Шлифовальный стол – подставка для сверлильного станка своими руками | Своими руками
Содержание ✓
- ✓ ШЛИФОВАЛЬНЫЙ СТОЛ — ПОДСТАВКА ДЛЯ СВЕРЛИЛЬНОГО СТАНКА СВОИМИ РУКАМИ
- ✓ ВИДЕО НА ЗАМЕТКУ – ШЛИФОВАЛЬНЫЙ БАРАБАН ДЛЯ СВЕРЛИЛЬНОГО СТАНКА СВОИМИ РУКАМИ
Как и большинство столяров, я обрабатываю фигурные кромки деталей на сверлильном станке с помощью шлифовальных барабанов различного размера. Чтобы избавиться от огромного количества мельчайшей древесной пыли, я соорудил специальный столик-подставку с коробом для сбора и отсоса пыли. Подставка представляет собой горизонтальную панель, закреплённую на прямоугольном герметичном коробе, в одной из боковых стенок которого вырезано отверстие для подключения шланга пылесоса.
Диаметр центрального отверстия в верхней панели я выбрал равным 84 мм, это примерно на 2 мм больше диаметра моего самого большого шлифовального барабана. В этот зазор между кромками отверстия и наружной поверхностью барабана и проходит отсос пыли. А для того, чтобы эффективность удаления пыли не снижалась при работе с барабанами меньшего размера, я использую шайбы-вставки, как на фрезерном станке.
ВСЕ ЧТО НЕОБХОДИМО ДЛЯ ЭТОЙ СТАТЬИ НАХОДИТСЯ ЗДЕСЬ >>>
Подставка практически полностью сделана из ДСП толщиной 18 мм. Две основные детали — верхняя и нижняя панели — соединены друг с другом герметичным коробом высотой 100 мм. На нижней панели я установил четыре Т-образные резьбовые втулки-гайки, с помощью которых подставка крепится к столу сверлильного станка.
На рисунке показана разметка заготовки на листе ДСП. Размеры могут быть изменены в зависимости от конкретной модели станка. Я использовал ДСП толщиной 18 мм, но если ваш станок имеет меньшие габариты, вполне можно сделать подставку и из многослойной фанеры толщиной 10-15 мм.
Разметка верхней и нижней панелей на одном листе ДСП даёт возможность вырезать продольные пазы на обеих панелях за один проход фрезой и таким образом гарантировать их точное совмещение.
При изготовлении верхней и нижней панелей начинать работу следует с выборки на заготовке продольных пазов шириной 18 и глубиной 6 мм. Если у вас есть торцевая пазовая фреза 018 мм, то каждый из пазов можно выбрать за один проход фрезерной машинки вдоль закреплённой струбцинами направляющей линейки. Если же такой фрезы нет, то выбирать пазы придётся фрезой меньшего диаметра в несколько проходов.
Несколько сложнее вырезать поперечные пазы. Приступая к этой работе, следует более внимательно и аккуратно выполнить разметку, а также проконтролировать точность установки направляющей линейки для фрезерной машинки. Поперечные пазы должны располагаться точно на одинаковых расстояниях друг от друга как на верхней, так и на нижней панели. Иначе собрать подставку будет затруднительно.
Когда все пазы будут выбраны, останется только разрезать заготовку на две детали — верхнюю и нижнюю панели, опилить их по размеченному контуру и обработать кромки, скруглив острые углы. Чтобы быстро и точно выполнить эту работу, нужно сначала вырезать одну из панелей, например, верхнюю, а затем, сложив обе детали вместе, вырезать нижнюю, используя верхнюю как шаблон.
Ширина боковых стенок короба зависит от необходимой его глубины, которая в свою очередь определяется максимальным размером (длиной) используемых для шлифования барабанов. Я сделал глубину короба равной 100 мм. Для этого потребовалось вырезать боковые стенки шириной 112 мм (100 мм — высота короба и по 6 мм на верхний и нижний пазы).
Разметка верхней и нижней панелей на одном листе ДСП.
В одной из боковых стенок короба надо вырезать отверстие для шланга пылесоса. В какой из боковых стенок и в каком месте его сделать, особого значения не имеет, лишь бы шланг не мешал работать.
С помощью этого же приспособления в верхней плите я вырезал и центральное отверстие 084 мм, которое выбрал за несколько неглубоких проходов. Чтобы не повредить фрезу на выходе, под плиту снизу нужно обязательно подложить пару дистанционных брусков, так как отверстие должно быть сквозным. Затем фрезой для выборки фальцев с направляющим подшипником вдоль верхней кромки отверстия выбрал фальц глубиной 6 мм для шайб-вставок.
