΡΡ ΠΏΠΎΡΠ»Π΅ ΠΈΠ·Π³ΠΎΡΠΎΠ²Π»Π΅Π½ΠΈΡ;
- ΠΏΡΠΎΡΠ΅ΡΡ ΡΠ°Π±ΠΎΡ Π±ΠΎΠ»Π΅Π΅ Β«ΡΠΈΡΡΡΠΉΒ», Π±Π΅Π· ΡΠ»Π΅Π΄ΠΎΠ² ΠΈ ΠΏΡΠΎΠ΄ΡΠΊΡΠΎΠ² Π³ΠΎΡΠ΅Π½ΠΈΡ Π½Π° ΠΌΠ΅ΡΠ°Π»Π»ΠΈΡΠ΅ΡΠΊΠΎΠΉ Π·Π°Π³ΠΎΡΠΎΠ²ΠΊΠ΅;
- ΠΏΡΠΎΡΡΠΎΡΠ° Π² ΠΈΡΠΏΠΎΠ»ΡΠ·ΠΎΠ²Π°Π½ΠΈΠΈ ΠΎΠ±ΠΎΡΡΠ΄ΠΎΠ²Π°Π½ΠΈΡ;
- Π²ΠΎΠ·ΠΌΠΎΠΆΠ½ΠΎΡΡΡ ΡΡΠ°ΡΠ΅Π½ΠΈΡ ΠΈΠ·Π΄Π΅Π»ΠΈΠΉ;
- ΡΠΊΠΎΠ½ΠΎΠΌΠΈΡΠ½ΠΎΡΡΡ.
ΠΠ΅ΡΠ°Π»Π» ΠΏΠΎΠ΄ Π²ΠΎΠ·Π΄Π΅ΠΉΡΡΠ²ΠΈΠ΅ΠΌ ΡΡΠ°Π½ΠΊΠΎΠ² ΡΡΠ°Π½ΠΎΠ²ΠΈΡΡΡ Π±ΠΎΠ»Π΅Π΅ ΠΏΡΠΎΡΠ½ΡΠΌ ΠΈ ΡΠ²ΡΡΠ΄ΡΠΌ, Π° ΡΠ°ΠΊΠΆΠ΅ ΠΏΡΠΈΠΎΠ±ΡΠ΅ΡΠ°Π΅Ρ Π·Π°ΡΠΈΡΡ ΠΎΡ ΠΊΠΎΡΡΠΎΠ·ΠΈΠΈ. ΠΠ»Ρ Ρ ΠΎΠ»ΠΎΠ΄Π½ΠΎΠΉ ΠΊΠΎΠ²ΠΊΠΈ ΡΠ°ΡΠ΅ Π²ΡΠ΅Π³ΠΎ ΠΏΡΠΈΠΌΠ΅Π½ΡΡΡ Π½ΠΈΠ·ΠΊΠΎΡΠ³Π»Π΅ΡΠΎΠ΄ΠΈΡΡΡΠΉ ΠΌΠ΅ΡΠ°Π»Π».
ΠΡΠΎΠΈΠ·Π²ΠΎΠ΄ΡΡΠ²ΠΎ ΠΈΠ·Π΄Π΅Π»ΠΈΠΉ Ρ ΠΎΠ»ΠΎΠ΄Π½ΠΎΠΉ ΠΊΠΎΠ²ΠΊΠΎΠΉ
ΠΡΠΎΡΠ΅ΡΡ ΠΏΠΎΠΏΡΠ»ΡΡΠ΅Π½ Π±Π»Π°Π³ΠΎΠ΄Π°ΡΡ ΡΠ²ΠΎΠ΅ΠΉ ΡΠΊΠΎΠ½ΠΎΠΌΠΈΡΠ½ΠΎΡΡΠΈ ΠΈ ΠΏΡΠΎΡΡΠΎΡΠ΅. Π§Π°ΡΠ΅ Π²ΡΠ΅Π³ΠΎ, Π΄Π°Π½Π½ΡΠΌ ΠΌΠ΅ΡΠΎΠ΄ΠΎΠΌ ΠΎΠ±ΡΠ°Π±Π°ΡΡΠ²Π°ΡΡ ΡΡΡΠ±Ρ Π½Π΅Π±ΠΎΠ»ΡΡΠΎΠ³ΠΎ ΡΠ΅ΡΠ΅Π½ΠΈΡ ΠΈ ΠΌΠ΅ΡΠ°Π»Π»ΠΈΡΠ΅ΡΠΊΠΈΠ΅ ΠΏΡΡΡΠΊΠΈ. ΠΡΠΎΡ ΠΌΠ΅ΡΠΎΠ΄ ΠΏΠΎΠ·Π²ΠΎΠ»ΡΠ΅Ρ Π±ΡΡΡΡΠΎ ΡΠΎΠ·Π΄Π°Π²Π°ΡΡ Π²Π½ΡΡΠΈΡΠ΅Π»ΡΠ½ΡΡ
ΡΠ°Π·ΠΌΠ΅ΡΠΎΠ² ΠΈΠ·Π΄Π΅Π»ΠΈΡ, ΠΏΠΎΡΡΠΎΠΌΡ ΠΏΠΎΠΏΡΠ»ΡΡΠ΅Π½ ΠΏΡΠΈ ΠΈΠ·Π³ΠΎΡΠΎΠ²Π»Π΅Π½ΠΈΠΈ Π·Π°Π±ΠΎΡΠΎΠ², Π²ΠΎΡΠΎΡ, Π±Π΅ΡΠ΅Π΄ΠΎΠΊ, ΠΎΠ³ΡΠ°Π΄, ΡΠ΅ΡΠ΅ΡΠΎΠΊ ΠΈ ΠΏΠ΅ΡΠΈΠ». Π’Π°ΠΊΠΈΠ΅ ΠΈΠ·Π΄Π΅Π»ΠΈΡ ΠΌΠΎΠΆΠ½ΠΎ ΠΈΡΠΏΠΎΠ»ΡΠ·ΠΎΠ²Π°ΡΡ Π΄Π»Ρ Π΄Π΅ΠΊΠΎΡΠ° ΡΠ°Π΄Π°, Π·Π°Π³ΠΎΡΠΎΠ΄Π½ΠΎΠ³ΠΎ ΡΡΠ°ΡΡΠΊΠ° ΠΈ Π΄Π°ΠΆΠ΅ ΡΠ°ΡΠ°Π΄Π° ΠΊΠΎΡΡΠ΅Π΄ΠΆΠ°.
ΠΠ»Π°Π²Π½ΡΠΌ ΠΏΠ»ΡΡΠΎΠΌ Π² ΠΎΡΠΎΡΠΌΠ»Π΅Π½ΠΈΠΈ ΠΏΠ°ΡΠΊΠΎΠ²ΡΡ Π·ΠΎΠ½ ΠΈ ΡΡΠ°ΡΡΠΊΠΎΠ², ΡΠ²Π»ΡΠ΅ΡΡΡ ΡΡΡΠΎΠΉΡΠΈΠ²ΠΎΡΡΡ ΠΈΠ·Π³ΠΎΡΠ°Π²Π»ΠΈΠ²Π°Π΅ΠΌΡΡ ΠΈΠ·Π΄Π΅Π»ΠΈΠΉ ΠΊ ΠΏΡΠΈΡΠΎΠ΄Π½ΡΠΌ ΡΠ²Π»Π΅Π½ΠΈΡΠΌ. ΠΠ½ΠΈ Π½Π΅ ΡΡΠ΅Π±ΡΡΡ Π΄ΠΎΠΏΠΎΠ»Π½ΠΈΡΠ΅Π»ΡΠ½ΠΎΠ³ΠΎ ΡΡ ΠΎΠ΄Π°, Π½ΡΠΆΠ½ΠΎ ΠΎΠ΄ΠΈΠ½ ΡΠ°Π· Π² Π΄Π²Π° Π³ΠΎΠ΄Π° ΠΎΠΊΡΠ°ΡΠΈΠ²Π°ΡΡ ΠΏΠΎΠ²Π΅ΡΡ Π½ΠΎΡΡΡ. ΠΠ΄Π½Π°ΠΊΠΎ Π½Π΅ ΠΈΡΠΊΠ»ΡΡΠ΅Π½Π° Π²ΠΎΠ·ΠΌΠΎΠΆΠ½ΠΎΡΡΡ ΡΠΎΠ·Π΄Π°Π½ΠΈΡ Π±ΠΎΠ»Π΅Π΅ ΠΈΠ·ΡΡΠ½ΡΡ ΡΠ»Π΅ΠΌΠ΅Π½ΡΠΎΠ² Π΄Π»Ρ ΠΈΠ½ΡΠ΅ΡΡΠ΅ΡΠ°. Π Π΅ΡΠ΅ΡΠΊΠΈ Π΄Π»Ρ ΠΊΠ°ΠΌΠΈΠ½Π°, ΡΠ²Π΅ΡΠΎΡΠ½ΡΠ΅ ΠΏΠΎΠ΄ΡΡΠ°Π²ΠΊΠΈ, ΠΌΠ°Π½Π³Π°Π»Ρ, ΠΊΡΠΎΠ½ΡΡΠ΅ΠΉΠ½Ρ Π΄Π»Ρ ΡΠΎΠ½Π°ΡΠ΅ΠΉ, Π΄Π΅ΠΊΠΎΡΠ°ΡΠΈΠ²Π½ΡΠ΅ Π²Π°Π·Ρ ΠΈΠ»ΠΈ ΡΠ°Π±ΡΡΠ΅ΡΡ. ΠΡΠΈΠ³ΠΈΠ½Π°Π»ΡΠ½ΡΠΉ Π΄Π΅ΠΊΠΎΡ ΠΌΠΎΠΆΠ½ΠΎ Π΄ΠΎΠΏΠΎΠ»Π½ΠΈΡΠ΅Π»ΡΠ½ΠΎ ΠΏΠΎΠΊΡΡΡΡ ΠΌΠ΅Π΄ΡΡ ΠΈΠ»ΠΈ Π·ΠΎΠ»ΠΎΡΡΠΌ Π½Π°ΠΏΡΠ»Π΅Π½ΠΈΠ΅ΠΌ.
ΠΡΠ΅ ΡΡΠΈ ΠΈΠ·Π΄Π΅Π»ΠΈΡ ΠΎΡΠ»ΠΈΡΠ°ΡΡΡΡ ΠΏΡΠΎΡΠ½ΠΎΡΡΡΡ, ΠΏΡΠΈ ΡΡΠΎΠΌ Π½Π΅ ΡΠ΅ΡΡΡΡ ΡΠ²ΠΎΠ΅Π³ΠΎ ΠΏΡΠ°ΠΊΡΠΈΡΠ΅ΡΠΊΠΎΠ³ΠΎ Π½Π°Π·Π½Π°ΡΠ΅Π½ΠΈΡ ΠΈ Π²ΡΠ³Π»ΡΠ΄ΡΡ ΠΊΠ°ΠΊ ΠΏΡΠΎΠΈΠ·Π²Π΅Π΄Π΅Π½ΠΈΠ΅ ΠΈΡΠΊΡΡΡΡΠ²Π°.
ΠΠ°ΠΊΠ°Π·Π°ΡΡ Ρ ΠΎΠ»ΠΎΠ΄Π½ΡΡ ΠΊΠΎΠ²ΠΊΡ ΠΌΠ΅ΡΠ°Π»Π»Π° Π² ΠΠΎΡΠΊΠ²Π΅ ΠΌΠΎΠΆΠ½ΠΎ Π½Π° ΡΠ°ΠΉΡΠ΅ Β«ΠΠ΅Π»ΡΠ½Π΄ Π‘ΡΠ°Π»ΡΒ». ΠΡ ΠΌΠΎΠΆΠ΅ΡΠ΅ ΠΎΡΡΠ°Π²ΠΈΡΡ Π·Π°ΡΠ²ΠΊΡ Π½Π° Π½Π°ΡΠ΅ΠΌ ΡΠ°ΠΉΡΠ΅ ΠΈΠ»ΠΈ ΠΏΠΎ ΡΠ΅Π»Π΅ΡΠΎΠ½Ρ.
Π§ΡΠΎ Π½ΡΠΆΠ½ΠΎ Π·Π½Π°ΡΡ ΠΎ ΠΊΠΎΠ²ΠΊΠ΅? ΠΡΠ»ΠΈΡΠΈΠ΅ Π₯ΠΎΠ»ΠΎΠ΄Π½ΠΎΠΉ ΠΊΠΎΠ²ΠΊΠΈ ΠΎΡ Π³ΠΎΡΡΡΠ΅ΠΉ ΠΊΠΎΠ²ΠΊΠΈ.
ΠΠΎΠ²ΠΊΠ° ΠΏΡΠ΅Π΄ΡΡΠ°Π²Π»ΡΠ΅Ρ ΡΠΎΠ±ΠΎΠΉ ΠΏΡΠΎΡΠ΅ΡΡ ΠΎΠ±ΡΠ°Π±ΠΎΡΠΊΠΈ ΡΠΏΠ΅ΡΠΈΠ°Π»ΡΠ½ΠΎΠΉ Π·Π°Π³ΠΎΡΠΎΠ²ΠΊΠΈ. ΠΠ΅ ΡΠ΅Π»Ρ ΠΏΡΠΈΠ΄Π°ΡΡ ΠΌΠ΅ΡΠ°Π»Π»Ρ ΡΡΠ΅Π±ΡΠ΅ΠΌΡΠ΅ ΡΠ°Π·ΠΌΠ΅ΡΡ Ρ ΡΠΎΡΠΌΠΎΠΉ. Π Π°Π·Π»ΠΈΡΠ°ΡΡ Π³ΠΎΡΡΡΡΡ ΠΊΠΎΠ²ΠΊΡ ΠΈ Ρ
ΠΎΠ»ΠΎΠ΄Π½ΡΡ.
ΠΠ°ΡΡΠ΅ΡΡ Π½ΡΠΆΠ½ΠΎ ΠΏΠΎΠ·Π½Π°ΠΊΠΎΠΌΠΈΡΡΡΡ Ρ ΠΎΠ±Π΅ΠΈΠΌΠΈ ΡΠ°Π·Π½ΠΎΠ²ΠΈΠ΄Π½ΠΎΡΡΡΠΌΠΈ, ΡΡΠΎΠ±Ρ Π·Π½Π°ΡΡ Π΄ΠΎΡΡΠΎΠΈΠ½ΡΡΠ²Π° ΠΈ Π½Π΅Π΄ΠΎΡΡΠ°ΡΠΊΠΈ ΠΊΠ°ΠΆΠ΄ΠΎΠΉ.
ΠΡΠΈ Π³ΠΎΡΡΡΠ΅ΠΌ ΡΠΏΠΎΡΠΎΠ±Π΅ ΠΌΠ΅ΡΠ°Π»Π»ΠΈΡΠ΅ΡΠΊΡΡ Π·Π°Π³ΠΎΡΠΎΠ²ΠΊΡ ΡΠΈΠ»ΡΠ½ΠΎ Π½Π°Π³ΡΠ΅Π²Π°ΡΡ. Π ΡΠ΅Π·ΡΠ»ΡΡΠ°ΡΠ΅ ΠΌΠ΅ΡΠ°Π»Π» ΡΡΠ°Π½ΠΎΠ²ΠΈΡΡΡ ΠΏΠ»Π°ΡΡΠΈΡΠ½ΡΠΌ. ΠΠΎΡΡΡΠ°Ρ ΠΊΠΎΠ²ΠΊΠ° ΠΏΡΠΈΠ΄Π°Π΅Ρ Π·Π°Π³ΠΎΡΠΎΠ²ΠΊΠ΅ Π½ΡΠΆΠ½ΡΠ΅ Π³Π°Π±Π°ΡΠΈΡΡ ΠΈ ΠΆΠ΅Π»Π°Π΅ΠΌΡΡ ΡΠΎΡΠΌΡ. ΠΠ°ΡΡΠ΅ΡΡ Π΄ΠΎΡΡΡΠΏΠ½Ρ ΡΠ°Π·Π½ΠΎΠΎΠ±ΡΠ°Π·Π½ΡΠ΅ Π²Π°ΡΠΈΠ°Π½ΡΡ ΡΠ°Π±ΠΎΡ.
Π£ Π½Π°Π³ΡΠ΅Π²Π° ΠΌΠ΅ΡΠ°Π»Π»ΠΈΡΠ΅ΡΠΊΠΎΠΉ Π·Π°Π³ΠΎΡΠΎΠ²ΠΊΠΈ ΠΈΠΌΠ΅ΡΡΡΡ ΠΈ ΡΠ²ΠΎΠΈ ΠΌΠΈΠ½ΡΡΡ. ΠΡΠ΅ΠΆΠ΄Π΅ Π²ΡΠ΅Π³ΠΎ, Π½Π΅ΠΎΠ±Ρ ΠΎΠ΄ΠΈΠΌΠΎ ΠΎΠ±ΡΡΡΡΠΎΠΈΡΡ ΡΠΏΠ΅ΡΠΈΠ°Π»ΡΠ½ΠΎΠ΅ ΠΏΠΎΠΌΠ΅ΡΠ΅Π½ΠΈΠ΅. ΠΠΎΡΡΠ΅Π±ΡΠ΅ΡΡΡ ΠΊΡΠΏΠΈΡΡ ΠΊΡΠ·Π½Π΅ΡΠ½ΡΠΉ Π³ΠΎΡΠ½, Π΄Π»Ρ ΠΊΠΎΡΠΎΡΠΎΠ³ΠΎ ΠΏΡΠΈΠ΄Π΅ΡΡΡ ΠΏΠΎΠΊΡΠΏΠ°ΡΡ ΡΠΎΠΏΠ»ΠΈΠ²ΠΎ.
ΠΠ΅ΠΎΠ±Ρ ΠΎΠ΄ΠΈΠΌΠΎ ΡΠΎΠ±Π»ΡΠ΄Π°ΡΡ ΠΏΡΠ°Π²ΠΈΠ»Π° ΠΏΠΎΠΆΠ°ΡΠ½ΠΎΠΉ Π±Π΅Π·ΠΎΠΏΠ°ΡΠ½ΠΎΡΡΠΈ, Π²Π°ΠΆΠ½ΠΎ, ΡΡΠΎΠ±Ρ ΠΌΠ°ΡΡΠ΅Ρ Π·Π½Π°Π», ΠΊΠ°ΠΊ ΡΠ°Π±ΠΎΡΠ°ΡΡ Ρ ΠΎΠ³Π½Π΅ΠΌ.
ΠΠΌΠ΅Ρ ΠΏΡΠ΅Π΄ΡΡΠ°Π²Π»Π΅Π½ΠΈΠ΅ ΠΎ ΡΠ΅ΠΌΠΏΠ΅ΡΠ°ΡΡΡΠ½ΡΡ ΡΠ΅ΠΆΠΈΠΌΠ°Ρ , ΠΈΡΠΏΠΎΠ»ΡΠ·ΡΠ΅ΠΌΡΡ Π² ΠΏΡΠΎΡΠ΅ΡΡΠ΅ ΠΊΠΎΠ²ΠΊΠΈ, Π±Π΅Π· ΡΡΡΠ΄Π° ΠΌΠΎΠΆΠ½ΠΎ Π²ΡΠ±ΡΠ°ΡΡ Π½ΡΠΆΠ½ΡΠΉ Π²ΠΈΠ΄ ΠΊΠΎΠ²ΠΊΠΈ.
Π₯ΠΎΠ»ΠΎΠ΄Π½Π°Ρ ΠΊΠΎΠ²ΠΊΠ° β ΡΡΠΎ ΡΡΡΠ΄ΠΎΠ·Π°ΡΡΠ°ΡΠ½ΡΠΉ ΠΏΡΠΎΡΠ΅ΡΡ. Π§ΡΠΎΠ±Ρ Π΄ΠΎΠ±ΠΈΡΡΡΡ ΠΎΡ ΠΌΠ΅ΡΠ°Π»Π»ΠΈΡΠ΅ΡΠΊΠΎΠΉ Π·Π°Π³ΠΎΡΠΎΠ²ΠΊΠΈ ΡΠΎΠΉ ΡΠΎΡΠΌΡ, ΠΊΠΎΡΠΎΡΠ°Ρ ΡΡΠ΅Π±ΡΠ΅ΡΡΡ, Π΅Π΅ ΠΈΠ·Π³ΠΈΠ±Π°ΡΡ, ΠΎΠΏΡΠ΅ΡΡΠΎΠ²ΡΠ²Π°ΡΡ ΠΈ ΡΠ²Π°ΡΠΈΠ²Π°ΡΡ. Π’Π΅Ρ
Π½ΠΈΠΊΠ° Π²ΡΠΏΠΎΠ»Π½Π΅Π½ΠΈΡ Π½Π΅ΠΌΠ½ΠΎΠ³ΠΎ ΠΏΡΠΎΡΠ΅ ΠΏΠΎ ΡΡΠ°Π²Π½Π΅Π½ΠΈΡ Ρ Π³ΠΎΡΡΡΠΈΠΌ ΡΠΏΠΎΡΠΎΠ±ΠΎΠΌ.
ΠΠ»Ρ ΠΌΠ°ΡΡΠ΅ΡΡΠΊΠΎΠΉ Π½Π΅ ΡΡΠ΅Π±ΡΠ΅ΡΡΡ ΠΌΠ½ΠΎΠ³ΠΎ ΠΌΠ΅ΡΡΠ°, Π° Π΄Π»Ρ Π΅Π΅ ΠΎΠ±ΡΡΡΡΠΎΠΉΡΡΠ²Π° Π½Π΅ ΠΏΠΎΠ½Π°Π΄ΠΎΠ±ΠΈΡΡΡ ΠΏΡΠΈΠΎΠ±ΡΠ΅ΡΠ°ΡΡ ΡΠΏΠ΅ΡΠΈΠ°Π»ΡΠ½ΡΠΉ Π³ΠΎΡΠ½, Π΄ΠΎΡΡΠ°ΡΠΎΡΠ½ΠΎ ΠΊΡΠΏΠΈΡΡ ΡΡΠ°Π½ΠΎΠΊ Π΄Π»Ρ ΠΊΠΎΠ²ΠΊΠΈ.
ΠΡΠΎΡΠ΅ΡΡ ΠΈΠ·Π³ΠΎΡΠΎΠ²Π»Π΅Π½ΠΈΡ ΠΈΠ·Π΄Π΅Π»ΠΈΡ ΠΏΡΠ΅Π΄ΠΏΠΎΠ»Π°Π³Π°Π΅Ρ ΡΠ°Π±ΠΎΡΡ Ρ Π·Π°Π³ΠΎΡΠΎΠ²ΠΊΠ°ΠΌΠΈ-ΠΏΠΎΠ»ΡΡΠ°Π±ΡΠΈΠΊΠ°ΡΠ°ΠΌΠΈ. ΠΡΠ»ΠΈ Π±ΡΠ»Π° Π΄ΠΎΠΏΡΡΠ΅Π½Π° ΠΎΡΠΈΠ±ΠΊΠ°, ΡΠΎ ΠΈΡΠΏΡΠ°Π²ΠΈΡΡ Π΅Π΅ Π½Π΅Π²ΠΎΠ·ΠΌΠΎΠΆΠ½ΠΎ.
ΠΠ»Ρ ΡΡΡΠ½ΠΎΠΉ ΠΊΠΎΠ²ΠΊΠΈ ΠΏΠΎΠ΄Ρ ΠΎΠ΄ΡΡ ΠΌΠ΅ΡΠ°Π»Π»Ρ, ΠΎΠ±Π»Π°Π΄Π°ΡΡΠΈΠ΅ ΠΎΠΏΡΠ΅Π΄Π΅Π»Π΅Π½Π½ΡΠΌΠΈ ΡΠ²ΠΎΠΉΡΡΠ²Π°ΠΌΠΈ. Π§Π΅ΠΌ ΠΏΠ»Π°ΡΡΠΈΡΠ½Π΅Π΅ ΠΌΠ΅ΡΠ°Π»Π», ΡΠ΅ΠΌ Π»Π΅Π³ΡΠ΅ ΠΈΠ·ΠΌΠ΅Π½ΠΈΡΡ Π΅Π³ΠΎ ΡΠΎΡΠΌΡ. ΠΠ΄Π½Π°ΠΊΠΎ ΠΏΠ»Π°ΡΡΠΈΡΠ½ΠΎΡΡΡ Π½Π΅ΡΠ°Π·ΡΡΠ²Π½ΠΎ ΡΠ²ΡΠ·Π°Π½Π° Ρ ΠΏΡΠΎΡΠ½ΠΎΡΡΡΡ.
Π£Π²Π΅Π»ΠΈΡΠ΅Π½ΠΈΠ΅ ΠΏΠΎΠΊΠ°Π·Π°ΡΠ΅Π»Ρ ΠΎΠ΄Π½ΠΎΠΉ Ρ Π°ΡΠ°ΠΊΡΠ΅ΡΠΈΡΡΠΈΠΊΠΈ Π½Π΅ΠΈΠ·Π±Π΅ΠΆΠ½ΠΎ Π²Π»Π΅ΡΠ΅Ρ Π·Π° ΡΠΎΠ±ΠΎΠΉ ΡΠΌΠ΅Π½ΡΡΠ΅Π½ΠΈΠ΅ Π΄ΡΡΠ³ΠΎΠΉ. ΠΠΎΠΊΡΠΏΠ°Ρ Π·Π°Π³ΠΎΡΠΎΠ²ΠΊΡ, ΠΌΠ°ΡΡΠ΅Ρ Π΄ΠΎΠ»ΠΆΠ΅Π½ ΡΠΎΡΠ½ΠΎ Π·Π½Π°ΡΡ, ΠΊΠ°ΠΊΠΎΠΉ Ρ Π½Π΅Π΅ ΡΠΎΡΡΠ°Π².
ΠΠ΅ΠΊΠΎΡΠ°ΡΠΈΠ²Π½ΡΠ΅ ΡΠ»Π΅ΠΌΠ΅Π½ΡΡ ΠΊΠΎΠ²ΠΊΠΈ ΠΌΠ°ΡΡΠ΅ΡΠ° Π΄Π΅Π»Π°ΡΡ ΠΈΠ· ΠΌΠ΅Π΄ΠΈ, ΡΡΠ°Π»ΠΈ, Π΄ΡΡΠ°Π»ΡΠΌΠΈΠ½ΠΈΡ ΠΈΠ»ΠΈ Π»Π°ΡΡΠ½ΠΈ. ΠΡΠΎΠΌΠ΅ ΡΠΎΠ³ΠΎ, ΠΌΠΎΠ³ΡΡ ΡΠ°ΠΊΠΆΠ΅ ΠΈΡΠΏΠΎΠ»ΡΠ·ΠΎΠ²Π°ΡΡΡΡ ΡΠΏΠ»Π°Π²Ρ. ΠΠ½ΡΠΎΡΠΌΠ°ΡΠΈΡ ΠΎ ΠΌΠ΅ΡΠ°Π»Π»Π°Ρ , ΠΊΠΎΡΠΎΡΡΠ΅ Π»Π΅Π³ΠΊΠΎ ΠΏΠΎΠ΄Π΄Π°ΡΡΡΡ ΠΊΠΎΠ²ΠΊΠ΅, ΠΌΠΎΠΆΠ½ΠΎ Π½Π°ΠΉΡΠΈ Π² ΠΠ°ΡΠΎΡΠ½ΠΈΠΊΠ΅ Π‘ΡΠ°Π»ΠΈ ΠΈ Π‘ΠΏΠ»Π°Π²ΠΎΠ².
ΠΠ°ΠΊΠΈΠ΅ Π΄Π»Ρ ΠΊΠΎΠ²ΠΊΠΈ Π½ΡΠΆΠ½Ρ ΠΈΠ½ΡΡΡΡΠΌΠ΅Π½ΡΡ
ΠΠ½Π²Π΅Π½ΡΠ°ΡΡ Π²Π°ΡΡΠΈΡΡΠ΅ΡΡΡ Π² Π·Π°Π²ΠΈΡΠΈΠΌΠΎΡΡΠΈ ΠΎΡ ΡΠΏΠΎΡΠΎΠ±Π° ΠΊΠΎΠ²ΠΊΠΈ. ΠΡΠ·Π½Π΅ΡΠ½ΡΠΉ Π³ΠΎΡΠ½ Ρ Π½Π°ΠΊΠΎΠ²Π°Π»ΡΠ½Π΅ΠΉ, ΠΌΠΎΠ»ΠΎΡΡ Ρ ΠΊΠ»Π΅ΡΠ°ΠΌΠΈ ΠΏΠΎΠ½Π°Π΄ΠΎΠ±ΡΡΡΡ Π΄Π»Ρ Π³ΠΎΡΡΡΠ΅ΠΉ ΠΊΠΎΠ²ΠΊΠΈ.
ΠΠ»Ρ Ρ ΠΎΠ»ΠΎΠ΄Π½ΠΎΠ³ΠΎ ΡΠΏΠΎΡΠΎΠ±Π° Π½ΡΠΆΠ΅Π½ ΠΈΠ½ΡΡΡΡΠΌΠ΅Π½Ρ Β«ΠΠ½ΡΡΠΈΠΊΒ», ΠΏΠΎΠ·Π²ΠΎΠ»ΡΡΡΠΈΠΉ ΠΈΠ·Π³ΠΈΠ±Π°ΡΡ Π·Π°Π³ΠΎΡΠΎΠ²ΠΊΡ ΠΏΠΎΠ΄ ΡΠ³Π»ΠΎΠΌ, ΠΈ ΡΡΠ°Π½ΠΎΠΊ Β«Π£Π»ΠΈΡΠΊΠ°Β» Π΄Π»Ρ ΠΊΠΎΠ²ΠΊΠΈ. ΠΠΎΡΠ»Π΅Π΄Π½ΠΈΠΉ ΡΡΠ°Π½ΠΎΠΊ ΠΏΠΎΠ·Π²ΠΎΠ»ΡΠ΅Ρ ΡΠΎΠ·Π΄Π°Π²Π°ΡΡ ΡΠ»Π΅ΠΌΠ΅Π½ΡΡ Π΄Π΅ΠΊΠΎΡΠ° Ρ ΡΠΎΡΠΌΠΎΠΉ Π² Π²ΠΈΠ΄Π΅ ΡΠΏΠΈΡΠ°Π»ΠΈ.
Π‘ΠΎΠ²ΡΠ΅ΠΌΠ΅Π½Π½ΡΠΉ ΡΡΠ½ΠΎΠΊ ΠΏΡΠ΅Π΄Π»Π°Π³Π°Π΅Ρ ΠΏΡΠΎΠΌΡΡΠ»Π΅Π½Π½ΡΠ΅ ΡΡΠ°Π½ΠΊΠΈ, ΠΏΡΠ΅Π΄Π½Π°Π·Π½Π°ΡΠ΅Π½Π½ΡΠ΅ Π΄Π»Ρ Π²ΡΠΏΠΎΠ»Π½Π΅Π½ΠΈΡ ΡΠ΅Ρ Π½ΠΎΠ»ΠΎΠ³ΠΈΡΠ΅ΡΠΊΠΈΡ ΠΎΠΏΠ΅ΡΠ°ΡΠΈΠΉ.
