Гриндер своими руками в домашних условиях (17 фото + описание)
Сделал самодельный станок гриндер в домашних условиях, без сварочных работ.
Привет всем! В мастерской без ленточного шлифовального станка, прожить конечно можно, но с ним намного удобней и быстрей можно делать многие работы, например точить ножи. А так как я планирую ещё делать ножи, то мне он становится крайне необходим.
Долго выбирал из чего сделать ролики, так как гриндер я решил сделать тестовый, просто проверить, что получится и учесть нюансы, то ролики покупать мне не хотелось для такого дела. В итоге покопавшись в гараже я нашел 2 ролика натяжителя, от автомобиля, на деле я спросил ещё по друзьям и набрал 5 штук с запасом.
Недостаток этих роликов том, что ролики нужной мне ширины оказались живые и крутились вязко создавая сопротивление, а это в свою очередь ведёт к потере мощности.
Двигателем послужил старый двигатель от стиральной машины, в стиральной машине он находился в разделе центрифуги. Двигатель долго находился на улице, пришлось его разбирать чистить, смазывать. Но в итоге в порядок я его привел. Мощность движка 180 Вт, что, как выяснилось в ходе работы вышло маловато.
Метал на каркас закупать я тоже не стал, так, как есть толстая фанера, и для жесткости конструкции при небольшой мощности её вполне хватает.
Теперь самое интересное, ролики то я нашел, а вот шкив на мотор просто так не найти. Я решил сделать его сам из фанеры. Так, как обороты двигателя у меня небольшие, то шкив должен быть не сильно маленький. Материал для его изготовления я выбрал всё туже фанеру, так как делать из метала без токарного станка практически нереально, искать токаря и покупать тоже не хотелось, так как смысл работы сделать гриндер без вложений.
И так, для начала я взял фанеру и напилил из неё круглых деталей нужного мне диаметра, напилить мне помог набор коронок по дереву. Для центровки я поставил в центр сверло и намазывая клея на каждый слой собрал из четырех кругляков что-то напоминающее шкив моего будущего станка.
После полного высыхания пришло время сверлить отверстие для шкива. Сверлильный станок я поленился доставать и просверлил отверстие немного кривовато, но это не страшно. Плотно набил шкив на вал мотора, я думал сначала просверлить отверстие в центре и нарезать резьбу, но не пришлось, шкив сел настолько плотно, что если придётся его снимать, то буду распиливать скорей всего.
Для выравнивая я решил попробовать обработать шкив болгаркой с лепестковым кругом, болгарка сама раскручивает мотор и получается ровно, но минус, раскручивает слишком сильно и приходится всё время останавливать двигатель, это видно на видео.
После 20 минут работы, шкив начал приобретать форму, но дальше болгаркой работать было неудобно. Мотор я прикрепил к доске проволокой, а доску к столу прикрепил струбциной. Подставил ещё несколько досок, взял стамеску и довел дело до конца.
Опыт на токарном станке по дереву у меня есть, это не сложно даже человеку вообще без опыта. Разница только во времени работы. И так шкив вышел отличным, без биений, гладенький и формы как я и хотел. Отличный способ сделать бюджетный шкив если что.
Затем я принялся вырезать основные элементы из фанеры, в этом мне помог лобзик и болгарка с универсальным диском. Дрелью я высверлил нужные отверстия для мотора, и немного рассверлил углубления, что бы болты не мешались выпирая. Болты я использовал, те что держат корпус мотора, поэтому искать ничего не пришлось.
И вот я прикрепил на свой каркас мотор, ролики, осталось сделать упор и ролик который натягивает ленту. Я взял так же фанеру, но толстая закончилась и я склеил из 2 мене толстых кусков фанеры элемент на котором держится третий ролик и пружина натяжения.
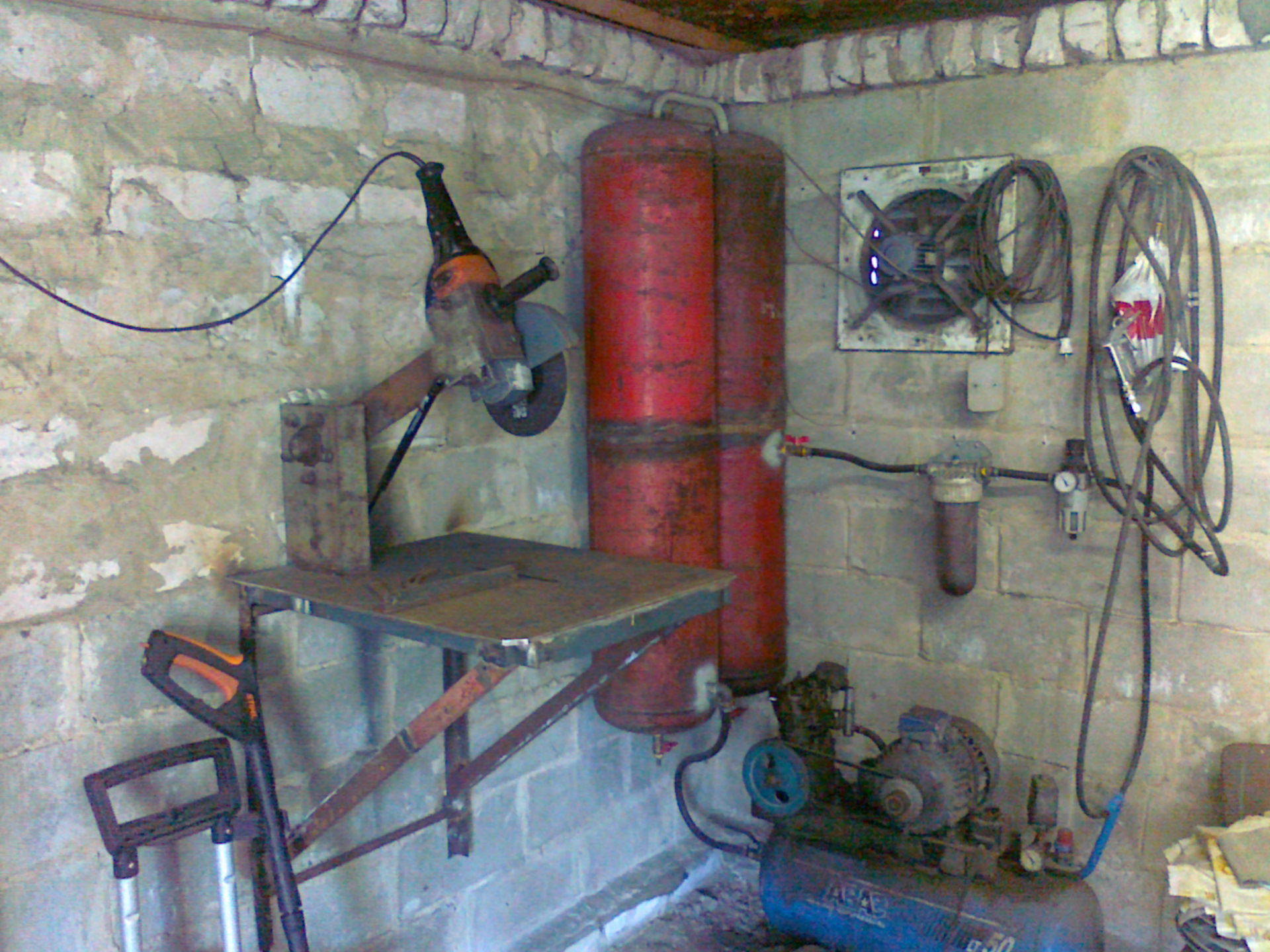
Теперь время сварки, во дворе нашел немного ржавый уголок, но через 20 минут работы с щеткой на дрели, уголок приобрел вид нового. Этот уголок, как раз то, что мне и было надо. Поискав получше я нашел ещё пластину металла толщиной 4 миллиметра. Всё разметив под прямыми углами я сварил в одну деталь. Регулируемый угол наклона, я делать не стал, так как гриндер по сути пробник. Прикрутив на болты упор к фанерному основанию работу можно считать завершенной.
