Основные определения и формулы
Скорость резания V (м/мин) – это окружная скорость перемещения режущих кромок фрезы. Эта величина определяет эффективность обработки и лежит в рекомендованных для каждого инструментального материала пределах. За один оборот фрезы точка режущей кромки, находящаяся на окружности фрезы диаметра D (мм), сможет пройти путь, равный длине окружности, то есть πD. Для того чтобы определить длину пути, пройденного точкой за одну минуту, нужно умножить длину пути за один оборот на частоту вращения фрезы, то есть πDN (мм/мин). Таким образом, формула для определения скорости резания будет следующей:
V = πDN/1000 (мм/мин).
Частота вращения шпинделя N (об/мин) равняется числу оборотов фрезы в минуту.
N = 1000V/nD (об/мин).
При фрезеровании различают минутную подачу, подачу на зуб и подачу наоборот фрезы.
Подача на зуб Fz (мм/зуб) – величина перемещения фрезы или рабочего стола с заготовкой за время поворота фрезы на один зуб.
Подача на оборот Fo (мм/об) – величина перемещения фрезы или рабочего стола с заготовкой за один оборот фрезы. Подача на оборот равняется произведению подачи на зуб на число зубьев фрезы Z:
Fo = FzZ (мм/об).
Минутной подачей Fm (мм/мин) называется величина относительного перемещения фрезы или рабочего стола с заготовкой за одну минуту. Минутная подача равняется произведению подачи на оборот на частоту вращения фрезы:
Fm = FoN = FzZN (мм/мин).
Глубиной фрезерования h (мм) называется расстояние между обработанной и необработанной поверхностями, измеряемое вдоль оси фрезы.
Шириной фрезерования b (мм) называется величина срезаемого припуска, измеренная в радиальном направлении, или ширина контакта заготовки и инструмента.
Производительность снятия материала Q (см3) – это объем удаляемого материала в единицу времени, определяемый глубиной, шириной обработки и величиной подачи.
Q = (h × b × Fm)/1000.
Определение режима резания при фрезеровании
ОПРЕДЕЛЕНИЕ РЕЖИМА РЕЗАНИЯ ПРИ ФРЕЗЕРОВАНИИ [c.350]В основе определения режимов резания при фрезеровании лежат те же экономические и технические критерии оптимизации, что и при токарной обработке, так что в данном случае достаточно только определить особенности и ограничения, накладываемые процессом фрезерования в сравнении с токарной обработкой. При фрезеровании инструмент совершает управляемое движение сразу по двум осям (X и К) в плоскости, параллельной этим осям.
Рис. 164. Определение режимов резания при фрезеровании (диаграмма последовательности операций) |
Выбор режимов резания при фрезеровании осуществляют главным образом для определения подачи на зуб фрезы и скорости резания, обеспечивающей требуемую стойкость, так как глубину резания и ширину фрезерования определяют видом фрезерования и припуском на обработку. [c.135]
Режимы резания при фрезеровании текстолита угловыми фрезами из быстрорежущей стали можно рассчитать по номограмме на рис. 199. На номограмме показан пример определения скорости резания для следующих условий обработки Г = 60 мин.
[c.204]
Номограмма для расчета режимов резания при фрезеровании гетинакса твердосплавными цилиндрическими фрезами дана на рис. 201. На номограмме показаны два примера определения скорости резания. [c.204]
Скорость резания при фрезеровании зависит от принятой стойкости фрезы. В таблицах рекомендуемых скоростей резания, а равно в руководящих материалах по режимам резания при фрезеровании исходят из определенных стойкостей фрезы. [c.454]
В гл. 9 приведены расчетные зависимости для определения режимов резания при точении, сверлении, зенкеровании, развертывании, протягивании, фрезеровании и шлифовании.
Расчетные зависимости для определения режимов резания при точении приведены в табл. 189—191 при сверлении, зенкеровании и развертывании- отверстий — в табл. 192—194 при протягивании—в табл. 195 при фрезеровании — в табл. 196—198 при шлифовании — в табл. 199—202. Поправочные коэффициенты на подачу и скорость резания, приведенные в зависимости, даны в соответствующих разделах справочника.
[c.371]
Выбор режимов резания при фрезеровании, так же как и при других способах обработки, должен начинаться с определения глубины фрезерования. Как правило, при величине припуска больше 3—4 мм обработку следует вести в два прохода — черновой и чистовой. При припусках лоЗ мм к обработке под последующее шлифование или другой вид окончательной обработки следует ограничиваться одним полу-чистовым проходом. Определив глубину резания и зная ширину фрезерования, устанавливают типоразмер фрезы и соответственно виду обработки величину подачи на одни зуб 8 г- [c.185]
Элементы режима резания при фрезеровании имеют следующие определения. [c.160]
Дайте определение элементов режима резания при фрезеровании. [c.173]
Для определения элементов режима резания при фрезеровании ( 2 и у) пользуются справочными таблицами или эмпирическими формулами. При этом порядок назначения наивыгоднейших режимов резания применяют следующий.
[c.231]
В этой главе излагаются методика и результаты опытов по определению силы резания при цилиндрическом и дисковом фрезеровании слоистых пластмасс твердосплавными фрезами. Устанавливается характер влияния режима резания, геометрических параметров режущей части фрез, износа фрезы на силу резания. Для сравнения приводятся результаты опытов по определению силы резания при фрезеровании слоистых пластмасс с различными наполнителями, а также при фрезеровании некоторых металлов.
Каждый электродвигатель рассчитан на определенную нагрузку, при которой он может работать продолжительное время. При этой нагрузке двигатель обладает так называемой нормальной или номинальной мощностью, развивает нормальный крутящий момент, имеет нормальное число оборотов и потребляет нормальную силу тока. При работе электродвигателя постоянно происходят изменения режима, связанные с изменением режимов резания при фрезеровании, а также с пуском, остановом, торможением и реверсированием механизмов станка.
[c.126]
Для определения скорости резания при заданных условиях пользуются справочными таблицами режимов резания [33 ] или соответствующими формулами. При фрезеровании зубчатых колес одно- [c.418]
В связи с этим приведенные в данной главе результаты исследования обрабатываемости текстолита фрезерованием имеют определенный практический интерес и позволяют более обоснованно выбирать режимы резания при обработке этого пластика цилиндрическими, пазовыми, угловыми и дисковыми фрезами. [c.67]
Раздел Резание металлов содержит сведения о процессе резания металлов, явлениях, возникающих в этом процессе, и классификации чистоты обработанных поверхностей. В этом разделе приведены необходимые справочные данные, формулы и таблицы для определения режимов резания, скорости резания, подачи, глубины резания, числа проходов при точении, строгании, сверлении, зенкеровании, развёртывании, фрезеровании, зубофрезеровании, резьбонарезании, протягивании, шлифовании и отделочной обработки (доводка брусками, притирка, отделка колеблющимися брусками).