Π§ΡΠΎΠ±Ρ Π·Π°Π³ΠΎΡΠΎΠ²ΠΊΠ° ΠΏΡΠΈΠΎΠ±ΡΠ΅Π»Π° Π½ΡΠΆΠ½ΡΡ ΡΠΎΡΠΌΡ, ΠΌΠ°ΡΡΠ΅Ρ Π΄ΠΎΠ»ΠΆΠ΅Π½ ΠΏΡΠΈΠΌΠ΅Π½ΡΡΡ Π² ΡΠ²ΠΎΠ΅ΠΉ ΡΠ°Π±ΠΎΡΠ΅ ΡΠ°Π·Π½ΡΠ΅ ΠΏΡΠΈΠ΅ΠΌΡ ΠΈ ΠΌΠ΅ΡΠΎΠ΄Ρ. ΠΠΎΠ½Π°Π΄ΠΎΠ±ΠΈΡΡΡ ΠΏΡΠΈΠΎΠ±ΡΠ΅ΡΡΠΈ ΡΠ°Π·Π»ΠΈΡΠ½ΡΠ΅ ΠΈΠ½ΡΡΡΡΠΌΠ΅Π½ΡΡ ΠΈ ΠΎΠ²Π»Π°Π΄Π΅ΡΡ ΡΠ°Π·Π½ΡΠΌΠΈ ΡΠ΅Ρ Π½ΠΎΠ»ΠΎΠ³ΠΈΡΠΌΠΈ.
Π₯ΠΎΠ»ΠΎΠ΄Π½ΡΠΉ ΡΠΏΠΎΡΠΎΠ± ΠΊΠΎΠ²ΠΊΠΈ Π½Π΅ ΡΡΠ΅Π±ΡΠ΅Ρ ΠΎΡ ΠΌΠ°ΡΡΠ΅ΡΠ° ΠΏΡΠΈΠ»ΠΎΠΆΠ΅Π½ΠΈΡ ΠΎΡΠΎΠ±ΡΡ ΡΡΠΈΠ»ΠΈΠΉ. Π ΡΠ°Π±ΠΎΡΠ΅ Π²ΡΠ΄Π΅Π»ΡΡΡΡΡ ΡΠ»Π΅Π΄ΡΡΡΠΈΠ΅ ΡΡΠ°ΠΏΡ:
ΡΠΎΠ·Π΄Π°Π½ΠΈΠ΅ ΡΠ΅ΡΡΠ΅ΠΆΠ° ΠΈΠ»ΠΈ Π²ΡΠΏΠΎΠ»Π½Π΅Π½ΠΈΠ΅ ΡΡΠΊΠΈΠ·Π° Π΄Π΅ΠΊΠΎΡΠ°ΡΠΈΠ²Π½ΠΎΠ³ΠΎ ΡΠ»Π΅ΠΌΠ΅Π½ΡΠ°
Π‘Π΅Π³ΠΎΠ΄Π½Ρ ΡΠ΅ΡΡΠ΅ΠΆ ΠΌΠΎΠΆΠ½ΠΎ ΡΠ΄Π΅Π»Π°ΡΡ Ρ ΠΏΠΎΠΌΠΎΡΡΡ ΠΊΠΎΠΌΠΏΡΡΡΠ΅ΡΠ½ΠΎΠΉ ΠΏΡΠΎΠ³ΡΠ°ΠΌΠΌΡ ΡΠ°ΠΌΠΎΡΡΠΎΡΡΠ΅Π»ΡΠ½ΠΎ ΠΈΠ»ΠΈ Π·Π°ΠΊΠ°Π·Π°ΡΡ ΠΏΡΠΎΡΠ΅ΡΡΠΈΠΎΠ½Π°Π»Π°ΠΌ. ΠΡΠΎΠ΅ΠΊΡ ΠΏΠΎΠ·Π²ΠΎΠ»ΠΈΡ Π΄ΠΎ Π½Π°ΡΠ°Π»Π° ΡΠ°Π±ΠΎΡΡ Π²ΡΡΠΈΡΠ»ΠΈΡΡ, ΡΠΊΠΎΠ»ΡΠΊΠΎ Π½ΡΠΆΠ½ΠΎ ΠΏΡΠΈΠΎΠ±ΡΠ΅ΡΡΠΈ ΠΌΠ΅ΡΠ°Π»Π»ΠΈΡΠ΅ΡΠΊΠΈΡ
Π·Π°Π³ΠΎΡΠΎΠ²ΠΎΠΊ. ΠΠ°ΠΊ Π΄Π΅Π»Π°Π΅ΡΡΡ Π΄Π΅ΡΠ΅Π²ΡΠ½Π½Π°Ρ Π±ΠΎΡΠΊΠ° ΡΠ²ΠΎΠΈΠΌΠΈ ΡΡΠΊΠ°ΠΌΠΈ: ΠΏΡΠΎΡΡΡΠ΅ ΠΏΠΎΡΠ°Π³ΠΎΠ²ΡΠ΅ ΠΈΠ½ΡΡΡΡΠΊΡΠΈΠΈ ΠΏΠΎ ΠΏΠΎΡΡΡΠΎΠΉΠΊΠ΅ ΡΡΠ°Π΄ΠΈΡΠΈΠΎΠ½Π½ΠΎΠΉ ΡΠ°ΡΡ Π’ΠΈΡΠΊΠΈ ΡΠ²ΠΎΠΈΠΌΠΈ ΡΡΠΊΠ°ΠΌΠΈ: ΡΠΎΠ·Π΄Π°Π΅ΠΌ ΡΠ°Π·Π½ΡΠ΅ ΡΠΈΠΏΡ Π·Π°ΠΆΠΈΠΌΠ½ΡΡ
ΡΡΡΡΠΎΠΉΡΡΠ².
ΠΡΠ½ΠΎΠ²Π½ΡΠ΅ ΠΊΠΎΠ²Π°Π½ΡΠ΅ ΡΠ»Π΅ΠΌΠ΅Π½ΡΡ ΠΏΡΠ΅Π΄ΡΡΠ°Π²Π»Π΅Π½Ρ ΡΠ»Π΅Π΄ΡΡΡΠΈΠΌΠΈ Π³ΡΡΠΏΠΏΠ°ΠΌΠΈ:
ΠΠ°ΠΏΠΊΠΈ. ΠΠΎΠ½ΡΡ ΠΌΠ΅ΡΠ°Π»Π»ΠΈΡΠ΅ΡΠΊΠΎΠ³ΠΎ ΠΏΡΡΡΠ° ΠΏΡΠΈΠ΄Π°Π΅ΡΡΡ ΠΎΠΏΡΠ΅Π΄Π΅Π»Π΅Π½Π½Π°Ρ ΡΠΎΡΠΌΠ°
ΠΠ°Π²ΠΈΡΠΊΠΈ. ΠΠΎΠ½ΡΡ ΠΏΡΡΡΠ° ΠΌΠΎΠ³ΡΡ Π±ΡΡΡ Π·Π°Π³Π½ΡΡΡ Π² ΠΎΠ΄Π½Ρ ΠΈΠ»ΠΈ Π΄Π²Π΅ ΡΡΠΎΡΠΎΠ½Ρ.
ΠΠΎΠ»ΡΡΠ°. ΠΠ»Π΅ΠΌΠ΅Π½ΡΡ Π΄Π΅ΠΊΠΎΡΠ° ΠΈΠ·Π³ΠΎΡΠ°Π²Π»ΠΈΠ²Π°ΡΡΡΡ ΠΈΠ· ΠΏΡΡΡΡΠ΅Π² Ρ ΠΊΠ²Π°Π΄ΡΠ°ΡΠ½ΡΠΌ ΠΈΠ»ΠΈ ΠΊΡΡΠ³Π»ΡΠΌ ΡΠ΅ΡΠ΅Π½ΠΈΠ΅ΠΌ.
ΠΡΡΡΠΆΠΊΠ° ΠΏΠΎΠ·Π²ΠΎΠ»ΡΠ΅Ρ ΡΠ²Π΅Π»ΠΈΡΠΈΠ²Π°ΡΡ Π΄Π»ΠΈΠ½Ρ ΠΌΠ΅ΡΠ°Π»Π»ΠΈΡΠ΅ΡΠΊΠΎΠΉ Π·Π°Π³ΠΎΡΠΎΠ²ΠΊΠΈ, ΡΠΌΠ΅Π½ΡΡΠ°Ρ Π·Π½Π°ΡΠ΅Π½ΠΈΠ΅ Π΅Π΅ ΡΠ΅ΡΠ΅Π½ΠΈΡ. ΠΠΈΠ±ΠΊΠ° Π΄Π°Π΅Ρ Π²ΠΎΠ·ΠΌΠΎΠΆΠ½ΠΎΡΡΡ Π·Π°Π³ΠΈΠ±Π°ΡΡ Π»ΡΠ±ΡΡ ΡΠ°ΡΡΡ Π·Π°Π³ΠΎΡΠΎΠ²ΠΊΠΈ ΠΏΠΎΠ΄ ΡΠ³Π»ΠΎΠΌ.
ΠΡΠ΅ ΡΠ»Π΅ΠΌΠ΅Π½ΡΡ ΡΠΎΠ±ΠΈΡΠ°ΡΡΡΡ Π²ΠΌΠ΅ΡΡΠ΅ ΠΈ Π·Π°ΠΊΡΠ΅ΠΏΠ»ΡΡΡΡΡ Ρ ΠΏΠΎΠΌΠΎΡΡΡ ΡΠ²Π°ΡΠΊΠΈ. ΠΡΠΈ ΠΎΠΏΠ΅ΡΠ°ΡΠΈΠΈ Π²ΡΠΏΠΎΠ»Π½ΡΡΡΡΡ Π½Π° ΡΠΏΠ΅ΡΠΈΠ°Π»ΡΠ½ΠΎΠΌ ΡΡΠΎΠ»Π΅.
ΠΠΈΡΡΠ΅, ΡΠΎΡΠΌΠΎΠ²ΠΊΠ° ΠΈ ΠΊΠΎΠ²ΠΊΠ° | ΠΡΡΠ½Π°Π» Gear Solutions ΠΠ°Ρ ΡΠ΅ΡΡΡΡ Π΄Π»Ρ ΠΏΡΠΎΠΈΠ·Π²ΠΎΠ΄ΠΈΡΠ΅Π»Π΅ΠΉ Π·ΡΠ±ΡΠ°ΡΡΡ ΠΊΠΎΠ»Π΅Ρ
ΠΡΠΎΠΈΠ·Π²ΠΎΠ΄ΠΈΡΠ΅Π»ΠΈ Π·ΡΠ±ΡΠ°ΡΡΡ ΠΊΠΎΠ»Π΅Ρ Π·Π°Π²ΠΈΡΡΡ ΠΎΡ ΠΈΠΌΠ΅ΡΡΠ΅Π³ΠΎΡΡ ΠΎΠ±ΠΎΡΡΠ΄ΠΎΠ²Π°Π½ΠΈΡ, ΡΠΏΠ΅ΡΠΈΡΠΈΠΊΠ°ΡΠΈΠΉ ΠΈΠ»ΠΈ ΡΡΠ΅Π±ΠΎΠ²Π°Π½ΠΈΠΉ ΠΊ ΠΊΠΎΠ½ΡΡΡΡΠΊΡΠΈΠΈ, ΡΡΠΎΠΈΠΌΠΎΡΡΠΈ ΠΏΡΠΎΠΈΠ·Π²ΠΎΠ΄ΡΡΠ²Π° ΠΈ ΡΠΈΠΏΠ° ΠΌΠ°ΡΠ΅ΡΠΈΠ°Π»Π°, ΠΈΠ· ΠΊΠΎΡΠΎΡΠΎΠ³ΠΎ Π΄ΠΎΠ»ΠΆΠ½ΠΎ Π±ΡΡΡ ΠΈΠ·Π³ΠΎΡΠΎΠ²Π»Π΅Π½ΠΎ Π·ΡΠ±ΡΠ°ΡΠΎΠ΅ ΠΊΠΎΠ»Π΅ΡΠΎ.
Π‘ΡΡΠ΅ΡΡΠ²ΡΠ΅Ρ ΠΌΠ½ΠΎΠΆΠ΅ΡΡΠ²ΠΎ ΠΌΠ΅ΡΠΎΠ΄ΠΎΠ² ΠΈΠ·Π³ΠΎΡΠΎΠ²Π»Π΅Π½ΠΈΡ Π·ΡΠ±ΡΠ°ΡΡΡ ΠΊΠΎΠ»Π΅Ρ, Π² ΡΠΎΠΌ ΡΠΈΡΠ»Π΅:
- ΠΡΠΎΡΠ΅ΡΡΡ ΡΠ΄Π°Π»Π΅Π½ΠΈΡ ΠΌΠ΅ΡΠ°Π»Π»Π° (ΠΎΠ±ΡΠ°Π±ΠΎΡΠΊΠ°, ΡΠΎΡΠΌΠΎΠ²ΠΊΠ°, ΡΡΠ΅Π·Π΅ΡΠΎΠ²Π°Π½ΠΈΠ΅, ΡΠ»ΠΈΡΠΎΠ²Π°Π½ΠΈΠ΅, ΡΠ»ΠΈΡΠΎΠ²Π°Π½ΠΈΠ΅, Ρ ΠΎΠ½ΠΈΠ½Π³ΠΎΠ²Π°Π½ΠΈΠ΅ ΠΈ ΠΏΡΠΈΡΠΈΡΠΊΠ°)
- Π Π°Π·Π»ΠΈΡΠ½ΡΠ΅ ΠΏΡΠΎΡΠ΅ΡΡΡ Π»ΠΈΡΡΡ ΠΊΠ°ΠΊ Π΄Π»Ρ ΠΏΡΠΎΠΈΠ·Π²ΠΎΠ΄ΡΡΠ²Π° Π·Π°Π³ΠΎΡΠΎΠ²ΠΎΠΊ Π·ΡΠ±ΡΠ°ΡΡΡ ΠΊΠΎΠ»Π΅Ρ, ΡΠ°ΠΊ ΠΈ Π΄Π»Ρ ΠΈΠ·Π³ΠΎΡΠΎΠ²Π»Π΅Π½ΠΈΡ Π·ΡΠ±ΡΠ°ΡΡΡ ΠΊΠΎΠ»Π΅Ρ
- Π¨ΡΠ°ΠΌΠΏΠΎΠ²ΠΊΠ° ΠΈ ΡΠΈΡΡΠΎΠ²Π°Ρ Π²ΡΡΡΠ±ΠΊΠ°
- Π₯ΠΎΠ»ΠΎΠ΄Π½ΠΎΠ΅ Π²ΠΎΠ»ΠΎΡΠ΅Π½ΠΈΠ΅ ΠΈ ΡΠΊΡΡΡΡΠ·ΠΈΡ
- ΠΠ±ΡΠ°Π±ΠΎΡΠΊΠ° ΠΏΠΎΡΠΎΡΠΊΠΎΠ²ΠΎΠΉ ΠΌΠ΅ΡΠ°Π»Π»ΡΡΠ³ΠΈΠΈ (P/M)
- ΠΠΈΡΡΠ΅ ΠΏΠΎΠ΄ Π΄Π°Π²Π»Π΅Π½ΠΈΠ΅ΠΌ
- ΠΡΠ±ΡΠ°ΡΠ°Ρ ΠΏΠ΅ΡΠ΅Π΄Π°ΡΠ°
- ΠΠΎΠΊΠΎΠ²ΠΊΠ° Π΄Π»Ρ ΠΈΠ·Π³ΠΎΡΠΎΠ²Π»Π΅Π½ΠΈΡ Π·Π°Π³ΠΎΡΠΎΠ²ΠΎΠΊ Π·ΡΠ±ΡΠ°ΡΡΡ ΠΊΠΎΠ»Π΅Ρ ΠΈ ΡΠΎΡΠ½ΠΎΠΊΠΎΠ²Π°Π½ΡΡ ΠΏΠΎΠ»ΡΠΊΡΡΠ³Π»ΡΡ ΠΈ ΡΠ΅ΡΡΠ°ΡΡΡ Π·ΡΠ±ΡΠ°ΡΡΡ ΠΊΠΎΠ»Π΅Ρ
ΠΠΎΠ»ΡΡΠΈΠ½ΡΡΠ²ΠΎ ΠΏΠ΅ΡΠ΅ΡΠΈΡΠ»Π΅Π½Π½ΡΡ
ΠΏΡΠΎΡΠ΅ΡΡΠΎΠ² ΠΏΠΎΠ΄Ρ
ΠΎΠ΄ΡΡ Π΄Π»Ρ Π·ΡΠ±ΡΠ°ΡΡΡ
ΠΏΠ΅ΡΠ΅Π΄Π°Ρ Ρ Π½ΠΈΠ·ΠΊΠΈΠΌΠΈ ΡΡΠ΅Π±ΠΎΠ²Π°Π½ΠΈΡΠΌΠΈ ΠΊ ΠΈΠ·Π½ΠΎΡΡ, Π½ΠΈΠ·ΠΊΠΎΠΉ ΠΏΠ΅ΡΠ΅Π΄Π°ΡΠ΅ΠΉ ΠΌΠΎΡΠ½ΠΎΡΡΠΈ ΠΈ ΠΎΡΠ½ΠΎΡΠΈΡΠ΅Π»ΡΠ½ΠΎ Π½ΠΈΠ·ΠΊΠΎΠΉ ΡΠΎΡΠ½ΠΎΡΡΡΡ ΠΏΠ΅ΡΠ΅Π΄Π°Π²Π°Π΅ΠΌΠΎΠ³ΠΎ Π΄Π²ΠΈΠΆΠ΅Π½ΠΈΡ [1]. ΠΠΎΠ³Π΄Π° ΠΏΡΠΈΠΌΠ΅Π½Π΅Π½ΠΈΠ΅ ΠΏΡΠ΅Π΄ΠΏΠΎΠ»Π°Π³Π°Π΅Ρ Π±ΠΎΠ»Π΅Π΅ Π²ΡΡΠΎΠΊΠΈΠ΅ Π·Π½Π°ΡΠ΅Π½ΠΈΡ ΠΎΠ΄Π½ΠΎΠΉ ΠΈΠ»ΠΈ Π½Π΅ΡΠΊΠΎΠ»ΡΠΊΠΈΡ
ΠΈΠ· ΡΡΠΈΡ
Ρ
Π°ΡΠ°ΠΊΡΠ΅ΡΠΈΡΡΠΈΠΊ, ΠΈΡΠΏΠΎΠ»ΡΠ·ΡΡΡΡΡ ΠΊΠΎΠ²Π°Π½ΡΠ΅ ΠΈΠ»ΠΈ Π²ΡΡΠ΅Π·Π°Π½Π½ΡΠ΅/ΠΎΠ±ΡΠ°Π±ΠΎΡΠ°Π½Π½ΡΠ΅ ΡΠ΅ΡΡΠ΅ΡΠ½ΠΈ. Π ΡΠ°Π±Π»ΠΈΡΠ΅ 1 ΠΏΠ΅ΡΠ΅ΡΠΈΡΠ»Π΅Π½Ρ Π΄ΠΎΠΏΡΡΠΊΠΈ ΠΏΠΎ ΠΏΠΎΠΊΠ°Π·Π°ΡΠ΅Π»ΡΠΌ ΠΊΠ°ΡΠ΅ΡΡΠ²Π° AGMA Π΄Π»Ρ ΡΠ°Π·Π»ΠΈΡΠ½ΡΡ
ΠΏΡΠΎΡΠ΅ΡΡΠΎΠ² ΠΈΠ·Π³ΠΎΡΠΎΠ²Π»Π΅Π½ΠΈΡ Π·ΡΠ±ΡΠ°ΡΡΡ
ΠΊΠΎΠ»Π΅Ρ [2].
ΠΠΈΡΡΠ΅
Π₯ΠΎΡΡ ΠΏΡΠΎΡΠ΅ΡΡ Π»ΠΈΡΡΡ ΡΠ°ΡΠ΅ Π²ΡΠ΅Π³ΠΎ ΠΈΡΠΏΠΎΠ»ΡΠ·ΡΠ΅ΡΡΡ Π΄Π»Ρ ΠΈΠ·Π³ΠΎΡΠΎΠ²Π»Π΅Π½ΠΈΡ Π·Π°Π³ΠΎΡΠΎΠ²ΠΎΠΊ Π΄Π»Ρ Π·ΡΠ±ΡΠ°ΡΡΡ ΠΊΠΎΠ»Π΅Ρ Ρ Π½Π°ΡΠ΅Π·Π°Π½Π½ΡΠΌΠΈ Π·ΡΠ±ΡΡΠΌΠΈ (ΡΠΈΡ. 1 ΠΈ ΡΠΈΡ. 2), ΡΡΡΠ΅ΡΡΠ²ΡΠ΅Ρ Π½Π΅ΡΠΊΠΎΠ»ΡΠΊΠΎ Π²Π°ΡΠΈΠ°Π½ΡΠΎΠ² ΠΏΡΠΎΡΠ΅ΡΡΠ° Π»ΠΈΡΡΡ, ΠΈΡΠΏΠΎΠ»ΡΠ·ΡΠ΅ΠΌΡΡ Π΄Π»Ρ ΠΈΠ·Π³ΠΎΡΠΎΠ²Π»Π΅Π½ΠΈΡ Π·ΡΠ±ΡΠ°ΡΡΡ ΠΊΠΎΠ»Π΅Ρ Ρ ΠΌΠΈΠ½ΠΈΠΌΠ°Π»ΡΠ½ΠΎΠΉ ΠΌΠ΅Ρ Π°Π½ΠΈΡΠ΅ΡΠΊΠΎΠΉ ΠΎΠ±ΡΠ°Π±ΠΎΡΠΊΠΎΠΉ ΠΈΠ»ΠΈ Π±Π΅Π· Π½Π΅Π΅.
Π ΠΈΡΡΠ½ΠΎΠΊ 1: ΠΠ°Π³ΠΎΡΠΎΠ²ΠΊΠ° ΡΠ΅ΡΡΠ΅ΡΠ½ΠΈ ΠΈΠ· Π»ΠΈΡΠΎΠΉ ΡΡΠ°Π»ΠΈ. ΠΠ΅Ρ: 478 ΠΊΠ³ (1053 ΡΡΠ½ΡΠ°). [3]Π ΠΈΡΡΠ½ΠΎΠΊ 2: ΠΠΎΠ»ΡΡΠ°Ρ Π»ΠΈΡΠ°Ρ ΡΡΠ°Π»ΡΠ½Π°Ρ ΡΠ΅ΡΡΠ΅ΡΠ½Ρ, ΠΎΠ±ΡΠ°Π±ΠΎΡΠ°Π½Π½Π°Ρ ΠΌΠ΅Ρ
Π°Π½ΠΈΡΠ΅ΡΠΊΠΎΠΉ ΠΎΠ±ΡΠ°Π±ΠΎΡΠΊΠΎΠΉ. [3] ΠΠ°ΠΏΡΠΈΠΌΠ΅Ρ, Π²Π½ΡΡΡΠ΅Π½Π½ΠΈΠ΅ ΡΠ΅ΡΡΠ΅ΡΠ½ΠΈ Ρ Π»ΠΈΡΡΠΌΠΈ Π·ΡΠ±ΡΡΠΌΠΈ (ΡΠΈΡ. 3) Π²ΡΠΏΡΡΠΊΠ°ΡΡΡΡ Π½Π΅ΡΠΊΠΎΠ»ΡΠΊΠΈΡ
ΡΠΈΠΏΠΎΡΠ°Π·ΠΌΠ΅ΡΠΎΠ² Π΄ΠΎ 1633 ΠΊΠ³ (3600 ΡΡΠ½ΡΠΎΠ²). ΠΠ½ΠΈ ΠΏΠΎΠ΄Π²Π΅ΡΠ³Π°ΡΡΡΡ ΡΠ΅ΡΠΌΠΎΠΎΠ±ΡΠ°Π±ΠΎΡΠΊΠ΅ Π΄ΠΎ ΡΡΠΎΠ²Π½Ρ ΠΏΡΠΎΡΠ½ΠΎΡΡΠΈ 689. ΠΠΠ° (100 ΡΡΠ½ΡΠΎΠ² Π½Π° ΠΊΠ²Π°Π΄ΡΠ°ΡΠ½ΡΠΉ Π΄ΡΠΉΠΌ), ΠΈ ΠΎΠ±ΡΠ°Π±ΠΎΡΠΊΠ° ΡΡΠΈΡ
ΡΠ΅ΡΡΠ΅ΡΠ΅Π½ Π½Π΅ ΡΡΠ΅Π±ΡΠ΅ΡΡΡ. Π ΠΎΠ±ΡΡΠΎΡΡΠ΅Π»ΡΡΡΠ²Π°Ρ
, ΠΊΠΎΠ³Π΄Π° Π½Π΅ΠΎΠ±Ρ
ΠΎΠ΄ΠΈΠΌΠ° ΠΌΠ΅Ρ
Π°Π½ΠΈΡΠ΅ΡΠΊΠ°Ρ ΠΎΠ±ΡΠ°Π±ΠΎΡΠΊΠ°, Π·Π°ΡΡΠ°ΡΡ Π½Π° ΠΌΠ΅Ρ
Π°Π½ΠΈΡΠ΅ΡΠΊΡΡ ΠΎΠ±ΡΠ°Π±ΠΎΡΠΊΡ ΡΠΎΠΊΡΠ°ΡΠ°ΡΡΡΡ Π·Π° ΡΡΠ΅Ρ Π»ΠΈΡΡΡ Π±Π»ΠΈΠΆΠ΅ ΠΊ ΠΎΠΊΠΎΠ½ΡΠ°ΡΠ΅Π»ΡΠ½ΠΎΠΉ ΡΠΎΡΠΌΠ΅.
ΠΡΡΠ³ΠΈΠΌ ΠΏΡΠΈΠΌΠ΅ΡΠΎΠΌ Π»ΠΈΡΠΎΠ³ΠΎ Π·ΡΠ±ΡΠ°ΡΠΎΠ³ΠΎ ΠΊΠΎΠ»Π΅ΡΠ° ΡΠ²Π»ΡΠ΅ΡΡΡ Π·ΡΠ±ΡΠ°ΡΠΎΠ΅ ΠΊΠΎΠ»Π΅ΡΠΎ, ΠΈΠ·Π³ΠΎΡΠΎΠ²Π»Π΅Π½Π½ΠΎΠ΅ ΠΈΠ· Π»ΠΈΡΠΎΠΉ Π²ΡΡΠΎΠΊΠΎΠΌΠ°ΡΠ³Π°Π½ΡΠΎΠ²ΠΈΡΡΠΎΠΉ (ΠΠ°Π΄ΡΠΈΠ»ΡΠ΄Π°) ΡΡΠ°Π»ΠΈ Π΄Π»Ρ ΠΊΠ°ΡΡΠ΅ΡΠ½ΠΎΠ³ΠΎ ΡΠ»Π΅ΠΊΡΡΠΈΡΠ΅ΡΠΊΠΎΠ³ΠΎ ΡΠΊΡΠΊΠ°Π²Π°ΡΠΎΡΠ°, ΠΏΠΎΠΊΠ°Π·Π°Π½Π½ΠΎΠ΅ Π½Π° ΡΠΈΡ. 4. ΠΡΠ±ΡΡ Π·ΡΠ±ΡΠ°ΡΠΎΠ³ΠΎ ΠΊΠΎΠ»Π΅ΡΠ° Π½Π΅ ΡΡΠ΅Π±ΠΎΠ²Π°Π»ΠΎΡΡ ΠΎΠ±ΡΠ°Π±Π°ΡΡΠ²Π°ΡΡ.
Π ΠΈΡ. 3. Π¨Π΅ΡΡΠ΅ΡΠ½ΠΈ Ρ Π»ΠΈΡΡΠΌΠΈ Π·ΡΠ±ΡΡΠΌΠΈ. ΠΠ΅Ρ Π΄ΠΎ 1633 ΠΊΠ³ (3600 ΡΡΠ½ΡΠΎΠ²). [3]Π ΠΈΡΡΠ½ΠΎΠΊ 4: Π¨Π΅ΡΡΠ΅ΡΠ½Ρ Ρ Π»ΠΈΡΡΠΌΠΈ Π·ΡΠ±ΡΡΠΌΠΈ Π΄Π»Ρ ΡΠ»Π΅ΠΊΡΡΠΈΡΠ΅ΡΠΊΠΎΠ³ΠΎ ΠΊΠ°ΡΡΠ΅ΡΠ½ΠΎΠ³ΠΎ ΡΠΊΡΠΊΠ°Π²Π°ΡΠΎΡΠ°. ΠΠ΅Ρ: 212 ΠΊΠ³ (468 ΡΡΠ½ΡΠΎΠ²). [3]
Π‘ΠΏΠ΅ΡΠΈΠ°Π»ΡΠ½ΡΠ΅ ΠΏΡΠΎΡΠ΅ΡΡΡ Π»ΠΈΡΡΡ

ΠΡΠΎΡΠ΅ΡΡ ΠΎΠ±ΠΎΠ»ΠΎΡΠΊΠΎΠ²ΠΎΠ³ΠΎ ΡΠΎΡΠΌΠΎΠ²Π°Π½ΠΈΡ ΠΎΡΠΎΠ±Π΅Π½Π½ΠΎ ΠΏΠΎΠ΄Ρ ΠΎΠ΄ΠΈΡ Π΄Π»Ρ ΠΎΡΠ»ΠΈΠ²ΠΎΠΊ, Π΄Π»Ρ ΠΊΠΎΡΠΎΡΡΡ :
- ΠΠΎΠ»Π΅Π΅ Π²ΡΡΠΎΠΊΠ°Ρ ΡΠΎΡΠ½ΠΎΡΡΡ ΡΠ°Π·ΠΌΠ΅ΡΠΎΠ², ΠΎΠ±Π΅ΡΠΏΠ΅ΡΠΈΠ²Π°Π΅ΠΌΠ°Ρ ΠΎΠ±ΠΎΠ»ΠΎΡΠΊΠΎΠ²ΡΠΌ ΡΠΎΡΠΌΠΎΠ²Π°Π½ΠΈΠ΅ΠΌ (ΠΏΠΎ ΡΡΠ°Π²Π½Π΅Π½ΠΈΡ Ρ ΠΎΠ±ΡΡΠ½ΡΠΌ ΡΠΎΡΠΌΠΎΠ²Π°Π½ΠΈΠ΅ΠΌ ΠΈΠ· ΡΡΡΠΎΠ³ΠΎ ΠΏΠ΅ΡΠΊΠ°), ΠΌΠΎΠΆΠ΅Ρ ΡΠΌΠ΅Π½ΡΡΠΈΡΡ ΠΎΠ±ΡΠ΅ΠΌ ΠΌΠ΅Ρ
Π°Π½ΠΈΡΠ΅ΡΠΊΠΎΠΉ ΠΎΠ±ΡΠ°Π±ΠΎΡΠΊΠΈ, Π½Π΅ΠΎΠ±Ρ
ΠΎΠ΄ΠΈΠΌΠΎΠΉ Π΄Π»Ρ Π·Π°Π²Π΅ΡΡΠ΅Π½ΠΈΡ Π΄Π΅ΡΠ°Π»ΠΈ.
