Шлифовальный барабан без токарного станка
Шлифовальный брусочек своими руками
Светильник из реек
- Опубликовано в Инструменты и приспособления, Мастеру
Мне тоже оказался до зарезу нужен шлифовальный барабан (потом покажу для чего). Просмотрев урок Дача Шульца, который я выкладывал чуть раньше, я решил сделать аналогичный, за некоторыми исключениями. Токарного станка у меня нет. Как я вышел из этого положения — смотрим ниже.
Материалом для изготовления была выбрана ножка от стола. Как показала дальнейшая обработка, она была сделана из сосны — не самый лучший материал, но, что было, то и пошло в дело… Ну что, поехали!
С помощью торцовки (да хоть ручной ножовки) отпиливаем заготовку под нужный размер.
С обеих сторон получившегося брусочка отметил центры
С одной стороны с помощью сверлильного станка (он играет ключевую роль во всем процессе) сверлим строго вертикальное отверстие по центру заготовки.
промазываем стенки отверстия и винта клеем (я использовал Титан)
и вворачиваем в винт по центру — он должен быть строго по оси заготовки. . Чтобы можно было завернуть винт я накрутил на него пару гаек, законтрив их.
С другой стороны наколол шилом центр. Для него напротив центра сверлильного патрона был установлен шип (дощечка в которую забит дюбель). Дощечка прижита к столу струбциной.
Этой же струбциной прижимается стальной уголок для подручника. Сам подручник — это еще один ровный обрезок ЛДСП, притянутый к уголку еще одной струбциной. Заготовку зажимаем в сверлильном патроне и опускаем на центральный шип (импровизированная задняя бабка)
из инструмента у меня были дедушкин майзель, самодельный реер, в который я переточил напильник и штангенциркуль.
А дальше я просто получал удовольствие, токарные работы, которые я люблю со школы, но по причине отсутствия токарника и острой в них необходимости я не выполнял.
Резцами скругляем заготовку
Затем бруском со шлифовальной бумагой доводим его до идеального цилиндра.
Периодически проверяем правильность цилиндра штангенциркулем.
Следующий шаг — покрытие заготовки эластическим покрытием. Для него я выбрал старый коврик для мыши.
Отрезаем полоску по ширине бобышки. Промазываем ее клеем.
Обматываем ее чем-нибудь (я использовал длинный кусок полиэтилена, который остался от упаковки Джокерной трубы и оставил на сутки высыхать.
Для изготовления пропила сделал простенький кондуктор (чтобы руки подальше от диска держать). Уголок из ЛДСП (я в нем собираю выдвижные ящики) к нему прикрутил обрезок с отверстием в которое гайкой затянул бобышку.
Паз получился глубиной около 5 мм (больше нельзя — треснет)
Вырезаем шкурку по размеру окружности (на 1 см больше(Заправляем края бумажки в паз, стараясь натянуть посильнее. Крепить бумагу я решил не клином, а резинкой. Для чего спер на работе катетер Фолея — отличная резинка. (Из них еще отличные рогатки получаются).
Растягиваем резинку и заводим ее в паз.
Проталкиваем его в паз отверткой (как показала практика, угольник или линейка лучше)
Все, резинка зафиксирована, можно пробовать.
В принципе, работает.. но в процессе эксплуатации резинку вырвало к чертям и заготовкой порвало мягкую подкладку. Поэтому конструкция фиксатора была доработана. Сверлом на 5 я высверлил в нижнем полюсе паза расширение для резинки.
Все манипуляции по креплению бумажки были повторены. Испытания прошли успешно. Резинка стоит, как влитая, удерживая бумагу.
Сейчас вырезал новый кусок коврика, промазал клеем и оставил сохнуть.
Конструкция с резинкой проще,чем клин, который использовал Дач Шульц, кроме того щель без абразива получается гораздо меньше. Преимущества же клина — 100% фиксация и отличное натяжение бумаги.
После проб я снова наклеил на барабан слой вспененного полиэтилена. Получилось вот так:
- шлифование
Станок по дереву своими руками
Изготовить станок по дереву своими руками можно, к примеру, из сгоревшего шлифовального станка. Оценив все плюсы и минусы сгоревшего заводского станка, можно приступать к изготовлению своего, который будет совсем не похож на заводской. Нужно обязательно все предусмотреть и сделать станок так, чтобы на нём можно было и фрезеровать, и шлифовать.
