Самодельный ЧПУ станок из принтеров своими руками — Часть 2
В предыдущей статье: Как собрать ЧПУ станка на Arduino своими руками за 3000 руб – Часть 1 Были рассмотренный основные этапы сборки станка ЧПУ из принтеров на Arduino. В данном обзоре расскажу из каких деталей и комплектующих собирался данный принтер. Покажу как устроены основные узлы. А также сделаем пуск станка на Arduino. Включим шпиндель.
Схема подключения драйверов L298n к Arduino NANO
Схема подключения шагового двигателя к L298n
Схема подключения с двумя двигателями на оси X:
Самое простоя программное обеспечение для запуска станка при такое схеме подключения смотрите тут. Данный пример очень простой но у него есть достаточно большое количества недостатков.
Для сборки ЧПУ станка из деталей от принтера были использовано:
- 3 Матричных принтера формата А3.
- Мебельные направляющие: 2 пары 500 мм. И одна пара на 300 мм.
- Доска 25х100, брусок 25х25, фанера толщиной 8 мм.
- Блок питания от компьютера.
- Arduino NANO
- Драйвера L298 4 шт.
- Строительные и мебельные уголки.
- Саморезы, винты, гайки и шпилька М10.
- Телефонные провода, провода из компьютера.
- Переменный резистор из автомобиля.
- Двигатель от автомобильного компрессора.
- Шаговый двигатель от сканера.
- Латунная цанга.
Кратко что для чего применялось в ЧПУ стнке:
Ось X Ч ПУ станка сделана из двух оснований от матричных принтеров формата А3. С помощью брусков 25х25 сделана обвязка оснований принтеров и на данные бруски закреплены две мебельные направляющие длиной 500 мм. На мебельные направляющие сверху закреплен лист фанеры польщенной 8 мм.
Ось Y станка на Arduino расположена на портале,который сделан из трех досок 25х100 мм. Для перемещения используется двигатель от матричного принтера и ременная передача. Направляющие также мебельные длиной 500 мм.
Ось Z ЧПУ закреплена на направляющие оси Y. Для перемещения был использован шаговый двигатель взятый из сканера. Передача винтовая сделанная из шпильки М10. Направляющи мебельные длиной 300 мм. Соединенные под углом 90 градусов для жесткости.
Шпиндель станка ЧПУ сделан из двигателя взятого из нерабочего автомобильного компрессора. На вал двигателя закреплена цанга.
Управляет станком Arduino NANO. Драйвера L298. Для понижения напряжения с 12 вольт до 8, используются транзисторы.
Смотрите также видео:
Фрезерование на самодельном фрезерном станке ЧПУ.
portal-pk.ru
Самодельный ЧПУ фрезерный станок / DIYtimes
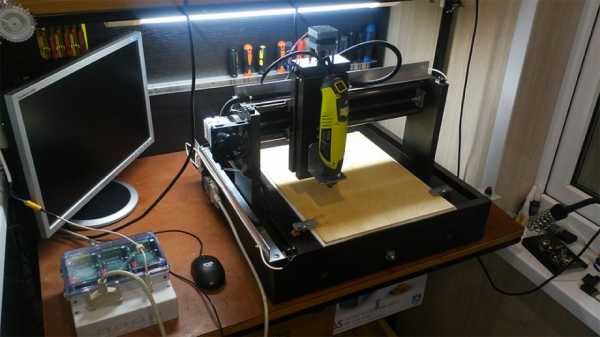
Эта статья покажет весь путь по изготовлению самодельного ЧПУ фрезеро-гравировального станка под управлением MACh4. Разберемся с конструкцией самоделки, подключения электрики и настойки программ.
Для сборки ЧПУ станка нам понадобятся направляющие из принетра EPSON – 4 штуки длинной 450 мм диаметром 14 мм и шаговые двигатели EM-181 в количестве 3 штук.
Размеры
Стол:
100х500 2шт.
100х420 2шт.
420х410 1шт.
Портал:
100х230 2шт.
100х420 1шт.
100х465 1шт.
Каретка “Z”
100х215 1шт.
95х210 1шь.
100х50 1шт.
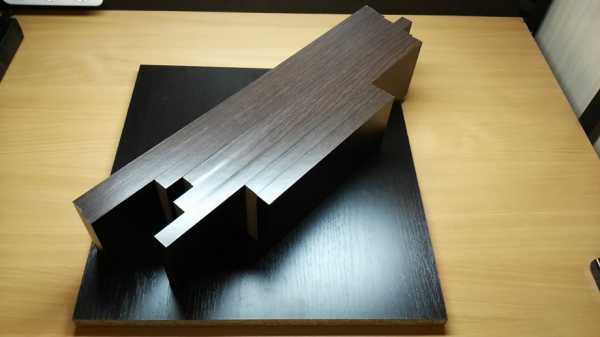
Корпус принтера будет из мебельной ДСП. Что бы улучшить эстетические характеристики нашего ЧПУ станка торцы ДСП с помощью утюга проклеим торцевой лентой. Купить ее как и ДСП можно в любом магазине мебельной фурнитуры. Детали скрепляем между собой саморезами или конфирмантами.
Для фрезерования отверстий под подшипники ходовых винтов я использовал перьевое сверло и дрель. Размер брал чуть меньше и доводил наждачкой для плотной посадки обоймы подшипника. Направляющие у меня были диаметром 14 мм, подшипники 22 мм в диаметре.
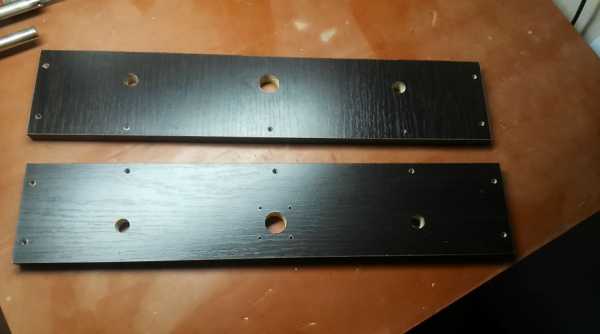
Направляющие я взял от принтера Epson с которого снял и сами валы. Сразу закреплять направляющие в корпусе не стал т.к. сложно сохранить их правильную ориентацию относительно валов, нужно иметь возможность регулировать. По тому взял сантехническую ПВХ трубу на 1/4 дюйма и зажимы для крепления на стену. Трубу разрезал на куски по 95 мм и тисками запрессовал в них направляющие. В таком виде их стало удобно регулировать и закреплять.
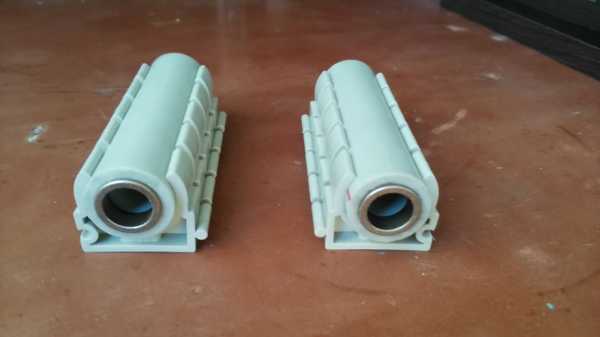
Теперь можно собрать основание ЧПУ станка. Основание лучше поставить на регулируемых ножках. Конструкция хоть и жесткая, но при точной настройке размеры могут заметно гулять если станок сдвинуть. Возможность регулировать длину ножек позволит избежать таких проблем при калибровке.
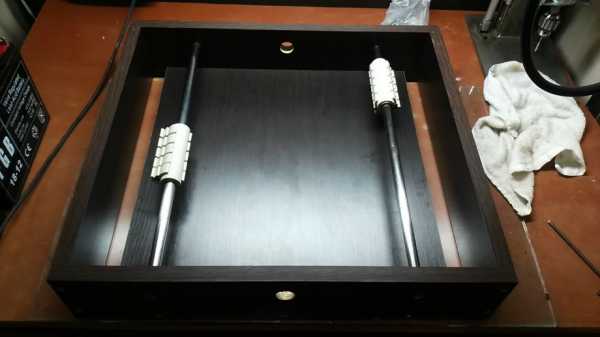
К нашим ПВХ трубкам с направляющим прикручиваем перекладину. Нужно добиться отсутствия перекосов, что бы при движении салазок по всей длине направляющих наша перекладина не подклинивала и двигался легко.
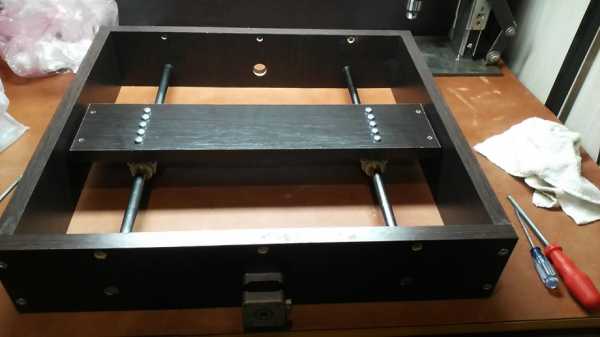
Аналогичным способом собирается вторая ось – Y. Высоту портала выбираем таким образом, что бы хватало места для закрепления фрезерного инструмента.
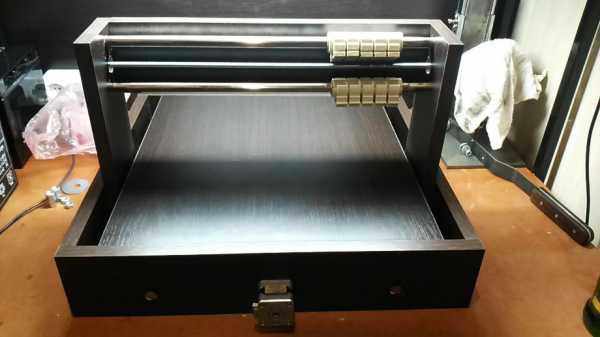
Не забываем, что хоть наш станок и деревянный, но есть детали установка которых требует высокой точности. Расстояние между установленными направляющими валами должно вымеряться штангенциркулем. Если непараллельность, то нужно растачивать отверстие шкуркой и ставить жестяные клинья. Добиваться максимальной параллельности.
Ходовые винты сделаны из обычной шпильки М8/М6. Соединение вала с шаговых двигателем выполнялось через самодельную трубчатую муфту, но лучше заказать специальные т.к. нельзя допускать жесткой фиксации валов – будут биения.