Режимы резания, выбору которых должно предшествовать определение операционных припусков (см. гл. 8), устанавливают по соответствующим нормативным таблицам. При пользовании этими таблицами необходимо обратить внимание на то, что в них наряду со значениями выбираемых параметров приводятся поправочные коэффициенты, а также отдельные данные в примечания.ч. Для определения требуемого параметра (с учетом конкретных условий обработки) табличные его значения необходимо умножать на поправочные коэффициенты. Последовательность выбора инструмента и режимов резания приведена в табл.
При фрезеровании выбор наивыгоднейшего режима резания заключается в определении наиболее рациональных глубины резания и числа проходов, подачи на один зуб фрезы и скорости резания. [c.103]
В целях возможности установления режимов резания, т. е. скоростей резания при определенных ширине и глубине фрезерования с различными подачами необходимо задаться экономической стойкостью. [c.445]
П )именение адаптивной системы управления на фрезерных головках обеспечивает возможность повышения производительности фрезерования торцов за счет сокращения машинного времени в 2 раза. Если при обычной обработке величина продольной подачи, устанавливаемая равной 330 мм/мин, остается все время постоянной, то при использовании САУ подача автоматически меняется в соответствии с глубиной и шириной фрезерования и на участках врезания и выхода фрезы = 350 н–т-920 мм/мин.
Таким образом, по нормативным таблицам выбирают скорость резания, число оборотов фрезы, подачу и мощность резания. Рекомендуемые в таблицах скорости резания, подачи и мощности рассчитаны на определенные условия эксплуатации. При изменении этих условий необходимо производить корректирование режимов резания, для чего вводят поправочные коэффициенты, которые учитывают изменение материала заготовки, состояние стали, характер заготовки и состояние ее поверхности, изменения периода стойкости фрезы и материала режущего инструмента, вид характера обработки, изменение ширины фрезерования и влияние охлаждения.

Выбранные скорость резания, число оборотов и минутную подачу умножают на все поправочные коэффициенты и затем увязывают с паспортными данными станка. По паспорту выбирают ближайшие значения числа оборотов и минутной подачи, имеющиеся на станке. После определения фактических режимов резания выбирают поправочные коэффициенты на нормативное значение эффективной мощности. Коэффициенты на эффективную мощность при работе концевых фрез учитывают изменения ширины фрезерования и скорости резания. Числовые значения этих поправочных коэффициентов являются общими для всех фрезерных работ и приведены в разделе обработки плоскостей цилиндрическими фрезами. [c.82]
С определенными трудностями сталкиваются также технологи и при назначении режимов фрезерования пластмасс ввиду отсутствия соответствующих технически и экономически обоснованных нормативных материалов, а также четкой методики по расчету режимов резания. [c.106]
Проверка выбранного режима по мощности. На работу, потребную для резания, расходуется при обычном фрезеровании 0,75—0,85, а при скоростных режимах 0,65—0,75 мощности N3 электродвигателя. Эф( ктивную мощность N3, потребную на фрезерование, определяют либо расчетом по методу, излагаемому в литературе (1, 2], либо по карте нормативов в зависимости от выбранного режима. Определенная эффективная мощность должна удовлетворять следующей зависимости N3 Л эЛ. с учетом к. п. д. станка Л- Если выбранный режим не отвечает этой зависимости, необходимо установленную минутную подачу зм снизить до величины, допускаемой мощностью электродвигателя станка, и соответственно уменьшить число оборотов шпинделя.
[c.491]
Номограмма на рис. 198 предназначена для расчета режимов резания при фрезеровании текстолита цилиндрическими фрезами из быстрорежущей стали. На номограмме показан пример определения скорости резания при следующих условиях обработки Т = 60 мин, t Ъ мм, = 0,1 мм1зуб, О = 100 мм. На шкале скоростей номограммы читаем соответствующую скорость резания 215 м1мин-
[c. 203]
Выбор технологического процесса обработки определяется не только необходимостью получения заданного класса чистоты, но и созданием определенного качества поверхностного слоя. В зависимости от режимов резания, применяемых при точении, фрезеровании, шлифовании и других видах обработки, изменяются физико-механические свойства поверхностного слоя. Скоростное точение, например, способствует упроченению поверхностного слоя. При шлифовании возможны структурные изменения поверхностного слоя и появление прижо-гов . Получили развитие упрочняющие технологические процессы обкатка шариками, роликами, обдувка дробью, также резко изменяющие состояние поверхностного слоя. [c.142]
При фрезеровании торцовыми фрезами следует иметь в виду, что для достижения производительных режимов резания должно соблюдаться определенное положение фрезы по отнбшению к заготовке для конструкционной стали необходимо врезание зуба фрезы с минимальной толщиной срезаемого слоя, что соответствует положению, изображенному на рис. 6,й вьом
[c.437]
Величина переднего угла оказывает влияние не только на износ передней грани. С увеличением переднего угла уменьшается радиус округления режущей кромки. Поэтому в тех случаях, когда инструмент изнашивается только по задней грани, увеличение переднего угла до его рационального значения снижает скорость износа задних граней инструмёнта. На, графике (фиг. 78) показано изменение износа задней грани и стойкости, концевой фрезы при обработке стал ОХМ на следующих режимах резания подача на один зуб 0,108 мм, скорость резания 35,5 mJmuh, глубина резания А мм, ширина фрезерования 16 мм. Здесь так же, как и случае износа по передней грани, наблюдается уменьшение износа и увеличение стойкости при увеличении переднего угла только до определенной величины (в данном случае 20°), а дальнейшее увеличение его сопровождается возрастанием износа и резким снижением стойкости. [c.95]
Начало научному исследованию микрогеометрии обработанной поверхности было положено русским ученым, проф. В. Л. Чебышевым, котврый в 1873 г. впервые в мире вывел формулу для определения высоты микронеровностей при цилиндрическом фрезеровании [92 ]. В этой формуле были учтены не только геометрические факторы (диаметр фрезы, угол между зубьями фрезы), но и элементы режима резания (подача, скорость резания). При содействии В. Л. Чебышева еще в 1893 г. на Тульском оружейном заводе были применены лекала, при помощи которых контролировали не только размеры детали, но и чистоту ее обработанной поверхности. Эти лекала были первыми в мире образцами (эталонами) чистоты поверхности, прообразом эталонов чистоты, применяемых в настоящее время.
