Назначение и способы сверления металла
Сверлением называется операция по выполнению отверстий в сплошном металле режущим инструментом — сверлом. Увеличение предварительно просверленного в детали отверстия с помощью сверла или зенкера называется рассверливанием.
При сверлении обрабатываемую деталь надежно закрепляют в станочных тисках, в специальном приспособлении, в кондукторе или планками на столе сверлильного станка, а сверлу сообщают два совместных движения (рис. 63, а) — вращательное по стрелке 1 и поступательное (направленное вдоль оси сверла) по стрелке 2. В результате этих двух, происходящих совместно движений (вращение сверла и подача его в металл) и совершается операция сверления. Вращательное движение сверла называется главным (рабочим) движением, или движением резания. Поступательное движение вдоль оси сверла называется движением подачи.
Рис. 63. Сверление
а — схема движений сверла; б — сверление по разметке; в — по шаблону; г — по кондуктору
Сверление сквозных и глухих отверстий диаметром до 80 мм на сверлильных станках выполняют с точностью пятого класса. Шероховатость обработанной поверхности отверстий — третьего-четвертого класса.
Выбор режимов резания при сверлении заключается в определении такой подачи скорости резания, чтобы процесс обработки детали был наиболее производительным и экономичным.
Теоретический расчет элементов режима резания производится в следующем порядке.
1. Выбирают подачу в зависимости от характера обработки, требуемого качества обработанной поверхности, прочности сверла и других технологических и механических факторов.
Подача, выбранная по справочным таблицам, корректируется по паспортным данным сверлильного станка (берется ближайшая меньшая).
2. Подсчитывают скорость резания в зависимости от обрабатываемого материала, материала режущей части сверла, диаметра сверла, подачи, стойкости сверла, глубины просверливаемого отверстия, формы заточки сверла и охлаждения по формуле
υ=[СυDzυ]/[TmSyυ] K м/мин,
где Сυ — постоянный коэффициент, характеризующий обрабатываемый материал, материал инструмента и условия обработки;
D—диаметр сверла, мм;
Т — стойкость сверла, мин;
S—подача, мм/об;
К — общий поправочный коэффициент, учитывающий конкретные условия обработки (обрабатываемый материал Кmυ, глубину сверления Klυ, материал режущей части сверла Кuυ и др.) K=Kmυ·Klυ·Kuυ…;
m, zυ, yυ — показатели степеней (по справочнику).
3. По найденной скорости резания подсчитывают число оборотов n:
где D — диаметр сверла, мм;
υu — скорость резания, м/мин; π — постоянная величина, равная 3,14. Полученное число оборотов корректируется по паспортным данным станка (принимается ближайшее меньшее или ближайшее большее, если оно не более чем на 5% расчетного).
4. Определяют действительную скорость резания υd, с которой будет производиться обработка;
υd = πDnd/1000 м/мин,
где nd — скорректированное по паспорту станка число оборотов.
5. Проверяются выбранные элементы режима резания по прочности слабого звена механизма главного движения и мощности электродвигателя станка.
Сверление отверстий по разметке (рис. 63, б) применяется при обработке единичных деталей. При сверлении отверстий по разметке важным является центровка сверла. Сверло устанавливают так, чтобы ось шпинделя станка, ось сверла и центр отверстия, намеченный керном, точно совпадали.
Сверление отверстий по шаблону (рис. 63, в) применяется при серийном изготовлении деталей. Для сверления отверстия по шаблону в пакет соединяют по 3—4 заготовки деталей, сверху заготовок накладывают шаблон, а затем их стягивают струбцинами.
Сверление отверстия через кондуктор (рис. 63, г) применяют при серийном изготовлении деталей, в которых требуется точно выдержать расстояние между центрами отверстий. Точность расположения отверстий гарантируется направлением сверла через закаленные втулки кондуктора.
Применение шаблонов и кондукторов позволяет сверлить отверстия без предварительной разметки.
Сверление отверстий в металле технология инструмент способы
Рассверливание металла — это одна из многочисленных операций, которая часто выполняется при слесарных работах. Сверление производится для различных разборных/неразборных соединений, когда требуются определенного диаметра отверстия для заклепочных, болтовых либо шпилечных креплений.
Сам по себе металл — высокопрочный материал, поэтому при работе с ним независимо от того, требуется его рассверлить или прорезать, используются режущие инструменты, которые намного прочнее его. Сверление металлических деталей может производиться как в специальных промышленных мастерских, так и в домашних условиях при проведении различных ремонтных работ, в гараже или небольшой мастерской. Для домашнего сверления обычно используется ручная электродрель.
Технология сверления
Просверливание отверстий в металлических заготовках или деталях — это определенная технология снятия тонких многочисленных слоев металла сверлом, вращающимся вокруг своей оси. При этом главным условием сверления является удержание сверла, закрепленного в патроне дрели, четко в перпендикулярном положении по отношению к просверливаемой заготовке.
Особенно это важно при сверлении толстого металла. Если во время работы сверло отклонится по отношению оси просверливаемого отверстия, оно просто сломается. Чтобы этого не произошло, дрель должна быть жестко зафиксирована. Для этого предусмотрены специальные приспособления, которые можно купить в магазине для инструментов или изготовить своими силами.
Режимы сверления
При работе со сверлом важно не только жестко его закрепить, но и
Для работы с металлами разной твердости рекомендуются и сверла, предназначенные для различных режимов работы. Режим скорости оборотов сверла напрямую зависит от толщины и твердости металла, а также диаметра самого сверла. Чем прочнее обрабатываемый материал и больше диаметр сверла, тем режим сверления должен быть медленнее. Показателем правильно выбранного режима является длинная, спиралевидная стружка.
Разметка керном, шаблон и кондуктор
Просверливать металл можно по выполненной керном разметке, использовать шаблон либо специальный кондуктор.
Керн — это остро заточенный металлический штырь, изготовленный из сверхпрочной стали. С его помощью на подготовленной для сверления металлической детали в месте, где планируется просверлить отверстие, делается небольшое углубление для сверла.
Для этого керн острым концом ставится в предполагаемую точку рассверливания, после чего по нему наносится сильный удар молотком. В оставленное керном углубление вставляется острие сверла и начинается сверление, при этом в начале работы сверло уже не сможет сместиться в сторону от размеченной точки.
Чтобы разметить центр заготовки цилиндрической формы, опытные слесари часто используют полоску жести, изогнутой под 90 градусов. При этом одно плечо должно соответствовать диаметру заготовки, оно накладывается на заготовку, после чего вдоль его края проводится линия карандашом. Операция проводится 2−3 раза, а точка пересечения линий будет указывать на центр цилиндра, где керном можно сделать углубление для сверла.
В случае когда нужна высокая точность и перпендикулярность просверливаемого канала или нужно строго выдержать расстояние между несколькими отверстиями, рекомендуется использовать кондуктор. Также кондуктор будет необходим при работе с тонкостенными трубами, когда керном будет невозможно сделать углубление для сверла.
