3.3. Сварочная проволока
3.3.1. Для автоматической и механизированной сварки под слоем флюса, а также для механизированной сварки в углекислом газе сталей всех марок, приведенных в п. 1.1.3 настоящего РД, применяется сварочная проволока сплошного сечения по ГОСТ 2246. Области применения сварочной проволоки для этих видов сварки приведены в табл. 3.5, химический состав — в приложении 6.
3.3.2. Для механизированной сварки порошковой проволокой применяются самозащитные порошковые проволоки, изготовленные по ГОСТ 26271 и соответствующим техническим условиям.
3.3.3. Марки порошковой
проволоки, которые могут быть применены
для сварки металлоконструкций,
изготовленных из стали с нормативным
пределом текучести не более 375 МПа (стали
марок, приведенных в приложении 1, которые
соответствуют обозначениям стали до
С375Д включительно), указаны в табл.
Возможность сварки порошковой проволокой более прочных сталей, а также марки порошковой проволоки для их сварки должны быть согласованы с проектной и материаловедческой организациями.
3.3.4. Каждая часть сварочной проволоки, отделенная от бухты (мотка), должна быть снабжена биркой, на которой указывается завод-изготовитель, марка, номер плавки и диаметр проволоки.
3.3.5. Сварочная проволока сплошного сечения должна храниться в условиях, исключающих ее загрязнение или коррозию. Перед употреблением проволока должна быть проконтролирована путем внешнего осмотра на предмет определения чистоты поверхности.
При необходимости проволоку очищают от ржавчины и грязи травлением в 5% растворе соляной или ингибированной (3% раствор уротропина в соляной кислоте) кислоты.
Можно очищать
проволоку, пропуская ее через специальные
механические устройства (в том числе
через устройства, заполненные сварочным
флюсом, кирпичом, осколками наждачных
кругов и войлочными фильтрами). Перед
очисткой бухту проволоки рекомендуется
прокалить при температуре 150—200°С в
течение 1,5–2 часов.
Разрешается также очищать проволоку наждачной шкуркой или любыми другими способами до металлического блеска. При очистке проволоки нельзя допускать ее резких перегибов (переломов), что может нарушить нормальный процесс подачи проволоки в зону сварки.
3.3.6. Порошковая проволока должна храниться в мотках в специальной таре, предупреждающей ее увлажнение. Перемотку порошковой проволоки производить запрещается.
Каждый моток порошковой проволоки должен быть проконтролирован путем внешнего осмотра на предмет определения чистоты поверхности проволоки, повреждения и переломов оболочки.
Перед применением
порошковая проволока должна быть
прокалена по режиму, приведенному в
табл. 3.4. После прокалки проволока может
быть использована в течение пяти суток,
если она хранится в соответствии с
требованиями п. 1.3.16 настоящего РД. По
истечении указанного срока порошковую
проволоку перед применением следует
вновь прокалить.
3.3.7. Каждая партия порошковой проволоки перед применением должна быть проверена на сварочно-технологические свойства путем наплавки валика на пластину и визуального контроля поверхности валика на наличие трещин, пор и неровностей. Наплавка валика производится на пластину толщиной 14—18 мм из углеродистой стали в нижнем положении по режиму, предписанному для данной марки проволоки. Сварочно-технологические свойства считаются удовлетворительными, если: на поверхности валика не будет обнаружено трещин; максимальный размер поры не превышает 1,2 мм, а число пор на любых 100 мм протяженности валика не превышает 5; глубина чешуйчатости не превышает 1,5 мм.
Таблица 3.5
Стальная сварочная проволока – Сварка металлов
Стальная сварочная проволока
Категория:
Сварка металлов
Стальная сварочная проволока
Стальная холоднотянутая сварочная проволока изготовляется по ГОСТ 2246—70. Из стальной сварочной проволоки изготовляют стержни электродов с покрытием для ручной дуговой сварки (штучные электроды). В маркировке такой проволоки будет присутствовать буква Э (электродная). При механизированных способах сварки под флюсом и в ереде защитных газов стальная сварочная проволока используется в качестве плавящегося электрода без покрытия.
Диаметры проволоки установлены следующие: 0,3; 0,5; 0,8; 1,0; 1,2; 1,4; 1,5; 1,6; 2,0, 2,5; 3,0; 4,0; 5,0; 6,0; 8,0; 10; 12 мм. Поставляется проволока в мотках весом 1,5—40 кг. Стальную сварочную проволоку по химическому составу делят на три группы: низко-углеродистая, легированная, высоколегированная.
Низкоуглеродистая сварочная проволока предназначена для сварки малоуглеродистых и некоторых среднеуглеродистых сталей, а также некоторых низколегированных сталей. Предусмотрено 6 марок такой проволоки: Св-08; Св-ША; Св-08АА; Св-08ГА; Св-ЮГА; Св-10Г2. Число указывает на содержание в проволоке углерода в сотых долях процента. Буква А указывает на повышенную чистоту металла сварочной проволоки по содержанию вредных примесей серы и фосфора — такая проволока обеспечивает наплавленный металл (металл шва) с повышенными пластическими свойствами.
Расшифруем одну из марок проволоки — Св-08ГА: Св — проволока сварочная; 08 — содержание углерода 0,08%; Г —в проволоке присутствует марганец, в среднем 1%; А — гарантируется повышенная пластичность наплавленного металла.
Легированная сварочная проволока предназначена для сварки низколегированных и легированных сталей. В этой группе предусмотрено 30 марок проволоки: Св-08ГС; Св-18ХГС; Св-10Х2СМД и др.
Высоколегированная сварочная проволока предназначена для сварки специальных высоколегированных сталей и для наплавки. В этой группе предусмотрено 39 марок проволоки: Св-06Х19Н9Т; Св-08Х14ГНТ; Св-13Х25Н18 и др.
Поверхность стальной сварочной проволоки должна быть чистой и гладкой, без окалины, ржавчины и масла, без заусениц и вмятин. Ннзкоуглеродистая и легированная сварочные проволоки могут выпускаться с омедненной поверхностью (О).
Пример маркировки стальной, сварочной проволоки на этикетке (бирке) мотка проволоки: Проволока 1,6 Св-08ГА ГОСТ 2246—70 (Проволока сварочная, диаметром 1,6 мм, марки Св-08ГА, предназначена для сварки). Проволока 3 Св-08А-Э-0 ГОСТ 2246—70 (Проволока сварочная, диаметром 3 мм, марки Св-08А, предназначена для изготовления электродов, с омедненной поверхностью).
Реклама:
Читать далее:
Электродные покрытия
Статьи по теме:
Сварочная проволока с нанокомпозиционным покрытием для сварки высокопрочных сталей
Предлагаемое изобретение относится преимущественно к машиностроению и может быть применено при дуговой сварке и наплавке металлических деталей в среде защитного газа и под флюсом.
Известен сварочный материал (см. Патон Б.Е., Мусияченко В.Ф., Кирьяков В.М. и др. Авторское свидетельство СССР №1447619 от 08.10.1986 г. Опубликовано 30.12.1988 г. Бюл. №48).
Известна сварочная проволока (см. Сидлин З.А., Строев B.C., Иванов В.А. и др. Сварочная проволока. Авторское свидетельство СССР №469565 от 05.09.1975 г. Опубликовано 05.05.1975 г. Бюл. №17). Состав проволоки содержит бор, лантан и церий, что позволяет измельчать дендритную микроструктуру, раскислять сварочную ванну и повышать пластичность сварочного шва.
Известна наноструктурированная сварочная проволока (см. Паршин С.Г. Наноструктурированная сварочная проволока. Патент РФ №2538228 от 01.07.2013 г. Опубликовано 10.01.2015 г. Бюл. №1), которая принята за прототип. Указанная проволока состоит из металлического стержня, на поверхность которого нанесено нанокомпозиционное покрытие. Покрытие выполнено электролитическим способом и включает металлическую матрицу с распределенными в ней наноразмерными частицами фторида металла и редкоземельных металлов. Проволока по прототипу позволяет улучшить капельный перенос электродного металла и механические свойства сварных соединений. Однако указанная проволока недостаточно эффективно влияет на модифицирование микроструктуры при сварке легированных высокопрочных сталей, что не позволяет повысить пластичность и ударную вязкость сварных швов.
Техническим результатом предлагаемого изобретения является повышение механических свойств сварных соединений легированных высокопрочных сталей за счет комплексного модифицирования и рафинирования сварочной ванны путем нанесения на поверхность сварочной проволоки нанокомпозиционного покрытия, содержащего наноразмерные частицы фторида и борида редкоземельного металла.
Сущность предлагаемого изобретения заключается в том, что на поверхности металлического стержня размещают нанокомпозиционное покрытие, состоящее из металлической матрицы, наноразмерных частиц фторидов и боридов редкоземельных металлов с размером частиц менее 1000 нм. В отличие от прототипа нанокомпозиционное покрытие содержит наноразмерные частицы фторида редкоземельного металла и борида редкоземельного металла при следующем соотношении объемов матрицы и наноразмерных частиц в покрытии, %:
Металлическая матрица – 55-96
Наноразмерные частицы фторида редкоземельного металла – 3-20
Наноразмерные частицы борида редкоземельного металла – 1-25.
В качестве фторида редкоземельного металла могут применяться: фторид лантана, фторид иттрия, фторид церия, фторид тория. В качестве борида редкоземельного металла могут применяться: борид лантана, борид иттрия, борид церия, борид тория.
При объеме фторида редкоземельного металла менее 3% отсутствует воздействие нанокомпозиционного покрытия на процесс капельного перехода и удаление водорода, а при увеличении объема более 20% снижается стабильность горения дуги. При объеме борида редкоземельного металла менее 1% снижается влияние покрытия на процессы модифицирования и улучшения микроструктуры наплавленного металла, а при увеличении объема более 25% происходит ухудшение механических свойств наплавленного металла и электрической проводимости композиционного покрытия.
Такое сочетание известных и новых признаков позволяет улучшить механические свойства сварного шва легированных высокопрочных сталей. Это становится возможным, поскольку проволока содержит систему комплексных модификаторов, которые обладают модифицирующим и рафинирующим воздействием. Для улучшения механических свойств в расплавленную сталь необходимо вводить комплексные модификаторы, которые содержат систему элементов, в которую могут входить бор, редкоземельные металлы, титан, цирконий и щелочноземельные металлы, например: La-B, Ti-B-Ca, Mg-Zr-Се, La-B-Ca и др. (см. Задиранов А.Н., Кац A.M. Теоретические основы кристаллизации металлов и сплавов. Москва: РУДН, 2008. – 225 с.).
Введение комплексных модификаторов позволяет одновременно измельчать и рафинировать микроструктуру легированных сталей. Модификация (измельчение) зерна за счет введения модификаторов основана на изменении поверхностной энергии на границе кристалл-расплав, уменьшении поверхностного натяжения расплава и увеличения количества центров кристаллизации. Одновременное введение фторида и борида редкоземельного металла позволяет изменить свойства поверхности на границе твердой и жидкой фазы, а также образовать дополнительные центры кристаллизации за счет тугоплавких боридов и образующихся нитридов. Введение фторида редкоземельного металла позволяет уменьшить количество остаточного диффузионного водорода в сварочном шве за счет связывания водорода H2 в плазме сварочной дуги в нерастворимые в сварочной ванне соединения HF.
Рафинирование заключается в удалении оксидов и сульфидов железа: FeO, FeS из сварочной ванны путем металлургических реакций с переходными металлами. Указанные реакции позволяют уменьшить количество легкоплавких эвтектик и ликваций в наплавленном металле сварного шва, что снижает межкристаллитную и межзеренную химическую неоднородность и приводит к повышению прочности межзеренных границ. Измельчение зерна в результате введения модификаторов приводит к увеличению протяженности межзеренных границ и уменьшению их ширины, что также увеличивает прочность межзеренных границ.
Увеличение прочности межзеренных границ в результате модифицирования микроструктуры, уменьшение количества остаточных газов H2, N2, O2 и рафинирование сварочной ванны по извлечению оксидов и сульфидов железа позволяет повысить пластичность, ударную вязкость сварных швов и их сопротивляемость хрупкому разрушению и возникновению холодным трещинам.
Термодинамические расчеты фазового состава металлургических систем при помощи программы FACT (Facility for the Analysis of Chemical Thermodynamics) показывают, что в равновесной системе Fe-LaF3-LaB6 при температуре сварочной ванны 1000-3000 K образуется значительное количество свободного лантана La и бора B в конденсированной фазе, табл. 1.
Аналогичное образование свободных элементов РЗМ: церия Ce, иттрия Y, тория Th и бора B в конденсированной фазе, согласно расчетам, отмечается в системах: Fe-(РЗМ)F3-CeB6, Fe-(РЗМ)F3-YB6, Fe-(РЗМ)F3-ThB6, основу которых составляют тугоплавкие гексабориды: LaB6(Тпл=2715°C), СеВ6(Тпл=2190°C), YB6(Тпл=2600°C), ThB6(Тпл=2450°C).
Термодинамические расчеты показывают, что наличие в сварочной ванне La и В приводит к образованию нитридов LaN, BN в системе N2-LaF3-LaB6, которые имеют высокие температуры плавления: LaN(Тпл=2450°C), BN(Тпл=3000°C), табл. 2.
Аналогичное образование нитридов РЗМ: церия Се, иттрия Y, тория Th и бора B в конденсированной фазе, согласно расчетам, отмечается в системах: Fe-(РЗМ)F3-CeB6, Fe-(РЗМ)F3-YB6, Fe-(РЗМ)F3-ThB6. Нитриды церия, иттрия, тория также имеют высокие температуры плавления: CeN(Тпл=2570°C), YN(Тпл=2670°C), ThN(Тпл=2820°C) (см. Двойные и тройные карбидные и нитридные системы переходных металлов. Холлек X. /пер. с нем. Под ред. Левинского Ю.М., М.: Металлургия, 1988. – 319 с.).