[c.74]
Выбор режимов резания. Настройка станка. После установки центровой оправки с фрезой и закрепления заготовки переходят к выбору и назначению режимов резания, которые должны обеспечить экономически наиболее выгодные условия изготовления конкретной детали при соблюдении заданных технических условий. Выбор режимов резания заключается в определении величин глубины резания, подачи, скорости резания и мощности резания. Необходимо также определить ширину фрезерования, диаметр и ширину фрезы, тип станка и другие данные. Выбор режимов резания зависит от многих факторов, взаимно влияющих друг на друга. При назначении режимов резания необходимо придерживаться определенной последовательности в выборе составляющих элементов при обязательном учете условий обработки. Выбор режимов резания производят по таблицам режимов резания, составленных на основе исследовательских работ и опыта передовых заводов. Таблицы режимов резания составлены для обработки черных и цветных металлов инструментами из быстрорежущей стали, твердых сплавов и минера-локерамики.
[c.60]
Проведенные авторами исследования по определению рациональных значений геометрических параметров режущей части цилиндрических твердосплавных фрез были выполнены на консольно-фрезерном станке мод. 6Н81 однозубой цилиндрической фрезой диаметром О = 225 мм, оснащенной сменным ножом из твердого сплава ВК4.
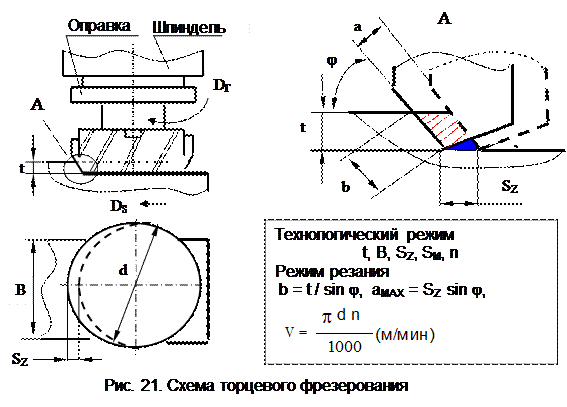
Настройка станка на режим фрезерования. Порядок определения элементов режима фрезерования аналогичен изложенному при обработке цилиндрической фрезой. Ширина фрезерования задала и равла 60 мм, глубина резания 3 мм. подача на зуб по условиям заданной чистоты поверхности может быть взята несколько большей, чем для цилиндрической фрезы, учитывая преи.мущества обработки торцовой фрезой, — она здесь задана равной (),1 мм/зуб-, скорость реза,ния 27 м мин, как для цилиндричеокой ф резы.
[c.122]
Номограмма построена по формуле (5) и состоит из трех квадрантов. В первом квадранте представлены периоды стойкости (Г) в пределах от 20 до 60 мин при разной ширине фрезерования (В), которые связаны определенной зависимостью со скоростью резания. Второй квадрант учитывает изменение подачи г от 0,0725 до 0,42 мм1зуб и третий квадрант представляет изменение диаметра О фрезы от 20 до 45 мм. Наклонные линии в этих квадрантах соответственно характеризуют влияние подачи и диаметра фрезы на скорость резания. Порядок расчета режимов по номограмме рассматривается на следующем примере. [c.117]
Назовите основные параметры режима резания при фрезеровании и типы образующихся стружек
Поверхностная обработка заготовок фрезерной обработкой может быть выполнена только после разработки технической карты с указанием основных режимов обработки.
Такая работа обычно выполняется специалистами со специальной подготовкой.
Условия резания во время фрезерования зависят от различных показателей, таких как тип материала и используемый инструмент.
- Основной индикатор фрезерного станка может быть установлен вручную, и индикатор также отображается в блоке числового программного управления.
Фрезерование резьбы требует особой осторожности, поскольку полученный продукт характеризуется рядом различных параметров. Изучите подробно характеристики выбора условий резания при фрезеровке.
Самый важный режим фрезерования называется скоростью резания. Определяет, как долго определенный слой материала удаляется с поверхности. Большинство машин имеют постоянную скорость резания. Тип материала заготовки учитывается при выборе соответствующего индикатора.
- При использовании нержавеющей стали скорость резания составляет 45-95 м / мин. При добавлении в состав различных химических элементов твердость и другие показатели будут меняться, снижая степень обрабатываемости.
Поскольку бронза считается более мягким составом, подобный режим при шлифовании может быть выбран в диапазоне 90-150 м / мин. Используется для изготовления широкого ассортимента продукции.
Латунь широко используется. Используется при изготовлении запорных элементов и различных клапанов. В зависимости от мягкости сплава скорость резания может быть увеличена до 130-320 м / мин. Латунь имеет тенденцию к повышению пластичности за счет мощного нагрева.
Сегодня алюминиевые сплавы очень распространены. В этом случае существует несколько версий с разными рабочими характеристиками. Именно поэтому режим фрезерования изменяется в диапазоне 200-420 м / мин. Имейте в виду, что алюминий относится к сплаву с низкой температурой плавления. Следовательно, если скорость обработки высока, пластичность может быть значительно улучшена.
Существует довольно много таблиц, которые используются для определения основного режима работы. Формула, определяющая вращение скорости резания: n = 1000 В / D. Рекомендуемая скорость резания и диаметр используемого резца учитываются. Аналогичная формула может быть использована для определения скорости вращения для всех типов обрабатываемого материала.
Рассматриваемый режим фрезерования измеряется в метрах в минуту на отрезанной части. Следует отметить, что специалисты не рекомендуют приводить шпиндель на максимальной скорости, поскольку износ может быть значительно увеличен, а инструменты могут быть повреждены. Поэтому результат уменьшается примерно на 10-15%. На основании этого параметра выбирается лучший инструмент.
Следующее определяется скоростью вращения инструмента.
Полученное качество поверхности. В заключительной технической операции выбирается самый большой параметр. Сколы слишком малы из-за вращения вала со многими вращениями. С другой стороны, при грубых технических операциях выбирается низкое значение, режущий инструмент медленно вращается и размер пластины увеличивается. Благодаря быстрому вращению достигается низкая шероховатость поверхности. С новейшим оборудованием и оборудованием вы можете получить зеркальную поверхность.
Производительность труда. При организации производства внимание также уделяется производительности используемого оборудования. Пример — мастерская на заводе по производству машин, где налажено массовое производство.
Если индекс режима обработки значительно уменьшается, производительность снижается. Самый оптимальный показатель значительно повышает производительность труда.
Степень износа установленного инструмента. Имейте в виду, что режущая кромка будет сильно изнашиваться, когда она будет тереться по обработанной поверхности.
- Чрезмерный износ может изменить точность продукта и снизить производительность труда. Как правило, износ связан с интенсивным нагревом поверхности. По этой причине оборудование, которое может подавать охлаждающую жидкость в зону удаления материала, используется в высокопроизводительных производственных линиях.
- Кроме того, этот параметр выбирается с учетом других показателей, таких как глубина подачи.
Маршрутизация поэтому составляется со всеми параметрами, выбранными одновременно.
