Электроды Сормайт
Во многих случаях сварочных работ приходится делать какие-то наплавки, напайки и т. п. Однако многие сварщики, которые имеют за своими плечами огромный опыт работы со свариваемым металлом, до сих пор выполняют наплавку металла обычными сварочными электродами. На самом деле это неправильно и мучительно долго, потому что если наплавка металла происходит с помощью обычных электродов, то существует вероятность прожога металла или просто некачественной наплавки.
Во избежание этих всех недостатков «умы мира» начали создание новых электродов, которые смогли бы удовлетворить потребность людей в качественных электродах для наплавки. И вот им удалось создать такие электроды, которые при наплавке выполняют свою часть работы качественно. Вторая часть работы лежит на плечах сварщика.
Именно электроды сормайт являются тем продуктом, которого так недоставало сварщикам. Несмотря на то, что многие люди говорят, что настоящий профессионал может выполнить работу качественно даже бракованным материалом.
Также опытные сварщики уже имеют опыт работы с такими электродами и остаются очень довольными. Они стараются посоветовать эти электроды и Вам, потому что наплавка металла может пригодиться и в том случае если Вам понадобится ремонт своего автомобиля, то сормайт будут как раз кстати. К примеру, на Вашем автомобиле может сноситься вал или какие-то другие детали. Да, действительно электроды сормайт очень нравятся профессиональным сварщикам
, поэтому они собирают львиную долю положительных отзывов.
Также электроды сормайт являются очень полезной вещью для железной дороги нашей страны. Железнодорожные составы имеют очень большой вес, поэтому на рельсы оказывается величайшее давление, вследствие которого рельсы подвергаются смятию и износу. По этим причинам концы рельс нуждаются в наплавке, потому что полностью заменять рельсы является нерентабельным.
Однако перед использованием данных электродов нужно провести с ними некоторую работу. Для начала их нужно поддать термической обработке при температуре 850 – 900 градусов по Цельсию в течение 3 – 4 часов. По прохождении указанного времени печь вместе с электродами остывает до 700 – 750 градусов, а потом снова разогревается до температуры около 900 градусов в течение 4 часов. Потом снова печь охлаждается, но уже до 600 градусов и снова идет нагревание до 900 градусов с последующим охлаждением до 35 градусов. Детали, которые были наплавлены сормайтом после нагревания до 950 градусов, закаляют в масле в течение 40 – 50 минут. После этого изделие готово к использованию.
Заказать электроды сормайт Вы можете через пункт меню «Контакты».
Сормайт – Справочник химика 21
Сталь Х5 (Х5Л ) с наплавкой наружной поверхности сормайтом Ло 1 (ГОСТ [c.19]Для повышения износоустойчивости втулок производят наплавку рабочих поверхностей гильз сормайтом или стеллитом. Если эти гюверхности не наплавляют твердым сплавом, то рекомендуется подвергнуть втулки термообработке, достигнув для легированных сталей твердости НВ — 350—400 и для углеродистых 260—320. [c.130]
Сталь с наплавкой стеллитом пли сормайтом Сталь с наплавкой сормайтом стали марок 4. Н и 40.x (после закалки) [c.153]
Затем партию колец растачивают в один размер с припуском 5 мм на диаметр с обязательной заваркой по фанице наплавленного слоя. Чем меньше пофешность заварки, тем выше качество окончательно обработанных колец. Кольцо с наплавленным слоем обтачивают по наружному диаметру по оправке с припуском на дальнейшую операцию 1,5 мм на диаметр. Для предотвращения скола сормайта на выходе резца при окончательной обточке обтачивают фаску на глубину снимаемого припуска. [c.110]
Уплотнительное кольцо 4 устанавливают фаской к передней бабке и зажимают гайкой 9. После включения станка упор-поводок 3 счет трения вращает деталь 4 и весь вращающий узел подшипника. Через отверстие во втулке 12 растачивают отверстие. Проверку осуществляют индикаторным нутромером. Через окно в. корпусе 1 обтачивают кольцо по слою сормайта со скоростью 0,08 мм/об. Скорость резания подрезным резцом 6 -8 м/мин, вспомогательный угол в плане ( = 30°.
Литые и порошкообразные смеси (Сормайт 1, ВК-3, Смена 2, КБХ) [c.375]
Толщина армированного слоя значительно влияет на износостойкость детали и определяется характером и условиями работы детали. Как показала практика [112], в зависимости от этих условий толщина слоя силава сормайт № 1 колеблется от 0,5 до [c.233]
Сормайт толщиной более 1,5 мм можно наплавлять несколькими слоями. Однако многослойной наплавки следует по возможности избегать слой необходимой толщины рекомендуется получать за один — два прохода. [c.233]
Сормайт 2 может подвергаться всем видам термической обработки. Это свойство очень важно, потому что иосле отжига детали, армированные этим сплавом, можио обрабатывать на металлорежущих станках. [c.234]
Снижение твердости наплавленного слоя после отжига до HR 30—35 позволяет армировать сормайтом № 2 детали, необходимую конфигурацию которых после наплавки можно получить режущим инструментом. [c.234]
После закалки деталей, армированных сормайтом № 2, твердость наплавленного слоя повыщается до HR 60—62. [c.234]
При работе с толчками и ударами возможно применение деталей, наплавленных сормайтом № 2 без термической обработки. В этом случае используется другое свойство сормайта № 2—его высокая вязкость. [c.234]
Для повышения долговечности деталей горячих центробежных насосов и детален клиновых задвижек их поверхности армируются твердым сплавом сормайт № 1 [101].
Наплавка твердого сплава сормайт. Металлургиздат, 1951, стр. 57. [c.389]
Стеллит, сормайт Серый с красной полосой но пери- [c.42]
Вал 7 в местах прохождения через набивку сальника защищен от износа съемными гильзами 15, на наружные поверхности которых направлен слой твердого сплава (сормайта или стеллита) для повышения износоустойчивости. [c.194]
Сормайт № 2 60-62 1,5—2,5 Не более 1,0 1,5—2,2 13,5-17,5 1,5-2,5 — — Остальное 0,07 0,07 [c.51]
Сталь марки 15, гост 1050-60, с наплавкой наруж ной поверхности сормайтом № 1 [c.378]
Уплотняющие кольца рабочих колес Ст. 1X13 с наплавкой сормайтом Ст.ЗХ13 без наплавки Углеродистая сталь с наплавкой сормайтом [c.61]
Для гильз, наплавленных сормайтом или стеллитом, допускается уменьшение наружного диаметра проточкой или шлифовкой до величины, обеспечивающей после проточки толщину наплавленного слоя не менее 0,5 —0,6 мм. При обычной его тол-и1,ине 1,8—2 мм наружный диаметр уменьшают на 3 мм. Для не-наплавленнь. х гильз проточка по наружному диаметру также допускается не более чем по 1,5 мм на сторону. [c.133]
Сталь с наплавкой сормайтом стали. марок 40ХН и ШХ-15 (после закалки) [c.153]
Защитные гильзы (втулки). Они служат для предохранения ва-лi от разрушения в местах установки сальниковых уплотнений и относятся к числу наиболее быстро изнашивающихся деталей цент-рс бежных насосов. Материалами для изготовления защитных гильз служат прокат углеродистых сталей (сталь 30, 40, 50), чугунное ЛР Тье, прокат легированных сталей (40Х, 1X13, 2X13, 3X13, Х5М). Для повышения износостойкости втулок производят наплавку их рабочих поверхностей сормайтом или стеллитом. Кроме того, втулки хромируют. Если поверхность стальных втулок не наплавляют твердым сплавом, то их подвергают термообработке.
На Ангарском нефтехимическом комбинате освоена механическая обработка уплотнительных колец насосов КВН из стали 20 и 15Х5М с наплавкой сормайтом. Кольца насосов КВН 55-70, КВН 55-120 и КВН 55-180 диаметром от 130 до 200 мм -тонкостенные, наплавленные сормайтом. Чистота обработки наружного и внутреннего диаметров – = 6,3. Допуск на раз-ностенность – в пределах 0,01 – 0,02 мм. Основной и наиболее сложной задачей является обеспечение точности отверстия (2-й класс) и разностенности в пределах 0,01 мм. Качество колец зависит от правильной их подготовки под наплавку, качества наплавки, термической обработки и равномерности слоя сор-майта. Предусмотрено несколько операций по постепенному уменьшению и стабилизации снимаемого припуска. [c.109]
Предварительные токарные операции выполняют на участке наплавки сормайтом в горячем состоянии при 700 – 800 °С. Нафев осуществляют в электропечах. Наплавленный сормайт обтачивают на токарном станке 1А62 в специальных конусных фибках, которые фиксируют кольцо по внутреннему диаметру. [c.109]
Наиболее широко для армирования ирнмеияются сплавы сормайт № I и сормайт Л Ь 2. [c.232]
Сормайт № 1 целесообразно применять прн армированин деталей простой конфигурации, работающих без резких толчков и ударов (детали центробежных насосов, клиновых за-двих ек, штампы для горячей штамповки, калибровочные кольца для труб, детали приспособлений для гибки труб и т. д.).
Сормайт № 2, обладающий, по сравнению с сормайт № 1, большей вязкостью, целесообразно применять для армирования деталей, работаю- щих с ударными нагрузками (клапаны и седла буровых насосов, вырубные штампы, матрицы и пуансоны для холодной штамповки и т. д.). Детали, наплавленные сормайтом № 2, после отжига обладают хорошей обрабатываемостью, что позволяет применять сормайт № 2 для армирования деталей сложной коифигура-цпи. [c.233]
Если армирование выполнено сплавом сормайт № I, то деталь подвергается термической обработке только лишь для повышения твердости и механических свойств основного металла, так как сормайт № 1 не принимает термическую обработку. В этом случае термическая обработка ведется ио оптимальным для каждой марки сталп или чугуна режимам. При закалке деталей, армиро-наиных сормайтом № 1, в качестве охлаждающей среды необходимо применять масло. Закалка в воде не рекомендуется, так как это может вызвать появление Tp HuiH в армированном слое. [c.234]
Армироваине сплавом сормайт № 1 высокохромистой сталп вызывает ряд трудностей, так как при резком перепаде температур в процессе армирования [c.240]
Лившиц Ф. Наплавка сормайтом № 1 гильз центробежных насосов и деталей клиновых задвилсек. Сб. статей по обмену опытом машииострои-телей-нефтяников, выи, 2, Гостоптехиздат, М., 1956, стр. 20—23. [c.388]
По условиям эксплуатации крекинг-насосы должны непрерывно работать в течение 30—40 суток, в связи с чем поверхности деталей, нод-верженные износу, наплавляют твердым снлавом (сормайтом или стеллитом). [c.196]
Сталь марки Х5 (трубы) по ЧМТУ 2968-51 с наплав кой наружной но верхности сормайтом № I (допускается замена стали Х5 на сталь марки Х5Т-Л) [c. 378]
Твердые сплавы
Подробности- Подробности
- Опубликовано 27.05.2012 13:23
- Просмотров: 21572
Твердые сплавы широко применяются в промышленности для наплавки быстроизнашивающихся поверхностей, для наплавки и напайки режущих инструментов.
Основой всех твердых сплавов являются тугоплавкие карбиды металлов, которые представляют собой химические соединения металла с углеродом.
Твердые сплавы можно разделить на следующие группы: П литые твердые сплавы, 2) порошкообразные твердые сплавы и 3) металл окерамические сверхтвердые сплавы.
Наибольшее распространение получили следующие твердые сплавы: сормайт, сталинит, вокар и победит.
Сормайт представляет собой литой сплав: изготовляется в виде прутков диаметром 3—8 мм и длиной до 450 мм. Применяется для наплавки быстроизнашивающихся частей деталей машин и инструментов. Наплавка производится ацетиленокислородным пламенем или электрической дугой по способу Славянова. Выпускается двух сортов: сормайт № 1 и сормайт № 2.
Сормайт № 1 имеет следующий химический состав: никеля 3— 5%, хрома 25—31%, марганца 1,5%, углерода 2,5—3,3%, кремния 2,8—4,2%, остальное — железо. Твердость HRC 48—52. Сормайт № 1 не требует термообработки после наплавки и может обрабатываться только шлифовкой карборундовыми камнями.
Сормайт № 2 содержит никеля 1,3—2,1 %, хрома 13—17,5%. марганца 1%, углерода 1,5—2%, кремния 1,5—2,2%, остальное — железо. Сплав сормайт № 2 после наплавки требует отжига, а затем закалки и отпуска. После отжига наплавленный сормайт № 2 может обрабатываться режущим инструментом.