При глубоком сверлении, чтобы жестко зафиксировать дрель в перпендикулярном положении к заготовке, применяются специальные приспособления.
Приспособления для сверления
Работа с металлом является довольно трудоемким процессом даже для опытных специалистов. Порой нужно длительное время удерживать дрель в строго одном положении к обрабатываемой детали. Чтобы облегчить труд и качественно просверлить металл, используется приспособление для сверления под прямым углом.
Такие приспособления бывают трех видов:
- Кондуктор для направления сверл.
- Направляющий фиксатор для дрели.
- Стойка для удержания дрели.
Кондуктор для направления сверл
Это устройство в виде коробки с установленными внутри направляющими втулками, которые изготовлены из сверхпрочной стали, не поддающейся воздействию сверла. Кондуктор можно использовать практически под все диаметры сверл до 20 мм. После установки этого приспособления над центром намеченного отверстия, сверло уже не уведет в сторону от его оси
Кондуктором удобно пользоваться для работы с трубами небольшим диаметром, когда невозможно для разметки воспользоваться керном.
Направляющий фиксатор для дрели
Этот механизм предназначен для удержания дрели в неподвижном состоянии при работе. Состоит из двух стоек, жестко закрепленных к подошве в виде большого круга. По стойкам двигается механизм, в который вставляется дрель и фиксируется к нему за шейку. Там же на стойках, под фиксирующим дрель механизмом находятся возвратные пружины.
По мере углубления сверла в металл, под усилием мастера, они сжимаются, но как только усилие прекращается, пружины распрямляются, и механизм, удерживающий дрель, по стойкам поднимается в исходное положение.
Стойка для удержания дрели
По сути, это упрощенный вертикальный станок для сверлильных работ, но с минимальными функциями.
Состоит из массивной плоской подошвы (платформы) и прикрепленной к ней жесткой штанги. Штанга закреплена к платформе строго под прямым углом. На ней же находится подвижная каретка с креплением для удержания дрели, и ручкой для ее управления.
Обрабатываемая деталь закрепляется на платформе при помощи струбцин или тисков. Мастер за ручку опускает каретку с дрелью вниз и удерживает ее во время всего процесса сверления.
Типы отверстий и методы их сверления
Просверленные отверстия в металле могут быть:
- Полностью сквозными.
- Заглушенными.
- Глубокими.
- С большим диаметром.
Сквозные отверстия: пронзают обрабатываемую деталь полностью насквозь. Особенность этого процесса заключается в защите поверхности верстака, на которой находиться заготовка, от повреждения при выходе сверла из детали. При этом может повредиться и сам режущий инструмент. Чтобы такого не произошло, можно использовать:
- Верстаки с отверстиями.
- Под обрабатываемую деталь подложить толстую деревянную прокладку.
- Уложить деталь на два металлических или деревянных бруса.
- На конечном этапе сверления снизить усилие на дрель и уменьшить скорость ее вращения.
Последний способ обычно должен использоваться при высверливании на месте, чтобы рядом расположенные детали не были повреждены.
Глухие отверстия: этот вид сверления выполняется не сквозным методом, а только на установленную глубину. Ограничение глубины высверливания устанавливается следующими способами:
- При помощи втулочного упора.
- Регулировочным упором патрона.
- Закрепленной на станок или дрель линейкой.
- Другими способами комбинирования в виде различных прокладок между дрелью и деталью.
Современные станки оборудованы автоматической подачей бура на заданную глубину, после чего работа прекращается.
Сверление глубоких отверстий: для этого обычно используется токарный станок. При этом если обрабатывается деталь цилиндрической формы, вращается не сверло, а сама заготовка. Во время работы сверло должно постоянно охлаждаться, а стружка из обрабатываемого прохода удаляться принудительно.
Для этой цели на поверхности глубинного бура расположены специальные канавки. Если они отсутствуют, он должен периодически извлекаться из тела детали и очищаться от металлической стружки. А в качестве охлаждающей жидкости можно использовать обыкновенную воду. Во время глубинного сверления в бытовых условиях нужно обязательно жестко закреплять дрель, иначе после поломки сверла, часть его останется в теле заготовки, которую можно считать испорченной.
Как просверлить отверстие большого диаметра в металле
Данная процедура намного сложнее глубинного бурения. Эта процедура при небольшой толщине металла выполняется специальной коронкой, или обыкновенными бурами для металла за несколько проходок.
Коронка
Состоит из комплекта, куда входит обычное сверло, ровно пробивающее канал в заготовке и самой коронки определенного диаметра. Рабочий процесс производится малыми оборотами дрели, при этом производиться принудительное охлаждение режущих кромок бура и коронки.
Многоэтапное сверление
При большой толщине детали необходимо иметь определенный запас буров, разница которых по диаметру должна быть по отношению друг к другу в пределах 25%. Работу следует начинать самым тонким сверлом. Как только им будет пробурен сквозной канал, производится замена сверла, у которого диаметр больше предыдущего. Таким образом, поэтапно, сверла меняются до диаметра заданного размера.
Ступенчато-конусный бур
Это комплект конусообразных сверл различных диаметров, находящихся на одной общей оси. Довольно удобный инструмент для работы со стальным листовым металлом. Принцип работы практически неотличим от обычного сверления.
Ступенчато-конусный бур заглубляется в заготовку, пока не достигается нужный размер просверливаемого отверстия.
Пробивка отверстий
Технология пробивки отверстий в металлических сплавах довольно распространенная. Она используется при работе с листовым металлом. Преимущества технологии в том, что отверстия пробиваются точно в заданной точке с четким диаметром и практически без потери определенного времени. Для этого используются специализированные прессовочные станки.
Для пробивки тонкого листового металла может использоваться ручной пробойник. Этот инструмент для пробивки отверстий в металле изготавливается из заостренной с одного конца стальной трубы. Для пробойника могут использоваться трубы различного диаметра. Для пробивки отверстия, пробойник приставляется к размеченной точке, после чего по нему наносится несколько сильных ударов молотком. В итоге получается аккуратно пробитое отверстие.
Советы мастеров
Работая с любыми электроинструментами, нужно всегда соблюдать технику безопасности и оберегать инструмент от преждевременного износа. Для этого рекомендуется принять во внимание несколько простых советов:
Перед началом работы следует всегда проверять прочность крепления сверла в патроне дрели.
- На одежде не должны болтаться свободно свисающие концы, которые могут намотаться на вращающиеся детали инструмента. Длинные волосы прячутся под головной убор, глаза защищаются очками.
- Бур должен вращаться, когда подносится к обрабатываемой поверхности, тогда он преждевременно не затупится.
- Вынимать бур из просверленного канала следует при включенной дрели, работающей на минимальных оборотах.
- Если режущая кромка бура не углубляется в заготовку, значит, сверло мягче данного металла и его следует заменить.
- Если сверло имеет небольшой диаметр и плохо держится в патроне дрели, на хвостовик, чтобы увеличить диаметр, следует намотать латунную проволоку.
