процесс обработки металла, типы станков, самодельное оборудование
Высокоточная обработка металлических предметов производится с применением нетрадиционных технологий и методик. К таковым можно отнести шлифовку, резку, а также закрепление посредством электроэрозионного влияния. Электроэрозионные станки появились довольно давно, однако, широкую популярность они получили лишь за последние 10−20 лет.
- Электроэрозионная обработка
- Резка металла
- Типы станков
- Проволочно-вырезные
- Прошивные
- Самодельное оборудование
Электроэрозионная обработка
Самое первое промышленное оборудование данного класса было разработано специалистами фирмы «CHARMILLES TECH» еще в середине минувшего столетия, а станок, оснащенный ЧПУ, увидел свет в конце 60-ых годов. В сравнении с общеизвестными методиками обработки металлических сплавов — шлифовкой, литьем, ковкой, электроискровую технологию можно назвать самой современной и инновационной.
Металлы — электропроводящие материалы, поэтому обрабатывающая процедура с использованием электротока подходит для любых сплавов. С помощью электроэрозионного станка может осуществлять очень обширный перечень мероприятий: начиная от
- Точечной шлифовкой;
- Восстановлением свойств поверхности;
- Повышением прочности;
- Имитацией;
- Напылением;
- Созданием гравировки.
Оборудование для электроэрозионной обработки основывается на особом принципе электродуги, приводящей к утрате вещества анодом и катодом. Непродолжительный электроимпульс способствует удалению вещества с анода, если же импульс будет более продолжительным, то вещество удаляется с катода. Электроэрозионный станок выдает обе разновидности электроимпульса. А обрабатываемые элементы и рабочие средства подключаются к отрицательному или же положительному полюсу.
В станках данного типа применяется исключительно постоянный электроток
.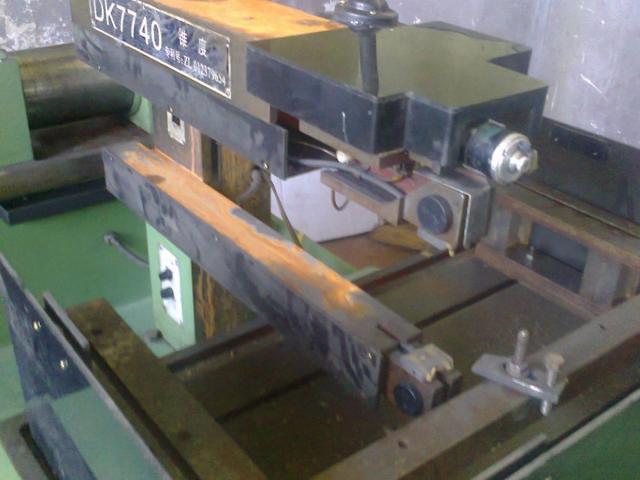
Обработка посредством электроимпульсной технологии, направленная на сверление или резание, осуществляется в особой жидкости — диэлектрике. В большинстве случаев при этом применяют керосин, масло или чистую воду. Манипуляции, связанные с укреплением, напылением и наращиванием поверхности, производятся в вакууме или в воздушной среде.
Резка металла
Такая обработка применяется при создании деталей со сложными контурами, в ювелирном искусстве и для создания элементов из очень твердых металлов. Ограничения, связанные с толщиной и габаритами заготовок, зависят лишь от параметров станка. Как правило, эта технология используется в крупносерийном производстве, где не нужна никакая дополнительная обработка деталей.
Кстати, электроэрозионное обрабатывающее оборудование можно сделать и своими руками. Но тут нужно учитывать тот факт, что в станках самодельного типа трудно воплотить в жизнь самые главные достоинства этой технологии: универсальность и точность. Ведь тугоплавкие металлические сплавы и металлы нуждаются в значительном расходе энергии.
В промышленности используется две разновидности устройств: вырезной (проволочный) и прошивной электроэрозионный станок. Первый тип применяется относительно толстых деталей, второй — для максимально точного исполнения, связанного с копированием тех или иных элементов.
Типы станков
Проволочно-вырезные
Такие станки используют в своей работе бесконтактную технологию взаимодействия специальной проволоки и заготовки. С их помощью можно обрабатывать самые разные сплавы. Данное оборудование характеризуется высочайшей точностью обработки, которая составляет примерно 0,011−0,012 миллиметра.