Сормайт № 2 отличается от сормайта № 1 более высокой прочностью, вязкостью и способностью подвергаться термической обработке. Торцы прутков из сормайта № 1 окрашиваются зеленой, а сормайта № 2 — красной краской. Если окраски нет, то марка сормайта определяется пробой на изгиб: сормайт № 1 ломается, а сормайт № 2 дает прогиб.
Ввиду различия свойств сормайт № 1 и сормайт № 2 применяют для наплавки деталей, работающих в различных условиях. Сормайт № 1 более твердый и не изменяет своих свойств с изменением температуры, поэтому он применяется для наплавки деталей несложной конфигурации, работающих при высокой температуре (до 1000° С) и не испытывающих в процессе работы ударных нагрузок.
Сормайт № 2 после отжига легко обрабатывается режущим инструментом, что позволяет применять его для наплавки деталей сложной конфигурации, требующих последующей механической обработки. Сормайт № 2 благодаря хорошей вязкости применяется для деталей, испытывающих ударные нагрузки. Этими сплавами можно наплавлять как стальные, так и чугунные детали.
Сталинит — порошкообразный сплав, представляющий собой черно-серую зернообразную массу с размером зерен 1—2 мм. Химический состав: углерода 8—10%, хрома 16—20%, марганца 13— 17%, кремния не более 3%, остальное — железо. Твердость наплавленного слоя HRC 75—78. Температура плавления сталинита 1300— 1350° С. Сталинит и другие порошкообразные твердые сплавы применяются для наплавки быстроизнашивающихся деталей, не требующих последующей чистовой обработки, например для наплавки щек камнедробилок, деталей землечерпалок и т. п.
Вокар также представляет собой порошкообразный твердый сплав с размером зерен 1—3 мм. Химический состав: вольфрама 85—87%, углерода 9—10%, кремния не более 3%, железа не более 2%. Твердость HRC 80—84. Температура плавления 2700°С. Вокар является дорогостоящим сплавом. Применяется при наплавке в виде прутков ТЗ, представляющих собой трубки из малоуглеродистой стали размером 6X0,5 мм, заполненные порошкообразным сплавом.
Наряду с высоколегированными сплавами можно с успехом применять в качестве твердых наплавок белый чугун марки КУ (ГОСТ 4834-49) и низколегированный белый чугун с 2% хрома марки ХЧ (разработан В НИИ автогеном)*.
Износ не наплавленных образцов превосходит износ образцов, наплавленных прутками из белого чугуна, в 3 раза, а наплавленных прутками из чугуна марки ХЧ — в 11 раз.
Победит — металлокерамический твердый сплав. Металлокерамические сплавы обладают особенно высокой твердостью. Победит изготовляется в виде пластинок различной формы и размера. Процесс изготовления сводится к следующему: мелкий порошок карбида вольфрама или другого тугоплавкого карбида и мелкий порошок связующего металла кобальта или никеля перемешиваются и затем прессуются в соответствующих формах. Спрессованные пластины спекаются при температуре, близкой к температуре плавления связующего металла, что дает очень плотный и твердый сплав.
Пластинки из этого сверхтвердого сплава применяются для изготовления металлорежущего и бурового инструмента. Пластинки напаиваются на державки режущего инструмента медью. Термообработка не требуется.
Читайте также
Добавить комментарий
Электроды Сормайт для наплавки: характеристики и особенности
Время чтения: 3 минуты
Электроды Сормайт (они же Сармайт, электроды сармайтовые) — это специализированные наплавочные стержни, применяемые для выполнения особо ответственных работ. Швы, выполненные с применением электродов Сормайт, способны продолжительное время противостоять коррозии, высоким температурам и ударным нагрузкам.
Данные электроды применяются в профессиональном промышленном производстве и ремонте. В этой статье мы подробно расскажем, какие технические характеристики и особенности у электродов Сормайт.
Содержание статьи
Общая информация
Основная характеристика электродов Сормайт — это их покрытие. Оно рутиловое, а это значит, что дуга будет гореть стабильно и легко поджигаться, в том числе повторно. Данные электроды предназначены для сварки чугуна. Выпускаются стержни диаметром от 5 до 7 мм. Основной производитель — Зеленоградский Электродный Завод.
Читайте также: Электроды с рутиловым покрытием
Есть две разновидности электродов Сормайт: №1 (марка ЦС-1) и №2 (марка ЦС-2). Отличаются они количеством легирующих элементов в составе, а так же эксплуатационными характеристиками. №2 прочнее и долговечнее, чем №1.
Электроды Сормайт — наплавочные. Это значит, что их используют не столько для формирования шва, сколько для формирования слоев, которых может быть несколько. В случае с электродами Сормайт не рекомендуется наплавлять более двух слоев одновременно. Если вам все же необходимо наплавить большее количество, то нижние слои нужно наплавить другими электродами, а два верхних слоя — электродами Сормайт.
Слои, наплавленные электродами Сормайт, устойчивы к абразивам и перепадам температур. Они хорошо переносят постоянную эксплуатацию. Даже, если наплавлялись части механизмов.
Особенности
Электроды для наплавки Сормайт необходимо прокалить перед сваркой. Установите температуру не более 900 градусов и прокаливайте в электрической печи не менее 3-х часов. После прокаливания не вынимайте электроды из печи. Подождите, пока температура сама опустится до 700 градусов. После чего снова включите печь и разогревайте электроды до 900 градусов по Цельсию в течение 4 часов. Повторите эту процедуру снова и в конце охладите стержни до 30-40 градусов.
Также есть ряд особенностей, связанных с деталями, которые вы варите с помощью Сормайтов. После сварочных работ детали нужно закалить в масле, разогретом до температуры 900 градусов. Закаливать нужно в течении 40 минут. После закалки деталь можно использовать.
Вместо заключения
Электроды Сормайт — это хороший выбор для тех, кто занимается сваркой профессионально. Эти наплавочные электроды хорошо зарекомендовали себя не только при сварке и ремонте чугуна, но и при работе с различными сталями. Их не найдешь в первом попавшемся магазине, но попробовать все же стоит. А вы когда-нибудь использовали электроды Сормайт в своей практике? Расскажите об этом в комментариях. Желаем удачи в работе!
Наплавка стеллитом и сормайтом | Сварка металлов и материалов
Область применения
Стеллиты – твердые сплавы на кобальтовой (иногда никелевой) основе- используются для наплавки деталей машин, станков и инструментов с целью повышения износостойкости. Важными свойствами стеллитов являются красностойкость и устойчивость против коррозии при высоком давлении газов и паров.
Для тех же целей, что и стеллиты, при ремонте деталей используется сормайт. Сормайтом называют группу литых высокоуглеродистых и высокохромистых железистых сплавов, содержащих также никель и кремний и отличающихся большой твердостью. Последнее позволяет отнести сормайт но свойствам к группе стеллитоподобных сплавов. Сормайт имеет низкую коррозионную устойчивость, так как содержит большое количество железа.
Стеллиты и сормайт используют для наплавкн в виде круглых электродов диаметром 3-7 мм и длиной 300- 400 мм. Общая толщина наплавленного слоя в зависимости от условий работы деталей может колебаться в пределах 0,5-5 мм.
Если после наплавки сормайтом требуется механическая обработка, то деталь подвергают отжигу. После наплавки стеллитом термообработка деталей не производится. Закалка и последующий отпуск детали, наплавленной сормайтом после механической ее обработки, заметно повышают твердость наплавленного слоя.
Процесс наплавки стеллитом
Процесс наплавки стеллита или сорманта во избежание окисления наплавленного слоя и выгорания углерода, вольфрама и хрома выполняют ацетилено-кислородным пламенем с избытком ацетилена. При наплавке горелку держат под углом к наплавляемой поверхности на расстоянии 15-20 мм. Поверхность нагревают до образования тонкой пленки расплавленного металла, затем быстро подводят стержень наплавляемого материала. Стержень в процессе наплавки необходимо держать в пламени горелки, чтобы капли сплава попадали только на расплавленную поверхность основного металла.
Детали крупных размеров при ремонте во избежание появления внутренних напряжений при наплавке рекомендуется предварительно подогревать до температуры 600-700° С, а затем после наплавки медленно охлаждать.
Поверхность, подлежащую наплавке, тщательно очищают от грязи, ржавчины и окалины металлической щеткой, напильником, шлифовальным кругом или с помощью пескоструйного аппарата. При сложной конфигурации детали очистку поверхности можно производить химическим способом: промывкой 10-15%-ным горячим раствором каустической соды, а затем теплым 15-20%-ным раствором серной кислоты.
При наплавке сормайта электрической дугой стержень электрода покрывают обмазкой, предохраняющей его от окисления и стабилизирующей дугу.
Наплавленную сормайтом поверхность можно обрабатывать резцами, оснащенными пластинками из металлокерамических сплавов марок ВК3 и ВК6 или шлифованием.
Похожие материалы
Сварочные электроды марки “Сормайт”
Очень часто, во время сварки приходится делать какие-то наплавки и напайки. Многие, даже очень опытные сварщики, выполняют такие простые манипуляции при помощи обычных сварочных электродов. На самом деле это неправильно и неудобно, потому делая наплавку обычным электродом, есть риск прожечь металл. Кроме того это очень долго, да и наплавка выйдет не качественной.
Чтобы облегчить такие процедуры как наплавка и напайка, инженеры начали создавать специальные электроды, при помощи которых можно было бы увеличить качество и скорость этих процессов.
Содержание статьи:
Для чего применяются электроды Сормайт?
Данные электроды применяются для вспомогательных работ. Конечно, сейчас многие скажут, что профессионал с большим опытом может работать с чем угодно и у него все будет выходить хорошо. Отчасти это так, однако если инструменты и оборудование плохо подходят для дела, сделать качественный продукт будет почти невозможно. К примеру, вы не можете закрутить болт или саморез без отвертки или шуруповерта или забить гвоздь без молотка. Все это можно попытаться сделать подручными средствами, но это будет не качественная работа.
Сварочные электроды “Сормайт” применяются почти повсеместно и многие мастера советуют обязательно иметь их под рукой. Такие электроды могут быть необходимы для ремонта машины. Например, у вас сносился вал или другие детали. Сварщики используют их во вспомогательных процедурах и сильно облегчают себе дальнейший труд.
Электроды “Сормайт” часто используются и на железной дороге. Рельсы испытывают большие нагрузки от постоянно проходящих по ним составам. Из-за этого они сильно изнашиваются и могут истончаться. При помощи “Сормайт” можно наплавлять недостающий металл. Это гораздо выгоднее, чем полностью менять рельсу.
Применение электродов
Поскольку данный вид электродов имеет узкую специализацию, работать с ними необходимо особенным образом. Первое, с чего следует начинать эксплуатацию таких изделий, это прокалка. Электроды помещаются в специальную печь, разогретую примерно до 900°С. Они должны прогреваться в течение 3,5 — 4 часов. По истечении этого времени, нужно дать печи остыть до 750°С и снова разогреть ее до 900°С, оставив электроды еще на 4 часа. Затем печь охлаждается вновь. На этот раз до 600°С. Нагрев печь до 900°С в третий раз, ее нужно охладить до 35°С.
Отдельную работу нужно провести также с деталями, на которые был наплавлен металл. Их следует разогреть до 950°С в масле. Делать это нужно в течение примерно 50 минут.
Электроды выпускаются в диаметрах от 3 до 7 мм. Модели “Сормайт т-590” используются для наплавки деталей, работающих в обычных условиях, а “Сормайт с27” для наплавки износостойких элементов.
Заключение
Электроды марки “Сормайт” применяются в самых разных сферах, где можно обойтись без длительного и затратного процесса варения. Вместо этого можно выполнить небольшие работы по наплавке и напайке небольших слоев металла. Профессионалы отмечают, что специализированные изделия подходят для таких работ гораздо лучше, чем обычные электроды.
определение и синонимы слова сормайт в словаре украинский языка
СОРМАЙТ – определение и синонимы слова сормайт в словаре украинский языкаEducalingo использует cookies для персонализации рекламы и получения статистики по использованию веб-трафика. Мы также передаем информацию об использовании сайта в нашу социальную сеть, партнерам по рекламе и аналитике.
ПРОИЗНОШЕНИЕ СЛОВА СОРМАЙТ
ЧТО ОЗНАЧАЕТ СЛОВО СОРМАЙТ
Нажмите, чтобы посмотреть исходное определение слова «сормайт» в словаре украинский языка.