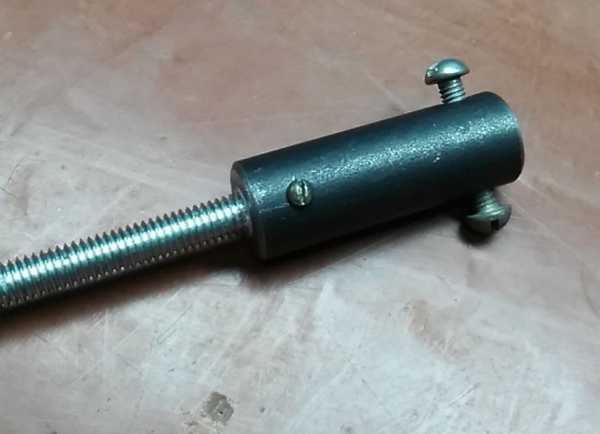
Для оси Z решено было использовать мебельные направляющие для шкафов. Они достаточно жесткие и легко монтируются. Те, что были у меня – двигались без заметного люфта.
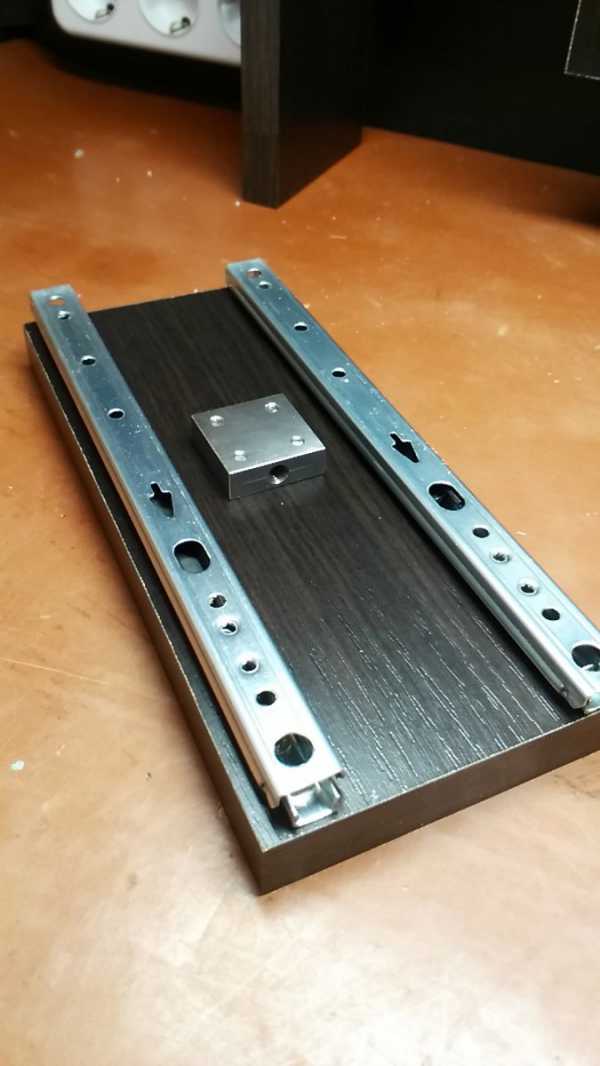
Двигатель вертикальной оси закрепляем на втулках что бы был доступ к муфте.
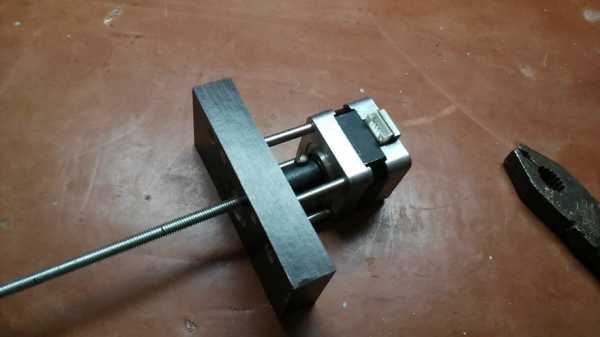
Собранная ось Z ЧПУ фрезера:
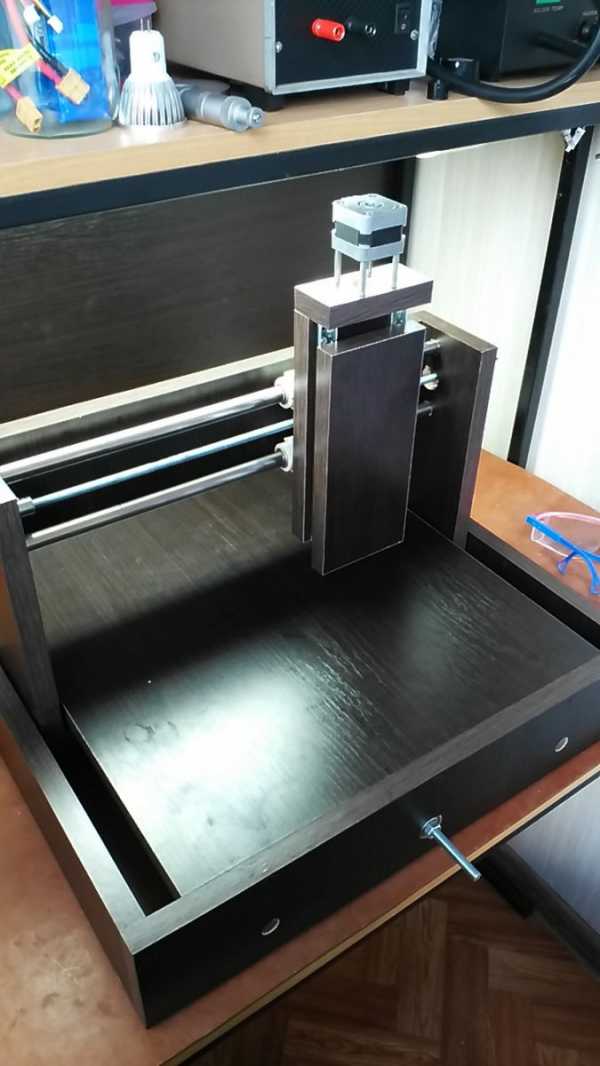
В качестве шпинделя был использован гравер-дремель. Его мощность позволяет обрабатывать дерево на малых подачах. Для более твердых материалов потребуется шпиндель большей мощности, но тогда и направляющие оси Z придется сменить.
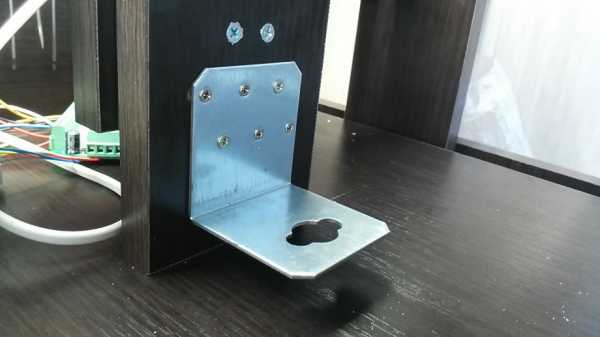
Гайки ходового винта были вытачены на токарном станке. Закреплены через строительный уголок.
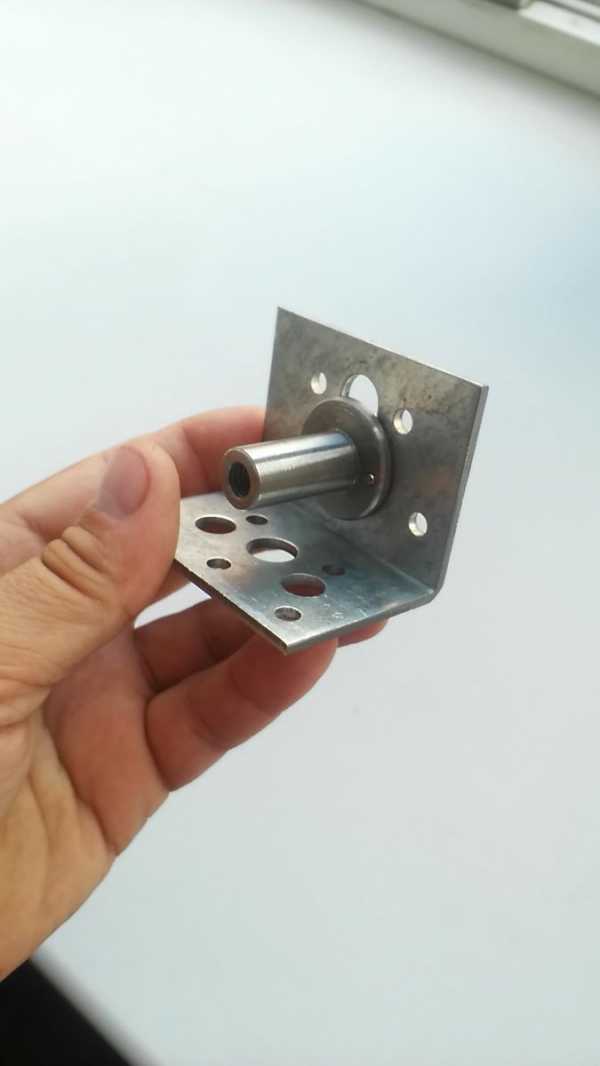
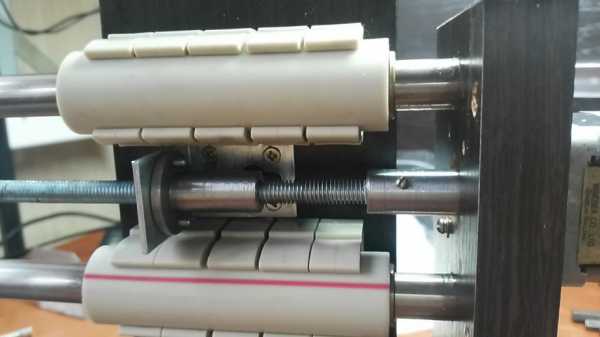
Теперь нам остается отрегулировать ходовую гайку и ходовой винт. Положение винта вымеряется так же штангенциркулем относительно направляющих валов, затягиваются. Ходовая гайка фиксируется в последний момент когда мы убедимся, что нет перекосов.