Тугоплавкие нитриды редкоземельных металлов (РЗМ) и бора увеличивают количество центров кристаллизации в сварочной ванне, что приводит к модифицированию (измельчению) микроструктуры сварного шва.
Наличие в сварочной ванне редкоземельного металла, например La, Се, Y, Th способствует интенсивным металлургическим реакциям по десульфурации – удалению сульфидов железа FeS путем связывания серы в тугоплавкие сульфиды редкоземельных металлов по реакциям:
Термодинамические расчеты констант равновесия металлургических реакций Kр показывают высокую вероятность указанных реакций по десульфурации в сварочной ванне при Т=1000-2000 K, табл. 3.
В результате реакций 1-4 в сварочной ванне уменьшается содержание легкоплавкого сульфида FeS(Тпл=1194°C) путем образования тугоплавких сульфидов РЗМ: La2S3(Tпл=2150°C), Ce2S3(Tпл=1890°C), Y2S3(Tпл=1925°C), Th2S3(Tпл=1950°C). Уменьшение растворенного сульфида FeS в сварочной ванне снижает концентрацию легкоплавких эвтектик при первичной кристаллизации, что снижает межкристаллитную и межзеренную химическую неоднородность. Это способствует увеличению прочности и пластичности металла сварного шва (см. Гуляев А.П. Металловедение. М.: Металлургия, 1986. – 272 с.).
Наличие в сварочной ванне редкоземельного металла позволяет интенсифицировать металлургические реакции по раскислению железа:
Термодинамические расчеты констант равновесия металлургических реакций Кр показывают высокую вероятность указанных реакций при Т=1000-2000 К, табл. 4.
В результате реакций раскисления образуются тугоплавкие оксиды РЗМ: La2O3(Тпл=2280°C), CeO2(Тпл=2600°C), Y2O3(Tпл=2430°C), ThO2(Тпл=3050°C). Образование оксидов РЗМ снижает концентрацию растворенного в сварочной ванне оксида железа FeO(Тпл=1377°C) и способствует увеличению дополнительных центров кристаллизации. Это также улучшает механические свойства сварного шва.
Одной из причин хрупкого разрушения и появления холодных трещин при сварке легированных высокопрочных сталей является наличие остаточного водорода и азота. Термодинамические расчеты показывают, что при дуговой сварке в диапазоне температур 1000-6000 K в газовой фазе при равновесной концентрации веществ в системах: H2-LaF3-LaB6, N2-LaF3-LaB6, парциальное давление молекулярного водорода и азота уменьшается, табл. 5.
Аналогичное уменьшение парциального давления молекулярного водорода и азота происходит в системах: H2-(РЗМ)F3-CeB6, N2-(РЗМ)F3-CeB6; H2-(РЗМ)F3-YB6, N2-(РЗМ)F3-YB6; H2-(РЗМ)F3-ThB6, N2-(РЗМ)F3-ThB6. Согласно закону Сивертса растворимость молекулярного водорода и азота в сварочной ванне пропорциональна квадратному корню из парциального давления газа, поэтому уменьшение парциального давления газов Н2, N2 над сварочной ванной уменьшает концентрацию остаточных газов в сварном шве, что улучшает сопротивляемость хрупкому разрушению.
Примером применения предлагаемой проволоки является механизированная сварка пластин толщиной 14 мм из стали 10ХСНД в среде смеси: аргон 75% + CO2 25% с применением полуавтомата ESAB Origo MIG L405. Для получения проволок с нанокомпозиционными покрытиями использовали сварочную проволоку Св-08Г2С без покрытия диаметром 1,2 мм. Нанокомпозиционные покрытия наносили электрохимическим способом из коллоидных никельсодержащих электролитов с нанодисперсными частицами фторида лантана LaB6 и гексаборида лантана LaB6. Для механических испытаний образцов по ГОСТ 6996-66 применяли разрывную машину «Super L 60», маятниковый копер РН450, твердомер «DuraScan-20», табл. 6.
Таким образом, предлагаемая проволока обеспечивает технический эффект, который выражается в улучшении механических свойств сварных соединений высокопрочных сталей, может быть изготовлена и применена с использованием известных в технике средств, следовательно, она обладает промышленной применимостью.
Сварочные материалы для газовой сварки
Газосварка представляет собой процесс, при котором кромки соединяемых элементов нагреваются сгоранием горючих газов в смеси с кислородом. Газовая сварка своими руками применяется для изготовления и ремонта изделий из листовой стали толщиной 1-5 мм, чугуна, латуни, меди, алюминия, исправления литьевых дефектов, наплавки твердых сплавов. Сварочные материалы для газовой сварки включают: горючий газ (ацетилен, пропан, водород), технически чистый кислород, присадочную проволоку, флюсы, в случае их потребности при работе с конкретным металлом или сплавом.
Сварочная проволока: разновидности и особенности применения
В большинстве случаев для сварки газом используют сварочную проволоку, близкую по химическому составу к металлу изделия. Ее поверхность должна быть гладкой, очищенной от окалины и других загрязнений. Температура плавления присадочной проволоки не должна превышать температуру плавления основного металла. Если для сварки цветных металлов и сплавов – меди, латуни, свинца – нет соответствующей проволоки, применяют нарезанные из свариваемого металла полоски. Сварочная проволока для газосварки
Способы ручной газосварки – левый или правый – выбирают в зависимости от положения шва в пространстве. При потолочном шве и правом способе сварочная проволока также играет роль препятствия для стекания металла.
Сварочная проволока для сварки газом изготавливается из:
- низкоуглеродистых и легированных сталей;
- алюминия и его сплавов;
- меди и ее сплавов.
Присадочные материалы для газовой сварки и наплавки чугуна выпускают в виде прутков, имеющих следующую маркировку:
- А – для горячей газосварки, предусматривающей общий подогрев изделия;
- Б – для сваривания изделий с местным подогревом;
- НЧ-1, НЧ-2 – для низкотемпературной сварки отливок с тонкими и толстыми стенками соответственно;
- БЧ, ХЧ – применяются для износостойкой наплавки.
Виды применяемых горючих газов
БаллонГазовая сварка цветных металлов и углеродистых сталей чаще всего осуществляется с использованием ацетилена. Это объясняется высокой температурой пламени и хорошей теплотой сгорания. Ацетилен представляет собой газ с характерным запахом, который придают присутствующие в нем примеси фтористого водорода и сероводорода. При нагревании до 500 градусов и при определенных концентрациях в смесях с кислородом и воздухом ацетилен становится взрывоопасным. Образование ацетилена происходит в результате реакции карбида кальция с водой. Сам карбид кальция образуется в результате сплавления обожженной извести и кокса.
В качестве горючих могут использоваться нефтяной и пиролизный газы. Они представляют собой газовые смеси, образующиеся при термическом разложении нефти и ее продуктов. Применяются для сваривания, резки и пайки стальных деталей толщиной, не превышающей 3 мм, и для сварки цветных металлов и их сплавов. Природный газ является продуктом разработки газовых месторождений и на 93-99% состоит из метана.
БаллонТехнический пропан и пропан-бутановая смесь являются побочными продуктами при добыче и переработке нефти и естественных нефтяных газов. Их применяют при сваривании деталей толщиной до 6 мм, в отдельных случаях – до 12 мм. С помощью этих газов можно сваривать и паять чугун, цветные металлы и сплавы, осуществлять кислородную и кислородно-флюсовую резку, наплавку, напыление пластмасс.
Сваривание металла в домашних условиях с помощью водорода стала возможна благодаря разработке специальных электролизеров, которые могут работать и от домашней двухфазной, и от трехфазной сети. В этих аппаратах вода разлагается на кислород и водород, причем, в нужных для сварочного процесса пропорциях. Размерный ряд выпускаемых электролизеров позволяет охватить практически все виды газовой сварки, пайки, наплавки, порошкового напыления, ручной и машинной кислородной резки. Аппараты разной мощности позволяют производить как микросварку и микропайку, так и резку листовой стали толщиной порядка 300 мм.
Виды флюсов для газосварки
Газовая сварка меди, алюминия, магния и их сплавов сопровождается активным образованием оксидов на поверхности свариваемых металлов под воздействием кислорода, содержащегося в воздухе. Тугоплавкие оксиды значительно затрудняют сварочный процесс.
С целью защиты металлов от окисления при сваривании используют флюсы для газовой сварки, которые представляют собой специальные сварочные порошки или пасты. В качестве флюсов используют борную кислоту и прокаленную буру. Их наносят на кромки свариваемого металла, на сварочную проволоку и прутки. При температуре сварки легкоплавкие флюсы образуют шлаки, всплывающие на поверхность расплавленного металла и предохраняющие его от окисления.
Для тех, кто постоянно варит при помощи ручной дуговой сварки, актуальным является вопрос, как варить полуавтоматом.
Создание аппарата для контактной сварки своими руками поможет сэкономить кругленькую сумму. Подробную инструкцию вы найдете в этой статье.
Хотите сварить алюминий или медь? Есть альтернативный способ! Подробнее по https://elsvarkin.ru/texnologiya/xolodnaya-svarka-metalla/ ссылке.
Основы теоретической подготовки специалистов по газовой сварке
Для студентов, изучающих курс “Технология газовой сварки”, реферат можно подготовить, используя следующую литературу:
- Глизманенко Д.
А. “Газовая сварка и резка металлов”;
- Багрянский К. В. “Теория сварочных процессов”;
- Геворкян В. Г. “Основы сварочного дела”.
По курсу “Газовая сварка” реферат должен отразить следующие основные моменты:
- назначение, преимущества и недостатки данного вид создания неразъемных соединений;
- необходимые для сварочного процесса материалы;
- используемое оборудование и аппаратуру;
- основные технологические моменты газосварки.
ArticleName | Влияние легирования сварочной проволоки скандием на механические свойства и структуру сварных соединений алюминиевых сплавов | ArticleAuthorData | АО «Арконик СМЗ», Москва, Россия: А. М. Дриц, директор по развитию бизнеса и новых технологий, эл. почта: Alexander.Drits@arconic.
ФГБОУ ВО «Московский политехнический университет», Москва, Россия:
АО «Опытный завод «Авиаль», Москва, Россия: | Abstract | Рассмотрено влияние скандия в присадочной проволоке на сопротивление образованию горячих трещин при аргонодуговой сварке алюминиевых сплавов 1420, 1565ч и 1901. Показано, что легирование присадочной проволоки скандием способствует увеличению критической скорости деформации по пробе МВТУ и почти полному подавлению образования горячих трещин по пробе «рыбий скелет». Установлено, что повышение механических свойств сварных соединений при введении скандия в присадочную проволоку достигается в результате измельчения кристаллической структуры шва и упроч нения твердого раствора скандием. Достижение наиболее выраженного эффекта от введения в сварочную проволоку скандия наблюдается при его концентрации 0,15–0,25 %. | References | 1. Рабкин Д. М. Металлургия сварки плавлением алюминия и его сплавов. — Киев : Наукова думка, 1986. — 256 с. |
Сварочная проволока и метизы — ООО ЮГМЕТИЗ
Наши преимущества перед другими металлоторгующими организациями — это богатый опыт работ, всесторонний подход к требованиям клиентов, а также идеальное соотношение стоимости сварочной проволоки и ее качества. Мы открыты для взимовыгодного партнерства и установления деловых отношений в области поставок сварочной проволоки и метизов. Постоянно увеличивающееся количество клиентов говорит о том, что мы осуществляем верные шаги и достойны их доверия.

Проволока пружинная по ГОСТ 1071-81 является термически обработанной и используется для производства пружин, навиваемых в холодном состоянии и не подвергаемых закалке. Сфера применения пружинной проволоки достаточно разнообразна — это и мебельная промышленность, и производство комплектующих для автомобилей, шариковые ручки, зажигалки — практически всё, что нас окружает.

Группа компании ЮгМетиз успешно работает на метизном рынке России с 1994 года. Офис ООО ЮгМетиз находится в Волгограде. Наш склад расположен рядом с оживленной транспортной магистралью. На складе всегда представлен широкий ассортимент метизной продукции. Наши товары: проволока ВР-1, проволока сварочная Св08Г2С, проволока вязальная, проволока вязальная оцинкованная, проволока пружинная, электроды, крепеж, гвозди, метизы, болты, гайки, шайбы, сетка сварная, сетка РАБИЦА, стропы, канаты.
Общая классификация и сварочно-технологические свойства флюсов
Классификация
Классификация сварочных флюсов имеет четыре критерия, которые разделяют присадочное средство. Заключаются они в следующих пунктах:
- назначение флюса;
- способ его изготовления;
- структура и физические параметры;
- химический состав.
Назначение
В зависимости от состава и свойств гранулированного средства, оно может быть применено для обеспечения сварочных процессов в работе с углеродистыми, легированными и цветными металлами. Его используют для электродуговой, газовой и электрошлаковой сварки, а также работах с неплавящимися электродами. Некоторые классы флюсов взаимозаменяемы. Так, флюс для сварки алюминия, может быть использован и для создания соединений на легированных сталях. В его состав входят натрий, калий и литий, которые будут положительно сказываться и на других металлах. «Алюминиевый» флюс хорошо подойдет для сварки угольными электродами. Другие гранулированные смеси узко специализированны и не пригодны для широкого применения.
Способ изготовления
В промышленности имеются три способа производства флюса:
- Плавленные. Для этого применяют электрические или угольные печи. Компоненты шихты разогревают до жидкого состояния и, сплавляясь, образуют полезную смесь. Брикеты и комки материала разбиваются до мелких частей. В готовом виде такие порошки имеют мелкодисперсную структуру серого цвета.
- Механические смеси. Это соединение нескольких видов флюса в один состав путем физического перемешивания гранул между собой.
Технология применяется для конкретных видом металлов. Постоянного состава не существует, а изготовление производится на заказ. Имеет существенный недостаток в виде разности веса и размера частиц, что приводит к их разделению при транспортировке и подаче из бункера.