- Π Π°Π·ΠΌΠ΅ΡΡ Π² ΡΠΎΡΡΠΎΡΠ½ΠΈΠΈ ΠΏΠΎΡΠ»Π΅ Π»ΠΈΡΡΡ Π½Π΅ ΡΠ²Π»ΡΡΡΡΡ ΠΊΡΠΈΡΠΈΡΠ΅ΡΠΊΠΈΠΌΠΈ, Π½ΠΎ Π³Π»Π°Π²Π½ΠΎΠΉ ΡΠ΅Π»ΡΡ ΡΠ²Π»ΡΡΡΡΡ Π³Π»Π°Π΄ΠΊΠΈΠ΅ ΠΏΠΎΠ²Π΅ΡΡ Π½ΠΎΡΡΠΈ (Π±ΠΎΠ»Π΅Π΅ Π³Π»Π°Π΄ΠΊΠΈΠ΅, ΡΠ΅ΠΌ ΠΏΡΠΈ Π»ΠΈΡΡΠ΅ Π² ΠΏΠ΅ΡΡΠ°Π½ΡΠ΅ ΡΠΎΡΠΌΡ). ΠΡΠΈΠΌΠ΅Ρ ΠΊΠΎΠ½ΠΈΡΠ΅ΡΠΊΠΎΠΉ ΠΏΠ΅ΡΠ΅Π΄Π°ΡΠΈ Ρ Π»ΠΈΡΡΠΌΠΈ Π·ΡΠ±ΡΡΠΌΠΈ ΠΈ ΠΏΡΠ΅Π²ΠΎΡΡ ΠΎΠ΄Π½ΡΠΌ ΠΊΠ°ΡΠ΅ΡΡΠ²ΠΎΠΌ ΠΏΠΎΠ²Π΅ΡΡ Π½ΠΎΡΡΠΈ, ΠΏΠΎΠ»ΡΡΠ΅Π½Π½ΠΎΠΉ ΠΏΡΡΠ΅ΠΌ ΡΠΎΡΠΌΠΎΠ²Π°Π½ΠΈΡ Π² ΠΊΠΎΠΆΡΡ , ΠΏΠΎΠΊΠ°Π·Π°Π½ Π½Π° ΡΠΈΡ. 5.9.0008
Π ΠΈΡ. 5. ΠΠΎΠ½ΠΈΡΠ΅ΡΠΊΠ°Ρ ΡΠ΅ΡΡΠ΅ΡΠ½Ρ Ρ Π»ΠΈΡΡΠΌΠΈ Π·ΡΠ±ΡΡΠΌΠΈ, ΠΈΠ·Π³ΠΎΡΠΎΠ²Π»Π΅Π½Π½Π°Ρ ΠΌΠ΅ΡΠΎΠ΄ΠΎΠΌ ΠΎΠ±ΠΎΠ»ΠΎΡΠ΅ΡΠ½ΠΎΠ³ΠΎ ΡΠΎΡΠΌΠΎΠ²Π°Π½ΠΈΡ Π΄Π»Ρ ΠΏΠΎΠ»ΡΡΠ΅Π½ΠΈΡ ΠΏΡΠ΅Π²ΠΎΡΡ
ΠΎΠ΄Π½ΡΡ
ΠΏΠΎΠ²Π΅ΡΡ
Π½ΠΎΡΡΠ΅ΠΉ ΠΈ ΠΆΠ΅ΡΡΠΊΠΈΡ
Π΄ΠΎΠΏΡΡΠΊΠΎΠ². [3] ΠΡΠΎΡΠ΅ΡΡ Π»ΠΈΡΡΡ ΠΏΠΎ Π²ΡΠΏΠ»Π°Π²Π»ΡΠ΅ΠΌΡΠΌ ΠΌΠΎΠ΄Π΅Π»ΡΠΌ ΡΠ°ΠΊΠΆΠ΅ ΠΈΠΌΠ΅Π΅Ρ ΠΎΠ³ΡΠ°Π½ΠΈΡΠ΅Π½Π½ΠΎΠ΅ ΠΏΡΠΈΠΌΠ΅Π½Π΅Π½ΠΈΠ΅ Π² ΠΏΡΠΎΠΈΠ·Π²ΠΎΠ΄ΡΡΠ²Π΅ Π·ΡΠ±ΡΠ°ΡΡΡ
ΠΊΠΎΠ»Π΅Ρ. ΠΠ³ΠΎ Π½Π°ΠΈΠ±ΠΎΠ»Π΅Π΅ ΠΎΡΠ΅Π²ΠΈΠ΄Π½Π°Ρ ΡΠ΅Π½Π½ΠΎΡΡΡ Π·Π°ΠΊΠ»ΡΡΠ°Π΅ΡΡΡ Π² ΠΈΠ·Π³ΠΎΡΠΎΠ²Π»Π΅Π½ΠΈΠΈ ΡΠΎΡΠ½ΡΡ
Π·ΡΠ±ΡΠ΅Π² ΡΠ΅ΡΡΠ΅ΡΠ½ΠΈ ΠΈΠ· ΠΌΠ°ΡΠ΅ΡΠΈΠ°Π»ΠΎΠ² Π½Π°ΡΡΠΎΠ»ΡΠΊΠΎ ΡΠ²Π΅ΡΠ΄ΡΡ
, ΡΡΠΎ Π·ΡΠ±ΡΡ Π½Π΅ ΠΌΠΎΠ³ΡΡ Π±ΡΡΡ Π»Π΅Π³ΠΊΠΎ ΠΈΠ·Π³ΠΎΡΠΎΠ²Π»Π΅Π½Ρ ΠΌΠ΅Ρ
Π°Π½ΠΈΡΠ΅ΡΠΊΠΎΠΉ ΠΎΠ±ΡΠ°Π±ΠΎΡΠΊΠΎΠΉ [4]. ΠΡΠΎΡ ΠΏΡΠΎΡΠ΅ΡΡ ΠΌΠΎΠΆΠ½ΠΎ ΠΈΡΠΏΠΎΠ»ΡΠ·ΠΎΠ²Π°ΡΡ Ρ ΡΠ°Π·Π»ΠΈΡΠ½ΡΠΌΠΈ ΡΡΠ°Π»ΡΠΌΠΈ, Π±ΡΠΎΠ½Π·Π°ΠΌΠΈ ΠΈ Π°Π»ΡΠΌΠΈΠ½ΠΈΠ΅Π²ΡΠΌΠΈ ΡΠΏΠ»Π°Π²Π°ΠΌΠΈ. Π‘ ΠΎΠ±ΡΠ°Π±Π°ΡΡΠ²Π°Π΅ΠΌΡΠΌΠΈ ΠΌΠ°ΡΠ΅ΡΠΈΠ°Π»Π°ΠΌΠΈ ΡΡΠΎΡ ΠΏΡΠΎΡΠ΅ΡΡ ΠΏΠΎ-ΠΏΡΠ΅ΠΆΠ½Π΅ΠΌΡ ΠΏΠΎΠ»Π΅Π·Π΅Π½, Π΅ΡΠ»ΠΈ Π·ΡΠ±ΡΠ°ΡΠΎΠ΅ ΠΊΠΎΠ»Π΅ΡΠΎ ΡΠ²Π»ΡΠ΅ΡΡΡ Π½Π΅ΠΎΡΡΠ΅ΠΌΠ»Π΅ΠΌΠΎΠΉ ΡΠ°ΡΡΡΡ ΡΠ»ΠΎΠΆΠ½ΠΎΠΉ ΡΠΎΡΠΌΡ, ΠΊΠΎΡΠΎΡΡΡ ΠΎΡΠ΅Π½Ρ ΡΡΡΠ΄Π½ΠΎ ΠΈΠ·Π³ΠΎΡΠΎΠ²ΠΈΡΡ ΠΌΠ΅Ρ
Π°Π½ΠΈΡΠ΅ΡΠΊΠΎΠΉ ΠΎΠ±ΡΠ°Π±ΠΎΡΠΊΠΎΠΉ.
ΠΠΎΠ»ΡΡΠΎΠ΅ ΠΊΠΎΠ»ΠΈΡΠ΅ΡΡΠ²ΠΎ Π½Π΅Π±ΠΎΠ»ΡΡΠΈΡ Π½Π΅Π΄ΠΎΡΠΎΠ³ΠΈΡ ΡΠ΅ΡΡΠ΅ΡΠ΅Π½ ΠΈΠ·Π³ΠΎΡΠ°Π²Π»ΠΈΠ²Π°Π΅ΡΡΡ ΠΌΠ΅ΡΠΎΠ΄ΠΎΠΌ Π»ΠΈΡΡΡ ΠΏΠΎΠ΄ Π΄Π°Π²Π»Π΅Π½ΠΈΠ΅ΠΌ Ρ Ρ ΠΎΠ»ΠΎΠ΄Π½ΠΎΠΉ ΠΊΠ°ΠΌΠ΅ΡΠΎΠΉ (ΠΎΡΠ»ΠΈΡΡΠ΅ ΠΏΠΎΠ΄ Π΄Π°Π²Π»Π΅Π½ΠΈΠ΅ΠΌ ΡΠ΅ΡΡΠ΅ΡΠ½ΠΈ ΠΎΠ±ΡΡΠ½ΠΎ ΠΈΠΌΠ΅ΡΡ Π΄ΠΈΠ°ΠΌΠ΅ΡΡ ΠΌΠ΅Π½Π΅Π΅ 150 ΠΌΠΌ (6 Π΄ΡΠΉΠΌΠΎΠ²) ΠΈ Π΄ΠΈΠ°ΠΌΠ΅ΡΡΠ°Π»ΡΠ½ΡΠΉ ΡΠ°Π³ ΠΎΡ 10 Π΄ΠΎ 48 (DP)). ΠΡΠ±ΡΠ°ΡΡΠ΅ ΠΊΠΎΠ»Π΅ΡΠ° ΡΠ»ΠΎΠΆΠ½ΠΎΠΉ ΡΠΎΡΠΌΡ, ΠΎΠ±ΡΠ°Π±ΠΎΡΠΊΠ° ΠΊΠΎΡΠΎΡΡΡ ΡΡΠ΅Π±ΡΠ΅Ρ Π±ΠΎΠ»ΡΡΠΈΡ Π·Π°ΡΡΠ°Ρ, ΠΌΠΎΠ³ΡΡ Π±ΡΡΡ ΠΈΠ·Π³ΠΎΡΠΎΠ²Π»Π΅Π½Ρ Π±ΡΡΡΡΠΎ ΠΈ Ρ Π½ΠΈΠ·ΠΊΠΈΠΌΠΈ Π·Π°ΡΡΠ°ΡΠ°ΠΌΠΈ Π² ΠΏΡΠΎΡΠ΅ΡΡΠ΅ Π»ΠΈΡΡΡ ΠΏΠΎΠ΄ Π΄Π°Π²Π»Π΅Π½ΠΈΠ΅ΠΌ. ΠΡΠ½ΠΎΠ²Π½ΡΠΌ Π½Π΅Π΄ΠΎΡΡΠ°ΡΠΊΠΎΠΌ ΠΏΡΠΎΡΠ΅ΡΡΠ° ΡΠ²Π»ΡΠ΅ΡΡΡ ΡΠΎ, ΡΡΠΎ Π»Π΅Π³ΠΊΠΎΠΏΠ»Π°Π²ΠΊΠΈΠ΅ ΠΌΠ΅ΡΠ°Π»Π»Ρ, ΠΏΡΠΈΠ³ΠΎΠ΄Π½ΡΠ΅ Π΄Π»Ρ Π»ΠΈΡΡΡ ΠΏΠΎΠ΄ Π΄Π°Π²Π»Π΅Π½ΠΈΠ΅ΠΌ, β Π°Π»ΡΠΌΠΈΠ½ΠΈΠΉ, ΡΠΈΠ½ΠΊ ΠΈ ΠΌΠ΅Π΄Ρ β Π½Π΅ ΠΎΠ±Π»Π°Π΄Π°ΡΡ Π΄ΠΎΡΡΠ°ΡΠΎΡΠ½ΠΎ Π²ΡΡΠΎΠΊΠΎΠΉ ΡΠ²Π΅ΡΠ΄ΠΎΡΡΡΡ Π΄Π»Ρ ΠΎΠ±Π΅ΡΠΏΠ΅ΡΠ΅Π½ΠΈΡ Π²ΡΡΠΎΠΊΠΎΠΉ Π½Π΅ΡΡΡΠ΅ΠΉ ΡΠΏΠΎΡΠΎΠ±Π½ΠΎΡΡΠΈ.
ΠΠ½ΠΎΠ³ΠΈΠ΅ ΡΠΈΠΏΡ Π·ΡΠ±ΡΠ°ΡΡΡ ΠΊΠΎΠ»Π΅Ρ ΠΌΠΎΠ³ΡΡ Π±ΡΡΡ ΠΎΡΠ»ΠΈΡΡ ΠΏΠΎΠ΄ Π΄Π°Π²Π»Π΅Π½ΠΈΠ΅ΠΌ, Π½Π°ΠΏΡΠΈΠΌΠ΅Ρ ΠΏΡΡΠΌΠΎΠ·ΡΠ±ΡΠ΅, ΡΠ΅ΡΠ²ΡΡΠ½ΡΠ΅, ΠΊΠ»Π°ΡΡΠ΅ΡΠ½ΡΠ΅ ΠΈ ΠΊΠΎΠ½ΠΈΡΠ΅ΡΠΊΠΈΠ΅. ΠΡΠΈΠΌΠ΅Π½Π΅Π½ΠΈΡ Π΄Π»Ρ ΡΡΠΈΡ ΡΠΈΠΏΠΎΠ² ΠΏΠ΅ΡΠ΅Π΄Π°Ρ Π²ΠΊΠ»ΡΡΠ°ΡΡ ΠΈΠ³ΡΡΡΠΊΠΈ, ΡΡΠΈΡΠ°Π»ΡΠ½ΡΠ΅ ΠΌΠ°ΡΠΈΠ½Ρ, ΠΌΠ΅Π»ΠΊΡΡ Π±ΡΡΠΎΠ²ΡΡ ΡΠ΅Ρ Π½ΠΈΠΊΡ, ΡΡΡΠ½ΡΠ΅ ΠΈΠ½ΡΡΡΡΠΌΠ΅Π½ΡΡ, ΠΊΠ°ΠΌΠ΅ΡΡ, Π±ΠΈΠ·Π½Π΅Ρ-ΠΌΠ°ΡΠΈΠ½Ρ ΠΈ ΠΏΠΎΠ΄ΠΎΠ±Π½ΠΎΠ΅ ΠΎΠ±ΠΎΡΡΠ΄ΠΎΠ²Π°Π½ΠΈΠ΅.
Π€ΠΎΡΠΌΠΎΠ²ΠΊΠ°
Π¨ΡΠ°ΠΌΠΏΠΎΠ²ΠΊΠ° ΠΈ ΡΠΈΡΡΠΎΠ²Π°Ρ Π²ΡΡΡΠ±ΠΊΠ°
Π¨ΡΠ°ΠΌΠΏΠΎΠ²ΠΊΠ° β ΡΡΠΎ ΠΌΠ΅ΡΠΎΠ΄ ΠΌΠ΅ΡΠ°Π»Π»ΠΎΠΎΠ±ΡΠ°Π±ΠΎΡΠΊΠΈ, ΠΊΠΎΡΠΎΡΡΠΉ ΡΡΠ°Π²Π½ΠΈΠ²Π°ΡΡ Ρ ΠΈΡΠΏΠΎΠ»ΡΠ·ΠΎΠ²Π°Π½ΠΈΠ΅ΠΌ ΡΠΎΡΠΌ Π΄Π»Ρ ΠΏΠ΅ΡΠ΅Π½ΡΡ. Π ΡΡΠΎΠΌ ΠΏΡΠΎΡΠ΅ΡΡΠ΅ Π»ΠΈΡΡ ΠΌΠ΅ΡΠ°Π»Π»Π° ΠΏΠΎΠΌΠ΅ΡΠ°Π΅ΡΡΡ ΠΌΠ΅ΠΆΠ΄Ρ Π²Π΅ΡΡ
Π½Π΅ΠΉ ΠΈ Π½ΠΈΠΆΠ½Π΅ΠΉ ΡΠ°ΡΡΡΠΌΠΈ ΠΌΠ°ΡΡΠΈΡΡ; Π²Π΅ΡΡ
Π½ΡΡ ΠΏΠ»Π°ΡΠΊΠ° Π²Π΄Π°Π²Π»ΠΈΠ²Π°Π΅ΡΡΡ Π² Π½ΠΈΠΆΠ½ΡΡ ΡΠ΅ΠΊΡΠΈΡ ΠΈ Β«ΡΠ½ΠΈΠΌΠ°Π΅ΡΒ» ΠΈΠ»ΠΈ Π²ΡΡΠ΅Π·Π°Π΅Ρ ΡΠ΅ΡΡΠ΅ΡΠ½Ρ ΠΈΠ· Π»ΠΈΡΡΠ°. ΠΡΠΎ Π½Π΅Π΄ΠΎΡΠΎΠ³ΠΎΠΉ ΠΈ Π²ΡΡΠΎΠΊΠΎΡΡΡΠ΅ΠΊΡΠΈΠ²Π½ΡΠΉ ΠΌΠ΅ΡΠΎΠ΄ ΠΈΠ·Π³ΠΎΡΠΎΠ²Π»Π΅Π½ΠΈΡ Π»Π΅Π³ΠΊΠΈΡ
Π·ΡΠ±ΡΠ°ΡΡΡ
ΠΊΠΎΠ»Π΅Ρ Π΄Π»Ρ ΡΠ°Π±ΠΎΡΡ Π±Π΅Π· Π½Π°Π³ΡΡΠ·ΠΊΠΈ ΠΈ Π² ΡΡΠ»ΠΎΠ²ΠΈΡΡ
ΡΡΠ΅Π΄Π½Π΅ΠΉ Π½Π°Π³ΡΡΠ·ΠΊΠΈ. Π¨ΡΠ°ΠΌΠΏΠΎΠ²ΠΊΠ° ΠΎΠ³ΡΠ°Π½ΠΈΡΠ΅Π½Π° ΡΠΎΠ»ΡΠΈΠ½ΠΎΠΉ Π·Π°Π³ΠΎΡΠΎΠ²ΠΊΠΈ ΠΈ ΠΈΡΠΏΠΎΠ»ΡΠ·ΡΠ΅ΡΡΡ Π² ΠΎΡΠ½ΠΎΠ²Π½ΠΎΠΌ Π΄Π»Ρ ΡΠΈΠ»ΠΈΠ½Π΄ΡΠΈΡΠ΅ΡΠΊΠΈΡ
Π·ΡΠ±ΡΠ°ΡΡΡ
ΠΊΠΎΠ»Π΅Ρ ΠΈ Π΄ΡΡΠ³ΠΈΡ
ΡΠΎΠ½ΠΊΠΈΡ
ΠΏΠ»ΠΎΡΠΊΠΈΡ
ΡΠΎΡΠΌ [5]. Π¨ΡΠ°ΠΌΠΏΠΎΠ²Π°Π½Π½ΡΠ΅ ΡΠ΅ΡΡΠ΅ΡΠ½ΠΈ ΠΈΠΌΠ΅ΡΡ ΡΠ°Π·ΠΌΠ΅Ρ ΠΎΡ 20 Π΄ΠΎ 120 DP ΠΈ ΡΠΎΠ»ΡΠΈΠ½Ρ ΠΎΡ 0,25 Π΄ΠΎ 3 ΠΌΠΌ (ΠΎΡ 0,010 Π΄ΠΎ 0,125 Π΄ΡΠΉΠΌΠ°) [6]. ΠΠΎ ΠΌΠ΅ΡΠ΅ ΡΠΎΠ³ΠΎ, ΠΊΠ°ΠΊ ΡΠ°Π³ ΡΡΠ°Π½ΠΎΠ²ΠΈΡΡΡ ΡΠΎΠ½ΡΡΠ΅, ΡΠΏΠ΅ΡΠΈΡΠΈΠΊΠ°ΡΠΈΡ ΠΌΠ°ΡΠ΅ΡΠΈΠ°Π»ΠΎΠ² Π΄ΠΎΠ»ΠΆΠ½Π° ΡΡΠ°Π½ΠΎΠ²ΠΈΡΡΡΡ ΡΠΎΠ½ΡΡΠ΅. Π Π’Π°Π±Π»ΠΈΡΠ΅ 2 ΠΏΠΎΠΊΠ°Π·Π°Π½Ρ ΡΠ΅ΠΊΠΎΠΌΠ΅Π½Π΄ΡΠ΅ΠΌΡΠ΅ Π·Π½Π°ΡΠ΅Π½ΠΈΡ ΡΠΎΠ»ΡΠΈΠ½Ρ Π·Π°Π³ΠΎΡΠΎΠ²ΠΊΠΈ Π΄Π»Ρ ΡΠ°Π·Π»ΠΈΡΠ½ΡΡ
ΡΠ°Π³ΠΎΠ², ΠΊΠΎΡΠΎΡΡΠ΅ ΠΎΠ±ΡΡΠ½ΠΎ ΠΈΡΠΏΠΎΠ»ΡΠ·ΡΡΡΡΡ ΠΈ Π½Π΅ ΡΡΠ΅Π±ΡΡΡ ΠΎΡΠΎΠ±ΠΎΠ³ΠΎ Π²Π½ΠΈΠΌΠ°Π½ΠΈΡ ΠΏΡΠΈ ΠΎΠ±ΡΠ»ΡΠΆΠΈΠ²Π°Π½ΠΈΠΈ ΠΌΠ°ΡΡΠΈΡΡ. ΠΠ°ΠΊ ΠΏΠΎΠΊΠ°Π·Π°Π½ΠΎ Π² Π’Π°Π±Π»ΠΈΡΠ΅ 1, Π΄ΠΎΠΏΡΡΠΊΠΈ Π΄Π»Ρ ΡΡΠ°ΠΌΠΏΠΎΠ²Π°Π½Π½ΡΡ
ΡΠ΅ΡΡΠ΅ΡΠ΅Π½ Ρ
ΠΎΡΠΎΡΠΈΠ΅, ΠΈ ΠΊΠ»Π°ΡΡ ΠΊΠ°ΡΠ΅ΡΡΠ²Π° AGMA 9.ΠΌΠΎΠΆΠ΅Ρ Π±ΡΡΡ Π΄ΠΎΡΡΠΈΠ³Π½ΡΡΠΎ Ρ ΠΎΡΠΎΠ±ΠΎΠΉ ΠΎΡΡΠΎΡΠΎΠΆΠ½ΠΎΡΡΡΡ.
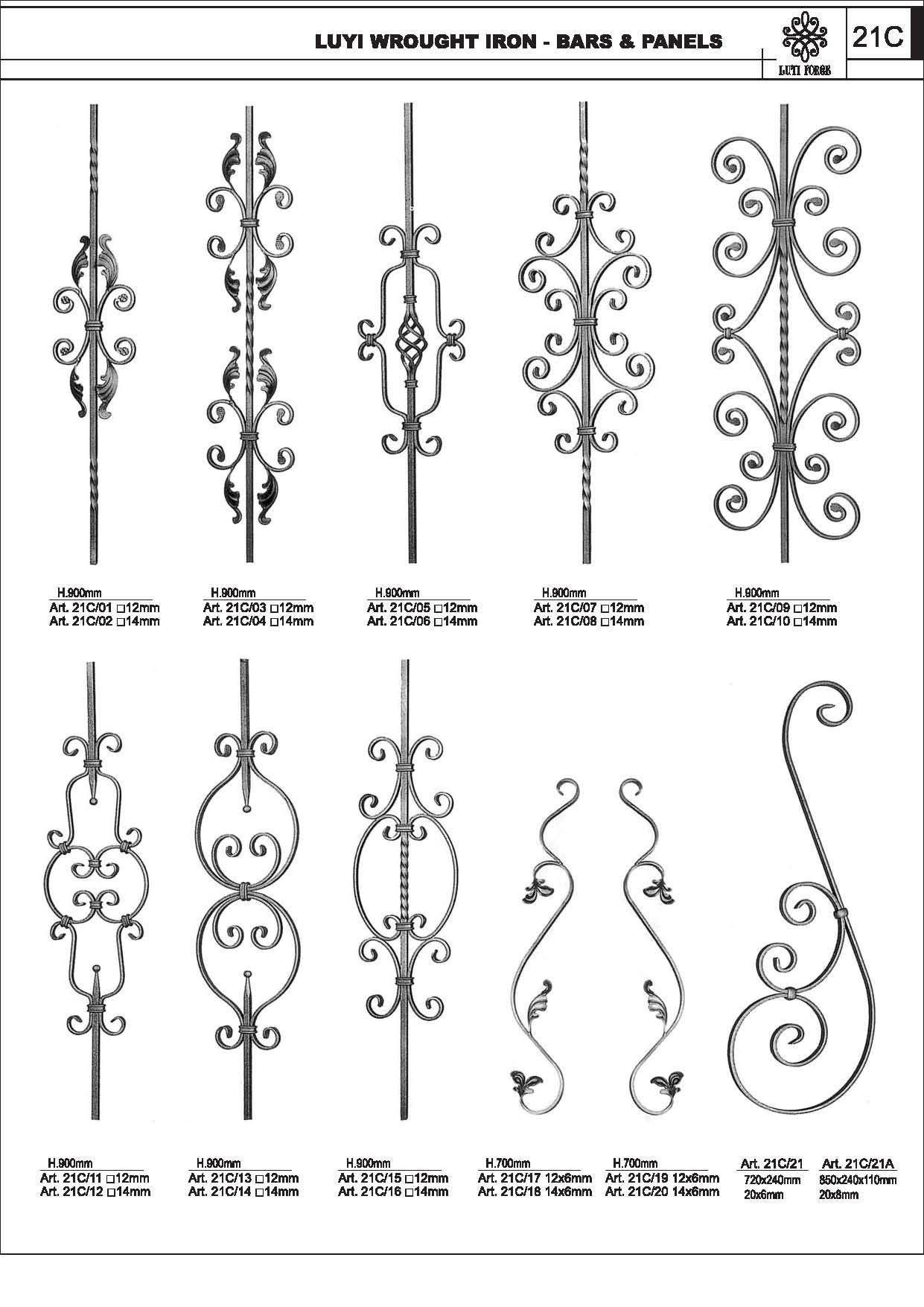
Π¨ΡΠ°ΠΌΠΏΠΎΠ²ΠΊΠΎΠΉ ΠΌΠΎΠΆΠ½ΠΎ ΠΎΠ±ΡΠ°Π±Π°ΡΡΠ²Π°ΡΡ ΡΠΈΡΠΎΠΊΠΈΠΉ ΡΠΏΠ΅ΠΊΡΡ ΠΌΠ°ΡΠ΅ΡΠΈΠ°Π»ΠΎΠ², Π²ΠΊΠ»ΡΡΠ°Ρ Π²ΡΠ΅ Π½ΠΈΠ·ΠΊΠΎ- ΠΈ ΡΡΠ΅Π΄Π½Π΅ΡΠ³Π»Π΅ΡΠΎΠ΄ΠΈΡΡΡΠ΅ ΡΡΠ°Π»ΠΈ, Π»Π°ΡΡΠ½ΠΈ ΠΈ Π½Π΅ΠΊΠΎΡΠΎΡΡΠ΅ Π°Π»ΡΠΌΠΈΠ½ΠΈΠ΅Π²ΡΠ΅ ΡΠΏΠ»Π°Π²Ρ. ΠΠ΅ΠΌΠ΅ΡΠ°Π»Π»ΠΈΡΠ΅ΡΠΊΠΈΠ΅ ΠΌΠ°ΡΠ΅ΡΠΈΠ°Π»Ρ ΡΠ°ΠΊΠΆΠ΅ ΠΌΠΎΠΆΠ½ΠΎ ΡΡΠ°ΠΌΠΏΠΎΠ²Π°ΡΡ. Π¨Π΅ΡΡΠ΅ΡΠ½ΠΈ, ΠΈΠ·Π³ΠΎΡΠΎΠ²Π»Π΅Π½Π½ΡΠ΅ Ρ ΠΏΠΎΠΌΠΎΡΡΡ ΡΡΠΎΠ³ΠΎ ΠΏΡΠΎΡΠ΅ΡΡΠ°, ΠΈΡΠΏΠΎΠ»ΡΠ·ΡΡΡΡΡ Π² ΠΈΠ³ΡΡΡΠΊΠ°Ρ , ΡΠ°ΡΠΎΠ²ΡΡ ΠΈ ΡΠ°ΠΉΠΌΠ΅ΡΠ½ΡΡ ΠΌΠ΅Ρ Π°Π½ΠΈΠ·ΠΌΠ°Ρ , ΡΠ°ΡΠ°Ρ , Π½Π΅Π±ΠΎΠ»ΡΡΠΈΡ Π±ΡΡΠΎΠ²ΡΡ ΠΏΡΠΈΠ±ΠΎΡΠ°Ρ , ΡΠ°ΠΊΠΈΡ ΠΊΠ°ΠΊ ΠΌΠΈΠΊΡΠ΅ΡΡ, Π±Π»Π΅Π½Π΄Π΅ΡΡ, ΡΠΎΡΡΠ΅ΡΡ ΠΈ ΠΊΠΎΠ½ΡΠ΅ΡΠ²Π½ΡΠ΅ Π½ΠΎΠΆΠΈ, Π° ΡΠ°ΠΊΠΆΠ΅ Π² Π±ΠΎΠ»Π΅Π΅ ΠΊΡΡΠΏΠ½ΡΡ ΡΡΡΡΠΎΠΉΡΡΠ²Π°Ρ , ΡΠ°ΠΊΠΈΡ ΠΊΠ°ΠΊ ΡΡΠΈΡΠ°Π»ΡΠ½ΡΠ΅ ΠΌΠ°ΡΠΈΠ½Ρ ΠΈ ΡΡΡΠΈΠ»ΠΊΠΈ.