Самое главное, что нужно для самодельного станка, это двигатель, который будет основой станка, и дальше все будет строиться на нем. Не нужно экономить, лучше сразу приобрести хороший двигатель.
Для работы с деревом вполне подойдет двигатель с подобными характеристиками – мощность примерно 3 кВт при 3000 оборотов в минуту, подключение 380 вольт. Такого количества оборотов должно хватить для фрезеровки. Еще одним значимым параметром двигателя является его вал диаметром 32 мм и длинной 70 мм.
Двигатель необходимо закрепить на станину, которую можно взять от старого станка. Станина вполне подходит для станка по дереву, так как она довольно тяжелая и на ней имеются все базовые плоскости для того, чтобы закрепить и сам двигатель, и площадку.
Пускатель и кнопка пуска установлены на станине справа, это очень удобно для работы. Кабель делается переносным, чтобы можно было включать его в розетку, расположенную на стене.
При самостоятельном изготовлении станка по дереву, необходимо тщательно продумать и предусмотреть все мелочи. Площадку нужно закрепить четырьмя болтами, которые должны быть утоплены. Перед установкой площадки необходимо выпилить в ней окошко под шлифовальный барабан, а затем с помощью шурупов закрепить две рейки, на которые впоследствии ляжет вторая площадка.
Вторая площадка будет регулируемой и сможет подниматься. Такое решение очень удобно.
Регулирующие бруски должны быть подложены между двумя площадками.
Шлифовальный барабан необходимо заказывать у токаря, но только у проверенного. Барабан должен быть изготовлен таким образом, чтобы он очень плотно садиться на вал и у него не было биений. Можно самому всё просчитать и дать токарю уже готовые чертежи.
Барабан должен иметь следующие размеры – высота — 21 см, посадка на вал – 7 см, стена после проточки – 7мм, проточка сквозная – 8 мм, диаметр – 145 мм и глубина проточки – 14 см.
Наждачное полотно должно заправляться и зажиматься внутри с помощью специальных прижимов. Замену можно будет произвести довольно легко и быстро. Для выполнения фрезеровки, необходимо снять площадку и барабан, затем установить другую площадку, кольцо или линейку и после этого начинать фрезеровку. Промышленные фрезы имеют посадочный размер 32 мм, так что они отлично встанут на вал. Также, легко может быть установлен и диск для того, чтобы делать пропилы. Подъем фрезы можно регулировать с помощью колец.
Такой станок способен прослужить вам много лет. На нем можно как фрезеровать, так и шлифовать. Как видно из данной статьи, станок по дереву своими руками сделать не трудно, нужны лишь подходящие материалы.
Самодельная шлифовальная машина для барабанов своими руками — WOODBREW
Все проектыПроекты с ЧПУМагазин проектовДеревообработка
Автор
Мы действительно сделали это, и это работает! Барабанная шлифовальная машина уже очень давно находится в нашем списке потребностей и пожеланий, и мы очень рады, что сделали ее своими руками! Эта самодельная барабанная шлифовальная машина очень поможет и сделает шлифование менее ужасным. Вы можете посмотреть видео ниже или прочитать и посмотреть!
Я хочу начать с того, что у нас есть набор планов , доступных здесь:
https://www.etsy.com/listing/851762604/drum-sander-build-plans?ref=shop_home_active_11
так что мы не будем давать точные размеры здесь. В этом подробном наборе чертежей указаны размеры этой 18-дюймовой барабанной шлифовальной машины, файл SketchUp и шаблоны.
Ремень: https://amzn.to/3eVIKGI
Опорные подшипники: https://amzn.to/2CIfWVc
Ключевой запас: https://amzn.to/3f3n8rM
3 Вал 9 : https://amzn.to/39s15Kr
Петля: https://amzn.to/2WVfFVu
Выключатель питания: https://amzn.to/3eXliIZ
Мы использовали инструмент Inventables X-Carve (http://bit.ly/2NtYwQm (партнерская ссылка)) для вырезания каждого патрона, чтобы получился барабан.
Мы использовали меламин для самой барабанной шлифовальной машины. Это будут все стороны, дно и шлифовальный стол (2). Мы вырезаем их на настольной пиле, но вы всегда можете использовать циркулярную пилу. Мы выбрали меламин, потому что стол должен быть гладким и прочным, а это самый доступный способ сделать это. Однако две из этих сторон будут обрезаны на X-Carve, чтобы они идеально подходили к болтам, которые будут крепиться к опорным блокам.