- Керамические. Соединение образовывается за счет скрепления порошкообразных веществ клеем, в роли которого выступает жидкое стекло. Альтернативным методом является спекание без сплавления. Компоненты шихты разогреваются до слипания в комки. После остывания они проходят процедуру измельчения. Благодаря недопущению сплавления сохраняются легирующие вещества.
Структура и параметры
Внешний вид и физическое строение порошкообразных средств для сварки может отличаться. Наиболее распространенными являются стекловидные зерна. Они имеют прозрачный цвет и круглую структуру. Отличаются более высокой насыпной массой, поэтому плотно укрывают соединение, защищая его от внешней среды.
Вторая категория флюсов создается в виде пемзообразного вещества. Это пенистые гранулы овальной или круглой формы. Цвет может варьировать от белого до коричневого. Порошок, из-за легкого веса, требует более высокого слоя присыпания соединения.
Химический состав
Из компонентов, входящих в состав порошкообразного вещества для присыпки сварного соединения, выделяются низкокремнистые смеси, где оксида последнего содержится меньше 35%. При этом участие марганца граничит на уровне 1%. Вторая группа — это флюсы с высоким содержанием оксида кремния, которое начинается от 35%. Третья категория называется бескислородной.
Отличаются флюсы и по степени взаимодействия с основным и присадочным металлами. Пассивные смеси только создают газовое облако, но никак не воздействуют на химический состав стали. Слаболегирующие порошки — это категория флюсов, производимая путем плавления, которые снабжают свариваемые материалы небольшим количеством кремния, марганца, и других полезных включений. Это придает шву большую прочность и ударную вязкость. Легирующие гранулированные составы обогащают металл в значительной степени, улучшая его физические и химические свойства. Швы после такой сварки лучше сопротивляются коррозии.
3.2 Марки
3.2.1 Флюсы для электрошлаковых технологий изготовляют следующих марок: АНФ – 1, АНФ – 1 – 1, АНФ – 1 – 2, АНФ – 1 – 3, АНФ – 6, АНФ – 6 – 1, АНФ – 6 – 2, АНФ – 6 – 3, АНФ – 6 – 4, АНФ – 6 – 5, АН – 291, АН – 295, АНФ – 25, АНФ – 28, АНФ – 29, АНФ – 32, АНФ – 35, ВГС, ВКС.
3.2.2 Химический состав флюсов должен соответствовать приведенному в таблице 1.
Таблица 1
Марка флюса | Массовая доля элемента, % | |||||||||||
кальция фторида | алюминия оксида | кальция оксида | магния оксида | кремния (IV) оксида | хрома оксида | марганца (II) оксида | углерода | железа (III) оксида | серы | фосфора | титана (IV) оксида | |
не более | ||||||||||||
АНФ – 1 | Не менее 90 | Не более 3 | Не более 5 | – | Не более 2,5 | – | – | 0,10 | 0,5 | 0,05 | 0,02 | 0,05 |
АНФ – 1 – 1 | Не менее 90 | Не более 3 | Не более 5 | – | Не более 2,5 | – | – | 0,05 | 0,5 | 0,05 | 0,02 | 0,05 |
АНФ – 1 – 2 | Не менее 85 | Не более 8 | Не более 8 | – | Не более 1,0 | – | – | 0,10 | 0,5 | 0,05 | 0,02 | 0,05 |
АНФ – 1 – 3 | Не менее 85 | Не более 8 | Не более 8 | – | Не более 1,0 | – | – | 0,05 | 0,5 | 0,05 | 0,02 | 0,05 |
АНФ – 6 | Основа | 25 – 31 | Не более 8 | – | Не более 2,5 | – | – | 0,10 | 0,5 | 0,05 | 0,02 | 0,05 |
АНФ – 6 – 1 | Основа | 25 – 31 | Не более 8 | – | Не более 2,5 | – | – | 0,05 | 0,5 | 0,05 | 0,02 | 0,05 |
АНФ – 6 – 2 | Основа | 25 – 31 | Не более 8 | – | Не более 1,0 | – | – | 0,10 | 0,5 | 0,05 | 0,02 | 0,05 |
АНФ – 6 – 3 | Основа | 25 – 31 | Не более 8 | – | Не более 1,0 | – | – | 0,05 | 0,5 | 0,05 | 0,02 | 0,05 |
АНФ – 6 – 4 | Основа | 28 – 34 | Не более 8 | – | Не более 2,5 | – | – | 0,10 | 0,5 | 0,05 | 0,02 | 0,05 |
АНФ – 6 – 5 | Основа | 25 – 37 | Сумма кальция оксида и магния оксида, не более 9 | 2 – 7 | 0,3 – 0,9 | – | 0,10 | 0,5 | 0,05 | 0,02 | – | |
АН – 291 | 10 – 20 | 35 – 45 | 20 – 28 | 17 – 27 | Не более 2,5 | – | – | 0,10 | 0,5 | 0,05 | 0,02 | 0,05 |
АН – 295 | 11 – 17 | 49 – 56 | 26 – 31 | Не более 6 | Не более 2,5 | – | – | 0,10 | 0,5 | 0,05 | 0,02 | 0,05 |
АНФ – 25 | 50 – 60 | 12 – 20 | 10 – 15 | 10 – 15 | 2 – 7 | – | – | 0,10 | 0,5 | 0,07 | 0,03 | – |
АНФ – 28 | 41 – 49 | Не более 5 | 26 – 32 | Не более 6 | 20 – 24 | – | – | 0,10 | 0,5 | 0,06 | 0,03 | – |
АНФ – 29 | 37 – 45 | 13 – 17 | 24 – 30 | 2 – 6 | 11 – 15 | – | – | 0,10 | 0,5 | 0,06 | 0,03 | – |
АНФ – 32 | 34 – 42 | 24 – 30 | 20 – 27 | 2 – 6 | 5 – 9 | – | 0,3 – 1,3 | 0,10 | 0,5 | 0,06 | 0,03 | – |
АНФ – 35 | 24 – 30 | 28 – 32 | 20 – 26 | 12 – 16 | 4 – 8 | – | Не более 0,5 | 0,10 | 0,5 | 0,06 | 0,03 | – |
ВГС | Не более 8 | 40 – 48 | 44 – 52 | Не более 5 | Не более 2,5 | – | – | 0,2 | 0,5 | 0,05 | 0,02 | – |
ВКС | 2 – 10 | Не более 5 | 34 – 52 | Не более 2 | 40 – 60 | – | – | 0,10 | 0,5 | 0,08 | 0,08 | – |
Примечание – Буквы и цифры в обозначении марок флюсов означают: АН – академия наук, Ф – фторидные, С – сплавленные, ВГ – высокоглиноземистые, ВК – высококремнистые; 1, 2, 3, 4 в марках АНФ – 1 и АНФ – 6 – пониженные массовые доли кремния и углерода, 5 – повышенная массовая доля хрома и кремния.
Пример условного обозначения фторидного флюса марки АНФ – 6 – 1:Флюс АНФ – 6 – 1 ГОСТ 30756 – 2001
Сварка под флюсом различных типов сталей
Сварка конструкционных углеродистых сталей
При сварке конструкционных малоуглеродистых сталей используют флюсы марок АН-348А,
ОСЦ-45, АНЦ-1 и другие в сочетании с малоуглеродистыми или марганцевыми проволоками
марок Св-08А, Св-08ГА, Св-10Г2.
Сварку среднеуглеродистых сталей выполняют при пониженных режимах, что существенно
сказывается на производительности, поэтому, при изготовлении конструкции из
среднеуглеродистых сталей данный вид сварки не нашёл широкого распространения
на практике.
Высокоуглеродистые конструкционные стали содержат 0,46-0,75% углерода и свариваемость
их затруднена. Для сварных конструкций эти стали не используются и необходимость
в их сваривании возникает, как правило, при ремонтных работах. В большинстве
случае, ремонт выполняют методом наплавки.
Сварка низколегированных сталей
К низколегированным сталям относят группу сталей, содержащих в составе менее
5% легирующих элементов. Оценивая
свариваемость сталей этой группы, можно сказать, что при сварке под флюсом
их свариваемость существенно не отличается от нелегированных малоуглеродистых
сталей. Но, легирующие элементы в составе стали повышают склонность сталей к
росту зёрен в
зоне термического влияния, а при высокой скорости охлаждения в них могут
возникать неоднородные структуры закалочного характера.
Для
сварки металлоконструкций из низколегированных сталей, с температурой эксплуатации
до -40°C, используют высококремнистые марганцевые флюсы марок АН-22, АН-22М,
АН-47, АН-67А и другие в сочетании с легированной сварочной проволокой марок
Св-10НМА, Св-08ХМ, Св-08МХ и др.
Сварка среднелегированных сталей
Среднелегированными являются стали, содержащие в составе 5-10% легирующих элементов.
Для современных среднелегированных сталей характерно легирование многокомпонентное,
комплексное. Легирование этих сталей только одним элементом применяется редко.
К сварным конструкциям из среднелегированных сталей предъявляются требования
повышенной прочности в условиях эксплуатации, а также, нередко, коррозионная
стойкость, стойкость к импульсным (резко возрастающим, мгновенным) нагрузкам.
Чем
выше содержание легирующих элементов, тем труднее сваривать сталь.
Одной из главных проблем свариваемости среднелегированных сталей является их
чувствительность к образованию
горячих трещин в сварных швах, поэтому при их сварке необходимо тщательно
выбирать композицию шва. Кроме этого, необходимо использовать технологические
приёмы и выбирать режимы, которые позволят получить хороший коэффициент формы
шва и снизить скорость охлаждения.
Для
сварки конструкций из среднелегированных сталей сварка под флюсом получила
достаточно широкое применение. Для такой сварки используются низкокремнистые
флюсы марок Ан-15, АН-15М, АН-17М и бескремнистые марок АН-30, ОФ-6, АВ-4 и
др.
Применение бескремнистых флюсов предпочтительно в тех случаях, когда к металлу
шва предъявляются повышенные требования по ударной вязкости. В сочетании с вышеуказанными
флюсами применяется сварочная проволока марок Св-20Х4ГМА, Св-08Х20Н9Г7Т, Св-10Х5М,
Св-10ХГСН2МТ.
Сварка высоколегированных сталей
Высоколегированными считаются стали, содержащие в составе более 10% легирующих
элементов. Сварка под флюсом высокоуглеродистых сталей нашла широкое применение
в химической и нефтяной промышленности, где требуется высокая коррозионная стойкость
сварных изделий и жаропрочность.
Своим широким применение для этих сталей сварка под флюсом получила благодаря
постоянству процесса сварки и, как следствие, химической однородности металла
шва
Это очень важно для высоколегированных сталей, учитывая, что даже незначительная
химическая неоднородность металла шва может стать причиной образования в нём
кристаллизационных трещин или заметно снизить коррозионную стойкость или жаропрочность
Сварка под флюсом способна обеспечить швы с гладкой поверхностью и плавным
переходом к основному металлу, что позволяет повысить стойкость к коррозии по
сравнению со сваркой электродами.
При сварке под флюсом высоколегированных сталей обычно применяют проволоку
диаметром 2-3мм. При этом могут использоваться почти все марки проволоки по
ГОСТ 224, а также многие марки проволоки, выпускаемые по ТУ, например, Св-12Х11НМФ,
Св-12Х13, Св-10Х17Т, Св-04Х19Н9, ЭП467, ЭП235, ЭП497 и другие.
Для
сварки жаропрочных высоколегированных сталей применяются фторидные флюсы
марок АНФ-5, АНФ-8, АНФ-24 и бескремнистые флюсы марок АНФ-17, АНФ-22. Для сварки
коррозионностойких высоколегированных сталей применяют флюсы с низким содержанием
кремния марок АН-26, АНФ-14.
Классификация сварочных флюсов
Основными признаками по которым разделяют флюсы — метод производства, химический состав и целевое предназначение. В зависимости от способа производства бывают плавленные и неплавленные флюсы.
Плавленные флюсы производят путем сплавления всех его компонентов и последующего дробления на мелкие зерна необходимой грануляции. Плавленные флюсы могут быть стекловидные и пемзовидные. Первые имеют вид прозрачных зерен разных оттенков, которые получают путем заливания горячего (1200°C) жидкого флюса в бак с водой. Пемзовидные флюсы — зерна пенистого материала получаемые при вливании жидкого флюса, нагретого до температуры 1600°C, в бак с водой. Когда пары воды подымаются, создают пемзовидный флюс. Размер зерен пензовидного флюса — от 0,2 до 4 мм. При использовании таких флюсом наблюдается лучшее формирование сварного шва. Более надежной защитой зоны сварки отличаются стекловидные флюсы.
Плавленные флюсы более дешевые в производстве и обеспечивают надежное формирование шва, защиту дуги, легкое отделение шлака. Хранить флюсы необходимо в сухих местах в бумажных мешках.
Неплавленный флюс производят путем смешивания мелких гранул компонентов входящих в флюс механическим путем без сплавления. Наиболее часто используют керамические флюсы.
Керамический флюс получают при смешивании компонентов с жидким стеклом и последующим протиранием сквозь сыто или с использованием специальных грануляторов. После дробление флюсу дают просохнуть при температуре 150-200°C и прожариваю при температуре 350°C. Керамические флюсы склонны поглощать влагу, поэтому их хранят в герметичных упаковках и жесткой таре через низкую прочность гранул. Их преимуществами считаются хорошая способность к легированию металла шва, низкая чувствительность к ржавчине и окалине.
По химическому составу различают оксидные, солевые и солеоксидные флюсы. Оксидные флюсы состоят с оксидов металлов из добавлением фторидных соединений. Из используют для сварки углеродистых и низколегированных сталей. Солевые флюсы состоят из фторидных и хлоридных солей металлов. Используют эти флюсы для сварки активных металлов. Солеоксидные флюсы, как можно понять, состоят из оксидов металлов и фторидов. Предназначены для сварки легированных сталей разного класса.
В зависимости от предназначения сварные флюсы делятся на несколько групп:
- для дуговой сварки углеродистых и низколегированных сталей;
- для дуговой сварки легированных сталей;
- для электрошлаковой сварки;
- для сварки цветных металлов и сплавов;
- флюсы для наплавки.