Шайбы-вставки можно вырезать из любого достаточно прочного листового материала. Я, например, их сделал из оргстекла толщиной 6 мм. Сначала нужно вырезать все шайбы по внешнему диаметру, а затем выбрать внутренние отверстия по размеру имеющихся в наличии шлифовальных барабанов. Желательно сразу сделать ещё пару шайб впрок – вдруг в будущем в дополнение к уже имеющимся в наличии придётся прикупить один-два барабана других размеров.
Если пазы в верхней и нижней панели вырезаны точно и безошибочно, то сборка подставки не займёт много времени. Сначала боковины короба вклеивают в пазы нижней панели, а затем сверху их накрывают верхней панелью. Все стыки стенок короба желательно дополнительно залить клеем-расплавом или каким-либо другим герметиком. Если зазор между внутренней кромкой отверстия сменных шайб и шлифовальным барабаном не превышает 1-2 мм, то благодаря герметичности короба удаление пыли идёт очень эффективно.
Подставку я устанавливаю на стол сверлильного станка и креплю самодельными болтами М8 с барашковой головкой. Для этого в нижней панели точно напротив отверстий в столе сверлильного станка запрессованы Т-образные резьбовые втулки-гайки М8. Такой способ крепления позволяет быстро превратить сверлильный станок в станок для шлифования кромок и так же быстро снять подставку, когда станок необходим для выполнения других работ.
Читайте также: Насадка на угловую шлифовальную машину для резьбы под дереву и отзывы мастера
ШЛИФОВАЛЬНЫЙ СТОЛ — ПОДСТАВКА ДЛЯ СВЕРЛИЛЬНОГО СТАНКА СВОИМИ РУКАМИ
Выборка продольных пазов по направляющей линейке. Ширина выбранных пазов должна быть точно равна используемой для изготовления подставки ДСП. В Если кромки деталей после раскроя заготовки получатся не слишком ровными, их можно обработать кромочной фрезой с упорным подшипником. И Кромки нижней панели обрезают, сложив обе детали вместе, используя верхнюю панель как шаблон.
Все углы и острые кромки верхней и нижней панелей желательно скруглить, обработав их профильной кромочной фрезой. EКомплект шайб-вставок, вырезанных из оргстекла толщиной 6 мм. Для их размещения предусмотрен фальц глубиной 6 мм.
Сначала боковины короба вклеивают в пазы нижней панели, а затем сверху их накрывают верхней панелью. Все стыки стенок короба желательно дополнительно залить клеем-расплавом или каким-либо другим герметиком.
Один из возможных вариантов крепления подставки на столе сверлильного станка – четырьмя самодельными винтами с барашковой головкой.
Читайте также: Насадка-стол для шлифовки болгаркой своими руками
ВИДЕО НА ЗАМЕТКУ – ШЛИФОВАЛЬНЫЙ БАРАБАН ДЛЯ СВЕРЛИЛЬНОГО СТАНКА СВОИМИ РУКАМИ
Шлифовальный барабан своими руками для сверлильного станка | DIY
Watch this video on YouTube
© Автор: Р. ФОКС, Канада
ИНСТРУМЕНТ ДЛЯ МАСТЕРОВ И МАСТЕРИЦ, И ТОВАРЫ ДЛЯ ДОМА ОЧЕНЬ ДЕШЕВО. БЕСПЛАТНАЯ ДОСТАВКА. ЕСТЬ ОТЗЫВЫ.Подпишитесь на обновления в наших группах и поделитесь.

Будем друзьями!
Стол для сверлильного станка своими руками – Строительство коттеджей и новые проекты домов
Хотя сверлильные станки незаменимы в столярных мастерских, столики большинства из них предназначены скорее для работы с металлом. Исправить положение вещей поможет удобный накладной столик с упорами. Он предоставит возможности, которых лишен стандартный чугунный столик станка.
Начните со столика
1. Для основания А выпилите два куска фанеры 12x368x750 мм (мы взяли березовую фанеру, так как она более гладкая и практически не имеет дефектов. Можно также использовать МДФ). Склейте оба куска вместе и зафиксируйте их струбцинами, выровняв края (рис. 1).
2. Из твердого оргалита толщиной 6 мм выпилите верхние боковые В, переднюю С и заднюю D накладки по указанным в «Списке материалов» размерам. Разметьте вырез радиусом 10 мм на переднем крае детали D (рис. 1). Выпилите вырез и отшлифуйте его края (вырез поможет легко извлекать пластину-вкладыш Е). Теперь нанесите клей на заднюю сторону накладок из оргалита и приклейте их к фанерной плите-основе (фото А).