Π§ΠΈΡΡΠΎΠ²Π°Ρ Π²ΡΡΡΠ±ΠΊΠ° (ΡΠ°ΠΊΠΆΠ΅ ΠΈΠ·Π²Π΅ΡΡΠ½Π°Ρ ΠΊΠ°ΠΊ Π²ΡΡΡΠ±ΠΊΠ° ΡΠΎΠ½ΠΊΠΈΡ
ΠΊΡΠΎΠΌΠΎΠΊ) Π½Π° ΡΠ°ΠΌΠΎΠΌ Π΄Π΅Π»Π΅ Π±ΠΎΠ»ΡΡΠ΅ ΠΏΠΎΡ
ΠΎΠΆΠ° Π½Π° Ρ
ΠΎΠ»ΠΎΠ΄Π½ΡΡ ΡΠΊΡΡΡΡΠ·ΠΈΡ, ΡΠ΅ΠΌ Π½Π° ΠΎΠΏΠ΅ΡΠ°ΡΠΈΡ ΡΠ΅Π·ΠΊΠΈ, ΡΠ°ΠΊΡΡ ββΠΊΠ°ΠΊ ΡΡΠ°ΠΌΠΏΠΎΠ²ΠΊΠ°. ΠΡΠΎΡΠ΅ΡΡ Π±Π΅ΡΠ΅Ρ ΠΌΠ΅ΡΠ°Π»Π» ΠΈΠ· Π»ΠΈΡΡΠ°, ΠΊΠ°ΠΊ ΡΡΠ°ΠΌΠΏΠΎΠ²ΠΊΠ°; Π½ΠΎ ΠΎΡΠ»ΠΈΡΠ°Π΅ΡΡΡ ΠΎΡ Π½Π΅Π³ΠΎ ΡΠ΅ΠΌ, ΡΡΠΎ ΠΈΡΠΏΠΎΠ»ΡΠ·ΡΠ΅Ρ Π΄Π²Π° ΡΡΠ°ΠΌΠΏΠ° ΠΈ ΡΠΎΡΠΌΠΈΡΡΠ΅Ρ Π·Π°Π³ΠΎΡΠΎΠ²ΠΊΡ, ΠΏΡΠΈΠ΄Π°Π²Π°Ρ Π΅ΠΉ ΠΆΠ΅Π»Π°Π΅ΠΌΡΡ ΡΠΎΡΠΌΡ. ΠΠ΅ΡΠ°Π»Π» Π²ΡΠ΄Π°Π²Π»ΠΈΠ²Π°Π΅ΡΡΡ Π² ΠΏΠΎΠ»ΠΎΡΡΠΈ ΡΡΠ°ΠΌΠΏΠ°, ΡΡΠΎΠ±Ρ ΡΡΠΎΡΠΌΠΈΡΠΎΠ²Π°ΡΡ ΠΆΠ΅Π»Π°Π΅ΠΌΡΡ ΡΠΎΡΠΌΡ. ΠΡΠΎΠΌΠ΅ ΡΠΎΠ³ΠΎ, Π² ΠΎΡΠ»ΠΈΡΠΈΠ΅ ΠΎΡ ΡΡΠ°ΠΌΠΏΠΎΠ²ΠΊΠΈ, ΡΠΈΡΡΠΎΠ²Π°Ρ Π²ΡΡΡΠ±ΠΊΠ° ΠΏΡΠ΅Π΄Π»Π°Π³Π°Π΅Ρ ΠΊΠΎΠ½ΡΡΡΡΠΊΡΠΎΡΡ ΠΎΠ³ΡΠ°Π½ΠΈΡΠ΅Π½Π½ΡΠ΅ ΡΡΠ΅Ρ
ΠΌΠ΅ΡΠ½ΡΠ΅ Π²ΠΎΠ·ΠΌΠΎΠΆΠ½ΠΎΡΡΠΈ ΠΈ, ΡΠ°ΠΊΠΈΠΌ ΠΎΠ±ΡΠ°Π·ΠΎΠΌ, ΠΌΠΎΠΆΠ΅Ρ ΠΈΡΠΏΠΎΠ»ΡΠ·ΠΎΠ²Π°ΡΡΡΡ Π΄Π»Ρ ΡΠΎΠ·Π΄Π°Π½ΠΈΡ ΡΠ°ΡΠΎΠΊ, ΠΌΠ½ΠΎΠΆΠ΅ΡΡΠ²Π΅Π½Π½ΡΡ
Π½Π°Π±ΠΎΡΠΎΠ² Π·ΡΠ±ΡΠ°ΡΡΡ
ΠΊΠΎΠ»Π΅Ρ ΠΈ Π΄ΡΡΠ³ΠΈΡ
ΡΠ»ΠΎΠΆΠ½ΡΡ
ΡΠΎΡΠΌ [5]. ΠΡΠ±ΡΠ°ΡΡΠ΅ ΠΊΠΎΠ»Π΅ΡΠ° Ρ ΡΠΎΠ½ΠΊΠΈΠΌΠΈ Π·Π°Π³Π»ΡΡΠΊΠ°ΠΌΠΈ ΠΌΠΎΠΆΠ½ΠΎ Π½Π°ΠΉΡΠΈ Π² ΡΠ°ΠΌΡΡ
ΡΠ°Π·Π½ΡΡ
ΠΎΠ±Π»Π°ΡΡΡΡ
, Π²ΠΊΠ»ΡΡΠ°Ρ Π°Π²ΡΠΎΠΌΠΎΠ±ΠΈΠ»Π΅ΡΡΡΠΎΠ΅Π½ΠΈΠ΅, Π±ΡΡΠΎΠ²ΡΡ ΡΠ΅Ρ
Π½ΠΈΠΊΡ, ΠΎΡΠ³ΡΠ΅Ρ
Π½ΠΈΠΊΡ, Π³ΠΈΠ΄ΡΠ°Π²Π»ΠΈΡΠ΅ΡΠΊΠΎΠ΅ ΠΈ ΠΌΠ΅Π΄ΠΈΡΠΈΠ½ΡΠΊΠΎΠ΅ ΠΎΠ±ΠΎΡΡΠ΄ΠΎΠ²Π°Π½ΠΈΠ΅.
Π₯ΠΎΠ»ΠΎΠ΄Π½ΠΎΠ΅ Π²ΠΎΠ»ΠΎΡΠ΅Π½ΠΈΠ΅ ΠΈ ΡΠΊΡΡΡΡΠ·ΠΈΡ
[6]ΠΡΠΎΡ ΠΏΡΠΎΡΠ΅ΡΡ ΡΡΠ΅Π±ΡΠ΅Ρ Π½Π°ΠΈΠΌΠ΅Π½ΡΡΠΈΡ Π·Π°ΡΡΠ°Ρ Π½Π° ΠΈΠ½ΡΡΡΡΠΌΠ΅Π½Ρ Π΄Π»Ρ ΠΌΠ°ΡΡΠΎΠ²ΠΎΠ³ΠΎ ΠΏΡΠΎΠΈΠ·Π²ΠΎΠ΄ΡΡΠ²Π° ΡΠ»Π΅ΠΌΠ΅Π½ΡΠΎΠ² ΡΠΈΠ»ΠΈΠ½Π΄ΡΠΈΡΠ΅ΡΠΊΠΈΡ Π·ΡΠ±ΡΠ°ΡΡΡ ΠΊΠΎΠ»Π΅Ρ ΠΈ ΡΡΠ΅Π·Π²ΡΡΠ°ΠΉΠ½ΠΎ ΡΠ½ΠΈΠ²Π΅ΡΡΠ°Π»Π΅Π½, ΠΏΠΎΡΠΊΠΎΠ»ΡΠΊΡ ΠΌΠΎΠΆΠ΅Ρ Π±ΡΡΡ ΠΈΠ·Π³ΠΎΡΠΎΠ²Π»Π΅Π½ ΠΏΡΠ°ΠΊΡΠΈΡΠ΅ΡΠΊΠΈ Π»ΡΠ±ΠΎΠΉ ΡΠΎΡΠΌΡ Π·ΡΠ±Π°. ΠΠ°ΠΊ ΡΠ»Π΅Π΄ΡΠ΅Ρ ΠΈΠ· Π½Π°Π·Π²Π°Π½ΠΈΡ, ΡΡΠ΅ΡΠΆΠ΅Π½Ρ ΠΏΡΠΎΡΡΠ³ΠΈΠ²Π°Π΅ΡΡΡ (Π²ΡΡΡΠ³ΠΈΠ²Π°Π΅ΡΡΡ) ΠΈΠ»ΠΈ ΠΏΡΠΎΡΠ°Π»ΠΊΠΈΠ²Π°Π΅ΡΡΡ (ΡΠΊΡΡΡΡΠ΄ΠΈΡΡΠ΅ΡΡΡ) ΡΠ΅ΡΠ΅Π· ΡΠ΅ΡΠΈΡ Π½Π΅ΡΠΊΠΎΠ»ΡΠΊΠΈΡ ΡΡΠ°ΠΌΠΏΠΎΠ², ΠΏΠΎΡΠ»Π΅Π΄Π½ΠΈΠΉ ΠΈΠ· ΠΊΠΎΡΠΎΡΡΡ ΠΈΠΌΠ΅Π΅Ρ ΠΎΠΊΠΎΠ½ΡΠ°ΡΠ΅Π»ΡΠ½ΡΡ ΡΠΎΡΠΌΡ ΠΆΠ΅Π»Π°Π΅ΠΌΠΎΠΉ ΡΠΎΡΠΌΡ Π·ΡΠ±Π°. ΠΠΎΠ³Π΄Π° ΠΌΠ°ΡΠ΅ΡΠΈΠ°Π» ΠΏΡΠΎΡ ΠΎΠ΄ΠΈΡ ΡΠ΅ΡΠ΅Π· ΡΡΠΈ ΠΌΠ°ΡΡΠΈΡΡ, ΠΎΠ½ ΡΠ°ΠΊΡΠΈΡΠ΅ΡΠΊΠΈ ΡΠΆΠΈΠΌΠ°Π΅ΡΡΡ Π² ΡΠΎΡΠΌΠ΅ ΠΌΠ°ΡΡΠΈΡΡ. ΠΠΎΡΠΊΠΎΠ»ΡΠΊΡ ΠΌΠ°ΡΠ΅ΡΠΈΠ°Π» ΡΠΌΠ΅ΡΠ°Π΅ΡΡΡ ΠΏΠΎΠ΄ Π΄Π°Π²Π»Π΅Π½ΠΈΠ΅ΠΌ, Π²Π½Π΅ΡΠ½ΡΡ ΠΏΠΎΠ²Π΅ΡΡ Π½ΠΎΡΡΡ Π½Π°Π³Π°ΡΡΠΎΠ²Π°Π½Π½Π°Ρ ΠΈ Π΄ΠΎΡΡΠ°ΡΠΎΡΠ½ΠΎ Π³Π»Π°Π΄ΠΊΠ°Ρ.
ΠΡΡΡΠΊΠΈ, ΠΊΠΎΡΠΎΡΡΠ΅ ΡΠ²Π»ΡΡΡΡΡ Β«Π·Π°Π³ΠΎΡΠΎΠ²ΠΊΠ°ΠΌΠΈΒ» Π΄Π»Ρ ΡΡΠΎΠ³ΠΎ ΠΏΡΠΎΡΠ΅ΡΡΠ°, ΠΎΠ±ΡΡΠ½ΠΎ ΠΈΠΌΠ΅ΡΡ Π΄Π»ΠΈΠ½Ρ ΠΎΡ 3 Π΄ΠΎ 3,7 ΠΌ (ΠΎΡ 10 Π΄ΠΎ 12 ΡΡΡΠΎΠ²). ΠΠΎΡΠ»Π΅ ΠΏΡΠΎΡ
ΠΎΠΆΠ΄Π΅Π½ΠΈΡ ΡΠ΅ΡΠ΅Π· ΠΌΠ°ΡΡΠΈΡΡ ΠΎΠ½ΠΈ ΠΈΠ·Π²Π΅ΡΡΠ½Ρ ΠΊΠ°ΠΊ ΡΠ°ΡΡΠ½Ρ-ΡΠ΅ΡΡΠ΅ΡΠ½ΠΈ ΠΈ ΡΠ°ΡΡΠΎ ΠΏΠΎΠΌΠ΅ΡΠ°ΡΡΡΡ Π² Π²ΠΈΠ½ΡΠΎΠ²ΡΠ΅ ΡΡΠ°Π½ΠΊΠΈ, ΠΊΠΎΡΠΎΡΡΠ΅ ΡΠΈΡΡΡΡ ΠΎΡΠ΄Π΅Π»ΡΠ½ΡΠ΅ ΡΠ΅ΡΡΠ΅ΡΠ½ΠΈ. ΠΠΏΡΡ ΠΏΠΎΠΊΠ°Π·Π°Π», ΡΡΠΎ Π±ΠΎΠ»Π΅Π΅ ΡΠΊΠΎΠ½ΠΎΠΌΠΈΡΠ½ΠΎ ΠΎΡΡΠ΅Π·Π°ΡΡ ΡΠ΅Π³ΠΌΠ΅Π½Ρ ΠΎΡ ΡΠΊΡΡΡΡΠ΄ΠΈΡΠΎΠ²Π°Π½Π½ΠΎΠ³ΠΎ ΡΡΠ΅ΡΠΆΠ½Ρ, ΡΠ΅ΠΌ ΠΎΡΡΠ΅Π·Π°ΡΡ ΠΎΡΠ΄Π΅Π»ΡΠ½ΠΎΠ΅ ΠΊΠΎΠ»Π΅ΡΠΎ. Π Π½Π΅ΠΊΠΎΡΠΎΡΡΡ
ΡΠ»ΡΡΠ°ΡΡ
Π±ΡΠ»ΠΎ Π±Ρ Π½Π΅Π²ΠΎΠ·ΠΌΠΎΠΆΠ½ΠΎ ΠΏΠΎΠ»ΡΡΠΈΡΡ ΠΆΠ΅Π»Π°Π΅ΠΌΡΡ ΡΠΎΡΠΌΡ ΡΠ΅ΡΡΠ΅ΡΠ½ΠΈ ΠΊΠ°ΠΊΠΈΠΌ-Π»ΠΈΠ±ΠΎ Π΄ΡΡΠ³ΠΈΠΌ ΡΠΏΠΎΡΠΎΠ±ΠΎΠΌ. ΠΠΎΠ³ΡΡ Π±ΡΡΡ ΠΏΠΎΠ»ΡΡΠ΅Π½Ρ ΡΠ°ΡΡΠ½Ρ Ρ ΡΠ΅ΡΡΠ΅ΡΠ½ΡΠΌΠΈ ΠΎΡ 16 Π΄ΠΎ 100 DP, Π½ΠΎ ΠΏΠΎ ΠΌΠ΅ΡΠ΅ ΡΠΎΠ³ΠΎ, ΠΊΠ°ΠΊ ΡΠ°Π³ ΡΡΠ°Π½ΠΎΠ²ΠΈΡΡΡ ΠΌΠ΅Π½ΡΡΠ΅, ΡΡΠ°Π½ΠΎΠ²ΠΈΡΡΡ Π²ΡΠ΅ ΡΡΡΠ΄Π½Π΅Π΅ ΠΏΠΎΠ»ΡΡΠΈΡΡ ΠΆΠ΅ΡΡΠΊΠΈΠ΅ Π΄ΠΎΠΏΡΡΠΊΠΈ, ΠΊΠΎΡΠΎΡΡΠ΅ ΠΈΠ½ΠΎΠ³Π΄Π° ΠΆΠ΅Π»Π°ΡΠ΅Π»ΡΠ½Ρ Π΄Π»Ρ ΡΠ΅ΡΡΠ΅ΡΠ΅Π½ Ρ ΠΌΠ΅Π»ΠΊΠΈΠΌ ΡΠ°Π³ΠΎΠΌ. ΠΡΠ±ΠΎΠΉ ΠΌΠ°ΡΠ΅ΡΠΈΠ°Π», ΠΎΠ±Π»Π°Π΄Π°ΡΡΠΈΠΉ Ρ
ΠΎΡΠΎΡΠΈΠΌΠΈ ΡΠ²ΠΎΠΉΡΡΠ²Π°ΠΌΠΈ Π²ΠΎΠ»ΠΎΡΠ΅Π½ΠΈΡ, ΡΠ°ΠΊΠΎΠΉ ΠΊΠ°ΠΊ Π²ΡΡΠΎΠΊΠΎΡΠ³Π»Π΅ΡΠΎΠ΄ΠΈΡΡΠ°Ρ ΡΡΠ°Π»Ρ, Π»Π°ΡΡΠ½Ρ, Π±ΡΠΎΠ½Π·Π°, Π°Π»ΡΠΌΠΈΠ½ΠΈΠΉ ΠΈ Π½Π΅ΡΠΆΠ°Π²Π΅ΡΡΠ°Ρ ΡΡΠ°Π»Ρ, ΠΌΠΎΠΆΠ΅Ρ Π±ΡΡΡ ΠΈΡΠΏΠΎΠ»ΡΠ·ΠΎΠ²Π°Π½ Π΄Π»Ρ ΡΡΠ½ΡΡΠΎΠΉ ΡΠ΅ΡΡΠ΅ΡΠ½ΠΈ.
Π¨Π΅ΡΡΠ΅ΡΠ½ΠΈ ΠΈ ΡΠ΅ΡΡΠ΅ΡΠ½ΠΈ, ΠΈΠ·Π³ΠΎΡΠΎΠ²Π»Π΅Π½Π½ΡΠ΅ Ρ ΠΏΠΎΠΌΠΎΡΡΡ ΡΡΠΎΠ³ΠΎ ΠΏΡΠΎΡΠ΅ΡΡΠ°, ΠΈΠΌΠ΅ΡΡ Π±ΠΎΠ»ΡΡΠΎΠ΅ ΡΠ°Π·Π½ΠΎΠΎΠ±ΡΠ°Π·ΠΈΠ΅ ΠΏΡΠΈΠΌΠ΅Π½Π΅Π½ΠΈΠΉ ΠΈ ΠΈΡΠΏΠΎΠ»ΡΠ·ΡΡΡΡΡ Π² ΡΠ°ΡΠ°Ρ , ΡΠ»Π΅ΠΊΡΡΠΈΡΠ΅ΡΠΊΠΈΡ ΡΠ°ΡΠ°Ρ , ΡΠ°ΡΠ°Ρ Ρ ΠΏΡΡΠΆΠΈΠ½Π½ΡΠΌ Π·Π°Π²ΠΎΠ΄ΠΎΠΌ, ΠΏΠΈΡΡΡΠΈΡ ΠΌΠ°ΡΠΈΠ½ΠΊΠ°Ρ , ΠΊΠ°ΡΠ±ΡΡΠ°ΡΠΎΡΠ°Ρ , ΠΌΠ°Π³Π½Π΅ΡΠΎ, ΠΌΠ°Π»ΡΡ Π΄Π²ΠΈΠ³Π°ΡΠ΅Π»ΡΡ , ΠΏΠ΅ΡΠ΅ΠΊΠ»ΡΡΠ°ΡΠ΅Π»ΡΡ , ΡΠ°ΠΊΡΠΎΠΌΠ΅ΡΡΠ°Ρ , ΠΊΠ°ΠΌΠ΅ΡΠ°Ρ , ΠΈΠ³ΡΠΎΠ²ΡΡ Π°Π²ΡΠΎΠΌΠ°ΡΠ°Ρ , Π²ΠΎ Π²ΡΠ΅Ρ Π²ΠΈΠ΄Ρ ΠΌΠ΅Ρ Π°Π½ΠΈΡΠ΅ΡΠΊΠΈΡ ΠΈΠ³ΡΡΡΠ΅ΠΊ ΠΈ ΠΌΠ½ΠΎΠ³ΠΈΠ΅ Π΄ΡΡΠ³ΠΈΠ΅ Π΄Π΅ΡΠ°Π»ΠΈ Π΄Π»Ρ ΠΌΠ°ΡΠΈΠ½ Π²ΡΠ΅Ρ Π²ΠΈΠ΄ΠΎΠ².
ΠΡΠ±ΡΠ°ΡΠΎΠ΅ ΠΊΠΎΠ»Π΅ΡΠΎ
Π¦ΠΈΠ»ΠΈΠ½Π΄ΡΠΈΡΠ΅ΡΠΊΠΈΠ΅ ΠΈ ΠΊΠΎΡΠΎΠ·ΡΠ±ΡΠ΅ Π·ΡΠ±ΡΠ°ΡΡΠ΅ ΠΊΠΎΠ»Π΅ΡΠ°, ΠΊΠ°ΠΊ ΠΈ ΡΠ»ΠΈΡΡ, ΠΏΡΠΎΡΠΈΠ»ΠΈΡΠΎΠ²Π°Π½Ρ (ΡΠ½ΠΎΡΠΊΠ° 1). ΠΠ»Π°Π³ΠΎΠ΄Π°ΡΡ ΡΡΠΎΠΌΡ ΠΏΡΠΎΡΠ΅ΡΡΡ Π΅ΠΆΠ΅Π³ΠΎΠ΄Π½ΠΎ ΠΏΡΠΎΠΈΠ·Π²ΠΎΠ΄ΡΡΡΡ ΠΌΠΈΠ»Π»ΠΈΠΎΠ½Ρ Π²ΡΡΠΎΠΊΠΎΠΊΠ°ΡΠ΅ΡΡΠ²Π΅Π½Π½ΡΡ
ΡΠ΅ΡΡΠ΅ΡΠ΅Π½; ΠΌΠ½ΠΎΠ³ΠΈΠ΅ ΡΠ΅ΡΡΠ΅ΡΠ½ΠΈ Π² Π°Π²ΡΠΎΠΌΠΎΠ±ΠΈΠ»ΡΠ½ΡΡ
ΡΡΠ°Π½ΡΠΌΠΈΡΡΠΈΡΡ
ΡΠ΄Π΅Π»Π°Π½Ρ ΡΠ°ΠΊΠΈΠΌ ΠΎΠ±ΡΠ°Π·ΠΎΠΌ. ΠΠ°ΠΊ ΠΏΠΎΠΊΠ°Π·Π°Π½ΠΎ Π½Π° ΡΠΈΡ. 6, ΠΏΡΠΎΡΠ΅ΡΡ Π² ΠΎΡΠ½ΠΎΠ²Π½ΠΎΠΌ ΡΠ°ΠΊΠΎΠΉ ΠΆΠ΅, ΠΊΠ°ΠΊ ΠΈ ΠΏΡΠΎΡΠ΅ΡΡ Π½Π°ΠΊΠ°ΡΡΠ²Π°Π½ΠΈΡ ΡΠ΅Π·ΡΠ±Ρ, Π·Π° ΠΈΡΠΊΠ»ΡΡΠ΅Π½ΠΈΠ΅ΠΌ ΡΠΎΠ³ΠΎ, ΡΡΠΎ Π² Π±ΠΎΠ»ΡΡΠΈΠ½ΡΡΠ²Π΅ ΡΠ»ΡΡΠ°Π΅Π² Π·ΡΠ±ΡΡ Π½Π΅ ΠΌΠΎΠ³ΡΡ Π±ΡΡΡ ΡΡΠΎΡΠΌΠΈΡΠΎΠ²Π°Π½Ρ Π·Π° ΠΎΠ΄ΠΈΠ½ ΠΎΠ±ΠΎΡΠΎΡ ΡΠΎΡΠΌΠΎΠ²ΠΎΡΠ½ΡΡ
Π²Π°Π»ΠΊΠΎΠ²; Π²Π°Π»ΠΊΠΈ ΠΏΠΎΡΡΠ΅ΠΏΠ΅Π½Π½ΠΎ ΠΏΠΎΠ΄Π°ΡΡΡΡ Π²Π½ΡΡΡΡ Π² ΡΠ΅ΡΠ΅Π½ΠΈΠ΅ Π½Π΅ΡΠΊΠΎΠ»ΡΠΊΠΈΡ
ΠΎΠ±ΠΎΡΠΎΡΠΎΠ².
Π ΠΈΡ. 6: Π‘ΠΏΠΎΡΠΎΠ± ΡΠΎΡΠΌΠΈΡΠΎΠ²Π°Π½ΠΈΡ Π·ΡΠ±ΡΠ΅Π² ΠΈ ΡΠ»ΠΈΡΠΎΠ² ΡΠ΅ΡΡΠ΅ΡΠ½ΠΈ ΠΌΠ΅ΡΠΎΠ΄ΠΎΠΌ Ρ ΠΎΠ»ΠΎΠ΄Π½ΠΎΠΉ ΡΡΠ°ΠΌΠΏΠΎΠ²ΠΊΠΈ. [1] ΠΠ·-Π·Π° Π²ΠΎΠ·Π½ΠΈΠΊΠ°ΡΡΠ΅Π³ΠΎ ΡΠ΅ΡΠ΅Π½ΠΈΡ ΠΌΠ΅ΡΠ°Π»Π»Π° Π²Π΅ΡΡ Π½ΠΈΠ΅ ΠΊΡΠΎΠΌΠΊΠΈ Π³Π½ΡΡΡΡ Π·ΡΠ±ΡΠ΅Π² Π½Π΅ ΡΠ²Π»ΡΡΡΡΡ Π³Π»Π°Π΄ΠΊΠΈΠΌΠΈ ΠΈ ΠΈΠΌΠ΅ΡΡ Π½Π΅ΡΠΎΠ²Π΅ΡΡΠ΅Π½Π½ΡΡ ΡΠΎΡΠΌΡ; ΡΠ°ΡΡΠΎ ΠΌΠΎΠΆΠ½ΠΎ ΡΠ²ΠΈΠ΄Π΅ΡΡ Π²Π΄Π°Π²Π»Π΅Π½Π½ΡΡ Π»ΠΈΠ½ΠΈΡ ΠΌΠ΅ΠΆΠ΄Ρ Π΄Π²ΡΠΌΡ Π½Π΅Π±ΠΎΠ»ΡΡΠΈΠΌΠΈ Π²ΡΡΡΡΠΏΠ°ΠΌΠΈ. ΠΠ΄Π½Π°ΠΊΠΎ, ΠΏΠΎΡΠΊΠΎΠ»ΡΠΊΡ Π²Π΅ΡΡ Π½ΡΡ Π³ΡΠ°Π½Ρ Π½Π΅ ΠΈΠ³ΡΠ°Π΅Ρ ΡΠΎΠ»ΠΈ Π² ΡΠ°Π±ΠΎΡΠ΅ Π·ΡΠ±ΡΠ΅Π² ΡΠ΅ΡΡΠ΅ΡΠ½ΠΈ, ΠΏΡΠΈ Π½Π°Π»ΠΈΡΠΈΠΈ Π΄ΠΎΡΡΠ°ΡΠΎΡΠ½ΠΎΠ³ΠΎ Π·Π°Π·ΠΎΡΠ° Π² ΡΠΎΠΏΡΡΠ³Π°Π΅ΠΌΠΎΠΉ ΡΠ΅ΡΡΠ΅ΡΠ½Π΅ ΡΡΠΎ Π½Π΅ Π²ΡΠ·ΡΠ²Π°Π΅Ρ Π·Π°ΡΡΡΠ΄Π½Π΅Π½ΠΈΠΉ. Π’Π°ΠΌ, Π³Π΄Π΅ ΡΡΠΎ ΠΆΠ΅Π»Π°ΡΠ΅Π»ΡΠ½ΠΎ, ΠΈΡΠΏΠΎΠ»ΡΠ·ΡΠ΅ΡΡΡ Π»Π΅Π³ΠΊΠΈΠΉ ΡΠΎΠΊΠ°ΡΠ½ΡΠΉ ΡΠ΅Π·, ΡΡΠΎΠ±Ρ ΠΎΠ±Π΅ΡΠΏΠ΅ΡΠΈΡΡ Π³Π»Π°Π΄ΠΊΡΡ Π²Π΅ΡΡ Π½ΡΡ ΡΠ°ΡΡΡ ΠΈ ΠΏΡΠ°Π²ΠΈΠ»ΡΠ½ΡΠΉ Π΄ΠΈΠ°ΠΌΠ΅ΡΡ ΠΏΡΠΈΠ΄Π°ΡΠΊΠ°.
ΠΠ°Π»ΡΡΠΎΠ²ΠΊΠ° ΠΏΡΠΎΠΈΠ·Π²ΠΎΠ΄ΠΈΡ Π·ΡΠ±ΡΠ°ΡΡΠ΅ ΠΊΠΎΠ»Π΅ΡΠ° Π² 50 ΡΠ°Π· Π±ΡΡΡΡΠ΅Π΅, ΡΠ΅ΠΌ Π½Π°ΡΠ΅Π·Π°Π½ΠΈΠ΅ Π·ΡΠ±ΡΠ°ΡΡΡ
ΠΊΠΎΠ»Π΅Ρ, Ρ Π³Π»Π°Π΄ΠΊΠΎΠΉ ΠΏΠΎΠ²Π΅ΡΡ
Π½ΠΎΡΡΡΡ 0,10 ΠΌΠΊΠΌ (4 ΠΌΠΈΠΊΡΠΎΠ΄ΡΠΉΠΌΠ°). ΠΠ΅ ΡΠΎΠ»ΡΠΊΠΎ ΠΏΡΠΎΠΊΠ°ΡΠΊΠ° ΠΎΠ±ΡΡΠ½ΠΎ Π½Π΅ ΡΡΠ΅Π±ΡΠ΅Ρ ΡΠΈΡΡΠΎΠ²ΠΎΠΉ ΠΎΠ±ΡΠ°Π±ΠΎΡΠΊΠΈ, Π½ΠΎ ΠΈ ΠΏΡΠΎΠΊΠ°ΡΠΊΠ° ΡΠ»ΡΡΡΠ°Π΅Ρ ΠΌΠΈΠΊΡΠΎΡΡΡΡΠΊΡΡΡΡ Π·Π°Π³ΠΎΡΠΎΠ²ΠΊΠΈ.
ΠΡΠΎΠΈΠ·Π²ΠΎΠ΄ΡΡΠ²Π΅Π½Π½Π°Ρ ΡΡΡΠ°Π½ΠΎΠ²ΠΊΠ° ΠΎΠ±ΡΡΠ½ΠΎ ΡΡΠ΅Π±ΡΠ΅Ρ ΡΠΎΠ»ΡΠΊΠΎ Π½Π°Π±ΠΎΡΠ° ΠΏΡΠΎΠΊΠ°ΡΠ½ΡΡ ΡΡΠ°ΠΌΠΏΠΎΠ² ΠΈ ΡΠΎΠΎΡΠ²Π΅ΡΡΡΠ²ΡΡΡΠ΅Π³ΠΎ ΠΏΡΠΈΡΠΏΠΎΡΠΎΠ±Π»Π΅Π½ΠΈΡ Π΄Π»Ρ ΠΎΡΠ½Π°ΡΠ΅Π½ΠΈΡ ΠΏΡΠΎΠΊΠ°ΡΠ½ΠΎΠ³ΠΎ ΡΡΠ°Π½ΠΊΠ°. ΠΠΈΠ±ΠΎ ΠΌΠ΅ΡΠΎΠ΄ΠΎΠΌ ΠΏΠΎΠ΄Π°ΡΠΈ (Π²ΡΠ΅Π·Π°Π½ΠΈΡ), Π»ΠΈΠ±ΠΎ ΠΌΠ΅ΡΠΎΠ΄ΠΎΠΌ ΡΠΊΠ²ΠΎΠ·Π½ΠΎΠΉ ΠΏΠΎΠ΄Π°ΡΠΈ ΠΏΡΠΎΠΊΠ°ΡΠ½ΡΠ΅ ΡΡΠ°ΠΌΠΏΡ ΠΏΠ΅ΡΠ΅ΠΌΠ΅ΡΠ°ΡΡ Π·Π°Π³ΠΎΡΠΎΠ²ΠΊΡ ΠΌΠ΅ΠΆΠ΄Ρ ΡΠΎΠ±ΠΎΠΉ, ΡΠΎΡΠΌΠΈΡΡΡ Π·ΡΠ±ΡΡ ΠΏΠΎΠ΄ Π΄Π°Π²Π»Π΅Π½ΠΈΠ΅ΠΌ.