В заключении скажу самоделка работает, но мотор от стиральной машины 180 ватт слабоват, хотя видел его во многих роликах, поэтому буду переделывать на более мощный двигатель. Работать этим можно, в, но не рекомендую использовать моторы слабей 300 ватт.
Смотрим видео:
Самодельные инструменты для работы.
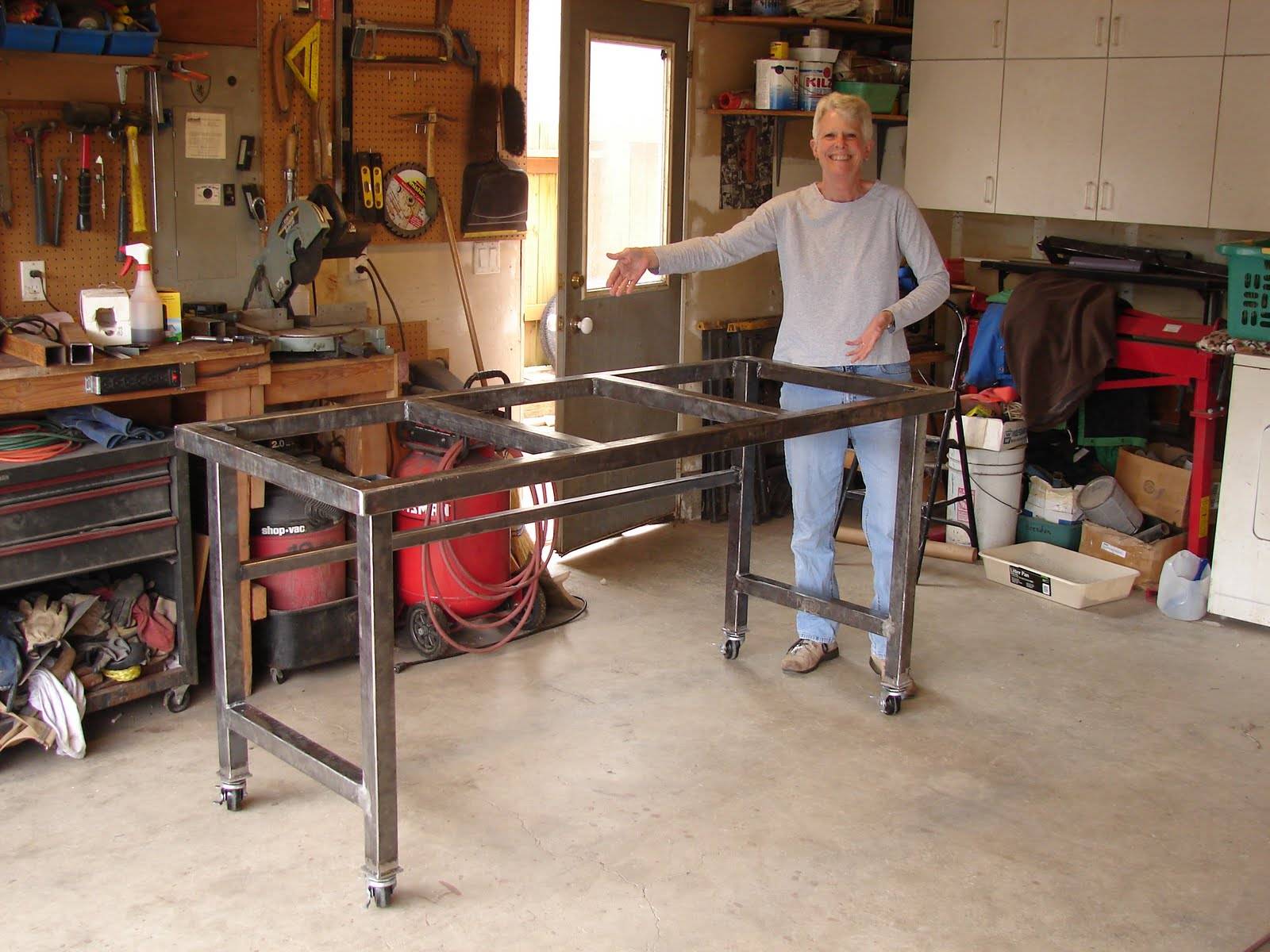
Для работы по дому или в гараже необходимы профессиональные инструменты. Но в некоторых случаях целесообразнее сделать оборудование своими руками. За основу можно взять заводские модели, адаптированные для выполнения конкретного типа работ в мастерской.