Нанеся клей на нижнюю сторону деталей В, С и D, разместите их на фанерной плите основания А. Для предотвращения сдвига соединяйте детали друг с другом и с основанием малярным скотчем. Затем сожмите склейку с помощью прокладок толщиной 19 мм и прижимных брусков сечением 40×80 мм.
3. Разметьте вырез радиусом 83 мм на заднем крае столика (рис. 1), выпилите его ленточной пилой или электролобзиком и гладко отшлифуйте.
4. Чтобы определить положение центрального выреза размером 89×89 мм в плите-основании столика, вставьте в патрон сверлильного станка сверло диаметром 3 мм, выровняйте относительно него чугунный столик станка и зафиксируйте его. Положите сверху накладной столик и выровняйте его так, чтобы сверло было нацелено в середину проема для вкладыша Е, образованного деталями В, С и D. Если чугунный столик выступает за передний край накладного столика, сдвиньте последний вперед, выровняв оба края. Зафиксируйте положение накладного столика струбцинами. Теперь просверлите сквозное отверстие диаметром 3 мм в фанерной плите-основании столика А. Снимите столик и переверните его. Разметьте вырез 89×89 мм, центрируя его относительно 3-миллиметрового отверстия. Затем просверлите в углах отверстия диаметром 10 мм и с помощью электролобзика выпилите вырез. Теперь выпилите пластину- вкладыш Е по указанным размерам.
5. Если металлический столик вашего станка имеет сквозные пазы, выпилите на нижней стороне накладного столика паз для вставки алюминиевого направляющего профиля (рис.1). Если в металлическом столике станка нет сквозных пазов, просверлите два монтажных отверстия диаметром 6 мм. Расположите их примерно посередине расстояния между центром и задним краем столика и на максимально возможном удалении друг от друга. Затем вновь зафиксируйте сверху накладной столик и отметьте положение отверстий на его нижней стороне. Выпилите паз для алюминиевого профиля, проходящий через эти отверстия.
6. Переверните накладной столик и выпилите или отфрезеруйте на его верхней стороне пазы для направляющих алюминиевых профилей (рис.2). Центры пазов должны совпадать со стыками деталей В, С и D. Примечание. Для комфортной роботы при шлифовке с помощью абразивных барабанов рекомендуем дополнительно оснастить столик системой удаления ныли, описанной в статье «Пылеудаление для шлифовального столика».
Теперь изготовьте упор
1. Выпилите по указанным размерам заготовки для опоры F, передней накладки G, нижней Н и верхней I деталей упора. Установите в пильный станок пазовый диск толщиной 10 мм и настройте продольный (параллельный) упор для выпиливания шпунтов точно посередине толщины деталей Н и I (рис. 3 и 4). Затем выпилите в этих деталях шпунты глубиной 5 мм и пометьте грани, которые прилегали к упору пильного станка. Выпиливая верхний и нижний шпунты на нижней летали, в обоих случаях направляйте заготовку вдоль упора одной и той же гранью. Теперь, не изменяя настроек, выпилите шпунт в заготовке опоры.
Прижимая детали помеченными гранями к задней стороне накладки G, склейте нижнюю Н и верхнюю I части упора друг с другом, с нижней опорой F и накладкой G. Струбцины должны сжимать склейку в двух направлениях.
2. Приклейте заготовку передней накладки G к заготовке опоры F (рис. 4). Убедитесь, что накладка приклеена к опоре точно под углом 90°. Когда клей высохнет, приклейте нижнюю Н и верхнюю I детали упора (фото В). Прежде чем клей высохнет, вставьте в квадратные отверстия стальные стержни диаметром 10 мм, пропустив их насквозь, чтобы удалить изнутри выдавленные излишки клея.
3. Выпилите на передней стороне накладки G шпунт 19×10 мм для установки направляющего алюминиевого профиля (рис. 4). Затем выпилите пылезащитный фальц 3×3 мм вдоль нижнего ребра накладки.
4. Ровно опилите один конец собранного упора, а затем распилите заготовку на три части (рис. 3), получив упор длиной 572 мм и два расширения-удлинителя по 89 мм. Затем отпилите на удлинителях часть опоры (рис. 4).
5. С помощью гибкого лекала разметьте полукруглые вырезы на верхнем крае упора и заднем крае опоры F (рис. 3). Выпилите вырезы электролобзиком или ленточной пилой и гладко отшлифуйте. Затем просверлите отверстия диаметром 6 мм для винтов, которыми упор крепится к столику, и отверстие для ключа сверлильного патрона в опоре, где указано.