ΠΠ³ΡΠ°Π½ΠΈΡΠ΅Π½ΠΈΡ
Π¦ΠΈΠ»ΠΈΠ½Π΄ΡΠΈΡΠ΅ΡΠΊΠΈΠ΅ ΡΠ΅ΡΡΠ΅ΡΠ½ΠΈ ΠΌΠΎΠΆΠ½ΠΎ Π½Π°ΠΊΠ°ΡΡΠ²Π°ΡΡ, Π΅ΡΠ»ΠΈ ΠΎΠ½ΠΈ ΠΈΠΌΠ΅ΡΡ 18 Π·ΡΠ±ΡΠ΅Π² ΠΈ Π±ΠΎΠ»Π΅Π΅. ΠΠ΅Π½ΡΡΠ΅Π΅ ΠΊΠΎΠ»ΠΈΡΠ΅ΡΡΠ²ΠΎ Π·ΡΠ±ΡΠ΅Π² ΠΏΡΠΈΠ²ΠΎΠ΄ΠΈΡ ΠΊ ΡΠΎΠΌΡ, ΡΡΠΎ ΡΠ°Π±ΠΎΡΠ° ΠΏΠ»ΠΎΡ ΠΎ ΠΊΠ°ΡΠΈΡΡΡ. ΠΠΎΡΠΎΠ·ΡΠ±ΡΠ΅ ΡΠ΅ΡΡΠ΅ΡΠ½ΠΈ ΠΌΠΎΠ³ΡΡ Π±ΡΡΡ ΠΏΡΠΎΠΊΠ°ΡΠ°Π½Ρ Ρ ΠΌΠ΅Π½ΡΡΠΈΠΌ ΠΊΠΎΠ»ΠΈΡΠ΅ΡΡΠ²ΠΎΠΌ Π·ΡΠ±ΡΠ΅Π², Π΅ΡΠ»ΠΈ ΡΠ³ΠΎΠ» Π½Π°ΠΊΠ»ΠΎΠ½Π° Π²ΠΈΠ½ΡΠΎΠ²ΠΎΠΉ Π»ΠΈΠ½ΠΈΠΈ Π΄ΠΎΡΡΠ°ΡΠΎΡΠ½ΠΎ Π²Π΅Π»ΠΈΠΊ.
ΠΠ±ΡΡΠ½ΠΎ Π½Π΅ΡΠ΅Π»Π΅ΡΠΎΠΎΠ±ΡΠ°Π·Π½ΠΎ Π½Π°ΠΊΠ°ΡΡΠ²Π°ΡΡ Π·ΡΠ±ΡΡ Ρ ΡΠ³Π»ΠΎΠΌ Π·Π°ΡΠ΅ΠΏΠ»Π΅Π½ΠΈΡ ΠΌΠ΅Π½Π΅Π΅ 20Β°. ΠΠΈΠΆΠ½ΠΈΠ΅ ΡΠ³Π»Ρ ΠΈΠΌΠ΅ΡΡ ΡΠΈΡΠΎΠΊΠΈΠ΅ Π»ΡΡΠΊΠΈ Π² ΠΎΡΠ½ΠΎΠ²Π°Π½ΠΈΠΈ ΠΈ Π½Π° Π³ΡΠ΅Π±Π½Π΅, ΡΡΠΎ ΡΡΠ΅Π±ΡΠ΅Ρ Π±ΠΎΠ»ΡΡΠ΅Π³ΠΎ Π΄Π°Π²Π»Π΅Π½ΠΈΡ ΠΏΡΠΈ ΠΏΡΠΎΠΊΠ°ΡΠΊΠ΅. ΠΠ΅Π½ΡΡΠΈΠ΅ ΡΠ³Π»Ρ ΡΠ°ΠΊΠΆΠ΅ ΠΏΡΠ΅ΠΏΡΡΡΡΠ²ΡΡΡ ΡΠ΅ΡΠ΅Π½ΠΈΡ ΠΌΠ΅ΡΠ°Π»Π»Π°. Π₯ΠΎΡΡ Π³Π°Π»ΡΠ΅Π»ΠΈ ΡΠ°Π΄ΠΈΡΡΠΎΠΌ 0,13 ΠΌΠΌ (0,005 Π΄ΡΠΉΠΌΠ°) ΠΌΠΎΠ³ΡΡ Π±ΡΡΡ ΠΏΡΠΎΠΊΠ°ΡΠ°Π½Ρ, ΠΌΠΈΠ½ΠΈΠΌΠ°Π»ΡΠ½ΡΠΉ ΡΠ°Π΄ΠΈΡΡ 0,25 ΠΌΠΌ (0,010 Π΄ΡΠΉΠΌΠ°) ΡΠ²Π»ΡΠ΅ΡΡΡ Π»ΡΡΡΠΈΠΌ. ΠΠ»Ρ Π±ΠΎΠ»ΡΡΠ΅ΠΉ ΡΠΎΡΠ½ΠΎΡΡΠΈ Π·Π°Π³ΠΎΡΠΎΠ²ΠΊΠΈ Π·ΡΠ±ΡΠ°ΡΡΡ
ΠΊΠΎΠ»Π΅Ρ ΠΏΠ΅ΡΠ΅Π΄ ΠΏΡΠΎΠΊΠ°ΡΠΊΠΎΠΉ ΡΠ»ΠΈΡΡΡΡ. Π€Π°ΡΠΊΠΈ Π΄ΠΎΠ»ΠΆΠ½Ρ Π±ΡΡΡ 30Β° ΠΈΠ»ΠΈ ΠΌΠ΅Π½ΡΡΠ΅.
Π‘ΡΠ°Π»ΠΈ Π΄Π»Ρ Π·ΡΠ±ΡΠ°ΡΠΎΠ³ΠΎ ΠΏΡΠΎΠΊΠ°ΡΠ° Π½Π΅ Π΄ΠΎΠ»ΠΆΠ½Ρ ΡΠΎΠ΄Π΅ΡΠΆΠ°ΡΡ Π±ΠΎΠ»Π΅Π΅ 0,13% ΡΠ΅ΡΡ ΠΈ ΠΆΠ΅Π»Π°ΡΠ΅Π»ΡΠ½ΠΎ Π½Π΅ ΡΠΎΠ΄Π΅ΡΠΆΠ°ΡΡ ΡΠ²ΠΈΠ½ΡΠ°. ΠΠ°Π³ΠΎΡΠΎΠ²ΠΊΠΈ Π½Π΅ Π΄ΠΎΠ»ΠΆΠ½Ρ Π±ΡΡΡ ΡΠ²Π΅ΡΠΆΠ΅ 28 HRC.
ΠΠΎΠΊΠΎΠ²ΠΊΠ°
ΠΠΎΠΊΠΎΠ²ΠΊΠ° ΡΠΆΠ΅ Π΄Π°Π²Π½ΠΎ ΠΈΡΠΏΠΎΠ»ΡΠ·ΡΠ΅ΡΡΡ Π² ΠΏΡΠΎΠΈΠ·Π²ΠΎΠ΄ΡΡΠ²Π΅ Π·ΡΠ±ΡΠ°ΡΡΡ
ΠΊΠΎΠ»Π΅Ρ. ΠΡΠΎ ΠΎΡΠΎΠ±Π΅Π½Π½ΠΎ Π²Π΅ΡΠ½ΠΎ Π΄Π»Ρ ΠΏΡΠΎΠΈΠ·Π²ΠΎΠ΄ΡΡΠ²Π° Π·Π°Π³ΠΎΡΠΎΠ²ΠΎΠΊ Π΄Π»Ρ Π·ΡΠ±ΡΠ°ΡΡΡ
ΠΊΠΎΠ»Π΅Ρ, ΠΊΠΎΡΠΎΡΡΠ΅ Π²ΠΏΠΎΡΠ»Π΅Π΄ΡΡΠ²ΠΈΠΈ Π±ΡΠ΄ΡΡ Π²ΡΡΠ΅Π·Π°Π½Ρ/ΠΎΠ±ΡΠ°Π±ΠΎΡΠ°Π½Ρ Π΄ΠΎ ΠΊΠΎΠ½Π΅ΡΠ½ΠΎΠΉ ΠΆΠ΅Π»Π°Π΅ΠΌΠΎΠΉ ΠΊΠΎΠ½ΡΠΈΠ³ΡΡΠ°ΡΠΈΠΈ. ΠΠ°Π³ΠΎΡΠΎΠ²ΠΊΠΈ Π·ΡΠ±ΡΠ°ΡΡΡ
ΠΊΠΎΠ»Π΅Ρ ΠΈΠ·Π³ΠΎΡΠΎΠ²Π»ΡΠ»ΠΈΡΡ ΠΌΠ΅ΡΠΎΠ΄Π°ΠΌΠΈ ΡΠ²ΠΎΠ±ΠΎΠ΄Π½ΠΎΠΉ ΠΊΠΎΠ²ΠΊΠΈ, ΡΠ²ΠΎΠ±ΠΎΠ΄Π½ΠΎΠΉ ΠΊΠΎΠ²ΠΊΠΈ (ΡΠΈΡ. 7) ΠΈ Π³ΠΎΡΡΡΠ΅ΠΉ ΠΎΡΠ°Π΄ΠΊΠΎΠΉ. ΠΠ° ΠΏΠΎΡΠ»Π΅Π΄Π½ΠΈΠ΅ 35 Π»Π΅Ρ Π±ΡΠ»ΠΈ ΠΏΡΠΎΠ²Π΅Π΄Π΅Π½Ρ Π·Π½Π°ΡΠΈΡΠ΅Π»ΡΠ½ΡΠ΅ ΠΈΡΡΠ»Π΅Π΄ΠΎΠ²Π°Π½ΠΈΡ ΠΈ ΡΠ°Π·ΡΠ°Π±ΠΎΡΠΊΠΈ, Π½Π°ΠΏΡΠ°Π²Π»Π΅Π½Π½ΡΠ΅ Π½Π° ΠΏΡΠΎΠΈΠ·Π²ΠΎΠ΄ΡΡΠ²ΠΎ Π·ΡΠ±ΡΠ°ΡΡΡ
ΠΊΠΎΠ»Π΅Ρ ΠΏΠΎΡΡΠΈ ΡΠ΅ΡΡΠ°ΡΠΎΠΉ ββΠΈΠ»ΠΈ ΡΠ΅ΡΡΠ°ΡΠΎΠΉ ββΡΠΎΡΠΌΡ ΠΏΡΡΠ΅ΠΌ ΠΏΡΠ΅ΡΠΈΠ·ΠΈΠΎΠ½Π½ΠΎΠΉ ΠΊΠΎΠ²ΠΊΠΈ. Π‘Π΅Π³ΠΎΠ΄Π½Ρ ΠΏΡΠ΅ΡΠΈΠ·ΠΈΠΎΠ½Π½ΡΠ΅ ΠΊΠΎΠ²Π°Π½ΡΠ΅ Π·ΡΠ±ΡΠ°ΡΡΠ΅ ΠΊΠΎΠ»Π΅ΡΠ°, ΡΡΠ΅Π±ΡΡΡΠΈΠ΅ ΠΌΠΈΠ½ΠΈΠΌΠ°Π»ΡΠ½ΠΎΠΉ ΡΠΈΡΡΠΎΠ²ΠΎΠΉ ΠΎΠ±ΡΠ°Π±ΠΎΡΠΊΠΈ ΠΈΠ»ΠΈ Π²ΠΎΠΎΠ±ΡΠ΅ Π½Π΅ ΡΡΠ΅Π±ΡΡΡΠΈΠ΅ Π΅Π΅ ΠΎΠ±ΡΠ°Π±ΠΎΡΠΊΠΈ, ΠΎΠ±ΡΡΠ½ΠΎ ΠΈΡΠΏΠΎΠ»ΡΠ·ΡΡΡΡΡ Π² Π°Π²ΡΠΎΠΌΠΎΠ±ΠΈΠ»ΡΠ½ΠΎΠΉ, Π³ΡΡΠ·ΠΎΠ²ΠΎΠΉ, Π²Π½Π΅Π΄ΠΎΡΠΎΠΆΠ½ΠΎΠΉ, Π°ΡΡΠΎΠΊΠΎΡΠΌΠΈΡΠ΅ΡΠΊΠΎΠΉ, ΠΆΠ΅Π»Π΅Π·Π½ΠΎΠ΄ΠΎΡΠΎΠΆΠ½ΠΎΠΉ, ΡΠ΅Π»ΡΡΠΊΠΎΡ
ΠΎΠ·ΡΠΉΡΡΠ²Π΅Π½Π½ΠΎΠΉ ΠΈ ΠΏΠΎΠ³ΡΡΠ·ΠΎΡΠ½ΠΎ-ΡΠ°Π·Π³ΡΡΠ·ΠΎΡΠ½ΠΎΠΉ ΠΎΡΡΠ°ΡΠ»ΡΡ
, Π° ΡΠ°ΠΊΠΆΠ΅ Π² ΡΠ½Π΅ΡΠ³Π΅ΡΠΈΠΊΠ΅ ΠΈ Π³ΠΎΡΠ½ΠΎΠ΄ΠΎΠ±ΡΠ²Π°ΡΡΠ΅ΠΉ ΠΏΡΠΎΠΌΡΡΠ»Π΅Π½Π½ΠΎΡΡΠΈ.
ΠΡΡΠΎΠΊΠΎΡΠ½Π΅ΡΠ³Π΅ΡΠΈΡΠ΅ΡΠΊΠ°Ρ ΠΊΠΎΠ²ΠΊΠ°
ΠΠ΄Π½ΠΈΠΌ ΠΈΠ· ΠΏΠ΅ΡΠ²ΡΡ ΠΏΡΠΎΡΠ΅ΡΡΠΎΠ² ΠΊΠΎΠ²ΠΊΠΈ Π΄Π»Ρ ΠΈΠ·Π³ΠΎΡΠΎΠ²Π»Π΅Π½ΠΈΡ Π·ΡΠ±ΡΠ°ΡΡΡ ΠΊΠΎΠ»Π΅Ρ ΠΏΠΎΡΡΠΈ ΠΈΠ»ΠΈ ΡΠ΅ΡΡΠ°ΡΠΎΠΉ ββΡΠΎΡΠΌΡ Π±ΡΠ» Π²ΡΡΠΎΠΊΠΎΡΠ½Π΅ΡΠ³Π΅ΡΠΈΡΠ΅ΡΠΊΠΈΠΉ ΠΏΡΠΎΡΠ΅ΡΡ ΠΊΠΎΠ²ΠΊΠΈ, ΠΊΠΎΡΠΎΡΡΠΉ ΠΏΡΠ΅Π΄ΡΡΠ°Π²Π»ΡΠ΅Ρ ΡΠΎΠ±ΠΎΠΉ ΠΏΡΠΎΡΠ΅ΡΡ Π³ΠΎΡΡΡΠ΅ΠΉ ΠΈΠ»ΠΈ Ρ ΠΎΠ»ΠΎΠ΄Π½ΠΎΠΉ ΡΡΠ°ΠΌΠΏΠΎΠ²ΠΊΠΈ Π² Π·Π°ΠΊΡΡΡΡΡ ΡΡΠ°ΠΌΠΏΠ°Ρ , ΠΏΡΠΈ ΠΊΠΎΡΠΎΡΠΎΠΌ ΡΠ°Π±ΠΎΡΠΈΠΉ ΠΌΠ΅ΡΠ°Π»Π» Π΄Π΅ΡΠΎΡΠΌΠΈΡΡΠ΅ΡΡΡ ΠΏΡΠΈ Π½Π΅ΠΎΠ±ΡΡΠ°ΠΉΠ½ΠΎ Π²ΡΡΠΎΠΊΠΈΠ΅ ΡΠΊΠΎΡΠΎΡΡΠΈ. Π ΠΈΠ΄Π΅Π°Π»Π΅ ΠΎΠΊΠΎΠ½ΡΠ°ΡΠ΅Π»ΡΠ½Π°Ρ ΠΊΠΎΠ½ΡΠΈΠ³ΡΡΠ°ΡΠΈΡ ΠΏΠΎΠΊΠΎΠ²ΠΊΠΈ ΠΏΠΎΠ»ΡΡΠ°Π΅ΡΡΡ Π·Π° ΠΎΠ΄ΠΈΠ½ ΡΠ΄Π°Ρ ΠΈΠ»ΠΈ, ΡΠ°ΠΌΠΎΠ΅ Π±ΠΎΠ»ΡΡΠ΅Π΅, Π·Π° Π½Π΅ΡΠΊΠΎΠ»ΡΠΊΠΎ ΡΠ΄Π°ΡΠΎΠ². Π‘ΠΊΠΎΡΠΎΡΡΡ ΠΏΠΎΠ»Π·ΡΠ½Π°, Π° Π½Π΅ Π΅Π³ΠΎ ΠΌΠ°ΡΡΠ°, ΡΠΎΠ·Π΄Π°Π΅Ρ ΠΎΡΠ½ΠΎΠ²Π½ΡΡ ΡΠΈΠ»Ρ ΠΊΠΎΠ²ΠΊΠΈ.
ΠΠΎΠΆΠ½ΠΎ ΠΏΡΠΎΠΈΠ·Π²ΠΎΠ΄ΠΈΡΡ ΡΠ΅ΡΡΠ΅ΡΠ½ΠΈ Ρ ΠΊΠΎΠ½ΡΡΡΠ½ΡΠΌ ΠΏΠΎΡΠΎΠΊΠΎΠΌ Π·Π΅ΡΠ΅Π½, ΠΏΠΎΠ²ΡΠΎΡΡΡΡΠΈΠΌ ΠΊΠΎΠ½ΡΠΈΠ³ΡΡΠ°ΡΠΈΡ Π·ΡΠ±ΡΠ΅Π², Ρ ΠΏΠΎΠΌΠΎΡΡΡ Π²ΡΡΠΎΠΊΠΎΡΠ½Π΅ΡΠ³Π΅ΡΠΈΡΠ΅ΡΠΊΠΎΠΉ ΠΊΠΎΠ²ΠΊΠΈ. Π ΡΠ»ΡΡΠ°Π΅ ΠΏΡΡΠΌΠΎΠ·ΡΠ±ΡΡ
Π·ΡΠ±ΡΠ°ΡΡΡ
ΠΊΠΎΠ»Π΅Ρ ΡΡΠΎ Π΄ΠΎΡΡΠΈΠ³Π°Π΅ΡΡΡ Π·Π° ΡΡΠ΅Ρ ΡΠΏΠ΅ΠΊΠ°Π½ΠΈΡ, Π²ΡΠ·ΡΠ²Π°ΡΡΠ΅Π³ΠΎ ΠΏΠΎΠΏΠ΅ΡΠ΅ΡΠ½ΠΎΠ΅ ΡΠ΅ΡΠ΅Π½ΠΈΠ΅ ΠΌΠ΅ΡΠ°Π»Π»Π° Π² ΠΌΠ°ΡΡΠΈΡΠ΅, ΠΈΠΌΠ΅ΡΡΠ΅ΠΉ ΠΆΠ΅Π»Π°Π΅ΠΌΡΡ ΠΊΠΎΠ½ΡΠΈΠ³ΡΡΠ°ΡΠΈΡ Π·ΡΠ±ΡΠ΅Π² Π½Π° Π΅Π΅ ΠΏΠ΅ΡΠΈΡΠ΅ΡΠΈΠΈ. Π Π΅Π»ΡΠ΅ΡΠ½ΠΎΠ΅ Π·Π΅ΡΠ½ΠΎ ΡΠ²Π΅Π»ΠΈΡΠΈΠ²Π°Π΅Ρ Π½Π΅ΡΡΡΡΡ ΡΠΏΠΎΡΠΎΠ±Π½ΠΎΡΡΡ Π±Π΅Π· ΡΠ²Π΅Π»ΠΈΡΠ΅Π½ΠΈΡ ΡΠ°Π·ΠΌΠ΅ΡΠ° Π·ΡΠ±Π°. ΠΡΠΎΠΌΠ΅ ΡΠΎΠ³ΠΎ, ΡΡΠΎΡ ΠΏΡΠΎΡΠ΅ΡΡ ΡΠ²ΠΎΠ΄ΠΈΡ ΠΊ ΠΌΠΈΠ½ΠΈΠΌΡΠΌΡ ΠΌΠ΅Ρ
Π°Π½ΠΈΡΠ΅ΡΠΊΡΡ ΠΎΠ±ΡΠ°Π±ΠΎΡΠΊΡ, Π½Π΅ΠΎΠ±Ρ
ΠΎΠ΄ΠΈΠΌΡΡ Π΄Π»Ρ ΠΏΡΠΎΠΈΠ·Π²ΠΎΠ΄ΡΡΠ²Π° Π³ΠΎΡΠΎΠ²ΠΎΠΉ ΡΠ΅ΡΡΠ΅ΡΠ½ΠΈ. Π₯ΠΎΡΡ ΠΏΡΡΠΌΠΎΠ·ΡΠ±ΡΠ΅ ΡΠ΅ΡΡΠ΅ΡΠ½ΠΈ Π»Π΅Π³ΡΠ΅ Π²ΡΠ΅Π³ΠΎ Π²ΡΠΊΠΎΠ²Π°ΡΡ, ΠΊΠΎΡΠΎΠ·ΡΠ±ΡΠ΅ ΠΈ ΡΠΏΠΈΡΠ°Π»ΡΠ½ΠΎ-ΠΊΠΎΠ½ΠΈΡΠ΅ΡΠΊΠΈΠ΅ ΡΠ΅ΡΡΠ΅ΡΠ½ΠΈ ΡΠ°ΠΊΠΆΠ΅ ΠΌΠΎΠΆΠ½ΠΎ Π²ΡΠΊΠΎΠ²Π°ΡΡ, Π΅ΡΠ»ΠΈ ΠΈΡ
ΠΊΠΎΠ½ΡΠΈΠ³ΡΡΠ°ΡΠΈΡ ΠΏΠΎΠ·Π²ΠΎΠ»ΡΠ΅Ρ Π²ΡΡΠΎΠ»ΠΊΠ½ΡΡΡ ΡΠ΅ΡΡΠ΅ΡΠ½Ρ ΠΈΠ· ΠΏΠΎΠ»ΠΎΡΡΠΈ ΡΡΠ°ΠΌΠΏΠ°. Π¨Π΅ΡΡΠ΅ΡΠ½ΠΈ ΠΊΠΎΠ²Π°Π»ΠΈ ΠΈΠ· Π½ΠΈΠ·ΠΊΠΎΠ»Π΅Π³ΠΈΡΠΎΠ²Π°Π½Π½ΠΎΠΉ ΡΡΠ°Π»ΠΈ, Π»Π°ΡΡΠ½ΠΈ, Π°Π»ΡΠΌΠΈΠ½ΠΈΠ΅Π²ΡΡ
ΡΠΏΠ»Π°Π²ΠΎΠ², Π½Π΅ΡΠΆΠ°Π²Π΅ΡΡΠ΅ΠΉ ΡΡΠ°Π»ΠΈ, ΡΠΈΡΠ°Π½Π° ΠΈ Π½Π΅ΠΊΠΎΡΠΎΡΡΡ
ΠΆΠ°ΡΠΎΠΏΡΠΎΡΠ½ΡΡ
ΡΠΏΠ»Π°Π²ΠΎΠ².
ΠΡΠ±ΡΠ°ΡΡΠ΅ ΠΊΠΎΠ»Π΅ΡΠ° Ρ DP ΠΎΡ 5 Π΄ΠΎ 20 ΠΎΠ±ΡΡΠ½ΠΎ Π²ΡΠΊΠΎΠ²ΡΠ²Π°ΡΡΡΡ Ρ Π½Π΅Π±ΠΎΠ»ΡΡΠΈΠΌ ΠΏΡΠΈΠΏΡΡΠΊΠΎΠΌ Π½Π° ΠΌΠ΅Ρ Π°Π½ΠΈΡΠ΅ΡΠΊΡΡ ΠΎΠ±ΡΠ°Π±ΠΎΡΠΊΡ ΠΈΠ»ΠΈ Π±Π΅Π· Π½Π΅Π³ΠΎ. Π‘ΡΠΎΠΊ ΡΠ»ΡΠΆΠ±Ρ ΡΡΠ°ΠΌΠΏΠ° Π·Π½Π°ΡΠΈΡΠ΅Π»ΡΠ½ΠΎ ΡΠ½ΠΈΠΆΠ°Π΅ΡΡΡ ΠΏΡΠΈ ΠΊΠΎΠ²ΠΊΠ΅ ΡΠ΅ΡΡΠ΅ΡΠ΅Π½ Ρ Π±ΠΎΠ»Π΅Π΅ ΠΌΠ΅Π»ΠΊΠΈΠΌ ΡΠ°Π³ΠΎΠΌ.
Π‘ΠΎΠΎΠ±ΡΠ°Π»ΠΎΡΡ ΠΎ ΠΏΠΎΠΊΠΎΠ²ΠΊΠ΅ Π·ΡΠ±ΡΠ°ΡΡΡ
ΠΊΠΎΠ»Π΅Ρ 5-DP Ρ ΡΠ²ΠΎΠ»ΡΠ²Π΅Π½ΡΠ½ΡΠΌ Π΄ΠΎΠΏΡΡΠΊΠΎΠΌ 0,013 ΠΌΠΌ (0,0005 Π΄ΡΠΉΠΌΠ°) ΠΈ ΠΎΠ±ΡΠ΅ΠΉ ΡΡΠΌΠΌΠ°ΡΠ½ΠΎΠΉ ΠΏΠΎΠ³ΡΠ΅ΡΠ½ΠΎΡΡΡΡ 0,08 ΠΌΠΌ (0,003 Π΄ΡΠΉΠΌΠ°). ΠΡΠΈ ΡΠ΅ΡΡΠ΅ΡΠ½ΠΈ Π±ΡΠ»ΠΈ Π²ΡΠΊΠΎΠ²Π°Π½Ρ Ρ ΠΎΡΠΊΠ»ΠΎΠ½Π΅Π½ΠΈΠ΅ΠΌ ΡΠ°ΡΡΡΠΎΡΠ½ΠΈΡ ΠΌΠ΅ΠΆΠ΄Ρ Π·ΡΠ±ΡΡΠΌΠΈ ΠΎΠΊΠΎΠ»ΠΎ 0,025 ΠΌΠΌ (0,001 Π΄ΡΠΉΠΌΠ°) ΠΈ ΠΎΠ±ΡΠΈΠΌ ΡΡΠΌΠΌΠ°ΡΠ½ΡΠΌ ΠΎΡΠΊΠ»ΠΎΠ½Π΅Π½ΠΈΠ΅ΠΌ 0,089 ΠΌΠΌ (0,0035 Π΄ΡΠΉΠΌΠ°). Π Π°Π·ΠΌΠ΅ΡΡ Π½Π°Π΄ ΡΡΠΈΡΡΠ°ΠΌΠΈ Π½Π° ΡΡΠΈΡ
ΡΠ΅ΡΡΠ΅ΡΠ½ΡΡ
Π²ΡΠ΄Π΅ΡΠΆΠΈΠ²Π°Π»ΠΈΡΡ Ρ ΡΠΎΡΠ½ΠΎΡΡΡΡ Β± 0,05 ΠΌΠΌ (0,002 Π΄ΡΠΉΠΌΠ°), Π° ΠΎΠ±ΡΠ°Ρ ΡΠΎΡΡΠ°Π²Π½Π°Ρ ΠΎΡΠΈΠ±ΠΊΠ° ΡΠΎΡΡΠ°Π²Π»ΡΠ»Π° ΠΎΠΊΠΎΠ»ΠΎ 0,20 ΠΌΠΌ (0,008 Π΄ΡΠΉΠΌΠ°).
Π‘ΠΎΠ±Π»ΡΠ΄Π΅Π½ΠΈΠ΅ ΠΎΡΠ΅Π½Ρ ΠΆΠ΅ΡΡΠΊΠΈΡ Π΄ΠΎΠΏΡΡΠΊΠΎΠ² Π½Π° ΡΠ°Π·ΠΌΠ΅ΡΡ Π·ΡΠ±ΡΠ°ΡΡΡ ΠΊΠΎΠ»Π΅Ρ ΠΌΠΎΠΆΠ΅Ρ ΠΈΡΠΊΠ»ΡΡΠΈΡΡ ΡΠΈΡΡΠΎΠ²ΡΡ ΠΎΠ±ΡΠ°Π±ΠΎΡΠΊΡ, Π½ΠΎ ΡΠΊΠΎΠ½ΠΎΠΌΠΈΡ ΠΌΠΎΠΆΠ΅Ρ Π±ΡΡΡ ΠΏΡΠ΅Π²ΡΡΠ΅Π½Π° ΠΈΠ·-Π·Π° Π±ΠΎΠ»Π΅Π΅ Π²ΡΡΠΎΠΊΠΈΡ Π·Π°ΡΡΠ°Ρ Π½Π° ΠΈΠ·Π³ΠΎΡΠΎΠ²Π»Π΅Π½ΠΈΠ΅/ΠΎΠ±ΡΠ»ΡΠΆΠΈΠ²Π°Π½ΠΈΠ΅ ΠΌΠ°ΡΡΠΈΡΡ. Π‘Π»Π΅Π΄ΠΎΠ²Π°ΡΠ΅Π»ΡΠ½ΠΎ, Π±ΠΎΠ»ΡΡΠΈΠ½ΡΡΠ²ΠΎ ΠΊΠΎΠ²Π°Π½ΡΡ ΡΠ΅ΡΡΠ΅ΡΠ΅Π½ ΠΈΠΌΠ΅ΡΡ ΠΏΡΠΈΠΏΡΡΠΊ Π½Π° ΠΌΠ΅Ρ Π°Π½ΠΈΡΠ΅ΡΠΊΡΡ ΠΎΠ±ΡΠ°Π±ΠΎΡΠΊΡ.
Π¦Π΅Π»Π΅ΡΠΎΠΎΠ±ΡΠ°Π·Π½Π° ΡΠ΅ΡΠΎΡ ΠΎΠ²Π°ΡΠΎΡΡΡ ΠΏΠΎΠ²Π΅ΡΡ Π½ΠΎΡΡΠΈ Π·ΡΠ±ΡΠ΅Π² ΡΠ΅ΡΡΠ΅ΡΠ½ΠΈ ΠΎΡ 0,5 Π΄ΠΎ 1,5 ΠΌΠΊΠΌ (ΠΎΡ 20 Π΄ΠΎ 60 ΠΌΠΈΠΊΡΠΎΠ΄ΡΠΉΠΌΠΎΠ²). ΠΠ΄Π½Π°ΠΊΠΎ Π΄Π°ΠΆΠ΅ ΠΏΡΠΈ ΡΠ΅ΡΠΎΡ ΠΎΠ²Π°ΡΠΎΡΡΠΈ 0,5 ΠΌΠΊΠΌ (20 ΠΌΠΈΠΊΡΠΎΠ΄ΡΠΉΠΌΠΎΠ²) Π»ΠΎΠΊΠ°Π»ΡΠ½ΡΠ΅ Π΄Π΅ΡΠ΅ΠΊΡΡ ΠΌΠΎΠ³ΡΡ ΡΠ²Π΅Π»ΠΈΡΠΈΠ²Π°ΡΡΡΡ Π² ΡΡΠ΅Π΄Π½Π΅ΠΌ Π΄ΠΎ 1,5 ΠΌΠΊΠΌ (60 ΠΌΠΈΠΊΡΠΎΠ΄ΡΠΉΠΌΠΎΠ²) ΠΈΠ»ΠΈ Π±ΠΎΠ»ΡΡΠ΅. ΠΠΎΡΡΠΎΠΌΡ Π±ΡΠ»ΠΎ Π±Ρ ΡΡΡΠ΄Π½ΠΎ ΠΏΠΎΠ΄Π΄Π΅ΡΠΆΠΈΠ²Π°ΡΡ Ρ ΠΎΡΠΎΡΠ΅Π΅ ΠΊΠ°ΡΠ΅ΡΡΠ²ΠΎ ΠΏΠΎΠ²Π΅ΡΡ Π½ΠΎΡΡΠΈ Π·ΡΠ±ΡΠ΅Π² ΡΠ΅ΡΡΠ΅ΡΠ½ΠΈ Π±Π΅Π· ΡΠ»ΠΈΡΠΎΠ²Π°Π½ΠΈΡ.
