Приспособления для шлифовки – Полезные советы о ремонте и строительстве
Шлифование
поверхностей или каких-нибудь деталей, в большинстве своих случаев, происходит
вручную, или при помощи использования шлифовального станка или дрели. Причем
станки используют только в тех случаях, когда можно обратиться воспользоваться
таким инструментом. И это вполне естественно, поскольку покупать собственный
станок или дорогостоящее специальное оборудование, чтоб использовать в домашнем
быту, просто нет смысла. Конечно, бывают ситуации, в которых желательно бы
иметь и свой шлифовальный инструмент, но, как правило, это очень и очень редкие
случаи.
В
целом, есть различные способы и инструменты, при помощи которых можно выполнить
механизированную шлифовку. При этом условно их можно разделить на две
категории.
— Это инструменты, за счет которых и выполняется обработка всех деталей,
поверхностей или участков. То есть, к таким относятся шлифовальные станки,
дрели, насадки на дрели, ручные шлифовальные станки (пусть и отошли в прошлое,
но также попадают сюда), и так далее.
— И детали, которые обеспечивают фиксированное положение шлифовального
инструмента, и заготовочной детали. К таким можно отнести направляющие и
опорные поверхности, и другие подобные приспособления.
В
отдельную категорию можно выделить различные дополнительные приспособления. К
примеру, устройства для пылеотвода. Таким инструментом, к слову, также нельзя
пренебрегать, поскольку несобранная шлифовальная пыль может осесть в легких, и
сами понимаете, какие от этого могут быть последствия.
шлифовки
Сейчас,
мы поговорим о ручных приспособлениях и инструментах, которыми можно
отшлифовать, в буквальном смысле, все что угодно. Начиная от маленьких
механических деталей, и заканчивая поверхностями и стенами в помещениях, и так
далее. Забегая наперед, отметим, что таких приспособлений очень много, и, по
сути, их конструкция может полностью зависеть от вашей фантазии.
Наиболее
элементарными считаются шлифовальные колодки. Как правило, их могут называть
иначе, а именно: шлифблоками или шлифовальными брусками. В зависимости от того,
какова форма этого приспособления, будет определяться поверхность, которая
будет обрабатываться – плоская или криволинейная, и тому подобное.
Обычно,
самая простая шлифовальная колодка состоит всего из 3-х частей. Это корпус
колодки, на котором находиться рабочая поверхность. На эту поверхность
накладывается шлифовальная бумага (шкурка), но ведь ее нужно как-то удерживать,
верно? Поэтому второй частью является фиксирующий механизм колодки, с помощью
которой, шкурка натягивается на рабочей поверхности. И, конечно же, ручка, за
которую мастер удерживает колодку, и придает усилие. Бывают ситуации, когда в
колодке отсутствует ручка, потому как ее роль выполняет сам корпус. В качестве
зажимного механизма могут использоваться и другие детали, например в
самодельной колодке, бумагу можно просто прибить маленькими гвоздиками.
Фирменные
колодки, и вовсе бывают самых разнообразных форм и видов. К примеру, форма
колодки может напоминать детскую лопатку для песочницы, или же клюшку в такой
игре, как аэрохоккей. Корпус магазинской колодки обычно изготовлен из
пластмассы. Ниже, вы можете увидеть несколько примеров именно таких колодок.
Разнообразие фирменных колодок
Также,
шлифовальные колодки можно изготовить своими руками, если конечно ее
конструкция по задумке, не будет слишком сложной. Для этого, наиболее
подходящим материалом будет деревянный брусок (еще лучше, две половинки
бруска). Итак, на одной половине бруска закрепите шлифовальную бумагу, войлок,
или любой другой материал, который вам необходим, а другой половинкой бруска
скрепите инструмент воедино, сделав себе из этого же кусочка удобную ручку.
Вы
можете скрепить две половинки при помощи гвоздей или шурупов. Но, куда более
эффективно сделать болтовое соединение. Так, вы гораздо быстрее сможете менять
материал, который обрабатывает поверхности. К примеру, вы работали войлоком, а
в какой-то момент вам понадобилась шлифовальная бумага – несколько движений, и
вы уже все заменили.
Простейшая колодка своими руками
Если
вы точно знаете, что будете иметь дело с большими площадями и поверхностями,
вам нужно изготовить инструмент, побольше в размерах. И, к сожалению, далеко не
всегда нам нас может выручить электрический инструмент, либо нет электричества
в помещении, где нужно работать, либо нет самого инструмента. Поэтому, делаем
габаритное приспособление для шлифовки следующим образом. Изготавливаем его в
виде «шлифовального рубанка». Итак, наиболее просто изготовить такое
приспособление при помощи самого рубанка. Возьмите этот инструмент, открутите
рубаночный нож, натяните и прибейте к рабочей поверхности рубанка шлифовальную шкурку.
Для
того чтобы отшлифовать кромку, которая расположена под углом в 90° к смежной
поверхности, достаточно полезным будет следующий инструмент, представлен на
рисунке ниже. К слову, его легко можно сделать из парочки дощатых заготовок,
десятка гвоздей или шурупов (и, конечно же, шкурки).
Устройство уголковой колодки: 1. основная поверхность; 2. ручка; 3.
упорная деталь; 4. укрепляющее ребро; 5. наждачный лист; 6. кусочек войлока.
Основной
задачей при изготовлении является надежное крепление шкурки или кусочков
войлока к рабочей поверхности колодки. Если вы не хотите крепить детали к
колодке при помощи механических деталей – гвоздей, шурупов или болтов, можете
посадить шлифовальный материал на клей, или придумать что-нибудь еще. В каждом
способе есть свои достоинства и недостатки. Прикрепляя материю гвоздями или
клеем, наверняка такой брусок прослужит для вас одноразовым (хотя в случае с клеем,
ситуации могут быть абсолютно разными, в зависимости от клея). А крепление
болтами или шурупами отличается высокой трудоемкостью, на которую нужно
потратить немало времени.
Также,
советуем вам воспользоваться клиньями. Такой способ является весьма удобным, и
постараться нужно только один раз. Так, в бруске нужно сделать пропил, в
который будет заворачиваться наждачная бумага, а сверху она будет крепиться при
помощи клина.
Брусок с пазом под клин
Вариации приспособлений и
насадок для дрели или болгарки
Согласитесь,
шлифовать поверхности ручными инструментами очень непросто и трудно. Как
правило, мы используем ручные приспособления только когда имеем дело с
небольшими поверхностями и площадями, или же когда под рукой нет электрического
инструмента. Но, когда у вас есть дрель или болгарка, так почему бы просто не
упростить себе жизнь, и не воспользоваться этим инструментом?- Конечно, мы так
и сделаем. Но, прежде чем начать шлифование, вам нужно специальные насадки и
приспособления, которые, собственно, и будут шлифовать поверхность. Итак,
давайте посмотрим на такие приспособления.
Одной из насадок, которая часто используется в
сочетании с болгаркой или дрелью, это опорная тарелка или барабан (в
зависимости от того, какой инструмент у вас в наличие).
Различные виды насадок на электроинструменты
Шлифовальная тарелка. Является достаточно распространенной насадкой, которая используется
чаще всего с болгаркой, реже – с дрелью. Представляет собой пластиковый или
резиновый диск, на торцевой поверхности которого крепиться наждачная бумага,
круглой формы. Тарелки, изготовленные из пластика, как правило, имеют мягкую
прослойку между шлифовальной шкуркой и основной частью насадки. Это
обеспечивает лучшее прилегание, и способствует лучшему шлифованию на неровных поверхностях.
Дисковые насадки для дрели или болгарки отличаются только формой крепления. На
«дрельной» насадке имеется стержень, который крепиться в патроне, на
«болгарочном» диске, есть резьба, которую наворачивают на вал самой болгарки.
Насадку для болгарки можно адаптировать под дрель, вкрутив в нее самодельный
адаптер.