Станки для обработки металлов
Самыми востребованными являются станки и оборудование для обработки металлических изделий. Они применяются не только для изготовления и ремонта, но и во время обслуживания другого инструмента.
В декабре идут большие шаги, а вместе с ним и возможность отпраздновать и одарить следующие подарки. Если вы находитесь на стадии завершения домашней мастерской, вы можете ожидать приятных сюрпризов, потому что инструменты – отличная и недорогая идея подарка.
Складной сантиметровый ковш – может быть из дерева, пластика или металла. Рулетка – она находится в кармане, вы также можете прикрепить ее к ремню. Цена от около 5 злотых за 5 метров измерительной ленты. Вы сами решите, какие инструменты вам нужны. Уровень – это очень полезно, и когда дело доходит до отделки, как остекление, это очень необходимо. Плоская щетка – используется в основном для небольших работ для обоев и ремонта лакокрасочных покрытий.
Помимо ручных приспособлений для комплектации ремонтной базы частного гаража или мастерской понадобятся мини-станки различных типов, сделанные своими руками. Речь идет не о профессиональном заводском оборудовании, а о его аналоге меньшей производительности. Однако несмотря на это она должна обладать оптимальным набором функций для осуществления всех типов работ.
Карпентерский карандаш – отлично рисует древесину, полезен для изготовления мебели, укладки пола и т.д. связывание связующего – необходимо для обоев, но также полезно для ремонтных и ремонтных работ. Металлический шпатель – полезен для очистки старой краски и обоев, для нанесения и сглаживания заполняющих заполняющих полостей. Присоединяйтесь к нам и следите за обновлениями.
Отвертки, простые и крестообразные, используются для завинчивания и скручивания винтов. Изолированная отвертка – необходима для электропроводки. Изоляционные ленты – для электромонтажных работ. Куб для подключения электрических проводов. Настенные монтажные штыри – полезны для подвешивания полки, шкафов и т.д. горячий клей. Абразивные лезвия – необходимы для точного шлифования поверхностей при ремонтных работах стен и мебели. Абразивная бумага – используется для шлифования. Стоит иметь документы разной градации.
Точильное оборудование
Станком первой необходимости считается точильное оборудование. Оно предназначено для обработки металлических поверхностей — заточка, шлифовка, полировка.
Для его изготовления своими руками потребуется минимум инструментов и комплектующих. Конструкция состоит из силового агрегата (электродвигатель) и точильных камней. Оптимальным вариантом станка является наличие двухстороннего вала.
Цена около 0, 20 злотых за лист. Универсальные плоскогубцы – полезны при ремонте и ремонте. Плоские угловые гаечные ключи – для винтов и скручивания винтов с шестигранной головкой. Трубчатый регулируемый ключ – полезен для работы с водой или отопления. Даже большие винтовые соединения легко удерживаются или отвинчиваются. Поскольку он захватывает довольно резко, он не заменит гаечный ключ, так как он повреждает гайки. Универсальный регулируемый гаечный ключ – используется для затяжки винтов; Благодаря регулировке расстояния он заменяет набор клавиш.
Комплектующие для изготовления мини-оборудования для гаража:
- электродвигатель мощностью от 0,8 до 1,5 кВт. Оптимальная частота оборотов — 800 об/мин;
- основание. Это может быть заводская станина или изготовленная самостоятельно. Важно чтобы она обеспечила устойчивость конструкции;
- блок крепления наждака. Заточные круги могут быть установлены на вал двигателя или в отдельном блоке.
Важно правильно подобрать виды наждака и другие приспособления. Для заточки инструментов, изготовленных из специальных сортов стали, чаще всего применяют корундовые или алмазные круги.
Инструменты для ручного строгания
Плоскогубцы – они полезны не только для рисования гвоздей. Этот многофункциональный инструмент – держит, захватывает и тянет. Цена от около 4 злотых. Пресс для плотника – сгладит склеенные поверхности, обеспечивая прочное соединение. Есть файлы, разорванные, полутрек и трекпад. Они имеют разные формы: полукруглые, треугольные, плоские или квадратные. Они будут работать на многих больших и малых предприятиях. Благодаря им вы можете ремонтировать двери, шкафы и книжные полки, а также делать что-то с нуля – садик, встроенную гардеробную стену или сборку кухонной мебели.
Для устойчивости самодельная конструкция должна иметь монтажные элементы, с помощью которых заточной станок будет крепиться на рабочий стол.
Фрезерный (сверлильный) станок по металлу
Другой разновидностью работы является сверление отверстий на поверхности металлических изделий. Для выполнения потребуется фрезерный станок. За основу можно взять чертеж заводской модели, которую в дальнейшем адаптируют для изготовления своими руками в мастерской.
Древесные инструменты – это основа
Все необходимые инструменты можно легко собрать на ближайшей строительной площадке за небольшую плату. Мы всегда начинаем с планирования. Сначала вы должны сделать эскиз, а затем определить порядок работы. После завершения деревянного здания элементы должны быть выложены плиткой до требуемого размера. Вам нужен карандаш и металлическая или деревянная отделка для направления линии резки. Когда мы используем угловую планку, мы также рисуем ее под прямым углом. Это базовые столярные инструменты.
Плотницкий инструмент: пороки, плоскогубцы и зажимы плотника
Будет полезен набор пороков. Они помогут стабилизировать деревянные элементы для резки, сверления, шлифования. Также сожмите два склеенных куска для времени склеивания. Распиловка была одним из самых важных инструментов в мастерской. Доступно несколько типов. плательщиками, скважинами, лопатами и пилами и скобами. Перед покупкой необходимо проверить свои зубы, потому что это зависит от того, как они организованы и закончены. Тонкие, плотно разнесенные зубы обеспечивают более точный и точный срез, чем большие, большие расстояния.
Так как приспособление будет выполнять ряд определенных функций — рекомендуется продумать компоновку инструмента. Чаще всего в качестве силового агрегата выбирают электродрель. Она устанавливается на съемный монтажный элемент и в случае надобности может быть оперативно демонтирована для выполнения других работ.
- в качестве подъемного механизма можно использовать рулевую рейку. Согласно его размерам рассчитываются остальные компоненты оборудования;
- для увеличения функциональности делают . После закрепления на нем детали он сможет смещаться относительно режущей части;
- дополнительно можно установить механизм углового фрезерного сверления.