- Чтобы отполированную поверхность детали случайно не повредить, на сверло нужно надеть фетровую или войлочную шайбу.
- Если отверстие сверлится не сквозное, на сверло можно надеть кусочек пенопласта, который будет одновременно играть роль измерителя глубины и сдувать с поверхности мелкую стружку.
obinstrumentah.info
это вид механической обработки материалов. Технология сверления. Оборудование для сверления
Сверление – это один из видов механической обработки материала резанием. В этом методе используется специальный режущий инструмент – сверло. С его помощью можно сделать отверстие разного диаметра, а также глубины. Кроме того, имеется возможность создания многогранных отверстий с разным сечением.
Назначение операции
Сверление – это необходимая операция, если требуется получить отверстие в металлическом изделии. Чаще всего для сверления имеется несколько следующих причин:
- требуется создать отверстие под нарезание резьбы, зенкерование, развертывание или растачивание;
- необходимо разместить в отверстиях электрические кабели, крепежные элементы, продеть через них анкерные болты и т. д.;
- отделение заготовок;
- ослабить разрушающиеся конструкции;
- в зависимости от диаметра отверстия, его можно использовать даже для закладки взрывчатки, к примеру, при добыче природного камня.
Данный список можно продолжать еще долго, но уже можно сделать вывод, что операция сверления – это одна из наиболее простых и в то же время довольно нужных и распространенных вещей.
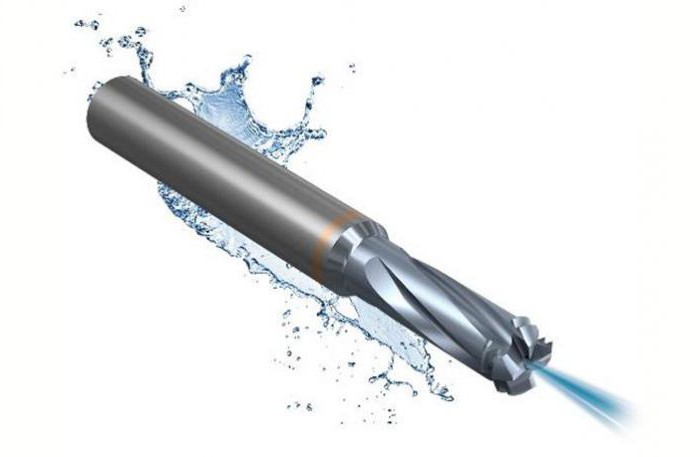
Расходные материалы
Естественно, что для осуществления процесса сверления необходимо иметь сверла. В зависимости от этого расходника будет меняться диаметр отверстия, а также количество его граней. Они могут быть круглого сечения, а могут быть многогранными – треугольными, квадратными, пятигранными, шестигранными и т. д.
Кроме того, сверление – это операция, при которой сверло будет нагреваться до высоких температур. По этой причине необходимо точно подбирать качество этого элемента, основываясь на требованиях материала, с которым придется работать.
- Довольно распространенный материал для производства приспособлений для сверления – углеродистая сталь. Элементы этой группы маркируются следующим образом: У8, У9, У10 и т. д. Основное предназначение таких расходников – это сверление отверстий в дереве, пластмассе, мягких металлах.
- Далее идут сверла, изготовленные из низколегированной стали. Они предназначаются для сверления тех же материалов, что и углеродистые, но их отличие заключается в том, что у этой марки элементов повышено значение теплостойкости до 250 градусов по Цельсию, а также увеличена скорость сверления.
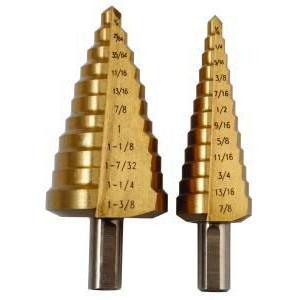
Улучшенные сверла
Имеется несколько типов сверл, которые предназначены для более качественных материалов:
- Первый тип сверл изготавливается из быстрорежущей стали. Теплостойкость этих расходников намного выше – 650 градусов по Цельсию, а предназначены они для сверления любых конструкционных материалов в незакаленном состоянии.
- Следующая группа – это сверла с твердыми сплавами. Применяются для того, чтобы делать отверстия в любых конструкционных незакаленных сталях, а также в цветном металле. Особенностью является то, что используется сверление на повышенных скоростях. По этой же причине теплостойкость повышена до 950 градусов по Цельсию.
- Одни из наиболее стойких элементов – это сверла с боразоном. Применяются для работ с чугуном, сталями, стеклом, керамикой, цветными металлами.
- Последняя группа – это сверла с алмазом. Применяются для сверления наиболее твердых материалов, стекла, керамики.
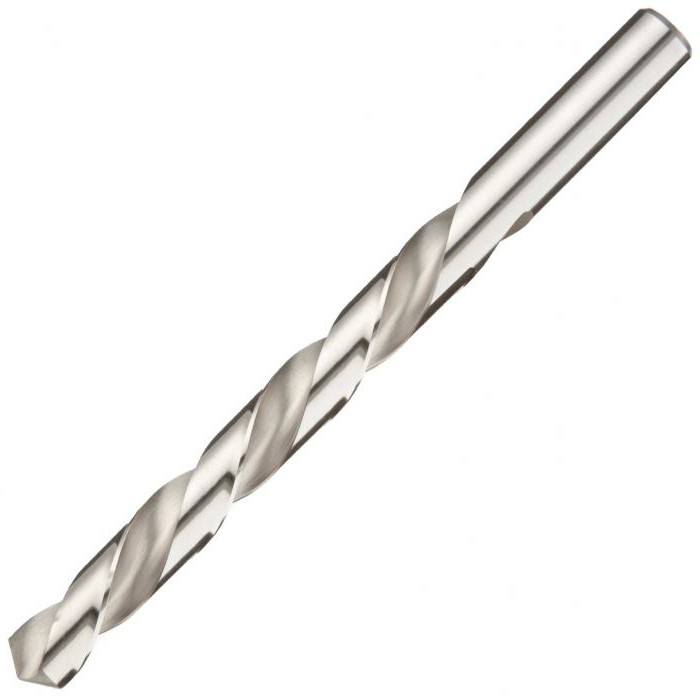
Типы станков для сверления
Для проведения операции сверления могут быть использованы следующие виды сверлильных станков:
- Вертикальные и горизонтальные сверлильные устройства. Сверление отверстий для таких машин – основная операция.
- Используются вертикальные и горизонтальные станки расточного типа. Сверление считается вспомогательными операциями для этих устройств.
- Вертикальные, горизонтальные и универсальные станки фрезеровочного типа. Для этих агрегатов сверление также является второстепенной операцией.
- Токарные и токарно-затыловочные станки. На первом типе устройств сверло является неподвижной частью, а вращается сама заготовка. Для второго типа устройства сверление не основная операция, а сверло является неподвижным элементом, как и в первом случае.