Стеллит
Стеліт
Стеллит – общее название высокоуглеродистых литейных твердых сплавов на основе кобальта, или никеля, или железа, обладающих повышенной твердостью 370 … 475 HV, высоким сопротивлением износу, коррозии а также способностью работать при высоких темепература. Сплав был создан Элвуд Гейнсом в 1907 году. Стелі́т — загальна назва високовуглецевих ливарних твердих сплавів на основі кобальту, чи нікелю, чи заліза, що відзначаються підвищеною твердістю 370…475 HV, високим опором зношуванню, корозії а також здатністю працювати при високих темепературах. Сплав було створено Елвудом Гейнсом у 1907 році.Значение слова сормайт в словаре украинский языка
сормайт, а ч. , мет. Очень твердый сплав, изготовленный на основе железа. Рабочие органы культиваторов наваривают сормайтом. Это обеспечивает самозатачивания их и более длительную службу (Сов. Укр., 26.IV 1961, 2). сормайт, а, ч., мет. Дуже твердий сплав, виготовлений на основі заліза. Робочі органи культиваторів наварюють сормайтом. Це забезпечує самозаточування їх і більш тривалу службу (Рад. Укр., 26.IV 1961, 2).
Синонимы и антонимы слова сормайт в словаре украинский языка
Перевод слова «сормайт» на 25 языков
ПЕРЕВОД СЛОВА СОРМАЙТ
Посмотрите перевод слова сормайт на 25 языков с помощью нашего многоязыкового переводчика c украинский языка.
Переводчик с украинский языка на
китайский язык sormayt1,325 миллионов дикторов
Переводчик с украинский языка на
испанский язык sormayt570 миллионов дикторов
Переводчик с украинский языка на
английский язык sormayt510 миллионов дикторов
Переводчик с украинский языка на
хинди язык sormayt380 миллионов дикторов
Переводчик с украинский языка на
арабский язык sormayt280 миллионов дикторов
Переводчик с украинский языка на
русский язык сормайт278 миллионов дикторов
Переводчик с украинский языка на
португальский язык sormayt270 миллионов дикторов
Переводчик с украинский языка на
бенгальский язык sormayt260 миллионов дикторов
Переводчик с украинский языка на
французский язык sormayt220 миллионов дикторов
Переводчик с украинский языка на
малайский язык sormayt190 миллионов дикторов
Переводчик с украинский языка на
немецкий язык sormayt180 миллионов дикторов
Переводчик с украинский языка на
японский язык sormayt130 миллионов дикторов
Переводчик с украинский языка на
корейский язык sormayt85 миллионов дикторов
Переводчик с украинский языка на
яванский язык sormayt85 миллионов дикторов
Переводчик с украинский языка на
вьетнамский язык sormayt80 миллионов дикторов
Переводчик с украинский языка на
тамильский язык sormayt75 миллионов дикторов
Переводчик с украинский языка на
маратхи язык sormayt75 миллионов дикторов
Переводчик с украинский языка на
турецкий язык sormayt70 миллионов дикторов
Переводчик с украинский языка на
итальянский язык sormayt65 миллионов дикторов
Переводчик с украинский языка на
польский язык sormayt50 миллионов дикторов
украинский сормайт
40 миллионов дикторов
Переводчик с украинский языка на
румынский язык sormayt30 миллионов дикторов
Переводчик с украинский языка на
греческий язык sormayt15 миллионов дикторов
Переводчик с украинский языка на
африкаанс язык sormayt14 миллионов дикторов
Переводчик с украинский языка на
шведский язык sormayt10 миллионов дикторов
Переводчик с украинский языка на
норвежский язык sormayt5 миллионов дикторов
Тенденции использования слова сормайт
ТЕНДЕНЦИИ ИСПОЛЬЗОВАНИЯ ТЕРМИНА «СОРМАЙТ»
На показанной выше карте показана частотность использования термина «сормайт» в разных странах.
Примеры использования в литературе на украинский языке, цитаты и новости о слове сормайт
КНИГИ НА УКРАИНСКИЙ ЯЗЫКЕ, ИМЕЮЩЕЕ ОТНОШЕНИЕ К СЛОВУ
«СОРМАЙТ» Поиск случаев использования слова сормайт в следующих библиографических источниках. Книги, относящиеся к слову сормайт, и краткие выдержки из этих книг для получения представления о контексте использования этого слова в литературе на украинский языке.1
Основы эксплуатации горных машин и оборудования. Учебное …Наряду с этим сплавом выпускают хромо-никелевые сплавы Сормайт No 1 и 2, в которых отсутствует вольфрами кобальт заменен железом. Сплавы ВКЗ и Сормайт No 1 успешно применяются для наплавки деталей, работающих …
Под ред. Гилёва А.В., 2015
2
Металловедение и термическая обработка стали: и чугуна; .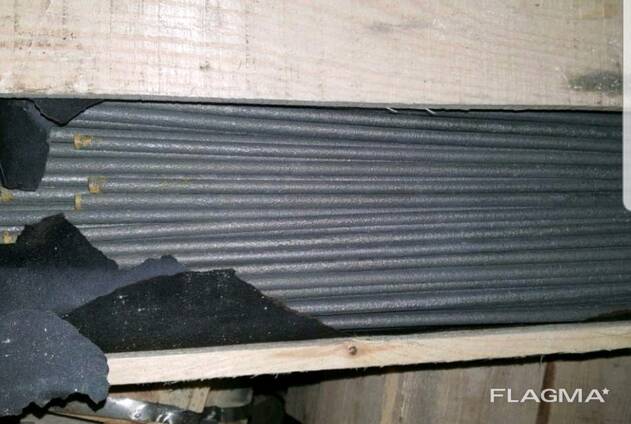
Микроструктуры сплавов сормайт No 1 в .N4 2: а — сормайт М 1; б — сормайт No 2 (по Раковскому и Андерс). Х1600 Составы сплавов сормайт (°о) Таблица 11 Свойства сормайта 5. ЗЕРНОВЫЕ СМЕСИ ДЛЯ …
Николай Тимофеевич Гудцов, 1956
3
Твердые сплавы в машиностроении: справочное пособиеВсе виды термической обработки наплавленных твердыми сплавами деталей, за исключением наплавленных сормайтом No 2, производятся по режимам, установленным для стали, из которой она изготовлены. Допускаемая …
В. С. Раковский, 1955
4
Технология металлов – Сторінка 244 Таблица 19 Химический состав литых твердых сплавов Стеллит представляет сплав на вольфрамо-хромо-кобальтовой основе, а сормайт — сплав на железо-хромовой основе. По структуре сплав сормайт 1 представляет …
Николай Васильевич Соколов, Моисей Ниссонович Ларин, Владимир Архипов, 1958
5
Справочник по машиностроительным материалам: Цветные …езохромоникелевые сплавы Сплавы этого типа выпускаются в СССР в виде прутков диаметром 5 — 7 мм и длиной 200 — 400 мм под наименованием сормайт [18], [19]. Состав сплавов двух выпускающихся марок …
Георгий Иванович Погодин-Алексеев, 1959
6
Сварка, резка и пайка металлов – Сторінка 278Сормайт представляет собой ж-слезохромистый сплав с небольт Шой добавкой никеля и не содержит вольфрама и кобальта. Твёрдость сормайту придаёт карбил хрома. Состав некоторых литых твёрдых сплавов приведён в …
К. К. Хренов, 2013
7
Спавохник электросварщика – Сторінка 243 М. М. Борт. 4. НАПЛАВКА ТВЕРДЫХ СПЛАВОВ Твердые сплавы можно разбить на три основные группы: 1) литые сплавы типа стеллитов — ВК-3, сормайт, «смена» и др.- 2) порошкообразные сплавы — вокар, сталинит и др
8
Металловедение и обработка металлов – Сторінка 58ИССЛЕДОВАНИЕ ТВЕРДОГО СПЛАВА ТИПА СОРМАЙТ, ЛЕГИРОВАННОГО БОРОМ Инж. Г. С. КАЧАЛ КИН Горьковский автозавод 0.1 0,2 0,3 0,1* 0,5 Количестдо бора Фиг. 1. Изменение механических свойств твердого сплава …
Совет Министров СССР. Государственный комитет по автоматизации и машиностроениû, 1958
9
Montazh, remont i smazka metallurgicheskogo oborudovanii͡a︡ Сормайтом наплавляют седла и тарелки клапанов, конусы засыпных аппаратов доменных печей; сталинитом — мундштуки хоботов завалочных машин, щеки дробилок, облицовочные плиты весовых воронок; порошковой ..
Nikolaĭ L’vovich Kasatkin, 1961
НОВОСТИ, В КОТОРЫХ ВСТРЕЧАЕТСЯ ТЕРМИН «СОРМАЙТ»
Здесь показано, как национальная и международная пресса использует термин сормайт в контексте приведенных ниже новостных статей.Пруток для наплавки сормайт Пр-С27 тип ПрН-У45Х28Н2СВМ …
Пруток для наплавки сормайт Пр-С27 тип ПрН-У45Х28Н2СВМ ГОСТ 21449-75 для наплавки износостойкого слоя на детали машин и оборудования, … «Бизнес-справочник “Пульс цен”, Июл 11»
Завод «ДимАл»: грузоподъемное оборудование, проверенное …
Ну а дабы клиенты завода «ДимАл» не переживали, что режущая кромка ножа быстро износится, на ней делается наплавка сплава Сормайт. Где и для … «www.equipnet.ru, Авг 10»
ССЫЛКИ
« EDUCALINGO. Сормайт [онлайн]. Доступно на <https://educalingo.com/ru/dic-uk/sormayt>. Фев 2021 ».
Крем перметрин: показания, побочные эффекты, предупреждения
Общее название: Крем с перметрином (на каждый рин METH)
Фирменное наименование: Acticin, Elimite
Проверено с медицинской точки зрения Drugs.com. Последнее обновление: 11 сентября 2020 г.
Использование крема перметрина:
- Применяется для лечения чесотки.
- Может быть передан вам по другим причинам. Поговорите с доктором.
Что мне нужно сказать своему врачу, прежде чем я приму крем перметрин?
- Если у вас аллергия на перметрин, хризантемы или любой другой компонент крема с перметрином.
- Если у вас аллергия на крем перметрин; любая часть крема перметрина; или любые другие лекарства, продукты питания или вещества. Расскажите своему врачу об аллергии и какие у вас были признаки.
Это лекарство может взаимодействовать с другими лекарствами или проблемами со здоровьем.
Расскажите своему врачу и фармацевту обо всех своих лекарствах (рецептурных или безрецептурных, натуральных продуктах, витаминах) и проблемах со здоровьем. Вы должны проверить чтобы убедиться, что для вас безопасно принимать крем с перметрином со всеми лекарствами и проблемами со здоровьем.Не начинать, не останавливать и не изменять дозу любой препарат без консультации с врачом.
Что мне нужно знать или делать, пока я принимаю крем перметрин?
- Сообщите всем своим поставщикам медицинских услуг, что вы принимаете крем с перметрином. Сюда входят ваши врачи, медсестры, фармацевты и стоматологи.
- Если перметрин крем принимается внутрь, немедленно обратитесь за медицинской помощью или позвоните в токсикологический центр.
- Не используйте для детей младше 2 месяцев без предварительной консультации с врачом.
- Сообщите своему врачу, если вы беременны, планируете беременность или кормите грудью. Вам нужно будет рассказать о преимуществах и рисках тебе и ребенку.
Как лучше всего принимать это лекарство (крем перметрин)?
Используйте крем с перметрином по назначению врача. Прочтите всю предоставленную вам информацию. Внимательно следуйте всем инструкциям.
- Не принимайте крем перметрин внутрь. Используйте только на коже.Не допускайте попадания в рот, нос и глаза (может вызвать ожог).
- Вымойте руки до и после использования.
- Нанести тонкий слой на кожу от шеи до пальцев ног. Разложите складки кожи, складки и промежутки между пальцами рук и ног.
- Обрезать ногти коротко.
- Нанесите крем под ногти зубной щеткой. Выбросьте зубную щетку после использования.
- Носите легкую одежду, пока на коже находится крем с перметрином.
- При нанесении крема не позволяйте вашей коже касаться чужой кожи.
- Через 8–14 часов полностью смойте крем с кожи теплой мыльной водой.
- Постирайте все постельное белье, полотенца и недавно ношенную одежду в горячей воде или отдайте их в химчистку.
Что мне делать, если я пропустил дозу?
- Введите пропущенную дозу, как только подумаете об этом.
По поводу каких побочных эффектов мне нужно немедленно позвонить врачу?