Если потребуется сверление с помощью вышеописанного станка заготовок большой толщины — лучше всего использовать мощный электродвигатель вместо дрели.
Зубила для дерева – необходимо выталкивать
Последнее, однако, делает процесс распиловки намного быстрее, хотя и менее точным. Форма зубов определяет, подходит ли пила для поперечной резки к древесным волокнам или продольным волокнам. Лучшая древесина – это пила с закаленными зубами. Деревянное долото – это не только инструмент для скульптора. Он также используется мастерами-умельцами и плотниками для вырезания канавок, отверстий неправильной формы, совместных столярных работ. Блейд – металлическая рабочая часть долота – может иметь трапецеидальное, прямоугольное или поперечное сечение.
Некоторые производители предлагают фрезерный стол с опорной стойкой, специально предназначенные для монтажа дрели.
Самодельные станки по дереву
Для работы по дереву необходимы три типа станков: отрезной, шлифовальный и токарный. При их наличии можно осуществлять все типы работ в домашних условиях. Однако следует учитывать конструктивные отличия, характерные для каждого типа оборудования.
Его ширина составляет от 4 до 40 мм. Зубило направлено под углом к поверхности дерева и ударяется молотком в конце рукоятки. С точным оврагом, так называемым. сбор, молот не понадобится. Прежде чем мы начнем вытирать, сделаем вертикальное долото с долотом вокруг запланированного углубления. Не забудьте сделать разрезы с интервалом 1-2 мм от обозначенной линии. Это запас, который мы удалим позже. В то время как строжка, это хорошая идея сделать равномерно разрезанные разрезы той же глубины, сформированные под углом, а затем отрезать результирующие чешуйки, ударив долото с противоположной стороны.
Перед выбором оптимальной модели следует определиться с видом выполняемых работ. На параметры будущей конструкции оказывают влияние размеры заготовки, необходимая степень ее обработки, породы древесины. Оптимальным вариантом инструмента будет изготовление универсального инструмента своими руками исходя из выполненного анализа и габаритов места в мастерской.
Самоделки для мастерской
Чтобы разрезать тонкую полоску дерева, понадобится самолет, обычно называемый пяткой. Мы разглаживаем лес, по краям, удаляем старый поврежденный слой, мы сделаем паз. Наиболее важным в струе является съемный нож. Скребок с сглаживающим валиком, прямолинейный профилировщик с профилированным скребком. Ножи можно обменять на определенную работу. Режущая кромка регулируется. Чем больше мы их вытаскиваем, тем толще древесина будет срезана. Перед строганием мы должны убедиться, что гвозди, скобы или винты не торчат из дерева.
Отрезные станки по дереву
Самая простая модель мини-отрезного оборудования для обработки древесины — электро или бензопила. С ее помощью можно делать резы различной точности и конфигурации. Однако из-за относительно больших физических нагрузок время работы будет ограничено. Поэтому для обработки больших объемов древесины рекомендуется делать пилорамы своими руками.
Как сделать приспособление для заточки сверла по металлу своими руками
Вам нужно удалить их, иначе они уничтожат клинок. Мы управляем плоскостями вдоль волокон – «с волосами». Они не будут измельчены, и поверхность станет гладкой. При работе плоскость должна быть хорошо прижата к материалу. Когда мы начинаем планировать с края элемента, акцент делается на передней части плоскости, и по мере приближения к краю мы увеличиваем противодавление. Чтобы сделать нас здоровыми, нож должен быть заточен. Резкий, вы можете легко недооценивать – в то время как строгание звучит отчетливым громким звуком.
Подобные станки могут быть нескольких видов:
- дисковая. Самый простой вариант приспособления, состоящий из опорного стола, режущего диска и силовой установки. Может применяться для реза листовых материалов, брусков и досок;
- . Предназначена для обработки стволов. Применяется для формирования досок и брусьев. Отличаются относительно небольшой сложностью изготовления;
- ленточная пилорама. Имеет те же функции, что и конструкции из бензопилы. Различие заключается в скорости обработки бревна.
Для фигурного реза можно использовать электролобзики. Однако изготовить этот инструмент своими руками будет проблематично.
Сверление по дереву – инструменты для плотницкого бурения
Дерево – довольно мягкий материал, и сверление в нем не составляет труда. Обычно используется для этой электрической дрели или даже ручного сверла. Однако наиболее важными являются взаимозаменяемые сверла и отвертки. Стоит выяснить, чем они служат. Если сверло не имеет центрирующего штыря, лучше всего сделать небольшую выемку в точке, где расположено отверстие для сверления, например, пуансон или гвоздь. При сверлении убедитесь, что отверстие не забито чипами. Удалим их, поскольку их накопление может вызвать растрескивание в отверстии, а иногда даже повреждение сверла, особенно при бурении во влажной, твердой или закаленной древесине.
При изготовлении самодельной пилорамы необходимо учитывать максимальный размер бревна — диаметр ствола и его длину. Исходя из этого рассчитывается оптимальный размер и характеристики приспособления.
Шлифовальное оборудование для обработки дерева
Когда мы удаляем сверло из отверстия, оно все равно должно двигаться. Если мы бурим в узкой плите или доске, и мы боимся, что сверло может сломать ее, то мы сжимаем часть в тисках между двумя деревянными блоками и начинаем бурение. Когда есть страх, что край дыры уродливый на другой стороне отверстия, давайте поместим там тонкий кусок дерева и надавим на него тиском. Затем мы сверляем отверстие через элемент и через блок одновременно. Открытие будет идеально с каждой стороны. Если мы пробурим толстый кусок дерева, а сверло слишком короткое, мы должны точно определить точки сверления с обеих сторон.
Для шлифовки дерева можно применять станки, сделанные своими руками, аналогичные устройствам для обработки металлов. Разница будет заключаться в абразивном материале, а также площади обработки.
Самая простая модель приспособления состоит из рабочего стола, двигателя и вертикального шлифовального вала. Последний может иметь лезвие либо монтажные элементы для установки абразивной ленты. С помощью этого оборудования можно обрабатывать торцевые края деревянных заготовок, выполнять их шлифовку.
