Самодельный токарный станок по металлу – Дом, дача, огород. – Каталог статей
Многие узлы и детали этого самодельного станка для обработки металлических деталей аналогичны тем, что были использованы в токарном станке по дереву. Поэтому по ходу описания будут ссылки к предыдущей публикации.
Два коротких 7 и два длинных швеллера 1 соединены между собой так, что образуют жесткую прямоугольную раму или, как ее еще называют, станину станка. На левом конце рамы укреплена неподвижная передняя бабка 9, а на правом конце опора 12. И передняя бабка, и опора имеют втулки, в которые вставлена ходовая труба 2. Она названа так потому, что по ней перемещаются задняя бабка 3 и суппорт 5.
Шпиндель передней бабки такой же, как и у токарного станка по дереву. Для закрепления деталей на нем устанавливаются поводковый патрон или планшайба 14. Приводится во вращение он от электрического двигателя 8 с помощью клиноременной передачи. Мощность двигателя 500 Вт или немного больше с частотой вращения вала до 3000 мин-1.
При обработке древесины токарь держит резец руками. При точении же металла поступать так нельзя — усилия, возникающие при снятии металлической стружки столь велики, что удержать резец не хватит силы. Поэтому его крепят в резцедержателе, который должен перемещаться как вдоль обрабатываемой детали от одной бабки к другой (обычно от задней к передней), так и поперек. Резцедержатель устанавливается на суппорте и перемещается поперек него по направляющим типа «ласточкин хвост», а суппорт движется вдоль станка вращением ходового винта 13, закрепленного в подшипниках на передней бабке 9 и опоре 12. На правом конце винта предусмотрен небольшой маховичок 5. Вращая его рукой, и перемещают суппорт в нужном направлении. А чтобы выдержать точность, за маховичком установлено кольцо с делениями. Шаг резьбы равен 2 мм, а при повороте ходового винта на одно деление суппорт переместится на 0,05 мм. Отсчитывать перемещение резца на большие расстояния будет удобнее, если около каждой четвертой риски (а их всего 40) нанести цифры 0,2, 0,4 мм и т.
Рис. 4. Детали самодельного токарного станка по металлу.
Кроме резцедержателя, на суппорте установлен лампа 10 в защитном колпаке-отражателе и сетчатый экран 11, защищающий токаря от стружки.
При точении длинных деталей трудно получить одинаковый диаметр по всей длине — от усилия резца дёталь прогибается. В этом случае рекомендуется использовать люнет 16, опорные кулачки которого подпирают обрабатываемую деталь. Люнет передвигается по опорной трубе вдоль детали и закрепляется в нужном положении, как и задняя бабка.
Для сбора стружки под рамой станка устанавливается поддон 4.
Рис. 5. Детали самодельного токарного станка по металлу.
Корпуса передней и задней бабок станка немного длиннее аналогичных корпусов токарного станка по дереву. Поэтому для прочности рекомендуется соединять детали корпуса между собой с помощью сварки. Чтобы избежать перекосов от внутренних напряжений в сварных швах, лучше сварить из двух швеллеров длинную колонну. Только потом от нее отрезаются заготовки нужной длины. На этих заготовках проводится разметка центров будущих отверстий. Особенно тщательно следует разметить отверстия под шпиндель, пиноль и втулки.
Шпиндель, детали его крепления и шкивы у станков одинаковые, поэтому делать новые необязательно, если вы построили токарный станок по дереву. Подойдет по своим характеристикам и электрический двигатель.
Возможности станка можно существенно увеличить, если в дополнение к уже имеющемуся сделать еще один шпиндель для крепления стандартного трехкулачкового патрона.
Рис. 6. Суппорт самодельного токарного станка по металлу.
В пиноли задней бабки целесообразно предусмотреть конические отверстия (так называемый конус Морзе). Они бывают разного размера. Для самодельного токарного станка подойдет отверстие под конус № 1. Его размеры приведены на рисунке 4. В него удобнее устанавливать различные приспособления и инструменты, имеющие конический хвостик. Конус Морзе проще всего изготовить специальной разверткой.