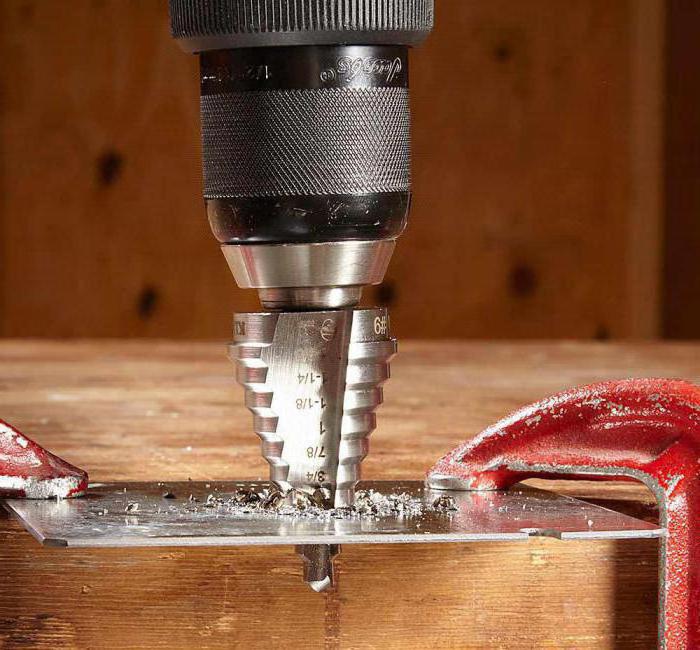
Это все типы сверлильных станков, на которых можно проводить все требуемые операции.
Ручные инструменты и вспомогательные операции
Для того чтобы облегчить процесс сверления, используются несколько вспомогательных операций. К ним можно отнести следующие:
- Охлаждение. При сверлении используются разнообразные смазочно-охлаждающие вещества. К ним относится, например, вода, эмульсии, олеиновая кислота. Также могут быть использованы газообразные вещества, к примеру углекислый газ.
- Ультразвук. Ультразвуковые вибрации, которые производит сверло, используются для увеличения производительности процесса, а также для усиления дробления стружки.
- Подогрев. Для того чтобы улучшить сверление металла, имеющего высокую плотность, его предварительно разогревают.
- Удар. Для работы с некоторыми поверхностями, например с бетоном, необходимо использовать ударно-поворотные движения, чтобы увеличить производительность.
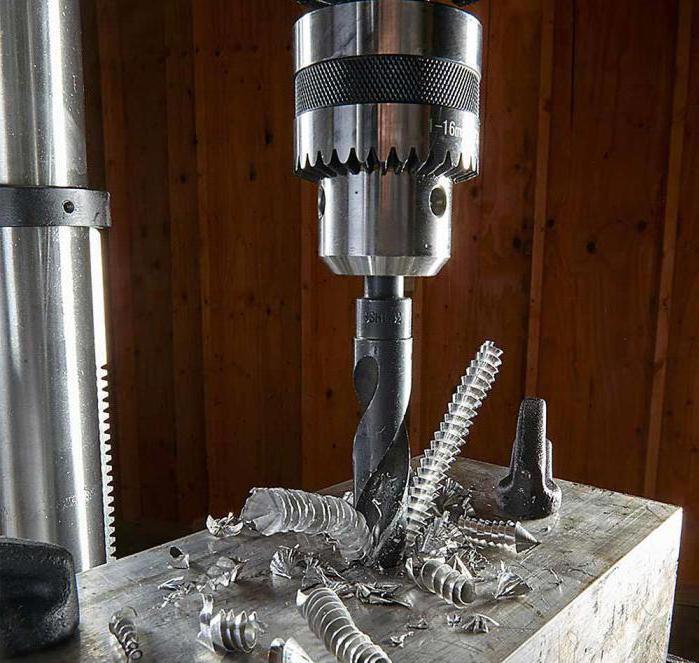
Осуществлять эту процедуру можно не только на станках в автоматическом режиме, но и на ручном оборудовании. Ручное сверление предполагает использование таких инструментов, как:
- Механическая дрель. Для сверления используется механическая сила человека.
- Электрическая дрель. Может осуществлять обычное и ударно-поворотное сверление. Работает от электрической сети.
Виды процедуры и охлаждение
Имеется несколько основных видов сверления – это оборудование цилиндрических отверстий, многогранных или же овальных, а также рассверливание уже имеющихся цилиндрических отверстий для увеличения их диаметра.
Основная проблема, которая возникает в процессе сверления металла, – это сильный нагрев расходуемого элемента, то есть сверла, а также места проведения работ. Температура материала может достигать 100 градусов по Цельсию и больше. Если она дойдет до определенных значений, то возможно возникновение горения или плавки. Здесь важно отметить, что множество сталей, которые используются для производства сверл, теряют свою твердость при нагреве, из-за чего трение будет только увеличиваться, поэтому элемент, к сожалению, будет изнашиваться быстрее.
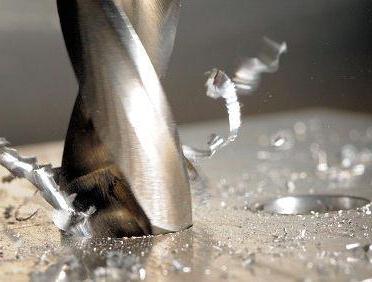
Для того чтобы бороться с этим недостатком, используют различные охлаждающие вещества. Чаще всего при вертикальном сверлении на станке имеется возможность организовать подачу охлаждающего вещества непосредственно к месту проведения работы. Если же она осуществляется с применением ручных приборов, то через определенный промежуток времени необходимо прерывать процесс и окунать сверло в жидкость.
Суть сверления
Технология сверления отверстий – это процесс образование канавок посредством снятия стружки в сплошном материале при помощи режущего инструмента. Данный элемент совершает вращательные и поступательные или же вращательно-поступательные движения одновременно, чем и образовывает отверстие.
Использование этого вида обработки материала используется для того, чтобы:
- получить неответственные отверстия с низкой степенью точности и классом шероховатости, используемые для крепежных болтов, заклепок и т. д.;
- получить отверстия под нарезание резьбы, развертывание и т. д.
Параметры обработки
Используя процедуру глубокого сверления или рассверливания можно получить отверстия, которые будут характеризоваться 10-й или 11-й степенью квалитета шероховатости поверхности. Если необходимо получить более качественное отверстие, то после завершения процесса обработки необходимо дополнительно зенкеровать и развертывать его.
Для того чтобы увеличить точность работы, в некоторых случаях можно прибегнуть к тщательному регулированию положения станка, правильно заточенному расходному элементу. Также применяется способ, при котором работа осуществляется через специальный прибор, повышающий точность. Данное устройство называется кондуктором. Также имеется разделение сверл на несколько классов. Бывают спиральные с прямыми канавками, перовые, используемые для глубокого или кольцевого сверления, а также центровочные сверла.
Описание конструкции сверла
Чаще всего для работы используется обычное спиральное сверло. Специальные используются намного реже.