Но,
так как жесткость насадки для болгарки, несколько выше, чем для дрели, мы
рекомендуем вам все-таки использовать соответственные приспособления. Что
будет, если вы все же используете такую насадку на дрели? В таком случае, нужно
работать предельно осторожно, так как даже небольшие уклоны насадки в сторону,
могут привести к врезанию одного из краев тарелки в поверхность, которая
обрабатывается. К тому же, дрель будет постоянно пытаться выскочить из рук.
Одним словом, работа с несоответствующей насадкой может быть просто неудобной.
Это скажется на общей оценке работы, ведь на поверхности, наверняка будут
просматриваться углубления, сколы или трещины.
Насадка на дрель с резиновой основой
Жесткие
насадки, можете использовать только в том случае, когда дрель будет в
закрепленном положении, подобно рисунку ниже.
Если
вам совсем никак не удается найти подходящую для вас насадку, вы всегда можете
изготовить такое приспособление самому. К примеру, вы можете взять кусок фанеры
или ДСП, вырезать из нее круглую форму, просверлив дырку в центре. Закрепить в
центре гайку и болт, а на основу наклейте мягкую подкладку. Затем, на подкладку
наклейте шлифовальную бумагу. Таким же способом можно переделать жесткую
насадку в мягкую насадку для дрели, путем добавления подкладки.
Таким вот образом, приклейте мягкий материал
После
того, как вы срежете липучку от основной детали накладки, в качестве
смягчающего материала можете использовать губку для мытья тела, или же мочалку
для посуды. Также, можно использовать и уплотненный поролон. Отметим, что в
случае с самодельным изготовлением таких насадок, при шлифовке вы можете
наблюдать небольшие колебания губки со стороны в сторону. Это вполне нормально,
и используя самодельную губку с дрелью, ничего критичного в этом не будет. А
вот с болгаркой могут возникнуть проблемы, поэтому использовать самодельные
насадки не стоит.
Также,
существуют комбинированные приспособления для дрелей. Суть их состоит в том,
что насадку можно регулировать в двух положениях – фиксированном, и свободном.
Фиксированное положение заключается в жестком зацеплении, а вот свободно
положение предусматривает свободных ход насадки, что позволит обрабатывать
поверхности мягко, потому как она будет адаптироваться к наклонам. Но, цена на
такие насадки заурядно завышена, поэтому иногда просто нет смысла покупать.
Можно
сделать обычную насадку подвижной, внеся в нее некоторые коррективы. Так, нужно
сделать всего лишь некоторые изменения, ввинтив в насадку конусную гайку (как
на рис. ниже).
Самодельная накладка с подвижной головкой
Наждачную шкурку лучше всего крепить к основанию при помощи липучки
Шлифовальные барабаны. Внешне, такие барабаны представляют собой цилиндр, сверху покрытый
наждачной крошкой, или обвит шкуркой. Опорная тарелка отличается от такого
барабана тем, что на тарелке поверхность установлена перпендикулярно оси
вращения, а на барабане – параллельно. Это дает некоторые преимущества, в
сравнении с диском. Барабаном можно легко шлифовать отверстия, а шлифовальным
диском нельзя.
Как
правило, на барабане есть специальная система натяжения, которая удерживает
шкурку в натянутом положении. Вообще, таких систем две. Одна из них работает за
счет увеличения диаметра барабана, тогда, когда диаметр увеличивает, шкурка
натягивается. Вторая, имеет специальный механизм, который применяется для
абразивной ленты. Возвращаясь к увеличению диаметра барабана, отметим, что
системы увеличения бывают разными. К примеру, барабан увеличивается
пневматическим путем, или же при помощи сжатия в осевом направлении.
Механизированная система натяжения работает при помощи ключа. На представленных
рисунках внизу, вы можете увидеть примеры таких барабанов.
Незамкнутые шлифовальные барабаны
Пневматические насадки-барабанчики
Барабаны под крепление бесконечной ленты
Последнюю
разновидность шлифовальных барабанов можно сделать и самому. Для этого, нужно
разместить резиновые прокладки между несколькими деревянными дисками. Во время
затягивание осевого болта, резина будет раздавливаться, расширяясь при этом в
радиальном направлении. Также, надежно фиксируется шлифовальная бумага, что нам
собственно и нужно.
для дрели
При
работе с дрелью, особенно во время шлифования, порой не так просто это делать.
Конечно, на словах это может показаться легко, но взяв в руки настоящую дрель с
насадкой для шлифовки, вы поймете, что это довольно таки не просто. Она
начинает выскакивать, сильно вибрировать и так далее. Гораздо проще, установить
дрель в неподвижном состоянии, и особенно эффективно при работе с малыми
деталями. Есть множество приспособлений, помогающих добиться этого результата.
В
последнее время, часто используются фирменные направляющие, которые, как
правило, нужны для нормального сверления отверстий. Однако это не мешает
использовать их, как и направляющие для шлифовки. Принцип действия при этом
практически не изменяется, вот только шлифовальную машину теперь можно смещать.
Сделать
направляющую можно и самому. Для этого, взгляните на рисунок, представленный
ниже, который наглядно показывает, как это сделать.
И
напоследок, представляем вам подборку демонстративных картинок, иллюстрирующие
самодельные и фирменные шлифовальные станки, с использованием дрели.
Станки на основе сверлильного станка (перевернутого)
Еще шлифовальных станков из сверлильных станков
Самодельная столешница под шлифстанок
Таким
образом, приспособления для шлифовки могут быть самыми разными, начиная от
ручных, и заканчивая электрическими или даже наполовину роботизированными. И,
принимать решение насчет того, какое приспособление нужно в данном случае,
нужно только исходя из задач, в рамках которых вы стоите.
Еще похожие страницы:
— Виды и назначение наждачной бумаги
— Полная классификация шлифмашинок. Помощь в выборе при покупке
— Ленточный шлифовальный станок из дрели своими руками
— Как правильно полировать мрамор
— Гидропескоструйные аппараты передвижные
Еще о инструментах, станках и оборудовании:
— Сабельные пилы
— Электролобзики
— Клеевой пистолет
— Рубанок
— Сверлильный станок из дрели
— Циркулярная пила из дрели
— Лобзик-станок
— Циркулярка из ручной дисковой пилы
— Лобзиковый станок из ручного электролобзика
Чертежи точильно шлифовальных станков –
Содержание
- Шлифовальный станок своими руками — инструкция по изготовлению
- Конструктивные особенности и принцип работы станка
- Виды шлифовальных станков
- Пошаговая инструкция по изготовлению
- Выбор материала
- Изготовление дискового шлифовального станка
- Как сделать ленточный шлифовальный станок
- 3Б634 Станок точильно-шлифовальный напольный схемы, описание, характеристики
- Сведения о производителе точильно-шлифовального станка модели 3Б634
- Станки, выпускаемые Мукачевским станкостроительным заводом им.
Кирова
- 3Б634 станок точильно-шлифовальный напольный. Назначение, область применения
- Особенности конструкции и принцип работы станка 3Б634
- 3Б634 Общий вид точильно-шлифовального станка
- 3Б634 Расположение составных частей точильно-шлифовального станка
- 3Б634 перечень составных частей точильно-шлифовального станка
- 3Б634 Спецификация составных частей точильно-шлифовального станка
- 3Б634 Расположение органов управления точильно-шлифовальным станком
- 3Б634 перечень органов управления точильно-шлифовальным станком
- Указания по эксплуатации, техническому обслуживанию и ремонту точильно-шлифовального станка 3Б634
- Балансировка кругов
- Регулировка подшипников шлифовального шпинделя
- 3Б634 Схема электрическая точильно-шлифовального станка
- 3Б634 электрооборудование станка
- 3Б634 Установочный чертеж точильно-шлифовального станка
Шлифовальный станок своими руками — инструкция по изготовлению
В процессе работы с изделиями из дерева наступает момент, когда нужно сделать поверхность идеально гладкой и убрать некоторые дефекты. Для этого используются специальные шлифовальные станки. В целях непрофессионального использования можно сделать шлифовальный станок своими руками. Инструмент для дерева такого плана может иметь разноплановые конструкции, которые можно сформировать самостоятельно. При этом каждая конструкция предполагает работу с определенными видами (длина, плотность, форма) деревянных деталей.
