Советский сварочный аппарат с питанием от бортсети
Когда сварочный аппарат выходит из строя, или зачастую просто лежит, без надобности, порой возникает желание просто сдать его на металлолом. Важно понимать, что привлекательность такого оборудования в плане приемки на лом заключается как раз в наличии внушительного количества цветного металла, в частности меди и алюминия. Но, чтобы принять решение о том, стоит сдавать агрегат на лом или нет, предлагается узнать, сколько меди в каждом сварочном аппарате, который может быть как выгодным для владельца, так и нет.
Кузовной цех во дворе: тест советского сварочного аппарата с питанием от бортсети
Давненько мы не обновляли экспозицию нашего редакционного музея советских автомобильных ретро-аксессуаров и гаджетов! Новым пополнением, очередной найденной на гаражных чердаках «капсулой времени», стало уникальное устройство – автомобильный сварочный аппарат!
Он представлял собой трехкилограммовую металлическую коробку отчаянно-красной масти с размерами 260х190х110 мм, с двумя мощными болтовыми клеммами для подключения сварочных проводов на передней панели. С помощью этого аппарата допускалось варить электродом с диаметром до 3 миллиметров в режиме «2,5 минуты сварка – 2,5 минуты отдых».
1 / 2
2 / 2
По моде наивной эпохи, когда каждое деревенское сельпо стремилось назвать себя «шопом» и «маркетом», надпись на приборе дублирована на английском. На передней же панели сварочного аппарата красуется крупное слово «АВТОВАЗ» и всем знакомый логотип тольяттинской «ладьи». Однако, разумеется, выпускал это устройство не сам автозавод, а его дочернее предприятие – ПТО ВАЗ, основанное в 1972 году, спустя шесть лет после запуска основного расшифровывалось как «Производство Технологического Оборудования» – это вспомогательное предприятие делало для основного жигулевского конвейера металлообрабатывающие станки, окрасочное и прочее технологическое оборудование, которое поставлялось в том числе и на другие автозаводы СССР.
В эпоху перестройки все госпредприятия были добровольно-принудительно ориентированы на расширение ассортимента в сторону «продукции народного потребления», в рамках чего на ПТО ВАЗ и был рожден автомобильный сварочный аппарат АСП-1 – для граждан и, как сказали бы сейчас, для «микробизнеса» – кооператоров, трудящихся в сфере мелких услуг населению. .
Огромный плафон красной лампочки на верхней крышке выглядит как некая кустарная доработка – странно и нелепо… Однако это штатный элемент конструкции, роль которого отражена в инструкции. Он ярко горит, пока электрическая дуга на электроде не зажжена, свидетельствуя о зарядке аккумулятора, и гаснет при начале сварки.
Почему вместо такого здоровенного «фонаря» не использовался светодиод или хотя бы миниатюрная индикаторная лампочка накаливания – непонятно…
На шильдике устройства выбита масса – «5 кг». Однако сам прибор весит около трех кило; пять – это масса со сварочными проводами, электрододержателем и «крокодилом» массы.
Знакомые с электроникой могут подумать, что под крышкой АСП-1 находится импульсный преобразователь-инвертор, как и внутри большинства современных инверторных сварочных аппаратов, работающих от сети 220 вольт… Но не забывайте – это самое начало десятилетия 90-х, когда большинство людей продолжало называть свою страну по привычке СССР, все машины были карбюраторными, а компьютеры встречались только в крупных НИИ… Мощная импульсная техника, а также соответствующие ей мощные силовые транзисторы и диоды редко встречались в то время в бытовых устройствах даже за рубежом – не то что во вчерашнем «совке». Так что все было гораздо проще!
Никаких преобразований напряжения внутри сварочника не происходило – из всей электроники он содержал только два мощных тиристора. Для того чтобы от бортсети легкового автомобиля можно было варить, АСП-1 делал, по сути, всего три простые вещи:
- Поднимал напряжение на генераторе, перехватывая роль штатного реле-регулятора.
- Подключал аккумулятор параллельно генератору, если силы тока не хватало.
- Автоматически переключался на зарядку аккумулятора, как только сварщик отрывал электрод от детали и прекращал работу.