Прошивные
Контактная же обработка основывается на работе точечного электрода. От него, в свою очередь, будет зависеть форма углубления, которое необходимо сделать в материале. Такие станки используются для обработки следующих материалов:
- Нержавейка;
- Инструментальные металлические сплавы;
- Сталь закаленного типа;
- Титан.
Но их в то же время можно использовать и для других сплавов, когда нужно сделать углубления или отверстия, придерживаясь максимальной точности.
Самодельное оборудование
Станки самодельного типа собираются в тех ситуациях, когда высокоточная обработка металлических сплавов производится довольно часто и в сравнительно крупных объемах. Сразу стоит отметить, что это оборудование сделать непросто. Такого рода начинание оправдывает себя лишь в мастерских и в цехах для обработки металлов.
В сети сейчас можно отыскать массу подробных инструкций, которые помогут реализовать эту задумку. Станки-самоделки нередко применяются для создания надписей, гравировки, резки тонколистового металла и некоторых иных целей.
Делаем настольное устройство для изготовления печатных плат в один клик / Хабр
В очередной раз отмывая раковину от рыжих пятен хлорного железа, после травления платы, я подумал, что пришло время автоматизировать этот процесс. Так я начал делать устройство для изготовления плат, которое уже сейчас можно использовать для создания простейшей электроники.
Ниже я расскажу о том, как делал этот девайс.
Базовый процесс изготовления печатной платы субтрактивным методом заключается в том, что на фольгированном материале удаляются ненужные участки фольги.
Сегодня большинство электронщиков используют технологии типа лазерно-утюжной для домашнего производства плат.
Мне хотелось поставить на стол некоторое устройство, в которое как в принтер можно отправить исходник платы, нажать кнопку и через какое-то время получить готовую плату.
Немного погуглив можно узнать, что люди, начиная с 70х годов прошлого века, начали разрабатывать настольные устройства для изготовления печатных плат. Первым делом появились фрезерные станки для печатных плат, которые вырезали дорожки на фольгированном текстолите специальной фрезой.
Желание немедленно купить специализированный станок прошло после изучения цен от поставщика. Выкладывать такие деньги за устройство я, как и большинство хоббийщиков, не готов. Поэтому решено было сделать станок самостоятельно.
Понятно, что устройство должно состоять из координатного стола, перемещающего режущий инструмент в нужную точку и самого режущего устройства.
В интернете достаточно примеров того, как сделать координатный стол на любой вкус. Например те же RepRap справляются с этой задачей (с поправками на точность).
С одного из моих предыдущих хобби-проектов по созданию плоттера у меня остался самодельный координатный стол. Поэтому основная задача заключалась в создании режущего инструмента.
Вполне логичным шагом могло стать оснащение плоттера миниатюрным гравером вроде Dremel. Но проблема в том, что плоттер, который можно дешево собрать в домашних условиях сложно сделать с необходимой жесткостью, параллельностью его плоскости к плоскости текстолита (при этом даже текстолит сам по себе может быть изогнутым). В итоге вырезать на нём платы более менее хорошего качества не представлялось бы возможным. К тому же не в пользу использования фрезерной обработки говорил тот факт, что фреза тупится со временем и утрачивает свои режущие свойства. Вот было бы здорово, если бы медь с поверхности текстолита можно было удалять бесконтактным способом.
Уже существуют лазерные станки немецкого производителя LPKF, в которых фольга просто испаряется мощным полупроводниковым лазером инфракрасного диапазона. Станки отличаются точностью и скоростью обработки, но их цена ещё выше чем у фрезерных, а собрать из доступных всем материалов такую вещь и как-то её удешевить пока не представляется простой задачей.
Из всего вышесказанного я сформировал некоторые требования к желаемому устройству:
- Цена сопоставимая со стоимостью среднего домашнего 3д-принтера
- Бесконтактное удаление меди
- Возможность собрать устройство из доступных компонентов самостоятельно в домашних условиях
Так я начал размышлять о возможной альтернативе лазеру в области бесконтактного удаления меди с текстолита. И наткнулся на метод электроискровой обработки, который давно применяется в металлообработке для изготовления точных металлических деталей.