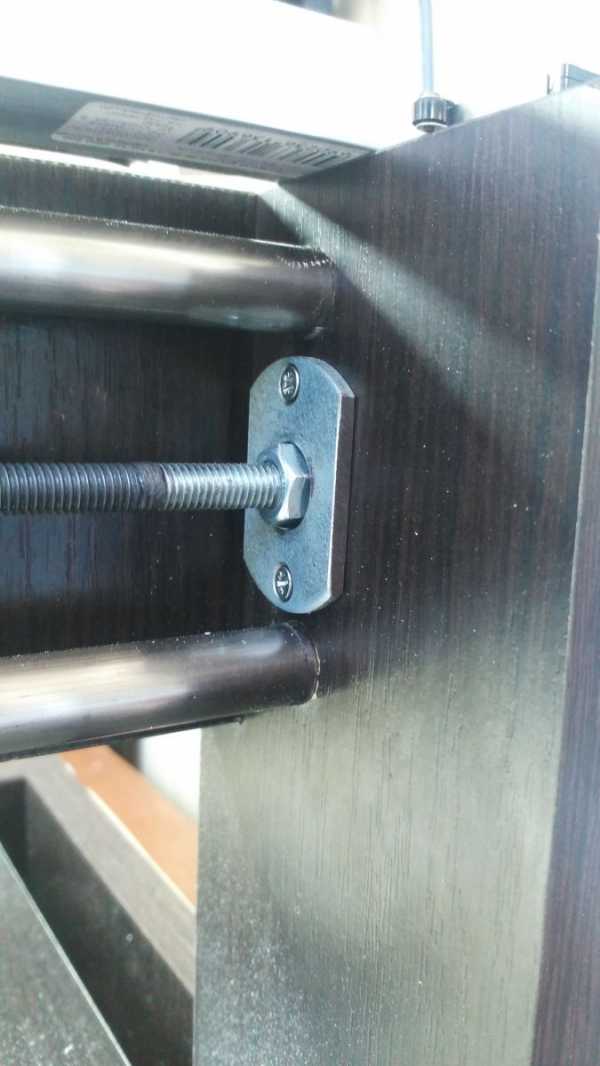
Обращу внимание, что подшипники на шпильку сажаем через подложку из жести. Зажимать гайками ее следует не сильно, что бы шпильку не выгибало в сторону. Само резьбовое соединение проклеивается бакситной смолой. Она устранит люфты и не даст раскручиваться во время работы станка.
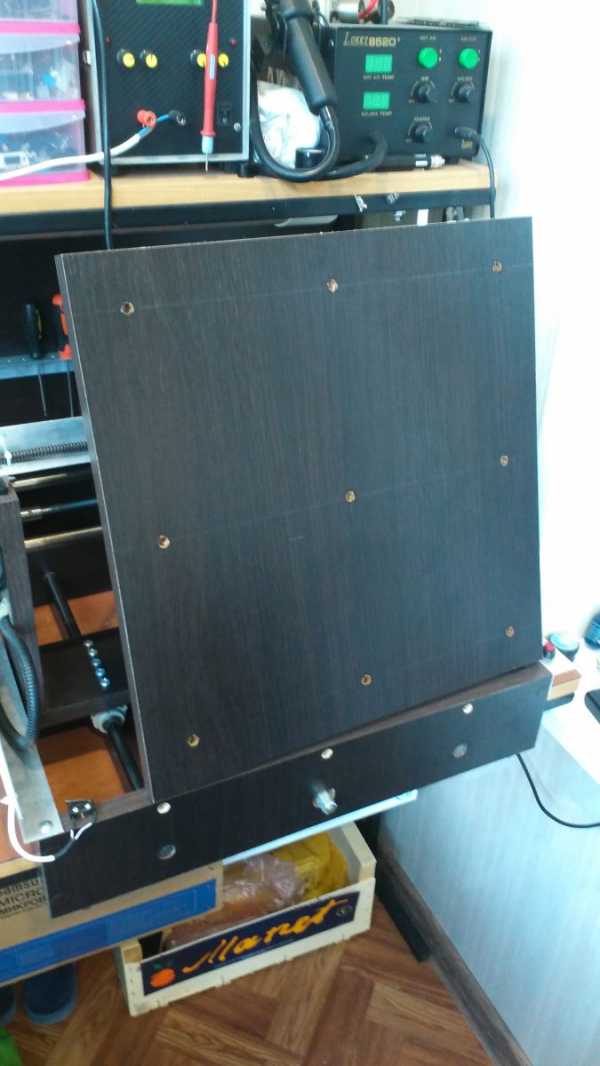
Далее нам предстоит размещение концевых выключателей (лимиты рабочего поля) подключение и настройка электроники. Изначально планировалось собирать электронику самостоятельно, но изучив схемы, стоимость комплектующих и необходимое время на изготовление плат было принято решение покупать готовое. Изучив предложения в интернете, сравнив цены были приобретены:
драйверы шаговых двигателей BL-TB6560-V2.0 $ 4.84 за 1 штуку.
Начнем с доработки двигателей. Двигатели EM-181 униполярные, это значит, что они имеют 4 обмотки соединенные определенным образом. Драйверы, которые мы используем, работают с биполярными двигателями, в которых 2 обмотки. Откручиваем 4 болта и снимаем заднюю крышку двигателя. Необходимо перерезать дорожку в обозначенном месте. Контакты обмотки 1 обозначены буквами “А” обмотки 2 буквами “В”.
Подробно описывать подключение всей электроники смысла нет, просто покажу фотографии из которых все предельно понятно. Одно только хочу заметить, что концевики не будут работать пока к плате опторазвязи кроме 5V от USB не будет подключено 12V. не знаю почему но нигде в описании я этого не нашел и долго не мог понять почему MACH не запускался.
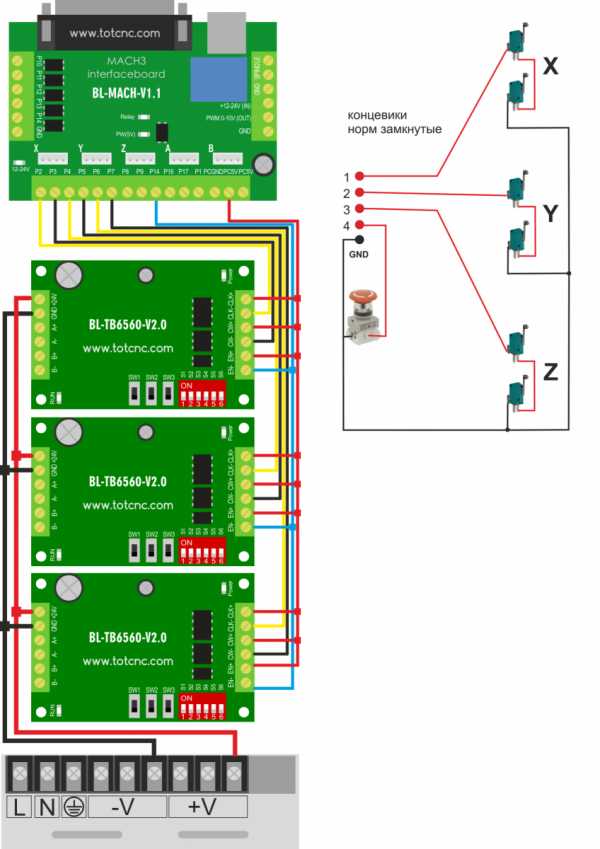
В качестве кабелеукладчика в автомагазине были приобретена пластиковая гофра диаметром около 10 мм. Кабель канал сделан из алюминиевого уголка.
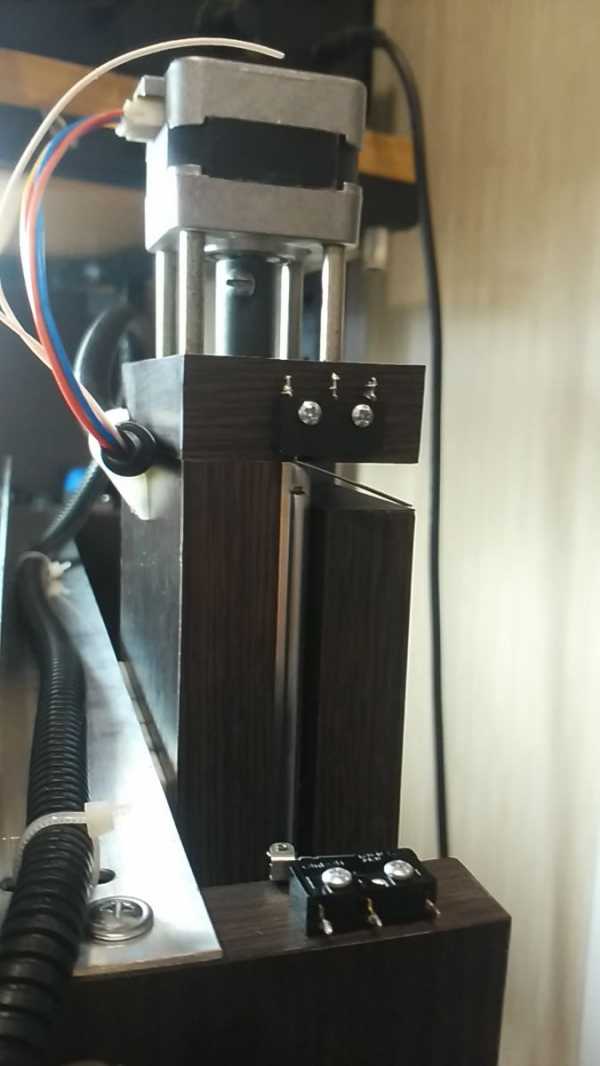
При пробных прогонах станка были неверно настроены драйверы, а точнее ток был выставлен на 3а что не понравилось двигателям и через 20 минут из них пошел дым. Для того чтобы это больше не повторилось, ток был ограничен на уровне 1.2а и были установлены радиаторы и вентиляторы охлаждения. (Позже в процессе эксплуатации выяснилось, что двигатели разогреваются сильно на малой подаче, при правильно выставленном значении тока и подаче в 10-15 мм/с. двигатели греются не сильно)
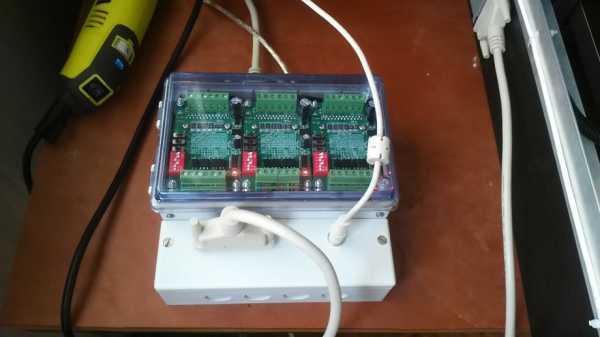
Электронику упаковываем в симпатичный корпус, нашел случайно на рынке, стоил 4$ подошел идеально.