То есть, в сущности, сварочным аппаратом на 90% являлся генератор автомобиля, плюсовой вывод которого напрямую подключался к сварочному электроду. Двигатель машины во время сварки должен был, разумеется, работать, и для обеспечения максимального выходного тока инструкция предписывала крутить коленвал до 2500 оборотов с помощью подсоса или помощника, нажимающего на педаль. А роль АСП-1 была «вспомогательно-коммутационная», если так можно выразиться…
Сварка с помощью АСП-1 достаточно проста. Запускается мотор машины, подсосом выставляются 2500 оборотов двигателя, к свариваемой детали подключается мощная клемма-«крокодил», в рукоятку-держак вставляется электрод, на глаза опускается щиток или маска, и процесс пошел.
Но если вы подумали, что перед этим нужно элементарно подключить питание аппарата «крокодилами» к аккумулятору, то вы серьезно ошиблись! Это – суровый советский жигулевский гаджет, а не современный литий-ионный пусковой бустер-пауэрбанк, с которым справится любая блондинка! Для подключения АСП-1 требовалось серьезное вмешательство в электропроводку под капотом.
Собственно, первый пункт процесса установки требовал закрепить сварочный аппарат стационарно под капотом «классики» или «девятки». Да-да, предполагалось, что сварочник станет постоянным «подкапотным жителем», как карбюратор или бензонасос, ибо электрическое его внедрение в электросистему автомобиля имело ряд особенностей. От генератора нужно было отсоединить силовой плюсовой выходной провод и подключить его к сварочному аппарату. Таким образом, сварочник включался между генератором и батареей. Затем предписывалось отключить от генератора реле-регулятор, роль которого брал на себя сварочный аппарат. Короче говоря, для подключения сварки автовладелец делал добрый десяток коммутаций в электропроводке машины – что-то размыкал, что-то наоборот – соединял перемычками. Все необходимое для этого, включая проводочки, клеммы и всякие кембрики, шло в комплекте поставки сварочного аппарата.
На первый взгляд может показаться, что даже для кратковременного использования собственного автомобиля в качестве сварочной установки требовалась длительная возня под капотом, а потом аналогичная возня в обратном порядке, чтобы вернуть проводку в прежнее состояние, дабы уехать. А вот и нет!
Не секрет, что советские инженеры при разработке товаров народного потребления зачастую по-спартански игнорировали вопросы элементарного комфорта в использовании, но только не в данном случае! В комплекте АСП-1 шла специальная косичка проводки с 8-штырьковым разъемом, которая и подключалась к электропроводке автомобиля. Когда вам надо было варить, вы втыкали в этот разъем штекер от сварочного аппарата, а когда надо было ехать – специальную замыкающую колодку. Колодка представляла собой ответную часть такого же разъема с перемычками в определенном порядке, и, будучи вставленной вместо сварки, полностью восстанавливала заводскую проводку автомобиля в штатном режиме!
Так что же такое АСП-1? Гениальная разработка, незаменимая в ряде экстремальных случаев, или странный выкидыш неповоротливой промышленности эпохи зарождающейся рыночной экономики? Почему подобные гаджеты не производятся сегодня, ведь периодическая необходимость в простой и легкой мобильной сварке там, где нет розетки, у многих по-прежнему возникает?
Будем откровенны: все же такое устройство – типичный продукт «смутного времени», типа кухонного половника из танковой бронестали от Уралвагонзавода… Надежность самого прибора была крайне высокой, но обмотки статоров и хиленькие советские выпрямительные диоды генераторов Жигулей и Москвичей работали со сваркой практически в режиме короткого замыкания, на пределе по току, да еще и с повышенным напряжением! Аккумулятор, который также постоянно включался в сварочный процесс, терял ресурс от больших токов разряда и заряда.
Сварка АСП-1 разрабатывалась и продавалась в эпоху карбюраторных автомобилей с минимумом электроники, и, как ни странно, несколько «опередила свое время», ибо сегодня даже на многих бюджетных машинах стоят генераторы на 120-160 ампер с куда более мощными диодами, которые как раз гораздо лучше подошли бы для использования совместно с электродом и маской… Но на современной насыщенной электроникой машине подобное внедрение в электросистему крайне опасно, а зачастую принципиально неприемлемо, поэтому аналогов АСП-1 в наши дни не выпускают и не продают. «Красная коробочка» перешла в разряд коллекционных курьезов…
Виды трехфазных устройств
Трехфазные сварочные аппараты бывают трех видов:
- трансформаторные;
- выпрямительные;
- инверторные.