6. Для установки резьбовых втулок в деталь I просверлите отверстия диаметром 11 мм, выходящие в верхнее квадратное отверстие упора (рис. 3 и 4). Нанесите на стенки этих отверстий эпоксидный клей и вставьте резьбовые втулки. Когда клей окончательно затвердеет, с помощью сверла диаметром 10 мм удалите его излишки, которые могли попасть в квадратные отверстия для стальных стержней. Дополнительные советы по установке резьбовых втулок приведены в «Совете мастера».
Совет мастера. Установка резьбовых втулок
В самодельных приспособлениях для мастерской часто используются различные винты для фиксации или регулировки. Чтобы они могли работать в деревянных и фанерных деталях, потребуются резьбовые втулки. Они выпускаются разных размеров (метрические — от М4 до М10). Существуют два основных типа — забивные и ввинчиваемые (футорки), как показано на левом фото внизу.
Используйте ввинчиваемые втулки в мягкой древесине и фанере, где крупные витки внешней резьбы легко сминают окружающую древесину. Просто просверлите отверстие, диаметр которого равен диаметру корпуса втулки-футорки, и вверните в него втулку. В твердой древесине, такой как дуб или клен, или когда втулка должна быть расположена у края детали и может расколоть древесину, просверлите отверстие диаметром чуть больше внешнего диаметра резьбы и вставьте в него втулку с эпоксидным клеем. Чтобы не испачкать клеем внутреннюю резьбу втулки, заклейте ее торец (фото справа вверху).
Забивные втулки с заусенцами на внешней стороне одинаково пригодны и для фанеры, и для твердой и мягкой древесины. Просверлите отверстие, диаметр которого равен диаметру корпуса втулки, и вставьте втулку с помощью струбцины или молотка и деревянного брусочка. В случаях, когда усилие прижимного винта вытягивает втулку из материала (например, винте ручкой-маховичком, фиксирующий стальные стержни удлинителей упора), просверлите отверстие такого диаметра, чтобы его стенок касались только кончики заусенцев, и вставьте в него втулку с эпоксидным клеем.
Завершение и сборка
1. Заклейте малярным скотчем дно пазов для установки алюминиевых профилей в столике и упоре. Затем нанесите на все детали отделочное покрытие (мы использовали полуматовый полиуретановый лак с межслойной шлифовкой наждачной бумагой зернистостью 220 единиц). Когда лак высохнет, удалите малярный скотч.
2. Через раззенкованные монтажные отверстия алюминиевых профилей просверлите направляющие отверстия в соответствующих деталях столика и упора. Нанесите на дно пазов эпоксидный клей, вставьте профили и закрепите их шурупами. Примечание. Некоторые направляющие профили имеют небольшой гребень вдоль одного внешнего края (рис. 4). Аля точного совмещения профилей в накладке упора а расширениях ориентируйте гребни в одном направлении во всех трех деталях.
3. Отпилите от стального стержня диаметром 10 мм четыре куска длиной 368 мм. Наждачной бумагой зернистостью 80 единиц грубо отшлифуйте один конец каждого стержня на длину 89 мм и с помощью эпоксидного клея закрепите эти концы в квадратных отверстиях удлинителей упора. Чтобы стержни оставались параллельными, вставьте их свободные концы в квадратные отверстия упора.
4. Чтобы сделать ручки-маховички для фиксации удлинителей упора (рис. 2), вверните винты длиной 32 мм с потайной головкой в гайки-маховички до половины. Нанесите под их головки эпоксидный клей, а затем вкрутите винты в гайки до конца.
5. Вставьте шестигранные головки двух винтов в нижний направляющий профиль накладного столика (рис. 2). Выровняйте накладной столик над металлическим столиком сверлильного станка и пропустите винты в сквозные пазы или отверстия. Добавьте шайбы и наверните пластиковые гайки-ручки.
Примечание. Пластиковые гайки-ручки имеют резьбовые отверстия глубиной около 16 мм. Возможно, вам потребуется укоротить 50-миллиметровые винты в соответствии с толщиной металлического столика вашего станка.
6. Вставьте шестигранные головки винтов в верхние направляющие профили. Совместите отверстия в основании упора с винтами, наденьте шайбы и закрепите упор гайками- маховичками. Вставьте стальные стержни удлинителей в квадратные отверстия упора и вверните фиксирующие винты с маховичками.
Добавьте регулируемый концевой упор-стопор
1. Чтобы сделать корпус упора-стопора J, выпилите из доски толщиной 19 мм два куска 51×73 мм и склейте их вместе лицом к лицу, выровняв торцы и кромки. Когда клей полностью высохнет, выпилите паз 6×5 мм посередине задней стороны корпуса (рис. 5).