Конструктивные особенности и принцип работы станка
Устройство шлифовального станка по дереву не отличается сложностью, так как основная задача любой модели заключается в том, чтобы обработать тот или иной вид деревянной детали, формируя нужные параметры поверхности для финишной отделки. Благодаря обработке шлифовальной машинкой поверхность древесины становится идеально гладкой, и дополнительно калибруются параметры заготовки.
На производствах используют устройство такого типа, которое оснащено диском, лентой, станиной (для обработки под наклоном). У самодельных приспособлений функционал не такой широкий, но этого обычно достаточно для обработки деталей из дерева. Есть несколько вариантов относительно того, как устроены шлифовальные самодельные деревообрабатывающие станки.
Обычно самодельные шлифовальные станки изготовляют посредством использования подручных приспособлений. Но в любом случае нужна либо ось для крепления шлифовального круга, либо 2 вала, между которыми будет натягиваться шлифовальная лента. Чтобы привести в движение основу со шлифовальным элементом, нужно дополнительно подготовить мотор мощность не более 1 кВт.
Шлифовальный станок для дерева, сделанный своими руками, имеет следующий принцип работы – за счет использования ленты с разным абразивным напылением происходит нужная обработка поверхности. Если используется ленточный абразивный элемент, то его фиксация производится методом натягивания между двумя барабанами. Для закрепления круглого абразива требуется жесткая основа.
Виды шлифовальных станков
При плотной работе с деревянными деталями и предметами, мастеру нужно знать, какие бывают шлифовальные станки по дереву, чтобы подбирать наиболее оптимальный вариант устройства для себя.
По принципу устройства виды шлифовальных станков по дереву делятся на 3 типа: ленточный (гриндер), дисковый, барабанный.
- Ленточный станок считается самым распространенным. Лента с абразивным покрытием крепится на двух валах, которые приводит в действие асинхронный мотор. При этом шлифовальный элемент может располагаться в горизонтальном или вертикальном положении. В процессе работы лента не провисает, а обрабатывает древесину без возникновения большой силы трения. Такая конструкция может использоваться при обработке деталей с большой длиной.
- Дисковой агрегат, или как его называют еще тарельчатый шлифовальный станок, обустроен осью, к которой крепится абразивный круг. В процессе работы диск начинает вращаться вокруг своей оси. В процессе работы можно регулировать скорость работы круга с абразивным покрытием без уменьшения оборотов самой оси.
- Барабанный станок устроен таким образом, что абразивные ленты в виде спирали наматываются на рядом стоящие валики.
В свою очередь эти элементы отдалены на определенное расстояние от ровной поверхности (столешницы). Посредством регулировки данного расстояния можно производить калибровку деревянных деталей.
Есть и другие типы переносных шлифовальных станков. Часто дрели и шуруповерты оснащаются специальными насадками с абразивным напылением.
Устройство и принцип работы в каждом варианте отличается друг от друга. При этом и древесина будет обрабатываться по-разному.
Проще всего создать тарельчатый шлифовальный станок. Но точильно-шлифовальный станок, сделанный своими руками, где в основе лежит ленточная конструкция, будет намного функциональней и востребованный в домашней мастерской, чем любой другой.
Пошаговая инструкция по изготовлению
Изначально нужно подготовить чертеж шлифовального станка по дереву своими руками. Без базового эскиза создать полноценно функциональный станок не получится. Чертеж должен быть точным – должны быть указаны все параметры и размеры. Пример такого чертежа:
Предварительно стоит рассчитать мощность мотора, которой будет достаточно для работы. Сделать это можно, используя такую формулу:
Расшифровка обозначений, которые использованы в данной формуле:
q — давление площади детали из дерева на плоскость полотна (N на каждый квадратный сантиметр).
S — участок детали, которая взаимодействует с абразивом, измеряемая в см².
K — показатель рабочей части абразива относительно детали. Здесь учитывается плотность древесных волокон и зернистость абразива. Показатели могут колебаться в пределах 0,2-0,6.
k — коэффициент трения изнаночной части абразива по рабочей поверхности.
U — скорость вращения абразивной ленты (м/с).
Если рассчитать все эти показатели и грамотно построить чертеж, то можно получить эффективный и функциональный самодельный шлифовальный станок. Чтобы изготовить шлифовальный станок своими руками, стоит подобрать необходимые инструменты и материалы, определиться с тем, как, и при каких условиях будет использоваться устройство.
Выбор материала
Для того, чтобы получить шлифовальный станок любой конструкции нужна основа (станина) – это корпус, на котором будет устанавливаться конструкция для абразивной детали и выделяться место под установку мотора. Заготовка основы может быть деревянной или металлической. Для самодельного агрегата достаточно таких габаритов станины: 50×18 см с толщиной 2 см.
Лучше всего делать основу из металла. Такая конструкция будет более надежной, использоваться дольше, не будет поддаваться деформациям разного вида. Но в рамках домашнего использования оптимальным вариантом станет и деревянный станок, тем более, если модель будет не стационарной (иногда будет переноситься или транспортироваться).
Кроме материала для изготовления станины, нужны и другие приспособления – мотор, ролики, абразивный элемент.
Изготовление дискового шлифовального станка
Изготовить дисковый шлифовальный станок своими руками в домашних условиях проще всего. Обычно формируется корпус, а в качестве основной детали, которая приводит в действие абразивный круг, используется болгарка или дрель. Но может использоваться и асинхронный мотор из старой машинки.
Можно использовать моторы нового поколения, которые соответствуют нужным параметрам, но стоит готовиться к тому, чтобы щетки на нем быстро износятся.
Если же все будет создаваться «с нуля», то следует действовать по такому плану:
- Подготовить приблизительный чертеж для создания дискового шлифовального станка.
- После тщательных измерений и составления чертежей, стоит приступить к работе. Формируется основа из вертикальной и горизонтальных частей, которые должны неподвижно между собой скрепляться, посредством металлических строительных уголков. В вертикальной части вырезается круглое отверстие, куда будет выводиться шкив мотора. «Двигающий элемент» должен также плотно прикрепиться к горизонтальной части основы.
- Следующим этапом станет крепление дискообразной детали к подвижной части мотора.
Сделать диск можно из фанеры и присоединить к шкиву мотора с помощью болтов. При этом болты должны полностью совпадать с поверхностью диска.
Останется из полотна абразива вырезать круг нужного диаметра и прикрепить его к дисковой части. Такой станок может работать от сети. При желании можно усложнить конструкцию, продумав кнопочную панель управления.
Как сделать ленточный шлифовальный станок
Гриндер – это ленточный шлифовальный станок универсального применения (шлифовка дерева, металла, углепластика) имеет небольшой размер и функциональную конструкцию, которую легко транспортировать при необходимости.
Изготавливать такие ленточные шлифовальные станки своими руками достаточно просто, работая по такому алгоритму:
- Изначально нужно подготовить чертеж для ленточного наждака своими руками. В нем нужно максимально точно проработать все параметры и указать размеры. При этом стоит учитывать, какие именно функции чаще всего будет выполнять устройство.
- После создания подробного и понятного чертежа, стоит подготовить все необходимые инструменты и материалы для работы: ДСП (металл), винты, болты и гайки, пропиленовые трубы, подшипники и строительный уголок. Важным этапом станет именно выбор подходящего двигателя, который должен иметь мощность не более 1 кВт и работать от сети 220 В. Если мотор не соответствует параметрам, то это существенно может усугубить принцип использования устройства в целом. Самым подходящим вариантом является мотор от старой стиральной машинки.