Сварочное оборудование первого вида в основе имеет трехфазный трансформатор. Первичная обмотка состоит из трех обмоток соединенных звездой, а вторичная понижающая обмотка соединяется треугольником.
Читать также: Расчет режимов резания для фрезерования
Если для сварки используется переменный ток, то с каждой фазы вторичной обмотки отдельным проводом к электроду через дроссель подается пониженное напряжение. По сравнению с однофазным сварочным трансформатором сварка получается более мягкой, электрическая дуга становится стабильней, просадка напряжения меньше.
Выпрямительные аппараты на выходе вторичной обмотки имеют три полумостовые схемы собранные из мощных диодов. Как и в первом случае с каждого выпрямителя ток подается на сварочный электрод.
Пульсации по сравнению с выпрямителем на одной фазе значительно меньше, соответственно сварочный ток более стабилен, что сказывается на качестве сварки.
В инверторах на три фазы при одинаковой мощности сварки можно использовать менее мощные диоды и транзисторы, но это практически так не делают. Наоборот применение трехфазного напряжения позволяет получать аппараты большой мощности при малых габаритах и массе.
Популярные модели
Сварочный инвертор полуавтомат 380 В – это наиболее распространенный прибор среди профессиональных аппаратов. В отличие от трансформаторных приборов они имеют небольшие габариты и массу.
Сварочный полуавтомат TESLA MIG 350 чешского производства хорошо зарекомендовал себя при работе в тяжелых условиях. При нестабильном или пониженном питающем напряжении обеспечивает стабильную сварочную дугу, работает от напряжения 380 В, а максимальный сварочный ток составляет 350 А.
Механизм подачи сварочной проволоки аппарата имеет два ролика, потребляемая мощность составляет 11,9 кВт. Запас мощности позволяет использовать длинные кабели до 20 м. Байонетные штекеры обеспечивают надежное и быстрое подключение горелки к аппарату. Производитель дает на оборудование трехгодичную гарантию.
Еще один пример профессионального трехфазного инвертора – это Сварог ARCTIC ARC 315 (R14). Он работает в жестких условиях, позволяет варить в интенсивном ручном режиме, выполнять наплавку. Благодаря использованию новейшей инверторной технологии аппарат может работать при температурах до -30 ⁰С. Имеется функция «горячий старт».
Раздельный монтаж силовых транзисторов повышает ремонтопригодность аппарата. При максимальном сварочном токе 315 А инвертор может использовать электроды диаметром 6 мм. Это позволяет сваривать металлы толщиной до 17 мм. При мощности 12 кВт имеет массу 22 кг.
Читать также: Графит температура плавления и кипения
Трехфазный инверторный сварочный аппарат «Ресанта САИ-315 380В» имеет примерно те же характеристики, что и «Сварог», но меньше дополнительных функций. Он более прост, поэтому дешевле и весит всего 10 кг.
Преимущества и недостатки
Все трехфазное оборудование для сварки относится к категории профессиональных устройств. Многие из них способны производить сварку в непрерывном режиме, то есть ПВ равно 100%. На строительстве трехфазные трансформаторные и выпрямительные сварочные аппараты до сих пор не имеют альтернатив.
Они не боятся пыли, грязи, работают при низких температурах, что противопоказано инверторам. Однофазные приборы трансформаторного типа тоже могут работать в таких же условиях, но у них мощность меньше и пульсации тока больше.
Соответственно, они не могут сравниться с трехфазными устройствами по качеству сварки, диаметру электродов и толщине свариваемого металла.
Использование трехфазного тока в инверторах, тоже имеет свои преимущества. Применяя одинаковую элементную базу, получают более мощный прибор с большими сварочными токами, что позволяет работать практически с любыми изделиями.
Схема прибора отличается незначительно. Используется тот же широтно-импульсный модулятор. Преобразование высокого в пониженное напряжение происходит на частоте порядка 40-100 кГц.
