16. Методы обработки отверстий.
После выполнения отверстий в сплошном материале производится их обработка для увеличения размеров и снижения шероховатости поверхностей, а также обработка предварительно полученных отверстий (например, литьем, продавливанием и т.п.).Обработка отверстий выполняется несколькими способами, в зависимости от того, какие параметры точности и шероховатости поверхности отверстия заданы чертежом. В соответствии с выбранным способом обработки выбирается и инструмент для ее осуществления. При обработке отверстий различают три основных вида операций: сверление, зенкерование, развертывание и их разновидности: рассверливание, зенкование, цекование.
Сверление –
это операция по образованию сквозных
и глухих отверстий в сплошном материале,
выполняемая при помощи режущего
инструмента – сверла. Различают сверление
ручное – ручными пневматическими и
электрическими сверлильными устройствами
(дрелями) и сверление на сверлильных
станках.
Одной из разновидностей
сверления является рассверливание –
увеличение диаметра отверстия,
просверленного ранее. В качестве
инструментов для рассверливания
отверстий, также как и для сверления,
используют сверла. Не рекомендуется
рассверливать отверстия, полученные в
заготовке методом литья, ковки или
штамповки. Такие отверстия имеют
различную твердость по поверхности
отверстия из-за окалины, образующейся
при литье, а также из-за неравномерной
концентрации внутренних напряжений в
металле на различных участках поверхности
отверстий, полученных методом ковки
или штамповки.
Зенкерованием называется
операция, связанная с обработкой
предварительно просверленных,
штампованных, литых или полученных
другими методами отверстий с целью
придания им более правильной геометрической
формы (устранение отклонений от круглости
и других дефектов), а также достижения
более высокой, по сравнению со сверлением,
точности (до 8-го квалитета) и более
низкой шероховатости (до Ra 1,25). Зенкерование
ведут либо
на настольных сверлильных станках (при
небольших диаметрах отверстий), либо
на стационарном сверлильном оборудовании,
устанавливаемом на фундаменте.
Виды отверстий и способы их обработки
Отверстия по способам обработки подразделяют на:
- крепежные отверстия в различных деталях (отверстия для крепежных болтов, винтов, шпилек, заклепок и т. п.). Точность изготовления таких отверстий невысокая (11…12-й квалитеты и грубее). Такие обычно сверлят на одно- или многошпиндельных сверлильных станках;
- ступенчатые или гладкие отверстия в деталях, представляющих собой тела вращения. Их обрабатывают сверлом (в ряде случаев с последующим зенкерованием или развертыванием) или резцом совместно с токарной обработкой наружных цилиндрических поверхностей;
- ответственные отверстия в корпусных деталях, точность обработки которых определяет правильность работы и долговечность узлов машины (например, редуктора) или качество работы всей машины (например, для шпинделей в корпусных деталях станков и т.
п.). Такие отверстия изготовляют обычно не хуже, чем по 7-му квалитету. Обрабатывают такие отверстия на различных станках универсальных или специального назначения;
- глубокие отверстия с отношением длины l к диаметру d больше пяти (l/d>5), например, отверстия шпинделей станков, пустотелых валов и т. п. Эти отверстия обрабатывают на станках специального назначения;
- конические и фасонные (с криволинейной образующей) отверстия, которые обрабатывают инструментом с коническими или криволинейными режущими кромками либо растачивают с помощью копирного приспособления;
- профильные (некруглого сечения) отверстия, обрабатываемые протягиванием, прошиванием и долблением.
В зависимости от назначения отверстий к ним могут предъявляться следующие требования: выдерживание размера отверстия по диаметру с заданной точностью, прямолинейность оси отверстия и образующей его поверхности, правильность цилиндрической формы отверстия (отсутствие конусности, овальности и огранки), перпендикулярность оси торцевым поверхностям детали.
Обработка отверстий круглого сечения производится на сверлильных, расточных, токарных, карусельных, револьверных станках, токарно-револьверных полуавтоматах и автоматах, протяжных и шлифовальных станках.