2. Выпилите по указанным размерам подвижный стопор К и приклейте его с помощью двухстороннего скотча к правой стороне корпуса J (рис. 5). Установите в патрон сверлильного станка сверло Форстнера диаметром 13 мм и высверлите в левой грани корпуса углубление-цековку глубиной 10 мм, как показано на рисунках и фото С. Затем, не сдвигая детали, установите сверло диаметром 6 мм и просверлите в центре углубления сквозное отверстие через обе детали.
3. Отделите стопор К от корпуса J. Сверлом Форстнера диаметром 19 мм высверлите в стопоре и корпусе углубления-цековки глубиной 10 мм точно над 6-миллиметровыми отверстиями (рис. 5). Для совмещения центров перед сверлением вставьте в отверстия шканты диаметром 6 мм. Затем, выровняв сверло диаметром 7 мм посередине 6-миллиметрового паза на задней стороне корпуса, просверлите сквозное отверстие, как указано на рисунке.
(Фото С) — Зафиксируйте детали, расположив стопор К внизу и прижав грань корпуса J с пазом к упору сверлильного столика. Высверлите углубление-цековку 13×10 мм в боковой грани корпуса. (Фото D) — Зафиксируйте подвижный стопор К на винте с помощью шайб и гайки, вставьте винт в отверстие корпуса J и вверните его в гайку, вклеенную эпоксидным клеем в углубление-цековку.
4. С помощью эпоксидного клея зафиксируйте гайку в 13-миллиметровом углублении-цековке корпуса J. Затем выпилите ползун L указанных размеров и вклейте в паз на задней стороне корпуса, вровень с его правой гранью (рис. 5).
5. Нанесите на все летали прозрачное отделочное покрытие. После просушки наденьте на винт с полукруглой головкой широкую 6-миллиметровую шайбу и вставьте его в отверстие стопора К. Наденьте на винт вторую шайбу, а затем наверните гайку. Затяните гайку так, чтобы стопор не покачивался, но винт мог вращаться. Теперь соедините стопор с корпусом J (фото D), вращая винт до соприкосновения обеих деталей.
6. С помощью эпоксидного клея зафиксируйте пластиковую гайку-маховичок на конце винта с полукруглой головкой. Вставьте винт с шестигранной головкой в отверстие корпуса J сзади, добавьте шайбу и гайку-маховичок спереди (рис. 5). Для использования регулируемого концевого упора- стопора сначала установите расстояние между корпусом и стопором около 12 мм. Двигая ползун с шестигранной головкой винта в направляющем алюминиевом профиле, с помощью рулетки или мерной линейки установите стопор на нужном расстоянии от сверла. Зафиксируйте его, затянув переднюю гайку-маховичок. Теперь точно отрегулируйте расстояние до сверла, вращая боковую гайку-маховичок. Стопорная гайка-маховичок и ползун L расположены точно по центру корпуса, поэтому вы сможете использовать регулируемый стопор справа и слева от сверла, просто перевернув его.
7. Соберите прижимы (рис. 2). Вставьте шестигранные головки их винтов в пазы направляющих алюминиевых профилей. Теперь сверлильный станок готов к настоящей работе и его по праву можно назвать столярным.
Точильный стол – подставка под сверлильный станок своими руками | DIY
Содержание ✓
- ✓ Столовая шлифовальная машина – подставьте для буровой машины с руками
- ✓ Видео -примечание – шлифовальный барабан для буровой машины с руками
детали на сверлильном станке с использованием шлифовальных барабанов различных размеров. Чтобы избавиться от огромного количества мельчайшей древесной пыли, я соорудил специальный стол-подставку с пылесборником и всасывающим коробом. Подставка представляет собой горизонтальную панель, закрепленную на прямоугольном герметичном коробе, в одной из боковых стенок которого имеется отверстие для подсоединения шланга пылесоса.
Диаметр центрального отверстия в верхней панели составляет 84 мм, что примерно на 2 мм больше диаметра моего самого большого шлифовального барабана. Именно в этот зазор между краями отверстия и наружной поверхностью барабана отсасывается пыль. А чтобы эффективность пылеудаления не снижалась при работе с барабанами меньшего размера, использую вставные шайбы, как на фрезерном станке.
ВСЕ НЕОБХОДИМОЕ ДЛЯ ЭТОЙ СТАТЬИ ЗДЕСЬ >>>
Подставка практически полностью изготовлена из ДСП толщиной 18 мм. Две основные части — верхняя и нижняя панели — соединяются между собой герметичным коробом высотой 100 мм. На нижней панели установил четыре Т-образные резьбовые втулки-гайки, которыми стойка крепится к столу сверлильного станка.