Единственный недостаток этих устройств заключается в том, что не всегда и не везде можно подключиться к трехфазному источнику питания на 380 В, и цена у них значительно выше, чем у однофазных аппаратов.
Сварочный аппарат в аренду в Советском округе, Липецк — 2 места 📍 (адреса, фото)
— 2 места
- Мы составили рейтинг 2 мест «сварочный аппарат в аренду» в Советском округе;
- Лучшая аренда сварочного аппарата: уровень цен, отзывы, фото;
- Аренда сварочного аппарата на карте: адреса, телефоны, часы работы;
Московская улица, 83, Советский округ • 8 (951) 301-93-49 • ежедневно с 09:00 до 18:00
Мы занимаемся продажей, прокатом и сервисным обслуживанием строительного инструмента и оборудования для частных лиц и компаний по Липецку, области и…
ул.
Фрунзе, 23, Советский округ • 8 (904) 680-61-44 • ежедневно с 09:00 до 18:00
Аренда и прокат строительного инструмента и оборудования для частных лиц и компаний по Липецку, области и России. ✔ ВЫГОДНЫЕ ЦЕНЫ (нал, безнал с НДС,…
Запрос в заведения — закажите услугу, уточните цену
Отправьте запрос — получите все предложения на почту:Не хотите обзванивать кучу заведений?
Интересные факты
Чаще всего люди ищут «сварочный аппарат в аренду», но встречаются и другие формулировки, например, аренда сварочного аппарата.
Самые популярные особенности найденных мест: аренда электрического отбойного молотка, аренда дрели, аренда компрессора, аренда шлифовальных машин для паркета, аренда циркулярной пилы, AEG, Bosch, Karcher, DEWALT, Makita.
Добавить бизнес — бесплатная реклама вашей организации на HipDir.
Военная техника: сварка советской брони
Приемка танков Т-34, сошедших с конвейера завода № 183 в Нижнем Тагиле. Источник: waralbum.ru
Все воюют с кряком!
Очень твердая гомогенная бронесталь 8С, являющаяся базой для среднего танка Т-34, доставила немало трудностей в процессе изготовления. Следует отметить, что столь прочная броня в период Второй мировой войны на танках использовалась только в Советском Союзе. И в этом, безусловно, были как положительные, так