Удивительно, но уже пора собираться. Мы предварительно просверлили отверстия для наших шурупов, а также добавили кромку из ПВХ со всех сторон меламиновых плит, которые будут видны. После того, как эти доски будут скреплены винтами, мы добавим фортепианную петлю сзади и на столешницу. Это сделано для того, чтобы стол можно было регулировать вверх и вниз в зависимости от толщины доски, которую вы хотите отшлифовать. Далее идет добавление на коммутатор. Мы просверлили отверстие спереди, чтобы провод, идущий к двигателю, мог пройти через него, и прикрутили переключатель прямо спереди. Вам придется снять одну сторону, чтобы установить барабан, так что вы можете надеть ее сейчас, чтобы правильно закрепить винты, или просто оставить ее снятой, пока барабан не встанет на место.
Двигатель уже должен быть внутри коробки, а сторона шкива должна торчать из отверстия.
Теперь, когда барабан готов и установлен на место, вы можете отрезать стержень доступа. Делайте то, что мы делали в видео, только если вам очень комфортно, мы включили машину и использовали ручную пилу для резки металла, чтобы медленно отрезать доступ. На противоположной стороне у вас тоже может остаться немного, у нас было достаточно места, чтобы использовать нашу портативную ленточнопильный станок для этой стороны. Что бы ни работало лучше всего!
Подъемный механизм Я не знаю, насколько хорошо я могу объяснить, как работает подъемник стола, поэтому я посоветую вам обратиться к видео для этой части. Это начинается в 7:40.
Мы сделали крышку барабана из МДФ таким образом, чтобы она сидела на болтах опорного блока и никогда не касалась наждачной бумаги. Мы также просверлили небольшую прорезь на стороне, противоположной двигателю, чтобы болт мог двигаться вверх и вниз внутри, когда ручка снаружи ослаблена. Это позволяет регулировать толщину материала при шлифовании и сохранять сбор пыли A1. Крышка для ремня также изготовлена из МДФ, и мы добавили только одну петлю, чтобы вы могли открывать и закрывать ее, когда вам нужно попасть внутрь, чтобы починить ремень или заменить его и т. д.
Наждачная бумага Мы наносим на барабан наждачную бумагу зернистостью 80 и 120. Мы не планируем когда-либо вставлять сюда всю 18-дюймовую доску, поэтому мы можем легко переключаться между наждачной бумагой с зернистостью 80 и 120 без необходимости снова надевать и снимать бумагу. Наждачная бумага помещается в канавку в барабане. , затем прикручивается небольшой скошенный кусок дерева, чтобы удерживать оба конца бумаги на месте.
Дилан впервые загружает доску в барабанную шлифовальную машину.
Вот и все! Честно говоря, очень удивлен, насколько хорошо работает эта самодельная барабанная шлифовальная машина. Мы не можем дождаться, чтобы начать больше проектов и действительно запустить это дело.
барабанный шлифовальный станок своими рукамикак сделать барабанный шлифовальный станоксделать свой собственный барабанный шлифовальный станоктолщина шлифовального станкаваритьдеревообработка
Как сделать шлифовальную машину своими руками [2022]: пошаговое руководство
Роберт Джонсон
Автор:
11 октября 2022 г. небольшая комиссия. Подробнее здесь.
Поделиться
Барабанные шлифовальные машины. Споры о том, является ли производство барабанной шлифовальной машины более рентабельным, чем покупка уже изготовленной, привели людей в замешательство и не позволили принять решение. Правда покупка барабанного шлифовального станка стоит немного дорого. Зачем тратить деньги, если можно построить по доступной цене? Здесь наши технические специалисты объясняют, как сделать портативную барабанную шлифовальную машину.
Инструменты и материалы
При сборке барабанной шлифовальной машины своими руками у вас есть возможность приобрести набор для самостоятельной сборки, в котором есть все материалы и конкретные инструкции. Generally, here are the essential tools and materials you will need for the project:
- ¾ Melamine sheets
- ¼ MDF
- Pulley
- Belt
- Motor
- Hinge
- Подшипники с блоками наволочки
- Переключатель мощности
- Вал
- Ключевой запас
Как создать свой собственный барабанщик
.