На рисунке представлена разметка заготовки на листе ДСП. Размеры могут отличаться в зависимости от конкретной модели машины. Я использовал ДСП 18 мм, но если ваш станок имеет меньшие габариты, то вполне можно сделать подставку из фанеры толщиной 10-15 мм.
Разметка верхней и нижней панелей на одном листе ДСП позволяет за один проход фрезой вырезать продольные пазы на обеих панелях и тем самым гарантировать их точное совмещение.
При изготовлении верхней и нижней панелей работу следует начинать с выборки на заготовке продольных пазов шириной 18 и глубиной 6 мм. Если у вас концевая фреза 018 мм, то каждый из пазов можно выбрать за один проход фрезерного станка по направляющей линейке, закрепленной струбцинами. Если такой фрезы нет, то канавки придется выбирать фрезой меньшего диаметра в несколько проходов.
Несколько сложнее нарезать поперечные канавки. Приступая к этой работе, следует более тщательно и аккуратно произвести разметку, а также проверить точность установки направляющей линии для фрезерного станка. Поперечные прорези должны располагаться точно на одинаковом расстоянии друг от друга как на верхней, так и на нижней панелях. В противном случае собрать подставку будет сложно.
Когда все пазы выбраны, остается только разрезать заготовку на две части – верхнюю и нижнюю панели, выпилить их по отмеченному контуру и обработать края, скруглив острые углы. Чтобы выполнить эту работу быстро и аккуратно, нужно сначала вырезать одну из панелей, например, верхнюю, а затем, сложив обе части вместе, вырезать нижнюю, используя верхнюю как шаблон.
Ширина боковых стенок ящика зависит от требуемой глубины, которая в свою очередь определяется максимальным размером (длиной) используемых для измельчения барабанов. Глубину короба я сделал равной 100 мм. Для этого пришлось вырезать боковые стенки шириной 112 мм (100 мм — высота коробки и по 6 мм на верхний и нижний пазы).
Разметка верхней и нижней панелей на одном листе ДСП.
В одной из боковых стенок ящика нужно вырезать отверстие для шланга пылесоса. В какой из боковых стенок и в каком месте она сделана, особого значения не имеет, главное, чтобы шланг не мешал работе.
Я также вырезал центральное отверстие диаметром 084 мм в верхней пластине с помощью того же инструмента, который я выбрал для нескольких неглубоких надрезов. Чтобы не повредить фрезу на выходе, обязательно под пластину снизу подложить пару распорных планок, так как отверстие должно быть сквозным. Затем фрезой для выбора фальца с направляющим подшипником по верхнему краю отверстия выделил фальц глубиной 6 мм для шайб-вкладышей.
Шайбы-вкладыши можно вырезать из любого достаточно прочного листового материала. Я, например, сделал их из оргстекла толщиной 6 мм. Сначала нужно вырезать все шайбы по внешнему диаметру, а затем подобрать внутренние отверстия под размеры имеющихся шлифовальных барабанов. Желательно сразу сделать еще пару шайб впрок – вдруг в будущем, помимо уже имеющихся, придется покупать один-два барабана других размеров.
Если пазы в верхней и нижней панелях вырезать точно и аккуратно, то сборка подставки не займет много времени. Сначала в пазы нижней панели вклеиваются бортики коробки, а затем сверху они закрываются верхней панелью. Все стыки стенок короба желательно дополнительно заполнить термоклеем или каким-либо другим герметиком. Если зазор между внутренней кромкой отверстия сменных шайб и шлифовальным барабаном не превышает 1-2 мм, то пылеудаление происходит очень эффективно за счет герметичности коробки.
Стойку устанавливаю на стол сверлильного станка и креплю самодельными болтами М8 с барашковой головкой. Для этого в нижнюю панель точно напротив отверстий в столе сверлильного станка запрессовываются Т-образные резьбовые втулки-гайки М8. Такой способ крепления позволяет быстро превратить сверлильный станок в кромкошлифовальный станок и так же быстро снять подставку, когда станок понадобится для другой работы.
См. также: Насадка к УШМ для резьбы по дереву и отзывы мастера
ШЛИФОВАЛЬНЫЙ СТОЛ – ПОДСТАВКА ДЛЯ СВЕРЛИЛЬНОГО СТАНКА СВОИМИ РУКАМИ
Выборка продольных канавок по направляющей линейке. Ширина выбранных пазов должна быть точно равна той, которая используется для изготовления подставки из ДСП. Б Если края деталей после резки заготовки получаются не слишком ровными, их можно обработать кромкорезом с подпятником. Края нижней панели обрезаются путем складывания обеих частей вместе, используя верхнюю панель в качестве шаблона.
Все углы и острые кромки верхней и нижней панелей желательно закруглить, обработав их профильным кромкорезом. E Набор шайб-вкладышей, вырезанных из оргстекла 6 мм. Для их размещения предусмотрена складка глубиной 6 мм.