Обработка точных отверстий всегда требует больших затрат станочного времени и средств на инструмент, чем аналогичная обработка таких же по размерам наружных поверхностей с той же степенью точности, так как режущий инструмент для обработки отверстий не обладает такой же жесткостью конструкции, особенно конструкции его крепления
(расточные оправки — борштанги, длинные расточные резцы и т. п.), как инструмент для обработки наружных цилиндрических поверхностей.Для повышения точности при обработке отверстий увеличивают число рабочих ходов, чтобы таким образом постепенно довести погрешности первоначальной обработки до допустимых размеров. Так, если для обтачивания гладкого вала по 8-му квалитету точности достаточно двух рабочих ходов, то для обработки отверстия того же диаметра и с той же точностью понадобится не менее четырех операций или переходов: сверление двумя сверлами, зенкерование и одно-или двукратное развертывание.
При обработке отверстий даже с относительно большим числом переходов в обычных условиях не удается достигнуть высокой точности по соосности обрабатываемого отверстия и какой-либо наружной цилиндрической поверхности обрабатываемой заготовки.
Отверстия диаметром до 80 мм в сплошном металле сверлят спиральными сверлами на сверлильных станках, а также на различных станках токарной группы. Для сверления отверстий диаметром свыше 80 мм применяют сверлильные головки специальных конструкций; эту операцию, как правило, выполняют на расточных станках.
Решение проблемы обработки отверстий, технология обработки нескольких отверстий
Отверстие является важной поверхностью коробки, кронштейна, втулки, кольца и диска, а также поверхностью, часто встречающейся при механической обработке. Когда точность обработки и шероховатость поверхности одинаковы, обрабатывать отверстия сложнее, чем обрабатывать наружную круглую поверхность, с низкой производительностью и высокой стоимостью.
Это связано с тем, что: 1) Размер инструмента, используемого для обработки отверстий, ограничен размером обрабатываемого отверстия, жесткость низкая, легко производить деформацию изгиба и вибрацию; 2) Когда отверстие обрабатывается фрезой фиксированного размера, размер отверстия обычно напрямую зависит от соответствующего размера фрезы. Производственная ошибка и износ фрезы напрямую влияют на точность обработки отверстия; 3) При обработке отверстия зона резания находится внутри заготовки, условия удаления стружки и отвода тепла плохие, а точность обработки и качество поверхности трудно контролировать.
Способы обработки отверстий включают сверление, развертывание, развертывание, растачивание, волочение, шлифование и чистовую обработку отверстий. Давайте изучим несколько видов технологии обработки отверстий, решим проблему обработки отверстий.
1. Сверление и развертывание
A. Сверление
Сверление — это первый процесс обработки отверстий в твердых материалах. Диаметр отверстия для сверления обычно составляет менее 80 мм. Существует два способа бурения: один — вращением долота; Другой – вращение заготовки. Ошибки, возникающие при использовании двух вышеуказанных методов бурения, неодинаковы. При бурении методом вращения долота, когда долото отклоняется из-за асимметричной режущей кромки и недостаточной жесткости долота, центральная линия обрабатываемого отверстия будет скошена или будет не прямой, но отверстие в основном не изменится. В режиме сверления с вращением заготовки, наоборот, отклонение сверла приведет к изменению апертуры, но центральная линия отверстия останется прямой.
Обычно используемые сверла имеют: спиральное сверло, центральное сверление, глубокое сверление и т. Д., Одним из наиболее часто используемых является спиральное сверло, его диаметр Φ 0,1-80 – мм.
Из-за ограничений конструкции жесткость бурового долота на изгиб и кручение низкая. Кроме того, из-за плохого центрирования точность обработки сверла низкая, которая в целом может достигать только IT13 ~ IT11. Шероховатость поверхности также была большой, Ra обычно составляла 50~12,5 мкм. Но скорость съема металла при сверлении велика, а эффективность резания высока. Сверление в основном используется для обработки отверстий с низкими требованиями к качеству, таких как отверстия под болты, нижние резьбовые отверстия, смазочные отверстия и т. д. Для отверстий с высокими требованиями к точности обработки и качеству поверхности они должны быть достигнуты путем развертывания, развертывания, растачивания или шлифовки. последующая механическая обработка.