Смотрите также:
Примеры решения задач по материаловедению
[1] | Юссеф, Х.А. и Эль-Хофи, Х., 2008, Технология обработки: станки и операции, CRC Press Taylor & Francis Group, стр. |
[2] | Joshi, PH, 2007, Справочник по станкам : Design and Operation , Tata McGraw-Hill Publishing Company Limited, Нью-Дели, стр.40-41. |
[3] | Миллер Р. и Миллер М. Р., Machine Shop Tools and Operations , All new 5 th edi., Willey Publishing Inc., New York, pp.253-254. |
[4] | Insperger, T., 2002 , «Анализ устойчивости периодических уравнений задержки – моделирование вибрации станка с помощью дифференциальных уравнений», докторская диссертация , Будапештский технологический и экономический университет .![]() |
[5] | Озоэгву, К.G., 2011 , «Дребезжание фрезерного станка с ЧПУ для пластика», диссертация магистра английского языка, Университет Ннамди Азикиве, Авка, . |
[6] | Gatti, PL, and Ferrari, V., 2003, Прикладные структурные и механические колебания: Теория, методы и измерительные приборы , Taylor & Francis e- Библиотека. |
[7] | He, J. и Fu, Z., 2001, Modal Analysis , Butterworth Heinemann, Oxford. |
[8] | Рао, С. С., 2004, Механические колебания (4 th ed.) , Дорлинг Киндерсли, Индия. |
[9] | Степан, Г., 1998, Модели дифференциальных уравнений с задержкой для вибрации станков: в нелинейной динамике обработки материалов и производства, под редакцией Ф. К.![]() |
[10] | Иуэзе, К. К. и Офочебе, С.М., 2011, «Конечный расчет для гидродинамического давления на погруженные движущиеся поверхности», Международный журнал механики и твердого тела, 6 (2), стр.115-128. |
[11] | Иуэзе, С.К., Ониечи, П.К., Агинам, Х. и Озоегву, К.Г., 2011, «Конечное проектирование против продольного изгиба конструкций при непрерывном гармоническом возбуждении», Международный журнал прикладных инженерных исследований, 6 (12), стр. 1445-1460. |
[12] | Иуэзе, К.К., Онечи, П.К., Агинам, Х. и Озоегву, К.Г., 2011, «Проектирование против динамического разрушения конструкций с балками и колоннами при возбуждении», Международный журнал теоретической и прикладной механики, 6 (2), стр.153– 164 |
[13] | Инспергер, Т., Манн, Б.П., Степан, Г., и Бейли, П.В., 2003 г., «Стабильность верхнего и нижнего фрезерования, часть 1: альтернативные аналитические методы. , ”Международный журнал станков и производства, 43, стр.25–34. |
[14] | Бобренков, О.А., Хасауна, Ф.А., Бутчер, Е.А. и Манн, Б.П., 2010, «Анализ динамики фрезерования для одновременно находящихся в зацеплении режущих зубьев», Journal of Sound and Vibration, 329, стр.585 –606. |
[15] | Бейли, П.В., Шмитц, Т.Л., Степан, Г., Манн, Б.П., Петерс, Д.А. и Инспергер, Т., 2002, «Влияние радиального погружения и направления резания на неустойчивость вибрации в конце. -milling », Труды IMECE’02 2002 Международная конференция и выставка по машиностроению ASME Новый Орлеан, Луизиана, 17-22 ноября. |
[16] | Райли, К. Ф., Хобсон, М. П. и Бенс, С. Дж., 1999, Математические методы для физики и инженерии , Low Prize ed. , Cambridge University Press , pp.185. |
[17] | Джайн, М. К., Айенгар, С. Р. К. и Джайн, Р. К., 2007, Численные методы научных и инженерных вычислений , Пятое изд. , New Age International (P) Limited Publishers, стр.352 и 357. |
Может ли возникать вибрация муфты мод при фрезеровании?
https://doi.org/10.1016/j.ijmachtools.2021.103738Получить права и контентОсновные моменты
- •
Представлена применимость вибрационного механизма муфты режимов при фрезеровании для гибких станков.
- •
Теория вибрации связи мод в нулевом и многочастотном режимах была описана и использована для определения границ устойчивости вибрации связи мод.
- •
Были проведены детальные испытания резания для проверки наличия границ устойчивости к вибрации при взаимодействии мод.
- •
Связь мод с нулевой частотой и границы устойчивости к регенеративному вибрации сравнивались друг с другом вместе с испытаниями на резку.
- •
В стабильности фрезерования преобладала регенеративная вибрация. Никаких следов вибрационных характеристик связи мод не наблюдалось.
Abstract
При фрезеровании сообщалось о двух различных самовозбуждающихся колебаниях; регенеративная вибрация и вибрация модовой муфты. Механизм регенеративной вибрации был тщательно изучен и подтвержден тестами, в то время как механизм вибрации связи режимов был известен давно для потоковых операций.Представленные модели вибрации связи мод были основаны только на текущих колебаниях системы, но не на задержанных колебаниях. С увеличением количества исследований, проводимых на роботизированных фрезерных операциях, многие исследователи утверждали, что низкочастотные сильные самовозбуждающиеся колебания при высоких скоростях шпинделя являются вибрацией связи мод. Однако обоснование механизма вибрации связи мод отсутствует в прогнозируемых границах устойчивости, и нет убедительных доказательств, отличающих его от механизма регенеративного вибрации.Кроме того, модели вибрации связи мод, применяемые к фрезерованию, основывались на операциях нарезания резьбы и, следовательно, не отражали характеристики прерывистого процесса фрезерования. Таким образом, в данной статье основное внимание уделяется диагностике вибрации связи мод в роботизированном фрезеровании. Принципы вибрации связи мод применяются к процессу фрезерования с учетом его прерывистых характеристик. Аппроксимация нулевого порядка для механизма вибрации связи мод адаптирована для фрезерования и расширена до многочастотного приближения.Границы устойчивости к вибрации модовой связи рассчитываются, исследуются с помощью тестов и сравниваются с границами устойчивости к регенеративной вибрации. Результаты показывают, что границы устойчивости к вибрации при соединении мод очень низкие и неопределенно зависят от скорости шпинделя. Это противоречит стабильности, наблюдаемой в экспериментальных тестах. Следовательно, можно сделать вывод, что вибрация при сопряжении мод при фрезеровании невозможна, поскольку предположение о том, что толщина стружки зависит только от текущих вибраций, не применимо к операциям фрезерования.Новизна представленной статьи заключается в теоретическом и экспериментальном обосновании того, что вибрация связи мод невозможна при фрезеровании.
Ключевые слова
Дребезжание связи мод
Регенеративное дребезжание
Роботизированное фрезерование
Рекомендуемые статьиЦитируемые статьи (0)
© 2021 Авторы. Опубликовано Elsevier Ltd.