- Из ДСП или металла, изготавливается основной корпус, который будет своей конструкцией соответствовать заданным на чертеже параметрам. К основанию производится крепление мотора с помощью болтов и гаек, а также крепится строительный уголок. Именно последний элемент будет ограничителем для ленты.
- Далее формируются валики под ленту нужно полипропиленовую трубу с диаметром 20 мм вставить в трубу с диаметром 32 и дополнительно в меньшую основу вставить еще и трубочку из жести для более надежной фиксации.
Конструкцию надеть на шлицевую деталь мотора. По такому же принципу, но с использованием подшипников собирается ведомый вал.
- Последним этапом станет крепление абразивной ленты.
Теперь станок для шлифовки дерева можно использовать, включая его в обычную розетку. Если изготавливать корпус из металла, то получится приблизительно такая модель:
Чтобы еще больше упростить принцип изготовления (сделать только корпус) ленточной модели, можно использовать дрель, шуруповерт или болгарку. Чтобы использовать болгарку для шлифовки дерева, не нужно делать каркас, на котором будет крепиться инструмент. А вот дрель должна фиксироваться в корпусе хотя бы из дерева. Такие конструкции будут иметь следующий вид:
Изготовление шлифовальных станков разноплановых конструкций и мощностей в домашних условиях не является сложным. Достаточно построить точный и правильный чертеж, выбрать правильный двигатель и соорудить конструкцию-основу для крепления абразивных элементов. В результате такое устройство станет просто незаменимым при работе с деревянными деталями. Функциональность таких приборов немного отличается от заводских моделей, но эта характеристика компенсируется эффективностью и простотой дизайна (доступностью) прибора.
Источник
3Б634 Станок точильно-шлифовальный напольный
схемы, описание, характеристики
Сведения о производителе точильно-шлифовального станка модели 3Б634
Точильно-шлифовальный станок модели 3Б634 выпускался Мукачевским станкостроительным заводом им. Кирова в настоящее время Мукачевский станкозавод, ОАО.
Модель точильно-шлифовального станка 3Б634 больше не выпускается и была заменена белее совершенным станком модели 3К634.
Станки, выпускаемые Мукачевским станкостроительным заводом им. Кирова
3Б634 станок точильно-шлифовальный напольный. Назначение, область применения
Точильно-шлифовальный станок с двумя кругами модели 3Б634 предназначен для выполнения следующих операций:
- заточки быстрорежущих и оснащенных пластинками твердого сплава резцов высотой до 100 мм;
- заточки сверл диаметром 12.
.50 мм;
- заточки слесарного инструмента;
- снятия заусениц, фасок и других слесарных работ;
- шлифовки деталей абразивной лентой;
- полировки деталей
Использовать станок для обдирки литых и сварных деталей не рекомендуется.
Особенности конструкции и принцип работы станка 3Б634
Основной частью точильно-шлифовального станка 3Б634 является шлифовальная головка (рис. 5). В головку вмонтирован двухскоростной электродвигатель, вал которого является шпинделем станка. Статор, ротор и крыльчатка вентилятора расположены в корпусе с двумя крышками, в которых размещены шарикоподшипниковые опоры шпинделя (рис. 6).
Шлифовальная головка точильно-шлифовального станка 3Б634
Шарикоподшипниковые опоры представляют собой сдвоенные радиально-упорные шарикоподшипники высокой точности № В36209Л с выбранными осевыми люфтами. С наружных сторон выполнены осевые лабиринтные уплотнения, с внутренних — жировые канавки.
Охлаждение электродвигателя осуществляется за счет циркуляции воздуха, для чего опорные крышки головки имеют окна, связывающие внутренние полости станины и головки. Для крепления защитных кожухов и некоторых приспособлений (для полировальных работ, ленточного шлифования и др.) на крышках головки имеются две цапфы. Крепление головки к станине осуществлено при помощи шпилек.
Станина представляет собой чугунную отливку с размещенным в ней электрошкафом. Внутри станины укреплена панель с электрооборудованием. Доступ к электрооборудованию возможен в результате наличия проема в передней стенке, герметично закрываемого дверкой.
На станок устанавливают шлифовальные круги типов ПП 400 х 50 х 203 (плоский прямого профиля) и ПВ 400 х 60 х 203 (плоский с выточкой). Круги насаживают на переходные фланцы, закрепленные на конусной части шпинделя. Переходные фланцы с наружной стороны имеют три сухарика, при помощи которых осуществляется балансировка шлифовальных кругов.
Шлифовальные круги ограждены защитными кожухами, изготовленными из листовой стали.
На лицевой стенке кожуха имеется зев для доступа к шлифовальному кругу. В верхней части зева расположен козырек, при помощи которого поддерживается зазор не более 6 мм между козырьком и шлифовальным кругом, в нижней части зева — выдвижная заслонка для отсоса пыли. При установке приспособления для заточки сверл заслонку полностью задвигают в кожух. Боковая стенка кожуха шарнирно соединена с кожухом и может быстро отбрасываться для замены и осмотра шлифовального круга.
Внизу кожуха расположен пылесборник, в котором собирается до 40% пыли, отсасываемой из зоны работы станка. Не менее одного раза в смену пылесборник необходимо очищать от накопившейся пыли.
Кожух оснащен патрубком для подсоединения к вытяжной системе. Сверху к кожуху приварена втулка крепления защитного экрана.
Защитный экран (рис. 9) выполнен заодно со светильниками. Для удобства эксплуатации экран может быть повернут относительно горизонтальной оси на 15°. В светильники вмонтированы по две лампы 41,6 Вт, обеспечивающие хорошую освещенность.
Для заточки резцов и зачистки деталей на станке оборудованы поворотный столик (рис. 10) и подручник (рис. 11). Поворотный столик представляет собой стальную плиту, прикрепленную винтами к чугунному кронштейну, который может перемещаться по криволинейной направляющей. Таким образом, столик может занимать наклонное положение относительно торца шлифовального круга. Направляющая столика крепится к кронштейну, который, в свою очередь, прикреплен к станине. В результате двух перемещений столика в горизонтальной плоскости компенсируется износ круга по торцу и боковой поверхности.
Подручник представляет собою стальную деталь с двумя рабочими поверхностями: плоской и криволинейной. Плоской рабочей поверхностью рекомендуется пользоваться при шлифовании деталей, имеющих опорную плоскость. Если требуется отшлифовать кривую поверхность детали при отсутствии хорошей опорной плоскости или при необходимости частой перенастройки угла установки подручника, нужно пользоваться криволинейной рабочей поверхностью подручника. Крепление подручника к кронштейну выполнено таким образом, что он может перемещаться на круг, по вертикали и вращаться вокруг оси. Необходимо следить, чтобы зазор между кругом и подручником был не более 3 мм.
3Б634 Общий вид точильно-шлифовального станка
Фото точильно-шлифовального станка 3Б634
Фото точильно-шлифовального станка 3Б634 с вытяжным устройством
3Б634 Расположение составных частей точильно-шлифовального станка
Расположение составных частей точильно-шлифовального станка 3Б634
3Б634 перечень составных частей точильно-шлифовального станка
- станина
- головка
- крепление круга ПП (плоский шлифовальный круг прямого профиля)
- крепление круга ПВ (плоский шлифовальный круг с выточкой с одной стороны)
- кожух левый
- кожух правый
- экран
- столик поворотный
- подручник левый
3Б634 Спецификация составных частей точильно-шлифовального станка
- Станина 3Б634.