и отрицательные стороны. цикла уже обсуждались многочисленные трещины, сопровождающие сварку башен и башен средних советских танков. При этом тяжелые КВ, а затем и ИСА были лишены этого: более пластиковая броня средней твердости гораздо легче переносит чрезмерные напряжения при сварке деталей. Инженеры “Бронетанкового института” с начала 19№ 42 предложен комплекс мероприятий по упрощению производства бронкобастеров и модернизации технологии сварки.
Сварщик за работой на Уральском танковом заводе в цехе сборки танков Т-34. Источник: waralbum.ru
Лобовая и бортовая части танка сваривались теперь по требованию ЦНИИ-48 только аустенитными электродами, лучше всего подходящими для трудносвариваемых сортов черного металла. Всего теперь до 10% (и более) всех электродов, необходимых для бронеавтомобиля, было аустенитным. Если ориентироваться на сведения, приведенные в книге Никиты Мельникова «Танковая промышленность СССР в годы Великой Отечественной войны», то на один танк Т-34-76 израсходовано около 400 электродов, причем 55 из них были аустенитными. Среди требований к применению таких электродов был запрет на их работу при повышенных рабочих токах до 320А. Превышение этого показателя грозит сильным нагревом зоны шва с последующей деформацией при остывании и растрескиванием.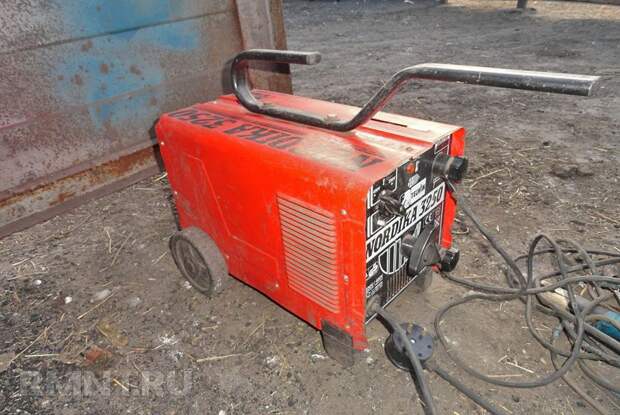
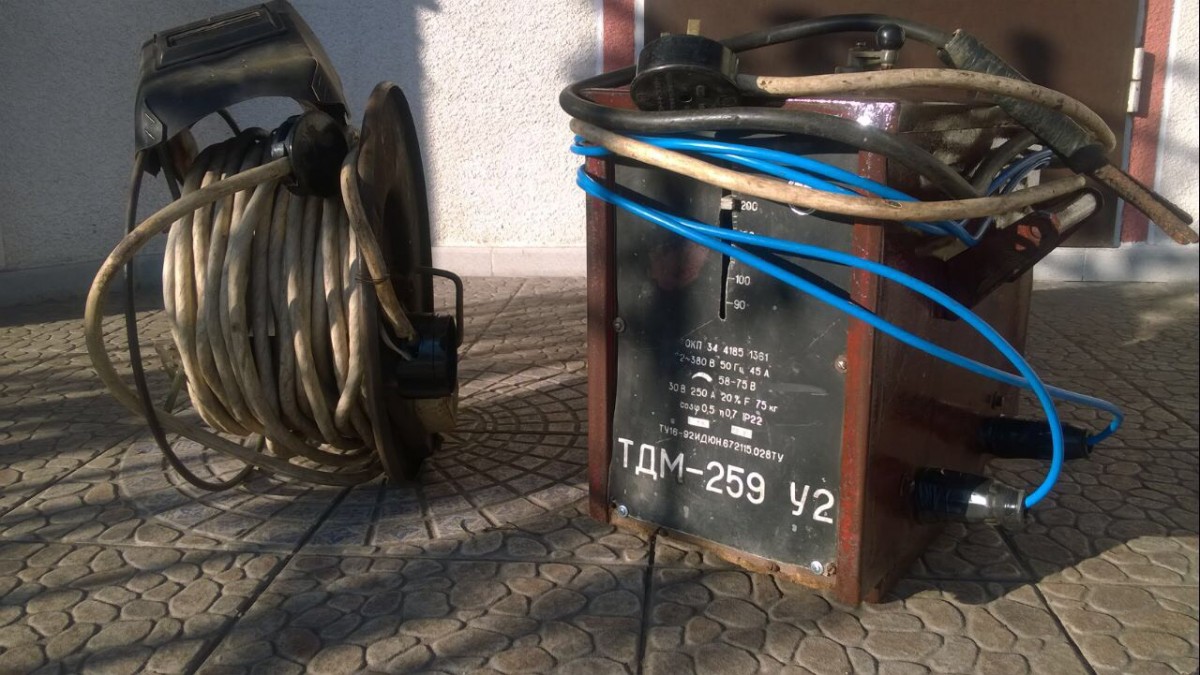
Рабочие Свердловского завода по сборке СУ-122. Источник: waralbum.ru
Приварка детали к крыше башни танка Автоматическая сварочная установка Т-34-85 на Уральском танковом заводе №183 в Нижнем Тагиле. Источник: waralbum.ru
Сварка корпуса танка Т-34 на Уральском танковом заводе №183 в Нижнем Тагиле. Источник: waralbum.ru
Если основной электрод и присадочная проволока были чрезмерно загрязнены серой, углеродом и фосфором (или, наоборот, в ней не хватало марганца или оксида марганца), это приводило к растрескиванию непосредственно в сварочном шве . Важно было тщательно подготовить сварку под флюсом. Требования были жесткими: детали