Сначала в пазы нижней панели вклеиваются борта коробки, а затем сверху они закрываются верхней панелью. Все стыки стенок короба желательно дополнительно заполнить термоклеем или каким-либо другим герметиком.
Один из возможных вариантов крепления подставки к столу сверлильного станка – четырьмя самодельными винтами с барашковой головкой.
Смотрите также: Приставка к столу болгарки своими руками
ВИДЕО ПРИМЕЧАНИЕ – ШЛИФОВАЛЬНЫЙ БАРАБАН ДЛЯ СВЕРЛИЛЬНОГО СТАНКА СВОИМИ РУКАМИ
Шлифовальный барабан для сверлильного станка своими руками | DIY
Посмотреть это видео на YouTube
© Автор: R. FOX, Канада
ИНСТРУМЕНТЫ ДЛЯ МАСТЕРОВ И ТОВАРЫ ДЛЯ ДОМА ОЧЕНЬ ДЕШЕВЫЕ. БЕСПЛАТНАЯ ДОСТАВКА. ЕСТЬ ОТЗЫВЫ.Подписывайтесь на обновления в наших группах и делитесь.
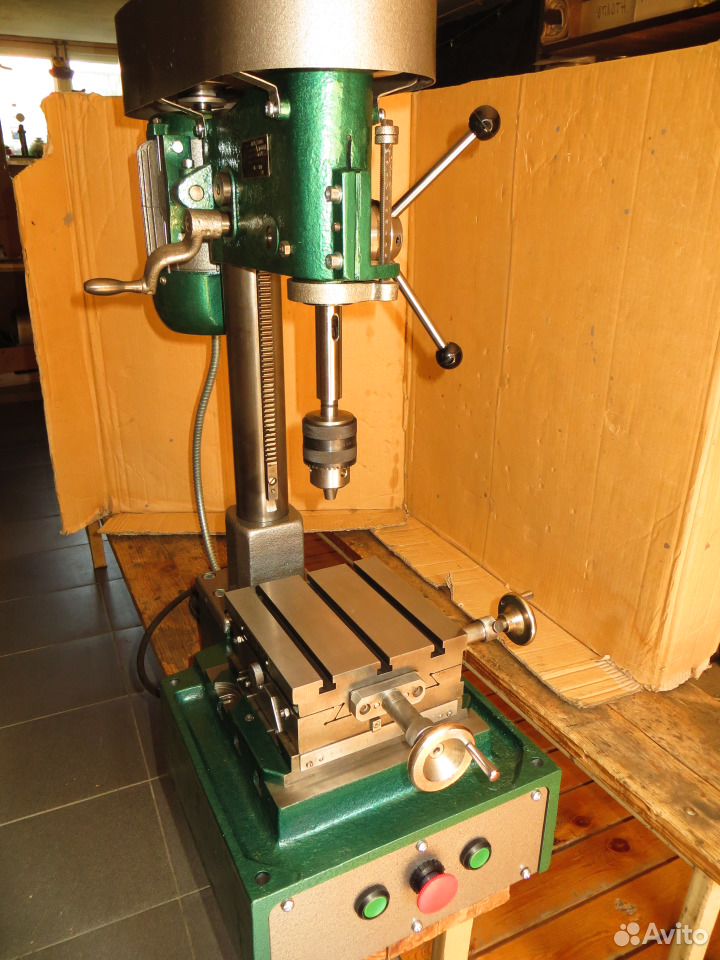
Давай дружить!
Схемы стола для шитья своими руками – как сделать дома
Работа на швейной машине – тяжелая работа. Вы должны все время концентрировать свое внимание на работе.
Таким образом, наличие организованного и просторного швейного стола является необходимостью для каждого энтузиаста шитья. Это не только украсит ваш стол, но и повысит вашу эффективность и создаст приятную рабочую атмосферу.
При планировании швейного стола необходимо помнить о некоторых основных вещах: места для хранения швейных принадлежностей, место для установки машины и так далее.
Вы можете использовать свой творческий потенциал, чтобы спланировать его так хорошо, как вы хотите, если это удобно в вашей работе. Тем не менее, чтобы помочь вам, ниже предлагаются несколько планов стола для шитья, чтобы вы могли почерпнуть идеи и спланировать свои!
Содержимое
- Схемы швейного стола «Сделай сам»
- Изготовление складного и передвижного швейного стола
- Подготовьте стол для шитья из ИКЕА
- Изготовьте простой стол для шитья из фанеры
- Превратите комод в стол для шитья!