Рекомендуемые статьи
Цитирующие статьи
Исследование износа инструмента и прогноз срока службы инструмента при микро-фрезеровании Ti-6Al-4V: Нанотехнологии и точное машиностроение: Том 1, № 4
3.6. Обсуждение износа инструмента
Износ инструмента – это необратимый процесс, который существенно влияет на качество готовой продукции и надежность обработки. Скорость износа инструмента напрямую зависит от твердости материала заготовки. В этом эксперименте титан, который, как известно, является труднообрабатываемым материалом, отбирается и обрабатывается с использованием концевых фрез из карбида вольфрама без покрытия. Влияние различных параметров обработки анализируется с использованием метода, предложенного Wang et al., 12 12. Ван CY, Xie YX, Qin Z и др. Износ и поломка твердосплавного инструмента с покрытием TiAlN и TiSiN при высокоскоростном фрезеровании закаленной стали. Одежда 2015; 336-337 : 29–42. https://doi.org/10.1016/j.wear.2015.04.018, в котором сравнивается прогрессия износа, измеренная на протяжении экспериментальной операции механической обработки, с основным режимом износа. Экспериментальные данные свидетельствуют о быстром износе концевых микроконцевиков, у которых основной режим износа имеет три различных стадии: первичную, вторичную и третичную.Графики измеренного радиуса режущей кромки (Рис. 10 и Рис. 11) иллюстрируют начальный значительный абразивный износ, который улучшается за счет высоких скоростей резания и низких скоростей подачи. Однако, с точки зрения измеренного изменения объема (рис. 14 и 15) при высоких скоростях резания, результаты показывают объемные потери 0,002 µ г при 70000 об / мин, что ниже, чем объемные потери 0,009 µ г при 30 000 об / мин. Более того, низкие объемные изменения происходят при высоких скоростях подачи, с 0.002 µ г при 150 мм / мин по сравнению с 0,007 µ г при 50 мм / мин. Этот результат указывает на непригодность низкой скорости подачи, поскольку она способствует высокому трению, что приводит к высокой температуре обработки в зоне резания. Данные об изменении объема указывают на начальную потерю объема и последующее увеличение объема. Из-за необратимого износа инструмента увеличение объема может быть результатом высокой температуры в зоне резания, что приводит к прилипанию материала заготовки к режущей поверхности инструмента, что эффективно снижает твердость инструмента и увеличивает скорость износа. .Износ по задней поверхности является преобладающим типом износа на вторичной и третичной стадиях обработки, где VB2 измеряется при разных скоростях обработки и подачах. На рис. 3 приведены измеренные средние значения износа по задней поверхности режущей кромки инструментов. Было подтверждено, что высокие скорости резания увеличивают скорость износа, поскольку график достигает пикового значения 60 µ м при 70 000 об / мин. Как показано на рис. 5, низкие скорости подачи, по-видимому, значительно улучшили скорость износа, поскольку VB2, измеренный после 400 мм обработки с использованием 50 мм / мин, составил 15 µ м, тогда как VB2, измеренный после 400 мм обработки с использованием 100 и 150 мм / мин. min составляет примерно 40 µ м.Стабильность обработки оценивается путем измерения шероховатости поверхности (рис. 12 и рис. 13) для различных скоростей резания и подачи. Измеренная шероховатость поверхности в диапазоне скоростей резания до 60 000 об / мин показывает постепенное ухудшение, тогда как быстрое изменение наблюдалось при 70 000 об / мин, что указывает на изменение производительности обработки. Шероховатость поверхности постепенно увеличивалась с длиной обработки до 300 мм, где она начала выравниваться.Однако быстрое увеличение шероховатости поверхности до 1000 нм измеряется для пазов, обработанных со скоростью 70 000 об / мин. Низкие скорости подачи привели к постепенному ухудшению шероховатости поверхности в процессе обработки. Между тем, график зависимости шероховатости поверхности от различных скоростей подачи, показанный на рис. 13, показывает почти идентичные характеристики обработки, указывая на то, что скорость подачи оказывает незначительное влияние на шероховатость поверхности.Режим резания при фрезеровании: расчет, определение, спецификации
Фрезерование – это далеко не простая операция по обработке металлов и других материалов, детали которой не всегда известны среднему человеку.Дело в том, что для этого процесса необходимо специальное приспособление, которое называется фрезой – его можно встретить на многих фабриках, фабриках, фабриках. Как происходит этот процесс? В этом случае задействованы режущий инструмент и заготовка. Режущим инструментом является сама фреза – она совершает вращательные движения, в отличие от самой заготовки, которая с помощью станка совершает поступательные движения в сторону фрезы. В результате получается такая обработка, которую сложно повторить с помощью любого другого инструмента.Однако эта статья не будет касаться информации о поверхности – этот материал предназначен для тех, кто уже более или менее знаком с процессом фрезерования. Основная и основная тема здесь – режим резания, то есть здесь будет производиться расчет и определение того, как должна работать фреза и какое сопло для нее использовать для конкретных видов металла разной твердости. Чтобы вам было легче понять данные, которые будут предоставлены позже, вы должны сразу знать, какие концепции будут здесь использоваться.
Все, что нужно знать
Итак, в каждом абзаце будет указано, какой материал рассматривается, а также его твердость по методу Бриннеля – наиболее известному и распространенному из всех методов определения твердости тел. Они измеряются в HB, то есть в единицах твердости по Бриннелю. Далее будет определена скорость резания, которая указывается в метрах в минуту (м / мин). Здесь следует обратить особое внимание на то, что это не скорость фрезы, а совсем другой параметр.Этот параметр будет рассмотрен на нескольких примерах – если материал, который обрабатывается резцом, не имеет дополнительного покрытия, и если резец имеет различные типы покрытия TI-NAMITE. И, конечно же, будет описан еще один очень важный параметр фрезерования – подача на зуб. Для людей, далеких от этой сферы, этот параметр может показаться довольно необычным, но если внимательно изучить его детали, все станет достаточно просто. Таким образом, этот параметр измеряется в миллиметрах на зуб и определяет, на сколько миллиметров перемещается заготовка при повороте фрезы на один зуб.Из этой подачи можно вычислить и другие – например, оборот и минуту, но именно кормление на зуб является ключевым фактором. И это также будет зависеть от диаметра используемого инструмента. Итак, все основные данные у вас есть – теперь пора выяснить, какой режим резки для фрезерования используется в каком случае.