Чтобы легче было извлекать инструмент, винт, перемещающий пиноль, необходимо удлинить, для чего на его конце необходимо проточить цилиндрический хвостовик диаметром 7 мм.
Задняя бабка фиксируется на раме специальной рукояткой. При повороте винт прижимает ее с помощью вкладыша к ходовой трубе. Такое же устройство используется для фиксирования пиноли и люнета. Все перечисленные узлы состоят из одинаковых деталей, и изготовить их не составит труда. Постарайтесь добиться, чтобы поверхность деталей была гладкая, с минимальными зазорами между собой.
Рис. 7. Измерения с помощью часового индикатора.
Корпуса обеих бабок, суппорта и опоры проще всего изготовить из швеллеров № 12 и 14 с плоскими полками. Для ходовой трубы подойдет стальная труба с наружным диаметром 70 мм и толщиной стенки 5 мм. Ходовые винты необходимо выточить из качественной стали. Подшипники для них изготавливаются из бронзы. Маховички могут быть сделаны из любого алюминиевого сплава. На прочие детали идет конструкционная сталь, например сталь Ст. 45. Отрезая заготовки, не забудьте оставить припуски на обработку и подгонку деталей.
Вы можете встретить затруднения при изготовлении суппорта, имеющего направляющие типа «ласточкин хвост». Но работу можно упростить, разделив сложную деталь на два отдельных, более простых элемента. Между собой они собираются на винтах М8 или М10 с потайной головкой.
Ходовые винты нарезаются плашкой. Если есть возможность использовать токарный винторезный станок, то лучше конечно, воспользоваться им и нарезать трапецеидальную резьбу. Такие винты и работают лучше, и меньше изнашиваются. Напоминаем, что на всех ходовых винтах резьба должна быть левой, чтобы при вращении маховичков резец перемещался в том же направлении, что и у заводских станков.
В конструкции станка есть детали, изготовленные из крупных заготовок. К ним относятся резцедержатель, узлы его перемещения, патрон и многие другие. Но можно поступить проще, сделав их составными.
Рис. 8. Детали к самодельному токарному станку по металлу.
Точность станка зависит не только от точности изготовления отдельных деталей, но и от точности сборки. Эту операцию следует проводить в следующей последовательности. Вначале в переднюю бабку установите узел шпинделя. Затем саму бабку закрепите на ходовой трубе болтом Ml0, для чего посередине опорной втулки просверлите отверстие и нарежьте резьбу. Оси шпинделя и ходовой трубы должны быть строго параллельны. Достигается это тщательной обработкой места крепления фланца опорной втулки и установкой прокладок. Параллельность измеряется с помощью часового индикатора, как показано на рисунке 7. Добившись необходимой точности, приступайте к сборке рамы станка. Она, как помните, состоит из двух коротких 7 и двух длинных швеллеров 1.
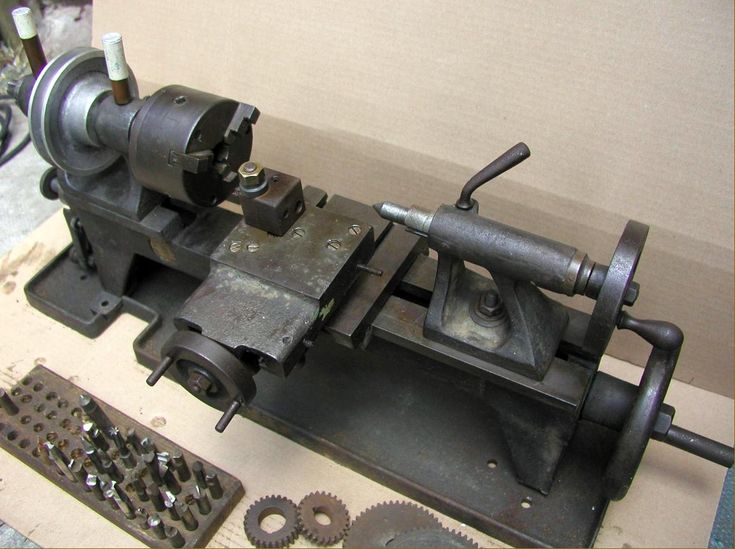
Рис. 9. Детали к самодельному токарному станку по металлу.