- Сделать недорогой стол для шитья
- Добавить специальные места для хранения
- Заключительные слова о чертежах столиков для шитья
- Связанные посты для Читатели чертежей столиков для шитья
Планы столов для шитья своими руками – Как сделать это дома
5 Сделай самИзготовление складного и передвижного швейного стола
Стол для шитья поразит вас своей эффективностью. Создание такого стола даст вам достаточную вместимость, а также использование пространства вашей комнаты.
Вы можете разложить стол, когда будете делать работу, которая, конечно, оторвется с большим пространством, а затем сложите его до исходного размера. Вы также можете перекатывать его, чтобы работать в любом месте, и хранить в углу, чтобы сэкономить место в комнате.
Читайте также: Лучшие бесплатные инструменты для тестирования скорости SSD и производительности жесткого диска 2022
Дорого ли это делать? Нисколько. Вам не понадобится какой-либо специальный инструмент, только несколько предметов домашнего обихода, и все готово.
В двенадцатиминутном видео вы найдете все инструкции, как это сделать.
Подготовьте стол для шитья из ИКЕА
В следующем видео показаны красивые самодельные идеи организации стола для шитья от ИКЕА. Как бы удивительно это ни выглядело, сделать такой не так уж и сложно. Все материалы и процедуры подробно описаны в видео, следуя которому вы тоже можете приготовить!
Вам понадобится несколько материалов, таких как фанера, сверлильный станок, шурупы, колеса и т. д. Такой дизайн, несомненно, поможет вам поддерживать порядок в своих вещах. Дама даже предложила хорошую настольную лампу для швейных работ, а также такие вещи, как держатели инструментов для хранения вещей. Следите за этим сейчас.
Изготовление простого столика для шитья из фанеры
Следуя этому видео, вы легко сможете самостоятельно изготовить стол для шитья из фанеры. Все, что вам нужно, это фанера и несколько инструментов для крафта, таких как сверлильный станок, электрическая отвертка, молоток и гвозди, электрический станок для резки дерева и т. д.
Можно собрать держатель станка и прикрепить его под столом, вырезая из древесины стола нужный участок, как это сделано на видео. После завершения изготовления покройте стол деревянным шпоном, чтобы придать ему гладкий и красивый вид.
На столе будет дополнительное место для хранения швейных принадлежностей. Он также легкий по весу, поэтому вы можете перемещать и размещать его в любом месте.
Превратите комод в швейный стол!
Да, вы не ослышались! Эта женщина переделала свой сломанный туалетный столик в швейный стол со съемными полками для хранения вещей. Если у вас есть туалетный столик, достаточно старый, чтобы его скоро выкинули, зачем его тратить? Как показано в этом видео, вы также можете использовать его для своего швейного стола.
Так просто, как кажется, его можно сделать из дерева. Выньте ящики и замените их деревянными досками измененного размера на направляющих, чтобы сделать хранилище. Вы можете использовать цветную бумагу, чтобы обернуть их, чтобы они выглядели красиво. Доски можно отсоединить, когда вы делаете свою работу на столе, и прикрепить обратно после того, как вы закончите.
Посмотрите видео, чтобы узнать, как это делается.
Сделать дешевый стол для шитья
Сделать дешевый стол для шитьяЭтот чертеж стола для шитья заставит вас задуматься. Вы не хотите тратить деньги на свой швейный стол? Ну вот и все. Ни один швейный стол не может быть дешевле этого. Эта дама в своих двух обучающих видеороликах показала, как она сделала свой стол для шитья из дешевых материалов, таких как пенопласт, пластиковый стол и даже кофейная кружка!
План стола также позволит вам скорректировать пространство на случай, если вам понадобится поработать над большим проектом из ткани. И так, чего же ты ждешь? Смотри видео и создавай прямо сейчас!
Добавление пользовательских единиц хранения
Дизайн этого швейного стола поражает как внешним видом, так и эффективностью. Если вы беспокоитесь о хранении ткани, катушек с нитками и других элементов, этот план стола идеально подходит для вас.
Вам не нужно беспокоиться о месте для множества ваших швейных инструментов. Этот план стола поставляется с множеством стеллажей, ящиков, где вы можете хранить свои вещи в организованном порядке так, как вы хотите. На видео показаны все процессы изготовления такого красивого столика. Давайте взглянем!
Читайте также: Почему экосольвентная бумага для термопереноса более популярна?
Заключительные слова о чертежах швейных столов
Хороший швейный стол поможет сохранить хорошее настроение во время работы и избавит вас от хаоса. Ткани и нитки могут превратиться в настоящий беспорядок, если их хранить в беспорядке. Таким образом, хороший план швейного стола – это то, что ищет каждый канализатор.