Сталь общего применения
Итак, первый материал, который рассматривается в данной статье, – это сталь общего применения. Какой режим резки использовать для этого материала? В первую очередь нужно определить твердость материала.Если твердость стали менее 150 единиц Бриннеля, то необходимо установить скорость от 150 до 210 метров в минуту в зависимости от покрытия. 150 соответственно при полном отсутствии покрытия и 210 – при наличии наиболее эффективного покрытия TI-NAMITE-A. Что касается опиливания на зуб, то здесь все зависит, как уже было сказано, от диаметра инструмента. Если его диаметр меньше трех миллиметров, подача на зуб будет от 0,012 до 0,018 миллиметра, при увеличении диаметра до 5 мм скорость подачи увеличится до 0.024 мм, если диаметр увеличивается до 9 мм, то подача увеличивается до 0,050 мм, при диаметре до 14 мм подача может подниматься до 0,080 мм, ну а при максимальном диаметре 25 миллиметров подача на зуб будет быть 0,18 мм. Эти данные также позволяют выбрать правильный режим резки. Но не забывайте, что бывают и более прочные сорта стали общего назначения. При твердости менее 190 единиц Бриннеля скорость должна составлять от 120 до 165 метров в минуту, а при твердости менее 240 единиц Бриннеля – от 90 до 125 метров в минуту.Естественно, питание зуба меняется. Он становится меньше и в первом случае может составлять от 0,01 до 0,1 миллиметра на зуб, а во втором – от 0,008 до 0,08 миллиметра на зуб. Естественно, это не единственный материал, который используется для фрезерования, поэтому стоит обратить внимание на другие металлы.
Спеченная сталь
Режимы резания при обработке цементированной стали будут зависеть от твердости материала. Если она меньше 235 единиц Бриннеля, то скорость резания будет соответствующей – от 100 до 140 метров в минуту.При твердости менее 285НВ показатель падает – от 80 до 110 метров в минуту. Но не забывайте о питании зубом. В принципе, о нем много не скажешь, потому что он ничем не отличается от того, что вы уже видели в предыдущем абзаце. В первом случае она будет иметь те же интервалы, что и при обработке обычной стали с твердостью менее 190NV, а во втором – такие же, как при обработке обычной стали с твердостью менее 240NV. Но нельзя сказать, что подача на зуб будет одинаковой, ведь для максимального диаметра инструмента в первом случае скорость подачи не равна 0.1, как в предыдущем примере, но 0,15. Именно поэтому расчет режимов резания – настолько сложная задача, что лучше всего соблюдать все нормы и в соответствии со строгими регламентами.
Азотированные стали
Расчет режимов резания при обработке нитридных сталей ничем не отличается от предыдущих случаев – только в этом случае материалы немного тверже предыдущих, поэтому не стоит удивляться, что скорость резания здесь будет от От 90 до 125 метров в минуту с менее твердой сталью и от 70 до 95 метров в минуту с более твердым материалом.Что касается подпиливания на зуб, то в первом случае здесь вполне стандартный шаг взлета – от 0,008 до 0,08 миллиметра, но если металл будет иметь большое количество единиц твердости по Бриннелю, это будет означать, что его подача уменьшится, и заметно . При минимальном диаметре инструмента он составит 0,006 миллиметра, а при максимальном – 0,06 миллиметра. На данный момент это самый низкий приток на зуб, рассмотренный в этой статье. Расчет режимов резания по этой информации обычно осуществляется по стандартной формуле, о которой пойдет речь в конце статьи.
Низкоуглеродистая сталь
Низкоуглеродистая сталь очень широко распространена, и самое главное – существует несколько различных уровней их твердости. И, естественно, у каждого из них будет своя скорость резания. Например, первые два вида стали имеют одинаковый показатель, если резец не имеет покрытия – 80 метров в минуту. Но при максимальном охвате первого типа скорость увеличивается до 110 метров в секунду, а у второго – всего до 85 метров в секунду. Но есть еще два типа, первый с твердостью менее 340НВ, а второй – менее 385НВ.Соответственно, первый параметр резания будет от 50 до 70 м / мин, а второй – от 35 до 50 м / мин. По сравнению с типами, которые вы видели ранее, это довольно низкая скорость. Соответственно, у этих видов стали и подача на зуб не слишком велика – отдельно стоит выделить последнюю твердость стали, которая при минимальном диаметре инструмента имеет невероятно низкую скорость подачи, всего 0,005 миллиметра. Сразу отметим, что здесь рассматривается фрезерование, а не режимы резания для токарной обработки.Как уже упоминалось выше, для расчета используется формула, с которой вы будете знакомы выше. Режимы резания для токарной обработки рассчитываются немного по другой формуле, поэтому не нужно пытаться применить один расчет ко всем видам работ.
Инструментальные стали
Инструментальные стали делятся по твердости на еще больше видов, чем среднеуглеродистые, поэтому режимы резания при фрезеровании инструментальной стали могут быть многочисленными. Если кратко рассказать об этой стали, то есть пяти видов твердости: менее 230НВ, менее 285НВ, менее 340НВ, менее 395НВ и более 395НВ.У каждого из них своя скорость резания: от 90 до 125 м / мин, от 70 до 95 м / мин, от 60 до 85 м / мин, от 45 до 65 м / мин и от 30 до 40 м / мин соответственно. . Собственно говоря, название этих данных будет уже на полпути к восполнению всех недостающих пространств при расчете формулы, по которой определяются режимы резания для фрезерования. Чтобы в формуле все переменные заменены числами, также необходимо знать диаметр инструмента (и полученные от него данные для подачи на зуб).
Как выбрать режим?
Выбор режимов резания довольно прост – каждая фреза имеет переключатель, позволяющий регулировать скорость резания. С помощью этого небольшого переключателя вы можете установить приблизительное значение оборотов в минуту, и тогда ваша машина будет работать на этом уровне. Строго говоря, это режим резания, но такой простой процесс требует большого количества вычислений, о которых речь пойдет ниже. Дело в том, что определение скорости вращения режущего инструмента фрезы должно быть максимально точным и редко, когда у вас есть достаточно времени и материала, чтобы выбрать режимы резания металла наугад.Вот почему существует теория, которую необходимо использовать перед практическим применением.
Формула скорости резания
Очень важно соблюдать нормы режимов резания, ведь дело здесь не только в том, что вы потратите очень много времени, а еще хуже, есть много материала, чтобы правильно выбрать режим вслепую. Это тоже может быть небезопасно. Поэтому лучше всего руководствоваться в первую очередь теоретическими знаниями. Итак, теперь вы узнаете формулу, по которой рассчитывается мода для конкретного металла.О том, как это можно использовать на практике, будет рассказано ниже. Сама формула предполагает, что скорость, выраженная в метрах в минуту, умножается на коэффициент преобразования 1000, а результат делится на произведение числа «пи», умноженного на диаметр мельницы. Это все элементы режима резания, необходимые для расчета скорости вращения фрезы.
Упрощенная формула
Нет смысла выполнять два умножения, если вы знаете, что число «пи» – это число без каких-либо переменных.Первоначально обычно укорачивают 1000 и 3,14, чтобы получить 318. 318 умножается на скорость, а затем результат делится на диаметр фрезы. Вот и все, эта формула уже намного проще предыдущей, и именно с ее помощью чаще всего производится определение режима резания.