Инструменты для шлифования древесины
Шлифовка – это последнее тянущееся дерево, которое закрашивает древесину перед покраской или лакировкой. Соответствующая гладкость достигается с помощью шлифовальной бумаги различной градации. Его листы можно поместить в ручные или электрические шлифовальные инструменты. Дешевая ручная шлифовальная машина будет создана, когда деревянный блок повернут с наждачной бумагой. Лучше осмотреть пластиковый абразивный шпатель, желательно для электрического шлифовального станка. Абразивная бумага или проволочные щетки и шлифовальные круги будут полезны для удаления старой краски, лака или другой древесины из дерева.
В видеоматериале показан оптимальный набор инструментов для работы по дому своими руками:
Примеры чертежей станков
Изготовление своими руками различных поделок, мебели, самостоятельный ремонт автомобиля, популярны не только по причине врожденной способности наших людей к созиданию. Это еще и неплохая экономия семейного бюджета.
Перед повторным шлифованием мы также наносим лакированную или окрашенную поверхность наждачной бумагой. Мы также придадим ему более резкость, что указано перед склеиванием. Для измельчения также используйте файлы и тары, чтобы изменить форму дерева, например, закруглить края. Мы ценим их особенно за небольшие или нерегулярные элементы. Тарки имеют небольшие всплески, а файлы – параллельные разрезы. Оба могут иметь разные формы: плоские, треугольные, дуговые, круглые.
Изготовление современного верстака
Ручные инструменты относятся к основному оборудованию каждой службы. Точный, прочный ключ в руках опытных и компетентных механиков является гарантией гладкой и безошибочной работы. Высокий уровень мастерства мастера – это не только свидетельство его навыков, но и инструменты, которые он использует. В конце концов, разные задачи требуют использования соответствующего оборудования. Вопрос о том, какие инструменты используются профессионалами и являются ли они всегда очень дорогими решениями? Оснащая головные уборы, мы можем стать владельцами надежных лифтов, ключей или электроинструментов, не перегружая ваш домашний бюджет.
Однако подобное хобби требует наличия специального оборудования. В любом доме есть элементарные ручные инструменты, в том числе электрические. Дрель, шуруповерт, болгарка, ручная дисковая пила, электролобзик.
Эти приспособления облегчают труд домашнего мастера, но с их помощью невозможно выполнять работу профессионально. Домашняя мастерская должна быть оборудована компактными станками.
Как выбрать автоподъемник?
Автомобильные лифты являются незаменимым компонентом каждой мастерской. Профессиональные услуги включают специализированные модели: колонны, пол или ножницы, а также переносные гидравлические подъемники. Эти последние не могут отсутствовать и в домашней комнате инструментов. Это незаменимый инструмент в любой ситуации, когда вам нужно поднимать автомобиль и ремонтировать тормоза, заменять подшипники или просто менять колесо. – Эти устройства доступны во многих вариантах. Они позволяют легко помещать устройство под машину, а когда вы устанавливаете его в нужное место, поднимите автомобиль, – добавляет эксперт.
Обзор самодельных станков для домашней мастерской — видео
Такая техника в изобилии предлагается специализированными магазинами.
Оснастив рабочее место таким арсеналом, вы сможете изготовить все, что угодно. Но высокая стоимость инструмента сводит на нет экономию при производстве поделок.
Остается одно – изготовить станки своими руками. Самодельное оборудование может работать ничуть не хуже заводского. К тому же, можно внести конструктивные ноу-хау для расширения возможностей.
Самодельные станки для домашней мастерской по дереву
Токарный станок по дереву
Его можно сделать из уже имеющихся инструментов. Достаточно крепкого стола, или просто массивной доски, установленной на ножки. Это будет станина.
Зажимной шпиндель для деревянных заготовок не обязателен. Равно как и отдельный двигатель привода. Есть простое комплексное решение – электродрель.
Если имеется регулятор оборотов – вообще замечательно. В патрон закрепляется перьевое сверло по дереву. Его необходимо доработать: заточить рабочую кромку в виде трезубца.
Следующий обязательный элемент – задняя бабка. В токарных станках по металлу, она необходима для поддержки длинных болванок. При обработке дерева на станке без зажимного шпинделя, задняя бабка является фиксирующим элементом. Она прижимает болванку к трезубцу, и поддерживает ее на оси вращения.
Типовая конструкция задней бабки на иллюстрации.
Резец в таком станке не закрепляется в суппорте. Деревянные заготовки обрабатываются ручной стамеской, которая опирается на подручник.
Самодельные фрезерные станки по дереву
Сложность инструмента зависит от вида производимых работ. Для элементарной торцевой обработки достаточно просто установить ручной фрезер под ровную столешницу. Электроинструмент крепится вверх ногами, рабочая насадка выступает над поверхностью. Такие самодельные станки широко распространены среди домашних мастеров.
Важно! Промышленные инструменты проектируются и создаются с учетом мер безопасности. Вращающийся фрезер может нанести серьезную травму, поэтому крепление должно быть надежным, а зона обработки иметь защиту от попадания конечностей оператора.
Если кронштейн для ручного фрезера снабдить устройством изменения высоты, вы получите полупрофессиональное оборудование.
Есть и более сложные конструкции. Если установить надежный подвес для ручного фрезера, вы сможете выполнять сложную фигурную обработку, в том числе и по шаблонам.
Самодельные сверлильные станки. Есть удобные приспособления для дрели, которые превращают ручной инструмент в стационарное оборудование. Но такие стойки опять же стоят денег.
Подобные приспособления несложно сделать своими руками. Один из вариантов – использование направляющих для мебельных ящиков. В сверлильном станке, главная задача обеспечить прямолинейное движение патрона по оси вращения.
Самый простой станок представляет собой направляющее приспособление, а перемещение осуществляется без дополнительных рычагов.
Одной рукой станок прижимается к заготовке, а второй – дрель опускается по направляющим. Для работы с деревом, такие станки самоделки подходят. Для обработки толстого металла, понадобится более тяжелая техника.
Как сделать самодельный сверлильный станок смотрите в этом видео
Наши «кулибины», научились использовать в качестве механизма сверлильного станка рулевые рейки от «Жигулей». Можно использовать ручную дрель, если закрепить хомутовый зажим на точках крепления рулевых рычагов.
Если вам нужен по-настоящему мощный станок, придется использовать отдельный электромотор. За основу берется та самая рулевая рейка, только вместо хомута и ручной дрели монтируется станина с патроном, ременным приводом, и мощным двигателем. Силовую установку можно взять от старой стиральной машинки, или мощного вентилятора.