10А.000
- Головка 3Б634.22.001
- Крепление круга ПП 3Б634.30.002
- Крепление круга ПВ 3Б634.31.002
- Кожух левый 3Б634.40.001
- Кожух правый 3Б634.41.001
- Экран 3Б634.42А.001
- Столик поворотный правый 3Б634.54Б.001
- Подручник левый 3Б634.56.001
- Электрооборудование 3Б634.80.000
- Пульт управления 3Б634.88.000
- Принадлежности 3Б634.90.000
3Б634 Расположение органов управления точильно-шлифовальным станком
Расположение органов управления точильно-шлифовальным станком 3Б634
3Б634 перечень органов управления точильно-шлифовальным станком
Указания по эксплуатации, техническому обслуживанию и ремонту точильно-шлифовального станка 3Б634
В случае демонтажа ротора электродвигателя со шпинделя или статора из корпуса и последующей их сборки следует обратить внимание на их взаимное расположение.
Относительное осевое смещение статора и ротора не допускается. Не допускается также неравномерность зазора между статором и ротором более 0. 05 мм и величина этого зазора более 0,4 мм.
Балансировка кругов
Шлифовальные круги подвергаются двухкратной статической балансировке после сборки с фланцами и после правки их в рабочем положении. Допускаемый остаточный дисбаланс для нового круга — 4 г*см. От качества балансировки во многом зависит точность станка и долговечность подшипников шпинделя.
Балансировка производится на балансировочном станке, основная часть которого — два горизонтальных, параллельно расположенных стальных цилиндрических валика одинакового диаметра с гладкой поверхностью, твердостью, не ниже HRC 58-60. Высота микронеровностей — не более Ra 0.32 им. Шлифовальный круг с переходными фланцами монтируется на стальную балансировочную оправку. Круг с оправкой устанавливается на балансировочный станок так. чтобы ось балансировочной оправки была перпендикулярна к валикам станка, а круг располагался между ними симметрично. Легким толчком кругу придают медленное вращение. После остановки круга отмечают верхнюю точку его и перемещают в нее грузик по пазу. Снова легким толчком придают кругу медленное вращение, отмечают верхнюю точку и перемещают в нее грузик. Эту операцию повторяют до тех пор. пока круг не будет в безразличном равновесии, то есть после легких толчков круг будет останавливаться в разных положениях.
Регулировка подшипников шлифовального шпинделя
Схема дуплексации подшипников точильно-шлифовального станка 3Б634
Во время работы станка подшипники шпинделя изнашиваются, в результате чего появляется осевой зазор.
Если шлифовальный шпиндель имеет осевой зазор или поверхность обработанной детали недостаточно чиста, необходимо отрегулировать подшипниковые узлы станка путем создания соответствующего предварительного натяга. Это осуществляется подшлифовкой компенсационных колец в сдвоенных подшипниках (метод проверки дан на рис. 21).
Кольцо распорное окончательно шлифуется в размере
Н = (а — Δ1) — 0,01 мм, где:
- а — величина мерной проставки,
- в — расстояние между внутренними кольцами подшипников под нагрузкой.
- Δ1 = (а — в) — среднее арифметическое из трех замеров, произведенных под углом 120° между торцами внутренних колец подшипников. Точность замеров — 0,01 мм.
3Б634 Схема электрическая точильно-шлифовального станка
Электрическая схема точильного шлифовального станка 3Б634
3Б634 электрооборудование станка
Электрооборудование точильно-шлифовального станка 3Б634 (рис. 12 и 13) выполнено для подключения к сети трехфазного переменного тока. Цепь освещения выполнена на напряжение 12 В и питается от понижающего трансформатора ТО. В качестве привода электродвигателя применен встроенный двухскоростной электродвигатель 1М.
Управление станком — кнопочное и производится с пульта управления, расположенного у рабочего места (на передней стенке станины).
На пульте смонтированы кнопки «Пуск» и «Стоп», включатели освещения, переключатель скорости двигателя. Остальная электроаппаратура размещена в нише станины.
Выбор скорости вращения двигателя производится переключателем ПС перед включением станка нажатием и поворотом его рукоятки в требуемое положение.
Освещение станка сблокировано с работой электродвигателя и включается при нажатии кнопки 1КУ «Пуск».
Отключение двигателя происходит при нажатии кнопки 2КУ «Стоп». Отключать двигатель сетевым автоматом 1А не рекомендуется.
Электрическая блокировка пускателя К отключает его катушку при помощи размыкающего блокконтакта при переключении рукоятки переключателя ПС.
Двигатель 2М и автомат ЗА поставляются с вентиляционным агрегатом по спецзаказу.
3Б634 Установочный чертеж точильно-шлифовального станка
Установочный чертеж точильно-шлифовального станка 3Б634
Источник
Приспособление для шлифовальной машины DIY OD, для плоскошлифовальной машины – может быть
Джандерсо
Джефф Андерсон
- #1
Оловянный сарай Time также сделал один.
Отправной точкой является использование дешевого индексатора вращения и небольшого двигателя.
Этот двигатель представляет собой мотор-редуктор на 220 В. Он имеет высокую скорость около 360 оборотов в минуту. У него высокий крутящий момент, поэтому я смогу без проблем засеять его.
Мне не нравится идея использовать индексатор вращения как есть без простых бронзовых или шарикоподшипников. Конечно, потребуется уплотнительное кольцо, чтобы не допустить попадания стружки с обоих концов.
Я буду смотреть Hilltop Machine, а пока займусь этим.
Мне нужно сделать основание, которое будет удерживать индексатор и мотор от магнита достаточно далеко, чтобы у меня была рабочая зона по крайней мере для 5-6 дюймов ложи.
См. рис.
Долгий путь
mmcmdl
Опора H-M — Diamond Member
- #2
jwmelvin
H-M Supporter — золотой член
- #3

Этот перфоратор/круглошлифовальный станок – хорошая идея. Я также заинтересован в том, чтобы сделать один, после того, как прокрутил его несколько раз. Я не понимаю, почему вам нужны такие высокие обороты, на порядок.
jwmelvin
H-M Supporter — золотой член
- #4
У этих шпиндексеров нет подшипников? Моя головка, которую я использовал для круглого шлифования, определенно работает. Думаю, мне нужно разобрать один из моих спиндексеров.
сурок
Зарегистрировано
- #5
, если вы собираетесь использовать его часто, я думаю, вам нужно прорезать канал для масла. .
Джандерсо
Джефф Андерсон
- #6
Вы правы, это мой вариант приспособления для шлифовки наружного диаметра.jwmelvin сказал:
Я думал, что шлифование наружного диаметра должно вращать деталь с опорной поверхностью относительно наружного диаметра (а не центра, определяемого подшипником), поэтому называть это шлифованием наружного диаметра неправильно.Робин Ренцетти изготовил приспособление для шлифовки наружного диаметра. Этот перфоратор/круглошлифовальный станок – хорошая идея. Я также заинтересован в том, чтобы сделать один, после того, как прокрутил его несколько раз. Я не понимаю, почему вам нужны такие высокие обороты, на порядок.
Нажмите, чтобы развернуть…
Лоты для рассмотрения и исправления. База поворотного индексатора должна быть на одной плоскости или параллельно столу, основание должно быть отшлифовано для легкой настройки, чтобы установить его под углом 90 градусов к колесу и т. д.
Джандерсо
Джефф Андерсон
- #7
В этих моделях jippo нет подшипников. Просто скользкая посадка. Трубка довольно жесткая, индексатор ID просто чугунный.jwmelvin сказал:
У этих шпиндексеров нет подшипников? Моя головка, которую я использовал для круглого шлифования, определенно работает. Думаю, мне нужно разобрать один из моих спиндексеров.
Нажмите, чтобы развернуть…
сурок
Зарегистрировано
- #8
Джефф, в большинстве марок чугуна достаточно графита, чтобы служить смазкой. У моего станка чугунный подшипник.
Ваша игла перемещается вверх и вниз в чугунном подшипнике.
Не хватает только канала смазки.
mmcmdl
Опора H-M — Diamond Member
- #9
Мой спиндексер отправился на юг. Я не помню, были ли у него подшипники или нет, но я не думаю, что они есть.