B. Расширение
Расширение относится к дальнейшей обработке отверстий, которые были просверлены, отлиты или выкованы с помощью расширяющего сверла, чтобы увеличить отверстие и улучшить качество обработки отверстия. Процесс развертывания может использоваться как предварительная обработка перед чистовой обработкой отверстия или как окончательная обработка отверстия с низкими требованиями. Расширяющее сверло похоже на спиральное сверло, но у него больше зубьев и нет горизонтального лезвия.
(1) сверло с большим количеством зубьев (3~8 зубьев), хорошая проводимость, относительно стабильное резание; (2) Без поперечной кромки и с хорошими условиями резания; (3) Небольшой припуск на обработку, канавка для удержания стружки может быть сделана неглубокой, стержень сверления может быть сделан толще, прочность и жесткость корпуса ножа хорошие. Точность развертывания обычно составляет IT11~IT10, а шероховатость поверхности Ra составляет 12,5~6,3 мкм. Рассверливание часто применяют для обработки отверстий диаметром менее 30 мм. При сверлении отверстия большего диаметра (D ≥30 мм) для предварительного сверления часто используется маленькое сверло (в 0,5–0,7 раза больше диаметра), а затем сверление и расширение отверстия соответствующего размера, что может улучшить обработку. качество и производительность скважины.
В дополнение к обработке цилиндрических отверстий различные отверстия для потайной головки и точечная торцевая обработка могут также обрабатываться с помощью различных зенкерных сверл специальной формы (также известных как зенкерное сверло). Передний конец бритвенного сверла обычно снабжен направляющей колонкой и направляется по выточенному отверстию.
2.Рассверливание
Рассверливание – один из методов чистовой обработки отверстия, который широко используется в производстве. Для небольших отверстий развертывание является более экономичным и практичным методом обработки по сравнению со шлифованием по внутреннему кругу и чистовым растачиванием.
A. Развертка
Развертка обычно делится на два типа: ручная развертка и машинная развертка. Ручка ручной развертки прямая, рабочая часть длиннее, направляющая функция лучше, ручная развертка имеет два типа конструкции: цельная и с регулируемым внешним диаметром. Развертка машины имеет два типа конструкции: одна с ручкой, а другая с втулкой. Разверткой можно обрабатывать не только круглые отверстия, но и конические отверстия.
B. Процесс развертывания и его применение
Припуск на развертывание оказывает большое влияние на качество развертывания. Припуск слишком велик, нагрузка на развертку слишком велика, режущая кромка быстро затупляется, и получить гладкую поверхность обработки непросто, а допуск на размер нелегко обеспечить; Запас слишком мал для удаления следов реза, оставленных верхним отростком, что, естественно, не улучшает качество обработки отверстия. Как правило, грубый шарнир составляет 0,35–0,15 мм, а тонкий шарнир — 0,15–0,05 мм.
Во избежание образования стружки развёртывание обычно выполняется на более низкой скорости резания (V < 8 м/мин для обработки стали и чугуна быстрорежущей развёрткой). Величина подачи связана с апертурой станка. Чем больше апертура, тем больше значение подачи. Когда развертка из быстрорежущей стали используется для обработки стали и чугуна, величина подачи обычно составляет 0,3~1 мм/об.
Развёртывание необходимо охлаждать, смазывать и очищать соответствующей смазочно-охлаждающей жидкостью для предотвращения образования отложений стружки и своевременного удаления стружки. По сравнению со шлифованием и растачиванием отверстий производительность развертывания выше, а точность отверстия легко гарантировать. Однако расширение отверстия не может исправить ошибку положения оси отверстия, и точность положения отверстия должна быть гарантирована предыдущей процедурой. Отверстие для развертывания не подходит для обработки ступенчатого отверстия и глухого отверстия.
Точность развертывания обычно составляет IT9 ~ IT7, а шероховатость поверхности Ra обычно составляет 3,2–0,8 мкм. Для отверстий среднего размера и высоких требований к точности (таких как прецизионные отверстия IT7) процесс сверления-расширения и развертывания является типичной схемой обработки, обычно используемой в производстве.