Π’ΠΈΠΏΠΎΠ²ΡΠ΅ ΠΏΠΎΠΊΠΎΠ²ΠΊΠΈ Π·ΡΠ±ΡΠ°ΡΡΡ ΠΊΠΎΠ»Π΅Ρ
Π¨Π΅ΡΡΠ΅ΡΠ½Ρ ΠΌΠ°ΡΡΠΎΠΉ 4,5 ΠΊΠ³ (10 ΡΡΠ½ΡΠΎΠ²), ΠΏΠΎΠΊΠ°Π·Π°Π½Π½Π°Ρ Π½Π° ΡΠΈΡ. 8, Π±ΡΠ»Π° Π²ΡΠΊΠΎΠ²Π°Π½Π° ΠΈΠ· ΡΡΠ°Π»ΡΠ½ΠΎΠΉ Π·Π°Π³ΠΎΡΠΎΠ²ΠΊΠΈ 8620 Π΄ΠΈΠ°ΠΌΠ΅ΡΡΠΎΠΌ 75 ΠΌΠΌ (3 Π΄ΡΠΉΠΌΠ°) ΠΈ Π΄Π»ΠΈΠ½ΠΎΠΉ 124 ΠΌΠΌ (4,9 Π΄ΡΠΉΠΌΠ°). Π£ΡΠΎΠ²Π΅Π½Ρ ΡΠ½Π΅ΡΠ³ΠΈΠΈ 353 000 ΠΠΆ (260 000 ΡΡΡ Β· ΡΡΠ½Ρ-ΡΠΈΠ»Π°) Π±ΡΠ» Π½Π΅ΠΎΠ±Ρ
ΠΎΠ΄ΠΈΠΌ, ΡΡΠΎΠ±Ρ Π²ΡΠΊΠΎΠ²Π°ΡΡ ΡΠ΅ΡΡΠ΅ΡΠ½Ρ Π·Π° ΠΎΠ΄ΠΈΠ½ ΡΠ΄Π°Ρ ΠΏΡΠΈ 1230 Β° C (2250 Β° F). ΠΠ΅ΡΠ΅ΠΏΠΎΠ½ΠΊΠ° Π½Π° ΡΠ΅ΡΡΠ΅ΡΠ½Π΅ Π±ΡΠ»Π° Π²ΡΠΊΠΎΠ²Π°Π½Π° Π΄ΠΎ ΠΊΠΎΠ½Π΅ΡΠ½ΠΎΠΉ ΡΠΎΠ»ΡΠΈΠ½Ρ; Π·ΡΠ±ΡΡ Π±ΡΠ»ΠΈ Π²ΡΠΊΠΎΠ²Π°Π½Ρ ΠΈΠ· ΠΏΡΠΈΠΏΡΡΠΊΠ° ΡΠΎΠ»ΡΠΈΠ½ΠΎΠΉ 0,51 ΠΌΠΌ (0,020 Π΄ΡΠΉΠΌΠ°) Π΄Π»Ρ ΡΠΈΡΡΠΎΠ²ΠΎΠΉ ΠΎΠ±ΡΠ°Π±ΠΎΡΠΊΠΈ.
ΠΡΡΠ°Π²ΠΊΠΈ ΡΡΠ°ΠΌΠΏΠΎΠ², ΠΈΠ·Π½Π°ΡΠ°Π»ΡΠ½ΠΎ ΠΈΡΠΏΠΎΠ»ΡΠ·ΠΎΠ²Π°Π²ΡΠΈΠ΅ΡΡ Π΄Π»Ρ ΠΊΠΎΠ²ΠΊΠΈ ΡΡΠΎΠΉ ΡΠ΅ΡΡΠ΅ΡΠ½ΠΈ, Π±ΡΠ»ΠΈ ΠΈΠ·Π³ΠΎΡΠΎΠ²Π»Π΅Π½Ρ ΠΈΠ· ΠΈΠ½ΡΡΡΡΠΌΠ΅Π½ΡΠ°Π»ΡΠ½ΠΎΠΉ ΡΡΠ°Π»ΠΈ h21 ΠΈΠ»ΠΈ h23. ΠΡΠ° ΡΡΠ°Π»Ρ ΠΎΠ±ΡΡΠ½ΠΎ ΡΠ°Π·ΠΌΡΠ³ΡΠ°Π»Π°ΡΡ ΠΏΠΎΡΠ»Π΅ ΠΈΠ·Π³ΠΎΡΠΎΠ²Π»Π΅Π½ΠΈΡ 20 ΡΠ΅ΡΡΠ΅ΡΠ΅Π½ ΠΈΠ·-Π·Π° ΡΠΎΠ³ΠΎ, ΡΡΠΎ Π΅Π΅ ΡΠ΅ΠΌΠΏΠ΅ΡΠ°ΡΡΡΠ° ΠΏΡΠ΅Π²ΡΡΠ°Π»Π° ΡΠ΅ΠΌΠΏΠ΅ΡΠ°ΡΡΡΡ ΠΎΡΠΏΡΡΠΊΠ° ΡΡΠ°Π»ΠΈ h23 565Β°C (1050Β°F). ΠΡΠ»ΠΎ ΠΎΠ±Π½Π°ΡΡΠΆΠ΅Π½ΠΎ, ΡΡΠΎ ΠΈΡΠΏΠΎΠ»ΡΠ·ΠΎΠ²Π°Π½ΠΈΠ΅ ΡΠΏΠ»Π°Π²Π° 718 (UNS N07718) ΡΠ²Π΅Π»ΠΈΡΠΈΠ²Π°Π΅Ρ ΡΡΠΎΠΊ ΡΠ»ΡΠΆΠ±Ρ Π²ΠΊΠ»Π°Π΄ΡΡΠ° ΠΌΠ°ΡΡΠΈΡΡ.
ΠΠ²ΡΠΎΠΌΠΎΠ±ΠΈΠ»ΡΠ½ΡΠΉ ΠΌΠ°Ρ
ΠΎΠ²ΠΈΠΊ, ΠΏΠΎΠΊΠ°Π·Π°Π½Π½ΡΠΉ Π½Π° ΡΠΈΡ. 9, Π΄ΠΈΠ°ΠΌΠ΅ΡΡΠΎΠΌ 272,49 ΠΌΠΌ (10,728 Π΄ΡΠΉΠΌΠ°) ΠΏΠΎ Π·ΡΠ±ΡΡΠΌ ΠΈ Π²Π΅ΡΠΎΠΌ 11 ΠΊΠ³ (24 ΡΡΠ½ΡΠ°), Π±ΡΠ» Π²ΡΠΊΠΎΠ²Π°Π½ ΠΈΠ· ΠΎΠ±ΡΠ°Π±ΠΎΡΠ°Π½Π½ΠΎΠΉ Π·Π°Π³ΠΎΡΠΎΠ²ΠΊΠΈ, ΠΎΡΠ»ΠΈΡΠΎΠΉ ΠΈΠ· ΡΠ΅ΡΠΎΠ³ΠΎ ΡΡΠ³ΡΠ½Π° ΠΊΠ»Π°ΡΡΠ° 40 (ΠΎΠ±ΡΡΠ½ΠΎ ΡΡΠΈΡΠ°ΡΡΠ΅Π³ΠΎΡΡ Π½Π΅ ΠΏΠΎΠ΄Π΄Π°ΡΡΠΈΠΌΡΡ ΠΊΠΎΠ²ΠΊΠ΅). ΠΠ΅Ρ
Π°Π½ΠΈΡΠ΅ΡΠΊΠΈ ΠΎΠ±ΡΠ°Π±ΠΎΡΠ°Π½Π½Π°Ρ Π·Π°Π³ΠΎΡΠΎΠ²ΠΊΠ°, ΡΠ΅ΡΠ΅Π½ΠΈΠ΅ ΠΊΠΎΡΠΎΡΠΎΠΉ ΠΏΠΎΠΊΠ°Π·Π°Π½ΠΎ Π½Π° ΡΠΈΡΡΠ½ΠΊΠ΅ 9., Π±ΡΠ» Π½Π°Π³ΡΠ΅Ρ Π΄ΠΎ 955 Β° C (1750 Β° F) ΠΈ Π²ΡΠΊΠΎΠ²Π°Π½ ΠΏΡΠΈ ΡΡΠΎΠ²Π½Π΅ ΡΠ½Π΅ΡΠ³ΠΈΠΈ 271 000 ΠΠΆ (200 000 ΡΡΡΠΎΠ² Β· ΡΡΠ½ΡΠΎΠ² ΡΠΈΠ»Ρ). ΠΡΠ° Π΄Π΅ΡΠ°Π»Ρ ΠΈΠΌΠ΅Π»Π° Π½Π°ΠΈΠΌΠ΅Π½ΡΡΡΡ ΡΠΏΠ΅ΡΠΈΡΠΈΠΊΠ°ΡΠΈΡ Π΄ΠΎΠΏΡΡΠΊΠ°. ΠΠΈΠ°ΠΌΠ΅ΡΡ Π½Π°Π΄ Π·ΡΠ±ΡΡΠΌΠΈ ΠΈ ΡΠΎΠ»ΡΠΈΠ½Π° ΠΊΠΎΡΠΏΡΡΠ° ΠΈΠΌΠ΅Π»ΠΈ Π΄ΠΎΠΏΡΡΠΊ +0,00 ΠΌΠΌ, -0,18 ΠΌΠΌ (+0,000 Π΄ΡΠΉΠΌΠ°, -0,007 Π΄ΡΠΉΠΌΠ°). ΠΠ°ΠΈΠ±ΠΎΠ»ΡΡΠΈΠΉ Π΄ΠΎΠΏΡΡΠΊ Π½Π° Π΄Π΅ΡΠ°Π»ΠΈ ΡΠΎΡΡΠ°Π²Π»ΡΠ» Β±1,02 ΠΌΠΌ (Β±0,040 Π΄ΡΠΉΠΌΠ°) Π½Π° Π΄ΠΈΠ°ΠΌΠ΅ΡΡ ΡΠ³Π»ΡΠ±Π»Π΅Π½ΠΈΡ. ΠΠΎΠΏΡΡΠΊΠΈ Π½Π° Π΄ΡΡΠ³ΠΈΠ΅ ΡΠ³Π»ΡΠ±Π»Π΅Π½ΠΈΡ ΡΠΎΡΡΠ°Π²Π»ΡΠ»ΠΈ Β±0,18 ΠΌΠΌ (Β±0,007 Π΄ΡΠΉΠΌΠ°) ΠΈ +0,48 ΠΌΠΌ, -0,00 ΠΌΠΌ (+0,019 Π΄ΡΠΉΠΌΠ°, -0,000 Π΄ΡΠΉΠΌΠ°). ΠΡΠ° ΡΠ΅ΡΡΠ΅ΡΠ½Ρ Π±ΡΠ»Π° Π²ΡΠΊΠΎΠ²Π°Π½Π° ΠΏΠΎ Π³ΠΎΡΠΎΠ²ΡΠΌ ΡΠ°Π·ΠΌΠ΅ΡΠ°ΠΌ.
ΠΡΠΊΠΎΠ²Π°Π½Ρ ΡΠ°Π·Π»ΠΈΡΠ½ΡΠ΅ ΡΠ΅ΡΡΠ΅ΡΠ½ΠΈ Ρ Π·ΡΠ±ΡΡΠΌΠΈ ΠΊΠ°ΠΊ ΡΠ΅Π»ΡΠ½ΠΎΠΉ ΡΠ°ΡΡΡΡ. ΠΠ½ΠΈ ΠΈΠΌΠ΅ΡΡ Π²Π½Π΅ΡΠ½ΠΈΠΉ Π΄ΠΈΠ°ΠΌΠ΅ΡΡ ΠΎΡ 64 Π΄ΠΎ 267 ΠΌΠΌ (ΠΎΡ 2,5 Π΄ΠΎ 10,5 Π΄ΡΠΉΠΌΠ°) ΠΈ Π²Π΅Ρ ΠΎΡ 0,54 Π΄ΠΎ 11 ΠΊΠ³ (ΠΎΡ 1,2 Π΄ΠΎ 24 ΡΡΠ½ΡΠΎΠ²). ΠΠΎΠ»ΡΡΠΈΠ½ΡΡΠ²ΠΎ ΠΈΠ· Π½ΠΈΡ
Π±ΡΠ»ΠΈ ΠΈΠ·Π³ΠΎΡΠΎΠ²Π»Π΅Π½Ρ Ρ ΠΏΡΠΈΠΏΡΡΠΊΠΎΠΌ ΠΎΡ 0,13 Π΄ΠΎ 0,51 ΠΌΠΌ (ΠΎΡ 0,005 Π΄ΠΎ 0,020 Π΄ΡΠΉΠΌΠ°) Π½Π° Π±ΠΎΠΊΠΎΠ²ΠΎΠΉ ΠΏΠΎΠ²Π΅ΡΡ
Π½ΠΎΡΡΠΈ ΠΊΠ°ΠΆΠ΄ΠΎΠ³ΠΎ Π·ΡΠ±Π° Π΄Π»Ρ ΡΠΈΡΡΠΎΠ²ΠΎΠΉ ΠΎΠ±ΡΠ°Π±ΠΎΡΠΊΠΈ ΠΈ ΡΠ»ΠΈΡΠΎΠ²ΠΊΠΈ. Π¨Π΅ΡΡΠ΅ΡΠ½ΠΈ, Π²ΡΠΊΠΎΠ²Π°Π½Π½ΡΠ΅ ΡΠΎ Π²ΡΡΡΠΎΠ΅Π½Π½ΡΠΌΠΈ Π·ΡΠ±ΡΡΠΌΠΈ, ΠΎΠ±ΡΡΠ½ΠΎ ΠΈΠΌΠ΅ΡΡ Π±ΠΎΠ»Π΅Π΅ Π΄Π»ΠΈΡΠ΅Π»ΡΠ½ΡΠΉ ΡΡΠΎΠΊ ΡΠ»ΡΠΆΠ±Ρ ΠΈ ΠΈΠ·Π½ΠΎΡΠΎΡΡΠΎΠΉΠΊΠΎΡΡΡ, ΡΠ΅ΠΌ ΡΠ΅ΡΡΠ΅ΡΠ½ΠΈ, ΠΈΠ·Π³ΠΎΡΠΎΠ²Π»Π΅Π½Π½ΡΠ΅ ΠΈΠ· ΠΊΠΎΠ²Π°Π½ΡΡ
Π·Π°Π³ΠΎΡΠΎΠ²ΠΎΠΊ, Π½Π° ΠΊΠΎΡΠΎΡΡΡ
Π·ΡΠ±ΡΡ Π·ΡΠ±ΡΠ°ΡΡΠ΅, ΠΏΡΠΎΡΠΈΠ»ΠΈΡΠΎΠ²Π°Π½Π½ΡΠ΅ ΠΈΠ»ΠΈ ΡΡΠ΅Π·Π΅ΡΠΎΠ²Π°Π½Π½ΡΠ΅.
ΠΡΠ΅ΡΠΈΠ·ΠΈΠΎΠ½Π½Π°Ρ ΠΊΠΎΠ²ΠΊΠ°
Π’Π΅ΡΠΌΠΈΠ½ Β«ΠΏΡΠ΅ΡΠΈΠ·ΠΈΠΎΠ½Π½Π°Ρ ΠΊΠΎΠ²ΠΊΠ°Β» Π½Π΅ ΠΎΠΏΡΠ΅Π΄Π΅Π»ΡΠ΅Ρ ΠΎΡΠ΄Π΅Π»ΡΠ½ΡΠΉ ΠΏΡΠΎΡΠ΅ΡΡ ΠΊΠΎΠ²ΠΊΠΈ, Π° ΡΠΊΠΎΡΠ΅Π΅ ΠΎΠΏΠΈΡΡΠ²Π°Π΅Ρ ΡΠΈΠ»ΠΎΡΠΎΡΡΠΊΠΈΠΉ ΠΏΠΎΠ΄Ρ ΠΎΠ΄ ΠΊ ΠΊΠΎΠ²ΠΊΠ΅. Π¦Π΅Π»ΡΡ ΡΡΠΎΠ³ΠΎ ΠΏΠΎΠ΄Ρ ΠΎΠ΄Π° ΡΠ²Π»ΡΠ΅ΡΡΡ ΠΏΠΎΠ»ΡΡΠ΅Π½ΠΈΠ΅ ΡΠΈΡΡΠΎΠΉ ΡΠΎΡΠΌΡ ΠΈΠ»ΠΈ, ΠΏΠΎ ΠΊΡΠ°ΠΉΠ½Π΅ΠΉ ΠΌΠ΅ΡΠ΅, ΠΏΠΎΡΡΠΈ ΡΠΈΡΡΠΎΠΉ ΡΠΎΡΠΌΡ Π² ΡΠΎΡΡΠΎΡΠ½ΠΈΠΈ ΠΏΠΎΡΠ»Π΅ ΠΊΠΎΠ²ΠΊΠΈ.
Π’Π΅ΡΠΌΠΈΠ½ Β«ΡΠ΅ΡΠΊΠ°Β» ΠΎΠ·Π½Π°ΡΠ°Π΅Ρ, ΡΡΠΎ ΠΏΠΎΡΠ»Π΅Π΄ΡΡΡΠ°Ρ ΠΌΠ΅Ρ
Π°Π½ΠΈΡΠ΅ΡΠΊΠ°Ρ ΠΎΠ±ΡΠ°Π±ΠΎΡΠΊΠ° ΠΈΠ»ΠΈ ΠΎΡΠ΄Π΅Π»ΠΊΠ° ΠΊΠΎΠ²Π°Π½ΠΎΠΉ ΠΏΠΎΠ²Π΅ΡΡ
Π½ΠΎΡΡΠΈ Π½Π΅ ΡΡΠ΅Π±ΡΠ΅ΡΡΡ. Π’Π°ΠΊΠΈΠΌ ΠΎΠ±ΡΠ°Π·ΠΎΠΌ, ΠΏΠΎΠΊΠΎΠ²ΠΊΠ° Π² ΡΠΎΡΠΌΠ΅ ΡΠ΅ΡΠΊΠΈ Π½Π΅ ΡΡΠ΅Π±ΡΠ΅Ρ Π΄ΠΎΠΏΠΎΠ»Π½ΠΈΡΠ΅Π»ΡΠ½ΠΎΠΉ ΠΎΠ±ΡΠ°Π±ΠΎΡΠΊΠΈ ΠΊΠ°ΠΊΠΎΠΉ-Π»ΠΈΠ±ΠΎ ΠΈΠ· ΠΊΠΎΠ²Π°Π½ΡΡ
ΠΏΠΎΠ²Π΅ΡΡ
Π½ΠΎΡΡΠ΅ΠΉ, Ρ
ΠΎΡΡ ΠΌΠΎΠ³ΡΡ ΠΏΠΎΡΡΠ΅Π±ΠΎΠ²Π°ΡΡΡΡ Π²ΡΠΎΡΠΈΡΠ½ΡΠ΅ ΠΎΠΏΠ΅ΡΠ°ΡΠΈΠΈ Π΄Π»Ρ ΠΏΠΎΠ»ΡΡΠ΅Π½ΠΈΡ ΠΌΠ΅Π»ΠΊΠΈΡ
ΠΎΡΠ²Π΅ΡΡΡΠΈΠΉ, ΡΠ΅Π·ΡΠ±Ρ ΠΈ Π΄ΡΡΠ³ΠΈΡ
ΠΏΠΎΠ΄ΠΎΠ±Π½ΡΡ
Π΄Π΅ΡΠ°Π»Π΅ΠΉ. ΠΠΎΠΊΠΎΠ²ΠΊΠ° Ρ ΠΏΠΎΡΡΠΈ ΡΠΈΡΡΠΎΠΉ ΡΠΎΡΠΌΠΎΠΉ ΠΌΠΎΠΆΠ΅Ρ Π±ΡΡΡ Π»ΠΈΠ±ΠΎ ΡΠ°ΠΊΠΎΠΉ, Π² ΠΊΠΎΡΠΎΡΠΎΠΉ Π½Π΅ΠΊΠΎΡΠΎΡΡΠ΅, Π½ΠΎ Π½Π΅ Π²ΡΠ΅ ΠΏΠΎΠ²Π΅ΡΡ
Π½ΠΎΡΡΠΈ ΡΠ²Π»ΡΡΡΡΡ ΡΠ΅ΡΡΠ°ΡΡΠΌΠΈ, Π»ΠΈΠ±ΠΎ ΡΠ°ΠΊΠΎΠΉ, Π² ΠΊΠΎΡΠΎΡΠΎΠΉ ΠΏΠΎΠ²Π΅ΡΡ
Π½ΠΎΡΡΠΈ ΡΡΠ΅Π±ΡΡΡ Π»ΠΈΡΡ ΠΌΠΈΠ½ΠΈΠΌΠ°Π»ΡΠ½ΠΎΠΉ ΠΌΠ΅Ρ
Π°Π½ΠΈΡΠ΅ΡΠΊΠΎΠΉ ΠΎΠ±ΡΠ°Π±ΠΎΡΠΊΠΈ ΠΈΠ»ΠΈ ΠΎΡΠ΄Π΅Π»ΠΊΠΈ. ΠΡΠ΅ΡΠΈΠ·ΠΈΠΎΠ½Π½Π°Ρ ΠΊΠΎΠ²ΠΊΠ° ΠΈΠ½ΠΎΠ³Π΄Π° ΠΎΠΏΠΈΡΡΠ²Π°Π΅ΡΡΡ ΠΊΠ°ΠΊ ΠΊΠΎΠ²ΠΊΠ° Ρ ΠΆΠ΅ΡΡΠΊΠΈΠΌΠΈ Π΄ΠΎΠΏΡΡΠΊΠ°ΠΌΠΈ, ΡΡΠΎΠ±Ρ ΠΏΠΎΠ΄ΡΠ΅ΡΠΊΠ½ΡΡΡ ΡΠ΅Π»Ρ Π΄ΠΎΡΡΠΈΠΆΠ΅Π½ΠΈΡ ΠΈΡΠΊΠ»ΡΡΠΈΡΠ΅Π»ΡΠ½ΠΎ Π·Π° ΡΡΠ΅Ρ ΠΎΠΏΠ΅ΡΠ°ΡΠΈΠΈ Π³ΠΎΡΡΡΠ΅ΠΉ ΠΊΠΎΠ²ΠΊΠΈ Π΄ΠΎΠΏΡΡΠΊΠΎΠ² Π½Π° ΡΠ°Π·ΠΌΠ΅ΡΡ ΠΈ ΡΠΈΡΡΠΎΡΡ ΠΏΠΎΠ²Π΅ΡΡ
Π½ΠΎΡΡΠΈ, ΡΡΠ΅Π±ΡΠ΅ΠΌΡΡ
Π² Π³ΠΎΡΠΎΠ²ΠΎΠΉ Π΄Π΅ΡΠ°Π»ΠΈ. Π ΠΏΠΎΡΠ»Π΅Π΄Π½ΠΈΠ΅ Π³ΠΎΠ΄Ρ ΠΌΠ΅ΡΠΎΠ΄Ρ Π°Π²ΡΠΎΠΌΠ°ΡΠΈΠ·ΠΈΡΠΎΠ²Π°Π½Π½ΠΎΠ³ΠΎ ΠΏΡΠΎΠ΅ΠΊΡΠΈΡΠΎΠ²Π°Π½ΠΈΡ ΠΈ ΠΏΡΠΎΠΈΠ·Π²ΠΎΠ΄ΡΡΠ²Π° (CAD/CAM) ΠΏΡΠΈΠΌΠ΅Π½ΡΠ»ΠΈΡΡ ΠΊ ΡΠ°Π·Π»ΠΈΡΠ½ΡΠΌ ΠΏΡΠΎΡΠ΅ΡΡΠ°ΠΌ ΠΊΠΎΠ²ΠΊΠΈ [7]. ΠΡΠΎΡ ΠΊΠΎΠΌΠΏΡΡΡΠ΅ΡΠΈΠ·ΠΈΡΠΎΠ²Π°Π½Π½ΡΠΉ ΠΏΠΎΠ΄Ρ
ΠΎΠ΄ ΠΏΡΠΈΠΌΠ΅Π½ΠΈΠΌ ΠΊ ΠΏΡΠ΅ΡΠΈΠ·ΠΈΠΎΠ½Π½ΠΎΠΉ Π³ΠΎΡΡΡΠ΅ΠΉ ΡΡΠ°ΠΌΠΏΠΎΠ²ΠΊΠ΅ ΡΠΏΠΈΡΠ°Π»ΡΠ½ΠΎ-ΠΊΠΎΠ½ΠΈΡΠ΅ΡΠΊΠΈΡ
, ΠΏΡΡΠΌΠΎΠ·ΡΠ±ΡΡ
ΠΈ Π²ΠΈΠ½ΡΠΎΠ²ΡΡ
Π·ΡΠ±ΡΠ°ΡΡΡ
ΠΊΠΎΠ»Π΅Ρ Π½Π° ΠΎΠ±ΡΡΠ½ΡΡ
ΠΏΡΠ΅ΡΡΠ°Ρ
, ΠΏΠΎΡΠΊΠΎΠ»ΡΠΊΡ ΠΎΠ½ ΠΏΠΎΠ·Π²ΠΎΠ»ΡΠ΅Ρ ΡΠ°Π·ΡΠ°Π±ΠΎΡΡΠΈΠΊΡ ΡΡΠ°ΠΌΠΏΠ° ΠΈΡΡΠ»Π΅Π΄ΠΎΠ²Π°ΡΡ Π²Π»ΠΈΡΠ½ΠΈΠ΅ ΡΠ°Π·Π»ΠΈΡΠ½ΡΡ
ΠΏΠ΅ΡΠ΅ΠΌΠ΅Π½Π½ΡΡ
ΠΏΡΠΎΡΠ΅ΡΡΠ° (Π½Π°Π³ΡΡΠ·ΠΎΠΊ, Π½Π°ΠΏΡΡΠΆΠ΅Π½ΠΈΠΉ ΠΈ ΡΠ΅ΠΌΠΏΠ΅ΡΠ°ΡΡΡΡ) Π½Π° ΠΊΠΎΠ½ΡΡΡΡΠΊΡΠΈΡ ΡΡΠ°ΠΌΠΏΠ°.