При таком методе металл удаляется электрическими разрядами, которые испаряют и разбрызгивают его с поверхности заготовки. Таким образом образуются кратеры, размер которых зависит от энергии разряда, его длительности и, конечно же, типа материала заготовки. В простейшем виде электрическую эрозию стали использовать в 40-х года XX века для пробивания отверстий в металлических деталях. В отличие от традиционной механической обработки отверстия можно было получить практически любой формы. В настоящее время данный метод активно применяется в металлообработке и породил целую серию видов станков.
Обязательной частью таких станков является генератор импульсов тока, система подачи и перемещения электрода — именно электрод (обычно медный, латунный или графитовый) является рабочим инструментом такого станка. Простейший генератор импульсов тока представляет собой простой конденсатор нужного номинала, подключенный к источнику постоянного напряжения через токоограничивающий резистор.
За вечер был изготовлен прототип эрозионного инструмента, представляющий собой соленоид, к якорю которого прикреплена медная проволочка. Соленоид обеспечивал вибрацию проволоки и прерывание контакта. В качестве источника питания был использован ЛАТР: выпрямленный ток заряжал конденсатор, а переменный питал соленоид. Эта конструкция была также закреплена в держателе ручки плоттера. В целом, результат оправдал ожидания, и головка оставляла на фольге сплошные полосы со рваными краями.
Способ явно имел право на жизнь, но требовалось решить одну задачу — компенсировать расход проволоки, которая расходуется при работе. Для этого требовалось создать механизм подачи и блок управления для него.
После этого, всё свободное время я начал проводить в одном из хакспейсов нашего города, где есть станки для металлообработки. Начались продолжительные попытки сделать приемлемое режущее устройство. Эрозионная головка состояла из пары шток-втулка, обеспечивающих вертикальную вибрацию, возвратной пружины и протяжного механизма. Для управления соленоидом потребовалось изготовить несложную схему состоящую из генератора импульса заданной длины на NE555, MOSFET-транзистора и индуктивного датчика тока. Первоначально предполагалось использовать режим автоколебаний, то есть подавать импульс на ключ сразу после импульса тока. При этом частота колебаний зависит от величины зазора и управление приводом производится согласно измерению периода автоколебаний. Однако стабильный автоколебательный режим оказался возможен в диапазоне амплитуд колебания головки, который составлял меньше половины максимального. Поэтому я принял решение использовать фиксированную частоту колебаний, генерируемых аппаратным ШИМом.
Закрепив режущую головку на плоттере, я начал опыты по прорезанию изолирующих дорожек на печатных платах. Первый результат достигнут и головка более-менее устойчиво обеспечивает непрерывный рез. Вот видео, демонстрирующее что получилось:
Принципиальная возможность изготавливать платы при помощи электроискровой обработки подтверждена. В ближайших планах повысить точность, увеличить скорость обработки и чистоту реза, а также выложить часть наработок в открытый доступ. Также планирую адаптировать модуль под использование с RepRap. Буду рад идеям и замечаниям в комментариях.
Самодельный электроэрозионный станок переходит от прототипа к серийному производству
- по: Дэн Мэлони
Из всех методов превращения больших кусков металла в более мелкие, пожалуй, нет более интересного, чем электроэрозионная обработка. Электроэрозионная обработка также заведомо суетлива из-за необходимости контролировать дуговой разряд при точном позиционировании инструмента относительно заготовки. Тем не менее, некоторым домашним геймерам это нравится, и мы любим делиться их успехами, например, этой незавершенной машиной EDM. (Видео, встроенное ниже.)
Мы связали первые видео [Энди] ниже перерыва, и мы ожидаем, что будет еще несколько, прежде чем все будет сказано и сделано. Но на самом деле, за то, что он начал проект довольно рано, [Энди] добился большого прогресса. EDM в основном использует электрическую дугу для удаления материала с заготовки, но, как и любой, кто непреднамеренно выполнил EDM, скажем, на отвертке, замкнув ее на клеммы в распределительной коробке под напряжением, процесс должен контролироваться, чтобы быть полезным.
Часть 1 показывает начало сборки с использованием старой машины для прожига кранов, 60-вольтового источника питания и простого генератора импульсов. Этого было достаточно, чтобы поэкспериментировать как с основами механического управления положением электродов, так и с электрическими аспектами получения устойчивого полезного разряда. Часть 2 продолжается усовершенствованиями, которые очень быстро привели к появлению первых полезных деталей, быстро и чисто обработанных из тонкой заготовки с использованием специального инструмента. Мы признаем, что были впечатлены — многие сборки EDM либо никогда не доходят до того, чтобы делать простые отверстия, либо останавливаются, когда продвижение за пределы этого первоначального успеха оказывается пугающим. Конечно, когда [Энди] упускает из виду тот факт, что он сделал кнопки для панели управления на своей самодельной машине для литья под давлением, возникает ощущение, что все возможно.