Далее приступайте к установке задней бабки. Проследите, чтобы не произошло смещения осей шпинделя и пиноли задней бабки, иначе при точении вместо цилиндрической будет получаться коническая поверхность. Добейтесь, чтобы оси шпинделя и пиноли лежали на одной прямой, которая, в свою очередь, должна быть параллельна поверхности ходовой трубы. Установите опорную планку, предохраняющую бабку от проворачивания. Грубая регулировка должна производиться передвижением планки, точная — подбором толщины стальных прокладок. При совмещении центр шпинделя должен совпасть с центром пиноли. Правильно отрегулированная бабка должна легко — от руки — перемещаться по ходовой трубе. Качество сборки проверьте часовым индикатором.
При сборке суппорта не требуется высокая точность. Прежде всего установите и отрегулируйте ходовые втулки так, чтобы горизонтальная поверхность корпуса при перемещении была параллельна оси ходовой трубы. Затем установите и отрегулируйте положение опорных планок. Если станок будет эксплуатироваться интенсивно, то для облегчения ремонта и регулирования сделайте планки разъемными — по типу тех, что установлены на задней бабке.
Далее приступайте к установке ходовой гайки и ходового винта. Для выполнения этой операции нужно осторожно снять передний длинный швеллер, чтобы не сбить настройку станины. Наверните гайку на винт и предварительно закрепите его на суппорте. Затем установите подшипники винта на передней опоре. Регулируя взаимное положение гайки, винта и подшипников, добейтесь легкости хода суппорта по всей длине. Последняя операция — установка механизма перемещения резцедержателя. Особой сложностью эта операция не отличается. Нужно только добиться, чтобы резцедержатель перемещался строго перпендикулярно оси ходовой трубы. Закончив работу, установите передний длинный швеллер на свое место.
Станок готов. Теперь следует его покрасить. Красить нужно осторожно, чтобы краска не попала на те детали станка, по которым скользят бабка и суппорт. Будет лучше, если перед покраской вы покроете их толстым слоем консистентной смазки.
Перед работой станок обязательно нужно закрепить на прочном массивном столе или верстаке. Нельзя начинать работу, не убедившись, что деталь в патроне зажата крепко. Для точения следует применять правильно и остро заточенные резцы. Не пытайтесь останавливать станок руками или какими-либо предметами. Нужно дождаться, пока шпиндель остановится сам. Перед работой наденьте на глаза очки и плотно застегните манжеты на рукавах. Работать в незастегнутой рубашке, в галстуке, с непокрытой головой недопустимо. Перед тем, как включить станок, проверьте, смазан ли он. Шпиндель смазывается жидкой смазкой, а пиноль и направляющие — консистентной. Окончив работу, уберите стружку и протрите ветошью все неокрашенные детали станка.
Приложение к «ЮТ» № 4 1986 г.
Делаем токарный станок по металлу и дереву своими руками
1 Токарный станок по дереву материалы
Сейчас можно купить токарный станок по дереву и по металлу на любой вкус (и за любую стоимость). Конечно же, добавляют к станку множество самых современных и дополнительных функций (которые чаще всего и не нужны).
Не спорю токарный станок – весьма нужная и полезная вещь для мастерской, но в 90% случаев он не стоит потраченных на него денег.
Так же можете изучить статью о создании столярной мастерской своими руками
Мы же хотим вам помочь сэкономить ваши финансы. Ради чего покупать модель с множеством ненужных функций, если можно сделать самостоятельно стандартную простую модель?