Основание станка должно быть массивным, чтобы тяжелый мотор не опрокинул конструкцию. Установив на патрон и электромотор шкивы нескольких диаметров, можно регулировать скорость вращения.
Важно! Меняя коэффициент передаточного числа шкивов, вы не только снижаете скорость. Одновременно увеличивается крутящий момент.
Пользуясь этим секретом, вы сможете использовать мощные сверла при наличии среднего мотора.
Кроме работы с прикладными инструментами, часто возникает необходимость выполнять механические работы при обслуживании автомобиля. При этом вовсе не обязательно закупать оборудование для автосервиса.
Самодельные приспособления для гаража
Пресс из гидравлического домкрата
Пожалуй, самый распространенный станок для гаража – это самодельный пресс. Вещь более чем необходимая. Есть типовая регламентная операция, за которую приходится платить автосервисам.
Запрессовка (извлечение) сайлентблоков. Процедура несложная, но требует усилия в сотни килограмм. Достаточно сварить из старого профиля рамку, и вы получаете мощный пресс с усилием, равным грузоподъемности домкрата.
Достаточно обзавестись кусочками труб разного диаметра (отлично подходят обоймы от подшипников), и профессиональный съемник для сайлентблоков готов.
Простой и наглядный пример пресса из домкрата для гаражных работ
Важно! Подобное оборудование может нанести травму. Приложенное усилие 2-10 тонн, незаметно «на глазок». Если криво поставленная деталь выскочит из рамки под давлением – беды не избежать.
Еще один несложный помощник – опора, или «фиксированный домкрат». Все автолюбители знают, что работать под автомобилем, когда он опирается на домкрат, опасно.
Поэтому следует подставлять опоры, предварительно подняв кузов домкратом. Чтобы не тратить средства на покупку, приспособление можно изготовить самостоятельно.
Необходима качественная труба квадратного сечения, и болты-шпильки прочностью не ниже 8,0. Иначе их срежет под весом автомобиля.
Съемник шаровых опор
Из куска трубы и обрезков стального листа, можно изготовить самодельный съемник шаровых опор. Вещь для гаража просто незаменимая.
А для правки сверл, отверток и ножей, можно изготовить самодельные заточные станки.
Съемник шаровых опор столь необходимая вещь в гараже. Подробности изготовления в этом видео.
Просто берем небольшой электромотор (для точила мощность не нужна), подбираем подходящую станину, и крепим подручник. Опора должна обеспечивать доступ, как к радиальной, так и к торцевой части наждачного круга.
На подручник можно закрепить любой кондуктор для заточки. Для сверл и отверток – это направляющий желоб. Для ножей – плоскость с фиксируемым углом наклона.
Итог:
Для изготовления любого станка или приспособления, не понадобится много времени. Могут понадобиться аналогичные обрабатывающие станки. Их можно взять напрокат, или попросить у знакомых мастеров.
Китай Производитель подъемных платформ, Ножничный подъемник, Поставщик мобильных ножничных подъемников
Домашний подъемник
Видео
Свяжитесь сейчас
Видео
Свяжитесь сейчас
Видео
Свяжитесь сейчас
Видео
Свяжитесь сейчас
Видео
Свяжитесь сейчас
Видео
Свяжитесь сейчас
Автомобильный поворотный стол
Видео
Свяжитесь сейчас
Видео
Свяжитесь сейчас
Видео
Свяжитесь сейчас
Видео
Свяжитесь сейчас
Видео
Свяжитесь сейчас
Видео
Свяжитесь сейчас
Домашний лифт для инвалидных колясок
Видео
Свяжитесь сейчас
Свяжитесь сейчас
Видео
Свяжитесь сейчас
Видео
Свяжитесь сейчас
Свяжитесь сейчас
Видео
Свяжитесь сейчас
Ножничный подъемник
Видео
Свяжитесь сейчас
Видео
Свяжитесь сейчас
Видео
Свяжитесь сейчас
Видео
Свяжитесь сейчас
Видео
Свяжитесь сейчас
Видео
Свяжитесь сейчас
Профиль компании
{{ util. each(imageUrls, функция(imageUrl){}}
{{ }) }}
{{ если (изображениеUrls.length > 1){ }}
{{ } }}
Вид бизнеса: | Производитель/Фабрика | |
Основные продукты: | Подъемная платформа , Ножничный подъемник , Мобильный ножничный подъемник , Гидравлический подъемник , Воздушная рабочая платформа | |
Количество работников: | 52 | |
Год основания: | 2014-08-05 | |
Сертификация системы менеджмента: | ISO9001:2015, сертификат IPMS | |
Среднее время выполнения: | Время выполнения в пиковый сезон: один месяц Время выполнения в межсезонье: один месяц |
Wemet Lift Machinery Co. , Ltd. в основном производит гидравлические подъемники, подъемные рабочие платформы и т. д., поставляя специализированное подъемное оборудование и схемы как для предприятий, так и для частных лиц.
Основная продукция: ножничный подъемник, мачтовый подъемник из алюминиевого сплава, четырехстоечный автомобильный подъемник, подъемник для инвалидных колясок, вертикальный грузовой подъемник, подъемник с шарнирно-сочлененной стрелой, гидравлический доклевеллер и другие специальные индивидуальные продукты. Дизайн продукта компании и производственный опыт в течение пятнадцати лет, серия специальных технологий, разработка …
Просмотреть все
Сертификаты
3 шт.Бизнес-лицензия
Пошлите Ваше сообщение этому поставщику
* Откуда:
* Кому:
г-жа Джулия
* Сообщение:
Введите от 20 до 4000 символов.
Это не то, что вы ищете? Опубликовать запрос на поставку сейчас
Этот 22-летний парень строит чипсы в гараже своих родителей
Сэм Зелуф завершил работу над этим самодельным компьютерным чипом из 1200 транзисторов, видимым под увеличительным стеклом, в августе 2021 года.
Комбайны Sam Zeloof Машины 1970-х годов с самодельными конструкциями. Его творения показывают, на что способны мелкие производители кремния.