3. Растачивание
Растачивание – это метод механической обработки, при котором предварительно изготовленные отверстия увеличиваются с помощью режущих инструментов. Растачивание можно производить как на сверлильном станке, так и на токарном станке.
A.Скучный путь
Сверлить можно тремя способами.
(1)Заготовка вращается и инструмент подается
Растачивание на токарных станках в основном относится к этому режиму расточки. Особенности процесса следующие: линия оси отверстия после обработки соответствует оси вращения заготовки, круглость отверстия в основном зависит от точности вращения шпинделя станка и осевой геометрической ошибки формы отверстие в основном зависит от точности направления подачи инструмента относительно оси вращения заготовки. Этот метод растачивания подходит для обработки отверстий с требуемой соосностью на поверхности внешнего круга.
(2)Инструмент вращается, и заготовка перемещает подачу
Шпиндель сверлильного станка приводит во вращение расточный резец, рабочий стол приводит в движение заготовку для выполнения движения подачи.
(3)Вращение инструмента и движение подачи
При использовании этого способа расточки изменяется длина подвески борштанги, также меняется деформация борштанги, близость к шпиндельной коробке апертуры велика , вдали от шпиндельной коробки отверстие небольшое, образующее конусное отверстие. Кроме того, с увеличением длины вывешивания расточной оправки будет увеличиваться изгибная деформация шпинделя из-за его собственного веса, и соответственно будет изгибаться ось обрабатываемого отверстия. Этот метод растачивания подходит только для более коротких отверстий.
B. Алмазное растачивание
По сравнению с обычным растачиванием, алмазное растачивание характеризуется малой обратной подачей, малой подачей, высокой скоростью резания, позволяет получить очень высокую точность обработки (IT7 ~ IT6) и очень чистую поверхность (Ra 0,4~0,05 м). Алмазное растачивание изначально обрабатывалось алмазным сверлильным инструментом, но теперь его обычно обрабатывают твердым сплавом, CBN и искусственным алмазным инструментом. В основном используется для обработки заготовок из цветных металлов, также может использоваться для обработки деталей из чугуна и стали.
Обычно используемые параметры резки алмазного растачивания следующие: обратная тяга 0,2~0,6 мм, окончательная расточка 0,1 мм; Количество подачи составляет 0,01~0,14 мм/об; Скорость резки составляет 100~250 м/мин для чугуна, 150~300 м/мин для стали и 300~2000 м/мин для цветного металла.
Чтобы гарантировать, что алмазное растачивание может обеспечить более высокую точность обработки и качество поверхности, станок (алмазный сверлильный станок) должен иметь более высокую геометрическую точность и жесткость, опору шпинделя станка обычно используют прецизионные радиально-упорные шарикоподшипники или статические подшипники скольжения. , высокоскоростные вращающиеся детали должны быть точно сбалансированы; Кроме того, движение механизма подачи должно быть очень плавным, чтобы стол мог выполнять плавное движение подачи на низкой скорости.
Алмазное сверление имеет хорошее качество обработки и высокую эффективность производства. Он широко используется при окончательной обработке прецизионных отверстий в большом количестве изделий, таких как отверстие цилиндра двигателя, отверстие поршневого пальца, отверстие главной оси на коробке шпинделя станка и т. д. Однако следует отметить, что: при обработке черного металлические изделия с алмазным растачиванием, только твердый сплав и CBN могут быть использованы для изготовления сверлильного инструмента, не могут быть использованы для изготовления сверлильного инструмента из алмаза, из-за сродства атомов углерода и элементов группы железа в алмазе срок службы инструмента низок.
C. Расточной инструмент
Расточный инструмент можно разделить на однолезвийный и двухкромочный
D. Технологические характеристики и область применения расточки
По сравнению с процессом сверления-расширения размер отверстия не ограничен в зависимости от размера инструмента, а расточка имеет сильную способность к исправлению ошибок, исходная ошибка отклонения оси отверстия может быть скорректирована с помощью нескольких перемещений инструмента, и может заставить поверхность расточки и позиционирования поддерживать более высокую точность позиционирования.