НАСТРОЙКА MACh4
Теперь пара слов о настройке программы управления MACh4.
Установка порта:
В меню “config”(«Конфигурации») выбираем “Port and Pins” (Порты и Пины) ставим галку на нужный порт.
Частоту ядра выбираем 25000Hz чтобы разогнать станок на нормальную скорость, на драйверах устанавливаем делитель 1:8
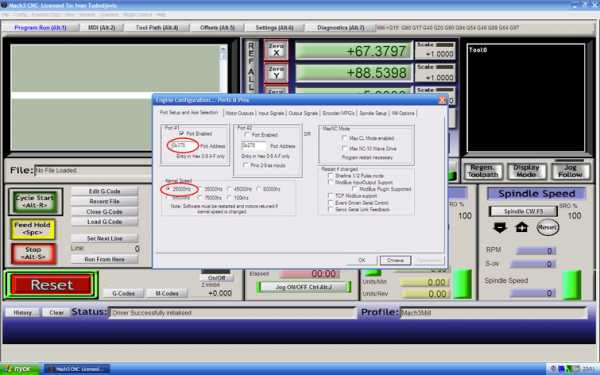
Настройка пинов управления двигателями:
Выберите вкладку “Motor Outputs”(«Выходы двигателей») Ставим галочки напротив осей X,Y,Z. Тем самым мы делаем их активными. Смотрим, к каким портам платы опторазвязки подключены наши драйверы и вписываем эти номера в поля “Step” (шаг) и “Dir” (направление) галочки “Step low active” отвечают за реверс вращения двигателей “step low active” шаг двигателя при положительном или отрицательном импульсе.
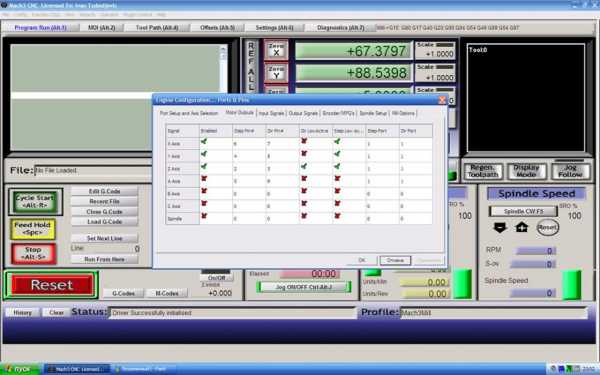
Концевые выключатели и кнопка экстренной остановки:
Концевики установленные на осях работают как индикатор достижения крайнего положения рабочего поля. Это предотвращает поломку механики. При срабатывании выключателя в процессе работы станок просто остановится.
В данном случае ось “X” подключена к 13 порту “Y” к 12 порту “Z” к 11 порту платы опторазвязки.
Кнопка E stop подключена к 15 порту и срабатывает при замыкании.
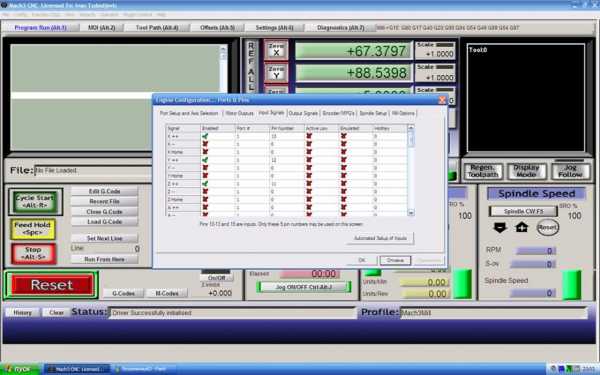
Теперь один очень важный момент. Даже если драйверы подключены правильно и пины управления подключены без ошибок двигатели не будут вращаться без команды включения. Переходим на вкладку ”output signale” и ставим, галочки напротив “enable” номер порта прописываем тот, к которому подключен контакт ”EN-” теоретически их можно подключить на один порт, но я все 3 драйвера подключен на порты 14-16-17
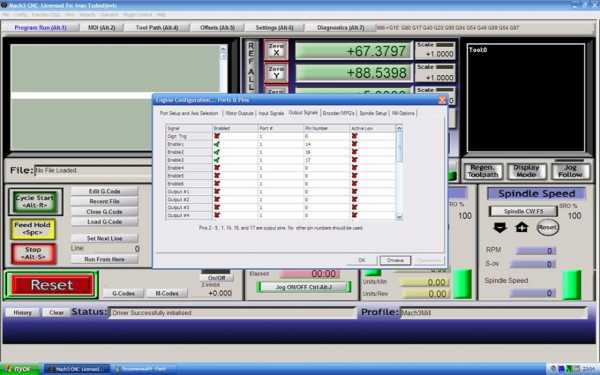
Вот и все, мы закончили настройки. Остался один маленький штрих. Ходовые гайки у нас без компенсации люфтов, и убрать их в таком исполнении убрать тяжело. Разработчики программы позаботились об этом и нам нужно всего лишь включить функцию компенсации и задать их величину. В меню “config”(«Конфигурации») выбираем “Backlash” Ставим галочку включить и прописываем значения для каждой оси.
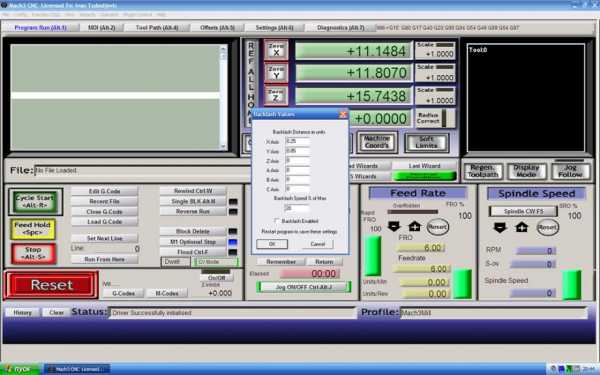
Работа в ArtCAM Чтобы статья получилась полноценной расскажу в вкратце как работать в программе “ArtCAM pro”. В качестве примера возьмем чертеж моторамы от самолета “MicroAngel” в формате *.dxf Открываем ArtCAM выбираем “файл” – “открыть” в поле тип файлов выбираем *.dxf
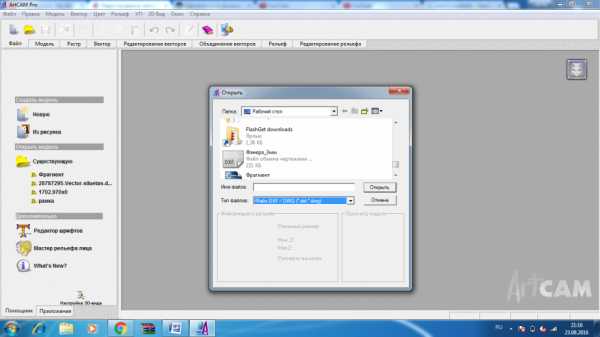
В меню “размер новой модели” задаем высоту и ширину нашей заготовки из фанеры, которую мы закрепили на рабочем столе. Чтобы не испортить стол станка заготовку я креплю прижимами на подложке из потолочной плитки или подложки для ламината. Задаем размер заготовки 300х300 и нажимаем 2 раза “ОК”
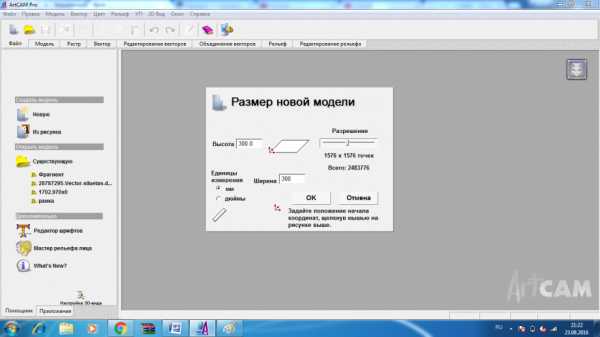
Компонуем элементы от нижнего левого угла, это по умолчанию нулевая точка.
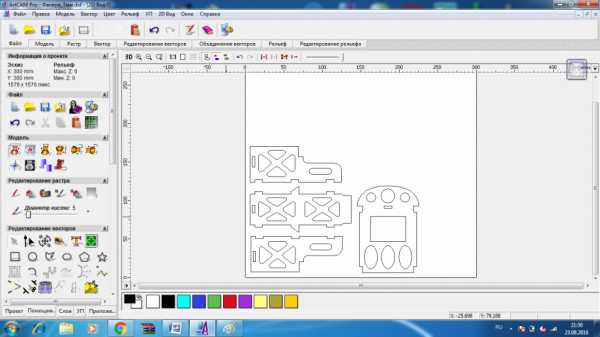
Вначале необходимо вырезать внутренние элементы. Для этого в нижнем левом углу панели инструментов выбираем “УП” Выделяем часть внутренних элементов и в разделе “2D УП” выбираем “обработка по профилю”
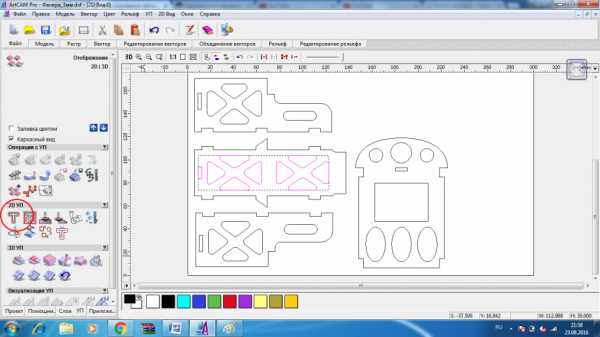
В поле “сторона обработки” выбираем внутри начальный проход оставляем “0” это верх нашей заготовки. Финишный проход ставим чуть больше толщины фанеры. В данном случае фанера 3мм. значит, в поле финишный проход ставим 3.2мм.