Спиральный элемент представляет собой двузубую режущую деталь, которая включает в себя всего две основных части – это хвостовик и рабочая часть.
Если говорить о рабочей части, то ее можно разделить на цилиндрическую и калибрующую. На первой части сверла располагаются две винтовые канавки друг напротив друга. Основное предназначение этой части – это отвод стружки, которая выделяется во время работы. Здесь важно отметить, что канавки обладают правильным профилем, который обеспечивает правильное образование режущих кромок сверла. Кроме того, создается и необходимое пространство, которое нужно для отвода стружки из отверстия.
Технология сверления
Здесь важно знать несколько определенных правил. Очень важно, чтобы форма канавок, а также угол наклона между направлением оси сверла и касательной к ленте были такими, чтобы обеспечить легкий отвод стружки, при этом не ослабив сечения зубьев. Однако же здесь стоит отметить, что эта технология, а особенно числовые значения, будет заметно меняться в зависимости от диаметра сверла. Все дело в том, что увеличение угла наклона приводит к ослаблению действия сверла. Этот недостаток проявляется тем сильнее, чем меньше диаметр элемента. По этой причине приходится подстраивать угол под сверло. Чем меньше сверло – тем меньше угол, и наоборот. Общий угол наклона канавок составляет от 18 до 45 градусов. Если речь идет о сверлении стали, то необходимо использовать сверла с углом наклона от 18 до 30 градусов. Если отверстия делаются в хрупких материалах, например, как латунь или бронза, то угол сокращается до 22-25 градусов.
Принципы проведения работы
Тут важно начать с того, что в зависимости от материала инструмента будет меняться и скорость резания. К примеру:
- Если сверление проводится с использованием элементов из инструментальной стали, то минимальная скорость составляет 25 м/мин, а максимальная – 35 м/мин.
- Если механическая обработка осуществляется сверлами, принадлежащими к категории быстрорежущих, то минимальная скорость – 12 м/мин, а максимальная – 18 м/мин.
- Если используются сверла их твердосплавных материалов, то значения равны 50 м/мин и 70 м/мин.
Здесь важно отметить, что технология сверления предполагает выбор скорости процедуры в зависимости от диаметра самого элемента и малой подачи (с увеличением диаметра растет и скорость).
Характерная особенность проведения работы – это использование стандартного угла при вершине для сверла, который равен 118 градусов. Если необходимо работать с сырьем, которое характеризуется высокой твердостью сплава, то угол нужно увеличить до 135 градусов.
Сохранность сверл
Одной из важных задач при проведении такого типа механической обработки стало то, что нужно сберечь режущие свойства расходника. Сохранность этих параметров напрямую зависит от того, какой способ эксплуатации был выбран и подходил ли он к данному материалу. Например, для того чтобы устранить поломку сверла на проходе, необходимо сильно уменьшать подачу в момент вывода сверла из отверстия.
Особое внимание технологии сверления нужно уделить в тех ситуациях, когда глубина отверстия превышает длину винтовой канавки расходника. В момент ввода сверла стружка все еще будет образовываться, а вот во время выхода ее уже не будет. Из-за этого сверла ломаются очень часто. Если никакого выхода из ситуации нет, то нужно периодически выводить сверло и вручную очищать его от ненужных элементов, то есть стружки.
Коронки для сверления
Для того чтобы проделать отверстие в определенном покрытии, необходимо использовать коронки. Однако и их тоже нужно выбрать правильно, основываясь на определенных параметрах. В настоящее время используется три основных вида материала для создания коронок – это алмаз, победит и карбидо-вольфрам. Особенностью алмазной коронки стало то, что она осуществляет безударное сверление. В таком случае получается более правильная геометрия отверстия.
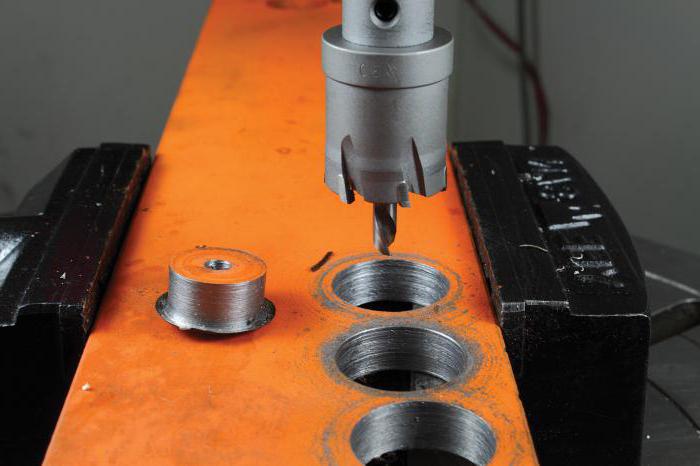
Основными преимуществами алмазных насадок стало следующее: возможность резки железобетонных материалов, низкий уровень шума и пыли, отсутствие нарушения структуры конструкции, так как технология не использует ударное усилие.
fb.ru
Способы сверления плитки без сколов: правила и рекомендации
После ремонтных работ иногда возникает необходимость просверлить отверстие в кафельной плитке. Чтобы не вызывать мастера, можно сделать это самостоятельно. Знание нюансов работы с материалом и правильный выбор инструмента помогут избежать трещин и сколов.
Особенности работы с кафелем
Главная трудность при сверлении кафельной плитки связана с ее фактурой. Плотность материала обусловлена его сложным составом. Плитка поддается резке с трудом, но при неосторожных работах легко трескается.
- Сверло для работы с кафелем должно быть острым и прочнее фактуры материала. Сверла по дереву или металлу непригодны.
- На дрели или шуруповерте выбрать скорость вращения от 200 до 900 об/мин. При определенных навыках можно увеличить до 1000 об/мин.
- Бурение отверстия в материале должно происходить не надавливанием на инструмент, а за счет низких оборотов дрели. Поспешность и применение усилия приведут к появлению трещин и сколов верхнего слоя.
- Сверло по отношению к поверхности кафеля должно располагаться под прямым углом на протяжении всего времени сверления. Уменьшение или увеличение угла наклона инструмента затрудняет работу, провоцирует повреждение поверхности. Неправильный наклон инструмента в начале работы провоцирует скольжение по поверхности.
- Высверливание отверстий на неустановленном изделии лучше всего производить на полу, используя кусок доски или ДСП.
Важно: если при работе кафель и сверло сильно нагреваются, охлаждают обыкновенной водой. От высоких температур поверхность трескается.
Инструмент для сверления
В зависимости от диаметра отверстия, которое необходимо просверлить, выбирают инструмент.
Главное условие – использование инструмента на малых оборотах. Маленькие отверстия легко пробурить ручной дрелью, более крупные – шуруповертом. Электродрель или перфоратор при сверлении используют с осторожностью, выбрав низкие обороты, и отключив ударный режим.
Важно: при работе с кафелем нельзя использовать режим реверса.