Мы с нетерпением ждем новых сведений об этой сборке. Мы видели несколько сборок EDM раньше, но ни одна из них не обладала таким большим потенциалом.
youtube.com/embed/AQCpueMkZ6o?version=3&rel=1&showsearch=0&showinfo=1&iv_load_policy=1&fs=1&hl=en-US&autohide=2&wmode=transparent” allowfullscreen=”true” sandbox=”allow-scripts allow-same-origin allow-popups allow-presentation”>Аппарат для электроэрозионной обработки – mikesworkshop
Аппарат для электроэрозионной обработки
С тех пор, как я сломал метчик при изготовлении Улучшенный патрон для метчиков , я подумывал сделать простой аппарат для электроэрозионной обработки. Делая шестигранное отверстие в рычаге блокировки пиноли мельницы, я снова подумал, что это еще одно приложение, где может помочь простой электроэрозионный станок. Я также вижу потенциальное применение в бурении HSS.
Мой интерес пробудился еще больше, когда я наткнулся на статью Дерека Лайнаса под названием «Простая самодействующая электроэрозионная машина» (http://www.stockportsme.co.uk/Membersprojects/Spark_eroder.html). Концепция этой машины очень проста. Он состоит из скользящего шпинделя, несущего инструмент, прикрепленного к якорю, приводимому в действие катушкой. Шпиндель соединен с конденсатором, который заряжается через катушку и внешний резистор. Когда конденсатор заряжается, зарядный ток активирует катушку и поднимает шпиндель. Когда конденсатор приближается к максимальному заряду, зарядный ток уменьшается, и в конечном итоге сила, удерживающая якорь в катушке, ослабевает настолько, что шпиндель освобождается, и он падает под действием силы тяжести. При ударе о заготовку конденсатор разряжается, вызывая искрение между инструментом и заготовкой. В то же время на катушку снова подается питание, и шпиндель отрывается от заготовки. Затем весь цикл повторяется. Конечным результатом является то, что искры разъедают металл и инструмент постепенно погружается в заготовку.
Во время использования заготовку и инструмент погружают в ванну с диэлектрической жидкостью. Обычно используют дистиллированную воду или керосин.
Я построил машину, как описано Дереком Лайнасом, и работал на ней от источника питания на 21 вольт. Я был разочарован скоростью эрозии, которая составляла около 1-2 мм/час с инструментом 3 мм. Версия Дерека работала от источника питания 50 В и, вероятно, достигла гораздо более высокой скорости эрозии. Я подумывал обновить свой блок питания до 50 В, но сначала решил посмотреть, можно ли улучшить производительность при 21 В.
Сначала я опишу механические части машины, а после опишу новую электрическую систему, которая значительно повышает производительность.
Блок состоит из катушки, показанной вверху фотографии. Под ним находится подшипниковый узел, в котором скользит шпиндель. Шпиндель заканчивается на верхнем конце якорем, который плотно входит в отверстие катушки. Обе эти части удерживаются на задней панели, которая изолирована от подставки черным блоком Delrin, который крепится к стержню с правой стороны.
Формирователь катушки был изготовлен из двух щек из плексигласа диаметром 40 мм с центральным отверстием 12 мм и трубки из делрина диаметром 13 мм и диаметром отверстия 10 мм. Концы делриновой трубки были загнуты внутрь щек. Первоначально катушка состояла из 1500 витков эмалированной медной проволоки 28 SWG, но впоследствии я уменьшил ее примерно до 1000 витков, чтобы уменьшить сопротивление катушки. Каркас из мягкой стали, окружающий катушку, образует магнитную цепь, и все это скрепляется винтами M3.
Верхняя пластина из мягкой стали имеет круглую стальную вставку размером 10 мм и толщиной 5 мм, которая входит в верхнюю часть змеевика. Нижняя поверхность покрыта диском диаметром 10 мм и толщиной 1 мм из резины EPDM. Этот резиновый диск служит трем целям. Он предотвращает прилипание якоря к стальной вставке, смягчает удар якоря при ударе о вставку и обеспечивает некоторый «отскок», позволяющий якорю отскакивать от вставки.