должны быть правильного размера, без нарушений допусков. В противном случае для сварки заготовку на стапеле приходилось «тянуть», создавая при этом серьезные внутренние напряжения. А простой сбой мощности и напряжения сварочного тока приводил к эффективности швов: пористости, непроварам и непроварам. Учитывая низкий уровень квалификации рабочих, допущенных к сварочным аппаратам, в возможность брака такого рода легко поверить.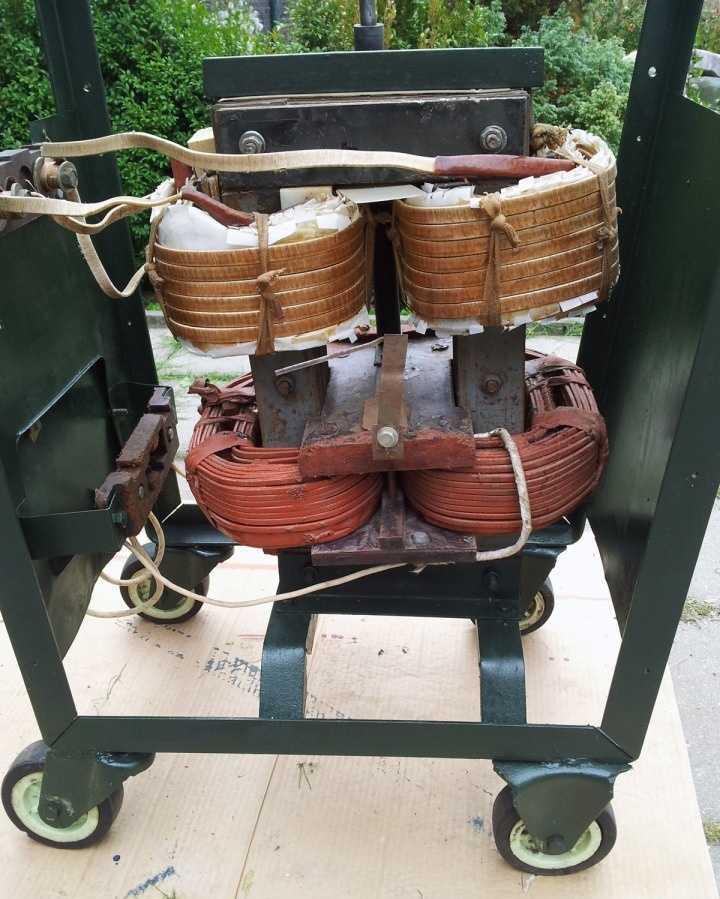
Сварочные корпуса СУ-122 и СУ-100 на Уральском заводе тяжелого машиностроения. Источник: waralbum.ru
Литая часть брони обменного пулемета ДТ. Завод № 183, 1942 год. Источник: Российский государственный архив экономики
Резкое увеличение производительности танковых заводов привело к 1943 году к одной неожиданной проблеме. Выяснилось, что остальная часть производства не успевала за танком. Станки работали очень тяжело, иногда отсутствовали амперметры для контроля силы тока на станках, не хватало качественных сварочных электродов. Все это вызывало периодические «всплески» треска серийного Т-34. Тушить эти волны брака предстояло оперативным техникам завода и инженерам из ЦНИИ-48.Обзор проекта
Жесткая броня и трещины в ней заставили инженеров изменить не только технологию автоматической сварки, но и ручной подход.
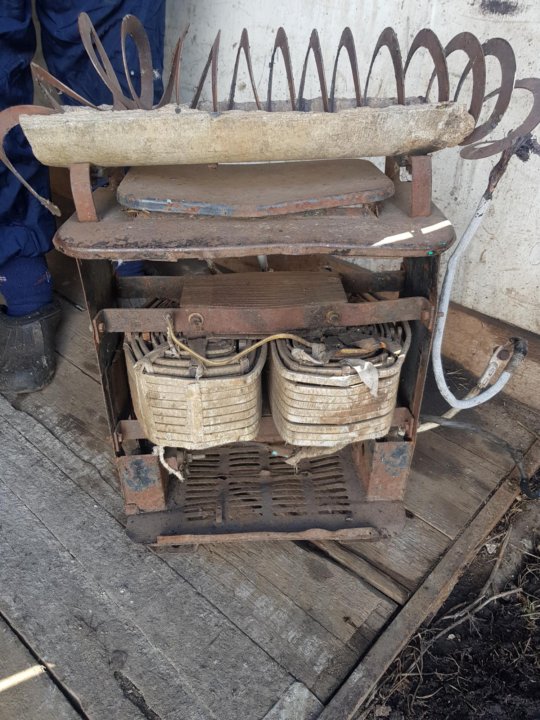
Источник: Российский государственный архив экономики
Изменились и технологические соединения корпусных частей танка Т-34. Изначально все соединения, кроме сопряжения ВЛД и НЛД, были как бы с чертежей, сделанных в квартале. Но вскоре после войны их поменяли на шпильки, но это не оправдалось — слишком много трещин появилось в местах прорезанных швов. Шиповое соединение для очень твердой брони было не очень подходящим из-за сильных местных усадочных напряжений после сварки. То, что было хорошей пластиковой немецкой броней, для российского Т-34 не подходило. Только в 1943 на «танке Победы» появился в окончательных версиях стык, довольный специалистами ЦНИИ-48, внахлест – стык и стык.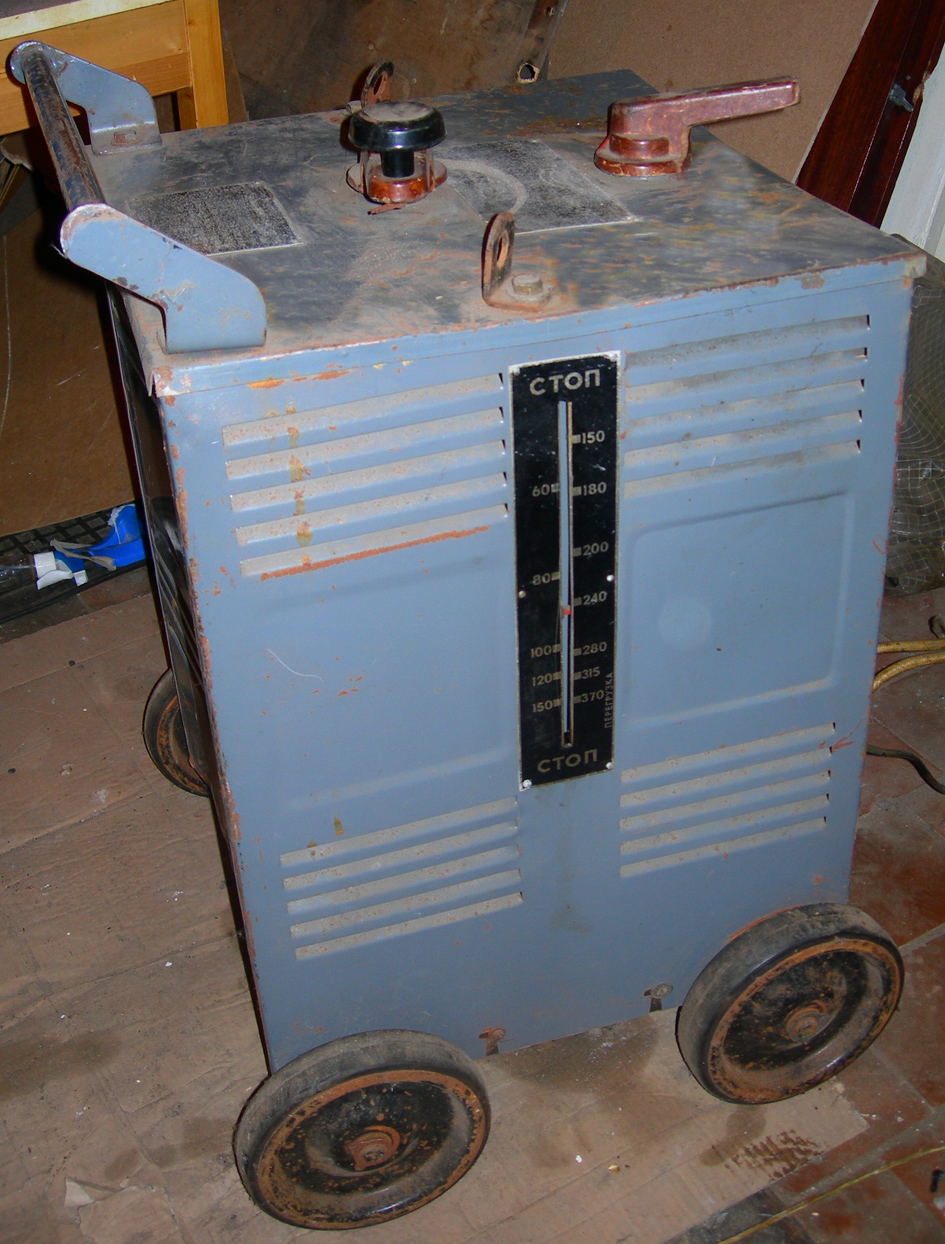