ΠΡΠ΅ΡΠΈΠ·ΠΈΠΎΠ½Π½ΡΠ΅ Π³ΠΎΡΡΡΠ΅ΠΊΠΎΠ²Π°Π½ΡΠ΅ Π·ΡΠ±ΡΠ°ΡΡΠ΅ ΠΊΠΎΠ»Π΅ΡΠ° ΠΈΠΌΠ΅ΡΡ ΡΠ΅ ΠΆΠ΅ ΠΏΡΠ΅ΠΈΠΌΡΡΠ΅ΡΡΠ²Π° ΠΏΠΎ ΡΡΠ°Π²Π½Π΅Π½ΠΈΡ Ρ Π·ΡΠ±ΡΠ°ΡΡΠΌΠΈ ΠΊΠΎΠ»Π΅ΡΠ°ΠΌΠΈ, ΡΡΠΎ ΠΈ Π΄ΡΡΠ³ΠΈΠ΅ ΡΠΎΡΠΌΠΎΠ²Π°Π½Π½ΡΠ΅ Π·ΡΠ±ΡΠ°ΡΡΠ΅ ΠΊΠΎΠ»Π΅ΡΠ° (Π»ΠΈΡΡΠ΅, ΠΎΠ±ΡΠ°Π±ΠΎΡΠ°Π½Π½ΡΠ΅ ΠΌΠ΅ΡΠΎΠ΄ΠΎΠΌ Π»ΠΈΡΡΡ ΠΏΠΎΠ΄ Π΄Π°Π²Π»Π΅Π½ΠΈΠ΅ΠΌ, Π»ΠΈΡΡΠ΅Π²ΡΠ΅), Π² ΡΠΎΠΌ, ΡΡΠΎ ΠΏΠΎΡΠ΅ΡΠΈ ΠΌΠ°ΡΠ΅ΡΠΈΠ°Π»Π° ΠΌΠΈΠ½ΠΈΠΌΠ°Π»ΡΠ½Ρ ΠΈΠ»ΠΈ ΠΎΡΡΡΡΡΡΠ²ΡΡΡ (ΡΠΈΡ. 10). ΠΡΠΎ ΡΠΊΠΎΠ½ΠΎΠΌΠΈΡ Ρ ΡΠΎΡΠΊΠΈ Π·ΡΠ΅Π½ΠΈΡ ΠΊΠ°ΠΊ ΡΡΠΎΠΈΠΌΠΎΡΡΠΈ ΡΠ°ΠΌΠΎΠ³ΠΎ ΠΌΠ°ΡΠ΅ΡΠΈΠ°Π»Π°, ΡΠ°ΠΊ ΠΈ, ΡΡΠΎ Π±ΠΎΠ»Π΅Π΅ Π²Π°ΠΆΠ½ΠΎ, ΡΡΠΎΠΈΠΌΠΎΡΡΠΈ ΠΌΠ΅Ρ
Π°Π½ΠΈΡΠ΅ΡΠΊΠΎΠΉ ΠΎΠ±ΡΠ°Π±ΠΎΡΠΊΠΈ. ΠΡΠΎΠΌΠ΅ ΡΠΎΠ³ΠΎ, ΠΏΡΠ΅ΡΠΈΠ·ΠΈΠΎΠ½Π½ΡΠ΅ ΠΊΠΎΠ²Π°Π½ΡΠ΅ ΡΠ΅ΡΡΠ΅ΡΠ½ΠΈ ΡΠ°ΠΊΠΆΠ΅ ΠΈΠΌΠ΅ΡΡ ΠΏΡΠ΅ΠΈΠΌΡΡΠ΅ΡΡΠ²ΠΎ ΠΏΠ΅ΡΠ΅Π΄ Π½Π°ΡΠ΅Π·Π½ΡΠΌΠΈ ΡΠ΅ΡΡΠ΅ΡΠ½ΡΠΌΠΈ ΠΏΠΎΠ²ΡΡΠ΅Π½Π½ΠΎΠΉ Π³ΡΡΠ·ΠΎΠΏΠΎΠ΄ΡΠ΅ΠΌΠ½ΠΎΡΡΠΈ. ΠΡΠ° Π΄ΠΎΠΏΠΎΠ»Π½ΠΈΡΠ΅Π»ΡΠ½Π°Ρ ΠΏΡΠΎΡΠ½ΠΎΡΡΡ Π² Π²ΠΈΠ΄Π΅ ΠΏΠΎΠ²ΡΡΠ΅Π½Π½ΠΎΠΉ ΡΡΡΠ°Π»ΠΎΡΡΠ½ΠΎΠΉ ΠΏΡΠΎΡΠ½ΠΎΡΡΠΈ ΠΎΠ±ΡΡΠ»ΠΎΠ²Π»Π΅Π½Π° ββΡΠ°Π·Π½ΠΈΡΠ΅ΠΉ Π² ΠΏΠΎΡΠΎΠΊΠ΅ Π·Π΅ΡΠ΅Π½ ΠΌΠ΅ΠΆΠ΄Ρ ΡΠ΅ΡΡΠ΅ΡΠ½ΡΠΌΠΈ, Π²ΡΡΠ΅Π·Π°Π½Π½ΡΠΌΠΈ ΠΈΠ· ΠΏΡΡΡΠΊΠΎΠ²ΠΎΠ³ΠΎ ΠΏΡΠΎΠΊΠ°ΡΠ°, ΠΈ ΠΊΠΎΠ²Π°Π½ΡΠΌΠΈ ΡΠ΅ΡΡΠ΅ΡΠ½ΡΠΌΠΈ. ΠΠΎΡΠΎΠΊ Π·Π΅ΡΠ΅Π½ Π² Π½Π°ΡΠ΅Π·Π½ΡΡ
Π·ΡΠ±ΡΠ°ΡΡΡ
ΠΊΠΎΠ»Π΅ΡΠ°Ρ
ΠΎΠΏΡΠ΅Π΄Π΅Π»ΡΠ΅ΡΡΡ ΠΎΡΠΈΠ΅Π½ΡΠ°ΡΠΈΠ΅ΠΉ Π³ΠΎΡΡΡΠ΅ΠΊΠ°ΡΠ°Π½ΠΎΠ³ΠΎ ΠΏΡΠΎΠΊΠ°ΡΠ° ΠΏΡΡΡΠΊΠΎΠ²ΠΎΠ³ΠΎ ΠΏΡΠΎΠΊΠ°ΡΠ° ΠΈ Π½Π΅ ΠΈΠΌΠ΅Π΅Ρ ΠΎΡΠ½ΠΎΡΠ΅Π½ΠΈΡ ΠΊ ΠΊΠΎΠ½ΡΡΡΡ Π·ΡΠ±ΡΠ΅Π² Π·ΡΠ±ΡΠ°ΡΠΎΠ³ΠΎ ΠΊΠΎΠ»Π΅ΡΠ°. ΠΠ° ΠΊΠΎΠ²Π°Π½ΡΡ
ΠΎΠ±ΡΠ°Π·ΡΠ°Ρ
ΠΏΠΎΡΠΎΠΊ Π·Π΅ΡΠ΅Π½ ΠΏΠΎΠ²ΡΠΎΡΡΠ΅Ρ ΠΊΠΎΠ½ΡΡΡ Π·ΡΠ±Π° Π² ΠΊΠ°ΠΆΠ΄ΠΎΠΌ Π·ΡΠ±Π΅ ΡΠ΅ΡΡΠ΅ΡΠ½ΠΈ. ΠΠ° ΡΠΈΡ. 11 ΡΡΠ°Π²Π½ΠΈΠ²Π°ΡΡΡΡ ΡΡΡΠ°Π»ΠΎΡΡΠ½ΡΠ΅ ΡΠ²ΠΎΠΉΡΡΠ²Π° Π½Π°ΡΠ΅Π·Π°Π½Π½ΡΡ
ΠΈ ΠΊΠΎΠ²Π°Π½ΡΡ
Π·ΡΠ±ΡΠ°ΡΡΡ
ΠΊΠΎΠ»Π΅Ρ [8].
ΠΡΠ±ΡΠ°ΡΡΠ΅ ΠΊΠΎΠ»Π΅ΡΠ° Ρ ΠΊΠ°ΡΠ΅ΡΡΠ²ΠΎΠΌ ΡΠΎΡΠΌΡ, Π±Π»ΠΈΠ·ΠΊΠΈΠΌ ΠΊ ΡΠΈΡΡΠΎΠΌΡ
ΠΠΎΠ»ΡΡΠΈΠ½ΡΡΠ²ΠΎ ΠΏΡΠΎΠΈΠ·Π²ΠΎΠ΄ΠΈΠΌΡΡ
ΡΠ΅Π³ΠΎΠ΄Π½Ρ ΠΊΠΎΠ²Π°Π½ΡΡ
Π·ΡΠ±ΡΠ°ΡΡΡ
ΠΊΠΎΠ»Π΅Ρ ΠΈΠΌΠ΅ΡΡ ΠΊΠΎΠ½ΡΠΈΠ³ΡΡΠ°ΡΠΈΡ, Π±Π»ΠΈΠ·ΠΊΡΡ ΠΊ ΡΠΈΡΡΠΎΠΉ. ΠΡΠ±ΡΡ ΡΠ΅ΡΡΠ΅ΡΠ½ΠΈ Π²ΡΠΊΠΎΠ²Π°Π½Ρ Ρ ΠΎΠ±ΠΎΠ»ΠΎΡΠΊΠΎΠΉ ΠΈΠ· ΠΌΠ°ΡΠ΅ΡΠΈΠ°Π»Π° (ΠΏΡΠΈΠΏΡΡΠΊ) Π²ΠΎΠΊΡΡΠ³ ΠΏΡΠΎΡΠΈΠ»Ρ Π·ΡΠ±Π°. ΠΡΠΎΡ ΠΊΠΎΠ½Π²Π΅ΡΡ Π²ΠΏΠΎΡΠ»Π΅Π΄ΡΡΠ²ΠΈΠΈ ΡΠ΄Π°Π»ΡΠ΅ΡΡΡ ΠΊΡΠ·Π½Π΅ΡΠ½ΡΠΌ ΡΠ΅Ρ
ΠΎΠΌ ΠΈΠ»ΠΈ Π·Π°ΠΊΠ°Π·ΡΠΈΠΊΠΎΠΌ, ΠΏΡΠΈΠΎΠ±ΡΠ΅ΡΠ°ΡΡΠΈΠΌ ΠΊΠΎΠ²Π°Π½ΡΠ΅ ΡΠ΅ΡΡΠ΅ΡΠ½ΠΈ.
ΠΠ° ΠΎΠ΄ΠΈΠ½ Ρ ΠΎΠ΄ ΡΡΠ°Π½Π΄Π°ΡΡΠ½ΡΠ΅ ΠΌΠ΅Ρ Π°Π½ΠΈΡΠ΅ΡΠΊΠΈΠ΅ ΠΊΠΎΠ²ΠΎΡΠ½ΡΠ΅ ΠΏΡΠ΅ΡΡΡ Ρ ΡΡΠΈΠ»ΠΈΠ΅ΠΌ ΠΎΡ 14 235 Π΄ΠΎ 53 375 ΠΊΠ (ΠΎΡ 1600 Π΄ΠΎ 6000 ΡΡ) ΡΠΎΡΠΌΠΈΡΡΡΡ ΡΠ΅ΡΡΠ΅ΡΠ½ΠΈ ΠΏΠΎΡΡΠΈ ΡΠΈΡΡΠΎΠΉ ΡΠΎΡΠΌΡ Ρ ΠΏΠΎΠ»Π½ΡΠΌ Π΄ΠΎΠΏΡΡΡΠΈΠΌΡΠΌ ΠΏΡΠΈΠΏΡΡΠΊΠΎΠΌ. Π¦Π΅Π»Ρ ΡΡΠΎΠΉ ΠΏΠ΅ΡΠ²ΠΎΠΉ ΠΎΠΏΠ΅ΡΠ°ΡΠΈΠΈ, ΠΊΠΎΡΠΎΡΠ°Ρ ΡΠΎΡΠΌΠΈΡΡΠ΅Ρ Β«Π±Π»ΠΈΠ½Β», ΡΠΎΡΡΠΎΠΈΡ Π² ΡΠΎΠΌ, ΡΡΠΎΠ±Ρ ΠΎΡΠΊΠΎΠ»ΠΎΡΡ ΠΎΠΊΠ°Π»ΠΈΠ½Ρ ΠΎΡ Π·Π°Π³ΠΎΡΠΎΠ²ΠΊΠΈ ΠΈ ΠΏΠΎΠ΄ΠΎΠ³Π½Π°ΡΡ Π½Π°ΡΡΠΆΠ½ΡΠΉ Π΄ΠΈΠ°ΠΌΠ΅ΡΡ ΡΠ°ΠΊ, ΡΡΠΎΠ±Ρ ΠΎΠ½ Π±ΡΠ» ΡΡΡΡ ΠΌΠ΅Π½ΡΡΠ΅ Π΄ΠΈΠ°ΠΌΠ΅ΡΡΠ° Π²ΠΏΠ°Π΄ΠΈΠ½Ρ Π·ΡΠ±ΡΠ°ΡΠΎΠΉ ββΠΌΠ°ΡΡΠΈΡΡ. ΠΠ°ΡΠ΅ΠΌ ΠΎΠΏΠ΅ΡΠ°ΡΠΎΡ ΠΏΠΎΠΌΠ΅ΡΠ°Π΅Ρ Π·Π°Π³ΠΎΡΠΎΠ²ΠΊΡ Π² ΡΠΈΡΡΠΎΠ²ΠΎΠΉ ΡΡΠ°ΠΌΠΏ.
ΠΠΎΡΠ»Π΅ ΠΊΠΎΠ²ΠΊΠΈ Π³ΠΈΠ΄ΡΠ°Π²Π»ΠΈΡΠ΅ΡΠΊΠ°Ρ Π²ΡΠ±ΠΈΠ²Π½Π°Ρ ΡΠΈΡΡΠ΅ΠΌΠ° Π½Π΅ΠΌΠ΅Π΄Π»Π΅Π½Π½ΠΎ ΠΈΠ·Π²Π»Π΅ΠΊΠ°Π΅Ρ ΡΠ΅ΡΡΠ΅ΡΠ½Ρ ΠΈΠ· ΡΠΈΡΡΠΎΠ²ΠΎΠ³ΠΎ ΡΡΠ°ΠΌΠΏΠ°. ΠΠΎΡΠ»Π΅ ΡΠΎΠ³ΠΎ, ΠΊΠ°ΠΊ Π½Π΅ΠΎΠ±ΡΠ°Π±ΠΎΡΠ°Π½Π½Π°Ρ ΠΊΠΎΠ²Π°Π½Π°Ρ ΡΠ΅ΡΡΠ΅ΡΠ½Ρ Π³ΠΈΠ΄ΡΠ°Π²Π»ΠΈΡΠ΅ΡΠΊΠΈ Π²ΡΡΠ°Π»ΠΊΠΈΠ²Π°Π΅ΡΡΡ ΠΈΠ· ΠΌΠ°ΡΡΠΈΡΡ, ΠΎΠ½Π° ΠΏΠΎΠΌΠ΅ΡΠ°Π΅ΡΡΡ Π² Π³Π½Π΅Π·Π΄ΠΎ Π΄Π»Ρ ΠΎΠ±ΡΠ΅Π·ΠΊΠΈ, Π³Π΄Π΅ ΠΏΡΠΎΠ±ΠΈΠ²Π°Π΅ΡΡΡ ΠΎΡΠ²Π΅ΡΡΡΠΈΠ΅. ΠΠ°ΡΠ΅ΠΌ Π΅ΠΌΡ Π΄Π°ΡΡ ΠΎΡΡΡΡΡ Π΄ΠΎ ΡΠ΅ΠΌΠΏΠ΅ΡΠ°ΡΡΡΡ ΠΎΠΊΡΡΠΆΠ°ΡΡΠ΅ΠΉ ΡΡΠ΅Π΄Ρ, ΡΡΠΎ ΠΎΠ±ΡΡΠ½ΠΎ Π·Π°Π½ΠΈΠΌΠ°Π΅Ρ Π΄ΠΎ 24 ΡΠ°ΡΠΎΠ². ΠΠΎΡΠ»Π΅ ΠΎΡ
Π»Π°ΠΆΠ΄Π΅Π½ΠΈΡ ΠΎΠ½ Π³ΠΎΡΠΎΠ² ΠΊ ΡΠΈΡΡΠΎΠ²ΠΎΠΉ ΠΎΠ±ΡΠ°Π±ΠΎΡΠΊΠ΅ (ΡΠΈΡ. 12).
ΠΡΠ±ΡΠ°ΡΡΠ΅ ΠΊΠΎΠ»Π΅ΡΠ° Ρ ΡΠΎΡΠΌΠΎΠΉ, Π±Π»ΠΈΠ·ΠΊΠΎΠΉ ΠΊ Π·Π°Π΄Π°Π½Π½ΠΎΠΉ, ΠΌΠΎΠ³ΡΡ Π±ΡΡΡ ΠΈΠ·Π³ΠΎΡΠΎΠ²Π»Π΅Π½Ρ Ρ ΠΈΡΠΏΠΎΠ»ΡΠ·ΠΎΠ²Π°Π½ΠΈΠ΅ΠΌ Π»ΡΠ±ΠΎΠΉ Π½Π°ΡΠ³Π»Π΅ΡΠΎΠΆΠΈΠ²Π°ΡΡΠ΅ΠΉ ΠΈΠ»ΠΈ ΠΈΠ½Π΄ΡΠΊΡΠΈΠΎΠ½Π½ΠΎΠΉ Π·Π°ΠΊΠ°Π»ΠΊΠΈ ΡΡΠ°Π»ΠΈ Π² ΠΏΡΡΠΈ ΠΎΡΠ½ΠΎΠ²Π½ΡΡ
ΠΊΠΎΠ½ΡΠΈΠ³ΡΡΠ°ΡΠΈΡΡ
: ΡΠΏΠΈΡΠ°Π»ΡΠ½ΠΎ-ΠΊΠΎΠ½ΠΈΡΠ΅ΡΠΊΠΈΠ΅, ΠΊΠΎΡΠΎΠ·ΡΠ±ΡΠ΅, ΠΏΡΡΠΌΡΠ΅ ΠΊΠΎΠ½ΠΈΡΠ΅ΡΠΊΠΈΠ΅, ΠΏΡΡΠΌΠΎΠ·ΡΠ±ΡΠ΅ Ρ ΠΏΡΠΈΠΏΡΡΠΊΠΎΠΌ 1 ΠΌΠΌ (0,04 Π΄ΡΠΉΠΌΠ°) ΠΈ ΠΏΡΡΠΌΠΎΠ·ΡΠ±ΡΠ΅ Ρ ΠΏΡΠΈΠΏΡΡΠΊΠΎΠΌ ΠΎΡ 0,1 Π΄ΠΎ ΠΏΡΠΈΠΏΡΡΠΊ 0,3 ΠΌΠΌ (ΠΎΡ 0,004 Π΄ΠΎ 0,012 Π΄ΡΠΉΠΌΠ°). ΠΡΠ±ΡΠ°ΡΡΠ΅ ΠΊΠΎΠ»Π΅ΡΠ° ΠΏΠΎΡΡΠΈ ΡΠΈΡΡΠΎΠΉ ΡΠΎΡΠΌΡ ΠΌΠΎΠ³ΡΡ Π±ΡΡΡ ΠΈΠ·Π³ΠΎΡΠΎΠ²Π»Π΅Π½Ρ Π΄ΠΈΠ°ΠΌΠ΅ΡΡΠΎΠΌ Π΄ΠΎ 425 ΠΌΠΌ (17 Π΄ΡΠΉΠΌΠΎΠ²) Ρ ΠΏΡΠΈΠΏΡΡΠΊΠ°ΠΌΠΈ ΠΎΡ 0,1 Π΄ΠΎ 1,5 ΠΌΠΌ (ΠΎΡ 0,004 Π΄ΠΎ 0,06 Π΄ΡΠΉΠΌΠ°).
- Π‘ΠΏΠΈΡΠ°Π»ΡΠ½ΡΠ΅ ΠΊΠΎΠ½ΠΈΡΠ΅ΡΠΊΠΈΠ΅ Π·ΡΠ±ΡΠ°ΡΡΠ΅ ΠΊΠΎΠ»Π΅ΡΠ° ΠΌΠΎΠ³ΡΡ ΠΈΠ·Π³ΠΎΡΠ°Π²Π»ΠΈΠ²Π°ΡΡΡΡ Π΄ΠΈΠ°ΠΌΠ΅ΡΡΠΎΠΌ Π΄ΠΎ 425 ΠΌΠΌ (17 Π΄ΡΠΉΠΌΠΎΠ²) Ρ ΠΌΠΈΠ½ΠΈΠΌΠ°Π»ΡΠ½ΡΠΌ ΠΏΡΠΈΠΏΡΡΠΊΠΎΠΌ 0,5 ΠΌΠΌ (0,02 Π΄ΡΠΉΠΌΠ°) Π½Π° Π±ΠΎΠΊΠΎΠ²ΡΡ ΡΡΠΎΡΠΎΠ½Ρ. ΠΠΎΡΡΠΈΠ³Π°Π΅ΡΡΡ ΠΌΠ°ΠΊΡΠΈΠΌΠ°Π»ΡΠ½ΡΠΉ ΡΠ³ΠΎΠ» ΡΠΏΠΈΡΠ°Π»ΠΈ 35Β° ΠΈ Π΄ΠΈΠ°ΠΏΠ°Π·ΠΎΠ½ ΡΠ°Π³Π° ΠΌΠ΅Π½Π΅Π΅ 7 DP
- ΠΡΡΠΌΡΠ΅ ΠΊΠΎΠ½ΠΈΡΠ΅ΡΠΊΠΈΠ΅ Π·ΡΠ±ΡΠ°ΡΡΠ΅ ΠΊΠΎΠ»Π΅ΡΠ° ΠΈΠΌΠ΅ΡΡ ΠΊΠΎΠ½ΡΠΈΠ³ΡΡΠ°ΡΠΈΡ/ΡΠ²ΠΎΠΉΡΡΠ²Π°, Π°Π½Π°Π»ΠΎΠ³ΠΈΡΠ½ΡΠ΅ ΡΠΏΠΈΡΠ°Π»ΡΠ½ΡΠΌ ΠΊΠΎΠ½ΠΈΡΠ΅ΡΠΊΠΈΠΌ Π·ΡΠ±ΡΠ°ΡΡΠΌ ΠΊΠΎΠ»Π΅ΡΠ°ΠΌ .
- ΠΠΎΡΠΎΠ·ΡΠ±ΡΠ΅ ΡΠ΅ΡΡΠ΅ΡΠ½ΠΈ ΠΌΠΎΠ³ΡΡ Π±ΡΡΡ ΠΈΠ·Π³ΠΎΡΠΎΠ²Π»Π΅Π½Ρ Π΄ΠΈΠ°ΠΌΠ΅ΡΡΠΎΠΌ Π΄ΠΎ 250 ΠΌΠΌ (10 Π΄ΡΠΉΠΌΠΎΠ²) ΠΈ Π²Π΅ΡΠΎΠΌ Π΄ΠΎ 40 ΠΊΠ³ (90 ΡΡΠ½ΡΠΎΠ²) Ρ ΠΌΠΈΠ½ΠΈΠΌΠ°Π»ΡΠ½ΡΠΌ ΠΏΡΠΈΠΏΡΡΠΊΠΎΠΌ 0,5 ΠΌΠΌ (0,02 Π΄ΡΠΉΠΌΠ°) Π½Π° Π±ΠΎΠΊΠΎΠ²ΡΡ ΡΡΠΎΡΠΎΠ½Ρ. ΠΠΎΡΡΠΈΠ³Π°Π΅ΡΡΡ ΠΌΠ°ΠΊΡΠΈΠΌΠ°Π»ΡΠ½ΡΠΉ ΡΠ³ΠΎΠ» Π½Π°ΠΊΠ»ΠΎΠ½Π° ΡΠΏΠΈΡΠ°Π»ΠΈ 25Β° ΠΈ Π΄ΠΈΠ°ΠΏΠ°Π·ΠΎΠ½ ΡΠ°Π³Π° ΠΎΡ 4 Π΄ΠΎ 12 DP
- Π¦ΠΈΠ»ΠΈΠ½Π΄ΡΠΈΡΠ΅ΡΠΊΠΈΠ΅ Π·ΡΠ±ΡΠ°ΡΡΠ΅ ΠΊΠΎΠ»Π΅ΡΠ° Ρ ΠΏΡΠΈΠΏΡΡΠΊΠΎΠΌ 1 ΠΌΠΌ (0,04 Π΄ΡΠΉΠΌΠ°) ΠΌΠΎΠ³ΡΡ Π±ΡΡΡ ΠΈΠ·Π³ΠΎΡΠΎΠ²Π»Π΅Π½Ρ Π΄ΠΈΠ°ΠΌΠ΅ΡΡΠΎΠΌ Π΄ΠΎ 400 ΠΌΠΌ (16 Π΄ΡΠΉΠΌΠΎΠ²) ΠΈ Π²Π΅ΡΠΎΠΌ Π΄ΠΎ 135 ΠΊΠ³ (300 ΡΡΠ½ΡΠΎΠ²) Ρ ΠΌΠΈΠ½ΠΈΠΌΡΠΌΠΎΠΌ 1 ΠΌΠΌ (0,04 Π΄ΡΠΉΠΌΠ°). Π·Π°ΠΏΠ°Ρ Π·Π°ΠΏΠ°ΡΠ° Π½Π° ΡΠ»Π°Π½Π³. ΠΠΈΠ°ΠΏΠ°Π·ΠΎΠ½ ΡΠ°Π³Π° ΠΌΠ΅Π½Π΅Π΅ 5 DP ΠΌΠΎΠΆΠ΅Ρ Π±ΡΡΡ Π΄ΠΎΡΡΠΈΠ³Π½ΡΡ. ΠΡΠΎΡ ΡΠΈΠΏ Π·ΡΠ±ΡΠ°ΡΠΎΠ³ΠΎ ΠΊΠΎΠ»Π΅ΡΠ° ΡΡΠ΅Π±ΡΠ΅Ρ ΡΠΈΡΡΠΎΠ²ΠΎΠΉ ΠΎΠ±ΡΠ°Π±ΠΎΡΠΊΠΈ Π·ΡΠ±ΠΎΡΡΠ΅Π·Π΅ΡΠΎΠ²Π°Π½ΠΈΠ΅ΠΌ, Π·ΡΠ±ΠΎΡΡΠ΅Π·Π΅ΡΠΎΠ²Π°Π½ΠΈΠ΅ΠΌ ΠΈ ΡΡΡΠΎΠ³Π°Π½ΠΈΠ΅ΠΌ, Π·ΡΠ±ΠΎΡΡΠ΅Π·Π΅ΡΠΎΠ²Π°Π½ΠΈΠ΅ΠΌ ΠΈ ΡΠ»ΠΈΡΠΎΠ²Π°Π½ΠΈΠ΅ΠΌ ΠΈΠ»ΠΈ ΡΠ»ΠΈΡΠΎΠ²Π°Π½ΠΈΠ΅ΠΌ
- Π¦ΠΈΠ»ΠΈΠ½Π΄ΡΠΈΡΠ΅ΡΠΊΠΈΠ΅ Π·ΡΠ±ΡΠ°ΡΡΠ΅ ΠΊΠΎΠ»Π΅ΡΠ° Ρ ΠΏΡΠΈΠΏΡΡΠΊΠΎΠΌ ΠΎΡ 0,1 Π΄ΠΎ 0,3 ΠΌΠΌ (ΠΎΡ 0,004 Π΄ΠΎ 0,012 Π΄ΡΠΉΠΌΠ°) ΠΌΠΎΠ³ΡΡ Π±ΡΡΡ ΠΈΠ·Π³ΠΎΡΠΎΠ²Π»Π΅Π½Ρ Π΄ΠΈΠ°ΠΌΠ΅ΡΡΠΎΠΌ Π΄ΠΎ 250 ΠΌΠΌ (10 Π΄ΡΠΉΠΌΠΎΠ²) ΠΈ ΠΌΠ°ΠΊΡΠΈΠΌΠ°Π»ΡΠ½ΠΎΠΉ ΡΠΈΡΠΈΠ½ΠΎΠΉ ΡΠΎΡΡΠ° Π΄ΠΎ 150 ΠΌΠΌ (6 Π΄ΡΠΉΠΌΠΎΠ²), Ρ ΠΏΡΠΈΠΏΡΡΠΊΠΎΠΌ ΠΎΡ 0,1 Π΄ΠΎ 0,12 Π΄ΡΠΉΠΌΠ°.
ΠΡΠΈΠΏΡΡΠΊ 0,3 ΠΌΠΌ (ΠΎΡ 0,004 Π΄ΠΎ 0,012 Π΄ΡΠΉΠΌΠ°) Π½Π° Π±ΠΎΠΊΠΎΠ²ΡΡ ΡΡΠΎΡΠΎΠ½Ρ. ΠΠΈΠ°ΠΏΠ°Π·ΠΎΠ½ ΡΠ°Π³Π° ΠΎΡ 4 Π΄ΠΎ 12 DP ΠΌΠΎΠΆΠ΅Ρ Π±ΡΡΡ Π΄ΠΎΡΡΠΈΠ³Π½ΡΡ. ΠΡΠΎΡ ΡΠΈΠΏ Π·ΡΠ±ΡΠ°ΡΠΎΠ³ΠΎ ΠΊΠΎΠ»Π΅ΡΠ° ΡΡΠ΅Π±ΡΠ΅Ρ ΡΠΈΠ½ΠΈΡΠ½ΠΎΠ³ΠΎ ΠΏΡΠΎΡΠ΅ΡΡΠ° ΡΠ»ΠΈΡΠΎΠ²ΠΊΠΈ ΠΈΠ»ΠΈ ΡΠ»ΠΈΡΠΎΠ²ΠΊΠΈ. ΠΠΎΠ·ΠΌΠΎΠΆΠ΅Π½ ΡΠΈΡΡΡΠΉ ΠΊΠΎΡΠ΅Π½Ρ.
Π‘ΡΡΠ»ΠΊΠΈ
- T.T. Krenzer and J.W. ΠΠΎΠ½ΠΈΠ»ΡΠΎ, ΠΡΠΎΠΈΠ·Π²ΠΎΠ΄ΡΡΠ²ΠΎ Π·ΡΠ±ΡΠ°ΡΡΡ ΠΊΠΎΠ»Π΅Ρ, ΠΎΠ±ΡΠ°Π±ΠΎΡΠΊΠ°, ΡΠΎΠΌ 16, Π‘ΠΏΡΠ°Π²ΠΎΡΠ½ΠΈΠΊ ΠΏΠΎ ASM, ASM International, 1989, ΡΡΡ. 330β355 .
- ΠΠΆ.Π. ΠΡΠ°Π»Π»Π°, Π‘ΠΏΡΠ°Π²ΠΎΡΠ½ΠΈΠΊ ΠΏΠΎ Π΄ΠΈΠ·Π°ΠΉΠ½Ρ ΠΏΡΠΎΠ΄ΡΠΊΡΠΈΠΈ Π΄Π»Ρ ΠΏΡΠΎΠΈΠ·Π²ΠΎΠ΄ΡΡΠ²Π°, ΡΠΎΠΌ 16, McGraw-Hill Book Company, 1986, ΡΡΡ. 355 .
- Π. ΠΠ»ΡΡ ΠΈ Π’.Π. Π‘ΡΠΈΠ²Π΅Π½Ρ, ΠΠ΄., Π‘ΠΏΡΠ°Π²ΠΎΡΠ½ΠΈΠΊ ΠΏΠΎ ΡΡΠ°Π»ΡΠ½ΠΎΠΌΡ Π»ΠΈΡΡΡ, ΡΠ΅ΡΡΠΎΠ΅ ΠΈΠ·Π΄Π°Π½ΠΈΠ΅, ΠΠ±ΡΠ΅ΡΡΠ²ΠΎ ΠΎΡΠ½ΠΎΠ²Π°ΡΠ΅Π»Π΅ΠΉ ΡΡΠ°Π»ΠΈ ΠΈ ASM International, 1995, ΡΡΡ. 2β34 .
- Π.Π. ΠΠ°Π΄Π»ΠΈ, ΠΠ΅ΡΠΎΠ΄Ρ ΠΈΠ·Π³ΠΎΡΠΎΠ²Π»Π΅Π½ΠΈΡ Π·ΡΠ±ΡΠ°ΡΡΡ ΠΊΠΎΠ»Π΅Ρ, Π‘ΠΏΡΠ°Π²ΠΎΡΠ½ΠΈΠΊ ΠΏΠΎ ΠΏΡΠ°ΠΊΡΠΈΡΠ΅ΡΠΊΠΎΠΌΡ ΠΏΡΠΎΠ΅ΠΊΡΠΈΡΠΎΠ²Π°Π½ΠΈΡ Π·ΡΠ±ΡΠ°ΡΡΡ ΠΊΠΎΠ»Π΅Ρ, McGraw-Hill Book Company, ΡΡΡ. 5.86
- Π. ΠΡΠΏΠ΅Ρ, ΠΡΠΎΠΈΠ·Π²ΠΎΠ΄ΡΡΠ²ΠΎ Π°Π»ΡΡΠ΅ΡΠ½Π°ΡΠΈΠ²Π½ΡΡ Π·ΡΠ±ΡΠ°ΡΡΡ ΠΊΠΎΠ»Π΅Ρ, Π’Π΅Ρ Π½ΠΎΠ»ΠΎΠ³ΠΈΡ Π·ΡΠ±ΡΠ°ΡΡΡ ΠΊΠΎΠ»Π΅Ρ. ΠΡΠ»Ρ / Π°Π²Π³ΡΡΡ 1998 Π³., ΡΡΡ. 9β16 .
- Π.Π. Π’Π°ΡΠ½ΡΠ΅Π½Π΄, ΠΠ΄., ΠΡΠ±ΡΠ°ΡΡΠ΅ ΠΊΠΎΠ»Π΅ΡΠ°, ΡΠ΄Π΅Π»Π°Π½Π½ΡΠ΅ ΡΡΠ°ΠΌΠΏΠ°ΠΌΠΈ, Π‘ΠΏΡΠ°Π²ΠΎΡΠ½ΠΈΠΊ ΠΠ°Π΄Π»ΠΈ ΠΏΠΎ Π·ΡΠ±ΡΠ°ΡΡΠΌ ΠΊΠΎΠ»Π΅ΡΠ°ΠΌ: ΠΏΡΠΎΠ΅ΠΊΡΠΈΡΠΎΠ²Π°Π½ΠΈΠ΅, ΠΏΡΠΎΠΈΠ·Π²ΠΎΠ΄ΡΡΠ²ΠΎ ΠΈ ΠΏΡΠΈΠΌΠ΅Π½Π΅Π½ΠΈΠ΅ Π·ΡΠ±ΡΠ°ΡΡΡ
ΠΊΠΎΠ»Π΅Ρ, Π²ΡΠΎΡΠΎΠ΅ ΠΈΠ·Π΄Π°Π½ΠΈΠ΅, McGraw Hill Book Company, 1992, ΡΡΡ.