Расчет
В таком материале без примера не обойтись. Ну, например, можно взять сталь общего назначения твердостью менее 150НВ и фрезу с покрытием TI-NAMITE и диаметром 10 мм. миллиметры.Итак, для начала нужно свериться с данными, которые были описаны в статье выше – при таких скоростях резания будет 175 м / мин, значит нужно 318 умножить на 175, получится 55650. Теперь нужно разделить по диаметру фрезы, то есть 10 – получается 5565. Это и есть искомое значение. Теперь вам нужно поставить его на свой автомат, а если установить такое значение невозможно, то рекомендуется взять чуть меньше.
Каталог зарубежных инструментов
Если вы воспользуетесь отечественным резаком, то, скорее всего, легко найдете необходимые данные для определения режима резания.Если у вас иностранный образец, у вас могут возникнуть проблемы. Вот почему при покупке иностранного фрезерного станка крайне необходимо запрашивать каталог со всеми необходимыми пояснениями, которые затем можно использовать в качестве теоретической основы при работе со станком.
Специальная графика
Настоящее спасение – это графики, которые созданы для более быстрого и удобного определения режима резания. Что такое график? Это набор прямых линий разного цвета, которые проходят между двумя осями – одна из них показывает скорость, то есть величину, которую вы знаете, поскольку вы знаете, с каким материалом вы работаете, а вторая – количество оборотов. в минуту вашей фрезы, то есть, говоря простым языком, режим ее работы.Почему линии разного цвета? Если вы не забыли, то количество оборотов в минуту нельзя рассчитать только по скорости резания – вам также нужен диаметр инструмента, и каждый цвет отвечает за его диаметр.
Как пользоваться расписанием?
Все, что от вас требуется, это найти в Таблице диаметр вашего инструмента и выбрать на графике прямую нужного цвета. Затем нужно определить скорость и провести прямую линию от оси y, то есть оси, на которой указаны значения этого параметра.От точки пересечения вашей линии с прямой линией выбранного цвета вы должны провести прямую линию до оси x, чтобы узнать точное количество оборотов в минуту.
p >>Техника фрезерования для резки | Режущие инструменты
Нажмите на изображение, чтобы увеличить
Тима Уилсона
Когда дело доходит до фрезерования, чтобы получить максимальную отдачу от вашего приложения, стоит знать некоторые хитрости. Например, при торцевом фрезеровании необходимо задействовать около 70 процентов фрезы.Это идеально для правильного стружкообразования и не выделяет слишком много тепла; однако бывают обстоятельства, при которых требуется полное зацепление, и это когда требуется более толстое покрытие CVD, чтобы выдерживать дополнительное выделяемое тепло.
Одним из методов повышения стойкости инструмента является метод накатки, который уменьшает толстую стружку на выходе из резания. При входе в деталь это снижает некоторые вибрации и, следовательно, растягивающие напряжения, возникающие при прямом входе в разрез.
«Техника вкатывания очень выгодна, – говорит Кевин Бертон, менеджер по фрезерным работам Sandvik Cormorant в Миссиссаге, Онтарио.«Особенно в сложных материалах, если вы входите прямо в деталь, это ухудшает стойкость инструмента».
Идея состоит в том, чтобы вращать фрезу по часовой стрелке, но без снижения скорости резания или скорости подачи. В результате не только меньше вибрации и больше тепла перемещается в стружку, но также удваивается или утроится срок службы инструмента.
«Золотое правило: от толстой к тонкой стружке», – говорит Бертон. «Если вы войдете прямо в компонент, у вас на входе будет толстая или толстая стружка, но если мы вкатимся, то на входе мы можем получить стружку от толстой до тонкой.”
Люди тоже меняют свою технику и имеют тенденцию приходить больше со стороны, с меньшим наклоном.
«Врезание в деталь было бы для закрытого кармана», – говорит Том Хаган, менеджер по фрезерной продукции Iscar Tools Inc. в Оквилле, Онтарио. «Вход сбоку будет использоваться для открытого кармана. Все зависит от формы детали, использование которой требует правильного применения ».
Hagan отмечает, что в такой большой компании, как Iscar, операторы, ищущие правильный угол, имеют поддержку электронного каталога, который предлагает тысячи комбинаций.
«Например, если вам нужна фреза на ½ дюйма, и вы используете полный паз на определенной глубине резания, каталог может рекомендовать четыре инструмента», – говорит Хаган. «Он даст вам данные о подаче и скорости, а также расскажет, как быстро нужно двигаться».
Нажмите на изображение, чтобы увеличить
Чтобы сделать это правильно, необходимо знать, как лучше всего работать в диапазоне параметров обработки. Глубина резания – это параметр, который претерпевает некоторые изменения. Операторы обнаруживают, что меньшая глубина резания при более высоких скоростях и большем количестве проходов дает реальные преимущества.
«Более высокая скорость и меньшая глубина резания позволяют машине легче», – говорит Хэган из Iscar. «Износ меньше, что имеет смысл для людей, которые выбирают машины меньшего размера, такие как CAT-40».
Для обработки карманов может также помочь спиральная траектория движения инструмента, так как она может как повысить стойкость инструмента, так и снизить – или практически устранить – вибрацию как в больших, так и в малых карманах.
«Этот метод в основном похож на калейдоскоп или штопор», – говорит Бертон. «Эта техника хороша для сложных материалов, таких как нержавеющая сталь и титан – обычно мы начинаем с очень небольшого радиального контакта.”
Spiral morph может использоваться вместо обычных методов фрезерования карманов. В отличие от этих других методов, высокая дуга зацепления не вызывает проблем с нагревом и отклонением.
«Преимущество в том, что при спиральном морфинге вы, как правило, сохраняете одно и то же взаимодействие по всему карману», – говорит Бертон.
Спиральное врезание также можно использовать для проделывания отверстий. Преимущество перед бурением в том, что для этого требуется меньше лошадиных сил и он более постоянен; это преимущество при обработке сложных материалов и снижает потребность во многих расточных инструментах.Этот метод поддерживается некоторыми программами, а также учитывает рекомендации поставщиков. Если предположить, что угол врезания и радиус определены, тогда можно получить правильный размер фрезы для диаметра отверстия.
«В наших каталогах есть таблица, показывающая диапазон размеров отверстий для определенного диаметра», – говорит Бертон. «Если разрез будет слишком маленьким, вы можете получить небольшой цилиндр посередине, что плохо. Кроме того, если разрез слишком большой, это может вызвать множество проблем, в частности, оплавление материалов на корпусе фрезы.”
Концевые фрезыс конической сферической головкой также могут поддерживать инновационные технологии. Благодаря жестким допускам на диаметр резания +/- .005 мм или .0002 дюйма, а также превосходному твердому сплаву и покрытиям, эти концевые фрезы обеспечивают исключительную функциональность как в трех-, так и в пятиосных средах.