Танковый корпус на кантователе. Источник: Российский государственный архив экономики
Наиболее простым способом оптимизации процесса сварки корпуса были тяжелые советские танки. Соединение бронелистов в четверть на ВЧ оставили без изменений, но внутренние угловые швы заменили внутренними треугольниками усиления. Уже в самый разгар войны для тяжелых танков (в первую очередь для снарядных атак) была выбрана наиболее оптимальная конфигурация сопряжения бронелистов. Если бы угол соединения был близок к 90 градусов лучше было использовать метод «шип» или четверть, а все остальные варианты или враспор в зуб. По результатам этих исследований в ЦНИИ-48 родилась своеобразная форма верхней части лобовой части корпуса танка ИС-2, когда при толщине брони 100-110 мм обеспечивается всеракурсная защита от 88 до 105 мм. обечайки сопрягаемых деталей в этой прочной конструкции были простыми, враспорными.Борис Патон об истории и развитии сварки.
Он один из величайших в истории сварки. Благодаря Борису Патону Советский Союз был одним из ведущих государств в области дуговой сварки во второй половине двадцатого века. Теперь эксперт делится с нами в блоге Perfect Welding своим взглядом на историю сварки и будущие проблемы, стоящие перед технологиями сварки.
Для профессора Бориса Патона невозможно переоценить важность сварки для развития человечества и качества нашей современной жизни. В конце концов, быстрый прогресс, достигнутый в нашем обществе, стал возможен только благодаря постоянному развитию и совершенствованию технологий соединения. «Вот что меня вдохновляет и завораживает, — говорит Патон в интервью блогу Perfect Welding. Сам Патон считается одним из самых важных пионеров в развитии сварки. Известный в Украине как герой, он возглавляет один из самых известных институтов электросварки: Институт им. Институт электросварки имени Патона в Киеве.