Для предотвращения провала сверла в стену при сверлении и случайного скола кафеля, применяется пластиковый ограничитель. Он устанавливается у самого основания дрели или шуруповерта. Служит одновременно упором и фиксатором прямого угла при сверлении.
Важно: чтобы установить метки для отверстий используют уровень, а выбрать нужный диаметр можно с помощью тонкой пластины -трафарета (кондуктора).
Для сверления кафеля применяют сверла с алмазным напылением, победитовые или специальные. Для отверстий под розетки используют круговые профессиональные сверла. Если при этом требуется сделать углубление в стене под кафелем, то используют перфоратор с буром из твердых сплавов.
Практические советы для домашнего сверления кафеля
Прежде чем приступить к работе, надо наметить будущее отверстие. Простукивая, определить есть ли пустоты под местом сверления. Полое пространство потребует очень аккуратной работы с инструментом: малейшее надавливание приведет к трещине. Ближе 2 см от краю плитки лучше не планировать сверление.
Важно: если отверстие необходимо сделать в шве, то располагать его следует по центру.
Избежать скольжения сверла поможет кусочек пластыря или малярного скотча.
На полу из пластилина устраивают валик, а середину наполняют водой. При работе круговым сверлом кафель сильно нагревается.
Чтобы избежать лишних расходов, лучше запастись специальным сверлом для кафеля – наконечник сверла треугольной формы, что само по себе предотвращает сколы и трещины. Если требуется дальше сверлить бетон, то сверло меняют.
Излишки пыли от кафеля во время сверления удаляют пылесосом.
Резка плитки болгаркой без СКОЛОВ (1 видео)
Способы сверления плитки без сколов (8 фото)
dekormyhome.ru
выбор инструмента, способы сверления, отверстие большого диаметра, советы, видео
Для того чтобы в ванной повесить полочку или вешалку, закрепить полотенцесушитель, установить трубы, нужно проделать отверстие в керамической плитке. Чтобы не повредить эмаль или не испортить хрупкий материал целиком, необходимы определённая сноровка и умение. Как грамотно это сделать собственными руками?
Выбор инструмента
При работе с кафелем важен выбор режущего инструмента.
Вот несколько подходящих вариантов:
- Ударная дрель. Это универсальный инструмент. Электрическая дрель с зубчатой передачей очень удобна в работе, но важно, чтобы она имела хотя бы двухскоростной регулятор вращения, так как работа с кафелем предполагает применение минимальной скорости с отключением ударного режима.
- Перфоратор. Хороший инструмент, обеспечивает максимальный результат при минимальных усилиях. Подойдёт при сверлении стены, на которую уложена плитка. Но нужно помнить, что сверлить нужно аккуратно.
- Шуруповерт. Можно использовать как аккумуляторный, так и сетевой. Скорость вращения сверла не должна превышать тысячи оборотов в минуту.
- Ручная дрель. Используется для проделывания отверстий, глубина которых не превышает 1,0 см.
Важен также выбор сверла, насадок. Кроме этого, необходимы малярная лента, разметчик, маркер и пылесос. Если нужно просверлить несколько отверстий, то дополнительно понадобятся ещё угольник и пузырьковый уровень.
При работе с кафелем важен выбор режущего инструмента
Также читайте материалы:
Если плитка не наклеена на стену или пол, то при сверлении нужно положить её на твердую ровную поверхность.
Вас может заинтересовать статья, в которой мы детально объясняем технологию монтажа керамической плитки на пол.
Способы сверления
В зависимости от конфигурации отверстия и самой рабочей поверхности можно применять такие способы сверления:
С применением сверла для стекла либо плитки
Оно приспособлено под скользкую, покрытую глазурью поверхность, где обычные сверла быстро тупятся. Его режущая часть имеет твердосплавную пластину с заострённым концом. Это обеспечивает точную его установку в выбранной точке. После разметки места сверления рекомендуется наклеить на него скотч либо малярную ленту. Если наклейка непрозрачная, то разметку делают прямо на ней. Благодаря такому приему сверло не будет скользить. После окончания работы скотч убирается.
Сверло для стекла приспособлено под скользкую, покрытую глазурью поверхность, где обычные сверла быстро тупятся
С использованием твердосплавного сверла для бетона
Этот способ самый распространенный, так как наборы разнокалиберных свёрл имеются практически в каждом доме. Сверление проводится с очень малой скоростью и с аналогичным способом достижения точности точки сверления. Оба эти способа применяются для образования отверстий малого диаметра под дюбели.
Сверление отверстий с использованием твердосплавного сверла для бетона проводится с очень малой скоростью и с аналогичным способом достижения точности точки сверления
Применение коронок с алмазным напылением
Такой метод используется для сверления больших отверстий под смеситель, розетку. На сверло надевается коронка, вращением которой обеспечивается правильное круглое отверстие. От характеристик напыления зависит качество произведенных работ. Данный метод из-за дороговизны насадки эффективен только при большом объеме работ.
Короноки с алмазным напылением используются для сверления больших отверстий под смеситель, розетку
Использование кругового сверла (балеринки)
Это сверло, напоминающее циркуль. Остриё размещается строго по центру, расстояние от него до резца меняется соответственно диаметру рассверливаемого отверстия. Инструмент настраивается на нужный диаметр благодаря возможности передвижения по штанге. Цена приспособления невелика, поэтому такой способ очень распространен. Сверление проводится на малой скорости. После прорезки плитки примерно на половину толщины сверло вставляется с обратной её стороны для досверливания до конца. К недостаткам этого метода можно отнести относительно небольшой срок службы сверла и большую вероятность сколов. Поэтому необходимо проводить эти работы особенно осторожно и тщательно.
Кругового сверло можно настроить на нужный диаметр благодаря возможности передвижения по штанге
Как сделать отверстие большого диаметра
Для отверстий очень большого диаметра применяют метод, отличный от всех предыдущих. Последовательность действий такова:
- Сначала размечают отверстие, прочертив его абрис на поверхности.
- Сверлом очень небольшого диаметра (желательно специальным, применяемым для плитки или стекла) просверливают по окружности как можно больше точечных отверстий.
- Осторожно убирают внутреннюю часть.
- Плоскогубцами удаляют заусеницы по контуру.
- Производят шлифовку внутреннего диаметра абразивом.
Для отверстий очень большого диаметра применяют сверло очень небольшого диаметра, которым просверливают по окружности как можно больше точечных отверстий
Чем сверлить плитку (видео)
Полезные советы
Вне зависимости от выбранного способа сверления, нужно использовать следующие нехитрые правила, чтобы безопаснее и качественнее выполнить эту работу:
- Перед началом работы необходимо хорошо смочить плитку, во время работы – периодически охлаждать инструмент и керамическую поверхность водой.
- Чтобы не ошибиться с глубиной сверления, на сверло надевают ограничитель или прикрепляют на определённом уровне кусок липкой ленты.
- Для предотвращения попадания осколков или пыли в глаза либо дыхательные пути надевают очки и респиратор.
