Обработка конических поверхностей
Общие сведения о конусах
Обработка деталей с конической поверхностью связана с образованием конуса, который характеризуется следующими размерами – рисунок слева а): меньшим d и большим D диаметрами и расстоянием L между плоскостями, в которых расположены окружности с диаметрами D и d. Угол α называется углом наклона конуса, а угол 2α – углом конуса. Отношение K=(D-d)/L называется конусностью и обычно обозначается со знаком деления (например, 1 : 20 или 1 : 50), а в некоторых случаях десятичной дробью (например, 0,05 или 0,02). Отношение y=(D-d)/(2L)=tg α называется уклоном.
Способы обработки конических поверхностей
При обработке валов часто встречаются переходы между обрабатываемыми поверхностями, имеющие
коническую форму.
Если длина конуса не превышает 50 мм, то его обработку
можно производить широким резцом – рисунок слева б). Угол наклона режущей кромки
резца в плане должен соответствовать углу наклона конуса на обрабатываемой
детали. Резцу сообщают подачу в поперечном или продольном направлении.
Для уменьшения искажения образующей конической поверхности и уменьшения
отклонения угла наклона конуса необходимо устанавливать режущую кромку
резца по оси вращения обрабатываемой детали. Следует учитывать, что при
обработке конуса резцом с режущей кромкой длиной более 10-15 мм могут
возникнуть вибрации, уровень которых тем выше, чем больше длина
обрабатываемой детали, меньше ее диаметр, меньше угол наклона конуса,
ближе расположен конус к середине детали, больше вылет резца и меньше
прочность его закрепления. В результате вибраций на обрабатываемой
поверхности появляются следы и ухудшается ее качество. При обработке
широким резцом жестких деталей вибрации могут отсутствовать, но при этом
возможно смещение резца под действием радиальной составляющей силы резания,
что приводит к нарушению настройки резца на требуемый угол наклона. Смещение
резца зависит от режима обработки и направления подачи.
Конические поверхности с большими уклонами можно обрабатывать при
повороте верхних салазок суппорта с резцедержателем – рисунок слева в), на угол
α, равный углу наклона обрабатываемого конуса.
Конические поверхности большой длины с
α=8-10 градусов можно обрабатывать при
смещении задней бабки – рисунок слева г), величина которого
h=L×sin α. Величину смещения задней
бабки определяют по шкале, нанесенной на торце опорной плиты со стороны
маховика, и риске на торце корпуса задней бабки. Цена деления на шкале
обычно 1 мм. При отсутствии шкалы на опорной плите величину смещения задней
бабки отсчитывают по линейке, приставленной к опорной плите. Способы
контроля величины смещения задней бабки показаны на рисунке справа.
В резцедержателе закрепляют упор, рисунок а) или индикатор, рисунок б).
В качестве упора может быть использована тыльная сторона резца.
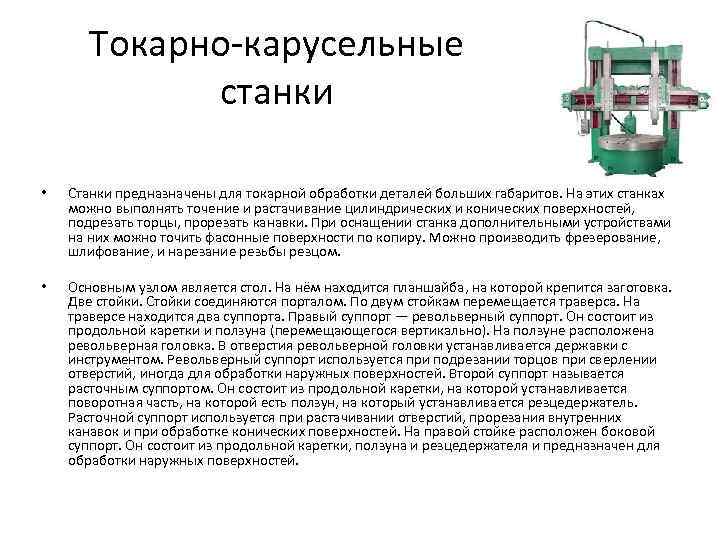
Для обеспечения одинаковой конусности партии деталей, обрабатываемых этим способом, необходимо, чтобы размеры заготовок и их центровых отверстий имели незначительные отклонения. Поскольку смещение центров станка вызывает износ центровых отверстий заготовок, рекомендуется обработать конические поверхности предварительно, затем исправить центровые отверстия и после этого произвести окончательную чистовую обработку. Для уменьшения разбивки центровых отверстий и износа центров целесообразно последние выполнять со скругленными вершинами.
Распространенной является обработка конических
поверхностей с применением копирных устройств. К станине станка крепится
плита 1, рисунок слева а), с копирной линейкой 2, по которой перемещается
ползун 5, соединенный с суппортом 6 станка тягой 7 с помощью зажима 8.
Для свободного перемещения суппорта в поперечном направлении необходимо
отсоединить винт поперечной подачи. При продольном перемещении суппорта 6
резец получает два движения: продольное от суппорта и поперечное от
копирной линейки 2. Величина поперечного перемещения зависит от угла
поворота копирной линейки 2 относительно оси 3 поворота. Угол поворота
линейки определяют по делениям на плите 1, фиксируют линейку болтами 4.
Подачу резца на глубину резания производят рукояткой перемещения верхних
салазок суппорта. Обработку конической поверхности 4, рисунок слева б),
производят по копиру 3, установленному в пиноли задней бабки или в
револьверной головке станка. В резцедержателе поперечного суппорта
устанавливают приспособление 1 с копирным роликом 2 и остроконечным
проходным резцом. При поперечном перемещении суппорта копирный ролик 2 в
соответствии с профилем копира 3 получает продольное перемещение, которое
передается (через приспособление 1) резцу. Наружные конические поверхности
обрабатываются проходными, а внутренние конические поверхности – расточными
резцами.