Сама конструкция состоит из следующих частей (смотрите на рисунке)
- Станина – является основой для станка, обычно изготовляется металлической и представляет собой несколько соединенных балок.
- Поперечная П — образная балка.
- Электрический двигатель – служит источником питания для правильного движения округ своей оси (подходят однофазные моторы мощностью от 200-400 Ватт).
- Токарный патрон.
- Опора для задней бабки.
- Элемент что крутится.
- Упор для заготовки или инструмента.
- Упор для подручника.
- Направляющие балки.
- Угол, стойка или опора для задней бабки.
- Обойма.
- Металлическая пластина под упор.
- Деталь поперечной направляющей.
- Винтики для закрепления.
- Опорная ось.
Прежде всего, можно не покупать новый мотор, а взять б-у, он обойдется вам значительно дешевле.
Элементы закрепляют на основе (№1 по рис.) 2 п -образных балки сваркой соединяют с двумя поперечными (№2 по рис.).
Направляющие сверху дополнительно фиксируются двумя углами (№10 по рис.), которые закрепляют к основной поверхности.
Двигатель (№3 по рис.) прикрепляют боковой части и закрепляют переднюю бабку.
В качестве основы задней бабки стоит использовать крутящийся центр (купить деталь от покупного варианта) закрепить его к опоре (№5 по рис. ) и приварить на площадке (№12 по рис.)
Упор ( №5) изготавливается из уголка и прикрепляется к опоре (№8) которая сама по себе закрепляется на обойме. Упор и обойму нанизывают на опорную ось (№15) а после этого приваривают к направляющим балкам.
Тот же упор (№5) и крутящийся элемент (№6) закрепляют на металлических пластинах (№12) которые содержат специальные движущиеся обоймы (№11).
Учтите что упор и задняя бабка – это подвижные элементы, которые должны без проблем двигаться по направляющим (№9).
Чтоб подвижные элементы были хорошо прикреплены к обоймам, в обоймах делаются предварительные отверстия (№14) и малейшая неточность снижает качество работы всего аппарата.
Сама сварка может повлечь за собой деформацию материала – сначала все материалы скрепляются точечной сваркой, а затем уже проводят полную работу.
Токарный станок по дереву видео youtube.com/embed/L2sUN8iNZTU” frameborder=”0″ allowfullscreen=”allowfullscreen”> Токарный станок по металлу материалыДля изготовления такого инструмента вам будет необходимо:
- Лист металла;
- П — образные балки из металла;
- Полоски из стали;
- Углы из стали;
- Электрический двигатель;
- Передаточный механизм;
- Несколько гаек и болтов для скрепления;
- Болгарка;
Отдельно стоит сказать о двигателе, он не обязательно должен быть новый, можно ограничиться и старым или б-у, его мощность должна составлять 2 кВт с количеством оборотов минуту в пределах 2000. Хотя это больше зависит от уровня вашей работы на этом станке.
Чем массивнее заготовки – тем мощнее должен быть двигатель, если вы хотите сделать компактный станок с малой мощностью – подойдет мотор даже от стиралки или электродрели.
Что касается передаточного механизма – можно отыскать через интернет или купить у знакомых старую коробку передач и снять с коробки муфту. Таким образом, вы получите механизм, который создает вашему станку несколько скоростей. А если установить дополнительный шкив – то можно улучшить количество оборотов.
Установку стоит начать с использования стальных углов и п-образной балки, из них (1 уголок и 1 балка) нужно сварить раму для основы.
Для этого нужно расклинить основу. Направляющие собирают из квадратных труб и стальных полосок.
Помимо этого их металлического листа делают коробку для кулачного патрона, после установки в ней помещаются подшипники с регулировкой.
Заднюю бабку нужно сварить из уголка и толстой пластинки, опорой которой будут служить направляющие.
Бабка должна легко, свободно перемещаться по направляющим. К верхней части бабки приварите гайки (чтоб фиксировать поддерживающий центр).