- Чтобы дрель при работе не раскачивалась, используется специальный штатив.
- Чрезмерный нажим на инструмент неизбежно приводит к повреждению поверхности сверления.
- Когда вы ошиблись в размерах при сверлении, то в случае, если размер отверстия меньше необходимого, нужно плоскогубцами подломать края. При большем размере отверстия излишки затирают фугой — белым цементом с разнообразными добавками. Причём этот раствор хорошо применять и для затирки межпанельных швов и трещин при сколах.
Чтобы дрель при работе не раскачивалась, используется специальный штатив
Сверление отверстий в кафельной плитке – дело нелёгкое и кропотливое. Здесь быстрота не всегда обеспечивает хорошее качество. Слишком уж капризен материал, в котором проделывается отверстие.
Если же вы прислушаетесь к перечисленным советам, выберете правильное сверло и соответствующий инструмент, то в этом хлопотном деле вас ждёт успех.
polaremont.ru
Обработка отверстий (сверление, цекование, развертывание и др.) и инструмент
Обработка отверстий – это целый ряд технологических операций, целью которых является доведение геометрических параметров, а также степени шероховатости внутренней поверхности предварительно выполненных отверстий до требуемых значений. Отверстия, которые обрабатываются при помощи таких технологических операций, могут быть предварительно получены в сплошном материале не только при помощи сверления, но также методом литья, продавливания и другими способами.
Обработка высверленного отверстия цилиндрическим зенкером
Конкретный способ и инструмент для обработки отверстий выбираются в соответствии с характеристиками необходимого результата. Различают три способа обработки отверстий – сверление, развертывание и зенкерование. В свою очередь эти методы подразделяются на дополнительные технологические операции, к которым относятся рассверливание, цекование и зенкование.
Чтобы понять особенности каждого из вышеперечисленных способов, стоит рассмотреть их подробнее.
Сверление
Чтобы обрабатывать отверстия, их необходимо предварительно получить, для чего можно использовать различные технологии. Наиболее распространенной из таких технологий является сверление, выполняемое с использованием режущего инструмента, который называется сверлом.
Основные части спирального сверла
При помощи сверл, устанавливаемых в специальных приспособлениях или оборудовании, в сплошном материале можно получать как сквозные, так и глухие отверстия. В зависимости от используемых приспособлений и оборудования сверление может быть:
- ручным, выполняемым посредством механических сверлильных устройств или электро- и пневмодрелей;
- станочным, осуществляемым на специализированном сверлильном оборудовании.
Физика сверления отверстий
Использование ручных сверлильных устройств является целесообразным в тех случаях, когда отверстия, диаметр которых не превышает 12 мм, необходимо получить в заготовках из материалов небольшой и средней твердости. К таким материалам, в частности, относятся:
- конструкционные стали;
- цветные металлы и сплавы;
- сплавы из полимерных материалов.
Если в обрабатываемой детали необходимо выполнить отверстие большего диаметра, а также добиться высокой производительности данного процесса, лучше всего использовать специальные сверлильные станки, которые могут быть настольными и стационарными. Последние в свою очередь подразделяются на вертикально- и радиально-сверлильные.
Рассверливание – тип сверлильной операции – выполняется для того, чтобы увеличить диаметр отверстия, сделанного в обрабатываемой детали ранее. Рассверливание также выполняется при помощи сверл, диаметр которых соответствует требуемым характеристикам готового отверстия.
Физика рассверливания отверстий
Такой способ обработки отверстий нежелательно применять для тех из них, которые были созданы методом литья или посредством пластической деформации материала. Связано это с тем, что участки их внутренней поверхности характеризуются различной твердостью, что является причиной неравномерного распределения нагрузок на ось сверла и, соответственно, приводит к его смещению. Формирование слоя окалины на внутренней поверхности отверстия, созданного с помощью литья, а также концентрация внутренних напряжений в структуре детали, изготовленной методом ковки или штамповки, может стать причиной того, что при рассверливании таких заготовок сверло не только сместится с требуемой траектории, но и сломается.
При выполнении сверления и рассверливания можно получить поверхности, шероховатость которых будет доходить до показателя Rz 80, при этом точность параметров формируемого отверстия будет соответствовать десятому квалитету.
Зенкерование
При помощи зенкерования, выполняемого с использованием специального режущего инструмента, решаются следующие задачи, связанные с обработкой отверстий, полученных методом литья, штамповки, ковки или посредством других технологических операций:
- приведение формы и геометрических параметров имеющегося отверстия в соответствие с требуемыми значениями;
- повышение точности параметров предварительно просверленного отверстия вплоть до восьмого квалитета;
- обработка цилиндрических отверстий для уменьшения степени шероховатости их внутренней поверхности, которая при использовании такой технологической операции может доходить до значения Ra 1,25.
При зенкеровании прикладывается меньшая сила реза, чем при сверлении, и отверстие получается более точное по форме и размерам
Если такой обработке необходимо подвергнуть отверстие небольшого диаметра, то ее можно выполнить на настольных сверлильных станках. Зенкерование отверстий большого диаметра, а также обработка глубоких отверстий выполняются на стационарном оборудовании, устанавливаемом на специальном фундаменте.
Ручное сверлильное оборудование для зенкерования не используется, так как его технические характеристики не позволяют обеспечить требуемую точность и шероховатость поверхности обрабатываемого отверстия. Разновидностями зенкерования являются такие технологические операции, как цекование и зенкование, при выполнении которых используются различные инструменты для обработки отверстий.
Зенкеры конусные по металлу
Специалисты дают следующие рекомендации для тех, кто планирует выполнить зенкерование.
- Зенкерование следует проводить в процессе той же установки детали на станке, при которой осуществлялось сверление отверстия, при этом из параметров обработки меняется только тип используемого инструмента.
- В тех случаях, когда зенкерованию подвергается необработанное отверстие в деталях корпусного типа, необходимо контролировать надежность их фиксации на рабочем столе станка.
- Выбирая величину припуска на зенкерование, надо ориентироваться на специальные таблицы.
- Режимы, на которых выполняется зенкерование, должны быть такими же, как и при осуществлении сверления.
- При зенкеровании должны соблюдаться те же правила охраны труда и техники безопасности, как и при сверлении на слесарно-сверлильном оборудовании.
Зенкование и цекование
При выполнении зенкования используется специальный инструмент – зенковка. При этом обработке подвергается только верхняя часть отверстия. Применяют такую технологическую операцию в тех случаях, когда в данной части отверстия необходимо сформировать углубление для головок крепежных элементов или просто снять с нее фаску.
Чем различаются зенкование и цекование
При выполнении зенкования также придерживаются определенных правил.
- Выполняют такую операцию только после того, как отверстие в детали будет полностью просверлено.
- Сверление и зенкование выполняются за одну установку детали на станке.
- Для зенкования устанавливают небольшие обороты шпинделя (не больше 100 оборотов в минуту) и применяют ручную подачу инструмента.