Для получения конического отверстия в сплошном материале, рисунок справа,
заготовку обрабатывают предварительно (сверлят, растачивают),
а затем окончательно (развертывают). Развертывание выполняют последовательно
комплектом конических разверток – рисунок внизу. Диаметр предварительно
просверленного отверстия на 0,5-1 мм меньше заходного диаметра развертки.
Формы режущих кромок и работа разверток: режущие кромки черновой развертки
– а) имеют форму уступов; получистовая развертка – б)
снимает неровности, оставленные черновой разверткой; чистовая развертка
– в) имеет сплошные режущие кромки по всей длине и калибрует
отверстие. Если требуется коническое отверстие высокой, точности, то его
перед развертыванием обрабатывают коническим зенкером, для чего в сплошном
материале сверлят отверстие диаметром на 0,5 мм меньше, чем диаметр конуса,
а затем применяют зенкер. Для уменьшения припуска под зенкерование иногда
применяют ступенчатые сверла разного диаметра.
На главную
методическая разработка открытого урока на тему «Технология обработки конической поверхности» Дисциплина МДК.04.02. «Технология металлообработки на токарных | Методическая разработка на тему:
МИНИСТЕРСТВО ОБРАЗОВАНИЯ ТУЛЬСКОЙ ОБЛАСТИ
Государственное профессиональное образовательное учреждение Тульской области
«Тульский государственный машиностроительный колледж им. Н. Демидова»
(ГПОУ ТО «ТГМК им. Н. Демидова»)
МЕТОДИЧЕСКАЯ РАЗРАБОТКА
НА ТЕМУ «Технология обработки конической поверхности»
Дисциплина МДК.04.02. «Технология металлообработки на
токарных станках»
ПМ.04 «Выполнение работ по одной или нескольким профессиям
рабочих, должностям служащих»
Тула 2016
Методическую разработку открытого занятия на тему «Технология обработки конической поверхности» по учебной дисциплине «Технология металлообработки на токарных станках» для студентов специальности 15.02.01 «Монтаж и техническая эксплуатация промышленного оборудования» подготовила преподаватель ГПОУ ТО «ТГМК им. Н. Демидова» – Воеводина Т.А
В методической разработке раскрыты особенности подготовки и проведения учебных занятий в современных условиях, применение методических приемов и методов на разных этапах занятия. Уровень учебного материала отвечает возрастным особенностям студентов и учебной программе по специальности 15.02.01 «Монтаж и техническая эксплуатация промышленного оборудования»
Введение
“Урок – это зеркало общей и педагогической культуры учителя, мерило его интеллектуального богатства, показатель его кругозора и эрудиции”
В.А. Сухомлинский
В настоящее время, как никогда раньше, повысились требования к учебному занятию – основной формы учебы и воспитания студентов.
Каким же в действительности должно быть учебное занятие на современном этапе? Как повысить его эффективность?
Вообще-то занятие зависит от многих составляющих. Но одним из важнейших условий повышения качества проведенных занятий есть разнообразие методов и приемов учебы, видов работы, которые выполняют студенты. Всяческое однообразие, в конечном итоге, порождает у подростков ощущение перегрузки. Оно возникает не столько от большого количества заданий, их сложности, сколько от однообразия, серости и будничности.
Предисловие
Комбинированное занятие по теме «Технология обработки конической поверхности» по учебной дисциплине «Технология металлообработки на токарных станках» проводится путем использования таких методов и форм проверки знаний студентов как фронтальный и индивидуальный опрос, тестирование по предыдущей теме, доклады студентов, работа в бригадах. Это помогает углубить и систематизировать знание по данной теме, достичь качественного усвоения студентами основных понятий, совершенствовать навыки логического мышления, и профессиональные задатки относительно экономического подхода к производственному процессу; воспитывать черты коллективизма при решении любых заданий, формированию общих и профессиональных компетенций:
ОК1. Понимать сущность и значимость своей будущей профессии, применять к ней устойчивый интерес.
ОК2. Организовывать собственную деятельность, выбирать типовые методы и способы выполнения профессиональных задач, оценивать их эффективность и качество.
ОК3. Принимать решения в стандартных и нестандартных ситуациях, нести за них ответственность.
ОК4. Осуществлять поиск и использование информации, необходимой для эффективного выполнения профессиональных задач, профессионального и личностного развития.
ОК5. Использовать информационно-коммуникационные технологии в проф.деятельности
ОК6. Работать в коллективе и команде, эффективно общаться с коллегами.
ОК7. Брать на себя ответственность за работу членов команды и результат выполнения заданий.
ПК 1.1. Использовать конструкторскую документацию при разработке технологических процессов изготовления деталей.
ППК 1.3. Составлять маршруты изготовления деталей и проектировать технологические операции.
ПК 1. 4. Разрабатывать и внедрять управляющие программы обработки деталей.
ПК 3.1. Участвовать в реализации технологического процесса по изготовлению деталей.
ПЛАН ЗАНЯТИЯ
Дата проведения: 01 марта 2016 г.
Группа: 100951
Специальность: 15.02.01 «Монтаж и техническая эксплуатация промышленного оборудования» (по отраслям)
Тема: «Технология обработки конусной поверхности»
Цель занятия :
Образовательная: Сформировать знания о сущности таких способов обработки как обработка конусов широким резцом, обработка конусов при повернутых верхних салазках суппорта, путем смещение задней бабки, обработка конических поверхностей при помощи конусной линейки
Развивающая: Содействовать развитию познавательного интереса к предмету, умению применять знания теории на практике. Развивать аналитическое мышление, умение отбирать из потока информации необходимую для данной ситуации; произвести навыки применения теоретических знаний путем прикладных упражнений (заданий).