Заточенный конус следует вмонтировать в балку, при этом соблюдая максимальную точность. Такой конус можно изготовить из любого болт, который подходить вам размером.
После этого собирают всю конструкцию, проверяют на легкость вращения шпинделя, регулирую передний и задний центры для создания ровной оси.
Теперь вы знаете, что построить станок для дерева или металла вполне реально и требует от вас немногих знаний и усилий, и при этом он вам обойдется значительно дешевле (да и в случае поломки вы сможете самостоятельно его починить).
В целом же изготовление такого станка вам поможет даже если вы и не часто занимаетесь такими работами, единственно такие механизма весьма громоздкие и нужно место для их хранения ( или можно сделать «карманные» модели).
Токарный станок по металлу видеоСамодельные инструменты для металлообработки – HomemadeTools.net , оправочный пресс, Arduino, сборка, автокузов, авиация, шило, ось, ленточная пила, брусок, база, аккумулятор, бортовой ролик, развальцовка, подшипник, ременный привод, ленточно-шлифовальный станок, ленточно-шлифовальный станок, шлифовальный станок, трубогиб, гибка, фаска, велосипед , черный оксид, кузнец, лезвие, воздуходувка, расточка, бурильный станок, домкрат для бутылок, открывалка для бутылок, коробка, тормоз, тормозная магистраль, пайка, протяжка, буфер, полировка, С-образный зажим, CAD, калькулятор, консервная дробилка, ролики ), литье, цемент, центровка, цепь, бензопила, фаска, шасси, шеви, долото, отрезная пила, патрон, круг, круговая резка, струбцина, очиститель, клипса, часы, ЧПУ, намотка катушки, цанга, шатун, контроллер, конверсия, копинг, медь, беспроводная, зенковка, коленчатый вал, кримпер, лом, отрезной круг, фреза, резка, режущий инструмент, резец g-горелка, цилиндр, удаление ржавчины, удаление заусенцев, съемник вмятин, штамп, напильник, шлифовальный станок, держатель штампа, пуансон, углубление, разборка, диск, дисковый шлифовальный станок, разделитель, тележки, тележка, дверь, дюбель, вытяжные штампы , тяговое устройство, инструмент для правки, дрель, сверло, сверлильный станок, сверление, краевой искатель, кромочный ролик, обрезной станок, электрика, электроника, гравер, травление, травление, травильный карандаш, расширитель, экстрактор, изготовление, сельскохозяйственные инструменты, забор, крылья, файл, Подшивка, Наполнитель, Конец, Пригонка, Крепление, Фланец, Вспышка, Мухобойка, маховик, Кузница, Ковка, Рамка, Фуллер, Шестерни, Мясорубка, Шлифование, Канавка, Охранять, руководство, Гильотинный инструмент, Оружейное дело, Ножовка, Забивать , ручной инструмент, ручка, выносливый, термообработка, шестигранник, петля, прижим, держатель, удерживающий, отверстие, коронка, перенос отверстия, крюки, шланг, ступица, гидравлический, двутавр, ударник, домкрат, ювелирный, кондуктор , электролобзик, полотно электролобзика, ключ, шпоночный паз, нож, накатка, токарный станок, газонокосилка, раскладка, свинец, листовая пружина, линишер, замок, стопорение, жалюзийный пресс, мехобработка, магнит, лупа , молоток, оправка, маркировка, измерение, металлообработка, металлообработка, микрометр, фреза, митра, модификация, формы, мотор, мотоцикл, крепление, мультитул, насечка, высекатель, масло, оптический, духовой шкаф, покраска, пантограф, пикет-твистер, шестерня , труба, трубогиб, рихтовочный молоток, плазма, плита, тигельный стол, обшивка, плоскогубцы, пневматический, полировальный станок, полировальный, переносной, позиционер, силовой молот, блок питания, пресс, пропан, протектор, монтировка, съемник, шкив, Pullmax, насос, пуансон, закалка, стойка, радиус, развертка, арматура, переработка, перегрузка, удаление, ремонт, восстановление, кольцевой ролик, заклепка, каркас безопасности, ролик, прокатный