Профессиягазосварщик
5.3. Флюсы
Сварочный флюс — материал, применяемый при сварке для химической очистки соединяемых поверхностей и улучшения качества шва.
Необходимость использования флюсов при сварке цветных металлов и сплавов, легированных сталей и чугуна продиктована тем, что при нагревании металлов до высокой температуры на их поверхности образуется пленка оксида, которая при расплавлении переходит в сварочную ванну и препятствует образованию высококачественного сварного шва.
Флюсы обеспечивают раскисление расплавленного металла сварочной ванны, а также удаление из него образовавшихся оксидов и неметаллических включений. Шлаки, всплывающие на поверхность сварочной ванны, предохраняют металл шва от воздействия атмосферного воздуха.
При сварке углеродистых сталей флюсы, как правило, не применяют.
Требования к флюсам:
- флюс должен быть более легкоплавким, чем основной и присадочный металлы;
- необходимо, чтобы расплавленный флюс обладал высокой жидкотекучестью;
- флюс должен активно раскислять оксиды, переводя их в шлаки;
- флюс не должен выделять вредные газы и вещества;
- необходимо, чтобы образовавшийся шлак хорошо отделялся;
- плотность флюса должна быть меньше плотности основного и присадочного металлов;
- необходимо, чтобы флюс сохранял свои свойства на протяжении всего процесса сварки.
Флюсы для сварки сталей. При создании сварных соединений на основе углеродистых сталей флюс используют при сварке сталей только высокоуглеродистых марок (с содержанием углерода более 0,6 %). Как правило, флюсом служит бура (тетраборат натрия — натриевая соль борной кислоты).
Что касается легированных сталей, то флюс применяют лишь при сварке хромистых и хромоникелевых сталей марок 03Х18Н9Т и 06X15Т толщиной до 2 мм.
Составы флюсов:
- 80 % плавикового шпата и 20 % ферротитана;
- 80 % буры и 20 % оксида кремния.
Флюс разводят в воде и в виде пасты наносят на кромки и обратную сторону шва за 15…20 мин до сварки.
Флюсы для сварки чугуна. Горячая сварка чугуна предполагает обязательное использование флюсов, действие которых тройственно. Во-первых, они предотвращают окисление кромок твердого металла, во-вторых, извлекают оксиды и неметаллические включения из расплавленного металла, а в-третьих, способствуют образованию пленки, защищающей сварочную ванну от воздействия газов пламени и воздуха.
Обычно применяют порошковые кислые флюсы, в состав которых входят боросодержащие вещества (табл. 5.1).
Таблица 5.1
Содержание, %, компонентов флюсов для горячей и холодной сварки чугуна
При низкотемпературной сварке чугуна с помощью чугунных прутков и латунных припоев, а также при пайко-сварке используют флюсы, характеристики которых приведены в табл. 5.2.
Таблица 5.2
Флюсы для низкотемпературной сварки и пайко-сварки чугуна
Снижение температуры при низкотемпературной газовой сварке чугуна до 670…750 °С достигается применением специальных флюсов, в то время как процессы пайко-сварки чугуна протекают при температуре 750…950°С.
Флюсы для сварки алюминия
При газовой сварке алюминия и его сплавов важное значение имеет состав флюса, поскольку он должен перевести тугоплавкую оксидную пленку (Аl203) на поверхности алюминия в легкоплавкие шлаковые включения, которые образуют корку, защищающую шов. Марки и состав флюсов для сварки приведены в табл
5. 3.
Таблица 5.3
Содержание, %, компонентов флюсов для газовой сварки алюминия и его сплавов
Флюсы для сварки меди. При газовой сварке медь окисляется с образованием на поверхности слоя Сu2O, который вызывает снижение механической прочности и пластичности сварного соединения, а также образование мелких трещин. Поэтому при газовой сварке меди необходимо использовать флюсы.
Рекомендуемые составы флюсов для сварки меди приведены в табл. 5.4.
Таблица 5.4
Содержание, %, компонентов флюсов для газовой сварки меди и ее сплавов
Роль флюсов заключается в растворении образующихся оксидов, в том числе оксида меди, переводе их в легкоплавкие шлаки и предотвращении окисления расплавленного металла.
* Флюс содержит 4% керосина (сверх 100%).
Принцип действия
Для начала, чтобы разобраться в принципе действия флюса, нужно понять, из чего состоит типичная зона сварки:
- Область дугового столба с внутренней температурой от 4-5 тысяч градусов по Цельсию.
- Область газового пузыря, которая образуется вследствие интенсивного атомарного испарения компонентов в кислородной среде.
- Область со шлаковым расплавом, располагающимся в верхней части газовой полости.
- Слой расплавленного металла в нижней части полости.
- Шлаковая корка, образующая твердую границу сварочной зоны.
Помимо упомянутых выше областей не менее важна сварочная проволока, она так же оказывает влияние на химическую активность.
Теперь, понимания из чего состоит сварочная зона, мы переходим к флюсу. Во время сварки поверхность детали активно окисляется и образуется шлаковая корка. Этих процессов можно избежать, если в зону сварки поступит легко плавящийся инертный материал. Таким материал как раз и является сварочный флюс. Он обезопасит деталь от окисления и поспособствует формированию качественного шва.
Чтобы эффективно использовать флюсы в своей работе нужно соблюсти следующие условия:
- Материал должен стабилизировать скорость работы, а не замедлять ее.
- Он не должен вступать в химическую реакцию с поверхностью свариваемых деталей или сварочной проволокой.
- Газовый пузырь должен быть изолирован от окружающей среды на протяжении всей работы.
- Если соблюдены все рекомендации, то остатки флюса должны легко удаляться после проведения сварочных работ. При этом большую часть удаленного материала можно будет использовать повторно (после очистки).
На практике оказывается, что соблюсти эти требования не так уж и просто. Флюс может отличаться по своему составу, равно как и технология его подачи в сварочную зону, поэтому нужно учитывать, какие именно металлы вы свариваете и какой вид сварки используете.
Виды флюсов
Как уже было сказано выше, флюс для сварки – это порошок с размерами гранул 0,2-4 мм. Его классификация зависит от многих показателей. Но есть основные характеристики, которые разделяют его на группы и классы.
По способу производства сварочные флюсы делятся на:
- плавленые: их компоненты сначала плавятся, затем гранулируются, прокаливаются и разделяются на фракции;
- неплавленые или керамические: это сухие ингредиенты, которые смешиваются с жидким стеклом, сушатся, гранулируются, прокаливаются и разделяются на фракции.
Производители и специалисты отмечают плавленый вариант, как лучший из двух представленных.
Разделение по химическому составу.
- Оксидные флюсы. В основе порошка содержатся оксиды металлов до 90% и остальное – это фторидные соединения. В этой группе есть подгруппы, которые определяют процентное содержание того или иного оксида. К примеру, оксид кремния. Если его содержится во флюсе до 1%, то такой порошок называется бескремнистый, если его содержание составляет 6-35% – низкокремнистый и больше 35% – высококремнистый. Оксидные флюсы предназначены для сварки низкоуглеродных и фтористых стальных заготовок.
- Солевые. В них нет оксидов металлов, основу составляют соли: фториды и хлориды. Такой порошок используется для сваривания активных металлов, к примеру, титан.
- Смешанные флюсы (солеоксидные). В них есть и оксиды и соли. Применяют их для соединения легированных сплавов.
Еще одна характеристика – активность флюсов. По сути, это скорость окисления порошка при его нагреве. Измеряется данный показатель от нуля до единицы и делит флюсы на четыре категории:
- Меньше 0,1 – это пассивные материалы.
- От 0,1 до 0,3 – малоактивные.
- От 0,3 до 0,6 – активные.
- Выше 0,6 – высокоактивные.
И последнее. Это деление по строению гранул. Здесь три позиции: стекловидные, пемзовидные и цементированные. Необходимо отметить, что сварка под стекловидным флюсом дает более широкий сварной шов, чем под пемзовидным. Если используется порошок с мелкими частицами, то шов под ним образуется глубокий и неширокий с высокими прочностными качествами.
Функционал гранулированного средства
Сварочные флюсы играют большую роль в обеспечении процесса соединения металлов. Их функции, в зависимости от состава вещества и свариваемого материала, могут заключаться в поддержании четырех действий.
Изоляция
Главной целью флюсов является создание непроницаемого газового облака, позволяющего основному и присадочному металлам беспрепятственно сплавляться в сварочной ванне. Чтобы порошок выполнял эту функцию необходима правильная дозировка вещества на линии соединения. Хорошими изоляционными газовыми свойствами обладают мелкие гранулы плотной структуры. Но возрастающая плотность укладки фракций на поверхности соединения отрицательно сказывается на формировании поверхности шва.
На изолирующую способность оказывает влияние не только размер посыпаемых частиц, но и их насыпная масса. Применяя специальные таблицы с данными можно устанавливать точную подачу стекловидного средства в сварочную зону.
Стабилизация
Кроме защитных свойств порошка, позволяющих вести сварочные работы без внешних газовых включений, флюсы создают благоприятную среду для горения электрической дуги, которая проявляется в разряде электрического тока между концом электрода и изделием. Расстояние между сторонами полюсов составляет около 5 мм. Для стабилизации горения дуги в состав гранул добавляют специальные вещества, позволяющие более устойчиво проходить электрическому разряду. Это дает возможность работать не только на постоянном, но и на переменном токе, и применять разнообразные режимы сварки.
Легирование
Благодаря воздействию высоких температур и взаимодействию основного и присадочного металлов, создается сварочный шов. Его химический состав зависит от используемых материалов. Из-за электрической дуги некоторые полезные элементы могут выгорать или передаваться с металла шва в шлаковые массы. Чтобы этого не произошло, в некоторые флюсы добавляют легирующие вещества, обогащающие шовный металл, и препятствующие насыщению шлака кремнием и марганцем. Для большего легирования используют соответствующую присадочную проволоку.
Формирование поверхности
Когда кристаллическая решетка в расплавленном металле только начинает образовываться, все, что соприкасается с ней, оказывает влияние на вид будущего шва. Флюсы, благодаря различной степени вязкости и межфазного натяжения, имеют сильные формирующие способности, благоприятно сказывающиеся на сварочном соединении.
Например, при работе на большой силе тока и толстых материалах, более практичны флюсы с долгим вязким состоянием. Такие порошки называют «длинными». Это позволяет глубоко прогретому сплаву постепенно кристаллизоваться и остыть, образуя гладкочешуйчатую структуру. Для сварки на малых токах, сильная жидкотекучесть будет мешать видеть сварочную ванну и качественно выполнять процесс, поэтому здесь применяются «короткие» флюсы, у которых вязкость быстро переходит в твердое состояние при снижении температуры.
Что такое сварка под защитными флюсами
По сути, это все тот же сварочный процесс с применением неплавящихся электродов и присадочной проволоки. Только вместо газа, который покрывает собою зону сварки, используется флюс – порошкообразный материал, засыпаемый поверх стыка двух металлических заготовок.
При высокой температуре сварки флюс расплавляется и выделяет все тот же защитный газ. При этом поверх зоны сваривания образуется прочная пленка, защищающая ее от негативного воздействия окружающего воздуха. Сгоревший порошок превращается в шлак, который легко снимается со сваренного шва. Остатки флюса можно собрать и использовать в другом месте.
Но самое главное, что все позиции, связанные с соединением стыкуемых деталей, точно такие же, как и в случае использования других сварочных технологий. А именно:
- правильный подбор режима сварки, который зависит от структуры соединяемых металлов;
- правильный выбор электрода;
- присадочной проволоки, которая по своим свойствам должна соответствовать свойствам основных металлов;
- грамотное формирование кромок;
- зачистка торцов деталей, их обезжиривание.
Но есть и одна отличительная особенность – правильный выбор флюса.
Неплавленые флюсы для автоматической сварки
Если плавленые флюсы изготавливают путём совместного сплавления их компонентов,
то неплавленые флюсы тщательно размалывают и смешивают между собой в строгом
соотношении в водном растворе жидкого стекла, которое является наиболее распространённым
связующим компонентом.
Получившуюся вязкую смесь протирают сквозь сито с определённым размером ячеек
для получения флюса с нужным размером зерна. Далее, сырые флюсовые гранулы повергаются
просушке в сушильных печах при температуре 150°C. Время просушки 15-20мин. Далее
гранулы прокаливают при температуре 300-350°C.
Неплавленые керамические флюсы
Неплавленые керамические флюсы в своё время были разработаны академиком Хреновым
К.К.. Такие флюсы значительно упрощают процесс легирования металла сварного
шва различными элементами. Для обеспечения этого, в состав флюса включают требуемое
количество легирующих элементов в виде порошковых металлов, минеральных и других
веществ.
Ещё одно преимущество керамического флюса является его достаточно высокая стойкость
к ржавчине, окалине и влаге на поверхности свариваемых изделий, по сравнению
с плавлеными флюсами. Такое преимущество особенно актуально при сварке
металлов на монтажно-строительной площадке под открытым небом.
В состав керамических флюсов, кроме минеральных шлакообразующих веществ, входят
и другие компоненты, которые хорошо раскисляют сварной шов и обеспечивают его
легирование. Это различные ферросплавы. Составы некоторых распространённых керамических
флюсов, в %, приведены в таблице:
Компонент: | К-2 | КС-1 | КВС-19 | К-1 |
Титановый концентрат | 55 | – | – | – |
Марганцевая руда | – | – | 54 | 60 |
Кварцевый песок | – | – | 30 | 20 |
Порошок алюминия | – | – | 2 | – |
Ферромарганец | 14 | 0,5 | – | – |
Ферросилиций | 8 | 0,8 | 7 | 10 |
Ферротитан | – | 6,0 | – | – |
Диоксид титана | – | 15,0 | – | – |
Мрамор | – | 57,7 | – | – |
Полевой шпат | 13 | – | – | – |
Плавиковый шпат | 10 | 20 | 7 | 10 |
Жидкое стекло, % от суммарной массы смеси | 13 | 15 | 15-17 | 17 |
Магнитные неплавленые флюсы
Магнитные флюсы являются разновидностью неплавленых флюсов. Технология изготовления
и область их использования такая же, как и у керамических неплавленых флюсов.