В августе производитель чипов Intel обнародовал новые подробности о своем плане построить «мегафабрику» на территории США, фабрику стоимостью 100 миллиардов долларов, где 10 000 рабочих будут производить новое поколение мощных процессоров, утыканных миллиардами транзисторов. В том же месяце 22-летний Сэм Зелуф объявил о своей вехе в области полупроводников. Это было сделано в одиночку в гараже его семьи в Нью-Джерси, примерно в 30 милях от того места, где в 1919 году в Bell Labs был изготовлен первый транзистор. 47.
Используя коллекцию утилизированного и самодельного оборудования, Zeloof изготовил микросхему с 1200 транзисторами. Он нарезал кремниевые пластины, нарисовал на них микроскопические узоры с помощью ультрафиолетового света и вручную погрузил их в кислоту, документируя процесс на YouTube и в своем блоге. «Возможно, это излишняя самоуверенность, но у меня менталитет, что другой человек понял это, поэтому я тоже могу, даже если это займет у меня больше времени», — говорит он.
Чип Зелуфа был его вторым. Первую, гораздо меньшую, он сделал в старшей школе в 2018 году; он начал делать отдельные транзисторы за год до этого. Его чипы отстают от процессоров Intel на технологические эпохи, но Зелуф лишь полушутя утверждает, что он добился более быстрого прогресса, чем полупроводниковая индустрия на заре своего существования. Его второй чип содержит в 200 раз больше транзисторов, чем его первый, и темпы роста опережают закон Мура — эмпирическое правило, придуманное одним из основателей Intel, согласно которому количество транзисторов на чипе удваивается примерно каждые два года.
Zeloof теперь надеется соответствовать масштабу революционного чипа Intel 4004 1971 года, первого коммерческого микропроцессора, который имел 2300 транзисторов и использовался в калькуляторах и других бизнес-машинах. В декабре он начал работу над временной схемой, способной выполнять простые сложения.
Зелуф говорит, что упрощение работы с полупроводниками будет способствовать появлению новых идей в области технологий.
Фотография: Sam Kang
За пределами гаража Zeloof пандемия вызвала глобальную нехватку полупроводников, что привело к замедлению поставок продукции от автомобилей до игровых консолей. Это вызвало новый интерес политиков к восстановлению мощностей США по производству собственных компьютерных чипов после десятилетий офшоринга.
Самые популярные
Микросхемы, собранные в гараже, не помогут вашей PlayStation, но Зелуф говорит, что его необычное хобби убедило его в том, что чипы принесут пользу обществу. сделать его более доступным для изобретателей без многомиллионных бюджетов. «Этот действительно высокий барьер для входа сделает вас очень склонным к риску, а это плохо для инноваций», — говорит Зелуф.
Зелуф начал делать свои собственные микросхемы в старшей школе в 2016 году. На него произвели впечатление видео на YouTube изобретателя и предпринимателя Джери Эллсуорт, в которых она делала свои собственные транзисторы размером с большой палец, в процессе, который включал шаблоны, вырезанные из виниловых наклеек, и бутылка от пятновыводителя ржавчины. Зелуф решил воспроизвести проект Эллсуорта и сделать следующий шаг, который ему казался логичным: перейти от одиночных транзисторов к интегральным схемам — скачок, который исторически занимал около десяти лет. «Он сделал квантовый скачок дальше», — говорит Эллсворт, ныне генеральный директор стартапа дополненной реальности под названием Tilt Five. «Огромная ценность в том, чтобы напомнить миру, что эти отрасли, которые кажутся настолько недосягаемыми, начинались с чего-то более скромного, и вы можете сделать это сами».
Производство компьютерных микросхем иногда называют самым сложным и точным производственным процессом в мире. Когда Зелуф начал вести блог о своих целях в отношении проекта, некоторые отраслевые эксперты написали ему по электронной почте, что это невозможно. «Причиной для этого была честность, потому что я думал, что это будет забавно», — говорит он. «Я хотел сделать заявление о том, что мы должны быть более осторожными, когда слышим, что что-то невозможно».
Семья Зелуфа поддерживала его, но в то же время была осторожна. Его отец попросил знакомого инженера-полупроводника дать несколько советов по безопасности. «Моей первой реакцией было то, что ты не можешь этого сделать. Это гараж», — говорит Марк Ротман, посвятивший 40 лет разработке микросхем, а сейчас работающий в компании, разрабатывающей технологии для OLED-экранов. Первоначальная реакция Ротмана смягчилась, когда он увидел прогресс Зелуфа. «Он сделал то, что я никогда бы не подумал, что люди могут сделать».
Проект Zeloof включает в себя как историю, так и инженерию. Производство современных микросхем происходит на предприятиях, чьи дорогие системы вентиляции и кондиционирования воздуха удаляют все следы пыли, которая может повредить их оборудованию стоимостью в миллиарды долларов. Зелуф не мог сравниться с этими методами, поэтому он читал патенты и учебники 1960-х и 70-х годов, когда инженеры компаний-первопроходцев, таких как Fairchild Semiconductor, изготавливали микросхемы на обычных верстаках. «Они описывают методы с использованием лезвий X-Acto, ленты и нескольких стаканов, а не «У нас есть эта машина стоимостью 10 миллионов долларов размером с комнату», — говорит Зелуф.
Зелуфу также пришлось оснастить свою лабораторию старинным оборудованием. На eBay и других аукционных сайтах он нашел готовую поставку дешевого оборудования 1970-х и 80-х годов, которое когда-то принадлежало закрытым калифорнийским технологическим компаниям. Большая часть оборудования требовала ремонта, но со старыми машинами легче возиться, чем с современными лабораторными. Одной из лучших находок Зелуфа был сломанный электронный микроскоп, который в начале 90-х стоил 250 000 долларов; он купил его за 1000 долларов и отремонтировал. Он использует его для проверки своих чипов на наличие дефектов, а также наноструктур на крыльях бабочки.
Самые популярные
Zeloof чинит устаревшее оборудование, купленное в Интернете, включая электронный микроскоп, для изготовления своих чипов.
Фотография: Сэм Канг
Иногда Zeloof приходилось импровизировать. Как и в настоящей фабрике микросхем, он хотел перенести свои микроскопически детализированные проекты на свои устройства, используя процесс, называемый фотолитографией. Он включает в себя покрытие будущего чипа светочувствительным материалом и использование такого устройства, как сверхточный проектор, для прожига шаблона, который будет направлять последующие этапы обработки. Машины для фотолитографии стоят дорого — до 150 миллионов долларов, — поэтому Зелуф сделал свое собственное, прикрутив модифицированный проектор для конференц-зала, купленный на Amazon, к микроскопу. Он проецирует его проекты в крошечном масштабе на кремниевые пластины, которые Зелуф покрывает материалом, чувствительным к ультрафиолетовому излучению.