ПРЕДУПРЕЖДЕНИЕ / ВНИМАНИЕ: хотя это может быть редким явлением, у некоторых людей могут возникать очень тяжелые, а иногда и смертельные побочные эффекты при приеме лекарства. Сказать твоему
Если у вас есть какие-либо из следующих признаков или симптомов, которые могут быть связаны с очень серьезным побочным эффектом, немедленно обратитесь за медицинской помощью:
- Признаки аллергической реакции в виде сыпи; крапивница; зуд; красная, опухшая, покрытая волдырями или шелушащаяся кожа с лихорадкой или без нее; хрипы; стеснение в груди или горле; затрудненное дыхание, глотание или разговор; необычная охриплость; или отек рта, лица, губ, языка, или горло.
- Чувство жжения или покалывания, которое не является нормальным.
- Раздражение глаз.
Каковы другие побочные эффекты Permethrin Cream?
Все препараты могут вызывать побочные эффекты. Однако у многих людей побочные эффекты отсутствуют или наблюдаются лишь незначительные побочные эффекты. Позвоните своему врачу или обратитесь за медицинской помощью помочь, если какие-либо из этих побочных эффектов или любые другие побочные эффекты беспокоят вас или не проходят:
- Зуд.
Поговорите с врачом о том, что делать.
- Раздражение при использовании крема с перметрином.
Это не все возможные побочные эффекты. Если у вас есть вопросы о побочных эффектах, позвоните своему врачу. Позвоните своему врачу за медицинской совет о побочных эффектах.
Вы можете сообщить о побочных эффектах в FDA по телефону 1-800-332-1088. Вы также можете сообщить о побочных эффектах по адресу https://www.fda.gov/medwatch.
Если есть подозрение на ПЕРЕДОЗИРОВКУ:
Если вы подозреваете, что произошла передозировка, немедленно позвоните в токсикологический центр или обратитесь за медицинской помощью.Будьте готовы рассказать или показать, что было взяли, сколько и когда это произошло.
Как хранить и / или выбрасывать крем перметрин?
- Хранить при комнатной температуре. Выбросьте все неиспользованные части после использования.
- Храните все лекарства в надежном месте. Храните все лекарства в недоступном для детей и домашних животных месте.
- Выбросьте неиспользованные или просроченные лекарства. Не спускайте воду в унитаз или в канализацию, если вам не сказали об этом.Свяжитесь со своим фармацевт, если у вас есть вопросы о том, как лучше всего выбросить лекарства. В вашем районе могут быть программы возврата наркотиков.
Использование информации для потребителей
- Если ваши симптомы или проблемы со здоровьем не улучшаются или ухудшаются, позвоните своему врачу.
- Не делитесь своими наркотиками с другими и не принимайте чужие лекарства.
- Для некоторых препаратов может быть другая брошюра с информацией для пациента.Проконсультируйтесь с фармацевтом. Если у вас есть какие-либо вопросы о креме с перметрином, обращайтесь
с вашим врачом, медсестрой, фармацевтом или другим поставщиком медицинских услуг.
- Если вы считаете, что произошла передозировка, немедленно позвоните в токсикологический центр или обратитесь за медицинской помощью. Будьте готовы рассказать или показать, что было взяли, сколько и когда это произошло.
Часто задаваемые вопросы
Дополнительная информация
Всегда консультируйтесь со своим врачом, чтобы убедиться, что информация, отображаемая на этой странице, применима к вашим личным обстоятельствам.
Заявление об отказе от ответственности за медицинское обслуживание
СодержаниеПлавка. Обработка расплава Афанасьев В.К., Попова М.В., Масляев М.В., Толстогузов В.Н., Чибряков М.В., Корнева О.В. Новый материал – электроды наросты из доменного чугуна без осадков графита Шумихин В.С., Щерецкий А.А. Кастовые композиты с аморфной матрицей Современные материалы Задруцкий С.П., Королев С.П., Шешко А.Г. Высокопроизводительные комплексные препараты для изготовления качественных отливок Малиновский В.С., Малиновский В.Д., Власова И.Б. Универсальные дуговые печи постоянного тока нового поколения для металлургии и машиностроения Нехамин С.М., Стомахин А.Ю., Черняк А.И., Филиппов А.К. Повышение эксплуатационных характеристик малотоннажных сталеплавильных электродуговых печей для литейного производства Технологии 21 века Кабалдин Ю.Г., Муравьев С.Н. Информационная модель самонаправленного синтеза наноматериалов – основы интеллектуальных нанотехнологий Марукович Е.И., Стеценко В.Ю., Ки-Янг Чой Непрерывное литье алюминиевых сплавов без применения модификаторов
Борисов Г.П. Некоторые аспекты положительной роли газовой пористости в управлении процессами формовки алюминиевых отливок |
(PDF) Использование серого чугуна для упрочнения почвообрабатывающего агрегата сельскохозяйственных машин
ITE 2019
IOP Conf. Серия: Материаловедение и инженерия 582 (2019) 012017
IOP Publishing
doi: 10.1088 / 1757-899X / 582/1/012017
5
Измерение микротвердости упрочненного слоя (рис.5) показывает, что поверхностный слой, нанесенный электродами из серого чугуна
и подвергнутый начальной термообработке, имеет более высокую твердость, чем базовый материал
, что позволяет сделать вывод о более высокой износостойкости.
Закаленные продукты прошли полевые испытания в хозяйствах Кемеровской области Российской Федерации
. Испытания показали эффективность использования упрочнения данным материалом для электроискровой сварки
, так как толщина и качество наплавленного слоя соответствуют необходимым требованиям износостойкости.
После работы почвообрабатывающих орудий в течение одного сезона наблюдались незначительные изменения геометрического размера
, которые можно восстановить известными методами.
3. Выводы
Использование серого чугуна в качестве сварочного материала, подвергнутого первичной термообработке с последующим нанесением
на поверхность деталей электроискровой сваркой, и работающих в среде абразивного износа
, дает возможность повысить эксплуатационный срок службы и снижение затрат на покупку новых деталей.
Литература
[1] Курбанова М.Г .; Черныш, А.П .; Санкина, О.В .; Бузиян О.Н. Повышение износостойкости
функциональной поверхности рабочих органов и механизмов измельчения и смешения биогазовой установки.
Достижения науки и техники АПК 2013. №5. С .: 79 – 80.
[2] Чибряков, М.В .; Санкина О.В. Дуговая сварка и электроискровая сварка деталей с нелегированным белым чугуном
. Новости международной академии аграрного образования 2018. Вестник №39 (2018). P .:
53 – 57.
[3] Шибе Винит, Чавла Викас, Характеристика сплавов для наплавки на основе Fe-C-Cr, Сделки
Индийского института металлов. Том: 71. Выпуск: 9. P .: 2211-2220
[4] Мартинацци, Дуглас; Lemos, Guilherme V. B .; Landell Renan M .; и др., Предварительное исследование эффекта
геометрии стержня в FHHP между чугуном с шаровидным графитом FE55006 и сталью SAE 8620, PERIODICO
TCHE QUIMICA. Объем: 16.Выпуск 31. Дата публикации: январь 2019 г. С. 642-649.
[5] Карсель-Карраско Франсиско-Хавьер; Паскуаль-Гийамон Мануэль; Салас-Висенте Фидель; и др., «Влияние
термической обработки на микроструктуру соединения чугуна с шаровидным графитом при использовании процесса сварки вольфрамом
в инертном газе с стержнями из перлитного серого чугуна в качестве присадочного материала, металлы».
Том: 9. Выпуск: 1. Номер статьи: 48. Опубликован: Янв 2019.
[6] Reisgen U .; Sharma R .; Виланд С. ; et al., Повышение коррозионной и износостойкости деталей из серого литого чугуна
путем поверхностной сварки дуплексной нержавеющей сталью с использованием регулируемой газовой дуги.
Сварка: Влияние разбавления на коррозионные свойства, MATERIALWISSENSCHAFT UND
WERKSTOFFTECHNIK. Том: 49. Выпуск: 12. Опубликован: декабрь 2018. С. 1520-1537.
[7] Виниченко Радослав; Качоровский Мечислав; Скибицкий Анджей, Микроструктуры,
, механические свойства и распределение температуры в сварном трением из чугуна с шаровидным графитом,
Журнал Бразильского общества механических наук и инженерии.Том: 40. Выпуск: 7.
Номер статьи: UNSP 347. Дата публикации: июль 2018 г.
[8] Сараев Ю.А. Гладковский С .; Лепихин С .; Каманцев И .; Лунев А .; Перовская М., Исследование
Влияние энергетического параметра сварки покрытым электродом на ударную вязкость
Характеристики и трещиностойкость полученных сварных соединений, Обработка металлов
Работа и материаловедение. Том: 20. Выпуск: 2. С .: 100-115
[9] Хамим М.; Трийоно; Дихарджо Кункоро, Влияние электрода и сварочного тока на физические и
механические свойства сварки чугуна, Международная конференция по технике, науке и нанотехнологиям
(ICESNANO) Место: Соло, ИНДОНЕЗИЯ Дата: 3–5 августа 2016 г. Книга Серия:
Материалы конференции AIP. Том: 1788. Опубликовано: 2017.
[10] Ambroza P .; Bockus S .; Каваляускене Л., Формирование микроструктуры наплавленных слоев дугой.
Автоматическая наплавка с использованием порошков вторичного сырья, Архив металлургии и
Материалы.Том: 58. Выпуск: 2. С .: 549-553. Опубликовано: 2013.
[11] Габец Д.А .; Марков А.М. Исследование влияния легирующих элементов на структуру и свойства
серого чугуна, работающего в условиях ударно-фрикционного износа. Обработка металлов
(технология, оборудование, инструменты), Металлообработка и материаловедение, 2019, т. 21,
нет. 1. С. 70–81.