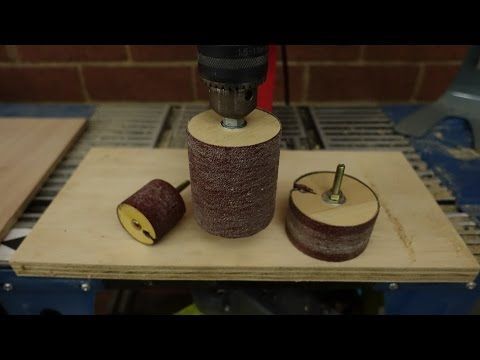
Первое, что нужно сделать, это получить правильный размер патронов барабана и стола. В Интернете доступно множество планов, в которых есть шаблоны для размеров. Но, если вы не хотите выбирать это, вы можете создать свои размеры по своему вкусу.
Шаг № 2: Вырежьте одинаковые детали для круглых барабанов
После получения размеров вырежьте детали для круглых барабанов на МДФ. Вы можете использовать Inventables X-Carve или любой другой режущий инструмент, чтобы вырезать размеры для барабанов. Наши эксперты предлагают вам создать закругления, достаточно большие для вашего вала и шпонки.
После того, как вы успешно сделали эти вырезы, вы должны склеить их вместе. Сначала наденьте кольцо, меламиновую доску, опорный блок и шкив на вал и шпонку. Отметьте, где расположен каждый материал, снимите их и склейте все вместе, чтобы они оставались прямыми. Чтобы они не развалились, склейте их пополам.
Шаг №3: Обрежьте детали стола
Для стола вашей барабанной шлифовальной машины своими руками вы должны использовать меламиновые листы. Обрежьте листы по длине с помощью циркулярной или настольной пилы, чтобы все стороны были точно вырезаны, чтобы соответствовать болтам, которые будут удерживать опорные блоки.
Шаг № 4: Соберите и соедините детали вместе
Просверлите несколько отверстий для винтов и наклейте кромку из ПВХ со всех сторон на меламиновую плиту. Как только вы это сделаете, вставьте шарнир пианино в заднюю часть и столешницу, чтобы стол можно было регулировать со всех сторон.
Далее необходимо просверлить отверстие в передней части платы для установки переключателя. Это позволит проводу удобно пройти через двигатель к выключателю на передней панели.
Теперь, когда вы закончили с переключателем, теперь нужно добавить барабан. Вам нужно будет снять одну сторону стола, чтобы интегрировать барабан и вставить винты. Перед этим прикрепите опорные блоки снаружи с помощью болтов и гаечных ключей ⅝, чтобы затянуть их [1]. Затем установите барабан на место.
Закрутите боковую сторону и затяните хомут. Теперь вставьте шкив внутрь и постучите им по кольцу. Заблокируйте шкив наружу.
Шаг № 5: Поместите двигатель внутрь
Затем поместите двигатель в коробку с петлей.
Шаг № 6. Добавьте барабаны и ремень
Двигатель и ремень должны быть выровнены так, чтобы двигатель мог тянуть ремень вниз. Это облегчит надевание и снятие ремня.
Шаг 7. Сборка крышек
Изготовьте крышки барабана и ленты из МДФ и убедитесь, что они не прилегают к наждачной бумаге. Вместо этого они должны сидеть на болтах опорного блока.
Шаг № 8. Оберните барабан наждачной бумагой по вашему выбору
Вы можете использовать наждачную бумагу с любой зернистостью на барабане, будь то зернистость 80, 120 или 2020. Поместите наждачную бумагу в канавку барабана и привинтите небольшие деревянные кусочки, чтобы закрепить оба конца наждачной бумаги.
Читайте также:
- Способы использования барабанной шлифовальной машины
- Способы отличить барабанную шлифовальную машину от рубанка
Вывод
Сделать своими руками барабанную шлифовальную машину проще простого. Но наша команда экспертов постаралась максимально упростить шаги и сделать каждый из них более понятным. Изготовление барабанной шлифовальной машины не только экономически выгодно, но и позволяет спроектировать инструмент в соответствии с вашими предпочтениями. Итак, соберите необходимые материалы и начните делать свой инструмент, следуя шагам, описанным в этом посте.
- Автор
- Последние сообщения
Роберт Джонсон
Роберт Джонсон — плотник, который с радостью делится своей страстью к творчеству с остальным миром. Его детище, Sawinery, позволило ему сделать это, а также связаться с другими мастерами. С тех пор он построил завидную мастерскую для себя и не менее впечатляющее онлайн-достижение: сайт с обширными ресурсами, который одинаково полезен как старожилам, так и новичкам.
Последние сообщения Роберта Джонсона (посмотреть все)
- Как отделать столешницу полиуретаном (пошаговое руководство) — 29 декабря 2022 г. Деревянные жалюзи — 28 декабря 2022 г.