Воспитательная: Используя коллективный метод работы, развивать чувство коллективизма и взаимопомощи как в процессе учебы, так и в дальнейшей производственной деятельности
Вид занятия : Комбинированное
Форма проведения занятия : Фронтальный опрос, тестирование, выступления студентов с докладами, запись основных положений под диктовку, работа в бригадах, решение производственных задач на определение технологии обработки конической поверхности
Межпредметные связи:
Обеспечивающие : – математика; физика; инженерная графика
Обеспечиваемые: – производственная практика
Методическое обеспечение: опорные конспекты, тесты, чертежи деталей
Технические обеспечение : компьютер, мультимедийный проектор, экран.
Литература: Обязательная:1. Багдасарова Т.А. Токарь: технология обработки: учебное пособие для нач. проф. образования. – М.: Издательский центр «Академия», 2013. – 80 с.
Дополнительная: Багдасарова Т.А. Токарь-универсал: учебное пособие для нач. проф. образования. – М.: Издательский центр «Академия», 2012 – 288с
Ход занятия
1 Организационный момент
Приветствие, проверка присутствующих и отсутствующих на занятии, подготовка к занятию, настрой на работу.
2 Ознакомление студентов с темой и учебными целями занятия
Запись темы занятия и основных заданий в конспекте по теме «Технология обработки конусной поверхности» .
Сегодня на занятии мы рассмотрим вопросы, которые пригодятся вам при выполнении практических заданий и в дальнейшей производственной деятельности. Для вас цель сегодняшнего занятия – это научиться применять полученные теоретические знания в простейших производственных ситуациях.
3 Актуализация опорных знаний
Фронтальный опрос
1. Какие виды движений осуществляются на токарном станке
2. Какое движение является главным
3. Какое движение является вспомогательным
4. Перечислить основные узлы станка
5. Перечислить инструмент, используемый для работы на токарном станке
6. Перечислить основные геометрические параметры резца
7. Из каких частей состоит резец
8. Какие имеются углы у резца
9. Что такое припуск на обработку
10. Перечислить элементы режимов резания
11. Какие из них устанавливаются на станке
Тестирование
Студенты выполняют тест с последующей проверкой друг друга и заполнением таблицы правильных ответов
Оценка за тестирование выставляется на следующем занятии, после проверки преподавателем.
ТЕСТ
Тема: Технология нарезание резьбы метчиками и плашками.
Вариант 1
1. Верно, ли что 1 дюйм равен 25,4 мм?
1. Да. 2. Нет.
2. Укажите, какая резьба прочнее:
1. Полученная резанием; 2. Полученная накаткой.
3. Сколько режущих частей имеет плашка?
1. Одну. 2. Две.
4. Как называются инструменты для комплексного контроля наружной резьбы?
1. Резьбовые калибр-кольца; 2. Резьбовые калибр-пробки.
5. Какую величину имеет угол при вершине дюймовой резьбы?
1. 30° 2. 40° 3. 50° 4. 55° 5. 60°
6 Каким инструментом нарезают наружную резьбу?
1плашки; 2 метчики; 3 воротки и плашкодержатели.
7. Укажите точное определение шага резьбы.
1. расстояние между соседними впадинами резьбы;
2. расстояние между соседними выступами резьбы;
3. расстояние между соседними выступами или впадинами резьбы.
8. Определите диаметр стержня dст под нарезание резьбы плашкой М24х1.
1. 23,86мм. 2. 24,5мм. 3. 23,5мм. 4. 23,9мм. 5. 23,0мм.
9. Определить диаметр сверла (Dсв) под нарезание резьбы метчиком М6-7G?
1. 5,9мм. 2. 5,8мм. 3. 5,5мм. 4. 4,5мм. 5. 5мм.
10. Какие из перечисленных причин послужат причиной брака рваная резьба?
1. Большое занижение диаметра; 4. Неправильный выбор СОТС;
2. Затупившийся инструмент; 5. Завышение скорости резания
3. Неправильная заточка инструмента;
Форма ответа:
1б | 1б | 1б | 1б | 1б | 1б | 1б | 1б | 1б | 1б |
1 | 2 | 3 | 4 | 5 | 6 | 7 | 8 | 9 | 10 |
10-9б – «5» 8-7 – «4» 6-5 – «3» 4 и менее «2»
Вариант 2
1 Диаметр отверстия под нарезание резьбы М12×1,5 метчиком составляет
1. 11,89мм 2.10,5мм 3.10,85мм 4. 11,85мм
2 Угол профиля метрической резьбы составляет
1. 500 2. 350 3. 550 4. 600
3 Где правильно обозначена метрическая резьба с крупным шагом?
1. М8х1; 2. М8х0,75; 3. М8.
4 Трубная резьба измеряется в
1 мм 2 см 3 дюймах 4 Количестве ниток на дюйм
5 Величина1 дюйма равна
1 24,5мм 2 25,4мм 3 23,5мм 4 25,5мм
6 Резьба какого типа чаще применяется при изготовлении крепежных деталей?
1 метрическая
2 упорная
3 трапецеидальная.