Но, кроме компонентов, содержащихся в керамических флюсах, в состав магнитных
входит железо в виде металлического порошка. Данный компонент придаёт флюсу
магнитные свойства и повышает производительность сварки.
Флюс подаётся с помощью дозирующее устройство сварочного автомата или полуавтомата.
Под воздействием магнитного поля электрической дуги, гранулы магнитного флюса
притягиваются к зоне сварки. При такой технологии
автоматической сварки расход флюса снижается и появляется возможность качественной
сварки
вертикальных сварных швов.
Далее рекомендуем перейти к статье “Флюсы
для автоматической сварки Ч.2 Виды сварочных флюсов”, в которой приведена
классификация имеющихся видов сварочных флюсов для автоматической сварки и рассказывается
про область их применения.
Дополнительные материалы по теме:
Технология | Техника |
(PDF) Газовая вольфрамовая дуговая сварка с использованием дугогасительной проволоки
Контрольные эксперименты и
Обсуждение
Экспериментальная система была создана для демонстрации возможности
процесса GTAW с электродуговой проволокой. Эта система
показана на рис. 5 с подробностями, приведенными в таблице 2
. Была проведена серия экспериментов. Как источник питания GTA, так и источник питания для нагрева проволоки
работали –
в режиме постоянного тока (CC), например,
, чтобы ток GTA (IGTA) и ток плавления проволоки
(IW) контролировались на уровне
.желаемых уровня.Чтобы доказать, что GTAW с дуговым разрядом
может разделять скорость осаждения
и энергию дуги, и что GTAW с дуговым разрядом
стабильна в относительно большом диапазоне
, были проведены эксперименты
с различными (IGTA, IW) комбинации.
IW был ограничен в пределах 200 А, потому что
предела возможностей источника питания для нагрева проволоки
. Заготовки, использованные в экспериментах
, представляли собой холоднокатаные стальные листы C1018 толщиной
толщиной 3⁄8 дюйма, а эксперименты
были выполнены в виде валика на пластину. Для этой толщины листа
, когда IGTA была ниже
, чем 100 А, внешний вид валика сварного шва
был неприемлемым, хотя процесс
все еще был стабильным, а проволока
была достаточно расплавленной. Следовательно, нижний предел
тока GTA, указанный в этом поиске re-
, равен 100 А. Для IW нижний предел был
установлен как 50 А.
Все эксперименты были разделены на
на три группы. по гта
ток.В группу 1 входят эксперименты 1–
4. В группу 2 входят эксперименты 5–8.
Группа 3 включает эксперименты 9–12.
Группа 1: эксперименты 1–4
В экспериментах 1–4 ток GTA
был установлен на уровне 200 А, а ток плавления проволоки
был установлен на 50, 100, 150 и 200 А,
соответственно. . Теплота плавления, общая подводимая теплота
и ρall увеличиваются с увеличением тока плавления
. Скорость подачи проволоки была отрегулирована
в соответствии с используемым током плавления проволоки
, чтобы проволока могла плавиться стабильно.
Условия эксперимента подробно описаны
в таблице 3, а зарегистрированные токи и напряжения
и изображения сварных швов
приведены на рис. 6–13. В легендах I1
и V1 относятся к току GTA и напряжению –
возрасту; а I2 и V2 – ток и напряжение плавления
проволоки.
Как видно на рис. 6–13, процесс
был стабильным во всех экспериментах.
Брызги отсутствуют, валик имеет однородную форму
и плотный.Наблюдается поверхностное окисление
, но его следует улучшить
за счет лучшего экранирования. Интегрированный комплект горелки
или увеличенная площадь экрана могут исключить возможное окисление
, и
следует рассматривать в возможных будущих усилиях по коммерциализации
.
Как видно, во всех случаях колебания тока и напряжения для
GTA (между основным металлом и заготовкой
шт.) Увеличились в дугогасительной проволоке GTAW
из автогенного металла. GTAW.Тем не менее, складки на
небольшие и почти не сравнимы с таковыми в типичном GMAW. Превосходная управляемость дуги
, связанная с
с обычной GTAW, разумно заменена
на GTAW с электродуговой проволокой. Используя измеренные напряжения
и требуемые токи, ρ
вычисляется для каждого эксперимента в группе
и перечисляется в таблице 3. Как видно,
процесс дугового разряда обеспечивает ρ в диапазоне
от 17 до 54 % просто изменяя ток провода
.Таким образом, демонстрируется управляемость дугой
и сварка предлагаемого процесса
и его удобство в достижении управляемости
.
Группа 2: Эксперименты 5–8
В экспериментах 5–8 ток GTA
был уменьшен до 150 А. Ток плавления проволоки
был установлен на 200, 150, 100 и 50 А,
соответственно. . Скорость подачи проволоки была отрегулирована в соответствии с током плавления проволоки
, чтобы проволока плавилась плавно
. Зарегистрированные значения тока и напряжения
, а также изображения сварных швов
приведены на рис. 14–21.
Как видно на рис. 14–21, процесс
был стабильным во всех экспериментах.
Брызги отсутствуют, валик имеет однородную форму
и плотный. Опять же, колебания тока и напряжения GTA
лишь немного увеличились. ρ демонстрируется
в диапазоне от 21 до 61%. Проверена возможность и управляемость процесса
для другого тока GTA.
Группа 3: эксперименты 9–12
В экспериментах 9–12 ток GTA
был снижен до 100 А, а ток плавления проволоки
был установлен на 50, 100, 150 и
200 А , соответственно. Скорость подачи проволоки
регулировалась в соответствии с током плавления проволоки
, чтобы проволока могла плавиться
стабильно. Зарегистрированные токи и напряжения
возраста, а также изображения сварных швов
приведены на рис. 22–29.
Как видно на рис. 22–29, процесс
также был стабильным. Нет брызг –
тер, валик однородный и плотный.
Слегка увеличенные колебания тока и напряжения
GTA по сравнению с
togenous GTAW еще раз подтверждают сохранение
управляемости дуги. ρ расширяется до
71%. Поскольку ρ можно легко сделать нулевым
без подачи проволоки, демонстрируется диапазон от 0 до
71% для ρ.Также можно продемонстрировать дальнейшее увеличение ρ на
, но для обеспечения соответствия
сварных швов типичным требованиям к геометрии шва
могут потребоваться соответствующие канавки
, такие как V-образная канавка или листы тонкого сечения,
вместо выполнения сварных швов относительно толщиной
пластин, как в этом предварительном исследовании, цель которого
– продемонстрировать осуществимость процесса
.
Анализ и обсуждение
Тепло, необходимое для плавления 1 кг различных сталей
ous от комнатной температуры, составляет
меньше, чем приблизительно 1000 кДж. Из
Рис. 2, GTAW с горячей проволокой требуется мощность дуги 10
кВт для достижения скорости наплавки
9 кг / ч. Тепло, используемое для плавления проволоки
, составляет 9000 кДж / ч. Общее количество тепла, подводимого к заготовке
, превышает тепловыделение, обеспечиваемое дугой
, что составляет 10 × 60 × 60 = 36000
кДж / ч, потому что источник питания из проволоки
также обеспечивает тепло. Коэффициент теплоты плавления в
, таким образом, общий подвод тепла ниже, чем
9000/36000 = 25%.Значение ρ в GTAW
с горячей проволокой несопоставимо с 71%, что было экспериментально продемонстрировано
для предлагаемого процесса GTAW
с электродуговой проволокой. Управляемость GTAW с дугой
значительно расширена по сравнению с GTAW с горячей проволокой
. 71% также для курса
, намного больше, чем для
GMAW (прямая полярность постоянного тока), который составляет
примерно 33%, потому что напряжение
катода на стали (заготовке) составляет около
. примерно вдвое больше, чем для напряжения
анода (стальная проволока) (см.23).
Управляемость сварного шва также может быть
используется другим способом в настраиваемом окне раметра pa-
, чтобы продемонстрировать, как показано
на рис. 30, где две координаты:
ток проволоки и ток GTA
соответственно.
Эта демонстрация кажется более легкой для понимания
с точки зрения приложения
. На рис. 30 показаны все эксперименты
, проведенные с каждым красным крестом, чтобы обозначить
набор параметров, который был мысленно подтвержден
для предложенной дуги
проволокой GTAW.
Как можно видеть, процесс дуговой сварки
GTAW считается применимым в
– полном окне параметров, разрешенном
используемым оборудованием. Это связано с тем, что ex-
, склоняющий красные кресты влево, так что
Iw = 0 не требует доказательства, поскольку это просто
слой автогенной GTAW; расширение красных крестов
вправо подпадает под ограничение
используемого оборудования; Для нижнего
красных крестов вниз требуется покрытие
, где требуются крайне низкое тепловложение
и высокая скорость наплавки, например
, наплавка в V-образной канавке, которая находится за пределами области видимости
этого технико-экономического обоснования;
повышение красного креста вверх означает высокий входной сигнал
с малым входом массы, что может быть легко выполнено с помощью холодной, горячей проволоки и дуги
с помощью GTAW. Распределение красных крестов
в прямоугольном окне
демонстрирует способность независимо обеспечивать выделенную массу и теплоотдачу.
Заключение и дальнейшие работы
Экспериментально продемонстрирован процесс
GTAW с применением инновационно модифицированного присадочного металла
для GTAW, т.е. процесс сварки дуговым разрядом
GTAW.
ОКТЯБРЬ 2012, ТОМ. 91
268-s
ИССЛЕДОВАНИЕ СВАРКИ
Chen 10-12_Layout 1 9/10/12 13:44 PM Page 268
A Обзор Dr.Аднан А. Угла, Хасан Дж. Хаудаир, Ахмед Р. Дж. Альмусави :: SSRN
Всемирная академия наук, инженерии и технологий Международный журнал машиностроения и материаловедения, Том 13, № 3, 2019 г.
14 стр. Добавлено: 7 ноя 2020
Просмотреть все статьи Dr.Аднан А. УглаКафедра машиностроения, Инженерный колледж, Исследовательская группа передовых производственных технологий, Университет Тикара, Аль-Насирия, Ирак – 64001
Кафедра машиностроения, Инженерный колледж, Исследовательская группа передовых производственных технологий , Университет Тикара, Аль-Насирия, Ирак – 64001
Багдадский университет / Инженерный колледж Аль-Хорезми / мехатроника, англ. Отдел
Дата написания: 3 февраля 2019 г.
Аннотация
Формованное осаждение металла (SMD) в аддитивной технологии послойного производства является многообещающей альтернативой традиционному производству, используемому для изготовления больших и дорогих металлических компонентов со сложной геометрией в дополнение к созданию свободных структур из строительных материалов в послойной технике.Настоящая статья представляет собой всесторонний обзор литературы и новейших технологий быстрого производства SMD-технологий. Целью данной статьи является всесторонний обзор наиболее важных фактов, с которыми столкнулись исследователи в методах SMD, особенно связанных с подачей холодной проволоки. Целью данного исследования является обзор литературы, представленной по процессам осаждения металлов и их классификациям, включая процесс SMD с использованием аддитивного производства проволоки + дуги (WAAM), который делится на проволоку + инертный газ вольфрама (TIG), инертный газ металла (MIG), или плазма. Это представленное литературное исследование охватывает обширные детали геометрии валика, параметров процесса и подводимого тепла или энергии дуги в результате процесса наплавки в обоих случаях MIG и Tandem-MIG в процессе SMD. Кроме того, SMD может выполняться с использованием сварки Single Wire-MIG (SW-MIG) и SMD с использованием сварки Dual Wire-MIG (DWMIG). Настоящий обзор показывает, что метод осаждения металлов при использовании процесса DW-MIG можно рассматривать как отличительный и недорогой метод для производства крупных металлических деталей из-за высоких скоростей наплавки, а также снижения воздействия высокой температуры, генерируемой во время осаждения. и уменьшить искажения.Однако точность и чистота поверхности MIGSMD ниже по сравнению с электронным и лазерным лучом.