«Наши концевые фрезы можно использовать в трехосевой среде для создания геометрии стенок, соответствующей углу инструмента, или на пятиосевом станке для создания практически любого угла или элемента поверхности», – говорит Стивен Джин, менеджер по продукции фрезерных инструментов. в Emuge Corp.в Западном Бойлстоне, Массачусетс.
«Кроме того, эти конические инструменты могут использоваться вместо концевых фрез со сферической головкой малого диаметра в тех случаях, когда при резке задействован только радиус инструмента, например, фрезерование следа или чистовая обработка. Благодаря прочной конструкции конуса, канавкам вдоль конуса и большему диаметру хвостовика, эти инструменты обеспечивают значительно большую стабильность, чем концевые фрезы со сферической головкой того же диаметра ».
В Emuge успехи в проектировании и разработке концевых фрез также привели к усовершенствованию режущих инструментов для черновой обработки.Например, концевые фрезы MULTI-Cut компании имеют смещенные канавки, а не типичное расположение канавок под углом 90 градусов на стандартной концевой фрезы с 4 зубьями. Кроме того, углы спирали варьируются от канавки к соседней канавке, что помогает устранить гармонические условия, вызывающие вибрации, приводящие к износу, и позволяет канавкам входить в резание с дополнительной стабильностью.
«Кроме того, режущая кромка« притуплена », чтобы обеспечить слегка отрицательную геометрию резания, что дополнительно помогает контролировать износ», – говорит Жан.«Это отличие от острой кромки, которая имеет тенденцию к сколам и трещинам, что способствует преждевременному износу».
Еще одна компания с технологией для поддержки передовых методов обработки – это OSG Canada, которая предлагает новые твердосплавные концевые фрезы VGx с переменным шагом для фрезерования без вибрации в различных областях, включая фрезерование пазов и боковых поверхностей стали, нержавеющих сталей и экзотических сплавов. , чугун и закаленные стали.
«OSG Canada недавно выпустила индексируемые режущие инструменты OSG Phoenix на канадский рынок, и результаты были очень положительными, – говорит Крейг Рэмси, менеджер по продукции OSG Canada.
Нажмите на изображение, чтобы увеличить
OSG Phoenix подходит для чернового и чистового фрезерования с режущими пластинами произвольной формы. Согласно OSG, это может обеспечить оптимальное чипообразование.
«Это обеспечивает эффективную работу во всех сферах фрезерования, включая прорезание пазов, фрезерование боковых сторон, спиральное фрезерование, а также трехмерное контурное фрезерование», – говорит Рамзи.
При наличии подходящих инструментов и хороших советов по технике, часто предлагаемых самими поставщиками, фрезерование может выйти за рамки ограниченных возможностей прошлых лет.Результат? Работа выполняется быстрее и проще, а инструменты служат дольше.
Вверх-фрезерование | Фрезерование вниз |
---|---|
При фрезеровании вверх фреза вращается против направления подачи стола. | При нижнем фрезеровании фреза вращается в направлении подачи стола. |
Нагрузка на зубья стружки (или толщина необрезанной стружки) постепенно увеличивается от нуля в точке зацепления до максимальной в точке выхода из зацепления. | Нагрузка на зубья стружки (или толщина необрезанной стружки) постепенно уменьшается от максимума в точке зацепления до нуля при расцеплении. |
Здесь происходит постепенная нагрузка на зуб, поскольку контакт начинается с нулевой стружкой. | Здесь зуб испытывает ударную нагрузку, поскольку зуб внезапно входит в зацепление с максимальной стружкой. |
На горизонтально-осевом фрезерном станке сила резания в режиме фрезерования вверх направлена вверх и, таким образом, она имеет тенденцию поднимать заготовку с рабочего стола.Соответственно, для надежного крепления заготовки требуется жесткое и дорогое приспособление. | В режиме нижнего фрезерования сила резания направлена вниз, и, таким образом, она имеет тенденцию прижимать заготовку, а не подниматься. Таким образом, можно использовать более дешевое приспособление. |
Образцы тонких заготовок при обработке в режиме фрезерования могут деформироваться из-за направленного вверх усилия резания. | Вероятность деформации образцов тонких заготовок меньше в режиме фрезерования снизу, если предусмотрена соответствующая опора снизу. |
Из-за постепенного увеличения количества стружки при дополнительном фрезеровании выделяется большое количество тепла. Таким образом, существует тенденция приваривания стружки зубьями. | Тенденция к сварке стружки меньше при фрезеровании снизу, но часто происходит повторное осаждение стружки на обработанной поверхности, что может ухудшить качество обработанной поверхности. |
Заусенец образуется только на необработанной поверхности перед подачей инструмента; однако большая часть таких заусенцев удаляется при последующих проходах. | Заусенец образуется на обработанной поверхности на противоположной стороне подачи инструмента.Таким образом, эти заусенцы не удаляются автоматически. Это приводит к ухудшению качества резки. |
В начале зацепления зубья трутся со следами укладки или подачи на обработанной поверхности. Это улучшает качество поверхности. | Никакого трения не происходит, поэтому следы укладки остаются на обработанной поверхности. |
Помимо улучшения качества поверхности, трение во время зацепления может привести к нежелательному деформационному упрочнению из-за значительного тепловыделения. | Вероятность деформационного упрочнения при пуховом фрезеровании минимальна. |
В режиме верхнего фрезерования на зубьях режущего инструмента не происходит выкрашивания из-за постепенного контакта. Соответственно, скорость износа инструмента относительно низкая. | Из-за ударной нагрузки при зацеплении происходит выкрашивание, которое может вызвать зазубринный износ. Таким образом, скорость износа инструмента высока. Также существует вероятность катастрофического отказа зубов. |
Глушитель люфта не требуется. | Требуется компенсатор люфта, особенно если фрезерный станок более старый. |
Если материал заготовки или фрезы хрупкий (например, керамика), всегда предпочтительнее фрезерование вверх. | Фрезерование вниз не является хорошим выбором, если материал заготовки хрупкий. |
Мы не можем найти эту страницу
(* {{l10n_strings.REQUIRED_FIELD}})
{{l10n_strings.CREATE_NEW_COLLECTION}} *
{{l10n_strings.ADD_COLLECTION_DESCRIPTION}}
{{l10n_strings.COLLECTION_DESCRIPTION}} {{addToCollection.description.length}} / 500 {{l10n_strings.TAGS}} {{$ item}} {{l10n_strings.PRODUCTS}} {{l10n_strings.DRAG_TEXT}}{{l10n_strings.DRAG_TEXT_HELP}}
{{l10n_strings.LANGUAGE}} {{$ select.selected.display}}{{article.content_lang.display}}
{{l10n_strings.AUTHOR}}{{l10n_strings.AUTHOR_TOOLTIP_TEXT}}
{{$ select.selected.display}} {{l10n_strings.CREATE_AND_ADD_TO_COLLECTION_MODAL_BUTTON}} {{l10n_strings.CREATE_A_COLLECTION_ERROR}} .