7 По назначению резьбы подразделяются
1 на треугольные и трапецеидальные
2 на цилиндрические и конические
3 на крепежные и ходовые
4 на многозаходные и однозаходные
8 Более прочная резьба получается при обработке методом
1 накатки
2 нарезания плашкой
3 нарезания резцом
4 нарезания метчиком
9 Угол профиля трубной резьбы составляет
1 600 2 300 3 550 4 650
10 Метрическая резьба М16х1,5 имеет профиль
1 трапецеидальный
2 прямоугольный
3 треугольный
4 круглый
Форма ответа:
1б | 1б | 1б | 1б | 1б | 1б | 1б | 1б | 1б | 1б |
1 | 2 | 3 | 4 | 5 | 6 | 7 | 8 | 9 | 10 |
10-9б – «5» 8-7 – «4» 6-5 – «3» 4 и менее «2»
Доклады (Приложение 1)
Студенты предварительно были разбиты на бригады и каждая бригада подготовила доклад –презентацию по определенной тематике и прежде чем приступить к изучению нового материала прослушаем подогтовленные доклады;
Тема 1 «Исторические факты о конусе» – это экскурс в прошлое.
Тема 2 «Конические поверхности в машиностроении»
Тема 3 ” Общие сведения о конусах” – повтор из курса математики
Лекционный материал
При обработке валов часто встречаются переходы между поверхностями, имеющие коническую форму.
Коническая поверхность характеризуется следующими параметрами (рис. 1): меньшим d и большим D диаметрами и расстоянием l между плоскостями, в которых расположены окружности диаметрами D и d. Угол α называется углом наклона конуса, а угол 2α — углом конуса.
Рисунок 1 Геометрия конуса
Конусностью называется отношение разности диаметров конуса к его длине. Обозначим конусность буквой K, тогда
(1)
Пример: Если конус имеет размеры: D =80 мм, d = 70 мм и l = 100 мм, то согласно формуле (1):
Это значит, что на длине 10 мм диаметр конуса уменьшается на 1 мм или на каждый миллиметр длины конуса разница между его диаметрами изменяется на
Иногда на чертеже вместо угла конуса указывается уклон конуса. Уклон конуса показывает, в какой мере отклоняется образующая конуса от его оси.
Уклон конуса определяется по формуле
(2)
где tg α — уклон конуса;
D — диаметр большого основания конуса в мм;
d — диаметр малого основания конуса в мм;
l — длина конуса в мм.
Пользуясь формулой (2), можно при помощи тригонометрических таблиц определить угол α уклона конуса.
Пример . Дано D = 80 мм; d=70мм; l= 100 мм. По формуле (2) имеем
По таблице тангенсов находим величину, наиболее близкую к tg α = 0,05, т. е. tg α = 0,049, которому соответствует угол уклона конуса α = 2°50′.
Следовательно, угол конуса 2α = 2•2°50′ = 5°40′.
Уклон конуса и конусность обычно выражают простой дробью, например: 1 : 10; 1 : 50, или десятичной дробью, например, 0,1; 0,05; 0,02 и т. д.
Технология обработки конической поверхности на токарном станке
На токарном станке обработка конических поверхностей производится одним из следующих способов:
1 с помощью широкого резца;
2 поворотом верхней части суппорта;
3 поперечным смещением корпуса задней бабки;
4 с помощью конусной линейки.
1 Обработка конических поверхностей широким резцом
Если длина конуса не превышает 25 мм, то его обработку можно производить широким резцом – рисунок 2).
Рисунок 2 Обработка конической поверхности широким резцом
Угол наклона режущей кромки резца в плане должен соответствовать углу наклона конуса на обрабатываемой детали. Резцу сообщают подачу в поперечном или продольном направлении. Для уменьшения искажения образующей конической поверхности и уменьшения отклонения угла наклона конуса необходимо устанавливать режущую кромку резца по оси вращения обрабатываемой детали. Следует учитывать, что при обработке конуса резцом с режущей кромкой длиной более 10-15 мм могут возникнуть вибрации, уровень которых тем выше, чем больше длина обрабатываемой детали, меньше ее диаметр, меньше угол наклона конуса, ближе расположен конус к середине детали, больше вылет резца и меньше прочность его закрепления. В результате вибраций на обрабатываемой поверхности появляются следы и ухудшается ее качество. При обработке широким резцом жестких деталей вибрации могут отсутствовать, но при этом возможно смещение резца под действием радиальной составляющей силы резания, что приводит к нарушению настройки резца на требуемый угол наклона. Смещение резца зависит от режима обработки и направления подачи.
2 Обработка конических поверхностей поворотом верхней части суппорта
При изготовлении на токарном станке коротких наружных и внутренних конических поверхностей с большим углом уклона нужно повернуть верхнюю часть суппорта относительно оси станка под углом α уклона конуса (рис. 3). При таком способе работы подачу можно производить только от руки, вращая рукоятку ходового винта верхней части суппорта, и лишь в наиболее современных токарных станках имеется механическая подача верхней части суппорта.
Рисунок 3 Поворот верхней части суппорта на требуемый
угол при помощи делений на опорном фланце
Для установки верхней части суппорта 1 на требуемый угол можно использовать деления, нанесенные на фланце 2 поворотной части суппорта (рис. 3). Если угол α уклона конуса задан по
чертежу, то верхнюю часть суппорта поворачивают вместе с его поворотной частью на требуемое число делений, обозначающих градусы. Число делений отсчитывают относительно риски, нанесенной на нижней части суппорта.
Если на чертеже угол α не дан, а указаны больший и меньший диаметры конуса и длина его конической части, то величину угла поворота суппорта определяют по формуле (1)
Пример . Даны диаметры конуса D = 80 мм, d = 66 мм, длина конуса l = 112 мм.
Имеем:
По таблице тангенсов находим приближенно: α = 3°35′. Следовательно, верхнюю часть суппорта необходимо повернуть на 3°35′.