Ключевые слова: формованная наплавка металла, аддитивное производство, двойная подача проволоки, проволока холодной подачи
Рекомендуемое цитирование: Предлагаемая ссылка
А.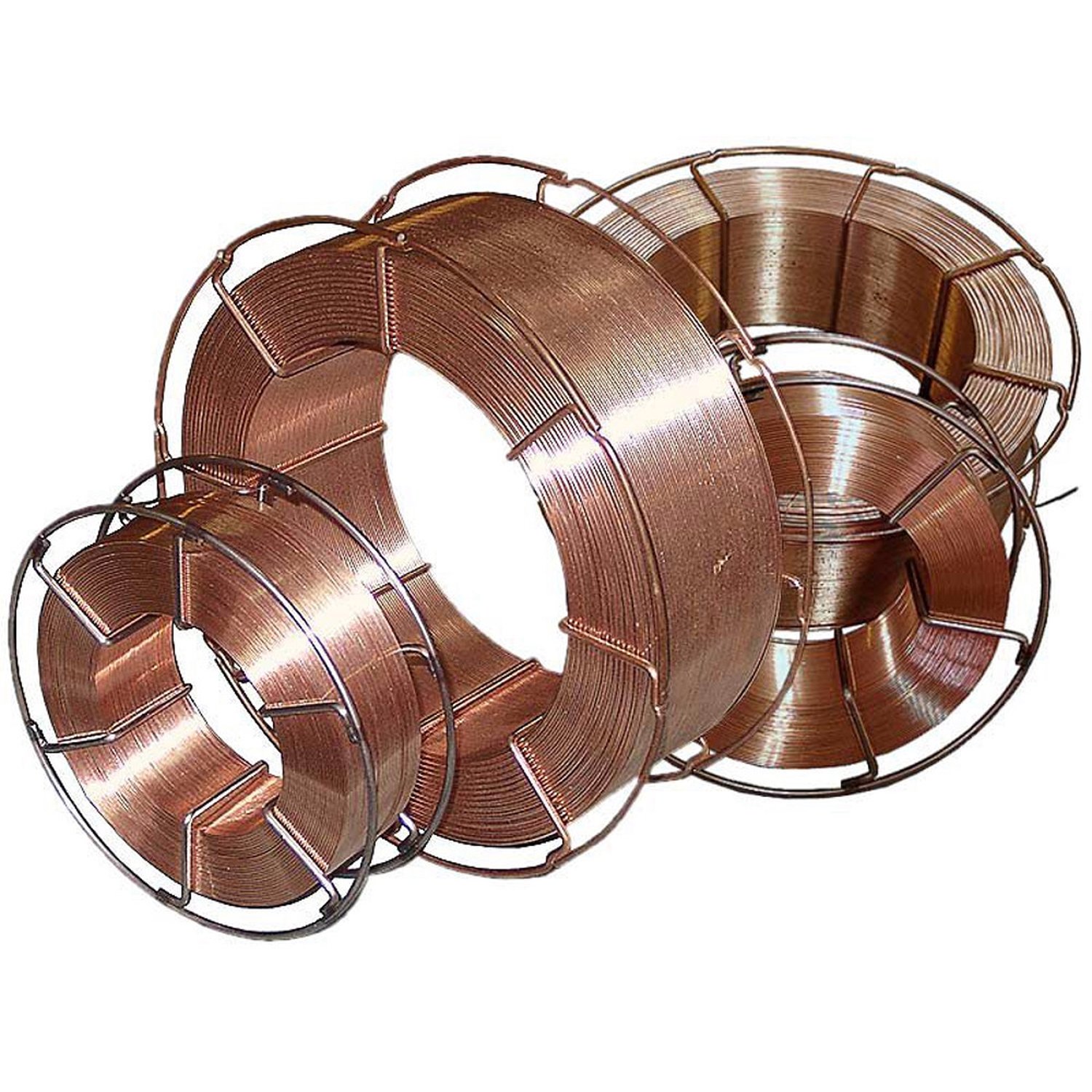
Поведение при интерференции дуги во время процесса двухпроводной газовой дуговой сварки
Для изучения интерференции дуги во время процесса двухпроводной газовой дуговой сварки была создана система синхронного сбора данных для получения мгновенной информации о профиле дуги, включая динамическое изменение длины дуги, как а также относительные сигналы напряжения и тока.Результаты показывают, что после добавления задней дуги (Т-дуга) к средней дуге (М-дуга) в стабильном процессе сварки ток М-дуги остается неизменным, в то время как перемешивание увеличивается; напряжение дуги М имеет явное увеличение; форма дуги M изменяется с увеличением ширины, длины и площади; частота переноса капли дуги М увеличивается, а сама капля становится меньше. Длина удлинения проволоки при двойной дуге оказывается меньше, чем при однодуговой сварке.
1. Введение
В последние годы большое количество исследований было сосредоточено на изучении сварочных материалов, технологии сварки и сварочного оборудования, особенно многопроволочной сварки, для повышения производительности сварки [1, 2].При двухпроводной или даже многопроволочной сварке MIG цель состоит в том, чтобы увеличить скорость сварки, при этом энергия линии остается постоянной. Поскольку одновременно плавятся несколько проволок, скорость наплавки, несомненно, выше, чем у одной.
Сварка сдвоенной проволокой привлекает большое внимание, поскольку позволяет повысить производительность сварки и улучшить сварочное образование. В настоящее время наиболее часто используемая двухпроволочная сварка в основном включает двухпроволочную газовую дуговую сварку [3], двухпроволочную сварку TANDEM [4] и дуговую сварку под флюсом (SAW) [5].Основная проблема при сварке двумя проволоками – это пересечение двух дуг, которое напрямую влияет на качество сварки [6]. Взаимодействие между двумя дугами вызывает изменение соответствующей морфологии дуги, что в свою очередь приводит к изменению распределения теплового пространства. Для получения идеального сварочного эффекта широко используется импульсный источник питания. В настройках управления для регулировки двух источников сварочного тока используются три режима: синхронный, переменный и случайный. Он может управлять сварочной дугой и относительной синхронизацией короткого замыкания, чтобы уменьшить взаимные помехи [7].
Безусловно, исследования явления прерывания дуги в двухпроводной проволоке в основном сосредоточены на методе сварки P-GMAW TANDEM. Уэяма и Охнава [8] использовали метод импульсного управления, в то время как явление дуговой интерференции и нестабильности напряжения все еще оставалось серьезным. Скотти и др. [7] воспользовались преимуществами высокоскоростной фотографии для анализа переноса двух капель плавления и поведения дуги в различных условиях путем изменения уровня тока и разной фазы. Ueyama et al. [9] также обнаружили, что конструкция сварочной горелки влияет на формирование сварного шва во время высокоскоростной импульсной сварки в режиме TANDEM.Результат показал, что использование специально сконструированных сварочных горелок может обеспечить стабильное горение дуги, увеличить скорость сварки и улучшить сварочное образование. Ueyama et al. В [4] изучали влияние расстояния между проволоками и состава защитного газа на интерференцию дуги во время импульсной сварки ТАНДЕМ. Юдодиброто и др. [10] представили индекс для оценки стабильности сварочной дуги TANDEM посредством статистики и расчета сварочного тока и анализа напряжения. Ueyama et al. [11] показали, как состояние поверхности сварочной ванны влияет на напряжение аномальной дуги, используя принцип минимального напряжения.
В этой статье интерференция дуги высокопрочной низколегированной стали в двухпроволочном GMAW была исследована путем наблюдения за изменением профиля дуги, а также измерения изменения электрических сигналов.
2. Методика эксперимента
Во время эксперимента первая проволока определяется как M-дуга вдоль направления сварки; следующий провод определяется как Т-образная дуга. Двойная дуговая сварка реализуется путем добавления Т-образной дуги в систему после того, как М-дуга постоянно горит. После того, как M- и T-дуги стабильно горят вместе в течение двух секунд, T-дуга удаляется из системы.Интерференция дуги анализируется в основном по четырем аспектам: электрический сигнал, форма дуги, частота переноса капель и длина удлинения проволоки. Экспериментальный процесс показан на рисунке 1. Высокоскоростная система камеры и система сбора электрического сигнала используются для наблюдения за процессом с целью получения информации о помехах. Профиль M-arc снят системой высокоскоростной фотосъемки. Вся экспериментальная система высокоскоростной сварки сдвоенной проволокой показана на рисунке 2.
2.1. Материалы
Образцом для сварочных испытаний является высокопрочная низколегированная сталь толщиной 15 мм. Химический состав материала показан в таблицах 1 и 2. В качестве присадочного материала в данном исследовании использовалась сварочная проволока 70MXH с суперпорошком диаметром 1,6 мм. В качестве защитного газа используется чистый CO 2 , широко используемый в судостроении.
|
(%)
(%)
(%)
(%)
(%)
(%)
(%)
(%)

2.2. Сварочное оборудование
Система экспериментального оборудования состояла из источника сварочного тока Panasonic YD-500GR3, платы сбора электрического сигнала, системы высокоскоростной камеры и т. Д.
2.3. Параметры сварки
Двойной электрод полностью положительный (сварочная горелка расположена рядом с анодом).Расстояние между горелкой, а также между соплом и основным металлом составляет 20 мм. А угол пересечения двух соседних горелок составляет 10 °. Сварка плоских поверхностей выполняется с потоком защитного газа CO 2 20 л / мин и скоростью сварки 500 мм / мин. Сила тока и напряжения М- и Т-дуг составляет 250 А / 27,5 В и 200 А / 25 В соответственно.
3.

3.1. Анализ формы сигналов двухпроводной сварки GMAW
Двойная дуговая сварка реализуется путем добавления Т-образной дуги в систему после того, как М-дуга постоянно горит.В этом процессе во время эксперимента измеряются ток и напряжение M- и T-дуги, которые показаны на рисунке 3. Диаграмма показывает, что как средние, так и действующие значения тока M-дуги не показывают очевидных изменений после добавления T-arc, в то время как напряжение M-arc значительно увеличивается, а напряжение T также выше уставки. Кроме того, стандартная разница увеличивает колебания тока и напряжения.
В эксперименте оба провода являются анодными.Следовательно, существуют серьезные помехи из-за электромагнитной силы, которая приводит к взаимному смещению в области дуги. Длина дуги также немного изменяется, что в дальнейшем приводит к изменению напряжения дуги. Это явление можно просто объяснить с помощью модели упрощения формулы отклонения, представленной на рисунке 4.
Смещение центра M- и L-дуг можно выразить с помощью следующих формул:
Приведенные выше выражения смещения показывают, что смещение одной дуги пропорционально току другой дуги и квадрату ее собственной длины дуги, но обратно пропорционально ее собственному току и расстоянию дуги.Кроме того, дуга смещается из-за электромагнитной силы.
3.2. Анализ характеристик профиля дуги M-Arc
Согласно изображению дуги, форма дуги M более стабильна, когда она горит отдельно. Эффект увлечения дуги приводит к небольшому смещению в противоположном направлении сварки. Как показано на Рисунке 5, после введения Т-образной дуги стабильность связанной дуги изменяется. Из-за притяжения между двумя дугами M-дуга имеет более очевидное смещение в сторону T-дуги.Используя программное обеспечение lab view, рассчитываются средние значения высоты, длины и площади M-дуги. В случае однопроволочной сварки ширина, длина и площадь М-дуги составляют 10,23 мм, 5,76 мм и 39,17 мм 2 соответственно. После добавления Т-образной дуги в систему форма связанной дуги изменится на 12,17 мм в ширину, 6,73 мм в длину и 52,09 мм в 2 по площади.
В соответствии с принципом минимального напряжения характеристика энергопотребления дуги имеет тенденцию к минимизации, и дуга является симметричной по оси, когда определены определенные условия тока и границы.Поскольку дуга находится в стабильном состоянии, диаметр столба дуги () и температура () должны обеспечивать минимальное значение напряженности электрического поля столба дуги ().
Когда Т-образная дуга приближается к М-дуге, это можно рассматривать как тот факт, что дуга вынуждена нагреваться окружающей средой. В соответствии с принципом минимального напряжения площадь поперечного сечения дуги будет автоматически увеличиваться, что приведет к снижению плотности тока, напряженности электрического поля и температуры электрической дуги.Когда рассеивание тепла устранено, дуга вырабатывает небольшое количество тепла для компенсации. Следовательно, производство тепла дугой происходит там, где ток остается неизменным и снижается. В соответствии с принципом минимального напряжения дуга имеет тенденцию к автоматическому спаду до минимального значения, что указывает на снижение способности рассеивания тепла до максимальной тенденции. Поэтому, когда дуга нагревается, дуга автоматически расширяется до определенного диаметра, и тогда напряженность электрического поля дуги становится максимальным уменьшением.
3.3. Анализ капельного переноса и длины удлинения проволоки M-Arc
В процессе сварки одиночной дугой частота капельного переноса M-дуги составляет около 30 Гц. После добавления Т-образной дуги частота капельного переноса М-дуги достигает примерно 40 Гц. Когда добавляется T-arc, режим капельного переноса M-arc, а также режим переноса отклонения остается неизменным. Частота переноса увеличивается, а размер капель становится меньше, как показано на рисунке 6. Тот факт, что после добавления T-дуги не происходит явных изменений в токе M-дуги, демонстрирует, что скорость подачи проволоки остается неизменной на протяжении всего эксперимента. .Это связано с тем, что скорость подачи сварочной проволоки определяет изменение тока. Кроме того, из-за эффекта нагрева сварочной проволоки для Т-образной дуги теплота плавления увеличивается, что увеличивает скорость плавления сварочной проволоки. Поскольку скорость подачи проволоки остается неизменной, размер капель становится меньше.
Длина удлинителя M-дуги рассчитывается, когда она горит отдельно, и после добавления T-дуги с использованием лабораторного обзора, соответственно. Как показано на Рисунке 7, длина удлинителя M-дуги уменьшается после добавления T-дуги.Длина удлинителя шины изменилась с 10,16 мм до 9,92 мм после добавления Т-образной дуги при условии A и A соответственно.
Уменьшение длины удлинения проволоки можно объяснить источником нагрева проволоки. Предыдущие исследования широко изучали механизм нагрева в процессе сварки и пришли к аналогичному мнению. Общий нагрев проволоки, вызывающий нагрев и плавление, состоит из двух основных частей: одна – это тепловыделение дуги вблизи электродной области, а другая – теплота сопротивления. Tichella et al. [12] отмечают, что тепло для нагрева и плавления сварочной проволоки в основном исходит от энергии анода, поглощающей электроны (обратно), что означает, что тепло дуги является основной энергией для плавления сварочной проволоки, в то время как Лесневич [13] считает, что теплота сопротивления удлинения проволоки является основной энергией для плавления сварочной проволоки даже в случае низкого сварочного тока. Увеличение длины удлинения проволоки и уменьшение площади ее поперечного сечения также приводит к увеличению скорости плавления проволоки.
Нет сомнений в том, что теплота плавления проволоки складывается из двух частей: тепла дуги и тепла сопротивления. Однако для сварки сдвоенной проволокой, нагреваемой соседней дугой, тепло для нагрева и плавления сварочной проволоки должно состоять из трех частей. Выражение выглядит следующим образом: где – общее количество теплоты для нагрева и плавления сварочной проволоки; – тепло дуги вблизи электродной области; – теплостойкость; – второй нагрев дуги; – сварочный ток; – эквивалентное напряжение дуговой плавки сварочной проволоки; – рабочее напряжение; – сопротивление длины удлинения провода; – сопротивление сварочной проволоки; – длина удлинителя провода; площадь провода.