стан, роторно-отрезной круг, поворотный стол, роторный инструмент, фрезер, фрезер стол, ржавчина, средство от ржавчины, удаление ржавчины, безопасность, мешок с песком, шлифовальный станок, шлифовальный блок, наждачная бумага, пила, козлы, шкала, скребок, удаление винтов, спиральная пила, формирователь, заточка, ножницы, листовой металл, щит, магазинный пресс, термоусадочная машина/ носилки, термоусадка, шлепалка, салазки, скользящий молоток, скользящий ролик, продольная пила, гнездо, шпиндель, с горшок, разбрасыватель, пружина, звездочка, угольник, накладка, штамп, подставка, люнет, упор, накопитель, прямая, ленточный дубликатор, шпилька, опора, поверхность, обжимной блок, переключатель, стол, настольная пила, задняя бабка, бак, конус, нарезание резьбы, шаблон, третья рука, резьбонарезной станок, наконечники, титан, инструмент, держатель инструмента, резцедержатель, подручник, горелка, трактор, трансмиссия, ножной молоток, дерево, труба, трубогиб, труборез, трубный ролик, трубка , подворачивание, тумблер, точение, клиновой блок, вакуум, вентиль, тиски, приспособления тисков, тиски-захваты, шайба, часовое дело, вес, сварщик, сварка, сварочный стол, колесо, лебедка, намотка, инструмент для зачистки проводов, верстак, верстак, ключ
самодельные инструменты для металлообработки | Блог GordsGarage
Опубликовано: 27 марта, 2012 в Механические работы, Инструменты и оборудование, Сварочные работы
Метки: трубогиб, Gord’s Garage, gordsgarage, самодельные металлообрабатывающие инструменты, самодельный спиральный гибочный станок, Механическая обработка, изготовление металла, металлообработка, декоративный, спиральный гибочный станок, сварка
Сгибатель прокрутки был в моем списке инструментов, которые я должен приобрести уже довольно давно. Я просмотрел все модели с ручным управлением, доступные для домашних парней и тех, у кого ограниченный бюджет. Все они работают примерно одинаково и не требуют ничего большего, чем сгибание плоского или круглого стержня вокруг матрицы прокрутки. Я постоянно колеблюсь между покупкой или созданием. Я думаю, что самая большая проблема при изготовлении одного из них – это создание самого кубика, как вы увидите, если будете читать дальше.
Обычно я начинаю свои сообщения с введения, продолжаю сборку и заканчиваю результатом. Ну сядь и держись, потому что сегодня я переключаю его! Давайте начнем с видео? Я покажу вам, что у меня получилось, а затем вы сможете решить, хотите ли вы читать дальше. Следующее видео, которое я снял после создания моей собственной версии сгибателя прокрутки. Я согнул кусок горячекатаного плоского проката размером ½” x 1/8”. Взглянем.
Итак, приступим к сборке. Каковы были критерии? Ну, я хотел, чтобы это была универсальная штуковина. Я не хотел создавать что-то, посвященное одному кубику, я хотел быть уверенным, что смогу что-то поменять, если понадобится. Я также хотел, чтобы мой рабочий конверт оставался чистым. Многие из имеющихся в продаже спиральных гибочных станков используют Т-образную рукоятку, прикрепленную к центру матрицы, чтобы оператор мог поворачивать матрицу. Я хотел придумать какой-нибудь способ сделать все как можно более ясным и открытым.
Итак, я начал рыться, чтобы посмотреть, что я ковыряю в поисках металла. У меня был кусок прямоугольной стальной трубы размером 3 x 1,5 x 0,065 дюйма, а также несколько старых велосипедных шестерен и цепь. Я также смог откопать старый сломанный удлинитель храповика на ½ дюйма, который может пригодиться. Похоже, у меня есть все, что мне нужно, за исключением пары подшипников с фланцем 5/8 дюйма, как у некоторых приводных ступиц 5/8 дюйма. Поездка к местному поставщику принесла мне оставшиеся компоненты, и я был готов к работе.