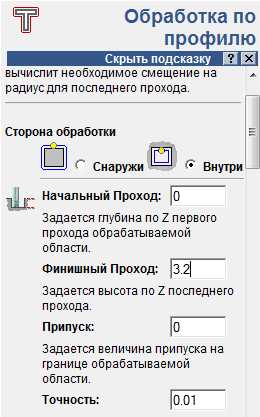
Далее “плоскость безопасности” тут все понятно, это высота перемещения инструмента над заготовкой. Следующий пункт выбор инструмента. Выбираем из библиотеки инструмент, при необходимости корректируем скорость подачи, скорость заглубления инструмента и максимальная глубина за проход. В данном случае фреза кукуруза диаметром 1мм. Подача инструмента 10 мм/с Заглубление 3мм/с Максимальная глубина за проход 1.1мм. При такой глубине заготовка будет прорезана за 3 прохода. Нажимаем “выбрать”
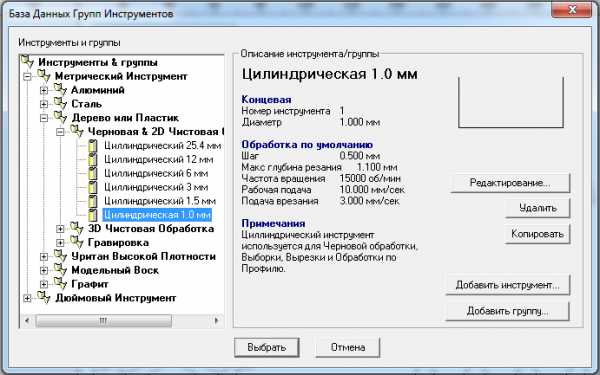
В поле “заготовка” нажимаем определить. Нулевую плоскость заготовки выбираем вверху, смещение вниз, высота заготовки 7мм. это толщина подложки 4мм. и 3мм. толщина фанеры.
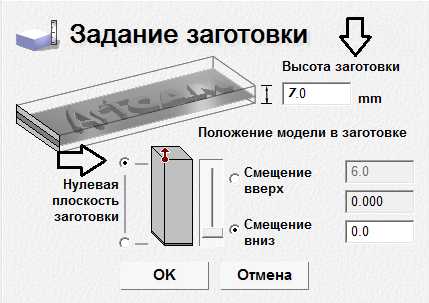
Далее пишем имя данного участка “УП” например №1 и нажимаем “сейчас” На чертеже по внутренней стороне обрисовывается вектор движения инструмента.
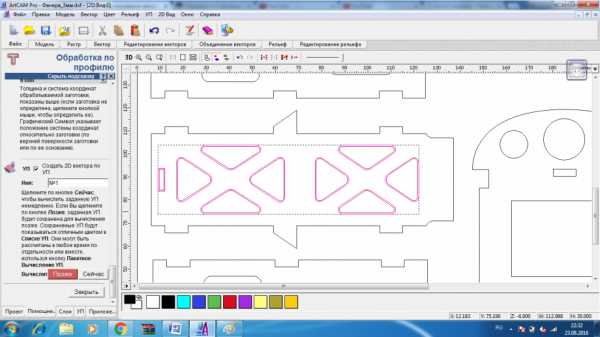
Выделяем остальные элементы внутри, а параметры обработки менять не будем. Каждому новому элементу задаем новое название.. Для обработки внешнего контура выбираем обработку по внешнему контуру, присваиваем имя и нажимаем “сейчас”. После завершения фрезировки деталь не должна вываливаться и для этого выделяем внешний вектор и выбираем функцию “создания переходов”. Высоту и ширину переходов задаем 1 мм, а в поле “постоянное количество” ставим 3-4 шт. Осталось только кликнуть “создать переходы”.
По завершению необходимо сохранить “УП” вверху нажимаем “УП” – “Сохранить УП”
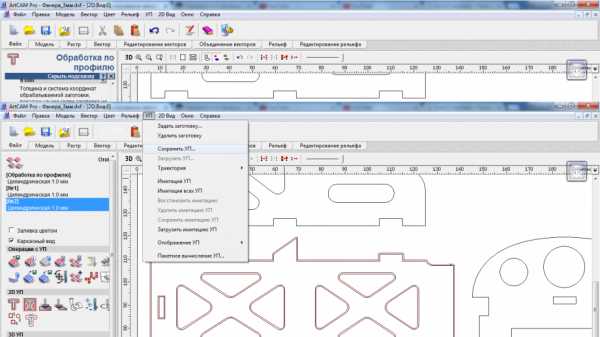
Слевой стороны список подпрограмм, которые сгенерировались для обработки детали под фрезу. В какой последовательности мы перенесем их в правое окно в такой, и будет, производится обработка. Переносим все вправо и нажимаем сохранить и присваиваем нашей программе имя. Все, наша программа готова к загрузке в “mach4”
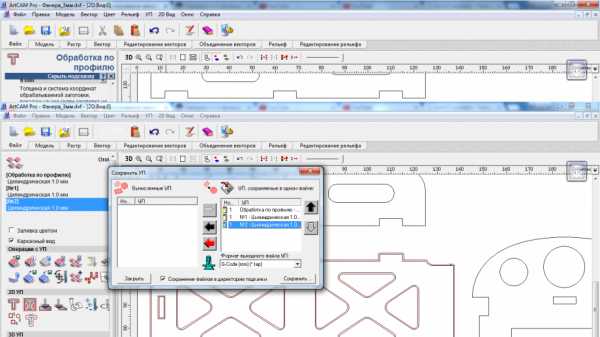
Программа для нашего станка готова. Крепим нашу заготовку из фанеры. Включаем станок, стрелками на клавиатуре перемещаем шпиндель в нулевую точку (у нас это левый нижний угол) кнопками “PgUp” “PgDn” опускаем фрезу так, чтобы она коснулась заготовки. Затем в меню “MACh4” устанавливаем нулевое положение по всем осям и загружаем нашу программу нажатием кнопки “Load G-Code”.
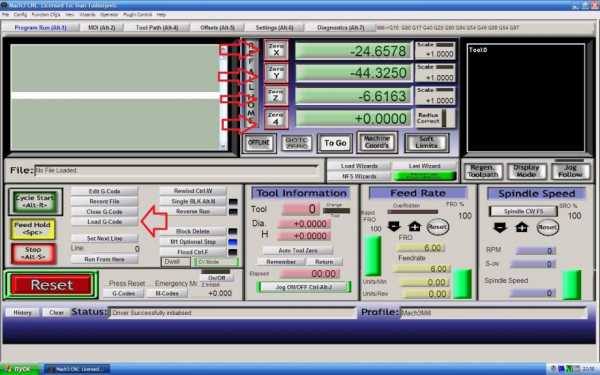
Включаем шпиндель, нажимаем кнопу “Cycle Start” и идем пить кофе.
Есть один важный момент. Фанера может быть кривая или при фиксации к столу ее может слегка выгнуть. На большой площади этот перепад может быть до 1мм. Станочек не сильно мощный и фрезы тонкие. Глубина обработки у нас выставлена 1мм за проход, а при изгибе фанеры заглубление может оказаться 1.5-2 мм. фреза начнет гореть или даже может сломаться. Поэтому я прогоняю фрезу над заготовкой и смотрю максимальную высоту и при обработке учитываю эту погрешность.
После того как фрезер закончит свою работу наслаждаемся результатом.
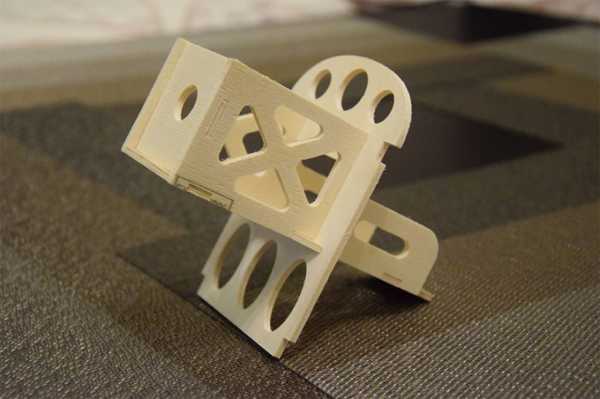
В качестве пробной детали была профрезирована рамка для фотографии.
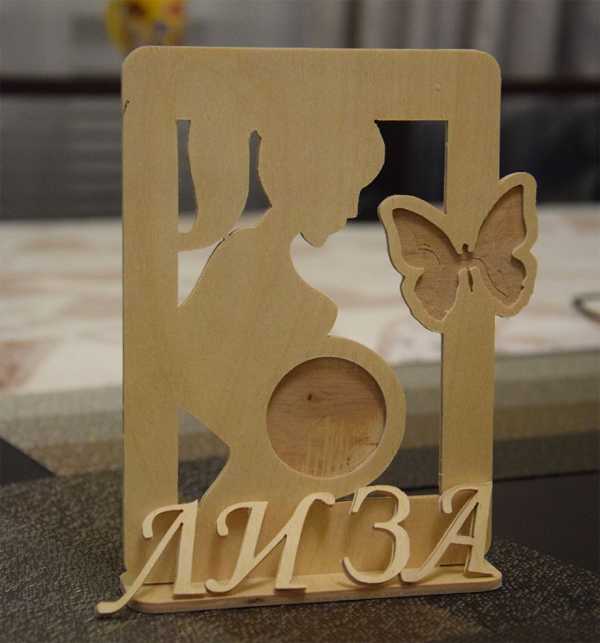
diytimes.ru
Самодельный станок с чпу | Все Станки
Сборка самодельного фрезерного ЧПУ станка занимает от одной до нескольких недель. Станина для него изготавливается из профильной трубы сечением 80х80 мм. Аппарат будет размещаться на верстаке, а мощное основание обеспечит лучшую устойчивость всей конструкции, предотвращая последствия вибраций. Направляющие фиксируются на подставке из профильных труб сечением 60х20 мм.
Конструкционные особенности
Собираем станину не с помощью сварки, а на резьбовых болтовых соединениях. В противном случае случаются силовые деформации. Резьбовая сборка позволит избежать люфтов и перекосов. После этого самодельный CNC агрегат сможет обрабатывать материал:
- дерево;
- пластик;
- листовой металл до 4 мм.
Оптимальным размером рабочей поверхности самодельного станка ЧПУ будет площадка 350х320 мм. В эти габариты укладывается большинство востребованных изделий. Диаметр направляющих валов для осей подбирают в пределах 10-20 мм. Для вертикальной оси он должен быть максимальным, так как она испытывает силовую нагрузку. Подшипники скольжения и направляющие подойдут от старых принтеров.