Сварочная проволока подсоединяется к аноду; таким образом, тепло для плавления сварочной проволоки в основном зависит от тепла, выделяемого резистивным нагревом в области анода. аналогично (рабочее напряжение) и связано с материалами. Для данного материала производство тепла на аноде связано только с током. За счет добавления сварочной проволоки, сварочная проволока получает соседний нагрев, при этом коэффициент плавления и остается неизменным. Поскольку и сохраняют инвариантность, и имеют относительную убыль. Следовательно, длина удлинения провода уменьшается.
4. Выводы
(1) Экспериментальная установка создана для изучения поведения интерференции между дугами из двух проволок, включая измерение синхронных сигналов тока и напряжения и наблюдение за профилем дуги, процессом переноса капель и изменением длины удлинения проволоки. . (2) Из-за давления дуги длина дуги и напряжение увеличиваются. Ток остается неизменным, в то время как перемешивание увеличивается в процессе сварки сдвоенной проволокой. (3) Из-за эффекта взаимодействия дуги частота переноса капли при сварке сдвоенной проволокой быстро увеличивается, а размер капли уменьшается.В то же время длина удлинения проволоки уменьшается, что указывает на изменение точки сварки.
Благодарность
Это исследование финансируется Национальным фондом естественных наук Китая (грант № 51275299).
Микроструктурные и механические свойства соединений проволоки из разнородного нитинола и нержавеющей стали, полученных с помощью микроэлектронно-лучевой сварки без присадочного материала
Применяя вышеупомянутые наборы параметров, можно было получить сварные швы без трещин для нитинола и 1.4310 стали разнородные сварные швы. На рис. 6а представлено изображение сварного образца методом BSE, а на рис. 6б – оптическая микрофотография. Макроскопически на свариваемых поверхностях дефектов не обнаружено.
Рис. 6Поверхность сварных швов: электронно-оптическое изображение (отраженные электроны) (a) и оптическая микрофотография (b)
На рис. 7 поперечное сечение сварного шва с использованием параметра «1c» из таблицы 3 , что означает сварку стальной проволоки со смещением оси луча на 150 мкм. Нержавеющая сталь находится справа, а нитинол – слева.На рис. 7 можно определить размер зоны сварки. Она составляет от 400 до 670 микрон в плоскости обзора (следует учитывать, что в зависимости от реальной анализируемой плоскости общая ширина сварного шва может отличаться до 20%).
Поперечное сечение образца, сваренного с параметром «1c»
На рисунке 8 показаны элементные схемы EDS для всей зоны сварного шва сопутствующего образца, сваренного с указанными выше параметрами, с указанием ожидаемых характерных особенностей.Ширина сварного шва немного отличается по сравнению с поперечным сечением на рис. 7, на что влияет подготовка образца, что приводит к небольшим различиям в плоскости обзора (как уже обсуждалось выше). Как показано на изображении SE на рис. 8, сталь расположена с правой стороны. Fe, Mn и Cr значительно обогащены в этой области, как можно вывести из каждой элементной карты на рис. 8. С левой стороны Ni и Ti значительно обогащены, и, таким образом, чистая нитиноловая проволока присутствует здесь в виде указано на изображении SE.В зоне сплавления очевидна довольно хорошая смесь всех зондируемых элементов, за небольшим исключением в середине сварного шва.
Отображение элементов EDS, полученное из зоны сварного шва
В дополнение к сопоставлениям элементов EDS на рис. 9 показаны результаты анализа линейного сканирования EDS. Сканирование показывает локальную эволюцию элементов обоих партнеров по сварке по всей зоне сварного шва. На уровне около 650 микрон эволюция линейного сканирования выявляет неоднородность, поскольку содержание Ti и Ni значительно увеличивается.Из обоих анализов, то есть элементарных сопоставлений, а также линейного сканирования, увеличение Ni и Ti становится очевидным между 600 и 700 мкм (контрольная точка, определенная на рис. 9). Это увеличение указывает на неоднородное распределение основных элементов, вносимых партнером по сварке нитинолом. В этой области сокращаются все основные элементы стального партнера по сварке. Возможное объяснение состоит в том, что в середине сварного шва, то есть в точке наибольшей глубины сварки, вводится наименьшее количество тепла на единицу объема, и, таким образом, как конвективный поток вокруг замочной скважины, так и поток Марангони менее выражены, в конечном итоге приводит к менее интенсивному перемешиванию элементов.Дополнительные подробности могут быть получены из дополнительного рассмотрения эволюции микроструктуры в зоне сварного шва, как будет рассмотрено ниже.
SE изображение зоны сварного шва ( a ) и линейная развертка EDS, полученная из зоны сварного шва ( b )
Из карты обратной полюсной диаграммы EBSD (Рис. 10a) и фазовой карты (Рис. 10b) можно вывести два основных аспекта. Во-первых, размер зерна в зоне сварного шва кажется значительно увеличенным по сравнению с основным материалом на правой и левой сторонах сварного шва. Это можно увидеть в правой части рис. 10b, обозначенной белыми стрелками. Кроме того, рост зерна кажется еще более выраженным на стороне с высоким содержанием никеля и титана (левая сторона), поскольку зерно выглядит более глобулярным по сравнению с микроструктурой в зоне зоны сварного шва рядом со сталью (правая сторона). Таким образом, во-вторых, на стороне, богатой Fe, Cr и Mn (справа), рост зерен, по-видимому, происходит иначе (отмечен белым овалом) по сравнению со стороной, богатой Ti и Ni. В прямом сравнении с отображениями EDS на рис.8, химическая неоднородность в середине зоны сварного шва, т.е. частичное обогащение Ni и Ti, по-видимому, связана с изменением локального затвердевания. Это можно вывести из результата EBSD, сосредоточив внимание на областях слева и справа от центра рис. 10. Различия в локально преобладающих режимах затвердевания, т. Е. Столбчатый и равноосный, могут быть связаны с разными термо- физические свойства аустенитного Ni-Ti и аустенитной стали. Из-за различий в теплопроводности и теплоемкости, а также незначительных различий в химическом составе эпитаксиальный рост, по-видимому, ускоряется локально (рис.
10).
EBSD-анализ зоны сварного шва параметра 1c. Карта обратной полюсной фигуры в направлении TD ( a ) и фазовая карта ( b ). В обоих случаях накладывается качество изображения (IQ).
В дополнение к микроскопическому анализу образцы были подвергнуты испытаниям на микротвердость. На рисунке 11 показан примерный профиль микротвердости образца, сваренного с набором параметров «1b». Измерения твердости показывают значительное увеличение твердости по всей зоне сварного шва, т.е.е. как со стороны 1.4310, так и со стороны нитинола. Предполагается, что образование очень мелких интерметаллических фаз, диспергированных по всей зоне сварки, может существенно повлиять на твердость, поскольку она более чем в два раза выше, чем у основных материалов. Все образцы показывают одинаковые значения твердости после сварки; однако градиенты, особенно на стороне нитинола, очень велики и, похоже, каким-то образом зависят от фактических параметров сварки.
Испытания на микротвердость сваренного образца с использованием набора параметров «1b»
Все сваренные образцы подвергались механическим испытаниям с акцентом на предел прочности при растяжении (UTS).Результаты показаны на рис. 12. В целом, UTS образцов, приваренных со смещением балки к соединительному элементу из нержавеющей стали (набор параметров 1a – 1d), показывают более высокие значения UTS по сравнению с образцами со смещением балки в сторону нитинола. (набор параметров 2a – 2e). Образцы, сваренные с выравниванием балки на стальной стороне 0,15 мм («1b») и 0,2 мм («1c»), показывают самый высокий UTS. Эти два образца достигли уровня сверхупругого напряжения, определенного примерно до 550 МПа. Тем не менее ни один из образцов не показал плато сверхупругих напряжений, что является характерной особенностью нитинола (рис.13).
Рис. 12Предел прочности при растяжении (UTS) сварных образцов (красная линия показывает предел прочности на сверхупругое плато используемого нитинольного материала)
Рис.
Диаграмма напряжения-деформации сваренных стандартных материалов и разнородного сварного образца с использованием набора параметров «1c»
На рис. 13 показаны диаграммы напряжения-деформации для эталонных сварных швов в аналогичных материалах, например, при сварке нитинол-нитинолом и 1.4310–1.4310 (рис. 13a), а также примерная кривая для разнородного сварного шва (нитинол -1.4310) с использованием набора параметров «1c» (рис. 13b), так как самый высокий предел прочности был найден для этого состояния (рис. 12). Соединения подобных материалов перед разрушением демонстрируют явную пластическую деформацию. Особенно в случае сварной проволоки Ni-Ti-Ni-Ti характерное плато напряжения наблюдается в сварном состоянии (при уровне напряжения около 530 МПа), обеспечивая деформацию при разрыве> 7%. Для 1.4310 перед разрушением наблюдается лишь незначительная пластическая деформация, а исходное состояние UTS не выполняется.Такое поведение можно рационализировать, исходя из самого начального состояния и местных эффектов сварки. Исходная проволока характеризуется очень высоким показателем UTS из-за того, что она поставляется в упрочненном состоянии. Как можно получить из испытаний на микротвердость и дальнейшей характеристики микроструктуры (не показано для краткости), все микроструктурные особенности, возникающие в результате холодной обработки, исчезают. Кроме того, наблюдается значительный рост зерна. Таким образом, при испытании на растяжение вся деформация локализуется в узкой зоне сварного шва, которая имеет значительно меньшую прочность по сравнению с окружающей высокопрочной проволокой в исходном состоянии.Эта локализация деформации и повреждения в очень ограниченном объеме всего испытанного образца проволоки приводит как к снижению прочности, так и к удлинению при разрыве (рис. 13а).
При сварке разнородных нитинола и 1.4310 преждевременное хрупкое разрушение произошло в упругом режиме на уровне напряжений, где можно было бы ожидать начала сверхупругого плато (рис. 13б). Поскольку эволюция микроструктуры сварного эталона Ni-Ti – Ni-Ti не кажется вредной в случае растягивающей нагрузки (как можно заключить из рис. 13a), т.е. мартенситное превращение, вызванное напряжением, наступает чуть выше 500 МПа, здесь необходимо учитывать дополнительные аспекты. Преждевременное разрушение образца, сваренного с параметром «1c», можно объяснить двумя аспектами: характерной микроструктурой, выявленной на картах EDS и EBSD (см. Рис. 8, 9 и 10), и интерметаллическими фазами, образовавшимися при сварке разнородных типов. нитинола и стали. Очевидно, что изменение микротвердости противоречит наблюдаемому росту зерна, поскольку предполагается, что меньший размер зерна характеризует более высокие значения твердости.Повышенная твердость в зоне сварного шва и, следовательно, увеличение общей прочности и хрупкости материала, соответственно, являются важным фактором для оценки доминирующего механизма разрушения. Общее увеличение твердости может быть объяснено только образованием интерметаллических фаз (Fe 2 Ti и NiTi 2 ), о которых неоднократно сообщалось в литературе, например, в [16,17,18,19]. Следует отметить, что локальное рассеяние твердости, показанное на рис.
11, должно быть связано с отдельными зернами, имеющими различную ориентацию (зерна в сварном шве на некоторых участках превышают размер отпечатков твердости).Анализ образцов с трещинами показал, что общие различия, наблюдаемые в значениях UTS для образцов «типа 1» и «типа 2», могут быть связаны с отдельными участками разрушения. В образцах «типа 2» разрушение наблюдается в разных местах сварного шва, в то время как в случае образцов «типа 1» разрушение всегда наблюдается в пограничном слое между сварным швом и нитиноловой проволокой (рис. 14). Поскольку образцы «типа 1», в которых смещение луча происходит на нержавеющей стали, показали более высокий UTS, основное внимание было уделено этим образцам.Полученные значения показывают, что начальный уровень мартенситного превращения в нитиноловой проволоке приводит к немедленному разрушению сварной конструкции. Поскольку анализ эволюции локальной деформации выходил за рамки настоящей работы, будущие испытания должны будут подтвердить следующее предположение: сварной шов представляет собой микроструктурную выемку.
Такая микроструктурная выемка приводит к локальному увеличению напряжения и, как следствие, к началу мартенситного превращения в этой области. Из-за крутого градиента твердости и присутствия охрупчивающих интерметаллических фаз, а также несовместимости деформаций из-за неоптимизированного градиента немедленно наступает преждевременный выход из строя.Однако на кривой “напряжение-деформация” нельзя получить никаких следов первоначального преобразования, поскольку преобразование затрагивает только очень небольшой объем всей проволоки. Анализ с помощью корреляции цифровых изображений (DIC), который будет проведен в ходе последующей работы и позволит в дальнейшем пролить свет на преобладающие механизмы деформации и повреждения.
Образец «типа 1» разрушился в пограничном слое между нитинолом и материалом шва (слева). Образец «типа 2», разрушенный в сварочном материале (справа)
Патенты на сварку и заявки на патенты (класс 219/136)
Номер патента: 9731373
Резюме: Способ осаждения твердой поверхности на алюминиевые металлические детали газотурбинного двигателя с использованием сварочного оборудования MIG, которое включает в себя генератор импульсного тока и импульсную подачу присадочной металлической проволоки, при этом напыление достигается с использованием присадочной металлической проволоки, состав которой такой же характер, как и состав алюминиевого сплава детали, подвергающейся осаждению на твердой поверхности, с импульсной подачей металлической проволоки и скоростью осаждения на металлическую деталь газотурбинного двигателя, адаптированными для осуществления осаждения без горячего растрескивания.
Тип: Грант
Зарегистрирован: 27 сентября 2012 г.
Дата патента: 15 августа 2017 г.
Правопреемников: SNECMA, НАЦИОНАЛЬНЫЙ НАУЧНЫЙ ЦЕНТР DE LA RECHERCHE SCIENTIFIQUE (CNRS), UNIVERSITE PARIS SUD (UPS), UNIVERSITE DE NANTES
Изобретателей: Жан-Батист Моттин, Жан-Франсуа Кастань, Тьерри Боден, Александр Янн, Мишель Бенуа, Паскаль Пайяр
Сварочная проволока | Научный.