Расшифровка SORMITE | Слова, расшифрованные из sormite
Расшифровка SORMITE | Слова, расшифрованные из сормитаЧто
7 букв слова можно составить из букв сормитСлово | Очки для скрэббла | Слова с друзьями баллов |
---|---|---|
эротизм | 9 | 10 |
влажный | 9 | 10 |
врезной | 9 | 10 |
трехкомпонентный | 9 | 10 |
Какие
6 буквенных слов можно составить из букв сормитСлово | Очки для скрэббла | Слова с друзьями баллов |
---|---|---|
изомер | 8 | 9 |
достоинства | 8 | 9 |
метро | 8 | 9 |
мистер | 8 | 9 |
митры | 8 | 9 |
митры | 8 | 9 |
муары | 8 | 9 |
Мойзер | 8 | 9 |
мотье | 8 | 9 |
motser | 8 | 9 |
remits | 8 | 9 |
римоза | 8 | 9 |
roesti | 6 | 6 |
смитер | 8 | 9 |
сомит | 8 | 9 |
вылет | 6 | 6 |
таймеры | 8 | 9 |
тиро | 6 | 6 |
истории | 6 | 6 |
триоза | 6 | 6 |
Какие
5 буквенных слов можно составить из букв сормитСлово | Очки для скрэббла | Слова с друзьями баллов |
---|---|---|
эмиры | 7 | 8 |
излучает | 7 | 8 |
estro | 5 | 5 |
шт.![]() | 7 | 8 |
мерис | 7 | 8 |
заслуга | 7 | 8 |
место | 7 | 8 |
метис | 7 | 8 |
метро | 7 | 8 |
болота | 7 | 8 |
мирос | 7 | 8 |
скупец | 7 | 8 |
митра | 7 | 8 |
клещи | 7 | 8 |
митра | 7 | 8 |
мерс | 7 | 8 |
муар | 7 | 8 |
влажный | 7 | 8 |
моит | 7 | 8 |
нравы | 7 | 8 |
Морзе | 7 | 8 |
мортс | 7 | 8 |
больше | 7 | 8 |
пылинки | 7 | 8 |
мотис | 7 | 8 |
омеров | 7 | 8 |
без | 7 | 8 |
ив | 5 | 5 |
рейст | 5 | 5 |
перевод | 7 | 8 |
повторно | 5 | 5 |
ресто | 5 | 5 |
Римс | 7 | 8 |
римс | 7 | 8 |
беспорядки | 5 | 5 |
обряды | 5 | 5 |
roist | 5 | 5 |
розетка | 5 | 5 |
розит | 5 | 5 |
рости | 5 | 5 |
ростов | 5 | 5 |
ротис | 5 | 5 |
поразить | 7 | 8 |
сморе | 7 | 8 |
удар | 7 | 8 |
стим | 7 | 8 |
шпиль | 5 | 5 |
магазин | 5 | 5 |
шторм | 7 | 8 |
стрим | 7 | 8 |
термины | 7 | 8 |
яруса | 5 | 5 |
таймер | 7 | 8 |
раз | 7 | 8 |
шины | 5 | 5 |
тирос | 5 | 5 |
туаз | 5 | 5 |
фолиантов | 7 | 8 |
торес | 5 | 5 |
торс | 5 | 5 |
торси | 5 | 5 |
попытки | 5 | 5 |
планки | 7 | 8 |
трио | 5 | 5 |
тройка | 5 | 5 |
Какие
4 буквенные слова можно составить из букв сормитСлово | Очки скрэббла | Слова с друзьями баллов |
---|---|---|
эмир | 6 | 7 |
излучать | 6 | 7 |
emos | 6 | 7 |
эрос | 4 | 4 |
erst | 4 | 4 |
Айрес | 4 | 4 |
товар | 6 | 7 |
мери | 6 | 7 |
метс | 6 | 7 |
болото | 6 | 7 |
миро | 6 | 7 |
мирс | 6 | 7 |
мисе | 6 | 7 |
мисо | 6 | 7 |
туман | 6 | 7 |
клещ | 6 | 7 |
больше | 6 | 7 |
моэс | 6 | 7 |
moit | 6 | 7 |
далее | 6 | 7 |
морс | 6 | 7 |
морт | 6 | 7 |
mose | 6 | 7 |
наибольшее | 6 | 7 |
пылинка | 6 | 7 |
моти | 6 | 7 |
шт.![]() | 6 | 7 |
или | 6 | 7 |
опустить | 6 | 7 |
руды | 4 | 4 |
орт | 4 | 4 |
рейса | 4 | 4 |
бэр | 6 | 7 |
реос | 4 | 4 |
остальное | 4 | 4 |
рец | 4 | 4 |
riem | 6 | 7 |
иней | 6 | 7 |
диски | 6 | 7 |
беспорядки | 4 | 4 |
подъем | 4 | 4 |
обряд | 4 | 4 |
rits | 4 | 4 |
косули | 4 | 4 |
ромов | 6 | 7 |
роза | 4 | 4 |
рост | 4 | 4 |
зубчатый | 4 | 4 |
роти | 4 | 4 |
гнили | 4 | 4 |
seir | 4 | 4 |
полу | 6 | 7 |
отец | 4 | 4 |
участок | 4 | 4 |
смир | 6 | 7 |
смит | 6 | 7 |
некоторые | 6 | 7 |
болячка | 4 | 4 |
сори | 4 | 4 |
сортировать | 4 | 4 |
шток | 6 | 7 |
stie | 4 | 4 |
стим | 6 | 7 |
перемешать | 4 | 4 |
ТЕМС | 6 | 7 |
термин | 6 | 7 |
уровень | 4 | 4 |
галстуки | 4 | 4 |
время | 6 | 7 |
шина | 4 | 4 |
тиро | 4 | 4 |
пальцы | 4 | 4 |
том | 6 | 7 |
тома | 6 | 7 |
тор | 4 | 4 |
тори | 4 | 4 |
торс | 4 | 4 |
тозе | 4 | 4 |
трес | 4 | 4 |
три | 4 | 4 |
накладка | 6 | 7 |
трио | 4 | 4 |
Какие
3-х буквенные слова можно составить из букв сормитСлово | Очки для скрэббла | Слова с друзьями баллов |
---|---|---|
эмо | 5 | 6 |
ems | 5 | 6 |
эм | 5 | 6 |
ers | 3 | 3 |
est | 3 | 3 |
ios | 3 | 3 |
ire | 3 | 3 |
ИЗМ | 5 | 6 |
iso | 3 | 3 |
свое | 3 | 3 |
мес | 5 | 6 |
до | 5 | 6 |
мир | 5 | 6 |
раз | 5 | 6 |
м н.![]() | 5 | 6 |
мои | 5 | 6 |
мор | 5 | 6 |
мес | 5 | 6 |
мотор | 5 | 6 |
oes | 3 | 3 |
ois | 3 | 3 |
Ом | 5 | 6 |
руда | 3 | 3 |
или | 3 | 3 |
орт | 3 | 3 |
ose | 3 | 3 |
рей | 3 | 3 |
рем | 5 | 6 |
рео | 3 | 3 |
рез.![]() | 3 | 3 |
рет | 3 | 3 |
обод | 5 | 6 |
рит | 3 | 3 |
икра | 3 | 3 |
п. | 5 | 6 |
гниль | 3 | 3 |
sei | 3 | 3 |
сер | 3 | 3 |
комплект | 3 | 3 |
сим | 5 | 6 |
сэр | 3 | 3 |
сид.![]() | 3 | 3 |
сом | 5 | 6 |
сот | 3 | 3 |
шри | 3 | 3 |
тес | 3 | 3 |
галстук | 3 | 3 |
тис | 3 | 3 |
палец | 3 | 3 |
том | 5 | 6 |
тор | 3 | 3 |
Что
2-х буквенное слово можно составить из букв сормитСлово | Очки для скрэббла | Слова с друзьями баллов |
---|---|---|
до | 4 | 5 |
и | 2 | 2 |
es | 2 | 2 |
и | 2 | 2 |
io | 2 | 2 |
это | 2 | 2 |
это | 2 | 2 |
мне | 4 | 5 |
миль | 4 | 5 |
мес | 4 | 5 |
oe | 2 | 2 |
или | 2 | 2 |
ом | 4 | 5 |
или | 2 | 2 |
ос | 2 | 2 |
re | 2 | 2 |
si | 2 | 2 |
так | 2 | 2 |
ул | 2 | 2 |
te | 2 | 2 |
ти | 2 | 2 |
до | 2 | 2 |
Результаты декодирования слов
Мы расшифровали анаграмму sormite и нашли 244 слова , которые соответствуют вашему поисковому запросу.
Совершенствование технологического процесса восстановления рабочих частей почвообрабатывающих машин – Справочник журналов открытого доступа (DOAJ)
Совершенствование технологического процесса восстановления рабочих частей почвообрабатывающих машин – Справочник журналов открытого доступа (DOAJ)Восточно-Европейский журнал корпоративных технологий (2020-04-01)
- Анатолий Дудников,
- Александра Горбенко,
- Антон Келемеш,
- Ольга Дрожчана
Принадлежности
- Анатолий Дудников
- Полтавская государственная аграрная академия
Сковороды, ул.
, 1/3, Полтава, Украина, 36003
- Александр Горбенко
- Полтавская государственная аграрная академия Ул. Сковороды, 1/3, Полтава, Украина, 36003
- Антон Келемеш
- Полтавская государственная аграрная академия Сковороды, ул., 1/3, Полтава, Украина, 36003
- Ольга Дрожчана
- Полтавская государственная аграрная академия
Ул.
Сковороды, 1/3, Полтава, Украина, 36003
- DOI
- https: // doi.org / 10.15587 / 1729-4061.2020.198962
- Том и выпуск журнала
- Vol. 2,
нет. 1 (104)
с. 72 – 77
Анализ износа деталей машин позволил установить характерные требования к технологическому процессу восстановления изношенных поверхностей. Экспериментальные исследования упрочнения рабочих поверхностей лемехов позволили определить параметры обработки: частоту колебаний обрабатывающего инструмента 1400 мин-1, амплитуду колебаний 0,5 мм и время обработки 20 с. Исследования влияния обычных и вибрационных работ на прочностные характеристики проводились сначала на моделях, а затем на реальных деталях. Новые акции послужили образцом. Экспериментальные исследования этих долей позволили установить характер износа режущего элемента.Сходство модели и реальной степени деформации детали обеспечивалось одинаковыми условиями прохождения процессов упрочнения. Достоверность результатов экспериментальных исследований оценивалась в соответствии с законом теоретического распределения при заданном значении доверительной вероятности α = 0,95. Исследования показали, что ширина лемеха 116–117,5 мм, оказывающая определенное влияние на эффективность лемеха, соответствует наибольшей вероятности 0,39. Экспериментально установлено, что степень упрочнения лемехов из стали Л-53 с наплавкой сормитом и виброупрочнением составляет 1.
В 85 раз больше, чем при традиционной обработке. Проведенные исследования позволили определить характер изменения формы лемеха и толщины режущей кромки и выбрать более эффективный процесс ее восстановления путем виброзащитного упрочнения. Предложен способ восстановления лемехов сваркой лент из стали 45 с автоматической наплавкой и виброупрочнением
Ключевые слова
Опубликовано в
Eastern-European Journal of Enterprise Technologies- ISSN
- 1729-3774 (печать)
- 1729-4061 (онлайн)
- Издатель
- Центр компьютерных технологий
- Страна издателя
- Украина
- Субъектов LCC
- Технология: Технология (Общие)
- Социальные науки: отрасли.
Землепользование. Рабочая сила: промышленность
- Сайт
- http://journals.uran.ua/eejet
О журнале
Интеллектуальный многофункциональный плуг | БИО Сеть конференций
BIO Web of Conferences 27 , 00003 (2020)Интеллектуальный многофункциональный пахотный агрегат
Геннадий Маслов, Елена Юдина * , Николай Малашихин и Гавриил Самурганов
Кубанский государственный аграрный университет имени И.Т. Трубилина, 350044 Краснодар, Россия
* Автор для переписки: [email protected]
Аннотация
Предложен многофункциональный пахотный агрегат, сочетающий в себе операцию внесения основного удобрения за один проход, вспашку отвала, дополнительное крошение и выравнивание почвы и обоснована его эффективность. Отличительным преимуществом нового агрегата является раздельное внесение удобрений на необходимую глубину в пахотном слое в соответствии с требованиями научно обоснованной системы земледелия: фосфорные удобрения вносятся специальной плуговой насадкой на дно вспаханной борозды, калийные удобрения азотные удобрения распределяются по пласту с помощью отвалов плуга.Дополнительное крошение и выравнивание вспаханной поверхности осуществляется одновременно с вспашкой приставкой, состоящей из комбинации кольцевидно-прямозубых и клиновидных дисков. В конструкции использовался корпус плуга известного уровня техники с правыми и левыми лемехами, что позволяет различать полевая доска, снижать сопротивление пахоте и увеличивать производительность агрегата. Рассчитаны и проанализированы технико-экономические показатели многофункционального агрегата. Также были проанализированы качественные показатели вспашки в сравнении с обычными серийными плугами.Предлагаемый многофункциональный агрегат, выполняющий основную задачу повышения производительности и снижения затрат, не увеличивает, а, скорее, снижает содержание пыли в пахотном слое по сравнению с дисковыми орудиями, тем самым снижая процессы эрозии.
© Авторы, опубликовано EDP Sciences, 2020
Это статья в открытом доступе, распространяемая в соответствии с условиями лицензии Creative Commons Attribution License 4.0, которая разрешает неограниченное использование, распространение и воспроизведение на любом носителе при условии правильного цитирования оригинальной работы.
1 Введение
Конкурентоспособность продукции растениеводства зависит от применяемых технологий [1–3] и интеллектуальных средств механизации [4, 5]. Ресурсосберегающие экологические технологии способствуют сохранению и повышению плодородия почв, повышению производительности труда и снижению затрат. На практике вышеперечисленные требования выполняются при строгом соблюдении научно обоснованных систем земледелия [6], сельскохозяйственные предприятия достигают высоких урожаев и являются рентабельными.Одним из основных способов обработки почвы в сельском хозяйстве является отвальная вспашка. Несмотря на высокую энергоемкость, себестоимость и низкую урожайность, он по-прежнему остается основным сельскохозяйственным методом борьбы с сорняками, болезнями растений и вредителями сельскохозяйственных культур [6]. Что касается негативного влияния вспашки на эрозию почвы, то результаты исследований КубГАУ [7] показали, что вспашка опрыскивает почву в 1,5 раза меньше, чем дисковые орудия. Перед вспашкой по системе земледелия [6] вносят основное удобрение. Его элементы – азот, калий и фосфор – равномерно распределены по всему пахотному слою.Он отрицателен для фосфора, так как фосфорные удобрения особенно необходимы в фазе созревания колосовых культур для получения высоких урожаев и должны вноситься на дно борозды во время вспашки [6]. Таким образом, при вспашке необходимо снизить энергоемкость, повысить урожайность и рациональное распределение отдельных видов удобрений в слоях вспаханной почвы. Решаем эту проблему в этой статье.
2 Материалы и методы
В работе использована методика математического моделирования процесса вспашки предлагаемым многофункциональным плужным агрегатом [8] и результаты сравнительных испытаний плугов различных конструкций [9].
Общие затраты энергии на процесс вспашки отвала, дополнительное измельчение и выравнивание почвы, а также внесение основного удобрения в почву были использованы в качестве целевой функции математической модели для оптимизации параметров предлагаемой пахотной установки. Этот процесс можно представить функцией (1):
(1)
, где E – общие затраты энергии на вспашку, МДж / га; Gtr – масса трактора, кг; Пистолет – масса агрегата, кг; Tatr , Taun – годовая нормативная нагрузка трактора и машины соответственно, ч; W – удельная мощность за 1 час сменного времени, га / ч; Ntep – мощность двигателя трактора, кВт; 42.7 – энергетический эквивалент израсходованного топлива, МДж / кг; 1,32 – энергозатраты человеческого труда, МДж / ч; 86,4 и 75 – эмпирические эквиваленты трактора и сельскохозяйственной машины соответственно, МДж / кг; 0,193; 0,38; 250 – эмпирические коэффициенты.