Способ обтачивания конических поверхностей поворотом верхней части суппорта имеет следующие недостатки: он допускает обычно применение только ручной подачи, что отражается на производительности труда и чистоте обработанной поверхности; позволяет обтачивать сравнительно короткие конические поверхности, ограниченные длиной хода верхней части суппорта.
3 Обработка конических поверхностей способом поперечного смещения корпуса задней бабки
Для получения конической поверхности на токарном станке необходимо при вращении заготовки вершину резца перемещать не параллельно, а под некоторым углом к оси центров. Этот угол должен равняться углу α уклона конуса. Наиболее простой способ получения угла между осью центров и направлением подачи — сместить линию центров, сдвинув задний центр в поперечном направлении. Путем смещения заднего центра в сторону резца (на себя) в результате обтачивания получают конус, у которого большее основание направлено в сторону передней бабки; при смещении заднего центра в противоположную сторону, т. е. от резца (от себя), большее основание конуса окажется со стороны задней бабки (рис. 4).
Рисунок 4 Обтачивание конической поверхности при поперечном
смещении корпуса задней бабки
Смещение корпуса задней бабки определяют по формуле
(3)
где S — смещение корпуса задней бабки от оси шпинделя передней бабки в мм;
D — диаметр большого основания конуса в мм;
d — диаметр малого основания конуса в мм;
L — длина всей детали или расстояние между центрами в мм;
l — длина конической части детали в мм.
Пример . Определить смещение центра задней бабки для обтачивания усеченного конуса, если D = 100 мм, d = 80 мм, L = 300 мм и l = 200мм. По формуле (3) находим:
Преимущество обработки конических поверхностей путем смещения корпуса задней бабки заключается в том, что этим способом можно обтачивать конусы большой длины и вести обтачивание с механической подачей.
Недостатки этого способа: невозможность растачивать конические отверстия; потеря времени на перестановку задней бабки; возможность обрабатывать лишь пологие конусы; перекос центров в центровых отверстиях, что приводит к быстрому и неравномерному износу центров и центровых отверстий и служит причиной брака при вторичной установке детали в этих же центровых отверстиях.
4 Обработка конических поверхностей с применением конусной линейки
Для обработки конических поверхностей с углом уклона α до 10—12° современные токарные станки обычно имеют особое приспособление, называемое конусной линейкой. Схема обработки конуса с применением конусной линейки приводится на рис. 5
Рисунок 5 Схема обработки конической поверхности
с применением конусной линейки
К станине станка прикреплена плита 11, на которой установлена конусная линейка 9. Линейку можно поворачивать вокруг пальца 8 под требуемым углом а к оси обрабатываемой детали. Для закрепления линейки в требуемом положении служат два болта 4 и 10. По линейке свободно скользит ползун 7, соединяющийся с нижней поперечной частью 12 суппорта при помо
щи тяги 5 и зажима 6. Чтобы эта часть суппорта могла свободно скользить по направляющим, ее отсоединяют от каретки 3, вывинчивая поперечный винт или отсоединяя от суппорта его гайку.
Если сообщить каретке продольную подачу, то ползун 7, захватываемый тягой 5, начнет перемещаться вдоль линейки 9. Так как ползун скреплен с поперечными салазками суппорта, то они вместе с резцом будут перемещаться параллельно линейке Благодаря этому резец будет обрабатывать коническую поверхность с углом уклона, равным углу α поворота конусной линейки.
После каждого прохода резец устанавливают на глубину резания с помощью рукоятки 1 верхней части 2 суппорта. Эта часть суппорта должна быть повернута на 90° относительно нормального положения, т. е. так, как это показано на рис 5
Если даны диаметры оснований конуса D и d и его длина l, то угол поворота линейки можно найти по формуле (2).
Подсчитав величину tg α, легко определить значение угла α по таблице тангенсов.
Применение конусной линейки имеет ряд преимуществ:
1) наладка линейки удобна и производится быстро;
2) при переходе к обработке конусов не требуется нарушать нормальную наладку станка, т. е. не нужно смещать корпус задней бабки; центры станка остаются в нормальном положении, т. е. на одной оси, благодаря чему центровые отверстия в детали и центры станка не срабатываются;
3) при помощи конусной линейки можно не только обтачивать наружные конические поверхности, но и растачивать конические отверстия;
4) возможна работа с продольным самоходом, что увеличивает производительность труда и улучшает качество обработки.
Недостатком конусной линейки является необходимость отсоединять салазки суппорта от винта поперечной подачи. Этот недостаток устранен в конструкции некоторых токарных станков, у которых винт не связан жестко со своим маховичком и зубчатыми колесами поперечного самохода.
Продолжение докладов (Приложение 1)
Тема 4 «Методы контроля конической поверхности»
Тема 5 «Обработка конической поверхности на станках с ЧПУ»
Вопросы для проверки усвоения нового материала и для подготовки к решению задач
1. Как вычисляется уклон конуса?
2.Какими способами можно обработать конические поверхности на токарных станках?
3. В каких случаях рекомендуется делать поворот верхней части суппорта?
4. Как вычисляется угол поворота верхней части суппорта для обтачивания конуса?
Работа в бригадах: Каждой бригаде выдается чертеж детали (Приложение 2), необходимо выбрать способ обработки, произвести необходимый расчет и обосновать выбор метода обработки
Комментарий работы студентов на занятии
- Общая характеристика работы студентов на занятии
- Определение недостатков в работе
- Определение лучших студентов
4 Выставление оценок
Итоги занятия
Сегодня на занятии мы познакомились со способами обработки конусов широким резцом, обработкой конусов при повернутых верхних салазках суппорта, путем смещение задней бабки, обработка конических поверхностей при помощи конусной линейки. Закрепили полученные знания, выполняя задания в бригадах.