По сравнению с расточкой и токарной обработкой, из-за плохой жесткости и деформации системы стержня инструмента, условия отвода тепла и удаления стружки плохие, тепловая деформация заготовки и инструмента относительно велика, качество обработки и эффективность производства расточки не так высока, как токарная обработка.
В заключение, из приведенного выше анализа видно, что расточка может использоваться для широкого спектра обработки и может использоваться для отверстий разных размеров и уровней точности. Для отверстий и систем с большой апертурой и повышенными требованиями к размерам и точности положения растачивание является практически единственным методом обработки. Точность обработки растачивания IT9.~ ИТ7. Сверление может использоваться в сверлильном станке, токарном станке, фрезерном станке и других станках, благодаря преимуществам гибкости производство широко используется. Для повышения эффективности растачивания в массовом производстве часто используются расточные штампы.
4.Хонинговальное отверстие
A.Принцип хонингования и хонинговальная головка
Хонингование – полирование отверстий хонинговальной головкой с точильным стержнем (бруском). При хонинговании заготовка фиксируется. Хонинговальная головка приводится в движение главным валом станка, чтобы вращаться и совершать возвратно-поступательные движения по прямой линии. Во время хонингования хонинговальный стержень прикладывается к поверхности заготовки под определенным давлением. С поверхности заготовки срезается очень тонкий слой материала. Чтобы избежать повторения движения абразивных зерен, обороты хонинговальной головки в минуту и возвратно-поступательное движение хонинговальной головки в минуту должны быть равными.
Для того чтобы стенку отверстия можно было обрабатывать равномерно, ход песчаной полосы должен превышать определенное значение на обоих концах отверстия. Чтобы обеспечить равномерность припуска на хонингование и уменьшить влияние ошибки вращения на точность обработки шпинделя станка, в основном используется плавающее соединение между хонинговальной головкой и шпинделем станка.
Радиальное расширение и регулировка шлифовальной ленты хонинговальной головки может производиться в ручных, пневматических и гидравлических конструкциях.
B. Технологические характеристики и область применения хонингования
(1)Хонингование позволяет достичь более высокой точности размеров и формы, а точность обработки составляет IT7~IT6. Погрешность круглости и цилиндричности отверстий можно контролировать в определенном диапазоне, но хонингование не может улучшить точность положения обрабатываемых отверстий.
(2)Более высокое качество поверхности можно получить путем хонингования, шероховатость поверхности Ra составляет 0,2~0,25 мкм, а глубина изношенного дефектного слоя поверхностного металла очень мала, 2,5~25 мкм.
(3)По сравнению со скоростью шлифования окружная скорость хонинговальной головки невелика (VC = 16~60 м/мин). Однако из-за большой площади контакта между песком и заготовкой и относительно высокой скорости возвратно-поступательного движения (VA = 8~20 м/мин) эффективность хонингования остается относительно высокой.
Хонингование широко применяется при обработке прецизионных отверстий в цилиндрах двигателей и различных гидравлических устройствах в крупном и серийном производстве. Его также можно использовать для обработки глубоких отверстий с соотношением сторон более 10. Однако хонингование не подходит для обработки отверстий на заготовках из цветных металлов с большой пластичностью, а также для обработки отверстий со шпоночными пазами, шлицевыми отверстиями и т. д.
5.Протяжка
A.Протяжка и протяжка
Протяжка – это высокопроизводительный метод отделки, который осуществляется на протяжном станине специальным протяжным устройством. Протяжная кровать делится на горизонтальную протяжную кровать и вертикальную протяжную кровать два, горизонтальная протяжная кровать является наиболее распространенной.
При протягивании протяжка движется только по прямой с низкой скоростью (основное движение). Протяжка при этом должна иметь количество зубьев не менее 3, иначе протяжка работает не стабильно, легко образуются кольцевые ряби на поверхности заготовки. Чтобы избежать чрезмерного усилия протяжки и заставить протяжку ломаться, протяжка работает, количество зубьев рабочего ножа в целом не должно превышать 6-8.