- В тех случаях, когда зенкование осуществляется цилиндрическим инструментом, диаметр цапфы которого больше диаметра обрабатываемого отверстия, работу выполняют в следующей последовательности: сначала сверлится отверстие, диаметр которого равен диаметру цапфы, выполняется зенкование, затем основное отверстие рассверливается на заданный размер.
Целью такого вида обработки, как цекование, является зачистка поверхностей детали, которые будут соприкасаться с гайками, головками болтов, шайбами и стопорными кольцами. Выполняется данная операция также на станках и при помощи цековки, для установки которой на оборудование применяются оправки.
Развертывание
Процедуре развертывания подвергаются отверстия, которые предварительно были получены в детали при помощи сверления. Обработанный с использованием такой технологической операции элемент может иметь точность, степень которой доходит до шестого квалитета, а также невысокую шероховатость – до Ra 0,63. Развертки делятся на черновые и чистовые, также они могут быть ручными или машинными.
Цилиндрические ручные развертки 24Н8 0150
Рекомендации, которых следует придерживаться при выполнении данного вида обработки, заключаются в следующем.
- Припуски в диаметре обрабатываемого отверстия выбираются по специальным таблицам.
- При использовании ручного инструмента, который вращают только по часовой стрелке, сначала выполняют черновое, а потом чистовое развертывание.
- Обработку стальных деталей выполняют с обязательным использованием СОЖ, чугунных – всухую.
- Машинное развертывание проводят сразу после сверления на станке – с одной установки детали.
- Для контроля качества результата используют специальные калибры.
Оценка статьи:
Загрузка…Поделиться с друзьями:
met-all.org
29. Сверление. Сущность процесса, назначение и область применения, применяемое оборудование (станок), инструмент, приспособления, точность размеров и шероховатость обрабатываемой поверхности.
Сверление– основной способ получения сквозных и глухих отверстий в сплошном материале заготовки. В качествеинструментаиспользуетсясверло. Обработка производится насверлильных и токарных станках. На сверлильных станках сверло совершает вращательное движение и продольное вдоль оси отверстия, а заготовка закреплена на столе станка. На токарных станках обрабатываемая деталь закрепляется в патрон и совершает вращательное движение, сверло крепится в заднюю бабку станка и совершает поступательное движение вдоль оси отверстия.
Рис.2. Схемы: а, б – сверления, в – рассверливания, г-зенкерования, д- развертывания
Диаметр просверливаемого отверстия можно увеличить сверлом большего размера. Такие операции называют рассверливанием. При сверлении обеспечивается сравнительно невысокая точность и качество поверхности.
Для получения отверстий более высокой точности и меньшей шероховатости поверхности выполняются зенкерование и развертывание. Зенкерованиемобрабатывают предварительно полученные отверстия многолезвийным инструментомзенкером, который имеет более жесткую рабочую часть. Число зубьев не менее трех.
Развертываниемможно исправить неточности формы отверстия.Развертки– многолезвийный инструмент, срезающий очень тонкие слои с обрабатываемой поверхности.
Назначение сверления: Сверление необходимая операция для получения отверстий в различных материалах при их обработке, целью которой является:
Изготовление отверстий под нарезание резьбы, зенкерование, развёртывание или растачивание.
Изготовление отверстий (технологических) для размещения в них электрических кабелей, анкерных болтов, крепёжных элементов и др.
Отделение (отрезка) заготовок из листов материала.
Ослабление разрушаемых конструкций.
Закладка заряда взрывчатого вещества при добыче природного камня.
Операции сверления производятся на следующих станках:
Вертикально-сверлильные станки.
Горизонтально-сверлильные станки.
Вертикально-расточные станки.
Горизонтально-расточные станки.
Вертикально-фрезерные станки.
Горизонтально-фрезерные станки.
Универсально-фрезерные станки.
Токарные станки (сверло неподвижно а обрабатываемая заготовка вращается).
Токарно-затыловочные станки (сверление вспомогательная операция, сверло неподвижно).
Для облегчения процессов резания материалов применяют следующее:
Охлаждение (вода, эмульсии, олеиновая кислота, углекислый газ, графит).
Ультразвук (ультразвуковые вибрации сверла увеличивают производительность и дробление стружки).
Подогрев (ослабляет твёрдость труднообрабатываемых материалов).
Удар (при ударно-поворотном сверлении (бурении) камня, бетона).
30. Протягивание. Сущность процесса, назначение и область применения, применяемое оборудование (станок), инструмент, приспособления, точность размеров и шероховатость обрабатываемой поверхности.
Протягивание– высокопроизводительный метод обработки деталей разнообразных форм, обеспечивающимвысокую точность формы и размеровобрабатываемой поверхности. Из-за высокой стоимостиинструмента – протяжки, протягивание применяют в крупносерийном производстве. В протяжке каждый режущий зуб больше последующего на определенную величину. Процесс резания при протягивании производится на протяжныхвертикального и горизонтального исполнений станкахпри поступательном движении инструмента относительно неподвижной заготовки за один проход.
Отверстия различной геометрической формы протягивают на горизонтально-протяжных станках для внутреннего протягивания. Размеры отверстий от 5 до 250 мм.
Рис. 6. Схемы протягирания: 1-обрабатываемая деталь,2 – протяжка; а…д- внутреннее протягивание; з…ж- наружнее протягивание
Цилиндрические отверстия протягивают после сверления, растачивания или зенкерования. Шпоночные и шлицевые пазы протягивают протяжками, форма которых в поперечном сечении соответствует профилю протягиваемого отверстия.
Наружные поверхности различной геометрической формы протягивают на вертикально-протяжных станках для наружного протягивания.
Протягивание применяется в крупносерийном и массовом производстве металлоизделий, и редко в мелкосерийном и единичном. Протяжки различных конструкций — наружные, внутренние, и дорны, являются одними из наиболее дорогих инструментов для выполнения металлообработки. Подчас каждая протяжка при своем изготовлении требует наивысшей точности и правильного расчета. Это обусловлено тем, что инструмент при протягивании работает в наиболее тяжёлых и суровых условиях огромных нагрузок (растяжение, сжатие, изгиб, абразивное и адгезионное выкрашивание лезвий протяжки). Протягиванию предшествуют подготовительные операции металлообработки, такие как сверление, зенкерование, развертывание, вырубка (т. е. для проведения протягивания требуется достаточно точно обработанная поверхность заготовки).
Дорнование(дорнирование) – вид обработки заготовок без снятия стружки. Сущность дорнования сводится к перемещению в отверстии заготовки с натягом жёсткого инструмента – дорна. Размеры поперечного сечения инструмента больше размеров поперечного сечения отверстия заготовки на величину натяга.
Станки для протягивания:
Горизонтально-протяжные станки: Все виды внутреннего и наружного протягивания заготовок.
Пресса: Обработка отверстий дорнами (прошивка, формообразование, калибровка).
Виды протягивания:
Внутреннее протягивание. Наружное протягивание. Дорнование. Накаливание.
studfile.net