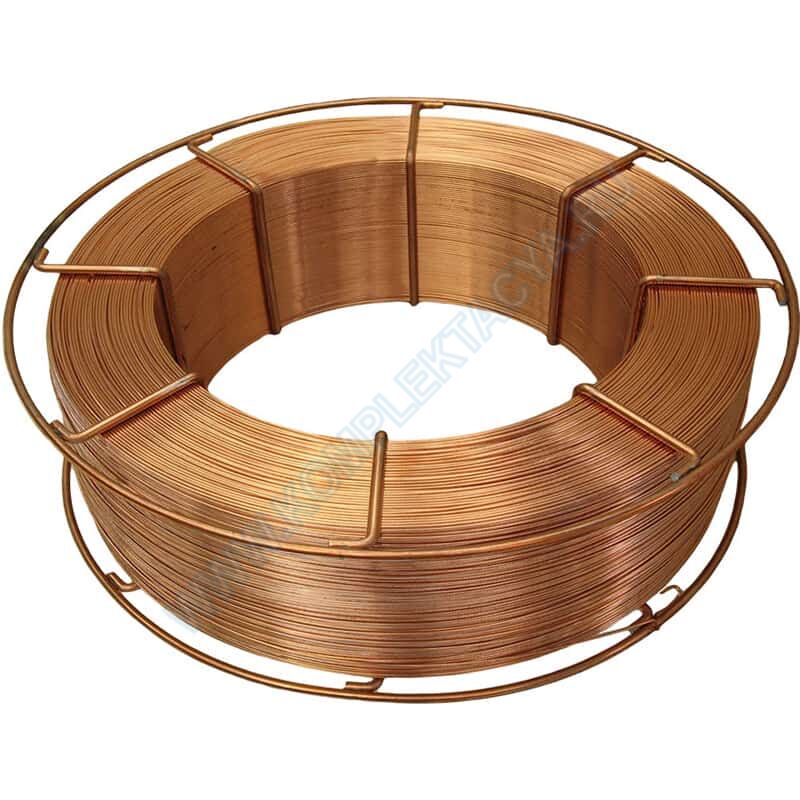
Авторы: Наталья Копцева, Юлия Ефимова, Михаил Чукин, Александр Песин, Н. Токарева, Алексей Ишимов
Аннотация: На комплексе GLEEBLE 3500 выполнено физическое моделирование непрерывного охлаждения стали Mn3Ni1CrMo с различными скоростями из аустенитного состояния.Проанализированы фазовые превращения и исследовано влияние скорости охлаждения на структуру и твердость. Построена диаграмма превращения при непрерывном охлаждении при распаде переохлажденного аустенита. Сделан вывод о возможности снижения твердости горячекатаной заготовки за счет снижения скорости охлаждения по сравнению с существующей при обработке на линии СТЕЛМОР ПАО «ММК», и это позволит исключить термическую обработку сварочной проволоки на аппаратная обработка.
99
Причины поломки сварочного стержня и проволокиАвторы: Александр Сычков, О. Тулупов Александр Мёллер
Аннотация: Проанализированы причины поломки сварочного прутка и проволоки при волочении. Показано, что основной причиной поломки является микрофизическая древовидная сегрегация, которая вызвана нерациональным добавлением борсодержащего материала при послепечной обработке, низкой эффективностью процесса непрерывной разливки стали, непроверенной технологией электромагнитного перемешивания металла в кристаллизаторе при непрерывное литье.Изучены особенности ликвации легированных элементов как в сварочном пруте, так и в проволоке. Показано, что неравномерность распределения бора, марганца и кремния в продольном и поперечном сечениях сварочного прутка станет основной причиной увеличения обрыва проволоки при дальнейшей волочении.
247
Физическое моделирование технологических режимов производства деформированных полуфабрикатов из экспериментальных алюминиевых сплавов, легированных скандиемАвторы: Владимир Баранов, Сергей Сидельников, Евгений Зенкин, Ольга Якивюк
Аннотация: Сочетание свариваемости, коррозионной стойкости и достаточной прочности позволяет использовать деформированные полуфабрикаты из сплавов системы Al-Mg для обшивки корпусов кораблей, в автомобилестроении, авиастроении и ракетостроении, а также в других областях. промышленность.Для повышения прочностных характеристик перспективно легирование их небольшими добавками металлов, таких как титан, цирконий, скандий и др. В данной работе были проведены исследования по получению деформированных полуфабрикатов (лент, прутков и проволоки) из алюминиевых сплавов, в которых содержание скандия варьировалось от 0,1 до 0,25%. Для этого в лаборатории Школы цветных металлов и материаловедения Сибирского федерального университета моделировали различные режимы обработки металлов.Для подготовки листовых полуфабрикатов смоделированы режимы горячей и холодной прокатки литой заготовки от толщины 40 мм до толщины 3 мм. Для изготовления листовых полуфабрикатов смоделированы режимы горячей и холодной прокатки литой заготовки от толщины 40 мм до толщины 1-3 мм. Для изготовления сварочной проволоки размером 2 × 2 мм был смоделирован процесс комбинированного литья и прокатки-экструзии (CCRE) для получения заготовки диаметром 9 мм и ее дальнейшей прокатки в квадратных калибрах.Пруток диаметром 9 мм производился на комбинированной технологической установке, а проволока – на прокатном стане с диаметром валка 130 мм. В соответствии с программой исследований измерены механические свойства горячедеформированных, холоднодеформированных и отожженных листовых полуфабрикатов. Затем полуфабрикаты сваривали вместе с полученной проволокой и оценивали качество и свойства сварного соединения, а также их коррозионную стойкость. В настоящее время результаты исследований используются для разработки промышленных технологий производства листов и пластин из экспериментальных сплавов системы Al-Mg, легированных скандием.
54
Феноменологическая модель упрочнения низкоуглеродистых сталей при многостадийной волочении.Авторы: А.В. Грушко, Владимир Владимирович Кухарь, Ю.О. Слободянюк
Аннотация: Полученная феноменологическая модель упрочнения низкоуглеродистой сварочной проволоки G3Si1 и Sb08-G2S при многоступенчатом волочении устанавливает зависимость коэффициентов кривой упрочнения (показателя упрочнения и модуля упрочнения) от интегральной деформации растяжения.Полученная модель позволяет рассчитывать кривую упрочнения, показатели прочности и пластичности металлических изделий по результатам испытаний катанки в состоянии поставки.
114
Определение температуры нагрева проволоки при импульсной дуговой сварке расчетно-графическим методомАвторы: А.Г. Крампит, М.А. Крампит
Аннотация: В статье авторы рассматривают аппарат для импульсной дуговой сварки, в котором в качестве сопротивления используется отрезок протяженного выступа электродной проволоки. Авторы представляют методику расчета температуры нагрева проволоки в импульсно-дуговом режиме.
392
Влияние обработки микролегированием сварочной проволоки 5183 на микроструктуру и свойство растяжения сварного соединенияАвторы: Сяо Мин Ван, Шэн Чжу, Чжи Хао Чжао, Ци Вэй Ван, Сяо Дун Чжао
Реферат: Сварочная проволока 5183, микролегированная с использованием Sc, Zr, Er и автоматической системы сварки MIG, применяется для сварки алюминиевого сплава 7A52.Оптический микроскоп и универсальная машина для испытаний на растяжение используются для исследования микроструктуры и свойств растяжения сварного соединения соответственно. Результаты показали, что зона сварки и зона плавления состояли из однородного изометрического кристалла и крошечного изометрического кристалла дендрита, когда сварное соединение было выполнено с использованием сварочной проволоки 5183, микролегированной через редкоземельный элемент, соответственно. Предел прочности на разрыв и удельное удлинение сварной зоны были максимально улучшены при микролегировании сварочной проволоки 5183 с использованием одного Sc или Zr соответственно.В результате микролегированной обработки сварочной проволоки 5183 с использованием Sc, Zr или Er в микропробах образовалось большое количество гранул Al3Sc, Al3Zr, Al3Er, которые сыграли роль гетерогенного зародышеобразования и улучшили микроструктуру зоны сварки. Между тем, появилась наноразмерная упрочняющая фаза A13Sc, A13Zr, Al3Er, диспергированная в зоне сварки, что привело к тому, что сварное соединение продемонстрировало высокую прочность на разрыв.
821
Подготовка и оценка романа АЛ-5.Сварочная проволока 4Si-0.5MgАвторы: Хао Ван, Чанг Шу Хэ, Донг Ван, Сян Чжао, Лян Цзо
Реферат: Присадочная проволока Al-5.4Si-0.5Mg была разработана и произведена методами прямого кокильного литья, экструзии, волочения в фильерах и отверстиях для сварки недавно разработанных Mg-содержащих алюминиевых сплавов с высоким содержанием Si. Пластины из сплава Al-12,7Si-0,7Mg были сварены встык методом дуговой сварки вольфрамовым электродом в среде инертного газа (TIG) с использованием сварочной проволоки в исходном состоянии.Микроструктура и механические свойства этих сварных соединений в различных условиях обработки твердым раствором и искусственным старением были изучены для оценки сварочных качеств новой сварочной проволоки. Результаты показали, что сварочная проволока Al-5,4Si-0,5Mg представляет собой идеальную специальную сварочную проволоку из сплава Al-12,7Si-0,7Mg, а присадочный металл поддается термической обработке. Сварные соединения показали значительно более высокие механические свойства после послесварочной термообработки (PWHT). Все это дает возможность широкого применения романа АЛ-5.Сварочная проволока 4Si-0,5Mg и сварные детали из сплава Al-12,7Si-0,7Mg.
176
Влияние сварочной проволоки на микроструктуру и механические свойства CO 2 Экранированный сварной шов дуговой сварки стали 30CrMnSiAАвторы: Хе Чен, Ченг Ган Ян, Ай Ву Ю, Цян Чжэн, Сяо Бинь Ю
Реферат: Сталь 30CrMnSiA сваривается дуговой сваркой в среде CO 2 с применением H08Mn2SiA и Ok Aristorod 12.5 сварочной проволокой соответственно. Изучено влияние сварочных составов на микроструктуру и механические свойства сварного соединения. Результаты показывают, что при использовании Ok Aristorod 12.5 для сварки микроструктура металла шва в основном состоит из игольчатого феррита, доэвтектоидного феррита и перлита, прочность сварного соединения на разрыв оставляет желать лучшего. При использовании H08Mn2SiA для сварки микроструктура металла шва в основном состоит из мелкозернистого феррита и игольчатого феррита, игольчатый феррит измельчается, а содержание игольчатого феррита увеличивается, поэтому прочность сварного соединения на растяжение повышается.С помощью этих двух сварочных проволок свариваются соединения, оба соединения имеют отличные свойства изгиба.
30
Влияние присадочного металла на микроструктуру и свойства сварного соединения 2519A / 7A52Авторы: Чжун Цзюй Ху, Хао Хуанг, Хун Ган Чжоу
Реферат: Алюминиевые сплавы 2519А / 7А52 сварены сварочными проволоками ЭР4043 и ЭР2319 методом МИГ.Изучены механические свойства, микроструктура, а также разрушение сварных соединений. Результаты показывают, что сварочная проволока из материала ER2319 благоприятна для измельчения зерна сварочных конструкций, а прочность и удлинение соединения лучше, чем при сварке сварочной проволокой ER4043. В то время как при использовании ER4043 прочность и пластичность соединения снижаются из-за образования хрупкой фазы с высоким содержанием кремния, и разрушение сварных деталей в основном является хрупким.
2136
Конструкция малого механизма подачи сварочной проволокиАннотация: Механизм подачи проволоки – это устройство подачи сварочной проволоки, широко используемое при сварке TIG и газовой сваркой CO2.Плавная подача проволоки напрямую влияет на качество сварки. Усовершенствован небольшой механизм подачи сварочной проволоки. Механизм подачи проволоки и пластина сварочной проволоки располагались по центру горелки. Это уменьшило сопротивление проводной передачи и увеличило мобильность. Практическое применение показало, что он обладает характеристиками стабильной и надежной подачи проволоки, высокой производительностью сварки, а также высоким качеством и стабильностью сварных соединений. Это существенно повлияет на улучшение существующей сварки и широкие перспективы применения в сварочном промышленном производстве.
309
Проволока для сварки интерметаллических сплавов и способ ее изготовления (Патент)
Сантелла, М. Л., и Сикка, В. К. Проволока для сварки интерметаллических сплавов и способ ее изготовления . США: Н. П., 1996.
Интернет.
Сантелла, М. Л., и Сикка, В. К. Проволока для сварки интерметаллических сплавов и способ ее изготовления . Соединенные Штаты.
Сантелла, М. Л., и Сикка, В. К. Вт.
«Проволока для сварки интерметаллических сплавов и способ ее изготовления». Соединенные Штаты.
@article {osti_242586,
title = {Проволока для сварки интерметаллических сплавов и способ ее изготовления},
author = {Сантелла, М. Л. и Сикка, В. К.},
аннотацияПримечание = {Сварочные проволоки для сварки интерметаллических сплавов алюминидов никеля, алюминидов никеля и железа, алюминидов железа или алюминидов титана, предпочтительно включающие дополнительные легирующие компоненты, изготавливаются в виде двухкомпонентных плакированных структур, в которых один компонент содержит первичный легирующий компонент. (s) за исключением алюминия, и другой компонент содержит алюминиевый компонент.Этот двухкомпонентный подход к изготовлению сварочной проволоки преодолевает трудности, связанные с механическим формированием сварочной проволоки из интерметаллических сплавов, которые обладают высокой прочностью и ограниченной пластичностью при повышенных температурах, обычно используемых в обычных процессах обработки металлов. Состав плакированной сварочной проволоки легко подбирается таким образом, чтобы состав сварочной проволоки при расплавлении образовывал сплав, определяемый наплавленным слоем сварного шва, который по существу соответствует составу соединяемого интерметаллического сплава.4 фиг.},
doi = {},
url = {https://www.osti.gov/biblio/242586},
journal = {},
number =,
объем =,
place = {United States},
год = {1996},
месяц = {6}
}