Существует три различных метода протягивания, которые описываются следующим образом:
(1)Послойное протягивание
Этот метод протяжки характеризуется протяжкой, вырезающей припуск на механическую обработку слой за слоем. Для облегчения ломки стружки на зубьях ножа имеются чередующиеся щели, разделяющие стружку. Протяжка, выполненная по принципу многослойной протяжки, называется обыкновенной протяжкой.
(2)ступенчатый
Особенностью этого метода протягивания является то, что каждый слой металла на обрабатываемой поверхности прорезается набором зубьев фрезы (обычно состоит из 2-3 зубьев каждой фрезы) одинакового размера, но чередуя друг друга. С каждого зуба срезается только один слой металла. Протяжка, разработанная блочной протяжкой, называется протяжкой для резки колеса.
(3)Композитное протягивание
Этот метод сочетает в себе преимущества послойного и кусочного протягивания. Грубая часть зубьев разделяется протяжкой, а тонкая часть разделяется протяжкой. Таким образом можно сократить длину протяжки, повысить производительность и получить лучшее качество поверхности. Протяжка, спроектированная по интегральной протяжке, называется интегрированной протяжкой.
Б. Технологические характеристики и область применения прошивки отверстий
(1)Протяжка – это многолезвийный инструмент, за один протяжной ход можно выполнить черновую обработку, чистовую обработку и чистовую обработку отверстий в последовательности, высокая эффективность производства.
(2)Точность протяжки отверстия в основном зависит от точности протяжки. В нормальных условиях точность протяжки отверстия может достигать IT9~IT7, а шероховатость поверхности Ra может достигать 6,3~1,6 мкм.
(3)При протягивании отверстий заготовка позиционируется самим обрабатываемым отверстием (ведущая часть протяжки является фиксирующим элементом заготовки). Обеспечить точность взаимного расположения отверстия и других поверхностей непросто. Для тех, кто внутри и снаружи круглой поверхности имеет соосность, требуется обработка вращающейся части тела, обычно сначала рисуется отверстие, а затем берется отверстие в качестве точки отсчета локализации, обрабатывающей другую поверхность.
(4)Протяжка может обрабатывать не только круглое отверстие, но также формировать отверстие, шлицевое отверстие.
(5)Протяжка представляет собой фрезу фиксированного размера сложной формы и высокой цены, которая не подходит для обработки больших отверстий.
Протяжка, обычно используемая в большом количестве массового производства, обрабатывает апертуру Ф от 10 до 80 мм, глубина отверстия не более чем в пять раз превышает апертуру отверстия на мелких и средних деталях.
Обработка мелких отверстий|Основная технология|Производство фильеры для текстильной и тонкой обработки|Сопло Kasen
- ВЕРХ
- Основная технология
- Чистовая обработка отверстий
Производство инструментов
Технология изготовления инструмента является вершиной основной технологии, которую насадки Kasen передавали из поколения в поколение на протяжении более 70 лет.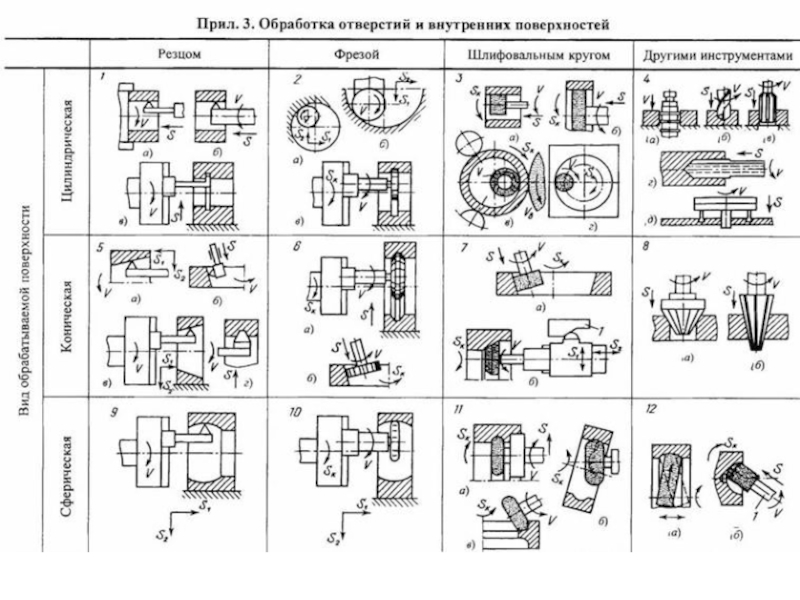
Эта технология обеспечивает сверление отверстий с субмикронной точностью. Микропоры, обработанные инструментами ручной работы, обеспечивают точность диаметра отверстия, шероховатость поверхности и округлость, что сложно при других методах обработки, таких как электроразряд, лазер и травление.