17.1β17.21
- Π.ΠΠΆ. ΠΡΠ»ΡΠΌΠ°Π½ ΠΈ Π.Π‘. Π Π°Π³Ρ ΡΠΏΠ°ΡΠΈ, ΠΡΠΎΠΈΠ·Π²ΠΎΠ΄ΡΡΠ²ΠΎ ΠΊΠΎΠ²Π°Π½ΡΡ ΠΈ ΡΠΊΡΡΡΡΠ΄ΠΈΡΠΎΠ²Π°Π½Π½ΡΡ Π·ΡΠ±ΡΠ°ΡΡΡ ΠΊΠΎΠ»Π΅Ρ, Gear Technol., ΠΈΡΠ»Ρ/Π°Π²Π³ΡΡΡ 1990 Π³., ΡΡΡ. 36β45 .
- Π’. Π Π°ΡΡΠ΅Π» ΠΈ Π. ΠΠ°Π½ΠΈΡ, ΠΡΠ΅ΡΠΈΠ·ΠΈΠΎΠ½Π½ΡΠ΅ ΠΊΠΎΠ²Π°Π½ΡΠ΅ Π·ΡΠ±ΡΠ°ΡΡΠ΅ ΠΊΠΎΠ»Π΅ΡΠ°, ΠΏΡΠΎΠΈΠ·Π²ΠΎΠ΄ΡΡΠ²ΠΎ ΠΈ Ρ Π°ΡΠ°ΠΊΡΠ΅ΡΠΈΡΡΠΈΠΊΠΈ Π·ΡΠ±ΡΠ°ΡΡΡ ΠΊΠΎΠ»Π΅Ρ, ΠΠΌΠ΅ΡΠΈΠΊΠ°Π½ΡΠΊΠΎΠ΅ ΠΎΠ±ΡΠ΅ΡΡΠ²ΠΎ ΠΌΠ΅ΡΠ°Π»Π»ΠΎΠ², 1974, ΡΡΡ. 229β239
ΠΠΎΡΠ΅ΠΌΡ Ρ ΠΎΠ»ΠΎΠ΄Π½ΠΎΠ΅ ΡΠΎΡΠΌΠΎΠ²Π°Π½ΠΈΠ΅? | Stabio North America
ΠΡΠΎΡ ΠΏΡΠΎΡΠ΅ΡΡ ΠΎΠ±ΡΠ°Π±ΠΎΡΠΊΠΈ ΠΌΠ΅ΡΠ°Π»Π»Π° ΡΡΠ±Π΅ΠΆΠ° Π²Π΅ΠΊΠΎΠ² ΡΠ°Π·Π²ΠΈΠ»ΡΡ ΠΈΠ· Π΅Π΄ΠΈΠ½ΡΡ
ΠΏΡΠΎΡΠ΅ΡΡΠΎΠ² ΠΊΠΎΠ²ΠΊΠΈ ΠΏΡΠΎΡΠ»ΠΎΠ³ΠΎ. Π‘ΠΎΠ²ΡΠ΅ΠΌΠ΅Π½Π½ΠΎΠ΅ ΠΎΠ±ΠΎΡΡΠ΄ΠΎΠ²Π°Π½ΠΈΠ΅ Π΄Π»Ρ Ρ
ΠΎΠ»ΠΎΠ΄Π½ΠΎΠΉ ΡΡΠ°ΠΌΠΏΠΎΠ²ΠΊΠΈ ΠΏΠΎΠ·Π²ΠΎΠ»ΡΠ΅Ρ ΠΈΠ·Π³ΠΎΡΠ°Π²Π»ΠΈΠ²Π°ΡΡ ΡΠ»ΠΎΠΆΠ½ΡΠ΅ Π΄Π΅ΡΠ°Π»ΠΈ Π½Π° ΡΠ΄ΠΈΠ²ΠΈΡΠ΅Π»ΡΠ½ΠΎ Π²ΡΡΠΎΠΊΠΈΡ
ΡΠΊΠΎΡΠΎΡΡΡΡ
ΠΈ Ρ Π½Π΅Π²Π΅ΡΠΎΡΡΠ½ΠΎΠΉ ΡΠΎΡΠ½ΠΎΡΡΡΡ. ΠΠ»Ρ ΠΊΠΎΠΌΠΏΠ°Π½ΠΈΠΉ, ΠΊΠΎΡΠΎΡΡΠ΅ Π² Π½Π°ΡΡΠΎΡΡΠ΅Π΅ Π²ΡΠ΅ΠΌΡ ΠΏΡΠΎΠΈΠ·Π²ΠΎΠ΄ΡΡ ΠΈΠ»ΠΈ ΠΏΠΎΠΊΡΠΏΠ°ΡΡ ΠΌΠ΅Ρ
Π°Π½ΠΈΡΠ΅ΡΠΊΠΈ ΠΎΠ±ΡΠ°Π±ΠΎΡΠ°Π½Π½ΡΠ΅ ΠΊΠΎΠΌΠΏΠΎΠ½Π΅Π½ΡΡ, ΠΏΡΠΎΡΠ΅ΡΡ Ρ
ΠΎΠ»ΠΎΠ΄Π½ΠΎΠΉ ΡΡΠ°ΠΌΠΏΠΎΠ²ΠΊΠΈ (ΡΠ°ΠΊΠΆΠ΅ Π½Π°Π·ΡΠ²Π°Π΅ΠΌΡΠΉ Ρ
ΠΎΠ»ΠΎΠ΄Π½ΠΎΠΉ Π²ΡΡΠ°Π΄ΠΊΠΎΠΉ) ΠΌΠΎΠΆΠ΅Ρ ΡΠ°ΡΡΠΌΠ°ΡΡΠΈΠ²Π°ΡΡΡΡ ΠΊΠ°ΠΊ ΡΠΊΠΎΠ½ΠΎΠΌΠΈΡΠ½Π°Ρ Π°Π»ΡΡΠ΅ΡΠ½Π°ΡΠΈΠ²Π° Π΄Π»Ρ ΠΊΠ°ΠΆΠ΄ΠΎΠΉ Π΄Π΅ΡΠ°Π»ΠΈ. Π₯ΠΎΡΡ Π½Π΅ΠΊΠΎΡΠΎΡΡΠ΅ ΠΊΠΎΠΌΠΏΠΎΠ½Π΅Π½ΡΡ ΠΌΠΎΠ³ΡΡ Π½Π΅ ΠΏΠΎΠ΄Π΄Π°Π²Π°ΡΡΡΡ ΠΏΡΠΎΡΠ΅ΡΡΡ Ρ
ΠΎΠ»ΠΎΠ΄Π½ΠΎΠΉ ΡΡΠ°ΠΌΠΏΠΎΠ²ΠΊΠΈ ΠΈΠ·-Π·Π° ΡΡΠ΅Π±ΠΎΠ²Π°Π½ΠΈΠΉ Π½Π΅Π±ΠΎΠ»ΡΡΠΎΠ³ΠΎ ΠΎΠ±ΡΠ΅ΠΌΠ° ΠΈΠ»ΠΈ Π½Π΅ΡΠΎΠ²ΠΌΠ΅ΡΡΠΈΠΌΡΡ
ΡΠΎΡΠΌ, ΠΏΡΠΈ ΠΏΡΠΎΠ΅ΠΊΡΠΈΡΠΎΠ²Π°Π½ΠΈΠΈ ΠΏΡΠΎΠΈΠ·Π²ΠΎΠ΄ΡΡΠ²Π΅Π½Π½ΠΎΠΉ Π΄Π΅ΡΠ°Π»ΠΈ ΡΠ»Π΅Π΄ΡΠ΅Ρ ΡΡΠΈΡΡΠ²Π°ΡΡ ΡΠ»Π΅Π΄ΡΡΡΠΈΠ΅ ΠΏΡΠ΅ΠΈΠΌΡΡΠ΅ΡΡΠ²Π°.
Π£Π½ΠΈΠ²Π΅ΡΡΠ°Π»ΡΠ½ΠΎΡΡΡ ΠΊΠΎΠ½ΡΡΡΡΠΊΡΠΈΠΈ
ΠΠ° ΠΏΡΠΈΠ²Π΅Π΄Π΅Π½Π½ΠΎΠΌ Π²ΡΡΠ΅ ΡΠΈΡΡΠ½ΠΊΠ΅ ΠΏΠΎΠΊΠ°Π·Π°Π½Π° ΠΎΠΏΠ΅ΡΠ°ΡΠΈΡ Ρ ΠΎΠ΄Π½ΠΈΠΌ ΡΡΠ°ΠΌΠΏΠΎΠΌ ΠΈ Π΄Π²ΡΠΌΡ ΡΠ΄Π°ΡΠ°ΠΌΠΈ, ΠΊΠΎΡΠΎΡΠ°Ρ Π΄ΠΎΠ²ΠΎΠ»ΡΠ½ΠΎ ΡΠ°ΡΠΏΡΠΎΡΡΡΠ°Π½Π΅Π½Π° Π² Π½Π°ΡΠ΅ΠΉ ΠΎΡΡΠ°ΡΠ»ΠΈ. ΠΠ΄Π½Π°ΠΊΠΎ Π² ΠΏΠΎΡΠ»Π΅Π΄Π½ΠΈΠ΅ Π³ΠΎΠ΄Ρ ΠΎΠ±ΠΎΡΡΠ΄ΠΎΠ²Π°Π½ΠΈΠ΅ Π΄Π»Ρ Ρ ΠΎΠ»ΠΎΠ΄Π½ΠΎΠΉ ΡΡΠ°ΠΌΠΏΠΎΠ²ΠΊΠΈ ΡΡΠ°Π»ΠΎ Π½Π°ΠΌΠ½ΠΎΠ³ΠΎ Π±ΠΎΠ»Π΅Π΅ ΡΠΎΠ²Π΅ΡΡΠ΅Π½Π½ΡΠΌ. Stabio North America ΠΈΠΌΠ΅Π΅Ρ ΡΠ»ΠΎΠΆΠ½ΠΎΠ΅ ΠΎΠ±ΠΎΡΡΠ΄ΠΎΠ²Π°Π½ΠΈΠ΅ Ρ ΡΠ΅ΡΡΡΡ ΠΏΡΠΎΠ³ΡΠ΅ΡΡΠΈΠ²Π½ΡΠΌΠΈ ΡΡΠ°ΠΌΠΏΠ°ΠΌΠΈ. ΠΡΠΈ ΡΠΎΡΠΌΠΎΠ²ΠΎΡΠ½ΡΠ΅ ΠΌΠ°ΡΠΈΠ½Ρ Ρ Π½Π΅ΡΠΊΠΎΠ»ΡΠΊΠΈΠΌΠΈ ΡΡΠ°Π½ΡΠΈΡΠΌΠΈ ΠΏΠΎΠ·Π²ΠΎΠ»ΡΡΡ Π½Π°ΠΌ ΠΏΡΠΎΠΈΠ·Π²ΠΎΠ΄ΠΈΡΡ ΡΠ»ΠΎΠΆΠ½ΡΠ΅ ΠΊΠΎΠΌΠΏΠΎΠ½Π΅Π½ΡΡ Ρ ΠΏΠΎΠΌΠΎΡΡΡ ΡΠ΅ΡΠΈΠΈ ΡΡΠ°Π½ΡΠΈΠΉ Π²ΡΡΠ°Π΄ΠΊΠΈ ΠΈ ΡΠΊΡΡΡΡΠ·ΠΈΠΈ.
ΠΡΠ°Π΄ΠΊΠ° (ΡΠ²Π΅Π»ΠΈΡΠ΅Π½ΠΈΠ΅ Π΄ΠΈΠ°ΠΌΠ΅ΡΡΠ° Π·Π°Π³ΠΎΡΠΎΠ²ΠΊΠΈ) ΠΈ ΡΠΊΡΡΡΡΠ·ΠΈΡ (ΡΠΌΠ΅Π½ΡΡΠ΅Π½ΠΈΠ΅ Π΄ΠΈΠ°ΠΌΠ΅ΡΡΠ° Π·Π°Π³ΠΎΡΠΎΠ²ΠΊΠΈ) Π½Π΅ΠΎΠ±Ρ ΠΎΠ΄ΠΈΠΌΡ Π΄Π»Ρ ΠΊΠΎΠ½ΡΡΠΎΠ»Ρ ΠΈ ΠΈΠ·ΠΌΠ΅Π½Π΅Π½ΠΈΡ ΠΊΠΎΠ½ΡΠΈΠ³ΡΡΠ°ΡΠΈΠΈ ΠΈΡΡ ΠΎΠ΄Π½ΠΎΠ³ΠΎ ΠΌΠ°ΡΠ΅ΡΠΈΠ°Π»Π° Π΄ΠΎ ΠΆΠ΅Π»Π°Π΅ΠΌΠΎΠΉ ΠΊΠΎΠ½Π΅ΡΠ½ΠΎΠΉ ΡΠΎΡΠΌΡ. Π‘ΡΠ°Π½ΠΊΠΈ Ρ Π½Π΅ΡΠΊΠΎΠ»ΡΠΊΠΈΠΌΠΈ ΡΡΠ°Π½ΡΠΈΡΠΌΠΈ ΠΏΠΎΠ·Π²ΠΎΠ»ΡΡΡ ΠΏΠ΅ΡΠ΅ΠΌΠ΅ΡΠ°ΡΡ ΡΠ°Π±ΠΎΡΡ ΡΠ΅ΡΠ΅Π· ΠΏΠΎΡΠ»Π΅Π΄ΠΎΠ²Π°ΡΠ΅Π»ΡΠ½ΠΎΡΡΡ ΡΡΠ°ΠΌΠΏΠΎΠ², Π° Π½Π΅ ΠΏΡΡΠ°ΡΡΡΡ ΡΡΠΎΡΠΌΠΈΡΠΎΠ²Π°ΡΡ Π΄Π΅ΡΠ°Π»Ρ Π²ΡΠ΅Π³ΠΎ Π·Π° Π½Π΅ΡΠΊΠΎΠ»ΡΠΊΠΎ ΡΠ΄Π°ΡΠΎΠ².
ΠΡΡΠΎΠΊΠ°Ρ ΠΏΡΠΎΠΈΠ·Π²ΠΎΠ΄ΠΈΡΠ΅Π»ΡΠ½ΠΎΡΡΡ ΠΈ ΠΏΠΎΠ²ΡΠΎΡΡΠ΅ΠΌΠΎΡΡΡ
ΠΡΠΎΡΠ΅ΡΡ Ρ
ΠΎΠ»ΠΎΠ΄Π½ΠΎΠΉ ΡΡΠ°ΠΌΠΏΠΎΠ²ΠΊΠΈ ΠΌΠΎΠΆΠ΅Ρ Π²ΡΠΏΠΎΠ»Π½ΡΡΡΡΡ Π² 100 ΡΠ°Π· Π±ΡΡΡΡΠ΅Π΅, ΡΠ΅ΠΌ ΠΌΠ΅Ρ
Π°Π½ΠΈΡΠ΅ΡΠΊΠ°Ρ ΠΎΠ±ΡΠ°Π±ΠΎΡΠΊΠ°, Π½ΠΎ ΠΏΡΠΈ ΡΡΠΎΠΌ ΠΎΠ±Π΅ΡΠΏΠ΅ΡΠΈΠ²Π°ΡΡ ΡΠ°ΠΊΡΡ ββΠΆΠ΅ ΡΠΎΡΠ½ΠΎΡΡΡ. ΠΠ°ΡΠΈΠ½Π° Ρ ΡΠ΅ΡΡΡΡ ΡΡΠ°Π½ΡΠΈΡΠΌΠΈ ΠΎΠ±ΡΠ°Π±Π°ΡΡΠ²Π°Π΅Ρ ΡΠ΅ΡΡΡ Π΄Π΅ΡΠ°Π»Π΅ΠΉ, ΠΊΠ°ΠΆΠ΄Π°Ρ ΠΈΠ· ΠΊΠΎΡΠΎΡΡΡ
Π½Π°Ρ
ΠΎΠ΄ΠΈΡΡΡ Π½Π° ΡΠ°Π·Π½ΡΡ
ΡΡΠ°Π΄ΠΈΡΡ
ΡΠ°Π·ΡΠ°Π±ΠΎΡΠΊΠΈ. Π‘ ΠΊΠ°ΠΆΠ΄ΡΠΌ Ρ
ΠΎΠ΄ΠΎΠΌ ΡΡΠ°Π½ΠΊΠ° Π³ΠΎΡΠΎΠ²Π°Ρ Π΄Π΅ΡΠ°Π»Ρ Π²ΡΡΠ°Π»ΠΊΠΈΠ²Π°Π΅ΡΡΡ ΠΈΠ· ΠΏΠΎΡΠ»Π΅Π΄Π½Π΅ΠΉ ΠΌΠ°ΡΡΠΈΡΡ, Π² ΡΠΎ Π²ΡΠ΅ΠΌΡ ΠΊΠ°ΠΊ Π½ΠΎΠ²Π°Ρ Π·Π°Π³ΠΎΡΠΎΠ²ΠΊΠ° ΠΎΠ±ΡΠ΅Π·Π°Π΅ΡΡΡ Π΄ΠΎ Π·Π°Π΄Π°Π½Π½ΠΎΠΉ Π΄Π»ΠΈΠ½Ρ ΠΈ ΠΏΠΎΠ΄Π°Π΅ΡΡΡ Π² ΠΏΠ΅ΡΠ²ΡΡ ΠΌΠ°ΡΡΠΈΡΡ β Π²ΡΠ΅ ΡΡΠΎ Π²ΡΠΏΠΎΠ»Π½ΡΠ΅ΡΡΡ ΡΠΎΡΠ½ΠΈ ΡΠ°Π· Π² ΠΌΠΈΠ½ΡΡΡ. ΠΡΠΎΠΌΠ΅ ΡΠΎΠ³ΠΎ, ΠΊΠΎΠ³Π΄Π° ΠΌΡ Π΄ΠΎΠ±Π°Π²Π»ΡΠ΅ΠΌ ΠΏΡΠΎΠΈΠ·Π²ΠΎΠ΄ΡΡΠ²Π΅Π½Π½ΡΠΉ ΠΎΠΏΡΡ, ΠΈΡΠΊΠ»ΡΡΠΈΡΠ΅Π»ΡΠ½ΡΡ ΠΊΠΎΠ½ΡΡΡΡΠΊΡΠΈΡ ΠΈΠ½ΡΡΡΡΠΌΠ΅Π½ΡΠ° ΠΈ ΠΈΡΠΏΠΎΠ»ΡΠ·ΠΎΠ²Π°Π½ΠΈΠ΅ ΠΏΡΠ΅ΡΠΈΠ·ΠΈΠΎΠ½Π½ΠΎΠΉ ΠΎΡΠ½Π°ΡΡΠΊΠΈ, Ρ
ΠΎΠ»ΠΎΠ΄Π½Π°Ρ Π²ΡΡΠ°Π΄ΠΊΠ° ΠΎΠ±Π΅ΡΠΏΠ΅ΡΠΈΠ²Π°Π΅Ρ ΠΏΡΠ΅Π²ΠΎΡΡ
ΠΎΠ΄Π½ΡΡ ΠΏΠΎΠ²ΡΠΎΡΡΠ΅ΠΌΠΎΡΡΡ.
Π£ΠΌΠ΅Π½ΡΡΠ΅Π½Π½ΡΠΉ Π±ΡΠ°ΠΊ
ΠΡΠΎΡΠ΅ΡΡ ΠΎΠ±ΡΠ°Π±ΠΎΡΠΊΠΈ Π½Π°ΡΠΈΠ½Π°Π΅ΡΡΡ Ρ ΠΏΡΡΡΠΊΠ° Π΄ΠΈΠ°ΠΌΠ΅ΡΡΠΎΠΌ, ΡΠΊΠ²ΠΈΠ²Π°Π»Π΅Π½ΡΠ½ΡΠΌ Π½Π°ΠΈΠ±ΠΎΠ»ΡΡΠ΅ΠΌΡ Π΄ΠΈΠ°ΠΌΠ΅ΡΡΡ ΠΎΠ±ΡΠ°Π±Π°ΡΡΠ²Π°Π΅ΠΌΠΎΠ³ΠΎ Π³ΠΎΡΠΎΠ²ΠΎΠ³ΠΎ ΠΊΠΎΠΌΠΏΠΎΠ½Π΅Π½ΡΠ°. ΠΡΠ° ΠΎΠΊΠΎΠ½ΡΠ°ΡΠ΅Π»ΡΠ½Π°Ρ ΡΠΎΡΠΌΠ° Π΄ΠΎΡΡΠΈΠ³Π°Π΅ΡΡΡ ΠΏΡΡΠ΅ΠΌ ΡΠ΄Π°Π»Π΅Π½ΠΈΡ ΠΏΡΡΡΠΊΠ°, ΡΡΠΎ ΡΠΌΠ΅Π½ΡΡΠ°Π΅Ρ Π΄ΠΈΠ°ΠΌΠ΅ΡΡ ΠΈ ΡΠΎΠ·Π΄Π°Π΅Ρ ΠΎΡΡ ΠΎΠ΄Ρ Π² Π²ΠΈΠ΄Π΅ ΡΡΡΡΠΆΠΊΠΈ. Π§Π΅ΠΌ Π²ΡΡΠ΅ ΡΠ΅Π½Π° ΡΡΡΡΡ (Π½Π°ΠΏΡΠΈΠΌΠ΅Ρ, ΠΌΠ΅Π΄ΠΈ, Π»Π°ΡΡΠ½ΠΈ ΠΈΠ»ΠΈ Π½Π΅ΡΠΆΠ°Π²Π΅ΡΡΠ΅ΠΉ ΡΡΠ°Π»ΠΈ), ΡΠ΅ΠΌ Π²ΡΡΠ΅ ΠΏΠΎΡΠ΅ΡΠΈ ΠΈΠ·-Π·Π° ΠΎΠ±ΡΠ°Π±ΠΎΡΠ°Π½Π½ΠΎΠ³ΠΎ Π»ΠΎΠΌΠ°.
ΠΠ°ΠΎΠ±ΠΎΡΠΎΡ, ΠΏΡΠΎΡΠ΅ΡΡ Ρ
ΠΎΠ»ΠΎΠ΄Π½ΠΎΠΉ ΡΡΠ°ΠΌΠΏΠΎΠ²ΠΊΠΈ Π½Π°ΡΠΈΠ½Π°Π΅ΡΡΡ ΡΠΎ ΡΠΏΠ΅ΡΠΈΠ°Π»ΡΠ½ΠΎΠΉ Π·Π°Π³ΠΎΡΠΎΠ²ΠΊΠΈ ΠΈ ΠΎΠ±ΡΠ°Π±Π°ΡΡΠ²Π°Π΅Ρ ΠΌΠ°ΡΠ΅ΡΠΈΠ°Π» ΡΠ΅ΡΠ΅Π· ΡΠ΅ΡΠΈΡ ΡΡΠ°ΠΌΠΏΠΎΠ². ΠΠΎΡΠ»Π΅Π΄ΠΎΠ²Π°ΡΠ΅Π»ΡΠ½ΠΎΡΡΡ ΡΠΎΡΠΌΠΎΠ²Π°Π½ΠΈΡ Π΄Π°ΡΡ ΠΎΠΊΠΎΠ½ΡΠ°ΡΠ΅Π»ΡΠ½ΡΡ ΡΠΎΡΠΌΡ Π·Π° ΡΡΠ΅Ρ ΡΠ΅ΠΊΠΎΠ½ΡΠΈΠ³ΡΡΠ°ΡΠΈΠΈ ΠΈΡΡ
ΠΎΠ΄Π½ΠΎΠΉ Π·Π°Π³ΠΎΡΠΎΠ²ΠΊΠΈ Π±Π΅Π· ΠΎΠ±ΡΠ°Π·ΠΎΠ²Π°Π½ΠΈΡ Π±ΡΠ°ΠΊΠ°! ΠΠ±ΡΠ΅ΠΌ Π³ΠΎΡΠΎΠ²ΠΎΠΉ Π΄Π΅ΡΠ°Π»ΠΈ ΡΠ°Π²Π΅Π½ ΠΎΠ±ΡΠ΅ΠΌΡ ΠΈΡΡ
ΠΎΠ΄Π½ΠΎΠΉ Π·Π°Π³ΠΎΡΠΎΠ²ΠΊΠΈ. ΠΡΠΎΡΠ΅ΡΡ Ρ
ΠΎΠ»ΠΎΠ΄Π½ΠΎΠΉ ΡΡΠ°ΠΌΠΏΠΎΠ²ΠΊΠΈ Π½Π΅ Π΄Π°Π΅Ρ ΠΎΡΡ
ΠΎΠ΄ΠΎΠ².
ΠΡΠΎΡΠ½ΠΎΡΡΡ ΠΏΡΠΎΠ΄ΡΠΊΡΠ°
ΠΡΠΈ ΠΎΠ±ΡΠ°Π±ΠΎΡΠΊΠ΅ ΠΊΡΠ΅ΠΏΠ΅ΠΆΠ° ΠΈΠ»ΠΈ ΠΊΠΎΠΌΠΏΠΎΠ½Π΅Π½ΡΠ° ΠΌΠ΅ΡΠ°Π»Π» ΡΡΠ΅Π·Π°Π΅ΡΡΡ Π΄Π»Ρ ΡΠΌΠ΅Π½ΡΡΠ΅Π½ΠΈΡ Π΄ΠΈΠ°ΠΌΠ΅ΡΡΠ°. Π£Π΄Π°Π»ΡΡ ΠΌΠ΅ΡΠ°Π»Π», Π²Ρ ΡΠ°ΠΊΠΆΠ΅ ΡΠ΄Π°Π»ΡΠ΅ΡΠ΅ ΠΈ Β«Π½Π°ΡΡΡΠ°Π΅ΡΠ΅Β» Π·Π΅ΡΠ½ΠΈΡΡΡΡ ΡΡΡΡΠΊΡΡΡΡ ΠΌΠ°ΡΠ΅ΡΠΈΠ°Π»Π°, ΡΠ΅ΠΌ ΡΠ°ΠΌΡΠΌ ΠΎΡΠ»Π°Π±Π»ΡΡ Π΄Π΅ΡΠ°Π»Ρ. ΠΠ΅ΡΠ°Π»Ρ Π±ΡΠ»Π° Π½Π° ΡΠ°ΠΌΠΎΠΌ Π΄Π΅Π»Π΅ ΠΏΡΠΎΡΠ½Π΅Π΅ Π½Π΅ΠΎΠ±ΡΠ°Π±ΠΎΡΠ°Π½Π½ΠΎΠ³ΠΎ ΠΏΡΡΡΠΊΠ°.
ΠΡΠ½ΠΎΠ²Π½ΡΠΌ ΠΏΡΠ΅ΠΈΠΌΡΡΠ΅ΡΡΠ²ΠΎΠΌ Ρ
ΠΎΠ»ΠΎΠ΄Π½ΠΎΠΉ ΡΡΠ°ΠΌΠΏΠΎΠ²ΠΊΠΈ ΡΠ²Π»ΡΠ΅ΡΡΡ ΠΏΠΎΠ²ΡΡΠ΅Π½Π½Π°Ρ ΠΏΡΠΎΡΠ½ΠΎΡΡΡ, ΠΏΡΠΈΠ΄Π°Π²Π°Π΅ΠΌΠ°Ρ ΠΊΠΎΠΌΠΏΠΎΠ½Π΅Π½ΡΡ Π·Π° ΡΡΠ΅Ρ ΡΠ΅ΠΊΠΎΠ½ΡΠΈΠ³ΡΡΠ°ΡΠΈΠΈ ΠΏΠΎΡΠΎΠΊΠ° Π·Π΅ΡΠ΅Π½. ΠΡΠΈ Ρ
ΠΎΠ»ΠΎΠ΄Π½ΠΎΠΉ ΡΡΠ°ΠΌΠΏΠΎΠ²ΠΊΠ΅ ΠΌΠ°ΡΠ΅ΡΠΈΠ°Π» Π½Π΅ ΡΠ΄Π°Π»ΡΠ΅ΡΡΡ, ΠΊΠ°ΠΊ Π² ΠΏΡΠΎΡΠ΅ΡΡΠ΅ ΠΎΠ±ΡΠ°Π±ΠΎΡΠΊΠΈ. ΠΠΌΠ΅ΡΡΠΎ ΡΡΠΎΠ³ΠΎ ΠΏΡΠΎΡΠ΅ΡΡΡ ΠΎΡΠ°Π΄ΠΊΠΈ ΠΈ ΡΠΊΡΡΡΡΠ·ΠΈΠΈ ΠΏΡΠΈΠ²ΠΎΠ΄ΡΡ ΠΊ ΡΠΏΠ»ΠΎΡΠ½Π΅Π½ΠΈΡ Π·Π΅ΡΠ΅Π½, Π° ΡΠ°ΠΌ ΠΏΠΎΡΠΎΠΊ Π·Π΅ΡΠ΅Π½ ΠΏΠΎΠ»ΠΎΠΆΠΈΡΠ΅Π»ΡΠ½ΠΎ ΠΈΠ·ΠΌΠ΅Π½ΡΠ΅ΡΡΡ Π² ΠΊΡΠΈΡΠΈΡΠ΅ΡΠΊΠΈΡ
ΠΎΠ±Π»Π°ΡΡΡΡ
Π΄Π΅ΡΠ°Π»ΠΈ. ΠΡΠ° ΠΏΠ΅ΡΠ΅Π³ΡΡΠΏΠΏΠΈΡΠΎΠ²ΠΊΠ° ΠΈ ΡΠΏΠ»ΠΎΡΠ½Π΅Π½ΠΈΠ΅ ΠΏΠΎΡΠΎΠΊΠ° Π·Π΅ΡΠ½Π° Π΄Π°Π΅Ρ Π΄Π΅ΡΠ°Π»ΠΈ, Π±ΠΎΠ»Π΅Π΅ ΡΡΡΠΎΠΉΡΠΈΠ²ΡΠ΅ ΠΊ ΡΡΡΠ°Π»ΠΎΡΡΠΈ. Π ΡΠ΅Π·ΡΠ»ΡΡΠ°ΡΠ΅ Π΄Π΅ΡΠ°Π»ΠΈ Ρ Ρ
ΠΎΠ»ΠΎΠ΄Π½ΠΎΠΉ Π³ΠΎΠ»ΠΎΠ²ΠΊΠΎΠΉ Π±ΡΠ΄ΡΡ ΠΈΠΌΠ΅ΡΡ Π±ΠΎΠ»Π΅Π΅ Π²ΡΡΠΎΠΊΠΈΠ΅ ΠΏΡΠ΅Π΄Π΅Π» ΠΏΡΠΎΡΠ½ΠΎΡΡΠΈ ΠΏΡΠΈ ΡΠ΄Π²ΠΈΠ³Π΅, ΡΠ°ΡΡΡΠΆΠ΅Π½ΠΈΠΈ ΠΈ ΡΠ΅ΠΊΡΡΠ΅ΡΡΠΈ.