Мотор и программное обеспечение
Передачу вращения от мотора на шпиндель осуществляет зубчатый ремень шириной не менее 10 мм. Плоские ремни в самодельном ЧПУ станке будут проскальзывать. Востребованным будет шаговый двигатель, имеющий крутящий момент не менее 18 кг/см. Мощность его будет 1,5 кВт.
В короб ставятся важные блоки:
- контроллер;
- материнская плата;
- частотный конвектор.
Пространство обеспечиваем хорошим продувом, так как в жаркую погоду наблюдается перегрев. Для подключения внешних устройств используется порт LPT. В программном обеспечении самодельных станков ЧПУ прописываются персональные драйвера для контроллеров. Последние выбираются четырехосного типа. Короб защищает также от возможных помех.
Важно знать, что контроллеры, оснащенные USB, не подойдут для станка с ЧПУ, использующего Linux.
Дополнительные факторы
В определенных случаях требуется установить систему охлаждения инструмента. Для этого ближе к шпинделю монтируют гибкий шланг. Второй его конец уходит в емкость с эмульсией. Для прокачки используется небольшая водяная помпа.
При выборе двигателя учитывается не только его мощность, но и скорость вращения, так как для инструментов небольшого диаметра требуются высокие обороты. В подобной ситуации выручает шаговый двигатель или коробка скоростей.
Предпочтительно выбирать готовые шпиндели, имеющие конус Морзе или возможность установки цангового патрона. В отличие от трехкулачковых патронов обеспечивается лучший захват инструмента при силовой нагрузке.
Представляем чертежи самодельных станков с габаритными размерами.
Электронная начинка оборудования
Управлять вашим станком с ЧПУ, сделанным своими руками, будет программное обеспечение, а его необходимо правильно подобрать. Выбирая такое обеспечение (его можно написать и самостоятельно), важно обращать внимание на то, чтобы оно было работоспособным и позволяло станку реализовывать все свои функциональные возможности. Такое ПО должно содержать драйверы для контроллеров, которые будут установлены на ваш фрезерный мини-станок.
В самодельном станке с ЧПУ обязательным является порт LPT, через который электронная система управления и подключается к станку. Очень важно, чтобы такое подключение осуществлялось через установленные шаговые электродвигатели.
Выбирая электронные комплектующие для своего станка, сделанного своими руками, важно обращать внимание на их качество, так как именно от этого будет зависеть точность технологических операций, которые на нем будут выполняться. После установки и подключения всех электронных компонентов системы ЧПУ нужно выполнить загрузку необходимого программного обеспечения и драйверов. Только после этого следуют пробный запуск станка, проверка правильности его работы под управлением загруженных программ, выявление недостатков и их оперативное устранение.
Все вышеописанные действия и перечисленные комплектующие подходят для изготовления своими руками фрезерного станка не только координатно-расточной группы, но и ряда других типов. На таком оборудовании можно выполнять обработку деталей со сложной конфигурацией, так как рабочий орган станка может перемещаться в трех плоскостях: 3d.
stankiwse.ru
Как сделать станок чпу своими руками?
СодержаниеСтанки, оснащенные числовым программным обеспечением (ЧПУ) представлены в виде современного оборудования для резки, точения, сверления или шлифования металла, фанеры, дерева пенопласта и других материалов.
Фрезерный станок с ЧПУ
Встроенная электроника на базе печатных плат «Arduino» обеспечивает максимальную автоматизацию работ.
Что собой представляет станок с ЧПУ?
Станки ЧПУ на базе печатных плат «Ардуино» способны в автоматическом режиме бесступенчато менять частоту вращения шпинделей, а также скорость подачи суппортов, столов и прочих механизмов. Вспомогательные элементы станка ЧПУ автоматически принимает нужное положение, и могут использоваться для резки фанеры или алюминиевого профиля.
В устройствах на основе печатных плат «Arduino» режущий инструмент (предварительно настроенный) также сменяется в автоматическом режиме.
Читайте также: как устроены 3D станки-фрезеры с ЧПУ по дереву и сверлильно-присадочные станки?
В устройствах ЧПУ на базе печатных плат «Ардуино» все команды подаются через контроллер.
Контроллер получает сигналы от программоносителя. Для такого оборудования для резки фанеры, металлического профили или пенопласта программоносителями являются кулачки, упоры или копиры.
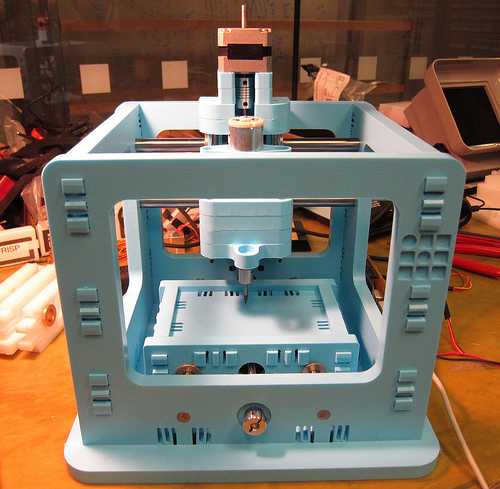
Самодельный станок на базе плат Ардуино
Читайте также: «Виды и особенности копировально-фрезерных станков» и «Как работают координатно-сверлильные станки с ЧПУ?».
Поступивший из программоносителя сигнал через контроллер подает команду на автомат, полуавтомат или копировальный станок. Если необходимо сменить лист фанеры или пенопласта для резки, то кулачки или копиры заменяются другими элементами.
Агрегаты с программным управлением на базе плат” Ардуино” в качестве программоносителя используют перфоленты, перфокарты или магнитные ленты в которых содержится вся необходимая информация. С применением плат «Arduino» весь процесс резки фанеры, пенопласта или другого материала полностью автоматизируется, сто минимизирует затраты труда.
Стоит отметить, что собрать станок ЧПУ для резки фанеры или пенопласта на базе плат Arduino своими руками можно без особых сложностей. Управление в агрегатах ЧПУ на основе «Ардуино» осуществляет контроллер, который передает как технологическую, так и размерную информацию.
Читайте также: сфера применения фрезерных станков с ЧПУ по металлу.
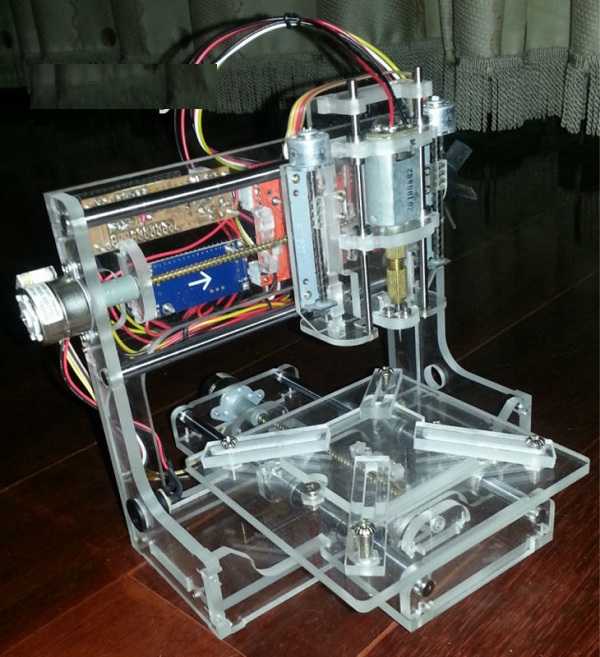
Самодельный гравировальный станок с ЧПУ на базе управления Ардуино
Применяя плазморезы с ЧПУ на базе плат «Ардуино» можно освободить большое число универсального оборудования и наряду с этим увеличить производительность труда. Основные преимущества станков на базе «Ардуино», собранных своими руками, выражаются в:
- высокой (по сравнению с ручными станками) производительностью;
- гибкости универсального оборудования в сочетании с точностью;
- снижении потребности в привлечении квалифицированных специалистов к работе;
- возможности изготовления взаимозаменяемых деталей по одной программе;
- сокращенных сроках подготовки при изготовлении новых деталей;
- возможности сделать станок своими руками.
Читайте также: «Разновидности и технология сварки швов — потолочных, горизонтальных, вертикальных».
к меню ↑
Процесс работы фрезерного станка с ЧПУ (видео)
к меню ↑
Разновидности ЧПУ станков
Читайте также: принцип работы зубофрезерного станка с ЧПУ и его модификации.
Представленные агрегаты для резки фанеры или пенопласта, использующие для работы платы «Arduino», делятся на классы по:
- технологическим возможностям;
- принципу смены инструмента;
- способу смены заготовки.
Любой класс такого оборудования можно сделать своими руками, а электроника «Arduino» обеспечит максимальную автоматизацию рабочего процесса. Наряду с классами, станки могут быть:
- токарными;
- сверлильно-расточными;
- фрезерными;
- шлифовальными;
- станки электрофизического ряда;
- многоцелевые.
Читайте также: как своими руками сделать фрезерный станок по металлу?
Токарные агрегаты на базе «Arduino» могут подвергать обработке наружные и внутренние поверхности всевозможных деталей.
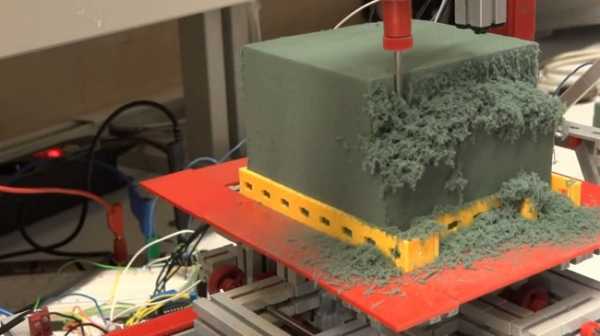
Станок с ЧПУ трехмерной резки под управлением Ардуино
Вращение заготовок может проводиться как в прямолинейных, так и в криволинейных контурах. Устройство также предназначается для резки наружной и внутренней резьбы. Фрезерные агрегаты на базе «Arduino» предназначаются для фрезерования простых и сложных деталей корпусного типа.
data-ad-client=”ca-pub-8514915293567855″
data-ad-slot=”5929285318″>
Кроме того они могут производить сверление и расточку. Шлифовальные станки, которые также можно сделать своими руками могут применяться для финишной обработки деталей.
В зависимости от вида обрабатываемых поверхностей агрегаты могут быть:
Читайте также: «О разновидностях плоскошлифовального оборудования».