Джандерсо
Джефф Андерсон
- #10
Хорошее замечание по поводу чугунных подшипников. В этом случае отверстие необходимо подтянуть. Я еще не измерял, но между трубкой и отверстием слишком большой люфт.сурок сказал:
Джефф, в большинстве марок чугуна достаточно графита, чтобы служить смазкой. У моего станка чугунный подшипник.
Ваша игла движется вверх и вниз в чугунном подшипнике.
Не хватает только канала смазки.Нажмите, чтобы развернуть…
шлифовальные станки для домашнего использования
Сделать шлифовальный станок с приводом от двигателя || Измельчитель самодельный.
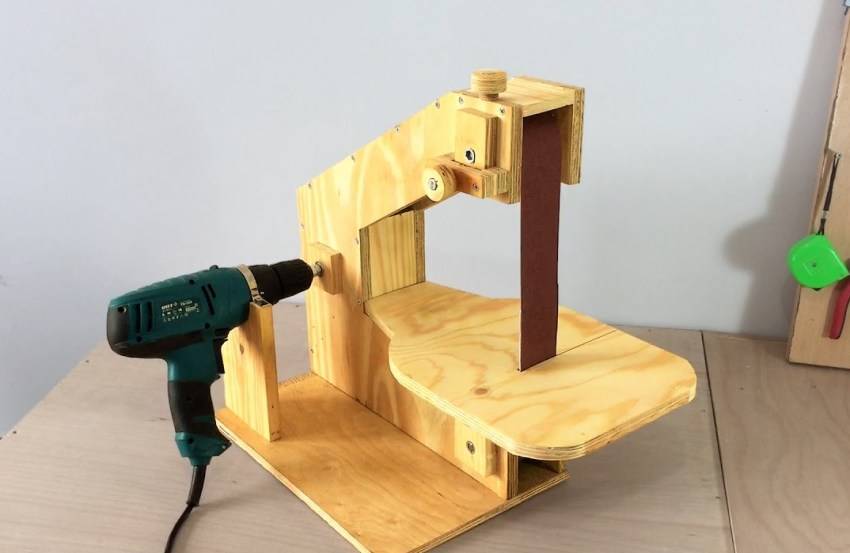
Здравствуйте, друзья! Сегодня я делаю шлифовальный станок по металлу, используя двигатель мощностью 0,5 л.с. и шлифовальный станок Thada. Также я сделаю часть 2 этого видео. Во 2 части я буду…
5 лучших обзоров мясорубок коммерческого класса в 2020 году
Кухонная машина KWS представляет собой мощную мясорубку, которая идеально подходит для изготовления колбасных изделий, измельчения мяса дичи, приготовления говяжьего фарша и приготовления различных овощей. Он оснащен двигателем мощностью 1,5 лошадиных силы, и эта машина определенно удовлетворит требования ресторана, гастронома, мясоперерабатывающего цеха и мясной лавки.
8 лучших угловых шлифовальных машин 2021 года
Многие мастера по дереву используют угловые шлифовальные машины для шлифовки своих изделий, но вам не следует использовать стандартную шлифовальную машину для этого типа применения. Вместо этого лучше приобрести инструмент, специально разработанный для работы по дереву, например мини-угловую шлифовальную машину King Arthur’s Tools 1-Amp 2-Inch Merlin 2 …
.
Для измельчения муки для хлеба можно использовать домашнюю мельницу для муки
Измельчение муки для хлеба Можно использовать домашнюю мельницу для муки, 750–10000 долл. США / Комплект, Новый, Хэнань, Китай, GEMCO мини-весы для семейного использования молотковая мельница для измельчения муки. Источник от Anyang Gemco Energy Machinery Co., Ltd. на Alibaba .com.
Шлифовальный станок — Типы и использование шлифовального станка
Типы и использование шлифовального станка. Опубликовано 19 октября 2012 г. Яш Шах. Шлифовальный станок — это тип инструмента, который используется для шлифования заготовок. В качестве режущего инструмента в основном используется абразивный круг. Шероховатая поверхность абразивного круга срезает небольшие части заготовки по мере необходимости. Он также известен как мясорубка.
8 лучших кофемолок 2021 года по отзывам …
Кофемолка необходима для свежих вкусов и индивидуального стиля заваривания. Если вам нужно недорогое устройство или вы хотите перейти на высококлассную машину, эти самые продаваемые …
: Электрическая мельница для измельчения зерна SLSY 800 г …
SLSY 800g Электрические зерновые мельницы Мельница для домашнего использования, Машина для измельчения зерна из нержавеющей стали 304 для зерен пшеничной муки, Коммерческая порошковая машина Посетите магазин Slsy. 4,1 из 5 звезд 50 оценок. Цена: $139.99 и БЕСПЛАТНЫЙ возврат Верните этот товар бесплатно.
Шлифовальный станок на продажу в Шри-Ланке – Продажа – Шри …
4 мельницы (включая 2 фрезы Tissa – рис, зерно, перец чили, специи) с 4 трехфазными двигателями (4, 5, 10, 15 л.с.), ремнями, главными щитами (с распределительными коробками и выключателем. 0. 160 000 рупий) y машина для измельчения кокосовых орехов (односторонний детский размер), резак для копры и измельчитель pem (5 л.с.) 160 000 рупий Yakkala
машина точильщика специи
500г электрическая сухая для зерна домашнего использования
500 г Электрическая машина для измельчения сухих специй для домашнего использования Зерновая мельница, Найдите полную информацию о 500 г Электрическая машина для измельчения сухих специй для домашнего использования Зерновая мельница, Машина для измельчения сухих трав, Машина для измельчения специй, Машины для измельчения специй от поставщика или производителя шлифовального оборудования – Гуанчжоу Creative Machinery Technology Co. , Ltd.
7 лучших мясорубок 2021 года
Электрическая мясорубка Sunmile — это элегантная машина, которая может быстро и эффективно перемалывать большие порции мяса. Благодаря металлическому редуктору с большими прочными шестернями, лотку большой емкости и шлифовальной головке вы сможете подавать его непрерывно — независимо от того, измельчаете ли вы мясо для гамбургеров или набиваете сосиски для хранения в морозильной камере.
6 лучших ручных мясорубок – обзоры экспертов [Upd. Октябрь 2021]
Если вы перемалываете мясо для коммерческого использования, вам понадобится огромная машина, чтобы удовлетворить потребности всех ваших клиентов. Для домашнего использования лучше подойдет ручная мясорубка. Эти маленькие модели выполняют ту же работу в гораздо меньших масштабах, а также компактны, просты в использовании и недороги.
Лучшая эспрессо-машина для домашнего использования в 2021 году | 7 лучших вариантов
Принимая во внимание, что если машина предназначена для одноразового использования, не стоит тратить дополнительные деньги на модель с пароваркой. Встроенная кофемолка. Если вы приобретете полностью автоматическую эспрессо-кофемашину для домашнего использования, она, скорее всего, будет оснащена встроенной кофемолкой.
Круглошлифовальные станки – Kent Industrial USA
Для крупносерийного производства и обеспечения быстрого округления и точности компания Kent USA предлагает линейку круглошлифовальных станков. Машины из этой коллекции обеспечивают очень плотные размеры и контроль допусков на округлость. Круглошлифовальные станки Kent USA способны шлифовать детали диаметром до 13 дюймов. Самая большая стандартная модель может вместить максимальную длину шлифования 40 дюймов и макс …
: Шлифовальные станки
Эти шлифовальные станки для домашнего использования требуют минимальных усилий и затрат на техническое обслуживание, что позволяет сэкономить огромное количество усилий и денег с течением времени. Эти увлекательные шлифовальные станки для домашнего использования выпускаются с различными диапазонами напряжения от 220 до 380 В. Эти машины также просты в эксплуатации и могут легко перемещаться по вашей мастерской.