Работа в бригадах использовалась и при выполнении домашнего задания. Подготовленные вами доклады показали, что вы умеете отбирать из потока информации сведения, необходимые для заданной темы. Содержание докладов содействовало развитию познавательного интереса к предмету.
Домашние задание
Багдасарова Т.А. Токарь: технология обработки: учебное пособие для нач. проф. образования. – М.: Издательский центр «Академия», 2013. Стр 55-62
Область применения конусов. Наряду с цилиндрическими деталями в машиностроении получили довольно широкое распространение детали с коническими поверхностями.
Однако область использования конусов не ограничивается режущими инструментами. Конические поверхности имеют многие детали машин.
Широкое использование конических соединений объясняется рядом их преимуществ.
1. Они обеспечивают высокую точность центрирования деталей.
2. При плотном соприкосновении пологих конусов получается неподвижное соединение.
3. Изменяя осевое положение деталей конического соединения, можно регулировать величину зазора между ними.
Ко́нус инструмента́льный — конический хвостовик инструмента (сверло, зенкер, фреза, развёртка, зажимной патрон, электрод контактной сварки) и коническое отверстие соответствующего размера (гнездо) в шпинделе или задней бабке, например, токарного станка. Предназначен для быстрой смены инструмента с высокой точностью центрирования и надёжностью крепления. Существуют много стандартов на различные конусы, различающиеся по конусности и исполнению
Конус Морзе — одно из самых широко применяемых креплений инструмента. Был предложен Стивеном А. Морзе (он же изобретатель спирального сверла) приблизительно в 1864 году
Конус Морзе подразделяется на восемь размеров, от КМ0 до КМ7 .
Наименьший конус Морзе № 0, а наибольший – № 6. Первые конусы Морзе изготовлялись в дюймовой системе,
Существует несколько исполнений хвостовика конуса: с лапкой, с резьбой, без оных. Некоторые конусы снабжаются системой отверстий и канавок для подачи смазочно-охлаждающей жидкости
Метрический конус По мере развития станкостроения понадобилось расширить диапазон размеров конусов Морзе как в большую, так и в меньшую стороны. При этом, для новых типоразмеров конуса, выбрали конусность ровно 1:20 (угол 1°25’56″) и назвали их метрическими конусами Типоразмер метрических конусов указывается по наибольшему диаметру конуса в миллиметрах. ГОСТ 25557-2006 также определяет уменьшенные метрические конуса № 4 и № 6 и большие метрические конуса № 80, 100, 120, 160, 200
Конструктивных различий между конусом Морзе и метрическим нет.
Широко распространённый инструментальный конус, в основном, для станков с ЧПУ с автоматической сменой инструмента.
Переходные втулки конусов Морзе.
Для уменьшения номенклатуры инструмента выпускаются разнообразные переходники из одних конусов в другие. Переходник типа наружный конус — внутренний конус именуют переходной втулкой. Переходник типа наружный конус — наружный конус именуют переходной оправкой.
ПРИЛОЖЕНИЕ
Наплавка – Mini-lathe.com
Наплавка – это процесс удаления металла с конца заготовки для получения плоской поверхности. Чаще всего заготовка имеет цилиндрическую форму, но с помощью 4-х кулачкового патрона можно обрабатывать заготовки прямоугольной или сложной формы для формирования кубов и других нецилиндрических форм.
Когда режущий инструмент токарного станка снимает металл, он прикладывает к заготовке значительную тангенциальную (т.е. боковую или боковую) силу. Для безопасного выполнения операции торцевания конец заготовки должен располагаться близко к кулачкам патрона. Заготовка не должна выступать из кулачков патрона более чем в 2-3 раза по диаметру, если только для поддержки свободного конца не используется люнет.
Скорости резания
Если вы прочитаете много книг по механической обработке, вы найдете много информации о правильной скорости резания для движения режущего инструмента относительно заготовки. Необходимо учитывать скорость вращения заготовки и движение инструмента относительно заготовки. По сути, чем мягче металл, тем быстрее резка. Не беспокойтесь слишком сильно об определении правильной скорости резания: работая на токарных станках 7x в хобби, вы быстро почувствуете, с какой скоростью вам следует двигаться.
Пока вы не почувствуете правильную скорость, начните с относительно низких скоростей и постепенно повышайте их. Одной из замечательных особенностей 7x является то, что вы можете регулировать скорость вращения, не останавливаясь, чтобы заменить ремни или шестерни. Большинство операций по резке будет выполняться на скорости в несколько сотен оборотов в минуту — с регулятором скорости, установленным ниже положения «12 часов», и с передачей HI/LO в диапазоне LO. Более высокие скорости, и особенно диапазон HI, используются для таких операций, как полировка, а не резка.
Подготовка к торцовке
Сначала убедитесь, что рычаг переключения передач на задней стороне передней бабки находится в нейтральном (среднем) положении, чтобы ходовой винт не вращался. Это очень важно, так как вы будете зажимать полугайку на ходовом винте во время операции торцевания, чтобы седло не отталкивалось от конца заготовки под действием силы операции резания.
Плотно зажмите заготовку в 3-х кулачковом патроне. Чтобы правильно отцентрировать работу, сомкните челюсти, пока они не коснутся поверхности работы, затем вручную поверните заготовку в челюстях, чтобы установить ее; затем сжать челюсти. Рекомендуется затягивать кулачки во всех трех положениях ключа патрона, чтобы обеспечить равномерный захват кулачками.