Многоцелевые агрегаты могут применяться для резки фанеры или пенопласта, выполнять сверление, фрезерование, расточку и токарную обработку деталей. Перед тем, как сделать станок с ЧПУ своими руками, важно учитывать, что деление оборудования производится и по способу смены инструмента. Замена может производиться:
- вручную;
- автоматически в револьверной головке;
- автоматически в магазине.
Если электроника (контроллер) может обеспечивать автоматическую смену заготовок с использованием специальных накопителей, то аппарат может длительное время работать без участия оператора.
Читайте также: «Как работает 3D станок для резьбы по дереву?».
к меню ↑
Рекомендации по сборке станка с ЧПУ
Для того, чтобы сделать представленный агрегат для резки фанеры или пенопласта своими руками, необходимо подготовить исходное оборудование. Для этого может быть пригоден бывший в употреблении сверлильный станок для печатных плат.
В нем рабочий орган заменяется на фрезу. Кроме того сделать механизм своими руками можно из кареток старого принтера.
Это позволит двигаться рабочей фрезе в направлении двух плоскостей. Далее к конструкции подключается электроника, ключевым элементом которой является контроллер и платы «Arduino».
Схема сборки позволяет сделать своими руками самодельный агрегат ЧПУ автоматическим. Такое оборудование может быть предназначено для резки пластика, пенопласта, фанеры или тонкого металла. Для того, чтобы устройство смогло выполнять более сложные виды работ, необходим не только контроллер, но и шаговый двигатель.
Читайте также: устройство и классификация фрезерно-гравировальных станков с ЧПУ.
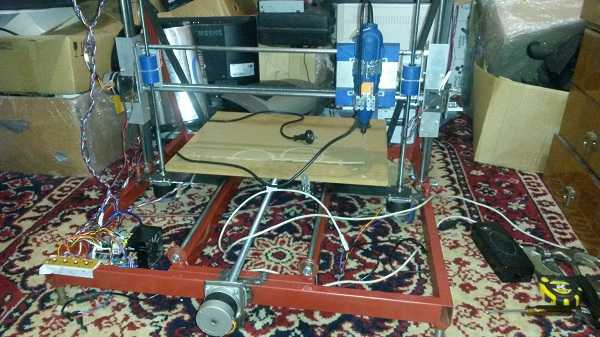
Самодельный станок с ЧПУ
Он должен обладать высокими мощностными показателями – не менее 40-50 ватт. Рекомендуется использовать обычный электродвигатель, так как с его применением отпадет необходимость в создании винтовой передачи, а контроллер будет обеспечивать своевременную подачу команд.
Нужное усилие на вал передачи в самодельном устройстве должно передаваться посредством зубчатых ремней. Если для передвижения рабочей фрезы самодельный станок с ЧПУ будет использовать каретки от принтеров, то для этой цели необходимо выбрать детали от принтеров больших размеров.
Основой будущего агрегата может послужить прямоугольная балка, которая должна быть прочно закреплена на направляющих. Каркас должен отличаться высокой степенью жесткости, но использовать сварку не рекомендуется. Лучше применять болтовое соединение.
Сварочные швы будут подвергаться деформации из-за постоянных нагрузок при работе станка. Элементы крепления при этом разрушаются, что приведет к сбою настроек, а контроллер будет работать некорректно.
Читайте также: «Как собрать самодельный шиномонтажный станок в домашних условиях?» и «Электроэрозионный станок своими руками для резки».
к меню ↑
О шаговых двигателях суппортах и направляющих
Агрегат с ЧПУ, собранный самостоятельно, должен быть оснащен шаговыми электродвигателями. Как уже упоминалось выше, для сборки агрегата лучше всего использовать двигатели от старых матричных принтеров.
Для эффективного функционирования устройства понадобится три отдельных двигателя шагового типа. Рекомендуется применять двигатели с пятью отдельными проводами управления. Это позволит увеличить функциональность самодельного аппарата в несколько раз.
При подборе двигателей для будущего станка нужно знать число градусов на один шаг, показатель рабочего напряжения и сопротивление обмотки. Впоследствии это поможет произвести корректную настройку всего программного обеспечения.
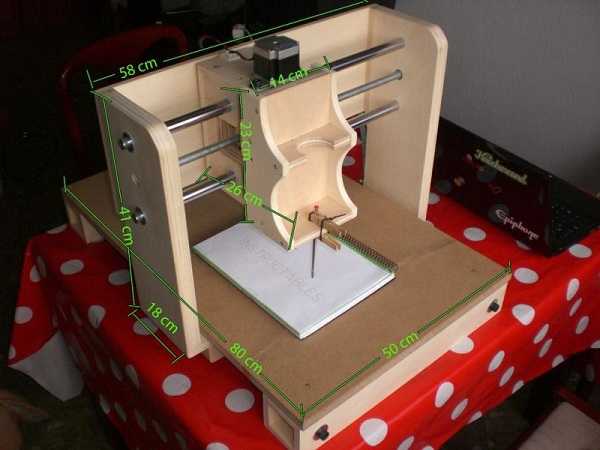
Деревянный станок с ЧПУ собранный своими руками
Крепление вала шарового двигателя производится с применением резинового кабеля, покрытого толстой обмоткой. Кроме того, с помощью такого кабеля можно присоединить двигатель к ходовой шпильке. Станину можно изготовить из пластмассы с толщиной в 10-12 мм.
Наряду с пластиком возможно применение алюминия или органического стекла.
Ведущие детали каркаса крепятся с помощью саморезов, а при использовании древесины можно крепить элементы клеем ПВА. Направляющие представляют собой стальные прутья с сечением в 12 мм и длиной в 20 мм. На каждую ось приходится по 2 прута.
Читайте также: «Как изготовить сварочный осциллятор своими руками?».
Суппорт изготавливают из текстолита, его размеры должны составлять 30×100х40 см. Направляющие части текстолита скрепляются винтами марки М6, а суппорты «Х» и «У» в верху должны иметь 4 резьбовых отверстия для закрепления станины. Шаговые электродвигатели устанавливаются с помощью крепежей.
Крепления можно сделать с использованием стали листового типа. Толщина листа должна составлять 2-3 мм. Далее винт соединяется с осью шагового двигателя посредством гибкого вала. С этой целью можно задействовать обычный резиновый шланг.
Любое гаечное соединение рекомендуется производить с помощью чугунных гаек.
data-full-width-responsive=”true”
data-ad-client=”ca-pub-8514915293567855″data-ad-slot=”8040443333″>
ostanke.ru
| |||||||||||||||||
| |||||||||||||||||
<< Первая < Предыдущая 1 2 3 4 5 6 7 8 9 10 Следующая > Последняя >> | |||||||||||||||||
Страница 1 из 30 |
homecnc.ru
Самодельный фрезерный станок с ЧПУ — libixur — Мой блог
Здравствуйте! В этой статье я расскажу про этапы создания своего станка с ЧПУ. Идеей станка я загорелся года два назад, когда в интернете наткнулся на видео таких станков.
Первые пробы сделать станок из металла вышли неудачными, и я как то забросил это дело. Но желание построить станок не оставляло меня, и в этом году просмотрев много сайтов и проектов станков я решил сделать его из фанеры. На этот выбор подтолкнул меня станок «АЙТО», автор Авилкин Дмитрий:
За основу я взял фанеру толщиной 10мм. Купил мебельные направляющие, и прикинув в голове размеры вырезал первые детали: боковые стенки и рабочий стол (ось X) .
Далее собрал уже вот такой вот «ящик», промежуточных фото к сожалению нет, но думаю из фото и так все понятно:
Ну можно сказать основа готова. Идем далее: я решил не делать никаких проставок под мотор, так как усилия небольшие и у него есть свой подшипник. Делаю отверстия под шаговый мотор и подшипник напротив для оси X. Подшипники использовал 627Z, моторы подобные тем что стоят в 5 дюймовых дисководах. Отверстия сверлил фрезой по дереву, вроде 22мм. Фото фрез и отверстий + установленный двигатель:
Аналогичные действия для оси Y. Упор для подшипника — это часть держащая лампочку в стоп-сигнале мотоцикла:
Установка направляющих и шпильки для оси Y:
Далее самое сложное — изготовление оси Z. Так как мебельные направляющие слишком большие, пришлось делать вручную. Тоже прикинув все в голове, приступил к изготовлению. Начал с «бочонков» которые бы ездили по направляющим. В бочонке есть 2 отверстия: одно с резьбой для закрепления, другое сквозное через которое будет проходить направляющая. В роли направляющих использовал тягу от какого-то грузового автомобиля (прочная штука, резьбу с трудом нарезал).
Изготовил 4 штуки. Кстати бочонки сделаны из старого болта на 10 или 12 (точно не помню). Далее все это закрепил на платформу которая будет ездить, сделал направляющие:
Теперь делаю подобный бочонок, но только в обоих отверстиях резьба. Т.е. так выглядит у меня винтовая гайка. Ну и потихоньку продолжаю делать ось Z:
На этом этапе фото оси Z заканчиваются, переходим к оси Y. Поскольку мебельные направляющие неидеальны, пришлось с обратной стороны сделать упор. Ну и тут же сделал гайку и поставил все это на станок:
Гайку для оси X изготовил из какого-то прочного ролика:
Как видно из фото я использовал строительные шпильки диаметром 6 мм. Но мне кажется нужно использовать хотя бы 8… Двигателя со шпильками я соединил кусочками твердой шлангочки:
Перейдем к электронике. Начну с драйвера шаговых двигателй, описывать тут его не буду, просто выложу пару фото. Описание можете почитать в статье: Драйвер шагового двигателя для станка с ЧПУ
Еще с самого начала я задумал для станка использовать отдельный компьютер, а точнее материнскую плату которая была куплена в интернете за 200грн (~25$). Так же еще перед тем как начать строить станок я задумал всю электронику поместить внутрь станка. Для этого и был сделан такой «ящик». Блок питания использовался естественно компьютерный который был изъят из корпуса и которому были укорочены провода. Купил жесткий диск на 3Гб, больше и не требуется, лишь бы винда влезла (которая у меня урезанная и весит ~300мБ). Все это дело было размещено на дне станка:
Материнка без видеокарты, она тут и не нужна. Станок управляется по сети через Radmin. Она также настроена на авто включение после того как появится питание. IDE шлейф был укорочен.