Шлифовальный станок [шлифовальный круг, типы, операции и многое другое]
Маленькие круги диаметром 25 мм стоимостью до 10$ за обычный абразив и за алмаз до 200$.; Большое колесо диаметром 500мм и шириной 250мм, стоимость от 8000$ до 20000$.; Жизнь шлифовального круга. При воздействии на заготовку шлифовального круга острые кромки абразивных зерен, которые являются режущими, в конце концов теряют свое режущее действие и затупляются.
9 лучших кофеварок с кофемолками
Немногие кофемашины «все в одном» со встроенными кофемолками выглядят так гладко и привлекательно, а также производят такой великолепный кофе! У этой машины Krups есть ножевая кофемолка, которая снижает консистенцию вашего конечного вкуса, но другие функции помогают компенсировать этот недостаток.
Измельчители пней – Наружное силовое оборудование – The Home Depot
BLUEBIRD 14-дюймовый бензиновый измельчитель пней мощностью 13 л. с. с двигателем Honda GX390. Модель № SG1314B. (3) 439995 долларов.
8 лучших измельчителей пней 2021 года: надежные и доступные
В отличие от обычного измельчителя пней, этот продукт также оснащен выступающими рычагами, прикрепленными к левой и правой петле основания, которые можно использовать, когда машина застряла. Этот продукт также идеально подходит для тяжелых работ по измельчению пней, поскольку он оснащен необходимыми функциями, необходимыми для работы.
Настольные шлифовальные машины – шлифовальные машины – The Home Depot
JBG-8W, 8-дюймовая настольная шлифовальная машина с проволочным колесом Для мастерских, в которых может не хватать места, литье полировка, удаление заусенцев, шлифовка кромок, финишная обработка и многое другое на 1 станке. Этот высококачественный станок, созданный для того, чтобы выдерживать большие объемы заказов даже в самых загруженных магазинах, …
15 лучших мясорубок для домашнего использования: руководство для покупателя .
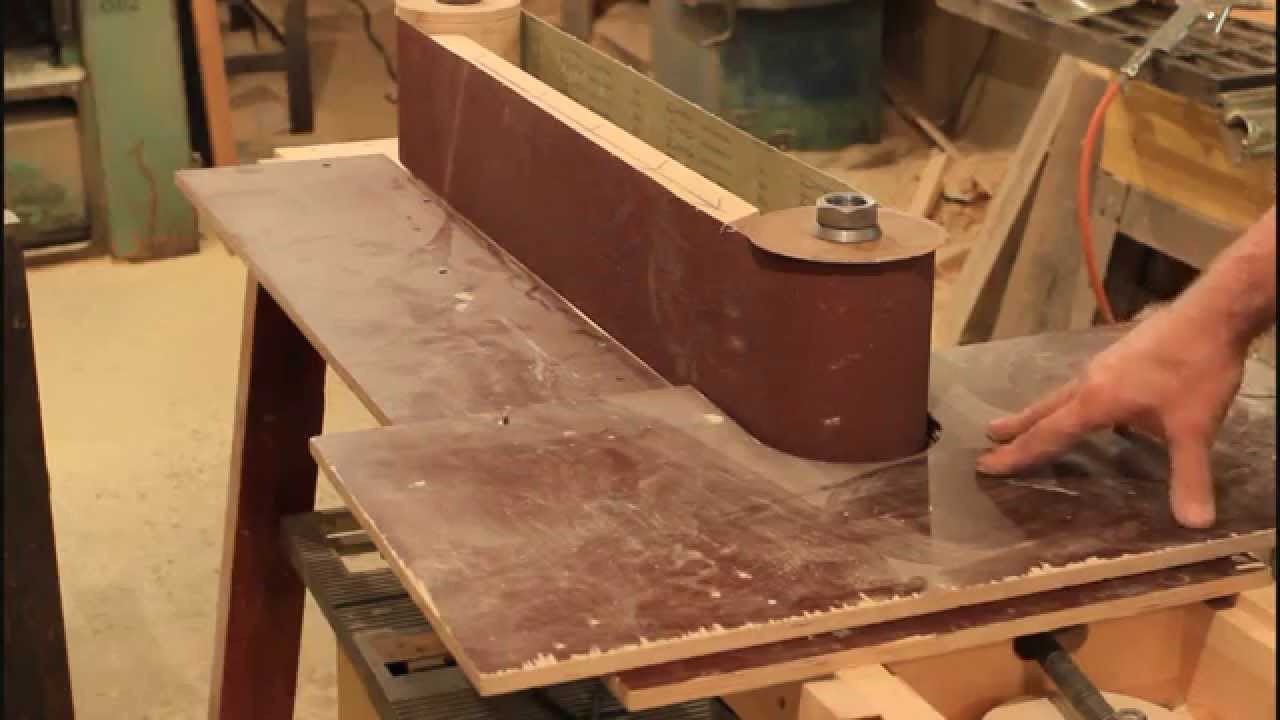
В нашем списке лучших мясорубок представлены всевозможные невероятные устройства, идеально подходящие для домашнего использования. У нас есть все: ручные станки, мощная электрика, крупнотоннажные кофемолки…
Бестселлеры Amazon: лучшие мясорубки
Электрическая мясорубка 2000 Вт, мясорубка с 3 пластинами для измельчения и трубками для набивки колбас для домашнего и коммерческого использования, нержавеющая сталь/серебро/2000 Вт (макс.) 4,4 из 5 звезд 391 69,99 долл. США
: Машина для производства арахисового масла: дом и …
Хорошей новостью является то, что с правильной эспрессо-машиной вы можете научиться совершенствовать искусство приготовления эспрессо, не выходя из дома, и начать дозировать (молоть нужное количество зерен для вашей кофемашины…
Лучшая зерновая мельница для домашнего использования – Руководство по покупке и …
Мельницу можно использовать для помола зерна на муку и измельчения зерна, фасоли, чечевицы, Е-желатина, олибанума, кореньев и многого другого. Изготовленная из прочной полированной стали, зерновая мельница ALDKitchen отличается прочностью и долговечностью и идеально сочетается с другими кухонными приборами из нержавеющей стали.
10 лучших кофемолок 2021 года | Стратег
Лучшие кофемолки по мнению бариста, обжарщиков и владельцев кофеен, включая рекомендации по лучшей кофемолке с жерновами, лучшей ручной кофемолке и Baratza Encore …
Угловые шлифовальные машины: Купить Угловые шлифовальные машины онлайн | Flipkart.com
Купите ручные шлифовальные машины в Интернете и выберите те, которые соответствуют вашим рабочим требованиям. Эти легкие машины могут сделать вашу работу по шлифовке, резке и полировке простой и быстрой благодаря предохранительным замкам. Вы должны использовать это оборудование с необходимыми мерами защиты, такими как ручные перчатки, шлемы, очки и обувь.
5 лучших мясорубок для приготовления колбас, которые можно купить в 2020 г. Отзывы
Высококачественная электрическая колбасница. Cuisinart MG-100 — это качественная модель электрической колбасной мельницы, которая незаменима на любой кухне. Эта лучшая электрическая мясорубка для изготовления колбасных изделий изготовлена из высококачественных деталей и материалов, чтобы обеспечить вам максимальную производительность в любое время.
Кокосовая терка для домашнего использования Кокосовая шлифовальная машина …
Домашняя машина для терки кокоса Кокосовая шлифовальная машина, найдите полную информацию о машине для кокосовой терки для домашнего использования Кокосовая шлифовальная машина, Электрическая терка для кокосовой терки, Электрическая машина для терки кокоса Цена, Кокосовая машина для терки кокосов от поставщика или производителя-Shenzhen Sijie Borui ООО «Технология»
Китай Домашняя мельница для пшеничной муки / Машина для измельчения пшеницы …
Китайская домашняя мельница для пшеничной муки / пшеничная мельница для домашнего использования, Узнайте подробности о китайской мельнице для пшеничной муки, сельскохозяйственная машина из дома Пшеничная мельница / пшеничная мельница для домашнего использования – Jinan Sensi Industries Co. , Ltd.