Заготовка не должна выступать из кулачков патрона более чем на 3 диаметра
Выберите режущий инструмент со слегка закругленным кончиком. Инструмент с острым концом прорежет небольшие канавки на лицевой стороне изделия и не позволит вам получить красивую гладкую поверхность.
Зажмите режущий инструмент в стойке и поверните стойку так, чтобы кончик режущего инструмента коснулся конца заготовки под небольшим углом. Важно, чтобы кончик режущего инструмента находился прямо на центральной линии токарного станка; если он слишком высокий или слишком низкий, у вас останется небольшая выпуклость в центре лица.
Зафиксируйте резцедержатель на месте и продвигайте каретку до тех пор, пока инструмент не окажется на одном уровне с концом заготовки. Убедитесь, что компаунд не полностью в конце пути к патрону; примерно на полпути в своем диапазоне путешествий это хорошо.
Установите токарный станок на самую низкую скорость и включите его. Убедитесь, что ходовой винт не вращается. Выключите токарный станок и нажмите рычаг полугайки вниз, чтобы зацепить полугайку с ходовым винтом. При правильном включении вы должны почувствовать, как рычаг защелкивается в почти горизонтальном положении.
Возможно, вам придется немного подвигать маховиком каретки вперед и назад, чтобы добиться хорошего зацепления. Фиксация полугайки на ходовом винте предотвратит движение каретки назад от заготовки во время торцевания. Если бы это произошло, конец заготовки имел бы форму легкого конуса, а не идеально плоский, или инструмент мог бы полностью перестать резать. Гораздо лучший способ зафиксировать каретку на месте — добавить замок каретки на ваш токарный станок, как описано на сайте Varmint Al и на моей странице модов для мини-токарных станков.
Начало обработки торца
Используйте составной маховик, чтобы продвигать кончик инструмента до тех пор, пока он не коснется конца заготовки. Используйте рукоятку поперечной подачи для отвода инструмента до тех пор, пока он не выйдет за пределы диаметра заготовки. Включите токарный станок и отрегулируйте скорость до нескольких сотен оборотов в минуту – около 10 часов на ручке управления скоростью.
Теперь медленно продвигайте маховик поперечной подачи, чтобы переместить инструмент к заготовке. Когда инструмент коснется заготовки, он должен начать снимать металл с конца. Продолжайте продвигать инструмент, пока он не достигнет центра заготовки, а затем поверните инструмент назад в противоположном направлении (к себе), пока он не окажется за краем заготовки.
Поскольку мы начали с того, что инструмент едва касался конца заготовки, вы, вероятно, удалили очень мало металла за этот проход. Это хорошая идея, пока вы не привыкнете к тому, насколько агрессивно вы можете снимать металл, не останавливая токарный станок. Кроме того, поскольку конец заготовки может быть очень неровным, вам следует избегать врезания инструмента в конец заготовки, если он попадает в высокое место.
Черновая обработка
С помощью составной рукоятки продвиньте инструмент к патрону примерно на 0,010″ (десять тысячных дюйма или одну сотую дюйма). Если состав установлен на 90 градусов к поперечному суппорту (именно так я обычно устанавливаю свой), то каждое деление, на которое вы поворачиваете рукоятку, будет продвигать инструмент на 0,001 (одну тысячную дюйма) к патрону.
Если компаунд установлен под другим углом, скажем, 30 градусов, к поперечному суппорту, то он будет продвигать инструмент менее чем на 0,001 на каждое деление. Точная сумма определяется по тригонометрическому синусу угла. Поскольку синус 30 градусов равен 0,5, инструмент будет продвигаться вперед на 0,0005 (пять десятитысячных или 1/2 одной тысячной дюйма) на каждое деление в этом примере. Всегда задавался вопросом, зачем нужен триггер? Теперь ты знаешь 😉
Вот изображение первого прохода операции торцевания. За этот проход я удаляю около 0,010 дюйма металла.
Резка на обратном проходе
Если вы повернете инструмент назад к себе после того, как он достигнет центра заготовки, вы заметите, что он удаляет небольшое количество металла на обратном проходе. Это связано с тем, что поверхность не идеально гладкая и удаляет металл с выступающих мест.
Если вам нужно удалить много металла, например, чтобы уменьшить заготовку до определенной длины, вы можете воспользоваться этим обратным резом, чтобы удалить больше металла за каждый проход, продвигая инструмент на небольшое расстояние в заготовку на обратный пропуск. Поскольку инструмент должен погружаться в поверхность заготовки, это лучше всего работает с достаточно острым инструментом.
Финишный рез
В зависимости от того, насколько грубым был конец заготовки в начале и насколько велик ее диаметр, вам может потребоваться сделать 3 или более проходов, чтобы получить хорошую гладкую поверхность по всей поверхности. Эти начальные проходы называются черновыми проходами и удаляют относительно большое количество металла.
Когда вы получите достаточно гладкую поверхность, вы можете сделать окончательный чистовой рез, чтобы удалить металл толщиной от 0,001 до 0,003″ и получить красивую гладкую поверхность. Финишный рез также можно выполнять на более высоких оборотах (скажем, 1500 об/мин), чтобы получить более гладкую поверхность.
Вот изображение чистовой резки в процессе удаления около 0,002 дюйма металла при скорости около 1000 об/мин.
Вот изображение готовой поверхности заготовки.
На рисунке справа показано, что происходит, если кончик вашего режущего инструмента находится ниже центральной линии токарного станка – в центре заготовки остается небольшой выступ. То же самое происходит, если инструмент слишком высок, но в этом случае утолщение будет иметь форму конуса.
Если инструмент слишком низкий, поместите прокладку подходящей толщины под инструмент в держателе инструмента. Если он слишком высок, отшлифуйте верх на несколько тысяч.