В 2018 году Зелуф разработал свой первый чип, простой усилитель с шестью транзисторами, во время урока физкультуры после того, как замещающий учитель направил учеников выполнять классную работу. Примерно через 12 часов работы и 66 шагов в гараже он получил Z1. На нем были изображены три танцующих медведя, которые являются символом Grateful Dead и теперь появляются на всех фишках Zeloof в знак благодарности Ротману, фанату группы.
В Z1 использовались транзисторы, которые Zeloof называет «прямо из 1970-х», с характеристиками размером всего 175 микрон, что примерно равносильно волоску. Он включил микросхемы в печатную плату, которая мигает одним светодиодом и гитарной педалью дисторшн.
В конце 2018 года Зелуф начал работать в Университете Карнеги-Меллона, взламывая части гаражного оборудования в своей комнате в общежитии, изучая электротехнику. Хотя он говорит, что соблюдал протоколы безопасности, университет возражал против рентгеновского аппарата в его комнате в общежитии. Во время поездок домой он модернизировал свою установку, готовясь к установке своего второго чипа, Z2. В нем используется транзистор с более быстрым переключением, основанный на пластинах кристаллического кремния, известного как поликремний, который стал доминирующим в 19 веке.70-е годы.
Самые популярные
Компания Zeloof скрутила вручную вырезанные полудюймовые квадраты поликремния, каждый из которых стал отдельным чипом, на небольшой самодельный поворотный стол на 4000 оборотов в минуту, чтобы покрыть их со светочувствительным материалом, необходимым для переноса его рисунка на поверхность. Затем его самодельная фотолитографическая машина сияла на его конструкции: сетка из 12 цепей, по 100 транзисторов в каждой (и танцующий медведь), всего 1200 транзисторов.
Первый чип Zeloof, Z1, был сделан в 2018 году, когда он еще учился в старшей школе, и состоит из шести транзисторов.
Фотография: Сэм Канг
Его второй чип, Z2, был закончен в августе 2021 года и имеет 1200 транзисторов.
Фотография: Сэм Канг
Zeloof работает над Z3, чипом, который будет способен складывать 1 + 1, как шаг к полноценному микропроцессору.
Фотография: Sam Kang
Затем каждый чип был протравлен кислотой и прокален в печи при температуре около 1000 градусов Цельсия, чтобы пропечь атомы фосфора, чтобы отрегулировать его проводимость. Еще три раунда под фотолитографической машиной, разделенные этапами, включая время в вакуумной камере, заполненной светящейся фиолетовой плазмой для вытравливания поликремния, завершили каждый чип. Сегодняшние коммерческие фабрики производят микросхемы в целом аналогичным образом, используя последовательность шагов для постепенного добавления и удаления материала в разных частях конструкции. Эти чипы намного сложнее, с миллиардами гораздо меньших транзисторов, тесно связанных друг с другом, и шаги выполняются машинами, а не вручную. Транзисторы на чипах Зелуфа второго поколения были примерно в 10 раз быстрее, чем на его первом, и имели характеристики всего 10 микрон, что немногим больше эритроцита.
В августе Зелуф протестировал Z2, подключив его к квадратному бежевому полупроводниковому анализатору, выпущенному Hewlett Packard примерно за два десятилетия до его рождения. Серия плавно нарастающих кривых ток-напряжение на светящемся зеленом экране сигнализировала об успехе. «На эту кривую было потрясающе смотреть, — говорит Зелуф, — первый признак жизни после того, как вы целый день окунаете этот маленький осколок кристалла в химический стакан».
Как отпраздновать, когда ваш самодельный чип заработал? «Твитни это!» — говорит Зелуф. Его проект получил множество подписчиков в Твиттере и миллионы просмотров на YouTube, а также несколько полезных советов от ветеранов 19-го века.Полупроводниковая промышленность 70-х годов.
Зелуф говорит, что не знает наверняка, чем он хочет заниматься после выпуска этой весной, но он думал о том месте, которое может занять самодельное производство микросхем в современной технологической экосистеме. Во многих отношениях самостоятельные эксперименты никогда не были более эффективными: робототехника и 3D-принтеры легко покупаются, а удобное для хакеров оборудование, такое как микроконтроллер Arduino и Raspberry Pi, хорошо зарекомендовало себя. «Но чипы по-прежнему производятся где-то на большом заводе, — говорит Зелуф. «Был небольшой прогресс в том, чтобы сделать это более доступным».
Эллсуорт, чьи самодельные транзисторы вдохновили Zeloof, говорит, что создание высококачественных чипов вручную может принести пользу. «Инструменты, которые у нас есть сегодня, могут сделать это доступным для небольших операций, и я думаю, что для некоторых проблем это имеет большой смысл», — говорит она. Эллсворт говорит, что технология чипов, которую ведущие фабрики считают устаревшей, все еще может быть полезна инженерам.
Zeloof недавно модернизировал свою фотолитографическую машину, чтобы печатать детали размером около 0,3 микрона или 300 нанометров, что примерно соответствует уровню производства коммерческих чипов в середине 90-х годов. 0 с. Теперь он думает о функциях, которые он мог бы встроить в чип в масштабе исторического Intel 4004. «Я хочу продвинуть гаражный кремний дальше и открыть умы людей для возможности того, что мы можем делать некоторые из этих вещей дома», — говорит он. .
Еще больше замечательных историй WIRED
- 📩 Последние новости о технологиях, науке и многом другом: получайте наши информационные бюллетени!
- Гонка за «зеленым» гелием
- Ковид станет эндемическим. Что происходит сейчас?
- Год спустя политика Байдена в отношении Китая очень похожа на политику Трампа
- 18 телешоу, которые мы с нетерпением ждем в 202
- Как защититься от смишинг-атак
- 👁️ Исследуйте искусственный интеллект, как никогда раньше, с нашей новой базой данных
- 📱 Разрываетесь между новейшими телефонами? Не бойтесь — ознакомьтесь с нашим руководством по покупке iPhone и любимыми телефонами Android
Том Симонит — старший редактор, который редактирует деловые новости WIRED.