Итак, как вы уже поняли из видео, я планировал интегрировать промежуточный вал для привода главного вала. Я использовал пару звездочек от старой велосипедной кассеты и обточил пару приводных ступиц, чтобы они подходили для звездочек. Затем звездочки были приварены к ступицам с помощью сварки TIG. Сварные швы ложились так хорошо, что вместо того, чтобы прибить первую звездочку, я намотал вокруг нее полный валик. Ошибка … Я должен был знать, что звездочка выглядела как переднее колесо моего горного велосипеда с тако после того, как я врезался в это дерево в прошлом году. Да… слишком много тепла для маленького парня, у него не было другого выбора, кроме как деформироваться. Нет проблем, много кассетных передач в запасе. Я вырезал волнистую звездочку и прикрепил новую, намного лучше. Что касается передачи, я не стал слишком научным. Гибочные станки обычно используют соотношение 1: 1 в сочетании с Т-образной рукояткой. Ручки-тройники не большие, так как не требуется большого механического усилия. Я использовал 24 зуба для ведущей звездочки и 28 зубьев для ведомой, что дало мне общее передаточное число 1,16: 1. Я полагал, что чуть меньше 1:1 будет более чем достаточно.
Для привода зубчатой передачи я решил приспособить удлинитель ½ дюйма к механизму приводной шестерни. У меня валялся старый сломанный удлинитель на ½ дюйма, поэтому я обточил удлинитель, чтобы он подходил к обработанной втулке на 5/8 дюйма. Эти двое были женаты, и судил сварщик TIG. Теперь ведущая ступица соединяется с ведущей шестерней через шпоночный вал 5/8 дюйма.
Позаботившись о зубчатой передаче и рычаге, пришло время перейти к изготовлению штампа. Мне нужно было поддерживать штампы, а также создавать что-то, что позволяло бы мне использовать различные инструменты. Я решил построить 9Основание диаметром 0,5 дюйма и толщиной 3/8 дюйма. Таким образом, я мог просверлить отверстия в пластине, необходимые для размещения различных штампов. Базовая пластина была вырезана плазмой из металлолома с помощью моего самодельного кругового резака. Края были зачищены, а в центре было просверлено отверстие 5/8 дюйма, чтобы пластина могла опираться на верхнюю часть ведомого вала 5/8 дюйма.
Следующими были штампы, и это оказалось огромной проблемой. Я не знаю способа математически построить прокрутку в AutoCAD, я уверен, что это возможно, за исключением того, что у меня нет ноу-хау. В конце концов я нашел изображение свитка, которое я смог увеличить на бумаге и вырезать его, чтобы он служил шаблоном. Мне потребовалось много времени, прежде чем я сообразил, что нужно разрезать свиток пополам, чтобы использовать его как кубик из двух частей. Когда дело дошло до изготовления штампа, чтобы обеспечить надлежащие зазоры прокручиваемого плоского стержня, также пришлось немного потрудиться.
С помощью пластины толщиной ½ дюйма я начертил свою матрицу прокрутки, схватил плазменный резак, глубоко вдохнул и начал выдувать расплавленный металл. Мой первоначальный план состоял в том, чтобы создать шаблон MDF в качестве руководства, но в конце концов я решил вырезать прокрутку самостоятельно. При резке стали толщиной ½ дюйма у меня немного больше времени на работу с резаком, чем при резке листового металла. Резка более толстого материала происходит намного медленнее, что дает мне больше времени и лучший контроль над резкой. С помощью грубой обрезки спиральной матрицы вручную я разрезал ее пополам и обрезал большую матрицу, чтобы обеспечить зазор изогнутого плоского стержня.