Чистовая обработка отверстий
Обработка микроотверстий является основной технологией сопла Kasen, которая образует два колеса производства инструментов. С помощью тонких инструментов, изготовленных с субмикронной точностью, достигается сверхвысокая точность сверления отверстий. В качестве выдающейся низкотехнологичной технологии мы предлагаем технологию обработки отверстий, которая соответствует вашим потребностям, включающую в себя передовые технологии, такие как электроэрозионная обработка и лазерная обработка, с упором на обработку и резку пластмасс. Он используется для управления светом, воздухом и жидкостью в качестве ключевой части для различных приложений, таких как апертуры электронного луча, промышленные струйные принтеры, различные отверстия и коллиматоры.
Обработка деформированного отверстия
Различные деформированные отверстия могут быть обработаны на порядка микрометров с использованием наших собственных инструментов.
Обрабатываемый материал и минимальный диаметр отверстия
Мы бросим вызов неопытным материалам и точности в соответствии с запросом клиента. В таблице ниже показана часть результатов производства, и если у вас нет результатов, пожалуйста, свяжитесь с нами каждый раз.
Материал | Мин.孔径 | |
---|---|---|
нержавеющая сталь | 5 мкм | |
Конструкционная сталь | 10 мкм | |
Инструментальная сталь | 10 мкм | |
“Высокая температура плавления Высокоустойчивые ингредиенты | платинаPt | 0,1 мкм |
Золотая платина Au-Pt | 10 мкм | |
молибден Mo | 1 мкм | |
Титаниум Ти | 2 мкм | |
танталTa | 5 мкм | |
Никелевый сплав Alloy-Ni | 10 мкм | |
вольфрамW | 10 мкм | |
Хрупкий материал | кремнийSi | 50 мкм |
Карбид кремния SiC | 60 мкм | |
СтеклоSiO2 | 10 мкм | |
Стеклоуглерод | 5 мкм | |
Обрабатываемая керамика | 30 мкм | |
Оксидная керамика | 60 мкм | |
пластик | Различные | 10 мкм |
■Пример фото
- Карбид кремния (SiC)/60 мкм
- Молибден (Mo)/5 мкм
- Стекло(SiO2)/10 мкм
- Платина (Pt)/0,1 мкм
Форма поперечного сечения
Благодаря опыту, накопленному в разработке и производстве прядильных сопел, мы можем предложить формы отверстий, подходящие для применения и условий.
В зависимости от формы поперечного сечения отверстия мы можем предложить форму, подходящую для сжатия электронного пучка, а также жидкости, такой как ламинарный поток, турбулентный поток и потеря давления.
Отделка кромок
Для прядильных насадок обработка краев отверстий оказывает существенное влияние на качество пряжи при прядении. У нас есть технология для обработки кромки в форме R или конусности, а также для удаления заусенцев и заусенцев, которые мы выращивали в течение многих лет при производстве прядильных сопел, поэтому мы обеспечиваем обработку кромки, которая соответствует применению продукта и условиям использования. Это возможно.
Высокий аспект
В дополнение к сверлению отверстий с большим радиусом действия, у нас также есть технология сверления отверстий с высокой прямолинейностью и гладкостью стенок.
Высокая зеркальная поверхность внутри отверстия может быть обработана на уровне, который трудно получить с помощью таких методов, как лазерная и электроэрозионная обработка.