Шпиндель представляет собой кусок стержня из мягкой стали диаметром 6 мм сарматура из мягкой стали мм на одном конце. Это два отдельных компонента, которые были разработаны компанией Loctited вместе.
Несущий блок изготовлен из куска стали 50 x 38 x 12 мм. Он был просверлен сверлом диаметром 6,5 мм, а концы расточены до 8 мм на глубину 10 мм. Две латунные вставки были рассверлены до 5,9 мм, а внешний диаметр уменьшен, чтобы обеспечить плотную посадку в зенкерных отверстиях. После запрессовки латунные вставки были рассверлены до 6 мм. Последней операцией является фрезерование центральной части блока.
Два отверстия в блоке предназначены для направляющей пластины, препятствующей вращению.
Кольцо, препятствующее вращению, изготовлено из куска круглой латуни диаметром 12 мм. Он был просверлен на 6 мм и прорезан щелью шириной 1 мм с помощью продольной пилы на глубину 1,5 мм. Под прямым углом к прорези в кольце просверлено поперечное отверстие и нарезана резьба M3 для винта, который фиксирует кольцо на шпинделе.
Крепежный винт также используется для электрического соединения шпинделя с помощью гибкого провода.
Направляющая пластина, препятствующая вращению, изготовлена из куска стали 6 x 25 мм. Вдоль одного края был сделан разрез шириной 1 мм и в него вклеен кусок листовой стали шириной 1 мм. Затем сталь подпиливали так, чтобы она выступала примерно на 1 мм.
Эта стальная полоса входит в прорезь стопорного кольца и предотвращает вращение шпинделя и инструмента.
Важно, чтобы шпиндель свободно скользил в опорном блоке и чтобы стопорное кольцо свободно скользило по стальной полосе. Шпиндель должен свободно падать при подъеме и отпускании.
Инструмент, в данном случае медный стержень диаметром 4 мм, крепится к концу шпинделя с помощью простого соединительного зажима. Инструмент может быть практически любой формы. Предпочтительным материалом является медь, так как она очень медленно подвергается эрозии, но также можно использовать и латунь.
Подставка представляла собой просто кусок 6-миллиметровой стальной пластины размером 125 x 75 мм с привинченным к ней куском 10-миллиметрового стального стержня.
В основании были просверлены различные отверстия для крепления изделия к основанию.
Латунный винт M6 в задней части устройства обеспечивает электрическое соединение со стойкой и заготовкой.
Электрические схемы
Базовая схема, описанная Дереком Лайнасом, показана выше с одной небольшой модификацией. В его схеме вместо лампы 12 В 50 Вт используется резистор 6,8 R мощностью 10 Вт. Когда к цепи подается питание, ток течет через катушку, чтобы зарядить конденсатор. Этот ток поднимает якорь и шпиндель. По мере того, как конденсатор заряжается, ток через катушку уменьшается до тех пор, пока якорь не перестанет в достаточной степени притягиваться к катушке, что позволяет шпинделю упасть. Это разряжает конденсатор, создавая искры на стыке инструмента и детали, которые разрушают изделие. Ток снова может течь через катушку, шпиндель поднимается, и весь цикл повторяется.
Причин замены резистора на лампу было несколько. Первым и самым важным было то, что резистор на 6,8 Ом, использовавшийся изначально, очень быстро сгорел (я не понимаю, почему это должно быть так, поскольку Дерек работает на своем устройстве от 50 Вольт, а ток через его резистор должен быть еще выше). Вторая причина изменения заключается в том, что лампы имеют очень низкое сопротивление в холодном состоянии. Это означает, что конденсатор может заряжаться быстрее, и, следовательно, потенциально рабочая частота должна быть выше. Третья причина замены резистора заключается в том, что яркость лампы обеспечивает визуальную индикацию тока в цепи.
Эта базовая схема обеспечивала низкую скорость эрозии, порядка 1-2 мм/ч, с помощью круглого латунного инструмента диаметром 3 мм. Чтобы попытаться улучшить это, была опробована следующая схема.