Я обработал кромки матрицы как шлифовальной машиной 4 ½ дюйма, так и ленточной шлифовальной машиной. Он получился довольно круглым, однако на нем было несколько плоских пятен. Глядя на матрицу, было совершенно очевидно, что это не ЧПУ или машина. Я полагал, что несколько плоских пятен не создадут особых проблем. Что ж, я ошибся… об этом позже.
Итак, мне нужно каким-то образом соединить мою стартовую матрицу со шпоночным валом 5/8 дюйма, а также придумать способ удерживать мой плоский стержень на месте во время выполнения изгиба. Я использовал другую втулку и вырезал в ней прорезь шириной ½ x 1/8 дюйма, чтобы можно было зацепить за нее плоский стержень. Мне удалось приварить ступицу TIG к меньшей секции штампа.
Затем пришло время прикрепить 2 штампа к опорной плите. В меньшей из них было просверлено отверстие диаметром 3/8 дюйма, а затем прорезано отверстие с резьбой в опорной пластине, которое позволило бы прикрепить меньшую матрицу к пластине болтами. Большую пластину нужно было установить и снять быстро и легко, чтобы можно было быстрее катить свитки. Я решил вдавить два холоднокатаных штифта 3/8 дюйма в матрицу, а затем просверлить сопрягаемые отверстия, чтобы штифты входили в опорную плиту. Я допустил немного помоев, чтобы гарантировать, что не потребуется привязывать или подглядывать.
Последним компонентом в повестке дня был опорный ролик, позволяющий изгибать плоский стержень. Я копался в своем барахле и нашел старый ролик ремня ГРМ, идеальный! У него была большая высота, чтобы можно было использовать более крупный плоский стержень, плюс он был не слишком большим в диаметре. Я выточил стальную прокладку, чтобы она крепилась болтами, что позволяло ролику свободно двигаться. В основании из стальной прямоугольной трубы было просверлено отверстие, позволяющее установить его как можно ближе к опорной плите диаметром 9,5 дюйма. В итоге я использовал стержень с резьбой 5/16 дюйма для крепления ролика, не зная, будет ли он достаточно тяжелым.
Итак, все компоненты изготовлены, пришло время испытать гибочный станок. Плотно зажав его в тисках, я пошел и нашел лом горячекатаного плоского проката размером ½” x 1/8”. Используя 48-дюймовую секцию, я отмечал деление через каждые 6 дюймов. Я хотел знать, сколько дюймов стержня требуется, чтобы сделать изгиб. Далее я помещаю конец плоского стержня в центральную часть ступицы с выемкой и начинаю проворачивать храповик ½”. Усилие согнуть было невероятно легким, никаких проблем. Фактическая форма плоского стержня с начальным изгибом? Не так здорово. Плоская планка не будет достаточно тугой 9Изгиб на 0 градусов в центральной прорези втулки, чтобы он мог хорошо и плотно прилегать к первой матрице. Хорошо… Я думаю, для гибки потребуется трехэтапный процесс. Раунд номер 2. На этот раз я начал с того, что согнул начальный изгиб под углом 90 градусов к концу моего плоского стержня. Все, что я сделал, это зажал его в тисках и с помощью молотка сделал себе чистый, четкий изгиб. Вернувшись к сгибателю прокрутки, и, зафиксировав плоский стержень в центральной втулке, я начал проворачивать. Штанга прекрасно облегает матрицу, даже слишком хорошо.
Ранее я ныл о том, что у меня были плоские пятна на плашках ручной резки. Ну я подумал, что пятна могут остаться незамеченными в процессе изгиба. Оказывается, я был неправ. Плоский стержень так плотно и плотно прилегает к штампам, что каждый дефект штампов становится очевидным в готовом изогнутом свитке. Ну что теперь? Думаю, у меня есть несколько вариантов. Во-первых, нужно создать углубления с помощью сварочного аппарата, а затем продолжить сглаживание кривых вручную или получить штампы с ЧПУ. Пока я выберу более дешевый из двух вариантов и потрачу некоторое время на переделку штампов.