Компоненты формулы (1):
Мощность двигателя трактора:
(2)
где R пр – сопротивление вспашке, кН; V w – рабочая скорость, км / ч.
Агрегат тягового сопротивления:
(3)
где кu – удельное тяговое сопротивление агрегата, кН / м 2 ;
B w – рабочая ширина агрегата, м.
Масса трактора Gtr и агрегата Gun соответственно:
(4)
(5)
Коэффициент использования рабочего времени смены:
(6)
Емкость агрегата:
(7)
Оптимальная рабочая ширина B w (м) агрегата, рабочая скорость Vw (км / ч), вместимость бункера для минеральных удобрений Vh ( 3 м), длина борозды Lf (км), удельный коэффициент трения почвы Ku (кН / м), коэффициент использования времени сдвига τ находятся по минимальному значению функции E (1).
3 Результаты и обсуждение
В предлагаемой многофункциональной установке учтены все прогрессивные конструктивные элементы оборотных плугов и различных устройств для внесения удобрений и дополнительного измельчения почвы [3]. Можно сравнить качество вспашки, выполняемой пахотными агрегатами без устройства для измельчения и выравнивания почвы одновременно с вспашкой с устройством на рисунках 1 и 2. Большая кусковатость вспашки (рисунок 1) потребует больших затрат на выравнивание почвы и завершение.
Среди отвальных плугов предпочтение отдается ПШКО (5 + 1 + 1) (рис. 3). Отличительные особенности конструкции корпуса плуга ПШКО-5-60 показаны на рисунке 4.
Плуг оборотный полуинтегральный ПШКО (5 + 1 + 1) (далее – плуг) предназначен для вспашки почв зерновых и технических культур на глубину до 30 см, без камней, плит и других препятствий, с удельная реакция грунта до 0,09 МПа (0,9 кгс / см 2 ) и твердость до 3.5 МПа (35 кгс / см 2 ).
Преимущества этих плугов заключаются в срезании, окучивании, измельчении и обертывании слоя почвы под углом 180 градусов. Они способствуют улучшению проникновения воды, воздуха и питательных веществ к корням растений, экономии топлива за счет устранения холостого хода трактора при вспашке (экономия топлива до 9 кг на каждый гектар). Захватывают ширину одного рабочего органа – 60 см, высоту стойки – 70 см, толщину – 30 мм. На ножи нанесено сормитовое покрытие, что продлевает срок службы оборудования.Ножи имеют две рабочие кромки. Корпуса плугов защищены от перегрузки защитными срезными болтами.
Недостатком плуга является отсутствие устройств для дополнительного измельчения почвы одновременно с вспашкой и устройств для внесения основных удобрений в соответствии с требованиями системы земледелия. Таким образом, авторы изобрели и разработали отсутствующие в этом плуге устройства.
Вспашка оборотными плугами характеризуется хорошим выравниванием, так как на плуге установлены правосторонние и левосторонние корпуса, однако приподнятый слой почвы необходимо сразу же измельчить, а поверхность почвы выровнять после прохода плуга (рис.2).
Промышленность разработала устройства к плугам для измельчения и выравнивания почвы, хотя нет устройств для внесения основного удобрения одновременно с вспашкой, и мы можем внедрить наше изобретение для удобрения [9]. В прошлом веке в России такие приспособления к плугам применялись. Для внесения удобрений использовали устройство ПКА-2, для измельчения почвы – ПВР-3,2 (к плугу ПЛН-8-35) и другие.
Аналогичное устройство можно использовать и с другими почвообрабатывающими машинами – с культиваторами, с рессорной бороной, роторными и другими агрегатами.Таким образом, многофункциональный комбинированный почвообрабатывающий агрегат ДКГП заслуживает внимания, но не оснащен перечисленными устройствами, что следует учитывать производителям.
Необходимость внесения основных удобрений для основной обработки в соответствии с системой земледелия объясняется особенностью фосфорных, калийных и азотных удобрений. Дело в том, что азотные удобрения подвижны, быстро растворяются в воде и под действием влаги переходят в нижние слои почвы, что не свойственно фосфорным и калийным удобрениям, которые необходимо сразу вносить на заданную глубину во время основной выращивание.При проведении поверхностной обработки почвы в последнюю обработку вносят фосфорные и калийные удобрения.
Предлагаемый многофункциональный пахотный агрегат (рис. 5) отличается не только наличием различных приспособлений к плугу, но и рациональным распределением элементов удобрений по глубине пахотного слоя. Азотные и калийные удобрения поступают на разбрасывающий диск 6 из бункеров 4 и 5, равномерно распределяются по поверхности поля и при прохождении плуга его корпусами 7 смешиваются с почвой по всему слою.Фосфорные удобрения из бункера 3 поступают в коллектор 8, а затем подаются воздуходувкой 9 по трубкам 10 для удобрений на каждый сброс корпусов плуга на дно борозды.
По технологии возделывания колосовых культур [6] также известно, что стартовая доза фосфорных удобрений (50 кг / га) вносится посадочной приставкой зерновой сеялки вместе с семенами и подкармливает растения в начале вегетации. фазы. Учитывая трудоемкость и дороговизну процесса вспашки, его применяют только после колосовых культур, особенно если они были заражены болезнями (корневая гниль) или после многолетних трав от предшественника [6].По сменной системе возделывания, в зависимости от типа почвы, часть колосовых культур возделывается после вспашки предшествующих культур с использованием поверхностной обработки почвы и даже без нее, по технологии no-till [10], но на небольших площадях поля.
Преимущество предлагаемого пахотного агрегата определяется совмещением технологических операций за один проход по полю, так как дает существенное преимущество по всем технико-экономическим показателям (таблица 1) и качеству работы (таблица 2).
Анализ технико-экономических показателей сравниваемых технологий вспашки показал существенное преимущество варианта использования многофункционального пахотного агрегата. Затраты на оплату труда снизились с 0,96 человеко-часа / га до 0,26 человеко-часа / га или в 3,7 раза, эксплуатационные расходы – в 1,6 раза, общие затраты на электроэнергию – с 581 МДж / га до – 262 или 2,2 раза, металлоемкость – в 1,9 раза. Срок окупаемости предложенного агрегата составил 1,5 года.
Преимущество предложенного плуга по качеству вспашки и расходу топлива хорошо видно по таблице 2, по результатам проведенных в КубНИИТиМ (Новокубанск) сравнительных испытаний по результатам различных конструкций плугов [9].
Наиболее предпочтительным агрегатом был в составе трактора К-701 и плуга ПБС-8-55 сравниваемых пахотных агрегатов. Конструкция последнего была применена в оборотном плуге ПШКО с основным преимуществом – отказ от левого борта за счет двухстороннего лемеха на корпусе. Плуг ПБС-8-55 (таблица 2) обеспечил максимальную рабочую скорость (8,9 км / ч), самый низкий расход топлива (12,3 кг / га) при достаточно высоком качестве крошения почвы. Сельскохозяйственным требованиям по качеству крошки не отвечали только плуги ПНУ-8-40 и СПЛ (табл. 2).Кроме того, эти два последних агрегата работали на небольшой скорости 6 и 7,7 км / ч, что сказывалось на их характеристиках. Большая глубина вспашки почвы (на 2 см) могла объяснить низкое качество крошения почвы плугом ПНУ-8-40, но он работал при более высокой влажности почвы (13,6%). Таким образом, конструкция плуга ПБС-8-55 является наиболее технологичной. В связи с этим в предложенном многофункциональном агрегате была использована конструкция корпуса.
Высокое качество крошения почвы плугами ПБС-8-55 и Kverneland (табл. 2) можно объяснить конструктивными особенностями их плуго-отвальной поверхности. Плуги ПНУ-8-40 и СПЛ-9 не соответствуют сельскохозяйственным требованиям по качеству крошения (65,6 и 75,2 процента, таблица 2), что свидетельствует о необходимости устройства к плугу для дополнительного измельчения и выравнивания почвы. Именно такое устройство предусмотрено в конструкции нашего многофункционального устройства (см. Рис. 1). В нашем приспособлении для плуга на валах установлены секции игольчатых и ножевых дисков, которые связаны между собой цепным приводом.
Из-за разного диаметра звездочек задний ряд ножевых дисков вращается в почве с большей скоростью.Это улучшает качество крошки и помогает очистить диски переднего ряда от пожнивных остатков, сорняков, а в случае повышенной влажности почвы – предотвратить ее налипание на рабочие органы. Высокое качество крошения почвы особенно важно при вспашке полупахотной земли, когда необходимо сохранить влажность почвы для будущего урожая и обеспечить условия для накопления новых осадков. На раме устройства, где закреплены секции игольчатых и ножевых дисков, предусмотрен балансир, величина которого для лучшего крошения зависит от твердости и влажности вспаханного грунта.
Рис. 1. Почва после прохождения плуга оборотного без приспособления |
Рис. 2. Пахотный агрегат с измельчителем почвы фирмы «LEMKEN» |
Рис. 3. Плуг оборотный ПШКО (5 + 1 + 1) |
Рис. 4. Конструкция корпуса плуга ПШКО-5-60 без бортика |
Инжир.5. Пахотный агрегат многофункциональный: 1 – трактор, 2 – плуг, 3,4,5 – бункеры для удобрений, 6 – разбрасывающий диск, 7 – корпус плуга, 8 – коллектор, 9 – коллектор. воздуходувка, 10 – трубка для удобрений |
Технико-экономические показатели плуга многофункционального
Таблица 2.Качественные показатели вспашки и удельный расход топлива различных конструкций плугов (данные КубНИИТиМ)
4 Заключение
В результате исследований предложен инновационный многофункциональный агрегат в составе оборотного энергосберегающего плуга без полевых досок, состоящий из агрегата для рационального распределения минеральных удобрений в пахотном слое почвы и агрегата для дополнительного измельчения и измельчения. выравнивание поверхности за плугом.Предлагаемый агрегат позволяет усовершенствовать технологию вспашки по сравнению с однооперационными машинами, которые отдельно осуществляют процесс внесения удобрений и завершение многослойной вспашки, и за счет своих преимуществ снижает трудозатраты в 3,7 раза, эксплуатационные расходы в 1,6 раза и потребление энергии в 2,2 раза. Срок окупаемости установки – 1,5 года.
Список литературы
- Технология возделывания кукурузы в Краснодарском крае / под ред.Петренко И. М. (Издательство «Агропромполиграфист», Краснодар, 2001), 89 с. [Google ученый]
- А.И. Трубилин, В. Гайдук, Э. Белкина, С.А. Калитко, А.Е.Горохова, Инфраструктура регионального агропродовольственного рынка: особенности функционирования и методы совершенствования, Espacios, 38 (33), статья No.
41 (2017) [Google ученый]
- Г.Г. Маслов, В. Лаврентьев, В. Цыбулевский, Е.М.Юдина, В. Ткаченко, Оптимизация параметров многофункционального агрегата на базе рессорной бороны // Прикл. J. инженера. и Адван. Technol. 9 (1), 1915–1918 (2019) [CrossRef] [Google ученый]
- ГРАММ.Маслов Г.
Трубилин, Инновационная система механизации обработки почвы, Монография (КубГАУ, Краснодар, 2019), 172 с. [Google ученый]
- D.R. Грифит, Дж. В. Мэннеринг, W.C. Запад, Уменьшенная обработка почвы – что произошло в планах 188 $ для 289, CES Paper No.209 (Purdue Univ., W / Lafayette, 1N, 1988) [Google ученый]
- Система земледелия Краснодарского края на агроландшафтной основе (Краснодар, 2015), 352 с. [Google ученый]
- А.
С. Найденов, В.В. Терещенко, Н. Бардак и др., Минимизация обработки почвы в полевом севообороте Кубани, Труды КубГАУ, 1 (52), 132 (2015) [Google ученый]
- А.А. Зангиев. Практикум по эксплуатации машинно-тракторного парка. М .: Колос, 2006. 320 с.[Google ученый]
- Омаров Р., Горлов И., Сложенкина М. и др. Применение методов математического моделирования в животноводстве // Междунар. J. of Innovat. Technol. и Explor. Инженер., 8 (12), 185–187 (2019) [Google ученый]
- Результаты испытаний сельхозтехники (сборник), вып.