В этой схеме добавлена вторая лампа, шунтирующая катушку. Это обеспечивает второй путь зарядки конденсатора, и опять же это должно увеличить ток в конденсаторе и, следовательно, рабочую частоту и скорость эрозии. Это привело к некоторому улучшению скорости эрозии, но оно не было значительным. Сопротивление шунта не может быть слишком низким, потому что тогда на катушке будет недостаточно напряжения, чтобы поднять якорь.
На скорость эрозии влияет ряд факторов. Во-первых, это количество заряда, хранящегося в конденсаторе. Это влияет на интенсивность искр. Однако существует предел того, насколько емкость может быть увеличена, потому что, если искры становятся слишком интенсивными, инструмент имеет тенденцию привариваться к заготовке. Вторым фактором, влияющим на скорость эрозии, является частота операций. На низких частотах это будет зависеть от значения сопротивления и емкости. Однако на более высоких частотах частота определяется скоростью, с которой шпиндель может подниматься и опускаться, т. е. собственной частотой колеблющегося шпинделя. На это, в свою очередь, влияет расстояние, на которое шпиндель должен подниматься и опускаться. Таким образом, более высокие частоты могут поддерживаться, когда расстояние до колебаний невелико. Заметно, что при использовании аппарата частота операций замедляется по мере проникновения инструмента в заготовку из-за увеличения пройденного пути. Понятно, что рабочие критерии эрозии сложны и постоянно меняются по мере возникновения эрозии.
Другие специалисты (например, Эрик Румбо в статье под названием «Простая электроэрозионная машина», Model Engineers’s Workshop 117, июль 2006 г.) пытались управлять соленоидом независимо от цепи заряда-разряда, используя нестабильный мультивибратор на основе микросхемы 555. Это позволяет оптимизировать цепь заряда-разряда для хорошего искрообразования, но при постоянной частоте привод катушки не использует время наилучшим образом, т. е. бывают моменты, когда частота привода может быть выше установленной частоты. Кроме того, цепь может терять ток, позволяя инструменту оставаться в контакте с заготовкой слишком долго.
Схема выше показывает метод, который я использовал для управления колебаниями шпинделя. Сеть RC находится слева. По мере зарядки конденсатора напряжение на шпинделе возрастает. Детектор напряжения справа отслеживает рост напряжения на шпинделе, и когда оно достигает определенного значения, он отключает ток на катушку, позволяя шпинделю падать и разряжать конденсатор во время работы. Если триггерное напряжение установлено низким, шпиндель будет колебаться быстро, тогда как если оно установлено высоким, то он будет работать медленно. Даже после выключения катушки конденсатор продолжает заряжаться при падении шпинделя, поэтому напряжение на конденсаторе в момент удара инструмента по заготовке будет значительно выше напряжения срабатывания. Преимущество этого подхода заключается в том, что конденсатор всегда заряжается, за исключением очень короткого периода (около 2 миллисекунд), когда инструмент фактически находится в контакте с заготовкой, и что частота колебаний всегда является самой высокой, которую можно поддерживать для установленного триггера. точка (т. е. время не теряется). На стороне RC цепи катушка не влияет на скорость заряда, а значения R и C можно оптимизировать для максимальной скорости эрозии, как указано ниже.
На приведенной выше схеме показан детектор напряжения. Два транзистора, Tr1 и Tr2, образуют классический дифференциальный усилитель с парой длинных хвостов, а Tr3 и Tr4 образуют выходной каскад, управляющий катушкой. Диод на катушке подавляет обратное напряжение на катушке, а светодиод обеспечивает визуальную индикацию среднего зарядного тока конденсатора С в цепи зарядки. В качестве детектора напряжения можно было бы использовать дешевый операционный усилитель, но для этого потребовался бы отдельный источник питания, поскольку максимальное рабочее напряжение операционного усилителя 714 составляет 18 В. Использование дискретных компонентов позволяет избежать этого осложнения
Эта схема без светодиода и последовательного резистора была собрана на небольшом куске полосовой платы, как показано ниже:
Ленточная плата установлена непосредственно на потенциометре. Для силового транзистора Tr4 радиатор не нужен, потому что он либо включен, либо выключен, и рассеивается небольшая мощность. Подключение к плате осуществляется через небольшой блок разъемов в левом нижнем углу.