В самом корпусе станка была сделана прорезь под разъемы материнки:
Так же на боковую стенку я вывел разъемы питания (3.3, 5, 12в) для питания различных инструментов. И еще тумблер который принудительно отключает питание шаговых двигателей, так как при простое они очень сильно греются:
Фото уже готового и рабочего станка. На заднюю стенку выведен разъем питания, шлейф для двигателя по оси Z взят от DVD плеера. Двигателя осей Z,Y соединены в один кабель и соединения закрыты коробочкой:
Ну и немного разных фото.
Двигателя которые применял для осей Y,Z:
Фото подшипников по осям X,Y:
Пара дополнительных фото оси Z:
Ну и на самый конец процесс роботы и первые результаты:
Выжигать пробовал точками и линиями. Поскольку фанера неровная, есть разница в оттенке.
Так же советую к прочтению новую статью с видеороликом: Проба гравера на самодельном станке с ЧПУ
На данный момент все! Надеюсь Вам было интересно!
Добавление: 31.03.2013
Уже не первый раз у меня спрашивают чертежи и размеры станка. Чертежей нет, так как делал все из головы. Вот только могу дать размеры боковины, из них должно быть все понятно. Ширина станка равна длине мебельных направляющих.
VN:F [1.9.20_1166]
Rating: 9.7/10 (116 votes cast)
Самодельный фрезерный станок с ЧПУ, 9.7 out of 10 based on 116 ratingsПоделиться ссылкой с друзьями:
libixur.ru
Фрезерный станок с ЧПУ по дереву своими руками: чертежи
Содержание статьи:
Для изготовления объемного рисунка на деревянной поверхности применяются заводские фрезерные станки с ЧПУ по дереву. Сделать аналогичную мини-модель своими руками в домашних условиях сложно, но возможно при детальном изучении конструкции. Для этого необходимо разобраться со спецификой, правильно подобрать комплектующие и выполнить их настройку.
Принцип работы фрезерного станка
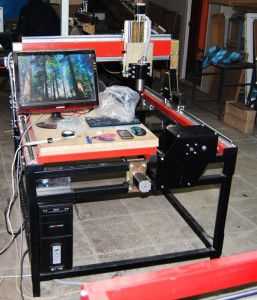
Оборудование для фрезерной обработки с ЧПУ
Современное деревообрабатывающее оборудование с блоком числового программного управления предназначено для формирования сложного рисунка по дереву. В конструкции должна присутствовать механическая электронная часть. В комплексе они позволят максимально автоматизировать процесс работы.
Для изготовления настольного мини-фрезерного станка по дереву своими руками следует ознакомиться с основными компонентами. Режущим элементом является фреза, которая устанавливается в шпиндель, расположенный на валу электродвигателя. Эта конструкция крепится на станину. Она может перемещаться по двум осям координат – x; y. Для фиксации заготовки необходимо сделать опорный столик.
Электронный блок управления соединяется с пошаговыми двигателями. Они обеспечивают смещение каретки относительно детали. По такой технологии можно сделать 3D рисунки на деревянной поверхности.
Последовательность работы мини-оборудования с ЧПУ, который можно изготовить своими руками.
- Написание программы, согласно которой будет выполнена последовательность перемещений режущей части. Для этого лучше всего использовать специальные программные комплексы, предназначенные для адаптации в самодельных моделях.
- Установка заготовки на стол.
- Вывод программы в ЧПУ.
- Включение оборудования, контроль за выполнением автоматических действий.
Для достижения максимальной автоматизации работы в 3D режиме потребуется правильно составить схему и выбрать соответствующие комплектующие. Специалисты рекомендуют изучить заводские модели, прежде чем сделать мини-фрезерный станок своими руками.
Для создания сложных рисунков и узоров на деревянной поверхности понадобится несколько видов фрез. Некоторые из них можно сделать самостоятельно, но для тонкой работы следует приобрести заводские.
Схема самодельного фрезерного станка с числовым управлением
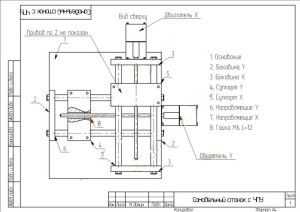
Схема фрезерного станка с ЧПУ
Самым сложным этапом является выбор оптимальной схемы изготовления. Она зависит от габаритов заготовки и степени ее обработки. Для домашнего использования желательно изготовить настольный мини-фрезерный станок с ЧПУ, сделанный своими руками, который будет иметь оптимальное число функций.
Конструкция трансмиссии
Оптимальным вариантом является изготовление двух кареток, которые будут двигаться по осям координат x; y. В качестве основания лучше всего использовать стальные шлифованные прутки. На них будут монтироваться каретки. Для создания трансмиссии необходимы шаговые электродвигатели и винты с подшипниками качения.
Для максимальной автоматизации процесса в конструкции мини-фрезерного станка с ЧПУ по дереву, сделанного своими руками, необходимо детально продумать электронную часть. Условно она состоит из следующих компонентов:
- блок питания. Необходим для подачи электроэнергии на шаговые электродвигатели и микросхему контроллера. Зачастую используют модель 12в 3А;
- контроллер. Он предназначен для подачи команд на электродвигатели. Для работы мини-фрезерного станка ЧПУ, изготовленного своими руками, достаточно простой схемы для контроля функционирования трех двигателей;
- драйвер. Также является элементом регулирования работы подвижной части конструкции.
Для управления рекомендуется использовать стандартные программные комплексы. Одним из них является KCam. Он имеет достаточно гибкую структуру для адаптации практически к любому контроллеру.
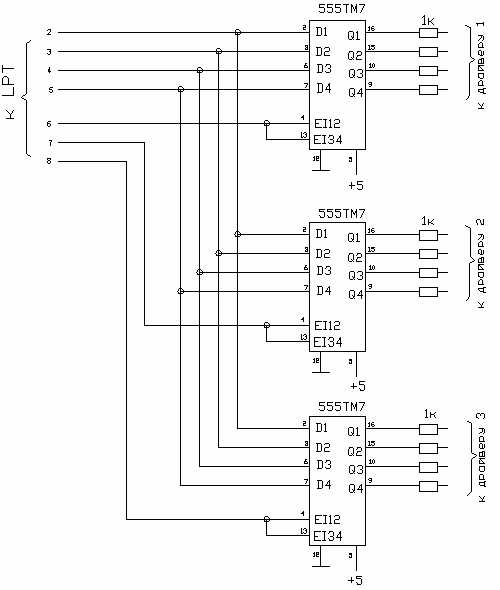
Схема контроллера на микросхемах 555TM7
Преимуществом этого комплекса является возможность импортирования исполняемых файлов самых распространенных форматов. С помощью специального приложения можно составить трехмерный чертеж детали для предварительного анализа. Шаговые двигатели будут работать с определенной частотой хода. Но для этого следует внести технические параметры в программу управления.
Во время составления программы рекомендуется сделать несколько отдельных блоков. Каждый из них будет предназначен для фрезерования, рисования, сверления или гравировки. Это позволит избежать холостых перемещений фрезы.
Выбор комплектующих для фрезерного станка с ЧПУ
Оборудование для фрезерной обработки из алюминиевой рамы
Следующим этапом является выбор компонентов для сборки самодельного оборудования. Оптимальным вариантом является использование подручных средств. В качестве основы для настольных моделей 3D станка можно использовать дерево, алюминий или оргстекло.
Для правильной работы всего комплекса необходимо разработать конструкцию суппортов. Во время их движения не должно возникать колебаний, это может привести к неточному фрезерованию. Поэтому перед сборкой все компоненты проверяются на совместимость друг с другом.
Рекомендации по выбору комплектующих для мини-фрезерного станка с ЧПУ, которые можно сделать своими руками:
- направляющие. Используются стальные шлифованные прутки диаметром 12 мм. Длина для оси x составляет 200 мм, для y — 90 мм;
- суппорт. Оптимальным вариантом является текстолит. Обычный размер площадки — 25*100*45 мм;
- шаговые двигатели. Специалисты рекомендуют использовать модели от принтера 24в, 5А. В отличие от приводов дисковода они имеют большую мощность;
- блок фиксации фрезы. Его также можно сделать из текстолита. Конфигурация напрямую зависит от имеющегося инструмента.
Блок питания лучше всего собрать заводской. При самостоятельном изготовлении возможны ошибки, которые впоследствии отразятся на работе всего оборудования.
Для пайки платы контроллера рекомендуется использовать резисторы и конденсаторы в SMD корпусах. Это позволит уменьшить габариты, оптимизировать внутреннее пространство в конструкции.
Порядок изготовления фрезерного станка с ЧПУ
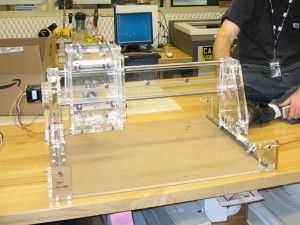
Фрезерный станок из оргстекла
После выбора всех компонентов можно сделать настольный мини фрезерный станок с ЧПУ по дереву самостоятельно своими руками. Предварительно еще раз проверяются все элементы, выполняется контроль их размеров и качества.
Для фиксации элементов оборудования необходимо использовать специальные крепежные детали. Их конфигурация и форма зависят от выбранной схемы.
Порядок действий по сборке настольного мини оборудования с ЧПУ по дереву с функцией 3D обработки.
- Монтаж направляющих суппорта, их фиксация на боковых частях конструкции. Эти блоки еще не устанавливаются на основание.
- Притирка суппортов. Их необходимо двигать по направляющим до тех пор, пока не получится плавный ход.
- Затяжка болтов для фиксации суппортов.
- Крепление компонентов на основание оборудования.
- Монтаж ходовых винтов вместе с муфтами.
- Установка ходовых двигателей. Они крепятся к винтам муфт.
Электронная часть располагается в отдельном блоке. Это способствует уменьшению вероятности сбоя в работе во время функционирования фрезера. Также важным моментом является выбор рабочей поверхности для установки оборудования. Она должна быть ровная, так как в конструкции не предусмотрены болты регулировки уровня.
После этого можно приступать к пробным испытаниям. Сначала рекомендуется задать несложную программу фрезерования по дереву. Во время работы необходимо сверять каждый проход фрезы — глубину и ширину обработки, в особенности это касается 3D режима.
В видеоматериале показан пример как собрать большой фрезерный станок с ЧПУ, изготовленный своими руками:
Примеры чертежей и самодельных конструкций
stanokgid.ru