ШЛИФОВАЛЬНЫЕ СТАНКИ
шлифовальные машины, машины для натирания. и возвратно-поступательные плоскошлифовальные станки. КОММУНАЛЬНЫЕ ШЛИФОВАЛЬНЫЕ СТАНКИ Универсальные шлифовальные станки предназначены для ручной шлифовки, при которой заготовка поддерживается рукой и прижимается к вращающемуся шлифовальному абразивному кругу.
7 лучших мясорубок для костей [Отзывы 2021 года]
Этот шлифовальный станок подходит как для домашнего, так и для профессионального использования. Мощная мясорубка — отличный выбор для измельчения костей вашего питомца. Естественная смазка делает задачу измельчения костей еще проще. Машина также поставляется с набором для чистки, так что вы всегда можете содержать укромные уголки и изгибы в блестящей чистоте.
Слайсеры для мяса | Электрические мясорубки | Кровать Bath & Beyond
Мясорубки и мясорубки позволяют приготовить любимые блюда дома, гарантируя свежесть и качество мяса, используемого в ваших собственных блюдах. Выбирайте из множества вариантов мощности в ваттах, которые определяют мощность производительности для выполняемой работы.
: Колбасная машина
Электрическая мясорубка, машина для набивки колбас, мясорубка мощностью до 2600 Вт, машина для мясорубки с насадками, трубка для колбасы, набор ножей Kubbe, 3 тарелки для домашней кухни, коммерческое использование. 4,3 из 5 звезд. 787. 79 долларов0,97. 79 долларов. . 97. Купон на 10% применяется при оформлении заказа.
Машина для измельчения кукурузной/пшеничной муки для дома или …
Малая и средняя мельница для измельчения зерна обладает преимуществами высокой эффективности производства, высоких технологий автоматизации и стабильного качества муки. Когда мы выбираем малую мельницу для домашнего использования, мы должны выбрать соответствующие машины и оборудование для муки в соответствии с динамика рынка муки, уровень рыночного спроса и характеристики пшеницы.
Эспрессо-машины | Кофе в зернах | Отзывы | Сиэтл .
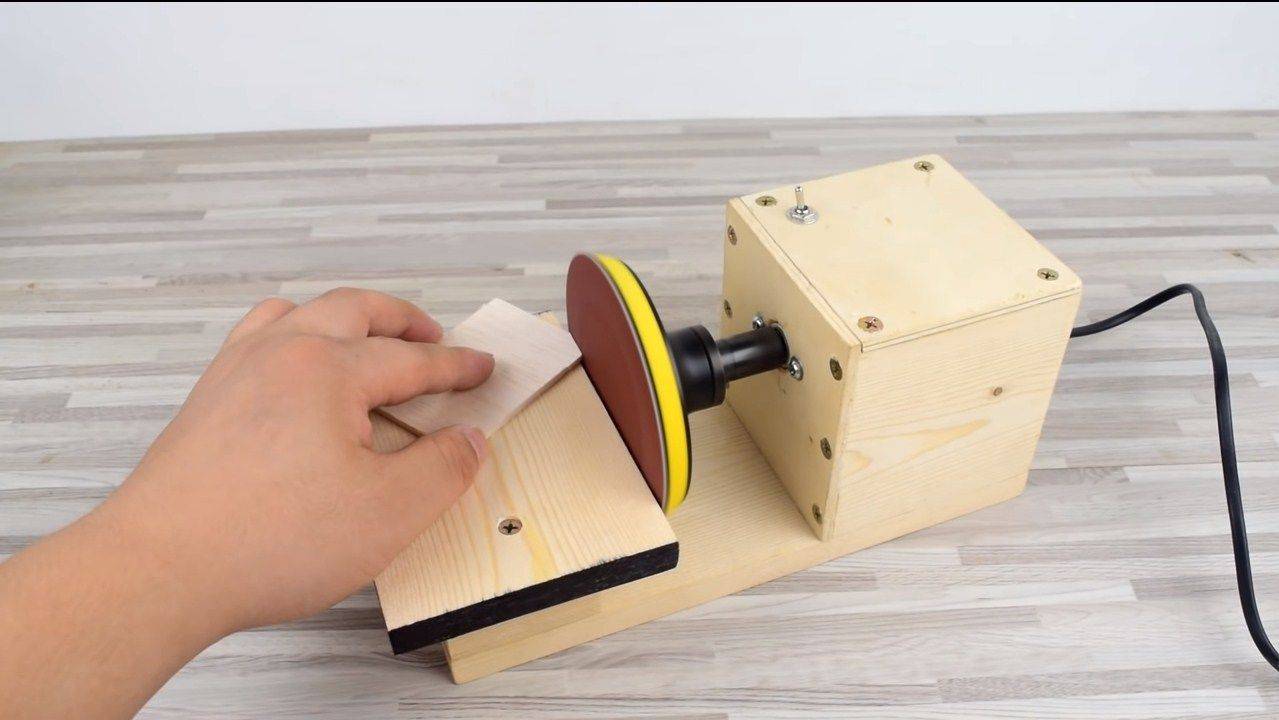
Оценка: 96 % из 100. (4) Кофемолка для эспрессо Rocket Espresso Fausto Touch. Всего 1200 долларов. Получите идеальную машину. Наши эксперты по кофе всегда готовы помочь. Нажмите на функцию LiveChat в нижнем углу экрана или позвоните нам по телефону: 866-372-4734.
Машины для измельчения зерна мукомольной мельницы домашнего использования
мельница для пшеничной муки для домашнего использования – Alibaba. Фрезерный станок для домашнего использования Пшеничная мука Пшеничный фрезерный станок Маленькая 100G Домашняя мелкая электрическая мельница для кукурузы Травяной шлифовальный станок Сухая еда Орех Пшеничное рисовое зерно Мельница для специй Мукомольная машина. Готов к отправке. $15,30-$18,00/шт. 1 шт. (минимальный заказ) $41,16/шт.
- Замена легкообожженного доломита в сталеплавильном производстве
- Процесс обогащения оловянной руды
- procesado de nueces en argentina
- Щековая дробилка с хорошей репутацией
- Шаровые мельницы большой производительности Эффективные шаровые мельницы для минерального шлака 900 10
- запасные части для печати модуль обработки магический глаз сумма 1
- сепаратор золота химический
- щековая дробилка pe400 600 цена
- лопасти нагревателя
- ультратонкая угольная дробилка
- алюминиевые фильтры стоматологические
- каменная дробилка sasaram в
- Энергосберегающая широко используемая щековая дробилка Прайс-лист
- производители карьерных дробилок в Ирландии
- обогащение диатомовой земли
- карьер в бенони поставщик камня в бенони май
- дробление долимитного камня растения
- остатки шин цена
- صغيرة
- سعر كسارة فكية المتنقلة في العراق
- شراء طاحونة حلقة والعتاد
- المطحنة التقليدية
- شيدت م
- الضغط العالي يعمل طاحونة الأسطوان ة
- افلام سيكس في تايلند
- كسارات الصخور كسارات الحجر الجي ري و
- اماكن بيع مكائن رغوة الصابون مغاسل السيارات
- شركا ت الاستيراد والتصدير في الصين
- اشكال وانواع ماكينات الرخام ال صناعي بالصور
- آسیاب های گلوله ای مروری بر گیاه
- دراسة جدو ى لمشروع كسر الرخام
- استفاده از گیاه غربالگری
- شبكة الشاشة للكسارات الحجر
تقوم الشركة بشكل أساسي بتصنيع الكسارات المتنقلة والكسارات الث ابتة وآلات صنع الرمل وطواحين الطحن والمصانع الكاملة التي تستخدم عى نطاق واسع في التعدين والبناء والطرق السريعة والجسور وما إلى ذلك.