Сварщик исторической важности Патон был особенно активен в области механизированной сварки и, таким образом, сыграл важную роль в дальнейшем развитии технологии сварки. «Самые захватывающие дух изменения были вызваны ручной дуговой сваркой металлом, дуговой сваркой под флюсом, сваркой вольфрамовым электродом в среде инертного газа, а также сваркой в среде инертного и активного газа», — объясняет Патон. Эксперт считает, что растущие потребности промышленности являются движущей силой новых разработок в области сварки. Промышленная потребность в новых методах и технологиях привела к развитию сварки переменным током, импульсных процессоров, настроек автокоррекции и процессов с цифровым управлением.
«Сварка ВИГ остается лучшим выбором, когда к качеству сварного шва предъявляются высокие требования», — говорит Патон. Эксперт даже предсказывает, что этот почтенный процесс сварки будет играть важную роль в сварке соединений в будущем, особенно в производственной сфере, особенно там, где используются роботы. Ключевая область применения — однопроходная сварка более толстых стенок толщиной от десяти миллиметров и более. Среди новаторских разработок в истории процесса TIG Патон выделяет использование активных веществ (активирующий флюс или «A-TIG»), высокочастотную сварку TIG (высокочастотный импульс или «HFP-TIG») и использование к активному газу добавляют инертный газ. Эти усовершенствования процесса сварки значительно повышают экономическую эффективность сварки TIG.
Несмотря на многочисленные разработки последних лет, эксперт видит большую потребность в новых сварочных системах, процессах и добавках. «Увеличивается количество конструкций и машин, которые достигли критического срока службы. Поэтому ремонтная сварка является важной темой. Нам необходимо наладить надежные процессы определения остаточного ресурса сварных соединений», — поясняет Патон. Кроме того, промышленность в настоящее время настаивает на дальнейшем развитии комбинаций, которые используются в гибридных процессах. Эксперт по сварке также видит потенциал для усовершенствования самого сварочного оборудования.