2, 40–41 (Росинформагротех, Москва, 2016). [Google ученый]
- М.Дудин, В. Секерин, С.В. Банк и др., Розничный брендинг в розничной торговле продуктами питания в России: маркетинговые продажи и инструменты коммуникации, Opcion, 34 (85), 1654–1663 (2018) [Google ученый]
Все таблицы
Таблица 1.Технико-экономические показатели плуга многофункционального
Таблица 2.Показатели качества вспашки и удельного расхода топлива различных конструкций плугов (данные КубНИИТиМ)
Все фигуры
Рис.![]() Пахотный агрегат многофункциональный: 1 – трактор, 2 – плуг, 3,4,5 – бункеры для удобрений, 6 – разбрасывающий диск, 7 – корпус плуга, 8 – коллектор, 9 – воздуходувка, 10 – трубка для удобрений | |
По тексту |
Структура и абразивный износ композиционного покрытия HSS M2 / WC
Исследованы особенности формирования фазовой структуры и абразивной износостойкости композиционных покрытий «Сталь WC-M2» на монокарбид вольфрама.Установлено, что добавление 20 мас.% WC к наплавленной порошковой смеси приводит к увеличению содержания карбида M 6 C. Эти карбиды демонстрируют мультимодальное распределение по размерам, состоящее из ~ 5,9 мкм мкм эвтектических карбидов по границам зерен, ~ 0,25 мкм мкм карбидов, диспергированных внутри зерен. Также обнаружено большее количество метастабильного аустенита ( ~ 88 об.%). Высокая абразивная износостойкость этих покрытий обеспечивается -мартенситным превращением и многомодальным распределением армирующих частиц по размерам.
1. Введение
Существует тенденция к разработке и созданию нового оборудования с меньшими затратами с использованием малолегированных низкоуглеродистых сталей, которые, однако, требуют упрочнения поверхности путем азотирования или карбонизации. Первоочередной задачей в этой ситуации является повышение как выносливости, так и надежности рабочих узлов машин и технологического оборудования. В этой связи решение связано не только с улучшением только износостойкости, но и со множеством проблем, включая, помимо прочего, коррозионную стойкость, контактную износостойкость, небольшую пластическую деформацию и термостойкость.
Эффективный подход к повышению износостойкости материалов – плакирование и модификация металлов концентрированными потоками энергии. Эти методы используются на практике и основаны на быстрой закалке ванны расплава при скоростях охлаждения от 10 4 до 10 9 К / с. Электронно-лучевая наплавка в вакууме – хороший кандидат для получения твердого покрытия на поверхности низкоуглеродистой подложки. Такая обработка дает некоторые преимущества [1], которые включают возможность подачи композиционных порошков для наплавки непосредственно в ванну расплава, вакуумную очистку расплавленного металла, постепенную и точную регулировку мощности электронного луча для обеспечения минимального проникновения расплава в подложку, постоянный химический состав и небольшой размер пула при плотности мощности электронного пучка до 10 5 Вт / см 2 .Все эти параметры могут быть оптимизированы для достижения перегрева ванны, необходимого для получения пересыщенного раствора легирующих элементов и мелкозернистых структур при охлаждении. Учитывая это, мы полагаем, что электронно-лучевая наплавка в вакууме может применяться для нанесения композиционного покрытия после окончательной термообработки и основного механического шлифования.
В современной практике для повышения износостойкости рабочих поверхностей деталей машин используются как твердые, так и сверхтвердые композиционные покрытия из стеллита, сормита или литого карбида вольфрама. Недостатком этих материалов является то, что они содержат от 30 до 90% мас. дорогостоящего карбида вольфрама. Также покрытия, полученные путем осаждения этих материалов, являются хрупкими из-за высокого содержания твердой фазы, неравномерного распределения этих частиц по всей массе покрытия, особенно из-за их содержания в диапазоне от 30 до 50 мас.%, И растрескивания сетки на поверхности покрытия. Все это не позволяет использовать их в ряде приложений, когда требуется совокупность этих свойств.
В частности, существует проблема быстрого выхода из строя валов-шестерен тяжелонагруженных редукторов из-за интенсивного износа азотированных шейек игольчатых подшипников.Конструктивная особенность редукторов заключается в том, что их валы-шестерни расположены в непосредственной близости друг от друга, и традиционная конструкция подшипников, состоящая из внешнего и внутреннего колец с роликами между ними, неприменима. Следовательно, необходимо сделать опорный подшипник непосредственно на поверхности вала-шестерни. Эти поверхности шейки должны обладать высокой износостойкостью, контактной износостойкостью, низкими пластическими деформациями, вязкостью разрушения, что диктует необходимость нанесения однородных многофункциональных покрытий.
Особенности покрытий, получаемых многопроходной электронно-лучевой наплавкой порошком стали М2, описаны в [2]. Установлено, что в карбидной подсистеме покрытия формируется многомодальное распределение армирующих частиц по размерам. Объемное содержание вторичного карбида M 6 C и остаточного аустенита можно регулировать в пределах от 4,5 до 7,5 мас.%. и от 5 до 30 мас.%, соответственно, в зависимости от условий термоциклирования, создаваемых при наплавке.Износостойкость покрытий улучшается с увеличением объемного содержания остаточного аустенита из-за вызванного деформацией мартенситного превращения и выделения мелких карбидов в зернах матрицы. Можно с уверенностью сказать, что чем выше содержание остаточного метастабильного аустенита в покрытии, тем выше износостойкость. Стоит пойти по пути добавления монокарбида вольфрама к порошку HSS. Поскольку WC имеет высокую растворимость в стальной матрице, он может обеспечивать от 80 до 90% об. содержание аустенита, а также более высокое объемное содержание выделившихся мелких карбидов.
Вклад деформационных фазовых превращений в абразивную износостойкость триповых сталей с метастабильным аустенитом оценен [3] на основе разработанной модели и экспериментальных данных. В рамках этой модели были выведены уравнения баланса энергии, которые затем служили для определения значений работы разрушения для образцов со стабильным или метастабильным аустенитом. Выявлено, что величина работы разрушения образцов с метастабильной аустенитной матрицей в 7 раз выше, чем у образцов без способности испытывать фазовое превращение, вызванное деформацией, при тех же условиях испытаний на износ.
Целью данной работы является изучение влияния содержания карбида вольфрама в исходной смеси на структуру, фазовое содержание и абразивную износостойкость композиционных покрытий HSS M2 / WC.
2. Материалы, оборудование и экспериментальные методы
Исходными материалами для электронно-лучевой наплавки были смеси порошков HSS M2 с добавлением от 5 до 350 мкм мкм порошка WC с содержанием 10, 15, 20, 25, 30, 40 и 50% масс. Химический состав стали М2 был следующим: C – 1%, Cr – 4%, W – 6.5%, Mo – 5%, V – 1,5%, Si <0,5%, Mn <0,55%, Ni <0,4%, S <0,03%, O 2 <0,03%, Fe - остальное. Композиционные смеси готовили путем смешивания вышеуказанных компонентов, прессования и спекания смесей в вакууме при парциальном давлении не выше 10 −2 Па с последующим измельчением и просеиванием кеков по фракциям. Наплавку проводили на плоских образцах из стали 0,3% С размером 20 × 30 × 200 мм, выполняя четыре прохода на каждую пластину. Длина строки сканирования 20 мм. Толщина плакированного металлического слоя за проход составляла 1 мм.Некоторые образцы были подвергнуты однократному или двойному отпуску, проводимому при 570 ± ° C в течение 1 часа.
Машина для электронно-лучевой наплавки в вакууме работала в автоматическом режиме: образцы загружались в ее камеру и закреплялись там в манипуляторах. Эти манипуляторы приводятся в движение в режимах вращения и перемещения от внешней системы электропривода. Из камеры откачивали воздух для достижения остаточного давления 10 -1 Па. Электронный луч, генерируемый электронной пушкой, сканировался по поверхности образца, создавая тем самым расплавленную ванну (рис. 1).Одновременно порошковая смесь подавалась в бассейн с помощью дозатора.
Ускоряющее напряжение, диаметр, длина развертки электронного луча и скорость подачи образца составляли 28 кВ, 1 мм и 20 мм, 2 мм / с, соответственно, и не изменялись во время эксперимента.
Микроструктуру нанесенных покрытий на продольных и поперечных шлифах исследовали с помощью оптического микроскопа (ОМ) Olympus GX 51 , оборудованного анализатором 700 SIAMS, прибором SEM Philips SEM 515 , оборудованным устройством микроанализа EDAX ECON IV , и прибор TEM Tecnai G2 FEI, оснащенный устройством для микроанализа.
В работе использовался традиционный метод подготовки микрошлифов – механическое шлифование и полирование алмазными пастами разных марок. Химическое травление проводили в 4% растворе HNO 3 в спирте. Определение количественных характеристик микроструктуры, включая количество, размер, форму и распределение различных фаз, было выполнено с использованием программного пакета SIAMS . Фольги ПЭМ толщиной 150 мкм м были вырезаны из покрытий на электроискровой машине.После механической и электролитической отделки для достижения толщины фольги от 70 до 90 мкм м было проведено окончательное ионное утонение для достижения толщины 200 нм.
Фазовый состав образцов как после наплавки, так и после испытаний на абразивный износ был исследован методом XRD с использованием дифрактометра Shimadzu XRD 6000 , работающего в диапазоне 2 ° от 30 до 120 градусов с шагом 0,02 ° и с фильтрованным излучением CoK α . Интегральные интенсивности дифракционных пиков использовали для количественного фазового анализа.Объемное содержание фазы в многокомпонентной системе определяли по следующему выражению: где “ и обозначают фазы, – угловой коэффициент, – коэффициент кратности, и – структурный фактор фазы и объем ячейки соответственно.
2.1. Микротвердость и износ
Числа микротвердости () как покрытия, так и подложки были измерены с помощью измерителя микротвердости ПМТ-3 с шагом 100 мкм м между вмятинами и нагрузкой 0.981 Н. Измерения проводились на двух параллельных траекториях отпечатка, смещенных на 50 μ м друг относительно друга в глубину. Расстояние между дорожками 200 μ м. Такая процедура позволила получить профили микротвердости по глубине с шагом 50 мкм м в покрытии.
Для определения скорости износа (мг / час) мы использовали метод рыхлых абразивных частиц (рис. 2) и измеряли потери массы ежечасно. Затем по пяти экспериментальным результатам была рассчитана средняя скорость износа.Граненые частицы кварцевого песка с острыми углами и краями и круглые частицы электрокорунда со средним размером до 300 мкм мкм использовали в качестве абразивного материала для испытаний на износ при 60 об / мин. Нормальная нагрузка составила 44,1 ± 0,25 Н. Анализ микроструктуры и микротвердости образцов после испытаний на износ проводился на конических сечениях, выполненных под углом 2 ° между верхней поверхностью и плоскостью сечения.
Анализ микроструктуры и микротвердости образцов после испытаний на износ проводился на конических сечениях, выполненных под углом 2 ° между верхней поверхностью и плоскостью сечения.
3. Результаты и обсуждение
Смеси HSS M2 + WC с содержанием WC 10, 15, 20, 25, 30, 40 и 50% мас. были приготовлены шаровой мельницей в течение 24 часов. Спекание смесей проводили в вакуумной печи при 1200 ° C в течение 1 часа. При использовании более низких температур частицы не спекаются друг с другом, и не получается качественный композитный спек. При температурах выше 1200 ° C лепешки очень трудно измельчать, а выход порошка слишком низкий. Полученные лепешки измельчали и просеивали до фракций по размеру частиц.Выход годного к употреблению измельченного композита от 30 до 350 мкм фракции мкм составил от 85 до 90%. Меньшие фракции частиц были отброшены.
Микроструктура композитной корки, предназначенной для наплавки, показана на рисунке 3. Как видно, изолированные частицы стали M2 окружены либо только фазой (а) островковой формы, либо частицами размером от 1 до 2 мкм мкм в сочетании с островки (б) в зависимости от содержания WC в смеси. Увеличение содержания исходного WC с 10 до 40% мас.приводит к увеличению количества угловатых частиц с 0 до 20–25% об. в торте.
Согласно данным XRD (рис. 4), два карбида, такие как WC и M 6 C, были обнаружены в спеках в дополнение к фазам матрицы и. Это означает, что частицы исходного порошка взаимодействуют друг с другом в процессе спекания с образованием композита. То, что это правда, подтверждается результатами, опубликованными в другом месте [4]. Авторы [4] показывают, что образование карбида M 6 C начинается после нагрева композитных смесей WC- (Ni-Al) и WC-NiTi до 700 ° C.Принимая во внимание морфологию, можно утверждать, что обнаруженная в кеках α -фаза имеет вид мартенситных игл.