Электроника смонтирована в коробке из МДФ, как показано здесь. Внизу справа находится трансформатор на 21 В с прикрепленными выпрямительными диодами. Выше показана схема платы, прикрепленная к потенциометру. Слева – зарядные компоненты для конденсатора. Они смонтированы на куске 3A «блока выбора». Он крепится к передней панели с помощью алюминиевого кронштейна. Последовательный резистор состоит из 4 последовательно соединенных вольфрамовых ламп накаливания 12 В 50 Вт. Два из них могут быть закорочены переключателем, чтобы обеспечить два выбираемых зарядных сопротивления. В правом нижнем углу блока шоколада находятся два конденсатора, используемые в RC-цепи. Это компоненты 470 мкФ 50 В. Один или оба могут быть выбраны переключателем, дающим две выбираемые емкости. Крайне слева от блока шоколада находится красный накопительный конденсатор емкостью 2200 мкФ, который подключается к диодам, установленным на трансформаторе.
Передняя панель устройства с расположением органов управления. Подключение к катушке осуществляется через гнездо для динамика DIN, а подключение к инструменту — через штекеры типа «банан» 4 мм.
Обратите внимание на квадратную переднюю панель. Бочкообразное искажение изображения — это артефакт камеры.
Здесь показана задняя часть блока управления. Вентилятор и вентиляционное отверстие обеспечивают охлаждение внутри коробки. Вентилятор представляет собой 50-мм вентилятор на 12 В, извлеченный из компьютера. Он подключен через две верхние лампы в цепи CR. Таким образом, по мере того, как ток и последующее тепло увеличиваются, увеличивается и скорость вращения вентилятора.
С этим контроллером возможна скорость эрозии около 9 мм в час при использовании латунного инструмента диаметром 3 мм. Это не быстро, но определенно удобнее, чем 1-2 мм/ч, достигаемые с помощью оригинальной схемы.
На этой фотографии показаны некоторые отверстия, «просверленные» с помощью электроэрозионного станка. Слева кусок стали толщиной 3 мм, посередине кусок листа толщиной 1 мм и справа кусок ножовочного полотна. Во всех случаях диаметр отверстия составляет 4 мм. Более толстому куску потребовалось около 30 минут, чтобы разрушить отверстие, в то время как другие были завершены за несколько минут.
В качестве диэлектрической жидкости я использовал дезодорированный керосин (уайт-спирит). Альтернативу, дистиллированную воду, я избегал из-за потенциальных проблем со ржавчиной.
Возможно дальнейшее усовершенствование аппарата. Источник питания с более высоким напряжением, несомненно, увеличит скорость эрозии. Механизм для опускания узла катушки/шпинделя во время эрозии для поддержания только короткой амплитуды вибрации также ускорит процесс.
Катастрофа!
В поисках более высоких скоростей эрозии мне удалось сжечь трансформатор. Это было рассчитано только на 1,2 ампера. Решил модернизировать трансформатор и впихнуть в схему амперметр. После проверки стоимости и размера модернизированного трансформатора на 4 ампера, оба из которых были значительными, я подумал об использовании импульсного источника питания 24 В для ноутбука. Подходящее устройство на 24 В и 100 Вт было куплено на ebay примерно за 8 фунтов стерлингов. В то же время на ebay был куплен амперметр 0-5A примерно за 4 фунта стерлингов.
Блок питания ноутбука имеет переключатель напряжения, позволяющий выбирать напряжение от 12 до 24 В. Он небольшой и автономный и может быть перемещен за пределы блока управления. Это создает достаточно места внутри существующей коробки для установки амперметра.
Версия Mk 2.
На фотографии выше показана новая передняя панель с установленным амперметром. Старая передняя панель была использована повторно. После отсоединения всех штекеров и т.д. он был снят и отверстие для амперметра вырезано с помощью коронки. Потенциометр переместили под амперметр и собрали блок. Никаких изменений в схему не вносилось, кроме снятия трансформатора и диодов. Блок питания ноутбука подключается к задней части коробки через розетку постоянного тока.
На этой фотографии показан блок питания ноутбука. Блок питания стабилизирован и имеет защиту от перегрузок.
Это изменение несколько повысило производительность устройства. Я думаю, что улучшение происходит потому, что напряжение нового блока не проседает в условиях высокой нагрузки.
Другие инновации.
В электроэрозионный станок были внесены еще две инновации. Они показаны на фото выше. К колеблющемуся валу добавлен груз. Это помогает преодолеть любое трение в подшипнике, что приводит к сокращению времени падения вала, а это, в свою очередь, увеличивает частоту колебаний.