Опиливание кромки
Операции торцевания оставляют довольно острую кромку на конце заготовки. Это хорошая идея, чтобы сгладить этот край напильником, чтобы придать ему хорошую фаску и не порезаться об него. Когда токарный станок работает на довольно низкой скорости, поднесите напильник с гладким срезом к концу заготовки под углом 45 градусов и слегка надавите на напильник.
Правая – левая рука держит конец напильника Неправильно: левая рука тянется за вращающийся патрон!
Обратите внимание, , что я держу хвостовик напильника в левой руке, а кончик в правой, чтобы моя левая рука не касалась вращающегося патрона. Спасибо Джону Чатему из группы по интересам 7×10 за этот важный совет по безопасности.
Убедитесь, что металлический конец напильника защищен деревянной ручкой или другим материалом. Без этой меры предосторожности существует опасность того, что хвостовик напильника может попасть обратно в ладонь или запястье с серьезными последствиями. Мой покрыт несколькими слоями термоусадочной трубки и скотча.
Я использую цветную ленту в различных комбинациях, чтобы помочь мне быстро найти нужный мне инструмент из моей рабочей кучи инструментов. Некоторые парни заменяют каждый инструмент на определенный держатель после его использования. Я не из тех парней. 😉
На этом фото показана обработанная поверхность и скошенный край. Вот каким должен быть хороший облицовочный срез: гладкая ровная поверхность без выпуклостей в центре. Положите точную линейку на поверхность лица, и вы не должны видеть никакого света под краем.
Если вы обнаружите слегка выпуклую форму, возможно, каретка отодвигается от передней бабки во время резки.
Какие обрабатывающие станки вы знаете об обработке с ЧПУ?
При механической обработке несколько операций выполняются в запланированной последовательности для достижения наилучших результатов. Мы рассмотрим три наиболее распространенных операции, включая токарную обработку, сверление и фрезерование. Обработка с ЧПУ — очень распространенный и универсальный производственный процесс. Таким образом, с помощью этих трех методов можно обрабатывать различные типы материалов. Металлы, пластмассы, композиты и дерево — все это возможные материалы для изготовления деталей.
I. Токарный станок Тип
В зависимости от использования и конструкции токарные станки в основном делятся на горизонтальные, напольные и вертикальные.
Револьверные станки, одношпиндельные автоматические станки, многошпиндельные автоматические и полуавтоматические станки, профилировочные станки и многофункциональные станки
Токарные станки и различные специализированные токарные станки, такие как токарные станки для распредвалов, токарные станки для коленчатых валов, колесные станки, зубчатые токарные станки. Среди всех токарных станков наибольшее распространение получили горизонтальные токарные станки. Размер горизонтальной обработки Уровень допуска может достигать IT8 ~ IT7, а значение Ra шероховатости поверхности может достигать 1,6 мкм.
II. Область применения токарного станка
1. Горизонтальный токарный станок, пригодный для токарной обработки внутренних и наружных цилиндрических поверхностей, конических поверхностей, формирования вращающихся поверхностей и кольцевых канавок, точения секций и различных резьб, сверления, развертывания, развертывания, нарезания резьбы, нарезания резьбы и накатки и другие процессы. Хотя степень автоматизации обычных горизонтальных токарных станков низкая, а вспомогательное время в процессе обработки также больше, но благодаря широкому диапазону обработки и хорошей общей производительности этот тип станка широко используется и популяризируется в механической обработке. промышленности, является одним из типичных представителей технологического оборудования в нашей машиностроительной промышленности, а также одним из незаменимых технологического оборудования в машиностроительной промышленности.
2. Вертикально-токарный станок, пригодный для обработки различных деталей каркаса и обечайки, а также пригодный для обработки внутренних и наружных цилиндрических поверхностей, конических поверхностей, торцевых поверхностей, пазов, резки, сверления, развальцовки и развертывания различных деталей А другая обработка, с помощью дополнительных устройств, также могут быть реализованы такие процессы обработки, как нарезание резьбы, токарная обработка, профилирование, фрезерование и шлифование.
III. Станочное оборудование
1. Сверлильный станок
Сверлильный станок подходит для плоского фрезерования и обработки отверстий в единичных или мелкосерийных деталях в механических мастерских. Конец шпиндельной коробки оснащен плоско вращающимся радиальным резцедержателем, который может точно сверлить большие отверстия и плоскости. Кроме того, можно выполнять сверление, развертывание и нарезание резьбы.
2.шлифовальный станок
Станки, в которых используются абразивы (шлифовальные круги, ленты, масляные камни или абразивы и т. д.) в качестве инструментов для обработки поверхности заготовки, в совокупности называются шлифовальными станками. Шлифовальный станок может обрабатывать различные поверхности, такие как внутренние и внешние цилиндрические и конические поверхности, плоские поверхности, поверхности профиля зуба шестерни, спиральные поверхности и поверхности различной формы и т. д. Он также может затачивать инструменты и резать и т. д. Диапазон процесса очень широкий. Поскольку в процессе шлифования легко получить высокую точность обработки и хорошее качество поверхности, шлифовальный станок в основном используется для чистовой обработки деталей, особенно для чистовой обработки деталей из закаленной стали и специальных материалов высокой твердости.
3. Токарный станок
Токарные станки в основном используются для обработки различных вращающихся поверхностей и торцов тел вращения. Таких как точение внутренних и наружных цилиндрических поверхностей, конических поверхностей, кольцевых канавок и формирование вращающихся поверхностей, точение торцов и различных часто используемых резьб, а также обработка различных поверхностей специальной формы технологическим оборудованием.