Изучая микроструктуру, а также данные XRD, полученные на образцах с наплавкой (рис.4), мы видим, что покрытия состоят из α -мартенсита, остаточного аустенита ( γ -фаза), 0,9 об. % карбидов VC размером 0,65 μ m и карбида M 6 C (Рисунок 5). Этот карбид M 6 C бывает двух морфологических типов.Первый тип I представлен дендритоподобными эвтектическими карбидами 3,8 μ мкм (рис. 5 (а) и 5 (б)), обнаруженными на границах зерен твердого раствора. Карбиды второго типа II выглядят как мелкие удлиненные частицы внутри зерен (рис. 5 (г)). В таблице 1 приведены данные о химическом составе структур, обнаруженных в точках, показанных на рисунках 5 (c) и 5 (d). Данные таблицы 1 позволяют сделать вывод о существенном снижении содержания ванадия во вторичных карбидах M 6 C по сравнению с эвтектическими карбидами.
|
При добавлении большего количества карбида вольфрама к исходной смеси количество карбида M 6 C увеличивается (рис. начиная с WC 30% мас. и выше, некоторое количество исходного WC сохраняется в дополнение к показанному выше. (Рисунки 6 (б) и 6 (в)). M 6 Карбид С в покрытиях, полученных из смесей с содержанием WC менее 30% мас. был обнаружен в виде дендритоподобных выделений на границах зерен аустенита, имеющих средний размер.9 мкм м и содержанием ~ 15 об.%. Кроме того, он существует в виде мелких осадков размером 0,24 мкм мкм внутри аустенитных зерен с общим содержанием ~ 8% об. Установлено, что для электронно-лучевой наплавки композитных покрытий с содержанием до 30% мас. WC может привести к образованию многомодального распределения частиц твердофазного карбида по размерам в покрытии.
Крупные ограненные частицы карбида M 6 C обнаружены в покрытиях, полученных из исходных порошковых смесей с содержанием WC 40% мас.(Рисунок 6 (c)). Эти частицы вырастают еще больше при увеличении содержания WC до 50% мас. (Рисунок 6 (d)). Кроме того, он существует в двух морфологических типах, таких как глобулярные и удлиненные (тромбоциты) частицы. Эти крупные частицы смешанного карбида образуют развитый каркас. Удерживаемые частицы WC окружены осадками M 6 C и встроены в каркас. Связующая фаза обнаружена в виде отдельных частиц. Трудно предположить, что такая каркасная структура армирующей фазы вряд ли послужит повышению износостойкости.Вероятно, крупные карбиды будут иметь положительное влияние на сопротивление абразивному износу. Износостойкость каркаса из мелких карбидов M 6 C будет определяться фазовым составом матрицы.
Зависимость количества аустенита от содержания карбида вольфрама в исходном порошке представляет собой кривую с максимумом в диапазоне от 20 до 25% мас. WC (рис. 7 (а)). Как однократный, так и двукратный отпуск нанесенного покрытия приводит к частичному мартенситному превращению.Установлено, что электронно-лучевая наплавка с напылением как чистого порошка стали М2, так и М2 + WC 40 до 50% мас. смеси дает всего от 3 до 4% об. остаточного аустенита. Однако, если мы использовали M2 + WC от 20 до 30% мас. смесей композиционные покрытия содержали от 30 до 40% об. остаточного аустенита даже после проведения двойного отпуска.
Следует отметить, что покрытия, сделанные с использованием M2 + WC от 0 до 30% мас. не выявили растрескивания сети на их поверхности.
Восходящая часть кривой на Рисунке 7 (а) показывает, что количество остаточного аустенита увеличивается до 82% об.с добавлением 20-25% WC мас. к исходной порошковой смеси. Такой эффект обеспечивается лучшей растворимостью WC и, следовательно, большим эффектом легирования твердого раствора γ как углеродом, так и карбидообразующими элементами.
Согласно данным EDAX, растворимость вольфрама в матрице покрытия возрастает с 3,5 до 11% мас. с содержанием WC в исходной смеси. Это включает снижение температуры начала мартенситного превращения и увеличение количества метастабильного остаточного аустенита после охлаждения (закалки).Из [5, 6] следует, что с увеличением температуры закалки HSS M2 одновременно увеличивается содержание углерода и легирующих элементов, что снижает точку мартенситного превращения. В нашей ситуации мы фактически имеем дело с закалкой из микропулка с жидкостью, что дополнительно сокращает интервал температур мартенситного превращения. Более высокое содержание остаточного аустенита обеспечивает минимальную твердость M2 + 20% мас. Композитные покрытия WC находятся на уровне 6 ГПа (рис. 7 (б), кривая 1).
Как видно из нисходящей части кривой на рисунке 7 (а), количество остаточного аустенита уменьшается, когда содержание WC в исходной смеси увеличивается с 30 до 50% масс. Обоснованием этого является неполное растворение как частиц M 6 C, так и частиц WC, которые затем служат либо зародышами кристаллизации, либо подложками для эпитаксиального роста смешанного карбида из аустенита. Одновременно тот же эффект снижает перегрев ванны расплава, а следовательно, и растворимость в ней карбидов.Кроме того, пониженное содержание фазы связующего в покрытии способствует релаксации напряжения, создаваемого разностью фазовых объемов α и γ фаз. Также это служит для более полного преобразования. Обсуждаемое здесь аномальное поведение аустенита в покрытиях должно влиять на их износостойкость.
3.1. Абразивный износ
Скорость износа частицами кварца быстро снижается для твердых покрытий, содержащих до 20% мас. WC, тогда как некоторый рост наблюдается от 25 до 30% мас.Покрытия для унитазов. Однако скорость износа продолжает падать с увеличением содержания WC (рис. 8 (а)). Максимум локальной скорости износа (рис. 8 (а)) может найти свое объяснение в структурных изменениях, происходящих в покрытии при нанесении 20% мас. Смеси WC порошковые. В этом случае начинает формироваться карбидная каркасная структура с участием исходных частиц WC. Также этому эффекту может способствовать использование граненой формы абразивных частиц кварца. При использовании электрокорунда скорость износа снижается с увеличением содержания WC.Особенно это касается покрытий, нанесенных от 20% мас. Смеси порошков WC (рис. 8 (б)). Другой аспект заключается в том, что использование более твердых абразивных частиц обеспечивает более высокую скорость износа в ~ 20 раз по сравнению с кварцевым песком.
Принимая во внимание микроструктуру на рисунках 5 и 6, объемное содержание аустенита на рисунке 7 (a), твердость (рисунок 7 (b)) и зависимости скорости износа на рисунке 8 в зависимости от содержания WC в исходной порошковой смеси , можно сказать, что износостойкость улучшается за счет большего количества аустенита в образцах, наплавленных для получения многомодального (, и) распределения по размерам упрочняющих карбидных фаз.Такое распределение служит для получения более тонких слоев межкарбидной связки и, таким образом, для уменьшения их избирательного износа и предотвращения отслаивания карбидов.
Кроме того, поскольку метастабильный аустенит способен к частичному мартенситному превращению, вызванному деформацией, это обеспечивает дополнительный эффект снятия напряжений во время износа. По данным РФА, количество β-фазы в покрытии M2 + 20% WC увеличилось на 40% об. после испытания на абразивный износ. Это мартенситное превращение в сочетании с субструктурным деформационным упрочнением приводит к увеличению твердости с 6 до 10 ГПа в подповерхностном слое покрытий на глубине 40 мкм м ниже изношенной поверхности (Рисунок 7 (b)).
Еще одним структурным фактором, важным для повышения износостойкости композиционного покрытия с метастабильной аустенитной матрицей, является его более высокая способность удерживать хрупкие карбидные фазы по сравнению с мартенситом и, таким образом, предотвращать их растрескивание как при микрошрезании, так и при усталостном износе. Это справедливо как для первичных дендритных карбидов, обнаруженных на границах зерен, так и для вторичных равноосных внутризеренных мелких карбидов [4]. Ни однократный, ни двукратный отпуск покрытий не могут изменить зависимость скорости изнашивания от содержания карбида вольфрама, хотя абсолютные значения несколько увеличиваются по сравнению с таковыми после наплавки (рисунки 8 (б), 8 (в) и 8 (г)). )).Такое поведение может быть связано с тем, что отпуск частично превращает аустенит в мартенсит и, следовательно, снижает влияние аустенита на снятие напряжений при превращении. С этой точки зрения отпуск – нежелательная термическая обработка после наплавки.
Износ М2 + 40% мас. На покрытие WC большое влияние оказывает термическая обработка. Микроструктура этого покрытия показывает карбидный каркас, состоящий из карбидов M 6 C и WC (рис. 6 (c)). Связующее только что нанесенное покрытие содержит около 50% об.аустенита (рис. 7 (а)), который положительно влияет как на снятие напряжений, так и на предотвращение скалывания частиц карбида.
Поскольку отпуск приводит к частичному превращению, он снижает как сопротивление выкрашиванию, так и удерживающую способность карбида. Наконец, степень износа М2 + 40% мас. Покрытия из WC увеличиваются на 40% за счет износа частицами электрокорунда.
Формирование карбидного каркаса наблюдается в M2 + 50% масс. покрытие (рисунок 6 (d)). Однако эти частицы карбида M 6 C более крупные по сравнению с частицами, обнаруженными в M2 + 40% масс.Покрытие WC (рис. 6 (c)). Связующая фаза находится в виде отдельных частиц и, следовательно, не оказывает большого влияния на износостойкость этого покрытия. Сравнивая износостойкость наплавленных и термообработанных покрытий, следует отметить, что в последнем случае скорость износа увеличилась на ~ 20%. Мы полагаем, что отслаивание крупных частиц карбидов нелегко, а карбидный каркас устойчив по отношению к чистому абразивному износу. Однако ударная нагрузка от абразивных частиц увеличит скорость износа как карбидного каркаса, так и более хрупкой матрицы.Также в наплавленном M2 + 50% мас. Образуется сетка карбидных трещин. Покрытия WC, которые улучшат процесс.
Отсюда следует, что высокая износостойкость показанных ранее композиционных покрытий обусловлена высоким содержанием остаточного аустенита. Такой вывод подтверждается многочисленными данными, содержащимися в литературных источниках [2, 4, 7, 8]. Еще одним фактором, способствующим износостойкости, является многомодальное распределение частиц карбида по размерам. Помимо остаточного аустенита, существуют другие важные факторы, определяющие износостойкость HSS, такие как происхождение, количество, характер распределения и размер карбидов [8–10]. Известно [11], что более высокая износостойкость литой HSS по сравнению с деформируемой HSS объясняется наличием твердого эвтектического карбидного каркаса, сформированного по границам твердого раствора γ . Было обнаружено, что карбидный каркас более эффективен для лучшей износостойкости по сравнению с изолированными крупными частицами карбида в условиях как абразивного, так и окислительного износа.
Для предотвращения износа относительно мягких зерен матрицы одним из возможных решений является усиление их мелкими карбидами.Литературный поиск, посвященный твердому металлу WC-Co [12–14], показывает, что при последовательном уменьшении размера карбидной фазы от микро- до субмикро-, а затем до наноразмеров, чтобы содержание Co оставалось постоянным, мы уменьшаем слой межкарбидной связки и одновременно увеличиваем твердость. Износостойкость увеличивается как при абразивном износе, так и при испытаниях на износ при скольжении за счет получения более мелких зерен карбида и более тонких слоев межкарбидной связки, которые служат для ограничения избирательного износа связки и дальнейшего скалывания частиц карбида [12, 13].
Таким образом, покрытие M2 + 20% WC является наиболее предпочтительным для наплавки шейки шестерни-вала, поскольку оно показывает хорошие уровни износостойкости, твердости, отсутствия трещин на поверхности, структурной однородности покрытия и большого количества остаточного аустенита, один из основных факторов снижения циклических внешних напряжений.
4. Выводы
(1) Установлено, что частицы WC взаимодействуют с частицами HSS M2 в порошковой смеси во время спекания порошковых корок и, таким образом, образуют карбид M 6 C.Содержание WC в исходной порошковой смеси увеличилось с 10 до 40% мас. соответствует содержанию WC от 20 до 25% об. в торте. (2) Как показано, добавление от 20 до 25% мас. WC в наплавочной смеси приводит к более высокому содержанию карбида M 6 C, обнаруженного в виде эвтектических 5,9 мкм мкм и мелких карбидов 0,25 мкм мкм внутри зерен (мультимодальное распределение по размерам) в дополнение к VC 0,65 мкм m карбидов и больше аустенита – 88% об.